Advantech EKI-1242ECMS Modbus RTU/TCP to EtherCAT Fieldbus Gateway Manual
Add to my manuals
68 Pages
advertisement
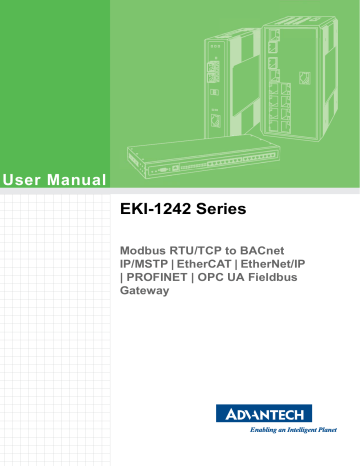
User Manual
EKI-1242 Series
Modbus RTU/TCP to BACnet
IP/MSTP | EtherCAT | EtherNet/IP
| PROFINET | OPC UA Fieldbus
Gateway
Copyright
The documentation and the software included with this product are copyrighted 2018 by Advantech Co., Ltd. All rights are reserved. Advantech Co., Ltd. reserves the right to make improvements in the products described in this manual at any time without notice. No part of this manual may be reproduced, copied, translated or transmitted in any form or by any means without the prior written permission of Advantech Co.,
Ltd. Information provided in this manual is intended to be accurate and reliable.
However, Advantech Co., Ltd. assumes no responsibility for its use, nor for any infringements of the rights of third parties, which may result from its use.
Acknowledgments
Intel and Pentium are trademarks of Intel Corporation.
Microsoft Windows and MS-DOS are registered trademarks of Microsoft Corp.
All other product names or trademarks are properties of their respective owners.
Product Warranty (5 years)
Advantech warrants to you, the original purchaser, that each of its products will be free from defects in materials and workmanship for five years from the date of purchase.
This warranty does not apply to any products which have been repaired or altered by persons other than repair personnel authorized by Advantech, or which have been subject to misuse, abuse, accident or improper installation. Advantech assumes no liability under the terms of this warranty as a consequence of such events.
Because of Advantech’s high quality-control standards and rigorous testing, most of our customers never need to use our repair service. If an Advantech product is defective, it will be repaired or replaced at no charge during the warranty period. For out of-warranty repairs, you will be billed according to the cost of replacement materials, service time and freight. Please consult your dealer for more details.
If you think you have a defective product, follow these steps:
1.
Collect all the information about the problem encountered. (For example, CPU speed, Advantech products used, other hardware and software used, etc.) Note anything abnormal and list any on screen messages you get when the problem occurs.
2.
Call your dealer and describe the problem. Please have your manual, product, and any helpful information readily available.
3.
If your product is diagnosed as defective, obtain an RMA (return merchandize authorization) number from your dealer. This allows us to process your return more quickly.
4.
Carefully pack the defective product, a fully-completed Repair and Replacement
Order Card and a photocopy proof of purchase date (such as your sales receipt) in a shippable container. A product returned without proof of the purchase date is not eligible for warranty service.
5.
Write the RMA number visibly on the outside of the package and ship it prepaid to your dealer.
Part No. 2009124200
Printed in Taiwan ii
Edition 1
October 2018
EKI-1242 Series User Manual
Declaration of Conformity
CE
This product has passed the CE test for environmental specifications. Test conditions for passing included the equipment being operated within an industrial enclosure. In order to protect the product from being damaged by ESD (Electrostatic Discharge) and EMI leakage, we strongly recommend the use of CE-compliant industrial enclosure products.
FCC Class A
Note: This equipment has been tested and found to comply with the limits for a Class
A digital device, pursuant to part 15 of the FCC Rules. These limits are designed to provide reasonable protection against harmful interference when the equipment is operated in a commercial environment. This equipment generates, uses, and can radiate radio frequency energy and, if not installed and used in accordance with the instruction manual, may cause harmful interference to radio communications.
Operation of this equipment in a residential area is likely to cause harmful interference in which case the user will be required to correct the interference at his own expense.
Technical Support and Assistance
1.
Visit the Advantech web site at www.advantech.com/support where you can find the latest information about the product.
2.
Contact your distributor, sales representative, or Advantech's customer service center for technical support if you need additional assistance. Please have the following information ready before you call:
– Product name and serial number
– Description of your peripheral attachments
– Description of your software (operating system, version, application software, etc.)
– A complete description of the problem
– The exact wording of any error messages
EKI-1242 Series User Manual iii
Warnings, Cautions, and Notes
Warning!
Warnings indicate conditions, which if not observed, can cause personal injury!
Caution!
Cautions are included to help you avoid damaging hardware or losing data. e.g.
There is a danger of a new battery exploding if it is incorrectly installed.
Do not attempt to recharge, force open, or heat the battery. Replace the battery only with the same or equivalent type recommended by the manufacturer. Discard used batteries according to the manufacturer's instructions.
Note!
Notes provide optional additional information.
Document Feedback
To assist us in making improvements to this manual, we would welcome comments and constructive criticism. Please send all such - in writing to: [email protected]
Packing List
Before setting up the system, check that the items listed below are included and in good condition. If any item does not accord with the table, please contact your dealer immediately.
1 x Fieldbus gateway
1 x DIN-Rail mounting bracket and screws
1 x Wall-mounting bracket iv EKI-1242 Series User Manual
Safety Instructions
Read these safety instructions carefully.
Keep this User Manual for later reference.
Disconnect this equipment from any DC outlet before cleaning. Use a damp cloth. Do not use liquid or spray detergents for cleaning.
For plug-in equipment, the power outlet socket must be located near the equipment and must be easily accessible.
Keep this equipment away from humidity.
Put this equipment on a reliable surface during installation. Dropping it or letting it fall may cause damage.
The openings on the enclosure are for air convection. Protect the equipment from overheating. DO NOT COVER THE OPENINGS.
Make sure the voltage of the power source is correct before connecting the equipment to the power outlet.
Position the power cord so that people cannot step on it. Do not place anything over the power cord.
All cautions and warnings on the equipment should be noted.
If the equipment is not used for a long time, disconnect it from the power source to avoid damage by transient overvoltage.
Never pour any liquid into an opening. This may cause fire or electrical shock.
Never open the equipment. For safety reasons, the equipment should be opened only by qualified service personnel.
If one of the following situations arises, get the equipment checked by service personnel:
– The power cord or plug is damaged.
– Liquid has penetrated into the equipment.
– The equipment has been exposed to moisture.
– The equipment does not work well, or you cannot get it to work according to the user's manual.
– The equipment has been dropped and damaged.
– The equipment has obvious signs of breakage.
DO NOT LEAVE THIS EQUIPMENT IN AN ENVIRONMENT WHERE THE
STORAGE TEMPERATURE MAY GO -40°C (-40°F) ~ 85°C (185°F). THIS
COULD DAMAGE THE EQUIPMENT. THE EQUIPMENT SHOULD BE IN A
CONTROLLED ENVIRONMENT.
The sound pressure level at the operator's position according to IEC 704-1:1982 is no more than 70 dB (A).
DISCLAIMER: This set of instructions is given according to IEC 704-1.
Advantech disclaims all responsibility for the accuracy of any statements contained herein.
The device is used for the restricted access location.
WARNING: USE CONDUCTORS WITH INSULATION RATED FOR AT LEAST
75°C.
AVERTISSEMENT : EMPLOYER DES CONDUCTEURS POUR AU MOINS
75°C.
BASE THE CONDUCTOR AMPACITY ON A MAXIMUM TERMINATION
TEMPERATURE OF 75°C.
LE COURANT ADMISSIBLE DU CONDUCTEUR DOIT ÊTRE DÉTERMINÉ EN
FONCTION D'UNE TEMPÉRATURE MAXIMALE AUX TERMINAISONS DE
75°C.
EKI-1242 Series User Manual v
CAUTION: FOR USE IN A CONTROLLED ENVIRONMENT. REFER TO
MANUAL FOR ENVIRONMENTAL CONDITIONS.
ATTENTION : POUR UTILISATION EN ATMOSPHÈRE CONTRÔLÉE.
CONSULTER LA NOTICE TECHNIQUE.
WARNING: EKI-1242 IS LIVE. RISK OF ELECTRIC SHOCK. DISCONNECT
POWER BEFORE SERVICING.
AVERTISSEMENT : EKI-1242 EST SOUS TENSION. RISQUE DE CHOC
ÉLECTRIQUE, COUPER LE COURANT AVANT L'ENTRETIEN.
WARNING: DISCONNECT ALL SOURCES OF SUPPLY BEFORE
SERVICING.
AVERTISSEMENT : COUPER TOUTES LES SOURCES D'ALIMENTATION
AVANT DE FAIRE L'ENTRETIEN ET LES RÉPARATIONS.
NEUTRAL FLOATING.
NEUTRE FLOTTANT.
IMPORTANT SAFETY INSTRUCTIONS
INSTRUCTIONS IMPORTANTES CONCERNANT LA SÉCURITÉ
– SAVE THESE INSTRUCTIONS - THIS MANUAL CONTAINS IMPORTANT
SAFETY INSTRUCTIONS.
CONSERVER CES INSTRUCTIONS. CETTE NOTICE CONTIENT DES
INSTRUCTIONS IMPORTANTES CONCERNANT LA SÉCURITÉ.
WARNING: SHOCK HAZARD. ONLY FOR MOUNTING IN A RACK OR
ENCLOSURE FULLY ENCLOSING ALL LIVE PARTS.
AVERTISSEMENT : RISQUE D'ÉLECTROCUTION. NE DOIT ÊTRE INSTALLÉ
QUE DANS UN BÂTI OU UN BOÎTIER RECOUVRANT ENTIÈREMENT
TOUTES LES PIÈCES SOUS TENSION.
WARNING: HOT SURFACE.
AVERTISSEMENT : SURFACE CHAUDE.
WARNING: PROPER VENTILATION IS REQUIRED TO REDUCE THE RISK
OF HAZARDOUS OR EXPLOSIVE GAS BUILDUP DURING INDOOR
CHARGING. SEE OWNERS MANUAL.
AVERTISSEMENT : UNE VENTILATION ADÉQUATE EST NÉCESSAIRE AFIN
DE RÉDUIRE LES RISQUES D'ACCUMULATION DE GAZ DANGEREUX OU
EXPLOSIFS DURANT LA RECHARGE À L'INTÉRIEUR. VOIR LE MANUEL
D'ENTRETIEN.
FOR USE WITH COPPER CONDUCTORS ONLY.
DESTINÉ À ÊTRE UTILISÉ AVEC DES CONDUCTEURS EN CUIVRE
SEULEMENT.
WARNING: HOT SURFACE(S).
AVERTISSEMENT : SURFACE(S) CHAUDE(S).
vi EKI-1242 Series User Manual
Safety Precaution - Static Electricity
Static electricity can cause bodily harm or damage electronic devices. To avoid damage, keep static-sensitive devices in the static-protective packaging until the installation period. The following guidelines are also recommended:
Wear a grounded wrist or ankle strap and use gloves to prevent direct contact with the device before servicing the device. Avoid nylon gloves or work clothes, which tend to build up a charge.
Always disconnect the power from the device before servicing it.
Before plugging a cable into any port, discharge the voltage stored on the cable by touching the electrical contacts to the ground surface.
EKI-1242 Series User Manual vii
Contents
Chapter 1
Product Overview
................................1
Front View..................................................................................... 3
Rear View ................................................................................... 11
Top View ..................................................................................... 12
Bottom View................................................................................ 13
Chapter 2
Fieldbus Gateway Installation
..........16
Connecting Hardware ................................................................. 17
Verifying Fieldbus Gateway Operation.................................................... 17
Installing the Fieldbus Gateway .............................................................. 18
DIN Rail Mounting....................................................................... 18
Wall-Mounting ............................................................................. 20
Connecting the Fieldbus Gateway to Ethernet Ports .............................. 22
RJ45 Ethernet Cable Wiring ....................................................... 22
MicroSD Card Installation ....................................................................... 23
Installing a MicroSD Card ........................................................... 23
Utilizing a MicroSD Card............................................................. 24
Power Supply Installation........................................................................ 25
Overview ..................................................................................... 25
Considerations ............................................................................ 26
Grounding the Device ................................................................. 26
Wiring a Relay Contact ............................................................... 27
Wiring the Power Inputs.............................................................. 28
Chapter 3
Managing Fieldbus Gateway
............30
Changing Default Password ....................................................... 31
Device Information ...................................................................... 32
Diagnose..................................................................................... 33
Data View.................................................................................... 34
IP Setting .................................................................................... 39
BACnet Setting ........................................................................... 45
EtherCAT Setting ........................................................................ 46
EtherNet/IP Setting ..................................................................... 46
PROFINET Setting...................................................................... 47
OPC UA Setting .......................................................................... 48
Modbus Setting ........................................................................... 49
Mapping Overview ...................................................................... 52
System Management .............................................................................. 53
Change Password....................................................................... 53
viii EKI-1242 Series User Manual
Backup Manager......................................................................... 53
Upgrade Manager....................................................................... 54
Reset System ............................................................................. 54
Reboot Device ............................................................................ 54
Apply Configuration .................................................................... 55
Modbus Traffic Catcher .............................................................. 56
EKI-1242 Series User Manual ix
List of Figures
Terminal Receptor: Relay Contact (EKI-1242BNMS/EKI-1242IBNMS) ...................... 27
Terminal Receptor: Relay Contact (EKI-1242BNMS/EKI-1242IBNMS) ...................... 28
Overview > Device Information > BACnet/IP | EtherNet/IP | PROFINET | OPC UA ... 33
EtherCAT Setting ......................................................................... 46
x EKI-1242 Series User Manual
System Management > Backup Manager > Backup Manager.................................... 53
System Management > Backup Manager > SD Card Backup .................................... 54
EKI-1242 Series User Manual xi
Chapter
1
Product Overview
1
1.1
Specifications
Specifications
Interface
Physical
LED Display
Environment
Description
I/O Port
EKI-1242BNMS/EKI-1242IBNMS: 2 x Modbus
TCP + 2 x BACnet IP + 1 x BACnet MSTP +
1 x RS-232/422/485
EKI-1242ECMS/EKI-1242IECMS: 2 x RJ45 +
2 x EtherCAT + 2 x RS-232/422/485
EKI-1242EIMS/EKI-1242IEIMS: 2 x RJ45 +
2 x EtherNet/IP + 2 x RS-232/422/485
EKI-1242PNMS/EKI-1242IPNMS: 2 x RJ45 +
2 x PROFINET + 2 x RS-232/422/485
EKI-1242OUMS/EKI-1242IOUMS: 2 x RJ45 +
2 x OPC UA + 2 x RS-232/422/485
Power Connector 6-pin removable screw terminal (power & relay)
MicroSD Card
Enclosure
Installation
Dimensions
(W x H x D)
System LED
Protocol LED
Configuration backup and restore
Metal with solid mounting hardware
DIN-rail, wall mount
42 x 140 x 95mm (1.66” x 5.52” x 3.75”)
Port LED
Operating
Temperature
Storage
Temperature
Ambient Relative
Humidity
P1, P2, Status
EKI-1242BNMS/EKI-1242IBNMS: BACnet IP
(BN), Modbus (MS)
EKI-1242ECMS/EKI-1242IECMS: EtherCAT
(EC), Modbus (MS)
EKI-1242EIMS/EKI-1242IEIMS: EtherNET/IP
(EI), Modbus (MS)
EKI-1242PNMS/EKI-1242IPNMS: PROFINET
(PN), Modbus (MS)
EKI-1242OUMS/EKI-1242IOUMS: OPC UA
(OU), Modbus (MS)
LAN: Speed, Link/Active
Serial: Tx, Rx
EtherCAT: Speed, Link/Active
(EKI-1242ECMS/EKI-1242IECMS only)
-10°C ~ 60°C (14°F ~ 140°F)
“I” models: -40°C ~ 75°C (-40°F ~ 167°F)
-40°C ~ 85°C (-40°F ~ 185°F)
10 ~ 95% (non-condensing)
EKI-1242 Series User Manual 2
Specifications Description
Power Power
Consumption
Power Input
Certifications EMC
1.2
Hardware Views
1.2.1
Front View
1.2.1.1
EKI-1242BNMS/EKI-1242IBNMS
5.2W
EKI-1242BNMS/EKI-1242IBNMS: 24 V
AC
, redundant dual power inputs
EKI-1242ECMS/EKI-1242IECMS: 12~48 V
DC
, redundant dual power inputs
EKI-1242EIMS/EKI-1242IEIMS: 12~48 V
DC
, redundant dual power inputs
EKI-1242PNMS/EKI-1242IPNMS: 12~48 V
DC
, redundant dual power inputs
EKI-1242OUMS/EKI-1242IOUMS:
12~48 V
DC
, redundant dual power inputs
CE, FCC Part 15 Subpart B (Class A)
1
2
3
4
1
P1 P2 Status
Default
2
1
BN MS
2
Rx Tx Rx Tx
5
1 2
Serial ports
EKI-1242BNMS
Figure 1.1 Front View
No. Item Description
1 System LED panel
See “LED Indicators” on page 4 for further details.
2 Default
3 ETH port
Press less than 5 seconds to restart the device. Press over 5 seconds to reset to factory default.
RJ45 port for Modbus/TCP and device configuration.
4 ETH port RJ45 port for BACnet/IP.
3 EKI-1242 Series User Manual
No. Item
5 Serial port
LED Indicators
LED Name
P1
P2
Status
BACnet (BN)
Modbus (MS)
Serial
Description
DB9 pinout. Port 1 supports BACnet MSTP and port 2 supports
RS-232/422/485.
LED Color Description
Green
Off
Green
Off
Orange
Off
Orange
Green
Orange
Green
Off
Orange
Green
Off
Power 1 is ON
Power 1 is off or power error condition exists
Power 2 is ON
Power 2 is off or power error condition exists
Blinking: System is ready
Solid:
– Restore config from SD card successfully to factory default state during booting
– Backup config to SD card successfully during booting
System is powered off
Reserved
Blinking: BACnet Daemon is not ready
Solid: BACnet Daemon is ready
Blinking: One of Modbus transaction query failed
Solid: All Modbus transactions query successfully
No Modbus transmission
Serial port is receiving data
Serial port is transmitting data
Data is not transmitted or received through the serial port
EKI-1242 Series User Manual 4
1.2.1.2
EKI-1242ECMS/EKI-1242IECMS
1
2
3
1
P1 P2 Status
Default
2
EC MS
4
Rx Tx Rx Tx
5
1 2
Serial ports
EKI-1242ECMS
Figure 1.2 Front View
No. Item Description
1 System LED panel
See “LED Indicators” on page 5 for further details.
2 Default
3 ETH port
Press less than 5 seconds to restart the device. Press over 5 seconds to reset to factory default.
RJ45 port for Modbus/TCP and device configuration.
4 ETH port
5 Serial port
RJ45 port for EtherCAT.
DB9 pinout supports RS-232/422/485.
LED Indicators
Catalog
System
LED
LED Name
P1
P2
Status
LED Color Description
Green
Off
Green
Off
Orange
Off
Power 1 is ON
Power 1 is off or power error condition exists
Power 2 is ON
Power 2 is off or power error condition exists
Blinking: System is ready
Solid:
– Restore config from SD card successfully to factory default state during booting
– Backup config to SD card successfully during booting
– Automatically Backup function is disabled
System is powered off
5 EKI-1242 Series User Manual
Catalog
Protocol
LED
LED Name
EtherCAT (EC)
Modbus (MS)
Port LED Serial
LED Color Description
Orange
Green
Heartbeat: Connect to EtherCAT failed
Blinking (500ms ON, 500ms OFF) :
EtherCAT is Error-State
Blinking (200ms ON, 200ms OFF):
EtherCAT is PreOP state
Blinking (200ms ON, 700ms OFF):
EtherCAT is SafeOP state
Solid: EtherCAT is OP state
Off
Orange
Green
Off
Orange
Green
Off
EtherCAT RJ45 Orange
RJ45
Green
Green
Orange/
Green
EtherCAT is Init-state
Blinking: One of Modbus transaction query failed
Solid: All Modbus transactions query successfully
No Modbus transmission
Serial port is receiving data
Serial port is transmitting data
Data is not transmitted or received through the serial port
Off: init
Flash 1x-12x: SafeOP 1x
Blinking: PreOP
Flickering: Bootstrap
On: Op
Off: No link
Blinking: Link and activity
On: Link without activity
Off: No link
Blinking: Link and activity
On: Link without activity
Off: no link
Solid Orange: Current link speed is 100M
Solid Green: Current link speed is 10M
EKI-1242 Series User Manual 6
1.2.1.3
EKI-1242EIMS/EKI-1242IEIMS
1
2
3
4
1
P1 P2 Status
Default
2
1
EI MS
2
Rx Tx Rx Tx
5
1 2
Serial ports
EKI-1242EIMS
Figure 1.3 Front View
No. Item Description
1 System LED panel
See “LED Indicators” on page 7 for further details.
2 Default
3 ETH port
Press less than 5 seconds to restart the device. Press over 5 seconds to reset to factory default.
RJ45 port for Modbus/TCP and device configuration.
4 ETH port
5 Serial port
RJ45 port for EtherNet/IP.
DB9 pinout supports RS-232/422/485.
LED Indicators
Catalog
System
LED
LED Name
P1
P2
Status
LED Color Description
Green
Off
Green
Off
Orange
Off
Power 1 is ON
Power 1 is off or power error condition exists
Power 2 is ON
Power 2 is off or power error condition exists
Blinking: System is ready
Solid:
– Restore config from SD card successfully to factory default state during booting
– Backup config to SD card successfully during booting
– Automatically Backup function is disabled
System is powered off
7 EKI-1242 Series User Manual
Catalog
Protocol
LED
LED Name
Modbus (MS)
Port LED Serial
RJ45
LED Color Description
EtherNET/IP (EI) Orange
Green
Orange
Green
Off
Orange
Green
Off
Green
Orange/
Green
Reserved
Blinking: IO connection do not establish
Solid: IO connection establish
Blinking: One of Modbus transaction query failed
Solid: All Modbus transactions query successfully
No Modbus transmission
Serial port is receiving data
Serial port is transmitting data
Data is not transmitted or received through the serial port
Off: No link
Blinking: Link and activity
On: Link without activity
Off: no link
Solid Orange: Current link speed is 100M
Solid Green: Current link speed is 10M
1.2.1.4
EKI-1242PNMS/EKI-1242IPNMS
1
2
3
4
1
P1 P2 Status
Default
2
1
PN MS
2
Rx Tx Rx Tx
5
1 2
Serial ports
EKI-1242PNMS
Figure 1.4 Front View
No. Item Description
1 System LED panel
See “LED Indicators” on page 9 for further details.
2 Default Press less than 5 seconds to restart the device. Press over 5 seconds to reset to factory default.
3 ETH port
4 ETH port
5 Serial port
RJ45 port for Modbus/TCP and device configuration.
RJ45 port for PROFINET.
DB9 pinout supports RS-232/422/485.
EKI-1242 Series User Manual 8
LED Indicators
Catalog
System
LED
Protocol
LED
LED Name
P1
P2
Status
Off
PROFINET (PN) Orange
Green
Modbus (MS)
Port LED Serial
RJ45
LED Color Description
Green
Off
Green
Off
Orange
Orange
Green
Off
Orange
Green
Off
Green
Orange/
Green
Power 1 is ON
Power 1 is off or power error condition exists
Power 2 is ON
Power 2 is off or power error condition exists
Blinking: System is ready
Solid:
– Restore config from SD card successfully to factory default state during booting
– Backup config to SD card successfully during booting
– Automatically Backup function is disabled
System is powered off
Blinking: PLC connection do not establish
Blinking: Indicated by TIA portal
Solid: IO connection establish
Blinking: One of Modbus transaction query failed
Solid: All Modbus transactions query successfully
No Modbus transmission
Serial port is receiving data
Serial port is transmitting data
Data is not transmitted or received through the serial port
Off: No link
Blinking: Link and activity
On: Link without activity
Off: no link
Solid Orange: Current link speed is 100M
Solid Green: Current link speed is 10M
9 EKI-1242 Series User Manual
1.2.1.5
EKI-1242OUMS/EKI-1242IOUMS
1
2
3
4
1
P1 P2 Status
Default
2
1
OU MS
2
Rx Tx Rx Tx
5
1 2
Serial ports
EKI-1242OUMS
Figure 1.5 Front View
No. Item Description
1 System LED panel
See “LED Indicators” on page 10 for further details.
2 Default
3 ETH port
Press less than 5 seconds to restart the device. Press over 5 seconds to reset to factory default.
RJ45 port for Modbus/TCP and device configuration.
4 ETH port
5 Serial port
RJ45 port for OPC UA.
DB9 pinout supports RS-232/422/485.
LED Indicators
Catalog
System
LED
LED Name
P1
P2
Status
LED Color Description
Green
Off
Green
Off
Orange
Off
Power 1 is ON
Power 1 is off or power error condition exists
Power 2 is ON
Power 2 is off or power error condition exists
Blinking: System is ready
Solid:
– Restore config from SD card successfully to factory default state during booting
– Backup config to SD card successfully during booting
– Automatically Backup function is disabled
System is powered off
EKI-1242 Series User Manual 10
Catalog
Protocol
LED
LED Name
OPC UA (OU)
Modbus (MS)
Port LED Serial
RJ45
LED Color Description
Green
Off
Orange
Green
Off
Orange
Green
Off
Green
Orange/
Green
OPC UA connection establish
OPC UA connection do not establish
Blinking: One of Modbus transaction query failed
Solid: All Modbus transactions query successfully
No Modbus transmission
Serial port is receiving data
Serial port is transmitting data
Data is not transmitted or received through the serial port
Off: No link
Blinking: Link and activity
On: Link without activity
Off: no link
Solid Orange: Current link speed is 100M
Solid Green: Current link speed is 10M
1.2.2
Rear View
1
Figure 1.6 Rear View
No. Item
1 DIN-Rail mounting plate
Description
Mounting plate used for the installation to a standard DIN rail.
11 EKI-1242 Series User Manual
1.2.3
Top View
1
No. Item
1 Wall mounting screws
2 Terminal block
3 Ground terminal
PWR2 1A@24V PWR1 DC12-48V
3
V2- V2+
P-Fail
V1- V1+
2
Figure 1.7 Top View
Description
Screws (x4) used in the installation of a wall mounting plate.
Connect cabling for power and alarm wiring.
Screw terminal used to ground chassis.
PWR2 1A@24V PWR1 AC 24V
1 3
N2 L2
P-Fail
N1 L1
2
Figure 1.8 Top View (EKI-1242BNMS/EKI-1242IBNMS)
2
3
No. Item
1 Wall mounting screws
Terminal block
Ground terminal
Description
Screws (x4) used in the installation of a wall mounting plate
Connect cabling for power and alarm wiring
Screw terminal used to ground chassis
EKI-1242 Series User Manual 12
1.2.4
Bottom View
1
2
Figure 1.9 Bottom View
No. Item Description
1 Wall mounting holes Screws holes (x4) used in the installation of a wall mounting plate
2 Component cover Open to access microSD card port (only supports FAT32 or exFAT file system).
1.3
Dimensions
11.60 [0.457]
33
[1.299]
15
[0.591]
35
[1.378]
20.53 [0.808]
42 [1.654] 30.50 [1.201]
104 [4.094]
95 [3.740]
40 [1.575] 42 [1.654]
47.05 [1.852]
47.95 [1.888]
95 [3.740]
Figure 1.10 Dimensions (EKI-1242BNMS/EKI-1242IBNMS)
13 EKI-1242 Series User Manual
42 [1.654]
20.53 [0.808]
11.60 [0.457]
33
[1.299]
15
[0.591]
35
[1.378]
30.50 [1.201]
104 [4.094]
95 [3.740]
40 [1.575] 42 [1.654]
47.05 [1.852]
47.95 [1.888]
95 [3.740]
42 [1.654]
20.53 [0.808]
Figure 1.11 Dimensions (EKI-1242ECMS/EKI-1242IECMS)
11.60 [0.457]
33
[1.299]
15
[0.591]
35
[1.378]
30.50 [1.201]
104 [4.094]
95 [3.740]
40 [1.575] 42 [1.654]
47.05 [1.852]
47.95 [1.888]
95 [3.740]
Figure 1.12 Dimensions (EKI-1242EIMS/EKI-1242IEIMS)
EKI-1242 Series User Manual 14
42 [1.654]
20.53 [0.808]
11.60 [0.457]
33
[1.299]
15
[0.591]
35
[1.378]
30.50 [1.201]
104 [4.094]
95 [3.740]
40 [1.575] 42 [1.654]
47.05 [1.852]
47.95 [1.888]
95 [3.740]
42 [1.654]
20.53 [0.808]
Figure 1.13 Dimensions (EKI-1242PNMS/EKI-1242IPNMS)
11.60 [0.457]
33
[1.299]
15
[0.591]
35
[1.378]
30.50 [1.201]
104 [4.094]
95 [3.740]
40 [1.575] 42 [1.654]
47.05 [1.852]
47.95 [1.888]
95 [3.740]
Figure 1.14 Dimensions (EKI-1242OUMS/EKI-1242IOUMS)
15 EKI-1242 Series User Manual
Chapter
2
Fieldbus Gateway
Installation
2
2.1
Installation Guidelines
The following guidelines are provided to optimize the device performance. Review the guidelines before installing the device.
Make sure cabling is away from sources of electrical noise. Radios, power lines, and fluorescent lighting fixtures can interference with the device performance.
Make sure the cabling is positioned away from equipment that can damage the cables.
Operating environment is within the ranges listed range, see “Specifications” on page 2.
Relative humidity around the fieldbus gateway does not exceed 95 percent
(noncondensing).
Altitude at the installation site is not higher than 10,000 feet.
In 10/100 and 10/100/1000 fixed port devices, the cable length from the fieldbus gateway to connected devices cannot exceed 100 meters (328 feet).
Make sure airflow around the fieldbus gateway and respective vents are unrestricted. Without proper airflow, the fieldbus gateway can overheat. To prevent performance degradation and damage to the fieldbus gateway, make sure there is clearance at the top and bottom and around the exhaust vents.
2.1.1
Connecting Hardware
In this instruction, it will explain how to find a proper location for your Fieldbus
Gateways, and how to connect to the network, hock up the power cable, and connect to the EKI-1242 Series.
2.2
Verifying Fieldbus Gateway Operation
Before installing the device in a rack or on a wall, power on the fieldbus gateway to verify that the fieldbus gateway passes the power-on self-test (POST). To connect
the cabling to the power source see “Power Supply Installation” on page 25.
At startup (POST), the System LED blinks green, while the remaining LEDs are a solidy green. Once the fieldbus gateway passes POST self-test, the System LED turns green. The other LEDs turn off and return to their operating status. If the fieldbus gateway fails POST, the System LED fieldbus gateways to an amber state.
After a successful self-test, power down the fieldbus gateway and disconnect the power cabling.
The fieldbus gateway is now ready for installation on its final location.
17 EKI-1242 Series User Manual
2.3
Installing the Fieldbus Gateway
2.3.1
DIN Rail Mounting
The DIN rail mount option is the quickest installation option. Additionally, it optimizes the use of rail space.
The metal DIN rail kit is secured to the rear of the fieldbus gateway. The device can be mounted onto a standard 35 mm (1.37”) x 7.5 mm (0.3”) height DIN rail. The devices can be mounted vertically or horizontally. Refer to the following guidelines for further information.
Note!
A corrosion-free mounting rail is advisable.
When installing, make sure to allow for enough space to properly install the cabling.
2.3.1.1
Installing the DIN-Rail Mounting Kit
1.
Position the rear panel of the fieldbus gateway directly in front of the DIN rail, making sure that the top of the DIN rail clip hooks over the top of the DIN rail, as shown in the following illustration.
Warning!
Do not install the DIN rail under or in front of the spring mechanism on the DIN rail clip to prevent damage to the DIN rail clip or the DIN rail.
Make sure the DIN rail is inserted behind the spring mechanism.
2.
Once the DIN rail is seated correctly in the DIN rail clip, press the front of the fieldbus gateway to rotate the fieldbus gateway down and into the release tab on the DIN rail clip.
If seated correctly, the bottom of the DIN rail should be fully inserted in the release tab.
EKI-1242 Series User Manual
DIN rail clip
DIN rail
DIN rail clip release tab
Figure 2.1 Installing the DIN-Rail Mounting Kit
18
See the following figure for an illustration of a completed DIN installation procedure.
Figure 2.2 Correctly Installed DIN Rail Kit
3.
Grasp the bottom of the fieldbus gateway and slightly rotate it upwards. If there is resistance, the fieldbus gateway is correctly installed. Otherwise, re-attempt the installation process from the beginning.
2.3.1.2
Removing the DIN-Rail Mounting Kit
1.
Ensure that power is removed from the fieldbus gateway, and disconnect all cables and connectors from the front panel of the fieldbus gateway.
2.
Push down on the top of the DIN rail clip release tab with your finger. As the clip releases, lift the bottom of the fieldbus gateway, as shown in the following illustration.
\
Figure 2.3 Removing the DIN-Rail
19 EKI-1242 Series User Manual
2.3.2
Wall-Mounting
The wall mounting option provides better shock and vibration resistance than the DIN rail vertical mount.
Note!
When installing, make sure to allow for enough space to properly install the cabling.
Before the device can be mounted on a wall, you will need to remove the DIN rail plate.
1.
Rotate the device to the rear side and locate the DIN mounting plate.
2.
Remove the screws securing the DIN mounting plate to the rear panel of the fieldbus gateway.
3.
Remove the DIN mounting plate. Store the DIN mounting plate and provided screws for later use.
4.
Remove the screws securing on the top and bottom of the device.
5.
Align the wall mounting plates on the rear side. The screw holes on the device and the mounting plates must be aligned, see the following illustration.
6.
Secure the wall mount plates with the provided screws, see the following figure.
Figure 2.4 Installing Wall Mount Plates
EKI-1242 Series User Manual 20
Once the wall mounting plates are secure on the device, you will need to attach the wall screws (x4).
7.
Locate the installation site and place the fieldbus gateway against the wall, making sure it is the final installation location.
8.
Use the wall mount plates as a guide to mark the locations of the screw holes.
9.
Drill four holes over the four marked locations on the wall, keeping in mind that the holes must accommodate wall sinks in addition to the screws.
To mount the wall plate, use screws of the size shown in the following illustration.
8.0 mm
4.0 mm
Figure 2.5 Wall Mounting Screw Dimensions
Note!
Make sure you use the recommended screw length for your particular application. The screws need to penetrate properly for the rated weight rating.
10.
Align the wall mount plate over the screws on the wall.
11.
Install the wall mount plate on the screws and slide it forward to lock in place, see the following figure.
2
1
2
Figure 2.6 Wall Mount Installation
12.
Once the device is installed on the wall, tighten the screws to secure the device.
21 EKI-1242 Series User Manual
2.4
Connecting the Fieldbus Gateway to Ethernet
Ports
2.4.1
RJ45 Ethernet Cable Wiring
For RJ45 connectors, data-quality, twisted pair cabling (rated CAT5 or better) is recommended. The connector bodies on the RJ45 Ethernet ports are metallic and connected to the GND terminal. For best performance, use shielded cabling.
Shielded cabling may be used to provide further protection.
Straight-thru Cable Wiring
Pin 1
Pin 2
Pin 3
Pin 6
Pin 1
Pin 2
Pin 3
Pin 6
Cross-over Cable Wiring
Pin 1
Pin 2
Pin 3
Pin 6
Pin 3
Pin 6
Pin 1
Pin 2
8
1
Figure 2.7 Ethernet Plug & Connector Pin Position
Maximum cable length: 100 meters (328 ft.) for 10/100BaseT.
2.5
Serial Connection
EKI-1242 Series provides eight ports DB9 (male) connectors. RS-232/422/485 pin assignments as below:
5
9
1
6
Pin
RS-232
RS-422
RS-485
1
DCD
TX-
DATA-
2
RX
Figure 2.8 DB 9 Pin Position
3
TX
4
DTR
TX+
DATA+
5 6 7 8
GND DSR RTS CTS
GND RX+
GND
9
RI
RX-
EKI-1242 Series User Manual 22
2.6
MicroSD Card Installation
The EKI-1242 Series provides an easy way to backup, restore, and deploy configuration settings. The fieldbus gateway provides a microSD card slot to support simple means to manage system configuration settings.
Only microSD cards with the FAT32 or exFAT file systems are supported.
2.6.1
Installing a MicroSD Card
1.
Before continuing, make sure the file system on the microSD card is set to
FAT32 or exFAT. If necessary, format the microSD card and then continue with the procedure.
2.
Remove the screw securing the component cover.
Figure 2.9 Removing the Component Cover Screw
3.
Open the component cover.
Figure 2.10 Opening the Component Cover
4.
The microSD card has a beveled edge. Align the microSD card with the slot making sure the card is aligned with the groove. If there is any resistance, remove the card and re-align it to the slot.
5.
Insert the microSD card and press it in until an audible click sounds.
Figure 2.11 Installing the MicroSD Card
23 EKI-1242 Series User Manual
6.
Close the component cover.
Figure 2.12 Closing the Component Cover
7.
Secure the component cover with the provided screw.
Figure 2.13 Installing the Component Cover Screw
2.6.2
Utilizing a MicroSD Card
1.
The device includes a microSD port to provide easy functionality to backup and deployment operations. The following information describes the supported uses when a microSD card (FAT32 or exFAT) is installed in the device.
Further information see “Backup Manager” on page 53 and “Upgrade Manager”
2.
The following functions are available:
– Deployment management:
– Reset configuration to factory default and power off.
– Insert a microSD card with a valid configuration file.
– Power on the device.
– The device uses the valid configuration settings in the microSD card.
– Backup management:
– Device setting is not factory default.
–
Enable Automatically Backup, see “Backup Manager” on page 53.
– Power off the device and insert a microSD card.
– Power on the device. The device’s current configuration settings are saved to the microSD card.
2.6.2.1
MicroSD Support
In the event of possible function errors, see the following information:
1.
Check that the microSD card file system is FAT32 or exFAT.
2.
Check that the microSD card has at least 20 Mbytes of free space.
3.
Check that the microSD card is not write-protected.
4.
Check that the file system is not corrupted.
5.
Check that the microSD card is not damaged.
If any of the events occur, the fieldbus gateway halts operation and the status LED begins flashing.
EKI-1242 Series User Manual 24
2.7
Power Supply Installation
2.7.1
Overview
Warning!
Power down and disconnect the power cord before servicing or wiring the fieldbus gateway.
Caution!
Do not disconnect modules or cabling unless the power is first switched off.
The device only supports the voltage outlined in the type plate. Do not use any other power components except those specifically designated for the fieldbus gateway device.
Caution!
Disconnect the power cord before installation or cable wiring.
The fieldbus gateways can be powered by using the same DC source used to power other devices. A DC voltage range of 12 to 48 V
DC
must be applied between the V1+ terminal and the V1- terminal (PW1), see the following illustrations. The chassis ground screw terminal should be tied to the panel or chassis ground. A redundant power configuration is supported by a secondary power supply unit to reduce network downtime as a result of power loss.
EKI-1242 Series support 12 to 48 V
DC
. Dual power inputs are supported and allow you to connect a backup power source.
Single DC Power Redundant DC Power
P2 P1 P2 P1
One DC Supply
Chassis
GND
(pane)
Dual DC Supplies
Chassis
GND
(pane)
Figure 2.14 Power Wiring for EKI-1242 Series
25 EKI-1242 Series User Manual
2.7.2
Considerations
Take into consideration the following guidelines before wiring the device:
The Terminal Block (CN1) is suitable for 12-24 AWG (3.31 - 0.205 mm
2
). Torque value 7 lb-in.
The cross-sectional area of the earthing conductors shall be at least 3.31 mm
2
.
Calculate the maximum possible current for each power and common wire.
Make sure the power draw is within limits of local electrical code regulations.
For best practices, route wiring for power and devices on separate paths.
Do not bundle together wiring with similar electrical characteristics.
Make sure to separate input and output wiring.
Label all wiring and cabling to the various devices for more effective management and servicing.
Note!
Routing communications and power wiring through the same conduit may cause signal interference. To avoid interference and signal degradation, route power and communications wires through separate conduits.
2.7.3
Grounding the Device
Caution!
Do not disconnect modules or cabling unless the power is first switched off.
The device only supports the voltage outlined in the type plate. Do not use any other power components except those specifically designated for the fieldbus gateway device.
Caution!
Before connecting the device properly ground the device. Lack of a proper grounding setup may result in a safety risk and could be hazardous.
Caution!
Do not service equipment or cables during periods of lightning activity.
Caution!
Do not service any components unless qualified and authorized to do so.
Caution!
Do not block air ventilation holes.
EKI-1242 Series User Manual 26
Electromagnetic Interference (EMI) affects the transmission performance of a device.
By properly grounding the device to earth ground through a drain wire, you can set up the best possible noise immunity and emissions.
P-Fail
V1- V1+ V2- V2+
Drain Wire with Lug
DC12-48V PWR1 1A@24V PWR2
Connection to
Grounding Point
Figure 2.15 Grounding Connection
By connecting the ground terminal by drain wire to earth ground the fieldbus gateway and chassis can be ground.
Note!
Before applying power to the grounded fieldbus gateway, it is advisable to use a volt meter to ensure there is no voltage difference between the power supply’s negative output terminal and the grounding point on the fieldbus gateway.
2.7.4
Wiring a Relay Contact
The following section details the wiring of the relay output. The terminal block on the
EKI-1242 Series is wired and then installed onto the terminal receptor located on the
EKI-1242 Series.
PWR2 1A@24V PWR1 DC12-48V
V2- V2+
P-Fail
V1- V1+
Figure 2.16 Terminal Receptor: Relay Contact
PWR2 1A@24V PWR1 AC 24V
N2 L2 N1 L1
P-Fail
Figure 2.17 Terminal Receptor: Relay Contact (EKI-1242BNMS/EKI-1242IBNMS)
The terminal receptor includes a total of six pins: two for PWR1, two for PWR2 and two for a fault circuit.
27 EKI-1242 Series User Manual
2.7.5
Wiring the Power Inputs
Caution!
Do not disconnect modules or cabling unless the power is first switched off.
The device only supports the voltage outlined in the type plate. Do not use any other power components except those specifically designated for the fieldbus gateway device.
Warning!
Power down and disconnect the power cord before servicing or wiring the fieldbus gateway.
There are two power inputs for normal and redundant power configurations. The power input 2 is used for wiring a redundant power configuration. See the following for terminal block connector views.
PWR2 1A@24V PWR1 DC12-48V
V2- V2+
P-Fail
V1- V1+
Figure 2.18 Terminal Receptor: Power Input Contacts
PWR2 1A@24V PWR1 AC 24V
N2 L2 N1 L1
P-Fail
Figure 2.19 Terminal Receptor: Relay Contact (EKI-1242BNMS/EKI-1242IBNMS)
To wire the power inputs:
Make sure the power is not connected to the fieldbus gateway or the power converter before proceeding.
1.
Loosen the screws securing terminal block to the terminal block receptor.
2.
Remove the terminal block from the fieldbus gateway.
EKI-1242 Series User Manual
Figure 2.20 Removing a Terminal Block
28
3.
Insert a small flat-bladed screwdriver in the V1+/V1- wire-clamp screws, and loosen the screws.
4.
Insert the negative/positive DC wires into the V+/V- terminals of PW1. If setting up power redundancy, connect PW2 in the same manner.
5.
Tighten the wire-clamp screws to secure the DC wires in place.
Loosening
Wire-clamp
Screws
Securing
Wire-clamp
Screws
Installing DC
Wires
Figure 2.21 Installing DC Wires in a Terminal Block
6.
Align the terminal block over the terminal block receptor on the fieldbus gateway.
7.
Insert the terminal block and press it in until it is flush with the terminal block receptor.
8.
Tighten the screws on the terminal block to secure it to the terminal block receptor.
If there is no gap between the terminal block and the terminal receptor, the terminal block is seated correctly.
Figure 2.22 Securing a Terminal Block to a Receptor
2.8
Default Button
Reset configuration to factory default:
Press and hold the Default button for 5 seconds.
System reboot:
Press and hold the Default button for 2 seconds.
Note!
Do NOT power off the fieldbus gateway when loading default settings.
29 EKI-1242 Series User Manual
Chapter
3
Managing Fieldbus
Gateway
3
3.1
Log In
To access the login window, connect the device to the network, see “Connecting the
Fieldbus Gateway to Ethernet Ports” on page 22. Once the fieldbus gateway is
installed and connected, power on the fieldbus gateway see the following procedures to log into your fieldbus gateway.
When the fieldbus gateway is first installed, the default network configuration is set to
DHCP enabled. You will need to make sure your network environment supports the fieldbus gateway setup before connecting it to the network.
1.
Launch your web browser on a computer.
2.
In the browser’s address bar type in the fieldbus gateway’s default IP address
(192.168.1.1). The login screen displays.
3.
Enter the default user name and password (admin/admin) to log into the management interface. You can change the default password after you have successfully logged in.
4.
Click Login to enter the management interface.
Figure 3.1 Login Screen
3.1.1
Changing Default Password
In keeping with good management and security practices, it is recommended that you change the default password as soon as the device is functioning and setup correctly. The following details the necessary steps to change the default password.
To change the password:
1.
Navigate to System Management > Change Password .
2.
In the Password field, type in the new password. Re-type the same password in the Confirmation field.
3.
Click Apply to change the current settings.
Figure 3.2 Changing a Default Password
After saving all the desired settings, perform a system save ( System Management >
Apply Configuration ). The changes are saved.
31 EKI-1242 Series User Manual
3.2
Overview
3.2.1
Device Information
The Device Information menu lists information pertaining to the system, such as
Model, Firmware version, MAC Address, and more. The information is for review only. To modify the device information, see the respective item within the user interface.
The following figures represent multiple supported devices. Some interface screens may represent specific device models.
To access this page, click Overview > Device Information .
Figure 3.3 Overview > Device Information > System
The following table describes the items in the previous figure.
Item
Model
Firmware Version
Uptime
Description
Displays the model name of the device.
Displays the current firmware version of the device.
Displays the accumulated time for continuous operation.
Figure 3.4 Overview > Device Information > Modbus/TCP
Item
MAC Address
Mode
IP Address
Subnet Mask
Gateway
Description
Displays the MAC address of the device.
Displays the IP address setting mode of the device.
Displays the assigned IP address of the device.
Displays the assigned subnet mask of the device.
Displays the assigned gateway of the device.
EKI-1242 Series User Manual 32
Figure 3.5 Overview > Device Information > BACnet/IP | EtherNet/IP |
PROFINET | OPC UA
The following table describes the items in the previous figure.
Item
MAC Address
Mode
IP Address
Subnet Mask
Gateway
Description
Displays the MAC address of the device.
Displays the IP address setting mode of the device.
Displays the assigned IP address of the device.
Displays the assigned subnet mask of the device.
Displays the assigned gateway of the device.
3.2.2
Diagnose
To access this page, click Overview > Diagnose .
The following tables are only available for EKI-1242BNMS/EKI-1242IBNMS.
The ensuing table for Modbus table settings is for reference only: Transaction
Name, Connect Status, Read Counter, Write Counter, Connect Error Counter,
Read Error Counter and Write Error Counter.
The following tables are only available for EKI-1242ECMS/EKI-1242IECMS.
The ensuing table for EtherCAT table settings is for reference only: Current
State, Port A (Input) and Port B (Output).
The ensuing table for Modbus table settings is for reference only: Transaction
Name, Connect Status, Read Counter, Write Counter, Connect Error Counter,
Read Error Counter and Write Error Counter.
The following tables are only available for EKI-1242EIMS/EKI-1242IEIMS.
The ensuing table for EtherNet/IP Instance table settings is for reference only:
AA, O->T Instance(Exclusive Owner), Exclusive Owner Data Size, O->T
Instance(Input Only), Input Only Data Size, T->O Instance and T->O Instance
Data Size.
The ensuing table for EtherNet/IP Overview table settings is for reference only:
Class3 connections, Class1 connections, Total TCP Transmit Packets, Total
TCP Receive Packets, Total UDP Transmit Packets and Total UDP Receive
Packets.
The ensuing table for I/O Connection table settings is for reference only: UP
Time, Originator, Receive Address, O->T Packets, T->O Packets, O->T
Connection ID, O->T RPI (ms), T->O Connection ID and T->O RPI (ms).
33 EKI-1242 Series User Manual
The following tables are only available for EKI-1242PNMS/EKI-1242IPNMS.
The ensuing table for PROFINET table settings is for reference only: Connect
Status, Connect Counter, Connected PLC MAC Address, Connected PLC IP
Address, PLC Operation Mode, Device Name and Send Clock (ms).
The ensuing table for Modbus table settings is for reference only: Transaction
Name, Connect Status, Read Counter, Write Counter, Connect Error Counter,
Read Error Counter and Write Error Counter.
The following tables are only available for EKI-1242OUMS/EKI-1242IOUMS.
The ensuing table for OPC UA Connection List table settings is for reference only: Index, IP Address and TCP Port.
The ensuing table for Modbus table settings is for reference only: Transaction
Name, Connect Status, Read Counter, Write Counter, Connect Error Counter,
Read Error Counter and Write Error Counter.
3.2.3
Data View
I/O Data View function allows for the display of exchanged data for all I/O modules.
Select data flow directions to obtain the correct data of EtherNet/IP data for EKI-
1242EIMS/EKI-1242IEIMS, monitor EtherCAT input data for EKI-1242ECMS/EKI-
1242IECMS and Profinet slot data for EKI-1242PNMS/EKI-1242IPNMS.
To access this page, click Overview > Data View .
The following figure displays the menu as found in the EKI-1242BNMS/EKI-
1242IBNMS.
EKI-1242 Series User Manual
Figure 3.6 Overview > Data View
34
The following figure displays the menu as found in the EKI-1242ECMS/EKI-
1242IECMS.
Figure 3.7 Overview > Data View
The following table describes the items in the previous figure.
Item
Auto Refresh
Description
Check the option to automatically have the table refresh the information.
35 EKI-1242 Series User Manual
The following figure displays the menu as found in the EKI-1242EIMS/EKI-
1242IEIMS.
Figure 3.8 Overview > Data View
The following table describes the items in the previous figure.
Item
Auto Refresh
Description
Check the option to automatically have the table refresh the information.
EKI-1242 Series User Manual 36
The following figure displays the menu as found in the EKI-1242PNMS/EKI-
1242IPNMS.
Figure 3.9 Overview > Data View
37 EKI-1242 Series User Manual
The following figure displays the menu as found in the EKI-1242OUMS/EKI-
1242IOUMS.
Figure 3.10 Overview > Data View
The following table describes the items in the previous figure.
Item
Auto Refresh
Description
Check the option to automatically have the table refresh the information.
EKI-1242 Series User Manual 38
3.3
Network Setting
3.3.1
IP Setting
The IP Setting menu allows you to select a static or DHCP network configuration.
The Static displays the configurable settings for the static option.
To access this page, click Network Setting > IP Setting .
The following figure displays the menu as found in the EKI-1242BNMS/EKI-
1242IBNMS.
Figure 3.11 Network Setting > IP Setting
The following table describes the items in the previous figure.
Item Description
Modbus/TCP IP Address Setting
Mode Click the drop-down menu to select the IP address setting mode:
Static address, or DHCP client.
IP Address
Subnet Mask
Enter a value to specify the IP address of the interface. The default is
192.168.1.1.
Enter a value to specify the IP subnet mask for the interface. The default is 255.255.255.0.
Gateway
Modbus/TCP and
BACnet/IP interface use the same IP address setting
Enter a value to specify the default gateway for the interface. The default is 192.168.1.254.
Check the option to use same IP address setting on Modbus/TCP and
BACnet/IP interface. In this mode, the BACnet ports of Modbus/TCP and BACnet/IP are bridged, so the traffic can be forwarded between these interfaces.
Unchecked the option to use two different IP subnet on Modbus/TCP and BACnet/IP interface. In this mode, the BACnet ports of Modbus/
TCP and BACnet/IP are not bridged, so the traffic can't be forwarded between these interfaces.
39 EKI-1242 Series User Manual
Item Description
BACnet/IP IP Address Setting
Mode Click the drop-down menu to select the IP Address Setting mode:
Static address, or DHCP client.
IP Address
Subnet Mask
Enter a value to specify the IP address of the interface. The default is
192.168.1.1.
Enter a value to specify the IP subnet mask for the interface. The default is 255.255.255.0.
Gateway Enter a value to specify the default gateway for the interface. The default is 192.168.1.254.
The following figure displays the menu as found in the EKI-1242ECMS/EKI-
1242IECMS.
Figure 3.12 Network Setting > IP Setting
The following table describes the items in the previous figure.
Item
Mode
IP Address
Subnet Mask
Gateway
Description
Click the drop-down menu to select the IP address setting mode:
Static address, or DHCP client.
Enter a value to specify the IP address of the interface. The default is
192.168.1.1.
Enter a value to specify the IP subnet mask for the interface. The default is 255.255.255.0.
Enter a value to specify the default gateway for the interface. The default is 192.168.1.254.
EKI-1242 Series User Manual 40
The following figure displays the menu as found in the EKI-1242EIMS/EKI-
1242IEIMS.
Figure 3.13 Network Setting > IP Setting
The following table describes the items in the previous figure.
Item Description
Modbus/TCP IP Address Setting
Mode
IP Address
Click the drop-down menu to select the IP address setting mode:
Static address, or DHCP client.
Enter a value to specify the IP address of the interface. The default is
192.168.1.1.
Subnet Mask
Gateway
Enter a value to specify the IP subnet mask for the interface. The default is 255.255.255.0.
Enter a value to specify the default gateway for the interface. The default is 192.168.1.254.
Modbus/TCP and
EtherNet/IP interface use the same IP address setting
Check the option to use same IP address setting on Modbus/TCP and
EtherNet/IP interface. In this mode, the Ethernet ports of Modbus/TCP and EtherNet/IP are bridged, so the traffic can be forwarded between these interfaces.
Unchecked the option to use two different IP subnet on Modbus/TCP and EtherNet/IP interface. In this mode, the Ethernet ports of Modbus/
TCP and EtherNet/IP are not bridged, so the traffic can't be forwarded between these interfaces.
EtherNet/IP IP Address Setting
Mode Click the drop-down menu to select the IP Address Setting mode:
Static address, or DHCP client.
41 EKI-1242 Series User Manual
Item Description
IP Address
Subnet Mask
Gateway
Enter a value to specify the IP address of the interface. The default is
192.168.1.1.
Enter a value to specify the IP subnet mask for the interface. The default is 255.255.255.0.
Enter a value to specify the default gateway for the interface. The default is 192.168.1.254.
The following figure displays the menu as found in the EKI-1242PNMS/EKI-
1242IPNMS.
Figure 3.14 Network Setting > IP Setting
The following table describes the items in the previous figure.
Item Description
Modbus/TCP IP Address Setting
Mode Click the drop-down menu to select the IP address setting mode:
Static address, or DHCP client.
IP Address
Subnet Mask
Enter a value to specify the IP address of the interface. The default is
192.168.1.1.
Enter a value to specify the IP subnet mask for the interface. The default is 255.255.255.0.
Gateway Enter a value to specify the default gateway for the interface. The default is 192.168.1.254.
PROFINET
Mode
IP Address
Subnet Mask
Gateway
Displays the IP address setting mode of the device.
Enter a value to specify the IP address of the interface. The default is
0.0.0.0.
Enter a value to specify the IP subnet mask for the interface. The default is 0.0.0.0.
Enter a value to specify the default gateway for the interface. The default is 0.0.0.0.
EKI-1242 Series User Manual 42
The following figure displays the menu as found in the EKI-1242OUMS/EKI-
1242IOUMS.
Figure 3.15 Network Setting > IP Setting
The following table describes the items in the previous figure.
Item Description
Modbus/TCP IP Address Setting
Mode
IP Address
Click the drop-down menu to select the IP address setting mode:
Static address, or DHCP client.
Enter a value to specify the IP address of the interface. The default is
192.168.1.1.
Subnet Mask
Gateway
Modbus/TCP and
OPC UA interface use the same IP address setting
Check the option to use same IP address setting on Modbus/TCP and
OPC UA interface. In this mode, the Ethernet ports of Modbus/TCP and OPC UA are bridged, so the traffic can be forwarded between these interfaces.
Unchecked the option to use two different IP subnet on Modbus/TCP and OPC UA interface. In this mode, the Ethernet ports of Modbus/
TCP and OPC UA are not bridged, so the traffic can't be forwarded between these interfaces.
OPC UA IP Address Setting
Mode
IP Address
Enter a value to specify the IP subnet mask for the interface. The default is 255.255.255.0.
Enter a value to specify the default gateway for the interface. The default is 192.168.1.254.
Click the drop-down menu to select the IP Address Setting mode:
Static address, or DHCP client.
Enter a value to specify the IP address of the interface. The default is
192.168.1.1.
43 EKI-1242 Series User Manual
Item
Subnet Mask
Gateway
Description
Enter a value to specify the IP subnet mask for the interface. The default is 255.255.255.0.
Enter a value to specify the default gateway for the interface. The default is 192.168.1.254.
3.4
Serial Settings
3.4.1
Port
,
To access this page, click Serial Settings > Port 1/Port 2 .
The following figure displays the menu as found in the EKI-1242BNMS/EKI-
1242IBNMS port 2 (Modbus), EKI-1242ECMS/EKI-1242IECMS, EKI-1242EIMS/EKI-
1242IEIMS, EKI-1242PNMS/EKI-1242IPNMS and EKI-1242OUMS/EKI-
1242IOUMS.
Figure 3.16 Serial Settings > Port 1/Port 2
The following table describes the items in the previous figure.
Item
Type
Baud Rate
Parity
Data Bits
Stop Bits
Flow Control
Submit
Description
Click the drop-down menu to select a serial interface: RS232, RS422 or RS485.
Enter a value to specify the baud rate. The value should conform to the current transmission speeds of connected devices when setting the baud rate.
Click the drop-down menu to select the parity: None, Odd, Even, Mark or Space.
Click the drop-down menu to select the data bits: 5, 6, 7, or 8.
Click the drop-down menu to select the stop bits: 1, 1.5 or 2.
Click the drop-down menu to select the flow control mode: None,
XOn/XOff or RTS/CTS.
Click Submit to save the values and update the screen.
EKI-1242 Series User Manual 44
The following figure displays the menu as found in the EKI-1242BNMS/EKI-
1242IBNMS port 1 (BACnet).
Figure 3.17 Serial Settings > Port 1
The following table describes the items in the previous figure.
Item
Baud Rate
Submit
Description
Click the drop-down menu to specify the baud rate. The value should conform to the current transmission speeds of connected devices when setting the baud rate.
Click Submit to save the values and update the screen.
3.5
Protocol Setting
3.5.1
BACnet Setting
The BACnet Setting page is only available for EKI-1242BNMS/EKI-1242IBNMS.
To access this page, click Protocol Setting > BACnet Setting .
Figure 3.18 Protocol Setting > BACnet Setting
The following table describes the items in the previous figure.
Item Description
Device Status/
Control Word in AI[0]/
AO[0]
When enabled, Device Status/Control Word should be in BACnet object AI[0]/AO[0]. Default value is Disabled .
Enter the name of the BACnet device.
BACnet Device
Name
Device Identifier Enter the value to specify the device identifier.
Mode
Max. Masters
Click the drop-down menu to select the BACnet mode: IP or MSTP.
Available under MSTP mode. Enter the variable defining the maximum number of masters.
45 EKI-1242 Series User Manual
Item
Max Info Frames
MAC Address
Submit
Description
Available under MSTP mode. Enter the variable defining the Max Info
Frames setting. The Max Info Frames setting should be high enough to allow for the transmission of at least as many MS/TP frame packets as there are available MS/TP frame buffers.
Available under MSTP mode. Enter the MAC address of the identified devices connected to the serial bus.
Click Submit to save the values and update the screen.
3.5.2
EtherCAT Setting
The EtherCAT Setting page is only available for EKI-1242ECMS/EKI-1242IECMS.
To access this page, click Protocol Setting > EtherCAT Setting .
Figure 3.19 Protocol Setting > EtherCAT Setting
The following table describes the items in the previous figure.
Item
Device Status/
Control Word in I/O
Map
Exception Code in I/
O Map
Submit
Description
Select Enabled to dedicate the first two I/O mapped bytes for status/ control information (default: Disabled ).
Select Enabled to dedicate the last 64 bytes of data from the
EtherCAT network stream (default: Disabled ).
Click Submit to save the values and update the screen.
3.5.3
EtherNet/IP Setting
On the EtherNet/IP network, the gateway transmits mapped data to scanner through
I/O data. The first two I/O mapped bytes in either direction can be dedicated for status/control information, and another 64 bytes of data coming from the Modbus/
TCP network can feature the Modbus exception codes.
The EtherNet/IP Setting page is only available for EKI-1242EIMS/EKI-1242IEIMS.
To access this page, click Protocol Setting > EtherNet/IP Setting .
Figure 3.20 Protocol Setting > EtherNet/IP Setting
EKI-1242 Series User Manual 46
The following table describes the items in the previous figure.
Item
Device Status/
Control Word in I/O
Map
Exception Code in I/
O Map
Submit
Description
Select Enabled to dedicate the first two I/O mapped bytes for status/ control information (default: Enabled ).
Select Enabled to dedicate the last 64 bytes of data from the
EtherNet/IP network stream (default: Enabled ).
Click Submit to save the values and update the screen.
3.5.4
PROFINET Setting
On the PROFINET network, the gateway transmits mapped data to PROFINET I/O
Slot.
There are two types of slot mappings as defined in the following figure.
The PROFINET Setting page is only available for EKI-1242PNMS/EKI-1242IPNMS.
To access this page, click Protocol Setting > PROFINET Setting .
Figure 3.21 Protocol Setting > PROFINET Setting
The following table describes the items in the previous figure.
Item
Device Status/
Control Word in Slot
Exception Code in
Slot
Read Only
Community
Read / Write
Community
Submit
Description
When enabled, Device Status/Control Word should be in PROFINET slot 1. The Modbus exception codes should be in PROFINET I/O slot
2.
When disabled, the Modbus exception codes should be in PROFINET
I/O slot 1.
Default value is Disabled .
Enable to use the Modbus exception code setting, see Device Status/
Control Word in Slot in the previous definition.
Enter the value for the SNMP Read Only Community string
(default: public).
Enter the value for the SNMP Read/Write Community string
(default: private).
Click Submit to save the values and update the screen.
47 EKI-1242 Series User Manual
3.5.5
OPC UA Setting
The OPC UA Setting page is only available for EKI-1242OUMS/EKI-1242IOUMS.
On the OPC UA network, the gateway transmits mapped data to the UPC UA nodes.
To access this page, click Protocol Setting > OPC UA Setting .
Figure 3.22 Protocol Setting > OPC UA Setting
The following table describes the items in the previous figure.
Item
Anonymous
Certificate Login
TCP Port
Maximum session
Session timeout
Submit
Description
Select Enabled to decided authentication setting in the OPC UA server (default: Enabled ).
When enabled, the server allowed anonymous login.
When disabled, the server needs username and password, the username and password same as Web UI username and password.
Select Enabled to enable the certificate login of cliens.
Client side can be select as below:
Security Policy:
None
Basic128Rsa15
– Sign
– Sign & Encrypt
Basic256Sha256
– Sign
– Sign & Encrypt
Enter the value to specify the OPC UA server listen port (default:
4840).
Enter the value to specify the OPC UA server maximum sessions
(default: 128).
Enter the value to specify the each session timeout (default: 600 sec.)
Click Submit to save the values and update the screen.
EKI-1242 Series User Manual 48
3.5.6
Modbus Setting
To communicate with remote Modbus/TCP slave devices, specify the Modbus command for each slave device. Each slave device may need more than one command for communication, so it is necessary to add all the commands manually.
To access this page, click Protocol Setting > Modbus Setting .
Figure 3.23 Protocol Setting > Modbus Setting
The following table describes the items in the previous figure.
Item
Start-up Mode
When Modbus/TCP error
Description
Click the drop-down menu to select the slave device’s mode at startup: Running or Idle (default: Running ).
Click the drop-down menu to select the command to initiate in the event of an error: Freeze Data or Clear Data.
Select Freeze Data to continue delivering the data most recently received from the Modbus-TCP network to the EtherNet/IP scanner.
Select Clear Data to clear any input entered into the data area and transmit only zeros to the EtherNet/IP scanner.
Click Submit to save the values and update the screen.
Submit
The ensuing table for Modbus Commands table settings is for reference only:
Allocated input size, output size, Index, Name, Mode, Slave ID, FC, Address/
Quantity, Trigger, Scan Interval, Data Swap, Response Timeout, I/O Disconnect,
Safe Value, Add (click to add a new transaction), Edit (click to modify existing transactions), Delete (click to delete existing transactions), Copy (click to copy an existing transaction) and FlowCtrl Status.
49 EKI-1242 Series User Manual
To add a new transaction:
Figure 3.24 Protocol Setting > Modbus Setting > Add
The following table describes the items in the previous figure.
Item
Name
Mode
Slave IP Address
Port
Serial Port
Slave ID
Description
Enter the name to identify the transaction, max length: 32 characters.
Click the drop-down menu to select Modbus protocol mode: TCP or
RTU.
TCP: Modbus TCP communication over TCP/IP networking.
RTU: Modbus RTU communication via the serial port.
Enter the IP address of the Modbus/TCP server on Modbus/TCP mode.
Enter the TCP port number of the remote slave device (default
Modbus-TCP port is 502), value range: 0 - 65535.
BNMS models: port 1 is dedicated for BACnet, port 2 is dedicated for Modbus.
Non BNMS models: select the serial interface where the remote
Modbus/RTU device is located.
Enter the Modbus/TCP server slave ID.
EKI-1242 Series User Manual 50
Item Description
Function Code
Trigger
The master device delivers packets to the slave device containing instructions as defined in the function code fields. The following is a list of the supported function codes.
01: Read coils
02: Read discrete inputs
03: Read holding registers
04: Read input register
05: Write single coil
06: Write single register
15: Write multiple coils
16: Write multiple registers
23: Read/Write multiple registers (Not available for on
EKI-1242BNMS/EKI-1242IBNMS models)
Click the drop-down menu to select the trigger setting.
Cyclic: The trigger function is set to read/write in a cyclical instance once the specified interval is reached, see Poll Interval field.
Data change: Checks for any data changes at the specified interval as defined the Poll Interval field. When a given change in the data area is noted, a write command is delivered.
Poll Interval
Data Swap
The Poll Interval value defines the frequency with which the Modbus command is re-issued.
The Data Swap field determines the order in which the particular bytes of the received/transmitted data are delivered.
None: Do not swap
Word: 0x01, 0x02 becomes 0x02, 0x01
Double Word: 0x01, 0x02, 0x03, 0x04 becomes 0x04, 0x03,
0x02, 0x01
NOTE:
When function code is set to 1, 2, 5, or 15, the available option is
None.
When function code is set to 6, the available options are None and Word.
When function code is set to 3, 4, 16, or 23, the quantity must be designated as an even integer.
Designate the read from/write to starting address for the Modbus registry.
Read Starting
Address
Read Quantity
I/O Map
Designate the number of read cycles.
Select Enabled to enable I/O map function (default: Enabled ). The function is only available for EKI-1242OUMS/EKI-1242IOUMS.
Response Timeout Define the span of time, in milliseconds, within which the server is required to produce a response to the exchange.
In I/O mapped write transaction, when EtherNet/IP does not exchange
I/O:
Clear data to Modbus server: Transmits only zeros.
Freeze data to Modbus server: Repeat the last stored data.
Write safe value: The value to transmit for each element.
Stop: The transmission of any and all data to the Modbus server is halted.
Submit Click Submit to save the values and update the screen.
Back Click Back to return the previous page.
51 EKI-1242 Series User Manual
3.5.7
Mapping Overview
The Mapping Overview function allows the viewing of data between Modbus RTU/
TCP to PROFINET Slot, EtherNet/IP I/O, EtherCAT PDI/PDO, BACnet/IP or BACnet/
MSTP.
To access this page, click Protocol Setting > Mapping Overview .
The following tables are only available for EKI-1242BNMS/EKI-1242IBNMS.
The ensuing table for Transaction table settings is for reference only: Name,
Quantity, and Access.
The ensuing table for BACnet Object Mapping - AI table settings is for reference only: Object identifier, Device name, Address and Object name.
The ensuing table for BACnet Object Mapping - AO table settings is for reference only: Object identifier, Device name, Address and Object name.
The ensuing table for BACnet Object Mapping - BI table settings is for reference only: Object identifier, Device name, Address and Object name.
The ensuing table for BACnet Object Mapping - BO table settings is for reference only: Object identifier, Device name, Address and Object name.
The following tables are available for EKI-1242ECMS/EKI-1242IECMS only.
The ensuing table for Input Mapping Overview table settings is for reference only: Input Data Byte buffer view, Input Data Name, Input Data Function Code,
Input Data Size (Byte) and Input Data Byte range.
The ensuing table for Output Mapping Overview table settings is for reference only: Output Data Byte buffer view, Output Data Name, Output Data Function
Code, Output Data Size (Byte) and Output Data Byte range.
The ensuing table for Gateway table settings is for reference only: Status,
Control and Exceptions.
The ensuing table for Transaction table settings is for reference only: Name,
Index, Bytes and Access.
The following tables are only available for EKI-1242EIMS/EKI-1242IEIMS.
The ensuing table for Input Mapping Overview table settings is for reference only: Input Data Byte buffer view, Master Name, Master Function Code, Master
Size (Byte) and Master Byte range.
The ensuing table for Output Mapping Overview table settings is for reference only: Output Data Byte buffer view, Adapter Name, Adapter Function Code,
Adapter Size (Byte) and Adapter Byte range.
The ensuing table for Transaction table settings is for reference only: Name,
Quantity, Class, Instance, Attribute and Access.
The following tables are only available for EKI-1242PNMS/EKI-1242IPNMS.
The ensuing table for PROFINET I/O table settings is for reference only: Slot,
Transaction Name, In Slot Range(bytes), Input Word and Output Word.
The ensuing table for Modbus Client table settings is for reference only: Name,
FC, Data Swap, Scan Time, Response Timeout, UID, Read/Write Starting
Address, Quantity and When PROFINET doesn't exchange I/O.
The following tables are only available for EKI-1242OUMS/EKI-1242IOUMS.
The ensuing table for Transaction table settings is for reference only: Name,
Data Type, Class, Quantity, Identifier and Access.
EKI-1242 Series User Manual 52
3.6
System Management
3.6.1
Change Password
The Change Password function allows you to easily update your current password from a single menu.
To access this page, click System Management > Change Password .
Figure 3.25 System Management > Change Password
The following table describes the items in the previous figure.
Item
Password
Confirmation
Submit
Description
Enter the character set to define a password.
Retype the password entry to confirm the profile password.
Click Submit to save the values and update the screen.
If you want to disable the password protection, change the password to the default option None (leave the password column blank). Be sure apply and reboot the system ( System Management > Apply Configuration ) to save the updates.
3.6.2
Backup Manager
The Backup Manager page allows you to backup configuration settings from the device or restores a configuration file to the device.
To access this page, click System Management > Backup Manager .
Figure 3.26 System Management > Backup Manager > Backup Manager
The following table describes the items in the previous figure.
Item
Backup
To
Restore Backup
Upload Archive
From
Description
Click Backup to backup configuration from the device.
Click the radio button to select the backup file destination.
Click Browse to select the configuration file.
Click Upload Archive to restore configuration to the device.
Click the radio-button to select upload file source.
53 EKI-1242 Series User Manual
Figure 3.27 System Management > Backup Manager > SD Card Backup
The following table describes the items in the previous figure.
Item
Automatically
Backup
Submit
Description
Click the radio-button to enable or disable the SD card automatically backup function.
Click Submit to save the values and update the screen.
3.6.3
Upgrade Manager
The Upgrade Manager page allows you to upgrade firmware.
To access this page, click System Management > Upgrade Manager .
Figure 3.28 System Management > Upgrade Manager
The following table describes the items in the previous figure.
Item
Browse File
Upload Archive
Description
Click Browse to select the firmware file.
Click Upload Archive to upgrade the firmware.
3.6.4
Reset System
To access this page, click System Management > Reset System .
Click Reset to have all configuration parameters reset to their factory default values.
All changes that have been made will be lost, even if you have issued a save.
Reset settings take effect after a system reboot.
Figure 3.29 System Management > Reset System
3.6.5
Reboot Device
To access this page, click System Management > Reboot Device .
EKI-1242 Series User Manual 54
Click Reboot to reboot the fieldbus gateway. Any configuration changes you have made since the last time you issued a save will be lost.
Figure 3.30 System Management > Reboot Device
3.6.6
Apply Configuration
To access this page, click System Management > Apply Configuration .
Click Apply and Reboot to have configuration changes you have made to be saved across a system reboot. All changes submitted since the previous save or system reboot will be retained by the device.
Figure 3.31 System Management > Apply Configuration
55 EKI-1242 Series User Manual
3.7
Tools
3.7.1
Modbus Traffic Catcher
The Modbus Traffic Catcher page shows only data sent and received by Modbus.
To access this page, click Tools > Modbus Traffic Catcher .
Figure 3.32 Tools > Modbus Traffic Catcher
The following table describes the items in the previous figure.
Item
Start
Stop
Export
Auto Scroll
Description
Click Start to start capturing the data.
Click Stop to stop capturing the data.
Click Export to export and download the captured data.
Check the option to cycle through all of the data screens automatically while start capturing data.
EKI-1242 Series User Manual 56
www.advantech.com
Please verify specifications before quoting. This guide is intended for reference purposes only.
All product specifications are subject to change without notice.
No part of this publication may be reproduced in any form or by any means, electronic, photocopying, recording or otherwise, without prior written permission of the publisher.
All brand and product names are trademarks or registered trademarks of their respective companies.
© Advantech Co., Ltd. 2018
advertisement
* Your assessment is very important for improving the workof artificial intelligence, which forms the content of this project
Related manuals
advertisement
Table of contents
- 13 Specifications
- 14 Hardware Views
- 14 Front View
- 22 Rear View
- 23 Top View
- 24 Bottom View
- 24 Dimensions
- 28 Installation Guidelines
- 28 Connecting Hardware
- 28 Verifying Fieldbus Gateway Operation
- 29 Installing the Fieldbus Gateway
- 29 DIN Rail Mounting
- 31 Wall-Mounting
- 33 Connecting the Fieldbus Gateway to Ethernet Ports
- 33 RJ45 Ethernet Cable Wiring
- 33 Serial Connection
- 34 MicroSD Card Installation
- 34 Installing a MicroSD Card
- 35 Utilizing a MicroSD Card
- 36 Power Supply Installation
- 36 Overview
- 37 Considerations
- 37 Grounding the Device
- 38 Wiring a Relay Contact
- 39 Wiring the Power Inputs
- 40 Default Button
- 42 Log In
- 42 Changing Default Password
- 43 Overview
- 43 Device Information
- 44 Diagnose
- 45 Data View
- 50 Network Setting
- 50 IP Setting
- 55 Serial Settings
- 56 Protocol Setting
- 56 BACnet Setting
- 57 EtherCAT Setting
- 57 EtherNet/IP Setting
- 58 PROFINET Setting
- 59 OPC UA Setting
- 60 Modbus Setting
- 63 Mapping Overview
- 64 System Management
- 64 Change Password
- 64 Backup Manager
- 65 Upgrade Manager
- 65 Reset System
- 65 Reboot Device
- 66 Apply Configuration
- 67 Tools
- 67 Modbus Traffic Catcher