advertisement
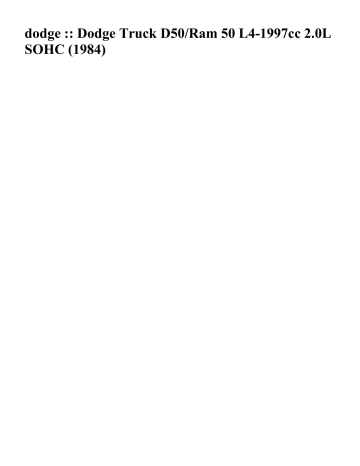
dodge :: Dodge Truck D50/Ram 50 L4-1997cc 2.0L
SOHC (1984)
> Relays and Modules > Relays and Modules - Lighting and Horns > Headlamp Relay > Component Information > Locations
Headlamp Relay: Locations
Left Side Front Fender Shield
Applicable to: 1981-84
> Relays and Modules > Relays and Modules - Powertrain Management > Relays and Modules - Computers and Control Systems > Powertrain Control Module <--> [Engine Control Module] > Component Information >
Locations
Powertrain Control Module: Locations
Under LH Side Of I/P
> Relays and Modules > Relays and Modules - Powertrain Management > Relays and Modules - Fuel Delivery and Air Induction > Throttle Control Vacuum Motor <--> [Engine Speed Governor Control Module] > Component
Information > Locations
Throttle Control Vacuum Motor: Locations
Under Center Of I/P
> Relays and Modules > Relays and Modules - Starting and Charging > Starter Relay > Component Information > Locations
Starter Relay: Locations
Inner Left Side Of Wheelwell
Applicable to: 1981-84
> Relays and Modules > Relays and Modules - Wiper and Washer Systems > Wiper Relay > Component Information > Locations
Wiper Relay: Locations
Left Side Of Fender Shield
Applicable to: 1981-84
> Sensors and Switches > Sensors and Switches - Cooling System > Engine - Coolant Temperature Sensor/Switch > Coolant Temperature Sensor/Switch (For Computer) > Component Information > Specifications
Coolant Temperature Sensor/Switch (For Computer): SpecificationsSwitch Torque
Switch Torque
Cooling Fan Switch 8-18 ft.lb
> Sensors and Switches > Sensors and Switches - Cruise Control > Clutch Switch, Cruise Control > Component Information > Locations
Clutch Switch: Locations
Under LH Side Of I/P
> Sensors and Switches > Sensors and Switches - Lighting and Horns > Brake Light Switch > Component Information > Service and Repair
Brake Light Switch: Service and Repair
Adjusting Stoplamp Switch Clearance
The stop light switch also serves as a brake pedal stopper and is located under the instrument panel, behind the brake pedal. Disconnect the wire, thenremove retaining nut from bracket and the switch. Reverse procedure to install. Ensure brake pedal height is correct, then adjust switch to obtain aclearance of .02 to .04 inch between switch housing and pedal stopper with pedal released.
> Sensors and Switches > Sensors and Switches - Lighting and Horns > Headlight Switch <--> [Headlamp Switch] > Component Information > Service and Repair
Headlight Switch: Service and Repair
On models equipped with dash mounted light switch, the switch is serviced with the instrument cluster. Refer to ``Instrument Cluster, Replace''procedure. On models equipped with turn signal mounted light switch, the switch is serviced with the turn signal/combination switch. Refer to ``VehicleLighting/Turn Signals/Turn Signal Switch/Service and Repair'' for procedure.
> Sensors and Switches > Sensors and Switches - Lighting and Horns > Turn Signal Switch > Component Information > Service and Repair
Turn Signal Switch: Service and Repair
1. Disconnect battery ground cable.2. Remove steering wheel using a suitable puller. Scribe alignment mark between steering wheel and shaft to ensure proper installation. On models with tilt steering columns, place column in lowest position during steering wheel removal.
3. Remove upper and lower steering column covers.4. Remove wiring harness retaining straps, if equipped, then disconnect electrical connectors.5. Remove column switch assembly.6. Reverse procedure to install, noting the following: a. Ensure column switch is properly aligned with steering shaft center.b. Attach switch wiring along column tube as close to center line as possible.c. Retain wiring using suitable retaining straps to prevent contact with other parts.
> Sensors and Switches > Sensors and Switches - Powertrain Management > Sensors and Switches - Computers and Control Systems > Coolant Temperature Sensor/Switch (For Computer) > Component Information >
Specifications
Coolant Temperature Sensor/Switch (For Computer): SpecificationsSwitch Torque
Switch Torque
Cooling Fan Switch 8-18 ft.lb
> Sensors and Switches > Sensors and Switches - Powertrain Management > Sensors and Switches - Ignition System > Ignition Switch > Component Information > Service and Repair
Ignition Switch: Service and Repair
The ignition switch is mounted in the rear of the steering column lock. When the key is turned to LOCK position and pulled out, the lock pinautomatically ejects from the cylinder and enters a groove in the steering shaft, locking the steering wheel. The heads of the bolts securing the steering lock assembly shear off when the bolts are tightened. Replacement of the steering lock assembly mayrequire that the steering column be removed, as these bolts must be cut or slotted to permit removal with a screwdriver. When the lock assembly isinstalled, new shear bolts must be used and the bolts should be tightened until the bolt heads twist off. However, the ignition switch can be serviced separately from the lock assembly using the following procedures.
1.
Disconnect battery ground cable, then remove upper and lower column covers.
2.
Remove bands securing switch harness and disconnect electrical connector.
Fig. 4 Ignition switch removal
3.
Loosen the bolt holding the switch and pull from lock assembly.
4.
Reverse procedure to install, first inserting key to check for proper operation.
> Sensors and Switches > Sensors and Switches - Starting and Charging > Clutch Switch > Component Information > Locations
Clutch Switch: Locations
Under LH Side Of I/P
> Sensors and Switches > Sensors and Switches - Starting and Charging > Ignition Switch > Component Information > Service and Repair
Ignition Switch: Service and Repair
The ignition switch is mounted in the rear of the steering column lock. When the key is turned to LOCK position and pulled out, the lock pinautomatically ejects from the cylinder and enters a groove in the steering shaft, locking the steering wheel. The heads of the bolts securing the steering lock assembly shear off when the bolts are tightened. Replacement of the steering lock assembly mayrequire that the steering column be removed, as these bolts must be cut or slotted to permit removal with a screwdriver. When the lock assembly isinstalled, new shear bolts must be used and the bolts should be tightened until the bolt heads twist off. However, the ignition switch can be serviced separately from the lock assembly using the following procedures.
1.
Disconnect battery ground cable, then remove upper and lower column covers.
2.
Remove bands securing switch harness and disconnect electrical connector.
Fig. 4 Ignition switch removal
3.
Loosen the bolt holding the switch and pull from lock assembly.
4.
Reverse procedure to install, first inserting key to check for proper operation.
> Sensors and Switches > Sensors and Switches - Starting and Charging > Neutral Safety Switch > Component Information > Service and Repair
Neutral Safety Switch: Service and Repair
1.
Loosen shift lever handle setscrew, then remove shift lever handle.
2.
Remove shift position indicator attaching screws, then the position indicator by lifting upward.
3.
Disconnect shift position indicator light from indicator assembly, then the neutral safety switch wiring.
4.
Loosen neutral safety switch adjustment screws, then remove attaching screws and switch.
5.
Reverse procedures to install, noting the following:
Fig. 8 Positioning selector lever for neutral safety switch installation. Ram Raider & 1984-86 Ram 50 a. Position selector lever as shown, install switch on selector lever bracket leaving screws loose, then connect suitable ohmmeter to switch terminals.
Fig. 9 Neutral safety switch clearance. Ram Raider & 1984-86 Ram 50 b. Move switch forward and backward through range of adjustment noting meter indication, and scribe alignment mark between switch and
are aligned, then tighten switch mounting screws.
> Maintenance > Alignment > System Information > Technical Service Bulletins > Alignment - Caster Adjustment Manual Revision
Alignment: Technical Service BulletinsAlignment - Caster Adjustment Manual Revision
Models
All Ram 50 Two & Four Wheel Drive Vehicles
Subject
Caster Adjustment - Service Manual Revision
Index
FRONT SUSPENSION
Date
03/18/85
No..
02-07-85
P-887C
Caster Adjustment
This bulletin is issued to supplement the service manual information regarding caster adjustment for Ram 50 pick-up trucks.
Caster
Two Wheel Drive
Four Wheel Drive
Specifications
2-1/2~ +/- 1~
2~ +/- 1~
NOTE:
POLICY:
CASTER DIFFERENCE BETWEEN LEFT HAND AND RIGHT HAND SIDES SHOULD NOT EXCEED 1/2~.
Information only
> Maintenance > Alignment > System Information > Technical Service Bulletins > Page 68
Alignment: Specifications
Caster Angle
4WD
+1 to +3 deg
Except 4WD
+1 1/2 to +3 1/2 deg
Desired Caster
Camber Angle
2 deg 2 1/2 deg
Front +1/2 to +1 1/2 deg +1/2 to +1 1/2 deg
1 deg
Desired Camber Angle Front ---
Rear 1 deg
---
Toe
Rear
Front .08-.35 in
Rear ---
---
.08 to .35 in
---
> Maintenance > Alignment > System Information > Service and Repair > Camber
Alignment: Service and RepairCamber
FRONT
WITH TWO WHEEL DRIVE
1. Using tool No. MB990805 to hold upper arm shaft to crossmember bolt in position, remove nut from engine compartment side and adjust the number of shims between upper arm shaft and crossmember.
2. The normal shim pack thickness is 0.16 inch. A change of 0.024 inch in thickness of the shim pack will provide a change of approximately 2/15 degree in camber adjustment.
WITH FOUR WHEEL DRIVE
Adjust number of shims between upper arm shaft and arm post of side frame. The normal shim package thickness is 0.12 inch. A change of 0.039 inchin thickness of shim pack will provide a change of approximately 13 minutes in camber adjustment. Camber adjusting shims are available inthicknesses of 0.039 and 0.079 inch.
REAR
Rear camber is pre-set during vehicle assembly and cannot be adjusted. If camber is not within specifications, check for worn or damaged suspensioncomponent, and damaged or deformed floor pan or body and repair as needed.
> Maintenance > Alignment > System Information > Service and Repair > Camber > Page 71
Alignment: Service and RepairCaster
Fig. 2 Caster adjustment. Ram Raider & 1984-86 Ram 50
Caster is adjusted by turning the upper control arm shaft as follows:1. Remove upper control arm.2. Rotate upper control arm shaft to alter caster setting. One half turn of the upper control arm shaft will cause the upper arm shaft to move approximately 0.049 inch forward or rearward, resulting in approximately 17 minute (17/60) change in caster setting.
3. Reinstall control arm and recheck caster.4. Repeat adjustment until caster is within specifications. Maximum variation between left and right sides should be less than 1/2.
> Maintenance > Alignment > System Information > Service and Repair > Camber > Page 72
Alignment: Service and RepairPreliminary Inspection
1. Road test vehicle noting any abnormal steering or handling characteristics.2. Ensure tires are the proper type, correctly inflated and that tires on each axle are the same size.3. Inspect ball joints, suspension arms, bushings and tie rods, and repair or replace any component that is damaged or excessively worn.4. Ensure wheel runout is not excessive, and that wheel bearings are properly adjusted.5. Jounce vehicle several times to settle suspension.6. Place vehicle on suitable alignment rack following manufacturer's instructions. On Ram 50 and Ram Raider models, remove hub cap and cotter pin
(2WD) or free wheeling hub (4WD), and attach alignment gauges to wheel hub.
7. Check and correct alignment angles in the following sequence: Rear toe and camber, caster, front camber and front toe.8. Correct any angle that is not within specifications. If no adjustment is possible, check for damaged or worn suspension components and/or damaged or distorted chassis and correct as needed.
> Maintenance > Alignment > System Information > Service and Repair > Camber > Page 73
Alignment: Service and RepairToe Adjustment
FRONT
On Colt models, remove outer bellows clip from tie rod before adjusting toe. After completing adjustment, reinstall clamp.The amount of toe-in of the left front wheel is reduced by turning the tie rod turnbuckle toward the front of the car and the amount of toe-in on theright front wheel is reduced by turning it toward the rear of the the car. After adjustment, the difference in length between the two tie rods should notexceed 0.2 inch (5 mm).
REAR
Rear toe is pre-set during vehicle assembly and cannot be adjusted. If toe is not within specifications, check for worn or damaged suspensioncomponents, and damaged or deformed floor pan or body and repair as needed.
> Maintenance > Tune-up and Engine Performance Checks > Fuel Pressure > System Information > Specifications
> Maintenance > Tune-up and Engine Performance Checks > Air/Fuel Mixture > System Information > Technical Service Bulletins > By Symptom for Air/Fuel Mixture: > 140884 > Jan > 84 > Propane Idle Set - Procedure
Air/Fuel Mixture: By SymptomPropane Idle Set - Procedure
Models
1984 MMC Import Vehicles All With Gasoline Fueled Engines, All Emission Markets (Except Vehicles With Turbo Chargers & Canada)
Subject
Propane Idle Set Procedure
Index
FUEL
Date
January 17, 1984
No..
14-08-84
P-94-C
The propane idle set procedure is authorized for 1984 subject model import vehicles.
The propane idle set method is to be used when "CO" meter procedure cannot be used, i.e., "CO" meter in for repair or is not available in the servicearea.
PROPANE IDLE CHECK & SET PROCEDURE
1.
Idle Setting Conditions: Lights, electric cooling fan, and all accessories are off, transmission in neutral, and front wheels in straight ahead position.
2.
If engine is cold, allow it to warm up until full operating temperature is reached (185 to 205~F).
NOTE:
PERFORM THE FOLLOWING STEPS 3 THROUGH 5 AND STEP 19 ONLY IF ENGINE IS EQUIPPED WITH A FEEDBACKCARBURETOR EMISSION SYSTEM.
3.
Turn off ignition switch.
4.
Disconnect the NEGATIVE cable from the battery for about 5 seconds. Then reconnect negative battery cable.
5.
Disconnect the connector of the exhaust oxygen sensor.
6.
Start and run engine for 5 seconds at an engine speed between 2,000 to 3,000 rpm.
7.
Then, allow engine to run at curb idle for 2 minutes.
> Maintenance > Tune-up and Engine Performance Checks > Air/Fuel Mixture > System Information > Technical Service Bulletins > By Symptom for Air/Fuel Mixture: >
140884 > Jan > 84 > Propane Idle Set - Procedure > Page 86
D50/Ram 50 L4-1997cc 2.0L SOHC (1984)
FIGURE 1
8.
Check engine idle speed and basic ignition timing. Adjust to specifications if necessary (Figure 1).
9.
Disconnect the air cleaner fresh air intake duct from the air cleaner snorkel.
Insert the propane supply hose into the air cleaner snorkel about 4 inches.
Make certain both valves on propane bottle are fully closed and the bottle is upright and in a safe location.
> Maintenance > Tune-up and Engine Performance Checks > Air/Fuel Mixture > System Information > Technical Service Bulletins > By Symptom for Air/Fuel Mixture: >
140884 > Jan > 84 > Propane Idle Set - Procedure > Page 87
D50/Ram 50 L4-1997cc 2.0L SOHC (1984)
FIGURE 3
10.
Open the propane bottle main valve fully, then slowly open the propane fine control valve to the position where maximum engine rpm is achieved.(Too much propane or too rich idle mixture will cause the engine to lose rpm as the fine control valve is opened.) (Figure 3.)
FIGURE 2
> Maintenance > Tune-up and Engine Performance Checks > Air/Fuel Mixture > System Information > Technical Service Bulletins > By Symptom for Air/Fuel Mixture: >
140884 > Jan > 84 > Propane Idle Set - Procedure > Page 88
D50/Ram 50 L4-1997cc 2.0L SOHC (1984)
Note the engine rpm increase. Specified values of each engine propane idle speed increase are outlined in Figure 2.
If the propane idle speed exceeds more than 25 rpm from the specified value in Figure 2 or the rpm does not increase at all, idle fuel mixtureshould be adjusted according to the propane assisted idle set procedure that follows.
FIGURE 4
11.
It is not necessary to remove carburetor from intake manifold to remove the idle mixture screw plug.
Drill out concealment plug on car. Remove vacuum connector from high altitude compensator (HAC) fittings on carburetor air horn (Figure 4).
Use a 1/4" diameter drill 8' long at the 11 o'clock position on the plug boss. Locate drill point 3/16" from end of boss.
Plug should pop out when the drill bit contacts it (Figure 4).
12.
Start engine and run for 1 minute at engine speed of 2500 rpm.
13.
Run engine at idle for 2 minutes.
> Maintenance > Tune-up and Engine Performance Checks > Air/Fuel Mixture > System Information > Technical Service Bulletins > By Symptom for Air/Fuel Mixture: >
140884 > Jan > 84 > Propane Idle Set - Procedure > Page 89
D50/Ram 50 L4-1997cc 2.0L SOHC (1984)
FIGURE 2
14.
Open the propane main valve and slowly open the fine control valve to the position where maximum engine speed is achieved. Use the idle speedadjusting screw to set the specified propane idle speed from Figure 2.
15.
Turn off propane main valve and adjust idle mixture screw to the specified idle set speed from Figure 2.
16.
17.
To recheck the maximum propane speed, open the main propane valve again. If the speed still differs more than 25 rpm from the specified propanespeed from Figure 2, repeat Steps 14 through 16.
18.
Remove the propane hose and replace fresh air duct on air cleaner snorkel.
19.
Reconnect the exhaust oxygen sensor (if engine is equipped with a feedback carburetor).
20.
Install Idle Mixture Screw Concealment Plug. (If new plug is needed, use PN MD606954.)
POLICY: Reimbursable within the provisions of the warranty
> Maintenance > Tune-up and Engine Performance Checks > Air/Fuel Mixture > System Information > Technical Service Bulletins > By Symptom for Air/Fuel Mixture: >
140884 > Jan > 84 > Propane Idle Set - Procedure > Page 90
D50/Ram 50 L4-1997cc 2.0L SOHC (1984)
FRONT WHEEL DRIVE LABOR OPERATION TIME SCHEDULE
FAILURE CODE: RO - Driveability
> Maintenance > Tune-up and Engine Performance Checks > Air/Fuel Mixture > System Information > Technical Service Bulletins > All Technical Service Bulletins for Air/Fuel Mixture: > 140884 > Jan > 84 > Propane Idle Set
- Procedure
Air/Fuel Mixture: All Technical Service BulletinsPropane Idle Set - Procedure
Models
1984 MMC Import Vehicles All With Gasoline Fueled Engines, All Emission Markets (Except Vehicles With Turbo Chargers & Canada)
Subject
Propane Idle Set Procedure
Index
FUEL
Date
January 17, 1984
No..
14-08-84
P-94-C
The propane idle set procedure is authorized for 1984 subject model import vehicles.
The propane idle set method is to be used when "CO" meter procedure cannot be used, i.e., "CO" meter in for repair or is not available in the servicearea.
PROPANE IDLE CHECK & SET PROCEDURE
1.
Idle Setting Conditions: Lights, electric cooling fan, and all accessories are off, transmission in neutral, and front wheels in straight ahead position.
2.
If engine is cold, allow it to warm up until full operating temperature is reached (185 to 205~F).
NOTE:
PERFORM THE FOLLOWING STEPS 3 THROUGH 5 AND STEP 19 ONLY IF ENGINE IS EQUIPPED WITH A FEEDBACKCARBURETOR EMISSION SYSTEM.
3.
Turn off ignition switch.
4.
Disconnect the NEGATIVE cable from the battery for about 5 seconds. Then reconnect negative battery cable.
5.
Disconnect the connector of the exhaust oxygen sensor.
6.
Start and run engine for 5 seconds at an engine speed between 2,000 to 3,000 rpm.
7.
Then, allow engine to run at curb idle for 2 minutes.
> Maintenance > Tune-up and Engine Performance Checks > Air/Fuel Mixture > System Information > Technical Service Bulletins > All Technical Service Bulletins for Air/
Fuel Mixture: > 140884 > Jan > 84 > Propane Idle Set - Procedure > Page 96
D50/Ram 50 L4-1997cc 2.0L SOHC (1984)
FIGURE 1
8.
Check engine idle speed and basic ignition timing. Adjust to specifications if necessary (Figure 1).
9.
Disconnect the air cleaner fresh air intake duct from the air cleaner snorkel.
Insert the propane supply hose into the air cleaner snorkel about 4 inches.
Make certain both valves on propane bottle are fully closed and the bottle is upright and in a safe location.
> Maintenance > Tune-up and Engine Performance Checks > Air/Fuel Mixture > System Information > Technical Service Bulletins > All Technical Service Bulletins for Air/
Fuel Mixture: > 140884 > Jan > 84 > Propane Idle Set - Procedure > Page 97
D50/Ram 50 L4-1997cc 2.0L SOHC (1984)
FIGURE 3
10.
Open the propane bottle main valve fully, then slowly open the propane fine control valve to the position where maximum engine rpm is achieved.(Too much propane or too rich idle mixture will cause the engine to lose rpm as the fine control valve is opened.) (Figure 3.)
FIGURE 2
> Maintenance > Tune-up and Engine Performance Checks > Air/Fuel Mixture > System Information > Technical Service Bulletins > All Technical Service Bulletins for Air/
Fuel Mixture: > 140884 > Jan > 84 > Propane Idle Set - Procedure > Page 98
D50/Ram 50 L4-1997cc 2.0L SOHC (1984)
Note the engine rpm increase. Specified values of each engine propane idle speed increase are outlined in Figure 2.
If the propane idle speed exceeds more than 25 rpm from the specified value in Figure 2 or the rpm does not increase at all, idle fuel mixtureshould be adjusted according to the propane assisted idle set procedure that follows.
FIGURE 4
11.
It is not necessary to remove carburetor from intake manifold to remove the idle mixture screw plug.
Drill out concealment plug on car. Remove vacuum connector from high altitude compensator (HAC) fittings on carburetor air horn (Figure 4).
Use a 1/4" diameter drill 8' long at the 11 o'clock position on the plug boss. Locate drill point 3/16" from end of boss.
Plug should pop out when the drill bit contacts it (Figure 4).
12.
Start engine and run for 1 minute at engine speed of 2500 rpm.
13.
Run engine at idle for 2 minutes.
> Maintenance > Tune-up and Engine Performance Checks > Air/Fuel Mixture > System Information > Technical Service Bulletins > All Technical Service Bulletins for Air/
Fuel Mixture: > 140884 > Jan > 84 > Propane Idle Set - Procedure > Page 99
D50/Ram 50 L4-1997cc 2.0L SOHC (1984)
FIGURE 2
14.
Open the propane main valve and slowly open the fine control valve to the position where maximum engine speed is achieved. Use the idle speedadjusting screw to set the specified propane idle speed from Figure 2.
15.
Turn off propane main valve and adjust idle mixture screw to the specified idle set speed from Figure 2.
16.
17.
To recheck the maximum propane speed, open the main propane valve again. If the speed still differs more than 25 rpm from the specified propanespeed from Figure 2, repeat Steps 14 through 16.
18.
Remove the propane hose and replace fresh air duct on air cleaner snorkel.
19.
Reconnect the exhaust oxygen sensor (if engine is equipped with a feedback carburetor).
20.
Install Idle Mixture Screw Concealment Plug. (If new plug is needed, use PN MD606954.)
POLICY: Reimbursable within the provisions of the warranty
> Maintenance > Tune-up and Engine Performance Checks > Air/Fuel Mixture > System Information > Technical Service Bulletins > All Technical Service Bulletins for Air/
Fuel Mixture: > 140884 > Jan > 84 > Propane Idle Set - Procedure > Page 100
D50/Ram 50 L4-1997cc 2.0L SOHC (1984)
FRONT WHEEL DRIVE LABOR OPERATION TIME SCHEDULE
FAILURE CODE: RO - Driveability
> Maintenance > Tune-up and Engine Performance Checks > Idle Speed > System Information > Technical Service Bulletins > By Symptom: > 140884 > Jan > 84 > Propane Idle Set - Procedure
Idle Speed: By SymptomPropane Idle Set - Procedure
Models
1984 MMC Import Vehicles All With Gasoline Fueled Engines, All Emission Markets (Except Vehicles With Turbo Chargers & Canada)
Subject
Propane Idle Set Procedure
Index
FUEL
Date
January 17, 1984
No..
14-08-84
P-94-C
The propane idle set procedure is authorized for 1984 subject model import vehicles.
The propane idle set method is to be used when "CO" meter procedure cannot be used, i.e., "CO" meter in for repair or is not available in the servicearea.
PROPANE IDLE CHECK & SET PROCEDURE
1.
Idle Setting Conditions: Lights, electric cooling fan, and all accessories are off, transmission in neutral, and front wheels in straight ahead position.
2.
If engine is cold, allow it to warm up until full operating temperature is reached (185 to 205~F).
NOTE:
PERFORM THE FOLLOWING STEPS 3 THROUGH 5 AND STEP 19 ONLY IF ENGINE IS EQUIPPED WITH A FEEDBACKCARBURETOR EMISSION SYSTEM.
3.
Turn off ignition switch.
4.
Disconnect the NEGATIVE cable from the battery for about 5 seconds. Then reconnect negative battery cable.
5.
Disconnect the connector of the exhaust oxygen sensor.
6.
Start and run engine for 5 seconds at an engine speed between 2,000 to 3,000 rpm.
7.
Then, allow engine to run at curb idle for 2 minutes.
> Maintenance > Tune-up and Engine Performance Checks > Idle Speed > System Information > Technical Service Bulletins > By Symptom: > 140884 > Jan > 84 > Propane
Idle Set - Procedure > Page 109
D50/Ram 50 L4-1997cc 2.0L SOHC (1984)
FIGURE 1
8.
Check engine idle speed and basic ignition timing. Adjust to specifications if necessary (Figure 1).
9.
Disconnect the air cleaner fresh air intake duct from the air cleaner snorkel.
Insert the propane supply hose into the air cleaner snorkel about 4 inches.
Make certain both valves on propane bottle are fully closed and the bottle is upright and in a safe location.
> Maintenance > Tune-up and Engine Performance Checks > Idle Speed > System Information > Technical Service Bulletins > By Symptom: > 140884 > Jan > 84 > Propane
Idle Set - Procedure > Page 110
D50/Ram 50 L4-1997cc 2.0L SOHC (1984)
FIGURE 3
10.
Open the propane bottle main valve fully, then slowly open the propane fine control valve to the position where maximum engine rpm is achieved.(Too much propane or too rich idle mixture will cause the engine to lose rpm as the fine control valve is opened.) (Figure 3.)
FIGURE 2
> Maintenance > Tune-up and Engine Performance Checks > Idle Speed > System Information > Technical Service Bulletins > By Symptom: > 140884 > Jan > 84 > Propane
Idle Set - Procedure > Page 111
D50/Ram 50 L4-1997cc 2.0L SOHC (1984)
Note the engine rpm increase. Specified values of each engine propane idle speed increase are outlined in Figure 2.
If the propane idle speed exceeds more than 25 rpm from the specified value in Figure 2 or the rpm does not increase at all, idle fuel mixtureshould be adjusted according to the propane assisted idle set procedure that follows.
FIGURE 4
11.
It is not necessary to remove carburetor from intake manifold to remove the idle mixture screw plug.
Drill out concealment plug on car. Remove vacuum connector from high altitude compensator (HAC) fittings on carburetor air horn (Figure 4).
Use a 1/4" diameter drill 8' long at the 11 o'clock position on the plug boss. Locate drill point 3/16" from end of boss.
Plug should pop out when the drill bit contacts it (Figure 4).
12.
Start engine and run for 1 minute at engine speed of 2500 rpm.
13.
Run engine at idle for 2 minutes.
> Maintenance > Tune-up and Engine Performance Checks > Idle Speed > System Information > Technical Service Bulletins > By Symptom: > 140884 > Jan > 84 > Propane
Idle Set - Procedure > Page 112
D50/Ram 50 L4-1997cc 2.0L SOHC (1984)
FIGURE 2
14.
Open the propane main valve and slowly open the fine control valve to the position where maximum engine speed is achieved. Use the idle speedadjusting screw to set the specified propane idle speed from Figure 2.
15.
Turn off propane main valve and adjust idle mixture screw to the specified idle set speed from Figure 2.
16.
17.
To recheck the maximum propane speed, open the main propane valve again. If the speed still differs more than 25 rpm from the specified propanespeed from Figure 2, repeat Steps 14 through 16.
18.
Remove the propane hose and replace fresh air duct on air cleaner snorkel.
19.
Reconnect the exhaust oxygen sensor (if engine is equipped with a feedback carburetor).
20.
Install Idle Mixture Screw Concealment Plug. (If new plug is needed, use PN MD606954.)
POLICY: Reimbursable within the provisions of the warranty
> Maintenance > Tune-up and Engine Performance Checks > Idle Speed > System Information > Technical Service Bulletins > By Symptom: > 140884 > Jan > 84 > Propane
Idle Set - Procedure > Page 113
D50/Ram 50 L4-1997cc 2.0L SOHC (1984)
FRONT WHEEL DRIVE LABOR OPERATION TIME SCHEDULE
FAILURE CODE: RO - Driveability
> Maintenance > Tune-up and Engine Performance Checks > Idle Speed > System Information > Technical Service Bulletins > All Technical Service Bulletins for Idle Speed: > 142084 > May > 84 > Engine Specifications -
Manual Corrections
Idle Speed: All Technical Service BulletinsEngine Specifications - Manual Corrections
Models
1984 Colt, Ram 50, & Conquest
Subject
Correction of 1984 Service Manuals on Engine Specifications
Index
FUEL
Date
May 21, 1984
No..
14-20-84
P-2112-C
This service bulletin is issued to correct the following 1984 Import Service Manuals.
^ Colt Service Manual Publication #81-270-4006
> Maintenance > Tune-up and Engine Performance Checks > Idle Speed > System Information > Technical Service Bulletins > All Technical Service Bulletins for Idle Speed:
> 142084 > May > 84 > Engine Specifications - Manual Corrections > Page 119
D50/Ram 50 L4-1997cc 2.0L SOHC (1984)
^ Ram-50 Service Manual Publication #81-370-4009
^ Conquest Service Manual Publication #81-270-4005
Corrections are highlighted in the attached specifications in bold type and should be entered in the respective model service manual.
POLICY: Information only
> Maintenance > Tune-up and Engine Performance Checks > Idle Speed > System Information > Technical Service Bulletins > All Technical Service Bulletins for Idle Speed: > 141984 > May > 84 > Carburetor - Idle Speed
Adjustment on A/C Install
Idle Speed: All Technical Service BulletinsCarburetor - Idle Speed Adjustment on A/C Install
Models
1984 Colt (W/O Turbo), Ram-50, Power Ram-50 (W/O Diesel) & Colt Vista
Subject
Idle-Up Speed Adjustment After Air Conditioning Installation and/or Service
Index
FUEL
Date
May 7, 1984
No.
14-19-84
P-1927-CThis procedure modifies the adjustment procedures in the subject model service manuals.
If difficulty is encountered in adjusting curb idle speed and/or idle-up speed after installation or servicing and adjustment of the air conditioning system,follow the adjustment procedure as outlined below:
ADJUSTMENT PROCEDURE
1.
Thoroughly warm up engine, turn off all accessories, front wheels in straight ahead position, transmission in neutral, parking brake set, andradiator cooling fan stopped.
FIGURE 1
> Maintenance > Tune-up and Engine Performance Checks > Idle Speed > System Information > Technical Service Bulletins > All Technical Service Bulletins for Idle Speed:
> 141984 > May > 84 > Carburetor - Idle Speed Adjustment on A/C Install > Page 124
D50/Ram 50 L4-1997cc 2.0L SOHC (1984)
FIGURE 2
2.
Check and adjust curb idle speed if necessary (see Figure 1 for specification) and make adjustment using SAS (speed adjusting screw) 1 (Figure2). On some models installation of air conditioner will change the curb idle speed already adjusted.
FIGURE 2
3.
Back off the idle-up speed adjusting screw for air conditioner one turn from fully tightened position (Figure 2).
4.
Lift the free lever by hand until it touches SAS 3 and record the engine speed ("N" = R.P.M.) obtained at this time (Figure 2).
> Maintenance > Tune-up and Engine Performance Checks > Idle Speed > System Information > Technical Service Bulletins > All Technical Service Bulletins for Idle Speed:
> 141984 > May > 84 > Carburetor - Idle Speed Adjustment on A/C Install > Page 125
D50/Ram 50 L4-1997cc 2.0L SOHC (1984)
FIGURE 1
FIGURE 2
5.. Turn on air conditioner switch. Adjust the idle-up speed while compressor is running to the specified rpm (Figure 1) by turning SAS 2 (Figure 2).When making this adjustment, be sure to record the turning direction and slot angle of SAS 2.
FIGURE 1
6.
Turn off air conditioner switch and make sure that the specified curb idle rpm is obtained (Figure 1).
7.
Race the engine at a speed of about 2000 rpm for five seconds.
8.
Turn on and then off the air conditioning switch repeatedly several times and make sure that with the compressor running that the engine is running
> Maintenance > Tune-up and Engine Performance Checks > Idle Speed > System Information > Technical Service Bulletins > All Technical Service Bulletins for Idle Speed:
> 141984 > May > 84 > Carburetor - Idle Speed Adjustment on A/C Install > Page 126
D50/Ram 50 L4-1997cc 2.0L SOHC (1984)
at the specified idle-up rpm (Figure 1).
Example:
FIGURE 2
If Sas 2 has been turned 180~ clockwise in Step 5, SAS 3 will be turned 360~ clockwise in Step 9. Then, lift thefree lever by hand until it touches SAS 3 and make sure that the engine rpm is "N" +/- 100 rpm (where "N" is therpm recorded in Step 4). If necessary, adjust using SAS 3.
FIGURE 2
SIMPLE ADJUSTMENT PROCEDURE FOR COLT VISTA ONLY
If the idle adjustment has been properly made before installation of the air conditioner, the following simple procedure may be used:
1.
Give one clockwise turn to SAS 2 (Figure 2).
2.
Give two clockwise turns to SAS 3 (Figure 2).
3.
Back off idle-up speed adjusting screw for air conditioner one turn from fully tightened position (Figure 2).
> Maintenance > Tune-up and Engine Performance Checks > Idle Speed > System Information > Technical Service Bulletins > All Technical Service Bulletins for Idle Speed:
> 141984 > May > 84 > Carburetor - Idle Speed Adjustment on A/C Install > Page 127
D50/Ram 50 L4-1997cc 2.0L SOHC (1984)
FIGURE 1
4.
Lastly, make sure that the curb idle speed and idle-up speed are properly adjusted (Figure 1).
FIGURE 2
If necessary, make fine adjustments with SAS 2 and SAS 3 (Figure 2).
POLICY: Reimbursable within the provisions of the warranty
FAILURE CODE: 31 - Rough Idle
> Maintenance > Tune-up and Engine Performance Checks > Idle Speed > System Information > Technical Service Bulletins > All Technical Service Bulletins for Idle Speed: > 140884 > Jan > 84 > Propane Idle Set - Procedure
Idle Speed: All Technical Service BulletinsPropane Idle Set - Procedure
Models
1984 MMC Import Vehicles All With Gasoline Fueled Engines, All Emission Markets (Except Vehicles With Turbo Chargers & Canada)
Subject
Propane Idle Set Procedure
Index
FUEL
Date
January 17, 1984
No..
14-08-84
P-94-C
The propane idle set procedure is authorized for 1984 subject model import vehicles.
The propane idle set method is to be used when "CO" meter procedure cannot be used, i.e., "CO" meter in for repair or is not available in the servicearea.
PROPANE IDLE CHECK & SET PROCEDURE
1.
Idle Setting Conditions: Lights, electric cooling fan, and all accessories are off, transmission in neutral, and front wheels in straight ahead position.
2.
If engine is cold, allow it to warm up until full operating temperature is reached (185 to 205~F).
NOTE:
PERFORM THE FOLLOWING STEPS 3 THROUGH 5 AND STEP 19 ONLY IF ENGINE IS EQUIPPED WITH A FEEDBACKCARBURETOR EMISSION SYSTEM.
3.
Turn off ignition switch.
4.
Disconnect the NEGATIVE cable from the battery for about 5 seconds. Then reconnect negative battery cable.
5.
Disconnect the connector of the exhaust oxygen sensor.
6.
Start and run engine for 5 seconds at an engine speed between 2,000 to 3,000 rpm.
7.
Then, allow engine to run at curb idle for 2 minutes.
> Maintenance > Tune-up and Engine Performance Checks > Idle Speed > System Information > Technical Service Bulletins > All Technical Service Bulletins for Idle Speed:
> 140884 > Jan > 84 > Propane Idle Set - Procedure > Page 132
D50/Ram 50 L4-1997cc 2.0L SOHC (1984)
FIGURE 1
8.
Check engine idle speed and basic ignition timing. Adjust to specifications if necessary (Figure 1).
9.
Disconnect the air cleaner fresh air intake duct from the air cleaner snorkel.
Insert the propane supply hose into the air cleaner snorkel about 4 inches.
Make certain both valves on propane bottle are fully closed and the bottle is upright and in a safe location.
> Maintenance > Tune-up and Engine Performance Checks > Idle Speed > System Information > Technical Service Bulletins > All Technical Service Bulletins for Idle Speed:
> 140884 > Jan > 84 > Propane Idle Set - Procedure > Page 133
D50/Ram 50 L4-1997cc 2.0L SOHC (1984)
FIGURE 3
10.
Open the propane bottle main valve fully, then slowly open the propane fine control valve to the position where maximum engine rpm is achieved.(Too much propane or too rich idle mixture will cause the engine to lose rpm as the fine control valve is opened.) (Figure 3.)
FIGURE 2
> Maintenance > Tune-up and Engine Performance Checks > Idle Speed > System Information > Technical Service Bulletins > All Technical Service Bulletins for Idle Speed:
> 140884 > Jan > 84 > Propane Idle Set - Procedure > Page 134
D50/Ram 50 L4-1997cc 2.0L SOHC (1984)
Note the engine rpm increase. Specified values of each engine propane idle speed increase are outlined in Figure 2.
If the propane idle speed exceeds more than 25 rpm from the specified value in Figure 2 or the rpm does not increase at all, idle fuel mixtureshould be adjusted according to the propane assisted idle set procedure that follows.
FIGURE 4
11.
It is not necessary to remove carburetor from intake manifold to remove the idle mixture screw plug.
Drill out concealment plug on car. Remove vacuum connector from high altitude compensator (HAC) fittings on carburetor air horn (Figure 4).
Use a 1/4" diameter drill 8' long at the 11 o'clock position on the plug boss. Locate drill point 3/16" from end of boss.
Plug should pop out when the drill bit contacts it (Figure 4).
12.
Start engine and run for 1 minute at engine speed of 2500 rpm.
13.
Run engine at idle for 2 minutes.
> Maintenance > Tune-up and Engine Performance Checks > Idle Speed > System Information > Technical Service Bulletins > All Technical Service Bulletins for Idle Speed:
> 140884 > Jan > 84 > Propane Idle Set - Procedure > Page 135
D50/Ram 50 L4-1997cc 2.0L SOHC (1984)
FIGURE 2
14.
Open the propane main valve and slowly open the fine control valve to the position where maximum engine speed is achieved. Use the idle speedadjusting screw to set the specified propane idle speed from Figure 2.
15.
Turn off propane main valve and adjust idle mixture screw to the specified idle set speed from Figure 2.
16.
17.
To recheck the maximum propane speed, open the main propane valve again. If the speed still differs more than 25 rpm from the specified propanespeed from Figure 2, repeat Steps 14 through 16.
18.
Remove the propane hose and replace fresh air duct on air cleaner snorkel.
19.
Reconnect the exhaust oxygen sensor (if engine is equipped with a feedback carburetor).
20.
Install Idle Mixture Screw Concealment Plug. (If new plug is needed, use PN MD606954.)
POLICY: Reimbursable within the provisions of the warranty
> Maintenance > Tune-up and Engine Performance Checks > Idle Speed > System Information > Technical Service Bulletins > All Technical Service Bulletins for Idle Speed:
> 140884 > Jan > 84 > Propane Idle Set - Procedure > Page 136
D50/Ram 50 L4-1997cc 2.0L SOHC (1984)
FRONT WHEEL DRIVE LABOR OPERATION TIME SCHEDULE
FAILURE CODE: RO - Driveability
> Maintenance > Tune-up and Engine Performance Checks > Idle Speed > System Information > Technical Service Bulletins > All Other Service Bulletins for Idle Speed: > 142084 > May > 84 > Engine Specifications - Manual
Corrections
Idle Speed: All Technical Service BulletinsEngine Specifications - Manual Corrections
Models
1984 Colt, Ram 50, & Conquest
Subject
Correction of 1984 Service Manuals on Engine Specifications
Index
FUEL
Date
May 21, 1984
No..
14-20-84
P-2112-C
This service bulletin is issued to correct the following 1984 Import Service Manuals.
^ Colt Service Manual Publication #81-270-4006
> Maintenance > Tune-up and Engine Performance Checks > Idle Speed > System Information > Technical Service Bulletins > All Other Service Bulletins for Idle Speed: >
142084 > May > 84 > Engine Specifications - Manual Corrections > Page 142
D50/Ram 50 L4-1997cc 2.0L SOHC (1984)
^ Ram-50 Service Manual Publication #81-370-4009
^ Conquest Service Manual Publication #81-270-4005
Corrections are highlighted in the attached specifications in bold type and should be entered in the respective model service manual.
POLICY: Information only
> Maintenance > Tune-up and Engine Performance Checks > Idle Speed > System Information > Technical Service Bulletins > All Other Service Bulletins for Idle Speed: > 141984 > May > 84 > Carburetor - Idle Speed
Adjustment on A/C Install
Idle Speed: All Technical Service BulletinsCarburetor - Idle Speed Adjustment on A/C Install
Models
1984 Colt (W/O Turbo), Ram-50, Power Ram-50 (W/O Diesel) & Colt Vista
Subject
Idle-Up Speed Adjustment After Air Conditioning Installation and/or Service
Index
FUEL
Date
May 7, 1984
No.
14-19-84
P-1927-CThis procedure modifies the adjustment procedures in the subject model service manuals.
If difficulty is encountered in adjusting curb idle speed and/or idle-up speed after installation or servicing and adjustment of the air conditioning system,follow the adjustment procedure as outlined below:
ADJUSTMENT PROCEDURE
1.
Thoroughly warm up engine, turn off all accessories, front wheels in straight ahead position, transmission in neutral, parking brake set, andradiator cooling fan stopped.
FIGURE 1
> Maintenance > Tune-up and Engine Performance Checks > Idle Speed > System Information > Technical Service Bulletins > All Other Service Bulletins for Idle Speed: >
141984 > May > 84 > Carburetor - Idle Speed Adjustment on A/C Install > Page 147
D50/Ram 50 L4-1997cc 2.0L SOHC (1984)
FIGURE 2
2.
Check and adjust curb idle speed if necessary (see Figure 1 for specification) and make adjustment using SAS (speed adjusting screw) 1 (Figure2). On some models installation of air conditioner will change the curb idle speed already adjusted.
FIGURE 2
3.
Back off the idle-up speed adjusting screw for air conditioner one turn from fully tightened position (Figure 2).
4.
Lift the free lever by hand until it touches SAS 3 and record the engine speed ("N" = R.P.M.) obtained at this time (Figure 2).
> Maintenance > Tune-up and Engine Performance Checks > Idle Speed > System Information > Technical Service Bulletins > All Other Service Bulletins for Idle Speed: >
141984 > May > 84 > Carburetor - Idle Speed Adjustment on A/C Install > Page 148
D50/Ram 50 L4-1997cc 2.0L SOHC (1984)
FIGURE 1
FIGURE 2
5.. Turn on air conditioner switch. Adjust the idle-up speed while compressor is running to the specified rpm (Figure 1) by turning SAS 2 (Figure 2).When making this adjustment, be sure to record the turning direction and slot angle of SAS 2.
FIGURE 1
6.
Turn off air conditioner switch and make sure that the specified curb idle rpm is obtained (Figure 1).
7.
Race the engine at a speed of about 2000 rpm for five seconds.
8.
Turn on and then off the air conditioning switch repeatedly several times and make sure that with the compressor running that the engine is running
> Maintenance > Tune-up and Engine Performance Checks > Idle Speed > System Information > Technical Service Bulletins > All Other Service Bulletins for Idle Speed: >
141984 > May > 84 > Carburetor - Idle Speed Adjustment on A/C Install > Page 149
D50/Ram 50 L4-1997cc 2.0L SOHC (1984)
at the specified idle-up rpm (Figure 1).
Example:
FIGURE 2
If Sas 2 has been turned 180~ clockwise in Step 5, SAS 3 will be turned 360~ clockwise in Step 9. Then, lift thefree lever by hand until it touches SAS 3 and make sure that the engine rpm is "N" +/- 100 rpm (where "N" is therpm recorded in Step 4). If necessary, adjust using SAS 3.
FIGURE 2
SIMPLE ADJUSTMENT PROCEDURE FOR COLT VISTA ONLY
If the idle adjustment has been properly made before installation of the air conditioner, the following simple procedure may be used:
1.
Give one clockwise turn to SAS 2 (Figure 2).
2.
Give two clockwise turns to SAS 3 (Figure 2).
3.
Back off idle-up speed adjusting screw for air conditioner one turn from fully tightened position (Figure 2).
> Maintenance > Tune-up and Engine Performance Checks > Idle Speed > System Information > Technical Service Bulletins > All Other Service Bulletins for Idle Speed: >
141984 > May > 84 > Carburetor - Idle Speed Adjustment on A/C Install > Page 150
D50/Ram 50 L4-1997cc 2.0L SOHC (1984)
FIGURE 1
4.
Lastly, make sure that the curb idle speed and idle-up speed are properly adjusted (Figure 1).
FIGURE 2
If necessary, make fine adjustments with SAS 2 and SAS 3 (Figure 2).
POLICY: Reimbursable within the provisions of the warranty
FAILURE CODE: 31 - Rough Idle
> Maintenance > Tune-up and Engine Performance Checks > Idle Speed > System Information > Technical Service Bulletins > Page 151
> Maintenance > Tune-up and Engine Performance Checks > Firing Order > Component Information > Specifications
FIRING ORDER 2.0L RWD & 2.6L
> Maintenance > Tune-up and Engine Performance Checks > Ignition Timing > Timing Marks and Indicators > System Information > Diagrams
Timing Marks and Indicators: Diagrams
TIMING MARK 1.6L RWD, 2.6L & 2.0L EX. VISTA
> Maintenance > Tune-up and Engine Performance Checks > Ignition Timing > Timing Marks and Indicators > System Information > Diagrams > Page 159
D50/Ram 50 L4-1997cc 2.0L SOHC (1984)
TIMING MARK 1981-85 5.2L & 5.9L
> Maintenance > Tune-up and Engine Performance Checks > Distributor, Ignition > Vacuum Advance Unit <--> [Distributor Advance Unit] > Component Information > Specifications > Electrical Specifications
Vacuum Advance Unit: Electrical Specifications
> Maintenance > Tune-up and Engine Performance Checks > Distributor, Ignition > Vacuum Advance Unit <--> [Distributor Advance Unit] > Component Information > Specifications > Electrical Specifications > Page 165
> Maintenance > Tune-up and Engine Performance Checks > Spark Plug > Component Information > Technical Service Bulletins > Customer Interest for Spark Plug: > 181788 > Oct > 88 > Spark Plugs - Oil Fouling/Misfire on
Hard Acceleration
Spark Plug: Customer InterestSpark Plugs - Oil Fouling/Misfire on Hard Acceleration
Models
1978-1989 MMC Engines With Jet Valves
Subject
Oil Fouled Spark Plug(s) Miss & Bucking Under Hard Acceleration
Index
FUEL
Date
October 17, 1988
No.
18-17-88
C18-21)This bulletin updates Technical Service Bulletin 5/14/88 and serves as a reminder that driveability problems may be caused by mechanical problems aswell as fuel system problems.
FIGURE 1
SYMPTOM/CONDITION
One or more (seldom occurs to more than one cylinder) spark plugs will be oil fouled and may show ground and center electrode erosion due tooverheating (Figure 1).
Under hard acceleration (wide open throttle) engine will miss and buck.
> Maintenance > Tune-up and Engine Performance Checks > Spark Plug > Component Information > Technical Service Bulletins > Customer Interest for Spark Plug: >
181788 > Oct > 88 > Spark Plugs - Oil Fouling/Misfire on Hard Acceleration > Page 174
D50/Ram 50 L4-1997cc 2.0L SOHC (1984)
FIGURE 2
This condition may result from a jet valve failure. The jet valve failure is characterized by one of the causes outlined below (refer to Figure 2 fordescription):
^ Oil leaking past the oil seal and valve stem.
^ Oil leaking past the valve body and oil seal.
^ Oil leaking past the O-ring seal between the valve body and cylinder head which may be caused by a torn or cut Oring.
FIGURE 1
DIAGNOSIS
Remove and inspect all spark plugs. If a spark plug is found to be heavily oil fouled and/or appears to have the electrodes eroded or overheated, proceedto jet valve removal procedure below (Figure 1).PARTS REQUIRED
Jet Valve Assembly (as required)
O-Ring (as required)
INSTALLATION PROCEDURE
PN MD009440
PN MD009786
1.
Remove only the jet valve of the cylinder showing the spark plug oiling or overheating. Follow the jet valve removal procedures outlined in therespective model year service manual using Miller Special Tool #MB-998310.
> Maintenance > Tune-up and Engine Performance Checks > Spark Plug > Component Information > Technical Service Bulletins > Customer Interest for Spark Plug: >
181788 > Oct > 88 > Spark Plugs - Oil Fouling/Misfire on Hard Acceleration > Page 175
D50/Ram 50 L4-1997cc 2.0L SOHC (1984)
FIGURE 2
2.
Push jet valve open and inspect the valve stem just under the valve head. If oil residue and excessive carbon buildup are present, the Jet ValveAssembly, PN MD009440, will have to be replaced (Figure 2).
If no residue or carbon buildup is present, inspect the O-ring for rips, tears, or deformity. O-ring can be replaced separately with PN MD009786.
FIGURE 3
3.
Inspect jet piece pocket by looking down into jet piece. If pocket has any buildup of burnt oil residue or carbon, it must be cleaned completelyusing the following procedure (Figure 3).
a.
Remove spark plug.
b.
Place piston on top dead center of compression stroke (both valves closed).
Use a thin stiff bristle brush to clean jet piece (a distributor cap terminal brush works well). A thin metal rod (coat hanger) can be used toloosen heavy deposits.
d.
Direct compressed air in jet piece. The loosened deposits will be blown out of the jet piece and spark plug hole. Eye protection isrecommended when performing this operation.
e.
Reinspect cleaned jet piece. If cracking or erosion is seen in the area of the jet air orifice (Figure 3) or the deposit cannot be cleanedadequately, the cylinder head will require replacement.
> Maintenance > Tune-up and Engine Performance Checks > Spark Plug > Component Information > Technical Service Bulletins > Customer Interest for Spark Plug: >
181788 > Oct > 88 > Spark Plugs - Oil Fouling/Misfire on Hard Acceleration > Page 176
D50/Ram 50 L4-1997cc 2.0L SOHC (1984)
4.
Install new spark plug of proper heat range and gap setting.
5.
Start engine and allow to fully warm up. Check for oil leaks and adjust idle speed if necessary.
POLICY: Information only
> Maintenance > Tune-up and Engine Performance Checks > Spark Plug > Component Information > Technical Service Bulletins > All Technical Service Bulletins for Spark Plug: > 181788 > Oct > 88 > Spark Plugs - Oil
Fouling/Misfire on Hard Acceleration
Spark Plug: All Technical Service BulletinsSpark Plugs - Oil Fouling/Misfire on Hard Acceleration
Models
1978-1989 MMC Engines With Jet Valves
Subject
Oil Fouled Spark Plug(s) Miss & Bucking Under Hard Acceleration
Index
FUEL
Date
October 17, 1988
No.
18-17-88
C18-21)This bulletin updates Technical Service Bulletin 5/14/88 and serves as a reminder that driveability problems may be caused by mechanical problems aswell as fuel system problems.
FIGURE 1
SYMPTOM/CONDITION
One or more (seldom occurs to more than one cylinder) spark plugs will be oil fouled and may show ground and center electrode erosion due tooverheating (Figure 1).
Under hard acceleration (wide open throttle) engine will miss and buck.
> Maintenance > Tune-up and Engine Performance Checks > Spark Plug > Component Information > Technical Service Bulletins > All Technical Service Bulletins for Spark
Plug: > 181788 > Oct > 88 > Spark Plugs - Oil Fouling/Misfire on Hard Acceleration > Page 182
D50/Ram 50 L4-1997cc 2.0L SOHC (1984)
FIGURE 2
This condition may result from a jet valve failure. The jet valve failure is characterized by one of the causes outlined below (refer to Figure 2 fordescription):
^ Oil leaking past the oil seal and valve stem.
^ Oil leaking past the valve body and oil seal.
^ Oil leaking past the O-ring seal between the valve body and cylinder head which may be caused by a torn or cut Oring.
FIGURE 1
DIAGNOSIS
Remove and inspect all spark plugs. If a spark plug is found to be heavily oil fouled and/or appears to have the electrodes eroded or overheated, proceedto jet valve removal procedure below (Figure 1).PARTS REQUIRED
Jet Valve Assembly (as required)
O-Ring (as required)
INSTALLATION PROCEDURE
PN MD009440
PN MD009786
1.
Remove only the jet valve of the cylinder showing the spark plug oiling or overheating. Follow the jet valve removal procedures outlined in therespective model year service manual using Miller Special Tool #MB-998310.
> Maintenance > Tune-up and Engine Performance Checks > Spark Plug > Component Information > Technical Service Bulletins > All Technical Service Bulletins for Spark
Plug: > 181788 > Oct > 88 > Spark Plugs - Oil Fouling/Misfire on Hard Acceleration > Page 183
D50/Ram 50 L4-1997cc 2.0L SOHC (1984)
FIGURE 2
2.
Push jet valve open and inspect the valve stem just under the valve head. If oil residue and excessive carbon buildup are present, the Jet ValveAssembly, PN MD009440, will have to be replaced (Figure 2).
If no residue or carbon buildup is present, inspect the O-ring for rips, tears, or deformity. O-ring can be replaced separately with PN MD009786.
FIGURE 3
3.
Inspect jet piece pocket by looking down into jet piece. If pocket has any buildup of burnt oil residue or carbon, it must be cleaned completelyusing the following procedure (Figure 3).
a.
Remove spark plug.
b.
Place piston on top dead center of compression stroke (both valves closed).
Use a thin stiff bristle brush to clean jet piece (a distributor cap terminal brush works well). A thin metal rod (coat hanger) can be used toloosen heavy deposits.
d.
Direct compressed air in jet piece. The loosened deposits will be blown out of the jet piece and spark plug hole. Eye protection isrecommended when performing this operation.
e.
Reinspect cleaned jet piece. If cracking or erosion is seen in the area of the jet air orifice (Figure 3) or the deposit cannot be cleanedadequately, the cylinder head will require replacement.
> Maintenance > Tune-up and Engine Performance Checks > Spark Plug > Component Information > Technical Service Bulletins > All Technical Service Bulletins for Spark
Plug: > 181788 > Oct > 88 > Spark Plugs - Oil Fouling/Misfire on Hard Acceleration > Page 184
D50/Ram 50 L4-1997cc 2.0L SOHC (1984)
4.
Install new spark plug of proper heat range and gap setting.
5.
Start engine and allow to fully warm up. Check for oil leaks and adjust idle speed if necessary.
POLICY: Information only
> Maintenance > Tune-up and Engine Performance Checks > Spark Plug > Component Information > Technical Service Bulletins > Page 185
> Maintenance > Tune-up and Engine Performance Checks > Compression Check > System Information > Specifications
Compression Check: Specifications
Pressure 170 psi
> Maintenance > Tune-up and Engine Performance Checks > Valve Clearance > System Information > Specifications
Valve Clearance: Specifications
Except Jet Valve Intake 0.006 in
1985-89 2.0L & 2.6L except jet valve have hydraulic lifters.
Jet Valve
Exhaust 0.01 in
Intake 0.006 in
> Maintenance > Tune-up and Engine Performance Checks > Valve Clearance > System Information > Specifications > Page 192
Valve Clearance: Adjustments
INTAKE & EXHAUST VALVES
Fig. 12 Adjusting valve clearance (Typical)
The jet valve must be adjusted before adjusting the intake valve.
1. With engine at operating temperature, remove rocker arm cover.2. Disconnect high tension lead from ignition coil.3. While observing rocker arms on No. 4 cylinder, rotate crankshaft until the exhaust valve is closing and the intake valve has just started to open
Fig. 12.
with crankshaft pulley mark aligned with TDC mark on timing chain case. At this position the No. 1 cylinder is at top dead center compressionstroke. Check and adjust valve clearance for both intake and exhaust valves of No. 1 cylinder, intake valve of No. 2 cylinder and exhaust valve ofNo. 3 cylinder, as necessary,
4. Rotate crankshaft 360 degrees and check and adjust valve clearance for exhaust valve of No. 2 cylinder, intake valve of No. 3 cylinder and intake and exhaust valves of No. 4 cylinder.
5. After completing adjustment, install rocker arm cover and connect ignition coil high tension lead.
JET VALVE
Fig. 13 Adjusting jet valve clearance
Exc. Models Equipped W/Hydraulic Lash Adjusters
Fig. 13.
Following procedure for intake and exhaust valve adjustment, position No. 1 cylinder at top dead center compression stroke. Loosen intake valveadjusting screw at least 2 turns, then loosen jet valve adjusting screw locknut. Rotate jet valve adjusting screw counterclockwise and insert a suitablefeeler gauge blade as specified in ``Valve Specification Chart,'' between jet valve stem and adjusting screw, Tighten jet valve adjusting screwuntil it contacts the feeler gauge blade, then while holding adjusting screw in position, tighten locknut. After jet valve adjustment has been completed,adjust intake valve clearance. Continue to follow intake and exhaust valve adjustment procedure and adjust jet valves as necessary.
> Maintenance > Timing Belt > Component Information > Adjustments
Timing Belt: Adjustments
1. Remove timing belt front upper cover.2. Carefully check the timing belt on its whole circumference for cracks and peeling.3. Turn crankshaft in normal direction (clockwise) until timing mark on camshaft sprocket is aligned with mating mark on cylinder head, so that piston in No. 1 cylinder is placed at top dead center on compression stroke.
CAUTION:
Do not turn crankshaft in opposite direction (counterclockwise) to align the timing mark with mating mark, otherwise an improper timing belt tension could result.
Timing Marks
4. Turn crankshaft in normal direction (clockwise) until second tooth past timing mark (punch) position on camshaft sprocket should be aligned with timing mark on cylinder head.
Access Cover Location
Removing Access Cover
5. Remove two access covers. Access cover can be easily removed by inserting screwdriver into groove from direction of embossed arrow and pry.6. Insert wrench through adjusting hole and loosen timing belt tensioner tightening bolt and nut.
CAUTION: 180 to 200 Loosen bolt and nut . If they are loosened more than necessary, they might fall into cover.
7. Insert plain screwdriver from top of timing belt cover. Slightly push tensioner bracket in tensioning direction, and then release. Now belt tension
> Maintenance > Timing Belt > Component Information > Adjustments > Page 196
D50/Ram 50 L4-1997cc 2.0L SOHC (1984)
will be automatically adjusted by tensile strength of tensioner spring.
CAUTION:
The purpose of pushing tensioner with screwdriver is to loosen tensioner mounting surface which might have stuck due to manyhours of being tightened
8. First tighten tensioner mounting bolt (bottom side) with wrench and then tighten mounting nut (top side).
CAUTION: Make sure that bolt (bottom side) is tightened first. If nut is tightened first, belt tension will vary (will become too tight).
Mounting Access Cover
9. Mount two access covers to respective adjusting holes. Access cover can be easily mounted by sliding in such a way that hook will pass between guide projections.
10. Install timing belt front upper cover.
> Maintenance > Timing Belt > Component Information > Adjustments > Page 197
Timing Belt: Service and Repair
Timing Belt Train
REMOVAL
Remove the parts in numerical order shown, paying attention to the following items.1. Place piston of No. 1 cylinder at top dead center of compression stroke.
> Maintenance > Timing Belt > Component Information > Adjustments > Page 198
D50/Ram 50 L4-1997cc 2.0L SOHC (1984)
Securing Tensioner Temporarily
2. Move tensioner fully toward water pump and temporarily secure it.3. If timing belt is to be reused, make an arrow mark which indicates turning direction to ensure that belt is reinstalled in same direction as before.
Preventing Rotation Of Left Silent Shaft
4. When oil pump sprocket nut is removed, first remove plug at left side of cylinder block and insert a screwdriver to keep left silent shaft in position.
8 mm (.3 in.) 60 mm (2.36 in) Screwdriver used for this purpose should have a shaft thick which can be inserted more than .
Removing Timing Belt B
5. Loosen right silent shaft sprocket mounting bolt unit it can be loosened by hand.6. Next, remove tensioner "B" and remove timing belt "B".
CAUTION: After timing belt "B" has been removed, do not attempt loosening bolt, while holding sprocket with pliers, etc.
INSPECTION
1. Check belt in detail if following flaws are evident, replace belt with a new one.
Checking Timing Belt a. Hardened back surface rubber back surface glossy. Nonelastic and so hard that even if a finger nail is forced into it, no mark is produced.
> Maintenance > Timing Belt > Component Information > Adjustments > Page 199
D50/Ram 50 L4-1997cc 2.0L SOHC (1984)
Checking Timing Belt b. Cracked back surface rubberc. Cracked or exfoliated canvasd. Cracked tooth bottome. Side of belt crackedf.
g. Side of belt badly worn
NOTE: Normal belt should have clear-cut sides as if cut with a sharp knife.
h. Badly worn teeth
Initial stage: Canvas on load side tooth flank worn (fluffy canvas fibers, rubber gone and color changed to white, and unclear canvas texture).Last stage: Canvas on load side tooth flank worn down and rubber exposed (tooth width reduced).
i. Missing tooth.
INSTALLATION
1. Install crankshaft sprocket, flange and spacer as shown, while paying attention to their mounting directions.
CAUTION: Pay special attention to direction of flange. If it is installed in wrong direction, a broken belt could result.
2. Temporarily secure tensioner at a position closest to water pump.3. install end A of spring to predetermined position on tensioner bracket.4. Install end B of spring to predetermined position on water pump.5. When spacer is installed to right silent shaft, direct spacer with its chamfered end toward shaft for protection of oil seal.
BELT INSTALLATION PROCEDURE
Aligning Timing Marks
1. Align timing mark on each sprocket with corresponding timing mark on front case.2. When timing belt "B" is installed, make certain that tension side has no slack.
> Maintenance > Timing Belt > Component Information > Adjustments > Page 200
D50/Ram 50 L4-1997cc 2.0L SOHC (1984)
Installing Tensioner "B"
3. install tensioner "B" with center of pulley located on left side of mounting bolt and with pulley flange directed toward front of engine.
Adjusting Belt Tension
4. Lift tensioner "B" with finger tip to tighten timing belt "B" so that its tension side will be taut. in this condition tighten bolt to secure tensioner
"B". When bolt is tightened, use care to prevent shaft from turning together. If shaft is turned together, belt will be overtensioned.
specification.
Belt deflection 5 to 7 mm (.2 to .3 in.) ..................................................................................................................................................................................
7. Move tensioner fully toward water pump and temporarily secure tensioner.
5. Check to ensure that timing marks are in alignment.6. Check to ensure that when center of span on tension side is depressed with index finger in direction of arrow, deflection of belt is up to
Mounting Timing Belt
> Maintenance > Timing Belt > Component Information > Adjustments > Page 201
D50/Ram 50 L4-1997cc 2.0L SOHC (1984)
8. Align timing mark on camshaft sprocket with that on cylinder head.9. Align timing mark on crankshaft sprocket with that on front case.
10. Align timing mark on oil pump sprocket with that on front case.
Preventing Rotation Of Left Silent Shaft
11. When timing mark on oil pump pulley is aligned with that on front case, be sure to remove plug on left side of cylinder block and insert a screw
8 mm (.3 in.) in 60 mm (2.36 in.)
25 mm(1 in.)
60 mm (2.36in.) driver having shaft diameter. If it can be inserted or more, alignment is correct. If it can be inserted only , turn oil pump sprocket through a turn and realign timing marks. Check to ensure that screwdriver can be inserted more than . Keep screw driver inserted until installation of timing belt is finished.
12. Install timing belt. While making sure that tension side of belt is not slackened, install timing belt onto crankshaft sprocket, oil pump sprocket and camshaft sprocket in that order.
13. Loosen tensioner mounting bolt and nut. By so doing, tensioner will be moved by spring and will apply tension to belt.14. Check that portion of belt which is indicated by arrow A to make sure that it is not floating up.15. Tighten tensioner mounting nut and bolt. Tighten slot side bolt before tightening fulcrum side nut. If fulcrum side nut is tightened earlier, tension bracket will be turned together and belt will be overtensioned.
16. Check to ensure that timing marks on all sprockets are in alignment with respective timing marks.17. Turn crankshaft.
CAUTION: Do not turn crankshaft in reverse direction. Crankshaft should be turned smoothly clockwise.
18. Loosen tensioner mounting nut and bolt.19. Tighten tensioner mounting nut and bolt. Be sure to tighten fulcrum side nut and bolt in Step 15.
Adjusting Timing Belt Tension
20. Check to ensure that when center of belt span on tension side and seal line of under cover are held between thumb and forefinger as illustrated, clearance C between belt and seal line is as follows:
Clearance C Approx. 14 mm. (.55 in.) ................................................................................................................................................................................
> Maintenance > Drive Belt > Component Information > Specifications
Drive Belt: Specifications
1981-84 ex. Diesel: One-fourth of a inch or 6-10 millimeter deflection at midpoint of belt between water pump & alternator, under a 22 lb load.
> Maintenance > Filters > Oil Filter, Engine > Component Information > Technical Service Bulletins > Oil Filter - Addition of Second Supplier
Oil Filter: Technical Service BulletinsOil Filter - Addition of Second Supplier
Models
1984 Colt, Vista, Conquest, D-50 Pick-Up Except With Diesel Engines
Subject
Addition of Second Oil Filter Supplier
Index
ENGINE
Date
December 10, 1984
No.
09-12-84Beginning in July, 1984, MMC began using a second supplier for oil filters in production on all car lines except D-50 pick-up trucks equipped withdiesel engines. The alternate filter is identified by PN
MD084963.
For service parts, use the present replacement filter, PN MD031805, as a replacement for either MD084963 or MD031805.
POLICY: Information only
> Maintenance > Hoses > Coolant Line/Hose > Component Information > Technical Service Bulletins > Carburetor Coolant Hose - Installation Procedure
Coolant Line/Hose: Technical Service BulletinsCarburetor Coolant Hose - Installation Procedure
Models
All 1984 Import MMC Vehicles With Carburetors Except 2.6L Engines
Subject
Correct Carburetor Coolant Hose Installation Procedure
Index
FUEL
Date
December 3, 1984
No.
14-62-84
P-5298-CThe procedure described in this bulletin should be utilized when servicing the coolant hose or carburetor for the wax pellet choke housing.
FIGURE 1
When installing the lower coolant hose on the wax pellet choke housing, the following steps should be followed to avoid interference of the tab end ofthe hose clamp with the accelerator cable (Figure 1).
1.. Lower coolant hose should only be pushed on up to the shoulder on choke housing nipple (Figure 1).
2.
Tab ends of the spring hose clamps for the lower coolant hose should be positioned downward (Figure 1).
POLICY: Information only
> Maintenance > Fluids > Coolant > Component Information > Technical Service Bulletins > Engine Coolant - Recycling Recommendations
Coolant: Technical Service BulletinsEngine Coolant - Recycling Recommendations
SUBJECT:
GROUP: COOLING
DATE: Dec. 21, 1990
MODELS:
All Domestic & Import Vehicles
DISCUSSION:
A number of systems are being marketed to "recycle" or "reconstitute" used ethylene glycol antifreeze/coolant in the dealership. Some of the systemshave been advertised as producing a recycled antifreeze "as good as" original and suggest the recycled product is suitable for use in Chrysler Corporationvehicles.
Tests, so far, indicate most of these systems merely remove suspended solids from the used antifreeze/coolant through the use of various size filters.These systems do not remove glycol degradation products, or dissolved solids, which can cause water pump seal wear.
These systems use a universal "reinhibitor package". The "reinhibitor package" can not restore every type antifreeze/coolant inhibitor system to a likenew condition.
Tests results indicate these "recycled" products do not consistently provide the protection required in Chrysler Corporation engines and cooling systems.
The use of these "reconstituted" antifreeze/coolants is not authorized in the performance of any repair covered under the provisions of the warranty.
> Maintenance > Fluids > Coolant > Component Information > Technical Service Bulletins > Page 220
Coolant: Specifications
1982-89 Ram 50
* 9.0 L (9.5 qts) Cooling System Capacity .............................................................................................................................................................................
* Includes 0.65 L (0.69 qts) for the coolant reserve tank.
> Maintenance > Fluids > Fluid - A/T > Component Information > Technical Service Bulletins > Automatic Transmission - New Fluid Type
Fluid - A/T: Technical Service BulletinsAutomatic Transmission - New Fluid Type
Models
All 1978-1985 Equipped With Automatic Transmission & Lock-Up Torque Converter
Subject
New Automatic Transmission Fluid
Index
TRANSMISSION
Date June 17, 1985
No.
21-04-85
P-2131A new automatic transmission fluid Type 7176, (PN 4318077 - quart and 4318079 - 55 gallon) has been released for all vehicles equipped withautomatic transmission and lock-up torque converter.
Aftermarket fluids can vary in terms of their friction characteristics and this in turn can affect the performance of the lock-up clutch, causing shudderand/or excessive slippage. Use of the new fluid will help to insure that the lock-up clutch will perform satisfactorily after the fluid has been replaced.
Type 7176 fluid should be used any time it is necessary to replace the fluid in a lock-up torque converter equipped transmission.
If a lock-up shudder condition is encountered, check all linkage adjustments and drain and refill the transmission with Type 7176 fluid prior toattempting any other repairs, especially if the fluid has been changed previously.
POLICY: Information only
> Maintenance > Fluids > Fluid - A/T > Component Information > Specifications > Transaxle/Transmission - Automatic
Fluid - A/T: SpecificationsTransaxle/Transmission - Automatic
AF, APCAPACITY, Refill*:
3.8 Liters 4.0 Quarts Type.............................................................................................................................................................................................................................. All ................................................................................................................................................................................................
*With the engine at operating temperature, shift transmission through all gears. Check fluid level in PARK and add fluid as needed.
> Maintenance > Fluids > Fluid - A/T > Component Information > Specifications > Transaxle/Transmission - Automatic > Page 227
Fluid - A/T: SpecificationsInitial Refill Capacity
AF, APCAPACITY, Refill*:
3.8 Liters 4.0 Quarts Type.............................................................................................................................................................................................................................. All ................................................................................................................................................................................................
*With the engine at operating temperature, shift transmission through all gears. Check fluid level in PARK and add fluid as needed.
> Maintenance > Fluids > Fluid - M/T > Component Information > Specifications
Fluid - M/T: Specifications
GL-4CAPACITY, Refill:
2.1 Liters 4.4 Pints Type......................................................................................................................................................................................................80W, 75W-85W 4-speed RWD...................................................................................................................................................................................
2.3 Liters 4.8 Pints 5-speed RWD...................................................................................................................................................................................
> Maintenance > Fluids > Fluid - Differential > Component Information > Specifications
Fluid - Differential: Specifications
GL-5* Limited-Slip ..................................................................................................................................................................................................................
GL-5 Other ...............................................................................................................................................................................................................................
CAPACITY, Refill:
1.1 Liters 2.3 Pints Above -10F (-23C), 90, 85-W-90, 80W-90; -30 to -10F (-34 to -23C), 80W, 80W-90; below -30F (-34C), 75W Front ................................................................................................................................................................................................
1.5 Liters 3.2 Pints Rear .................................................................................................................................................................................................
LIMITED-SLIP IDENTIFICATION:Lift rear of vehicle, turn one wheel and the other will turn in the same direction
> Maintenance > Fluids > Fluid - Transfer Case > Component Information > Specifications
Fluid - Transfer Case: Specifications
GL-4CAPACITY, Refill:
2.2 Liters 4.6 Pints Type......................................................................................................................................................................................................80W, 75W-85W All models .......................................................................................................................................................................................
> Maintenance > Fluids > Engine Oil > Component Information > Technical Service Bulletins > Engine Oil - New `SG' Level Oil
Engine Oil: Technical Service BulletinsEngine Oil - New `SG' Level Oil
Models
All 1989 And Earlier Domestic & Import Vehicles
Subject
New "SG" Quality Engine Oil
Index
LUBRICATION
Date
April 24, 1989
No.
10-01-89
(C10-01-9)BODY CODE LEGEND
ALL 1989 AND EARLIER CHRYSLER/PLYMOUTH & DODGE DOMESTIC & IMPORT VEHICLES
"SG" QUALITY ENGINE OIL
The quality of engine oil recommended for use in all Chrysler Motors' vehicles has been upgraded to an "SG" level. The new "SG" quality engine oilscan provide significant improvements concerning sludge, varnish and wear control. These new quality oils may also be used in older vehicles wherelower quality oils (SE, SF, SF/CC) were recommended. Specific recommendations for all 1989 vehicles may be found in the vehicle "Owners Manual".
The new "SG" engine oils are currently being introduced into the MOPAR product line in addition to being commercially available through manyautomotive supply outlets.
POLICY: Information only
> Maintenance > Fluids > Engine Oil > Component Information > Technical Service Bulletins > Engine Oil - New `SG' Level Oil > Page 241
Engine Oil: Technical Service BulletinsEngine - Oil Application
Models
All Domestic & Import Vehicles Except Turbocharged
Subject
Use of 5W-30 Engine Oil
Index
ENGINE
Date
September 16, 1985
No.
09-17-85
P-3398-CMopar Max 5W-30 SF/CC oil is now available through Parts Supply.
1.
5W-30 engine oil is recommended for all normal driving conditions up to 100~F ambient temperatures except as noted in (2). This oil providesbetter engine starting and faster lubrication to engine components at low temperatures than 10W30 or 15W40 oils. 5W-30 oil also provides betterfuel economy.
2.
SAE 5W-30 and 5W-40 oils are not recommended for use in turbocharged engines, domestic vehicles equipped with the 1.6L engine, nor in trucks(including the Voyager, Caravan & Mini-Ram Van) above 60~F. In addition, these oils are not recommended in cars with 318-4BBL engines atany temperature (police vehicles).
The part numbers for Mopar "Max" oil are:
5W-30 SF/CC (quart)
5W-30 SF/CC (drum)
PN 4318075
PN 4318076
5W-30 oil is now used as the factory fill in most Chrysler Corporation vehicles.
POLICY: Information only
> Maintenance > Fluids > Engine Oil > Component Information > Technical Service Bulletins > Page 242
Engine Oil: Specifications
SE, SF, SG Type Gasoline engine ............................................................................................................................................................................................
CAPACITY, Refill:
2-wheel drive:
3.5 Liters 3.7 Quarts 4.5 Liters 4.7 Quarts 2.0-liter eng. ............................................................................................................................................................................2.6-liter eng. ............................................................................................................................................................................
4-wheel drive:
4.5 Liters 4.7 Quarts 5.3 Liters 5.6 Quarts 2.0-liter eng.............................................................................................................................................................................2.6-liter eng.............................................................................................................................................................................
Capacity shown is without filter. When replacing filter, additional oil may be needed
Gasoline engines:1981
1982-84 Above 32F (0C) .........................................................................................................................................................................20W-20, 20W-40, 20W-50Above -10F (-23) .......................................................................................................................................................................10W-30, 10W-40, 10W-50Below 32F (0C) .........................................................................................................................................................................................................5W-40Below 10F (-12C) ................................................................................................................................................................................5W-20, 5-30, 5W-40
Above 32F (0C) .........................................................................................................................................................................20W-20, 20W-40, 20W-50Above -10F (-23) .......................................................................................................................................................................10W-30, 10W-40, 10W-50Below 60F (16C) ...........................................................................................................................................................................5W-20*, 5W-30, 5W-40*Not recommended for sustained high-speed driving
> Maintenance > Fluids > Refrigerant > Component Information > Specifications > Capacity Specifications
Refrigerant: Capacity Specifications
A/C Refrigerant Specifications
Capacity .................................................................................................................................................................................................... 34 oz (2.13 lbs)
> Maintenance > Fluids > Refrigerant > Component Information > Specifications > Capacity Specifications > Page 247
Refrigerant: Fluid Type Specifications
Fluid Type specifications
Type ................................................................................................................................................................................................. Refrigerant 12 (R-12)
> Maintenance > Fuses and Circuit Breakers > Fuse Block > Component Information > Diagrams > Diagram Information and Instructions
Fuse Block: Diagram Information and Instructions
Group Index
Alphabetic Index to Wiring Diagrams Electrical When trying to find the diagram for a specific component or system, use the information or the under
Group Index Diagrams By Sheet Number
Diagrams By Figure Number Whenever a reference exists to another sheet or figure, find the corresponding diagram using the , , or . The reference number for the subsequent diagram will match a listed group shown.
> Maintenance > Fuses and Circuit Breakers > Fuse Block > Component Information > Diagrams > Diagram Information and Instructions > Page 253
Fuse Block: Electrical Diagrams
TRUCKFuse Block..............................................Left Kick Panel Below Hood Release
Fusible Link...........................................Battery Positive Terminal
> Maintenance > Service Reminder Indicators > System Information > Service Precautions
Service Reminder Indicators: Service Precautions
SERVICE PRECAUTION
All Service Reminder Indicators should be investigated or serviced immediately. Vehicle damage may result if the indicator is ignored.
> Maintenance > Wheels and Tires > Wheel Bearing > Component Information > Adjustments
Wheel Bearing: Adjustments
Install hub bearings on spindle, then install hub nut and torque to 22 ft. lbs. to seat bearings. Loosen hub nut, then torque nut to 6 ft. lbs. Install nutretainer cap and cotter pin. If cotter pin holes are not aligned, loosen nut to align holes. The nut may be loosened to a maximum of 30 to align cotterpin holes. Check to ensure hub assembly rotates freely without play.
> Maintenance > Wheels and Tires > Wheel Bearing > Component Information > Service and Repair > Removal
Wheel Bearing: Service and RepairRemoval
Fig. 8 Hub & wheel bearing assembly exploded view. Shown w/manual locking hub
Fig. 9 Automatic (free wheeling) locking hub
> Maintenance > Wheels and Tires > Wheel Bearing > Component Information > Service and Repair > Removal > Page 263
D50/Ram 50 L4-1997cc 2.0L SOHC (1984)
1. Remove wheel and tire assembly, then remove brake caliper assembly leaving brake hose connected. Suspend caliper assembly from frame using a wire hook to prevent damage to brake hose.
2. Place hub in free position, then remove free wheeling hub cover. On models with automatic locking hubs, ensure hub is in "free wheeling" position by placing transfer case lever in 2H position and moving in reverse 4-7 feet. If cover cannot be removed by hand, loosen cover with suitable strapwrench, taking care not to damage cover.
3. Remove snap ring securing drive axle, then the adjusting shims.4. Remove free wheeling hub assembly from front hub, using tool MD998360 or equivalent to remove bolts securing automatic locking hub.
Fig. 10 Spindle nut removal & installation
5. Remove lock washer, then remove hub locknut using tool No. MB990954.6. Pull front hub with brake disc from knuckle, using care not to drop outer wheel bearing inner race.7. Remove grease from inside front hub, then using a suitable drift, drive bearing races from hub.8. Place alignment marks on brake disc and hub, then separate hub and disc as necessary.
> Maintenance > Wheels and Tires > Wheel Bearing > Component Information > Service and Repair > Removal > Page 264
Wheel Bearing: Service and RepairInspection
HUB, SPINDLE & BEARINGS
1. Clean components with suitable solvent and blow dry with compressed air.
Fig. 11 Checking spindle for wear
2. Inspect spindle for wear and damage and measure spindle bearing seating area diameter. Diameter should be 1.7805 to 1.7812 inch.3. Inspect bearings for damage excessive wear, overheating and scoring, and replace as needed.4. Check fit of bearing outer races in hub. If races are loose, hub should be replaced.
MANUAL LOCKING HUB
Fig. 8 Hub & wheel bearing assembly exploded view. Shown w/manual locking hub
1. Inspect hub ring, inner hub and hub body, and the clutch. If components are damaged or worn, assembly should be replaced.2. Inspect tension spring and compression spring, and replace if collapsed or deteriorated.3. Check operation of control handle and replace as needed.
> Maintenance > Wheels and Tires > Wheel Bearing > Component Information > Service and Repair > Removal > Page 265
D50/Ram 50 L4-1997cc 2.0L SOHC (1984)
Fig. 9 Automatic (free wheeling) locking hub
AUTOMATIC LOCKING HUB
DISASSEMBLY
1. Press in on brake B, then remove housing C-ring.2. Remove brake B, brake B and brake spring from housing, then remove housing snap ring.3. Mount assembly in press, lightly compress drive gear, then remove retainer B C-ring, noting the following: a. Place protective cloth under cover mating surface.b. Because return spring is approximately 1.57 inches long, ensure press stroke is more than 1.57 inches.c. Do not apply more than 441 lbs. pressure to drive gear.d. After removing C-ring, slowly reduce press force until return spring relaxes completely.
4. Remove retainer B, return spring, slide gear assembly and drive gear assembly from housing.5. Remove and discard drive gear snap ring.6. Press in on slide gear cam and remove slide gear C-ring.
INSPECTION
1. Check slide and drive gear splines for damage.2. Check cam portion of retainer A for wear or damage.3. Check cam for wear and damage.4. Check slide gear and housing tooth surfaces for wear and damage.5. Check retainer B and housing contact surfaces for wear and damage.6. Check brake wear as follows:
Fig. 12 Measuring brake assembly. Automatic locking hub a. Assemble brake A and brake B, then measure thickness of assembly at two lugs on brake A.b. Standard thickness is 0.413 inch and minimum thickness is 0.378 inch.
> Maintenance > Wheels and Tires > Wheel Bearing > Component Information > Service and Repair > Removal > Page 266
D50/Ram 50 L4-1997cc 2.0L SOHC (1984)
7. Inspect return and shift springs as follows:
Fig. 13 Measuring spring free length. Automatic locking hub a. Measure free length of spring as shown.b. Minimum return spring free length is 1.38 inches.c. Minimum shift spring free length is 1.18 inches.
8. Replace any components that are damaged, excessively worn, or that are not within specifications.
ASSEMBLY
Apply Mopar grease 2525035 or equivalent to mounting surfaces of all components and reverse disassembly procedure, noting the following:1. Pack grooves of retainer B with specified grease.2. Install return spring with smaller diameter coil toward cam.3. Pack grooves of brake B with specified grease.
> Maintenance > Wheels and Tires > Wheel Bearing > Component Information > Service and Repair > Removal > Page 267
Wheel Bearing: Service and RepairInstallation
1. Drive outer races into front hub using a suitable drift, then evenly coat inner wall of front hub with grease.2. Pack inner and outer bearings with suitable grease. Apply grease to oil seal lip.3. Position inner bearing and oil seal on hub, then install oil seal using tool No. MB990985.
Fig. 8 Hub & wheel bearing assembly exploded view. Shown w/manual locking hub
Fig. 14 Checking front hub rotating torque
4. If removed, install brake disc on front hub, tightening attaching bolts alternately and evenly to 36-44 ft. lbs. After assembling, check brake disc runout. Brake disc runout should not exceed 0.006 inch.
5. Carefully install front hub on steering knuckle spindle.6. Install outer bearing on spindle, then install spindle nut.7. Adjust wheel bearings as follows: a. Torque bearing locknut to 94-145 ft. lbs. while rotating hub to seat bearings.b. Loosen spindle nut and retighten to 18 ft. lbs., then back off 30.c. Install lock washer. If hole in lock washer is not aligned with hole in spindle nut, the nut may be loosened up to an additional 20 to obtain
> Maintenance > Wheels and Tires > Wheel Bearing > Component Information > Service and Repair > Removal > Page 268
D50/Ram 50 L4-1997cc 2.0L SOHC (1984)
proper alignment.
d. Using a suitable spring scale or torque wrench, measure force required to rotate front hub.e. The force required to rotate the front hub assembly should be 1.1-4.0 lbs. (spring scale) or 3-11 inch lbs. (torque wrench), and endplay should be less than 0.002 inch. If rotating force is not within specifications, repeat adjustment.
f. When adjustment is correct, secure washer with retaining screws.
8. On models with automatic locking hubs, measure brake contact surface depth as follows:
Fig. 15 Measuring brake contact surface depth. Automatic locking hub a. Measure dimension A, in two places using suitable depth gauge.b. Average of two readings should be 0.46-0.48 inch. If depth is greater than specified, install suitable shims. If depth is less than specified, recheck hub and bearing installation.
9. Apply grease to inner surface of free wheeling hub body assembly.
10. Apply semi-dry sealant to front hub surface to which the free wheeling hub body assembly is attached.11. Align tab on free wheel hub with groove on spindle, install free wheeling hub body assembly on front hub, then torque attaching bolts to 37-43 ft.
lbs.
12. Reverse remaining procedure to complete installation.
> Maintenance > Wheels and Tires > Wheel Hub > Axle Nut > Component Information > Technical Service Bulletins > Rear Axle Shaft - Retaining Nut Lock Washers
Axle Nut: Technical Service BulletinsRear Axle Shaft - Retaining Nut Lock Washers
Models
1979-89 PB/B4 And SJ/B6 Vehicles
Subject
Lock Washer For Rear Axle Shaft Retaining Nut
Index
REAR AXLE
Date
April 17, 1989
No.
03-01-89
(CO0-02-9)
AXLE SHAFT RETAINING NUT LOCK WASHER
BODY CODE LEGEND
PB/B4 - RAM 50 PICKUP SJ/B6 - RAM RAIDER
AXLE SHAFT RETAINING NUT LOCK WASHER
When axle service requires removal of the axle shaft retaining nut and lock washer (Figure 1), the lock washer must not be reused. The lock washer, P/NMB092433, must be replaced when reassembling the axle.
> Maintenance > Wheels and Tires > Wheel Hub (Locking) > Component Information > Technical Service Bulletins > Automatic Locking Hubs - Racheting Noise
Wheel Hub (Locking): Technical Service BulletinsAutomatic Locking Hubs - Racheting Noise
Models
1984-1985 Dodge Power Ram 50 Pick-Up
Subject
Racheting Noise in Automatic Locking Hubs
Index
FRONT AXLE
Date
November 19, 1984
No.
02-10-84 P-5120-CSYMPTOM/CONDITION
Racheting noise in automatic locking hubs during low temperature operation or after shifting from "4H" to "2H".
DIAGNOSIS/CORRECTION
Use the attached chart to determine the corrective action necessary.
POLICY: Information Only
SYMPTOM RESOLUTION
Noise is generated after start-up with shift lever in "2H" position under low temperature.
free-wheeling hub.
Noise is generated after shift lever is changed from "4H"
(lock) "2H" (free) position.
Drive the vehicle with the lever in "4H" position for a while to warm up oil in transfer case and then drive with the lever in "2H" position.
When shifting "4H" (lock) to
"2H" (free) position, first stop vehicle, change shift lever from "4H" to "2H" position, and then slowly drive vehicle straight backward for 10 to 20 feet.
CAUSE
Under low temperature, oil in transfer case gets stiff and it accordingly rotates front drive shaft which causes racheting effect* of automatic
If shifting is done while vehi- cle is turning, only one side of free-wheeling hub will be freed resulting in the racheting effect.*
*Racheting effect is caused when slide gear and housing gear are not engaged and there is difference of revolution speed between those two gears. Noiseis caused by this revolutional difference.
The racheting of the hubs is not detrimental to the components or operation of the vehicle. The 1985 owners manual will advise the customer of thecondition.
> Engine, Cooling and Exhaust > Engine > Compression Check > System Information > Specifications
Compression Check: Specifications
Pressure 170 psi
> Engine, Cooling and Exhaust > Engine > Camshaft, Lifters and Push Rods > Camshaft, Engine > Component Information > Specifications
Camshaft: Specifications
Cap Bolt Torque 14-15 ft.lb
> Engine, Cooling and Exhaust > Engine > Camshaft, Lifters and Push Rods > Camshaft, Engine > Component Information > Specifications > Page 287
Camshaft: Service and Repair
Removal
1.
Disconnect battery ground cable and remove air cleaner.
2.
Disconnect spark plug wires and remove accessory drive belts, as needed.
3.
Mark and disconnect necessary electrical connectors and vacuum hoses, then remove timing belt upper cover and rocker arm cover.
Fig. 5 Camshaft timing marks. 2000cc engine
4.
Rotate crankshaft in normal direction of rotation until No. 1 cylinder is at TDC and crankshaft and camshaft timing marks are aligned,.
5.
6.
Do not rotate crankshaft after sprocket is removed from camshaft.
Place chalk mark between timing belt and camshaft sprocket, remove camshaft sprocket bolt, separate sprocket from camshaft leaving belt in placeon sprocket, then secure sprocket and belt on lower timing cover. Take care that sprocket does not disengage from belt and fall, and maintaintension on belt to maintain proper timing.
Evenly loosen camshaft bearing cap/rocker arm retaining bolts in crossing pattern, remove bearing caps and rocker shafts as an assembly, thenremove camshaft.
> Engine, Cooling and Exhaust > Engine > Camshaft, Lifters and Push Rods > Camshaft, Engine > Component Information > Specifications > Page 288
D50/Ram 50 L4-1997cc 2.0L SOHC (1984)
Fig. 21 Rocker arms, rocker shafts & camshaft exploded view. 2000cc engines
7.
Fig. 21, Disassemble components in numerical order, noting position for installation.
Installation
1.
Coat camshaft with suitable assembly lubricant and position cam in head, with camshaft aligned so that valves for No. 1 cylinder are closed (TDCon compression stroke).
Fig. 17 Rocker arm shaft installation, 1600cc, 2000cc engines
2.
Fig.17. Insert rocker shafts into front bearing cap, installing shaft with oil hole side down and noting that front end of shaft has a cut .16 inch wide,
> Engine, Cooling and Exhaust > Engine > Camshaft, Lifters and Push Rods > Camshaft, Engine > Component Information > Specifications > Page 289
D50/Ram 50 L4-1997cc 2.0L SOHC (1984)
Fig. 22 Assembling rocker arms & rocker arm shafts. 2000cc engine
3.
Fig. 22,
Apply engine oil to I.D. of rocker arms prior to assembly. Assemble rocker arms, springs and remaining bearing caps on rocker shafts, inpositions noted during disassembly.
Fig. 23 Hydraulic lash adjuster & retaining clip installation. 1985-88 2000cc & 2600cc engines
4.
Fig. 23, On models with hydraulic lash adjusters, insert each adjuster into rocker arm taking care not to spill fluid from adjuster. Retain adjusters usingsuitable clips, to prevent them from falling out during installation.
5.
On all models, install assembly onto cylinder head and evenly tighten bolts in crossing pattern until bearing caps are seated. When caps are seated,torque bolts to specifications in crossing pattern.
6.
Install sleeve over camshaft and press oil seal into place using suitable driver.
7.
Install camshaft sprocket and timing belt, then ensure timing marks are properly aligned.
8.
Adjust valves to specifications as outlined, then temporarily install rocker cover.
9.
Reverse remaining procedure to complete installation, then check timing belt tension as outlined. After engine reaches normal operatingtemperature, recheck valve clearances and adjust as needed.
Fig. 24 Applying sealant to semi-circular packing
10.
Fig. 24,
When installing rocker cover after checking valve clearances, apply suitable sealer to semi-circular packing and cylinder head, then installrocker cover.
> Engine, Cooling and Exhaust > Engine > Camshaft, Lifters and Push Rods > Rocker Arm Assembly > Component Information > Service and Repair
Rocker Arm Assembly: Service and Repair
REMOVAL
1. Disconnect battery ground cable and remove air cleaner.2. Disconnect spark plug wires and remove accessory drive belts, as needed.3. Mark and disconnect necessary electrical connectors and vacuum hoses, then remove timing belt upper cover and rocker arm cover.
Fig. 5 Camshaft timing marks. 2000cc engine
Fig. 5. 4. Rotate crankshaft in normal direction of rotation until No. 1 cylinder is at TDC and crankshaft and camshaft timing marks are aligned, 5. Place chalk mark between timing belt and camshaft sprocket, remove camshaft sprocket bolt, separate sprocket from camshaft leaving belt in place
Do not rotate crankshaft after sprocket is removed from camshaft.
on sprocket, then secure sprocket and belt on lower timing cover. Take care that sprocket does not disengage from belt and fall, and maintaintension on belt to maintain proper timing.
6. Evenly loosen camshaft bearing cap/rocker arm retaining bolts in crossing pattern, remove bearing caps and rocker shafts as an assembly, then remove camshaft.
> Engine, Cooling and Exhaust > Engine > Camshaft, Lifters and Push Rods > Rocker Arm Assembly > Component Information > Service and Repair > Page 293
D50/Ram 50 L4-1997cc 2.0L SOHC (1984)
Fig. 21 Rocker arms, rocker shafts & camshaft exploded view. 2000cc engines
Fig. 21, 7. Disassemble components in numerical order, noting position for installation.
INSTALLATION
1. Coat camshaft with suitable assembly lubricant and position cam in head, with camshaft aligned so that valves for No. 1 cylinder are closed (TDC on compression stroke).
Fig. 17 Rocker arm shaft installation, 1600cc, 2000cc engines
Fig.
2. Insert rocker shafts into front bearing cap, installing shaft with oil hole side down and noting that front end of shaft has a cut .16 inch wide,
17.
Fig. 22 Assembling rocker arms & rocker arm shafts. 2000cc engine
Fig. 22, 3. Apply engine oil to I.D. of rocker arms prior to assembly. Assemble rocker arms, springs and remaining bearing caps on rocker shafts, in positions noted during disassembly.
Fig. 23 Hydraulic lash adjuster & retaining clip installation. 1985-88 2000cc & 2600cc engines
4. On models with hydraulic lash adjusters, insert each adjuster into rocker arm taking care not to spill fluid from adjuster. Retain adjusters using
Fig. 23, suitable clips, to prevent them from falling out during installation.
5. On all models, install assembly onto cylinder head and evenly tighten bolts in crossing pattern until bearing caps are seated. When caps are seated,
> Engine, Cooling and Exhaust > Engine > Camshaft, Lifters and Push Rods > Rocker Arm Assembly > Component Information > Service and Repair > Page 294
D50/Ram 50 L4-1997cc 2.0L SOHC (1984)
torque bolts to specifications in crossing pattern.
6. Install sleeve over camshaft and press oil seal into place using suitable driver.7. Install camshaft sprocket and timing belt, then ensure timing marks are properly aligned.8. Adjust valves to specifications as outlined, then temporarily install rocker cover.9. Reverse remaining procedure to complete installation, then check timing belt tension as outlined. After engine reaches normal operating temperature, recheck valve clearances and adjust as needed.
Fig. 24 Applying sealant to semi-circular packing
Fig. 24, 10. When installing rocker cover after checking valve clearances, apply suitable sealer to semi-circular packing and cylinder head, then install rocker cover.
> Engine, Cooling and Exhaust > Engine > Cylinder Block Assembly > Connecting Rod Bearing > Component Information > Service and Repair
Connecting Rod Bearing: Service and Repair
Fig. 50 Piston & rod assembly
Fig. 50.
This piston and rod is assembled with the indented arrow on the piston and the embossed numeral on the rod facing toward front of engine,
PISTON, PINS & RINGS
0.010, 0.020, 0.030 and 0.039 inch Pistons and rings are available in standard size and oversizes of . Oversize pins are not available.
MAIN & ROD BEARINGS
0.010, 0.020 and 0.030 inch Main and rod bearings are available in undersizes of .
The main bearing caps are installed with arrows facing front of engine.
> Engine, Cooling and Exhaust > Engine > Cylinder Block Assembly > Connecting Rod, Engine > Component Information > Specifications
Connecting Rod: Specifications
Connecting Rod Cap Bolts 33-34 ft.lb
> Engine, Cooling and Exhaust > Engine > Cylinder Block Assembly > Connecting Rod, Engine > Component Information > Specifications > Page 302
Connecting Rod: Service and Repair
Fig. 50 Piston & rod assembly
Fig. 50.
This piston and rod is assembled with the indented arrow on the piston and the embossed numeral on the rod facing toward front of engine,
PISTON, PINS & RINGS
0.010, 0.020, 0.030 and 0.039 inch Pistons and rings are available in standard size and oversizes of . Oversize pins are not available.
MAIN & ROD BEARINGS
0.010, 0.020 and 0.030 inch Main and rod bearings are available in undersizes of .
The main bearing caps are installed with arrows facing front of engine.
> Engine, Cooling and Exhaust > Engine > Cylinder Block Assembly > Crankshaft Main Bearing > Component Information > Service and Repair
Crankshaft Main Bearing: Service and Repair
Fig. 50 Piston & rod assembly
Fig. 50.
This piston and rod is assembled with the indented arrow on the piston and the embossed numeral on the rod facing toward front of engine,
PISTON, PINS & RINGS
0.010, 0.020, 0.030 and 0.039 inch Pistons and rings are available in standard size and oversizes of . Oversize pins are not available.
MAIN & ROD BEARINGS
0.010, 0.020 and 0.030 inch Main and rod bearings are available in undersizes of .
The main bearing caps are installed with arrows facing front of engine.
> Engine, Cooling and Exhaust > Engine > Cylinder Block Assembly > Crankshaft, Engine > Component Information > Specifications > Crankshaft Journal Tolerances
Crankshaft: Specifications
Rod Journal Diameter 1.772 in
Main Journal Diameter 2.244 in
Shaft End Play 0.002-0.007 in
> Engine, Cooling and Exhaust > Engine > Cylinder Block Assembly > Crankshaft, Engine > Component Information > Specifications > Crankshaft Journal Tolerances > Page 310
Crankshaft: Specifications
Crankshaft Main Bearing Caps 61 ft.lb
> Engine, Cooling and Exhaust > Engine > Cylinder Block Assembly > Harmonic Balancer - Crankshaft Pulley > Component Information > Technical Service Bulletins > Engine - Torque Specifications, Manual Correction
Harmonic Balancer - Crankshaft Pulley: Technical Service BulletinsEngine - Torque Specifications, Manual Correction
Models
1984 Ram 50, Power Ram 50
Subject
Service Manual Correction Engine Torque Specifications
Index
ENGINE
Date July 30, 1984
No.
09-10-84
P-3050-C
FIGURE 1
> Engine, Cooling and Exhaust > Engine > Cylinder Block Assembly > Harmonic Balancer - Crankshaft Pulley > Component Information > Technical Service Bulletins >
Engine - Torque Specifications, Manual Correction > Page 315
D50/Ram 50 L4-1997cc 2.0L SOHC (1984)
FIGURE 2
Errors in the tightening torques for the engine crankshaft pulley shown in the 1984 Ram 50 Service Manual, Publication #81-370-4009, have beencorrected as described in Figures 1 and 2.
> Engine, Cooling and Exhaust > Engine > Cylinder Block Assembly > Harmonic Balancer - Crankshaft Pulley > Component Information > Technical Service Bulletins > Page 316
Harmonic Balancer - Crankshaft Pulley: Specifications
Vibration Damper Or Pulley 11-15 ft.lb
> Engine, Cooling and Exhaust > Engine > Cylinder Block Assembly > Piston, Engine > Component Information > Specifications
Piston: Specifications
Piston Clearance .0008-.0016 in
> Engine, Cooling and Exhaust > Engine > Cylinder Block Assembly > Piston, Engine > Component Information > Specifications > Page 320
Piston: Service and Repair
Fig. 50 Piston & rod assembly
Fig. 50.
This piston and rod is assembled with the indented arrow on the piston and the embossed numeral on the rod facing toward front of engine,
PISTON, PINS & RINGS
0.010, 0.020, 0.030 and 0.039 inch Pistons and rings are available in standard size and oversizes of . Oversize pins are not available.
MAIN & ROD BEARINGS
0.010, 0.020 and 0.030 inch Main and rod bearings are available in undersizes of .
The main bearing caps are installed with arrows facing front of engine.
> Engine, Cooling and Exhaust > Engine > Cylinder Block Assembly > Piston Ring, Engine > Component Information > Specifications
Piston Ring: Specifications
Ring End Gap Top Ring 0.010 in
Note: Fit rings in tapered bores for clearance listed in tightest portion of ring travel.
2nd Ring 0.008 in
Oil Ring 0.008 in
> Engine, Cooling and Exhaust > Engine > Cylinder Block Assembly > Piston Ring, Engine > Component Information > Specifications > Page 324
Piston Ring: Service and Repair
Fig. 50 Piston & rod assembly
Fig. 50.
This piston and rod is assembled with the indented arrow on the piston and the embossed numeral on the rod facing toward front of engine,
PISTON, PINS & RINGS
0.010, 0.020, 0.030 and 0.039 inch Pistons and rings are available in standard size and oversizes of . Oversize pins are not available.
MAIN & ROD BEARINGS
0.010, 0.020 and 0.030 inch Main and rod bearings are available in undersizes of .
The main bearing caps are installed with arrows facing front of engine.
> Engine, Cooling and Exhaust > Engine > Cylinder Head Assembly > Valve Clearance > System Information > Specifications
Valve Clearance: Specifications
Except Jet Valve Intake 0.006 in
1985-89 2.0L & 2.6L except jet valve have hydraulic lifters.
Jet Valve
Exhaust 0.01 in
Intake 0.006 in
> Engine, Cooling and Exhaust > Engine > Cylinder Head Assembly > Valve Clearance > System Information > Specifications > Page 329
Valve Clearance: Adjustments
INTAKE & EXHAUST VALVES
Fig. 12 Adjusting valve clearance (Typical)
The jet valve must be adjusted before adjusting the intake valve.
1. With engine at operating temperature, remove rocker arm cover.2. Disconnect high tension lead from ignition coil.3. While observing rocker arms on No. 4 cylinder, rotate crankshaft until the exhaust valve is closing and the intake valve has just started to open
Fig. 12.
with crankshaft pulley mark aligned with TDC mark on timing chain case. At this position the No. 1 cylinder is at top dead center compressionstroke. Check and adjust valve clearance for both intake and exhaust valves of No. 1 cylinder, intake valve of No. 2 cylinder and exhaust valve ofNo. 3 cylinder, as necessary,
4. Rotate crankshaft 360 degrees and check and adjust valve clearance for exhaust valve of No. 2 cylinder, intake valve of No. 3 cylinder and intake and exhaust valves of No. 4 cylinder.
5. After completing adjustment, install rocker arm cover and connect ignition coil high tension lead.
JET VALVE
Fig. 13 Adjusting jet valve clearance
Exc. Models Equipped W/Hydraulic Lash Adjusters
Fig. 13.
Following procedure for intake and exhaust valve adjustment, position No. 1 cylinder at top dead center compression stroke. Loosen intake valveadjusting screw at least 2 turns, then loosen jet valve adjusting screw locknut. Rotate jet valve adjusting screw counterclockwise and insert a suitablefeeler gauge blade as specified in ``Valve Specification Chart,'' between jet valve stem and adjusting screw, Tighten jet valve adjusting screwuntil it contacts the feeler gauge blade, then while holding adjusting screw in position, tighten locknut. After jet valve adjustment has been completed,adjust intake valve clearance. Continue to follow intake and exhaust valve adjustment procedure and adjust jet valves as necessary.
> Engine, Cooling and Exhaust > Engine > Cylinder Head Assembly > Rocker Arm Assembly > Component Information > Service and Repair
Rocker Arm Assembly: Service and Repair
REMOVAL
1. Disconnect battery ground cable and remove air cleaner.2. Disconnect spark plug wires and remove accessory drive belts, as needed.3. Mark and disconnect necessary electrical connectors and vacuum hoses, then remove timing belt upper cover and rocker arm cover.
Fig. 5 Camshaft timing marks. 2000cc engine
Fig. 5. 4. Rotate crankshaft in normal direction of rotation until No. 1 cylinder is at TDC and crankshaft and camshaft timing marks are aligned, 5. Place chalk mark between timing belt and camshaft sprocket, remove camshaft sprocket bolt, separate sprocket from camshaft leaving belt in place
Do not rotate crankshaft after sprocket is removed from camshaft.
on sprocket, then secure sprocket and belt on lower timing cover. Take care that sprocket does not disengage from belt and fall, and maintaintension on belt to maintain proper timing.
6. Evenly loosen camshaft bearing cap/rocker arm retaining bolts in crossing pattern, remove bearing caps and rocker shafts as an assembly, then remove camshaft.
> Engine, Cooling and Exhaust > Engine > Cylinder Head Assembly > Rocker Arm Assembly > Component Information > Service and Repair > Page 333
D50/Ram 50 L4-1997cc 2.0L SOHC (1984)
Fig. 21 Rocker arms, rocker shafts & camshaft exploded view. 2000cc engines
Fig. 21, 7. Disassemble components in numerical order, noting position for installation.
INSTALLATION
1. Coat camshaft with suitable assembly lubricant and position cam in head, with camshaft aligned so that valves for No. 1 cylinder are closed (TDC on compression stroke).
Fig. 17 Rocker arm shaft installation, 1600cc, 2000cc engines
Fig.
2. Insert rocker shafts into front bearing cap, installing shaft with oil hole side down and noting that front end of shaft has a cut .16 inch wide,
17.
Fig. 22 Assembling rocker arms & rocker arm shafts. 2000cc engine
Fig. 22, 3. Apply engine oil to I.D. of rocker arms prior to assembly. Assemble rocker arms, springs and remaining bearing caps on rocker shafts, in positions noted during disassembly.
Fig. 23 Hydraulic lash adjuster & retaining clip installation. 1985-88 2000cc & 2600cc engines
4. On models with hydraulic lash adjusters, insert each adjuster into rocker arm taking care not to spill fluid from adjuster. Retain adjusters using
Fig. 23, suitable clips, to prevent them from falling out during installation.
5. On all models, install assembly onto cylinder head and evenly tighten bolts in crossing pattern until bearing caps are seated. When caps are seated,
> Engine, Cooling and Exhaust > Engine > Cylinder Head Assembly > Rocker Arm Assembly > Component Information > Service and Repair > Page 334
D50/Ram 50 L4-1997cc 2.0L SOHC (1984)
torque bolts to specifications in crossing pattern.
6. Install sleeve over camshaft and press oil seal into place using suitable driver.7. Install camshaft sprocket and timing belt, then ensure timing marks are properly aligned.8. Adjust valves to specifications as outlined, then temporarily install rocker cover.9. Reverse remaining procedure to complete installation, then check timing belt tension as outlined. After engine reaches normal operating temperature, recheck valve clearances and adjust as needed.
Fig. 24 Applying sealant to semi-circular packing
Fig. 24, 10. When installing rocker cover after checking valve clearances, apply suitable sealer to semi-circular packing and cylinder head, then install rocker cover.
> Engine, Cooling and Exhaust > Engine > Cylinder Head Assembly > Valve Cover > Component Information > Specifications
Valve Cover: Specifications
Rocker Arm Cover 4-5 ft/lb ft.lb
> Engine, Cooling and Exhaust > Engine > Cylinder Head Assembly > Valve Guide > Component Information > Service and Repair
Valve Guide: Service and Repair
Fig. 29 Valve guide & guide bore oversizes
1.
2.
3.
Press old valve guide from cylinder head toward lower surface using pushrod from valve guide replacement kit, tool No. MD998115 and a suitablepress.
Fig. 29.
Ream each valve guide bore in cylinder head to the O.D. of replacement valve guide,
4.
Press fit new valve guide into top of cylinder head using tool No. MD998115. This tool installs valve guide to a predetermined height. If astandard size valve guide has been removed, replacement valve guide should be oversized. New valve guide should be installed at roomtemperature.
After installation of new valve guides, insert valve and check for proper clearance. If clearance is not correct, ream guide until proper clearance isobtained. Refer to ``Valve Specifications'' for stem to guide clearance.
> Engine, Cooling and Exhaust > Engine > Cylinder Head Assembly > Valve Seat > Component Information > Specifications
Valve Seat: SpecificationsSeat Angle
Seat Angle
Valve Seat Angle 45 deg
> Engine, Cooling and Exhaust > Engine > Cylinder Head Assembly > Valve Spring > Component Information > Specifications
Valve Spring: SpecificationsSpring Height and Pressure
Spring Height and Pressure
Installed Height 1.590 in
Note: Jet valve spring installed height, .846 inch.
Valve Spring Pressure 62 lbf at 1.591 in
> Engine, Cooling and Exhaust > Engine > Cylinder Head Assembly > Valve, Intake/Exhaust > Component Information > Specifications
Valve: Specifications
Valve Face Angle 45 deg
Stem Clearance Intake .0012-.0024 in
Exhaust .0020-.0035 in
Stem Diameter Intake 0.315 in
Exhaust 0.315 in
Jet Valve 0.1693 in
> Engine, Cooling and Exhaust > Engine > Drive Belts, Mounts, Brackets and Accessories > Drive Belt > Component Information > Specifications
Drive Belt: Specifications
1981-84 ex. Diesel: One-fourth of a inch or 6-10 millimeter deflection at midpoint of belt between water pump & alternator, under a 22 lb load.
> Engine, Cooling and Exhaust > Engine > Engine Lubrication > Engine Oil > Component Information > Technical Service Bulletins > Engine Oil - New `SG' Level Oil
Engine Oil: Technical Service BulletinsEngine Oil - New `SG' Level Oil
Models
All 1989 And Earlier Domestic & Import Vehicles
Subject
New "SG" Quality Engine Oil
Index
LUBRICATION
Date
April 24, 1989
No.
10-01-89
(C10-01-9)BODY CODE LEGEND
ALL 1989 AND EARLIER CHRYSLER/PLYMOUTH & DODGE DOMESTIC & IMPORT VEHICLES
"SG" QUALITY ENGINE OIL
The quality of engine oil recommended for use in all Chrysler Motors' vehicles has been upgraded to an "SG" level. The new "SG" quality engine oilscan provide significant improvements concerning sludge, varnish and wear control. These new quality oils may also be used in older vehicles wherelower quality oils (SE, SF, SF/CC) were recommended. Specific recommendations for all 1989 vehicles may be found in the vehicle "Owners Manual".
The new "SG" engine oils are currently being introduced into the MOPAR product line in addition to being commercially available through manyautomotive supply outlets.
POLICY: Information only
> Engine, Cooling and Exhaust > Engine > Engine Lubrication > Engine Oil > Component Information > Technical Service Bulletins > Engine Oil - New `SG' Level Oil > Page 359
Engine Oil: Technical Service BulletinsEngine - Oil Application
Models
All Domestic & Import Vehicles Except Turbocharged
Subject
Use of 5W-30 Engine Oil
Index
ENGINE
Date
September 16, 1985
No.
09-17-85
P-3398-CMopar Max 5W-30 SF/CC oil is now available through Parts Supply.
1.
5W-30 engine oil is recommended for all normal driving conditions up to 100~F ambient temperatures except as noted in (2). This oil providesbetter engine starting and faster lubrication to engine components at low temperatures than 10W30 or 15W40 oils. 5W-30 oil also provides betterfuel economy.
2.
SAE 5W-30 and 5W-40 oils are not recommended for use in turbocharged engines, domestic vehicles equipped with the 1.6L engine, nor in trucks(including the Voyager, Caravan & Mini-Ram Van) above 60~F. In addition, these oils are not recommended in cars with 318-4BBL engines atany temperature (police vehicles).
The part numbers for Mopar "Max" oil are:
5W-30 SF/CC (quart)
5W-30 SF/CC (drum)
PN 4318075
PN 4318076
5W-30 oil is now used as the factory fill in most Chrysler Corporation vehicles.
POLICY: Information only
> Engine, Cooling and Exhaust > Engine > Engine Lubrication > Engine Oil > Component Information > Technical Service Bulletins > Page 360
Engine Oil: Specifications
SE, SF, SG Type Gasoline engine ............................................................................................................................................................................................
CAPACITY, Refill:
2-wheel drive:
3.5 Liters 3.7 Quarts 4.5 Liters 4.7 Quarts 2.0-liter eng. ............................................................................................................................................................................2.6-liter eng. ............................................................................................................................................................................
4-wheel drive:
4.5 Liters 4.7 Quarts 5.3 Liters 5.6 Quarts 2.0-liter eng.............................................................................................................................................................................2.6-liter eng.............................................................................................................................................................................
Capacity shown is without filter. When replacing filter, additional oil may be needed
Gasoline engines:1981
1982-84 Above 32F (0C) .........................................................................................................................................................................20W-20, 20W-40, 20W-50Above -10F (-23) .......................................................................................................................................................................10W-30, 10W-40, 10W-50Below 32F (0C) .........................................................................................................................................................................................................5W-40Below 10F (-12C) ................................................................................................................................................................................5W-20, 5-30, 5W-40
Above 32F (0C) .........................................................................................................................................................................20W-20, 20W-40, 20W-50Above -10F (-23) .......................................................................................................................................................................10W-30, 10W-40, 10W-50Below 60F (16C) ...........................................................................................................................................................................5W-20*, 5W-30, 5W-40*Not recommended for sustained high-speed driving
> Engine, Cooling and Exhaust > Engine > Engine Lubrication > Oil Filter, Engine > Component Information > Technical Service Bulletins > Oil Filter - Addition of Second Supplier
Oil Filter: Technical Service BulletinsOil Filter - Addition of Second Supplier
Models
1984 Colt, Vista, Conquest, D-50 Pick-Up Except With Diesel Engines
Subject
Addition of Second Oil Filter Supplier
Index
ENGINE
Date
December 10, 1984
No.
09-12-84Beginning in July, 1984, MMC began using a second supplier for oil filters in production on all car lines except D-50 pick-up trucks equipped withdiesel engines. The alternate filter is identified by PN
MD084963.
For service parts, use the present replacement filter, PN MD031805, as a replacement for either MD084963 or MD031805.
POLICY: Information only
> Engine, Cooling and Exhaust > Engine > Engine Lubrication > Oil Filter Housing > Component Information > Technical Service Bulletins > Oil Filter Bracket & Oil Pump - Modification
Oil Filter Housing: Technical Service BulletinsOil Filter Bracket & Oil Pump - Modification
Models
1984-1987 NF45Z (Colt Vista) & PB (Ram 50) With 2.0L Engine
Subject
Modification of Oil Pump & Oil Filter Bracket
Index
ENGINE
Date
June 29, 1987
No.
09-05-87 (C2-09)
P-2315SYMPTOM/CONDITION
The oil pump gears, oil pump cover, and oil filter bracket assembly for the subject model vehicles have been modified, effective with vehicles producedsince November, 1986, as follows:
1
1
1
1
Rear Wheel Drive - Engine #FC8526 and beyond Front Wheel Drive - Engine #FC8530 and beyond
Following are the replacement parts for servicing these modified oil pumps:
Oil Pump Drive Gear
Oil Pump Driven Gear
Front Case Assembly
Oil Filter Bracket Assembly:
Ram 50
Vista
PN MD096269
PN MD041089
PN MD102415
PN MD122260
PN MD122261
These parts can be used on earlier built engines if both gears, front case assembly, and oil filter bracket assembly are replaced together.
POLICY: Information only
> Engine, Cooling and Exhaust > Engine > Engine Lubrication > Oil Pan, Engine > Component Information > Service and Repair
Oil Pan: Service and Repair
On some models it may be necessary to remove engine from vehicle to gain access to oil pan.
1.
Raise and support vehicle, remove engine splash pan, if equipped, then drain crankcase.
2.
Remove the oil pressure sender unit, if necessary, and on turbocharged models, disconnect oil drain hose and remove oil drain pipe.
3.
Remove the oil pan bolts and oil pan.
4.
Remove oil pump pickup if necessary.
5.
Reverse procedure to install.
> Engine, Cooling and Exhaust > Engine > Engine Lubrication > Oil Pump, Engine > Component Information > Technical Service Bulletins > Oil Filter Bracket & Oil Pump - Modification
Oil Pump: Technical Service BulletinsOil Filter Bracket & Oil Pump - Modification
Models
1984-1987 NF45Z (Colt Vista) & PB (Ram 50) With 2.0L Engine
Subject
Modification of Oil Pump & Oil Filter Bracket
Index
ENGINE
Date
June 29, 1987
No.
09-05-87 (C2-09)
P-2315SYMPTOM/CONDITION
The oil pump gears, oil pump cover, and oil filter bracket assembly for the subject model vehicles have been modified, effective with vehicles producedsince November, 1986, as follows:
1
1
1
1
Rear Wheel Drive - Engine #FC8526 and beyond Front Wheel Drive - Engine #FC8530 and beyond
Following are the replacement parts for servicing these modified oil pumps:
Oil Pump Drive Gear
Oil Pump Driven Gear
Front Case Assembly
Oil Filter Bracket Assembly:
Ram 50
Vista
PN MD096269
PN MD041089
PN MD102415
PN MD122260
PN MD122261
These parts can be used on earlier built engines if both gears, front case assembly, and oil filter bracket assembly are replaced together.
POLICY: Information only
> Engine, Cooling and Exhaust > Engine > Engine Lubrication > Oil Pump, Engine > Component Information > Technical Service Bulletins > Page 376
Oil Pump: Service and Repair
To remove oil pump pickup, refer to ``Oil Pan, Replace.''
Fig. 54 Oil pump assembly. 2000cc engines
The oil pump is of the gear type. The oil pump is also used to drive the left counterbalance shaft. The oil pump drive gear has a sprocket driven by a timing belt. The counterbalance shaft is mounted to the oil pump driven gear and rotates in the opposite direction of crankshaft rotation.
1.
Remove timing case as outlined under ``Timing Case, Replace'' procedure.
2.
Remove oil pump gears and left counterbalance shaft from case.
Fig. 55 Oil pump gear timing marks. 2000cc engines
3.
Install oil pump gear in timing case, aligning timing marks.
4.
Insert left counterbalance shaft into driven gear.
5.
Install timing case.
> Engine, Cooling and Exhaust > Engine > Intake Manifold > Component Information > Specifications
Intake Manifold: Specifications
Intake Manifold 11-14 ft.lb
> Engine, Cooling and Exhaust > Engine > Seals and Gaskets, Engine > Crankshaft Main Bearing Seal > Component Information > Service and Repair
Crankshaft Main Bearing Seal: Service and Repair
Fig. 51 Disassembled view of rear seal
1.
Remove transmission, clutch assembly and flywheel or flex plate, as equipped.
2.
Fig. 51.
Remove rear oil seal case and separate into three parts: oil seal, separator and case,
Fig. 52 Installing rear seal into case
3.
Fig. 52.
Drive in oil seal from inside of case, using suitable tool, Ensure the oil seal plate fits properly in the inner contact surface of the seal case,if equipped.
4.
Install separator with the oil hole facing the bottom of the case, if equipped.
5.
Apply engine oil to oil seal lips.
6.
Install the oil seal case in the cylinder block.
> Engine, Cooling and Exhaust > Engine > Timing Components > Timing Belt > Component Information > Adjustments
Timing Belt: Adjustments
1. Remove timing belt front upper cover.2. Carefully check the timing belt on its whole circumference for cracks and peeling.3. Turn crankshaft in normal direction (clockwise) until timing mark on camshaft sprocket is aligned with mating mark on cylinder head, so that piston in No. 1 cylinder is placed at top dead center on compression stroke.
CAUTION:
Do not turn crankshaft in opposite direction (counterclockwise) to align the timing mark with mating mark, otherwise an improper timing belt tension could result.
Timing Marks
4. Turn crankshaft in normal direction (clockwise) until second tooth past timing mark (punch) position on camshaft sprocket should be aligned with timing mark on cylinder head.
Access Cover Location
Removing Access Cover
5. Remove two access covers. Access cover can be easily removed by inserting screwdriver into groove from direction of embossed arrow and pry.6. Insert wrench through adjusting hole and loosen timing belt tensioner tightening bolt and nut.
CAUTION: 180 to 200 Loosen bolt and nut . If they are loosened more than necessary, they might fall into cover.
7. Insert plain screwdriver from top of timing belt cover. Slightly push tensioner bracket in tensioning direction, and then release. Now belt tension
> Engine, Cooling and Exhaust > Engine > Timing Components > Timing Belt > Component Information > Adjustments > Page 388
D50/Ram 50 L4-1997cc 2.0L SOHC (1984)
will be automatically adjusted by tensile strength of tensioner spring.
CAUTION:
The purpose of pushing tensioner with screwdriver is to loosen tensioner mounting surface which might have stuck due to manyhours of being tightened
8. First tighten tensioner mounting bolt (bottom side) with wrench and then tighten mounting nut (top side).
CAUTION: Make sure that bolt (bottom side) is tightened first. If nut is tightened first, belt tension will vary (will become too tight).
Mounting Access Cover
9. Mount two access covers to respective adjusting holes. Access cover can be easily mounted by sliding in such a way that hook will pass between guide projections.
10. Install timing belt front upper cover.
> Engine, Cooling and Exhaust > Engine > Timing Components > Timing Belt > Component Information > Adjustments > Page 389
Timing Belt: Service and Repair
Timing Belt Train
REMOVAL
Remove the parts in numerical order shown, paying attention to the following items.1. Place piston of No. 1 cylinder at top dead center of compression stroke.
> Engine, Cooling and Exhaust > Engine > Timing Components > Timing Belt > Component Information > Adjustments > Page 390
D50/Ram 50 L4-1997cc 2.0L SOHC (1984)
Securing Tensioner Temporarily
2. Move tensioner fully toward water pump and temporarily secure it.3. If timing belt is to be reused, make an arrow mark which indicates turning direction to ensure that belt is reinstalled in same direction as before.
Preventing Rotation Of Left Silent Shaft
4. When oil pump sprocket nut is removed, first remove plug at left side of cylinder block and insert a screwdriver to keep left silent shaft in position.
8 mm (.3 in.) 60 mm (2.36 in) Screwdriver used for this purpose should have a shaft thick which can be inserted more than .
Removing Timing Belt B
5. Loosen right silent shaft sprocket mounting bolt unit it can be loosened by hand.6. Next, remove tensioner "B" and remove timing belt "B".
CAUTION: After timing belt "B" has been removed, do not attempt loosening bolt, while holding sprocket with pliers, etc.
INSPECTION
1. Check belt in detail if following flaws are evident, replace belt with a new one.
Checking Timing Belt a. Hardened back surface rubber back surface glossy. Nonelastic and so hard that even if a finger nail is forced into it, no mark is produced.
> Engine, Cooling and Exhaust > Engine > Timing Components > Timing Belt > Component Information > Adjustments > Page 391
D50/Ram 50 L4-1997cc 2.0L SOHC (1984)
Checking Timing Belt b. Cracked back surface rubberc. Cracked or exfoliated canvasd. Cracked tooth bottome. Side of belt crackedf.
g. Side of belt badly worn
NOTE: Normal belt should have clear-cut sides as if cut with a sharp knife.
h. Badly worn teeth
Initial stage: Canvas on load side tooth flank worn (fluffy canvas fibers, rubber gone and color changed to white, and unclear canvas texture).Last stage: Canvas on load side tooth flank worn down and rubber exposed (tooth width reduced).
i. Missing tooth.
INSTALLATION
1. Install crankshaft sprocket, flange and spacer as shown, while paying attention to their mounting directions.
CAUTION: Pay special attention to direction of flange. If it is installed in wrong direction, a broken belt could result.
2. Temporarily secure tensioner at a position closest to water pump.3. install end A of spring to predetermined position on tensioner bracket.4. Install end B of spring to predetermined position on water pump.5. When spacer is installed to right silent shaft, direct spacer with its chamfered end toward shaft for protection of oil seal.
BELT INSTALLATION PROCEDURE
Aligning Timing Marks
1. Align timing mark on each sprocket with corresponding timing mark on front case.2. When timing belt "B" is installed, make certain that tension side has no slack.
> Engine, Cooling and Exhaust > Engine > Timing Components > Timing Belt > Component Information > Adjustments > Page 392
D50/Ram 50 L4-1997cc 2.0L SOHC (1984)
Installing Tensioner "B"
3. install tensioner "B" with center of pulley located on left side of mounting bolt and with pulley flange directed toward front of engine.
Adjusting Belt Tension
4. Lift tensioner "B" with finger tip to tighten timing belt "B" so that its tension side will be taut. in this condition tighten bolt to secure tensioner
"B". When bolt is tightened, use care to prevent shaft from turning together. If shaft is turned together, belt will be overtensioned.
specification.
Belt deflection 5 to 7 mm (.2 to .3 in.) ..................................................................................................................................................................................
7. Move tensioner fully toward water pump and temporarily secure tensioner.
5. Check to ensure that timing marks are in alignment.6. Check to ensure that when center of span on tension side is depressed with index finger in direction of arrow, deflection of belt is up to
Mounting Timing Belt
> Engine, Cooling and Exhaust > Engine > Timing Components > Timing Belt > Component Information > Adjustments > Page 393
D50/Ram 50 L4-1997cc 2.0L SOHC (1984)
8. Align timing mark on camshaft sprocket with that on cylinder head.9. Align timing mark on crankshaft sprocket with that on front case.
10. Align timing mark on oil pump sprocket with that on front case.
Preventing Rotation Of Left Silent Shaft
11. When timing mark on oil pump pulley is aligned with that on front case, be sure to remove plug on left side of cylinder block and insert a screw
8 mm (.3 in.) in 60 mm (2.36 in.)
25 mm(1 in.)
60 mm (2.36in.) driver having shaft diameter. If it can be inserted or more, alignment is correct. If it can be inserted only , turn oil pump sprocket through a turn and realign timing marks. Check to ensure that screwdriver can be inserted more than . Keep screw driver inserted until installation of timing belt is finished.
12. Install timing belt. While making sure that tension side of belt is not slackened, install timing belt onto crankshaft sprocket, oil pump sprocket and camshaft sprocket in that order.
13. Loosen tensioner mounting bolt and nut. By so doing, tensioner will be moved by spring and will apply tension to belt.14. Check that portion of belt which is indicated by arrow A to make sure that it is not floating up.15. Tighten tensioner mounting nut and bolt. Tighten slot side bolt before tightening fulcrum side nut. If fulcrum side nut is tightened earlier, tension bracket will be turned together and belt will be overtensioned.
16. Check to ensure that timing marks on all sprockets are in alignment with respective timing marks.17. Turn crankshaft.
CAUTION: Do not turn crankshaft in reverse direction. Crankshaft should be turned smoothly clockwise.
18. Loosen tensioner mounting nut and bolt.19. Tighten tensioner mounting nut and bolt. Be sure to tighten fulcrum side nut and bolt in Step 15.
Adjusting Timing Belt Tension
20. Check to ensure that when center of belt span on tension side and seal line of under cover are held between thumb and forefinger as illustrated, clearance C between belt and seal line is as follows:
Clearance C Approx. 14 mm. (.55 in.) ................................................................................................................................................................................
> Engine, Cooling and Exhaust > Engine > Timing Components > Timing Belt Tensioner > Component Information > Adjustments
Timing Belt Tensioner: Adjustments
Fig. 49 Positioning camshaft sprocket for timing belt adjustment. 1500cc engine, 1600cc & 2000cc engines similar
1. On Colt models, turn steering wheel all the way to left lock, support engine with suitable jack and remove left engine mount bracket to provide clearance to rotate crankshaft.
2. Remove timing belt upper front cover and the spark plugs.3. Rotate crankshaft clockwise (normal direction of rotation) and inspect timing belt. If belt is satisfactory, continue rotating crankshaft until No. 1
Cylinder is at TDC on compression stroke and timing mark on camshaft sprocket is aligned with mark on belt cover or cylinder head.
Fig. 49.
4. Rotate crankshaft clockwise until mark on camshaft sprocket is 2 teeth away from mark on cover or cylinder head, This causes spring
Do not rotate crankshaft counterclockwise, as belt tension willbe adversely affected. pressure of No. 2 exhaust valve to apply specific tension to tension timing belt.
5. Remove accessory drive belts and pulleys as needed, then the two adjusting port covers, inserting a screwdriver into slot on timing belt cover and prying timing port covers off.
Do not loosen bolt or nut more than 3/4 6. Insert 14 mm socket through adjusting port, loosen timing belt tensioner nut and bolt 1/2 - 3/4 turn. turn, as fastener may fall out into cover .
7. Check to ensure that tensioner is not sticking, by inserting a screwdriver through opening on top of lower timing belt cover and pushing tensioner toward timing belt. Release tensioner and remove screwdriver. Spring tension of the timing belt tensioner will automatically adjust the timing belt.
8. Tighten tensioner adjuster bolt, then the pivot bolt. Always tighten slotted adjuster bolt or nut first to prevent tensioner from rotating out of position.
9. Install adjusting port covers, then install timing belt upper front cover.
> Engine, Cooling and Exhaust > Engine > Timing Components > Timing Cover > Component Information > Service and Repair
Timing Cover: Service and Repair
1.
Remove timing belt as described under ``Timing Belt, Replace.''
2.
Remove camshaft sprocket, crankshaft sprocket and flange.
3.
Remove timing belt tensioner.
Fig. 32 Locking left silent shaft. 2000cc engines
4.
Fig. 32.
Remove oil pump sprocket. When the oil pump sprocket nut is removed, first remove plug at bottom of left side of cylinder block, then insert asuitable screwdriver to keep the left counterbalance shaft in position,
Fig. 33 Silent shaft timing belt (B) & tensioner. 2000cc engines
5.
Fig. 33, Loosen counterbalance shaft sprocket mounting bolt then remove tensioner ``B,'' and timing belt ``B.''
6.
Fig. 33, Remove crankshaft sprocket ``B,'' and the counterbalance shaft sprocket.
7.
Remove timing belt upper under and lower under covers.
8.
Remove water pump.
9.
Remove cylinder head assembly.
10.
Remove oil pan, oil screen and oil pump cover.
> Engine, Cooling and Exhaust > Engine > Timing Components > Timing Cover > Component Information > Service and Repair > Page 400
D50/Ram 50 L4-1997cc 2.0L SOHC (1984)
Fig. 34 Oil pump driven gear removal. 2000cc engines
11.
Fig. 34.
Insert a screwdriver through plug hole in left side of cylinder block to hold counterbalance shaft in position, then loosen oil pump driven gearmounting bolt,
12.
Remove timing case with left counterbalance shaft attached.
13.
Reverse procedure to install. Refer to ``Timing Belt or Chain, Replace'' procedure for timing belt installation.
> Engine, Cooling and Exhaust > Engine > Tune-up and Engine Performance Checks > Fuel Pressure > System Information > Specifications
> Engine, Cooling and Exhaust > Engine > Tune-up and Engine Performance Checks > Air/Fuel Mixture > System Information > Technical Service Bulletins > By Symptom for Air/Fuel Mixture: > 140884 > Jan > 84 > Propane
Idle Set - Procedure
Air/Fuel Mixture: By SymptomPropane Idle Set - Procedure
Models
1984 MMC Import Vehicles All With Gasoline Fueled Engines, All Emission Markets (Except Vehicles With Turbo Chargers & Canada)
Subject
Propane Idle Set Procedure
Index
FUEL
Date
January 17, 1984
No..
14-08-84
P-94-C
The propane idle set procedure is authorized for 1984 subject model import vehicles.
The propane idle set method is to be used when "CO" meter procedure cannot be used, i.e., "CO" meter in for repair or is not available in the servicearea.
PROPANE IDLE CHECK & SET PROCEDURE
1.
Idle Setting Conditions: Lights, electric cooling fan, and all accessories are off, transmission in neutral, and front wheels in straight ahead position.
2.
If engine is cold, allow it to warm up until full operating temperature is reached (185 to 205~F).
NOTE:
PERFORM THE FOLLOWING STEPS 3 THROUGH 5 AND STEP 19 ONLY IF ENGINE IS EQUIPPED WITH A FEEDBACKCARBURETOR EMISSION SYSTEM.
3.
Turn off ignition switch.
4.
Disconnect the NEGATIVE cable from the battery for about 5 seconds. Then reconnect negative battery cable.
5.
Disconnect the connector of the exhaust oxygen sensor.
6.
Start and run engine for 5 seconds at an engine speed between 2,000 to 3,000 rpm.
7.
Then, allow engine to run at curb idle for 2 minutes.
> Engine, Cooling and Exhaust > Engine > Tune-up and Engine Performance Checks > Air/Fuel Mixture > System Information > Technical Service Bulletins > By Symptom for Air/Fuel Mixture: > 140884 > Jan > 84 > Propane Idle Set - Procedure > Page 413
D50/Ram 50 L4-1997cc 2.0L SOHC (1984)
FIGURE 1
8.
Check engine idle speed and basic ignition timing. Adjust to specifications if necessary (Figure 1).
9.
Disconnect the air cleaner fresh air intake duct from the air cleaner snorkel.
Insert the propane supply hose into the air cleaner snorkel about 4 inches.
Make certain both valves on propane bottle are fully closed and the bottle is upright and in a safe location.
> Engine, Cooling and Exhaust > Engine > Tune-up and Engine Performance Checks > Air/Fuel Mixture > System Information > Technical Service Bulletins > By Symptom for Air/Fuel Mixture: > 140884 > Jan > 84 > Propane Idle Set - Procedure > Page 414
D50/Ram 50 L4-1997cc 2.0L SOHC (1984)
FIGURE 3
10.
Open the propane bottle main valve fully, then slowly open the propane fine control valve to the position where maximum engine rpm is achieved.(Too much propane or too rich idle mixture will cause the engine to lose rpm as the fine control valve is opened.) (Figure 3.)
FIGURE 2
> Engine, Cooling and Exhaust > Engine > Tune-up and Engine Performance Checks > Air/Fuel Mixture > System Information > Technical Service Bulletins > By Symptom for Air/Fuel Mixture: > 140884 > Jan > 84 > Propane Idle Set - Procedure > Page 415
D50/Ram 50 L4-1997cc 2.0L SOHC (1984)
Note the engine rpm increase. Specified values of each engine propane idle speed increase are outlined in Figure 2.
If the propane idle speed exceeds more than 25 rpm from the specified value in Figure 2 or the rpm does not increase at all, idle fuel mixtureshould be adjusted according to the propane assisted idle set procedure that follows.
FIGURE 4
11.
It is not necessary to remove carburetor from intake manifold to remove the idle mixture screw plug.
Drill out concealment plug on car. Remove vacuum connector from high altitude compensator (HAC) fittings on carburetor air horn (Figure 4).
Use a 1/4" diameter drill 8' long at the 11 o'clock position on the plug boss. Locate drill point 3/16" from end of boss.
Plug should pop out when the drill bit contacts it (Figure 4).
12.
Start engine and run for 1 minute at engine speed of 2500 rpm.
13.
Run engine at idle for 2 minutes.
> Engine, Cooling and Exhaust > Engine > Tune-up and Engine Performance Checks > Air/Fuel Mixture > System Information > Technical Service Bulletins > By Symptom for Air/Fuel Mixture: > 140884 > Jan > 84 > Propane Idle Set - Procedure > Page 416
D50/Ram 50 L4-1997cc 2.0L SOHC (1984)
FIGURE 2
14.
Open the propane main valve and slowly open the fine control valve to the position where maximum engine speed is achieved. Use the idle speedadjusting screw to set the specified propane idle speed from Figure 2.
15.
Turn off propane main valve and adjust idle mixture screw to the specified idle set speed from Figure 2.
16.
17.
To recheck the maximum propane speed, open the main propane valve again. If the speed still differs more than 25 rpm from the specified propanespeed from Figure 2, repeat Steps 14 through 16.
18.
Remove the propane hose and replace fresh air duct on air cleaner snorkel.
19.
Reconnect the exhaust oxygen sensor (if engine is equipped with a feedback carburetor).
20.
Install Idle Mixture Screw Concealment Plug. (If new plug is needed, use PN MD606954.)
POLICY: Reimbursable within the provisions of the warranty
> Engine, Cooling and Exhaust > Engine > Tune-up and Engine Performance Checks > Air/Fuel Mixture > System Information > Technical Service Bulletins > By Symptom for Air/Fuel Mixture: > 140884 > Jan > 84 > Propane Idle Set - Procedure > Page 417
D50/Ram 50 L4-1997cc 2.0L SOHC (1984)
FRONT WHEEL DRIVE LABOR OPERATION TIME SCHEDULE
FAILURE CODE: RO - Driveability
> Engine, Cooling and Exhaust > Engine > Tune-up and Engine Performance Checks > Air/Fuel Mixture > System Information > Technical Service Bulletins > All Technical Service Bulletins for Air/Fuel Mixture: > 140884 >
Jan > 84 > Propane Idle Set - Procedure
Air/Fuel Mixture: All Technical Service BulletinsPropane Idle Set - Procedure
Models
1984 MMC Import Vehicles All With Gasoline Fueled Engines, All Emission Markets (Except Vehicles With Turbo Chargers & Canada)
Subject
Propane Idle Set Procedure
Index
FUEL
Date
January 17, 1984
No..
14-08-84
P-94-C
The propane idle set procedure is authorized for 1984 subject model import vehicles.
The propane idle set method is to be used when "CO" meter procedure cannot be used, i.e., "CO" meter in for repair or is not available in the servicearea.
PROPANE IDLE CHECK & SET PROCEDURE
1.
Idle Setting Conditions: Lights, electric cooling fan, and all accessories are off, transmission in neutral, and front wheels in straight ahead position.
2.
If engine is cold, allow it to warm up until full operating temperature is reached (185 to 205~F).
NOTE:
PERFORM THE FOLLOWING STEPS 3 THROUGH 5 AND STEP 19 ONLY IF ENGINE IS EQUIPPED WITH A FEEDBACKCARBURETOR EMISSION SYSTEM.
3.
Turn off ignition switch.
4.
Disconnect the NEGATIVE cable from the battery for about 5 seconds. Then reconnect negative battery cable.
5.
Disconnect the connector of the exhaust oxygen sensor.
6.
Start and run engine for 5 seconds at an engine speed between 2,000 to 3,000 rpm.
7.
Then, allow engine to run at curb idle for 2 minutes.
> Engine, Cooling and Exhaust > Engine > Tune-up and Engine Performance Checks > Air/Fuel Mixture > System Information > Technical Service Bulletins > All Technical
Service Bulletins for Air/Fuel Mixture: > 140884 > Jan > 84 > Propane Idle Set - Procedure > Page 423
D50/Ram 50 L4-1997cc 2.0L SOHC (1984)
FIGURE 1
8.
Check engine idle speed and basic ignition timing. Adjust to specifications if necessary (Figure 1).
9.
Disconnect the air cleaner fresh air intake duct from the air cleaner snorkel.
Insert the propane supply hose into the air cleaner snorkel about 4 inches.
Make certain both valves on propane bottle are fully closed and the bottle is upright and in a safe location.
> Engine, Cooling and Exhaust > Engine > Tune-up and Engine Performance Checks > Air/Fuel Mixture > System Information > Technical Service Bulletins > All Technical
Service Bulletins for Air/Fuel Mixture: > 140884 > Jan > 84 > Propane Idle Set - Procedure > Page 424
D50/Ram 50 L4-1997cc 2.0L SOHC (1984)
FIGURE 3
10.
Open the propane bottle main valve fully, then slowly open the propane fine control valve to the position where maximum engine rpm is achieved.(Too much propane or too rich idle mixture will cause the engine to lose rpm as the fine control valve is opened.) (Figure 3.)
FIGURE 2
> Engine, Cooling and Exhaust > Engine > Tune-up and Engine Performance Checks > Air/Fuel Mixture > System Information > Technical Service Bulletins > All Technical
Service Bulletins for Air/Fuel Mixture: > 140884 > Jan > 84 > Propane Idle Set - Procedure > Page 425
D50/Ram 50 L4-1997cc 2.0L SOHC (1984)
Note the engine rpm increase. Specified values of each engine propane idle speed increase are outlined in Figure 2.
If the propane idle speed exceeds more than 25 rpm from the specified value in Figure 2 or the rpm does not increase at all, idle fuel mixtureshould be adjusted according to the propane assisted idle set procedure that follows.
FIGURE 4
11.
It is not necessary to remove carburetor from intake manifold to remove the idle mixture screw plug.
Drill out concealment plug on car. Remove vacuum connector from high altitude compensator (HAC) fittings on carburetor air horn (Figure 4).
Use a 1/4" diameter drill 8' long at the 11 o'clock position on the plug boss. Locate drill point 3/16" from end of boss.
Plug should pop out when the drill bit contacts it (Figure 4).
12.
Start engine and run for 1 minute at engine speed of 2500 rpm.
13.
Run engine at idle for 2 minutes.
> Engine, Cooling and Exhaust > Engine > Tune-up and Engine Performance Checks > Air/Fuel Mixture > System Information > Technical Service Bulletins > All Technical
Service Bulletins for Air/Fuel Mixture: > 140884 > Jan > 84 > Propane Idle Set - Procedure > Page 426
D50/Ram 50 L4-1997cc 2.0L SOHC (1984)
FIGURE 2
14.
Open the propane main valve and slowly open the fine control valve to the position where maximum engine speed is achieved. Use the idle speedadjusting screw to set the specified propane idle speed from Figure 2.
15.
Turn off propane main valve and adjust idle mixture screw to the specified idle set speed from Figure 2.
16.
17.
To recheck the maximum propane speed, open the main propane valve again. If the speed still differs more than 25 rpm from the specified propanespeed from Figure 2, repeat Steps 14 through 16.
18.
Remove the propane hose and replace fresh air duct on air cleaner snorkel.
19.
Reconnect the exhaust oxygen sensor (if engine is equipped with a feedback carburetor).
20.
Install Idle Mixture Screw Concealment Plug. (If new plug is needed, use PN MD606954.)
POLICY: Reimbursable within the provisions of the warranty
> Engine, Cooling and Exhaust > Engine > Tune-up and Engine Performance Checks > Air/Fuel Mixture > System Information > Technical Service Bulletins > All Technical
Service Bulletins for Air/Fuel Mixture: > 140884 > Jan > 84 > Propane Idle Set - Procedure > Page 427
D50/Ram 50 L4-1997cc 2.0L SOHC (1984)
FRONT WHEEL DRIVE LABOR OPERATION TIME SCHEDULE
FAILURE CODE: RO - Driveability
> Engine, Cooling and Exhaust > Engine > Tune-up and Engine Performance Checks > Idle Speed > System Information > Technical Service Bulletins > By Symptom: > 140884 > Jan > 84 > Propane Idle Set - Procedure
Idle Speed: By SymptomPropane Idle Set - Procedure
Models
1984 MMC Import Vehicles All With Gasoline Fueled Engines, All Emission Markets (Except Vehicles With Turbo Chargers & Canada)
Subject
Propane Idle Set Procedure
Index
FUEL
Date
January 17, 1984
No..
14-08-84
P-94-C
The propane idle set procedure is authorized for 1984 subject model import vehicles.
The propane idle set method is to be used when "CO" meter procedure cannot be used, i.e., "CO" meter in for repair or is not available in the servicearea.
PROPANE IDLE CHECK & SET PROCEDURE
1.
Idle Setting Conditions: Lights, electric cooling fan, and all accessories are off, transmission in neutral, and front wheels in straight ahead position.
2.
If engine is cold, allow it to warm up until full operating temperature is reached (185 to 205~F).
NOTE:
PERFORM THE FOLLOWING STEPS 3 THROUGH 5 AND STEP 19 ONLY IF ENGINE IS EQUIPPED WITH A FEEDBACKCARBURETOR EMISSION SYSTEM.
3.
Turn off ignition switch.
4.
Disconnect the NEGATIVE cable from the battery for about 5 seconds. Then reconnect negative battery cable.
5.
Disconnect the connector of the exhaust oxygen sensor.
6.
Start and run engine for 5 seconds at an engine speed between 2,000 to 3,000 rpm.
7.
Then, allow engine to run at curb idle for 2 minutes.
> Engine, Cooling and Exhaust > Engine > Tune-up and Engine Performance Checks > Idle Speed > System Information > Technical Service Bulletins > By Symptom: >
140884 > Jan > 84 > Propane Idle Set - Procedure > Page 436
D50/Ram 50 L4-1997cc 2.0L SOHC (1984)
FIGURE 1
8.
Check engine idle speed and basic ignition timing. Adjust to specifications if necessary (Figure 1).
9.
Disconnect the air cleaner fresh air intake duct from the air cleaner snorkel.
Insert the propane supply hose into the air cleaner snorkel about 4 inches.
Make certain both valves on propane bottle are fully closed and the bottle is upright and in a safe location.
> Engine, Cooling and Exhaust > Engine > Tune-up and Engine Performance Checks > Idle Speed > System Information > Technical Service Bulletins > By Symptom: >
140884 > Jan > 84 > Propane Idle Set - Procedure > Page 437
D50/Ram 50 L4-1997cc 2.0L SOHC (1984)
FIGURE 3
10.
Open the propane bottle main valve fully, then slowly open the propane fine control valve to the position where maximum engine rpm is achieved.(Too much propane or too rich idle mixture will cause the engine to lose rpm as the fine control valve is opened.) (Figure 3.)
FIGURE 2
> Engine, Cooling and Exhaust > Engine > Tune-up and Engine Performance Checks > Idle Speed > System Information > Technical Service Bulletins > By Symptom: >
140884 > Jan > 84 > Propane Idle Set - Procedure > Page 438
D50/Ram 50 L4-1997cc 2.0L SOHC (1984)
Note the engine rpm increase. Specified values of each engine propane idle speed increase are outlined in Figure 2.
If the propane idle speed exceeds more than 25 rpm from the specified value in Figure 2 or the rpm does not increase at all, idle fuel mixtureshould be adjusted according to the propane assisted idle set procedure that follows.
FIGURE 4
11.
It is not necessary to remove carburetor from intake manifold to remove the idle mixture screw plug.
Drill out concealment plug on car. Remove vacuum connector from high altitude compensator (HAC) fittings on carburetor air horn (Figure 4).
Use a 1/4" diameter drill 8' long at the 11 o'clock position on the plug boss. Locate drill point 3/16" from end of boss.
Plug should pop out when the drill bit contacts it (Figure 4).
12.
Start engine and run for 1 minute at engine speed of 2500 rpm.
13.
Run engine at idle for 2 minutes.
> Engine, Cooling and Exhaust > Engine > Tune-up and Engine Performance Checks > Idle Speed > System Information > Technical Service Bulletins > By Symptom: >
140884 > Jan > 84 > Propane Idle Set - Procedure > Page 439
D50/Ram 50 L4-1997cc 2.0L SOHC (1984)
FIGURE 2
14.
Open the propane main valve and slowly open the fine control valve to the position where maximum engine speed is achieved. Use the idle speedadjusting screw to set the specified propane idle speed from Figure 2.
15.
Turn off propane main valve and adjust idle mixture screw to the specified idle set speed from Figure 2.
16.
17.
To recheck the maximum propane speed, open the main propane valve again. If the speed still differs more than 25 rpm from the specified propanespeed from Figure 2, repeat Steps 14 through 16.
18.
Remove the propane hose and replace fresh air duct on air cleaner snorkel.
19.
Reconnect the exhaust oxygen sensor (if engine is equipped with a feedback carburetor).
20.
Install Idle Mixture Screw Concealment Plug. (If new plug is needed, use PN MD606954.)
POLICY: Reimbursable within the provisions of the warranty
> Engine, Cooling and Exhaust > Engine > Tune-up and Engine Performance Checks > Idle Speed > System Information > Technical Service Bulletins > By Symptom: >
140884 > Jan > 84 > Propane Idle Set - Procedure > Page 440
D50/Ram 50 L4-1997cc 2.0L SOHC (1984)
FRONT WHEEL DRIVE LABOR OPERATION TIME SCHEDULE
FAILURE CODE: RO - Driveability
> Engine, Cooling and Exhaust > Engine > Tune-up and Engine Performance Checks > Idle Speed > System Information > Technical Service Bulletins > All Technical Service Bulletins for Idle Speed: > 142084 > May > 84 >
Engine Specifications - Manual Corrections
Idle Speed: All Technical Service BulletinsEngine Specifications - Manual Corrections
Models
1984 Colt, Ram 50, & Conquest
Subject
Correction of 1984 Service Manuals on Engine Specifications
Index
FUEL
Date
May 21, 1984
No..
14-20-84
P-2112-C
This service bulletin is issued to correct the following 1984 Import Service Manuals.
^ Colt Service Manual Publication #81-270-4006
> Engine, Cooling and Exhaust > Engine > Tune-up and Engine Performance Checks > Idle Speed > System Information > Technical Service Bulletins > All Technical
Service Bulletins for Idle Speed: > 142084 > May > 84 > Engine Specifications - Manual Corrections > Page 446
D50/Ram 50 L4-1997cc 2.0L SOHC (1984)
^ Ram-50 Service Manual Publication #81-370-4009
^ Conquest Service Manual Publication #81-270-4005
Corrections are highlighted in the attached specifications in bold type and should be entered in the respective model service manual.
POLICY: Information only
> Engine, Cooling and Exhaust > Engine > Tune-up and Engine Performance Checks > Idle Speed > System Information > Technical Service Bulletins > All Technical Service Bulletins for Idle Speed: > 141984 > May > 84 >
Carburetor - Idle Speed Adjustment on A/C Install
Idle Speed: All Technical Service BulletinsCarburetor - Idle Speed Adjustment on A/C Install
Models
1984 Colt (W/O Turbo), Ram-50, Power Ram-50 (W/O Diesel) & Colt Vista
Subject
Idle-Up Speed Adjustment After Air Conditioning Installation and/or Service
Index
FUEL
Date
May 7, 1984
No.
14-19-84
P-1927-CThis procedure modifies the adjustment procedures in the subject model service manuals.
If difficulty is encountered in adjusting curb idle speed and/or idle-up speed after installation or servicing and adjustment of the air conditioning system,follow the adjustment procedure as outlined below:
ADJUSTMENT PROCEDURE
1.
Thoroughly warm up engine, turn off all accessories, front wheels in straight ahead position, transmission in neutral, parking brake set, andradiator cooling fan stopped.
FIGURE 1
> Engine, Cooling and Exhaust > Engine > Tune-up and Engine Performance Checks > Idle Speed > System Information > Technical Service Bulletins > All Technical
Service Bulletins for Idle Speed: > 141984 > May > 84 > Carburetor - Idle Speed Adjustment on A/C Install > Page 451
D50/Ram 50 L4-1997cc 2.0L SOHC (1984)
FIGURE 2
2.
Check and adjust curb idle speed if necessary (see Figure 1 for specification) and make adjustment using SAS (speed adjusting screw) 1 (Figure2). On some models installation of air conditioner will change the curb idle speed already adjusted.
FIGURE 2
3.
Back off the idle-up speed adjusting screw for air conditioner one turn from fully tightened position (Figure 2).
4.
Lift the free lever by hand until it touches SAS 3 and record the engine speed ("N" = R.P.M.) obtained at this time (Figure 2).
> Engine, Cooling and Exhaust > Engine > Tune-up and Engine Performance Checks > Idle Speed > System Information > Technical Service Bulletins > All Technical
Service Bulletins for Idle Speed: > 141984 > May > 84 > Carburetor - Idle Speed Adjustment on A/C Install > Page 452
D50/Ram 50 L4-1997cc 2.0L SOHC (1984)
FIGURE 1
FIGURE 2
5.. Turn on air conditioner switch. Adjust the idle-up speed while compressor is running to the specified rpm (Figure 1) by turning SAS 2 (Figure 2).When making this adjustment, be sure to record the turning direction and slot angle of SAS 2.
FIGURE 1
6.
Turn off air conditioner switch and make sure that the specified curb idle rpm is obtained (Figure 1).
7.
Race the engine at a speed of about 2000 rpm for five seconds.
8.
Turn on and then off the air conditioning switch repeatedly several times and make sure that with the compressor running that the engine is running
> Engine, Cooling and Exhaust > Engine > Tune-up and Engine Performance Checks > Idle Speed > System Information > Technical Service Bulletins > All Technical
Service Bulletins for Idle Speed: > 141984 > May > 84 > Carburetor - Idle Speed Adjustment on A/C Install > Page 453
D50/Ram 50 L4-1997cc 2.0L SOHC (1984)
at the specified idle-up rpm (Figure 1).
Example:
FIGURE 2
If Sas 2 has been turned 180~ clockwise in Step 5, SAS 3 will be turned 360~ clockwise in Step 9. Then, lift thefree lever by hand until it touches SAS 3 and make sure that the engine rpm is "N" +/- 100 rpm (where "N" is therpm recorded in Step 4). If necessary, adjust using SAS 3.
FIGURE 2
SIMPLE ADJUSTMENT PROCEDURE FOR COLT VISTA ONLY
If the idle adjustment has been properly made before installation of the air conditioner, the following simple procedure may be used:
1.
Give one clockwise turn to SAS 2 (Figure 2).
2.
Give two clockwise turns to SAS 3 (Figure 2).
3.
Back off idle-up speed adjusting screw for air conditioner one turn from fully tightened position (Figure 2).
> Engine, Cooling and Exhaust > Engine > Tune-up and Engine Performance Checks > Idle Speed > System Information > Technical Service Bulletins > All Technical
Service Bulletins for Idle Speed: > 141984 > May > 84 > Carburetor - Idle Speed Adjustment on A/C Install > Page 454
D50/Ram 50 L4-1997cc 2.0L SOHC (1984)
FIGURE 1
4.
Lastly, make sure that the curb idle speed and idle-up speed are properly adjusted (Figure 1).
FIGURE 2
If necessary, make fine adjustments with SAS 2 and SAS 3 (Figure 2).
POLICY: Reimbursable within the provisions of the warranty
FAILURE CODE: 31 - Rough Idle
> Engine, Cooling and Exhaust > Engine > Tune-up and Engine Performance Checks > Idle Speed > System Information > Technical Service Bulletins > All Technical Service Bulletins for Idle Speed: > 140884 > Jan > 84 >
Propane Idle Set - Procedure
Idle Speed: All Technical Service BulletinsPropane Idle Set - Procedure
Models
1984 MMC Import Vehicles All With Gasoline Fueled Engines, All Emission Markets (Except Vehicles With Turbo Chargers & Canada)
Subject
Propane Idle Set Procedure
Index
FUEL
Date
January 17, 1984
No..
14-08-84
P-94-C
The propane idle set procedure is authorized for 1984 subject model import vehicles.
The propane idle set method is to be used when "CO" meter procedure cannot be used, i.e., "CO" meter in for repair or is not available in the servicearea.
PROPANE IDLE CHECK & SET PROCEDURE
1.
Idle Setting Conditions: Lights, electric cooling fan, and all accessories are off, transmission in neutral, and front wheels in straight ahead position.
2.
If engine is cold, allow it to warm up until full operating temperature is reached (185 to 205~F).
NOTE:
PERFORM THE FOLLOWING STEPS 3 THROUGH 5 AND STEP 19 ONLY IF ENGINE IS EQUIPPED WITH A FEEDBACKCARBURETOR EMISSION SYSTEM.
3.
Turn off ignition switch.
4.
Disconnect the NEGATIVE cable from the battery for about 5 seconds. Then reconnect negative battery cable.
5.
Disconnect the connector of the exhaust oxygen sensor.
6.
Start and run engine for 5 seconds at an engine speed between 2,000 to 3,000 rpm.
7.
Then, allow engine to run at curb idle for 2 minutes.
> Engine, Cooling and Exhaust > Engine > Tune-up and Engine Performance Checks > Idle Speed > System Information > Technical Service Bulletins > All Technical
Service Bulletins for Idle Speed: > 140884 > Jan > 84 > Propane Idle Set - Procedure > Page 459
D50/Ram 50 L4-1997cc 2.0L SOHC (1984)
FIGURE 1
8.
Check engine idle speed and basic ignition timing. Adjust to specifications if necessary (Figure 1).
9.
Disconnect the air cleaner fresh air intake duct from the air cleaner snorkel.
Insert the propane supply hose into the air cleaner snorkel about 4 inches.
Make certain both valves on propane bottle are fully closed and the bottle is upright and in a safe location.
> Engine, Cooling and Exhaust > Engine > Tune-up and Engine Performance Checks > Idle Speed > System Information > Technical Service Bulletins > All Technical
Service Bulletins for Idle Speed: > 140884 > Jan > 84 > Propane Idle Set - Procedure > Page 460
D50/Ram 50 L4-1997cc 2.0L SOHC (1984)
FIGURE 3
10.
Open the propane bottle main valve fully, then slowly open the propane fine control valve to the position where maximum engine rpm is achieved.(Too much propane or too rich idle mixture will cause the engine to lose rpm as the fine control valve is opened.) (Figure 3.)
FIGURE 2
> Engine, Cooling and Exhaust > Engine > Tune-up and Engine Performance Checks > Idle Speed > System Information > Technical Service Bulletins > All Technical
Service Bulletins for Idle Speed: > 140884 > Jan > 84 > Propane Idle Set - Procedure > Page 461
D50/Ram 50 L4-1997cc 2.0L SOHC (1984)
Note the engine rpm increase. Specified values of each engine propane idle speed increase are outlined in Figure 2.
If the propane idle speed exceeds more than 25 rpm from the specified value in Figure 2 or the rpm does not increase at all, idle fuel mixtureshould be adjusted according to the propane assisted idle set procedure that follows.
FIGURE 4
11.
It is not necessary to remove carburetor from intake manifold to remove the idle mixture screw plug.
Drill out concealment plug on car. Remove vacuum connector from high altitude compensator (HAC) fittings on carburetor air horn (Figure 4).
Use a 1/4" diameter drill 8' long at the 11 o'clock position on the plug boss. Locate drill point 3/16" from end of boss.
Plug should pop out when the drill bit contacts it (Figure 4).
12.
Start engine and run for 1 minute at engine speed of 2500 rpm.
13.
Run engine at idle for 2 minutes.
> Engine, Cooling and Exhaust > Engine > Tune-up and Engine Performance Checks > Idle Speed > System Information > Technical Service Bulletins > All Technical
Service Bulletins for Idle Speed: > 140884 > Jan > 84 > Propane Idle Set - Procedure > Page 462
D50/Ram 50 L4-1997cc 2.0L SOHC (1984)
FIGURE 2
14.
Open the propane main valve and slowly open the fine control valve to the position where maximum engine speed is achieved. Use the idle speedadjusting screw to set the specified propane idle speed from Figure 2.
15.
Turn off propane main valve and adjust idle mixture screw to the specified idle set speed from Figure 2.
16.
17.
To recheck the maximum propane speed, open the main propane valve again. If the speed still differs more than 25 rpm from the specified propanespeed from Figure 2, repeat Steps 14 through 16.
18.
Remove the propane hose and replace fresh air duct on air cleaner snorkel.
19.
Reconnect the exhaust oxygen sensor (if engine is equipped with a feedback carburetor).
20.
Install Idle Mixture Screw Concealment Plug. (If new plug is needed, use PN MD606954.)
POLICY: Reimbursable within the provisions of the warranty
> Engine, Cooling and Exhaust > Engine > Tune-up and Engine Performance Checks > Idle Speed > System Information > Technical Service Bulletins > All Technical
Service Bulletins for Idle Speed: > 140884 > Jan > 84 > Propane Idle Set - Procedure > Page 463
D50/Ram 50 L4-1997cc 2.0L SOHC (1984)
FRONT WHEEL DRIVE LABOR OPERATION TIME SCHEDULE
FAILURE CODE: RO - Driveability
> Engine, Cooling and Exhaust > Engine > Tune-up and Engine Performance Checks > Idle Speed > System Information > Technical Service Bulletins > All Other Service Bulletins for Idle Speed: > 142084 > May > 84 >
Engine Specifications - Manual Corrections
Idle Speed: All Technical Service BulletinsEngine Specifications - Manual Corrections
Models
1984 Colt, Ram 50, & Conquest
Subject
Correction of 1984 Service Manuals on Engine Specifications
Index
FUEL
Date
May 21, 1984
No..
14-20-84
P-2112-C
This service bulletin is issued to correct the following 1984 Import Service Manuals.
^ Colt Service Manual Publication #81-270-4006
> Engine, Cooling and Exhaust > Engine > Tune-up and Engine Performance Checks > Idle Speed > System Information > Technical Service Bulletins > All Other Service
Bulletins for Idle Speed: > 142084 > May > 84 > Engine Specifications - Manual Corrections > Page 469
D50/Ram 50 L4-1997cc 2.0L SOHC (1984)
^ Ram-50 Service Manual Publication #81-370-4009
^ Conquest Service Manual Publication #81-270-4005
Corrections are highlighted in the attached specifications in bold type and should be entered in the respective model service manual.
POLICY: Information only
> Engine, Cooling and Exhaust > Engine > Tune-up and Engine Performance Checks > Idle Speed > System Information > Technical Service Bulletins > All Other Service Bulletins for Idle Speed: > 141984 > May > 84 >
Carburetor - Idle Speed Adjustment on A/C Install
Idle Speed: All Technical Service BulletinsCarburetor - Idle Speed Adjustment on A/C Install
Models
1984 Colt (W/O Turbo), Ram-50, Power Ram-50 (W/O Diesel) & Colt Vista
Subject
Idle-Up Speed Adjustment After Air Conditioning Installation and/or Service
Index
FUEL
Date
May 7, 1984
No.
14-19-84
P-1927-CThis procedure modifies the adjustment procedures in the subject model service manuals.
If difficulty is encountered in adjusting curb idle speed and/or idle-up speed after installation or servicing and adjustment of the air conditioning system,follow the adjustment procedure as outlined below:
ADJUSTMENT PROCEDURE
1.
Thoroughly warm up engine, turn off all accessories, front wheels in straight ahead position, transmission in neutral, parking brake set, andradiator cooling fan stopped.
FIGURE 1
> Engine, Cooling and Exhaust > Engine > Tune-up and Engine Performance Checks > Idle Speed > System Information > Technical Service Bulletins > All Other Service
Bulletins for Idle Speed: > 141984 > May > 84 > Carburetor - Idle Speed Adjustment on A/C Install > Page 474
D50/Ram 50 L4-1997cc 2.0L SOHC (1984)
FIGURE 2
2.
Check and adjust curb idle speed if necessary (see Figure 1 for specification) and make adjustment using SAS (speed adjusting screw) 1 (Figure2). On some models installation of air conditioner will change the curb idle speed already adjusted.
FIGURE 2
3.
Back off the idle-up speed adjusting screw for air conditioner one turn from fully tightened position (Figure 2).
4.
Lift the free lever by hand until it touches SAS 3 and record the engine speed ("N" = R.P.M.) obtained at this time (Figure 2).
> Engine, Cooling and Exhaust > Engine > Tune-up and Engine Performance Checks > Idle Speed > System Information > Technical Service Bulletins > All Other Service
Bulletins for Idle Speed: > 141984 > May > 84 > Carburetor - Idle Speed Adjustment on A/C Install > Page 475
D50/Ram 50 L4-1997cc 2.0L SOHC (1984)
FIGURE 1
FIGURE 2
5.. Turn on air conditioner switch. Adjust the idle-up speed while compressor is running to the specified rpm (Figure 1) by turning SAS 2 (Figure 2).When making this adjustment, be sure to record the turning direction and slot angle of SAS 2.
FIGURE 1
6.
Turn off air conditioner switch and make sure that the specified curb idle rpm is obtained (Figure 1).
7.
Race the engine at a speed of about 2000 rpm for five seconds.
8.
Turn on and then off the air conditioning switch repeatedly several times and make sure that with the compressor running that the engine is running
> Engine, Cooling and Exhaust > Engine > Tune-up and Engine Performance Checks > Idle Speed > System Information > Technical Service Bulletins > All Other Service
Bulletins for Idle Speed: > 141984 > May > 84 > Carburetor - Idle Speed Adjustment on A/C Install > Page 476
D50/Ram 50 L4-1997cc 2.0L SOHC (1984)
at the specified idle-up rpm (Figure 1).
Example:
FIGURE 2
If Sas 2 has been turned 180~ clockwise in Step 5, SAS 3 will be turned 360~ clockwise in Step 9. Then, lift thefree lever by hand until it touches SAS 3 and make sure that the engine rpm is "N" +/- 100 rpm (where "N" is therpm recorded in Step 4). If necessary, adjust using SAS 3.
FIGURE 2
SIMPLE ADJUSTMENT PROCEDURE FOR COLT VISTA ONLY
If the idle adjustment has been properly made before installation of the air conditioner, the following simple procedure may be used:
1.
Give one clockwise turn to SAS 2 (Figure 2).
2.
Give two clockwise turns to SAS 3 (Figure 2).
3.
Back off idle-up speed adjusting screw for air conditioner one turn from fully tightened position (Figure 2).
> Engine, Cooling and Exhaust > Engine > Tune-up and Engine Performance Checks > Idle Speed > System Information > Technical Service Bulletins > All Other Service
Bulletins for Idle Speed: > 141984 > May > 84 > Carburetor - Idle Speed Adjustment on A/C Install > Page 477
D50/Ram 50 L4-1997cc 2.0L SOHC (1984)
FIGURE 1
4.
Lastly, make sure that the curb idle speed and idle-up speed are properly adjusted (Figure 1).
FIGURE 2
If necessary, make fine adjustments with SAS 2 and SAS 3 (Figure 2).
POLICY: Reimbursable within the provisions of the warranty
FAILURE CODE: 31 - Rough Idle
> Engine, Cooling and Exhaust > Engine > Tune-up and Engine Performance Checks > Idle Speed > System Information > Technical Service Bulletins > Page 478
> Engine, Cooling and Exhaust > Engine > Tune-up and Engine Performance Checks > Firing Order > Component Information > Specifications
FIRING ORDER 2.0L RWD & 2.6L
> Engine, Cooling and Exhaust > Engine > Tune-up and Engine Performance Checks > Ignition Timing > Timing Marks and Indicators > System Information > Diagrams
Timing Marks and Indicators: Diagrams
TIMING MARK 1.6L RWD, 2.6L & 2.0L EX. VISTA
> Engine, Cooling and Exhaust > Engine > Tune-up and Engine Performance Checks > Ignition Timing > Timing Marks and Indicators > System Information > Diagrams >
Page 486
D50/Ram 50 L4-1997cc 2.0L SOHC (1984)
TIMING MARK 1981-85 5.2L & 5.9L
> Engine, Cooling and Exhaust > Engine > Tune-up and Engine Performance Checks > Distributor, Ignition > Vacuum Advance Unit <--> [Distributor Advance Unit] > Component Information > Specifications > Electrical
Specifications
Vacuum Advance Unit: Electrical Specifications
> Engine, Cooling and Exhaust > Engine > Tune-up and Engine Performance Checks > Distributor, Ignition > Vacuum Advance Unit <--> [Distributor Advance Unit] > Component Information > Specifications > Electrical
Specifications > Page 492
> Engine, Cooling and Exhaust > Engine > Tune-up and Engine Performance Checks > Spark Plug > Component Information > Technical Service Bulletins > Customer Interest for Spark Plug: > 181788 > Oct > 88 > Spark Plugs
- Oil Fouling/Misfire on Hard Acceleration
Spark Plug: Customer InterestSpark Plugs - Oil Fouling/Misfire on Hard Acceleration
Models
1978-1989 MMC Engines With Jet Valves
Subject
Oil Fouled Spark Plug(s) Miss & Bucking Under Hard Acceleration
Index
FUEL
Date
October 17, 1988
No.
18-17-88
C18-21)This bulletin updates Technical Service Bulletin 5/14/88 and serves as a reminder that driveability problems may be caused by mechanical problems aswell as fuel system problems.
FIGURE 1
SYMPTOM/CONDITION
One or more (seldom occurs to more than one cylinder) spark plugs will be oil fouled and may show ground and center electrode erosion due tooverheating (Figure 1).
Under hard acceleration (wide open throttle) engine will miss and buck.
> Engine, Cooling and Exhaust > Engine > Tune-up and Engine Performance Checks > Spark Plug > Component Information > Technical Service Bulletins > Customer
Interest for Spark Plug: > 181788 > Oct > 88 > Spark Plugs - Oil Fouling/Misfire on Hard Acceleration > Page 501
D50/Ram 50 L4-1997cc 2.0L SOHC (1984)
FIGURE 2
This condition may result from a jet valve failure. The jet valve failure is characterized by one of the causes outlined below (refer to Figure 2 fordescription):
^ Oil leaking past the oil seal and valve stem.
^ Oil leaking past the valve body and oil seal.
^ Oil leaking past the O-ring seal between the valve body and cylinder head which may be caused by a torn or cut Oring.
FIGURE 1
DIAGNOSIS
Remove and inspect all spark plugs. If a spark plug is found to be heavily oil fouled and/or appears to have the electrodes eroded or overheated, proceedto jet valve removal procedure below (Figure 1).PARTS REQUIRED
Jet Valve Assembly (as required)
O-Ring (as required)
INSTALLATION PROCEDURE
PN MD009440
PN MD009786
1.
Remove only the jet valve of the cylinder showing the spark plug oiling or overheating. Follow the jet valve removal procedures outlined in therespective model year service manual using Miller Special Tool #MB-998310.
> Engine, Cooling and Exhaust > Engine > Tune-up and Engine Performance Checks > Spark Plug > Component Information > Technical Service Bulletins > Customer
Interest for Spark Plug: > 181788 > Oct > 88 > Spark Plugs - Oil Fouling/Misfire on Hard Acceleration > Page 502
D50/Ram 50 L4-1997cc 2.0L SOHC (1984)
FIGURE 2
2.
Push jet valve open and inspect the valve stem just under the valve head. If oil residue and excessive carbon buildup are present, the Jet ValveAssembly, PN MD009440, will have to be replaced (Figure 2).
If no residue or carbon buildup is present, inspect the O-ring for rips, tears, or deformity. O-ring can be replaced separately with PN MD009786.
FIGURE 3
3.
Inspect jet piece pocket by looking down into jet piece. If pocket has any buildup of burnt oil residue or carbon, it must be cleaned completelyusing the following procedure (Figure 3).
a.
Remove spark plug.
b.
Place piston on top dead center of compression stroke (both valves closed).
Use a thin stiff bristle brush to clean jet piece (a distributor cap terminal brush works well). A thin metal rod (coat hanger) can be used toloosen heavy deposits.
d.
Direct compressed air in jet piece. The loosened deposits will be blown out of the jet piece and spark plug hole. Eye protection isrecommended when performing this operation.
e.
Reinspect cleaned jet piece. If cracking or erosion is seen in the area of the jet air orifice (Figure 3) or the deposit cannot be cleanedadequately, the cylinder head will require replacement.
> Engine, Cooling and Exhaust > Engine > Tune-up and Engine Performance Checks > Spark Plug > Component Information > Technical Service Bulletins > Customer
Interest for Spark Plug: > 181788 > Oct > 88 > Spark Plugs - Oil Fouling/Misfire on Hard Acceleration > Page 503
D50/Ram 50 L4-1997cc 2.0L SOHC (1984)
4.
Install new spark plug of proper heat range and gap setting.
5.
Start engine and allow to fully warm up. Check for oil leaks and adjust idle speed if necessary.
POLICY: Information only
> Engine, Cooling and Exhaust > Engine > Tune-up and Engine Performance Checks > Spark Plug > Component Information > Technical Service Bulletins > All Technical Service Bulletins for Spark Plug: > 181788 > Oct > 88
> Spark Plugs - Oil Fouling/Misfire on Hard Acceleration
Spark Plug: All Technical Service BulletinsSpark Plugs - Oil Fouling/Misfire on Hard Acceleration
Models
1978-1989 MMC Engines With Jet Valves
Subject
Oil Fouled Spark Plug(s) Miss & Bucking Under Hard Acceleration
Index
FUEL
Date
October 17, 1988
No.
18-17-88
C18-21)This bulletin updates Technical Service Bulletin 5/14/88 and serves as a reminder that driveability problems may be caused by mechanical problems aswell as fuel system problems.
FIGURE 1
SYMPTOM/CONDITION
One or more (seldom occurs to more than one cylinder) spark plugs will be oil fouled and may show ground and center electrode erosion due tooverheating (Figure 1).
Under hard acceleration (wide open throttle) engine will miss and buck.
> Engine, Cooling and Exhaust > Engine > Tune-up and Engine Performance Checks > Spark Plug > Component Information > Technical Service Bulletins > All Technical
Service Bulletins for Spark Plug: > 181788 > Oct > 88 > Spark Plugs - Oil Fouling/Misfire on Hard Acceleration > Page 509
D50/Ram 50 L4-1997cc 2.0L SOHC (1984)
FIGURE 2
This condition may result from a jet valve failure. The jet valve failure is characterized by one of the causes outlined below (refer to Figure 2 fordescription):
^ Oil leaking past the oil seal and valve stem.
^ Oil leaking past the valve body and oil seal.
^ Oil leaking past the O-ring seal between the valve body and cylinder head which may be caused by a torn or cut Oring.
FIGURE 1
DIAGNOSIS
Remove and inspect all spark plugs. If a spark plug is found to be heavily oil fouled and/or appears to have the electrodes eroded or overheated, proceedto jet valve removal procedure below (Figure 1).PARTS REQUIRED
Jet Valve Assembly (as required)
O-Ring (as required)
INSTALLATION PROCEDURE
PN MD009440
PN MD009786
1.
Remove only the jet valve of the cylinder showing the spark plug oiling or overheating. Follow the jet valve removal procedures outlined in therespective model year service manual using Miller Special Tool #MB-998310.
> Engine, Cooling and Exhaust > Engine > Tune-up and Engine Performance Checks > Spark Plug > Component Information > Technical Service Bulletins > All Technical
Service Bulletins for Spark Plug: > 181788 > Oct > 88 > Spark Plugs - Oil Fouling/Misfire on Hard Acceleration > Page 510
D50/Ram 50 L4-1997cc 2.0L SOHC (1984)
FIGURE 2
2.
Push jet valve open and inspect the valve stem just under the valve head. If oil residue and excessive carbon buildup are present, the Jet ValveAssembly, PN MD009440, will have to be replaced (Figure 2).
If no residue or carbon buildup is present, inspect the O-ring for rips, tears, or deformity. O-ring can be replaced separately with PN MD009786.
FIGURE 3
3.
Inspect jet piece pocket by looking down into jet piece. If pocket has any buildup of burnt oil residue or carbon, it must be cleaned completelyusing the following procedure (Figure 3).
a.
Remove spark plug.
b.
Place piston on top dead center of compression stroke (both valves closed).
Use a thin stiff bristle brush to clean jet piece (a distributor cap terminal brush works well). A thin metal rod (coat hanger) can be used toloosen heavy deposits.
d.
Direct compressed air in jet piece. The loosened deposits will be blown out of the jet piece and spark plug hole. Eye protection isrecommended when performing this operation.
e.
Reinspect cleaned jet piece. If cracking or erosion is seen in the area of the jet air orifice (Figure 3) or the deposit cannot be cleanedadequately, the cylinder head will require replacement.
> Engine, Cooling and Exhaust > Engine > Tune-up and Engine Performance Checks > Spark Plug > Component Information > Technical Service Bulletins > All Technical
Service Bulletins for Spark Plug: > 181788 > Oct > 88 > Spark Plugs - Oil Fouling/Misfire on Hard Acceleration > Page 511
D50/Ram 50 L4-1997cc 2.0L SOHC (1984)
4.
Install new spark plug of proper heat range and gap setting.
5.
Start engine and allow to fully warm up. Check for oil leaks and adjust idle speed if necessary.
POLICY: Information only
> Engine, Cooling and Exhaust > Engine > Tune-up and Engine Performance Checks > Spark Plug > Component Information > Technical Service Bulletins > Page 512
> Engine, Cooling and Exhaust > Engine > Tune-up and Engine Performance Checks > Compression Check > System Information > Specifications
Compression Check: Specifications
Pressure 170 psi
> Engine, Cooling and Exhaust > Engine > Tune-up and Engine Performance Checks > Valve Clearance > System Information > Specifications
Valve Clearance: Specifications
Except Jet Valve Intake 0.006 in
1985-89 2.0L & 2.6L except jet valve have hydraulic lifters.
Jet Valve
Exhaust 0.01 in
Intake 0.006 in
> Engine, Cooling and Exhaust > Engine > Tune-up and Engine Performance Checks > Valve Clearance > System Information > Specifications > Page 519
Valve Clearance: Adjustments
INTAKE & EXHAUST VALVES
Fig. 12 Adjusting valve clearance (Typical)
The jet valve must be adjusted before adjusting the intake valve.
1. With engine at operating temperature, remove rocker arm cover.2. Disconnect high tension lead from ignition coil.3. While observing rocker arms on No. 4 cylinder, rotate crankshaft until the exhaust valve is closing and the intake valve has just started to open
Fig. 12.
with crankshaft pulley mark aligned with TDC mark on timing chain case. At this position the No. 1 cylinder is at top dead center compressionstroke. Check and adjust valve clearance for both intake and exhaust valves of No. 1 cylinder, intake valve of No. 2 cylinder and exhaust valve ofNo. 3 cylinder, as necessary,
4. Rotate crankshaft 360 degrees and check and adjust valve clearance for exhaust valve of No. 2 cylinder, intake valve of No. 3 cylinder and intake and exhaust valves of No. 4 cylinder.
5. After completing adjustment, install rocker arm cover and connect ignition coil high tension lead.
JET VALVE
Fig. 13 Adjusting jet valve clearance
Exc. Models Equipped W/Hydraulic Lash Adjusters
Fig. 13.
Following procedure for intake and exhaust valve adjustment, position No. 1 cylinder at top dead center compression stroke. Loosen intake valveadjusting screw at least 2 turns, then loosen jet valve adjusting screw locknut. Rotate jet valve adjusting screw counterclockwise and insert a suitablefeeler gauge blade as specified in ``Valve Specification Chart,'' between jet valve stem and adjusting screw, Tighten jet valve adjusting screwuntil it contacts the feeler gauge blade, then while holding adjusting screw in position, tighten locknut. After jet valve adjustment has been completed,adjust intake valve clearance. Continue to follow intake and exhaust valve adjustment procedure and adjust jet valves as necessary.
> Engine, Cooling and Exhaust > Engine > Water Pump > Component Information > Service and Repair
Water Pump: Service and Repair
1.
Disconnect battery ground cable and drain cooling system.
2.
Remove fan shroud, then disconnect lower radiator hose.
3.
Remove drive belt cooling fan and pulley.
4.
Place No. 1 piston at top dead center, compression stroke.
5.
Remove camshaft pulley, timing belt covers, timing belt, camshaft sprocket, upper under cover and timing belt tensioner.
6.
Remove water pump mounting bolts and the water pump.
7.
Reverse procedure to install.
> Engine, Cooling and Exhaust > Cooling System > Coolant > Component Information > Technical Service Bulletins > Engine Coolant - Recycling Recommendations
Coolant: Technical Service BulletinsEngine Coolant - Recycling Recommendations
SUBJECT:
GROUP: COOLING
DATE: Dec. 21, 1990
MODELS:
All Domestic & Import Vehicles
DISCUSSION:
A number of systems are being marketed to "recycle" or "reconstitute" used ethylene glycol antifreeze/coolant in the dealership. Some of the systemshave been advertised as producing a recycled antifreeze "as good as" original and suggest the recycled product is suitable for use in Chrysler Corporationvehicles.
Tests, so far, indicate most of these systems merely remove suspended solids from the used antifreeze/coolant through the use of various size filters.These systems do not remove glycol degradation products, or dissolved solids, which can cause water pump seal wear.
These systems use a universal "reinhibitor package". The "reinhibitor package" can not restore every type antifreeze/coolant inhibitor system to a likenew condition.
Tests results indicate these "recycled" products do not consistently provide the protection required in Chrysler Corporation engines and cooling systems.
The use of these "reconstituted" antifreeze/coolants is not authorized in the performance of any repair covered under the provisions of the warranty.
> Engine, Cooling and Exhaust > Cooling System > Coolant > Component Information > Technical Service Bulletins > Page 528
Coolant: Specifications
1982-89 Ram 50
* 9.0 L (9.5 qts) Cooling System Capacity .............................................................................................................................................................................
* Includes 0.65 L (0.69 qts) for the coolant reserve tank.
> Engine, Cooling and Exhaust > Cooling System > Coolant Line/Hose > Component Information > Technical Service Bulletins > Carburetor Coolant Hose - Installation Procedure
Coolant Line/Hose: Technical Service BulletinsCarburetor Coolant Hose - Installation Procedure
Models
All 1984 Import MMC Vehicles With Carburetors Except 2.6L Engines
Subject
Correct Carburetor Coolant Hose Installation Procedure
Index
FUEL
Date
December 3, 1984
No.
14-62-84
P-5298-CThe procedure described in this bulletin should be utilized when servicing the coolant hose or carburetor for the wax pellet choke housing.
FIGURE 1
When installing the lower coolant hose on the wax pellet choke housing, the following steps should be followed to avoid interference of the tab end ofthe hose clamp with the accelerator cable (Figure 1).
1.. Lower coolant hose should only be pushed on up to the shoulder on choke housing nipple (Figure 1).
2.
Tab ends of the spring hose clamps for the lower coolant hose should be positioned downward (Figure 1).
POLICY: Information only
> Engine, Cooling and Exhaust > Cooling System > Engine - Coolant Temperature Sensor/Switch > Coolant Temperature Sensor/Switch (For Computer) > Component Information > Specifications
Coolant Temperature Sensor/Switch (For Computer): SpecificationsSwitch Torque
Switch Torque
Cooling Fan Switch 8-18 ft.lb
> Engine, Cooling and Exhaust > Cooling System > Heater Core > Component Information > Service and Repair
Heater Core: Service and Repair
Fig. 23 Heater core & blower motor. 1984-86 Ram 50
1. Disconnect battery ground cable, then place temperature control lever in Off position and drain cooling system.2. Remove parcel tray, center ventilation duct and grille and defroster duct.3. Disconnect heater hoses from heater core. Plug heater core fittings to prevent coolant spillage.4. Disconnect wire connector from blower motor.5. Remove bolts and nuts attaching heater assembly to dash panel, then the heater assembly.6. Remove heater core from heater assembly.7. Reverse procedure to install.
> Engine, Cooling and Exhaust > Cooling System > Sensors and Switches - Cooling System > Engine - Coolant Temperature Sensor/Switch > Coolant Temperature Sensor/Switch (For Computer) > Component Information >
Specifications
Coolant Temperature Sensor/Switch (For Computer): SpecificationsSwitch Torque
Switch Torque
Cooling Fan Switch 8-18 ft.lb
> Engine, Cooling and Exhaust > Cooling System > Water Pump > Component Information > Service and Repair
Water Pump: Service and Repair
1.
Disconnect battery ground cable and drain cooling system.
2.
Remove fan shroud, then disconnect lower radiator hose.
3.
Remove drive belt cooling fan and pulley.
4.
Place No. 1 piston at top dead center, compression stroke.
5.
Remove camshaft pulley, timing belt covers, timing belt, camshaft sprocket, upper under cover and timing belt tensioner.
6.
Remove water pump mounting bolts and the water pump.
7.
Reverse procedure to install.
> Engine, Cooling and Exhaust > Exhaust System > Catalytic Converter > Component Information > Description and Operation
Catalytic Converter: Description and Operation
Fig. 32 Single & Twin Catalytic Converters
Fig. 32.
The catalytic converter is an emission control device added to the exhaust system to effectively reduce the levels of carbon monoxide andhydrocarbons entering the atmosphere. There are two types of catalytic converters used on these vehicles. The two types are, pellet type and monolithic type. The pellet type converter wasused on early models and incorporates palladium coated pellets to control emissions. On later models, the monolithic type converter is used. Thisconverter contains a honeycomb insert that is coated with palladium catalytic material,
> Engine, Cooling and Exhaust > Exhaust System > Exhaust Manifold > Component Information > Specifications
Exhaust Manifold: Specifications
Exhaust Manifold 11-14 ft.lb
> Powertrain Management > Relays and Modules - Powertrain Management > Relays and Modules - Computers and Control Systems > Powertrain Control Module <--> [Engine Control Module] > Component Information >
Locations
Powertrain Control Module: Locations
Under LH Side Of I/P
> Powertrain Management > Relays and Modules - Powertrain Management > Relays and Modules - Fuel Delivery and Air Induction > Throttle Control Vacuum Motor <--> [Engine Speed Governor Control Module] >
Component Information > Locations
Throttle Control Vacuum Motor: Locations
Under Center Of I/P
> Powertrain Management > Sensors and Switches - Powertrain Management > Sensors and Switches - Computers and Control Systems > Coolant Temperature Sensor/Switch (For Computer) > Component Information >
Specifications
Coolant Temperature Sensor/Switch (For Computer): SpecificationsSwitch Torque
Switch Torque
Cooling Fan Switch 8-18 ft.lb
> Powertrain Management > Sensors and Switches - Powertrain Management > Sensors and Switches - Ignition System > Ignition Switch > Component Information > Service and Repair
Ignition Switch: Service and Repair
The ignition switch is mounted in the rear of the steering column lock. When the key is turned to LOCK position and pulled out, the lock pinautomatically ejects from the cylinder and enters a groove in the steering shaft, locking the steering wheel. The heads of the bolts securing the steering lock assembly shear off when the bolts are tightened. Replacement of the steering lock assembly mayrequire that the steering column be removed, as these bolts must be cut or slotted to permit removal with a screwdriver. When the lock assembly isinstalled, new shear bolts must be used and the bolts should be tightened until the bolt heads twist off. However, the ignition switch can be serviced separately from the lock assembly using the following procedures.
1.
Disconnect battery ground cable, then remove upper and lower column covers.
2.
Remove bands securing switch harness and disconnect electrical connector.
Fig. 4 Ignition switch removal
3.
Loosen the bolt holding the switch and pull from lock assembly.
4.
Reverse procedure to install, first inserting key to check for proper operation.
> Powertrain Management > Tune-up and Engine Performance Checks > Fuel Pressure > System Information > Specifications
> Powertrain Management > Tune-up and Engine Performance Checks > Air/Fuel Mixture > System Information > Technical Service Bulletins > By Symptom for Air/Fuel Mixture: > 140884 > Jan > 84 > Propane Idle Set -
Procedure
Air/Fuel Mixture: By SymptomPropane Idle Set - Procedure
Models
1984 MMC Import Vehicles All With Gasoline Fueled Engines, All Emission Markets (Except Vehicles With Turbo Chargers & Canada)
Subject
Propane Idle Set Procedure
Index
FUEL
Date
January 17, 1984
No..
14-08-84
P-94-C
The propane idle set procedure is authorized for 1984 subject model import vehicles.
The propane idle set method is to be used when "CO" meter procedure cannot be used, i.e., "CO" meter in for repair or is not available in the servicearea.
PROPANE IDLE CHECK & SET PROCEDURE
1.
Idle Setting Conditions: Lights, electric cooling fan, and all accessories are off, transmission in neutral, and front wheels in straight ahead position.
2.
If engine is cold, allow it to warm up until full operating temperature is reached (185 to 205~F).
NOTE:
PERFORM THE FOLLOWING STEPS 3 THROUGH 5 AND STEP 19 ONLY IF ENGINE IS EQUIPPED WITH A FEEDBACKCARBURETOR EMISSION SYSTEM.
3.
Turn off ignition switch.
4.
Disconnect the NEGATIVE cable from the battery for about 5 seconds. Then reconnect negative battery cable.
5.
Disconnect the connector of the exhaust oxygen sensor.
6.
Start and run engine for 5 seconds at an engine speed between 2,000 to 3,000 rpm.
7.
Then, allow engine to run at curb idle for 2 minutes.
> Powertrain Management > Tune-up and Engine Performance Checks > Air/Fuel Mixture > System Information > Technical Service Bulletins > By Symptom for Air/Fuel
Mixture: > 140884 > Jan > 84 > Propane Idle Set - Procedure > Page 586
D50/Ram 50 L4-1997cc 2.0L SOHC (1984)
FIGURE 1
8.
Check engine idle speed and basic ignition timing. Adjust to specifications if necessary (Figure 1).
9.
Disconnect the air cleaner fresh air intake duct from the air cleaner snorkel.
Insert the propane supply hose into the air cleaner snorkel about 4 inches.
Make certain both valves on propane bottle are fully closed and the bottle is upright and in a safe location.
> Powertrain Management > Tune-up and Engine Performance Checks > Air/Fuel Mixture > System Information > Technical Service Bulletins > By Symptom for Air/Fuel
Mixture: > 140884 > Jan > 84 > Propane Idle Set - Procedure > Page 587
D50/Ram 50 L4-1997cc 2.0L SOHC (1984)
FIGURE 3
10.
Open the propane bottle main valve fully, then slowly open the propane fine control valve to the position where maximum engine rpm is achieved.(Too much propane or too rich idle mixture will cause the engine to lose rpm as the fine control valve is opened.) (Figure 3.)
FIGURE 2
> Powertrain Management > Tune-up and Engine Performance Checks > Air/Fuel Mixture > System Information > Technical Service Bulletins > By Symptom for Air/Fuel
Mixture: > 140884 > Jan > 84 > Propane Idle Set - Procedure > Page 588
D50/Ram 50 L4-1997cc 2.0L SOHC (1984)
Note the engine rpm increase. Specified values of each engine propane idle speed increase are outlined in Figure 2.
If the propane idle speed exceeds more than 25 rpm from the specified value in Figure 2 or the rpm does not increase at all, idle fuel mixtureshould be adjusted according to the propane assisted idle set procedure that follows.
FIGURE 4
11.
It is not necessary to remove carburetor from intake manifold to remove the idle mixture screw plug.
Drill out concealment plug on car. Remove vacuum connector from high altitude compensator (HAC) fittings on carburetor air horn (Figure 4).
Use a 1/4" diameter drill 8' long at the 11 o'clock position on the plug boss. Locate drill point 3/16" from end of boss.
Plug should pop out when the drill bit contacts it (Figure 4).
12.
Start engine and run for 1 minute at engine speed of 2500 rpm.
13.
Run engine at idle for 2 minutes.
> Powertrain Management > Tune-up and Engine Performance Checks > Air/Fuel Mixture > System Information > Technical Service Bulletins > By Symptom for Air/Fuel
Mixture: > 140884 > Jan > 84 > Propane Idle Set - Procedure > Page 589
D50/Ram 50 L4-1997cc 2.0L SOHC (1984)
FIGURE 2
14.
Open the propane main valve and slowly open the fine control valve to the position where maximum engine speed is achieved. Use the idle speedadjusting screw to set the specified propane idle speed from Figure 2.
15.
Turn off propane main valve and adjust idle mixture screw to the specified idle set speed from Figure 2.
16.
17.
To recheck the maximum propane speed, open the main propane valve again. If the speed still differs more than 25 rpm from the specified propanespeed from Figure 2, repeat Steps 14 through 16.
18.
Remove the propane hose and replace fresh air duct on air cleaner snorkel.
19.
Reconnect the exhaust oxygen sensor (if engine is equipped with a feedback carburetor).
20.
Install Idle Mixture Screw Concealment Plug. (If new plug is needed, use PN MD606954.)
POLICY: Reimbursable within the provisions of the warranty
> Powertrain Management > Tune-up and Engine Performance Checks > Air/Fuel Mixture > System Information > Technical Service Bulletins > By Symptom for Air/Fuel
Mixture: > 140884 > Jan > 84 > Propane Idle Set - Procedure > Page 590
D50/Ram 50 L4-1997cc 2.0L SOHC (1984)
FRONT WHEEL DRIVE LABOR OPERATION TIME SCHEDULE
FAILURE CODE: RO - Driveability
> Powertrain Management > Tune-up and Engine Performance Checks > Air/Fuel Mixture > System Information > Technical Service Bulletins > All Technical Service Bulletins for Air/Fuel Mixture: > 140884 > Jan > 84 >
Propane Idle Set - Procedure
Air/Fuel Mixture: All Technical Service BulletinsPropane Idle Set - Procedure
Models
1984 MMC Import Vehicles All With Gasoline Fueled Engines, All Emission Markets (Except Vehicles With Turbo Chargers & Canada)
Subject
Propane Idle Set Procedure
Index
FUEL
Date
January 17, 1984
No..
14-08-84
P-94-C
The propane idle set procedure is authorized for 1984 subject model import vehicles.
The propane idle set method is to be used when "CO" meter procedure cannot be used, i.e., "CO" meter in for repair or is not available in the servicearea.
PROPANE IDLE CHECK & SET PROCEDURE
1.
Idle Setting Conditions: Lights, electric cooling fan, and all accessories are off, transmission in neutral, and front wheels in straight ahead position.
2.
If engine is cold, allow it to warm up until full operating temperature is reached (185 to 205~F).
NOTE:
PERFORM THE FOLLOWING STEPS 3 THROUGH 5 AND STEP 19 ONLY IF ENGINE IS EQUIPPED WITH A FEEDBACKCARBURETOR EMISSION SYSTEM.
3.
Turn off ignition switch.
4.
Disconnect the NEGATIVE cable from the battery for about 5 seconds. Then reconnect negative battery cable.
5.
Disconnect the connector of the exhaust oxygen sensor.
6.
Start and run engine for 5 seconds at an engine speed between 2,000 to 3,000 rpm.
7.
Then, allow engine to run at curb idle for 2 minutes.
> Powertrain Management > Tune-up and Engine Performance Checks > Air/Fuel Mixture > System Information > Technical Service Bulletins > All Technical Service
Bulletins for Air/Fuel Mixture: > 140884 > Jan > 84 > Propane Idle Set - Procedure > Page 596
D50/Ram 50 L4-1997cc 2.0L SOHC (1984)
FIGURE 1
8.
Check engine idle speed and basic ignition timing. Adjust to specifications if necessary (Figure 1).
9.
Disconnect the air cleaner fresh air intake duct from the air cleaner snorkel.
Insert the propane supply hose into the air cleaner snorkel about 4 inches.
Make certain both valves on propane bottle are fully closed and the bottle is upright and in a safe location.
> Powertrain Management > Tune-up and Engine Performance Checks > Air/Fuel Mixture > System Information > Technical Service Bulletins > All Technical Service
Bulletins for Air/Fuel Mixture: > 140884 > Jan > 84 > Propane Idle Set - Procedure > Page 597
D50/Ram 50 L4-1997cc 2.0L SOHC (1984)
FIGURE 3
10.
Open the propane bottle main valve fully, then slowly open the propane fine control valve to the position where maximum engine rpm is achieved.(Too much propane or too rich idle mixture will cause the engine to lose rpm as the fine control valve is opened.) (Figure 3.)
FIGURE 2
> Powertrain Management > Tune-up and Engine Performance Checks > Air/Fuel Mixture > System Information > Technical Service Bulletins > All Technical Service
Bulletins for Air/Fuel Mixture: > 140884 > Jan > 84 > Propane Idle Set - Procedure > Page 598
D50/Ram 50 L4-1997cc 2.0L SOHC (1984)
Note the engine rpm increase. Specified values of each engine propane idle speed increase are outlined in Figure 2.
If the propane idle speed exceeds more than 25 rpm from the specified value in Figure 2 or the rpm does not increase at all, idle fuel mixtureshould be adjusted according to the propane assisted idle set procedure that follows.
FIGURE 4
11.
It is not necessary to remove carburetor from intake manifold to remove the idle mixture screw plug.
Drill out concealment plug on car. Remove vacuum connector from high altitude compensator (HAC) fittings on carburetor air horn (Figure 4).
Use a 1/4" diameter drill 8' long at the 11 o'clock position on the plug boss. Locate drill point 3/16" from end of boss.
Plug should pop out when the drill bit contacts it (Figure 4).
12.
Start engine and run for 1 minute at engine speed of 2500 rpm.
13.
Run engine at idle for 2 minutes.
> Powertrain Management > Tune-up and Engine Performance Checks > Air/Fuel Mixture > System Information > Technical Service Bulletins > All Technical Service
Bulletins for Air/Fuel Mixture: > 140884 > Jan > 84 > Propane Idle Set - Procedure > Page 599
D50/Ram 50 L4-1997cc 2.0L SOHC (1984)
FIGURE 2
14.
Open the propane main valve and slowly open the fine control valve to the position where maximum engine speed is achieved. Use the idle speedadjusting screw to set the specified propane idle speed from Figure 2.
15.
Turn off propane main valve and adjust idle mixture screw to the specified idle set speed from Figure 2.
16.
17.
To recheck the maximum propane speed, open the main propane valve again. If the speed still differs more than 25 rpm from the specified propanespeed from Figure 2, repeat Steps 14 through 16.
18.
Remove the propane hose and replace fresh air duct on air cleaner snorkel.
19.
Reconnect the exhaust oxygen sensor (if engine is equipped with a feedback carburetor).
20.
Install Idle Mixture Screw Concealment Plug. (If new plug is needed, use PN MD606954.)
POLICY: Reimbursable within the provisions of the warranty
> Powertrain Management > Tune-up and Engine Performance Checks > Air/Fuel Mixture > System Information > Technical Service Bulletins > All Technical Service
Bulletins for Air/Fuel Mixture: > 140884 > Jan > 84 > Propane Idle Set - Procedure > Page 600
D50/Ram 50 L4-1997cc 2.0L SOHC (1984)
FRONT WHEEL DRIVE LABOR OPERATION TIME SCHEDULE
FAILURE CODE: RO - Driveability
> Powertrain Management > Tune-up and Engine Performance Checks > Idle Speed > System Information > Technical Service Bulletins > By Symptom: > 140884 > Jan > 84 > Propane Idle Set - Procedure
Idle Speed: By SymptomPropane Idle Set - Procedure
Models
1984 MMC Import Vehicles All With Gasoline Fueled Engines, All Emission Markets (Except Vehicles With Turbo Chargers & Canada)
Subject
Propane Idle Set Procedure
Index
FUEL
Date
January 17, 1984
No..
14-08-84
P-94-C
The propane idle set procedure is authorized for 1984 subject model import vehicles.
The propane idle set method is to be used when "CO" meter procedure cannot be used, i.e., "CO" meter in for repair or is not available in the servicearea.
PROPANE IDLE CHECK & SET PROCEDURE
1.
Idle Setting Conditions: Lights, electric cooling fan, and all accessories are off, transmission in neutral, and front wheels in straight ahead position.
2.
If engine is cold, allow it to warm up until full operating temperature is reached (185 to 205~F).
NOTE:
PERFORM THE FOLLOWING STEPS 3 THROUGH 5 AND STEP 19 ONLY IF ENGINE IS EQUIPPED WITH A FEEDBACKCARBURETOR EMISSION SYSTEM.
3.
Turn off ignition switch.
4.
Disconnect the NEGATIVE cable from the battery for about 5 seconds. Then reconnect negative battery cable.
5.
Disconnect the connector of the exhaust oxygen sensor.
6.
Start and run engine for 5 seconds at an engine speed between 2,000 to 3,000 rpm.
7.
Then, allow engine to run at curb idle for 2 minutes.
> Powertrain Management > Tune-up and Engine Performance Checks > Idle Speed > System Information > Technical Service Bulletins > By Symptom: > 140884 > Jan > 84
> Propane Idle Set - Procedure > Page 609
D50/Ram 50 L4-1997cc 2.0L SOHC (1984)
FIGURE 1
8.
Check engine idle speed and basic ignition timing. Adjust to specifications if necessary (Figure 1).
9.
Disconnect the air cleaner fresh air intake duct from the air cleaner snorkel.
Insert the propane supply hose into the air cleaner snorkel about 4 inches.
Make certain both valves on propane bottle are fully closed and the bottle is upright and in a safe location.
> Powertrain Management > Tune-up and Engine Performance Checks > Idle Speed > System Information > Technical Service Bulletins > By Symptom: > 140884 > Jan > 84
> Propane Idle Set - Procedure > Page 610
D50/Ram 50 L4-1997cc 2.0L SOHC (1984)
FIGURE 3
10.
Open the propane bottle main valve fully, then slowly open the propane fine control valve to the position where maximum engine rpm is achieved.(Too much propane or too rich idle mixture will cause the engine to lose rpm as the fine control valve is opened.) (Figure 3.)
FIGURE 2
> Powertrain Management > Tune-up and Engine Performance Checks > Idle Speed > System Information > Technical Service Bulletins > By Symptom: > 140884 > Jan > 84
> Propane Idle Set - Procedure > Page 611
D50/Ram 50 L4-1997cc 2.0L SOHC (1984)
Note the engine rpm increase. Specified values of each engine propane idle speed increase are outlined in Figure 2.
If the propane idle speed exceeds more than 25 rpm from the specified value in Figure 2 or the rpm does not increase at all, idle fuel mixtureshould be adjusted according to the propane assisted idle set procedure that follows.
FIGURE 4
11.
It is not necessary to remove carburetor from intake manifold to remove the idle mixture screw plug.
Drill out concealment plug on car. Remove vacuum connector from high altitude compensator (HAC) fittings on carburetor air horn (Figure 4).
Use a 1/4" diameter drill 8' long at the 11 o'clock position on the plug boss. Locate drill point 3/16" from end of boss.
Plug should pop out when the drill bit contacts it (Figure 4).
12.
Start engine and run for 1 minute at engine speed of 2500 rpm.
13.
Run engine at idle for 2 minutes.
> Powertrain Management > Tune-up and Engine Performance Checks > Idle Speed > System Information > Technical Service Bulletins > By Symptom: > 140884 > Jan > 84
> Propane Idle Set - Procedure > Page 612
D50/Ram 50 L4-1997cc 2.0L SOHC (1984)
FIGURE 2
14.
Open the propane main valve and slowly open the fine control valve to the position where maximum engine speed is achieved. Use the idle speedadjusting screw to set the specified propane idle speed from Figure 2.
15.
Turn off propane main valve and adjust idle mixture screw to the specified idle set speed from Figure 2.
16.
17.
To recheck the maximum propane speed, open the main propane valve again. If the speed still differs more than 25 rpm from the specified propanespeed from Figure 2, repeat Steps 14 through 16.
18.
Remove the propane hose and replace fresh air duct on air cleaner snorkel.
19.
Reconnect the exhaust oxygen sensor (if engine is equipped with a feedback carburetor).
20.
Install Idle Mixture Screw Concealment Plug. (If new plug is needed, use PN MD606954.)
POLICY: Reimbursable within the provisions of the warranty
> Powertrain Management > Tune-up and Engine Performance Checks > Idle Speed > System Information > Technical Service Bulletins > By Symptom: > 140884 > Jan > 84
> Propane Idle Set - Procedure > Page 613
D50/Ram 50 L4-1997cc 2.0L SOHC (1984)
FRONT WHEEL DRIVE LABOR OPERATION TIME SCHEDULE
FAILURE CODE: RO - Driveability
> Powertrain Management > Tune-up and Engine Performance Checks > Idle Speed > System Information > Technical Service Bulletins > All Technical Service Bulletins for Idle Speed: > 142084 > May > 84 > Engine
Specifications - Manual Corrections
Idle Speed: All Technical Service BulletinsEngine Specifications - Manual Corrections
Models
1984 Colt, Ram 50, & Conquest
Subject
Correction of 1984 Service Manuals on Engine Specifications
Index
FUEL
Date
May 21, 1984
No..
14-20-84
P-2112-C
This service bulletin is issued to correct the following 1984 Import Service Manuals.
^ Colt Service Manual Publication #81-270-4006
> Powertrain Management > Tune-up and Engine Performance Checks > Idle Speed > System Information > Technical Service Bulletins > All Technical Service Bulletins for
Idle Speed: > 142084 > May > 84 > Engine Specifications - Manual Corrections > Page 619
D50/Ram 50 L4-1997cc 2.0L SOHC (1984)
^ Ram-50 Service Manual Publication #81-370-4009
^ Conquest Service Manual Publication #81-270-4005
Corrections are highlighted in the attached specifications in bold type and should be entered in the respective model service manual.
POLICY: Information only
> Powertrain Management > Tune-up and Engine Performance Checks > Idle Speed > System Information > Technical Service Bulletins > All Technical Service Bulletins for Idle Speed: > 141984 > May > 84 > Carburetor - Idle
Speed Adjustment on A/C Install
Idle Speed: All Technical Service BulletinsCarburetor - Idle Speed Adjustment on A/C Install
Models
1984 Colt (W/O Turbo), Ram-50, Power Ram-50 (W/O Diesel) & Colt Vista
Subject
Idle-Up Speed Adjustment After Air Conditioning Installation and/or Service
Index
FUEL
Date
May 7, 1984
No.
14-19-84
P-1927-CThis procedure modifies the adjustment procedures in the subject model service manuals.
If difficulty is encountered in adjusting curb idle speed and/or idle-up speed after installation or servicing and adjustment of the air conditioning system,follow the adjustment procedure as outlined below:
ADJUSTMENT PROCEDURE
1.
Thoroughly warm up engine, turn off all accessories, front wheels in straight ahead position, transmission in neutral, parking brake set, andradiator cooling fan stopped.
FIGURE 1
> Powertrain Management > Tune-up and Engine Performance Checks > Idle Speed > System Information > Technical Service Bulletins > All Technical Service Bulletins for
Idle Speed: > 141984 > May > 84 > Carburetor - Idle Speed Adjustment on A/C Install > Page 624
D50/Ram 50 L4-1997cc 2.0L SOHC (1984)
FIGURE 2
2.
Check and adjust curb idle speed if necessary (see Figure 1 for specification) and make adjustment using SAS (speed adjusting screw) 1 (Figure2). On some models installation of air conditioner will change the curb idle speed already adjusted.
FIGURE 2
3.
Back off the idle-up speed adjusting screw for air conditioner one turn from fully tightened position (Figure 2).
4.
Lift the free lever by hand until it touches SAS 3 and record the engine speed ("N" = R.P.M.) obtained at this time (Figure 2).
> Powertrain Management > Tune-up and Engine Performance Checks > Idle Speed > System Information > Technical Service Bulletins > All Technical Service Bulletins for
Idle Speed: > 141984 > May > 84 > Carburetor - Idle Speed Adjustment on A/C Install > Page 625
D50/Ram 50 L4-1997cc 2.0L SOHC (1984)
FIGURE 1
FIGURE 2
5.. Turn on air conditioner switch. Adjust the idle-up speed while compressor is running to the specified rpm (Figure 1) by turning SAS 2 (Figure 2).When making this adjustment, be sure to record the turning direction and slot angle of SAS 2.
FIGURE 1
6.
Turn off air conditioner switch and make sure that the specified curb idle rpm is obtained (Figure 1).
7.
Race the engine at a speed of about 2000 rpm for five seconds.
8.
Turn on and then off the air conditioning switch repeatedly several times and make sure that with the compressor running that the engine is running
> Powertrain Management > Tune-up and Engine Performance Checks > Idle Speed > System Information > Technical Service Bulletins > All Technical Service Bulletins for
Idle Speed: > 141984 > May > 84 > Carburetor - Idle Speed Adjustment on A/C Install > Page 626
D50/Ram 50 L4-1997cc 2.0L SOHC (1984)
at the specified idle-up rpm (Figure 1).
Example:
FIGURE 2
If Sas 2 has been turned 180~ clockwise in Step 5, SAS 3 will be turned 360~ clockwise in Step 9. Then, lift thefree lever by hand until it touches SAS 3 and make sure that the engine rpm is "N" +/- 100 rpm (where "N" is therpm recorded in Step 4). If necessary, adjust using SAS 3.
FIGURE 2
SIMPLE ADJUSTMENT PROCEDURE FOR COLT VISTA ONLY
If the idle adjustment has been properly made before installation of the air conditioner, the following simple procedure may be used:
1.
Give one clockwise turn to SAS 2 (Figure 2).
2.
Give two clockwise turns to SAS 3 (Figure 2).
3.
Back off idle-up speed adjusting screw for air conditioner one turn from fully tightened position (Figure 2).
> Powertrain Management > Tune-up and Engine Performance Checks > Idle Speed > System Information > Technical Service Bulletins > All Technical Service Bulletins for
Idle Speed: > 141984 > May > 84 > Carburetor - Idle Speed Adjustment on A/C Install > Page 627
D50/Ram 50 L4-1997cc 2.0L SOHC (1984)
FIGURE 1
4.
Lastly, make sure that the curb idle speed and idle-up speed are properly adjusted (Figure 1).
FIGURE 2
If necessary, make fine adjustments with SAS 2 and SAS 3 (Figure 2).
POLICY: Reimbursable within the provisions of the warranty
FAILURE CODE: 31 - Rough Idle
> Powertrain Management > Tune-up and Engine Performance Checks > Idle Speed > System Information > Technical Service Bulletins > All Technical Service Bulletins for Idle Speed: > 140884 > Jan > 84 > Propane Idle Set -
Procedure
Idle Speed: All Technical Service BulletinsPropane Idle Set - Procedure
Models
1984 MMC Import Vehicles All With Gasoline Fueled Engines, All Emission Markets (Except Vehicles With Turbo Chargers & Canada)
Subject
Propane Idle Set Procedure
Index
FUEL
Date
January 17, 1984
No..
14-08-84
P-94-C
The propane idle set procedure is authorized for 1984 subject model import vehicles.
The propane idle set method is to be used when "CO" meter procedure cannot be used, i.e., "CO" meter in for repair or is not available in the servicearea.
PROPANE IDLE CHECK & SET PROCEDURE
1.
Idle Setting Conditions: Lights, electric cooling fan, and all accessories are off, transmission in neutral, and front wheels in straight ahead position.
2.
If engine is cold, allow it to warm up until full operating temperature is reached (185 to 205~F).
NOTE:
PERFORM THE FOLLOWING STEPS 3 THROUGH 5 AND STEP 19 ONLY IF ENGINE IS EQUIPPED WITH A FEEDBACKCARBURETOR EMISSION SYSTEM.
3.
Turn off ignition switch.
4.
Disconnect the NEGATIVE cable from the battery for about 5 seconds. Then reconnect negative battery cable.
5.
Disconnect the connector of the exhaust oxygen sensor.
6.
Start and run engine for 5 seconds at an engine speed between 2,000 to 3,000 rpm.
7.
Then, allow engine to run at curb idle for 2 minutes.
> Powertrain Management > Tune-up and Engine Performance Checks > Idle Speed > System Information > Technical Service Bulletins > All Technical Service Bulletins for
Idle Speed: > 140884 > Jan > 84 > Propane Idle Set - Procedure > Page 632
D50/Ram 50 L4-1997cc 2.0L SOHC (1984)
FIGURE 1
8.
Check engine idle speed and basic ignition timing. Adjust to specifications if necessary (Figure 1).
9.
Disconnect the air cleaner fresh air intake duct from the air cleaner snorkel.
Insert the propane supply hose into the air cleaner snorkel about 4 inches.
Make certain both valves on propane bottle are fully closed and the bottle is upright and in a safe location.
> Powertrain Management > Tune-up and Engine Performance Checks > Idle Speed > System Information > Technical Service Bulletins > All Technical Service Bulletins for
Idle Speed: > 140884 > Jan > 84 > Propane Idle Set - Procedure > Page 633
D50/Ram 50 L4-1997cc 2.0L SOHC (1984)
FIGURE 3
10.
Open the propane bottle main valve fully, then slowly open the propane fine control valve to the position where maximum engine rpm is achieved.(Too much propane or too rich idle mixture will cause the engine to lose rpm as the fine control valve is opened.) (Figure 3.)
FIGURE 2
> Powertrain Management > Tune-up and Engine Performance Checks > Idle Speed > System Information > Technical Service Bulletins > All Technical Service Bulletins for
Idle Speed: > 140884 > Jan > 84 > Propane Idle Set - Procedure > Page 634
D50/Ram 50 L4-1997cc 2.0L SOHC (1984)
Note the engine rpm increase. Specified values of each engine propane idle speed increase are outlined in Figure 2.
If the propane idle speed exceeds more than 25 rpm from the specified value in Figure 2 or the rpm does not increase at all, idle fuel mixtureshould be adjusted according to the propane assisted idle set procedure that follows.
FIGURE 4
11.
It is not necessary to remove carburetor from intake manifold to remove the idle mixture screw plug.
Drill out concealment plug on car. Remove vacuum connector from high altitude compensator (HAC) fittings on carburetor air horn (Figure 4).
Use a 1/4" diameter drill 8' long at the 11 o'clock position on the plug boss. Locate drill point 3/16" from end of boss.
Plug should pop out when the drill bit contacts it (Figure 4).
12.
Start engine and run for 1 minute at engine speed of 2500 rpm.
13.
Run engine at idle for 2 minutes.
> Powertrain Management > Tune-up and Engine Performance Checks > Idle Speed > System Information > Technical Service Bulletins > All Technical Service Bulletins for
Idle Speed: > 140884 > Jan > 84 > Propane Idle Set - Procedure > Page 635
D50/Ram 50 L4-1997cc 2.0L SOHC (1984)
FIGURE 2
14.
Open the propane main valve and slowly open the fine control valve to the position where maximum engine speed is achieved. Use the idle speedadjusting screw to set the specified propane idle speed from Figure 2.
15.
Turn off propane main valve and adjust idle mixture screw to the specified idle set speed from Figure 2.
16.
17.
To recheck the maximum propane speed, open the main propane valve again. If the speed still differs more than 25 rpm from the specified propanespeed from Figure 2, repeat Steps 14 through 16.
18.
Remove the propane hose and replace fresh air duct on air cleaner snorkel.
19.
Reconnect the exhaust oxygen sensor (if engine is equipped with a feedback carburetor).
20.
Install Idle Mixture Screw Concealment Plug. (If new plug is needed, use PN MD606954.)
POLICY: Reimbursable within the provisions of the warranty
> Powertrain Management > Tune-up and Engine Performance Checks > Idle Speed > System Information > Technical Service Bulletins > All Technical Service Bulletins for
Idle Speed: > 140884 > Jan > 84 > Propane Idle Set - Procedure > Page 636
D50/Ram 50 L4-1997cc 2.0L SOHC (1984)
FRONT WHEEL DRIVE LABOR OPERATION TIME SCHEDULE
FAILURE CODE: RO - Driveability
> Powertrain Management > Tune-up and Engine Performance Checks > Idle Speed > System Information > Technical Service Bulletins > All Other Service Bulletins for Idle Speed: > 142084 > May > 84 > Engine
Specifications - Manual Corrections
Idle Speed: All Technical Service BulletinsEngine Specifications - Manual Corrections
Models
1984 Colt, Ram 50, & Conquest
Subject
Correction of 1984 Service Manuals on Engine Specifications
Index
FUEL
Date
May 21, 1984
No..
14-20-84
P-2112-C
This service bulletin is issued to correct the following 1984 Import Service Manuals.
^ Colt Service Manual Publication #81-270-4006
> Powertrain Management > Tune-up and Engine Performance Checks > Idle Speed > System Information > Technical Service Bulletins > All Other Service Bulletins for Idle
Speed: > 142084 > May > 84 > Engine Specifications - Manual Corrections > Page 642
D50/Ram 50 L4-1997cc 2.0L SOHC (1984)
^ Ram-50 Service Manual Publication #81-370-4009
^ Conquest Service Manual Publication #81-270-4005
Corrections are highlighted in the attached specifications in bold type and should be entered in the respective model service manual.
POLICY: Information only
> Powertrain Management > Tune-up and Engine Performance Checks > Idle Speed > System Information > Technical Service Bulletins > All Other Service Bulletins for Idle Speed: > 141984 > May > 84 > Carburetor - Idle
Speed Adjustment on A/C Install
Idle Speed: All Technical Service BulletinsCarburetor - Idle Speed Adjustment on A/C Install
Models
1984 Colt (W/O Turbo), Ram-50, Power Ram-50 (W/O Diesel) & Colt Vista
Subject
Idle-Up Speed Adjustment After Air Conditioning Installation and/or Service
Index
FUEL
Date
May 7, 1984
No.
14-19-84
P-1927-CThis procedure modifies the adjustment procedures in the subject model service manuals.
If difficulty is encountered in adjusting curb idle speed and/or idle-up speed after installation or servicing and adjustment of the air conditioning system,follow the adjustment procedure as outlined below:
ADJUSTMENT PROCEDURE
1.
Thoroughly warm up engine, turn off all accessories, front wheels in straight ahead position, transmission in neutral, parking brake set, andradiator cooling fan stopped.
FIGURE 1
> Powertrain Management > Tune-up and Engine Performance Checks > Idle Speed > System Information > Technical Service Bulletins > All Other Service Bulletins for Idle
Speed: > 141984 > May > 84 > Carburetor - Idle Speed Adjustment on A/C Install > Page 647
D50/Ram 50 L4-1997cc 2.0L SOHC (1984)
FIGURE 2
2.
Check and adjust curb idle speed if necessary (see Figure 1 for specification) and make adjustment using SAS (speed adjusting screw) 1 (Figure2). On some models installation of air conditioner will change the curb idle speed already adjusted.
FIGURE 2
3.
Back off the idle-up speed adjusting screw for air conditioner one turn from fully tightened position (Figure 2).
4.
Lift the free lever by hand until it touches SAS 3 and record the engine speed ("N" = R.P.M.) obtained at this time (Figure 2).
> Powertrain Management > Tune-up and Engine Performance Checks > Idle Speed > System Information > Technical Service Bulletins > All Other Service Bulletins for Idle
Speed: > 141984 > May > 84 > Carburetor - Idle Speed Adjustment on A/C Install > Page 648
D50/Ram 50 L4-1997cc 2.0L SOHC (1984)
FIGURE 1
FIGURE 2
5.. Turn on air conditioner switch. Adjust the idle-up speed while compressor is running to the specified rpm (Figure 1) by turning SAS 2 (Figure 2).When making this adjustment, be sure to record the turning direction and slot angle of SAS 2.
FIGURE 1
6.
Turn off air conditioner switch and make sure that the specified curb idle rpm is obtained (Figure 1).
7.
Race the engine at a speed of about 2000 rpm for five seconds.
8.
Turn on and then off the air conditioning switch repeatedly several times and make sure that with the compressor running that the engine is running
> Powertrain Management > Tune-up and Engine Performance Checks > Idle Speed > System Information > Technical Service Bulletins > All Other Service Bulletins for Idle
Speed: > 141984 > May > 84 > Carburetor - Idle Speed Adjustment on A/C Install > Page 649
D50/Ram 50 L4-1997cc 2.0L SOHC (1984)
at the specified idle-up rpm (Figure 1).
Example:
FIGURE 2
If Sas 2 has been turned 180~ clockwise in Step 5, SAS 3 will be turned 360~ clockwise in Step 9. Then, lift thefree lever by hand until it touches SAS 3 and make sure that the engine rpm is "N" +/- 100 rpm (where "N" is therpm recorded in Step 4). If necessary, adjust using SAS 3.
FIGURE 2
SIMPLE ADJUSTMENT PROCEDURE FOR COLT VISTA ONLY
If the idle adjustment has been properly made before installation of the air conditioner, the following simple procedure may be used:
1.
Give one clockwise turn to SAS 2 (Figure 2).
2.
Give two clockwise turns to SAS 3 (Figure 2).
3.
Back off idle-up speed adjusting screw for air conditioner one turn from fully tightened position (Figure 2).
> Powertrain Management > Tune-up and Engine Performance Checks > Idle Speed > System Information > Technical Service Bulletins > All Other Service Bulletins for Idle
Speed: > 141984 > May > 84 > Carburetor - Idle Speed Adjustment on A/C Install > Page 650
D50/Ram 50 L4-1997cc 2.0L SOHC (1984)
FIGURE 1
4.
Lastly, make sure that the curb idle speed and idle-up speed are properly adjusted (Figure 1).
FIGURE 2
If necessary, make fine adjustments with SAS 2 and SAS 3 (Figure 2).
POLICY: Reimbursable within the provisions of the warranty
FAILURE CODE: 31 - Rough Idle
> Powertrain Management > Tune-up and Engine Performance Checks > Idle Speed > System Information > Technical Service Bulletins > Page 651
> Powertrain Management > Tune-up and Engine Performance Checks > Firing Order > Component Information > Specifications
FIRING ORDER 2.0L RWD & 2.6L
> Powertrain Management > Tune-up and Engine Performance Checks > Ignition Timing > Timing Marks and Indicators > System Information > Diagrams
Timing Marks and Indicators: Diagrams
TIMING MARK 1.6L RWD, 2.6L & 2.0L EX. VISTA
> Powertrain Management > Tune-up and Engine Performance Checks > Ignition Timing > Timing Marks and Indicators > System Information > Diagrams > Page 659
D50/Ram 50 L4-1997cc 2.0L SOHC (1984)
TIMING MARK 1981-85 5.2L & 5.9L
> Powertrain Management > Tune-up and Engine Performance Checks > Distributor, Ignition > Vacuum Advance Unit <--> [Distributor Advance Unit] > Component Information > Specifications > Electrical Specifications
Vacuum Advance Unit: Electrical Specifications
> Powertrain Management > Tune-up and Engine Performance Checks > Distributor, Ignition > Vacuum Advance Unit <--> [Distributor Advance Unit] > Component Information > Specifications > Electrical Specifications >
Page 665
> Powertrain Management > Tune-up and Engine Performance Checks > Spark Plug > Component Information > Technical Service Bulletins > Customer Interest for Spark Plug: > 181788 > Oct > 88 > Spark Plugs - Oil Fouling/
Misfire on Hard Acceleration
Spark Plug: Customer InterestSpark Plugs - Oil Fouling/Misfire on Hard Acceleration
Models
1978-1989 MMC Engines With Jet Valves
Subject
Oil Fouled Spark Plug(s) Miss & Bucking Under Hard Acceleration
Index
FUEL
Date
October 17, 1988
No.
18-17-88
C18-21)This bulletin updates Technical Service Bulletin 5/14/88 and serves as a reminder that driveability problems may be caused by mechanical problems aswell as fuel system problems.
FIGURE 1
SYMPTOM/CONDITION
One or more (seldom occurs to more than one cylinder) spark plugs will be oil fouled and may show ground and center electrode erosion due tooverheating (Figure 1).
Under hard acceleration (wide open throttle) engine will miss and buck.
> Powertrain Management > Tune-up and Engine Performance Checks > Spark Plug > Component Information > Technical Service Bulletins > Customer Interest for Spark
Plug: > 181788 > Oct > 88 > Spark Plugs - Oil Fouling/Misfire on Hard Acceleration > Page 674
D50/Ram 50 L4-1997cc 2.0L SOHC (1984)
FIGURE 2
This condition may result from a jet valve failure. The jet valve failure is characterized by one of the causes outlined below (refer to Figure 2 fordescription):
^ Oil leaking past the oil seal and valve stem.
^ Oil leaking past the valve body and oil seal.
^ Oil leaking past the O-ring seal between the valve body and cylinder head which may be caused by a torn or cut Oring.
FIGURE 1
DIAGNOSIS
Remove and inspect all spark plugs. If a spark plug is found to be heavily oil fouled and/or appears to have the electrodes eroded or overheated, proceedto jet valve removal procedure below (Figure 1).PARTS REQUIRED
Jet Valve Assembly (as required)
O-Ring (as required)
INSTALLATION PROCEDURE
PN MD009440
PN MD009786
1.
Remove only the jet valve of the cylinder showing the spark plug oiling or overheating. Follow the jet valve removal procedures outlined in therespective model year service manual using Miller Special Tool #MB-998310.
> Powertrain Management > Tune-up and Engine Performance Checks > Spark Plug > Component Information > Technical Service Bulletins > Customer Interest for Spark
Plug: > 181788 > Oct > 88 > Spark Plugs - Oil Fouling/Misfire on Hard Acceleration > Page 675
D50/Ram 50 L4-1997cc 2.0L SOHC (1984)
FIGURE 2
2.
Push jet valve open and inspect the valve stem just under the valve head. If oil residue and excessive carbon buildup are present, the Jet ValveAssembly, PN MD009440, will have to be replaced (Figure 2).
If no residue or carbon buildup is present, inspect the O-ring for rips, tears, or deformity. O-ring can be replaced separately with PN MD009786.
FIGURE 3
3.
Inspect jet piece pocket by looking down into jet piece. If pocket has any buildup of burnt oil residue or carbon, it must be cleaned completelyusing the following procedure (Figure 3).
a.
Remove spark plug.
b.
Place piston on top dead center of compression stroke (both valves closed).
Use a thin stiff bristle brush to clean jet piece (a distributor cap terminal brush works well). A thin metal rod (coat hanger) can be used toloosen heavy deposits.
d.
Direct compressed air in jet piece. The loosened deposits will be blown out of the jet piece and spark plug hole. Eye protection isrecommended when performing this operation.
e.
Reinspect cleaned jet piece. If cracking or erosion is seen in the area of the jet air orifice (Figure 3) or the deposit cannot be cleanedadequately, the cylinder head will require replacement.
> Powertrain Management > Tune-up and Engine Performance Checks > Spark Plug > Component Information > Technical Service Bulletins > Customer Interest for Spark
Plug: > 181788 > Oct > 88 > Spark Plugs - Oil Fouling/Misfire on Hard Acceleration > Page 676
D50/Ram 50 L4-1997cc 2.0L SOHC (1984)
4.
Install new spark plug of proper heat range and gap setting.
5.
Start engine and allow to fully warm up. Check for oil leaks and adjust idle speed if necessary.
POLICY: Information only
> Powertrain Management > Tune-up and Engine Performance Checks > Spark Plug > Component Information > Technical Service Bulletins > All Technical Service Bulletins for Spark Plug: > 181788 > Oct > 88 > Spark Plugs
- Oil Fouling/Misfire on Hard Acceleration
Spark Plug: All Technical Service BulletinsSpark Plugs - Oil Fouling/Misfire on Hard Acceleration
Models
1978-1989 MMC Engines With Jet Valves
Subject
Oil Fouled Spark Plug(s) Miss & Bucking Under Hard Acceleration
Index
FUEL
Date
October 17, 1988
No.
18-17-88
C18-21)This bulletin updates Technical Service Bulletin 5/14/88 and serves as a reminder that driveability problems may be caused by mechanical problems aswell as fuel system problems.
FIGURE 1
SYMPTOM/CONDITION
One or more (seldom occurs to more than one cylinder) spark plugs will be oil fouled and may show ground and center electrode erosion due tooverheating (Figure 1).
Under hard acceleration (wide open throttle) engine will miss and buck.
> Powertrain Management > Tune-up and Engine Performance Checks > Spark Plug > Component Information > Technical Service Bulletins > All Technical Service
Bulletins for Spark Plug: > 181788 > Oct > 88 > Spark Plugs - Oil Fouling/Misfire on Hard Acceleration > Page 682
D50/Ram 50 L4-1997cc 2.0L SOHC (1984)
FIGURE 2
This condition may result from a jet valve failure. The jet valve failure is characterized by one of the causes outlined below (refer to Figure 2 fordescription):
^ Oil leaking past the oil seal and valve stem.
^ Oil leaking past the valve body and oil seal.
^ Oil leaking past the O-ring seal between the valve body and cylinder head which may be caused by a torn or cut Oring.
FIGURE 1
DIAGNOSIS
Remove and inspect all spark plugs. If a spark plug is found to be heavily oil fouled and/or appears to have the electrodes eroded or overheated, proceedto jet valve removal procedure below (Figure 1).PARTS REQUIRED
Jet Valve Assembly (as required)
O-Ring (as required)
INSTALLATION PROCEDURE
PN MD009440
PN MD009786
1.
Remove only the jet valve of the cylinder showing the spark plug oiling or overheating. Follow the jet valve removal procedures outlined in therespective model year service manual using Miller Special Tool #MB-998310.
> Powertrain Management > Tune-up and Engine Performance Checks > Spark Plug > Component Information > Technical Service Bulletins > All Technical Service
Bulletins for Spark Plug: > 181788 > Oct > 88 > Spark Plugs - Oil Fouling/Misfire on Hard Acceleration > Page 683
D50/Ram 50 L4-1997cc 2.0L SOHC (1984)
FIGURE 2
2.
Push jet valve open and inspect the valve stem just under the valve head. If oil residue and excessive carbon buildup are present, the Jet ValveAssembly, PN MD009440, will have to be replaced (Figure 2).
If no residue or carbon buildup is present, inspect the O-ring for rips, tears, or deformity. O-ring can be replaced separately with PN MD009786.
FIGURE 3
3.
Inspect jet piece pocket by looking down into jet piece. If pocket has any buildup of burnt oil residue or carbon, it must be cleaned completelyusing the following procedure (Figure 3).
a.
Remove spark plug.
b.
Place piston on top dead center of compression stroke (both valves closed).
Use a thin stiff bristle brush to clean jet piece (a distributor cap terminal brush works well). A thin metal rod (coat hanger) can be used toloosen heavy deposits.
d.
Direct compressed air in jet piece. The loosened deposits will be blown out of the jet piece and spark plug hole. Eye protection isrecommended when performing this operation.
e.
Reinspect cleaned jet piece. If cracking or erosion is seen in the area of the jet air orifice (Figure 3) or the deposit cannot be cleanedadequately, the cylinder head will require replacement.
> Powertrain Management > Tune-up and Engine Performance Checks > Spark Plug > Component Information > Technical Service Bulletins > All Technical Service
Bulletins for Spark Plug: > 181788 > Oct > 88 > Spark Plugs - Oil Fouling/Misfire on Hard Acceleration > Page 684
D50/Ram 50 L4-1997cc 2.0L SOHC (1984)
4.
Install new spark plug of proper heat range and gap setting.
5.
Start engine and allow to fully warm up. Check for oil leaks and adjust idle speed if necessary.
POLICY: Information only
> Powertrain Management > Tune-up and Engine Performance Checks > Spark Plug > Component Information > Technical Service Bulletins > Page 685
> Powertrain Management > Tune-up and Engine Performance Checks > Compression Check > System Information > Specifications
Compression Check: Specifications
Pressure 170 psi
> Powertrain Management > Tune-up and Engine Performance Checks > Valve Clearance > System Information > Specifications
Valve Clearance: Specifications
Except Jet Valve Intake 0.006 in
1985-89 2.0L & 2.6L except jet valve have hydraulic lifters.
Jet Valve
Exhaust 0.01 in
Intake 0.006 in
> Powertrain Management > Tune-up and Engine Performance Checks > Valve Clearance > System Information > Specifications > Page 692
Valve Clearance: Adjustments
INTAKE & EXHAUST VALVES
Fig. 12 Adjusting valve clearance (Typical)
The jet valve must be adjusted before adjusting the intake valve.
1. With engine at operating temperature, remove rocker arm cover.2. Disconnect high tension lead from ignition coil.3. While observing rocker arms on No. 4 cylinder, rotate crankshaft until the exhaust valve is closing and the intake valve has just started to open
Fig. 12.
with crankshaft pulley mark aligned with TDC mark on timing chain case. At this position the No. 1 cylinder is at top dead center compressionstroke. Check and adjust valve clearance for both intake and exhaust valves of No. 1 cylinder, intake valve of No. 2 cylinder and exhaust valve ofNo. 3 cylinder, as necessary,
4. Rotate crankshaft 360 degrees and check and adjust valve clearance for exhaust valve of No. 2 cylinder, intake valve of No. 3 cylinder and intake and exhaust valves of No. 4 cylinder.
5. After completing adjustment, install rocker arm cover and connect ignition coil high tension lead.
JET VALVE
Fig. 13 Adjusting jet valve clearance
Exc. Models Equipped W/Hydraulic Lash Adjusters
Fig. 13.
Following procedure for intake and exhaust valve adjustment, position No. 1 cylinder at top dead center compression stroke. Loosen intake valveadjusting screw at least 2 turns, then loosen jet valve adjusting screw locknut. Rotate jet valve adjusting screw counterclockwise and insert a suitablefeeler gauge blade as specified in ``Valve Specification Chart,'' between jet valve stem and adjusting screw, Tighten jet valve adjusting screwuntil it contacts the feeler gauge blade, then while holding adjusting screw in position, tighten locknut. After jet valve adjustment has been completed,adjust intake valve clearance. Continue to follow intake and exhaust valve adjustment procedure and adjust jet valves as necessary.
> Powertrain Management > Computers and Control Systems > Coolant Temperature Sensor/Switch (For Computer) > Component Information > Specifications
Coolant Temperature Sensor/Switch (For Computer): SpecificationsSwitch Torque
Switch Torque
Cooling Fan Switch 8-18 ft.lb
> Powertrain Management > Computers and Control Systems > Powertrain Control Module <--> [Engine Control Module] > Component Information > Locations
Powertrain Control Module: Locations
Under LH Side Of I/P
> Powertrain Management > Computers and Control Systems > Idle Up Control Valve > Component Information > Description and Operation
Idle Up Control Valve: Description and Operation
Fig. 19 Throttle opener system. 1982-86 models except 1982 Champ & Colt (federal) w/1400cc engine & manual transaxle
1982-88 Models exc. 1982 Champ & Colt (federal) w/1400cc engines & manual transaxle
Fig. 19,
This system, consists of a throttle opener assembly, a solenoid valve, an engine speed sensor and the air conditioning compressor switch. When the compressor is switched on, the speed sensor detects a drop in engine speed, and activates the solenoid valve. The solenoid valve thentransfers intake manifold vacuum to the throttle opener, which opens the throttle valve via the throttle opener lever. The engine speed, therefore, isbalanced against the air conditioning compressor load, resulting in improved idle and decreased levels of exhaust pollutants.
> Powertrain Management > Computers and Control Systems > Idle Up Control Valve > Component Information > Description and Operation > Page 703
Idle Up Control Valve: Adjustments
Fig. 19 Throttle opener system. 1982-86 models except 1982 Champ & Colt (federal) w/1400cc engine & manual transaxle
1.
Start engine and allow to reach normal operating temperature.
2.
Ensure that all electrical accessories are ``Off,'' then position transmission in ``Neutral.''
3.
Set curb idle to specifications.
4.
5.
With air conditioning system ``Off,'' disconnect vacuum hose from throttle opener nipple, then apply 20 inches Hg vacuum to throttle opener witha suitable vacuum pump.
Fig. 19, Adjust engine speed with throttle opener setting screw, to the following specifications: a. On 1982 Champ & Colt (1600cc engine), set engine speed to 900 50 RPM for automatic transaxle equipped vehicles, or 850 50 RPM for manual transaxle equipped vehicles. b. On 1982 Challenger, Sapporo & Pickup, set engine speed to 900 50 RPM.c. On 1983 Challenger & Sapporo, set engine speed to 1050 50 RPM.d. On 1983 Colt, set engine speed to 1100 50 RPM for manual transaxle equipped vehicles, or 1150 50 RPM for automatic transaxle equipped vehicles.
> Powertrain Management > Computers and Control Systems > Information Bus > Component Information > Testing and Inspection > Diagnostic Trouble Code Descriptions
Information Bus: Diagnostic Trouble Code Descriptions
For Information regarding diagnosis of all B, C, P, U and Manufacturer Codes
> Powertrain Management > Computers and Control Systems > Information Bus > Component Information > Testing and Inspection > Diagnostic Trouble Code Descriptions > Page 708
Information Bus: Diagnostic Trouble Code Tests and Associated Procedures
For Information regarding diagnosis of all B, C, P, U and Manufacturer Codes
> Powertrain Management > Computers and Control Systems > Relays and Modules - Computers and Control Systems > Powertrain Control Module <--> [Engine Control Module] > Component Information > Locations
Powertrain Control Module: Locations
Under LH Side Of I/P
> Powertrain Management > Computers and Control Systems > Sensors and Switches - Computers and Control Systems > Coolant Temperature Sensor/Switch (For Computer) > Component Information > Specifications
Coolant Temperature Sensor/Switch (For Computer): SpecificationsSwitch Torque
Switch Torque
Cooling Fan Switch 8-18 ft.lb
> Powertrain Management > Emission Control Systems > Secondary Air Supply <--> [Air Injection] > Air Diverter Valve > Component Information > Description and Operation
Air Switching Valve System 1982-84 Pickup w/2000cc & 2600cc engines
> Powertrain Management > Emission Control Systems > Catalytic Converter > Component Information > Description and Operation
Catalytic Converter: Description and Operation
Fig. 32 Single & Twin Catalytic Converters
Fig. 32.
The catalytic converter is an emission control device added to the exhaust system to effectively reduce the levels of carbon monoxide andhydrocarbons entering the atmosphere. There are two types of catalytic converters used on these vehicles. The two types are, pellet type and monolithic type. The pellet type converter wasused on early models and incorporates palladium coated pellets to control emissions. On later models, the monolithic type converter is used. Thisconverter contains a honeycomb insert that is coated with palladium catalytic material,
> Powertrain Management > Emission Control Systems > Slow Cut Solenoid Valve <--> [Deceleration Valve] > Component Information > Description and Operation
Slow Cut Solenoid Valve: Description and Operation
Fig. 16 Deceleration spark advance system
Fig. 19b Air Switching Valve System
> Powertrain Management > Emission Control Systems > Slow Cut Solenoid Valve <--> [Deceleration Valve] > Component Information > Description and Operation > Page
728
D50/Ram 50 L4-1997cc 2.0L SOHC (1984)
Fig. 18a Coasting Air Valve System
Fig. 18a. Fig. 19a.
Fig. 16,
Fig. 17.
Fig. 16.
The deceleration system used on some 1982-84 models includes a coasting air valve system, and an air switching valve system, Some 1981-88 models incorporate a deceleration spark advance system, and/or a dashpot, The coasting air valve system and air switching valve system are used to reduce HC emissions during deceleration. The engine speed sensor whichcontrols the solenoid valve, will prevent the coasting air valve or air switching valve from operating at or below a specified engine RPM by opening thesolenoid valve. On 1400, 1600 and 2,000 cc engines, the specified engine speed is 1800 RPM (+/- 200 RPM). On 2,600cc engines, the specified enginespeed is 1600 RPM (+/- 200 RPM). This is done to prevent poor idling or engine stalling at lower engine speeds. The coasting air valve suppliesadditional air to the intake manifold at engine speeds within the specified range, from a port located below the secondary throttle valve. The airswitching valve supplies additional air to the intake manifold at engine speeds within the specified range, from the idle mixture adjusting screw passagelocated below the primary throttle valve. The coasting air valve and air switching valve are built into the carburetor. The deceleration spark advance system consists of an engine speed sensor and a solenoid valve, During deceleration, ignition timing isadvanced by intake manifold vacuum acting upon the distributor vacuum advance unit diaphragm, which is routed through the solenoid valve. At orbelow a specified engine RPM, the engine speed sensor will activate the solenoid valve, changing vacuum acting upon the distributor vacuum advanceunit diaphragm from intake manifold vacuum to carburetor ported vacuum. On some models a dashpot is used to delay throttle valve closure during deceleration to its normal idle speed position to reduce HC emissions.
> Powertrain Management > Emission Control Systems > Slow Cut Solenoid Valve <--> [Deceleration Valve] > Component Information > Description and Operation > Page 729
Slow Cut Solenoid Valve: Adjustments
Top Of Engine
> Powertrain Management > Emission Control Systems > Evaporative Emissions System > Evaporative Emission Control Canister > Component Information > Locations > Evaporative Emission Control Canister
Evaporative Emission Control Canister: LocationsEvaporative Emission Control Canister
A sealed, maintenance free, charcoal canister is used on all engines and is located in the wheel well area of the engine compartment.
> Powertrain Management > Emission Control Systems > Evaporative Emissions System > Evaporative Emission Control Canister > Component Information > Locations > Evaporative Emission Control Canister > Page 735
Evaporative Emission Control Canister: LocationsCheck Valve
Top Of Fuel Tank
> Powertrain Management > Emission Control Systems > Evaporative Emissions System > Liquid Vapor Separator, Evaporative System > Component Information > Locations
Liquid Vapor Separator: Locations
Top Of Fuel Tank
> Powertrain Management > Emission Control Systems > Exhaust Gas Recirculation > EGR Valve > Component Information > Locations
EGR Valve: Locations
Top Of Engine
> Powertrain Management > Emission Control Systems > Positive Crankcase Ventilation > Component Information > Description and Operation
Positive Crankcase Ventilation: Description and Operation
Positive Crankcase Ventilation (PCV) System. 1982-86 2600cc engine & 1982-86 2000cc engine
DESCRIPTION
Exc. 1983-85 Pickup w/ Diesel Engine
Fig. 2.
This system incorporates a PCV valve which is located at the rocker arm cover, With this system, fresh air is routed from the air cleaner tothe front of the valve cover and into the crankcase where the fresh air is mixed with the blow-by gasses. The mixture of fresh air and blow-bygasses then passes through the PCV valve and is drawn through a hose to the intake manifold and to the combustion chamber. Under high speed orduring acceleration conditions, the blow-by gasses are drawn through the PCV valve to the intake manifold and through the breather to the aircleaner and routed into the combustion chamber.
SYSTEM TESTING
Fig. 2.
1. Check if hoses or PCV valve is clogged.2. Check air flow through hoses as shown in
> Powertrain Management > Emission Control Systems > Positive Crankcase Ventilation > Component Information > Description and Operation > Page 746
Positive Crankcase Ventilation: Testing and Inspection
Positive Crankcase Ventilation (PCV) System. 1982-86 2600cc engine & 1982-86 2000cc engine
DESCRIPTION
Exc. 1983-85 Pickup w/ Diesel Engine
Fig. 2.
This system incorporates a PCV valve which is located at the rocker arm cover, With this system, fresh air is routed from the air cleaner tothe front of the valve cover and into the crankcase where the fresh air is mixed with the blow-by gasses. The mixture of fresh air and blow-bygasses then passes through the PCV valve and is drawn through a hose to the intake manifold and to the combustion chamber. Under high speed orduring acceleration conditions, the blow-by gasses are drawn through the PCV valve to the intake manifold and through the breather to the aircleaner and routed into the combustion chamber.
SYSTEM TESTING
Fig. 2.
1. Check if hoses or PCV valve is clogged.2. Check air flow through hoses as shown in
> Powertrain Management > Emission Control Systems > Thermostatic Air Cleaner > Component Information > Description and Operation
Thermostatic Air Cleaner: Description and Operation
Fig. 3 Heated air intake (HAIS) system
DESCRIPTION
Exc. Diesel & Turbocharged Engines
Fig. 3,
84 F
84 F 113 F
113 F
In this system, the hot air control valve is controlled by a vacuum motor/temperature sensor combination system which responds to intakemanifold vacuum and temperature inside the air cleaner housing. When temperature inside air cleaner is below , air bleed valve remainsclosed, forcing intake manifold vacuum to be applied to diaphragm of vacuum motor which then opens air control valve and allows heated air toenter. If air cleaner temperature is between and , air flow will occur through both hot and cold air circuits. When air cleanertemperature is above , the air bleed valve is fully opened, causing air control valve to close fully regardless of intake manifold vacuum,thereby allowing only cold air to flow.
VACUUM SYSTEM TESTING
84 F
113 F 1. Check that heat cowl to air cleaner and all vacuum hoses are properly attached and in good condition.2. With cold engine and ambient temperature of less than , air control valve should be in up position.3. With engine warmed up and running, check temperature of air entering air cleaner. When air temperature exceeds , the air control valve should be in down position.
84 F 15 in.Hg (380 mmHg) 4. Remove air cleaner from engine and allow to cool down to under . Apply vacuum to sensor and check that valve is in up position. If valve does not rise, check vacuum motor for proper operation.
10 in.Hg (250 mmHg) 5. To test vacuum motor, apply of vacuum using tool C-4207 or equivalent. Valve should be in full up position. If vacuum motor fails to operate properly, replace air cleaner housing assembly.
> Powertrain Management > Emission Control Systems > Thermostatic Air Cleaner > Component Information > Description and Operation > Page 750
Thermostatic Air Cleaner: Testing and Inspection
Fig. 3 Heated air intake (HAIS) system
DESCRIPTION
Exc. Diesel & Turbocharged Engines
Fig. 3,
84 F
84 F and 113 F
113 F
In this system, the hot air control valve is controlled by a vacuum motor/temperature sensor combination system which responds to intakemanifold vacuum and temperature inside the air cleaner housing. When temperature inside air cleaner is below , air bleed valve remainsclosed, forcing intake manifold vacuum to be applied to diaphragm of vacuum motor which then opens air control valve and allows heated air toenter. If air cleaner temperature is between , air flow will occur through both hot and cold air circuits. When air cleanertemperature is above , the air bleed valve is fully opened, causing air control valve to close fully regardless of intake manifold vacuum,thereby allowing only cold air to flow.
VACUUM SYSTEM TESTING
84 F
113 F 1. Check that heat cowl to air cleaner and all vacuum hoses are properly attached and in good condition.2. With cold engine and ambient temperature of less than , air control valve should be in up position.3. With engine warmed up and running, check temperature of air entering air cleaner. When air temperature exceeds , the air control valve should be in down position.
84 F 15 in.Hg (380 mmHg) 4. Remove air cleaner from engine and allow to cool down to under . Apply vacuum to sensor and check that valve is in up position. If valve does not rise, check vacuum motor for proper operation.
10 in.Hg (250 mmHg) 5. To test vacuum motor, apply of vacuum using tool C-4207 or equivalent. Valve should be in full up position. If vacuum motor fails to operate properly, replace air cleaner housing assembly.
> Powertrain Management > Fuel Delivery and Air Induction > Fuel Pressure > System Information > Specifications
> Powertrain Management > Fuel Delivery and Air Induction > Idle Speed > System Information > Technical Service Bulletins > By Symptom: > 140884 > Jan > 84 > Propane Idle Set - Procedure
Idle Speed: By SymptomPropane Idle Set - Procedure
Models
1984 MMC Import Vehicles All With Gasoline Fueled Engines, All Emission Markets (Except Vehicles With Turbo Chargers & Canada)
Subject
Propane Idle Set Procedure
Index
FUEL
Date
January 17, 1984
No..
14-08-84
P-94-C
The propane idle set procedure is authorized for 1984 subject model import vehicles.
The propane idle set method is to be used when "CO" meter procedure cannot be used, i.e., "CO" meter in for repair or is not available in the servicearea.
PROPANE IDLE CHECK & SET PROCEDURE
1.
Idle Setting Conditions: Lights, electric cooling fan, and all accessories are off, transmission in neutral, and front wheels in straight ahead position.
2.
If engine is cold, allow it to warm up until full operating temperature is reached (185 to 205~F).
NOTE:
PERFORM THE FOLLOWING STEPS 3 THROUGH 5 AND STEP 19 ONLY IF ENGINE IS EQUIPPED WITH A FEEDBACKCARBURETOR EMISSION SYSTEM.
3.
Turn off ignition switch.
4.
Disconnect the NEGATIVE cable from the battery for about 5 seconds. Then reconnect negative battery cable.
5.
Disconnect the connector of the exhaust oxygen sensor.
6.
Start and run engine for 5 seconds at an engine speed between 2,000 to 3,000 rpm.
7.
Then, allow engine to run at curb idle for 2 minutes.
> Powertrain Management > Fuel Delivery and Air Induction > Idle Speed > System Information > Technical Service Bulletins > By Symptom: > 140884 > Jan > 84 >
Propane Idle Set - Procedure > Page 763
D50/Ram 50 L4-1997cc 2.0L SOHC (1984)
FIGURE 1
8.
Check engine idle speed and basic ignition timing. Adjust to specifications if necessary (Figure 1).
9.
Disconnect the air cleaner fresh air intake duct from the air cleaner snorkel.
Insert the propane supply hose into the air cleaner snorkel about 4 inches.
Make certain both valves on propane bottle are fully closed and the bottle is upright and in a safe location.
> Powertrain Management > Fuel Delivery and Air Induction > Idle Speed > System Information > Technical Service Bulletins > By Symptom: > 140884 > Jan > 84 >
Propane Idle Set - Procedure > Page 764
D50/Ram 50 L4-1997cc 2.0L SOHC (1984)
FIGURE 3
10.
Open the propane bottle main valve fully, then slowly open the propane fine control valve to the position where maximum engine rpm is achieved.(Too much propane or too rich idle mixture will cause the engine to lose rpm as the fine control valve is opened.) (Figure 3.)
FIGURE 2
> Powertrain Management > Fuel Delivery and Air Induction > Idle Speed > System Information > Technical Service Bulletins > By Symptom: > 140884 > Jan > 84 >
Propane Idle Set - Procedure > Page 765
D50/Ram 50 L4-1997cc 2.0L SOHC (1984)
Note the engine rpm increase. Specified values of each engine propane idle speed increase are outlined in Figure 2.
If the propane idle speed exceeds more than 25 rpm from the specified value in Figure 2 or the rpm does not increase at all, idle fuel mixtureshould be adjusted according to the propane assisted idle set procedure that follows.
FIGURE 4
11.
It is not necessary to remove carburetor from intake manifold to remove the idle mixture screw plug.
Drill out concealment plug on car. Remove vacuum connector from high altitude compensator (HAC) fittings on carburetor air horn (Figure 4).
Use a 1/4" diameter drill 8' long at the 11 o'clock position on the plug boss. Locate drill point 3/16" from end of boss.
Plug should pop out when the drill bit contacts it (Figure 4).
12.
Start engine and run for 1 minute at engine speed of 2500 rpm.
13.
Run engine at idle for 2 minutes.
> Powertrain Management > Fuel Delivery and Air Induction > Idle Speed > System Information > Technical Service Bulletins > By Symptom: > 140884 > Jan > 84 >
Propane Idle Set - Procedure > Page 766
D50/Ram 50 L4-1997cc 2.0L SOHC (1984)
FIGURE 2
14.
Open the propane main valve and slowly open the fine control valve to the position where maximum engine speed is achieved. Use the idle speedadjusting screw to set the specified propane idle speed from Figure 2.
15.
Turn off propane main valve and adjust idle mixture screw to the specified idle set speed from Figure 2.
16.
17.
To recheck the maximum propane speed, open the main propane valve again. If the speed still differs more than 25 rpm from the specified propanespeed from Figure 2, repeat Steps 14 through 16.
18.
Remove the propane hose and replace fresh air duct on air cleaner snorkel.
19.
Reconnect the exhaust oxygen sensor (if engine is equipped with a feedback carburetor).
20.
Install Idle Mixture Screw Concealment Plug. (If new plug is needed, use PN MD606954.)
POLICY: Reimbursable within the provisions of the warranty
> Powertrain Management > Fuel Delivery and Air Induction > Idle Speed > System Information > Technical Service Bulletins > By Symptom: > 140884 > Jan > 84 >
Propane Idle Set - Procedure > Page 767
D50/Ram 50 L4-1997cc 2.0L SOHC (1984)
FRONT WHEEL DRIVE LABOR OPERATION TIME SCHEDULE
FAILURE CODE: RO - Driveability
> Powertrain Management > Fuel Delivery and Air Induction > Idle Speed > System Information > Technical Service Bulletins > All Technical Service Bulletins for Idle Speed: > 142084 > May > 84 > Engine Specifications -
Manual Corrections
Idle Speed: All Technical Service BulletinsEngine Specifications - Manual Corrections
Models
1984 Colt, Ram 50, & Conquest
Subject
Correction of 1984 Service Manuals on Engine Specifications
Index
FUEL
Date
May 21, 1984
No..
14-20-84
P-2112-C
This service bulletin is issued to correct the following 1984 Import Service Manuals.
^ Colt Service Manual Publication #81-270-4006
> Powertrain Management > Fuel Delivery and Air Induction > Idle Speed > System Information > Technical Service Bulletins > All Technical Service Bulletins for Idle
Speed: > 142084 > May > 84 > Engine Specifications - Manual Corrections > Page 773
D50/Ram 50 L4-1997cc 2.0L SOHC (1984)
^ Ram-50 Service Manual Publication #81-370-4009
^ Conquest Service Manual Publication #81-270-4005
Corrections are highlighted in the attached specifications in bold type and should be entered in the respective model service manual.
POLICY: Information only
> Powertrain Management > Fuel Delivery and Air Induction > Idle Speed > System Information > Technical Service Bulletins > All Technical Service Bulletins for Idle Speed: > 141984 > May > 84 > Carburetor - Idle Speed
Adjustment on A/C Install
Idle Speed: All Technical Service BulletinsCarburetor - Idle Speed Adjustment on A/C Install
Models
1984 Colt (W/O Turbo), Ram-50, Power Ram-50 (W/O Diesel) & Colt Vista
Subject
Idle-Up Speed Adjustment After Air Conditioning Installation and/or Service
Index
FUEL
Date
May 7, 1984
No.
14-19-84
P-1927-CThis procedure modifies the adjustment procedures in the subject model service manuals.
If difficulty is encountered in adjusting curb idle speed and/or idle-up speed after installation or servicing and adjustment of the air conditioning system,follow the adjustment procedure as outlined below:
ADJUSTMENT PROCEDURE
1.
Thoroughly warm up engine, turn off all accessories, front wheels in straight ahead position, transmission in neutral, parking brake set, andradiator cooling fan stopped.
FIGURE 1
> Powertrain Management > Fuel Delivery and Air Induction > Idle Speed > System Information > Technical Service Bulletins > All Technical Service Bulletins for Idle
Speed: > 141984 > May > 84 > Carburetor - Idle Speed Adjustment on A/C Install > Page 778
D50/Ram 50 L4-1997cc 2.0L SOHC (1984)
FIGURE 2
2.
Check and adjust curb idle speed if necessary (see Figure 1 for specification) and make adjustment using SAS (speed adjusting screw) 1 (Figure2). On some models installation of air conditioner will change the curb idle speed already adjusted.
FIGURE 2
3.
Back off the idle-up speed adjusting screw for air conditioner one turn from fully tightened position (Figure 2).
4.
Lift the free lever by hand until it touches SAS 3 and record the engine speed ("N" = R.P.M.) obtained at this time (Figure 2).
> Powertrain Management > Fuel Delivery and Air Induction > Idle Speed > System Information > Technical Service Bulletins > All Technical Service Bulletins for Idle
Speed: > 141984 > May > 84 > Carburetor - Idle Speed Adjustment on A/C Install > Page 779
D50/Ram 50 L4-1997cc 2.0L SOHC (1984)
FIGURE 1
FIGURE 2
5.. Turn on air conditioner switch. Adjust the idle-up speed while compressor is running to the specified rpm (Figure 1) by turning SAS 2 (Figure 2).When making this adjustment, be sure to record the turning direction and slot angle of SAS 2.
FIGURE 1
6.
Turn off air conditioner switch and make sure that the specified curb idle rpm is obtained (Figure 1).
7.
Race the engine at a speed of about 2000 rpm for five seconds.
8.
Turn on and then off the air conditioning switch repeatedly several times and make sure that with the compressor running that the engine is running
> Powertrain Management > Fuel Delivery and Air Induction > Idle Speed > System Information > Technical Service Bulletins > All Technical Service Bulletins for Idle
Speed: > 141984 > May > 84 > Carburetor - Idle Speed Adjustment on A/C Install > Page 780
D50/Ram 50 L4-1997cc 2.0L SOHC (1984)
at the specified idle-up rpm (Figure 1).
Example:
FIGURE 2
If Sas 2 has been turned 180~ clockwise in Step 5, SAS 3 will be turned 360~ clockwise in Step 9. Then, lift thefree lever by hand until it touches SAS 3 and make sure that the engine rpm is "N" +/- 100 rpm (where "N" is therpm recorded in Step 4). If necessary, adjust using SAS 3.
FIGURE 2
SIMPLE ADJUSTMENT PROCEDURE FOR COLT VISTA ONLY
If the idle adjustment has been properly made before installation of the air conditioner, the following simple procedure may be used:
1.
Give one clockwise turn to SAS 2 (Figure 2).
2.
Give two clockwise turns to SAS 3 (Figure 2).
3.
Back off idle-up speed adjusting screw for air conditioner one turn from fully tightened position (Figure 2).
> Powertrain Management > Fuel Delivery and Air Induction > Idle Speed > System Information > Technical Service Bulletins > All Technical Service Bulletins for Idle
Speed: > 141984 > May > 84 > Carburetor - Idle Speed Adjustment on A/C Install > Page 781
D50/Ram 50 L4-1997cc 2.0L SOHC (1984)
FIGURE 1
4.
Lastly, make sure that the curb idle speed and idle-up speed are properly adjusted (Figure 1).
FIGURE 2
If necessary, make fine adjustments with SAS 2 and SAS 3 (Figure 2).
POLICY: Reimbursable within the provisions of the warranty
FAILURE CODE: 31 - Rough Idle
> Powertrain Management > Fuel Delivery and Air Induction > Idle Speed > System Information > Technical Service Bulletins > All Technical Service Bulletins for Idle Speed: > 140884 > Jan > 84 > Propane Idle Set -
Procedure
Idle Speed: All Technical Service BulletinsPropane Idle Set - Procedure
Models
1984 MMC Import Vehicles All With Gasoline Fueled Engines, All Emission Markets (Except Vehicles With Turbo Chargers & Canada)
Subject
Propane Idle Set Procedure
Index
FUEL
Date
January 17, 1984
No..
14-08-84
P-94-C
The propane idle set procedure is authorized for 1984 subject model import vehicles.
The propane idle set method is to be used when "CO" meter procedure cannot be used, i.e., "CO" meter in for repair or is not available in the servicearea.
PROPANE IDLE CHECK & SET PROCEDURE
1.
Idle Setting Conditions: Lights, electric cooling fan, and all accessories are off, transmission in neutral, and front wheels in straight ahead position.
2.
If engine is cold, allow it to warm up until full operating temperature is reached (185 to 205~F).
NOTE:
PERFORM THE FOLLOWING STEPS 3 THROUGH 5 AND STEP 19 ONLY IF ENGINE IS EQUIPPED WITH A FEEDBACKCARBURETOR EMISSION SYSTEM.
3.
Turn off ignition switch.
4.
Disconnect the NEGATIVE cable from the battery for about 5 seconds. Then reconnect negative battery cable.
5.
Disconnect the connector of the exhaust oxygen sensor.
6.
Start and run engine for 5 seconds at an engine speed between 2,000 to 3,000 rpm.
7.
Then, allow engine to run at curb idle for 2 minutes.
> Powertrain Management > Fuel Delivery and Air Induction > Idle Speed > System Information > Technical Service Bulletins > All Technical Service Bulletins for Idle
Speed: > 140884 > Jan > 84 > Propane Idle Set - Procedure > Page 786
D50/Ram 50 L4-1997cc 2.0L SOHC (1984)
FIGURE 1
8.
Check engine idle speed and basic ignition timing. Adjust to specifications if necessary (Figure 1).
9.
Disconnect the air cleaner fresh air intake duct from the air cleaner snorkel.
Insert the propane supply hose into the air cleaner snorkel about 4 inches.
Make certain both valves on propane bottle are fully closed and the bottle is upright and in a safe location.
> Powertrain Management > Fuel Delivery and Air Induction > Idle Speed > System Information > Technical Service Bulletins > All Technical Service Bulletins for Idle
Speed: > 140884 > Jan > 84 > Propane Idle Set - Procedure > Page 787
D50/Ram 50 L4-1997cc 2.0L SOHC (1984)
FIGURE 3
10.
Open the propane bottle main valve fully, then slowly open the propane fine control valve to the position where maximum engine rpm is achieved.(Too much propane or too rich idle mixture will cause the engine to lose rpm as the fine control valve is opened.) (Figure 3.)
FIGURE 2
> Powertrain Management > Fuel Delivery and Air Induction > Idle Speed > System Information > Technical Service Bulletins > All Technical Service Bulletins for Idle
Speed: > 140884 > Jan > 84 > Propane Idle Set - Procedure > Page 788
D50/Ram 50 L4-1997cc 2.0L SOHC (1984)
Note the engine rpm increase. Specified values of each engine propane idle speed increase are outlined in Figure 2.
If the propane idle speed exceeds more than 25 rpm from the specified value in Figure 2 or the rpm does not increase at all, idle fuel mixtureshould be adjusted according to the propane assisted idle set procedure that follows.
FIGURE 4
11.
It is not necessary to remove carburetor from intake manifold to remove the idle mixture screw plug.
Drill out concealment plug on car. Remove vacuum connector from high altitude compensator (HAC) fittings on carburetor air horn (Figure 4).
Use a 1/4" diameter drill 8' long at the 11 o'clock position on the plug boss. Locate drill point 3/16" from end of boss.
Plug should pop out when the drill bit contacts it (Figure 4).
12.
Start engine and run for 1 minute at engine speed of 2500 rpm.
13.
Run engine at idle for 2 minutes.
> Powertrain Management > Fuel Delivery and Air Induction > Idle Speed > System Information > Technical Service Bulletins > All Technical Service Bulletins for Idle
Speed: > 140884 > Jan > 84 > Propane Idle Set - Procedure > Page 789
D50/Ram 50 L4-1997cc 2.0L SOHC (1984)
FIGURE 2
14.
Open the propane main valve and slowly open the fine control valve to the position where maximum engine speed is achieved. Use the idle speedadjusting screw to set the specified propane idle speed from Figure 2.
15.
Turn off propane main valve and adjust idle mixture screw to the specified idle set speed from Figure 2.
16.
17.
To recheck the maximum propane speed, open the main propane valve again. If the speed still differs more than 25 rpm from the specified propanespeed from Figure 2, repeat Steps 14 through 16.
18.
Remove the propane hose and replace fresh air duct on air cleaner snorkel.
19.
Reconnect the exhaust oxygen sensor (if engine is equipped with a feedback carburetor).
20.
Install Idle Mixture Screw Concealment Plug. (If new plug is needed, use PN MD606954.)
POLICY: Reimbursable within the provisions of the warranty
> Powertrain Management > Fuel Delivery and Air Induction > Idle Speed > System Information > Technical Service Bulletins > All Technical Service Bulletins for Idle
Speed: > 140884 > Jan > 84 > Propane Idle Set - Procedure > Page 790
D50/Ram 50 L4-1997cc 2.0L SOHC (1984)
FRONT WHEEL DRIVE LABOR OPERATION TIME SCHEDULE
FAILURE CODE: RO - Driveability
> Powertrain Management > Fuel Delivery and Air Induction > Idle Speed > System Information > Technical Service Bulletins > All Other Service Bulletins for Idle Speed: > 142084 > May > 84 > Engine Specifications -
Manual Corrections
Idle Speed: All Technical Service BulletinsEngine Specifications - Manual Corrections
Models
1984 Colt, Ram 50, & Conquest
Subject
Correction of 1984 Service Manuals on Engine Specifications
Index
FUEL
Date
May 21, 1984
No..
14-20-84
P-2112-C
This service bulletin is issued to correct the following 1984 Import Service Manuals.
^ Colt Service Manual Publication #81-270-4006
> Powertrain Management > Fuel Delivery and Air Induction > Idle Speed > System Information > Technical Service Bulletins > All Other Service Bulletins for Idle Speed: >
142084 > May > 84 > Engine Specifications - Manual Corrections > Page 796
D50/Ram 50 L4-1997cc 2.0L SOHC (1984)
^ Ram-50 Service Manual Publication #81-370-4009
^ Conquest Service Manual Publication #81-270-4005
Corrections are highlighted in the attached specifications in bold type and should be entered in the respective model service manual.
POLICY: Information only
> Powertrain Management > Fuel Delivery and Air Induction > Idle Speed > System Information > Technical Service Bulletins > All Other Service Bulletins for Idle Speed: > 141984 > May > 84 > Carburetor - Idle Speed
Adjustment on A/C Install
Idle Speed: All Technical Service BulletinsCarburetor - Idle Speed Adjustment on A/C Install
Models
1984 Colt (W/O Turbo), Ram-50, Power Ram-50 (W/O Diesel) & Colt Vista
Subject
Idle-Up Speed Adjustment After Air Conditioning Installation and/or Service
Index
FUEL
Date
May 7, 1984
No.
14-19-84
P-1927-CThis procedure modifies the adjustment procedures in the subject model service manuals.
If difficulty is encountered in adjusting curb idle speed and/or idle-up speed after installation or servicing and adjustment of the air conditioning system,follow the adjustment procedure as outlined below:
ADJUSTMENT PROCEDURE
1.
Thoroughly warm up engine, turn off all accessories, front wheels in straight ahead position, transmission in neutral, parking brake set, andradiator cooling fan stopped.
FIGURE 1
> Powertrain Management > Fuel Delivery and Air Induction > Idle Speed > System Information > Technical Service Bulletins > All Other Service Bulletins for Idle Speed: >
141984 > May > 84 > Carburetor - Idle Speed Adjustment on A/C Install > Page 801
D50/Ram 50 L4-1997cc 2.0L SOHC (1984)
FIGURE 2
2.
Check and adjust curb idle speed if necessary (see Figure 1 for specification) and make adjustment using SAS (speed adjusting screw) 1 (Figure2). On some models installation of air conditioner will change the curb idle speed already adjusted.
FIGURE 2
3.
Back off the idle-up speed adjusting screw for air conditioner one turn from fully tightened position (Figure 2).
4.
Lift the free lever by hand until it touches SAS 3 and record the engine speed ("N" = R.P.M.) obtained at this time (Figure 2).
> Powertrain Management > Fuel Delivery and Air Induction > Idle Speed > System Information > Technical Service Bulletins > All Other Service Bulletins for Idle Speed: >
141984 > May > 84 > Carburetor - Idle Speed Adjustment on A/C Install > Page 802
D50/Ram 50 L4-1997cc 2.0L SOHC (1984)
FIGURE 1
FIGURE 2
5.. Turn on air conditioner switch. Adjust the idle-up speed while compressor is running to the specified rpm (Figure 1) by turning SAS 2 (Figure 2).When making this adjustment, be sure to record the turning direction and slot angle of SAS 2.
FIGURE 1
6.
Turn off air conditioner switch and make sure that the specified curb idle rpm is obtained (Figure 1).
7.
Race the engine at a speed of about 2000 rpm for five seconds.
8.
Turn on and then off the air conditioning switch repeatedly several times and make sure that with the compressor running that the engine is running
> Powertrain Management > Fuel Delivery and Air Induction > Idle Speed > System Information > Technical Service Bulletins > All Other Service Bulletins for Idle Speed: >
141984 > May > 84 > Carburetor - Idle Speed Adjustment on A/C Install > Page 803
D50/Ram 50 L4-1997cc 2.0L SOHC (1984)
at the specified idle-up rpm (Figure 1).
Example:
FIGURE 2
If Sas 2 has been turned 180~ clockwise in Step 5, SAS 3 will be turned 360~ clockwise in Step 9. Then, lift thefree lever by hand until it touches SAS 3 and make sure that the engine rpm is "N" +/- 100 rpm (where "N" is therpm recorded in Step 4). If necessary, adjust using SAS 3.
FIGURE 2
SIMPLE ADJUSTMENT PROCEDURE FOR COLT VISTA ONLY
If the idle adjustment has been properly made before installation of the air conditioner, the following simple procedure may be used:
1.
Give one clockwise turn to SAS 2 (Figure 2).
2.
Give two clockwise turns to SAS 3 (Figure 2).
3.
Back off idle-up speed adjusting screw for air conditioner one turn from fully tightened position (Figure 2).
> Powertrain Management > Fuel Delivery and Air Induction > Idle Speed > System Information > Technical Service Bulletins > All Other Service Bulletins for Idle Speed: >
141984 > May > 84 > Carburetor - Idle Speed Adjustment on A/C Install > Page 804
D50/Ram 50 L4-1997cc 2.0L SOHC (1984)
FIGURE 1
4.
Lastly, make sure that the curb idle speed and idle-up speed are properly adjusted (Figure 1).
FIGURE 2
If necessary, make fine adjustments with SAS 2 and SAS 3 (Figure 2).
POLICY: Reimbursable within the provisions of the warranty
FAILURE CODE: 31 - Rough Idle
> Powertrain Management > Fuel Delivery and Air Induction > Idle Speed > System Information > Technical Service Bulletins > Page 805
> Powertrain Management > Fuel Delivery and Air Induction > Air/Fuel Mixture > System Information > Technical Service Bulletins > By Symptom for Air/Fuel Mixture: > 140884 > Jan > 84 > Propane Idle Set - Procedure
Air/Fuel Mixture: By SymptomPropane Idle Set - Procedure
Models
1984 MMC Import Vehicles All With Gasoline Fueled Engines, All Emission Markets (Except Vehicles With Turbo Chargers & Canada)
Subject
Propane Idle Set Procedure
Index
FUEL
Date
January 17, 1984
No..
14-08-84
P-94-C
The propane idle set procedure is authorized for 1984 subject model import vehicles.
The propane idle set method is to be used when "CO" meter procedure cannot be used, i.e., "CO" meter in for repair or is not available in the servicearea.
PROPANE IDLE CHECK & SET PROCEDURE
1.
Idle Setting Conditions: Lights, electric cooling fan, and all accessories are off, transmission in neutral, and front wheels in straight ahead position.
2.
If engine is cold, allow it to warm up until full operating temperature is reached (185 to 205~F).
NOTE:
PERFORM THE FOLLOWING STEPS 3 THROUGH 5 AND STEP 19 ONLY IF ENGINE IS EQUIPPED WITH A FEEDBACKCARBURETOR EMISSION SYSTEM.
3.
Turn off ignition switch.
4.
Disconnect the NEGATIVE cable from the battery for about 5 seconds. Then reconnect negative battery cable.
5.
Disconnect the connector of the exhaust oxygen sensor.
6.
Start and run engine for 5 seconds at an engine speed between 2,000 to 3,000 rpm.
7.
Then, allow engine to run at curb idle for 2 minutes.
> Powertrain Management > Fuel Delivery and Air Induction > Air/Fuel Mixture > System Information > Technical Service Bulletins > By Symptom for Air/Fuel Mixture: >
140884 > Jan > 84 > Propane Idle Set - Procedure > Page 814
D50/Ram 50 L4-1997cc 2.0L SOHC (1984)
FIGURE 1
8.
Check engine idle speed and basic ignition timing. Adjust to specifications if necessary (Figure 1).
9.
Disconnect the air cleaner fresh air intake duct from the air cleaner snorkel.
Insert the propane supply hose into the air cleaner snorkel about 4 inches.
Make certain both valves on propane bottle are fully closed and the bottle is upright and in a safe location.
> Powertrain Management > Fuel Delivery and Air Induction > Air/Fuel Mixture > System Information > Technical Service Bulletins > By Symptom for Air/Fuel Mixture: >
140884 > Jan > 84 > Propane Idle Set - Procedure > Page 815
D50/Ram 50 L4-1997cc 2.0L SOHC (1984)
FIGURE 3
10.
Open the propane bottle main valve fully, then slowly open the propane fine control valve to the position where maximum engine rpm is achieved.(Too much propane or too rich idle mixture will cause the engine to lose rpm as the fine control valve is opened.) (Figure 3.)
FIGURE 2
> Powertrain Management > Fuel Delivery and Air Induction > Air/Fuel Mixture > System Information > Technical Service Bulletins > By Symptom for Air/Fuel Mixture: >
140884 > Jan > 84 > Propane Idle Set - Procedure > Page 816
D50/Ram 50 L4-1997cc 2.0L SOHC (1984)
Note the engine rpm increase. Specified values of each engine propane idle speed increase are outlined in Figure 2.
If the propane idle speed exceeds more than 25 rpm from the specified value in Figure 2 or the rpm does not increase at all, idle fuel mixtureshould be adjusted according to the propane assisted idle set procedure that follows.
FIGURE 4
11.
It is not necessary to remove carburetor from intake manifold to remove the idle mixture screw plug.
Drill out concealment plug on car. Remove vacuum connector from high altitude compensator (HAC) fittings on carburetor air horn (Figure 4).
Use a 1/4" diameter drill 8' long at the 11 o'clock position on the plug boss. Locate drill point 3/16" from end of boss.
Plug should pop out when the drill bit contacts it (Figure 4).
12.
Start engine and run for 1 minute at engine speed of 2500 rpm.
13.
Run engine at idle for 2 minutes.
> Powertrain Management > Fuel Delivery and Air Induction > Air/Fuel Mixture > System Information > Technical Service Bulletins > By Symptom for Air/Fuel Mixture: >
140884 > Jan > 84 > Propane Idle Set - Procedure > Page 817
D50/Ram 50 L4-1997cc 2.0L SOHC (1984)
FIGURE 2
14.
Open the propane main valve and slowly open the fine control valve to the position where maximum engine speed is achieved. Use the idle speedadjusting screw to set the specified propane idle speed from Figure 2.
15.
Turn off propane main valve and adjust idle mixture screw to the specified idle set speed from Figure 2.
16.
17.
To recheck the maximum propane speed, open the main propane valve again. If the speed still differs more than 25 rpm from the specified propanespeed from Figure 2, repeat Steps 14 through 16.
18.
Remove the propane hose and replace fresh air duct on air cleaner snorkel.
19.
Reconnect the exhaust oxygen sensor (if engine is equipped with a feedback carburetor).
20.
Install Idle Mixture Screw Concealment Plug. (If new plug is needed, use PN MD606954.)
POLICY: Reimbursable within the provisions of the warranty
> Powertrain Management > Fuel Delivery and Air Induction > Air/Fuel Mixture > System Information > Technical Service Bulletins > By Symptom for Air/Fuel Mixture: >
140884 > Jan > 84 > Propane Idle Set - Procedure > Page 818
D50/Ram 50 L4-1997cc 2.0L SOHC (1984)
FRONT WHEEL DRIVE LABOR OPERATION TIME SCHEDULE
FAILURE CODE: RO - Driveability
> Powertrain Management > Fuel Delivery and Air Induction > Air/Fuel Mixture > System Information > Technical Service Bulletins > All Technical Service Bulletins for Air/Fuel Mixture: > 140884 > Jan > 84 > Propane Idle
Set - Procedure
Air/Fuel Mixture: All Technical Service BulletinsPropane Idle Set - Procedure
Models
1984 MMC Import Vehicles All With Gasoline Fueled Engines, All Emission Markets (Except Vehicles With Turbo Chargers & Canada)
Subject
Propane Idle Set Procedure
Index
FUEL
Date
January 17, 1984
No..
14-08-84
P-94-C
The propane idle set procedure is authorized for 1984 subject model import vehicles.
The propane idle set method is to be used when "CO" meter procedure cannot be used, i.e., "CO" meter in for repair or is not available in the servicearea.
PROPANE IDLE CHECK & SET PROCEDURE
1.
Idle Setting Conditions: Lights, electric cooling fan, and all accessories are off, transmission in neutral, and front wheels in straight ahead position.
2.
If engine is cold, allow it to warm up until full operating temperature is reached (185 to 205~F).
NOTE:
PERFORM THE FOLLOWING STEPS 3 THROUGH 5 AND STEP 19 ONLY IF ENGINE IS EQUIPPED WITH A FEEDBACKCARBURETOR EMISSION SYSTEM.
3.
Turn off ignition switch.
4.
Disconnect the NEGATIVE cable from the battery for about 5 seconds. Then reconnect negative battery cable.
5.
Disconnect the connector of the exhaust oxygen sensor.
6.
Start and run engine for 5 seconds at an engine speed between 2,000 to 3,000 rpm.
7.
Then, allow engine to run at curb idle for 2 minutes.
> Powertrain Management > Fuel Delivery and Air Induction > Air/Fuel Mixture > System Information > Technical Service Bulletins > All Technical Service Bulletins for Air
/Fuel Mixture: > 140884 > Jan > 84 > Propane Idle Set - Procedure > Page 824
D50/Ram 50 L4-1997cc 2.0L SOHC (1984)
FIGURE 1
8.
Check engine idle speed and basic ignition timing. Adjust to specifications if necessary (Figure 1).
9.
Disconnect the air cleaner fresh air intake duct from the air cleaner snorkel.
Insert the propane supply hose into the air cleaner snorkel about 4 inches.
Make certain both valves on propane bottle are fully closed and the bottle is upright and in a safe location.
> Powertrain Management > Fuel Delivery and Air Induction > Air/Fuel Mixture > System Information > Technical Service Bulletins > All Technical Service Bulletins for Air
/Fuel Mixture: > 140884 > Jan > 84 > Propane Idle Set - Procedure > Page 825
D50/Ram 50 L4-1997cc 2.0L SOHC (1984)
FIGURE 3
10.
Open the propane bottle main valve fully, then slowly open the propane fine control valve to the position where maximum engine rpm is achieved.(Too much propane or too rich idle mixture will cause the engine to lose rpm as the fine control valve is opened.) (Figure 3.)
FIGURE 2
> Powertrain Management > Fuel Delivery and Air Induction > Air/Fuel Mixture > System Information > Technical Service Bulletins > All Technical Service Bulletins for Air
/Fuel Mixture: > 140884 > Jan > 84 > Propane Idle Set - Procedure > Page 826
D50/Ram 50 L4-1997cc 2.0L SOHC (1984)
Note the engine rpm increase. Specified values of each engine propane idle speed increase are outlined in Figure 2.
If the propane idle speed exceeds more than 25 rpm from the specified value in Figure 2 or the rpm does not increase at all, idle fuel mixtureshould be adjusted according to the propane assisted idle set procedure that follows.
FIGURE 4
11.
It is not necessary to remove carburetor from intake manifold to remove the idle mixture screw plug.
Drill out concealment plug on car. Remove vacuum connector from high altitude compensator (HAC) fittings on carburetor air horn (Figure 4).
Use a 1/4" diameter drill 8' long at the 11 o'clock position on the plug boss. Locate drill point 3/16" from end of boss.
Plug should pop out when the drill bit contacts it (Figure 4).
12.
Start engine and run for 1 minute at engine speed of 2500 rpm.
13.
Run engine at idle for 2 minutes.
> Powertrain Management > Fuel Delivery and Air Induction > Air/Fuel Mixture > System Information > Technical Service Bulletins > All Technical Service Bulletins for Air
/Fuel Mixture: > 140884 > Jan > 84 > Propane Idle Set - Procedure > Page 827
D50/Ram 50 L4-1997cc 2.0L SOHC (1984)
FIGURE 2
14.
Open the propane main valve and slowly open the fine control valve to the position where maximum engine speed is achieved. Use the idle speedadjusting screw to set the specified propane idle speed from Figure 2.
15.
Turn off propane main valve and adjust idle mixture screw to the specified idle set speed from Figure 2.
16.
17.
To recheck the maximum propane speed, open the main propane valve again. If the speed still differs more than 25 rpm from the specified propanespeed from Figure 2, repeat Steps 14 through 16.
18.
Remove the propane hose and replace fresh air duct on air cleaner snorkel.
19.
Reconnect the exhaust oxygen sensor (if engine is equipped with a feedback carburetor).
20.
Install Idle Mixture Screw Concealment Plug. (If new plug is needed, use PN MD606954.)
POLICY: Reimbursable within the provisions of the warranty
> Powertrain Management > Fuel Delivery and Air Induction > Air/Fuel Mixture > System Information > Technical Service Bulletins > All Technical Service Bulletins for Air
/Fuel Mixture: > 140884 > Jan > 84 > Propane Idle Set - Procedure > Page 828
D50/Ram 50 L4-1997cc 2.0L SOHC (1984)
FRONT WHEEL DRIVE LABOR OPERATION TIME SCHEDULE
FAILURE CODE: RO - Driveability
> Powertrain Management > Fuel Delivery and Air Induction > Altitude Compensator > Component Information > Diagrams
High Altitude Compensator (HAC) system. 1983-86 Pickup w/2000cc 2000 & 2600cc engines; 1984 1400cc, 1600cc Non-turbocharged
> Powertrain Management > Fuel Delivery and Air Induction > Altitude Compensator > Component Information > Diagrams > Page 832
Altitude Compensator: Description and Operation
Fig. 24 High altitude compensation system.
Fig. 24,
HIGH ALTITUDE VEHICLE This system, is used to maintain the correct air/fuel mixture should the vehicle encounter atmospheric conditions normally present during highaltitude operation. A small bellows chamber, mounted in the engine compartment, is connected to the carburetor through hoses and is vented to atmosphere. Atmosphericpressure expands or contracts the bellows as necessary. A brass tapered seat valve is used to regulate the air flow accordingly. When a rarefied atmosphere is encountered, the air/fuel mixture becomes increasingly rich. At a pre-determined atmospheric pressure, the bellowsexpands, causing the tapered seat valve to lift off its seat and allow additional air to enter the main air bleeds. This additional air, when combined withthe air available, provides the system with the proper amount of air necessary to maintain the correct air/fuel mixture. When encountering differentaltitudes, the system provides varying amounts of air as needed. Once sufficient atmospheric pressure is restored, the tapered valve closes, enabling thesystem to return to its normal operational mode. Some models equipped with automatic transmission use a vacuum delay valve to delay the vacuum signal to the secondary throttle valve diaphragmchamber. This delay helps to decrease carbon monoxide and hydrocarbon emissions during vehicle acceleration.
> Powertrain Management > Fuel Delivery and Air Induction > Carburetor > Carburetor Jet > Component Information > Technical Service Bulletins > High Altitude Conversion Packages
Carburetor Jet: Technical Service BulletinsHigh Altitude Conversion Packages
Models
Subject
High Altitude Conversion Packages
Index
EMISSIONS
Date
April 9, 1984
No..
25-01-84
P-1423-CA package is now available to accommodate a customer who wishes to convert his 1984 low altitude emission package to the high altitude (over 4,000feet above sea level) emission package.
Vehicles with the low altitude package transferred to service in high altitude areas may exhibit undesirable driveability. However, the installation of ahigh altitude conversion package is voluntary and at the customer's expense.
The high altitude field conversion packages and procedures outlined below have been authorized in the following 1984 non-altitude equipped enginefamilies in service at altitudes above 4,000 feet above sea level.
CONVERSION INSTRUCTIONS
Sea Level to High Altitude
Altitude performance improvement adjustments for 1984 model year Ram-50 and Power Ram-50 trucks are as follows:
Gasoline Fueled Vehicles
1.
Advance basic timing as outlined below using the procedure in the 1984 Ram-50 service manual.
Engine Low Altitude High Altitude
2.0L
2.6 L (All)
5~ +/- 2~ BTDC
7~ +/- 2~ BTDC
10~ +/- 2~ BTDC
12~ +/- 2~ BTDC
2.
Remove air cleaner cover from the air cleaner assembly.
FIGURE 1
> Powertrain Management > Fuel Delivery and Air Induction > Carburetor > Carburetor Jet > Component Information > Technical Service Bulletins > High Altitude
Conversion Packages > Page 838
D50/Ram 50 L4-1997cc 2.0L SOHC (1984)
FIGURE 2
3.
Replace carburetor main (primary) air jet with jet supplied in the respective kit (Figure 1). Be sure to use the proper screwdriver (Figure 2).
4.
Reinstall air cleaner cover.
FIGURE 1
FIGURE 6
5.
Install emission control information update label supplied in kit (Figure 1) to properly cleaned location on the hood as indicated in Figure 6.
Performance Adjustments
The following procedure applies to vehicles returned to service at low altitude (below 4,000 feet above sea level) which previously had the high altitudekit installed. This procedure does not remove any components installed in high altitude kit.
1.
Remove complete air cleaner assembly from engine (cover and filter housing).
> Powertrain Management > Fuel Delivery and Air Induction > Carburetor > Carburetor Jet > Component Information > Technical Service Bulletins > High Altitude
Conversion Packages > Page 839
D50/Ram 50 L4-1997cc 2.0L SOHC (1984)
FIGURE 4
2.
Remove jet air bypass screw "B" and install screw "A" from low altitude kit PN MD080351 (Figure 4). Place screw "B" in owners manual packetin glove compartment for reinstallation if vehicle is returned to high altitude operation at a later date.
3.
Reinstall air cleaner assembly.
FIGURE 3
FIGURE 6
4.
Install low altitude emission control update label supplied in kit, PN MD080351, to properly cleaned location on the hood as indicated in Figure 6.
> Powertrain Management > Fuel Delivery and Air Induction > Carburetor > Carburetor Jet > Component Information > Technical Service Bulletins > High Altitude
Conversion Packages > Page 840
D50/Ram 50 L4-1997cc 2.0L SOHC (1984)
(Do not remove high altitude emission update label.)
5.
Check the ignition timing and curb idle RPM according to the specified timing and idle setting procedure per the 1984 D-50, Power Ram-50 Truckservice manual.
FIGURE 5
IMPORTANT:
SHOULD THE VEHICLE BE RETURNED TO SERVICE AT HIGH ALTITUDE (ABOVE 4,000 FEET ABOVE SEALEVEL), SCREW "A" SHOULD BE REMOVED AND SCREW "B" REINSTALLED AND THE LOW ALTITUDEEMISSION UPDATE LABEL SHOULD BE REMOVED.
Diesel Power Vehicles
Vehicles taken from low altitude service to high altitude service should have the injection timing advanced from 5~ +/- 2~ ATC to 3~ +/- 2~ ATC.
Use injection timing procedure outlined in 1984 Ram-50, Power Ram-50 service manual, publication #81-370-4009, pages 14-26 through 14-28.
POLICY: Information only
> Powertrain Management > Fuel Delivery and Air Induction > Dashpot > Component Information > Locations
Dashpot: Locations
On Carburetor, Top Of Engine
Top Of Engine
> Powertrain Management > Fuel Delivery and Air Induction > Fuel > Component Information > Technical Service Bulletins > Fuel - Alcohol Fuel Recommendations
Fuel: Technical Service BulletinsFuel - Alcohol Fuel Recommendations
Models
All Gasoline Fueled
Subject
Alcohol Blend Fuels
Index
FUEL
Date
October 22, 1984 No..
14-52-84
P-4644-CThe increasing availability of gasolines containing alcohol has resulted in the need to provide additional information relative to driveability problems thatmay be experienced with the use of gasolines containing alcohol. Chrysler's 1984 and 1985 Owner's Manual statement on gasolines containing alcoholreads as follows:
Gasolines Containing Alcohol
Some gasolines sold at service stations contain alcohol, although they may not be so identified. Use of fuels containing alcohol is not recommended,unless the nature of the blend can be determined as being satisfactory.
Gasohol A mixture of 10% Ethanol (grain alcohol) and 90% unleaded gasoline may be used in your vehicle. If driveability problems are experienced as a result of using gasohol, it is recommended that thevehicle be operated on gasoline.
Methanol Do not use gasolines containing Methanol (wood alcohol). Use of this type of alcohol can result in vehicle performance deterioration and damage critical parts in the fuel pump, carburetor, and other fuel system components. Fuel system damage and vehicle performance problems, resulting from the use of gasolines containing Methanol, may not be covered by the new vehicle warranty.
The following comments do not appear in the owners manuals.
Although gasohol is not recommended, it may be used. However, driveability problems may be experienced, such as longer starting times,hesitation/stumble on accelerations, and/or loss of power on accelerations resulting from fuel foaming/vapor lock due primarily to the increased volatilityof the gasohol.For customer complaints of this nature, and if the customer is using gasohol or a fuel of unknown corn position, it is strongly recommended that thevehicle be returned to 100% unleaded gasoline to obtain maximum driveability, performance, and fuel economy.
You can easily test the fuel for the presence and percentage of alcohol by using Miller Tool #C-4846. This special tool is listed in your Miller ToolCatalog.
It is our recommendation that customers are made aware of the cautionary fuel statement in the Owner's Manual in order to avoid unnecessarydriveability complaints.
Customers may question the availability of alcohol-free fuel. As of the date this bulletin was printed 22 states will have passed alcohol labeling lawswhich require a label on the pump if alcohol is present in the gasoline.
The attached is a partial list of where the major fuel suppliers stand on alcohol blended fuels. Discretionary use of alcohol blends by independentretailers, however, may occur and should be recognized.
POLICY: Information only
> Powertrain Management > Fuel Delivery and Air Induction > Fuel > Component Information > Technical Service Bulletins > Fuel - Alcohol Fuel Recommendations > Page
848
D50/Ram 50 L4-1997cc 2.0L SOHC (1984)
ALCOHOL BLENDS: WHERE THE MAJORS STAND
COMPANY
Amoco
MARKET
Iowa, Eastern Nebraska, Southeastern South
Dakota and Kansas.
Arco
Ashland
About 1,400 branded jobber and dealer outlets in
New York and Pennsylvania; wholesales to small refiners, unbranded distributors; owns a 200 million gallon a year methanol plant.
Kentucky, Ohio, Michigan, Indiana, and Iowa; joint
Chevron
Conoco
BLEND
10% Ethanol
Oxinol: 4.75%
Methanol, 4.57%
Co-solvents
10% Ethanol venture partner in a 60 gallon a year ethanol plant at Southpoint, Ohio.
About 1,000 stations in Kentucky and Tennessee; 10% Ethanol
83% interest in a 21 million gallon a year Kentucky ethanol plant.
Wholesales ethanol at terminals in Missouri, 10% Ethanol
Exxon
Getty
Illinois, Nebraska, and Kansas. Jobbers sell blends in Nebraska and Iowa and the company sells blends through its subsidiary, Western Stores in Iowa.
None None
Three small regions in Omaha, Nebraska; 10% Ethanol
Gulf
Northeastern Iowa, and Western Kansas. Owns 100 million gallon a year methanol plant in Delaware (but not blending).
Last year considered owning part of an ethanol plant in North Carolina.
None
Marathon
Mobil
Phillips
Shell
None
None
Illinois, Indiana, Missouri, and Iowa.
None
Sohio
COMPANY
None
MARKET
Southland Markets ethanol blends in 14 states, primarily
California, Florida, Illinois, Indiana, Iowa,
Kansas, New Mexico, Ohio, Tennessee, and Utah. Testing oxinol in Houston.
Sun Test marketed oxinol at about 200 branded stations in Pennsylvania.
None
None
10% Ethanol
None
None
BLEND
10% Ethanol,
Oxinol
None
Tenneco
Texaco
Tennessee and Florida, owns a 135 million gallon a year methanol plant in Texas, but does not blend methanol.
10% Ethanol
Illinois, Indiana, Kentucky, Western Tennessee, 10% Ethanol and St. Louis. Owns 50% of 60 million gallon a year ethanol plant in Illinois.
None None Union
Sources: Information Resources, Inc., Washington, D.C.
> Powertrain Management > Fuel Delivery and Air Induction > Fuel Pressure Control Solenoid > Component Information > Locations
Fuel Pressure Control Solenoid: Locations
Top Of Engine
> Powertrain Management > Fuel Delivery and Air Induction > Fuel Pump > Fuel Pressure > System Information > Specifications
> Powertrain Management > Fuel Delivery and Air Induction > Fuel Shut-off Solenoid > Component Information > Locations
Fuel Shut-off Solenoid: Locations
Top Of Engine
> Powertrain Management > Fuel Delivery and Air Induction > Throttle Control Vacuum Motor <--> [Engine Speed Governor Control Module] > Component Information > Locations
Throttle Control Vacuum Motor: Locations
Under Center Of I/P
> Powertrain Management > Fuel Delivery and Air Induction > Idle Speed Control (Linkage) > Component Information > Adjustments
Idle Speed Control (Linkage): Adjustments
Fig. 19 Throttle opener system. 1982-86 models except 1982 Champ & Colt (federal) w/1400cc engine & manual transaxle
1.
Start engine and allow to reach normal operating temperature.
2.
Ensure that all electrical accessories are ``Off,'' then position transmission in ``Neutral.''
3.
Set curb idle to specifications.
4.
5.
With air conditioning system ``Off,'' disconnect vacuum hose from throttle opener nipple, then apply 20 inches Hg vacuum to throttle opener witha suitable vacuum pump.
Fig. 19, Adjust engine speed with throttle opener setting screw, to the following specifications: a. On 1982 Champ & Colt (1600cc engine), set engine speed to 900 50 RPM for automatic transaxle equipped vehicles, or 850 50 RPM for manual transaxle equipped vehicles. b. On 1982 Challenger, Sapporo & Pickup, set engine speed to 900 50 RPM.c. On 1983 Challenger & Sapporo, set engine speed to 1050 50 RPM.d. On 1983 Colt, set engine speed to 1100 50 RPM for manual transaxle equipped vehicles, or 1150 50 RPM for automatic transaxle equipped vehicles.
> Powertrain Management > Fuel Delivery and Air Induction > Idle Up Control Valve > Component Information > Description and Operation
Idle Up Control Valve: Description and Operation
Fig. 19 Throttle opener system. 1982-86 models except 1982 Champ & Colt (federal) w/1400cc engine & manual transaxle
1982-88 Models exc. 1982 Champ & Colt (federal) w/1400cc engines & manual transaxle
Fig. 19,
This system, consists of a throttle opener assembly, a solenoid valve, an engine speed sensor and the air conditioning compressor switch. When the compressor is switched on, the speed sensor detects a drop in engine speed, and activates the solenoid valve. The solenoid valve thentransfers intake manifold vacuum to the throttle opener, which opens the throttle valve via the throttle opener lever. The engine speed, therefore, isbalanced against the air conditioning compressor load, resulting in improved idle and decreased levels of exhaust pollutants.
> Powertrain Management > Fuel Delivery and Air Induction > Idle Up Control Valve > Component Information > Description and Operation > Page 868
Idle Up Control Valve: Adjustments
Fig. 19 Throttle opener system. 1982-86 models except 1982 Champ & Colt (federal) w/1400cc engine & manual transaxle
1.
Start engine and allow to reach normal operating temperature.
2.
Ensure that all electrical accessories are ``Off,'' then position transmission in ``Neutral.''
3.
Set curb idle to specifications.
4.
5.
With air conditioning system ``Off,'' disconnect vacuum hose from throttle opener nipple, then apply 20 inches Hg vacuum to throttle opener witha suitable vacuum pump.
Fig. 19, Adjust engine speed with throttle opener setting screw, to the following specifications: a. On 1982 Champ & Colt (1600cc engine), set engine speed to 900 50 RPM for automatic transaxle equipped vehicles, or 850 50 RPM for manual transaxle equipped vehicles. b. On 1982 Challenger, Sapporo & Pickup, set engine speed to 900 50 RPM.c. On 1983 Challenger & Sapporo, set engine speed to 1050 50 RPM.d. On 1983 Colt, set engine speed to 1100 50 RPM for manual transaxle equipped vehicles, or 1150 50 RPM for automatic transaxle equipped vehicles.
> Powertrain Management > Fuel Delivery and Air Induction > Relays and Modules - Fuel Delivery and Air Induction > Throttle Control Vacuum Motor <--> [Engine Speed Governor Control Module] > Component Information
> Locations
Throttle Control Vacuum Motor: Locations
Under Center Of I/P
> Powertrain Management > Fuel Delivery and Air Induction > Rollover/Pressure Relief Valve <--> [Rollover Valve, Fuel Tank] > Component Information > Locations
Rollover/Pressure Relief Valve: Locations
Top Of Fuel Tank
> Powertrain Management > Ignition System > Firing Order > Component Information > Specifications
FIRING ORDER 2.0L RWD & 2.6L
> Powertrain Management > Ignition System > Ignition Timing > Timing Marks and Indicators > System Information > Diagrams
Timing Marks and Indicators: Diagrams
TIMING MARK 1.6L RWD, 2.6L & 2.0L EX. VISTA
> Powertrain Management > Ignition System > Ignition Timing > Timing Marks and Indicators > System Information > Diagrams > Page 884
D50/Ram 50 L4-1997cc 2.0L SOHC (1984)
TIMING MARK 1981-85 5.2L & 5.9L
> Powertrain Management > Ignition System > Distributor, Ignition > Vacuum Advance Unit <--> [Distributor Advance Unit] > Component Information > Specifications > Electrical Specifications
Vacuum Advance Unit: Electrical Specifications
> Powertrain Management > Ignition System > Distributor, Ignition > Vacuum Advance Unit <--> [Distributor Advance Unit] > Component Information > Specifications > Electrical Specifications > Page 890
> Powertrain Management > Ignition System > Pick-Up Coil, Ignition > Component Information > Specifications
> Powertrain Management > Ignition System > Sensors and Switches - Ignition System > Ignition Switch > Component Information > Service and Repair
Ignition Switch: Service and Repair
The ignition switch is mounted in the rear of the steering column lock. When the key is turned to LOCK position and pulled out, the lock pinautomatically ejects from the cylinder and enters a groove in the steering shaft, locking the steering wheel. The heads of the bolts securing the steering lock assembly shear off when the bolts are tightened. Replacement of the steering lock assembly mayrequire that the steering column be removed, as these bolts must be cut or slotted to permit removal with a screwdriver. When the lock assembly isinstalled, new shear bolts must be used and the bolts should be tightened until the bolt heads twist off. However, the ignition switch can be serviced separately from the lock assembly using the following procedures.
1.
Disconnect battery ground cable, then remove upper and lower column covers.
2.
Remove bands securing switch harness and disconnect electrical connector.
Fig. 4 Ignition switch removal
3.
Loosen the bolt holding the switch and pull from lock assembly.
4.
Reverse procedure to install, first inserting key to check for proper operation.
> Powertrain Management > Ignition System > Spark Plug > Component Information > Technical Service Bulletins > Customer Interest for Spark Plug: > 181788 > Oct > 88 > Spark Plugs - Oil Fouling/Misfire on Hard
Acceleration
Spark Plug: Customer InterestSpark Plugs - Oil Fouling/Misfire on Hard Acceleration
Models
1978-1989 MMC Engines With Jet Valves
Subject
Oil Fouled Spark Plug(s) Miss & Bucking Under Hard Acceleration
Index
FUEL
Date
October 17, 1988
No.
18-17-88
C18-21)This bulletin updates Technical Service Bulletin 5/14/88 and serves as a reminder that driveability problems may be caused by mechanical problems aswell as fuel system problems.
FIGURE 1
SYMPTOM/CONDITION
One or more (seldom occurs to more than one cylinder) spark plugs will be oil fouled and may show ground and center electrode erosion due tooverheating (Figure 1).
Under hard acceleration (wide open throttle) engine will miss and buck.
> Powertrain Management > Ignition System > Spark Plug > Component Information > Technical Service Bulletins > Customer Interest for Spark Plug: > 181788 > Oct > 88
> Spark Plugs - Oil Fouling/Misfire on Hard Acceleration > Page 906
D50/Ram 50 L4-1997cc 2.0L SOHC (1984)
FIGURE 2
This condition may result from a jet valve failure. The jet valve failure is characterized by one of the causes outlined below (refer to Figure 2 fordescription):
^ Oil leaking past the oil seal and valve stem.
^ Oil leaking past the valve body and oil seal.
^ Oil leaking past the O-ring seal between the valve body and cylinder head which may be caused by a torn or cut Oring.
FIGURE 1
DIAGNOSIS
Remove and inspect all spark plugs. If a spark plug is found to be heavily oil fouled and/or appears to have the electrodes eroded or overheated, proceedto jet valve removal procedure below (Figure 1).PARTS REQUIRED
Jet Valve Assembly (as required)
O-Ring (as required)
INSTALLATION PROCEDURE
PN MD009440
PN MD009786
1.
Remove only the jet valve of the cylinder showing the spark plug oiling or overheating. Follow the jet valve removal procedures outlined in therespective model year service manual using Miller Special Tool #MB-998310.
> Powertrain Management > Ignition System > Spark Plug > Component Information > Technical Service Bulletins > Customer Interest for Spark Plug: > 181788 > Oct > 88
> Spark Plugs - Oil Fouling/Misfire on Hard Acceleration > Page 907
D50/Ram 50 L4-1997cc 2.0L SOHC (1984)
FIGURE 2
2.
Push jet valve open and inspect the valve stem just under the valve head. If oil residue and excessive carbon buildup are present, the Jet ValveAssembly, PN MD009440, will have to be replaced (Figure 2).
If no residue or carbon buildup is present, inspect the O-ring for rips, tears, or deformity. O-ring can be replaced separately with PN MD009786.
FIGURE 3
3.
Inspect jet piece pocket by looking down into jet piece. If pocket has any buildup of burnt oil residue or carbon, it must be cleaned completelyusing the following procedure (Figure 3).
a.
Remove spark plug.
b.
Place piston on top dead center of compression stroke (both valves closed).
Use a thin stiff bristle brush to clean jet piece (a distributor cap terminal brush works well). A thin metal rod (coat hanger) can be used toloosen heavy deposits.
d.
Direct compressed air in jet piece. The loosened deposits will be blown out of the jet piece and spark plug hole. Eye protection isrecommended when performing this operation.
e.
Reinspect cleaned jet piece. If cracking or erosion is seen in the area of the jet air orifice (Figure 3) or the deposit cannot be cleanedadequately, the cylinder head will require replacement.
> Powertrain Management > Ignition System > Spark Plug > Component Information > Technical Service Bulletins > Customer Interest for Spark Plug: > 181788 > Oct > 88
> Spark Plugs - Oil Fouling/Misfire on Hard Acceleration > Page 908
D50/Ram 50 L4-1997cc 2.0L SOHC (1984)
4.
Install new spark plug of proper heat range and gap setting.
5.
Start engine and allow to fully warm up. Check for oil leaks and adjust idle speed if necessary.
POLICY: Information only
> Powertrain Management > Ignition System > Spark Plug > Component Information > Technical Service Bulletins > All Technical Service Bulletins for Spark Plug: > 181788 > Oct > 88 > Spark Plugs - Oil Fouling/Misfire on
Hard Acceleration
Spark Plug: All Technical Service BulletinsSpark Plugs - Oil Fouling/Misfire on Hard Acceleration
Models
1978-1989 MMC Engines With Jet Valves
Subject
Oil Fouled Spark Plug(s) Miss & Bucking Under Hard Acceleration
Index
FUEL
Date
October 17, 1988
No.
18-17-88
C18-21)This bulletin updates Technical Service Bulletin 5/14/88 and serves as a reminder that driveability problems may be caused by mechanical problems aswell as fuel system problems.
FIGURE 1
SYMPTOM/CONDITION
One or more (seldom occurs to more than one cylinder) spark plugs will be oil fouled and may show ground and center electrode erosion due tooverheating (Figure 1).
Under hard acceleration (wide open throttle) engine will miss and buck.
> Powertrain Management > Ignition System > Spark Plug > Component Information > Technical Service Bulletins > All Technical Service Bulletins for Spark Plug: >
181788 > Oct > 88 > Spark Plugs - Oil Fouling/Misfire on Hard Acceleration > Page 914
D50/Ram 50 L4-1997cc 2.0L SOHC (1984)
FIGURE 2
This condition may result from a jet valve failure. The jet valve failure is characterized by one of the causes outlined below (refer to Figure 2 fordescription):
^ Oil leaking past the oil seal and valve stem.
^ Oil leaking past the valve body and oil seal.
^ Oil leaking past the O-ring seal between the valve body and cylinder head which may be caused by a torn or cut Oring.
FIGURE 1
DIAGNOSIS
Remove and inspect all spark plugs. If a spark plug is found to be heavily oil fouled and/or appears to have the electrodes eroded or overheated, proceedto jet valve removal procedure below (Figure 1).PARTS REQUIRED
Jet Valve Assembly (as required)
O-Ring (as required)
INSTALLATION PROCEDURE
PN MD009440
PN MD009786
1.
Remove only the jet valve of the cylinder showing the spark plug oiling or overheating. Follow the jet valve removal procedures outlined in therespective model year service manual using Miller Special Tool #MB-998310.
> Powertrain Management > Ignition System > Spark Plug > Component Information > Technical Service Bulletins > All Technical Service Bulletins for Spark Plug: >
181788 > Oct > 88 > Spark Plugs - Oil Fouling/Misfire on Hard Acceleration > Page 915
D50/Ram 50 L4-1997cc 2.0L SOHC (1984)
FIGURE 2
2.
Push jet valve open and inspect the valve stem just under the valve head. If oil residue and excessive carbon buildup are present, the Jet ValveAssembly, PN MD009440, will have to be replaced (Figure 2).
If no residue or carbon buildup is present, inspect the O-ring for rips, tears, or deformity. O-ring can be replaced separately with PN MD009786.
FIGURE 3
3.
Inspect jet piece pocket by looking down into jet piece. If pocket has any buildup of burnt oil residue or carbon, it must be cleaned completelyusing the following procedure (Figure 3).
a.
Remove spark plug.
b.
Place piston on top dead center of compression stroke (both valves closed).
Use a thin stiff bristle brush to clean jet piece (a distributor cap terminal brush works well). A thin metal rod (coat hanger) can be used toloosen heavy deposits.
d.
Direct compressed air in jet piece. The loosened deposits will be blown out of the jet piece and spark plug hole. Eye protection isrecommended when performing this operation.
e.
Reinspect cleaned jet piece. If cracking or erosion is seen in the area of the jet air orifice (Figure 3) or the deposit cannot be cleanedadequately, the cylinder head will require replacement.
> Powertrain Management > Ignition System > Spark Plug > Component Information > Technical Service Bulletins > All Technical Service Bulletins for Spark Plug: >
181788 > Oct > 88 > Spark Plugs - Oil Fouling/Misfire on Hard Acceleration > Page 916
D50/Ram 50 L4-1997cc 2.0L SOHC (1984)
4.
Install new spark plug of proper heat range and gap setting.
5.
Start engine and allow to fully warm up. Check for oil leaks and adjust idle speed if necessary.
POLICY: Information only
> Powertrain Management > Ignition System > Spark Plug > Component Information > Technical Service Bulletins > Page 917
> Powertrain Management > Ignition System > Spark Control System <--> [Thermal Vacuum Valve, Vacuum/Dist. Advance] > Component Information > Description and Operation
Spark Control System: Description and Operation
Fig. 18 Idling Spark Advance System
Fig. 18,
The vacuum chamber used in this system, is of the dual diaphragm type. The main diaphragm uses ported vacuum in the conventional mannerto advance ignition timing. The sub-diaphragm, however, is actuated by manifold vacuum tapped below the throttle valve and provides additional timingadvance during periods of deceleration and idle. This additional timing advance results in decreased levels of hydrocarbons entering the atmosphere viathe exhaust system.
> Transmission and Drivetrain > Automatic Transmission/Transaxle > Case, A/T > Component Information > Technical Service Bulletins > Transmission Vent Assembly - Relocation
Case: Technical Service BulletinsTransmission Vent Assembly - Relocation
Models
1984 Power Ram 50 Four Wheel Drive Pick-Up
Subject
Revised Transmission/ Vent Assembly
Index
TRANSMISSION
Date
October 1, 1984
No.
21-05-84
P-4394-/ P-4394-C
The transmission vent assembly on the subject model vehicles has been changed. The new vent has been relocated rearward and higher on thetransmission adapter housing. Relocation of the vent helps prevent oil "weepage" out the vent during low temperature operation.
> Transmission and Drivetrain > Automatic Transmission/Transaxle > Case, A/T > Component Information > Technical Service Bulletins > Transmission Vent Assembly -
Relocation > Page 927
D50/Ram 50 L4-1997cc 2.0L SOHC (1984)
FIGURE 1
FIGURE 2
The location of the new vent assembly is shown in Figure1, as compared to the location of the old vent in Figure 2.
Install the vent with the index notch toward the front of the vehicle. The vent part numbers are:
Old New
MD712895
NOTE:
MD715206
THE VENTS ARE NOT INTERCHANGEABLE.
POLICY: Information only
> Transmission and Drivetrain > Automatic Transmission/Transaxle > Fluid - A/T > Component Information > Technical Service Bulletins > Automatic Transmission - New Fluid Type
Fluid - A/T: Technical Service BulletinsAutomatic Transmission - New Fluid Type
Models
All 1978-1985 Equipped With Automatic Transmission & Lock-Up Torque Converter
Subject
New Automatic Transmission Fluid
Index
TRANSMISSION
Date June 17, 1985
No.
21-04-85
P-2131A new automatic transmission fluid Type 7176, (PN 4318077 - quart and 4318079 - 55 gallon) has been released for all vehicles equipped withautomatic transmission and lock-up torque converter.
Aftermarket fluids can vary in terms of their friction characteristics and this in turn can affect the performance of the lock-up clutch, causing shudderand/or excessive slippage. Use of the new fluid will help to insure that the lock-up clutch will perform satisfactorily after the fluid has been replaced.
Type 7176 fluid should be used any time it is necessary to replace the fluid in a lock-up torque converter equipped transmission.
If a lock-up shudder condition is encountered, check all linkage adjustments and drain and refill the transmission with Type 7176 fluid prior toattempting any other repairs, especially if the fluid has been changed previously.
POLICY: Information only
> Transmission and Drivetrain > Automatic Transmission/Transaxle > Fluid - A/T > Component Information > Specifications > Transaxle/Transmission - Automatic
Fluid - A/T: SpecificationsTransaxle/Transmission - Automatic
AF, APCAPACITY, Refill*:
3.8 Liters 4.0 Quarts Type.............................................................................................................................................................................................................................. All ................................................................................................................................................................................................
*With the engine at operating temperature, shift transmission through all gears. Check fluid level in PARK and add fluid as needed.
> Transmission and Drivetrain > Automatic Transmission/Transaxle > Fluid - A/T > Component Information > Specifications > Transaxle/Transmission - Automatic > Page 934
Fluid - A/T: SpecificationsInitial Refill Capacity
AF, APCAPACITY, Refill*:
3.8 Liters 4.0 Quarts Type.............................................................................................................................................................................................................................. All ................................................................................................................................................................................................
*With the engine at operating temperature, shift transmission through all gears. Check fluid level in PARK and add fluid as needed.
> Transmission and Drivetrain > Clutch, M/T > Clutch Pedal Assembly > Component Information > Adjustments
Clutch Pedal Assembly: Adjustments
Fig. 1 Clutch pedal adjustment specifications
MODELS W/CABLE RELEASE SYSTEM
Fig. 2 Clutch pedal height & freeplay measurement
1. Measure clutch pedal height (A). If height is not within specifications, adjust with pedal stopper bolt. If pedal height is not within specifications on models without stopper bolt, check pedal stop and pedal support for damage and wear and repair as needed.
2. Measure clutch pedal freeplay (B). If freeplay is not within specifications, adjust as follows:
> Transmission and Drivetrain > Clutch, M/T > Clutch Pedal Assembly > Component Information > Adjustments > Page 939
D50/Ram 50 L4-1997cc 2.0L SOHC (1984)
Fig. 3 Clutch cable adjustment a. Pull outer cable away from cable retainer at toe board and turn adjusting wheel until clearance (C), is 0.12-0.16 inch for Ram 50, 0.2-0.24
inch for Colt or 0-0.04 inch for Colt Vista.
b. Depress clutch pedal several times and recheck pedal freeplay.c. Repeat adjustment as needed until freeplay is within specifications.
Fig. 4 Clutch release point measurement
3. After adjusting pedal height and freeplay, measure height of clutch pedal from floorboard at clutch release point (D).4. If release point is less than value specified in chart, check clutch assembly and release mechanism and repair as needed.
Fig. 2 Clutch pedal height & freeplay measurement
> Transmission and Drivetrain > Clutch, M/T > Clutch Pedal Assembly > Component Information > Adjustments > Page 940
D50/Ram 50 L4-1997cc 2.0L SOHC (1984)
MODELS W/HYDRAULIC RELEASE SYSTEM
1. Measure clutch pedal height (A).2. Check clutch pedal clevis pin play. It should be 0.04-0.12 inch, measured at pedal.3. If clutch pedal height is not within specifications, turn either the clutch switch or adjusting bolt to bring height within specifications. If clevis pin
Do not press pushrod intomaster cylinder when adjusting clevis pin clearance. play is not within specifications, adjust clutch master cylinder pushrod as necessary to bring play within specifications.
4. Check clutch pedal freeplay and clutch release point. If either dimension is not within specifications, hydraulic system requires bleeding or clutch is faulty.
> Transmission and Drivetrain > Clutch, M/T > Clutch Switch > Component Information > Locations
Clutch Switch: Locations
Under LH Side Of I/P
> Transmission and Drivetrain > Clutch, M/T > Pilot Bearing > Component Information > Technical Service Bulletins > Clutch Splines & Pilot Bushing - Lubrication
Pilot Bearing: Technical Service BulletinsClutch Splines & Pilot Bushing - Lubrication
Models
AA, AB, AD, AG, AH, AJ, AK, AL, AN, AP, AQ, AS Bodies Through 1989
Subject
Clutch Splines/Pilot Bushing Lubrication
Index
CLUTCH
Date
January 16, 1989
No.
06-01-89
P-0046 (C06-01-9)BODY CODE LEGEND
AA - Spirit/Acclaim
AD - Dodge Ram Pickup/Ram Charger
AH - LeBaron/LeBaron GTS
AK - Aries/Reliant
AN - Dodge Dakota/Dakota Sport
AQ - Chrysler TC
AB - Dodge Ram Van/Wagon
AG - Daytona
AJ - LeBaron
AL - Omni/Horizon
AP - Shadow/Sundance
AS - Caravan/Voyager
This Technical Service Bulletin supersedes ALL previous Service Technical Publications through 1989 covering the lubrication of the clutch splines andpilot bushing. The procedures outlined in this bulletin apply to all domestic cars and trucks equipped with manual transmissions and transaxles.
SERVICE PROCEDURE
NOTE:
CLUTCH SPLINES
1.
Thoroughly clean the input shaft clutch splines and clutch disc splines, they must be free of any dirt or rust.
2.
Apply a light coat of wheel bearing grease PN 4318064 evenly to the entire length of the exposed input shaft splines. Be sure all excessivelubricant is removed.
NOTE:
THE USE OF ALTERNATIVE OIL BASED LUBRICANTS IS NOT RECOMMENDED AS THESE LUBRICANTS WILLEVENTUALLY DRY UP OR BURN OFF LEAVING ONLY A DRY RESIDUE.
REAR WHEEL DRIVE VEHICLES - PILOT BUSHING
1.
Thoroughly clean the pilot bearing journal at the end of the input shaft and the inside of the pilot bushing.
2.
Apply a light coat of multi-purpose grease PN 4318063 to the inside of the pilot bushing.
THIS PROCEDURE SHOULD BE PERFORMED ANYTIME THE TRANSMISSION/TRANSAXLE IS REMOVED FROM THEENGINE AND/OR CLUTCH SERVICE IS PERFORMED.
NOTE:
POLICY:
FAILURE TO PERFORM THIS PROCEDURE MAY RESULT IN ONE OR MORE OF THE FOLLOWINGSYMPTOMS/CONDITIONS - HIGH SHIFTING EFFORT INTO FIRST AND SECOND GEAR, GEAR CLASH INTOREVERSE AND LOW GEARS, PILOT BUSHING NOISE AND CLUTCH DRAG.
INFORMATION ONLY
> Transmission and Drivetrain > Clutch, M/T > Pressure Plate > Component Information > Specifications
Pressure Plate: Specifications
> Transmission and Drivetrain > Differential Assembly > Differential Carrier > Carrier Bearings > Component Information > Adjustments
Carrier Bearings: Adjustments
Front Drive Axle
1. Press side bearing inner race on to differential unit using tool No. MB990802.2. Install side bearing adjusting shims at each side of differential, then position differential into differential carrier.
Fig. 21 Measuring clearance between differential carrier & side bearing adjusting shim. Front driving axle
3. Push differential carrier to one side and measure clearance between side bearing shim and differential carrier.4. Measure thickness of side bearing shims that were used when measuring clearance between side bearing shims and differential carrier.5. Select two pairs of shims with a thickness equal to those used during clearance measurement plus 1/2 the clearance measure plus 0.002 inch.
Fig. 22 Installing side bearing adjusting shims. Front driving axle
6. Install one pair of side bearing adjusting shim to each side of differential, and check to ensure that there is no clearance between shim and carrier.
Rear Drive Axle
5. Measure drive gear to drive pinion backlash using a dial indicator. Drive gear to drive pinion backlash should be 0.005-0.007 inch. If backlash is less than specified, loosen side bearing nut on rear side of drive gear, then tighten side bearing nut on tooth side an equal amount.
6. After adjustment, tighten each side bearing nut by 1/2 distance of two adjacent holes on side bearing nut.
> Transmission and Drivetrain > Differential Assembly > Differential Carrier > Carrier Bearings > Component Information > Adjustments > Page 956
D50/Ram 50 L4-1997cc 2.0L SOHC (1984)
Fig. 23 Lock plate installation
7. Ensure backlash is within specifications, then install a suitable lock plate and torque attaching bolt to 11 to 16 ft. lbs..
> Transmission and Drivetrain > Differential Assembly > Fluid - Differential > Component Information > Specifications
Fluid - Differential: Specifications
GL-5* Limited-Slip ..................................................................................................................................................................................................................
GL-5 Other ...............................................................................................................................................................................................................................
CAPACITY, Refill:
1.1 Liters 2.3 Pints Above -10F (-23C), 90, 85-W-90, 80W-90; -30 to -10F (-34 to -23C), 80W, 80W-90; below -30F (-34C), 75W Front ................................................................................................................................................................................................
1.5 Liters 3.2 Pints Rear .................................................................................................................................................................................................
LIMITED-SLIP IDENTIFICATION:Lift rear of vehicle, turn one wheel and the other will turn in the same direction
> Transmission and Drivetrain > Differential Assembly > Pinion Bearing, Differential > Component Information > Adjustments
Pinion Bearing: Adjustments
Fig. 20 Measuring drive pinion bearing preload
1. The adjustment of the drive pinion bearing preload should be performed after the adjustment of the pinion height. Remove the end yoke and insert the bearing preload adjusting shim between the pinion spacer and the bearing, and torque the end yoke nut to 116-159 ft. lbs. on front drive axles.On rear drive axles, torque nut to 137 to 181 ft. lbs. Pinion bearing preload should be within specifications. In case of using a torque wrench, adaptthe socket (use 1/2" 3/8" adapter) to the box.
2. Remove the end yoke, apply a thin coat of grease to the outside of the oil seal, then drive it into the gear carrier. Subsequently apply grease required to the oil seal lip contact surface of the end yoke shaft. Insert the end yoke, then torque the end yoke nut to 116-159 ft. lbs. on front driveaxles. On rear drive axles, torque nut to 137 to 181 ft. lbs.
> Transmission and Drivetrain > Differential Assembly > Pinion Gear, Differential > Component Information > Adjustments
Pinion Gear: Adjustments
1. Press front and rear bearing outer races into gear carrier using a press or a hammer and a suitable drift. Ensure outer race makes full contact with gear carrier and does not tilt during installation.
2. Attach spacer, washer and nut to tool No. MB990819 or equivalent, then install front and rear drive pinion bearings into gear carrier. Tighten nut on installation tool until front and rear bearing preload is 6-9 inch lbs. on 1984-85 models or 3.5-4.3 inch lbs on 1986-88 models, without oil seal.Apply a suitable lubricant to washer during installation.
Fig. 16 Installed position of tool for checking drive pinion height
3. Install drive pinion bearings and tools from kit C-4626, into gear carrier according to tool manufacturer's instructions. Gradually tighten tool adjusting nut, until front and rear bearing preload is 6-9 inch lbs. on 1984-85 models or 3.5-4.3 inch lbs on 1986-88 models.
Fig. 17 Positioning tool in side bearing seat
Fig. 18 Drive pinion height selective shim chart
4. On all models, mount tool MB990552 or equivalent, in gear carrier side bearing seat, then select a suitable shim from chart, which corresponds to clearance between tools C-4626 and MB990552 or equivalents on. When installing tool MB990552, ensure side bearing seat is clean and cut outportion of tool is positioned as shown.
> Transmission and Drivetrain > Differential Assembly > Pinion Gear, Differential > Component Information > Adjustments > Page 966
D50/Ram 50 L4-1997cc 2.0L SOHC (1984)
Fig. 19 Installing drive pinion rear bearing
5. Install selected shim between rear bearing and drive pinion, then press rear bearing onto drive pinion. If gear is to be replaced, install new shims of same thickness as shims used on drive pinion. In determining thickness of shim pack, the amount of shim pack compression and bearing wearshould be taken into account.
> Transmission and Drivetrain > Differential Assembly > Ring Gear <--> [Ring Gear, Differential] > Component Information > Adjustments
Ring Gear: Adjustments
Fig. 24 Measuring ring gear backlash
1. Install a dial indicator on the back of the ring gear, and measure the amount of runout. Runout should be less than 0.002 inch. If the ring gear indicates excessive runout over the limits, change the position of the assembly with the differential case and measure the runout again. If the runoutis still excessive, replace the ring gear or the differential case as necessary.
2. Measurement of backlash of the drive pinion against the ring gear should be measured at 4 points on the ring gear with the drive pinion fixed securely to its final position. Install a dial indicator to the ring gear tooth edges. Backlash should be within specifications.
3. If the measured backlash is greater than specified, shift shims in an appropriate thickness of the ring gear teeth side to the other side (back of the ring gear) to obtain the proper backlash.
4. If the measured backlash is smaller than specified, reverse shifting of shims stated above.
> Transmission and Drivetrain > Drive Axles, Bearings and Joints > Axle Shaft Assembly > Axle Shaft > Component Information > Service and Repair > Constant Velocity Type Axle Shaft Assembly
Axle Shaft: Service and RepairConstant Velocity Type Axle Shaft Assembly
Removal & Installation
Fig. 6 Drive axle assembly exploded view
Do not allow caliper to 1. Remove wheel and brake caliper assembly, leaving brake hose connected, and hang caliper from body or suspension arm. hang by brake hose.
Support lower control arm with suitable jack prior to disconnecting ball joints from 2. Remove hub cover assembly, then remove snap ring from drive axle.3. Remove knuckle and front hub assembly as a unit. steering knuckle.
4. To remove left drive axle, slowly lower jack supporting control arm, then pull drive axle from differential carrier.5. To remove right drive axle, raise right lower control arm with jack and proceed as follows:
Do not remove lifting a. Remove upper mounting nuts from right shock absorber, then remove shock absorber from arm post of side frame. device from lower arm until shock absorber has been reconnected.
b. Remove four nuts connecting right drive axle to inner shaft assembly, then remove right drive axle.
> Transmission and Drivetrain > Drive Axles, Bearings and Joints > Axle Shaft Assembly > Axle Shaft > Component Information > Service and Repair > Constant Velocity
Type Axle Shaft Assembly > Page 976
D50/Ram 50 L4-1997cc 2.0L SOHC (1984)
6. Remove inner shaft from differential shaft carrier assembly.7. Remove dust seal.8. Reverse procedure to install noting the following: a. Torque right drive axle to inner shaft assembly bolts to 37-43 ft. lbs.b. On 1984 models, tighten shock absorber upper mounting nut until protrusion of stud above bottom of nut is 0.8 inch. On 1985-88 models, tighten shock absorber upper mounting nut until protrusion of stud above top of nut is 0.5 inch for 1985 models or 0.27-0.31 inch for 1986Ram 50 4 X 4 and 1987-88 Ram Raider. On 1987-88 Ram 50 4 X 4, tighten nut to end of threads. On all models, install jam nut and torque to9-13 ft. lbs.
c. Mount knuckle and front hub assembly together and check drive axle endplay as follows: Install snap ring onto drive axle. Position dial indicator on end of drive axle and turn drive axle in axial direction. Drive axle endplay should be 0.008-0.020 inch. Install proper spacer tobring endplay into specification.
Disassembly
1. Remove boot bands from Birfield joint and double offset joint boots. Discard bands and replace with new bands at reassembly.2. Remove circlip from double offset joint outer race.3. Remove drive axle from double offset joint outer race.4. Clean grease from outer race, then remove balls from cage.5. Turn double offset joint cage 30 degrees from position at which balls were installed and push cage down toward Birfield joint until it is off inner race.
6. Remove inner race snap ring, inner race and cage from end of drive axle.7. Remove snap ring from drive axle, then remove double offset joint boot and Birfield boot. Tape end of drive axle so splines do not damage boots as they are removed.
Do not disassemble Birfield joint. 8. Remove dust cover. 9. Using suitable tool and press, remove bearing from inner shaft.
Inspection
1. Inspect outer race of double offset joint for excessive wear or damage.2. Inspect bearing for damage to races.3. Inspect drive axle and inner shaft for damage to splines.4. Inspect drive and inner shaft for bending or other damage.5. Inspect Birfield joint for damage to balls, water contamination, rust and other foreign material.6. Inspect dust cover for proper shape and damage.7. Inspect Birfield joint and double offset joint boots for deterioration, tears or cracks.8. Inspect double offset joint inner race, balls and cage for damage, wear or rust.
Assembly
1. Press dust cover onto inner shaft.2. Press inner bearing onto shaft using tool No. MD990560.3. Press dust covers onto Birfield joints and double offset joints.4. Apply grease to drive axle.
Fig. 7 Driveshaft boot and band identification
5. Install Birfield joint boot, all boot bands and double offset joint boot on drive axle and Birfield joint.6. Install double offset joint cage onto drive axle with smaller diameter end of cage toward Birfield joint. Install snap ring, inner race and circlip onto drive axle.
7. Apply grease to double offset joint inner race and cage, then fit balls into cage.8. Apply 2-3 ounces of grease to outer race, then install race on drive axle.
> Transmission and Drivetrain > Drive Axles, Bearings and Joints > Axle Shaft Assembly > Axle Shaft > Component Information > Service and Repair > Constant Velocity
Type Axle Shaft Assembly > Page 977
D50/Ram 50 L4-1997cc 2.0L SOHC (1984)
9. Apply 2-3 ounces of grease to outer race, then install circlip.
10. Apply as much grease as was removed from Birfield joint during inspection, then install boot. Birfield joint boot should measure 3 inches in length from outer band to inner band.
> Transmission and Drivetrain > Drive Axles, Bearings and Joints > Axle Shaft Assembly > Axle Shaft > Component Information > Service and Repair > Constant Velocity Type Axle Shaft Assembly > Page 978
Axle Shaft: Service and RepairConventional Fixed/Floating Axle Shaft
Axle Assembly Removal and Installation
EXC. MODELS EQUIPPED WITH INDEPENDENT REAR SUSPENSION
1. Raise vehicle and support at frame. Support rear axle with a suitable jack.2. Remove wheels and propeller shaft. Place matching mark on propeller shaft flange yoke and companion yoke for reassembly.3. Disconnect brake hose from brake line.4. Disconnect parking brake cable from both wheels and remove the parking brake cable lever on axle housing.5. Remove shock absorbers.6. Remove coil springs (if so equipped) or leaf springs as outlined.7. If equipped with coil springs, remove lower control arm, assist link and upper control arm.8. Remove rear axle assembly from vehicle.9. Reverse procedure to install.
Axle Shaft Removal and Installation
REMOVAL
Fig. 1 Rear axle shaft assembly exploded view. Ram 50 & Ram Raider
1. Raise and support rear of vehicle, then remove rear wheel and brake drum.2. Disconnect rear parking brake cable at equalizer and remove cable retaining bolts and heat shields as needed.3. Disconnect brake tube from wheel cylinder and plug line and open fitting.4. Remove 4 nuts securing bearing case, then remove axle shaft, bearing case and brake backing plate as an assembly. Use suitable slide hammer, if necessary, to free assembly from axle housing.
5. Remove O-ring and shims for preloading bearing. Retain shims for reassembly.
> Transmission and Drivetrain > Drive Axles, Bearings and Joints > Axle Shaft Assembly > Axle Shaft > Component Information > Service and Repair > Constant Velocity
Type Axle Shaft Assembly > Page 979
D50/Ram 50 L4-1997cc 2.0L SOHC (1984)
Fig. 2 Axle shaft bearing locknut removal & installation. Ram 50 & Ram Raider
6. Disengage lock washer then remove locknut using tool No. MB990785.
Fig. 3 Rear axle shaft bearing case removal. Ram 50 & Ram Raider
7. Reinstall locknut on axle shaft approximately 3 turns, then install tool No. MB990787-A and washers. Turn nuts with equal pressure to ensure smooth removal of bearing and remove bearing case from shaft.
8. Using hammer and suitable drift, remove bearing outer race from bearing case.9. Remove inner axle shaft oil seal from housing using suitable puller, and drive outer seal from bearing housing.
INSTALLATION
1. Apply wheel bearing grease to outer surface of bearing outer race and to lip of outer oil seal, then drive them into bearing case.2. Place backing plate, bearing case and bearing over rear axle shaft, then apply bearing grease to bearing rollers and install bearing race.3. Install washer, lock washer and locknut. Torque locknut to 130 - 159 ft. lbs. (177 - 216 Nm) using tool No. MB990785, then bend tab on lock washer into groove on locknut. If lock washer does not engage with locknut, slightly retighten locknut.
4. Apply bearing grease to lip of inner oil seal and drive seal into rear axle housing using tool No. C-4572.5. Adjust axial play of rear axle shaft as follows: a. Remove any rust or old sealer from mating surface of bearing case and housing.
> Transmission and Drivetrain > Drive Axles, Bearings and Joints > Axle Shaft Assembly > Axle Shaft > Component Information > Service and Repair > Constant Velocity
Type Axle Shaft Assembly > Page 980
D50/Ram 50 L4-1997cc 2.0L SOHC (1984)
Fig. 1 Rear axle shaft assembly exploded view. Ram 50 & Ram Raider b. Insert 1 mm shim and O-ring into left side of housing, and apply silicone rubber sealant to mating face of bearing case.c. Install left side axle shaft into left side housing and torque bearing case nuts to 36 - 43 ft. lbs. (49 - 59 Nm).d. Install right side axle shaft into right side housing, without shim or O-ring, and temporarily torque bearing case nuts to 0.4 ft. lbs. (.6 Nm).
Measure and record gap between bearing case and housing using feeler gauge.
e. Remove axle shaft from housing, then select a shim with thickness of measured gap of step "d" and a shim with thickness from 0.05 - 0.20
mm (0.002 - 0.007 inch). Insert selected shims and O-ring into housing and apply silicone sealer to mating face of bearing case.
f.
6. Connect brake tube to wheel cylinder and install rear brake drum and wheel.
Install right side axle shaft into right side housing and torque bearing case nuts to 36 - 43 ft. lbs. (49 - 59 Nm). Then, using a dial indicator,check axial play as shown. The axial play should be 0.002 - 0.007 inch (0.05 - 0.20 mm). If specified play is not obtained, change thicknessof selected shims and reassemble.
> Transmission and Drivetrain > Drive Axles, Bearings and Joints > Wheel Bearing > Component Information > Adjustments
Wheel Bearing: Adjustments
Install hub bearings on spindle, then install hub nut and torque to 22 ft. lbs. to seat bearings. Loosen hub nut, then torque nut to 6 ft. lbs. Install nutretainer cap and cotter pin. If cotter pin holes are not aligned, loosen nut to align holes. The nut may be loosened to a maximum of 30 to align cotterpin holes. Check to ensure hub assembly rotates freely without play.
> Transmission and Drivetrain > Drive Axles, Bearings and Joints > Wheel Bearing > Component Information > Service and Repair > Removal
Wheel Bearing: Service and RepairRemoval
Fig. 8 Hub & wheel bearing assembly exploded view. Shown w/manual locking hub
Fig. 9 Automatic (free wheeling) locking hub
> Transmission and Drivetrain > Drive Axles, Bearings and Joints > Wheel Bearing > Component Information > Service and Repair > Removal > Page 986
D50/Ram 50 L4-1997cc 2.0L SOHC (1984)
1. Remove wheel and tire assembly, then remove brake caliper assembly leaving brake hose connected. Suspend caliper assembly from frame using a wire hook to prevent damage to brake hose.
2. Place hub in free position, then remove free wheeling hub cover. On models with automatic locking hubs, ensure hub is in "free wheeling" position by placing transfer case lever in 2H position and moving in reverse 4-7 feet. If cover cannot be removed by hand, loosen cover with suitable strapwrench, taking care not to damage cover.
3. Remove snap ring securing drive axle, then the adjusting shims.4. Remove free wheeling hub assembly from front hub, using tool MD998360 or equivalent to remove bolts securing automatic locking hub.
Fig. 10 Spindle nut removal & installation
5. Remove lock washer, then remove hub locknut using tool No. MB990954.6. Pull front hub with brake disc from knuckle, using care not to drop outer wheel bearing inner race.7. Remove grease from inside front hub, then using a suitable drift, drive bearing races from hub.8. Place alignment marks on brake disc and hub, then separate hub and disc as necessary.
> Transmission and Drivetrain > Drive Axles, Bearings and Joints > Wheel Bearing > Component Information > Service and Repair > Removal > Page 987
Wheel Bearing: Service and RepairInspection
HUB, SPINDLE & BEARINGS
1. Clean components with suitable solvent and blow dry with compressed air.
Fig. 11 Checking spindle for wear
2. Inspect spindle for wear and damage and measure spindle bearing seating area diameter. Diameter should be 1.7805 to 1.7812 inch.3. Inspect bearings for damage excessive wear, overheating and scoring, and replace as needed.4. Check fit of bearing outer races in hub. If races are loose, hub should be replaced.
MANUAL LOCKING HUB
Fig. 8 Hub & wheel bearing assembly exploded view. Shown w/manual locking hub
1. Inspect hub ring, inner hub and hub body, and the clutch. If components are damaged or worn, assembly should be replaced.2. Inspect tension spring and compression spring, and replace if collapsed or deteriorated.3. Check operation of control handle and replace as needed.
> Transmission and Drivetrain > Drive Axles, Bearings and Joints > Wheel Bearing > Component Information > Service and Repair > Removal > Page 988
D50/Ram 50 L4-1997cc 2.0L SOHC (1984)
Fig. 9 Automatic (free wheeling) locking hub
AUTOMATIC LOCKING HUB
DISASSEMBLY
1. Press in on brake B, then remove housing C-ring.2. Remove brake B, brake B and brake spring from housing, then remove housing snap ring.3. Mount assembly in press, lightly compress drive gear, then remove retainer B C-ring, noting the following: a. Place protective cloth under cover mating surface.b. Because return spring is approximately 1.57 inches long, ensure press stroke is more than 1.57 inches.c. Do not apply more than 441 lbs. pressure to drive gear.d. After removing C-ring, slowly reduce press force until return spring relaxes completely.
4. Remove retainer B, return spring, slide gear assembly and drive gear assembly from housing.5. Remove and discard drive gear snap ring.6. Press in on slide gear cam and remove slide gear C-ring.
INSPECTION
1. Check slide and drive gear splines for damage.2. Check cam portion of retainer A for wear or damage.3. Check cam for wear and damage.4. Check slide gear and housing tooth surfaces for wear and damage.5. Check retainer B and housing contact surfaces for wear and damage.6. Check brake wear as follows:
Fig. 12 Measuring brake assembly. Automatic locking hub a. Assemble brake A and brake B, then measure thickness of assembly at two lugs on brake A.b. Standard thickness is 0.413 inch and minimum thickness is 0.378 inch.
> Transmission and Drivetrain > Drive Axles, Bearings and Joints > Wheel Bearing > Component Information > Service and Repair > Removal > Page 989
D50/Ram 50 L4-1997cc 2.0L SOHC (1984)
7. Inspect return and shift springs as follows:
Fig. 13 Measuring spring free length. Automatic locking hub a. Measure free length of spring as shown.b. Minimum return spring free length is 1.38 inches.c. Minimum shift spring free length is 1.18 inches.
8. Replace any components that are damaged, excessively worn, or that are not within specifications.
ASSEMBLY
Apply Mopar grease 2525035 or equivalent to mounting surfaces of all components and reverse disassembly procedure, noting the following:1. Pack grooves of retainer B with specified grease.2. Install return spring with smaller diameter coil toward cam.3. Pack grooves of brake B with specified grease.
> Transmission and Drivetrain > Drive Axles, Bearings and Joints > Wheel Bearing > Component Information > Service and Repair > Removal > Page 990
Wheel Bearing: Service and RepairInstallation
1. Drive outer races into front hub using a suitable drift, then evenly coat inner wall of front hub with grease.2. Pack inner and outer bearings with suitable grease. Apply grease to oil seal lip.3. Position inner bearing and oil seal on hub, then install oil seal using tool No. MB990985.
Fig. 8 Hub & wheel bearing assembly exploded view. Shown w/manual locking hub
Fig. 14 Checking front hub rotating torque
4. If removed, install brake disc on front hub, tightening attaching bolts alternately and evenly to 36-44 ft. lbs. After assembling, check brake disc runout. Brake disc runout should not exceed 0.006 inch.
5. Carefully install front hub on steering knuckle spindle.6. Install outer bearing on spindle, then install spindle nut.7. Adjust wheel bearings as follows: a. Torque bearing locknut to 94-145 ft. lbs. while rotating hub to seat bearings.b. Loosen spindle nut and retighten to 18 ft. lbs., then back off 30.c. Install lock washer. If hole in lock washer is not aligned with hole in spindle nut, the nut may be loosened up to an additional 20 to obtain
> Transmission and Drivetrain > Drive Axles, Bearings and Joints > Wheel Bearing > Component Information > Service and Repair > Removal > Page 991
D50/Ram 50 L4-1997cc 2.0L SOHC (1984)
proper alignment.
d. Using a suitable spring scale or torque wrench, measure force required to rotate front hub.e. The force required to rotate the front hub assembly should be 1.1-4.0 lbs. (spring scale) or 3-11 inch lbs. (torque wrench), and endplay should be less than 0.002 inch. If rotating force is not within specifications, repeat adjustment.
f. When adjustment is correct, secure washer with retaining screws.
8. On models with automatic locking hubs, measure brake contact surface depth as follows:
Fig. 15 Measuring brake contact surface depth. Automatic locking hub a. Measure dimension A, in two places using suitable depth gauge.b. Average of two readings should be 0.46-0.48 inch. If depth is greater than specified, install suitable shims. If depth is less than specified, recheck hub and bearing installation.
9. Apply grease to inner surface of free wheeling hub body assembly.
10. Apply semi-dry sealant to front hub surface to which the free wheeling hub body assembly is attached.11. Align tab on free wheel hub with groove on spindle, install free wheeling hub body assembly on front hub, then torque attaching bolts to 37-43 ft.
lbs.
12. Reverse remaining procedure to complete installation.
> Transmission and Drivetrain > Drive Axles, Bearings and Joints > Wheel Hub > Axle Nut > Component Information > Technical Service Bulletins > Rear Axle Shaft - Retaining Nut Lock Washers
Axle Nut: Technical Service BulletinsRear Axle Shaft - Retaining Nut Lock Washers
Models
1979-89 PB/B4 And SJ/B6 Vehicles
Subject
Lock Washer For Rear Axle Shaft Retaining Nut
Index
REAR AXLE
Date
April 17, 1989
No.
03-01-89
(CO0-02-9)
AXLE SHAFT RETAINING NUT LOCK WASHER
BODY CODE LEGEND
PB/B4 - RAM 50 PICKUP SJ/B6 - RAM RAIDER
AXLE SHAFT RETAINING NUT LOCK WASHER
When axle service requires removal of the axle shaft retaining nut and lock washer (Figure 1), the lock washer must not be reused. The lock washer, P/NMB092433, must be replaced when reassembling the axle.
> Transmission and Drivetrain > Drive Axles, Bearings and Joints > Wheel Hub (Locking) > Component Information > Technical Service Bulletins > Automatic Locking Hubs - Racheting Noise
Wheel Hub (Locking): Technical Service BulletinsAutomatic Locking Hubs - Racheting Noise
Models
1984-1985 Dodge Power Ram 50 Pick-Up
Subject
Racheting Noise in Automatic Locking Hubs
Index
FRONT AXLE
Date
November 19, 1984
No.
02-10-84 P-5120-CSYMPTOM/CONDITION
Racheting noise in automatic locking hubs during low temperature operation or after shifting from "4H" to "2H".
DIAGNOSIS/CORRECTION
Use the attached chart to determine the corrective action necessary.
POLICY: Information Only
SYMPTOM RESOLUTION
Noise is generated after start-up with shift lever in "2H" position under low temperature.
free-wheeling hub.
Noise is generated after shift lever is changed from "4H"
(lock) "2H" (free) position.
Drive the vehicle with the lever in "4H" position for a while to warm up oil in transfer case and then drive with the lever in "2H" position.
When shifting "4H" (lock) to
"2H" (free) position, first stop vehicle, change shift lever from "4H" to "2H" position, and then slowly drive vehicle straight backward for 10 to 20 feet.
CAUSE
Under low temperature, oil in transfer case gets stiff and it accordingly rotates front drive shaft which causes racheting effect* of automatic
If shifting is done while vehi- cle is turning, only one side of free-wheeling hub will be freed resulting in the racheting effect.*
*Racheting effect is caused when slide gear and housing gear are not engaged and there is difference of revolution speed between those two gears. Noiseis caused by this revolutional difference.
The racheting of the hubs is not detrimental to the components or operation of the vehicle. The 1985 owners manual will advise the customer of thecondition.
> Transmission and Drivetrain > Flywheel > Component Information > Specifications
Flywheel: Specifications
Flywheel to Crankshaft 94-101 ft.lb
> Transmission and Drivetrain > Manual Transmission/Transaxle > Case, M/T > Component Information > Technical Service Bulletins > Transmission Vent Assembly - Relocation
Case: Technical Service BulletinsTransmission Vent Assembly - Relocation
Models
1984 Power Ram 50 Four Wheel Drive Pick-Up
Subject
Revised Transmission/ Vent Assembly
Index
TRANSMISSION
Date
October 1, 1984
No.
21-05-84
P-4394-/ P-4394-C
The transmission vent assembly on the subject model vehicles has been changed. The new vent has been relocated rearward and higher on thetransmission adapter housing. Relocation of the vent helps prevent oil "weepage" out the vent during low temperature operation.
> Transmission and Drivetrain > Manual Transmission/Transaxle > Case, M/T > Component Information > Technical Service Bulletins > Transmission Vent Assembly -
Relocation > Page 1009
D50/Ram 50 L4-1997cc 2.0L SOHC (1984)
FIGURE 1
FIGURE 2
The location of the new vent assembly is shown in Figure1, as compared to the location of the old vent in Figure 2.
Install the vent with the index notch toward the front of the vehicle. The vent part numbers are:
Old New
MD712895
NOTE:
MD715206
THE VENTS ARE NOT INTERCHANGEABLE.
POLICY: Information only
> Transmission and Drivetrain > Manual Transmission/Transaxle > Fluid - M/T > Component Information > Specifications
Fluid - M/T: Specifications
GL-4CAPACITY, Refill:
2.1 Liters 4.4 Pints Type......................................................................................................................................................................................................80W, 75W-85W 4-speed RWD...................................................................................................................................................................................
2.3 Liters 4.8 Pints 5-speed RWD...................................................................................................................................................................................
> Transmission and Drivetrain > Manual Transmission/Transaxle > Input Shaft, M/T > Component Information > Technical Service Bulletins > Clutch Splines & Pilot Bushing - Lubrication
Input Shaft: Technical Service BulletinsClutch Splines & Pilot Bushing - Lubrication
Models
AA, AB, AD, AG, AH, AJ, AK, AL, AN, AP, AQ, AS Bodies Through 1989
Subject
Clutch Splines/Pilot Bushing Lubrication
Index
CLUTCH
Date
January 16, 1989
No.
06-01-89
P-0046 (C06-01-9)BODY CODE LEGEND
AA - Spirit/Acclaim
AD - Dodge Ram Pickup/Ram Charger
AH - LeBaron/LeBaron GTS
AK - Aries/Reliant
AN - Dodge Dakota/Dakota Sport
AQ - Chrysler TC
AB - Dodge Ram Van/Wagon
AG - Daytona
AJ - LeBaron
AL - Omni/Horizon
AP - Shadow/Sundance
AS - Caravan/Voyager
This Technical Service Bulletin supersedes ALL previous Service Technical Publications through 1989 covering the lubrication of the clutch splines andpilot bushing. The procedures outlined in this bulletin apply to all domestic cars and trucks equipped with manual transmissions and transaxles.
SERVICE PROCEDURE
NOTE:
CLUTCH SPLINES
1.
Thoroughly clean the input shaft clutch splines and clutch disc splines, they must be free of any dirt or rust.
2.
Apply a light coat of wheel bearing grease PN 4318064 evenly to the entire length of the exposed input shaft splines. Be sure all excessivelubricant is removed.
NOTE:
THE USE OF ALTERNATIVE OIL BASED LUBRICANTS IS NOT RECOMMENDED AS THESE LUBRICANTS WILLEVENTUALLY DRY UP OR BURN OFF LEAVING ONLY A DRY RESIDUE.
REAR WHEEL DRIVE VEHICLES - PILOT BUSHING
1.
Thoroughly clean the pilot bearing journal at the end of the input shaft and the inside of the pilot bushing.
2.
Apply a light coat of multi-purpose grease PN 4318063 to the inside of the pilot bushing.
THIS PROCEDURE SHOULD BE PERFORMED ANYTIME THE TRANSMISSION/TRANSAXLE IS REMOVED FROM THEENGINE AND/OR CLUTCH SERVICE IS PERFORMED.
NOTE:
POLICY:
FAILURE TO PERFORM THIS PROCEDURE MAY RESULT IN ONE OR MORE OF THE FOLLOWINGSYMPTOMS/CONDITIONS - HIGH SHIFTING EFFORT INTO FIRST AND SECOND GEAR, GEAR CLASH INTOREVERSE AND LOW GEARS, PILOT BUSHING NOISE AND CLUTCH DRAG.
INFORMATION ONLY
> Transmission and Drivetrain > Transfer Case > Fluid - Transfer Case > Component Information > Specifications
Fluid - Transfer Case: Specifications
GL-4CAPACITY, Refill:
2.2 Liters 4.6 Pints Type......................................................................................................................................................................................................80W, 75W-85W All models .......................................................................................................................................................................................
> Transmission and Drivetrain > Transfer Case > Shift Fork, Transfer Case > Component Information > Technical Service Bulletins > Transfer Case Shift Lever - Redesigned
Shift Fork: Technical Service BulletinsTransfer Case Shift Lever - Redesigned
Models
1984 Power Ram 50 4-Wheel Drive Equipped With KM145 & KM146 Transmissions
Subject
New Transfer Case Shift Lever, Lug & Shift Fork
Index
TRANSMISSION
Date
12/10/84
No.
21-16-84
P-5389C
FIGURE 1
FIGURE 2
Approximately early July, 1984 a new transfer case shift lever entered production on 4-wheel drive Power Ram 50 trucks (Figure 1). The new lever has a
> Transmission and Drivetrain > Transfer Case > Shift Fork, Transfer Case > Component Information > Technical Service Bulletins > Transfer Case Shift Lever - Redesigned
> Page 1025
D50/Ram 50 L4-1997cc 2.0L SOHC (1984)
larger nylon coated lower end where it engages the shift lug and fork. The lug and fork were also changed to accommodate the new lever (Figure 2).
NOTE:
THE NEW SHIFT LEVER, LUG, AND FORK CAN BE USED IN PRIOR MODELS ONLY AS AN ASSEMBLY. DO NOTMIX COMPONENT PARTS.
Part
Lever Assembly, Control
New PN
MD718050
Old PN
MD704221
Lug, Shift (2WD-4WD) MD716798 MD711153
Fork, Shift (High-Low)
POLICY: Information only
MD716797 MD700702
> Transmission and Drivetrain > Transfer Case > Shifter Transfer Case > Component Information > Technical Service Bulletins > Transfer Case Shift Lever - Redesigned
Shifter Transfer Case: Technical Service BulletinsTransfer Case Shift Lever - Redesigned
Models
1984 Power Ram 50 4-Wheel Drive Equipped With KM145 & KM146 Transmissions
Subject
New Transfer Case Shift Lever, Lug & Shift Fork
Index
TRANSMISSION
Date
12/10/84
No.
21-16-84
P-5389C
FIGURE 1
FIGURE 2
Approximately early July, 1984 a new transfer case shift lever entered production on 4-wheel drive Power Ram 50 trucks (Figure 1). The new lever has a
> Transmission and Drivetrain > Transfer Case > Shifter Transfer Case > Component Information > Technical Service Bulletins > Transfer Case Shift Lever - Redesigned >
Page 1030
D50/Ram 50 L4-1997cc 2.0L SOHC (1984)
larger nylon coated lower end where it engages the shift lug and fork. The lug and fork were also changed to accommodate the new lever (Figure 2).
NOTE:
THE NEW SHIFT LEVER, LUG, AND FORK CAN BE USED IN PRIOR MODELS ONLY AS AN ASSEMBLY. DO NOTMIX COMPONENT PARTS.
Part
Lever Assembly, Control
New PN
MD718050
Old PN
MD704221
Lug, Shift (2WD-4WD) MD716798 MD711153
Fork, Shift (High-Low)
POLICY: Information only
MD716797 MD700702
> Brakes and Traction Control > Disc Brake System > Brake Caliper > Component Information > Service and Repair > Sliding Type Caliper
Brake Caliper: Service and RepairSliding Type Caliper
Fig. 7 Sliding type caliper exploded view. Front disc brake
CALIPER & BRAKE PAD REMOVAL
1.
Remove wheel, then retainer clip and stopper plug.
2.
Loosen caliper mounting and remove caliper.
3.
Remove anti-squeak shims, then brake pad from caliper support.
CALIPER SERVICE
1.
Remove brake pads as previously outlined.
2.
Remove hose clip from strut area and disconnect brake hose from caliper, then remove caliper.
3.
Keep fingersaway from piston area to prevent injury. Remove dust boot, then cover outer surface of caliper with cloth. Apply compressed air through brake hose fitting to remove piston.
4.
Remove piston seal taking care not to damage caliper cylinder.
5.
Clean all parts using brake fluid.
6.
Apply rubber grease to piston seal and install into caliper cylinder.
7.
Lubricate piston and piston bore with brake fluid, then insert piston into bore taking care not to twist seal.
8.
Apply RX-2 grease or equivalent to dust boot attaching groove in caliper, then insert dust boot.
9.
Install brake pad, then apply Plastilube #2 or equivalent grease to stopper plug and caliper sliding surface. Install caliper and retainer clip.
10.
Connect and tighten brake hose, then bleed brakes.
Fig. 8 Sliding caliper brake pad clip installation. Front disc brake
BRAKE PAD INSTALLATION
1.
Clean exposed part of piston, then push piston into original position using hammer handle. If piston is difficult to move, open bleeder screw andpiston will move easily. Be sure to bleed brakes.
> Brakes and Traction Control > Disc Brake System > Brake Caliper > Component Information > Service and Repair > Sliding Type Caliper > Page 1037
D50/Ram 50 L4-1997cc 2.0L SOHC (1984)
2.
Apply Plastilube grease or equivalent to both faces of outer pad anti-squeak shim, then install both brake pads with anti-squeak shims into calipersupport. Install clip B and inner and outer clips in proper directions.
3.
Install caliper, then stopper plug and retainer clip.
> Brakes and Traction Control > Disc Brake System > Brake Caliper > Component Information > Service and Repair > Sliding Type Caliper > Page 1038
Brake Caliper: Service and RepairTwo Piece Pin Type Caliper
Fig. 1 Two piece pin type caliper exploded view
BRAKE PAD REMOVAL
1.
Remove the wheel.
2.
Remove the protector, by prying up the edge of the clip at the center of the pad protector with a screwdriver.
3.
Holding the center of the M-clip with fingers, detach the M-clip from the pad and the ends from the retaining pins.
4.
Pull the retaining pins from the caliper assembly and remove the K-spring.
5.
Remove the brake pad assembly by holding the backing plate area of the pad with pliers.
CALIPER REMOVAL
1.
Remove the brake pads as outlined previously.
2.
Remove the brake hose clip from the strut area, then disconnect the brake hose from the caliper.
3.
Remove the caliper assembly by loosening torque plate and adapter mounting bolts.
CALIPER OVERHAUL
1.
Loosen caliper attaching bridge bolts and separate the outer caliper from the inner caliper.
2.
Do not apply high pressure suddenlysince the piston may cause personal injury. After the removal of the dust seal, remove the piston by applying compressed air at the brake hose fitting.
3.
Remove the piston seal, using care not to damage the cylinder.
4.
Clean all parts using clean brake fluid.
5.
Apply rubber grease to the piston seal and apply brake fluid to the cylinder bore. Insert the piston seal into the piston carefully to preventdistortion.
6.
7.
Whenever the torque plate has been removed from the inner caliper, it is necessary to clean the torque plate shaft and the shaft bore of the caliperand apply suitable grease to the rubber bushing, wiper seal inner surface and torque plate shaft before assembly. Apply sufficient grease to thethreaded portion of the torque plate shaft.
CALIPER INSTALLATION
1.
Install caliper on adapter.
2.
Torque the caliper assembly (torque plate) to the adapter bolts to 58-72 ft. lbs.
3.
Torque the brake hose to 9-12 ft. lbs.
> Brakes and Traction Control > Disc Brake System > Brake Caliper > Component Information > Service and Repair > Sliding Type Caliper > Page 1039
D50/Ram 50 L4-1997cc 2.0L SOHC (1984)
Fig. 2 Brake pad installation. Two piece pin type caliper
BRAKE PAD INSTALLATION
1.
Spread the piston, using the special tool, Piston Spreader (C-3992) or equivalent, then insert the brake shoe through the shim.
2.
Install the K-spring and M-clip.
3.
Install the pad protector.
Fig. 3 Installing K-spring & M-clip. Two piece pin type caliper
> Brakes and Traction Control > Disc Brake System > Brake Disc <--> [Brake Rotor/Disc] > Component Information > Specifications
Brake Disc: Specifications
Front Nominal Thickness 0.79 in
Minimum Thickness 0.72 in
Runout (T.I.R.) 0.006 in
> Brakes and Traction Control > Drum Brake System > Brake Drum > Component Information > Specifications
Brake Drum: Specifications
2WD 4WD
Rear Inside Diameter 9.5 in 10.0 in
> Brakes and Traction Control > Drum Brake System > Brake Drum > Component Information > Specifications > Page 1047
Fig. 3 Rear Drum Brake Assembly Exploded View - Ram Raider & 1984-88 Ram 50
> Brakes and Traction Control > Drum Brake System > Brake Shoe > Component Information > Diagrams
Fig. 3 Rear Drum Brake Assembly Exploded View - Ram Raider & 1984-88 Ram 50
> Brakes and Traction Control > Drum Brake System > Brake Shoe > Component Information > Diagrams > Page 1051
Brake Shoe: Adjustments
These brakes are equipped with self adjusting mechanisms, therefore periodic adjustments are not necessary. If stopping power is insufficient, or if brakepedal travel is excessive, brakes should be cleaned and inspected, and the self-adjusting mechanisms should be checked.
After performing brake service, adjust brake shoes as follows:
1.
Ensure shoes are centered on backing plate and measure width of brake shoes using suitable caliper. On Colt Vista models, also measure insidediameter of brake drum.
2.
Adjust width of brake shoes to approximately 7.06 inches for Colt or 9.97 inches for Ram 50 and Ram Raider. On Colt Vista, adjust brake shoes toa width approximately 0.060 inch less than inside diameter of brake drum.
3.
Install brake drums and adjust parking brake as outlined.
4.
If shoeactuating lever is pulled by parking brake cable, self-adjusters will not operate. After adjusting parking brake, release parking brake lever and ensure that shoe actuating lever is not being pulled by parking brake cable.
> Brakes and Traction Control > Hydraulic System, Brakes > Brake Caliper > Component Information > Service and Repair > Sliding Type Caliper
Brake Caliper: Service and RepairSliding Type Caliper
Fig. 7 Sliding type caliper exploded view. Front disc brake
CALIPER & BRAKE PAD REMOVAL
1.
Remove wheel, then retainer clip and stopper plug.
2.
Loosen caliper mounting and remove caliper.
3.
Remove anti-squeak shims, then brake pad from caliper support.
CALIPER SERVICE
1.
Remove brake pads as previously outlined.
2.
Remove hose clip from strut area and disconnect brake hose from caliper, then remove caliper.
3.
Keep fingersaway from piston area to prevent injury. Remove dust boot, then cover outer surface of caliper with cloth. Apply compressed air through brake hose fitting to remove piston.
4.
Remove piston seal taking care not to damage caliper cylinder.
5.
Clean all parts using brake fluid.
6.
Apply rubber grease to piston seal and install into caliper cylinder.
7.
Lubricate piston and piston bore with brake fluid, then insert piston into bore taking care not to twist seal.
8.
Apply RX-2 grease or equivalent to dust boot attaching groove in caliper, then insert dust boot.
9.
Install brake pad, then apply Plastilube #2 or equivalent grease to stopper plug and caliper sliding surface. Install caliper and retainer clip.
10.
Connect and tighten brake hose, then bleed brakes.
Fig. 8 Sliding caliper brake pad clip installation. Front disc brake
BRAKE PAD INSTALLATION
1.
Clean exposed part of piston, then push piston into original position using hammer handle. If piston is difficult to move, open bleeder screw andpiston will move easily. Be sure to bleed brakes.
> Brakes and Traction Control > Hydraulic System, Brakes > Brake Caliper > Component Information > Service and Repair > Sliding Type Caliper > Page 1057
D50/Ram 50 L4-1997cc 2.0L SOHC (1984)
2.
Apply Plastilube grease or equivalent to both faces of outer pad anti-squeak shim, then install both brake pads with anti-squeak shims into calipersupport. Install clip B and inner and outer clips in proper directions.
3.
Install caliper, then stopper plug and retainer clip.
> Brakes and Traction Control > Hydraulic System, Brakes > Brake Caliper > Component Information > Service and Repair > Sliding Type Caliper > Page 1058
Brake Caliper: Service and RepairTwo Piece Pin Type Caliper
Fig. 1 Two piece pin type caliper exploded view
BRAKE PAD REMOVAL
1.
Remove the wheel.
2.
Remove the protector, by prying up the edge of the clip at the center of the pad protector with a screwdriver.
3.
Holding the center of the M-clip with fingers, detach the M-clip from the pad and the ends from the retaining pins.
4.
Pull the retaining pins from the caliper assembly and remove the K-spring.
5.
Remove the brake pad assembly by holding the backing plate area of the pad with pliers.
CALIPER REMOVAL
1.
Remove the brake pads as outlined previously.
2.
Remove the brake hose clip from the strut area, then disconnect the brake hose from the caliper.
3.
Remove the caliper assembly by loosening torque plate and adapter mounting bolts.
CALIPER OVERHAUL
1.
Loosen caliper attaching bridge bolts and separate the outer caliper from the inner caliper.
2.
Do not apply high pressure suddenlysince the piston may cause personal injury. After the removal of the dust seal, remove the piston by applying compressed air at the brake hose fitting.
3.
Remove the piston seal, using care not to damage the cylinder.
4.
Clean all parts using clean brake fluid.
5.
Apply rubber grease to the piston seal and apply brake fluid to the cylinder bore. Insert the piston seal into the piston carefully to preventdistortion.
6.
7.
Whenever the torque plate has been removed from the inner caliper, it is necessary to clean the torque plate shaft and the shaft bore of the caliperand apply suitable grease to the rubber bushing, wiper seal inner surface and torque plate shaft before assembly. Apply sufficient grease to thethreaded portion of the torque plate shaft.
CALIPER INSTALLATION
1.
Install caliper on adapter.
2.
Torque the caliper assembly (torque plate) to the adapter bolts to 58-72 ft. lbs.
3.
Torque the brake hose to 9-12 ft. lbs.
> Brakes and Traction Control > Hydraulic System, Brakes > Brake Caliper > Component Information > Service and Repair > Sliding Type Caliper > Page 1059
D50/Ram 50 L4-1997cc 2.0L SOHC (1984)
Fig. 2 Brake pad installation. Two piece pin type caliper
BRAKE PAD INSTALLATION
1.
Spread the piston, using the special tool, Piston Spreader (C-3992) or equivalent, then insert the brake shoe through the shim.
2.
Install the K-spring and M-clip.
3.
Install the pad protector.
Fig. 3 Installing K-spring & M-clip. Two piece pin type caliper
> Brakes and Traction Control > Hydraulic System, Brakes > Brake Master Cylinder > Component Information > Specifications
Brake Master Cylinder: Specifications
Cylinder Bore Diameter 0.87 in
> Brakes and Traction Control > Hydraulic System, Brakes > Brake Master Cylinder > Component Information > Specifications > Page 1063
Brake Master Cylinder: Service and Repair
1.
Disconnect the brake tube from the master cylinder.
2.
On 1984 Colt Hatchback, disconnect level sensor electrical connector.
3.
On models equipped with manual brakes remove clevis pin connecting pushrod to brake pedal.
4.
Remove the attaching bolts from the toe-board or power brake assembly.
5.
Reverse procedure to install. Torque attaching bolts to 6-9 ft. lbs. Torque brake tube flare nut to 9.5-12 ft. lbs. If the car is equipped with powerbrakes, check clearance between the back of the master cylinder piston and the power brake pushrod. It should be 0 to 0.03 in. If clearance is notcorrect, adjust the length of the pushrod.
> Brakes and Traction Control > Parking Brake System > System Information > Adjustments
Parking Brake System: Adjustments
1.
Apply parking brake with a force of approximately 66 lbs. while counting number of clicks. Lever should pull out 16-17 notches.
2.
If pull stroke is not as specified, loosen cable adjuster to release parking brake cable then depress brake pedal several times to ensure shoe to drumclearance is properly maintained by self-adjusters.
3.
If adjusting nut istightened excessively, self-adjuster mechanism will be inoperative. Tighten adjusting nuts or turnbuckle until brake lever stroke is 16-17 notches with a pulling force of approximately 66 lbs.
4.
After adjustment, ensure that brake equalizer on 1984-86 2 wheel drive models is nearly parallel with centerline of vehicle. On 1984-86 4 wheeldrive models and all 1987 models, ensure equalizer and joint are at right angles to each other.
> Brakes and Traction Control > Power Booster <--> [Power Brake Assist] > Vacuum Brake Booster > Component Information > Service and Repair
Vacuum Brake Booster: Service and Repair
1.
Remove master cylinder as outlined previously.
2.
Disconnect vacuum hose from power brake unit.
3.
Remove pin connecting power brake rod with brake pedal.
4.
Remove power brake unit attaching nuts and the power brake unit.
5.
Reverse procedure to install.
> Starting and Charging > Sensors and Switches - Starting and Charging > Clutch Switch > Component Information > Locations
Clutch Switch: Locations
Under LH Side Of I/P
> Starting and Charging > Sensors and Switches - Starting and Charging > Ignition Switch > Component Information > Service and Repair
Ignition Switch: Service and Repair
The ignition switch is mounted in the rear of the steering column lock. When the key is turned to LOCK position and pulled out, the lock pinautomatically ejects from the cylinder and enters a groove in the steering shaft, locking the steering wheel. The heads of the bolts securing the steering lock assembly shear off when the bolts are tightened. Replacement of the steering lock assembly mayrequire that the steering column be removed, as these bolts must be cut or slotted to permit removal with a screwdriver. When the lock assembly isinstalled, new shear bolts must be used and the bolts should be tightened until the bolt heads twist off. However, the ignition switch can be serviced separately from the lock assembly using the following procedures.
1.
Disconnect battery ground cable, then remove upper and lower column covers.
2.
Remove bands securing switch harness and disconnect electrical connector.
Fig. 4 Ignition switch removal
3.
Loosen the bolt holding the switch and pull from lock assembly.
4.
Reverse procedure to install, first inserting key to check for proper operation.
> Starting and Charging > Sensors and Switches - Starting and Charging > Neutral Safety Switch > Component Information > Service and Repair
Neutral Safety Switch: Service and Repair
1.
Loosen shift lever handle setscrew, then remove shift lever handle.
2.
Remove shift position indicator attaching screws, then the position indicator by lifting upward.
3.
Disconnect shift position indicator light from indicator assembly, then the neutral safety switch wiring.
4.
Loosen neutral safety switch adjustment screws, then remove attaching screws and switch.
5.
Reverse procedures to install, noting the following:
Fig. 8 Positioning selector lever for neutral safety switch installation. Ram Raider & 1984-86 Ram 50 a. Position selector lever as shown, install switch on selector lever bracket leaving screws loose, then connect suitable ohmmeter to switch terminals.
Fig. 9 Neutral safety switch clearance. Ram Raider & 1984-86 Ram 50 b. Move switch forward and backward through range of adjustment noting meter indication, and scribe alignment mark between switch and
are aligned, then tighten switch mounting screws.
> Starting and Charging > Relays and Modules - Starting and Charging > Starter Relay > Component Information > Locations
Starter Relay: Locations
Inner Left Side Of Wheelwell
Applicable to: 1981-84
> Starting and Charging > Battery > Component Information > Technical Service Bulletins > Battery - Checking Procedure Revision
Battery: Technical Service BulletinsBattery - Checking Procedure Revision
Models
All MMC Vehicles
Subject
Battery Checking Procedures
Index
ELECTRICAL
Date
December 5, 1988
No.
08-10-88
P-4983
(C08-11)
SYMPTOM/CONDITION
The battery checking procedure has been revised for all MMC vehicles. The following procedure should be used when checking the condition of thebattery.
POLICY: Information only
> Starting and Charging > Battery > Component Information > Technical Service Bulletins > Battery - Checking Procedure Revision > Page 1090
D50/Ram 50 L4-1997cc 2.0L SOHC (1984)
^ BATTERY TESTING PROCEDURE
> Starting and Charging > Battery > Component Information > Specifications > Electrical Specifications
Battery: Electrical Specifications
Canada, Standard Battery
Canada, Standard Battery
BCI Group Number 24
Cranking Performance 500 A
Except Canada, Standard Battery
Except Canada, Standard Battery
BCI Group Number 25
Cranking Performance 430 A
> Starting and Charging > Battery > Component Information > Specifications > Electrical Specifications > Page 1093
Battery: Mechanical Specifications
Canada, Standard Battery
Canada, Standard Battery
BCI Group Number 24
Cranking Performance 500 A
Except Canada, Standard Battery
Except Canada, Standard Battery
BCI Group Number 25
Cranking Performance 430 A
> Starting and Charging > Charging System > Generator <--> [Alternator] > Component Information > Specifications
Generator: SpecificationsRated & Test Output
Rated & Test Output
Rated Output 45 A
Test Output 41 A at 3000 rpm
> Starting and Charging > Charging System > Generator <--> [Alternator] > Component Information > Testing and Inspection > Charging Voltage Test
Generator: Testing and InspectionCharging Voltage Test
Fig. 1 Alternator charging voltage test connection. Exc. Battery voltage sensing type alternator
Exc. Battery Voltage Sensing Type
1.
With ignition switch in the "Off" position, disconnect battery positive cable, then connect an ammeter between cable and battery positive post.
2.
Connect a voltmeter between alternator terminal L and ground. Ensure voltage reading is zero. If a reading or needle deflection is indicated on thevoltmeter, either the alternator or alternator wiring is defective.
3.
Place ignition switch in the "On" position, then note voltmeter reading. Voltmeter should indicate a reading considerably less than battery voltage.If reading indicates battery voltage, the alternator may be defective.
4.
Connect jumper cable between battery positive post and battery positive cable, then start engine. This will prevent starting current from beingapplied to ammeter.
5.
Remove jumper cable connected between battery positive post and cable, then increase engine speed to 2000 to 3000 RPM and note ammeterreading. If reading is 5 amps or less (10 amps or less for 1987-88 models), note voltage reading. If reading is above 5 amps (10 amps or less for1987-88 models), either continue to charge battery until reading drops to 5 amps or less (10 amps or less for 1987-88 models) or install a fullycharged battery. The charging current may also be limited by installing a {1/4} ohm resistor in series with the battery.
6.
Charging voltage should be as listed in the "Alternator and Regulator Specification Chart."
Fig. 2 Alternator charging voltage test connection. Battery voltage sensing type alternator
Battery Voltage Sensing Type
1.
With ignition switch in the "Off" position, disconnect battery ground cable and connect a digital voltmeter between alternator S terminal, andground.
2.
Disconnect alternator output wire from alternator B terminal, then connect a DC ammeter in series between the B terminal and the disconnectedoutput wire. Connect positive lead of ammeter to B terminal. Connect negative lead to the disconnected output wire.
3.
Set engine tachometer and reconnect battery ground cable.
4.
5.
Place ignition switch in the "On" position and note voltmeter. The reading should be equal battery voltage. If reading is 0, there is either an opencircuit in the wire between alternator S terminal and battery positive terminal or a blown fusible link.
Start engine, keeping all accessories and lights off. Run engine at a constant 2500 RPM and read voltmeter when alternator output current drops to10 amps or less. Voltage reading should be as listed in the "Alternator and Regulator Specification Chart."
> Starting and Charging > Charging System > Generator <--> [Alternator] > Component Information > Testing and Inspection > Charging Voltage Test > Page 1100
Generator: Testing and InspectionOutput Current Test
Fig. 3 Alternator output test connection
1.
With ignition switch in the "Off" position, disconnect battery cables.
2.
Disconnect wire from terminal B of alternator, then connect an ammeter between battery positive cable and alternator B terminal.
3.
Connect a voltmeter between B terminal and ground.
4.
Connect battery ground cable to battery ground post, then note voltmeter reading. The voltmeter should indicate battery voltage.
5.
Connect a tachometer to engine, then start engine and turn on lights.
6.
Operate engine at approximately 2500 RPM and note ammeter reading. After engine has been started, the ammeter reading will gradually decreaseas the battery approaches a fully charged condition. Read the ammeter indication at its maximum value while increasing engine RPM. Refer to "Alternator and Regulator Specification Chart."
> Starting and Charging > Charging System > Voltage Regulator > Component Information > Specifications
Voltage Regulator: SpecificationsSystem Operating Voltage
System Operating Voltage
Voltage Setting 14.1-14.7 V at 68 deg F
Note: At Test Temperature
> Starting and Charging > Starting System > Clutch Switch > Component Information > Locations
Clutch Switch: Locations
Under LH Side Of I/P
> Starting and Charging > Starting System > Ignition Switch > Component Information > Service and Repair
Ignition Switch: Service and Repair
The ignition switch is mounted in the rear of the steering column lock. When the key is turned to LOCK position and pulled out, the lock pinautomatically ejects from the cylinder and enters a groove in the steering shaft, locking the steering wheel. The heads of the bolts securing the steering lock assembly shear off when the bolts are tightened. Replacement of the steering lock assembly mayrequire that the steering column be removed, as these bolts must be cut or slotted to permit removal with a screwdriver. When the lock assembly isinstalled, new shear bolts must be used and the bolts should be tightened until the bolt heads twist off. However, the ignition switch can be serviced separately from the lock assembly using the following procedures.
1.
Disconnect battery ground cable, then remove upper and lower column covers.
2.
Remove bands securing switch harness and disconnect electrical connector.
Fig. 4 Ignition switch removal
3.
Loosen the bolt holding the switch and pull from lock assembly.
4.
Reverse procedure to install, first inserting key to check for proper operation.
> Starting and Charging > Starting System > Neutral Safety Switch > Component Information > Service and Repair
Neutral Safety Switch: Service and Repair
1.
Loosen shift lever handle setscrew, then remove shift lever handle.
2.
Remove shift position indicator attaching screws, then the position indicator by lifting upward.
3.
Disconnect shift position indicator light from indicator assembly, then the neutral safety switch wiring.
4.
Loosen neutral safety switch adjustment screws, then remove attaching screws and switch.
5.
Reverse procedures to install, noting the following:
Fig. 8 Positioning selector lever for neutral safety switch installation. Ram Raider & 1984-86 Ram 50 a. Position selector lever as shown, install switch on selector lever bracket leaving screws loose, then connect suitable ohmmeter to switch terminals.
Fig. 9 Neutral safety switch clearance. Ram Raider & 1984-86 Ram 50 b. Move switch forward and backward through range of adjustment noting meter indication, and scribe alignment mark between switch and
are aligned, then tighten switch mounting screws.
> Starting and Charging > Starting System > Starter Motor > Component Information > Specifications
> Starting and Charging > Starting System > Starter Motor > Component Information > Specifications > Page 1117
Starter Motor: Service and Repair
1.
Disconnect battery ground cable and remove air cleaner, as needed, to gain access to starter.
2.
Disconnect starter wiring.
3.
Remove starter mounting bolts, then the starter. On truck models, brake pipes, steering joint or A/C lines may prevent lifting starter from enginecompartment. If so, remove splash shield and remove starter from under vehicle.
4.
Before mounting starter, clean the mating surfaces of starter and the engine.
5.
Install starter and tighten mounting bolts so the starter motor shaft is perfectly parallel with the central axis of the engine in all directions. Torquemounting bolts to 16-23 ft. lbs.
6.
Connect starter wiring and battery ground cable.
> Starting and Charging > Starting System > Starter Relay > Component Information > Locations
Starter Relay: Locations
Inner Left Side Of Wheelwell
Applicable to: 1981-84
> Starting and Charging > Power and Ground Distribution > Fuse Block > Component Information > Diagrams > Diagram Information and Instructions
Fuse Block: Diagram Information and Instructions
Group Index
Alphabetic Index to Wiring Diagrams Electrical When trying to find the diagram for a specific component or system, use the information or the under
Group Index Diagrams By Sheet Number
Diagrams By Figure Number Whenever a reference exists to another sheet or figure, find the corresponding diagram using the , , or . The reference number for the subsequent diagram will match a listed group shown.
> Starting and Charging > Power and Ground Distribution > Fuse Block > Component Information > Diagrams > Diagram Information and Instructions > Page 1126
Fuse Block: Electrical Diagrams
TRUCKFuse Block..............................................Left Kick Panel Below Hood Release
Fusible Link...........................................Battery Positive Terminal
> Power and Ground Distribution > Fuse Block > Component Information > Diagrams > Diagram Information and Instructions
Fuse Block: Diagram Information and Instructions
Group Index
Alphabetic Index to Wiring Diagrams Electrical When trying to find the diagram for a specific component or system, use the information or the under
Group Index Diagrams By Sheet Number
Diagrams By Figure Number Whenever a reference exists to another sheet or figure, find the corresponding diagram using the , , or . The reference number for the subsequent diagram will match a listed group shown.
> Power and Ground Distribution > Fuse Block > Component Information > Diagrams > Diagram Information and Instructions > Page 1132
Fuse Block: Electrical Diagrams
TRUCKFuse Block..............................................Left Kick Panel Below Hood Release
Fusible Link...........................................Battery Positive Terminal
> Steering and Suspension > Alignment > System Information > Technical Service Bulletins > Alignment - Caster Adjustment Manual Revision
Alignment: Technical Service BulletinsAlignment - Caster Adjustment Manual Revision
Models
All Ram 50 Two & Four Wheel Drive Vehicles
Subject
Caster Adjustment - Service Manual Revision
Index
FRONT SUSPENSION
Date
03/18/85
No..
02-07-85
P-887C
Caster Adjustment
This bulletin is issued to supplement the service manual information regarding caster adjustment for Ram 50 pick-up trucks.
Caster
Two Wheel Drive
Four Wheel Drive
Specifications
2-1/2~ +/- 1~
2~ +/- 1~
NOTE:
POLICY:
CASTER DIFFERENCE BETWEEN LEFT HAND AND RIGHT HAND SIDES SHOULD NOT EXCEED 1/2~.
Information only
> Steering and Suspension > Alignment > System Information > Technical Service Bulletins > Page 1138
Alignment: Specifications
Caster Angle
4WD
+1 to +3 deg
Except 4WD
+1 1/2 to +3 1/2 deg
Desired Caster
Camber Angle
2 deg 2 1/2 deg
Front +1/2 to +1 1/2 deg +1/2 to +1 1/2 deg
1 deg
Desired Camber Angle Front ---
Rear 1 deg
---
Toe
Rear
Front .08-.35 in
Rear ---
---
.08 to .35 in
---
> Steering and Suspension > Alignment > System Information > Service and Repair > Camber
Alignment: Service and RepairCamber
FRONT
WITH TWO WHEEL DRIVE
1. Using tool No. MB990805 to hold upper arm shaft to crossmember bolt in position, remove nut from engine compartment side and adjust the number of shims between upper arm shaft and crossmember.
2. The normal shim pack thickness is 0.16 inch. A change of 0.024 inch in thickness of the shim pack will provide a change of approximately 2/15 degree in camber adjustment.
WITH FOUR WHEEL DRIVE
Adjust number of shims between upper arm shaft and arm post of side frame. The normal shim package thickness is 0.12 inch. A change of 0.039 inchin thickness of shim pack will provide a change of approximately 13 minutes in camber adjustment. Camber adjusting shims are available inthicknesses of 0.039 and 0.079 inch.
REAR
Rear camber is pre-set during vehicle assembly and cannot be adjusted. If camber is not within specifications, check for worn or damaged suspensioncomponent, and damaged or deformed floor pan or body and repair as needed.
> Steering and Suspension > Alignment > System Information > Service and Repair > Camber > Page 1141
Alignment: Service and RepairCaster
Fig. 2 Caster adjustment. Ram Raider & 1984-86 Ram 50
Caster is adjusted by turning the upper control arm shaft as follows:1. Remove upper control arm.2. Rotate upper control arm shaft to alter caster setting. One half turn of the upper control arm shaft will cause the upper arm shaft to move approximately 0.049 inch forward or rearward, resulting in approximately 17 minute (17/60) change in caster setting.
3. Reinstall control arm and recheck caster.4. Repeat adjustment until caster is within specifications. Maximum variation between left and right sides should be less than 1/2.
> Steering and Suspension > Alignment > System Information > Service and Repair > Camber > Page 1142
Alignment: Service and RepairPreliminary Inspection
1. Road test vehicle noting any abnormal steering or handling characteristics.2. Ensure tires are the proper type, correctly inflated and that tires on each axle are the same size.3. Inspect ball joints, suspension arms, bushings and tie rods, and repair or replace any component that is damaged or excessively worn.4. Ensure wheel runout is not excessive, and that wheel bearings are properly adjusted.5. Jounce vehicle several times to settle suspension.6. Place vehicle on suitable alignment rack following manufacturer's instructions. On Ram 50 and Ram Raider models, remove hub cap and cotter pin
(2WD) or free wheeling hub (4WD), and attach alignment gauges to wheel hub.
7. Check and correct alignment angles in the following sequence: Rear toe and camber, caster, front camber and front toe.8. Correct any angle that is not within specifications. If no adjustment is possible, check for damaged or worn suspension components and/or damaged or distorted chassis and correct as needed.
> Steering and Suspension > Alignment > System Information > Service and Repair > Camber > Page 1143
Alignment: Service and RepairToe Adjustment
FRONT
On Colt models, remove outer bellows clip from tie rod before adjusting toe. After completing adjustment, reinstall clamp.The amount of toe-in of the left front wheel is reduced by turning the tie rod turnbuckle toward the front of the car and the amount of toe-in on theright front wheel is reduced by turning it toward the rear of the the car. After adjustment, the difference in length between the two tie rods should notexceed 0.2 inch (5 mm).
REAR
Rear toe is pre-set during vehicle assembly and cannot be adjusted. If toe is not within specifications, check for worn or damaged suspensioncomponents, and damaged or deformed floor pan or body and repair as needed.
> Steering and Suspension > Steering > Ball Stud <--> [Front Steering Knuckle] > Component Information > Service and Repair
Ball Stud: Service and Repair
Fig. 1 Front suspension exploded view
1. Raise and support front of vehicle, and place suitable jack under lower control arm to relieve spring tension from knuckle.2. Remove hub assembly as outlined, then remove brake rotor dust cover.3. Remove cotter pin and retaining nut, then disconnect tie rod from knuckle using suitable puller.4. Remove cotter pins and nuts, disconnect upper and lower ball joints, then remove knuckle.5. Reverse procedure to install.
> Steering and Suspension > Steering > Steering Column > Component Information > Diagrams
Fig. 9 Exploded view of steering column assembly. 1984-86 Ram 50
> Steering and Suspension > Steering > Steering Gear > Component Information > Service and Repair > Manual Steering Gear Service
Steering Gear: Service and RepairManual Steering Gear Service
Fig. 1 Disassembled view of manual steering gear, except rack & pinion
Disassembly
Prior to disassembly, note starting torque required to rotate mainshaft.
1. Place alignment marks on pitman arm and mainshaft, then remove nut and pull pitman arm from shaft, using tool No. C3894A.2. Remove breather plug and allow lubricant to drain from steering gear.3. Remove upper cover attaching bolts, then loosen adjuster bolt locknut and back off adjusting bolt 2 to 3 turns.4. Place mainshaft and cross shaft in the straight ahead position, then using a soft faced mallet tap on bottom of cross shaft and remove cross shaft and upper cover as an assembly. When removing components, use care not to damage cross shaft oil seal.
Do not 5. Position upper cover in a soft jawed vise, then remove adjusting bolt and separate upper cover from cross shaft. Retain spacer for reassembly.6. Remove end cover and mainshaft adjusting shims, then remove mainshaft and bearings. Retain mainshaft adjusting shims for assembly. disassemble mainshaft or ball nut assembly.
7. Remove cross shaft and mainshaft oil seals from steering gear housing.
Inspection
1. Check cross shaft and mainshaft bearings for wear and damage and replace as necessary. If cross shaft bearing is found to be worn or damaged, replace cross shaft, bearing and steering gear housing as an assembly.
> Steering and Suspension > Steering > Steering Gear > Component Information > Service and Repair > Manual Steering Gear Service > Page 1155
D50/Ram 50 L4-1997cc 2.0L SOHC (1984)
2. Check ball nut and mainshaft for smooth operation. If operation is not smooth or excessive freeplay is indicated, replace mainshaft and ball nut as an assembly.
3. Check to ensure that hole in breather plug is not clogged. A needle may be used to clear breather plug passage.
Assembly & Adjustment
1. Apply grease to mainshaft and cross shaft oil seal lips, then install seals on steering gear housing.2. Position steering gear housing in soft jawed vise, then position mainshaft into housing.3. Install gasket, mainshaft shims (same as removed) and end cover onto steering gear housing. Torque end cover attaching bolts to 11-14 ft. lbs.
Apply suitable sealer to end cover gasket and cover attaching bolts.
4. Using an inch pound torque wrench and tool No. CT1108, check mainshaft preload. Mainshaft preload should be 3-4.8 inch pounds. If preload is less than specified, remove adjusting shims to increase preload. If preload is more than specified, add shims to reduce preload. Adjusting shims areavailable in thickness from 0.002-0.020 inch.
5. Install adjusting bolt and spacer into groove on upper end of cross shaft. Use spacers to adjust axial play to 0-.002 inch. Spacers are available in thickness of 0.077-0.083 inch.
6. Carefully insert cross shaft into gear housing, meshing ball nut rack with cross shaft gear. Before installing, apply a small amount of gear oil to ball nut, cross shaft and cross shaft gear. Also apply a small amount of grease to cross shaft seal before installing cross shaft.
7. Apply suitable sealer to upper cover attaching bolts, except the breather plug, then install upper cover and torque attaching bolts to 11-14 ft. lbs.8. Align marks on Pitman arm and mainshaft, then install Pitman arm and tighten retaining nut.9. Measure steering gear backlash as follows: a. Insert a small amount of gear oil into steering gear through breather plug.b. Tighten adjusting bolt until it contacts gear teeth.c. Cycle Pitman arm left and right several times to mesh gear teeth.
Fig. 2 Steering gear backlash measurement. Manual steering gear, except rack & pinion
10. After completing assembly, measure mainshaft preload. Mainshaft preload should be 5.6-7.4 inch pounds. If not within specifications, check cross shaft, cross shaft bearing and end cover for proper installation. Also check adjusting bolt for improper adjustment.
11. Fill steering gear housing with 0.19 quarts of gear oil.
> Steering and Suspension > Steering > Steering Gear > Component Information > Service and Repair > Manual Steering Gear Service > Page 1156
Steering Gear: Service and RepairPower Steering Gear Service
Fig. 4 Power steering gear exploded view
Disassembly
1. Remove adjusting locknut, then side cover bolts and turn in adjusting bolt 2 or 3 turns.2. With gear in neutral (center) position, tap bottom of cross shaft with plastic hammer to remove shaft.3. Remove valve housing nut using tool No. MB990667 for large gear and No. MB990852 for small gear, then valve housing bolts. While holding rack piston to avoid rotation, remove valve housing and rack piston.
> Steering and Suspension > Steering > Steering Gear > Component Information > Service and Repair > Manual Steering Gear Service > Page 1157
D50/Ram 50 L4-1997cc 2.0L SOHC (1984)
Fig. 5 Measurement of rack piston backlash
4. Secure valve housing in vise with dial indicator as shown, then move rack and piston up and down to check backlash between groove of rack piston and the balls. Backlash should be 0.0039 inch for large gear and 0.080 inch for small gear maximum. Measure backlash with piston fullytightened and loosened 2 turns. If backlash exceeds limit, replace ball screw unit and rack piston as an assembly.
Do not lose any of the 26 balls.
5. Remove rack piston from valve housing by turning counterclockwise.
Fig. 6 Removal of top cover
6. Remove top cover of valve housing using tool No. MB990853 for small gear or special spanner wrench as shown.
Fig. 7 Components of rack piston
7. Remove circulator holder, circulator, seal ring and O-ring from rack piston.8. Remove thrust unit, thrust needle roller bearing, seal rings and O-rings from input worm unit.9. To disassemble subassembly components, proceed as follows:
Do not lose any needle bearing rollers. a. Turn in adjusting bolt at tip of cross shaft and remove side cover. b. Remove adjusting bolt and plate, O-ring and needle bearing from side cover. Do not remove O-ring and sealing at rear of needle bearing if no oil leaks from thread of adjusting bolt. Also, do not remove bleeder plug unless necessary.
c. Remove seal ring and O-ring from valve housing.d. Remove ball bearing and oil seal from top cover.e. Remove snap ring at bottom of gearbox, then back-up ring and oil seal. Pull out seal housing.f.
10. To assemble subassembly components, proceed as follows. Replace O-rings, seal rings and oil seals whenever disassembled.
a. Apply thin coat of multi-purpose grease to bearing surface of needle bearing and install rollers into side cover, then apply grease to bottom of side cover.
b. Insert adjusting bolt and plate into "T" slot on top of cross shaft, and adjust play to 0-.002 inch by selecting proper adjusting plate. When installing adjusting plate, place chamfered portion of plate to contact surface of cross shaft.
> Steering and Suspension > Steering > Steering Gear > Component Information > Service and Repair > Manual Steering Gear Service > Page 1158
D50/Ram 50 L4-1997cc 2.0L SOHC (1984)
c. Install O-ring into side cover.d. Align cross shaft with side cover and tighten with adjusting bolt, then tighten lock bolt temporarily.e. Apply thin coat of multipurpose grease to lip of oil seal and press into top cover, then press fit ball bearing.f.
Apply thin coat of ATF to O-ring and seal ring, then insert into seal housing. Install seal housing straight into gear box with O-ring sidepositioned near mainshaft.
g. Apply thin coat of multipurpose grease to lip of oil seal, then press into gear box using tool No. CT-1008. Install back-up ring and snap ring.
Assembly
Do not apply excessive force.
1. Apply thin coat of ATF to input worm unit O-rings and install O-rings and seal rings alternately onto worm unit. 2. Install thrust plate, thrust needle bearing and thrust plate to both ends of worm unit in that order, then apply thin coat of ATF to each.3. Install O-ring and seal ring into groove of valve housing and apply thin coat of ATF to each.
Fig. 8 Tightening of top cover
4. Install input worm unit into valve housing, then O-ring into top cover and top cover with bearing and oil seal onto valve housing. While turning worm unit, tighten by using spring scale and special spanner wrench as shown. Rotate worm unit to check for uniform movement.
5. Install valve housing nut and tighten temporarily using tool No. MB990667 for large gear and No. MB990852 for small gear. Do not allow top cover to rotate. The final tightening will occur during total starting torque measurement later in assembly procedure.
6. Measure starting torque by using tool No. CT-1108 and torque wrench while turning input worm unit, ensure preload is 3.5-6.9 in. lbs. If necessary, readjust by loosening valve housing nut as in steps 4-5.
7. Install O-ring and seal ring to rack piston and apply thin coat of ATF to each.8. Install rack piston into worm shaft until piston contacts worm shaft end, then insert 19 balls into groove through 2 openings on top of piston. Do not rotate worm unit and piston while inserting balls. Do not allow hole to offset or turn during insertion of balls so balls will not fall into wronggroove. After insertion of all balls, ensure balls reach approximately 0.080 inch for large gear, or 0.5 inch for small gear below end of piston.Excessive clearance is an indication that a ball has fallen into wrong groove. If so, remove rack piston and insert balls.
9. Insert 7 balls into rack piston circulator. Apply multipurpose grease to balls to prevent them from falling from circulator. Install circulator and holder into rack piston.
10. Secure gear box in vise, then install valve housing and rack piston assembly into gear box and torque bolts to 33-40 ft. lbs. After installation, rotate
Do not force rack piston into gearbox as seal ring may be damaged.
assembly to move rack piston to neutral (center) position.
11. Apply thin coat of ATF to teeth and shaft of rack piston and multipurpose grease to oil seal lip of gear box, then install cross shaft assembly into gearbox and torque side cover bolts to 33-40 ft. lbs.
Fig. 9 Measurement of total starting torque
12. Measure total starting torque of input worm shaft at neutral (center) position using tool No. CT-1108 and adjust to 3.6-7.1 in. lbs. for large gear or
4.3-7.8 in. lbs. for small gear by turning adjusting bolt. Torque valve housing nut to 130-166 ft. lbs. using tool No. MB990667 for large gear or
> Steering and Suspension > Steering > Steering Gear > Component Information > Service and Repair > Manual Steering Gear Service > Page 1159
D50/Ram 50 L4-1997cc 2.0L SOHC (1984)
No. MB990852 for small gear. Check input worm shaft for smooth rotation throughout its operation range.
Fig. 10 Installation position of Pitman arm
13. Align slit of cross shaft with marking of pitman arm and install pitman arm, then torque nut to 94-108 ft. lbs. Check clearance between center of gearbox bolt and pitman arm. Clearance should be 0.77 inch.
> Steering and Suspension > Steering > Steering Gear > Component Information > Service and Repair > Manual Steering Gear Service > Page 1160
Steering Gear: Service and RepairSteering Gear Replacement
Manual Steering Gear Replacement
1. Disconnect steering shaft from steering gear main shaft.2. Disconnect tie rod from relay rod and pitman arm from relay rod using tool No. C3894A.3. Remove air cleaner and disconnect pressure and return hose from steering gear. Remove under cover.4. Remove starter from transmission.5. Remove steering gear. Use tool No. CT1106 if pitman arm is removed.6. Reverse procedure to install. Torque pressure hose to 40-47 ft. lbs., return hose to 29-36 ft. lbs., tie rod socket and relay rod connection to 26-32 ft. lbs. and steering gear to 40-47 ft. lbs.
7. Remove the clamp bolt connecting the steering shaft with the steering gear housing mainshaft.8. Using Pitman and idler arm puller (C-3894), disconnect the pitman arm and the relay rod.9. Remove the steering gear assembly from the body frame.10. Using the pitman arm puller (Special Tool CT-1106), remove the pitman arm from the cross shaft.11. Reverse procedure to install.
Power Steering Gear Replacement
1. Disconnect steering shaft from steering gear main shaft.2. Disconnect tie rod from relay rod and pitman arm from relay rod using tool No. C3894A.3. Remove air cleaner and disconnect pressure and return hose from steering gear. Remove under cover.4. Remove starter from transmission.5. Remove steering gear. Use tool No. CT1106 if pitman arm is removed.6. Reverse procedure to install. Torque pressure hose to 40-47 ft. lbs., return hose to 29-36 ft. lbs., tie rod socket and relay rod connection to 26-32 ft. lbs. and steering gear to 40-47 ft. lbs.
7. Disconnect steering shaft from steering gear mainshaft.8. Remove retaining nuts, then disconnect tie rod from relay rod and pitman arm from relay rod using puller C-3894A.9. Disconnect pressure and return hoses from steering gear, then remove steering gear mounting bolts and steering gear. On Pickup models with automatic transmission, it may be necessary to disconnect throttle linkage and remove splash shield. On Pickup models with manual transmission,it may be necessary to remove starter motor to permit steering gear removal.
10. Reverse procedure to install.
> Steering and Suspension > Suspension > Ball Joint > Component Information > Service and Repair > Lower Ball Joint Replacement
Ball Joint: Service and RepairLower Ball Joint Replacement
UPPER BALL JOINT
Ram 50 4 X 2
1. Remove upper control arm.2. Remove snap ring and dust cover from ball joint, then using tools Nos. MB990799 and MB990800, press ball joint from arm.3. Using a torque wrench, check torque required to start upper ball joint in motion. The torque required should be 0.6-2.5 ft. lbs. Inspect ball joint cover for wear and damage.
4. If ball joint is to be reused, lubricate with grease.5. Align ball joint and control alignment marks, then press ball joint into control arm using tools Nos. MB990799 and MB990800. The initial
If standard pressure is not obtained when pressing in balljoint, replace ball joint and/or control arm as necessary. pressure to install the ball joint to a depth of 0.12-0.24 inch is 1550 lbs. or above.
6. Using snap ring pliers, position snap ring into groove on ball joint case.7. Install dust cover and ring into groove on ball joint.8. Install upper control arm as outlined.
Ram 4 X 4
The following procedures are given for control arms removed from vehicle.
1. Remove rebound stop. Remove ring, dust cover and snap ring from upper ball joint.2. Remove upper ball joint using tool Nos. MB990799 and MB990800.3. Reverse procedure to install. Align ball joint and control alignment marks and press ball into upper arm using tool Nos. MB990799 and
MB990800. Initial pressure to install ball joint to a depth of 0.12-0.24 inch is 1500 lbs. minimum. If minimum ball joint pressure is not obtainedwhen pressing in ball joint, replace ball joint or upper arm as necessary.
LOWER BALL JOINT
Ram 50 4 X 2
1. Remove lower control arm as outlined.2. Remove snap ring and dust cover from ball joint.3. Remove ball joint to lower control arm attaching bolts, then remove ball joint.4. Check ball joint for axial play. Ball joint axial play should not exceed 0.02 inch.5. Lubricate ball joint with grease, then install ball joint dust cover and snap ring.6. Position ball joint on lower control arm, then install attaching bolts and torque to 22-30 ft. lbs.7. Install lower control arm as outlined.
Ram 4 X 4
The following procedures are given for control arms removed from vehicle.
1. Remove four lower ball joint retaining nuts and remove lower ball joint.2. Reverse procedure to install. Torque lower ball joint to lower arm nuts to 40-54 ft. lbs.
> Steering and Suspension > Suspension > Ball Joint > Component Information > Service and Repair > Lower Ball Joint Replacement > Page 1166
Ball Joint: Service and RepairUpper Ball Joint Replacement
UPPER BALL JOINT
Ram 50 4 X 2
1. Remove upper control arm.2. Remove snap ring and dust cover from ball joint, then using tools Nos. MB990799 and MB990800, press ball joint from arm.3. Using a torque wrench, check torque required to start upper ball joint in motion. The torque required should be 0.6-2.5 ft. lbs. Inspect ball joint cover for wear and damage.
4. If ball joint is to be reused, lubricate with grease.5. Align ball joint and control alignment marks, then press ball joint into control arm using tools Nos. MB990799 and MB990800. The initial
If standard pressure is not obtained when pressing in balljoint, replace ball joint and/or control arm as necessary. pressure to install the ball joint to a depth of 0.12-0.24 inch is 1550 lbs. or above.
6. Using snap ring pliers, position snap ring into groove on ball joint case.7. Install dust cover and ring into groove on ball joint.8. Install upper control arm as outlined.
Ram 4 X 4
The following procedures are given for control arms removed from vehicle.
1. Remove rebound stop. Remove ring, dust cover and snap ring from upper ball joint.2. Remove upper ball joint using tool Nos. MB990799 and MB990800.3. Reverse procedure to install. Align ball joint and control alignment marks and press ball into upper arm using tool Nos. MB990799 and
MB990800. Initial pressure to install ball joint to a depth of 0.12-0.24 inch is 1500 lbs. minimum. If minimum ball joint pressure is not obtainedwhen pressing in ball joint, replace ball joint or upper arm as necessary.
LOWER BALL JOINT
Ram 50 4 X 2
1. Remove lower control arm as outlined.2. Remove snap ring and dust cover from ball joint.3. Remove ball joint to lower control arm attaching bolts, then remove ball joint.4. Check ball joint for axial play. Ball joint axial play should not exceed 0.02 inch.5. Lubricate ball joint with grease, then install ball joint dust cover and snap ring.6. Position ball joint on lower control arm, then install attaching bolts and torque to 22-30 ft. lbs.7. Install lower control arm as outlined.
Ram 4 X 4
The following procedures are given for control arms removed from vehicle.
1. Remove four lower ball joint retaining nuts and remove lower ball joint.2. Reverse procedure to install. Torque lower ball joint to lower arm nuts to 40-54 ft. lbs.
> Steering and Suspension > Suspension > Control Arm > Component Information > Service and Repair
Control Arm: Service and Repair
Fig. 1 Front suspension exploded view
> Steering and Suspension > Suspension > Control Arm > Component Information > Service and Repair > Page 1170
D50/Ram 50 L4-1997cc 2.0L SOHC (1984)
Fig. 4 Front suspension. Ram 50 4 X 2
1. Remove front wheel, brake caliper assembly and front hub assembly.2. Remove dust covers from anchor arm assemblies.3. Place alignment mark on torsion bar with mark on anchor arm B.4. Remove anchor arm assembly, then remove torsion bar from anchor arm assembly B.5. Remove stabilizer bar from lower arm, then remove shock absorber.6. Remove cotter pins and nuts from upper and lower ball joint studs at tie rod end.7. Disconnect tie rod from knuckle using tool C3894-A.8. Separate upper ball joint from knuckle using tool No. MB990635.
> Steering and Suspension > Suspension > Control Arm > Component Information > Service and Repair > Page 1171
D50/Ram 50 L4-1997cc 2.0L SOHC (1984)
9. Separate upper ball joint from knuckle using tool No. C3894-A.
10. Remove bolts connecting upper arm shaft to arm post of side frame, then remove upper arm assembly.11. Remove two bolts attaching lower arm then remove lower arm.12. Reverse procedure to install, noting the following: a. Refer to torque specifications.b. Torque shock absorber lower mounting bolts to 6 to 8 ft. lbs. On 1984 models, tighten shock absorber upper mounting nut until protrusion of stud above bottom of nut is 0.8 inch. On 1985-88 models, tighten shock absorber upper mounting nut until protrusion of stud above top of nutis 0.5 inch for 1985 models or 0.27-0.31 inch for 1986 Ram 50 and 1987-88 Ram Raider. On 1987-88 Ram 50, tighten nut to end of threads.On all models, install jam nut and torque to 9-13 ft. lbs.
Fig. 2 Torsion bar anchor bolt installation. Ram 50 4 X 4, Ram Raider similar c. Refer to image and check dimension A when torsion bar and anchor arm are assembled. Standard value is 5.6-5.8 inch for left side and
5.4-5.6 inch for right side on Ram 50, or 5.32-5.64 inches for left side and 4.9-5.2 inches for right side on Ram Raider.
Fig. 3 Torsion bar anchor bolt specifications. Ram Raider d. Torque anchor bolt until protrusion is to specification shown for Ram 50 or for Ram Raider.e. On 1984 models, tighten stabilizer bar to lower arm nut until protrusion of stud above bottom of nut is 0.63-0.71 inch. On 1985-88 models, tighten stabilizer bar to lower arm nut until protrusion of stud above top of nut is 0.24-0.31 inch.
Fig. 4 Dimension between bump stop and bump stop bracket
> Steering and Suspension > Suspension > Control Arm > Component Information > Service and Repair > Page 1172
D50/Ram 50 L4-1997cc 2.0L SOHC (1984)
f.
With installation procedure complete and vehicle lowered to ground, torque lower arm to bracket of side frame to 102-115 ft. lbs. Measuredistance A. Measured distance should be 2.8 inch. If measurement is out of specification, turn adjusting nut of torsion bar anchor bolt untilmeasurement comes into specification.
> Steering and Suspension > Suspension > Cross-Member > Component Information > Service and Repair
Cross-Member: Service and Repair
Fig. 5 Location front suspension crossmember bolts
1. Install suitable jack under differential carrier.2. Remove front suspension crossmember from differential carrier assembly and from support bracket of side frame.3. Reverse procedure to install. Torque front suspension crossmember to support bracket of side frame bolt to 73-86 ft. lbs. Torque front suspension crossmember to bracket bolt to 22-30 ft. lbs.
> Steering and Suspension > Suspension > Ball Stud <--> [Front Steering Knuckle] > Component Information > Service and Repair
Ball Stud: Service and Repair
Fig. 1 Front suspension exploded view
1. Raise and support front of vehicle, and place suitable jack under lower control arm to relieve spring tension from knuckle.2. Remove hub assembly as outlined, then remove brake rotor dust cover.3. Remove cotter pin and retaining nut, then disconnect tie rod from knuckle using suitable puller.4. Remove cotter pins and nuts, disconnect upper and lower ball joints, then remove knuckle.5. Reverse procedure to install.
> Steering and Suspension > Suspension > Stabilizer Bar, Sway Control > Component Information > Service and Repair > Front
Stabilizer Bar: Service and RepairFront
Fig. 8 Positioning strut bar bushing retaining nuts (Typical)
RAM 50 4 X 2
1. Raise and support front of vehicle, then remove wheel and tire assembly.2. Disconnect stabilizer bar and strut bar from lower control arm.3. Remove strut bar bracket to body attaching bolts, then remove stabilizer bar and strut bar from strut bar bracket. When removing strut bar bushings note position and direction of bushings and washers for reassembly.
4. Reverse procedure to install, noting the following: a. When assembling strut bar to bracket and set clearance between end of strut bar and retaining nut. Clearance should be 3.8 inches for 1984
Ram 50 4 X 2 or 2.9 inches for 1985-88 Ram 50 4 X 2.
b. After installing strut bar bushings, temporarily tighten outer retaining nut, as nut will be tightened to specified torque after vehicle has been lowered.
c. When connecting stabilizer bar to lower control arm, set clearance between end of bolt and retaining nut to 0.87-0.94 inch for Ram 50 4 X 2.d. Tighten components to the following torque: Stabilizer bar bracket bolts, 6-8 ft. lbs. Stabilizer bar to lower control arm: Ram 50 4 X 2, 18-25 ft. lbs. Strut bar to bracket nuts, 54-61 ft. lbs. Strut bar to lower control arm: Ram 50 4 X 2, 51-61 ft. lbs. Strut bar bracket to frame, 25-33 ft.lbs.
> Steering and Suspension > Suspension > Stabilizer Bar, Sway Control > Component Information > Service and Repair > Front > Page 1183
Stabilizer Bar: Service and RepairRear
1. Remove stabilizer bar from stabilizer link assembly and lower arm.2. Reverse procedure to install, noting the following: a. On 1984 models tighten stabilizer link to No. 1 crossmember until protrusion of stud above bottom of nut is 0.63-0.71 inch. b. On 1984 models, tighten stabilizer bar to lower arm nut until protrusion of stud above bottom of nut is 0.63-0.71 inch.
> Steering and Suspension > Suspension > Suspension Spring ( Coil / Leaf ) > Component Information > Service and Repair > Front Coil Spring Replace
Suspension Spring ( Coil / Leaf ): Service and RepairFront Coil Spring Replace
Fig. 7 Separating upper & lower ball joints from steering knuckle. Ram 50 4 X 2
RAM 50 4 X 2
1. Remove wheel and tire assembly, then remove caliper and rotor.2. Loosen nut at end of strut bar, then disconnect strut bar and stabilizer bar from lower control arm.3. Remove shock absorber, then install suitable spring compressor and compress coil spring.4. Remove cotter pin and nut from lower control arm, then using tool No. C-3564A, separate lower ball joint from steering knuckle.5. Carefully loosen spring compressor and remove coil spring.6. Reverse procedure to install. Torque lower ball joint nut to 87-130 ft. lbs., then install cotter pin. Torque brake strut bar nut to 54-61 ft. lbs. and strut bar to lower control arm attaching bolts to 51-61 ft. lbs. Torque stabilizer bar bolts to 18-5 ft. lbs.
> Steering and Suspension > Suspension > Suspension Spring ( Coil / Leaf ) > Component Information > Service and Repair > Front Coil Spring Replace > Page 1188
Suspension Spring ( Coil / Leaf ): Service and RepairLeaf Spring Replacement
Fig. 10 Leaf spring rear suspension. Ram 50 & Ram Raider
1. Raise rear of vehicle and position jackstands under frame side rails, then remove wheel and tire assembly. Lower jack and allow vehicle to rest on jackstands.
2. Disconnect parking brake cable bracket from leaf spring.3. Disconnect shock absorber from upper and lower mounting.4. Loosen U-bolt nuts, then raise rear axle housing until axle clears U-bolt seat, and remove U-bolt seat.5. Remove spring pin from spring front mounting and shackle pin from spring rear mounting, then remove leaf spring assembly.
> Steering and Suspension > Suspension > Suspension Strut / Shock Absorber > Component Information > Service and Repair > Front
Suspension Strut / Shock Absorber: Service and RepairFront
RAM 50 4 X 2
Disconnect shock absorber at upper and lower mountings, then remove shock absorber from vehicle. When installing, torque shock absorber upperattaching bolts to 9-13 ft. lbs. and lower attaching bolts to 6-9 ft. lbs.
RAM 50 4 X 4
1. Detach shock absorber from upper and lower mounting, then remove shock absorber.2. Reverse procedure to install. Torque shock absorber lower mounting bolts to 6 to 8 ft. lbs. On 1984 models, tighten shock absorber upper mounting nut until protrusion of stud above bottom of nut is 0.8 inch. On 1985-88 models, tighten shock absorber upper mounting nut untilprotrusion of stud above top of nut is 0.5 inch for 1985 models or 0.27-0.31 inch for 1986 Ram 50 4 X 4 and 1987-88 Ram Raider. On 1987-88Ram 50 4 X 4, tighten nut to end of threads. On all models, install jam nut and torque to 9-13 ft. lbs.
> Steering and Suspension > Suspension > Suspension Strut / Shock Absorber > Component Information > Service and Repair > Front > Page 1193
Suspension Strut / Shock Absorber: Service and RepairRear
Fig. 10 Leaf spring rear suspension. Ram 50 & Ram Raider
1. Raise rear of vehicle and position jackstands under frame side sills.2. Remove wheel and tire assembly, then disconnect shock absorber at upper and lower mounting and remove from vehicle.3. Reverse procedure to install. Torque upper and lower mounting nuts to 13-18 ft. lbs.
> Steering and Suspension > Suspension > Wheel Bearing > Component Information > Adjustments
Wheel Bearing: Adjustments
Install hub bearings on spindle, then install hub nut and torque to 22 ft. lbs. to seat bearings. Loosen hub nut, then torque nut to 6 ft. lbs. Install nutretainer cap and cotter pin. If cotter pin holes are not aligned, loosen nut to align holes. The nut may be loosened to a maximum of 30 to align cotterpin holes. Check to ensure hub assembly rotates freely without play.
> Steering and Suspension > Suspension > Wheel Bearing > Component Information > Service and Repair > Removal
Wheel Bearing: Service and RepairRemoval
Fig. 8 Hub & wheel bearing assembly exploded view. Shown w/manual locking hub
Fig. 9 Automatic (free wheeling) locking hub
> Steering and Suspension > Suspension > Wheel Bearing > Component Information > Service and Repair > Removal > Page 1199
D50/Ram 50 L4-1997cc 2.0L SOHC (1984)
1. Remove wheel and tire assembly, then remove brake caliper assembly leaving brake hose connected. Suspend caliper assembly from frame using a wire hook to prevent damage to brake hose.
2. Place hub in free position, then remove free wheeling hub cover. On models with automatic locking hubs, ensure hub is in "free wheeling" position by placing transfer case lever in 2H position and moving in reverse 4-7 feet. If cover cannot be removed by hand, loosen cover with suitable strapwrench, taking care not to damage cover.
3. Remove snap ring securing drive axle, then the adjusting shims.4. Remove free wheeling hub assembly from front hub, using tool MD998360 or equivalent to remove bolts securing automatic locking hub.
Fig. 10 Spindle nut removal & installation
5. Remove lock washer, then remove hub locknut using tool No. MB990954.6. Pull front hub with brake disc from knuckle, using care not to drop outer wheel bearing inner race.7. Remove grease from inside front hub, then using a suitable drift, drive bearing races from hub.8. Place alignment marks on brake disc and hub, then separate hub and disc as necessary.
> Steering and Suspension > Suspension > Wheel Bearing > Component Information > Service and Repair > Removal > Page 1200
Wheel Bearing: Service and RepairInspection
HUB, SPINDLE & BEARINGS
1. Clean components with suitable solvent and blow dry with compressed air.
Fig. 11 Checking spindle for wear
2. Inspect spindle for wear and damage and measure spindle bearing seating area diameter. Diameter should be 1.7805 to 1.7812 inch.3. Inspect bearings for damage excessive wear, overheating and scoring, and replace as needed.4. Check fit of bearing outer races in hub. If races are loose, hub should be replaced.
MANUAL LOCKING HUB
Fig. 8 Hub & wheel bearing assembly exploded view. Shown w/manual locking hub
1. Inspect hub ring, inner hub and hub body, and the clutch. If components are damaged or worn, assembly should be replaced.2. Inspect tension spring and compression spring, and replace if collapsed or deteriorated.3. Check operation of control handle and replace as needed.
> Steering and Suspension > Suspension > Wheel Bearing > Component Information > Service and Repair > Removal > Page 1201
D50/Ram 50 L4-1997cc 2.0L SOHC (1984)
Fig. 9 Automatic (free wheeling) locking hub
AUTOMATIC LOCKING HUB
DISASSEMBLY
1. Press in on brake B, then remove housing C-ring.2. Remove brake B, brake B and brake spring from housing, then remove housing snap ring.3. Mount assembly in press, lightly compress drive gear, then remove retainer B C-ring, noting the following: a. Place protective cloth under cover mating surface.b. Because return spring is approximately 1.57 inches long, ensure press stroke is more than 1.57 inches.c. Do not apply more than 441 lbs. pressure to drive gear.d. After removing C-ring, slowly reduce press force until return spring relaxes completely.
4. Remove retainer B, return spring, slide gear assembly and drive gear assembly from housing.5. Remove and discard drive gear snap ring.6. Press in on slide gear cam and remove slide gear C-ring.
INSPECTION
1. Check slide and drive gear splines for damage.2. Check cam portion of retainer A for wear or damage.3. Check cam for wear and damage.4. Check slide gear and housing tooth surfaces for wear and damage.5. Check retainer B and housing contact surfaces for wear and damage.6. Check brake wear as follows:
Fig. 12 Measuring brake assembly. Automatic locking hub a. Assemble brake A and brake B, then measure thickness of assembly at two lugs on brake A.b. Standard thickness is 0.413 inch and minimum thickness is 0.378 inch.
> Steering and Suspension > Suspension > Wheel Bearing > Component Information > Service and Repair > Removal > Page 1202
D50/Ram 50 L4-1997cc 2.0L SOHC (1984)
7. Inspect return and shift springs as follows:
Fig. 13 Measuring spring free length. Automatic locking hub a. Measure free length of spring as shown.b. Minimum return spring free length is 1.38 inches.c. Minimum shift spring free length is 1.18 inches.
8. Replace any components that are damaged, excessively worn, or that are not within specifications.
ASSEMBLY
Apply Mopar grease 2525035 or equivalent to mounting surfaces of all components and reverse disassembly procedure, noting the following:1. Pack grooves of retainer B with specified grease.2. Install return spring with smaller diameter coil toward cam.3. Pack grooves of brake B with specified grease.
> Steering and Suspension > Suspension > Wheel Bearing > Component Information > Service and Repair > Removal > Page 1203
Wheel Bearing: Service and RepairInstallation
1. Drive outer races into front hub using a suitable drift, then evenly coat inner wall of front hub with grease.2. Pack inner and outer bearings with suitable grease. Apply grease to oil seal lip.3. Position inner bearing and oil seal on hub, then install oil seal using tool No. MB990985.
Fig. 8 Hub & wheel bearing assembly exploded view. Shown w/manual locking hub
Fig. 14 Checking front hub rotating torque
4. If removed, install brake disc on front hub, tightening attaching bolts alternately and evenly to 36-44 ft. lbs. After assembling, check brake disc runout. Brake disc runout should not exceed 0.006 inch.
5. Carefully install front hub on steering knuckle spindle.6. Install outer bearing on spindle, then install spindle nut.7. Adjust wheel bearings as follows: a. Torque bearing locknut to 94-145 ft. lbs. while rotating hub to seat bearings.b. Loosen spindle nut and retighten to 18 ft. lbs., then back off 30.c. Install lock washer. If hole in lock washer is not aligned with hole in spindle nut, the nut may be loosened up to an additional 20 to obtain
> Steering and Suspension > Suspension > Wheel Bearing > Component Information > Service and Repair > Removal > Page 1204
D50/Ram 50 L4-1997cc 2.0L SOHC (1984)
proper alignment.
d. Using a suitable spring scale or torque wrench, measure force required to rotate front hub.e. The force required to rotate the front hub assembly should be 1.1-4.0 lbs. (spring scale) or 3-11 inch lbs. (torque wrench), and endplay should be less than 0.002 inch. If rotating force is not within specifications, repeat adjustment.
f. When adjustment is correct, secure washer with retaining screws.
8. On models with automatic locking hubs, measure brake contact surface depth as follows:
Fig. 15 Measuring brake contact surface depth. Automatic locking hub a. Measure dimension A, in two places using suitable depth gauge.b. Average of two readings should be 0.46-0.48 inch. If depth is greater than specified, install suitable shims. If depth is less than specified, recheck hub and bearing installation.
9. Apply grease to inner surface of free wheeling hub body assembly.
10. Apply semi-dry sealant to front hub surface to which the free wheeling hub body assembly is attached.11. Align tab on free wheel hub with groove on spindle, install free wheeling hub body assembly on front hub, then torque attaching bolts to 37-43 ft.
lbs.
12. Reverse remaining procedure to complete installation.
> Steering and Suspension > Suspension > Wheel Hub > Axle Nut > Component Information > Technical Service Bulletins > Rear Axle Shaft - Retaining Nut Lock Washers
Axle Nut: Technical Service BulletinsRear Axle Shaft - Retaining Nut Lock Washers
Models
1979-89 PB/B4 And SJ/B6 Vehicles
Subject
Lock Washer For Rear Axle Shaft Retaining Nut
Index
REAR AXLE
Date
April 17, 1989
No.
03-01-89
(CO0-02-9)
AXLE SHAFT RETAINING NUT LOCK WASHER
BODY CODE LEGEND
PB/B4 - RAM 50 PICKUP SJ/B6 - RAM RAIDER
AXLE SHAFT RETAINING NUT LOCK WASHER
When axle service requires removal of the axle shaft retaining nut and lock washer (Figure 1), the lock washer must not be reused. The lock washer, P/NMB092433, must be replaced when reassembling the axle.
> Steering and Suspension > Suspension > Wheel Hub (Locking) > Component Information > Technical Service Bulletins > Automatic Locking Hubs - Racheting Noise
Wheel Hub (Locking): Technical Service BulletinsAutomatic Locking Hubs - Racheting Noise
Models
1984-1985 Dodge Power Ram 50 Pick-Up
Subject
Racheting Noise in Automatic Locking Hubs
Index
FRONT AXLE
Date
November 19, 1984
No.
02-10-84 P-5120-CSYMPTOM/CONDITION
Racheting noise in automatic locking hubs during low temperature operation or after shifting from "4H" to "2H".
DIAGNOSIS/CORRECTION
Use the attached chart to determine the corrective action necessary.
POLICY: Information Only
SYMPTOM RESOLUTION
Noise is generated after start-up with shift lever in "2H" position under low temperature.
free-wheeling hub.
Noise is generated after shift lever is changed from "4H"
(lock) "2H" (free) position.
Drive the vehicle with the lever in "4H" position for a while to warm up oil in transfer case and then drive with the lever in "2H" position.
When shifting "4H" (lock) to
"2H" (free) position, first stop vehicle, change shift lever from "4H" to "2H" position, and then slowly drive vehicle straight backward for 10 to 20 feet.
CAUSE
Under low temperature, oil in transfer case gets stiff and it accordingly rotates front drive shaft which causes racheting effect* of automatic
If shifting is done while vehi- cle is turning, only one side of free-wheeling hub will be freed resulting in the racheting effect.*
*Racheting effect is caused when slide gear and housing gear are not engaged and there is difference of revolution speed between those two gears. Noiseis caused by this revolutional difference.
The racheting of the hubs is not detrimental to the components or operation of the vehicle. The 1985 owners manual will advise the customer of thecondition.
> Steering and Suspension > Wheels and Tires > Wheel Bearing > Component Information > Adjustments
Wheel Bearing: Adjustments
Install hub bearings on spindle, then install hub nut and torque to 22 ft. lbs. to seat bearings. Loosen hub nut, then torque nut to 6 ft. lbs. Install nutretainer cap and cotter pin. If cotter pin holes are not aligned, loosen nut to align holes. The nut may be loosened to a maximum of 30 to align cotterpin holes. Check to ensure hub assembly rotates freely without play.
> Steering and Suspension > Wheels and Tires > Wheel Bearing > Component Information > Service and Repair > Removal
Wheel Bearing: Service and RepairRemoval
Fig. 8 Hub & wheel bearing assembly exploded view. Shown w/manual locking hub
Fig. 9 Automatic (free wheeling) locking hub
> Steering and Suspension > Wheels and Tires > Wheel Bearing > Component Information > Service and Repair > Removal > Page 1220
D50/Ram 50 L4-1997cc 2.0L SOHC (1984)
1. Remove wheel and tire assembly, then remove brake caliper assembly leaving brake hose connected. Suspend caliper assembly from frame using a wire hook to prevent damage to brake hose.
2. Place hub in free position, then remove free wheeling hub cover. On models with automatic locking hubs, ensure hub is in "free wheeling" position by placing transfer case lever in 2H position and moving in reverse 4-7 feet. If cover cannot be removed by hand, loosen cover with suitable strapwrench, taking care not to damage cover.
3. Remove snap ring securing drive axle, then the adjusting shims.4. Remove free wheeling hub assembly from front hub, using tool MD998360 or equivalent to remove bolts securing automatic locking hub.
Fig. 10 Spindle nut removal & installation
5. Remove lock washer, then remove hub locknut using tool No. MB990954.6. Pull front hub with brake disc from knuckle, using care not to drop outer wheel bearing inner race.7. Remove grease from inside front hub, then using a suitable drift, drive bearing races from hub.8. Place alignment marks on brake disc and hub, then separate hub and disc as necessary.
> Steering and Suspension > Wheels and Tires > Wheel Bearing > Component Information > Service and Repair > Removal > Page 1221
Wheel Bearing: Service and RepairInspection
HUB, SPINDLE & BEARINGS
1. Clean components with suitable solvent and blow dry with compressed air.
Fig. 11 Checking spindle for wear
2. Inspect spindle for wear and damage and measure spindle bearing seating area diameter. Diameter should be 1.7805 to 1.7812 inch.3. Inspect bearings for damage excessive wear, overheating and scoring, and replace as needed.4. Check fit of bearing outer races in hub. If races are loose, hub should be replaced.
MANUAL LOCKING HUB
Fig. 8 Hub & wheel bearing assembly exploded view. Shown w/manual locking hub
1. Inspect hub ring, inner hub and hub body, and the clutch. If components are damaged or worn, assembly should be replaced.2. Inspect tension spring and compression spring, and replace if collapsed or deteriorated.3. Check operation of control handle and replace as needed.
> Steering and Suspension > Wheels and Tires > Wheel Bearing > Component Information > Service and Repair > Removal > Page 1222
D50/Ram 50 L4-1997cc 2.0L SOHC (1984)
Fig. 9 Automatic (free wheeling) locking hub
AUTOMATIC LOCKING HUB
DISASSEMBLY
1. Press in on brake B, then remove housing C-ring.2. Remove brake B, brake B and brake spring from housing, then remove housing snap ring.3. Mount assembly in press, lightly compress drive gear, then remove retainer B C-ring, noting the following: a. Place protective cloth under cover mating surface.b. Because return spring is approximately 1.57 inches long, ensure press stroke is more than 1.57 inches.c. Do not apply more than 441 lbs. pressure to drive gear.d. After removing C-ring, slowly reduce press force until return spring relaxes completely.
4. Remove retainer B, return spring, slide gear assembly and drive gear assembly from housing.5. Remove and discard drive gear snap ring.6. Press in on slide gear cam and remove slide gear C-ring.
INSPECTION
1. Check slide and drive gear splines for damage.2. Check cam portion of retainer A for wear or damage.3. Check cam for wear and damage.4. Check slide gear and housing tooth surfaces for wear and damage.5. Check retainer B and housing contact surfaces for wear and damage.6. Check brake wear as follows:
Fig. 12 Measuring brake assembly. Automatic locking hub a. Assemble brake A and brake B, then measure thickness of assembly at two lugs on brake A.b. Standard thickness is 0.413 inch and minimum thickness is 0.378 inch.
> Steering and Suspension > Wheels and Tires > Wheel Bearing > Component Information > Service and Repair > Removal > Page 1223
D50/Ram 50 L4-1997cc 2.0L SOHC (1984)
7. Inspect return and shift springs as follows:
Fig. 13 Measuring spring free length. Automatic locking hub a. Measure free length of spring as shown.b. Minimum return spring free length is 1.38 inches.c. Minimum shift spring free length is 1.18 inches.
8. Replace any components that are damaged, excessively worn, or that are not within specifications.
ASSEMBLY
Apply Mopar grease 2525035 or equivalent to mounting surfaces of all components and reverse disassembly procedure, noting the following:1. Pack grooves of retainer B with specified grease.2. Install return spring with smaller diameter coil toward cam.3. Pack grooves of brake B with specified grease.
> Steering and Suspension > Wheels and Tires > Wheel Bearing > Component Information > Service and Repair > Removal > Page 1224
Wheel Bearing: Service and RepairInstallation
1. Drive outer races into front hub using a suitable drift, then evenly coat inner wall of front hub with grease.2. Pack inner and outer bearings with suitable grease. Apply grease to oil seal lip.3. Position inner bearing and oil seal on hub, then install oil seal using tool No. MB990985.
Fig. 8 Hub & wheel bearing assembly exploded view. Shown w/manual locking hub
Fig. 14 Checking front hub rotating torque
4. If removed, install brake disc on front hub, tightening attaching bolts alternately and evenly to 36-44 ft. lbs. After assembling, check brake disc runout. Brake disc runout should not exceed 0.006 inch.
5. Carefully install front hub on steering knuckle spindle.6. Install outer bearing on spindle, then install spindle nut.7. Adjust wheel bearings as follows: a. Torque bearing locknut to 94-145 ft. lbs. while rotating hub to seat bearings.b. Loosen spindle nut and retighten to 18 ft. lbs., then back off 30.c. Install lock washer. If hole in lock washer is not aligned with hole in spindle nut, the nut may be loosened up to an additional 20 to obtain
> Steering and Suspension > Wheels and Tires > Wheel Bearing > Component Information > Service and Repair > Removal > Page 1225
D50/Ram 50 L4-1997cc 2.0L SOHC (1984)
proper alignment.
d. Using a suitable spring scale or torque wrench, measure force required to rotate front hub.e. The force required to rotate the front hub assembly should be 1.1-4.0 lbs. (spring scale) or 3-11 inch lbs. (torque wrench), and endplay should be less than 0.002 inch. If rotating force is not within specifications, repeat adjustment.
f. When adjustment is correct, secure washer with retaining screws.
8. On models with automatic locking hubs, measure brake contact surface depth as follows:
Fig. 15 Measuring brake contact surface depth. Automatic locking hub a. Measure dimension A, in two places using suitable depth gauge.b. Average of two readings should be 0.46-0.48 inch. If depth is greater than specified, install suitable shims. If depth is less than specified, recheck hub and bearing installation.
9. Apply grease to inner surface of free wheeling hub body assembly.
10. Apply semi-dry sealant to front hub surface to which the free wheeling hub body assembly is attached.11. Align tab on free wheel hub with groove on spindle, install free wheeling hub body assembly on front hub, then torque attaching bolts to 37-43 ft.
lbs.
12. Reverse remaining procedure to complete installation.
> Steering and Suspension > Wheels and Tires > Wheel Hub > Axle Nut > Component Information > Technical Service Bulletins > Rear Axle Shaft - Retaining Nut Lock Washers
Axle Nut: Technical Service BulletinsRear Axle Shaft - Retaining Nut Lock Washers
Models
1979-89 PB/B4 And SJ/B6 Vehicles
Subject
Lock Washer For Rear Axle Shaft Retaining Nut
Index
REAR AXLE
Date
April 17, 1989
No.
03-01-89
(CO0-02-9)
AXLE SHAFT RETAINING NUT LOCK WASHER
BODY CODE LEGEND
PB/B4 - RAM 50 PICKUP SJ/B6 - RAM RAIDER
AXLE SHAFT RETAINING NUT LOCK WASHER
When axle service requires removal of the axle shaft retaining nut and lock washer (Figure 1), the lock washer must not be reused. The lock washer, P/NMB092433, must be replaced when reassembling the axle.
> Steering and Suspension > Wheels and Tires > Wheel Hub (Locking) > Component Information > Technical Service Bulletins > Automatic Locking Hubs - Racheting Noise
Wheel Hub (Locking): Technical Service BulletinsAutomatic Locking Hubs - Racheting Noise
Models
1984-1985 Dodge Power Ram 50 Pick-Up
Subject
Racheting Noise in Automatic Locking Hubs
Index
FRONT AXLE
Date
November 19, 1984
No.
02-10-84 P-5120-CSYMPTOM/CONDITION
Racheting noise in automatic locking hubs during low temperature operation or after shifting from "4H" to "2H".
DIAGNOSIS/CORRECTION
Use the attached chart to determine the corrective action necessary.
POLICY: Information Only
SYMPTOM RESOLUTION
Noise is generated after start-up with shift lever in "2H" position under low temperature.
free-wheeling hub.
Noise is generated after shift lever is changed from "4H"
(lock) "2H" (free) position.
Drive the vehicle with the lever in "4H" position for a while to warm up oil in transfer case and then drive with the lever in "2H" position.
When shifting "4H" (lock) to
"2H" (free) position, first stop vehicle, change shift lever from "4H" to "2H" position, and then slowly drive vehicle straight backward for 10 to 20 feet.
CAUSE
Under low temperature, oil in transfer case gets stiff and it accordingly rotates front drive shaft which causes racheting effect* of automatic
If shifting is done while vehi- cle is turning, only one side of free-wheeling hub will be freed resulting in the racheting effect.*
*Racheting effect is caused when slide gear and housing gear are not engaged and there is difference of revolution speed between those two gears. Noiseis caused by this revolutional difference.
The racheting of the hubs is not detrimental to the components or operation of the vehicle. The 1985 owners manual will advise the customer of thecondition.
> Heating and Air Conditioning > Blower Motor > Component Information > Service and Repair
Blower Motor: Service and Repair
Fig. 23 Heater core & blower motor. 1984-86 Ram 50
1. Disconnect battery ground cable.2. Remove instrument cluster outlined.3. Disconnect cable between blower motor and heater unit at connector.4. Working through instrument cluster panel mounting area, remove blower motor attaching bolts.5. Remove blower motor.6. Reverse procedure to install.
> Heating and Air Conditioning > Heater Core > Component Information > Service and Repair
Heater Core: Service and Repair
Fig. 23 Heater core & blower motor. 1984-86 Ram 50
1. Disconnect battery ground cable, then place temperature control lever in Off position and drain cooling system.2. Remove parcel tray, center ventilation duct and grille and defroster duct.3. Disconnect heater hoses from heater core. Plug heater core fittings to prevent coolant spillage.4. Disconnect wire connector from blower motor.5. Remove bolts and nuts attaching heater assembly to dash panel, then the heater assembly.6. Remove heater core from heater assembly.7. Reverse procedure to install.
> Heating and Air Conditioning > Refrigerant > Component Information > Specifications > Capacity Specifications
Refrigerant: Capacity Specifications
A/C Refrigerant Specifications
Capacity .................................................................................................................................................................................................... 34 oz (2.13 lbs)
> Heating and Air Conditioning > Refrigerant > Component Information > Specifications > Capacity Specifications > Page 1246
Refrigerant: Fluid Type Specifications
Fluid Type specifications
Type ................................................................................................................................................................................................. Refrigerant 12 (R-12)
> Restraint Systems > Seat Belt Systems > Seat Belt Extension > Component Information > Technical Service Bulletins > Seat Belt Extender - Types/Identification
Seat Belt Extension: Technical Service BulletinsSeat Belt Extender - Types/Identification
Models
1983-1987 MMC Manufactured Vehicles (Imported For Chrysler) Except Sapporo/Challenger Models
Subject
Seat Belt Extender
Index
BODY
Date
September 15, 1986
No.
23-08-86
P-3235The front seat belt extender is intended for use only when the current seat belt is not long enough to fit around an occupant. It must be removed andstored when not required by that occupant.
Incorrect use of the seat belt extender, or any other extender which is not specified, may result in serious injury.
Four types of extenders have been released to be used in the combinations shown in the chart on page 2.
FIGURE 1
Install the seat belt extenders as shown in Figure 1.PARTS REQUIRED
Part No.
Type
Seat Belt Extender
Seat Belt Extender
*See chart on page 2
MB544778
MB544779
POLICY:
Model Year
Vehicle Model
Conquest
Information only
1983 1984
Type A
C*
D*
1985
Type A
1986
Type B
1987
(Not provided
> Restraint Systems > Seat Belt Systems > Seat Belt Extension > Component Information > Technical Service Bulletins > Seat Belt Extender - Types/Identification > Page
1253
D50/Ram 50 L4-1997cc 2.0L SOHC (1984)
Colt
Raider
Ram 50, Power Ram 50
Colt Vista
Type A
Type A
Type A Type A Type B
Type A
Type D
Type A
Type D
Type B
Type C due to adoption of automatic seat belt)
Type B
Type B
Type B
Type C
> Restraint Systems > Seat Belt Systems > Seat Belt Reminder Buzzer > Component Information > Technical Service Bulletins > Customer Interest for Seat Belt Reminder Buzzer: > 082684 > Nov > 84 > Radio - Speaker Noise
When Warning Buzzers Are ON
Seat Belt Reminder Buzzer: Customer InterestRadio - Speaker Noise When Warning Buzzers Are ON
Models
1984 Vehicles Equipped With Standard AM/FM (Sales Code RAL) Radio
Subject
Radio Noise From Warning Buzzer on AM Band
Index
ELECTRICAL
Date
November 23, 1984
No..
08-26-84
P-4992SYMPTOM/CONDITION
Subject vehicles may exhibit excessive noise on the AM band when seat belt, headlamp on, key in warning buzzer is operated.
REPAIR PROCEDURE
Replace Warning Buzzer, PN 3747751, (grey case) with new Suppressed Warning Buzzer, PN 4221730, (green case).
Verify operation of all buzzer functions.
POLICY: Reimbursable within the provisions of the warranty
TIME ALLOWANCE: Refer to Labor Operation Time Schedule for Labor Operation and Time Allowance.
> Restraint Systems > Seat Belt Systems > Seat Belt Reminder Buzzer > Component Information > Technical Service Bulletins > All Technical Service Bulletins for Seat Belt Reminder Buzzer: > 082684 > Nov > 84 > Radio -
Speaker Noise When Warning Buzzers Are ON
Seat Belt Reminder Buzzer: All Technical Service BulletinsRadio - Speaker Noise When Warning Buzzers Are ON
Models
1984 Vehicles Equipped With Standard AM/FM (Sales Code RAL) Radio
Subject
Radio Noise From Warning Buzzer on AM Band
Index
ELECTRICAL
Date
November 23, 1984
No..
08-26-84
P-4992SYMPTOM/CONDITION
Subject vehicles may exhibit excessive noise on the AM band when seat belt, headlamp on, key in warning buzzer is operated.
REPAIR PROCEDURE
Replace Warning Buzzer, PN 3747751, (grey case) with new Suppressed Warning Buzzer, PN 4221730, (green case).
Verify operation of all buzzer functions.
POLICY: Reimbursable within the provisions of the warranty
TIME ALLOWANCE: Refer to Labor Operation Time Schedule for Labor Operation and Time Allowance.
> Restraint Systems > Seat Belt Systems > Seat Belt Warning Timer > Component Information > Locations
Seat Belt Warning Timer: Locations
Under LH Side Of I/P
Applicable to: 1981-84
> Accessories and Optional Equipment > Antenna > Component Information > Technical Service Bulletins > Radio - No AM/Weak FM Reception
Antenna: Technical Service BulletinsRadio - No AM/Weak FM Reception
Models
All 1984 Vehicles Equipped With Standard AM-FM Mux Radio (Sales Code RAL)
Subject
No AM and Weak FM Radio Reception
Index
ELECTRICAL
Date
February 14, 1984
No.
08-08-84
P-536SYMPTOM/CONDITION
Radio reception coming in weak on FM stations and not at all on AM stations may be due to the antenna plug short circuiting inside the radio. Thiscondition is similar to a failed antenna.
DIAGNOSIS
To determine whether the radio or antenna is at fault:
1.
To gain access to the back of the radio, slide the radio out of the instrument panel without disconnecting any wires.
2.
Turn radio on and tune to a local AM station.
> Accessories and Optional Equipment > Antenna > Component Information > Technical Service Bulletins > Radio - No AM/Weak FM Reception > Page 1275
D50/Ram 50 L4-1997cc 2.0L SOHC (1984)
FIGURE 1
3.
Pull the antenna plug out of the ferrule about 1/8" (Figure 1).
If the radio starts playing, remove radio and send to a warranty repair station. Mark the repair order:
ANTENNA FERRULE PROBLEM
If the radio does not play when the antenna plug was pulled out 1/8", substitute a known good antenna to determine if the car antenna is defective.
POLICY: Information only
> Accessories and Optional Equipment > Radio, Stereo, and Compact Disc > Radio/Stereo > Component Information > Technical Service Bulletins > Radio - No AM/Weak FM Reception
Radio/Stereo: Technical Service BulletinsRadio - No AM/Weak FM Reception
Models
All 1984 Vehicles Equipped With Standard AM-FM Mux Radio (Sales Code RAL)
Subject
No AM and Weak FM Radio Reception
Index
ELECTRICAL
Date
February 14, 1984
No.
08-08-84
P-536SYMPTOM/CONDITION
Radio reception coming in weak on FM stations and not at all on AM stations may be due to the antenna plug short circuiting inside the radio. Thiscondition is similar to a failed antenna.
DIAGNOSIS
To determine whether the radio or antenna is at fault:
1.
To gain access to the back of the radio, slide the radio out of the instrument panel without disconnecting any wires.
2.
Turn radio on and tune to a local AM station.
> Accessories and Optional Equipment > Radio, Stereo, and Compact Disc > Radio/Stereo > Component Information > Technical Service Bulletins > Radio - No AM/Weak
FM Reception > Page 1281
D50/Ram 50 L4-1997cc 2.0L SOHC (1984)
FIGURE 1
3.
Pull the antenna plug out of the ferrule about 1/8" (Figure 1).
If the radio starts playing, remove radio and send to a warranty repair station. Mark the repair order:
ANTENNA FERRULE PROBLEM
If the radio does not play when the antenna plug was pulled out 1/8", substitute a known good antenna to determine if the car antenna is defective.
POLICY: Information only
> Accessories and Optional Equipment > Radio, Stereo, and Compact Disc > Radio/Stereo > Component Information > Technical Service Bulletins > Page 1282
Radio/Stereo: Service and Repair
1.
Disconnect battery ground cable.
2.
Remove instrument cluster bezel as outlined in "Instrument Cluster, Replace."
3.
Remove radio bracket to instrument panel attaching screws, then the bracket.
4.
Pull radio slightly outward and disconnect antenna, speaker and feed leads, then remove radio from instrument panel.
5.
Reverse procedure to install.
> Accessories and Optional Equipment > Towing / Trailer System > Trailer Adapter Kit > Component Information > Technical Service Bulletins > Trailer Tow Wiring/Components - Installation Cautions
Trailer Adapter Kit: Technical Service BulletinsTrailer Tow Wiring/Components - Installation Cautions
NO.: 08-05-91
GROUP: ELECTRICAL
DATE: Apr. 22, 1991
SUBJECT: Trailer Tow Wiring Installation
MODELS:
ALL DODGE TRUCKS
DISCUSSION:
Improper installation of trailer tow wiring or electrical components can cause erratic operation of the vehicles electrical system. When installing wiringor additional components, or diagnosing a vehicle with erratic electrical operation, observe the following guidelines.
^
Inspect trailer wiring for bare or broken wires, corroded splices and terminals, shorted lamp sockets, poor or insufficient grounding between thetrailer wiring system and trailer frame.
^
When connecting lighting circuits, use a factory trailer tow wiring harness or a Mopar service kit if available. Mopar kits include matingconnectors and do not require cutting or splicing of vehicle wiring. If cutting or splicing is required, the attached Wiring Procedure should befollowed.
^
When installing any electrical equipment (such as electric brakes, battery chargers, lighting, and winches) make sure that the tow vehicleselectrical ground is hard wired to the trailer electrical ground. Ground wires should be attached to a clean, bare metal surface, not to a paintedsurface. DO NOT rely on the trailer hitch coupling for ground.
^ When using butt splice connectors, test the splice integrity by pulling on the wires after crimping.
^ DO NOT use insulation displacement or insulation piercing crimp type terminals.
^ Some electrical equipment will require splicing into the vehicle wiring. Follow the attached Wiring Procedure when installing these components.
WIRING PROCEDURE
1.
With the ignition key in the OFF position, disconnect the battery.
2.
Remove one inch of insulation from each wire to be connected.
3.
Slide a piece of heat shrink tubing (PN 4419644) onto one wire.
> Accessories and Optional Equipment > Towing / Trailer System > Trailer Adapter Kit > Component Information > Technical Service Bulletins > Trailer Tow Wiring/
Components - Installation Cautions > Page 1288
D50/Ram 50 L4-1997cc 2.0L SOHC (1984)
4.
Spread the strands of each wire apart (Example 1).
5.
Push the ends of the wire together until the strands are close to the insulation (Example 2).
6.
Twist the wires together (Example 3).
7.
Solder the twisted wire ends using a ROSIN CORE SOLDER.
8.
Slide the piece of heat shrink tubing down to cover the splice. Be careful to center the tubing on the splice. Using a heat gun, heat the tubing untilit shrinks and seals the splice.
9.
Connect the battery.
> Body and Frame > Bumper > Component Information > Technical Service Bulletins > Synthetic Resin Bumpers - Painting
Bumper: Technical Service BulletinsSynthetic Resin Bumpers - Painting
Models
All 1984 & 1985 Imports
Subject
Index
BODY
Date
November 18, 1984
No..
23-21-84
P-5119-CService replacement bumpers available through Parts Supply are finished in a neutral (off white) shade. Proper preparation of these synthetic-resin(polyurethane and polypropylene) bumpers prior to painting is necessary.
NOTE: PLEASE ASSURE THAT YOUR BODY SHOP FOREMAN AND/OR PAINTER HAS THIS INFORMATION.
REFINISHING PROCEDURES
1.
Attach bumper to bumper core or support.
2.
Mask all areas which are not to be painted.
3.
Carefully water sand entire bumper area which is to be painted, using #400 or #600 water resistant sandpaper.
DO NOT REMOVE OFF WHITE PAINTED SURFACE FROM BUMPER.
4.
Degrease surface with wax and grease remover.
5.
Spray color coat onto bumper following paint manufacturer's instructions.
6.
Allow color coat to dry naturally (at room temperature) for approximately ten minutes, if clear coat is to be used.
CAUTION: DO NOT ALLOW DUST OR OTHER FOREIGN MATTER TO ADHERE TO PAINTED SURFACE.
7.
Spray clear coat onto bumper following paint manufacturer's instructions.
NOTE: STEPS (6) AND (7) ARE ONLY USED FOR PAINT COATS WITH METALLIC FINISH.
8.
Allow paint to dry.
CAUTION: IF PAINT IS GOING TO BE QUICK DRIED (OVEN OR HEAT LAMP), FIRST ALLOW IT TO AIR DRY FOR
APPROXIMATELY 15 MINUTES.
POLICY: Information only
> Body and Frame > Frame > Cross-Member > Component Information > Service and Repair
Cross-Member: Service and Repair
Fig. 5 Location front suspension crossmember bolts
1. Install suitable jack under differential carrier.2. Remove front suspension crossmember from differential carrier assembly and from support bracket of side frame.3. Reverse procedure to install. Torque front suspension crossmember to support bracket of side frame bolt to 73-86 ft. lbs. Torque front suspension crossmember to bracket bolt to 22-30 ft. lbs.
> Body and Frame > Frame > Trailer Adapter Kit > Component Information > Technical Service Bulletins > Trailer Tow Wiring/Components - Installation Cautions
Trailer Adapter Kit: Technical Service BulletinsTrailer Tow Wiring/Components - Installation Cautions
NO.: 08-05-91
GROUP: ELECTRICAL
DATE: Apr. 22, 1991
SUBJECT: Trailer Tow Wiring Installation
MODELS:
ALL DODGE TRUCKS
DISCUSSION:
Improper installation of trailer tow wiring or electrical components can cause erratic operation of the vehicles electrical system. When installing wiringor additional components, or diagnosing a vehicle with erratic electrical operation, observe the following guidelines.
^
Inspect trailer wiring for bare or broken wires, corroded splices and terminals, shorted lamp sockets, poor or insufficient grounding between thetrailer wiring system and trailer frame.
^
When connecting lighting circuits, use a factory trailer tow wiring harness or a Mopar service kit if available. Mopar kits include matingconnectors and do not require cutting or splicing of vehicle wiring. If cutting or splicing is required, the attached Wiring Procedure should befollowed.
^
When installing any electrical equipment (such as electric brakes, battery chargers, lighting, and winches) make sure that the tow vehicleselectrical ground is hard wired to the trailer electrical ground. Ground wires should be attached to a clean, bare metal surface, not to a paintedsurface. DO NOT rely on the trailer hitch coupling for ground.
^ When using butt splice connectors, test the splice integrity by pulling on the wires after crimping.
^ DO NOT use insulation displacement or insulation piercing crimp type terminals.
^ Some electrical equipment will require splicing into the vehicle wiring. Follow the attached Wiring Procedure when installing these components.
WIRING PROCEDURE
1.
With the ignition key in the OFF position, disconnect the battery.
2.
Remove one inch of insulation from each wire to be connected.
3.
Slide a piece of heat shrink tubing (PN 4419644) onto one wire.
> Body and Frame > Frame > Trailer Adapter Kit > Component Information > Technical Service Bulletins > Trailer Tow Wiring/Components - Installation Cautions > Page
1302
D50/Ram 50 L4-1997cc 2.0L SOHC (1984)
4.
Spread the strands of each wire apart (Example 1).
5.
Push the ends of the wire together until the strands are close to the insulation (Example 2).
6.
Twist the wires together (Example 3).
7.
Solder the twisted wire ends using a ROSIN CORE SOLDER.
8.
Slide the piece of heat shrink tubing down to cover the splice. Be careful to center the tubing on the splice. Using a heat gun, heat the tubing untilit shrinks and seals the splice.
9.
Connect the battery.
> Body and Frame > Paint, Striping and Decals > Paint > System Information > Technical Service Bulletins > Synthetic Resin Bumpers - Painting
Paint: Technical Service BulletinsSynthetic Resin Bumpers - Painting
Models
All 1984 & 1985 Imports
Subject
Index
BODY
Date
November 18, 1984
No..
23-21-84
P-5119-CService replacement bumpers available through Parts Supply are finished in a neutral (off white) shade. Proper preparation of these synthetic-resin(polyurethane and polypropylene) bumpers prior to painting is necessary.
NOTE: PLEASE ASSURE THAT YOUR BODY SHOP FOREMAN AND/OR PAINTER HAS THIS INFORMATION.
REFINISHING PROCEDURES
1.
Attach bumper to bumper core or support.
2.
Mask all areas which are not to be painted.
3.
Carefully water sand entire bumper area which is to be painted, using #400 or #600 water resistant sandpaper.
DO NOT REMOVE OFF WHITE PAINTED SURFACE FROM BUMPER.
4.
Degrease surface with wax and grease remover.
5.
Spray color coat onto bumper following paint manufacturer's instructions.
6.
Allow color coat to dry naturally (at room temperature) for approximately ten minutes, if clear coat is to be used.
CAUTION: DO NOT ALLOW DUST OR OTHER FOREIGN MATTER TO ADHERE TO PAINTED SURFACE.
7.
Spray clear coat onto bumper following paint manufacturer's instructions.
NOTE: STEPS (6) AND (7) ARE ONLY USED FOR PAINT COATS WITH METALLIC FINISH.
8.
Allow paint to dry.
CAUTION: IF PAINT IS GOING TO BE QUICK DRIED (OVEN OR HEAT LAMP), FIRST ALLOW IT TO AIR DRY FOR
APPROXIMATELY 15 MINUTES.
POLICY: Information only
> Body and Frame > Paint, Striping and Decals > Paint > System Information > Technical Service Bulletins > Synthetic Resin Bumpers - Painting > Page 1308
Paint: Technical Service BulletinsPaint - Codes/Cross References
Models
All 1984 Domestic & Import Passenger Car & Truck
Subject
1984 Standard Colors
Index
BODY
Date
Sept, 1983
(current) No.
23-13-83Attached sheets list the Chrysler paint codes which are located on the vehicle body code plate. For location of the code plate see service manual. Asample domestic passenger car plate is enclosed for reference only. First three spaces on second line designates whether vehicle is monotone, two-tonecar, or two-tone truck.
APA - Monotone APB - Two-Tone Car APC - Two-Tone Truck
> Body and Frame > Paint, Striping and Decals > Paint > System Information > Technical Service Bulletins > Synthetic Resin Bumpers - Painting > Page 1309
D50/Ram 50 L4-1997cc 2.0L SOHC (1984)
> Body and Frame > Paint, Striping and Decals > Paint > System Information > Technical Service Bulletins > Synthetic Resin Bumpers - Painting > Page 1310
D50/Ram 50 L4-1997cc 2.0L SOHC (1984)
> Body and Frame > Paint, Striping and Decals > Paint > System Information > Technical Service Bulletins > Synthetic Resin Bumpers - Painting > Page 1311
D50/Ram 50 L4-1997cc 2.0L SOHC (1984)
> Body and Frame > Paint, Striping and Decals > Paint > System Information > Technical Service Bulletins > Synthetic Resin Bumpers - Painting > Page 1312
D50/Ram 50 L4-1997cc 2.0L SOHC (1984)
The next four spaces will be used to designate primary paint color (for 1984 only three spaces will be used). The first letter will always be a "P".
The next four spaces will be used to designate secondary paint color (for 1984 only three spaces will be used). The first letter will always be a "Q".
In both cases the additional letter and digit will correspond to the letter and digit on the following sheets. These sheets cover all domestic and import carsand trucks for 1984... Various paint manufacturer's reference paint codes can be found listed to the right of the Chrysler code.
These paint manufacturers have service representatives who are thoroughly experienced in the latest refinishing processes and painting techniques, whocan assist your body shop personnel with recommended preparation and application procedures.
> Body and Frame > Paint, Striping and Decals > Paint > System Information > Technical Service Bulletins > Synthetic Resin Bumpers - Painting > Page 1313
D50/Ram 50 L4-1997cc 2.0L SOHC (1984)
Color chip charts are available from the respective vendors through their local outlets or service representatives.
NOTE: PLEASE FURNISH YOUR BODY SHOP FOREMAN AND/OR PAINTER WITH THIS INFORMATION.
POLICY: Information only
BODY CODEPLATE
The Body Code Plate is located on the Left Front Side Shield or Wheel Housing or on the Upper Radiator Support. The Plate contains 7 rows of data.The bottom 3 rows are reserved for specific information as depicted below. Starting at the fourth row, (following the reserved portion), other SalesCodes used to build a specific vehicle are listed in the ascending order by Alpha sequence.
> Body and Frame > Seats > Component Information > Technical Service Bulletins > Upholstery - Cleaning Procedure
Seats: Technical Service BulletinsUpholstery - Cleaning Procedure
Models
All ChryslerPlymouth & Dodge Vehicles
Subject
Cloth Seat Cleaning Procedure
Index
BODY
Date
February 6, 1989
No.
23-03-89
P-367 (C23-02-9)The following is the recommended procedure for the cleaning of soiled cloth seat upholstery. Use of improper cleaning materials or procedures mayresult in swelling or deterioration of foam, discoloration of fabric, or loosening the bond between the seat fabric and foam.
NOTE: USE ONLY THE APPROVED MOPAR CLEANERS OR EQUIVALENT OR A MILD SOAP SOLUTION.
PARTS REQUIRED
Super Kleen or
Total Clean
REPAIR PROCEDURE
PN 4318015
PN 4318019
1.
Apply approved cleaner to soiled area with cloth after wringing out excess cleaner.
2.
Do not soak upholstery, even with recommended cleaners.
3.
Wipe soiled area with a lifting motion.
4.
Wipe off immediately with a clean, dry towel or rag.
NOTE:
POLICY:
DO NOT USE CARPET TYPE CLEANING APPARATUS THAT BLOWS IN SOLVENT OR STEAM, NOR ANY HOUSEHOLDCLEANERS NOT SPECIFICALLY RECOMMENDED FOR CLOTH UPHOLSTERY.
Information only
> Cruise Control > Clutch Switch, Cruise Control > Component Information > Locations
Clutch Switch: Locations
Under LH Side Of I/P
> Cruise Control > Sensors and Switches - Cruise Control > Clutch Switch, Cruise Control > Component Information > Locations
Clutch Switch: Locations
Under LH Side Of I/P
> Instrument Panel, Gauges and Warning Indicators > Instrument Cluster / Carrier > Component Information > Service and Repair
Instrument Cluster / Carrier: Service and Repair
1.
Disconnect battery ground cable.
2.
Pull off radio and heater control knobs.
3.
Remove adjusting nuts from radio and heater control stalks.
4.
Remove ashtray, then the ashtray bracket.
5.
Remove two cluster to dashboard attaching screws, then draw out cluster panel from lower left corner.
6.
Disconnect cluster wiring and speedometer cable, then remove cluster.
7.
Reverse procedure to install.
> Instrument Panel, Gauges and Warning Indicators > Odometer > Component Information > Technical Service Bulletins > Instrument Cluster - Odometer Memory Chip Service
Odometer: Technical Service BulletinsInstrument Cluster - Odometer Memory Chip Service
Models
All Domestic Passenger Cars Equipped With Electronic Instrument Cluster
Subject
Instrument Cluster/ Odometer Memory Chip Service
Index
ELECTRICAL
Date
March 19, 1984
No.
08-01-84
Electronic instrument clusters contain an odometer memory chip to record the vehicle mileage. Since the chip is relatively small and delicate, certain caremust be exercised in handling the device during cluster or chip service. Refer to the procedure below for proper memory chip removal and installationprocedures.
DIAGNOSIS
Prior to servicing the instrument cluster, utilize the "Self-Diagnostic Test" procedure provided in the service manual to determine whether the cluster orthe memory chip is faulty.
^
A code of 1, 2 or 3 during the first test and the word "Fail" displayed in the odometer area, indicates the cluster is defective. Replace the cluster,retaining the memory chip for installation in the replacement cluster so as to maintain the vehicle mileage. This electronic memory device containsthe current accumulated vehicle mileage. Follow the procedure below to transfer the memory chip.
^
A code of "4" and the word "Fail" displayed in the odometer area indicates a probable odometer memory chip failure. Order a replacement chippackage and install per the following instructions.
NOTE:
REPLACEMENT OF THE ODOMETER CHIP IS PERMISSIBLE ONLY WHERE ORIGINAL MILEAGE MAY BE POSTED ON ADOOR JAMB LABEL. IN AREAS WHERE LAWS REQUIRE ORIGINAL MILEAGE TO BE DISPLAYED IN ODOMETER,CONTACT HUNTSVILLE ON 1-800-328-6121.
PARTS REQUIRED
Odometer NVM Chip Package PN 4342218
Consists of:
1 - NVM Chip with Asterisk (*Indicates not original mileage) 1 - Instruction Sheet 1 - Speedometer Door Jamb Label
REPAIR PROCEDURE
1.
Remove instrument cluster per service manual procedures.
2.
If service replacement chip will be used, record original mileage on speedometer door jamb label and attach to door jamb (if dashes, record lastknown mileage).
3.
Select a clean work area.
4.
Wash hands to insure that grease and dirt will not be left on the odometer chip contact pins.
5.
Place the cluster front side down on a soft clean cloth.
6.
Insure that the cluster is with the bottom toward the person intending to remove and install the odometer chip.
> Instrument Panel, Gauges and Warning Indicators > Odometer > Component Information > Technical Service Bulletins > Instrument Cluster - Odometer Memory Chip
Service > Page 1334
D50/Ram 50 L4-1997cc 2.0L SOHC (1984)
7.
Open the odometer chip access door by pressing the latch ears toward the center of the door.
FIGURE 1
8.
Notice that the odometer chip located just inside the access door has a distinctive notch. Be sure to install the chip in the same direction it was inthe original cluster. When installed properly, the odometer chip notch should be on the left (Figure 1).
FIGURE 2
FIGURE 3
9.
Using Miller Special Tool #C-4817 (Figure 2), grasp the chip between the tool jaws under the ends of the odometer chip. Carefully rock the chipalong its longitudinal axis as you pull gently. The odometer chip should extract easily (Figure 3).
NOTE:
IF THE ODOMETER CHIP WILL NOT BE IMMEDIATELY INSTALLED IN THE NEW CLUSTER, PROTECT THE ODOMETERCHIP FROM DAMAGE BY PLACING IT IN AN ENVELOPE WITH THE VEHICLE VIN NUMBER AND MILEAGE.
> Instrument Panel, Gauges and Warning Indicators > Odometer > Component Information > Technical Service Bulletins > Instrument Cluster - Odometer Memory Chip
Service > Page 1335
D50/Ram 50 L4-1997cc 2.0L SOHC (1984)
FIGURE 4
10.
Before inserting replacement odometer chip into cluster (or transferring existing odometer chip to new cluster), inspect pins of chip to assure theyare straight and perpendicular to chip body. If not, align pins before attempting to install in cluster (Figure 4).
11.
The odometer chip should now be placed lightly in the socket with the notch to the left. Note that each of the 14 contact pins is in contact with thelip of the socket pin. If all 14 pins are not started in the socket, gently reform the pins to match the socket holes. Press the odometer chip intoposition with Miller Special Tool #C-4817.
12.
Verify that the odometer chip notch is toward the left when the cluster is face down, and bottom of cluster is toward installer.
13.
Replace access door and install cluster in vehicle per service manual procedures.
14.
If odometer chip was transferred to new cluster or original mileage odometer chip was obtained, verify that the mileage is the same as wasrecorded.
This bulletin is released in advance of parts availability. The parts listed in this bulletin will be available in mid-March, 1984.
POLICY: Reimbursable within the provisions of the warranty
FAILURE CODE:
0.4 Hrs.
08-70-02-02 Memory Chip With Original Mileage 0.4 Hrs.
58 - Internal Defect
TIME ALLOWANCE:Labor Operation No. 08-70-02-01 Memory Chip With Zero Mileage
> Instrument Panel, Gauges and Warning Indicators > Seat Belt Reminder Buzzer > Component Information > Technical Service Bulletins > Customer Interest for Seat Belt Reminder Buzzer: > 082684 > Nov > 84 > Radio -
Speaker Noise When Warning Buzzers Are ON
Seat Belt Reminder Buzzer: Customer InterestRadio - Speaker Noise When Warning Buzzers Are ON
Models
1984 Vehicles Equipped With Standard AM/FM (Sales Code RAL) Radio
Subject
Radio Noise From Warning Buzzer on AM Band
Index
ELECTRICAL
Date
November 23, 1984
No..
08-26-84
P-4992SYMPTOM/CONDITION
Subject vehicles may exhibit excessive noise on the AM band when seat belt, headlamp on, key in warning buzzer is operated.
REPAIR PROCEDURE
Replace Warning Buzzer, PN 3747751, (grey case) with new Suppressed Warning Buzzer, PN 4221730, (green case).
Verify operation of all buzzer functions.
POLICY: Reimbursable within the provisions of the warranty
TIME ALLOWANCE: Refer to Labor Operation Time Schedule for Labor Operation and Time Allowance.
> Instrument Panel, Gauges and Warning Indicators > Seat Belt Reminder Buzzer > Component Information > Technical Service Bulletins > All Technical Service Bulletins for Seat Belt Reminder Buzzer: > 082684 > Nov > 84
> Radio - Speaker Noise When Warning Buzzers Are ON
Seat Belt Reminder Buzzer: All Technical Service BulletinsRadio - Speaker Noise When Warning Buzzers Are ON
Models
1984 Vehicles Equipped With Standard AM/FM (Sales Code RAL) Radio
Subject
Radio Noise From Warning Buzzer on AM Band
Index
ELECTRICAL
Date
November 23, 1984
No..
08-26-84
P-4992SYMPTOM/CONDITION
Subject vehicles may exhibit excessive noise on the AM band when seat belt, headlamp on, key in warning buzzer is operated.
REPAIR PROCEDURE
Replace Warning Buzzer, PN 3747751, (grey case) with new Suppressed Warning Buzzer, PN 4221730, (green case).
Verify operation of all buzzer functions.
POLICY: Reimbursable within the provisions of the warranty
TIME ALLOWANCE: Refer to Labor Operation Time Schedule for Labor Operation and Time Allowance.
> Instrument Panel, Gauges and Warning Indicators > Volt Meter Gauge > Component Information > Technical Service Bulletins > Voltmeter - Explanation for High Readings
Volt Meter Gauge: Technical Service BulletinsVoltmeter - Explanation for High Readings
Models
All 1984 Models Equipped With Magnetic Voltmeter Instrument Clusters
Subject
High Voltmeter Readings
Index
ELECTRICAL
Date
March 19, 1984-C
No.
08-11-84
P-982-CSYMPTOM/CONDITION
The magnetic type of voltmeters used in subject 1984 vehicles are sensitive to heat build up inside the instrument cluster housing. The increased heat thatbuilds up places the voltmeter indicator toward the high end of the "normal" operating portion of the meter or, under the right conditions, may just enterthe "high warning" portion of the meter.
The conditions causing this high reading are as follows:
^
An hour or more of continuous driving at cold ambient temperatures (cold temperature operation causes the voltage regulator output to be higherthan hot temperature operation).
^ Instrument cluster illumination lamps and/or heater/defroster on, which increases temperatures around the voltmeter.
A defective voltage regulator (overcharging) will normally cause the voltmeter to read well into the warning area (full scale) and will occur immediately,not over a period of an hour or more.
POLICY: Information only
If a high voltmeter reading exists, verify battery and charging system are operating normally per service manual procedures. If system meetsspecifications, assure customer that system is operating properly. Do not replace voltage regulator or voltmeter if test results meet service manualspecifications.
> Lighting and Horns > Brake Light Switch > Component Information > Service and Repair
Brake Light Switch: Service and Repair
Adjusting Stoplamp Switch Clearance
The stop light switch also serves as a brake pedal stopper and is located under the instrument panel, behind the brake pedal. Disconnect the wire, thenremove retaining nut from bracket and the switch. Reverse procedure to install. Ensure brake pedal height is correct, then adjust switch to obtain aclearance of .02 to .04 inch between switch housing and pedal stopper with pedal released.
> Lighting and Horns > Hazard Warning Lamps > Hazard Warning Flasher > Component Information > Locations
Hazard Warning Flasher: Locations
Under LH Side Of I/P
Applicable to: 1981-84
> Lighting and Horns > Headlamp > Headlamp Relay > Component Information > Locations
Headlamp Relay: Locations
Left Side Front Fender Shield
Applicable to: 1981-84
> Lighting and Horns > Headlamp > Headlight Switch <--> [Headlamp Switch] > Component Information > Service and Repair
Headlight Switch: Service and Repair
On models equipped with dash mounted light switch, the switch is serviced with the instrument cluster. Refer to ``Instrument Cluster, Replace''procedure. On models equipped with turn signal mounted light switch, the switch is serviced with the turn signal/combination switch. Refer to ``VehicleLighting/Turn Signals/Turn Signal Switch/Service and Repair'' for procedure.
> Lighting and Horns > Horn > Component Information > Technical Service Bulletins > Customer Interest for Horn: > 082284 > Aug > 84 > Horn - Intermittently Inoperative
Horn: Customer InterestHorn - Intermittently Inoperative
Models
All 1983-1984 Equipped with Tilt Steering
Subject
Intermittent Horn Operation on Tilt Column
Index
ELECTRICAL
Date
August 6, 1984
No..
08-22-84
P-3277-CSYMPTOM/CONDITION
Intermittent horn operation on tilt steering column.
Since there is no rotation between the steering wheel pick-up ring and the mating horn brush on a tilt column, any grease present may act as an insulator.
REPAIR PROCEDURE
1.
Tilt Column Only
Remove the ignition key from the key cylinder. Rotate the steering wheel to insure that the column is locked.
2.
Remove the steering wheel.
3.
Thoroughly remove all lube from the steering wheel pick-up ring and the mating horn brush using mineral spirits. It is very important that bothsurfaces be cleaned thoroughly. Do not sand the ring or relube it.
4.
Replace the steering wheel.
5.
Check horn operation.
POLICY: Reimbursable within the provisions of the warranty
0.2 Hrs.
FAILURE CODE: 61 - Intermittent Operation
> Lighting and Horns > Horn > Component Information > Technical Service Bulletins > All Technical Service Bulletins for Horn: > 082284 > Aug > 84 > Horn - Intermittently Inoperative
Horn: All Technical Service BulletinsHorn - Intermittently Inoperative
Models
All 1983-1984 Equipped with Tilt Steering
Subject
Intermittent Horn Operation on Tilt Column
Index
ELECTRICAL
Date
August 6, 1984
No..
08-22-84
P-3277-CSYMPTOM/CONDITION
Intermittent horn operation on tilt steering column.
Since there is no rotation between the steering wheel pick-up ring and the mating horn brush on a tilt column, any grease present may act as an insulator.
REPAIR PROCEDURE
1.
Tilt Column Only
Remove the ignition key from the key cylinder. Rotate the steering wheel to insure that the column is locked.
2.
Remove the steering wheel.
3.
Thoroughly remove all lube from the steering wheel pick-up ring and the mating horn brush using mineral spirits. It is very important that bothsurfaces be cleaned thoroughly. Do not sand the ring or relube it.
4.
Replace the steering wheel.
5.
Check horn operation.
POLICY: Reimbursable within the provisions of the warranty
0.2 Hrs.
FAILURE CODE: 61 - Intermittent Operation
> Lighting and Horns > Relays and Modules - Lighting and Horns > Headlamp Relay > Component Information > Locations
Headlamp Relay: Locations
Left Side Front Fender Shield
Applicable to: 1981-84
> Lighting and Horns > Sensors and Switches - Lighting and Horns > Brake Light Switch > Component Information > Service and Repair
Brake Light Switch: Service and Repair
Adjusting Stoplamp Switch Clearance
The stop light switch also serves as a brake pedal stopper and is located under the instrument panel, behind the brake pedal. Disconnect the wire, thenremove retaining nut from bracket and the switch. Reverse procedure to install. Ensure brake pedal height is correct, then adjust switch to obtain aclearance of .02 to .04 inch between switch housing and pedal stopper with pedal released.
> Lighting and Horns > Sensors and Switches - Lighting and Horns > Headlight Switch <--> [Headlamp Switch] > Component Information > Service and Repair
Headlight Switch: Service and Repair
On models equipped with dash mounted light switch, the switch is serviced with the instrument cluster. Refer to ``Instrument Cluster, Replace''procedure. On models equipped with turn signal mounted light switch, the switch is serviced with the turn signal/combination switch. Refer to ``VehicleLighting/Turn Signals/Turn Signal Switch/Service and Repair'' for procedure.
> Lighting and Horns > Sensors and Switches - Lighting and Horns > Turn Signal Switch > Component Information > Service and Repair
Turn Signal Switch: Service and Repair
1. Disconnect battery ground cable.2. Remove steering wheel using a suitable puller. Scribe alignment mark between steering wheel and shaft to ensure proper installation. On models with tilt steering columns, place column in lowest position during steering wheel removal.
3. Remove upper and lower steering column covers.4. Remove wiring harness retaining straps, if equipped, then disconnect electrical connectors.5. Remove column switch assembly.6. Reverse procedure to install, noting the following: a. Ensure column switch is properly aligned with steering shaft center.b. Attach switch wiring along column tube as close to center line as possible.c. Retain wiring using suitable retaining straps to prevent contact with other parts.
> Lighting and Horns > Turn Signals > Turn Signal Flasher > Component Information > Locations
Turn Signal Flasher: Locations
Under LH Side Of I/P
Applicable to: 1981-84
> Lighting and Horns > Turn Signals > Turn Signal Switch > Component Information > Service and Repair
Turn Signal Switch: Service and Repair
1. Disconnect battery ground cable.2. Remove steering wheel using a suitable puller. Scribe alignment mark between steering wheel and shaft to ensure proper installation. On models with tilt steering columns, place column in lowest position during steering wheel removal.
3. Remove upper and lower steering column covers.4. Remove wiring harness retaining straps, if equipped, then disconnect electrical connectors.5. Remove column switch assembly.6. Reverse procedure to install, noting the following: a. Ensure column switch is properly aligned with steering shaft center.b. Attach switch wiring along column tube as close to center line as possible.c. Retain wiring using suitable retaining straps to prevent contact with other parts.
> Wiper and Washer Systems > Relays and Modules - Wiper and Washer Systems > Wiper Relay > Component Information > Locations
Wiper Relay: Locations
Left Side Of Fender Shield
Applicable to: 1981-84
> Wiper and Washer Systems > Wiper Blade > Component Information > Technical Service Bulletins > Customer Interest for Wiper Blade: > 23-014-06 > Mar > 06 > Wipers/Washers - Wipers Smear or Streak Windshield
Wiper Blade: Customer InterestWipers/Washers - Wipers Smear or Streak Windshield
NUMBER: 23-014-06
GROUP: Body
DATE: March 8, 2006
SUBJECT:Windshield Wiper Blade/Element Maintenance
All Chrysler Group Vehicles MODELS:All All
DISCUSSION:
Windshield wiper blades/elements are frequently replaced unnecessarily. Because of the environmental conditions vehicles can be operated in, a film canbuild up on both the windshield and the windshield wiper elements that will cause poor cleaning/streaking of the windshield, and in some instances, achattering condition as the wipers blades travel across the windshield.
Replacement of the wiper blades/elements is normally NOT required to correct streaking issues. A simple NORMAL MAINTENANCE cleaning of thewiper blades/elements and windshield is all that is required.
If the wipe pattern appears to be streaky or if there is chatter and no damage to the wiper blades/elements is obvious, the following steps should beperformed:
1.
Use a soft cloth or sponge & squeegee and MOPAR Windshield Washer Solvent (p/n 04318067AB, 16 Oz. bottle or p/n 04318068AB, 32 Oz.bottle), MOPAR Glass Cleaner (p/n 04897623AB, 16 Oz. bottle) or a solution of 50/50 alcohol and water, to wash the windshield.
2.
Raise the wiper blades off the glass and clean the wiper blade elements (rubber insert) with MOPAR Windshield Washer Solvent or a solution of50/50 alcohol and water and a soft cloth, paper towel or sponge.
3.
Return the wiper blades to their normal operating position and function the washer system. If the wiper blades/elements are not streaking thewindshield or chattering, replacing the blade assembly(ies) is not necessary. If the wipe pattern is still objectionable, repeat step 2 several times. Ifthe wipe pattern is still objectionable, replace the wiper blades/elements.
POLICY:Information Only
Disclaimer :
This bulletin is supplied as technical information only and is not an authorization for repair.
> Wiper and Washer Systems > Wiper Blade > Component Information > Technical Service Bulletins > All Technical Service Bulletins for Wiper Blade: > 23-014-06 > Mar > 06 > Wipers/Washers - Wipers Smear or Streak
Windshield
Wiper Blade: All Technical Service BulletinsWipers/Washers - Wipers Smear or Streak Windshield
NUMBER: 23-014-06
GROUP: Body
DATE: March 8, 2006
SUBJECT:Windshield Wiper Blade/Element Maintenance
All Chrysler Group Vehicles MODELS:All All
DISCUSSION:
Windshield wiper blades/elements are frequently replaced unnecessarily. Because of the environmental conditions vehicles can be operated in, a film canbuild up on both the windshield and the windshield wiper elements that will cause poor cleaning/streaking of the windshield, and in some instances, achattering condition as the wipers blades travel across the windshield.
Replacement of the wiper blades/elements is normally NOT required to correct streaking issues. A simple NORMAL MAINTENANCE cleaning of thewiper blades/elements and windshield is all that is required.
If the wipe pattern appears to be streaky or if there is chatter and no damage to the wiper blades/elements is obvious, the following steps should beperformed:
1.
Use a soft cloth or sponge & squeegee and MOPAR Windshield Washer Solvent (p/n 04318067AB, 16 Oz. bottle or p/n 04318068AB, 32 Oz.bottle), MOPAR Glass Cleaner (p/n 04897623AB, 16 Oz. bottle) or a solution of 50/50 alcohol and water, to wash the windshield.
2.
Raise the wiper blades off the glass and clean the wiper blade elements (rubber insert) with MOPAR Windshield Washer Solvent or a solution of50/50 alcohol and water and a soft cloth, paper towel or sponge.
3.
Return the wiper blades to their normal operating position and function the washer system. If the wiper blades/elements are not streaking thewindshield or chattering, replacing the blade assembly(ies) is not necessary. If the wipe pattern is still objectionable, repeat step 2 several times. Ifthe wipe pattern is still objectionable, replace the wiper blades/elements.
POLICY:Information Only
Disclaimer :
This bulletin is supplied as technical information only and is not an authorization for repair.
> Wiper and Washer Systems > Windshield Wiper Transmission <--> [Wiper Gear Box] > Component Information > Service and Repair
Windshield Wiper Transmission: Service and Repair
EXC. 1984 COLT HATCHBACK
1. Remove wiper motor as outlined under "Windshield Wiper Motor, Replace."2. Position wiper motor shaft at right angles to the linkage and remove linkage while holding shaft.3. Reverse procedure to install, noting the following: a. Ensure shaft bracket positioning boss is properly located in access hole.b. Mount wiper arm so that when motor is in park position distance between wiper blade and bottom of windshield is 0.6 inch on left side and
0.8 inch on right side for 1985-88 Colt, 1.2 inch on left side and 1 inch on right side for Colt Vista, 0.5 inch on both sides for Conquest, 0.6-1inch on both sides for Ram 50 and 1.5-1.9 inch on both sides for Ram Raider.
> Wiper and Washer Systems > Wiper Motor > Component Information > Service and Repair
Wiper Motor: Service and Repair
FRONT WIPER
1. Disconnect battery ground cable and remove wiper motor access hole cover, located on the left hand side of the front deck, if applicable.2. Raise covers and remove nuts securing wiper arms to pivot shafts, note installation position of arms, then remove wiper arms.3. Remove cowl moldings, as needed, to gain access to pivot shaft fasteners.4. Remove wiper pivot shaft attaching bolts or nuts, then push pivots inwards.5. Remove wiper motor attaching bolts or nuts, pull motor out slightly and disconnect linkage. Mark relationship of wiper motor crank arm to driveshaft prior to disconnecting linkage to ensure proper stop angle after installation.
6. Remove wiper motor.7. Reverse procedure to install. When installing crank arm on wiper motor, ensure reference marks made during removal are aligned, then install wiper arms as outlined in "Windshield Wiper Transmission, Replace."
> Wiper and Washer Systems > Wiper Relay > Component Information > Locations
Wiper Relay: Locations
Left Side Of Fender Shield
Applicable to: 1981-84
advertisement
Related manuals
advertisement
Table of contents
- 2 Relays and Modules
- 2 Relays and Modules - Lighting and Horns
- 2 Headlamp Relay
- 2 Component Information
- 2 Locations
- 4 Relays and Modules - Powertrain Management
- 4 Relays and Modules - Computers and Control Systems
- 4 Powertrain Control Module <--> [Engine Control Module]
- 4 Component Information
- 4 Locations
- 6 Relays and Modules - Fuel Delivery and Air Induction
- 6 Throttle Control Vacuum Motor <--> [Engine Speed Governor Control Module]
- 6 Component Information
- 6 Locations
- 8 Relays and Modules - Starting and Charging
- 8 Starter Relay
- 8 Component Information
- 8 Locations
- 10 Relays and Modules - Wiper and Washer Systems
- 10 Wiper Relay
- 10 Component Information
- 10 Locations
- 12 Sensors and Switches
- 12 Sensors and Switches - Cooling System
- 12 Engine - Coolant Temperature Sensor/Switch
- 12 Coolant Temperature Sensor/Switch (For Computer)
- 12 Component Information
- 12 Specifications
- 14 Sensors and Switches - Cruise Control
- 14 Clutch Switch, Cruise Control
- 14 Component Information
- 14 Locations
- 16 Sensors and Switches - Lighting and Horns
- 16 Brake Light Switch
- 16 Component Information
- 16 Service and Repair
- 18 Headlight Switch <--> [Headlamp Switch]
- 18 Component Information
- 18 Service and Repair
- 20 Turn Signal Switch
- 20 Component Information
- 20 Service and Repair
- 22 Sensors and Switches - Powertrain Management
- 22 Sensors and Switches - Computers and Control Systems
- 22 Coolant Temperature Sensor/Switch (For Computer)
- 22 Component Information
- 22 Specifications
- 24 Sensors and Switches - Ignition System
- 24 Ignition Switch
- 24 Component Information
- 24 Service and Repair
- 26 Sensors and Switches - Starting and Charging
- 26 Clutch Switch
- 26 Component Information
- 26 Locations
- 28 Ignition Switch
- 28 Component Information
- 28 Service and Repair
- 30 Neutral Safety Switch
- 30 Component Information
- 30 Service and Repair
- 32 Maintenance
- 32 Alignment
- 32 System Information
- 32 Technical Service Bulletins
- 32 Alignment - Caster Adjustment Manual Revision
- 34 Page 68
- 36 Service and Repair
- 36 Camber
- 38 Page 71
- 40 Page 72
- 42 Page 73
- 44 Tune-up and Engine Performance Checks
- 44 Fuel Pressure
- 44 System Information
- 44 Specifications
- 46 Air/Fuel Mixture
- 46 System Information
- 46 Technical Service Bulletins
- 46 By Symptom for Air/Fuel Mixture:
- 46 140884
- 46 Jan
- 46 84
- 46 Propane Idle Set - Procedure
- 47 Page 86
- 49 Page 87
- 51 Page 88
- 53 Page 89
- 55 Page 90
- 58 All Technical Service Bulletins for Air/Fuel Mixture:
- 58 140884
- 58 Jan
- 58 84
- 58 Propane Idle Set - Procedure
- 59 Page 96
- 61 Page 97
- 63 Page 98
- 65 Page 99
- 67 Page 100
- 70 Idle Speed
- 70 System Information
- 70 Technical Service Bulletins
- 70 By Symptom:
- 70 140884
- 70 Jan
- 70 84
- 70 Propane Idle Set - Procedure
- 71 Page 109
- 73 Page 110
- 75 Page 111
- 77 Page 112
- 79 Page 113
- 82 All Technical Service Bulletins for Idle Speed:
- 82 142084
- 82 May
- 82 84
- 82 Engine Specifications - Manual Corrections
- 83 Page 119
- 86 141984
- 86 May
- 86 84
- 86 Carburetor - Idle Speed Adjustment on A/C Install
- 87 Page 124
- 89 Page 125
- 91 Page 126
- 93 Page 127
- 96 140884
- 96 Jan
- 96 84
- 96 Propane Idle Set - Procedure
- 97 Page 132
- 99 Page 133
- 101 Page 134
- 103 Page 135
- 105 Page 136
- 108 All Other Service Bulletins for Idle Speed:
- 108 142084
- 108 May
- 108 84
- 108 Engine Specifications - Manual Corrections
- 109 Page 142
- 112 141984
- 112 May
- 112 84
- 112 Carburetor - Idle Speed Adjustment on A/C Install
- 113 Page 147
- 115 Page 148
- 117 Page 149
- 119 Page 150
- 122 Page 151
- 124 Firing Order
- 124 Component Information
- 124 Specifications
- 126 Ignition Timing
- 126 Timing Marks and Indicators
- 126 System Information
- 126 Diagrams
- 127 Page 159
- 130 Distributor, Ignition
- 130 Vacuum Advance Unit <--> [Distributor Advance Unit]
- 130 Component Information
- 130 Specifications
- 130 Electrical Specifications
- 132 Page 165
- 134 Spark Plug
- 134 Component Information
- 134 Technical Service Bulletins
- 134 Customer Interest for Spark Plug:
- 134 181788
- 134 Oct
- 134 88
- 134 Spark Plugs - Oil Fouling/Misfire on Hard Acceleration
- 135 Page 174
- 137 Page 175
- 139 Page 176
- 142 All Technical Service Bulletins for Spark Plug:
- 142 181788
- 142 Oct
- 142 88
- 142 Spark Plugs - Oil Fouling/Misfire on Hard Acceleration
- 143 Page 182
- 145 Page 183
- 147 Page 184
- 150 Page 185
- 152 Compression Check
- 152 System Information
- 152 Specifications
- 154 Valve Clearance
- 154 System Information
- 154 Specifications
- 156 Page 192
- 158 Timing Belt
- 158 Component Information
- 158 Adjustments
- 159 Page 196
- 162 Page 197
- 163 Page 198
- 165 Page 199
- 167 Page 200
- 169 Page 201
- 172 Drive Belt
- 172 Component Information
- 172 Specifications
- 174 Filters
- 174 Oil Filter, Engine
- 174 Component Information
- 174 Technical Service Bulletins
- 174 Oil Filter - Addition of Second Supplier
- 176 Hoses
- 176 Coolant Line/Hose
- 176 Component Information
- 176 Technical Service Bulletins
- 176 Carburetor Coolant Hose - Installation Procedure
- 178 Fluids
- 178 Coolant
- 178 Component Information
- 178 Technical Service Bulletins
- 178 Engine Coolant - Recycling Recommendations
- 180 Page 220
- 182 Fluid - A/T
- 182 Component Information
- 182 Technical Service Bulletins
- 182 Automatic Transmission - New Fluid Type
- 184 Specifications
- 184 Transaxle/Transmission - Automatic
- 186 Page 227
- 188 Fluid - M/T
- 188 Component Information
- 188 Specifications
- 190 Fluid - Differential
- 190 Component Information
- 190 Specifications
- 192 Fluid - Transfer Case
- 192 Component Information
- 192 Specifications
- 194 Engine Oil
- 194 Component Information
- 194 Technical Service Bulletins
- 194 Engine Oil - New `SG' Level Oil
- 196 Page 241
- 198 Page 242
- 200 Refrigerant
- 200 Component Information
- 200 Specifications
- 200 Capacity Specifications
- 202 Page 247
- 204 Fuses and Circuit Breakers
- 204 Fuse Block
- 204 Component Information
- 204 Diagrams
- 204 Diagram Information and Instructions
- 206 Page 253
- 208 Service Reminder Indicators
- 208 System Information
- 208 Service Precautions
- 210 Wheels and Tires
- 210 Wheel Bearing
- 210 Component Information
- 210 Adjustments
- 212 Service and Repair
- 212 Removal
- 213 Page 263
- 216 Page 264
- 217 Page 265
- 219 Page 266
- 222 Page 267
- 223 Page 268
- 226 Wheel Hub
- 226 Axle Nut
- 226 Component Information
- 226 Technical Service Bulletins
- 226 Rear Axle Shaft - Retaining Nut Lock Washers
- 228 Wheel Hub (Locking)
- 228 Component Information
- 228 Technical Service Bulletins
- 228 Automatic Locking Hubs - Racheting Noise
- 230 Engine, Cooling and Exhaust
- 230 Engine
- 230 Compression Check
- 230 System Information
- 230 Specifications
- 232 Camshaft, Lifters and Push Rods
- 232 Camshaft, Engine
- 232 Component Information
- 232 Specifications
- 234 Page 287
- 235 Page 288
- 237 Page 289
- 240 Rocker Arm Assembly
- 240 Component Information
- 240 Service and Repair
- 241 Page 293
- 243 Page 294
- 246 Cylinder Block Assembly
- 246 Connecting Rod Bearing
- 246 Component Information
- 246 Service and Repair
- 248 Connecting Rod, Engine
- 248 Component Information
- 248 Specifications
- 250 Page 302
- 252 Crankshaft Main Bearing
- 252 Component Information
- 252 Service and Repair
- 254 Crankshaft, Engine
- 254 Component Information
- 254 Specifications
- 254 Crankshaft Journal Tolerances
- 256 Page 310
- 258 Harmonic Balancer - Crankshaft Pulley
- 258 Component Information
- 258 Technical Service Bulletins
- 258 Engine - Torque Specifications, Manual Correction
- 259 Page 315
- 262 Page 316
- 264 Piston, Engine
- 264 Component Information
- 264 Specifications
- 266 Page 320
- 268 Piston Ring, Engine
- 268 Component Information
- 268 Specifications
- 270 Page 324
- 272 Cylinder Head Assembly
- 272 Valve Clearance
- 272 System Information
- 272 Specifications
- 274 Page 329
- 276 Rocker Arm Assembly
- 276 Component Information
- 276 Service and Repair
- 277 Page 333
- 279 Page 334
- 282 Valve Cover
- 282 Component Information
- 282 Specifications
- 284 Valve Guide
- 284 Component Information
- 284 Service and Repair
- 286 Valve Seat
- 286 Component Information
- 286 Specifications
- 288 Valve Spring
- 288 Component Information
- 288 Specifications
- 290 Valve, Intake/Exhaust
- 290 Component Information
- 290 Specifications
- 292 Drive Belts, Mounts, Brackets and Accessories
- 292 Drive Belt
- 292 Component Information
- 292 Specifications
- 294 Engine Lubrication
- 294 Engine Oil
- 294 Component Information
- 294 Technical Service Bulletins
- 294 Engine Oil - New `SG' Level Oil
- 296 Page 359
- 298 Page 360
- 300 Oil Filter, Engine
- 300 Component Information
- 300 Technical Service Bulletins
- 300 Oil Filter - Addition of Second Supplier
- 302 Oil Filter Housing
- 302 Component Information
- 302 Technical Service Bulletins
- 302 Oil Filter Bracket & Oil Pump - Modification
- 304 Oil Pan, Engine
- 304 Component Information
- 304 Service and Repair
- 306 Oil Pump, Engine
- 306 Component Information
- 306 Technical Service Bulletins
- 306 Oil Filter Bracket & Oil Pump - Modification
- 308 Page 376
- 310 Intake Manifold
- 310 Component Information
- 310 Specifications
- 312 Seals and Gaskets, Engine
- 312 Crankshaft Main Bearing Seal
- 312 Component Information
- 312 Service and Repair
- 314 Timing Components
- 314 Timing Belt
- 314 Component Information
- 314 Adjustments
- 315 Page 388
- 318 Page 389
- 319 Page 390
- 321 Page 391
- 323 Page 392
- 325 Page 393
- 328 Timing Belt Tensioner
- 328 Component Information
- 328 Adjustments
- 330 Timing Cover
- 330 Component Information
- 330 Service and Repair
- 331 Page 400
- 334 Tune-up and Engine Performance Checks
- 334 Fuel Pressure
- 334 System Information
- 334 Specifications
- 336 Air/Fuel Mixture
- 336 System Information
- 336 Technical Service Bulletins
- 336 By Symptom for Air/Fuel Mixture:
- 336 140884
- 336 Jan
- 336 84
- 336 Propane Idle Set - Procedure
- 337 Page 413
- 339 Page 414
- 341 Page 415
- 343 Page 416
- 345 Page 417
- 348 All Technical Service Bulletins for Air/Fuel Mixture:
- 348 140884
- 348 Jan
- 348 84
- 348 Propane Idle Set - Procedure
- 349 Page 423
- 351 Page 424
- 353 Page 425
- 355 Page 426
- 357 Page 427
- 360 Idle Speed
- 360 System Information
- 360 Technical Service Bulletins
- 360 By Symptom:
- 360 140884
- 360 Jan
- 360 84
- 360 Propane Idle Set - Procedure
- 361 Page 436
- 363 Page 437
- 365 Page 438
- 367 Page 439
- 369 Page 440
- 372 All Technical Service Bulletins for Idle Speed:
- 372 142084
- 372 May
- 372 84
- 372 Engine Specifications - Manual Corrections
- 373 Page 446
- 376 141984
- 376 May
- 376 84
- 376 Carburetor - Idle Speed Adjustment on A/C Install
- 377 Page 451
- 379 Page 452
- 381 Page 453
- 383 Page 454
- 386 140884
- 386 Jan
- 386 84
- 386 Propane Idle Set - Procedure
- 387 Page 459
- 389 Page 460
- 391 Page 461
- 393 Page 462
- 395 Page 463
- 398 All Other Service Bulletins for Idle Speed:
- 398 142084
- 398 May
- 398 84
- 398 Engine Specifications - Manual Corrections
- 399 Page 469
- 402 141984
- 402 May
- 402 84
- 402 Carburetor - Idle Speed Adjustment on A/C Install
- 403 Page 474
- 405 Page 475
- 407 Page 476
- 409 Page 477
- 412 Page 478
- 414 Firing Order
- 414 Component Information
- 414 Specifications
- 416 Ignition Timing
- 416 Timing Marks and Indicators
- 416 System Information
- 416 Diagrams
- 417 Page 486
- 420 Distributor, Ignition
- 420 Vacuum Advance Unit <--> [Distributor Advance Unit]
- 420 Component Information
- 420 Specifications
- 420 Electrical Specifications
- 422 Page 492
- 424 Spark Plug
- 424 Component Information
- 424 Technical Service Bulletins
- 424 Customer Interest for Spark Plug:
- 424 181788
- 424 Oct
- 424 88
- 424 Spark Plugs - Oil Fouling/Misfire on Hard Acceleration
- 425 Page 501
- 427 Page 502
- 429 Page 503
- 432 All Technical Service Bulletins for Spark Plug:
- 432 181788
- 432 Oct
- 432 88
- 1 Spark Plugs - Oil Fouling/Misfire on Hard Acceleration
- 433 Page 509
- 435 Page 510
- 437 Page 511
- 440 Page 512
- 442 Compression Check
- 442 System Information
- 442 Specifications
- 444 Valve Clearance
- 444 System Information
- 444 Specifications
- 446 Page 519
- 448 Water Pump
- 448 Component Information
- 448 Service and Repair
- 450 Cooling System
- 450 Coolant
- 450 Component Information
- 450 Technical Service Bulletins
- 450 Engine Coolant - Recycling Recommendations
- 452 Page 528
- 454 Coolant Line/Hose
- 454 Component Information
- 454 Technical Service Bulletins
- 454 Carburetor Coolant Hose - Installation Procedure
- 456 Engine - Coolant Temperature Sensor/Switch
- 456 Coolant Temperature Sensor/Switch (For Computer)
- 456 Component Information
- 456 Specifications
- 458 Heater Core
- 458 Component Information
- 458 Service and Repair
- 460 Sensors and Switches - Cooling System
- 460 Engine - Coolant Temperature Sensor/Switch
- 460 Coolant Temperature Sensor/Switch (For Computer)
- 460 Component Information
- 460 Specifications
- 462 Water Pump
- 462 Component Information
- 462 Service and Repair
- 464 Exhaust System
- 464 Catalytic Converter
- 464 Component Information
- 464 Description and Operation
- 466 Exhaust Manifold
- 466 Component Information
- 466 Specifications
- 468 Powertrain Management
- 468 Relays and Modules - Powertrain Management
- 468 Relays and Modules - Computers and Control Systems
- 468 Powertrain Control Module <--> [Engine Control Module]
- 468 Component Information
- 468 Locations
- 470 Relays and Modules - Fuel Delivery and Air Induction
- 470 Throttle Control Vacuum Motor <--> [Engine Speed Governor Control Module]
- 470 Component Information
- 470 Locations
- 472 Sensors and Switches - Powertrain Management
- 472 Sensors and Switches - Computers and Control Systems
- 472 Coolant Temperature Sensor/Switch (For Computer)
- 472 Component Information
- 472 Specifications
- 474 Sensors and Switches - Ignition System
- 474 Ignition Switch
- 474 Component Information
- 474 Service and Repair
- 476 Tune-up and Engine Performance Checks
- 476 Fuel Pressure
- 476 System Information
- 476 Specifications
- 478 Air/Fuel Mixture
- 478 System Information
- 478 Technical Service Bulletins
- 478 By Symptom for Air/Fuel Mixture:
- 478 140884
- 478 Jan
- 478 84
- 478 Propane Idle Set - Procedure
- 479 Page 586
- 481 Page 587
- 483 Page 588
- 485 Page 589
- 487 Page 590
- 490 All Technical Service Bulletins for Air/Fuel Mixture:
- 490 140884
- 490 Jan
- 490 84
- 490 Propane Idle Set - Procedure
- 491 Page 596
- 493 Page 597
- 495 Page 598
- 497 Page 599
- 499 Page 600
- 502 Idle Speed
- 502 System Information
- 502 Technical Service Bulletins
- 502 By Symptom:
- 502 140884
- 502 Jan
- 502 84
- 502 Propane Idle Set - Procedure
- 503 Page 609
- 505 Page 610
- 507 Page 611
- 509 Page 612
- 511 Page 613
- 514 All Technical Service Bulletins for Idle Speed:
- 514 142084
- 514 May
- 514 84
- 514 Engine Specifications - Manual Corrections
- 515 Page 619
- 518 141984
- 518 May
- 518 84
- 518 Carburetor - Idle Speed Adjustment on A/C Install
- 519 Page 624
- 521 Page 625
- 523 Page 626
- 525 Page 627
- 528 140884
- 528 Jan
- 528 84
- 528 Propane Idle Set - Procedure
- 529 Page 632
- 531 Page 633
- 533 Page 634
- 535 Page 635
- 537 Page 636
- 540 All Other Service Bulletins for Idle Speed:
- 540 142084
- 540 May
- 540 84
- 540 Engine Specifications - Manual Corrections
- 541 Page 642
- 544 141984
- 544 May
- 544 84
- 544 Carburetor - Idle Speed Adjustment on A/C Install
- 545 Page 647
- 547 Page 648
- 549 Page 649
- 551 Page 650
- 554 Page 651
- 556 Firing Order
- 556 Component Information
- 556 Specifications
- 558 Ignition Timing
- 558 Timing Marks and Indicators
- 558 System Information
- 558 Diagrams
- 559 Page 659
- 562 Distributor, Ignition
- 562 Vacuum Advance Unit <--> [Distributor Advance Unit]
- 562 Component Information
- 562 Specifications
- 562 Electrical Specifications
- 564 Page 665
- 566 Spark Plug
- 566 Component Information
- 566 Technical Service Bulletins
- 566 Customer Interest for Spark Plug:
- 566 181788
- 566 Oct
- 566 88
- 566 Spark Plugs - Oil Fouling/Misfire on Hard Acceleration
- 567 Page 674
- 569 Page 675
- 571 Page 676
- 574 All Technical Service Bulletins for Spark Plug:
- 574 181788
- 574 Oct
- 574 88
- 574 Spark Plugs - Oil Fouling/Misfire on Hard Acceleration
- 575 Page 682
- 577 Page 683
- 579 Page 684
- 582 Page 685
- 584 Compression Check
- 584 System Information
- 584 Specifications
- 586 Valve Clearance
- 586 System Information
- 586 Specifications
- 588 Page 692
- 590 Computers and Control Systems
- 590 Coolant Temperature Sensor/Switch (For Computer)
- 590 Component Information
- 590 Specifications
- 592 Powertrain Control Module <--> [Engine Control Module]
- 592 Component Information
- 592 Locations
- 594 Idle Up Control Valve
- 594 Component Information
- 594 Description and Operation
- 596 Page 703
- 598 Information Bus
- 598 Component Information
- 598 Testing and Inspection
- 598 Diagnostic Trouble Code Descriptions
- 600 Page 708
- 602 Relays and Modules - Computers and Control Systems
- 602 Powertrain Control Module <--> [Engine Control Module]
- 602 Component Information
- 602 Locations
- 604 Sensors and Switches - Computers and Control Systems
- 604 Coolant Temperature Sensor/Switch (For Computer)
- 604 Component Information
- 604 Specifications
- 606 Emission Control Systems
- 606 Secondary Air Supply <--> [Air Injection]
- 606 Air Diverter Valve
- 606 Component Information
- 606 Description and Operation
- 608 Catalytic Converter
- 608 Component Information
- 608 Description and Operation
- 610 Slow Cut Solenoid Valve <--> [Deceleration Valve]
- 610 Component Information
- 610 Description and Operation
- 611 Page 728
- 614 Page 729
- 616 Evaporative Emissions System
- 616 Evaporative Emission Control Canister
- 616 Component Information
- 616 Locations
- 616 Evaporative Emission Control Canister
- 618 Page 735
- 620 Liquid Vapor Separator, Evaporative System
- 620 Component Information
- 620 Locations
- 622 Exhaust Gas Recirculation
- 622 EGR Valve
- 622 Component Information
- 622 Locations
- 624 Positive Crankcase Ventilation
- 624 Component Information
- 624 Description and Operation
- 626 Page 746
- 628 Thermostatic Air Cleaner
- 628 Component Information
- 628 Description and Operation
- 630 Page 750
- 632 Fuel Delivery and Air Induction
- 632 Fuel Pressure
- 632 System Information
- 632 Specifications
- 634 Idle Speed
- 634 System Information
- 634 Technical Service Bulletins
- 634 By Symptom:
- 634 140884
- 634 Jan
- 634 84
- 634 Propane Idle Set - Procedure
- 635 Page 763
- 637 Page 764
- 639 Page 765
- 641 Page 766
- 643 Page 767
- 646 All Technical Service Bulletins for Idle Speed:
- 646 142084
- 646 May
- 646 84
- 646 Engine Specifications - Manual Corrections
- 647 Page 773
- 650 141984
- 650 May
- 650 84
- 650 Carburetor - Idle Speed Adjustment on A/C Install
- 651 Page 778
- 653 Page 779
- 655 Page 780
- 657 Page 781
- 660 140884
- 660 Jan
- 660 84
- 660 Propane Idle Set - Procedure
- 661 Page 786
- 663 Page 787
- 665 Page 788
- 667 Page 789
- 669 Page 790
- 672 All Other Service Bulletins for Idle Speed:
- 672 142084
- 672 May
- 672 84
- 672 Engine Specifications - Manual Corrections
- 673 Page 796
- 676 141984
- 676 May
- 676 84
- 676 Carburetor - Idle Speed Adjustment on A/C Install
- 677 Page 801
- 679 Page 802
- 681 Page 803
- 683 Page 804
- 686 Page 805
- 688 Air/Fuel Mixture
- 688 System Information
- 688 Technical Service Bulletins
- 688 By Symptom for Air/Fuel Mixture:
- 688 140884
- 688 Jan
- 688 84
- 688 Propane Idle Set - Procedure
- 689 Page 814
- 691 Page 815
- 693 Page 816
- 695 Page 817
- 697 Page 818
- 700 All Technical Service Bulletins for Air/Fuel Mixture:
- 700 140884
- 700 Jan
- 700 84
- 700 Propane Idle Set - Procedure
- 701 Page 824
- 703 Page 825
- 705 Page 826
- 707 Page 827
- 709 Page 828
- 712 Altitude Compensator
- 712 Component Information
- 712 Diagrams
- 714 Page 832
- 716 Carburetor
- 716 Carburetor Jet
- 716 Component Information
- 716 Technical Service Bulletins
- 716 High Altitude Conversion Packages
- 717 Page 838
- 719 Page 839
- 721 Page 840
- 724 Dashpot
- 724 Component Information
- 724 Locations
- 726 Fuel
- 726 Component Information
- 726 Technical Service Bulletins
- 726 Fuel - Alcohol Fuel Recommendations
- 727 Page 848
- 730 Fuel Pressure Control Solenoid
- 730 Component Information
- 730 Locations
- 732 Fuel Pump
- 732 Fuel Pressure
- 732 System Information
- 732 Specifications
- 734 Fuel Shut-off Solenoid
- 734 Component Information
- 734 Locations
- 736 Throttle Control Vacuum Motor <--> [Engine Speed Governor Control Module]
- 736 Component Information
- 736 Locations
- 738 Idle Speed Control (Linkage)
- 738 Component Information
- 738 Adjustments
- 740 Idle Up Control Valve
- 740 Component Information
- 740 Description and Operation
- 742 Page 868
- 744 Relays and Modules - Fuel Delivery and Air Induction
- 744 Throttle Control Vacuum Motor <--> [Engine Speed Governor Control Module]
- 744 Component Information
- 744 Locations
- 746 Rollover/Pressure Relief Valve <--> [Rollover Valve, Fuel Tank]
- 746 Component Information
- 746 Locations
- 748 Ignition System
- 748 Firing Order
- 748 Component Information
- 748 Specifications
- 750 Ignition Timing
- 750 Timing Marks and Indicators
- 750 System Information
- 750 Diagrams
- 751 Page 884
- 754 Distributor, Ignition
- 754 Vacuum Advance Unit <--> [Distributor Advance Unit]
- 754 Component Information
- 754 Specifications
- 754 Electrical Specifications
- 756 Page 890
- 758 Pick-Up Coil, Ignition
- 758 Component Information
- 758 Specifications
- 760 Sensors and Switches - Ignition System
- 760 Ignition Switch
- 760 Component Information
- 760 Service and Repair
- 762 Spark Plug
- 762 Component Information
- 762 Technical Service Bulletins
- 762 Customer Interest for Spark Plug:
- 762 181788
- 762 Oct
- 762 88
- 762 Spark Plugs - Oil Fouling/Misfire on Hard Acceleration
- 763 Page 906
- 765 Page 907
- 767 Page 908
- 770 All Technical Service Bulletins for Spark Plug:
- 770 181788
- 770 Oct
- 770 88
- 770 Spark Plugs - Oil Fouling/Misfire on Hard Acceleration
- 771 Page 914
- 773 Page 915
- 775 Page 916
- 778 Page 917
- 780 Spark Control System <--> [Thermal Vacuum Valve, Vacuum/Dist. Advance]
- 780 Component Information
- 780 Description and Operation
- 782 Transmission and Drivetrain
- 782 Automatic Transmission/Transaxle
- 782 Case, A/T
- 782 Component Information
- 782 Technical Service Bulletins
- 782 Transmission Vent Assembly - Relocation
- 783 Page 927
- 786 Fluid - A/T
- 786 Component Information
- 786 Technical Service Bulletins
- 786 Automatic Transmission - New Fluid Type
- 788 Specifications
- 788 Transaxle/Transmission - Automatic
- 790 Page 934
- 792 Clutch, M/T
- 792 Clutch Pedal Assembly
- 792 Component Information
- 792 Adjustments
- 793 Page 939
- 795 Page 940
- 798 Clutch Switch
- 798 Component Information
- 798 Locations
- 800 Pilot Bearing
- 800 Component Information
- 800 Technical Service Bulletins
- 800 Clutch Splines & Pilot Bushing - Lubrication
- 802 Pressure Plate
- 802 Component Information
- 802 Specifications
- 804 Differential Assembly
- 804 Differential Carrier
- 804 Carrier Bearings
- 804 Component Information
- 804 Adjustments
- 805 Page 956
- 808 Fluid - Differential
- 808 Component Information
- 808 Specifications
- 810 Pinion Bearing, Differential
- 810 Component Information
- 810 Adjustments
- 812 Pinion Gear, Differential
- 812 Component Information
- 812 Adjustments
- 813 Page 966
- 816 Ring Gear <--> [Ring Gear, Differential]
- 816 Component Information
- 816 Adjustments
- 818 Drive Axles, Bearings and Joints
- 818 Axle Shaft Assembly
- 818 Axle Shaft
- 818 Component Information
- 818 Service and Repair
- 818 Constant Velocity Type Axle Shaft Assembly
- 819 Page 976
- 821 Page 977
- 824 Page 978
- 825 Page 979
- 827 Page 980
- 830 Wheel Bearing
- 830 Component Information
- 830 Adjustments
- 832 Service and Repair
- 832 Removal
- 833 Page 986
- 836 Page 987
- 837 Page 988
- 839 Page 989
- 842 Page 990
- 843 Page 991
- 846 Wheel Hub
- 846 Axle Nut
- 846 Component Information
- 846 Technical Service Bulletins
- 846 Rear Axle Shaft - Retaining Nut Lock Washers
- 848 Wheel Hub (Locking)
- 848 Component Information
- 848 Technical Service Bulletins
- 848 Automatic Locking Hubs - Racheting Noise
- 850 Flywheel
- 850 Component Information
- 850 Specifications
- 852 Manual Transmission/Transaxle
- 852 Case, M/T
- 852 Component Information
- 852 Technical Service Bulletins
- 852 Transmission Vent Assembly - Relocation
- 853 Page 1009
- 856 Fluid - M/T
- 856 Component Information
- 856 Specifications
- 858 Input Shaft, M/T
- 858 Component Information
- 858 Technical Service Bulletins
- 858 Clutch Splines & Pilot Bushing - Lubrication
- 860 Transfer Case
- 860 Fluid - Transfer Case
- 860 Component Information
- 860 Specifications
- 862 Shift Fork, Transfer Case
- 862 Component Information
- 862 Technical Service Bulletins
- 862 Transfer Case Shift Lever - Redesigned
- 1 Page 1025
- 866 Shifter Transfer Case
- 866 Component Information
- 866 Technical Service Bulletins
- 866 Transfer Case Shift Lever - Redesigned
- 867 Page 1030
- 870 Brakes and Traction Control
- 870 Disc Brake System
- 870 Brake Caliper
- 870 Component Information
- 870 Service and Repair
- 870 Sliding Type Caliper
- 871 Page 1037
- 874 Page 1038
- 875 Page 1039
- 878 Brake Disc <--> [Brake Rotor/Disc]
- 878 Component Information
- 878 Specifications
- 880 Drum Brake System
- 880 Brake Drum
- 880 Component Information
- 880 Specifications
- 882 Page 1047
- 884 Brake Shoe
- 884 Component Information
- 884 Diagrams
- 886 Page 1051
- 888 Hydraulic System, Brakes
- 888 Brake Caliper
- 888 Component Information
- 888 Service and Repair
- 888 Sliding Type Caliper
- 889 Page 1057
- 892 Page 1058
- 893 Page 1059
- 896 Brake Master Cylinder
- 896 Component Information
- 896 Specifications
- 898 Page 1063
- 900 Parking Brake System
- 900 System Information
- 900 Adjustments
- 902 Power Booster <--> [Power Brake Assist]
- 902 Vacuum Brake Booster
- 902 Component Information
- 902 Service and Repair
- 904 Starting and Charging
- 904 Sensors and Switches - Starting and Charging
- 904 Clutch Switch
- 904 Component Information
- 904 Locations
- 906 Ignition Switch
- 906 Component Information
- 906 Service and Repair
- 908 Neutral Safety Switch
- 908 Component Information
- 908 Service and Repair
- 910 Relays and Modules - Starting and Charging
- 910 Starter Relay
- 910 Component Information
- 910 Locations
- 912 Battery
- 912 Component Information
- 912 Technical Service Bulletins
- 912 Battery - Checking Procedure Revision
- 913 Page 1090
- 916 Specifications
- 916 Electrical Specifications
- 918 Page 1093
- 920 Charging System
- 920 Generator <--> [Alternator]
- 920 Component Information
- 920 Specifications
- 922 Testing and Inspection
- 922 Charging Voltage Test
- 924 Page 1100
- 926 Voltage Regulator
- 926 Component Information
- 926 Specifications
- 928 Starting System
- 928 Clutch Switch
- 928 Component Information
- 928 Locations
- 930 Ignition Switch
- 930 Component Information
- 930 Service and Repair
- 932 Neutral Safety Switch
- 932 Component Information
- 932 Service and Repair
- 934 Starter Motor
- 934 Component Information
- 934 Specifications
- 936 Page 1117
- 938 Starter Relay
- 938 Component Information
- 938 Locations
- 940 Power and Ground Distribution
- 940 Fuse Block
- 940 Component Information
- 940 Diagrams
- 940 Diagram Information and Instructions
- 942 Page 1126
- 944 Power and Ground Distribution
- 944 Fuse Block
- 944 Component Information
- 944 Diagrams
- 944 Diagram Information and Instructions
- 946 Page 1132
- 948 Steering and Suspension
- 948 Alignment
- 948 System Information
- 948 Technical Service Bulletins
- 948 Alignment - Caster Adjustment Manual Revision
- 950 Page 1138
- 952 Service and Repair
- 952 Camber
- 954 Page 1141
- 956 Page 1142
- 958 Page 1143
- 960 Steering
- 960 Ball Stud <--> [Front Steering Knuckle]
- 960 Component Information
- 960 Service and Repair
- 962 Steering Column
- 962 Component Information
- 962 Diagrams
- 964 Steering Gear
- 964 Component Information
- 964 Service and Repair
- 964 Manual Steering Gear Service
- 965 Page 1155
- 968 Page 1156
- 969 Page 1157
- 971 Page 1158
- 973 Page 1159
- 976 Page 1160
- 978 Suspension
- 978 Ball Joint
- 978 Component Information
- 978 Service and Repair
- 978 Lower Ball Joint Replacement
- 980 Page 1166
- 982 Control Arm
- 982 Component Information
- 982 Service and Repair
- 983 Page 1170
- 985 Page 1171
- 987 Page 1172
- 990 Cross-Member
- 990 Component Information
- 990 Service and Repair
- 992 Ball Stud <--> [Front Steering Knuckle]
- 992 Component Information
- 992 Service and Repair
- 994 Stabilizer Bar, Sway Control
- 994 Component Information
- 994 Service and Repair
- 994 Front
- 996 Page 1183
- 998 Suspension Spring ( Coil / Leaf )
- 998 Component Information
- 998 Service and Repair
- 998 Front Coil Spring Replace
- 1000 Page 1188
- 1002 Suspension Strut / Shock Absorber
- 1002 Component Information
- 1002 Service and Repair
- 1002 Front
- 1004 Page 1193
- 1006 Wheel Bearing
- 1006 Component Information
- 1006 Adjustments
- 1008 Service and Repair
- 1008 Removal
- 1009 Page 1199
- 1012 Page 1200
- 1013 Page 1201
- 1015 Page 1202
- 1018 Page 1203
- 1019 Page 1204
- 1022 Wheel Hub
- 1022 Axle Nut
- 1022 Component Information
- 1022 Technical Service Bulletins
- 1022 Rear Axle Shaft - Retaining Nut Lock Washers
- 1024 Wheel Hub (Locking)
- 1024 Component Information
- 1024 Technical Service Bulletins
- 1024 Automatic Locking Hubs - Racheting Noise
- 1026 Wheels and Tires
- 1026 Wheel Bearing
- 1026 Component Information
- 1026 Adjustments
- 1028 Service and Repair
- 1028 Removal
- 1029 Page 1220
- 1032 Page 1221
- 1033 Page 1222
- 1035 Page 1223
- 1038 Page 1224
- 1039 Page 1225
- 1042 Wheel Hub
- 1042 Axle Nut
- 1042 Component Information
- 1042 Technical Service Bulletins
- 1042 Rear Axle Shaft - Retaining Nut Lock Washers
- 1044 Wheel Hub (Locking)
- 1044 Component Information
- 1044 Technical Service Bulletins
- 1044 Automatic Locking Hubs - Racheting Noise
- 1046 Heating and Air Conditioning
- 1046 Blower Motor
- 1046 Component Information
- 1046 Service and Repair
- 1048 Heater Core
- 1048 Component Information
- 1048 Service and Repair
- 1050 Refrigerant
- 1050 Component Information
- 1050 Specifications
- 1050 Capacity Specifications
- 1052 Page 1246
- 1054 Restraint Systems
- 1054 Seat Belt Systems
- 1054 Seat Belt Extension
- 1054 Component Information
- 1054 Technical Service Bulletins
- 1054 Seat Belt Extender - Types/Identification
- 1055 Page 1253
- 1058 Seat Belt Reminder Buzzer
- 1058 Component Information
- 1058 Technical Service Bulletins
- 1058 Customer Interest for Seat Belt Reminder Buzzer:
- 1058 082684
- 1058 Nov
- 1058 84
- 1058 Radio - Speaker Noise When Warning Buzzers Are ON
- 1060 All Technical Service Bulletins for Seat Belt Reminder Buzzer:
- 1060 082684
- 1060 Nov
- 1060 84
- 1060 Radio - Speaker Noise When Warning Buzzers Are ON
- 1062 Seat Belt Warning Timer
- 1062 Component Information
- 1062 Locations
- 1064 Accessories and Optional Equipment
- 1064 Antenna
- 1064 Component Information
- 1064 Technical Service Bulletins
- 1064 Radio - No AM/Weak FM Reception
- 1065 Page 1275
- 1068 Radio, Stereo, and Compact Disc
- 1068 Radio/Stereo
- 1068 Component Information
- 1068 Technical Service Bulletins
- 1068 Radio - No AM/Weak FM Reception
- 1069 Page 1281
- 1072 Page 1282
- 1074 Towing / Trailer System
- 1074 Trailer Adapter Kit
- 1074 Component Information
- 1074 Technical Service Bulletins
- 1074 Trailer Tow Wiring/Components - Installation Cautions
- 1075 Page 1288
- 1078 Body and Frame
- 1078 Bumper
- 1078 Component Information
- 1078 Technical Service Bulletins
- 1078 Synthetic Resin Bumpers - Painting
- 1080 Frame
- 1080 Cross-Member
- 1080 Component Information
- 1080 Service and Repair
- 1082 Trailer Adapter Kit
- 1082 Component Information
- 1082 Technical Service Bulletins
- 1082 Trailer Tow Wiring/Components - Installation Cautions
- 1083 Page 1302
- 1086 Paint, Striping and Decals
- 1086 Paint
- 1086 System Information
- 1086 Technical Service Bulletins
- 1086 Synthetic Resin Bumpers - Painting
- 1088 Page 1308
- 1089 Page 1309
- 1091 Page 1310
- 1093 Page 1311
- 1095 Page 1312
- 1097 Page 1313
- 1100 Seats
- 1100 Component Information
- 1100 Technical Service Bulletins
- 1100 Upholstery - Cleaning Procedure
- 1102 Cruise Control
- 1102 Clutch Switch, Cruise Control
- 1102 Component Information
- 1102 Locations
- 1104 Sensors and Switches - Cruise Control
- 1104 Clutch Switch, Cruise Control
- 1104 Component Information
- 1104 Locations
- 1106 Instrument Panel, Gauges and Warning Indicators
- 1106 Instrument Cluster / Carrier
- 1106 Component Information
- 1106 Service and Repair
- 1108 Odometer
- 1108 Component Information
- 1108 Technical Service Bulletins
- 1108 Instrument Cluster - Odometer Memory Chip Service
- 1109 Page 1334
- 1111 Page 1335
- 1114 Seat Belt Reminder Buzzer
- 1114 Component Information
- 1114 Technical Service Bulletins
- 1114 Customer Interest for Seat Belt Reminder Buzzer:
- 1114 082684
- 1114 Nov
- 1114 84
- 1114 Radio - Speaker Noise When Warning Buzzers Are ON
- 1116 All Technical Service Bulletins for Seat Belt Reminder Buzzer:
- 1116 082684
- 1116 Nov
- 1116 84
- 1 Radio - Speaker Noise When Warning Buzzers Are ON
- 1118 Volt Meter Gauge
- 1118 Component Information
- 1118 Technical Service Bulletins
- 1118 Voltmeter - Explanation for High Readings
- 1120 Lighting and Horns
- 1120 Brake Light Switch
- 1120 Component Information
- 1120 Service and Repair
- 1122 Hazard Warning Lamps
- 1122 Hazard Warning Flasher
- 1122 Component Information
- 1122 Locations
- 1124 Headlamp
- 1124 Headlamp Relay
- 1124 Component Information
- 1124 Locations
- 1126 Headlight Switch <--> [Headlamp Switch]
- 1126 Component Information
- 1126 Service and Repair
- 1128 Horn
- 1128 Component Information
- 1128 Technical Service Bulletins
- 1128 Customer Interest for Horn:
- 1128 082284
- 1128 Aug
- 1128 84
- 1128 Horn - Intermittently Inoperative
- 1130 All Technical Service Bulletins for Horn:
- 1130 082284
- 1130 Aug
- 1130 84
- 1130 Horn - Intermittently Inoperative
- 1132 Relays and Modules - Lighting and Horns
- 1132 Headlamp Relay
- 1132 Component Information
- 1132 Locations
- 1134 Sensors and Switches - Lighting and Horns
- 1134 Brake Light Switch
- 1134 Component Information
- 1134 Service and Repair
- 1136 Headlight Switch <--> [Headlamp Switch]
- 1136 Component Information
- 1136 Service and Repair
- 1138 Turn Signal Switch
- 1138 Component Information
- 1138 Service and Repair
- 1140 Turn Signals
- 1140 Turn Signal Flasher
- 1140 Component Information
- 1140 Locations
- 1142 Turn Signal Switch
- 1142 Component Information
- 1142 Service and Repair
- 1144 Wiper and Washer Systems
- 1144 Relays and Modules - Wiper and Washer Systems
- 1144 Wiper Relay
- 1144 Component Information
- 1144 Locations
- 1146 Wiper Blade
- 1146 Component Information
- 1146 Technical Service Bulletins
- 1146 Customer Interest for Wiper Blade:
- 1146 23-014-06
- 1146 Mar
- 1146 06
- 1146 Wipers/Washers - Wipers Smear or Streak Windshield
- 1148 All Technical Service Bulletins for Wiper Blade:
- 1148 23-014-06
- 1148 Mar
- 1148 06
- 1148 Wipers/Washers - Wipers Smear or Streak Windshield
- 1150 Windshield Wiper Transmission <--> [Wiper Gear Box]
- 1150 Component Information
- 1150 Service and Repair
- 1152 Wiper Motor
- 1152 Component Information
- 1152 Service and Repair
- 1154 Wiper Relay
- 1154 Component Information
- 1154 Locations