- Computers & electronics
- Audio & home theatre
- Audio amplifiers
- Cisco
- Compact Reverse Transmitters 9008x with FP, DFB or CWDM Lasers
- User manual
Cisco Compact Reverse Transmitters 9008x with FP, DFB or CWDM Lasers Broadband Node Installation and Operation Guide
Add to My manuals110 Pages
advertisement
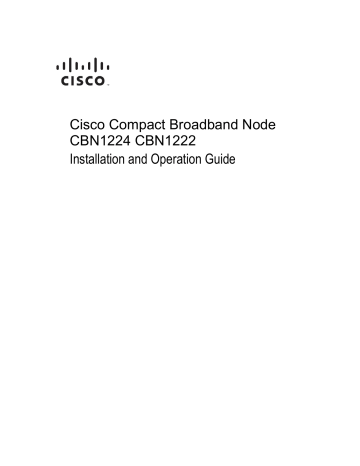
OL-30326-02
Cisco Compact Broadband Node
CBN1224 CBN1222
Installation and Operation Guide
For Your Safety
Explanation of Warning and Caution Icons
Avoid personal injury and product damage! Do not proceed beyond any symbol until you fully understand the indicated conditions.
The following warning and caution icons alert you to important information about the safe operation of this product:
You may find this symbol in the document that accompanies this product.
This symbol indicates important operating or maintenance instructions.
You may find this symbol affixed to the product. This symbol indicates a live terminal where a dangerous voltage may be present; the tip of the flash points
to the terminal device.
You may find this symbol affixed to the product. This symbol indicates a
protective ground terminal.
chassis terminal (normally used for equipotential bonding).
You may find this symbol affixed to the product. This symbol indicates an optional ground terminal (only used in some particular cases).
You may find this symbol affixed to the product. This symbol warns of a
potentially hot surface.
You may find this symbol affixed to the product and in this document. This symbol indicates an infrared laser that transmits intensity-modulated light and emits invisible laser radiation or an LED that transmits intensity-
modulated light.
Important
Please read this entire guide. If this guide provides installation or operation instructions, give particular attention to all safety statements included in this guide.
Notices
Trademark Acknowledgments
Cisco and the Cisco logo are trademarks or registered trademarks of Cisco and/or its affiliates in the U.S. and other countries. To view a list of cisco trademarks, go to this
URL: www.cisco.com/go/trademarks.
Third party trademarks mentioned are the property of their respective owners.
The use of the word partner does not imply a partnership relationship between
Cisco and any other company. (1110R)
Publication Disclaimer
Cisco Systems, Inc. assumes no responsibility for errors or omissions that may appear in this publication. We reserve the right to change this publication at any time without notice. This document is not to be construed as conferring by implication, estoppel, or otherwise any license or right under any copyright or patent, whether or not the use of any information in this document employs an invention claimed in any existing or later issued patent.
Copyright
© 2016 Cisco and/or its affiliates. All rights reserved. Printed in the United States of
America.
Information in this publication is subject to change without notice. No part of this publication may be reproduced or transmitted in any form, by photocopy, microfilm, xerography, or any other means, or incorporated into any information retrieval system, electronic or mechanical, for any purpose, without the express permission of Cisco Systems, Inc.
Contents
Important Safety Instructions
Laser Safety
Introduction
General Information
Installation
Operating
Customer Support Information
Glossary
Index
26
44
65
95
v
xv
19
97
105
iii
Important Safety Instructions
Read and Retain Instructions
Carefully read all safety and operating instructions before operating this equipment, and retain them for future reference.
Follow Instructions and Heed Warnings
Follow all operating and use instructions. Pay attention to all warnings and cautions in the operating instructions, as well as those that are affixed to this equipment.
Terminology
The terms defined below are used in this document. The definitions given are based on those found in safety standards.
Service Personnel - The term service personnel applies to trained and qualified individuals who are allowed to install, replace, or service electrical equipment. The service personnel are expected to use their experience and technical skills to avoid possible injury to themselves and others due to hazards that exist in service and restricted access areas.
User and Operator - The terms user and operator apply to persons other than service personnel.
Ground(ing) and Earth(ing) - The terms ground(ing) and earth(ing) are synonymous.
This document uses ground(ing) for clarity, but it can be interpreted as having the same meaning as earth(ing).
Electric Shock Hazard
This equipment meets applicable safety standards.
WARNING:
To reduce risk of electric shock, perform only the instructions that are included in the operating instructions. Refer all servicing to qualified service
personnel only. v
vi
Electric shock can cause personal injury or even death. Avoid direct contact with dangerous voltages at all times.
Know the following safety warnings and guidelines:
Only qualified service personnel are allowed to perform equipment installation or replacement.
Only qualified service personnel are allowed to remove chassis covers and access any of the components inside the chassis.
Equipment Placement
WARNING:
Avoid personal injury and damage to this equipment. An unstable mounting
surface may cause this equipment to fall.
To protect against equipment damage or injury to personnel, comply with the following:
Install this equipment in a restricted access location (access restricted to service personnel).
Make sure the mounting surface or rack is stable and can support the size and weight of this equipment.
Strand (Aerial) Installation
CAUTION:
Be aware of the size and weight of strand-mounted equipment during the
installation operation.
Ensure that the strand can safely support the equipment’s weight.
Pedestal, Service Closet, Equipment Room or Underground Vault Installation
WARNING:
Avoid the possibility of personal injury. Ensure proper handling/lifting techniques are employed when working in confined spaces with heavy
equipment.
Ensure this equipment is securely fastened to the mounting surface or rack where necessary to protect against damage due to any disturbance and subsequent fall.
Ensure the mounting surface or rack is appropriately anchored according to manufacturer’s specifications.
Ensure the installation site meets the ventilation requirements given in the equipment’s data sheet to avoid the possibility of equipment overheating.
Ensure the installation site and operating environment is compatible with the equipment’s International Protection (IP) rating specified in the equipment’s data sheet.
Connecting to Utility AC Power
Important: If this equipment is a Class I equipment, it must be grounded.
If this equipment plugs into an outlet, the outlet must be near this equipment, and must be easily accessible.
Connect this equipment only to the power sources that are identified on the equipment-rating label, which is normally located close to the power inlet connector(s).
This equipment may have two power sources. Be sure to disconnect all power sources before working on this equipment.
If this equipment does not have a main power switch, the power cord connector serves as the disconnect device.
Always pull on the plug or the connector to disconnect a cable. Never pull on the cable itself.
Connection to Network Power Sources
Refer to this equipment’s specific installation instructions in this manual or in companion manuals in this series for connection to network ferro-resonant AC power sources.
AC Power Shunts
AC power shunts may be provided with this equipment.
Important: The power shunts (where provided) must be removed before installing modules into a powered housing. With the shunts removed, power surge to the components and RF-connectors is reduced. vii
viii
CAUTION:
RF connectors and housing seizure assemblies can be damaged if shunts are not removed from the equipment before installing or removing modules from
the housing.
Grounding (Utility AC Powered Equipment in Pedestals, Service Closets, etc.)
This section provides instructions for verifying that the equipment is properly grounded.
Safety Plugs (USA Only)
This equipment is equipped with either a 3-terminal (grounding-type) safety plug or a 2-terminal (polarized) safety plug. The wide blade or the third terminal is provided for safety. Do not defeat the safety purpose of the grounding-type or polarized safety plug.
To properly ground this equipment, follow these safety guidelines:
Grounding-Type Plug - For a 3-terminal plug (one terminal on this plug is a protective grounding pin), insert the plug into a grounded mains, 3-terminal outlet.
Note: This plug fits only one way. If this plug cannot be fully inserted into the outlet, contact an electrician to replace the obsolete 3-terminal outlet.
Polarized Plug - For a 2-terminal plug (a polarized plug with one wide blade and one narrow blade), insert the plug into a polarized mains, 2-terminal outlet in which one socket is wider than the other.
Note: If this plug cannot be fully inserted into the outlet, try reversing the plug.
If the plug still fails to fit, contact an electrician to replace the obsolete 2-terminal outlet.
Grounding Terminal
If this equipment is equipped with an external grounding terminal, attach one end of an 18-gauge wire (or larger) to the grounding terminal; then, attach the other end of the wire to a ground, such as a grounded equipment rack.
Safety Plugs (European Union)
Class I Mains Powered Equipment – Provided with a 3-terminal AC inlet and requires connection to a 3-terminal mains supply outlet via a 3-terminal power cord for proper connection to the protective ground.
Note: The equipotential bonding terminal provided on some equipment is not designed to function as a protective ground connection.
Class II Mains Powered Equipment – Provided with a 2-terminal AC inlet that may be connected by a 2-terminal power cord to the mains supply outlet. No connection to the protective ground is required as this class of equipment is provided with double or reinforced and/or supplementary insulation in addition to the basic insulation provided in Class I equipment.
Note: Class II equipment, which is subject to EN 50083-1, is provided with a chassis mounted equipotential bonding terminal. See the section titled
Equipotential Bonding for connection instructions.
Equipotential Bonding
If this equipment is equipped with an external chassis terminal marked with the IEC
60417-5020 chassis icon ( ), the installer should refer to CENELEC standard EN
50083-1 or IEC standard IEC 60728-11 for correct equipotential bonding connection instructions.
General Servicing Precautions
WARNING:
Avoid electric shock! Opening or removing this equipment’s cover may
expose you to dangerous voltages.
CAUTION:
These servicing precautions are for the guidance of qualified service personnel only. To reduce the risk of electric shock, do not perform any servicing other than that contained in the operating instructions unless you
are qualified to do so. Refer all servicing to qualified service personnel.
Be aware of the following general precautions and guidelines:
Servicing - Servicing is required when this equipment has been damaged in any way, such as power supply cord or plug is damaged, liquid has been spilled or objects have fallen into this equipment, this equipment has been exposed to rain or moisture, does not operate normally, or has been dropped.
Wristwatch and Jewelry - For personal safety and to avoid damage of this equipment during service and repair, do not wear electrically conducting objects such as a wristwatch or jewelry.
Lightning - Do not work on this equipment, or connect or disconnect cables, ix
x during periods of lightning.
Labels - Do not remove any warning labels. Replace damaged or illegible warning labels with new ones.
Covers - Do not open the cover of this equipment and attempt service unless instructed to do so in the instructions. Refer all servicing to qualified service personnel only.
Moisture - Do not allow moisture to enter this equipment.
Cleaning - Use a damp cloth for cleaning.
Safety Checks - After service, assemble this equipment and perform safety checks to ensure it is safe to use before putting it back into operation.
Electrostatic Discharge
Electrostatic discharge (ESD) results from the static electricity buildup on the human body and other objects. This static discharge can degrade components and cause failures.
Take the following precautions against electrostatic discharge:
Use an anti-static bench mat and a wrist strap or ankle strap designed to safely ground ESD potentials through a resistive element.
Keep components in their anti-static packaging until installed.
Avoid touching electronic components when installing a module.
Fuse Replacement
To replace a fuse, comply with the following:
Disconnect the power before changing fuses.
Identify and clear the condition that caused the original fuse failure.
Always use a fuse of the correct type and rating. The correct type and rating are indicated on this equipment.
Rating: Rated Voltage 250VAC, Rated Current 4A
Breaking capacity: UL: 10 In @ 250 VAC / 50 A @ 63 VDC
Type: T4AL
Batteries
This product may contain batteries. Special instructions apply regarding the safe use and disposal of batteries:
Safety
Insert batteries correctly. There may be a risk of explosion if the batteries are incorrectly inserted.
Do not attempt to recharge ‘disposable’ or ‘non-reusable’ batteries.
Please follow instructions provided for charging ‘rechargeable’ batteries.
Replace batteries with the same or equivalent type recommended by manufacturer.
Do not expose batteries to temperatures above 100°C (212°F).
Disposal
The batteries may contain substances that could be harmful to the environment
Recycle or dispose of batteries in accordance with the battery manufacturer’s instructions and local/national disposal and recycling regulations.
The batteries may contain perchlorate, a known hazardous substance, so special handling and disposal of this product might be necessary. For more information about perchlorate and best management practices for perchlorate-containing substance, see www.dtsc.ca.gov/hazardouswaste/perchlorate.
Modifications
This equipment has been designed and tested to comply with applicable safety, laser safety, and EMC regulations, codes, and standards to ensure safe operation in its intended environment. Refer to this equipment's data sheet for details about regulatory compliance approvals.
Do not make modifications to this equipment. Any changes or modifications could void the user’s authority to operate this equipment. xi
xii
Modifications have the potential to degrade the level of protection built into this equipment, putting people and property at risk of injury or damage. Those persons making any modifications expose themselves to the penalties arising from proven non-compliance with regulatory requirements and to civil litigation for compensation in respect of consequential damages or injury.
Accessories
Use only attachments or accessories specified by the manufacturer.
Electromagnetic Compatibility Regulatory Requirements
This equipment meets applicable electromagnetic compatibility (EMC) regulatory requirements. Refer to this equipment's data sheet for details about regulatory compliance approvals. EMC performance is dependent upon the use of correctly shielded cables of good quality for all external connections, except the power source, when installing this equipment.
Ensure compliance with cable/connector specifications and associated installation instructions where given elsewhere in this manual.
EMC Compliance Statements
Where this equipment is subject to USA FCC and/or Industry Canada rules, the following statements apply:
FCC Statement for Class A Equipment
This equipment has been tested and found to comply with the limits for a Class A digital device, pursuant to Part 15 of the FCC Rules. These limits are designed to provide reasonable protection against harmful interference when this equipment is operated in a commercial environment.
This equipment generates, uses, and can radiate radio frequency energy and, if not installed and used in accordance with the instruction manual, may cause harmful interference to radio communications. Operation of this equipment in a residential area is likely to cause harmful interference in which case users will be required to correct the interference at their own expense.
Industry Canada - Industrie Canadiene Statement
This apparatus complies with Canadian ICES-003.
Cet appareil est confome à la norme NMB-003 du Canada.
CENELEC/CISPR Statement with Respect to Class A Information Technology Equipment
This is a Class A equipment. In a domestic environment this equipment may cause radio interference in which case the user may be required to take adequate measures. xiii
Laser Safety
Introduction
This equipment contains an infrared laser that transmits intensity-modulated light and emits invisible radiation.
Warning: Radiation
WARNING:
Avoid personal injury! Use of controls, adjustments, or procedures other than those specified herein may result in hazardous radiation exposure.
Avoid personal injury! The laser light source on this equipment (if a transmitter) or the fiber cables connected to this equipment emit invisible laser radiation. Avoid direct exposure to the laser light source.
Avoid personal injury! Viewing the laser output (if a transmitter) or fiber cable with optical instruments (such as eye loupes, magnifiers, or
microscopes) may pose an eye hazard.
Do not apply power to this equipment if the fiber is unmated or unterminated.
Do not stare into an unmated fiber or at any mirror-like surface that could reflect light emitted from an unterminated fiber.
Do not view an activated fiber with optical instruments (e.g., eye loupes, magnifiers, microscopes).
Use safety-approved optical fiber cable to maintain compliance with applicable laser safety requirements.
Warning: Fiber Optic Cables
WARNING:
Avoid personal injury! Qualified service personnel may only perform the procedures in this manual. Wear safety glasses and use extreme caution when handling fiber optic cables, particularly during splicing or terminating operations. The thin glass fiber core at the center of the cable is fragile when exposed by the removal of cladding and buffer material. It easily fragments into glass splinters. Using tweezers, place splinters immediately in a sealed waste container and dispose of them safely in accordance with local
regulations. xv
Safe Operation for Software Controlling Optical Transmission Equipment
If this manual discusses software, the software described is used to monitor and/or control ours and other vendors’ electrical and optical equipment designed to transmit video, voice, or data signals. Certain safety precautions must be observed when operating equipment of this nature.
For equipment specific safety requirements, refer to the appropriate section of the equipment documentation.
For safe operation of this software, refer to the following warnings.
WARNING:
Ensure that all optical connections are complete or terminated before using this equipment to remotely control a laser device. An optical or laser device can pose a hazard to remotely located personnel when operated
without their knowledge.
Allow only personnel trained in laser safety to operate this software.
Otherwise, injuries to personnel may occur.
Restrict access of this software to authorized personnel only.
Install this software in equipment that is located in a restricted access area. xvi
Maximum Laser Power
The maximum laser power that can be produced through this product, due to misalignment or component failure, is 6 mW.
Laser Aperture Label
The following label is located on the node fiber tray cover. The end of the fiber represents the only laser aperture of this equipment.
Chassis Warning Label
The following labels are located on this equipment. xvii
1
Chapter 1
Introduction
Overview
This chapter introduces you to the 1.2 GHz Compact Broadband Node and describes its main components, configuration options, and accessories.
Purpose
This guide provides instructions for installing, configuring, setting up, and troubleshooting of the 1.2 GHz Compact Broadband Node.
Who Should Use This Document
This document is intended for authorized service personnel who have experience working with similar equipment. The service personnel should have appropriate background and knowledge to complete the procedures described in this document.
Qualified Personnel
WARNING:
Allow only qualified and skilled personnel to install, operate, maintain, and service this product. Otherwise, personal injury or equipment damage may occur.
Only appropriately qualified and skilled personnel should attempt to install, operate, maintain, and service this product.
19
Scope
This guide discusses the following topics.
Description of the 1.2 GHz Compact Broadband Node
Procedures for strand (aerial) and pedestal installation
Configuring the Node launch amplifier and major modules
Balancing the forward and reverse signal paths
Troubleshooting the 1.2 GHz Compact Broadband Node
Descriptions of configuration options and accessories
Document Version
This is the first release of this guide.
20
On Copyright
No part of this manual may be reproduced or communicated to the public by any means or in any form, or distributed by sale or otherwise, for any purpose, without the express prior written consent of CISCO.
CISCO assumes no responsibility for errors or omissions that may appear in this manual. This manual may not and shall not to be construed as conferring any license or right under any copyright or patent.
On Icons
Indicates information of assistance
Indicates condition that could cause confusion
Indicates an infrared laser that transmits intensity-modulated light and emits invisible laser radiation or an LED that transmits intensity-modulated light.
Informs about electrostatic discharge (ESD) damage
In General
CISCO warrants proper functioning of the CBN 1224 as long as it is operated in compliance with this manual.
CISCO warrants that the CBN 1224 meets applicable safety standards. The CBN 1224 has been designed and tested to comply with applicable safety, laser safety, and
EMC regulations, codes, and standards to ensure safe operation in its intended environment. As this is a Class B Information Technology Equipment it may cause radio interference (CENELEC Statement).
However CISCO shall not be held liable under the warranty or otherwise for any personal injury or equipment damage resulting from improper installation or operation of the CBN 1224. The same applies in case of any modifications or alterations performed by any third party to CISCO.
CISCO strongly recommends to read this manual before installing the CBN 1224.
21
22
On Inspection
CISCO recommends to inspect the CBN 1224 before installation. Should any problems arise during the inspection, CISCO advises contact with its sales office for assistance.
Retention of shipping boxes is advisable.
On Storage
The CBN 1224 can be stored without any degradation of parameters for a period of
18 months after manufacturing.
Standard atmospheric conditions of storage according to the IEC60068-2-48 norm: temperature 15 to 35°C, humidity 25 to 70%, pressure 860 to 1060hPa.
On Installation and Operation
Important: In order to reduce the risk of electric shock, it is advisable that:
Only qualified service personnel shall be allowed to perform installation or replacement as the installation must conform to all local codes and regulations.
Only qualified service personnel shall be allowed to remove chassis covers and access any of the components inside the chassis.
The protective grounding shall not be violated by using an extension cable, power cable, or autotransformer without a protective ground conductor.
Care shall be taken to maintain the protective grounding during service or repair and to re-establish the protective grounding before putting the CBN 1224 back into operation.
Important: In order to procure a proper installation site it is advisable that:
The protective ground lead of the building’s electrical installation complies with national and local requirements.
The installation site is dry, clean, and ventilated. The CBN 1224 must not contact water. The CBN 1224 must be operated in an environment as described in the
CBN 1224’s technical specifications to be found on this Product’s data sheet.
Important: In order to protect against damage or injury to personnel, it is advisable to:
Install the CBN 1224 in a restricted access location.
Do not install the CBN 1224 near any heat sources such as radiators, heat registers, stoves, or other heat-producing equipment.
Place the CBN 1224 close enough to a main AC outlet to accommodate the length of its power cord.
Route all power cords so as to avoid walking on, placing objects on, or leaning objects against them.
Use only with a cart, stand, tripod, bracket, or table specified by the manufacturer, or sold with the CBN 1224.
Make sure the mounting surface or rack is stable and can support the size and weight of the CBN 1224.
Anchor the mounting surface or rack according to manufacturer’s specifications.
Ensure the CBN 1224 is securely fastened to the mounting surface or rack where necessary to protect against damage due to any disturbance and subsequent fall.
On Warnings and Cautions
Electrostatic discharge
Electrostatic discharge (ESD) damage, which can occur when electronic cards or components are improperly handled, results in complete or intermittent failures. Electromagnetic interference (EMI) shielding and connectors are integral components of the carrier. Although the metal carrier helps to protect the board from ESD, it is advisable to use a preventive antistatic strap during handling.
Important: In order to prevent ESD damage it is advisable to:
Always use an ESD wrist or ankle strap and ensure that it makes good skin contact.
Connect the CBN 1224 end of the strap to an unfinished chassis surface.
Use any available ejector levers or captive installation screws when removing a component.
Handle carriers by available handles or edges only – avoid touching the printed circuit boards or connectors;
Place a removed circuit board component-side-up on an antistatic surface or in a static shielding container. If you plan to return the component to the manufacturer, immediately place it in a static shielding container;
23
24
Avoid contact between the printed circuit boards and clothing. The wrist strap only protects components from ESD voltages on the body; ESD voltages on clothing can still cause damage;
Never attempt to remove the printed circuit board from the metal carrier.
Radiation
The CBN 1224 contains an infrared laser transmitting intensity-modulated light and emitting invisible radiation. In order to avoid hazardous radiation exposure it is advisable to:
Do not apply power to the CBN 1224 if the fiber is unmated or unterminated.
Do not stare into an unmated fiber or at any mirror-like surface that could reflect light that is emitted from an unterminated fiber.
Do not view an activated fiber with optical instruments (e.g., eye loupes, magnifiers, microscopes).
Use safety-approved optical fiber cable to maintain compliance with applicable laser safety requirements.
Fiber Optic Cables
It is advisable to wear safety glasses and use extreme caution when handling fiber optic cables, particularly during splicing or terminating operations. The thin glass fiber core at the center of the cable is fragile when exposed by the removal of cladding and buffer material. It easily fragments into glass splinters.
Using tweezers, place splinters immediately in a sealed waste container and dispose of them safely in accordance with local regulations.
On Modification
It is not allowed to make modifications to the CBN 1224 on pain of losing authority to operate the unit.
Furthermore modifications may degrade the level of protection built into the CBN
1224, putting people and property at risk of injury or damage. Any Person, who performs any modifications, exposes him/herself to the penalties arising from proven non-compliance with regulatory requirements and to civil litigation for compensation in respect of consequential damages or injury.
In order to replace a fuse, it is advised to:
Disconnect the power before changing fuses.
Identify and clear the condition that caused the original fuse failure.
Use a fuse of the correct type and rating as indicated on the CBN 1224.
25
2
Chapter 2
General Information
26
Introduction
The CBN 1224 described in this document is a segmentable optical node 2x4.
This modern device with low power consumption is distinguished by a compact housing and can be used in various network applications.
This modular equipment may be installed in a standard HFC application as well as in Fiber Deep Networks.
Details of the node configuration required for each of these applications are described throughout this document.
The CBN 1224 meets CENELEC, EN 607-28-3, EN 50083-2, EN 60728-11 requirements and ensures electromagnetic compatibility and user safety.
This symbol on the device indicates that the device should not be disposed of as normal household garbage. Do not dispose of your device as unsorted municipal waste. The device should be handed over to a certified collection point for recycling or proper disposal at the end of its life. For more detailed information about the recycling of the device or batteries, contact your local city office, the household waste disposal service, or the retail store where you purchased this device.
The disposal of this device is subject to the Waste from Electrical and Electronic
Equipment (WEEE) Directive of the European Union (2002/96/EC). The purpose for separating WEEE and batteries from other waste is to minimize any environmental impact and health hazard due to the presence of hazardous substances.
27
28
2.1.
Features of the CBN 1224
1.2 GHz technology
An extended bandwidth product with available downstream bandwidth up to 1218 MHz; DOCSIS 3.1 standard compliant
200 MHz technology
Capable of extending bandwidth in upstream up to 204 MHz; DOCSIS 3.1 standard compliant
GaN Technology
The Output parameters for analog and digital carriers improved for lower power consumption
Electronic control
Product set up is conducted using electronic control. No plug in pads or equalizers are required
VMC (CISCO Mobile Configuration)
Convenient and user-friendly remote configuration through mobile devices
LED Indicator
Easy local configuration of the product using buttons and LED Indicator
NMS transponder (DOCSIS/EuroDOCSIS)
Reduced operating costs thanks to the remote monitoring and configuration
VIG (CISCO INGRESS GUARD) system compliant
Verification and elimination of the source of ingress in the network
Integration of optical passives
A possibility of installing CWDM/DWDM/WDM filters inside the housing
GREEN mode – Intelligent Power Consumption
A significant reduction of power use through design optimization of its consumption
29
2.2.
Overview Diagram
Block diagram of the CBN 1224 node.
30
2.3.
General modules location
31
32
1.
DCM/EDCM Module
2.
HF – high pass filter
3.
CISCO Ingress Guard system
4.
NMS indicator
5.
LED indicator
6.
Keyboard
7.
Output equalizers EQ 3, EQ 4
8.
SP 4 T or TO or JP – taps
9.
LF/LPBL – low pass filter or BF/RBPL – band pass filter
10.
Fuses
11.
RF Ports
12.
DF – diplex filter
13.
AT 1, AT 2 – interstage attenuator; EQ 1, EQ 2 – interstage equalizer
14.
Communication port
1.
Field replaceable power supply
2.
Up to 4 configurable RF ports with current passing
3.
Fiber management tray
4.
Assembly WDM/CWDM
5.
Up to 4 return path transmitters
Passing current Fuses
The maximum input current to the node is 12A. Remove the fuses protecting the unused ports, otherwise the 75 terminators may be damaged. The fuse jumpers are installed instead of fuses, as standard. They should be replaced by fuses with proper current values if the overload protection is needed.
Version 30-65 V AC.
33
Please verify that proper grounding exists before connecting the power supply! There is a possibility of electrical shock which can cause injury or death.
The CBN 1224 optical node can be powered via any RF port (any RF output or input). The node can also be powered through an additional local power input. The node accepts quasi-square or sinusoidal voltage in the range of 30-65 V AC.
The node is powered by a switched mode power supply which generates all the DC voltages necessary for proper operation of the node. A Fuse is inside the power supply module.
The node can be configured in such a way that it can transfer the remote powering from any one port to another or outside via the local power inserter. The current transferred via any port (bypass current) cannot exceed 12 A. The maximum current for the power inserter is 12 A. It means that the current exceeding 12 A cannot be inserted to any RF port. The local power supply port (power inserter) can insert the current up to 15 A. The supply current flow between the ports depends on the installed fuses (fuse jumpers).
Fuse jumpers are installed as standard. If overcurrent protection is required, it is possible to install time lag fuses with ratings depending on the overcurrent protection requirements for a given port. Additionally, all ports are protected against overvoltage to increase node reliability. The advanced solution of the switched mode power supply gives high efficiency and low power consumption for a broad range of input voltage 30-65 V AC.
The tables below show power consumption depending on input voltage in three node configurations:
34
with one transmitter and two receivers with monitoring module
with four transmitters, two receivers with monitoring module
35
with four transmitters, two receivers without monitoring module
36
2.4.
Plug-in Modules
Thanks to the modular design of the CBN 1224 broadband node one can use various modules allowing simple configuration of the node and flexible tailoring of the node functionalities to the operator’s needs.
CWDM optical transmitter module
Danger! Infrared laser sources with invisible (1310-1610nm range) laser radiation have continuous power of about 2mW. This radiation can cause harmful, irreversible damage to your eyes. Never look into an open fiber end / connector with a laser source connected to the fiber, neither directly nor with optical instruments.
Caution: Electrostatic discharge (ESD) damage, which can occur when electronic cards or components are improperly handled, results in complete or intermittent failures. Electromagnetic interference (EMI) shielding and connectors are integral components of the carrier. Although the metal carrier helps to protect the board from ESD, use a preventive antistatic strap during handling.
The table below shows the technical specification of the CBN-RTX-x-yyyy module with OMI stabilization (x describe the output power in dBm and yyyy describes the
CWDM wavelength = 1310, 1330, 1350, 1370, 1390, 1410, 1430, 1450, 1470, 1490, 1510,
1530, 1550, 1570, 1590, 1610 nm. As a standard the module comes with a SC/APC connector. ).
37
38
Parameter
Laser type
Value
DFB
Wavelength
1310 + 1, - 2
1330 + 1, - 2
1350 + 1, - 2
1370 + 1, - 2
1390 + 1, - 2
1410 + 1, - 2
1430 + 1, - 2
1450 + 1, - 2
1470 + 1, - 2
1490 + 1, - 2
1510 + 1, - 2
1530 + 1, - 2
1550 + 1, - 2
1570 + 1, - 2
1590 + 1, - 2
1610 + 1, - 2
Wavelength temperature coefficient
0.1
Node operation temperature range
- 40 to +60
Comment
Isolated
3 dBm
3 dBm
16 wavelengths typical, max. 0,12
Output optical power 3 ± 0.5;
3 dBm @16 wavelenghts
(1310÷1610nm)
Bandwidth
Minimum input level for
NPR > 30dB
5 to 204
-10
Dynamic range for NPR
> 35dB
Optical connector type
>16
SC/APC
AT3=AT4=AT5=AT6=5dB
AT3=AT4=AT5=AT6=5dB
Test point RF - directional - 20
Stabilized optical power ± 0.5
Relative to RF signal feeding the laser diode
Unit nm
Nm/0C
°C dBm
MHz dBµV/Hz dB dB dBm
OMI change in temperature function
Power consumption:
CBN-RTX-3-yyyy
± 0.5
1.5 dB
W
NPR CWDM 1610nm CBN 12XX, AT3=AT4=AT5=AT6=0, INGRESS=0 5-65 MHz OPTICAL
LINK ~12 dB -15 km FIBER + PASSIVE ATT
NPR VS INPUT NOISE POWER
DF XXXX T – Diplex filter module
The DF XXXX T diplex filter module is used when the CBN 1224 optical node is applied in a bi-directional HFC access network for separation of forward and return path signals. The DF XXXX T module (XXXX is the maximum frequency of the return path) can be installed in the DIPLEX FILTER slots. The available filter versions are DF 65-85 T, DF 85-105 T and DF 204-258 T.
39
The CBN 1224 optical node design allows changing the operation band for the forward and return paths according to the user requirements. The band change is done by means of the plug-in modules. Depending on the modules installed, the operation band can be shared between the forward and return paths as follows:
Return path band [MHz] Forward path band [MHz] Cisco PID
5 - 65 85 - 1218 CBNA-DPL6585
5 - 85
5 - 204
105 - 1218
258 - 1218
CBNA-DPL-85105
CBNA-DPL-204258
SP 4 T / TO XX T / JP 0 T – Taps
40
These plug-in modules are used to distribute the downstream signal to the output ports of the CBN1224. Different splits values are available
The table below presents the available options
TYPE RANGE
ATTENUATION
INPUT
TO OUT1/OUT4
JP-0-T 5 - 1218 MHz 0 dB
ATTENUATION
INPUT
TO OUT2/OUT3
NC *
SP 4 T 5 - 1218 MHz 4.5 dB 4.5 dB
Cisco PID
CBN-LNK-00
CBN-SPL-12-04
TO 6 T
TO 8 T
TO 10 T
TO 13 T
TO 15 T
TO 17 T
5 - 1218 MHz
5 - 1218 MHz
5 - 1218 MHz
5 - 1218 MHz
5 - 1218 MHz
5 - 1218 MHz
4.2 dB
2.5 dB
2.2 dB
2.2 dB
1.5 dB
1.5 dB
6.3 dB
8.0 dB
10.2 dB
13.0 dB
15.0 dB
17.0 dB
CBN-SPL-12-06
CBN-SPL-12-08
CBN-SPL-12-10
CBN-SPL-12-13
CBN-SPL-12-15
CBN-SPL-12-17
(*) Using JP 0 T jumper module the RF signal is provided directly to the OUT1 or
OUT4.
LF XXXX T / LPBL – Low-pass filter
The low pass filter is used to limit the upstream frequency band present at the reverse transmitter. The filter need to be selected in accordance with the selected diplex filter.
The table below presents the available options
LF – Low-pass filter / LPBL Return path band [MHz]
LF 65T / LPBL 65G 5 - 65
LF 85T / LPBL 85G
LF 204 T
5 - 85
5 - 204
Cisco PID
CBN-LPF-65
CBN-LPF-85
CBN-LPF-204
BF XXXX T / RBPL – Reverse path filter
41
The band pass filter has the same functionality as the above low pass filter, but will block the lower edge of the upstream frequency band to reduce disturbance from ingress noise. The filter need to be selected in accordance with the selected diplex filter.
The table below presents the available options
BF – Reverse path filter /
RBPL
BF 15-65T / RBPL 15-65
BF 15-85T / RBPL 15-85
BF 15-204 T
Return path band [MHz]
15 - 65
15 - 85
15 - 204
Cisco PID
CBN-BPF-1565
CBN-BPF-1585
CBN-BPF-15205
HF – High-pass filter
The high pass filter is used to configure the downstream frequency band of the
CBN1224. The filter need to be selected in accordance with the selected diplex filter.
The table below presents the available options
HF – High pass filter / HPB Return path band [MHz]
HF 85 T 85
HF 110 T
HF 258 T
110
258
Cisco PID
CBN-HPF-FW85
CBN-HPF-FW105
CBN-HPF-FW258
42
EQ – Pivot point for forward equalizer
The equalizer is used to set the pivot point of electronic controlled forward equalizer. The CBN1224 can be configured for operation up to 1006MHz or
1218MHz.
The table below presents the available options
EQ - equalizer Pivot point for forward equalizer
EQ 1006 ET 1006 MHz
EQ 1218 ET 1218 MHz
Cisco PID
CBN-EQL-1218
CBN-EQL-1006
43
3
Chapter 3
Installation
44
3.1.
Tools, Accessories, Turning moments
Before you start the installation, make sure you have the following tools and equipment to connect and configure the Compact Node CBN 1224.
You need a…
4mm hexagon key
Torx 30 hexalobular key
To…
Tighten and loosen the lid.
Install the base
3 mm x 0,8 mm flat tip screwdriver Install AC wires, Pins.
5mm x 1 mm flat tip screwdriver Add transmitters
8mm x 1,2 mm flat tip screwdriver Open AC hole plug
Torx 10
Flat key 22mm
Perform Fiber management
PG11/IEC/F
Flat key 24mm PG16 Fiber choke
The table below presents the turning moments according to the norm DIN/VDE
0619, point 7. Turning moment kept IP class 67 (5 bar).
Material
Metal Plastic
Element
Turning moments in Nm
PG 9
PG11
PG16
ORTB screw
RF pins screw
AC IN screw
Fiber management screw
Lid screw
6.25
6.25
7.5
1.5-1.7
1.5
0.5
0.5
4
-
-
-
-
3.75
3.75
5.0
-
45
3.2.
Site requirements
The housing protects the circuitry from environmental influence and node overheating. The aluminum housing makes the node operation possible in a wide range of temperatures (-40 - 60°C). The amplifier has a very high IP 67 protection class, so it is possible to mount the housing outdoors. The rubber gasket makes the housing airtight and the additional metal gasket provides electromagnetic compatibility.
46
3.3.
Mounting the Node
The optical node should be mounted in a vertical position so that the signal cables would go down. Unless the condition is fulfilled, the air circulation may be disturbed.
The compact housing of the optical node requires little mounting space, so it can be mounted in street cabinets as well as in building cabinets. Universal mounting brackets enable easy installation of the node. The node has 4 RF ports, one optical port on the housing bottom and a local supply port on the left side of the housing.
The node lid is mounted with M5 hexagon socket head screws.
The housing view of the CBN 1224.
Note: The top two mounting brackets are shipped in the vertical position and may be used as is, or rotated as shown in the diagram below.
47
48
3.4.
To Mount the Node
Preparation for mounting
Inspect the housing carefully before node installation. Pay attention to possible damages of the heat sink, RF/optical ports or lid screws and make sure that there are three universal mounting brackets inside the packaging.
Installation
Before optical node installation mount the universal brackets in the right position. Mount the node to the wall or mounting plate with max. 6 mm screws.
The optical node should be mounted in a vertical position so that the signal cables would go down. Unless the condition is fulfilled, the air circulation may be disturbed.
During the normal operation (proper mounting and air circulation) the node can heat up to 35°C (for the ambient temperature 20°C).
To Open and Tighten the Housing
To open or close the lid, tighten the screws in the following order:
1, 2, 3, 4 or 4, 3, 2, 1
Installation is to be done by a qualified personnel in accordance with local and national regulations.
The outer conductor of the coax cable is intended to be grounded/earthed at the front end and adequate current limiter is to be provided to control short circuit current.
Equipment connected to the protective earthing of the building installation through the mains connection or through other equipment with a connection to protective earthing – and to a cable distribution system using coaxial cable, may in
49
some circumstances create a fire hazard. Connection to a cable distribution system has therefore to be provided through a device providing electrical isolation below a certain frequency range (galvanic isolator, see EN 60728-11).
NOTE In Norway, due to regulation for installations of cable distribution systems, and in Sweden, a galvanic isolator shall provide electrical insulation below 5 MHz.
The insulation shall withstand a dielectric strength of 1,5 kV r.m.s., 50 Hz or 60 Hz, for 1 min.
“Utstyr som er koplet til beskyttelsesjord via nettplugg og/eller via annet jordtilkoplet utstyr – og er tilkoplet et kabel-TV nett, kan forårsake brannfare. For å unngå dette skal det ved tilkopling av utstyret til kabel-TV nettet installeres en galvanisk isolator mellom utstyret og kabel- TV nettet.”
”Utrustning som är kopplad till skyddsjord via jordat vägguttag och/eller via annan utrustning och samtidigt är kopplad till kabel-TV nät kan i vissa fall medfőra risk főr brand. Főr att undvika detta skall vid anslutning av utrustningen till kabel-
TV nät galvanisk isolator finnas mellan utrustningen och kabel-TV nätet.”
50
Lid screw tightening order
51
3.5.
To Mount Other Modules
DCM/EDCM Module
Monitoring module DCM/EDCM is an outstanding solution for HFC network management and monitoring. Thanks to a built-in DOCSIS/EuroDOCSIS modem, it simplifies implementation of a management system for optical nodes and broadband amplifiers. The solution uses an existing DOCSIS/EuroDOCSIS environment and equipment, significantly driving down costs of the Network Management System implementation.
The DCM/EDCM module enables optical node management and monitoring using a web browser, no proprietary software required and access to the node’s web page is free. Through a Simple Network Management Protocol (SNMP) interface, standard MIBs are used for efficient network monitoring and management. The
SNMP standard enables cooperation with open monitoring systems using access to
MIB base.
Configurable parameters, such as signal levels and slope, AGC or redundancy and segmentation, can be adjusted remotely through the module, without interruption to signal transmission.
The DCM/EDCM module enables remote upgrading of the node or amplifier firmware.
52
Remember to mount DCM/EDCM module when the power is OFF.
Caution: Electrostatic discharge (ESD) damage, which can occur when electronic cards or components are improperly handled, result in complete or intermittent failures. Electromagnetic interference (EMI) shielding and connectors are integral components of the carrier. Although the metal carrier helps to protect the board from ESD, use a preventive antistatic strap during handling.
Optical Transmitter Modules
The return path optical signal can be transmitted if at least one ORTB optical transmitter module is installed in the optical node. If you need the return path with two or more outputs, you should install additional optical transmitters. Pay attention to the correct installation of fiber optic cables - See Fiber management.
Follow the procedure shown in the figures below in order to install the optical transmitter modules. Gently insert the transmitter board-edge connector into the appropriate black lid receptacle, then screw it down using 0.5 Nm turning moment.
Make sure that the fiber is not damaged or cut during installation.
1. Screw mounting the optical transmitter Tx1
2. Screw mounting the optical transmitter Tx2
53
3. Screw mounting the optical transmitter Tx3
4. Screw mounting the optical transmitter Tx4
Mounting of ORTB optical transmitter modules
There is a possibility to mount max. 4 x 3dBm Tx or 2 x 6 dBm Tx or 2 x 3 dBm Tx and 1 x 6 dBm Tx.
If only one optical transmitter is used (Tx1), the configuration of the return path should be established in RF combining (See Return Path configuration) and TX 1 slot should be used.
Caution: Electrostatic discharge (ESD) damage, which can occur when electronic cards or components are improperly handled, results in complete or intermittent failures. Electromagnetic interference (EMI) shielding and connectors are integral components of the carrier. Although the metal carrier helps to protect the board from ESD, use a preventive antistatic strap during handling.
Fiber and Fiber Management
This section describes how to install optical transmitters and associated fiber cables and fiber connectors.
Remember to clean fiber connectors after installation or reinstallation using proper tools. It is necessary to clean all fiber connectors (existing and incoming). See pictures below
54
Remember to protect unused connectors. Do not pull fibers. Bend radius of fibers have to be > 25 mm.
The picture below presents a view of the standard optical node without additional plugins. Note that the receivers are factory installed under the main circuit board.
55
56
Step 1
The picture below presents instruction on how to install the optical transmitter:
Repeat this action with the second screw.
Step 2
57
Step 3
Step 4
Step 5
58
Step 8
Step 7
Step 6
59
60
Step 9
Step 10
Step 11
61
Procedure for installing additional optical transmitters is the same as for the first one.
Carefully route fibers as shown below:
62
General overview
RF connectors
This chapter presents how to properly install the RF PG11 connectors.
To install RF connectors follow the below steps:
Make sure that the pin’s length is min 26 mm max 29 mm
63
Screw the PG11 into the housing. Picture below presents case with 4 outputs version.
64
Remember to use the 75 Ohm terminator in unused outputs.
While screwing PG 11 connectors and pins use proper turning moments.
Grounding the Node
To ensure safe operation of the node it should be connected to the ground.
There is a grounding connector on the left side of the node. The node should be grounded with a 4 mm² copper wire.
Please check the proper grounding before connecting the power supply! An electric shock can be dangerous to life or health.
4
Chapter 4
Operating
65
4.1.
Configuration Modes
Adjustment - Control panel
The CBN 1224 optical node has a microcontroller which controls the values of the controlled elements, changes the configuration of the node and measures the input optical power.
The node can be controlled from the control panel consisting of the LED displays and two pairs of the function buttons:
Menu buttons - / + are used for scrolling and choosing the position to change/control.
UP/DOWN buttons are used for changing the values of the element which has been previously chosen by the menu buttons -/+. The value changes automatically and does not require any confirmation.
3-segment LED display – shows the current element value or its configuration.
LED Display
66
Normal mode – gives an access to the functions necessary for the maintenance of the node, i.e. related to attenuator and equalizer values, and measures the optical input power.
Service mode – gives an access to the configuration functions, like AGC or GREEN configuration.
Access to the service mode is limited and requires pressing and holding the -
/+ buttons concurrently for 2 seconds. The service menu can be activated only when the LED display shows the neutral position.
The service menu will change into the normal menu after waiting approx. 2 min. without any operation in the service mode or by choosing the neutral position SE and pressing both -/+ buttons for 2 seconds.
67
4.2.
Electronic adjustment for CBN 1224 – menu tree
68
Normal mode
In the normal menu one can choose the following functions (using -/+ menu buttons):
r1 – indicates optical input power level on first receiver
r2 – indicates optical input power level on second receiver
Possible values:
Lo – input power level is too low
Hi – input power level is too high
0.7 – positive power (indicated with no sign before number)
-0.7 – negative power (indicated with minus sign before number)
69
A1 – defines value of the AT 1 attenuator. Can be set from the range 0 – 20 dB with step 0.5 dB
E1 – defines value of the EQ 1 equalizer. Can be set from the range 0 – 20 dB with step 0.5 dB
A2 – defines value of the AT 2 attenuator. Can be set from the range 0 – 20 dB with step 0.5 dB
E2 – defines value of the EQ 2 equalizer. Can be set from the range 0 – 20 dB with step 0.5 dB
70
A3 – defines value of the AT 3 attenuator. Can be set from the range 0 – 20 dB with step 0.5 dB
A4 – defines value of the AT 4 attenuator. Can be set from the range 0 – 20 dB with step 0.5 dB
A5 – defines value of the AT 5 attenuator. Can be set from the range 0 – 20 dB with step 0.5 dB
71
72
A6 – defines value of the AT 6 attenuator. Can be set from the range 0 – 20 dB with step 0.5 dB
In1 – defines value of the first Ingress Switch with possible settings:
0 – no attenuation
-6 – attenuation of 6 dB
-∞ – attenuation of 40 dB
In2 – defines value of the second Ingress Switch with possible settings
0 – no attenuation
-6 – attenuation of 6 dB
-∞ – attenuation of 40 dB
In3 – defines value of the third Ingress Switch with possible settings:
0 – no attenuation
-6 – attenuation of 6 dB
-∞ – attenuation of 40 dB
In4 – defines value of the fourth Ingress Switch with possible settings:
0 – no attenuation
73
74
-6 – attenuation of 6 dB
-∞ – attenuation of 40 dB
S1 – defines which output is connected to the first test point. Possible settings:
1 – first output
2 – second output
S2 – defines which output is connected to the second test point. Possible settings:
3 – third output
4 – fourth output
Service mode
In the normal menu one can choose the following functions (using -/+ menu buttons):
FC – defines how forward path is configured:
S1 – forward path is configured as follows:
Port 1
Rx 1
Port 2
Port 3
DS Matrix
Port 4 r1 – receivers Rx1 and Rx2 operate in redundancy mode
75
Rx 1
Rx 2
DS Matrix
S. – receivers Rx1 and Rx2 operate in the segmentation mode:
Port 1
Port 2
Port 3
Port 4
Rx 1 Port 1
Port 2
Port 3
Rx 2
Port 4
DS Matrix
76
rc -defines how return path is configured:
C1 – all ports are combined to Tx1:
Port 1
Tx 1
Port 2
Port 3
Port 4
US Matrix
C14 – ports 1 and 2 are combined to Tx1, ports 3 and 4 are combined to Tx2
Tx 1
Port 1
Tx 4
Port 2
Port 3
Port 4
US Matrix
77
78
R1 – Tx4 behaves as a redundancy for Tx1
Tx 1
Port 1
Port 2
Tx 4
Port 3
Port 4
US Matrix
R14 – Tx2 operates as a redundancy for Tx1, Tx3 operates as a redundancy for Tx4
Tx 1 Port 1
Tx 2
Port 2
Tx 3 Port 3
Tx 4 Port 4
US Matrix
S. – transmitters are working in a segmentation mode:
Tx 1 Port 1
Tx 2 Port 2
Tx 3 Port 3
Tx 4 Port 4
US Matrix
C1S. – port 1 and 2 are combined to Tx1, Tx2 and Tx4 works in a segmentation mode:
79
S.C4 – T x
1 and T x
2 work in a segmentation mode, port 3 and 4 are combined to T x
4
80
If only one optical transmitter is used (Tx1), the configuration of the return path should be established in position combining (C1)
tHl – redundancy threshold low – the level at which the “low receiver” will be switched on. It can be set from the range: - 9dBm - 1dBm
tHH – redundancy threshold high – the level at which the “high receiver” will be switched on. It can be set from the range: - 9dBm - 1dBm
Ac1 – defines AGC circuit of R x
1. May be switched on/off or acting as attenuator while choosing a number from the range 0 – 20 dB (with step 0.5 dB)
81
82
Ac2 – defines AGC circuit of R x
2. May be switched on/off or acting as attenuator while choosing a number from the range 0 – 20 dB (with step 0.5 dB):
ʎ - defines optical level meter calibration and can be chosen from the following options:
13 – 1310 nm
15 – 1550 nm
The node shows the current value of the receiver input power. To accept this level as a reference level for AGC, press and hold down two UP/DOWN buttons at the same time. The node will confirm that this value is saved in the memory and will use it as a reference level during the optical power compensation.
Gr1 – defines power consumption for Rx1 and can be chosen from the following options:
0 – max power consumption
1 – typical power consumption
2 – minimal power consumption
Gr1 – defines power consumption for Rx2 and can be chosen from the following options:
0 – max power consumption
1 – typical power consumption
2 – minimal power consumption
83
84
bn – defines operating bandwidth (its upper band). Possible settings:
1 GHz
1.2 GHz
Pay attention to use proper pivot point equalizer for forward configuration
(EQ 1006 ET or EQ 1218 ET)
Tr1 – T x
1 laser ON/OFF control :
Tr2 – T x
2 laser ON/OFF control :
Tr3 – T x
3 laser ON/OFF control :
Tr4 – T x
4 laser ON/OFF control :
Fr – indicates current software version
85
SE – service mode
dS – default settings
86
Table of default settings: r1 r2
Gr2 bn
Tr1
Tr2
Tr3
Tr4 rC tHL tHH
λ
Ac1
Ac2
Gr1
A5
A6
In1
In2
A1
E1
A2
E2
A3
A4
In3
In4
S1
S2
FC
-
-
0
Hi on on on on
C1
-5
-1
13
ON
ON
0
17
17 oo oo
10
0
10
0
17
17 oo oo
1
4
S1
87
Forward Configuration
It is not allowed to connect the modulated optical signal (full channel raster,
4% OMI) with an optical power for which the output level of the optical node exceeds 118 dBuV with minimum values of AT1 and AT2. The level of the input optical power should not be higher than 0dBm (with AGC switched off). If the output level is higher than 118 dBuV, the optical node can be damaged!
The optical node has a system to protect the inter stage amplifiers. If the optical receiver is provided more optical power than the catalogue range, the uC will automatically increase AGC attenuator to maximum.
Optical receivers LED Indicator
Both receivers are connected to LED receiver indicators on the main board. They show the status of the receivers and present optical power. The picture below describes possible states and enciphered information where color shows present optical power and active receiver.
88
Red – optical power > 0,1 dBm
Red – optical power < - 8,1 dBm
Green – optical power < - 0,1 dBm
Green – optical power > - 7,9 dBm
Automatic gain control AGC
There are two available adjustment modes:
Manual - AGC is turned off; attenuation values can be chosen from the 0 - 20 dB range in 1 dB step.
89
90
Automatic - the AGC circuit automatically changes the attenuation value within the range of +/- 3 dBm on the basis of the input optical power changes. When the AGC is on, it introduces an additional max. 14 dB attenuation of the RF path. This attenuation is necessary for obtaining the proper operation dynamics. The pictures above describe conditions of AGC working range and attenuations and show the examples of AGC calibration for each type of optical receiver.
Forward path amplifier
The modern GaN technology, implemented in the input stage as well as in both output stages, guarantees high RF levels at the optical node output and low levels of intermodulation distortion.
Interstage adjustment
Interstage adjustment is done by the AT1 attenuator and the EQ1 interstage equalizer which are common for PORT 1/2. The path attenuation/gain and slope control is done electronically from the control panel in the range (measured in the bandwidth: 47 MHz – 1 GHz or 47 MHz – 1,2 GHz):
AT1 – from 0 to 20 dB with 0.5 dB step
EQ1 - from 0 to 20 dB with 0.5 dB step
Additionally, there is another AT2 attenuator and the EQ2 interstage equalizer which are common for PORT 3/4. The path attenuation/gain and slope control is done electronically from the control panel in the range (measured in the bandwidth:
47 MHz – 1 GHz or 47 MHz – 1,2GHz):
AT2 - from 0 to 20 dB with 0.5 dB step
EQ2 - from 0 to 20 dB with 0.5 dB step
Pivot point for forward equalizer for both paths is done by:
EQ 1006 ET – for bandwidth 47 MHz – 1006 MHz
EQ 1218 ET - for bandwidth 47 MHz – 1218 MHz
Interstage equalization allows to increase the output level without deterioration of the intermodulation parameters of the node.
The equalizer circuit has a concave shape to compensate PIII 700 Comscope cable.
The slope value is specified between markers on 47 and 1G/1.2G MHz. If one changes bandwidth of the node from 1.2 GHz to 1006 MHz the slope displayed on the LED will be recalculated.
Outputs
The optical node has two amplification paths and four output ports. There are four diplex filters after the output stages. The diplex filter splits the forward and return path signals. The Ports 1 and 4 are treated as the main ports while Ports 2 and 3 can be optionally configured by the passive TO 10XX T plug-in module. If Port 2 and 3 are unused, both should apply the JP 0 T jumper module.
Reverse Configuration
The CBN 1224 optical node has a set of switches on the main board for return path configuration. It is possible to obtain the following path configurations.
The Tx1 transmitter is the primary transmitter. If only one optical transmitter is used it must be installed in slot corresponding to (Tx1). Configuration of the return path should be established in position C1.
In the sockets described as US FILTER 1; US FILTER 2; US FILTER 3 and US FILTER
4 one can install the BF 15-204 T or LF 204 T filters reducing interference in the return path.
Return path adjustment
On each of four return path inputs there are attenuators marked as AT 6 – for
Port#4, AT 5 – for Port#3, AT 4 - for Port#2 and AT 3 - for port#1, which allows adjustment of the signal entering the return path transmitters depending on the chosen configuration and RF input power levels.
91
Selection of the proper attenuation value of the path depends on the input port signal levels and the channel plan.
Ingress switch
The IS ingress switch permits diagnosis of unwanted interfering signals entering the network (ingress) in the return path band. It contains an attenuator with three possible values (0 dB, 6 dB and OFF) which can be preset locally from the control panel or remotely by means of the monitoring system. It is used to localize ingress sources fast and remotely in the distributed network architecture and remove the ingress source immediately by the network operator’s technical service.
92
4.3.
Diplex filters
The diplex filters in the CBN 1224 optical node are designed as plug-in modules DF
XXXX T. These filters are placed at the node output. This modular solution allows changing the return path maximum frequency.
Changing the return path’s maximum frequency requires an exchange of DF
XXXX T, HF, LF/LPBL, BF/RBPL for the appropriate band and reverse transmitter.
93
94
4.4.
Test points
In the input and output signal paths there are directional test points (TP) with SMB connectors (-20 dB).
The TP 1 test point is for forward path signal measurement for Ports 1 and 2 and inserting the sweep signal for the return path – with an SMB connector, -20 dB signal level.
The TP 2 test point is for forward path signal measurement for Ports 3 and 4 and inserting the sweep signal for the return path – with an SMB connector, -20 dB signal level.
Each transmitter has its own SMB test point.
The usage of directional test points allows precise measurement of signal levels.
Customer Support Information
If You Have Questions
If you have technical questions, call Cisco Services for assistance.
Follow the menu options to speak with a service engineer.
Access your company's extranet site to view or order additional technical publications. For accessing instructions, contact the representative who handles your account. Check your extranet site often as the information is updated frequently.
95
Glossary
A
A ampere. A unit of measure for electrical current. ac, AC alternating current. An electric current that reverses its direction at regularly recurring intervals.
AC/RF alternating current radio frequency.
AGC automatic gain control. A process or means by which gain is automatically adjusted in a specified manner as a function of input level or other specified parameters. attenuation
The difference between transmitted and received signal strength due to loss through equipment, lines, or other transmission medium. Usually expressed in decibels. attenuator
A passive device designed to reduce signal strength without distorting the waveform.
Usually specified in dB.
AUX auxiliary.
B blanking level
The amplitude of the front and back porches of the composite video signal. The blanking level separates the range containing picture information from the range containing synchronization information.
97
Glossary
Bps bits per second. The total number of bits sent in a second of time.
BW bandwidth. A measure of the information-carrying capacity of a communications channel, for example the range of usable frequencies that can be carried by a CATV system. The bandwidth corresponds to the difference between the lowest and highest frequency that can be carried by the channel.
C
CCW counterclockwise.
CF continuous feed.
CW continuous wave.
D dB decibel. One tenth of a bel, the number of decibels denoting the ratio of two amounts of power being ten times the common logarithm of this ratio.
DC directional coupler. dc, DC direct current. An electric current flowing in one direction only and substantially constant in value. diplex filter
A filter which divides the frequency spectrum into a high frequency segment and a low frequency segment so that two different signals can be sent down the same transmission path. distribution system
The part of a CATV system consisting of the transmission medium (coaxial cables, fiber optic cables, etc.) used to carry signals from the headend system to subscriber terminals.
98
Glossary
DPU digital processing unit.
E
EC
European Community. emission designer
An FCC or CCIR code that defines the format of radiation from a transmitter.
EQ equalizer.
F equalization
The process of compensating for an undesired result. For example, equalizing tilt in a distribution system.
FM frequency modulation. A transmission technique in which the frequency of the carrier varies in accordance with the modulating signal. frequency
The number of similar shapes in a communications or electrical path in a unit of time. For example, the number of sine waves moving past a fixed point in a second. frequency response
The effect that changing the frequency has on the magnitude of a signal. ft-lb foot-pound. A measure of torque defined by the application of one pound of force on a lever at a point on the lever that is one foot from the pivot point.
G gain
A measure of the increase in signal level, relative to a reference, in an amplifier. Usually expressed in decibels.
99
Glossary
H
Hertz
A unit of frequency equal to one cycle per second.
HGBT high gain balanced triple.
HGD high gain dual.
I
I/O input/output.
IC integrated circuit.
IEC
International Electro-technical Commission.
IF intermediate frequency. The common frequency which is mixed with the frequency of a local oscillator to produce the outgoing radio frequency (RF) signal. in-lb inch-pound. A measure of torque defined by the application of one pound of force on a lever at a point on the lever that is one inch from the pivot point.
K
K
Kelvin. A measure of temperature. Zero degrees K equals –273 degrees Centigrade or –459 degrees Fahrenheit.
L
LED light-emitting diode. An electronic device that lights up when electricity passes through it.
100
Glossary
M
LEI, LEII, LEIII line extender I, line extender II, line extender III.
Mbps megabits per second. A unit of measure representing a rate of one million bits (megabits) per second.
N nanosecond
One thousandth of a microsecond. (One billionth of a second.)
Nm
Newton meter. A measure of torque defined by the application of one Newton of force on a lever at a point on the lever that is one meter from the pivot point. (1 Nm = 0.737561 ft-lb)
P
PCB printed circuit board.
PROM
PWB printed wiring board.
R
RCVR receiver. reverse path
Signal flow direction toward the headend.
RF programmable read-only memory. A memory chip on which data can be written only once.
Once data has been written onto a PROM, it cannot be written to again. radio frequency. The frequency in the portion of the electromagnetic spectrum that is above the audio frequencies and below the infrared frequencies, used in radio transmission systems.
101
Glossary
RFI radio frequency interference.
RMA return material authorization. A form used to return products.
RX receive or receiver.
S
S/N or SNR signal-to-noise ratio. The ratio, in decibels, of the maximum peak-to-peak voltage of the video signal, including synchronizing pulse, to the root-mean-square voltage of the noise. Provides a measure and indication of signal quality.
SA system amplifier.
SAI, SAII, SAIII system amplifier I, system amplifier II, system amplifier III.
SM status monitor.
SMC status monitoring and control. The process by which the operation, configuration, and performance of individual elements in a network or system are monitored and controlled from a central location.
SMIU status monitor interface unit.
SNMP simple network management protocol. A protocol that governs network management and the monitoring of network devices and their functions.
102
Glossary splitter
A device which divides a signal or power from an input to deliver multiple outputs.
T sweep generator
A signal source which can automatically vary its frequency continuously from one frequency to another. torque
A force that produces rotation or torsion. Usually expressed in lb-ft (pound-feet) or N-m
(Newton-meters). The application of one pound of force on a lever at a point on the lever that is one foot from the pivot point would produce 1 lb-ft of torque.
TX transmit or transmitter.
U uV microvolt. One millionth of a volt.
V
V volt.
W
W watt. A measure of electrical power required to do work at the rate of one joule per second. In a purely resistive load, 1 Watt = 1 Volt x 1 Amp.
103
Index
A
AC shunt power directors • 4 accessories miscellaneous • 8 adjusting received amplitude • 72 ampere capability • 19 amplifier
AC shunt power directors • 4 customer installable accessories • 6 miscellaneous accessories • 8 power supply • 4 amplifier only compensation mode • 68 attaching connectors • 27
B balancing forward path • 53 forward path for AGC stations • 62 reverse path • 72
Before You Begin • 133 blue label • 19
C characteristics of power supply • 4 charts linear tilt • 106 manual backoff • 55 closing the housing • 17 connecting coaxial cable • 27 connector description • 90 connectors, attaching • 27
E
EDR Receiver Module • 126
EDR Transmitter Module • 123
EDR Transmitter Status Indicators • 140 electric heat gun applicator • 14
Enhanced Digital Return (EDR) System
Installation • 133
Enhanced Digital Return System Overview • 120
Equipment • 144 equipment for troubleshooting procedures • 84
F
Features • 120 features of power supply • 4 fiber optic ferrule cleaner • 84
105
Index final setup procedure • 80 forward data carrier • 72 forward path balancing
AGC stations • 53 thermal setup mode • 62 thermal stations using amplifier only compensation mode • 68 using trim networks • 71
G
GainMaker
AC shunt power directors • 4 customer installable accessories • 6 illustrations • 8 miscellaneous accessories • 8 power supply • 4 generating test signals • 72
H housing attaching • 29 attaching connectors • 27 base • 19 blue label • 19 connecting coaxial cable • 27 measurements • 15 strand mounting • 29 trimming center conductor • 27
106
I illustrations torque sequence • 18 injection of test signals • 72 input signal level • 53 installing
AC shunt power directors • 39
Installing the EDR Receiver • 138
Introduction • 141
L linear tilt charts
1 GHz • 106
870 MHz • 106 lint free wipes • 84
M manual backoff chart • 55 measurements • 15
Method of Generating and Monitoring Test
Signals • 141 miscellaneous problems • 97 monitoring received amplitude • 72 monitoring test signals • 72 multiple CW signal generator • 72
N no AC power • 86
O opening the housing • 17
Operating Environment • 133
P power direction settings • 39 power supply characteristics • 4 propane torch • 14
R
Receiver Operating Modes • 128 removing AC shunt power directors • 39
Reverse Balancing and Alignment Procedure •
142 reverse balancing procedure • 73
Reverse Balancing the Node with the Enhanced
Digital Return (EDR) Modules • 141 reverse path balancing adjusting • 72 completing • 80 generating test signals • 72 introduction • 72 monitoring • 72 monitoring test signals • 72 received amplitude • 72 sequence • 72 test signal injection • 72 reverse sweep receiver • 72 reverse sweep transmitter • 72
S setting
Index power direction • 39 signal level meter • 72 size • 15 spectrum analyzer • 72 strand mounting • 29
System Block Diagram • 122
System Functional Diagrams • 121
T testing input signal levels • 53 tilt charts, linear • 106
To Install the Transmitter Module • 134 tools, required • 14 torque sequence • 18
Transmitter Module Setup Procedure • 139
Transmitter Module Troubleshooting Chart • 145 trim networks forward path balancing using • 71 trimming the center conductor • 27
Troubleshooting • 144
107
Americas Headquarters
Cisco Systems, Inc.
170 West Tasman Drive
San Jose, CA 95134-1706
USA http://www.cisco.com
Tel: 408 526-4000
800 553-6387
Fax: 408 527-0883
This document includes various trademarks of Cisco Systems, Inc. Please see the Notices section of this document for a list of the Cisco Systems, Inc. trademarks used in this document.
Product and service availability are subject to change without notice.
© 2016 Cisco and/or its affiliates. All rights reserved.
First Published: August 2016
advertisement
Related manuals
advertisement