Diamond technologies DT7000 User Manual
Add to My manuals22 Pages
Diamond technologies DT7000 is a high-quality communication I/O gateway giving you plenty of options to connect different industrial networks, serial devices, and more. Here are some of its capabilities:
- Supports various fieldbus networks, including Profibus, DeviceNet, CANopen, EtherCat, EtherNet/IP, MODBUS-TCP, and more.
- Offers four serial ports for MODBUS-RTU master/slave or generic serial driver support.
- Provides digital and analog I/O with 8 digital outputs, 8 digital inputs, 4 analog outputs, and 8 analog inputs.
- Allows for customization through a user application written in C, enabling you to implement data translation, local control, or specific protocols.
advertisement
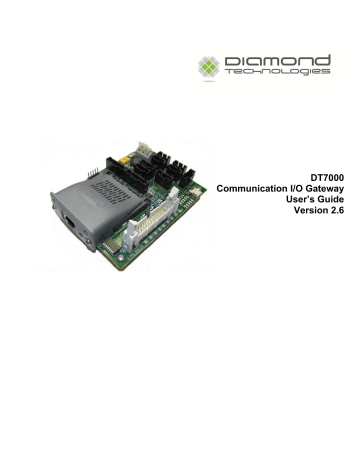
DT7000
Communication I/O Gateway
User’s Guide
Version 2.6
6 Clock Tower Place
Suite 100
Maynard, MA 01754
USA
Tel: (866) 837-1931
Tel: (978) 461-1140
FAX: (978) 461-1146 http://www.diamondt.com/
Liability
Diamond Technologies Inc. shall not be liable for technical or editorial errors or omissions contained herein, nor for incidental or consequential damages resulting from the use of this material. Those responsible for the use of this device must ensure that all necessary steps have been taken to verify that the applications meet all performance and safety requirements including any applicable laws, regulations, codes, and standards.
There are many applications of this product. The examples and illustrations in this document are included solely for illustrative purposes. Because of the many variables and requirements associated with any particular implementation,
Diamond Technologies Inc. cannot assume responsibility for actual use based on these examples and illustrations.
Diamond Technologies Inc., reserves the right to modify our products in line with our policy of continuous product development. The information in this document is subject to change without notice and should not be considered as a commitment by Diamond Technologies Inc.
Intellectual Property Rights
© 2011 Diamond Technologies Inc. * ALL RIGHTS RESERVED.* Protected to the fullest extent under
U.S. and international laws. Copying, or altering of this document is prohibited without express written consent from
Diamond Technologies Inc.
Diamond Technologies Inc. has intellectual property rights relating to technology embodied in the product described in this document. These intellectual property rights may include patents and pending patent applications in the US and other countries.
Diamond Technologies Inc. and the Diamond Technologies logo are trademarks of Diamond Technologies Inc. All other trademarks are the property of their respective holders.
DT7000 Gateway User’s Guide 2.61 Page 2 of 22
i Revision History
Version Date
1.0 09/28/08
2.0 01/21/09
Original
Description
Version
Update for Version 2.x Firmware
2.1
2.2
2.3
2.4
07/12/10
10/01/10
02/15/11
08/11/11
Update CANopen support.
Separated Network Supplements.
Fixed bit numbering in Generic Serial Driver
Minor text updates
Updated
2.61 05/05/14
ii Reference Documents iii Table of Contents
i Revision History .................................................................................................................................................................... 3 ii Reference Documents ........................................................................................................................................................... 3 iii Table of Contents ................................................................................................................................................................. 3
1.0 Introduction ........................................................................................................................................................................ 4
2.0 DT7000 – Module .............................................................................................................................................................. 4
2.1 Module Layout .............................................................................................................................................................. 5
2.2 Module Mounting .......................................................................................................................................................... 5
2.3 Input Power ................................................................................................................................................................... 5
2.4 Serial Port Connections ................................................................................................................................................. 6
2.5 Digital I/O Connections ................................................................................................................................................. 7
2.6 Analog I/O Connections ................................................................................................................................................ 9
2.7 Fieldbus Connection ...................................................................................................................................................... 9
2.8 Mating Connectors ........................................................................................................................................................ 9
2.9 Module Indicators ....................................................................................................................................................... 10
2.10 Module DIP Switches ................................................................................................................................................ 10
3.0 Communications .............................................................................................................................................................. 11
3.1 Serial Communications Settings ...................................................................................................................................... 11
3.2 Fieldbus Data Format ....................................................................................................................................................... 12
3.2 Generic Serial Driver ....................................................................................................................................................... 14
4.0 Supported Networks ......................................................................................................................................................... 15
4.1 MODBUS-RTU (Native Serial Ports) .............................................................................................................................. 16
5.0 Diagnostic Interface ......................................................................................................................................................... 17
5.1 Startup ......................................................................................................................................................................... 18
5.2 Interface Menu ........................................................................................................................................................... 20
5.3 Updating the Module Firmware .................................................................................................................................. 21
6.0 Technical Specifications .................................................................................................................................................. 22
DT7000 Gateway User’s Guide 2.61 Page 3 of 22
1.0 Introduction
This document covers Diamond Technologies DT7000 Communications I/O Gateway . This module provides a gateway between industrial networks, and serial devices as well as providing digital and analog I/O and local control capabilities.
The DT7000 utilizes one of the available Anybus CompactCom modules for the desired fieldbus. This module can be replaced with any of the other available Anybus CompactCom modules to provide a gateway to most industrial fieldbus networks.
As standard the device supports MODBUS-RTU through the serial ports, and can be a MODBUS master and/or a
MODBUS slave. Also the module supports a generic serial driver which allows any serial data to be passed through the serial device to the installed fieldbus. The module also includes digital and analog I/O which can be accessed through the fieldbus.
A version of the module is available with an Ethernet interface. The Ethernet interface provides communication to the module via Ethernet. This Ethernet interface is in addition to the CompactCom interface which also may be
Ethernet based.
A user application, developed in C can be installed in the module to provide data translation and local control.
This allows for instance ASCII serial data sent by a serial device to be converted to real number values on the fieldbus, or a digital output to be set when an analog input value exceeds a limit. Simple C applications are installed on top of the DT7000 standard firmware to implement virtually any control or interface application supported by the DT7000 interfaces.
2.0 DT7000 – Module
The DT7000 module includes four serial ports (PORT A, B, C and D). These ports can be configured as master or slave using the standard MODBUS-RTU protocol. Alternatively the ports can be configured to support the generic serial driver to allow control of serial devices over the fieldbus network with protocols implemented on the host. With an installed user application any serial protocol can be implemented in the module by the user. The module includes 8 digital outputs, 8 digital inputs, 4 analog outputs and 8 analog inputs. The I/O data, serial data, or any local control data generated by the user application, is mapped onto the installed fieldbus according to the user configuration. Different Anybus-CompactCom modules can be installed in the DT7000 module to connect to the various fieldbus networks. The following fieldbus networks are currently supported by the DT7000.
Profibus
DeviceNet
CANopen
EtherCat
EtherNet/IP
MODBUS-TCP
Profinet-IO
MODBUS-RTU
ControlNet
DT7000 Gateway User’s Guide 2.61 Page 4 of 22
2.1 Module Layout
The figure below, shows the module layout, and can be used to identify the components listed in the following sections.
DT7000 Board Layout
2.2 Module Mounting
The DT7000 provides four mounting holes (Z1, Z2, Z3, and Z4). These are 0.120” diameter holes with a surrounding pad of 0.200”. Mounting hole Z2 is connected to Earth Ground. The other holes are not connected.
Various DIN rail and enclosure mounting options are available for the DT7000. Contact the factory for information.
2.3 Input Power
The DT7000 requires input power of 9 to 40 VDC (24 VDC nominal), at the terminal block connector (J19).
Alternatively for some applications a 3 pin pluggable connector (J17) is used for power in.
Refer to the following table for the power connections.
DT7000 Gateway User’s Guide 2.61 Page 5 of 22
Input Power:
J19 Pin J17 Pin SIGNAL
Power for the I/O devices is supplied through the I/O connector (J10). The I/O supports voltages from 5 to 40
VDC. Two jumpers on the board (R67, and R68) can be installed to tie the input power to the I/O connector. This defeats the optical isolation but allows driving I/O devices with the power supplied to the module.
2.4 Serial Port Connections
The DT7000 includes four serial ports. Each serial port is either RS232 or RS485. For B versions of the module, only the RS232 connectors are included. Refer to the following tables, for connecting serial devices to the
DT7000.
DT7000 Serial Connections
RS232:
PORT A (J7) PORT B (J16) PORT C (J26) PORT D (J25) SIGNAL
RS485:
PORT A (J13) PORT B (J4) PORT C (J28) PORT D (J29) SIGNAL
If the ENB signal on the RS232 connector is tied to GND, the RS232 is active and the RS485 is disabled. If not, the RS485 is active, and the RS232 is disabled. Pins 4 and 5 should be connected on the RS232 (J13, J4) connector to enable the RS232. Alternatively the ports can be forced to RS232 via the configuration, eliminating the need to connect pins 4 and 5.
The GND and +5V on the RS485connectors can be used for biasing resistors if desired. Refer to the RS485 specification for information on terminating and biasing the RS485 network. No more then 50 mA should be drawn from the 5V on the RS485 connector. A termination resistor can be installed on the board if desired.
The port A and port B RS485 ports can be built as isolated RS485. Contact the factory for more information if isolated RS485 is desired.
DT7000 Gateway User’s Guide 2.61 Page 6 of 22
2.5 Digital I/O Connections
The digital I/O is accessed through the 26 pin connector (J10). The module provides 8 digital outputs and 8 digital inputs. The digital inputs and outputs are optically isolated and can be ordered as either sinking or sourcing.
The output transistors are N channel MOSFET transistors capable of sinking or sourcing up to 1.5A. (Note current for the entire module should be limited to 6 A). They include over temperature, over current, transient voltage, and ESD protection. They are suitable for driving relays or other inductive loads directly.
When configured as sinking the output transistors are open drain with source tied to the I/O GND.
Digital Outputs (8X) Sinking:
When configured as sourcing the output transistors are open source with the drain tied to IO power.
Digital Outputs (8X) Sourcing:
When the inputs are configured as source in, they require a current source on the input pin to turn on.
Digital Input (8X) (Source in):
When they are configured as sink in they require a current sink on the input pin to turn on.
DT7000 Gateway User’s Guide 2.61 Page 7 of 22
Digital Input (8X) (Sink in):
The I/O configuration (sourcing or sinking) is not user configurable and must be specified at order. If required, any combination of sourcing and sinking inputs and outputs can be configured on the same module. Contact the factory for special configurations.
Refer to the following table for connecting the Digital I/O.
Digital I/O:
J10 Pin Signal J10 Pin Signal
1 OUT-0 2 XV
3 OUT-1 4 XV
5 OUT-2 6 XV
7 OUT-3 8 XV
9 OUT-4 10 XV
11 OUT-5 12 IN-0
13 OUT-6 14 IN-1
15 OUT-7 16 IN-2
17 XGND 18 IN-3
19 XGND 20 IN-4
21 XGND 22 IN-5
23 XGND 24 IN-6
25 XGND 26 IN-7
All inputs and outputs are rated for 5 to 40 VDC. If jumpers R67 and R68 are installed the input voltage to the module is connected to the XV pins on the connector. This voltage can then be used to power I/O devices. Note the total current draw of all the I/O devices must be limited to 3 Amps if R67 and R68 are installed.
Alternatively jumpers R67 and R68 can be removed and any voltage from 5 to 40 VDC can be supplied to the XV pins on the connector. This allows the I/O to operate at a voltage different then the module supply voltage. With jumpers R67 and R68 removed the inputs and outputs are optically isolated from the module power. With R67 and R68 removed the current draw of all the I/O devices must be limited to 6 Amps.
Each input and output has a status LED (D6-D13) numbered 0-7 on the board silkscreen. Each LED includes a green element which is illuminated when the corresponding input is on, and a yellow element which is illuminated when the corresponding output is on.
The XV LED (D4) shows the status of the external I/O voltage. This will be illuminated green if I/O voltage is present. It will be red if I/O voltage is connected with polarity reversed.
DT7000 Gateway User’s Guide 2.61 Page 8 of 22
2.6 Analog I/O Connections
The analog I/O is accessed through the 8 pin connectors (J18 and J21). The module provides 2 analog outputs and
4 analog inputs on each of the connectors (4 analog outputs and 8 analog inputs total).
Analog outputs are 0 to 10 volt, 10 bit outputs. If required the board can be configured for 0 to 5 volt outputs or 0 to 20 mA outputs. Analog inputs are 0 to 10 volt 10 bit inputs. If required the board can be configured for 0 to 5 volt or 0 to 20 mA inputs. Custom configurations are possible. Please contact the factory for custom analog configurations. (The 0 to 20 mA inputs/outputs can be used to for 4 to 20 mA signals with a corresponding loss of resolution).
Refer to the following table for connecting the analog I/O.
Analog I/O:
J18 Pin Signal J21 Pin Signal
8 ANOUT-0 8 ANOUT-2
7 ANOUT-1 7 ANOUT-3
6 +5V 6 +5V
5 GND 5 GND
4 ANIN-0 4 ANIN-4
3 ANIN-1 3 ANIN-5
2 ANIN-2 2 ANIN-6
1 ANIN-3 1 ANIN-7
The analog I/O can be mapped to the fieldbus data as needed via the user configuration. Additionally a user application can be used to calibrate, average, and convert analog values as needed.
The +5V available on the connector can be used to power external signal conditioning hardware if needed. No more the 200 mA should be drawn +5V supply.
2.7 Fieldbus Connection
The fieldbus connects to the fieldbus connector on the Anybus-CompactCom module. This connector is fieldbus specific. There are also LEDs on the Anybus-CompactCom module. Refer to the ABCC module documentation for information on the fieldbus connection, and the LEDs on the module.
2.8 Mating Connectors
The serial and analog connectors on the DT7000 are Molex latching connectors. The digital connector is a 26 pin header connector, suitable for ribbon cable or discrete wire connectors. The following table lists the recommended mating connectors.
DT7000 Mating Connectors
Type
RS232
RS485
Analog
Ref
J7,J16,J26,J25
J13,J4,J28,J29
J18,J21
Digital J10
Mating Connector
Molex 50-57-9405
Molex 50-57-9404
Molex 50-57-9408
Amp 102387-6
Crimp Pin
Molex 90119-2109
Molex 90119-2109
Molex 90119-2109
Amp 1-87756-8
DT7000 Gateway User’s Guide 2.61 Page 9 of 22
2.9 Module Indicators
There are four power LEDs on the module. They are listed in the table below.
DT7000 Power LEDs
Ref
D1
Green Red
+24V Pow OK Reverse Input Power
D2
D3
D4
+5V Pow OK
+3.3V Pow OK
IO Pow OK
Resettable Fuse Tripped
-
Reverse I/O Power
D1 indicates 24 V power is applied to the module. D2 and D3 indicate the internal voltages are being generated.
All (3) LEDs will be on green when the module is operating properly. D4 indicates the I/O power is applied to the module and will be illuminated green when I/O power is present.
There is a red/green dual color status LED (D5) on the module. On power up the LED flashes alternately red and green to indicate the module is starting up. Once the module is initialized, the status LED has the following meaning.
DT7000- Status LED Indications
D5 – State Indication
Flashing RED
Flashing GREEN
Flashing mostly off
(RED or GREEN)
Not Communicating to Serial Device
Communicating to Serial Device
Not Communicating on Fieldbus
Flashing mostly on
(RED or GREEN)
Solid RED
Communicating on Fieldbus
Module failure
2.10 Module DIP Switches
There is an 8 position DIP switch on the module. The 8 switches are used to set the network address on the fieldbus. These switches set an address in binary. A switch in the up (OFF) position corresponds to a 1 bit.
Example: Address 05.
1 2 3 4 5 6 7 8
05 up dn up dn dn dn dn dn
If the switches are all down (0 value), then the module will read the fieldbus address from the EEPROM on the
CompactCom module. This should also be used if the fieldbus address will be set over the network by a network configuration tool. The fieldbus address in the EEPROM can also be set through the diagnostics port. The switches can be used to reset all configurable parameters in the DT7000 to factory default values, and to erase the user application. If the switches are all up (255 value) on power up, the status LED (D5) will flash red for 5 seconds, and on the diagnostic port a message (*** Change Switches to Reset to Factor Defaults ***) will be displayed. Changing any switch value at this time will reset the module to a factory default state. If the switches remain unchanged, the module will start with a switch value of 255.
DT7000 Gateway User’s Guide 2.61 Page 10 of 22
The meaning of the address and the valid range is fieldbus specific. Refer to the specific fieldbus supplement for the exact meaning of the dip switch settings.
If the module is configured as a MODBUS master or MODBUS slave, the MODBUS master and MODBUS slave device IDs are kept in FLASH. By default a master module will attempt to communicate to MODBUS device ID
1, and a slave module will respond to requests to MODBUS device ID 1. Other MODBUS device IDs can be set and stored through the diagnostics port. If no CompactCom module is installed, the DIP switches will set the
MODBUS salve device ID.
3.0 Communications
The DT7000 provides communications through 4 serial ports. The serial ports can be configured for various functions including Diagnostic port, MODBUS slave, MODBUS master, MODBUS route port, Generic serial driver, or custom protocol.
The Anybus CompactCom module provides connectivity to any of the available fieldbus protocols. As a slave I/O device to a PLC or host computer, any of the fieldbus protocols can be used, as supported by the host.
For users wishing to develop an application on a host PC to communicate with the DT7000, MODBUS-RTU or
MODBUS-TCP can be used. ActiveX components implementing MODBUS are readily available and can be used to simplify application development.
For Ethernet communications to the DT7000, MODBUS-TCP can be used with the MODBUS-TCP
CompactCom module.
For serial communications including USB or Bluetooth, to the DT7000, MODBUS-RTU can be used. A host application can communicate to one of the 4 serial ports through MODBUS-RTU without the need for a
CompactCom module. Alternatively the MODUB-RTU CompactCom module can be used leaving all 4 serial ports available. The USB or Bluetooth CompactCom modules can be used, along with a virtual com port driver, allowing MODBUS-RTU communications through USB or Bluetooth to the DT7000.
3.1 Serial Communications Settings
The communications settings for the serial ports are configured for the application. The module is configured by default with the following settings.
Port Default Settings
Port BAUD Data Bits Parity
Port A 115200
Port B 115200
8
8
None
None
Port C 115200
Port D 115200
8
8
None
None
Function
MODBUS Salve
Available
Generic Serial
Diagnostics
Many of the serial settings can be configured through the diagnostic port. These include enabling or disabling the
Generic Serial driver on each port, defining the buffers sizes for the Generic Serial driver, and setting the communication parameters, including BAUD rate and parity. Some settings can only be configured through a user application, including enabling MODBUS master functionality or custom serial protocols on a serial port.
DT7000 Gateway User’s Guide 2.61 Page 11 of 22
3.2 Fieldbus Data Format
The digital I/O, analog I/O, and serial data are mapped to the field bus data and can be accessed over the installed fieldbus. This mapping can be configured through the diagnostic port.
The following table lists the default mapping of the data on the fieldbus for this version of the module.
Output Data (Sent from Host to DT7000).
Word Byte Register Function
0
1
2
3
4
5
6
7
8
9
10
11
12
13
14
15
24
25
26
27
28
29
30
31
16
17
18
19
20
21
22
23
8
9
10
11
12
13
14
15
4
5
6
7
0 Digital Outputs (Outputs 0-7)
1 Reserved
2
3
Analog Output 0
Analog Output 1
Analog Output 2
Analog Output 3
Port A, Driver Control
Port A, Send Length
Port A, Send Byte 0
Port A, Send Byte 1
Port A, Send Byte 2
Port A, Send Byte 3
Port A, Send Byte 4
Port A, Send Byte 5
Port A, Send Byte 6
Port A, Send Byte 7
Port A, Send Byte 8
Port A, Send Byte 9
Port A, Send Byte 10
Port A, Send Byte 11
Port A, Send Byte 12
Port A, Send Byte 13
Port A, Send Byte 14
Port A, Send Byte 15
Port A, Send Byte 16
Port A, Send Byte 17
Port A, Send Byte 18
Port A, Send Byte 19
DT7000 Gateway User’s Guide 2.61 Page 12 of 22
Input Data (Sent from DT7000 to Host).
Word
0
1
2
3
4
5
6
7
8
Byte Register Function
8
9
10
11
12
13
14
15
16
17
4
5
6
7
0 Digital Inputs (Inputs 0-7)
1 Reserved
2
3
Analog Input 0
Analog Input 1
Analog Input 2
Analog Input 3
Analog Input 4
Analog Input 5
Analog Input 6
Analog Input 7
19
11
12
13
14
15
16
17
18
19
20
21
29
30
31
32
33
34
35
36
21
22
23
24
25
26
27
28
37
38
39
40
41
42
43
Port A, Driver Status
Port A, Receive Length
Port A, Receive Byte 0
Port A, Receive Byte 1
Port A, Receive Byte 2
Port A, Receive Byte 3
Port A, Receive Byte 4
Port A, Receive Byte 5
Port A, Receive Byte 6
Port A, Receive Byte 7
Port A, Receive Byte 8
Port A, Receive Byte 9
Port A, Receive Byte 10
Port A, Receive Byte 11
Port A, Receive Byte 12
Port A, Receive Byte 13
Port A, Receive Byte 14
Port A, Receive Byte 15
Port A, Receive Byte 16
Port A, Receive Byte 17
Port A, Receive Byte 18
Port A, Receive Byte 19
Depending on the particular fieldbus, and the allowed configurations of the Anybus-CompactCom module on that fieldbus, this data may be represented differently at the host. In all cases some set of input and output modules
DT7000 Gateway User’s Guide 2.61 Page 13 of 22
will be defined to form the equivalent of the mapped input words, output words. For some hosts and masters the byte order of word data might be reversed. The host must account for these differences.
With an installed user application the data presented on the fieldbus is completely controlled by the application.
This can include, MODBUS master registers, averaged or processed analog data, or data generated internally by the user application.
3.2 Generic Serial Driver
The generic serial driver allows connection of a serial device to the fieldbus network. The driver allows any data to be sent to and received from the serial device. This allows specific communications protocols to be implemented by the host through the fieldbus. A user application also accesses the serial channels through the generic serial driver, accessing the DT input and output arrays in the same manner as a host.
The generic serial driver defines in the input data array a STATUS word, and an input buffer, and in the output data array a CONTROL word and an output buffer. The STATUS word and CONTROL word are used to coordinate the flow of data through the serial driver. The input buffer stores serial data received from the serial device presented on the fieldbus, and the output buffer stores data placed on the fieldbus to be sent to the serial device.
The STATUS and CONTROL words include a length field in the upper byte and handshake bits in the lower byte, as defined below.
Status Word Definition
15-8 7-4 3 2 1 0
RX Length Reserved MORE SYNCACK TXACK RXDAT
RXDAT – Toggles when received serial data is available on the fieldbus.
TXACK – Toggles when output data has been sent to serial device.
SYNCACK – Set to 1 to acknowledge a Synch request.
MORE – Set to 1 if additional data has been received beyond what is in the Input buffer. This indicates the received data has been fragmented to fit in the input buffer and more data needs to be read after this input buffer is read.
Control Word Definition
15-8 7-4 3 2 1 0
TX Length Reserved MORE SYNC TXDAT RXACK
RXACK – Toggled by host to acknowledge receive serial data has been read. When this is toggled the input buffer will be cleared and filled with more serial data if available.
TXDAT – Toggled by host to indicate data in output buffer is available to be sent to the serial device.
SYNC – Set to 1 to request a synchronization. The input buffer is cleared and all status word bits are set to 0.
MORE – Set to 1 if data has been fragmented to fit in output buffer, and more data needs to be sent immediately after the output buffer has been sent.
The host should follow the procedure outlined here to send and receive data from the serial device.
DT7000 Gateway User’s Guide 2.61 Page 14 of 22
Sending data to the serial device:
1.
Place data to be sent in the output buffer.
2.
Place length of data to be sent in TX Length field.
3.
If data has been fragmented set MORE bit.
4.
Toggle the TXDAT bit.
5.
Wait for the TXACK bit to toggle to match the TXDAT bit.
6.
If more data is to be sent repeat from step 1.
Receiving data from the serial device:
1.
Wait for the RXDAT bit to toggle to be different then the RXACK bit.
2.
Read the serial data from the input buffer.
3.
If the MORE bit is set the data is a fragment and can be reassembled with additional data to follow.
4.
Toggle the RXACK bit to match the RXDAT bit indicating data has been read.
5.
Input buffer will be cleared, and/or filled with additional data if available.
6.
Repeat from step 1.
Note: If the serial device can send data unsolicited the host must monitor the STATUS word and read data as it becomes available to avoid data loss.
4.0 Supported Networks
The following fieldbus networks are currently supported. The corresponding Anybus CompactCom module is installed to support a given fieldbus network. Support for additional fieldbus networks will be added in the future.
Profibus
DeviceNet
CANopen
EtherCat
EtherNet/IP
Profinet-IO
ControlNet
MODBUS-TCP
MODBUS-RTU
In addition to the fieldbus networks the following passive Anybus CompactCom modules are available and supported by the DT7000.
USB
Bluetooth
The passive modules provide a serial pass through connection between the DT7000 and a host, over a different media. The passive modules internally connect to port C of the DT7000, disabling the port C connectors J26 and
J16. With a passive module installed, a serial protocol (such as MODBUS RTU) enabled on port C will pass through the installed media (USB or Bluetooth) to the host.
Information on configuring the DT7000 for use on a specific fieldbus with the associated CompactCom can be found in the respective network supplement for the fieldbus.
DT7000 Gateway User’s Guide 2.61 Page 15 of 22
4.1 MODBUS-RTU (Native Serial Ports)
The DT700 supports the Anybus-CompactCom Modbus-RTU module for MODBUS-RTU connectivity.
Information regarding using this module can be found in the Modbus-RTU network supplement.
It is also possible to communicate to the DT7000 through one of the 4 serial ports using MODBUS-RTU, by enabling this protocol on the desired port. Since the CompactCom passive modules (USB and Bluetooth) are a pass through to port C, MODBUS-RTU is supported through these modules via port C.
Through the native MODBUS interface the input and output arrays are accessible. In addition it is possible to access other memory areas in the DT7000. When a user application is installed, the DT arrays and the FB arrays are both accessible at different address ranges. In addition the AP data array is accessible. Finally the configuration block is accessible allowing the module to be configured through the MODBUS interface.
The following notes apply to the native MODBUS interface:
The default parameters for the native serial ports are 115200,N,8,1, and can be set through the diagnostics port.
The native serial ports only support RTU, and do not support MODBUS-Ascii.
Only the function codes listed in the table below are supported through the native serial ports.
The function codes access the various data areas in the DT7000. If no user application is installed, the DT input array is copied to the FB input array and the FB output array is copied to the DT output array. This means the same input data can be accessed either through the DTInArray or the FBInArray (these are identical). If the field bus is active, then the field bus master controls the output data and writing to the output arrays has no effect. If the field bus is not active and no user application is installed, then the output data can be written through the
DTOutArray (writing to the FBOutArray has no effect). With a user application installed writing to the
DTOutArray is always possible, and to the FBOutArray when the field bus is not active. Note that it is possible to access the same data with different function codes. The following table shows the mapping of DT7000 memory areas to the various MODBUS function codes and addresses.
DT7000 Gateway User’s Guide 2.61 Page 16 of 22
Function Code
1 – Read Coils
5 - Write Single Coil
2 – Read Discrete Inputs
Absolute
Address
0-2047
Modicon 5-digit
Address
00001-02048
5000-7047 05001-07048
0-2047 10001-12048
5000-7047 15001-17048
DT7000 Mapping
DTOutArray 0-127 (As Bits)
FBOutArray 0-127 (As Bits)
DTInArray 0-127 (As Bits)
FBInArray 0-127 (As Bits)
3 - Read holding Registers
6 - Write Single Register
16 - Write Multiple Registers
1024-2432 41025-42433 Ap Data Array 0-1407
5000-5127 45001-45128 FBOutArray
5256-5383 45257-45384 FBInArray
6001-6383 46001-46384 Config Data 0-383
4 - Read Input Registers 0-127 30001-30128 DTInArray 0-127
5000-5127 35001-35128 FBInArray
The output arrays, AP data array, and configuration block have read/write access as holding registers and can be accessed with function codes which access the Holding Registers (3, 6, 16). Bit level access to bits in the output array words is possible with the Read Coil, and Write Coil function codes (1, 5).
The input array has read only access (except as noted below). Attempts to write to registers in the input array that are assigned to functions (writing to the corresponding holding register) will produce an illegal address exception.
Bit level access to bits in the input array words is possible with the Read Discrete Inputs function code (2). Word level access to the input array is possible with the Read Holding Registers, and Read Input Registers, function codes (3, 4).
It is possible to use the DT7000 module as a MODBUS-RTU to fieldbus gateway. Through the native serial ports writing to input array registers that are not assigned to other functions, using function code 6, or 16 to address
40257-40512 is allowed, and will modify values in the input array. The input array can then be read through the fieldbus. Values written by the fieldbus into the output array can be read using function code 3 to address 40001-
40255. This allows a communications path through the DT7000 from one device which is accessing the DT7000 through the installed fieldbus, and another device which is accessing the DT7000 through MODBUS-RTU through one of the native serial ports.
5.0 Diagnostic Interface
The diagnostics interface allows for checking the input and output values of the module as well as changing some of the settings. The diagnostic interface can be used with terminal emulation software such as Hyperterminal
(included with Windows XP), or the open source software, Tera Term which is compatible with Windows 7 and many other operating systems ( www.logmett.com
).
DT7000 Gateway User’s Guide 2.61 Page 17 of 22
By default Port D is the diagnostic interface. On power up, diagnostic information will be sent through this port.
Any port, not assigned to another function can be used as a diagnostic port. Connecting to a port that is not assigned to another function, and pressing ESC, will set this as the diagnostic port and display the main menu. To save the current diagnostic port for future startup information, update the flash configuration with the ‘U’ command.
The following shows the configuration in Hyperterminal to connect to the diagnostic interface.
DT7000 Gateway User’s Guide 2.61 Page 18 of 22
5.1 Startup
When the DT7000 first powers up, the following data will be displayed through the diagnostic interface. This data varies depending on the installed fieldbus and the application.
DT7000 Ver 2.15 I/O Gateway, Diamond Technologies (c) 2011
DT7 Module Type - B
DIP Switches: 0
SwapBytes: 0
CC Exists Type: Active
Port A - : 232
Port B - : 232
Port C - : 232
Port D - : 232
InArrayWords: 22
OutArrayWords: 16
Port A - Modbus Slave Driver Initialized - MOD ID: 1
Port C - Generic Serial Gateway - In[10] Out[10]
AB: Mod type: 0401 - (Anybus CompactCom)
AB: FW Ver: 3.3.1
AB: Net type: 0080 - Modbus-TCP
AB: Param supp: 1
AB: Net Data Fmt: 0
AB: DHCP: 0
AB: Subnet: 0.0.0.0
AB: IP: 0.0.0.0
AB: Run (1537)
Following this, dots will be displayed across the screen indicating the module is operational.
DT7000 Gateway User’s Guide 2.61 Page 19 of 22
5.2 Interface Menu
By pressing Esc the main menu will appear. This menu varies depending on the installed fieldbus, and the application.
DT7000 Rev 02.15 - Diagnostics Interface (PortD)
7 - Set Module type
N - Network IO array
S - Display Scan Statistics
O - Set Outputs
X - Configure Standard Inputs
Y - Configure Standard Outputs
Z - Configure IO Array Sizes
Q - Configure Serial IO
P - Configure Serial Port Function
G - Load Gateway Logic Code
W - Swap bytes in Field Bus words
L - Configure Diagnostic Logging
I - Set IP Address
K - Set Subnet Mask
D - Set DHCP
U - Update Flash Config
F - Reset to Factory Defaults (Clear Logic Code)
Menu options can be selected by pressing the number of letter in front of the option. Configuration values can be changed as desired.
The input and output array values can be displayed by selecting the ‘N’ option.
The digital outputs can be set by selecting the ‘O’ option. This however is only possible if the fieldbus is not controlling the outputs. On most networks, unplugging the network cable releases control of the outputs by the fieldbus, and they can be set with the ‘O’ option.
Configuration of the module can be done with the ‘X’, ‘Y’, ‘Z’, ‘Q’, and ‘P’ options. Once the configuration is changed it can be stored to flash with the ‘U’ option.
DT7000 Gateway User’s Guide 2.61 Page 20 of 22
5.3 Updating the Module Firmware
The DT7000 standard module firmware can be updated through the diagnostic interface. This procedure is for updating the main firmware, not for loading a user application. The following instructions assume Hyperterminal is the terminal interface being used.
From the menu screen press CNTRLF. This will bring up the following screen:
DT7000 BootLoader Ver 2.3, Diamond Technologies (c) 2010
LoadPort 04 DiagPort 04 LoadMode 01
Flash Erase size: 0800, Flash Write size: 0100
Loader Location: 0001e800 - 0001ffff
DT7000 Current Firmware Version: 2.15
Waiting for Flash Load - ESC to abort
In Hyperterminal go to Transfer and then Load Text File. Browse to and select the firmware file to be loaded.
(Note the firmware file is a .HEX file. Changing Files of Type: to All will allow you to select the .HEX file)
Load the firmware file. The address being loaded, along with dots will be displayed on the screen as the file is loaded. It will take a few minutes. When the update is finished the DT7000 module will restart.
DT7000 Gateway User’s Guide 2.61 Page 21 of 22
6.0 Technical Specifications
Module:
Operating Temperature: 0 Deg C to 70 Deg C.
Input Voltage: 9 – 40 VDC (24 VDC Nominal).
Input Current: 300 mA max, 100 mA typ.
(@24VDC).
1
RoHS compliant.
Serial Channels:
Electrical: RS232 or RS485 (Isolated, Optional)
Protocol: MODBUS master, slave. Or custom.
Baud Rate: 9600 to 384000. Configurable.
USB Channel:
Version 2.0: Full Speed
Windows Virtual Com Port Driver
Diagnostic and Configuration port
Custom protocols optional
Ethernet Channel:
RJ45, 10/100 Mbit, Autosensing.
Protocol: MODBUS-TCP master or slave.
Embedded diagnostic webpage
Windows Virtual Com Port Driver
Diagnostics and configuration port.
Fieldbus:
Via Anybus CompactCom.
Active and Passive Modules supported.
Digital Outputs:
Channels: 8 o 1.5 Amp Max 2 o Integrated clamp diode for Inductive loads. o Current limited. o Overvoltage, overtemp protection.
Polarity: Sinking or Sourcing 3
Voltage: 5 to 40 VDC.
Digital Inputs:
Channels: 16
Polarity: Sinking or Sourcing 3
Voltage: 5 to 40 VDC.
Analog Outputs:
Channels: 2 or 4 o Voltage: 0-10 VDC (0-5VDC optional) o Current: 0-20 mA
Resolution: 10 bit.
4
Relative Accuracy: +/- 3 LSB 5
Analog Inputs:
Channels: 4 or 8 o Voltage: 0–10 VDC (0-5VDC optional) o Current: 0-20mA 4
Resolution: 10 bit.
Relative Accuracy: +/- 1 LSB 5
1 With Jumper R67, R68 removed. If R67, R68 installed, I/O load is added to input supply.
2 Max current entire module, 6 Amps with R67, R68 removed, 3 Amps with R67, R68 installed.
3 Modules built with sourcing or sinking inputs and outputs. Not user selectable.
4 0-20 mA analog channels can be used for 4-20 mA with corresponding reduction in resolution.
5 Gain and offset errors can be calibrated out in software.
DT7000 Gateway User’s Guide 2.61 Page 22 of 22
advertisement
Related manuals
advertisement
Table of contents
- 3 i Revision History
- 3 ii Reference Documents
- 3 iii Table of Contents
- 4 1.0 Introduction
- 4 2.0 DT7000 – Module
- 5 2.1 Module Layout
- 5 2.2 Module Mounting
- 5 2.3 Input Power
- 6 2.4 Serial Port Connections
- 7 2.5 Digital I/O Connections
- 9 2.6 Analog I/O Connections
- 9 2.7 Fieldbus Connection
- 9 2.8 Mating Connectors
- 10 2.9 Module Indicators
- 10 2.10 Module DIP Switches
- 11 3.0 Communications
- 11 3.1 Serial Communications Settings
- 12 3.2 Fieldbus Data Format
- 14 3.2 Generic Serial Driver
- 15 4.0 Supported Networks
- 16 4.1 MODBUS-RTU (Native Serial Ports)
- 17 5.0 Diagnostic Interface
- 18 5.1 Startup
- 20 5.2 Interface Menu
- 21 5.3 Updating the Module Firmware
- 22 6.0 Technical Specifications