- Home
- Domestic appliances
- Climate control
- Split-system air conditioners
- Carrier
- 58MTA120F10120
- Installation Guide
advertisement
▼
Scroll to page 2
of 52
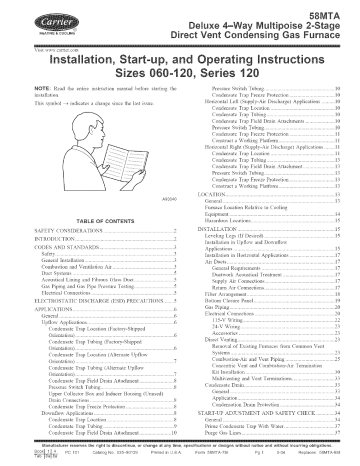
88MTA DeMu×e 4-Way NuMtipoise 2-Stage Direct Vent Condensing Gas Furnace HEATUNG & COOUNG \isit x__ v_.carrier.com tnstammation, Start-up, and Operating tnstructions Sizes 060-120, Series 120 NOTE: Read theentire instruction manual be%re starting the installation. Pressure Switch Tubing ..................................................... Condensate Trap Freeze Protection ................... Horizontal Left (Supply-Air Discharge) Applications ..... Condensate Trap Location ........................ Condensate Trap Tubing ............................ Condensate Trap Field Drain Attachments .............. Pressure Switch Tubing .......................... Condensate Trap Freeze Protection .................. Construct a Working Platform ......................... Horizontal Right (Supply=Air Discharge) Applications ........ Condensate Trap Location .......................... Condensate Trap Tubing ............................ Condensate Trap Field Drain Attachment .............. Pressure Switch Tubing ........................... Condensate Trap Freeze Protection .................. Construct a Working Platform ...................... This symbol --> indicates a change since the last issue, A93040 TABLE OF CONTENTS SAFETY ( ONSIDERATIONS ..................................................... 2 INTRODU( TION 2 (?ODES AND STANDARDS ............................ 3 Safety ......................................................................................... General Installation ................................................................... Confhustion and Ventilation Air .............................................. Duct Systems ............................................................................ Acoustical Lining and Fibrous Glass Duct Gas Piping and Gas Pipe Pressure Testing ................. Electrical ( onnections ............................. ELECTROSTATIC DISCHARGE (ESD) PRE(AUTIONS .... 3 3 3 5 5 5 5 6 6 6 Condensate Trap Freeze Protection ................... Downftow Applications ............................. Condensate Trap Location ......................... Condensate Trap Tubing ........................... Condensate Trap Field Drain Attachment .............. 8 8 8 9 10 Manufacturer reserves PC 101 the right to disoontinue, Catalog No. 535-80129 or change 13 13 INSTALLATION ..................................... Leveling Legs (If* Desired) ........................... Installation in Up flow and Down flow Applications ...................................... Installation in Horizontal Applications .................. Air Ducts ......................................... i5 15 6 6 7 7 8 8 8 14 15 General Requirements ........................... Ductwork Acoustical Treatment .................... 17 17 Supply Air Connections .......................... Return Air ( onnections .......................... 17 17 18 19 Gas Piping ...................................... Electrical ( onnections .............................. 20 20 115=V Wiring ................................. 24-V Wiring ................................... Accesso*ies .................................... Direct Venting ...................................... Removal of Existing Furnaces flora Common Vent Systems .......................................... Combustion-Air and Vent Piping ....................... Concentric Vent and Combustion-Air Termination Kit Installation ................................... Multiventing and Vent Terminations .................. Condensate D*ain ................................. General ...................................... Application .................................... Condensation Drain Protection ..................... 22 23 23 23 START=UP ADJUSTMENT AND SAFETY (HE(K General ........................................... Prime (ondensate Trap With Warm ................... Purge Gas Lines .................................. Form 15 17 17 Elite* Arrangement .................................... Bottom Closure Panel .............................. at any time, specifications Printed in USA 13 13 I3 13 13 LO( ATION .......................................... General ......................................... Furnace Location Relative to (ooling Equipment ....................................... Hazardous Locations ............................... 5 APPLI( ATIONS ..................................... General ............................................. Lpflow Applications ............................... Condensate Trap Location (Factory=Shipped Orientation) ....................................... Condensate Trap Tubing (Factou=Shipped Orientation) ...................................... Condensate Trap Location (Alternate Upflow Orientation) ..................................... Condensate Trap Tubing (Alternate Upflow Orientation) ...................................... Condensate Trap Field Drain Attachment ............... Pressure Switch Tubing ................................ Upper Collector Box and Inducer Housing (Unused) Drain ( onnections .............................. 10 10 l0 10 10 l0 l0 11 11 or des}gns 58MTA-7SI without notice Pg 1 and without 5-04 ........ 23 25 30 33 33 33 34 34 34 34 37 37 inourring obligations. Replaces: 58MTA-6SI such as cleaning and replacing be performed by heating equipment, on labels attached precautions These instructions or cover national instructions especially to shipped those the minimmn standards safety C[TS unit and exceed requirements and safkty codes. certain other safety local codes and conform In some and instances, ordinances, that may not have kept up with changing tial construction practices. We minimum fbr a saf_ installation. Wear with must working on on tags, and that may apply. to existing these air filters. All other operations trained sma'ice personnel When observe precautions in literatme, glasses and work AND ABRASION require these residen= instructions as a gloves HAZARD Failure to %llow this caution may result in personal iaju W. Sheet metal parts may have sharp edges or bun's Use care and wear appropriate protective clothing and gloves when ban= dling parts. Have a fire extinguisher available during start-up and adjustment procedures and service calls ; I Recognize safkty information. This is the safety-alert symbol When you see this symbol on the unit and in instructions manuals, be almt to the potential for personal inju W or Understand these signal words: DANGER, WARNING, (AU= TION, and NOTE. These words are used with the safkty=alert symbol. DANGER identifies the most serious hazards which will result in severe personal injury or death. WARNING signifies hazards which could result in personal injury or death. (AUTION is used to identify unsafe practices which may result in minor personal injury or prodact and property damage. NOTE is used to highlight suggestions which will result in enhanced installation, reliability', or operation. REGISTERED QUALITY SYSTEM AIRFLOW SAFETY FURNA(E Improper RELIABILITY installation 4> CONSIDERATIONS HAZARD or misapplication of" furnace can require excessive servicing or cause premature component failure Application of this i\u'nace should be indoors with special attention given to vent sizing temperature rise, and material, unit leveling, and unit sizing FIRE, EXPLOSION, ELECTRICAL SHOCK AND CARBON MONOXIDE POISONING HAZARD Failme to follow this warning could result in electrical shock, firQ personal ir{jnry, or death. Improper installation, ad}ustn_ent, alteration service, mainte= nance, o* use can cause carbon monoxide poisoning, explo= sion, fire, electrical shock, o* other conditions which may cause personal injury or property damage. Consuh a qualified installer, smwice agency, local gas supplier, or your distribu= tot or branch fbr information or assistance. The qualified installer or agency must use only fi_ctmy=authorized and listed kits or accessories when modif}'ing this product. Installing and servicing gas electrical and personnel should Untrained personnel heating equipment components. install, can repair, perform p gas input rate, air Only can be hazardous trained or service basic and heating maintenance due to qualified equipment. fhnctions AIRFLOW AIRFLOW © AIRFLOW A93041 Fig. 1--MuRipoise Orientations INTRODUCTION The model 5SMTA, 2=Stage, 4=way multipoise, Gas=Fired, Cat= egory IV, direct vent condensing fhrnace is available in model sizes ranging in high-stage gas input rates of 60,000 to 120,000 Btuh This furnace is CSA. (fbm_erly AGA and CGA) design= certified l\_r natnral and propane gases (see furnace rating plate) and fbr installation in alcoves, attics, basements, closets, utility rooms, crawlspaces, and garages. This furnace is factory=shipped %r use with natural gas conversion propane A (,SA (%rmerly kit is required gas to convert shall not be installed proper furnace installation blower con_partrnent. directly %r use with combustible material downflow installations, a fi_ctory accessory when installed on combustible base is not required manul:acmrer's other on carpeting, any other Special This f;arnace gas, This furnace used AGA and CGA) listed d-ian wood materials coil assembly of the 58MTA furnace AGA certified installation and (CA) vehicles, installation completed in a structure at final 1. Combustion must section coil box User's Information (fbm_erly mobile Warranty homes, is suitable building cially available soap solution and "Start=Up, in Use a commer- made specifically Adjustment, and Safety install furnace temperature-rise external to operate range static with pressure a \mace circulated is installed containing system Box or condensate so that air shall casing which has range, supply an as speci= ducts plate. Drain tube coupting 1 Drain tube coupling grommet 1 Vent and combustion-air 2 the space containing also be handled and terminating For accesso_ instruction by duct(s) outside the space temperature Remove Follow all nationM is designed must for not exceed continuous This is shipped nected for UPFLOW quired when used return=air dh. Failure re['cr to the accesso_- materials AND before operating \mace. STANDARDS and local codes and standards The installation must comply instructions. installation in addition to with regulations having with of as shown must LEFT atmosphere the &ain (supply-air be installed discharge and flue and con= are re= (combustion kit. In a installation. and ( anada, follow to the outdoor vent-air intake National Installation and all authorities all codes and standards fbr 2--General Systems ANSI NFPA Standard of Canada, (ode (NSCNGPI() 90B Natural C SA B149 Gas Installation or for only the NFG( 400 N (apitol, N.W., contact the American Gas Washington DC 20001 CANADA: NSCNGPIC For a copy, contact Standard CSA International., 178 Rexdale Boulevard, Etobicoke onto), Step * arid 1-00 US: NFG( arid the NFPA 90B. For copies, contact the National Fire Protection Association Inc., Batterymarch Park, Quincy, MA 02269; Association, air fiom the for proper * appli- tem_ination accessory below US: National Fuel Gas (ode (NFGC) NFPA 54-2002 ANSI Z223,1-2002 and the Installation Standards, Warm Air Heating Step section. is taken directly factory listed l--Safety CANADA: RIGHT, direction) in Applications gases are discharged States and Air (onditioning these tubes HORIZONTAL and a factor T accessory kit instructions * motors modifications with a direct=vent all air for combustion furnace to follow and pressure Minor in Fig. 1. See details and flue gas) system system, with codes the following: Propane applications. the national jurisdiction. n_ininmm of heat exchangers, in DOWNFLOW, or HORIZONTAL See 85°F may af_bct reliability (See Fig. 4.) furnace all shipping CODES these detail, comply air limits termination 1 1" furnace fbr installation in a residential garage must as specified in the warning box in the "Location" and controls. atmosphere. 2 disk assembly of the ser_-ing gas supplier, local building, heating, plumbing, and other codes. In absence of local codes, the installation must temperature of 60°F db or intetw_ittent operation down to 55°F dh such as when used with a night setback them_ostat. Return-air outdoor intake pipe perforated installation NOTE: Step furnace direct=vent 3 intake hote filler plug ONLY supplied with some furnaces. In the United This filrnace intake pipe support trap hole filler plug carl T air 6. The furnace is not to be used for tempora W heating buildings or structures under construction. cations 1 the fi_rnace. 5. A gas-fired be installed section, return trap extension tube 1 2 Combustion-air sec= intended See fl_rnace rating to areas outside d_e remm sealed to the furnace the furnace's the allowable section. by the furnace the \mace, within a duct within fled in the "Adjustments" This Quantity 1 Vent and combustion-air in the "Gas Check" Manual Vent Pipe Extension 3. Always in in the main Inducer housing drain tube 1/2-in CPVC street elbow Condensate for the detec- as specified to assist Certificate Collector (onnect only, as specified flame. materials are shipped Loose Parts Bag includes: Pressure tube extension for instructions with an open materials Installation, Startup, and Operating Instructions Service and Maintenance Instructions on the outdoors. vent system tion of leaks to check all connections, 4. When in furnace be discharged of these test for gas leaks Piping" rich. is installed on site or a manufSctured to an approved the "Venting" 2. Never built This the %llowing These Installer Packet includes: site. products this \mace %r or outdoors. be flooring. is not C.S.A. with For must or when the manufacturer's is used. The design recreational base and wood when this \mace is shipped tile, o1" flooring. floor furnace Ontario, M9W a--Combustion US: Section Ventilation CANADA: Supply 83 1R3, Canada and of the Ventilation Air NFGC, fbr Part 7 of due NSCNGPIC, for Appliances Sales, (Tor- Air Venting Cornbustion Systems arid and Air O AIRFLOW TYP CONDENSATE DRAIN TRAP LOCATION (DOWNFLOW & HORIZONTAL LEFT) z- OUTL CONDENSATE DRAIN TRAP LOCATION _ {DOWNFLOW & HORIZONTAL RIGHT) OR ALTERNATE _NN DIA GAS CONN ?_-IN DIA POWER CONN POWER !'NN D_A THERMOSTAT ENTRY 22 Hid _s-IN DIA ACCESSORY POWER ENTRY 24 SIDE INLET 9 _" TYP INLET CONDENSATE DRAIN LOCATION (UPFLOW) 1½_, 11 i¢ ,,,4_,. DRAIN LOCATION (UPFLOW) DIMPLE LOCATORS FOR HORIZON ]:AL HANGING NOTES: BOTTOM INLET I. Minimum return-air openings at furnace, based on metal duct. If flex duct is used, see flex duct manufacturer's recommendations for equivalent diameters. 2. Minimum return-air opening at furnace: a. For 800 CFM-16qn. round or 14% x 12qn. rectangle. b. For 1200 CFM-20qn. round or 14V2x 19VNn, rectangle. c. For t600 CFM-22-in. round or 14Y=x 23%-in. rectangle. d. For airflow requirements above 1800 CFM, see Air Delivery table in Product Data literature for specific use of single side inlets, The use of both side inlets, a combination of I side and the bottom, or the bottom only will ensure adequate return air openings for airflow requirements above 1800 CFM at 0.5 W.C. ESP. DiMENSiONS (iN.) UNIT SIZE A D E 060-t2 17-1/2 15-7/8 16 080-t2 17-1/2 15-7/8 16 080-t6 17-1/2 15-7/8 100-t6 21 19-3/8 191/2 19-3/8 191/2 100-20 21 120-20 24-1/2 22J/8 16 23 A02149 Fig. 2--DimensionaB Drawing ENTRY 39 (_' 30 %2" DRAIN TRAP LOCANON (ALTERNATE UPFLOW} CONN This furnace isforindoor installatioo inabuilding constructed onsite. This [umace may beinstalled inamanufactured (mobile) home when stated onrating plate and using factor)/authorized kit..oncombustible This furnace may beinstalled flooring inalcove ordoset atMinimum Inches Clearance ToCombustible Construction asdescribed below. This furnace requires aspecial venting system. Refer totheinstallation instructions forparts listand method ofinstallation. This furnace isforuse with schedule-40 PVC, PVC-DV\h/, CPVC, or24 Ainches BS-D_J_/pipe, and must not bevented incommon with other gas4ired appliances. Construction through which vent/air intake pipes may be installed ismaximum (600 ram), minimum 3/4 inches (19mm) thickness (including roofing materials). Cette fournaise 8airpuls@ estequip@e pour utilisation avec gaz naturel etaltitudes comprises entre 0 - 3,050m (0 - 10,000 pi),exsept@ qseles fournalses de 140 taille soot pour altitudes comprises entre 0 - 2J35m (0 - 7,000pi). Utiliser use trousse de conversion, foumie par le fabrican_ pour passer au gaz propane ou pour certaines installations au gaz naturel. Cette foumaise a air puls@ est pour fas_allation _ I'interieur dons un b_timent construit sur place. Cette fournalse _ air pulse peut @treinstallee dons une maison pr@fabriquee (maisoo mobile) si prescrit par la plaque signalCtique et si I' on utilise une trousse speblfiee par le fabric.ant _ette foumaise peut _tre install@esur un pfancher combustible dons un enfoncement ou un placard en observant les Degagement Minimum En Pouces Avec Era#merits De Construction CombustibUes. Cette fournaise n@cessite un syst@me d'@vacuation sp@cial. La m@thode d'inslallation et la Ilste des piCces n@cessaires figurent dons les instructions d'install4on. Cette foumalse dolt s'utillser avecla tuyauterie des nomenclatures 40 PVC, PVC-DWV, CPVC, ou ABS-DVW et elle ne peut pas @treventilee conjointment avec d'autres appareils a gaz. Epeisseur de la construction au travers de laquelle il est possible de faire passer les tayaux d'aeration (admission/evacuation): 24 pc (600 ram) maximum, 3/4 pc (19mm) minimum (y compris la toiture). For upflow and do\_,_]llowapplicatbns, furnace must be installed level, or pRcbed within 1/Z' of favel. For a horizontal application, the furnace must be pi_.chedminimum 1/4" to maximum of 1/2" fo_vard for proper drainage. See h_stall4oo Manual [or IMPORTANT unit support details on horizontal applications. MIN 1/4" TO 1/2" MAX Pour des applicatior_s de flux ascendant et descendant, la foumaise deit @treinstall@ede niveau ou inclin@e_5 pos plus de I/Z' du niveau. Pour une application t_rizontale, lafournaise deit @treinclin@eentre minimum 1/4" et maximum 1/Z' du niveau pour le drainage approprie. En cos d'installatioo en position horizontale, consulter les rerL_eignementa IMPOR]IANTS sur le support dans b manuel d'insfallddon. HORIZONTAL MINIMUM INCHES CLEARANCE TO CONBUSTtBLE CONSTRUCTION ALL POSITIONS: Minimum front clearance for service 24 inches (610ram). ¢ t 140 size furnaces require 1 inch back clearance to combustible DOWNFLOW POSITIONS: This furnace is approved for UPFLOW, DOWNFLOW and HOR_ONTAL installalises. Cetfa faumalse est approuvee pour Iinstaliatbn HORIZONTALE et la drculation d'air VERS LE HAUT et VERS LE BAS, materials, Clearance arrows do not change with furnace orientation, t For installation or] combustible floors only when installed on special base No. KGASB0201ALL, Coil Assembly, Part No. CD5 or CK5, or Coil Casing, Part No. KCAKC. HORIZONTAL POSITIONS: ne change pas avsc I'orientat_a_de la gen@abur d "a_rchaed, Line contact is permissible only between lines formed by intersections of top and two sides of furnace jacket, and building joists, studs, or framing. Clearance shown is for air inlet and air outlet ends. O 120 and 140 size furnaces require 1 inch bottom clearance to combustible materials. DEGAGEMENT MINIMUM EN POUCES AVEC ELEMENTS DE CONSTRUCT!ON COMBUSTIBLES POUR TOUS LES POSITIONS: D@gagement avant minimum de 610mm (24 pc) pour I'entretien. t ¢ Pour les fournaises de 140 taille, 1 pc (25mm) degagement des materiaux combustibles est requis au-arriere. POUR LA POSITION COURANT DESCENDANT: t Pour I'irkstallation sur le plancher combustible seulement quand on utilise la base spg_ciale, piece n o KGASB0201ALL, I'erksemble serpentin, piece n° CD5 ou CKS, ou le carter de serpentin, piece n o KC/_XC. POUR LA POSITIONHORIZONTALE: Le contact n'est permis q0ente les lignes formees par les intersections du deseus et des deuxcCtes de la chemise de la foun]aise, et des selives, des montants ou de la charpente du batiment. § La distance indiquee concerne I'extremit6 du tuyau d'aniv@e d'air et I'extremit6 du tuyau de sortie d'air. O Pour les fournaises de 120 et 140 taille, 1 pc (25mm) degagement des materiaux combusitbles est requis au-dessous. ti/ent clearance to combustibles 0". Clearance in inches Degagement (pc}, 0 (pc) Degagement d'evsnt avec combJstibles, 328066-201 REV. B LIT TOP A_02_Tf{:F -j -_ Fig. 3--Clearances Step * 4-==Duct Systems US and CANADA: (ACCA) Manual tractors National Air Conditioning Contractors * 5--Acoustical US and (ANADA: Lining . g--Gas US: NF'G(7 codes Fibrous cmTent edition tested by UL Standard Step and Piping and chapters Gas Pipe ConSoci- Engineers 34 I Rigid NFPA 90B as Air Ducts Pressure plumbing must * When flexible connectors not exceed 36 inches. * 7--Electrical US: National be installed by a licensed are used, Parts 36 3, 4, 5, A, B, E, G, and H. Connections Electrical Canadian ELECTROSTATIC Erse this procedure ESD service to prevent ---> In the state of Massachusetts: This product fitter. Step NSCNGPIC are used they shall not exceed Code (NE() Electrical ANSIiNFPA Code CSA D_SCHARGE (ESD) PROCEDURE 70-2002 C22.1 PRECAUTIONS Testing 5, 6, 7, and 12 and national * CANADA: CANADA: G_ass Duct of SMACNA, 181 for (lass When lever type gas shutof£s inches. Association D, Sheet Metal and Air Conditioning Association (SMACNA), or American ety of Heating, Reti'igeration, and Air Conditioning (ASHRAE) 2001 Fundamentals Handbook Chapter Step to CombustibJes plumber the maximum length or gas shall for all installed kit (available EBD damage. and uninstalled from commercial sources) _i_rnaces. An may be used APPUCATIONS MINOR MAX 85°F PROPERTY Failure to fbllow DAMAGE this caution may result in minor property damage, Local codes application or over a finished In Canada, NS(NGPIC Step l--General Some assembly ! RETURN R °I .C "_ pressure tubes are connected instructions 2--Upflow In an upflow Fig. 4_Retum-Air section, and be are accordance required shown as shown in for with t\u'naces in Fig. 1. All drain and in Fig. 6. See appropriate for these procedures. Applications application_ the blower and conditioned CONDENSATE Temperature modifications in any of the 4 applications Step A93042 installations shall and/or local codes. and entire furnace f_lrnace is used in an attic ceiling. installed application III a drain pan under trap when a condensing NOTE: cun'ent MIN 55°F may require condensate is located air is discharged TRAP LOCATION below the burner upwards, (FACTORY-SHIPPED ORIENTATION) The ,-f UNIT DAMAGE Failure " _ 1 this caution may result in damage to unit Follow below during furnace static discharge can the Electronic fiom electronic Precautions installation control discharges affect Discharge _itmace electronic the f_/rnace, electrostatic and servicing Precautions personnel and hand the control, to protect will prevent tools and the person CONDENSATE listed the NOTE: confirm electIo° which are will help to discharge by TRAP at the same tubes should pressure switch grounding 3. After the chassis, or connecting recharge your ungrounded 4. [f you held in hand during will be discharged. touching control Tools by a color ibllows: &ain label bo@ objects, touch as you to smwice d_e do nothing to wires as long or shuffling feet, touching objects, firmly touch a clean, etc.). ungrounded 5. Lse this procedure may proceed (moving unpainted metal surface contlol or wires. of the [:urnace robe label), again before touching and uninstalled your (violet body's electrostatic control from furnace, follow or yourself a new control damage. items in contact into containers 7. An ESD service also be used charge to ground If the control 1 through before touching bringing attached to condensate trap and applications. connection location tubes are identified inducer port NOTE: robe connection must be extended for the *\allowing: of field drain connection. (See Fig. 2 or If internal filter or side Filter/Media (abinet b. Remove and discard desired side. &ain loose parts drain coupling &ain robe coupling grommet hole plug grommet bag) in selected bag) through blower. e. (ement tube casing casing 2 factory=supplied button in loose street CPV( Put all used and new Fig. be ungrounded cemented objects 6.) These NOTE: Failure prevent draining. elbows to condensate to use CPVC must from (factory-supplied tong end of coupling 1/2-in. duct in hole. (_i_ctory=supplied ensuring is used. &ain fiorn return on the condensate may (green label). robe should be located to opposite side of casing attachment to assist in filter removal. the conhol sources) as housing Tube drain by doing location relief robe (pink These and also 6.) the in a Port, and the rigid drain tube connection from commercial ESD damage. to protect Relief or molded), switch trap field attachment discharge is to be installed 4 before with the t:urnace. kit (available to prevent t'rom its container, Drain, robe. These label door to Housing by their Trap Drain condensate d. Slide removing controls The (ungrounded) fLlITlaC eS, 6. Be%re *\_r drain robe label on main [:urnace box &ain robe (blue label), and pressure c. Install _br installed section for use in upflow on each collector a. Determine you and (FACTORY-SHIPPED be factory tea@ can be identified 2. (ondensate metal surti_c¢ of the t'urnace which is close to the control. shelf A _hctory-supplied trap drain connection to the attachment. See Condensate See Fig. 6 or tube routing location of these tubes. These 1, Disconnect all power to the t_urnace Muhiple disconnects may be require& DO NOT TOUCH THE CONTROL OR ANY WIRE CONNE( TED TO THE CONTROL PRIOR TO DIS° (HARGING YOUR BODY'S ELECTROSTATI( CHARGE TO GROUND. chassis TUBING 1. Collector Box Drain, Inducer Pressure Switch Tubes potential. touch the clean, unpainted, in the blowe* applications. ORIENTATION) tubes 2. Firefly installed components Procedure held during the procedure These precautions avoid exposing d-le control to electrostatic putting is factory for UPFLOW Trap Tubing (Factory-Shipped Orientation) extension details. (See Fig. 5.) components Electrostatic trap connected robe is used to extend the condensate desired t\lrnace side for field drain HAZARD to follow condensate factory cemented parts [itces elbows to trap. (See together and trap drain connection elbows may allow &ain to kink and t--- BLOWER SHELF / / /J- / / _ FURNACE X DOOR CONDENSATE \ TRAP (INSIDE) ]-- CONDENSATE TRAP FURNACE / / X \ ] FURNACE S,Dy IDE OOR / _ FIELD 2 '4 \ _-ALTERNATE DRAIN \ TUBE LOCATION \ CONDENSATE TRAP --& F'ELDJ 1 '2 DRAIN FURNACE --"1------ DRAIN CONN CONN SIDE VIEW ! END VIEW FRONT VIEW FRONT VIEW DRAIN TUBE LOCATION UPFLOW DOWNFLOW AND EXTERNAL UPFLOW APPLICATIONS HORIZONTAL APPLICATIONS ALTERNATE APPLICATIONS S OT#O 7 'So:< (OPTIONAL) ._111/2 /40D COLLECTOR TRAP RELIEF / / BOX TO PORT %OD INDUCER HOUSING DRAIN CONNECTION /80D COLLECTOR BOX DRAIN CONNECTION 71/8 SCREW HOLE FOR UPFLOW OR DOWNFLOW APPLICATIONS (OPTIONAL) 7/8 2 GUIDES (WHEN : V2-1N PVC OR CPVC USED) FRONT VIEW SIDE VIEW A93026 Fig. 8--Condensate fl <onnect larger supplied diameter in loose drain parts bag) tube and clamp to condensate (factory- trap and clamp FIRE, INJURY OR DEATH HAZARD Failure to £_llow this warning could result in electrical shock, fire, personal inju_ or death. ( asing hole filler cap must be installed in blower shelf hole when condensate trap is relocated. securely. g. Route robe to coupling h. Attach and cut to appropriate robe to coupling CONDENSATE TRAP and clamp LOCATION length. securely. (ALTERNATE UPFLOW ORIENTATION) An ahemate of casing. NOTE: location fbr the condensate (See Fig the fi_ctory-connected nected Upflow left°hand &ain and modified (Alternate relocate ing: and relief Orientation) 3 tubes 2. Remove trap from blower casing connected location side is used, section fbr tubing Trap Tubing attachment To side, per_:brm the follow- to condensate trap shelf by gently pushing tabs inward t_ap hole filler bag) into blower shelf 4. Install condensate tlap into left-hand side casing hole by inserting tube connection stubs through casing hole and rotating until tabs snap into locking position. 5 Fill unused condensate tlap casing holes with plastic filler caps (bactory-supplied in loose parts bag). port robes must be disconSee < ondensate tlap to the left-hand 1. Remove 3. Instail side of casing for attachment. condensate and rotating trap is the left-hand 2 and 7) If the alternate Trap cap (fi_ctory-supplied hole where in loose trap was removed parts CONDENSATE TRAP TUBING (ALTERNATE ORIENTATION) UPFLOW NOTE: See Fig. 7 or robe routing label on main ['urnace door to confirm location of these robes 1 Collector Box Drain Tube Connect collector box &ain robe (blue label) to condensate trap. NOTE: On 17-1/2 in wide furnaces ONLY, cut robe between CmTugated sections to prevent kinks from occmring PLUG --_ CAP DRAIN TUBE & WHITE COLLECTOR BOX _,DRAIN TUBE (BLUE & WHITE STRIPED) (BLUE STRIPED) TUBE COLLECTOR BOX _'_ TUBE (PINK) "N (PINK) COLLECTOR TUBE TUBE BOX -- (GREEN) (GREEN) INDUCER DRAIN (MOLDED) TUBE (BLUE) DRAIN TUBE (BEHIND COLLECTOR BOX DRAIN TUBE) O TRAP DRAIN TUBE O (BLUE) HOUSING DRAIN FACTORY-SUPPLIED DRAIN TUBE COUPLING (LEFT DRAIN OPTION) TUBE (VIOLET) A01031 FIELDqNSTALLED FACTORY-SUPPLIED DRAIN TUBE £ Fig. FACTOR_SUPPLIED ½-1NCPVC STREET ELBOWS(2) FOR LEFT DRAIN OPTION 7--ARernate FIELD-INSTALLED FACTORY-SUPPLIED DRAIN TUBE NOTE: See Fig to check fbr proper COUPLING (RIGHT DRAIN OPTION) UPPER A01030 Upflow Configuration Location 6 or 7 or robe routing label on main furnace BOX _Sctory°installed 2, Inducer Housing Drain Tube a, Remove and discard LOWER (molded) inducer housing &ain tube which was previously connected to condensate t_ap, AND INDU(ER corrugated, striped label). leakage in this application. This robe plugged HOUSING Ensure See Fig. 6 or 7 or tube routing to check tbr proper 2. Upper housing to (blue to prevent and is a white condensate this tube is plugged. label on main furnace door connections. inducer Attached connection robe is plugged NOTE: b, Lse inducer housing &ain extension robe (violet label and f5ctow-supplied in toose parts bag) to connect LOWER inducer housing &ain connection to the condensate trap door DRAIN" (ONNECTIONS 1. Upper collector box &ain connection Attached to the UPPER collector box drain Fig. 6--Factory-Shipped Upflow Tube Configuration (Shown with Blower Access Panel Removed} Trap connections. (OLLECTOR (t NUSED) and the drain connection UPPER (urmsed) connection is a cap and clamp. condensate leakage inducer housing This cap is used in this application. Ensure &aia to prevent this connection is capped. c, Detem_ine approp*iate tength, cut, and connect robe d, (lamp robe to prevent any condensate leakage, 3, Relief Port Tube a, (onnect NOTE: See Fig. 6 or 7 or tube routing to check fbr proper CONDENSATE relief port tube (green label) to condensate trap, TRAP FREEZE Refer to (ondensate b, Extend this tube (iI'required) by splicing to small diameter tube (fitctow=supplied in toose parts bag) tions and procedures. Step 3--Downflow c, Determine appropriate length, cut, and connect robe In a downflow fhrnace burner and conditioned (ONDENSATE TRAP FIELD DRAIN ATTACHMENT Re_kr to Condensate procedures Drain section %r recommendations section, label on main furnace door connections. Drain PROTE( Protection TION section for recommenda- Applications application, CONDENSATE TRAP The condensate trap must the blower is located air is discharged above the downwards. LO(ATION and blowe* shelf location PRESSURE SWITCH TUBING as shown The LOWER collector box pressm'e robe (pink 1abel) is factory connected to the High Pressure Switch and should not require any modification, To ti"om the fhcto_--installed in selected application tocation in Fig. 2, g, or 9. relocate location, be removed and relocated condensate per%m_ 1, Remove trap fi'om the blower shelf the following: 3 tubes connected to condensate t_ap, to desired 4. h_stall casing COLLECTOR DRAIN TUBE was (BLUE) PLUG COLLECTOR TUBE ren'lo'_ FIRE, INJURY, Failure to fbllow fire, personal BOX (GREEN) Casing COLLECTOR EXTENSION BOX TUBE _-_ COLLECTOR TUBE BOX (PINK) --_ COLLECTOR & WHITE HAZARD could result in electrical hole filler cap must shock, condensate trap in blower into desired stubs through into locking CONDENSATE be installed shelf hole t*ap is relocated tube connection BOX TUBE OR DEATH this warning when condensate 5. h_stall trap inju U o1"death tabs snap DRAIN hole filler cap into blox_ er shetf hole where ed TRAP casing casing hole by inserting hole and rotating until label on main fl/rnace door position. TUBING (BLUE STRIPED) COLLECTOR EXTENSION BOX_ NOT_:: See Fig. 8 or 9 or robe routing to check for proper Relocate robes as described connections TUBE 1 (ollector a Box Drain Remove below. Tube factory-installed plug from LOWER collector box and plug into UPPER collector box which was connected to condensate drain robe (blue and white TRAP b. Install removed clamp &ain tube (blue label) striped label). trap. INDUCER DRAIN TUBE HOUSING c (VIOLET) Connect densate A01023 (1.) LOWER collector (b) Trap Located LOWER Clamp PLUG F F COLLECTOR DRAIN TUBE COLLECTOR TUBE (PINK) collector box drain tube (blue Trap Located (blue and white ously plugged. large* supplied in loose COLLECTOR BOX DRAIN TUBE (BLUE & WHITE STRIPED) (d) COUPLING A01024 Fig. 9--Downflow Tube Configuration (Right-Hand Trap Installation) 2. Remove trap from blower shelf by gently pushing tabs inward and rotating tlap 3. Remove casing hole filler cap from casing hole. (See Fig. 2, 8, or 9) coupling collectm striped label) box bag) shown (f) Dote*mine Clamp Honsing inducer b. Remove box in Fig (e.) (onnect 2. Inducer collector collector robe appropriate previ- (facto Wtube cou- robe _br robe directly to condensate tlap as lengd_ and cut tlap. tube to prevent any condensate leakage. Tube gtctory=installed housing drain robe 9 to condensate Drain was to drain box drain drain in drain which drain parts teakage. Side of Casing (factouosupplied into diameter extended fl'om a. Remove TM bag) (onnect (c.) Route TRAP COLLECTOR BOX EXTENSION DRAIN TUBE robe parts COLLECTOR BOX TUBE (GREEN) COLLECTOR BOX EXTENSION TUBE (VIOLET) CONDENSATE &ain loose trap. Tube any condensate on Right pling, extending collector box connection to condensate trap BOX _I._A_D RAI N TUBE TUBE (b) BOX (BLUE) COLLECTOR BOX EXTENSION TUBE INDUCER HOUSING DRAIN to con- on Left Side of Casing robe to prevent (ondensate (a.) Install O connection and white striped label) to condensate does not need to be cut. (2.) © drain trap Condensate (a.) Connect Fig. 8--Downflow Tube Configuration (Left-Hand Trap Installation) box cap and clamp fl'om LOWER inducer housing drain connection. and discard &ain robe which UPPER (molded) was previonsly connected to condensate trap. c. Install cap and clamp on UPPER inducer housing connection where molded &ain robe was removed. d. Use inducer supplied housing e. Connect housing in loose drain &ain tube (violet parts connection inducer housing bag) label to connect drain and factow- LOWER inducer to the condensate trap. drain to condensate connection trap (1.) (ondensate Trap Located on Left Side of (asing (a) Determine appropriate length andcut (b.)(onnect robetocondensate trap (c) Clamp robe toprevent anycondensate leakage. (2) (ondensate Trap Located on Right Side of Casing (a) Route inducer directly as shown 3. Relief housing &ain from inducer in Fig (b.) Determine (c) (onnect (d.) (lamp robe (violet housing 2. Remove 3. Install robe to condensate tube to prevent to INJURY, Failure to tPllow trap Casing Switch Tubing FIELD DRAIN section to TRAP Condensate Drain section _br connection SWIT(H One collector box pressure High Pressure upflow recommendations and robe (pink label) is filctoly connected for use when This tube MUST tbr the condensate trap relief port robe. The other pressure robe (green label) which was _tctory connected condensate trap relief port connection MUST be connected High Pressure RIGHT Switch in DOWNFLOW or in until a box tu the to tl_e tot proper tahel on main furnace b. Connect High collector c. Route 2. Extend large parts tube (green to condensate to small diameter label) which 2. Inducer was collector box connected pressure robe to High Pressure small diameter (pink label) Switch which was by splicing robe (gtctory=supplied to this extended 6. Determine robe (pink label) robe to relief TRAP Retkr to Condensate tions and procedures. Step 4--Horizontal in loose parts to condensate trap relief length, cut, and connect robe. CONDENSATE and which clamp to condensate Drain any condensate parts was (factoryextend° trap and cut leakage. Tube LOWER (molded) was previously inducer connected Protection Left (Supply-Ak housing to condensate housing appropriate _br recommenda= collector trap application_ the blower and conditioned air is discharged to the PRESSURE The and relocated from in selected trap from the box robe (green LOWER collector appropriate TRAP Drain in loose was previ= to small parts bag). robe to relief port trap. cut, and connect any condensate FIELD which hap by splicing bux pressure length, robe to prevent SWITCH label) DRAIN section robe. leakage. ATTACHMENTS fbr recommendations and TUBING collector box pressure robe (pink label) is fScto W application nected, extended, switch in HORIZONTAL heating input blower location shelf to desired NOTE: to condensate leakage. the factor-installed the tbllowing: 3 robes connected tlap. robe. connected to the High Pressure Switch fbr use when fhrnace is installed in UPFLOW applications. This tube MUST be discon= in Fig. 2 or 10. condensate LOWER cut, and connect any condensate on the condensate Condensate procedures. LOCATION must be removed to to the label and to connect to the condensate to the condensate extended CONDENSATE is located robe (violet bag) robe (fi_ctury=supplied c. Detem_ine Discharge) parts length, robe to prevent connection section &ain extension Port Tube d. (lamp section, shelf location perform housing &ain connection b. Route PROTECTION Drain TRAP The condensate 1. Remove in loose label) trap robe inducer diameter port connection. FREEZE left furnace right of the burner left. location, drain in loose a. Extend Refkr To relocate tube (blue to condensate and discard d. Clamp Applications as shown (ti_ctory=supplied bux drain tube (blue label) ously connected appropriate CONDENSATE blower filler length. Housing c. Detem_ine port cunnection. In a horizontal plastic label on main fire, ace door to fhctory=supplied 3. Relief 7. (lamp with bag). box &ain robe. b. Use inducer bag). 5. Route holes trap. previously remaining by and Tube diameter drain robe which in loose collector box pressure robe (green label) to High Switch connection labeled COLLE(TOR BOX. 4. Extend hole hole position. casing in loose parts robe to prevent a. Remove bag). 3. (onnect Pressure casing casing to trap relief port connection robe (factory-supplied side through TUBING extended d. Clamp box pressure connected by splicing tube (pink label) attached Switch. collectur previously box pressure shelf hole door connections. Pressure shock, in loose parts bag) to drain robe coupling, to appropriate 1. Disconnect trap connected ing collector See Fig. 8 or 9 or robe routing leEr-hand stubs &ain tube coupling previously HORIZONTAL in blower tabs snap into locking into collector supplied NOTE: into condensate Box Drain Install bag) applications tu check trap TRAP 1. Collector and used collector be installed NOTE: See Fig 10 or tube ruuting check for proper connections to f_ul_ace is installed be disconnected HAZARD could result in electrical connection caps (ti_ctory=supplied TUBING Switch applications. parts trap is relocated tube CONDENSATE PRESSURE in loose trap was removed. or death. condensate 5. Fill unused procedures the injury inserting ATTA(HMENT for OR DEATH this warning hole filler cap must rotating CONDENSATE cap (tilctoly-supplied shelf hole where when condensate leakage 4. Install Pressure hole filler FIRE, procedore. Retkr casing fire, persunal Port Tube Refer tabs inward trap and cut. any condensate pushing label) to condensate length shelf by gently trap. bag) into blower 9 appropriate trap from blower and rotating trap. check 10 rerouted, and then reconnected LEFT applications tu the pressure for 060 and 080 fi/rnaces. See Fig. 10 or tube routing for proper connections. label on main Nrnace door to PLUG AUXILIARY BOX DRAtN TUBE (BLUE AND WHITE STRtPED) "J" BOX --_ O O © CONDENSATE TRAP \ \ X \_-- BOX EXTENSION DRAIN TUBE COLLECTOR BOX _ DRAIN TUBE (VIOLET) COLLECTOR BOX DRAIN TUBE (BLUE) \ EXTENS,ON TUBE XX DRAIN TUBE COUPLING RELOCATE TUBE BETWEEN BLOWER SHELF AND INDUCER HOUSING FOR 040, 060, AND 080 HEATING iNPUT FURNACES A01029 Fig. 10--Horizontal Modif}" robe as described 1. Disconnect High robe (factory-supplied tube disconnected extended in item in loose Refhr to Condensate tribe to High BOX. MINOR platfbm_ section for recommendao Local Failure to follow operation The condensate PLATFORM where all required furnace this caution may result in intem_ittent codes may require or over Combustion-air n_um length drain sloped below fire, ace. See connection to condensate to an open &ain. NOTE: with and vent pipes of 5 ft. (See Table A 12_in. minimum short (5 to 8 it) vent when In (anada, NSCNGPI( may result to offset pipe are restricted section This property as shown is recommended recommendation is to junction and in attic ceiling. box (JoBox) MUST Fig. with be relocated 120 See to Electrical LOCATION must be removed and relocated condensate perfbrm from in selected the fhctoryoinstalled application location trap fiom the blower shelf to desired the following: 1. Remove 3 tribes connected 2. Remove trap from blower and rotating 11 is used in Fig. 2 or 12. relocate location, to a mini° trap shelf location entire furnace fhmace installations shall be in accordance Installation Codes and/or local codes TRAP condensate blower 7.) systems. in minor a drain pan under a condensing a finished The auxiliary CONDENSATE unit To NOTE: is located to air is discharged DAMAGE opposite side of t:t_rnace casing. (See Connection section for JoBox relocation. be installed The trap must also be properly the blower and conditioned this caution application The trap MUST to fbllow trap NOTE: cun'ent clearances OPERATE Fig. 5 tbr dimensions. section, condensate NOT[[: NOT Discharge) damage are met. (See Fig. 3 and 11.) [TNIT MAY {Supply=Air right t'uInace application, PROPERTY Failure PROTECTION Protection A WORKING Constlq.lct working the vent pipe. housing. tions and procedt/res. CONSTRU(T fi'om exiting the right. FREEZE Drain droplets Right the tef_ of" the homer shelf and inducer TRAP 5--Horizontal In a horizontal 1. 4. Detem_ine appropriate length, cut, and reconnect Pressure Switch connection labeled COLLE(TOR CONDENSATE condensate 11 or 35) Applications parts housing. blower excessive (See Fig to robe: indtlcer b. Between tube (pink label) attached Step diameter bag) to extend a. Behind reduce box pressure Switch. smaller 3. Route below: collector Pressure 2. Use Left Tube Configuration t_ap to condensate shelf by gently t_ap. pushing tabs inward COMBUSTION INTAKE VENT 12-1N. MIN HORIZONTAL PIPE SECTION IS RECOMMENDED WITH SHORT (5 TO 8 FT) VENT SYSTEMS TO REDUCE EXCESSIVE CONDENSATE DROPLETS FROM EXITING THE VENT PIPE. SHUTOFF GAS VALVE ACCESS OPENING FOR TRAP SEDIMENT TRAP DRAIN CONDENSATE TRAP NOTE: LOCAL CODES MAY REQUIRE A DRAIN PAN UNDER THE FURNACE AND CONDENSATE TRAP WHEN A CONDENSING FURNACE IS INSTALLED ABOVE FINISHED CEILINGS. A93031 Fig. 11--Attic Location and Working Platform TUBE (BLUE) COLLECTOR BOX TUBE (GREEN) BOX EXTENSION COLLECTOR TUBE BOX TUBE (PINK) AUXILARY "J" BOX RELOCATED HERE ÷ TRAP COLLECTOR BOX DRAIN TUBE (BLUE AND WHITE STRIPED) DRAIN TUBE (VIOLET) COLLECTOR BOX EXTENSION TUBE A01028 Fig. 12--Horizontal Right Tube Configuration 12 3. Instal! casing hole filler bag) into blower shelf cap (_actory-supplied hole where in loose parts 1 Disconnect trap was removed High collector Pressure 2. Extend collector previously FIRE, ]INJURY, Failure to _bllow this warning fire, personal Casing OR DEATH cap m_/st be installed condensate 4. Install trap robe connection rotating 5. Fill until unused into tabs snap check stubs trap caps (_hctoryosupplied NOTE: label) removed condensate c. Connect with plastic label on main _i/rnace door to plug fiom LOWER striped collector collector label) connected which was previously collector Drain housing box IN]IT trap. Tube Failure does not need to be previously (factor'-supplied box pressure connected to robe (pink length, robe to relief TRAP in robe (pink High label) Pressure to condensate cut, and connect robe. port connection. FREEZE Drain PROTECTION Protection A WORKING working MAY section for recommenda- PLATFORM platfom_ NOT to _bllow The condensate leakage. where all required furnace clearances OPERATE this caution may result and clamp from in intem_ittent nnit below See NOTE: f\ Clamp extension robe (violet cut, NOTE: &ain robe Step Switch Tubing TRAP FIELD DRAIN fbr connection procedure. CONDENSATE [o Condensate Drain ATTACHMENT section for recommendations One collector Pressure UPFLOW applications. for the condensate tube fbr use when trap relief fhnaace label) port robe. The which port connection Switch in was other factory MUST DOW_NFLOW in and used collector See Fig. 12 or tube routing box directly wood (refer flooring exiting is to the vent pipe. material other than CONSIDERATIONS). ° be provided with ample space _br servicing and cleaning. Always comply with minin?um fire protection clearances shown on the l:urnace clearance to combustibles label. may be located for dilution For upflowidownflow or pitched operation. For horizontal from in a confined or ventilation it is level 1i2oin. maxinmm 13 on any combustible to SAFETY from be attached to an air distribution system and be located as close to the center of the distribution system as possible. Refer to Air Ducts section. NOTE: below. are protected ° provisions door to components be located where available electric power and gas supplies specifications on the J:_t_rnace rating plate. This _i/rnace HORIZONTAL so the electrical not be installed to the connections. robes as described be installed water be connected label on main fi/rnace fiom must to the applications. for proper droplets is recommended i--General connected or condensate section This recommendation ° to is installed This tube MUST be disconnected trap relief (green Pressure robe (pink label) is fi_ctory connected Switch pipe systems. be located so combustion-air and vent pipe maximma_ are not exceeded. Re_?r to Table 7. TUBING box pressure the High excessive to a mini- ° and procedures. SWITCH offset (5 to 8 ft) vent are restricted 7.) to leakage. section and vent pipes A 12oin. minimum This furnace * Pressure to an open drain. LOCATION Port Tube: to t\N'nace. to condensate (See Fig. 11 or 34.) LOWER trap. and connect any condensate sloped of 5 ft. (See Table short rednce trap. robe to prevent (ombustionoair mma_ length label and in loose parts bag) to connect &ain connection to condensate length, connection LOWER drain connection. &ain be installed The drain trap must also be properly cap appropriate trap MUST Fig. 5 for dimensions. Tube: housing condensate Relocate in loose to with e. Determine check was are met. (See Fig. 3 and 1 i.) box drain robe (blue and white any condensate fitctoryoinstalled _hctory-supplied inducer housing NOTE: robe collector this extended to Condensate Construct clamp and plug into UPPER robe to prevent & Use inducer RIGHT robe (flactov-supplied diameter appropriate CONSTRUCT box label). c. Install cap and clamp on UPPER inducer housing connection where molded &ain robe was removed. High was Rome CONDENSATE trap. condensate smaller bag) to extend which 5. Detem_ine b. Remove and discard UPPER (molded) inducer housing &ain robe which was previously connected to condensate pressure which tions and procedures to condensate Housing PRESSURE label) trap relief port connection operation. inducer Refhr robe (green trap relief port connection. filler Tube: LOWER a. Remove Refer to tlap. label) & (lamp 3. Relief parts Switch. Refer and white tube (blue 2. Inducer and position. holes attached collector box pressure tube (green label) to High Switch connection labeled COLLECTOR BOX. 6. Clamp _hctoryoinstalled drain robe (blue striped cut. hole connections. a. Remove &ain loose TUBING Box Drain b. Install casing pressure to condensate to small diameter remaining by hole parts bag). See Fig. 12 or tube routing 1. (ollector side casing through casing in loose TRAP for proper 3. Connect Pressure hole 4. Use right_hand into locking condensate CONDENSATE shelf trap is relocate& condensate inserting in blower robe (pink label) parts bag). shocL ir_im'y or death hole filler when in electrical box connected by splicing HAZARD could result box pressure Switch. secondary forward within install furnace 1i2oin. for proper applications pitch to ensure proper heat exchangers. without meet special air. applications _brward space lengths 1/4-in. mininmm condensate (See Fig. 13.) so that _itrnace to &ainage t LEVEL (0") TO 1/2" MAX V2" MAX UPFLOW OR DOWNFLOW HORIZONTAL A02146 Fig. 13--Proper Condensate BACK Drainage A When a fk/rnace is installed so dlat supply ducts carry air circulated by the f_lrnace to areas outside the space return also be handled by ducts air must The ducts ensure nlent terminate a negative roolTl outside pressure the space condition containing sealed the t:urnace, to furnace containing FRONI A93043 casing. Fig. 14--Prohibit the t:t_mace to will not occur within 1 INJURY Failure OR to fbllow injury, DEATH Failure HAZARD this warning could result install fhmace on its back. iu fire, personal control operation will be adversely return-air ducts to back of _hrnace. (See Fig. affected. 14) If this filmace the Safkty Never to %llow HAZARD this caution may result in minor property or unit damage. or death Do not on Back space or [TNIT DAMAGE FIRE, Installation equip° protection connect Step is installed ambient in an unconditioned temperatures measures 2--Furnace may be 32°F must be taken. Location or (See Fig. Relative space lower, where i?eeze 15.) to Cooling Equipment ]"he cooling UNIT DAMAGE This gas furnace that: -The furnace wiring, may be used _br construction is permanently piping, venting installed and dt/cting installed heat provided with all installed electrical according the condition flame furnace. as created rollout This prevents a negative by the circulating an&or drawing parallel condensation with a fi/rnace, with o1"oi1 downstream in heat dampers exchanger. or other means When used to equipped to the damper with a means to prevent is in t:ull-heat operation or fhll°coot of either unit unless position. pressure air blower, combustion parallel to avoid control flow of air shal! be adequate to prevent chilled air from entering t:tmtace. If dampers are manually operated, they must be these installation instructions. A remm air duct is provided, sealed to the f:urcmce casing, and terminated outside the space containing coil must be installed side of ft_mace HAZARD causing products into a the sWt/eture, -The t'umace is controlled wired" to provide heat thermostatic control. -(lean outside minimize air is provided the coi_'osive const_-acdon dwwall by a thermostat. continuously materials. of _ilrnace -The temperature for combustion effkcts of adhesives, It also prevents dust into combustion plugging It may not be "hot to the structure without This is to sealers and other the entrainment air, which can cause of fouling and components. of d'*e remm air to the furnace is no less than 55°F, with no evening setback or shutdown. The use of the fimlace while the structure is under consha/ction is _;_M_'F deemed to be instructions. intermittent operation rise is within furnace and the firing nameplate -The MINIMUM plate, the rated rise range rate has been INSTALLED installation OR FREEZE on the OTECTION set to the REQUIRED value. filters construction cleaned our BLENT -The air temperature rating per used to clean process must the circulating be either changed air during the or thoroughly prior to occupancy. -The Nmace, ductwork remove &ywall system components and filters are cleaned dust and construction utter construction as necessa V to debris fiom all HVAC A93058 is completed. Fig. 15--Freeze 14 Protection Step 3--Hazardous Locations 18-1N. MINIMUM TO BURNERS A93044 Fig. 16--Installation in a Garage A89014 FIRE, EXPLOSION, INJURY OR DEATH HAZARD Improper location or inadequate protection could result in fire or explosion When the fhmace is installed in a residential garage_ the bu*ners and ignition sources nll.lst be located at least 18 in. above the floor. The f_/rnace must be tocated or protected to avoid physical damage by vehicles. When the fhmace is installed in a public garage, airplane hangar, or other building having a hazardous atmosphere, the furnace must be installed in accordance with the NFGC or NSCNGPIC (See Fig 16.) Step l--Leveling Fig. 17--Leveling Legs INSTALLATION Legs {If Desired) When f_tmace is used in upgow position with side inlet(s), leveling tegs may be desire& (See Fig. I7) Install field-supplied, cmTosion-resistant 5/16=in machine bolts and nuts. NOTE: The maximum length of bolt should not exceed l= 1/2 in l. Position furnace on its back. Locate and &ill a 5716=in. diameter hole in each bottom corner of furnace (See Fig. 17) Holes in bottom closure panel may be used as guide locations 2. For each hole, install nut on bolt and then install bolt and nut in hole. (Install fiat washer it"desired) A96283 3. Install another nut on other side of thmace base (Install flat washer it"desired) Fig. 18--Floor 4. Adjust outside nut to provide desired height, and tighten inside nut to secure arrangement. NOTE: Bottom closure must be used when 1cycling legs are used See Bottom Closure Panel section Step 2--hstaHation Applications 4 in Opflow and Downfiow subbase (KGASB) Opening is used, Fig. 19. If (?oil Assembly Part No Part No install as shown NOTE: K(AK( Remove is used, [:urnace perforated, Dimensions install as shown in CD5 or CK5 or Coil Box supply=air in Fig 20. duct flanges when they interfere with mating flanges on coil or downflow subbase. To remove perforated, supply-air duct flanges, use wide duct pliers, NOTE: For downt'tow applications, this _amace is approved for use on combustible flooring when special base (available t'rom manui:acmrer) Part No. KGASB0201ALL is used. Special base is not required when this %mace is installed on manuthcmrer's (Toil Assembly Part No. CD5 or CK5, or (oil Box Part No. K(AK( is used. duct flange until 1. Determine application being installed t'rom Table 1. 2. (onstruct hole in floor per dimensions specified in Table 1 and Fig. 18. 3. (onstruct 18. If downflow and Plenum plenum to dimensions specified in Table 1 and Fig. 15 tool, it breaks or hand seamers off Be careful to bend flange of sharp edges. back (See Fig and forth 2!0 TABLE FURNACE CASBNG WIDTH 1--OPENING D_MENS_ONS (iN.) PLENUM OPENING FLOOR OPEMNG APPLICATION A Upflow Applications Downflow Applications Downflow Applications on Non-Combustible on Combustible Flooring D 24-1/8 B 16-5/8 24-3/4 15-7/8 19 16-1/2 19-5/8 15-1/8 19 16-3/4 20-3/8 15-1/2 19 16-1/2 20 19-1/2 24-1/8 20-1/8 24-3/4 19-3/8 19 20 19-5/8 18-5/8 19 20-1/4 20-3/8 19 19 20 20 Flooring Using KGASB Subbase Furnace with or without CD5 or CK5 Coil Assembly or KCAKC Coil Box 17-112 C 16 Downflow Applications on Combustible Flooring NOT Using KGASB Subbase Furnace with or without CD5 or CK5 Coil Assembly or KCAKC Coil Box Upflow Applications Downflow Applications Downflow Applications on Non-Combustible on Combustible Flooring Flooring Using KGASB Subbase Furnace with or without CD5 or CK5 Coil Assembly or KCAKC Coil Box 21 Downflow Applications on Combustible Flooring NOT Using KGASB Subbase Furnace with or without CD5 or CK5 Coil Assembly or KCAKC Coil Box Upflow Applications Downflow Applications Downflow Applications on Non-Combustible on Combustible Flooring 24-1/8 23-5/8 24-3/4 19 23-1/2 19-5/8 22-1/8 19 23-3/4 20-3/8 22-1/2 19 23-1/2 20 Flooring Using KGASB Subbase Furnace with or without CD5 or CK5 Coil Assembly or KCAKC Coil Box 24-112 23 22-7/8 Downflow Applications on Combustible Flooring NOT Using KGASB Subbase Furnace with or without CD5 or CK5 Coil Assembly or KCAKC Coil Box FURNACE FURNACE (OR COIL CASING WHEN USED) CD5 OR CK5 COIL ASSEMBLY OR KCAKC COIL BOX /_ ,---.----- DOWNFLOW SUBBASE SHEET METAL ._p,_ PLENUM SHEET METAL PLENUM -- COMBUSTIBLE FLOORING COMBUSTIBLE FLOORING FLOOR OPENING FLOOR -OPENING A96284 A96285 Fig. 19--Furnace, Pienum_ and Subbase on a Combustible Floor Fig. 20--Furnace, Pmenum, and Coil Assembly Coil Box Installed on a Combustible Floor Installed 16 or When DISCHARGE FLANGE a fllrnace is installed DUCT the fhrnace fl_rnace NO Secure Seal / connections a 1=in. clearance ductwork t'or a distance 90B or local Fmanges assistance operation o1" per_bm_ance Do not bend cycling completely shown in Fig. 21. Step or bend it inward pad. Furnace and angle in Horizontal can be suspended iron supports. 3/8-in. all=thread 3/8-in. shown rod) unit Metal 2! This Remove a minimum SMACNA acoustical or installed fiom each on suitable corner to desired lock washers, length. and 3/8-in. are provided Use bolts 1 X 3/8=in. fbr hole locations. or outlet. bolts ductwork and Ductwork insulated passing to enhance is used, materials a vapor to supply air from the fl/rnace. See can fbr possible be inserted shall prevent STICAL openings using fbr sampling the air leaks. TREATMENT that do not have a 90 degree first branch take=off elbow may and l0 fl require internal standard and fibrous supply=air flat fibrous glass ducts. shall comply 181 for Class duct to 3/4-in. The supply-air casing on ductwork Both with NFPA 1 Rigid air ducts. Furnaces to fl_mace supply-/outlet-air (when flange duct attachment used) duct flanges DO NOT on l_rnace must ONLY supply-air be connected or air conditioning cut main fl/rnace casing coil to attach supply side air duct, humidifie*, or other accessories All accessories METST be connected external to fl/rnace main casing. rods as (See Downflow Fig. 2.) Connect Furnaces supply-air supply-air duct to supply-air duct attachment must opening ONLY on fhmace. be connected The to fltrnace supply/outlet or air conditioning coil casing (when used), when installed on non=combustible material. When installed on combus- [TNIT MAY NOT OPERATE Failure to follow this caution may result in intem_ittent unit operation or per_bm_ance satisfaction. The entire tength of flmlace MUST be supported when flu'nace is used in a horizontal position to ensure proper draining. When suspended, bottom brace supports sides and center blower shelf When unit is supported fi'om the ground, blocks o1"pad shoutd support sides and center blower shelf area.. Step 4--Air code with a cooling coil, the outlet duct shall construction Connect (4 each nuts on hanger used. with AIR CONNECTIONS Upflow can blocks by hanger be fl'om combustible attachment ACO[ lining SUPPLY d_e furnace between should can be viewed duct to the duct in either horizontal In a crawlspace, the code for further requirements. duct systems of 210 ° as Applications (See Fig. 22.) Cut hanger in Fig. 22. Dimples air acoustical lining. As an alternative, fibrous ductwork may be used if constructed and installed in accordance with the latest edition of and may cause limit thilure. horizontally position. t'rom floor joist washers, in Fig used of vibration. 90B as tested by UL Standard can be installed be hung as shown exchanger left o1" right discharge either inward heat a--Installation These furnaces The cover of main across }*eat exchangers or premature flange in intem_ittent satisfaction duct flanges will affect airflow may result to fl_mace air conditioning or a probe D[ CTWORK OPERATE this caution *;or type of dttctwork of 36 in. horizontally that d_e heat exchanger stleam. NOT be space Maintain light to follow carry be provided with a removable access panel. This opening shal! be accessible when the furnace is installed and shall be of such a size A93029 MAY ducts the space containing connections should For a t:urnace not equipped Fig. 21--Duct fhsteners perfbrmance. When is recommended. NFPA outside transmission unconditioned system barrier YES with proper and return=duct to prevent through / Failure the supply tape or duct sealer. fltrnace 210° MIN and terminating ductwork Flexible YES casing supply= approved UNIT so that circulated by the fllrnace to areas outside the space containing the furnace, the return air must also be handled by a duct(s) sealed to tible material, nected must approved D() NOT cut main t\lmace humidifier, air duct, be connected Connect or other external duct flanges Horizontal must casing ONLY to attach accessories. m furnace be modified be con- air conditionsupply Al! accessories main casing. Supply air per Fig. 21. Furnaces supply=air supply-air duct to supply duct attachment supply/outlet The duct system should be designed and sized according to accepted national standa*ds such as those published by: Air Conditioning Contractors Association (ACCA), Sheet Metal and Air Conditioning (out*actors National Association (SMACNA) or American Society of Heating, Refligerating and Air Conditioning Engineers (ASHRAE), or consult The Air Systems Design Guide= tines reference tables available fi'om your tocal distributor. The duct system should be sized to handle the required system design CFM at the design static pressure attachment or factory side opening GENERAL REQUIREMENTS duct subbase ing coil casing. MUST Duets supply=air to an accessory must or air conditioning air opening ONLY on furnace. be connected coil casing (when used). The to furnace DE) NOT cut main furnace casing to attach supply side air duct, humidifier, or other accessories. All accessories MUST be connected external to fl/rnace main casing. RETURN AIR (()NNECTIONS The fitrnace installed cannot affect mix products 17 and its return so that negative another air system pressure created appliance's of combustion designed and by the air circulating shall fan congbustion with circulating be air supply or act to air, and that the air 3/8-1N. ROD ANGLE IRON OR EQI ALTERNATE SUPPORT LOCATION 4-IN. MIN 8-IN MAX (B) (A) ROD LOCATION USING DIMPLE LOCATORS (SEE DIMENSIONAL DWG FOR LOCATIONS) __) 3/8-1N. HEX & WASHER (4) REQD PER ROD (A) PREFERRED ROD LOCATION (B) ALTERNATE ROD LOCATION (B) 13/16-1N.MAX ALTERNATE SUPPORT LOCATION FROM BACK (B) NOTES: 1. A 1 In. clearance minimum between top of furnace and combustible material. 2. The entire length of furnace must be supported when furnace is used in horizontal position to ensure proper drainage. A93304 Fig. 22--Craw{space circulating nicating type, fan of the fhrnace, with another shall be operable opening in an enclosure appliance only when in the _hmace on ducts if installed fhel-buming in the closed Step commu- ApNication 5--FHter covering or in a remm N an air plenum --5 position. FIRE, CARBON HAZARD Failure to follow injury FIRE to _bllow injuv_ Never this warning or death connect return-air Return-air upflow [pflow result to the back on _hmace of the t\u'nace side(s) permitted air filter orientation., in external only. arrangement filter Filter/Media blower must be connected right), or a combination of bottom casing. Bypass may be attached air portion return-air Downflow The and Horizontal portion be made duct DO NOT of return-air at ductwork must and side(s) sides of main into unused (left or Factory instructions t_umace side remm any portion of be casing or coil casing in fire, personal a filter or with filter access door will type. vary The cabinet due to application, filter may be tl_mace installed (if provided) or the furnace supplied washable filters are shipped external Filter/Media in an blower in the its application, packaged with the cabinet. with bactory-supplied the disposable cabinet assembly, and The Filter Media washable filter is provided, installation cabinet are can be used or a fitcto_-specified filter (see cabinet instructions). casing If installing mine connected Bypass for high-eNciency Furnaces cut into duct to bottom, DO NOT connect duct to back of furnace return-air provide& humidifier of the ftm_ace casing. co_dd result comparm_ent If a factory-supplied duct this warning unit without and comparm_ent Furnaces The return-air AND POISONING in fire_ personal The ducts duct connections applications could MONOXIDE or death. Never operate removed. HAZARD Failure Arrangement not of the direct-vent any door or panel _im con_partrnent Horizonta{ sides humidifier to return-air or back to attach connections sides exterior opening necessary. any filter should bottom 18 fbr See Table location. shipped to fiul_ace. the filter location with Table in the fimaace filter and 2 to determine 2 indicates this Nrnace. and side return-air blower relocate filter compartment, filter correct retaining filter if size for desired size, location, See Fig. 2 fbr location openings. deter= wire and quantity and size of Table 2--FILTER AiR FILTER LOCATED 171/2-1N. WIDE CASINGS ONLY: INSTALL FELD-SUPPLIED FILTER FILLER STRIP UNDER FILTER. INFORMATION IN BLOWER COMPARTMENT FILTER SIZE (IN.)* FILTER FURNACE CASBNG WIDTH (iN.) Side Return Bottom Return TYPE 17-112 (1) 16 X 25 X It (1) 16 X 25 X 17 Cteaeabte (1) 16X25X (1) 20X25X 17 Cteanable (1) 24X25X 17 Cieanabte 21 24-112 1 (1 or 2) 16X25X1 * Filters may be field modified by cutting filter matedal and support rods (3) in filters Alternate sizes and additional filters may be ordered from your dealer ? Factory-provided with furnace. (.'ITS AND ABRAS!ON Failure to %llow HAZARD this caution may result in minor personal injury Use care when cutting flying pieces rods in filters to protect against and sharp rod ends. Wear safety glasses, gloves, and appropriate support protective clothing. i UN!T MAY Failure NOT to follow operation OPERATE this caution or perfbmaance For airflow may result in intem_ittent unit WASHABLE FILTER satisfaction. requirements above 1800 CFM, see Air Delivew table in Product Data literature fbr specific use of single side inlets. The use of both side inlets, a combination of 1 side and the bottom, openings NOTE: or the bottom for airflow Side return=air configurations. only will ensure requirements above adequate return air 1800 CFM. openings can ONLY be used in [ PFLOW filter(s) as in Fig. Install shown 23 Bottom '\\ retmYPair opening may be used with all 4 orientations. Filter may need to be cut to fit some furnace widths. Install filter as shown in Fig \ FILTER RETAINER FILTER SUPPORT 24. A00213 Fig. 24_Bottom WASHABLE FILTER To remove bottolTl clostlre FHter Arrangement panel, perfbm_ 1. Tilt or raise [_urnace and remove panel. (See Fig. 25.) FILTER RETAINER 2 Rotate 3 Remove 4. Reinstall fi'ont filler panel bottom closure downward the following: 2 screws holding to release fi'ont filler holding tabs. panel front filler panel and screws. \ A93045 Fig. 23--FHter NOTE: Remove inlet is used. Step 6--Bottom F'his furnace installed and discard Closure is shipped bottom return-air opening. remm air is used. bottom for Side inlet closure panel when bottom Panel with bottom closure panel installed BOTTOM CLOSURE PANEL in This panel MUST be in place when side FRONT FILLER PANEL A93047 Fig. 25--Removing 19 Bottom Closure Panel Step 7--Gas Piping GAS Gas piping must be installed in accordance with national and local codes Refer to cun'ent edition of NFGC in the United States SUPPLY MANUAL Canadian installations must be made in accordance with NSCNG= PIC and all authorities having jm'isdiction. _/ II vSHUTOFF_ Gas supply line should be a separate tine running directly flora meter to _i/rnace, it" possible Refer to Table 3 for recommended gas pipe sizing. Table a--MAXiMUM NOMINAL IRON PIPE SBZE (IN.) 1,'2 CAPACITY OF PIPE* LENGTH OF PIPE (FT) tNTr=RNAL DIAM_aTER ON.) 10 20 30 40 50 0.622 175 120 97 82 73 a/4 0.824 360 250 200 170 151 t 1.049 680 465 375 320 285 1-114 1.380 1400 950 770 660 580 1-1/2 1.610 2100 1460 1180 990 900 A93324 Fig. 26--Typical Piping Cubic ft of gas per hr for gas _ressuresof 05 psig (14-in wc) orless and a pressure drop of 05-in wc (based on a 0.60 specific gravity gas) Ref: Table 9.2 NFGC. should and national exceeds tested in accordance and gas codes befbre In (anada, the pressure Risers must be used to connect to _hrnace and to meter. Support all gas piping with appropriate straps, hangers, etc Use a minimum of 1 hanger eve_ 6 t't. Joint compound (pipe dope) should be applied sparingly and only to male threads of joints. Pipe dope must be resistant to propane gas. be pressure plumbing connected Gas Pipe Arrangement refer to cun'ent 05 psig (14-in. edition fi'om the fimaace test pressure is equal to or less than 05 After shutoff shutoff and capped have been made, befbre If pipe must be pressure tesL If psig (14=in. wc), mm off switch located on furnace valve before test. all connections local has been of NSCNGPI( wc), gas supply disconnected electric manual with NFGC, the furnace gas valve and accessible purge lines and check %r leakage. NOTE: --> FIRE OR EXPLOSION Failure to fbllow personal injury, = Connect HAZARD this warning could result using a backup wrench switch MUST be fitcing _:bmard exceed 05 maximum tap connection providing psig (14=in is suitable test pressure wc) stated NOT on gas valve (See to avoid The gas or tilted minimma_ inlet supply pressures marked on the rating the fi/rnace burners ON at HI-HEAT and OFF. supply pressure shall be within to DOES 53.) gas contlols = Gas valve shutoff connection Fig or death gas pipe to fhmace damaging in fire, explosion, The gas valve inlet pressure use as test gauge the maximum and plate with upward. = Never purge a gas line into a combustion test t'or gas leaks with an open flame. Use available soap solution made specifically leaks to check all connections. = Use proper mani_bld. length = If a flexible connector having jurisdiction, tiu'nace gas valve Nrnace casing. Install a sediment installed by level of gas iron and extend trap in riser control manifold If local codes always use a new listed connector. has previously An accessible _hmace tapping, casing riser and manual served manual another shutoff and within Trap can be to t\u'nace connect should joint at valve. below between (See Fig gas appliance valve MUST be installed A li8=in connection, of gas supply shutoff valve and 52A-H 115-v and 24-v connections for field wiring wiring Check diagram all _hctow showing and field for tightness 26.) which to NPT plugged MiST connection external be installed to furnace SHOCK Failm'e to follow or death, this warning Blower access cont_oi No component switch door switch HAZARD could opens operation result in personal ll5-v power inju W to furnace can occur, Do not bypass or with panel removed, Field=supplied wiring shall con%rm with the limitations of 63_T rise. gas connector, Do not use a connector 6 ft of filrnace. 27, 28, field ELECTRICAL close a capped extend union so gas appliance _br test gauge upstream of manual installed of 2 in. outside Then nipple gas shutoff typical Connections by authority be leading allow the use of a flexible accessible immediately downst*eam shall to ihmace. a ground See Fig. of electrical of tee is vertical Place 8--Electrical on gas control a n_inin-mm end of tee. (apped contIots. a commercially or allowed leading Step Never for the detection stress pipe a tee to section into lower to avoid is required black connecting straight-through nipple of pipe chamber. and 2O .... .... --- FIELD 24-V WIRING FIELD 115-, 208/230-, 460-V WIRING FACTORY24-V WIRING FACTORY1I5-V WIRING FIELD-SUPPLIED FUSED DISCONNECT 208/230- OR PHASE 208/230-V SINGLE 115-V FUSED DISCONNECT SWITCH (WHEN REQUIRED) CONDENSING UNIT NOTES: 1. Connect Y-terminal as shown for proper operation. 2. Some thermostats require a "C" terminal connection as shown. 3. If any of the original wire, as supplied, must be replaced, use same type or equivalent wire. A99071 Fig. 27--Typical Heating and Cooling Application Wiring Diagram 1-Stage Thermostat .... .... --- and Condensing Unit FIELD 24-V WIRING FIELD 115-, 208/230-, 460-V WIRING FACTORY 24-V WIRING FACTORY 115-V WIRING 2-STAGE THERMOSTAT TERMINALS S_IEN _ t THREE_WIRE-,_11 HEATING__ ONLY _ (_ II (_ (_) (_ (_(_ II FIELD-SUPPLIED _ _k F-TI I i I i FUSED DISCONNECT _ i 208/230- OR 460-v PHASE 208/230-V SINGLE 'PHASE JUNCTION 115-V FUSED DISCONNECT BOX SWITCH (WHEN REQUIRED) CONTROL BOX @ 2-SPEED CONDENSING UNIT @ N-VTERMINAL BLOCK FURNACE NOTES: 1. Connect Y-terminal as shown for proper operation. 2. Some thermostats require a "C" terminal connection as shown. 3. tfany of the original wire, as supplied, must be replace& use same type or equivalent wire. A99072 Fig. 28--Typical Heating and Cooling Application Wiring 2i Diagram 2-Stage Thermostat and Condensing Unit Table5--APPROVED ASTM SPECNCATION (MARKED ON MATER_AL) D1827 COMBUSTION-NR B4ATER_AL PiPE FITTINGS ABS Pipe -- PVC Pipe -- D1785 AND VENT PIPE, FITTNG SOLVENT CEMENT AND PRNERS Schedule-40 Solvent Cement D2238 For ABS -- D2241 PVC Pipe -- SDR-21 & SDR-26 D2488 PVC -- Fittings Schedule-40 D2488 ABS -- Fittings -- For ABS Schedule-40 Solvent Cement D8884 For PVC -- -- D2881 ABS Pipe Fittings D2888 PVC Pipe Fittings DWV F488 CPVC -- Fittings Schedule-40 F441 CPVC Pipe -- Schedule-40 F442 CPVC Pipe -- F498 For CPVC -- -- F628 F688 ABS For PVC Pipe -- --- F891 PVC Pipe -- MAY Failure For PVC DWV at Schedule-40 NOT to follow For CPVC Cellular Core DWV at Schedule-40 Primer in intermittent unit within Furnace control control will green/yellow box screw. lock WIRING Befbre proceeding power plate. Also, for proper (ontrol is to gas valve and phase supply equipment ouL with electrical fiequency, f_/mace rating be grounded wire routed 115-V by must check grounded connections, and burner make certain to that specified to be sure that service to handle load or through ( 4erminal correspond is sufficient operation imposed Rd.'_r to rating plate or Table 4 for equipment that A disconnecting f'rom and readily NOTE: Proper polarity is incorrect, contlol rapidly and I:urnace will NOT --€ FIRE polarity must means accessible be maintained LED stares dtis to _bllow and fi/rnace. electrical for l15-v indicator be located wiring. If light will flash operate. this warning could result operation or perfi_rmance satisfaction Do not connect aluminum wire between provided must to ftlrnace HAZARD Failure on the by sight & DWV branch electrical circuit containing a properly sized breaker for this J:ilrnace. See Table 4 for wire size and filse specifications may result IPS sizes For PVC Cellular Core Schedule40 OPERATE this caution tPS sizes SDR Solvent Cement operation. voltage, DESCRBPTBON Schedule-40 Use a separate fuse or circuit [?NIT AND CEMENT MATERIALS Use only copper wire. in intermittent disconnect switch (See Fig. 29.) specifications. For U.S. installations, dance with National make all electrical Electrical (;ode (NE() connections ANSIiNFPA in accoro 70-2002 and any local codes or ordinances that might apply. For Canadian installations, all electrical connections must be made in accordance with Canadian Electrical (?ode (SA C22.1 or authorities having jurisdiction. Table 4_ELECTRICAL OPERATNG VOLTAGE RANGE UNT S_ZE VOLTS-HERTZ-PHASE Max* Min* MAX UNT AMPS 080=12 115-60-1 127 104 8.4 080=12 115-60-1 127 104 080=18 115-60-1 127 100=16 115-60-1 100=20 115-60-1 t20=20 115-60-1 DATA NIN WNE SRZE MAX WNE LENGTH (FT)J; MAX FUSE OR CKT EKR AMPS** 11.3 14 83 15 8.1 10.8 14 84 15 104 11.6 15.3 12 87 20 127 104 11.6 15.4 12 37 20 127 104 13.3 17.5 12 33 20 127 104 12.9 16.8 12 84 20 UNT AMPACITYt Permissible limits of voltage range at which unit will operate satisfactorily. 1 Unit ampacity = 125 percent of largest operating components full load amps plus 100 percent of all other potential operating components' load amps $ Length shown is measured 1 way along wire path between unit and service panel for maximum 2 percent voltage drop. ** Time-delay type is recommended 22 (EAC, humidifier, etc ) full ELECTRIC DISCONNECT SWITCH ALTERNATE -FIELD LOCATION S ACTORY INSTALLED LOCATION ® (_/"/ A93033 Fig. 29--Disconnect Switch ELECTRICAL SHOCK Failure to follow this warning AND FIRE and Furnace Y HAZARD coud result in electrical shock, fire, or death The furnace casing MUST have an unintem/pted or unbroken A00212 ground according to NEC ANSINFPA 70-2002 and (arm= dian Electrical (}ode CSA (}22 1 or local codes to minimize personal injury if an electrical consist of electrical ground when codes. wire installed £mlt should or conduit in accordance Do not use gas piping occur. approved Fig. 30--Relocating This may for electrical with existing as an electlical 2 electrical Hmalidifier Connect ground. (HEM) an accessory Co_>24V screw terminal The HUM 1, Remove 2 screws holding auxiliary J=box, (See Fig 300 OR ELECTRICAL SHOCK to fbllow this warning operation or perfbmaance in intermittent -9 on f:urnace, not contact field for proper similar 24=v connections Connect cooling at 24=v terminal terminal operation. Y/Y2 contains control during installation, block as shown in Fig Use only AWG No an amomotive-type, (See Fig service, size/type. is required, The control on furnace. shorts of 24-v wiring could cause this fuse to use ONLY a 3-amp will flash code 24 when fuse of fi/se needs connect terminals connection. are during blower fbr EAC energized motor with marked l15=v (See f_amace terminal device. may result control HUM on Thermidistaff See Themlidistat-f_L component terminal M, Zone Zone manufitcturer's in unit to HEM Controller Conholler, instructions or ff*ermo= for proper EAC-1 Fig. (1.0=amp Venting an existing original are this caution REMOVAL OF EXISTING EL RNACES FROM COMMON VENT SYSTEMS (EAC) Two male quick=connect provided relay connected to operation is desired The 58MTA fi/mace requires a dedicated (one 5SMTA furnace only) direct-vent system In a direct=vent system, all air for combustion is taken directty fi'om outdoor atnlosphere, and alt flue gases are discharged to outdoor atmosphere fi/se located When Air Cleaner is energized. HAZARD to follow Step 9--Direct A( CESSORIES terminals DAMAGE stat, or controller connection, 27 and 28 replacement 1. Electronic gas valve 18, color=coded, 3-amp 32) Any direct or maintenance If ftlse replacement identical when strip. operation. (humidifier) The 24-v circuit blow. UNIT damage. DO NOT copper themlostat wire fbr lengths up to 100 ft For wire lengths over 100 it, use AWG No. 16 wire. on furnace blower Failure or gas components (See Fig. 32) is energized and board them_ostat unit satisfaction. 24=V WIRING Make terminal on the control humidifier HUM terminal HAZARD could result If manual disconnect switch is to be mounted select a location where a drill or fhstener will electrical amp n_aximum NOTE: A field=supplied, 115 v controlled EAC terminals may be added if humidifier during Failure 05 (See Fig. 31 or 32.) 2, Rotate J-box 180 ° and attach box to left sidQ using holes provided FIRE 24 VA(, (if used) to the 1/4=in. male quick=connect J=BOX RELOCATION -9 J=Box venting and EAC-2 the remaining 32.) I venting These n_axirnum) furnace operation. 23 attached system and vent, and spillage Category system I furnace is removed may no longer appliances could cause leakage of combustion be sized An improperly the formation of condensate products or replaced, to properly sized (ategoLv of condensate and combustion into the living the vent in the products, space, etc. CONNECTIONDIAGRAM RED FIRS M CAP-2 FIELD-DISCONNECT 112 BREAKER & DISCONNECT SV_ITCH SCHEMATIC NOTE #2 DIAGRAM (NATURALGAS& PROPANE) BLU -- _OM NEUTT%' L_jNo_ R HI NOTE #3 _._GR_JYEI TO 115VAC FUSE OR CIRCUIT LS HP IHBLOR BRN BRN ORNJ X'_/LGPS0'M4ENUSED) x'_/LPS I ? I HS] !, , I - t I T I I iF .... PL5 p[4 4 LO 1 SELECT C}@,RT 4T SWI LO4tT BL(N"_R i ONLY OFF-I_LAy il * ON NORN OFF'HEAr _ _2C 3 90 i_; PL3 ' I_HT/CLR SoN RA_, i c'i° 1 kO _2C 3 180 _SEC * FACTORY SEThNGS L2 SPARE-1 I-MED LO HI HEAT-_,_D OTE #10 CAP-1 _L I,- _=DHI HI STAR BLK _!- -2-_ PL1 ON OFF P[2 COOKING SFA_-2 BIWR i'180 1_ BHBLOR L1 u 3 ACRDJ @ J o GRNJYEL BRN L2 L., PM-6 FU1 SEC 1 TRAN = MED HI-- V_q" _rrr RED PL1-12 E_U 4_ ACR ACRDJ BHI/LOR BHT/CLR AIR CONDFIONING RELAY SPST (NO) AIR CONDITIONING RELAY DISABLE JUMPER BLOWER MOTOR SPEED CHANGE RELAY SPDT BLOWER MOTOR SPEED C HANGE RELAY SPDT BLWR BLWM CAP 1 2 CPU DHUM EAC 1 EAC 2 FRS FS_ FU1 FU2 GND GV GVR 1.2 BLOWER MOTOR RELAY. SPST (NO) BLOWER MOTOR¸ PERMANEN_SPUT CAPACITOR CAPACITOR MICROPROCESSOR AND CIRCUITRY DHUM CONNECTION ELECTRONIC AIR CLEANER CONNECTION (115 VAC 10 AMP MAX¸) ELECTRONIC AIR CLEANER CONNECTION (COMMON) FLAME ROLLOUT SW MANUAL RESE_SPST (NC) FLAME PROVING ELECTRODE FUSE 3 AMP AUTOMOTIVE BLADE TYPE FACTORY INSTALLED FUSEOR CIRCUIT BREAKER CURRENT INTERRUPTDEVICE (FIELD SUPPLIEDAND INSTALLED) EQUIPMENT GROUND GAS VALVE REDUNDANT GAS VALVE RELAY DPS,r(N O ) HPS HPSR HSI HSIR HUN1 IDM IDR IHI/LOR ILK JB LED HIGH HEAT PRESSURESWFCH,SPSF (NO) HIGH HEAT PRESSURESWITCH RELAY. SPSF (NC) HOT SURFACE IGNITER (115VAC) HOT SURFACE IGNITER RELAY SPST (NO) 24VAC HUMIDIFIER CONNECTION (05 AN1P MAX) INDUCED DRAH MOTOR 2 SPEED_SHADED POLE INDUCED DRAFT NIOTOR RELAY SPSN(N O) INDUCER MOTOR SPEED CHANGE RELAY SPDF BLOWER ACCESS PANEL INTERLOCK SWITCH SPS_(N O) JUNCTION BOX UG HT EMITIING DIODE FOR SFATUSCODES AMBER LGPS LPS IS OL PCB LOW GAS PRESSURESWFCH SPSN(N O) LOW HEAT PRESSURE SWFCH SPST (NO) LIMIT SWFCH AUTO RESELSPST (N C) AUTO RESETINTERNAL MOTOR OVERLOAD TEMPERATURE SWITCH (NC) PRINTED CIRCUIT BOARD CONTROL PM PL2 12 CIRCUIT PCB CON NECTOR 3 CIRCUIT PCB HSI& IDM CONNECTOR PL3 PL4 PLS PLT 6 4 2 3 TRAN TEST/IWIN TRANSFORMER 115VAC/24VAC COMPONENT TEST & TWIN NING TERMINAL CIRCUIT CIRCUIT CIRCUIT CIRCUIT ICNI MOTOR CONNECTOR (NOT SHOWN) IDM CONNECTOR HSI CONNECTOR fACTORY TESTCONNECTOR $)PL1-4 PL1G NOTE #_i_J (WHENLGPS USE HPS $ PLI-lO JUNCTION O TERMINAL CONTROL .... PCB TERMINAL FACTORY POWER FACTORY CONTROL )'PL1-9 WI RING (24VAC) FIELDCONTROL WIRING (115VAC) FIELDCONTROL WIRING (24VAC) CONDUCTOR (_ WIRING (115VAC) ON CONTROL PCB i_ NOTE #5 PCB FIELD WIRING SCREW TERMINAL --L FIELD EARTH GROUND EQUIPMENT GROUND FIELD SPUCE _) _ PLUG RECEPTACLE A02176 Fig. 31--Wiring Diagram Combustim>air CARBON Failure MONOXIDE to follow connected the steps outlined to the ver*tir*g system could result The in carbon fol!owing connected while POISONING steps shall below for each appliance placed poisoning be for each beir*g placed connected See Table Furnace tached appliance to the x enting system 2. Inspect the venting system pitch, as required Z223H=2002NFPA some are Installation cmxosion and other ur*safe condition. 3. As far as practical, cor*nected spaces or restriction, deficiencies, which close all buildir*g between the space to the ver.tir.g could doors in which system are --€ leakage, cause an ar*d aindows the appliance(s) located and other of the building. 4. Close fireplace dryers and any appliance the ver.ting system. range and bathroom hoods 6. Follm_ speed. into hood Place Adjust exhaust the appliance Slope the them?ostat combustion-air relief opening ver.ting after andor ver.ting When at the of main system that each appliance properly remm doors, vents aboxe, dampers and any other gas-fired conditions of use. NOT or vent cor*nectors when or connector using burner Gas and _ir*dows, tested exhaust appliance as it passes is used dards vent systems fhns, in Table INIT CORROSION which to their AND table VENT fbtmd For ar*y inside include as possible National and American Society minimum in the NFGC star*dards. See Table See Table 7 for maximum 5 for approved piping primers, Standards for Testing must (ANSI) and Materials star*° (ASTM) for use in the U.S.A. ar*d Fig. 37, 38, 39, 40, and CARBON Failure to damage, personal cement. combustior*°air SDR and vent sized for 2-it*. pipe. Ar*y pipe size change furnace drainage casing pipe must 8 with Am_aflex-type fieezir*g, space or when be insulated a as insulation. HAZARD air is fi'equently fluorides, contaminated chlorides, products air may structure by halogens, bromides, and iodides. detergents, adhesives, bleaches, pair*t, ar*d Locate corr*bustion-air inlet as far pool and swimming pool pump an'angements. pipe Furr*ace below an unheated FIRE AND EXPLOSION HAZARD Failure to %llow this wamir*g could result in fire, property damage, persona! irljnry, or death. Solvent cemer*ts are combustible Keep away fi'om heal sparks, and open flame Use or*ly in well ver*tilated areas Avoid breathing in vapor or allowing contact with skirl or eyes DWV pipe Canada. NOTE: unit size as and vent pipes fbr this unit PVC, PVC-DWV or ABS= pipe it* intem_ittent to temperatures through from swimmir*g It* Canada, construct all combustion-air of CSA or ULC listed schedule-40 and may result or NSC= ar*d solvents Ir*stimte materials pipe lengths "N honse, PIPING and vent pipe, fittings, m These elemer*ts are _bund in aerosols, clear*ir*g solvents, salts, air _?esher*ers, or vent connectors, must be sized to approach to Americar* 41 _br exterior toward 0 as a raceway, shown because General cot*form in ft with no sags between Excessive exposure to contaminated combustior* result in safety and perfbrmance related problems. (ombustion air must r*ot be taken fiom inside connected when may r*eed to be resized. resizing appropriate COMBUSTION=AIR Combustion-air downward and OPERATE vent pipe is exposed other household determined NGPIC and vent pipes of 1/4 in. per linear to _bllow this caution chimney (7ode. fireplace prexions system to be relocated any of the above B 149.1, Natural outlined appliances cap may need or candle. during (SA 9. After it has been determined other be at- operation. so appli= appliances 5 minutes of a match is observed 54-2002 MAY such as when fl'om draft hood equipped Installation system must intake plug fitting MINOR PROPERTY DAMAGE Failure to fbllow this caution may result in water damage f?om cor*der*sate drippir*g. When combustion-air pipe is instal!ed above a suspended ceiling, pipe must be ir*sulated with 3iSqn. thick Armaflex= type insulation (ombustion-air pipe should also be insulated when it passes through wam_, humid space to prevent condensate fi'om dripping l:i'om the combustion°air pipe Failure being NFPA Vent connections applications. UNIT fan. 2002 the vent . so they are operating a summer fl_e venting system must be cotxected in accordance the National Fuel Gas (?ode. ANSI Z223A= to alternate as tests, with Propane housing to rims, such continuously. Use the flame 8. If improper r*ot cor*nected any exhaust exhausts, operation. 7. Test for spillage operation. on instructions. ar*ce is operating draft Turn Do r*ot operate fl_e lighting ir*spected (roof dampers. 5. Turn on clothes at maximum in same hangers. size ar*d horizontal (?ode ar*d these ir*structions. that there is no blockage ar*d all doors and vent pipe in Fig. 34. Combustion=air furr*ace a minimum system. fbr proper together in the National Fuel Gas (!ode, ANSI 54°2002 or the CSA B149.1. Natural Gas and Propane Detem?ine it* xenting terminate clearances. combustion=air NOTE: openir*gs must zone, either through roof or sidewall using accessory termir*ation kit 6 for required as shown indr*cer Jr*to operation, not in operation: 1. Seal any unused and vent pipes pressure preferred), into operation or death fbllowed to the ver*ting system al! other appliances HAZARD being monoxide atmospheric tem_inatior* in vertical pipe. is NOT pipe should approved connections in All are follow combustion-air this POISONING warning proper of vent condensate. 25 HAZARD could result in property irljury, or death. ar*d vent pipes watertight Pipes must also tem_inate 37, 38, 39, 40, or 41. be made outside (See Fig. 330 This allows MONOXIDE must exactly be airtight and as shown in Fig. \ A _ item A Clearance Description Clearance Canadian above grade, veranda, porch, deck, balcony, or anticipated B Installation AREA WHERE TERMINAL iS NOT PERMITED (1) U.S Installation 12" (30cm) # (2) 12" (30 cm) snow level Clearance to a window or door that may be opened to a permanently 9"(23 cm) for appliances > 10,O00 Btuh (3 kW) regulator assembly 3" (91 cm) within 15"(4.5 m) above the meter/regulator assembly 3'(91 cm)within assembly D Vertical clearance to a ventilated soffit located above the closed window distance of 2"(61cm) from the E Clearance to an unven61ated soffit F Clearance to an outside corner G Clearance to an inside corner H Clearance to each side of the centedine meter or gas service extended above I Clearance to service regulator vent oufiet 3" (91 cm) J Clearance to non-mechanical air supply inlet to building or 9" (23 cm)for appliances the combustion > 10,000 Btuh (3 kW) and < 50,000 Btuh (15kW), 12" (30 cm) for appliances > 50,006 Btuh (15 kW) Clearance terminal within a horizontal centedine of the terminal 12" (30 cm) for appliances and < 1O0,OO6Btuh (30 kW), 36" (91 cm) for appflances > 160.600 Btuh (30 kW) C electrical E_ (_) AIR SUPPLY INLET VENT TERMINAL air inlet to any other appliance 9"(23 cm) for appliances > 10,000 Btuh (3 kW) and > 16,000 Btuh (3 kW) and < 50.600 Btuh (15kW), 12" (30 cm) for appliances 6" (1.83 m) 3' (91 cm) above if within 10"(3m)horizontally Clearance to a mechanical L Clearance under a veranda, porch, deck, or balcony 12" (30 cm) + M Clearance to each side of the centerline 12" (30 cm) 12" (30 cm) 3" (91 cm) 3' (91 cm) 3" (91 cm) 3' (91 cm) extended above or m) above the meter/regulator < 100,000 Btuh (30kW) and < 50.000 Btuh (15 kW), 12" (36 cm) for appliances > 56,066 Btuh (15 kW) K air supply inlet 15'(45 > 50,006 Btuh (15 kW) below vent terminal of the furnace to a dryer or water heater vent. or other appliance's Clearance direct vent intake or exhaust to the vent terminal vent, or other appliances Clearance of a dryer vent, water heater direct vent intake or exhaust. from a plumbing vent stack (1) In accordance with the current CSA B149 1. Natural Gas and Propane lnstaHafon (2) In accordance with the current ANSI Z223.1/NFPA 54, National Fuel Gas Code Code # 18 " (46 cm) above roof surface + Permitted only if veranda, porch, deck. or balcony is fully open on a minimum of two sides beneath the floor. For clearances not specified in ANSI Z223.1/N F PA 54 or CSA B 149.1, clearances shall be in accordance manufacturer's installation instructions with local install ation codes and the req ui remen ts of the gas su pplier and the Notes: 1 2 The vent for this appliance shaft not terminate a. Over public walkways; or b Near soffit vents or crawl space vents or other areas where condensate c. Where condensate When locating vent terminations, Recirculafon 3 vapor could cause damage or could be detrimental considerafon can cause poor combustion, of regulators, relief valves, or other equipment must be given to prevailing winds, location, and other conditions which may cause recirculation inlet condensate Avoid venting under a deck or large overhang or vapor could create a nusaince or hazard or property damage; or to the operation Recircutation problems, and accelerated of the combustion products of adjacent vents corrosion of the heat exchangers. could occur and cause performance or system problems. A04117 -_ Table 6--Direct Vent Termination 26 Clearance SETUP SWITCHES LOW-HEAT ONLY AND BLOWER OFF-DELAY x TWINNING AND/OR COMPONENT TEST TERMINAL N N N J \ J / / ACRDJ - AIR CONDITIONING RELAY DISABLE JUMPER y 24-V-THERMOSTAT TERMINALS TRANSFORMER 24-VAC CONNECTIONS HUMIDIFIER TERMINAL (24-VAC 0.5 AMP MAX.) ....................... PL1 - LOW VOLTAGE MAIN HARNESS CONNECTOR 3-AMP FUSE LED OPERATION & J J: DIAGNOSTIC LIGHT PL3 115-VAC (L2) NEUTRAL-Jr CONNECTIONS B_,iOR J I HEAT B.TCL_ E SPARE-1 / BLOWER SPEED'__ BLW_ 1 SPARE-2 COOL SELECTION TERMINALS \ PL2 - HOT SURFACE IGNITER & INDUCER MOTOR CONNECTOR VOLTAGE CONNECTION 115-VAC (L1) LINE EAC-1 TERMINAL __.j (115-VAC 1.0 AMP MAX,) A02017 Fig. 32--Control Center 2 When installing vent systems of short pipe length, use the smallest allowable pipe diameter, Do not use pipe size greater than required or incomplete combustion_ flame disturbance_ or flame sense lockout may occur, FURNACE NOTE: Do not count elbows or pipe sections in tem_inations or within [_umace, See shaded areas in Fig, 37, 38, 39, 40, and 41, NOT IN HORIZONTAL SECTION EXAMPLE: An 080-12 lis, elevation 650 t't above application with TRANSITION IN VERTICAL SECTION 5 elbows indicates pipe, requiring used but require for both required same NOTE: The minimum for fl_ese fi/maces water &oplets. combustion-air is 5 ft, Short pipe lengths These droplets minimum offset pipe section to reduce excessive Combustion-Air Determine 1, Using and vent pipe length droplets and Vent combustion-air Table combustion-air 7, is recommended, 2-1/2 combustion were in AlbuquerquQ installation would pipe, 2-in. pipe is only good 2-1/2 in, pipe is good since larger f_r both pipes. If elevation 5250 f_ require At 500I- air pipe pipe must be pipes be used 2ol/2 in to 6000-ft for 17 ft with 5 elbows, fbr 70 ft with 7 vent but only 30 fl in diameter always tion, Combustion-Air and vent pipe diameter, detem_ine and vent pipe diameters combustion-air sea level, must Table vent elevaand 5 elbows, vent pipe outlet, Pick the larger of these 2 pipe diameters _br both in Fig, 35_ Pipe Diameter individually in diameter Therefore, diameter pipe, along allow a 2-in. diameter fbr 35 t't with 3 elbows, pipe and combustion-air and a 12-in, as shown would a 2-1/2 in an and 32 ft of vent pipQ vent and combustion-air installation above (5-8 ft) may discharge may be undesirable, fi'om exiting (each) in Indianapo- and 34 ft of confbustion-air this application with 5 elbows). Fig. 33--Combust{on-Air and Vent P{pe Diameter Transition Location and Elbow Configuration located sea level, could be installed 3 elbows (2-ira pipe is good A93034 size _lmace allowed NOTE: the smallest All pipe joints combustion-air fbr each pipe, necessary and use this diameter 1 and vent pipes, 27 and Vent Pipe Attachment Attach must be cemented pipe to inlet housing to remove except connection_ attachment pipe _br servicing combustion-air of since it may be pipe to ftmaace as follows: NOTE: Select 1 vent pipe connection and 1 combustion-air pipe connection. NOTE: Select 1 vent pipe connection and 1 combustion-air pipe connection. AIR COMBUSTION-AIR _ COMBUSTION-AIR VENT COMBUSTIONAIR UPFLOW _;_ DOWNFLOW COMBUSTIONAIR COMBUSTIONAIR VENT HORIZONTAL-LEFT COMBUSTIONAIR AIR FLOW VENT DISCHARGE HORIZONTAL-RIGHT DISCHARGE A96187 Fig. 34--Combustion-Air and Vent Pipe Connections a. Detem_ine tocation of" combustion-air intake pipe connec= tion to con_bostion=air intake housing as shown in Fig. 34 for application. using RTV sealant, oI by drilling a hole in fitting, using hole in intake housing as a guide Install a field-supplied No. 6 or No. 8 sheet metal screw. b. Reposition combustion=air intake housing plug fitting in appropriate unused intake housing connection. NOTE: DO NOT OVERTIGHTEN S(REW. Breakage of intake housing or fitting may cause air teakage to occur c. It" required (See Table 7), insert perfPrated disk assembly (factory=supplied in loose parts bag) in intake housing where combustion=air intake pipe will be connected. If half disk set is required, install with shoulder of disk against stop in combustion=air inlet. A plugged &ain connection has been provided on this fitting £br use when moisture is fbund in combustion-air intake pipe and combustion box NOTE: Moisture improper d. Install pipe support (fhctow-supplied in loose parts bag) into selected fhmac¢ casing combustion-air pipe hole. Pipe support should be positioned at bottom of casing hole in termination. tion is similar combustion=air Ensure intake combustion-air may be result of intake pipe termina- to that shown in Fig 37, 38, 39, 40, and 41 so it will not be susceptible to areas where moisture could be pulled in light snow or other sources of e. Insert 2-in. diameter pipe into intake housing. If use of this drain connection NOTE: A 2=in. diameter pipe must be used within the furnace casing. Make all pipe diameter transitions outside furnace casing. with a 3/16-in. robe should f Install casing hole filler plug (factow-supplied in loose parts bag) in unused combustiomair pipe casing hole. g. Drill a 1/8-in. hole in 2=ira combustiomair in intake laousing as a guide h. Install a field=supplied No. 6 or No into combustion-air pipe. be routed AiC (if'used), 2. Attach pipe using hole location as shown b. Reposition and clamp tion. Tighten NOTE: Do not attach combustion-air intake pipe permanently to combustion=air intake housing since it may be necessary to remove pipe for service of igniter or flame sensor. Combustion=Air Intake Housing Plug Fitting The combustion-air intake plug fitting must be installed in unused combustion=air intake housing. This fitting must be attached by 2g drill out fitting's a field=supplied condensate be trapped. vent pipe to fitmace housing NOTE: DO NOT OVERTIGHTEN SCREW. Breakage of intake housing or fitting may cause air leakage to occur. to open and should a Determine g sheet metal screw is desired, &ill and connect &ain (See Fig tap plug 3/8-in. tube. This for f_./mace and 36.) as follows: of vent pipe connection to inducer in Fig. 34 for application elastomeric to appropriate clamp. (rubber) unused inducer inducer housing housing outlet cap connec= 121,M,4 1 _._ VENT PIPE 12" MI N -_--_ l HORIZONTAL TO ROOF HORIZONTAL _ P,PE f PIPE TO SIDEWALL COMBUSTION-AIR COMBUSTION-AIR COMBUS_IO_N-AIR PIPE VENT PIPE 12"MIN ::_' 12" MIN ,,_D VENT PIPE VERTICAL TO ROOF VERTICAL TO SIDEWALL NOTE: A 12 In. minimum offset pipe section is recommended with short (5 to 8 ft) vent systems. This recommendation is to reduce excessive condensate droplets from exiting the vent pipe. A96230 Fig. 35_hort Vent (5 to 8 ft) System I --> UNIT DAMAGE HAZARD Failure to follow this caution may result coupling in unit component elastomeric (rubber) both clamps Inducer housing against inducer housing. any condensate leakage c. h_stall into outlet pipe Clamp and fully seated must be tightened the clamp to prevent e Install parts support selected should cap must be installed (_i_ctory=supplied _lmace casing be positioned in loose vent pipe hole. at bottom of casing parts Pipe bag) Vent support by 12-in. UNIT DAMAGE this caution may result in unit component pipe must internal condensate NOTE: casing filler Furnaces This pipe on ALL NOT_:: See label upflow be installed and fillly seated stop, Clamp must be tightened against extension inducer to prevent 3 any pipe must all pipe diameter d. Be certain that mating be used a'ansitions within outside Tighten Tighten with 100,000 vent extension channel and larger to assist vent pipe is supplied, vent pipe and downflow Btuh hole. pipe (2-in. diameter d_is vent extension the field in loose pipe casing to [\N'nace it inducer applications on vent extension sur_i_ces of inducer housing coupling, and 2=in diameter clean Assemble the dry robe to field installed Working [i'om fi/rnace pipe fbr proper if an elbow is used installation. to connect vent vent pipe. to outside, cut pipe to required elastomeric 4 Deburr inside and outside 5 (hamfcr outside and cement, 6 (;lean of pipe. the [:urnace [:umace tion, elastomeric and the hous- length(s) teakage, A 2=in. diameter Make stop housing (fi_ctory=supplied has a built-in When to connect housing plug combustion-air This pipe may be shortened damage. housing be used on the internal the pipe to inducer with a PV( disposal housing to 15 in =lb. of torque. hole Pipe: inducer vent pipe through HAZARD Failure to follow Vent screws onto and _hlly into inducer until it bottoms casing tong). condensate must coupling bag) in unused Extension clamps) the 2=in diameter to secure inputs are supplied hole. 2 loose Insert ing connection damage. --> (with connection casing. edge of pipe _br better distribution of primer connec= vent pipe are (rubber) vent 7. Check 29 and dU all sur_tces to be joined dry fit of pipe and mark insertion depth on pipe. TABLE 7--MAXIMUM ALTITUDE (FT} UNIT SBZE 060-12 080-12 080-16 0 to 2000 100-16 100-20 120-20 ALTITUDE (FT} UNIT SIZE (FT} notes at end 2 Pipe or 2-in Concentric 2 Pipe or 2-in Concentric OF 90 ° ELBOWS 1 2 3 4 5 6 1-1/2 20 15 10 5 NA NA 2 70 70 70 70 70 70 1-1/2 10 NA NA NA NA NA 20 2 55 50 35 30 30 2-1/2 70 70 70 70 70 70 2 5 NA NA NA NA NA 2-1/2 40 30 20 20 10 NA 3 70 70 70 70 70 70 2-1/2 one disk 10 NA NA NA NA NA 31 45 40 35 30 25 20 31 no disk 70 70 70 70 70 70 2 Pipe or 3-in Concentric 2 Pipe or 3-in. Concentric TERMINATION TYPE NUMBER OF 90 ° ELBOWS PIPE DIA 1 2 3 4 5 6 17 12 7 NA NA NA 2 70 67 66 61 61 61 080-12 080-16 2 Pipe or 2-in Concentric 2 49 44 30 25 25 15 2-1/2 70 70 70 70 70 70 100-16 100-20 2 Pipe or 3-in Concentric 2-1/2 35 26 16 16 6 NA 3 70 70 70 70 66 61 3 14 0 NA NA NA NA 31 no disk 70 70 63 56 50 43 41- no disk 70 70 70 70 70 70 2 Pipe or 3-in. Concentric 1 2 3 4 5 6 2 Pipe or 2-in Concentric 1-1/2 16 11 6 NA NA NA 2 68 63 62 57 57 56 080-12 080-16 2 Pipe or 2-in Concentric 2 46 41 28 23 22 13 2-1/2 70 70 70 70 70 70 100-16 100-20 2 Pipe or 3dn Concentric 2-1/2 33 24 15 14 5 NA 3 70 70 70 66 61 56 2 Pipe or 3-in. Concentric 31. no disk 65 58 51 44 38 31 41. no disk 70 70 70 70 70 70 UNIT SIZE TERMINATION TYPE NUMBER OF 90 ° ELBOWS PIPE DIA (IN.)* 120-20 See ON.)* 1-1/2 060-12 3001 to 4000 NUMBER PIPE OmA (IN.)* 120-20 ALTITUDE TERMINATION TYPE PiPE LENGTH {FT) 2 Pipe or 2-in Concentric 060-12 2001 to 3000 ALLOWABLE of table NOTE: It is recommended that all pipes be c_lt, prepare& and preassembled be:_bre pem'tamer,tly cementing ar*y.joint. Combustion-air factory and vent pipes accessory termination kit must outside A structure in 1 of the be installed installations shown in Fig. 37, 38, 39, 40, and 41. Four tem_ination kits are available. 8, After pipes have been cut and preassembled_ apply generous layer of cement primer to pipe fitting socket and end of pipe to insertion mark. Quickly apply approved cement to end of pipe and fitdng socket (over primer) Apply cement in a light, uniform coat on inside of socket to prevent buildnp of excess cement Apply second coat See Table 1. The 6 %r additional 2-in. termination 2-ira diameter 2. The 9. While cement is still wet, twist pipe into socket with 1/4 mm Be sure pipe is fl41y inserted into fitting socket 2-pipe 3-in. termination 4-in. diameter in., 2-in. in%rmation. kit is _br 1-in., bracket kit is for 2ol/2 NOTE: Shaded to be tem_ination. These when determining pipe 14. Lse appropriate methods to seal openings where vent and combustion=air pipes pass through roof or side wall. CONCENTRIC VENT AND COMBE STION=AIR TERMINATION KIT INSTALLATION since it is less susceptible parts and in, and 3-in., systems termination pipe kit is fo* l-in, systems when 1-1/2 single is desired. vent/air termination 3-in., and 4-in. diameter pipe systems of wall or roof is desired. 13. Slope combustion-air and vent pipes downward toward fi/rnace a minimum of 174-in per linear _'twith no sags between hangers 1ol/2 in., systems in. diameter of wall or roof 4. The 3-in. concentric 12. Support combustion-air and vent piping a minimnm of eve W 5 ft (3 k for SDR-21 or -26 PVC) using perfbrated metal hanging strap bracket termination vent/air and 2-!/2 penetration 11. Handle pipe joints careflflly until cement sets ternxination 2=pipe termination 3. The 2-in. concentric 10. Wipe excess cement fi'om.joint. A continuous bead of cement will be visible around perimeter of a properly made joint. NOTE: If" these instructions dif_:kr from those packaged tern_ination kit, follow kit instructions must terminate kit is for 2ol/2 when single in., penetration in Fig. 37, 38, 39, 40, and 41 are considered components diameter. should Roof to damage, NOT temaination has reduced be counted is prefmTed chances to take in contaminants, and has tess visible vent vapors. (See Fig 37 or 38.) Sidewall termination may require sealing or shielding of with 30 building surfi_ces con'osive combustion with a CmTOSiVe resistance products of vent system. material due to TABLE 7--MAXINUN ALTITUDE (FT) UNIT SIZE 4001 to 5000_ (FT) (FT) (FT) 3 4 5 6 15 10 5 NA NA NA 52 2 64 59 58 53 52 2 44 39 26 21 20 11 2-1/2 70 70 70 70 70 70 100-16 100-20 2 Pipe or 3dn Concentric 2-1/2 31 22 13 12 NA NA 3 70 70 67 62 57 52 2 Pipe or 3-in. Concentric 3t no disk 53 46 40 33 26 20 41- no disk 70 70 70 70 70 70 TERMiNATiON TYPE PIPE DtA (iN.)* 1 2 3 4 5 6 14 9 NA NA NA NA 47 NUMBER OF 90 ° ELBOWS 060-12 2 Pipe or 2-in Concentric 1-1/2 2 60 55 54 49 48 080-12 080-16 2 Pipe or 2-in Concentric 2 41 36 23 18 17 8 2-1/2 70 70 70 70 70 70 100-16 100-20 2 Pipe or 3-in Concentric 2-1/2 29 21 12 11 NA NA 3 70 67 62 57 52 47 2 Pipe or 3-in. Concentric 31- no disk 42 35 29 22 15 9 41- no disk 70 70 70 70 70 70 TERMiNATiON TYPE PIPE DtA (IN.)* 1 2 3 4 5 6 13 8 NA NA NA NA 43 NUMBER OF 90 ° ELBOWS 060-12 2 Pipe or 2-in Concentric 1-1/2 2 57 52 50 45 44 080-12 080-16 2 Pipe or 2-in Concentric 2 38 33 21 16 15 6 2-1/2 70 70 68 67 66 64 100-16 100-20 2 Pipe or 3-in Concentric 2-1/2 27 19 10 9 NA NA 3 68 63 58 53 48 43 2 Pipe or 3-in. Concentric 31- no disk 31 24 18 11 NA NA 41- no disk 70 70 70 70 67 62 TERMINATION TYPE PIPE DtA UNIT SiZE 7001 to 8000_ 2 2 Pipe or 2-in Concentric 120-20 ALTITUDE 1 080-12 080-16 UNIT SiZE 6001 to 7000_ OF 90 ° ELBOWS {IN.}* 2 Pipe or 2-in Concentric 120-20 ALTITUDE NUMBER PIPE DmA 060-12 UNIT SiZE 5001 to GO00_ TERMINATION TYPE PIPE LENGTH (FT) (Continued} 1-1/2 120-20 ALTITUDE ALLOWABLE NUMBER OF 90 ° ELBOWS (IN.)* 1-1/2 1 2 3 4 5 6 12 7 NA NA NA NA 2 53 48 46 41 40 38 2 36 31 19 14 12 NA 060-12 2 Pipe or 2-in Concentric 080-12 080-16 2 Pipe or 2-in Concentric 2-1/2 66 65 63 62 60 59 100-16 100-20 2 Pipe or 3-in Concentric 2-1/2 25 17 8 7 NA NA 3 63 58 53 48 43 38 2 Pipe or 3-in. Concentric 31- no disk 20 13 7 NA NA NA 41- no disk 61 56 51 46 41 36 120-20 See notes at end of table Extended Exposed Sidewall Pipes b thickness affected allow be positioned plants/shrubs kit should by wind eddy recirculation where vent vapors or air conditioning equip- be positioned so that it will not be (such as inside building of flue gases, airborne corners) leaves, or or light snow d tbr exposed pipe Terns!nation kit should damaged by or subjected balls, ere, NOTE: Pipe length(k) specified [br maximum pipe lengths to= cared in unconditioned spaces Pipes located in unconditioned space cannot exceed total allowable pipe length as specified in Table 7, Two=Pipe Termination kit should c, Termination 2, Lsing winter design temperature (used in load ca!culations), find appropriate temperature [br your application and [:m'nace model insulation Termination wil! not damage ment, 1, Detem_ine combustion-air and vent pipe diameters, as stated above, using torn! pipe tength and number of elbows, 3, Detem_ine required lengths as stated in Table a. Comply with all clearance requirements 6 Sidewall combustion-air and vent pipe terns!nations may be extended beyond area shown in Fig. 40 or 41 in outside ambient by insulating pipes as indicated in Table g, e Terns!nation kit should be positioned to foreign where objects, be positioned it will not be suck* as stones, where vent vapors are not objectionable, 2 Kit Cut 2 holes, being 1, Detem_ine location for termination. Consider the /bllowing when determining an appropriate location for termination kit, 3 Loosely insta!l combustion=air 31 1 for each pipe, of appropriate size for pipe size used elbow pipe in bracket and place assembly on TABLE 7--MAXIMUM ALTITUDE TERMINATION TYPE UNiT SBZE (FT} 800t to 9000@ dN.)* 1 2 3 4 5 6 11 6 NA NA NA NA 2 Pipe or 2-in Concentric 2 49 44 42 37 35 34 080-12 080-16 2 Pipe or 2-in Concentric 2 33 28 17 12 10 NA 2-1/2 62 60 58 56 55 53 2 Pipe or 3-in Concentric 2-1/2 23 15 7 5 NA NA 3 59 54 49 44 39 34 2 Pipe or 3-in. Concentric 3t no disk 10 NA NA NA NA NA 4t no disk 35 30 25 20 15 10 TERMINATION TYPE UNIT SIZE 9001 to 10,000_ NUMBER OF 90 ° ELBOWS PIPE DmA 060-12 100-16 100-20 (FT) PIPE LENGTH {FT) (Continued) 1-1/2 120-20 ALTITUDE ALLOWABLE 060-12 2 Pipe or 2-in Concentric 080-12 080-16 2 Pipe or 2-in Concentric 100-16 100-20 2 Pipe or 3-in Concentric 120-20 2 Pipe or 3-in. Concentric NUMBER OF 90 ° ELBOWS PIPE DtA (IN.)* 1 2 3 4 5 6 2 45 40 38 33 31 29 2 30 25 14 9 7 NA 2-1/2 57 55 53 51 49 47 2-1/2 21 13 5 NA NA NA 3 54 49 44 30 34 29 41- no disk 10 5 NA NA NA NA * Disk usage-Unless otherwise specified, use perforated disk assembly (factory-supplied in loose parts bag) If one disk is stated, separate 2 halves of perforated disk assembly and use shouldered disk half When using shouldered disk half, install screen side toward inlet box. 1 Wide radius elbow $ Vent sizing for Canadian installations over 4500 fl (1370 m) above sea level are subject to acceptance by the local authorities having jurisdiction. NA-Not AHowed; pressure switch will not make. NOTES: 1 Do not use pipe size greater than those specified in tab{e or incomplete combustion, flame disturbance, or flame sense _ockout may occur 2 Size both the combustion-air and vent pipe independently, determine the smallest diameter allowed by the chart for each pipe, then use the larger of these two diameters for both pipes 3 Assume two 45 ° elbows equal one 90 ° elbow Long radius elbows are desirable and may be required in some cases 4 Elbows and pipe sections within the furnace casing and at the vent termination should not be included in vent length or elbow count. 5 The minimum pipe length is 5 ft for all applications 6 Use the 3-in. diameter vent termination kit for installafions requiring 4-in diameter pipe i_k_ 3/8" ID TUBE OMBUSTION TAKE "-'- (oncentlic - AIR HOUSING 1. Detet_nine BURNER a \ oRtL Tem_ination location Comply 6 kit should will not damage ment. c. Teilnination kit should or light damaged Fig. 36--Air Intake Housing Plug Fitting Drain balls, install cut vent pipe Coupling mount as shown in Fig must 37. be positioned For applications using by dashed in Fig. 37, install lines making Sidewall 41. pipe coupling combustion-air U-fitfing. so bracket pipe option, 90 c>street A 180 ° [?-fitting terminations-Install bracket on properly using lines in Fig. 40, rotate vent pipe option will kit should into 3. Loosely 90 c> in Fig. 40 or vent elbow 90 _>fi'om position procedures 5. (beck loose pipe fittings. as used required for system dimensions Clean and cement using not be comers) or airborne leaves, be positioned where it will not be to foreign ok{iects, such as stones, where vent vapors are hole fbr 2qn. kit, or one 5-in. diameter by dashed inside shown in using same in Fig. 37, 40, or 41. Do not allow insulation termination terminations-Locate priate height as shown assembly in Fig Sidewall terminations-Locate with rain shield positioned 39, or other materials when installing Roof in Fig vent/air components in kit. kit with rain shield REMOVED of pipe assembly shown 32 concentric instructions 4. Slide assembled piping. as shown so it will building of flue gases, kit should be positioned assemble together Fig. 40. 4. Disassemble be positioned equip- etc. 2. Cut one 4qn. diameter hole fbr 3qn. kit. may be used. indicated vapors not objectionable. NOTE: For applications vent indicated elbow as shown where or air conditioning ed@ (snch as inside by or subjected e. Tem?ination terminations-Loosely as stated in Table snow. d. Tem?ination A93035 elbow, be positioned of the an appropriate requirements that may allow recirculation OPEN DRAIN (onsideration determining plants/shrubs aJTected by wind Roof tem_ination. with all clearance b. Termination TRAP!_ TO %r Kit fbllowing should be made when location fbr termination kit. BOX 3/16 Vent/Air it through through through hole. to accumulate hole, roof to appro- through sidewall 38, assembly no more than 1-in, from wall as AIR AND VENT 8 3/4" FOR 3"KIT 6 3/4" FOR 2" KIT MAINTAIN 12 IN. CLEARANCE ABOVE HIGHEST ANTICIPATED SNOW LEVEL. MAXIMUM OF 24 IN. ABOVE ROOF. A87224 Fig. 37--Roof Fig. 38--Concentric Vent and Combustion-Air Termination (Preferred} Termination (Preferred} 12 IN. CLEARANCE ABOVE HIGHEST ANTICIPATED SNOW LEVEL OR GRADE, WHICHEVER IS GREATER. Roof A93055 Fig. 39--Concentric 5. Disassemble loose pipe fitnngs. procedures as used _br system Clean and cement using same required dimensions MULTIVENTING When 2 or more 58MTA shown near each other, each vented. NEVER When 2 or more common 58MTA UNIT vent or furnaces may be installed that 36 vent in from terminations recirculation of flue gases. 47 represents distance 2-in. n_axinmm away Dimension between be first made 2 terminations. as shown Drain as OPERATE Unit must not be installed, left in an unoccupied It is temperature to avoid as touching NOT to _bllow this caution may result in intermittent unit operation. &ain A in Fig. 43, 44, 45, 46, and pipes or rain shields, MAY Failure 43, 44, 45, 46, or 47, but the next vent termination l"n_ast be at least 10--Condensate 38 or 39. TERMINATIONS near each other, 2 vent terminations in Fig important in Fig i'L_maces are vented furnace must be individually breach vent 58MTA _hrnaces are vented as shown AND VENT Side piping. Step 6. Check Vent and Combustion-Air Termination &ops or and then turned during to 32°F and below line have adequate Maintenance operated, structure Instl_actions unless _?eeze protection. _:br winterizing off and cold weather drain trap See Service procedure. when and and (See Fig. 42) separation. GENERAL Condensate trap is shipped connected _br UPFLOW RELO(ATED for use installed in the blower shelf and titctoI 7 applications. (ondensate trap must be in DOVv%'FLOW and HORIZONTAL applications. Condensate 33 trap MUST be used for all applications. Furnace condensate is mildly 32 to 45. Due to corrosive pH neutralizing acidic, nature typically filter may be desired. to determine if a pH neutralizer in the pH range of this condensatQ Check of a condensate with local authorities is required APPLICATION The _lmace, drained A/C, supplied trap connections IN. SEPARATION BOTTOM OF :'COMBUSTION AIR AND OF VENT The AiC prior to the (t:umace, Ai(, drains &ain may be combined must fi/rnace have &ain an open or vented drain as close possible to prevent siphoning and an external, connection. or humidifier) field= All &ain must be temlinated into to the respective equipment of the equipment's See Fig. 48 _br example of possible 1/2=in. CPVC or PVC tee _br vent as drain. field drain attachment and AiC or humidifier using &ain connection. 12 IN. CLEARANCE ABOVE HIGHEST ANTICIPATED SNOW LEVEL OR GRADE, WHICHEVER IS GREATER. COMBUSTION-AIR and humidifier together. Outdoor draining codes. ti'eeze --9 A87225 of the fi/mace (audon should be is permissible taken &ain pipe and prohibit PERSONAL INJURY when if allowed fi'eezing. by local Ambient may &aining. AND PROPERTY DAMAGE HAZARD Fig. 40--Sidewall Termination OVERHANG of 12 in. or More OR ROOF Failure to fbllow this warning and personal J-f (aution should conditions jjj / ..... _ .... j 12" MINIMUM _ be taken damage where Excessive soil conditions slippe_ condensate which may result to plants. CONDENSATE cause draining injuries. may cause saturated in damage Freezing to prevent may cause personal draining _/_" could result in property irtiury or death DRAIN condensate cracks, PROTE(TION left in condensate and possible water trap damage and drain may line may occur. If fi'eeze protection is required, use condensate freeze protection accessory or equivalent 3 to 6 watt per ft at 120-v and 40°F self=regulating, shielded, IN. SEPARATION BOTTOM OF :'COMBUSTION AIR AND OF VENT trap is not required when connecting 1 wrap using £hcturer's confPrm to ASTM PVC drain pipe, When D2564 In Canada, fittings_ a condensate approved trap or drain robe coupling) PVC, or 5/g-in. ID tube select Primer must cont'om_ or UL( listed schedule is required, furnace MAY a pump with select an overflow a pump To avoid trap to ASTM NOT Furnace control control will Step or which Wire sides. ties can be (See Fig. 49.) heat tape, approximately heat tape, _bllow heat for all other installation ADJUSTMENT to follow tape manu= guidelines. AND SAFETY CHECK OPERATE this caution may result in intem_ittent unit must lock be grounded out. (ontrol connected for proper is operation, grounded to gas valve or throngh C=terminal and l--General The _hrnace applications. field=supplied green@ellow wire burner box screw and must 40 CPVC tape in place. (See operation. and cement. pump fbr condensing sate spillage, or F493 use CSA heat of condensate insm/ctions START-UP Failure F656. in notches trap back. per ft. 5. When UNIT Instructions recommenda- on itself 3 times. 4. Wrap field drain pipe with remaining the field drain to Drain pipe and fittings must confPm_ to ANSI standards ASTM D1785, D2466 or D2846 CPVC or PVC cement See Installation sides of condensate ties to secure positioned trap The field drain connection (condensate is sized for ti2-in. (PVC, 1/2-in. connection. tape. tape in half and wrap 3. Use wire Fig. 41--Raised Sidewall Termination when Walt Penetration is Less than 12 in. Above Snow or Grade this condensate heat or heat tape manufhcmrer's 2. Locate heat tape between Fig. 49.) CLEARANCE ABOVE HIGHEST ANTICIPATED SNOW LEVEL OR GRADE, WHICHEVER IS GREATER. A87226 An external with accessory 1. Fold heat !2 IN. / COMBUSTION-AIR (ELBOW PARALLEL TO WALL) and waterproof supplied tions must have a 115-v power supply properly connected and grounded. is NOTE: conden- polarity switch. Proper and the Nmace 34 polarity is incorrect, must control be maintained status indicator will not operate. for ll5-v wiring. light will flash rapidly If TABLE 8--MAXIMUM ALLOWABLE EXPOSED VENT P{PE LENGTH (FT) WITH AND W_THOUT {NSULAT{ON IN WINTER DESIGN TEMPERATURE AMBIENT* WINTER DESBGN TEMPERATURE (OF) 20 UNiT SIZE 060 080 100 120 MAX PiPE DIAMETER (IN.) 2 WITHOUT W_TH 318=iN. OR INSULATION 44 THICKER INSULATIONt 70 0 2 21 70 -20 2 20 57 20 2 55 55 0 2 30 55 -20 2 16 55 20 2.5 58 70 0 2.5 29 70 -20 2.5 14 67 20 2.5 40 40 0 2.5 38 40 -20 2.5 21 40 20 3 63 70 0 3 30 70 -20 3 12 70 20 3 70 70 0 3 38 70 -20 3 19 70 20 4 65 70 0 4 26 70 -20 4 5 * Pipe length (fl) specified for maximum pipe lengths located in unconditioned as specified in Table 7. ? Insulation thickness based on R value of 35 per in. 65 spaces. Pipes located in unconditioned space cannot exceed total allowable pipe length length of previous heating on and off cycles, when to operate in tow- and high° gas heat _br optimum com£_rt Setup switch=l (SW-1) must be in the fi_ctou=shipped OFF position See Fig. 3! and Table 9A and B for setup switch information, Table 9A--Furnace SETUP SWITCH NO. SWITCH NAME \t / DESCRIPTION OF USE NORMAL POSITION Adaptive Heat SWol Setup SwRch Description When off, aflows 2-stage operation with a single-stage thermostat. Turn on when using 2-stage thermostat to allow Low Heat operation when R to W/W1 closes and High Heat operation when R to W/W1 and W2 close. OFF Mode 32°F //\ Blower OFF delay SWo2 , Blower OFF SWo3 Natural gas service 42--Freeze pressure and be no less than 016 Them_ostat required 2-stage cooling, wire psig _br gas heating heating heat pumps, made at the 24-_ This Nmace a 2-stage operation. and some terminal BLOWER-OFF MODE SETUP SWITCH DELAY (SEC} SW-2 SW-3 OFF be connected for and G are required for 90 OFF must be 120 OFF ON 150 ON OFF 180 ON ON on the control. These (See Fig. 320 a single=stage heating or them_ostat. thermostats, £urnace tem_inal single-stage W2 must with either DESIRED HEATING are the minimum clock thermostats. block For single=stage control Control blower OFF delay time Used in conjunction with SW-2 See Table 9B. Table 9B--Blower Off Delay Setup Switch (SW) 2-Stage Units with PSC Blower Motors wc), _c), CoM, Y¥2, can be installed heating (4,5-in, 05 psig (14=in at R and W/W1 thermostats. ON or OFF Protect{on must not exceed connections Control blower OFF dMay time Used in conjunction with SW-3 See Table 9B. delay A93058 F{g. ON or OFF them_ostats, connect block. the (See control thermostat Fig. wilt 27 W to WW1 and determine, 52H.) based If a 2-stage at For position on control 35 heating at end process thermostat of furnace _br selecting is to be used, installation. high This move SW-1 o\errides and tox_ fire to ON built=in and allows the A96128 Fig. 43--Rooftop Termination (Dimension "A" is Touching or 2-in. Maximum COMBUSTION AIR Separation) AIR COMBUSTION / A93056 Fig. 44--Concentric Vent and Combustion-Air Roof Termination (Dimension "A" is Touching or 2-in. Maximum Separation) A96129 Fig. 46--Raised SidewNl Termination when Walt Penetration is 12 in. or Less Above Snow or Grade (Dimension "A" is Touching or 2-in. Maximum Separation} VENT A93057 Fig. 45--Concentric Vent and Combustion-Air Side Termination (Dimension "A" is Touching or 2-in. Maximum Separation} A96130 2-stage thermostat to select gas heating modes _he W2 f_'om thermostat must be connected to W2 on control tem_inal block Fig. 47--Sidewall Termination (Dimension "A" is Touching Separation) (See Fig. 28 and 52AoG.) BeJ:bre operating fi_mace, switch fbr continuity. switch. complete The blower check If necessary, compartment the 115-v circuit each flame rollout press and release door must be manual button reset to reset in place to to the ft_rnace. 36 of More than 12 in. or 2qn Maximum / \ OPEN STAND --7 PIPE FOR / A/COR/ HUMIDIFIER ,L DRAIN TEE U h_ A94054 Fig. 48--ExamNe of Field Drain Attachment A99118 Fig. 50--Inducer Housing Drain Cap CONDENSATE FIRE HAZARD Failure to fbllow operation this caution or perfbm_ance This flmaace the burner "_ is equipped with a manual if a flame occurs in the burner switch. Correct Step (3 WRAPS 2--Prime rollout enclosure inadequate nent fhilure, or restricted the switch. HEAT in intem_ittent unit reset limit switch in box area. The switch will open and shut off power to the gas valve WIRE TIE(S)_ may result satisfaction or overheating area. combustion-air Trap bypass supply, flue gas passageway Condensate condition DO NOT With the compo= betbre resetting Water TAPE_ MINIMUM)_ INIT MAY Failure operation A93036 Trap Heat Tape OPERATE this caution or perfbm_ance ( ondensate Fig. 49--Condensate NOT to fbllow trap must be PRIMED occur The condensate ONLY be primed of condensate 1 may result Remove in intermittent unit satisfaction or proper trap has internal by pouring draining chambers may not which water into the inducer can drain side trap. upper inducer housing &ain 1/2-in. ID connection cap. (See Fig. 50) 2 (onnect field=supplied housing drain 3. Insert field=supplied 4 1 quart Pour through into open field t'unnet housing, a--Purge and Gas After all connections check for leaks. 37 to upper inducer into tube, into t\mnetimbe. overfill Water condensate should tIap, run and flow drain. (See Fig. 51.) drain connection Step fhnnel of water inducer 5. Remove robe connection. robe fiom inducer housing and replace cap and clamp. Lines have been made, purge the gas lines and NOTE: Low-heat=only switch, SW-I, selects either the tow=heat- only operation mode when ON, or adaptive heating OFF, in response to a call _br heat (See Fig. 32.) This furnace can operate thermostat because adaptive sequence history of the length t'mnace will start up in either tow-gas heat on time 0 to ld minutes) (fi'om is interrupted, the stored the control minutes and then switch to "call starts Period= the tow-heat pressure control begins CPU pressure control IDM motor high=heat pressure The and are open, and CPU selects IDM comes LPS closes, re-closes up to speed, and the prepurge prepurge IDM inducer closes. motor a 15=second If the furnace on the tow=heat If the [_umace control switch motor circuit verifies LPS and HPS switch a 15=second the inducer is based in high speed. the inducer will begin Trap contacts IDM this as the thermostat selection [br heat", R=WiWI switch When low=heat for up to 16 as long a self check, operation low-heat the times. Prepurge low-heat Condensate "calls motor 1. Inducer If d-_e is permitted is erased. Subsequent cycle perfbm_s pressure inducer which select to high-heat, _br heat." of thermostat control high-heat heat. CPU determines history CPU will initially When wall thermostat furnace the to high-heat. happens, history low-gasupon on/off periods tow= or high=gas heat, the control stored selects is based gas heating starts up iu low=gas continues a programmed which selection of previous a single=stage includes furnace If power Fig. 51--FNing This with when thermostat. be_bre switching A99119 CPU operation, operation of the single-stage The control of controlled heat or high-gas-heat stored as a 2=stage furnace _hmace mode period. the t\trnace period, furnace A_ler control the CPU and continue to run at high=speed. CPU selects remains switch high=heat operatiom the running at high-speed, and the relay HPSR is de=energized to close the N( contact When sufficient pressure is available laigl>heat pressure switch HPS closes, and the high-heat FIRE AND EXPLOSION Failure personal Never for HAZARD to t'ollow this warning valve solenoid could result in a fire, exptosiou, injury_ or death purge gas a gas line into a combustion leaks with an open flame. chamber. Use Never test and Safety a commercially (beck" sections switch If the high-heat 4--Sequence l_sing schematic operation very through the different If power or W/W1 blower during intetxuption and W2), the contloi off detay period still calling Read the sequence and _bllow for gas heating this period, respond blower through door blower must TRAN, hot surface igniter diagram A_er motor the gas valve the Hot Igniter Surface HSI. Five period the will 12 2=second as motor flame proving 4. Flame-Proving-When will to be conducted blower the the sensor switches to tow=speed BLWM, flame GV. period electrode contlol continues (PU to hold is not proved begins. begins ignition before sequence going automatically (See Fig. 27 for them_ostat connectious) 115 vac power 38 after sensed is proved the running the or gas by GVR will until the two seconds, hours, motor at high-speed, GV-M for up to three at the flame- inducer the blower-ON to Ignition-Lockout. a_:_er three The The HSI igniter is flame the gas valve within opens. begins. FSE, unless pe- GVR close where it is ignited close the gas valve GV=M, and the control TWO-STAGE HEATING WITH SINGLE-STAGE THERMOSTAT (ADAPTIVE MODE) the igniter warm-up contacts seconds flame burner proving fi/mace CPU, period, a 17-sec GV, the gas valve gas flow to the burners until control HPS fails of 2 minutes the igniter valve GV permits flame for power IDM, Sequence-When energized code fbr the main gas valve relay a 2=second the _hruace switch prepurge is energized remain ILK to furnace HSL and gas valve HSI closes, this perio& switch end of the inducer Igniter is flash CPU pressure period. to energize for the selected the LED will be ON continuous be installed inducer Warm-Up-At Surface riod is completed normally door interlock trans_:bm_er LED pressure closes for a maximum if the thermostat is restored, The amber a_ler which to the thermostat will run the blower switch 3. Trial-For-Ignition of occurs dtlring "call t'or heat" (WiW 1 a_ler power long as no _Sults are detected. The modes. %llow care_hlly NOTE: pressure warm-up 31, control after the low-heat of 2. Igniter in Fig. The thruace period after ignition. of Operation diagram LPS closes. high=heat Hot Step is energized. prepurge to close and the tow=heat pressure switch LPS closes, thrnace will operate at tow-heat gas flow rate until available soap solution made specifically for d_e detection of leaks to check al! connections, as specified in "Gas Piping" and "Start=up Adjustment, these iusm/ctions. GV-HI begins a 15-second the gas more delay open. IDM and the period and If the burner the control CPU will CPU will repeat the Trials=For-Ignition Lockout by momentarily to the [:umace, or by inten'upting will be reset interropting 24 vac power atSEC1 orSE(2tothefurnace control (PU(notatW/W1, G, 2. Switching R, etc.). If flame is prm'ed fhrnace contlol operate the indncer longer when (PU BLWM not nmde Delayqfbumer HEAT flanm is proven the blower 66 sec after gas valve GV=M blower motor BLWM is energized IDM motor BLWM Simultaneously, energized is energized the electronic and remains BLWM is energized. (7. Switching From CPU switches CPU will energized will Low- To High- the inducer high=heat Heat- speed COOLING is motor If the fhmace contlol the furnace control to high-heat, motor pressure energized to close the NC contact. available the high-heat high=heat gas valve pressure solenoid IDM switch speed relay When sufficient switch GV-HI HPS is closes, is energized. five seconds "calls The thermostat circuit is starts not switch R=to=W used. ti'om high=heat circuit closes delay- circuit stopping humidifier When is opened, gas flow terminal remain energized selection WITH R-to=W1 circuits TWO-STAGE the low-heat circuit. always Closing causes includes control furnace performs the inducer nmtor contacts IDM to the R to Wl circuit for circuits fbr high=heat. The verifies the low-heat and are open, 1 above apply switching fi'om low- to high=heat heating nmde described as well, in item except for switch low to high. The de=energized to close sure is available the high=heat the inducer high-heat the N( the high=heat gas valve motor pressure contact. pressure solenoid IDM speed switch relay When suftlcient switch HPS closes, GV-HI is energized. blower nmtor BLWM will switch to HI HEAT seconds after the R to W2 circuit closes. speed an the connections.) cooling the fhmace cooling relay sequence of contlolled period of the single-stage disable jumper nmde in place A(RDJ the Nmace unit to high-cooling. tow- control CPU (PU to energize can start up the cooling or high-cooling. If starting the [_trnace conkol time 0 to 20 minutes) (fi'om ACR determines to a control relay the outdoor must in response tem_inal and switch a CPU or high-cooling opthe stored history of cooling (See Fig. 32.) When unit with control the unit the low-cooling which in up in low-cooling, is permitted onbefbre to high-cooling. is interrupted, the Nrnace control 20 minutes and then to energize CPU the stored history will select energize cycle relay and switch the outdoor as tong as the themmstat of the thermostat and fbr up to the air conditioning the Y/Y2 temlinal Subsequent is erased tow-cooling selection continues is based to on stored times. The wall themmstat "calls fbr cooling", closing the R to G-and-Y circuits. The R to Y1 circuit starts the outdoor unit on low-cooling the furnace fi'om HPSR lbr can tm_a on the air conditioning histo_ and vice versa. speed Thermostat adaptive the adaptive call for cooling. From Low- To High- Heat-If t!_e thermostat R to is closed and the R to W2 circuit closes, the furnace CPU will to enable unit to high-cooling, and delays are nmtor to reduce Y/Y2 A(R in high-speed. circuits (See Fig. 32.) because of previous If the power and with blower (OOL a two-speed a programmed switching LPS and HPS f:unctions 2=stage of speed. CPU either R=to=Wl= regardless R-to-Y circuits is energized to DHUM and Single-Stage can operate The furnace switch. a selftcheck, switch The start=up and shutdown 1. S_itehing WI circuit thermostat on Y/Y2 to 5 seconds. The air conditioning be connected the The on COOL EAC-1 operating Jumper themmstat the length themmstat be ON to to closing operation, "calls for heat", closing pressure must BLWM terminal operation, which selects low=cooling eration. This selection is based upon THERMOSTAT switch the high=heat or closing the R to W1 and-W2 control The will connections). only connec- Mode) single-stage blower-OFF mode in response circuits. unit will stop, and Nrnace Cooling call for cooling. fbr thernmstat of the low-heat=only high-heat offtdelay This fhmace (depending The will opens. or E for themmstat (See Fig. 27 and 52A=H for themmstat MODE) only operation The wall themmstat furnace switches). fbr a 120-second HEATING In this nmde, tow-heat delay pressure GV-M nmtor BLWM is operating. is satisfied, the R-to-G-and-Y sec. the will NOTE: HEATING select the tow=heat the setting period. EA(-I motor and R-to-G-and-YiY2 motor continue 90 (Adaptive GV-M, de-energizing nmtor IDM fbr 90, 120, 150, or 180 seconds (See Fig. 28 and 52A-G and=W2 cooling is the R to gas valve a 15=second post-purge and air cleaner terminal is factor-set (NON-ADAPTIVE themmstat themmstat will additional unit, air cleaner The outdoor BLWM will the themmstat is satisfied, the bmlaers, and The inducer at blower-OFF CPU TWO-STAGE NOTE: the thernmstat to the HUM. energized for motor BLWM control delay. while a single=stage de-energizing remain blower on when (, R-to-G-and-Y blower The electronic 2. Two-Speed 8. Blower-Off W to tow-heat is closed (PU high-heat solenoid after the R to W2 circuit the outdoor start the furnace and the The blower control the the inducer tions.) opened. To Low- Heat-The HPSR fbr cooling" high=heat. High- the gas valve relay de-energize Cooling nmtor BLWM will switch to HI HEAT speed five seconds after the furnace control (PU switches ti'om tow-heat to From The and When sufficiently, open. 115-v when blower When the themmstat 7. Switching GV-HI. (See Fig. 27 or 28 and 52A, de= pressure solenoid switch contact MODE The themmstat fi'om tow to HPSR pressure the N( pressnre HPS HEAT EAC-I as long as the blower R to remain energized as long as the low-heat pressure switch LPS remains closed. The blower nmtor BLWM will switch to LO at LO speed. terminal gas valve 1. Single-Speed [_'om tow=heat switch The at HI HEAT air cleaner to open reduces switch speed. Hi-heat=The If the thermostat fi'om high to low. The high-heat is opened. is energized To Low- Heat- the motor IDM on high speed until flame is no is energized High- and be present, high-heat Low-heat=The starts should prm'ed. 5. Blower-On high. flame will lock out of Gas=Heating From W2 circuit opens, and the R to Wl circuit remains closed, the fhmace control (PU will switch the inducer nmtor IDM speed speed is presand The five 39 spee& blower and the R to G-and-Y1 motor as LO HEAT). BLWM at low-cool circuits starts speed (same THERMIDISTAT TWO-STAGE FURNACE NOTE HEAT STAGE SINGLE-SPEED AIR CONDITIONER THERMIDISTAT TWO-STAGE FURNACE SINGLE-SPEED HEAT PUMP 11 2 RVSCOOLING_ N/A NOTE11 HEATSTAGE3 (FURNACEHi)_ HEAT STAGE 1 COOL STAGE 1 HEAT STAGE 2 [_ (FURNACE LO) HEAT/COOL STAGE (COMPRESSOR) FAN [_ 24 VAC HOT [_ DEHUMIDIFY [_ 24 VAC COMM [_ [Z2_ 1 FAN [_ HOT [_ / ......... 24 VAC DEHUMIDIFY 24 VAC COMM [_ [_ HUM [_ HUM HUMIDIFIER HUMIDIFY [_ (24 VAC) HUMIDIFY N/A ..../ 4VAC/ I _[ HUMIDIFIER ...... N/A [_ OUTDOOR _/_c coS_S°,%_ [2_ [ OUTDOOR SENSOR _,, OONNEDT'ON _[2_ See notes 2, 5, 7, 10, and 11 See notes 1, 2, 4, 6, 7, 9,10,11, and 15 A00277 A00275 Fig. 82A--Two-Stage Furnace with Single-Speed Conditioner THERMIDISTAT TWO-STAGE FURNACE Fig. 52C--Two-Stage Furnace with Single-Speed Pump (Dual Fue{) Air TWO-SPEED AIR CONDITIONER THERMIDISTAT Heat TWO-STAGE TWO-SPEED FURNACE HEATPUMP NOTE11 HEAT STAGE 2 COOL STAGE 1 HEAT STAGE t COOL STAGE 2 RVS COOLING HEA(_CMOpQRLSsl AGLEo1) _ NOTE12 HEA_FSTAGEE3 _ FAN [_ 24 VAC HOT [_ DEHUMIDIFY [_ 24 VAC COMM [_ ...... NEAT/COOLSTAGE 2_ (COMPRESSORHI) _ ...... "fiTE_2 _ ..... FAN[_ ...................... [_ _ HUMIDIFY ....... [_ _ HUM "'"-. _VACHO_[_ .......... [_ DEHOM'D'FY_ .......................... _4MAOOOMM[2 _ ............. [_: ............. [_ HUM ......4VAC, i / HUMIDIFIER ..... HUMIDIFY ............... HUMIDIFIER(24 VAC) N/A [_ N/A [_ OUTDOOR SENSOR Os_00_ _ OUTDOOR _1:_ DONNEOT,ON See notes 2, 5, 8,10, coS_Sc°,_o, l[2_ I1, and 12 See notes 1,2, 3, 4, 6, 8, 9, t0,12,13, and 15 A00278 A00276 Fig. 52B--Two-Stage Furnace with Conditioner Two-Speed Air Fig. 82D--Two-Stage Furnace with Two-Speed Pump (Dual Fue{) 40 Heat DUAL FUEL TWO-STAGE THERMOSTAT SINGLE-SPEED FURNACE HEAT TWO-STAGE PUMP TWO-STAGE THERMOSTAT TWO-SPEED FURNACE NOTE 11 NOTE 12 AIR CONDITIONER RVS COOLING NOTE 11 E2_ HEAT STAGE 3 { URNACE HI) HEAT STAGE 2 (FURNACE LO) HEAT/COOL STAGE 1 (COMPRESSOR) FAN [_ 24 VAC 24VAC HOT E2_ [_ COMM [_ N/A 1] HUM RVS SENSING OUTDOOR !_ See notes 2, tl, and 12 A00281 CONNECTION ![_ See notes 1, 2, 4,11,14,15, and Fig. 52G--Two-Stage Thermostat With Two-Stage Furnace and Two=Speed Air Conditioner 16 A00279 Fig. 52E--Dual Fuel Thermostat Furnace and Single-Speed DUAL FUEL THERMOSTAT RVS with Two-Stage Heat Pump TWO-STAGE FURNACE TWO-SPEED HEAT PUMP S;NGLE-STAGE TWO-STAGE THERMOSTAT FURNACE TWO-SPEED AIR CONDITIONER COOLING HEA_o%O%_s_oA_,.%I _ ..................... _ ..... HEA_FSuTRANGAcEE3 _ HEAT/COOL STAGE (COMPRESSOR _4 VAC ................ 2 _ HI) HOT [2_ NOTE 12 ....... [2_ _4VAOCOMM [_ ...................... [2_ ] N/A RVS SENSING [2_ B [_ See O T sOCR notes 1 and 2 A00282 OUTDOOR SENSOR _/_ Fig. 52H--Single-Stage Thermostat With Two-Stage Furnace and Two-Speed Air Conditioner CONNECT'O"/[2_ See notes HUM HUM 1,2, 3, 4, 12,13, 14, 15, and 17 A00280 Fig. 52F--Dual FuemThermostat With Two-Stage Furnace and Two-Speed Heat Pump 41 Notes for Fig. 52A-H: 1. Heat pump 2. Refer MUST to outdoor have a high pressure equipment 3. Select the "ZONE" 4. Outdoor switch Installation position on the two=speed Air Temperature Sensor _br dual _fiel applications, Inst_/ctions must for additional heat pump be attached No.1 on Thermidistat No. 1 on Them_idistat should be set in ON position 7. Dip switch No. 2 on Them_idistat should be set in OFF should be set in ON position No. 2 on Thermidistat Option 10. NO connection No. should connection. must Sensing 15. DO NOT SELECT board, to control to control control 14. The RVS 16. Dip switch position for air conditioner for heat pump position installations. This is _hctolw deJhult. installations. for single-speed its own high-stage terminal terminal furnace compressor operation. jumper operation INTERFACE" internally D on Dual Fuel Thermostat when using 1 on furnace operation. t:hel applications. a Thermidistat. contIol should be set in ON position staging. not be connected the "F[ RNACE compressor ON in all daal on Nrnace control should be removed via fm'nace control algorithm to allow unit staging. heating "L" should This is controlled HUM ACRDJ outdoor for two-speed must be turned dip switch No. If wire is connected, Them_idistatiThem_ostat 13. Furnace Fuel Selection" If wire is connected, ThermidistatiThem_ostat 12. Optional control 10 "Dual be made to the furnace connection. to allow be see in OFF delimit. 9. Configuration 11. Optional procedure. control. 6. Dip switch 8. Dip switch and setup in all dual iq/el applications. 5. Dip switch This is fhctow should in_brmation This is internally or "BALANCE by the Them_idistatiDual shoutd be set in OFF position shoutd be set in ON position This is Pactory used to sense defi'ost POINT" option deihult. operation on the two-speed heat pump Fuel The*mostat. ibr single-speed compressor operation This is fhcto W defhult 17. Dip switch D on Dual Fuel Thermostat If the fmTmCe control CPU switches from low-cooling high=cooling, the fhmace control (PU conditioning relay When the air conditioning ACR ACR. is energized will energize the R to Yl-and=Y2 circuits relay the outdoor unit to high=cooling speed, and the R to G-andYl-and=YiY2 circuits switch the furnace blower motor BLWM to COOL NOTE: When outdoor unit BLWM continues LO-HEAT) high compressor until THERMIDISTAT flora tow-cooling will run shut down at tow=cool the outdoor unit to high-cooling for 1 minute while tl_e speed speed as compressor (same comes air cleaner terminal When there is a dehumidif}" demand, the DHUM input is activated, which means 24 vac signal is removed fi'om the DHUM input terminal. In other words, the DHUM input logic is reversed. The DHUM input is turned ON when no dehumidify,' demand exists. Once 24 vac is detected by tl_e fi.maace contlol on tl_e DHUM input, the furnace control operates in The*midistat mode. If the DHUM input is low or OFF for more than 48 hours, the furnace control reverts back to non-Them_idistat mode. The cooling operation described above also applies to operation with a Them_idistat The exceptions are listed below: back on at EA(= 1 is energized are opened. The outdoor BLWM and electronic energized to DHUM with unit stops, and the fttrnace blower air cleaner terminal EAC=I will for an additional to reduce 90 seconds. the cooling off=delay Jumper Y1 to 5 seconds. (See Fig. 32.) 3. Two-Speed CoMing and Two-Stage (See Fig. 28 and Fig. 52A-G NOTE: The ACRDJ must control of the outdoor unit The thermostat low-cooling closes or closes kbr high=cooling. on low-cooling the speed, as LO HEAT). connections) to allow thermostat (See Fig. 32.) R to G=and-Yl circuits the R to G=and-Yl=and-Y2 The R to YI circuit the _amace blower speed _br thermostat staging. a When the R demand _br BLWM will speed as LO Thermostat be disconnected and the R to G-and=Y1 motor BLWM on low=cool The R to Yl-and=Y2 unit circuit starts speed (same circuits start the outdoor unit on high-cooling speed, and the R to G-andY/Y2 circuits start the fhrnace blower motor BLWM on COOL speed. The electlonic air cleaner tem_inal EAC- 1 is energized to G-and=Y1 circuit is dosed and there is a ddaumidificatiom the _hmace blower motor continue running at low-cool speed (same HEAT). b. When the R to G-and Y/Y2 circuit is closed and there is a demand for dehumidification, the furnace blower motor BLWM will &op the blower speed from COOL to HI HEAT fbr a maximum of 10 minmes before reverting back to COOL speed. If there is still a demand tbr dehun_idifi= cation after 20 minutes, the _hrnace control (PU will &op the blower speed back to HI HEAT speed. This alternating 10-minute cycle wilt continue as tong as there is a call for cooling. for circuits starts the outdoor connections.) The dehumidification output, DHI_M on the Thermidistat should be connected to the _hrnace control thermostat terminal DHUM. 115 vac whenever the blower motor BLWM is operating. When the tl',ermostat is satisfied, the R to G-and=Y circuit remain MODE (See Fig. 52A=D _br Thermidistat tl_e speed The electronic operation, speed. transitioning to compressor G-and-Yl-and-Y2 circuits are opened. The outdoor unit stops, and the fire, ace blower BLWM and electronic air cleaner terminal EAC=I will remain energized £,r an additional 90 seconds Juniper YI to DHUM to reduce the cooling off-delay to 5 _econ&. (See Fig. 32.) to the air switch for two-speed c. When the "call for cooling" is satisfied and there is a demand for dehumidification, the cooling blower-off delay is decreased I'rom 90 seconds to 5 seconds. with 115 vac whenever the blower motor BLWM is operating. When the thermostat is satisfied, the R to G-and-Y1 or R to 42 (ONTINL When O[ S BLOWER the R to G circuit motor BLWM HI HEAT, HEAT Tem_inal speed BLWM During by the thermostat, on continuous-blower or COOL EAC-! (17 seconds), BLWM speed befbre When the thermostat speed reverting (PU during will hold the blower the selected to continuous-blower speed to operate at tow=cool LO HEAT). When the thetl_aostat is satisfied, the blower motor BLWM operate an additional 90 seconds on tow-cool speed BLWM will satisfied, seconds blower When "calls speed operate at COOL speed. motor BLWM on COOL speed befbre (same motor speed as continue operating blower Continuous When the will operate reverting them_ostat back HUM is energized diagnose a system to continuons= 5 seconds, if no other _kmction BLWM BLWM will from speeds Thermostat from problem SHOCK Failure to fbltow this warning personal injm% access -To the room panel board must be taken when thermo= Disconnect 3 Manually 4 For approximately themmstat to COOL. blower turning off the shift speed from (OOL to HI HEAT FAN again to LO HEAT as many times as desired to be auton_atically used following the continuous- of LO HEAT switch will shift the continuous-blower Repeating the procedure will be changed HEAT will at the speed fi'om HI HEAT shift the continuous- speed. The selection blowe* could result in electrical door switch opens operation manually can access is shock, closing l15-v power can occur this switch to Caution l;or service door. them_ostat R lead fi'om furnace close blower on control until control. door switch. 2 sec, short (_umper) to the TEST/TWIN on control and is stored in the memov a power The pro'poses. 2 CPU helps _ilure. HAZARD No component fi/mace setting The EAC=I This feature or death. operating. control reasons is energized. Self:Test: Remove Momentarily motor delay period in case of a component ELECTRICAL contlol Selection fbr safkty when blower 1 speed. the blower blower-OFF speed. are not energized Compmlent Blower operation. fi'om the facto_ the G signal, SELF-TEST tm_a off the FAN switch or push-button on the for 1-3 seconds a_ler the blower motor BLWM is The leaving on fbr the selected stat, momentarily room thermostat speed delay Y2 or R to WiWl=and-Yl-and- 90 for an additional continuous=blower blower the blower is an additional motor Speed timQ blower-OFF motor the blower Blower different at the same on for the selected to continuous-blower temlinal To Begin the blower is opened, motor disappear, will remain terminal speed. the R to G circuit disappear remain post-purge speed afier a 3 second or R to WiW l-an&Y 1- component test f?ature will not operate if any thet_aostat signal present at control and not until all time delays are completed. speed. for high-cooling", the blower requires select the blower back to continuous-blower the themmstat a nom_al indncer NOTE: The furnace control component test allows all components to run ibr a short time; except the gas valve and humidifier delay switch be_bre reverting signals ( OMPONENT motor blowe>OFF _br low-cooling", will will If the R to WiWl=and-Y then switch at signals BLWM BLWM delay "calls will Y/Y2 to heat up more delay period begins respectively the fk/rnace control period When motor igniter and blower-ON heat exchangers at the end of the blower-ON at HI HEAT BLWM and=YiY2=and=G is LO will stop doting (7 seconds), the furnace or HI HEAT In high=heat, BLWM delimit as long as the blower period. ignifion allowing then restarts LO HEAT tl_e blower speed (can be set Factor- the I_urnace control period arid the blower switches to (OOL delay If the R to WiW 1-and=YiY2-and=G is energized (66 seconds), quickly, speed) is energized a call _br heat, the blower warm=up disappears, is closed will operate to LO HEAT, motor MODE 3/16=in. LED rams off the Cov-24v tem_inal quick=connect tem_inal Remove jumper fi'om termi- nals. (See Fig. 320 interruption. NOTE: longer P/MP If TEST/TWIN and than 2 sec, LED will Co_>24v terminals flash rapidly are jumpered and ignore component test request. (See Fig. 52C-F When installed fbr themmstat connections) Component with a heat pm_ap, the furnace changes the timing demand del:i'ost sequence cycles. control to avoid long blower When automatically ofttimes during the R to WiWl=and-Y1 or R to blower speed motor as LO HEAT), BLWM perio& then HEAT speed. When control begins remains and=G BLWM shut signals will remain the W/W1 inducer disappear then come post-purge speed. back at the period on at LO the furnace and the blower If the R to WiWl-and-Yl= same on _br the selected If the R to WiWl=and=Y1 the blower motor BLWM cycle. The input signal disappears_ at LO HEAT will remain a low-heat on until the end of the prepurge off for 24 seconds a normal running arid begin time, the blower blower-OFF signals disappear, leaving the G signal, will remain on fbr the selected blowerto continuous-blower R to WiWl-and-Y to WiWl=and-Yl=and-YY2, or R to WiWl=and-Yl=and-Y and=G circuits are energized to or mrn on the blower a high=heat cycle. BLWM The blower the end of the prepurge come back the furnace motor motor perio& on at HI HEAT control at COOL BLWM speed. Y2=and-G, speed, When R the W/W1 d Blowe* e igniter motor and continues for 15 see, then off on LO-HEAT Blower motor operates on HI-HEAT E Blower motor operates on COOL g. Indtlcer motor 6. Operate _/mace 7. Verify l_m_ace goes to low=speed speed speed speed then Follmv fumace signal 43 down _br 10 sec for 10 see. for 10 see. for 10 sec, then stops. tape from blower by on outer door. lowering themmstat setting temperature. that ftlrnace restarts by raising thermostat setting above temperature. OPERATE on until per instruction shut to run test sequence. is energized operates is as follows: code 4 times. motto" sta*ts on high-speed Hot sm'face roonl arid begin input _hmace status Step g of component c 8. Verify Y2= then slmt off _br 24 seconds speed. Inducer below room CPU will switch will remain b _br 2-stage previous 5. Reconnect R lead to £i/mace cont_ot, remove door switch, and re-install blower door. motor delay period. OFF delay period then switch When the R to WiWI-an&YiY2, LED will display until WiWl-and-Yl=and-G circuits are energized, the furnace contlol CPU will switch to or tmla on the blower motor BLWM at tow cool speed (same test sequence a FURNA( procedures E on operating instructions label attached to TABLE 10--MODEL 58MTA ORIFICE SiZE AND HIGH/LOW-HEAT FOR CORRECT INPUTS NANIFOLD PRESSURES FOR USE WITH 060 THROUGH 120 SIZE FURNACES ONLY (TABULATED DATA BASED ON 20,000/13,000 BTUH PER BURNER, DERATED 2 PERCENT FOR EACH 1000 FT ABOVE SEA LEVEL)* SPECIFIC ALTITUDE RANGE {FT) AVG GAS NEAT VALUE (BTUIOU FT) 0.58 GRAVITY 0.60 OF NATURAL Manifold Pressure Orifice no. Manifold Pressure Orifice no. Manifold Pressure Orifice no. 850 43 3.7/1.5 43 3.8/1.6 42 3.2/1.4 875 43 3.5/1.5 43 3.6/1.5 43 3.7/1.6 900 44 3.7/1.6 43 3.4/1.4 43 925 44 3.5/1.5 44 3.7/1.6 950 44 3.4/1.4 44 2000 975 44 3.2/1.3 0% derate 1000 45 1025 o Orifice no. Manifold Pressure 42 3.3/1.4 42 3.4/1.4 43 3.8/12.6 42 3.2/1.4 3.5/1.5 43 3.6/1.5 43 3.7/1.6 44 3.8/1.6 43 3.4/1.4 43 3.5/1.5 3.5/1.5 44 3.6/1.5 44 3.7/1.6 44 3.8/1.6 44 3.3/1.4 44 3.4/1.4 44 3.5/1.5 44 3.6/1.5 3.7/1.6 45 3.8/1.6 44 3.2/1.4 44 3.4/1.4 44 3.5/1.5 45 3.5/1.5 45 3.6/1.5 45 3.7/1.6 44 3.2/1.3 44 3.3/1.4 1050 45 3.%1.4 45 3.4/1.5 45 3.6/1.5 45 3.7/1.6 45 3.8/1.6 1075 45 3.2/1.3 45 3.3/1.4 45 3.4/1.4 45 3.5/1.5 45 3.6/1.5 1100 47 3.6/1.5 47 3.7/1.6 45 3.2/I .4 45 3.4/1.4 45 3.5/1.5 SPECIFIC GRAVITY ALTrUDE RANGE {FT) AVG GAS HEAT VALUE (BTU/CU FT) 0.62 Orifice no. Manifold Pressure Orifice no. Manifold Pressure Orifice no. Manifotd Pressure 775 43 3.8/1.6 42 3.2/1.4 42 3.3/1.4 42 3.4/1.4 42 3.5/1.5 8OO 43 3.5/1.5 43 3.7/1.5 43 3.8/1.6 42 3.2/1.4 42 3.%1.4 825 44 3.8/1.6 43 3.4/1.5 43 3.6/1.5 43 3.7/1.5 43 3.8/1.6 85O 44 3.6/1.5 44 3.7/1.6 44 3.8/1.6 43 3.5/1.5 43 3.6/1.5 875 44 3.4/1.4 44 3.5/1.5 44 3.6/1.5 44 3.7/1.6 43 3.4/1.4 9OO 44 3.2/1.4 44 3.3/1.4 44 3.4/1.4 44 3.5/1.5 44 3.6/1.5 925 45 3.7/1.5 45 3.8/1.6 44 3.2/1.4 44 3.3/1.4 44 3.4/1.5 95O 45 3.5/1.5 45 3.6/1.5 45 3.7/1.6 45 3.8/1.6 44 3.3/1.4 975 45 3.3/1.4 45 3.4/1.4 45 3.5/1.5 45 3.6/1.5 45 3.8/1.6 1000 47 3.7/1.6 45 3.2/1.4 45 3.4/1.4 45 3.5/1.5 45 3.6/1.5 1025 47 3.6/1.5 47 3.7/1.6 45 3.2/1.3 45 3.3/1.4 45 3.4/1.4 or SPECIFIC GRAVITY AVG GAS HEAT VALUE {FT) 0.66 Manifold Pressure 3ooo ALTITUDE RANGE 0.64 Orifice no. to <' _, 0.60 GAS Manifold Pressure U.S. Canada Altitudes 2001 to 4500 5% derate 0.58 OF NATURAL Orifice no. Altitudes 2001 0 0.66 Manifold Pressure to _= 0.64 Orifice no. o r_ GAS 0.62 0.58 0.60 OF NATURAL GAS 0.62 0.64 0.66 (BTU/CU FT) Orifice no. Manifold Pressure Orifice no. Manifold Pressure Orifice no. Manifold Pressure Orifice no. Manifold Pressure Orifice no. Manifotd Pressure 75O 43 3.7/1.6 43 3.8/1.6 42 3.3/1.4 42 3.4/1.4 42 3.5/1.5 775 43 3.5/1.5 43 3.6/1.5 43 3.7/1.6 43 3.8/1.6 42 3.2/1.4 8OO 44 3.7/1.6 43 3.4/1.4 43 3.5/1.5 43 3.6/1.5 43 3.7/1.6 825 44 3.5/1.5 44 3.6/1.5 44 3.8/1.6 43 3.4/1.4 43 3.5/1.5 85O 44 3.3/1.4 44 3.4/1.4 44 3.5/1.5 44 3.7/1.5 44 3.8/1.6 875 45 3.8/1.6 44 3.2/1.4 44 3.3/1.4 44 3.5/1.5 44 3.6/1.5 9OO 45 3.6/1.5 45 3.7/1.6 45 3.8/1.6 44 3.3/1.4 44 3.4/1.4 925 45 3.4/1.4 45 3.5/1.5 45 3.6/1.5 45 3.7/1.6 44 3.2/1.3 95O 45 3.2/1.4 45 3.3/1.4 45 3.4/1.5 45 3.5/1.5 45 3.7/1.5 975 47 3.6/1.5 45 3.2/1.3 45 3.3/1.4 45 3.4/1.4 45 3.5/1.5 1000 47 3.5/1.5 47 3.6/1.5 45 3.7/1.6 45 3.2/1.4 45 3.%1.4 3001 to 4000 7% derate Orifice numbers shown in shading are factory installed NOTE: Percents of derate are based on midpoints of U.S. altitude ranges FURNACE RESTART In the L .S.A. reduced With f'umace operating, set thermostat below room temperature and observe that furnace goes off, Set themxostat above room temperature Step and observe that furnace the input ratings by 2 percent fbr each %r altitudes above 1000 ft above In Canada, the input ratings must be derated ahimdes of 200! ft to 4500 t't above sea level. restarts. Adjust 5--Adjustments Furnace SET GAS IN'PET RATE rating manifold plate adjusted 1. Detem_ine Furnace gas input rate on rating plate is for installations at altitudes up to 2000 ft For Con'ect 44 pressure to obtain input rate must be within Natural Input. 2000 ft must be sea level by 5 percent for input rate. ÷ 2 percent of input on Ihrnace fbr altitude. Gas Orifice Size And Manifbld Pressure TABLE 10--MODEL 58MTA ORIF_CE SIZE AND HIGHILOW-HEAT MANIFOLD PRESSURES FOR CORRECT iNPUTS (Continued} FOR USE WiTH 060 THROUGH 120 SIZE FURNACES ONLY(TABULATED DATA BASED ON 20,000f13,000 BTUH PER BURNER, DERATED 2 PERCENT FOR EACH 1000 FT ABOVE SEA LEVEL}* SPECIFIC ALTITUDE RANGE {FT) 0.58 GRAVITY 0.60 OF NATURAL Manifold Pressure Orifice no. Manifold Pressure Orifice no. Manifold Pressure Orifice no. Manifold Pressure 725 43 3.7/1.5 43 3.8/1.6 42 3.2/1.4 42 3.3/1.4 42 3.4/1.4 750 44 3.4/1.4 43 3.5/1.5 43 3.7/1.5 43 3.8/1.6 42 3.2/1.4 775 44 3.7/1.6 44 3.8/1.6 43 3.4/1.4 43 3.5/1.5 43 3.7/1.5 4001 800 44 3.5I .5 44 3.6/1.5 44 3.7/1.6 44 3.8/1.6 43 3.4/1.4 to 825 44 3.2/1.4 44 3.4/1.4 44 3.5/1.5 44 3.6/1.5 44 3.7/1.6 850 45 3.5/1.5 45 3.8/1.6 44 3.3/1.4 44 3.4/1.4 44 3.5/1.5 875 45 3.3/1.4 45 3.6/1.5 45 3.7/1.6 44 3.2/1.3 44 3.3/1.4 900 45 3.3/1.4 45 3.4/1.4 45 3.5/1.5 45 3.6/1.5 45 3.8/1.6 925 47 3.7/1.6 45 3.2/1.4 45 3.3/1.4 45 3.4/1.5 45 3.6/1.5 95O 47 3.5/1.5 47 3.6/1.5 45 3.2/1.3 45 3.3/1.4 45 3.4/1.4 AVG GAS HEAT VALUE (BTU/CU FT) 0.58 0.60 OF NATURAL GAS 0.62 0.64 0.66 Orifice no. Manifotd Pressure Orifice no. Manifold Pressure Orifice no. Manifold Pressure Orifice no. Manifold Pressure Orifice no. Manifold Pressure 7OO 43 3.6/1.5 43 3.7/1.6 42 3.2/1.3 42 3.3/1.4 42 3.4/1.4 725 43 3.4/I .4 43 3.5/1.5 43 3.6/1.5 43 3.7/1.6 43 3.8/1.6 75O 44 3.6/1.5 44 3.7/1.6 43 3.4/1.4 43 3.5/1.5 43 3.6/1.5 775 44 3.4/I .4 44 3.5/1.5 44 3.6/1.5 44 3.7/1.6 43 3.4/1.4 5001 8OO 44 3.2/1.3 44 3.3/1.5 44 3.4/1.4 44 3.5/1.5 44 3.6/1.5 to 825 45 3.6/1.5 45 3.7/1.6 44 3.2/1.4 44 3.3/1.4 44 3.4/1.4 85O 45 3.4/1.4 45 3.5/1.5 45 3.6/1.5 45 3.8/1.6 44 3.2/1.4 875 45 3.2/1.4 45 3.3/1.4 45 3.4/1.5 45 3.6/1.5 45 3.7/1.5 9OO 47 3.6/1.5 47 3.7/1.6 45 3.3/1.4 45 3.4/1.4 45 3.5/1.5 925 47 3.4/1.4 47 3.5/1.5 47 3.7/1.5 45 3.2/1.3 45 3.3/1.4 95O 48 3.7/1.6 48 3.8/1.6 47 3.5/1.5 47 3.6/1.5 47 3.7/1.6 975 48 3.5/1.5 48 3.6/1.5 48 3.8/1.6 47 3.4/1.4 47 3.5/1.5 1000 48 3.3/1.4 48 3.5/1.5 48 3.6/1.5 48 3.7/1.6 48 3.8/1.6 6000 11% derate ALTBTUDE RANGE SPECIFIC GRAVITY AVG GAS HEAT VALUE 0.58 0.60 OF NATURAL GAS 0.62 0.64 0.66 (BTU/CU FT) Orifice no. Manifold Pressure Orifice no. Manifold Pressure Orifice no. Manifold Pressure Orifice no. Manifold Pressure Orifice no. Manifold Pressure 65O 42 3.2/1.3 42 3.3/1.4 42 3.4/1.4 42 3.5/1.5 42 3.6/1.6 675 43 3.6/1.5 43 3.7/1.6 43 3.8/1.6 42 3.2/1.4 42 3.3/1.4 7O0 44 3.8/1.6 43 3.4/1.5 43 3.6/1.5 43 3.7/1.6 43 3.8/1.6 6001 725 44 3.6/1.5 44 3.7/1.6 44 3.8/1.6 43 3.4/1.4 43 3.5/1.5 to 75O 44 3.3/1.4 44 3.4/1.5 44 3.6/1.5 44 3.7/1.6 44 3.8/1.6 775 45 3.8/I .6 44 3.2/1.4 44 3.3/1.4 44 3.4/1.5 44 3.5/1.5 8OO 45 3.5/1.5 45 3.7/1.5 45 3.8/1.6 44 3.2/1.4 44 3.3/1.4 825 45 3.3/1.4 45 3.4/1.5 45 3.6/1.5 45 3.7/1.6 45 3.8/1.6 85O 47 3.7/1.6 45 3.2/1.4 45 3.4/1.4 45 3.5/1.5 45 3.6/1.5 875 47 3.5/1.5 47 3.6/1.5 45 3.2/1.3 45 3.3/1.4 45 3.4/1.4 (FT) :.5 0.66 Orifice no. ALTITUDE RANGE {FT) :.5 0.64 Manifotd Pressure SPECIFIC GRAVITY _>" GAS 0.62 Orifice no. 5000 9% derate :.5 AVG GAS NEAT VALUE (BTUICU FT) 7000 13% derate * Orifice numbers shown in shading are factory instNled NOTE: Percents of derate are based on midpoints of US altitude ranges a Obtain average gas heat value (at installed altitude) from local gas supplier, L Follow heat intersection settings b, Obtain average gas specific gravity' fiom local gas supplier, c Verify furnace model and size Table 10 can only be used _Z_r model 58MTA furnaces with heating inputs o1" 20,000/13,000 (High/Low) Btuh per burner, d, Find installation altimde in Table 10, NOTE: For Canada altitudes of 200! to 4500 k, use I_,SA altitudes of 200! to 3000 ft in Table 10, e Find closest natural gas heat value and specific gravity on Table 10, 45 vahle and specific to find for proper orifice operation size gravity and lines to point manil"old of pressure TABLE 10--MODEL 58MTA ORIFICE SIZE AND HIGH/LOW-HEAT NANIFOLD PRESSURES FOR CORRECT INPUTS (Continued) FOR USE WITH 060 THROUGH 120 SIZE FURNACES ONLY (TABULATED DATA BASED ON 20,000/13,000 BTUH PER BURNER, DERATED 2 PERCENT FOR EACH 1000 FT ABOVE SEA LEVEL)* SPECIFIC ALTITUDE RANGE (FT) AVG GAS HEAT VALUE (BTUiCU FT) 0.58 GRAVITY 0.60 0.66 Orifice no. Manifold Pressure Orifice no. Manifold Pressure Orifice no. Manifold Pressure Orifice no. Manifold Pressure 825 43 3.8/1.6 42 3.3/1.4 42 3.4/1.4 42 3.5/1.5 42 3.6/1.5 65O 43 3.5/1.5 43 3.7/1.6 43 3.8/1.6 42 3.2/1.4 42 3.3/1.4 675 44 3.8/1.6 43 3.4/1.4 43 3.5/1.5 43 3.6/1.5 43 3.7/1.6 7001 to 7OO 44 3.5/1.5 44 3.6/1.5 44 3.8/1.6 43 3.4/1.4 43 3.5/1.5 725 44 3.3/1.4 44 3.4/1.4 44 3.5/I .5 44 3.6/1.5 44 3.7/1.6 8000 15% derate 750 45 3.7/1.6 45 3.8/1.6 44 3.3/1.4 44 3.4/1.4 44 3.5/1.5 775 45 3.5/1.5 45 3.6/1.5 45 3.7/1.6 45 3.8/1.6 44 3.3/1.4 8OO 45 3.3/1.4 45 3.4/1.4 45 3.5/1.5 45 3.6/1.5 45 3.7/1.6 825 47 3.6/1.5 45 3.2/1.3 45 3.3/1.4 45 3.4/1.4 45 3.5/1.5 85O 47 3.4/1.4 47 3.5/1.5 47 3.7/1.5 45 3.2/1.3 45 3.3/1.4 Altitudes 8001 to 9000 17% derate ALTITUDE RANGE AVG GAS HEAT VALUE (BTU/CU FT) 0.58 0.60 OF NATURAL GAS 0.62 0.64 0.66 Orifice no. Manifold Pressure Orifice no. Manifold Pressure Orifice no. Manifotd Pressure Orifice no. Manifold Pressure Orifice no. Manifold Pressure 6OO 43 3.8/1.6 42 3.3/1.4 42 3.4/1.4 42 3.5/1.5 42 3.6/1.5 625 43 3.5/1.5 43 3.6/1.5 43 3.8/1.6 42 3.2/1.4 42 3.3/1.4 65O 44 3.7/1.6 43 3.4/1.4 43 3.5/1.5 43 3.6/1.5 43 3.7/1.6 675 44 3.5/1.5 44 3.6/1.5 44 3.7/1.6 44 3.8/1.6 43 3.4/1.5 7OO 44 3.2/1.4 44 3.3/1.4 44 3.4/1.5 44 3.6/1.5 44 3.7/1.6 725 45 3.6/1.5 45 3.8/1.6 44 3.2/1.4 44 3.3/1.4 44 3.4/1.4 75O 45 3.4/1.4 45 3.5/1.5 45 3.6/1.5 45 3.8/1.6 44 3.2/1.4 775 45 3.2/1.3 45 3.3/1.4 45 3.4/1.4 45 3.5/1.5 45 3.6/1.5 8OO 47 3.6/1.5 47 3.7/1.6 45 3.2/1.3 45 3.3/1.4 45 3.4/1.4 SPECIFIC GRAVITY AVG GAS HEAT VALUE 0.58 0.60 OF NATURAL GAS 0.62 0.64 0.66 (BTU/CU FT) Orifice no. Manifold Pressure Orifice no. Manifold Pressure Orifice no. Manifold Pressure Orifice no. Manifold Pressure Orifice no. Manifold Pressure 575 43 3.8/1.6 42 3.2/1.4 42 3.3/1.4 42 3.3/1.5 42 3.6/1.5 6OO 43 3.5/1.5 43 3.6/1.5 43 3.7/1.6 42 3.2/1.3 42 3.3/1.4 625 44 3.7/1.6 44 3.8/1.6 43 3.5/1.5 43 3.6/1.5 43 3.7/1.6 to 65O 44 3.4/1.4 44 3.5/1.5 44 3.7/1.5 44 3.8/1.6 43 3.4/1.4 10,000 675 44 3.8/1.6 44 3.3/1.4 44 3.4/1.4 44 3.5/1.5 44 3.6/1.5 7OO 45 3.6/1.5 45 3.7/1.6 45 3.8/1.6 44 3.3/1.4 44 3.4/1.4 725 45 3.3/1.4 45 3.4/1.5 45 3.6/1.5 45 3.7/1.6 45 3.8/1.6 75O 47 3.7/1.6 45 3.2/1.4 45 3.3/1.4 45 3.4/1.5 45 3.5/1.5 775 47 3.5/1.5 47 3.6/1.5 47 3.7/1.6 45 3.2/1.4 45 3.3/1.4 (FT) 4 0.64 Manifold Pressure ALTITUDE RANGE (FT) .=_ GAS Orifice no. SPECIFIC GRAVITY >, "E O <,' _, OF NATURAL 0.62 9001 19% derate _Orifice numbers shown in shading are factory installed. NOTE: Percents of derate are based on midpoints of U.S. altitude ranges 2, Adjust Manifold Pressure To Obtain Input Rate, a Remove burner enclosure fiont EXAMPLE: (0=2000 ff altitude using Table 10) Heating value 1050 Btuicu ff Specific gravity 062 Therefbre: Orifice No 45 Manifbld pressure 3,6-in, wc for high heat 1.5-in. wc for tow heat * Furnace is shipped with No, 45 orifices, In thisexample all main burner ori_:_cesare the cmTect size and do not need to be changed to obtain the proper input rate, NOTE: Manifold pressure MUST burner enclosure fiont REMOVED always be measured with b, Remove regulator seal caps that conceal adjustment screws for low=and high-heat gas valve pressure regulators, (See Fig. 53.) c. Move setup switch SW=I on control center to ON position, This keeps furnace locked in tow-heat operation. d, Jumper R and WiWI tlaermostat connections on control to start _iu_ace, g. (beck and verify burner orifice size in furnace NEVER ASSUME ORIFICE SIZE: ALWAYS CHECK AND VERIFY, e Turn low-heat adjusting screw (3/32 hex Allen wrench) counterclockwise (ou0 to decrease input rate or clock=wise (in) to increase input rate 46 BURNER FLAME --_ _'- /_[ (PROPANE WHITE= NATURAL INLET BURNER 13 5 TURNS SILVER 12 TURNS) / (PROPANE NAT JRAL WHITE 9 5 TURNS S LVER 9 5 TURNS) MANIFOLD J A89020 A04048 --> Fig. 83--Redundant NOTE: DO NOT Automatic set tow-heat mani%ld we or more than 1.%in. wc %r natural outside this range, change main Fig. 54--Burner Gas Control Valve pressure less than 1.3=in. gas. If mani%ld burner orifices Flame pressure to obtain is pressure in this range. --> FIRE HAZARD Failure to %llow tifk, property DO NOT this cmldon damage, bottom may result personal out gas vah'e This can result in unregulated excess overfire injury, in reduced regulator manitbld and heat exchanger fire, ace and death adjusting pressure screw BURNER and result in U NOTE: If orifice hole appears damaged been re&illed, check orifice hole with cmTect size. aligned orifice Never re&ill fl Move setup switch tow=heat to OFF position and squarely A93059 characteristics. Fig. BB--Bumer contlol. and W2 (See 32) This Fig. them_ostat keeps connections fl/mace pipes, in by clocking locked a adjusting counterclockwise (in) to increase screw (3/32 (out) to decrease hex Allen wrench) input rate or clockwise manifold pressure adjustment be clea* blue, almost jumper DAMAGE to damage is obtained, regulator j. Remove Failure %llow due to R-to=W1 replace sinews. caps Calculate UNITED high-altitude STATES above derate and Table Main transparent that conceal burner adjustment vent input (if required). 2000 ft, _his furnace for each has been approved 1000 fi above 11 for derate multiplier Derate flame (See Fig. 54) and W2. sea level See factor. d_is flame caution may result impingement in component of burners and re&ill orifices. Improper Natural Gas Input &illing excessive (burrs, burner heat Rate By Clocking out-of: noise Furnace Input Rate Furnace Input Rate at Sea Level X Multiplier Factor = at Installation Attitude 100,000 X 0.91 = 91,000 CANADA At installation altitudes [i'om 2001 to 4500 fl, this :h_mace must be derated 5 pmcent by an authorized Gas Conversion Station or Dealer To determine COITect input rate %r altitude, see exampte above and use 095 as derate multiplier fi_ctor, HAZARD round holes, etc.) can cause misdirection of burner flames. 3. Veri_- and EXAMPLE: exchangers. DO NOT combustion-air 100,000 Btuh input furnace installed at 4300 ft. CmTect input gas valve UNIT robing, fi'ont are in place when checking gas meter Example less than 3.2=in. in this range. --> all pressure enclosure for 2 percent we or more than 3.8-in. wc for natural gas. It" mani%ld pressure is outside this range, change main burner orifices to obtain pressure should sure and burner At altitudes rate. DO NOT set high=heat i. When Be on operation high-heat Orifice after completing NOTE: R and W1 high=heat NOTE: flame adjustment g. Jumper h, Turn A bun'-flee for proper SW-I ORIFICE or it is suspected to have a numbered &ill bit of an orifice. hole is essential J failures and b Reinstall burner box cover, NOTE: Clocking gas input rate MUST the burner box cover INSTALLED Gas Meter 47 ahvays be per%m_ed with TABLE 11--ALTITUDE DERATE MULTIPLIER U.S.A. FOR SECONDS ALTITUDE (FT) 0=2000 PERCENT OF DERATE 0 DERATE MULTIPLIER FACTOR FOR U.S.A.* 1.00 2001 =3000 4-8 0.95 3001 =4000 6-8 TABLE SIZE FOR 1 REVOLUTION 0.93 12--GAS OF TEST 1 Cu DIAL 2 Ft Cu RATE (CU FTfHR) SECONDS 5 Ft Ca SIZE FOR 1 REVOLUTION Ft OF TEST DIAL 2 5 Ca Ft 1 Cu Ft Cu Ft 10 360 720 1800 50 72 144 360 11 327 655 1636 51 71 141 355 12 300 600 1500 52 69 138 346 13 277 555 1385 53 68 136 340 14 257 514 1286 54 67 133 333 15 240 480 1200 55 65 131 327 16 225 450 1125 56 64 129 321 17 212 424 1059 57 63 126 316 18 200 400 1000 58 62 124 310 305 4001=5000 8-10 0.91 5001 =6000 10-12 0.89 8001 =7000 12-14 0.87 7001 =8000 14-16 0.85 8001=8000 16-18 0.83 9001=10,000 18-20 0.81 19 189 379 947 59 61 122 factor is based on midpoint altitude for NtRude range. 20 180 360 900 60 60 120 300 21 171 343 857 62 58 116 290 22 164 327 818 64 56 112 281 23 157 313 783 66 54 109 273 24 150 300 750 68 53 106 265 25 144 288 720 70 51 103 257 26 138 277 692 72 50 100 250 27 133 267 667 74 48 97 243 28 129 257 643 76 47 95 237 29 124 248 621 78 46 92 231 30 120 240 600 80 45 90 225 31 116 232 581 82 44 88 220 32 113 225 563 84 43 86 214 33 109 218 545 86 42 84 209 34 106 212 529 88 41 82 205 35 103 206 514 90 40 80 200 38 100 200 500 92 39 78 196 37 97 195 486 94 38 76 192 38 95 189 474 96 38 75 188 39 92 185 462 98 37 74 184 40 90 180 450 100 36 72 180 41 88 176 439 102 35 71 178 42 86 172 429 104 35 69 173 43 84 167 419 106 34 68 170 44 82 164 409 108 33 67 167 45 80 160 400 110 33 65 164 46 78 157 391 112 32 64 161 47 76 153 383 116 31 62 155 48 75 150 375 120 30 60 150 46 73 147 367 124 29 58 145 * Derate multiplier c. Check proper that gas valve adjustment input to be clocke& & Obtain yearly heat value NOTE: Be sure heating correct fbr your altitude. adjustment average value are in place fbr local of gas (onsnh of gas beating caps used local gas %r gas supply. for calculations utility is fbr altitude value. e. (hock and verify orifice size in furnace. NEVER ASSUME THE ORIFICE SIZE. ALWAYS CHECK AND VERIFY. £ Turn off all other gas appliances and pilots. g. Move setup switch SW=I to ON position, fm'nace tocked in low=heat ope*ation h, Jumper This keeps R=to=WiWl i, Let t::urcmce run for 3 minutes .i, Measure in low-heat time (in sec) fbr gas meter operation, to complete 1 revolu= tion, Note reading k, Refe* to Table 1, Multiply m Move Wl switch and SW=I W2 locked through T for high-heat EXAMPLE: (0=2000 in high=heat input Heating value of gas Time for 1 revolution Gas rate input plate Btuicu is 100,000 975 Bmicu ft of 2=cu ft dial Table 103 X 975 'i' Bmh SET TEMPERATURE is within +2 percent of the f_/rnace pressure Btuh. In this adjustment input rate DAMAGE Failure to %llow per that stated above when installed W2 rating plate Recommended range or slightly high jumper gas heat. must specified or* 5k_mace is at midpoint Jumper R to W/W1 05" rise and W2 to check rise. To check low-gas-heat Do not plate operate specified on the furnace as fbllows: 48 limits operation to W2. Determine on unit rating furnace the exchanger above temperature and tow specified This be within SW=I in ON position rise. remove thermostat in overheating flue gases in heat for condensate rise must Place may result or condensing Temperatuie high-gas-heat R, W/W1, and call for heat. HAZARD this caution areas not designed altitudes. n. Remove jumper across connections to tern?inure [SNIT heat exchangers gas inputs (high=heat and tow=heat) must be of that stated on furnace rating plate when at sea level or derated RISE 70 sec 100,425 size and manifold at higher items 12) the orifice installed Repeat keeps ft X cu ft&r example, NOTE: Measured within +2 pc*cent This R operation. 103 cu ftihr (from Bm heating and jumper connections. operation. ft), ft altitude) input from rating Bm heating value (Btuicu to OFF position thermostat furnace Furnace k of gas pc* hr, gas rate cu ftihr by heating setup and 12 fbr cubic air temperature exceed temperatnre temperature rise for both rise ranges fbr high and low gas heat within the temperature rating plate. Determine rise ranges the air temperature a Place duct themmmeters in return and s_/pply ducts as to thruace as possible Be sure then_ometers do not heat exchangers so that radiant heat does not affect mometer readings. This is particularly important straight run ducts close 'see' ther= with TaNe 1a-Speed SPEED White Common COM B_ack High Coot b. When thermometer readings stabilize, subtlact return-air temperature t'rom supply=air tempe*ature to determine tern= peramre rise. AS SHIPP_=D Yellow Med-High Orange1" Blue Med SPARE High-Gas Med-Low Low* Red If"the temperature rise is outside this range, check the tk_llowing: a Gas input for low- and high gas heat operation Semection LEAD COLOR * Continuous b_ovcer ? Available on 5-speed Heat Spare/High-Gas Heat Low-Gas Heat speed blowers only b. De*ate for altitude it"applicable. c Return and supply ducts fbr excessive restrictions causing static pressures greater than 0.50=in we. provide greater com%rt. See Table 9 %r positiou of switches and Fig 31 or 32 %r location of switches on control center SET THERMOSTAT HEAT ANTICIPATOR d. Adjust temperature rise by adjusting blower speed. In= crease blower speed to reduce temperature rise. Decrease blower speed to increase temperature rise. ELECTRICAL --> When using a nonelectronic thermostat, the them_ostat heatanticipator must be set to match the amp draw of the electrical components in R=WiWl circuit. Accurate amp draw readings can be obtained at them_ostat subbase terminals R and W. SHOCK HAZARD Fig. 56 illustrates an easy method of obtaining actual amp &aw. The amp reading should be taken after blower motor has started and furnace is operating in low heat. To operate t\u'nace in tow=heat, first move SW-I to ON position, then connect ammeter wires as shown in Fig. 56. The them_ostat anticipator should NOT be in the circuit while measuring current. If them_ostat has no subbase, the thermostat mttst be disconnected from R and WiWI wires during cmTent measurement Return SW-1 to final desired location after completing the reading. Failure to %llow this waraiug could result in personal inju W or death. Disconnect 115-v electrical power before changing speed tap For high=heat, on cmmol: the %llowing a. Me&high b. Med & 4-speed --> -Available only ou 5-speed motors. FactoQ" for these motors. c. Me&Low 80K can be made at HI HEAT (Yellow) (()range) setting connections (Blue) - Do NOT 120K Btuh input Ng_ : HI GAS-HEAT on models. Factow for setting TERMINALS WITH THERMOSTAT REMOVED HOOK-AROUND VOLT/AMMETER motors. UNIT DAMAGE HAZARD Failure to %llow this caution exchangers use Nr 0 may result in damage due to over temperature to the heat or condensate corrosion 1 NEVER connect Low Speed (Red) wire to "HI HEAT" 2 Do NOT connect Medium Low Speed (Blue) wire to "HI -HEAT" on 80,000 Btuh and 120,000 For tow-heat, d-_e %llowiug -HEAT on control: a Med (Orange) b. Me&Low change remove -Available can be only on 5=speed made at LO 10 TURNS motors FROM UNIT 24-VOLT TERMINAL BLOCK - Factou- blower blower connections sizes (Blue) c Low (RED) To Bmh input model motor motor setting speed selections lead flora control for heating HI-HEAT EXAMPLE: mode, tem_iual. terminal. Follow Reconnect this same procedure LO-HEAT and COOL speed selection. Set Blower Off Delay original ibr FOR THERMOSTAT SETTING A80201 Fig. 56--Amp lead on SPARE proper = 0.5 AMPS (See Fig 32) Select desired blower motor speed lead t'rom one of d_e other motor leads and relocate it to HI-HEAT terminal. See Table 13 ibr lead color identification 50 AMPS ON AMMETER 10 TURNS AROUND JAWS selection See of thermostat anticipator Draw Check with Ammeter manuii_cturer's and for varying When using an electronic instrllctions heating cycle thermostat, %r adjustiug heat length. set cycle rate for 3 cycles per l'lo_.N" a Remove Blower Access Door if installed Step b. Turn Dip switch delay. ADJUST See Table BLOWER 2 and 3 ON or OFF %r desired the main lengthened or shortened off blower when off (HEAT time operating the MODE) delay period in the heating 6--Check This sectiou 9A and B or Fig. 3i and 32. OFF DELAY If desired, blower may be mode to as part 1 49 Controls covers the safety contlols installation pressure Safety is complete The switch were all checked of rmrmal Check Primary operation. Limit Contlol that must be checked flame sensor, befbre gas valve, in the Start=up procedure and section Thiscontrolshutsoff gascontlolsystem andenergizes air-circulating blower motorif ihmace overheats. Recommended method of checking thislimitcontrol is to gradually block offremm airafterfurnace hasbeen operating ibraperiod ofatleast 5minutes. Assoon aslimitcontrol has shutoffburners, return-air opening should betmblocked to permit nom_al aircirculation Byusing thismethod tocheck limitcontrol, it canbeestablished thatlimitis functioning properly andoperates if there isarestricted return-air supply ormotorfailureIf limitcontrol does notfunction during this test,cause must bedetermined andcon'ected 2. Check Pressure This connol operation a, Turn proves off l15-v power inducer. (beck switch door on 115-v power pressure should not induce* motor to Ihrnace. is Nnctioning glow, is disconnected, shut mine reason pressure con'ect condition. off 115=v power inducer code ignitor furnace switch and wait 1 minute. properly, and status Code 32. If hot surfhce f Reconnect and disconnect to "call for heat" switch ensure hot surface LED flashes glows when down immediately. did not function When igniter a Status inducer motor Deter- properly and to furnace. motor and mrn on 115-v power leads, reinstall main furnace door, supply. 5O tools and instruments SW-1 through desired blower-OFF SW-3 settings delay 3. Verify flame 4. Verify that blower after ibr (SW-2 rollout Clean up debris completing thermostat manual reset switch and outer doors test furnace with room them_ostat operation of accessories per literature Guide with packet installation (SW-1) to and owner. near furnace has continuity. are properly 6. (heck tions. Users type and SW-3). 5. Cycle 8. Leave flora wire harness. d. Set thermostat e. Turn of draft to fhmace, outer/hrnace lead wires 2. (heck 7. Review operation as follows: b. Remove c. Turn Switch CHECKLmST l. Put away installed. manuihcmrer's instruc- CH ECKLmST--BNSTALLATION LOAD CALCULATION Condensate Drain Heating Load (Btuh) Unit Level or Pitched Forward Cooling Load (Btuh) Internal Tubing Connections and Traps Furnace Model Selection COMBUSTION External Drain Connection Sloped AND VENT PiPiNG Termination Free of Kinks Leak Tight and Location Condensate Trap Primed before Start-Up Roof or Sidewall Heat Tape Installed if Required Termination Kit -- 2 Pipe or Concentric Combustion-Air CHECKLIST--START-UP Pipe Length Gas Input Rate (Set Within 2 percent of Rating Plate) Combustion-Air Pipe Elbow Quantity Temperature Vent Pipe Length Thermostat Rise Adjusted Anticipator Vent Pipe Elbow Quantity Anticipator Setting Adjusted or Pipe Diameter Determined from Sizing Table Cycte Rate (3 Cyctes per Hr) Selected Pipe Sloped To Furnace Safety Controls Check Pipe Insulation Primary Limit Over Ceitings Pressure Switch Low-Ambient Exposed Pipes 5i Operation Copyright 2004 CARRIER Manufacturer reserves Book 1 4 Tab 6a 8a PC 101 Corp. _ 7310 W. Morris St • Mdianapolis, the right to discontinue, CataMg No. 535-80129 or change IN 46231 58mta7si at any time, specifications Printed in USA Form or designs 58MTA-7SI without notice Pg 52 and without 5-04 incurring obligations, Replaces: 58MTA-6SI
advertisement
* Your assessment is very important for improving the workof artificial intelligence, which forms the content of this project