advertisement
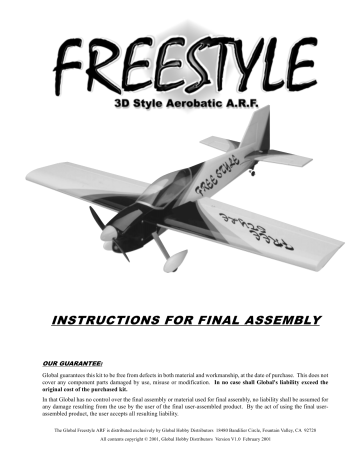
INSTRUCTIONS FOR FINAL ASSEMBLY
OUR GUARANTEE:
Global guarantees this kit to be free from defects in both material and workmanship, at the date of purchase. This does not cover any component parts damaged by use, misuse or modification. In no case shall Global's liability exceed the original cost of the purchased kit.
In that Global has no control over the final assembly or material used for final assembly, no liability shall be assumed for any damage resulting from the use by the user of the final user-assembled product. By the act of using the final userassembled product, the user accepts all resulting liability.
The Global Freestyle ARF is distributed exclusively by Global Hobby Distributors 18480 Bandilier Circle, Fountain Valley, CA 92728
All contents copyright © 2001, Global Hobby Distributors Version V1.0 February 2001
1
TABLE OF CONTENTS
Safety Warning ............................................................... 2
Introduction .................................................................... 3
Our Recommendations ................................................... 4
Additional Items Required ............................................. 5
Tools and Supplies Required ......................................... 5
Metric Conversion Chart ................................................ 5
Kit Contents .................................................................... 6
Replacement Parts .......................................................... 7
A Note About Covering ................................................. 8
Wing Assembly .............................................................. 8
Installing the Dihedral Brace ................................... 8
Joining the Wing Halves .......................................... 9
Wing Mounting .............................................................. 9
Installing the Wing Bolt Doubler ............................ 9
Mounting the Wing ................................................ 10
Belly Pan ...................................................................... 10
Aligning the Belly Pan ........................................... 10
Installing the Belly Pan .......................................... 11
Horizontal Stabilizer .................................................... 11
Aligning the Horizontal Stabilizer ........................ 11
Mounting the Horizontal Stabilizer ....................... 12
Vertical Stabilizer ......................................................... 13
Aligning the Vertical Stabilizer ............................. 13
Mounting the Vertical Stabilizer ........................... 13
Control Surface Hinging .............................................. 14
Hinging the Ailerons .............................................. 14
Hinging the Elevator Halves ................................. 14
Hinging the Rudder ................................................ 15
Tail Wheel .................................................................... 15
Assembling the Bracket ......................................... 16
Installing the Tail Wheel Bracket .......................... 16
Installing the Tail Wheel ........................................ 17
Main Landing Gear ...................................................... 17
Installing the Aluminum Strut ............................... 17
Installing the Wheels and Wheel Pants ................. 18
Aligning the Wheel Pants ...................................... 19
Engine Installation ....................................................... 19
Installing the Engine Mount Beams ...................... 19
Aligning the Engine ............................................... 19
Servo Installation ......................................................... 20
Installing the Servos .............................................. 20
Throttle Control System ............................................... 21
Installing the Pushrod Tube ................................... 21
Installing the Pushrod ............................................ 22
Installing the Servo Connector .............................. 22
Adjusting the Throttle Pushrod ............................. 23
Elevator Control System .............................................. 23
Installing the Control Horns .................................. 23
Installing the Pushrod ............................................ 24
Adjusting the Pushrod ........................................... 25
Rudder Control System ................................................ 25
Installing the Control Rod ..................................... 25
Installing the Pull-Pull Cables ............................... 26
Adjusting the Pull-Pull Cables .............................. 27
Aileron Control System ............................................... 28
Installing the Control Horns .................................. 28
Installing the Pushrods ........................................... 28
Adjusting the Pushrods .......................................... 29
Fuel Tank ...................................................................... 30
Assembling the Stopper ......................................... 30
Installing the Stopper Assembly ............................ 30
Installing the Fuel Tank ......................................... 31
Cowling ........................................................................ 31
Aligning the Cowling ............................................ 31
Installing the Cowling ............................................ 33
Installing the Propeller and the Spinner ................ 33
Canopy ......................................................................... 33
Aligning the Canopy .............................................. 33
Installing the Canopy ............................................. 34
Final Assembly ............................................................. 34
Applying the Decals .............................................. 34
Installing the Wing Skids ....................................... 34
Installing the Switch .............................................. 35
Installing the Receiver and the Battery ................. 35
Balancing ...................................................................... 35
Balancing the Freestyle ARF ................................. 35
Lateral Balancing ......................................................... 36
Control Throws ............................................................ 36
Preflight Check ............................................................. 36
Safety Guidelines ......................................................... 37
Flying the Freestyle ARF ............................................. 37
3D Aerobatic Flying Setup .......................................... 38
Radio Setup for 3D Flying ........................................... 39
Trim Chart .................................................................... 40
Product Evaluation Sheet ............................................. 43
SAFETY WARNING
This R/C airplane is not a toy! If misused, it can cause serious bodily injury and/or damage to property. Fly only in open areas and preferably at a dedicated R/C flying site. We suggest having a qualified instructor carefully inspect your airplane before its first flight. Please carefully read and follow all instructions included with this airplane, your radio control system and any other components purchased separately.
2
INTRODUCTION
Thank you for choosing the Global Freestyle ARF. Get ready to experience the most outrageous flying .46 size airplane you've ever encountered!
The Global Freestyle ARF is a prebuilt .46 size airplane designed specifically for 3D style aerobatics. What makes this airplane so great is that this style of flying can be done using any sport .46 size ball bearing two stroke engine! Most airplanes that are designed for 3D aerobatics are either big, expensive behemoths that are difficult to transport or they are profile kits that are made from heavy plywood and don't look good. The Global Freestyle ARF changes all of this.
Look closely at the Freestyle ARF and you will notice that it is built extremely light, yet is very strong. The fuselage is built up from lightweight balsa and plywood and the tail surfaces are built-up balsa. The wing panels are foam core with balsa sheeting and utilize open-bay construction to reduce weight. Ready-to-fly weight is minimal so you can understand why a sport .46 ball bearing engine flies the Freestyle ARF so well.
The Freestyle ARF comes with a complete hardware package that includes a clear canopy, fiberglass wheel plants, heavy duty aluminum landing gear, wheels, fuel tank, tail wheel assembly, motor mounts and all of the necessary nuts and bolts. Also included is a clear cowling template that makes it easy to align the cooling holes without damaging the prepainted fiberglass cowling - and remember, the Freestyle ARF is covered by master craftsmen using real iron-on covering material, not cheap "shelf paper" like some other manufacturers use.
We hope you enjoy your new Global Freestyle ARF as much as we have enjoyed designing and building it for you. If you have any questions or comments, please feel free to contact us. We have also included a product survey in the back of this instruction manual. Please take the time to fill it out and send it to us. We always enjoy hearing any comments or suggestions you may have.
This instruction manual is designed to guide you through the entire final assembly process of your new Global
Freestyle ARF in the least amount of time possible. Along the way you'll learn how to properly assemble your new airplane and also learn tips that will help you in the future. We have listed some of our recommendations below.
Please read through them before going any further.
✔ Please read through each step before beginning assembly. You should find the layout very complete and straight forward. Our goal is to guide you through assembly without any of the headaches and hassles that you might expect.
✔ There are check boxes next to each step. After you complete a step, check off the box. This will help prevent you from losing your place.
✔ Cover your work table with brown paper or a soft cloth, both to protect the table and to protect the individual parts.
✔ Keep a couple of small bowls or jars handy to put the small parts in after you open the accessory bags.
✔ We're all excited to get a new airplane in the air, but take your time. This will ensure you build a straight, strong and great flying airplane.
✔ If you come across this symbol
☛
, it means that this is an important point or an assembly hint.
✔ For your convenience we have included complete
3D aerobatic flying setup information and a trimming chart beginning on page # 37.
If you should find a part missing or damaged, or have any questions about assembly, please contact us at the address below:
Global Customer Care
18480 Bandilier Circle
Fountain Valley CA 92728
Phone: (714) 963-0329 Fax: (714) 964-6236 E-mail: [email protected]
Global sells a complete line of replacement parts for the Freestyle ARF. If you should ever require things like wing sets, cowlings or wheel pants, please contact us using the information above. We'll be happy to help you out. For your convenience we have a complete replacement parts list on page # 6.
3
OUR RECOMMENDATIONS
The following section describes our recommendations to help you in deciding which types of accessories to purchase for your new Global Freestyle ARF. First, decide on the type of flying you want to do, then look at which items you'll need.
SPORT FLYING
While the Freestyle ARF is designed for 3D aerobatics, it also makes an excellent sport flyer for those pilots who are accomplished at flying low wing sport airplanes. If you decide you want only to fly basic aerobatics with the Freestyle then these items are well suited:
Radio System:
A standard four channel radio system with five standard servos and a Y-harness will work fine. The ailerons use two separate servos, so the Y-harness is necessary to link them together.
Engine and Propeller:
A ball bearing .46 size two stroke engine with a standard muffler will be more than enough power for sport flying.
Use a 10 x 6 or 11 x 6 propeller for the best performance.
We Recommend:
Hitec Focus 4 FM Radio w/4 HS-300 Standard Servos
QTY. 1 P/N 444107 Cirrus CS-71 Standard Servo
QTY. 1 P/N 444728 Cirrus Y-Harness Extension
QTY. 1 P/N 210746 Magnum XL .46ARNV Engine
QTY. 1 P/N 115493 Thunderbolt R/C Long Glow Plug
QTY. 1 P/N 608460 APC 10 x 6 Propeller or
QTY. 1 P/N 608560 APC 11 x 6 Propeller
3D Aerobatic Flying
This is what the Freestyle was designed for. While the Freestyle is an excellent sport flyer, it's even better at 3D aerobatics. If that's what you want to do then these items are the most well suited:
Radio System:
A four or more channel computer radio with mixing capabilities will be required. Since there are two separate aileron servos used, they can be plugged separately into the receiver, allowing you the capability of flaperon or spoileron mixing and differential. The Freestyle is not a big, heavy airplane, so it's not necessary to use high-torque servos.
Five standard size dual ball bearing servos will work fine.
Engine and Propeller:
A ball bearing .46 size two stroke engine with a standard muffler or a .61 size four stroke engine would be an excellent choice. For 3D flying and extreme vertical performance, use a 12.25 x 3.75 APC propeller on your two stroke engine or a 12 x 6 or 13 x 5 on your four stroke engine.
We Recommend:
Hitec Flash 5X FM Radio w/4 HS-422 Deluxe Servos
QTY. 1 P/N 444110 Cirrus CS-71 2BB Professional Servo
QTY. 1 P/N 210746 Magnum XL .46ARNV Engine
QTY. 1 P/N 115493 Thunderbolt R/C Long Glow Plug
QTY. 1 P/N 608684 APC 12.25 x 3.75 Propeller
If You're Using a Four Stroke Engine:
QTY. 1 P/N 210985 Magnum XL .61RFS Engine
QTY. 1 P/N 115490 Thunderbolt 4-Cycle Glow Plug
QTY. 1 P/N 608680 APC 12 x 8 Propeller or
QTY. 1 P/N 609288 APC 13 x 6 Propeller
4
ADDITIONAL ITEMS REQUIRED
The items listed below are required in addition to the items recommended in the previous section. Those items will vary depending upon the setup you choose - either the sport flying setup or the 3D aerobatics setup.
❑ Dubro 1/4" Foam Rubber # 868638
❑ Global XX Silicon Fuel Line # 115923
❑ Dubro In-Line Fuel Filter # 568900
These Are Optional Items:
❑ Ernst Charging Jack # 223730
❑ Cirrus On-Board Voltage Indicator # 444762
❑ Magnum 2-1/4" Chrome Spinner # 237153
TOOLS AND SUPPLIES REQUIRED
❑ Kwik Bond Thin C/A # 887500
❑ Kwik Bond Thick C/A # 887510
❑ Kwik Bond 5 Minute Epoxy # 887560
❑ Kwik Bond 30 Minute Epoxy # 887565
❑ Kwik Bond C/A Debonder # 887545
❑ Wilhold Silicon Sealant # 335407
❑ Pacer Formula 560 Canopy Glue
❑ # 0 Phillips Head Screwdriver
❑ # 1 Phillips Head Screwdriver
❑ # 2 Phillips Head Screwdriver
❑ 4mm Hex Driver
❑ Adjustable Wrench
❑ Wire Cutters
❑ Needle Nose Pliers
❑ Excel Modeling Knife # 692801
❑ Promax Curved Scissors for Plastic # 361120
The part numbers for the Cirrus servos and Y-harness listed in the previous section, and the Ernst Charging
Jack and the Cirrus On-Board Voltage Indicator listed to the left are for use with Hitec and JR radio control systems. These items are also available with connectors that are compatible with Futaba and Airtronics radio control systems. Please check with your dealer for part numbers and pricing.
❑ Electric Drill
❑ Assorted Drill Bits
❑ Dubro T-Pins # 567685
❑ Ernst Airplane Stand # 223977
❑ Ruler
❑ Pencil
❑ Dremel Tool w/Assorted Bits
❑ Builder's Triangle
❑ 220 Grit Sandpaper w/Sanding Block
❑ Masking Tape
❑ Paper Towels
❑ Rubbing Alcohol
❑ NHP Epoxy Mixing Sticks # 864204
❑ NHP Epoxy Mixing Cups # 864205
METRIC CONVERSION CHART
To convert inches into millimeters: Inches x 25.4 = mm
1/64"
1/32"
1/16"
3/32"
1/8"
5/32"
=
=
=
=
=
=
.4mm
.8mm
1.6mm
2.4mm
3.2mm
4.0mm
3/16" =
1/4" =
3/8"
1/2"
4.8mm
6.4mm
= 9.5mm
= 12.7mm
5/8"
3/4"
= 15.9mm
= 19.0mm
1"
2"
3"
6"
12"
18"
= 25.4mm
= 50.8mm
= 76.2mm
= 152.4mm
= 304.8mm
= 457.2mm
21"
24"
30"
36"
= 533.4mm
= 609.6mm
= 762.0mm
= 914.4mm
5
KIT CONTENTS
We have organized the parts as they come out of the box for easier identification during assembly. Before you begin assembly, group the parts like we list them below. This will ensure that you have all of the parts before you begin assembly and it will also help you become familiar with each part.
AIRFRAME ASSEMBLIES
❑ {1} Fuselage
❑ {1} Right Wing Half w/Aileron
❑ {1} Left Wing Half w/Aileron
❑ {1} Horizontal Stabilizer w/Elevator Halves
❑ {1} Vertical Stabilizer w/Rudder
❑ {1} Belly Pan
❑ {1} Fiberglass Molded Cowling
❑ {1} Clear Molded Canopy
MAIN GEAR ASSEMBLY
❑ {1} Aluminum Main Gear Strut
❑ {2} 55mm Diameter Wheels
❑ {2} Fiberglass Molded Wheel Pants
❑ {2} 25mm Square Plywood Plates
❑ {2} 3mm x 38mm Threaded Axle Bolts
❑ {4} 3mm Flat Washers
❑ {6} 3mm Hex Nuts
❑ {2} 2.5mm x 18mm Wood Screws
❑ {2} 4mm x 20mm Machine Screws
TAIL WHEEL ASSEMBLY
❑ {1} Prebent Tail Wheel Wire
❑ {1} 25mm Diameter Wheel
❑ {1} Molded Nylon Tail Wheel Bracket
❑ {1} Molded Nylon Tail Wheel Tiller Arm
❑ {2} 2mm Wheel Collars
❑ {2} 2mm x 5mm Machine Screws
❑ {2} 2mm Brass Collets
❑ {3} 3mm x 18mm Wood Screws
❑ {1} 2mm x 30mm Steel Pin
THROTTLE CONTROL SYSTEM
❑ {1} 1mm x 500mm Pushrod Wire w/Z-Bend
❑ {1} 4mm x 380mm Plastic Tube
❑ {1} Adjustable Servo Connector Assembly
6
RUDDER CONTROL SYSTEM
❑ {1} Stranded Pull-Pull Cable
❑ {4} 2mm Threaded Brass Couplers
❑ {4} 1mm Brass Collets
❑ {4} Nylon Clevises
❑ {1} 3mm x 50mm Threaded Rod
❑ {2} 3mm Flat Washers
❑ {2} 3mm Hex Nuts
❑ {2} Nylon Adjustable Control Horns
❑ {4} C/A Style Hinges
AILERON CONTROL SYSTEM
❑ {2} 2mm x 80mm Pushrod Wires w/Z-Bends
❑ {2} Nylon Control Horns
❑ {2} Nylon Control Horn Backplates
❑ {2} Nylon Clevises
❑ {4} 2mm x 25mm Machine Screws
❑ {10} C/A Style Hinges
ELEVATOR CONTROL SYSTEM
❑
{1} Hardwood Split Elevator Pushrod
❑ {2} Nylon Control Horns
❑ {2} Nylon Control Horn Backplates
❑
{2} Nylon Clevises
❑ {4} 2mm x 25mm Machine Screws
❑ {1} Adjustable Servo Connector Assembly
❑
{6} C/A Style Hinges
MOTOR MOUNT ASSEMBLY
❑ {2} Engine Mount Beams
❑ {1} Plywood Thrust Plate
❑ {4} 4mm x 30mm Socket Head Screws
❑ {4} 4mm Flat Washers - Large O.D.
❑ {4} 4mm x 35mm Machine Screws
❑ {4} 4mm Flat Washers - Small O.D.
❑ {4} 4mm Split Washers
❑ {4} 4mm Hex Nuts
FUEL TANK ASSEMBLY
❑ {1} 280cc Fuel Tank
❑ {1} Nylon Fuel Tank Cap
❑ {1} Rubber Stopper
❑ {1} Nylon Stopper Backplate
❑ {1} Silicon Fuel Tubing
❑ {1} Weighted Fuel Pick-Up
❑ {1} 4mm x 40mm Nylon Fuel Pick-Up Tube
❑ {2} 4mm 90º Nylon Vent Tubes
❑ {1} 3mm x 22mm Self-Tapping Screw
❑ {1} Nylon Fuel Filler Housing
❑ {1} Nylon Fuel Filler Snap-Ring
❑ {1} Nylon Fuel Filler Plug
MISCELLANEOUS PARTS
❑ {1} Plywood Dihedral Brace
❑ {1} Spinner Assembly
❑ {1} 10 x 6 Composite Propeller
❑ {2} Nylon Molded Wing Skids
❑ {1} Clear Molded Cowling Template
❑ {1} 25mm x 55mm Plywood Plate
❑ {2} 4mm x 40mm Socket Head Screws
❑ {2} 4mm Flat Washers - Large O.D.
❑ {4} 3mm x 18mm Wood Screws
❑ {4} 3mm Flat Washers
❑ {6} 2mm x 8mm Wood Screws
❑ {1} Decal Set
REPLACEMENT PARTS
☛
Global carries a complete line of replacement parts for the Freestyle ARF. Listed below are the replacement parts that are available along with their respective part numbers for easy ordering convenience. These replacement parts can be ordered through your local hobby dealer or directly from Global by calling 1-714-964-0329.
170472 - Instruction Manual
170473 - Wing Set
170474 - Fuselage Set
170475 - Stabilizer Set
170523 - Engine Mount Set
170581 - Fuel Tank Assembly
170481 - Aluminum Landing Gear Strut
170482 - Molded Fiberglass Wheel Pants
170476 - Molded Fiberglass Cowling 170483 - Spinner Assembly
170477 - Clear Molded Cowling Template 170484 - Decal Set
170478 - Clear Molded Canopy
170479 - Belly Pan
170480 - Hardware Package
170599 - 10 x 6 Composite Propeller
856901 - Tail Wheel Assembly
7
A NOTE ABOUT COVERING
The covering material used on the Freestyle ARF is real iron-on heat shrink covering material, not cheap "shelf paper."
Because of this, it is possible with heat and humidity changes that the covering on your airplane may wrinkle or sag. This trait is inherent in all types of heat shrink material. To remove any wrinkles that might be visible you will need to purchase, or borrow from a fellow modeler, a heat iron. If you need to purchase one, the Global Heat Sealing Iron # 360900 is recommended.
Follow these simple steps to remove the wrinkles:
❑ 1) Plug in and turn on the sealing iron to the medium-high temperature setting. Allow the iron to heat up for approximately 5 - 7 minutes.
❑ 2) After the iron has reached temperature, lightly apply the iron to the wrinkled section of the covering. Move the iron slowly over the wrinkled section until the covering tightens and the wrinkles disappear. You will notice that the color of the covering will darken when it is heated. When the covering cools back down, it will return to its normal color.
☛
If the color layer smears from any of the seams the temperature of the iron is too hot. Turn the temperature dial down and wait about 5 minutes for the iron to adjust to the lower temperature. You can remove any excess color streaks using a paper towel soaked with a small quantity of Acetone.
WING ASSEMBLY
ITEMS REQUIRED
❑ {1} Right Wing Half
❑ {1} Left Wing Half
❑ {1} Plywood Dihedral Brace
TOOLS AND SUPPLIES REQUIRED
❑ Kwik Bond 30 Minute Epoxy
❑ Excel Modeling Knife
❑ Ruler
❑ Pencil
❑ 220 Grit Sandpaper w/Sanding Block
❑ Masking Tape
❑ Paper Towels
❑ Rubbing Alcohol
❑ NHP Epoxy Mixing Sticks
❑ NHP Epoxy Mixing Cups
INSTALLING THE DIHEDRAL BRACE
❑ 1) Look carefully at the surface of each root rib on both wing halves. Notice that there is excess covering material overlapping onto them.
❑ 2) Using a modeling knife, carefully cut away and remove the excess covering material from both of the root ribs. Leave about 1/16" of covering material overlapping so it does not pull away later.
8
☛
Removing most of the covering material from the two root ribs will expose more of the wood. This will result in a stronger joint when the wing halves are epoxied together later. See photo # 1 below.
Photo # 1
❑ 3) Using a ruler and a pencil, locate and mark the centerline of the plywood dihedral brace. Draw a vertical line, one on each side of the dihedral brace, at this location. See photo # 2 below.
Photo # 2
❑ 4) Test fit the plywood dihedral brace into the plywood dihedral brace box in each wing half. The brace
should slide into each wing half up to the centerline you drew. If it does not, remove the dihedral brace and use
220 grit sandpaper with a sanding block to lightly sand the edges and tips of the brace until you are satisfied with the fit. See photo # 3 below.
Photo # 3
☛
The dihedral brace is symmetrical, so it can be installed in any orientation. There is no top or bottom.
❑ 5) Test fit both of the wing halves together with the dihedral brace temporarily installed (without using glue).
Look carefully at the center section joint: the wing halves should fit together tightly with few or no gaps in the joint.
See photo # 4 below.
Photo # 4
❑ 6) If the center section joint is not tight, remove the wing halves and the dihedral brace, and lightly sand the edges and tips of the brace. Test fit the wing halves together with the dihedral brace installed again and repeat until you are satisfied with the fit. Once you are satisfied with the fit, remove the wing halves and the dihedral brace.
☛
It is important that the wing halves fit together firmly.
The better the fit, the stronger the center section joint will be.
❑ 7) Following the instructions on the packaging, mix a generous amount of Kwik Bond 30 Minute Epoxy. Mix the epoxy for about 1 minute. This will ensure that both parts are thoroughly incorporated.
❑ 8) Working with only one wing half for now, apply a thin layer of epoxy inside the plywood dihedral brace box and to only half of the dihedral brace. Make sure to cover the top and bottom, as well as the sides, and use enough epoxy to fill any gaps.
❑ 9) Slide the dihedral brace into the wing half up to its centerline. Remove any excess epoxy before it dries, using a paper towel and rubbing alcohol. Allow the epoxy to set up before proceeding.
JOINING THE WING HALVES
❑ 10) Once the epoxy has set up, trial fit both wing halves together again to double check that the wing halves still fit together properly.
❑ 11) Mix a generous amount of Kwik Bond 30
Minute Epoxy. Apply a thin layer of epoxy to the exposed half of the dihedral brace, the inside of the second wing half, and the entire surface of both root ribs, in-
cluding the dowel pin. Make sure to use enough epoxy to fill any gaps.
❑ 12) Slide the two wing halves together and realign them. Wipe away any excess epoxy, using a paper towel and rubbing alcohol, and use several pieces of masking tape to hold the two wing halves aligned until the epoxy fully cures.
❑
13) Once the epoxy has fully cured, remove the masking tape and double-check the center section joint.
If any gaps are present, mix a small amount of Kwik Bond
30 Minute Epoxy and carefully fill any remaining gaps.
Remove any excess epoxy using a paper towel and rubbing alcohol, and allow the epoxy to thoroughly cure.
WING MOUNTING
ITEMS REQUIRED
❑ {1} 25mm x 55mm Plywood Plate
❑ {2} 4mm x 40mm Socket Head Screws
❑ {2} 4mm Flat Washers - Large O.D.
TOOLS AND SUPPLIES REQUIRED
❑ Kwik Bond Thick C/A
❑ 4mm Hex Driver
❑ Excel Modeling Knife
❑ Electric Drill
❑ 11/64" Drill Bit
❑ Ernst Airplane Stand
❑ Ruler
❑ Pencil
INSTALLING THE WING BOLT DOUBLER
❑ 1) Using a modeling knife, remove the covering from over the top and bottom of the two predrilled wing mounting holes in the trailing edge of the wing. The holes are located 7/16" in front of the trailing edge and 13/16" out from each side of the centerline.
9
❑ 2) Using a ruler and a pencil, carefully draw a vertical centerline on one side of the 25mm x 55mm plywood plate. See photo # 5 below.
Photo # 5
MOUNTING THE WING
❑ 8) Place the wing into the wing saddle and secure it into place using two 4mm x 40mm socket head screws and two 4mm flat washers. See Photo # 8 below.
Photo # 8
❑ 3) Set the plywood plate onto the bottom of the wing. The rear edge of the plate should be flush with the trailing edge of the wing and the centerline of the plate should be lined up with the centerline of the wing. See photo # 6 below.
Photo # 6
❑ 4) While holding the plywood plate firmly in place, use a pencil to draw an outline of the plate onto the wing's surface.
❑ 5) Remove the plate. Using a modeling knife, carefully cut away and remove the covering material from inside the outline you drew. See photo # 7 below.
Photo # 7
❑ 6) Apply a bead of Kwik Bond Thick C/A to the bottom of the plywood plate. Set the plate back into place and realign it. Hold it in place until the C/A fully cures.
❑ 7) After the C/A has cured, use a drill with an 11/64" drill bit to open the two wing mounting holes through the plywood plate. Use the holes that were predrilled through the wing as a guide.
10
☛
Two blind nuts have been preinstalled into the bottom of the plywood wing mounting block in the fuselage for the socket head screws to thread into.
☛
Do not overtighten the socket head screws. You don't want to crush the wing.
BELLY PAN
ITEMS REQUIRED
❑ {1} Belly Pan
TOOLS AND SUPPLIES REQUIRED
❑ Kwik Bond 30 Minute Epoxy
❑ 4mm Hex Driver
❑ Excel Modeling Knife
❑ Ernst Airplane Stand
❑ Ruler
❑ Pencil
❑ 220 Grit Sandpaper w/Sanding Block
❑ Masking Tape
❑ Paper Towels
❑ Rubbing Alcohol
❑ NHP Epoxy Mixing Sticks
❑ NHP Epoxy Mixing Cups
ALIGNING THE BELLY PAN
❑ 1) Using a modeling knife, cut away and remove the covering material from over the precut notch in the front of the belly pan.
❑ 2) Using a modeling knife, cut away and remove the covering material from over the precut wing bolt access hole in the bottom of the belly pan. The hole is located
1-3/4" in front of the back edge of the belly pan and it is
1/2" wide and 1-1/4" long.
❑ 3) With the wing installed on the fuselage, set the belly pan into place and push it down firmly. Align both the front and back of the belly pan with the sides and bottom of the fuselage and use several pieces of masking tape to hold it firmly in place. See photo # 9 below.
Photo # 9
☛
If the front of the belly pan does not line up with the sides of the fuselage, use a modeling knife to widen the notch in the belly pan. That will give you more room to move the belly pan from side to side.
❑ 4) When satisfied with the alignment, hold the belly pan firmly in place and use a pencil to outline the sides of the belly pan onto the bottom of the wing.
❑ 5) Remove the masking tape and the belly pan from the wing. Using a modeling knife, carefully cut away and remove the covering material from inside the outline you drew. See photo # 10 below.
Photo # 10
❑ 6) Using a modeling knife, carefully cut away and remove the covering material from the bottom edges of the belly pan. See photo # 11 below.
Photo # 11
☛
Removing the covering material from the gluing surfaces will result in a stronger bond for the epoxy.
INSTALLING THE BELLY PAN
❑ 7) Mix a small quantity of Kwik Bond 30 Minute
Epoxy. Apply a thin layer of epoxy to only the gluing surfaces of the belly pan.
❑ 8) Set the belly pan back into place and realign it.
Use several pieces of masking tape to hold it securely in place and remove any excess epoxy using a paper towel and rubbing alcohol.
❑ 9) After the epoxy has fully cured, remove the masking tape, but leave the wing in place for now.
HORIZONTAL STABILIZER
ITEMS REQUIRED
❑ {1} Horizontal Stabilizer w/Elevator Halves
TOOLS AND SUPPLIES REQUIRED
❑ Kwik Bond 30 Minute Epoxy
❑ Excel Modeling Knife
❑ Dubro T-Pins
❑ Ernst Airplane Stand
❑ Ruler
❑ Pencil
❑ 220 Grit Sandpaper w/Sanding Block
❑ Masking Tape
❑ Paper Towels
❑ Rubbing Alcohol
❑ NHP Epoxy Mixing Sticks
❑ NHP Epoxy Mixing Cups
ALIGNING THE
HORIZONTAL STABILIZER
❑ 1) Set the two elevator halves aside for now. You won't need them at this time.
❑ 2) Using a modeling knife, cut away and remove the covering material from both sides of the horizontal stabilizer mounting slot. The slot is 4-3/8" long and 3/8" wide. The front of the slot is 5" in front of the trailing edge of the fuselage.
☛
The trailing edge of the fuselage is beveled forward to allow for more rudder control deflection.
❑ 3) Slide the stabilizer into the mounting slot. To align the stabilizer, start by doing the following:
❑ A) Center the stabilizer from side to side in the slot. If you measure from each side of the fuselage to
11
each tip of the stabilizer, both measurements will be the same when the stabilizer is centered. See figure # 1 below.
Figure # 1
❑ F) With the stabilizer held firmly in place, look from the front of the airplane at both the wing and the stabilizer. When aligned properly, the stabilizer should be parallel with the wing. See figure # 3 below.
Figure # 3
A=A-1
❑ B) When you are satisfied that the stabilizer is centered, use a pencil to draw a couple of marks on each side of the stabilizer where it and the back of the fuselage sides meet. See photo # 12 below.
Photo # 12
❑ C) With the back of the stabilizer aligned with the marks you drew, use a T-pin to secure the stabilizer to the fuselage at the trailing edge only.
☛
The front of the stabilizer should be able to pivot from side to side and the back should stay firmly in place.
❑ D) Using a ruler, measure the distance between the tips of the stabilizer and the tips of the wing. Pivot the front of the stabilizer until both of these measurements are equal. See figure # 2 below.
Figure # 2
C=C-1
☛
If the stabilizer is out of alignment, remove it and use
220 grit sandpaper with a sanding block to sand down the higher side of the stabilizer mounting slot. Reinstall the stabilizer and check the alignment once more. Repeat this procedure until you are satisfied with the alignment.
MOUNTING THE
HORIZONTAL STABILIZER
❑ 4) With the stabilizer properly aligned, use a pencil to draw a line on each side of the stabilizer were it meets the fuselage sides. Do this on both the top and bottom.
❑ 5) Remove the stabilizer. Using a modeling knife, cut away and remove the covering material from between the lines you drew. See photo # 13 below.
Photo # 13
B=B-1
❑ E) When you are satisfied that the stabilizer is aligned, use a pencil to draw a couple of marks on each side of the front of the stabilizer where it and the fuselage sides meet, then use a couple of pieces of masking tape to hold the stabilizer firmly in place.
12
☛
When cutting through the covering to remove it, cut with only enough pressure to cut through only the covering itself. Cutting down into the balsa structure could weaken the stabilizer.
❑ 6) Mix a generous amount of Kwik Bond 30 Minute
Epoxy. Apply a generous amount of epoxy to only the top and bottom of the gluing surface on the stabilizer.
☛
Because the stabilizer has to slide in place through the fuselage, apply epoxy only to the stabilizer. This will prevent the epoxy from spreading over the entire length of one half of the stabilizer when you slide it into place.
❑ 7) Slide the stabilizer into place and realign it, double checking all of your measurements once more
before the epoxy sets up. Wipe away any excess epoxy using a paper towel and rubbing alcohol, and hold the stabilizer in place using several pieces of masking tape.
Allow the epoxy to fully cure before proceeding.
❑ 8) After the epoxy has cured, remove the masking tape. Look closely at the glue joint. If there are any gaps between the stabilizer and the fuselage, fill them using
Kwik Bond 30 Minute Epoxy. Remove any excess epoxy using a paper towel and rubbing alcohol and allow the epoxy to set up before proceeding.
VERTICAL STABILIZER
ITEMS REQUIRED
❑
{1} Vertical Stabilizer w/Rudder
TOOLS AND SUPPLIES REQUIRED
❑ Kwik Bond 30 Minute Epoxy
❑ Excel Modeling Knife
❑ Ernst Airplane Stand
❑ Ruler
❑ Pencil
❑ Builder's Triangle
❑ Masking Tape
❑ Paper Towels
❑ Rubbing Alcohol
❑ NHP Epoxy Mixing Sticks
❑ NHP Epoxy Mixing Cups
ALIGNING THE
VERTICAL STABILIZER
❑ 1) Slide the vertical stabilizer into the mounting slot in the top of the fuselage. When the stabilizer is aligned properly, the rear edge of the stabilizer should be even with the rear edge of the fuselage and the stabilizer should be pressed down firmly
❑ 2) While holding the vertical stabilizer firmly in place, use a pencil to draw a line on each side of the vertical stabilizer where it meets the top of the fuselage. See photo # 14 below.
Photo # 14
❑ 3) Remove the stabilizer and hold it up to a bright light. Look carefully at the stabilizer and you will see the inner structural framework.
❑ 4) Using a modeling knife, cut away and remove the covering material (on both sides) from over only the solid balsa structure that is below the lines you drew.
Remove the covering material from the bottom edge of the stabilizer also. See photo # 15 below.
Photo # 15
☛
Do not cut directly below the lines you drew or you will be cutting right into the open framework.
☛
When cutting through the covering to remove it, cut with only enough pressure to cut through only the covering itself. Cutting down into the balsa structure could weaken the stabilizer.
❑ 5) Slide the vertical stabilizer back into place and realign it. Using a builder's triangle, check to make sure that the vertical stabilizer is aligned 90º to the horizontal stabilizer. See figure # 4 below.
Figure # 4
MOUNTING THE
VERTICAL STABILIZER
❑ 6) Mix a generous amount of Kwik Bond 30 Minute
Epoxy. Apply a generous amount of epoxy to the exposed gluing surfaces of the stabilizer and to the sides and top of the stabilizer mounting slot in the fuselage.
❑ 7) Slide the stabilizer into place and realign it, double checking all of your measurements once more before the epoxy sets up. Wipe away any excess epoxy using a paper towel and rubbing alcohol and hold the stabilizer in place using several pieces of masking tape. Allow the epoxy to fully cure before proceeding.
13
❑ 8) After the epoxy has cured, remove the masking tape. Look closely at the glue joint. If there are any gaps between the stabilizer and the fuselage, fill them using
Kwik Bond 30 Minute Epoxy. Remove any excess epoxy using a paper towel and rubbing alcohol and allow the epoxy to set up before proceeding.
CONTROL SURFACE HINGING
TOOLS AND SUPPLIES REQUIRED
❑ Kwik Bond Thin C/A
❑ Kwik Bond C/A Debonder
❑ Excel Modeling Knife
❑ Ernst Airplane Stand
❑ Paper Towels
☛
Because of the large size of the control surfaces on the Freestyle ARF it is absolutely imperative that the hinges be glued properly. This includes both having a tight hinge gap and using plenty of C/A glue.
HINGING THE AILERONS
❑ 1) Locate the five precut hinge slots in the trailing edge of each half of the wing and the leading edge of each aileron.
❑ 2) Test fit the C/A hinges into the hinge slots in each aileron. Each hinge should be inserted far enough into the slots so that the centerline of the hinges is flush with the leading edges of the ailerons. If the hinges cannot be inserted deeply enough, use a modeling knife to cut the hinge slots deeper.
❑ 3) With each of the hinges centered in the hinge slots, apply 5-6 drops of Kwik Bond Thin C/A to the joint where the hinges and the ailerons meet. Allow a few seconds between drops for the C/A to "wick" into the hinges, then turn the ailerons over and repeat this procedure on the other side of each hinge. Let the C/A dry for about 10 minutes before proceeding. See photo # 16 below.
Photo # 16
☛
If any C/A gets onto the aileron, it can be removed promptly using a paper towel soaked with a small quantity of Kwik Bond C/A Debonder.
14
❑ 4) Working with one aileron for now, slide the aileron and its hinges into the hinge slots in the trailing edge of the wing. Adjust the aileron so that the tip of the aileron is even with the tip of the wing.
❑ 5) While holding the aileron tight against the wing, pivot the aileron down about 45º. Apply 5-6 drops of
Kwik Bond Thin C/A to the exposed area of each hinge.
Turn the wing over and repeat for the other side of the hinges. See photo # 17 below.
Photo # 17
☛
If any C/A runs down the length of the hinge line, it can be removed promptly using a paper towel soaked with a small quantity of Kwik Bond C/A Debonder.
❑ 6) Allow the C/A to dry completely - about 15 minutes. When you are sure that the C/A has completely cured, pivot the aileron up and down about five times to free up the hinges.
❑ 7) Gently grasp the aileron and pull on it like you are trying to pull out the hinges. The hinges should hold securely. If one or more hinges feels loose, apply more
C/A and allow it to completely cure.
❑ 8) Repeat steps # 4 through # 7 to install the second aileron on the other half of the wing.
HINGING THE ELEVATOR HALVES
❑ 9) Locate the three precut hinge slots in the trailing edge of each half of the stabilizer and the leading edge of each elevator half.
❑ 10) Test fit the C/A hinges into the hinge slots in each elevator half. Each hinge should be inserted far enough into the slots so that the centerline of the hinges is flush with the leading edges of the elevator halves. If the hinges cannot be inserted deeply enough, use a modeling knife to cut the hinge slots deeper.
❑ 11) With each of the hinges centered in the hinge slots, apply 5-6 drops of Kwik Bond Thin C/A to the joint where the hinges and the elevator halves meet. Allow a few seconds between drops for the C/A to wick into the hinges, then turn the elevator halves over and repeat this procedure on the other side of each hinge. Let the C/A dry for about 10 minutes before proceeding.
☛
If any C/A gets onto the elevator halves, it can be removed promptly using a paper towel soaked with a small quantity of Kwik Bond C/A Debonder.
❑ 12) Working with one elevator half for now, slide the elevator and its hinges into the hinge slots in the trailing edge of the stabilizer. Adjust the elevator so that there is no more than a 1/16" gap between the elevator counterbalance and the tip of the stabilizer.
❑ 13) While holding the elevator tight against the stabilizer, pivot the elevator down about 45º. Apply 5-6 drops of Kwik Bond Thin C/A to the exposed area of each hinge. Turn the fuselage over and repeat for the other side of the hinges.
☛
If any C/A runs down the length of the hinge line, it can be removed promptly using a paper towel soaked with a small quantity of Kwik Bond C/A Debonder.
❑ 14) Allow the C/A to dry completely - about 15 minutes. When you are sure that the C/A has completely cured, pivot the elevator up and down about five times to free up the hinges.
❑ 15) Gently grasp the elevator and pull on it like you are trying to pull out the hinges. The hinges should hold securely. If one or more hinges feels loose, apply more
C/A and allow it to completely cure.
❑ 16) Repeat steps # 12 through # 15 to install the second elevator half on the other half of the stabilizer.
HINGING THE RUDDER
❑ 17) Locate the four precut hinge slots in the trailing edge of both the vertical stabilizer and fuselage, and the leading edge of the rudder.
❑ 18) Test fit the C/A hinges into the hinge slots in the rudder. Each hinge should be inserted far enough into the slots so that the centerline of the hinges is flush with the leading edges of the rudder. If the hinges cannot be inserted deeply enough, use a modeling knife to cut the hinge slots deeper.
❑ 19) With each of the hinges centered in the hinge slots, apply 5-6 drops of Kwik Bond Thin C/A to the joint where the hinges and the rudder meet. Allow a few seconds between drops for the C/A to wick into the hinges, then turn the rudder over and repeat this procedure on the other side of each hinge. Let the C/A dry for about 10 minutes before proceeding.
☛
If any C/A gets onto the rudder, it can be removed promptly using a paper towel soaked with a small quantity of Kwik Bond C/A Debonder.
❑ 20) Slide the rudder and its hinges into the hinge slots in the trailing edge of the stabilizer and the fuselage.
Adjust the rudder so that there is no more than a 1/16" gap between the rudder counter-balance and the tip of the stabilizer.
❑ 21) While holding the rudder tight against the stabilizer and fuselage, pivot the rudder to the right about
45º. Apply 5-6 drops of Kwik Bond Thin C/A to the exposed area of each hinge. Turn the fuselage over and repeat for the other side of the hinges.
☛
If any C/A runs down the length of the hinge line, it can be removed promptly using a paper towel soaked with a small quantity of Kwik Bond C/A Debonder.
❑ 22) Allow the C/A to dry completely - about 15 minutes. When you are sure that the C/A has completely cured, pivot the rudder back and forth about five times to free up the hinges.
❑ 23) Gently grasp the rudder and pull on it like you are trying to pull out the hinges. The hinges should hold securely. If one or more hinges feels loose, apply more
C/A and allow it to completely cure.
TAIL WHEEL
ITEMS REQUIRED
❑ {1} Prebent Tail Wheel Wire
❑ {1} 25mm Diameter Wheel
❑ {1} Molded Nylon Tail Wheel Bracket
❑ {1} Molded Nylon Tail Wheel Tiller Arm
❑ {2} 2mm Wheel Collars
❑ {2} 2mm x 5mm Machine Screws
❑ {2} 2mm Brass Collets
❑ {3} 3mm x 18mm Wood Screws
❑ {1} 2mm x 30mm Steel Pin
TOOLS AND SUPPLIES REQUIRED
❑ Kwik Bond Thick C/A
❑ Kwik Bond C/A Debonder
❑ # 0 Phillips Head Screwdriver
❑ # 1 Phillips Head Screwdriver
❑ Electric Drill
❑ 5/64" Drill Bit
❑ Ernst Airplane Stand
❑ Ruler
❑ Pencil
❑ Dremel Tool w/Cutting Disc
❑ Masking Tape
15
ASSEMBLING THE BRACKET
❑ 1) Push one of the brass collets into the top and one into the bottom of the nylon tail wheel bracket. Install the collets with the flanges facing the outer surfaces of the bracket. See photo # 18 below.
Photo # 18
❑ 6) Using a Dremel Tool with a cutting disc attachment, carefully cut off the top of the tail wheel wire flush with the top of the tiller arm.
INSTALLING THE
TAIL WHEEL BRACKET
❑ 7) Place the tail wheel bracket onto the bottom of the fuselage. To align the assembly, the pivot point of the tiller arm should be even with the rudder hinge line and the bracket should be centered in the middle of the fuselage. See photo # 21 below.
Photo # 21
❑
2) Push one 2mm wheel collar into the molded recess in the nylon tail wheel tiller arm. Carefully rotate the wheel collar until the threaded hole in the collar lines up with the molded hole in the side of the tiller arm.
❑
3) Partially thread one 2mm x 5mm machine screw through the tiller arm and into the wheel collar. See photo # 19 below.
Photo # 19
❑ 4) Push the tail wheel wire up through the bottom of the tail wheel bracket, then slide the tiller arm over the tip of the wire and push it down into the molded recess in the tail wheel bracket.
❑ 5) Turn the tail wheel wire so that the coil faces the front of the bracket and adjust the tiller arm so that it faces the back of the bracket. While holding everything in alignment, tighten the 2mm x 5mm machine screw using a # 0 phillips screwdriver. See photo # 20 below.
Photo # 20
❑ 8) When satisfied with the alignment, hold the bracket in place and use a pencil to mark the locations of the three mounting screws onto the fuselage.
❑
9) Remove the tail wheel bracket. Using a drill with a 5/64" drill bit, drill three pilot holes through the fuselage at the marks you drew.
❑ 10) Set the bracket back into place and realign it.
Secure it to the fuselage using three 3mm x 18mm wood screws. Tighten the screws firmly using a # 1 phillips screwdriver.
❑ 11) Use a couple of pieces of masking tape, taped between the rudder and vertical stabilizer, to hold the rudder centered.
❑ 12) Rotate the tiller arm so that it is centered over the bottom edge of the rudder. Use a pencil to draw a mark on the bottom edge of the rudder, directly below the middle of the slot in the tiller arm. See photo # 22 below.
Photo # 22
16
❑ 13) Rotate the tiller arm out of the way. Using a drill with a 5/64" drill bit, drill a 3/4" deep hole into the bottom of the rudder at the mark you drew.
☛
Make sure you drill the hole 90º to the bottom of the rudder and make sure that it's centered.
❑ 14) Squeeze a small amount of Kwik Bond Thick
C/A down into the hole. Rotate the tiller arm back into place and slide the 2mm x 30mm steel pin through the slot in the tiller arm and into the hole in the rudder. Adjust the depth of the pin so that there is 1/4" sticking above the tiller arm. See photo # 23 below.
Photo # 23
☛
Any C/A that squeezes out of the hole can be removed promptly using a paper towel soaked with a small quantity of Kwik Bond C/A Debonder.
INSTALLING THE TAIL WHEEL
❑ 15) Partially thread one 2mm x 5mm machine screw into the remaining 2mm wheel collar.
❑ 16) Slide the 25mm diameter tail wheel onto the tail wheel wire, followed by the wheel collar. Push the wheel collar against the wheel and, using a # 0 phillips screwdriver, tighten the machine screw to secure the wheel into place. See photo # 24 below.
Photo # 24
☛
Double check that the tail wheel spins freely. It should not bind.
❑ 17) Using a # 0 phillips screwdriver, loosen the machine screw in the side of the tiller arm. With the rudder still centered, rotate the tail wheel wire until it is centered with the rudder. When satisfied with the alignment, tighten the machine screw firmly.
MAIN LANDING GEAR
ITEMS REQUIRED
❑
{1} Aluminum Main Gear Strut
❑ {2} 55mm Diameter Wheels
❑ {2} Fiberglass Molded Wheel Pants
❑
{2} 25mm Square Plywood Plates
❑ {2} 3mm x 38mm Threaded Axle Bolts
❑ {4} 3mm Flat Washers
❑
{6} 3mm Hex Nuts
❑ {2} 2.5mm x 18mm Wood Screws
❑ {2} 4mm x 20mm Machine Screws
TOOLS AND SUPPLIES REQUIRED
❑ Kwik Bond Thin C/A
❑ Kwik Bond 5 Minute Epoxy
❑ # 1 Phillips Head Screwdriver
❑ Adjustable Wrench
❑ Needle Nose Pliers
❑ Excel Modeling Knife
❑ Electric Drill
❑ 5/64" & 5/32" Drill Bits
❑ Ernst Airplane Stand
❑ Ruler
❑ Pencil
❑
Dremel Tool w/Cutting Disc
❑ 220 Grit Sandpaper w/Sanding Block
❑ Masking Tape
❑ Paper Towels
❑ Rubbing Alcohol
❑ NHP Epoxy Mixing Sticks
❑ NHP Epoxy Mixing Cups
INSTALLING THE ALUMINUM STRUT
❑ 1) Using a modeling knife, cut away and remove the covering material from over the two predrilled main gear access holes in the bottom of the fuselage. The two holes are located 3/4" in front of the wing saddle and they are both 5/8" in diameter.
☛
Look carefully at the aluminum main gear strut from one end and you will notice that one side is straight and the other side is angled.
❑ 2) Slide the main gear strut into the precut slot, making sure that the straight side is toward the back of the fuselage. Align the predrilled holes in the strut with the predrilled holes in the fuselage.
17
❑ 3) When satisfied with the alignment, secure the strut into place using two 4mm x 20mm machine screws.
Tighten the screws firmly using a # 1 phillips screwdriver.
INSTALLING THE WHEELS
AND WHEEL PANTS
❑ 4) Test fit one 25mm square plywood plate into one wheel pant. The plate should be centered over the molded recess in the side of the pant. See photo # 25 below.
Photo # 25
❑ 10) Using a Dremel Tool with a cutting disc attachment, carefully cut a slot from the hole you drilled down to the bottom of the wheel pant. See photo # 27 below.
Photo # 27
❑ 11) Slide one 55mm diameter wheel onto one of the 3mm x 38mm threaded axle bolts. Thread one 3mm hex nut onto the axle bolt and up against the wheel. See photo # 28 below.
Photo # 28
❑
5) Remove the plywood plate and set it aside. Using 220 grit sandpaper, carefully roughen the fiberglass only where the plate will be glued into place.
❑ 6) Mix a small quantity of Kwik Bond 5 Minute
Epoxy and apply a generous layer to the gluing surface of the plywood plate.
❑ 7) Set the plate back into place and realign it. Remove any excess epoxy using a paper towel and rubbing alcohol, and hold the plate firmly in place until the epoxy sets up.
❑ 8) Hold the wheel pant up to the landing gear bracket. Center the molded recess in the side of the wheel pant over the end of the bracket, and using a pencil, mark the location of the axle hole onto the side of the wheel pant. See photo # 26 below.
Photo # 26
☛
Don't tighten the nut against the wheel. The wheel should be able to spin freely, but not be too loose.
❑ 12) Carefully apply a couple of drops of Kwik Bond
Thin C/A to the nut to lock it firmly into place. Allow the
C/A to fully cure before proceeding.
❑ 13) Slide one 3mm flat washer up against the hex nut. Slide the wheel assembly into the slot in the wheel pant, making sure the washer is on the inside of the wheel pant (up against the plywood plate).
❑ 14) Slide the end of the axle bolt through the predrilled hole in the landing gear bracket. Slide one 3mm flat washer up against the bracket and thread one 3mm hex nut onto the bolt. See photo # 29 below.
Photo # 29
☛
So that the wheel pant will be at the proper height, the bottom edge of the pant should be 1/8" above the bottom edge of the landing gear bracket.
❑
9) Using a drill with a 5/32" drill bit, drill a hole through the wheel pant at the mark you drew.
18
❑ 15) While holding the hex nut inside the wheel pant with needle nose pliers, tighten the outer hex nut firmly using an adjustable wrench.
❑ 16) Thread a second 3mm hex nut onto the axle bolt, and using an adjustable wrench, tighten it firmly up against the first hex nut.
❑ 17) Repeat steps # 4 through # 16 to install the second wheel and wheel pant assembly
ALIGNING THE WHEEL PANTS
❑ 18) With the airplane sitting on a level surface, carefully pivot each wheel pant until the bottom rear portion of each pant is parallel with the ground.
❑ 19) When satisfied with the alignment, use a drill with a 5/64" drill bit and drill one pilot hole through the side of each wheel pant, using the predrilled holes in the landing gear bracket as a guide.
❑ 20) Install and tighten one 2.5mm x 18mm wood screw in each wheel pant to lock them into place.
ENGINE INSTALLATION
ITEMS REQUIRED
❑ {2} Engine Mount Beams
❑
{1} Plywood Thrust Plate
❑ {4} 4mm x 30mm Socket Head Screws
❑ {4} 4mm Flat Washers - Large O.D.
❑
{4} 4mm x 35mm Machine Screws
❑ {4} 4mm Flat Washers - Small O.D.
❑ {4} 4mm Split Washers
❑
{4} 4mm Hex Nuts
TOOLS AND SUPPLIES REQUIRED
❑ # 2 Phillips Head Screwdriver
❑ 4mm Hex Driver
❑ Adjustable Wrench
❑ Electric Drill
❑ 1/8" & 11/64" Drill Bits
❑ Ernst Airplane Stand
❑ Ruler
❑ Pencil
INSTALLING THE ENGINE MOUNT BEAMS
☛
The references in the next step are taken from the consideration that you are looking at the front of the airplane with the airplane right-side up.
❑ 1) Install the two nylon engine mount beams, along with the plywood thrust plate, using four 4mm x 30mm socket head screws and four 4mm large O.D. flat washers. Tighten the screws firmly using a 4mm hex driver to secure the mounting beams and thrust plate in place. See photo # 30 below.
Photo # 30
☛
The engine mount beams should be installed with the longer side of both beams toward the lower left portion of the fuselage. The thrust plate should be installed with the thicker portion on the right side of the airplane. Remember, these references are as if you were looking at the front of the airplane, with the airplane right-side up.
ALIGNING THE ENGINE
☛
The engine mount spacing is set from the factory to accept either the Magnum XL .46ARNV two stroke engine or the Magnum XL .61RFS four stroke engine.
Other engine brands that have a maximum crankcase width of no more than 35mm will also work.
These instructions will detail the installation of the
Magnum XL .46ARNV engine. Please note that the drive washer spacing will be the same for whichever different engine you may choose.
❑ 2) Remove the muffler, carburetor (two stroke only) and rear needle valve assembly (if applicable) from your engine and set them aside.
❑ 3) Set the engine on the engine mounting beams.
Using a ruler, measure the distance that the front of the drive washer is from the back of the motor mount beams.
Adjust the depth of the engine until the measurement is
4-5/8". See photo # 31 below.
Photo # 31
19
❑ 4) While holding the engine firmly in place, use a pencil to mark the four engine mounting screw locations onto the engine mounting beams. See photo # 32 below.
Photo # 32
❑ 5) Remove the engine and set it aside. Using a drill with a 1/8" drill bit, drill a pilot hole through the engine mounting beams at each of the four locations you marked.
☛
Because of the consistency of the engine mounting beams, it's best to drill pilot holes before drilling the larger holes. This will prevent the drill from "creeping" and distorting the holes.
❑ 6) Set the engine back into place and realign it.
Check to ensure that the holes in the engine mounting lugs still line up with the pilot holes in the beams.
❑ 7) Remove the engine and set it aside. Using a drill with an 11/64" drill bit, enlarge the four pilot holes in the engine mounting beams.
❑ 8) Install the engine using four 4mm x 35mm machine screws, four 4mm small O.D. flat washers, four 3mm split washers and four 3mm hex nuts. Tighten the hex nuts and machine screws firmly using a # 2 phillips screwdriver and an adjustable wrench. See photo # 33 below.
Photo # 33
SERVO INSTALLATION
TOOLS AND SUPPLIES REQUIRED
❑ # 1 Phillips Head Screwdriver
❑ Excel Modeling Knife
❑ Electric Drill
❑ 1/16" Drill Bit
❑ Ernst Airplane Stand
❑ Ruler
❑ Pencil
INSTALLING THE SERVOS
❑ 1) Locate the five servos you intend to use for the elevator, rudder, throttle and aileron controls.
❑ 2) Carefully install the four rubber grommets and four brass collets onto each of the servo mounting lugs.
☛
For proper vibration reduction, the brass collets should be inserted into the rubber grommets with the flanges facing the bottom of the servo mounting lugs.
See figure # 5 below.
Figure # 5
❑ 3) Position three servos into the fuselage servo tray, making sure that you run the servo wires below the tray and out toward the front of the fuselage.
☛
Pay close attention to the positions of the servo output shafts. They should face the directions shown in the photo. See photo # 34 below.
Photo # 34
☛
Both the flat washers and split washers are installed on the bottoms of the engine mounting beams.
❑ 9) Following the instructions that were included with your engine, install the carburetor and rear needle valve assembly (if applicable) onto your engine at this time. Do not install the muffler yet.
20
❑ 4) Using a drill with a 1/16" drill bit, drill pilot holes through the servo tray for each of the servo mounting screws (included with your radio system).
❑ 5) Using a # 1 phillips screwdriver, install and tighten the mounting screws to hold the servos in place.
See photo # 35 below.
Photo # 35
❑ 6) Set the fuselage aside for now. Using a modeling knife, cut away and remove the covering material from over the servo exit holes in the top of the wing.
Both holes are located 3-1/2" in front of the trailing edge and 1/2" out from the centerline. Each hole is 5/8" in diameter.
❑ 7) Working with one servo for now, slide the servo lead through the precut channel in the wing (from within the servo cutout) and pull the lead out through the exit hole in the top of the wing. See photo # 36 below.
Photo # 36
❑ 8) Position the servo onto the servo rails, noting the position of the servo output shaft. It should face the trailing edge of the wing. See photo # 37 below.
Photo # 37
❑ 11) Repeat steps # 7 through # 10 to install the second aileron servo in the other half of the wing.
THROTTLE CONTROL SYSTEM
ITEMS REQUIRED
❑ {1} 1mm x 500mm Plain Pushrod Wire w/Z-Bend
❑ {1} 4mm x 380mm Plastic Tube
❑ {1} Adjustable Servo Connector Assembly
TOOLS AND SUPPLIES REQUIRED
❑ Kwik Bond Thin C/A
❑ Kwik Bond Thick C/A
❑ # 0 Phillips Head Screwdriver
❑ Adjustable Wrench
❑ Wire Cutters
❑ Excel Modeling Knife
❑ Electric Drill
❑ 5/64" & 7/64" Drill Bits
❑ Ernst Airplane Stand
❑ Ruler
❑ Pencil
❑ 220 Grit Sandpaper w/Sanding Block
INSTALLING THE PUSHROD TUBE
❑ 1) Using a pencil, draw a mark on the firewall to locate the position of the throttle pushrod. The mark should be drawn just to the outside of the motor mount beam to prevent any possibility of the pushrod tube interfering with the fuel tank when it is installed later.
❑ 2) Using a drill with a 7/64" drill bit, carefully drill a hole through the firewall at the mark you drew. See photo # 38 below.
Photo # 38
❑ 9) Using a drill with a 1/16" drill bit, drill pilot holes through the servo tray for each of the servo mounting screws (included with your radio system).
❑ 10) Using a # 1 phillips screwdriver, install and tighten the mounting screws to hold the servos in place.
❑ 3) Using a ruler and a modeling knife, measure and cut the 380mm plastic tube to a length of 10-1/4".
❑ 4) Using 220 grit sandpaper, lightly sand about 1/2" of one end of the plastic tube to roughen the surface.
21
☛
Roughening the smooth plastic will help the C/A adhere to it better.
❑ 5) Slide the plastic tube through the hole you drilled in the firewall. Adjust the tube so that 1/8" of it extends past the front of the firewall.
❑ 6) When satisfied with the alignment, use Kwik
Bond Thick C/A to glue the tube only to the firewall at this time. Allow the C/A to fully cure before proceeding.
❑ 7) After the C/A has fully cured, use a modeling knife to cut the tube off flush with the front of the firewall.
INSTALLING THE PUSHROD
❑ 8) Carefully remove the throttle arm from your engine's carburetor. Insert the Z-Bend in the end of the
1mm x 500mm pushrod wire into the outermost hole in the throttle arm. See photo # 39 below.
Photo # 39
❑ 11) Using a drill with a 5/64" drill bit, enlarge the third hole out from the center of the servo arm.
❑ 12) Install one adjustable servo connector through the third hole out from the center of the servo arm. When you thread on the nut, don't tighten it completely. You don't want the connector loose, but you do want it to be able to rotate without binding. See photo # 41 below.
Photo # 41
❑ 9) Slide the plain end of the pushrod wire into the plastic tube until the throttle arm lines up with your engine's carburetor. Reattach the throttle arm and rotate the throttle barrel into the fully closed position.
☛
Check for the smooth operation of the pushrod wire.
It should not bind. You may need to make about a 1/4" bend between the throttle arm and firewall so that the pushrod lines up better. See photo # 40 below.
Photo # 40
☛
Apply a drop or two of Kwik Bond Thin C/A to the connector nut and allow the C/A to fully cure. This will prevent the connector nut from loosening during flight.
❑ 13) Per your radio system guide, plug the battery into the switch, the switch into the receiver, and the throttle servo lead into the proper slot in the receiver. Turn on the radio system.
❑ 14) Check to ensure that the throttle servo output shaft is rotating in the correct direction. When the throttle control stick on the transmitter is moved forward, from the idle to the full throttle position, the servo output shaft should rotate counterclockwise. If it doesn't, flip the servo reversing switch on your transmitter.
❑ 15) Position the throttle control stick and the throttle trim lever on your transmitter at their lowest positions.
Slide the adjustable servo connector/servo horn assembly over the plain end of the throttle pushrod wire.
☛
You may need to cut the pushrod wire about 1" shorter to make the end of it more accessible.
❑ 16) After making sure that the carburetor is in the fully closed position, angle the servo horn back about 45º from center and attach it to the servo output shaft. The servo connector should be facing the side of the fuselage.
See photo # 42 below.
Photo # 42
INSTALLING THE SERVO CONNECTOR
❑ 10) Locate one plastic "4-point" servo horn that came with your servo. Each of the arms should have at least three holes in it. Use wire cutters to cut away and remove all but one of the arms.
22
☛
Before gluing the plastic tube into place in the next step, use 220 grit sandpaper to roughen only the gluing surface of the tube.
❑ 17) Using Kwik Bond Thick C/A, glue the plastic tube to the side of the fuselage. When gluing the tube into place make sure that the middle of the tube is below the wing saddle. See photo # 43 below.
Photo # 43
❑ 18) While holding the carburetor barrel fully closed, use a # 0 phillips screwdriver to tighten the machine screw in the top of the adjustable servo connector.
❑ 19) Using a # 0 phillips screwdriver, install and tighten the servo horn retaining screw, provided with your servo, to secure the servo horn into place. Use wire cutters to cut away and remove the excess pushrod wire.
ADJUSTING THE THROTTLE PUSHROD
❑ 20) When the throttle linkage is adjusted properly, the carburetor barrel should be fully closed when the throttle control stick and the throttle trim lever are at their lowest positions. Moving the throttle trim lever up should open the carburetor barrel about 25%. Moving the throttle control stick all of the way forward should open the throttle barrel completely.
☛
All of these movements should be done without any binding present in the linkage. If you hear the servo "buzzing" at either end-point, there is probably binding present in the linkage - see next step.
❑ 21) Sometimes the servo will bind at the fully closed and/or the fully opened throttle positions. If this happens, and your radio is equipped with End Point Adjustments
(EPA), make those adjustments using the transmitter (see your radio guide for further details). If your radio does not have this feature you can still adjust the linkage manually. For more travel, move the Z-Bend to a hole closer to the center of the throttle arm. For less travel, move the servo connector to a hole closer to the center of the servo arm. Ideally, you don't want the servo to bind while at either the idle or the full throttle positions.
ELEVATOR CONTROL SYSTEM
ITEMS REQUIRED
❑
{1} Hardwood Split Elevator Pushrod
❑ {2} Nylon Control Horns
❑ {2} Nylon Control Horn Backplates
❑
{2} Nylon Clevises
❑ {4} 2mm x 25mm Machine Screws
❑ {1} Adjustable Servo Connector Assembly
TOOLS AND SUPPLIES REQUIRED
❑ Kwik Bond Thin C/A
❑ # 0 Phillips Head Screwdriver
❑ Wire Cutters
❑ Adjustable Wrench
❑ Excel Modeling Knife
❑ Electric Drill
❑ 5/64" Drill Bit
❑ Ernst Airplane Stand
❑ Ruler
❑ Pencil
INSTALLING THE CONTROL HORNS
❑ 1) Using a ruler and a pencil, measure out 7/8" from the inside edge of each elevator half, at the hinge line, and draw a mark on each elevator half. Do not measure out from the fuselage sides.
❑ 2) Working with one elevator half for now, position one nylon control horn onto the bottom of the elevator, aligning the centerline of the control horn with the mark you drew. Angle the control horn toward the fuselage side so that the base of the control horn is parallel with the hinge line. Adjust the control horn so that the clevis attachment holes are directly over the hinge line. See photo # 44 below.
Photo # 44
❑ 3) When satisfied with the alignment, use a pencil to mark the locations of the two control horn mounting screws.
23
❑ 4) Remove the control horn and set it aside. Using a drill with a 5/64" drill bit, carefully drill two holes through the elevator at the marks you drew.
☛
Be careful not to drill the holes crooked. They should be drilled at a 90º angle to the elevator.
❑ 5) Set the control horn back into place and realign it. Push two 2mm x 25mm machine screws into the base of the control horn and through the elevator.
❑ 6) Place the nylon control horn backplate onto the machine screws, aligning the two holes in the backplate with the two screws. Using a # 0 phillips screwdriver, evenly tighten both machine screws to draw the backplate into place. Be careful not to overtighten the screws. You don't want to crush the wood.
❑ 7) Repeat steps # 2 through # 6 to install the control horn on the other elevator half.
INSTALLING THE PUSHROD
❑ 8) Using a modeling knife, cut away and remove the covering material from over the two elevator pushrod exit slots in the back of the fuselage. One slot is located on each side of the fuselage, 6" in front of the rudder hinge line. Each slot is 1-1/2" long and 3/16" wide.
❑ 9) Slide the split elevator pushrod assembly through the fuselage, carefully feeding the two threaded wires out the two pushrod exit holes.
☛
When installing the pushrod, make sure that the plain pushrod wire (at the front of the pushrod) is toward the bottom of the fuselage. This will prevent the dowel from
"snagging" on the plywood wing hold down block.
☛
If you're having problems feeding the threaded wires out of the fuselage, drop two pieces of string through the exit holes and into the servo bay. Tie one piece of string to each wire and carefully pull the strings. This will guide the pushrod wires out of the exit holes quickly and easily.
❑ 10) Using a modeling knife and a ruler, measure and cut off two 1/4" pieces of Global XX Silicon Fuel Tubing. Slide one piece of tubing onto the base of each nylon clevis. See photo # 45 below.
Photo # 45
❑ 11) Thread one nylon clevis onto the threaded end of each pushrod wire. For security, thread the clevises on no less than 5/16".
❑ 12) Carefully snap each clevis into the fifth hole out from the base of each control horn and slide the pieces of silicon tubing up over the clevises to secure them into place. See photo # 46 below.
Photo # 46
❑
13) Use a couple of pieces of masking tape, taped between both elevator halves and the stabilizer, to hold both elevator halves centered.
❑ 14) Locate one plastic "4-point" servo horn that came with your servo. Each of the arms should have at least three holes in it. Use wire cutters to cut away and remove all but one of the arms.
❑ 15) Using a drill with a 5/64" drill bit, enlarge the third hole out from the center of the servo arm.
❑
16) Install one adjustable servo connector through the third hole out from the center of the servo arm. When you thread on the nut, don't tighten it completely. You don't want the connector loose, but you do want it to be able to rotate without binding. See photo # 47 below.
Photo # 47
☛
Apply a drop or two of Kwik Bond Thin C/A to the connector nut, allowing the C/A to fully cure. This will prevent the connector nut from loosening during flight.
❑ 17) Per your radio system guide, plug the battery into the switch, the switch into the receiver, and the elevator servo lead into the proper slot in the receiver. Turn on the radio system.
24
❑ 18) Slide the adjustable servo connector/servo horn assembly over the plain end of the pushrod wire. Attach the servo horn to the servo output shaft, making sure that the servo horn is centered and that the servo connector is facing the middle of the fuselage. See photo # 48 below.
Photo # 48
❑ 19) With both of the elevator halves and the servo arm centered, use a # 0 phillips screwdriver to tighten the machine screw in the top of the adjustable servo connector.
❑ 20) Using a # 0 phillips screwdriver, install and tighten the servo horn retaining screw, provided with your servo, to secure the servo horn into place. Use wire cutters to cut away and remove the excess pushrod wire.
ADJUSTING THE PUSHROD
❑ 21) With your radio system plugged in and turned on, check the direction the elevator control surfaces move and the amount of control deflection. To do this pull back on the elevator control stick. Both elevator halves should move up. If they do not, flip the servo reversing switch on your transmitter to change the direction. (Refer to your radio guide for more information on this function.)
❑ 22) Pull back completely on the elevator control stick. While holding the control stick completely back, use a ruler and measure the amount the trailing edge of each elevator half moves up. This measurement should be 1-3/8" measured from the widest point of each elevator half. See figure # 6 below.
Figure # 6
❑ 24) If the elevator halves are moving more than
1-3/8", move the adjustable connector in one hole toward the center of the servo horn to decrease the control deflection. If the elevator halves are moving less than 1-3/8", move both clevises one hole closer to the base of the control horns to increase the control deflection. When adjusted properly, both elevator halves should move 1-3/8" both up and down.
RUDDER CONTROL SYSTEM
ITEMS REQUIRED
❑ {1} Stranded Pull-Pull Cable
❑ {4} 2mm Threaded Brass Couplers
❑ {4} 1mm Brass Collets
❑ {4} Nylon Clevises
❑ {1} 3mm x 50mm Threaded Rod
❑ {2} 3mm Flat Washers
❑ {2} 3mm Hex Nuts
❑ {2} Nylon Adjustable Control Horns
TOOLS AND SUPPLIES REQUIRED
❑ Kwik Bond Thin C/A
❑ # 0 Phillips Head Screwdriver
❑
Adjustable Wrench
❑ Wire Cutters
❑ Needle Nose Pliers
❑
Excel Modeling Knife
❑ Electric Drill
❑ 5/64 & 9/64" Drill Bits
❑
Ernst Airplane Stand
❑ Ruler
❑ Pencil
INSTALLING THE CONTROL ROD
❑ 1) Using a ruler and a pencil, measure up 1-1/2" from the bottom of the rudder, at the hinge line, and draw a mark. Measure back 3/8" from the rudder hinge line, at the mark you just drew, and draw another mark. See photo # 49 below.
Photo # 49
❑ 23) If the control surface deflection is more or less than 1-3/8" it must be changed. If your radio is equipped with End Point Adjustments (EPA), make those adjustments using the transmitter. (Refer to your radio guide for further details.) If your radio does not have this feature, you can still make the adjustments to the pushrod manually - see next step.
25
❑ 2) Using a drill with a 9/64" drill bit, drill a hole through the rudder where the two marks intersect.
☛
Be careful not to drill the hole crooked. Drill the hole at a 90º angle to the rudder.
❑ 3) Slide the 3mm x 50mm threaded rod through the hole. Slide one 3mm flat washer over each end of the rod and push them against the sides of the rudder.
❑ 4) Thread one 3mm hex nut onto each end of the threaded rod. Thread the nuts up against the flat washers while keeping the threaded rod centered. There should be about 5/8" of threaded rod beyond each of the nuts.
See photo # 50 below.
Photo # 50
❑ 10) Working with one length of cable for now, slide one brass collet, non-flange side first, over one end of the cable.
❑ 11) While holding the collet in place so it doesn't slide off, carefully thread the same end of the cable through the predrilled hole in one threaded coupler.
❑ 12) Loop the cable around the coupler and slide the end of it back through the collet. Using needle nose pliers, carefully crimp the collet to lock the cable in place.
See photo # 51 below.
Photo # 51
❑ 5) While keeping the threaded rod centered, tighten the hex nuts using an adjustable wrench.
☛
Do not overtighten the hex nuts. You don't want to crush the wood.
❑ 6) Carefully apply a couple of drops of Kwik Bond
Thin C/A to both of the hex nuts. Allow the C/A to fully cure before proceeding.
☛
The C/A will lock the hex nuts in place and prevent the threaded rod from turning.
❑ 7) After the C/A has cured, thread one nylon adjustable control horn onto each end of the threaded rod.
Thread the control horns on until the ends of the control horns are flush with the ends of the rod.
INSTALLING THE PULL-PULL CABLES
❑ 8) Using a modeling knife, cut away and remove the covering material from over the two rudder cable exit slots in the fuselage sides. One slot is located on each side of the fuselage, 5-1/2" in front of the rudder hinge line and 1-3/4" up from the bottom of the fuselage.
❑ 9) Using a pair of wire cutters, carefully cut the stranded pull-pull cable exactly in half.
☛
If the ends of the cable begin to unravel, use your fingers to twist the ends back into shape.
26
❑ 13) Carefully apply a couple of drops of Kwik Bond
Thin C/A to the brass collet.
☛
The C/A will "wick" between the collet and the cable, making the joint even stronger. Do not omit this step.
❑ 14) Repeat steps # 10 through # 12 to install the threaded coupler onto the end of the second length of cable.
❑ 15) Using a modeling knife and a ruler, measure and cut off two 1/4" pieces of Global XX Silicon Fuel Tubing. Slide one piece of tubing onto the base of two nylon clevises.
❑ 16) Thread one nylon clevis onto each of the two threaded couplers. For security, thread the clevises on no less than 5/16". Carefully snap each clevis onto the adjustable control horns and slide the pieces of silicon tubing up over the clevises to secure them into place.
See photo # 52 below.
Photo # 52
❑ 17) Locate one plastic "2-point" servo horn that came with your servo. Each of the arms should have at least four holes in it.
❑ 18) Using a drill with a 5/64" drill bit, enlarge the third hole out from the center of each servo arm.
❑ 19) Using a modeling knife and a ruler, measure and cut off two 1/4" pieces of Global XX Silicon Fuel Tubing. Slide one piece of tubing each onto the bases of two nylon clevises.
❑ 20) Thread one nylon clevis onto each of the two remaining threaded couplers. For security, thread the clevises on no less than 5/16". Carefully snap each clevis into the enlarged holes in the servo arms and slide the pieces of silicon tubing up over the clevises to secure them into place.
❑ 21) Per your radio system guide, plug the battery into the switch, the switch into the receiver, and the rudder servo lead into the proper slot in the receiver.
Turn on the radio system.
❑ 22) Attach the servo horn to the servo output shaft, making sure that the servo horn is centered. See photo # 53 below.
Photo # 53
❑ 23) Use a couple of pieces of masking tape, taped between the rudder and the stabilizer, to hold the rudder centered. Working with the cable on the right side for now, slide one brass collet, non-flange side first, over the end of the cable.
❑ 24) While holding the collet in place so it doesn't slide away, carefully thread the end of the cable through the predrilled hole in the threaded coupler on the right side.
❑ 25) Pull the cable to remove any slack, then loop the cable around the coupler and slide it back through the collet. Using needle nose pliers, carefully crimp the collet to lock the cable in place. See photo # 54 below.
Photo # 54
❑ 26) Carefully apply a couple of drops of Kwik Bond
Thin C/A to the brass collet.
☛
The C/A will "wick" between the collet and the cable, making the joint even stronger. Do not omit this step.
❑ 27) Repeat steps # 23 through # 25 to install the remaining length of cable to the second threaded coupler.
☛
Look carefully into the back of the fuselage to make sure that the pull-pull cables are not wrapped around each other or around the elevator pushrod.
❑ 28) Using a # 0 phillips screwdriver, install and tighten the servo horn retaining screw, provided with your servo, to secure the servo horn into place. Use wire cutters to remove the excess cable.
❑ 29) Remove the pieces of masking tape from the rudder. With your radio system turned on, double check to ensure that both the rudder and the rudder servo are still centered.
ADJUSTING THE PULL-PULL CABLES
❑ 30) With your radio system plugged in and turned on, check the direction the rudder control surface moves and the amount of control deflection. To do this push right on the rudder control stick. The rudder should move right. If it does not, flip the servo reversing switch on your transmitter to change the direction. (Refer to your radio guide for more information on this function.)
❑ 31) Check the tension of the pull-pull cables. To do this do the following: move the rudder control stick to one side. Let the control stick go and check to see if the rudder returns to center. Do this a couple of times in each direction. If the rudder does not come back to center, one or both pull-pull cables are too tight. You can adjust the tension of the cables by adjusting the clevises. Ideally, the cables should be as tight as possible, while still allowing the rudder to center. The cables should not have slack in them, yet they should not be so tight that the linkage and/or the servo bind.
❑ 32) Push right completely on the rudder control stick. While holding the control stick completely right, use a ruler to measure the amount the trailing edge of the rudder moves right. This measurement should be
2-3/8" measured from the widest point of the rudder. See figure # 7 below.
Figure # 7
27
❑ 33) If the control surface deflection is more or less than 2-3/8" it must be changed. If your radio is equipped with End Point Adjustments (EPA), make those adjustments using the transmitter. (Refer to your radio guide for further details.) If your radio does not have this feature, you can still make the adjustments to the pull-pull cables manually.
❑ 34) If the rudder is moving more than 2-3/8", move both clevises in one hole toward the center of the servo horn to decrease the control deflection. If the rudder is moving less than 2-3/8", thread both nylon adjustable control horns closer to the rudder to increase the control deflection. When adjusted properly, the rudder should move 2-3/8" both right and left.
AILERON CONTROL SYSTEM
ITEMS REQUIRED
❑ {2} 2mm x 80mm Pushrod Wires w/Z-Bends
❑ {2} Nylon Control Horns
❑ {2} Nylon Control Horn Backplates
❑ {2} Nylon Clevises
❑ {4} 2mm x 25mm Machine Screws
TOOLS AND SUPPLIES REQUIRED
❑ # 0 Phillips Head Screwdriver
❑ Wire Cutters
❑ Needle Nose Pliers
❑ Excel Modeling Knife
❑ Electric Drill
❑ 5/64" Drill Bit
❑ Ruler
❑ Pencil
INSTALLING THE CONTROL HORNS
❑ 1) Using a ruler and a pencil, measure out 3-3/4" from the inside edge of each aileron, at the hinge line, and draw a mark. Do not measure out from the sides of the belly pan.
❑ 2) Working with one aileron for now, position one nylon control horn onto the bottom of the aileron, aligning the centerline of the control horn with the mark you drew. The control horn should be aligned perpendicular to the hinge line and the clevis attachment holes should be directly over the hinge line.
❑ 3) When satisfied with the alignment, use a pencil to mark the locations of the two control horn mounting screws onto the aileron.
28
❑ 4) Remove the control horn and set it aside. Using a drill with a 5/64" drill bit, carefully drill two holes through the aileron at the marks you drew.
☛
Be careful not to drill the holes crooked. The holes should be drilled straight down through the aileron.
❑ 5) Set the nylon control horn back into place and realign it. Push two 2mm x 25mm machine screws into the base of the control horn and through the aileron. See photo # 55 below.
Photo # 55
❑ 6) Place the nylon backplate onto the machine screws, aligning the two holes in the backplate with the two screws. Using a # 0 phillips screwdriver, evenly tighten both machine screws to draw the backplate into place. Be careful not to overtighten the screws. You don't want to crush the wood.
❑ 7) Repeat steps # 2 through # 6 to install the control horn on the second aileron.
INSTALLING THE PUSHRODS
❑ 8) Using a modeling knife and a ruler, measure and cut off two 1/4" pieces of Global XX Silicon Fuel Tubing. Slide one piece of tubing onto the base of two nylon clevises.
❑ 9) Thread one nylon clevis onto the threaded end of each 2mm x 80mm pushrod wire. For security, thread the clevises on no less than 5/16".
❑ 10) Working with one aileron for now, use a couple of pieces of masking tape, taped between the aileron and the wing, to hold the aileron centered.
❑ 11) Locate one plastic "4-point" servo horn that came with your servo. Each of the arms should have at least four holes in it. Use wire cutters to cut away and remove all but one of the arms.
❑ 12) Using a drill with a 5/64" drill bit, enlarge the third hole out from the center of the arm.
❑ 13) Install the Z-Bend in the end of one pushrod wire into the hole that you enlarged in the servo arm. Install the wire so that the long portion of the wire comes out on the top of the servo arm. See photo # 56 below.
Photo # 56
❑ 14) Per your radio system guide, plug the battery into the switch, the switch into the receiver, and the aileron servo lead into the proper slot in the receiver. Turn on the radio system.
❑ 15) Attach the servo horn to the servo output shaft, making sure that the servo horn is centered and is facing out toward the tip of the wing. See photo # 57 below.
Photo # 57
❑ 18) Repeat steps # 10 through # 17 to install the second aileron pushrod.
ADJUSTING THE PUSHRODS
❑ 19) With your radio system plugged in and turned on, check the direction the aileron control surfaces move and the amount of control deflection. To do this push right on the aileron control stick. The right-hand aileron should move up and the left-hand aileron should move down (looking from the back of the wing with the wing right-side up). If they do not, flip the servo reversing switch on your transmitter to change the direction.
(Refer to your radio guide for more information on this function.)
❑ 20) Push right completely on the aileron control stick. While holding the control stick completely right, use a ruler and measure the amount the trailing edge of each aileron moves up and down. Both ailerons should move up 1-1/8" and down 1-1/8". These measurements should be measured from the widest point of each aileron. See figure # 8 below.
Figure # 8
❑ 16) With both the servo horn and the aileron still centered, adjust the clevis until it lines up with the control horn. Snap the clevis into the fourth hole out from the base of the control horn and slide the piece of silicon tubing up over the clevis to secure it into place. See photo # 58 below.
Photo # 58
❑ 17) Using a # 0 phillips screwdriver, install and tighten the servo horn retaining screw, provided with your servo, to secure the servo horn into place. Remove the pieces of masking tape from the aileron.
❑
21) If the control surface deflection is more or less than 1-1/8" it must be changed. If your radio is equipped with End Point Adjustments (EPA), make those adjustments using the transmitter. (Refer to your radio guide for further details.) If your radio does not have this feature, you can still make the adjustments to the pushrods manually.
❑ 22) If the ailerons are moving more than 1-1/8", move the Z-Bends in one hole toward the center of the servo horns to decrease the control deflection. If the ailerons are moving less than 1-1/8", move both clevises one hole closer to the base of the control horns to increase the control deflection. When adjusted properly, both ailerons should move 1-1/8" both up and down.
☛
Now that you've finished the basic control system setup, don't forget to read the section starting on page
# 37 if you plan on 3D flying. That section details more specific control surface deflections, transmitter setups and mixing recommendations.
29
FUEL TANK
ITEMS REQUIRED
❑
{1} 280cc Fuel Tank
❑ {1} Nylon Fuel Tank Cap
❑ {1} Rubber Stopper
❑
{1} Nylon Stopper Backplate
❑ {1} Silicon Fuel Tubing
❑ {1} Weighted Fuel Pick-Up
❑
{1} 4mm x 40mm Nylon Fuel Pick-Up Tube
❑ {2} 4mm 90º Nylon Vent Tubes
❑ {1} 3mm x 22mm Self Tapping Screw
TOOLS AND SUPPLIES REQUIRED
❑ Wilhold Silicon Sealant
❑ # 1 Phillips Head Screwdriver
❑ Excel Modeling Knife
❑ Ernst Airplane Stand
❑ Ruler
❑ Pencil
ASSEMBLING THE STOPPER
❑ 1) Using a ruler and a modeling knife, measure and cut the silicon fuel tubing to 3-3/4" long. Attach one end of the silicon tubing to the weighted fuel pick-up.
☛
There are three molded holes in the rubber stopper.
Two holes are opened and one is covered by a thin layer of rubber at the front of the stopper. Using a modeling knife, cut away and remove the thin layer of rubber to completely open the third hole.
❑ 2) Push the straight 4mm x 40mm nylon fuel pick-up tube through one hole in the rubber stopper until 1/2" of the tube sticks out from the front of the stopper. Slide the nylon backplate over the tube at the back of the stopper.
See photo # 59 below.
Photo # 59
❑ 3) Push one 4mm 90º nylon vent tube into the nylon backplate and through the stopper until the end of the tube sticks out 1/2" in front of the stopper.
30
❑ 4) Using a modeling knife, cut away and remove part of the second nylon vent tube, leaving 1/4" beyond the bend. This will be the fill tube.
☛
You have to cut the fill tube shorter so that the stopper assembly will fit into the fuel tank opening.
❑ 5) Push the fill tube into the nylon backplate and through the rubber stopper until the end of the tube sticks out 1/2" in front of the stopper. Orientate the two tubes as shown. See photo # 60 below.
Photo # 60
❑ 6) Slide the nylon fuel cap over the three tubes at the front of the stopper. Push the 3mm x 22mm self tapping screw into the center hole in the cap and through the rubber stopper and use a # 1 phillips screwdriver to begin tightening the screw, but do not completely tighten it yet.
❑ 7) Slide the silicon fuel tubing, with the weighted pick-up attached, onto the back of the nylon fuel pick-up tube. See photo # 61 below.
Photo # 61
INSTALLING THE STOPPER ASSEMBLY
❑ 8) Push the stopper assembly into the molded fuel tank opening and rotate the stopper so that the nylon vent tube is pointing straight up toward the top of the fuel tank.
☛
You can identify the top of the fuel tank because it is a shorter distance from the middle of the fuel tank opening.
☛
If you hold the fuel tank assembly up against a bright light, you can see into the tank to check the orientation of the stopper assembly.
❑ 9) Check to make sure that the weighted fuel pick-up moves freely within the tank. The end of the fuel pick-up should be about 3/8" in front of the back of the tank.
❑ 10) When satisfied with the alignment of the stopper assembly, use a # 1 phillips screwdriver to tighten the
3mm x 22mm self tapping screw until the stopper expands and seals the fuel tank opening. See photo # 62 below.
Photo # 62
☛
Make sure that the fuel tank is right-side up. The top of the fuel tank should be toward the top of the fuselage.
❑ 15) Using a modeling knife, cut out several pieces of Dubro 1/4" Foam Rubber. Push the back of the fuel tank down against the forward bulkhead and use the pieces of foam rubber to secure the fuel tank in position. See photo # 63 below.
Photo # 63
☛
Do not overtighten the self tapping screw. Doing so could cause the fuel tank to split.
INSTALLING THE FUEL TANK
❑ 11) Using a modeling knife, cut three 10" long pieces of Global XX Silicon Fuel Tubing.
❑ 12) Install the pieces of fuel tubing onto the three nylon tubes at the front of the fuel tank. Use a pencil to label the ends of the tubing either Vent, Fuel Pick-Up or
Fuel Filler.
☛
Labeling the different pieces of tubing will prevent you from mixing them up later on.
☛
We do not recommend permanently installing the fuel tank at this time. Depending on the engine you have decided to use, it's possible that you may have to install the receiver battery in the fuel tank compartment.
If you do, you will have to remove the fuel tank. After balancing, we suggest coming back to these steps and permanently installing the fuel tank.
❑ 13) Carefully apply a generous bead of Wilhold
Silicon Sealant around the seam between the front of the fuel tank and the fuel tank cap.
☛
The Silicon Sealant will seal the gaps between the fuel tank cap and the predrilled hole in the firewall.
❑ 14) Feed the ends of the fuel tubing through the predrilled hole in the firewall and slide the fuel tank into the fuel tank compartment. Push the fuel tank up against the back of the firewall making sure that the fuel tank cap is seated in the predrilled hole.
COWLING
ITEMS REQUIRED
❑ {1} Fiberglass Molded Cowling
❑ {1} Spinner Assembly
❑ {1} 10 x 6 Composite Propeller
❑ {1} Clear Molded Cowling Template
❑ {4} 3mm x 18mm Wood Screws
❑
{4} 3mm Flat Washers
❑ {1} Nylon Fuel Filler Housing
❑ {1} Nylon Fuel Filler Snap-Ring
❑
{1} Nylon Fuel Filler Plug
TOOLS AND SUPPLIES REQUIRED
❑ # 0 Phillips Head Screwdriver
❑ # 1 Phillips Head Screwdriver
❑ Adjustable Wrench
❑ Excel Modeling Knife
❑ Electric Drill
❑ 5/64", 1/8", 1/4" & 3/8" Drill Bits
❑ Ernst Airplane Stand
❑ Ruler
❑ Pencil
❑ Dremel Tool w/Cutting Disc & Sanding Drum
❑ 220 Grit Sandpaper w/Sanding Block
❑ Masking Tape
ALIGNING THE COWLING
❑ 1) Remove the needle valve, detent spring and muffler assembly from your engine and set them aside.
31
❑ 2) Remove the tape from the clear molded cowling template so that you have a right and left half.
❑ 3) Using a # 0 phillips screwdriver, remove the two wood screws that hold the spinner cone to the spinner backplate. Set the spinner cone and screws aside.
❑ 4) Slide the spinner backplate onto your engine, making sure that it is firmly pushed up against the drive washer. See photo # 64 below.
Photo # 64
☛
If any part of the template is touching the engine, remove the template and adjust the sizes of the cutouts until you are satisfied with the fit. There should be a minimum space of 3/32" between the engine and the template.
❑ 10) Slide the template and the spinner backplate back into place and realign them. Use several pieces of masking tape to hold the template to the fuselage.
❑ 11) Using a pencil, mark the locations of the four mounting screws onto the template. Two screws should be located on each side of the template, equally spaced apart. They will thread into the edges of the firewall, so position the marks 1/8" behind the front edge of the firewall. See photo # 66 below.
Photo # 66
❑ 5) With the fuselage in your airplane stand, hold the right half of the clear molded cowling template up against the side of the fuselage, aligning the best you can the front of the template with the back of the spinner.
❑ 6) While holding the template in place, use a pencil to outline on the template the parts of the engine that need to be removed for clearance.
❑ 7) Using a Dremel Tool with first a cutting disc then a sanding drum, cut away the template from within the outlines you drew. Remove small amounts of material at a time, checking your work often.
❑
8) After you have finished rough cutting the clearance holes, use a couple of pieces of masking tape to join the two template halves back together.
❑ 9) Remove the spinner backplate from the engine.
Slide the template over the engine and reinstall the backplate. Check the alignment of the template: there should be a 3/32" space between the template and the backplate, and the front of the template should be centered around the backplate. No part of the template should touch the engine, either. See photo # 65 below.
Photo # 65
❑ 12) While holding the template firmly in place, use a drill with a 5/64" drill bit to drill four pilot holes through the template and into the edges of the firewall.
❑ 13) Using a pencil, mark the locations of the high and low speed needle valves onto the template.
❑ 14) Remove the spinner backplate and the template.
Using a drill with a 5/16" drill bit, drill access holes through the template for the high and low speed needle valves, then use a 1/8" drill bit to enlarge the four pilot holes in only the template - not the fuselage.
❑ 15) Using a Dremel Tool with first a cutting disc then a sanding drum, cut a 1" diameter air-intake hole in the front of the template. See photo # 67 below.
Photo # 67
❑ 16) Install the muffler onto your engine. Slide the spinner backplate and the cowling template back into place and realign them. Check to make sure the cowling does not touch the muffler.
32
☛
If you are using a four stroke engine you may need to cut away and remove some of the template to clear the muffler's exhaust header.
❑ 17) Using a drill with a 3/8" drill bit, carefully drill a hole through the side of the template for the fuel filler housing.
❑ 18) Use 220 grit sandpaper to smooth out all of the cutouts, being careful to remove any burrs or sharp points.
☛
If there are any burrs or sharp points on the cowling template, they may scratch the paint when you slide it over the fiberglass cowl.
INSTALLING THE COWLING
❑ 19) Slide the cowling template over the fiberglass cowling and press them both firmly against each other.
Using a pencil, carefully trace all of the cutouts and the holes onto the fiberglass cowl.
❑ 20) Remove the cowling template and carefully cut out the fiberglass cowl using the same technique as you did previously. Make sure to drill the holes for the cowl mounting screws, high and low speed needle valves and the fuel filler housing.
❑ 21) Push the fuel filler housing into the 3/8" hole you drilled and snap the nylon snap-ring over the housing from inside the cowling. See figure # 9 below.
Figure # 9
❑ 22) Using a modeling knife, cut to length and attach the vent tube to the muffler pressure nipple and the fuel pick-up tube to the fuel nipple on the carburetor (if using a standard carburetor engine) or to the fuel nipple on the needle valve assembly (if using an engine equipped with a remote mounted needle valve assembly).
❑ 23) Slide the fuel filler tube through the fuel filler housing mounted in the cowl. Leave about 1" of the tube beyond the outside of the cowl and cut off the remainder.
Attach the nylon fuel filler plug to the end of the tubing and push the plug into the housing.
❑
24) Slide the cowling into place and align it. Using a # 1 phillips screwdriver install and tighten four 3mm x
18mm wood screws and four 3mm flat washers to secure the cowling firmly into place.
INSTALLING THE
PROPELLER AND THE SPINNER
❑ 25) Slide the spinner backplate onto the engine's crankshaft, followed by the propeller and the propeller washer.
❑ 26) Turn the propeller until it touches the two molded posts in the backplate. While holding the propeller in place, install and tighten the propeller nut using an adjustable wrench.
❑ 27) Test fit the spinner cone over the propeller.
Depending on the size of the propeller you are using, the spinner cone may not fit over it. If this is the case, use a modeling knife to carefully enlarge the two cutouts in the spinner cone.
☛
It is important that the spinner cone not touch any part of the propeller when it is in place.
❑ 28) When satisfied with the fit, slide the spinner cone over the propeller. Using a # 0 phillips screwdriver, install and tighten the two wood screws (that you removed previously) to secure the spinner cone into place.
CANOPY
ITEMS REQUIRED
❑ {1} Clear Molded Canopy
❑ {6} 2mm x 8mm Wood Screws
TOOLS AND SUPPLIES REQUIRED
❑ Pacer Formula 560 Canopy Glue
❑
# 0 Phillips Head Screwdriver
❑ Electric Drill
❑ 1/16" Drill Bit
❑
Promax Lexan Canopy Scissors
❑ Ernst Airplane Stand
❑ Ruler
❑
Pencil
❑ 220 Grit Sandpaper w/Sanding Block
❑ Masking Tape
ALIGNING THE CANOPY
❑ 1) Using Promax Lexan Canopy Scissors, carefully cut out the canopy along the molded scribe line.
❑ 2) Using 220 grit sandpaper with a sanding block, carefully sand the edges of the canopy smooth and straight.
☛
Be careful not to let the sandpaper scratch the clear parts of the canopy.
33
❑ 3) Using a ruler and a pencil, measure back 1-5/8" from the back edge of the cockpit cutout, at the top of the fuselage, and draw a mark.
❑ 4) Set the canopy on the fuselage, aligning the back edge of the canopy with the mark you drew.
❑ 5) Look from the front of the fuselage and carefully center the canopy. When satisfied with the alignment, use a couple of pieces of masking tape to hold the canopy firmly in place. See photo # 68 below.
Photo # 68
INSTALLING THE CANOPY
❑ 6) Using a pencil, mark the locations of the six canopy hold down screws. Three screws should be located on each side of the canopy frame - one at the front, one at the back and one in the middle.
❑ 7) Using a drill with a 1/16" drill bit, drill pilot holes through the canopy and into the fuselage at the six marks you drew.
❑ 8) Remove the pieces of masking tape and the canopy. Carefully apply a thin bead of Pacer Formula
560 Canopy Glue around the base of the canopy.
❑ 9) Set the canopy back into place and realign it.
Using a # 0 phillips screwdriver, install and tighten the six 2mm x 8mm wood screws to hold the canopy in place.
See photo # 69 below.
Photo # 69
☛
Before the Formula 560 Canopy Glue dries, use a paper towel soaked with water to remove any excess glue that might squeeze out onto the fuselage. If any glue has squeezed out inside the canopy, don't worry. The glue dries clear so you won't see it.
34
FINAL ASSEMBLY
ITEMS REQUIRED
❑
{2} Nylon Molded Wing Skids
❑ {1} Decal Set
TOOLS AND SUPPLIES REQUIRED
❑ Kwik Bond 5 Minute Epoxy
❑ # 0 Phillips Head Screwdriver
❑ Excel Modeling Knife
❑ Promax Curved Scissors for Plastic
❑ Electric Drill
❑ 5/64" & 1/8" Drill Bits
❑ Ernst Airplane Stand
❑ Ruler
❑ Pencil
❑ Masking Tape
❑ Paper Towels
❑ Rubbing Alcohol
❑ NHP Epoxy Mixing Sticks
❑ NHP Epoxy Mixing Cups
APPLYING THE DECALS
❑ 1) Using a clean cloth, wipe the airframe down completely to remove dust, debris and oil.
❑ 2) Working with one decal at a time, use a pair of scissors and carefully cut out the decal along its outer edges.
❑ 3) Remove the protective backing from the decal and stick the decal to the airplane (use the box cover photos to position the decals). Lightly rub the decal with a soft cloth to remove any trapped air from beneath it.
☛
If any air bubbles form in the decal you can "prick" the bubbles with a straight pin to release the air.
❑ 4) Repeat the steps above to install the remaining decals. Rub each decal down thoroughly to adhere it into place.
INSTALLING THE WING SKIDS
❑ 5) Using a ruler and a pencil, measure forward 6" from the aileron hinge line, at the wing tip, and draw a mark. Measure in 3/8" from the wing tip, at the mark you just drew, and draw a second mark. Where these two marks intersect is the location of the wing skid.
❑ 6) Set the nylon wing skid in place and use a pencil to mark the locations of the three mounting pins onto the bottom of the wing.
❑ 7) Using a drill with a 1/8" drill bit, drill shallow holes into the wing at the three locations you marked.
☛
Be careful not to drill through the top of the wing.
❑ 8) Mix a small quantity of Kwik Bond 5 Minute
Epoxy and apply a thin layer to the bottom of the wing skid and to the three mounting pins. Push the wing skid into place and remove any excess epoxy using a paper towel and rubbing alcohol. See photo # 70 below.
Photo # 70
❑ 15) Set the receiver and the battery pack into the fuselage. When you balance the airplane in the next section you will need to move the battery and receiver forward or aft to balance the airplane. When you are ready to install them permanently, use a couple of pieces of Dubro
1/4" foam rubber and scrap balsa glued between the fuselage sides to wedge them into place.
☛
If you are using a two stroke engine you will most likely need to install the battery pack inside the fuel tank compartment and the receiver behind the fuel tank.
If this is the case, you will need to remove the fuel tank and use several pieces of Dubro 1/4" foam rubber to wedge the battery in place between the tank and the fuselage floor.
☛
If you are using a four stroke engine you will most likely need to install both the flight battery and the receiver behind the fuel tank.
❑ 16) After you have installed the receiver, use a drill with a 5/64" drill bit and drill a hole through the left side of the fuselage, opposite the receiver. Unwrap the receiver antenna and feed it out through the hole.
❑ 17) Using a modeling knife, carefully make an antenna mount out of an extra servo horn. Cut the arm into the shape shown. Use the modified servo arm and a rubber band to secure the end of the antenna to the tail wheel wire. See figure # 10 below.
Figure # 10
❑ 9) Repeat steps # 5 through # 8 to install the wing skid on the other half of the wing.
INSTALLING THE SWITCH
❑ 10) The switch should be mounted in the left side of the fuselage in front of the servo tray and below the bottom edge of the canopy. Use the faceplate of the switch itself to locate and mark the switch cutout and the two mounting holes.
❑ 11) Using a modeling knife, cut out the hole for the switch. Using a drill with a 5/64" drill bit, drill the two pilot holes through the fuselage side.
❑ 12) Mount the switch using the two machine screws provided with your radio system. Use a # 0 phillips screwdriver to tighten the screws.
INSTALLING THE
RECEIVER AND THE BATTERY
❑ 13) Using a modeling knife, cut out two pieces of
Dubro 1/4" foam rubber large enough to be wrapped around the receiver and the battery pack.
❑ 14) Wrap the receiver and the battery pack in the foam rubber, using several long pieces of masking tape, wrapped around the parts, to hold the foam in place.
☛
Do not wrap the foam too tightly or it will reduce its vibration dampening quality.
BALANCING
TOOLS AND SUPPLIES REQUIRED
❑ 4mm Hex Driver
❑ Ruler
❑ Masking Tape
BALANCING THE FREESTYLE ARF
❑ 1) It is critical that your airplane be balanced correctly. Improper balance will cause your airplane to lose control and crash.
The Center of Gravity is located 3-3/4" back from the leading edge of the wing, at the fuselage sides.
35
☛
This location is recommended for initial test flying.
The C.G. can be moved fore or aft up to 1/2", but it is not recommended that the C.G. be located any farther back than 4-1/4" behind the leading edge of the wing, at the fuselage sides.
☛
The Freestyle should be balanced with the fuel tank empty.
❑ 2) Install the wing onto the fuselage. Apply two short pieces of masking tape on the top of the wing, 3-3/4" back from the leading edge, at the fuselage sides.
❑ 3) Turn the airplane upside down, place your fingers on the masking tape and carefully lift the airplane.
If the nose of the airplane falls, the airplane is nose heavy.
To correct this, move the battery pack and/or receiver back far enough to bring the airplane into balance. If the tail of the airplane falls, the airplane is tail heavy. To correct this, move the battery pack and/or receiver forward enough to bring the airplane into balance. When balanced correctly, the airplane should sit level or slightly nose down when you lift it up with your fingers at the
C.G. location.
☛
Once you have flown and become familiar with the flight characteristics of the Freestyle, the balance point
(C.G.) can be moved fore or aft up to 1/2" in each direction to change the flight performance. Moving the balance point back will cause the airplane to be more responsive, but less stable. Moving the balance point forward will cause the airplane to be more stable, but less responsive.
Do not fly the Freestyle beyond the recommended balance range or an uncontrollable crash could result!
LATERAL BALANCING
☛
Lateral balancing will make the airplane easier to trim and will make it track straighter in the air. It is highly recommended.
❑ 4) Turn the airplane upside down and tie one length of string to the propeller shaft and one length of string to the tail wheel wire.
❑ 5) With someone helping you, carefully lift the airplane up by the two pieces of string. Watch how the wing reacts. If one side of the wing drops, that side is heavier than the other. To correct this, stick a small piece of self adhesive lead to the bottom of the lighter wing half.
❑ 6) Repeat the procedure a couple of more times to double check your findings. When done properly the wing should stay level when you lift the airplane.
36
CONTROL THROWS
❑ 1) We recommend setting up the Freestyle using the control throws we recommended in the pushrod installation steps. Those control throws are suggested for initial test flying. If you haven't set up the control throws yet, we have listed them here again. Please refer back to those pages for the proper technique for adjusting the control throws. These settings will allow the airplane to fly smoother and make it easier to control.
Elevator:
Ailerons:
Rudder:
TEST FLYING
1-3/8" Up
1-1/8" Up
1-3/8" Down
1-1/8" Down
2-3/8" Right 2-3/8" Left
❑ 2) After you have become familiar with the flying characteristics of the Freestyle, you may want to increase the control throws to the settings listed below. These throws will provide greater aerobatic performance.
Elevator:
Ailerons:
Rudder:
SPORT FLYING
1-9/16" Up 1-9/16" Down
1-1/4" Up 1-1/4" Down
2-5/8" Right 2-5/8" Left
IMPORTANT
The control throws listed above are the maximum we would recommend for sport flying. If you want to do
3D aerobatics with the Freestyle, please completely read and understand the section "3D Aerobatic Flying Setup" beginning on page # 38. That section talks about important setup tips and control throw recommendations that should not be ignored.
PREFLIGHT CHECK
❑ 1) Completely charge the transmitter and receiver batteries before your first day of flying.
❑ 2) Check every bolt and every glue joint in the
Freestyle to ensure that everything is tight and well bonded. This should include all of the control surface hinges as well.
❑ 3) Double check the balance of the airplane. Do this with the fuel tank empty.
❑ 4) Check the control surfaces. They should all move in the correct direction and not bind.
❑ 5) If your radio transmitter is equipped with dual rate switches double check that they are on the low rate setting for your first few flights.
❑ 6) Check to ensure that all of the control surfaces are moving the proper amount in both low and high rate settings.
❑ 7) Check the receiver antenna. It should be fully extended and not coiled up inside the fuselage.
❑ 8) Properly balance the propeller. A propeller that is out of balance will cause excessive vibration which could lead to engine and/or airframe failure and it will reduce engine efficiency and power.
SAFETY
The following are our general guidelines for your safety and the safety of others. Please read and understand these safety guidelines before going out to the flying field for the first time.
❑ 1) Do not test fly your model for the first time without first having it safety-checked by an experienced modeler.
❑ 2) Do not fly your model higher than approximately
400 feet within 3 miles of an airport without having an observer with you. The observer should tell you about any full-size aircraft in your vicinity and you should always give the right-of-way to full-scale aircraft.
❑ 3) When flying at a flying field with established rules, you should abide by those rules. You should not deliberately fly your model in a reckless and/or dangerous manner.
❑ 4) While flying, you should not deliberately fly behind the flight line. If your model should inadvertently fly behind the flight line, you should change course immediately.
❑ 5) You should complete a successful range check of your radio equipment prior to each new day of flying, or prior to the first flight of a new or repaired model.
❑ 6) You should perform your initial turn after take off away from the flightline and/or spectator area.
❑ 7) You should not knowingly operate your R/C radio system within 3 miles of a preexisting model club flying field without a frequency sharing agreement with that club.
FLYING THE FREESTYLE
The Freestyle is designed for those pilots who are experienced at flying sport models. It is not a trainer. If you do not feel comfortable that you are able to test fly the airplane, don't hesitate to ask someone for some help test flying and trimming it.
When set up for test flying or general sport flying, the Freestyle is much like flying any other sport airplane.
The Freestyle is a nimble flier. It's very lightweight, has a thick airfoil and a low wing loading, which makes it very predictable during slow flight and landing. Because it uses very large control surfaces for its size you need to remember not to over-control. For general flying, you will not need to move the sticks very far.
TAKE OFF
Because the Freestyle is light and has a lot of power, it sometimes seems like it wants to take off by itself. Do be aware that it's still important to let the airplane get up to flying speed before lifting off the ground. Lifting the airplane off the ground too fast will cause the airplane to stall and crash. You should allow the airplane to roll out until the tail is completely off the ground and flying and then gently pull it off the ground and into a shallow climb.
Because of the torque of the engine, the airplane will have a natural tendency to pull to the left when it is accelerating down the runway. You will need to compensate for this by applying and holding right rudder during the takeoff roll. Once the airplane lifts off the ground, you can release the right rudder.
IN THE AIR
In the air the Freestyle is as smooth and docile or as wild and aerobatic as you want it to be. What's to say:
It's made for aerobatics and that's what it does best. Pretty much anything you can do, the Freestyle will do like no other .40 size airplane you've flown before.
LANDING
Because of the Freestyle's light weight and low wing loading, landings are very smooth and predictable. There is no tendency to tip stall, but we do recommend that you land with a small amount of power. It's not good practice to just chop the power and dive the airplane to the runway. Because it glides so well you will probably find that you will have to reduce power near the beginning of your downwind leg to give the airplane a chance to slow down.
Use small control inputs so you don't over-control and gently flair for a three point landing.
37
3D AEROBATIC FLYING SETUP
When setting up an airplane for 3D flying, there are some points that you should be aware of. If you're a veteran of high performance aerobatics, you've probably heard this information before but, if this is your first high performance 3D airplane, this information will be very important to you.
HINGE GAPS
Because of the large control surface area it is imperative that the aileron and elevator hinge gaps be sealed. Failure to do this can lead to control surface flutter, which in turn can cause your airplane to crash. Sealing the hinge gaps will also provide crisper control response and the model will fly straighter and truer, making trimming much easier. Hinge gaps can be sealed using heat shrink covering material or clear vinyl tape. To seal the hinge gaps follow these steps:
❑ 1) Cut a piece of covering material 1" wide and the same length as the hinge line.
❑ 2) Fold the length of covering material in half lengthwise so that there is a sharp crease down the middle of the material.
❑ 3) Remove the protective backing from the covering material. With the control surface fully deflected in the "UP" position, place the length of covering material over the hinge line, making sure that the crease is completely down in the hinge line.
❑ 4) With the control surface fully deflected in the
"UP" position, use a heat sealing iron to carefully adhere the covering material to both the trailing edge of the flying surface and the leading edge bevel of the control surface. Use a modeling knife to trim the excess covering material flush with the surfaces.
❑ 5) Pivot the control surface up and down several times to check for free movement.
CONTROL SURFACE LINKAGES
If you don't maintain the proper mechanical advantage on the control surfaces, control surface flutter may result, which in turn can cause your airplane to lose control and crash. What mechanical advantage means in our case is the distance that the pushrod attachment points (pivot points) are from the servos and the control surfaces.
☛
Keeping the pushrods as close to the center of the servo arms as possible will increase the servo's resolution. What this means is that when you move the control sticks, the servo arms will have to travel farther to achieve the desired control inputs. This makes the resolution higher, therefore causing the control surface deflection to be more precise. We don't recommend moving the pushrods any farther away from the center of the servo arms than absolutely necessary.
☛
Keeping the pushrod as far away as possible from the control surface is better than moving it closer. The mechanical advantage is greatly reduced the closer the pushrod is moved toward the control surface. We don't recommend moving the pushrods any closer to the control surfaces than absolutely necessary.
THROTTLE MANAGEMENT
It is very important that you understand throttle management. In a nutshell, this means no full throttle dives. Full throttle dives should be avoided so as not to cause control surface flutter. When the nose of the airplane drops, decrease the throttle, just as in full-scale aerobatics.
Continued on Next Page
38
RADIO SETUP FOR 3D FLYING
Although you don't have to use a computer radio to enjoy the flying qualities of the Freestyle, if you're planning on doing
3D aerobatics it is recommended. Before making any adjustments, please read and understand your radio's setup manual.
EXPONENTIAL
Expo, as it's more commonly referred to, softens the control feel around neutral. This is especially helpful when flying an airplane that uses a lot of control throw, like the Freestyle. Softening the neutral point makes the airplane fly smoother and makes it more likely that you won't over-control. Obviously you may want to change the expo settings to suit your flying style, but here are some good starting points:
Elevator:
Ailerons:
Rudder:
SPORT FLYING
30%
35%
25%
3D FLYING
60%
50%
50%
☛
If you are not used to flying with expo, we suggest starting with lower percentages until you become more accustomed to the feel of the controls.
DIFFERENTIAL MIXING
Differential mixing allows you to control different amounts of both up and down aileron control throws. This eliminates the adverse yaw that is noticeable in some airplanes, making the airplane roll straighter and truer.
Ailerons:
Ailerons:
SPORT FLYING
1-1/4" Up 1-1/8" Down
3D FLYING
1-7/16" Up 1-5/16" Down
FLAPERON AND SPOILERON MIXING
Because the Freestyle uses individual aileron servos, they can be plugged separately into the receiver and will allow the use of flaperons (both ailerons down at the same time) and spoilerons (both ailerons up at the same time). These functions can then be mixed with the elevator for extreme pitch changes useful in 3D maneuvers.
Elevator:
Elevator:
1-3/8" Up and Flaperons (down) 1/2"
1-3/8" Down and Spoilerons (up) 1/2"
☛
We do not recommend using flaperon and spoileron to elevator mixing during general sport flying, especially during takeoff and landing. This mixing should only be used for 3D maneuvers.
3D FLYING CONTROL SURFACE THROWS
Elevator:
Ailerons:
Rudder:
1-3/4" Up 1-3/4" Down
1-7/16" Up 1-5/16" Down
3" Right 3" Left
☛
The 3D control surface throws are our preferences. The airplane flies very good using them; however, these recommendations are not set in stone. Feel free to make adjustments to suit your flying style. Have fun experimenting!
39
TRIM CHART
After you have test flown and done the initial trim changes to the aircraft, use the Trim Chart below to begin trimming your airplane. Following and adhering to this chart will result in the ability to diagnose trim problems and correct those problems using the simple adjustments shown below. Making these observations and related corrections will result in a straighter and truer flying airplane.
TRIM FEATURE
Control Centering
Control Throws
Engine Thrust Angle*
Center of Gravity and
Longitudinal Balance
Yaw**
Lateral Balance
Aileron Rigging
MANEUVER
Fly general circles and random maneuvers
Fly random maneuvers
From straight and level flight, chop the throttle quickly
From level flight, roll to a 45º bank and neutralize the controls
Into the wind, do inside loops using only elevator.
Repeat test doing outside loops from an inverted entry
Into the wind, do tight inside loops
Wing the wings level pull to a vertical climb and neutralize the controls
OBSERVATION
Try for hands off straight and level flight
A) Too sensitive, jerky controls
B) Not sufficient control
A) Airplane continues in a level path for a short distance
B) Airplane pitches nose up
C) Airplane pitches nose down
A) Airplane continues in the bank for a moderate distance
B) The nose pitches up
C) The nose drops
A) Wings are level throughout
B) Yaws to right in both inside and outside loops
C) Yaws to left in both inside and outside loops
D) Yaws to the right on inside loops and yaws to the left on outside loops
E) Yaws to the left on inside loops and yaws to the right on outside loops
A) Wing are level and plane falls to either side
B) Falls off to the left in loops.
Worsens as loops tighten
C) Fall off to the right in loops.
Worsens as loops tighten
A) Climb continues along the same path
B) Nose tends to go toward an inside loop
C) Nose tends to go toward an outside loop
CORRECTION
Readjust linkages so the transmitter trim levers are centered
If A) Adjust linkages to reduce control throws
If B) Adjust linkages to increase control throws
If A) Engine thrust angle is correct
If B) Decrease down-thrust
If C) Increase down-thrust
If A) Trim settings are good
If B) Add nose weight
If C) Remove nose weight
If A) Trim settings are good
If B) Add left rudder trim
If C) Add right rudder trim
If D) Add left aileron trim
If E) Add right aileron trim
If A) Trim settings are good
If B) Add weight to right wing tip
If C) Add weight to left wing tip
If A) Trim settings are good
If B) Raise both ailerons very slightly
If C) Lower both ailerons very slightly
*Engine thrust angle and center of gravity interact. Check both.
**Yaw and lateral balance produce similar symptoms. Note that the fin may be crooked. Make certain both elevator halves are even with each other and that they both produce the same amount of control deflection throughout the complete deflection range. Right and left references are as if you were in the cockpit.
40
41
42
P R ODUCT EV A L U A TION SHEET
Telling us what you like and don't like determines what model kits we make and how we make them. We would appreciate it if you would take a few minutes of your time to answer the following questions about this kit. Simply fold this form on the dotted lines, seal with tape and mail it to us. Do not use staples and make sure our address faces
out.
1) Kit:
Global Freestyle ARF
2) Where did you learn about this kit?
❑ Magazine Ads ❑ Friend
❑ Hobby Shop
❑ Internet
❑ Other
3) What influenced you the most to buy this kit?
❑ Magazine Ads ❑ Price
❑ Type of Model
❑ Recommendation
❑ Internet
❑
❑
Box Art
Other
4) Did you have any trouble understanding the written instructions? If yes, please explain.
❑ Yes ❑ No
________________________________________
________________________________________
________________________________________
________________________________________
5) Did you have any trouble understanding any of the photographs? If yes, please explain.
❑ Yes ❑ No
________________________________________
________________________________________
________________________________________
________________________________________
6) Were any of the kit parts:
❑ Damaged
❑ Missing
❑ Wrong Size
❑ Wrong Shape
If you checked any of the boxes above, did you contact our Customer Service Department to resolve the problem?
❑ Yes ❑ No
7) Was any of the assembly difficult for you? If yes, please explain.
❑ Yes ❑ No
________________________________________
________________________________________
________________________________________
________________________________________
8) What did you like most about this kit?
❑ Assembly Manual ❑ Parts Fit
❑ Hardware Supplied
❑ Other
❑ Price
________________________________________
________________________________________
________________________________________
9) What did you like least about this kit?
❑ Assembly Manual ❑ Parts Fit
❑ Hardware Supplied
❑ Other
❑ Price
________________________________________
________________________________________
________________________________________
10) Are you satisfied with the finished model? If no, please explain.
❑ Yes ❑ No
________________________________________
________________________________________
________________________________________
________________________________________
11) How does this kit compare to similar kits by other manufacturers?
❑ Better
❑ Not as Good
❑ As Good
Additional Comments: ______________________________________________________________________
________________________________________________________________________________________
________________________________________________________________________________________
________________________________________________________________________________________
________________________________________________________________________________________
43
44
_____________________________
_____________________________
_____________________________
(Return Address Here)
Fold along dotted line
Global Hobby Distributors
Attn: Customer Care
18480 Bandilier Circle
Fountain Valley CA 92728-8610
Fold along dotted line
Post Office will not deliver without proper postage
advertisement
* Your assessment is very important for improving the workof artificial intelligence, which forms the content of this project
Related manuals
advertisement
Table of contents
- 2 Safety Warning
- 3 Introduction
- 4 Our Recommendations
- 5 Additional Items Required
- 5 Tools and Supplies Required
- 5 Metric Conversion Chart
- 6 Kit Contents
- 7 Replacement Parts
- 8 A Note About Covering
- 8 Wing Assembly
- 8 Installing the Dihedral Brace
- 9 Joining the Wing Halves
- 9 Wing Mounting
- 9 Installing the Wing Bolt Doubler
- 10 Mounting the Wing
- 10 Belly Pan
- 10 Aligning the Belly Pan
- 11 Installing the Belly Pan
- 11 Horizontal Stabilizer
- 11 Aligning the Horizontal Stabilizer
- 12 Mounting the Horizontal Stabilizer
- 13 Vertical Stabilizer
- 13 Aligning the Vertical Stabilizer
- 13 Mounting the Vertical Stabilizer
- 14 Control Surface Hinging
- 14 Hinging the Ailerons
- 14 Hinging the Elevator Halves
- 15 Hinging the Rudder
- 15 Tail Wheel
- 16 Assembling the Bracket
- 16 Installing the Tail Wheel Bracket
- 17 Installing the Tail Wheel
- 17 Main Landing Gear
- 17 Installing the Aluminum Strut
- 18 Installing the Wheels and Wheel Pants
- 19 Aligning the Wheel Pants
- 19 Engine Installation
- 19 Installing the Engine Mount Beams
- 19 Aligning the Engine
- 20 Servo Installation
- 20 Installing the Servos
- 21 Throttle Control System
- 21 Installing the Pushrod Tube
- 22 Installing the Pushrod
- 22 Installing the Servo Connector
- 23 Adjusting the Throttle Pushrod
- 23 Elevator Control System
- 23 Installing the Control Horns
- 24 Installing the Pushrod
- 25 Adjusting the Pushrod
- 25 Rudder Control System
- 25 Installing the Control Rod
- 26 Installing the Pull-Pull Cables
- 27 Adjusting the Pull-Pull Cables
- 28 Aileron Control System
- 28 Installing the Control Horns
- 28 Installing the Pushrods
- 29 Adjusting the Pushrods
- 30 Fuel Tank
- 30 Assembling the Stopper
- 30 Installing the Stopper Assembly
- 31 Installing the Fuel Tank
- 31 Cowling
- 31 Aligning the Cowling
- 33 Installing the Cowling
- 33 Installing the Propeller and the Spinner
- 33 Canopy
- 33 Aligning the Canopy
- 34 Installing the Canopy
- 34 Final Assembly
- 34 Applying the Decals
- 34 Installing the Wing Skids
- 35 Installing the Switch
- 35 Installing the Receiver and the Battery
- 35 Balancing
- 35 Balancing the Freestyle ARF
- 36 Lateral Balancing
- 36 Control Throws
- 36 Preflight Check
- 37 Safety Guidelines
- 37 Flying the Freestyle ARF
- 38 3D Aerobatic Flying Setup
- 39 Radio Setup for 3D Flying
- 40 Trim Chart
- 43 Product Evaluation Sheet