- Home
- Do-It-Yourself tools
- Hand tools
- Measuring & layout tools
- Endres+Hauser
- Micropilot FMR66B
- Operating instructions
advertisement
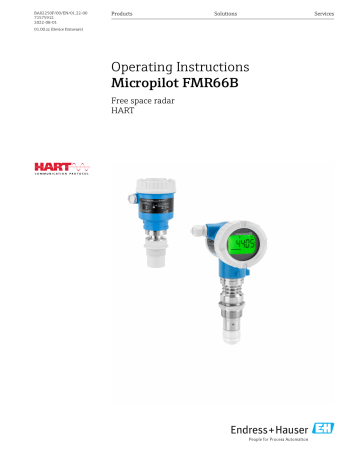
BA02250F/00/EN/01.22-00
71575912
2022-08-01
01.00.zz (Device firmware)
Products Solutions
Operating Instructions
Micropilot FMR66B
Free space radar
HART
Services
2
Micropilot FMR66B HART
1.
Order code:
Ser. no.:
Ext. ord. cd.:
XXXXX-XXXXXX
XXXXXXXXXXXX
XXX.XXXX.XX
Serial number
2.
www.endress.com/deviceviewer
Endress+Hauser
Operations App
3.
A0023555
• Make sure the document is stored in a safe place such that it is always available when working on or with the device
• Avoid danger to individuals or the facility: read the "Basic safety instructions" section carefully, as well as all other safety instructions in the document that are specific to working procedures
The manufacturer reserves the right to modify technical data without prior notice. The
Endress+Hauser sales organization will supply you with current information and updates to these instructions.
Endress+Hauser
Micropilot FMR66B HART Table of contents
Table of contents
1 Document information . . . . . . . . . . . . . . 5
Purpose of this document . . . . . . . . . . . . . . . . .
Symbols . . . . . . . . . . . . . . . . . . . . . . . . . . . . . .
Safety symbols . . . . . . . . . . . . . . . . . .
Symbols for certain types of information and graphics . . . . . . . . . . .
Documentation . . . . . . . . . . . . . . . . . . . . . . . .
Technical Information (TI) . . . . . . . . .
Brief Operating Instructions (KA) . . . . .
Safety Instructions (XA) . . . . . . . . . . . .
Functional Safety Manual (FY) . . . . . . .
List of abbreviations . . . . . . . . . . . . . . . . . . . . .
Registered trademarks . . . . . . . . . . . . . . . . . . .
2 Basic safety instructions . . . . . . . . . . . . 8
Requirements for personnel . . . . . . . . . . . . . . .
Intended use . . . . . . . . . . . . . . . . . . . . . . . . . .
Workplace safety . . . . . . . . . . . . . . . . . . . . . . .
Operational safety . . . . . . . . . . . . . . . . . . . . . .
Product safety . . . . . . . . . . . . . . . . . . . . . . . . .
Functional Safety SIL (optional) . . . . . . . . . . . .
IT security . . . . . . . . . . . . . . . . . . . . . . . . . . . .
Device-specific IT security . . . . . . . . . . . . . . .
3 Product description . . . . . . . . . . . . . . . . 11
Product design . . . . . . . . . . . . . . . . . . . . . . . .
4 Incoming acceptance and product identification . . . . . . . . . . . . . . . . . . . . . 12
Incoming acceptance . . . . . . . . . . . . . . . . . . .
Product identification . . . . . . . . . . . . . . . . . . .
Nameplate . . . . . . . . . . . . . . . . . . . .
Manufacturer address . . . . . . . . . . . .
Storage and transport . . . . . . . . . . . . . . . . . .
Storage conditions . . . . . . . . . . . . . . .
Transporting the product to the measuring point . . . . . . . . . . . . . . . .
5 Installation . . . . . . . . . . . . . . . . . . . . . . . 14
General instructions . . . . . . . . . . . . . . . . . . . .
Mounting requirements . . . . . . . . . . . . . . . . .
Internal vessel fittings . . . . . . . . . . . .
Avoiding interference echoes . . . . . . .
Vertical alignment of antenna axis . . .
Radial alignment of the antenna . . . .
Optimization options . . . . . . . . . . . . .
Mounting the measuring device . . . . . . . . . . .
PVDF40 mm (1.5 in) . . . . . . . . . . . . .
50 mm (2 in) . . . . . . . . . . . . . . . . . .
Turning the housing . . . . . . . . . . . . .
Endress+Hauser
Turning the display module . . . . . . . .
Changing the installation position of the display module . . . . . . . . . . . . . .
Closing the housing covers . . . . . . . . .
Post-mounting check . . . . . . . . . . . . . . . . . . .
6 Electrical connection . . . . . . . . . . . . . . 21
Connecting requirements . . . . . . . . . . . . . . .
Cover with securing screw . . . . . . . . .
Potential equalization . . . . . . . . . . . .
Connecting the device . . . . . . . . . . . . . . . . . .
Supply voltage . . . . . . . . . . . . . . . . .
Cable specification . . . . . . . . . . . . . . .
4 to 20 mA HART . . . . . . . . . . . . . . .
Overvoltage protection . . . . . . . . . . .
Wiring . . . . . . . . . . . . . . . . . . . . . . .
Terminal assignment . . . . . . . . . . . .
Cable entries . . . . . . . . . . . . . . . . . . .
Available device plugs . . . . . . . . . . . .
Ensuring the degree of protection . . . . . . . . .
Cable entries . . . . . . . . . . . . . . . . . . .
Post-connection check . . . . . . . . . . . . . . . . . .
7 Operation options . . . . . . . . . . . . . . . . . 29
Overview of operating options . . . . . . . . . . . .
Operating keys and DIP switches on the
HART electronic insert . . . . . . . . . . . . . . . . . .
User roles and related access authorization . . . . . . . . . . . . . . . . . .
Device display (optional) . . . . . . . . . .
Operation via Bluetooth® wireless technology (optional) . . . . . . . . . . . .
Access to the operating menu via the operating tool . . . . . . . . . . . . . . . . . . . . . . . .
DeviceCare . . . . . . . . . . . . . . . . . . . . . . . . . .
Function scope . . . . . . . . . . . . . . . . .
FieldCare . . . . . . . . . . . . . . . . . . . . . . . . . . . .
Function scope . . . . . . . . . . . . . . . . .
8 System integration . . . . . . . . . . . . . . . . 33
Overview of device description files . . . . . . . . .
Measured variables via HART protocol . . . . . .
9 Commissioning . . . . . . . . . . . . . . . . . . . . 34
Preliminaries . . . . . . . . . . . . . . . . . . . . . . . .
Function check . . . . . . . . . . . . . . . . . . . . . . .
Establishing a connection via FieldCare and
DeviceCare . . . . . . . . . . . . . . . . . . . . . . . . . .
Via HART protocol . . . . . . . . . . . . . . .
3
Table of contents Micropilot FMR66B HART
Via service interface (CDI) . . . . . . . . .
Configuring the device address via software . .
Setting the operating language . . . . . . . . . . .
Local display . . . . . . . . . . . . . . . . . . .
Operating tool . . . . . . . . . . . . . . . . . .
Device configuration . . . . . . . . . . . . . . . . . . .
Level measurement in bulk solids . . . .
Commissioning wizard . . . . . . . . . . .
Recording the Echo curve . . . . . . . . . . . . . . . .
"Simulation" submenu . . . . . . . . . . . . . . . . . . .
10 Operation . . . . . . . . . . . . . . . . . . . . . . . . . 38
10.1 Reading off the device locking status . . . . . . .
10.2 Reading off measured values . . . . . . . . . . . . .
10.3 Adapting the device to process conditions . . . .
10.4 Heartbeat Technology (optional) . . . . . . . . . .
10.4.1 Heartbeat Verification . . . . . . . . . . . .
10.4.2 Heartbeat Verification/Monitoring . .
11 Diagnostics and troubleshooting . . . 39
11.1 General troubleshooting . . . . . . . . . . . . . . . . .
11.1.1 General errors . . . . . . . . . . . . . . . . . .
11.2 Error - SmartBlue operation . . . . . . . . . . . . . .
11.3 Diagnostic information on local display . . . . . .
11.3.1 Diagnostic message . . . . . . . . . . . . . .
11.4 Diagnostic event in the operating tool . . . . . . .
11.5 Adapting the diagnostic information . . . . . . .
11.6 Queued diagnostic messages . . . . . . . . . . . . .
11.7 Diagnostic list . . . . . . . . . . . . . . . . . . . . . . . .
11.8 List of diagnostic events . . . . . . . . . . . . . . . . .
11.9 Event logbook . . . . . . . . . . . . . . . . . . . . . . . .
11.9.1 Event history . . . . . . . . . . . . . . . . . . .
11.9.2 Filtering the event logbook . . . . . . . .
11.9.3 Overview of information events . . . . .
11.10 Resetting the device . . . . . . . . . . . . . . . . . . . .
11.10.1 Resetting the device via the operating tool . . . . . . . . . . . . . . . . . .
11.10.2 Resetting the device via keys on the electronic insert . . . . . . . . . . . . . . . .
11.11 Device information . . . . . . . . . . . . . . . . . . . .
11.12 Firmware history . . . . . . . . . . . . . . . . . . . . . .
. . . . . . . . . . . . . . . .
12 Maintenance . . . . . . . . . . . . . . . . . . . . . . 49
12.1 Exterior cleaning . . . . . . . . . . . . . . . . . . . . . .
12.2 Seals . . . . . . . . . . . . . . . . . . . . . . . . . . . . . . .
13 Repair . . . . . . . . . . . . . . . . . . . . . . . . . . . . 50
13.1 General information . . . . . . . . . . . . . . . . . . .
13.1.1 Repair concept . . . . . . . . . . . . . . . . .
13.1.2 Repair of Ex-certified devices . . . . . . .
13.2 Spare parts . . . . . . . . . . . . . . . . . . . . . . . . . .
13.3 Replacement . . . . . . . . . . . . . . . . . . . . . . . . .
13.3.1 HistoROM . . . . . . . . . . . . . . . . . . . . .
13.4 Return . . . . . . . . . . . . . . . . . . . . . . . . . . . . . .
13.5 Disposal . . . . . . . . . . . . . . . . . . . . . . . . . . . .
14 Accessories . . . . . . . . . . . . . . . . . . . . . . . 52
14.1 Weather protection cover 316L . . . . . . . . . . .
14.2 Plastic weather protection cover . . . . . . . . . . .
14.3 Adjustable flange seal . . . . . . . . . . . . . . . . . .
14.3.1 Seal, adjustable, DN80 . . . . . . . . . . . .
14.3.2 Seal, adjustable, DN100 . . . . . . . . . . .
14.3.3 Seal, adjustable, DN150 . . . . . . . . . . .
14.3.4 Seal, adjustable, ASME 3"/ JIS 80A . . .
14.3.5 Seal, adjustable, ASME 4" . . . . . . . . . .
14.3.6 Seal, adjustable, ASME 6"/ JIS 150A . .
14.4 Mounting bracket, adjustable . . . . . . . . . . . . .
14.5 M12 socket . . . . . . . . . . . . . . . . . . . . . . . . . .
14.6 Remote display FHX50B . . . . . . . . . . . . . . . . .
14.7 Commubox FXA195 HART . . . . . . . . . . . . . . .
14.8 HART Loop Converter HMX50 . . . . . . . . . . . .
14.9 FieldPort SWA50 . . . . . . . . . . . . . . . . . . . . . .
14.10 Wireless HART adapter SWA70 . . . . . . . . . . .
14.11 Fieldgate FXA42 . . . . . . . . . . . . . . . . . . . . . .
14.12 Field Xpert SMT70 . . . . . . . . . . . . . . . . . . . . .
14.13 DeviceCare SFE100 . . . . . . . . . . . . . . . . . . . .
14.14 FieldCare SFE500 . . . . . . . . . . . . . . . . . . . . .
14.15 Memograph M . . . . . . . . . . . . . . . . . . . . . . .
14.16 RN42 . . . . . . . . . . . . . . . . . . . . . . . . . . . . . .
15 Technical data . . . . . . . . . . . . . . . . . . . . 61
15.1 Input . . . . . . . . . . . . . . . . . . . . . . . . . . . . . . .
15.2 Output . . . . . . . . . . . . . . . . . . . . . . . . . . . . .
15.3 Environment . . . . . . . . . . . . . . . . . . . . . . . . .
15.4 Process . . . . . . . . . . . . . . . . . . . . . . . . . . . . .
Index . . . . . . . . . . . . . . . . . . . . . . . . . . . . . . . . . . 72
4 Endress+Hauser
Micropilot FMR66B HART Document information
1 Document information
1.1 Purpose of this document
These Operating Instructions contain all the information that is required in the various phases of the life cycle of the device: from product identification, incoming acceptance and storage, to mounting, connection, operation and commissioning through to troubleshooting, maintenance and disposal.
1.2 Symbols
1.2.1 Safety symbols
DANGER
This symbol alerts you to a dangerous situation. Failure to avoid this situation will result in serious or fatal injury.
WARNING
This symbol alerts you to a dangerous situation. Failure to avoid this situation can result in serious or fatal injury.
CAUTION
This symbol alerts you to a dangerous situation. Failure to avoid this situation can result in minor or medium injury.
NOTICE
This symbol contains information on procedures and other facts which do not result in personal injury.
1.2.2 Symbols for certain types of information and graphics
Permitted
Procedures, processes or actions that are permitted
Preferred
Procedures, processes or actions that are preferred
Forbidden
Procedures, processes or actions that are forbidden
Tip
Indicates additional information
Reference to documentation
Reference to graphic
Notice or individual step to be observed
1.
,
2.
,
3.
Series of steps
Result of a step
Operation via local display
Operation via operating tool
Endress+Hauser 5
Document information
6
Micropilot FMR66B HART
Write-protected parameter
1, 2, 3, ...
Item numbers
A, B, C, ...
Views
Safety instructions
Observe the safety instructions contained in the associated Operating Instructions
1.3 Documentation
The following types of documentation are available in the Download Area of the Endress
+Hauser website ( www.endress.com/downloads ):
For an overview of the scope of the associated Technical Documentation, refer to the following:
• Device Viewer ( www.endress.com/deviceviewer ): Enter serial number from nameplate.
• Endress+Hauser Operations app : Enter serial number from nameplate or scan matrix code on nameplate.
1.3.1 Technical Information (TI)
Planning aid
The document contains all the technical data on the device and provides an overview of the accessories and other products that can be ordered for the device.
1.3.2 Brief Operating Instructions (KA)
Guide that takes you quickly to the 1st measured value
The Brief Operating Instructions contain all the essential information from incoming acceptance to initial commissioning.
1.3.3 Safety Instructions (XA)
Depending on the approval, the following Safety Instructions (XA) are supplied with the device. They are an integral part of the Operating Instructions.
The nameplate indicates the Safety Instructions (XA) that are relevant to the device.
1.3.4 Functional Safety Manual (FY)
Depending on the SIL approval, the Functional Safety Manual (FY) is an integral part of the Operating Instructions and applies in addition to the Operating Instructions, Technical
Information and ATEX Safety Instructions.
The different requirements that apply for the protective function are described in the
Functional Safety Manual (FY).
1.4 List of abbreviations
BA
Document type "Operating Instructions"
KA
Document type "Brief Operating Instructions"
Endress+Hauser
Micropilot FMR66B HART Document information
TI
Document type "Technical Information"
SD
Document type "Special Documentation"
XA
Document type "Safety Instructions"
PN
Nominal pressure
MWP
Maximum working pressure
The MWP is indicated on the nameplate.
ToF
Time of Flight
FieldCare
Scalable software tool for device configuration and integrated plant asset management solutions
DeviceCare
Universal configuration software for Endress+Hauser HART, PROFIBUS, FOUNDATION
Fieldbus and Ethernet field devices
DTM
Device Type Manager
ε r
(Dk value)
Relative dielectric constant
Operating tool
The term "operating tool" is used in place of the following operating software:
• FieldCare / DeviceCare, for operation via HART communication and PC
• SmartBlue app, for operation using an Android or iOS smartphone or tablet
BD
Blocking Distance; no signals are analyzed within the BD.
PLC
Programmable logic controller (PLC)
1.5 Registered trademarks
HART®
Registered trademark of the FieldComm Group, Austin, Texas, USA
Bluetooth®
The Bluetooth® word mark and logos are registered trademarks owned by the Bluetooth
SIG, Inc. and any use of such marks by Endress+Hauser is under license. Other trademarks and trade names are those of their respective owners.
Apple®
Apple, the Apple logo, iPhone, and iPod touch are trademarks of Apple Inc., registered in the U.S. and other countries. App Store is a service mark of Apple Inc.
Android®
Android, Google Play and the Google Play logo are trademarks of Google Inc.
KALREZ®, VITON®
Registered trademarks of DuPont Performance Elastomers L.L.C., Wilmington, DE USA
Endress+Hauser 7
Basic safety instructions
8
Micropilot FMR66B HART
2 Basic safety instructions
2.1 Requirements for personnel
The personnel for installation, commissioning, diagnostics and maintenance must fulfill the following requirements:
‣ Trained, qualified specialists must have a relevant qualification for this specific function and task.
‣ Personnel must be authorized by the plant owner/operator.
‣ Be familiar with federal/national regulations.
‣ Before starting work: personnel must read and understand the instructions in the manual and supplementary documentation as well as the certificates (depending on the application).
‣ Personnel must follow instructions and comply with general policies.
The operating personnel must fulfill the following requirements:
‣ Personnel are instructed and authorized according to the requirements of the task by the facility's owner-operator.
‣ Personnel follow the instructions in this manual.
2.2 Intended use
Application and media
The measuring device described in these Operating Instructions is intended for continuous, non-contact level measurement primarily in bulk solids. Because of its operating frequency of approx. 80 GHz, a maximum radiated peak power of 6.3 mW and an average output power of 63 µW, unrestricted use outside of closed, metallic vessels is also permitted (for example over heaps). Operation does not pose any danger whatsoever to humans and animals.
If the limit values specified in the "Technical data" and the conditions listed in the instructions and additional documentation are observed, the measuring device may be used for the following measurements only:
‣ Measured process variables: level, distance, signal strength
‣ Calculable process variables: volume or mass in any shape of vessel
To ensure that the measuring device remains in proper condition for the operation time:
‣ Use the measuring device only for media against which the process-wetted materials are adequately resistant.
‣ Observe the limit values in the "Technical data".
Incorrect use
The manufacturer is not liable for damage caused by improper or non-intended use.
Avoid mechanical damage:
‣ Do not touch or clean device surfaces with pointed or hard objects.
Clarification of borderline cases:
‣ For special fluids and fluids for cleaning, Endress+Hauser is glad to provide assistance in verifying the corrosion resistance of fluid-wetted materials, but does not accept any warranty or liability.
Residual risks
Due to heat transfer from the process as well as power loss in the electronics, the temperature of the electronics housing and the assemblies it contains (e.g. display module, main electronics module and I/O electronics module) may rise to 80 °C (176 °F). When in operation, the sensor may reach a temperature close to the medium temperature.
Danger of burns from contact with surfaces!
‣ For elevated fluid temperatures, ensure protection against contact to prevent burns.
Endress+Hauser
Micropilot FMR66B HART Basic safety instructions
2.3 Workplace safety
When working on and with the device:
‣ Wear the required personal protective equipment according to federal/national regulations.
‣ Switch off the supply voltage before connecting the device.
2.4 Operational safety
Risk of injury!
‣ Operate the device only if it is in proper technical condition, free from errors and faults.
‣ The operator is responsible for the interference-free operation of the device.
Modifications to the device
Unauthorized modifications to the device are not permitted and can lead to unforeseeable dangers:
‣ If modifications are nevertheless required, consult with the manufacturer.
Repair
To ensure continued operational safety and reliability:
‣ Carry out repairs on the device only if they are expressly permitted.
‣ Observe federal/national regulations pertaining to the repair of an electrical device.
‣ Use only original spare parts and accessories from the manufacturer.
Hazardous area
To eliminate danger to persons or the installation when the device is used in the hazardous area (e.g. explosion protection, pressure vessel safety):
‣ Check the nameplate to verify whether the ordered device can be put to its intended use in the hazardous area.
‣ Observe the specifications in the separate supplementary documentation, which is an integral part of this manual.
2.5 Product safety
This device is designed in accordance with good engineering practice to meet state-of-theart safety requirements, has been tested, and left the factory in a condition in which it is safe to operate.
It meets general safety standards and legal requirements. It also complies with the EC directives listed in the device-specific EC Declaration of Conformity. Endress+Hauser confirms this by affixing the CE mark to the device.
2.6 Functional Safety SIL (optional)
The Functional Safety Manual must be strictly observed for devices that are used in functional safety applications.
2.7 IT security
We only provide a warranty if the device is installed and used as described in the
Operating Instructions. The device is equipped with security mechanisms to protect it against any inadvertent changes to the device settings. IT security measures in line with operators' security standards and designed to provide additional protection for the device and device data transfer must be implemented by the operators themselves.
Endress+Hauser 9
Basic safety instructions Micropilot FMR66B HART
2.8 Device-specific IT security
The device offers specific functions to support protective measures by the operator. These functions can be configured by the user and guarantee greater in-operation safety if used correctly. An overview of the most important functions is provided in the following section:
• Write protection via hardware write protection switch
• Access code (applies for operation via display, Bluetooth or FieldCare, DeviceCare, ASM,
PDM)
10 Endress+Hauser
Micropilot FMR66B HART
3 Product description
3.1 Product design
1
Product description
2 3
4 4
1 Design of the Micropilot FMR66B
1 Electronics housing
2 Encapsulated antenna, PVDF, 40 mm (1.5 in), threaded process connection
3 Encapsulated antenna, PVDF, 40 mm (1.5 in), flange process connection
4 Drip-off antenna 50 mm (2 in), threaded process connection
5 Drip-off antenna 50 mm (2 in), flange process connection
A0046664
Endress+Hauser 11
Incoming acceptance and product identification Micropilot FMR66B HART
4 Incoming acceptance and product identification
4.1 Incoming acceptance
DELIVERY NOTE
1 = 2
A0016870
Check the following during incoming acceptance:
• Is the order code on the delivery note (1) identical to the order code on the product sticker (2)?
• Are the goods undamaged?
• Do the data on the nameplate correspond to the order specifications and the delivery note?
• Is the documentation provided?
• If required (see nameplate): are the Safety Instructions (XA) provided?
If one of these conditions is not met, please contact the manufacturer's sales office.
4.2 Product identification
The following options are available for the identification of the measuring device:
• Nameplate specifications
• Extended order code with breakdown of the device features on the delivery note
‣ Device Viewer ( www.endress.com/deviceviewer ); manually enter the serial number from the nameplate.
All the information about the measuring device is displayed.
‣ Endress+Hauser Operations app ; manually enter the serial number indicated on the nameplate or scan the 2D matrix code on the nameplate.
All the information about the measuring device is displayed.
4.2.1 Nameplate
The information that is required by law and is relevant to the device is shown on the nameplate, e.g.:
• Manufacturer identification
• Order number, extended order code, serial number
• Technical data, degree of protection
• Firmware version, hardware version
• Approval-related information, reference to Safety Instructions (XA)
• DataMatrix code (information about the device)
12 Endress+Hauser
Micropilot FMR66B HART Incoming acceptance and product identification
4.2.2 Manufacturer address
Endress+Hauser SE+Co. KG
Hauptstraße 1
79689 Maulburg, Germany
Place of manufacture: See nameplate.
4.3 Storage and transport
4.3.1 Storage conditions
• Use the original packaging
• Store the device in clean and dry conditions and protect from damage caused by shocks
Storage temperature range
See Technical Information.
4.3.2 Transporting the product to the measuring point
L WARNING
Incorrect transport!
The housing or sensor can be damaged or pull off. Risk of injury!
‣ Transport the device to the measuring point in its original packaging or by the process connection.
‣ Always secure lifting equipment (slings, eyes, etc.) at the process connection and never lift the device by the electronic housing or sensor. Pay attention to the center of gravity of the device so that it does not tilt or slip unintentionally.
Endress+Hauser 13
Installation Micropilot FMR66B HART
5 Installation
5.1 General instructions
L WARNING
Loss of protection rating if the device is opened in a wet environment.
‣ Only open the device in a dry environment!
1. Install the device or turn the housing so that the cable entries do not point upwards.
2. Always firmly tighten the housing cover and the cable entries.
3. Counter-tighten the cable entries.
4. A drip loop must be provided when laying the cables.
5.2 Mounting requirements
5.2.1 Internal vessel fittings
A0029263
α
14
A0031814
Avoid internal fittings (point level switches, temperature sensors, struts, vacuum rings, heating coils, baffles etc.) inside the signal beam. Pay attention to the beam angle α .
Endress+Hauser
Micropilot FMR66B HART
5.2.2 Avoiding interference echoes
Installation
Endress+Hauser
A0031817
Metal deflector plates, installed at an angle to scatter the radar signals, help prevent interference echoes.
5.2.3 Vertical alignment of antenna axis
Align the antenna so that it is perpendicular to the product surface.
The maximum reach of the antenna can be reduced, or additional interference signals can occur, if the antenna is not installed perpendicular to the product.
5.2.4 Radial alignment of the antenna
Based on the directional characteristic, radial alignment of the antenna is not necessary.
5.2.5 Optimization options
Mapping
Measurement can be optimized by electronically suppressing interference echoes.
See the Confirm distance parameter.
5.3 Mounting the measuring device
5.3.1 Encapsulated antenna, PVDF40 mm (1.5 in)
Information concerning threaded connections
• When screwing in, turn by the hex bolt only.
• Tool: open-ended wrench 55 mm
• Maximum permissible torque: 50 Nm (36 lbf ft)
15
Installation
16
Micropilot FMR66B HART
Information about the mounting nozzle
The maximum nozzle length H max
depends on the nozzle diameter D .
Maximum nozzle length H max
as a function of the nozzle diameter D
D
50 to 80 mm (2 to 3.2 in)
80 to 100 mm (3.2 to 4 in)
100 to 150 mm (4 to 6 in)
≥ 150 mm (6 in)
H max
600 mm (24 in)
1 000 mm (24 in)
1 250 mm (50 in)
1 850 mm (74 in)
øD
In the case of longer nozzles, reduced measuring performance must be expected.
Please note the following:
• The end of the nozzle must be smooth and free from burrs.
• The edge of the nozzle should be rounded.
• Mapping must be performed.
• Please contact the manufacturer's support department for applications with nozzles that are higher than indicated in the table.
5.3.2 Drip-off antenna PTFE 50 mm (2 in)
Information concerning threaded connections
• When screwing in, turn by the hex bolt only.
• Tool: open-ended wrench 55 mm
• Maximum permissible torque: 50 Nm (36 lbf ft)
Information about the mounting nozzle
The maximum nozzle length H max
depends on the nozzle diameter D .
Maximum nozzle length H max
as a function of the nozzle diameter D
D
50 to 80 mm (2 to 3.2 in)
80 to 100 mm (3.2 to 4 in)
100 to 150 mm (4 to 6 in)
≥150 mm (6 in)
H max
750 mm (30 in)
1 150 mm (46 in)
1 450 mm (58 in)
2 200 mm (88 in)
øD
In the case of longer nozzles, reduced measuring performance must be expected.
Please note the following:
• The end of the nozzle must be smooth and free from burrs.
• The edge of the nozzle should be rounded.
• Mapping must be performed.
• Please contact the manufacturer's support department for applications with nozzles that are higher than indicated in the table.
Endress+Hauser
Micropilot FMR66B HART Installation
5.3.3 Turning the housing
The housing can be rotated up to 380° by loosening the locking screw.
Your benefits
• Easy installation due to optimum alignment of housing
• Easily accessible device operation
• Optimum readability of the local display (optional)
A B C D
1 1 1
A Plastic single compartment housing (no locking screw)
B Aluminum single compartment housing
C Dual compartment housing
D Dual compartment housing, L-form
1 Locking screw
NOTICE
The housing cannot be unscrewed fully.
‣ Loosen the external locking screw by a maximum of 1.5 turns. If the screw is unscrewed too much or completely (beyond the screw anchor point), small parts
(counter disk) can become loose and fall out.
‣ Tighten the securing screw (hexagon socket 4 mm (0.16 in)) with maximum
3.5 Nm (2.58 lbf ft) ± 0.3 Nm (0.22 lbf ft).
5.3.4 Turning the display module
L WARNING
Supply voltage switched on!
Risk of electric shock and/or explosion!
‣ Switch off the supply voltage before opening the measuring device.
A0046660
3.
1.
4 0.7 Nm
2.
4.
A0038224
1. If fitted: release the screw of the cover lock for the electronics compartment cover using the Allen key.
2. Unscrew the electronics compartment cover from the transmitter housing and check the cover seal.
3. Press the release mechanism and remove the display module.
Endress+Hauser 17
Installation Micropilot FMR66B HART
4. Turn the display module to the desired position: maximum 4 × 90 ° in each direction.
Fit the display module on the electronics compartment in the desired position until it clicks into place. Screw the electronics compartment cover back onto the transmitter housing. If fitted: tighten the screw of the cover lock using the Allen key
0.7 Nm (0.52 lbf ft)±0.2 Nm (0.15 lbf ft).
5.3.5 Changing the installation position of the display module
The installation position of the display can be changed in the case of the dual compartment housing, L-form.
A0048401
L WARNING
Supply voltage switched on!
Risk of electric shock and/or explosion!
‣ Switch off the supply voltage before opening the measuring device.
1 → 2 → 3 →
2 x
4 mm 2.
2.
1.
0.7 Nm
1.
A0046831
‣ If fitted: release the screw of the cover lock for the display cover using the Allen key.
A0046832
‣ Unscrew the display cover and check the cover seal.
A0046833
‣ Press the release mechanism, remove the display module.
18 Endress+Hauser
Micropilot FMR66B HART Installation
4 → 5 →
2 x
4 mm
0.7 Nm
6 →
1.
2.
‣ Release the connection.
7 →
A0046834 A0046923
‣ If fitted: release the screw of the cover lock for the connection compartment cover using the Allen key.
A0046924
‣ Unscrew the connection compartment cover, check the cover seal. Screw this cover onto the electronics compartment instead of the display cover. If fitted: tighten the screw of the cover lock using the Allen key
8 y pla
Dis
2.
Endress+Hauser
1.
A0048406
‣ Plug in the connection for the display module in the connection compartment.
‣ Fit the display module in the desired position until it clicks into place.
A0046928
‣ Screw the display cover firmly back onto the housing. If fitted: tighten the screw of the cover lock using the Allen key
0.7 Nm (0.52 lbf ft).
5.3.6 Closing the housing covers
NOTICE
Thread and housing damaged from dirt!
‣ Remove dirt (e.g. sand) on the cover and housing thread.
‣ If you encounter resistance when closing the cover, check the thread for dirt and clean it.
Housing thread
The thread of the electronics and connection compartment is coated with lubricant varnish.
Avoid additional lubrication.
5.4 Post-mounting check
Is the device free from damage (visual inspection)?
Are the measuring point identification and labeling correct (visual inspection)?
19
Installation Micropilot FMR66B HART
Is the measuring device protected against precipitation and sunlight?
Are the securing screws and cover lock tightened securely?
Does the measuring device comply with the measuring point specifications?
For example:
• Process temperature
• Process pressure
• Ambient temperature
• Measuring range
20 Endress+Hauser
Micropilot FMR66B HART Electrical connection
6 Electrical connection
6.1 Connecting requirements
6.1.1 Cover with securing screw
In the case of devices for use in the hazardous area with a certain type of protection, the cover is sealed by a securing screw.
NOTICE
If the securing screw is not positioned correctly, the cover cannot provide secure sealing.
‣ Open the cover: slacken the screw of the cover lock with a maximum of 2 turns so that the screw does not fall out. Fit the cover and check the cover seal.
‣ Close the cover: screw the cover securely onto the housing, making sure that the securing screw is positioned correctly. There should not be any gap between the cover and housing.
2 x
4
0.7 Nm
A0039520
2 Cover with securing screw
6.1.2 Potential equalization
The protective ground on the device must not be connected. If necessary, the potential matching line can be connected to the outer ground terminal of the transmitter before the device is connected.
A B C D
Endress+Hauser
1 1 1
A Single compartment housing, plastic
B Single compartment housing, aluminum
C Dual compartment housing
D Dual compartment housing, L-form
1 Ground terminal for connecting the potential matching line
1
A0046583
L WARNING
Explosion Hazard!
‣ Please refer to the separate documentation on applications in hazardous areas for the safety instructions.
For optimum electromagnetic compatibility:
• Keep the potential matching line as short as possible
• Observe a cross-section of at least 2.5 mm 2 (14 AWG)
21
Electrical connection
6.2 Connecting the device
A B
1 1
C
1
Micropilot FMR66B HART
D
1
A0046659
A Plastic single compartment housing
B Aluminum single compartment housing
C Dual compartment housing
D Dual compartment housing, L-form
1 Connection compartment cover
Housing thread
The thread of the electronics and connection compartment is coated with lubricant varnish.
Avoid additional lubrication.
6.2.1 Supply voltage
The supply voltage depends on the selected type of device approval
Non-hazardous, Ex d, Ex e 10.5 to 35 V
DC
Ex i 10.5 to 30 V
DC
Nominal current 4 to 20 mA
The power unit must be tested to ensure it meets safety requirements (e.g., PELV,
SELV, Class 2) and must comply with the relevant protocol specifications.
A suitable circuit breaker must be provided for the device in accordance with
IEC/EN61010-1
Device display and Bluetooth
Depending on the supply voltage and current consumption (see the chart)
• the background lighting is switched on or off
• the Bluetooth function (order option) can be switched on or off optionally
22 Endress+Hauser
Micropilot FMR66B HART
Endress+Hauser
Electrical connection
U
18.5
17.5
16.5
15.5
14.5
13.5
12.5
11.0
C
10.5
3.6
3.8
B
4
A
4.2
4.4
4.6
4.8
5 5.2
5.4
I
LOOP
A0047056
A Display lighting switched on, Bluetooth can be switched on optionally
B Display lighting switched off, Bluetooth can be switched on optionally
C Display lighting switched off and Bluetooth not active
6.2.2 Cable specification
Rated cross-section
• Supply voltage
0.5 to 2.5 mm 2 (20 to 13 AWG)
• Protective earth or grounding of the cable shield
> 1 mm 2 (17 AWG)
• External ground terminal
0.5 to 4 mm 2 (20 to 12 AWG)
Cable outer diameter
The cable outer diameter depends on the cable gland used
• Coupling, plastic:
⌀5 to 10 mm (0.2 to 0.38 in)
• Coupling, nickel-plated brass:
⌀7 to 10.5 mm (0.28 to 0.41 in)
• Coupling, stainless steel:
⌀7 to 12 mm (0.28 to 0.47 in)
6.2.3 4 to 20 mA HART
1 2
3
Y
I
+
-
+
mA
4
A0028908
3 Block diagram of HART connection
1 Device with HART communication
2 HART communication resistor
3 Power supply
4 Multimeter or ammeter
The HART communication resistor of 250 Ω in the signal line is always necessary in the case of a low-impedance power supply.
Take the voltage drop into consideration:
Maximum 6 V for a 250 Ω communication resistor
23
Electrical connection
24
Micropilot FMR66B HART
6.2.4 Overvoltage protection
The overvoltage protection can optionally be ordered as a "Mounted accessory" via the product structure
Devices without optional overvoltage protection
Equipment from Endress+Hauser fulfills the requirements of the product standard IEC /
DIN EN 61326-1 (Table 2 Industrial Environment).
Depending on the type of port (DC power supply, input/output port) different testing levels according to IEC / DIN EN 61326-1 against transient overvoltages (Surge) are applied
(IEC / DIN EN 61000-4-5 Surge):
Test level on DC power ports and input/output ports is 1 000 V line to earth
Devices with optional overvoltage protection
• Spark-over voltage: min. 400 V
DC
• Tested according to IEC / DIN EN 60079-14 sub chapter 12.3 (IEC / DIN EN 60060-1 chapter 7)
• Nominal discharge current: 10 kA
Overvoltage category
Overvoltage category II
6.2.5 Wiring
L WARNING
Supply voltage might be connected!
Risk of electric shock and/or explosion!
‣ If the device is used in hazardous areas, make sure to comply with national standards and the specifications in the Safety Instructions (XAs). The specified cable gland must be used.
‣ The supply voltage must match the specifications on the nameplate.
‣ Switch off the supply voltage before connecting the device.
‣ If necessary, the potential matching line can be connected to the outer ground terminal of the device before the power supply lines are connected.
‣ A suitable circuit breaker should be provided for the device in accordance with IEC/EN
61010.
‣ The cables must be adequately insulated, with due consideration given to the supply voltage and the overvoltage category.
‣ The connecting cables must offer adequate temperature stability, with due consideration given to the ambient temperature.
‣ Only operate the measuring device with the covers closed.
Connect the device in the following order:
1. Release the cover lock (if provided).
2. Unscrew the cover.
3. Guide the cables into the cable glands or cable entries.
4. Connect the cables.
5. Tighten the cable glands or cable entries so that they are leak-tight. Counter-tighten the housing entry.
6. Screw the cover securely back onto the connection compartment.
7. If provided: tighten the screw of the cover lock using the Allen key
0.7 Nm (0.52 lbf ft) ±0.2 Nm (0.15 lbf ft).
Endress+Hauser
Micropilot FMR66B HART
6.2.6 Terminal assignment
Single compartment housing
3
2
1
-
+
4 Connection terminals and ground terminal in the connection compartment
1 Positive terminal
2 Negative terminal
3 Internal ground terminal
Dual compartment housing
Electrical connection
A0042594
+
3 2 1
5 Connection terminals and ground terminal in the connection compartment
1 Positive terminal
2 Negative terminal
3 Internal ground terminal
A0042803
Endress+Hauser 25
Electrical connection
Dual compartment housing, L-form
Micropilot FMR66B HART
26
+
3 2 1
6 Connection terminals and ground terminal in the connection compartment
1 Positive terminal
2 Negative terminal
3 Internal ground terminal
6.2.7 Cable entries
A
1 1
B
1
C
1
D
A0045842
2 2 2 2
A0046584
A Single compartment housing, plastic
B Single compartment housing, aluminum
C Dual compartment housing
D Dual compartment housing, L-form
1 Cable entry
2 Dummy plug
The type of cable entry depends on the device version ordered.
Always route connecting cables downwards so that moisture cannot penetrate the connection compartment.
If necessary, create a drip loop or use a weather protection cover.
6.2.8 Available device plugs
In the case of devices with a plug, it is not necessary to open the housing for connection purposes.
Use the enclosed seals to prevent the penetration of moisture into the device.
Endress+Hauser
Micropilot FMR66B HART Electrical connection
Devices with M12 plug
4 3
1 2
1 Signal +
2 Not assigned
3 Signal –
4 Ground
Measuring devices with Harting plug Han7D
A B –
A0011175
+
+ –
2
3
8 7 6
1
4
5
Han7D
+ –
A Electrical connection for devices with Harting plug Han7D
B View of the plug-in connection on the device
Brown
Green/yellow
+ Blue
Material
CuZn, gold-plated plug-in jack and plug contacts
A0041011
6.3 Ensuring the degree of protection
6.3.1 Cable entries
• Gland M20, plastic, IP66/68 NEMA TYPE 4X/6P
• Gland M20, nickel-plated brass, IP66/68 NEMA TYPE 4X/6P
• Gland M20, 316L, IP66/68 NEMA TYPE 4X/6P
• Thread M20, IP66/68 NEMA TYPE 4X/6P
• Thread G1/2, IP66/68 NEMA TYPE 4X/6P
If the G1/2 thread is selected, the device is delivered with an M20 thread as standard and a G1/2 adapter is included with the delivery, along with the corresponding documentation
• Thread NPT1/2, IP66/68 TYPE 4X/6P
• Dummy plug transport protection: IP22, TYPE 2
• HAN7D plug, 90 degrees, IP65 NEMA Type 4X
• M12 plug
• When housing is closed and connecting cable is plugged in: IP66/67, NEMA Type 4X
• When housing is open or connecting cable is not plugged in: IP20, NEMA Type 1
Endress+Hauser 27
Electrical connection Micropilot FMR66B HART
NOTICE
Plug M12 and plug HAN7D: incorrect mounting can invalidate the IP protection class!
‣ The degree of protection only applies if the connecting cable used is plugged in and screwed tight.
‣ The degree of protection only applies if the connecting cable used is specified according to IP67, NEMA Type 4X.
‣ The IP protection classes are only maintained if the dummy cap is used or the cable is connected.
6.4 Post-connection check
Are the device or cables undamaged (visual inspection)?
Do the cables used comply with the requirements?
Do the mounted cables have strain relief?
Cable glands mounted, securely tightened and leak-tight?
Does the supply voltage correspond to the specifications on the nameplate?
No reverse polarity, terminal assignment correct?
Cover screwed down correctly?
Cover lock tightened correctly?
28 Endress+Hauser
Micropilot FMR66B HART Operation options
7 Operation options
7.1 Overview of operating options
• Operation via operating keys and DIP switches on the electronic insert
• Operation via optical operating keys on the device display (optional)
• Operation via Bluetooth® wireless technology (with optional device display with
Bluetooth) with Smartblue app or FieldXpert, DeviceCare
• Operation via operating tool (Endress+Hauser FieldCare/DeviceCare, handheld terminal,
AMS, PDM, ...)
7.2 Operating keys and DIP switches on the HART electronic insert
1
2
Display
4 3
Endress+Hauser
A0046129
7 Operating keys and DIP switches on the HART electronic insert
1 Operating key for reset password (for Bluetooth login and Maintenance user role)
1+2 Operating keys for device reset (as-delivered state)
2 Operating key II (only for factory reset)
3 DIP switch for alarm current
4 DIP switch for locking and unlocking the device
The setting of the DIP switches on the electronic insert has priority over the settings made via other operation methods (e.g. FieldCare/DeviceCare).
7.3 Structure and function of the operating menu
The differences between the structure of the operating menus of the local display and the
Endress+Hauser FieldCare or DeviceCare operating tools can be summarized as follows:
The local display is suitable for configuring simple applications.
The operating tools (FieldCare, DeviceCare, SmartBlue, AMS, PDM, ...) can be used to configure the parameters of wide-ranging applications.
Wizards help the user to commission the various applications. The user is guided through the individual configuration steps.
7.3.1 User roles and related access authorization
The two user roles Operator and Maintenance (as-delivered state) have different write access to the parameters if a device-specific access code has been defined. This access code protects the device configuration from unauthorized access.
29
Operation options Micropilot FMR66B HART
If an incorrect access code is entered, the user obtains the access rights of the Operator role.
7.4 Access to the operating menu via the local display
7.4.1 Device display (optional)
Possible to operate the optical operating keys through the cover. No need to open the device.
Functions:
• Display of measured values and fault and notice messages
• Background lighting, which switches from green to red in the event of an error
• The device display can be removed for easier operation
Backlighting is switched on or off depending on the supply voltage and the current consumption.
The device display is also optionally available with Bluetooth® wireless technology.
30
-
ESC
+
E
1
A0039284
8 Graphic display with optical operating keys (1)
• Key
• Navigate downwards in the picklist
• Edit the numerical values or characters within a function
• Key
• Navigate upwards in the picklist
• Edit the numerical values or characters within a function
• Key
• Change from main display to main menu
• Confirm entry
• Jump to the next item
• Select a menu item and activate the edit mode
• Unlock/lock the display operation
• Press and hold the key to display a short description of the selected parameter (if available)
• key and key (ESC function)
• Exit edit mode for a parameter without saving the changed value
• Menu at a selection level: pressing the keys simultaneously takes the user back up a level in the menu
• Press and hold the keys simultaneously to return to the upper level
Endress+Hauser
Micropilot FMR66B HART Operation options
7.4.2 Operation via Bluetooth® wireless technology (optional)
Requirement
• Device with device display including Bluetooth
• Smartphone or tablet with Endress+Hauser SmartBlue app or PC with DeviceCare from version 1.07.05 or FieldXpert SMT70
The range of the connection is up to 25 m (82 ft). The range can vary depending on environmental conditions such as attachments, walls or ceilings.
The operating keys on the display are locked as soon as the device is connected via
Bluetooth.
A flashing Bluetooth symbol indicates that a Bluetooth connection is available.
SmartBlue app
1. Scan the QR code or enter "SmartBlue" in the search field of the App Store or Google
Play.
A0039186
2. Start the SmartBlue app.
3. Select device from livelist displayed.
4. Login:
Enter the user name: admin
Password: serial number of the device.
5. Change the password after logging in for the first time!
Prerequisites
System requirements
The SmartBlue app is available to download for smartphones or tablets.
• Devices with iOS: iPhone 5S or higher as of iOS11; iPad 5th generation or higher as of iOS11; iPod Touch 6th generation or higher as of iOS11
• Devices with Android: from Android 6.0 and Bluetooth® 4.0
Initial password
The serial number of the device serves as the initial password when the connection is established for the first time.
Please note the following
If the Bluetooth display is removed from one device and installed in another device:
• All the log-in data are only saved in the Bluetooth display and not in the device
• The password changed by the user is also saved in the Bluetooth display
7.5 Access to the operating menu via the operating tool
Access via the operating tool is possible:
• Via HART communication, e.g. Commubox FXA195
• Via Endress+Hauser Commubox FXA291
With the Commubox FXA291, a CDI connection can be established with the device interface and a Windows PC/notebook with a USB port
Endress+Hauser 31
Operation options Micropilot FMR66B HART
7.6 DeviceCare
7.6.1 Function scope
Tool for connecting and configuring Endress+Hauser field devices.
The fastest way to configure Endress+Hauser field devices is with the dedicated
"DeviceCare" tool. Together with the device type managers (DTMs), DeviceCare presents a convenient, comprehensive solution.
For details, see Innovation Brochure IN01047S
7.7 FieldCare
7.7.1 Function scope
FDT-based plant asset management tool from Endress+Hauser. FieldCare can configure all smart field devices in a system and helps you manage them. By using the status information, FieldCare is also a simple but effective way of checking their status and condition.
Access is via:
• CDI service interface
• HART communication
Typical functions:
• Parameterization of transmitters
• Loading and saving of device data (upload/download)
• Documentation of the measuring point
• Visualization of the measured value memory (line recorder) and event logbook
For additional information about FieldCare, see Operating Instructions BA00027S and BA00059S
32 Endress+Hauser
Micropilot FMR66B HART System integration
8 System integration
8.1 Overview of device description files
• Manufacturer ID: 17 (0x0011)
• Device type ID: 0x11C1
• HART specification: 7.6
• DD files, information and files can be found at:
• www.endress.com
• www.fieldcommgroup.org
8.2 Measured variables via HART protocol
The following measured values are assigned to the device variables at the factory:
Device variable
Primary variable (PV)
Secondary variable (SV)
Tertiary variable (TV)
Quaternary variable (QV)
Measured value
Level linearized
Distance
Absolute echo amplitude
Relative echo amplitude
The assignment of the measured values to the device variables can be changed in the following submenu:
Application → HART output → HART output
In a HART Multidrop loop, only one device may use the analog current value for signal transmission. For all other devices in the "Loop current mode" parameter , select the
Disable option.
Endress+Hauser 33
Commissioning Micropilot FMR66B HART
9 Commissioning
All configuration tools provide a commissioning assistant that supports the user when setting the most important configuration parameters ( Guidance menu
Commissioning wizard).
9.1 Preliminaries
The measuring range and the unit in which the measured value is transmitted correspond to the data on the nameplate.
L WARNING
The settings of the current output are relevant for safety!
This can result in product overflow.
‣ The setting for the current output depends on the setting in the Assign PV parameter.
‣ After changing the setting of the current output, check the setting of the span (Lower range value output and Upper range value output) and change it if necessary!
9.2 Function check
Before commissioning the measuring point, check whether the post-mounting and postconnection checks (checklist) have been performed:
•
A
"Post-mounting check" section
•
A
"Post-connection check" section
9.3 Establishing a connection via FieldCare and
DeviceCare
9.3.1 Via HART protocol
9
2 3 6 8
34
1 4 5 7
9 Options for remote operation via HART protocol
1 PLC (programmable logic controller)
2 Transmitter power supply unit, e.g., RN42
3 Connection for Commubox FXA195 and AMS Trex TM device communicator
4 AMS Trex TM device communicator
5 Computer with operating tool (e.g., DeviceCare/FieldCare, AMS Device View, SIMATIC PDM)
6 Commubox FXA195 (USB)
7 Field Xpert SMT70
8 Bluetooth modem with connecting cable (e.g., VIATOR)
9 Transmitter
A0044334
Endress+Hauser
Micropilot FMR66B HART
9.3.2 Via service interface (CDI)
1 2
Commissioning
3
1 Computer with FieldCare/DeviceCare operating tool
2 Commubox FXA291
3 Service interface (CDI) of the measuring device (= Endress+Hauser Common Data Interface)
9.4 Configuring the device address via software
See "HART address" parameter
Enter the address to exchange data via the HART protocol.
• Guidance → Commissioning → HART address
• Application → HART output → Configuration → HART address
9.5 Setting the operating language
9.5.1 Local display
Setting the operating language
To set the operating language, the display first needs to be unlocked:
1. Press the key for at least 2 s.
A dialog box appears.
2. Unlock the display operation.
3. Select the Language parameter in the main menu.
4. Press the key.
5. Select the desired language with the or key.
6. Press the key.
Display operation locks automatically (except in the Safety mode wizard):
• after 1 min on the main page if no key has been pressed
• after 10 min within the operating menu if no key has been pressed
9.5.2 Operating tool
Set display language
System → Display → Language
Selection in the Language parameter; Visibility depends on order options or device settings
A0039148
Endress+Hauser 35
Commissioning
36
Micropilot FMR66B HART
9.6 Device configuration
9.6.1 Level measurement in bulk solids
R
BD
E F
D
L
100%
0%
A0016934
10 Configuration parameters for level measurement in bulk solids
R Reference point of measurement
D Distance
L Level
E "Empty calibration" parameter (= 0%)
F "Full calibration" parameter (= 100%)
9.6.2 Commissioning with the Commissioning wizard
In FieldCare, DeviceCare, SmartBlue and on the display, the Commissioning wizard is available to guide the user through the initial commissioning steps.
Complete this wizard to commission the device.
For each parameter, enter the appropriate value or select the appropriate option.
NOTE
If you exit the wizard before completing all required parameters, the changes you made will be saved. For this reason, the device may be in an undefined state!
In this case, a reset to the default settings is recommended.
9.7 Recording the Echo curve
Record the current Echo curve as a reference echo curve for subsequent diagnostic purposes
After the measurement has been configured, it is recommended to record the current Echo curve as a reference echo curve.
The Save reference curve parameter in the Echo curve submenu is used to record the
Echo curve.
Diagnostics → Echo curve → Save reference curve
‣ Under the Save reference curve parameter, activate the Customer reference curve option
Endress+Hauser
Micropilot FMR66B HART
9.8 "Simulation" submenu
Simulation of a process variable, a pulse output or a diagnostic event.
Commissioning
Endress+Hauser 37
Operation Micropilot FMR66B HART
10 Operation
10.1 Reading off the device locking status
Displaying active write protection in the Locking status parameter
• Local display :
The symbol appears on the main page
• Operating tool (FieldCare/DeviceCare) :
Navigation: System → Device management → Locking status
10.2 Reading off measured values
All the measured values can be read off using the Measured values submenu.
Navigation: Application menu → Measured values submenu
10.3 Adapting the device to process conditions
The following menus are available for this purpose:
• Basic settings in the Guidance menu
• Advanced settings in:
• Diagnostics menu
• Application menu
• System menu
10.4 Heartbeat Technology (optional)
10.4.1 Heartbeat Verification
"Heartbeat Verification" wizard
This wizard is used to start an automatic verification of the device functionality. The results can be documented as a verification report.
• The wizard can be used via the operating tools and the display
The wizard can be started on the display but only shows the Passed option or Failed option result.
• The wizard guides the user through the entire process for creating the verification report
10.4.2 Heartbeat Verification/Monitoring
The Heartbeat submenu is only available when operating via FieldCare, DeviceCare or the SmartBlue app. It contains the wizards that are provided with the Heartbeat
Verification and Heartbeat Monitoring application packages.
Documentation on the Heartbeat Technology: Endress+Hauser website: www.endress.com
→ Downloads.
38 Endress+Hauser
Micropilot FMR66B HART Diagnostics and troubleshooting
11 Diagnostics and troubleshooting
11.1 General troubleshooting
11.1.1 General errors
Device is not responding
• Possible cause: Supply voltage does not match the specification on the nameplate
Remedial action: Apply the correct voltage
• Possible cause: The polarity of the supply voltage is wrong
Remedial action: Correct the polarity
• Possible cause: The connecting cables are not in contact with the terminals
Remedial action: Check the electrical contact between cables and correct if necessary
• Possible cause: Load resistance too high
Remedial action: Increase the supply voltage to reach the minimum terminal voltage
Values not visible on the display
• Possible cause: Display setting is too bright or too dark
Remedial action:
Use the Contrast display parameter to increase or reduce contrast
Navigation path: System → Display → Contrast display
• Possible cause: The plug of the display cable is not connected correctly
Remedial action: Connect the plug correctly
• Possible cause: Display is defective
Remedial action: Replace the display
"Communication error" is indicated on the display when the device is started or the display is connected
• Possible cause: Electromagnetic interference influence
Remedial action: Check grounding of the device
• Possible cause: Defective cable connection or display plug
Remedial action: Replace the display
Communication via CDI interface not working
Possible cause: Wrong setting of the COM port on the computer
Remedial action: Check the setting of the COM port on the computer and correct it if necessary
Device measuring incorrectly
Possible cause: Parameter configuration error
Remedial action: Check and correct the parameter configuration
11.2 Error - SmartBlue operation
Operation via SmartBlue is only possible on devices that have a display with Bluetooth
(optionally available).
Endress+Hauser 39
Diagnostics and troubleshooting Micropilot FMR66B HART
Device is not visible in the live list
• Possible cause: No Bluetooth connection available
Remedial action: Enable Bluetooth in the field device via display or software tool and/or in the smartphone/tablet
• Possible cause: Bluetooth signal outside range
Remedial action: Reduce distance between field device and smartphone/tablet
The connection has a range of up to 25 m (82 ft).
Operating radius with intervisibility 10 m (33 ft)
• Possible cause: Geopositioning is not enabled on Android devices or is not permitted for the SmartBlue app
Remedial action: Enable/permit the geopositioning service on Android device for the
SmartBlue app
• Display does not have Bluetooth
Device appears in the live list but a connection cannot be established
• Possible cause: The device is already connected with another smartphone/tablet via
Bluetooth
Only one point-to-point connection is permitted
Remedial action: Disconnect the smartphone/tablet from the device
• Possible cause: Incorrect user name and password
Remedial action: The standard user name is "admin" and the password is the device serial number indicated on the device nameplate (only if the password was not changed by the user beforehand)
If the password has been forgotten, contact Endress+Hauser Service
( www.addresses.endress.com
)
Connection via SmartBlue not possible
• Possible cause: Incorrect password entered
Remedial action: Enter the correct password, paying attention to lower/upper case
• Possible cause: Forgotten password
Remedial action: Contact Endress+Hauser Service ( www.addresses.endress.com
)
Login via SmartBlue not possible
• Possible cause: Device is being put into operation for the first time
Remedial action: Enter the user name "admin" and the password (device serial number), paying attention to lower/upper case
• Possible cause: The electric current and voltage are not correct.
Remedial action: Increase the supply voltage.
Device cannot be operated via SmartBlue
• Possible cause: Incorrect password entered
Remedial action: Enter the correct password, paying attention to lower/upper case
• Possible cause: Forgotten password
Remedial action: Contact Endress+Hauser Service ( www.addresses.endress.com
)
• Possible cause: Operator option has no authorization
Remedial action: Change to Maintenance option
11.3 Diagnostic information on local display
11.3.1 Diagnostic message
Measured value display and diagnostic message in alarm condition
Faults detected by the self-monitoring system of the device are displayed as a diagnostic message in alternation with the unit.
40 Endress+Hauser
Micropilot FMR66B HART Diagnostics and troubleshooting
1 X
2
A0043759
1 Status signal
2 Status symbol with diagnostic event
Faults detected by the self-monitoring system of the device are displayed as a diagnostic message in alternation with the measured value display.
X X X X X X X X X
S801
X X X X X X X X X
S i
1
2
3
A0043103
1 Status signal
2 Status symbol with diagnostic event
3 Event text
Status signals
F
"Failure (F)" option
A device error has occurred. The measured value is no longer valid.
C
"Function check (C)" option
The device is in the service mode (e.g. during a simulation).
S
"Out of specification (S)" option
The device is being operated:
• Outside of its technical specifications (e.g. during startup or a cleaning)
• Outside of the configuration performed by the user (e.g. sensor frequency outside the configured span)
M
"Maintenance required (M)" option
Maintenance required. The measured value remains valid.
Diagnostic event and event text
The fault can be identified by means of the diagnostic event. The event text helps you by providing information about the fault. In addition, the corresponding status symbol is displayed in front of the diagnostic event.
Endress+Hauser 41
Diagnostics and troubleshooting
42
Micropilot FMR66B HART
X X X X X X X X X
S801
X X X X X X X X X
S 1
2
3 5 6
4
A0038013
1 Status signal
2 Event text
3 Status symbol
4 Diagnostic event
5 Status signal
6 Event number
If two or more diagnostic events occur simultaneously, only the diagnostic message with the highest priority is shown.
"Active diagnostics" parameter
Key
Opens the message about the remedial measures.
Key
Acknowledge warnings.
Key
Back to operating menu.
11.4 Diagnostic event in the operating tool
If there is a diagnostic event in the device, the status signal appears on the top left in the status section of the operating tool together with the associated icon for event behavior according to NAMUR NE 107:
• Failure (F)
• Function check (C)
• Out of specification (S)
• Maintenance required (M)
Click the status signal to see the detailed status signal.
The diagnostic events and remedial measures can be printed in the Diagnostic list submenu.
11.5 Adapting the diagnostic information
The event level can be configured:
Navigation: Diagnostics → Diagnostic settings → Configuration
11.6 Queued diagnostic messages
The display alternates between the queued diagnostic messages and the measured value.
Queued diagnostic messages can also be displayed in the Active diagnostics parameter.
Navigation: Diagnostics → Active diagnostics
Endress+Hauser
Micropilot FMR66B HART Diagnostics and troubleshooting
11.7 Diagnostic list
In the Diagnostic list submenu submenu, up to 5 currently pending diagnostic messages can be displayed. If more than 5 messages are pending, the messages with the highest priority are shown on the display.
Navigation path
Diagnostics → Diagnostic list
Calling up and closing the remedial measures
1. Press .
The message for the remedial measures for the selected diagnostic event opens.
2. Press + simultaneously.
The message about the remedial measures closes.
11.8 List of diagnostic events
Diagnostic number
Short text Remedy instructions
Diagnostic of sensor
062
151
168
Sensor connection faulty Check sensor connection
Sensor electronic failure
Build-up detected
Replace sensor electronic module
Check process conditions
F
F
M
Status signal
[from the factory]
Diagnostic of electronic
203 HART Device
Malfunction
204
242
HART Electronic Defect
Check device specific diagnosis.
Check device specific diagnosis.
Firmware incompatible 1. Check software
2. Flash or change main electronic module
252
270
272
Module incompatible 1. Check if correct electronic module is plugged
2. Replace electronic module
Main electronics defective
Replace main electronics
Main electronics faulty 1. Restart device
2. Contact service
S
F
F
F
F
F
273
282
283
287
388
Main electronics defective
Replace main electronics
Data storage inconsistent Restart device
Memory content inconsistent
1. Restart device
2. Contact service
Memory content inconsistent
Electronics and
HistoROM defective
1. Restart device
2. Contact service
1. Restart device
2. Replace electronics and
HistoROM
3. Contact service
Diagnostic of configuration
410 Data transfer failed 1. Retry data transfer
2. Check connection
F
F
F
M
F
F
Diagnostic behavior
[from the factory]
Alarm
Alarm
Warning
Warning
Alarm
Alarm
Alarm
Alarm
Alarm
Alarm
Alarm
Alarm
Warning
Alarm
Alarm
Endress+Hauser 43
Diagnostics and troubleshooting Micropilot FMR66B HART
Diagnostic number
412
420
421
431
435
437
438
441
484
Short text
Processing download
HART Device
Configuration Locked
Remedy instructions
Download active, please wait
Check device locking configuration. S
HART Loop Current fixed Check Multi-drop mode or current simulation.
C
S
Status signal
[from the factory]
Trim required
Linearization faulty
Configuration incompatible
Dataset different
Carry out trim
Check linearization table
1. Update firmware
2. Execute factory reset
C
F
F
M
Current output out of range
Failure mode simulation active
1. Check data set file
2. Check device parameterization
3. Download new device parameterization
1. Check process
2. Check current output settings
Deactivate simulation
S
C
C 485
491
495
Process variable simulation active
Current output simulation active
Diagnostic event simulation active
Configuration Sensor
Unit invalid
Deactivate simulation
Deactivate simulation
Deactivate simulation
538
585
586
Simulation distance
Record map
1. Check sensor configuration
2. Check device configuration
Deactivate simulation
Recording of mapping please wait
Diagnostic of process
801
802
805
Supply voltage too low
Supply voltage too high
Loop current faulty
Increase supply voltage
Decrease supply voltage
1. Check wiring
2. Replace electronics
806
807
825
826
846
847
848
Loop diagnostics 1. Check supply voltage
2. Check wiring and terminals
Increase supply voltage No Baseline due to insuf.
volt. at 20 mA
Electronics temperature 1. Check ambient temperature
2. Check process temperature
Sensor temperature out of range
1. Check ambient temperature
2. Check process temperature
Check device specific diagnosis.
HART Non-Primary
Variable Out of Limit
HART Primary Variable
Out of Limit
HART Device Variable
Alert
Check device specific diagnosis.
Check device specific diagnosis.
C
S
F
C
C
F
S
F
M
M
S
S
S
S
S
941 Echo lost Check parameter 'DC value' S
Diagnostic behavior
[from the factory]
Warning
Warning
Warning
Warning
Alarm
Alarm
Warning
Warning
Warning
Warning
Warning
Warning
Alarm
Warning
Warning
Alarm
Warning
Alarm
Warning
Warning
Warning
Warning
Warning
Warning
Warning
Warning
44 Endress+Hauser
Micropilot FMR66B HART Diagnostics and troubleshooting
Diagnostic number
Short text Remedy instructions
S
Status signal
[from the factory]
Diagnostic behavior
[from the factory]
Warning
942
952
968
In safety distance
Foam detected
Level limited
1) Diagnostic behavior can be changed.
1. Check level
2. Check safety distance
3. Reset self holding
Check process conditions
1. Check level
2. Check limit parameters
C
S
Warning
Warning
11.9 Event logbook
11.9.1 Event history
A chronological overview of the event messages that have occurred is provided in the
Event logbook submenu. This submenu only exists if operating via the local display. In the case of operation via FieldCare, the event list can be displayed with the "Event List /
HistoROM" functionality of FieldCare.
Navigation:
Diagnostics → Event logbook → Event list
A maximum of 100 event messages can be displayed in chronological order.
The event history includes entries for:
• Diagnostic events
• Information events
In addition to the operating time when the event occurred, each event is also assigned a symbol that indicates whether the event has occurred or is finished:
• Diagnostic event
• : Occurrence of the event
• : End of the event
• Information event
: Occurrence of the event
Calling up and closing the remedial measures
1. Press .
The message for the remedial measures for the selected diagnostic event opens.
2. Press + simultaneously.
The message about the remedial measures closes.
11.9.2 Filtering the event logbook
Filters can be used to determine which category of event messages is displayed in the
Event list submenu.
Navigation: Diagnostics → Event logbook
Filter categories
• All
• Failure (F)
• Function check (C)
Endress+Hauser 45
Diagnostics and troubleshooting
• Out of specification (S)
• Maintenance required (M)
• Information
11.9.3 Overview of information events
I1444
I1445
I1461
I1512
I1513
I1514
I1157
I1256
I1264
I1335
I1397
I1398
I1440
I1515
I1551
I1552
I1554
I1555
I1556
I1956
I1000
Info number
I1079
I1089
I1090
I1091
I11074
I1110
I11104
I1151
I1154
I1155
--------(Device ok)
Sensor changed
Power on
Configuration reset
Configuration changed
Device verification active
Write protection switch changed
Loop diagnostics
History reset
Reset terminal voltage min/max
Reset electronics temperature
Memory error event list
Display: access status changed
Safety sequence aborted
Firmware changed
Fieldbus: access status changed
CDI: access status changed
Main electronic module changed
Device verification passed
Device verification failed
Sensor verification failed
Download started
Download finished
Upload started
Upload finished
Assignment error fixed
Failed: Main electronic verification
Safety sequence started
Safety sequence confirmed
Safety mode off
Reset
Info name
Micropilot FMR66B HART
46
11.10 Resetting the device
11.10.1 Resetting the device via the operating tool
Reset the device configuration - either entirely or in part - to a defined state
Navigation: System → Device management → Reset device
Endress+Hauser
Micropilot FMR66B HART Diagnostics and troubleshooting
Reset device parameter
For details see the "Description of device parameters" documentation.
11.10.2 Resetting the device via keys on the electronic insert
Reset the password
15 s
I I I I
Display
I
II
Endress+Hauser
2×
A0050210
11 Sequence - resetting the password
Deleting/resetting the password
1. Press operating key I three times.
The Reset Password function is started, the LED flashes.
2. Press operating key I once within 15 s.
The password is reset, the LED flashes briefly.
If operating key I is not pressed within 15 s, the action is canceled and the LED is no longer lit.
Resetting the device to the factory setting
12 s
Display II
I
I
II
12 Operating keys on the electronic insert
Resetting the device to the factory setting
‣ Press operating key I and operating key II simultaneously for at least 12 s.
Device data are reset to the factory setting, the LED flashes briefly.
50 ms
A0050009
11.11 Device information
All the device information is contained in the Information submenu.
Navigation: System → Information
47
Diagnostics and troubleshooting Micropilot FMR66B HART
For details see the "Description of device parameters" documentation.
11.12 Firmware history
The firmware version can explicitly be ordered via the product structure. This makes it possible to ensure the compatibility of the firmware version with an existing or planned system integration.
11.12.1 Version 01.00.zz
Original software
48 Endress+Hauser
Micropilot FMR66B HART Maintenance
12 Maintenance
No special maintenance work is required.
12.1 Exterior cleaning
Notes on cleaning
• The cleaning agents used should not corrode the surfaces and the seals
• Observe the degree of protection of the device
12.2 Seals
The process seals, located on the process connection of the device, should be replaced periodically. The interval between changes depends on the frequency of the cleaning cycles, the cleaning temperature and the medium temperature.
Endress+Hauser 49
Repair
50
Micropilot FMR66B HART
13 Repair
13.1 General information
13.1.1 Repair concept
Endress+Hauser repair concept
• The devices have a modular design
• Repairs can be carried out by Endress+Hauser Service or by appropriately trained customers
• Spare parts are grouped into logical kits with the associated replacement instructions
For more information on service and spare parts, please contact your Endress+Hauser sales representative.
13.1.2 Repair of Ex-certified devices
L WARNING
Incorrect repair can affect electrical safety!
Explosion Hazard!
‣ Only specialist personnel or the Endress+Hauser service team may carry out repairs on
Ex-certified devices.
‣ Relevant standards and national regulations on hazardous areas, safety instructions and certificates must be observed.
‣ Use only original Endress+Hauser spare parts.
‣ Please note the device designation on the nameplate. Only identical parts may be used as replacements.
‣ Carry out repairs according to the instructions.
‣ Only the Endress+Hauser service team is permitted to modify a certified device and convert it to another certified version.
‣ All repairs and modifications must be documented.
13.2 Spare parts
• Some replaceable device components are identified by a spare part nameplate. This contains information about the spare part.
• All the spare parts available for the measuring device are listed in the Device Viewer
( www.endress.com/deviceviewer ) along with the order code and can be ordered. If available, users can also download the associated Installation Instructions.
Device serial number or QR code:
Located on the device and spare part nameplate.
13.3 Replacement
L CAUTION
Data upload/download is not permitted if the device is used for safety-related applications.
‣ After an entire device or an electronics module has been replaced, the parameters can be downloaded to the device again via the communication interface. For this, the data must have been uploaded to the PC beforehand using the "FieldCare/DeviceCare" software.
Endress+Hauser
Micropilot FMR66B HART Repair
13.3.1 HistoROM
It is not necessary to perform a new device calibration after replacing the display or transmitter electronics.
The spare part is supplied without HistoROM.
After removing the transmitter electronics, remove HistoRom and insert it into the new spare part.
13.4 Return
The requirements for safe device return can vary depending on the device type and national legislation.
1. Refer to the web page for information: http://www.endress.com/support/return-material
Select the region.
2. Return the device if repairs or a factory calibration are required, or if the wrong device was ordered or delivered.
13.5 Disposal
If required by the Directive 2012/19/EU on waste electrical and electronic equipment
(WEEE), the product is marked with the depicted symbol in order to minimize the disposal of WEEE as unsorted municipal waste. Do not dispose of products bearing this marking as unsorted municipal waste. Instead, return them to the manufacturer for disposal under the applicable conditions.
Endress+Hauser 51
Accessories Micropilot FMR66B HART
14 Accessories
14.1 Weather protection cover 316L
The weather protection cover can be ordered together with the device via the "Accessory enclosed" product structure.
It is used to protect against direct sunlight, precipitation and ice.
Weather protection cover 316L is suitable for the dual compartment housing made of aluminum or 316L. The delivery includes the holder for direct mounting on the housing.
228.9 (9.01)
136.4 (5.37) 92.5 (3.64) 170.5 (6.71)
52
!65 (2.56)
81 (3.19)
103 (4.06)
A0039231
13 Dimensions. Unit of measurement mm (in)
Material
• Weather protection cover: 316L
• Clamping screw: A4
• Holder: 316L
Order number for accessories:
71438303
14.2 Plastic weather protection cover
The weather protection cover can be ordered together with the device via the "Accessory enclosed" product structure.
It is used to protect against direct sunlight, precipitation and ice.
The plastic weather protection cover is suitable for the single compartment housing made of aluminum. The delivery includes the holder for direct mounting on the housing.
!115 (4.53)
140 (5.51)
165 (6.5)
14 Dimensions. Unit of measurement mm (in)
32 (1.26)
140 (5.51)
A0038280
Endress+Hauser
Micropilot FMR66B HART Accessories
Material
Plastic
Order number for accessories:
71438291
14.3 Adjustable flange seal
The adjustable flange seal is used to align the sensor to the surface of the product. It can be ordered directly with the device via the product structure "Accessory enclosed" or individually via the specific order number.
14.3.1 Seal, adjustable, DN80
The seal, adjustable, DN80 is compatible with flanges EN DN80 PN10/PN40
±8°
ø89 (3.5)
ø142 (5.59)
Technical data
• Material: EPDM
• Recommended screw size: M14
• Recommended screw length: 100 mm (3.9 in)
• Process pressure: –0.1 to 0.1 bar (–1.45 to 1.45 psi)
• Process temperature:–40 to +80 °C (–40 to +176 °F)
Ordering information
• The flange seal can be ordered together with the device via the "Accessory enclosed" product structure.
• Order number: 71074263
14.3.2 Seal, adjustable, DN100
The seal, adjustable, DN100 is compatible with flanges EN DN100 PN10/PN16
±8°
A0046695
ø115 (4.53)
ø162 (6.38)
A0046696
Endress+Hauser 53
Accessories
54
Micropilot FMR66B HART
Technical data
• Material: EPDM
• Recommended screw size: M14
• Recommended screw length: 100 mm (3.9 in)
• Process pressure: –0.1 to 0.1 bar (–1.45 to 1.45 psi)
• Process temperature:–40 to +80 °C (–40 to +176 °F)
Ordering information
• The flange seal can be ordered together with the device via the "Accessory enclosed" product structure.
• Order number: 71074264
14.3.3 Seal, adjustable, DN150
The seal, adjustable, DN150 is compatible with flanges EN DN150 PN10/PN19 and JIS
10K 150A
±8°
ø169 (6.65)
ø218 (8.58)
A0046697
Technical data
• Material: EPDM
• Recommended screw size: M18
• Recommended screw length: 110 mm (4.3 in)
• Process pressure: –0.1 to 0.1 bar (–1.45 to 1.45 psi)
• Process temperature:–40 to +80 °C (–40 to +176 °F)
Ordering information
• The flange seal can be ordered together with the device via the "Accessory enclosed" product structure.
• Order number: 71074265
14.3.4 Seal, adjustable, ASME 3"/ JIS 80A
The seal, adjustable, ASME 3"/ JIS 80A is compatible with flanges ASME 3" 150 lbs and JIS
80A 10K
±8°
ø89 (3.5)
ø133 (5.2)
A0046698
Endress+Hauser
Micropilot FMR66B HART Accessories
Technical data
• Material: EPDM
• Recommended screw size: M14
• Recommended screw length: 100 mm (3.9 in)
• Process pressure: –0.1 to 0.1 bar (–1.45 to 1.45 psi)
• Process temperature:–40 to +80 °C (–40 to +176 °F)
Ordering information
• The flange seal can be ordered together with the device via the "Accessory enclosed" product structure.
• Order number: 71249070
14.3.5 Seal, adjustable, ASME 4"
The seal, adjustable, ASME 4" is compatible with flanges ASME 4" 150 lbs
±8°
ø115 (4.53)
ø171 (6.7)
A0046699
Technical data
• Material: EPDM
• Recommended screw size: M14
• Recommended screw length: 100 mm (3.9 in)
• Process pressure: –0.1 to 0.1 bar (–1.45 to 1.45 psi)
• Process temperature:–40 to +80 °C (–40 to +176 °F)
Ordering information
• The flange seal can be ordered together with the device via the "Accessory enclosed" product structure.
• Order number: 71249072
14.3.6 Seal, adjustable, ASME 6"/ JIS 150A
The seal, adjustable, ASME 6"/ JIS 150A is compatible with flanges ASME 6" 150 lbs and
JIS 150A 10K
±8°
ø168 (6.6)
ø219 (8.6)
A0046700
Endress+Hauser 55
Accessories Micropilot FMR66B HART
Technical data
• Material: EPDM
• Recommended screw size: M18
• Recommended screw length: 100 mm (3.9 in)
• Process pressure: –0.1 to 0.1 bar (–1.45 to 1.45 psi)
• Process temperature:–40 to +80 °C (–40 to +176 °F)
Ordering information
• The flange seal can be ordered together with the device via the "Accessory enclosed" product structure.
• Order number: 71249073
14.4 Mounting bracket, adjustable
The device can be mounted on a wall or ceiling with the mounting bracket.
The device can be aligned with the product surface with the swivel function.
The mounting bracket can be ordered together with the device via the product structure
"Accessory enclosed".
A0048745
15 Ceiling or wall mounting
56 Endress+Hauser
Micropilot FMR66B HART
156 (6.14) 35 (1.38)
Accessories
Endress+Hauser
3 (0.12)
65 (2.56)
32.5 (1.28)
6 (0.24) !9 (0.35)
A0048769
16 Dimensions of mounting bracket. Unit of measurement mm (in)
Scope of delivery:
• 1 × mounting bracket, 316L (1.4404)
• 2 × holder, 316L (1.4404)
• 6 × screws, A4
• 4 × lock washer, A4
Suitable for device with:
• Single compartment housing
• Dual compartment housing, L-form and:
• Encapsulated antenna, PVDF, 40 mm (1.5 in)
• Drip-off antenna 50 mm (2 in), threaded process connection
FMR6xB mounting device order number: 71523849
There is no conductive connection between the mounting bracket and the transmitter housing. The bracket should be included in local potential equalization to prevent any electrostatic charge.
Fasten only to stable materials (e.g. metal, brick, concrete) with suitable fastening fixtures (provided by the customer).
14.5 M12 socket
M12 socket, straight
• Material:
Body: PBT; union nut: nickel-plated die-cast zinc; seal: NBR
• Degree of protection (fully locked): IP67
• Pg coupling: Pg7
• Order number: 52006263
57
Accessories
58
Micropilot FMR66B HART
M12 socket, angled
• Material:
Body: PBT; union nut: nickel-plated die-cast zinc; seal: NBR
• Degree of protection (fully locked): IP67
• Pg coupling: Pg7
• Order number: 71114212
M12 socket, angled, 5 m (16 ft) cable
• M12 socket material:
• Body: TPU
• Union nut: nickel-plated die-cast zinc
• Cable material:
PVC
• Cable Li Y YM 4×0.34 mm 2 (20 AWG)
• Cable colors
• 1 = BN = brown
• 2 = WH = white
• 3 = BU = blue
• 4 = BK = black
• Order number: 52010285
14.6 Remote display FHX50B
The remote display is ordered via the Product Configurator.
If the remote display is to be used, the device version Prepared for display FHX50B must be ordered.
C
A
D
B
E
A0046692
A Plastic single compartment housing, remote display
B Aluminum single compartment housing, remote display
C Device side, plastic single compartment housing prepared for remote display
D Device side, aluminum single compartment housing prepared for remote display
E Device side, dual compartment housing, L-form, prepared for remote display
Material of single compartment housing, remote display
• Aluminum
• Plastic
Degree of protection:
• IP68 / NEMA 6P
• IP66 / NEMA 4x
Endress+Hauser
Micropilot FMR66B HART
Connecting cable:
• Connecting cable (option) up to 30 m (98 ft)
• Standard cable provided by customer onsite up to 60 m (196 ft)
Ambient temperature:
• –40 to +80 °C (–40 to +176 °F)
• Option: –50 to +80 °C (–58 to +176 °F)
14.7 Commubox FXA195 HART
For intrinsically safe HART communication with FieldCare via the USB interface
For details, see "Technical Information" TI00404F
Accessories
Endress+Hauser
14.8 HART Loop Converter HMX50
Is used to evaluate and convert dynamic HART process variables to analog current signals or limit values.
Order number:
71063562
For details, see "Technical Information" TI00429F and Operating Instructions
BA00371F
14.9 FieldPort SWA50
Intelligent Bluetooth® and/or WirelessHART adapter for all HART field devices
For details, see "Technical Information" TI01468S
14.10 Wireless HART adapter SWA70
The WirelessHART adapter is used for the wireless connection of field devices. It can be easily integrated into field devices and existing infrastructures, offers data protection and transmission safety and can be operated in parallel with other wireless networks.
For details, see Operating Instructions BA00061S
14.11 Fieldgate FXA42
Fieldgates enable communication between connected 4 to 20 mA, Modbus RS485 and
Modbus TCP devices and SupplyCare Hosting or SupplyCare Enterprise. The signals are transmitted either via Ethernet TCP/IP, WLAN or mobile communications (UMTS).
Advanced automation capabilities are available, such as an integrated Web-PLC, OpenVPN and other functions.
For details, see "Technical Information" TI01297S and Operating Instructions
BA01778S.
14.12 Field Xpert SMT70
Universal, high-performance tablet PC for device configuration in Ex Zone 2 and non-Ex areas
For details, see "Technical Information" TI01342S
59
Accessories Micropilot FMR66B HART
14.13 DeviceCare SFE100
Configuration tool for HART, PROFIBUS and FOUNDATION Fieldbus field devices
Technical Information TI01134S
14.14 FieldCare SFE500
FDT-based plant asset management tool
It can configure all smart field units in your system and helps you manage them. By using the status information, it is also a simple but effective way of checking their status and condition.
Technical Information TI00028S
14.15 Memograph M
The Memograph M graphic data manager provides information on all the relevant process variables. Measured values are recorded correctly, limit values are monitored and measuring points analyzed. The data are stored in the 256 MB internal memory and also on an SD card or USB stick.
Technical Information TI00133R and Operating Instructions BA00247R
14.16 RN42
Single-channel active barrier with wide-range power supply for safe electrical isolation of
4 to 20 mA standard signal circuits, HART transparent.
Technical Information TI01584K and Operating Instructions BA02090K
60 Endress+Hauser
Micropilot FMR66B HART
Measured variable
Measuring range
Technical data
15 Technical data
15.1 Input
The measured variable is the distance between the reference point and the product surface. The level is calculated based on "E", the empty distance entered.
The start of the measuring range is the point where the beam hits the floor. Levels below this point cannot be measured, particularly in the case of conical outlets. An alignment unit can be used to increase the maximum measuring range in such applications.
Maximum measuring range
The maximum measuring range depends on the antenna size and design.
Antenna
Encapsulated, PVDF, 40 mm (1.5 in)
Drip-off, PTFE, 50 mm (2 in)
Maximum measuring range
22 m (72 ft)
50 m (164 ft)
Usable measuring range
The usable measuring range depends on the antenna size, the medium's reflective properties, the installation position and any possible interference reflections.
In principle, measurement is possible up to the tip of the antenna.
Depending on the position of the product (angle of repose) and to avoid any material damage from abrasive media and deposit buildup on the antenna, the end of the measuring range should be selected 10 mm (0.4 in) before the tip of the antenna A .
Endress+Hauser 61
Technical data Micropilot FMR66B HART
100%
Operating frequency
Transmission power
Output signal
0%
C
A0031829
A Antenna tip + 10 mm (0.4 in)
B Smallest possible measuring range
C Distance above silo floor = 50 to 80 mm (1.97 to 3.15 in)
H Silo height > 0.7 m (2.3 ft)
For the dielectric constants (DC values) of many media commonly used in industry, please refer to:
• Dielectric constant (DC value) Compendium CP01076F
• The Endress+Hauser "DC Values app" (available for Android and iOS)
Approx. 80 GHz
Up to 8 devices can be installed in a tank without the devices mutually influencing one another.
• Peak power: 6.3 mW
• Average output power: 63 µW
15.2 Output
HART
Signal coding:
FSK ±0.5 mA over current signal
Data transmission rate:
1 200 Bit/s
Galvanic isolation:
Yes
Current output
4 to 20 mA with superimposed digital communication protocol HART, 2-wire
62 Endress+Hauser
Micropilot FMR66B HART
Signal on alarm
Linearization
Technical data
The current output offers a choice of three different operating modes:
• 4.0 to 20.5 mA
• NAMUR NE 43: 3.8 to 20.5 mA (factory setting)
• US mode: 3.9 to 20.8 mA
Current output
Failure mode (according to NAMUR Recommendation NE 43):
• Minimum alarm (= factory setting): 3.6 mA
• Maximum alarm: 22 mA
Local display
Status signal (according to NAMUR Recommendation NE 107):
Plain text display
Operating tool via service interface (CDI)
Status signal (according to NAMUR Recommendation NE 107):
Plain text display
Operating tool via HART communication
Status signal (according to NAMUR Recommendation NE 107):
Plain text display
The linearization function of the device allows the conversion of the measured value into any unit of length, weight, flow or volume.
Pre-programmed linearization curves
Linearization tables for calculating the volume in the following vessels are preprogrammed into the device:
• Pyramid bottom
• Conical bottom
• Angled bottom
• Horizontal cylinder
• Sphere
Other linearization tables of up to 32 value pairs can be entered manually.
Endress+Hauser 63
Technical data
Load
Protocol-specific data
Micropilot FMR66B HART
4 to 20 mA HART
R
L max
1065
848
3 R
L max £
U – 10.5 V
23 mA
10.5
30 35
U
[V]
1
2
1 Power supply 10.5 to 30 VDC Ex i
2 Power supply 10.5 to 35 VDC, for other types of protection and non-certified device versions
3 R
Lmax
maximum load resistance
U Supply voltage
Operation via handheld terminal or PC with operating program: take minimum communication resistor of 250 Ω into consideration.
A0039232
HART
Manufacturer ID:
17 (0x11{hex})
Device type ID:
0x11C1
Device revision:
1
HART specification:
7
DD version:
1
Device description files (DTM, DD)
Information and files under:
• www.endress.com
On the product page for the device: Documents/Software → Device drivers
• www.fieldcommgroup.org
HART load:
Min. 250 Ω
HART device variables
The following measured values are assigned to the device variables at the factory:
Device variable
Assign PV
Assign SV
Measured value
Level linearized
Distance
64 Endress+Hauser
Micropilot FMR66B HART
Wireless HART data
1)
Device variable
Assign TV
Assign QV
The PV is always applied to the current output.
Choice of HART device variables
• Level linearized
• Distance
• Terminal voltage
• Electronics temperature
• Sensor temperature
• Absolute echo amplitude
• Relative echo amplitude
• Area of incoupling
• Build-up index
• Build-up detected
• Foam index
• Foam detected
• Percent of range
• Loop current
• Terminal current
• Not used
Supported functions
• Burst mode
• Additional transmitter status
• Device locking
Minimum start-up voltage:
10.5 V
Start-up current:
< 3.6 mA
Starting time:
< 15 s
Minimum operating voltage:
10.5 V
Multidrop current:
4 mA
Time to establish connection:
< 30 s
Measured value
Absolute echo amplitude
Relative echo amplitude
Technical data
Endress+Hauser 65
Technical data Micropilot FMR66B HART
15.3 Environment
Ambient temperature range
The following values apply up to a process temperature of +85 °C (+185 °F). At higher process temperatures, the permitted ambient temperature is reduced.
• Without LCD display:
• Standard: –40 to +85 °C (–40 to +185 °F)
• Optionally available: –50 to +85 °C (–58 to +185 °F) with restricted operating life and performance
• Optionally available: –60 to +85 °C (–76 to +185 °F) with restricted operating life and performance; below –50 °C (–58 °F): devices can be damaged permanently
• With LCD display: –40 to +85 °C (–40 to +185 °F) with limitations in optical properties such as display speed and contrast. Can be used without limitations up to
–20 to +60 °C (–4 to +140 °F)
If operating outdoors in strong sunlight:
• Mount the device in the shade.
• Avoid direct sunlight, particularly in warm climatic regions.
• Use a weather protection cover (see accessories).
Ambient temperature limits The permitted ambient temperature (T a process temperature range.
) depends on the selected housing material and
In the event of temperature (T p temperature (T a
) is reduced.
) at the process connection, the permitted ambient
The following information only takes functional aspects into consideration. Additional restrictions may apply for certified device versions.
Plastic housing material
Process temperature range: –40 to +80 °C (–40 to +176 °F)
P1
T a
P2
P5
P3
P4
T p
17 Plastic housing material; process temperature range: –40 to +80 °C (–40 to +176 °F)
P1 = T p
: –40 °C (–40 °F) | T a
: +76 °C (+169 °F)
P2 = T p
: +76 °C (+169 °F) | T a
: +76 °C (+169 °F)
P3 = T
P4 = T p p
: +80 °C (+176 °F) | T
: +80 °C (+176 °F) | T a
: +75 °C (+167 °F) a
: –40 °C (–40 °F)
P5 = T p
: –40 °C (–40 °F) | T a
: –40 °C (–40 °F)
In the case of devices with plastic housings and CSA C/US approval, the selected process temperature range of –40 to +80 °C (–40 to +176 °F) is limited to
0 to +80 °C (+32 to +176 °F).
Process temperature range: 0 to +80 °C (+32 to +176 °F), with CSA C/US approval
A0032024
66 Endress+Hauser
Micropilot FMR66B HART
Endress+Hauser
Technical data
T a
P1 P2
P5
P3
P4
T p
18 Plastic housing material; process temperature range: 0 to +80 °C (+32 to +176 °F) with CSA C/US approval
P1 = T p
: 0 °C (+32 °F) | T a
: +76 °C (+169 °F)
P2 = T p
P3 = T p
: +76 °C (+169 °F) | T
: +80 °C (+176 °F) | T a
: +76 °C (+169 °F) a
: +75 °C (+167 °F)
P4 = T p
P5 = T p
: +80 °C (+176 °F) | T
: 0 °C (+32 °F) | T a
: 0 °C (+32 °F) a
: 0 °C (+32 °F)
A0048826
Process temperature range: –40 to +130 °C (–40 to +266 °F)
P1
T a
P2
P5
P3
P4
T p
19 Plastic housing material; process temperature range: –40 to +130 °C (–40 to +266 °F)
P1 = T p
: –40 °C (–40 °F) | T a
: +76 °C (+169 °F)
P2 = T p
P3 = T p
: +76 °C (+169 °F) | T
: +130 °C (+266 °F) | T a
: +76 °C (+169 °F) a
: +52 °C (+126 °F)
P4 = T p
: +130 °C (+266 °F) | T a
: –40 °C (–40 °F)
P5 = T p
: –40 °C (–40 °F) | T a
: –40 °C (–40 °F)
In the case of devices with plastic housings and CSA C/US approval, the selected process temperature range of –40 to +130 °C (–40 to +266 °F) is limited to
0 to +130 °C (+32 to +266 °F).
Process temperature range: 0 to +130 °C (+32 to +266 °F), with CSA C/US approval
A0032024
T a
P1 P2
P5
P3
P4
T p
20 Plastic housing material; process temperature range: 0 to +130 °C (+32 to +266 °F) with CSA C/US approval
P1 = T
P2 = T p p
: 0 °C (+32 °F) | T a
: +76 °C (+169 °F)
: +76 °C (+169 °F) | T a
: +76 °C (+169 °F)
P3 = T p
: +130 °C (+266 °F) | T a
: +52 °C (+126 °F)
P4 = T p
P5 = T p
: +130 °C (+266 °F) | T
: 0 °C (+32 °F) | T a
: 0 °C (+32 °F) a
: 0 °C (+32 °F)
A0048826
Aluminum housing material
Order option; process temperature range: –40 to +80 °C (–40 to +176 °F)
67
Technical data
Storage temperature
Micropilot FMR66B HART
P1
T a
P2
P5
P3
P4
T p
21 Aluminum housing material; process temperature range: –40 to +80 °C (–40 to +176 °F)
P1 = T p
P2 = T p
: –40 °C (–40 °F) | T a
: +79 °C (+174 °F)
: +79 °C (+174 °F) | T a
: +79 °C (+174 °F)
P3 = T
P4 = T p p
: +80 °C (+176 °F) | T
: +80 °C (+176 °F) | T a
: +79 °C (+174 °F) a
: –40 °C (–40 °F)
P5 = T p
: –40 °C (–40 °F) | T a
: –40 °C (–40 °F)
Order option; process temperature range: –40 to +130 °C (–40 to +266 °F)
P1
T a
P2
P5
P3
P4
T p
22 Aluminum housing material; process temperature range: –40 to +130 °C (–40 to +266 °F)
P1 = T p
P2 = T p
: –40 °C (–40 °F) | T a
: +79 °C (+174 °F)
: +79 °C (+174 °F) | T a
: +79 °C (+174 °F)
P3 = T
P4 = T p p
: +130 °C (+266 °F) | T
: +130 °C (+266 °F) | T a
: +55 °C (+131 °F) a
: –40 °C (–40 °F)
P5 = T p
: –40 °C (–40 °F) | T a
: –40 °C (–40 °F)
316L housing material
Order option; process temperature range: –40 to +80 °C (–40 to +176 °F)
P1
T a
P2
P5
P3
P4
T p
23 316L housing material; process temperature range: –40 to +80 °C (–40 to +176 °F)
P1 = T p
: –40 °C (–40 °F) | T a
: +77 °C (+171 °F)
P2 = T p
: +77 °C (+171 °F) | T
P3 = T p
: +80 °C (+176 °F) | T a
: +77 °C (+171 °F) a
: +77 °C (+171 °F)
P4 = T p
: +80 °C (+176 °F) | T
P5 = T p
: –40 °C (–40 °F) | T a a
: –40 °C (–40 °F)
: –40 °C (–40 °F)
• Without LCD display: –40 to +90 °C (–40 to +194 °F)
• With LCD display: –40 to +85 °C (–40 to +185 °F)
A0032024
A0032024
A0032024
68 Endress+Hauser
Micropilot FMR66B HART Technical data
Climate class
Installation height as per
IEC61010-1 Ed.3
Degree of protection
Vibration resistance
Electromagnetic compatibility (EMC)
DIN EN 60068-2-38 (test Z/AD)
• Generally up to 2 000 m (6 600 ft) above sea level
• Over 2 000 m (6 600 ft) under the following conditions:
• Supply voltage < 35 V
DC
• Power supply, overvoltage category 1
Test as per IEC 60529 and NEMA 250-2014
Housing and process connection
IP66/68, TYPE 4X/6P
(IP68: (1.83 mH
2
O for 24 h))
Cable entries
• Gland M20, plastic, IP66/68 TYPE 4X/6P
• Gland M20, brass nickel plated, IP66/68 TYPE 4X/6P
• Gland M20, 316L, IP66/68 TYPE 4X/6P
• Thread M20, IP66/68 TYPE 4X/6P
• Thread G1/2, IP66/68 TYPE 4X/6P
If the G1/2 thread is selected, the device is delivered with an M20 thread as standard and a G1/2 adapter is included with the delivery, along with the corresponding documentation
• Thread NPT1/2, IP66/68 TYPE 4X/6P
• HAN7D plug, 90 degrees, IP65 NEMA Type 4X
• M12 plug
• When housing is closed and connecting cable is plugged in: IP66/67 NEMA Type 4X
• When housing is open or connecting cable is not plugged in: IP20, NEMA Type 1
NOTICE
Plug M12 and plug HAN7D: incorrect mounting can invalidate the IP protection class!
‣ The degree of protection only applies if the connecting cable used is plugged in and screwed tight.
‣ The degree of protection only applies if the connecting cable used is specified according to IP67 NEMA Type 4X.
‣ The IP protection classes are only maintained if the dummy cap is used or the cable is connected.
DIN EN 60068-2-64 / IEC 60068-2-64 for 5 to 2 000 Hz: 1.5 (m/s 2 ) 2 /Hz
• Electromagnetic compatibility as per EN 61326 series and NAMUR recommendation
EMC (NE21)
• With regard to the safety function (SIL), the requirements of EN 61326-3-x are satisfied
• Maximum measured error during EMC testing: < 0.5 % of the span.
For more details refer to the EU Declaration of Conformity.
Endress+Hauser 69
Technical data
Process pressure range
Micropilot FMR66B HART
15.4 Process
L WARNING
The maximum pressure for the device depends on the lowest-rated component with regard to pressure (components are: process connection, optional mounted parts or accessories).
‣ Only operate the device within the specified limits for the components!
‣ MWP (Maximum Working Pressure): The MWP is specified on the nameplate. This value refers to a reference temperature of +20 °C (+68 °F) and may be applied to the device for an unlimited time. Note temperature dependence of MWP. For flanges, refer to the following standards for the permitted pressure values at higher temperatures:
EN 1092-1 (with regard to their stability/temperature property, the materials 1.4435
and 1.4404 are grouped together under EN 1092-1; the chemical composition of the two materials can be identical), ASME B16.5, JIS B2220 (the latest version of the standard applies in each case). MWP data that deviate from this are provided in the relevant sections of the Technical Information.
‣ The Pressure Equipment Directive (2014/68/EU) uses the abbreviation PS . This corresponds to the maximum working pressure (MWP) of the device.
The following tables show the dependencies between the seal material, process temperature (T
P
) and process pressure range for each process connection that can be selected for the antenna used.
Encapsulated antenna, PVDF, 40 mm (1.5 in)
Process connection thread 1-½"
A0047831
Seal
PVDF encapsulated
T p
–40 to +80 °C
(–40 to +176 °F)
Process pressure range
–1 to 3 bar (–14.5 to 43.5 psi)
PVDF encapsulated –40 to +130 °C
(–40 to +266 °F)
–1 to 3 bar (–14.5 to 43.5 psi)
The following temperature restriction applies for devices with the dust ignition-proof approval category 1D, 2D or 3D
PVDF encapsulated –20 to +80 °C (–4 to +176 °F) –1 to 3 bar (–14.5 to 43.5 psi)
Process connection UNI flange PP
A0047947
Seal
PVDF encapsulated
T p
–40 to +80 °C
(–40 to +176 °F)
Process pressure range
–1 to 3 bar (–14.5 to 43.5 psi)
The following temperature restriction applies for devices with the dust ignition-proof approval category 1D, 2D or 3D
PVDF encapsulated –20 to +80 °C (–4 to +176 °F) –1 to 3 bar (–14.5 to 43.5 psi)
The pressure range may be further restricted in the event of a CRN approval.
70 Endress+Hauser
Micropilot FMR66B HART Technical data
Drip-off antenna 50 mm (2 in)
Process connection thread
Seal T p
FKM Viton GLT –40 to +150 °C (–40 to +302 °F)
FKM Viton GLT –40 to +200 °C (–40 to +392 °F)
Process pressure range
–1 to 16 bar (–14.5 to 232 psi)
–1 to 16 bar (–14.5 to 232 psi)
A0047447
Process connection UNI flange PP
Seal T p
FKM Viton GLT –40 to +80 °C (–40 to +176 °F)
Process pressure range
–1 to 3 bar (–14.5 to 43.5 psi)
Dielectric constant
A0047726
Process connection UNI flange 316L
Seal T p
FKM Viton GLT –40 to +150 °C (–40 to +302 °F)
FKM Viton GLT –40 to +200 °C (–40 to +392 °F)
Process pressure range
–1 to 3 bar (–14.5 to 43.5 psi)
–1 to 3 bar (–14.5 to 43.5 psi)
A0047726
The pressure range may be further restricted in the event of a CRN approval.
For bulk solids
ε r
≥ 1.6
Contact Endress+Hauser for applications with lower dielectric constants than indicated.
Endress+Hauser 71
Index Micropilot FMR66B HART
Index
A
Access authorization to parameters
Read access . . . . . . . . . . . . . . . . . . . . . . . . . . . . . 29
Write access . . . . . . . . . . . . . . . . . . . . . . . . . . . . . 29
Access code . . . . . . . . . . . . . . . . . . . . . . . . . . . . . . . . 29
Incorrect input . . . . . . . . . . . . . . . . . . . . . . . . . . . 29
Application . . . . . . . . . . . . . . . . . . . . . . . . . . . . . . . . . 8
B
Bluetooth® wireless technology . . . . . . . . . . . . . . . . . 31
C
CE mark (Declaration of Conformity) . . . . . . . . . . . . . . 9
Cleaning . . . . . . . . . . . . . . . . . . . . . . . . . . . . . . . . . . 49
Climate class . . . . . . . . . . . . . . . . . . . . . . . . . . . . . . . 69
D
Declaration of Conformity . . . . . . . . . . . . . . . . . . . . . . 9
Device locking, status . . . . . . . . . . . . . . . . . . . . . . . . 38
Device Viewer . . . . . . . . . . . . . . . . . . . . . . . . . . . . . . 50
DeviceCare . . . . . . . . . . . . . . . . . . . . . . . . . . . . . . . . 32
Diagnostic event . . . . . . . . . . . . . . . . . . . . . . . . . . . . 41
In the operating tool . . . . . . . . . . . . . . . . . . . . . . . 42
Diagnostic events . . . . . . . . . . . . . . . . . . . . . . . . . . . 40
Diagnostic list . . . . . . . . . . . . . . . . . . . . . . . . . . . . . . 43
Diagnostic message . . . . . . . . . . . . . . . . . . . . . . . . . . 40
Diagnostics
Symbols . . . . . . . . . . . . . . . . . . . . . . . . . . . . . . . . 40
Display values
For locking status . . . . . . . . . . . . . . . . . . . . . . . . . 38
Disposal . . . . . . . . . . . . . . . . . . . . . . . . . . . . . . . . . . 51
Document
Purpose . . . . . . . . . . . . . . . . . . . . . . . . . . . . . . . . . 5
E
Event history . . . . . . . . . . . . . . . . . . . . . . . . . . . . . . . 45
Event list . . . . . . . . . . . . . . . . . . . . . . . . . . . . . . . . . . 45
Event text . . . . . . . . . . . . . . . . . . . . . . . . . . . . . . . . . 41
Exterior cleaning . . . . . . . . . . . . . . . . . . . . . . . . . . . . 49
F
Field of application
Residual risks . . . . . . . . . . . . . . . . . . . . . . . . . . . . . 8
FieldCare . . . . . . . . . . . . . . . . . . . . . . . . . . . . . . . . . 32
Function . . . . . . . . . . . . . . . . . . . . . . . . . . . . . . . 32
Filtering the event logbook . . . . . . . . . . . . . . . . . . . . 45
Functional Safety Manual (FY) . . . . . . . . . . . . . . . . . . . 6
FV (HART variable) . . . . . . . . . . . . . . . . . . . . . . . . . . 33
H
HART integration . . . . . . . . . . . . . . . . . . . . . . . . . . . 33
HART protocol . . . . . . . . . . . . . . . . . . . . . . . . . . . . . 34
HART variables . . . . . . . . . . . . . . . . . . . . . . . . . . . . . 33
I
Intended use . . . . . . . . . . . . . . . . . . . . . . . . . . . . . . . . 8
72
L
Local display see Diagnostic message see In alarm condition
M
Media . . . . . . . . . . . . . . . . . . . . . . . . . . . . . . . . . . . . . 8
O
Operating elements
Diagnostic message . . . . . . . . . . . . . . . . . . . . . . . 42
Operation . . . . . . . . . . . . . . . . . . . . . . . . . . . . . . . . . 38
Operational safety . . . . . . . . . . . . . . . . . . . . . . . . . . . . 9
P
Product safety . . . . . . . . . . . . . . . . . . . . . . . . . . . . . . . 9
Purpose of this document . . . . . . . . . . . . . . . . . . . . . . 5
PV (HART variable) . . . . . . . . . . . . . . . . . . . . . . . . . . 33
R
Read access . . . . . . . . . . . . . . . . . . . . . . . . . . . . . . . . 29
Reading off measured values . . . . . . . . . . . . . . . . . . . 38
Registered trademarks . . . . . . . . . . . . . . . . . . . . . . . . . 7
Repair concept . . . . . . . . . . . . . . . . . . . . . . . . . . . . . 50
Requirements concerning the staff . . . . . . . . . . . . . . . . 8
Return . . . . . . . . . . . . . . . . . . . . . . . . . . . . . . . . . . . 51
S
Safety instructions
Basic . . . . . . . . . . . . . . . . . . . . . . . . . . . . . . . . . . . 8
Safety Instructions (XA) . . . . . . . . . . . . . . . . . . . . . . . . 6
Securing screw . . . . . . . . . . . . . . . . . . . . . . . . . . . . . 21
Service interface (CDI) . . . . . . . . . . . . . . . . . . . . . . . . 35
Settings
Adapting the measuring device to the process
conditions . . . . . . . . . . . . . . . . . . . . . . . . . . . . . . 38
Spare parts . . . . . . . . . . . . . . . . . . . . . . . . . . . . . . . . 50
Nameplate . . . . . . . . . . . . . . . . . . . . . . . . . . . . . . 50
Status signals . . . . . . . . . . . . . . . . . . . . . . . . . . . . . . 41
Submenu
Event list . . . . . . . . . . . . . . . . . . . . . . . . . . . . . . . 45
SV (HART variable) . . . . . . . . . . . . . . . . . . . . . . . . . . 33
T
Troubleshooting . . . . . . . . . . . . . . . . . . . . . . . . . . . . 39
Turning the display module . . . . . . . . . . . . . . . . . . . . 17
TV (HART variable) . . . . . . . . . . . . . . . . . . . . . . . . . . 33
U
Use of the measuring device see Intended use
Use of the measuring devices
Borderline cases . . . . . . . . . . . . . . . . . . . . . . . . . . . 8
Incorrect use . . . . . . . . . . . . . . . . . . . . . . . . . . . . . 8
W
Workplace safety . . . . . . . . . . . . . . . . . . . . . . . . . . . . 9
Endress+Hauser
Micropilot FMR66B HART
Write access . . . . . . . . . . . . . . . . . . . . . . . . . . . . . . . 29
Index
Endress+Hauser 73
*71575912*
71575912 www.addresses.endress.com
advertisement
* Your assessment is very important for improving the workof artificial intelligence, which forms the content of this project
Related manuals
advertisement
Table of contents
- 5 Document information
- 8 Basic safety instructions
- 11 Product description
- 12 identification
- 14 Installation
- 21 Electrical connection
- 29 Operation options
- 33 System integration
- 34 Commissioning
- 38 Operation
- 39 Diagnostics and troubleshooting
- 49 Maintenance
- 50 Repair
- 52 Accessories
- 61 Technical data
- 72 Index