advertisement
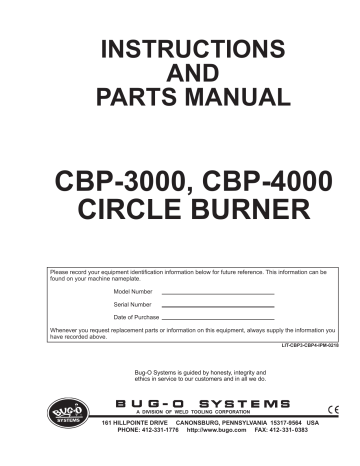
INSTRUCTIONS
AND
PARTS MANUAL
CBP-3000, CBP-4000
CIRCLE BURNER
Please record your equipment identification information below for future reference. This information can be found on your machine nameplate.
Model Number
Serial Number
Date of Purchase
Whenever you request replacement parts or information on this equipment, always supply the information you have recorded above.
LIT-CBP3-CBP4-IPM-0218
Bug-O Systems is guided by honesty, integrity and ethics in service to our customers and in all we do.
A DIVISION OF WELD TOOLING CORPORATION
161 HILLPOINTE DRIVE CANONSBURG, PENNSYLVANIA 15317-9564 USA
PHONE: 412-331-1776 http://www.bugo.com FAX: 412-331- 0383
SAFETY
PROTECT YOURSELF AND OTHERS FROM SERIOUS INJURY OR DEATH. KEEP
CHILDREN AWAY. BE SURE THAT ALL INSTALLATION, OPERATION, MAINTENANCE
AND REPAIR PROCEDURES ARE PERFORMED ONLY BY QUALIFIED INDIVIDUALS.
2
ELECTRIC SHOCK CAN KILL.
1) The equipment is not waterproof. Using the unit in a wet environment may result in serious injury. Do not touch equipment when wet or standing in a wet location.
2) The unused connectors have power on them. Always keep the unused connectors covered with the supplied protective panels. Operation of the machine without the protective panels may result in injury.
3) Never open the equipment without first unplugging the power cord or serious injury may result.
4) Verify the customer supplied power connections are made in accordance with all applicable local and national electrical safety codes. If none exist, use
International Electric Code (IEC) 950.
5) Never remove or bypass the equipment power cord ground. Verify the equipment is grounded in accordance with al applicable local and national electrical safety codes. In none exist, use
International Electric Code (IEC) 950.
READ INSTRUCTIONS.
Read the instruction manual before installing and using the equipment.
EQUIPMENT DAMAGE
POSSIBLE.
1) Do not plug in the power cord with out first verifying the equipment is OFF and the cord input voltage is the same as required by the machine or serious damage may result.
2) Always verify both the pinion and wheels are fully engaged before applying power or equipment damage may occur.
3) Do not leave the equipment unattended.
4) Remove from the work site and store in a safe location when not in use.
FALLING EQUIPMENT can cause serious personal injury and equipment damage.
Faulty or careless user installation is possible. As a result, never stand or walk underneath equipment.
MOVING PARTS can cause serious injury.
1) Never try to stop the pinion from moving except by removing power or by using the STOP control.
2) Do not remove any protective panels, covers or guards and operate equipment.
HIGH FREQUENCY WARNINGS
SPECIAL PRECAUTIONS ARE REQUIRED WHEN USING PLASMA,
TIG OR ANY WELDING PROCESS THAT USES HIGH FREQUENCY
TO STRIKE AN ARC.
WARNING : HIGH FREQUENCY CAN EFFECT MACHINE
OPERATION AND THEREFORE, WELD QUALITY.
Read the precautions below before installing and using the equipment.
PRECAUTIONS:
1) Some plasma or welding cables are strong sources of high frequency interference.
NEVER lay a plasma or welding cable across the controls of the machine.
2) Always physically separate the plasma or welding cable leads from the machine cables. For example, the plasma or welding cable leads should NEVER be bundled with a pendant cable or the machine power cord. Maximize the separation between any machine cables and the plasma or welding cables.
3) Strictly follow the grounding procedures specified for the plasma or welding unit.
NOTE: Some plasma and welding units produce exceptionally large amounts of high frequency noise. They may require a grounding rod be driven into the earth within six feet (2 meters) of the plasma or welding unit to become compatible with an automatic cutting or welding process.
4) If the high frequency is produced using a spark gap, adjust the points so the gap is as small as possible. The larger the gap, the higher the voltage and the higher the interference.
5) Some plasma or welding units will inject high frequency interference into the AC power line. Use separate power line branches whenever possible to power the plasma or welding source and the machine. Do not plug them into the same outlet box.
6) High frequency noise may enter the machine through the plasma or welding supply remote contactor leads. Some plasma and welding sources can produce noise spikes of up to several thousand volts. These sources are not compatible with automated cutting and welding equipment. It is recommended that the remote contactor leads on these plasma or welding sources not be connected to the machine.
An alternate solution is to purchase a separate remote contactor isolation box.
3
4
CBP-3000, CBP-4000 CIRCLE BURNER
INSTRUCTIONS AND PARTS MANUAL
TABLE OF CONTENTS
PAGE
6 ............ Set-Up and Operation
7 ............ BUG-6050 Pendant Control
10 ........... Technical Data / Dimensions / CBP-3000 Circle Burner
11 ............ Technical Data / Dimensions / CBP-4000 Circle Burner
12 ........... CBP-1550-F Control Box
13 ........... CBP-3000 Circle Burner / Exploded View / Parts List
14 ........... CBP-4000 Circle Burner / Exploded View / Parts List
14 ........... CWO-3073 CBP-3000 Frame / Exploded View / Parts List
15 ........... CBP-3000, CBP-4000 Circle Burner / Wiring Diagram
16 ........... CBP-3000, CBP-4000 Circle Burner / Electrical Component Chart
17 ........... CBP-1675 Motorized Racker / Exploded View / Parts List
18 ........... CWP-1635 Motorized Racking System / Exploded View / Parts List
18 ........... CBP-1590 Drive Box / Exploded View / Parts List
19 ........... CWO-1690 Large Horizontal Racker / Exploded View / Parts List
20 ........... CWO-3193 Housing Assembly / Exploded View / Parts List
20 ........... CWO-3358 Motor & Transmission Plate / Exploded View / Parts List
21 ........... CBP-1535-18 Encoder Assembly / Exploded View / Parts List / Wiring Diagram
22 ........... CWO-3361 P.M. Motor Assembly #147 / Exploded View / Parts List
23 ........... CWO-3501 Shaft Assembly / Exploded View / Parts List
23 ........... CWO-3920 Slide Bar Mounting Assembly / Exploded View / Parts List
24 ........... CWO-3960 Small Brush Assembly / Exploded View / Parts List
24 ........... CWO-3961 Small Retainer Block / Detail View
25 ........... CBP-1550-F (CBP-1502) Control Box / Exploded View / Parts List
26 ........... CBP-1550-F (CBP-1502) Control Box / Wiring Diagram
27 ........... CBP-1550-F (CBP-1502) Control Box / Electrical Component Chart
28 ........... CWO-3744 Manipulator Bracket / Exploded View / Parts List
29-30 ....... Preventive Maintenance
INTRODUCTION
The CBP-3000 (CBP-3002) Circle Burner uses oxy-fuel for square or beveled hole cuts using a single cutting pass. The CBP-3000 is mounted on a special frame with a releasable permanent magnet base specially designed for use on vessels and large diameter pipe.
The CBP-4000 (CBP-4002) Circle Burner also uses oxy-fuel for single pass, square or beveled hole cuts. Mounted on a column and boom, manipulator or fixture, the CBP-4000 is designed for use on vessels, large diameter pipe, domed heads and flat plate.
FEATURES
• 1-1/2 h.p. P.M. Motor and rotational speed control
• Rotation speed of 0.1-2 r.p.m.
• 100% duty cycle
• Adjustable vertical and horizontal torch positioning system
• 2 hose machine torch w / tip adjuster, includes tips
• Cutting capacities: 1.5"- 42" (38-1067 mm) bevel cut holes, 4"- 48" (102-1219 mm) square cut holes
• Brushes and collector rings for all controls, eliminates cable and hose wrap
• Encoder controlled rise and fall of torch
5
6
SETUP AND OPERATION
**All page numbers referred to in this section are from this manual unless otherwise specified.**
POWER SUPPLY: CBP-3000, CBP-4000 use standard 120/50-60/1 VAC.
CBP-3002, CBP-4002 use 220/50-60/1 VAC.
OXY-FUEL CUTTING TORCH: The CBP-3000, CBP-4000 Circle Burner is equipped with a Victor 2-Hose Machine Oxy-Fuel Torch model 204-A w/rack. Refer to the Victor Oxy-Fuel
Cutting Torch instruction manual supplied with this machine for general operation and set-up information.
FIXTURING: The CBP-4000 series of circle burners have to be fixtured in some manner from the top of the shaft. This may be achieved in one of the following; column & boom, manipulator or a fixture devise.
OXYGEN / FUEL CONNECTIONS: The CBP-3000, CBP-4000 Circle Burner is designed to accept standard oxy-fuel hose fitting connections. These connections are located at the top of the shaft on all models.
WHEEL ADJUSTMENT: The CBP-3000, CBP-4000 Racking System is equipped with adjustable wheels. Always check these components for proper wheel adjustment before using the machine. The wheels need adjustment if you can cock or wiggle the components out of alignment. The wheels should be snug but not prohibit movement along the path of travel.
The wheels with the hex stand off are adjustable. To adjust the wheels loosen the hex bolt (A) until the adjustable bushing (B) can be rotated.
Correct the wheel alignment by rotating the adjustable bushing (B). Once adjusted, hold the adjustable bushing (B) while tightening the hex bolt (A).
Recheck alignment.
B A
MACHINE CONTROLS: Various speed and directional capabilities can be controlled using the
CBP-1550 Control Box. Please refer to CBP-1550 Control Box (page 12) section in this manual.
BUG-6050 PENDANT CONTROL
The handheld terminal with keypad and text display or pendant control is used for entering the dimension and weld parameter data. It plugs into the Pendant connection on the CBP-1550 control box.
ALPHA KEYS: Press keys A, B, C, D, E, or F for the desired program function.
DIGIT KEYS: Use the digit keys to enter pipe diameters or dimensions.
ENTER: Push the enter button to store the numeric value keyed.
BACKSPACE: The backspace key removes the last digit keyed in before pushing the enter button, if a correction is required.
SHIFT : The blank key at the top right corner of the keypad is the SHIFT key. Use this key to access additional programming options.
ARROW KEYS: Used to Jog vertical axis during auto-run program to set new torch position.
7
8
PROGRAMMING
ALPHA KEYS
Dimensions and weld parameter data is entered on the handheld terminal with keypad and text display.
The alpha keys used are listed below, with their functions:
A : To enter dimensions.
C : To change Program Number in memory (0 – 99).
D : To display all programmed parameters for the current program.
E : To enter the number of passes (1 – 99)
F : To enter the start angle, so cut can start at the preferred point around the joint (see page 12).
Three other useful key functions are:
Shift 9 : Set units, english (inch) or metric (meters)
Shift 8 : Test drives & encoders
Shift E : Version number (have this information ready when calling for service)
DATA REQUIRED
The following five (5) parameters are entered for each program:
1. Small diameter (diameter of cut) - inches X 100 or mm X 10.
2. Large diameter (work O.D.) - inches X 100 or mm X 10.
3. Offset - inches X 100 or mm X 10. Enter “0” if nozzle is on centerline of vessel.
4. Overlap (additional rotation on end of pass) - degrees X 100.
5. Start Angle - degrees X 100. Enter “0” for top dead center.
In addition, background parameters that are retained for all programs, and are individually set are:
• Number of Passes (when multiple passes required. Default setting is 1).
NOTE: If the STOP / RESUME button is pressed, the machine will be in pause mode, and cannot be programmed. Press the RESET button to get back to the ready mode for programming.
On-center Nozzle
(Offset = 0)
Hillside or
Offset Nozzle
PROGRAMMING, CONT’D.
DATA ENTRY
When entering data with the pendant keypad, multiply inches, degrees, or seconds by 100 and enter the number without a decimal point. For metric dimensions, multiply mm X 10 or cm X 100.
Example: 350 for 3.5 inches,
800 for 80 mm, on metric machines
Press “ENTER” on the keypad after the number is entered.
SAVING PROGRAMS
The machine has 100 storage areas or cut programs, numbered 0 to 99 in memory. Push the “C” button on the pendant keypad to change (or set) the program number and enter the desired number. Program data is retained until reprogrammed. At any time, one of these numbers is selected, it will stay selected even when power is shut off and turned back on, it will not change until the program number is changed by the operator. Settings for time delay and number of passes are not saved as part of a program.
MAKING A CUT:
1.
torch is at the appropriate position, standoff distance and angle.
2.
3.
metal must be preheated to a bright cherry red. When the red spot appears, depress the cutting
oxygen lever slowly and firmly.
Start cutting rotation (forward or reverse) by pressing the Cycle Start button (“L” on pg. 12)
located on the CWP-1550 Control Box.
The machine will then run the complete cut program.
WARNING: IT IS NECESSARY TO USE CORRECT EYE, HEAD, AND BODY PROTECTION.
9
TECHNICAL DATA: CBP-3000 CIRCLE BURNER
Rotation speed: 0.1 - 2 r.p.m.
Cam Range: 0 - 7" (0 - 178 mm)
Cutting Radius:
For Square Cut Holes: 2" - 24" (51 - 610 mm)
For Bevel Cut Holes: 0.75" - 21" (20 - 534 mm)
Height: 34.5" (877 mm)
Net Weight: 125 lbs. (56.7 kg)
Shipping weight: 230 lbs. (104.3 kg)
DIMENSIONS:
40"
(1016 mm)
20.25"
(515 mm)
36.5"
(928 mm)
Max Cutting Radius
(See Above)
10
TECHNICAL DATA: CBP-4000 CIRCLE BURNER
Rotation speed: 0.1 - 2 r.p.m.
Cam Range:
Cutting Radius:
0 - 7" (0 - 178 mm)
For Square Cut Holes: 2" - 24" (51 - 610 mm)
For Bevel Cut Holes: 0.75" - 21" (20 - 534 mm)
Height: 37" (940 mm)
Net Weight: 210 lbs. (95.3 kg)
Shipping weight: 290 lbs. (132 kg)
DIMENSIONS:
53”
(1347 mm)
34.5”
(877 mm)
Max Cutting Radius
(See Above)
27”
(686 mm)
11
CBP-1550-F CONTROL BOX
M A
1
6
N
B
2
7
L
K
J
C
3 8
D
4
9
H
E
F
5 10
G
(FRONT VIEW)
A. DIGITAL READOUT - Displays rotation speed as a reference value.
B. SPEED CONTROL - Increases or decreases the rotation speed.
C. RESET - Resets Home or weld start position.
D. HORIZONTAL JOG Drives the horizontal racker left and right.
E. HORIZONTAL SPEED CONTROL Increases or decreases speed of horizontal racker.
F. PILOT LIGHT - Illuminated when power is ON to rotation control box.
G. ON/OFF SWITCH - Enables / disables power to the rotation control box.
H. ROTATION DIRECTION SWITCH - Changes rotation direction.
J.
MANUAL JOG - Manually drives the torch tip while machine is stopped or paused.
K.
STOP/PAUSE - Stops cut program and rotation.
L. START/RESUME - Starts cut program and rotation.
M. VAC On/Off switch for flux recovery vacuum
(welding models only).
N. HOT/COLD SWITCH Changes whether the
12 rotation control uses the wire feeder (welding models only).
(REAR VIEW)
1. Y-DRIVE - Connects to Vertical Racking Motor
2. X-ENCODER Connects to Encoder
3. HORIZ - Connects to Horizontal Racker Motor
4. X-MOTOR Connects to Terminal Block
Assembly
5. 120 VAC - Input power
6. PENDANT Connects to Pendant
7. CONTACTOR - Connects to welding power source.
8. VAC Connects to vacuum pump for flux recovery.
9. FUSE Access to 5 Amp fuse.
10. CIRCUIT BREAKER RESET Press to reset circuit breaker after overload.
CBP-3000 CIRCLE BURNER / EXPLODED VIEW / PARTS LIST
14
15
16
17
18
19
20
21
22
6
7
8
9
10
11
12
13
ITEM QTY PART NO.
1
2
3
4
5
1 BUG-1259
1 BUG-1298
1 CWP-1635
1 CWO-1690
1 CWO-3137
1 CWO-3193
1 CBP-1595
1 CWO-3358
DESCRIPTION
Adjustable Tip Adaptor
2-Hose Mechanical Torch
Racking Group
Large Horizontal Racker
Plastic Guard Assembly
Housing Assembly
Encoder Assembly
Motor & Transmission Plate Assembly
1 CBP-1550-F Control Box w/ Flux Recovery
1 CWO-3361
1 CWO-3366
1 CWO-3445
1 CWO-3501
1 CWO-3920
1 CWO-3935
1 CWO-3960
1 CWO-3996
1 CWO-3997
1 CWO-4050
1 CWO-4340
1 CWO-4910
1 CWO-5074
P.M. Motor Assembly #147
Collector Ring Assembly
Top Gear, Alum, CBP-3000
Shaft Assembly
Slide Bar Mounting Assembly
Terminal Block Assembly
Small Brush Retainer
28" Oxygen Hose Assembly
28" Fuel Hose Assembly
1" Bearing w/Fasteners
1-1/2" Flange Bearing
16.5# Load Spring Assembly
1-1/2" I.D. Trantorque
5
13
22
7
8
12
3
16
15
11
20
6
9
10
18
17
21
19
2
1
14
4
13
CBP-4000 CIRCLE BURNER / EXPLODED VIEW / PARTS LIST
ITEM QTY PART NO.
1
2
1
1
CBP-3000*
CBO-3073
DESCRIPTION
Programmable Circle Burner
CB-2 Frame
2
* See page 13 for exploded view / parts list
1
CWO-3073 CBP-3000 FRAME / EXPLODED VIEW / PARTS LIST
1
2 4
2
3
4
5
6
7
8
ITEM QTY PART NO.
1 1
2
1
3
8
4
1
8
CWO-3072
CWO-3777
CWO-4590
FAS-0495
FAS-1390
FAS-2396-FT
FAS-2398
WAS-0262
DESCRIPTION
Frame Weldment
T-Handle, Knob 5/16-18 x .98"
Magnet / CBP-3000 Frame
Set Scr 3/8-16 x 1/2” Cup Point
Hex Nut 3/8-16
Hex Hd Cap Scr 3/8-16 x 2-1/4"
Hex Hd Cap Scr 3/8-16 x 3"
3/8" Split Lock Washer Zinc Plated
3
6
8
5
8
5
14
7
CBP-3000, CBP-4000 CIRCLE BURNER / WIRING DIAGRAM
HT BLK
HT BL
HT BLK GR
15
CBP-3000, CBP-4000 CIRCLE BURNER / ELECTRICAL COMPONENT CHART
ITEM DESCRIPTION
7
8
5
6
3
4
1
2
Pendant
Collector Ring
Control Box
P.M. Motor Assembly
Terminal Block
Small Brush Retainer
Motor Cable
Control Cable
CBP-1550
120 VAC
BUG-6050
CWO-3366
CBP-1550
CWO-3361
CWO-3935
CWO-3960
CBP-1533
CWO-3394
16
CBP-1675 MOTORIZED RACKER / EXPLODED VIEW / PARTS LIST
6
4
A
3
F
A
F
2
8
5
10
A = Adjustable Wheel Placement
F = Fixed Wheel Placement
7
9,11
ITEM QTY PART NO.
1
2
3
4
5
6
7
8
9
10
11
1 CBP-1590
1 CWO-1677
2
2
1
2
2
2
2
3
2
CWO-1680
CWO-1681
CWO-1682
CWO-1694
FAS-0555
FAS-0557
FAS-0559
FAS-2551
WAS-0240
DESCRIPTION
Drive Box
Mount Plate
W2 Fixed Leg & Wheel Assembly
W2 Adj. Leg & Wheel Assembly
Racker Mount Bar
Stand-Off
Screw, Soc Hd Cap 1/4-20 x 1/2
Screw, Soc Hd Cap 1/4-20 x 3/4
Screw, Soc Hd Cap 1/4-20 x 1
Screw, Soc Hd Cap 1/4-20 x 1 1/4
Washer, SAE 1/4
1
17
CWP-1635 MOTORIZED RACKING SYSTEM / EXPLODED VIEW / PARTS LIST
3 1
6
ITEM QTY PART NO.
1
2
3
4
5
6
1
1
1
1
1
1
ABR-1050
ABR-1070
CBP-1675
CWO-1695
DESCRIPTION
V-Guide Way, 40"
V-Guide Way, 19"
Motorized Racker
Attachment Block
BUG-5188-10 Torch Holder
CWO-3460 33# Load Spring Assembly 5
4
CBP-1590 DRIVE BOX / EXPLODED VIEW / PARTS LIST
9
5
4
10
2
3
7
11
6
1
8
ITEM QTY PART NO. DESCRIPTION
1
2
3
4
5
6
7
8
9
10
11
1 BUG-1550 Gear Motor (150:1)
1 BUG-6040 Gear / Encoder Assembly
1 BUG-9909 Panel Connector, 6-T, M
1 CBP-1585 Drive Box Enclosure
1 CBP-1586 Drive Plate
4 AFR-1015 Spacer Washer
4 FAS-0204
4 FAS-0519
4 FAS-0527
4 FAS-1305
Screw, Rnd Hd Slt 4-40 x 3/8
Screw, Soc Hd Cap 6-32 x 1
Screw, Soc Hd Cap 8-32 x 3/4
Hex Nut 4-40
1 GOF-3014 Drive Pinion
18
CWO-1690 LARGE HORIZONTAL RACKER / EXPLODED VIEW / PARTS LIST
1
15
12
18
16
2
17
13
4
14
F
A
F
A
5
11
3
10 6
8
A
A
F
F
7
9
A = Adjustable Leg & Wheel Assembly
F = Fixed Leg & Wheel Assembly
6
7
8
9
10
11
12
13
14
15
16
17
18
ITEM QTY PART NO.
1
2
3
4
5
1 BUG-2032
1 CWO-1678
1 CWO-1679
2 CWO-1680
2 CWO-1681
1 CWO-1687
2 CWO-4326
2 CWO-4326
2 FAS-0557
1 FAS-1307
1 MUG-1141
1 MUG-1142
1 MUG-1144
2 MUG-1453
1 MUG-1579
3 WAS-0204
1 CWO-1671
2 FAS-0559
DESCRIPTION
Knob, Black
Racker Plate
Pinion 11T
W2 Fixed Leg & Wheel Assembly
W2 Adj. Leg & Wheel Assembly
Mount Plate (Large Racker)
Fixed Leg & Wheel Assembly
Adj. Leg & Wheel Assembly
Soc Hd Cap Scr 1/4-20 x 3/4"
Hex Jam Nut 3/4-16
Bearing Collet
Knob, Locking
Shaft
Stand-Off
Retaining Ring
1/4" SAE Washer
Racker Shield
Soc Hd Cap Scr 1/4-20 x 1"
19
CWO-3193 HOUSING ASSEMBLY / EXPLODED VIEW / PARTS LIST
7
4
6
10
5
2
6
9
8
10
7 3
6
ITEM QTY PART NO.
1
2
3
4
5
6
7
8
9
1 BUG-9096
1 BUG-9097
1
1
2
2
3
3
8
CWO-5839
CWO-5854
CWO-5974
ARV-1113
CWO-9339
FAS-0535
FAS-0548
DESCRIPTION
1/4" Fitting Oxy #32
1/4" Fitting Gas #33
Center Tubing Housing CBP-3000
Top Housing Plate
Insert 1.875 O.D. x 1.625 I.D.
1/4 NPT 90 Degree st. elbow
Angle For Guard
Soc Hd Cap Scr 10-24 x 1/2"
Soc Hd Cap Scr 10-32 x 3/4"
CWO-3358 MOTOR & TRANSMISSION PLATE / EXPLODED VIEW / PARTS LIST
7
2
9
1
5
9
8
5
3
9
4
ITEM QTY PART NO.
1
2
3
4
5
6
7
8
9
20
10
1 BUG-1338
1 CWO-5885 Transmission & Motor Plate
1
2
CWO-5886
FAS-0359
8 FAS-1351
3 FAS-2372
4 FAS-2554
4 WAS-0241
10 WAS-0243
3 WAS-0251
DESCRIPTION
Nameplate
End Plate
Hex Hd Cap Scr 1/4-20 x 1"
Hex Nut 1/4-20
Hex Hd Cap Scr 5/16-18 x 1-1/4"
Soc Hd Cap Scr 1/4-20 x 1-3/4"
1/4" USS Zinc Flat Washer
1/4" Split Lockwasher
5/16" Split Lockwasher
6
10
6
10
CBP-1535-18 ENCODER ASSEMBLY / EXPLODED VIEW / PARTS LIST /
WIRING DIAGRAM
2
13
12 3
11
1
1
4
5
14
10
21
2
6
18 11
20
5
1
19
9
7
15
16
17
2
2
2
2
1
4
1
2
3
4
1
1
1
1
1
1
1
2
1
10
11
12
13
14
15
16
17
18
19
20
21
ITEM QTY PART NO.
1
2
3
4
5
6
7
8
9
1
1
CBP-1603
CBP-1549
MUG-1592
BUG-6044
SFX-1218
MUG-1593
CBP-1601
CBP-1602
CBP-1593
CAP-1105M
CON-1305P
FAS-0204
FAS-0124
FAS-0115
WAS-0240
WAS-0243
FAS-2351
FAS-0559
FAS-0227
FAS-1305
CBP-1598
DESCRIPTION
Encoder Enclosure For CWP-18
Encoder, 512 CPR
Bracket
Flexible Coupling
Bearing-Flg 1/4 ID x 3/8 OD x 5/16 Lg
Pod
Encoder Mount Plate For CWP-18
Encoder Mounting Bar For CWP-18
Gear Shaft Assembly
1Uf 50V 10% Radial
Panel Connector, 5-T, M
Rnd Hd Slt Scr 4-40 x 3/8 Zinc
8/32 x 3/8 Pan Hd, Di-Chrome
6-32 x 1/2 Pan Head, Zinc
1/4 SAE Flat Washer
1/4" Split Lock Washer
Hex Hd Cap Scr 1/4-20 x 1-1/4
Soc Hd Cap 1/4-20 x 1
Rnd Hd Scr 8-32 x 3/4
Hex Nut 4-40
Connector Cable
21
CWO-3361 P.M. MOTOR ASSEMBLY #147 / EXPLODED VIEW / PARTS LIST
ITEM QTY PART NO.
1
2
3
4
5
1 CWO-4067
1 CWO-4147
1 CWO-5767
1 FAS-0454
DESCRIPTION
P.M. Motor #147
P.M. Motor Bracket #970
Gear, P.M. Motor #147
Set Scr 1/4-20 x 3/8"
1 TER-WTE-1508 #8 Fork Blue 14RB-8FL-T&B
5
4 1
2
3
22
CWO-3501 SHAFT ASSEMBLY / EXPLODED VIEW / PARTS LIST
2
4
5 5 7 5 5
6
1
3 ITEM QTY PART NO.
1
2
3
4
5
6
7
8
1 BUG-1296
1 BUG-1297
1
1
BUG-9096
BUG-9097
DESCRIPTION
90 0 Hose Adaptor, Oxygen
90 0 Hose Adaptor, Fuel
Outlet Bushing, Oxygen
Outlet Bushing, Fuel
4 CWO-4049 O-Ring, Oxygen, Fuel
1 CWO-3502 CB-1P, CBP-3000 Pointer
1 CWO-5577 Shaft
1 FAS-0539 Soc Hd Cap Scr 10-24 x 1"
8
CWO-3920 SLIDE BAR MOUNTING ASSEMBLY / EXPLODED VIEW / PARTS LIST
3
5
3
5
1
4
6 2
6
4
2
ITEM QTY PART NO.
1
DESCRIPTION
1 CWO-3912 Slide Bar Assembly
2
3
4
5
6
2 CWO-9035 Top/Bottom Vert Slide Plate
4 FAS-2372
4
4
4
FAS-2391
WAS-0251
WAS-0262
Hex Hd Cap Scr 5/16-18 x 1-1/4"
Hex Hd Cap Scr 3/8-16 x 1-1/4"
5/16" Split Lock Washer
3/8" Split Lock Washer
23
CWO-3960 SMALL BRUSH ASSEMBLY / EXPLODED VIEW / PARTS LIST
1
9
10
11
2
8
ITEM QTY PART NO.
1
2
3
4
5
6
7
8
9
10
11
12
1 CWO-3961
1 CWO-9076
2 CWO-5831
2 CWO-5874
2 CWO-5875
2 CWO-5876
1 CWO-9108
2 FAS-0539
1 FAS-2551
1 WAS-0240
1 WAS-0243
DESCRIPTION
CBP-3000 Small Retainer Block
Small Retainer Support
1/8" x 1/8" x 7/8" Brush
1/8" Brush Holder
Cap
Clip
CBP-3000 Small Brush Block
Soc Hd Cap Scr 10-24 x 1"
Soc Hd Cap Scr 1/4-20 x 1-1/4"
1/4" SAE Washer
1/4" Split Lock Washer
2 TERM WTE-0602 #6 Fork Blue
CWO-3961 SMALL RETAINER BLOCK / DETAIL VIEW
24
CBP-1550-F (CBP-1502) CONTROL BOX / EXPLODED VIEW / PARTS LIST
2
5
4
3
6
4
7
8
9,10
15
42
16 32
43
17,18 27
19,20
1
11
38
52
12 15
42
31 22
30
21
23
47
46
34
42
29
24,25
37
48
49
28
26
35
36
50
51
ITEM QTY PART NO. DESCRIPTION
1
2
3
4
5
1 CBP-1556 Rear Legend Plate
1 BUG-9446 Cord Grip
6
7
8
9
2 BUG-9856 Panel Connector, 2-T, F
2 MUG-1156 Panel Connector, 4-T, F
1 BUG-9909 Panel Connector, 6-T, M
1 BUG-9902 Panel Connector, 6-T, F
1 BUG-9486 Panel Connector, 2-T, M
1 FHO-0188 Fuse Holder, Panel Mount
1 BUG-2923 Circuit Breaker, 0.7 Amp
10 1 BUG-2924 Reset Seal, Transparent
11 1 CBP-6030 Control Module
12 1 BUG-6029 Bracket
13 1 BUG-6031 Filter
14 1 BUG-6028 Terminal Block, Kulka
15 2 BUG-1770 Motor Control Board
16 1 CBP-1557 Control Case
17 1 BUG-1764 Meter Display Board Ass’y
18 1 MDS-1011 Display Bezel
19 1 BUG-1562 Potentiometer, 10k, 3 Turn
20 1 BUG-5757 Knob, Black
21 1 SWT-1112 Push Button Switch, Red
22 1 SWT-1111 Push Button Switch, Black
23 1 MUG-1199 Toggle Switch, DPDT
24 1 BUG-9677 Potentiometer, 10k ohms
25 1 MDS-1044 Knob, Yellow
26 1 CWO-6206 Red Neon Lamp, 125V
* 1 BUG-1428 Pilot Light, 240V
ITEM QTY PART NO. DESCRIPTION
27 1 CBP-1553 Front Legend Plate
28 1 ARM-2279 Toggle Switch, DPST
29 1 SWT-3601 Toggle Switch, 4PDT
30 1 PRS-1065 Joystick
31 1 SWT-1113 Push Button Switch, Green
32 1 ABP-1069 Toggle Switch, SPST
33 1 CWO-6520 4-Quadrant Speed Control
34 1 CBP-1511 Transformer Bracket
35 1 CBP-1551 Control Cover
36 1 CWO-6417 Wire Feeder Mount Plate
37 1 MUG-1589 Hole Plug, 0.500"
38 34 FAS-0204 Screw, Rnd Hd Slt, 4-40 x 3/8
39 30 FAS-1305 Hex Nut, 4-40
40 2 FAS-0115 Screw, Pan Hd, 6-32 x 1/2
41 2 FAS-1310 Hex Nut, 6-32
42 6 FAS-0224 Screw, Rnd Hd, 8-32 x 3/8
43 4 FAS-0104 Screw, Pan Hd, 4-40, Black
44 4 FAS-0244 Screw, Rnd Hd, 10-32 x 3/8
45 4 FAS-1340 Hex Nut, 10-32
46 2 FAS-0525 Screw, Soc Hd Cap, 8-32 x 1/2
47 10 SCW WTE 0264 Screw, #6 x 1/4" Pan Hd
48 2 FAS-0253 Screw, Rnd Hd, 1/4-20 x 5/16"
49 2 WAS-0242 1/4" External Star Lockwasher
50 2 WAS-0243 1/4" Split Lock Washer
51 2 FAS-0356 Screw, Hex Hd Cap, 1/4-20x5/8
52 1 BUG-5218 Transformer, 117V 50/60 HZ
* 1 BUG-5231 Transformer, 240 VAC
* Not Shown 25
CBP-1550-F (CBP-1502) CONTROL BOX / WIRING DIAGRAM
{
EN CO
G -15V
26
223
223
BLU
TAN
TAN
YEL W TAN BL TAN W
BRN ORG
A B
CN3 SO
ORG ORG PNK PNK G
RY BRN
CBP-1550-F (CBP-1502) CONTROL BOX / ELECTRICAL COMPONENT CHART
ITEM DESCRIPTION
CB Circuit Breaker
PL Pilot Light
T Transformer
VT Volt Trap
MC1 4-Quadrant Speed Control
CM Control Module
CN1 Connector (Pendant)
CN2 Connector (Solenoid)
CN3 Connector (Motor Arm)
CN4 Connector (Aux.)
CN5 Connector (Rot. Motor)
CN6 Connector (Racker)
CN7 Connector (Vacuum)
DSP Digital Display
LF Line Filter
MC2 Motor Control Board
MC3 Speed Control (Racker)
P Potentiometer
P2 Potentiometer (Racker)
SW1 Toggle Switch (Power)
SW2 PB Switch (Start)
SW3 PB Switch (Stop)
SW4 PB Switch (Reset)
SW5 Joystick Switch
SW6 Switch (Racker)
SW7 Mirror Switch
SW8 Switch (Vacuum)
SW9 Switch (Dry Run)
TB1 Terminal Block
F1,F2 5A Fuse
BUG-6031
BUG-1770
CAS-1770
BUG-1562
BUG-9677
ARM-2279
SWT-1113
SWT-1112
SWT-1111
PRS-1065
MUG-1199
BUG-2626
ABP-1069
ARM-2279
BUG-6028
CWO-7076
CBP-1550-F
120 VAC
BUG-2923
LED-2111
BUG-5218
BUG-1393
CWO-6520
CBP-6030
BUG-9902
MUG-1156
CON-06RP06F
CON-1305S
CON-03RS03F
BUG-9856
BUG-9486
BUG-1764
CBP-1502
240 VAC
BUG-1428
BUG-5231
BUG-1563
27
ACCESSORIES
CWO-3744 MANIPULATOR BRACKET
The Manipulator Bracket is a mounting devise that was designed to be used on some Circle Welders and Circle Burners. It attaches to an existing fixture and can be easily adjusted to make sure that the Circle Welder/Burner remains square on the work piece.
CWO-3744 MANIPULATOR BRACKET / EXPLODED VIEW / PARTS LIST
5
4
3
7
6
9
8
9
1
8
28
ITEM QTY PART NO.
1
2
3
4
5
6
7
8
9
1 CWO-3740
1 CWO-3777
1
1
1
1
2
8
12
CWO-4127
CWO-4421
CWO-5551
CWO-5982
FAS-0495
FAS-1301
WAS-0280
DESCRIPTION
Manipulator Bracket / Weldment
T-Handle, Knob 5/16-18 x .98"
Locking Collar
1/2-13 x 2-1/2" All Thread Rod
Bracket / Mount Plate
Oillite Thrust Bearing
Set Scr 3/8-16 x 1/2"
Hex Nut 1/2-13
1/2" Washer
2
PREVENTIVE MAINTENANCE / CBP-3000, CBP-4000 CIRCLE BURNER
CAUTION: Make sure the input power to the Rotation Control is disconnected from the power source.
AFTER DAILY USE:
Refer to CBP-3000, CBP-4000 Exploded View Parts List (Page 13).
Racking System (Item #3): Inspect gear rack; hardened ways and wheels (remove all dirt, grease, and rust). Check hardened ways for nicks and replace if necessary. Lubricate with a dry spray lubricant. Adjust wheels for snug fit and smooth operation. Lubricate racker pinion with a dry teflon or graphite spray lubricant.
Large Horizontal Racker (Item #4): Inspect wheels (remove all dirt, grease, and rust). Adjust wheels for snug fit and smooth operation. Lubricate racker pinion and wheels with a dry Teflon or graphite spray lubricant.
Slide Bar Mounting Assembly (Item #14): Inspect hardened ways (remove all dirt, grease, and rust). Check hardened ways for nicks and replace if necessary. Lubricate the hardened ways with a dry Teflon or graphite spray lubricant.
Refer to CBP-3000, CBP-4000 Electrical Wiring Diagram (Page 15).
Collector Ring (Item #2): Inspect cable connections for damages and that the connector is not cracked. Ensure that the connector is fastened properly to the Top Aluminum Gear (Item #12) on the CBP-3000, CBP-4000 Exploded View Parts List.
EVERY SIX MONTHS:
Refer to CBP-3000, CBP-4000 Exploded View Parts List (Page 13).
Top Aluminum Gear (Item #12): Do not grease this gear. Inspect gear teeth (remove all dirt, grease, and rust). Lubricate with a dry Teflon or graphite spray lubricant. Replace gear if excessively worn.
P.M. Motor Assembly (Item #10): Do not grease this pinion. Inspect the drive pinion (remove all dirt, grease, and rust). Lubricate with a dry Teflon or graphite spray lubricant. Replace pinion if excessively worn. Check set screw and tighten if necessary. Adjust motor assembly using the four adjustable mounting fasteners so that proper gear mesh is achieved between the Top
Aluminum Gear (Item #12) and the motor drive pinion.
29
PREVENTIVE MAINTENANCE / CBP-3000, CBP-4000 CIRCLE BURNER
Control Box (Item #9): Open control box use an air hose to blow out dust and dirt. Check all wires for breaks and replace if necessary. Check all electrical connectors and plugs if an electrical component fails refer to CBP-1550 Rotation Control electrical component chart (page
27) for replacement parts or return for service.
Small Brush Retainer (Item #16): Inspect black brush holders for cracks and replace if needed.
Check and make sure all wires are soldered properly to the holders. Replace the brushes when their length is less than ½ inch long. Remove the brushes and sand them to ensure a smooth contact surface. Make sure all fasteners are tight.
Terminal Block Assembly (Item #15): Inspect the plastic terminal strip make sure it is not cracked, replace if necessary. Make sure all terminal connections are tight. Make sure all ground wires are connected to the mounting screws of the terminal strip.
EVERY TWELVE MONTHS:
Refer to CBP-3000, CBP-4000 Exploded View Parts List (Page 13).
1" Bearing with Fasteners (Item #19): Do not grease the bearing it is greased for life by the manufacturer. If the grease fitting has not been removed and plugged we suggest that you do so now. Earlier models may not have been plugged at time of assembly.
1-1/2" Flange Bearing (Item #20): Do not grease the bearing it is greased for life by the manufacturer. If the grease fitting has not been removed and plugged we suggest that you do so now. Earlier models may not have been plugged at time of assembly.
P.M. Motor Assembly (Item #10): Bodine gear motor lubrication. Fill gear motor to oil level indicator with worm gear oil conforming to AGMA#5EP compounded (SAE#90) oil or Bodine lubricant #LO-23. Do not overfill.
Refer to CBP-3000 CBP-4000 Electrical Component Chart (Page 16).
Collector (Item #2): The collector ring should be sanded once a year. If the collector ring is pitted too badly it should be replaced. Inspect all wires coming out of the collector ring for cut or missing insulation. All wires should be fastened to the center shaft with a nylon cable tie. Tighten four set screws if needed.
30
WARRANTY
Limited 3-Year Warranty
Model _________________________________
Serial No. ______________________________
Date Purchased: ________________________
Where Purchased: _______________________
For a period ending one (1) year from the date of invoice, Manufacturer warrants that any new machine or part is free from defects in materials and workmanship and Manufacturer agrees to repair or replace at its option, any defective part or machine. HOWEVER, if the invoiced customer registers the Product
Warranty by returning the Warranty Registration Card supplied with the product within 90 days of the invoice date, or by registering on-line at www.bugo.com, Manufacturer will extend the warranty period an additional two (2) years which will provide three (3) total years from the date of original invoice to customer. This warranty does not apply to machines which, after Manufacture’s inspection are determined by Manufacturer to have been damaged due to neglect, abuse, overloading, accident or improper usage. All shipping and handling charges will be paid by the customer.
The foregoing express warranty is exclusive and Manufacturer makes no representation or warranty
(either express or implied) other than as set forth expressly in the preceding sentence. Specifically,
Manufacturer makes no express or implied warranty of merchantability or fitness for any particular purpose with respect to any goods. Manufacturer shall not be subject to any other obligations or liabilities whatsoever with respect to machines or parts furnished by Manufacturer.
Manufacturer shall not in any event be liable to Distributor or any customer for any loss of profits, incidental or consequential damages or special damages of any kind. Distributor’s or customer’s sole and exclusive remedy against Manufacturer for any breach of warranty, negligence, strict liability or any other claim relating to goods delivered pursuant hereto shall be for repair or replacement (at
Manufacturer’s option) of the machines or parts affected by such breach.
Distributor’s Warranty:
In no event shall Manufacturer be liable to Distributor or to any customer thereof for any warranties, representations or promises, express or implied, extended by Distributor without the advance written consent of Manufacturer, including but not limited to any and all warranties of merchantability or fitness for a particular purpose and all warranties, representations or promises which exceed or are different from the express limited warranty set forth above. Distributor agrees to indemnify and hold Manufacturer harmless from any claim by a customer based upon any express or implied warranty by Distributor which exceeds or differs from Manufacturer’s express limited warranty set forth above.
HOW TO OBTAIN SERVICE:
If you think this machine is not operating properly, re-read the instruction manual carefully, then call your Authorized BUG-O dealer/distributor. If they cannot give you the necessary service, write or phone us to tell us exactly what difficulty you have experienced. BE SURE to mention the MODEL and SERIAL numbers.
31
advertisement
Related manuals
advertisement