advertisement
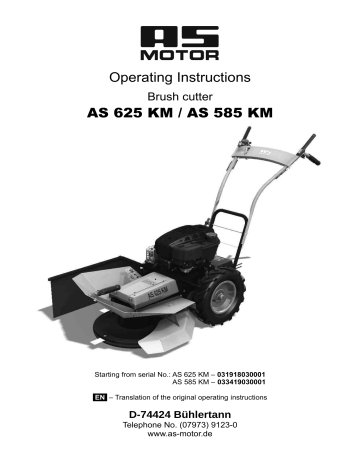
Operating Instructions
Brush cutter
AS 625 KM / AS 585 KM
Starting from serial No.: AS 625 KM – 031918030001
AS 585 KM – 033419030001
EN
– Translation of the original operating instructions
D-74424 Bühlertann
Telephone No. (07973) 9123-0 www.as-motor.de
Contents
1 Operating Instructions
2 Attached illustrations
3 EC Declaration of Conformity
AS 625 KM / AS 585 KM
4
16
22
Basic Information
Ask your retailer to unpack your machine and provide instructions, as part of its pre-sale service!
Type designation (Type)
Engine Type
AS 625 KM
AS 585 KM
BRIGGS & STRATTON 875EXi Series
TM
ZONGSHEN XP200
Date of delivery - Sale
Vendor (stamp)
We recommend that you make a copy of this page with the purchased purchase data in case the original
Operation Instructions get lost.
1 Add the number from the machine's ID plate or attach its ID label.
3
EN English
1 Operating Instructions
Contents
1 Operating Instructions 4
1.1 Introduction....................................................................5
1.1.1 Special Warning......................................................5
1.2 Operational Safety...........................................................5
1.2.1 Safety Regulations..................................................5
1.2.2 Noise and Vibrations Levels.....................................6
1.2.3 Safety Pictograms...................................................6
1.3 Basic Information............................................................7
1.3.1 Expected use..........................................................7
1.3.1.1 Technical Data...............................................7
1.3.1.2 Engine Information........................................8
1.3.2 Description of the Machine and its Components........8
1.4 Operating Instructions.....................................................8
1.4.1 Machine Assembly..................................................8
1.4.1.1 Machine Assembly Procedure..........................8
1.4.2 Commissioning.......................................................9
1.4.2.1 Cutting disk starting.......................................9
1.4.2.2 Machine Start (Travel)....................................9
1.4.2.3 Machine Stopping.........................................10
1.4.2.4 Travel Speed Selection..................................10
1.4.3 Working with the Machine.....................................10
1.4.3.1 The Machine Working Width.........................10
1.4.3.2 Growth Cutting Method................................10
1.4.3.2.1 Mowing Troubles.................................10
1.5 Maintenance, Care, Storage...........................................11
1.5.1 Travel Wheels.......................................................11
1.5.1.1 Tyre Pressure...............................................11
1.5.2 Machine Lubrication..............................................11
1.5.2.1 Engine Oil Change........................................11
1.5.2.2 Lubrication Points.........................................11
1.5.3 Sharpening and Replacement of Working Blades.....12
1.5.4 Belt Transmissions - Automatic Brake.....................12
1.5.4.1 Adjusting of tension pulleys..........................12
1.5.4.1.1 V-Belt Change.....................................13
1.5.4.2 Brake function check and adjustment............13
1.5.5 Servicing intervals.................................................13
1.5.6 Troubleshooting....................................................14
1.5.7 Storage................................................................14
1.5.7.1 Machine Washing and Cleaning.....................14
1.5.8 Disposal of Packaging and the Machine at the End of its Service Life.................................................................15
The manufacturer reserves the right to implement technical changes and innovations not affecting the operability and safety of the machine. These changes may not show in these Operating Instructions.
Typographical errors reserved.
4
AS 625 KM / AS 585 KM
1.1 Introduction
Dear customer,
Congratulations to your purchasing decision. With your AS brush cutter, you have received a reliable, high-quality machine that has proven itself during years of operation. We always strive to further improve our machines. Wherever you want to cut any tall grass, weeds and scrub, either on meadows, in orchards, on horse pastures or community grounds, you may count on the reliable assistance of your new brush cutter. The AS shrub cutter is a specialist in such tasks. It cuts large fields with dense and tall grass in the shortest time, handling uneven surfaces as easily as slopes and embankments.
To be able to work with your brush cutter safely, get familiar with its control, please. For this we have developed these operating instructions for you. Definitely read the safety instructions in the next chapter! They are to protect your health. In the next chapters, you will learn everything critical about your AS brush cutter, including its use and care. Your AS brush cutter will only perform best and work for many years if you treat it properly and follow the few maintenance and care instructions. If you have any questions about your brush cutter, contact your dealer or directly AS-Motor, please. We are happy to help you, and we are also grateful for suggestions for improvement.
One more wish: Be nice to your neighbours and cut grass only on weekdays between 07:00 a.m. and 01:00 p.m. and between 03:00 and 07:00 p.m. According to the noise protection regulations of 1 August, 1987, it is not allowed to cut grass on Sundays, holidays and outside of the specified times. Different regional regulations may apply as well (siesta). We now wish you a pleasant work with your AS brush cutter.
These operating instructions define the right, left, front, and rear sides from the operator's location and view. The operator stands in the machine’s travel direction, behind the brush cutter handlebars.
1.1.1 Special Warning
The user must read these Operating Instructions and follow all the machine operating instructions in order to prevent any health risks or property damage to the user or other persons.
The safety instructions specified in these operating instructions do not cover all the possible conditions and situations, which may occur in practice. Safety factors, such as a reasonable approach, care, and caution are not included in these operating instructions, but it is assumed that every person using the machine or doing any maintenance work on it is able to sufficiently use them.
Only mentally and physically fit persons may operate this machine. Should this machine be used commercially, the owner of the machine is bound to provide operators with work safety training and instruct them regarding its operation, and keep records of such training.
If you find any part of these operating instructions unclear, feel free to contact
your dealer 2 or directly the machine manufacturer 3 .
The operating instructions attached to this machine are its integral part. They must be available at all times, stored at an accessible place where they cannot get destroyed. When selling the machine to another person, the operating instructions must be handed over to the new owner. The manufacturer bears no responsibility for the risks, hazards, accidents, or injuries resulting from operation of the machine if the above-mentioned conditions have not been met.
The manufacturer bears no responsibility for the damage caused by unauthorized use, inappropriate operation, and any damage caused by any modification of the machine without the manufacturer’s approval.
During work it is necessary to follow safety regulations to avoid any injury to yourself or other persons present nearby and to avoid any property damage. These instructions are marked in the operating instructions by the following warning symbol:
If you see this symbol in the operating instructions, carefully read the statement following after it!
This international safety symbol indicates important instructions concerning safety.
When you see this symbol, be alert to the possibility of your or other persons’ injury and carefully read the following statement.
Table 1: Symbols
If not indicated otherwise, the description is valid for both machines
1.2 Operational Safety
The machine is designed to protect the operator as much as possible against any flying pieces of mowed growth. Do not remove any passive or active security features. You would expose yourself to the risk of injury.
1.2.1 Safety Regulations
The machine operator must be over 18 years of age . He is obliged to familiarize himself with the instructions for the use of the machine and to be familiar with the general principles of occupational safety.
Always make sure that no part (especially the working mechanism or its cover) is damaged or loose before using the machine .
Identified defects must be immediately eliminated . Use only original spare parts during repairs.
2
3
Fill-in the dealer’s address in the table provided at the beginning of these operating instructions (unless already filled-in by the dealer).
For the address of the manufacturer, see the end of these operating instructions
5
EN English
Do not start the engine in confined spaces! Take extra care when handling the machine. When the engine is turned OFF, the exhaust silencer remains hot. When filling the fuel make sure that no leak occurs and you do not spill the fuel over the engine parts. If it be to the contrary, dry the affected parts or wait until the petrol evaporates.
Always switch OFF the engine and wait for the cutting disc to stop before you perform any activity in the close vicinity of the machine! Always switch OFF the engine before leaving the machine!
Never leave the engine running at full speed or idling for a long time when the cutting disk drive clutch and travel wheels drive clutch are OFF! Parts of the drive train (V-belt, belt pulley, coupling pulley, etc.) may get damaged!
Cut growth must be free of solid items (such as stones, wires, loose debris, etc.) before using the machine. These items could be thrown out or could damage the machine. If they cannot be removed, avoid such spots.
The machine is fitted with a rotating working tool. The maximum circumferential speed is 64 m.s
-1 . Make sure that other people stay at a safe distance when you are working with your machine (the possibility of flying off the chopped or ejected solid items)!
When working with the machine, all other people ( especially children ) and animals must stay outside the machine's work area.
They operator may only continue working after they reach a safe 4 distance.
Observe the safe distance from the machine given by the handle.
Use work equipment approved per EN 166 or EN 1731 (tight fit clothes, firm footwear, work gloves, and safety glasses) at work.
Protect your hearing with suitable protective equipment per EN 352-1 (ear muffs) or EN 352-2 (earplug ear protectors). Please ask your dealer for this equipment.
Do not use your machine on wet grass. You must always move on safe terrain. While working, always walk. Do not ever run. Be especially careful when changing your direction on the slopes. Do not stand on heavily sloping slopes. Do not hold your machine if you fall down - release it!
It is forbidden to remove any protective devices and covers from the machines.
All the repairs, adjustments, lubrication, and cleaning of the machine must be carried out while the engine is on idle and spark plug disconnected.
1.2.2 Noise and Vibrations Levels
Declared emission sound pressure level A
Guaranteed sound power level
AS 625 KM
L pAd
= 84,0+4,0 [dB] L pAd
L
WA,G
= 98 [dB]
AS 585 KM
L
= 84,0+4,0 [dB]
WA,G
= 98 [dB]
Declared cumulative value of acceleration of vibrations transmitted to the
a hvd
= 8,5+3,4 [m.s
-2 ] a hvd
= 8,5+3,4 [m.s
-2 ]
With regard to the value of the declared sound pressure level at the work station, it is necessary to use one's personal protective equipment against noise, which is effective for the aforementioned noise level.
With respect to the declared values of vibrations transmitted to the operator’s hand-arm, it is necessary to adjust the working procedures for this type of machine by selecting appropriate technological breaks to reduce vibration exposure.
1.2.3 Safety Pictograms
The user is obliged to keep the pictograms on the machine in a readable state and, in case of any damage, ensure their replacement.
4 The EN 12733 standards provide for the designation of the outer security zone A around the work area B. It is necessary to prevent access to this area by means of appropriate banning marks. The distance between the sides of areas A and B must not be less than 50 m . Once a person or animal enters this hazardous area of the machine, the operator must immediately release the gear lever and wait with any other work until the area is free again.
5 Short term = up to one minute.
6 per ČSN EN 12733+A1 , Annex B and ČSN EN ISO 11201 : April 2010
7 per government decree No. 9/2002 Coll.
or Directive 2000/14/EC , Annex No. 3, part B, item 33, and ISO 3744
8 per ČSN EN 12733+A1 , Annex C , and EN ISO 20643
6
AS 625 KM / AS 585 KM
Position:
A combined sticker located at
the back of the frame. ( Fig. 3)
Number: Description:
1 Before using the machine, refer to the operating instructions .
2
3
During your machine maintenance, danger of cutting.
disconnect the cable from the ignition spark plug
It is forbidden to reach with a hand or step into the cutting blade working area -
.
4
5
6
Dangerous flying fragments, cuttings, ejected objects, etc. may hit a person . Other persons and animals - keep a safe distance from the machine.
While working, observe the machine’s maximum allowed safe slope accessibility .
Use eye and ear protection.
A separate sticker on the
Sticker on the control lever on
Sticker on the control lever on
Sticker attached to the cutting
Sticker attached to the cutting
-
-
-
-
Tool turning direction arrow
Turning ON the cutting disc drive.
0
0
= cutting disk not rotating,
Machine travel start.
= machine is still,
Prohibited space machine.
Guaranteed
1
1 = lock ON,
= machine is moving
2 = cutting disk rotating
for other persons and animals. Minimum safe distance from the
sound power
- Right (Clockwise) level .
Table 2: Safety Pictograms
1.3 Basic Information
1.3.1 Expected use
The AS 625 KM brush cutter is designed and manufactured according to the latest findings concerning small garden and agricultural technology. It features its great easy-to-use, quiet, powerful and fuel-efficient Briggs&Stratton engine and trouble-free maintenance.
The AS 585 KM brush cutter is technically based on AS 625 KM, however it is equipped with a Zongshen engine and a single-speed wheel axle.
in the woods and on the meadow up to the
areas. The areas must not feature any solid items in the growth or rough terrain. The cutter is
not designed for park landscaping.
The use for purposes other than the intended purpose is; therefore, to be considered a use for an unspecified purpose!
The machine may operate in all the inclined positions defined by the engine manufacturer in the event that the operator is able to safely guide the machine, both in relation to himself and the surroundings.
The protective devices comply with the requirements of EN 12733. These standards primarily take account of the operator's safety since he cannot be hit by any stones or other objects thrown by the machine's rotating mechanism during the machine’s regular travel. Therefore, the operator must always be in the regular control position, i.e. behind the machine, and with both hands firmly holding the handle.
It is forbidden to remove any protective devices and covers from the machines.
9 The brush cutter is not designed to cut any woody growth thicker than 5 mm! A failure to observe this policy will damage the machine.
10 The area growth must be cut and raked at least once a year!
7
EN English
1.3.1.1 Technical Data
AS 620KM Unit
Length x Width (including the side cover) x Height
Weight
The machine's maximum working width
Safe slope operation
Blade peripheral speed
Travel speed
Gearbox oil volume
Gearbox oil quality
Table 3: Technical information on the brush cutter
1.3.1.2 Engine Information
Engine
Type
Displacement
Bore x stroke
Max. output/RPM (HP)
Maximum (set) speed of the motor
Fuel consumption (Torque = 75%)
Specific fuel consumption
Maximum (permanent) tilting of the motor
Maximum (short term 14 ) tilting of the motor
Fuel
Motor oil filling
Oil grade
Spark plug
Unit cm 3 mm kW/min -1 (HP)
N.m/min -1 min -1 l (litre).h
-1 /min -1 g/kW.h (l.h
-1 )
l (litre) petrol (unleaded) l (litre)
SAE
mm kg cm
min -1 m.s
-1 km.h
-1 m 2 .h
-1 l (litre)
API / SAE
Value
AS 625 KM AS 585 KM
1755 x 795 x 1190
67 66
62,2
10°
1964
64
2,0 – 2,7
1244 - 1680
0,05
GL-4 (GL-5) / 90 (80W-90)
2,4
1502
Value
Briggs & Stratton 875EXi Series TM
190
68,3 x 51,8
3,56/3200 (4,77)
11,87/2600
3200 ± 100
1,4 /2600
-
15°
30°
1 oct. No. 91-95
0,6
SAE 30 or 10W-30
CHAMPION RC12YC
Zongshen XP200
196
70 x 51
3,6/3800 (4,82)
10/3000
-
≤ 395 (1,1)
LG F6RTC
Table 4: Engine technical information
1.3.2 Description of the Machine and its Components
controls ( 14 ,
17 , 18 , 19 and 20 ) are located on the handlebars. The handlebars are attached to the frame by means of a bolt 7 and they are height-adjustable in 6 positions. The handles 16 are used to firmly grip and guide the machine at work. The left hand side of the handlebar features the travel 19 clutch lever that controls the machine’s forward travel. The right hand side features the disk 17 drive clutch lever that turns ON (OFF) the cutting disk drive. The two control levers return to the starting position after releasing the handlebars in an emergency and cut the engine power transmission. The cutting disk 4 features its
automatic brake 16 , which stops it. The
engine speed control 8 is controlled by the gas lever 20 . The travel is ensured by a worm gearbox with a belt clutch that provides a smooth force transmission (the machine starts moving smoothly) to the wheels 15 . The clutch gearbox is covered by its plastic cover 13 . At the front, there is the cutting disk 4 with four steel blades 5 . The operator is protected against flying cut growth items by a sheet metal cover ( 1 and 10 ) of the cutting disk, meeting EN 12733 . The cut growth line spacing is secured by a removable side cover 3 , which is attached by a screw 9 .
11 Actual speed of unloaded disc including the loss in the belt transmission.
12 The machine’s surface power depends on the mowed growth type.
13 Measured per Society of Automotive Engineers (SAE) J1940
14 Short term - up to one minute.
15 Measured per Society of Automotive Engineers (SAE) J1349
16 The automatic brake is an active safety feature that increases the machine safety.
8
AS 625 KM / AS 585 KM
1 Cutting disk top cover
2 Front handle
3 Side cover with a holder
4 Cutting disk
5 Blade (4 pcs)
6 Drive cover
7 Bolt
8 Engine
9 Side cover screw
11
12
13
14
Machine frame
Tank cap
Gearbox cover
Strap with cables
10 Cutting disk bottom cover 15 Wheels
16 Handle
17 Disk drive clutch lever
18 Lock button
19 Travel clutch lever
20 Gas lever
Table 5:
1.4 Operating Instructions
1.4.1 Machine Assembly
Ask your dealer to unpack your machine and provide instructions, as part of its pre-sale service!
Gripping points for unpacking from the box (per
Fig. 1): grab the cutting disk at the front or use hole under the gearbox cover
1 , and the machine frame tube in the rear 2 .
1.4.1.1 Machine Assembly Procedure
Assemble the machine per the following procedure: (We recommend completing the assembly by two persons)
1.
Per Fig. 1 - take out both halves of the disk cover
5 , bag 6 , bolt 4 , cover support 9 , both side cover components 7 , and bottom disk cover 8 . Remove the cardboard insert between the handlebars and the engine from the box.
2.
Grab the machine, using its gripping points at the front 1 and in the back 2 and remove it from the box.
3.
Lift the handlebars 3
Fig. 1, turn them a attach per Fig. 10 step
>1 to the frame (select one of the 3 holes in the heightadjusting handlebars and one of the two holes in the frame). Following >1 , pass the screw through, attach the flat washer, and firmly tighten the handlebars with the wing nut A . The bowden cables of the control levers must not be crossed - this would reduce their service life! Remove the tightening straps from the bag and attach the bowden cables to the handlebars at the top end of the handlebar tube bend. To fasten, 2 strapping tapes are sufficient. Cut the loose ends of the straps.
4.
>3 , attach the bottom disk cover 2 to the left side of the frame by means of 4 screws B and fasten it.
Tighten the screws.
5.
>3 , fit the screw B into the hole in the right rear part of the frame, but do not tighten it. Insert the right
(bigger) part of the cover 3 between the bottom plastic cover of the disk and machine frame, so the screws B and C in the frame fit into the three grooves in the cover marked with an arrow. Manually tighten the screw connection B . Do not tighten the screw connection C for the time being. Attach the right side of the cover by three screws B per >4 . Manually tighten the screw connection B per >4 .
6.
>5 , insert a screw B into the rear part hole and slide the smaller left part of the cover towards the frame from the machine’s left side and fasten it with two screws B per >6 . Manually tighten the screws B . Connect both halves of the cover together in the front section per >3 by means of the two connections D . Tighten the screw connection D .
7.
>7 , fit the handle holder 5 onto the left cover reinforcement and secure it with two screw connections D .
Attach the rubber handle component 6 to the fixed holder.
8.
Tighten all the screw connections B and C per >2 , >3 , >4 , >5 and >6 !
9.
>8 , attach the rear (shorter) side cover to its shorter holder arm 8 , and then attach the side (longer) cover to its longer holder arm 7 . Pull the strapping tapes E through the cover holder holes and secure both covers 7 and 8 against sliding by tightening the tapes. Please shorten the loose ends of the tapes. Slide the shorter arm of the cover holder into the hole in the frame. Tighten the fastening screw 9
per Fig. 2 and make sure the side cover does not spontaneously fall.
1.4.2 Commissioning
The machine may be shipped without its engine operating fluids (depending on different national regulations)!
1.
Check the engine oil level or fill the engine with the specified type and amount of oil. Fill the tank with the prescribed quantity and type of petrol.
2.
AS 625 KM – Move the accelerator lever to its CHOKE or
position. The accelerator lever positions are described in Fig. 9.
All four of the main positions described are locked by a simple, protruding system in the lever body.
AS 585 KM – Move the accelerator lever to its MAX position. When the engine is cold, press the PRIMER three times to inject
the fuel to the carburettor 19
Even when the engine is warm, it may be necessary to inject the fuel. For starting a warm engine, it is sufficient to press the PRIMER only once.
3.
Start the engine by pulling on the hand starter cord 20 .
4.
AS 625 KM – Let the new or cold engine run for about 30 seconds with the choke engaged (accelerator lever in the CHOKE
position) 21 . After that, move the accelerator lever to the
MAX position. Let the engine run in this position for about 30 seconds.
17 The original operating instructions and their Czech translation are attached to the machine.
18 The MAX position is used in the case of an automatic choke engine. For more information, see the engine operating instructions, please.
19 The engine startup instructions are described in detail in the engine operating instructions.
20 The engine startup instructions are described in detail in the engine operating instructions.
21 In the case of an engine with automatic choke, let the engine run for about 30 seconds with the accelerator lever in the MAX position.
9
EN English
Do not leave the machine unattended!
When starting the engine, both control levers ( 17 and 19
in Fig. 2) must be in the OFF position (they must not
be pressed to the handles)!
1.4.2.1 Cutting disk starting
Make sure that all persons, animals, children are at a safe distance from the machine! Otherwise, do not continue in this activity!
1.
speed for approx. 1 minute to warm up.
2.
Grab the left handle of the handlebar with your left hand. With your right hand, following
Fig. 11, move the control lever
1 to its top position until it is inserted into the strap with cables 2 .
3.
Following Fig. 11, press the lock button
3 on the strap 2 . Hold the button until the control lever 1 starts to move the strap with cables 2 while moving down to the handle.
4.
Then, with a slow, slow movement of your right hand, press the control lever 1 on the right handle.
Press the lever smoothly and slowly so that the cutting disc may spin and the engine does not stop.
5.
After starting the cutting disk, press the lever fully against the handle and hold it firmly.
The cutting disk start is accompanied by partial slipping of the V-belt and associated accompanying phenomena (knocking, whistling). When the belt has been run in, these effects usually disappear.
Note:
With a new or cold engine, the engine may go out during the first few starts of the cutting disk drive. When the motor has warmed up, this will no longer happen. If the cutting disk drive can not be started even after warming up the engine, make sure that there is no fault per
1.4.2.2 Machine Start (Travel)
The travel is activated by the lever ( 19
in Fig. 2) on the left handle. Push the lever to the handle, and the machine will immediately
move forward. Once you press the lever and the machine starts moving forward, adjust your walking speed to the machine speed.
The travel clutch is a belt one, so you may press the clutch lever slowly - the machine does not move with a jerk, but smoothly.
Always press the clutch lever to the handlebar handle. If the lever is not fully pressed, the V-belt gets damaged.
The travel clutch lever cannot control the travel speed!
Never back with the travel clutch lever pressed!
1.4.2.3 Machine Stopping
To stop the machine travel, release the lever on the left handle. The machine travel will stop, but the cutting disc will continue to rotate.
The cutting disc drive will stop after you release the lever on the right handle.
The automatic brake will brake the cutting disc. Move the accelerator lever to the MIN or STOP position.
Always turn OFF the engine and wait for the cutting disk to stop before performing any work in the close vicinity of the machine! Always switch the engine OFF before leaving the machine!
Never leave the engine running at full speed or idling for a long time when the cutting disk drive clutch and travel wheels drive clutch are OFF! Parts of the drive train (V-belt, belt pulley, coupling pulley, etc.) may get damaged!
1.4.2.4 Travel Speed Selection – AS 625 KM only
The machine features two travel speeds. A lower one TURTLE for dense, moist or tall growth, and higher one HARE for thin, dry or short growth.
It is always necessary to adjust the travel speed to the growth type!
unit, there is a helpful sticker with a picture of the belt positions in the pulleys on the gearbox and the axle.
When changing speed, the engine must always be switched OFF and the throttle lever in the STOP position!
1.
Following Fig. 12, loosen the plastic nut
1 and lift the top gearbox cover 2 . Push in the direction of the arrow on the bottom of the gearbox cover at the centre of the rear of the frame until the bottom cover 3 releases and jumps from the projection in the frame.
2.
Slide the V-belt completely out of the pulley on the gearbox to the right into the slot in the frame between the pulley and the machine frame tube.
3.
Slide the V-belt forward for about 1.5 cm, and then move it to the wedge groove in the axle pulley per the selected gear. Check visually and by touching whether the belt fits to the selected pulley groove.
4.
Insert the V-belt into the groove in the gearbox pulley, corresponding to the selected gear. Make sure that the belt is seated
straight in the correct pulleys per the gear selected per Fig. 14. The belt must not cross!
22 The engine startup instructions are described in detail in the engine operating instructions.
10
AS 625 KM / AS 585 KM
5.
Refit the two covers. Insert the top plastic cover 2
per Fig. 12 sideways under the engine plate, lock it, and tighten the plastic
nut 1 . Deflect the bottom plastic cover 3 upwards, and place the hole in the cover foot on the frame projection. Release the cover deflection, and the cover snaps into place.
1.4.3 Working with the Machine
1.4.3.1 The Machine Working Width
It is always necessary to adjust the working width to the growth density!
machine through the terrain sufficiently straight and accurately to cut the growth stand over the full width of the disk. We recommend that
the machine be guided partially through cut growth per the arrow in Fig. 13.
1.4.3.2 Growth Cutting Method
The growth must be free of solid items (such as stones, wires, loose debris, etc.) before using the machine. These items could be thrown out or could damage the machine. If they cannot be removed, avoid such spots.
When mowing in uneven terrain, care must be taken to ensure that the bottom disc continuously slides over the ground and does not bounce. Disc bouncing results in a low-quality of growth mowing and uneven stubble.
Set the maximum engine speed, let the cutting disc spin at maximum speed, and then drive against the growth that you want to mow.
The mowed growth is ejected by the cutting disc to the right, on the side cover that defines rows.
When mowing, move through the growth so that the growth that is not mowed yet is always on the left side of the machine
When mowing on slopes, it is best to ride along the slope contour lines.
Observe safe slope access ( Table 3)!
If the cut growth is very dense, prickly, rotten or beaten, it is necessary to reduce the machine’s working width proportionally in such a way that there is no significant reduction in cutting disk speed and thus reduced mowing quality.
1.4.3.2.1 Mowing Troubles
Pay special caution when lifting and backing the machine!
The engine must always be OFF when cleaning the area under the top cover!
Always only tilt the machine backwards on the handlebar by pushing the handlebar downwards. Always pay extra caution when moving in the area under the raised machine! Secure it against spontaneous movement!
Take extra care when cleaning the space underneath the top cover. Blade cutting edges are sharp. When cleaning, protect your hands with work gloves or use a suitable item, such as a tree branch.
Always wait for the cutting disc to stop before proceeding with any activity on or around the machine.
1.
The disc loses speed, the engine loses speed, but does not stop.
Immediately stop the machine travel and slightly back-up with the machine front gently lifted (pushing the handlebar downwards). The space underneath the top cover partially cleans itself from the excessive grass mass. Then move again against the growth.
2.
The drive stopped, the engine turned OFF.
Release both levers on the handlebars and lift the front of the machine by pushing on the handlebars. Slide the machine slightly backward. Clean the area under the top cover and spread the grass mass on the surface. Start the engine, turn on the cutting disk drive, and start moving against the growth.
1.5 Maintenance, Care, Storage
Owing to the weight of the machine, all maintenance and adjustment shall be performed by two people.
To secure a long-term satisfaction with our product, it is necessary to provide it with due care and maintenance. By providing regular maintenance you will prevent its rapid wear and you will secure correct operation of all its parts.
Observe all instructions concerning maintenance and adjusting intervals. We recommend that you keep records of operating hours and the conditions under which the machine is used (these may be useful for servicing centres). We recommend that you have the post-season maintenance implemented by one of our authorized service centres; the same applies to standard maintenance if you are not certain of your technical capabilities.
Before each use of the machine, check the tightening of the screws securing the blades in the upper disk and also the screws fixing the lower disk to the flange.
1.5.1 Travel Wheels
The travel wheels are an important part of the machine. The wheels carry the entire weight of the machine, transmit the engine power, and engage the machine. The wheels contain tubes.
1.5.1.1 Tyre Pressure
For proper operation and to ensure a long service life of the travel wheels, especially the tyres, it is necessary to check the tyre pressure.
Perform the check before starting to work with the machine. Before the machine is shut down for a long time, apply the maximum tyre pressure.
Keep the same pressure in the left and right wheels – the machine better holds a straight track.
11
EN English
Do not exceed the maximum tyre pressure – there is a risk of the tyre explosion!
MAX imum ( recommended) tyre pressure: 23 PSI ( 160 kPa or 1,6 bar or 1,57 atm or 0,16 MPa )
MIN
imum 23 allowed tyre pressure:
18 PSI (124,1 kPa or 1,24 bar or 1,22 atm or 0,124 MPa)
If there is a permanent tyre pressure leakage, make sure that there is no defect on the tyre tube – repair it if necessary.
If you are not sufficiently manually skilled, have the operations done by an authorized service centre.
1.5.2 Machine Lubrication
When working with lubricants, observe the basic hygiene regulations and observe the environmental protection regulations and laws.
If you are not sufficiently manually skilled, have the operations done by an authorized service centre.
In order to secure trouble-free and easy movement of all mechanical parts, it is necessary to pay adequate attention to lubrication. A few drops of oil are usually enough (e.g. oil for bicycles). The gearbox is already factory-filled with a sufficient amount of oil, which is not necessary to change over the life of the machine. Check the oil level and refill oil in case of any leakage.
1.5.2.1 Engine Oil Change
If you are not manually skilled enough, entrust this work to a specialist workshop.
Follow the instructions stated in the motor operating instructions. Shorten the change interval to one half, if you are to use your machine in a dusty environment. When pouring oil out of the engine, tilt the machine to the side where the oil spout is fitted or disassemble the entire engine.
1.5.2.2 Lubrication Points
There is no need to remove any covers from the machine to lubricate the bowden cables on the handlebar. The other lubrication points may be reached after removing the plastic covers. From a wide range of oils, any engine or gear oil or spray oil is suitable for lubrication. When selecting plastic lubricants (grease) any lubricant intended for water pump lubrication is sufficient. However, its application usually requires the dismantling of the respective slide.
Note: When using plastic grease with graphite ingredient, the lubrication intervals may be extended during the season up to 25 hours .
Lubrication point - description
Bowden cables and lock button
Disk drive pulleys
Interval within season at least 2x (5 drops) every 10 hours (2 drops)
Travel clutch pulley
Brake key
Screwed connections every 10 hours (2 drops) every 10 hours (1 drop)
-
After season yes
Lubricant oil yes yes yes yes grease grease oil grease
Figure Note
Cable entry into the bowden and moving parts.
Casing after removing the pulley holder.
Frame contact surface.
>1 and >8 Bolt and side cover screw.
Table 6: Lubrication intervals
1.5.3 Sharpening and Replacement of Working Blades
If you are not manually skilled enough, entrust this work to a specialist workshop.
Note: In the case of any unprofessional repair of blades using other than original parts, the manufacturer is not liable for any damages on the machine or caused by your machine. The blade is embossed with a sign that indicates the manufacturer and is a check mark that the blade is an original spare part.
The machine must be placed on a hard horizontal surface and must be secured so that there is good access to the blade and machine would not start moving unexpectedly.
Take special care when removing the blades. Blade cutting edges are sharp. Protect your hands with working gloves.
The engine must be switched OFF and the spark plug cable end removed!
1) Hold the top disc to prevent it from rotating and remove the blade screw connection with a tubular spanner No. 16 ( 2 , 3 and
4 ). First unscrew the nut 2 and then the screw 3 .
2) Remove the blade 1 and blade mounting parts from the cutting disk. Straighten the edges and sharpen the blade cutting edges.
The inclination of the sharpened edge should be 30° with respect to the blade’s bottom plane.
3) Make sure all the blade mounting parts feature no visible damage. Otherwise, replace damaged parts with new ones.
4) Screw the blade screw assembly back in. The screw 3
must be tightened 25 firmly. Lock the screw with its nut
2 .
23 If the tyre pressure is lower than the minimum, the tyre-casing structure will be damaged and the service life will be significantly reduced.
24 The blades have two edges - they may be rotated as needed. In any case, the blade must be undamaged.
25 Insufficient screw tightening leads in most cases to the destruction of the hardened pad around which the blade rotates.
12
AS 625 KM / AS 585 KM
If any blade is bent or excessively worn, you must always replace all the cutting disc blades!
1.5.4 Belt Transmissions - Automatic Brake
The machine is equipped with modern design belts that do not require special care. It is only necessary to check them regularly, and when there are cracks or tears on the belt surface, replace them. The factory setting of the tensioning pulleys must be checked after the first approximately 5 hours of operation when the belt is breaking in. During breaking in, it is necessary to check the function of the tensioning pulleys to prevent the tensioning pulley from being damaged due to the extension of the belt to its damage. It is also necessary to check the automatic brake function during the run-in.
You may verify the correct function of belt drives in a simple way: a) The machine with its travel turned ON has to overcome the terrain unevenness of 10 cm high - curb is suitable, for example.
b) The engine that is started when the drive drive clutch is pressed quickly goes OFF. The belt starts to drive (the disc starts to rotate) already at the 1/3 of the drive lever clutch step.
If at least one of the checks failed, it is necessary to adjust the tensioning pulleys!
1.5.4.1 Adjusting of tension pulleys
If you are not manually skilled enough, entrust this work to a specialist workshop.
Per a):
the terrain inequality and visually check which belt is slipping.
1) If the belt A slips on the machine's right side , tension it through unscrewing the screw 1
in the direction of the arrow (away from the frame) for about 1 mm and repeat the check per 1.5.4 a). Continue with the tensioning until condition 1.5.4 a) is met, and the machine is not moving forward when the travel clutch lever is released.
If it is no longer possible to unscrew the bolt 1 , screw it fully against the direction of the arrow and hook the spring at the end of the cable into the distal hole in the pulley arm. Then, repeat the belt tensioning till condition 1.5.4 a) is met.
2) If the belt B slips between the engine and gearbox , tension it with the tensioning pulley. Release the tensioning pulley by releasing the nut 4 located on the motor plate and tension the pulley in the direction of the arrow, using a suitable tool
(such as a screwdriver). Once tensioned, tighten the nut. Then check the correct travel gear operation.
As soon as you cannot adjust the tensioning pulleys so that the belt does not slip, the belt must be replaced.
Per b):
Remove the front plastic cover to see the drive belt and disk drive pulley ( Fig. 16). (Labels
2 and 3
20 are common and belong to the same bowden cable.)
1)
Tension the belt by unscrewing the crew 27
3
for Fig. 20 about 1 mm in the arrow direction (away from the frame) and repeat
the check per 1.5.4 b). Continue with the tensioning till condition 1.5.4 b) is met. When the disk drive clutch lever is turned OFF the belt must be at rest, and it must not vibrate or move.
If the screw 3
3
Always check the automatic brake function after any adjustment!
1.5.4.1.1 V-Belt Change
sufficiently by the operation that it can no longer be tensioned with its tensioning pulleys. The exact process of changing the individual belts
path around all the guide elements!
If you are not manually skilled enough, entrust this work to a specialist workshop.
1.5.4.2 Brake function check and adjustment
Check the automatic brake function after every 10 hours of operation. (You may perform a continuous check at work.) Whenever the disk drive clutch lever is released, the automatic brake must stop the spinning disk within 5 seconds.
Do not continue working with the machine until you clear the automatic brake fault.
If you are not manually skilled enough, entrust this work to a specialist workshop.
If the brake does not stop the spinning disk in the aforementioned time range, the brake bowden cable adjusted 2
The adjustment screw that secures the brake bowden cable 2 to the machine frame in
Fig. 20 must be screwed in against the arrow
direction (towards the frame), so that the axle clearance of the bowden bolt in the adjustment screw is 1 mm. Then check the automatic brake function. If it is not possible to achieve sufficient brake performance by screwing the bolt 2 , fully, screw the brake bolt adjusting screw on the handlebar so that the axle clearance of the bowden bolt in the adjusting screw is 1 mm and then check the automatic brake
26 Můžete využít i šroubu na opačném konci bowdenu upevněného k příčce řídítek. V tomto případě ho šroubujte směrem od příčky řídítek.
27 You can also use the screw on the opposite end of the Bowden cable attached to the handlebar traverse. In such an event, screw it away from the handlebar traverse.
28 Use exclusively genuine replacement parts. Proper gear function cannot be guaranteed when using V-belts from different manufacturers.
29 May be performed in the opposite way – first screw in (towards the handlebar traverse) Brake bowden cable screw on the handles so the axial clearance is 1 mm in the adjustment screw.
30 The condition of the axial clearance of the brake cable in the adjusting screw is met.
13
EN English
1.5.5 Servicing intervals
Activity
Checking engine oil level
Engine air filter cleaning
Washing
Removing dirt and mowed growth debris
Blade sharpening
Blade inspection and storage
Checking that the cutting disc is tightened
Checking tightening of screwed connections
Lubrication
V-belts check
-
-
yes
Before mowing yes checked yes yes
checking the condition
During the season per the engine operating instructions every 10 hours
2x after every mowing yes yes as needed yes immediate replacement upon damage yes
every 5 hours
Before storage yes yes yes yes
every 20 hours yes
Table 7: Servicing intervals
1.5.6 Troubleshooting
Problem Cause
The cutting disc is not rotating The engine has not started
The disk drive clutch lever is not pressed
Insufficient belt tension
Torn belt
The machine is not moving
The belt has come off
Other defect
The engine has not started
The travel clutch lever is not pressed
Insufficient belt tension
The engine will not start
The brake does not brake
Torn belt
The belt has come off
Other defect
The petrol tank is empty
The petrol supply line is closed
Other defect
There is no axial clearance in the bowden cable, the cable is stretched
The brake key is not loose
Brake lining is worn - brake cannot be adjusted
The machine travel will not stop Broken travel pulley spring
The inner Bowden cable is stiff; bent Bowden cable
The cutting disc will not stop
The control levers do not return back
The tension pulley does not return back to its position
The tension pulley does not return back to its position
The inner Bowden cable is stiff; bent Bowden cable
Broken return spring
Other defect
Other defect
Solution
Start the engine
Press the lever
Adjust the tension pulley
Replace the belt
Re-mount the belt
Visit a service centre
Start the engine
Press the lever
Adjust both the tension pulleys
Replace the belt
Re-mount the belt
Visit a service centre
Add petrol
Open the petrol supply line
Visit a service facility
Adjust the brake
Lubricate
Visit a service facility
Replace with a new one
Lubricate or replace the Bowden cable
Lubricate
Lubricate
Lubricate or replace the Bowden cable
Replace with a new one
Visit a service facility
Visit a service facility
Table 8: Troubleshooting
14
AS 625 KM / AS 585 KM
1.5.7 Storage
Prior to any long-term storage (e.g. at the season end) remove all the dirt and plant residues from the machine. Prevent unauthorized persons from access to the machine. Protect the machine against weather impacts, but do not use any leakproof protection due to the possibility of increased corrosion.
Make sure the working blades are not damaged, sharpen blade cutting edges (or replace them, if damaged).
We strongly recommend the following steps:
Preserve the cutting disc blades.
Remove all the dirt and plant residues from the machine.
Repair any paint damage.
Drain the fuel from the fuel tank and carburettor (further instructions in the engine operating instructions).
Perform the post-season machine lubrication according to the
Check the tyre pressure and inflate the tyres per 1.5.1.1 to the
MAX pressure value.
1.5.7.1 Machine Washing and Cleaning
When washing and cleaning the machine, proceed so as to observe valid provisions and laws regarding protection of water courses and other water resources against pollution or contamination by chemical agents.
Never wash the engine by a water jet! During starting, the engine electric system could malfunction.
Do not ever wash your machine with any pressure washer Fig. 22.
1.5.8 Disposal of Packaging and the Machine at the End of its Service Life
When you unpack the machine you are bound to dispose of the packaging material according to national laws and decrees concerning waste disposal.
When disposing of the machine at the end of its service life, we recommend proceeding as follows:
Demount from your machine all the parts that may still be used.
Remove the plastic and non-ferrous metal parts.
The remaining machine and its removed demounted parts are to be disposed of according to national laws and decrees concerning waste disposal.
31 The respective local authority will inform you of the disposal centre location.
15
EN English
2 Attached illustrations
3
5
6
7
Fig. 1: Machine Unpacking
1 4
2
9
8
7
8
9
1
2
3
4
5
6
Fig. 2: Main Machine Components
1 2 3 4 5
11
12
13
14
15
10
6
16
17
18 19
20
Pictogram locations on the machine
Fig. 3: Safety labels – Combined sticker
16
AS 625 KM / AS 585 KM
Fig. 4: Safety pictogram
- Disk starting
Pictogram locations on the machine Fig. 5: Safety pictogram -
Machine travel
Pictogram locations on the machine
Fig. 6: Safety pictogram - Direction of rotation arrow
Fig. 7: Safety pictogram - Dangerous area
Fig. 8: Safety pictogram - Guaranteed level
1
STOP position
The engine is not running.
It is used to turn off a running engine.
Engine shutdown.
Refuelling.
Machine transport.
2
MIN position
The engine runs at its idle speed.
(Turtle sign)
Short work brake.
1
2
Fig. 9: Accelerator lever position
3
4
Pictogram locations on the machine
3
MAX position
The engine runs at its maximum speed. (Hare sign)
Working position
4
3
4
CHOKE position
The engine choke is engaged.
Cold engine start.
It is not used in automatic choke engines.
2
1
17
EN English
Step > >1
1
A
>4
B
B
B
D
D
5
>7
6
>2 >3
B
B
2
B
B
B
>5
B
4
3
C
D
D
B
B
C
>6
>8
E
>9
E
8
7
Legend:
A B C D E
Fig. 10: Machine Assembly Procedure
18
AS 625 KM / AS 585 KM
1
2
3
Fig. 11: Disk starting
OIL
1
3
Fig. 12: Gearbox Cover Removal
2
Fig. 13: The Machine Working Width
2 nd gear
HARE
1 st gear
TURTLE
Fig. 14: Gears
OIL
OIL
OIL
OIL
Fig. 15: Lubrication point
OIL
Fig. 18: Lubrication point
OIL
OIL
OIL
2
Fig. 16: Bowden cables installation
3
Fig. 17: Lubrication point
4
B
1
2
OIL
1
3
Fig. 19: Blade replacement
4
2
3
Fig. 20: Bowden Cable Adjustment
A
19
EN English
Fig. 21: V-belts paths Fig. 22: Pressure washing forbidden
Fig. 23: PRIMER
20
AS 625 KM / AS 585 KM
3 EC Declaration of Conformity
Address:
Product (machine) – type:
Serial No.:
Description:
EC Declaration of Conformity
AS-MOTOR GERMANY GmbH & Co. KG
Ellwanger Straße 15; D-74424 Bühlertann
AS 625 KM AS 585 KM from 031918030001 From 033419030001
Machine type
AS 625 KM Brush Cutter
Engine
BRIGGS & STRATTON 875EXi Series TM
Power
3,56 kW/3200 min -1
Operation width
62,2 cm
AS 585 KM Brush Cutter Zongshen XP200 3,6 kW/3800 min -1 62,2 cm
This brush cutter is designed for the cutting of tall thin-grassed growths and woody undergrowth in the woods and on the meadow up to the maximum height of 80 cm in maintained areas. There must be no foreign objects and surface unevenness on the cut surfaces. The cutter is not intended for park and lawn maintenance.
All the respective provisions met by the product:
Harmonized technical standards used for conformity assessment:
Other technical standards and specifications used for conformity assessment:
Machinery Directive 2006/42/EC
Noise Emission Directive 2000/14/ EC
Electromagnetic Compatibility Directive 2014/30/EC
EN 12733 + A1, EN 55012:2007
EN ISO 12100-2, EN 1050
Persons involved in the conformity assessment:
Conformity assessment procedure used:
Measured acoustic power level: A L
WA
= 97 dB
Authorized Body No. 255
Notified body č. 1016
The Government Testing Laboratory of Machines J.S.C.
Třanovského 622/11, 163 04 Prague 6 - Řepy, CZ
Noise Emission Directive 2000/14/ EC, annex VI
Guaranteed acoustic performance level:
A L
WA,G
= 98 dB
We declare that the equipment specified above is in conformity with the requirements of the above-mentioned directives.
Note: All regulations have been used as amended at the moment of issuing of this declaration without expressly specifying the amendments.
Place of issue:
Date of issue:
Name:
Eberhard Lange
Bühlertann
20.3.2019
Person authorized to sign on behalf of the manufacturer:
Position:
Company director
Signature:
32 The manufacturer also prepares and archives all technical documents regarding all directives relevant to the present EC declaration of conformity
21
A blank page must be in here.
A blank page must be in here.
AS-Motor Germany GmbH & Co. KG
Ellwanger Straße 15
D-74424 Bühlertann www.as-motor.de
THE HIGH GRASS MOWER AND 2 STROKE ENGINE MANUFACTURE
AS-Motor is your premium manufacturer for lawn and high grass mowers as well as 2 stroke engines. We offer our customers professional technology for steep slopes, rough terrain, and lawn care. Our extensive product range which includes hand-held entry-level devices up to the world’s first all-wheel ride-on mower with remote control will always offer private customers, municipalities service providers the right product. For more than 60 years, we have been developing and producing with a high production depth in Southern Germany and supply our dealer network in more than 30 countries all over the world.
Mulching mower
Mulching mower – the time-saving alternative!
AS-Motor mulching mowers shred the grass to create such a fine mulch, almost an “invisible” fertiliser, that sinks right away back into the lawn.
Disposal of the cuttings is not required.
Professional lawn mower Professional lawn mowers with rear or side discharge for every requirement, even with all-wheel drive, brake and reverse gear.
Allmäher® brush cutter
Flail mower
Allmäher® ride-on brush cutter
Rotary mower
Weed remover
An agile lawn mower for maintenance of extensive grassed areas. The
Allmäher® reliably mows and mulches metre-high grass, brushes and weeds.
High grass with undergrowth, steep slope or extensive areas in unknown terrain? The movably mounted flail blades of the AS-Motor flail mower give way to rocks and obstacles and chop the cuttings several times over.
If extensive areas, weeds and undergrowth up to 1.2 m, the AS-Motor allwheel mowers are also perfect for steep and even extremely steep terrain.
Ease of use and high area performance combined in one compact ride-on mower. For more safety, comfort and efficiency in difficult terrain we have developed the innovative and the world’s first remote controlled ride-on mower.
The cost-effective alternative to the cutter-bar mower. Also ideal for feed production. The grass is not shredded but deposited in straight rows as a windrow next to the machine.
Careful and chemical-free weed removal. The AS-Motor weed removers
“WeedHex” mechanically clean paved areas and curb stones from growing weeds – quickly, safely, and efficiently.
Text and figures © 2019
VL-31-2019
CSKV: 63006500071
Release: 11.2.2020
V1.0 EN
advertisement
* Your assessment is very important for improving the workof artificial intelligence, which forms the content of this project
Related manuals
advertisement