advertisement
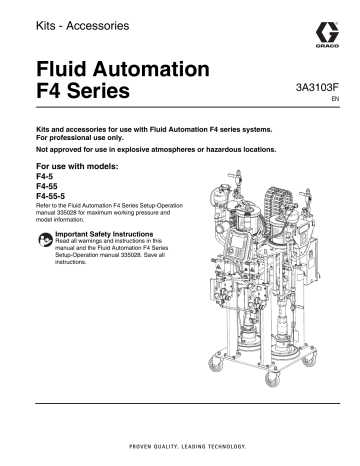
Kits - Accessories
Fluid Automation
F4 Series
Kits and accessories for use with Fluid Automation F4 series systems.
For professional use only.
Not approved for use in explosive atmospheres or hazardous locations.
For use with models:
F4-5
F4-55
F4-55-5
Refer to the Fluid Automation F4 Series Setup-Operation manual 335028 for maximum working pressure and model information.
Important Safety Instructions
Read all warnings and instructions in this manual and the Fluid Automation F4 Series
Setup-Operation manual 335028. Save all instructions.
3A3103F
EN
Related Manuals
Related Manuals
Refer to Fluid Automation F4 Series Setup-Operation manual 335028 for the complete list of related manuals.
2
Contents
Related Manuals . . . . . . . . . . . . . . . . . . . . . . . . . . . 2
Warnings . . . . . . . . . . . . . . . . . . . . . . . . . . . . . . . . . 3
Installation . . . . . . . . . . . . . . . . . . . . . . . . . . . . . . . . 6
Pressure Relief Procedure . . . . . . . . . . . . . . . . . 6
F4-55 Caster Kit, 24X218 . . . . . . . . . . . . . . . . . . 7
Dual Press Kit, 25A102 . . . . . . . . . . . . . . . . . . . . 7
Second Press Cable Kit, 25A106 . . . . . . . . . . . . 9
Mixing Stacks Supported . . . . . . . . . . . . . . . . . 10
Material In-line Filters . . . . . . . . . . . . . . . . . . . . 15
Material Regulators . . . . . . . . . . . . . . . . . . . . . . 17
Colorant Tank Kits . . . . . . . . . . . . . . . . . . . . . . 19
Color Flow Meter Kits . . . . . . . . . . . . . . . . . . . . 21
Color Injector Kits . . . . . . . . . . . . . . . . . . . . . . . 21
Continuous Level Sensor Kits . . . . . . . . . . . . . . 23
5-Gallon Pail Girdle, 25A160 . . . . . . . . . . . . . . 25
Pressure Transducer Kit, 25C237 . . . . . . . . . . . 26
Parts . . . . . . . . . . . . . . . . . . . . . . . . . . . . . . . . . . . . 29
F4-55 Caster Kit, 24X218 . . . . . . . . . . . . . . . . . 29
Dual Press Kit, 25A102 . . . . . . . . . . . . . . . . . . . 30
Second Press Cable Kit, 25A106 . . . . . . . . . . . 31
Straight Thread Multi-pass Mixing Stack,
25A990-993 . . . . . . . . . . . . . . . . . . . . . . . . 32
Straight Thread Single-pass Mixing Stack,
25A995-998 . . . . . . . . . . . . . . . . . . . . . . . . 34
Multi-pass Stack Mixer, 25A876 . . . . . . . . . . . . 36
Single-pass Stack Mixer, 25C003 . . . . . . . . . . . 37
In-line Filter Replacement Kits . . . . . . . . . . . . . 38
Manifold Assembly, 25B014 . . . . . . . . . . . . . . . 39
Shut-off Valve, 25A987 . . . . . . . . . . . . . . . . . . . 43
Two-pass Mixer Assembly, 25B016 . . . . . . . . . 44
Material In-line Filter, 25A983 . . . . . . . . . . . . . . 45
Material Regulator, 25A892 and 25A899 . . . . . 46
Color Injector, 25C478 . . . . . . . . . . . . . . . . . . . 48
Mini Single-pass Mixing Stack, 25C794/99 . . . . 50
Mixer-Material Regulator Component, 25C792/93
Stack Bracket Kit, 25C998 . . . . . . . . . . . . . . . . 54
Stack Adapter Kit, 25D011 . . . . . . . . . . . . . . . . 55
Tapered Thread Mixing Stack, 24R681 . . . . . . 56
Tapered Thread Mixing Stack, 25A169 . . . . . . . 59
Tapered Thread Mixing Stack, SK556 and
SK556-2A . . . . . . . . . . . . . . . . . . . . . . . . . . 61
Manifold Assembly, SA914-3A/-5A . . . . . . . . . . 63
Material In-line Filter, SA925-1A . . . . . . . . . . . . 66
Material In-line Filter, SA926-1A . . . . . . . . . . . . 67
Material Regulators, SA920-G and SA921-G . . 68
Color Injector Kit, 25A108 . . . . . . . . . . . . . . . . . 69
Color Injector Assembly, SN751-1A . . . . . . . . . 70
Colorant Tank Kit, 25A104 . . . . . . . . . . . . . . . . 72
Colorant Tank Kit, 25A105 . . . . . . . . . . . . . . . . 74
Color Flow Meter Kits, 25A103 and 25A161 . . . 76
Continuous Level Sensor Kit, 25A100 . . . . . . . . 77
Continuous Level Sensor Kit, 25A101 . . . . . . . . 78
5-Gallon Pail Girdle, 25A160 . . . . . . . . . . . . . . . 79
Pressure Transducer Kit, 25C237 . . . . . . . . . . . 80
Technical Data . . . . . . . . . . . . . . . . . . . . . . . . . . . . 81
Graco Standard Warranty . . . . . . . . . . . . . . . . . . . 82
3A3103F
Warnings
Warnings
The following warnings are for the setup, use, grounding, maintenance, and repair of Fluid Automation F4 Series equipment. The exclamation point symbol alerts you to a general warning and the hazard symbols refer to procedure-specific risks. When these symbols appear in the body of this manual or on warning labels, refer back to these
Warnings. Product-specific hazard symbols and warnings not covered in this section may appear throughout the body of this manual where applicable.
ELECTRIC SHOCK HAZARD
This equipment must be grounded .
Improper grounding, setup, or usage of the system can cause electric shock.
• Turn off and disconnect power cord before servicing equipment.
• Connect only to grounded electrical outlets.
• Use only 3-wire extension cords.
• Ensure ground prongs are intact on power and extension cords.
• Do not expose to rain. Store indoors
SKIN INJECTION HAZARD
High-pressure fluid from dispensing device, hose leaks, or ruptured components will pierce skin. This may look like just a cut, but it is a serious injury that can result in amputation. Get immediate surgical treatment.
• Do not point dispensing device at anyone or at any part of the body.
• Do not put your hand over the fluid outlet.
• Do not stop or deflect leaks with your hand, body, glove, or rag.
• Follow the Pressure Relief Procedure when you stop dispensing and before cleaning, checking, or servicing equipment.
• Tighten all fluid connections before operating the equipment.
• Check hoses and couplings daily. Replace worn or damaged parts immediately.
MOVING PARTS HAZARD
Moving parts can pinch, cut or amputate fingers and other body parts.
• Keep clear of moving parts.
• Do not operate equipment with protective guards or covers removed.
• Pressurized equipment can start without warning. Before checking, moving, or servicing equipment, follow the Pressure Relief Procedure and disconnect all power sources.
3A3103F 3
Warnings
4
FIRE AND EXPLOSION HAZARD
Flammable fumes, such as solvent and paint fumes, in work area can ignite or explode. Paint or solvent flowing through the equipment can cause static sparking. To help prevent fire and explosion:
• Use equipment only in well ventilated area.
• Eliminate all ignition sources; such as pilot lights, cigarettes, portable electric lamps, and plastic drop cloths (potential static arc).
• Ground all equipment in the work area. See Grounding instructions.
• Never spray or flush solvent at high pressure.
• Keep work area free of debris, including solvent, rags, and gasoline.
• Do not plug or unplug power cords, or turn power or light switches on or off when flammable fumes are present.
• Use only grounded hoses.
• Hold gun firmly to side of grounded pail when triggering into pail. Do not use pail liners unless they are anti-static or conductive.
• Stop operation immediately if static sparking occurs or you feel a shock .
Do not use equipment until you identify and correct the problem.
• Keep a working fire extinguisher in the work area.
EQUIPMENT MISUSE HAZARD
Misuse can cause death or serious injury.
• Do not operate the unit when fatigued or under the influence of drugs or alcohol.
• Do not exceed the maximum working pressure or temperature rating of the lowest rated system component. See Technical Data in all equipment manuals.
• Use fluids and solvents that are compatible with equipment wetted parts. See Technical Data in all equipment manuals. Read fluid and solvent manufacturer’s warnings. For complete information about your material, request MSDS from distributor or retailer.
• Do not leave the work area while equipment is energized or under pressure.
• Turn off all equipment and follow the Pressure Relief Procedure when equipment is not in use.
• Check equipment daily. Repair or replace worn or damaged parts immediately with genuine manufacturer’s replacement parts only.
• Do not alter or modify equipment. Alterations or modifications may void agency approvals and create safety hazards.
• Make sure all equipment is rated and approved for the environment in which you are using it.
• Use equipment only for its intended purpose. Call your distributor for information.
• Route hoses and cables away from traffic areas, sharp edges, moving parts, and hot surfaces.
• Do not kink or over bend hoses or use hoses to pull equipment.
• Keep children and animals away from work area.
• Comply with all applicable safety regulations.
TOXIC FLUID OR FUMES HAZARD
Toxic fluids or fumes can cause serious injury or death if splashed in the eyes or on skin, inhaled, or swallowed.
• Read SDSs to know the specific hazards of the fluids you are using.
• Store hazardous fluid in approved containers, and dispose of it according to applicable guidelines.
PERSONAL PROTECTIVE EQUIPMENT
Wear appropriate protective equipment when in the work area to help prevent serious injury, including eye injury, hearing loss, inhalation of toxic fumes, and burns. Protective equipment includes but is not limited to:
• Protective eyewear, and hearing protection.
• Respirators, protective clothing, and gloves as recommended by the fluid and solvent manufacturer
3A3103F
3A3103F
Warnings
PRESSURIZED ALUMINUM PARTS HAZARD
Use of fluids that are incompatible with aluminum in pressurized equipment can cause serious chemical reaction and equipment rupture. Failure to follow this warning can result in death, serious injury, or property damage.
• Do not use 1,1,1-trichloroethane, methylene chloride, other halogenated hydrocarbon solvents or fluids containing such solvents.
• Do not use chlorine bleach.
• Many other fluids may contain chemicals that can react with aluminum. Contact your material supplier for compatibility.
BURN HAZARD
Equipment surfaces and fluid that’s heated can become very hot during operation. To avoid severe burns:
• Do not touch hot fluid or equipment.
5
6
Installation
Installation
NOTICE
To prevent thread damage, apply POLY-TEMP ceramic tape or equivalent to all National Pipe
Threads (NPTs) when installing.
®
NOTE: Some installation steps reference numbers in parentheses that refer to call outs in parts drawings. See the Parts section in this manual for part identification.
Pressure Relief Procedure
Follow the Pressure Relief Procedure whenever you see this symbol.
2. Open the prime ball valves for both the A and B pumps.
Prime Ball
Valve
The F4 Series equipment stays pressurized until pressure is manually relieved. To help prevent serious injury from pressurized fluid, such as skin injection, splashing fluid and moving parts, follow the
Pressure Relief Procedure before cleaning, checking, or servicing the equipment.
NOTE: Always place an empty container under the prime valves and the ratio check valves before using them to keep material from dispensing onto the machine.
NOTE: There is pressure on each side of both the A and
B dosing valves. Pressure must be relieved on the pump side and the stack side of the dosing valves.
1. To relieve pressure at the pump, turn off the system air slider valve.
3. To relieve pressure on the side leading out to the stack from the dosing valves, ensure the material outlet valves are open on the A and B side.
Material Outlet Valves
Ratio Check Valves
4. Open the ratio check valve on both the A and B side to relieve pressure.
NOTE: This procedure relieves air pressure from the entire system.
3A3103F
Installation
F4-55 Caster Kit, 24X218
This kit is for attaching casters to the F4-55 and F4-55-5 models that do not have casters installed at the factory.
See page
Parts for part identification.
1. Lift the machine until it is at least 3 in. (8 cm) off the floor.
Dual Press Kit, 25A102
This kit is needed when using a second press with any of the F4 Series machines.
NOTE: The kit contains one material outlet ball valve.
The second press connection uses the outlet ball valve that is already installed on the machine.
Injury may occur if the machine is lifted and not secured to prevent falling. Rest the machine on stands or blocks while installing the caster kit.
2. Align the four holes in the white bracket (1) with the holes on the caster (2).
3. Mount the caster to the bracket by inserting four of the hex screws (3) included in the kit through the top of the bracket and securing them to the caster underneath with four hex nuts (4).
4. Torque the nuts to 30-35 ft-lbs (41-47 N•m).
5. Fasten the bracket to the base frame using four of the hex screws (3).
6. Torque the hex screws to 30-35 ft-lbs (41-47 N•m).
7. Repeat steps 2-6 for the remaining three casters.
1. Remove the material outlet ball valve and adapter fitting from the machine where you are installing the dual press kit.
Material Outlet
Ball Valve and Adapter
3A3103F 7
Installation
NOTE: Apply tape to all male threads as needed.
2. Attach the valve and the adapter to the dual press kit.
This kit includes a 3/8 in. air line tee that needs to be installed at the machine’s air line outlet port when connecting the air lines to the stacks. See
on page
for more information.
Location of air line outlet port on the F4-5.
3. Attach the dual press kit to the material outlet connection on the machine where you removed the original outlet ball valve.
4. Tighten all connections.
5. Connect the material hoses to the dual press kit.
The material hose connections are 12 JIC flared connections.
NOTE: Do not connect the material hoses to the mixing stacks until after the pumps and material lines have been primed.
Location of air line outlet port on the F4-55 and F4-55-5.
8 3A3103F
Installation
Second Press Cable Kit, 25A106
This kit contains cables for making connections from the electronic enclosure to the mixing stack and the press when using a second press with the F4 Series
in Parts for part identification.
3. Connect the cable for the mixing stack (201) to the electronic enclosure at the connection marked
Stack 2.
Connection at
Electronic
Enclosure
Press Cable
Connection at Press
Connection at
Electronic
Enclosure
Step 3
Mixing Stack
Cable Assembled
Step 1
Connection at Stack
4. Connect the mixing stack cable to the harness splitter (202), and connect the splitter to the two cords
(203) in the kit.
5. Connect the cord labeled stack valve 1A to the stack’s solenoid block A connector and the cord labeled stack valve 1B to the B connector.
1. Connect the press cable (204) to the electronic enclosure at the connection marked Press 2.
2. Refer to the Fluid Automation F4 Series
Setup-Operation manual 335028 for information about connecting the cable to the press.
3A3103F
B C1
A
Cords Connect Here
NOTE: The number of solenoid block connectors varies depending on which mixing stack you are using.
9
Installation
Mixing Stacks Supported
There are two types of mixing stack products available with the F4 Series:
• Straight thread stacks
• Tapered thread stacks
Mixing Stacks with Straight Threads
The straight thread mixing stacks offer multi-pass and single-pass mixing options. These stack kits include material in-line filters. For information about in-line fil-
On all configurations of the straight thread mixing stacks, the material lines from the F4 machine are connected to the 12 JIC inlets on the stack. If coolant lines
(normally chilled water) are being used, they are connected to the 5/16 in (8 mm) water jacket fittings on the mixers. The JIC outlets of the mixer can be adapted as needed to connect to the press or to the material regulator, which would then be connected to the press.
Multi-pass Mixing Stack
The multi-pass stack includes multiple mixing elements to optimize mixing of the material. Three configurations of the mixing stack are available to meet the specific needs of your system.
Kit 25A990 has a manifold, mixer, and regulator but does not include manifold on/off valves, a solenoid block, or a connection for a color injector. The material inlet connections on the manifold are 12 JIC, the water jacket elbow fittings are 5/16 in. (8 mm), and the outlet is
08 JIC.
Kit 25A992 has the same components as kit 25A990 and also includes manifold on/off valves and a solenoid block with two solenoids that is designed for systems that are not using a color injector. This kit uses 5/16 in.
(8 mm) air line tubing for the air connection between the solenoid block and the manifold valves. There is also a
3/8 in. (10 mm) connection for the stack air inlet.
3/8 in.
(10 mm)
12 JIC
Inlet
5/16 in.
(8 mm)
08 JIC
Outlet
Kit 25A993 has all of the components from kit 25A992 and also includes a color injector (with adapter) and a solenoid block with three solenoids that is designed for use with the color injector. See Color Injector Kits on page
for more information.
The third solenoid in this kit has two 1/4 in. (6 mm) connections for air line tubing from the color injector.
3/8 in.
(10 mm)
5/16 in.
(8 mm)
12 JIC
Inlet
08 JIC
Outlet
12 JIC
Inlet
5/16 in.
(8 mm)
08 JIC
Outlet
10 3A3103F
Installation
Single-pass Mixing Stack
This single-pass stack is designed for systems that require a higher flow rate. Three configurations are available to meet the specific needs of your system.
NOTE: The air line, material, and water jacket connections are the same for the single-pass mixing stack as the multi-pass stacks.
Kit 25A995 has a manifold, mixer, and regulator but does not include manifold on/off valves, a solenoid block, or a connection for a color injector. The material inlet connections are 12 JIC, the water jacket fittings are
5/16 in. (8 mm), and the outlet is 08 JIC.
This kit uses 5/16 in. (8 mm) air line tubing for the air connection between the solenoid block and the manifold valves. There is also a 3/8 (10 mm) connection for the stack air inlet.
Kit 25A998 has all of the components from kit 25A997 and also includes a color injector (with adapter) and a solenoid block with three solenoids that is designed for use with the color injector. See Color Injector Kits on
The third solenoid in this kit has two 1/4 in. (6 mm) connections for air line tubing from the color injector.
3/8 in.
(10 mm)
5/16 in.
(8 mm)
12 JIC
Inlet
08 JIC
Outlet
12 JIC
Inlet
Kit 25A997 has the same components as kit 25A995 and also includes manifold on/off valves and a solenoid block with two solenoids that is designed for systems that are not using a color injector.
3/8 in.
(10 mm)
* On other side
5/16 in.
(8 mm)*
08 JIC
Outlet
12 JIC
Inlet
* On other side
3A3103F
5/16 in.
(8 mm)*
08 JIC
Outlet
11
Installation
Mini Single-pass Mixing Stack
The mini single-pass mixing stack is intended for applications that require dispensing mini-shots of material.
This stack has 1/4 in. mixing elements, holds less amounts of material in the mixer to reduce material waste, and provides continuous cooling of the mixed material.
This stack has 12 JIC material inlet connections and a
5/16 in. (8 mm) water jacket fitting. The outlet is an 06
JIC connector.
A unique feature of this stack is that it includes a combined mixer-material regulator component.
Kit 25C794 includes a third valve that provides additional control for dispensing material based on the needs of your system. This valve has 5/32 in. (4 mm) air fittings.
3/8 in.
(10 mm)
5/16 in.
(8 mm)
Kit 25C792 , which is included as part of kit 25C794, can be purchased and used separately. This kit has the combined mixer-material regulator component with the third valve, but does not include the manifold on/off valves, a solenoid block, or gauges.
5/16 in.
(8 mm)
5/32 in.
(4mm)
12 JIC
Inlet
06 JIC
Outlet
Kit 25D011 is an option for use with kit 25C792 depending on the needs of your system. Kit 25D011 can also be used with kits 25A990 (see page
page
). Two 12 JIC to 08 JIC reducing adapters are included in kit 25D011 for systems requiring them. You can also purchase JIC adapters separately. See the part numbers for these adapters on page
12 JIC
Inlet
5/32 in.
(4mm)
06 JIC
Outlet
12 JIC Reducers
08 JIC
Kit 25C799 has the same components as kit 25C794 except it does not include the third valve for controlling material dispensing.
12 JIC
Inlet
3/8 in.
(10 mm)
5/16 in.
(8 mm)
Plug
12 JIC
06 JIC
Outlet
Kit 25C998 is a bracket that can be used to mount kit
25C792 on a press or other location. After the bracket is mounted to the mixer-material regulator component, use
5/16 in. (8 mm) screws (not included) to mount the
bracket in the desired location. See page 54 for mount-
ing slot dimensions and the location where the bracket is mounted on 25C792.
12 3A3103F
Installation
Mixing Stacks with Tapered Threads
There are three models of mixing stacks that have tapered threads and come without in-line filters. Each of these stacks uses 1/4 in. (6 mm) air line tubing for the air connection between the solenoid block and the manifold valves. The material line inlet connections are 12
JIC and the water jacket elbow fittings for the coolings lines are 1/4 in. (6 mm) for all three models.
The mixing stack you choose depends on the needs of your system.
Kit 24R681 has a mixer with 24 5/8 in. (16 mm) mixing elements and a high flow rate. This stack kit has a 3/4 in. (19 mm) outlet fitting for connecting to the press.
Kit SK556 has a mixer with 12 5/8 in. (16 mm) mixing elements that provides a higher flow rate. This stack kit has a 3/4 in. (19 mm) outlet fitting for connecting to the press.
3/8 in.
(10 mm)
12 JIC
Inlet
1/4 in.
(6 mm)
3/4 in. (19 mm)
Outlet
1/4 in. (6 mm)
12 JIC
Inlet
3/4 in. (19 mm)
Outlet
Kit 25A169 also has 24 3/8 in. (10 mm) mixing elements but the mixer is smaller, which results in a lower flow rate. This stack kit has a 1/2 in. (13 mm) outlet fitting for connecting to the press. There is also a 3/8 (10 mm) connection for the stack air inlet.
3/8 in.
(10 mm)
SK556-2A Option
Each of these three stack kits have a port for at least one color injector. Mixing stack SK556 also has an option available for a second color injector solenoid on the solenoid block.
12 JIC
Inlet
1.2 in.
Outlet
3A3103F
1/4 in. (6 mm)
Installing the Stack Kits
The installation steps are similar on all models of the mixing stacks. Mounting the stack onto the press varies depending on the type of press being used.
NOTE: For information about using the material in-line filters or the material regulators as part of the installa-
for the in-line filters and page
for the material regulators.
13
Installation
1. If you choose a stack with a solenoid block, it comes already mounted on the stack. If you need to install or replace a solenoid block, ensure that is mounted on the opposite side of the stack from the pressure gauge faces.
2. Run the 3/8 in. (10 mm) air inlet tubing included in the kit from the machine and connect it to the air inlet on the stack. (Stack 25A169 is shown below.)
Stack Air Inlet
4. After the pumps and material lines have been primed, connect both the A and B material outlet hoses to the stack. See the Fluid Automation F4
Series Setup-Operation manual 335028 for more information. (Stack 25A992 is shown below.)
Material Line Connections
NOTE: If two stacks are being used with a dual press setup, use the 3/8 in. air line tee included with the dual press kit (25A102) for the connection at the machine.
See
on page
for information.
3. The 1/4 in. (6 mm) or 5/16 in. (8 mm) air line tubes
(depending on the model) are already connected at the stack. To replace or reinstall the air line tubes, connect them as follows when looking at the side of the stack opposite from the pressure gauge faces.
(Stack 24R68 is shown below.)
• Connect the air line tubes from the forward solenoid ports to the two closer fittings on the manifold on/off valves.
• Connect the air line tubes from the back ports to the two fittings at the ends of the manifold on/off valves.
5. Connect the cables from the electronic enclosure to the solenoids as shown below. Always use the
Stack 1 connection at the electronic enclosure if
only using one press. See page 9 for a diagram of
the electronic enclosure’s connections.
B C1 A
Stack Cables
Color 1 Cable
NOTE: The solenoid block on mixing stack kit
SK556-2A has an extra solenoid for a second color injector (C2). Connect the cable from Color 2 on the electronic enclosure to the C2 connection.
NOTE: Mixing stacks 25A992, 25A997, 25C794, and
25C799, are configurations that do not utilize a color injector. With these models, there are only two solenoids on the solenoid block for stack cable connections.
Solenoid add-on kit 25B009 can be used to add another solenoid to the block if needed.
NOTE: All of the stacks have push-to-connect fittings to circulate fluid for presses that use chillers.
14 3A3103F
Installation
Using Straight Thread Mixers with Tapered Thread
Stacks
The multi-pass and single-pass mixing elements included with the straight thread mixing stacks can be used with tapered thread mixing stacks using an optional adapter (part no. 17M397).
Adapter
Connect the 1-1/14 in. end of the adapter to the tapered thread stack’s manifold and the 1-3/8 in. end of the adapter to the mixer (25C003 shown). Tighten the connections at both ends until secure.
See Manifold Assembly, SA914-3A/-5A on page
for part information.
Material In-line Filters
Material in-line filters are installed between the mixing stack and the press. They filter the material coming from the stack to help prevent clogging.
The straight thread mixing stacks include a fac-
here are used with the mixing stacks as shown below.
In-line Filter Mixing Stacks
SA925-1A (3/4 in.)
SA926-1A (1/2 in.)
24R681, 25A169, SK556
24R681, 25A169, SK556
25A983* 25A990, 25A992, 25A993,
25A995, 25A997, 25A998
* Replaces the factory-installed in-line filters.
NOTE: In-line filter 25A983 cannot be used with the mini single-pass mixing stacks.
In-line Filter, SA925-1A
NOTE: Material in-line filter SA925-1A can only be used with tapered thread mixing stacks.
This filter is for a 3/4 in. NPT connection (both input and output). If a material regulator is used, the filter should be installed between the stack and the regulator.
NOTE: The 3/4 in. material filter provides a higher flow rate than the 1/2 in. filter.
Top of Filter
Stack Connects
Here
3A3103F 15
Installation
Bottom of Filter
To Press
In-line Filter, 25A983
NOTE: Material in-line filter 25A983 can only be used with straight thread mixing stacks.
This filter provides a high flow rate and can be installed on both the multi-pass and single-pass mixing stacks, except for the mini single-pass stack. The input and output connections for the filter are 1-3/8 in. (35 mm).
Top of Filter
Stack Connects Here
Bottom of Filter
To Press
In-line Filter, SA926-1A
NOTE: Material in-line filter SA926-1A can only be used with tapered thread mixing stacks.
This filter is for a 1/2 in. NPT connection (both input and output). If a material regulator is used, the filter should be installed between the stack and the regulator.
Top of Filter
Stack Connects Here
This filter is installed at the end of the mixer, between the mixer and a material regulator.
Installing in-line filter 25A983 on the straight thread mixing stack kits requires first removing the factory-installed in-line filter.
1. Loosen the nut at the bottom of the mixer and disconnect it from the 08 JIC filter fitting.
2. Remove the three screens and the filter support as shown below. Leave the o-ring when installing the new in-line filter.
Bottom of Filter
To Press
16 3A3103F
Installation
3. Connect the 08 JIC filter fitting to the bottom of in-line air filter 25A983.
4. Attach the top of the filter to the stack’s mixer.
5. Attach material regulator 25A986 to the 08 JIC filter fitting.
Material Regulators
Material regulators help to reduce pressure fluctuations and provide a more consistent material feed pressure into the press. The regulator is installed between the mixing stack and the press. If an in-line filter is used, the regulator is installed after (below) the filter.
NOTE: The mini mixing stacks 25C792, 25C794, and
25C799 do not require a material regulator as each kit includes a combined mixer-material regulator component.
Material Regulator, 25A986
NOTE: Material regulator 25A986 is used with straight thread mixing stacks.
Two configuration options are available for this material regulator. The only difference between the two configurations is that one includes a gauge to monitor outbound pressure and the other does not include the gauge.
The input and output connections for this material regulator are 08 JIC.
Parts for more information.
8 JIC
NOTE: Replacement kits are available for the factory-installed in-line filters. See
In-line Filter Replacement Kits on page 38
.
3A3103F 17
Installation
Two regulator options are offered for the tapered thread mixing stacks 24R681, 25A169, and SK556. Both regulators include a gauge for monitoring pressure
Material Regulator, SA921-G
NOTE: Material regulator SA921-G is used with tapered thread mixing stacks.
This regulator is for a 3/4 in. NPT connection (both input and output) and would be used with material in-line filter
SA925-1A.
Material Regulator Features
All four of the material regulators described in this section have a pressure adjustment control that allows you to manually increase or decrease output pressure. Turn the adjustment control clockwise to increase pressure and counterclockwise to decrease pressure.
Material Regulator, SA920-G
NOTE: Material regulator SA920-G is used with tapered thread mixing stacks.
This regulator is for a 1/2 in. NPT connection (both input and output) and would be used with material in-line filter
SA926-1A.
Pressure Adjustment
On all of the regulator models, the input line is connected to the port marked IN and the output line is connected to the port marked OUT. All models include a ball valve for bleeding the line, if needed.
Also, the regulators have push-to-connect fittings to circulate fluid for press configurations that use chillers.
NOTE: A diaphragm isolator is located between the gauge and fluid regulator. This is to prevent material from curing inside the gauge. Material still may cure inside the diaphragm isolator on the fluid regulator side, which could prevent accurate pressure readings. Periodic maintenance helps to ensure proper functionality.
18 3A3103F
Installation
Colorant Tank Kits
There are two sizes of colorant tanks available, one for the F4-5 and one for the F4-55 and F4-55-5.
Colorant Tank Kit, 25A104
2. Connect the tank to the bracket using the screw
(3611) and nut (3612) provided in the kit.
3. Ensure all screws are tight to secure the tank.
Colorant Tank Kit, 25A105
This colorant tank is for use with the F4-5 and holds up to 3 qt (3 liters) of color material. See page
Parts for part identification.
1. To mount the tank to the F4-5, remove two of the existing bolts on a ram cylinder and attach the colorant tank bracket (3610) using the two screws
(3609) provided in the kit.
This colorant tank is for use with the F4-55 and F4-55-5 and holds up to 3 gal. (11 liters) of color material. See
Parts for part identification.
1. To mount the tank to the machine, attach the white tank bracket (3813) to a ram cylinder using the four hex screws (3806) included in the kit.
White Tank Bracket
3A3103F
Bracket
Tank Mounting Bracket
19
Installation
2. Attach the tank mounting bracket (3809) to the white tank bracket using two hex screws (3812) included in the kit.
3. Ensure all screws are tight to secure the tank.
4. Attach the colorant tank to the mounting bracket using two socket head screws (3810) included in the kit.
3. Connect the other end of the 1/4 in. tubing to the colorant tank air regulator on the top of the tank.
Tank Air Line Connection
4. Connect the color material line to the 06 JIC connector at the bottom of the tank.
Air Line and Color Material Line
Connections
The air line and material line connections are handled the same way for both tank kits.
1. At the machine, remove the 3/8 in. plug from one of the air line connections and replace it with the 3/8 in. x 1/4 in. reducer included in the kit.
Material Line Connection
NOTE: The connection for the material line depends on
if you are using a color flow meter or not. See Color
Flow Meter Kits and Color Injector Kits on page 21
to complete installation.
2. Connect the 1/4 in. tubing that is included with the kit to the reducer at the machine.
20 3A3103F
Installation
Color Flow Meter Kits
The color flow meter provides feedback to the system about the flow of the color material and automatically adjusts to maintain the color setpoint, based on the feedback and the settings in the Advanced Display Module (ADM).
NOTE: There are two color flow meter kits available for use with the F4 Series. Kit 25A103 can be used for most color materials. Kit 25A161 should be used for high viscosity material.
NOTE: See the Fluid Automation F4 Series Setup-Operation manual 335028 for information about calibrating the color flow meter and color injector.
1. Connect the colorant tank’s material line to the 06
JIC inlet connection on the color flow meter. See
Colorant Tank Kits on page 19 .
2. Connect the color material line from the color injector to the 06 JIC outlet connection on the flow meter.
3. Connect the cable included with the color flow meter kit to the cable connection on the flow meter.
Cable to
Electronic
Enclosure
Inlet
Connection
Outlet
Connection
NOTE: Always use Color F/M 1 if you are only using one press. Color F/M 2 can be used for the second connection in a dual press configuration, or if two injectors are used on a single press.
Color Injector Kits
The color injector connects to the mixing stack and is used to add color to the silicone material so it can be mixed in the stack prior to being dispensed by the press.
NOTE: There are two color injector kits available for use with the F4 Series. Kit 25C478 is used with straight thread mixing stacks and kit 25A108 is used with tapered thread stacks.
Install 25C478
Two configurations (25A993 and 25A998) of the straight thread mixing stacks come with color injectors already installed. If you need to replace the color injector or want to install a color injector on another straight thread stack, use kit 25C478.
Mount color injector 25C478 onto the stack as shown below. (Stack 25A993 is shown.)
1. Loosen the nut (part no. 17L385) at the top of the mixer and separate the mixer from the manifold assembly.
2. Connect the color injector kit to the mixer and manifold assembly and torque the nuts to 25-30 ft-lbs
(30-40 N•m).
4. Connect the other end of the cable to the electronic enclosure at one of the Color F/M connections. See page
for a diagram of the electronic enclosure’s connections.
3A3103F 21
Installation
Install 25A108
Color injector 25A108 is connected onto the stack at the mixer as shown below. (Stack 24R681 is shown.) Apply ceramic tape to the NPT threads on the color injector prior to mounting it on the mixer.
2. Connect the 1/4 in. air line tubes from the color injector to the injector solenoid on the stack.
Inject Color Air Hose
Connects Here
Retract Injector Air Hose
Connects Here
Color Injector Connections
The following steps apply to both 25C478 and 25A108.
1. Attach the color material line from either the colorant tank or the color flow meter (depending on the configuration) to the color injector using the 06 JIC quick disconnect.
3. Connect the cord included with the kit to the stack’s
solenoids at C1. See page 48 (25C478) or page
(25A108) in Parts for part identification.
Color 1 Cable
Color Material
Line
Retract Color Injector Air Hose Connection
Inject Color Air Hose Connection
NOTE: The disconnect has a check mechanism on both sides to prevent colorant from pouring out when not attached.
B C1 A
Stack Cables
4. Connect the other end of the cord to the cable included in the kit and connect the cable to the electronic enclosure at the Color 1 connection. See page
for a diagram of the electronic enclosure’s connections.
22 3A3103F
Installation
Continuous Level Sensor Kits
Do not install these sensors while the machine is operating or when air is supplied to the system.
Removing hex nuts from the ram assemblies while the machine is operating could cause personal injury or damage the machine. Follow the Pressure Relief
Procedure on page
installation.
The continuous level sensors are designed to measure the amount of material left in the drums and provide feedback to the system. The material ratio can then be adjusted so the drums are emptied at the same time.
Continuous Level Sensor, 25A100
This sensor kit is for the F4-55 and F4-55-5. It includes two sensors, each with a bracket and hardware for mounting the sensors to the machine. This kit also includes cables for connecting each sensor to the continuous level cables running from the electronic enclo-
Parts for part identification.
3. Mount the sensor with the bracket as shown below and attach and tighten the hex nuts on the ram beams until secure.
Ram Beam Hex Nuts
4. Connect the cables (4104) included in the kit to the top of the string pot sensors (4101).
5. These cables then attach to pre-installed cables that run from the electronic enclosure through the cable track and hose guide. Look for the cables marked E located near the A and B air motors. Connect them to the cables (4104) running from the sensors.
String Pot
Bracket for String
Pot Connection
Follow these steps to install the sensors on both the A and B sides.
1. Remove the hex nut from the bolt on the end of each ram beam nearest to the electronic enclosure.
2. Using the screws (4103) included in the kit, attach each of the string pot sensors (4103) to the brackets
(4101).
6. Attach the string pots (4102) to the string connection brackets located on the electronic enclosure brace.
Use the screws (4103) included in the continuous level sensor kit to attach the string to the bracket on each side.
3A3103F 23
Installation
7. Adjust the height of the pre-installed leveling clamps to 5.38 in. (137 mm) from the bottom of each ram beam to the top of the leveling clamps.
These sensors are mounted on the ram motor plates behind the ADM and light tower.
1. Remove the hex nuts from the bolts on each ram motor plate closest to the ADM.
2. Using the screws (4205) included in the kit, attach each of the string pot sensors (4203) to the brackets
(4201).
5.38 in.
(137 mm)
Secondary Bracket Bolts
Leveling
Clamps
Continuous Level Sensor, 25A101
This sensor kit is for the F4-5 and includes two sensors, each with a bracket for mounting to the machine and another bracket for connecting the string pot. This kit also includes cables for connecting each sensor to the continuous level cables running from the electronic enclosure. See page
in Parts for part identification.
Motor Plate Hex Nuts
3. Mount each sensor with the bracket as shown above and reattach the ram motor plate hex nuts, but do not fully tighten them.
4. Add the secondary bracket bolts (4204) included in the kit to orient the sensors as shown above.
Secure the bolt with the nuts (4206) included in the kit.
5. Tighten the ram hex nuts until secure.
6. Connect the cables (4207) included in the kit to the top of the string pot sensors (4203).
7. These cables then attach to pre-installed cables that run from the electronic enclosure through the cable track and hose guide. Look for the cables marked E located near the A and B air motors. Connect them to the cables (4207) running from the sensors.
24 3A3103F
Installation
8. Remove the screws from the ram brackets next to the piston rods.
String Connection Bracket String Pot
9. Place the string connection brackets (4202) on the ram brackets as shown above and replace and tighten the screws until secure.
10. Attach the string pots (4203) to the brackets. Use the screws (4205) included in the kit to attach the string to the bracket on each side.
11. Adjust the height of the pre-installed leveling clamps to 3.75 in. (95 mm) from the bottom of each ram motor plate to the top of the leveling clamps.
NOTE: See the Fluid Automation F4 Series Setup and
Operation manual 335028 for information about setting up and calibrating the sensors in the ADM software.
5-Gallon Pail Girdle, 25A160
This is intended for use with the F4-55 machine. The pail girdle is placed around 5-gallon pails that are used to contain material dispensed from the machine. The pail girdle reinforces the pail to help keep it from cracking or breaking during use.
To place the girdle on a pail, loosen the three clamp handles until the pail fits inside the girdle. Slide the pail into the girdle and tighten the clamp handles until secure.
NOTE: Do not over-tighten the girdle as it could damage the pail.
3.75 in.
(95 mm)
Leveling
Clamps
3A3103F 25
Installation
Pressure Transducer Kit, 25C237
The pressure transducer kit is used to monitor mixing stack pressure through the system instead of using the stack’s gauges. Pressure information is transmitted by the pressure transducer to the system’s ADM.
NOTE: This kit can be used with straight thread or tapered thread stacks. The 1/2 NPT x 08 JIC adapter
(4410) included in the kit is required when connecting to a straight thread stack.
There are two pressure transducers in each kit. One end of each is connected to the stack (pressure A and pressure B) and the other end is connected to Fluid Control
Module 2 (FCM 2) in the electronic enclosure.
NOTE: A second pressure transducer kit can be used to monitor additional pressures in the system or a second stack. On the ADM, these connections are pressure C and pressure D. When using a second kit, pressure A and B must still be connected to FCM 2 and pressure C and D must be connected to FCM 1.
Follow these steps to install the pressure transducer kit.
in Parts for part identification.
1. Remove both gauges from the stack.
a. For tapered thread stacks, install the two pressure sensors by connecting the 1/2 in. NPT pressure transducer adapters (4405) to the stack where the gauges were removed. Use ceramic tape on the NPT fittings.
b. For straight thread stacks, install the 1/2 NPT x
08 JIC adapters (4410) to the stack where the gauges were removed. Then connect the two
NPT pressure transducers to the adapters.
Install Adapter
Connect Pressure Transducer
NOTE: The pressure transducers can also be used with
the stack adapter kit 25D011 (see page 12 ). Remove
the gauges and install the pressure sensors (4403) directly into where the gauges were removed, as shown below. Do not use the pressure transducer adapters
(4405) or the 1/2 NPT x 08 JIC adapters (4410) for this installation.
A B
26
Remove Gauge
Connect Pressure Transducer
2. Connect each pressure sensor (4403) to the cables
(4404) included in the kit and run the cables to the machine’s electronic enclosure.
3A3103F
Installation
3. Insert the cables through an available opening in the
F4 Series machine’s electronic enclosure and connect the cable from pressure A on the stack to port 6 and the cable from pressure B on the stack to port 7 on FCM 2.
Using Small Shot Mode
If the pressure transducer kit is being installed to run in small shot mode, the custom software blue token included in the kit must be inserted into FCM2. See the
Fluid Automation F4 Series Setup and Operation manual 335028 for more information.
Also, the restrictor that comes with the kit needs to be installed between the outlet of the dosing valve and the stainless steel u-tube that connects to the flow meter on the F4 series machine.
1. Loosen and remove the fittings that connect the u-tube to the dosing valve and flow meter.
2. Insert the restrictor (4108) into the tube with the flange near the top as shown below.
4. If a second pressure transducer is being used on the F4 System, connect the cable into port 6 for pressure C and port 7 for pressure D on FCM 1 as shown below.
Restrictor
FCM1
Port 7
FCM2
Port 7
U-tube
Port 6
C D
Port 6
A B
5. Insert the custom software blue token included in the kit into FCM2. This is required to run the machine in small shot mode.
NOTE: See the Fluid Automation F4 Series Setup and
Operation manual 335028 for information about the pressure sensor operation in the ADM software.
NOTE: If there is material in the tube, clean out enough of it to allow the restrictor to be completely inserted into the tube.
3. Reattach the u-tube to the dosing valve and flow meter and tighten the fittings until secure.
The dosing valve’s JIC adapter should fit tightly against the top of the restrictor.
NOTE: When you are using small shot mode, the pressure transducer kit can only be used with a single press.
It cannot be used with the dual press kit.
NOTE: See the Fluid Automation F4 Series Setup and
Operation manual 335028 for information about running the F4 series machine in small shot mode.
3A3103F 27
Installation
NOTES:
28 3A3103F
Parts
F4-55 Caster Kit, 24X218
3 1
1
3 2
Parts
4 2
2
F IG . 1: Casters
1
2
3
4
Ref Part
24X217
121495
127048
127076
Description
BRACKET, caster, white
CASTER, swivel, w/brake, 800 lbs
SCREW, machine, hex, flange, m10 x1.5 x 25
NUT, hex, flange, serrated, m10
Quantity
4
4
32
16
1
2
Apply sealant to all male threads as needed.
Torque items to 30-35 ft-lbs (41-47 N•m).
3A3103F 29
Parts
Dual Press Kit, 25A102
1. Apply tape to all male threads as needed.
114
115
113
112
107
106
111
110
109
105
104
101
F IG . 2: Dual Press
103
102
Ref Part Description
101 123980
102 113833
FITTING, swivel, 3/4 x 1/2, mf, sst, 3.5
TEE, pipe, female
103 15428-5-SS FITTING, elbow, 90, 1/4 npt, mm, ss, 4k, 3
104 FAA081100 VALVE, check 3/4 npt, fxf, 4410 psi, ss
105 16R883
106 24P719
107 94/1027/98
109 128058
FITTING, nipple, reducing, 3/4 x 1/2
VALVE, 1/2 in. ball
ADAPTER, jic 12 x 1/2 in. npt, mm, ss, 3k, 316
FITTING, tee, 3/8 in. od, push
110 502570
111 114373
112 128055
113 128054
114 256459*
115 256460*
FITTING, tee, 1/2 in. npt
FITTING, nipple, 1/2 npt, sst hex
FITTING, bushing, 1/2 npt x 1/8 npt, ss
FITTING, elbow, st, 90, 1/8 npt, ss
KIT, A side valve (Red)
KIT, B side valve (Blue)
* Ensure you are using use the correct color-coded part for each side.
4
4
2
2
2
1
4
4
Quantity
2
2
4
4
4
2
105
104
103
30 3A3103F
Second Press Cable Kit, 25A106
201
202 203
Parts
204
F IG . 3: Second Press Cable
Ref Part Description
201 128197
202 127949
CABLE, cga, m12, 5 pin, fxm 8, 4 pin, m
HARNESS, splitter, m12
203 24M122 CORD, set, euro/male, din/female, rev
204 128441 CABLE, cga, m12, spin, m, 4m, pigtail
Quantity
1
1
2
1
3A3103F 31
Parts
Straight Thread Multi-pass Mixing Stack, 25A990-993
308 309
310
310
306
307
305
301
309
304
309
317
326
324
3
3
3
302
3 325
323
328
327
3 Torque items to 25-30 ft-lbs (30-40 N•m).
F IG . 4. Straight Thread Multi-pass Stack
32 3A3103F
Ref Part Description
301
25B014*
25A918*
302 25A876
304 172479
305 25A920
306 551295
307
25B000
25B001
MANIFOLD, assy, valve, 12 jic
MANIFOLD, assy, chck vlvs, 12 jic
MIXER, assy, 5 pass, sst
TAG, warning
BRACKET, valve, stack, white
SCREW, mach, pan hd
MANIFOLD, assy, stack, 2-valve
MANIFOLD, assy, stack, 3-valve
308 117126
309 17L943
SCREW, shcs m5 x16
LABEL, identification, stack
310 61/0027/88 TUBE, 0.313 od, polyflo, nat
323 17L352 SUPPORT, screen, filter
324 040768†
325 040769†
326 040770†
327 25C478
328 17L384
SCREEN, woven wire, 1 in. dia, 80 mesh
SCREEN, woven wire, 1 in. dia, 100 mesh
SCREEN, woven wire, 1 in. dia, 200 mesh
KIT, color, injection
FITTING, filter, 8 jic
Quantity 25A990 25A992 25A993
1
1
1
1
1
2
1
3 ft
1
1
1
1
4
1
1
1
1
* Assembly 25B014 includes manifold 25A918. Mixing stack kit 25A990 uses only 25A918.
Replacement Danger and Warning labels, tags, and cards are available at no cost.
† Parts are available in rebuild kit 25A915.
Parts
3A3103F 33
Parts
Straight Thread Single-pass Mixing Stack, 25A995-998
408 409
410
410
406
405
407 401
409
3
409
404
3
3
402
427
3 Torque items to 25-30 ft-lbs (30-40 N•m).
F IG . 5: Straight Thread Single-pass Stack
426
424
34
3 425
423
428
3A3103F
Ref Part
25B014*
401
25A918*
Description
MANIFOLD, assy, valve, 12 jic
402 25C003
404 172479
405 25A920
MANIFOLD, assy, chck vlvs, 12 jic
MIXER, assy, 12 element, sst, large
TAG, warning
BRACKET, valve, stack, white
406 107530 SCREW, mach, pan, hd
407
25B000
25B001
408 117126
MANIFOLD, assy, stack, 2-valve
MANIFOLD, assy, stack, 3-valve
SCREW, shcs m5 x 16
409 17L943 LABEL, identification, stack
410 61/0027/88 TUBE, 0.313 od, polyflo, nat
423 17L352
424 040768†
425 040769†
426 040770†
427 25C478
428 17L384
SUPPORT, screen, filter
SCREEN, woven wire, 1 in. dia, 80 mesh
SCREEN, woven wire, 1 in. dia, 100 mesh
SCREEN, woven wire, 1 in. dia, 200 mesh
KIT, color, injection
FITTING, filter, 8 jic
† Parts are available in rebuild kit 25A915.
Quantity 25A995 25A997 25A998
1
1
1
1
1
1
2
4
1
1
3 ft
1
1
1
1
1
1
* Assembly 25B014 includes manifold 25A918. Mixing stack kit 25A995 uses only 25A918.
Replacement Danger and Warning labels, tags, and cards are available at no cost.
Parts
3A3103F 35
Parts
Multi-pass Stack Mixer, 25A876
For straight thread mixing stacks.
512 (x15)
516
518
4
503 (x2)
6
506 (x10)
507 (x2)
513 (x2)
4
504 (x2)
514 (x2)
508 (x2)
5 1
F IG . 6: Straight Thread Multi-pass Mixer
515 (x2)
502 (x2)
Ref Part Description
501 17L156
502 17L157
HOUSING, mixer, 5 pass, sst, 1/2 in. bore
CAP, mixer, 5 pass, sst, 1/2 in. bore
503 C20272† PACKING, o-ring
504 120901† O-RING
505 17L339† SEAL, .375 x .25o x .25 long
506 112556 SCREW, cap, sch
507 25B010† SEAT, 8 jic
508 17L353 HOUSING, screen, filter, 8 jic
509 17L340
512 ---*
CYLINDER, water jacket, 2.5 x 4.23 lg
MIXER, cartridge
513 17L385 NUT, housing, filter
514 559013† O-RING, (-024) fluoroelastomer-75 duro
515 116197 FITTING, elbow, 5/16 od x 1/8 nptf
--- Not available for individual sale.
† Parts are available in rebuild kit 25B005.
* Available in pack of 30 (part no. 25B003) or pack of 150 (part no. 25B004).
2
2
2
2
2
1
15
Quantity
1
2
2
2
2
10
36
501
505 (x2)
509
1
4
5
Torque items to 27-39 ft-lbs (37-53 N•m).
Do not over tighten.
Apply a light coating of lubricant.
6
Apply red thread sealant to threads as needed. Wipe off any excess adhesive.
Torque to 10-12 ft-lbs (13-16 N•m).
3A3103F
Parts
Single-pass Stack Mixer, 25C003
For straight thread mixing stacks.
614
608 (x2) 4
607 (x2)
4
603 (x2)
602 (x2)
1 5
609 (x2)
4
F IG . 7: Straight Thread Single-pass Mixer
605
Ref Part Description
601 17L946
602 17L945
603 17L385
TUBE, mixer, sst, 12 element, lg
ADAPTER, flange to 1 1/8-16
NUT, housing, filter
604 129169
605 17L947
RING, retaining, od, 1.437
CYLINDER, water jacket
606 ---* CARTRIDGE, mixer
607 122237† PACKING, o-ring, 029, solvent resist
608 121370† PACKING, o-ring 022
609 559013† O-RING, (-024) fluoroelastomer-75 duro
614 116197 FITTING, elbow, 5/16 od x 1/8 nptf
Quantity
1
2
1
6
2
2
2
2
2
2
--- Not available for individual sale.
† Parts are available in rebuild kit 25B008.
* Available in pack of 24 (part no. 25B006) or pack of 120 (part no. 25B007).
601
604 (x2)
606 (x6)
1
4
5
Torque items to 25-30 ft-lbs (30-40 N•m).
Apply a light coating of lubricant to o-rings. Use sparingly.
Apply red thread sealant to threads as needed.
3A3103F 37
Parts
In-line Filter Replacement Kits
For straight thread mixing stacks.
701
702
703
704
705
706
707
708
F IG . 8: In-line Filter Replacement Kits
Ref Part Description
701 17L385 NUT, housing, filter
702 17L353 HOUSING, screen, filter, 8 jic
703 040770 SCREEN, woven wire, 1in. dia, 200 mesh
704 040769 SCREEN, woven wire, 1 in. dia,100 mesh
705 040768 SCREEN, woven wire, 1 in. dia, 80 mesh
706 17L352 SUPPORT, screen, filter
707 559013 O-RING, (-024) fluoroelastomer-75 duro
708 17L384 FITTING, filter, 8 jic
--- Not available for individual sale.
Quantity 25A909 25A985 25A915
1
1
1
1
1
1
1
1
38 3A3103F
Parts
Manifold Assembly, 25B014
For straight thread mixing stacks.
806
1 808 1
2
801
2
2
806 1
2
802 2
1 804
807
1 Torque items to 27-39 ft-lbs (37-53 N•m). Do not over tighten.
2
3
Apply red thread sealant to threads as needed.
Torque items to 25-30 ft-lbs (30-40 N•m).
4
Apply ceramic tape to tapered male threads as
F IG . 9: Straight Thread Manifold Assembly
803
3
Ref Part Description
801 25A918 MANIFOLD, assy, chck vlvs, 8 flange
802 129298 FITTING, connector, 1/4 bspt, 5/16 t
803 123129 NUT, tube, 3/4 jic
804 129134 ADAPTER, jic 8 x 1/4 npt, mxf, ss
805 113654 GAUGE, pressure, fluid, sst
806 129133 ADAPTER, jic 12 x jic 8, mxm, ss
807 24Z119 VALVE, 2-way, pneu, sst, 3k max
808 17L656 FITTING, adapter, 8 jic x 12 jic flange
Quantity
1
4
2
2
2
2
2
2
805 4
1 804
2
802
807
3A3103F 39
Parts
Manifold, 25A918
For straight thread mixing stacks.
903
1 2
2 906
906a
903b
902
1
2
Apply food grade lubricant to threads as needed and torque to 65-70 ft-lbs (88-95 N•m).
Apply food grade lubricant to threads and o-ring and torque to 30-40 in-lb (3.5-4.5 N•m).
F IG . 10: Straight Thread Manifold
Ref Part Description
901
902
17L430
25B012
MANIFOLD, sst,12 jic to 1 3/8-20
SEAT, 10 jic
903 25A913 VALVE, check,12 jic
903a 126959 BALL, ceramic, si-n
903b 121084
903c 17L415
SPRING
RETAINER, spring, check valve, 12 jic
906 25C012 PLUG, needle, injector, assy
906a 168518 PACKING, o-ring
Quantity
1
2
1
1
2
1
1
1
40
901
903c
903a
3A3103F
Parts
Manifold On/Off Valves, 24Z119
For straight thread mixing stacks
1016
1008
1009
1 1011
1010
1004
1003
4 5
1017
1005
6
1016
1007
1
2
3
Place seal into bearing with spring facing outward.
Apply food grade lubricant to the chamber on shaft. Press shaft through bearing and seal using retainer to hold seal in place.
Clean threads on shaft and tapped hole in ball holder. Apply blue thread sealant and torque to 41 in-lbs (4.6 N•m).
F IG . 11: Straight Thread Manifold On/Off Valves
1013
3
1015
1004
1006 2
1002
1001
5
4
5
6
Clean threads on coupling and tapped hole in air cylinder.
Apply blue thread sealant. Tighten until seated.
Torque to 140 in-lbs (16 N•m).
Torque to 85 in-lbs (9.5 N•m).
Ref.
Part
1001 117083
1002 129040
1003 17L407
1004 17L391
1005 121194
Description
SCREW, shcs m6 x 70
CYLINDER, air, 50 mm bore, 5 mm stroke
RETAINER, shaft, valve, shut-off ball
SPACER, air cylinder
SCREW, shcs, m5 .8 x 30, ms
1006 17L406‡ SHAFT, valve, shut-off ball
1007 17L381 PLATE, valve, mounting
1008 25C005‡ BODY, valve, shut-off w/seat
1009 17L388‡ BEARING, valve shaft
1010 127734† SEAL, double lip, pe, .187 x .437
1011 17L390 DISK, seal retainer
1013 106553† PACKING, o-ring
1015 24Z118‡ BALL, socket assy, .406 dia
1016 25B010† SEAT, 8 jic
1017 15H108 LABEL, safety, warning, pinch
Quantity
4
1
1
4
4
1
1
1
1
1
1
1
1
3
2
Replacement Danger and Warning labels, tags, and cards are available at no cost.
† Parts are available in repair kit 25B017.
‡ Parts are available in repair kit 25B015.
3A3103F 41
Parts
Stack Solenoid Blocks, 25B000 and 25B001
For straight thread mixing stacks.
1102
1108(x2)
25B001
1104(x4)
1106
1
1103
1105
1 Apply pipe sealant to all male threads as needed.
1101(x3)
1105
25B009
25B000
1101(x2)
F IG . 12: Straight Thread Solenoid Blocks
Ref Part Description
1101 060247† SOLENOID, pneumatic, 1/8 in. npt
1102 060255 PLATE, end, kit
1103 100721 PLUG, pipe
1104 129138 CONNECTOR, 1/8 npt x 5/16 tube, mxf, pltd
1105 121021 MUFFLER, 1/4 npt
1106 121018 FITTING, elbow, male, swivel, 1/4 npt
1107 070408 SEALANT, pipe, sst
1108 123371† FITTING, connector, 1/4 tub x 1/8 npt, b
† Parts are available in Solenoid Add-On Kit 25B009
25B000
Quantity
2
1
1
4
2
1
1
25B001
Quantity
3
1
1
4
2
1
1
2
42 3A3103F
Shut-off Valve, 25A987
For straight thread mixing stacks.
1
1205
2
1204
2
1
2
Torque to 27-39 ft-lbs (37-53 N•m).
Apply red sealant to tapered threads as needed.
F IG . 13: Straight Thread Shut-off Valve
Ref Part Description
1201 24Z119 VALVE, 2-way, pneu, sst, 3k max
1202 125781 FITTING, union, 8 jic x 8 jic, sst
1203 123598 ADAPTER, 8 jic x 1/4 in. npt
1204 129132 PLUG, hex, 8 jic, ss
1205 129298 CONNECTOR, 5/16 tube x r1/4, f x m, brs
Quantity
1
1
1
1
2
1203 2
1201
1202
1
Parts
3A3103F 43
Parts
Two-pass Mixer Assembly, 25B016
For straight thread mixing stacks.
2
1302 1
1303 1304
2
F IG . 14: Straight Thread Two-pass Mixer
Ref Part Description
1301 SM396-324 MIXER, 2 pass, 16 cartridges, 1/4 np
1302 SK513
1303 17L955
1304 17L385
JACKET, water, 322, 324, 2 pass
FITTING, adapter, 8 jic x 1/2 npt, m
NUT, housing, filter
Quantity
1
1
2
2
1301
1
Apply a light coating of anti-seize lubricant to all male threads as needed.
2
Apply ceramic tape to all male fluid fittings as needed. Do not use dope.
44 3A3103F
Parts
Material In-line Filter, 25A983
For straight thread mixing stacks
1402
1403
1401(x8)
1
1404
1406
1407
1
Torque to 29 ft-lbs (39 N•m).
F IG . 15: Straight thread In-line Filter
Ref Part Description
1401 121167
1402 17L792
SCREW, shcs, m8 x 40
CAP, inlet, 2.5 dia. filter
1403 FAA040512† SCREEN, filter, 2.5 od, 80 mesh, sst
1404 FAA040513† SCREEN, filter, 2.5 od, 100 mesh, sst
1405 FAA040514† SCREEN, filter, 2.5 od, 200 mesh, sst
1406 17L940
1407 109458†
SUPPORT, filter, 2.5 in. dia, 303 ss
PACKING, o-ring
1408 17L793
1409 108526†
1410 112887
CAP, outlet, 2.5 dia. filter
PACKING, o-ring, ptfe
TOOL, wrench, spanner
Not shown.
† Parts are available in repair kit 25B018.
Quantity
8
1
1
1
1
1
1
1
1
1
3A3103F
1405
1409
1408
45
Parts
Material Regulator, 25A892 and 25A899
For straight thread mixing stacks.
1511 (x6)
1516
1507
1502
1514
1522 (x4)
1506
1501
1518 (x2)
1508 (x6)
1
1519
1526
6
1529
1509
1515
4
1510
1525
1504
1517
1503
1513
1505
1512
1530 6
1528
1527
6
1
4
6
Torque to 28-30 ft-lbs (38-40 N•m). Tightening sequence should be in a star pattern.
Apply a light coating lubricant to spherical end as needed.
Apply tape to all male NPT threads as needed.
F IG . 16: Straight Thread Material Regulators
Ref Part Description
1501 C38312‡
1502 ---†
1503 ---†
O-RING, -019 fluoroelastomer a 75 duro
DIAPHRAGM, regulator, polypropylene
DIAPHRAGM, regulator, ptfe
1504 FAA040308 SPRING,COMP, 1.43 od x 2.13 lg, 7, 921
1505 FAA040309‡ BALL, 11/32 dia, tc, gr 25, 92 rc
1506 FAA040310‡ SPRING, comp, conical, sa921
1507 FAA040480 NUT, nlock, hex, 1/4-28, gr 2, zin
1508 109114 SCREW, cap, sch
1509 FAA040484 NUT, jam, hex, 5/16-24, gr 5, zink
1510 25A911 COVER, assy, regulator
1511 108788
1512 17L382
WASHER, m8
HOUSING, regulator
1513 SA920005‡ VALVE, assy, retainer, seat
1514 SA920006‡ SCREW, stem, valve, cs, chrome
1515 SA920007 SCREW, hhc, 5/16-24 x 1.88, cs, cust
1516 SA920008
1517 SA921005
CAP, retainer/guide, spring, cs
PLATE, oscillator, spring, cs, zink
1
1
1
1
1
1
6
1
1
6
25A899
With
Gauge
1
1
1
1
1
1
1
1
1
1
1
1
1
6
1
1
6
25A892
Without
Gauge
1
1
1
1
1
1
1
46 3A3103F
1518 25B010
1519 121399
1522 116197
1525 C20272†
1526 080690
1527 121907
1528 080803
1529 166866
1530
17L895
15K815
SEAT, 8 jic
PACKING, o-ring 012 f x 75
FITTING, elbow, 5/16 od x 1/8 nptf
PACKING, o-ring
GAUGE, press, 0-1k psi, 1/4 nptm, bm
FITTING, nipple, hex, 1/4 npt, sst, swv
VALVE, ball, 1/4 in. f, 2k psi, 316 ss
FITTING, elbow, street
ADAPTER, regulator, gauge
PLUG, dummy, transducer
--- Not available for individual sale.
† Parts are available in kit 25A914.
‡ Parts are available in repair kit 25B013.
4
1
1
2
1
1
1
1
1
4
1
2
1
1
Parts
3A3103F 47
Parts
Color Injector, 25C478
For straight thread mixing stacks.
1601
4
1607
1606 (other side)
1605
1608
1604 1
1603
2
4
1 Apply red sealant to threads and torque item to
27-39 ft-lbs (37-53 N•m).
Apply ceramic tape to NPT threads as needed.
Cut to 18 inches long each.
1613
2
1611
F IG . 17: Straight Thread Color Injector
Ref Part Description
1601 SN751-1A
1602 17M441
1603 25B010
INJECTOR, assy, color
ADAPTER, 1-3/8 in. x jic 8
SEAT, 8 jic
1604 17L353
1605 17L385
HOUSING, screen, filter, 8 jic
NUT, housing, filter
1606 17L943 LABEL, identification, stack
1607 61/0001/88 TUBE, 250 od, poly
1608 559013
1611 081076
O-RING, (-024) fluoroelastomer-75 duro
HOUSING, body, qd, 1/4 nptm, crplt, brs
1612 080071
1613 24E899
1614 125750
FITTING, elbow, 90, jic 6 x 1/4 npt, mf
CABLE, 5 pin, mf, 4.0, molded
CORD SET, euro/male, din/female, rev
Quantity
1
1
1
1
1
1
3
1
1
1
1
1
48
1602
1612
1614
3A3103F
NOTES:
Parts
3A3103F 49
Parts
Mini Single-pass Mixing Stack, 25C794/99
1716
1716
1705 (x2)
1
1704
2
1703 (x2) 3
1715
1
1702 (x2)
1701
1
1706 (x2)
2
2
1714
1711
1710
1713 (x4)
1716
1707 (x2)
4
2
3
4
1
Torque to 27-39 ft-lbs (37-53 N•m). Do not over-tighten.
Apply sealant to threads as needed.
Torque items to 25-30 ft-lbs (34-40 N•m).
Apply ceramic tape to all male threads as needed.
F IG . 18: Mini Single-pass Stack Mini-shots
1708
1709
1712 (x4)
50 3A3103F
Ref Part
1701
25C792
25C793
1702 17L656
1703 123129
1704 129133
1705 24Z119
1706 129134
1707 080103
1708 17S280
1709 25C797
1710 25A920
1711 25B000
1712 117029
1713 107530
1714 117126
1715 61/0027/88
1716 17L943
Description
REGULATOR, chilled, w/shut off valve
REGULATOR, chilled, w/o shut off valve
FITTING, adapter, 8 jic x 12 jic flange
NUT, tube, 3/4 jic
ADAPTER, jic (12) x jic (08), mxm, ss
VALVE, 2-way, pneu, sst, 3k max
ADAPTER, jic (08) x 1/4 pt, mxf, ss
GAUGE, 5000, psi, liquid, 2.5 in.
INSULATOR, valve
BRACKET, valve, white
BRACKET, valve, stack, white
MANIFOLD, assy, stack, 2-valve
SCREW, shcs m6 x 25
SCREW, cap, sch, hex
SCREW, shcs m5 x 16
TUBE, 0.313 od, polyflo, nat
LABEL, identification, stack
2
1
1
1
2
2
Quantity 25C794 25C799
1
1
2
2
2
4
2
1
4
4 ft
1
Parts
3A3103F 51
Parts
Mixer-Material Regulator Component, 25C792/93
1812
1844
1806
1805
1813
7
1803
1817
1804
1816
1810
1809
1815 4
1841
1825
1801
1842 1814
1802
1807
1808 1
1811
1843 1822
1844
7 8
1837
1860
1844
1847
1849
7 1851
1840 7
1858 7 8
1857
1822
8
1839
7 1819
7 1854
1856
1838
1835
1836
7 1850
1835
7 1819
7
1859
1857
1850 7
1846
1848
1851 7
1858 7
1855 7
8
1853 8
1852 7 8
1854 7
1861
1
Torque to 28-30 ft-lbs (38-40 N•m). Tightening sequence should be in a crisscrossing pattern.
4
Apply a light coating of lubricant to spherical end as needed.
6.
Apply tape to all male npt threads as needed.
7 Apply high-temperature lubricant to O.D. thread and o-rings.
8 Torque items to 65-70 ft-lbs (88-95 N•m).
F IG . 19: Mixer-Material Regulator
52 3A3103F
Parts
Ref Part Description
1825 C20272†
1835 109450
1836 15U932
1837
17S226
17S227
1838 106553
1839 15Y627
1840 256210
1841 25D114
1842 125779
1843 110475
1844 110208
1846 17L352
1847 040768‡
1848 040769‡
1849 040770‡
1850 103413
1851 559013‡
1852 17S230
1853 17L385
1854 GC2057
1855 17S228
1856 17S225
1801 C38312
1802 ---†
1803 ---†
O-RING, -019 fluoroelastomer a 75 duro
DIAPHRAGM, regulator, polypropylene
DIAPHRAGM, regulator, ptfe
1804 FAA040308 SPRING, comp, 1.43 od x 2.13 lg, 7, 921
1805 15W305 BALL, carbide, 25 cc, 50 cc
1806 FAA040310 SPRING, comp, conical, sa921
1807 FAA040480 NUT, nlock, hex, 1/4-28, gr 2, zin
1808 109114 SCREW, cap, sch
1809 FAA040484 NUT, jam, hex, 5/16-24, gr 5, zink
1810 25A911
1811 108788
1812 17S224
1813 SA920005
COVER, assy, regulator
WASHER, flat
HOUSING, regulator, w/valve, sst
VALVE, assy, retainer, seat
1814 SA920006
1815 SA920007
1816 SA920008
1817 SA921005
1819 556555
1822 116197
SCREW, stem, valve, cs, chrome
SCREW, hhc, 5/16-24 x 1.88, cs, cust
CAP, retainer/guide, spring, cs
PLATE, oscillator, spring, cs, zink
O-RING, -012 fluoroelastomer-a 75 duro
FITTING, elbow, 5/16 od x 1/8 nptf
PACKING, o-ring
PACKING, o-ring
SEAT, valve needle, high press
RETAINER, seat, valve
RETAINER, seat, no valve
PACKING, o-ring
PACKING, o-ring #2-116, ptfe
VALVE, dispense, hp
SEAT, 6 jic
FITTING, union, 06 jic x 06 jic, sst
FITTING, street, tee
PLUG, pipe, headless
SUPPORT, screen, filter
SCREEN, woven wire, 1 in. dia, 80 mesh
SCREEN, woven wire, 1 in. dia, 100 mesh
SCREEN, woven wire, 1 in. dia, 200 mesh
PACKING, o-ring
O-RING, (-024) fluoroelastomer-75 duro
ADAPTER, mixer, regualtor
NUT, housing, filter
O-RING, o-ring, fluoroelastomer, 2-013
TUBE, plastic mixer,12 x .25 dia
HOUSING, adapter, mixer
1
1
3
3
2
1
1
1
1
1
1
1
5
1
2
1
1
2
2
1
1
1
1
1
1
6
1
1
6
1
1
1
1
1
1
1
1
Quantity 25C792 25C793
1
1
1
1
1
3A3103F 53
Parts
Ref Part
1857 25B012
1858 25A913
1859 512532
1860 517269
1861 172479
Description
SEAT, 12 jic
VALVE, check, 12 jic
ELEMENT, mixer static
VALVE, drain cock
TAG, warning
--Not available for individual sale.
‡ Parts are available in rebuild kit 25A915.
Quantity 25C792
2
2
1
1
1
Replacement Danger and Warning labels, tags, and cards are available at no cost.
† Parts are available in kit 25A914.
25C793
Stack Bracket Kit, 25C998
1.5 in.
(38.1 mm)
1.13 in.
(28.7 mm)
1902
1901
NOTE: 25C792 shown for mounting purposes only.
1903 (x4)
F IG . 20: Stack Bracket Kit
Ref Part Description
1901 17S279 INSULATOR, regulator
1902 25C796 BRACKET, regulator, white
1903 120913 SCREW
Quantity
1
1
4
54 3A3103F
Parts
Stack Adapter Kit, 25D011
2005 (x2) 2007 1 2
2008
2004
2003 (x2)
2006
2002
2001 3
F IG . 21: Stack Adapter Kit
Ref Part Description
2001 080103 GAUGE, 5000, psi, liquid, 2.5 in.
2002 17T095 FITTING, adapter
2003 111457 PACKING, o-ring
2004 17T096 FITTING, adapter
2005 25B010 SEAT, 8 jic
2006 123129 NUT, tube, 3/4 jic
2007 17L656 FITTING, adapter, 8 jic x 12 jic flange
2008 17T211 FITTING, reducer, 08 jic x 12 jic, fxm, s
Quantity
2
2
2
2
2
2
2
2
JIC Adapters (
Sold Individually
)
Part Description Image
17T211 FITTING, reducer, 08 jic x 12 jic, fxm, s
125781 FITTING, union, 08 jic x 08 jic, sst
128442 FITTING, adapter, 12 jic x 08 jic, fm, ss
2008
2004
1 Torque to 27-39 ft-lbs (37-53 N•m).
Do not over-tighten.
2 Apply sealant to threads as needed.
3 Apply ceramic tape to all male threads as needed.
3A3103F 55
Parts
Tapered Thread Mixing Stack, 24R681
2103
2118
2102
2118
2104
2110
2101
2108
2109
2119
F IG . 22: Tapered Thread Stack 24R681
Ref Part Description
2101 SA914-5A
2102 96/0105/99
2103 SK579
2104 61/0001/88
MANIFOLD, mixer, assy, gun, 1/2 npt
SCREW, shc, 1/4-20 x 1.50, ms, e
MANIFOLD, pneumatic, 3-solenoid, rh
TUBE, 1/4 in. od, poly
2108 114373
2109 SM396-324
2110 SK513
2114 172479
2118 94/1027/98
FITTING, nipple, 1/2 npt, sst hex
MIXER, 2 pass, 16 cartridges, 1/4 npt
JACKET, water, 322, 324, 2 pass
TAG, warning
ADAPTER, jic 12 x 1/2 npt, mm, ss, 3k, 316
2119 114496 FITTING, nipple, 1/2 npt x 3/4 npt, ss, 5k
2120 61/0002/88 TUBE, 3/8 in. od, poly
Quantity
1
2
1
4.7 ft
1
1
1
1
2
1
15 ft
Replacement Danger and Warning labels, tags, and cards are available at no cost.
Not shown.
2114
1. Use ceramic sealant tape on all male fluid fitting threads; do not use pipe dope.
2. Use PTFE thread seal tape and/or pipe sealant on all male air fitting threads.
56 3A3103F
Parts
Water Jacket, SK513
For tapered thread mixing stacks.
2201
2203 2201
2202 1 2
2205
2202
1 2
2204
2205
1 Apply a light coating of anti-seize lubricant to all male threads as needed.
2 Apply ceramic tape to all male threads as needed.
NOTE: 2 x ref. 1802 are located on the other end of the water jacket.
F IG . 23: Tapered Thread Water Jacket for Mixer
Ref Part Description
2201 FAA040560 SCREW, shcs, 10-32 x 3.5, sst
2202 101970 PLUG, skt hd, 1/4 npt, ss
2203 SM321003 JACKET, water, 16 cartridge
2204 SM321005 JACKET, water, 16 cartridge
2205 94/0704-1/96 FITTING, elbow, swvl, 1/4 tube x 1/4 npt
Quantity
4
4
1
1
4
3A3103F 57
Parts
Tapered Thread Mixer SM396-322
For tapered thread mixing stacks.
2304
2307
2305
2302 (inside) 2303
4
2309
2301
2
2305
2301
2
2306
2303
4
2
4
Apply a light coating of lubricant to seals.
Apply ceramic tape to all male threads as needed.
F IG . 24: Tapered Thread Mixer
Inside SK513
Ref Part
2301 555690
2302 ---*
2303 101970
Description
O-RING, -120 fluoroelastomer-a 75 duro
CARTRIDGE, mixer
PLUG, skt hd, 1/4 npt, ss
2304 SM396004 CAP, 2 pass, mixer, top, sm396-324
2305 SM321001 TUBE, element, 1.0 in. od x 16.0, sst
2306 SM396002 CAP, 2 pass, mixer, bot, sm396-322
2307 SM396003 ROD, tie, sm 396-322, 324, 3/8-16
2308 112913
2309 103975
NUT, hex
WASHER, lock, 3/8
Quantity
4
16
2
1
2
1
2
2
2
* Available in pack of 24 (part no. 25B006) or pack of 120 (part no. 25B007).
23108
58 3A3103F
Tapered Thread Mixing Stack, 25A169
2406
2404 2404
510
2407
2401
2413
2412
2402
2403
1. Use ceramic sealant tape on all male fluid fitting threads; do not use pipe dope.
2. Use PTFE thread seal tape and/or pipe sealant on all male air fitting threads.
F IG . 25: Tapered Thread Stack 25A169
Ref Part Description
2401 SA914-5A
2402 114373
2403 SM370-24
MANIFOLD, mixer, assy, gun, 1/2 npt
FITTING, nipple, 1/2 npt, sst hex
MIXER, 2 pass, 24 elements
2404 94/1027/98
2406 61/0001/88
ADAPTER, jic 12 x 1/2 npt, mm, ss, 3k, 316
TUBE, 1/4 in. od, poly
2407 SK579 MANIFOLD, pneumatic, 3-solenoid, lh
2408 61/0002/88 TUBE, 3/8 in. od, poly
2412 96/0105/99
2413 172479
SCREW, shc, 1/4-20 x 1.50, ms, e
TAG, warning
Quantity
1
2
1
2
4.7 ft
1
15 ft
2
1
Replacement Danger and Warning labels, tags, and cards are available at no cost.
Not shown.
Parts
3A3103F 59
Parts
Water Jacket and Mixer, SM370-24
For tapered thread mixing stacks.
2515
2503 2507
2509
2501
2 2502
2
Apply a light coating of lubricant to seals.
3
4
Apply sealant to threads as needed.
Apply ceramic tape to all male threads as needed.
6 Pipe plug ref 2105 must be flush to ref. 2109.
2508
3 6
2505
2501 2
2506
4 2504
2501
2
2511
F IG . 26: Tapered Thread Water Jacket and Mixer
2509
Ref Part Description
2501 115719 PACKING, o-ring, 015,v iton
2502 FAA040231 MIXER, 0.363 x 12 el, sst
2503 500171
2504 124588
2505 110208
SCREW, shcs, 1/4-20 x 1.75, ss
SCREW, cap, sh, 1/4-20 x 1.25 lg, sst
PLUG, pipe, 1/8 npt, ss
2506 104071 PLUG, pipe, 1/16 npt, ss
2507 SM370001 CAP, 2 pass,mixer, top, sm370-24
2508 SM370002 CAP, 2 pass, mixer, bot, sm370-24
2509 SM370003 HOUSING, 2 pass, mixer, sm370-24
2511 101970
2515 125412
PLUG, pipe, 1/4 npt, ss
FITTING, elbow, male, swivel
Quantity
4
2
4
2
1
4
2
1
1
2
2
2501
2 2506
4 2508
60 3A3103F
Parts
Tapered Thread Mixing Stack, SK556 and SK556-2A
2609
2602
2610 2610
2602A
2601
2604
2611
1. Use ceramic sealant tape on all male fluid fitting threads; do not use pipe dope.
2. Use PTFE thread seal tape and/or pipe sealant on all male air fitting threads.
F IG . 27: Tapered Thread Stack SK556
2603
SK556
Ref Part Description
2601 SA914-3A MANIFOLD, mixer, assy, gun, 1-1/4 - 18th
2602 SK579 MANIFOLD, pneumatic, 3-solenoid, lh
2603 SM327-WJ MIXER, water, jacket, medical
2604 SM327-12
2605 172479
MIXER, 12 element, medical
TAG, warning
2609 61/0001/88 TUBE, 1/4 in. od, poly
2610 94/1027/98 ADAPTER, jic 12 x 1/2 npt, mm, ss, 3k, 316
2611 96/0105/99 SCREW, shc, 1/4-20 x 1.50, ms, e
2618 61/0002/88 TUBE, 3/8 in. od, poly
SK556-2A
Ref Part
2602A SK579-2A
Description
MANIFOLD, pneumatic, 4-solenoid, lh
Quantity
1
1
1
1
1
4.7 ft
2
2
15 ft
Quantity
1
Replacement Danger and Warning labels, tags, and cards are available at no cost.
Not shown.
3A3103F
2605
61
Parts
Water Jacket, SM327-WJ, and Mixer, SM327-12
For tapered thread mixing stacks.
SM327-WJ
2703
2704
2702
2701
2704
2701 (inside)
SM327-12
2703
2704
2702 (inside)
F IG . 28: Tapered Thread Water Jacket and Mixer
SM327-WJ
Ref Part
2701 112781
2702 24P868
2703 040644
2704 154662
Description
ELBOW, swivel, 90 deg
KIT, housing, mixer, water, jacket
RETAINER, ring, external, ss
PACKING, o-ring
SM327-12 - Inside SM327-WJ
Ref Part Description
2701 FAA040586 MIXER, 12 element, ss
2702 040704 SCREW, hollow, lock, steel
2703 94/0370/98 PLUG, skt hd, 1/4 npt, ss
2704 SM327003 HOUSING, mixer, assy, 16 mmx 12 el
Not shown.
Quantity
2
1
1
2
Quantity
1
1
2
1
62 3A3103F
Parts
Manifold Assembly, SA914-3A/-5A
For tapered thread mixing stacks.
2805 2806
2801
2805 2801
2803
2804
2802
2807 (inside)
2808
F IG . 29: Tapered Thread Manifold Assembly
SA914-3A
Ref Part Description
2801 SG263-1A GUN, shut off, single, mat'l
2802 080103 GAUGE, 5000 psi, liquid, 2.5 in.
2803 16C633 FITTING, nipple, hex, 1/2 x 1/4, m x m, ss
2804 108417
2805 080856
2806 24P867
2807 108519
ELBOW, female, 1/4 npt, fxf, 5k, sst
VALVE, check, 25#, ss, 1/2 in. nptm
KIT, manifold, base, 3-way, assy
PACKING, o-ring
SA914-5A - Parts above and the following:
Ref Part Description
2808 SA914007 ADAPTER, sa 914, 1/2 in. nptf
Adapter for straight thread mixers:
Ref Part Description
2808A 17M397 ADAPTER, 1-3/8 in. x 1-1/4 in.
Order separately.
Quantity
2
2
2
2
2
1
1
Quantity
1
Quantity
1
3A3103F
2808A
2803
2804
2802
63
Parts
Manifold On/Off Valves, SG263-1A
For tapered thread mixing stacks.
2907
2904 (x3)
2905
2917
2911
2914
2913
2912
2902
2919
2903
2
2920
2906
1 2918 (x4)
2901
2908
2909
1
2915
1
2910
F IG . 30: Tapered Thread Manifold On/Off Valves
2921
2922
1
2
Lubricate air cylinder ID and seals with lithium grease.
Apply fluid seals with white mineral oil fluid.
Ref Part Description
2901 107204† PACKING, o-ring
2902 SG263008† SEAT, carbide, .500 ball,. 999 od
2903 01161S† SEAL, poly, 9/16 od, 5/16 id, 1/8 cs
2904 FAA041448 SCREW, set, hex, socket, 10-24
2905 SG263004 WASHER, gun, single, mat'l
2906 SG263003 CYLINDER, gun, single, mat'l
2907 123371 FITTING, connector, 1/4 tub x 1/8 npt, b
2908 SG263002 PISTON, gun, single, mat'l
2909 156641†
2910 00095B†
PACKING, o-ring
O-RING, packing, o-ring, buna
2911 SG263001 CAP, gun, single, mat'l
2912 112781 ELBOW, swivel, 90 deg
2913 112756
2914 C19277
SCREW, cap, socket hd
WASHER, lock, split, hi-collar
2915 C20145† PACKING, o-ring, buna-n
2917 SG263005† PLUNGER, gun, single, mat'l
2918 297862 SCREW, cap, flat head
2919 SG263006† BEARING, gun, single, mat'l
2920 SG263007 BODY, gun, single, mat'l
2921 SG263009 FITTING, gun, single, 1-3/16-12th dm,
2922 172479 TAG, warning
† Parts are available in repair kit 25A173.
Replacement Danger and Warning labels, tags, and cards are available at no cost.
1
1
1
1
1
1
1
1
Quantity
1
1
1
3
1
1
1
1
1
1
1
4
1
64 3A3103F
Parts
Solenoid Blocks, SK579/-2A
For tapered thread mixing stacks.
3004 1
SK579
3006
3007
3002
1 Apply pipe sealant to all male threads as needed.
3003 1
SK579-2A
3005
3009
3008 3001
3008
F IG . 31: Tapered Thread Solenoid Block
Ref Part Description
3001 060247
3002 060255
3003 100721
3004 123371
3005 080111
3006 121018
SOLENOID, pneumatic, 1/8 in., npt
PLATE, end, kit
PLUG, pipe
FITTING, connector, 1/4 tub x 1/8 npt, b
MUFFLER, 1/4 in. npt, brass
FITTING, elbow, male, swivel, 1/4 npt
3007 21604-01 PLUG, plug, tube, plastic, 1/4 in. dia.
3008
SR645006 PLATE, solenoid, base
SR645010 PLATE, mounting, 4-valve
3009 15D256 SCREW, cap, sch
SK579
Quantity
3
1
2
6
2
1
1
1
SK579-2A
Quantity
4
1
2
8
1
1
4
2
1
2
3009
3A3103F 65
Parts
Material In-line Filter, SA925-1A
For tapered thread mixing stacks.
3108
3104
3102
1
3101
3107
3103
3105
3109
3101
1
3 2
3110
3106
1
2
Apply a light coating of lubricant to seals.
Apply a light coating of anti-seize lubricant to threads.
3 Apply ceramic tape to all male threads.
F IG . 32: Tapered Thread In-line Filter SA925-1A
Ref Part Description
3101 112245 PACKING, o-ring
3102 FAA040512 SCREEN, filter, 2.5 od, 80 mesh, sst
3103 FAA040513 SCREEN, filter, 2.5 od,100 mesh, sst
3104 FAA040514 SCREEN, filter, 2.5 od, 200 mesh, sst
3105 FAA040540 NUT, hex, 5/16-18, cs, gr8, u-coat
3106 FAA040541 SCREW, hhc, 5/16-18 x 2.50, cs, gr8, u
3107 SA925001 HOUSING, outlet, 3/4 npt
3108 SA925003 HOUSING, inlet, 3/4 npt
3109 SA925006 SUPPORT, screen
3110 123111 FITTING, nipple, hex, 3/4 npt, 3k, ss
Quantity
2
1
1
1
4
4
1
1
1
1
66 3A3103F
Parts
Material In-line Filter, SA926-1A
For tapered thread mixing stacks.
3205
3
1 3201
2
3206
3203
3208
3204
3202
3209
3207
3 2
1
2
Apply a light coating of lubricant to seals.
Apply a light coating of anti-seize lubricant to threads.
3 Apply ceramic tape to all male threads.
F IG . 33: Tapered Thread In-line Filter SA926-1A
Ref Part Description
3201 103413
3202 040768†
3203 040769†
3204 040770†
3205 114238
PACKING, o-ring
SCREEN, woven wire, 1 in. dia, 80 mesh
SCREEN, woven wire, 1in. dia, 100 mesh
SCREEN, woven wire, 1 in. dia, 200 mesh
SCREW, cap, hex hd
3206 101970 PLUG, pipe, hdls
3207 SA926001 HOUSING, outlet, 1/2 in. npt
3208 SA926002 HOUSING, inlet, 1/2 in. npt
3209 SA926003 SUPPORT, screen
† Parts are available in rebuild kit 25A915.
Quantity
2
1
4
1
1
1
1
1
1
3A3103F 67
Parts
Material Regulators, SA920-G and SA921-G
For tapered thread mixing stacks.
3301
3303 3302
3304
3310
3312
3314
3315
3309
3319
3318
3307
3317
3305
3306
3326
3327
3328
3325 (x4)
F IG . 34: Tapered Thread Material Regulators
3313
Ref Part Description
3301 --
3302 --
O-RING, -019 fluoroelastomer a 75 duro
DIAPHRAGM, polypropylene, sa92x
3303 -- DIAPHRAGM, ptfe, sa92x
3304 FAA040308 SPRING, comp, 1.43 od x 2.13 lg, zinc
3305 FAA040309 BALL, 11/32 dia, tc, gr 25, 92 rc
3306 FAA040310 SPRING, comp, conical, sa921
3307 FAA040480 NUT, nlock, hex, 1/4-28, gr 2, zin
3308 --SCREW, shc, 10-32 x 0.88, ss
3309 FAA040484 NUT, jam, hex, 5/16-24, gr 5, zinc
3310 SA920001
3311 SA920002
3312
SA920003
SA921001
CHAMBER, spring, cap, sst
PLUG, spring, cap, cs
BASE, material, regulator (SA920-G)
BASE, in/out, matl, 3/4 npt (SA921-G)
3313 SA920005
3314 SA920006
3315 SA920007
3316 SA920008
3317 SA921005
3318 ---
3319 080690
3325 ---
3326 121907
3327 080803
3328 ---
VALVE, assy, retainer, seat
SCREW, stem, valve, cs, chrome
SCREW, hhc, 5/16-24 x 1.88, ss, cust
CAP, retainer/guide, spring, cs
PLATE, oscillator, spring, cs, zinc
FITTING, nipple, 1/4 mpt x .875 sst
GAUGE, press, 0-1 kpsi, 1/4 nptm, bm
FITTING, elbow, swvl, 1/4 tube x 1/4 npt
FITTING, nipple, hex, 1/4 npt, sst, swv
VALVE, ball, 1/4 in. f, 2k psi, 316 ss
FITTING, elbow, street
1
1
1
1
20
1
1
1
Quantity
1
1
1
1
1
1
1
1
1
1
1
4
1
1
1
1
3311
3316
3318
3308 (x20)
3312 Bottom View
--- Not available for individual sale.
Parts are available in kit SA920K.
68 3A3103F
Color Injector Kit, 25A108
For tapered thread mixing stacks.
3401
1 Apply pipe sealant to all male threads as needed.
1
3402
3403
3405
F IG . 35: Tapered Thread Color Injector
Ref Part Description
3401 SN751-1A INJECTOR, assy, color
3402 081076 HOUSING, body, qd, 1/4 npt m, crplt, brs
3403 080071 FITTING, elbow, 90, jic 6 x 1/4 npt, mf
3405 24E899
3406 125750
CABLE, 5 pin, male/female, 4.0 m
CORD SET, euro/male, din/female, rev
Quantity
1
1
1
1
1
3406
Parts
3A3103F 69
Parts
Color Injector Assembly, SN751-1A
3510
8 3529
3521
3530
3513 1
3507
2 3518
3532
8
3531
4 3
3545
7 6
3525
3533
3519
3503
3534
6 7
3527
3511
1
3501
5 3
3535
3524
3 5
3551
3509
1
3514
3504
3516
1
3508
3513
1
3506
3505
3515
1
3502
3517
1
3550
3512
1
3523
3526
3528
3546
3
4
1
2
Apply a light coating of lubricant to seals.
Apply a light coating of lubricant to piston.
Apply a light coating of anti-seize lubricant to threads.
Torque fasteners to 16-18 in-lbs or 2 ft-lbs (2 N•m).
F IG . 36: Injector Assembly
7
8
5
6
Torque fasteners to 95-98 in-lbs or 8 ft-lbs (11 N•m).
Apply a light coating of anti-seize lubricant to all male threads.
Apply ceramic tape to all male threads.
Apply PTFE tape to all male threads.
Ref Part Description
3501 SN750002
3502 SN751002
3503 SN751003
3504 SN751004
3505 SN751005
3506 SN751006
3507 SN751007
3508 SN751008
3509 SN751009
3510 17E105
3511 556553
3512 106555
3513 559013
3514 160516
3515 555684
INJECTOR, screw, color, injector
BLOCK, color, injector
INSERT, color, injector
PIN, color, injector
CAP, front, color, injector
SEAL, retainer, color, injector
PISTON, color, injector
CYLINDER, color, injector
CAP, rear, color, injector
ROD, push, color
O-RING, -008 fluoroelastomer-a 75 duro
PACKING, o-ring
O-RING, (-024) fluoroelastomer-75 duro
PACKING, o-ring, 214
O-RING, -018 fluoroelastomer-a 75 duro
3516 01070B
3517 01071U
SEAL, poly, 9/16 od, 5/16 id, 1/4 cs
SEAL, poly, 7/16 od, 3/16 id, 1/4 cs
3518 020080 BEARING, sleeve, 7/16 in., od x 5/16in.
3519 FAA040247 WIPER, d, style, 5/16 in. od, buna
70
1
1
1
1
1
1
1
1
1
2
Quantity
1
1
1
1
1
1
1
1
1
3A3103F
3521 17E104
3523 040652
3524 556511
3525 080006
3526 080431
3527 080268
3528 080270
3529 080503
3530 080502
3531 080143
3532 080459
3533 080504
3534 SN751001
3535 C19810
3545 102410
3546 SN751021
3550 172479
3551 7606-08
RING, lock, rotation
SCREW, bleeder, 1/4-28 x 59/64 lg
SCREW 1/4-20 x 4.50 soc hd cap
VALVE, check, 1/4 npt x 1/4 npt, sst
SPRING, 50 psi, ss
VALVE, insert, ss
POPPET, ss
COUPLING, qc, 1/8in. nptm x 1/8 in. flow
COUPLING, 1/8 in. flow x 1/4 in. od (.170 in. id)
FITTING, 1/8 in. nptm x 1/8 in. qc
HOSE, 1/8 in. x 1/4 in. od (.170 in. id)
COUPLING, qc, 1/4 in. nptf x 1/4 in. flow
BODY, valve, color, injector
SCREW, cap, socket hd
SCREW, cap socket hd, #6
CAP, nose, injector, color
TAG, warning
O-RING, o-ring, buna n, 2-011
3
1
1
1
1
1
1
4
1
1
1
1
4
1
1
1
1
1
Replacement Danger and Warning labels, tags, and cards are available at no cost.
Parts
3A3103F 71
Parts
Colorant Tank Kit, 25A104
3605
3601
1 Apply pipe sealant to all male threads as needed.
3603
1
1
3602
F IG . 37: Colorant Tank 25A104
Ref Part Description
3601 ST802
3602 16A006
3603 122991
TANK, 3-quart, feed, cs, nkl-plt
FITTING, elbow, street, sst
ADAPTER, jic 6 x 1/4, mm, ss, 6k, 316
3604 123112 FITTING, t, 1/4 tube, prestolock, brs
3605 61/0001/88 TUBE, 1/4 in. od, poly
3607 23210-01
3609 128457
FITTING, reducer, tube, 3/8 x 1/4 tube
SCREW, mach, hex flange, hd
3610 25A110
3611 111195
3612 801020
BRACKET, tank, 3l
SCREW, cap, flange, hd
NUT, lock, hex
Quantity
1
1
1
1
10 ft
1
2
1
1
1
3607
3604
3611
3609
3610
3612
72 3A3103F
Parts
3-quart Tank, ST802
3705
3706
3704
3707
3711
3713
3702
3703
3710
3701
3712
3712
3709
3708
3714
3717
3718
F IG . 38: 3-quart Tank
Ref Part Description
3701 00181B O-RING, buna, 254, 70 d
3702 94/0762/99 VALVE, relief, 1/4 npt, m, 115 psi, sil
3703 080003
3704 555443
REGULATOR, air, 0-100 psi, 1/4" npt
FITTING, nipple 1/4 npt x .875 sst
3705 121022
3706 113911
3707 ST802002
3708 ---
FITTING, elbow, male, 1/4 npt
GAUGE, pressure, air
TANK, lid, feed, 3-qt, (2)1/4 npt
KIT, tank, main, feed, 3-qt, 1/2 npt
3709 ST802003 PLATE, follow, 3-quart, uhmw
3710 96/0445/99 SCREW, shc, 3/8-16 x 2.00, ms, e
3711 109058
3712 104123
SCREW, cap, hex head
WASHER, lock, spring
3713 102025 NUT, full, hex, regular
3714 L0000095 LABEL, plte, warning-do not service
3717 16C633
3718 080803
FITTING, nipple, hex, 1/2 x 1/4, mxm, ss
VALVE, ball, 1/4 in. f, 2k psi, 316 ss
--- Not available for individual sale.
Quantity
1
1
1
1
1
1
1
1
1
4
1
2
2
1
1
1
Replacement Danger and Warning labels, tags, and cards are available at no cost.
3A3103F 73
Parts
Colorant Tank Kit, 25A105
3805
3807
1 Apply pipe sealant to all male threads as needed.
3804
3801
3810 (x2)
3809
1
3802
F IG . 39: Colorant Tank 25A105
3803
1
Ref Part Description
3801 ST830
3802 16A006
3803 122991
TANK, 3 gallon, feed
FITTING, elbow, street, sst
ADAPTER, jic 06 x 1/4, mm, ss, 6k, 316
3804 123112 FITTING, t, 1/4 tube, prestolock, brs
3805 61/0001/88 TUBE, 1/4 in. od, poly
3806 114182
3807 23210-01
3809 24P891
3810 121112
SCREW, mach, hex flange
FITTING, reducer, tube, 3/8 x 1/4 tube
KIT, bracket, mount, tank
SCREW, cap, socket head
3811 C19843 SCREW, cap, socket head
3812 ST830007 BLOCK, mount, tank
3813 25A114
3814 127048
BRACKET, tank, 11 l, white
SCREW, mach, hex, flange, m10 x 1.5 x 2
Quantity
1
1
1
1
10 ft
4
1
2
1
1
2
1
2
74
3813
3806
3814
3812
3811
3A3103F
Parts
3-gallon Tank, ST830
3903
3904
3905
3907
3911
3913
3906
3902
3912
3912
3910
3901
3909
3908
3914
3917
3918
F IG . 40: 3-gallon Tank
Ref Part Description
3901 00192B O-RING, 2-265
3902 94/0762/99 VALVE, relief, 1/4 npt, m, 115 psi, sil
3903 080003
3904 555443
3905 121022
REGULATOR, air, 0-100 psi, 1/4" npt
FITTING, nipple 1/4 npt x .875 sst
FITTING, elbow, male, 1/4 npt
3906 113911 GAUGE, pressure, air
3907 ST830001 TANK, lid, feed
3908 --KIT, tank, main, feed
3909 ST830005 TANK, plate, feed
3910 96/0445/99 SCREW, shc, 3/8-16 x 2.00, ms, e
3911 109058 SCREW, cap, hex head
3912 104123
3913 102025
WASHER, lock, spring
NUT, full, hex, regular
3914 L0000095 LABEL, plte, warning-do not service
3917 16C633
3918 080803
FITTING, nipple, hex, 1/2 x 1/4, mxm, ss
VALVE, ball, 1/4 in. f, 2k psi, 316 ss
--- Not available for individual sale.
Quantity
1
1
1
1
1
1
1
1
1
4
1
2
2
1
1
1
Replacement Danger and Warning labels, tags, and cards are available at no cost.
3A3103F 75
Parts
Color Flow Meter Kits, 25A103 and 25A161
1 Apply pipe sealant to all male threads as needed.
1
4002
4004
F IG . 41: Color Flow Meter
Ref Part Description
4001
---
---
METER, gear, assy, G3000HR
METER, gear, assy, G3000
4002 122991 ADAPTER, jic 6 x 1/4, mm, ss, 6k, 316
4003 122961 ADAPTER, swvl, jic 6 x 1/4 npt, fm, ss, 5
4004 17E305 CABLE, m12 x cir, 5p x 3p, mxf, 4m
--- Not available for individual sale.
Quantity
1
1
1
1
1
25A103
25A161
4001
4003
1
76 3A3103F
Continuous Level Sensor Kit, 25A100
4104 (x2)
4103 (x10)
F IG . 42: Continuous Level Sensor 25A100
Ref Part Description
4101 25A257 BRACKET, sensor, assy, white
4102 17E314 SENSOR, pot, string
4103 116475 SCREW, shcs, m 4 x 12
4104 17E317 CABLE, gca, 5p x 6p, mxf
Quantity
2
2
10
2
4101 (x2)
4102 (x2)
Parts
3A3103F 77
Parts
Continuous Level Sensor Kit, 25A101
4207
4203
4205
4202
F IG . 43: Continuous Level Sensor 25A101
Ref Part Description
4201 25A328 BRACKET, sensor, assy, 5 gal, white
4202 25A345 BRACKET, string, sensor, white
4203 17E314 SENSOR, pot, string
4204 127048 SCREW, mach, hex, flange, m 10 x 1.5 x 2
4205 116475 SCREW, shcs, m 4 x 12
4206 109209 NUT, lock, hex
4207 17E317 CABLE, gca, 5p x 6p, mxf
Quantity
2
2
2
2
10
2
2
4204
4206
4201
78 3A3103F
5-Gallon Pail Girdle, 25A160
4302
4301
4303
F IG . 44: Pail Girdle
Ref Part Description
4301 FAA040220 ROD, jig latch bolt, 3/8-16 thds
4302 FAA040518 SCREW, shc, shldr, 3/8 x 1, ss
4303 FAA040540 NUT, hex, 5/16-18, cs, gr8, u-coat
4304 ---
4305 24R368
KIT, pail, girdle, weldment
KIT, clamp, tee, handle
--- Not available for individual sale.
Quantity
3
3
3
1
3
4304
4305
Parts
3A3103F 79
Parts
Pressure Transducer Kit, 25C237
4409 4408
4404
4403
F IG . 45: Pressure Transducer
Ref Part Description
4402 121399 PACKING, o-ring, 012 f x 75
4403 16A093 SENSOR, pressure, fluid outlet
4404 124409 CABLE, m12, 5 pin, rev key, m/f, 3m
4405 16G492 ADAPTER, pressure transducer, hlf
4407 128648 PROTECTOR, wire, corrugated, 1 in.
4408 17M919 INSERT, restrictor, .078
4409 25C443 TOKEN, gca, key, lsr, small shot
4410 126975 FITTING, adapter, 1/2 nptf x 8 jicm, ss
Not shown.
Quantity
2
2
2
2
10 ft
2
1
2
4410
4402
4405
80 3A3103F
Technical Data
Technical Data
Fluid Automation F4 Series
Mixing Stacks: 25A990, 992, 993; 25A995, 997, 998; 25C792, 794, 799;
Material Regulators: 25A892, 25A899; Material Filters: 25A909, 25A983
US
Maximum Operating Pressure - all except
25A983
3000 psi
Maximum Operating Pressure - 25A983
Maximum Air Pressure
Maximum Coolant Pressure
Viscosity range
Wetted parts (fluid)
Metric
241 bar, 24.1 MPa
2610 psi
145 psi
180 bar, 18.0 MPa
10 bar, 1 MPa
100 psi
50,000 to 5,000,000 cps
7 bar, 0.7 MPa
50,000 to 5,000,000 MPa-s
303/304 SST, 17-4 H1150 SST, acetal (POM), HDPE, UHMWPE, tungsten carbide, silicon nitride, flouroelastomer
Wetted parts (coolant)
303/304 SST, nickel-plated brass, buna-n, acetal (POM), flouroelastomer, epoxy composite
Inlet/Outlet Sizes
Fluid Inlet (Mixing Stacks)
Fluid Outlet (Mixing Stacks)
Fluid Inlet/Outlet (Material Regulators)
Coolant Inlet/Outlet (Mixers)
12 JIC(m)
06 JIC(m) - 25C792, 794, 799
08 JIC(m) - all others listed above
08 JIC(f)
5/16 in tube 8 mm tube
3A3103F 81
Graco Standard Warranty
Graco warrants all equipment referenced in this document which is manufactured by Graco and bearing its name to be free from defects in material and workmanship on the date of sale to the original purchaser for use. With the exception of any special, extended, or limited warranty published by Graco, Graco will, for a period of twelve months from the date of sale, repair or replace any part of the equipment determined by
Graco to be defective. This warranty applies only when the equipment is installed, operated and maintained in accordance with Graco’s written recommendations.
This warranty does not cover, and Graco shall not be liable for general wear and tear, or any malfunction, damage or wear caused by faulty installation, misapplication, abrasion, corrosion, inadequate or improper maintenance, negligence, accident, tampering, or substitution of non-Graco component parts. Nor shall Graco be liable for malfunction, damage or wear caused by the incompatibility of Graco equipment with structures, accessories, equipment or materials not supplied by Graco, or the improper design, manufacture, installation, operation or maintenance of structures, accessories, equipment or materials not supplied by Graco.
This warranty is conditioned upon the prepaid return of the equipment claimed to be defective to an authorized Graco distributor for verification of the claimed defect. If the claimed defect is verified, Graco will repair or replace free of charge any defective parts. The equipment will be returned to the original purchaser transportation prepaid. If inspection of the equipment does not disclose any defect in material or workmanship, repairs will be made at a reasonable charge, which charges may include the costs of parts, labor, and transportation.
THIS WARRANTY IS EXCLUSIVE, AND IS IN LIEU OF ANY OTHER WARRANTIES, EXPRESS OR IMPLIED, INCLUDING BUT NOT
LIMITED TO WARRANTY OF MERCHANTABILITY OR WARRANTY OF FITNESS FOR A PARTICULAR PURPOSE .
Graco’s sole obligation and buyer’s sole remedy for any breach of warranty shall be as set forth above. The buyer agrees that no other remedy
(including, but not limited to, incidental or consequential damages for lost profits, lost sales, injury to person or property, or any other incidental or consequential loss) shall be available. Any action for breach of warranty must be brought within two (2) years of the date of sale.
GRACO MAKES NO WARRANTY, AND DISCLAIMS ALL IMPLIED WARRANTIES OF MERCHANTABILITY AND FITNESS FOR A
PARTICULAR PURPOSE, IN CONNECTION WITH ACCESSORIES, EQUIPMENT, MATERIALS OR COMPONENTS SOLD BUT NOT
MANUFACTURED BY GRACO . These items sold, but not manufactured by Graco (such as electric motors, switches, hose, etc.), are subject to the warranty, if any, of their manufacturer. Graco will provide purchaser with reasonable assistance in making any claim for breach of these warranties.
In no event will Graco be liable for indirect, incidental, special or consequential damages resulting from Graco supplying equipment hereunder, or the furnishing, performance, or use of any products or other goods sold hereto, whether due to a breach of contract, breach of warranty, the negligence of Graco, or otherwise.
FOR GRACO CANADA CUSTOMERS
The Parties acknowledge that they have required that the present document, as well as all documents, notices and legal proceedings entered into, given or instituted pursuant hereto or relating directly or indirectly hereto, be drawn up in English. Les parties reconnaissent avoir convenu que la rédaction du présente document sera en Anglais, ainsi que tous documents, avis et procédures judiciaires exécutés, donnés ou intentés, à la suite de ou en rapport, directement ou indirectement, avec les procédures concernées.
Graco Information
Sealant and Adhesive Dispensing Equipment
For the latest information about Graco products, visit www.graco.com
.
For patent information, see www.graco.com/patents .
TO PLACE AN ORDER, contact your Graco distributor, go to www.graco.com
and select
“Where to Buy” in the top blue bar, or call to find the nearest distributor.
If calling from the US: 800-746-1334
If calling from outside the US: 0-1-330-966-3000
All written and visual data contained in this document reflects the latest product information available at the time of publication.
Graco reserves the right to make changes at any time without notice.
For patent information, see www.graco.com/patents.
Original instructions.
This manual contains English. MM 3A3103
Graco Headquarters: Minneapolis
International Offices: Belgium, China, Japan, Korea
GRACO INC. AND SUBSIDIARIES • P.O. BOX 1441 • MINNEAPOLIS MN 55440-1441 • USA
Copyright 2015, Graco Inc. All Graco manufacturing locations are registered to ISO 9001.
www.graco.com
Revision F, November 2017
advertisement
Related manuals
advertisement
Table of contents
- 2 Related Manuals
- 3 Warnings
- 6 Installation
- 6 Pressure Relief Procedure
- 7 F4-55 Caster Kit, 24X218
- 7 Dual Press Kit, 25A102
- 9 Second Press Cable Kit, 25A106
- 10 Mixing Stacks Supported
- 15 Material In-line Filters
- 17 Material Regulators
- 19 Colorant Tank Kits
- 21 Color Flow Meter Kits
- 21 Color Injector Kits
- 23 Continuous Level Sensor Kits
- 25 5-Gallon Pail Girdle, 25A160
- 26 Pressure Transducer Kit, 25C237
- 29 Parts
- 29 F4-55 Caster Kit, 24X218
- 30 Dual Press Kit, 25A102
- 31 Second Press Cable Kit, 25A106
- 32 Straight Thread Multi-pass Mixing Stack, 25A990-993
- 34 Straight Thread Single-pass Mixing Stack, 25A995-998
- 36 Multi-pass Stack Mixer, 25A876
- 37 Single-pass Stack Mixer, 25C003
- 38 In-line Filter Replacement Kits
- 39 Manifold Assembly, 25B014
- 43 Shut-off Valve, 25A987
- 44 Two-pass Mixer Assembly, 25B016
- 45 Material In-line Filter, 25A983
- 46 Material Regulator, 25A892 and 25A899
- 48 Color Injector, 25C478
- 50 Mini Single-pass Mixing Stack, 25C794/99
- 52 Mixer-Material Regulator Component, 25C792/93
- 54 Stack Bracket Kit, 25C998
- 55 Stack Adapter Kit, 25D011
- 56 Tapered Thread Mixing Stack, 24R681
- 59 Tapered Thread Mixing Stack, 25A169
- 61 Tapered Thread Mixing Stack, SK556 and SK556-2A
- 63 Manifold Assembly, SA914-3A/-5A
- 66 Material In-line Filter, SA925-1A
- 67 Material In-line Filter, SA926-1A
- 68 Material Regulators, SA920-G and SA921-G
- 69 Color Injector Kit, 25A108
- 70 Color Injector Assembly, SN751-1A
- 72 Colorant Tank Kit, 25A104
- 74 Colorant Tank Kit, 25A105
- 76 Color Flow Meter Kits, 25A103 and 25A161
- 77 Continuous Level Sensor Kit, 25A100
- 78 Continuous Level Sensor Kit, 25A101
- 79 5-Gallon Pail Girdle, 25A160
- 80 Pressure Transducer Kit, 25C237
- 81 Technical Data
- 82 Graco Standard Warranty