- Computers & electronics
- Networking
- Gateways/controllers
- Danfoss
- VLT Soft Starter MCD 600
- Installation Guide
Danfoss VLT Soft Starter MCD 600 Installation Guide
Add to My manuals34 Pages
Danfoss VLT Soft Starter MCD 600 is a compact and powerful soft starter designed to provide smooth starting and stopping of electric motors, reducing mechanical stress on equipment and extending motor life. It features an intuitive user interface, built-in protection functions, and the ability to communicate via various protocols, including Modbus TCP, making it suitable for integration into industrial networks and automation systems.
advertisement
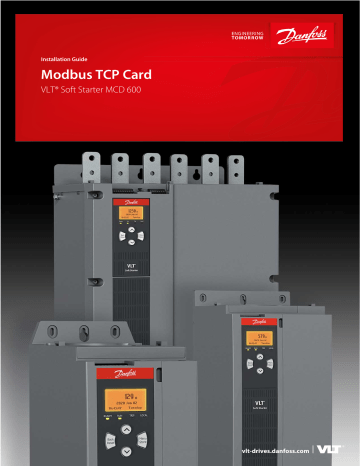
Installation Guide
Modbus TCP Card
VLT® Soft Starter MCD 600
vlt-drives.danfoss.com
Modbus TCP Card
Installation Guide
Contents
1
1.1
1.2
2
2.1
2.2
2.3
3
3.1
3.2
3.3
3.4
3.2.1
3.2.2
3.2.3
4
4.3
4.4
4.5
4.1
4.2
4.6
Parameters for Configuring Network Settings
4.5.1
4.5.2
4.5.2.1
4.5.3
4.5.4
4.5.2.2
4.5.4.1
4.5.4.2
4.6.1
Identifying the Device with Ethernet Device Configuration Tool
5
5.1
Configuration Requirements for PLC
Danfoss A/S © 2022.10
Contents
AN353424224484en-000201/130R0946 | 3
Modbus TCP Card
Installation Guide
6
6.1
Requirements for Successful Operation
6.2
6.3
6.4
Ensuring Safe and Successful Control
7
7.1
7.2
Command and Configuration Registers (Read/Write)
7.3
7.4
7.5
7.6
7.3.1
Writing Parameters to the Soft Starter
Status Reporting Registers (Read Only)
7.5.1
7.5.2
8
8.1
8.2
8.3
Connect the CT to the Ground Fault Inputs
Configure Ground Fault Protection Settings
9
9.1
9.2
9.3
9.4
10
10.1
10.2
10.3
10.4
10.5
4 | Danfoss A/S © 2022.10
Contents
AN353424224484en-000201/130R0946
Modbus TCP Card
Installation Guide Safety
1 Safety
1.1 Disclaimer
The examples and diagrams in this manual are included solely for illustrative purposes. The information contained in this manual is subject to change at any time and without prior notice. Responsibility or liability is never accepted for direct, indirect, or consequential damage resulting from the use or application of this equipment.
1.2 Warnings
W A R N I N G
-
SHOCK HAZARD
Attaching or removing accessories while the soft starter is connected to mains voltage may cause personal injury.
Before attaching or removing accessories, isolate the soft starter from mains voltage.
W A R N I N G
-
-
RISK OF PERSONAL INJURY AND EQUIPMENT DAMAGE
Inserting foreign objects or touching the inside of the soft starter while the expansion port cover is open may endanger personnel and can damage the soft starter.
Do not insert foreign objects in the soft starter with the port cover open.
Do not touch the inside of the soft starter with the port cover open.
Danfoss A/S © 2022.10
AN353424224484en-000201 / 130R0946 | 5
Modbus TCP Card
Installation Guide Introduction
2 Introduction
2.1 Product Design
The Modbus TCP Card allows the soft starter to connect to an Ethernet network and be controlled or monitored using an Ethernet communication model.
Familiarity with Ethernet protocols and networks is required to operate the device successfully. For difficulties arising from using this device with 3 rd -party products, including PLCs, scanners, and commissioning tools, contact the relevant supplier.
2.2 Compatibility
This communication expansion card is suitable for use with VLT® Soft Starter MCD 600.
The card is available in 2 versions:
•
• 175G0130: VLT® Soft Starter MCD 600 Modbus TCP Card
175G0030: VLT® Soft Starter MCD 600 Modbus TCP Card with Ground Fault Protection.
This manual is suitable for use with both versions.
This Installation Guide is intended for use with version 2.x of the VLT® Soft Starter MCD 600 Modbus TCP Card. Version 1.x of the
Modbus TCP Card does not support custom users, TCP connection, or IoT operation.
2.3 Network Connection
Table 1: Supported Protocols
Protocols
Modbus TCP
TCP
MQTT
OPC UA
Industrial Ethernet via Modbus TCP
Transmission control protocol to connect to port 4000 of a PC
Message queue telemetry transport
Open platform communications unified architecture
3
2
4
1
READY RUN TRIP LOCAL
Exit
Reset
Menu
Store
Soft Starter
2/T1
1/L1
4/T2
3/L2
6/T3
5/L3
Illustration 1: Overview of Network Connections
5
6 | Danfoss A/S © 2022.10
AN353424224484en-000201 / 130R0946
Modbus TCP Card
Installation Guide
1
2
3
Soft starter
Network switch
IoT connection (MQTT/OPC UA)
Introduction
4
5
Industrial Ethernet connection to programmable logic controller
TCP connection to VLT® Motion Control Tool MCT
10. Refer to the VLT® Motion Control Tool MCT 10
Operating Guide for connection details.
Danfoss A/S © 2022.10
AN353424224484en-000201 / 130R0946 | 7
Modbus TCP Card
Installation Guide
3 Installation
3.1 Installing the Expansion Card
1 2
Installation
Illustration 2: Installing the Expansion Card
Procedure
1.
Push a small flat-bladed screwdriver into the slot in the center of the expansion port cover and ease the cover away from the soft starter.
2.
Align the card with the expansion port. Gently push the card along the guide rails until it clicks into the soft starter.
3.2 Network Connections
3.2.1 Ethernet Ports
The device has 2 Ethernet ports. If only 1 connection is required, either port can be used.
•
•
•
•
3.2.2 Cables
When connecting to the device, make sure that the cables are of 1 of the following categories:
Category 5
Category 5e
Category 6
Category 6e
3.2.3 EMC Precautions
To minimize electromagnetic interference, Ethernet cables should be separated from motor and mains cables by 200 mm (7.9 in).
If the Ethernet cable must cross motor or mains cables, the crossing should be at an angle of 90°.
3.3 Network Establishment
The controller must establish communications directly with each device before the device can participate in the network.
•
•
3.4 Addressing
Each device in a network is addressed using a MAC address and an IP address.
The device can be assigned a static IP address during configuration or can be configured to accept a dynamic IP address (via
DHCP).
The MAC address is fixed within the device and is printed on a label on the front of the device.
8 | Danfoss A/S © 2022.10
AN353424224484en-000201 / 130R0946
Modbus TCP Card
Installation Guide Device Configuration
4 Device Configuration
4.1 Before Configuring the Device
N O T I C E
The error LED flashes whenever the device is receiving power but is not connected to a network. The error LED will flash occasionally during the configuration process.
N O T I C E
At power-up, the communication card loads the IP address stored in the soft starter.
•
•
•
4.2 Configuration Methods
Network communication parameters for the communication card can be set via the soft starter or via the on-board web server.
The card uses a static IP address by default. To enable DHCP addressing, set parameter 12–20 DHCP to Enable or change the setting via the on-board web server.
The IP address can be set via the programmable parameters of the soft starter.
The web server can configure the IP address and messaging settings for MQTT/OPC UA operation.
4.3 Parameters for Configuring Network Settings
Use parameters 12-8 to 12-21 to configure the network address. The parameters can be set via the Main Menu, via the Setup Tools, or by uploading a configuration file via USB Save & Load.
Parameter Default
12-8 Gateway Address
12-9 Gateway Address 2
12-10 Gateway Address 3
12-11 Gateway Address 4
12-12 IP Address
12-13 IP Address 2
12-14 IP Address 3
12-15 IP Address 4
12-16 Subnet Mask
12-17 Subnet Mask 2
12-18 Subnet Mask 3
12-19 Subnet Mask 4
12-20 DHCP
12-21 Location ID
168
0
2
255
255
255
0
Disable
192
168
0
100
192
0
Danfoss A/S © 2022.10
AN353424224484en-000201 / 130R0946 | 9
Modbus TCP Card
Installation Guide Device Configuration
4.4 Enabling Network Control
N O T I C E
If the reset input is active, the soft starter does not operate. If a reset switch is not required, use parameter 7-9 to set the reset input to normally open or fit a link across terminals RESET, COM+ on the soft starter.
Procedure
1.
Set parameter 1-1 Command Source to Network for the soft starter to accept commands from the Modbus TCP Card.
4.5 On-board Web Server
4.5.1 Connect to the Device
To configure settings using the on-board web server, the Modbus TCP Card must be installed in a soft starter, control power must be available, and the card and computer must both be connected to the Ethernet network.
The computer must use a fixed IP address (not DHCP) and the same subnet mask as the card. The default IP address for the card is
192.168.0.2. The default subnet mask is 255.255.255.0.
Once connected, the web server reports basic information about the card and the soft starter.
10 | Danfoss A/S © 2022.10
AN353424224484en-000201 / 130R0946
Modbus TCP Card
Installation Guide
Modbus TCP
Modbus TCP
MCD 600
Device Configuration
4.5.2 Manage Users and Passwords
N O T I C E
-
-
For security reasons, define a custom administrator ID and password. The default username and password are:
Username: danfoss_admin
Password: danfoss_admin
N O T I C E
Version 1.x of the Modbus TCP Card does not support custom users.
•
•
•
The Modbus TCP Card supports multiple users and levels of privilege.
Users can view the home screen and IP settings.
Supervisors can view the home screen and IP settings, and they can change configuration settings.
Administrators can view the home screen, change configuration settings, and add or delete users.
Danfoss A/S © 2022.10
AN353424224484en-000201 / 130R0946 | 11
Modbus TCP Card
Installation Guide
4.5.2.1 Adding a User
1
2
3
4
Procedure
1.
Connect to the web server and click Administration.
2.
3.
Click Create new user .
Enter the new username and password.
4.
5.
6.
Click Create an account
Save changes .
.
Set privileges (user, supervisor, administrator) as appropriate.
Click
4.5.2.2 Deleting a User
Procedure
1.
Connect to the web server and click Administration .
2.
3.
Select the required entry in the user list and click Delete .
Click Delete again to confirm the action.
5
6
Device Configuration
12 | Danfoss A/S © 2022.10
AN353424224484en-000201 / 130R0946
Modbus TCP Card
Installation Guide Device Configuration
4.5.3 Configuring the IP Address
N O T I C E
For version 1.x of the Modbus TCP Card, changes made via the web server are not stored in the soft starter and will be lost when control power is cycled.
1
2
3
Procedure
1.
2.
Connect to the web server and click IP Setting .
Edit settings as required. To enable DHCP addressing, tick the DHCP checkbox.
3.
Click Submit to send the new settings to the device.
4.5.4 Configure IoT Settings
The Modbus TCP Card supports soft starter status monitoring via IoT. The card cannot control or program the soft starter.
N O T I C E
Version 1.x of the Modbus TCP Card does not support IoT operation.
Danfoss A/S © 2022.10
AN353424224484en-000201 / 130R0946 | 13
Modbus TCP Card
Installation Guide
4.5.4.1 Configuring MQTT Settings
Device Configuration
Procedure
1.
Connect to the web server and click Configuration .
2.
3.
Select MQTT Client
Tick the Enable
.
checkbox to enable MQTT client operation.
4.
5.
6.
The MQTT client is enabled by default.
Click Connection and configure the settings as required.
Click Connections ⇒ Actions to select which information the card should publish.
Click Submit to save all settings in the card.
14 | Danfoss A/S © 2022.10
AN353424224484en-000201 / 130R0946
Modbus TCP Card
Installation Guide
4.5.4.2 Configuring OPC UA Settings
Device Configuration
Procedure
1.
Connect to the web server and click Configuration .
2.
3.
Select OPC UA Server
Tick the Enable
.
checkbox to enable OPC UA client operation.
4.
5.
6.
The OPC UA client is enabled by default.
Click Server Configuration and configure the settings as required.
Select Actions to select the actions for different object instances.
Click Submit to save all settings in the card.
4.6 Scanning the Network
If there is no connection to the web server and the soft starter cannot be accessed physically, use the Ethernet Device Configuration
Tool to scan the network and identify the device. Changes made via the Ethernet Device Configuration Tool cannot be stored permanently in the device and will be lost when the control power is cycled.
Download the Ethernet Device Configuration Tool from www.danfoss.com
under the sections Service and Support/Downloads .
N O T I C E
If the PC has a firewall enabled, add the tool to the list of authorized programs.
Danfoss A/S © 2022.10
AN353424224484en-000201 / 130R0946 | 15
Modbus TCP Card
Installation Guide
4.6.1 Identifying the Device with Ethernet Device Configuration Tool
Procedure
1.
2.
Start the Ethernet Device Configuration Tool.
Click Search Devices .
Device Configuration
3.
The software searches for connected devices.
Use the IP address to connect to the device via the web server.
16 | Danfoss A/S © 2022.10
AN353424224484en-000201 / 130R0946
Modbus TCP Card
Installation Guide
5 PLC Configuration
5.1 Configuration Requirements for PLC
The PLC must be configured to map registers within the communication card to addresses within the PLC.
The device must be configured directly in the PLC. No extra files are required.
PLC Configuration
Danfoss A/S © 2022.10
AN353424224484en-000201 / 130R0946 | 17
Modbus TCP Card
Installation Guide Operation
6 Operation
6.1 Requirements for Successful Operation
The Modbus TCP Card must be controlled by a Modbus client (such as a PLC), which complies with the Modbus Protocol Specification. For successful operation, the client must also support all functions and interfaces described in this manual.
N O T I C E
The available features and parameter details may vary according to the model and software version of the soft starter. Refer to the VLT® Soft Starter MCD 600 Operating Guide for details of parameters and supported features.
6.2 Device Classification
The Modbus TCP Card is a Modbus server and must be managed by a Modbus client over Ethernet.
6.3 Ensuring Safe and Successful Control
Data written to the device remains in its registers until the data is overwritten or the device is reinitialized. If the soft starter is controlled via parameter 7-1 Command Override or is disabled via the reset input (terminals RESET, COM+), fieldbus commands should be cleared from the registers. If a command is not cleared, it is re-sent to the soft starter once fieldbus control resumes.
6.4 Feedback LEDs
Port 1 Port 2
TX/RX2 TX/RX1 STATUS
LINK 2 LINK 1 ERROR
Keypad
Table 2: LED Descriptions
LED name
Error
Status
Link x
TX/RX x
LED state
Off
Flashing
On
Off
Slow flash
Fast flash
Off
On
Flashing
Off
Description
No error.
System error.
Communication error.
The device is not powered up.
The device is ready but not configured.
Communication has been established.
No network connection.
Connected to a network.
Transmitting or receiving data.
No network connection.
18 | Danfoss A/S © 2022.10
AN353424224484en-000201 / 130R0946
Modbus TCP Card
Installation Guide Modbus Registers
7 Modbus Registers
7.1 Important Information
N O T I C E
The available features and parameter details may vary according to the model and software version of the soft starter. Refer to the VLT® Soft Starter MCD 600 Operating Guide for details of parameters and supported features.
N O T I C E
All references to registers mean the registers within the communication card unless otherwise stated.
7.2 Command and Configuration Registers (Read/Write)
Table 3: Details of Command and Configuration Registers
Register Description Bits Details
40001 Command (single write) 0–7 To send a command to the soft starter, write the required value:
00000000 = Stop
00000001 = Start
00000010 = Reset
00000100 = Quick stop (coast to stop)
00001000 = Forced communication trip
00010000 = Start using Parameter Set 1
00100000 = Start using Parameter Set 2
01000000 = Reserved
10000000 = Reserved
8–14 Reserved
15 Must = 1
40002
40003
40004
40005
Reserved
Reserved
Reserved
Reserved
40006
40007
Reserved
Reserved
40008 Reserved
40009–40xxx Parameter management (single/multiple read or multiple write)
0–15 Manage soft starter programmable parameters.
7.3 Parameter Management
Parameters can be read from and written to the soft starter. When writing parameters to the soft starter, every parameter is updated to match the values in the PLC.
N O T I C E
While parameters are being written, the soft starter cannot start/stop the motor.
Danfoss A/S © 2022.10
AN353424224484en-000201 / 130R0946 | 19
Modbus TCP Card
Installation Guide Modbus Registers
The Modbus TCP protocol limits read/write operations to a maximum of 123 registers at one time. The registers must be consecutive.
To avoid loss of communications due to an unintentional change of network configuration, write the network address parameter settings before writing start/stop parameter settings.
7.3.1 Writing Parameters to the Soft Starter
N O T I C E
For reliable operation, the parameter block containing network configuration settings must be written first.
Procedure
1.
Configure all soft starter parameter values in the PLC as required, including IP address, gateway address, subnet mask, and
DHCP configuration.
2.
3.
Write the parameter block that includes the network parameter settings from the PLC to the soft starter.
Write the other parameter blocks from the PLC to the soft starter until all parameter values have been written.
7.4 Status Reporting Registers (Read Only)
N O T I C E
For models MCD6-0063B and smaller (soft starter model ID 1~4), the current reported via communications registers is 10 times greater than the actual value.
Table 4: Description of Read Registers
Register Description
30003
30004
30005
30006
30007
30008
30600
Reserved
Reserved
Reserved
Reserved
Reserved
Reserved
Product information
Bits Details
30601 Model number
0–5
6–8
Binary protocol version
Parameter list major version
9–15 Product type code: 15 = MCD 600
0–7 Reserved
8–15 Soft starter model ID
30602
30603
30604
Reserved
Reserved
Starter state 0–4
0 = Reserved
1 = Ready
2 = Starting
3 = Running
4 = Stopping
5 = Not ready (restart delay, restart temperature check, run simulation, reset input is open)
20 | Danfoss A/S © 2022.10
AN353424224484en-000201 / 130R0946
Modbus TCP Card
Installation Guide
Register Description
30605
30606
30607
30608
Current
Current
Motor temperature
Power
30609
30610
% Power factor
Voltage
30611
30612
Current
Current
30613 Current
Danfoss A/S © 2022.10
Modbus Registers
5
6
Bits Details
6 = Tripped
7 = Programming mode
8 = Jog forward
9 = Jog reverse
1 = Warning
0 = Uninitialized
1 = Initialized
8
9
7 Command source
0 = Remote LCP, Digital Input, Clock
1 = Network
Reserved
0 = Negative phase sequence
1 = Positive phase sequence
10–15 Reserved
0–13 Average rms current across all 3 phases
14–15 Reserved
0–9 Current (% motor FLC)
10–15 Reserved
0–7 Motor thermal model (%)
8–15 Reserved
0–11 Power
12–13 Power scale
0 = Multiply power by 10 to get W
1 = Multiply power by 100 to get W
2 = Power (kW)
3 = Multiply power by 10 to get kW
14–15 Reserved
0–7 100% = power factor of 1
8–15 Reserved
0–13 Average rms voltage across all 3 phases
14–15 Reserved
0–13 Phase 1 current (rms)
14–15 Reserved
0–13 Phase 2 current (rms)
14–15 Reserved
0–13 Phase 3 current (rms)
AN353424224484en-000201 / 130R0946 | 21
Modbus TCP Card
Installation Guide Modbus Registers
Register
30614
30615
30616
30617
30618
30619
Description
Voltage
Bits Details
14–15 Reserved
0–13 Phase 1 voltage
Voltage
14–15 Reserved
0–13 Phase 2 voltage
14–15 Reserved
0–13 Phase 3 voltage Voltage
14–15 Reserved
Parameter list version number 0–7 Parameter list minor revision
Digital input state
8–15 Parameter list major version
0–15
For all inputs, 0 = open, 1 = closed (shorted)
0 = Start/Stop
1 = Reserved
2 = Reset
3 = Input A
4 = Input B
5–15 = Reserved
Trip code 0–15 See the chapter Trip Codes.
8–15 Reserved
30620–30631 Reserved
N O T I C E
The reset input is normally closed by default. If parameter 7-9 Reset/Enable Logic is set to normally open, the reported state is inverted (0 = closed, 1 = open).
7.5 Legacy Mode
The Modbus TCP Card can also operate in Legacy Mode, which uses the same registers as the clip-on Modbus RTU Module supplied by Danfoss for use with older soft starters. Some registers differ from those specified in the Modbus protocol specification.
•
•
7.5.1 Initializing Legacy Mode
If the card has been operating in Standard Mode, it must be reset before communicating in Legacy Mode. To initialize the card for
Legacy Mode, either: cycle control power, or reset register 40001 to 0 (write 0 to bits 0–15).
7.5.2 Registers
N O T I C E
For models MCD6-0063B and smaller, the current and frequency reported via communications registers are 10 times greater than the actual value.
22 | Danfoss A/S © 2022.10
AN353424224484en-000201 / 130R0946
Modbus TCP Card
Installation Guide Modbus Registers
Table 5: Description of Registers in Legacy Mode
Register Description
40001
40002
Reserved
Command (single write)
Bits Details
40003 Soft starter state
0–2
To send a command to the starter, write the required value:
1 = Start
2 = Stop
3 = Reset
4 = Quick stop (coast to stop)
5 = Forced communication trip
6 = Start using Parameter Set 1
7 = Start using Parameter Set 2
3–15 Reserved
0–3 1 = Ready
2 = Starting
3 = Running
4 = Stopping (including braking)
5 = Restart delay (including temperature check)
6 = Tripped
7 = Programming mode
8 = Jog forward
9 = Jog reverse
4
5
6
1 = Positive phase sequence (only valid if bit 6 = 1)
1 = Current exceeds FLC
0 = Uninitialized
1 = Initialized
7–15 Reserved
40004
40005
40006
Reserved
Motor current
Motor temperature
0–7 Average 3-phase motor current (A)
8–15 Reserved
0–7 Motor thermal model (%)
8–15 Reserved
40007
40008
Reserved
Reserved
40009–40xxx Parameter management (single or multiple read/ write)
40600 Version
0–7
8–15 Reserved
0–5 Binary protocol version
6–8
9–15
Manage soft starter programmable parameters. See the VLT® Soft
Starter MCD 600 Operating Guide for a complete parameter list.
Parameter list version number
Product type code:
Danfoss A/S © 2022.10
AN353424224484en-000201 / 130R0946 | 23
Modbus TCP Card
Installation Guide
Register Description
40601 Model number
40602
40603
40604
Reserved
Reserved
Starter state
40605
40606
40607
40608
Current
Current
Motor temperature
Power
24 | Danfoss A/S © 2022.10
Modbus Registers
Bits Details
15 = MCD 600
0–7 Reserved
8–15 Soft starter model ID
0–4 0 = Reserved
1 = Ready
2 = Starting
3 = Running
4 = Stopping
5 = Not ready (restart delay, restart temperature check, run simulation, reset input is open)
6 = Tripped
7 = Programming mode
8 = Jog forward
9 = Jog reverse
1 = Warning 5
6
0 = Uninitialized
1 = Initialized
8
9
7
Command source
0 = Remote LCP, Digital Input, Clock
1 = Network
Reserved
0 = Negative phase sequence
1 = Positive phase sequence
10–15 Reserved
0–13 Average rms current across all 3 phases
14–15 Reserved
0–9 Current (% motor FLC)
10–15 Reserved
0–7 Motor thermal model (%)
8–15 Reserved
0–11 Power
12–13 Power scale
0 = Multiply power by 10 to get W
1 = Multiply power by 100 to get W
2 = Power (kW)
3 = Multiply power by 10 to get kW
AN353424224484en-000201 / 130R0946
Modbus TCP Card
Installation Guide Modbus Registers
Register
40609
40610
40611
40612
40613
40614
40615
40616
40617
40618
40619
Description
% Power factor
Voltage
Current
Current
Bits Details
14–15 Reserved
0–7 100% = power factor of 1
8–15 Reserved
0–13 Average rms voltage across all 3 phases
14–15 Reserved
0–13 Phase 1 current (rms)
14–15 Reserved
0–13 Phase 2 current (rms)
14–15 Reserved
0–13 Phase 3 current (rms) Current
Voltage
Voltage
14–15 Reserved
0–13 Phase 1 voltage
14–15 Reserved
0–13 Phase 2 voltage
Voltage
14–15 Reserved
0–13 Phase 3 voltage
14–15 Reserved
Parameter list version number 0–7 Parameter list minor revision
Digital input state
8–15 Parameter list major version
0–15 For all inputs, 0 = open, 1 = closed (shorted)
0 = Start/Stop
1 = Reserved
2 = Reset
3 = Input A
4 = Input B
5–15 = Reserved
Trip code 0–7 See the chapter Trip Codes
8–15 Reserved
40620–40631 Reserved
N O T I C E
The reset input is normally closed by default. If parameter 7-9 Reset/Enable Logic is set to normally open, the reported state is inverted (0 = closed, 1 = open).
Danfoss A/S © 2022.10
AN353424224484en-000201 / 130R0946 | 25
Modbus TCP Card
Installation Guide
30
31
28
29
26
27
23
24
35
36
33
34
19
20
16
18
14
15
12
13
10
11
8
9
6
7
4
5
7.6 Trip Codes
Code Description
2
3
255
1
No trip
Excess start time
Motor overload
Motor thermistor
Current imbalance
Frequency
Phase sequence
Overcurrent
Power loss
Undercurrent
Heat sink overtemperature
Motor connection
Input A trip
FLC too high
Unsupported option (function not available in inside delta)
Communications card fault
Network communication
Overvoltage
Undervoltage
Ground fault
Parameter out of range
Input B trip
L1 phase loss
L2 phase loss
L3 phase loss
L1-T1 shorted
L2-T2 shorted
L3-T3 shorted
Time-overcurrent (bypass overload)
SCR overtemperature
Battery/clock
Thermistor circuit
26 | Danfoss A/S © 2022.10
Modbus Registers
AN353424224484en-000201 / 130R0946
Modbus TCP Card
Installation Guide
80
81
78
79
76
77
74
75
82
83
84–96
71
72
60
70
58
59
56
57
Code
47
48
Description
Overpower
Underpower
LCP disconnected
Zero speed detect
SCR Itsm
Instantaneous overcurrent
Rating capacity
Current Read Err L1
Current Read Err L2
Current Read Err L3
Motor connection T1
Motor connection T2
Motor connection T3
Firing fail P1
Firing fail P2
Firing fail P3
VZC fail P1
VZC fail P2
VZC fail P3
Low control volts
Internal fault x. Contact the local supplier with the fault code (x).
Modbus Registers
Danfoss A/S © 2022.10
AN353424224484en-000201 / 130R0946 | 27
Modbus TCP Card
Installation Guide Ground Fault Protection
8 Ground Fault Protection
8.1 Overview
N O T I C E
Ground fault protection is only available on ground fault enabled option cards with soft starters running a compatible version of software. Contact the supplier for assistance.
The Modbus TCP Card can detect ground current and trip before the equipment is damaged.
Ground fault protection requires a 1000:1 or 2000:1 current transformer (not supplied). The CT should be rated 1 VA or 5 VA. The soft starter can be configured to trip at 1–50 A. If ground fault current rises above 50 A, the soft starter trips immediately.
Parameter 40-3 Ground Fault Trip Active selects when ground fault protection is active.
8.2 Connect the CT to the Ground Fault Inputs
To use ground fault protection, a common-mode current transformer (CT) must be installed around all 3 phases.
Procedure
1.
2.
Use a 1000:1 or 2000:1 CT with a rating of 1 VA or 5 VA.
Set parameter 40-5 Ground Fault CT ratio to match the CT.
3.
Connect the CT to the ground fault terminals (G1, G2, G3).
For maximum protection, the CT should be installed on the input side of the soft starter.
8.3 Configure Ground Fault Protection Settings
Ground fault protection settings must be set in the soft starter.
Parameter Description
Parameter 40-1 Ground Fault Level
Parameter 40-2 Ground Fault Delay
Sets the trip point for ground fault protection.
Shows the response of the Modbus TCP Card to ground fault variation, avoiding trips due to momentary fluctuations.
Parameter 40-3 Ground Fault Trip Active Selects when a ground fault trip can occur.
Parameter 40-4 Ground Fault Action Selects the response of the soft starter to the protection event.
Parameter 40-5 Ground Fault CT Ratio Set to match the ratio of the ground current measuring CT.
28 | Danfoss A/S © 2022.10
AN353424224484en-000201 / 130R0946
Modbus TCP Card
Installation Guide
9 Network Design
9.1 Star Topology
In a star network, all controllers and devices connect to a central network switch.
Network Design
Illustration 3: Example of Star Topology
9.2 Line Topology
In a line network, the controller connects directly to 1 port of the 1 st card. The 2 nd Ethernet port connects to another card, which in turn connects to another device until all devices are connected.
Illustration 4: Example of Line Topology
N O T I C E
The device has an integrated switch to allow data to pass through in line topology. The device must be receiving control power from the soft starter for the switch to operate.
N O T I C E
If the connection between 2 devices is interrupted, the controller cannot communicate with devices after the interruption point.
Danfoss A/S © 2022.10
AN353424224484en-000201 / 130R0946 | 29
Modbus TCP Card
Installation Guide Network Design
N O T I C E
Each connection adds a delay to the communication with the next device. The maximum number of devices in a line network is
32. Exceeding this number may reduce the reliability of the network.
9.3 Ring Topology
In a ring topology network, the controller connects to the 1 st card via a network switch. The 2 nd Ethernet port of the card connects to another device, which in turn connects to another device until all devices are connected. The final device connects back to the switch.
The device supports beacon-based ring node configuration.
Illustration 5: Example of Ring Topology
N O T I C E
The network switch must support loss of line detection.
9.4 Combined Topologies
A single network can include both star and line components.
30 | Danfoss A/S © 2022.10
AN353424224484en-000201 / 130R0946
Modbus TCP Card
Installation Guide
Illustration 6: Example of Combined Topologies
Network Design
Danfoss A/S © 2022.10
AN353424224484en-000201 / 130R0946 | 31
Modbus TCP Card
Installation Guide
10 Specifications
10.1 Connections
Soft starter
Contacts
Network
10.2 Settings
IP address
Device name
10.3 Network
Link speed
Full duplex
Auto crossover
10.4 Power
Consumption (steady state, maximum)
Reverse polarity protected
Galvanically isolated
10.5 Certification
RCM
CE
Specifications
6-way pin assembly
Gold flash
RJ45
Automatically assigned, configurable
Automatically assigned, configurable
10 Mbps, 100 Mbps (auto-detect)
35 mA@24 V DC
IEC 60947-4-2
EN 60947-4-2
32 | Danfoss A/S © 2022.10
AN353424224484en-000201 / 130R0946
Modbus TCP Card
Installation Guide Specifications
Danfoss A/S © 2022.10
AN353424224484en-000201 / 130R0946 | 33
Danfoss A/S
Ulsnaes 1
DK-6300 Graasten vlt-drives.danfoss.com
Danfoss can accept no responsibility for possible errors in catalogs, brochures, and other printed material. Danfoss reserves the right to alter its products without notice. This also applies to products already on order provided that such alterations can be made without subsequential changes being necessary in specifications already agreed. All trademarks in this material are property of the respective companies. Danfoss and the Danfoss logotype are trademarks of Danfoss A/S. All rights reserved.
*130R0946*
Danfoss A/S © 2022.10
*M0025601* AN353424224484en-000201 / 130R0946
advertisement
Related manuals
Frequently Answers and Questions
What is the purpose of the Modbus TCP Card?
What are the network connection options for the Modbus TCP Card?
How do I configure the network settings for the Modbus TCP Card?
Can I control the soft starter using the Modbus TCP Card?
How do I access the on-board web server of the Modbus TCP Card?
How do I secure the on-board web server of the Modbus TCP Card?
What are the user privilege levels supported by the Modbus TCP Card?
advertisement