advertisement
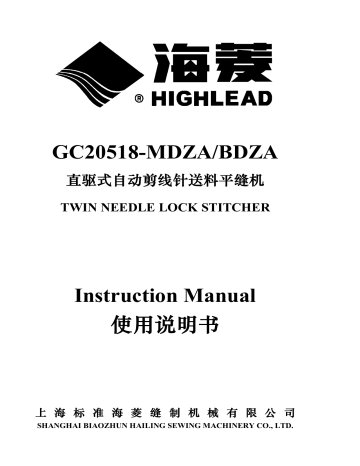
GC20518-MDZA/BDZA
直驱式自动剪线针送料平缝机
TWIN NEEDLE LOCK STITCHER
Instruction Manual
使用说明书
上 海 标 准 海 菱 缝 制 机 械 有 限 公 司
SHANGHAI BIAOZHUN HAILING SEWING MACHINERY CO., LTD.
1.PRECAUTIONS BEFORE STARTING OPERATION
1)Safety precautions:
( 1 ) When turning the power on, keep your hands and fingers away from the area around/under the needle and the area around the pulley.
( 2 ) Power must be turned off when the machine is not in use, or when the operator leaves the seat.
( 3 ) Power must be turned off when tilting the machine head, installing or removing the “V” belt, adjusting the machine, or when replacing.
( 4 ) Avoid placing fingers, hairs, bars etc., near the pulley, “V” belt, bobbin winder pulley, or motor when the machine is in operation.
( 5 ) Do not insert fingers into the thread take-up cover, under/around the needle, or pulley when the machine is in operation.
( 6 ) If a belt cover, finger guard, eye guard are installed, do not operate the machine without these safety devices.
2)Precautions before starting operation:
( 1 ) If the machine’s oil pan has an oil sump, never operate the machine before filling it.
( 2 ) If the machine is lubricated by a drop oiler, never operate the machine before lubricating.
( 3 ) When a new sewing machine is first turned on, verify the rotational direction of the pulley with the power on. (The pulley should rotate counterclockwise when viewed from the pulley)
( 4 ) Verify the voltage and (single or three) phase with those given on the machine nameplate.
3)Precautions for operating conditions:
( 1 ) Avoid using the machine at abnormally high temperatures ( 35 ℃ or higher ) or low temperatures ( 5 ℃ or lower ) .
( 2 ) Avoid using the machine in dusty conditions.
2.SPECIFICATIONS
Max.sewing speed
Application
Stitch length
Presser-foot stroke
By hand
By pneumatic
Needle size
4000r.p.m
Light weight
0-5mm
DP×5 14#
3000r.p.m
Medium weight
0-7mm
8mm
16mm
DP×5 21#
Needle gauge
— 1 —
6.4Standard
3.LUBRICATION
1) Oiling(1)
Fill the oil reservoir with oil up to oil level mark.Oil level should be periodically checked.
If oil level is found below the level replenish oil to the oil level mark.
Use white spindle oil.
2) Oiling(2)
When a new sewing machine is used for the first time,or sewing machine left out of use for considerably long time is used again,replenish a suitable amount of oil to the portions indicated by arrow in the below figure.
Adjustment of oiling to rotating hook.
3) Oiling condition
See dripping of oil through the oil sight window to check oiling condition during operation.
4.PRECAUTIONS OPERATION
(1) When the power is turned on or off,keep foot away from the pedal.
(2) It should be noted that the brake may not work when the power is interrupted or power failure occurs during sewing machine operation.
(3) Since dust in the control box might cause malfunction or control troubles,be sure to keep the control box cover close during operation.
(4) Do not apply a multimeter to the control circuit for checking,otherwise voltage of multimerter might damage semiconductor components in the circuit.
5.ADJUSTMENT OF NEEDLE
BAR STOP POSITION
When the pedal is kicked down by heel,the machine stop at“UP”position.If the marks deviate larger than 3mm,adjust as follows:
— 2 —
Release the set screw of the magnet positioned piece, adjust the position of magnet positioning piece, until the machine stops in the needle up position (the marker on the pulley and the reference line of motor cover to coincide), then tighten the screws.
6.INSTALLING NEEDLE
Note:Before installing the needle,be sure to turn off the power.
To install the needle, turn the machine pulley over toward operator(or counter-clockwise)until the needle bra moves up to its highest point,put the needle up into the needle bar(or needle clamp) as deeply as it will go,with the long groove of the needle face to face.Tighten the needle set screw securely.
7.WINDING BOBBIN THREAD
Note:When bobbin thread is wound, keep the presser foot lifted.
Thread tension : Particularly in the case of nylon or polyester thread,wind the bobbin loosely.
( 1 ) Press the bobbin onto the thread winding shaft.
( 2 ) Pass the thread for winding thread as shown in the figure, and wind the end of the thread clockwise around the bobbin several times, then wind the thread on the thread adjuster side counter-clock wise several times.
( 3 ) Press lever 1 in the direction of the arrow, and start the sewing machine.
( 4 ) The operation will automatically stop when winding is completed.
( 5 ) Adjustment of thread winding strength, adjust with the thread adjuster nut 2.
( 6 ) Adjustment of thread winding amount, adjust by loosening screw 3 and moving adjustment plate 4:
The thread winding amount will increase when moved in the direction of a.
The thread winding amount will decrease when moved in the direction of b.
8.SELECTION OF THREAD
It is recommended to use”S”twist thread in the left needle(viewed from front),and “Z”twist thread in the right needle.When discriminate use “Z”twist thread in both the needles.For bobbin thread,”S”twist thread as well as “Z”twist thread can be used.
9.THREADING
( 1 ) Pass each thread through thread guide A.
— 3 —
Note: When thin slippery thread (polyester thread) is used pass the thread through thread guide B as show in figure.
( 2 ) Thread take-up lever to the highest position, pass each thread in the order in figure.
Note: Pressing the tension releasing handlebar , the thread can be pulled out easily.
10.ADJUSTMENT OF STITCH LENGTH AND REVERSE SEWING
Rotate the stitch length adjusting dial to change the stitch length.
When press the feed reversing lever, reverse sewing will take place.Loose the lever, reverse sewing will disappear.
11.SETTING OF BOBBIN
( 1 ) Pulling out 5cm thread tail from the bobbin.
( 2 ) Hold the bobbin so that the bobbin thread is would in right direction and put it into the hook.
12.LIFTING THE BOBBIN THREAD
( 1 ) Put the hook into the bobbin case and press down the latch 1.
The thread end should be left on the bed.
— 4 —
( 2 ) While holding the thread by left hand,rorate the balance wheel one turn by right hand.
By pulling up the needle thread,as shown in the figure,the bobbin thread will be lifted.The combination of bobbin thread and needle thread should be aligned and led backward.
13.BALANCE OF THREAD TENSION
14.ADJUSTMENT OF THREAD TENSION
There is virtually no need to adjust the bobbin thread tension, except for special kind of the thread, when slight adjustment will be necessary.
Turning the adjusting screw clockwise will increase the tension of bobbin thread, otherwise, the tension of bobbin thread will decrease.
Needle thread tension should be adjusted in reference to bobbin thread tension.
To adjust needle thread tension,turn each tension adjusting nut.
Needle thread tension can be also adjusted for special fabric and thread by changing intensity and movable range of slack thread adjusting spring.
15.ADJUSTMENT OF PRESSER FOOT PRESSURE
Pressure of presser foot is to be adjusted in accordance with thickness of materials to be sewn.
— 5 —
First loosen lock nut. For heavy materials, turn the adjust bolt to increase the pressure, while for light materials, turn the adjust bolt to decrease the pressure as shown in Fig.
After the adjustment. Tighten the lock nut.
16.TIMING BETWEEN ROTATING HOOK MOTION AND NEEDLE
MOTION
( 1 ) Set the stitch length on the stitch length dial shown table.
( 2 ) When the needle is lifted A shown table, from the lowest position, as shown in Fig. The following positional relationship should be maintained: a . The lower edge of needle eye should be 1.0-1.6mm below the hook point. b . The hook point should be located the center of the needle axis. c . Gap between the hook point and the side face of needle should be 0.05mm.
Note:Positioning of hook point
( 1 ) When the needle is at DOWN position,the smaller gear should be engaged with the large gear so that the “S”screw of the latter gear on the reverse side.
( 2 ) Tighten each “S”screw,where is punched for set screw,on the hook shaft.
( 3 ) Approximate position of hook “C”screw of hook should be found close to the needle when the needle is at DOWN position.
To finely adjust timing between the needle motion and hook
Stitch length
Needle lift A
3
2.2mm
4.5
2.4mm
— 6 —
motion,loosen the set screw of large gear and move the hook saddle in lower shaft axial direction within a rang from 1mm to 2mm.
Note:Position adjustment of needle point
Adjust needle position so that gap between the lower edge of needle is
1.0-1.6mm when the needle is lifted by A mm from its lowest position.
( 1 ) Remove the face plate,loosen the set screw of needle bar bracket and vertically move the bar to adjust.
( 2 ) After the adjustment, tighten the set screw.
17.ADJUSTMENT OF FEED DOG HEIGHT
Height of feed dog and pressure of presser foot should be adjusted for individual fabric(s) with the following cautions:
( 1 ) Fabric will be damaged if the feed dog extends too high,or pressure foot is too large.
( 2 ) Even stitch length cannot be assured if the feed dog is too low or pressure foot is too small.
( 3 ) Feed dog height should be measured at the point where the needle is at the top position.
For light fabrics: Approx. 0.8mm from throat plate
For usual fabrics: Approx. 1.0mm from throat plate
For heavy fabrics:Apporx.1.2mm from throat plate
Adjustment procedure a.Lean the machine head backward. b.Turn the pulley by hand and stop when the feed dog rises to the maximum height. c.Loosen the feed bar set screw. d.Vertically move the feed bar(in the direction indicated by arrow in the figure)to adjust it to adequate height. e.After the adjustment,tighten the feed bar set screw.
The feed dog height is factory-adjusted to 1.2mm.
18.RELATIONSHIP BETWEEN
ROTATING HOOK MOTION AND
TAKE-UP LEVER MOTION
When the timing belt was removed for its replacement,for example,the relationship between relating hook motion and take-up lever motion should be adjusted as follows:
— 7 —
( 1 ) Turn the balance wheel and stop when the take-up lever is lifed to its upper dead point.
( 2 ) Lean the machine head backward and make sure the arrow(timing mark)put on the timing belt is in line with the black line on the boss of lower shaft.
( 3 ) If the timing mark is not in the line with the black,remove the timing belt and install it again to adjust.
19.RELATIONSHIP BETWEEN HOOK
MOTION AND OPENER MOTION
( 1 ) Turn the balance wheel by hand and stop when the opener holder is located most remotely from the throat plate.
( 2 ) Make sure the gap between the bobbin case holder
A and the opener is approximately 0.2mm.
( 3 ) If the gap is too large or small,loosen the opener holder set screw B and adjust position of the opener.
20.RELATIONSHIP BETWEEN NEEDLE MOTION AND FEED DOG
MOTION
( 1 ) Set feed length to “0”on the feed setting dial.
( 2 ) Lean the machine head backward.
( 3 ) Loosen the feed lifting rock shaft crank set screw
A and B.
( 4 ) Set the needle at the lowest position.
( 5 ) Adjust the distance between presser rod and vibration prevention rod to 13.5mm and temporarily tighten the feed lifting rock shaft crank set screws A and B.
( 6 ) If the connection is not at right angle,remove the back cover,loosen screw C and move the right link to adjust.
( 7 ) After the completion of adjustment,fully tighten the screw A,B,C.
Note:At the same time make certain that needle can enter the feed dog needle hole at the center of the hole.
— 8 —
21.SAFETY CLUTCH DEVICE
Safety clutch device is installed to prevent the hook and cog belt from damage in case the thread is caught into the hook when the machine is loaded abnormally during operation.
1) Function of safety clutch
( 1 ) When the safety clutch acts,the belt pulley will be unloaded,then the rotation of hook shaft will stop.The arm shaft only will rotate.Stop the operation of machine.
( 2 ) Clean the thread thoroughly which is caught into the hook.
( 3 ) Turn the pulley bushing by hand,and check whether the hook shaft rotates lightly and properly,place the clutch device as follows.
2) How to set the safety clutch
( 1 ) While pressing down the push button on the opposite side of bed by left hand,turn the balance wheel slowly by right hand away from you as shown in the figure.
( 2 ) The balance wheel will stop by the gear plate,but turn the balance wheel more firmly.
( 3 ) Release the push button.
( 4 ) As shown in the figure,the safety clutch device is set.
3) Force applied to the safety clutch
( 1 ) The force applied to the safety clutch is the smallest when the white mark of the eccentric pin faces the center of the lower shaft.The force proportionally increase as the white mark faces the outside.
( 2 ) To adjust the force slide the timing belt,loosen the set screw,and turn the eccentric pin.
After the adjustment,make sure to tighten the set screw.
22.ADJUSTMENT OF THE UPPER
FEED
If the uneven feeding occurs according to the fabric.Adjust the long hole of the horizontal feed shaft crank(right)to adjust the upper feed length.Adjust as follows:
( 1 ) Loosen the bolt.
( 2 ) Move the bolt upward to increase upper feed.
— 9 —
( 3 ) Move the special bolt downward to decrease the upper feed.The upper feed and the lower feed theoretically becomes equal at the reference line on the feed connection crank(right).
Securely tighten the bolt after adjustment.
23. ADJUSTMENT THE STITCH TOLERANCE
Screwing the pin that connects the link of back-sewing with the crank of back-sewing(down)can adjust the tolerance of between the stitches.Screwing the pin in clockwise can increase the stitch of forward sewing,otherwise,the stitch of back-sewing will be increased.
24.INSTALLATION OF MOVABLE KNIFE
1) Installation of movable knife
( 1 ) Turn the balance wheel and lower the needle bar to the lowest position.
( 2 ) Push the cam follower crank so that the cam roller enters into the thread trimmer cam groove.
( 3 ) Turn the balance wheel until the black mark point on the arm meets the white mark point on the balance wheel.Set the cam follower crank at this position with a screwdriver temporarily preventing the cam roller coming out from the cam groove.
( 4 ) Loosen the thread trimmer rocking crank clamp bolts A and B.
( 5 ) Adjust the movable knife so that the movable knife end slant portion protrudes 0-0.5mm from the fixed knife,as shown in figure and tighten the bolts A and B.
— 10 —
2) Gap between movable knife and bobbin case holder stopper
( 1 ) Turn the balance wheel by hand until needle reaches the lowest position.
( 2 ) With the needle at the lowest position,depress cam follower crank,turn the balance wheel until the movable knife reaches the extremity of its stroke.
( 3 ) Manually rotate the inner hook in the direction indicated by arrow in figure and adjust gap between the movable knife and the inner hook stopper to about 0.5mm(the screws A and B should be loosen for this adjustment).
25.ADJUSTMENT OF
THREAD TRIMMER CAM
( 1 ) Turn the balance wheel by hand until the needles reach the lowest position.
( 2 ) Maintaining the needle position,depress the cam follower crank and put the cam roller into the groove of thread trimmer cam.
( 3 ) Turning the balance wheel by hand,adjust the thread trimmer cam so that the movable knife starts moving when the green mark point on the balance wheel comes in line with the black mark point on the arm.
Note:To adjust,loosen two thread trimmer cam clamp screws
A.
26.ADJUSTMENT OF SCISSORING
PRESSURE OF MOVABLE KNIFE AND
FIXED KNIFE
( 1 ) Loosen the fixed knife bracket clamp bolt A.
( 2 ) Turn the vertical position adjusting screw B to adjust meshing pressure and then righter the hexagon socket head cap screw A.
Note:Since excess pressure cause large torque to the thread trimming mechanism and trimming failure,adjust it so that thread can be trimmed with minimum pressure.
( 3 ) Move the movable knife and check that the thread can be sharply trimmed.
27.SHARPING OF FIXED KNIFE
When the knives dull,the fixed knife should be sharpened as illustrated in figure.Since it is very difficult to sharpen the movable knife,replace it with a new one when it dulls .
— 11 —
28.ADJUSTMENT FOR CHANGE OF NEEDLE GAUGE PARTS
( 1 ) Replace the throat plate, feed dog and needle clamp.(Since the throat plate and feed dog are special parts designed for thread trimming machine, be sure to use those specified by us.)
( 2 ) Lean the machine head backward.
( 3 ) Loosen two connecting link clamp bolts J.
( 4 ) Remove the spring M.
( 5 ) Loosen the hook bracket clamp screws A and B and adjust gap between each needle and hook.
( 6 ) When the needles and hooks have been adjusted, install the spring M.
( 7 ) Contact the rocking cranks C and D to the stopper pins E and F and tighten the connecting link clamp bolt J.
( 8 ) Turn the balance wheel by band until the needles reach the lowest position.
( 9 ) Loosen the nuts G and H.
( 10 ) Depress the cam follower crank K and adjust the connecting rod L so that the cam roller can smoothly enter the groove of thread trimmer cam.
( 11 ) Adjustment of the cam groove and the cam roller a.Push the cam follower crank K so that the cam roller enters into the cam groove. b.Turn the connecting rod L and adjust the clearance between the cam roller and the cam groove surface N as small as possible, and tighten the nuts G and H. c.Push the cam follower crank K again and check that the cam roller enters into the thread trimmer cam groove smoothly.
— 12 —
29.SPECIFICATIONS OF THE OPERATION PANEL
The operation panel is integrated with the motor cover.The operation panel LCD module will display the sewing mode,specifications,bartacking,foot lifting,needle stop position,thread trimmer and low-speed start. Each key on the operation panel diagram as shown. (Left : standard control operation panel Right : integrated control operation panel)
Bartacking
(ON/OFF)
Bartacking
(ON/OFF)
30.VALVE COMPLETE
This machine is designed with mini valve complete that installed integrately by several valves. The function of the valves as shown in Fig.(Left: standard control system.Right :integrated control system)
C.Feed reversing D.Presser foot lifting E.Thread tension releasing
— 13 —
上 海 标 准 海 菱 缝 制 机 械 有 限 公 司
SHANGHAI BIAOZHUN HAILING SEWING MACHINERY CO., LTD.
地址 : 上海市松江区书林路 850 号
ADD: 850, Shulin Road, Songjiang District Shanghai, P.R.China
邮编 : 201612
Zip Code: 201612
内销业务:电话
: 86-21-64061284
传真
: 86-21-64462799
零件服务:电话 : 86-21-64851424 传真 : 86-21-64069792
Overseas Business: TEL: 86-21-64853303 FAX: 86-21-64854304
ADD:RM105,Bld.5 Yuan Zhong Industry Park, No.2007 Hongmei Road,
Shanghai, P.R.China 201103
E-mail:[email protected] http://www.highlead.com.cn
制造商保留因技术改进而更改内容的权利,恕不另行通知
2017
年
12
月印制
advertisement
* Your assessment is very important for improving the workof artificial intelligence, which forms the content of this project