advertisement
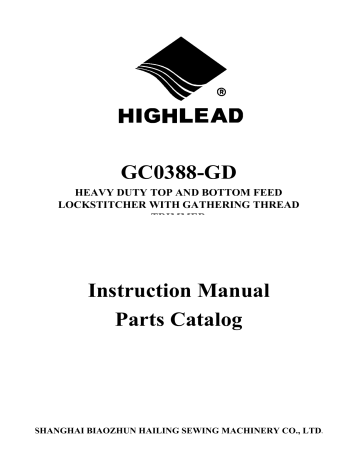
GC0388-GD
HEAVY DUTY TOP AND BOTTOM FEED
LOCKSTITCHER WITH GATHERING THREAD
TRIMMER
Instruction Manual
Parts Catalog
SHANGHAI BIAOZHUN HAILING SEWING MACHINERY CO., LTD.
CONTENTS
1. Instruction Manual
1. Safety precautions ················································································································· 1
2. Precautions before starting operation ·········································································· 1
3. Precautions for operating conditions ············································································ 1
4. Specifications ··············································································································· 1
5. Power cable connection ······························································································· 1
6. Installing the belt ·········································································································· 2
7. Adjustment of needle bar stop position ········································································ 2
8. Installing the knee lifter································································································· 3
9. Lubrication ··················································································································· 3
10. Condition of oil lubrication ·························································································· 3
11. Adjustment of the hook lubrication ·············································································· 3
12. Adjustment of oil pump ······························································································· 4
13. Periodical cleaning ····································································································· 4
14. Handling instructions ·································································································· 4
15. Installation of belt cover ····························································································· 5
16. How to wind the lower thread ····················································································· 5
17. How to attach a needle ······························································································ 5
18. How to route the upper thread···················································································· 5
19. Adjustment of stitch length and reverse sewing ························································· 6
20. Adjusting the thread tension ······················································································· 6
21. Upper thread tension ·································································································· 6
22. Lower thread tension ·································································································· 6
23. Adjustment of presser pressure·················································································· 7
24. Feed dog height ········································································································· 7
25. Adjustment of feed dog inclination ·············································································· 7
26. Adjustment of stitch length and forward/backward sewing ········································· 8
27. Presser bar lifter ········································································································· 8
28. Adjustment of walking foot and presser foot ······························································· 8
29. Adjustment of feed timing ························································································· 10
30. Adjustment of thread trimmer mechanism ································································ 10
31. Adjustment of top Differential regulation of devices ·················································· 12
32. Ruffling sewing reset ································································································ 13
33. Use of the Differential partition ················································································· 13
34. Adjustment of the presser of retral presser foot mechanism ···································· 13
35. Wearing reinforcing belt ··························································································· 14
36. Install the stand of Reinforcing belt ·········································································· 14
37. Adjustment of front back positions for presser foot··················································· 14
38. Adjustment of the air pressure of decompressing relief ············································ 15
2. Parts Catalog
A. Arm bed and its accessories ······················································································ 16
B. Sewing mechanism ···································································································· 19
C. Sewing mechanism&Feed rock lower shaft ······························································· 22
D. Stitch length mechanism ···························································································· 25
E. Upper feed rock shaft mechanism ············································································· 28
F. Upper feed lifting rock shaft mechanism····································································· 30
G. Presser foot mechanism ···························································································· 33
H. Differential mechanism ······························································································ 35
I . Knife actuating mechanism ························································································ 37
J. Touch back & Detector mechanism ············································································ 40
K. Oil lubrication mechanism ·························································································· 42
L. Accessories ················································································································ 44
1
、
Safety precautions
:
1 ) When turning the power on, keep your hands and fingers away from the area around/under the needle and the area around the pulley.
2 ) Power must be turned off when the machine is not in use, or when the operator leaves the seat.
3 ) Power must be turned off when tilting the machine head, installing or removing the “V” belt, adjusting the machine, or when replacing.
4 ) Avoid placing fingers, hairs, bars etc., near the pulley, “V” belt, bobbin winder pulley, or motor when the machine is in operation.
5) Do not insert fingers into the thread take-up cover, under/around the needle, or pulley when the machine is in operation.
6) If a belt cover, finger guard, eye guard are installed, do not operate the machine without these safety devices.
2
、
Precautions before starting operation
:
1) Never operate the machine before filling the machine’s oil pan.
2) When a new sewing machine is first turned on, verify the rotational direction of the pulley with the power on.
3) Verify the voltage and phase (single or three) with those given on the machine nameplate.
3
、
Precautions for operating conditions
:
1) Avoid using the machine at abnormally high temperatures ( 35 ℃ or higher ) or low temperatures ( 5 ℃ or lower ) .
2) Avoid using the machine in dusty conditions.
4
、
Specifications:
Model
Specifications
Max. sewing speed
Stitch length
Alternating movement ruffling sewing ratio
Adjust the ratio of ruffling sewing
Thread take-up lever stroke
Needle bar stroke
Presser foot stroke
Needle
By hand
By knee
Hook
Lubrication system
Thread trimmer
GC0388-GD
2,000 rpm
0-5.0mm
( Ordinary sewing 0 — 8.0 mm )
2.0-3.0mm
( Ordinary sewing 2.0-5.0 mm )
1:1-2:1
Dial
73.0 mm
38.0 mm
DP × 17 22#
6.0 mm
16.0 mm
Fully rotating automatic lubricaton(for thread trimmer) Large
Automatic
○
5
、
Power cable connection
:
— 1 —
Each connector(plug) should be completely set in the corresponding receptacle of the control box after checking the connector shape and mating direction.
(1) When a three-phase motor is used, connect ”U” phase to the red lead, ”V” phase to the white lead,
“W” phase to the black lead. Motor rotation direction depends on the internal switch setting in the control box.
Note: The green wire must be connected to the ground terminal in order to properly ground the motor.
(2) The appropriate power fuse capacity is as follows:
Three-phase power source: 200-240V : 10A
Single-phase power source: 100-120V : 15A
6
、
Installing the belt (Fig.1):
1) Use a V-belt for sewing machine use, type M.
2) To adjust the belt tension, change the motor height by turning the tension adjust nuts so that the belt sinks about 15mm when depressed by hand at the center of the belt span. If the tension is too low, the speed may not be consistent in the low or medium range, or the needle may not stop in the proper position. If the tension is too high, the motor bearings will deteriorate more rapidly.
Fig.1 Fig.2
7
、
Adjustment of needle bar stop position(Fig2, Fig3, Fig4):
Fig.3 Fig.4
1 ) Adjustment of “UP” position
When the pedal is kicked down by heel to cut the thread, the machine stops in the “UP” position. If the marks deviate more than 3mm, adjust as follows:
( 1 ) Disconnect the plug (12 pins) from the control panel;
( 2 ) Run the machine and stop in the “UP” position;
— 2 —
( 3 ) While holding the pulley, insert the adjusting tool into the two holes marked “A”, then rotate the pulley.
2 ) Adjustment of “DOWN” position
When the pedal is returned to the neutral position, the machine stops in the “DOWN” position. If the marks deviate more than 3mm, adjust as follows:
( 1 ) Disconnect the plug (12 pins) from the control panel;
( 2 ) Run the machine and stop in the “DOWN” position;
( 3 )
3) Confirm the stop operation then the plug (12 pins) coming from the machine head into the receptacle.
8
、
Installing the knee lifter (Fig.5) :
1 ) Pull out the knee lifter shafts (on the right and left) as far as possible, and properly set them.
2 ) Install the drive arm on each shaft.
3 ) Set a link between the right and left drive arms to connect them.
4 ) Install the knee lifter lever on the left drive arm.
Fig.5 Fig.6 Fig.7
9
、
Lubrication (Fig.6):
Pour oil up to position “A” of the oil tank.
During operation, check the oil level periodically, and in cases where the oil level is below position “B”, replenish the oil supply up to position “A”.
Use white spindle oil.
10
、
Condition of oil lubrication (Fig.7):
While operating the machine, check the condition of oil lubrication through the oil check window.
11
、
Adjustment of the hook lubrication (Fig.8):
Fig.8 Fig.9
Adjustment can be done by turning screw “A”.
(1) When the screw has been fully tightened …… Maximum
— 3 —
(2) When the screw has been fully loosened …… Maximum
Note : After adjustment of this screw, the machine should be operated for at least 30 seconds, then check the oil mist from the hook.
12
、
Adjustment of oil pump ( Fig.
9):
The standard adjustment is as follows:
The adjusting plate keeps the bypass hole fully closed. To decrease splashing, open the bypass hole appropriately.
13
、
Periodical cleaning (Fig.10, Fig.11, Fig.12):
Clean the feed dog, hook and oil pump periodically.
Maintenance of motor: Remove dust from the motor filter every one or two months.
Control box: Remove dust from the connector.
Fig.10 Fig.11 Fig.12
14
、
Handling instructions (Motor and control box ):
1) Keep your feet away from the pedal when turning the power on or off.
2) Always turn the power off when leaving your seat.
3) The brakes may fail if the power is switched off or power failure occurs during operation of the sewing machine.
4) The control box cover must be kept closed during machine operation to prevent misfunction caused by the entry of dirt.
5) The control circuitry must not be checked with a multimeter to protect the semiconductor parts from voltage.
6) The power switch must be turned off before tilting the machine head or touching the needle.
7) The three-phase motor must be grounded using ground wire (GREEN). The single-phase motor must not be wired to a starburst connection.
8 ) When manipulating the switch in the control box, first turn off the power switch, then open the front cover (Fig.16). If you have to open the bottom cover, wait for 10 minutes after the power switch has been turned off, since a high voltage is applied inside the box. (This is vital to discharge the built-in capacitors).
9) Use the motor away from high noise sources such as high-frequency welders.
10) A suitable capacity is 15A for a single-phase, and 10A for three-phase motor respectively.
11) The detector uses an optical detecting element. Do not allow dirt, dust, oil etc., to attach to the detecting plate when the machine pulley has been removed for adjustment. If dirty, gently wipe it off while avoiding scratching the plate. Also, care should be taken to avoid oil soaking into the crevices in the plate.
— 4 —
15
、
Installation of belt cover:
Be sure to install the belt cover for safety.
16
、
How to wind the lower thread (Fig.13):
Strength of winding : Particularly in the case of nylon or polyester thread, wind the bobbin loosely.
Uneven winding: If the bobbin is wound unevenly, slide the thread guide toward the less wound portion of bobbin.
Winding amount: When the bobbin is wound excessively, loosen the adjusting screw. When the bobbin is wound insufficiently, tighten the adjusting screw.
Fig.13
17
、
How to attach a needle (Fig.14):
Note: Before attach the needle, be sure to turn the power switch off.
Note: If thread snapping occurs during reverse sewing with polyester, it may be avoided by fitting the needle with the long groove shifted to the front side. Normally, avoid fitting the needle with the groove facing backward.
Fig.14
18
、
How to route the upper thread (Fig.15):
Raise the thread take-up lever to its highest possible position, and route the upper thread in the order illustrated below.
— 5 —
Fig.15
19
、
Adjustment of stitch length and reverse sewing (Fig.16):
1 ) To change the stitch length, rotate the stitch length adjusting dial while pressing the “push ” lever.( the max. stitch length is 5mm while ruffling sewing , the max. stitch length is 8mm while Ordinary sewing)
2 ) Pressing the stitch length adjusting lever for reverse stitching.( Sew with automatic reverse sewing when ruffling sewing)
Fig.16
20
、
Adjusting the thread tension (Fig.17):
Fig.17
21
、
Upper thread tension (Fig.18):
1 ) The upper thread can be adjusted based on the lower thread tension.
2 ) For special fabric sewing with special thread, the desired tension can be obtained by adjusting the strength and operating range of thread take-up spring.
22
、
Lower thread tension (Fig.19):
Lower thread tension can be adjusted by rotating screw “A”.
— 6 —
Fig.18 Fig.19
23
、
Adjustment of presser pressure (Fig.20):
1 ) Pressure should be adjusted according to the material to be sewn.
2 ) Pressure on both the walking foot and the presser foot can be adjusted.
3 ) Sewing pressure should be adjusted to the minimum required strength.
Fig.20
24
、
Feed dog height (Fig.21):
1 ) Feed dog should be 1.0mm higher than the throat plate.
2 ) To adjust the dog height as follows:
(1) Loosen the screw “A”, move the feed bar upward and downward.
( 2 ) When adjustment is completed, tighten the screw “A”.
Fig.21 Fig.22
25
、
Adjustment of feed dog inclination (Fig.22):
If necessary, adjust the inclination according to the material to be sewn as follows:
1) Loosen the screw “A”.
2) Rotate the eccentric shaft clockwise or counterclockwise with screw driver.
3) Tighten the screw “A”.
— 7 —
26
、
Adjustment of stitch length and forward/backward sewing (Fig.23):
1 ) Loosen the set screws located in the bracket.
2) Rotate the stitch length adjusting pin until the desired length is reached as follows:
(1) Clockwise: Increases the stitchlength in forward sewing, and decreases the stitch length in backward sewing.
(2) Counterclockwise: Decreases the stitch length in forward sewing, and increases the stitch length in backward sewing.
Fig.23 Fig.24
27
、
Presser bar lifter (Fig.24):
Rotate the presser bar lifter in the direction of the arrow. This raises the presser foot.
28
、
Adjustment of walking foot and presser foot:
1) Adjustment of alternating movement (Fig25):
(1) The alternating movement on the walking foot and presser foot can be adjusted by using adjusting dial located on the top cover.
(2) Adjusting the locking device to the max number(5mm).Adjusting the locking device to the same number marked on the alternating movement adjusting.
(3)Face the desired number printed on the dial to the matching mark located on the top cover. The number printed on the dial represents the possible protrusion of the walking foot and presser foot from the throat plate when the alternating movements on these are evenly set.
(4) The alternating movements can be readjusted up to 2.0-5.0mm. While doing ruffling sewing, the foot interactive volume should be 2.0-3.0mm at the scope of regulation
2) To change the balance of the alternating movements between the walking foot and presser foot (Fig.26):
(1) To increase the rise of the walking foot and decrease the rise of the presser foot:
① Remove the rubber plug of top cover.
② Rotate the pulley until the presser foot is slightly raised from the throat plate.
③ Loosen screw “A” (on the right side)
— 8 —
④ The built-in spring pulls down the presser foot until it makes contact with the throat plate.
Tighten the screw “A”.
⑤ After this adjustment, the protrusion of the presser foot has been decreased by a set distance.
And the vertical motion of the walking foot has been increased by the same distance.
(2) As a contrary case (1) , to decrease the rise of the walking foot and increase the rise of presser foot as follows:
Fig.25 Fig.26
Fist, rotate the pulley until the walking foot is slightly raised from the throat plate. Next, loosen screw “A”. Finally, tighten screw “A”. This decreases the rise of the walking foot.
3) Installing the feed regulator bracket (Fig.27):
Fig.27 Fig.28
Note: If the feed regulator bracket is poorly positioned, the resultant alternating movements may be too short or long, causing defective machine operation.
(1) Set the clearance between special screw “A” located on the regulator stud and the side wall of the machine arm to 26.5mm as Fig.27.
(2) With the feed regulator stud held as explained is step (1) above, adjust the feed regulator bracket.
This adjustment should insure a clearance of 12mm between the periphery of pin “B” located on the feed regulator bracket and the top cover mounting face located on the arm. Tighten screw “C”.
4) Feed pitch adjustment of walking foot (Fig.28):
— 9 —
Momentum regulation must be put differential subscript circled up to the minimum (non-differential under feeding status), then the upper and lower feed ratio should be adjusted to 1: 1 to ensure the accuracy of devices on adjustment differential
Upper position → Feed pitch → Small Lower position → Feed pitch → Large
29
、
Adjustment of feed timing (Fig.29):
Fig.29
1) The standard position of the eccentric feed cam and eccentric feed lifting cam are illustrated to Fig.29
2) Open the top cover, properly slide the eccentric ring to adjust the position. The eccentric feed cam can also be adjusted by removing the rubber plug located on the top cover. In the latter case, however, the built-in bevel gear is concealed; care should be taken when adjusting.
30
、
Adjustment of thread trimmer mechanism:
Fig.30
1 ) The thread trimmer mechanism illustrated as Fig.30.
2 ) Relation between the fixed blade and movable knife (left) edge:
( 1 ) The standard position is illustrated as Fig.31.
( 2 ) The distance between the fixed blade and movable knife is 0.3mm.
( 3 ) The correct position of fixed blade bracket or fixed blade can be adjusted according to Fig.31.
Fig.31
— 10 —
3 ) Knife driving shaft:
(1) The standard position is illustrated as Fig.32.
(2) When assembling, the knife driving shaft must first be put through the drive arm.
(3) Cam follower crank 1 must be positioned as illustrated to the right, and secured on the recess located on the knife driving shaft.
(4) The stopper must be secured on the recess in such a way that the knife driving shaft is snug and smoothly rotates in the shaft direction.
Fig.32
4 ) Installing the thread trimmer solenoid unit (Fig.33):
Fig.33
( 1 ) Operation stroke of the thread trimmer solenoid: a. Standard operation stroke is 6.0mm.
b. This stroke can be adjusted by using nut “A”.
( 2 ) Installing the unit: a. The unit can be mounted by using screws “B” and “C”. b. Clearance of 1.0mm must be insured between the driving lever and cam follower crank 2 with stopper nut “A” made contact with solenoid. c. In such a situation, activating the solenoid should create a clearance of 0.5mm between cam follower crank 1 and 2. This situation is standard. To meet this standard, slide the solenoid mounting bracket in the direction of the arrow as illustrated, if adjustment is needed.
5 ) Installing the thread trimming cam (Fig.34):
(1) Face the 2nd timing mark “A” (GREEN) located on the pulley to the matching mark on the arm.
(2) With the thread trimmer solenoid activated, rotate the thread trimmer cam forward until the cam makes contact with the roller. Then, secure the cam.
( 3 ) With the thread trimmer solenoid deactivated, allow the cam follower crank 2 to return to its
— 11 —
original position. This should create a clearance of 0.5mm-1.0mm between the cam and roller end. This distance is standard.
Fig.34
6 ) Adjustment of knife engagement (Fig.35):
(1) Position of movable knife (left) and fixed blade:
See the Fig.35, the standard distances from the needle center are 7.5mm and 5mm from the movable knife (left) and fixed blade respectively.
(2) Adjustment of knife engagement:
Fig.35
With the solenoid activated, turn on the machine. This rotates the thread trimming cam which rotates the movable knife (left). When the movable knife (left) has moved to its farthest distance, the standard engagement of the blade is 1.5mm-2.0mm. The engagement can be adjusted by properly mounting the drive arm.
(3) Adjustment of knife engagement pressure: a. If a thread is poorly cut, particularly when it is thick, slightly increase the engaging pressure. This should solve the problem. b. The engaging pressure can be adjusted in this way: Loosen lock nut “B” and adjust it by using adjusting screw “A”.
31
、
Adjustment of top Differential regulation of devices
(
Fig. 37
、
38
)
1 ) If adjusting the differential momentum, you should first press the differential reset button
(Figure 38) ,on differential device in a state of non-shrink joints, and then press as shown in Figure 37
— 12 —
the "push" on positioning plate, at last rotate the differential Momentum conditioning standard dial
2) when the differential Momentum conditioning standard dial turn right, reducing the charge on delivery, turn left, increased charge on delivery.when Rotating conditioning standard dial to the minimum , the ratio with the volume of the cloth sending up and down is 1:1 ,when the number of marked scale in rotating dial switch to the "10" ,the ratio with the volume of the cloth sending up and down is 2:1
3) Doing flat seam for Long time, dial superscript circled of the differential momentum standard up to the minimum.
Fig. 37 Fig. 38
32
、
Ruffling sewing reset
(
Fig. 38
)
If you want make a period of ruffling sewing and a period of Ordinary sewing at a piece of suture material, the steps are:
Ruffling sewing - press the reset button - Ordinary sewing
Ordinary sewing - press the reset button - ruffling sewing ruffling sewing after restoration, remove the differential partition, the model can be used for general feed lockstitcher, the largest stitch length can arrive to 8mm, interactive capacity of pressure foot adjust between 2-5mm
33
、
Use of the Differential partition
(
Fig.39
)
During ruffling sewing, differential pressure partition below the top feed dog, the upper and lower suture material can sew separating by differential partition ; During Ordinary sewing sewing , put away the differential partition and placed it where do not affect the sewing.
34
、
Adjustment of the presser of retral presser foot mechanism (Fig.40)
Fig. 39 Fig. 40
1) release the nut, rotating the feed adjusting knob.the presser to the retral feed dog will become stronger when turning the knob clockwise,and weaker when turning counterclockwise.
— 13 —
2)adjust the presser of retral presser foot mechanism in accordance with the plasticity of suture material , sewing soft material, the presser of retral presser foot mechanism properly tune small, there is conducive to feeding;sewing rigid materials, the presser of retral presser foot mechanism properly tune big, and is conducive to the formation of folds and feed.
3) If the presser of presser foot mechanism is too much big, presser foot mechanism will rise from the feed dog, causing material damage to joints, so the above circumstances occur, the pressure not to pin too much stress.
35
、
Wearing reinforcing belt (Fig.41)
Referring to Figure 41 fot how to wear reinforcing belt, First make reinforcing belt going through spring (damping trough), then going through the zone plate with two long trough, finally put reinforcing belt into the long trough of press foot.
Fig. 41 Fig. 42
36
、
Install the stand of Reinforcing belt (Fig.42)
First put bolt in the chassis left side of face tightened, and then put the parts using tie-in of bending connecting rod installed on the machine ,the way how to adjust the resistance of Reinforcing belt is to compress on both sides of the spring.
37
、
Adjustment of front back positions for presser foot (Fig.43)
1) Adjust the stitch length to 5mm, and adjust the differential Momentum conditioning standard dial to the "10";
2) Release the bolt A, put the foot after the external pressure placed on the plane with machine needle cylindrical Pinzi position (as shown in Figure 43), tighten the screw A
— 14 —
Fig. 43 Fig. 44
38
、
Adjustment of the air pressure of decompressing relief (Fig.44)
Air pressure of decompressing relief should be raised at 0.40-0.50mpa to ensure the regulation of stability in differential momentu and the life of differential momentum swing rod.if the air pressure is too large,it is too big wallop to Feed regulator when the cylinder works.and it is easily to deform the Feed regulator. if the air pressure is too small,it will affect the stability of adjustment with differential momentum.
— 15 —
A.ARM BED MECHANISM
— 16 —
A.ARM BED MECHANISM
Fig.
No.
Part No.
Description
A01 HA300B2090 Rubber plug
A02 HA300B2110 Rubber plug
A03 HA300B2170 Screw
A04 HM22B18001 Arm side cover
A05 H6029B8001 Gasket for arm side cover
A06 HA307B0673 Rubber plug
A07 HA700F2100 Screw
A08 H6017B8001 Thread guide
A09 H6022B8001 Coil spring for upper feed lifting
A10 H6023B8001 Stopper pin for upper feed lifting
A11 H431040060 Set screw
A12 H6025B8001 Dial for upper feed lifting
A13 H6026B8001 Plate for upper feed lifting
A14 HA309B0069 Oil check window
A15 HA111G0683 Screw
A16 H6015B8001 Top cover
A17 H6016B8001 Gasket for top cover
A18 H6030B8001 Rubber plug
A19 H6031B8001 Rubber plug
A20 H6032B8001 Rubber plug
A21 H6020B8001 Upper feed lifting regulator cam
A22 HA600C2020 Thread take-up cover
A23 HA100B2110 Set screw
A24 HA300B2100 Rubber plug
A25 H005008060 Spring washer
A26 HA100B2220 Leg
A27 HA710B0671 Pre-tension adjusting nut
A28 HA710B0672 Thread tension spring
A29 HA112B0693 Thread tension disc
A30 HA710B0673 Thread tension stud
A31 HA710B0674 Thread guide
A32 HA106B0676 Screw
A33 HA600B2050 Thread guide
A34 HA300B2080 Set screw
A35 HA300B2130 Screw
A36 H2000B2040 Cloth guide plate
A37 HA307B0674 Rubber plug
A38 HA114I0674 Screw
A39 HA500C2060 Thread guide
A40 HA115B7011 O-ring
A41 HA310B0703 Thread tension regulator bushing
A42 HA806B0671 Thread take-up spring
A43 H6725B8001 Thread releasing pin
— 17 —
Pcs.
Remarks
1
3 GB/T93 6
3
1 SM11/64(40)
1
2
1 SM11/64(40)×31
1
2 SM9/64(40)×6
1
1 SM15/64(28)×6.8
2 SM11/64(40)×5.5
1
1
1
1
1 SM9/64(40)×4.5
1
1 S15
1
4 φ 8.8
1 φ 5.7
4
1
1
3 φ 11.8
1 SM11/64(40)×7
1
2
2
2 GB/T80 M4×6
2
1
1
2
1
1
8 SM11/64(40)×12
1
1
2
1
1 SM11/64(40)×5.5
A.ARM BED MECHANISM
Fig.
No.
Part No.
Description
A44 HA806B0673 Thread tension stud
A45 HA310B0705 Thread tension disc
A46 HA310B0702 Thread tension releasing disc
A47 H2206B0671 Thread tension spring
A48 HA115B7010 Thumb nut revolution stopper
A49 HA310B0701 Thumb nut
A50 HA115B0708 Screw
A51 HA607B0671 Thread guide
A52 HA124B0713 Screw
A53 HA124B0712 Plate spring for slide plate
A54 H6812B8001 Slide plate
A55 HA500B2030 Needle plate
A56 H2000B2050 Screw
A57 HA700B2030 Screw
A58 H5341B8001 Screw
A59 HM21B28001 Face plate
A60 HM20B58001 Arm
A61 H6027B8001 Plate for upper feed lifting
A62 H6409B8001 Arm bed cover
A63 H6410B8001 Gasket for arm bed cover
A64 HA300B2160 Screw
A65 HM22B27101 Screw
A66 HA106B0676 Screw
A67 HM22B08001 Strap guide
A68 H003001060 Nut
A69 HM21B38001 Washer
A70 H409060200 Screw
A71 HM21B58001 Strap guide
A72 H3410C301L Screw
A73 HM22B58001 Stopper
A74 HA115B0702 Nut
A75 HK810H8001 Spring
A76 H7342G8001 Washer
A77 HK809H8001 Screw
A78 HK806H8001 Gauge bearing bracket stopper
A79 H7362G8001 Washer
A80 H6644C8001 Washer
A81 HM22B48001 Clapboard
A82 HM22B78001 Strap guide
A83 HA500C2070 Screw
A84 H6644C8001 Washer
A85 HM21B68001 Strap guide
A86 HM22B68001 Arm sidecover baffle
— 18 —
Pcs.
Remarks
1
1 M6
1
1 M6×20
1
4 SM9/64(40)×4
1
1 SM1/4(40)
1
1
1 SM11/64(40)×7.5
1
1
1
1
2
1
1
4 SM9/64(40)×5
2
1 SM1/4(40)×49
2
1
1
1
1
1 SM9/64(40)×6
1
2 SM3/32(56)×2.2
1
1
1
2 SM11/64(40)×8.85
1
1
1
2 SM11/64(40)×20
1 SM11/64(40)×26
1
1
5 SM11/64(40)×12
1
1 SM9/64×40/6
B.SEWING MECHANISM
B.SEWING MECHANISM
Fig.
No.
Part No.
Description
B01 HA300B2090 Rubber plug
B02 H2009B0067 Needle bar bushing (upper)
B03 H6005C8001 Needle bar
B04 H6006C8001 Needle bar bushing (lower)
B05 H2000G2020 Thread guide
B06 H2000G2030 Needle
B07 HA100C2170 Set screw
B08 HA100C2020 Screw
B09 HA700H2040 Felt
B10 HA804H0651 Oil shade cap
B11 H6007C7101 Thread take-up lever assay
B12 H4967K8001 Screw
B13 HA100C2200 Slide block
B14 H2205C0661 Needle bar connecting link guide
B15 HA307C0662 Set screw
B16 H6023C8001 Needle bar crank
B17 HA100C2060 Screw
B18 HA705C0662 O-ring
B19 HA100C2070 Set screw
B20 H6011C8001 Upper shaft bushing (upper)
B21 H6013C8001 Upper feed lifting cam
B22 H6016C8001 Upper feed rock crank (left)
B23 H6015C8001 Balance weight
B24 HA100D2040 Upper shaft bushing (middle)
B25 HA3411D308 Screw
B26 HA108G0661 Collar for upper shaft
B27 HA105D0662 Screw
B28 HA112D3012 C-type retaining ring
B29 H6020C8001 Crank rock
B30 H6019C8001 Upper feed rock crank (right)
B31 H6018C8001 Upper feed lifting cam (right)
B32 H6021C8001 Upper shaft bushing (right)
B33 HA306D0066 Oil seal
B34 HA108C0663 Screw
B35 HA113D2112 Upper shaft gear
B36 HA113D2122 Vertical shaft gear (upper)
B37 HA100D2110 Vertical shaft bushing (upper)
B38 HA100C2020 Screw
B39 H6022C8001 Vertical shaft
B40 HA600D2010 Vertical shaft bushing (lower)
B41 HA113D2222 Vertical shaft gear (lower)
B42 HA113D2212 Lower shaft gear
B43 HA104D0652 Rubber plug
— 20 —
Pcs.
Remarks
1
1 SM15/64(28)×7
1
2 SM1/4(40)×4
1 20
1
1
1
1
1
8 SM1/4(40)×7
1
1
1
1
1
1
1
1
2 SM15/64(28)×10
1
1
1
1
1
1 DP×17 #22
1 SM1/8(44)×4.5
1 SM15/64(28)×10
1
1
1
2 SM11/64(40)×7.2
1
1
1
1
1
1
2 SM1/4(40)×6
1
1 SM9/32(28)×13
1
1 SM9/32(28)×14
B.SEWING MECHANISM
Fig.
No.
Part No.
Description
B44 H6010C8001 Upper shaft
B45 HA704C0653 Felt
B46 HA7121C104 Oil amount adjusting pin assay
Pcs.
1
1
1
Remarks
— 21 —
C.SEWING MECHANISM &FEED ROCK LOWER SHAFT
C.SEWING MECHANISM &FEED ROCK LOWER SHAFT
Fig.
No.
Part No.
Description
C01 HA300C2030 Screw
C02 HA705J0654 Shaft for feed bar (eccentric)
C03 HA104G0011 Feed rock shaft crank
C04 HA104G0012 Screw
C05 HA104G0656 Washer
C06 HA104G0654 Screw
C07 H6005D8001 Feed dog
C08 HA705J0021 Feed bar assay
C09 H1204D0651 Feed lifting rock shaft fork
C10 HA111G0683 Screw
C11 H6010D8001 Upper feed rock shaft
C12 HA300C2030 Screw
C13 H6011D8001 Connecting rod for upper feed
C14 H6012D8001 Upper feed rock shaft
C15 H4722G8001 Square block
C16 HA113F0684 Screw
C17 HA800F2020 Screw
C18 H6008D8001 Feed rock shaft crank (right)
C19 H6009D8001 Pin
C20 H6006D8001 Feed rock shaft
C21 HA105D0661 Collar for feed rock shaft
C22 HA105D0662 Screw
C23 HA100G2040 Bushing for feed rock shaft
C24 H007009150 C-type retaining ring
C25 HA900E2030 Bobbin case
C26 HA600E2060 Bobbin
C27 HA100E2150 Screw
C28 H2100E2010 Hook positioner
C29 H2200C2050 Rotating hook
C30 HA1111E104 Screw
C31 HA1111E204 Oil felt for hook shaft
C32 HA700E2030 Oil seal
C33 HA704B0654 Bushing for hook shaft (left)
C34 HA704B0653 Bushing for hook shaft (middle)
C35 H6015D8001 Hook shaft
C36 HA305E0662 Screw
C37 HA305E0661 Collar for hook shaft
C38 HA311E0671 Bushing for hook shaft (right)
C39 HA100C2020 Screw
C40 HA300E2100 Plunger
C41 HA300E2110 Coil spring
C42 HA300E2040 Guide plate
C43 HA104F0654 Screw
Pcs.
Remarks
1 GB/T894.1 15
1
1
1 SM11/64(40)×10
1
1
1
1
1
1 SM3/16(32)×9.7
1
1
2 SM15/64(28)×4.5
1
1
1 SM15/64(28)×10
1
1
1
1 SM15/64(28)×10
1 SM11/64(40)×8
1
1
2 SM3/16(28)×12
1
2 SM1/8(44)×6
1
1
1
1 SM11/64(40)×12
1
1 SM11/64(40)×8
1
1
2
1 SM15/64(28)×8.5
1 SM15/64(28)×13.5
1
1
1
2
4 SM1/4(40)×4
1
— 23 —
C.SEWING MECHANISM &FEED ROCK LOWER SHAFT
Fig.
No.
Part No.
Description
C44 HA705K0661 Feed lifting rock shaft crank (right)
C45 HA104G0012 Screw
C46 HA100G2070 Pin
C47 H6013D8001 Feed lifting rock shaft
C48 HA100G2120 Bushing for feed lifting shaft
C49 HA100G2130 Washer
C50 HA710E0692 Screw
C51 HA710E0691 Thread trimmer cam
Pcs.
Remarks
1
2 SM3/16(28)×12
1
1
1
1
2 SM1/4(40)×10
1
— 24 —
D.STITCH LENGTH MECHANISM
D.STITCH LENGTH MECHANISM
Fig.
No.
Part No.
Description
D01 HA108G0661 Collar for reverse bar
D02 HA105D0662 Screw
D03 HA100G2040 Bushing for reverse bar
D04 HA100B2110 Screw
D05 HA100C2020 Screw
D06 H6007E8001 Bracket pin
D07 H6008E8001 Pin
D08 H6006E8001 Reverse bar
D09 H4723G8001 Guide plate
D10 HA300C2030 Screw
D11 HA700B2120 Rubber plug
D12 HA100F2040 Pin
D13 HA704B0655 Bushing for feed regulator
D14 HA3411D308 Screw
D15 H6012E8001 Washer
D16 H007013040 E-type ring
D17 H6010E8001 Link
D18 H6013E8001 Pin
D19 HA113F0684 Screw
D20 H6009E8001 Feed regulator
D21 H6018E8001 Spring retainer
D22 HC01360 O-ring
D23 H6015E8001 Bracket
D24 HA100E2150 Screw
D25 HA100F2090 Spring for stopper pin
D26 HA700F2030 Stopper pin
D27 HA113F3022 O-ring
D28 H6017E8001 Feed regulator pin
D29 HA109F0674 O-ring
D30 HA720F0681 Screw bar
D31 HA720F0687 Coil spring
D32 HA720F0683 Stopper pin releasing lever
D33 HA7421F120 Dial
D34 H2205D0661 Plate for stitch length
D35 HA720F0685 Bushing
D36 HA720F0686 Screw
D37 HA113F0683 Screw
D38 HA104F0654 Screw
D39 HA309F0671 Feed reversing lever
D40 HA100F2110 Spring washer
D41 H3008F0671 Feed reversing lever shaft
D42 HA113F3022 O-ring
D43 H6020E7101 Crank for feed reversing lever
— 26 —
Pcs.
Remarks
1
1
1
1
1
1
1
1
1
4 SM11/64(40)×10
1
1
1
1
1
1
1
1 SM3/16(28)×18
1 SM3/16(28)×6.5
2 SM15/64(28)×10
1
2 SM1/4(40)×4
1
1 SM11/64(40)×5.5
1 SM15/64(28)×10
1
1
1
1
1
1
2
6 SM11/64(28)×8
1 SM15/64(28)×7
2
2 GB/T896 4
1
2
1 SM15/64(28)×8.5
1
1
1 GB3452.1 36
1
D.STITCH LENGTH MECHANISM
Fig.
No.
Part No.
D44 HA100F2130 Screw
D45 H6023E8001 Spring
D46 HA800F2010 Spring holder
D47 HA800F2020 Screw
D48 HA806C0675 Spring holder
D49 HA806C0674 Coil spring
D50 H6011E8001 Link for reserve feed
Description Pcs.
Remarks
1
1
1
1 SM15/64(28)×14.5
1
1
1 SM15/64(28)×13.5
— 27 —
E.UPPER FEED ROCK SHAFT MECHANISM
E.UPPER FEED ROCK SHAFT MECHANISM
Fig.
No.
Part No.
Description
E01 H6006F8001 Upper feed rock shaft crank (left)
E02 H431060050 Screw
E03 HA100B2110 Screw
E04 H6008F8001 Bushing for upper feed rock shaft crank
E05 H2013N0067 Nut
E06 H2013J0065 Washer
E07 H2121I0065 Feed connecting slick block
E08 HM20F68001 Upper feed rock shaft
E09 HA108G0661 Collar
E10 HA105D0662 Screw
E11 H6018F8001 O-ring
E12 HK852H8001 Upper feed rock shaft crank
E13 HA3411D308 Screw
E14 H6010F8001 Hinge pin
E15 H6015F8001 Feed connecting lever
E16 H2004J0662 Screw
E17 H6016F8001 Walking foot connecting rod
E18 H2004J0067 Screw
E19 HA100I2050 Spring washer
E20 H2004J0661 Feed arm
Pcs.
Remarks
1
2
2 SM11/64(40)×5.5
2
1 SM1/4×24
1 6
1
1
1
2 SM1/4(40)×4
1
1
1 SM15/64(28)×7
1
1
2 SM1/4(40)×5
1
2 SM9/64(40)×7
2 3.5
1
— 29 —
F.UPPER FEED LIFTING ROCK SHAFT MECHANISM
— 30 —
F.UPPER FEED LIFTING ROCK SHAFT MECHANISM
Fig.
No.
Part No.
Description
F01 H6005G8001 Upper feed lifting rock shaft
F02 HA100B2110 Screw
F03 H6006G8001 Bushing for upper feed lifting rock shaft (left)
F04 H6007G8001 Bushing for upper feed lifting rock shaft (right)
F05 H6009G8001 Upper feed lifting rock crank
F06 H5336H8001 Screw
F07 H6010G8001 Upper feed lifting rock crank shaft
F08 H6011G8001 Link
F09 H6039G8001 Screw
F10 H6013G8001 Upper feed regulator bracket
F11 HA7311C606 Screw
F12 H6014G8001 Shaft for upper feed lifting rock shaft
F13 H6015G8001 Crank for upper feed lifting rock crank
F14 H007009100 C-type ring
F15 H6016G8001 Pin
F16 H6020G8001 Cam follower
F17 HA100G2040 Bushing for upper feed shaft
F18 H6019G8002 Upper feed regulator shaft
F19 H6021G8002 Spring
F20 HA108G0661 Collar
F21 HA105D0662 Screw
F22 H2004J0662 Screw
F23 H6023G8001 Link for feed lifting rock shaft
F24 H007013060 E-type ring
F25 H6022G8001 Pin
F26 H6024G8001 Bell crank
F27 H6027G8001 Link
F28 H6028G8001 Pin
F29 H6029G8001 Stud screw
F30 H6030G8001 Bell crank support
F31 H6040G8001 Nut
F32 H6031G8001 Bell crank support shaft
F33 HA110D0672 Screw
F34 HA300B2110 Rubber plug
F35 H2010J0065 Thumb screw
F36 H2010J0066 Nut
F37 H6032G8001 Presser regulating bracket
F38 HA300C2030 Screw
F39 H6038G8001 Spring
F40 H6034G7101 Spring guide bar assay
F41 H6037G8001 Bushing for walking foot guide link
F42 H6036G8001 Walking foot guide link
F43 H6033G8001 Spring guide bar holder
Pcs.
Remarks
2 GB/T896 6
1
1
1
1
1 SM15/64(28)×5
1
1 SM15/64(28)
1
1 SM15/64(28)×12
1
1 SM9/32(28)×35
1
1
1
1
1
1 SM9/32(28)
1
2 SM11/64(40)×8
1
4 SM11/64(40)×5.5
1
1
1
1 SM15/64(28)×13.5
1
1
2 SM11/64(40)×3.8
1
4 SM11/64(40)×15
1
1
2
1
1
1 GB/T894.1 10
1
2 SM15/64(28)×10
1
2 SM1/4(40)×4
2 SM1/4(40)×5
1
— 31 —
F.UPPER FEED LIFTING ROCK SHAFT MECHANISM
Fig.
No.
Part No.
Description
F44 H2000I2050 Screw
F45 H2000N0040 Washer
F46 HA111G0683 Screw
F47 H2000N0030 Walking foot guide bracket
F48 HM20G68001 Walking foot
F49 HM20G78001 Knife
Pcs.
Remarks
1
1
3 SM9/64(40)×8
2
2 SM11/64(40)×12
1
— 32 —
G.PRESSER FOOT MECHANISM
G.PRESSER FOOT MECHANISM
Fig.
No.
Part No.
Description
G01 HA700F2100 Screw
G02 H6023H8001 Thread guide
G03 H6027H8001 Presser bar guide bracket
G04 HA3411D308 Screw
G05 H2400G2140 Thumb screw
G06 HA117H0692 Nut
G07 H6020H8001 Presser bar spring
G08 HA107H0662 Screw
G09 H6013H8001 Knee lifter rod
G10 H6017H8001 Spring
G11 HA100H2050 Stud bolt
G12 H6016H8001 Knee lifter lever
G13 H6009H7101 Presser bar lifting cam
G14 HA305E0662 Screw
G15 H6008H8001 Spring
G16 H6007H8001 Presser bar lifting shaft
G17 HA300H2080 O-ring
G18 H6006H8001 Presser bar lifter
G19 H6018H8001 Knee lifter connecting rod
G20 HA107H1013 Screw
G21 H6014H8001 Knee lifter lever (left)
G22 HA305H6611 Tension releasing cam
G23 HA100H2050 Stud bolt
G24 H6037B8001 Thread releasing pin
G25 HM20H68001 Presser bar
G26 HA704B0651 Bushing for presser bar
G27 HM21H08001 Presser foot
G28 HM21H18001 Presser foot
G29 HM21H28001 guide apparatus
G30 HM21H48001 Walking foot guard cover
G31 HD707F8001 Screw
G32 HM022F8001 Spring
G33 HM21H38001 Pin
G34 H2400G2160 Nut
G35 H2400G2150 Screw
Pcs.
Remarks
1 SM11/64(40)×7
1
1
1 SM15/64(28)×7
1 SM1/2(28)×41.5
1 SM1/2(28)
1
2 SM3/16(28)×3.5
1
1
1 SM15/64(28)×5.2
1
1
1
1
1
2 SM15/64(28)×4.5
1
1
1 SM11/64(40)×6.5
1
1
1 SM15/64(28)×6.7
1
1
1
1
1
1
1
2 M4×0.7/15.8
1
1
1 SM11/64×40
1 SM11/64×40/31
— 34 —
H.DIFFERENTIAL MECHANISM
H.DIFFERENTIAL MECHANISM
Fig.
No.
Part No.
Description
H01 HA720F0686 Screw
H02 HA720F0685 Bush
H03 HM308F8001 Plate for stitch length
H04 HA7421F120 Dial
H05 HA720F0683 Stopper pin releasing lever
H06 HA720F0687 Coil spring
H07 HM20L68001 Screw bar
H08 HM22L28001 Feed regulator spindle
H09 HA705C0662 O-ring
H10 HM21L98001 Washer
H11 H431050050 Screw
H12 H2010J0066 Nut
H13 HK830H8001 Screw
H14 H2013N0651 Slide block
H15 H007013040 E-type ring
H16 HM21L78001 Feed driver connecting rod
H17 HM21L58001 link rod
H18 HM21L68001 Pin
H19 HM22L58001 Pin
H20 HM22L68001 Washer
H21 H007013040 E-type ring
H22 HM23L18001 windpipe
H23 HM23L08001 Bracket
H24 HA300B2160 Screw
H25 HM22L98001 reset button
H26 HF937E8001 Windpipe joint
H27 HEE4218001 Windpipe joint
H28 HF15404013 Cylinder
H29 H2004J0662 Screw
H30 HM22L48001 Coupling
H31 H431050050 Screw
H32 HM22L08001 Coil spring
H33 H431050050 Screw
H34 HM21L48001 Feed regulator
H35 HA100F2090 Spring for stopper pin
H36 HA700F2030 Stopper pin
H37 JGD0100011 Reducing valve and solenoid valve
Pcs.
Remarks
1
2
1
1
1
1
2
1
2
1
1
1
1
1
1
1
1
1
1
1
1
1
1
2
1
1
1
1
1
1
1
2 SM11/64×40/10
1
1
1
1 GJ2D16D-T1247-15(SMC)
1
— 36 —
I.KNIFE ACTUATING MECHANISM
I.KNIFE ACTUATING MECHANISM
Fig.
No.
Part No.
Description
I01 HA712N0698 Thread trimmer driving lever
I02 HA712N6910 Flexible wire holder
I03 HA712N0699 Stud screw
I04 HA712N6911 Flexible wire presser
I05 HA712N6912 Screw
I06 HA712N0695 Stud screw
I07 HA712N0697 Trimmer lever spring
I08 HA712N0696 Spring support collar
I09 HA7311CC06 Screw
I10 HA100E2150 Screw
I11 HA710N0683 Nut
I12 H2208H0068 Thread trimmer solenoid
I13 HA700N0080 Screw
I14 HA300C2030 Screw
I15 HA708P0668 Cord holder
I16 HA7641B319 Terminal pin
I17 H6005J8001 Flexible wire
I18 HA300H2080 O-ring
I19 H6004J7101 Flexible wire assay
I20 H003003050 Nut
I21 HA712N6913 Holder
I22 HA7121N604 Screw
I23 HA7121N704 Nut
I24 HA7121N104 Bracket for fixed blade
I25 H22121H204 Thread guide
I26 HA7311CH06 Screw
I27 HA7121N304 Screw
I28 H22121H104 Fixed blade
I29 HA704N1111 Knife holding bracket saddle
I30 HA7111N304 Nut
I31 HA704N1112 Knife base (left)
I32 HA7111N504 Nut
I33 HA7111N604 Knife driving crank
I34 HA7111N204 Screw
I35 HA7111N404 Link
I36 HA704N1114 Screw
I37 HA704N1113 Thrust washer
I38 H2204H0651 Movable knife (left)
I39 HA7111N704 Screw
I40 H6006J8001 Knife driving shaft
I41 HA706N0066 Cam follower crank assay
I42 HA700N0050 Bushing
I43 HA700N0040 Coil spring
— 38 —
Pcs.
Remarks
1
1
1 SM9/64(40)×8
1 SM9/64(40)×5
1
1
2
1
1
1
2 SM11/64(40)×6.2
1
1
1
3 SM1/8(44)×6
1
1
2 SM11/64(40)×7
1
1
1
1
1 SM11/64(40)×8
1
2 SM1/8(44)×7
1
1
1
2 SM9/64(40)×8.5
1 SM11/64(40)×10
1
1
4 SM15/64(28)×12
1
1
1
7 SM11/64(40)×8
1
2
2 GB/T6171 M5
1
1 SM9/64(40)×8.5
1 SM9/64(40)
I.KNIFE ACTUATING MECHANISM
Fig.
No.
Part No.
I44 HA710N0682 Lever stopper plate
I45 HA113F0684 Screw
I46 HA906N0661 Stopper
I47 HA700N0110 Coil spring
I48 HA105D0662 Screw
I49 HA715N0071 Collar
I50 HA7411N110 Screw
Description Pcs.
Remarks
1
1 SM15/64(28)×11.3
1
1
1 SM1/4(40)×4
1
1 SM15/64(28)×23
— 39 —
J.TOUCH BACK MECHANISM & DETECTOR MECHANISM
J.TOUCH BACK AND DETECTOR MECHANISM
Fig.
No.
Part No.
Description
J01 HA300B2160 Screw
J02 H6005K8001 Bracket
J03 HA7221P508 Screw
J04 HA704O0657 Rubber plug
J05 HA704O0659 Screw
J06 HA704O0654 Spring plate
J07 H2205I0661 Bracket for touch switch
J08 H6006K7101 Vinyl cap-tire cable for touch switch
J09 HA7641B319 Terminal pin (male)
J10 HA704O0021 Push button
J11 H007013030 E-type ring
J12 HA704O0065 Spring
J13 HA704O6510 Screw
J14 HA704O0655 Micro switch
J15 HA704O0658 Insulator set
J16 HA705Q0065 Ground wire
J17 HA700Q0030 Cord holder
J18 H6009K8001 Solenoid assay for touch back
J19 H2006I0672 Gasket
J20 H6010K8001 Arm side cover
J21 HA300C2030 Screw
J22 H6011K8001 Gasket
J23 H007013040 E-type ring
J24 HA712N0692 Pin
J25 H6012K8001 Stud screw
J26 H2204G0652 Rubber ring
J27 HA703R0065 Detector bracket assay
J28 HA703R0067 Washer
J29 HA703R0066 Detector bracket supporter
J30 HA111G0683 C-type ring
J31 HA700R0060 Washer
J32 HA700R0050 Supporter spring
J33 HA700R0040 Spacer B
J34 HA700R0020 Speed command disc (up)
J35 HA700R0030 Spacer A
J36 HA700R0010 Speed command disc (down)
J37 HA110D0672 Screw
J38 H2204I0651 Pulley
Pcs.
Remarks
2
1
1
8 SM11/64(40)×10
1
2
1
1
5
1
2 GB/T896 3
1
2 M2×8
1
1
1
2 HP-5N
1
1
1
2
1
7 SM11/64(40)×8
1
1
2
1
1
1
1
1
1
1
1
1
1
2 SM15/64(28)×12
1
— 41 —
K.OIL LUBRICATION MECHANISM
K.OIL LUBRICATION MECHANISM
Fig.
No.
Part No.
Description
K01 H6019I8001 Oil wick
K02 HA700B2150 Oil felt
K03 H6019I8001 Oil wick
K04 H6016I8001 Upper shaft oil tube
K05 HA116I0682 Bushing
K06 H6006I8001 Oil pump
K07 HA100I2090 Screw
K08 H6010I8001 Rooter
K09 H6011I8001 Slider
K10 H6012I8001 Oil pump cover
K11 HA100I2070 Oil adjusting plate
K12 HA100I2050 Spring washer
K13 HA100I2040 Screw
K14 HA111I0065 Oil pump filter
K15 HA113I0661 Bushing
K16 H6014I8001 Lower shaft oil tube
K17 HA110E0672 Oil pipe for lower shaft bushing
K18 H6018I8001 Oil return tube
K19 HA300I2030 Oil return tube clip
K20 HA300E2030 Oil adjusting screw
K21 HA100E2060 Oil adjusting spring
K22 HA305G0664 Oil wick
K23 HA304G0655 Oil wick
K24 HA300I2060 Oil felt holder
K25 HA106B0676 Screw
K26 H6009I8001 Oil wick holder
Pcs.
Remarks
1
1
1
1
1
1
3 SM11/64(40)×13
1
1
1
1
1 3.5
3 SM1/8(44)×13
1
1
1
1 SM1/2(28)
1
1
1
1
1 SM15/64(28)×25.5
1
1
1 SM9/64(40)×6
1
— 43 —
L.ACCESSORIES
L.ACCESSORIES
Fig.
No.
Part No.
Description
L01 HA505B0672 Thread take-up spring
L02 H2000G2030 Needle
L03 H3200L0060 Socket wrench 3
L04 HA704S0653 Socket wrench 2
L05 HA300J2230 Washer for wood screw
L06 H801045200 Wood screw
L07 HA300J2200 Screw driver (middle)
L08 HA300J2210 Screw driver (small)
L09 HA100J2160 Spanner
L10 HA704S0654 Speed command disc adjusting disc
L11 HA100J2110 Oil with oiler
L12 HA600E2060 Bobbin
L13 HA307J0067 Hinge with rubber cushion
L14 HA100J2090 Vibration preventing rubber (large)
L15 H3200L0030 Vibration preventing rubber (small)
L16 HA100J2120 Magnet block
L17 HA300J2370 Thread stand assay
L18 HA905S0066 Bobbin winder assay
L19 H4954N7101 Belt guard assay
L20 HA100J2180 Cover
L21 HA300J2070 Screw driver (large)
L22 H6017L8001 Screw
L23 H6005L8001 Link
L24 H6006L8001 Knee lifter driving crank
L25 HA106J0664 Bolt
L26 HA106J0667 Bolt
L27 HA106J0666 Knee lifter plate stopper
L28 HA106J0665 Knee lifter plate
L29 HA106J0668 Knee lifter cover
L30 HA106J0662 Knee lifter shaft
L31 H6015L8001 Knee lifter shaft
L32 HA104J0657 Coil spring
L33 HA104J0658 Knee lifter
L34 HA100F2130 Screw
L35 HA104J6510 Nut
L36 HA104J0659 Set screw
L37 H007013090 E-type ring
L38 H6016L8001 Collar
L39 HA100C2090 Screw
L40 H6008L8001 Oil reservoir
L41 HA104J0652 Screw
L42 HA104J0653 Seal washer
L43 H6009L8001 Gasket for oil reservoir
— 45 —
Pcs.
Remarks
1
1
1
2
3 SM5/16(18)×13
1 SM15/64(28)×8
1
2
1
1
1 SM15/64(28)×14.5
2 SM15/64(28)
2
2
2 SM15/64(28)×28
1 GB/T896 9
1
2 SM15/64(28)×4.5
1
2 SM5/16(28)×10
1
4
2
1
1
1
1
4 DP×17 #22
1
1
4
4 GB/T99 4.5×20
1
2
2
1
1 GXJ-2A
1
1
1
1
2 SM1/4(24)×10.7
1
L.ACCESSORIES
Fig.
No.
Part No.
Description
L44 HA106J0661 Knee lifter lifting pin
L45 HA600J2060 Gasket
L46 HA600J2040 Screw
L47 HA600J2050 Drainage tube
L48 HA300J2170 Oil tank
L49 HM21M08001 Nut
L50 HM21M18001 Baffle
L51 HM20M98001 Thread stand pole
L52 HA106J0663 Knee lifter driving crank
L53 HM20M78001 Screw
L54 HA106J0664 Screw
L55 HM20M88001 Thread stand
L56 HE027B8001 Spring
Pcs.
4
1
2
1
2
1
1
1
2
1
1
1
1
Remarks
— 46 —
SHANGHAI BIAOZHUN HAILING SEWING MACHINERY CO., LTD.
ADD: NO.850 Shulin Road, Songjiang District Shanghai, P.R.China
Zip Code: 201612
Overseas Business: TEL: 86-21-64853303 FAX: 86-21-64854304
E-mail:[email protected] http://www.highlead.com.cn
The description covered in this manual is subject to change for improvement of the commodity without notice
2019.5. Printed
advertisement
* Your assessment is very important for improving the workof artificial intelligence, which forms the content of this project