- Home
- Home security & automation
- Security device components
- onsemi
- FUSB307BGEVB Type-C Port Controller IC Evaluation Board
- User manual
onsemi FUSB307BGEVB Type-C Port Controller IC Evaluation Board User Manual
Add to My manuals16 Pages
advertisement
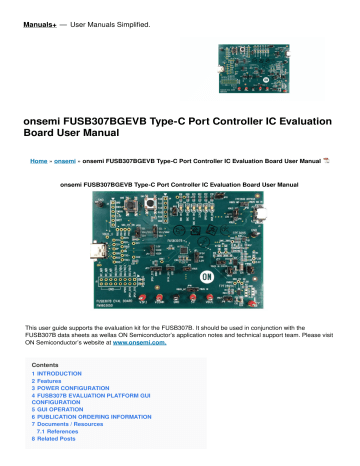
Manuals+ — User Manuals Simplified.
onsemi FUSB307BGEVB Type-C Port Controller IC Evaluation
Board User Manual
Home » onsemi » onsemi FUSB307BGEVB Type-C Port Controller IC Evaluation Board User Manual onsemi FUSB307BGEVB Type-C Port Controller IC Evaluation Board User Manual
This user guide supports the evaluation kit for the FUSB307B. It should be used in conjunction with the
FUSB307B data sheets as wellas ON Semiconductor’s application notes and technical support team. Please visit
ON Semiconductor’s website at www.onsemi.com.
Contents
4 FUSB307B EVALUATION PLATFORM GUI
6 PUBLICATION ORDERING INFORMATION
8 Related Posts
INTRODUCTION
The FUSB307B evaluation board and included software allows customers a complete platform to evaluate the
Type−C interface detection solution the FUSB307B provides. The evaluation board is designed for both standalone operation and connection to test equipment for specific testing requirements. The FUSB307B software provides both fully automatic control and manual control of the FUSB307B functions. With a single connection to a
PC and a couple configurations in the GUI, the evaluation board can function as a Source, Sink, or Dual Role port.
Description
The FUSB307B targets system designers looking to implement up to four USB Type−C port controllers (TCPC) with USB−PD capabilities.
This solution provides integrated Type−C Rev 1.3 detection circuitry enabling manual attach/detach detection.
Time critical Power Delivery functionality is handled autonomously, offloading the Processor or Type−C Port
Manager (TCPM). The FUSB307B complies with the USB−PD Interface Specification.
Figure 2. Block Diagram
Features
USB−PD Interface Spec Rev 1.0 Ver. 1.2 Compatible
USB Type−C Rev 1.3 Compatible
USB−PD Rev 3.0 Ver. 1.1 Compatible
Fast Role Swap
Sink Transmit
Extended Data Messages (Chunked)
Dual−Role Functionality
Manual Type−C Detection
Automatic DRP Toggling
USB−PD Interface Specification Support
Automatic GoodCRC Packet Response
Automatic Retries of Sending Packet
All SOP* Types Supported
VBUS Source and Sink Control
Integrated 3 W Capable VCONN to CCx Switch
10-bit VBUS ADC
Programmable GPIOs
4 Selectable I2C Addresses
Dead Battery Operation
Powered from VBUS
LDO Output provides power to TCPM
Packaging
16-pin WQFN (3.0 × 3.0 mm)
Figure 3. Evaluation Board Layout
POWER CONFIGURATION
The FUSB307B evaluation board is designed to be able to be powered from just the PC connection or powered externally based on the testing requirements. To use the external VDD to the device, take the jumper off of JP1 and connect external VDD to the middle post of JP1, which is FUSB307B VDD.
Power Supplied from Board
The FUSB307B can fully operate from the VBUS input of the micro-B USB receptacle J3. To operate the evaluation board, the USB power should be provided to the board over the micro-B USB. Then, the on board regulator (LDO) generates VDD, which is 3.3 V for device supply. Once valid USB power is provided, the indicator
LED, 3.3 V, is turned on.
I²C Connection
Direct I2C Connection Customers that want to directly connect their I2C masters to the evaluation board can connect the I2C master signals to the SCL, SDA, and INT_N test points.
PC I2C Connection
The evaluation board uses an STM32F072CB micro-controller-unit (mcu) as an I2C master to control the
FUSB307B. This is the communication method used by the FUSB307B GUI. By connecting the PC to the micro-B
USB receptacle J3, the evaluation board automatically powers the microcontroller and connects the I2C master to the FUSB307B.
TYPE−C SIGNAL CONNECTIONS
The FUSB307B evaluation board allows different ways of connecting to another Type−C device or controlling the signals of the Type−C receptacle based on the type of testing that is required.
CC Pins
The Type−C CC1 and CC2 pins are directly connected to the Type−C receptacle J1 on the board. Each CC pin has a series jumper (JP7, JP14) which is useful to measure voltage and current. Note that the FUSB307B evaluation board contains the minimum cReceiver capacitance specified in the USB PD specification for the CC pins which is 220 pF. This capacitance is C27 and C28 in the schematic.
VBUS 5 V
VBUS is used differently based on the Type−C port type. The FUSB307B controls an integrated load switch
(FPF3695) for Sink and Source path depending on what device is connected. In each case, an LED indicator (SNK
ON and SRC ON) tells which VBUS power path is established. A test point for VBUS voltage sensing (VBUS_S) is located near J1. The EVB is designed to supply 5.0 V VBUS from PC USB power or an external supply. This option can be configurable by JP16 as shown below.
Figure 4. V5P0 Power Selection
Jumper on VBUS_MC: PC USB power to V5P0
Jumper off: external power (5 V test point) to V5P0
Jumper on VBUS IN: VBUS SRC (from source device) power to V5P0.
VBUS Greater Than 5 V
To offer VBUS greater than 5 V, the 12 V test point can be used as an input for a VBUS level of 9 V, 12 V, 15 V, or
20 V. This input is controlled by the FPF2895C load switch and the SRV_HV_ON signal from the mcu. If this high voltage VBUS will be used, the JP8 jumper needs to be shorted so that this high voltage VBUS can be switched onto the VBUS rail to the Type−C connector at J1.
VCONN
VCONN can be supplied to the FUSB307B externally through the VCONN test point found along the External
Power Inputs test points.
USB2.0 and SBU
They are left open in the Type−C connector with no connections to other circuitry on the board. Test points are near the Type−C connector J1.
STATUS LED’S
The following status LEDs are provided on the evaluation board. All of the LEDs can be disconnected by JP11 and JP12.
D1
D2
D3
D4
D5
D6
Figure 5. LED Indicators
Table 1. STATUS LED’S
LED on when GPIO2 is active (low) on when DBG_N is in active (low) on when SNK_ON is active (high) on when SRC_ON is active (high) on when SRC_HV_ON is active (high) on when V3P3_SYS is present (high)
Status
Figure 6. FUSB307B Evaluation Board FM160305D Schematic (1/2)
Figure 7. FUSB307B Evaluation Board FM160305D Schematic (2/2)
FUSB307B EVALUATION PLATFORM GUI CONFIGURATION
GUI Installation
Instructions for installing ON Semiconductor FUSB307B Control Software
1. Locate and extract the file “FUSB307B_gui_1_1_0_Customer.exe” (versions of the file will include the release
number) from the archive file “FUSB307B_gui_1_1_0_Customer.7z”. The .exe can be located in any location you prefer. Double-click the .exe file to start the GUI.
2. Plug the STD−A end of the USB Cable into the USB port of your PC.
3. Plug the Micro−B end of the USB Cable into the GUI Interface (J3 at the top right corner of the board) on the
Evaluation Board. V3P3_SYS LED will illuminate if properly connected.
4. Wait for the USB Port to connect with a message in the lower left hand corner of the GUI that states “USB
Device: VID:0x1057 PID:0x0133” and “Device Connected v1.1.1” in the lower right corner (or a newer version if applicable). If the message states “Disconnected”, then there is a connection problem.
Upgrading the GUI Software:
1. Simply delete the previous version of the .exe.
2. Repeat the installation process above.
GUI OPERATION
Program Startup
To operate the FUSB307B Evaluation Platform, perform the following steps:
1. Install the FUSB307B GUI software as described in the previous section.
2. Connect the FUSB307B board to your computer with a micro-USB cable.
3. Start the GUI software by double-clicking the .exe file from the location you saved it to.
4. The base operation GUI will appear as shown in Figure 8 below.
5. The lower right part of the screen will now indicate “Device Connected v1.1.1” (the version number may be different as newer firmware is released). If this is not shown, there is a likely a power configuration issue with the FUSB307B device. If power is supplied correctly, check that the firmware was programmed correctly. The document for firmware download is posted separately. You can now read, write, and configure the FUSB307B.
Accessories can be plugged in and used.
Figure 8. Initial Page of FUSB307B GUI
USING THE GUI
There are two basic modes to control/monitor the FUSB307B. Pre-programmed firmware on the mcu can control the FUSB307B and then the GUI can work with the firmware to control/monitor the FUSB307B. The GUI can also be used with the Register Map and Script tabs to manually control/monitor the FUSB307B. These two modes should not be used together, as it will interfere with the autonomous mode state machine. By default, the USB
Type−C state machine is enabled. The checkbox has to be de-selected to use the device manually. Status information is shown in the top half of the window, as well as in the “PD Control” tab and the “State Logs” tab.
Scripts can also be loaded in the “Script” tab for easier loading of multiple sequential steps.
More information on specific operation of each section of the GUI is provided in the following sections.
File Menu
“File”
Click “Exit” to exit the FUSB307B GUI program
“Preferences”
Select “Auto Poll” to automatically update the GUI with the FUSB307B status
Help”
“About” provides GUI version information
General
General This tab provides the overall device status. The lower third of this tab is the “Control” section. When the
FUSB307B EVB is initially connected to the PC, this section will automatically update itself. At any time after that, the “Read Config” button should be used before making any changes to this section. The port type can be set to either DRP, Sink, or Source, and other features can be enabled or disabled here. After making any changes, press “Write Config” to update the device with any changes.
Figure 9. General Tab
PD Control
This tab logs any PD activity with PD Message History Box. The log file can be expanded or collapsed to show more or less detail of the PD packets. The other control boxes indicate the current state of the PD state machine and what contract was negotiated. When connected as a sink, it displays the source capabilities of the source that is attached. The user can select different capabilities and make the requests. The user can also manually send different PD messages through the pull-down menu and the click buttons.
Figure 10. PD Control Tab
State Logs
Events can be logged in the software by checking the “Auto Poll” option in the Preferences menu. These logs can be useful in debugging and in checking the timing of various operations. Each log message has the timestamp
(with 100 s resolution). To stop logging, click the “Auto Poll” option in the Preferences menu.
An example of a Type−C attach and the PD communication flow is shown below.
To support debug efforts, the “Set State” button can be used to force a specific state machine state. The state can be selected in the pull down menu to the left of the “Set State” button.
The screens can be cleared with the “Clear State Log” and “Clear PD State Log” buttons to the right of each window. Either Type−C State log or Policy Engine State log can be saved to a text log file using the “Save TC Log” and/or “Save PD log” buttons.
Figure 11. State Logs Tab
Capabilities
The “Capabilities” tab is to set-up PD functionality of the EVB. The settings in this tab dictate how the PD state machine will respond once a connection is made. It is the programmed source and sink capabilities of the device and the charging algorithm that is used to automatically select a source capability when connected to a source.
Note, the “Read Src Caps”, “Read Sink Caps”, and “Read Settings” buttons need to be clicked to reflect the default settings of the PD state machine.
Figure 12. Capacitance Tab
Register Map
The “Register Map” tab enables reading and writing any value to any register in the FUSB307B. When performing
a register write, the selected register/registers is/are read back again to confirm the write action. So the write button actually performs a write and then a read operation.
The “Device Poll” option tells the GUI to automatically check the DEVICE_ID register for the I2C address selected in the “Addr” pull down box and display the “Device Connected …” or “ No Device” message in the lower right corner of the GUI.
The “Register Poll” option tells the GUI to constantly poll the FUSB307B registers and update the register values.
This should be used only for debugging since it can disrupt the timing operations of the firmware.
Figure 13. Register Map Tab
Scripting
This tab enables the use of scripts to configure the FUSB307B. The window in the left side of the tab controls the scripting.
Scripts can be added through the GUI using normal copy/paste methods or imported from an external file using the “Load” button. After achieving a desired setup, a script can also be exported to a file using the “Save” button.
Each line of the script should be formatted as follows:
Command, port, I2C addr, # bytes, register addr, data1, , dataN, optional comment
The Command is: “r” or “w”
The port is always 0
The I2C addr is any connected device I2C address
The # bytes is the number of bytes to read or write
The register addr is the starting register address
The data1, …, dataN are for writing values to registers
And optional comment is just informational
Each field can be separated with a space (“ ”), a comma (“,”), or a semicolon (“;”).
The Run button will execute all the lines of the script. The Step button will execute the highlighted line. The
Loop feature will loop the entire script up to 99 times. Setting Loop count to 0 will loop indefinitely. Some
example script commands are given below: r 0, 0xA0, 2, 0x04; Read DeviceID r 0, 0xA0, 1, 0x1A; Read RoleControl w 0, 0xA0, 1, 0x1A, 0x1B; Set Rp 1.5A
w 0, 0xA0, 3, 0x51, 0x02, 0x47, 0x06; Write PD Byte
Count and Header for GetSourceCaps w 0, 0xA0, 1, 0x50, 0x30; Write Transmit SOP command
Results of an executed script are shown in the box on the right side of the tab. These results can be exported to a file using normal copy and paste functions.
Figure 14. Script Tab
Figure 15. Example Script and Results
VDM
This tab enables supports Vendor Defined Messages (VDM). The “Configuration” section is used for configuring the FUSB307B. The upper left “FUSB305” section window is used for displaying and modifying or adding VDM information to the EVB. Right-clicking on the Sop field allows you to add SVIDs. Right-clicking on an SVID allows you to remove the SVID or add a Mode. Right-clicking on a Mode allows you to remove it. Retrieving VDM information from a connected device can be done in the lower left “Other” section window. Right-clicking on Sop allows you to request Discover Identity or Discover SVIDs. Right-clicking on a SVID allows you to request
Discover Modes. Right-clicking on a Mode allows you to request to Enter or Exit that Mode.
Figure 16. VDM Tab
Arm and Cortex are registered trademark of Arm Limited (or its subsidiaries) in the US and/or elsewhere. USB
Type−C and USB−C are trademarks of USB Implementers Forum. ON Semiconductor is licensed by the Philips
Corporation to carry the I2C bus protocol.
onsemi, , and other names, marks, and brands are registered and/or common law trademarks of Semiconductor
Components Industries, LLC dba “onsemi” or its affiliates and/or subsidiaries in the United States and/or other countries. onsemi owns the rights to a number of patents, trademarks, copyrights, trade secrets, and other intellectual property. A listing of onsemi’s product/patent coverage may be accessed at www.onsemi.com/site/pdf/Patent−Marking.pdf
. onsemi is an Equal Opportunity/Affirmative Action Employer.
This literature is subject to all applicable copyright laws and is not for resale in any manner.
The evaluation board/kit (research and development board/kit) (hereinafter the “board”) is not a finished product and is not available for sale to consumers. The board is only intended for research, development, demonstration and evaluation purposes and will only be used in laboratory/development areas by persons with an engineering/technical training and familiar with the risks associated with handling electrical/mechanical components, systems and subsystems. This person assumes full responsibility/liability for proper and safe handling. Any other use, resale or redistribution for any other purpose is strictly prohibited.
THE BOARD IS PROVIDED BY ONSEMI TO YOU “AS IS” AND WITHOUT ANY REPRESENTATIONS OR
WARRANTIES WHATSOEVER. WITHOUT LIMITING THE FOREGOING, ONSEMI (AND ITS
LICENSORS/SUPPLIERS) HEREBY DISCLAIMS ANY AND ALL REPRESENTATIONS AND WARRANTIES IN
RELATION TO THE BOARD, ANY MODIFICATIONS, OR THIS AGREEMENT, WHETHER EXPRESS, IMPLIED,
STATUTORY OR OTHERWISE, INCLUDING WITHOUT LIMITATION ANY AND ALL REPRESENTATIONS
AND WARRANTIES OF MERCHANTABILITY, FITNESS FOR A PARTICULAR PURPOSE, TITLE,
NON−INFRINGEMENT, AND THOSE ARISING FROM A COURSE OF DEALING, TRADE USAGE, TRADE
CUSTOM OR TRADE PRACTICE.
onsemi reserves the right to make changes without further notice to any board.
You are responsible for determining whether the board will be suitable for your intended use or application or will achieve your intended results. Prior to using or distributing any systems that have been evaluated, designed or tested using the board, you agree to test and validate your design to confirm the functionality for your application.
Any technical, applications or design information or advice, quality characterization, reliability data or other services provided by onsemi shall not constitute any representation or warranty by onsemi, and no additional obligations or liabilities shall arise from onsemi having provided such information or services.
onsemi products including the boards are not designed, intended, or authorized for use in life support systems, or any FDA Class 3 medical devices or medical devices with a similar or equivalent classification in a foreign jurisdiction, or any devices intended for implantation in the human body. You agree to indemnify, defend and hold harmless onsemi, its directors, officers, employees, representatives, agents, subsidiaries, affiliates, distributors, and assigns, against any and all liabilities, losses, costs, damages, judgments, and expenses, arising out of any claim, demand, investigation, lawsuit, regulatory action or cause of action arising out of or associated with any unauthorized use, even if such claim alleges that onsemi was negligent regarding the design or manufacture of any products and/or the board.
This evaluation board/kit does not fall within the scope of the European Union directives regarding electromagnetic compatibility, restricted substances (RoHS), recycling (WEEE), FCC, CE or UL, and may not meet the technical requirements of these or other related directives.
FCC WARNING – This evaluation board/kit is intended for use for engineering development, demonstration, or evaluation purposes only and is not considered by onsemi to be a finished end product fit for general consumer use. It may generate, use, or radiate radio frequency energy and has not been tested for compliance with the limits of computing devices pursuant to part 15 of FCC rules, which are designed to provide reasonable protection against radio frequency interference. Operation of this equipment may cause interference with radio communications, in which case the user shall be responsible, at its expense, to take whatever measures may be required to correct this interference.
onsemi does not convey any license under its patent rights nor the rights of others.
LIMITATIONS OF LIABILITY: onsemi shall not be liable for any special, consequential, incidental, indirect or punitive damages, including, but not limited to the costs of re qualification, delay, loss of profits or goodwill, arising out of or in connection with the board, even if onsemi is advised of the possibility of such damages. In no event shall onsemi’s aggregate liability from any obligation arising out of or in connection with the board, under any theory of liability, exceed the purchase price paid for the board, if any
The board is provided to you subject to the license and other terms per onsemi’s standard terms and conditions of sale. For more information and documentation, please visit www.onsemi.com.
PUBLICATION ORDERING INFORMATION
LITERATURE FULFILLMENT
Email Requests to: [email protected]
onsemi Website: www.onsemi.co
TECHNICAL SUPPORT
North American Technical Support
Voice Mail: 1 800−282−9855 Toll Free USA/Canada
Phone: 011 421 33 790 2910
Europe, Middle East and Africa Technical Support
Phone: 00421 33 790 2910
For additional information, please contact your local Sales Representative
Documents / Resources
onsemi FUSB307BGEVB Type-C Port Controller IC Evaluation Board [pdf] User Manual
FUSB307BGEVB Type-C Port Controller IC Evaluation Board, FUSB307BGEVB, Type-C Port
Controller IC Evaluation Board, Controller IC Evaluation Board, IC Evaluation Board, Evaluation
Board, Board
References
required.cc - This website is for sale! - required Resources and Information.
Intelligent Power and Sensing Technologies | onsemi
Manuals+,
advertisement
Related manuals
advertisement