advertisement
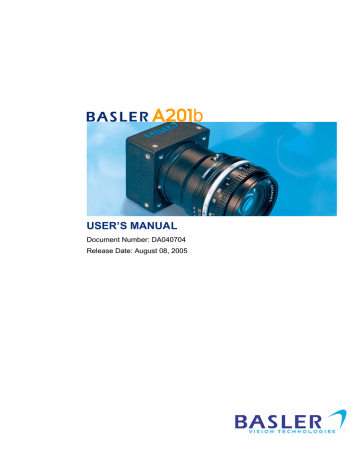
USER’S MANUAL
Document Number: DA040704
Release Date: August 08, 2005
For customers in the U.S.A.
This equipment has been tested and found to comply with the limits for a Class A digital device, pursuant to Part 15 of the FCC Rules. These limits are designed to provide reasonable protection against harmful interference when the equipment is operated in a commercial environment. This equipment generates, uses, and can radiate radio frequency energy and, if not installed and used in accordance with the instruction manual, may cause harmful interference to radio communications. Operation of this equipment in a residential area is likely to cause harmful interference in which case the user will be required to correct the interference at his own expense.
You are cautioned that any changes or modifications not expressly approved in this manual could void your authority to operate this equipment.
The shielded interface cable recommended in this manual must be used with this equipment in order to comply with the limits for a computing device pursuant to Subpart J of Part 15 of FCC
Rules.
For customers in Canada
This apparatus complies with the Class A limits for radio noise emissions set out in Radio Interference Regulations.
Pour utilisateurs au Canada
Cet appareil est conforme aux normes Classe A pour bruits radioélectriques, spécifiées dans le
Règlement sur le brouillage radioélectrique.
Life Support Applications
These products are not designed for use in life support appliances, devices, or systems where malfunction of these products can reasonably be expected to result in personal injury. Basler customers using or selling these products for use in such applications do so at their own risk and agree to fully indemnify Basler for any damages resulting from such improper use or sale.
Warranty Note
Do not open the housing of the camera. The warranty becomes void if the housing is opened.
All material in this publication is subject to change without notice and is copyright Basler
Vision Technologies.
Contacting Basler Support Worldwide
Europe:
Basler AG
An der Strusbek 60 - 62
22926 Ahrensburg
Germany
Tel.: +49-4102-463-500
Fax.: +49-4102-463-599 [email protected]
Americas:
Basler, Inc.
740 Springdale Drive, Suite 100
Exton, PA 19341
U.S.A.
Tel.: +1-877-934-8472
Fax.: +1-877-934-7608 [email protected]
Asia:
Basler Asia PTe. Ltd
25 Internat. Business Park
#04-15/17 German Centre
Singapore 609916
Tel.: +65-6425-0472
Fax.: +65-6425-0473 [email protected]
www.basler-vc.com
DRAFT
Table of Contents
Table of Contents
1 Introduction
2 Camera Interface
2.3.1 ExSync: Controls Line Readout and Exposure Time . . . . . . . . . . . . . . . . . . 2-4
2.3.1.1 RS-644/RS-422 Compatibility . . . . . . . . . . . . . . . . . . . . . . . . . . . . . 2-4
2.4.7.1 Operation in Single 10 Bit or Single 8 Bit Output Mode . . . . . . . . . 2-10
2.4.7.2 Operation in Dual 10 Bit or Dual 8 Bit Output Mode. . . . . . . . . . . . 2-13
2.8 Converting Channel Link Video Output to RS-644 with a BIC. . . . . . . . . . . . . . . . 2-17
3 Basic Operation and Features
3.1.1.1 Integrated IR Cut Filter on C-Mount Equipped Cameras . . . . . . . . . 3-3
BASLER A201 b i
ii
Table of Contents
DRAFT
3.3.1 ExSync, Level-controlled Mode with Exposure Start After Image Transfer
3.3.2 ExSync, Level-controlled Mode with Exposure Start During Image Transfer
3.3.3 ExSync, Programmable Mode with Exposure Start After Image Transfer
3.3.4 ExSync, Programmable Mode with Exposure Start During Image Transfer
3.3.5 Free-run, Programmable Mode with Exposure Start After Image Transfer
3.3.6 Free-run, Programmable Mode with Exposure Start During Image Transfer
3.5.2 Balancing the Gain and Offset on Odd and Even Lines . . . . . . . . . . . . . . . 3-15
3.7.2 Changes to the Maximum Frame Rate with Area of Interest. . . . . . . . . . . . 3-26
4 Configuring the Camera
4.1 Configuring the Camera with the Camera Configuration Tool. . . . . . . . . . . . . . . . . 4-2
4.2 Configuring the Camera with Binary Programming Commands . . . . . . . . . . . . . . . 4-4
4.2.1 Command Frame and Response Format . . . . . . . . . . . . . . . . . . . . . . . . . . . 4-4
4.2.3.3 Calculating the Block Check Character . . . . . . . . . . . . . . . . . . . . . . 4-8
4.2.4 Commands for Setting Camera Parameters . . . . . . . . . . . . . . . . . . . . . . . . . 4-9
BASLER A201 b
DRAFT
Table of Contents
4.2.4.1 Video Data Output Mode . . . . . . . . . . . . . . . . . . . . . . . . . . . . . . . . . 4-9
4.2.4.2 Exposure Time Control Mode. . . . . . . . . . . . . . . . . . . . . . . . . . . . . 4-10
4.2.4.6 Area of Interest Starting Column . . . . . . . . . . . . . . . . . . . . . . . . . . 4-13
4.2.4.7 Area of Interest Width in Columns . . . . . . . . . . . . . . . . . . . . . . . . . 4-14
4.2.4.9 Area of Interest Height in Lines . . . . . . . . . . . . . . . . . . . . . . . . . . . 4-16
4.2.7.1 Read Microcontroller Firmware Version . . . . . . . . . . . . . . . . . . . . . 4-20
4.2.7.2 Read FPGA Firmware Version. . . . . . . . . . . . . . . . . . . . . . . . . . . . 4-20
4.2.7.3 Read Vendor Information . . . . . . . . . . . . . . . . . . . . . . . . . . . . . . . . 4-20
4.2.7.7 Read Gain and Offset Reference Values . . . . . . . . . . . . . . . . . . . . 4-22
4.2.8 Commands for Manipulating Configuration Sets . . . . . . . . . . . . . . . . . . . . . 4-23
4.2.8.1 Copy the Factory Set or a User Set into the Work Set. . . . . . . . . . 4-23
4.2.8.2 Copy Work Set into a User Set . . . . . . . . . . . . . . . . . . . . . . . . . . . 4-24
5 Mechanical Considerations
6 Troubleshooting
BASLER A201 b iii
iv
Table of Contents
DRAFT
Appendix A Using the Camera with a BIC
A.1.3.1 Temperature and Humidity . . . . . . . . . . . . . . . . . . . . . . . . . . . . . . . A-3
A.3.1 Channel Link Cable Between the Camera and the BIC . . . . . . . . . . . . . . . . A-9
A.3.2 Video Data Cable Between the BIC and the Frame Grabber . . . . . . . . . . . . A-9
A.3.3 RS-232 Cable Between the BIC and the PC. . . . . . . . . . . . . . . . . . . . . . . . A-10
A.4 Video Data and Control Signals Between the BIC and the Frame Grabber . . . . . A-10
A.4.1 Signals Input to the BIC by the Frame Grabber . . . . . . . . . . . . . . . . . . . . . A-10
A.4.1.1 ExSync: Controls Frame Readout and Exposure Time . . . . . . . . . A-10
A.4.2 Signals Output from the BIC to the Frame Grabber . . . . . . . . . . . . . . . . . . A-11
A.4.2.1 FVAL: Indicates a Valid Frame . . . . . . . . . . . . . . . . . . . . . . . . . . . A-11
A.4.2.2 LVAL: Indicates a Valid Line . . . . . . . . . . . . . . . . . . . . . . . . . . . . . A-11
A.4.2.3 Pixel Clock: Indicates a Valid Pixel . . . . . . . . . . . . . . . . . . . . . . . . A-11
A.4.2.5 BIC Operation with Attached Camera in Single 10 Bit or
Single 8 Bit Output Mode . . . . . . . . . . . . . . . . . . . . . . . . . . . . . . . . A-11
A.4.2.6 BIC Operation with Attached Camera in Dual 8 Bit Output Mode . A-14
A.4.3.1 RS-644/RS-422 Compatibility . . . . . . . . . . . . . . . . . . . . . . . . . . . . A-16
A.8.1 Making Connections (BIC Directly Attached to Camera) . . . . . . . . . . . . . . A-19
A.8.2 Making Connections (BIC and Camera Mated with a Cable) . . . . . . . . . . . A-21
BASLER A201 b
DRAFT
Table of Contents
Revision History . . . . . . . . . . . . . . . . . . . . . . . . . . . . . . . . . . . . . . . . . . . . . . i
Feedback . . . . . . . . . . . . . . . . . . . . . . . . . . . . . . . . . . . . . . . . . . . . . . . . . . . iii
Index . . . . . . . . . . . . . . . . . . . . . . . . . . . . . . . . . . . . . . . . . . . . . . . . . . . . . . . v
BASLER A201 b v
Table of Contents
DRAFT vi
BASLER A201 b
DRAFT
1 Introduction
Introduction
The Basler A201 b high resolution, progressive scan cameras are versatile cameras designed for industrial use. Superb image sensing features are combined with a robust, high-precision machined housing.
Important features are:
• High spacial resolution
• High sensitivity
• Anti-blooming
• Asynchronous full frame shutter via electronic exposure control
• Square sensor cells
• High Signal-to-Noise ratio
• Programmable via an RS-232 serial port
• Area of interest (AOI) scanning
• Correlated double sampling
• Industrial housing manufactured with high planar, parallel and angular precision
• Compact Size
1.1 Camera Models
There are two camera models: the A201 b monochrome version and a color version designated as the A201 bc . Throughout this manual, the camera will be called the A201 b . Passages that are only valid for a specific model will be so indicated.
BASLER A201 b 1-1
Introduction
DRAFT
1.2 Performance Specifications
Category
Sensor
Pixels
Pixel Size
Photosensitive Area
Fill Factor
Spectral Response
Photo Response Non-uniformity
Photo Response Non-linearity
Pixel Clock Speed
Max. Frame Rate
Video Output Type
Video Output Formats
Synchronization
Exposure Time Control
Gain and Offset
Connector
Power Requirements
Lens Adapters
Housing Size (L x W x H)
Weight
Specification
Interline Transfer Progressive Scan CCD Sensor
1008 (H) x 1018 (V)
9 µm x 9 µm
9.1 mm (H) x 9.2 mm (V)
55%
Monochrome Camera:
Color Camera:
± 5% (typical)
± 5% (typical)
42 MHz in single output mode or 21 MHz in dual output mode
30 Frames/sec.
Channel Link LVDS (RS-644 LVDS when the camera is used with an optional Basler Interface Converter)
Single 8 Bit, Single 10 Bit, Dual 8 Bit, or Dual 10 Bit
Via external ExSync signal or free-run
Level-controlled, programmable, or free-run
Programmable via a serial link
One, 26 pin, high-density, D-Sub plug
12 VDC (± 10%), max. 8 W, < 1% ripple
C-mount or F-mount without lens adapter: with C-mount adapter: with F-mount adapter: without lens adapter: with C-mount adapter: with F-mount adapter:
CE, FCC
38.1 mm x 62 mm x 62 mm
40.6 mm x 62 mm x 62 mm
69.6 mm x 62 mm x 62 mm
~ 155 g.
~ 200 g.
~ 265 g.
Conformity
Table 1-1: A201 b Performance Specifications
1-2 BASLER A201 b
DRAFT
Introduction
40
35
30
25
20
15
10
5
0
400 450 500 550 600 650 700 750 800 850
Wavelength (nm)
900 950 1000
Figure 1-1: Spectral Response - A201 b Monochrome Camera
50
45
40
35
30
25
20
15
10
5
0
400 500 600
Red
700
Wavelength (nm)
Green
800
Blue
900
Figure 1-2: Spectral Response - A201 bc Color Camera
L
Cameras equipped with a C-mount lens adapter contain an integrated IR cut filter.
On cameras equipped with an F-mount adapter, use of a suitable IR cut filter is recommended to maintain spectral balance and optimum MTF.
1-3 BASLER A201 b
Introduction
DRAFT
1.3 Environmental Requirements
1.3.1 Temperature and Humidity
Housing temperature during operation:
Humidity during operation:
0° C ... + 50° C (+ 32° F ... + 122° F)
20% ... 80%, relative, non-condensing
1.3.2 Ventilation
Allow sufficient air circulation around the camera to prevent internal heat build-up in your system and to keep the camera housing temperature during operation below 50° C. Provide additional cooling such as fans or heat sinks if necessary.
Warning!
Without sufficient cooling, the camera can get hot enough during operation to cause burning when touched.
1-4 BASLER A201 b
DRAFT
Introduction
1.4 Precautions
Power
Caution!
Be sure that all power to your system is switched off before you make or break connections to the camera. Making or breaking connections when power is on can result in damage to the camera.
Read the manual
Read the manual carefully before using the camera.
Keep foreign matter outside of the camera
Do not open the casing. Touching internal components may damage them.
Be careful not to allow liquid, flammable, or metallic material inside the camera housing. If operated with any foreign matter inside, the camera may fail or cause a fire.
Electromagnetic Fields
Do not operate the camera in the vicinity of strong electromagnetic fields. Avoid electrostatic charging.
Transporting
Only transport the camera in its original packaging. Do not discard the packaging.
Cleaning
Avoid cleaning the surface of the CCD sensor if possible. If you must clean it, use a soft, lint free cloth dampened with a small quantity of pure alcohol. Do not use methylated alcohol.
Because electrostatic discharge can damage the CCD sensor, you must use a cloth that will not generate static during cleaning (cotton is a good choice).
To clean the surface of the camera housing, use a soft, dry cloth. To remove severe stains, use a soft cloth dampened with a small quantity of neutral detergent, then wipe dry.
Do not use volatile solvents such as benzine and thinners; they can damage the surface finish.
BASLER A201 b 1-5
Introduction
DRAFT
1-6 BASLER A201 b
DRAFT
2 Camera Interface
Camera Interface
2.1 Connections
2.1.1 General Description
The A201 b is interfaced to external circuitry via a single, high density, 26 pin D-Sub plug located
on the back of the camera. Figure 2-1 shows the plug and the two status LEDs which indicate
signal integrity and power OK.
Yellow LED
(signal integrity)
Green LED
(power OK)
Figure 2-1: A201 b Connector and LEDs
BASLER A201 b
D-Sub HD
26 Pin Plug
2-1
Camera Interface
DRAFT
2.1.2 Pin Assignments
The pin assignments for the D-Sub HD 26 plug used to interface video data, control signals and
Pin
Number
Signal
Name
Direction Level Function
1, 9, 18,
19, 25, 26 1
DC Gnd
Input Ground DC Ground
2, 20 2
22
24
+12 VDC
RxD
TxD
Input
Input
Output
12 VDC ± 10%
RS-232
RS-232
DC Power
RS-232 Serial Communication Data Receive
RS-232 Serial Communication Data Transmit
21, 23
1
11
Signal Gnd
ExSync+
ExSync-
Reserved+
Input
Input
Ground
RS-644
LVDS
Signal Ground
External Trigger
10
13
Reserved-
TxClkOut+
Input RS-644
LVDS
Reserved LVDS Input
12
17
TxClkOut-
TxDataOut3+
Output Channel Link
LVDS
Transmit Clock from Channel Link Transmitter
16
8
TxDataOut3-
TxDataOut2+
Output Channel Link
LVDS
Data from Channel Link Transmitter
7
6
TxDataOut2-
TxDataOut1+
Output Channel Link
LVDS
Data from Channel Link Transmitter
5
15
TxDataOut1-
TxDataOut0+
Output Channel Link
LVDS
Data from Channel Link Transmitter
14
4 Output Channel Link
LVDS
Data from Channel Link Transmitter
3 TxDataOut0-
1
Pins 1, 9, 18, 19, 25, 26, 21 and 23 are all tied together inside of the camera.
2
Pins 2 and 20 are tied together inside of the camera.
Table 2-1:A201 b Pin Assignments for the D-Sub HD 26-pin Plug
The camera housing is not grounded and is electrically isolated from the circuit boards inside of the camera.
The camera has no reverse power protection. Therefore, always observe
the polarity as indicated in Table 2-1.
The camera has no overvoltage protection. Therefore, always observe the
power requirements as described in Section 2.6
.
2-2 BASLER A201 b
DRAFT
Camera Interface
Figure 2-2: A201 b Pin Numbering
1
10
19 26
9
18
2.1.3 Plug Source Information
At the time this manual was published, Basler’s sources for the 26 pin, high density plug used on the camera are FCT Electronic (Part CT15-26P1-L228) and AMP (Part HDP-22 Size-2 26-
Position). Basler will use plugs from either of these suppliers or the equivalent.
2.2 Cable Information
The cable between the camera and the frame grabber must meet the specifications shown in
Characteristic
Maximum Length
Specification
10 meters
1
100 ± 10 Ω Individually Shielded Twisted Pair
Characteristic Impedance
Conductor Size 28 AWG Stranded
1
The maximum cable length was tested with a Sumitomo IEE6-99135 cable. It will decrease when used
in an area with severe ambient electromagnetic interference.
Table 2-2: Cable Specifications
BASLER A201 b 2-3
Camera Interface
DRAFT
2.3 Input Signals
The ExSync input signal can be used to control the A201 b . ExSync is an LVDS signal as specified
describes the ExSync input signal.
2.3.1 ExSync: Controls Line Readout and Exposure Time
The camera can be programmed to function under the control of an externally generated sync signal in either of two exposure time control modes. In these modes, level-controlled and programmable, the ExSync signal is used to control exposure time and frame read out. For more detailed information on the two modes, see Section
ExSync can be a periodic or non-periodic function. The frequency of the ExSync signal determines the camera’s frame rate. Note that ExSync is edge sensitive and therefore must toggle. Minimum high time for the ExSync signal is 1 µs.
The A201 b uses a National Semiconductor DS90LV048A differential line receiver to receive the
ExSync input signal. A detailed spec sheet for this RS-644 LVDS device is available at the
National Semiconductor web site (www.national.com).
Figure 2-3 shows a basic schematic for the input stage of the A201
b .
2.3.1.1 RS-644/RS-422 Compatibility
The input voltage tolerance for the RS-644 receiver used in the A201 b is 0.0 V to 3.9 V. On typical
RS-422 transmitters, the output voltage can range as high as 4.0 V. As you see, the output voltage of a typical RS-422 transmitter can exceed the input voltage tolerance of the RS-644 receiver in the A201 b . Therefore, RS-422 signals should not be input directly into the A201 b .
2-4
Figure 2-3: A201 b DC Power and RS-644 Input Connections
BASLER A201 b
DRAFT
Camera Interface
2.4 Output Signals
Data is output from the A201 b using Channel Link LVDS technology.
2.4.1 Channel Link Basics
Channel Link is an LVDS (Low Voltage Differential Signaling) technology for transmitting digital data. Channel Link uses a parallel-to-serial transmitter and a serial-to-parallel receiver to transmit data at rates up to 1.8 Gbps.
As shown in Figure 2-4, the Channel Link Transmitter converts 28 bits of CMOS/TTL data into four
LVDS data streams. A phase-locked pixel clock is transmitted in parallel with the data streams over a fifth LVDS link. With each cycle of the pixel clock, 28 bits of input data are sampled and transmitted. The Channel Link receiver converts the data streams back into 28 bits of CMOS/TTL data.
Channel Link was developed by National Semiconductor and is a registered trademark of that company.
Transmitter Receiver
Data (LVDS)
Data (LVDS)
Data (LVDS)
Data (LVDS)
Transmit Clock
PLL Clock (LVDS) PLL
Receive Clock
Figure 2-4: Channel Link Block Diagram
BASLER A201 b 2-5
Camera Interface
DRAFT
2.4.2 Channel Link Implementation in the A201 b
The A201 b uses a National Semiconductor DS90C383 as a Channel Link transmitter. For a
Channel Link receiver, we recommend that you use the National Semiconductor DS90CF386, the
National Semiconductor DS90CR288 or an equivalent. Detailed data sheets for these components are available at the National Semiconductor web site (www.national.com). The data sheets contain all of the information that you need to implement Channel Link, including application notes.
The schematic in Figure 2-5 shows the configuration of the output from the Channel Link
transmitter in the A201 b and a typical implementation for the Channel Link receiver in a frame grabber. During normal operation, 28 bits of TTL data are input to the transmitter on TX inputs 0 through 27 and the pixel clock is input on TxCLKIN. After transmission, the 28 bits appear as TTL signals on the corresponding RX outputs of the receiver.
L
Note that the timing used for sampling the data at the Channel Link receiver in the frame grabber varies from device to device. On some receivers, TTL data must be sampled on the rising edge of the receive clock, and on others, it must be sampled on the falling edge. Also, some devices are available which allow you to select either rising edge or falling edge sampling. Please consult the data sheet for the receiver that you are using for specific timing information.
2-6 BASLER A201 b
DRAFT
Camera Interface
BASLER A201 b 2-7
2-8
Camera Interface
DRAFT
2.4.3 Pixel Clock
As shown in Figure 2-5 and in Table 2-3, the pixel clock is assigned to the TxClkIn (transmit clock)
pin of the Channel Link transmitter. The pixel clock is used to time the sampling and transmission of pixel data as shown in Figures
2-9 . The Channel Link transmitter used in A201
b cameras requires pixel data to be sampled and transmitted on the falling edge of the clock.
The frequency of the pixel clock varies depending on the output mode of the camera. The available output modes are explained in detail in Sections
L
Note that the timing used for sampling the data at the Channel Link receiver in the frame grabber varies from device to device. On some receivers, data must be sampled on the rising edge of the pixel clock (receive clock), and on others, it must be sampled on the falling edge. Also, some devices are available which allow you to select either rising edge or falling edge sampling. Please consult the data sheet for the receiver that you are using for specific timing information.
2.4.4 Frame Valid Bit
As shown in Figures
through 2-9 , the frame valid bit indicates that a valid frame is being
transmitted.
2.4.5 Line Valid Bit
As shown in Figures
through
, the line valid bit indicates that a valid line is being transmitted. Pixel data is only valid when the frame valid bit and the line valid bit are both high.
2.4.6 Video Data
Table 2-3 lists the assignment of pixel data bits to the input pins on the Channel Link transmitter
in the camera and the corresponding output pins on the Channel Link receiver in the frame grabber. As shown in the table, the bit assignments for pixel data varies depending on the output mode setting of the camera. The available output modes are explained in more detail in Sections
.
Table 2-3 also shows the assignment for the frame valid bit, the line valid bit and the pixel clock.
These assignments are constant for all output modes.
BASLER A201 b
DRAFT
Camera Interface
Camera
TxIN0
TxIN1
TxIN2
TxIN3
TxIN4
TxIN5
TxIN6
TxIN7
TxIN8
TxIN9
TxIN10
TxIN11
TxIN12
TxIN13
TxIN14
Frame
Grabber
RxOUT0
RxOUT1
RxOUT2
RxOUT3
RxOUT4
RxOUT5
RxOUT6
RxOUT7
RxOUT8
RxOUT9
RxOUT10
RxOUT11
RxOUT12
RxOUT13
RxOUT14
TxIN15
TxIN16
TxIN17
TxIN18
TxIN19
TxIN20
TxIN21
TxIN22
TxIN23
TxIN24
TxIN25
TxIN26
TxIN27
TxCLKIn
RxOUT15
RxOUT16
RxOUT17
RxOUT18
RxOUT19
RxOUT20
RxOUT21
RxOUT22
RxOUT23
RxOUT24
RxOUT25
RxOUT26
RxOUT27
RxCLKOut
Table 2-3: Bit Assignments
Reserved
Reserved
Reserved
Reserved
Reserved
Reserved
Reserved
Reserved
Reserved
Line Valid
Frame Valid
Reserved
Pixel Bit 6
Pixel Clock
Single 10 Bit
Output Mode
Pixel Bit 0
Pixel Bit 1
Pixel Bit 2
Pixel Bit 3
Pixel Bit 4
Pixel Bit 7
Pixel Bit 5
Pixel Bit 8
Pixel Bit 9 (MSB)
Reserved
Reserved
Reserved
Reserved
Reserved
Reserved
Single 8 Bit
Output Mode
Pixel Bit 0
Pixel Bit 1
Pixel Bit 2
Pixel Bit 3
Pixel Bit 4
Pixel Bit 7 (MSB)
Pixel Bit 5
Reserved
Reserved
Reserved
Reserved
Reserved
Reserved
Reserved
Reserved
Reserved
Reserved
Reserved
Reserved
Reserved
Reserved
Reserved
Reserved
Reserved
Line Valid
Frame Valid
Reserved
Pixel Bit 6
Pixel Clock
Dual 10 Bit
Output Mode
Odd Pixel Bit 0
Odd Pixel Bit 1
Odd Pixel Bit 2
Odd Pixel Bit 3
Odd Pixel Bit 4
Odd Pixel Bit 7
Odd Pixel Bit 5
Odd Pixel Bit 8
Odd Pixel Bit 9
(MSB)
Reserved
Reserved
Reserved
Reserved
Even Pixel Bit 8
Even Pixel Bit 9
(MSB)
Even Pixel Bit 0
Even Pixel Bit 6
Even Pixel Bit 7
Even Pixel Bit 1
Even Pixel Bit 2
Even Pixel Bit 3
Even Pixel Bit 4
Even Pixel Bit 5
Reserved
Line Valid
Frame Valid
Reserved
Odd Pixel Bit 6
Pixel Clock
Dual 8 Bit
Output Mode
Odd Pixel Bit 0
Odd Pixel Bit 1
Odd Pixel Bit 2
Odd Pixel Bit 3
Odd Pixel Bit 4
Odd Pixel Bit 7
(MSB)
Odd Pixel Bit 5
Even Pixel Bit 0
Even Pixel Bit 1
Even Pixel Bit 2
Even Pixel Bit 6
Even Pixel Bit 7
(MSB)
Even Pixel Bit 3
Even Pixel Bit 4
Even Pixel Bit 5
Reserved
Reserved
Reserved
Reserved
Reserved
Reserved
Reserved
Reserved
Reserved
Line Valid
Frame Valid
Reserved
Odd Pixel Bit 6
Pixel Clock
BASLER A201 b 2-9
Camera Interface
DRAFT
2.4.7 Video Data Output Modes
The L201 b can operate in Single 10 Bit, Single 8 Bit, Dual 10 Bit, or Dual 8 Bit output mode. These
modes are described in detail in Sections 2.4.7.1
and
.
2.4.7.1 Operation in Single 10 Bit or Single 8 Bit Output Mode
In Single 10 Bit mode, the pixel clock operates at 42 MHz. On each clock cycle, the camera transmits 10 bits of pixel data, a frame valid bit, and a line valid bit. The assignment of the bits is
The pixel clock is used to time data sampling and transmission. As shown in Figures
the camera samples and transmits data on each falling edge of the pixel clock.
The frame valid bit indicates that a valid frame is being transmitted.
The line valid bit indicates that a valid line is being transmitted. Pixel data is only valid when the frame valid bit and the line valid bit are both high.
Operation in Single 8 Bit mode is similar to Single 10 Bit mode except that the two least significant bits output from each ADC are dropped and only 8 bits of data per pixel is transmitted.
L
The data sequence outlined below, along with Figures
what is happening at the inputs to the Channel Link transmitter in the camera.
Note that the timing used for sampling the data at the Channel Link receiver in the frame grabber varies from device to device. On some receivers, data must be sampled on the rising edge of the pixel clock (receive clock), and on others, it must be sampled on the falling edge. Also, some devices are available which allow you to select either rising edge or falling edge sampling. Please consult the data sheet for the receiver that you are using for specific timing information.
2-10
Video Data Sequence
1
When the camera is not transmitting valid data, the frame valid and line valid bits sent on each cycle of the pixel clock will be low. Once the camera has completed frame acquisition, it will begin to send valid data:
• On the pixel clock cycle where frame data transmission begins, the frame valid bit will become high.
• On the pixel clock cycle where data transmission for line one begins, the line valid bit will become high. Ten of the bits transmitted during this clock cycle will contain the data for pixel number one in line one.
• On the next cycle of the pixel clock, the line valid bit will be high. Ten of the bits transmitted during this clock cycle will contain the data for pixel number two in line one.
• On the next cycle of the pixel clock, the line valid bit will be high. Ten of the bits transmitted during this clock cycle will contain the data for pixel number three in line one.
• This pattern will continue until all of the pixel data for line one has been transmitted. (A total of 1008 cycles.)
• After all of the pixels in line one have been transmitted, the line valid bit will become low indicating that valid data for line one is no longer being transmitted.
____________________
1 The data sequence assumes that the camera is operating in 10 bit mode. If the camera is operating in 8 bit mode, only 8 bits of data per pixel will be transmitted.
BASLER A201 b
DRAFT
Camera Interface
• On the pixel clock cycle where data transmission for line two begins, the line valid bit will become high. Ten of the bits transmitted during this clock cycle will contain the data for pixel number one in line two.
• On the next cycle of the pixel clock, the line valid bit will be high. Ten of the bits transmitted during this clock cycle will contain the data for pixel number two in line two.
• On the next cycle of the pixel clock, the line valid bit will be high. Ten of the bits transmitted during this clock cycle will contain the data for pixel number three in line two.
• This pattern will continue until all of the pixel data for line two has been transmitted. (A total of
1008 cycles.)
• After all of the pixels in line two have been transmitted, the line valid bit will become low indicating that valid data for line two is no longer being transmitted.
• The camera will continue to transmit pixel data for each line as described above until all of the lines in the frame have been transmitted. After all of the lines have been transmitted, the frame valid bit will become low indicating that a valid frame is no longer being transmitted.
Figure 2-6 shows the data sequence when the camera is operating in level-controlled exposure
mode. Figure 2-7 shows the data sequence when the camera is operating in programmable
exposure mode.
This diagram is not drawn to scale.
The diagram assumes that the area of interest feature is not being used. With the area of interest feature enabled, the number of lines transferred and the number of pixels in each line could be smaller.
Figure 2-6: Single 10 Bit or Single 8 Bit Output Mode with Level Controlled Exposure
____________________
1 The Line Valid low time alternates between 6.2 µs and 7.4 µs. The first low time is 6.2 µs, the next is 7.4 µs, the next is 6.2 µs, the next 7.4 µs, and so on. This pattern will continue until all of the pixel data for a line has been transmitted.
2 Depending on the Line Valid low time, the Line Valid cycle is either 30.2 µs or 31.4 µs.
BASLER A201 b 2-11
Camera Interface
DRAFT
This diagram is not drawn to scale.
The diagram assumes that the area of interest feature is not being used. With the area of interest feature enabled, the number of lines transferred and the number of pixels in each line could be smaller.
Figure 2-7: Single 10 Bit or Single 8 Bit Output Mode with Programmable Exposure
2-12
____________________
1 The Line Valid low time alternates between 6.2 µs and 7.4 µs. The first low time is 6.2 µs, the next is 7.4 µs, the next is 6.2 µs, the next 7.4 µs, and so on. This pattern will continue until all of the pixel data for a line has been transmitted.
2 Depending on the Line Valid low time, the Line Valid cycle is either 30.2 µs or 31.4 µs.
BASLER A201 b
DRAFT
Camera Interface
2.4.7.2 Operation in Dual 10 Bit or Dual 8 Bit Output Mode
In Dual 10 Bit mode, the pixel clock operates at 21 MHz. On each clock cycle, the camera transmits 10 bits of pixel data for two pixels, a frame valid bit, and a line valid bit. The assignment
of the bits is shown in Table 2-3.
The pixel clock is used to time data sampling and transmission. As shown in Figures
the camera samples and transmits data on each falling edge of the pixel clock.
The frame valid bit indicates that a valid frame is being transmitted.
The line valid bit indicates that a valid line is being transmitted. Pixel data is only valid when the frame valid bit and the line valid bit are both high.
Operation in Dual 8 Bit mode is similar to Dual 10 Bit mode except that the two least significant bits output from each ADC are dropped and only 8 bits of data per pixel is transmitted.
L
The data sequence outlined below, along with Figures
what is happening at the inputs to the Channel Link transmitter in the camera.
Note that the timing used for sampling the data at the Channel Link receiver in the frame grabber varies from device to device. On some receivers, data must be sampled on the rising edge of the pixel clock (receive clock), and on others, it must be sampled on the falling edge. Also, some devices are available which allow you to select either rising edge or falling edge sampling. Please consult the data sheet for the receiver that you are using for specific timing information.
Video Data Sequence
1
When the camera is not transmitting valid data, the frame valid and line valid bits sent on each cycle of the pixel clock will be low. Once the camera has completed frame acquisition, it will begin to send valid data:
• On the pixel clock cycle where frame data transmission begins, the frame valid bit will become high.
• On the pixel clock cycle where data transmission for line one begins, the line valid bit will become high. Ten of the bits transmitted during this clock cycle will contain the data for pixel number one in line one and ten of the bits will contain data for pixel number two in line one.
• On the next cycle of the pixel clock, the line valid bit will be high. Ten of the bits transmitted during this clock cycle will contain the data for pixel number three in line one and ten of the bits will contain data for pixel number four in line one.
• On the next cycle of the pixel clock, the line valid bit will be high. Ten of the bits transmitted during this clock cycle will contain the data for pixel number five in line one and ten of the bits will contain data for pixel number six in line one.
• This pattern will continue until all of the pixel data for line one has been transmitted. (A total of 504 cycles.)
• After all of the pixels in line one have been transmitted, the line valid bit will become low indicating that valid data for line one is no longer being transmitted.
• On the pixel clock cycle where data transmission for line two begins, the line valid bit will become high. Ten of the bits transmitted during this clock cycle will contain the data for pixel number one in line two and ten of the bits will contain data for pixel number two in line two.
____________________
1 The data sequence assumes that the camera is operating in 10 bit mode. If the camera is operating in 8 bit mode, only 8 bits of data per pixel will be transmitted.
2-13 BASLER A201 b
Camera Interface
DRAFT
• On the next cycle of the pixel clock, the line valid bit will be high. Ten of the bits transmitted during this clock cycle will contain the data for pixel number three in line two and ten of the bits will contain data for pixel number four in line two.
• On the next cycle of the pixel clock, the line valid bit will be high. Ten of the bits transmitted during this clock cycle will contain the data for pixel number five in line two and ten of the bits will contain data for pixel number six in line two.
• This pattern will continue until all of the pixel data for line two has been transmitted. (A total of
504 cycles.)
• After all of the pixels in line two have been transmitted, the line valid bit will become low indicating that valid data for line two is no longer being transmitted.
• The camera will continue to transmit pixel data for each line as described above until all of the lines in the frame have been transmitted. After all of the lines have been transmitted, the frame valid bit will become low indicating that a valid frame is no longer being transmitted.
Figure 2-8 shows the data sequence when the camera is operating in level-controlled exposure
mode. Figure 2-9 shows the data sequence when the camera is operating in programmable
exposure mode.
This diagram is not drawn to scale.
The diagram assumes that the area of interest feature is not being used. With the area of interest feature enabled, the number of lines transferred and the number of pixels in each line could be smaller.
Figure 2-8: Dual 10 Bit or Dual 8 Bit Output Mode with Level Controlled Exposure
2-14
____________________
1 The Line Valid low time alternates between 6.2 µs and 7.4 µs. The first low time is 6.2 µs, the next is 7.4 µs, the next is 6.2 µs, the next 7.4 µs, and so on. This pattern will continue until all of the pixel data for a line has been transmitted.
2 Depending on the Line Valid low time, the Line Valid cycle is either 30.2 µs or 31.4 µs.
BASLER A201 b
DRAFT
Camera Interface
This diagram is not drawn to scale.
The diagram assumes that the area of interest feature is not being used. With the area of interest feature enabled, the number of lines transferred and the number of pixels in each line could be smaller.
Figure 2-9: Dual 10 Bit or Dual 8 Bit Output Mode with Programmable Exposure
____________________
1 The Line Valid low time alternates between 6.2 µs and 7.4 µs. The first low time is 6.2 µs, the next is 7.4 µs, the next is 6.2 µs, the next 7.4 µs, and so on. This pattern will continue until all of the pixel data for a line has been transmitted.
2 Depending on the Line Valid low time, the Line Valid cycle is either 30.2 µs or 31.4 µs.
BASLER A201 b 2-15
Camera Interface
DRAFT
2.5 RS-232 Serial Communication
The A201 b is equipped for RS-232 serial communication. The RS-232 serial connection is used to issue commands to the camera for changing modes and parameters. The serial link can also be used to query the camera about its current setup.
The Basler Camera Configuration Tool is a convenient, graphical interface that can be used to change camera modes and parameters via the serial connection. The configuration tool is installed as part of the camera installation. A booklet describing how to install the configuration
tool is shipped with the camera. Section 4.1
provides some basic information about the configuration tool. Detailed instructions for using the tool are included in the on-line help file that is installed with the tool.
Basler has also developed a binary command protocol that can be used to change camera modes and parameters directly from your application via the serial connection. See Section
for details on the binary command format.
2.5.1 Making the Serial Connection
You will use a serial port on your PC for RS-232 communication with the camera. Make sure that the following requirements are met:
• Make sure that pin 3 on the PC serial port is wired to pin 22 on the camera.
• Make sure that pin 2 on the PC serial port is wired to pin 24 on the camera.
• Make sure that pin 5 on the serial port is wired to pin 21 or 23 on the camera.
• Make sure that the port is set for 8N1 (8 data bits + no parity + 1 stop bit) and a baud rate of
9600 bps.
2.6 DC Power
The A201 b requires 12 VDC (± 10%) power. The camera has no overvoltage protection. An input voltage higher than 14 VDC will damage the camera.
The camera’s maximum power consumption is approximately 8 watts.
Ripple must be less than 1%.
The camera has no reverse power protection. Therefore, always observe
the polarity as indicated in Table 2-1 on page 2 .
2-16 BASLER A201 b
DRAFT
Camera Interface
2.7 Status LEDs
Green LED
When the green LED on the back of the camera is not lit, it means that no voltage or a voltage below 10.4 V is present. When the green LED is lit, it means that a voltage of 10.4 V or higher is present.
The camera has no overvoltage protection. Therefore, always observe the power requirements as
.
Yellow LED
The yellow LED on the back of the camera indicates signal integrity. At power up, the LED will light for several seconds as the microprocessor in the camera boots up. If all is OK, the LED will then remain lit continuously.
If an error condition is detected at any time after the microprocessor boots up, the LED will begin
to blink an error code. See Section 6 for details.
2.8 Converting Channel Link Video Output to RS-644 with a BIC
As mentioned in Section
, video data is output from the A201
b in Channel Link LVDS format.
The video output from the camera can be converted to RS-644 LVDS by using a Basler Interface
Converter (BIC). The BIC is a small device which attaches to the A201 b . For complete information on installing and using the BIC, refer to Appendix A.
BASLER A201 b 2-17
Camera Interface
DRAFT
2-18 BASLER A201 b
DRAFT
Basic Operation and Features
3 Basic Operation and Features
3.1 Functional Description
The A201 b area scan camera employs a CCD-sensor chip which provides features such as electronic exposure time control and anti-blooming. Exposure time is normally controlled via an externally generated trigger signal (ExSync). The ExSync signal facilitates periodic or nonperiodic pixel readout.
When exposure is controlled by an ExSync signal, exposure time can be either level-controlled or programmable. In level-controlled mode, charge is accumulated when the ExSync signal is low and a rising edge of ExSync triggers the readout of accumulated charges. In programmable mode, exposure time can be programmed to a predetermined time period. In this case, exposure begins on the rising edge of ExSync and accumulated charges are read out when the programmed exposure time ends.
A free-run mode that allows the camera to operate without an ExSync signal is also available. In free-run mode, the camera generates its own internal control signal and the internal signal is used to control exposure and charge read out. When operating in free-run, the camera outputs frames continuously.
At readout, accumulated charges are transported from the light-sensitive sensor elements (pixels) to the CCD vertical shift registers. The charges from the bottom two lines of pixels in the CCD
array are then moved into two horizontal shift registers as shown in Figure 3-1. As charges move
out of the two horizontal shift registers, they are converted to voltages proportional to the size of each charge. Shifting is clocked according to the camera's 42 MHz internal data rate.
The voltages moving out of each shift register are amplified by a Variable Gain Control (VGC) and then digitized by a 10 bit, Analog-to-Digital converter (ADC). The digitized video data is transmitted from the camera to the frame grabber using a Channel Link LVDS transmission format
(see Section
for details). Lines are output sequentially in a progressive scan until one full frame is obtained.
If the camera is an A201 bc , a color interpolation can be done to obtain full RGB information for each pixel (see Section
For optimal digitization, gain and offset are programmable via a serial port.
3-1 BASLER A201 b
Basic Operation and Features
DRAFT
Figure 3-1: A201 b Sensor Architecture
3-2 BASLER A201 b
DRAFT
Basic Operation and Features
3.1.1 Color Creation in the A201 bc
The CCD sensor used in the A201 bc is equipped with an additive color separation filter known as a Bayer filter. With the Bayer filter, each individual pixel is covered by a micro-lens which allows
the figure illustrates, in each block of four pixels, one pixel is struck by red light, one is struck by blue light and two pixels are struck by green light.
Since each individual pixel gathers information on only one color, an interpolation must be made from the surrounding pixels to get full RGB data for the pixel. A DLL that can be used to convert the output from the A201 bc into RGB color information is available through Basler support. The support contact numbers appear on the title page of this manual.
Line 1018
Line 1017
Line 1016
Line 1015
Line 1014
Line 1013
G R G R G
B G B G B
G R G R G
B G B G B
G R G R G
B G B G B
R
G
R
G
R
G
G R G
B G B
G R G
B G B
G R G
B G B
R
G
R
G
R
G
Line 6
Line 5
Line 4
Line 3
Line 2
Line 1
Pixel
G R G R G
B G B G B
G R G R G
B G B G B
G R G R G
B G B G B
R
G
R
G
R
G
1 2 3 4 5 6
Figure 3-2: Bayer Filter Pattern
G R G
B G B
G R G
B G B
G R G
B G B
R
G
R
G
R
G
1005 1006 1007 1008
3.1.1.1 Integrated IR Cut Filter on C-Mount Equipped Cameras
Cameras equipped with a C-mount lens adapter contain an IR cut filter inside of the camera. The location of the IR filter limits the thread length of the lens that is used on the camera. See Section
for more details on lens thread length.
Cameras equipped with an F-mount lens adapter do not contain an IR cut filter.
BASLER A201 b 3-3
Basic Operation and Features
DRAFT
3.2 Exposure Time Control Mode Basics
The A201 b can operate under the control of an external trigger signal (ExSync) or can operate in
“free-run.” In free-run, the camera generates its own internal control signal and does not require an ExSync signal.
3.2.1 ExSync Controlled Operation
In ExSync operation, the camera’s frame rate and exposure time are controlled by an externally generated (ExSync) signal. The ExSync signal is typically supplied to the camera by a frame grabber board. You should refer to the manual supplied with your frame grabber board to determine how to set up the ExSync signal that is being supplied to the camera.
When the camera is operating under the control of an ExSync signal, the length of the ExSync signal period determines the camera’s frame rate. Exsync can be periodic or non-periodic.
When the camera is operating with an ExSync signal, it has two modes of exposure time control available: level-controlled mode and programmable mode.
• In ExSync, level-controlled mode, the exposure time is determined by the time between the falling edge of ExSync and the next rising edge. The pixels are exposed and charge is accumulated only when ExSync is low. The frame is read out and transferred on the rising edge of
the ExSync signal (see Figure 3-3).
ExSync Period
Exposure
ExSync
Frame Read Out
Figure 3-3: ExSync, Level-controlled Mode
• In ExSync, programmable mode, the rising edge of ExSync triggers exposure and charge accumulation for a pre-programmed period of time. The frame is read out and transferred at
the end of the pre-programmed period. The falling edge of ExSync is irrelevant (see Figure 3-
A parameter called "Timer 1" is used to set the length of the pre-programmed exposure period.
ExSync Period
ExSync
Exposure
(Timer 1)
Figure 3-4: ExSync, Programmable Mode
Frame Read Out
3-4 BASLER A201 b
DRAFT
Basic Operation and Features
You can set the camera to operate in one of the ExSync controlled exposure modes using either
the Camera Configuration Tool (see Section 4.1
) or binary commands (see Section
).
With the Camera Configuration Tool, you use the Exposure Tab to set the camera for ExSync operation and to select the level-controlled or programmable exposure time control mode. If you select the programmable mode, you must also enter an exposure time. When you enter an exposure time, the configuration tool will automatically set the “Timer 1” parameter to the correct value.
With binary commands, you must use the Exposure Time Control Mode command to select
ExSync edge-controlled or ExSync programmable mode. If you choose the programmable mode, you must also use the Timer 1 command to set the exposure time.
L
ExSync must toggle.
The minimum ExSync period is 33.3 ms.
ExSync must remain high for at least 1 µs.
The minimum exposure time is 1 µs.
BASLER A201 b 3-5
3-6
Basic Operation and Features
DRAFT
3.2.2 Free-run
In free-run, no ExSync signal is required. The camera generates a continuous internal control signal based on two programmable parameters: "Timer 1" and "Timer 2." Timer 1 determines how long the internal signal will remain low and the Timer 2 determines how long the signal will remain high.
When the camera is operating in free-run, the length of the control signal period determines the camera’s frame rate. (The control signal period is equal to Timer 1 plus Timer 2.)
When the camera is operating in free-run, it exposes and outputs frames continuously.
In free-run, only the programmable mode of exposure time control is available.
• In free-run, programmable mode, the pixels are exposed and charge is accumulated when the internal control signal is low. The frame is read out and transferred on the rising edge of
internal control signal (see Figure 3-5).
In this mode, the exposure time can programmed as desired by varying the setting of the
"Timer 1" parameter.
Control Signal Period
Internal
Control
Signal
Timer 2 Timer 1
Exposure frame read out
Figure 3-5: Free-run, Programmable Mode
You can set the camera to operate in free-run using either the Camera Configuration Tool (see
) or binary commands (see Section
With the Camera Configuration Tool, you use the Exposure Tab to set the camera for free-run and to select the programmable exposure time control mode. If you choose to operate the camera in free-run, the tool will require you to enter a frame rate and an exposure time on the Exposure Tab.
The configuration tool will automatically set the Timer 1 and Timer 2 parameters so that the camera will operate with the frame rate and exposure time that you enter.
With binary commands you must use the Exposure Time Control Mode command to select the free-run, programmable mode. You must also use the Timer 1 command to set Timer 1 and the
Timer 2 command to set Timer 2.
L
In free-run mode, the period of the internal control signal is equal to the sum of the Timer 1 setting plus the Timer 2 setting. The sum of the Timer 1 setting plus the Timer 2 setting must be greater than 33.3 ms.
The minimum setting for Timer 1 is 1 µs.
The minimum setting for Timer 2 is 1 µs.
BASLER A201 b
DRAFT
Basic Operation and Features
3.3 Exposure Time Control Modes in Detail
3.3.1 ExSync, Level-controlled Mode with Exposure Start After
Image Transfer (Frame Valid Low)
This timing diagram is not drawn to scale.
Figure 3-6: ExSync, Level-controlled Mode - Exposure Start with Frame Valid Low
The falling edge of ExSync begins exposure. At the start of exposure, a single, 9 µs discharge pulse is generated and this pulse discharges the CCD array. Effective exposure starts at the end of the discharge pulse.
The rising edge of ExSync triggers charge readout. Readout starts 10 µs after the rising edge of
ExSync. Readout takes 5 µs during which exposure continues.
• Effective exposure = n + 6.0 µs (n = exposure set by ExSync)
L
FVAL must be low for at least 32 ns before the ExSync signal goes low.
ExSync must remain high for a minimum of 1 µs.
The minimum ExSync signal period is 33.3 ms.
With very low exposures, use flash light to prevent smearing.
3-7 BASLER A201 b
Basic Operation and Features
DRAFT
3.3.2 ExSync, Level-controlled Mode with Exposure Start During
Image Transfer (Frame Valid High)
This timing diagram is not drawn to scale.
3-8
Figure 3-7: ExSync, Level-controlled Mode - Exposure Start with Frame Valid High
Whenever a frame is being transferred, regularly spaced discharge pulses are generated.
If the falling edge of ExSync occurs while a frame is being transferred, it is not possible to generate a discharge pulse asynchronously. In this case, exposure starts at the end of the last regular discharge pulse. The discharge pulses scheduled during exposure are suppressed.
The rising edge of ExSync triggers readout. Readout starts after a delay of 10 µs and takes 5 µs.
Exposure continues during readout.
• Effective exposure = n + d + 15.0 µs (n = exposure set by ExSync)
(d = time to last discharge pulse
d ≤ 45 µs in normal operation
d ≤ 49 µs when AOI is used)
L
Frame valid must be low for at least 1 ns before the ExSync signal rises.
ExSync must remain high for a minimum of 1 µs.
The minimum ExSync signal period is 33.3 ms.
With very low exposures, use flash light to prevent smearing.
BASLER A201 b
DRAFT
Basic Operation and Features
3.3.3 ExSync, Programmable Mode with Exposure Start After
Image Transfer (Frame Valid Low)
This timing diagram is not drawn to scale.
Figure 3-8: ExSync, Programmable Mode - Exposure Start with Frame Valid Low
The rising edge of ExSync begins exposure. At the start of exposure, a single, 9 µs discharge pulse is generated and this pulse discharges the CCD array. Effective exposure starts at the end of the discharge pulse.
The end of the exposure triggers readout. Readout starts after a delay of 10 µs and takes 5 µs.
Exposure continues during readout.
• Effective exposure = n + 6.0 µs (n = Timer 1)
L
FVAL must be low for at least 32 ns before the ExSync signal rises.
ExSync must remain high for a minimum of 1 µs.
The minimum ExSync signal period is 33.3 ms.
With very low exposures, use flash light to prevent smearing.
BASLER A201 b 3-9
Basic Operation and Features
DRAFT
3.3.4 ExSync, Programmable Mode with Exposure Start During
Image Transfer (Frame Valid High)
This timing diagram is not drawn to scale.
3-10
Figure 3-9: ExSync, Programmable Mode - Exposure Start with Frame Valid High
Whenever a frame is being transferred, regularly discharge pulses are generated.
If ExSync rises while a frame is being transferred, it is not possible to generate a discharge pulse asynchronously. In this case, the start of exposure is shifted to the end of the last regular discharge pulse. The discharge pulses during exposure are suppressed.
The microcontroller detects the shift in the start of exposure and it makes a corresponding shift in the end of the exposure. The end of the shifted exposure triggers readout. Readout occurs after a delay of 10 µs. Readout takes 5 µs during which exposure continues.
• Effective exposure = n + 15.0 µs (n = Timer 1)
L
FVAL must be low for at least 1 ns before the end of the shifted exposure.
ExSync must remain high for a minimum of 1 µs.
The minimum ExSync signal period is 33.3 ms.
With very low exposures, use flash light to prevent smearing.
BASLER A201 b
DRAFT
Basic Operation and Features
3.3.5 Free-run, Programmable Mode with Exposure Start After
Image Transfer (Frame Valid Low)
This timing diagram is not drawn to scale.
Figure 3-10: Free-run, Programmable Mode - Exposure Start with Frame Valid Low
The control signal going low begins exposure. At the start of exposure, a single, 9 µs discharge pulse is generated and this pulse discharges the CCD array. Effective exposure starts at the end of the discharge pulse.
The end of exposure triggers readout. Readout starts after a delay of 10 µs and takes 5 µs.
Exposure continues during readout.
• Effective exposure = n + 6.0 µs (n = Timer 1)
L
FVAL must be low for at least 32 ns before the internal sync signal goes low.
The internal control signal must remain high for a minimum of 1 µs.
The minimum period for the internal control signal is 33.3 ms.
With very low exposures, use flash light to prevent smearing.
3-11 BASLER A201 b
Basic Operation and Features
DRAFT
3.3.6 Free-run, Programmable Mode with Exposure Start During
Image Transfer (Frame Valid High)
This timing diagram is not drawn
3-12
Figure 3-11: Free-run, Programmable Mode - Exposure Start with Frame Valid High
Whenever a frame is being transferred, regularly spaced discharge pulses are generated.
If the control signal goes low while a frame is being transferred, it is not possible to generate a discharge pulse asynchronously. In this case, the start of exposure is shifted to the end of the last regular discharge pulse. The discharge pulses scheduled during exposure are suppressed.
The microcontroller detects the shift in the start of exposure and it makes a corresponding shift in the end of the exposure. The end of the shifted exposure time triggers readout. Readout occurs after a delay of 10 µs. Readout takes 5 µs during which exposure continues.
• Effective exposure = n + 15.0 µs (n = Timer 1)
L
FVAL must be low for at least 1 ns before the end of the shifted exposure.
The internal control signal must remain high for a minimum of 36 µs.
The minimum period for the internal control signal is 33.3 ms.
With very low exposures, use flash light to prevent smearing.
BASLER A201 b
DRAFT
Basic Operation and Features
3.4 Video Data Output Modes
The A201 b can output video data using four different modes: Single 10 Bit mode, Single 8 Bit mode, Dual 10 Bit mode, or Dual 8 Bit mode. These modes are described in detail in Section
.
You can select the video data output mode using either the Camera Configuration Tool (see
) or binary commands (see Section
). With the Camera Configuration Tool, you use the Output Version Tab to select the data output mode and with binary commands you use the
Video Data Output Mode command.
3.5 Gain and Offset
The major components in the A201 b electronics include: a CCD sensor, two VGCs (Variable Gain
Controls), and two ADCs (Analog to Digital
Converters). The pixels in the CCD sensor output voltage signals when they are exposed to light. These voltages are amplified by the VGCs and transferred to the ADCs which convert the voltages to digital output signals.
Two parameters, gain and offset are associated with
each VGC. As shown in Figures 3-12 and 3-13
, increasing or decreasing the gain increases or decreases the amplitude of the signal that is input to the ADC. Increasing or decreasing the offset moves the signal up or down the measurement scale but does not change the signal amplitude.
Figure 3-12: Gain
The default gain and offset are set so that with optimal lighting and exposure, the linear output range of the
CCD sensor maps to the input range of the ADC. Under these conditions, black will produce a gray value of 1 from the ADC and white will produce a gray value of
254 (in 8 bit output mode) or 1023 (in 10 bit output mode).
For most applications, black should have a gray value of 1 and white should have a gray value of 254 (in 8 bit output mode) or 1023 (in 10 bit output mode). Attempt to achieve this by varying exposure and illumination rather than changing the camera’s gain. The default gain is the optimal operating point (minimum noise) and should be used if possible.
Figure 3-13: Offset
Internally, the A201 b processes odd and even lines separately in two different data channels (see
Figure 3-1). Consequently, gain must be adjusted separately for the odd lines and for the even
lines. Due to variations in the camera's electronics, the gain needed on the odd channel to correctly map the output from the VGC to the input of the ADC may be different from the gain needed on the even channel. Gain balance between the odd and even channels is important to
BASLER A201 b 3-13
Basic Operation and Features
DRAFT maintain uniform output data with minimal gray value differences between odd and even lines.
for more detailed information on balancing the gain.
L
Because increasing gain increases both signal and noise, the signal to noise ratio does not change significantly when gain is increased.
You can set the gain and offset using either the Camera Configuration Tool (see Section 4.1
binary commands (see Section 4.2
With the Camera Configuration Tool, you use the slide controls on the Gain and Offset Tab to easily adjust gain and offset.
With binary commands, you must use the Odd Line Gain and Even Line Gain commands to set the gain and the Odd Line Offset and Even Line Offset commands to set the offset.
3.5.1 Gain Settings in More Detail
The output signals from the pixels in the CCD sensor normally range from 0 Volts when the pixels are exposed to no light to 0.35 Volts when they are exposed to bright light. Within that range, the sensor characteristics are linear. Saturation starts at 0.35 Volts. Further exposure results in a higher sensor output signal but linearity is no longer guaranteed.
The default factory gain is set for an amplification factor of 5.7 (15 dB). At this setting, the sensor’s normal linear output range of 0 V - 0.35 V is amplified to 0 V - 2.0 V. The peak-to-peak input range of the ADC is 0 V - 2.0 V. Thus when the gain is at factory default, the amplified output of the sensor maps directly to the input voltage range of the ADC.
Gain is adjustable and can be programmed on a decimal scale that ranges from 0 to 1023 (0x0000 to 0x03FF). The settings result in the following amplification:
• 0 = 3.7 dB
• 1023 = 40.0 dB
• The gain can be adjusted in steps of approximately 0.0354 dB.
The desired 15 dB default gain is achieved when the gain is programmed to 376 (0x0178). You should find that the default gain setting on your camera is near to this value.
Reducing the gain below 376 results in mapping more than the linear operating range of the sensor to the ADC. Increasing the gain to more than 376 maps a smaller portion of the sensor’s linear output signal to the ADC.
If you know the decimal number (DN) setting for the gain on your camera, the equivalent decibel value can be calculated by using one of the following two equations: dB = 20 log
10
658 DN
+ 3.7
Where DN = 0 to 511 dB = ( 0.0354
) DN + Where DN = 512 to 1023
BASLER A201 b 3-14
DRAFT
Basic Operation and Features
3.5.2 Balancing the Gain and Offset on Odd and Even Lines
Internally, the A201 b processes odd and even lines separately in two different data channels (see
Figure 3-1). Consequently, the gain and offset must be adjusted separately for the odd lines and
for the even lines. Due to variations in the camera's electronics, the gain and offset needed to correctly map the output from the odd lines to the odd channel ADC may be different from the gain and offset needed to map the output from the even lines to the even channel ADC. Gain alignment between the channels is important to maintain uniform output data with minimal gray value differences between odd and even lines.
Basler performs a calibration procedure on each camera before it leaves the factory and the results of the procedure are stored in the camera. The results of the calibration procedure can be used to calculate gain and offset settings that will keep the odd and even channels in balance. If you use the Camera Configuration Tool (see Section
) to set the gain and offset on your
camera, the “auto-balance” feature on the Gain and Offset Tab will automatically use the stored
calibration values to keep the channels in balance. If you use binary commands (see Section 4.2
to set gain and offset, you can use the calibration values to calculate gain and offset settings that will keep the channels in balance.
The calibration procedure is performed as follows:
A standard black and white test pattern is placed in the camera’s field of view.
The test pattern is illuminated with a very bright light source. The gain and offset on each channel are set so that the camera returns a gray value of 1 for black and 254 for white. These settings are stored in the camera as the odd line low gain setting, the odd line low offset setting, the even line low gain setting, and the even line low offset setting.
The test pattern is illuminated with a very dim light source. The gain and offset on each channel are set so that the camera returns a gray value of 1 for black and 254 for white. These settings are stored in the camera as the odd line high gain setting, the odd line high offset setting, the even line high gain setting, and the even line high offset setting.
The results of the calibration procedure are shown graphically in Figure 3-14. As you will notice,
when the illumination is high, low gain and offset settings are needed to achieve gray values of 1 and 254. When the illumination is low, high gain and offset values are needed. Between these two extremes, the relationship between the illumination and the required gain and offset is assumed to be linear. The area between these two extremes is defined as the “normally available gain/offset
range” as shown in Figure 3-15.
If you use the Camera Configuration Tool with the “auto-balance” feature selected, the left end and the right end of the slides on the Gain and Offset tab correspond to the low end and the high end of the normally available gain and offset range. As you move the slides from left to right, you are moving through the normal gain/offset range and the configuration tool is using the reference values from the calibration procedure to keep the channels in balance. For example, suppose that you have “auto- balance” on, and that you move the sliders so that they are 40% of the way from left to right. In this case, the configuration tool will use the reference values to calculate the gain and offset needed for the camera to operate at 40% of the normal gain/offset range while keeping
the channels balanced. This situation is shown graphically in Figure 3-16.
BASLER A201 b 3-15
Basic Operation and Features
DRAFT
Gain needed to achieve
1-254
Odd
Even
Offset needed to achieve
1-254
High
Light
Illumination
Low
Light
Odd
Even
Note: The differences between the odd channel and the even channel are exaggerated so that they will show clearly in the graphs.
High
Light
Illumination
Low
Light
Figure 3-14: Graph of Balanced Odd and Even Channel Gain and Offset Settings
Gain
Odd
Even
Offset
Odd
Even
3-16
0%
Normal Gain/Offset Range
100%
Figure 3-15: Normal Gain/Offset Range
BASLER A201 b
DRAFT
Odd Channel Gain Setting for 40% of Normal Range
Gain
Even Channel Gain Setting for 40% of Normal Range
Basic Operation and Features
Odd
Even
Odd Channel Offset Setting for 40% of Normal Range
Offset
Even Channel Offset Setting for 40% of Normal Range
Odd
Even
0%
Figure 3-16: Settings at 40% of the Normal Range
40%
100%
If you want to change the gain and offset using binary commands, you can keep the channels in balance by using the stored gain and offset reference values when you make your changes. To do this, you must select a percentage of the normally available gain/offset range and then use the reference values along with the formula shown below to calculate the required settings for the odd line gain and offset and for the even line gain and offset. You can then enter the calculated settings into the camera using the appropriate commands.
Setting =
100
BASLER A201 b 3-17
Basic Operation and Features
DRAFT
Example of Setting Balanced Gain and Offset with Binary Commands:
Assume that you want to keep the odd lines and the even lines balanced and that you want to set the gain and offset for 40% of the normal operating range.
1. Use the “Read gain and offset reference values” command to read the values that were stored during the camera’s calibration procedure. For our example, we will assume that the camera returned the following reference values:
Odd line high gain
Odd line low gain
Even line high gain
Even line low gain
0x02d5
0x017c
0x02de
0x0180
Odd line high offset
Odd line low offset
0x0020
0x0010
Even line high offset 0x0025
Even line low offset 0x0010
2. The reference values are hexadecimal. Convert them to decimal:
Odd line high gain
Odd line low gain
Even line high gain
Even line low gain
725
380
734
384
Odd line high offset
Odd line low offset
32
16
Even line high offset 37
Even line low offset 16
3. Use the odd line high gain and odd line low gain reference values to calculate the gain for the odd lines:
Odd line gain setting =
100
Odd line gain setting = 518
4. Use the odd line high offset and odd line low offset reference values to calculate the offset for the odd lines:
Odd line offset setting =
100
Odd line offset setting = 22.4 (round to 22)
5. Use the even line high gain and even line low gain reference values to calculate the gain for the even lines:
Even line gain setting =
100
Even line gain setting = 524
6. Use the even line high offset and even line low offset reference values to calculate the offset for the even lines:
Even line offset setting =
100
Even line offset setting = 24.4 (round to 24)
7. Convert the results to hexadecimal:
Odd line gain setting of 518 decimal = 0x0206
Odd line offset setting of 22 decimal = 0x0016
Even line gain setting of 524 decimal = 0x020c
Even line offset setting 0f 24 decimal = 0x0018
3-18 BASLER A201 b
DRAFT
Basic Operation and Features
8. Use the odd line gain, odd line offset, even line gain, and even line offset binary commands to set the gain and offset to the calculated values.
After you use the commands to enter the calculated values, the camera will be operating at 40% of the normally available gain/offset range and the odd and even lines will be balanced.
L
For special applications, gain and offset can be set to different percentages of the normal gain/offset range. Just make sure that the gain for the odd and the even lines is set to the same percentage and that the offset for the odd and the even lines is set to the same percentage. For example, if you wanted to set the gain to 60% and the offset to 40%, make sure that the odd line gain and the even line gain are both set to 60% of the normal range and that the odd line offset and the even line offset are both set to 40% of the normal range.
Setting the gain and the offset to significantly different percentages may substantially reduce image quality.
BASLER A201 b 3-19
Basic Operation and Features
DRAFT
3.6 Digital Shift
The “digital shift” feature allows you to change the group of bits that is output from each ADC.
Using the digital shift feature will effectively multiply the output of the camera by 2 times, 4 times or 8 times. Section
describes how digital shift works when the camera is operating in 10 bit
output mode and Section
describes how digital shift works when the camera is operating in
8 bit output mode.
You can set digital shift using either the Camera Configuration Tool (see Section 4.1
) or binary commands (see Section
). With the Camera Configuration Tool, you use the Features Tab to set digital shift and with binary commands you use the Digital Shift command.
3.6.1 Digital Shift in 10 bit Output Mode
No Shift
b uses 10 bit
ADCs to digitize the output from the CCD sensor.
When the camera is operating in 10 bit output mode, by default, the camera transmits the 10 bits that are output from each ADC.
ADC bit
9 bit
8 bit
7 bit
6 bit
5 bit
4 bit
3 bit
2 bit
1 bit
0
M
S
B Not Shifted
L
S
B
Shift Once
When the camera is set to shift once, the output from the camera will include bit 8 through bit 0 from each ADC along with a zero as an LSB.
The result of shifting once is that the output of the camera is effectively doubled. For example, assume that the camera is set for no shift, that it is viewing a uniform white target, and that under these conditions the reading for the brightest pixel is 100.
If you changed the digital shift setting to shift once, the reading would increase to 200.
ADC bit
9 bit
8 bit
7 bit
6 bit
5 bit
4 bit
3 bit
2 bit
1 bit
0
“0”
M
S
B Shifted Once
L
S
B
L
Note that if bit 9 is set to 1, all of the other bits will automatically be set to 1.
This means that you should only use the shift once setting when your pixel readings in 10 bit mode with no digital shift are all below 512.
3-20 BASLER A201 b
DRAFT
Basic Operation and Features
Shift Twice
When the camera is set to shift twice, the output from the camera will include bit 7 through bit 0 from each ADC along with two zeros as LSBs.
The result of shifting twice is that the output of the camera is effectively multiplied by four. For example, assume that the camera is set for no shift, that it is viewing a uniform white target, and that under these conditions the reading for the brightest pixel is 100. If you changed the digital shift setting to shift twice, the reading would increase to 400.
ADC bit
9 bit
8 bit
7 bit
6 bit
5 bit
4 bit
3 bit
2 bit
1 bit
0
“0” “0”
M
S
B Shifted Twice
L
S
B
L
Note that if bit 9 or bit 8 is set to 1, all of the other bits will automatically be set to 1. This means that you should only use the shift twice setting when your pixel readings in 10 bit mode with no digital shift are all below 256.
Shift Three Times
When the camera is set to shift three times, the output from the camera will include bit 6 through bit 0 from each ADC along with three zeros as LSBs.
The result of shifting three times is that the output of the camera is effectively multiplied by eight. For example, assume that the camera is set for no shift, that it is viewing a bit
9 bit
8 uniform white target, and that under these conditions the reading for the brightest pixel is 100. If you changed the digital shift setting to shift three times, the reading would increase to 800.
bit
7 bit
6
M
S
B
ADC bit
5 bit
4 bit
3 bit
2 bit
1 bit
0
Shifted 3 Times
“0” “0” “0”
L
S
B
L
Note that if bit 9, bit 8 or bit 7 is set to 1, all of the other bits will automatically be set to 1. This means that you should only use the shift three times setting when your pixel readings in 10 bit mode with no digital shift are all below 128.
3-21 BASLER A201 b
Basic Operation and Features
DRAFT
3.6.2 Digital Shift in 8 bit Output Modes
No Shift
As mentioned in Section
, the A201 b uses 10 bit
ADCs to digitize the output from the CCD sensor. When the camera is operating in 8 bit output mode, by default, it drops the least two significant bits from each ADC and transmits the 8 most significant bits (bit 9 through bit 2).
ADC bit
9 bit
8 bit
7 bit
6 bit
5 bit
4 bit
3 bit
2 bit
1 bit
0
M
S
B Not Shifted
L
S
B
Shift Once
When the camera is set to shift once, the output from the camera will include bit 8 through bit 1 from each
ADC.
The result of shifting once is that the output of the camera is effectively doubled. For example, assume that the camera is set for no shift, that it is viewing a uniform white target and that under these conditions the reading for the brightest pixel is 20. If you changed the digital shift setting to shift once, the reading would increase to 40.
ADC bit
9 bit
8 bit
7 bit
6 bit
5 bit
4 bit
3 bit
2 bit
1 bit
0
M
S
B Shifted Once
L
S
B
L
Note that if bit 9 is set to 1, all of the other bits will automatically be set to 1.
This means that you should only use the shift once setting when your pixel readings in 8 bit mode with no digital shift are all below 128.
3-22 BASLER A201 b
DRAFT
Shift Twice
When the camera is set to shift twice, the output from the camera will include bit 7 through bit 0 from each
ADC.
The result of shifting twice is that the output of the camera is effectively multiplied by four. For example, assume that the camera is set for no shift, that it is viewing a uniform white target, and that under these conditions the reading for the brightest pixel is 20. If you changed the digital shift setting to shift twice, the reading would increase to 80.
Basic Operation and Features
ADC bit
9 bit
8 bit
7 bit
6 bit
5 bit
4 bit
3 bit
2 bit
1 bit
0
M
S
B Shifted Twice
L
S
B
L
Note that if bit 9 or bit 8 is set to 1, all of the other bits will automatically be set to 1. This means that you should only use the shift twice setting when your pixel readings in 8 bit mode with no digital shift are all below 64.
Shift Three Times
When the camera is set to shift three times, the output from the camera will include bit 6 through bit 0 from each ADC along with a zero as the
LSB.
The result of shifting three times is that the output of the camera is effectively multiplied by eight.
For example, assume that the camera is set for no shift, that it is viewing a uniform white target and that under these conditions the reading for the brightest pixel is 20. If you changed the digital shift setting to shift three times, the reading would increase to 160.
ADC bit
9 bit
8 bit
7 bit
6 bit
5 bit
4 bit
3 bit
2 bit
1 bit
0
“0”
M
S
B
Shifted 3 Times
L
S
B
L
Note that if bit 9, bit 8 or bit 7 is set to 1, all of the other bits will automatically be set to 1. This means that you should only use the shift once setting when your pixel readings in 8 bit mode with no digital shift are all below 32.
BASLER A201 b 3-23
Basic Operation and Features
DRAFT
3.6.3 Precautions When Using Digital Shift
There are several checks and precautions that you must follow before using the digital shift feature. The checks and precautions differ depending on whether you will be using the camera in
10 bit output mode or in 8 bit output mode.
If you will be using the camera in 10 bit output mode, make this check:
1. Use binary commands or the Output Version Tab on the configuration tool to put the camera in 10 bit output mode.
2. Use binary commands or the Features Tab to set the camera for no digital shift.
3. Check the output of the camera under your normal lighting conditions with no digital shift and note the readings for the brightest pixels.
• If any of the readings are above 512, do not use digital shift.
• If all of the readings are below 512, you can safely use the 2X digital shift setting.
• If all of the readings are below 256, you can safely use the 2X or 4X digital shift setting.
• If all of the readings are below 128, you can safely use the 2X, 4X or 8X digital shift setting.
If you will be using the camera in 8 bit output mode, make this check:
1. Use binary commands or the Output Version Tab on the configuration tool to put the camera in 8 bit output mode.
2. Use the binary commands or the Features Tab to set the camera for no digital shift.
3. Check the output of the camera under your normal lighting conditions with no digital shift and note the readings for the brightest pixels.
• If any of the readings are above 128, do not use digital shift.
• If all of the readings are below 128, you can safely use the 2X digital shift setting.
• If all of the readings are below 64, you can safely use the 2X or 4X digital shift setting.
• If all of the readings are below 32, you can safely use the 2X, 4X or 8X digital shift setting.
3-24 BASLER A201 b
DRAFT
Basic Operation and Features
3.7 Area of Interest (AOI)
The area of interest feature allows you to specify a portion of the CCD array and during operation, only the pixel information from the specified portion is transferred out of the camera.
The size of the area of interest is defined by declaring a starting column, a width in columns, a starting line and a height in lines. For example, suppose that you specify the starting column as
11, the width in columns as 16, the starting line as 5 and the height in lines as 10. As shown in
Figure 3-17, the camera will only transmit pixel data from within the defined area.
Information from the pixels outside of the area of interest is discarded.
Width in Columns
Starting Column
Height in
Lines
Starting
Line
Line 20
Line 19
Line 18
Line 17
Line 16
Line 15
Line 14
Line 13
Line 12
Line 11
Line 10
Line 9
Line 8
Line 7
Line 6
Line 5
Line 4
Line 3
Line 2
Line 1
Column 1 2 3 4 5 6 7 8 9 10 11 12 13 14 15 16 17 18 19 20 21 22 23 24 25 26 27 28 29 30 31 32
The camera will only transmit the pixel data from this area.
Figure 3-17: Area of Interest
You can set the area of interest using either the Camera Configuration Tool (see Section 4.1
) or
binary commands (see Section 4.2
). With the Camera Configuration Tool, you use the Features
Tab to set the area of interest. With binary commands, you use the Area of Interest Starting
Column, Area of Interest Width in Columns, Area of Interest Starting Line, and Area of Interest
Height in Lines commands.
BASLER A201 b 3-25
Basic Operation and Features
DRAFT
3.7.1 Area of Interest Setup Rules
When setting up the area of interest, several rules must be followed. The setup rules are listed below.
• The setting for the “width in columns” must be divisible by 2.
• The setting for the “height in lines” must be divisible by 2.
• The sum of the setting for the Starting Column plus the setting for the Width in Columns can not exceed 1009.
• The sum of the setting for the Starting Line plus the setting for the Height in Lines can not exceed 1019.
In normal operation, the camera is set to use all of the pixels in the array. To use all of the pixels, the starting column should be set to 1, the width in columns should be set to 1008, the starting line should be set to 1, and the height in lines should be set to 1018.
3.7.2 Changes to the Maximum Frame Rate with Area of Interest
When the area of interest feature is used, the camera’s maximum achieveable frame rate increases. The amount that the maximum frame rate increases depends on the number of lines included in the area of interest. The fewer the number of lines in the area of interest, the higher the maximum frame rate. The maximum achieveable frame rate can be calculated using the following formula:
Maximum Frames per Second =
2
+ [ (1018 - LI) x 6 µs +
Where: LI = the number of lines included in the area of interest
3-26 BASLER A201 b
DRAFT
Basic Operation and Features
3.8 Test Image
The test image mode is used to check the camera’s basic functionality and its ability to transmit an image via the video data cable. The test image can be used for service purposes and for failure diagnostics. In test mode, the image is generated with a software program and the camera’s digital devices and does not use the optics, CCD sensor, VGCs or ADCs.
The test image consists of lines with repeated gray scale gradients ranging from 0 to 255. The first line starts with a gray value of 0 on the first pixel. The second line starts with a gray value of
1 on the first pixel. The third line starts with a gray value of 2 on the first pixel, and so on.
The mathematical expression for the test image is: gray level = [x + y] MOD 256. This expres-
sion is shown graphically in Figure 3-19.
If the camera is set for an exposure mode that uses an ExSync signal, an ExSync signal is required to output the test image. If the camera is set for free-run, each cycle of the camera’s internal sync signal will trigger the output of a test image. Figure 3-18: Test Image
Figure 3-19: Formation of Test Image
L
When the test image is active, the gain, offset, and exposure time have no effect on the image.
Digital shift makes the test image appear very light, therefore, digital shift should be disabled when the test image is active.
You can put the camera in test image mode using either the Camera Configuration Tool (see
) or binary commands (see Section
). With the Camera Configuration Tool, you use the Test Image Tab to select the test image. With binary commands you use Test Image command.
BASLER A201 b 3-27
Basic Operation and Features
DRAFT
3.9 Configuration Sets
The camera’s adjustable parameters are stored in configuration sets and each configuration set contains all of the parameters needed to control the camera.
There are three different types of configuration sets: the
Work Set, the Factory Set, and User Sets.
Work Set
The Work Set contains the current camera settings and thus determines the camera’s present performance, that is, what your image currently looks like. The Work
Set is stored in the camera RAM. The configuration parameters in the Work Set can be altered directly using the Camera Configuration Tool or using binary programming commands.
Figure 3-20: Config Sets
Factory Set
When a camera is manufactured, a test set up is performed on the camera and an optimized configuration is determined. The Factory Set contains the camera’s factory optimized configuration. The Factory Set is stored in non-volatile memory on the EEPROM and can not be altered.
User Sets
User Sets are also stored in the non-volatile EEPROM of the camera. The camera has 15 User
Sets. Each User Set initially contains factory settings but User Sets can be modified. Modification is accomplished by making changes to the Work Set and then copying the Work set into one of the User Sets. The Camera Configuration Tool or binary commands can be used to copy the Work
Set into one of the User Sets.
Startup Pointer
When power to the camera is switched off, the Work set in the RAM is lost. At the next power on, a configuration set is automatically copied into the Work Set. The Startup Pointer is used to specify which of the configuration sets stored in the EEPROM will be copied into the Work Set at power on. The Startup Pointer is initially set so that the Factory Set is loaded into the Work Set at power on. This can be changed using the Camera Configuration Tool or binary commands. The Startup
Pointer can be set to the Factory Set or to any one of the User Sets. So, for example, if the Startup
Pointer is set to User Set 13, then User Set 13 will be copied into the Work Set at power on.
You can work with configuration sets and the startup pointer using either the Camera
Configuration Tool (see Section
) or binary commands (see Section
With the Camera Configuration Tool, you can use the Sets Tab to copy the Work Set to a User Set, to Copy a User Set or the Factory Set to the Work Set, or to set the Startup Pointer.
With binary commands you use the Copy Work Set to User Set command, the Copy Factory Set or User Set to Work Set command, and the Select Startup Pointer command to manipulate configuration sets.
3-28 BASLER A201 b
DRAFT
Basic Operation and Features
3.10 Camera Status
The A201 b monitors its status by performing a regular series of self checks. The current status of the camera can be viewed in several ways:
• with the Camera Configuration Tool. You can use the Status Tab (see Section
configuration tool’s on-line help) to check a list of several possible errors and an indication of whether those errors are present.
• with binary commands. You can use the Camera Status command (see Section
) to check if the camera has detected any errors.
• by checking the yellow LED on the back of the camera. If certain error conditions are present,
the yellow LED will blink (see Section 6.1
).
BASLER A201 b 3-29
Basic Operation and Features
DRAFT
3-30 BASLER A201 b
DRAFT
Configuring the Camera
4 Configuring the Camera
The A201 b comes factory-set so that it will work properly for most applications with only minor changes to the camera’s settings. For normal operation, the following settings are usually configured by the user:
• Exposure time control mode
• Exposure time (for ExSync programmable mode or free-run programmable mode)
To customize operation for your particular application, the following settings can also be configured:
• Gain
• Offset
• Area of Interest
• Digital Shift
The A201 b is programmable via the serial port. Two methods can be used to change the cameras’s settings. The first and easier approach is to change the settings using the Camera Configuration
and the configuration tool’s on-line help file for instructions on using the
configuration tool. You can also change the settings directly from your application using binary commands. Section
lists the commands and provides instructions for their use.
BASLER A201 b 4-1
Configuring the Camera
DRAFT
4.1 Configuring the Camera with the Camera
Configuration Tool
The Camera Configuration Tool (CCT) is a Windows ® based program used to easily change the camera’s settings. The tool communicates via the serial interface and automatically generates the
binary programming commands that are described in Section 4.2
. For instructions on installing the tool, see the CCT installation booklet that was shipped with the camera.
This manual assumes that you are familiar with Microsoft Windows ® and that you have a basic knowledge of how to use programs. If not, please refer to your Microsoft Windows ® manual.
4.1.1 Opening the Configuration Tool
1. Make sure that the serial interface is connected to your camera and that the camera has power.
2. To start the Camera Configuration Tool, click Start, click Basler Vision Technologies, and then click Camera Config Tool (default installation).
If start-up was successful, the Model Tab is displayed.
If start-up was not successful the Connection Tab or a Select Camera dialog box will appear.
Refer to the CCT installation booklet that was delivered with your camera for possible causes and solutions.
4.1.2 Closing the Configuration Tool
Close the Configuration Tool by clicking on the button in the upper right corner of the window.
4.1.3 Configuration Tool Basics
The RAM memory in the camera contains the set of parameters that controls the current operation of the camera. This set of parameters is known as the Work Set (see
). The Camera Configuration Tool is used to view the present settings for the parameters in the Work Set or to change the settings. The configuration tool organizes the parameters into related groups and displays each related group on a tab. For example, the Features Tab contains all of the parameters related to the Area of Interest feature and the Digital Shift feature.
When the configuration tool is opened, it queries the camera and displays the current settings for the parameters in the Work Set.
Figure 4-1: Features Tab
4-2 BASLER A201 b
DRAFT
Configuring the Camera
Using the Refresh and Apply Buttons
Two buttons always appear at the bottom of the configuration tool window, the Refresh button and the Apply button.
Typically, if you make a change to one or more of the settings on a tab, you must click the Apply button for that change to be transmitted from the configuration tool to the camera’s Work Set. Because the parameters in the Work Set control the current operation of the camera, when you click the Apply button, you will see an immediate change in the camera’s operation.
The Refresh button can be used at any time to make sure that the configuration tool is displaying the current settings for the parameters in the Work Set. When you click the Refresh button, the configuration tool queries the camera to determine the current setting for each parameter in the
Work Set and updates the display on each tab.
L
Keep in mind that the Work Set is stored in a volatile memory. Any changes you make to the Work Set using the configuration tool will be lost when the camera is switched off. To save changes you make to the Work Set, go to the
Sets Tab and save the modified Work Set into one of the camera’s 15 User
Sets. The User Sets are stored in non-volatile memory and will not be lost when
the camera is switched off (see Section 3.9
).
If you want your changes to be loaded into the Work Set at the next power on, go to the Sets Tab and set the Startup Pointer to the User Set where you saved your changes.
4.1.4 Configuration Tool Help
The Camera Configuration Tool includes a complete on-line help file which explains how to use each tab and how the settings on each tab will effect the camera’s operation. To access on-line help, press the F1 key whenever the configuration tool is active.
BASLER A201 b 4-3
Configuring the Camera
DRAFT
4.2 Configuring the Camera with Binary
Programming Commands
Commands can be issued to the A201 b via the RS-232 serial connection using a binary protocol.
With this protocol, data is placed into a frame and sent to the camera. Once the data is received it is checked for validity. If valid, the data is extracted and the command is executed.
If the command issued to the camera was a read command, the camera will respond by placing the requested data into a frame and sending it to the host computer.
4.2.1 Command Frame and Response Format
4-4
Figure 4-2: Representation of a Command Frame and Response
STX Identifies the start of the frame text
Size = 1 Byte
(The value of the STX byte is always 0x02)
DESC Descriptor
Size = 2 Bytes
The bits in the descriptor are assigned as follows:
8 bits
Command ID
1 bit
Read/Write Flag
( 0 = write, 1 = read )
7 bits
Data Length
(in Bytes)
The MSB of the descriptor is on the left (highest bit of the command ID) and the LSB of the descriptor is on the right (lowest bit of the data length).
DATA Data field
Size = Number of bytes indicated in the Data Length portion of the descriptor.
BASLER A201 b
BCC
DRAFT
Configuring the Camera
Block check character
Size = 1 Byte
The block check character is the exclusive-or sum (XOR sum) of the bytes in the descriptor field and the data field.
ETX Identifies the end of the frame text
Size = 1 Byte
(The value of the ETX byte is always 0x03)
ACK/NAK Response Positive frame acknowledge/negative frame acknowledge
Size = 1 byte
(The value for a positive frame acknowledgement is 0x06 and for a negative frame acknowledgement is 0x15.)
L
All values are formatted as little endian (Intel format).
BASLER A201 b 4-5
4-6
Configuring the Camera
4.2.2 Error Checking
DRAFT
4.2.2.1 ACK/NAK
When the camera receives a frame, it checks the order of the bytes in the frame and checks to see if the XOR sum of the bytes in the descriptor and the data fields matches the block check character. The camera also checks to see if the number of bytes in the data field is equal to the number specified in the descriptor.
If all checks are correct, an ACK is send to the host. If any check is incorrect, a NAK is sent.
4.2.2.2 Time-outs
Byte Time-out
The camera checks the time between the receipt of each byte in the frame. If the time between any two bytes exceeds 1 second, the camera enters a “garbage state” and discards any more incoming bytes. The camera remains in this state until it sees 1.5 seconds of silence. Once the camera sees 1.5 seconds of silence, it goes into an idle state (looking for an STX).
4.2.2.3 Read Command
In the normal case, when a read command is sent to the camera, the camera responds with an
ACK and a frame. The frame will contain the data requested in the read command.
If the camera receives a read command with an unknown command ID in the descriptor, it will respond with an ACK but will not send a frame.
If the host sends a read command and gets no ACK/NAK, the host can assume that no camera is present.
If the host sends a read command and gets an ACK/NAK but does not receive a frame within 500 ms, the host can assume that there was a problem with the read command.
4.2.2.4 Write Command
In the normal case, when a write command is sent to the camera, the camera responds with an
ACK.
If the camera receives a write command with an unknown command ID in the descriptor, it will respond with an ACK but will not perform the write.
After a write command has been issued by the host, the host can verify the write by issuing a corresponding read command and checking that the returned data is as expected. The host can
also issue a camera status read command (see Section 4.2.9
) and check the returned data to see if an error condition has been detected.
L
For many of the write commands listed in the tables on pages 5-9 through 5-
27, only data within a specified range or a specified group of values is valid.
The camera does not perform a check to see if the data in the write command is within the allowed range or specified group of allowed values.
BASLER A201 b
DRAFT
Configuring the Camera
4.2.3 Example Commands
4.2.3.1 Read Command
An example of the command message used to read the camera status is:
0x02, 0x43, 0x82, 0xC1, 0x03
0x02 - is the STX. The STX is always 0x02.
0x43 - is the first byte of the descriptor. The first byte of the descriptor is the command ID.
Command IDs can be found in the tables on pages 5-9 through 5-27. If you check the
table on page 5-26, you will find that the ID for the camera status read command is
0x43.
0x82 - is the second byte of the descriptor. The MSB in this byte represents the read/write flag and since this is a read command, the bit should be set to a 1. The other seven bits of this byte represent the data size (in bytes) that will be transferred using this
command. If you check the table on page 5-26, the data size for the camera status
command is 2 bytes. So the arrangement of the bits in the second byte of the descriptor should be 1000 0010 which translates to 0x82.
Note that for read commands, the data size specified in the descriptor represents the number of bytes of data that you expect to see in the response. No data bytes are actually included in the read command.
0xC1 - is the block check character (BCC). See page 5-8 for instructions on calculating a
BCC.
0x03 - is the ETX. The ETX is always 0x03.
4.2.3.2 Write Command
An example of the command message used to copy the Work Set to User Set 2 is:
0x02, 0x46, 0x01, 0x02, 0x45, 0x03
0x02 - is the STX. The STX is always 0x02.
0x46 - is the first byte of the descriptor. If you check the table on page 5-24, you will find that
the ID for the command to copy the Work Set to a User Set is 0x46.
0x01 - is the second byte of the descriptor. The MSB in this byte represents the read/write flag and since this is a write command, the bit should be set to a 0. The other seven bits of this byte represent the data size (in bytes) that will be transferred using this
command. If you check the table on page 5-24, the data size for the copy Work Set to
User Set command is 1 byte. So the arrangement of the bits in the second byte of the descriptor should be 0000 0001 which translates to 0x01.
0x02 - is the data byte. If you check the table on page 5-24, you will find that to copy the Work
Set to User Set 2, the data byte must be set to 0x02.
0x45 - is the block check character (BCC). See page 5-8 for instructions on calculating a
BCC.
0x03 - is the ETX. The ETX is always 0x03.
BASLER A201 b 4-7
Configuring the Camera
DRAFT
4.2.3.3 Calculating the Block Check Character
The block check character in any A201 b command is the exclusive-or sum (XOR sum) of the bytes in the descriptor and the data fields. For the write command example shown in Section
the block check character is 0x45. Let’s consider how this block check character was calculated.
In this case, we must find the XOR sum of three bytes. This is done by finding the XOR sum of the first two bytes and then by taking the result and finding the XOR sum of the result plus the third byte.
Calculating XOR sums is most easily understood when numbers are shown in their binary form, so in the sample calculations shown below, the hexadecimal digits in our command have been converted to binary.
To find the XOR sum of two binary numbers, you must add the two digits in each column using the following rules:
If both digits are 0, the result is 0.
If both digits are 1, the result is 0.
If one of the digits is a 1 and the other is a 0, the result is 1.
With all of this in mind, here is how the BCC for the write command shown in Section
would be calculated:
0 1 0 0 0 1 1 0 = the binary representation of 0x46
0 0 0 0 0 0 0 1 = the binary representation of 0x01
0 1 0 0 0 1 1 1 = the XOR sum of the first two bytes
0 1 0 0 0 1 1 1 = The XOR sum of the first two bytes
0 0 0 0 0 0 1 0 = the binary representation of 0x02
0 1 0 0 0 1 0 1 = The XOR sum
0 1 0 0 0 1 0 1 = 0x45 = the block check character
4-8 BASLER A201 b
DRAFT
4.2.4 Commands for Setting Camera Parameters
4.2.4.1 Video Data Output Mode
Configuring the Camera
Purpose: To set the video data output mode or to read the current video data output mode setting. See
Sections
for an explanation of the available video data output modes.
Type: This is a read or write command.
Read Command:
Response:
Cmd-ID
0xC0
Cmd-ID
0xC0
R/W-Flag
1
R/W-Flag
0
Write Command:
Response:
Data Format:
Cmd-ID
0xC0
None
Byte 1
R/W-Flag
0
Data Length
(see the table below).
1
Data Length
1
Data Length
1
An ID that specifies the data output mode
Data
-
Data
1 Byte
Data
1 Byte
ID
0x00
0x01
0x02
0x03
Output Mode
Single 8 Bit mode
Dual 8 Bit mode
Single 10 Bit mode
Dual 10 Bit mode
BASLER A201 b 4-9
Configuring the Camera
DRAFT
4.2.4.2 Exposure Time Control Mode
Purpose: To set the exposure time control mode or to read the current exposure time control mode setting. See Section
for an explanation of exposure time control modes.
Type: This is a read or write command.
Read Command:
Response:
Cmd-ID
0xA0
Cmd-ID
0xA0
R/W-Flag
1
R/W-Flag
0
Write Command:
Response:
Data Format:
Cmd-ID
0xA0
None
Byte 1
R/W-Flag
0
Data Length
(see the table below).
1
Data Length
1
Data Length
1
An ID that specifies the exposure mode
Data
-
Data
1 Byte
Data
1 Byte
ID
0x00
0x04
0x05
Exposure Time Control Mode
Free-run, Programmable
ExSync, Level-controlled
ExSync, Programmable
4-10 BASLER A201 b
DRAFT
Configuring the Camera
4.2.4.3 Timer 1
Purpose: To set Timer 1 or to read the current Timer 1 setting. Timer 1 is used when the camera is
operating in ExSync programmable mode or in free-run mode. See Section 3.2
Type: This is a read or write command.
Read Command:
Response:
Cmd-ID
0xA6
Cmd-ID
0xA6
R/W-Flag
1
R/W-Flag
0
Write Command: Cmd-ID
0xA6
None
R/W-Flag
0
Response:
Data Format:
Data Length
3
Data Length
3
Data Length
3
Data
-
Data
3 Bytes
Data
3 Bytes
Data Range:
Byte 1
Byte 2
Byte 3
Low byte of the Timer 1 setting
Mid byte of the Timer 1 setting
High byte of the Timer 1 setting
Timer 1 settings can range from 0x000001 to 0xFFFFFF µs.
4.2.4.4 Timer 2
Purpose: To set Timer 2 or read the current Timer 2 setting. Timer 2 is used when the camera is operating in free-run mode. See Section
Type: This is a read or write command.
Read Command:
Response:
Cmd-ID
0xA7
Cmd-ID
0xA7
R/W-Flag
1
R/W-Flag
0
Write Command: Cmd-ID
0xA7
None
R/W-Flag
0
Response:
Data Format:
Data Length
3
Data Length
3
Data Length
3
Data
-
Data
3 Bytes
Data
3 Bytes
Data Range:
Byte 1
Byte 2
Byte 3
Low byte of the Timer 2 setting
Mid byte of the Timer 2 setting
High byte of the Timer 2 setting
Timer 2 settings can range from 0x000001 to 0xFFFFFF µs.
BASLER A201 b 4-11
Configuring the Camera
4.2.4.5 Digital Shift
DRAFT
Purpose: To enable or disable digital shift. See Section
for an explanation of digital shift.
Type: This is a read or write command.
Read Command:
Response:
Write Command:
Response:
Data Format:
Cmd-ID
0xA5
Cmd-ID
0xA5
Cmd-ID
0xA5
None
Byte 1
R/W-Flag
1
R/W-Flag
0
R/W-Flag
0
Data Length
(see the table below).
1
Data Length
1
Data Length
1
An ID that specifies the digital shift status
Data
-
Data
1 Byte
Data
1 Byte
ID Digital Shift
0x00 No digital shift
0x01 Digital shift once
0x02 Digital shift twice
0x03 Digital Shift by three
(multiples output 2X)
(multiples output 4X)
(multiples output 8X)
L
shift.
for precautions that you must consider when using digital
4-12 BASLER A201 b
DRAFT
Configuring the Camera
4.2.4.6 Area of Interest Starting Column
Purpose: To set the starting column for the area of interest or to read the current setting. See Section
for details on the area of interest.
Type: This is a read or write command.
Read Command:
Response:
Cmd-ID
0xA9
Cmd-ID
0xA9
R/W-Flag
1
R/W-Flag
0
Write Command: Cmd-ID
0xA9
None
R/W-Flag
0
Response:
Data Format:
Data Length
2
Data Length
2
Data Length
2
Data
-
Data
2 Bytes
Data
2 Bytes
Data Range:
Byte 1
Byte 2
Low byte of the starting column setting
High byte of the starting column setting
The starting column setting can range from 0x0000 to 0x03EF.
(When using binary commands, the starting column = n +1 where n is the setting made using this binary command.
For example, if you wish to define column 100 as starting colunm, set 99 with the help of this command.)
L
or a list of rules which must be followed when entering the
settings for the area of interest.
BASLER A201 b 4-13
Configuring the Camera
DRAFT
4.2.4.7 Area of Interest Width in Columns
Purpose: To set the width in columns for the area of interest or to read the current setting. See
Section
for details on the area of interest.
Type: This is a read or write command.
Read Command:
Response:
Cmd-ID
0xAB
Cmd-ID
0xAB
R/W-Flag
1
R/W-Flag
0
Write Command: Cmd-ID
0xAB
None
R/W-Flag
0
Response:
Data Format:
Data Length
2
Data Length
2
Data Length
2
Data
-
Data
2 Bytes
Data
2 Bytes
Data Range:
Byte 1
Byte 2
Low byte of the width in columns setting
High byte of the width in columns setting
The width in columns setting can range from 0x0001 to 0x03F0.
L
See Section
for a list of rules which must be followed when entering the settings for the area of interest.
4-14 BASLER A201 b
DRAFT
Configuring the Camera
4.2.4.8 Area of Interest Starting Line
Purpose: To set the starting line for the area of interest or to read the current setting. See Section
for details on the area of interest.
Type: This is a read or write command.
Read Command:
Response:
Cmd-ID
0xA8
Cmd-ID
0xA8
R/W-Flag
1
R/W-Flag
0
Write Command: Cmd-ID
0xA8
None
R/W-Flag
0
Response:
Data Format:
Data Length
2
Data Length
2
Data Length
2
Data
-
Data
2 Bytes
Data
2 Bytes
Data Range:
Byte 1
Byte 2
Low byte of the starting line setting
High byte of the starting line setting
The starting line setting can range from 0x0000 to 0x03F9.
(When using binary commands, the starting line = n +1 where n is the setting made using this binary command.
For example, if you wish to define line 50 as starting line, set 49 with the help of this command.)
L
or a list of rules which must be followed when entering the
settings for the area of interest.
BASLER A201 b 4-15
Configuring the Camera
DRAFT
4.2.4.9 Area of Interest Height in Lines
Purpose: To set the height in lines for the area of interest or to read the current setting. See Section
for details on the area of interest.
Type: This is a read or write command.
Read Command:
Response:
Cmd-ID
0xAA
Cmd-ID
0xAA
R/W-Flag
1
R/W-Flag
0
Write Command: Cmd-ID
0xAA
None
R/W-Flag
0
Response:
Data Format:
Data Length
2
Data Length
2
Data Length
2
Data
-
Data
2 Bytes
Data
2 Bytes
Data Range:
Byte 1
Byte 2
Low byte of the height in lines setting
High byte of the height in lines setting
The height in lines setting can range from 0x0001 to 0x03FA
L
or a list of rules which must be followed when entering the
settings for the area of interest.
4-16 BASLER A201 b
DRAFT
Configuring the Camera
4.2.4.10 Odd Line Gain
Purpose: To set the gain for the odd lines or to read the current odd line gain setting. See Section
for more information on gain.
Type: This is a read or write command.
Read Command:
Response:
Cmd-ID
0x80
Cmd-ID
0x80
R/W-Flag
1
R/W-Flag
0
Write Command: Cmd-ID
0x80
None
R/W-Flag
0
Response:
Data Format:
Data Length
2
Data Length
2
Data Length
2
Data
-
Data
2 Bytes
Data
2 Bytes
Data Range:
Byte 1
Byte 2
Low byte of odd line gain setting
High byte of odd line gain setting
Odd line gain settings can range from 0x0000 to 0x03FF.
4.2.4.11 Odd Line Offset
Purpose: To set the offset for the odd lines or to read the current odd line offset setting. See Section
for more information on offset.
Type: This is a read or write command.
Read Command:
Response:
Cmd-ID
0x84
Cmd-ID
0x84
R/W-Flag
1
R/W-Flag
0
Write Command: Cmd-ID
0x84
None
R/W-Flag
0
Response:
Data Format:
Data Length
2
Data Length
2
Data Length
2
Data
-
Data
2 Bytes
Data
2 Bytes
Data Range:
Byte 1
Byte 2
Low byte of odd line offset setting
High byte of odd line offset setting
Odd line offset settings can range from 0x0000 to 0x03FF
BASLER A201 b 4-17
Configuring the Camera
4.2.4.12 Even Line Gain
DRAFT
Purpose: To set the gain for the even lines or to read the current even line gain setting. See Section
Type: This is a read or write command.
Read Command:
Response:
Cmd-ID
0x82
Cmd-ID
0x82
R/W-Flag
1
R/W-Flag
0
Write Command: Cmd-ID
0x82
None
R/W-Flag
0
Response:
Data Format:
Data Length
2
Data Length
2
Data Length
2
Data
-
Data
2 Bytes
Data
2 Bytes
Data Range:
Byte 1
Byte 2
Low byte of even line gain setting
High byte of even line gain setting
Even line gain settings can range from 0x0000 to 0x03FF
4.2.4.13 Even Line Offset
Purpose: To set the offset for the even lines or to read the current even line offset setting. See Section
for more information on offset.
Type: This is a read or write command.
Read Command:
Response:
Cmd-ID
0x86
Cmd-ID
0x86
R/W-Flag
1
R/W-Flag
0
Write Command: Cmd-ID
0x86
None
R/W-Flag
0
Response:
Data Format:
Data Length
2
Data Length
2
Data Length
2
Data
-
Data
2 Bytes
Data
2 Bytes
Data Range:
Byte 1
Byte 2
Low byte of even line offset setting
High byte of even line offset setting
Even line offset settings can range from 0x0000 to 0x03FF
4-18 BASLER A201 b
DRAFT
4.2.5 Test Image Command
Configuring the Camera
Purpose: To enable or disable a test image. See Section
for an explanation of the test image.
Type: This is a read or write command.
Read Command:
Response:
Write Command:
Response:
Data Format:
Cmd-ID
0xA1
Cmd-ID
0xA1
Cmd-ID
0xA1
None
Byte 1
R/W-Flag
1
R/W-Flag
0
R/W-Flag
0
Data Length
(see the table below).
1
Data Length
1
Data Length
1
An ID that specifies the test image
Data
-
Data
1 Bytes
Data
1 Byte
ID
0x00
0x01
Test Image
No test image
Test Image (gradient pattern)
4.2.6 Camera Reset Command
Purpose: Initiates a camera reset. The behavior is similar to a power up reset.
Type: This is a write only command.
Write Command:
Response:
Data Format:
Cmd-ID
0x42
None
Byte 1
Byte 2
R/W-Flag
0
Low byte
High byte
Data Length
2
Data
0x07, 0xCF
0xCF is always used
0x07 is always used
BASLER A201 b 4-19
Configuring the Camera
DRAFT
4.2.7 Query Commands
4.2.7.1 Read Microcontroller Firmware Version
Purpose: To read the microcontroller firmware version.
Type: This is a read only command.
Read Command:
Response:
Data Format:
Cmd-ID
0x40
Cmd-ID
0x40
Byte 1
Byte 2
Byte 3
R/W-Flag
1
R/W-Flag
0
Data Length
3
Data Length
3
Low byte of firmware version
High byte of firmware version
Protocol Version
Data
-
Data
3 Bytes
BCD coded
BCD coded
4.2.7.2 Read FPGA Firmware Version
Purpose: To read the FPGA firmware version.
Type: This is a read only command.
Read Command:
Response:
Data Format:
Cmd-ID
0x41
Cmd-ID
0x41
Byte 1
Byte 2
Byte 3
R/W-Flag
1
R/W-Flag
0
Data Length
3
Data Length
3
Low byte of firmware version
High byte of firmware version undefined - 0x00 is always used
Data
-
Data
3 Bytes
BCD coded
BCD coded
4.2.7.3 Read Vendor Information
Purpose: To read the camera vendor’s name.
Type: This is a read only command.
Read Command:
Response:
Data Format:
Cmd-ID
0x01
Cmd-ID
0x01
R/W-Flag
1
R/W-Flag
0
Data Length
16
Data Length
16
Data
-
Data
16 Bytes
Zero terminated string if less than 16 bytes are needed for the vendor information. Unterminated string if all 16 bytes are needed.
4-20 BASLER A201 b
DRAFT
4.2.7.4 Read Model Information
Configuring the Camera
Purpose: To read the camera’s model number.
Type: This is a read only command.
Read Command:
Response:
Data Format:
Cmd-ID
0x02
Cmd-ID
0x02
R/W-Flag
1
R/W-Flag
0
Data Length
16
Data Length
16
Data
-
Data
16 Bytes
Zero terminated string if less than 16 bytes are needed for the model information. Unterminated string if all 16 bytes are needed.
4.2.7.5 Read Product ID
Purpose: To read the camera’s product ID number.
Type: This is a read only command.
Read Command:
Response:
Data Format:
Cmd-ID
0x03
Cmd-ID
0x03
R/W-Flag
1
R/W-Flag
0
Data Length
16
Data Length
16
Data
-
Data
16 Bytes
Zero terminated string if less than 16 bytes are needed for the product ID information. Unterminated string if all 16 bytes are needed.
4.2.7.6 Read Serial Number
Purpose: To read the camera’s serial number.
Type: This is a read only command.
Read Command:
Response:
Data Format:
Cmd-ID
0x04
Cmd-ID
0x04
R/W-Flag
1
R/W-Flag
0
Data Length
16
Data Length
16
Data
-
Data
16 Bytes
Zero terminated string if less than 16 bytes are needed for the serial number information. Unterminated string if all 16 bytes are needed.
BASLER A201 b 4-21
Configuring the Camera
DRAFT
4.2.7.7 Read Gain and Offset Reference Values
Purpose: To read the gain and offset reference values that are determined during the camera’s factory calibration procedure (see Section
Type: This is a read only command.
Read Command:
Response:
Cmd-ID
0x08
Cmd-ID
0x08
Data Format: Byte 1
Byte 2
Byte 3
Byte 4
Byte 5
Byte 6
Byte 7
Byte 8
Byte 9
Byte 10
Byte 11
Byte 12
Byte 13
Byte 14
Byte 15
Byte 16
R/W-Flag
1
R/W-Flag
0
Data Length
16
Data Length
16
Data
-
Data
16 Bytes
Low byte of the odd line low gain reference value
High byte of the odd line low gain reference value
Low byte of the even line low gain reference value
High byte of the even line low gain reference value
Low byte of the odd line low offset reference value
High byte of the odd line low offset reference value
Low byte of the even line low offset reference value
High byte of the even line low offset reference value
Low byte of the odd line high gain reference value
High byte of the odd line high gain reference value
Low byte of the even line high gain reference value
High byte of the even line high gain reference value
Low byte of the odd line high offset reference value
High byte of the odd line high offset reference value
Low byte of the even line high offset reference value
High byte of the even line high offset reference value
4-22 BASLER A201 b
DRAFT
Configuring the Camera
4.2.8 Commands for Manipulating Configuration Sets
4.2.8.1 Copy the Factory Set or a User Set into the Work Set
Purpose: To copy the Factory Set or one of the 15 User Sets into the Work Set. See Section
explanation of configuration sets.
The write command will cause the selected set to be copied into the Work Set and the set will become active immediately.
The read command returns the ID of the set that was last copied into the Work Set. (If nothing has been copied to the Work Set since the last power up or reset, the read command will return the ID for “no active set.” This condition indicates that no valid Factory Set or User Sets were found. It will also cause the yellow LED on the back of the camera to show six pulses.)
Type: This is a read or write command.
Read Command:
Response:
Cmd-ID
0x45
Cmd-ID
0x45
R/W-Flag
1
R/W-Flag
0
Write Command:
Response:
Data Format:
Cmd-ID
0x45
None
Byte 1
R/W-Flag
0
Data Length
An ID that specifies the set.
(see the table below).
1
Data Length
1
Data Length
1
Data
-
Data
1 Byte
Data
1 Byte
Set ID Set
0x00 Factory Set
0x01
0x02
User Set 1
User Set 2
0x03
0x04
0x05
0x06
User Set 3
User Set 4
User Set 5
User Set 6
0x07
0x08
User Set 7
User Set 8
0x09 User Set 9
0x0A User Set 10
0x0B User Set 11
0x0C User Set 12
0x0D User Set 13
0x0E User Set 14
0x0F User Set 15
0xFF No active set
BASLER A201 b 4-23
Configuring the Camera
DRAFT
4.2.8.2 Copy Work Set into a User Set
Purpose: To copy the Work Set into one of the 15 User Sets. See Section
configuration sets.
Type: This is a write only command.
Write Command:
Response:
Cmd-ID
0x46
None
R/W-Flag
0
Data Format: Byte 1
Data Length
1
An ID that specifies the user set.
(see the table below).
Data
1 Byte
Set ID Set
0x01
0x02
User Set 1
User Set 2
0x03
0x04
0x05
0x06
User Set 3
User Set 4
User Set 5
User Set 6
0x07
0x08
User Set 7
User Set 8
0x09 User Set 9
0x0A User Set 10
0x0B User Set 11
0x0C User Set 12
0x0D User Set 13
0x0E User Set 14
0x0F User Set 15
4-24 BASLER A201 b
DRAFT
4.2.8.3 Select the Startup Pointer
Configuring the Camera
Purpose: The Startup Pointer is used to tag the configuration set that will be copied into the Work Set
The write command is used to set the Startup Pointer to the Factory Set or to one of the User
Sets.
The read command returns the Set ID for the current setting.
Type: This is a read or write command.
Read Command:
Response:
Cmd-ID
0x47
Cmd-ID
0x47
R/W-Flag
1
R/W-Flag
0
Write Command:
Response:
Data Format:
Cmd-ID
0x47
None
Byte 1
R/W-Flag
0
Data Length
An ID that specifies the set.
(see the table below).
1
Data Length
1
Data Length
1
Data
-
Data
1 Byte
Data
1 Byte
Set ID Set
0x00 Factory Set
0x01
0x02
User Set 1
User Set 2
0x03
0x04
0x05
0x06
User Set 3
User Set 4
User Set 5
User Set 6
0x07
0x08
User Set 7
User Set 8
0x09 User Set 9
0x0A User Set 10
0x0B User Set 11
0x0C User Set 12
0x0D User Set 13
0x0E User Set 14
0x0F User Set 15
BASLER A201 b 4-25
Configuring the Camera
DRAFT
4.2.9 Camera Status Command
Purpose: The camera has been programmed to detect several error conditions. When an error condition is detected, a flag is set. The status command allows you to read the error flags.
Type: This is a read only command.
Read Command:
Response:
Cmd-ID
0x43
Cmd-ID
0x43
Data Format: Byte 1
Byte 2
R/W-Flag
1
R/W-Flag
0
Data Length
2
Data Length
2
Data
-
Data
2 Bytes
Each bit specifies an error condition (see table below).
If a bit is set to 1, the error condition assigned to that bit is present. If the bit is set to 0, the error is not present.
Each bit specifies an error condition (see table below).
If a bit is set to 1, the error condition assigned to that bit is present. If the bit is set to 0, the error is not present.
Byte 1
Bit 0
Bit 1
Bit 2
Bit 3
Bit 4
Bit 5
Bit 6
Bit 7
No ExSync signal in the last 5 seconds
A reset has occurred.
The camera is unlocked
Reserved
Unknown command ID specified in a read or write command
A read or write command could not be executed; access denied
The length member of the last command does not match the defined length
Parameter error
(currently has no meaning - reserved for future use)
Byte 2
Bit 0
Bit 1
Bit 2
Bit 3
Bit 4
Bit 5
Bit 6
Bit 7
FPGA; general error
FPGA; no FPGA firmware available
No FPGA/ADC command list available
Error in FPGA/ADC command list item
User set is erroneous
Factory set is erroneous
EEPROM checksum error (this is a checksum used to determine if the contents of the EEPROM are valid)
No EEPROM command list available
4-26 BASLER A201 b
4.2.10 Bitrate Command
DRAFT
Configuring the Camera
Purpose: To set the bitrate of the serial communications link. The bitrate is changed immediately after the successful receipt of this command. (The default bitrate is 9600.)
Type: This is a write only command.
Write Command:
Response:
Cmd-ID
0x44
None
R/W-Flag
0
Data Length
4
Data
4 Bytes
Data Format: Byte 1
Byte 2
Byte 3
Byte 4
ID
0x12
0x13
0x14
Bitrate
4800
9600
14400
0x15
0x17
19200
38400
0x19 57600
0x1A 76800
0x1B 115200
An ID that specifies the bitrate (see table below).
undefined - always write 0x00 undefined - always write 0x00 undefined - always write 0x00
L
When changing the bitrate for serial communication, use the following procedure:
1. Issue the write command with the new bitrate.
2. Wait one second.
3. Change the bitrate on the serial port that the camera is connected to.
4. Restart the PC and the camera.
5. Resume communication.
4-27 BASLER A201 b
Configuring the Camera
DRAFT
4-28 BASLER A201 b
DRAFT
Mechanical Considerations
5 Mechanical Considerations
5.1 Camera Dimensions and Mounting Facilities
The A201 b camera housing is manufactured with high precision. Planar, parallel, and angular sides guarantee precise mounting with high repeatability.
The A201 b camera is equipped with four M4 mounting holes on the front and two M4 mounting
holes on each side as indicated in Figure 5-1.
Caution!
To avoid collecting dust on the sensor, mount a lens on the camera immediately after unpacking it.
BASLER A201 b 5-1
Mechanical Considerations
DRAFT
5-2
Figure 5-1: A201 b Mechanical Dimensions (in mm)
BASLER A201 b
DRAFT
5.2 C-Mount Adapter Dimensions
Mechanical Considerations
Figure 5-2: C-Mount Adapter Dimensions (in mm)
5.3 F-Mount Adapter Dimensions
Figure 5-3: F-Mount Adapter Dimensions (in mm)
BASLER A201 b 5-3
Mechanical Considerations
DRAFT
5.4 Positioning Accuracy of the Sensor Chip
Positioning accuracy of the sensor chip in the horizontal and vertical direction is ± 0.2 mm.
Rotational positioning accuracy is as shown in Figure 5-4. Reference position is the center of the
camera housing.
Since the translatory and rotational positioning tolerance depend on each other, the worse case of maximum rotational and horizontal/vertical mis-positioning can not occur at the same time.
Figure 5-4: Rotational Positioning Accuracy
5.5 Maximum Lens Thread Length
Caution!
When a C-mount lens is used on an A201 bc
, the thread length on the lens must be less than 7.5 mm. If a lens with a longer thread length is used, the camera will be damaged and will no longer operate.
As shown in Figure 5-5, when a C-mount lens is
used on an A201 bc , the thread length on the lens must be less than 7.5 mm. The A201 bc is equipped with an internal IR cut filter. If a lens with a longer thread length is used, the IR cut filter will be damaged or destroyed and the camera will no longer operate.
Cameras equipped with F-mount lens adapters do not have an internal IR cut filter.
5-4
Figure 5-5: C-mount Lens Thread
BASLER A201 b
DRAFT
6 Troubleshooting
Troubleshooting
6.1 Fault Finding Using Camera LEDs
6.1.1 Yellow LED
The A201 b regularly performs self tests. Detected errors are signaled by blinking of the yellow LED on the back of the camera. The number of pulses indicate the detected error. If several error states are present, the LED outputs the error codes in succession.
See Table 6-1 for the description of the pulses and the error states.
LED
On
Continuous
3 pulses
Description
The camera is OK.
5 pulses
6 pulses
7 pulses
8 pulses
ExSync has not changed state for 5 seconds or longer. If you are not supplying an ExSync signal to the camera, this is a normal condition and should be ignored.
Otherwise check the cable and the ExSync generating device.
The Work Set could not be stored into a User set.
Please contact Basler technical support.
A User Set or the Factory Set could not be loaded into the Work Set.
Please contact Basler technical support.
A valid list of commands was not available.
Please contact Basler tech support.
The FPGA could not be configured. Please contact Basler Technical Support
Table 6-1: Camera Status Indications
6.1.2 Green LED
Green LED
When the green LED on the back of the camera is not lit, it means that no voltage or a voltage below 10.4 V is present. When the green LED is lit, it means that a voltage of 10.4 V or higher is present.
The camera has no overvoltage protection. Therefore, always observe the power requirements as
.
BASLER A201 b 6-1
Troubleshooting
DRAFT
6.2 Troubleshooting Charts
The following pages contain several troubleshooting charts which can help you find the cause of problems that users sometimes encounter. The charts assume that you are familiar with the camera’s features and settings and with the settings for your frame grabber. If you are not, we suggest that you review the manuals for your camera and frame grabber before you troubleshoot a problem.
6.2.1 No Image
Use this chart if you see no image at all when you attempt to capture an image with your frame grabber (in this situation, you will usually get a message from the frame grabber such as “timeout”). If you see a poor quality image, a completely black image, or a completely white image, use the chart in Section
Always switch off power to the system before making or breaking any connection.
Are you using a Basler Interface
Converter (BIC) with the camera?
Yes
No
Use a voltmeter to check the power source for the BIC. Make sure that the power source meets the specs shown in Section
Is the power source OK?
No
Yes
Replace the power source
Connect the power source to the BIC and then check the green
LED on the BIC.
Is the green LED lit?
Yes
No
Replace the BIC
Check the green
LED on the camera.
Is the green LED lit?
No
Yes
Is the BIC attached directly to the camera or is it attached with a cable?
Cable
Directly
Remove the BIC from the camera. Use a volt meter to check the voltage between pin
2 (+) and pin 1 (-) on the BIC.
Is 12 VDC present?
No Yes
Replace the BIC
Replace the
Camera
Use a voltmeter to check the power source for the camera. Make sure that the power source
meets the specs shown in Section 2.6
Is the power source OK?
No
Remove the cable from the 26 pin connector on the front of the BIC. Use a volt meter to check the voltage between pin 2 (+) and pin 1 (-) on the BIC.
Is 12 VDC present?
Yes
Check the cable between the camera and the BIC for broken wires and poor connections.
Is the cable OK?
Yes
Replace the Camera
No
No
Yes
Replace the power source
Connect the power source to the camera and then check the green LED on the camera.
Is the green LED lit?
No
Yes
Replace the camera
Replace the BIC
Replace the cable
6-2 BASLER A201 b
DRAFT
Troubleshooting
Check the Yellow LED on the Camera.
Is the yellow LED flashing?
No. the LED is either on constantly or it is off constantly.
Yes. It is flashing
3 pulses.
Yes. It is flashing
5, 6, 7 or 8 pulses.
The camera is not detecting an
ExSync signal. Check the ExSync signal or set the camera for Free-
).
Call Basler Technical Support for assistance. (The contact numbers appear on the title page of this manual.)
Check to make sure that the RS-232 serial connection is working OK. You can do this by starting the Camera Configuration Tool and seeing which tab appears. If a Model Tab appears, the connection is OK. If a Connection Tab appears, there is a problem with the serial connection.
Is the serial connection OK?
No
Yes
Go to the
RS-232 serial communications troubleshooting chart.
Are you controlling the camera with an ExSync signal or is the camera in free-run?
ExSync signal.
Free-run.
Did you set up free-run using the exposure tab on the camera configuration tool or with binary commands?
Check the setup on your frame grabber and make sure that the
ExSync signal is not too short. The period of the ExSync signal must be greater than 33.3 ms.
(On many frame grabbers, the period of the ExSync signal is adjusted by changing a setting for the “frame rate”. Your frame rate should not exceed 30 fps.)
Is the ExSync period OK?
No
Yes
Check your exposure setting.
The exposure time must be less than the ExSync period.
Is the exposure OK?
Yes
No
Correct the settings.
Correct the settings.
Switch on the test image.
Can the test image be seen?
Yes
No
Go to the interfacing troubleshooting chart.
Config.
Tool
Binary
Commands
Check to make sure that:
Timer 1 is set no lower than
1 µs.
Timer 2 is set no lower than 1
µs.
The sum of the Timer 1 setting plus the Timer 2 setting is greater than 33.3 ms.
Are the settings OK?
No
Yes
Switch on the test image.
Can the test image be seen?
Yes
No
Correct the settings.
Go to the interfacing troubleshooting chart.
Replace the camera.
Replace the camera.
BASLER A201 b 6-3
Troubleshooting
DRAFT
6.2.2 Poor Quality Image
Use this chart if the image is poor quality, is completely white, or is completely black. If you get no image at all when you attempt to capture an image with the frame grabber, use the chart that
Put the camera into test image mode. Use your frame grabber to capture an image and examine the image carefully. (Most frame grabbers include software tools that allow you to see the individual values of each pixel in the image and histograms that display distributions of the pixel values in the image.)
The pixel values in your captured test image should be exactly as described in
Section
. Also, if you capture several test images, the pixel values should be the same in all of the captured test images.
Are the test images OK?
Yes
No
Go to the interfacing troubleshooting chart.
Use the Sets Tab on the configuration tool to copy the
Factory Set to the Work Set. Take the camera out of test image mode and capture a normal image.
Is the problem still present?
Yes
No
One of the camera’s settings was significantly misadjusted. Review the camera manual to make sure that you are setting the camera correctly.
Images are too bright or too dark.
Images look noisy.
Images have a color problem.
Other image problems.
Do the following:
Make sure that the lens cap has been removed.
Check the lens aperture. If the images are too dark, try opening the aperture. Try closing the aperture if they are too bright.
Check the exposure time. If the images are too dark try increasing the exposure. Try decreasing the exposure if they are too bright.
Check your light source. If the images are too dark, try increasing your light intensity. Try decreasing the intensity if they are too bright.
Check your gain setting. If the images are too dark, try increasing the gain. Try decreasing the gain if they are too bright.
Has the problem been corrected?
Do the following:
Make sure that you are using a DC light source. Using an AC light source can make images appear noisy.
Make sure that the camera has proper ventilation. If the camera becomes extremely hot, it may produce noisy images.
Check the exposure time. If you use an extremely long exposure time, the images can become noisy.
Check your gain setting. Using a very low or a very high gain setting can cause noisy images.
Examine the objects that you are imaging. Objects with characteristics such as changing surface texture or reflectance will produce images that appear noisy.
Has the problem been corrected?
Yes
No
Yes
No
Exit this chart.
Do the following:
If most colors look OK but some colors look odd or muddy, try using an IR cut filter. (This only applies to cameras with F-mount lens adapters. Cameras with Cmount lens adapters have a builtin IR cut filter.)
If colors appear to be swapped
(for example, things that should be red are green), check the x-offset and y-offset settings on the frame grabber.
If the captured images appear to be tinted, do a white balance.
Most frame grabbers include a white balance tool.
Has the problem been corrected?
Yes
Exit this chart.
No
Exit this chart.
Contact Basler Technical Support. The contact numbers appear on the title page of this manual.
Before you call for support, be sure to make note of the camera settings and the frame grabber settings you are using. You should also have a captured live image and a captured test image available. Technical support will frequently request that you e-mail copies of these captured images.
6-4 BASLER A201 b
DRAFT
Troubleshooting
6.2.3 Interfacing
Use the interfacing troubleshooting charts if you think that there is a problem with the cables between your devices or if you have been directed here from another chart. Go to Chart A if you are using the camera without a Basler Interface Converter (BIC) or go to Chart B if you are using the camera with a BIC.
Interfacing Chart A
(without a BIC)
Always switch off power to the system before making or breaking any connection.
Reseat all of the cable connections at the camera, the frame grabber, and the PC.
After you reseated the connections, is the problem still present?
Yes
No
Exit this chart.
Use a voltmeter to check the power source for the camera. The output must be 12 VDC (± 10%). Also, the power source must be rated for at least 8 W?
Is the power source OK?
Yes
No
Replace the power source
If extra hardware is available, try to locate the problem by substitution. (Substitute only one piece of hardware at a time and retry the system after each substitution.)
After you finished making substitutions, is the problem still present?
Yes
No
Exit this chart.
Check the DCF (configuration) file that you are using with your frame grabber. Make sure that it is the correct file for the Basler A201 b . Be aware that sometimes different DCF files must be used depending on which of the camera’s features you have enabled.
DCF files for many types of frame grabbers are available at the Basler web site: www.basler-vc.com. These files have all been tested with the A201 b and we suggest that you use them if one is available for your type of frame grabber.
After you checked the DCF file, is the problem still present?
Yes
No
Check all of the cables in the system:
of this manual and make sure that you are using a cable that has the right characteristics and is not too long. It is extremely important to use the proper cables when you are working with Channel Link based cameras.
Use an ohm meter to check each wire to see of it is broken or shorted to any of the other wires in the cable.
Examine the terminations on each end of the cable. Look for broken pins, poor crimps or poor solder joints.
Check the pinout chart that appears in Section
diagrams in your frame grabber manual. Make sure that your cables are correctly wired.
After you checked the cables, is the problem still present?
Yes
No
Exit this chart.
Exit this chart.
Contact Basler Technical Support. The contact numbers appear on the title page of this manual.
Before you call for support, be sure to make note of the camera settings and the frame grabber settings you are using. You should also have a captured live image and a captured test image available. Technical support will frequently request that you e-mail copies of these captured images.
BASLER A201 b 6-5
Troubleshooting
DRAFT
Interfacing Chart B
(with a BIC
)
Always switch off power to the system before making or breaking any connection.
6-6
Reseat all of the cable connections at the camera, the BIC, the frame grabber, and the PC.
After you reseated the cables, is the problem still present?
Yes
Use a voltmeter to check the power source for the
BIC. The output must be 24 VDC (± 10%). Also, the power source must be rated for at least 10 W?
Is the power source OK?
Yes
No
No Exit this chart.
Replace the power source
If extra hardware is available, try to locate the problem by substitution. (Substitute only one piece of hardware at a time and retry the system after each substitution.)
After you finished making substitutions, is the problem still present?
Yes
No Exit this chart.
Check the DCF (configuration) file that you are using with your frame grabber. Make sure that it is the correct file for the Basler A201 b . Be aware that sometimes different DCF files must be used depending on which of the camera’s features you have enabled.
DCF files for many types of frame grabbers are available at the Basler web site: www.basler-vc.com. These files have all been tested with the A201 b and we suggest that you use them if one is available for the frame grabber that you are using.
After you checked the DCF file, is the problem still present?
Yes
No
Check all of the cables in the system:
of this manual and make sure that you are using cables
that have the right characteristics and are not too long. It is extremely important to use the proper cables when you are working with Channel Link based cameras.
Use an ohm meter to check each wire to see of it is broken or shorted to any of the other wires in the cable.
Examine the terminations on each end of the cable. Look for broken pins, poor crimps or poor solder joints.
Check the pinout charts that appear in Section 2.1.2
and check the pinout diagrams in your frame grabber manual. Make sure that your cables are correctly wired.
After you checked the cables, is the problem still present?
Yes
No
Exit this chart.
Exit this chart.
Contact Basler Technical Support. The contact numbers appear on the title page of this manual.
Before you call for support, be sure to make note of the camera settings and the frame grabber settings you are using. You should also have a captured live image and a captured test image available. Technical support will frequently request that you e-mail copies of these captured images.
BASLER A201 b
DRAFT
Troubleshooting
6.2.4 RS-232 Serial Communication
Use the serial communication troubleshooting charts if you think that there is a problem with RS-
232 serial communication or if you have been directed here from another chart. Go to Chart A if you are using the camera without a Basler Interface Converter (BIC) or go to Chart B if you are using the camera with a BIC.
Serial Communication Chart A
(without a BIC)
Always switch off power to the system before making or breaking any connection.
Check the COM port that you are using for serial communications. Make sure that the port is set for
8 data bits, no parity, 1 stop bit, and 9600 baud.
After the port settings correct?
No
Correct the settings and then restart your computer.
Yes
Check the PC and make sure that the serial cable is plugged into the correct connector. (On PCs with multiple serial port connectors, it is easy to plug the cable into the wrong connector.)
Is the cable plugged into the correct connector?
No
Yes
Change the connection
Check the wiring between the camera and the serial port on the computer.
The wiring should be as described in
Section
serial connection should be no more than 15 meters long.
Is the cable the correct length and is it wired correctly.
No
Yes
Replace the cable.
Try using a different COM port on your computer. For example, if you have been using
COM port 1, try using COM port 2 instead.
When you do this, make sure that the port is set for 8N1 and 9600 baud. Also make sure that the serial cable is plugged into the correct connector on the computer. Be sure to restart your computer after you make the port change.
Is the problem still present after you changed the port?
Yes
No
Exit this chart.
Contact Basler Technical Support.
The contact numbers appear on the title page of this manual.
BASLER A201 b 6-7
Troubleshooting
DRAFT
Serial Communication Chart B
(with a BIC)
Always switch off power to the system before making or breaking any connection.
Check the COM port that you are using for serial communications. Make sure that the port is set for 8 data bits, no parity, 1 stop bit, and
9600 baud.
After the port settings correct?
Yes
No
Check the PC and make sure that the serial cable is plugged into the correct connector. (On PCs with multiple serial port connectors, it is easy to plug the cable into the wrong connector.)
Is the cable plugged into the correct connector on the PC?
Yes
No
Correct the settings and then restart your computer.
Change the connection
Check the wiring on the serial cable between the computer and the BIC. (This cable should be a null modem cable
and should be wired as shown on page A-9.) Also, make
sure that the cable is no longer than 15 meters.
Is the cable the correct length and is it wired correctly.
Yes
No
Try using a different COM port on your computer. For example, if you have been using COM port 1, try using COM port 2 instead. When you do this, make sure that the port is set for 8N1 and 9600 baud. Also make sure that the serial cable is plugged into the correct connector on the computer. Be sure to restart your computer after you make the port change.
Is the problem still present after you changed the port?
Yes
No
Contact Basler Technical Support.
The contact numbers appear on the title page of this manual.
Replace the cable.
Exit this chart.
6-8 BASLER A201 b
DRAFT
Troubleshooting
6.3 Before Calling Basler Technical Support
To help you as quickly and efficiently as possible when you have a problem with a Basler camera, it is important that you collect several pieces of information before you contact technical support.
Copy the form that appears on this and the next page (or download it from the support section of www.basler-vc.com), fill it out, and fax the pages to your local dealer or to your nearest Basler support center. Or, you can write an e-mail listing the requested pieces of information and with the requested files attached. Our technical support contact numbers are shown in the front section of this manual.
1 The camera’s product ID:
2 The camera’s serial number:
3 The operating system:
4 Frame grabber that you use with the camera:
5 CCT version that you use with the camera:
6 Describe the problem in as much detail as possible:
(If you need more space, use an extra sheet of paper.)
7 If known, what’s the cause of the problem?
8 When did the problem occur?
After start.
While running.
After a certain action (e.g., a change of parameters):
BASLER A201 b 6-9
Troubleshooting
9 How often did/does the problem occur?
DRAFT
Once.
Regularly when:
Occasionally when:
Every time.
10 How severe is the problem?
Camera can still be used.
Camera can be used after I take this action:
6-10
Camera can no longer be used.
11 Did your application ever run without problems?
Yes No
12 Parameter set
It is very important for Basler Technical Support to get a copy of the exact camera parameters that you were using when the problem occurred.
To make a copy of the parameters, open the parameter set in the CCT and save or dump the settings to a file. Send the generated file to Basler Technical Support.
If you cannot access the camera, please try to state the following parameter settings:
Video data output mode:
Exposure time control mode:
Exposure time:
Gain:
Offset:
13 Live image/test image
If you are having an image problem, try to generate and save live images that show the problem. Also generate and save test images. Please save the images in BMP format, zip them, and send them to Basler Technical Support.
BASLER A201 b
DRAFT
Troubleshooting
BASLER A201 b 6-11
Troubleshooting
DRAFT
6-12 BASLER A201 b
DRAFT
Using the Camera with a BIC
Appendix A
Using the Camera with a BIC
A.1 Introduction
As mentioned in Section
, video data is output from the A201 b in a Channel Link LVDS format.
The video output from the camera can be converted to LVDS as specified for RS-644 by using a
Basler Interface Converter (BIC). The BIC is a small device that attaches to the A201 b .
A.1.1 BIC Functional Description
As shown in the block diagram in Figure A-1, a channel link receiver in the BIC receives the output
data from the camera in Channel Link LVDS format. The receiver converts the Channel Link signals to TTL level signals and passes the TTL signals to a group of RS-644 LVDS transmitters.
The LVDS transmitters convert the TTL level signals to standard LVDS signals as specified for
RS-644 and transmit the signals out of the BIC.
The A201 b can accept an ExSync input signal in RS-644 LVDS format. The ExSync signal from the frame grabber is passed through the BIC to the camera using a straight through connection with no active circuitry.
Configuration commands and responses are transmitted between the camera and the host computer via an RS-232 serial connection. RS-232 commands and responses are passed through the BIC using a straight through connection with no active circuitry.
The BIC requires a 24 VDC power input. The A201 b , however, requires 12 VDC power. The BIC converts incomming 24 VDC to 12 VDC and supplies 12 VDC to the camera.
BASLER A201 b A-1
Using the Camera with a BIC
DRAFT
Basler Interface Converter
Configuration Commands to Camera in
RS-232 Format
Command Responses from Camera
Video Data from Camera in Channel
Link LVDS
Format
Channel
Link
Receiver
ExSync Signal to Camera in
RS-644 LVDS
Format
12 VDC to Camera
Figure A-1: BIC Block Diagram
DC/DC
Converter
RS-644 LVDS
Transmitter
RS-644 LVDS
Transmitter
RS-644 LVDS
Transmitter
RS-644 LVDS
Transmitter
Configuration Commands to Camera in
RS-232 Format
Command Responses from Camera
Video Data
To Frame
Grabber in
RS-644 LVDS
Format
ExSync Signal in
RS-644 LVDS
Format
24
VDC
A.1.2 BIC Specifications
Category
Video Input
Video Output
Pixel Clock Speed
Power Requirements
Size
Weight
Table A-1: BIC Specifications
Specification
Channel Link LVDS
RS-644 LVDS
42 MHz when the attached A201 b is operating in single output mode
21 MHz when the attached A201 b is operating in dual output mode
24 VDC (± 10%), max. 10 W (when attached to an A201 b
), < 1% ripple
35.5 mm x 59.5 mm x 59.5 mm (L x W x H)
~ 110 g
A-2 BASLER A201 b
DRAFT
Using the Camera with a BIC
A.1.3 BIC Environmental Requirements
A.1.3.1 Temperature and Humidity
Housing temperature during operation:
Humidity during operation:
A.1.3.2 Ventilation
0° C ... + 50° C (+ 32° F ... + 122° F)
20% ... 80%, relative, non-condensing
Allow sufficient air circulation around the BIC to prevent internal heat build-up in your system and to keep the BIC housing temperature during operation below 50° C. Provide additional cooling such as fans or heat sinks if necessary.
Warning!
Without sufficient cooling the BIC can get hot enough during operation to cause burning when touched.
A.1.4 BIC Precautions
Power
Caution!
Be sure that all power to your system is switched off before you make or break connections to the BIC. Making or breaking connections when power is on can result in damage to the BIC.
Read the manual
Read the manual carefully before using the BIC.
Keep foreign matter outside of the BIC
Do not open the housing. Touching internal components may damage them.
Be careful not to spill water or other liquids on the BIC. Do not allow flammable or metallic material inside the BIC housing. If used with any foreign matter inside, the BIC may fail or cause a fire.
Electromagnetic Fields
Do not operate the BIC in the vicinity of strong electromagnetic fields. Avoid electrostatic charging.
Transporting
Only transport the BIC in its original packaging. Do not discard the packaging.
Cleaning
To clean the surface of the BIC housing, use a soft, dry cloth. To remove severe stains, use a soft cloth dampened with a small quantity of neutral detergent, then wipe dry.
Do not use volatile solvents such as benzine and thinners; they can damage the surface finish.
BASLER A201 b A-3
Using the Camera with a BIC
DRAFT
A.2 BIC Interface Description
A.2.1 Connections
A.2.1.1 General Description
The BIC is interfaced to external circuitry via one connector on its front and three connectors on
its back. Figure A-2 shows the connector types used on the BIC and shows the location of the
BIC
FRONT
VIEW
BIC
REAR
VIEW
Green
LED
D-Sub HD
44 Pin
Receptacle
Subminiature
Round
4 pin plug
D-Sub HD
26 Pin Receptacle
Figure A-2: BIC Connector Types
D-Sub
9 pin plug
A-4 BASLER A201 b
Connection to Camera
Front View
DRAFT
Using the Camera with a BIC
Rear View
Serial Port:
RXD, TXD
Green LED:
Power OK
EXSYNC In
Digital Video Out
FVAL Out
LVAL Out
Pixel Clock Out
+ 24 V Power In
Figure A-3: BIC Connectors and Signals
19
10
1
26
18
9
Rear View
Front View
15
30
44
1
6 9
5
1
2
4
3
1
16
31
Figure A-4: BIC Pin Numbering
A.2.1.2 Pin Assignments
The D-Sub HD 26-pin receptacle on the front of the BIC is used to interface video data and control
signals with the camera. The pin assignments for the receptacle are shown in Table A-2.
BASLER A201 b A-5
Using the Camera with a BIC
DRAFT
Pin
Number
Signal
Name
Direction Level Function
1, 9, 18,
19, 25, 26
1
2, 20
2
22
24
21, 23 1
11
10
13
12
15
14
6
5
4
3
8
7
17
16
DC Gnd
+12 VDC
TxD
RxD
Signal Gnd
Output
Output
Output
Input
Output
Ground
12 VDC ± 10%
RS-232
RS-232
Ground
DC Ground
DC Power Output to the Camera
RS-232 Serial Communication
RS-232 Serial Communication
Signal Ground
ExSync+
ExSync-
Reserved+
Reserved-
RxClkIn+
RxClkIn-
RxDataIn3+
RxDataIn3-
RxDataIn2+
RxDataIn2-
RxDataIn1+
RxDataIn1-
RxDataIn0+
RxDataIn0-
Output
Output
Input
Input
Input
Input
Input
RS-644 LVDS
RS-644 LVDS
Channel Link
LVDS
Channel Link
LVDS
Channel Link
LVDS
Channel Link
LVDS
Channel Link
LVDS
External Trigger
Reserved LVDS Output
Receive Clock to Channel Link Receiver
Data to Channel Link Receiver
Data to Channel Link Receiver
Data to Channel Link Receiver
Data to Channel Link Receiver
1 Pins 1, 9, 18, 19, 25, 26, 21 and 23 are all tied together inside of the BIC.
2 Pins 2 and 20 are tied together inside of the BIC.
Table A-2: Pin Assignments for the D-sub HD 26-pin Receptacle
A-6
L
The BIC housing is not grounded and is electrically isolated from the circuit boards inside of the BIC.
The D-Sub 9-pin plug on the back of the BIC is used for RS-232 communication between the host
computer and the camera. The pin assignments for the plug are shown in Table A-3.
BASLER A201 b
DRAFT
Using the Camera with a BIC
Pin
Number
7
8
5
6
9
3
4
1
2
Signal
Name
RxD
TxD
Signal Gnd
Direction Level
Input
Output
Input
RS-232
RS-232
Ground
Table A-3: Pin Assignments for the D-sub 9-pin Plug
Function
Not Connected
RS-232 Serial Communication
RS-232 Serial Communication
Tied to pin 6 internally
Signal Ground
Tied to pin 4 internally
Tied to pin 8 internally
Tied to pin 7 internally
Not Connected
The subminiature, round 4-pin plug on the back of the BIC is used for input power. The pin
assignments for the plug are shown in Table A-4.
Pin
Number
1
2
3
4
Signal
Name
DC Gnd
Direction Level Function
+24 VDC
Input
Input
Ground
24 VDC ± 10%
DC Ground
Tied to pin 1 internally
DC Power input for the BIC
Tied to pin 3 internally
Table A-4: Pin Assignments for the Subminiature, Round 4-pin Plug
BASLER A201 b A-7
Using the Camera with a BIC
DRAFT
The D-Sub HD 44-pin receptacle on the back of the BIC is used to interface video data and control
signals with the frame grabber. The pin assignments for the receptacle are shown in Table A-5.
As shown in the table, the assignment of pixel data varies depending on the output mode setting of the camera that is attached to the BIC.
A-8
Pin
Number
7
8
5
6
3
4
1
2
Signal
Name
DOUT 0
DOUT 1
DOUT 2
DOUT 3
DOUT 4
DOUT 5
DOUT 6
DOUT 7
Direction
Output
Output
Output
Output
Output
Output
Output
Output
Level
RS-644 LVDS
RS-644 LVDS
RS-644 LVDS
RS-644 LVDS
RS-644 LVDS
RS-644 LVDS
RS-644 LVDS
RS-644 LVDS
Single 10 Bit
Output Mode
Pixel Bit 0
Pixel Bit 1
Pixel Bit 2
Pixel Bit 3
Pixel Bit 4
Pixel Bit 5
Pixel Bit 6
Pixel Bit 7
/DOUT 1
/DOUT 2
/DOUT 3
/DOUT 4
/DOUT 5
/DOUT 6
/DOUT 7
/DOUT 8
DOUT 8
DOUT 9
DOUT 10
DOUT 11
DOUT 12
DOUT 13
DOUT 14
/DOUT 0
/DOUT 9
/DOUT 10
/DOUT 11
/DOUT 12
/DOUT 13
/DOUT 14
21
22
23
24
17
18
19
20
13
14
15
16
9
10
11
12
25
26
27
28
29
30
Output
Output
Output
Output
Output
Output
Output
Output
Output
Output
Output
Output
Output
Output
Output
Output
Output
Output
Output
Output
Output
Output
RS-644 LVDS Pixel Bit 8
RS-644 LVDS Pixel Bit 9 (MSB)
RS-644 LVDS
RS-644 LVDS
Not Used
Not Used
RS-644 LVDS
RS-644 LVDS
RS-644 LVDS
RS-644 LVDS
Not Used
Not Used
Not Used
/Pixel Bit 0
RS-644 LVDS
RS-644 LVDS
RS-644 LVDS
RS-644 LVDS
RS-644 LVDS
RS-644 LVDS
RS-644 LVDS
RS-644 LVDS
/Pixel Bit 1
/Pixel Bit 2
/Pixel Bit 3
/Pixel Bit 4
/Pixel Bit 5
/Pixel Bit 6
/Pixel Bit 7
/Pixel Bit 8
RS-644 LVDS
RS-644 LVDS
RS-644 LVDS
RS-644 LVDS
RS-644 LVDS
RS-644 LVDS
/Pixel bit 9
Not Used
Not Used
Not Used
Not Used
Not Used
Table A-5: Pin Assignments for the D-sub HD 44-pin Receptacle
/Pixel Bit 1
/Pixel Bit 2
/Pixel Bit 3
/Pixel Bit 4
/Pixel Bit 5
/Pixel Bit 6
/Pixel Bit 7
Not Used
Not Used
Not Used
Not Used
Not Used
Not Used
Not Used
Not Used
/Pixel Bit 0
Not Used
Not Used
Not Used
Not Used
Not Used
Not Used
Single 8 Bit
Output Mode
Pixel Bit 0
Pixel Bit 1
Pixel Bit 2
Pixel Bit 3
Pixel Bit 4
Pixel Bit 5
Pixel Bit 6
Pixel Bit 7 (MSB)
Dual 8 Bit
Output Mode
Odd Pixel Bit 0
Odd Pixel Bit 1
Odd Pixel Bit 2
Odd Pixel Bit 3
Odd Pixel Bit 4
Odd Pixel Bit 5
Odd Pixel Bit 6
Odd Pixel Bit 7
(MSB)
Even Pixel Bit 0
Even Pixel Bit 1
Even Pixel Bit 2
Even Pixel Bit 3
Even Pixel Bit 4
Even Pixel Bit 5
Even Pixel Bit 6
/Odd Pixel Bit 0
/Odd Pixel Bit 1
/Odd Pixel Bit 2
/Odd Pixel Bit 3
/Odd Pixel Bit 4
/Odd Pixel Bit 5
/Odd Pixel Bit 6
/Odd Pixel Bit 7
/Even Pixel Bit 0
/Even Pixel Bit 1
/Even Pixel Bit 2
/Even Pixel Bit 3
/Even Pixel Bit 4
/Even Pixel Bit 5
/Even Pixel Bit 6
BASLER A201 b
DRAFT
Using the Camera with a BIC
Pin
Number
31
Signal
Name
DOUT 15
Direction
Output
Level
RS-644 LVDS
Single 10 Bit
Output Mode
Not Used
32
33
34
35
36
37
38
/DOUT 15
LVAL
/LVAL
PClk
/PClk
SyncIn
/SyncIn
Output
Output
Output
Output
Output
Input
Input
RS-644 LVDS
RS-644 LVDS
RS-644 LVDS
RS-644 LVDS
RS-644 LVDS
RS-644 LVDS
RS-644 LVDS
Not Used
Line Valid
/Line Valid
Pixel Clock
/Pixel Clock
External
Trigger
/External
Trigger
Frame Valid
/Frame Valid
39
40
41
FVAL Output
/FVAL
Not Connected
Output
RS-644 LVDS
RS-644 LVDS
42
43
Not Connected
Signal
Gnd
Output Ground
44 Tied to pin 43 internally
/ means an inverted signal with the low signal being active
Signal Ground
Table A-5: Pin Assignments for the D-sub HD 44-pin Receptacle
Signal Ground
Not Used
Line Valid
/Line Valid
Pixel Clock
/Pixel Clock
External
Trigger
/External
Trigger
Frame Valid
/Frame Valid
Single 8 Bit
Output Mode
Not Used
Dual 8 Bit
Output Mode
Even Pixel Bit 7
(MSB)
/Even Pixel Bit 7
Line Valid
/Line Valid
Pixel Clock
/Pixel Clock
External
Trigger
/External
Trigger
Frame Valid
/Frame Valid
Signal Ground
A.3 Cable Information
A.3.1 Channel Link Cable Between the Camera and the BIC
The BIC can be attached directly to a Channel Link based camera or a cable can be used between the camera and the BIC. In cases where a cable is used between the camera and the BIC, the cable must meet the specifications shown in Section
A.3.2 Video Data Cable Between the BIC and the Frame Grabber
The video data cable between the BIC and the frame grabber must made with 28 gauge AWG twisted pair wire and have a characteristic impedance of 100 ohms.
The maximum length of the cable is 11 meters when the A201 b attached to the BIC is operating in single output mode and 18 meters when the attached camera is operating in dual output mode.
BASLER A201 b A-9
Using the Camera with a BIC
DRAFT
A.3.3 RS-232 Cable Between the BIC and the PC
The RS-232 cable between the nine pin plug on the BIC and the serial port connector on the PC
can be a null modem cable or a simple three wire connection as illustrated in Figure A-5. The
maximum length of the cable is 15 meters.
Figure A-5: BIC to PC RS-232 Interface Cable
L
The cable between the BIC and the PC must contain a twist so that pin 2 on the BIC connects to pin 3 on the PC and pin 3 on the BIC connects to pin 2 on the PC.
A.4 Video Data and Control Signals Between the BIC and the Frame Grabber
All video data and control signals transmitted between the BIC and the frame grabber use LVDS
technology as specified for RS-644. Detailed information on RS-644 appears in Section A.4.3
.
A.4.1 Signals Input to the BIC by the Frame Grabber
A.4.1.1 ExSync: Controls Frame Readout and Exposure Time
The camera attached to the BIC can be programmed to function in several exposure time control modes. In some of these modes, an ExSync signal is used to control exposure time and frame read out. For more detailed information on exposure control modes and the use of the ExSync
ExSync can be a periodic or a non-periodic function. The frequency of the Exsync signal determines the camera’s frame rate.
A-10 BASLER A201 b
DRAFT
Using the Camera with a BIC
The BIC accepts the ExSync signal from the frame grabber and passes it through to the camera using a straight through connection with no active circuitry.
A.4.2 Signals Output from the BIC to the Frame Grabber
A.4.2.1 FVAL: Indicates a Valid Frame
Frame valid (FVAL) indicates a valid frame as shown in Figures A-6
and
valid if FVAL is high.
A.4.2.2 LVAL: Indicates a Valid Line
Line valid (LVAL) indicates a valid line of data as illustrated in Figures A-6 and A-7
. Video data is only valid if LVAL is high.
A.4.2.3 Pixel Clock: Indicates a Valid Pixel
Pixel clock (PClk) indicates a valid pixel of data as illustrated in Figures
LVAL, and PClk signals are used to clock the digital video output data into external circuitry. Digital data is valid on the rising edge of pixel clock with FVAL and LVAL high.
The frequency of the pixel clock output from the BIC varies depending on the output mode of the
attached camera. See Sections A.4.2.5
A.4.2.4 Video Data
The assignment of pixel data bits to the output pins of the BIC and the output sequence of the pixel
data varies depending on the output mode of the attached camera. Table A-5 shows how the pixel
data bits are assigned for each camera output mode. Sections
and
describe the data output sequence for each camera output mode.
L
The A201 b attached to the BIC must be set for Single 10 Bit, Single 8 Bit, or
Dual 8 Bit output mode. The BIC can not accept Dual 10 Bit output from the camera.
A.4.2.5 BIC Operation with Attached Camera in Single 10 Bit or
Single 8 Bit Output Mode
When the camera attached to the BIC is operating in Single 10 Bit output mode, the pixel clock output from the BIC will be 42 MHz. On each clock cycle, the BIC will transmit 10 bits of pixel data.
The assignment of the bits is shown in Table A-5.
When the camera attached to the BIC is operating in Single 8 Bit output mode, the pixel clock output from the BIC will be 42 MHz. On each clock cycle, the BIC will transmit 8 bits of pixel data.
(The two least significant bits output from each ADC are dropped.)
Video Data Sequence
1
When the camera is not transmitting valid pixel data, the frame valid and line valid signals on each cycle of the pixel clock will be low. Once the camera has completed frame acquisition, it will begin to send valid data:
• On the pixel clock cycle where frame data transmission begins, FVAL will become high.
A-11 BASLER A201 b
Using the Camera with a BIC
DRAFT
• On the pixel clock cycle where data transmission for line one begins, LVAL will become high.
During this cycle, 10 bits of data for pixel number one in line one will be transmitted.
• On the next cycle of the pixel clock, LVAL will be high. During this cycle, 10 bits of data for pixel two in line one will be transmitted.
• On the next cycle of the pixel clock, LVAL will be high. During this cycle, 10 bits of data for pixel three in line one will be transmitted.
• This pattern will continue until all of the pixel data for line one has been transmitted. (A total of 1008 cycles.)
• After all of the pixels in line one have been transmitted, LVAL will become low indicating that valid line data for line one is no longer being transmitted.
• On the pixel clock cycle where data transmission for line two begins, LVAL will become high.
During this cycle, 10 bits of data for pixel number one in line two will be transmitted.
• On the next cycle of the pixel clock, LVAL will be high. During this cycle, 10 bits of data for pixel two in line two will be transmitted.
• On the next cycle of the pixel clock, LVAL will be high. During this cycle, 10 bits of data for pixel three in line two will be transmitted.
• This pattern will continue until all of the pixel data for line two has been transmitted. (A total of
1008 cycles.)
• After all of the pixels in line two have been transmitted, LVAL will become low indicating that valid line data for line two is no longer being transmitted.
• The camera will continue to transmit pixel data for each line as described above until all of the lines in the frame have been transmitted. After all of the lines have been transmitted,
FVAL will become low indicating that a valid frame is no longer being transmitted.
exposure mode.
A-12
____________________
1 The data sequence assumes that the camera attached to the BIC is operating in 10 bit mode. If the attached camera is operating in 8 bit mode, only 8 bits of data per pixel will be transmitted.
BASLER A201 b
DRAFT
Using the Camera with a BIC
This diagram is not drawn to scale.
The diagram assumes that the area of interest feature is not being used. With the area of interest feature enabled, the number of lines transferred and the number of pixels in each line could be smaller.
Figure A-6: Single 10 Bit or Single 8 Bit Output Mode with Level Controlled Exposure
This diagram is not drawn to scale.
The diagram assumes that the area of interest feature is not being used. With the area of interest feature enabled, the number of lines transferred and the number of pixels in each line could be smaller.
Figure A-7: Single 10 Bit or Single 8 Bit Output Mode with Programmable Exposure
____________________
1 The Line Valid low time alternates between 6.2 µs and 7.4 µs. The first low time is 6.2 µs, the next is 7.4 µs, the next is 6.2 µs, the next 7.4 µs, and so on. This pattern will continue until all of the pixel data for a line has been transmitted.
2 Depending on the Line Valid low time, the Line Valid cycle is either 30.2 µs or 31.4 µs.
BASLER A201 b A-13
Using the Camera with a BIC
DRAFT
A.4.2.6 BIC Operation with Attached Camera in Dual 8 Bit Output Mode
When the camera attached to the BIC is operating in Dual 8 Bit output mode, the pixel clock output from the BIC will be 21 MHz. On each clock cycle, the BIC will transmit 8 bits of data for two pixels.
The assignment of the bits is shown in Table A-5.
Video Data Sequence
When the camera is not transmitting valid pixel data, the frame valid and line valid signals on each cycle of the pixel clock will be low. Once the camera has completed frame acquisition, it will begin to send valid data:
• On the pixel clock cycle where frame data transmission begins, FVAL will become high.
• On the pixel clock cycle where data transmission for line one begins, LVAL will become high.
During this cycle, 8 bits of data for pixel number one in line one and 8 bits of data for pixel number two in line one will be transmitted.
• On the next cycle of the pixel clock, LVAL will be high. During this cycle, 8 bits of data for pixel three in line one and 8 bits of data for pixel four in line one will be transmitted.
• On the next cycle of the pixel clock, LVAL will be high. During this cycle, 8 bits of data for pixel five in line one and 8 bits of data for pixel six in line one will be transmitted.
• This pattern will continue until all of the pixel data for line one has been transmitted. (A total of 504 cycles.)
• After all of the pixels in line one have been transmitted, LVAL will become low indicating that valid line data for line one is no longer being transmitted.
• On the pixel clock cycle where data transmission for line two begins, LVAL will become high.
During this cycle, 8 bits of data for pixel number one in line two and 8 bits of data for pixel number two in line two will be transmitted.
• On the next cycle of the pixel clock, LVAL will be high. During this cycle, 8 bits of data for pixel three in line two and 8 bits of data for pixel four in line two will be transmitted.
• On the next cycle of the pixel clock, LVAL will be high. During this cycle, 8 bits of data for pixel five in line two and 8 bits of data for pixel six in line two will be transmitted.
• This pattern will continue until all of the pixel data for line two has been transmitted. (A total of
504 cycles.)
• After all of the pixels in line two have been transmitted, LVAL will become low indicating that valid line data for line two is no longer being transmitted.
• The camera will continue to transmit pixel data for each line as described above until all of the lines in the frame have been transmitted. After all of the lines have been transmitted,
FVAL will become low indicating that a valid frame is no longer being transmitted.
exposure mode.
A-14 BASLER A201 b
DRAFT
Using the Camera with a BIC
This diagram is not drawn to scale. The diagram assumes that the area of interest feature is not being used. With the area of interest feature enabled, the number of lines transferred and the number of pixels in each line could be smaller.
Figure A-8: Dual 8 Bit Output Mode with Level Controlled Exposure
This diagram is not drawn to scale. The diagram assumes that the area of interest feature is not being used. With the area of interest feature enabled, the number of lines transferred and the number of pixels in each line could be smaller.
Figure A-9: Dual 8 Bit Output Mode with Programmable Exposure
____________________
1 The Line Valid low time alternates between 6.2 µs and 7.4 µs. The first low time is 6.2 µs, the next is 7.4 µs, the next is 6.2 µs, the next 7.4 µs, and so on. This pattern will continue until all of the pixel data for a line has been transmitted.
2 Depending on the Line Valid low time, the Line Valid cycle is either 30.2 µs or 31.4 µs.
BASLER A201 b A-15
Using the Camera with a BIC
DRAFT
A.4.3 RS-644 LVDS Information
All video data and control signals output from the BIC and the ExSync control signal input to the
BIC use LVDS technology as specified for RS-644.
As shown in Figure A-10, the BIC uses National Semiconductor DS90LV047A differential line
drivers to generate the LVDS output signals DOut0 through DOut15, FValOut, LValOut, and
PClkOut.
The ExSync control signal input to the BIC passes straight through the BIC and into the camera.
The camera uses a National Semiconductor DS90LV048A differential line receiver to receive the
ExSync input signal.
Detailed spec sheets for these devices are available at the National Semiconductor web site
(www.national.com).
A.4.3.1 RS-644/RS-422 Compatibility
Outputs From the BIC
The output voltage level for the RS-644 differential line drivers used in the BIC can range from a low of 0.90 V to a high of 1.6 V. The typical voltage swing for these devices is ± 0.31 V.
The receive threshold for typical RS-422 receivers is well within the ± 0.31 V swing generated by the RS-644 line drivers. Also, the input voltage tolerance for typical RS-422 receivers is well above the output voltage generated by the RS-644 devices. For these reasons, typical RS-422 receivers are compatible with the RS-644 signals output from the BIC.
Inputs To the BIC
As shown in Figure A-10, the ExSync signal input to the BIC passes directly through the BIC and
on to the camera. The input voltage tolerance for the RS-644 receiver used in the camera is 0.0
V to 3.9 V.
On typical RS-422 transmitters, the output voltage can range as high as 4.0 V. As you see, the output voltage of a typical RS-422 transmitter can exceed the input voltage tolerance of the RS-
644 receiver used in the camera. Therefore, RS-422 signals should not be input directly into the
BIC.
A-16 BASLER A201 b
DRAFT
Using the Camera with a BIC
Figure A-10: BIC Power, RS-232, and Video Data Connections
BASLER A201 b A-17
Using the Camera with a BIC
DRAFT
A.5 RS-232 Serial Connection
, configuration commands and responses are transmitted between the camera and the host computer via an RS-232 serial connection. RS-232 commands and responses are passed through the BIC using a straight through connection with no active circuitry.
A.6 Power Supply
The BIC requires a 24 VDC (± 10%) power supply. The maximum wattage required for a BIC attached to an A201 b is approximately 10 W. Ripple must be less than 1%.
L
The BIC operates on 24 VDC, but the A201 b operates on 12 VDC. The BIC will convert its 24 VDC input to 12 VDC and will supply 12 VDC to the camera.
DO NOT apply 24 VDC to the camera.
A.7 Status LED
Green LED
When the green LED on the BIC is lit, it indicates that power is being supplied to the BIC.
A.8 Installing the Camera and the BIC
The camera and BIC can be installed in two ways: the BIC can be attached directly to the camera or the BIC can be connected to the camera with a cable. If you are installing a system with the BIC
directly attached to the camera, start your installation with Section A.8.1
. If you are installing a system with the BIC and camera connected with a cable, start your installation with Section
A-18 BASLER A201 b
DRAFT
Using the Camera with a BIC
A.8.1 Making Connections (BIC Directly Attached to Camera)
Caution!
Be sure that all power to your system is switched off before you make or break connections to the camera or the BIC. Making or breaking connections when power is on can result in damage to the camera or the BIC.
1. Remove the six-sided standoffs on each side of the 26-pin plug on the back of the camera
and on each side of the 26-pin receptacle on the front of the BIC (see Figure A-11). Replace
the standoffs with pan head screws from the BIC installation kit.
2. Remove two screws from the back of the camera as shown in Figure A-11. Replace the
screws with six-sided standoffs from the BIC installation kit.
Front of the BIC
Back of the Camera
Remove these screws and replace them with standoffs
Figure A-11: Changing the Screws
Remove these six-sided standoffs and replace them with pan head screws
3. Hold the camera and the BIC so that the 26 pin plug on the back of the camera is aligned with the 26 pin receptacle on the front of the BIC.
4. Press the camera and the BIC together.
5. Get two 20 mm long screws from the BIC installation kit. Insert the screws through the BIC
(see Figure A-12) and screw them into the back of the camera. This will lock the BIC and the
camera together.
BASLER A201 b A-19
Using the Camera with a BIC
DRAFT
Camera
20 mm
Screw
BIC
D-Sub
9 pin Plug
D-Sub HD
44 pin
Receptacle
20 mm
Screw
Subminiature
Round
4 pin plug
Figure A-12: BIC Mated Directly to Camera
6. Attach one end of your video data/control signal cable to the 44 pin receptacle on the BIC and the other end to your frame grabber.
7. Attach one end of a null modem cable to the nine pin plug on the BIC and the other end to a serial port on your computer.
8. Make sure that the power source you will be using to supply the BIC meets the requirements
9. Attach the output connector from your power source to the four pin plug on the BIC.
10. Switch on the power to your system.
to continue the installation.
L
The BIC operates on 24 VDC, but the A201 b operates on 12 VDC. The BIC will convert its 24 VDC input to 12 VDC and will supply 12 VDC to the camera.
A-20 BASLER A201 b
DRAFT
Using the Camera with a BIC
A.8.2 Making Connections (BIC and Camera Mated with a Cable)
Caution!
Be sure that all power to your system is switched off before you make or break connections to the camera or the BIC. Making or breaking connections when power is on can result in damage to the camera or the BIC.
1. Connect a straight-through Channel Link Cable from the 26 pin plug on the back of the
camera to the 26 pin receptacle on the front of the BIC (see Figure A-13).
Camera BIC
D-Sub HD
44 Pin
Receptacle
D-Sub HD
26 Pin Plug
Subminiature
Round
4 pin plug
Straight Through
Channel Link Cable
Figure A-13: Attaching a Cable to the Camera and the BIC
D-Sub
9 pin plug
2. Attach one end of your video data/control signal cable to the 44 pin receptacle on the back of the BIC and the other end to your frame grabber.
3. Attach one end of a null modem cable to the nine pin plug on the back of the BIC and the other end to a serial port on your computer.
4. Make sure that the power source you will be using to supply the BIC meets the requirements
5. Attach the output connector from your power source to the four pin plug on the BIC.
6. Switch on the power to your system.
to continue the installation.
L
The BIC operates on 24 VDC, but the A201 b operates on 12 VDC. The BIC will convert its 24 VDC input to 12 VDC and will supply 12 VDC to the camera.
A-21 BASLER A201 b
Using the Camera with a BIC
DRAFT
A.8.3 Setting Up the Serial Port
The RS-232 serial connection between your computer and the camera is used to issue commands to the camera for changing camera modes and parameters. In order for your camera to receive commands, it must be connected to a serial port and the serial port must be set up correctly.
Make sure that the serial port your camera is connected to has the following settings:
• 8 data bits
• no parity
• 1 stop bit
• baud rate = 9600 bps
You must use the computer’s “control panel” to set up the serial port. If you are not familiar with setting up a serial port on your computer, refer to the manual or help files for your computer’s operating system.
Once you have set up the serial port, go on to Section
A.8.4 Installing the Camera Configuration Tool
The Camera Configuration Tool (CCT) is a Windows® based program used to easily change the camera’s settings. The tool communicates with the camera via the serial connection.
For instructions on installing the tool, see the CCT installation booklet that was shipped with the camera.
A.8.5 Next Steps
• Look at each of the Tabs in the Camera Configuration Tool and look through the on-line help included with the tool. This is a good way to familiarize yourself with the camera’s features and settings.
• Read the manual for your Basler camera. You will get the most from your camera if you understand how the camera’s features work and what happens when you change camera settings.
• Read the supporting material included with your frame grabber and make sure that the frame grabber is properly configured to work with your Basler camera. In order to capture images, your frame grabber must be properly configured to work with your Basler camera.
L
In addition to configuring the camera and the frame grabber, you must also set up other system components such as light sources, optics and the host computer. Only a complete, careful setup will guarantee optimum performance.
A-22 BASLER A201 b
A.9 BIC Dimensions
DRAFT
Using the Camera with a BIC
Figure A-14: BIC Dimensions (in mm)
BASLER A201 b A-23
Using the Camera with a BIC
DRAFT
A-24 BASLER A201 b
DRAFT
Revision History
Revision History
Doc. ID Number
DA 040701
DA 040702
DA 040703
DA 040704
Date
Dec. 21, 2000
June 12, 2001
July 13, 2001
Changes
Initial release.
Made numerous small changes to grammar and phrasing.
Added ripple specification to Table 1-1 and Sections 2.6
Added note on reverse power and overvoltage protection to Sections
.
Added maximum cable length specification to Section
.
Added information on absolute maximum voltage to Section 2.6
.
Added a more detailed specification of the green LED to Section
Section
.
Changed timing diagrams shown in Figure 2-6, Figure 2-7, Figure 2-8
Changed timing diagrams shown in Figure 3-6, Figure 3-7, Figure 3-8,
Figure 3-9, Figure 3-10, Figure 3-11 and respective formulas for calculat-
ing the effective exposure.
Changed CMD-IDs in Section 4.2.4.1
Changed timing diagrams shown in Figure A-6, Figure A-7, Figure A-8 and Figure A-9.
Removed the “Camera Installation“ section. Camera installation is described in the camera‘s Installation Guide only.
Removed information on camera configuration tool installation. Installation is described in the tool‘s Installation Guide only.
August 08, 2005 Replaced front page.
Added „Contacting Basler Support Worldwide“ page.
Replaced Figure 1-1 and Figure 1-2.
Replaced Figure 3-2.
Changed Data Format in section „Camera Reset Command“.
Added section "Before Calling Basler Technical Support".
BASLER A201 b i
Revision History
DRAFT ii BASLER A201 b
DRAFT
Feedback
Feedback
Your feedback will help us improve our documentation. Please click the link below to access an online feedback form. Your input is greatly appreciated.
http://www.baslerweb.com/umfrage/survey.html
BASLER A201 b iii
Feedback
DRAFT iv BASLER A201 b
DRAFT
Index
A
apply button ........................................................ 4-3
area of interest
explained ................................................... 3-25
setting with binary commands ..........4-13, 4-15
B
Basler Interface Converter
Bayer filter .......................................................... 3-3
BIC......................................................................A-1
BIC output signals
binary command frame....................................... 4-4
binary commands
error checking.............................................. 4-4
examples ..................................................... 4-7
explained ..................................................... 4-4
bitrate
setting with binary commands ................... 4-27
block check character
calculating ................................................... 4-8
defined......................................................... 4-5
C
cable specifications
BIC ..............................................................A-9
camera ........................................................ 2-3
camera configuration tool
apply button................................................. 4-3
closing the tool ............................................ 4-2
installing ....................................................A-22
opening the tool........................................... 4-2
refresh button .............................................. 4-3
camera status
channel link
explained ..................................................... 2-5
implementation information ......................... 2-6
cleaning the camera and sensor ................ 1-5, A-3
C-mount adapter................................................. 5-3
commands
configuration sets
explained ................................................... 3-28
manipulating with binary commands 4-23, 4-24
configuration tool
configuring the camera
with binary commands ................................ 4-4
with the config tool ...................................... 4-2
D
data output mode
digital shift
explained................................................... 3-20
setting with binary commands................... 4-12
dimensions ......................................................... 5-1
BIC ............................................................A-23
camera ........................................................ 5-2
C-mount adapter ......................................... 5-3
F-mount adapter ......................................... 5-3
E
environmental requirements
BIC ..............................................................A-3
camera ........................................................ 1-4
exposure time
relation to exp. time control modes .... 3-4–3-12
exposure time control mode(s)
explained..................................................... 3-4
setting with binary commands................... 4-10
ExSync signal...................................................A-10
explained.............................................. 2-4, 3-4
RS-644 specs for ........................................ 2-4
F
factory set
copying to the work set ............................. 4-23
explained................................................... 3-28
fill factor.............................................................. 1-2
F-mount adapter................................................. 5-3
frame rate
basic specification....................................... 1-2
changes with area of interest .................... 3-26
free-run
explained..................................................... 3-6
setting with binary commands................... 4-10
functional description
BIC ..............................................................A-1
camera ........................................................ 3-1
FVAL ................................................................A-11
G
gain
explained................................................... 3-13
setting with binary commands.......... 4-17, 4-18
Index
BASLER A201 b v
vi
Index
DRAFT
H
humidity requirements
BIC ..............................................................A-3
camera ........................................................ 1-4
I
input signals
to the BIC ..................................................A-10
to the camera .............................................. 2-4
installing
the camera with a BIC ...............................A-18
the configuration tool .................................A-22
interfacing the BIC ..............................................A-4
interfacing the camera ........................................ 2-1
IR cut filter ............................................1-3, 3-3, 5-4
L
LEDs
on the BIC ......................................... A-4, A-18
on the camera ....................................2-17, 6-1
lens thread length ............................................... 5-4
level-controlled exposure mode
explained ..............................................3-4, 3-6
setting with binary commands ................... 4-10
LVAL.................................................................A-11
M
microcontroller firmware version
reading with binary commands.................. 4-20
model number
viewing with commands ............................ 4-21
model tab............................................................ 4-3
mounting facilities ............................................... 5-1
O
offset
explained ................................................... 3-13
setting with binary commands ..........4-17, 4-18
output mode
output signals
from the BIC ..............................................A-11
from the camera .......................................... 2-5
P
photo response non-uniformity ........................... 1-2
pin assignments
BIC ..............................................................A-5
camera ........................................................ 2-2
pin numbering
BIC ..............................................................A-5
camera ........................................................ 2-3
pixel clock
on the BIC .................................................A-11
on the camera ............................................. 2-8
pixel size ............................................................ 1-2
plug source information...................................... 2-3
positioning accuracy of sensor chip ................... 5-4
power requirements
BIC ..............................................................A-2
camera ........................................................ 1-2
precautions
BIC ..............................................................A-3
camera ........................................................ 1-5
programmable exposure mode
explained..................................................... 3-4
setting with binary commands................... 4-10
R
read command
error checking ............................................. 4-6
example ...................................................... 4-7
refresh button ..................................................... 4-3
resetting the camera with binary commands.... 4-19
RS-232 serial connection ................ 2-16, A-1, A-18
RS-644
S
sensor type......................................................... 1-2
serial connection
serial number, camera
viewing with binary commands ................. 4-21
serial port
setting up ..................................................A-22
specifications
BIC ..............................................................A-2
camera ........................................................ 1-2
spectral response............................................... 1-3
startup pointer
explained................................................... 3-28
setting with binary commands................... 4-25
status
checking with binary commands ............... 4-26
checking with the yellow LED ..................... 6-1
T
temperature requirements
BIC ..............................................................A-3
camera ........................................................ 1-4
test image
explained................................................... 3-27
setting with binary commands................... 4-19
timer 1
BASLER A201 b
DRAFT
explained ..............................................3-4, 3-6
setting with binary commands ................... 4-11
timer 2
explained ..................................................... 3-6
setting with binary commands ................... 4-11
troubleshooting ................................................... 6-1
troubleshooting chart
interfacing.................................................... 6-5
no image...................................................... 6-2
poor quality image ....................................... 6-4
RS-232 serial communication ..................... 6-7
U
user sets
copying to the work set.............................. 4-23
explained ................................................... 3-28
V
ventilation
BIC ..............................................................A-3
camera ........................................................ 1-4
video data output mode(s)
explained ................................................... 2-10
setting with binary commands ..................... 4-9
W
weight
BIC ..............................................................A-2
camera ........................................................ 1-2
work set
copying to a user set ................................. 4-24
explained ................................................... 3-28
relationship to the config tool....................... 4-2
write command
error checking.............................................. 4-6
example....................................................... 4-7
Index
BASLER A201 b vii
Index
DRAFT viii BASLER A201 b
advertisement
Related manuals
advertisement
Table of contents
- 23 1.1 Camera Models
- 23 1.2 Performance Specifications
- 23 1.3 Environmental Requirements
- 23 1.3.1 Temperature and Humidity
- 23 1.3.2 Ventilation
- 23 1.4 Precautions
- 24 2.1 Connections
- 24 2.1.1 General Description
- 24 2.1.2 Pin Assignments
- 24 2.1.3 Plug Source Information
- 24 2.2 Cable Information
- 24 2.3 Input Signals
- 24 2.3.1 ExSync: Controls Line Readout and Exposure Time
- 24 2.3.1.1 RS-644/RS-422 Compatibility
- 24 2.4 Output Signals
- 24 2.4.1 Channel Link Basics
- 24 2.4.2 Channel Link Implementation in the A201b
- 24 2.4.3 Pixel Clock
- 24 2.4.4 Frame Valid Bit
- 24 2.4.5 Line Valid Bit
- 24 2.4.6 Video Data
- 24 2.4.7 Video Data Output Modes
- 24 2.4.7.1 Operation in Single 10 Bit or Single 8 Bit Output Mode
- 24 2.4.7.2 Operation in Dual 10 Bit or Dual 8 Bit Output Mode
- 24 2.5 RS-232 Serial Communication
- 24 2.5.1 Making the Serial Connection
- 24 2.6 DC Power
- 24 2.7 Status LEDs
- 24 2.8 Converting Channel Link Video Output to RS-644 with a BIC
- 25 3.1 Functional Description
- 25 3.1.1 Color Creation in the A201bc
- 25 3.1.1.1 Integrated IR Cut Filter on C-Mount Equipped Cameras
- 25 3.2 Exposure Time Control Mode Basics
- 25 3.2.1 ExSync Controlled Operation
- 25 3.2.2 Free-run
- 25 3.3 Exposure Time Control Modes in Detail
- 69 (Frame Valid Low)
- 69 (Frame Valid High)
- 69 (Frame Valid Low)
- 69 (Frame Valid High)
- 69 (Frame Valid Low)
- 69 (Frame Valid High)
- 69 3.4 Video Data Output Modes
- 69 3.5 Gain and Offset
- 69 3.5.1 Gain Settings in More Detail
- 69 3.5.2 Balancing the Gain and Offset on Odd and Even Lines
- 69 3.6 Digital Shift
- 69 3.6.1 Digital Shift in 10 bit Output Mode
- 69 3.6.2 Digital Shift in 8 bit Output Modes
- 69 3.6.3 Precautions When Using Digital Shift
- 69 3.7 Area of Interest (AOI)
- 69 3.7.1 Area of Interest Setup Rules
- 69 3.7.2 Changes to the Maximum Frame Rate with Area of Interest
- 69 3.8 Test Image
- 69 3.9 Configuration Sets
- 69 3.10 Camera Status
- 70 4.1 Configuring the Camera with the Camera Configuration Tool
- 70 4.1.1 Opening the Configuration Tool
- 70 4.1.2 Closing the Configuration Tool
- 70 4.1.3 Configuration Tool Basics
- 70 4.1.4 Configuration Tool Help
- 70 4.2 Configuring the Camera with Binary Programming Commands
- 70 4.2.1 Command Frame and Response Format
- 70 4.2.2 Error Checking
- 70 4.2.2.1 ACK/NAK
- 70 4.2.2.2 Time-outs
- 70 4.2.2.3 Read Command
- 70 4.2.2.4 Write Command
- 70 4.2.3 Example Commands
- 70 4.2.3.1 Read Command
- 70 4.2.3.2 Write Command
- 70 4.2.3.3 Calculating the Block Check Character
- 70 4.2.4 Commands for Setting Camera Parameters
- 95 4.2.4.1 Video Data Output Mode
- 95 4.2.4.2 Exposure Time Control Mode
- 95 4.2.4.3 Timer
- 95 4.2.4.4 Timer
- 95 4.2.4.5 Digital Shift
- 95 4.2.4.6 Area of Interest Starting Column
- 95 4.2.4.7 Area of Interest Width in Columns
- 95 4.2.4.8 Area of Interest Starting Line
- 95 4.2.4.9 Area of Interest Height in Lines
- 95 4.2.4.10 Odd Line Gain
- 95 4.2.4.11 Odd Line Offset
- 95 4.2.4.12 Even Line Gain
- 95 4.2.4.13 Even Line Offset
- 95 4.2.5 Test Image Command
- 95 4.2.6 Camera Reset Command
- 95 4.2.7 Query Commands
- 95 4.2.7.1 Read Microcontroller Firmware Version
- 95 4.2.7.2 Read FPGA Firmware Version
- 95 4.2.7.3 Read Vendor Information
- 95 4.2.7.4 Read Model Information
- 95 4.2.7.5 Read Product ID
- 95 4.2.7.6 Read Serial Number
- 95 4.2.7.7 Read Gain and Offset Reference Values
- 95 4.2.8 Commands for Manipulating Configuration Sets
- 95 4.2.8.1 Copy the Factory Set or a User Set into the Work Set
- 95 4.2.8.2 Copy Work Set into a User Set
- 95 4.2.8.3 Select the Startup Pointer
- 95 4.2.9 Camera Status Command
- 95 4.2.10 Bitrate Command
- 96 5.1 Camera Dimensions and Mounting Facilities
- 96 5.2 C-Mount Adapter Dimensions
- 96 5.3 F-Mount Adapter Dimensions
- 96 5.4 Positioning Accuracy of the Sensor Chip
- 96 5.5 Maximum Lens Thread Length
- 97 6.1 Fault Finding Using Camera LEDs
- 97 6.1.1 Yellow LED
- 97 6.1.2 Green LED
- 97 6.2 Troubleshooting Charts
- 97 6.2.1 No Image
- 97 6.2.2 Poor Quality Image