advertisement
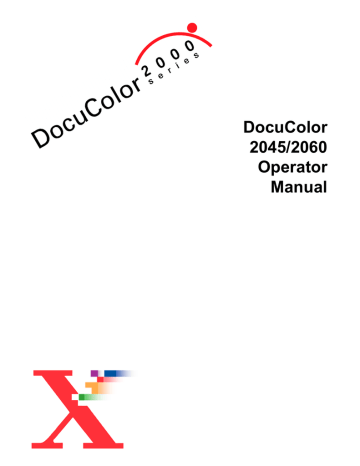
DocuColor
2045/2060
Operator
Manual
© 1999, 2000, 2001 Xerox Corporation. All rights reserved.
Copyright protection claimed includes all forms and matters of copyrightable material and information now allowed by statutory or judicial law or hereinafter granted, including without limitation, material generated from the software programs that are displayed on the screen such as styles, templates, icons, screen displays, looks, etc.
Xerox
®
, The Document Company
®
, the digital X
®
, and all Xerox product names and product numbers mentioned in this publication are registered trademarks of Xerox Corporation.
Xerox Canada is a licensee of all the trademarks. Other company brands and product names may be trademarks or registered trademarks of their respective companies and are also acknowledged.
Changes are periodically made to this document. Technical updates will be included in subsequent editions.
Printed in the United States of America.
Table of Contents
T A B L E O F C O N T E N T S
D O C U C O L O R 2 0 6 0 / 2 0 4 5 O P E R A T O R M A N U A L iii
T A B L E O F C O N T E N T S
Quality Starts with the Original . . . . . . . . . . . . . . . . . . . . . . . . . . . . . . . 1–2
How Input Determines Outpu . . . . . . . . . . . . . . . . . . . . . . . . . . . . . . . . . 1–3
Grain/Image Size . . . . . . . . . . . . . . . . . . . . . . . . . . . . . . . . . . . . . . . 1–5
Getting the Color You Expect . . . . . . . . . . . . . . . . . . . . . . . . . . . . . . . . . 1–5
Adding and Replacing Gray to Improve Color . . . . . . . . . . . . . . . . . . . . . . . . 1–9
Halftone Dots and Screen Angles . . . . . . . . . . . . . . . . . . . . . . . . . . . . . . . . 1–10
Digital Image Manipulation . . . . . . . . . . . . . . . . . . . . . . . . . . . . . . . . . 1–13
Sharpening. . . . . . . . . . . . . . . . . . . . . . . . . . . . . . . . . . . . . . . . . . . 1–13
Important Additional Tips . . . . . . . . . . . . . . . . . . . . . . . . . . . . . . . . . . . 1–13
Output Considerations . . . . . . . . . . . . . . . . . . . . . . . . . . . . . . . . . . . . . 1–14
Anti-aliasing . . . . . . . . . . . . . . . . . . . . . . . . . . . . . . . . . . . . . . . . . 1–16
Duplex Settings . . . . . . . . . . . . . . . . . . . . . . . . . . . . . . . . . . . . . . . 1–17
iv D O C U C O L O R 2 0 6 0 / 2 0 4 5 O P E R A T O R M A N U A L
T A B L E O F C O N T E N T S
Right Angle Fold . . . . . . . . . . . . . . . . . . . . . . . . . . . . . . . . . . . . . . 1–19
Accordion Fold . . . . . . . . . . . . . . . . . . . . . . . . . . . . . . . . . . . . . . . . 1–19
Nested Signature and Binders Creep . . . . . . . . . . . . . . . . . . . . . . 1–20
Gathered Signature . . . . . . . . . . . . . . . . . . . . . . . . . . . . . . . . . . . . 1–20
Saddle Stitching . . . . . . . . . . . . . . . . . . . . . . . . . . . . . . . . . . . . . . 1–21
Perfect Binding . . . . . . . . . . . . . . . . . . . . . . . . . . . . . . . . . . . . . . . 1–21
Mechanical Binding . . . . . . . . . . . . . . . . . . . . . . . . . . . . . . . . . . . . 1–21
Looseleaf Binding . . . . . . . . . . . . . . . . . . . . . . . . . . . . . . . . . . . . . 1–21
Embossing . . . . . . . . . . . . . . . . . . . . . . . . . . . . . . . . . . . . . . . . . . . 1–22
Dry Ink/Toner Waste Bottle . . . . . . . . . . . . . . . . . . . . . . . . . . . . . . . . . . 2–7
Ground Fault Indicator (GFI) Circuit Breaker . . . . . . . . . . . . . . . . . . . . . . 2–8
Message Area . . . . . . . . . . . . . . . . . . . . . . . . . . . . . . . . . . . . . . . . . 2–9
Tabs/Buttons/Icons . . . . . . . . . . . . . . . . . . . . . . . . . . . . . . . . . . . . . 2–9
Touch Screen Button Types and Functions. . . . . . . . . . . . . . . 2–11
D O C U C O L O R 2 0 6 0 / 2 0 4 5 O P E R A T O R M A N U A L v
T A B L E O F C O N T E N T S
Power Saver. . . . . . . . . . . . . . . . . . . . . . . . . . . . . . . . . . . . . . . . . . 2–21
Machine Status . . . . . . . . . . . . . . . . . . . . . . . . . . . . . . . . . . . . . . . 2–22
Meters . . . . . . . . . . . . . . . . . . . . . . . . . . . . . . . . . . . . . . . . . . 2–23
Job Monitor . . . . . . . . . . . . . . . . . . . . . . . . . . . . . . . . . . . . . . . . . . 2–30
Audio Tones . . . . . . . . . . . . . . . . . . . . . . . . . . . . . . . . . . . . . . . . . . 2–31
Alert Screens . . . . . . . . . . . . . . . . . . . . . . . . . . . . . . . . . . . . . . . . . 2–32
Maintenance . . . . . . . . . . . . . . . . . . . . . . . . . . . . . . . . . . . . . . . . . 2–33
Duplex Automatic Document Feeder (DADF) . . . . . . . . . . . . . . . . . . . . 2–34
Paper Path in the Digital Press . . . . . . . . . . . . . . . . . . . . . . . . . . . . . . . 2–39
Relocating the DocuColor 2060/2045 . . . . . . . . . . . . . . . . . . . . . . . . . . . . . 2–41
vi D O C U C O L O R 2 0 6 0 / 2 0 4 5 O P E R A T O R M A N U A L
T A B L E O F C O N T E N T S
Recommended Papers and Special Materials . . . . . . . . . . . . . . . . . . . . . . . . 3–1
Paper Tray Special Features . . . . . . . . . . . . . . . . . . . . . . . . . . . . . . . . . . 3–7
Transparency Guidelines. . . . . . . . . . . . . . . . . . . . . . . . . . . . . . . . . . . . . 3–9
Simplex Print Jobs . . . . . . . . . . . . . . . . . . . . . . . . . . . . . . . . . . . . . 3–10
Duplex Print Jobs. . . . . . . . . . . . . . . . . . . . . . . . . . . . . . . . . . . . . . 3–10
Non-standard Size Paper . . . . . . . . . . . . . . . . . . . . . . . . . . . . . . . . . . . 3–11
Specific Weight Conversion . . . . . . . . . . . . . . . . . . . . . . . . . . . . . . . . . 3–17
Weight Conversion Ranges. . . . . . . . . . . . . . . . . . . . . . . . . . . . . . . . . . 3–18
Duplex Automatic Document Feeder (DADF) . . . . . . . . . . . . . . . . . . . . . 4–4
Document Specifications. . . . . . . . . . . . . . . . . . . . . . . . . . . . . . . . . 4–4
Identifying Duplex Automatic Document Feeder (DADF) Parts. . . . . 4–5
Using the Duplex Automatic Document Feeder (DADF) . . . . . . . . . 4–6
Clearing a DADF Jam . . . . . . . . . . . . . . . . . . . . . . . . . . . . . . . . . . . 4–7
White Border Edges on Copies . . . . . . . . . . . . . . . . . . . . . . . . . . . . . . . . 4–8
Message Area . . . . . . . . . . . . . . . . . . . . . . . . . . . . . . . . . . . . . . . . . 4–9
Tabs/Buttons/Icons . . . . . . . . . . . . . . . . . . . . . . . . . . . . . . . . . . . . 4–10
Touch Screen Button Types and Functions. . . . . . . . . . . . . . . 4–11
D O C U C O L O R 2 0 6 0 / 2 0 4 5 O P E R A T O R M A N U A L vii
T A B L E O F C O N T E N T S
Features (Digital Press with Scanner Only) . . . . . . . . . . . . . . . . . . . . . . . . . 4–13
Color Mode . . . . . . . . . . . . . . . . . . . . . . . . . . . . . . . . . . . . . . . . . . 4–14
Auto . . . . . . . . . . . . . . . . . . . . . . . . . . . . . . . . . . . . . . . . . . . . 4–14
Full Color. . . . . . . . . . . . . . . . . . . . . . . . . . . . . . . . . . . . . . . . . 4–15
3 Pass Color . . . . . . . . . . . . . . . . . . . . . . . . . . . . . . . . . . . . . . 4–15
Black Only. . . . . . . . . . . . . . . . . . . . . . . . . . . . . . . . . . . . . . . . 4–15
Single Color . . . . . . . . . . . . . . . . . . . . . . . . . . . . . . . . . . . . . . 4–16
Collated . . . . . . . . . . . . . . . . . . . . . . . . . . . . . . . . . . . . . . . . . 4–18
Uncollated . . . . . . . . . . . . . . . . . . . . . . . . . . . . . . . . . . . . . . . 4–18
More... . . . . . . . . . . . . . . . . . . . . . . . . . . . . . . . . . . . . . . . . . . 4–18
Reduce/Enlarge . . . . . . . . . . . . . . . . . . . . . . . . . . . . . . . . . . . . . . . 4–19
100% . . . . . . . . . . . . . . . . . . . . . . . . . . . . . . . . . . . . . . . . . . . 4–20
Auto%. . . . . . . . . . . . . . . . . . . . . . . . . . . . . . . . . . . . . . . . . . . 4–20
Third Button . . . . . . . . . . . . . . . . . . . . . . . . . . . . . . . . . . . . . . 4–20
Fourth Button . . . . . . . . . . . . . . . . . . . . . . . . . . . . . . . . . . . . . 4–20
More... . . . . . . . . . . . . . . . . . . . . . . . . . . . . . . . . . . . . . . . . . . 4–21
Common Percentage Conversions . . . . . . . . . . . . . . . . . . . . . 4–26
Paper Supply . . . . . . . . . . . . . . . . . . . . . . . . . . . . . . . . . . . . . . . . . 4–27
Auto Paper . . . . . . . . . . . . . . . . . . . . . . . . . . . . . . . . . . . . . . . 4–27
2 Sided Output . . . . . . . . . . . . . . . . . . . . . . . . . . . . . . . . . . . . . . . . 4–28
1-1. . . . . . . . . . . . . . . . . . . . . . . . . . . . . . . . . . . . . . . . . . . . . . 4–29
1-2. . . . . . . . . . . . . . . . . . . . . . . . . . . . . . . . . . . . . . . . . . . . . . 4–29
2-1. . . . . . . . . . . . . . . . . . . . . . . . . . . . . . . . . . . . . . . . . . . . . . 4–30
2-2. . . . . . . . . . . . . . . . . . . . . . . . . . . . . . . . . . . . . . . . . . . . . . 4–31
Image Shift . . . . . . . . . . . . . . . . . . . . . . . . . . . . . . . . . . . . . . . . . . 4–32
No Shift . . . . . . . . . . . . . . . . . . . . . . . . . . . . . . . . . . . . . . . . . 4–32
Auto Center . . . . . . . . . . . . . . . . . . . . . . . . . . . . . . . . . . . . . . 4–33
Margin Shift . . . . . . . . . . . . . . . . . . . . . . . . . . . . . . . . . . . . . . 4–34
Unrestricted Shift . . . . . . . . . . . . . . . . . . . . . . . . . . . . . . . . . . 4–35
Corner Shift . . . . . . . . . . . . . . . . . . . . . . . . . . . . . . . . . . . . . . 4–36
Auto . . . . . . . . . . . . . . . . . . . . . . . . . . . . . . . . . . . . . . . . . . . . 4–37
Manual Input . . . . . . . . . . . . . . . . . . . . . . . . . . . . . . . . . . . . . 4–38
Mixed Size Originals . . . . . . . . . . . . . . . . . . . . . . . . . . . . . . . 4–39
Bound Originals . . . . . . . . . . . . . . . . . . . . . . . . . . . . . . . . . . . . . . . 4–40
viii D O C U C O L O R 2 0 6 0 / 2 0 4 5 O P E R A T O R M A N U A L
T A B L E O F C O N T E N T S
Edge Erase for Drilled Paper . . . . . . . . . . . . . . . . . . . . . . . . . 4–44
Border Erase . . . . . . . . . . . . . . . . . . . . . . . . . . . . . . . . . . . . . . 4–45
Edge/Center Erase . . . . . . . . . . . . . . . . . . . . . . . . . . . . . . . . . 4–46
Stored Programming . . . . . . . . . . . . . . . . . . . . . . . . . . . . . . . . . . . 4–48
Store Programming. . . . . . . . . . . . . . . . . . . . . . . . . . . . . . . . . 4–48
Recall Programming . . . . . . . . . . . . . . . . . . . . . . . . . . . . . . . . 4–49
Delete Programming. . . . . . . . . . . . . . . . . . . . . . . . . . . . . . . . 4–50
Original Type . . . . . . . . . . . . . . . . . . . . . . . . . . . . . . . . . . . . . . . . . 4–52
Auto Photo & Text . . . . . . . . . . . . . . . . . . . . . . . . . . . . . . . . . 4–53
Text . . . . . . . . . . . . . . . . . . . . . . . . . . . . . . . . . . . . . . . . . . . . . 4–54
Photo. . . . . . . . . . . . . . . . . . . . . . . . . . . . . . . . . . . . . . . . . . . . 4–55
Map . . . . . . . . . . . . . . . . . . . . . . . . . . . . . . . . . . . . . . . . . . . . 4–56
Dark Edges . . . . . . . . . . . . . . . . . . . . . . . . . . . . . . . . . . . . . . . 4–57
Define Area . . . . . . . . . . . . . . . . . . . . . . . . . . . . . . . . . . . . . . 4–59
Lighten/Darken . . . . . . . . . . . . . . . . . . . . . . . . . . . . . . . . . . . . . . . 4–63
Sharpness . . . . . . . . . . . . . . . . . . . . . . . . . . . . . . . . . . . . . . . . . . . 4–64
Image Tone Presets . . . . . . . . . . . . . . . . . . . . . . . . . . . . . . . . . . . . 4–65
Normal . . . . . . . . . . . . . . . . . . . . . . . . . . . . . . . . . . . . . . . . . . 4–65
Lively. . . . . . . . . . . . . . . . . . . . . . . . . . . . . . . . . . . . . . . . . . . . 4–66
Sharp . . . . . . . . . . . . . . . . . . . . . . . . . . . . . . . . . . . . . . . . . . . 4–66
Warm . . . . . . . . . . . . . . . . . . . . . . . . . . . . . . . . . . . . . . . . . . . 4–67
Cool. . . . . . . . . . . . . . . . . . . . . . . . . . . . . . . . . . . . . . . . . . . . . 4–67
Background Erase. . . . . . . . . . . . . . . . . . . . . . . . . . . . . . . . . . 4–68
Color Balance. . . . . . . . . . . . . . . . . . . . . . . . . . . . . . . . . . . . . . . . . 4–69
D O C U C O L O R 2 0 6 0 / 2 0 4 5 O P E R A T O R M A N U A L ix
T A B L E O F C O N T E N T S
Transparency Options . . . . . . . . . . . . . . . . . . . . . . . . . . . . . . . . . . 4–82
Booklet Creation . . . . . . . . . . . . . . . . . . . . . . . . . . . . . . . . . . . . . . 4–85
Mirror Image . . . . . . . . . . . . . . . . . . . . . . . . . . . . . . . . . . . . . . . . . 4–89
Negative Image . . . . . . . . . . . . . . . . . . . . . . . . . . . . . . . . . . . . . . . 4–90
Repeat Image. . . . . . . . . . . . . . . . . . . . . . . . . . . . . . . . . . . . . . . . . 4–91
Paper Stock Specifications . . . . . . . . . . . . . . . . . . . . . . . . . . . . . . . . . . . 5–5
Loading Special Stock in Tray 4 . . . . . . . . . . . . . . . . . . . . . . . . . . . . . . . 5–7
Tabbed Inserts . . . . . . . . . . . . . . . . . . . . . . . . . . . . . . . . . . . . . . . . . 5–7
Non-standard Size Paper . . . . . . . . . . . . . . . . . . . . . . . . . . . . . . . . . 5–8
Coated Paper . . . . . . . . . . . . . . . . . . . . . . . . . . . . . . . . . . . . . . . . . . 5–8
Digital Press Paper Reliability. . . . . . . . . . . . . . . . . . . . . . . . . . . . . . . . 5–14
Cleaning Tray 4 . . . . . . . . . . . . . . . . . . . . . . . . . . . . . . . . . . . . . . . 5–14
Loss of Power . . . . . . . . . . . . . . . . . . . . . . . . . . . . . . . . . . . . . . . . 5–18
Electrical Requirements. . . . . . . . . . . . . . . . . . . . . . . . . . . . . . . . . 5–19
Power Consumption. . . . . . . . . . . . . . . . . . . . . . . . . . . . . . . . . . . . 5–19
Heat Output . . . . . . . . . . . . . . . . . . . . . . . . . . . . . . . . . . . . . . . . . . 5–19
x D O C U C O L O R 2 0 6 0 / 2 0 4 5 O P E R A T O R M A N U A L
T A B L E O F C O N T E N T S
Environmental Requirements . . . . . . . . . . . . . . . . . . . . . . . . . . . . . . . . 5–20
Atmosphere Requirements . . . . . . . . . . . . . . . . . . . . . . . . . . . . . . 5–20
Noise Levels . . . . . . . . . . . . . . . . . . . . . . . . . . . . . . . . . . . . . . . . . 5–20
Ozone Emissions . . . . . . . . . . . . . . . . . . . . . . . . . . . . . . . . . . . . . . 5–20
Tray Capacity . . . . . . . . . . . . . . . . . . . . . . . . . . . . . . . . . . . . . . . . . 5–21
Throughput. . . . . . . . . . . . . . . . . . . . . . . . . . . . . . . . . . . . . . . . . . . 5–21
Tray 4 Weight. . . . . . . . . . . . . . . . . . . . . . . . . . . . . . . . . . . . . . . . . 5–21
Floor Space Requirements. . . . . . . . . . . . . . . . . . . . . . . . . . . . . . . 5–21
Identifying High Capacity Stacker Parts . . . . . . . . . . . . . . . . . . . . . . . . 5–22
Control Panel . . . . . . . . . . . . . . . . . . . . . . . . . . . . . . . . . . . . . . . . . 5–23
Paper Stock Specifications . . . . . . . . . . . . . . . . . . . . . . . . . . . . . . . . . . 5–25
Selecting High Capacity Stacker Features . . . . . . . . . . . . . . . . . . . . . . 5–27
Stacker Mode . . . . . . . . . . . . . . . . . . . . . . . . . . . . . . . . . . . . . . . . 5–29
Offset Mode. . . . . . . . . . . . . . . . . . . . . . . . . . . . . . . . . . . . . . . . . . 5–29
Top Tray Mode . . . . . . . . . . . . . . . . . . . . . . . . . . . . . . . . . . . . . . . . 5–29
Unloading the High Capacity Stacker . . . . . . . . . . . . . . . . . . . . . . . . . . 5–30
High Capacity Stacker Maintenance . . . . . . . . . . . . . . . . . . . . . . . . . . 5–33
Cleaning the High Capacity Stacker . . . . . . . . . . . . . . . . . . . . . . . 5–33
Loss of Power . . . . . . . . . . . . . . . . . . . . . . . . . . . . . . . . . . . . . . . . 5–35
High Capacity Stacker Stapler (HCSS) . . . . . . . . . . . . . . . . . . . . . . . . . . . . . 5–36
Identifying High Capacity Stacker Stapler Parts. . . . . . . . . . . . . . . . . . 5–36
Control Panel . . . . . . . . . . . . . . . . . . . . . . . . . . . . . . . . . . . . . . . . . 5–37
Electrical/Environmental Requirements . . . . . . . . . . . . . . . . . . . . . . . . 5–38
Paper Stock Specifications . . . . . . . . . . . . . . . . . . . . . . . . . . . . . . . . . . 5–38
D O C U C O L O R 2 0 6 0 / 2 0 4 5 O P E R A T O R M A N U A L xi
T A B L E O F C O N T E N T S
Using the High Capacity Stacker Stapler . . . . . . . . . . . . . . . . . . . . . . . . 5–41
Hints and Tips . . . . . . . . . . . . . . . . . . . . . . . . . . . . . . . . . . . . . . . . 5–41
Stapling Hints . . . . . . . . . . . . . . . . . . . . . . . . . . . . . . . . . . . . . . . . 5–41
Feeding 3 Hole Drilled Paper . . . . . . . . . . . . . . . . . . . . . . . . . 5–44
Stapling from the Fiery EX2000 . . . . . . . . . . . . . . . . . . . . . . . 5–45
Paper Specifications for Stapling. . . . . . . . . . . . . . . . . . . . . . 5–46
Stapling Capacity for Different Paper Types and Weights . . . . . . . . . . 5–47
Unloading the High Capacity Stacker Stapler . . . . . . . . . . . . . . . . . . . 5–47
Ordering and Loading Staples . . . . . . . . . . . . . . . . . . . . . . . . . . . . . . . 5–49
High Capacity Stacker Stapler Maintenance . . . . . . . . . . . . . . . . . . . . 5–50
Cleaning the High Capacity Stacker Stapler . . . . . . . . . . . . . . . . . 5–50
Loss of Power . . . . . . . . . . . . . . . . . . . . . . . . . . . . . . . . . . . . . . . . 5–53
DADF Jam Clearance . . . . . . . . . . . . . . . . . . . . . . . . . . . . . . . . . . . . . . 6–15
Transport Module Jam . . . . . . . . . . . . . . . . . . . . . . . . . . . . . . . . . . . . . 6–21
Right/Left Door Paper Path Jams . . . . . . . . . . . . . . . . . . . . . . . . . . . . . 6–25
Registration, Vacuum Transport and Fuser . . . . . . . . . . . . . . . . . . 6–25
Horizontal Transport (2-Sided Printing Only) . . . . . . . . . . . . . . . . . 6–28
Electrical Power Requirements (200/240 - 50/60 Hz). . . . . . . . . . . . . . . 7–1
Specifications . . . . . . . . . . . . . . . . . . . . . . . . . . . . . . . . . . . . . . . . . 7–1
Power Consumption. . . . . . . . . . . . . . . . . . . . . . . . . . . . . . . . . . . . . 7–1
Air Exchange Rate . . . . . . . . . . . . . . . . . . . . . . . . . . . . . . . . . . . . . . 7–2
Energy Star/Sleep Mode . . . . . . . . . . . . . . . . . . . . . . . . . . . . . . . . . 7–2
xii D O C U C O L O R 2 0 6 0 / 2 0 4 5 O P E R A T O R M A N U A L
T A B L E O F C O N T E N T S
Environmental Requirements . . . . . . . . . . . . . . . . . . . . . . . . . . . . . . . . . 7–2
Noise Levels . . . . . . . . . . . . . . . . . . . . . . . . . . . . . . . . . . . . . . . . . . 7–3
Ozone Emissions . . . . . . . . . . . . . . . . . . . . . . . . . . . . . . . . . . . . . . . 7–3
Warm-up Time . . . . . . . . . . . . . . . . . . . . . . . . . . . . . . . . . . . . . . . . . 7–3
First Print Out Time . . . . . . . . . . . . . . . . . . . . . . . . . . . . . . . . . . . . . 7–3
Digital Press Size . . . . . . . . . . . . . . . . . . . . . . . . . . . . . . . . . . . . . . . 7–5
Digital Press Weight . . . . . . . . . . . . . . . . . . . . . . . . . . . . . . . . . . . . 7–5
Floor Space Requirements. . . . . . . . . . . . . . . . . . . . . . . . . . . . . . . . 7–5
Duplex Automatic Document Feeder (DADF) Specifications . . . . . . . . . 7–5
Document Feeding Method . . . . . . . . . . . . . . . . . . . . . . . . . . . . . . . 7–5
DADF Capacity . . . . . . . . . . . . . . . . . . . . . . . . . . . . . . . . . . . . . . . . . 7–5
Power Source. . . . . . . . . . . . . . . . . . . . . . . . . . . . . . . . . . . . . . . . . . 7–6
Dimensions . . . . . . . . . . . . . . . . . . . . . . . . . . . . . . . . . . . . . . . . . . . 7–6
Floor Space Requirements. . . . . . . . . . . . . . . . . . . . . . . . . . . . . . . . 7–6
Cleaning the Document Glass Cover . . . . . . . . . . . . . . . . . . . . . . . . . . . . . . . 8–3
Replacing a Dry Ink/Toner Cartridge. . . . . . . . . . . . . . . . . . . . . . . . . . . . 8–4
Changing the Waste Dry Ink/Toner Bottle . . . . . . . . . . . . . . . . . . . . . . 8–10
D O C U C O L O R 2 0 6 0 / 2 0 4 5 O P E R A T O R M A N U A L xiii
T A B L E O F C O N T E N T S
This page is intentionally left blank.
xiv D O C U C O L O R 2 0 6 0 / 2 0 4 5 O P E R A T O R M A N U A L
Safety Notes
Electrical Safety
This Xerox digital press and the recommended supplies have been designed and tested to meet strict safety requirements. Attention to the following notes will ensure the continued safe operation of your digital press.
• Use only the power cord supplied with this equipment.
• Plug the power cord directly into a correctly grounded electrical outlet. Do not use an extension cord. If you do not know whether or not an outlet is grounded, consult a qualified electrician.
• Do not use a ground adapter plug to connect this equipment to an electrical outlet that lacks a ground connection terminal.
WARNING: You may get a severe electrical shock if the outlet is not correctly grounded.
• Do not place the press where people may step on or trip on the power cord.
Do not place objects on the power cord.
• Do not override or disable electrical or mechanical interlocks.
• Do not obstruct the ventilation openings. These openings are provided to prevent overheating of the machine.
D O C U C O L O R 2 0 6 0 / 2 0 4 5 O P E R A T O R M A N U A L xv xv
S A F E T Y N O T E S
WARNING: Never push objects of any kind into slots or openings on this equipment. Making a contact with a voltage point or shorting out a part could result in fire or electrical shock.
• If any of the following conditions occur, immediately switch off the power to the machine and disconnect the power cord from the electrical outlet. Call an authorized Xerox service representative to correct the problem.
– The machine emits unusual noises or odors.
– The power cord is damaged or frayed.
– A wall panel circuit breaker, fuse, or other safety device has been tripped.
– Liquid is spilled into the press.
– The machine is exposed to water.
– Any part of the machine is damaged.
Disconnect Device
The power cable is the disconnect device for this equipment. It is attached to the back of the machine as a plug-in device. To remove all electrical power from the machine, disconnect the power cable from the electrical outlet.
xvi D O C U C O L O R 2 0 6 0 / 2 0 4 5 O P E R A T O R M A N U A L
Laser Safety
S A F E T Y N O T E S
Use of controls, adjustments, or procedures other than those specified in this documentation may result in a hazardous exposure to laser radiation.
This equipment complies with international safety standards.
With specific regard to laser safety, the equipment complies with performance standards for laser products set by government, national, and international agencies as a Class 1 laser product. It does not emit hazardous light, as the beam is totally enclosed during all phases of customer operation and maintenance.
D O C U C O L O R 2 0 6 0 / 2 0 4 5 O P E R A T O R M A N U A L xvii
S A F E T Y N O T E S
Maintenance Safety
• Do not attempt any maintenance procedure that is not specifically described in the documentation that is supplied with your press.
• Do not use aerosol cleaners. The use of supplies that are not approved may cause poor performance of the press, and could create a dangerous condition.
• Use the supplies and cleaning materials only as directed in this manual.
Keep all of these materials out of the reach of children.
• Do not remove the covers or guards that are fastened with screws. There are no parts behind these covers that you can maintain or service.
Do not perform any maintenance procedures unless you have been trained to do them by a Xerox representative, or unless a procedure is specifically described in one of the manuals included with your press.
xviii D O C U C O L O R 2 0 6 0 / 2 0 4 5 O P E R A T O R M A N U A L
Operational Safety
S A F E T Y N O T E S
Your Xerox equipment and supplies were designed and tested to meet strict safety requirements. These include safety agency examination, approval, and compliance with established environmental standards.
Your attention to the following safety guidelines will help ensure the continued safe operation of your digital press:
• Use the materials and supplies specifically designed for your digital press.
The use of unsuitable materials may result in poor performance of the machine and possibly a hazardous situation.
• Follow all warnings and instructions that are marked on or supplied with the machine.
• Place the machine in a room that provides adequate space for ventilation and servicing.
• Place the machine on a level, solid surface (not on a thick pile carpet) that has adequate strength to support the weight of the machine.
• Do not attempt to move the machine. A leveling device that was lowered when your machine was installed may damage the carpet or floor.
• Do not set up the machine near a heat source.
• Do not set up the machine in direct sunlight.
• Do not set up the machine in line with the cold air flow from an air conditioning system.
• Do not place containers of coffee or other liquid on the machine.
• Do not block or cover the slots and openings on the machine. Without adequate ventilation, the machine may overheat.
• Do not attempt to override any electrical or mechanical interlock devices.
WARNING: Be careful when working in areas identified with this warning symbol. These areas may be very hot and could cause personal injury.
If you need any additional safety information concerning the machine or materials, contact your Xerox representative.
D O C U C O L O R 2 0 6 0 / 2 0 4 5 O P E R A T O R M A N U A L xix
S A F E T Y N O T E S
Ozone Safety
This product produces ozone during normal operation. The ozone is heavier than air, and the quantity is dependent on print volume. Providing the correct environmental parameters, as specified in the Xerox installation procedures, ensures that concentration levels meet safe limits.
If you need additional information about ozone, request the Xerox publication,
OZONE, 600P83222, by calling 1-800-828-6571 in the USA. For a French language version, call 1-800-828-6571 in the USA, then press 2.
xx D O C U C O L O R 2 0 6 0 / 2 0 4 5 O P E R A T O R M A N U A L
Notices
Radio Frequency Emissions
FCC in the USA
This equipment has been tested and found to comply with the limits for a Class A digital device, pursuant to Part 15 of the Federal Communications Commission
Rules. These limits are designed to provide reasonable protection against harmful interference when the equipment is operated in a commercial environment. This equipment generates, uses, and can radiate radio frequency energy and, if not installed and used in accordance with the instruction manual, may cause harmful interference to radio communications. Operation of this equipment in a residential area is likely to cause harmful interference in which case the user will be required to correct the interference at his/her own expense.
Changes or modifications to this equipment not specifically approved by the
Xerox Corporation may void the user’s authority to operate this equipment.
Shielded cables must be used with this equipment to maintain compliance with
FCC regulations.
In Canada
This digital apparatus does not exceed the Class A limits for radio noise emissions from digital apparatus as defined in the Radio interference regulations of Industry Canada.
D O C U C O L O R 2 0 6 0 / 2 0 4 5 O P E R A T O R M A N U A L xxi xxi
N O T I C E S
Safety Extra Low Voltage Approval
This Xerox digital press is in compliance with various governmental agencies and national safety regulations. All system ports meet the Safety Extra Low Voltage
(SELV) circuits for connection to customer-owned devices and networks.
Additions of customer-owned or third-party accessories that are attached to the press must meet or exceed the requirements previously listed. All modules that require external connection must be installed per the installation procedure.
Certifications in Europe
The CE marking that is applied to this product symbolizes Xerox Europe’s
Declaration of Conformity with the following applicable Directives of the
European Union as of the dates indicated:
January 1, 1995: - Council Directive 73/23/EEC amended by Council Directive 93/
68/EEC, approximation of the laws of the member states related to low voltage equipment.
January 1, 1996: - Council Directive 89/336/EEC, approximation of the laws of the member states related to electromagnetic compatibility.
Changes or modifications to this equipment not specifically approved by Xerox
Europe may void the user’s authority to operate the equipment.
Shielded cables must be used with this equipment to maintain compliance with the EMC Directive 89/336/EEC.
This equipment is not primarily intended for use in a domestic environment.
A full declaration defining the relevant Directives and referenced standards can be obtained from your Xerox Europe representative.
WARNING: In order to allow this equipment to operate in proximity to
Industrial, Scientific and Medical (ISM) equipment, the external radiation from
ISM equipment may have to be limited or special mitigation measures taken.
WARNING: This is a Class A product. In a domestic environment, this product may cause radio interference, in which case the user may be required to take adequate measures.
xxii D O C U C O L O R 2 0 6 0 / 2 0 4 5 O P E R A T O R M A N U A L
N O T I C E S
It’s Illegal in the USA
Congress, by statute, has forbidden the reproduction of the following subjects under certain circumstances. Penalties of fine or imprisonment may be imposed on those guilty of making such reproductions.
1.
Obligations or Securities of the United States Government, such as:
Certificates of Indebtedness National Bank Currency
Coupons from Bonds
Silver Certificates
United States Bonds
Federal Reserve Notes
Federal Reserve Bank Notes
Gold Certificates
Treasury Notes
Fractional Notes
Certificates of Deposit Paper Money
Bonds and Obligations of certain agencies of the government, such as
FHA, etc.
Bonds. (U.S. Savings Bonds may be photographed only for publicity purposes in connection with the campaign for the sale of such bonds.)
Internal Revenue Stamps. (If it is necessary to reproduce a legal document on which there is a canceled revenue stamp, this may be done provided the reproduction of the document is performed for lawful purposes.)
Postage Stamps, canceled or uncanceled. (For philatelic purposes, Postage
Stamps may be photographed, provided the reproduction is in black and white and is less than 75% or more than 150% of the linear dimensions of the original.)
Postal Money Orders.
Bills, Checks, or Drafts of money drawn by or upon authorized officers of the
United States.
Stamps and other representatives of value, of whatever denomination, which have been or may be issued under any Act of Congress.
D O C U C O L O R 2 0 6 0 / 2 0 4 5 O P E R A T O R M A N U A L xxiii
N O T I C E S
2.
Adjusted Compensation Certificates for Veterans of the World Wars.
3.
Obligations or Securities of any Foreign Government, Bank, or Corporation.
4.
Copyrighted material, unless permission of the copyright owner has been obtained or the reproduction falls within the “fair use” or library reproduction rights provisions of the copyright law. Further information of these provisions may be obtained from the Copyright Office, Library of
Congress, Washington, D.C. 20559. Ask for Circular R21.
5.
Certificates of Citizenship or Naturalization. (Foreign Naturalization
Certificates may be photographed.)
6.
Passports. (Foreign Passports may be photographed.)
7.
Immigration Papers.
8.
Draft Registration Cards.
9.
Selective Service Induction Papers that bear any of the following
Registrant’s information:
Earnings or Income
Court Record
Dependency Status
Previous military service
Physical or mental condition
Exception: United States military discharge certificates may be photographed.
10. Badges, Identification Cards, Passes, or Insignia carried by military personnel, or by members of the various Federal Departments, such as FBI,
Treasury, etc. (unless photograph is ordered by the head of such department or bureau.)
Reproducing the following is also prohibited in certain states:
Automobile Licenses - Drivers’ Licenses - Automobile Certificates of Title.
The above list is not all inclusive, and no liability is assumed for its completeness or accuracy. In case of doubt, consult your attorney.
xxiv D O C U C O L O R 2 0 6 0 / 2 0 4 5 O P E R A T O R M A N U A L
N O T I C E S
It’s Illegal in Canada
Parliament, by statute, has forbidden the reproduction of the following subjects under certain circumstances. Penalties of fines or imprisonment may be imposed on those guilty of making such copies.
1.
Current bank notes or current paper money.
2.
Obligations or securities of a government or bank.
3.
Exchequer bill paper or revenue paper.
4.
The public seal of Canada or of a province, or the seal of a public body or authority in Canada, or of a court of law.
5.
Proclamations, orders, regulations or appointments, or notices thereof (with intent to falsely cause same to purport to have been printed by the Queen’s
Printer for Canada, or the equivalent printer for a province).
6.
Marks, brands, seals, wrappers or designs used by or on behalf of the
Government of Canada or of a province, the government of a state other than Canada or a department, board, Commission or agency established by the Government of Canada or of a province or of a government of a state other than Canada.
7.
Impressed or adhesive stamps used for the purpose of revenue by the
Government of Canada or of a province or by the government of a state other than Canada.
8.
Documents, registers or records kept by public officials charged with the duty of making or issuing certified copies thereof, where the reproduction falsely purports to be a certified copy thereof.
9.
Copyrighted material or trademarks of any manner or kind without the consent of the copyright or trademark owner.
The above list is provided for your convenience and assistance, but it is not all inclusive, and no liability is assumed for its completeness or accuracy. In case of doubt, consult your solicitor.
D O C U C O L O R 2 0 6 0 / 2 0 4 5 O P E R A T O R M A N U A L xxv
N O T I C E S
Environmental Notices for the USA
As an ENERGY STAR
®
partner, Xerox Corporation has determined that this digital press model meets the ENERGY STAR
®
guidelines for energy efficiency.
ENERGY STAR
®
is a US registered trademark.
The ENERGY STAR program is a team effort between the Environmental
Protection Agency and the office equipment industry to promote energy-efficient personal computers, monitors, printers, digital presses, fax machines and copiers. Reducing the energy consumption of this equipment will help combat smog, acid rain and long-term changes to the climate by decreasing the emissions that result from generating electricity.
Environmental Notices for Canada
As a participant in the Environmental Choice program, Xerox Corporation has determined that this digital press model meets the Environmental Choice guidelines for energy efficiency.
Environment Canada established the Environmental Choice program in 1988 to help consumers identify environmentally responsible products and services.
Copier, printer, digital press, and fax products must meet energy efficiency and emissions criteria, and exhibit compatibility with recycled supplies. Currently,
Environmental Choice has more than 1600 approved products and 140 licensees.
Xerox has been a leader in offering EcoLogo approved products. In 1996, Xerox became the first company licensed to use the Environmental Choice EcoLogo for its copiers, printers, and fax machines.
xxvi D O C U C O L O R 2 0 6 0 / 2 0 4 5 O P E R A T O R M A N U A L
Symbols
C O N V E N T I O N S
Conventions
Standardized conventions have been used in this manual to assist you in visually locating and identifying information quickly.
CAUTION: This symbol alerts you to an action that may cause damage to hardware, software, or result in the loss of data.
WARNING: Warnings alert you to an action that may cause bodily injury.
WARNING: This symbol identifies an area on the machine that is HOT and may cause burn injuries.
WARNING: This symbol indicates a laser is being used in the machine and alerts you to refer to the appropriate safety information.
D O C U C O L O R 2 0 6 0 / 2 0 4 5 O P E R A T O R M A N U A L xxvii
KEY POINT: This symbol identifies information that is being emphasized and is important for you to remember.
2
3
1
The 1 2 3... symbol indicates the beginning of a task or work process you should use to complete a procedure and is followed by the first step of a numbered procedure, task, or work process.
NOTE: This symbol calls your attention to information that is helpful, but not essential to complete a procedure or task.
Writing Style Conventions
• Bold type indicates the name of a button to press or touch.
• Underlining is used to emphasize a word or term.
• Italic type is used for the text associated with symbols such as Cautions,
Notes, Key Points, etc. to visually bring the information to your attention.
• Italic type is also used to indicate names, such as the name of a chapter, or the name of a screen.
• Procedures direct you to press buttons located on the Control Panel, and touch buttons located on the Touch Screen.
• Text referring to illustrations or screen samples precedes the image.
D O C U C O L O R 2 0 6 0 / 2 0 4 5 O P E R A T O R M A N U A L xxviii xxviii
1.
About Color Printing
Overview
Traditional offset printing requires time, people, materials, and many steps to produce quality color output. Digital technology is changing the way the printing industry works. All the steps that used to be performed for offset printing have now been digitized and can be performed on your computer. The DocuColor
2060/2045 digital color press makes it possible for you to print fast, offsetquality images.
The flexibility and control offered by digital technologies and software applications can give you excellent results. Understanding the variables that affect the output image quality. These variables include: the quality of the original that is scanned into a computer, resolution, color management, imaging technology and a variety of other factors, are some of the things you need to understand to maximize your results.
To help you use all this new digital desktop technology, this chapter provides you with information about how to produce color images that will give you highquality output prints.
D O C U C O L O R 2 0 6 0 / 2 0 4 5 O P E R A T O R M A N U A L 1 1–1
A B O U T C O L O R P R I N T I N G
Image Quality
When creating a document with color images, you first need to understand the capabilities, strengths, and weaknesses of the software you are using. This applies to both the PC and Mac platforms of software such as QuarkXPress ® ,
Adobe FrameMaker ® , Adobe Illustrator ® , Macromedia FreeHand ® , and Adobe
Photoshop ® , to mention just a few of the applications available today. Having a thorough knowledge of these programs will assist you in creating your files correctly.
The following sections describe the different variables that affect the output image quality. These variables include: the quality of the original, resolution, color management, and a variety of other factors.
Quality Starts with the Original
Whether your original image is a scanned transparency, a photograph, or a digital file, the image characteristics you start with will have a major impact on the end results. As an image goes through the production process, it is displayed in many different ways: as digital information in the scanned image file; as pixels of red, green, and blue (RGB) light on the computer screen; and as dots of cyan, magenta, yellow, and black (CMYK) dry ink/toner on paper. During each step of the process, the colors of the original are transformed to meet the needs of these different technologies and the output media.
1–2 D O C U C O L O R 2 0 6 0 / 2 0 4 5 O P E R A T O R M A N U A L
A B O U T C O L O R P R I N T I N G
How Input Determines Output
Scanners
Successful reproduction of color images depends on a number of factors, starting with the differences in how the various technologies that affect the image translate and display the color.
Scanners are able to capture colors only as red, green, and blue (RGB). Two types of scanners are used today: drum and flatbed scanners. A flatbed scanner does not have as much color range as a drum scanner.
• A drum scanner uses a photomultiplier tube (PMT) that is very sensitive and accurate. The original document is attached to the drum which is rotated past a group of sensors - one each for red, green, and blue, and a fourth that sharpens the digital image. An internal computer usually performs the RGB to CMYK (cyan, magenta, yellow, black) conversion.
• Flatbed scanners use a less expensive and less accurate charge coupled device (CCD) sensor. The original is placed on a flat glass surface and the array of CCD sensors passes by the original, and collects the red, green, and blue data. RGB to CMYK conversion is usually performed on a computer workstation.
KEY POINT: The resolution at which the image is initially scanned and digitized determines the quality of the final output and limits the degree to which the image can be enlarged without loss of final printed quality.
D O C U C O L O R 2 0 6 0 / 2 0 4 5 O P E R A T O R M A N U A L 1–3
A B O U T C O L O R P R I N T I N G
Image Key
Some scanners, especially low-end desktop models, tend to compress the tonal range of an image and increase the contrast or difference between light and dark areas. If the contrast of your original is too high or too low, detail could be lost when it is reproduced. Images that have few dark areas or shadow tones are called high key. In contrast, a low key image consists of large areas of shadow and darker midtones (the tones that fall in between).
Some scanners allow you to manually override automatic exposure controls in those cases in which the images have these characteristics.
Imaging software applications use histograms or graphic displays to show the distribution of pixels inside the different tonal ranges of an image.
1–4 D O C U C O L O R 2 0 6 0 / 2 0 4 5 O P E R A T O R M A N U A L
A B O U T C O L O R P R I N T I N G
Grain/Image Size
The size of an original scanned image is also important to the clarity of the output image. If an image is enlarged too much, the grain of the image may become obvious, detracting from the image quality. In digital photographs, the grain introduced by scanning limits how large an image can be successfully enlarged.
The guidelines below show the maximum recommended enlargement for a few standard sizes.
Original Size
4 x 5 inch
8 x 10 inch
Print Size
11 x 17 inch/
A3
24 x 36 inch
Getting the Color You Expect
Our eyes are sensitive enough to perceive thousands of different colors in the spectrum of visual light, including many colors that cannot be displayed on a color monitor. The color range, or color gamut, that can be printed with dry ink/ toner is even more limited.
Understanding the color gamut is especially important when you compare how different technologies and output devices use light to reflect color images with what we see on a printed page. As colors move from the scanner to the screen to the press, they are converted from one color model to another so you do not get in print exactly the same colors you see on the screen.
For this reason, when you are designing for printed output, you always need to think about what can be reproduced with dry ink/toner on paper and not what you see on your monitor.
D O C U C O L O R 2 0 6 0 / 2 0 4 5 O P E R A T O R M A N U A L 1–5
A B O U T C O L O R P R I N T I N G
Additive color
Subtractive color
Media
Raster Image Processors
Computer monitors work with energized phosphors that glow red, green, or blue on the face of a picture tube. If accurate color reproduction is important to you, your monitor should be calibrated on a regular basis. Calibration adjusts and corrects the gamma, white and black points, and color balance of the monitor.
Monitors display color with impressive accuracy, but they can never match the printed page perfectly because of the physics of color involved. Monitors display additive color space RGB, and printing devices use CMYK, which is subtractive color space.
Printing is based on the subtractive color process. Cyan, magenta, and yellow dry ink/toner is placed on white reflective paper. Each color then absorbs, or subtracts, its opposing counterpart from the reflected white light. This process controls the amount of red, green, and blue light that is reflected from the white paper. The CMYK colors are printed as layers of halftone dots in various sizes and at various angles to create the illusion of different colors. The varying dot sizes create an effect similar to the varying intensities of the red, green and blue phosphors of a monitor.
The paper on which the image has printed significantly affects color reproduction. Paper reflects unabsorbed light back to the eye of the viewer.
Therefore, the more reflective the surface of the paper, the wider the range of colors that can be produced.
Refer to the Color Materials Usage Guide included in your Customer
Documentation package for more information on how paper influences image quality.
Once a file is ready to print, it is sent to a Raster Image Processor (RIP) to be processed for output. RIP units typically offer a wide range of functionality, including electronic collation, RIP while printing, color management, automatic trapping, and calibration.
Refer to your Raster Image Processor (RIP) User Documentation for more information on the functionality of your RIP unit.
1–6 D O C U C O L O R 2 0 6 0 / 2 0 4 5 O P E R A T O R M A N U A L
A B O U T C O L O R P R I N T I N G
Color Gamut
A color gamut is a range of colors. The gamut that the human eye can see is much larger than can be produced in a photograph. The photograph gamut is much larger than that of an RGB monitor. The RGB monitor gamut is larger than the CMYK gamut of a Xerox DocuColor system press. The CMYK gamut of offset printing is significantly less than that of a Xerox DocuColor system. The figure below compares the color gamuts of the DocuColor 40 and the DocuColor 2060/
2045.
Comparison of 6 Point (C,M,Y,R,G,B) (A*, B* Color Gamuts: DC40 vs DC2060/2045
Yellow
Red
Green
Magenta
Blue
DC2045/2060
DC40
Cyan
D O C U C O L O R 2 0 6 0 / 2 0 4 5 O P E R A T O R M A N U A L 1–7
A B O U T C O L O R P R I N T I N G
Color Models
Video technology (computer monitors, scanners, and television screens) sees color as transparent light and uses an RGB model to display colors. To display color appropriately on video technology, captured images are broken down into pixels (picture elements) that are projected as rays of red, green, and blue light.
Printers see color as reflective light, which reacts much differently on hard copy printed images and bounces off non-transparent surfaces. Colors are translated into combinations of cyan, magenta, yellow, and black, using a CMYK color model, to get true colors.
1–8 D O C U C O L O R 2 0 6 0 / 2 0 4 5 O P E R A T O R M A N U A L
A B O U T C O L O R P R I N T I N G
Adding and Replacing Gray to Improve Color
There are limitations to achieving the exact colors when converting from RGB (for video display) to CMY (for print). For example, CMY pigments aren’t capable of producing consistent black or gray tones.
In cases in which the three ink or toner colors overlap heavily, software applications automatically vary the percentages of cyan, magenta, and yellow to enhance image quality and improve printability. This technique is known as undercolor removal, or UCR, in which black ink is used to replace cyan, magenta, and yellow ink in neutral areas only (that is, areas with equal amounts of cyan, magenta, and yellow). This uses less ink and provides greater depth in shadows. UCR is generally used for newsprint and uncoated stock
Another form of undercolor removal is called Gray Component
Replacement (GCR). To compensate for the neutral or grey tones created during the conversion of RGB to CMYK, black ink replaces portions of cyan, magenta, and yellow ink in colored areas, as well as in neutral areas. GCR separations tend to reproduce dark, saturated colors somewhat better than UCR separations do, and they maintain gray balance better in print.
Light GCR
Medium GCR
Maximum GCR
D O C U C O L O R 2 0 6 0 / 2 0 4 5 O P E R A T O R M A N U A L 1–9
A B O U T C O L O R P R I N T I N G
Color Management
Since the color on a screen differs from the color produced by the press, it is necessary to have a Color Management System (CMS). The CMS identifies and bridges the gap between the RGB and CMYK color spaces belonging to your monitor, press, and scanner. Mac and Mac OS compatible computers use the
Apple ColorSync CMS to implement and handle the profiles of these devices. For
Windows - based PCs, refer to your PC Operator Manual for the compatible CMS.
Without a color management system, one image will appear different when reproduced on different devices due to inconsistencies in color gamuts.
A color management system helps you obtain more consistent results by aligning the color gamuts used by different devices.
Halftone Dots and Screen Angles
Halftone Screens
105 o
90 o
75 o
45 o
0 o
To produce continuous tone images on an output device, bitmaps and process color graphics must be broken into a series of dots of various sizes and colors.
This creates a halftone screen. Halftone screens combine cyan, magenta, yellow, and black dots at different screen angles to form a four-color image. The structure and patterns by which the colors are combined are the halftone screens. When a certain color is required, the halftone screen determines the dots to color, the color to use, and the degree to which each dot is colored. The figure on the left illustrates a halftone screen.
1–10 D O C U C O L O R 2 0 6 0 / 2 0 4 5 O P E R A T O R M A N U A L
A B O U T C O L O R P R I N T I N G
Halftone Dots
Halftone dots are combinations of spots that create a printed dot. The dots shown here demonstrate different print resolutions. The illustration on the left contains 25 possible printer dot cells, which can create different gray values. The illustration on the right contains 256 printer dot cells, which allows for a greater range of grays. To print a visually convincing halftone image, you need at least
150 shades of gray.
Halftone Dot Shapes
Because toner reacts differently with different paper surfaces, the characteristics of your paper generally determine the screen ruling you should use (for example, dry ink/toner tends to spread on rough, absorbent grades of paper). Different dot shapes can enhance and improve output quality.
Solid Background Printing
Media
Image quality is affected by the capabilities of your output device and the type of paper, or media, you are using. Keep in mind the following regarding the
DocuColor 2060/2045:
• The maximum dry ink/toner coverage is 270 percent.
• The maximum color depth is 256 levels per color.
• The maximum color resolution is 600 dpi.
To obtain sharp and uniform prints, paper stocks should be smooth and be composed of uniformly distributed fibers. Paper formation is determined by the uniformity of paper fiber distribution. In color printing, paper formation influences the tendency to mottle, produce uneven spotty toner coverage, and in solid backgrounds it determines the sharpness of the color and its saturation.
Xerox media have been designed with evenly distributed fibers in its structure to yield crisp and mottle-free prints.
Paper quality can vary from one side to another. Good quality paper reduces these differences. Many suppliers use arrows on the paper ream label to indicate the preferred side for imaging.
D O C U C O L O R 2 0 6 0 / 2 0 4 5 O P E R A T O R M A N U A L 1–11
A B O U T C O L O R P R I N T I N G
Electronic Digital File
Calibration
Calibration is essential to insuring good color quality. The purpose of calibration is to measure how the DocuColor 2060/2045 is printing the requested colors and to then make any corrections that are required.
Calibration at the RIP should be done daily, or any time there is the possibility that the digital press colors may have changed from what they were in an earlier calibration. Some of the reasons to calibrate are:
• Color displays differently on identical press models produced by the same manufacturer.
• The temperature of machinery as it warms up affects color intensity.
• Image quality and color reproduction on uncalibrated equipment results in unpredictable, unreliable results.
To properly predict, manage, and minimize color variables, hardware and software must be calibrated before production begins.
Refer to the DocuColor 2060/2045 System Administration Guide for information on calibrating the digital press.
Refer to the manuals that came with your Raster Image Processor for information on calibrating that unit.
1–12 D O C U C O L O R 2 0 6 0 / 2 0 4 5 O P E R A T O R M A N U A L
A B O U T C O L O R P R I N T I N G
Digital Image Manipulation
Although image reproduction can be a complex process, one of the primary advantages of capturing an image digitally is that it can be manipulated until you have achieved the desired output. Imaging software applications are continually improving image manipulation capabilities to simplify the process.
Sizing
When digitally enlarging an image, the pixels or cells may become visible. The resulting staircasing, or aliasing, in diagonal lines can be corrected using your software application to add pixels before resizing.
Sharpening
When converting or scanning an RGB image to a CMYK image, the image may become fuzzy. Use the sharpen option of your software application to adjust the clarity of the image.
Color Cast
Color cast is the modification of a hue by the addition of a trace of another hue, such as yellowish green, pinkish blue, etc. This effect can be added or removed by adding black, white, or shades of gray points using the color balance option of your software application.
Important Additional Tips
• Determine the file format.
• Calibrate equipment for the best output, if necessary.
• Include all files, fonts, and linked art.
• Determine the best way to store your data for reprint capability.
• Determine whether the data can be compressed for storage without degrading print quality to unacceptable levels. If quality is unacceptable after compression, consider storage methods that do not require compression.
D O C U C O L O R 2 0 6 0 / 2 0 4 5 O P E R A T O R M A N U A L 1–13
A B O U T C O L O R P R I N T I N G
Output Considerations
Mottle
Mottling is uneven spotty toner coverage that occurs when printing large, solid areas of flat color. Paper choice can be critical in avoiding this problem. To obtain sharp and uniform images, use only paper stock that is smooth and has uniformly distributed fibers.
Mottle No Mottle
Registration
Trapping or overprinting can compensate for gaps or shifts as the paper passes through the printing cycle.
Registered Misregistered
1–14 D O C U C O L O R 2 0 6 0 / 2 0 4 5 O P E R A T O R M A N U A L
A B O U T C O L O R P R I N T I N G
Trapping
Trapping compensates for misregistration by slightly overprinting adjacent colors.
No Trap Trap
Halo
Haloes are light areas around an object that occur when printing a darker color dry ink/toner on a lighter color dry ink/toner background. Printing on pastel or gray paper eliminates this problem.
Halo No Halo
Opacity
Opacity is a measure of how much light can pass through paper. When producing
2-sided output, choose a paper with high opacity so the print from side 1 does not show through on side 2.
D O C U C O L O R 2 0 6 0 / 2 0 4 5 O P E R A T O R M A N U A L 1–15
A B O U T C O L O R P R I N T I N G
Anti-aliasing
Anti-aliasing is a graphics software feature that eliminates or softens the jaggedness of low resolution curved edges.
Anti-aliased Not
Anti-aliased
Knockout
Knockout prints a shape or object by removing (knocking out) all underlying colors.
Knockout
Overprint
Overprint allows an element to print over the top of underlying elements, rather than knocking them out. This feature is often used with black text.
Overprint
1–16 D O C U C O L O R 2 0 6 0 / 2 0 4 5 O P E R A T O R M A N U A L
A B O U T C O L O R P R I N T I N G
Duplex Settings
To ensure that the image orientation is correct on both sides of the page, the correct duplex setting must be indicated in the print driver window. If the setting is incorrect, your document could print with the image data on one side of the page rotated 180 o from the other side.
File Formats
Computer graphics created in different graphics software applications provide varying levels of output quality. They are typically described in two ways: pixelbased or bitmap (bits of information or raster files); or mathematically described object-oriented graphics (vector graphics).The most commonly used file formats include Tagged Image File Format (TIFF) and encapsulated PostScript (EPS).
TIFF is a pixel-based, or bitmap, format that can be read by a wide range of applications across multiple platforms. This format is especially useful for viewing and outputting images used with standard office applications, such as
Microsoft Word and PowerPoint.
EPS is an object-oriented format that provides the highest quality images your output device is capable of printing. It is the most reliable and comprehensive file format for desktop publishing and graphics programs because it is device - independent.
Resolution
Resolution is the number of dots available to represent a bitmapped image. PC monitors have a resolution of 72 dpi. Choosing the right image capture resolution is key to getting the most out of your image. It is important to remember that an image can be printed only at the resolution available on your output device. The
DocuColor 2060/2045 has a print capability of 600 dpi.
D O C U C O L O R 2 0 6 0 / 2 0 4 5 O P E R A T O R M A N U A L 1–17
A B O U T C O L O R P R I N T I N G
Raster Image Processors
Raster Image Processors (RIPs) are connected to your network and drive color output devices. Each time an image is sent to a printer, the RIP connected to the printer converts, or rasterizes, the data in the file into dots which can be printed by the target output device. Each dot is assigned a specific location, color, and density level.
RIPs optimize the color of a document by manipulating the dots which make up the image so that it matches the gamut of the printer.
Image quality functions typically associated with a RIP include:
• RIP while printing allows the RIP to concurrently submit pages to the output device while processing new images for printing.
• Advanced text and line art quality controls provide anti-aliasing capabilities for high-quality text and graphics.
• Color Management System facilitates optimizations of images and offset ink/toner simulations.
• Document storage keeps the rasterized file resident on the RIP for future processing.
For further information, refer to the documentation that came with your RIP.
1–18 D O C U C O L O R 2 0 6 0 / 2 0 4 5 O P E R A T O R M A N U A L
A B O U T C O L O R P R I N T I N G
Finishing
There are two types of finishing: the finishing that the DocuColor 2060/2045 can do and the preparation for finishing other than what the DocuColor 2060/2045 can perform.
The finishing options for the DocuColor 2060/2045 are the Offset Catch Tray
(OCT), which offsets sets for easy separation, or the High Capacity Stacker (HCS), which collates and offsets stacks received from the press.
To prepare output for finishing other than what the DocuColor 2060/2045 can perform, you must first understand the various folding techniques, binding methods, and finishing touches available. You must also have software such as
DK&A, Ultimate Technographics, Scenicsoft, Press Wise, etc. to enable you to correctly prepare the document for printing.
Folding Techniques
Parallel Fold
A parallel fold means that the paper is folded parallel to either the long edge or short edge of the paper.
Right Angle Fold
The Right Angle Fold is a fold that falls at a right angle to the previous fold. A right edge fold takes the parallel fold one step further.
Accordion Fold
An Accordion fold is two or more parallel folds in opposite directions.
Gate Fold
Gate Folds create a pair of foldouts that can be imaged upon. They are especially useful for brochures and book covers.
D O C U C O L O R 2 0 6 0 / 2 0 4 5 O P E R A T O R M A N U A L 1–19
A B O U T C O L O R P R I N T I N G
Binding Preparation
Nested Signature and Binders Creep
The effects of binders creep are most obvious when thick paper is folded or multiple signatures are nested with each other. After trimming, the innermost signatures will have a smaller page size than the outermost.
Gathered Signature
Gathered signatures are folded, placed on top of one another, and bound together. This process minimizes the effects of binders creep.
Bottling
Bottling occurs when signatures are not folded at precise right angles.
1–20 D O C U C O L O R 2 0 6 0 / 2 0 4 5 O P E R A T O R M A N U A L
A B O U T C O L O R P R I N T I N G
Binding Methods
Saddle Stitching
Saddle Stitching is accomplished using a stapler or a high-speed binding machine that inserts and bends thin wire through the spine of a document. This wire leaves the document looking like it has been stapled. The maximum number of sheets that can be saddle stitched is 32.
Perfect Binding
Providing an unprinted area on the inside cover of a perfect bound book gives an area for the glue to adhere to and allows it to wrap around some of the inside pages.
Mechanical Binding
Mechanical binding allows pages to be flat, so it is often used for technical manuals, notebooks, and calendars.
Looseleaf Binding
Looseleaf bindings are ideal for documents that undergo frequent updates because pages can be inserted and removed easily.
D O C U C O L O R 2 0 6 0 / 2 0 4 5 O P E R A T O R M A N U A L 1–21
A B O U T C O L O R P R I N T I N G
Final Finishing Touches
Die Cutting
In die cutting, shapes are cut out of a page with sharp knives. It is most often used to create attention-getting documents, or for packaging with unique shapes, like video box covers.
Lamination
Laminated documents are encased in a thin, washable plastic coating to protect frequently handled documents from the elements and human wear and tear.
Varnish
Varnishing protects documents from the elements and can also be used as a design to enhance a document. Depending on the desired effect, gloss or matte
(dull) varnish can be applied to an entire document (flood coverage) to give it a smooth overall finish, or to specific portions of a page (spot coverage) to highlight some parts of the document while de emphasizing others.
Embossing
When a document is embossed, it is pressed between two dies (or molds) to create a raised or lowered texture on the sheet. This works best on uncoated cover weight papers.
1–22 D O C U C O L O R 2 0 6 0 / 2 0 4 5 O P E R A T O R M A N U A L
2.
Overview
The DocuColor 2060/2045 is a full color/black and white digital press operating at a speed of 60/45 prints per minute. This chapter provides the location, name, and function of the various digital press components including:
• External parts
• Internal parts
• The Control Panel
• The Help system
D O C U C O L O R 2 0 6 0 / 2 0 4 5 O P E R A T O R M A N U A L 2–1
O V E R V I E W
Identifying the External Parts
Use the illustration below to identify components of the external parts listed in the table.
Power On/Off
Switch
Control Panel
Touch Screen
Dry Ink/Toner
Compartment
Duplex
Automatic
Document
Feeder
Upper
Door
Tray 1
Tray 2
Offset
Catch
Tray
Exit Module
Tray 3
Transport
Module
Left Front
Door
Right Front Door
Figure 1. Key External Parts of the Digital Press
Part
Paper Tray 1
Paper Tray 2
Paper Tray 3
Description
Holds 550 sheets of paper of 24 pound (90 g/m
2
) paper.
Holds 550 sheets of paper of 24 pound (90 g/m
2
) paper.
Holds 2200 sheets of paper of 24 pound (90 g/m
2
) paper.
2–2 D O C U C O L O R 2 0 6 0 / 2 0 4 5 O P E R A T O R M A N U A L
O V E R V I E W
Part Description
Upper Door
Transport
Module
Transport
Module
Duplex
Automatic
Document
Feeder (DADF)
The Upper Door Transport Module paper path transports paper from the Paper Trays to the Transport Module.
The Transport Module carries the paper from the paper trays to the upper paper path of the digital press. It also routes the paper from the lower paper path of the digital press to the upper paper path of the digital press when duplexing.
The DADF automatically feeds originals to be scanned as Simplex or Duplex. The DADF is an option with a capacity of up to 50 same size or mixed size, 16 to
32 pound (64 to 128 g/m
2
) documents. The DADF is not on the printer-only configuration.
Scanner Scans the original to be copied.
Document Glass An original can be placed on the Document Glass to scan for copying.
ON/OFF
ON
OFF
Press the Power Switch to the On position to switch the digital press on.
A screen message advises of a short wait while the
Fuser warms up and the digital press runs a system check. You can program the digital press for a job during this time and the printing process will start automatically when the digital press is ready.
Press the Power Switch to the Off position to switch the digital press off.
Allow the digital press to remain off for a minimum of 20 seconds before switching the power on again.
Touch Screen Allows selections to be made by simply touching the selections on the screen.
D O C U C O L O R 2 0 6 0 / 2 0 4 5 O P E R A T O R M A N U A L 2–3
O V E R V I E W
Part
Control Panel
Description
Allows keypad selection of features. Refer to the Control
Panel section in this chapter.
Contains the Dry Ink/Toner cartridges.
Dry Ink/Toner
Compartment
Offset Catch
Tray (OCT)
Right/Left Front
Doors
Exit Module
Ground Fault
Indicator (GFI)
Circuit Breaker
Receives completed print job. Sets are offset for easy separation. Maximum capacity is 500 sheets of 24 pound (90 g/m
2
) paper.
Houses the image transfer system for simplex and duplex printing. Open to clear jams in the paper path in the Printing Module and at the Fuser. Follow the instructions precisely for clearing a jam in the Fuser.
CAUTION: The Fuser is extremely hot and will cause injury if clearing jam instructions are not followed.
Contains the decurler and the inverter. The decurler removes any curl from the printed page. The inverter is used when duplexing or face down output is selected.
Not shown in Figure 1, refer to Figure 5. This device trips if an interruption is detected in the power to the digital press.
2–4 D O C U C O L O R 2 0 6 0 / 2 0 4 5 O P E R A T O R M A N U A L
O V E R V I E W
Ecology Module
The Ecology Module connected to the back of the DocuColor 2060/2045 contains the environmental components (ozone and dust filters). The Ecology Module is maintained by the Xerox service representative.
Figure 2. Ecology Module
D O C U C O L O R 2 0 6 0 / 2 0 4 5 O P E R A T O R M A N U A L 2–5
O V E R V I E W
Electrical Module
The Electrical Module houses software, printed wiring boards, and power supplies. The Xerox service representative connects their laptop to the Electrical
Module to load software or run diagnostics.
Figure 3. Electrical Module
CAUTION: DO NOT block the vents of the Electrical Module. Excessive heat buildup may damage the DocuColor 2060/2045.
WARNING: Do not remove the covers or guards that are fastened with screws. There are no parts behind these covers that you can maintain or service.
2–6 D O C U C O L O R 2 0 6 0 / 2 0 4 5 O P E R A T O R M A N U A L
O V E R V I E W
Dry Ink/Toner Waste Bottle
The Dry Ink/Toner Waste Bottle collects the waste dry ink/toner in the printing process. The Dry Ink/Toner Waste Bottle is customer replaceable and located in the rear of the Exit Module.
Refer to the Maintenance Chapter of this manual for instructions on changing the
Dry Ink/Toner Waste Bottle.
Dry Ink/
Toner Waste
Bottle
Figure 4. Dry Ink/Toner Waste Bottle
D O C U C O L O R 2 0 6 0 / 2 0 4 5 O P E R A T O R M A N U A L 2–7
O V E R V I E W
Ground Fault Indicator (GFI) Circuit Breaker
The DocuColor 2060/2045 is equipped with an additional safety circuit breaker called a Ground Fault Indicator. This device trips if the power to the digital press is interrupted.
Ecology
Module
GFI
Figure 5. Digital Press GFI Circuit Breaker
The digital press should be powered on as soon as possible after the power is restored, and a print should be made to ensure that no damage to the DocuColor
2060/2045 has occurred.
If power to the digital press is interrupted, do the following:
1
Locate the circuit breaker on the back of the digital press on the electrical module next to the toner waste bottle.
2
If the device has been tripped, the switch will be in the Off position (down). Flip the switch up.
NOTE: If the device trips again, or if power is not restored by the above procedure, call your Xerox service representative.
CAUTION: The Pressure Pad in the Fuser remains in a up position if power to the digital press is interrupted while the digital press is in use. The Pressure Pad will not be released from this position until the power is restored, the Power
Switch is in the On position, and the Start button is pressed.
If the Pressure Pad remains in the up position for a prolonged period of time, print quality defects will occur.
2–8 D O C U C O L O R 2 0 6 0 / 2 0 4 5 O P E R A T O R M A N U A L
O V E R V I E W
Touch Screen
Use the Touch Screen to select features and options for the scanned output.
It also displays messages that indicate the status of the digital press during idle, run, or fault conditions.
The Touch Screen displays the default screen selected in the Tools Mode by your
System Administrator. The default screen can be either the Basic Features, Job
Status, or Machine Status screen.
Message Area
The message area at the top of the Touch Screen displays messages concerning the digital press status, programming conflicts, or errors. Messages may also provide instructions for the operator.
Tabs/Buttons/Icons
Some screens on the Touch Screen display tabs which contain various selectable options. Refer to the example on the following page.
Features and options are initially set to the factory default settings. These settings can be changed by your System Administrator in Tools Mode.
Ask your System Administrator for more information regarding these selections, or refer to the System Administration Guide.
D O C U C O L O R 2 0 6 0 / 2 0 4 5 O P E R A T O R M A N U A L 2–9
O V E R V I E W
Message Area
Tab
Option
Button
Figure 6. Message Area, Tabs, and Option Buttons
2–10 D O C U C O L O R 2 0 6 0 / 2 0 4 5 O P E R A T O R M A N U A L
O V E R V I E W
Touch Screen Button Types and Functions
Selectable Touch Screen buttons are in color and shadowed. These buttons change appearance when selected. The standard button types include:
• Option buttons
Option buttons are blank with words or graphics to the side.
Some features have more options associated with them than can be displayed on one screen. Touching a More... button displays a screen with all further options.
• Icon buttons
Icon buttons are Option buttons that display icons.
• Arrow buttons
Arrow buttons allow you to change values for features such as Variable
Reduce/Enlarge.
Touch the up arrow to increase the value; touch the down arrow to decrease the value. Changes are displayed in the value boxes.
Values on the DocuColor 2060/2045 are set in millimeters (mm) and inches.
• Fixed selection buttons
Fixed selection buttons allow you to select preset (default) values indicated on the Touch Screen.
D O C U C O L O R 2 0 6 0 / 2 0 4 5 O P E R A T O R M A N U A L 2–11
O V E R V I E W
• Cancel and Save buttons
The Cancel button allows you to cancel selected feature options without saving them.
The Save button allows you to save selected feature options.
Cancel
Button
Save
Button
Icon
Button
Fixed
Option
Figure 7. Screen Button Types
Arrows to set values
2–12 D O C U C O L O R 2 0 6 0 / 2 0 4 5 O P E R A T O R M A N U A L
O V E R V I E W
Control Panel
Your DocuColor 2060/2045 has one of two Control Panels: a Control Panel with words, as shown below, or a panel with international symbols, as shown on the following page. The function of each button is described in the table on the following pages. Not all of the functions are activated for the digital press configuration without the Scanner.
Figure 8. DocuColor 2060/2045 Control Panel with words
D O C U C O L O R 2 0 6 0 / 2 0 4 5 O P E R A T O R M A N U A L 2–13
O V E R V I E W
Figure 9. DocuColor 2060/2045 Control Panel with international symbols
2–14 D O C U C O L O R 2 0 6 0 / 2 0 4 5 O P E R A T O R M A N U A L
Name
Features
Power Saver
Job Status
Language
Access
Machine Status
Word
O V E R V I E W
Symbol Function
Displays the screen containing the Basic
Features, Added Features, Image Quality, and
More tabs. Appears on digital press with scanner only.
Puts the digital press in a standby status mode, in which the Fuser temperature is lowered.
Displays a list and the current status of all jobs submitted on the Touch Screen. You can also hold, release, promote, delete, and see the options selected for each job in the digital press queue.
Allows you to select one of two languages to be displayed on the Touch Screen.
Allows access to the password-protected
Tools Mode and the Auditron Mode.
Gives Paper Tray, Machine Details, Error Log, and Maintenance information. Machine Status is where you will find the serial number for the
DocuColor 2060/2045, the customer support phone numbers, and the meters that show the count for color, black and white, color large size, and total output.
D O C U C O L O R 2 0 6 0 / 2 0 4 5 O P E R A T O R M A N U A L 2–15
O V E R V I E W
Name
Review
Help
Clear All
Interrupt
Word Symbol Function
Displays the job programming choices that are selected. Digital press with scanner only.
Displays additional information useful in completing a task.
Clears all job programming and returns the digital press to the default settings. Clear All cannot be used while printing is in progress.
Digital press with scanner only.
Interrupts the printing in process to allow a priority job to be scanned. The Interrupt indicator lamp lights up. Press the Interrupt button after the job is completed to return to printing the previous job. Interrupt cannot be selected while using the Poster feature. While running a job in Interrupt, Define Area in the
Original Type/Dark Edges feature cannot be selected. Also, Stored Programming and
Added Features cannot be used while running a job in Interrupt. Digital press with scanner only.
2–16 D O C U C O L O R 2 0 6 0 / 2 0 4 5 O P E R A T O R M A N U A L
Name
Pause
Word
Start
Keypad
C
O V E R V I E W
Symbol Function
Press the Pause button to stop the scanning process. You cannot run another job while in the Pause mode. You must press Pause again to resume the original job or to press Clear All to cancel the job. Digital press with scanner only.
Press the Start button to start the scanning process. The Start button is also used in the
Tools Mode for certain settings.
Use the keypad to enter your password for access to Tools Mode. Use the keypad to enter the number of copies desired for a job.
Press the C (Clear) button to return the selected quantity to 1. Digital press with scanner only.
D O C U C O L O R 2 0 6 0 / 2 0 4 5 O P E R A T O R M A N U A L 2–17
O V E R V I E W
Features
When the Features button is pressed, the following screen is displayed. Tray 4 appears in the Paper Supply column only when an optional Tray 4 is connected to the digital press. Auto Paper does not show for all configurations.
The Features screen can be set as the initial screen default by your System
Administrator.
2–18
Figure 10. Features Initial Screen
Tab Description
Basic Features
Added Features Displays choices to program for 2-Sided Output, Image
Shift, Original Input, Bound Originals, Edge Erase, and
Stored Programming.
Image Quality
Displays the choices to program for Color Mode, Output,
Reduce/Enlarge, and Paper Supply.
Displays Image Quality options, including Original Type,
Lighten/Darken, Sharpness, Image Tone Presets, Color
Balance, Color Shift, Chroma, and Color Bar.
More...
Displays the tabs for Output Format, Job Assembly, and
Back (takes you back to the Basic Features screen).
D O C U C O L O R 2 0 6 0 / 2 0 4 5 O P E R A T O R M A N U A L
O V E R V I E W
Job Status
When you press the Job Status button, the Job Status screen, shown in
Figure 10, is displayed. The Job Status screen can be set as the initial screen default by your System Administrator. Information about the job includes Job
Type, Current Status, Paper Size, Output Quantity (refers to the output in sheets for a single page job and in sets or stacks for a multiple page job), and total
Number of Pages.
Jobs are numbered in the order they are received for processing. Job order in the queue may be modified by an automatic Hold (something has to be done to the digital press before continuing), a Manual Hold (at user request), Promotion of one or more jobs, or Delete a job.
To perform one of the following functions, you must first touch the desired job to select it, then touch one of the buttons below.
• Touch Hold Job for a manual hold. When a job is in Hold Job status in the queue, it will not print when it reaches the top of the job queue. It will be skipped until it is released or deleted.
• Touch Release Job to reactivate a job that is on hold in the queue. If the job is being held due to a resource (paper, dry ink/toner, etc.) problem, the job is not released until the resource is provided. A job that is held due to user request can be released by touching the Release button.
• Touch Promote Job to advance a selected job in the queue to be processed after the job that is currently printing. Jobs are processed on a first-in/firstout basis when multiple jobs are promoted. Once a job has been promoted, it cannot be skipped by jobs promoted after it.
• Touch Delete Job to delete a selected job from the queue. You must answer
“Yes” when confirmation of the delete is requested.
• Touch Job Details for detailed information about a selected job such as
Number of Images processed, Color Mode, Paper Tray in use, Paper Type, and Finishing.
Job names will be truncated to 16 characters on the Job Status screen, which may be fewer characters than are displayed on your RIP.
D O C U C O L O R 2 0 6 0 / 2 0 4 5 O P E R A T O R M A N U A L 2–19
O V E R V I E W
Name
Job List
Hold Job
Release Job
Promote Job
Delete Job
Job Details
Up/Down Arrows
Figure 11. Job Status Screen
Function
Shows all jobs submitted.
Holds a job in the print queue until released.
Releases a Hold Job to be printed.
Enables a job to be moved in front of other jobs in the queue.
Deletes a selected job.
Shows the programmed options for a selected job.
Enables scrolling through job list.
2–20 D O C U C O L O R 2 0 6 0 / 2 0 4 5 O P E R A T O R M A N U A L
O V E R V I E W
Power Saver
The Power Saver button puts the digital press in a standby status mode, in which the Fuser temperature is lowered. The factory default is 60 minutes. The Power
Saver time out can be changed in Tools to reflect a value from 1 to 240 minutes .
Refer to the System Administration Guide for further information.
Language
The Language button toggles the Touch Screen between two preset languages.
Access
The Access button brings up a screen that requires a password to enter the Tools and Auditron Modes. Refer to the System Administration Guide for further information on these two Modes.
D O C U C O L O R 2 0 6 0 / 2 0 4 5 O P E R A T O R M A N U A L 2–21
O V E R V I E W
Machine Status
When the Machine Status button is pressed, the following screen is displayed.
The Machine Status screen can be set as the initial screen default by your
System Administrator. Tray 4 appears in the Paper Supply column when an optional Tray 4 has been connected to the digital press.
2–22
Figure 12. Machine Status Initial Screen
Screen Name Function
Paper Trays
Machine Details Displays the customer support phone number, the serial number of the machine, and access to the Meters screen.
Error Log
Shows the trays available, and the size, type, weight and level of the paper in the trays.
Shows all error codes to assist your Xerox service representative in solving problems with the DocuColor 2060/
2045.
Maintenance Displays the status of the Dry Ink/Toner Cartridges, Dry Ink/
Toner Waste Bottle, Fuser Oil, and Fuser Web. A green check mark indicates that the status is Okay. A yellow check mark indicates a Warning. A red circle indicates a Fault.
NOTE: The Fuser Web is to be changed only by your
Xerox service representative.
D O C U C O L O R 2 0 6 0 / 2 0 4 5 O P E R A T O R M A N U A L
O V E R V I E W
Meters
The meters keep track of print counts. To view the print count touch the Meters button on the Machine Details screen. The Billing Meters screen is displayed.
Figure 13. Machine Details Screen
D O C U C O L O R 2 0 6 0 / 2 0 4 5 O P E R A T O R M A N U A L 2–23
O V E R V I E W
To reset the Meters to zero, follow this procedure:
1
Touch the Resettable Meters button on the Billing Meters screen.
Figure 14. Billing Meters Screen
2–24 D O C U C O L O R 2 0 6 0 / 2 0 4 5 O P E R A T O R M A N U A L
2
Touch the Reset button on the Resettable Meters screen.
The numbers reset to 0.
O V E R V I E W
Figure 15. Resettable Meters screen
3
Touch Close until you reach the primary Machine Details screen.
D O C U C O L O R 2 0 6 0 / 2 0 4 5 O P E R A T O R M A N U A L 2–25
O V E R V I E W
Review
The Review button displays the Review screen, which allows you to review the information programmed for a scanner job. Use the up and down arrow buttons on the right side of the screen to scroll down through all of the features.
• Touch the All Features button to display the information for each feature.
• Touch the Invoked Features button to display only the information for the features programmed for a particular job.
• Touch the Features Off Default button to display only the information for the features whose settings are not the default settings.
Figure 16. Review Screen for Digital Press with Scanner
2–26 D O C U C O L O R 2 0 6 0 / 2 0 4 5 O P E R A T O R M A N U A L
O V E R V I E W
Figure 17. Review Screen for Digital Press with Scanner continued
Figure 18. Review Screen for Digital Press with Scanner continued
D O C U C O L O R 2 0 6 0 / 2 0 4 5 O P E R A T O R M A N U A L 2–27
O V E R V I E W
Figure 19. Review Screen for Digital Press with Scanner continued
2–28 D O C U C O L O R 2 0 6 0 / 2 0 4 5 O P E R A T O R M A N U A L
O V E R V I E W
Help
Press Help for an overview of the different options displayed in the various tabs on the Touch Screen.
Clear All
Press Clear All to cancel all programmed selections and restore the defaults.
Interrupt
Press Interrupt to interrupt a scan or print job that is running, to program and run another job, and then to resume scanning or printing the original job. A green light to the left of the interrupt button indicates that interrupt has been selected.
Pause
Press the Pause button to stop the job that is running. On the Job Status screen, touch Delete Job to cancel the job or Resume Scan to continue the job.
D O C U C O L O R 2 0 6 0 / 2 0 4 5 O P E R A T O R M A N U A L 2–29
O V E R V I E W
Job Monitor
The Job Monitor screen displays the options selected for the current job and allows you to program features for the next job while the current job is running. If there is more than one job programmed in the digital press, the last job programmed appears on the Job Monitor, not the job that is currently running.
Figure 20. Job Monitor Screen
The digital press may be programmed to accept Additional Originals. This selection is activated in the Tools Mode. Refer to the System Administration
Guide for instructions.
If Additional Originals is activated, the digital press looks for more originals to be fed for a job until the Scanning Complete button is pressed on the Job Monitor screen.
2–30 D O C U C O L O R 2 0 6 0 / 2 0 4 5 O P E R A T O R M A N U A L
O V E R V I E W
Audio Tones
There are three audio tones:
• Attention:
The Attention Tone indicates that the button you press cannot be selected.
• Button Selection:
The Button Selection Tone indicates that the button you press can be selected.
• Fault:
The Fault Tone indicates that the digital press is in a fault condition and will not operate until the fault is cleared.
The Audio Tones can be activated or deactivated through the Tools Mode. For more information, refer to the System Administration Guide.
D O C U C O L O R 2 0 6 0 / 2 0 4 5 O P E R A T O R M A N U A L 2–31
O V E R V I E W
Alert Screens
An Alert screen has a red bar across the screen when a consumable product, such as Dry Ink/Toner, needs to be replaced. An Alert screen also indicates that the digital press is unable to make prints because of a fault condition. Follow the instructions on the Touch Screen to resolve the problem and resume printing.
Figure 21. Alert Screen
2–32 D O C U C O L O R 2 0 6 0 / 2 0 4 5 O P E R A T O R M A N U A L
O V E R V I E W
Maintenance
The Maintenance screen displays a green check mark if the level of the consumable listed is adequate. A yellow triangle alerts you that the level is low and a red circle indicates that the consumable is depleted. The DocuColor 2060/
2045 will automatically interrupt the current job and will not restart until the consumable is replaced.
Figure 22. Maintenance Screen
D O C U C O L O R 2 0 6 0 / 2 0 4 5 O P E R A T O R M A N U A L 2–33
O V E R V I E W
Duplex Automatic Document Feeder (DADF)
Figure 23. DADF
The DADF automatically feeds up to 50 same size or mixed size documents.
1
Place documents face up in the Duplex Automatic Document Feeder and ensure that the paper guide is against the documents.
The Document Feed Lamp displays a green arrow when a document is inserted correctly into the feeder. This light can also indicate a document jam.
2
Press the Start button to begin the scan operation. The original is fed from the top of the stack to the Document Glass to be scanned then face down to the
DADF output tray on the right.
KEY POINT: Do not use excessive force to press down on the Duplex
Automatic Document Feeder when scanning bound documents.
KEY POINT: You may not use the Auto Color option if the Duplex Automatic
Document Feeder must remain open during copying. The digital press with scanner will not operate until you make a different selection under the Color
Mode feature.
2–34 D O C U C O L O R 2 0 6 0 / 2 0 4 5 O P E R A T O R M A N U A L
O V E R V I E W
Document Glass
Figure 24. Orientation of Original
1
Lift the DADF and place the original face down in the upper-left corner using the same orientation on the Document Glass as the paper in the chosen paper tray
(Long Edge Feed (LEF) on the glass if the paper in the chosen paper tray is LEF.
Short Edge Feed (SEF) on the glass if the paper in the chosen paper tray is SEF).
CAUTION: When copying a bound document, DO NOT apply excessive force to close the DADF.
2
Lower the Duplex Automatic Document Feeder.
3
Press the Start button to begin the scan operation.
The maximum scanned image size is 11 x 17 inches or A3. To copy an image of this size onto 12 x 17.7 inch or SRA3 paper, you must select 102
% enlargement.
Refer to the Paper and Paper Trays Chapter of this manual for more information on programming the system for the various paper sizes.
KEY POINT: You may not use the Auto Color option if the Duplex Automatic
Document Feeder must remain open during copying. The digital press with scanner will not operate until you make a different selection under the Color
Mode feature.
D O C U C O L O R 2 0 6 0 / 2 0 4 5 O P E R A T O R M A N U A L 2–35
O V E R V I E W
Identifying the Internal Parts
Document
Glass
Upper
Door
Tray 1
Tray 2
Tray 3
Dry Ink/Toner
Cartridges
Transport
Paper Path
Serial
Number
Label
Digital Press
Paper Path
Exit Module
Paper
Figure 25. Internal view of the DocuColor 2060/2045
Path
Dry Ink/Toner Cartridges
The colors in the DocuColor 2060/2045, from left to right, are black, cyan, magenta, and yellow. Refer to the Maintenance Chapter of this manual for instructions on changing the cartridge.
Serial Number Label
If the DocuColor 2060/2045 has a loss of power, and it is impossible to access the Machine Details tab to get the serial number, open the two main front doors.
The serial number label is in the center of the bottom frame of the digital press.
2–36 D O C U C O L O R 2 0 6 0 / 2 0 4 5 O P E R A T O R M A N U A L
Upper Door
O V E R V I E W
The Upper Door Transport Module paper path transports paper from Trays 1 and
2, and optional Tray 4 to the Transport Module.
From
Tray 4
Figure 26. Upper Door
Tray 1
Tray 2
Tray 3
Transport
Module
To the digital press
From
Horizontal
(Duplex)
Transport
Figure 27. Paper Path
D O C U C O L O R 2 0 6 0 / 2 0 4 5 O P E R A T O R M A N U A L 2–37
O V E R V I E W
Transport Module
The upper paper path in the Transport Module carries the paper from the Paper
Trays to the upper paper path of the digital press.
The lower paper path in the Transport Module carries the paper from the lower paper path in the digital press to the upper paper path in the digital press when duplexing.
Paper from Trays
1, 2 and 4
Takeaway
Transport
Paper from Tray 3
Upper
Transport
To the Digital
Press
Lower
Transport
Single Sided prints from the Horizontal
Transport
Figure 28. Transport Module Paper Path
Figure 29. Transport Module
2–38 D O C U C O L O R 2 0 6 0 / 2 0 4 5 O P E R A T O R M A N U A L
O V E R V I E W
Paper Path in the Digital Press
The Paper Path in the digital press transfers an image to the paper and fuses it for both the simplex and duplex selections. It has two areas, the upper Paper
Path and the lower Paper Path. The upper Paper Path is used for both simplexing and duplexing. The lower Paper Path is used for duplexing only. Horizontal
Transport 1 decurls the paper when printing duplex.
From Transport Module
To Transport Module
Alignment
Transport
Fuser
Transport
Vacuum Transport
Inverter Transport
Inverter
Gate
To Exit
Module
Horizontal Transport 2
Horizontal Transport 1
From
Duplex
Inverter
Transport
Figure 30. Digital Press Paper Path
D O C U C O L O R 2 0 6 0 / 2 0 4 5 O P E R A T O R M A N U A L 2–39
O V E R V I E W
Exit Module
A completed print passes through the Exit Module to the Offset Catch Tray.
The Exit Module contains a Decurler that removes paper curl caused by the fusing process.
The Exit Module also contains an Inverter which turns the paper over so that side
2 can print when duplexing or when face down output is selected.
To the output device
Decurler
From Digital Press
To Inverter Transport Duplex Inverter
Transport
To Digital Press
Figure 31. Exit Module Paper Path
Figure 32. Exit Module
2–40 D O C U C O L O R 2 0 6 0 / 2 0 4 5 O P E R A T O R M A N U A L
O V E R V I E W
Relocating the DocuColor 2060/2045
If the DocuColor 2060/2045 must be relocated, call your Xerox customer representative. The Installation Planning procedure must be conducted for every new site.
D O C U C O L O R 2 0 6 0 / 2 0 4 5 O P E R A T O R M A N U A L 2–41
O V E R V I E W
This page is intentionally left blank.
2–42 D O C U C O L O R 2 0 6 0 / 2 0 4 5 O P E R A T O R M A N U A L
3.
Paper and Paper Trays
Recommended Papers and Special Materials
Refer to the Color Materials User Guide and the Recommended Materials List for paper guidelines. The Recommended Materials List is a downloadable file on www.xerox.com. Use the search parameters DC 2060 or DC2045 and follow the path until you reach the files that can be downloaded.
Paper Handling
For the best performance load paper with the seam side down in Trays 1 and 2 and seam side up in Tray 3. The seam side is where the ream of paper is sealed.
NOTE: Many suppliers use arrows on the product labels to indicate the preferred side to image first. Use this side (as signaled by the arrow) as equivalent to the seam side when loading the paper.
Many factors affect the performance of paper, including room temperature, humidity, paper quality, dust, and the size of the image area. If jams or paper curl problems occur, remove the paper from the paper tray, turn it over, place it back in the paper tray, and resume printing. If the problem is rectified, continue to load your paper in the same manner. If the problem is not rectified, load a new ream of paper and try the process again. If the problem persists, your System
Administrator can go into the Tools Mode and try the different decurler settings.
If, after trying all the previous suggestions, the problem still persists, call your
Xerox representative.
D O C U C O L O R 2 0 6 0 / 2 0 4 5 O P E R A T O R M A N U A L 13 3–1
P A P E R A N D P A P E R T R A Y S
For reliable digital press operation and good print quality, Xerox recommends the following:
• Store Paper:
• On a flat surface. Do not store paper directly on the floor, since that increases the possibility of moisture absorption. Paper should be stored on pallets, or shelves or in cabinets in an area protected from extremes of temperature and humidity.
• In a low dust area.
• In a low humidity area. Humidity is one of the most important steps to promote proper paper characteristics. Optimum paper storage conditions include a relative humidity of 35% to 55%. An increase in humidity can cause paper to develop wavy edges. This occurs because the edges absorb moisture while the rest of the ream remains unaffected. Wavy edges can cause jams and misfeeds.
• In an air-tight moisture proof container.
• In controlled temperature. The temperature in the room where paper is stored can have a significant effect on how that paper performs in the machine. Optimum paper storage temperature is 68 to 76 degrees F (20 to 24.4 degrees C).
For additional paper handling information, refer to the Color Materials Usage
Guide.
• Cutting and Trimming Paper
Proper cutting of the paper is important. Mills offering paper in cut sizes cut their papers using state-of-the-art rotary slitters on high performance systems. Slitting and edge trimming by circular knives with dust removal at every cutting point prevents contamination of the paper.
Trimming papers from parent sheets to get the desired output size may generate dust if dull knives are used. The recommendation is to delay trimming until printing has been finalized to prevent paper dust generation and contamination.
If pre-printing is imperative, an in-house maintenance program, including knife sharpness maintenance and dust removal with a vacuum or air system, are key to achieving good results.
3–2 D O C U C O L O R 2 0 6 0 / 2 0 4 5 O P E R A T O R M A N U A L
P A P E R A N D P A P E R T R A Y S
Paper Trays 1, 2, and 3
Paper Trays 1, 2, and 3 are standard Paper Trays and hold the paper supply for the
DocuColor 2060/2045.
Tray 1
Tray 2
Tray 3
Figure 1. Trays 1, 2, and 3
D O C U C O L O R 2 0 6 0 / 2 0 4 5 O P E R A T O R M A N U A L 3–3
P A P E R A N D P A P E R T R A Y S
The following figure shows the paper paths for Trays 1, 2, and 3.
From
Tray
4
Transport
Module
Tray 1
Tray 2
Tray 3
To the digital press
From
Horizontal
(Duplex)
Transport
Figure 2. Paper Path of Trays 1, 2 and 3
3–4 D O C U C O L O R 2 0 6 0 / 2 0 4 5 O P E R A T O R M A N U A L
P A P E R A N D P A P E R T R A Y S
Paper Guidelines
For the best results, remember the following:
• Do not load paper or other materials above the MAX line.
• Do not use wrinkled, torn, curled, or folded paper.
• Use the recommended paper sizes and weights.
• Do not mix sizes or weights of paper in a paper tray.
• Ensure that the tray indicator LEDs are set for the correct weight range.
• Follow the Recommended Materials List suggestions found at: www.xerox.com
Copy paper is fed into the digital press in one of two positions. One position is called long edge feed (LEF). Long edge refers to the long edge of your copy paper.
When you see LEF, position your copy paper so the long edge is fed first. The other position is called short edge feed (SEF). Short edge refers to the short edge of your copy paper. When you see SEF, position your copy paper so the short edge is fed first.
NOTE: It is imperative that you load paper with the paper guides adjusted properly. If the paper is NOT loaded properly, it will skew and jams will occur.
D O C U C O L O R 2 0 6 0 / 2 0 4 5 O P E R A T O R M A N U A L 3–5
P A P E R A N D P A P E R T R A Y S
Paper
Paper Size
Paper Weight Range
Transparencies
Labels
Transfer Paper
Coated Paper
Tabbed Inserts**
Drilled
64 - 220 g/m
2
No
No
No
No
No
Yes
Tray 1/Tray2
JIS B5 (LEF/SEF)
8.5 x 11 inch/A4 (LEF/SEF)
JIS B4 (SEF)
ISO B4
8 x 10 inch (LEF)
8.5 x 13 inch (SEF)
8.5 x 14 inch (SEF)
11 x 17 inch/A3 (SEF)
12 x 18 inch (SEF)*
12.6 x 17.7 inch/SRA3 (SEF)*
Tray 3
Yes
Yes
Yes
Yes
JIS B5 (LEF/SEF)
8.5 x 11 inch/A4 (LEF/SEF)
JIS B4 (SEF)
ISO B4
8 x 10 inch (LEF)
8.5 x 13 inch (SEF)
8.5 x 14 inch (SEF)
11 x 17 inch/A3 (SEF)
12 x 18 inch (SEF)
12.6 x 17.7 inch/SRA3 (SEF)
12.6 x 19.2 inch (SEF)
64 - 280 g/m
2
Yes
Yes
Table 1. Paper Guidelines
*Requires a Paper Guide to be removed to run these sizes.
Call your Xerox service representative for the Side Guide removal.
**Refer to Non-standard Size Paper in this chapter.
NOTE: If you have an optional High Capacity Stacker (HCS), the back sometimes comes off when printing labels with the Stack Mode selected. Use the Top Tray Mode when printing labels to avoid this problem.
KEY POINT: When feeding paper short edge feed and you have an optional
High Capacity Stacker (HCS), the output must be sent to the High Capacity
Stacker Top Tray.
3–6 D O C U C O L O R 2 0 6 0 / 2 0 4 5 O P E R A T O R M A N U A L
P A P E R A N D P A P E R T R A Y S
Paper Tray Special Features
Special features help control the environmental conditions in the paper trays to ensure optimum print capability:
• Paper Trays 1 and 2 have optional heater kits available.
• Paper Tray 3 has a heater underneath the paper tray that can be activated by your Xerox service representative.
• Paper Tray 3 has two blowers. The lead edge blower is on at all times and produces heated air if the following selections are made: coated paper, transparencies, or plain paper 106 g/m
2
or heavier. The trail edge blower is on at all times and does not produce heated air.
• Paper Tray 3 has air adjust levers on the drawer to regulate the amount of air disbursed. If the paper weight is 150 g/m
2 or less, the position of the air adjust levers should be toward the front of the tray. If the paper weight is 150 g/m
2 or more, the position of the air adjust levers should be toward the rear of the tray.
Figure 3. Trail Edge and Lead Edge Blowers
D O C U C O L O R 2 0 6 0 / 2 0 4 5 O P E R A T O R M A N U A L 3–7
P A P E R A N D P A P E R T R A Y S
Tray Capacity
Paper Trays 1 and 2 have a capacity of 550 sheets of 24 pound (90 g/m
2
) paper.
Paper Tray 3 has a capacity of 2200 sheets of 24 pound (90 g/m
2
) paper.
Curl
When the paper is exposed to heat, the paper loses moisture and curls toward the heat source. High coverage jobs tend to curl more due to the toner plastification effect on the paper surface. The system tries to reduce this by using mechanical devices within the paper path called decurlers.
Your system has been designed with an automatic curl control system that uses information such as: the amount of coverage on the page, paper weight, whether the paper is coated or uncoated, and the current humidity and temperature to determine the amount of pressure needed at the different decurlers to reduce output curl.
If you are experiencing excessive curl, remove the paper from the tray, turn it over and replace it in the tray. If the curl is still excessive, refer to the System
Administration Guide, Tools Mode chapter, to change the decurler settings to accommodate the environmental and paper conditions.
Duplexing
The DocuColor 2060/2045 duplexes prints from all paper trays up to 220 g/m
2
.
The system does not duplex media heavier than 220 g/m
2
or larger than 12.6 x
18” (321.1 x 458.1 mm).
3–8 D O C U C O L O R 2 0 6 0 / 2 0 4 5 O P E R A T O R M A N U A L
P A P E R A N D P A P E R T R A Y S
Transparency Guidelines
Transparencies can be run ONLY from Tray 3.
Use only the transparencies recommended:
• Xerox Removable Paper Stripe: USA and Canada, 3R5765; Xerox
Europe, 3R93179.
• Load transparencies into Tray 3 with the paper stripe side facing DOWN and with the stripe as the leading edge. (The leading edge is the edge that feeds into the digital press first.)
• Do not mix paper and transparencies in Tray 3. Jams may occur.
• Ensure that Transparency is selected in the weight section on the paper tray.
Tabbed Inserts
Tabbed Inserts can be loaded into Tray 3 as non-standard paper.
• Tabbed inserts can be run from, but are not recommended for, optional Tray 4 as non-standard paper.
• When loading, the non-tabbed, short edge of the tabbed insert should be the lead edge to the digital press.
• If a jam occurs while running tabbed sets, there is no recovery procedure.
• You have to manually reassemble your originals and prints, determine where the job left off, and resume printing or cancel the job and start again.
• The size of the tabbed insert should be 9 x 11 inch (229 x 279 mm) for letter size tabs (223.5 x 296 mm for A4 equivalent tabs).
• The proper weight of the insert should be selected on the tray.
• Select Non-standard size and input 11 inches or 296 mm for A4 as the X axis and 9 inches or 223.5 mm for A4 as the Y axis dimensions for SEF.
Refer to the System Administration Guide for the procedure to program nonstandard size paper.
D O C U C O L O R 2 0 6 0 / 2 0 4 5 O P E R A T O R M A N U A L 3–9
P A P E R A N D P A P E R T R A Y S
Drilled Paper
3-hole drilled paper can be run only from Trays 1, 2, and 3. 3-hole drilled paper does not run reliably from the optional Tray 4.
Drilled paper should be run in the Simplex (1-sided) and Duplex (2-sided) orientations shown below to avoid paper jams caused by the holes not aligning correctly with the paper sensor in the press.
Simplex Print Jobs
Load the drilled paper into Trays 1, 2, or 3 Long Edge Feed (LEF) with the holes at the lead edge position. Refer to the following illustration:
Trays 1 and 2
Rear of paper tray
Left side
Front of paper tray
Paper tray guides
Tray 3
Paper tray guides
Rear of paper tray
Right side
Front of paper tray
Duplex Print Jobs
Load drilled paper into Trays 1, 2, or 3 with the holes positioned toward the rear of the paper tray. Refer to the following illustration:
Trays 1, 2, and 3
Rear of paper tray
Paper tray guides
Front of paper tray
NOTE: If you are stapling 3-hole drilled paper with the optional High Capacity
Stacker Stapler, refer to the Accessories chapter for paper loading instructions, based on the position of the staple.
3–10 D O C U C O L O R 2 0 6 0 / 2 0 4 5 O P E R A T O R M A N U A L
P A P E R A N D P A P E R T R A Y S
Letterhead
Different inks and dry inks/toners are used to produce preprinted letterhead that may not pass through the digital press intact.
Refer to the Specialty Media Guide that came with your documentation for information on using preprinted letterhead paper.
Non-standard Size Paper
Non-standard Size Paper (7.2 to 12.6 (LEF) or 7.2 to 19.2 (SEF)) can be loaded into
Tray 3 and optional Tray 4. Ensure that Non-standard Size Paper is selected on
Tray 3 and optional Tray 4. Refer to the System Administration Guide for the procedure to program Non-standard Size Paper.
Oversize Paper
Oversize paper (12 x 18” (SEF) or 12.6 x 17.7”/SRA3 (SEF)) can be loaded in Trays
1 and 2 after the paper guides are removed by a Xerox service representative.
Refer to the System Administration Guide for the procedure to program oversize paper.
D O C U C O L O R 2 0 6 0 / 2 0 4 5 O P E R A T O R M A N U A L 3–11
P A P E R A N D P A P E R T R A Y S
Auto Tray Switching
When Auto Tray Switching (ATS) (this feature may not be available with your configuration) is activated in the Tools Mode, the digital press automatically switches to another tray containing paper of the identical size, weight, type, and feeding orientation (SEF or LEF) when the tray being used is empty. Refer to the
System Administration Guide for the instruction on enabling ATS.
Auto Paper
Auto Paper automatically senses the size of the original and selects the proper paper tray for output. Refer to the System Administration Guide for information on how to activate Auto Paper Supply.
Figure 4. Basic Features Screen
3–12 D O C U C O L O R 2 0 6 0 / 2 0 4 5 O P E R A T O R M A N U A L
Loading Paper
P A P E R A N D P A P E R T R A Y S
1
Pull out the tray slowly until it stops.
2
Load the correct size paper into the tray in the correct feeding orientation. Refer to the orientation labels on each tray.
NOTE: Do not load materials above the MAX line located on the Edge Guide.
• Load the paper seam side (the side on which the ream of paper is sealed) down in Tray 1 and Tray 2.
• Load the paper seam side (the side on which the ream of paper is sealed) up in Tray 3.
NOTE: Many suppliers use arrows on the product labels to indicate the preferred side to image first. Use this side (as signaled by the arrow) as equivalent to the seam side when loading the paper.
Figure 5. Paper Orientation for Trays 1 and 2
D O C U C O L O R 2 0 6 0 / 2 0 4 5 O P E R A T O R M A N U A L 3–13
P A P E R A N D P A P E R T R A Y S
Figure 6. Paper Orientation for Tray 3
3
Adjust the paper guides by pressing in the guide release and carefully moving the
Edge Guide until it lightly touches the edge of the material in the tray.
3–14 D O C U C O L O R 2 0 6 0 / 2 0 4 5 O P E R A T O R M A N U A L
P A P E R A N D P A P E R T R A Y S
4
Although Trays 1, 2, and 3 have auto size detection capability, the paper weight
(g/m
2
) range must be selected on the Weight Indicator. Selecting the correct paper weight range affects the feed performance and Image Quality. Press the
selection button until the light next to the correct weight is illuminated.
Tray 1 has a chart which converts pounds into g/m
2 for easy selection, or refer to the Paper Weight Conversion Tables in this chapter.
NOTE: The Indicator light will illuminate for the paper weight selected. The
Indicator is on the frame of the digital press to the right of the tray and can only be seen when the tray is pulled out.
Selection
Button
Figure 7. Paper Trays 1 and 2 Weight Indicator on the Frame
D O C U C O L O R 2 0 6 0 / 2 0 4 5 O P E R A T O R M A N U A L 3–15
P A P E R A N D P A P E R T R A Y S
5
In addition to designating the correct paper weight for Tray 3, select Non-
Standard or Standard paper and Coated or Uncoated paper.
Figure 8. Paper Tray 3 Indicator
6
Close the tray slowly to avoid shifting the paper stack.
KEY POINT: If you hear paper being crumpled or torn, stop closing the tray.
Remove all pieces of any damaged paper and close the tray slowly.
3–16 D O C U C O L O R 2 0 6 0 / 2 0 4 5 O P E R A T O R M A N U A L
P A P E R A N D P A P E R T R A Y S
Paper Weight Conversion Tables
Specific Weight Conversion
176
200
203
216
135
150
158
163
220
259
280
80
90
105
120
50
60
64
75
Grammage g/m
2
59
66
74
47
53
54
57
35
40
42
43
21
24
28
32
13
16
17
20
Xerographic
Bond,
Writing, pounds
17 x 22 inch-
500 sheets
Offset, Text,
Book, pounds
107
110
119
135
70
80
90
100
137
146
149
169
189
43
50
54
60
25 x 38 inch -
500 sheets
34
41
Cover, pounds Index, pounds
20 x 26 inch -
500 sheets
18
22
24
28
30
33
39
44
50
55
58
60
65
74
75
80
81
92
104
Bristol and Tag, pounds
87
90
97
110
58
66
75
83
112
119
122
140
155
35
41
44
50
25.5 x 30.5 inch -
500 sheets
28
33
72
74
80
91
48
55
62
67
93
98
100
114
128
29
34
36
41
22.5 x 28.5 inch -
500 sheets
23
27
Yellow shading indicates grades widely used for this classification
D O C U C O L O R 2 0 6 0 / 2 0 4 5 O P E R A T O R M A N U A L 3–17
P A P E R A N D P A P E R T R A Y S
Weight Conversion Ranges
Grammage g/m
2
Xerographic
Bond, Writing, pounds
Offset, Text,
Book, pounds
17 x 22 inch -
500 sheets
25 x 38 inch -
500 sheets
64 - 80
81 - 105
106 - 135
136 - 150
151 - 220
221 - 280
17 - 21
22 - 28
29 - 36
37 - 40
41 - 59
60 - 74
43 - 54
55 - 70
71 - 90
91 - 100
101 - 149
150 - 189
Cover, pounds Index, pounds
20 x 26 inch -
500 sheets
24 - 30
31 - 39
40 - 44
45 - 55
56 - 81
82 - 104
25.5 x 30.5 inch -
500 sheets
35 - 44
45 - 58
59 - 75
76 - 83
84 - 122
123 - 166
Bristol and Tag, pounds
22.5 x 28.5 inch-
500 sheets
29 - 36
37 - 48
49 - 62
63 - 67
68 - 100
101 - 128
3–18 D O C U C O L O R 2 0 6 0 / 2 0 4 5 O P E R A T O R M A N U A L
4.
Scanner
Scanning
The Scanner and Duplex Automatic Document Feeder (DADF) are optional accessories for the DocuColor 2060/2045. This chapter will familiarize you with the scanner features you can use for scan-to-print jobs. The following scanner functions are discussed:
• Basic Scanning Steps
• The DADF
• Conditions such as Auto Rotation, White Border, etc.
• Basic Features
• Added Features
• Image Quality
• Output Format
• Job Assembly
D O C U C O L O R 2 0 6 0 / 2 0 4 5 O P E R A T O R M A N U A L
S C A N N E R
Basic Scanning Steps
If the DADF belt is dirty and the original is a thin or transparent document, background may appear on the copy. This may also occur when copies are made using the Document Glass. Place a white sheet of paper of the same size on top of the document being copied to eliminate background until the belt is cleaned.
Use the following steps for one-sided copies. Refer to the Basic Features section for two-sided copies.
1
Touch the Basic Features tab.
2
Press the Clear All button to clear any previous programming.
3
Lift the DADF and place the original face down on the Document Glass and close the DADF. Do not press down on the DADF with excessive force when scanning thick originals such as books.
4
Ensure that the document is registered using the same orientation on the
Document Glass as the paper in the chosen paper tray (that is, LEF on the glass if the paper in the chosen paper tray is LEF; SEF on the glass if the paper in the chosen paper tray is SEF).
4–2
Figure 1. Original Registration on the Document Glass
D O C U C O L O R 2 0 6 0 / 2 0 4 5 O P E R A T O R M A N U A L
S C A N N E R
• The digital press with scanner will have difficulty recognizing the size of the original if the following are placed on the Document Glass.
• Highly transparent originals, such as transparencies or tracing paper.
• Originals with dark edges.
• Photographs with dark edges and without a white border.
• Shiny originals.
• Originals with dark backgrounds.
• Thick originals such as books.
• Originals copied with the DADF open, and the area housing the digital press is brightly lit.
Refer to Document Type/Dark Edges in Image Quality to scan originals with dark edges.
5
Enter the required quantity of copies using the keypad.
If you enter an incorrect quantity, press the C (Clear) button.
6
Select any other required features by touching the button corresponding to the feature. Some screens require that you touch Save to save your selections or
Cancel if the selection made is incorrect.
7
Press the Start button.
You can press Start while the digital press is warming up. The scanning process begins automatically at the end of the warm-up time.
To stop the scan process, press the Pause button.
KEY POINT: Do not use excessive force to press down on the Duplex
Automatic Document Feeder when scanning bound documents.
KEY POINT: You may not use the Auto Color option if the Duplex Automatic
Document Feeder must remain open during scanning. The digital press with scanner will not operate until you make a different selection under the Color
Mode feature.
For additional information on materials, refer to the Color Materials User Guide and the Recommended Materials List for paper guidelines. The Recommended
Materials List is a downloadable file on www.xerox.com. Use the search parameters DC 2060 or DC2045 and follow the path until you reach the files that can be downloaded.
D O C U C O L O R 2 0 6 0 / 2 0 4 5 O P E R A T O R M A N U A L 4–3
S C A N N E R
Duplex Automatic Document Feeder (DADF)
Document Specifications
Documents should meet the guidelines for optimum operation. Document jams may occur if originals other than those recommended are used. Jams may damage the originals.
• The original should be uncoated paper and the weight of the original should be from 16 to 32 pound (64 to 128 g/m
2
).
• 8.5 x 5.5 inches, 8.5 x 11 inches, 8.5 x 14 inches, 11 x 17 inches, A5, A4, A3, and 8.5 x 13 inches are recommended original sizes.
If the DADF senses documents in the feeder other than those recommended, a message displays and the digital press stops. Place the original documents on the Document Glass, or enter the document size by using the Original Size feature in the Added Features tab.
If the input document is slightly smaller or larger than a standard size document, the Duplex Automatic Document Feeder may detect it as a standard size document. Dark areas or image loss along the edges may occur. Enter the document size by using the Original Size feature or the Edge Erase feature in the
Added Features tab.
The following document types cause document jams or malfunction of the DADF.
Make copies of these documents by placing them directly on the Document
Glass.
• Book, pamphlet, and booklet documents
• Broken, creased, or paste-up documents
• Documents with clips and staples
• Transparent documents (the document size cannot be detected automatically or the DADF belt is copied)
• Documents with black carbon
• Documents smaller than A5 size (8.5 x 5.5 inches)
• Paper weight heavier than 32 pound (128 g/m
2
)
• Coated paper
KEY POINT: If you are using the Duplex Automatic Document Feeder (DADF) to scan more than 50 originals, you can use the Additional Originals option to scan the entire stack of originals as one scan to print job. The Additional
Originals feature must be enabled in Tools Mode. Refer to the System
Administration Guide for information on how to enable this feature.
4–4 D O C U C O L O R 2 0 6 0 / 2 0 4 5 O P E R A T O R M A N U A L
S C A N N E R
Identifying Duplex Automatic Document Feeder
(DADF) Parts
Document Feed Lamp Output Tray
Output Tray
Extension
DADF
Paper
Guide
Figure 2. DADF
Part
Document Feed Lamp
Paper Guide
Output Tray
Output Tray Extension
Description
Lights when the original is properly seated in the
DADF and ready to be scanned.
Must be adjusted lightly against the original.
After the original is scanned it is fed to the Output
Tray.
If you have an 8.5 x 14 inch or larger original, pull out the Output Tray Extension to help support the output.
D O C U C O L O R 2 0 6 0 / 2 0 4 5 O P E R A T O R M A N U A L 4–5
S C A N N E R
Using the Duplex Automatic Document Feeder
(DADF)
1
Remove any paper clips or staples from the documents.
2
Place up to 50 same size or mixed size from 16 to 32 pound (64 to 128 g/m
2
) documents face up in the DADF Tray. Slide the documents to the left until the green Document Feed Lamp is lit.
3
Ensure that the paper guide is against the document.
4
Extend the DADF Output Tray to accommodate longer length output.
5
Press the Clear All button to clear any previous programming.
6
Touch the Basic Features tab.
7
Enter the required quantity of copies using the keypad.
If you enter an incorrect quantity, press the C (Clear) button.
8
Select any other required features by touching the button corresponding to the feature. Some screens require that you touch Save to capture your selections.
9
Press the Start button to begin the scan operation. The original is fed from the top of the stack to the Document Glass to be scanned then face down to the
DADF output tray on the right.
NOTE: If the DADF belt is dirty and the original is a thin or transparent document, background may appear on the copy. This may also occur when copies are made using the Document Glass. Place a white sheet of paper of the same size on top of the document being copied to eliminate background until the belt is cleaned.
For additional information on materials, refer to the Color Materials User Guide and the Recommended Materials List for paper guidelines. The Recommended
Materials List is a downloadable file on www.xerox.com. Use the search parameters DC 2060 or DC2045 and follow the path until you reach the files that can be downloaded.
4–6 D O C U C O L O R 2 0 6 0 / 2 0 4 5 O P E R A T O R M A N U A L
Clearing a DADF Jam
S C A N N E R
Figure 3. Left Cover of the DADF
1
Open the left cover of the DADF.
2
Carefully remove the jammed original. If the original tears, ensure all pieces are removed.
3
Follow all instructions on the Touch Screen.
4
Press Start to resume the job.
D O C U C O L O R 2 0 6 0 / 2 0 4 5 O P E R A T O R M A N U A L 4–7
S C A N N E R
Auto Image Rotation
The DocuColor 2060/2045 offers an automatic rotation feature for 8.5 x 11 inch, or A4, original documents input from both the Duplex Automatic Document
Feeder and the Document Glass. This feature must be activated through Tools
Mode. Refer to the System Administration Guide for the procedure.
If the scanner detects that the orientation of the original document is different from the orientation of the paper tray selected, an orientation mismatch message appears and asks if you want to rotate the image. Select “Yes” to rotate the image.
If you do not want to rotate the image, select “No”. Use the Reduce/Enlarge feature, on the Basic Features tab, to fit the image onto the paper orientation selected.
White Border Edges on Copies
All copies made on the DocuColor 2060/2045 have white border edges on four sides of the output. There is a factory setting which removes 2 mm from all four edges of the scanned original. This factory setting cannot be altered.
If the white border edges result in image loss on your copies, select the Auto% option in the Reduce/Enlarge feature to minimize the image loss. The Auto% option automatically reduces or enlarges the copy, based on the size and orientation of the document and the paper tray selected. This option is applied only to standard size documents.
You may also use the Auto Center feature to ensure the original is centered on your output. For more information on Auto Center, refer to the Edge Erase feature in the Added Features section.
4–8 D O C U C O L O R 2 0 6 0 / 2 0 4 5 O P E R A T O R M A N U A L
S C A N N E R
Touch Screen
Use the Touch Screen to select features and options that specify the appearance of the scanned output.
The Touch Screen also displays messages that indicate the status of the digital press during idle, run, or fault conditions.
The Touch Screen displays the default screen selected in the Tools Mode by your
System Administrator. The default screen can be the Basic Features, Job Status or Machine Status screen.
Message Area
The message area at the top of the Touch Screen displays messages concerning the digital press status, programming conflicts, or errors. The messages may also provide instructions for the operator.
D O C U C O L O R 2 0 6 0 / 2 0 4 5 O P E R A T O R M A N U A L 4–9
S C A N N E R
Message
Area
Tab
Option
Button
Tabs/Buttons/Icons
Some screens on the Touch Screen display tabs which contain selectable options.
Features and options are initially set to the factory default settings. These settings can be changed by your System Administrator in Tools Mode.
Ask your System Administrator for more information regarding these selections, or refer to the Tools chapter of the System Administration Guide.
Figure 4. Message Area, Tabs and Option Buttons
4–10 D O C U C O L O R 2 0 6 0 / 2 0 4 5 O P E R A T O R M A N U A L
S C A N N E R
Touch Screen Button Types and Functions
Selectable Touch Screen buttons are in color and shadowed. These buttons change appearance when selected. The standard button types are described as follows:
• Option buttons
Option buttons are blank with words or graphics to the side.
Some features have more options associated with them than can be displayed on one screen. Touching a More... button displays a screen with more options.
• Icon buttons
Icon buttons are Option buttons that display icons.
• Arrow buttons
Arrow buttons allow you to change values for features such as Variable
Reduce/Enlarge.
Touch the up arrow to increase the value; touch the down arrow to decrease the value. Changes are displayed in the value boxes.
Values on the DocuColor 2060/2045 are set in millimeters (mm) and inches.
• Fixed selection buttons
Fixed selection buttons allow you to select preset (default) values indicated on the Touch Screen.
D O C U C O L O R 2 0 6 0 / 2 0 4 5 O P E R A T O R M A N U A L 4–11
S C A N N E R
• Cancel and Save buttons
The Cancel button allows you to cancel selected feature options without saving them.
The Save button allows you to save selected feature options.
Cancel
Button
Save
Button
Icon
Button
Fixed
Option
Figure 5. Screen Button Types
Arrows to set values
4–12 D O C U C O L O R 2 0 6 0 / 2 0 4 5 O P E R A T O R M A N U A L
S C A N N E R
Features (Digital Press with Scanner Only)
Features and options discussed follow the factory default settings. You may see different settings, depending on the options your System Administrator has selected in Tools Mode.
Basic Features
The Basic Features tab contains the basic selections necessary for scanning a document. Touch the feature button desired. Tray 4 appears in the Paper Supply column only when an optional Tray 4 has been connected to the digital press.
Auto Paper does not show for all configurations.
Figure 6. Basic Features Screen
D O C U C O L O R 2 0 6 0 / 2 0 4 5 O P E R A T O R M A N U A L 4–13
S C A N N E R
Color Mode
Auto
The Auto feature, located in the Color Mode column on the Basic Features screen, enables the DocuColor 2060/2045 to automatically sense if the original document is in color or black and white. If the original is in color, the DocuColor
2060/2045 automatically uses Full Color. If the original is in black and white, the
DocuColor 2060/2045 automatically uses Black Only, which reduces color dry ink used.
Gold, silver, and fluorescent colors cannot be copied accurately. The dry inks
(toners) do not contain the metallic particles necessary to accurately reproduce gold and silver colors or the fluorescent properties that are required to reproduce fluorescent colors.
With the Auto Color option, some very dark colors may be sensed as black and therefore copied as black. In these cases, select the Full Color option.
For the scanner to accurately sense the presence of color on a document during the prescan cycle, the color area on the document must be greater than 2 inches x 2 inches (approximately 50 mm x 50 mm). If the color area is less than 2 inches x 2 inches (approximately 50 mm x 50 mm), select the Full Color option.
4–14 D O C U C O L O R 2 0 6 0 / 2 0 4 5 O P E R A T O R M A N U A L
S C A N N E R
Full Color
Select the Full Color option, located in the Color Mode column on the Basic
Features screen, when the original contains color and black. In the Full Color
Mode, he DocuColor 2060/2045 uses all four colors: cyan, magenta, yellow, and black for the output document.
3 Pass Color
Select the 3 Pass Color option, located in the Color Mode column on the Basic
Features screen, when the document contains very little black, or when Process
Black is acceptable over a true reproduction black (used with photographs, for example). The DocuColor 2060/2045 uses only cyan, magenta, and yellow to produce the output image.
Process Black is a combination of cyan, magenta, and yellow. The three dry inks
(toners) are combined together in equal amounts to produce black. No Black dry ink (toner) is used.
Black Only
In the Black Only mode, the digital press uses only black dry ink (toner) and the output is black only regardless of the colors in the original. The Black Only feature is located in the Color Mode column on the Basic Features screen.
D O C U C O L O R 2 0 6 0 / 2 0 4 5 O P E R A T O R M A N U A L 4–15
S C A N N E R
Single Color
Select from the color palette displayed. In the Single Color Mode, the percentages of cyan, magenta, and yellow can be adjusted to vary the output hue.
1
Touch the Single Color... button on the Basic Features screen. The Single Color
Palette screen is displayed.
4–16
Figure 7. Single Color Palette Screen
2
Select the desired color from the color palette.
3
Touch the Color Adjust button. The Color Adjust screen is displayed.
D O C U C O L O R 2 0 6 0 / 2 0 4 5 O P E R A T O R M A N U A L
S C A N N E R
4
If you want to adjust the hue, press the up/down buttons to adjust the percentages of cyan, magenta, and yellow. The box reflecting the overall color changes as the color is adjusted. Touch Save when the desired hue has been achieved.
Figure 8. Color Adjust Screen
5
Continue selecting options for your job.
6
When you are finished selecting options, press the Start button.
D O C U C O L O R 2 0 6 0 / 2 0 4 5 O P E R A T O R M A N U A L 4–17
S C A N N E R
Output
Collated
Collated refers to copies that are delivered as sets and offset in the output device.
Each set is in the order in which the originals were placed in the DADF (1, 2, 3...,
1, 2, 3).
The Collated option is located in the Output column on the Basic Features screen.
Uncollated
Uncollated refers to copies that are delivered to the output device in the order in which they were copied (1, 1, 1,..., 2, 2, 2,..., 3, 3, 3,...).
The Uncollated option is located in the Output column on the Basic Features screen.
More...
The More... button, located in the Output column on the Basic Features screen, gives access to the following options:
• Auto The digital press selects the optimal output orientation automatically.
• Face Up: Output is delivered to the output device face up.
• Face Down: Output is delivered to the output device face down.
Output Assembly has two options: Collated and Uncollated.
4–18
Figure 9. Output, More... Screen
D O C U C O L O R 2 0 6 0 / 2 0 4 5 O P E R A T O R M A N U A L
S C A N N E R
Reduce/Enlarge
The Reduce/Enlarge feature, located on the Basic Features screen, allows you to select the size of the output image from preset values or through independent ratios for the image length and width. The DocuColor 2060/2045 can also be set up for automatic reduction or enlargement.
Depending on what the System Administrator has selected, you see several percentage options for reduction or enlargement.
For example, 78% reduces an 8.5 x 14 inch image to fit on 8.5 x11 inch paper.
Copies may be reduced to 25% or enlarged to 400%.
If the image on the document extends to the edge of the page, press the More... button in the Reduce/Enlarge column, and select Whole Image to minimize the image loss on the copies.
Figure 10. Basic Features Screen
D O C U C O L O R 2 0 6 0 / 2 0 4 5 O P E R A T O R M A N U A L 4–19
S C A N N E R
100%
100%, located in the Reduce/Enlarge column on the Basic Features screen, ensures that the entire original is copied if the paper tray selected and the original are the same size.
Auto%
The Auto% option, located in the Reduce/Enlarge column on the Basic Features screen, automatically reduces or enlarges the image, based on the size and orientation of the document and the paper tray selected. This option is applied only to standard size documents.
Select Auto% when the original document and the copy paper are different sizes.
KEY POINT: A factory default setting of 2 mm edge erase applies to making copies. This setting cannot be altered.
The image is reduced or enlarged in the same proportions for the X (horizontal) and Y (vertical) directions.
The Auto Paper option in Paper Supply is not available when Auto% is selected and may not be available for your configuration.
Third Button
The third button in the Reduce/Enlarge column is set to a factory default. 129% is an example of how the value can be set. This factory default can be changed in the Tools Mode. For more information on how to change this default, refer to the
System Administration Guide.
Fourth Button
The fourth button in the Reduce/Enlarge column is set to a factory default. 64% is an example of how the value can be set. This factory default can be changed in the Tools Mode. For more information on how to change this default, refer to the
System Administration Guide.
4–20 D O C U C O L O R 2 0 6 0 / 2 0 4 5 O P E R A T O R M A N U A L
S C A N N E R
More...
• 100%:
100% ensures that the entire original is copied if the paper tray selected and the original are the same size.
Figure 11. Reduce/Enlarge, More... Screen
• Auto%:
The Auto% option automatically reduces or enlarges the copy, based on the size and orientation of the document and the paper tray selected. This option is applied only to standard size documents.
D O C U C O L O R 2 0 6 0 / 2 0 4 5 O P E R A T O R M A N U A L 4–21
S C A N N E R
• Preset/Variable:
Preset is the quickest way to select a desired magnification. Up to six
Presets are available at one point in time, and the values of Presets can be changed in Tools Mode. Refer to the System Administration Guide for procedures.
You can set Variable values using the arrows or you can input the numeric value from the keypad for values from 25 to 400%.
1
Touch the More... button on the Basic Features screen
2
Touch the Preset/Variable button. The Preset/Variable screen is displayed.
4–22
Figure 12. Preset/Variable Screen
3
If you select a Preset percentage. Press Save. If you choose to input a variable percentage, either press the up/down arrows to the desired percentage or enter the number by using the keypad. Press Save.
4
Continue selecting options for your job.
5
When the option selections are complete, press Start.
D O C U C O L O R 2 0 6 0 / 2 0 4 5 O P E R A T O R M A N U A L
S C A N N E R
• Custom:
To customize, 25 to 400% can be selected independently on both the X and Y axis using the up and down arrows.
Auto Custom automatically reduces or enlarges the width and length of the image on the original by different percentages. The percentage is based on the prescanned size of the original document in relation to the size of the paper selected.
1
Touch the More... button on the Basic Features screen.
2
Touch the Custom button. The Custom screen is displayed.
X X/Y Y
Figure 13. Custom Screen
3
Select an independent variable percentage for the X axis using the X up and down arrow buttons. Select an independent variable percentage for the Y axis using the Y up and down arrows, OR select the percentage simultaneously for the X and Y axis using the X/Y up and down arrow buttons.
4
Press Save.
5
Continue selecting options for your job.
6
When the option selections are complete, press Start.
D O C U C O L O R 2 0 6 0 / 2 0 4 5 O P E R A T O R M A N U A L 4–23
S C A N N E R
• % by Length:
Input the Length of the Original from 0.1 to 17 inches and the Length of the
Copy Paper from 0.1 to 17 inches. The digital press compares the length and width of the original to the length and width of the paper in the tray selected, and then calculates the correct magnification to produce the desired output.
1
Touch the More... button on the Basic Features screen.
2
Touch the % by Length button. The % by Length screen is displayed.
4–24
Figure 14. % by Length Screen
3
Input the length of the original using the up and down arrow buttons.
4
Input the length of the copy paper using the up and down arrow buttons.
5
Press the Save button.
6
Continue selecting options for your job.
7
When you have finished selecting options, press Start.
D O C U C O L O R 2 0 6 0 / 2 0 4 5 O P E R A T O R M A N U A L
S C A N N E R
• Whole Image:
The Whole Image feature prevents a loss of image at the edges of your print by automatically fractionally reducing a bleed edge original image. Use
Whole Image when you have selected 100% or Auto% in the Reduce/
Enlarge feature.
Set the Edge Erase feature to 0mm.
Whole Image cannot be used with the following features. (These features may not be available for your configuration.)
• Image Shift
• 12 x 18 inch setting on Tray 3
• Repeat Image
• Poster
• Color Bar
• N-Up
• Mirror Image
• Booklet Creation
D O C U C O L O R 2 0 6 0 / 2 0 4 5 O P E R A T O R M A N U A L
Figure 15. Whole Image Screen
4–25
S C A N N E R
Common Percentage Conversions
Percentage
64%
129%
70%
78%
141%
154%
220%
Paper sizes
11 x 17 inch to 8.5 x 11 inch
8.5 x 11 inch to 11 x 17 inch
A3 to A4
8.5 x 14 inch to 8.5 x 11 inch
A4 to A3
5.5 x 8.5 inch to 8.5 x 11 inch
3.5 x 8.5 inch to 8.5 x 11 inch
Table 1. Common Percentage Conversions
4–26 D O C U C O L O R 2 0 6 0 / 2 0 4 5 O P E R A T O R M A N U A L
S C A N N E R
Paper Supply
There are three standard paper trays standard with the digital press. Tray 4 is an optional high capacity feeder. Paper size is set by adjusting the paper guides in each tray. Refer to Paper and Paper Trays for tray paper weight selection. The
Paper Supply also indicates how much paper is remaining in the paper trays.
Follow the procedure below to choose the desired Paper Tray.
1
Touch the Basic Features tab.
2
Touch the tray loaded with the appropriate paper for the job (Tray 1, Tray 2, Tray
3, or optional Tray 4).
Tray 4 will only appear if you have an optional Tray 4 connected to your Digital
Press.
3
Continue selecting options for your job.
4
When you are finished selecting options, press Start.
Auto Paper
Auto Paper automatically senses the size of the original and selects the proper paper tray for output. For more information on how to activate Auto Paper, refer to the System Administration Guide.
D O C U C O L O R 2 0 6 0 / 2 0 4 5 O P E R A T O R M A N U A L 4–27
S C A N N E R
Added Features
The Added Features tab gives you more selections for additional complex copy jobs.
Figure 16. Added Features Screen
2 Sided Output
Use the 2 Sided Output feature to scan 1-sided or 2-sided originals for 1-sided or
2-sided output.
The 2 Sided Output feature can be used with 16 through 28 pound (64 through
105 g/m
2
) paper, or for standard paper sizes smaller than 12 x 18 inches (A3).
4–28 D O C U C O L O R 2 0 6 0 / 2 0 4 5 O P E R A T O R M A N U A L
1-1
This scans a 1-sided original and produces 1-sided output.
S C A N N E R
Figure 17. 1-1 Sided Screen
1-2
This scans 1-sided originals and creates 2-Sided output. Indicate the orientation of the copies to be Head to Head or Head to Toe.
D O C U C O L O R 2 0 6 0 / 2 0 4 5 O P E R A T O R M A N U A L
Figure 18. 1-2 Sided Screen
4–29
S C A N N E R
2-1
This scans a 2-sided original and produces 1-sided copies. Indicate whether the original is Head to Head or Head to Toe orientation.
Figure 19. 2-1 Sided Screen
4–30 D O C U C O L O R 2 0 6 0 / 2 0 4 5 O P E R A T O R M A N U A L
S C A N N E R
2-2
This scans a 2-sided original and creates 2-sided output. Indicate whether the original is Head to Head or Head to Toe orientation. Also indicate the orientation of the copy to be Head to Head or Head to Toe.
Figure 20. 2-2 Sided Screen
D O C U C O L O R 2 0 6 0 / 2 0 4 5 O P E R A T O R M A N U A L 4–31
S C A N N E R
Image Shift
Image Shift enables specific kinds of image repositioning on output. When using
2-Sided Output, the Image Shift options can be set independently for each side.
The Image Shift feature is located on the Added Features screen.
No Shift
If No Shift is selected, the digital press assumes that the original document is registered in the upper left corner of the Document Glass. If the document is offset from this registration point, the image on the output copy will be offset by the same amount. No adjustment is made to your copies.
Figure 21. No Shift Screen
4–32 D O C U C O L O R 2 0 6 0 / 2 0 4 5 O P E R A T O R M A N U A L
S C A N N E R
Auto Center
Auto Center automatically places the scanned image in the center of the output paper size. The original should be smaller than the output paper, or the image should be reduced if the original is larger than the output paper.
In some cases, the original image center is shifted slightly on the output copy.
The orientation of the output image is determined by the placement of the document on the Document Glass and the orientation of the selected paper supply.
Figure 22. Auto Center Screen
D O C U C O L O R 2 0 6 0 / 2 0 4 5 O P E R A T O R M A N U A L 4–33
S C A N N E R
Margin Shift
Use the Margin Shift feature to create a margin for binding one edge of a document by shifting the image away from that edge.
The Margin Shift feature enables you to center a document image, shift the image to one edge slightly, or move the image to a specified edge (0 to 50 mm
Left/Right or Top/Bottom) of the output copy.
1
Touch the Image Shift button on the Added Features screen.
2
Touch the Margin Shift button. The Margin Shift screen is displayed.
4–34
Figure 23. Margin Shift Screen
Choose Top/Bottom or Left/Right (only one choice can be made), and input the
Margin Shift in mm using the up and down arrow buttons.
3
Press Save.
4
Continue selecting options for your job.
5
When you are finished selecting options, press Start.
D O C U C O L O R 2 0 6 0 / 2 0 4 5 O P E R A T O R M A N U A L
S C A N N E R
Unrestricted Shift
Unrestricted Shift allows independent shifting of the image horizontally and/or vertically. The limit is the maximum dimension of the paper. The X axis can be shifted 0 to 432 mm and the Y axis can be shifted 0 to 297 mm.
1
Touch the Image Shift button on the Added Features screen.
2
Touch the Unrestricted Shift button. The Unrestricted Shift screen is displayed.
X
Figure 24. Unrestricted Shift Screen
3
Input the X axis in mm using the X up and down arrow buttons.
4
Input the Y axis in mm using the Y up and down arrow buttons.
5
Press Save.
6
Continue selecting options for your job.
7
When you are finished making selections, press Start.
Y
D O C U C O L O R 2 0 6 0 / 2 0 4 5 O P E R A T O R M A N U A L 4–35
S C A N N E R
Corner Shift
Corner Shift enables shifting of the image to each of the four corners of the paper or to the center of each of the four sides of the paper (eight positions total).
Corner Shift may not be evident on your output if you copy your original document at 100%.
The orientation of the image on the copies is determined by the placement of the document on the Document Glass and by the orientation of the selected paper supply.
1
Touch the Image Shift button on the Added Features screen.
2
Touch the Corner Shift button. The Corner Shift screen is displayed.
4–36
Selection Arrows
Figure 25. Corner Shift Screen
3
Touch the arrow that corresponds to the location in which you would like to place the image.
4
Press Save.
5
Continue selecting options for your job.
6
When you are finished selecting options, press Start.
D O C U C O L O R 2 0 6 0 / 2 0 4 5 O P E R A T O R M A N U A L
S C A N N E R
Original Input
The Original Input feature, located on the Added Features screen, enables you to specify the size of the original document to be scanned. You may select a standard international size, standard US paper size, or a non-standard size. This feature also allows you to specify automatic feed (DADF) or manual feed
(Document Glass).
Figure 26. Original Input Screen
Auto
Auto automatically detects the size of the original document. The Mixed Size
Originals selection is off (default). There is a loss of productivity if Auto and
Mixed Size Originals are both selected due to the need for a prescan of each document.
D O C U C O L O R 2 0 6 0 / 2 0 4 5 O P E R A T O R M A N U A L 4–37
S C A N N E R
Manual Input
When you use the Manual Input option, place the documents on the Document
Glass one at a time. The machine prescans each document for size so it is not necessary to select Mixed Size Originals. There is no loss of productivity, however, if Mixed Size Originals is selected with Manual Input. When you select a size from one of eight standard sizes or you customize the size of the original on the X (0.4 - 17 inches) and Y (0.4 - 11.7 inches) axis, the size you choose will apply to all the documents for that job.
1
Touch the Original Input button on the Added Features screen.
2
Touch the Manual Input button. The Manual Input screen is displayed.
4–38
Figure 27. Manual Input Screen
3
Press the button for the appropriate Standard Size. To Customize the size, press the Custom Size button, and use the up and down arrow buttons to enter both the X and Y axis. If you select Custom Size, the Custom Size screen appears.
D O C U C O L O R 2 0 6 0 / 2 0 4 5 O P E R A T O R M A N U A L
S C A N N E R
Figure 28. Manual Input, Custom Size Screen
4
Press Save.
5
Continue selecting options for your job.
6
When you are finished selecting options, press Start.
Mixed Size Originals
You can copy jobs with mixed size originals when you use the Duplex Automatic
Document Feeder (DADF). When you select the Mixed Size Originals feature and
Auto Paper Supply (this feature may not be available with your configuration), the scanner automatically identifies the document size and selects the correct paper supply.
You may use as many different sized originals for Mixed Sized Originals as you wish providing you are using standard size paper and have the appropriate paper in the Paper Trays.
D O C U C O L O R 2 0 6 0 / 2 0 4 5 O P E R A T O R M A N U A L 4–39
S C A N N E R
Bound Originals
The Bound Originals feature allows you to copy bound documents such as books, magazines, journals, notebooks, glued forms, or stapled sets. When you select this feature, each page is copied onto a separate sheet of paper. If you select Left
Page, only the page on the left side of the bound original is scanned and copied.
If you select Right Page, only the page on the right side of the bound original is scanned and copied. Selecting Both Pages scans and copies the pages on both sides of the bound original.
1
Touch the Bound Originals button on the Added Features screen. The Bound
Originals screen is displayed.
4–40
Figure 29. Bound Originals Screen
D O C U C O L O R 2 0 6 0 / 2 0 4 5 O P E R A T O R M A N U A L
S C A N N E R
2
Touch the Left Page button to scan and copy the left page. Touch the Right
Page button to scan and copy the right page. Touch the Both Pages button to scan and copy both pages.
3
If you select Left Page or Right Page, use the up and down arrow buttons to indicate the desired amount of Binding Erase in millimeters (0-50 mm).
Figure 30. Left Page Bound Originals Screen
D O C U C O L O R 2 0 6 0 / 2 0 4 5 O P E R A T O R M A N U A L 4–41
S C A N N E R
4
If you select Both Pages, indicate the amount of binding erase using the up and down arrow buttons. Indicate the Reading Order by touching either the Left or
Right button.
• Touch the Left button to have output delivered in sequential order: 1, 2, 3...
• Touch the Right button to have output delivered in reverse order: 3, 2, 1...
Figure 31. Both Pages Bound Originals Screen
5
Touch the Save button.
6
Continue selecting options for your job.
7
When you are finished selecting options, press the Start button.
4–42 D O C U C O L O R 2 0 6 0 / 2 0 4 5 O P E R A T O R M A N U A L
S C A N N E R
Edge Erase
The Edge Erase feature, located on the Added Features screen, allows you to erase images around the border of a document. Edge Erase also deletes center streaks caused by a gap between the spine of a bound document and the
Document Glass.
To deactivate the option, select “Off.”
Figure 32. Edge Erase Off Screen
D O C U C O L O R 2 0 6 0 / 2 0 4 5 O P E R A T O R M A N U A L 4–43
S C A N N E R
Edge Erase for Drilled Paper
Edge Erase can be used to erase the black holes created when copying an original that is printed on drilled paper. This can be used for 1-Sided and 2-Sided scan to print jobs from the Duplex Automatic Document Feeder (DADF).
Using the Edge Erase feature for this purpose may cause some image loss on the opposite side of the document.
Use the following procedure to use Edge Erase to erase black holes on output:
1
Choose the appropriate paper tray in the Paper Supply column on the Basic
Features screen.
2
Select Original Input on the Added Features screen. Select Manual Input and
Custom Size.
3
Make sure that the Y dimension is set to equal the length of the original being copied.
4
Change the X dimension to a size equal to the width of the original minus the edge amount for the holes.
For example, for an 8.5”x11” original, input 8” for the X dimension.
5
Press the Save button.
6
If you are have a 2-Sided scan to print job, select 2 Sided Output on the Added
Features screen. Select 2-2 Sided. Select Head to Head in both the Images on
Original and Images on Copy columns.
7
Press the Save button. Select any other features needed for the job.
8
Place the originals into the DADF in the short edge feed direction with the holes facing the user.
You will get an Image Orientation Mismatch fault when the originals are being scanned. Select Yes to rotate the image.
9
Another screen will appear asking if you want to continue with the job, select
Resume Scan.
The scan to print job will then be output.
4–44 D O C U C O L O R 2 0 6 0 / 2 0 4 5 O P E R A T O R M A N U A L
S C A N N E R
Border Erase
The Border Erase feature makes it possible to specify the size of border to create on all four sides of a print. You can erase the border in 1 mm increments from a minimum of 0 mm up to a maximum of 50 mm.
Border Erase and Edge Erase work independently of each other.
The default value for Border Erase is 2 mm and may be changed in Tools Mode.
Refer to the System Administration Guide for instructions.
Figure 33. Border Erase Screen
D O C U C O L O R 2 0 6 0 / 2 0 4 5 O P E R A T O R M A N U A L 4–45
S C A N N E R
Edge/Center Erase
Edge/Center Erase allows you to erase the Left/Right edge, Top/Bottom edge, and Center from 0 to 50 mm in increments of 1 mm. Left/Right and Top/Bottom can be set independently.
Edge Erase is proportional to Reduce/Enlarge. For example, if Edge Erase is set for 30 mm and 50% reduction is programmed then the amount of Edge Erase will be 15 mm on the output.
When using 2-Sided Output, the same amount of erasure applies to sides 1 and 2.
Center Erase erases the shadow line from scanning the spine of a bound original
(for example a book or a magazine). It is also useful for erasing the boundary line between two documents placed side by side on the Document Glass.
Center Erase may be specified between 0-50 mm in increments of 2 mm. When you specify a value, each side of the center is erased by half of the specified value. A Center Erase value of 30 mm results in 15 mm being erased from either side of the center.
For some original image sizes, Edge/Center Erase does not occur exactly in the center of the output image. Center Erase default is 0 mm, which can be changed in Tools Mode. Refer to the System Administration Guide for more information on how to change this setting.
4–46 D O C U C O L O R 2 0 6 0 / 2 0 4 5 O P E R A T O R M A N U A L
S C A N N E R
1
Touch the Edge Erase button on the Added Features screen.
2
Touch the Edge/Center Erase button. The Edge/Center Erase screen is displayed.
Figure 34. Edge/Center Erase Screen
3
Input the Left/Right, Top/Bottom, and Center Erase as desired using the appropriate up and down arrow buttons.
4
Press Save.
5
Continue selecting options for your job.
6
When you are finished selecting options, press Start.
D O C U C O L O R 2 0 6 0 / 2 0 4 5 O P E R A T O R M A N U A L 4–47
S C A N N E R
Stored Programming
The Stored Programming feature, located on the Added Features screen, enables you to store up to 10 scan to print jobs in memory. Store Programming, Recall
Programming, and Delete Programming are available in both Interrupt and
Normal Modes. Use the up and down arrow buttons to select a storage location, then select one of the choices described below:
Store Programming
Store Programming saves the current job programming selections. Use Store
Programming to save complex feature settings that you use frequently.
Figure 35. Store Programming Screen
4–48 D O C U C O L O R 2 0 6 0 / 2 0 4 5 O P E R A T O R M A N U A L
S C A N N E R
Recall Programming
Recall Programming retrieves stored jobs and applies their programming features to a new copy job.
Figure 36. Recall or Delete Programming Screen
D O C U C O L O R 2 0 6 0 / 2 0 4 5 O P E R A T O R M A N U A L 4–49
S C A N N E R
Delete Programming
Delete Programming erases the contents of a stored job and frees that memory position when you select Yes on the Delete Stored Programming Confirmation screen.
.
Figure 37. Delete Stored Programming Confirmation Screen
Use the job number buttons to assign, access, or delete the jobs that have been stored in the digital press memory and to indicate the next available memory position.
4–50 D O C U C O L O R 2 0 6 0 / 2 0 4 5 O P E R A T O R M A N U A L
S C A N N E R
Image Quality
Image Quality allows you to select options to enhance and modify the original image to reach your desired output.
Figure 38. Image Quality Screen
D O C U C O L O R 2 0 6 0 / 2 0 4 5 O P E R A T O R M A N U A L 4–51
S C A N N E R
Original Type
The Original Type feature enables you to define the kind of original document you wish to copy. The digital press automatically makes fine adjustments to optimize the copy sharpness based on document type. Specifying an Original Type increases the probability that your output will be an accurate reproduction of your original document.
1
Touch the Original Type button on the Image Quality screen. The Original Type screen is displayed.
4–52
Figure 39. Original Type Screen
2
Select the appropriate original type from the descriptions on the following pages.
3
Press Save.
4
Continue selecting options for your job.
5
When you are finished selecting options, press Start.
D O C U C O L O R 2 0 6 0 / 2 0 4 5 O P E R A T O R M A N U A L
S C A N N E R
Auto
Photo & Text
Use Auto Photo & Text for original documents that contain pictures and printed text. The default for column 2 (Photo, Halftone, or Xerographic Copy) can be selected in the Tools Mode. Refer to your System Administration Guide for more information on how to change this setting.
In the Auto Photo & Text mode, the digital press copies the text areas with the
Text option and the photo areas with the selection from Column 2 (Photo,
Halftone, or Xerographic Copy) to optimize the output. Output copies will be made using the best sharpness and density levels for pictures and charts combined with the best levels for text.
Figure 40. Auto Photo & Text Screen
• Photo refers to an original photograph (continuous tone). Photo is the best selection when true reproduction of light skin colors, light colors, or gray areas is important. The Photo option is appropriate for very high quality halftone documents.
• Halftone refers to the type of photograph found in most magazines. The
Halftone option uses a fine screen that varies the darkness and density of dots that make up the copied image.
• Xerographic Copy refers to the type of image produced by copying a photograph on a xerographic copier or text that has already been reproduced and is not an original document.
D O C U C O L O R 2 0 6 0 / 2 0 4 5 O P E R A T O R M A N U A L 4–53
S C A N N E R
Text
Text documents are composed of fine line characters or other high contrast documents with bright, dense colors. Text suppresses background color.
The following options allow you to optimize your output:
• Select Normal (the default) if the text on the original document is of normal darkness.
• Select Light Text (pencil text) if the text on the original document is light and needs to be darkened, or is indistinct or in pencil and should be enhanced to be reproduced. Light Text can only be selected when Black Only is selected in Color Mode.
Figure 41. Text Screen
4–54 D O C U C O L O R 2 0 6 0 / 2 0 4 5 O P E R A T O R M A N U A L
S C A N N E R
Photo
The Photo option is for photographs or lithographs including paintings that contain a variety of pastel colors. The default for column 2 (Photo, Halftone, or
Xerographic Copy) can be selected in the Tools Mode. Refer to your System
Administration Guide for the procedure.
The Photo option provides the most accurate color and density copy for continuous tone documents that contain a wide range of densities from very dark to very light images.
You must make a selection from Column 2 (Photo, Halftone, or Xerographic Copy) to optimize the output.
• Photo is the best selection when true reproduction of light skin colors, light colors, or gray areas is important. The Photo option is appropriate for very high quality halftone documents.
• The Halftone option uses a fine screen that varies the darkness and density of dots that make up the copied image.
• Xerographic Copy refers to the type of image produced by copying a photograph on a xerographic copier or text that has already been reproduced and is not an original document.
D O C U C O L O R 2 0 6 0 / 2 0 4 5 O P E R A T O R M A N U A L
Figure 42. Photo Screen
4–55
S C A N N E R
Map
Use the Map option to optimize the reproduction of detailed graphics, maps, or map-like originals.
With this option, text on a light-colored background is enhanced more than if you used the Photo option or the Text option.
Figure 43. Map Screen
4–56 D O C U C O L O R 2 0 6 0 / 2 0 4 5 O P E R A T O R M A N U A L
S C A N N E R
Dark Edges
The scanner cannot detect the size of an original when there is no white border.
Touch the Dark Edges button on the Original Type screen when documents such as photos or text extend to the edge of the original. When Dark Edges is on, it is possible to specify the size of the original document
Figure 44. Original Type Screen
D O C U C O L O R 2 0 6 0 / 2 0 4 5 O P E R A T O R M A N U A L 4–57
S C A N N E R
When you select On, standard sizes appear. Touch the original size, and touch the Save button so that the full document is scanned.
Figure 45. Dark Edges On Screen
OR
Touch Custom Size to input the size of the original on the X (0.4 - 17 inches) and
Y (0.4 - 11.7 inches) axis. The size you select applies to all the documents for that job. Touch the Save button.
4–58
Figure 46. Custom Size Screen
D O C U C O L O R 2 0 6 0 / 2 0 4 5 O P E R A T O R M A N U A L
S C A N N E R
Define Area
Select Define Area when it is necessary to define different areas as different types on the same document. The total number of rectangular areas that can be defined is four. X can be defined 0 - 432 mm and Y can be defined 0 - 297 mm from the upper right corner of the document as you are reading it.
When areas overlap, the area you defined last has priority. Areas that are not defined are copied in the Document Type (Text, Photo, or Map) that is selected for the entire document.
You can enter up to four coordinates, change coordinates, delete an area, define the next area, or check the entries made for the previous area.
1
Touch the Original Type button on the Image Quality screen.
2
Touch the Define Area button. The Define Area screen is displayed.
D O C U C O L O R 2 0 6 0 / 2 0 4 5 O P E R A T O R M A N U A L
Figure 47. Define Area Screen
4–59
S C A N N E R
3
Touch the document type for the area (Text, Photo, or Map) to be defined.
4
Use the up and down arrows to enter the size of the area for the starting points,
X1 and Y1, and the ending points, X2 and Y2. Measure the area to be defined using a ruler with millimeters.
Measure from the registration edges of the document to obtain the X and Y values.
5
Press the Enter Coordinates button.
6
Touch Next Area to define any additional areas with the same document type
(up to four areas). Press the Enter Coordinates button after each set of coordinates is selected.
7
Repeat steps 3 through 6 until all areas are input.
8
Press the Save button.
9
If you need to change the type of document for another area, touch the document type for the area (Text, Photo, or Map) to be defined.
10
Continue selecting job options for your job.
11
When you are finished selecting options, press the Start button.
4–60 D O C U C O L O R 2 0 6 0 / 2 0 4 5 O P E R A T O R M A N U A L
S C A N N E R
• Change Coordinates
Use Change Coordinates to redefine a defined area using the up and down arrows.
1
Touch the Change Coordinates button on the Define Area screen.
Figure 48. Define Area Screen
2
Touch either the Next Area or Previous Area button until the desired area is displayed.
3
Touch the Enter Coordinates button to input the new coordinates. To cancel your changes, touch the Cancel button.
4
Touch the Save button.
5
Continue selecting options for your job.
6
When you are finished selecting options, press the Start button.
D O C U C O L O R 2 0 6 0 / 2 0 4 5 O P E R A T O R M A N U A L 4–61
S C A N N E R
• Deleting an Area
After a Document Type has been selected for a document area, and the area has been defined, it may be that the area is not needed or it is incorrect. Delete the area or change the Document Type by pressing the Delete Area button on the
Define Area screen.
1
Touch the document type for the area (Text, Photo, or Map) to be defined. To cancel the selected Document Type, touch the Cancel button on the Define Area screen.
4–62
Figure 49. Define Area Screen
2
To delete an area, touch either the Next Area or Previous Area button until the desired area is displayed.
3
Touch the Delete Area button. All of the displayed coordinates change back to
0. Touch the Cancel button to restore the deleted area or areas.
4
Touch the Save button.
5
Continue selecting options for your job.
6
When you are finished selecting options, press the Start button.
D O C U C O L O R 2 0 6 0 / 2 0 4 5 O P E R A T O R M A N U A L
S C A N N E R
Lighten/Darken
The Lighten/Darken feature, located on the Image Quality screen, enables Auto or Manual selection from among the 13 density levels available for desired output. Auto or Manual may be set as the default in Tools Mode. Refer to your
System Administration Guide for instructions.
When the Auto option is selected, the digital press determines the overall density of the document and adjusts the level accordingly. This feature is more effective for black and white copying. If Auto is selected, you can change to
Manual by pressing one of the arrows.
The Normal (0) level is the digital press default for Lighten/Darken. Use the
Normal setting to copy original documents that have the desired overall lightness or darkness. There are six levels of darker and six levels of lighter to select to enhance the output copy.
Figure 50. Lighten/Darken Screen
D O C U C O L O R 2 0 6 0 / 2 0 4 5 O P E R A T O R M A N U A L 4–63
S C A N N E R
Sharpness
The Sharpness feature, located on the Image Quality screen, allows you to adjust the amount of image definition on your copies.
Normal (0) is best for most copies.
Adjust for sharpness when you require copies with crisp lines and fine definition.
Adjust for softness when you require copies with softer, less focused images.
Figure 51. Sharpness Screen
4–64 D O C U C O L O R 2 0 6 0 / 2 0 4 5 O P E R A T O R M A N U A L
S C A N N E R
Image Tone Presets
The Image Tone Presets feature, located on the Image Quality screen, changes
Image Quality settings to produce balanced image tones described below.
The Image Tone Preset feature also lets you enable Background Erase.
Normal
The Normal option makes no changes to image quality and produces copies with the same quality and density as those of the original. The Image Tone Preset default is Normal.
Figure 52. Image Tone Presets Screen
D O C U C O L O R 2 0 6 0 / 2 0 4 5 O P E R A T O R M A N U A L 4–65
S C A N N E R
Lively
The Lively option uses the highest color saturation to produce rich, vivid output colors. The option increases the Color Saturation to the most vivid setting and adjusts the Lighten/Darken setting one step lighter
4–66
Before After
Sharp
The Sharp option produces a sharp, clear image on the copy; increases the color saturation; and selects the highest Sharpness setting.
Before After
D O C U C O L O R 2 0 6 0 / 2 0 4 5 O P E R A T O R M A N U A L
S C A N N E R
Warm
The Warm option produces a soft image on the copy adding a warm reddish tint to low density colors. Use this setting to apply a light pink tone to skin colors and to give a soft tone to dark, warm colors.
Before After
Cool
The Cool option produces a strong, clear blue tone on the copy. This setting makes blue color stronger and makes dark, cold colors clearer.
D O C U C O L O R 2 0 6 0 / 2 0 4 5 O P E R A T O R M A N U A L
Before After
4–67
S C A N N E R
Background Erase
Background Erase prevents undesired marks or images that are printed on the back of an original from appearing on the output copy.
This feature is similar to Lighten/Darken but Lighten/Darken removes less of the background.
Before After
4–68 D O C U C O L O R 2 0 6 0 / 2 0 4 5 O P E R A T O R M A N U A L
S C A N N E R
Color Balance
The Color Balance feature, located on the Image Quality screen, allows you to adjust the balance for areas of high, medium, and low density image areas for
Cyan, Magenta, Yellow, and Black.
For each color there are three density levels (low, medium, and high). There are three higher settings, three lower settings, and the normal setting within each density level.
Each color can be adjusted independently and in any combination. It is important to remember that adjusting the amount of any of the process colors has an effect on the other colors.
The default value for Color Balance may be set in Tools Mode. Refer to the
System Administration Guide for more information on how to change this setting.
Figure 53. Color Balance Screen
D O C U C O L O R 2 0 6 0 / 2 0 4 5 O P E R A T O R M A N U A L 4–69
S C A N N E R
Color Shift
The Color Shift feature, located on the Image Quality screen, allows you to shift all hues in an image simultaneously in order to make the overall character of the output image warmer or cooler.
The illustration on the Color Shift screen helps you anticipate the results of the requested shift. The lower bar illustrates the relationship between colors and adjacent hues. The top bar shifts to the left or right to reflect your choice. When
Normal is selected, the upper bar is centered above the lower bar.
The default value for Color Shift may be set in Tools Mode. Refer to the System
Administration Guide for more information on how to change this setting.
Figure 54. Color Shift Screen
4–70 D O C U C O L O R 2 0 6 0 / 2 0 4 5 O P E R A T O R M A N U A L
S C A N N E R
Chroma
The Chroma feature, located on the Image Quality screen, allows you to adjust the overall color saturation of the copy. The higher the color saturation, the more vivid the color. The lower the color saturation, the more subtle the color. Normal
Chroma results in the output colors that match the colors of the original document.
The default value for Chroma may be set in Tools Mode. Refer to the System
Administration Guide for more information on how to change this setting.
Figure 55. Chroma Screen
D O C U C O L O R 2 0 6 0 / 2 0 4 5 O P E R A T O R M A N U A L 4–71
S C A N N E R
Color Bar
The Color Bar option places a color bar on the printed output, which enables you to determine if image quality needs to be adjusted. When this feature is turned on, a Color Bar image appears on the lead edge of the output, as long as the distance between the leading edge of the paper and the leading edge of the image is greater than or equal to 15mm. The Color Bar continues to appear on all output that contains enough space until the feature is turned off.
You must select a specific Paper Tray on the Basic Features screen for the Color
Bar button to be selectable.
1
Touch the Color Bar button on the Image Quality screen. The Color Bar screen is displayed.
4–72
Figure 56. Color Bar Screen
2
Touch either the On or Off button.
3
Touch the Save button.
4
Continue selecting options for your job.
5
When you are finished selecting options, press the Start button.
D O C U C O L O R 2 0 6 0 / 2 0 4 5 O P E R A T O R M A N U A L
S C A N N E R
More...
Touching the More... tab allows you to select the features on the Output Format and Job Assembly screens.
Output Format
The Output Format tab contains features associated with the organization of the finished product. It is recommended that you run a Proof Set (refer to Job
Assembly in this chapter for the procedure) to ensure that all job settings are correct and that they produce the desired output.
Figure 57. Output Format Screen
D O C U C O L O R 2 0 6 0 / 2 0 4 5 O P E R A T O R M A N U A L 4–73
S C A N N E R
Covers
The Covers option allows you to run covers from any tray loaded with the proper paper. You may run Front Covers and Back Covers from different trays for the same job. Paper used for Covers must be the same size and orientation as that used for the body of the job.
If the Covers require 2-sided output, paper used for Covers must be the same weight and material as paper used for the body of the job. Heavyweight paper or transparencies may be used for 1-sided Covers only.
You must select Collated and a specific Paper Tray on the Basic Features screen for the Covers button to be selectable. The Covers feature may not be used in combination with the N-Up, Transparency Options, Booklet Creation, Repeat
Image, or Poster features.
1
Touch the Covers button on the Output Format screen. The Covers screen is displayed.
4–74
Figure 58. Covers Screen
D O C U C O L O R 2 0 6 0 / 2 0 4 5 O P E R A T O R M A N U A L
S C A N N E R
2
Touch No Covers, Front Cover Only, Back Cover Only, or Front and Back
Covers.
3
If you select Front Cover Only, you must indicate if there is an image on the cover. Touch None for no image and Front Only if there is an image on the front side of the Front Cover.
Figure 59. Front Cover Only Screen
D O C U C O L O R 2 0 6 0 / 2 0 4 5 O P E R A T O R M A N U A L 4–75
S C A N N E R
If you select Back Cover Only, you must indicate if there is an image on the cover. Touch None for no image and Back Only if there is an image on the back side of the Back Cover.
Figure 60. Back Cover Only Screen
4–76 D O C U C O L O R 2 0 6 0 / 2 0 4 5 O P E R A T O R M A N U A L
S C A N N E R
If Front and Back Covers has been selected, you must indicate if there is an image on either cover. Touch None for no image, Front Only if there is an image on the front side of the Front Cover, Back Only if there is an image on the back side of the Back Cover, or Front & Back for an image on the exterior side of both covers.
Figure 61. Front and Back Covers Screen
4
If Front Cover Only, Back Cover Only, or Front and Back Covers have been selected, you must indicate the tray from which the cover stock is fed.
5
Touch the Save button.
6
Continue selecting options for your job.
7
When you are finished selecting options, press the Start button.
D O C U C O L O R 2 0 6 0 / 2 0 4 5 O P E R A T O R M A N U A L 4–77
S C A N N E R
Inserts
Inserts allows you to insert blank or preprinted sheets into a job after predetermined pages. Inserts must be the same size and orientation as the paper used for the body of the job and can be loaded into any of the available trays. An image cannot be printed on an insert. Inserts are not subject to billing.
Up to 10 inserts can be placed in a single set of a job. Up to 300 inserts can be inserted into the sets of a job. (For example: If you choose to have 10 inserts placed in a single set of output for a job, you will be able to run 30 sets of the job.)
You cannot place more than one insert in the same predetermined location.
Automatic Tray Switching may be used in combination with the Inserts option.
Output must be Collated, and a specific Paper Tray must be selected on the Basic
Features screen for the Inserts button to appear. Inserts may not be used in combination with the N-Up, Transparency Options, Booklet Creation, Repeat
Image, or Poster features.
1
Touch the Inserts button on the Output Format screen. The Inserts screen is displayed.
4–78
Figure 62. Inserts Screen
D O C U C O L O R 2 0 6 0 / 2 0 4 5 O P E R A T O R M A N U A L
S C A N N E R
2
Choose the tray that holds the Inserts.
3
Using the keypad on the Control Panel, select the page number after which you want to place an insert. Confirm the Entry Line or Clear the Selected Line and reinput the page number.
4
Repeat step 3 up to 10 times.
5
Touch the Save button.
6
Continue selecting options for your job.
7
When you are finished selecting options, press the Start button.
D O C U C O L O R 2 0 6 0 / 2 0 4 5 O P E R A T O R M A N U A L 4–79
S C A N N E R
N-Up
N-Up allows you to print multiple document images, in a specified order, on a single sheet of paper. The images may be printed 2-Up, 4-Up, or 8-Up. If you have an odd number of images, add a blank image to make it an even number. A graphic representation appears on the right side of the display depicting your choice.
You must specify the orientation of the original document, the original image, and the paper in the chosen tray. You may select only one Original Type that will apply to all originals for the job.
Each image will be centered within its position on the output page. Edge Erase is used for the individual images in their section of the output page. When Auto is selected in Lighten/Darken (refer to Image Quality), the setting of the first image applies to the rest of the images.
Mixed Size Originals may be used in combination with N-Up, but image loss may occur. The N-Up feature cannot be used in combination with the Interrupt,
Inserts, Covers, Booklet Creation, Mirror Image, Negative Image, Repeat Image,
Poster, Bound Originals, or Image Shift features.
1
Touch the N-Up button on the Output Format screen. The N-Up screen is displayed.
4–80
Figure 63. N-Up Screen with 2-Up selected
D O C U C O L O R 2 0 6 0 / 2 0 4 5 O P E R A T O R M A N U A L
S C A N N E R
2
Choose the number of images required (2-Up, 4-Up, or 8-Up).
3
Touch either Portrait or Landscape for the Original Document Orientation.
4
Indicate the Original Image Orientation.
5
Touch either Portrait or Landscape to indicate the Copy Paper Orientation.
6
Using the arrow buttons, indicate the Image Placement. (Refer to the Output display at the top of the screen for image placement and orientation.)
7
Touch the Save button.
8
Continue selecting options for your job.
9
When the option selections are complete, press the Start button.
D O C U C O L O R 2 0 6 0 / 2 0 4 5 O P E R A T O R M A N U A L 4–81
S C A N N E R
Transparency Options
Transparency Options allows you to do the following:
• Transparency Set produces a single set of transparencies with a designated number of sets of paper output. Only one set of transparencies is produced regardless of the number of paper sets requested.
• Transparency Set + Dividers produces a single set of transparencies + dividers with a designated number of sets of paper output. Only one set of transparencies is produced regardless of the number of paper sets required.
• Dividers Only produces a continuous stream of dividers to be incorporated into a job programmed for transparencies only. This is the option to choose if you are running multiple sets of transparencies and require a divider to be inserted between each set.
Off is the permanent default for Transparency Options. The default cannot be changed in Tools Mode.
Tray 3 is automatically selected when Transparency Options is selected.
Transparencies should be run from Tray 3 ONLY. If you have an optional Tray 4 you can run transparencies but it is not recommended. Any other tray may be selected for Dividers. If Transparency Options is selected and paper is in Tray 3, a message appears in the message area on the Touch Screen indicating that transparencies must be loaded into Tray 3.
Collated must be selected on the Basic Features screen for the Transparency
Options button to appear. The Transparency Options feature cannot be used in combination with the Covers, Inserts, Booklet Creation, or Poster features.
4–82 D O C U C O L O R 2 0 6 0 / 2 0 4 5 O P E R A T O R M A N U A L
S C A N N E R
1
Touch the Transparency Options button on the Output Format screen. The
Transparency Options screen is displayed.
Figure 64. Transparency Options Screen
2
Select the type of transparency job required (Transparency Set, Transparency
Set + Dividers, or Dividers Only).
D O C U C O L O R 2 0 6 0 / 2 0 4 5 O P E R A T O R M A N U A L 4–83
S C A N N E R
3
If a finishing device is attached to your configuration, select where to feed the output. It is recommended that the transparencies be output to the Top Tray even though both selections are valid.
Figure 65. Transparency Set + Dividers Screen
4
If Transparency Set + Dividers or Dividers Only is selected, indicate the paper tray where the dividers are loaded.
5
Touch the Save button.
6
Continue selecting options for your job.
7
When you are finished selecting options, press the Start button.
4–84 D O C U C O L O R 2 0 6 0 / 2 0 4 5 O P E R A T O R M A N U A L
S C A N N E R
Booklet Creation
Booklet Creation allows you to create multi-page booklets from an ordered set of
1-Sided or 2-Sided originals. When Auto% is selected, the digital press reduces or enlarges the image as required. Any other Reduce/Enlarge selection could result in image loss.
When Booklet Creation is selected, the output is automatically set to 1 - 2 Sided.
The selected paper tray must have the paper oriented SEF. Auto Paper is not available with Booklet Creation. The orientation of the original, whether you use the DADF or the Document Glass, must be LEF. The maximum paper size used is
8.5 x 11 inches (A4). There is a maximum output of 25 sheets, including covers, per booklet.
Output must be Collated, and a specific Paper Tray must be selected on the Basic
Features screen for the Booklet Creation button to be selectable. The Booklet
Creation feature cannot used in combination with the Covers, Inserts, N-Up,
Transparency Options, Mirror Image, Repeat Image, Poster, 2-Sided Output, Color
Bar, Bound Originals, or Image Shift features.
1
Touch the Booklet Creation button on the Output Format screen. The Booklet
Creation screen is displayed.
D O C U C O L O R 2 0 6 0 / 2 0 4 5 O P E R A T O R M A N U A L
Figure 66. Booklet Creation Screen
4–85
S C A N N E R
2
Touch the On button.
3
Indicate whether the original documents are 1-Sided, 2-Sided Head to Head, or 2-Sided Head to Toe.
4
Touch the Binding Margin button and input the Binding Margin in millimeters.
Figure 67. Binding Margin Screen
4–86 D O C U C O L O R 2 0 6 0 / 2 0 4 5 O P E R A T O R M A N U A L
S C A N N E R
5
Touch Back Cover Image and On if required. (The default is Off. This option puts the last scanned image on the last booklet page when there are more booklet pages than scanned images.). If a Binding Margin is set, you may not select this option.
Figure 68. Back Cover Image Screen
6
Touch Select Tray for Cover and On if required. (The default is Off. Since the
Cover for the Booklet Creation is 8.5 x 11 inch maximum size sheet of paper, the front and back option does not appear here.) Touch the Paper Tray where the
Covers are loaded.
D O C U C O L O R 2 0 6 0 / 2 0 4 5 O P E R A T O R M A N U A L
Figure 69. Select Tray for Cover Screen
4–87
S C A N N E R
7
Touch Printed Output. Touch the button for the final output orientation (Left
Bound Head to Head, Right Bound Head to Head, or Top Bound Head to
Toe).
Figure 70. Printed Output Screen
8
Touch the Save button.
9
Continue selecting options for your job.
10
When you are finished selecting options, press the Start button.
4–88 D O C U C O L O R 2 0 6 0 / 2 0 4 5 O P E R A T O R M A N U A L
S C A N N E R
Mirror Image
Mirror Image enables you to make a mirror image (reversed image) copy of an original document.
Mirror Image cannot be used with N-Up, Booklet Creation, Repeat Image, 2-
Sided Output, Poster, or any of the Image Shift options.
1
Touch the Mirror Image button on the Output Format screen. The Mirror Image screen is displayed.
Figure 71. Mirror Image Screen
2
Touch either the On or Off button.
3
Touch the Save button.
4
Continue selecting options for your job.
5
When you are finished selecting options, press the Start button.
D O C U C O L O R 2 0 6 0 / 2 0 4 5 O P E R A T O R M A N U A L 4–89
S C A N N E R
Negative Image
Negative Image allows you to create a negative of an original document. The output color depends on the selections you choose in Basic Features, Color
Mode. If you select Black Only, the black and white on the original is reversed. If you select a single color, the color and white on the original is reversed. If you choose Full Color or 3 Color in the Color Mode, the output produced is in complimentary colors.
The Negative Image feature cannot be used in combination with the N-Up,
Repeat Image, or Bound Originals features.
1
Touch the Negative Image button on the Output Format screen. The Negative
Image screen is displayed.
4–90
Figure 72. Negative Image Screen
2
Touch either the On or Off button.
3
Touch the Save button.
4
Continue selecting options for your job.
5
When you are finished selecting options, press the Start button.
D O C U C O L O R 2 0 6 0 / 2 0 4 5 O P E R A T O R M A N U A L
S C A N N E R
Repeat Image
Repeat Image enables you to print a single image repeatedly on a single sheet of paper or transparency up to 15 times in both the horizontal and vertical directions for any desired quantity of output.
• Auto automatically computes and place as many images in the horizontal and vertical directions as will fit within the limits calculated for the image size (document size x magnification) and paper size. You must choose a reduction ratio before this option has any effect on your output.
• Manual allows you to choose from 1 to 15 repetitions in both the horizontal and vertical directions.
A specific Paper Tray must be selected on the Basic Features screen for the
Repeat Image button to be selectable. Repeat Image cannot be used in combination with Corner Shift, Image Shift, Margin Shift, 2-Sided Output, N-Up,
Poster, Booklet Creation, Center Erase, Negative Image, Bound Originals, Covers, or Inserts.
1
Touch the Repeat Image button on the Output Format screen. The Repeat Image screen is displayed.
D O C U C O L O R 2 0 6 0 / 2 0 4 5 O P E R A T O R M A N U A L
Figure 73. Repeat Image Screen
4–91
S C A N N E R
2
Select Auto or Manual.
Figure 74. Manual Repeat Image Screen
3
If you select Auto, ensure that a reduction ratio has been chosen. If you select
Manual, indicate the number of images (1 to 15) in both the horizontal and vertical directions.
4
Touch the Save button.
5
Continue selecting options for your job.
6
When you are finished selecting options, press the Start button.
4–92 D O C U C O L O R 2 0 6 0 / 2 0 4 5 O P E R A T O R M A N U A L
S C A N N E R
Poster
Poster allows you to create a multi-page enlargement of an original. The number of copies is automatically set at one for this feature.
The arrangement of the image on the output depends on the document orientation (portrait or landscape) and the paper orientation (LEF or SEF).
Poster size is specified in two ways:
• Preset, specifies the output poster size by indicating the number of sheets of the paper size that will make up the finished Poster.
• Enlarge%, which permits independent specification of the X and Y axis percentages (100% to 400%) using the X and Y up and down arrows OR by selecting the percentage simultaneously for the X and Y axis using the center X/Y up and down arrows.
Output must be Collated, and a specific Paper Tray must be selected on the Basic
Features screen for the Poster button to be selectable. The Poster feature cannot be used in combination with the Image Shift, N-Up, Repeat Image, Booklet
Creation, Bound Originals, Mirror Image, Transparency Options, Mixed Size
Originals, 2-Sided Output, Covers, or Inserts options.
1
Touch the Poster button on the Output Format screen. The Poster screen is displayed.
D O C U C O L O R 2 0 6 0 / 2 0 4 5 O P E R A T O R M A N U A L
Figure 75. Poster Screen
4–93
S C A N N E R
2
Touch the On button.
3
Choose either Presets or Enlarge%.
4
If you select Presets, select the number of sheets for the output size indicated by touching the desired button.
Figure 76. Poster Presets Screen
4–94 D O C U C O L O R 2 0 6 0 / 2 0 4 5 O P E R A T O R M A N U A L
S C A N N E R
If you select Enlarge%, input the X and Y axis enlargement values (100% to
400%) independently or simultaneously.
Figure 77. Poster Enlarge% Screen
5
Touch the Save button.
6
Continue selecting options for your job.
7
When you are finished selecting options, press the Start button.
D O C U C O L O R 2 0 6 0 / 2 0 4 5 O P E R A T O R M A N U A L 4–95
S C A N N E R
Job Assembly
Job Assembly allows you to build individual jobs and to print a proof set to ensure all settings for your job are correct.
Figure 78. Job Assembly Screen
4–96 D O C U C O L O R 2 0 6 0 / 2 0 4 5 O P E R A T O R M A N U A L
S C A N N E R
Build Job
Build Job allows you to program, scan, and store individual job segments of a large or complex copy job, and then print all the segments as one complete job.
This feature is useful when you have copy jobs containing more than fifty originals. Segments are programmed as if they were ordinary, independent jobs, and scanning is initiated for each segment by pressing the Start button.
When you press the Save button, the Build Job screen closes, and control reverts to the Basic Features screen. A new button, Build Job Controls, appears at the top right of all primary screens. Press this button to access features that are available after a segment is saved.
Output must be Collated, and a specific Paper Tray must be selected on the Basic
Features screen for the Build Job button to appear on the Job Assembly screen.
The Build Job feature cannot be used in combination with the Inserts, Covers, or
Poster options.
1
Touch the Build Job button on the Job Assembly screen. The Build Job screen is displayed.
D O C U C O L O R 2 0 6 0 / 2 0 4 5 O P E R A T O R M A N U A L
Figure 79. Build Job Screen
4–97
S C A N N E R
2
Touch the On button. The Build Job On screen is displayed.
4–98
Figure 80. Build Job On Screen
3
Touch either the On or Off button (under Blank Page Insertions) to have a blank page placed at the end of the job.
4
Touch either the On or Off button (under Segment Separators) to have a separator inserted between segments.
5
Touch the Save button to save your settings and return to the Basic Features screen.
6
Continue selecting options for this segment just as you would for any ordinary scan to print job.
NOTE: Options are programmed independently for each individual segment.
Therefore, after this segment is programmed and the Start button is pressed, all options will return to the default settings. You will have to program the desired options each time you scan a segment.
7
When you are finished selecting options for this segment, press the Start button.
Repeat steps 6 and 7 for each segment or press the Build Job Controls button, described in steps 8 through 10, to access features available after each segment is scanned.
D O C U C O L O R 2 0 6 0 / 2 0 4 5 O P E R A T O R M A N U A L
S C A N N E R
8
Press the Build Job Controls button at the top-right corner of the screen. The
Build Job Controls screen is displayed.
Figure 81. Build Job Controls Screen
9
Choose the desired Segment Option:
• Touch the Proof Segment button to print out a proof set of the last segment that was scanned.
• Touch the Delete Segment button to delete the last segment that was scanned.
• Touch the Save Segment Programming button to save the programming options for the last scanned segment for later use in the build job.
• Touch the Recall Segment Programming button to recall programming that was saved for a previously scanned segment. This button is only selectable after the first segment is scanned.
10
Choose the desired Job Preview/Completion option:
• Touch the Proof Set button to print out a proof set of all the segments scanned for this build job.
• Touch the Cancel Job button to cancel the entire build job and exit the
Build Job feature.
• Touch the Build Job Complete button when you are finished compiling the build job. The entire build job will be output to the printer.
11
When all segments are completed, press the Build Job Complete button. Every segment that you programmed for this build job will be output to the printer as one complete job.
D O C U C O L O R 2 0 6 0 / 2 0 4 5 O P E R A T O R M A N U A L 4–99
S C A N N E R
Proof Set
Proof Set outputs one full set of a job, allowing you to ensure that all job settings are correct and to produce the desired output.
Collated must be selected on the Basic Features screen in order for the Proof Set button to appear on the Job Assembly screen. The Proof Set feature cannot be used in combination with the Poster option.
1
Touch the Proof Set button on the Job Assembly screen. The Proof Set screen is displayed.
Figure 82. Proof Set Screen
4–100 D O C U C O L O R 2 0 6 0 / 2 0 4 5 O P E R A T O R M A N U A L
S C A N N E R
2
Touch the On button. One full set of your job is output, and the Proof Set Job
Completion screen is displayed.
Figure 83. Proof Set Job Completion Screen
3
Touch the Continue Printing button to finish printing the job. Touch the Change
Quantity button, and use the numeric keypad on the Control Panel change the number of sets to be output. Touch the Color Balance button to change the image quality.
4
If you select Change Quantity or Color Balance, touch the Continue Printing button to finish printing the job.
5
Touch either the Save Job or Cancel Job button.
Back
Selecting the Back... tab returns you to the Basic Features screen.
D O C U C O L O R 2 0 6 0 / 2 0 4 5 O P E R A T O R M A N U A L 4–101
S C A N N E R
This page is intentionally left blank.
4–102 D O C U C O L O R 2 0 6 0 / 2 0 4 5 O P E R A T O R M A N U A L
5.
Accessories
Tray 4
Tray 4 is an optional high capacity paper tray with a capacity of 2500 sheets of 24 pound (64 - 80 g/m
2
) paper.
Refer to the Color Materials User Guide and the Recommended Materials List for paper guidelines. The Recommended Materials List is a downloadable file at www.xerox.com. Use the search parameters DC 2060 or DC2045 and follow the path until you reach the files that can be downloaded.
Identifying Tray 4 Parts
Control
Panel
Left Door
Right Door
Figure 1. Tray 4
D O C U C O L O R 2 0 6 0 / 2 0 4 5 O P E R A T O R M A N U A L 1Tray 4 5–1
A C C E S S O R I E S T R A Y 4
Tray 4
Horizontal
Transport behind the
Right Door
Paper Tray
From
Tray
4
Figure 2. Internal View of Tray 4
Tray 1
Tray 2
Tray 3
Transport
Module
To the digital press
From
Horizontal
(Duplex)
Transport
Figure 3. Paper Path of Tray 4
5–2 D O C U C O L O R 2 0 6 0 / 2 0 4 5 O P E R A T O R M A N U A L
T R A Y 4
Control Panel
A C C E S S O R I E S
Figure 4. Tray 4 Control Panel
Symbol Function
Left Door: Misfeed jam indicator. Also blinks when
Tray 4 is out of paper and the tray is open.
Right Door: Open to clear jams for the Tray 4
Horizontal Transport and the Digital Press Left Side
Door.
Ready.
D O C U C O L O R 2 0 6 0 / 2 0 4 5 O P E R A T O R M A N U A L 5–3
A C C E S S O R I E S T R A Y 4
Symbol Function
Tray Unlock: Use to load paper or lower the paper tray.
Ready to open.
Wait. The paper tray is in motion, wait until the light goes out.
Red
Orange
Green
Paper level indicator. The far left indicator is red: Tray
4 will not function until paper is loaded. The second indicator is orange, warning of a low paper level. The other indicators are green, which indicates the level of paper in the tray.
When Tray 4 is turned on, the display flashes, then the software version number is shown. After initialization, a green indicator light appears in the lower left corner of the screen. All other codes shown are for the Xerox representative to run diagnostics when servicing Tray
4. If there is a problem that you can rectify, the problem and the corrective action appears on the digital press Touch Screen.
The keypad under the door at the right of the Control
Panel is for the Xerox representative to run diagnostics when servicing the unit.
5–4 D O C U C O L O R 2 0 6 0 / 2 0 4 5 O P E R A T O R M A N U A L
T R A Y 4 A C C E S S O R I E S
Paper Stock Specifications
There are two positions in which paper is fed into the digital press. One of the positions is called long edge feed (LEF). Long edge refers to the long edge of your paper. When you see LEF, position your paper so that the long edge is fed first.
The other position is called short edge feed (SEF). Short edge refers to the short edge of your paper. When you see SEF, position your paper so that the short edge is fed first.
Tray 4 handles paper from a minimum of 64 g/m
2
up to 220 g/m
2
, either coated or uncoated. It accepts all standard paper sizes supported by the DocuColor 2060/
2045, with the exception of JIS B5 LEF (Asian standard size).
Non standard sizes from 182 to 320mm (7.2 to 12.6") across the feed direction, and 203 to 488 mm (8.0 to 19.2") in the feed direction, with the exception of some long narrow paper sizes are also accepted by Tray 4. Paper longer than 305 mm
(12") in the feed direction must measure at least 210 mm (8.3") across the feed direction.
Special paper stock for Tray 4:
• Letterhead (refer to Letterhead procedure in this section).
• 3 hole drilled paper is not recommended.
• Colored paper.
• Coated/Non-coated paper (coated paper less than 100 g/m
2
may not feed as reliably as coated paper greater than 100 g/m
2
.
• Tabbed Inserts can be run but are not recommended for Tray 4. Refer to
Tabbed Inserts procedure in this section.
Tray 4 holds a maximum of 2500 sheets of 24 pound (64 - 80 g/m
2
) paper (five reams). DO NOT fill above the MAX line.
For further instructions on loading special stock, refer to the Loading Special
Stock section in this chapter.
D O C U C O L O R 2 0 6 0 / 2 0 4 5 O P E R A T O R M A N U A L 5–5
A C C E S S O R I E S T R A Y 4
.
Paper
Paper Size
Paper Weight Range
Transparencies
Transfer Paper
Coated Paper
Tabbed Inserts
Tray 4
JIS B5 (SEF)
8.5 x 11 inch/A4 (LEF/SEF)
JIS B4 (SEF)
11 x 17 inch/A3 (SEF)
8 x 10 inch (SEF)
8.5 x 13 inch (SEF)
8.5 x 14 inch (SEF)
12 x 18 inch (SEF)
SRA3, 320 x 450 mm (SEF)
12.6 x 19.2 inch (SEF)
64 - 220 g/m
2
No
No
Yes
Can be run but is not recommended
KEY POINT: When feeding 8.5 x 11" and A4 paper to the optional High
Capacity Stacker Stack Tray, the paper must be fed LEF.
5–6 D O C U C O L O R 2 0 6 0 / 2 0 4 5 O P E R A T O R M A N U A L
T R A Y 4 A C C E S S O R I E S
Tray 4 Special Features
Special features help control the environmental conditions in the paper tray to ensure optimum print capability:
• Paper Tray 4 has an optional heater kit available.
Loading Special Stock in Tray 4
To ensure that the output is correct follow the orientation shown on the Tray 4 indicator when loading special stock.
Tabbed Inserts
Tabbed Inserts can be run from Tray 4 but it is not recommended. Load the nontabbed, short edge of the tabbed insert as the lead edge, and select nonstandard paper. If a jam occurs while running tabbed sets, there is no recovery procedure. You have to manually reassemble your originals and prints, determine where the job left off and resume printing or cancel the job and start again.
The size of the tabbed insert should be 9 x 11 inch (229 x 279 mm) for letter size tabs (223.5 x 296 mm for A4 equivalent tabs). Select the proper weight of the insert on the tray. Select Non-standard size and input 11 inches or 296 mm for A4 as the X axis and 9 inches or 223.5 mm for A4 as the Y axis dimensions for SEF.
Refer to the System Administration Guide, Tools Mode chapter, for programming non-standard size paper.
KEY POINT: If you are using drilled Tabbed Inserts, you may experience sporadic jams caused by the holes passing over the sensors.
D O C U C O L O R 2 0 6 0 / 2 0 4 5 O P E R A T O R M A N U A L 5–7
A C C E S S O R I E S T R A Y 4
Non-standard Size Paper
Non-standard size paper (7.2 to 12.6 (LEF) or 7.2 to 19.2 (SEF)) can be loaded into
Tray 4. Ensure that Non-standard size paper is selected on Tray 4. Refer to the
System Administration Guide, Tools Mode chapter, for programming nonstandard size paper.
Letterhead
Different inks and dry inks/toners are used to produce preprinted letterhead that may not pass through the digital press intact.
Refer to the Specialty Media Guide that came with your documentation for information on using preprinted letterhead paper.
Coated Paper
Follow the directions on the ream of paper when loading coated paper.
NOTE: Remove any remaining sheets from the Elevator Tray before loading a different paper stock.
5–8 D O C U C O L O R 2 0 6 0 / 2 0 4 5 O P E R A T O R M A N U A L
T R A Y 4
Loading Paper in Tray 4
Side
Guide
End
Guides
A C C E S S O R I E S
Figure 5. Tray 4 Left Door Open
Front Edge Paper Stop
Figure 6. Tray 4 Paper Guides
1
Press the Tray Unlock button.
2
Wait until the Ready to Open indicator is illuminated.
3
Open the Tray 4 Door.
D O C U C O L O R 2 0 6 0 / 2 0 4 5 O P E R A T O R M A N U A L 5–9
A C C E S S O R I E S T R A Y 4
4
Remove any remaining sheets from the Elevator Tray if you are changing paper stock.
5
Load the paper seam side (the side where the ream of paper is sealed) up in
Tray 4.
Load the paper onto the Elevator Tray with the sheets even against the front and lead edge registration guides. DO NOT fill above the MAX line. Ensure that the side edge and end guides are against the paper. Incorrect loading of paper can result in excessive sheet skew, misfeeds, or multiple feeds due to paper guides not being aligned properly.
KEY POINT: Tray 4 is an accessory shared with other printers. The Front
Edge Paper Stop button is used for smaller sized paper that can be run on other printers. It has no functional use on the DocuColor 2060/2045.
Although Tray 4 has auto size detection capability, the paper weight (g/m
2
) range must be selected on the Weight Indicator. Selecting the correct paper weight range affects the feed performance and Image Quality.
6
Press the button until the light next to the correct weight is illuminated.
KEY POINT: When the tray elevator lowers while loading paper, or after clearing a jam in Tray 4, make sure that the paper is registered evenly against the front and lead edge guides. This is most important when the tray is full of paper because the tray can tilt to compensate for curl or other conditions, and the top of the stack moves away from the front edge guides.
5–10 D O C U C O L O R 2 0 6 0 / 2 0 4 5 O P E R A T O R M A N U A L
T R A Y 4 A C C E S S O R I E S
7
Select Standard or Non-Standard paper, the g/m
2
of the paper, Coated or
Uncoated paper, and adjust the Paper Guides until they lightly touch the paper.
The Tray 4 will have one of the two labels below depending on the market area.
Paper
Guides
Orientation
Paper
Guides
Non-
Standard
Size
Standard
Size
Weights
Coated Uncoated
Figure 7. Tray 4 Label without Words
8
Close the Tray 4 Door.
Figure 8. Tray 4 Label with Words
If the door seems to be locked in the out position, give it a firm push.
KEY POINT: If you hear paper crumpling or tearing, stop closing the tray.
Remove all pieces of any damaged paper and close the tray slowly.
The Elevator Tray automatically rises and stops at the correct feeding height.
D O C U C O L O R 2 0 6 0 / 2 0 4 5 O P E R A T O R M A N U A L 5–11
A C C E S S O R I E S
Selecting Tray 4
T R A Y 4
Tray 4 can be selected on the digital press Touch Screen for scan jobs, or for networked jobs as a selection through the Raster Image Processor.
The following instructions are for scanned jobs. Refer to the Printing Guide that came with your RIP for information on selecting Tray 4.
1
Touch Tray 4 in the Paper Supply column on the Basic Features screen.
5–12
Figure 9. Basic Features Screen
2
Continue selecting any other desired options for your job.
3
When you are finished selecting options, press Start.
D O C U C O L O R 2 0 6 0 / 2 0 4 5 O P E R A T O R M A N U A L
T R A Y 4 A C C E S S O R I E S
Jam Clearance
A paper jam in Tray 4 is indicated by a message on the digital press Touch
Screen. Follow the instructions displayed.
Perform the following steps to clear a Tray 4 jam and resume printing.
1
The Tray 4 icon on the Tray 4 Control Panel will indicate which door on the Tray 4 to open. Open the doors indicated.
2
Press the Tray Unlock button.
3
Wait until the Ready to Open indicator is illuminated.
4
Open the Tray 4 Left Door.
5
Remove any misfed paper from the Tray 4 Paper Tray.
6
Open the Right Door, and remove any paper from the Tray 4 Horizontal Transport by lifting the green handle and turning the green knob in the direction of the arrow.
7
Open the Left Side Door of the digital press and remove any paper found in the digital press. Refer to the Left Side Door Jam Clearance section in the Problem
Solving chapter in this manual.
8
Close the Left Side Door of the digital press.
9
Close the Tray 4 Doors.
The Elevator Tray automatically rises and stop at the correct feeding height.
10
Follow the instructions displayed in the Touch Screen to resume printing.
D O C U C O L O R 2 0 6 0 / 2 0 4 5 O P E R A T O R M A N U A L 5–13
A C C E S S O R I E S
Digital Press Paper Reliability
T R A Y 4
The Best performance is obtained by using the baseline/centerline paper for which the system has been designed.
North America: Xerox Digital Color Xpressions 94, 24 lb.
Europe: Xerox Colotech+ 90 g/m
2
.
Refer to the Recommended Paper List found on the Internet at: http://www.xerox.com
Use the search parameters DC 2060 or DC 2045 and follow the path until you reach the files that can be downloaded.
Tray 4 Maintenance
Cleaning Tray 4
Do not clean any area inside of Tray 4. If the exterior of Tray 4 requires cleaning, dampen a paper towel or soft, clean cloth with a liquid, nonabrasive glass cleaner or water.
WARNING: To avoid damage to Tray 4, DO NOT pour or spray the cleaner or water directly onto Tray 4. Always apply the liquid to the cloth first.
WARNING: DO NOT use any other cleaners or solvents on Tray 4 or they may interact with the paint on the covers, eventually causing the paint to peel.
5–14 D O C U C O L O R 2 0 6 0 / 2 0 4 5 O P E R A T O R M A N U A L
T R A Y 4 A C C E S S O R I E S
Problem Solving
Tray 4 has an altitude sensor that detects the curl of the paper and adjusts the
Elevator Tray accordingly. If misfeeds and jams occur repeatedly:
• Find the problem in the Problem column.
• Follow the suggestion in the Suggested Solutions column until the situation is corrected.
Problem
Fault Code 052-310
Communication problem
Fault Code 052-320
Unexpected connection
Fault Code 052-210
No response from Tray 4
Fault Code 007-532
Tray 4 not ready to print
Fault Code 007-236
Tray 4 Tray Tilt Fault
Fault Code 007-239
Volt Failure
Fault Code 008-201
Drive motor problem
Fault Code 007-242
Air drive motor fault
Fault Code 007-243
Vacuum Valve fault
Fault Code 007-290
Internal software problem
No power to Tray 4
Suggested Solutions
• Cancel or save the job.
• Power off the digital press. Wait 15 seconds and power on.
• Cancel or save the job.
• Power off the digital press. Wait 15 seconds and power on.
• Cancel or save the job.
• Power off the digital press. Wait 15 seconds and power on.
• Cancel or save the job.
• Power off the digital press. Wait 15 seconds and power on. If problem persists, use another tray and call for service.
• Cancel or save the job.
• Power off the digital press. Wait 15 seconds and power on. If problem persists, use another tray and call for service.
• Cancel or save the job.
• Power off the digital press. Wait 15 seconds and power on. If problem persists, use another tray and call for service.
• Cancel or save the job.
• Power off the digital press. Wait 15 seconds and power on. If problem persists, use another tray and call for service.
• Cancel or save the job.
• Power off the digital press. Wait 15 seconds and power on. If problem persists, use another tray and call for service.
• Cancel or save the job.
• Power off the digital press. Wait 15 seconds and power on. If problem persists, use another tray and call for service.
• Cancel or save the job.
• Power off the digital press. Wait 15 seconds and power on. If problem persists, use another tray and call for service.
• Check that the Tray 4 power cord is connected.
• Test the Ground Fault Indicator according to the instructions in this chapter.
D O C U C O L O R 2 0 6 0 / 2 0 4 5 O P E R A T O R M A N U A L 5–15
A C C E S S O R I E S T R A Y 4
Problem Suggested Solutions
Repeated Tray 4 misfeeds.
• Turn the paper stack around or over in the Elevator Tray.
• Replace the paper in the tray with paper from a new package.
• Keep paper in the original wrapper and store it flat in a dry environment when not in use.
• Fan the paper at all four corners. Change it if it has uneven edges.
• Lightweight or heavyweight paper may not feed with as much reliability as papers that are
64 to 220 g/m
2
.
• Remove a few sheets from the top and the bottom of the ream in the Elevator Tray.
• Ensure that the paper is loaded evenly to the edge of the tray and not overloaded.
• Check to ensure that the side guides are lightly against the paper and not too tight.
• If the environment is high humidity (50 to 85%) and coated paper is being used, the Tray 4
Heater Kit may have to be installed.
Tray 4 does not feed.
Misfeeds occur with lightweight paper.
Prints are skewed.
• The digital press should be set to feed from Tray 4.
Use a heavier weight paper.
Touch Screen displays
"Add Paper" message and there is paper in the tray selected
Ensure that the Rear and Side Guide Adjustment Levers are in the correct position.
If the Coated Paper button at the front of Tray 4 is selected and Uncoated Paper is not programmed on the Touch Screen or in the RIP print driver screen, an incorrect message, "Add
Paper" is displayed. Change the settings so they are consistent.
For additional help, call your Xerox representative.
Follow the instructions below before calling for service.
1
Be prepared to provide a complete description of the problem to the service operator. Defining the problem accurately may help you and the operator solve the problem over the phone and minimize downtime. If the problem cannot be solved by telephone, a service representative will be dispatched to your site promptly.
2
Record the displayed Fault Codes.
5–16 D O C U C O L O R 2 0 6 0 / 2 0 4 5 O P E R A T O R M A N U A L
T R A Y 4 A C C E S S O R I E S
3
Record the Machine Serial Number. Press the Machine Status button on the
Control Panel. Touch the Machine Details tab and the serial number is displayed.
4
If copy quality is a problem, take a copy sample to the telephone with you to help you describe the problem or to assist you when answering the questions from the service operator about the defects.
5
If possible, use a phone near the press when calling for assistance. Follow the instructions provided by the operator.
6
For system support, user help, and service support, call the appropriate number:
US: 1-800-821-2797
Canada: 1-800-939-3769
Europe: _________________________
Latin America:_________________________
D O C U C O L O R 2 0 6 0 / 2 0 4 5 O P E R A T O R M A N U A L 5–17
A C C E S S O R I E S T R A Y 4
Loss of Power
Tray 4 is equipped with an additional safety feature, the ground fault indicator
(GFI). The ground fault indicator is located at the bottom center of the back cover of Tray 4.
If power to Tray 4 is interrupted:
• Ensure the power cord is plugged in to the proper wall receptacle (the ground fault indicator must be plugged in to reset).
• Check to see if the GFI switch was tripped. Press and release the RESET button. Power should be restored to Tray 4.
• If the device interrupts power to Tray 4 immediately, or if the power has not been restored by the above procedure, call Xerox Customer Support.
Also call your Xerox service representative if the loss of power to Tray 4 seems to be frequent or excessive.
GFI
Figure 10. Tray 4 GFI
5–18 D O C U C O L O R 2 0 6 0 / 2 0 4 5 O P E R A T O R M A N U A L
T R A Y 4 A C C E S S O R I E S
Tray 4 Specifications
Electrical Requirements
Western Hemisphere: 115 VAC, 15 amp for 60 Hz. and 220 VAC, 10 amp for 50
Hz installations.
Europe: 200/240 Volt, 10 amp 50 Hz service outlet.
Tray 4 requires a single power source separate from the digital press.
Power Consumption
Standby - 1.5 KVA
Run - 1.5 KVA
Heat Output
Standby - 5100 BTU
Run - 5100 BTU
D O C U C O L O R 2 0 6 0 / 2 0 4 5 O P E R A T O R M A N U A L 5–19
A C C E S S O R I E S
Environmental Requirements
T R A Y 4
Atmosphere Requirements
Temperature: 10º C (50º F) Min.
Relative Humidity (% RH): 15% Min.
Altitude: N/A
32º C (90º F) Max.
85%
Greater than 2000 meters (6560 ft.) above sea level may require field adjustments.
Better performance is achieved when conditions are maintained between
20-25º C (68-77º F).
Noise Levels
Standby
IOT Operation
Full System Operation
Continuous Noise
49.5 dBa
64.0 dBa
72.0 dBa
Impulse Noise
N/A
72.0 dBa
72.0 dBa
Ozone Emissions
Not to exceed 0.02 PPM (maximum)
Imaging material: No unpleasant odor
Dust
Dust concentration during continuous run should be 0.1mg/cubic meter.
5–20 D O C U C O L O R 2 0 6 0 / 2 0 4 5 O P E R A T O R M A N U A L
T R A Y 4 A C C E S S O R I E S
Capabilities
Tray Capacity
Paper Tray 4 (optional) has a capacity of 2500 sheets.
Throughput
Tray 4 (optional): Inches/JIS B5 (LEF/SEF) to 12.6 x 19.2 inch (320 x 487mm)
SEF.
Physical Characteristics
Tray 4 Size
48.07 inches/1221 mm (W) x 29.53 inches/750 mm (D) x 55.6 inches /
1412 mm (H).
Tray 4 Weight
425 pounds/192.95 Kg.
Floor Space Requirements
Ask your Xerox representative to refer to the DocuColor 2060/2045 Installation
Planning Guide.
D O C U C O L O R 2 0 6 0 / 2 0 4 5 O P E R A T O R M A N U A L 5–21
A C C E S S O R I E S
High Capacity Stacker (HCS)
H I G H C A P A C I T Y S T A CK E R ( H C S )
The High Capacity Stacker (HCS) is an optional finishing device that provides stacking and offsetting capabilities for output into a stacker cart. The HCS connects to the right end of the digital press and replaces the Offset Catch Tray on the press.
The stacker cart has a capacity of 3500 sheets of 64 - 80 g/m
2
coated or uncoated paper. You can select the Offset mode on the digital press Touch Screen when sets are sent to the stacker cart. This provides offset separation between the stacked sets. The High Capacity Stacker can also send documents to the Top
Tray. The Top Tray has a capacity of 250 sheets of 64 - 80 g/m
2
paper.
Identifying High Capacity Stacker Parts
Top Tray
Back
Control Panel
Right Side
Left Side
Front Door access to stacker cart
Docking plate to digital press
Front
Figure 11. High Capacity Stacker
5–22 D O C U C O L O R 2 0 6 0 / 2 0 4 5 O P E R A T O R M A N U A L
H I G H C A P A C I T Y S T A CK E R ( H C S )
Control Panel
A C C E S S O R I E S
Figure 12. HCS Control Panel
1
2
3
Name Function
Ready Indicator The Ready Indicator blinks when the digital press is being initialized. The Ready Indicator is constant when in use or in standby.
Table Down
Switch
Press once to lower the elevator and unlock the front
HCS door. Press again to stop the elevator from lowering. If pressed while running a job, all sheets in the paper path are delivered before the elevator will lower.
Ready To Open Illuminates when the elevator has reached the down position and the Stacker Door can be opened.
D O C U C O L O R 2 0 6 0 / 2 0 4 5 O P E R A T O R M A N U A L 5–23
A C C E S S O R I E S H I G H C A P A C I T Y S T A CK E R ( H C S )
4
5
6
Name
Please Wait
Fault Codes
Main Tray
7
8
9
10
Baffle Area
Entry
Top Tray
Horizontal
Transport
Function
Please Wait will illuminate while the elevator is in motion.
When there is a fault in the HCS, the Fault Code appears here. Refer to the Touch Screen for further information.
Illuminates when paper is being delivered to the elevator tray. Blinks when the cart is full or not in place.
The indicator is OFF when the Stacker is in standby mode.
Illuminates when paper is being stacked. Blinks when there is a jam. The indicator is OFF when the Stacker is in standby mode.
Blinks when there is a jam in baffle area 1. The indicator is OFF when the Stacker is in standby mode. Refer to
Jam Clearance in this section.
Illuminates when in Top Tray Mode. Blinks when the tray is full. The indicator is OFF when the Stacker is in standby mode.
Blinks when there is a jam in the registration area or in the baffle areas. The indicator is OFF when the Stacker is in standby mode. Refer to Jam Clearance in this section
5–24 D O C U C O L O R 2 0 6 0 / 2 0 4 5 O P E R A T O R M A N U A L
H I G H C A P A C I T Y S T A CK E R ( H C S )
Paper Stock Specifications
A C C E S S O R I E S
The following papers are considered to be baseline/centerline and are recommended to ensure you receive the best quality from your HCS:
Uncoated Xerox Digital Color Xpressions 94, 24 lbs. In Europe, Xerox Colotech+
90 g/m 2 .
Coated Xerox Digital Color Xpressions GlossCoated Text (120 g/m
2
/80 lbs.) In
Europe, Xerox ColoTech Gloss Coated 120 g/m
2
.
NOTE: Manufacturers of coated stock do not recommend its use when the ambient relative humidity exceeds 60%.
The Stack Tray accepts the following papers:
• Paper weights from a minimum of 64 g/m 2 up to 220 g/m 2 - either coated or uncoated stock. It also accepts paper from 221 g/m
2
up to 280 g/m 2 with the possibility of degraded stack quality and an increased jam rate.
• All standard media sizes supported by the digital press with the exception of JIS B5 LEF (Asian standard size) and 8.5 x 11"/A4 SEF
• Non-standard sizes from 182 to 320 mm (7.2 to 12.6") across the feed direction, and 203 to 488 mm (8.0 to 19.2") in the feed direction.
• 3 hole drilled 8.5 x 11" and A4 paper must be run LEF to the Stack Tray.
The Top Tray accepts the following papers:
• All media types, sizes, and weights that are supported by the digital press.
• Duplexed 3 hole drilled paper must be fed short edge first, therefore must be sent to the Top Tray.
D O C U C O L O R 2 0 6 0 / 2 0 4 5 O P E R A T O R M A N U A L 5–25
A C C E S S O R I E S H I G H C A P A C I T Y S T A CK E R ( H C S )
Media Types Accepted: Coated or uncoated stocks, drilled stock,
Transparencies and labels (labels can be sent only to the Top Tray).
Paper Weight Range for Trays: Stack Tray = 64 – 220 g/m
2
,
Top Tray = 64 – 280 g/m
2
.
Special Notes:
• Special materials may not run as reliably as the baseline paper
• Transparencies may be run to either the Top Tray or the Stack Tray. Stack height should be limited to 100 transparencies.
• Coated paper lighter than 100 g/m
2
may not run as reliably as coated paper heavier than 100 g/m
2
.
• Papers that are 80 g/m
2
or lighter require 210 mm (8.3") minimum measurement in the feed direction.
• Non-standard papers longer than 305 mm (12") in the feed direction require 210 mm (8.3") minimum measurement across the feed direction.
Top Tray Mode
Stack
Mode
Figure 13. HCS Paper Path
5–26 D O C U C O L O R 2 0 6 0 / 2 0 4 5 O P E R A T O R M A N U A L
H I G H C A P A C I T Y S T A CK E R ( H C S )
Selecting High Capacity Stacker Features
A C C E S S O R I E S
Use the following instructions to select the High Capacity Stacker when using the digital press scanner to make prints.
If sending a job through the network, refer to the Printing Guide that came with your Raster Image Processor for information on how to set the job Properties/
Parameters when using the HCS.
1
Touch More... on the Basic Features screen in the Copy Output column on the digital press Touch Screen.
Figure 14. Basic Features Screen
2
On the next screen, make the desired selections under Output Delivery and
Output Assembly, then touch the Stacker button.
D O C U C O L O R 2 0 6 0 / 2 0 4 5 O P E R A T O R M A N U A L 5–27
A C C E S S O R I E S H I G H C A P A C I T Y S T A CK E R ( H C S )
Figure 15. Output, More... Screen
3
Select the desired Output Catch Tray and your choice under Offset (refer to the descriptions on the following pages).
5–28
Figure 16. Output Device, Stacker Screen
D O C U C O L O R 2 0 6 0 / 2 0 4 5 O P E R A T O R M A N U A L
H I G H C A P A C I T Y S T A CK E R ( H C S )
4
Touch Save.
5
Select any other options for your job.
6
Press the Start button on the digital press Control Panel.
Stacker Mode
A C C E S S O R I E S
The Stacker Mode stacks collated sets sent from the digital press. The stacker tray has a capacity of 3500 sheets of 64 - 80 g/m
2
paper.
NOTE: Labels should not be sent to the Stack Tray.
.
Figure 17. Stacker Paper Path
Offset Mode
The Offset Mode offsets each set of sheets by 15 mm (0.6 inches) for easy separation.
Top Tray Mode
The High Capacity Stacker diverts sheets that are too small or too large to be stacked to the Top Tray. Any sheets that need to be purged after a paper jam are also sent to the Top Tray.
NOTE: Only use the Top Tray when printing labels.
Figure 18. Top Tray Paper Path
D O C U C O L O R 2 0 6 0 / 2 0 4 5 O P E R A T O R M A N U A L 5–29
A C C E S S O R I E S
Unloading the High Capacity Stacker
H I G H C A P A C I T Y S T A CK E R ( H C S )
When the High Capacity Stacker is full, or you want to retrieve a job that has been completed, the operator may unload the stacker by performing the following steps.
1
Press the Table Down Switch.
2
Wait until the elevator stops and the Please Wait indicator is OFF. The Ready To
Open indicator illuminates.
3
Open the High Capacity Stacker front door.
4
Position the securing bar onto the stacker cart handle as shown below.
Figure 19. Positioning the Stacker Cart Handle
5–30 D O C U C O L O R 2 0 6 0 / 2 0 4 5 O P E R A T O R M A N U A L
H I G H C A P A C I T Y S T A CK E R ( H C S ) A C C E S S O R I E S
5
Ensure that the handle is in the proper position on the top of the paper stack so that the stack will not move when the stacker cart is pulled out.
6
Pull the stacker cart straight out and remove the paper.
7
Push the empty stacker cart straight into the High Capacity Stacker.
8
Return the securing bar back into position as shown below.
Figure 20. Securing Bar Storage Position
9
Close the High Capacity Stacker front door.
10
Follow the instructions displayed on the digital press Touch Screen to resume printing.
D O C U C O L O R 2 0 6 0 / 2 0 4 5 O P E R A T O R M A N U A L 5–31
A C C E S S O R I E S
Jam Clearance
H I G H C A P A C I T Y S T A CK E R ( H C S )
A paper jam in the High Capacity Stacker will be indicated by a message on the digital press Touch Screen. Follow the instructions displayed. The image on the
HCSS Control Panel will flash showing the area where the jam is located.
Perform the following steps to clear the High Capacity Stacker jam and resume printing.
5–32
Figure 21. HCS Jam Clearance Areas
1
Lift the High Capacity Stacker Top Cover.
2
Lift the green handle, or handles, indicated on the Touch Screen and remove all paper in this area. Remove paper only from the areas indicated.
3
Close each green handle.
4
Close the High Capacity Stacker Top Cover.
5
If the Touch Screen indicates there is a jam in the digital press, follow the instructions on the screen to remove any paper in the area indicates. Refer to the
Jam Clearance section in the Problem Solving chapter in this manual.
6
Follow the instructions displayed on the digital press Touch Screen to resume printing.
D O C U C O L O R 2 0 6 0 / 2 0 4 5 O P E R A T O R M A N U A L
H I G H C A P A C I T Y S T A CK E R ( H C S )
High Capacity Stacker Maintenance
A C C E S S O R I E S
Cleaning the High Capacity Stacker
Do not clean any area inside the High Capacity Stacker. If the covers or Front
Door require cleaning, dampen a paper towel or soft, clean cloth with a liquid, nonabrasive glass cleaner or water.
To avoid damage to the High Capacity Stacker, do not pour or spray the cleaner or water directly onto the High Capacity Stacker. Always apply the liquid to the cloth first.
Do not use any other cleaners or solvents on the High Capacity Stacker or they may interact with the paint on the covers, eventually causing the paint to peel.
D O C U C O L O R 2 0 6 0 / 2 0 4 5 O P E R A T O R M A N U A L 5–33
A C C E S S O R I E S
Problem Solving
H I G H C A P A C I T Y S T A CK E R ( H C S )
If, after following the recommended solutions, the problem persists, call for assistance.
The Fault Codes described below appear on the HCS display panel.
Problem
Fault 052-311
Fault 212-252
Fault 212-253
Fault 212-251
Fault 212-254
Ready Indicator does not illuminate
Poor Stacking
Cause Solution
Communication problem
HCS Flipper wheel problem.
HCS Flipper wheel problem.
HCS Stacking Height problem
• Cancel or save the job.
• Power off the digital press. Wait 15 seconds and power on.
• Open Top Cover.
• Clear the paper path.
• If the fault code is still displayed, save or cancel the job, then power off the digital press. Wait 15 seconds and power on.
• Open Top Cover.
• Clear the paper path.
• If the fault code is still displayed, save or cancel the job, then power off the digital press. Wait 15 seconds and power on.
• Open Top Cover.
• Clear the paper path.
• If the fault code is still displayed, save or cancel the job, then power off the digital press. Wait 15 seconds and power on.
HCS Registration problem • Open Top Cover.
• Clear the paper path.
• If the fault code is still displayed, save or cancel the job, then power off the digital press. Wait 15 seconds and power on.
No power • Check the power cord connected to the power source.
• Check that the GFI circuit breaker is not tripped (rear cover).
• Check that the main switch is on.
Mixed sizes of paper
High paper curl
Run separate jobs and empty stacker.
• Adjust digital press decurler.
• Flip paper in digital press paper tray(s).
• Rotate paper in the digital press paper tray(s).
• Switch to heavier paper.
5–34 D O C U C O L O R 2 0 6 0 / 2 0 4 5 O P E R A T O R M A N U A L
H I G H C A P A C I T Y S T A CK E R ( H C S ) A C C E S S O R I E S
Poor Stacking continued:
Paper Jams:
Elevator does not go up.
Mixed sizes of paper
High paper curl
High paper curl
8 1/2 x 11 inch, 8 1/2 x 14 inch, A4 paper sizes
Mechanical obstruction
Lower paper path
High paper curl
Handle not in correct position.
Run separate jobs and empty stacker.
• Adjust digital press decurler.
• Flip paper in digital press paper tray(s).
• Rotate paper in the digital press paper tray(s).
• Switch to heavier paper.
• Adjust digital press decurler.
• Flip paper in digital press paper tray(s).
• Rotate paper in the digital press paper tray(s).
• Check that paper in the digital press is loaded short edge feed
(SEF).
• Check for obstruction in the stacker paper path.
• Ensure that all transports and baffles are properly seated.
• Ensure that the cart is properly seated.
Deselect offset or restart job.
• Adjust digital press decurler.
• Flip paper over in the paper tray being used.
• Rotate the paper in the paper tray being used.
• Switch to heavier paper.
• Open the front door and position the handle correctly.
Loss of Power
If power is interrupted to the High Capacity Stacker:
• Ensure the power cord is plugged in to the proper wall receptacle.
• Ensure that the digital press power is on.
• If the power has not been restored by the above procedure, call Xerox
Customer Support.
Also call your Xerox service representative if the loss of power to the High
Capacity Stacker seems to be frequent or excessive.
D O C U C O L O R 2 0 6 0 / 2 0 4 5 O P E R A T O R M A N U A L 5–35
A C C E S S O R I E S
High Capacity Stacker Stapler (HCSS)
H I G H C A P A C I T Y S T A CK E R S T A P L E R ( H C S S )
The High Capacity Stacker Stapler is an optional finishing device which provides stacking with offset and single or dual stapling output capabilities. Sets of up to
50 sheets of 64 - 80 g/m
2
may be stapled.
The High Capacity Stacker Stapler must be connected to the right end of the digital press, replacing the Offset Catch Tray. The Stack Tray has a capacity of
2000 sheets of 64 - 80 g/m
2
paper. The HCSS also has an Offset mode which provides separation between the stacked sets sent to the Stack Tray. The High
Capacity Stacker can also send output (not stapled) of 250 sheets of
64 - 80 g/m
2
paper to the Top Tray.
Banner sheets can be used with your Fiery RIP. The banner sheets must be printed on LEF 8.5" x 11" paper. Refer to the EX2000 Printing Guide for more information on how to turn this feature on.
Identifying High Capacity Stacker Stapler Parts
Top (or Purge) Tray
Offset Stacker
Stapler Tray
Figure 22. High Capacity Stacker Stapler
5–36 D O C U C O L O R 2 0 6 0 / 2 0 4 5 O P E R A T O R M A N U A L
H I G H C A P A C I T Y S T A CK E R S T A P L E R ( H C S S )
Control Panel
A C C E S S O R I E S
4
5
3
1 2
Figure 23. HCSS Control Panel
3
4
5
1
2
Name Function
Ready Indicator The Ready Indicator blinks when the digital press is being initialized. The Ready Indicator is constant when in use or in standby.
Staple Indicator The Staple Indicator blinks when the staple level in the stapler is low. The Staple Indicator is constant when the stapler is empty.
Keypad The keypad, including the C button, is used only by the
Xerox service representative.
Shows the fault codes.
Message
Display
Jam Indicator Area illuminates to indicate the location of a jam in the
HCSS.
D O C U C O L O R 2 0 6 0 / 2 0 4 5 O P E R A T O R M A N U A L 5–37
A C C E S S O R I E S H I G H C A P A C I T Y S T A CK E R S T A P L E R ( H C S S )
Electrical/Environmental Requirements
Western Hemisphere: 115 VAC, 15 amp, for 60 Hz. and 220 VAC, 10 amp for 50
Hz installations.
Europe: 200-240 Volt 10 amp 50 Hz service outlet.
The HCSS requires a separate power source from the digital press.
Temperature: 10º C (50º F) Min.
Relative Humidity (% RH): 15% Min.
Altitude: N/A
32º C (90º F) Max.
85%
Greater than 2000 meters (6560 ft.) above sea level may require field adjustments.
Better performance is achieved when conditions are maintained between
20-25º C (68-77º F).
Paper Stock Specifications
The High Capacity Stacker Stapler Top Tray accepts all media types, sizes, and weights supported by the DocuColor 2060/2045. The Stack Tray accepts all standard media sizes supported by the DocuColor 2060/2045 with the exception of sizes greater than A3/11 x 17".
Refer to the chart on the following page for information on accepted media types.
5–38 D O C U C O L O R 2 0 6 0 / 2 0 4 5 O P E R A T O R M A N U A L
H I G H C A P A C I T Y S T A CK E R S T A P L E R ( H C S S ) A C C E S S O R I E S
Name
JIS B5
A4
Inches
7.2x10.1
8.3x11.7
Letter
JIS B4
A3
SRA3
B5
8.5x11
8.5x13
8.5x14
10.1x14.33
11x17
11.7x16.5
12x18
12.6x17.7
12.6x19.2
7.2x10.1
8x10
Paper Size
MM
182 x 257
210 x 297
216 x 279
216 x 330
216 x 256
257 x 364
279 x 432
297 x 420
305 x 457
320 x 450
320 x 488
182 x 257
203 x 254
SEF
SEF
SEF
SEF
SEF
SEF
LEF
LEF
Orientation
SEF
SEF/LEF
SEF/LEF
SEF
SEF
Output
Stack Tray
50 sheet maximum for Stapling*
Yes
Yes
Yes
No
No
No
Yes
1
Yes
1
64 - 220 g/m
2
Staple Position
Yes
Yes
Yes
Yes
Yes
Portrait
Portrait/
Landscape
Portrait/
Landscape
Portrait/
Landscape
Portrait/
Landscape
Portrait
Portrait/Dual
Portrait/
Dual
–
–
–
Portrait
Portrait
Top Tray
64 - 280 g/m
2
Yes
Yes
Yes
Yes
Yes
Yes
Yes
Yes
Yes
Yes
Yes
Yes
1
The digital press cannot feed paper less than 8.3” (203 mm) in the feed direction below 80 g/m
2
.
* Refer to the table on page 5-48 for information on the stapling capacity for various paper types and weights.
D O C U C O L O R 2 0 6 0 / 2 0 4 5 O P E R A T O R M A N U A L 5–39
A C C E S S O R I E S
Paper Path
H I G H C A P A C I T Y S T A CK E R S T A P L E R ( H C S S )
Control Panel
Top Tray
Offset Stacker
Stapler Tray
Staple Cartridge
Figure 24. HCSS Paper Path
As media enters the HCSS, it is fed to the Top Tray or to the Offset Stacker
Stapler Tray, depending on your selections.
5–40 D O C U C O L O R 2 0 6 0 / 2 0 4 5 O P E R A T O R M A N U A L
H I G H C A P A C I T Y S T A CK E R S T A P L E R ( H C S S )
Using the High Capacity Stacker Stapler
A C C E S S O R I E S
Use the HCSS either by scanning documents and making your selections on the
Touch Screen, or by sending a document through the network and making your selections under Job Properties/Parameters.
• Use the following instructions to select the High Capacity Stacker
Stapler when scanning prints on the digital press.
• If sending a job through the network, refer to the Printing Guide that came with your Raster Image Processor for information on how to set the job Properties/Parameters when using the HCSS.
Hints and Tips
The HCSS cannot staple jobs with mixed sizes of paper.
The stacking may be skewed on the output from mixed size paper jobs.
You can mix coated and uncoated stock.
The HCSS accepts jobs of mixed weight papers below 220 g/m
2
.
Only clear paper jams at the area indicated on the HCSS Control Panel. Do not remove paper from any other areas of the paper path.
Stapling Hints
There are three stapling options:
• Single Staple Position 1
• Single Staple Position 2
• Dual Staple
If you select Single Staple, the screen in Figure 25 displays. Selecting Position 1 places a staple in the upper left corner of SEF or LEF sets. Position 2 places a staple in the bottom left corner of SEF sets only.
Selecting Dual Staple places two staples closer to the top/bottom center of the sheets than a single staple.
D O C U C O L O R 2 0 6 0 / 2 0 4 5 O P E R A T O R M A N U A L 5–41
A C C E S S O R I E S H I G H C A P A C I T Y S T A CK E R S T A P L E R ( H C S S )
Figure 25. Output Device, Single Staple Screen
Read the following procedure for more information on how to use the HCSS.
1
Touch More... in the Copy Output column on the Basic Features screen.
.
5–42
Figure 26. Basic Features Screen
D O C U C O L O R 2 0 6 0 / 2 0 4 5 O P E R A T O R M A N U A L
H I G H C A P A C I T Y S T A CK E R S T A P L E R ( H C S S ) A C C E S S O R I E S
2
On the next screen, make the desired selections under Output Delivery and
Output Assembly, then touch the Stapler/Stacker button.
.
Figure 27. Output, More... Screen
3
Select the desired Output Catch Tray and Stapling option. Then select Offset or
No Offset.
.
Figure 28. Output Device, Stapler/Stacker Screen
D O C U C O L O R 2 0 6 0 / 2 0 4 5 O P E R A T O R M A N U A L 5–43
A C C E S S O R I E S H I G H C A P A C I T Y S T A CK E R S T A P L E R ( H C S S )
4
Touch Save.
5
Select any other options for your job.
6
Press the Start button on the digital press Control Panel.
Feeding 3 Hole Drilled Paper
If you are stacking unstapled 3 hole drilled paper, the following is recommended:
• Send LEF Simplex (one sided) jobs to the Stack Tray.
• Send SEF Duplex (two sided) jobs to the Top Tray.
Using the Stack Tray for SEF Duplex jobs leads to an increase in uneven stacking caused by an interference between the holes and corners of subsequent sheets.
You can minimize uneven stacking by loading 3 hole drilled paper SEF in the paper tray with the holes toward the back of the digital press, and selecting Collated sets.
Refer to the following chart only when sending stapled jobs through the Fiery
EX2000. Selections are made in the Print Driver window, or in Job Properties at the Command Workstation.
When sending jobs scanned on the digital press to the HCSS for stapling, follow the feeding instructions for both plain and 3 hole drilled paper in the Paper and
Paper Trays chapter.
5–44 D O C U C O L O R 2 0 6 0 / 2 0 4 5 O P E R A T O R M A N U A L
H I G H C A P A C I T Y S T A CK E R S T A P L E R ( H C S S )
Stapling from the Fiery EX2000
A C C E S S O R I E S
Plain Paper
Simplex LEF @ 60 ppm
1. Load any Tray with LEF plain paper.
2. Select Front/Dual staple position.
3. Select HCSS Stack Tray as the output destination.
3 Hole Drilled Paper
Simplex LEF @ 60 ppm
1. Load Trays 1, 2, or 3 LEF with 3 hole drilled paper
(holes to the left in Trays 1 and 2, holes to the
right in Tray 3.)
2. Select Front/Dual staple position.
3. Select HCSS Stack Tray as the output destination.
Duplex LEF @ 30 ppm
1. Load any Tray with LEF plain paper.
2. Select Head to Head orientation.
3. Select Front/Dual staple position.
4. Select HCSS Stack Tray as the output destination.
Simplex SEF @ 45 ppm
1. Load any Tray with SEF plain paper.
2. Select Front staple position.
3. Select HCSS Stack Tray as the output destination.
Duplex SEF @ 22.5 ppm
1. Load Trays 1, 2, or 3 SEF with holes toward the back of the digital press.
2. Select Head to Head Duplex orientation.
3. Select Rear staple position.
4. Select HCSS Stack Tray as the output destination.
Note: Dual staple not available.
Simplex SEF @ 45 ppm
1. Load Trays 1, 2, or 3 SEF with 3 hole paper (holes
toward the front of the press.)
2. Select Front staple position.
3. Select HCSS Stack Tray as the output destination.
Duplex SEF @ 22.5 ppm
1. Load any Tray with SEF plain paper.
2. Select Head to Head orientation.
3. Select Front staple position.
4. Select HCSS Stack Tray as the output destination.
Simplex SEF @ 45 ppm
1. Load any Tray with SEF plain paper.
2. Select Front staple position.
3. Select HCSS Stack Tray as the output destination.
Duplex SEF @ 22.5 ppm
1. Load Trays 1, 2, or 3 SEF with holes toward the front of the digital press.
2. Select Head to Head Duplex orientation.
3. Select Front staple position.
4. Select HCSS Stack Tray as the output destination.
Simplex LEF @ 60 ppm
1. Load Trays 1, 2, or 3 LEF with 3 hole drilled paper
(holes to the left in Trays 1 and 2, holes to the
right in Tray 3.)
2. Select Front/Dual staple position.
3. Select HCSS Stack Tray as the output destination.
Duplex SEF @ 22.5 ppm
1. Load any Tray with SEF plain paper.
2. Select Front staple position.
3. Select Head to Head orientation.
4. Select HCSS Stack Tray as the output destination.
Duplex SEF @ 22.5 ppm
1. Load Trays 1, 2, or 3 SEF with holes toward the back of the digital press.
2. Select Head to Head Duplex orientation.
3. Select Rear staple position.
Note: Dual staple not available.
Sample Output
Note: ppm = pages per minute.
D O C U C O L O R 2 0 6 0 / 2 0 4 5 O P E R A T O R M A N U A L 5–45
A C C E S S O R I E S H I G H C A P A C I T Y S T A CK E R S T A P L E R ( H C S S )
Paper Specifications for Stapling
The following chart shows the stapling details for paper size, orientation, destination, and staple position. Numbers have been rounded up or down.
Staple Positions marked with an "O" may be selected in the position indicated.
Positions marked with an "x" are not available for stapling.
Items followed by an asterisk (*) have the following limitation. Papers that are
210 mm (8.3") in the feed direction must be greater than 80 g/m
2
in weight.
Inches MM
7.2 x 10.1
8.3 x 11.7
8.5 x 11
8.5 x 13
8.5 x 14
10.1 x 14.3
JIS B5 (182 x
257)
A4 (210 x 297)
216 x 279
216 x 330
216 x 356
JIS B4 (257 x
364)
SEF
11 x 17 279 x 432
11.7 x 16.5
A3 (297 x 420)
12 x 18 305 x 457
12.6 x 17.7
320 x 450
7.2 x 10.1
8 x 10
8.3 x 11.7
8.5 x 11
10.5 x 15.3
10.5 x 7.6
B5 (182 x 257)
203 x 254
LEF
LEF
A4 (210 x 297) LEF
216 x 279
Kai 8 (267 x 388)
Asian market size
Kai 16 (267 x
194) Asian market size
LEF
SEF
LEF
SEF
SEF
SEF
SEF
SEF
SEF
SEF
SEF
SEF
Sheet
Orientation
Output
Destination
HCSS Stack
Tray
64-220 g/m
2
(stapling)
Yes
Yes *
Yes *
Yes *
Yes
Yes
Yes
Yes
Yes
No
No
Yes
Yes
Yes
Yes
Yes
Front corner
O
Staple Position
Rear corner x
Dual x
HCSS Top Tray
64-280 g/m
2
(no stapling)
Yes
Output
Destination
O
O
O
O
O
O
O
--
--
O
O
O
O
O
O
O
O
O
O x x x
--
-x x x x x x x x x x x
O
O
--
-x x
O
O x x Yes *
Yes
Yes
Yes
Yes
Yes
Yes *
Yes *
Yes
Yes
Yes
Yes
Yes
Yes
Yes
5–46 D O C U C O L O R 2 0 6 0 / 2 0 4 5 O P E R A T O R M A N U A L
H I G H C A P A C I T Y S T A CK E R S T A P L E R ( H C S S ) A C C E S S O R I E S
NOTE: Stapled sets of large paper (A3, 11 x 17" and greater) may stack slightly skewed. The stapled sets will be of high quality.
Stapling Capacity for Different Paper Types and Weights
Following is the staple capacity for various types and weights of paper.
Paper Weight
64–80 g/m
2
81–105g/m
2
106–135 g/m
2
136–150 g/m
2
151–220 g/m
2
221–280 g/m
2
Transparencies
31
26
50
42
18
No *
No
Coated Uncoated
31
26
50
42
18
No *
No
No
No
No
No
No
Mix Sizes
No
No
* 221 to 280 g/m
2
paper, either coated or uncoated, cannot be stapled. These weights will be stacked in the Top Tray.
Unloading the High Capacity Stacker Stapler
To ensure consistent quality, unload sets of less than four sheets and lighter weight paper after 50 sets are made, or when the curl of the sets inhibits the ability of the sets to exit the HCSS.
When the Stack Tray is full, Fault Code 112-550 appears in the message display on the HCSS. The digital press Touch Screen displays a message, "Unload the
Main Tray of the Finisher".
The HCSS continues to stack sheets into the Stack Tray after the message appears, but excess sheets may have a degraded stacking quality. For best performance, unload the tray when 2,000 sheets have been stacked.
D O C U C O L O R 2 0 6 0 / 2 0 4 5 O P E R A T O R M A N U A L 5–47
A C C E S S O R I E S
Jam Clearance
H I G H C A P A C I T Y S T A CK E R S T A P L E R ( H C S S )
A paper jam in the High Capacity Stacker Stapler is indicated by a message on the digital press Touch Screen. The HCSS Control Panel display illuminates the area where the jam has occurred.
1
2
3
5–48
Figure 29. HCSS Jam Clearance Areas
Read the following steps for more information on how to clear a jam.
1
Open the HCSS Front Door. There are three possible jam areas as indicated in the photo above. Handle one moves down, handle two moves to the right, and handle three moves up.
2
Remove all jammed paper only from the area indicated on the Touch Screen and the HCSS Control Panel Display. Do not remove paper from any other areas.
3
Reposition the handle.
4
Close the HCSS Front Door.
5
Follow any instructions on the Touch Screen to restart your print job.
D O C U C O L O R 2 0 6 0 / 2 0 4 5 O P E R A T O R M A N U A L
H I G H C A P A C I T Y S T A CK E R S T A P L E R ( H C S S )
Ordering and Loading Staples
A C C E S S O R I E S
You can order new staple cartridges through the system you normally use for ordering Xerox supplies. The cartridge number to order is 8R12799. You should keep a supply on hand so production is not interrupted while you are waiting for staples to be shipped.
2
1
Grey
Handle
Figure 30. Staple Cartridge
1
Open the front door of the High Capacity Stacker Stapler.
2
Push the yellow (1) lever down with your left hand. Grasp the grey handle on the cartridge unit and pull it towards you until it stops. Release the yellow level and the unit will lock into place.
3
Grasp the yellow staple cartridge and pull it towards you. The entire unit will move forward, then the staple cartridge only will pull free of the unit.
4
Insert a new cartridge into the unit, and push it until you hear it click into place.
5
Push the yellow lever down and the cartridge unit automatically swings back into place.
D O C U C O L O R 2 0 6 0 / 2 0 4 5 O P E R A T O R M A N U A L 5–49
A C C E S S O R I E S H I G H C A P A C I T Y S T A CK E R S T A P L E R ( H C S S )
High Capacity Stacker Stapler Maintenance
Cleaning the High Capacity Stacker Stapler
Do not clean any area inside of the High Capacity Stacker Stapler. If the High
Capacity Stacker Stapler covers require cleaning, dampen a paper towel or soft, clean cloth with a liquid, nonabrasive glass cleaner or water.
To avoid damage to the High Capacity Stacker Stapler, do not pour or spray the cleaner or water directly onto the High Capacity Stacker Stapler. Always apply the liquid to the cloth first.
Do not use any other cleaners or solvents on the High Capacity Stacker Stapler or they may interact with the paint on the covers, eventually causing the paint to peel.
5–50 D O C U C O L O R 2 0 6 0 / 2 0 4 5 O P E R A T O R M A N U A L
H I G H C A P A C I T Y S T A CK E R S T A P L E R ( H C S S )
Problem Solving
A C C E S S O R I E S
If after reviewing the Problems and following the recommended solutions the problem persists, call for assistance.
Problem
Fault Code 112-100
Jam indicated in HCSS, but actually is in the Exit
Module.
Fault Code 112-100
Jam indicated in HCSS.
No visible jams in HCSS because sheet is located over the Exit Module sensor.
Fault Code 112-130
Jam indicated in HCSS, but is also in Exit Module.
Fault Code 112-130
Jam indicated in HCSS.
Fault Code 112-110
Fault Code 052-310
Cause Solution
Jammed Paper not visible in
HCSS, and fault code does not clear after opening and closing HCSS door.
Paper jammed between Exit
Module and HCSS sensors
Paper is jammed over both the
Exit Module and HCSS sensors.
Paper is jammed between the
Exit Module and the HCSS sensors.
Paper jammed in the HCSS and the Exit Module during a purge of sheets to the Top
Tray.
Communication problem
• Open the HCSS door.
• Jammed paper is not visible in the area indicated. Close the
HCSS door.
• The Touch Screen indicates a jam in the Exit Module. Open the Exit Module and clear any visible sheets.
• Open and close the HCSS door.
• Clear any other areas indicated on the Touch Screen.
• Open the HCSS door.
• Jammed paper is not visible in the area indicated. Close the
HCSS door.
• If the fault code remains, open the Exit Module. No jammed sheets are visible.
• Undock the HCSS. Find the jammed sheet between the Exit
Module and the HCSS. Refer to the Note below this table for information on how to undock the HCSS.
• Clear any other areas indicated on the Touch Screen.
• Open the HCSS door.
• Clear any visible jams.
• If no jammed paper is visible in the HCSS area indicated, open the Exit Module door and clear any jammed paper. Close the Exit Module door.
• Open and close the HCSS door.
• Open the HCSS door.
• If no jammed paper is visible in the area indicated, open the
Exit Module door and clear any jammed paper. Close the Exit
Module door.
• Open and close the HCSS door.
• If the fault persists, undock the HCSS and clear the jammed paper between the Exit Module and the HCSS. Refer to the
Note below this table for information on how to undock the
HCSS.
• Clear the jammed paper from the HCSS.
• Clear the jammed paper from the Exit Module.
• Open and close the HCSS door.
• Resume job.
• Cancel or save the job.
• Power off the digital press. Wait 15 seconds and power on.
D O C U C O L O R 2 0 6 0 / 2 0 4 5 O P E R A T O R M A N U A L 5–51
A C C E S S O R I E S H I G H C A P A C I T Y S T A CK E R S T A P L E R ( H C S S )
Problem
Fault Code 052-321
Fault Code 052-320
Fault Code 052-312
Paper Jams:
Cause
Connection problem
Unexpected connection
Communication problem
Ready Indicator does not illuminate
Poor Stacking:
No power
Mixed sizes of paper
High paper curl
Mechanical obstruction
Use Top Tray
High paper curl
Solution
• Cancel or save the job.
• Power off the digital press. Wait 15 seconds and power on.
• Cancel or save the job.
• Power off the digital press. Wait 15 seconds and power on.
• Cancel or save the job.
• Power off the digital press. Wait 15 seconds and power on.
• Check the power cord connected to the power source.
• Check that the main switch is on.
Run separate jobs and empty stacker.
• Adjust digital press decurler.
• Flip paper in digital press paper tray(s).
• Rotate paper in the digital press paper tray(s).
• Check for obstruction in the stacker stapler paper path.
• Ensure that all transports and baffles are properly seated.
Deselect offset or restart job to the Top Tray.
• Adjust digital press decurler.
• Flip paper in digital press paper tray(s).
• Rotate paper in the digital press paper tray(s).
• Switch to heavier paper.
NOTE: To undock the HCSS from the digital press, reach into the circular area near the bottom of the HCSS for the Undocking Lever. Refer to the picture below.
5–52
Undocking Lever inside here
Figure 31. HCSS Undocking Lever
Pull the lever toward you and hold it in position while moving the HCSS a small distance (25.4mm, 1") away from the press. Release the lever and continue to move the HCSS as far as required.
D O C U C O L O R 2 0 6 0 / 2 0 4 5 O P E R A T O R M A N U A L
H I G H C A P A C I T Y S T A CK E R S T A P L E R ( H C S S )
Loss of Power
A C C E S S O R I E S
If power is interrupted to the High Capacity Stacker Stapler:
• Ensure the power cord is plugged in to the proper wall receptacle.
• Ensure that the digital press power is on.
• If the power has not been restored by the above procedure, call Xerox
Customer Support.
Also call your Xerox service representative if the loss of power to the High
Capacity Stacker seems to be frequent or excessive.
D O C U C O L O R 2 0 6 0 / 2 0 4 5 O P E R A T O R M A N U A L 5–53
A C C E S S O R I E S H I G H C A P A C I T Y S T A CK E R S T A P L E R ( H C S S )
This page is intentionally left blank.
5–54 D O C U C O L O R 2 0 6 0 / 2 0 4 5 O P E R A T O R M A N U A L
6.
Problem Solving
General Problems
When a problem occurs with your DocuColor 2060/2045, instructions appear on the Touch Screen. Refer to the information in this chapter to help resolve the problem.
If the DocuColor 2060/2045 has a loss of power and you cannot access the
Machine Details tab to get the serial number, open the two main front doors. The serial number label is in the center of the bottom frame of the digital press.
This chart lists problems and suggested solutions that apply to your DocuColor
2060/2045. If the problem persists after following all instructions, call your Xerox representative.
Problem
The digital press does not power on.
(Continued on next page.)
Suggested solutions
• Ensure the power cord is plugged into the receptacle correctly.
• Ensure the power switch inside the front left door is set to the on position.
NOTE: If the RIP indicates that the digital press has a fault and the touch screen does not readily display a message, press the Machine Status button and touch Error Log to display the fault history.
D O C U C O L O R 2 0 6 0 / 2 0 4 5 O P E R A T O R M A N U A L 16 6–1
P R O B L E M S O L V I N G
Problem
The digital press does not power on
(continued).
Prints are not on desired paper size.
Suggested solutions
• Check the GFI circuit breaker switch.
• If the power in your location is working properly, you have tried the suggested solutions, and the digital press power does not power on, call for assistance.
• Ensure that the proper paper is loaded in the paper trays.
• Select the paper size, tray and weight through the digital press options on your PC.
• Ensure that the correct weight is selected on the tray.
• Ensure that “Fit to Paper” or an equivalent selection is not selected in your print driver.
• Go into Tools Mode and adjust registration.
Refer to the Tools Mode in the System
Administration Guide.
Misregistration of the scan to print image from the Document
Glass.
Paper is misfed or wrinkles repeatedly.
• If a message appears on the Touch Screen, follow the instructions displayed and refer to the information in this chapter.
• Ensure the proper paper (refer to the Paper chapter of this manual and the Recommended
Materials List) is loaded correctly and not filled above the MAX line.
• Turn the paper stack around and/or over in the selected paper tray.
• Remove a few sheets from the top and the bottom of the stack in the paper tray.
• Fan all four edges of the paper in the selected paper tray.
• Replace the paper in the selected paper tray with paper from a new package.
• Remove any partially fed paper from the trays.
• Ensure the paper you are using had been stored properly.
6–2 D O C U C O L O R 2 0 6 0 / 2 0 4 5 O P E R A T O R M A N U A L
P R O B L E M S O L V I N G
Problem Suggested Solution
The Control Panel
Touch Screen does not respond to a touch command.
You cannot program a job while a screen is open.
Digital press with scanner features are not selectable.
• Press Clear All on the Control Panel.
• Touch a selectable button on the Touch Screen.
A slight pressure is required to cause the digital press with scanner to react.
• If the problem persists, open the Front Door of the digital press with scanner. Close the Front
Door and make a selection on the Touch
Screen. If the Touch Screen does not respond to any touch commands, switch off the power.
Wait 15 seconds. Then switch on the power.
Reprogram the digital press with scanner for the copy features that are desired.
Jobs cannot be programmed or copies made while some screens, such as administration screens, jam clearance screens, or consumable status information screens, are open. Follow the directions on the information screen. Then program the desired job.
Certain features cannot be selected because of the previous selections. Generally, features or buttons you can select appear selectable to indicate you can use them with the previous selections. Refer to the “Overview” chapter for more information about buttons.
D O C U C O L O R 2 0 6 0 / 2 0 4 5 O P E R A T O R M A N U A L 6–3
P R O B L E M S O L V I N G
Problem
Transparencies
Transparencies are too oily.
Multiple sheets feed from the paper trays.
Suggested Solution
• Load the transparencies by following the instructions in Chapter 3, “Paper and Paper
Trays.
• Make 5 blank sheet copies with the Full Color option on paper stock to purge excess oil from system. Reload the transparencies and continue the copying job.
• Refer to the Recommended Materials List and the Color Materials Usage Guide for more information about transparencies.
• Do not fill the paper trays above the MAX fill line indicator.
• Remove the paper from the tray and fan the sheets to separate the joined sheets.
• Predrilled sheets may stick together at the holes. Remove the paper from the tray and fan the sheets to separate the joined sheets.
• Paper and transparencies may stick together if environmental conditions are too dry and cause excessive static. Increase the humidity level in the room to minimize static.
• Gently fan transparencies to separate the sheets before you load them.
6–4 D O C U C O L O R 2 0 6 0 / 2 0 4 5 O P E R A T O R M A N U A L
P R O B L E M S O L V I N G
Problem
Sheets will not feed from Paper Tray 4
Paper jams when exiting the Paper
Trays
Output jams when exiting the digital press to the Offset
Catch Tray
Copies originating from Paper Tray 4 are skewed. Jams may be occurring.
Digital press with scanner does not make copies when
Auto Paper is selected.
Suggested Solution
• Ensure that the height of the stack does not exceed the MAX fill line.
• Check that the paper guide is not too tight. The paper guide should be adjusted to fit snug against the paper stack.
• Ensure that the edge guides of the paper tray fit snugly against the paper stack.
• Do not fill the paper trays above the MAX fill line indicator.
• Close the tray slowly to avoid shifting the paper stack.
• When no other output device is present, the
Offset Catch Tray can hold up to 500 sheets of
24 pound (90 g/m
2
) paper. Empty the catch tray when output approaches this limit to ensure continuous production.
• Ensure the first sheet is not blocking the paper exit, particularly for 11 x 17 inch (A3) output.
The paper guides on Paper Tray 4 may not be set correctly or may be too tight against the paper stack. Ensure that the paper guide lightly touches the paper stack.
For the Auto Paper selection to function correctly, the size of the original document must be the same size as the paper supply that is loaded in at least one of the trays. If not, select the paper tray size that best meets your needs. Or, if you wish to continue to use the Auto Paper feature, load one of the trays with the same size paper as the original document.
D O C U C O L O R 2 0 6 0 / 2 0 4 5 O P E R A T O R M A N U A L 6–5
P R O B L E M S O L V I N G
Problem
Fresh copies used as original documents cause jams in the
Duplex Automatic
Document Feeder.
Excessive paper curl
(continued on the next page).
Suggested Solution
This problem is caused by the oil used in the fusing process. The problem can be reduced or eliminated by allowing output to sit for awhile so oil can evaporate before using them as original documents.
Paper curl may be a result of:
• Ensure that the correct paper weight and paper type are selected.
• The mass of dry ink (toner) coverage on the copy - the greater the toner mass, the greater the paper curl.
• The paper weight.
• The humidity conditions at the digital press with scanner.
• You can sometimes minimize curl problems by flipping the paper over in the tray and making the copies again. If excessive curl is still present, use a heavier paper.
• Attempt to minimize the amount of dry ink on the copy paper by selecting the Photo feature as the Document Type and/or the lighter and/ or less chroma image quality options.
• Select the Full Color option instead of 3 Pass
Color to minimize the amount of dry ink on the copy paper.
• Empty the output device when output approaches this limit to ensure continuous production.
6–6 D O C U C O L O R 2 0 6 0 / 2 0 4 5 O P E R A T O R M A N U A L
P R O B L E M S O L V I N G
Problem
Excessive paper curl
(continued).
Moiré patterns on the copies
Suggested Solution
Paper curl may be a result of:
• Allow output to sit for awhile so any excess oil can evaporate before using them as original documents.
• Copying high density background areas or documents with alternating high and low density areas results in more curl. Attempt to reduce the amount of curl by adjusting the image quality controls to reduce the amount of dry ink on the copies.
• Place the digital press with scanner and paper in a room with air conditioning and low humidity to minimize the moisture in the environment.
• Attempt to copy on thicker paper or on paper stock that is less sensitive to moisture.
• This problem sometimes occurs when original documents have halftone images. Perform the following suggested solutions in the following order:
• Select Halftone as the Original Type. If selecting Halftone does not solve the problem, select Map as the Original Type.
• Rotate the original on the Document Glass by
180 degrees.
• Reduce or enlarge the output by 5%.
• Use the Sharpness feature to select Softer options until the moiré patterns are not visible.
D O C U C O L O R 2 0 6 0 / 2 0 4 5 O P E R A T O R M A N U A L 6–7
P R O B L E M S O L V I N G
Problem
The entire document is not being copied
Scattered, very light show-through images occur when copying a document that is on thin paper.
A black border appears.
Suggested Solution
• Enter the Original Input.
• Reduce the image.
• Select the Background Erase option in the
Image Tone Presets feature in the Image
Quality tab.
• To eliminate the unwanted show-through images, place the thin (translucent) document on the Document Glass. Cover the document with a black (or very dark) sheet of paper that is the same size as the document you are copying.
• Place the 2-sided original document on the
Document Glass with a blank sheet of paper on top of it.
• Adjust the Lighten/Darken control to Lighten.
• Select the Photo & Text or Text document type and the Lighten/Darken feature or Background
Erase in the Image Tone Presets feature of the
Image Quality tab.
• Select the Auto Center option in the Image
Shift feature or the Edge Erase feature of the
Added Features tab.
Or:
• Program the Original Input in the Added
Features tab for the dark bordered document that you wish to copy.
6–8 D O C U C O L O R 2 0 6 0 / 2 0 4 5 O P E R A T O R M A N U A L
P R O B L E M S O L V I N G
Problem
The edge of the original image is deleted from the copies.
Copies made from photographs show color or background on output edges
Copies made using the 100% Reduce/
Enlarge feature do not include the entire image along the edge of the document.
Output is too light.
Output is too dark.
Output has too much contrast.
Output has low contrast.
Suggested Solution
• Edge deletion on all sides of the copy is normal, and is greatest on the lead edge of the copy. Set the Edge Erase feature, Variable
Erase option, to 4 mm to minimize the deletion.
Select the size for the original document in the
Added Features tab and an appropriate setting from the Reduce/Enlarge option.
• Moisture may be present in the paper. Load a fresh supply of paper into the trays.
• Some deletions may be caused by small pieces of paper remaining in the digital press with scanner components after a paper jam has been cleared. When clearing a paper jam, be sure to look for and remove any paper fragments.
Most emulsions used to develop photographs have color. Sometimes this color shows on the border of the photograph. To prevent the color from being copied as part of the image or as background, use the Edge Erase feature on the Added Features tab to deliberately erase the unwanted color or background.
Select the Original Input feature and program the exact size of the dark bordered document that you wish to copy.
Use the Lighten/Darken feature to select a darker level. Select the Text or Maps option in the Original
Type feature.
Use the Lighten/Darken feature to select a lighter level. Select the Photo option in the Original Type feature.
Select less Chroma (toward Pastel) in the Image
Quality tab.
Select more Chroma (toward Vivid) in the Image
Quality tab. Select the Maps option in the Original
Type feature.
D O C U C O L O R 2 0 6 0 / 2 0 4 5 O P E R A T O R M A N U A L 6–9
P R O B L E M S O L V I N G
Problem
Background on the copies.
Suggested Solution
• Examine the input document for the source of the problem.
• Ensure that the document is held flat on the
Document Glass and that the document cover is closed.
• From the Image Quality tab, adjust the Lighten/
Darken control to Lighten.
• When making Black copies, select Black Only as the Color Mode. Reduce the Color Balance so the background does not appear on the copies.
• When copying colors, set the Color Mode to
Auto and set the Image Tone Preset
Background Erase option so that the background does not appear on the copies.
• Determine the type of document you are copying. From the Original Type feature, indicate whether the original is Photo & Text,
Text, Photo, or Maps for best image quality.
NOTE: Use the Photo option for documents that contain areas of different density, from light to dark, when all levels of density need to be copied.
6–10 D O C U C O L O R 2 0 6 0 / 2 0 4 5 O P E R A T O R M A N U A L
P R O B L E M S O L V I N G
Problem
The copies are blurred when copying thick documents, threedimensional objects, or books.
The image quality gradually degrades on successive copies, or copies made with settings used previously are significantly worse than copies you are making now.
Copies have dark bands on the lead edge and a corner when 100% Reduce/
Enlarge is selected.
Suggested Solution
• Increase the Sharpness.
• Select the Text or Maps option in the Original
Type feature.
• Ensure that the document is held flat on the
Document Glass and that the document cover is closed as much as possible. DO NOT force the cover closed.
• The internal process control function of the digital press with scanner has degraded.
• Place a white sheet of paper on the Document
Glass and run 35 blank copies using Full Color in the Color Mode feature. Make a copy of the document again. Ensure that the image quality selections are set properly.
• If the problem persists, contact your System
Administrator or refer to the System
Administrator Guide.
• The bands may be caused by curled edges on the document or by misregistration of the document on the Document Glass. Ensure that the document is registered correctly.
• Ensure that the Edge Erase is at No Erase (2 mm). Increasing the amount of Edge Erase should remove more of the dark bands but could cause image loss.
D O C U C O L O R 2 0 6 0 / 2 0 4 5 O P E R A T O R M A N U A L 6–11
P R O B L E M S O L V I N G
Problem
Copies have dark bands on the lead edge and a corner when 100% Reduce/
Enlarge is selected and the DADF is used.
Corner Shift appears in the wrong area on the copy.
Large black borders appear on the copies with documents smaller than the copy paper size.
The image density of the copy seems lighter toward the trail edge.
Suggested Solution
The bands may be caused by curled edges on the document or by misregistration of the document by the DADF. Ensure that the Edge Erase is at No Erase
(2 mm). Increasing the amount of Edge Erase should remove more of the dark bands but could cause image loss.
Ensure the document is positioned on the
Document Glass and the correct Corner Shift is selected.
• No shift is selected. Select the Auto Center feature to eliminate the black borders.
• Also, select the Auto Center feature to eliminate the black borders for digital press with scanners equipped with the Duplex
Automatic Document Feeder (DADF).
This defect is noticeable only when the input document has large solid areas. To reduce or eliminate this defect, select the Photo option in the
Original Type feature of the Image Quality tab.
6–12 D O C U C O L O R 2 0 6 0 / 2 0 4 5 O P E R A T O R M A N U A L
P R O B L E M S O L V I N G
Problem
Copies made from a newspaper, a map, or a photograph have background when
Original Type is defined as Maps or
Photo.
It is difficult to perform secondary operations on the copies, such as writing on them or using adhesives.
Greyish spots appear when scanning a glossy photo or glossy original.
Suggested Solution
• The DocuColor 2060/2045 digital press with scanner detects low densities of color and reproduces them. This is especially true with the Maps and Photo options.
• Use the Background Erase option in the Image
Tone Presets feature in the Image Quality tab.
• Newspaper show-through can be reduced or eliminated by backing the document with a black sheet of paper.
• The background can be reduced or eliminated by adjusting the Lighten/Darken feature toward lighten.
This problem is caused by the oil used in the fusing process. The problem can be reduced or eliminated by setting the copies aside for one or two hours before performing a secondary operation on them.
Rubbing the copy surface with a soft, clean cloth or eraser may also help.
Place a transparency on the Document Glass then place the glossy photo or glossy original face down on the transparency to reduce the glare.
D O C U C O L O R 2 0 6 0 / 2 0 4 5 O P E R A T O R M A N U A L 6–13
Left
Side
Door
Upper
Door
Tray 1
Tray 2
Tray 3
P R O B L E M S O L V I N G
Jam Clearance
DADF
If a jam occurs, the DocuColor 2060/2045 stops printing and a message is displayed on the Touch Screen. Follow all instructions displayed completely and in sequence. Refer to this chapter for additional information to resolve the problem.
If power is interrupted during the printing process, it is imperative that you clear all other jam areas before you open and clear areas behind the Right and Left
Front Doors of the digital press. Figure 1 illustrates the various parts of the digital press. Follow the jam clearance instructions on the Touch Screen.
Touch Screen
Offset
Catch
Tray
Exit
Module
Transport
Module
Left Front
Door
Right Front Door
Figure 1. DocuColor 2060/2045
6–14 D O C U C O L O R 2 0 6 0 / 2 0 4 5 O P E R A T O R M A N U A L
P R O B L E M S O L V I N G
DADF Jam Clearance
When a document jam occurs in the Duplex Automatic Document Feeder, the
Document Feed Lamp lights and instructions for clearing the jam appear on the
Touch Screen.
Document Feed Lamp
Left
Cover
Figure 2. DADF
1
Open the Left Cover by lifting it to the left.
2
Remove the jammed documents. Check for and remove any torn pieces of paper.
3
Close the Left Cover.
D O C U C O L O R 2 0 6 0 / 2 0 4 5 O P E R A T O R M A N U A L 6–15
P R O B L E M S O L V I N G
4
Slide the Document Guide away from the stack of documents.
5
Raise the DADF and remove any documents from the Document Glass.
6
Remove any paper that is on the DADF belt.
7
Close the DADF.
8
Check the documents for damage, creases, and/or folds before reloading them into the Document Feeder Tray.
NOTE: If a document is damaged, you may have to use Interrupt mode to make a copy from the Document Glass. You can then return to the original job and use the copy instead of the damaged document in the stack of documents you are copying.
9
Check the message on the screen to ensure that all jams are cleared.
10
Reload the stack of documents into the Duplex Automatic Document Feeder according to the instructions on the Touch Screen. Reposition the document guide.
11
Press the Start button to restart your copy job.
6–16 D O C U C O L O R 2 0 6 0 / 2 0 4 5 O P E R A T O R M A N U A L
P R O B L E M S O L V I N G
Left Side Door Jam
Digital
Press
Rear
Figure 3. Left Side Door (Area 1)
Digital
Press
Front
1
Open the Left Side Door of the DocuColor 2060/2045. If you have an optional Tray
4 (refer to the Accessories chapter in this manual), open the Tray 4 Right Door, then open the Left Side Door of the digital press.
2
Carefully remove all jammed paper, ensuring that all pieces are removed if the paper rips.
3
Close the Left Side Door. If you have an optional Tray 4, close the Tray 4 Right
Door.
D O C U C O L O R 2 0 6 0 / 2 0 4 5 O P E R A T O R M A N U A L 6–17
P R O B L E M S O L V I N G
Trays 1, 2 and 3 Jams
CAUTION: The Feed Heads and the Feed Rolls are delicate and can be damaged if this procedure is not followed precisely.
From
Tray 4
Transport
Module
Tray 1
Tray 2
Tray 3
Figure 4. Paper Path of Trays 1, 2 and 3
To the
Digital
Press
From
Horizontal
(Duplex)
Transport
1
Perform the Left Side Door Jam procedure on the previous page before opening
Trays 1 and 2.
2
Open Tray 1.
6–18 D O C U C O L O R 2 0 6 0 / 2 0 4 5 O P E R A T O R M A N U A L
P R O B L E M S O L V I N G
3
Carefully remove all jammed paper.
4
Close Tray 1.
5
Open Tray 2.
6
Carefully remove all jammed paper.
7
Close Tray 2.
8
Perform the Transport Module Jam procedure later in this chapter before opening
Tray 3.
9
Open Tray 3.
10
Carefully remove all jammed paper.
11
Close Tray 3.
12
Follow the instructions on the Touch Screen to resume your print job.
D O C U C O L O R 2 0 6 0 / 2 0 4 5 O P E R A T O R M A N U A L 6–19
P R O B L E M S O L V I N G
Upper Door Jam
2
Figure 5. Upper Door
1
Open the Upper Door above Tray 1.
2
Lower the Feed Transport by pulling down on green handle 2.
3
Carefully remove all jammed paper.
4
Raise the Feed Transport back into its original position.
NOTE: The front door will not close if the Feed Transport handle is not seated properly.
5
Close the Upper Door.
6
Follow the instructions on the Touch Screen to resume your print job.
6–20 D O C U C O L O R 2 0 6 0 / 2 0 4 5 O P E R A T O R M A N U A L
P R O B L E M S O L V I N G
Transport Module Jam
Paper from Trays
1, 2, and 4
Takeaway
Transport
Paper from
Tray 3
Upper
Transport
To the Digital
Press
Lower
Transport
Single Sided prints from the Horizontal
Transport
Figure 6. Transport Module Paper Path
3a
7b
Figure 7. Transport Module
3b
7a
D O C U C O L O R 2 0 6 0 / 2 0 4 5 O P E R A T O R M A N U A L 6–21
P R O B L E M S O L V I N G
1
Open the Transport Module door.
2
When printing 1-Sided or 2-Sided, grasp the green handle 3a, squeeze and move it to the right.
3
Carefully remove all jammed paper.
4
Reposition the green handle 3a.
5
Lift green handle 3b.
6
Carefully remove all jammed paper and return handle 3b to the original position.
7
When printing 2-Sided, also lift handle 7a and remove all jammed paper. Return handle 7a to the original position.
8
When a Tray 3 misfeed occurs, release handle 7b and remove all jammed paper.
Return handle 7b to the original position.
9
Close the Transport Module door.
10
Follow the instructions on the Touch Screen to restart your print job.
6–22 D O C U C O L O R 2 0 6 0 / 2 0 4 5 O P E R A T O R M A N U A L
Exit Module Jams
P R O B L E M S O L V I N G
8e
8c
8d
8f
8g
Decurler
From Digital Press
To Inverter Transport Duplex Inverter
Transport
To Digital Press
Figure 8. Exit Module Paper Path
8a
8b
Figure 9. Exit Module
D O C U C O L O R 2 0 6 0 / 2 0 4 5 O P E R A T O R M A N U A L 6–23
P R O B L E M S O L V I N G
1
Open the Exit Module door.
2
When printing 1-Sided or 2-Sided, squeeze and open green handle 8a.
3
Squeeze and open green handle 8b.
4
Squeeze and open green handle 8c.
5
Squeeze and open green handle 8d.
6
Squeeze and open green handle 8f.
7
Carefully remove all jammed paper. Turn green knob 8e to free any immovable paper.
8
Reposition the green handle 8a and ensure the handle is seated properly.
9
Reposition the green handle 8b and ensure the handle is seated properly.
10
Reposition the green handle 8c and ensure the handle is seated properly.
11
Reposition the green handle 8d and ensure the handle is seated properly.
12
Reposition the green handle 8f and ensure the handle is seated properly.
13
When printing 2-Sided or face down output, lift handle 8g.
14
Carefully remove all jammed paper.
15
Reposition the green handle 8g and ensure the handle is seated properly.
16
Close the Exit Module door.
17
Follow the instructions on the Touch Screen to restart your print job.
6–24 D O C U C O L O R 2 0 6 0 / 2 0 4 5 O P E R A T O R M A N U A L
P R O B L E M S O L V I N G
Right/Left Door Paper Path Jams
Registration, Vacuum Transport and Fuser
From Transport Module
To Transport Module
Alignment
Transport
Fuser
Transport
Vacuum Transport
Inverter Transport
Inverter
Gate
To Exit
Module
Horizontal Transport 2
Horizontal Transport 1
Figure 10. Right/Left Door Paper Path
From
Duplex
Inverter
Transport
Figure 11. Right and Left Doors Open
D O C U C O L O R 2 0 6 0 / 2 0 4 5 O P E R A T O R M A N U A L 6–25
P R O B L E M S O L V I N G
4a
Fuser
4b
4
4c
4d
4e
Figure 12. Alignment, Vacuum and Fuser Transport
KEY POINT: It is imperative that you clear all other jam areas before you open and clear the Right and Left Front Door areas.
CAUTION: The Fuser area is extremely hot and injury will occur if not handled correctly.
1
Open the Right and Left Front Doors.
2
Grasp handle 4 and move it in the direction of the arrow.
3
Slowly pull the Paper Transport straight out until it stops.
4
Lift handle 4a and carefully remove all jammed paper, ensuring that all pieces are removed if the paper is torn. Turn the green handle 4b to free any immovable paper.
6–26 D O C U C O L O R 2 0 6 0 / 2 0 4 5 O P E R A T O R M A N U A L
P R O B L E M S O L V I N G
5
Reposition green handle 4a.
6
The Fuser area is on the right hand side of the Paper Transport. Lift handle 4c on the right hand side and lay the Inverter Transport back.
7
Lift handle 4d and clear all jammed paper. Rotate knob 4e counterclockwise to clear any immovable paper.
NOTE: Occasionally a sheet of paper wraps around the heat roll. (The heat roll is visible when handle 4d is up.) DO NOT attempt to remove this sheet of paper because the stripper fingers may be damaged if you attempt this procedure. Call your Xerox service representative to remove this piece of paper.
8
Reposition green handle 4d and close the Inverter Transport 4c. Ensure the magnets are in place front and back.
9
Slowly push in the Paper Transport until it stops. Ensure that the green handle is seated properly.
10
Close the Right and Left Front Doors.
11
Follow the instructions on the Touch Screen to restart your print job.
D O C U C O L O R 2 0 6 0 / 2 0 4 5 O P E R A T O R M A N U A L 6–27
P R O B L E M S O L V I N G
Horizontal Transport (2-Sided Printing Only)
When printing 2-Sided output, perform the following in addition to steps 2 through 8 of the Registration, Vacuum Transport, and Fuser procedure.
6–28
5
6
Figure 13. Digital Press Horizontal Transport
CAUTION: The Fuser area is extremely hot and injury will occur if not handled correctly.
1
Lift both of the Horizontal Transport handles 5 and 6.
2
Apply pressure to the handles to securely latch them.
CAUTION: The paper can rip if the paper is not pushed before removing it from under the lip of the Transport.
3
Push the paper back until you see the edge of the paper, then remove the paper.
4
Reposition handles 5 and 6.
5
Close the Right and Left Front Doors.
6
Follow the instructions on the Touch Screen to restart your print job.
D O C U C O L O R 2 0 6 0 / 2 0 4 5 O P E R A T O R M A N U A L
Fault Codes
P R O B L E M S O L V I N G
When there is a problem with the digital press or an accessory, refer to the Touch
Screen where the Fault Code and a solution will be displayed. Follow all steps until the problem is corrected. If the problem persists, call the following number for assistance.
Follow the instructions below before calling for service.
1
Be prepared to provide a complete description of the problem to the service operator. Defining the problem accurately may help you and the operator solve the problem over the phone and minimize downtime. If the problem cannot be solved by telephone, a service representative will be dispatched to your site promptly.
2
Record the displayed Fault Codes.
3
Record the Machine Serial Number. Press the Machine Status button on the
Control Panel. Touch the Machine Details tab and the serial number is displayed.
4
If copy quality is a problem, take a copy sample to the telephone with you to help you describe the problem or to assist you when answering the questions from the service operator about the defects.
5
If possible, use a phone near the press when calling for assistance. Follow the instructions provided by the operator.
6
For system support, user help, and service support, call the appropriate number:
US: 1-800-821-2797
Canada: 1-800-939-3769
Europe: _________________________
Latin America:_________________________
D O C U C O L O R 2 0 6 0 / 2 0 4 5 O P E R A T O R M A N U A L 6–29
P R O B L E M S O L V I N G
This page is intentionally left blank.
6–30 D O C U C O L O R 2 0 6 0 / 2 0 4 5 O P E R A T O R M A N U A L
7.
Technical Data
Raster Image Processor (RIP)
Refer to the documentation that comes with your RIP.
Digital Press Specifications
Electrical Power Requirements (200/240 - 50/60 Hz)
Specifications
Single phase - Three wire plus safety ground
Current service - 30 Amp sole use @ 200V to 240V
20 Amp sole use @ 220V to 240V
Range (line to neutral) - 200 V minimum to 240 V maximum
Frequency - 50/60 Hz
Power Consumption
Standby - 2.6 KVA maximum
Run - 4.8 KVA maximum
Power Saver - 1.9 KVA maximum
D O C U C O L O R 2 0 6 0 / 2 0 4 5 O P E R A T O R M A N U A L 17 7–1
T E CH N I C A L D A T A
Heat Output
Standby - 7936 BTU
Run - 12,300.8 BTU
Air Exchange Rate
Standby - 6143 cubic feet
Run - 21,609.72 cubic feet
Power Saver - 1059.3 cubic feet
Energy Star/Sleep Mode
Standby - 2.3 KW
Run - 3.6 KW
Power Saver - 45 W
Environmental Requirements
As an ENERGY STAR Partner, Xerox Corporation has determined that this product meets the ENERGY STAR guidelines for energy efficiency.
Operating Temperatures:
Minimum: 50°F (10°C) at 15 percent relative humidity
Maximum: 90°F (32°C) at 85 percent relative humidity
NOTE: Above 82°F (28°C), reduced humidity is required to maintain the specified performance.
Altitude
Normal configuration: maximum 10,000 feet (3000 meters).
7–2 D O C U C O L O R 2 0 6 0 / 2 0 4 5 O P E R A T O R M A N U A L
T E CH N I C A L D A T A
Noise Levels
Standby
IOT Operation
Full System Operation
Continuous Noise
49.5 dBa
64.0 dBa
72.0 dBa
Impulse Noise
N/A
72.0 dBa
72.0 dBa
Ozone Emissions
Not to exceed 0.02 PPM (maximum)
Imaging material: No unpleasant odor
Dust
Dust concentration during continuous run should be 0.1mg/cubic meter.
Capabilities
Tray Capacity
Paper Trays 1 and 2 have a capacity of 550 sheets.
Paper Tray 3 has a capacity of 2200 sheets.
Throughput
Tray 1/Tray 2: Inches/JIS B5 (LEF/SEF) to 11 x 17 inch/A3 SEF
Tray 3: Inches/JIS B5 (LEF/SEF) to 12.6 x 19.2 inch (320 x 487mm) SEF
Warm-up Time
7 minutes
First Print Out Time
16 seconds
D O C U C O L O R 2 0 6 0 / 2 0 4 5 O P E R A T O R M A N U A L 7–3
T E CH N I C A L D A T A
:
Print Rates
Use the Productivity Setting in the Tools Mode to optimize the throughput speed for the type of paper you run most frequently. This feature is available only for the DocuColor 2060.
• Selecting Auto selects a Fuser temperature based on the paper weight selected on the paper tray, improving average power consumption, but slowing operation while the Fuser heats up or cools down.
• Selecting Light Weight sets the Fuser temperature to 160 o
C, which optimizes the throughput speed for light weight papers, and uses less power.
• Selecting Heavy Weight sets the Fuser temperature to 175 o
C, which optimizes the throughput speed for heavier papers, and uses more power.
Refer to the Systems Administrator Guide for the procedure.
The DocuColor 2045 speeds for each paper weight are listed in this table and cannot be changed.
Substrate
64 - 80 g/m
2
81 - 105 g/m
2
106 - 135 g/m
2
136 - 150 g/m
2
151 - 220 g/m
2
221 - 280 g/m
2
Transparencies
45 ppm*
45 ppm
30 ppm
30 ppm
22.5 ppm
22.5 ppm
22.5 ppm
DocuColor
2045
DocuColor 2060
Heavy Weight
45 ppm
Light Weight
45 ppm
45 ppm
60 ppm
30 ppm
30 ppm
22.5 ppm
22.5 ppm
60 ppm
30 ppm
30 ppm
22.5 ppm
22.5 ppm
22.5 ppm
Auto
45 ppm
60 ppm
60 ppm
30 ppm
30 ppm
22.5 ppm
22.5 ppm
Table 1. Substrate Print Speeds
*ppm = prints per minute
7–4 D O C U C O L O R 2 0 6 0 / 2 0 4 5 O P E R A T O R M A N U A L
T E CH N I C A L D A T A
Physical Characteristics
Digital Press Size
92.3 inches/2380 mm (W) x 37.4 inches/950 mm (D) x 55.6 inches /
1412 mm (H)
Digital Press Weight
1870 pounds/850 Kg
Floor Space Requirements
Minimum space requirements for the basic configuration of the digital press, including the RIP: 178.5 inches/4505mm L x 165.4 inches/3167mm W.
Duplex Automatic Document Feeder (DADF) Specifications
Document Feeding Method
Face-up, top feed method.
Sizes
Minimum: 8.5 x 11 inches (216 x 279 mm)/A4 (SEF)
Maximum:11 x 17 inches (279 x 432 mm)/A3 (SEF)
DADF Capacity
50 for 38 - 100 g/m
2
documents.
40 for 101 - 128 g/m
2
D O C U C O L O R 2 0 6 0 / 2 0 4 5 O P E R A T O R M A N U A L 7–5
T E CH N I C A L D A T A
Speed
40 black and white copies per minute (A4 or 8.5 x 11 inch. LEF)
12 black and white copies per minute (A3 or 11 x 17)
Power Source
Supplied from the Digital Press.
Noise
Run: 68 dB(A)
Dimensions
25.19 inches/640 mm (W) x 21.06 inches/535 mm (D) x 5.11inches/130 mm (H)
Weight
28.7 lbs. (14 kg)
Floor Space Requirements
Refer to the DocuColor 2060/2045 Installation Planning Guide.
7–6 D O C U C O L O R 2 0 6 0 / 2 0 4 5 O P E R A T O R M A N U A L
Metric Conversion Chart
NOTE: Note that most numbers are rounded off.
T E CH N I C A L D A T A
0.3
0.5
0.6
0.7
0.8
1
0.15
0.2
0.25
0.28
0.01
0.04
0.05
0.1
4
5
2
2.3
2.5
3
1.4
1.5
1.7
1.9
Inches
15
18
7
13
20
25.4
6
7
4
5
1
3
0.254
1
64
76
51
58
43
48
36
38
104
127
Millimeters
(mm)
8.5
8.7
9.0
10.0
10.5
10.8
7.8
8.0
8.3
8.4
6
7.2
7.3
7.5
11.8
11.85
12.5
13.0
11.0
11.1
11.15
11.5
13.4
13.45
Inches
216
221
229
254
267
274
198
203
211
213
153
183
185
190
300
301
318
330
279
282
283
292
340
342
Millimeters
(mm)
Inches/
International
Sizes
13.5
14.0
8.0
15.75
16.9
17.0
24.0
Millimeters
429
432
610
343
356
203
400
(mm)
5 x 8
8 x 10
8 x 11
A4
8.5 x 11
8.5 x 13
8.5 x 14
8.7 x 14
9 x 11
9 x 14
11 x 17
A3
12 x 17
12 x 18
SRA3
12.6 x 17.7
127 x 203
203 x 254
203 x 279
210 x 297
216 x 279
216 x 330
216 x 356
221 x 356
229 x 279
229 x 356
279 x 432
297 x 420
305 x 432
305 x 457
320 x 450
Celsius (°C)
10
32
100
200
204
218
Kilograms
1.0
0.454
Fahrenheit
50
90
212
392
400
425
(°F)
Pounds
2.205
1.0
D O C U C O L O R 2 0 6 0 / 2 0 4 5 O P E R A T O R M A N U A L 7–7
T E CH N I C A L D A T A
This page is intentionally left blank.
7–8 D O C U C O L O R 2 0 6 0 / 2 0 4 5 O P E R A T O R M A N U A L
8.
Maintenance
This chapter describes the consumable supply replenishment procedures necessary for keeping your DocuColor 2060/2045 operating reliably.
For troubleshooting problems, refer to the Problem Solving Section of this manual. Problems that cannot be solved need to be referred to your Xerox service representative. Use the procedure in this section when it becomes necessary to request a service call.
The procedure for ordering supplies and a list of the supplies you should keep onhand are also included in this chapter.
Cleaning the Touch Screen
Clean the Touch Screen during the digital press warm-up cycle at the start of each day. Remove all dust and fingerprints by wiping the Touch Screen with a clean, lint-free cloth.
CAUTION: To avoid damage, do not use any Xerox cleaner, water, or commercial cleaner on the Touch Screen.
D O C U C O L O R 2 0 6 0 / 2 0 4 5 O P E R A T O R M A N U A L 18 8–1
M A I N T E N A N C E
Cleaning the Document Glass
Keep the Document Glass clean to ensure that prints are the best quality. Clean the Document Glass at the beginning of each day and during the day as needed.
1
Slightly dampen a clean, lint-free cloth with Xerox Lens and Mirror Cleaner or a glass cleaner that is not abrasive.
CAUTION: To avoid damage, do not pour or spray the cleaner directly onto the
Document Glass.
2
Clean the Document Glass by wiping the glass in the lengthwise direction. Keep your fingers off the glass.
3
Use a clean, dry, lint-free cloth to wipe off any excess moisture.
4
Repeat these steps until there are no visible marks or streaks on the Document
Glass.
8–2 D O C U C O L O R 2 0 6 0 / 2 0 4 5 O P E R A T O R M A N U A L
M A I N T E N A N C E
Cleaning the Document Glass Cover
Keep the Document Glass cover clean at all times. Any white foreign substance on the surface of the cushion may cause the digital press to calculate the actual document size or its position incorrectly, resulting in an unsatisfactory print.
Clean the Document Glass Cover at the beginning of each day and during the day as needed.
1
Lift the Document Glass Cover.
2
Slightly dampen a clean lint-free cloth with Film Remover.
3
Wipe the underside of the Document Glass Cover until it is clean and dry.
4
Close the Document Glass Cover.
Replacing Consumable Supplies
A message is displayed on the Touch Screen when a consumable item is nearing the replacement time. Another message is displayed when you must replace consumable items. The press will not continue to run after this message is displayed until the item is replaced.
You should keep a supply available of the following consumable items:
• Dry Ink/Toner cartridges in all four colors
• Fuser Oil
• An empty Waste Dry Ink/Toner bottle.
D O C U C O L O R 2 0 6 0 / 2 0 4 5 O P E R A T O R M A N U A L 8–3
M A I N T E N A N C E
Replacing a Dry Ink/Toner Cartridge
Refer to the following procedure when a message to replace a Dry Ink/Toner
Cartridge is displayed on the Touch Screen. There are also instructions on labels that are affixed to the compartment containing the cartridges.
CAUTION: To prevent spillage, remove Dry Ink/Toner cartridges only when the
“Replace the Dry Ink Cartridge” message is displayed on the Touch Screen.
1
Place a drop cloth below the Dry Ink/Toner area.
2
Open the Dry Ink/Toner Compartment.
Dry Ink Compartment Door
Figure 1. Dry Ink Compartment
8–4 D O C U C O L O R 2 0 6 0 / 2 0 4 5 O P E R A T O R M A N U A L
M A I N T E N A N C E
3
Rotate the empty cartridge counter-clockwise until the arrow on the cartridge is aligned with the unlocked padlock on the compartment label.
4
Pull the cartridge completely out of the compartment. Dispose of the empty cartridge according to local regulations.
CAUTION: Do not use warm or hot water, or cleaning solvents, to remove Dry
Ink/Toner from your skin or clothing. This will set the Dry Ink/Toner and make it difficult to remove. If any Dry Ink/Toner gets on your skin or clothing, use a brush to remove it, blow it off, or wash it off with cold water and mild soap.
Figure 2. Removing a Cartridge
D O C U C O L O R 2 0 6 0 / 2 0 4 5 O P E R A T O R M A N U A L 8–5
M A I N T E N A N C E
5
Remove a new cartridge from the box.
CAUTION: Dry Ink/Toner settles and compacts during shipping and must be loosened before inserting the cartridge into the machine. Failure to completely loosen the material may cause damage to the gear at the end of the cartridge.
KEY POINT: Vigorously shake and/or slap the new cartridge with your hand until the Dry Ink/Toner is completely loosened. To determine if the material is loose, place your finger tips on the flat side of the gear cogs at the back of the cartridge and turn the gear clockwise. When the gear turns freely, the material is loose and the cartridge can be inserted into the compartment.
Figure 3. Turning the Cartridge Gear
8–6 D O C U C O L O R 2 0 6 0 / 2 0 4 5 O P E R A T O R M A N U A L
M A I N T E N A N C E
6
To insert the cartridge into the compartment, align the arrow on the cartridge with the unlocked padlock on the compartment and slide the cartridge into the compartment.
CAUTION: If more than one cartridge needs to be replaced at the same time, ensure that the cartridges are replaced in their correct color locations. From left to right, the cartridge colors are black, cyan, magenta, and yellow.
7
Rotate the cartridge clockwise until the arrow on the cartridge is aligned with the locked padlock on the compartment.
Figure 4. Inserting a Cartridge
8
Close the Dry Ink/Toner compartment.
D O C U C O L O R 2 0 6 0 / 2 0 4 5 O P E R A T O R M A N U A L 8–7
M A I N T E N A N C E
Adding Fuser Oil
A message appears on the Touch Screen advising you when to add Fuser Oil. Use the following procedure to replenish the Fuser Oil supply.
1
Open the Right Front Door of the digital press.
2
Place a drop cloth on the floor under the Fuser area. Any oil spilled on a hard floor will make the floor slippery.
3
Refer to the following figure for the location of the Fuser Oil Reservoir Cap.
Fuser Oil Cap
8–8
Figure 5. Fuser Oil Cap
D O C U C O L O R 2 0 6 0 / 2 0 4 5 O P E R A T O R M A N U A L
M A I N T E N A N C E
4
To open the Reservoir Cap, grasp the tab at the back of the cap and pull it forward.
5
Remove the cap from the bottle of Fuser Oil and replace it with the Filler Spout
Cap. This cap was provided to you when your digital press was installed. Contact your Xerox service representative if you cannot locate the Filler Spout Cap and need another one.
6
Carefully insert the Filler Spout into the opened Fuser Oil Reservoir and squeeze the bottle until the oil reaches the maximum fill level tab visible inside the
Reservoir.
7
Remove the Filler Cap from the bottle and place it on a cloth or paper towel to drain. Return the original cap to the bottle of Fuser Oil.
8
Close the Reservoir Cap, ensuring that it snaps into place.
9
Close the Right Front Door of the digital press.
D O C U C O L O R 2 0 6 0 / 2 0 4 5 O P E R A T O R M A N U A L 8–9
M A I N T E N A N C E
Changing the Waste Dry Ink/Toner Bottle
A message appears on the Touch Screen advising you when to replace the Waste
Dry Ink/Toner Bottle.
The bottle is located at the back of the Exit Module. Refer to the following figure.
Exit Module
Waste Dry Ink/
Toner Bottle location
Figure 6. Waste Dry Ink/Toner Bottle location
To order consumable supplies, refer to Consumable Supplies in this chapter.
8–10 D O C U C O L O R 2 0 6 0 / 2 0 4 5 O P E R A T O R M A N U A L
M A I N T E N A N C E
1
Open the Waste Dry Ink/Toner door at the back of the Exit Module. Refer to the following figure.
Figure 7. Waste Bottle Door opened
2
Grasp the handle of the full bottle and pull it out of the machine.
3
Remove the cap from the cap holder on the side of the full bottle and press the cap securely into the open hole on the top of the full bottle.
Open hole
Cap in holder
Figure 8. Waste Dry Ink/Toner Bottle
4
Dispose of the full bottle according to your local regulations.
5
Remove an empty bottle from the carton and insert it into the machine. Ensure that the hole on the top of the bottle is open.
6
Close the Waste Dry Ink/Toner Bottle door.
D O C U C O L O R 2 0 6 0 / 2 0 4 5 O P E R A T O R M A N U A L 8–11
M A I N T E N A N C E
Calling for Service
Refer to the Touch Screen when there is a problem with the digital press or an accessory. A status code and suggested solutions are displayed on the screen.
Follow all steps in the suggested solutions until the problem is corrected. If the problem persists, call for assistance.
Follow the instructions below before calling for service.
1
Be prepared to provide a complete description of the problem to the service operator. Defining the problem accurately may help you and the operator solve the problem over the phone and minimize downtime. If the problem cannot be solved by telephone, a service representative will be dispatched to your site promptly.
2
Record the displayed Fault Codes.
3
Record the Machine Serial Number. Press the Machine Status button on the
Control Panel. Touch the Machine Details tab and the serial number is displayed. (If for some reason the serial number is not displayed, open the Right/
Left Front Doors of the digital press. The serial number is also on a white label on the bottom front frame.)
4
If copy quality is a problem, take a copy sample to the telephone with you to help you describe the problem or to assist you when answering the questions from the service operator about the defects.
5
If possible, use a phone near the press when calling for assistance. Follow the instructions provided by the operator.
6
For system support, user help, and service support, call the appropriate number:
US: 1-800-821-2797
Canada: 1-800-939-3769
Europe: _________________________
Latin America:_________________________
8–12 D O C U C O L O R 2 0 6 0 / 2 0 4 5 O P E R A T O R M A N U A L
M A I N T E N A N C E
Consumable Supplies
The following items are shipped with the DocuColor 2060/2045. It is recommended that you have a supply of these items available to eliminate downtime when they need to be replaced.
Supply Item
Dry Ink/Toner (Black)
Dry Ink/Toner (Cyan)
Dry Ink/Toner (Magenta)
Dry Ink/Toner (Yellow)
Developer (Black)
Developer (Cyan)
Developer (Magenta)
Developer (Yellow)
Fuser Oil
*Waste Dry Ink/Toner Container
Paper
Supply
Number
Eastern
Hemisphere
6R90289
6R90290
6R90291
6R90292
5R90246
5R90247
5R90248
5R90249
8R4004
8R90352
Colotech+
Supply
Number
Western
Hemisphere
6R975
6R976
6R977
6R978
5R629
5R630
5R631
5R632
8R3993
8R12662
Brightwhite 94
Supply Unit
Shipped with digital press/
Reorder
Quantity
1
1
1
1
1
1
1
1
1
1
2 reams
Approximate Print
Yield/Carton (Full
Color Prints*)
19K
29K
29K
29K
100K
100K
100K
100K
200K
50k
* Please call your Xerox service representative if you need to reorder Waste Dry Ink/Toner Containers. Only Xerox service representatives are able to reorder Waste Dry Ink/Toner Containers.
D O C U C O L O R 2 0 6 0 / 2 0 4 5 O P E R A T O R M A N U A L 8–13
M A I N T E N A N C E
Store supply items and Xerox parts in their original packages in a convenient location.
* Dry Ink/Toner yield projections are based on 15 percent area coverage per color
(4 colors = 60 percent) at standardized conditions on 8.5 x 11 inch Xerox Digital
Color Brightwhite 94 (previously Xerox Color Xpressions) 24 lb. (90 g/m
2
) and
Colotech+ 90 g/m
2 reference paper.
NOTE: Actual yields vary greatly, depending on color intensity, area coverage, paper stock, and run mode selected.
To order consumable supplies, call the appropriate number:
US: 1-800-822-2200
Canada: French: 1-800-668-0133, English: 1-800-668-0199
Europe: _________________________
Latin America:_________________________
8–14 D O C U C O L O R 2 0 6 0 / 2 0 4 5 O P E R A T O R M A N U A L
I N D E X
9.
Index
Numerics
100%
1-Sided Output
Drilled Paper
2-Sided Output
Drilled Paper
1-1
1-2
2-1
2-2
Paper Trays 1, 2, and 3
A
Accepted Paper Types
High Capacity Stacker (HCS) 5–26
Access Button
Accessories
High Capacity Stacker (HCS) 5–22
High Capacity Stacker Stapler (HCSS)
Added Features Screen
Bound Originals
Stored Programming
Adding Fuser Oil
D O C U C O L O R 2 0 6 0 / 2 0 4 5 O P E R A T O R M A N U A L 9–1
I N D E X
9–2
Additional Finishing Options 1–22
Die Cutting
Embossing
Varnish
Arrow Buttons
Audio Tones
Auto Paper Supply
B
Back...Tab
Auto
Color Mode
Output
Reduce/Enlarge
Basic Scanning Steps
Looseleaf Binding
Mechanical Binding
Perfect Binding
Saddle Stitching
Binding Preparation
Bottling
Gathered Signature
Nested Signature and Binders Creep
Border Erase
Bound Originals
Build Job
D O C U C O L O R 2 0 6 0 / 2 0 4 5 O P E R A T O R M A N U A L
I N D E X
C
C (Clear) Button
Calibration
Calling for Service
Capabilities
Print Rates
Throughput
Tray Capacity
Warm-up Time
Capturing an Image Digitally
Additional Tips
Calibration
Output Considerations
Certifications in Europe
Changing the Waste Dry Ink/Toner Bottle
Chapter 1 About Color Printing
Chapter 2 Overview
Chapter 3 Paper and Paper Trays
Chapter 4 Scanner
Chapter 5 Accessories
Chapter 7 Technical Data
Chapter 8 Maintenance
Chroma
Clear All Button
Coated Paper
Paper Tray 4
Color Balance
Color Bar
Color Management
Color Mode
3 Pass Color
Auto
Black Only
Full Color
Single Color
D O C U C O L O R 2 0 6 0 / 2 0 4 5 O P E R A T O R M A N U A L 9–3
I N D E X
9–4
Color Printing Overview
Color Range
Color Shift
Color Translation
Consumable Supplies
Access Button
C (Clear) Button
Clear All Button
Features Button
Interrupt Button
Job Status Button
Keypad
Language Button
Machine Status
Machine Status Button
Pause Button
Power Saver Button
Start Button
Conventions
Symbols
Writing Style Conventions xxviii
Covers
Cutting and Trimming Paper 3–2
D
Dark Edges
Deleting an Area
Delete Programming
D O C U C O L O R 2 0 6 0 / 2 0 4 5 O P E R A T O R M A N U A L
I N D E X
Digital Press
Calling for Service
Consumable Supplies
Maintenance
Replacing Consumable Supplies 8–3
Digital Press Capabilities
Print Rates
Throughput
Tray Capacity
Warm-up Time
Digital Press Electrical Power Requirements 7–1
Air Exchange Rate
Heat Output
Power Consumption
Specifications
Digital Press Environmental Requirements
Dust
Noise Levels
Ozone Emissions
Digital Press Paper Path
Digital Press Physical Characteristics
Size
Digital Press Specifications
Disconnect Device
Document Glass
Document Specifications
Drilled Paper
1-Sided Print Jobs
2-Sided Print Jobs
Duplex Print Jobs
High Capacity Stacker Stapler (HCSS)
Overview
D O C U C O L O R 2 0 6 0 / 2 0 4 5 O P E R A T O R M A N U A L 9–5
I N D E X
9–6
Dry Ink/Toner Cartridges
Dry Ink/Toner Waste Bottle 2–7
Duplex Automatic Document Feeder (DADF)
Clearing a DADF Jam
Document Specifications
Identifying Duplex Automatic Document Feeder (DADF) Parts 4–5
Jam Clearance
Using the Duplex Automatic Document Feeder (DADF) 4–6
Duplex Automatic Document Feeder (DADF) Specifications
Capacity
Dimensions
Document Feeding Method
Noise
Sizes
E
Ecology Module
Border Erase
Electrical Module
Electrical Power Requirements
Air Exchange Rate
Heat Output
Power Consumption
Specifications
Electrical Safety
Environmental Notices for Canada
Environmental Notices for the USA
Exit Module
D O C U C O L O R 2 0 6 0 / 2 0 4 5 O P E R A T O R M A N U A L
I N D E X
F
Factors Affecting Color Output
Additive Color
Paper Type
Raster Image Processors (RIP) 1–6
Subtractive Color
Factors Affecting Image Quality 1–11
Paper
Factors Affecting Image Reproduction
Color Contrast
Scanners
Fault Codes
FCC in the USA
Features Button
Fiery EX2000 stapling hints
File Formats
Finishing Options
Additional Finishing Options 1–22
Binding Preparation
Folding Techniques
Fixed Selection Buttons
Folding Techniques
Accordion Fold
Parallel Fold
Right Angle Fold
Halftone Dot Shapes
Halftone Dots
Halftone Screens
G
General Problems
Ground Fault Indicator (GFI) Circuit Breaker
D O C U C O L O R 2 0 6 0 / 2 0 4 5 O P E R A T O R M A N U A L 9–7
I N D E X
9–8
H
High Capacity Stacker (HCS) 5–22
Identifying High Capacity Stacker (HCS) Parts
Jam Clearance
Loss of Power
Maintenance
Paper Guidelines
Problem Solving
Selecting High Capacity Stacker (HCS) Features 5–27
Special Notes
Stack Tray
Stacker Mode
Top Tray
Top Tray Mode
Unloading
High Capacity Stacker Stapler (HCSS)
Electrical/Environmental Requirements
Feeding Drilled Paper
Hints and Tips
Identifying High Capacity Stacker Stapler (HCSS) Parts
Jam Clearance
Loss of Power
Maintenance
Ordering and Loading Staples
Paper Guidelines
Paper Path
Paper Specifications for Stapling 5–46
Problem Solving
Stapling Capacity by Paper Weight/Type
Stapling from the Fiery EX2000
Stapling Hints
Unloading
Using the High Capacity Stacker Stapler (HCSS)
Hold Job Button
Horizontal Transport (2-Sided Printing Only)
D O C U C O L O R 2 0 6 0 / 2 0 4 5 O P E R A T O R M A N U A L
I N D E X
I
Icon Buttons
Identifying Duplex Automatic Document Feeder (DADF) Parts 4–5
Identifying High Capacity Stacker (HCS) Parts
Identifying High Capacity Stacker Stapler (HCSS) Parts
Identifying the Digital Press External Parts
Document Glass
Dry Ink/Toner Waste Bottle 2–7
Duplex Automatic Document Feeder (DADF)
Ecology Module
Electrical Module
Exit Module
Ground Fault Indicator (GFI) Circuit Breaker
Power Switch
Scanner
Touch Screen
Upper Door
Identifying the Digital Press Internal Parts
Dry Ink/Toner Cartridges
Exit Module
Paper Path
Serial Number Label
Upper Door
Identifying Tray 4 Parts
Modifying the Color
Sharpening an Image
Image Quality of the Original
Image Quality Overview
D O C U C O L O R 2 0 6 0 / 2 0 4 5 O P E R A T O R M A N U A L 9–9
I N D E X
9–10
Image Quality Screen
Chroma
Color Balance
Color Bar
Color Shift
Image Tone Presets
Sharpness
Unrestricted Shift
Image Tone Presets
Background Erase
Lively
Normal
Sharp
Warm
Inserts
Interrupt Button
It’s Illegal in Canada
It’s Illegal in the USA
J
Jam Clearance
Duplex Automatic Document Feeder (DADF)
Exit Module Jams
High Capacity Stacker (HCS) 5–32
High Capacity Stacker Stapler (HCSS)
Horizontal Transport (2-Sided Printing Only)
Left Side Door Jam
Overview
Paper Tray 4
D O C U C O L O R 2 0 6 0 / 2 0 4 5 O P E R A T O R M A N U A L
I N D E X
Right/Left Door Paper Path Jams 6–25
Transport Module Jam
Upper Door Jam
Job Assembly Screen
Build Job
Proof Set
Job List Screen 2–20
Job Monitor Screen
Job Status
Job Status Button
Hold Job Button
Job List Screen 2–20
Promote Job Button
Release Job Button
Up/Down Arrow Buttons 2–20
K
Keypad
L
Labels
Language Button
Laser Safety
Letterhead Paper
Paper Tray 4
Paper Trays 1, 2, and 3
Loading Paper
Paper Tray 4
Paper Trays 1, 2, and 3
Loading Staples
Loss of Power
High Capacity Stacker (HCS) 5–35
High Capacity Stacker Stapler (HCSS) 5–53
Paper Tray 4
D O C U C O L O R 2 0 6 0 / 2 0 4 5 O P E R A T O R M A N U A L 9–11
I N D E X
9–12
M
Machine Status
Meters
Machine Status Button
Machine Details Tab
Meters Screen
Maintenance Tab
Maintenance
Digital Press
Adding Fuser Oil
Changing the Waste Dry Ink/Toner Bottle
Cleaning the Document Glass Cover
Cleaning the Document Screen
Cleaning the Touch Screen
Replacing a Dry Ink/Toner Cartridge
High Capacity Stacker (HCS) 5–33
Cleaning the High Capacity Stacker (HCS)
High Capacity Stacker Stapler (HCSS)
Cleaning the High Capacity Stacker Stapler (HCSS)
Paper Tray 4
Cleaning Tray 4
Maintenance Safety
Map
Meters Screen
Metric Conversion Chart
Modifying the Color
More... Button
More...Tab
D O C U C O L O R 2 0 6 0 / 2 0 4 5 O P E R A T O R M A N U A L
I N D E X
N
Negative Image
Non-standard Size Paper
Paper Tray 4
Paper Trays 1, 2, and 3
Notices
Certifications in Europe
Environmental Notices for Canada
Environmental Notices for the USA
It’s Illegal in Canada
It’s Illegal in the USA
Radio Frequency Emissions
N-Up
O
Operational Safety
Option Buttons
Ordering Staples
Auto
Dark Edges
Map
Photo
Text
Output
Uncollated
D O C U C O L O R 2 0 6 0 / 2 0 4 5 O P E R A T O R M A N U A L 9–13
I N D E X
9–14
Output Considerations
2-Sided Output Settings
File Formats
Halo
Jagged Edges
Knockout
Overprint
Registration
Output Format Screen
Covers
Inserts
Negative Image
N-Up
Repeat Image
Transparency Options
Oversize Paper
Paper Trays 1, 2, and 3
Ozone Safety
P
Paper Guidelines
High Capacity Stacker (HCS) 5–25
Accepted Paper Types
Paper Weight Range
Special Notes
Stack Tray
Top Tray
High Capacity Stacker Stapler (HCSS)
Paper Specifications for Stapling 5–46
Staple Capacity by Paper Weight/Type
D O C U C O L O R 2 0 6 0 / 2 0 4 5 O P E R A T O R M A N U A L
I N D E X
Paper Tray 4
Paper Size
Paper Weight Range
Transfer Paper
Paper Trays 1, 2, and 3
Drilled Paper
Paper Size
Paper Weight Range
Transfer Paper
Paper Handling
Cutting and Trimming Paper 3–2
Paper Storage
Store Paper
Paper Path in the Digital Press
Paper Path of Paper Tray 4 5–2
Paper Path of Trays 1, 2, and 3 3–4
Paper Size
Paper Tray 4
Paper Specifications for Stapling 5–46
Paper Stock Specifications
Special Paper Stock for Tray 4
Paper Storage
Auto Paper Supply
Paper Tray 4
Identifying Tray 4 Parts
Jam Clearance
Loading Paper
D O C U C O L O R 2 0 6 0 / 2 0 4 5 O P E R A T O R M A N U A L 9–15
I N D E X
9–16
Loss of Power
Maintenance
Non-standard Size Paper
Paper Guidelines
Paper Path
Paper Reliability
Problem Solving
Selecting Tray 4
Tray 4 Environmental Requirements
Tray 4 Physical Characteristics 5–21
Tray 4 Specifications
Paper Trays
1, 2, and 3
4
Paper Trays 1, 2 and 3
Paper Guidelines
Paper Trays 1, 2, and 3
2-Sided Printing
Drilled Paper
Loading Paper
Non-standard Size Paper
Oversize Paper
Paper Path
Transparency Guidelines
Tray Capacity
Paper Weight Conversion Ranges
Paper Weight Conversion Tables
Paper Weight Conversion Ranges
Specific Paper Weight Conversion
Specific Weight Conversion 3–17
D O C U C O L O R 2 0 6 0 / 2 0 4 5 O P E R A T O R M A N U A L
I N D E X
Paper Weight Range
High Capacity Stacker (HCS) 5–26
Paper Tray 4
Pause Button
Percentage Conversions
Photo
Power Saver Button
Power Switch
Print Rates
Auto
Problem Solving
General Problems
High Capacity Stacker (HCS) 5–34
High Capacity Stacker Stapler (HCSS)
Loss of Power
Paper Tray 4
Promote Job Button
Proof Set
R
Radio Frequency Emissions
FCC in the USA
Raster Image Processor (RIP)
Recall Programming
Recommended Papers and Special Materials 3–1
Paper Handling
www.xerox.com
D O C U C O L O R 2 0 6 0 / 2 0 4 5 O P E R A T O R M A N U A L 9–17
I N D E X
9–18
Reduce/Enlarge
100%
Auto%
More... Button
% by Length
100%
Auto%
Preset/Variable
Third Button
Registration, Vacuum Transport and Fuser
Release Job Button
Relocating the DocuColor 2060/2045 2–41
Repeat Image
Replacing a Dry Ink/Toner Cartridge
Replacing Consumable Supplies 8–3
S
Safety Extra Low Voltage Approval
Save Buttons
Scanner
Added Features Screen
Duplex Automatic Document Feeder (DADF)
Image Quality Screen
Job Assembly Screen
Output Format Screen
Overview
Touch Screen
White Border Edges on Copies
Serial Number Label
Sharpening an Image
Sharpness
Specific Paper Weight Conversion
D O C U C O L O R 2 0 6 0 / 2 0 4 5 O P E R A T O R M A N U A L
I N D E X
Stacker Mode
Staple Capacity by Paper Weight/Type
Stapling from the Fiery EX2000
Start Button
Store Programming
Stored Programming
Delete Programming
Recall Programming
Store Programming
Supplies
Symbols
T
Tabbed Inserts
Overview
Paper Tray 4
Text
Top Tray Mode
Touch Screen
Tabs/Buttons/Icons
Touch Screen Button Types and Functions
Touch Screen Button Types and Functions
Transfer Paper
Paper Tray 4
Transparencies
Paper Tray 4
Transparency Guidelines
Transparency Options
Tray 4 Capabilities
Throughput
Tray Capacity
Tray 4 Environmental Requirements
Atmosphere Requirements
Dust
Noise Levels
Ozone Emissions
D O C U C O L O R 2 0 6 0 / 2 0 4 5 O P E R A T O R M A N U A L 9–19
I N D E X
Tray 4 Physical Characteristics
Size
Tray 4 Specifications
Environmental Requirements
Heat Output
Power Consumption
Tray Capacity
Paper Trays 1, 2, and 3
U
Uncollated
Unloading the High Capacity Stacker (HCS) 5–30
Unloading the High Capacity Stacker Stapler (HCSS)
Unrestricted Shift
Up/Down Arrow Buttons 2–20
Upper Door
Using the Duplex Automatic Document Feeder (DADF) 4–6
Using the High Capacity Stacker Stapler (HCSS)
W
Ways to Improve Color
White Border Edges on Copies
Writing Style Conventions xxviii
www.xerox.com.
9–20 D O C U C O L O R 2 0 6 0 / 2 0 4 5 O P E R A T O R M A N U A L
701P36797
March 2001
Xerox Corporation
Global Knowledge and Language Services
780 Salt Road
Webster, New York 14580
advertisement
Related manuals
advertisement
Table of contents
- 3 Table of Contents
- 15 Safety Notes
- 15 Electrical Safety
- 16 Disconnect Device
- 17 Laser Safety
- 18 Maintenance Safety
- 19 Operational Safety
- 20 Ozone Safety
- 21 Notices
- 21 Radio Frequency Emissions
- 21 FCC in the USA
- 21 In Canada
- 22 Safety Extra Low Voltage Approval
- 22 Certifications in Europe
- 23 It’s Illegal in the USA
- 25 It’s Illegal in Canada
- 26 Environmental Notices for the USA
- 26 Environmental Notices for Canada
- 27 Conventions
- 27 Symbols
- 28 Writing Style Conventions
- 29 1. About Color Printing
- 29 Overview
- 30 Image Quality
- 30 Quality Starts with the Original
- 31 How Input Determines Output
- 32 Image Key
- 33 Grain/Image Size
- 33 Getting the Color You Expect
- 35 Color Gamut
- 36 Color Models
- 37 Adding and Replacing Gray to Improve Color
- 38 Color Management
- 38 Halftone Dots and Screen Angles
- 38 Halftone Screens
- 39 Halftone Dots
- 39 Halftone Dot Shapes
- 39 Solid Background Printing
- 40 Electronic Digital File
- 40 Calibration
- 41 Digital Image Manipulation
- 41 Sizing
- 41 Sharpening
- 41 Color Cast
- 41 Important Additional Tips
- 42 Output Considerations
- 42 Mottle
- 42 Registration
- 43 Trapping
- 43 Halo
- 43 Opacity
- 44 Anti-aliasing
- 44 Knockout
- 44 Overprint
- 45 Duplex Settings
- 45 File Formats
- 45 Resolution
- 46 Raster Image Processors
- 47 Finishing
- 47 Folding Techniques
- 47 Parallel Fold
- 47 Right Angle Fold
- 47 Accordion Fold
- 47 Gate Fold
- 48 Binding Preparation
- 48 Nested Signature and Binders Creep
- 48 Gathered Signature
- 48 Bottling
- 49 Binding Methods
- 49 Saddle Stitching
- 49 Perfect Binding
- 49 Mechanical Binding
- 49 Looseleaf Binding
- 50 Final Finishing Touches
- 50 Die Cutting
- 50 Lamination
- 50 Varnish
- 50 Embossing
- 51 2. Overview
- 52 Identifying the External Parts
- 55 Ecology Module
- 56 Electrical Module
- 57 Dry Ink/Toner Waste Bottle
- 58 Ground Fault Indicator (GFI) Circuit Breaker
- 59 Touch Screen
- 59 Message Area
- 59 Tabs/Buttons/Icons
- 61 Touch Screen Button Types and Functions
- 63 Control Panel
- 68 Features
- 69 Job Status
- 71 Power Saver
- 71 Language
- 71 Access
- 72 Machine Status
- 73 Meters
- 76 Review
- 79 Help
- 79 Clear All
- 79 Interrupt
- 79 Pause
- 80 Job Monitor
- 81 Audio Tones
- 82 Alert Screens
- 83 Maintenance
- 84 Duplex Automatic Document Feeder (DADF)
- 85 Document Glass
- 86 Identifying the Internal Parts
- 86 Dry Ink/Toner Cartridges
- 86 Serial Number Label
- 87 Upper Door
- 88 Transport Module
- 89 Paper Path in the Digital Press
- 90 Exit Module
- 91 Relocating the DocuColor 2060/2045
- 93 3. Paper and Paper Trays
- 93 Recommended Papers and Special Materials
- 93 Paper Handling
- 95 Paper Trays 1, 2, and 3
- 97 Paper Guidelines
- 99 Paper Tray Special Features
- 100 Tray Capacity
- 100 Curl
- 100 Duplexing
- 101 Transparency Guidelines
- 101 Tabbed Inserts
- 102 Drilled Paper
- 102 Simplex Print Jobs
- 102 Duplex Print Jobs
- 103 Letterhead
- 103 Non-standard Size Paper
- 103 Oversize Paper
- 104 Auto Tray Switching
- 104 Auto Paper
- 105 Loading Paper
- 109 Paper Weight Conversion Tables
- 109 Specific Weight Conversion
- 110 Weight Conversion Ranges
- 111 4. Scanner
- 111 Scanning
- 112 Basic Scanning Steps
- 114 Duplex Automatic Document Feeder (DADF)
- 114 Document Specifications
- 115 Identifying Duplex Automatic Document Feeder (DADF) Parts
- 116 Using the Duplex Automatic Document Feeder (DADF)
- 117 Clearing a DADF Jam
- 118 Auto Image Rotation
- 118 White Border Edges on Copies
- 119 Touch Screen
- 119 Message Area
- 120 Tabs/Buttons/Icons
- 121 Touch Screen Button Types and Functions
- 123 Features (Digital Press with Scanner Only)
- 123 Basic Features
- 124 Color Mode
- 124 Auto
- 125 Full Color
- 125 3 Pass Color
- 125 Black Only
- 126 Single Color
- 128 Output
- 128 Collated
- 128 Uncollated
- 128 More...
- 129 Reduce/Enlarge
- 130 100%
- 130 Auto%
- 130 Third Button
- 130 Fourth Button
- 131 More...
- 136 Common Percentage Conversions
- 137 Paper Supply
- 137 Auto Paper
- 138 Added Features
- 138 2 Sided Output
- 139 1-1
- 139 1-2
- 140 2-1
- 141 2-2
- 142 Image Shift
- 142 No Shift
- 143 Auto Center
- 144 Margin Shift
- 145 Unrestricted Shift
- 146 Corner Shift
- 147 Original Input
- 147 Auto
- 148 Manual Input
- 149 Mixed Size Originals
- 150 Bound Originals
- 153 Edge Erase
- 154 Edge Erase for Drilled Paper
- 155 Border Erase
- 156 Edge/Center Erase
- 158 Stored Programming
- 158 Store Programming
- 159 Recall Programming
- 160 Delete Programming
- 161 Image Quality
- 162 Original Type
- 163 Auto Photo & Text
- 164 Text
- 165 Photo
- 166 Map
- 167 Dark Edges
- 169 Define Area
- 173 Lighten/Darken
- 174 Sharpness
- 175 Image Tone Presets
- 175 Normal
- 178 Background Erase
- 179 Color Balance
- 180 Color Shift
- 181 Chroma
- 182 Color Bar
- 183 More...
- 183 Output Format
- 184 Covers
- 188 Inserts
- 190 N-Up
- 192 Transparency Options
- 195 Booklet Creation
- 199 Mirror Image
- 200 Negative Image
- 201 Repeat Image
- 203 Poster
- 206 Job Assembly
- 207 Build Job
- 210 Proof Set
- 211 Back
- 213 5. Accessories
- 213 Tray 4
- 213 Identifying Tray 4 Parts
- 215 Control Panel
- 217 Paper Stock Specifications
- 219 Tray 4 Special Features
- 219 Loading Special Stock in Tray 4
- 219 Tabbed Inserts
- 220 Non-standard Size Paper
- 220 Letterhead
- 220 Coated Paper
- 221 Loading Paper in Tray 4
- 224 Selecting Tray 4
- 225 Jam Clearance
- 226 Digital Press Paper Reliability
- 226 Tray 4 Maintenance
- 226 Cleaning Tray 4
- 227 Problem Solving
- 230 Loss of Power
- 231 Tray 4 Specifications
- 231 Electrical Requirements
- 231 Power Consumption
- 231 Heat Output
- 232 Environmental Requirements
- 232 Atmosphere Requirements
- 232 Noise Levels
- 232 Ozone Emissions
- 232 Dust
- 233 Capabilities
- 233 Tray Capacity
- 233 Throughput
- 233 Physical Characteristics
- 233 Tray 4 Size
- 233 Tray 4 Weight
- 233 Floor Space Requirements
- 234 High Capacity Stacker (HCS)
- 234 Identifying High Capacity Stacker Parts
- 235 Control Panel
- 237 Paper Stock Specifications
- 239 Selecting High Capacity Stacker Features
- 241 Stacker Mode
- 241 Offset Mode
- 241 Top Tray Mode
- 242 Unloading the High Capacity Stacker
- 244 Jam Clearance
- 245 High Capacity Stacker Maintenance
- 245 Cleaning the High Capacity Stacker
- 246 Problem Solving
- 247 Loss of Power
- 248 High Capacity Stacker Stapler (HCSS)
- 248 Identifying High Capacity Stacker Stapler Parts
- 249 Control Panel
- 250 Electrical/Environmental Requirements
- 250 Paper Stock Specifications
- 252 Paper Path
- 253 Using the High Capacity Stacker Stapler
- 253 Hints and Tips
- 253 Stapling Hints
- 256 Feeding 3 Hole Drilled Paper
- 257 Stapling from the Fiery EX2000
- 258 Paper Specifications for Stapling
- 259 Stapling Capacity for Different Paper Types and Weights
- 259 Unloading the High Capacity Stacker Stapler
- 260 Jam Clearance
- 261 Ordering and Loading Staples
- 262 High Capacity Stacker Stapler Maintenance
- 262 Cleaning the High Capacity Stacker Stapler
- 263 Problem Solving
- 265 Loss of Power
- 267 6. Problem Solving
- 267 General Problems
- 280 Jam Clearance
- 281 DADF Jam Clearance
- 283 Left Side Door Jam
- 284 Trays 1, 2 and 3 Jams
- 286 Upper Door Jam
- 287 Transport Module Jam
- 289 Exit Module Jams
- 291 Right/Left Door Paper Path Jams
- 291 Registration, Vacuum Transport and Fuser
- 294 Horizontal Transport (2-Sided Printing Only)
- 295 Fault Codes
- 297 7. Technical Data
- 297 Raster Image Processor (RIP)
- 297 Digital Press Specifications
- 297 Electrical Power Requirements (200/240 - 50/60 Hz)
- 297 Specifications
- 297 Power Consumption
- 298 Heat Output
- 298 Air Exchange Rate
- 298 Energy Star/Sleep Mode
- 298 Environmental Requirements
- 298 Altitude
- 299 Noise Levels
- 299 Ozone Emissions
- 299 Dust
- 299 Capabilities
- 299 Tray Capacity
- 299 Throughput
- 299 Warm-up Time
- 299 First Print Out Time
- 300 Print Rates
- 301 Physical Characteristics
- 301 Digital Press Size
- 301 Digital Press Weight
- 301 Floor Space Requirements
- 301 Duplex Automatic Document Feeder (DADF) Specifications
- 301 Document Feeding Method
- 301 Sizes
- 301 DADF Capacity
- 302 Speed
- 302 Power Source
- 302 Noise
- 302 Dimensions
- 302 Weight
- 302 Floor Space Requirements
- 303 Metric Conversion Chart
- 305 8. Maintenance
- 305 Cleaning the Touch Screen
- 306 Cleaning the Document Glass
- 307 Cleaning the Document Glass Cover
- 307 Replacing Consumable Supplies
- 308 Replacing a Dry Ink/Toner Cartridge
- 312 Adding Fuser Oil
- 314 Changing the Waste Dry Ink/Toner Bottle
- 316 Calling for Service
- 317 Consumable Supplies
- 319 9. Index