- No category
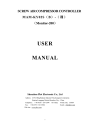
advertisement
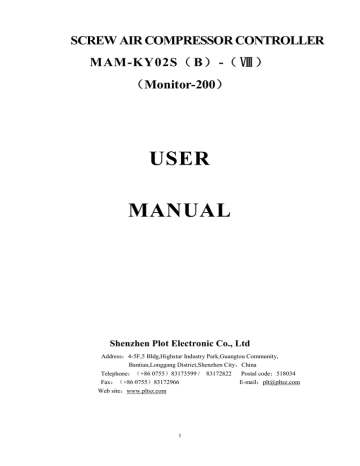
SCREW AIR COMPRESSOR CONTROLLER
MAM-KY02S( B) -( Ⅷ )
(Monitor-200)
USER
MANUAL
Shenzhen Plot Electronic Co., Ltd
Address:4-5F,5 Bldg,Highstar Industry Park,Guangtou Community,
Bantian,Longgang District,Shenzhen City,China
Telephone:(+86 0755)83173599 / 83172822 Postal code:518034
Fax:(+86 0755)83172966 E-mail:[email protected]
Web site:www.pltsz.com
1
VOTE OF THANKS
Thank you for your trustworthy and select of PLOT air compressor controller !
Shenzhen Plot Electronic Co., Ltd specializes on the manufacture and R&D of air compressor controller. We are devoted to win customer trust through our high quality products and service.
We try our best to ensure the completeness and correctness of the manual, but
PLOT Company shall reserve the rights for continuous research and improvement on its products and assume no obligation for the modification and improvement on the previously delivered products. The design of products is subject to the change without notice.
Please feel free to contact our after-sale service center if you encounter any problem with our product.
You are always welcome to make suggestions and advices!
2
NOTICE
Please read all the operation manual before operating the set and keep this manual for further reference.
Installation of MAM—KY** compressor controller can be performed only by professional technicians.
Installation position shall be considered carefully in order to ensure good ventilation and reduce electromagnetic interference
.
Wiring shall be performed respectively according to regulations for heavy and weak current to reduce electromagnetic interference.
RC snubber must be connected to the two terminals of coil (such as AC contactor ,valve, etc),which are controlled by relay output.
Port connection shall be inspected carefully before power on.
Correct ground connection (the third ground)can help increase product capacity of resisting signal interference.
Set rated current of motor: the max current of motor/1.2.
Features:
● Chinese / English display.
● Short circuit, current block, current open phase, current overload, current unbalance protection for motor
● On-off control and running control of motor.
● Prevention for air compressor reversal
● Temperature measurement , control and protection
● Control pressure balance by adjust load rate automatically
● High integration , high reliability ,high cost performance.
● Remote control/Local control.
● Block mode/Independent mode.
● RS-485 communication function,
3
Contents
1,Basic Operation..................................................................................................................................................... 5
1.1, Button Explanation................................................................................................................................... 5
1.2, Status Display and Operation .................................................................................................................. 6
2, Contoller Function and Technical Parameter ................................................................................................. 12
3, Model and Specification .................................................................................................................................... 12
3.1, Model explanation .................................................................................................................................. 12
3.2Power specification sheet for corresponding motor. .............................................................................. 13
4, Installation.......................................................................................................................................................... 13
4.1, Mechanical Installation .......................................................................................................................... 13
4.2, Electrical Connections ............................................................................................................................ 15
5, Alarm Function .................................................................................................................................................. 16
5. 1、Monitor Indication............................................................................................................................... 16
5.2,Controller Indicator ................................................................................................................................ 16
6,Controller Protection.......................................................................................................................................... 17
7, Troubleshooting ................................................................................................................................................. 18
7.1、This Fault Review ................................................................................................................................. 18
7.2、Common Failures and Causes: ............................................................................................................ 18
8, Schematic Diagram:........................................................................................................................................ 20
4
1,Basic Operation
1.1, Button Explanation
Picture 1
I——Start Button:
1,When compressor is at stop status, press this button to start the compressor.
2,When compressor is set as master ( No.1 ) in block mode ,press this button to start the compressor and activate block mode function at the same time.
O——Stop Button:
1,When the compressor is at running status, press this button to stop the compressor;
2,When compressor is set as master (No.1 ) in block mode ,press this button to stop compressor and block mode function as well.
——Load / unload Button:
When the compressor is at running status ,press this button to load or unload ;
S——
Set Button:
1. When modifying data, press this button after modification to save and confirm the modified data.
2. When the compressor is at password setting status ,press this button to save and confirm the password
——Move up button/Increasing button:
1,when viewing the menu, press this button to move upward the cursor ;
2,When modifying data, press this button to increase the data at current position .
——Move down button / Decreasing button:
5
1, When viewing the menu, press this button to move downward the cursor;
2,When modifying data, press this button to decrease the data at current position.
——Shift button /Enter button:
1,When modifying data, press this button to move to the next data bit;
2,when select menu, press this button to switch to submenu. If no submenu available, the controller will shift to data setting mode.
C——Return button / Reset button:
1, When modifying data, press this button to exist data setting mode;
2, When viewing the menu, press this button to return to previous-menu;
3, When the controller is at failure stop status, long press this button to reset.
1.2, Status Display and Operation
The display screen will show as below after power on::
WELCOME
SCREW COMPRESSOR
After 5 seconds, the menu will switch as below:
DISC T:20℃
AIR P:0.60Mpa
RUN STATUS:NORMAL STOP
ADD:001 LOCAL
Press “” to enter into Selection Menu:
RUN PARAMETER
CALENDAR
CUSTOMER
PARAMETER
1.2.1, Operating Parameter and Menu
Press“” or“” to move the cursor to “RUN PARAMETER”, then press“” to switch to secondary menu:
MOTOR、FAN CURR
TOTAL RUN TIME
THIS RUN TIME
MAINTENANCE PARA
Move the cursor to “MOTOR,FAN CURR” ,press“” to switch to secondary menu:
CURR(A):R S T
6
MOTOR: 56.1 56.2 56.0
FAN: 4.1 4.1 4.1
Press “RESET”, to return to the previous menu or the main menu. If no operation at the current menu for 120 seconds , controller will automatically return to the main menu and turn off the back light simultaneously.
According to above method, use move down “” ,move up button“”, enter button“”and return button
“RESET” to check TOTAL RUN TIME,THIS RUN TIME,MAINTENANCE PARA,FAULT RECORD,
PROD.DATE、SERIAL,THIS FAULT and return to previous menu.
1.2.2, Calendar
Check and set time of controller
TIME
2004-2-22
WEEK0
12:46:59
1.2.3, Customer Parameter
A, Customer parameter view and modification
It is not allowed to modify CUSTOMER PARAMETER and FACTORY PARAMETER in running status and
STOP DELAY
The check and modification of CUSTOMER PARAMETER is similar with RUN PARAMETER. Take
UNLOAD P as example: Move “”or“”to CUSTOMER PARAMETER and then press “”to switch to below menu
SET P、T
SET TIME
OPERATION MODE
BLOCK PARAMETER SET press“” to switch to below menu
LOAD P:00.65MPa
UNLD P:00.80MPa
FAN START T:0080℃
FAN STOP T:0070℃
Move the cursor to item LOAD P, then press “”
to switch to the following menu which requires a user password input.
INPUT PASSWORD
****
Note: User password can be modified in customer parameter and FACTORY PARAMETER
7
is fixed as
In this menu, the first data bit of password starts blinking,press “”or“” to modify the first bit of password,Press “” to move the cursor to the next data bit, modify the second data of password in accordance with the above , and modify the third and fourth data of password in sequence. Press“S” to confirm the input data and the menu will switch to the following menu after verification:
UNLD P:00.80MPa
FAN START T:0080℃
FAN STOP T:0070℃ indicates that the data is at a setting status
In the menu above , press “”, the first data of LOAD P starts blinking ,user can press “”or“”to modify the present data in accordance with the above method .Press“” to move to next data and modify the target data in sequence. When finished, press “S” to confirm and save the data.
B, Customer Parameter Sheet and Function
First menu
SET P、T
SET TIME
Second menu
LOAD P
UNLD P
FAN START T
FAN STOP T
MOTOR START
TIME
FAN
TIME
START
Preset Data Function
00.65MPa
00.80MPa
0080℃
0070℃
0008S
0003S
1,In AUTO load mode , compressor will load if pressure is below this set data
2,In STANDBY mode, compressor will start if the pressure is below this set data
1,Compressor will unload automatically if air pressure is above this set data
2.This data should be set above LOAD P ,also should be set below UNLD P LIM
Fan will start if DISC T is above this set data
Fan will stop if DISC T is below this set data
Set the MOTOR START TIME. Record time when motor is activated, controller will not start overload protection during this time to avoid impulse starting current stopping the motor.
Set the FAN START TIME. Record time when fan is activated, controller will not start overload protection during this time to avoid impulse starting current stopping the fan.
STAR DELAY
TIME
LOAD DELAY
TIME
0006S
0002S
Interval time from star start to delta start.
Unloading in this set time after enter delta running
STANDBY
DELAY
STOP DELAY
0600S
0010S
When unloading continuously, compressor will automatically stop and enter to standby status if over this set time
For NORMAL STOP operation, compressor will stop after it continuously unloads over this set time
8
OPERATION
MODE
BLOCK
PARAMETER
SET
RE-START
DELAY
OTHER
DRAIN OPEN
TIME
DRAIN CLOSE
TIME
0100S
0000S
0002S
0060H
START MODE
LOAD MODE
COM MODE
COM ADD
Machine can start only over this set time at any case(after normal stop, standby or alarm &stop)
Additional function
Auto drain control, continuously drain time
LOCAL/
REMOTE
AUTOMATI
CAL/MANU
AL
DISABLE/
BLOCK/
COMPUTER
0001
Auto drain control, continuously drain interval time
LOCAL :only the button on the controller can turn on and turn off the machine.
REMOTE: both the button on the controller and the remote control button can turn on and turn off the machine;
MANUAL : only when the pressure is above
UNLD P, compressor will unload automatically .For any other case ,the
Load/Unload function can only be executed by pressing “load/unload” key.
AUTOMATICAL: the load/unload function can be executed by the fluctuation of AIR P automatically
DISABLE: communication function is not activated.
COMPUTER: compressor can communicate with computer or DCS as slave according to
MODBUS-RTU.
BLOCK: compressors can work in a net
Set the communication address in COMPUTER or
BLOCK mode. This address is unique for every controller in net
BLOCK STATUS
BLOCK ON/OFF
TURN TIME
BLOCK
NUMBER
MASTER/
SLAVE
ORDER/
ALONG
0002H
0002
BLOCK LOAD P 00.63MPa
1.When service as master in BLOCK, master controls slave; the COM ADD should be set as
No.1
2.When service as slave in BLOCK, slave is controlled by master
When master pressure is between BLOCK
LOAD P and BLOCK UNLD P, master determines slave to work alternatively after working over this set time
Number of air compressors in block net
In BLOCK mode, one compressor will start or load when master AIR P is below this set data
9
O/A
SEPERATOR
CLR
MAINTENANCE
TIME
AIR FILTER
LUBE
BLOCK UNLD P
OIL FILTER
O/A
SEPERATOR
GREASE
CHINESE/
ENGLISH
00.78MPa
0000H
0000H
0000H
0000H
2000H
MAX LIFE TIME
LANGUAGE
PHASE PRO
BLOCK DELAY
GREASE
OIL FILTER
AIR FILTER
LUBE
0020S
0000H
2000H
2000H
2000H
2000H
ENGLISH
ENABLE/
DISABLE
10
In BLOCK mode, one compressor will stop or unload when master AIR P is above this set data
In BLOCK mode, when master sends two commands continuously, second command signal delays for this set data
Record total running time of oil filter. If changing new oil filter, the data should be reset by manual operation.
Record total running time of O/A separator. If changing new O/A separator, the data should be reset by manual operation
Record total running time of air filter .If changing new air filter, the data should be reset by manual operation
Record total running time of lubricant. If changing new lubricant, the data should be reset by manual operation
Record total running time of grease. If changing new grease, the data should be reset by manual operation
1, Alarm prompt when total running time of oil filter is above the set data .
2,Set this data to “0000” , alarm function for oil filter running time is not activated
1, Alarm prompt when total running time of
O/A separator is above the set data.
2,Set this data to “0000” ,alarm function for
O/A separator running time is not activated
1, Alarm prompt when total running time of air filter is above the set data.
2,Set this data to “0000” , alarm function for air filter running time is not activated
1, Alarm prompt when total running time of lubricant is above the set data.
2, Set this data to “0000”, alarm function for lubricant running time is not activated.
1, Alarm prompt when total running time of grease is above the set data.
2,Set this data to “0” , alarm function for grease running time is not activated
ENGLISH: Displays in English
CHINESE: Displays in Chinese
Enable: PHASE PRO function is activated
Disable: PHASE PRO function is not activated
NEW
PASSWORD
USER
**** ****
User could modify the user password by old user password or factory password
1.2.4,Factory Parameter
The view and modification of factory parameter requires a factory password, The modification step is same as customer parameter modification. Main function is as below:
PARAMETER
Initial Data Function
MOTOR RATED
CURR
FAN
CURR
RATED
ALARM DISC T
STOP DISC T
STOP AIR P
UNLD P LIM
Maximum motor overload data /1.2
Maximum fan overload data/1.2
105℃
110℃
00.90MPa
0.85MPa
When the current of motor is more than 1.2 times of the set data , the unit will stop for overload feature. (see table2.1.1)
When the current of fan is more than 1.2 times than the set data , the unit will stop for overload feature.
When discharge temperature reaches this set data, compressor will alarm
When the discharge temperature reaches this set data, compressor will alarm and stop
When pressure reaches this set data ,compressor will alarm and stop
This data is the maximum of UNLD P. The UNLD P in the customer parameter must be set no higher than this data.
TOTAL LOAD
TIME
TOTAL RUN
TIME
FAULT
RECORD RESET
000095 H
000100 H
****
Modify the TOTAL LOAD TIME
Modify the TOTAL RUN TIME
CURR
UNBALANCE
OPEN PHASE
PROT
FREQ SEL
OPEN PHASE
PROT
PROD.DATE
SERIAL NO.
0006
002.0S
50Hz/60Hz
002.0S
9999-99-99
9999999999
Input”8888”and press “set“ button to clear all the history fault record.
When MAX -MIN CURRENT >=(1+ SET
DATA*MIN CURRENT/10
),the unbalance protection is activated ,compressor will alarm and stop, reporting MOTOR CURR UNBAL
If the set data ≥ 15, the unbalance protection will not be activated.
If OPEN PHASE protection ≥20 seconds, OPEN
PHASE protection is not activated
Choose operation power frequency.(This parameter influences the sample current value. When this data is set incorrectly, the actual current is 1.2 times different from displayed current value)
If OPEN PHASE protection ≥20 seconds, OPEN
PHASE protection is not activated
Production date set by manufacturer
Serial No. set by manufacturer
11
2, Contoller Function and Technical Parameter
2.1,Digital input &output:9 points of digital input,10 points of digital relay output
2.2,Analog input& output: 2 points of Pt100 temperature input,2 points of 4~20mA pressure signal input,2 groups of three phases current input (CT provided);
2.3,Input voltage of phases:three phase 380V;
2.5,Measurement :
2.5.1Oil temperature:—20~150℃;A
ccuracy
:±1℃
2.5.2Discharge temperature:—20~150℃;A
ccuracy
:±1℃
2.5.3Running time:0~999999H
2.5.4Current:0~999.9A
2.5.5Pressure:0~1.60MPa A
ccuracy
:0.01Mpa
2.6,Phase protection: When compressor is at stop mode and detects open phase, response time≤2s;
2.7,Motor protection: This controller provides open phase, unbalance and overload protection to motor and fan.
2.7.1Open phase protection:When any phase opens, the response time equals to set time;This function is not activated when OPEN PHASE PROTECTION time is set over 20s
2.7.2Unbalance protection: when MAX-MIN current >= SET DATA *MIN current/10 ,respond time is
5s;
2.7.3Protection features of overload (time unit: second),please see following table(table 2.1.1)for your reference. Multiple=Iactual/Iset ,response time is shown in following table (table 2.1.1) according to overload multiples from 1.2 times and 3.0 times .
I
actual
/
I
set
Time parameter
≥1.2 ≥1.3 ≥1.5 ≥1.6 ≥2.0 ≥3.0
Response time(S) 60 48 24 8 5 1
Table 2 curve table for protection of motor
2.8, Temperature protection: when actual temperature measured is higher than temperature set; response time≤2s
2.9, Contact capacity of output relay: 250V,5A;Contact endurance :500000 times;
2.10, Current error is less than 1.0%.;
2.11,RS—485communication
3, Model and Specification
3.1, Model explanation
Control modeⅧ
T:RS—485communication
B:Pressure transmitter;K:pressure switch
Motor max operating current
V:Vane compressor;S:Screw compressor
02 controller(LCD display)
Model
12
3.2Power specification sheet for corresponding motor.
Current range
Corresponding
Specification main motor
(A) power (KW)
Remark
KY02(20)
KY02(40)
KY02(100)
8~20
16~40
100
Below 11
11-18.5
22-45
KY02(200)
KY02(400)
KY02(600/5)
200
400
600/5
55-90
110
200-250 With CT
Description
Fan has three levels of current, such as 0.2-2.5A,
1-5A and 4-10A, determined by current of motor
4, Installation
4.1, Mechanical Installation
4.1.1, CT Installation
The CT shall be installed at a place where the current of motor cable can be measured, thus, controller can be set according to instructions on motor nameplate, and the detailed dimension is shown as below:
A
B
Picture1、CT1 Structural dimension of CT1(ф36 hole) Picture2、CT1 Installation dimension
A
B
Picture 3、Structural dimension of CT2(ф10 hole) Picture 4、CT2 Installation dimension
13
4.1.2,Controller Installation
When install the controller, room should be left around controller for wiring. The specific dimension is shown as below:
The corresponding digital input terminal of 00、01、02、03、
04、05、06、07 is 20、 19、18、
17、16、15、14、13.
2、Indicator(OUT)
The corresponding digital input terminal of 00、01、02、03、
04、05、06、07、08、09 is 27、28、 29、30、31、35、
36、37、38、39
3、Power Indicator:PWR
4、Run indicator:RUN
5、Error indicator:ERR
Picture 5、Controller structure dimension
4.1.3,Panel Function and Installation Panel Structure 165
╳
102
╳
50(mm)
250
50
I
后 油
冷 冷
却
器
却
器
排气温度:80C
供压:0.80MPa
运行状态:设备已停止
0秒 本地
O
S
Picture 6,Panel Dimension
Picture 7, Hole dimension
14
22
3
14
4.2, Electrical Connections
Picture 8、Terminal arrangement diagram
Monitor connection terminal:
There are five connection cables and a communication cable which are used for display connection , RS-485 communication ,24V power supply.
Controller connection terminal:
Communication cable is used to connect monitor and controller.
1.2.3 CT1:Motor current transformer
23、24、25 Phase input
4.5.6
27
CT2:Fan transformer current
Motor contactor
7、9
28
Discharge temperature input
Star contactor
29
34
39
43,44
Delta contactor
Outlet valve
Alarm indicator
220V
30
37
40
Inlet valve
Run indicator
31
38
Communication port 2 42
Fan
Error indicator
GND(analog)
*
Note : Electromagnetism coil shall be connected nearest with RC snubber during wiring, Dotted line is for extra function
15
5, Alarm Function
5. 1、Monitor Indication
5.1.1, Air Filter Alarm
①. Air filter block check.
The monitor displays AIR BLOCK by checking pressure differential switch close.
②. Air filter running time alarm
The text displays AIR TIME END when running time of the air filter is exhausted.
5.1.2, Oil Filter Alarm
①. Oil filter block check.
The monitor displays OIL BLOCK by checking pressure differential switch close.
②. Oil filter running time alarm
The text displays OILTIME END when running time of the oil filter is exhausted.
5.1.3, O/A Separator Alarm
①. O/A separator block check.
The monitor displays O/A BLOCK by checking pressure differential switch close.
②. O/A filter running time alarm
The text displays O/A TIME END when running time of the oil filter is exhausted.
5.1.4, Lubricant Alarm
The text displays LUBE TIME END when running time of the lubricant is exhausted.
5.1.5, Grease Alarm
The text displays GREASE TIME END when running time of the grease is exhausted.
5.1.6, Discharge Temperature High Alarm
The text displays DISC T HIGH when DISC T is higher than ALARM DISC T set in FACTORY
PARAMETER.
5.2,Controller Indicator
Indicator Meaning and function Indicator status
Power
Run
Error
Digital input
Controller power on
Controller run
Failure and stop
Terminal 26~18 digital input
PWR indicator on
RUN indicator on
ERR indicator blink
IN00~08corresponding indicator on. Indicator will not be illuminated if input has no function
Digital output
Terminal 39、40、41、42、43、46、
47、49、50、51digital output
OUT00~09 corresponding indicator on
Data storage Data and time set PWR blink once
16
6,Controller Protection
6.1,,Motor protection
MAM—KY02Scompressor controller provide short circuit ,block, overload, lack phase, unbalance protection to motor.
Electronic failure
Failure display Reason
Short circuit Display “Motor/FAN OVER LOAD” Short circuit or wrong current set
Current Block Display “Motor/FAN BLOCK”
Overload
Lack phase
Unbalance
Display “Motor/FAN OVERLOAD”
Display “Motor/FAN *LACK PHASE”
Display “Motor/FAN UNBALANCE”
Overload, bearing wear and other mechanica l failure
Overload, bearing wear and other mechanica l failure
Power supply, contactor and open phase of motor
Poor contact of contactor, inside open-loop of motor
6.2,Protection of Discharge Temperature High
When DISC T is above the STOP DISC T, the controller will alarm and stop the machine. THIS FAULT displays DISC T HIGH
6.3,Protection of Air Compressor anti-reversal
When compressor is at stop status and three phases sequence is not in order, THIS FAULT displays PHASE
WRONG1, and the controller cannot start the motor. Change the position of any arbitrary two phase power lines and check the rotation of motor.
6.4,Protection of Air Pressure High
When the AIR P is above the MAX LIM P, the controller will alarm and stop the machine. THIS FAULT displays HIGH P.
6.5, Protection of Sensor Fault
When pressure sensor or temperature sensor is disconnected, the controller will alarm and stop the machine.
THIS FAULT displays **SENSOR FAULT.
6.6, Protection of Air compressor Open Phase
When compressor is at stop status and open phase is detected, THIS FAULT displays PHASE WRONG2, and the controller cannot start the compressor. Check the three phase.
17
7, Troubleshooting
7.1、This Fault Review
Alarm and stop caused by the external parts of controllers may be removed by checking THIS FAULT or
FAULT RECORD, method is shown as below:
Press“” to move the cursor to “RUN PARAMETER” menu, then press“”,the secondary menu will show as below:
MOTOR FAN CURR
TOTAL RUN TIME
THIS RUN TIME
MAINTENANCE
FAULT RECORD
PROD.DATE、SERIAL
THIS FAULT
Move the cursor to “THIS FAULT” menu Then press“”to switch to the following menu(display failure):
STOP: DISC T SENSOR
FAULT
170℃
User can reset fault according to the information prompted
7.2、Common Failures and Causes:
Failure Reason Solution
High discharge temperature
Temperature Sensor
Failure
Bad vent condition, Oil shortage etc.
Cable broken or PT100 failure
Check the vent condition and lubricant amount etc.
Check the wiring and PT100
High Pressure
Pressure Sensor Failure
Pressure too high or the pressure sensor failure
Cable broken, Sensor failure or the cables connect reversely
Check the pressure and the pressure sensor
Check the wiring and pressure transmitter
Lack water Water pressure switch failure Check water pressure switch
Open Phase
Overload
Power open phase or the contactor failure
Voltage too low, tubes block, bearing wear off or other
Check the power and contactors
Check the set data, voltage, bearings, tubes and other mechanical system.
18
Unbalance
Wrong Phase Sequence
Fan fail to run
Motor overload during start
Main Contactor shakes frequently mechanical failure or wrong set data etc.
Current unbalance, contactor failure or the internal open loop of the motor
Phase sequence reversal or open phase
Fan failure, contactor failure,no control output
Check the power, contactor and the motor
Check the wiring
Check wiring
Master start time set to less than the star delta delay time
The emergency stop button is loose or controller is reset by interference
Reset the master start time longer than star delay + 2 seconds
Check if the coil of contactor connects with
RC snubber or not
19
8, Schematic Diagram:
20
advertisement
* Your assessment is very important for improving the workof artificial intelligence, which forms the content of this project
Related manuals
advertisement