advertisement
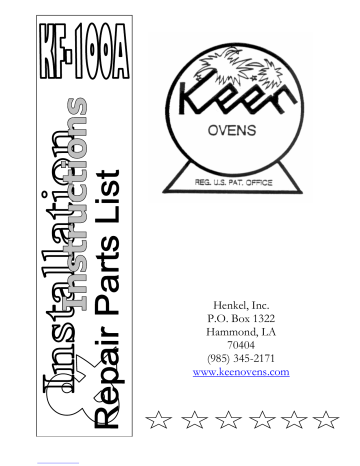
Henkel, Inc.
P.O. Box 1322
Hammond, LA
70404
(985) 345-2171
www.keenovens.com
Henkel, Inc.
P.O. Box 1322 * Hammond, Louisiana * 70404 * (985) 345-2171
www.keenovens.com
Models KF-100A Flux Holding Oven
Installation Instructions & Repair Parts List
One Year Limited Warranty
Henkel, Inc. warrants its products against defects in material and workmanship. Henkel,
Inc. will either repair or replace without charge any properly installed product which fails under normal operating conditions within one year from date of installation, provided it is returned to our factory, transportation prepaid, and our inspection determined it to be defective under the terms of this warranty. The warranty covers only equipment manufactured by Henkel, Inc., and does not extend to transportation, installation, or replacement charges at the buyers’ facility; nor does it apply to any other equipment of another manufacturer used in conjunctions with Henkel, Inc. equipment. No other warranty, expressed or implies exists beyond that included in this statement.
Keen Ovens
Model KF-100A Flux Holding Oven
Specifications
Voltage (Specify)
Wattage
Thermostat
Temperature
Insulation
Interior Dimensions
Net Weight
Shipping Weight
Shipping Dimensions
120V 240V
500W 500W
Factory Preset/ Field Adjustable
Preset 275ºF : Range 100ºF-400ºF
2" Thermal Insulating Wool
12" X 16" X 22"
95 lbs.
170 lbs.
30" X 48" X 30"
Recommended Spare Parts
When it is critical to have continuous operation of this unit; we suggest having the following spare parts on hand:
Heating Element Assemblies
Thermostat
General Information
The model KF-100A is a portable hopper style flux oven capable of storing 125 pounds of welding flux. Flux is top loaded by way of a removable door and discharged through a slide valve located on the bottom of the unit.
Safety Precautions
Read all instructions completely before attempting to operate this unit.
*** SAVE THESE SAFETY INSTRUCTIONS ***
To reduce the risk of electrical shock, fire, or personal injury follow the guidelines below:
•
Before connecting unit to a power source, be sure the voltage supplied is the same as that specified on the nameplate of the unit.
•
Check outlet to ensure proper grounding of the electrical cable. Have a licensed electrician check the
A/C power outlet if you are not sure.
•
Use this unit for its intended purpose as described by literature.
•
Make sure power cord is located so that it will not be stepped on, tripped over, or otherwise subjected to stress of heat, oil, or sharp edges. Do not close doors on the cord.
•
To reduce the risk of damage to the electric plug and cord, disconnect by plug rather than by the cord.
•
Do not use this unit if cord or plug is in poor condition. If it has been exposed to weather or immersed in water, have a qualified serviceman inspect and replace parts as necessary.
•
•
•
WARNING! NEVER HANDLE PLUG, CORD, OR UNIT WITH WET HANDS OR WHILE
STANDING IN WATER.
Use special care when moving heavily loaded units.
Do not store combustible material on or around the unit.
•
Do not operate this unit empty.
•
When using the unit at a distance where an extension cord becomes necessary, a 3-conductor grounding cord of adequate size must be used for safety, and to prevent loss of power and overheating. Use only a UL listed extension cord suitable for outdoor use. Make certain wire size is large enough for A/C amperage rating of unit.
Operation
Load oven with flux. To turn unit on, simply plug the power cord into the appropriate single phase A/C power source. (See oven nameplate for voltage rating.) Indicating light glows when power is being supplied to the heating elements. Plugs are not supplied on 240-volt models due to the many different receptical configurations in the field. All units meet electrical code requirements when used with a grounded power source.
***CAUTION: DO NOT USE ON D/C POWER SUPPLY! ***
The KF-100A is designed to vent around the perimeter of the lid. In instances where there is high moisture content in the flux, the interior of the lid is designed to channel condensation into the well built into the top lip of the oven.
Temperature Setting
The thermostat on the model KF-100A is factory preset at approximately 275ºF but has a range of
100º - 400ºF. To adjust temperature setting, disconnect oven from power source, then remove snap-in plug from element cover. This exposes thermostat adjustment screw. Using a small screwdriver, adjust set screw until desired temperature is attained. (Turning set screw counter clockwise increases temperature, turning set screw clockwise decreases temperature.) One-quarter turn equals approximately
35ºF. Replace snap-in plug and reconnect oven to power source.
Guide to Storage
See the enclosed guide to storage. This guide may be used in the absence of storage information from the flux manufacturer. In critical situations, contact your flux manufacturer.
Functional Description
The model KF-100A is a portable hopper style flux oven designed to hold 125 pounds of welding flux at moderate optimum temperature. Temperature is regulated by a field adjustable thermostat with an indicating pilot light, and monitored with a bimetal thermometer. This oven may be used as a portable unit or may be readily attached from its carrier and mounted directly to the welding manipulator. The model KF-100A is insulated with a full 2” of thermal insulating wool and is equipped with lifting lugs.
Scheduled Maintenance
The manufacturer recommends that the operator periodically clean all flux residue from heating elements and brackets. Excessive flux buildup on elements may cause hot spots and shorten element life.
Troubleshooting
The Keen oven model KF-100A requires a minimal amount of electrical knowledge to repair if necessary.
IF OVEN FAILS TO OPERATE – NO HEAT
1.
Check power source.
2.
Check power cord continuity. Replace cord assembly if faulty. (Strain relief may have to be removed from power cord to gain access.)
3.
If cord and power supply check okay, remove leads from thermostat terminals and check for continuity across terminals. If continuity is not present across thermostat terminals, replace thermostat.
4.
If thermostat is good, check continuity of elements and element wiring. If elements or wiring are faulty, replace.
IF OVEN OVERHEATS
1.
If oven overheats, adjust thermostat. (See “Temperature Setting” section.)
2.
If thermostat calibration fails to lower temperature, replace thermostat. (See “Corrective
Maintenance” section.)
IF OVEN HEATS BUT FAILS TO REACH TEMPERATURE
1 . Calibrate thermostat. (See “Temperature Setting” section.)
Corrective Maintenance
CHANGING THE HEATING ELEMENTS
1.
Disconnect power source and empty oven of flux.
2.
Remove element cover and leads from elements (Note: power cord strain relief may have to be removed to gain clearance.)
3.
From interior of oven, remove elements from clips and pull elements free of hopper wall.
4.
Replace new elements and electrical leads being sure terminals are not shorted to oven body. Replace element cover.
CHANGING THE THERMOSTAT
1.
Disconnect from the power source.
2.
Remove element cover (Note: power cord strain relief may have to be removed to gain clearance).
3.
Remove electrical leads from thermostat and remove thermostat from mounting bolt.
4.
Replace and rewire new thermostat being sure terminals are not shorted to oven body. Do not over tighten elements mounting bolt.
KF –100A 120V / 500W
Wiring Diagram
KF –100A 240V / 500W
Wiring Diagram
Model KF-100A Repair Parts List
ITEM # QUANTITY DESCRIPTION PART NUMBER
1
3
1
1
* Elements 120V
W/T 240V
Power Cord
301023
301026
301018
6
7
4
5
1
2
1
1
Strain Relief
Thermometer
Pilot Light
Wheel
301043
301127
301085
460106
2 1 Thermostat 301024
** Please state model number and serial number and specify voltage and wattage when ordering repair parts, spare parts, or accessory parts. All necessary attaching hardware is supplied with each part ordered.
(Item numbers refer to pictorial drawings below for repair parts.)
HENKEL, INC.
Manufacturer of KEEN Ovens
Quality Since 1923.
Phone (985) 345-2171
Fax (985) 345-5653
PO Box 1322
Hammond, Louisiana
70401
Flux and Electrode Stabilizing Guide
Type (AWS
)
Standard
EXX10
EXX11
EXX12
EXX13
EXX20
EXX30
Iron Powder
EXX14
EXX24
EXX27
Iron Powder -
Low Hydrogen
EXX18
EXX28
Low Hydrogen
EXX15
EXX16
Low
-
Hydrogen
High Tensile
EXXX15
EXXX16
Stainless
Inconel
Monel
Nickel
Brasses
Bronzes
Hard Surfacing
Special Alloys
Granulated or
Agglomerated
Flux
Air Conditioned
Storage
Before Opening
80
°
F
±
20
°
60%
±
10% RH
90
°
F
±
20
°
50% RH max
90
°
F
±
20
°
50% RH max
90
°
F
±
20
°
50% RH max
90
°
F
±
20
°
50% RH max
90
°
F
±
20
°
50% RH max
90
°
F
±
20
°
50% RH max
Dry Rod
Oven Holding
After Opening
140
°
F
±
30
°
140
°
F
±
30
°
400
°
F
±
50
°
400
°
F
±
50
°
400
°
F
±
50
°
225
°
F
±
50
°
240
°
F
±
50
°
180
°
F
±
25
° two hours
After Exposure to Moisture a
Sufficient Time to affect Weld Quality
Recondition
Step 1
Rebake
Step 2
240
°
F
±
25
° one hour
Three hour total
180
°
F
±
25
° two hours
180
°
F
±
25
° two hours
180
°
F
±
25
° two hours
180
°
F
±
25
° two hours
180
°
F
±
25
° one hour
Not required
325
°
F
±
25
° one hour
Three hour total
700
°
F
±
100
° one-half hour
Two & one-half hour total
600
°
F
±
100
° one-half hour
Two & one-half hour total
700
°
F
±
100
° one-half hour
Two & one-half hour total
350
°
F
±
50
° one hour
Two hour total
700
°
F
±
100
° ∅ two hours
CONTACT YOUR ELECTRODE MANUFACTURER FOR SPECIFIC INFORMATION INVOLVING
CRITICAL OPERATIONS.
Electrode coating should not be exposed to the rebaking temperature without first having been reconditioned at a lower temperature. Failure to observe this rule will result in breakdown of electrode coatings.
After rebake, lower temperature to holding level until reissue .
IMPORTANT:
This table is offered as a guide to proper storage and oven holding temperatures for the most common electrodes in use today. In addition, recondition/rebake procedures for electrode coatings that have been exposed to moisture for a sufficient period of time to affect the weld quality are included.
Good judgment and the manufacturer’s recommendations should be your guide.
Note: In the HTS
Stainless electrode groups, and 15 & 16 type coatings, there can be a greater difference in the maximum temperature requirements for rebaking than those shown. This can be handled by special request to the particular manufacturer involved.
advertisement
* Your assessment is very important for improving the workof artificial intelligence, which forms the content of this project
Related manuals
advertisement