advertisement
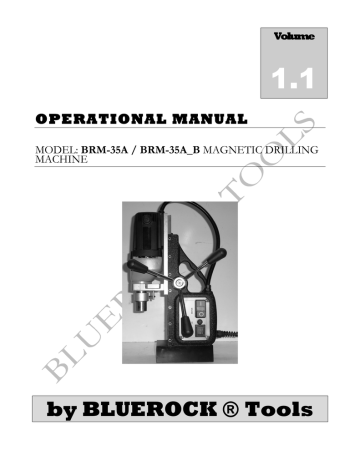
Volume
1.1
OPERATIONAL MANUAL
MODEL: BRM-35A / BRM-35A_B MAGNETIC DRILLING
MACHINE
by BLUEROCK ® Tools
M W S - B R M - 3 5 A / B M A G D R I L L
UNPACKING THE ITEM
Caution: This machine is packed together with items that may be sharp, oily and overly heavy objects.
Remove the machine from the packaging in a safe manner. Check to ensure all accessories are included with the item while unpacking. If any parts are found to be missing, contact the retailer as soon as possible. Do not throw away the packaging until the item is out of the guarantee period. Dispose of the packaging in an environmentally responsible manner. Recycle if possible. Keep all plastic bags away from children due to risk of suffocation.
WEEE - Waste Electrical & Electronic Equipment. Note this machine should be disposed of as electrical & electronic waste.
© THE NEWMAN TRADING COMPANY LLC DBA BLUEROCK® TOOLS 2016
1100 SW 16
th
St • Suite D
Renton, WA 98057
Phone 206.604.8363 • Fax 425.572.5167 www.bluerocktools.com
B R M - 3 5 A / B M A G D R I L L
Table of Contents
SAFETY
PRE-OPERATIONAL SAFETY CHECKS
OPERATIONAL SAFETY CHECKS
SPECIFICATIONS
INCLUDED ACCESSORIES
ADDITIONAL AVAILABLE ACCESSORIES 5
A
DDITIONAL ACCESSORIES FOR THIS MACHINE CAN BE FOUND IN
BLUEROCK ® T
OOLS ONLINE SHOP AT
WWW
.
BLUEROCKTOOLS
.
COM OR FROM YOUR LOCAL RETAILER
.
5
4
4
1
1
1
OPERATIONS
PURPOSE
OPERATIONAL PRINCIPLES
MACHINE COMPONENTS
TRANSPORTING THE MACHINE
RUNNING THE MACHINE
INSTALLING ANNULAR CUTTERS
TROUBLESHOOTING
GENERAL MAINTENANCE
OCCASIONAL MAINTENANCE
PARTS LIST
BREAKDOWN VIEW
12
13
14
6
6
6
6
7
8
10
11
12
B R M - 3 5 A / B M A G D R I L L Chapter
1
Safety
DO NOT USE THIS MACHINE UNLESS YOU HAVE READ THE
OPERATING INSTRUCTIONS!
Safety glasses must be worn at all times in work areas.
Appropriate footwear must be worn.
Long and loose hair must be contained.
Close fitting/protective clothing must be worn.
Safety gloves should be worn at all times and jewelry must not be worn.
Hard-hat must be worn while using machine.
Hearing protection should be worn when using this machine.
Dust mask must be worn while using this machine.
Read operational manual prior to use.
PRE-OPERATIONAL SAFETY CHECKS
Ø Examine the power cord and plug for damage. This tool is supplied with a ground plug and
must always be used with the proper grounded circuit.
Ø Examine the body of the machine and inspect for damage or defects.
OPERATIONAL SAFETY CHECKS
Ø ONLY to be operated by qualified personal who have read instructions. o NOTE: Failure to read and follow instructions could result in electrical shock, fire,
property damage and/or serious injury!
Ø DO ensure all non-essential people are clear of the immediate work area.
Ø DO keep body parts, clothing & power cords clear of turning/cutting pieces. Stay alert and
use common since when using this tool.
1
B R M - 3 5 A / B M A G D R I L L
Ø DO allow machine to reach operating speed before starting a hole.
Ø
DO unplug machine while changing or adjusting cutting bits so as not to accidentally turn
machine on.
Ø DO remove adjusting keys or hex wrenches prior to turning the machine on.
Ø DO use cutting paste (instead of cutting oil) when using this drill in an inverted position to
prevent oils from entering the electrical system and for ease of cutting.
Ø DO tie a loop in any extension cord connections to prevent cords coming apart and a loss of
power.
Ø
DO guard against electric shock by preventing body contact with grounded surfaces such as
pipes, radiators, ranges, refrigerators, etc.
Ø DO be mindful that power tools can expose an operator to vibrations transmitted trough
contact with the machine. Prolonged exposure can lead to medical issues which should be discussed with a medical professional.
Ø
DO tie in a drip loop in the power cord to prevent cutting fluid from running into the power
receptacle.
Ø DO use a dust extraction system for cutting materials that create dust such as cast iron. The
operator should also wear a protective respiratory device.
Ø DO NOT make adjustments to machine while the machine is running.
Ø DO NOT switch off the machine when it is under load, except in an emergency.
Ø DO NOT remove or modify grounding plug. Only to be used on a properly grounded circuit.
Ø DO NOT leave the machine running when not in use.
Ø DO NOT hold the work piece by hand or using body. Always mechanically clamp or secure
work piece.
Ø DO NOT allow coolant oil to enter the machine’s ventilation system.
Ø DO NOT operate machine outside of machine specifications.
Ø DO NOT touch moving parts while the machine is running as death or dismemberment could
occur.
Ø DO NOT remove machine metals panels while machine is connected to a power source. Only
to be removed for service by qualified personal and put back on the machine after service is complete.
Ø DO NOT allow children or untrained personal to operate machine.
Ø DO NOT use this machine in the rain or a wet environment. If using outdoors, make sure the
adhering surface is clean and dry.
Ø DO NOT operate in the presence of explosive materials as power tools create sparks which
may ignite dust or fumes.
Ø DO NOT drill into an area that may contain a live electrical wire/circuit.
2
B R M - 3 5 A / B M A G D R I L L
Ø DO NOT operate this machine on the same work surface where welding is being performed.
This could result in severe damage to the machine or personal injury to the user.
Ø DO NOT use this machine without the safety chain or safety strap.
Ø DO NOT operate this machine on a lower voltage as it may result in the electromagnet being
at a reduced power level and the machine could become unstable while cutting. This could also limit the motor life.
o NOTE: Use of long small gauge power extension cords can result in decreased
voltage. As local voltages can vary, it may be a good idea to test the voltage at the end of the extension cord to ensure proper voltage requirements are met. You might also consult an electrician to make sure the length of cord matches up with the proper wire gauge for this size motor. Make sure to use outdoor cords when operating outdoors.
3
B R M - 3 5 A / B M A G D R I L L
Chapter
2
Specifications
ELECTRICAL DATA
Voltage
Current
Motor Size
Power Connection
120V, 50-60Hz
10 Amps
1200W
US Standard 3 Prong Type B Plug
MECHANICAL DATA
Cutter Range
Cutting Depth
Cutting Speed
Tool Holder
Magnetic Adhesion
Stroke
SHIPPING DATA
Shipping Weight
Shipping Carton
Annular Cutter: 7/16” Min to 1.5” Max (12mm - 35mm)
Twist Drill Bit: 1” Max
2” Max Depth
595 RPM One Speed Gearbox
Direct Arbor with ¾” Weldon Shank
2600 Lbs (13000N)
6.5” - Only short twist drill bits can be used with this drill.
40 Lbs
19” x 8” x 15”
Included Accessories
DESCRIPTION
Instruction Manual
Coolant/Oil Bottle
Feed Handles
Chuck, Adapter and Key
Safety Chain
Plastic Case (for protection during shipping)
Hex Wrench
QTY
1
1
3
1 ea
1
1
2
4
B R M - 3 5 A / B M A G D R I L L
Note
UPON RECEIPT, CHECK CAREFULLY TO ENSURE THAT THE
MACHINE IS IN GOOD CONDITION AND HAS ALL
ACCESSORIES LISTED ABOVE.
Additional Available Accessories
Additional accessories for this machine can be found in BLUEROCK ® Tools online shop at www.bluerocktools.com or from your local retailer.
DESCRIPTION
13 Pc 2” Depth HSS Annular Cutter Set with Centering Pin
6 Pc 2” Depth HSS Annular Cutter Set with Centering Pin
6 Pc 1” Depth HSS Annular Cutter Set with Centering Pin
5/8” Screw In Chuck HD Heavy Duty and Key
5/8” Taper Chuck HD Heavy Duty and Key
5/8” Taper Chuck Black Medium Duty and Key
5
B R M - 3 5 A / B M A G D R I L L
Chapter
3
Operations
Note
THOROUGHLY READ THROUGH THE ENTIRE MANUAL BEFORE
OPERATING THIS MACHINE!
PURPOSE
Ø
The purpose of the BRM-35A is to drill through steel using annular cutters or
standard twist drill bits (when using the optional drill chuck).
Ø These drills are designed to magnetically adhere to a ferrous surface using their
electromagnetic base. Generally these drills are designed and used to drill through mild steel. This magnetic base will not work without a power connection.
o NOTE: The entire magnetic base must cover the work area to have full
magnetic adhesion. Using only a portion of the magnet is dangerous! Make sure the base fits completely on the surface.
Ø These machines can be used vertically, horizontally or overhead (inverted) provided
strong enough magnetic adhesion and an acceptable work environment. NOTE: For safety, the safety chain should always be used incase of an accidental power failure or other loss of magnetic adhesion.
OPERATIONAL PRINCIPLES
Ø
The main drilling shaft rotates in the forward direction. The main drilling motor
connects to the tool holder to make contact with a surface and slowly bore a hole.
Using the feed handles on the side of the drill, the user can raise or lower the drilling motor.
MACHINE COMPONENTS
Ø The main components of the BRM-35A are the tool holder, gearbox, motor, frame and
magnetic base. The tool holder is driven by the transfer case and the motor.
o These components must be not be removed except by a qualified technician.
Power must be disconnected prior to any service.
6
B R M - 3 5 A / B M A G D R I L L
Ø This machine has one primary adjusting point for the travel between the magnetic
base frame and the drill frame slide. The main way to increase or decrease the users ability to move the drill by hand is with this system. These are the black hex bolts on the side of the machine that have a locking nut around them. These are generally used to tighten up the travel as the brass slides wear over time. Be mindful to evenly adjust these so that the travel is even and smooth. The ideal travel generally keeps the drill in place when the user is not using the drill (this is usually on the tighter side) although individual users needs may vary.
1) Carbon Brush Holder
2) Drill Motor
3) Gearbox
4) ¾” Weldon Shank Tool Holder
5) Optional Annular Cutter (not included)
6) Drill Frame Slide
7) Magnetic Base
8) Feed Handle
9) Motor On Switch
10) Motor Off Switch
11) Magnet On/Off Switch
TRANSPORTING THE MACHINE
Ø When transporting the machine, always use the carrying handle.
Ø Ensure the drilling head is at the lowest position.
Ø DO NOT transport the machine with cutters or bits in the tool holder.
Ø
If the coolant bottle is connected, ensure the valve is in the “off” position or the
coolant has been drained.
Ø If transporting inside a vehicle, it is recommended to transport it on its side so as to
avoid the item falling over.
Ø If possible, transport in a case.
Ø DO NOT carry the machine by the cord.
Ø DO NOT allow the cord or plug to drag along the floor when transporting.
7
B R M - 3 5 A / B M A G D R I L L
RUNNING THE MACHINE
Ø Do all pre-operational and operational safety checks from Chapter 1.
Ø Consider your security and stability as well as the orientation of the machine in the
work area.
o Consider the work surface material, condition, strength, density and rigidity.
These factors directly affect the tools magnetic adhesion. Magnetic adhesion diminishes with thinner material and rough surface. Full magnetic spec’d adhesion is considered on 1” material. When using on material 3/8” or less, the drill should be mechanically clamped to the work-piece.
Ø After placing the machine in work area, connect the safety chain. o The safety chain should attach to the machine (preferably through the
carrying handle) as well as attached to the work area in such a manner that prevents the machine from detaching or falling from the work area in the event of magnetic deactivation or lost adhesion.
Ø Ensure the feed handles are securely attached to the feed spindle.
Ø Ensure the work surface and bottom of magnet are free of debris, oil, etc.
Ø Select appropriate size tool holder, chuck or adapters.
Ø Select and set up oiling method or cutting pastes. o If drilling overhead or horizontal use cutting paste liberally applied to the
cutting bit.
Ø If using the machine horizontally with the oil bottle, connect bottle to the side of the
machine using the two set screws located on the drill frame.
o Connect the oil bottle tube into the side of the tool holder by firmly pressing
in the hose.
§ To remove the hose later, press in the plastic piece around the hose
towards the tool holder while simultaneously pulling the plastic hose away from the tool holder.
o Make sure the oil bottle valve is in the off position.
§
This is generally at a 90 degree angle from the valve hose. o Fill the oil bottle with cutting fluid.
Ø Select appropriate size annular cutter or standard twist drill bit. o The ¾” Weldon shank uses two Allen head bolts. The annular cutters will go
in the shank and be secured on the two flat sides by the two Allen head screws. See next section below for more specifics on using annular cutters.
o If using a standard twist drill bit you will can use the drill chuck with a ¾”
Weldon shank adapter. Secure the chuck into the Weldon shank using the same method as standard annular cutters. Tighten the bit into the chuck.
8
B R M - 3 5 A / B M A G D R I L L
Ø Plug the machine into power source. o Form a loose knot in the power cord close to the plug connection to prevent
cutting fluid from running down the cord and into the power receptacle.
Ø Engage the magnet by pressing the magnet button on the control panel. o Check that the machine is firmly attached to the work area. o NOTE: The motor will not start unless magnet is on.
Ø Turn feed handle raising the cutter until the bit is above the work surface.
Ø Open the oil bottle valve to allow oil to come out to the work surface. o You may have to gently squeeze or shake the bottle to get the oil to start
flowing.
Ø Turn the machine on. o Start the machine by pressing the green “on” switch. Stop the machine by
pressing the red “off” switch.
Ø Very slowly engage the cutting bit with the material surface by lightly engaging the
hand crank down towards the material.
Ø After about 1/16” of cutting has been achieved in the work surface, slightly more
force can be applied. This will be the normal amount of force the rest of the hole.
o NOTE: Do not force the hole. Let the machine do most of the work.
Excessive physical effort should be avoided as it can cause damage to the machine or the user.
o If the unit jams in a hole, stop the drill immediately to prevent injury.
Disconnect the drill from the power supply and loosen the cutter by turning drill spindle counterclockwise. Never attempt to free cutter by starting motor!
Ø Make sure to keep the cutting material adequately lubricated.
Ø Ease up on feed pressure as the cutter starts breaking through the backside of the
material.
o If using annular cutters with a centering pin, the slug should eject using the
spring-loaded mechanism in the drill shank. Be mindful that this slug can eject at a rapid rate, so be sure all is clear on the output side of this slug to prevent injury to persons or property.
Ø Finish drilling the hole.
Ø
Turn the motor off and disconnect power once the drill is safely back up in the non-
drilling position.
o Remove metal chips wrapped around cutter and tool holder. Use a leather
glove or pliers as these metal pieces can be sharp.
Ø Disconnect safety chain and move the drill to a new drilling location.
9
B R M - 3 5 A / B M A G D R I L L
INSTALLING ANNULAR CUTTERS
Ø WARNING: Annular cutters are extremely sharp and should only be handled with a
thick glove so as not to cut the user during installation or removal.
Ø Check that the cutters are sharp and not damaged. o Annular cutters that are dull or damaged should not be used.
Ø Insert the pilot pin into the center of the annular cutter you have chosen. o NOTE: The pilot pin helps in locating the center of the hole as well as ejecting
the metal slug after the cut.
Ø Make certain the machine is unplugged from power.
Ø Raise the tool holder to ensure ample room to install the cutter.
Ø Insert the annular cutter into the ¾” adapter.
Ø Align the two “flat” sides of the annular cutter with the flat sides of the adapter. o CAUTION: Make certain the hex screw is seated into the flat side and not
simply on the round side of the cutter shank.
Ø Tighten one of the hex screws while slowly rotating the cutter forward and
backwards.
o Continue to tighten the screw until fully tightened.
Ø Tighten the 2
nd
hex screw.
Ø The annular cutter is ready to use.
1) ¾” Adapter Hex Set Screws (2 total)
2) Annular Cutter (not included)
3) ¾” Weldon Shank Tool Holder
10
B R M - 3 5 A / B M A G D R I L L
Troubleshooting
Note
SERVICING SHOULD ONLY BE DONE BY A QUALIFIED TECHNICIAN.
DON’T FORGET TO UNPLUG POWER TO UNIT PRIOR TO SERVICE!
Chapter
4
PROBLEM SOLUTION
Motor does not turn on. 1) Magnet not turned on. Magnet has to be engaged prior to motor working.
2) Check external power source (extension cord, breaker, etc).
3) Loose internal wire. Check and secure if necessary.
4) Motor brushes defective. Replace if necessary.
5) Check the fuse at the control panel. If it is blown, replace with same size.
6) Check the back of the internal PC board for a short. Replace if necessary.
7) Check the relays on the PC board to see if there are any shorts.
Replace if necessary.
8) Check to ensure the motor on/off switch is operable. Replace if necessary.
Motor turns on when the magnet is turned on.
Excessive sparking when motor is running.
1) PC board has a short or relays are fused in closed position.
Check and replace PC board/relay if necessary.
1) This may indicate the presence of debris in the motor or worn out carbon brushes. Check the brushes for unusual wear and replace if necessary. Clean out the internal motor armature if necessary.
2) Armature has a rough edge. Inspect and replace if necessary.
Magnetic does not hold to work area.
Hole is not cutting.
1) Work surface thickness is too small. A minimum of 3/8” (10mm) continuous ferrous steel must be used for magnetic adhesion.
NOTE: It is normal to be able to push these drills off their adhesion if pushing from the top side. CAUTION: These drills do not work on sheet metal!
2) Entire magnet base is not on the work surface.
3) Voltage is low at the machine. Check voltage.
4) There is debris or excess material between the work area and the magnetic base. Clean work area surface.
1) Cutter is dull. Sharpen or replace.
2) Work area material is not appropriate for cutter type. High carbon type steels require special cutting bits (tungsten carbide tip, etc).
11
B R M - 3 5 A / B M A G D R I L L
Chapter
5
General Maintenance
Ø Inspect electrical cords and electrical connections.
Ø Keep machine clean and free of debris.
Ø
Check for misalignment, binding and breakage of all moving parts. If damaged, repair tool
before use.
Ø
Keep cutting tools sharp and clean. Sharp cutters are less likely to bind and are easier to
control.
Occasional Maintenance
Ø Have the power tool serviced by a qualified service technician using identical replacement
parts.
o Change motor brushes:
1) Disconnect drill from power.
2) Unscrew left and side brush holder caps.
3) Take out old brushes.
4) Replace with exact same size new brushes.
5) Screw in brush holder caps tightly.
o Adjusting slides:
1) Periodically check, lubricate and adjust slides as necessary.
2) Use hex wrench to loosen the lock nuts and hex screws.
3) Adjust the screws evenly while moving the handle up and down so that there’s no free play yet not binding anywhere through its range of travel.
4) Retighten the lock nuts.
12
B R M - 3 5 A / B M A G D R I L L
Chapter
6
Parts List
1. Flexible cable 25. M6×16 screw 49. Drill holder plate 73. Bearing 6004
2. Magnetic switch 26. Screw plate 50. Out slide 74. Spindle
3. Fuse cap
4. Fuse
27. Magnetic base
28. M5 screw nut
51. M6×12 screw
52. Drill holder
75. Screw M8×8
76. Connect
5. Fuse holder
6. Motor starter
29. M5×16 screw 53. M6×30 screw
30. Bearing 54. Brush cap
7. Cable protector 31. Bearing
8. Cable holder 32. Internal slide
55. Brush
56. Brush holder
77. Oil holder
78. O ring
79. Spring
80. Spring stop
9. Plate
10. M4×8 screw
11. Handle holder
12. Handle
13. 4×10 key
14. Axle
15. 5×15 key
16. Gear
33. Slide
34. Slide
35. M5×8 screw
36. Plate
37. Rack
38. M6×20 screw 62. Bearing 6008
39. Hook
40. Tank
57. M5×65 screw
58. Motor holder
59. Field core
60. M5×65 screw
61. Wind catcher
63. Motor
64. Bearing 6009
81. Catch spring
82. 5mm hex wrench
83. 4mm hex wrench
84. Chuck
85. Chuck key
86. Chuck connect
87. Safety strain
88.
17. Stop plate 41. Valve 65. Gear box cap
18. Cable protector 42. M6×10 screw 66. Bearing 627
19. Cable holder 43. Screw plate
20. Machine holder 44. Screw plate
67. Gear
68. Bearing 627
21. M5×8 screw
22. Cable fixer
23. M4×10 screw
24. Controller
45. Cable holder
47. Screw plate
48. Screw plate
69. Gear box
46. M5×10 screw 70. Catch spring
71. Gear
72. Bearing 6003
89.
90.
91.
92.
93.
94.
95.
96.
13
B R M - 3 5 A / B M A G D R I L L
Breakdown View
14
advertisement
* Your assessment is very important for improving the workof artificial intelligence, which forms the content of this project