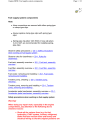
advertisement
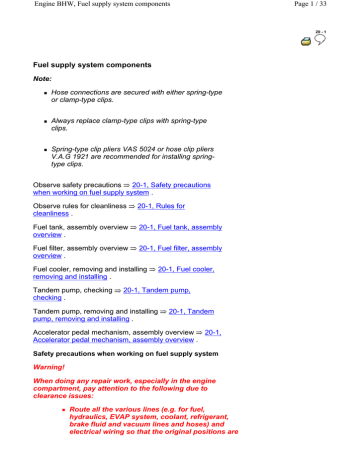
Engine BHW, Fuel supply system components
Fuel supply system components
Note:
Hose connections are secured with either spring-type or clamp-type clips.
Always replace clamp-type clips with spring-type clips.
Spring-type clip pliers VAS 5024 or hose clip pliers
V.A.G 1921 are recommended for installing springtype clips.
Observe safety precautions 20-1, Safety precautions when working on fuel supply system .
Observe rules for cleanliness 20-1, Rules for cleanliness .
Fuel tank, assembly overview 20-1, Fuel tank, assembly overview .
Fuel filter, assembly overview 20-1, Fuel filter, assembly overview .
Fuel cooler, removing and installing 20-1, Fuel cooler, removing and installing .
Tandem pump, checking 20-1, Tandem pump, checking .
Tandem pump, removing and installing 20-1, Tandem pump, removing and installing .
Accelerator pedal mechanism, assembly overview 20-1,
Accelerator pedal mechanism, assembly overview .
Safety precautions when working on fuel supply system
Warning!
When doing any repair work, especially in the engine compartment, pay attention to the following due to clearance issues:
Route all the various lines (e.g. for fuel, hydraulics, EVAP system, coolant, refrigerant, brake fluid and vacuum lines and hoses) and electrical wiring so that the original positions are
Page 1 / 33
20 - 1
Fuel supply system components
restored.
Caution!
Ensure sufficient clearance to all moving or hot components.
The fuel or fuel lines in the fuel system can become very hot (danger of scalding)!
In addition, the fuel system is under pressure!
Before opening the system, place rags around the connection area and release pressure by carefully loosening the connection!
Wear protective goggles and protective gloves when working on the fuel system!
Always observe the following when removing and installing the Fuel Level Sensor or the Fuel Pump (FP) from full or partially filled fuel tanks:
Before starting work, switch on exhaust extraction system and place an extraction hose close to the installation opening of fuel tank to extract escaping fuel fumes. If no exhaust extraction system is available, a radial fan (as long as motor is not in air flow) with a displacement greater than 15 m
3
/h can be used.
Prevent fuel from contacting skin! Wear fuel-resistant gloves!
Rules for cleanliness
When working on the fuel supply/injection system, pay careful attention to the following "6 rules" :
Thoroughly clean all connections and the surrounding area before disconnecting.
Place parts that have been removed on a clean surface and cover them. Do not use fluffy cloths!
Carefully cover over opened components or seal, if
Page 2 / 33
Fuel supply system components repairs are not performed immediately.
Only install clean components: Only unpack replacement parts immediately prior to installation.
Do not use parts that have been stored loose (e.g. in tool boxes etc.).
When the system is open: Avoid working with compressed air if possible. Do not move vehicle unless absolutely necessary.
Do not let diesel fuel flow onto coolant hoses. If necessary, the hoses must be cleaned again immediately. Replace corroded hoses.
Fuel tank, assembly overview
Page 3 / 33
Cap
Fuel supply system components
Oil seal
Replace if damaged
Bolt
Gravity/expansion valve
To remove valve unclip upward out of support
Check valve for through-flow,
Valve vertical: Open; Valve angled at 45 : Closed
Angle piece
O-ring
Replace if damaged
Breather valve
To remove valve unclip sideways out of support
Before installing, unscrew cap
Item - 1 -
breather valve
Ground connection
Ensure seated tightly
Supply line
To fuel filter Item - 2 -
Clipped in at fuel tank
Ensure seated tightly
Black
Return line
From fuel filter Item - 1 -
Clipped in at fuel tank
Page 4 / 33
Fuel supply system components
Ensure seated tightly
Blue or with blue marking
Fuel Level Sensor G
Clipped onto baffle housing in fuel tank
Removing and installing
20-1, Fuel Level Sensor, removing and installing
Oil seal
To install, place into opening of fuel tank dry
Replace if damaged
Moisten with fuel only when installing flange
Union nut, 80 Nm
Use ring nut wrench 3217 for removal and installation
Connector
Black, 4-pin
Flange
Note installed position on fuel of the fuel gauge sender
Fuel delivery unit
Removing and installing
20-1, Fuel delivery unit, removing and installing
Check fuel pump 20-1,
Fuel pump, checking
Clean strainer if soiled
Page 5 / 33
Fuel supply system components
Outer part of baffle housing
With suction jet pump
Component of fuel tank
Vent line
Ensure seated tightly
25 Nm
Fuel tank
Fuel tank, emptying 20-1,
Fuel tank, emptying
Support with engine/transmission jack
V.A.G 1383/A when removing
Removing and installing
20-1, Fuel tank, removing and installing
Securing strap
Observe varying lengths
Bracket
For securing straps
25 Nm
Tank flap unit
With rubber cup
Page 6 / 33
Fuel supply system components
Installed location of the fuel gauge sender
Marking on sender must align with marking on fuel tank -
arrow - .
Note:
After installing the fuel gauge sender, verify that the fuel supply and return lines at the fuel tank are still clipped in.
Checking breather valve
Lever in rest position: Closed
Lever pushed in direction of arrow: Open
Note:
Before installing bleeder valve, unscrew cap from fuel tank.
Fuel filter, assembly overview
Page 7 / 33
Fuel supply system components
Note:
When installing, make sure that the fuel filter is not installed with the water drain plug sitting on the oil filter bracket. This could loosen and begin leaking.
Install the fuel filter so that accessibility to the water drain plug is ensured.
Page 8 / 33
Return line
To fuel cooler 20-1, Fuel cooler, removing and installing
Blue or with blue marking
Ensure seated tightly
Supply line
Fuel supply system components
From fuel tank 20-1, Fuel tank, assembly overview
White or with white markings
Ensure seated tightly
Retaining clip
Regulator valve
Installed location: direction of arrow to fuel tank
When changing filter, remove retaining clip and take off regulator valve with fuel lines attached.
When under + 15 C: flowthrough to filter is open
When over +31 C: flowthrough to filter is closed
O-ring
Replace
Return line
From tandem pump Item -
16 -
Ensure seated tightly
Blue or with blue marking
Fuel line
Fuel Temperature Sensor G81
Supply line
To tandem pump Item - 15
-
Ensure seated tightly
White or with white markings
Page 9 / 33
Fuel supply system components
Fuel filter
Before installing, fill with diesel fuel
Direction of flow is marked with arrows
Do not interchange connections
Replace if damaged
Seal
Replace if damaged
Water drain plug
To vent, remove retaining clip for regulator valve and take off regulator valve with fuel lines attached
Loosen and allow approx. 100 cm
3
of fluid to drain
Fuel cooler, removing and installing
Special tools, testers and auxiliary items required
Torque wrench (5 to 50 Nm) V.A.G 1331
Removing
Observe rules for cleanliness 20-1, Rules for cleanliness .
Page 10 / 33
Fuel supply system components
Note:
The fuel cooler is located in the return line to the fuel tank. It is attached to the underbody of the vehicle.
Page 11 / 33
- Remove retaining clip - C - and bolt - B - and take off cover - A - .
- Separate fuel lines at fuel cooler.
- Remove nuts - arrows - .
Installing
Installation is performed in reverse order. When doing this note the following:
Tightening torque of nuts for fuel cooler: 15 Nm
Fuel tank, emptying
Special tools, testers and auxiliary items required
Fuel supply system components
Fuel siphoning unit VAS 5190
Work sequence
- Observe safety precautions before performing repair supply system
- Open fuel tank flap.
- Push suction hose - arrow - of fuel extractor VAS 5190 into fuel filler neck and extract fuel.
Note:
When no more fuel can be extracted, the tank is emptied only enough for the sender flanges to be opened without danger. The tank may be removed while containing the remaining fuel.
Fuel tank, removing and installing
Special tools, testers and auxiliary items required
Page 12 / 33
Fuel supply system components
Engine/transmission jack V.A.G 1383/A
Torque wrench (5 to 50 Nm) V.A.G 1331
Plug tool for additive tank T10249 (engine code BGW only)
Removing
Note:
The fuel tank must not be more than 1/4 full.
Empty fuel tank using fuel siphoning unit VAS 5190
20-1, Fuel tank, emptying .
Observe safety precautions before performing repair fuel supply system .
- Check whether a coded radio is installed. If necessary, obtain anti-theft coding.
Page 13 / 33
Fuel supply system components
- Disconnect battery Ground (GND) strap with ignition switched off.
- Remove wheelhousing liner, right rear:
Repair Manual, Body Exterior, Repair Group 66,
Wheelhousing liner, removing and installing
- Unscrew securing bolts and remove tank flap unit with rubber cup.
- Remove securing bolt on filler neck.
Warning!
During all repair procedures be aware of the following:
Route all the various lines (e.g. fuel lines, as well as electrical wiring) so that the original positions are restored.
Always perform repair procedures on open systems in rooms with adequate ventilation only!
- Remove tensioning strap while supporting fuel tank with engine/transmission jack V.A.G 1383/A .
Caution!
The fuel or fuel lines in fuel system can become very hot (danger of scalding)!
Ensure sufficient clearance to all moving or hot components.
In addition, the fuel system is under pressure.
Before opening the system, place rags around the connection area and release pressure by carefully loosening the connection.
Wear protective goggles and protective gloves when working on the fuel system!
- Lower engine/transmission jack V.A.G 1383/A only so far until supply and return lines and connector on fuel level sensor can be disconnected.
Note:
Page 14 / 33
Fuel supply system components
Press in securing ring to disengage the fuel lines.
- Unclip supply and return lines at fuel tank and separate connector for fuel level sensor.
- Lower fuel tank.
Installing
Installation is performed in reverse order. When doing this note the following:
Route the vent hoses kink-free.
Route the fuel hoses kink-free.
Secure fuel lines with clamps.
Do not interchange supply and return hose (return hose blue or blue markings, supply hose black).
Clip in the supply and return lines at fuel tank.
Fuel pump, checking
Special tools, testers and auxiliary items required
Page 15 / 33
Hand multimeter V.A.G 1526 B or multimeter V.A.G
1715
Fuel supply system components
Voltage tester V.A.G 1527 B
Connector test set V.A.G 1594 C
Conditions
The fuses must be OK.
Battery voltage must be at least 11.5 Volts.
All electrical consumers such as lights and rear window defroster must be switched off.
Checking function and voltage supply
- Switch ignition on. Fuel pump must run for approx. 1 second.
- Switch ignition off.
If fuel pump does not activate:
- Remove luggage compartment floor cover.
- Connect voltage tester V.A.G 1527 B with adapter cables
Page 16 / 33
Fuel supply system components from test adapter kit V.A.G 1594 C to outer contacts of connector.
- Switch ignition on again, LED must illuminate for approx.
1 second.
- Switch ignition off.
If LED does not illuminate:
- Check actuation of fuel pump relay and check wiring for open circuits and short circuits:
Vehicle Diagnosis,
Testing and Information System VAS 5051 Vehicle
diagnosis, testing information system VAS 5051
LED lights up (voltage supply OK):
- Remove fuel delivery unit 20-1, Fuel delivery unit, removing and installing .
- Check if electrical wiring between flange and fuel pump is connected and has continuity.
If no open circuits are found:
- Replace fuel delivery unit 20-1, Fuel delivery unit, removing and installing .
Checking current draw of Fuel Pump (FP)
- Pull connector off of flange of fuel delivery unit.
Page 17 / 33
- Set multimeter to measuring range 20 A and connect it inline between contacts - 1 - of connector and fuel pump using adapter cables from connector test set V.A.G 1594
C .
Note:
Also, the current clamp of the multimeter V.A.G 1715 can be attached to an adapter cable between the contacts - 1 - of the connector and the fuel pump.
Fuel supply system components
- Connect contacts - 4 - of connector and fuel pump with an adapter cable from connector test set V.A.G 1594 C .
- Start engine and run at idle speed.
- Measure current draw of fuel pump: Specification: 3.5 to
4.5 Amps.
If the measured value lies outside the specified value:
- Replace fuel delivery unit 20-1, Fuel delivery unit, removing and installing .
Fuel delivery unit, removing and installing
Page 18 / 33
Special tools, testers and auxiliary items required
Ring nut wrench 3217
Fuel pump wrench 3307
Fuel supply system components
Torque wrench (40 to 200 Nm) V.A.G 1332
Removing
Note:
The fuel tank must not be more than 1/4 full.
Empty fuel tank if necessary 20-1, Fuel tank, emptying .
Observe safety precautions before performing repair fuel supply system .
- Check whether a coded radio is installed. If necessary, obtain anti-theft coding.
- Disconnect battery Ground (GND) strap with ignition switched off.
- Remove luggage compartment floor cover.
- Pull supply line - 1 - and return line - 2 - , as well as 4-pin connector - 3 - off of flange.
Page 19 / 33
- Separate connector - 4 - .
Caution!
Fuel supply lines are under pressure! Before removing from hose connection wrap a cloth around the connection. Then release pressure by carefully pulling hose off connection.
Fuel supply system components
- Use Ring nut spanner 3217 to remove union nut.
- Pull flange and seal out of opening in fuel tank.
- Pull off fuel return line - 2 - and connector for fuel gauge sender on underside of flange - 1 - .
- Pull off connection piece of return hose at inner part of baffle housing in direction of arrow.
Page 20 / 33
Fuel supply system components
- While pressing retaining tab, pull out Fuel Level Sensor G from baffle housing in fuel tank - arrows - .
- Press release buttons - arrows - and separate fuel hose at Y-fitting.
Page 21 / 33
- Turn fuel delivery unit approx. 15 counter-clockwise onto stop using Fuel pump wrench 3307 and remove with flange.
Fuel supply system components
Note:
If the delivery unit is to be replaced then drain old delivery unit before disposal.
Installing
Page 22 / 33
- Insert fuel pump into baffle housing in fuel tank so that notch - 1 - at fuel pump aligns with marking - 2 - at baffle housing.
Note:
Baffle housing is shown without fuel tank for the sake of illustration.
- Turn fuel delivery unit approx. 15 clockwise onto stop using fuel pump wrench 3307 .
Fuel supply system components
Notch - 1 - aligns with marking - 3 - (bayonet connection).
- Push fuel hose onto Y-fitting and push together until retaining tabs - arrows - engage.
- Place Y-fitting with fuel hoses into fuel tank toward right rear.
Note:
Make sure that the fuel hose from the baffle housing to the Y-fitting is hooked into the retainer at the outer part of the baffle housing.
- Clip in fuel return line at inner part of baffle housing.
- Insert fuel gauge sender in guide at baffle housing and press down until it engages.
- Reconnect fuel gauge sender connector and fuel return line to flange.
Note:
Insert dry seal of fuel pump into opening of fuel tank.
Only coat seal with fuel when installing Fuel Pump
(FP).
Page 23 / 33
Fuel supply system components
- With flange in installation position, turn clockwise and insert into fuel tank.
Page 24 / 33
- Check that marking on flange aligns with marking on fuel tank - arrow - .
- Tighten union nut. Tightening torque: 80 Nm
The rest of the assembly is basically a reverse of the disassembling sequence.
Note:
Do not switch supply and return hoses (return line blue- or with blue markings).
Ensure fuel hoses are seated securely.
Fuel Level Sensor, removing and installing
Removing
Note:
The fuel tank must not be more than 1/4 full.
Empty fuel tank if necessary 20-1, Fuel tank, emptying .
Observe safety precautions before performing repair fuel supply system .
- Remove flange 20-1, Fuel delivery unit, removing and installing , Fuel delivery unit, removing.
Fuel supply system components Page 25 / 33
- While pressing retaining tab, pull out Fuel Level Sensor G from baffle housing in fuel tank - arrows - .
Installing
- Insert Fuel Level Sensor G in guide on baffle housing and press down until it engages.
- Install flange of fuel delivery unit 20-1, Fuel delivery unit, removing and installing , Fuel delivery unit, removing and installing.
Accelerator pedal mechanism, assembly overview
Fuel supply system components Page 26 / 33
Bracket
Connector
Black, 6-pin
10 Nm
Throttle Position (TP) Sensor
G79
Not adjustable
Throttle position sensor transmits driver control to engine control module
To remove, remove footwell cover
Bracket
Fuel supply system components
For footwell cover
Clipped to throttle position sensor
Tandem pump, checking
Special tools, testers and auxiliary items required
Pressure gauge VAS 5187
Torque wrench (5 to 50 Nm) V.A.G 1331
Vehicle diagnostic, testing, and information system
VAS 5051
Diagnostic cable VAS 5051/6A
Conditions
Coolant temperature must be at least 85 C.
Page 27 / 33
Fuel supply system components
Pump-Injector units O.K.
Fuel filter and fuel lines must not be plugged.
Fuel level sensor must be OK.
Work sequence
- Loosen charge air tube and set aside.
Page 28 / 33
- Remove locking bolt - arrow - .
- Install pressure gauge VAS 5187 as shown.
- Secure charge air tube in place again.
- Start engine and run at idle speed.
- Connect vehicle diagnostic, testing, and information system VAS 5051 and select operating mode "Vehicle self-
Fuel supply system components diagnosis" .
- Press button "01 - Engine electronics" on display.
- Press diagnostic function "08 - Read measured value block" .
- Using number keypad, enter display group "1" and acknowledge entry with Q-key.
- Read idle RPM in display field "1" .
- Increase engine speed to 4000 RPM.
- Observe displayed pressure on pressure gauge.
Specification: min. 7.5 bar
- Return engine to idle speed.
If the specification is not obtained:
- Clamp return line closed between fuel filter and tandem pump with a hose clamp.
- Increase engine speed to 4000 RPM.
- Observe displayed pressure on pressure gauge.
Specification: min. 7.5 bar
- Return engine to idle speed.
If the specification is now obtained:
Pressure loss at Pump-Injector unit.
- Replace O-rings of Pump-Injector unit.
If the specification is not obtained:
- Replace tandem pump 20-1, Tandem pump, removing and installing , Tandem pump, removing and installing.
Note:
After removing the pressure gauge, fasten the locking bolt to 25 Nm. Always replace the seal.
Tandem pump, removing and installing
Tandem pump must not be disassembled under any circumstances, since it may otherwise cause the vacuum component to malfunction. The result would
Page 29 / 33
Fuel supply system components
be a failure of the brake booster.
Page 30 / 33
Special tools, testers and auxiliary items
required
Torque wrench (5 to 50 Nm) V.A.G
1331
Hand vacuum pump V.A.G 1390
Hand vacuum pump reservoir
V.A.G 1390/1
Pliers for spring type clips VAS
5024
Removing
Fuel supply system components
- Pull off supply hose - 1 - (white marking) and return hose -
2 - (blue marking) from fuel filter.
- Connect hand vacuum pump V.A.G 1390 with hand vacuum pump reservoir V.A.G 1390/1 to return hose.
- Operate hand vacuum pump until no more fuel runs from return hose. Make sure that no fuel is sucked into hand vacuum pump.
- Loosen charge air tube and set aside.
- Drain coolant 19-1, Cooling system, draining and filling .
- Disconnect coolant hoses from connection Item - 12 - .
- Remove connection Item - 12 - .
- Pull vacuum line - 1 - from brake booster off of tandem pump - 4 - .
- Disconnect central connector for Pump-Injector unit.
- Pull supply hose - 2 - (white marking) off of tandem pump
- 4 - .
- Remove bolts - arrows - .
- Remove the tandem pump - 4 - from the cylinder head.
Page 31 / 33
Fuel supply system components
- Pull tandem pump - 4 - slightly upward, pull off return hose - 3 - (blue marking) and remove tandem pump - 4 - .
Installing
Installation is performed in the reverse order of removal, note the following:
Note:
Make sure that the tandem pump is properly seated in the camshaft.
Always replace the seals of the tandem pump.
Page 32 / 33
- Connect return hose - 3 - (blue marking) to return connection on tandem pump.
- Install tandem pump and tighten upper bolts to 20 Nm.
- Tighten lower bolts to 10 Nm.
- Connect supply hose - 2 - (white marking) to supply connection and vacuum line - 1 - from brake booster to tandem pump - 4 - .
- Connect central connector for Pump-Injector unit.
- Install charge air tube.
Fuel supply system components
- Connect supply hose - 1 - (white marking) to fuel filter.
- Connect hand vacuum pump V.A.G 1390 with hand vacuum pump reservoir V.A.G 1390/1 to return hose - 2 -
(blue marking) of fuel filter.
- Operate hand vacuum pump, until fuel runs from return hose. Make sure that no fuel is sucked into hand vacuum pump.
- Connect return hose - 2 - (blue marking) to fuel filter.
Page 33 / 33
advertisement
* Your assessment is very important for improving the workof artificial intelligence, which forms the content of this project
Related manuals
advertisement