- Home
- Domestic appliances
- Sewing & ironing
- Sewing machines
- Baby Lock
- A-LINE Lauren BL450A
- Reference guide
Baby Lock A-LINE Lauren BL450A Reference Guide
Add to my manuals
28 Pages
Baby Lock A-LINE Lauren BL450A is a fully-featured serger with a wide range of capabilities, from overlock sewing to flatlock seams, blind hemming, and pin tucking. It has 4, 3, or 2-thread capability, adjustable stitch length, differential feed, and adjustable pressure on fabric. The BL450A also features a free arm for sewing cuffs, sleeves, and pant legs. It comes with a built-in needle threader and an extension table for larger projects.
advertisement
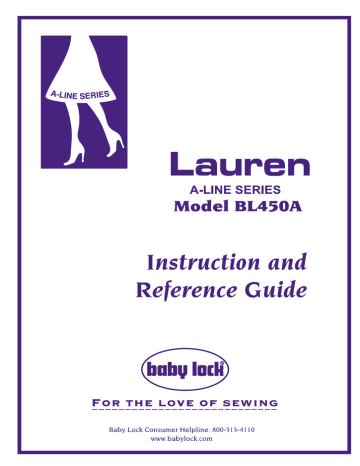
INSTRUCTION AND REFERENCE GUIDE
This sewing machine is intended for household use.
IMPORTANT SAFETY INSTRUCTIONS
When using a sewing machine, basic safety precautions should always be followed, including the following.
Read all instructions before using.
DANGER
- To reduce the risk of electric shock:
1. Never leave unattended when plugged in. Always unplug this machine from the electric outlet immediately after using and before cleaning.
2. Always unplug before relamping. Replace bulb with same type rated 10 Watts.
WARNING
- To reduce the risk of burns, fire, electric shock, or injury to persons:
1. Do not allow to be used as a toy. Close attention is necessary when this sewing machine is used by or near children.
2. Use this sewing machine only for its intended use as described in this manual. Use only attachments recommended by the manufacturer as contained in this manual.
3. Never operate this sewing machine if it has a damaged cord or plug, if it is not working properly, if it has been dropped or damaged, or dropped into water. Return the sewing machine to the nearest authorized retailer or service center for examination, repair, electrical or mechanical adjustment.
4. Never operate the sewing machine with any air openings blocked. Keep ventilation openings of the sewing machine and foot controller free from the accumulation of lint, dust, and loose cloth.
5. Never drop or insert any object into any opening.
6. Do not use outdoors.
7. Do not operate where aerosol (spray) products are being used or where oxygen is being administered.
8. To disconnect, turn the power switch to the off position, then remove plug from outlet.
9. Do not unplug by pulling on cord. To unplug, grasp the plug, not the cord.
10. Keep fingers away from all moving parts. Special care is required around the sewing machine needle and knives.
11. Always use the proper needle plate. The wrong plate can cause the needle to break.
12. Do not use bent needles.
13. Do not pull or push fabric while stitching. It may deflect the needle causing it to break.
14. Switch the sewing machine off when making any adjustments in the needle area, such as threading needle or loopers, changing needle, blade, or needle plate.
15. Always unplug the sewing machine from the electrical outlet when removing covers, lubricating, or when making any other user servicing adjustments mentioned in this manual.
SAVE THESE INSTRUCTIONS
TABLE OF CONTENTS
SPECIFICATIONS ..................................................... 1
GETTING TO KNOW YOUR SERGER ..................... 2
ACCESS TO THREAD GUIDES AND FREE ARM .... 3
ELECTRICAL CONNECTION .................................... 4
ACCESSORIES ......................................................... 4
INSERTING THE NEEDLE ........................................ 5
NEEDLE, THREAD AND FABRIC CHART ................ 5
THREADING THE MACHINE .................................... 6
extension bar .......................................................... 6
threading the upper looper ..................................... 7
threading the lower looper ...................................... 8
threading the right and left needles ........................ 9
easy thread changing -Tying On method ............... 9
BEFORE STARTING TO SEW ................................ 10
starting to sew ...................................................... 10
presser foot markings ........................................... 10
end of seam ......................................................... 10
when thread breaks .............................................. 10
OVERLOCK SEWING (2-needle, 4-thread) ............. 11
FOUR THREAD TENSION ...................................... 11
SETTING STITCH LENGTH .................................... 12
ADJUSTING THE DIFFERENTIAL FEED ............... 12
SETTING THE SEAM WIDTH ................................. 12
ADJUSTING THE PRESSURE ON FABRIC ........... 13
OVERLOCK SEWING (1-needle, 3-thread) ............. 13
three thread tension ............................................. 13
NARROW AND ROLLED HEMMING ...................... 14
changing the needle plate .................................... 14
setting controls ..................................................... 14
NARROW HEM-Method A ....................................... 15
thread tension-Method A ...................................... 15
ROLLED HEMMING-Method B ................................ 15
thread tension-Method B ...................................... 15
TWO THREAD SERGING ....................................... 16
to convert from 3-thread to 2-thread sewing ........ 16
thread tension ...................................................... 17
to convert from 2-thread to 3- or 4- thread sewing 17
FREE ARM SEWING ............................................... 17
BLIND HEMMING .................................................... 18 changing the presser foot .................................... 18 setting controls .................................................... 18 sewing ................................................................. 18
SEWING WITH THE UPPER BLADE DISENGAGED .. 19 sewing ................................................................. 19
FLATLOCK SEAM ................................................... 20 setting controls .................................................... 20 thread tension ...................................................... 20 sewing ................................................................. 20
PIN TUCKING .......................................................... 21 sewing ................................................................. 21
DECORATIVE OVERLOCK ..................................... 21
TURNING CORNERS .............................................. 22
outside corner ...................................................... 22 inside corners ...................................................... 22
outside curves ...................................................... 22
CLEANING AND MAINTENANCE ........................... 23
cleaning ................................................................ 23
oiling ..................................................................... 23
changing the sewing light ..................................... 23
changing the lower blade ..................................... 23
BEFORE YOU CALL FOR SERVICE ...................... 24
STITCH SELECTION CHART ................................. 25
SPECIFICATIONS
Stitch length
Differential feed ratio
Seam width
Needle bar stroke
Presser foot
Presser foot lift
Needle
Number of threads
Dimensions
Net weight
1-4 mm
0.7-2.0
Left needle: 6.2-7.2 mm, Right needle: 4.0-5.0 mm
27 mm
Hinged, Snap on type
5 mm
Type Schmetz ELx705 or Organ HAx1, size 75-90/11-14
4, 3, 2
Width: 290 mm x Depth: 230 mm x Height: 320 mm
6.7 kg
1
GETTING TO KNOW YOUR SERGER
11
12
13
14
9
10
8 7 6 5 4 3 2 1
17
16
1. Thread Guide Hanger
2. Extension Bar
3. Lower Looper Thread Tension Dial
(Blue)
4. Upper Looper Thread Tension Dial
(Green)
5. Thread Guide and Pretension Disc
6. Right Needle Thread Tension Dial
(Yellow)
7. Left Needle Thread Tension Dial
(Red)
8. Pressure Regulator
9. Thread Take-up Lever
10. Presser Foot Lifter
11. Presser Foot Releasing Lever
12. Presser Foot
13. Free Arm
14. Extension Table
15. Extension Table Lock/Release Lever
16. Front Cover
17. Stitch Length Window
15
FRONT VIEW
27
26
25
24
18. Differential Feed Indicator
19. Stitch Length Regulator Dial
(outside dial)
20. Differential Feed Regulator Dial
(inside dial)
21. Handwheel
22. Light & Power Switch
23. Terminal Box
24. Spool Stand
25. Spool Pin
26. Cone Holders
27. Handle
18
19
20
21
22
23
REAR VIEW
2
INSIDE OF FRONT COVER AND FREE ARM
COVER
1. Needle Clamp
2. Upper Blade Holder
3. Upper Blade
4. Needle Plate
5. Seam Width Knob
6. Upper Looper
7. Lower Looper
8. Lower Blade
1
2
3
4
5
ACCESS TO THREAD GUIDES AND FREE ARM
1. Place thumb in hollow of front cover and slide it to the right as far as possible; pull cover down toward you.
2. To close, lift cover up and it will snap into place.
3. Be sure that the cover is properly closed before starting to sew.
Opening the Extension Table Removing the Free Arm Cover
6
7
8
1. To unlock side cover, turn lever located on left side of Extension Table towards front of machine.
2. Pull Extension Table out to open.
3. To close and lock, push cover shut and turn lever toward back of machine. This locks the Extension
Table to Free Arm Cover.
Swing Extension Table out with lever in locked position and Free Arm Cover will stay attached to the Extension
Table.
3
ELECTRICAL CONNECTION
Connect the electrical cord to the machine by inserting the threehole plug into the terminal box located on the right side of the machine.
Connect the cord plug into an electrical outlet.
Power Line
Plug
POLARIZED PLUG INFORMATION
This appliance has a polarized plug (one prong wider than the other). To reduce the risk of electric shock, this plug is intended to fit in a polarized outlet only one way. If the plug does not fit fully in the outlet, reverse the plug. If it still does not fit, contact a qualified electrician to install the proper outlet. Do not modify the plug in any way.
Light and
Power
Switch
Foot
Control
LIGHT AND POWER SWITCH
The light and power switch is located on right side of machine in front of the terminal box. To turn power on, push the front side of the switch.
Turning on the power, lights up the stitching area. The machine will not operate unless the switch is on.
FOOT CONTROL (Model YC-482)
This foot control was designed exclusively for this machine, and is not to be used on any other machine, nor should any other foot control be connected to this machine.
Place Foot control on floor where it is easy to reach with your foot.
To make machine go faster, press down on foot control; to slow down the sewing speed, let up slightly on the foot control.
CAUTION:
Disconnect the electrical cord from the wall outlet when machine is not in use or when it is being cleaned.
Turn the power switch to the “OFF” position before changing needles or needle plates, and before connecting the cord. This will help prevent accidents.
ACCESSORIES
Needles
ELx705/Organ HAx1
(#11 x 2)
Thread Caps
(#14 x 3)
Tweezers
Extra Lower
Blade
Subsidiary
Looper
(for 2-thread sewing)
Subsidiary
Looper Case
Blind Hem
Presser Foot
4
Oiler Brush
Allen
Wrench
Screw
Driver
Rolled Hem
Needle Plate Thread Nets Accessory Case
INSERTING THE NEEDLE
Select the proper type and size needle for fabric used. (See below “NEEDLE, THREAD AND FABRIC CHART”.)
Left Needle
Clamp Screw
Right Needle
Clamp Screw
Tighten
Flat Side
Loosen
OFF
1. Turn electrical power off.
2. Turn handwheel toward you until the needle comes to its highest point.
3. Use the allen wrench to loosen the Left and/or Right needle clamp screw, and remove the needle.
4. Place flat side of needle toward back of the machine, and insert in needle clamp as far as it will go.
5. Retighten the screw.
NEEDLE, THREAD AND FABRIC CHART
The chart shows size and type of thread, and needle size for various weights and types of fabrics. Size means the fineness of both needle and thread.
FABRICS
LIGHTWEIGHT: organdy, voile, taffeta, lawn, crepe.
MEDIUM WEIGHT: gingham, satin, seersucker, linen, velveteen, gabardine, broadcloth.
HEAVY WEIGHT: denim, tweed, corduroy, pile fabrics.
KNIT tricot jersey wool
THREADS
Cotton #100
Silk #100
Spun #80-100
Tetron #90
Cotton #60-80
Silk #50
Spun #60-90
Tetron #60-80
Cotton #40-60
Silk #40-50
Spun #60-90
Tetron #50-60
Spun #60-80
Tetron #60-80
Woolly Nylon
Spun #60-80
Tetron #60
Woolly Nylon
Spun #60-80
Tetron #50-60
Woolly Nylon
Woolly Tetron
NEEDLE SIZES
Schmetz ELx705; 80/12 or
Organ HAx1; 75/11
Schmetz ELx705; 80/12,
90/14 or
Organ HAx1; 75/11, 90/14
Schmetz ELx705; 90/14 or
Organ HAx1; 90/14
Schmetz ELx705; 90/14 or
Organ HAx1; 75/11
Schmetz ELx705; 80/12 or 90/14
Organ HAx1; 75/11, 90/14
Schmetz ELx705; 90/14 or
Organ HAx1; 90/14
5
THREADING THE MACHINE
When threading, be sure to follow the directions given below. The machine must be threaded in the proper sequence in order to sew. An illustration for correct threading is inside the front cover of the machine.
The thread guides are identified with color markings corresponding to the thread to which they belong.
Always thread the upper and lower loopers before threading the needles.
Threading Sequence
1. Upper Looper (Green)
2. Lower Looper
3. Right Needle
(Blue)
(Yellow)
4. Left Needle (Red)
Stopper
extension bar
1. Pull the Extension Bar up as far as it will go.
2. Rotate the Thread Guide Hanger so that the Thread
Guides are right above the spool pins. Stopper pegs will snap into position.
3. Place the spools or thread cones on spool pins.
Lower
Looper
Thread
Upper
Looper
Thread
Right
Needle
Thread
Left
Needle
Thread
When using thread on cones, place the cone over the cone holders on the spool pin.
Thread spool nets are useful for synthetic threads which tend to drop off its holder.
Cover the thread cones with the thread nets provided with the accessories.
Bring thread end to the top of the machine.
6
Thread caps are also provided with the accessories.
They are used when sewing with regular spools.
Insert the stem of cap into the spool hole opposite the end with notch.
threading the upper looper
Open the front cover and thread upper looper thread as illustrated below in steps 1 to 9.
Follow thread guides with green color markings on machine.
1. Pass thread through top guide from back to front.
1
1
3
2
2
2. Bring thread down and pass through thread guide and under pretension disc.
3 9
8
7
6
4
5
9
Threading chart inside front cover
8
7
4
6
5
3. Bring thread straight down through the slot so that it passes between the tension discs.
4. Hook thread from the left side.
5. Hook thread from the right side.
6. Hook thread from the bottom side and pull thread up.
7. Hook thread from the top side.
8. Hook thread from the bottom side and pull thread up.
9. Use tweezers to pass thread through the upper looper hole front to back. Pull at least 7 cm (3 inches) of thread through the upper looper.
7
threading the lower looper
Swing the extension table, with free arm attached, out to the left. Thread lower looper thread as illustrated below in steps A to H. Follow thread guides with blue color markings on machine.
A
A. Pass thread through guide from back to front.
B. Bring thread down and pass through thread guide and under pretension disc.
C. Bring thread straight down along the slot so that the thread passes between the tension discs.
C
B
C
G
H
F
E
D
G
H
F
D
E
D. Hook thread from the right side and pull thread towards left.
E. Hook thread from the bottom side.
F. Hook thread from the bottom side and pull thread towards left.
G. Turn handwheel toward you until the lower looper is in extreme left side position. Pass thread through hole using the tweezers.
H. Turn handwheel until the lower looper is in extreme right position. Use the tweezers to pass thread through hole front to back. Pull at least
7 cm (3 inches) of thread through lower looper.
8
threading the right and left needles
B
A
C b c a
Thread right needle as illustrated below in steps a to i.
Thread guides with yellow color marking on machine.
f i g h e d a-c. Thread same sequence as threading upper and lower looper thread.
d. Hook thread into guide and pull it towards left.
e. Hook thread into back opening of guide.
f.
Hook into guide by sliding thread across top and down into hole.
g. Position thread into right side opening of guide.
h. Pass thread behind right side of guide plate.
i.
Pass through right needle eye front to back. Pull at least 7 cm
(3 inches) of thread through the needle eye.
E f
F
G
H i g h
D e d
Thread left needle as illustrated below in steps A to H.
Thread guides with red color marking on machine.
G
F
E
H
D
A-C. Thread same sequence as threading upper and lower looper thread.
D. Hook thread into front opening of guide and pull thread up.
E. Hook into guide by sliding thread across top and down into hole.
F. Position thread into left side opening of guide.
G. Pass thread under left side of guide plate.
H. Use the tweezers to pass thread through left needle eye front to back.
Pull at least 7 cm (3 inches) of thread through the needle eye.
easy thread changing -Tying On method
1. Cut the thread near the spools.
2. Exchange the spool with a new one and tie end to remaining thread making knot as small as possible.
3. Make note of the tension setting numbers on each Thread Tension Dial.
4. Turn Thread Tension Dials to the smallest number.
5. Lightly pull thread tails behind presser foot and press Foot Control to run machine until upper and lower thread knot comes through looper hole.
6. Stop needle thread knot before passing through eye of needle. Pull needle threads near the needle eye and cut thread knots.
7. Pass threads through needle eye manually.
8. Return tension dials to original tension settings.
9
BEFORE STARTING TO SEW
When the machine is plugged in properly and threaded correctly it is ready for sewing. To insure good stitches, make several sewing tests using the same fabric and thread on which you will sew. Make the proper adjustments while test sewing.
Close front cover before beginning any sewing project.
starting to sew
1. Pull all threads under the presser foot and toward the back.
2. Lower the presser foot.
3. Turn handwheel toward you 2 or 3 times and check the thread chain.
4. Press Foot Control lightly pulling threads toward back and make thread chain about 5 cm (2 inches).
5. Place a scrap of fabric under the toe of the presser foot at the position to be stitched.
6. Hold end of thread with your left hand when starting to sew.
presser foot markings
The markings on the front of the presser foot line up directly in front of the needles for guiding your fabric.
• Left mark for the left needle.
• Right mark for the right needle.
The toe opening in the presser foot is designed to guide a stabilizing tape, narrow elastic or decorative ribbon into the stitching.
Insert the tape or elastic into the slot and under the back of the foot.
end of seam
1. When the needle reaches the end of seam, chain off by running the machine until the thread chain is 6-7 cm (2-3 inches) long.
2. Stop the machine and cut the thread chain leaving 3-4 cm (1-
2 inches) attached to the machine. Tie small knots in thread ends and treat with dot of seam sealant. Let dry and trim close to knot.
3. For neater finish, pull thread ends back through seam using hook or yarn needle.
when thread breaks
If the thread breaks while sewing, remove fabric from machine and rethread as indicated below.
• Upper Looper Thread; turn handwheel toward you until the upper looper is in the lowest position. Pass thread through the looper hole.
• Lower Looper Thread; cut the needle threads near needle hole; rethread the lower looper; rethread the needle/needles.
To begin sewing, place material 3-4 cm (1-2 inches) behind point where thread broke.
10
OVERLOCK SEWING (2-needle, 4-thread)
Your machine will sew overlock stitches and simultaneously trim the fabric.
It is delivered from the factory preset to sew a 4-thread overlock stitch.
This machine can also sew 1-needle, 3-thread overlock stitch by removing one needle. (See page 13 “OVER-
LOCK SEWING 1-needle, 3-thread”.)
The 2-needle, 4-thread stitch offers a stronger seam for some areas of your sewing. It is recommended for most woven fabrics and clothes that will receive harder wear and/or frequent washings.
FOUR THREAD TENSION
Bottom side of fabric
Correct 4-thread tension
Top side
of
fabric
Lower
Looper
Thread
The stitch quality depends on proper balance between the four thread tensions. The tensions may require adjustment depending on the type of fabric, heaviness of fabric and size of thread used.
The table below is a guide for adjusting the thread tension.
Note: Be sure that the thread is passing between the tension discs.
Fabric
Light Weight
Left
Needle
Thread
2.5-4.5
Right
Needle
Thread
1.5-3.5
Upper
Looper
Thread
2.0-4.0
Lower
Looper
Thread
2.0-4.0
Medium Weight 2.5-4.5
1.5-3.5
2.0-4.0
2.0-4.0
Heavy Weight 2.5-4.5
1.5-3.5
2.0-4.0
2.0-4.0
Turning thread tension dial
5
Increase
Upper
Looper
Thread
Left
Needle
Thread
Right
Needle
Thread
NOTE:
This table is a guide for thread tensions when sewing with #80 to #90 polyester spun threads.
Decrease
TO INCREASE, turn tension dial to a higher number.
TO DECREASE, turn tension dial to a lower number.
The charts below are illustrations of stitches needing adjustment in the thread tension.
Left needle thread is too loose. (Clearly visible on the bottom side of fabric.)
Right needle thread is too loose.
Upper looper thread crossed on bottom side of fabric.
Lower looper thread crossed on top side of fabric.
Increase Left Needle Thread
Tension and/or Decrease
Upper and Lower Looper
Thread Tensions evenly.
Increase Right Needle
Thread Tension.
Increase Upper Looper
Thread Tension and/or
Decrease Lower Looper
Thread Tension.
Increase Lower Looper
Thread Tension and/or
Decrease Upper Looper
Thread Tension.
11
SETTING STITCH LENGTH
The stitch length can be adjusted between 1 and 4 mm.
• For shortest stitch, turn dial to 1. (fig.12-A)
• For longest stitch, turn dial to 4.
As a rule, light weight fabrics take a shorter stitch.
Heavy weight fabrics need longer stitches.
Most normal sewing is done with stitch length dial set at 3. This produces a medium length stitch which makes a strong seam and is suitable for most fabrics.
ADJUSTING THE DIFFERENTIAL FEED
fig. 12-A
Rear
Shorter
Longer
N
This machine has two feed dogs - a front feed dog and a rear feed dog, which move independently and can be adjusted separately.
This Differential Feed prevents waving in stretch fabrics and insures pucker-free seams in light weight woven fabrics.
The rear feed motion (main feed) is adjusted by turning the stitch length regulator dial. The front feed motion is adjusted by turning the differential feed regulator dial which is located inside the stitch length regulator dial. (fig. 12-B) fig. 12-C
Front
0.7
fig. 12-B
“pucker free” seams
• For normal sewing, set the differential feed regulator dial to
“N”. Both feed dogs will move together and feed evenly.
• For pucker-free seams in delicate or closely woven fabrics, turn the dial to “0.7”. The front feed dog motion will be shorter than the rear feed dog motion. The front feed dog will hold back the fabric enabling the rear feed dog to take it up behind the needle without any puckering. (fig. 12-C)
• When sewing stretch or knit fabrics, turn the dial towards
“2”. The front feed dog motion will be longer than the rear feed dog motion and in this manner the fabric can be sewn without stretching. (fig. 12-D) fig. 12-D without without
The differential feed can be used for gathering or lettuce edging.
• For gathering, set the dial towards “2”. (fig. 12-E)
• For lettuce edging, set the dial towards “0.7”. (fig. 12-F) no “wavy” seams
2 with with
SETTING THE SEAM WIDTH
Overedge seam width can be adjusted from 6.2 mm (right needle 4.0 mm) to 7.2 mm (right needle 5.0 mm) stitch.
Normally the machine is set at 6.2 mm which is the width most frequently used.
For heavy weight fabrics, set control knob to wider stitch.
1. Turn power switch off.
2. Open front cover and Free Arm Cover.
3. Push the Upper Blade Holder to the right and turn the
Width Indicator Knob downward to select wider stitch width. For smaller width turn knob in opposite direction.
When adjusting the width, use the markings on the needle plate as guide and line up with left edge of lower blade width indicator.
The numbers marked on the needle plate are the width from the fabric's cut edge to the right needle, and the distance between needles is 2.2 mm. Therefore the width to left needle is an additional 2.2 mm.
12 fig. 12-E
4 5
Lower
Blade
Width
Indicator
Push
Width
Indicator
Knob fig. 12-F
2.2 mm
4-5 mm
ADJUSTING THE PRESSURE ON FABRIC
The pressure on the foot can be adjusted for different weight fabrics. The fabric should move along smoothly and evenly without slipping.
Stitches should be uniform in size.
The pressure on this machine is set for sewing medium weight fabrics.
Increase
• For sewing light weight fabrics, decrease the pressure (turn screw to left).
• For heavy weight fabrics, increase the pressure (turn screw to right).
OVERLOCK SEWING
Correct 3thread tension
(1-needle, 3-thread )
This machine can also sew 1-needle, 3-thread overlock stitching by removing either needle, depending on the seam width you desire.
This is the standard overlock stitch and is suitable for most fabrics.
Bottom side of fabric
To convert your machine to a wide 3-thread stitch (7.2 mm -
6.2 mm), snip the right needle thread just above the eye of the needle.
Remove the thread from the “yellow” color coded thread guides. Remove the right needle and tighten the right needle clamp screw. This stitch width is suitable for sewing heavier fabrics.
Lower
Looper
Thread
Top side of
fabric
Decrease
Upper
Looper
Thread
Needle
Thread
To convert your machine to a narrow 3-thread stitch (5 mm - 4 mm), snip the left needle thread just above the eye of the needle. Remove the thread from the “red” color coded thread guides. Remove the left needle and tighten the left needle clamp screw. This stitch width is suitable for sewing lightweight to medium weight fabrics.
Fabric
Weight
Both seam widths can be adjusted by turning the width indicator knob. (See page 12 “SETTING SEAM
WIDTH”.)
Light
three thread tension
Medium
Heavy
(Left)
(Right)
(Left)
(Right)
(Left)
(Right)
6.2 mm
Needle Thread
(Left or Right)
2.0-4.0
1.5-3.5
2.0-4.0
1.5-3.5
2.5-4.5
1.5-3.5
Upper
Looper
Thread
2.0-4.0
2.5-5.0
2.0-4.0
2.5-5.0
2.0-4.0
2.5-5.0
4.0 mm
Lower
Looper
Thread
2.0-4.0
2.0-4.0
2.0-4.0
2.0-4.0
2.0-4.0
2.0-4.0
Use the chart to the right as a guide in setting tension.
Note: Be sure that the thread is passing between the tension discs.
The illustrations below are examples of stitches which need adjusting.
NOTE:
This table is a guide for thread tensions when sewing with #80 to #90 polyester spun threads.
Needle thread is too loose. (Clearly visible on the bottom side of fabric.)
Upper looper thread crossed on bottom side of fabric.
Lower looper thread crossed on top side of fabric.
Increase Needle Thread Tension and/or Decrease Upper and Lower
Looper Thread Tension.
Increase Upper Looper Thread
Tension and/or Decrease Lower
Looper Thread Tension.
Increase Lower Looper Thread
Tension and/or Decrease Upper
Looper Thread Tension.
13
NARROW AND ROLLED HEMMING
By changing the needle plate to “Rolled Hem Needle Plate” and using right needle only, the machine trims fabric, folds back the edge and sews a narrow hem (overedge). The width of the narrow overedge is 1.5 mm (about
1/16") and is used for overedging light and medium weight fabrics.
Two variations of the rolled overedge hem can be sewn with this machine by changing the thread tension.
Both methods are used with light and medium weight fabrics.
Method B gives a softer finish by pulling the interlocking threads to the wrong side.
changing the needle plate
The machine comes with a standard overedge needle plate set to the machine.
Change the needle plate when sewing rolled overedge.
4 - 5
Standard Overedge
Needle Plate
Stitch fingers
Rolled Hem
Needle Plate
Stitch fingers
OFF
1. Turn power switch off.
2. Turn handwheel toward you until needle is at its highest point.
3. Lift presser foot lifter.
4. Clear stitches off the stitch fingers.
5. Open Extension Table and Free
Arm Cover (See page 3).
6. Loosen the front side screw.
7. Lift the Needle Plate off and replace with Rolled Hemming
Plate. (Be sure that thread is not caught under plate.)
8. Retighten the screw and replace
Free Arm Cover.
setting controls
Set the controls as follows.
1. Use right needle only. (Remove the left needle.)
2. Fabric, Thread & Needle Size
Refer to Page 5 “NEEDLE, THREAD & FABRIC
CHART”, for selecting suitable thread and needle sizes for sewing on light and medium weight fabrics.
3. Stitch Length Regulator
Set stitch length between 1 and 2 mm.
4. Width Indicator Knob
The seam width for sewing rolled overedge is normally
1.5 mm (about 1/16").
Turn width indicator knob and adjust so that the left side of Lower Blade Width Indicator is aligned with the mark of the Rolled Hem Needle Plate. (See page 12).
14
1 - 2
Right Needle Stitch Length Seam Width
NARROW HEMMING -Method A
Pull the excess threads gently toward the back and begin sewing.
Although the stitch width is set at 1.5 mm, you will actually need 3.5 mm
(about 1/8") to provide enough fabric for the fold back.
thread tension -Method A
Use the chart below as a guide in setting tension.
The tension adjustments for Method A are the same as 1-needle, 3-thread overlock. See page 13 if adjustments are needed.
Fabric
Light & Medium
Needle
Thread
(Right)
1.5-3.5
Upper
Looper
Thread
2.0-4.0
Lower
Looper
Thread
2.0-4.0
Correct 3-thread narrow overedge tension
1.5 mm
3.5 mm
Right side of fabric
Upper
Looper
Thread
NOTE:
This table is a guide for thread tensions when sewing with #80 to #90 polyester spun threads.
ROLLED HEMMING -Method B
Regulate the tension dials using guide below.
Fabric
Needle
Thread
(Right)
Upper
Looper
Thread
Lower
Looper
Thread
Light & Medium 1.5-3.5
2.0-4.0
4.0-7.0
Wrong side of fabric
Lower
Looper
Thread
Correct 3-thread rolled hem tension
Right side
of fabric
Needle
Thread
The upper looper thread encases the fabric edge in Method B rolled hem, creating a softer finish.
Settings and sewing of Method B rolled hem are the same as the Method A narrow hem except for thread tension.
(See below)
thread tension -Method B
Upper
Looper
Thread
Needle
Thread
NOTE:
This table is a guide for thread tensions when sewing with #80 to #90 polyester spun threads.
Needle thread is too loose.
Wrong side of fabric
Upper looper thread is too loose.
Lower
Looper
Thread
Lower looper thread is too loose.
Increase Needle Thread Tension and/or Decrease Upper Thread
Tension.
Increase Upper Looper Thread
Tension.
Increase Lower Looper Thread
Tension and/or Decrease Upper
Looper Thread Tension.
15
TWO THREAD SERGING
Two thread serging provides a decorative, yet functional seam known as the flatlock seam. You can flatlock garments ranging from lingerie to fake fur coats. When sewing with two threads you can achieve a flat, bulk-free seam. Using it to seam fake-fur fabrics and hand knit fabrics you will find that the “stitches” disappear into the nap. Enhance the appearance of flatlock stitch with the use of decorative threads through the looper.
Correct thread tension
Top of fabric
Bottom of fabric
Lower
Looper
Thread
Besides flatlock seaming, two thread serging also provides a sturdy means of overedging all fabrics.
This can be combined with speciality threads for decorative edges on ruffles, hemlines, and borders.
Needle thread
Two thread sewing is accomplished through the elimination of two threads
- the upper looper and either needle. NOTE: Use the LEFT needle for a wide flatlock stitch; use the RIGHT needle for a narrow flatlock stitch.
Needle and lower looper threads are crossing on the edge of fabric.
to convert from 3-thread to 2-thread sewing
1. Open the front cover and rotate the handwheel to bring the upper looper to its lowest position.
2. Cut the upper looper thread just behind the eye of the upper looper.
(A)
3. Remove the lower looper thread from the thread guide (A).
(B)
4. Hook the lower looper thread to the thread guide (B).
5. Insert the subsidiary looper into the hole at the top of the upper looper shaft.
6. Push on the subsidiary looper with your finger and rotate it to the left until the tip of the subsidiary looper is securely positioned into the eye of the upper looper.
16
thread tension
When you are doing two thread serging for the first time use a medium weight fabric to sew a test sample for determining the correct tension setting. Begin by adjusting the needle tension to “1” and the lower looper tension to “4”. Sew a sample. If the threads are not balanced make necessary adjustments according to the illustrations.
Needle thread laps around over the top of fabric.
Lower looper thread laps around over the bottom of fabric.
Increase Needle Thread Tension and/or Decrease Lower Looper
Thread Tension.
Increase Lower Looper Thread
Tension and/or Decrease Needle
Thread Tension.
to convert from 2-thread to 3- or 4- thread sewing
1. Open the front cover and bring the upper looper to its lowest position.
2. With your finger, push back on the subsidiary looper, and rotate clockwise (up) to disengage from the eye of the upper looper.
3. Remove subsidiary looper from the upper looper shaft and place in accessory box.
4. Remove the lower looper thread from the thread guide (B) and hook to the thread guide (A).
5. Re-thread upper looper thread guides which may have been unthreaded and back through the eye of the upper looper.
6. For four thread sewing, replace the second needle and its corresponding thread.
7. Rebalance tensions - tighten needle thread, re-adjust lower looper if necessary.
(A) (B)
FREE ARM SEWING
This machine will convert to free arm sewing by simply opening the Extension Table. It is used for sewing sleeves, trousers or similar places that are difficult to sew on a flat bed machine.
Turn lever located on left side of extension table to the front of machine and swing table out.
17
BLIND HEMMING
By changing the presser foot to “Blind Hem Presser Foot”, you can sew blind stitches while trimming fabric.
It produces a durable hem which is almost invisible on the right side of the article sewn. It is useful for sewing cuffs, trouser bottoms, pockets etc,.
changing the presser foot
REMOVING THE PRESSER FOOT
1. Turn the handwheel toward you until the needle is at its highest point.
2. Lift up the presser foot by raising the presser foot lifter.
3. Push the presser foot releasing lever towards you, and presser foot will disengage.
4. Pull up the presser foot spring and remove the presser foot.
2
3
1
Spring
REPLACING THE PRESSER FOOT
1. Pull up the presser foot spring and place the presser foot below the presser foot holder so that the pin on the foot fits into the hollow of presser foot holder.
2. Lower the presser bar with the presser foot lifter and the presser foot will snap into place.
2
1
setting controls
Attach the blind hem presser foot and remove the left needle (leave the right needle).
Set the machine to sew 1-needle, 3-thread overlock and adjust the thread tensions as shown on the right.
sewing
Pin
Set tension dials for normal 3-thread overlocking.
Needle Thread
(Right)
Slightly Decrease
Needle
Right
Upper Looper
Thread
Slightly Increase
Lower Looper
Thread
Slightly Decrease
Stitch Length
3 - 4
Presser Foot
Blind Hem
Needle Plate
Standard
Seam Width
4
First sew a test sample on a scrap of fabric and adjust the seam guide and thread tension.
1-2 cm
Guide
Right side of fabric
Wrong side of fabric
1. Fold hem up as desired, fold it back toward right side of the fabric. Leave 1 to 2 cm seam allowance to the right.
Screw
2. The plastic guide on the presser foot ensures even feeding of the fabric when blind hemming. This guide is adjusted by turning the screw.
3. Raise the presser foot.
4. With the wrong side up, place the fabric under the presser foot so that the plastic guide is just touching the folded edge.
5. Adjust the guide so that the needle pierces just the folded edge.
18
6. Lower the presser foot and sew hem, guiding fabric evenly along the plastic guide.
7. When hem is completed, open the fabric and press hem.
CORRECT THREAD TENSION
The upper and lower looper threads are crossed on the cut edge of fabric.
SEWING WITH UPPER BLADE DISENGAGED
When sewing without trimming, disengage the moving blade as shown below.
Use the blind hem presser foot to insure even seam width.
NOTE: When using the blind hem foot, always remove the left needle.
1. Unplug the machine.
2. Open the front cover.
3. Turn handwheel toward you until the upper blade is at its lowest point.
4. Push the upper blade to the right as far as it will go and turn knob in opposite direction until it clicks into position.
5. To re-engage, push blade holder to right and turn blade towards you until it clicks into position.
sewing
Adjust the plastic guide by turning the screw so that the stitches are just over the folded edge.
19
FLATLOCK SEAM
Using the blind hem presser foot and disengaging the upper blade, you can sew decorative top stitching “Flatlock
Seam” as shown on the sketch.
setting controls
Flatlock Seam (Correct thread tension)
Set the machine controls as below.
Needle
Right
Stitch Length
2-3
Presser Foot
Blind Hem
Upper Blade
Disengage
Needle Plate
Standard
thread tension
Test Sample
Set tension dials for normal 3-thread overcasting.
Needle Thread
(Right)
Decrease
Upper Looper
Thread
Normal
Lower Looper
Thread
Increase
Upper
Looper
Thread
Needle
Thread
Lower
Looper
Thread
1. First sew test sample for adjusting the thread tensions.
2. Fold fabric with wrong sides together.
3. Adjust the plastic guide on blind hem foot so that the stitches just overcast the folded edge.
4. Adjust the thread tensions until the needle thread comes to folded edge and the lower looper thread formes nearly a straight line on the edge.
sewing
1. Fold fabric with wrong sides together.
2. Adjust the plastic guide so that the stitches hang halfway over the folded edge.
3. Lower the presser foot and sew.
20
4. When stitching is completed, pull fabric flat and press the stitches from the wrong side of fabric.
PIN TUCKING
Pin tucking is a useful decorative stitch for blouses and children’s wear.
Set the machine controls as shown on the right.
Slightly increase the looper thread tension.
Right
Needle
Presser Foot
Blind Hem
Stitch Length
2-3
Upper Blade
Disengage
Needle Plate
Standard
sewing
1. Fold fabric with wrong sides together.
2. Adjust the plastic guides so that the stitches just overcast the folded edge.
3. Lower the presser foot and sew.
4. Sew as many rows as desired and press them to lay flat on one side.
DECORATIVE OVERLOCK
When you change the Upper Looper Thread to heavier thread or yarn, you can produce decorative overlock stitching.
Try using various types of thread to create attractive combinations experiment with different tension adjustments to produce a variety of decorative effects.
examples;
1-needle, 3-thread Rolled hem Method B 2-thread Flatlock
Upper Looper
Thread:
Heavy thread or Yarn
Upper Looper
Thread:
Woolly Nylon;
Rayon; metallics
21
TURNING CORNERS outside corner
1. Cut the corner about 5-6 cm (2-3 inches) along the cutting line.
2. Sew to the end of fabric and stop machine.
3. Raise needle and presser foot.
4. Pull fabric slightly towards the back and pull out tangled thread from
Needle plate.
5. Turn fabric and position the fabric by lining up the cut line and blade.
Lower the Presser Foot.
6. Resume sewing.
inside corners
1. Snip to corner of seam line.
2. Sew desired seam line until blade reaches corner.
3. When you approach the corner, slow down.
Lower the needle.
3. Straighten the seam line out in front of the blade.
Continue stitching to complete the edge.
outside curves
The machine can continue sewing when rounding a curve. There is no need to stop the machine and pivot.
Push excess fabric toward the presser foot giving the machine more fabric and continue sewing as if sewing a straight seam.
22
CLEANING AND MAINTENANCE cleaning
Brush around the fabric feed dog
Fabric, thread scraps and dust may accumulate around moving parts and effect the functioning of machine.
Unplug cord and clean machine with the brush provided with the accessories.
Brush inside of the front cover
oiling
Critical parts used in this machine are made of special material that does not require oiling. Only the parts indicated with arrows shown below need oiling. Depending on use these should be oiled once or twice a month.
2-3 drops
changing the sewing light
If the sewing light does not light when power switch is turned on, replace the bulb.
1. Unplug sewing machine from the wall receptacle.
2. Remove the Light Cover by loosening the screw.
3. After bulb is cool to the touch, carefully unscrew bulb to remove.
4. Replace with new bulb of same size wattage and size.
5. Replace the Light Cover.
2-3 drops
changing the lower blade
Replace the Lower Blade as shown below when it becomes dull. An extra blade is provided with the accessories.
1. Unplug the machine.
2. Open the front cover.
3. Disengage the upper blade. (See page 19)
4. Loosen the Lower Blade Screw and take out the blade.
5. Install new blade by inserting it into the groove of the blade holder. Be sure that the tip of the lower blade is lined up with the surface of
Needle Plate, and tighten screw.
6. Re-engage the Upper Blade to cutting position. Close the front cover.
Needle Plate
The upper blade is made of special hard material and should not require replacement under normal use. If it should chip or need replacement, call for your retailer.
Lower Blade
Lower Blade
Holder
23
BEFORE YOU CALL FOR SERVICE
Your new serger was carefully inspected and tested at the factory and was in perfect working order when shipped.
Under normal conditions, if you carefully follow instructions for threading, operating and maintenance, your machine will give you years of trouble-free service.
Occasional difficulties are usually caused by a condition that can be easily remedied with a minor adjustment.
Some possible problems, their causes and corrections are given here.
PROBLEM
THREAD BREAKS
MACHINE SKIPS
STITCHES
NEEDLE BREAKS
CAUSE CORRECTION REF. PAGE
• Needle inserted incorrectly
• Thread tensions are too tight
• Bent or blunt needle
• Machine not properly threaded
• Threads are caught in incorrect guide
Reset needle
Loosen thread tensions
Insert new needle
Rethread machine
Rethread machine
5
11, 13, 15, 17
5
6-9
6-9
• Bent or blunt needle
• Needle inserted incorrectly
• Pressure on foot insufficient
• Incorrect needle size or type
• Machine incorrectly threaded
• Tensions set too high
Insert new needle
Reset needle
Increase pressure
Insert correct needle
Rethread machine
Loosen thread tensions
5
5
13
5
6-9
11, 13, 15, 17
• Pulling fabric while sewing
• Incorrect size needle or thread for fabric being sewn
• Needle inserted incorrectly
Do not pull fabric
Choose correct needle and thread
Reset needle
• Pressure on presser foot insufficient Increase pressure
10
5
5
13 MACHINE DOES NOT
FEED PROPERLY
FABRIC PUCKERS
• Lower blade is dull
• Stitch length not suitable for fabric
• Differential feed not suitable
• Thread tensions are too tight
• Seam width not suitable for fabric
• Tensions not adjusted properly LOOSE STITCHES OR
LOOPS FORMED
MACHINE RUNS HEAVILY • Dirt or lint in stitching mechanism
Change lower blade
Readjust stitch length
Readjust differential feed
Loosen thread tensions
Readjust seam width
Check thread tensions
Clean the machine
MACHINE WILL NOT SEW • Cord not plugged into electrical outlet
• Light and power switch not on
Check plug
Turn on the switch
23
12
12
11, 13, 15, 17
12
11, 13, 15, 17
23
4
4
24
STITCH SELECTION CHART
STITCH
(Correct thread tension)
2-needle, 4-thread
NEEDLE NEEDLE PLATE
Both
4 - 5
Standard
SEAM WIDTH STITCH LENGTH
1-4 mm
4 5
6.2-7.2 mm
(align 4-5 mm line)
Refer to Page
11 for Tension
Adjustment.
1-needle, 3-thread (Wider)
1-4 mm
4 5
Left
4 - 5
Standard
6.2-7.2 mm
(align 4-5 mm line)
Refer to Page
13 for Tension
Adjustment.
1-needle, 3-thread (Narrower)
1-4 mm
4 5
Right
4 - 5
Standard 4-5 mm
Refer to Page
13 for Tension
Adjustment.
Narrow Hemming-Method A
1-2 mm
Right Rolled Hem
1.5 mm
(Actually 3.5 mm)
Refer to Page
15 for Tension
Adjustment.
Narrow Hemming-Method B
1-2 mm
4 - 5
Standard
Refer to Page
15 for Tension
Adjustment.
Two thread (Wider or Narrower)
Right Rolled Hem
Remove Upper Looper Thread and attach Subsidiary Looper.
1.5 mm
(Actually 3.5 mm)
4 5
Left (Wider) or
Right (Narrower)
1-4 mm
6.2-7.2 mm (Wider)
(align 4-5 mm line)
4-5 mm (Narrower)
Refer to Page
17 for Tension
Adjustment.
25
62180 BL450A B8
advertisement
* Your assessment is very important for improving the workof artificial intelligence, which forms the content of this project