RVR tank instructions 2011.02.24.pdf
Advertisement
Advertisement
Installation and operating instructions
RVR 200L, 250L AND 300L
316 STAINLESS STEEL WATER HEATERS
INSTALLATION AND OPERATING INSTRUCTIONS
READ CAREFULLY BEFORE INSTALLING THE WATER HEATER.
LEAVE THESE INSTRUCTIONS WITH THE END USER.
Approval Number: 1003062
Version 20110224
Installation and operating instructions
Table of Contents
Page Title
3
3
3
4
4
5
6
1.0 Introduction
1.1 Reading the instructions
1.2 Guarantee
2.0 Technical Specifications
2.1 Capacity and Performance
2.2 Dimensions
2.3 Installation options
6
8
9
10
10
2.3.1 Unvented System
2.3.2 Open / Vented System
3.0 Recirculation
4.0 Installation General Requirements
5.0 Discharge Pipes from Safety Valves
10
11
12
5.1 Tundish Installation
5.2 High Level Termination of discharge
5.3 Discharge pipe sizing example
13
14
14
15
12
13
13
13
6.0 Electrical requirements
7.0 Maintenance Procedures
7.1 Draining and filling the system
7.2 Checking the expansion vessel
7.3 Checking the operation of safety valves
8.0 Commissioning
9.0 Risk of Bacterial Growth/Legionella
10.0 Troubleshooting
2
Installation and operating instructions
1.0 Introduction
1.1 READING THE INSTRUCTIONS
Please read and ensure that you fully understand these instructions prior to installing the water heater.
Following installation and commissioning the operation of the heater should be explained to the customer and these instructions left with them for future reference.
1.2 Guarantee
This water heater is guaranteed for a period of five years provided that:
It has been installed in accordance with these instructions and all the necessary inlet controls and safety valves have been fitted correctly.
Any valves or controls are approved by RVR.
The unit has not been tampered with and has been regularly maintained as detailed in these instructions.
The unit has been used only for heating potable water.
The unit is registered in writing with RVR Energy Technology Ltd (a form is provided with the delivery) and written confirmation of registration is received. Where the unit is not registered the guarantee is limited to
12 months from date of delivery.
The unit is NOT guaranteed against damage by frost or due to the build up of scale.
This guarantee does not affect the statutory rights of the consumer.
The policy of RVR Energy Technology is that of continuous improvement and development, therefore the right is reserved to change specification without notice.
All water heaters must be installed by a competent and qualified person, in accordance with relevant clauses of applicable standards and recommendations.
These include but may not be limited to the following:-
EN12897: 2006 Water Supply—Specification for indirectly heated unvented (closed) storage water heaters.
All relevant Building Regulations
Local Water Bye Laws
IEE Wiring Regulations
Health & Safety legislation
3
Installation and operating instructions
2.0 Technical Specifications
2.1 Capacity and Performance
Nominal Capacity
Litres
Max. Normal DHW Pressure bar
Max. Normal Primary Pressure bar
Max. Operating Temperature
° C
Standing Heat Loss
Dedicated Solar Volume kWh/24h
Litres
Upper Coil information:
Upper Coil Performance kW
Upper Coil Water Content
Upper Coil Pressure Drop
Upper Coil Flow Rate
Reheat Time
Lower Coil information:
Lower Coil Performance
Upper Coil Water Content
Lower Coil Pressure Drop
Lower Coil Flow Rate
Reheat Time
Litres kpa
Litres/s minutes kW
Litres kpa
Litres/s minutes
4.5
19.5
0.17
15
16.5
5.7
32.0
0.20
23
RVR 200L RVR 250L RVR 300L
200 250 300
5.5 5.5 5.5
4 4 4
90
1.21
122
90
1.48
155
90
1.74
178
14.1 15.2 18.6
5.4
25.4
0.18
18
18.5
6.65
34.0
0.22
29
6.3
28.2
0.22
18
20.8
7.6
39.3
0.25
32
Table 1 - Technical information
4
Installation and operating instructions
2.2 Dimensions
Figure 1 - Connections
Dimensions
A
B
C
D
E
F
G
H
I
J
Dry Weight
Full Weight mm mm mm mm mm mm mm mm mm mm kg kg
200L
1480
520
320
180
260
390
825
1138
1220
1300
57
257
Table 2– Dimensions of Water Heater
250L
1835
520
320
180
270
400
1000
1417
1555
1655
66
316
300L
2170
520
320
200
290
492
1147
1682
1867
1970
72
372
Figure 2 - Dimensions of water heater
5
Installation and operating instructions
2.3 Installation Options
This water heater may be used in either open vented systems or in unvented installations. In unvented installations, the optional unvented kit (RVR Stock No: ACW018) must be used to ensure a safe installation. The unvented kit contains items 2, 3, 5, 6 and 11 as shown in figure 3 together with an expansion vessel hose and pressure gauge. Other items such as mixing valve and zone valves are available from RVR.
2.3.1 Unvented System
1. Stop Valve
2. Combined Pressure Reducing Valve and cold fill manifold
3. Expansion vessel
4. Drain Valve
5. Tundish
6. Temperature and Pressure Relief Valve
7. Mixing Valve
8. Upper Coil Temperature Sensor Dry
9. Zone Valve
10. Lower Coil Temperature sensor Dry
11. Pressure Gauge
Figure 3 - Unvented system schematic to comply with BS7206:1990
6
Installation and operating instructions
WARNING: All water heaters must be fitted with temperature control to ensure that the domestic water is not heated to temperatures above 60°C
The following safety devices must be fitted to the water heater when used in an unvented system:
1
2
Stop Valve: This allows the system to be isolated from the cold water supply.
3
4
5
6
7
8
Combined Pressure Reducing Valve and Cold Fill Manifold: The PRV is designed to stabilise the inlet water pressure at 3 bar. The unit comprises the PRV and a manifold containing a check valve, a cold water balancing port and a preset pressure relief valve. The pressure relief valve is set at 6bar.
Expansion vessel: Expansion must be accommodated using an Expansion vessel. The Expansion vessel must be sized to accommodate the maximum expansion of the system and should be suitable for use with potable water.
Drain Valve: This allows the water heater to be drained for service or removal.
Tundish: The Tundish must be fitted to the discharge of the safety valves. It provides an air break and allows the user to see the release of water from the valves.
Temperature and Pressure Relief valve (T&P valve): this ensures that the temperature of the stored water cannot exceed 100 o
C and in this scenario will vent any excess pressure.
Blending (Mixing) Valve: The blending valve limits the temperature of the delivered water by mixing it with cold water as required. The delivered water temperature should not exceed 50°C.
Upper Coil Temperature Sensor Dry Pocket: This is used for the insertion of the high limit and thermostat control. It is essential that suitable temperature controls are used to prevent the water from reaching excessive temperature. A high limit thermostat with a manual reset device is also supplied to
9 allow interruption of the energy supply when the water temperature reaches 90°C. The correct installation and wiring of this device is essential for the safe operation of the water heater.
Zone Valve: The recommended water storage temperature is 60°C. The water heater thermostat should be wired to ensure that the energy supply to the water heater is interrupted if the water temperature exceeds 60°C. The zone valve is used for this purpose.
10 Lower Coil Temperature Sensor Dry Pocket: This is used to insert temperature sensor for the control of the lower coil. In a solar water heating system, the solar water heater sensor will normally be fitted here. It is essential that suitable temperature controls are used to prevent the water temperature exceeding 60°C.
11 Pressure Gauge: This is used to monitor pressure in the system from 0-6 bar.
Failure to fit these essential safety devices will invalidate the warranty and may cause a dangerous installation leading to property damage, injury or loss of life.
7
Installation and operating instructions
2.3.2 Open / Vented System
1. Stop Valve
2. Drain Valve
3. Mixing Valve
4. Zone Valve
5. Cold Water Cistern
6. Vent Pipe
7. Lower Coil Temperature sensor Dry Pocket
8. Upper Coil Temperature
Sensor Dry Pocket
WARNING: All water heaters must be fitted with temperature control to ensure that the domestic water is not heated to excessive temperatures.
A blending (mixing) valve must be fitted to all installations to ensure water does not exceed
50°C at the point of use.
Figure 4 - Open system schematic
The following safety devices must be fitted to the water heater when used in an open system:
1
2
3
4
5
6
7
8
Stop Valve: This allows the system to be isolated from the cold water supply.
Drain Valve: This allows the water heater to be drained for service or removal.
Blending (Mixing) Valve: The blending valve limits the temperature of the delivered water by mixing it with cold water as required. The delivered water temperature should not exceed 50°C.
Zone Valve: The recommended water storage temperature is 60°C. The water heater thermostat should be wired to ensure that the energy supply to the water heater is interrupted f the water temperature exceeds 60°C. The zone valve is used for this purpose.
Cold Water Cistern: This is the cold water storage cistern. The Vent pipe is also returned to the cistern.
Vent pipe: This is also referred to as the expansion pipe and is used to safely vent expansion of the heated water.
Lower Coil Temperature Sensor Dry Pocket: This is used to insert temperature sensor for the control of the lower coil. In a solar water heating system, the solar water heater sensor will normally be fitted here.. It is essential that suitable temperature controls are used to prevent the water temperature exceeding 60°C.
Upper Coil Temperature Sensor Dry Pocket: This is used for the insertion of the high limit and thermostat control. It is essential that suitable temperature controls are used to prevent the water temperature exceeding 60°C. A high limit thermostat with a manual reset device is also supplied to allow interruption of the energy supply when the water temperature reaches 90°C. The correct installation and wiring of this device is essential for the safe operation of the water heater.
Failure to fit these essential safety devices will invalidate the warranty and may cause a dangerous installation.
8
Installation and operating instructions
3.0 Recirculation
A secondary return may be fitted.
A non-return valve must be fitted to prevent back-flow and a bronze recirculation pump will be needed in conjunction with a pipe thermostat to circulate the hot water.
Almost all installations will be fitted with a blending valve. Special care must be taken when connecting a secondary return in conjunction with a blending valve. Please refer to Figures 5 below for information on how the secondary return should be connected. It is very important that the connection to the cold water port of the mixing valve is connected downstream of the fill manifold as shown. It must not be connected to the
‘balanced cold water outlet’.
Hot Water Outlet
4
1. Recirculation Pump
2. Thermostat
3. Check Valve
4. Mixing Valve
1 2
3
Balanced Cold Water Outlet
Cold Water Inlet
Figure 5—Recirculation layout
9
Installation and operating instructions
4.0 Installation - General Requirements:
Check the load bearing capacity of any floors or walls to ensure that they can support the weight of the water heater when filled to capacity. Refer to table 2 for full weight of the water heater.
Enough space should be left at the top and sides of the unit for pipe connections and access to the safety controls and valves. Refer to Figure 1 and the Dimensions Table 2 to determine a suitable position for the heater.
DO NOT install the water heater where the unit may freeze.
Refer to the section IMPORTANT INSTALLATION POINTS to determine which valves and accessories are required. Plumb the valves as shown in the relevant diagrams ( Figures 3 & 4). An isolating valve must be fitted on the cold water supply to the heater. Several hot water outlets can be served.
Do not use solder joints as this will damage the heater and may prevent servicing under warranty.
5.0 Discharge Pipes from Safety Valves
5.1 Tundish Installation
The discharge pipes must be routed to a tundish. The discharge pipework from both relief valves may be joined together.
The pipe diameter must be at least one pipe size larger than the nominal outlet size of the safety device, unless its’ total equivalent hydraulic resistance exceeds that of a straight pipe 9m long.
I.e. Discharge pipes between 9m and 18m equivalent resistance length should be at least 2 sizes larger than the nominal outlet size of the safety device. Between 18m and 27m at least 3 larger, and so on.
Bends must be taken into account in calculating the flow resistance.
For more information please see FIG. 4, TABLE 3 and SECTION 3.3
Valve outlet size Minimum size of discharge pipe D1
G 1/2
G 3/4
G 1
15mm
22mm
28mm
Minimum size of discharge pipe D2 from tundish
22mm
28mm
35mm
28mm
35mm
42mm
35mm
42mm
54mm
Maximum Resistance allowed (expressed as a length of straight pipe)
Up to 9m
Up to 18m
Up to 27m
Up to 9m
Up to 18m
Up to 27m
Up to 9m
Up to 18m
Up to 27m
Resistance created by each elbow or bend
0.8m
1.0m
1.4m
1.0m
1.4m
1.7m
1.4m
1.7m
2.3m
Table 3 – Discharge Pipe Sizing
Tundish - The tundish must be positioned vertically within 500 mm of the unit, clearly visible to the user and away from electrical devices. The minimum size of the discharge pipe downstream of the tundish is given in
TABLE 3.
10
Installation and operating instructions
The discharge pipework from the tundish:
Must fall continuously through its length.
Must be of a heat resistant material, e.g. metal.
Must not be fitted with any valves or taps.
Must discharge to a safe visible position, e.g. onto the surface of an external wall or into a gulley.
Must have a minimum of 300 mm straight pipework directly from the tundish.
Note: Where children may play or otherwise come into contact with discharges, a wire cage or similar guard must be positioned to prevent contact whilst maintaining visibility.
The diagrams on this page show recommended methods of routing and terminating the discharge pipe safely.
Where a single pipe serves a number of discharges, such as in blocks of flats, the number served should be limited to not more than 6 systems so that any tundish installation can be traced easily.
If a single common discharge pipe is used then it should be at least one pipe size larger than the largest individual discharge pipe to be connected. If the system is installed where discharges from safety devices may not be apparent, i.e. in dwellings occupied by blind, infirm or disabled people, consideration should be given to the installation of an electronically operated device to warn when discharge takes place.
Figure 6 - Discharge Pipe routing
Figure 7 - Tundish installation
300mm minimum
D1
D2
Option A
Tundish
300mm minimum
D1
D2
Option B
Tundish
Pipe close to wall to allow water to fan out safely
100mm max.
70mm min.
Ground level
300mm minimum
D1
D2
Option C
Tundish
Type ‘A’
Air Gap
Gulley if available
End of pipe clearly visible
5.2 High Level Termination of Discharge
At high level, discharge onto a roof is acceptable providing the roof is capable of withstanding high temperatures and there is a distance of 3 m from any plastic guttering systems that would collect such discharge.
Note: The discharge may consist of scalding water and steam. Asphalt, roofing felt and non-metallic materials may be damaged by such discharges.
11
Installation and operating instructions
5.3 Discharge Pipe Sizing Example
This example shows how to select pipe diameter for a given discharge pipe.
For this example we will assume we are using a G½ temperature relief valve and require 4 elbows in the discharge pipe run. The length of the pipe run from tundish to point of discharge is 7 metres.
Begin by calculating whether 22mm pipe would be sufficient
Consult Table 3 and look up the maximum resistance allowed for this pipe size (9 metres)
Consult Table 3 and look up the resistance of an elbow in this pipe size (0.8 m) As we have 4 elbows or bends, multiply (0.8m * 4m) = 3.2m
Subtract the resistance of the elbows from the maximum resistance (9m—3.2m) = 5.8m.
Is your length of pipe run less than or equal to the maximum permissible resistance for this pipe run?
7 metres is not less than or equal to 5.8m, so 22mm pipe is not acceptable. Repeat the steps above using
28mm pipe (18m max resistance—4m of resistance from elbows = 14m. 7m < 14m, so 28mm is acceptable). If
28mm is not acceptable, repeat the steps above using 35mm pipe.
6.0 Installation - Electrical Requirements
WARNING: This water heater must be earthed
The water heater may be optionally fitted with a high limit and control thermostat. See RVR Stock No AMS960 for more information. Wiring for RVR Model AMS960 is shown in figure 8. Where fitted, it is essential that the energy source to the water heater is under the control of this device.
Figure 8—Thermostat/High Limit Control
Figure 9—Typical Wiring Scheme
The water heater may be optionally fitted with an electrical immersion heater. The immersion heater thread size is 1
1/4”
. Ensure that any electric immersion heater is fitted with a high limit and control thermostat.
Where an immersion heater is fitted, the following information is relevant.
Disconnect the electrical supply before removing the terminal cover. Installation must be in accordance with the current I.E.E. Wiring Regulations.
The electricity supply should be fused to protect the immersion heater circuit and it should be possible to isolate it via a double pole isolating switch with a contact separation of at least 3mm in both poles.
12
Installation and operating instructions
Draining and cleaning:
Ensure provision is made for draining and cleaning the water heater. If the water heater is fitted with a drain point, then connect to drain via a suitable valve to allow purging and cleaning. The drain point may be fitted with a plug which will need to be removed before connecting the drain pipe.
See example schematic below:
Protection against water damage:
This product should not be installed in a location where water leakage is likely to cause damage.
If it is necessary to install this product in such a location such as an attic or higher floor of a building, a 'tanked', waterproof chamber should be created to ensure that any potential leaks from the product and associated fittings or pipes are contained and drained away safely.
See example schematic below:
13
Installation and operating instructions
7.0 Maintenance Procedures
7.1 Draining and Refilling the System
Draining
1. Switch off electrical power to immersion heater(s) and/or solar station and/or shut down the boiler.
2. Close the Stop Valve.
3. Open a hot water tap in order to reduce pressure in the water heater.
4. Drain from the drain cock at the base of the water heater.
Refilling
1. DO NOT switch on the immersion heaters or solar station or boiler until the system has been completely refilled.
2. Close the drain valve.
3. With hot tap open, turn on pumped cold water supply. When water flows from the hot tap allow to flow for a short while to purge air and to flush through any disturbed particles.
4. Close hot tap and then open successive hot taps in system to purge any air.
The electrical supply can now be switched on.
7.2 Checking the expansion vessel
The charge pressure of the expansion vessel should be checked annually.
Method
Switch off power to immersion heater(s) and shut down boiler.
Close the Stop Valve.
Open a hot water tap in order to reduce pressure in the cylinder.
Remove the black cap on the end of the expansion vessel.
The charge pressure can then be checked against the vessel nameplates by using a good tyre gauge. If it is low then replenish it by using a nitrogen gas bottle with regulating valve, or a foot pump. The pressure will normally be set to 3.5 bar.
Any fluid escaping from the expansion vessel valve indicates a leaking diaphragm and the vessel should be replaced.
7.3 Checking the operation of safety valves
Manually operate the valve lever on the Temperature & Pressure Relief Valve for a few seconds.
Check that water is discharged and that it flows freely through the tundish and discharge pipework.
Check that the valve reseats correctly when released.
Repeat the procedure for the Expansion Relief Valve.
Note: The water discharged may be very hot.
Important: After servicing, preliminary electrical system checks must be carried out to ensure electrical safety (i.e. polarity, earth continuity, resistance to earth and short circuit).
14
Installation and operating instructions
8.0 Commissioning
It is important to follow the steps outlined below during commissioning.
Do not switch on the electrical supply, solar station or boiler until the unit has been filled with water and checked for leaks.
Check that all installation, electrical and discharge pipe requirements have been met.
Check that all water and electrical connections are tight and properly connected.
Open a hot water tap, turn on mains water supply to the heater.
Allow unit to fill and leave hot tap running for a short while to purge any air and flush out the pipe-work.
Close the hot tap and check the system for leaks.
Manually test the operation of the Temperature/Pressure Relief Valve and Pressure Relief Valve. Ensure water flows freely from the valve(s) and through the discharge pipes.
Switch on the electrical supply and boiler.
Verify that water is heated and that the thermostatic controls work correctly.
9.0 Risk of Bacterial Growth/Legionella
Hot water storage cylinders that maintain a temperature of 60oC throughout the whole storage vessel for a period of one hour daily should achieve satisfactory control of Legionella bacteria, in line with recommendations in HSE CoP L8.
The solar heating system should be designed so as to prevent the risks associated with bacterial growth, low water flow rates and scale formation whilst preventing risk of scalding due to high water temperatures. Legionella bacteria grow readily at temperatures in the range 20oC to 45oC.
In order to reduce the risk of colonization of a water system the temperature of cold water in pipes and cisterns should not exceed 20oC, and hot water should be stored and distributed at a temperature of not less than 60oC with a temperature at the discharge point of 50oC after one minute. Systems should be designed and operated to provide appropriate temperature control of water storage. Information and guidance should be provided to the homeowner on the correct operation of these systems during normal operation and after periods of non use. For further guidance, refer to national guidelines on the control of legionellosis.
Cold and hot water pipe work should be as short as practicable, especially where it only serves infrequently used taps and fittings. In all cases minimum hot and maximum cold water temperatures should be reached at all draw-off points after a maximum period of one minute running at full flow. Due consideration should be given to the selection of braided or flexible hoses and the suitability of materials in contact with water.
Measures shall be taken in the design and installation of cold and hot water systems to prevent the colonization of the system with legionella. These shall include the avoidance of:
• Stagnation of water in pipes, cisterns and other storage vessels;
• Water temperatures in the range of 20oC to 45oC;
•
•
Use of materials that can harbour or provide nutrients for bacteria and other organisms, inside cisterns.
Fittings where there is a potential for aerosol formation.
15
Installation and operating instructions
10.0 Troubleshooting
FAULT
Water not heating
POSSIBLE CAUSES
Electrical supply fault
REMEDIAL MEASURES
Check electrical supply. Verify the operation of boiler and controls.
Discharge of water from
Pressure Relief Valve
(continuously)
Thermal cut-out tripped
Thermostat fault
Excessive supply water pressure
Check cut-out. If it has activated then reset and check thermostat operation.
If necessary replace thermostat/thermal cut-out (see Wiring Diagram)
Check thermostat operation, replace if necessary
Fit Pressure Reducing Valve (see
IMPORTANT INSTALLATION
POINTS)
Check valve is seating properly. Replace if necessary. Failure of Pressure Relief Valve
Discharge of water from
Pressure Relief Valve
(intermittently) Inadequate expansion in system
Water supply pressure exceeds 3.5 bar
Check expansion vessel size and precharge pressure.
Fit a pressure reducing valve with integral line strainer (See Important installation points)
Water or steam from
Pressure Relief Valve
No water flow
Thermostat and thermal cut-out fault
Inlet valves incorrectly fitted
Supply water not turned on
Blockage in water supply
Milky water Oxygenated water
Table 4 - Faults and remedial measures
Replace thermostat and thermal cutout
Check all valves are correctly installed in accordance with flow direction arrows
Check water supply is on
Check for obstructions. If a pressure reducing valve is fitted check strainer is not blocked.
Water from a pressurised system releases oxygen bubbles when flowing.
The milkiness will disappear after a short time.
16
Installation and operating instructions
Manufacturer details:
17
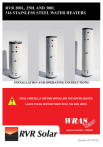
Download
Advertisement