- No category
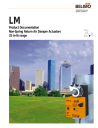
advertisement
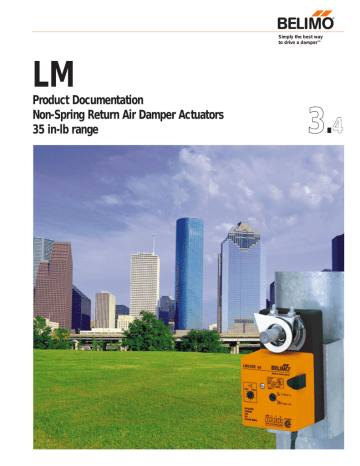
LM
Product Documentation
Non-Spring Return Air Damper Actuators
35 in-lb range
Simply the best way to drive a damper™
®
3
.
4
Belimo Product Range
Quality, Performance, Flexibility — Belimo offers the most complete actuator range.
®
Non-Spring Return
Actuators
35 in-lb for damper areas up to 8 sq.ft.
70 in-lb for damper areas up to 18 sq.ft.
160 in-lb for damper areas up to 40 sq.ft.
266 in-lb for damper areas up to 70 sq.ft.
Open/Close
Floating
Proportional
Open/Close
Floating
Proportional
Open/Close
Floating
Proportional
Open/Close
Floating
Proportional
24 V 24 V
LM24
LM24-S
LM24-10P
(10 K
Ω
Pot.)
LM24-5P0-T
(5 K
Ω
Pot.)
LM24-T
LMC24*
LM24SR
(2–10 VDC)
LM24SR-T
LMC24-SR*
LMC24-SR-T*
-S = built-in auxiliary switch
-T = terminal strip
* = 25 to 35 sec run time,
27 in-lb torque
24 V
NM24
24 V
NM24-SR
(2–10 VDC)
NM24-SRS
(start point/ span adjust.)
NM24-PWM
(pulse width modulation)
Add-on auxiliary switches:
SN1 (1 switch)
SN2 (2 switches)
24 V 24 V
AM24
AM24-S
(with built-in aux. switch)
AM24-SR
AM24-PWM*
(pulse width modulation)
AM24-SRS*
(3 control range options)
Add-on auxiliary switches for proportional actuators only:
SA1 (1 switch) SA2 (2 switches)
Add-on feedback potentiometer: PA...
24 V
GM24
24 V
GM24-SR
(2–10 V DC)
Add-on auxiliary switches:
S1 (1 switch) S2 (2 switches)
Add-on mid-position switch: SZS
Add-on feedback potentiometer: P...
2
ON THE COVER: The Exxon building in dowtown Houston Texas has nearly 4000 Belimo LM actuators installed.
®
Belimo Product Range
35 in-lb for damper areas up to 8 sq.ft.
Spring Return
Actuators
60 in-lb for damper areas up to 15 sq.ft.
133 in-lb for damper areas up to 35 sq.ft.
Open/Close
Floating
Proportional Open/Close Proportional
Open/Close
Floating
Proportional
24 V
LF24
LF24-S
LF24-3
LF24-3-S
(Floating point)
120V/230V
LF120
LF120-S
LF230
LF230-S
24 V
LF24-SR
LF24-SR-S
(2–10 VDC)
LF24-SR-MP*
(6-9 VDC)
LF24-SR-S-MP*
(6-9 VDC)
24 V
NF24
NF24-S
120 V
NF120
NF120-S
24 V
NF24-SR
(2–10 VDC)
-S = built-in auxiliary switch
-3 = floating point control
* = output auxiliary power supply 20 VDC
Proportional actuators can accept 4–20 mA control signal with the addition of a 500
Ω resistor.
Damper areas based on 4 in-lb/ft 2 damper torque loading. Parallel blade. No edge seals.
AF24
AF24-S
AF24-3
(Floating point)
AF24-3-S
(Floating point)
120V/230V
AF120
AF120-S
AF230
AF230-S
24 V
AF24-SR
(2–10 VDC)
AF24-SR-S
(2–10 VDC)
AF24-SR95
(0–135
Ω
)
AF24-PWM
(Pulse Width
Modulation)
3
LM Series Direct Coupled Actuator
Small Yet Powerful
●
Minimum 35 in-lb torque in a compact package.
For damper areas up to 8 sq-ft.
Areas of Application
VAV Units and Small Zone Dampers
Quiet Plus ® VAV terminal unit by
Warren Technology
Rack and pinion type actuator replaced by direct coupled LM.
For applications where a linear stroke is needed, use a KM actuator with the ZH accessory or a NM actuator with a crankarm.
Replacement LM24 compatible with existing control system.
Existing pneumatic actuator requires linkage.
Replacement Belimo actuator (LM type) direct couples to VAV
By-Pass damper shaft.
4
LM Series - at a glance
Torque: 35 in-lb
Power supply : 24 VAC/DC
Control signal: on-off/floating point
Control signal: proportional 2 to 10 VDC
Feedback signal: 2 to 10 VDC
10k
Ω feedback potentiometer
5k
Ω feedback potentiometer
Run time, 80 to 110 sec for 0 to 35 in-lb
Left/Right rotation switch
Angle of rotation limiting (mechanical)
Angle of rotation limiting (electronic)
Plenum rated cable, 18 GA
Screw terminal strip
Manual override push-button
Built-in auxiliary switch
LM24
US
LM24-T
US
LM24-S
US
LM24-10P
US
LM24-5P0-T
US
LM24SR
US
LM24SR-T
US
● ● ● ● ● ● ●
●
●
●
●
●
●
●
●
●
●
● ●
●
●
●
●
●
●
●
●
●
●
●
●
●
●
●
●
●
●
●
●
●
●
●
● ● ●
●
●
●
●
● ●
●
●
●
● ●
●
●
®
®
BENEFITS…
●
Cut labor costs with simple direct coupling.
●
Check damper position from a distance with clear position indication.
●
Don’t worry about actuator burn-out.
Belimo is overload-proof throughout rotation.
●
Enjoy added flexibility with easy mechanical stops to adjust angle of rotation.
(LM24SR has electronic rotation limiting.)
●
Easy-to-operate auxiliary switch offers feedback option or signal for additional device.
●
Easily accessible manual override push-button helps you get up and running faster.
●
Need to change control direction?
Do it easily with a simple switch.
●
3 ft. plenum rated cable eases installation
(external terminal strip also available)
LM Series Direct Coupled Actuator
LISTED
94D5
TEMP. IND &
REG. EQUIP
.
UL
B e li m o’ s C ommitmen t to
Q u a li ty
ISO
Since
The Belimo Difference
●
Customer Commitment.
Extensive product range. Competitive project pricing. Application assistance.
Same-day shipments. Free technical support. Unconditional warranty.
●
Low Installation and Life-Cycle Cost.
Easy installation. Accuracy and repeatability.
Low power consumption. No maintenance.
●
Long Service Life.
Components tested before assembly. Every product tested before shipment.
20+ years direct coupled actuator design.
Bulk Packaging Offers Big Value for Large Jobs, Stocking Orders.
5
LM24 Series on-off/floating point control direct coupled actuator
On-off/ floating point control, 24 V
Torque min. 35 in-lb, for control of damper surfaces up to 8 sq ft.
LM24
US
LM24-S
US
LM24-10P
US
LM24-5P0-T
US
LM24-T
US
LISTED
94D5
TEMP. IND &
REG. EQUIP
.
UL
®
Application
For on-off and floating point control of dampers in HVAC systems. Actuator sizing should be done in accordance with the damper manufacturer’s specifications. The actuator mounts directly to the damper operating shaft with a universal V-bolt clamp assembly.
LM24-S
US
LM24-T
US
Technical Data
Power supply
Power consumption
Transformer sizing
Electrical connection
Overload protection
LM24… on-off/floating point
24 VAC ± 20% 50/60 Hz 24 VDC ± 10%
2 W
3 VA (Class 2 power source)
3 ft, 18 GA, UL CL2P plenum cable
Electronic throughout 0 to 95° rotation
Angle of rotation
Torque max 95°, adjust. with mechanical stops min 35 in-lb [4 Nm]
Direction of rotation reversible w/switch L/R (not on “-T” models)
Position indication clip-on indicator (not on “-T” models)
Running time
Manual override
80 to 110 sec. for 0 to 35 in-lb external push button
Humidity 5 to 95% RH, noncondensing
Ambient temperature -22°F to +122°F [-30°C to +50°C]
Storage temperature
Housing type
-40°F to +176°F [-40°C to +80°C]
NEMA type 2 (-T models NEMA 1)
Housing material rating UL94-5V
Noise level less than 35 dB (A)
Servicing
Agency listings
Quality standard
Weight maintenance free
UL873 listed, CSA 4813 02 certified, CE
ISO 9001
1.2 lbs [0.55 kg]
Operation
The actuator is not provided with and does not require any limit switches, but is electronically protected against overload. The angle of rotation is mechanically limited to 95°. When reaching the damper or actuator end position, the actuator automatically stops. The gears can be manually disengaged with a button on the actuator cover. The position of the actuator is indicated by a visual pointer. The anti-rotation strap supplied with the actuator will prevent lateral movement.
Accessories
LM-P T-type anti-rotation bracket
ZG-LMSA Shaft adaptor for short shafts
Tool-02 8 mm wrench
LM24-S
US
Auxiliary switch Adj. 0° to 95°, SPDT 6 A (2.5A) @ 24 VAC
LM24-10P
US
Feedback 10 k
Ω
, 1W potentiometer
LM24-5P0-T
US bulk pack only
Feedback 5 k
Ω
, 1W potentiometer
Direction of rotation Reverse wires terminals 2 and 3
LM24-T
US bulk pack only
Electrical connection Screw terminal (for 26 to 14 GA wire)
Direction of rotation
6
Reverse wires terminals 2 and 3
Dimensions
All ratings in brackets are metric.
1/4” to 5/8” [6 to 16]
1/4” to 7/16” [6 to 11]
®
LM24 Series on-off/floating point control direct coupled actuator
On-off/ floating point control, 24 V
1
24 VAC Transformer
Line
Volts
●
2
3
Blk
(1)
Common
Red
(2)
+
a open a closed
●
● a
The indication of direction is valid for switch position R.
4
On-off control
Wht
(3)
+
LM24 (-S)
US
LM24-10P
US
1
24 VAC Transformer
2
Line
Volts
●
●
●
6
5
3
●
●
1 Common
2 +
●
3 +
4
1
Line
Volts
24 VAC Transformer
2
●
●
●
6
The indication of direction is valid for switch position R.
4
Floating point or on-off control
5
Org (P1)
4
Blue (P2)
Yel (P3)
3
Blk
(1)
Common
Red
(2)
+
Wht
(3)
+
LM24 (-S)
LM24-10P
0
10 k
Ω
/5k
Ω
Feedback potentiometer
10/5
7
7
LM24-10P
US
LM24-5P0-T
US
US
US
Floating point or on-off control of LM24-T
LM24-5P0-T
US
US and
S1
S2
NC
●
S3
●
NO
●
0° to 95°
LM24-S
US
Auxiliary switch wiring for LM24-S
US
Notes
1
2
Provide overload protection and disconnect as required.
Actuators may also be powered by 24 VDC
3
Actuators are provided with color coded wires. Wire numbers are provided for reference.
4
For position indication, the LM24-10P
US is provided with a 10 k
Ω feedback potentiometer and the LM24-5P0-T
US is provided with a 5 k
Ω feedback potentiometer.
5
The LM24-T
US and LM24-5P0-T
US are provided with a numbered screw terminal strip instead of cable.
6
Switch wires 2 and 3 to change rotation direction of
LM24-T
US and LM24-5P0-T
US
(does not have L/R external switch).
7
Value based on resistance between (P1) and (P2).
indicates direction of rotation of actuator.
Feedback potentiometer wiring for LM24-10P
US and
LM24-5P0-T
US
LM24… on-off/floating - Typical Specification:
Control damper actuators shall be electronic direct coupled type which require no crank arm and linkage. Actuators shall be UL and CSA listed, have a 2 year warranty, and be manufactured under ISO 9001 International Quality Control
Standards. Actuators shall have reversing switch and manual override on the cover, and be protected from overload at all angles of rotation. If required, actuator will be provided with screw terminal strip for electrical connections (LM24-T
US and
LM24-5P0-T
US
). If required, one adjustable SPDT auxiliary switch shall be provided (LM24-S
US
). If required, actuators shall be provided with a built-in 10 k
Ω feedback potentiometer (LM24-
10P
US
) or 5k
Ω
(LM24-5P0-T). Actuators shall be as manufactured by Belimo.
L-Type anti-rotation bracket. Included with each actuator.
Bulk packaging LM24 on-off/floating
Bulk Pack No.
LM24.1
US
LM24-T.1
US
LM24-5P0-T.1
US
Actuator Type
LM24
US
LM24-T
US
LM24-5P0-T
US
Quantity/Pack
32
48
48
7
LM24SR Series proportional control direct coupled actuator
Proportional control, 24 V, for 2 to 10 VDC and 4 to 20 mA control signal
Torque min. 35 in-lb, for control of damper surfaces up to 8 sq ft.
LM24SR
US
LM24SR-T
US
LISTED
94D5
TEMP. IND &
REG. EQUIP
.
UL
®
LM24SR
US
LM24SR-T
US
Technical Data
Power supply
Overload protection
Control signal ‘Y’
Input impedance
Operating range
Feedback output ‘U’
LM24SR
US
24 VAC ± 20% 50/60 Hz
24 VDC ± 10%
2 W Power consumption
Transformer sizing
Electrical connection
Angle of rotation
Torque
Direction of rotation
Position indication
Running time
Manual override
4 VA (Class 2 power source)
LM24SR
US
: 3 ft, 18 GA, UL CL2P plenum cable
Electronic throughout 0 to 95° rotation
0 to 10 VDC, 0 to 20 mA
100 k
Ω
(0.1 mA), 500
Ω
2 to 10 VDC, 4 to 20 mA
2 to 10 VDC (max. 0.7 mA )
(not available on LM24SR-T
US
) max 95°, electronically adjustable
20 to 100% on LM24SR
US min 35 in-lb reversible with switch L/R
L = CW with an increase in voltage
R = CCW witn an increase in voltage clip-on indicator (not on “-T” models)
80 to 110 sec. for 0 to 35 in-lb external push button
Humidity 5 to 95% RH, noncondensing
Ambient temperature -22°F to +122°F [-30°C to +50°C]
Storage temperature
Housing type
-40°F to +176°F [-40°C to +80°C]
NEMA type 2 (-T models Nema type1)
Housing material rating UL 94-5V
Noise level less than 35 dB (A)
Servicing
Agency listings maintenance free
UL 873 listed, CSA 4813 02 certified, CE
Quality standard
Weight
ISO 9001
1.2 lbs [0.55 kg]
Application
For proportional modulation of dampers in HVAC systems.
Actuator sizing should be done in accordance with the damper manufacturer’s specifications. The actuator mounts directly to the damper operating shaft with a universal V-bolt clamp assembly. The actuator operates in response to a 2 to 10 VDC or, with the addition of a 500
Ω resistor, a 4 to 20 mA input signal from an electronic controller or positioner. A 2 to 10 VDC feedback signal is provided for position indication or master slave applications. (Not available on “-T” versions)
The LM24SR
US provides an electronic angle of rotation adjustment to limit the actuators rotation 20% to 100% while still using the full input signal and feedback control range. (Not available on LM24SR-T
US
)
Operation
The anti-rotation strap supplied with the actuator will prevent lateral movement of the actuator. The damper actuator is not provided with and does not require any limit switches, but is protected electronically against overload. The angle of rotation is mechanically limited to 95°. When reaching the damper or actuator end position, the actuator automatically stops. The gears can be manually disengaged by pressing a button on the actuator cover. The position of the actuator is indicated by a visual pointer.
Accessories
LM-P T-type anti-rotation bracket
IRM-100 Input scaling module
ZG-LMSA Shaft adaptor for short shafts
PTA-250 Pulse width modulating interface
SGA24
SGF24
Tool-02
Min. and/or manual positioner in NEMA 4 housing
Min. and/or manual positioner for flush panel mount
8 mm wrench
ZAD24
ZG-R01
Digital position indication
500
Ω resistor for 4 to 20 mA
Dimensions
All ratings in brackets are metric.
1/4” to 5/8” [6 to 16]
1/4” to 7/16” [6 to 11]
LM24SR-T
US bulk pack only
Electrical connection Screw terminals (for 26 to 14 GA wire)
Angle of rotation
Housing
Feedback
8 max 95°, adjust. with mechanical stops
NEMA type 1
No feedback with the LM24SR-T
US
®
LM24SR Series proportional control direct coupled actuator
Proportional control, 24 V, for 2 to 10 VDC and 4 to 20 mA control signal
1
24 VAC Transformer
●
Line
Volts
7
2 to 10 VDC
Control Signal
(–)
(+)
2 to 10 VDC
Feedback Signal
(–)
(+)
6
2 to 10 VDC control of LM24SR
US
2
Blk
(1)
Common
Red
(2)
+ Hot
Wht
(3)
Y 2 to 10V Input
Grn
(5)
U 2 to 10V Output
LM24SR
US
1
24 VAC Transformer
7
Line
Volts
●
2 to 10 VDC
Control Signal
4 to 20 mA w/500
Ω
resistor
(–)
(+)
6
●
●
Ω
500
Ω
●
8
4
●
●
1 Common
●
3 Y 2 to 10V Input
5
LM24SR-T
US
2 to 10 VDC and 4 to 20 mA control of LM24SR-T
US
1
24 VAC Transformer
●
Line
Volts
7
●
●
Ω
500
Ω
●
8
4 to 20 mA
Control Signal
(–)
(+)
2 to 10 VDC
Feedback Signal
(–)
(+)
6
2
Blk
(1)
Common
Red
(2)
+ Hot
Wht
(3)
Y 2 to 10V Input
Grn
(5)
U 2 to 10V Output
LM24SR
4 to 20 mA control of LM24SR
US with 2 to 10 VDC feedback output
US
LM24SR(-T)
US
- Typical Specification:
Control damper actuators shall be electronic direct coupled type which require no crank arm and linkage. Actuators shall be UL and CSA listed, have a 2 year warranty, and be manufactured under ISO 9001 International Quality Control
Standards. Actuators shall have reversing switch and gear disengagement button on the cover, and be electronically protected from overload at all angles of rotation. Actuators shall respond to 2 to 10VDC output relative to position regardless of the amount of damper rotation. A 2 to 10 VDC feedback signal shall be provided for position indication or master-slave applications. Actuators shall be as manufactured by Belimo.
An electronic angle of rotation adjustment shall be provided to reduce the actuators rotation from 100 to 20% while still using the full input signal and feedback control range. (LM24SR
US
)
If required, actuator will be provided with screw terminal strip for electrical connections (LM24SR-T
US
).
Notes
1
2
Provide overload protection and disconnect as required.
Actuators are provided with color coded wires. Wire numbers are provided for reference.
4
The LM24SR-T
US is provided a screw terminal instead of cable.
5
The LM24SR-T
US does not have feedback.
6
Connect actuator common (Wire 1) to Negative (–) leg of control circuits only.
7 Actuators may also be powered by 24 VDC.
8
A 500
Ω resistor (ZG-R01) must be added for 4 to 20 mA control.
L-Type anti-rotation bracket. Included with each actuator.
Bulk packaging LM24SR
US and LM24SR-T
US
Bulk Pack No.
LM24SR.1
US
LM24SR-T.1
US
Actuator Type
LM24SR
US
LM24SR-T
US
Quantity/Pack
32
48
9
LMC24 (SR) Fast running direct coupled actuator
24 V, 25 to 35 sec. running time
Torque min. 27 in-lb, for control of damper surfaces up to 6 sq ft.
LMC24
US
(on/off, floating)
LMC24-SR
US
(proportional)
LMC24-SR-T
US
(proportional)
LISTED
94D5
TEMP. IND &
REG. EQUIP
.
UL
®
Application
For on-off and floating point control of dampers in HVAC systems (LMC24
US
). For proportional modulation of dampers in
HVAC systems (LMC24-SR-T
US
). Actuator sizing should be done in accordance with the damper manufacturer’s specifications. The actuator mounts directly to the damper operating shaft with a universal V-bolt clamp assembly.
LMC24
US LMC24-SR
US
Technical Data
Power supply
Power consumption
Transformer sizing
Electrical connection
Overload protection
Angle of rotation
Torque
Control signal ‘Y’
Input impedance
Feedback output ‘U’
Direction of rotation
LMC24 (-SR)
US
…
24 VAC ± 20% 50/60 Hz 24 VDC ± 10%
LMC24
US
2.0 W
LMC24-SR
US
2.5 W
LMC24
US
3 VA
LMC24-SR
US
4 VA
3 ft, 18 GA, UL CL2P plenum cable
Electronic throughout 0 to 95° rotation max 95°, adjust. with mechanical stops
(LMC24
US
), electronically adjustable
20 to 100% on LMC24-SR
US only min 27 in-lb [3 Nm]
0 to 10 VDC, 0 to 20 mA (LMC24-SR-T
US
)
100 k
Ω
(0.1 mA), 500
Ω
(LMC24-SR-T
US
)
2 to 10 VDC (max. 0.7 mA )
(LMC24-SR-T
US
) reversible with switch “CCW-CW”
LMC24-SR-T
US
:
CW with a decrease in voltage
CCW with a decrease in voltage clip-on indicator Position indication
Running time
Manual override
25 to 35 sec. for 0 to 27 in-lb external push button
Humidity 5 to 95% RH, noncondensing
Ambient temperature -22°F to +122°F [-30°C to +50°C]
Storage temperature
Housing type
-40°F to +176°F [-40°C to +80°C]
NEMA type 2
Housing material rating UL94-5V
Noise level less than 35 dB (A)
Servicing
Agency listings
Quality standard
Weight maintenance free
UL873 listed, CSA 4813 02 certified, CE
ISO 9001
1.2 lbs [0.55 kg]
The LMC24-SR-T
US actuator operates in response to a 2 to 10
VDC or, with the addition of a 500
Ω resistor, a 4 to 20 mA input signal from an electronic controller or positioner. A 2 to 10 VDC feedback signal is provided for position indication or master slave applications. The LMC24-SR
US provides an electronic angle of rotation adjustment (not available in the LMC24-SR-T
US
) to limit the actuators rotation 20% to 100% while still using the full input signal and feedback control range.
Operation
The actuator is not provided with and does not require any limit switches, but is electronically protected against overload. The angle of rotation is mechanically limited to 95°. When reaching the damper or actuator end position, the actuator automatically stops. The gears can be manually disengaged with a button on the actuator cover. The position of the actuator is indicated by a visual pointer. The anti-rotation strap supplied with the actuator will prevent lateral movement.
Accessories
LM-P
IRM-100
Dimensions
T-type anti-rotation bracket
Input scaling module (For LMC24-SR-T
US only)
ZG-LMSA Shaft adaptor for short shafts
PTA-250 Pulse width modulating interface
SGA24
(For LMC24-SR-T
US only)
Min. and/or manual positioner in NEMA 4 housing
SGF24
Tool-02
ZAD24
ZG-R01
(For LMC24-SR-T
US only)
Min. and/or manual positioner for flush panel mount
(For LMC24-SR-T
US only)
8 mm wrench
Digital position indication (For LMC24-SR-T
US only)
500
Ω resistor for 4 to 20 mA
(For LMC24-SR-T
US only)
All ratings in brackets are metric.
1/4” to 5/8” [6 to 16]
1/4” to 7/16” [6 to 11]
LMC24-SR-T
US
Electrical connection
Angle of rotation
Housing
10
Screw terminals (for 26 to 14 GA wire) max 95°, adjust. with mechanical stops
NEMA type 1
®
24 V, 25 to 35 sec. running time
LMC24 (SR) Fast running direct coupled actuator
1
24 VAC Transformer
2
Line
Volts
● a open a closed
●
● a
3
Blk
(1)
Common
Red
(2)
+
Wht
(3)
+
The indication of direction is valid for switch position CW.
On-off control
CCW CW
LMC24
US
1
24 VAC Transformer
2
Line
Volts
●
●
●
The indication of direction is valid for switch position CW.
3
Blk
(1)
Common
Red
(2)
+
Wht
(3)
+
CCW CW
LMC24
US
Floating point or on-off control
1
24 VAC Transformer
●
Line
Volts
2
2 to 10 VDC
Control Signal
(–)
(+)
2 to 10 VDC
Feedback Signal
(–)
(+)
4
2 to 10 VDC control of LMC24-SR-T
US
3
Blk
(1)
Common
Red
(2)
+ Hot
6
Wht
(3)
Y 2 to 10V Input
Grn
(5)
U 2 to 10V Output
CCW CW
LMC24-SR-T
US
1
24 VAC Transformer
●
Line
Volts
4 to 20 mA
Control Signal
(–)
(+)
2 to 10 VDC
Feedback Signal
(–)
(+)
4
2
●
●
Ω
500
Ω
●
5
3
Blk
(1)
Common
Red
(2)
+ Hot
6
Wht
(3)
Y 2 to 10V Input
Grn
(5)
U 2 to 10V Output
CCW CW
LMC24-SR-T
US
4 to 20 mA control of LMC24-SR-T
US with 2 to 10 VDC feedback output
Notes
1
2
Provide overload protection and disconnect as required.
Actuators may also be powered by 24 VDC
3
Actuators are provided with color coded wires. Wire numbers are provided for reference.
4
5
Connect actuator common (Wire 1) to Negative (–) leg of control circuits only.
A 500
Ω resistor (ZG-R01) must be added for 4 to 20 mA control.
6
LMC24-SR-T
US does not have a cable. Numbers shown are terminal numbers.
LMC24… - Typical Specification:
Control damper actuators shall be electronic direct coupled type which require no crank arm and linkage. Actuators shall be UL and CSA listed, have a 2 year warranty, and be manufactured under ISO 9001 International Quality Control
Standards. Actuators shall have reversing switch and manual override on the cover, and be protected from overload at all angles of rotation. Actuator shall have a nominal running time of 30 seconds for 95° rotation. Proportional actuators shall respond to 2 to 10VDC output relative to position regardless of the amount of damper rotation. A 2 to 10 VDC feedback signal shall be provided for position indication or master-slave applications.
(LMC24-SR
US
An electronic angle of rotation adjustment only) shall be provided to reduce the actuators rotation from 100 to 20% while still using the full input signal and feedback control range. Actuators shall be as manufactured by Belimo.
L-Type anti-rotation bracket. Included with each actuator.
11
Installation Instructions
Quick-Mount Visual Instructions
min.
1.5”
[38]
L-bracket
1
2
L-bracket
3
1. Turn damper blade to its fully closed position.
2. With manual override button depressed, rotate actuator clamp to about 1/16” - 1/8” between actuator stop and clamp, depending on damper seal design. Slide actuator over shaft and finger-tighten nuts.
3. Slide anti-rotation bracket up under actuator engaging center cut-out on actuator back. Secure bracket with self-tapping screws. Tighten the two nuts on the universal clamp with
8 mm wrench, 3-5 ft-lb torque. (On dampers with edge seals, actuator will compress damper blades when reaching end position for air-tight damper.)
4. Adjust end stops, if required.
4
®
12
®
Actuator sizing/preliminary steps
Installation Instructions
Basic Formula for Actuator Sizing
Consult the damper manufacturer for rated torque loading. Call your Belimo representative for help in determining torque loading with linkage applications.
Damper Area
(2 ft
2
) x x
Rated Torque Loading of Damper
(4 in-lb/ft
2
)
=
=
Total in-lb Required
(8 in-lb) Belimo LM 35 in-lb
Duct Diameter (inches)
4”
5”
6”
7”
8”
9”
CONVERSION OF DUCT DIAMETER AREA
Area (square feet)
.09
Duct Diameter (inches)
10”
.19
.20
.27
.35
.44
11”
12”
14”
16”
18”
Formula for conversion of duct diameter area: A =
π
r
2
(
π
= 3.14, r = radius)
144
Area (square feet)
.55
.66
.79
1.07
1.40
1.77
When rated loading of damper is not available:
The following general selection guide may be used when it is not possible to obtain the damper manufacturer’s rated torque loading.
Note multiplier for face velocity (feet per minute, FPM).
Damper Type
Torque Loading in-lb/ft
2
< 1000 FPM/2 in w.g. 1000-2500 FPM/3 in w.g. (x 1.5) 2500-3000 FPM/4 in w.g. (x 2.0)
Air-tight application
Round blade/edge seals
Parallel blade/edge seals
Opposed blade/edge seals
10
7
5
15
10.5
7.5
20
14
10
Normal close-off application
Round blade/metal seat
Parallel blade/no edge seals
Opposed blade/no edge seals
5
4
3
7.5
6
4.5
10
8
6
Preliminary steps
1.
Belimo actuators should be mounted indoors in dry, relatively clean environment free from corrosive fumes. If the actuator is to be mounted outdoors, a protective enclosure must be used to shield the actuator. (See Belimo Mechanical Accessories Doc. 5.2)
2.
For new construction work, order dampers with extended shafts. Instruct the installing contractor to allow space for mounting and service of the Belimo actuator on the shaft.
3.
The LM Series actuator requires a minimum shaft length of 1.5”.
Use the ZG-LMSA for short shaft installations on 1/2” diameter shafts.
13
Installation Instructions
General Wiring
WARNING The wiring technician must be trained and experienced with electronic circuits. Disconnect power supply before attempting any wiring connections or changes. Make all connections in accordance with wiring diagrams and follow all applicable local and national codes. Provide disconnect and overload protection as required. Use copper, twisted pair, conductors only.
Always read the controller manufacturer's installation liter-
ature carefully before making any connections. Follow all instructions in this literature. If you have any questions, contact the controller manufacturer and/or Belimo.
Transformer(s)
The LM Series actuators require a 24 VAC transformer and draw a maximum of 4 VA.
CAUTION: It is good practice to power electronic or digital controllers from a separate power transformer than that used for actuators or other end devices. The power supply design in our actuators and other end devices use half wave rectification.
Some controllers use full wave rectification. When these two different types of power supplies are connected to the same power transformer and the DC commons are connected together, a short circuit is created across one of the diodes in the full wave power supply, damaging the controller. Only use a single power transformer to power the controller and actuator if you know the controller power supply uses half wave rectification.
Multiple actuators, one transformer
Multiple actuators may be powered from one transformer provided the following rules are followed:
1. The TOTAL current draw of the actuators (VA rating) is less than or equal to the rating of the transformer.
2. Polarity on the secondary of the transformer is strictly followed.
This means that all No. 1 wires from all actuators are connected to the common leg on the transformer and all
No 2 wires from all actuators are connected to the hotleg.
Mixing wire No. 1 & 2 on one leg of the transformer will result in erratic operation or failure of the actuator and or controls.
Multiple actuators, multiple transformers
Multiple actuators positioned by the same control signal may be powered from multiple transformers provided the following rules are followed:
1. The transformers are properly sized.
2. All No. 1 wires from all actuators are tied together and tied to the negative leg of the control signal. See wiring diagram.
Wire length for LM Series actuators
Keep power wire runs below the limits listed in the Fig. 1. If more than one actuator is powered from the same wire run, divide the allowable wire length by the number of actuators to determine the maximum run to any single actuator.
Maximum wire length:
Wire Size Max. Feet.
16 Ga 1225 Ft.
18 Ga 725 Ft.
Fig. 1
Wire Size Max. Feet
20 Ga
22 Ga
400 Ft
200 Ft
Example for LM…
US
: 3 actuators, 18 Ga wire
725 Ft ÷ 3 Actuators = 241.6 Ft. Maximum wire run.
Wire Type and Wire Installation Tips
For most installations, 18 or 16 Ga. cable works well with the
LM24 type actuators. Use code approved wire nuts, terminal strips or solderless connectors where wires are joined. It is good practice to run control wires unspliced from the actuator to the controller. If splices are unavoidable, make sure the splice can be reached for possible maintenance. Tape and/or wire tie the splice to reduce the possibility of the splice being inadvertently pulled apart.
LM Series Actuators with Terminal Strip
LM…-T actuators feature an external screw terminal strip on the top of the actuator housing (instead of cable). Connections are numbered and a wiring schematic is shown next to the terminal strip. The terminals are designed for 26 to 14 GA wire.
Overload protection
All Belimo actuators are electronically protected against overload. In the LM series an electronic circuit maintains the current at a level which will not damage the motor while providing adequate holding torque.
Manual Override
A button on the actuator cover disengages the gear train so the damper shaft can be moved manually. Release the button and the gear train is re-engaged.
Use the manual override to test the installation without power. For tight shut-off the damper should close with 5° of actuator stroke left.
0 1
Gear release button
0 1
14
®
®
Feature Operation
Installation Instructions
Direction of Rotation Switch (All LM except LM24-T
US
, LM24-5P0-T
US
)
LM actuators have a reversing switch on the cover labeled “L-R”.
Switch position indicates start point. For the LM24SR(-T), with the switch in position “L”, the actuator rotates clockwise with an increase in voltage or current. With the switch in position “R”, the actuator rotates counterclockwise with an increase in voltage or current.
During checkout, the switch position can be temporarily reversed and the actuator will reverse its direction. This allows the technician a fast and easy way to check the actuator operation without having to switch wires or change settings on the thermostat.
When the check-out is complete, make sure the switch is placed back to its original position.
The LM24 (-S)
US and LM24-10P
US rotate clockwise when the switch is in the “R” position and power is applied to wire #2. When power is applied to wire #3 the actuator rotates counter clockwise.
Rotating the “L/R” switch to “L” reverses the control logic.
2 VDC 10 VDC 10 VDC 2 VDC
L
L
The LM24-T and LM24-5P0-T
US do not have a switch. They rotate clockwise when power is applied to wire #3, and counterclockwise when power is applied to wire #2.
R
Clockwise
0 1
Counter
Clockwise
R
0 1
Direction of rotation switch. Position indicates start point.
Mechanical Angle of Rotation Limiting (LM Series, On-Off/Floating and LM24SR-T
US
)
The adjustable stops are needed when there is no damper stop or if you want the damper to halt rotating before it reaches its stops. The LM actuator can be indefinitely stalled in any position without harm.
1. Loosen the two end stops with a No. 2 Phillips head screwdriver being careful not to unscrew the captive nut under the slot.
2. Move the stops (in 2.5° steps) to the desired position and retighten the screws.
0
Adjust angle-of-rotation in steps of 2.5
°
1
Electronic Angle of Rotation Limiting (LM24SR
US
)
With the LM24SR
US proportional actuator, you can adjust the angle of rotation (95°) anywhere between 20% and 100% using an external adjustment. A potentiometer limits rotation while allowing the full control input and feedback range (2 to 10
VDC), providing higher control resolution within the limited angle of rotation.
2 VDC
L
R
0
Limitation set at 50%
Angle of rotation = 45
°
Control signal = 10 VDC
0
20% 100%
1
20% 100%
L
Feedback signal will also be adjusted 2 to 10 VDC
R
0
10 VDC
45
°
/50% Limit
10 VDC
45
°
/50% Limit
1
1
2 VDC
Adjustable Auxiliary Switch (LM24-S
US
)
The LM24-S
US actuator is equipped with an adjustable auxiliary switch used to indicate damper position or to interface additional controls or equipment. Switching positions can be set over the full scale of 0 to 95° simply by setting switch on the actuator cover.
Method A
1. Set desired switch position. (Example 60%)
2. As the actuator rotates, the switch indicator moves from
60% toward 0%. When the indicator passes 0 the switch contact between S1 and S3 is broken and the contact between S1 and S2 is made.
Method B
1. Use manual override to position universal clamp to desired switch position.
2. Turn switch pointer to “0”.
60%
0%
S2
S3
S1
S2
0 S3
S1
1
24 VAC
6A (2.5A)
S1 S2 S3
Desired switch position set at
60%
0
100%
1
15
Special Wiring Diagrams
16
Line
Volts
24 VAC Transformer
●
1
●
Control Signal
0 to 10 VDC
Controller A
(–)
(+)
●
2
3
1
2
Common
+ Hot
Control Signal
0 to 10 VDC
Controller B
(–)
(+)
1
3
Y
1
Input, 0 to 10 V
4
4
LM24SR(-T)
US
1
IN4001, IN4003 diode or equivalent, observe polarity.
Explanation: The diode allows the positive (+) signal to pass through it and does not allow a higher level positive signal to back feed to the other controller. Only the highest controller signal is seen by the actuator. There is a .7 VDC voltage loss across the diode. This makes the actual voltage range 2.7 to 10.7 VDC.
2
Actuators are provided with color coded wires. Wire numbers are provided for reference.
3
The LM24SR-T
US is provided a screw terminal instead of cable.
4
The LM24SR-T
US does not have feedback.
Operating 1 LM24SR (-T)
US with the higher of two 0 to 10
VDC control signals.
}
1
2
3
Stop
– +
+ –
●
●
1
●
2 3
1 Common
2 +
3 +
Note: Direction of rotation shown for the R position.
LM24(-T)
US
IN4001, IN4003 diode or equivalent, observe polarity.
Actuators are provided with color coded wires. Wire numbers are provided for reference.
The LM24(-T)
US is provided a screw terminal instead of cable.
Floating point control of LM24(-T) control signal.
US using a 2-wire DC
24 VAC
HOT max
4A (T)
COM
24 VAC
HOT max
4A (T)
COM
+
NSV-BAT (2) or equiv.
–
2 3 10 9 2 3 10 9
NSV-BAT (2) or equiv.
+
–
1 11 NSV 24 1 11 NSV 24
3 2 1
~ ~
COM
( + ) ( + ) ( – )
LM24…
US on-off/floating point
3 2 1
Y1
HOT COM
( + ) ( – )
LM24SR (-T)
US
3 2 1
~ ~
COM
( + ) ( + ) ( – )
LM24…
US on-off/floating point
Note: Fail-safe direction must have normally closed contact.
To other actuators
3 2 1
Y1
HOT COM
( + ) ( – )
LM24SR (-T)
US
To other actuators
Battery back up for fail-safe operation.
Up to 30 actuators can be powered with one NSV24 and 2 batteries.
Line
Volts
24 VAC Transformer
●
●
2 to 10 VDC
Control Signal
(–)
(+)
●
2
●
Damper #1
Blk
(1)
Common
Red
(2)
+ Hot
20% 100%
Wht
(3)
Y
Grn
(5)
U
Limitation set at 100%
Angle of rotation = 90
LM24SR
US
Using the LM24SR actuator electronic rotation adjustment, both dampers will change position in proportion to each other.
E.G. With a 50% position signal from the controller (6 VDC), damper #1 will rotate to 45°, damper #2 will rotate to 22.5°.
Damper #2
Blk
(1)
Common
Red
(2)
+ Hot
Wht
(3)
Y
Grn
(5)
U
20% 100%
Limitation set at 50%
Angle of rotation = 45
°
LM24SR
US
Parallel control of two LM24SR
US actuators with different angles of rotation
®
®
Startup and Checkout
LM24SR(-T)
US
Electrical check-out procedure
Step
1.
Procedure
Control signal is applied to actuator.
2.
3.
4.
5.
6.
7.
Check power wiring. Correct any problems. See Note 1.
Turn reversing switch to the correct position.
Expected Response
Actuator will move to its “Control
Signal” position.
Gives Expected
Response
Go To Step…
Actuator operates properly
Step 8
Power supply rating should be
≥ the total power requirement of the actuator(s). Minimum voltage of 19.2 VAC or 21.6 VDC.
Actuator will move to its “Control
Signal” position.
Power wiring corrected, actuator begins to drive
Step 1
Actuator operates properly.
Step 8
Actuator operates properly.
Step 8
Does Not Give
Expected Response
Go To Step…
No response at all
Step 2
Operation is reversed
Step 3
Does not drive toward "Control
Signal Position"
Step 4
Power wiring corrected, actuator still does not drive
Step 4
Does not drive toward “Control
Signal Position”
Step 4
Step 5
Make sure the control signal positive
(+) is connected to Wire No 3 and control signal negative (-) is connected to wire No. 1. Most control problems are caused by reversing these two wires. Verify that the reversing switch is all the way CCW or CW.
Drives to “Control Signal” position
Check input signal with a digital volt meter (DVM). Make sure the input is within the range of the actuator. For
LM24SR(-T)
US this is 0 to 10 VDC or
0 to 20 mA.
Note: The input signal must be above the 2 VDC or 4 mA to have the actuator move.
Input voltage or current should be ±1% of what controller's adjustment or programming indicate.
Use the manual override button to move the damper by hand from fully closed to fully open.
Damper will go from fully closed to fully open.
Check damper torque requirement.
Torque requirement is
≤ actuator’s minimum torque.
Controller output
(actuator input) is correct. Input
Polarity Correct.
Step 6
Damper moves properly
Step 7
Defective Actuator.
Replace Actuator -
See Note 2
Reprogram, adjust repair or replace controller as needed.
Step 1
Find cause of damper jam and repair.
Step 1
Recalculate actuator requirement and correct installation.
8.
Actuator works properly. Test controller by following controller manufacturer's instructions.
Note 1
Check that the transformer(s) are sized properly.
• If a common transformer is used, make sure that polarity is observed on the secondary. This means connect all No. 1 wires to one leg of the transformer and all No. 2 wires to the other leg of the transformer.
• If multiple transformers are used with one control signal, make sure all No. 1 wires are tied together and tied to control signal negative (-).
• Controllers and actuators must have separate 24 VAC/VDC power sources.
Note 2
If failure occurs within 5 years from original installation date, notify Belimo and give details of the application.
17
Simply the best way to drive a damper™
Serving HVAC Professionals
Throughout the Americas
®
Visit us at www.belimo.com
BELIMO AIRCONTROLS (USA), INC.
Corporate Headquarters/Distribution Center/Customer Support
Latin American Customer Support
43 OLD RIDGEBURY ROAD, P.O. BOX 2928
DANBURY, CT 06813
(203) 791-9915 • (800) 543-9038 • FAX (203) 791-9919
TOLL FREE FAX ORDER LINE: 1-800-ACTUATE
(1-800-228-8283)
Western USA Distribution Center/Customer Support
4900 MILL STREET, UNIT #9
RENO, NV 89502
(702) 857-4243 • (800) 987-9042 • FAX (702) 857-4255
TOLL FREE FAX ORDER LINE: 1-800-987-8875
BELIMO AIRCONTROLS (CAN), INC.
Corporate Headquarters/Distribution Center/Customer Support
5716 COOPERS AVE, UNITS 14 & 15
MISSISSAUGA, ONTARIO L4Z 2E8
(905) 712-3118 • FAX (905) 712-3124
BELIMO SERVOMOTEUR, INC.
Corporate Headquarters/Customer Support
2790 CHEMIN DU LAC
LONGUEUIL, QUÉBEC J4N 1B8
(450) 928-1440 • FAX (450) 928-0050
Overview
Doc. 1.0
The Most Complete Documentation Available for Damper Actuators
Product Guide and Company Profile
Spring Return Actuators
Doc. 2.1
Doc. 2.2
Doc. 2.3
AF Series, 133 in-lb
NF Series, 60 in-lb
LF Series, 35 in-lb
Non-Spring Return Actuators
Doc. 3.1
Doc. 3.2
GM Series, 266 in-lb
AM Series, 166 in-lb
Doc. 3.3
Doc. 3.4
NM Series, 70 in-lb
LM Series, 35 in-lb
Accessories
Doc. 4.1
Doc. 4.2
Electronic Accessories
Mechanical Accessories
Application Information
Doc. 5.1
Doc. 5.2
Mounting Methods Guide
Wiring Guide
Doc. 5.3
Doc. 5.4
Damper Applications Guide
Pneumatic vs Electric Actuation
Submittal Sheets AF, NF, LF, GM, AM, NM, LM
News
Belimo Direct
Product Newsletter
Belimo Feedback Application Newletter
Subject to change 3.30199
advertisement
* Your assessment is very important for improving the workof artificial intelligence, which forms the content of this project