advertisement
▼
Scroll to page 2
of 32
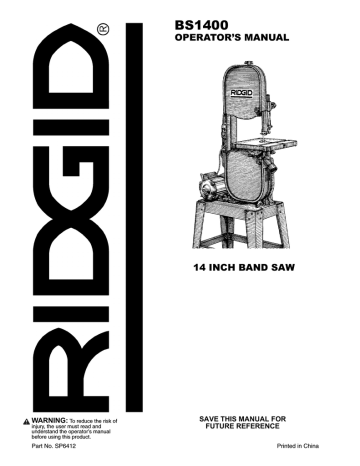
%6 23(5$725·60$18$/ ,1&+%$1'6$: WARNING: To reduce the risk of injury, the user must read and understand the operator’s manual before using this product. Part No. SP6412 SAVE THIS MANUAL FOR FUTURE REFERENCE Printed in China Table of Contents Section Page Safety Instructions For Band Saw ................................. 2 Safety Signal Words ................................................... 2 Before Using The Saw ................................................ 2 When Installing Or Moving The Saw ........................... 3 Before Each Use ......................................................... 3 To Reduce The Risk Of Injury From Jams, Slips Or Thrown Pieces Or Broken Blades ............................. 4 Plan Ahead To Protect Your Eyes, Hands, Face and Ears .................................................................... 4 Whenever Saw Is Running ......................................... 5 Before Leaving The Saw ............................................. 5 Glossary Of Terms For Woodworking ........................... 5 Motor Specifications and Electrical Requirements ........ 6 Power Supply and Motor Specifications ..................... 6 General Electrical Connections ................................... 6 110-120 Volt, 60 Hz. Tool Information ........................ 6 Changing Motor Voltage .............................................. 7 Motor Safety Protection .............................................. 7 Wire Sizes ................................................................... 7 Unpacking and Checking Contents ............................... 8 Tools Needed .............................................................. 8 Unpacking ................................................................... 8 List of Loose Parts ...................................................... 8 List of Loose Parts in Bag ........................................... 9 Assembly .....................................................................10 Attaching Leveling Feet ............................................ 10 Assembling Leg Set .................................................. 10 Attaching Band Saw to Leg Set ................................ 11 Adjusting Leveling Feet ............................................. 11 Mounting The Motor .................................................. 12 Mounting Blade Hangers ...........................................13 Mounting the Pulley Cover ........................................ 13 Mounting the Switch Box .......................................... 13 Mounting the Dust Chute .......................................... 14 Mounting the Table Trunnion Support ...................... 14 Mounting Bevel Scale ................................................ 14 Mounting the Table ................................................... 15 Section Page Installing Bevel Scale Indicator.................................. 15 Getting to Know Your Band Saw ................................. 16 Alignments and Adjustments ....................................... 18 Tilting the Table ........................................................ 18 Adjusting 90° Table Stop .......................................... 18 Changing Blades ...................................................... 18 Adjusting Blade Tension ........................................... 19 Adjusting Blade Tracking .......................................... 19 Adjusting Upper Blade Guide Assembly ................... 19 Adjusting Upper Blade Guides and Blade Support Bearing .................................................................... 20 Adjusting Lower Blade Guides and Blade Support Bearing .................................................................... 20 Safety Instructions for Basic Band Saw Operation ...... 21 Before Each Use ....................................................... 21 To Reduce The Risk Of Injury From Jams, Slips Or Thrown Pieces Or Broken Blades ........................... 21 Plan Ahead To Protect Your Eyes, Hands, Face and Ears .................................................................. 21 Whenever Saw Is Running ....................................... 22 Before Leaving The Saw .......................................... 21 Basic Saw Operations ................................................. 23 General Cutting ......................................................... 23 Circle Cutting ............................................................ 23 Maintenance ................................................................ 24 Tires .......................................................................... 24 Adjusting The Upper Blade Guide Travel ................. 24 General Maintenance ............................................... 24 Motor ......................................................................... 24 Lubrication ................................................................ 24 RIDGID Recommends the Following Accessories ....... 24 Troubleshooting ........................................................... 25 Motor ......................................................................... 25 General ..................................................................... 26 Wiring Diagram ............................................................ 26 Repair Parts ................................................................ 27 Safety Instructions For Band Saw WARNING: indicates a potentially hazardous situation which, if not avoided, could result in death or serious injury. CAUTION: indicates a potentially hazardous situation which, if not avoided, may result in minor or moderate injury. It may also be used to alert against unsafe practices that may cause property damage. NOTE: Advises you of information or instructions vital to the operation or maintenance of the equipment. The purpose of safety symbols is to attract your attention to possible dangers. The safety symbols, and the explanations with them, deserve your careful attention and understanding. The safety warnings do not by themselves eliminate any danger. The instructions or warnings they give are not substitutes for proper accident prevention measures. Safety Symbols DANGER: indicates an imminently hazardous situation which, if not avoided, will result in death or serious injury. Before Using The Saw WARNING: Do not attempt to use the tool until you have read thoroughly and understand completely the operator’s manual. Pay close attention to the safety rules, including Dangers, Warnings, and Cautions. If you use this tool properly and only for what it is intended, you will enjoy years of safe, reliable service. 2 WARNING: To reduce the risk of mistakes that could cause serious, permanent injury, do not plug the saw in until the following steps have been completed. • Review and understand all safety instructions and operating procedures in this manual. • Review the maintenance methods for this saw. • Find and read all the warning labels found on the front of the saw (shown below). • Completely assemble and align saw (see “Assembly” and “Alignment and Adjustments” section within). • Learn the use and function of the ON-OFF switch, table tilt lock knobs, blade guides, backup bearings, blade guard support adjustment knob and blade guard. When Installing Or Moving The Saw heavy boards. • Turn saw off and unplug cord before moving the saw. To reduce the risk of injury from electrical shock. • Make sure your fingers do not touch the plug’s metal prongs when plugging in or unplugging the saw. To reduce the risk of back injury. • Get help when you need to move the saw. Always get help if you need to lift the saw. • Never stand on tool. Serious injury could occur if the tool tips or you accidentally hit the cutting tool. Do not store any items above or near the tool where anyone might stand on the tool to reach them. Reduce the risk of dangerous environment. • Use the saw in a dry, indoor place protected from rain. • Keep work area well lighted. To reduce the risk of injury from unexpected saw movement. • Put the saw on a firm level surface where there is plenty of room to handle and properly support the workpiece. • Support the saw so the table is level and the saw does not rock. • Bolt the saw to the floor or work surface if it tends to slip, walk or slide during operations like cutting long, Before Each Use Inspect your saw. • To reduce the risk of injury from accidental starting, turn the switch off, unplug the saw, and remove the switch key before changing the setup, removing covers, guards or blade. • Check for alignment of moving parts, binding of moving parts, breakage of parts, saw stability, and any other conditions that may affect the way the saw works. • If any part is missing, bent or broken in any way, or any electrical part does not work properly, turn the saw off and unplug the saw. • Replace damaged or missing parts before using the saw again. • Maintain tools with care. Keep the saw clean for best and safest performance. Follow instructions for lubricating. • Remove adjusting keys and wrenches. Form a habit of checking for and removing keys and adjusting wrenches from table top before turning it on. 3 Safety Instructions For Band Saw (continued) To Reduce The Risk Of Injury From Jams, Slips Or Thrown Pieces Or Broken Blades Inspect your blade. • Choose the right blade size, style and cutting speed for the material and the type of cutting you plan to do. • Make sure the blade teeth point downward, toward the table. • Make sure the blade guides and thrust bearings are properly adjusted. • Make sure the blade tension is properly adjusted. • Make sure the bevel clamp is tight and no parts have excessive play. • To reduce the risk of accidental blade contact, minimize blade breakage and provide maximum blade support, always adjust the upper blade guide and blade guard to just clear the workpiece. Inspect your work area. • Keep work area clean. • Cluttered areas and benches invite accidents. Floor must not be slippery from wax or sawdust. • To reduce the risk of burns or other fire damage, never use the saw near flammable liquids, vapors or gases. Plan your work • Use the right tool. Don’t force tool or attachment to do a job it was not designed to do. • Use this band saw to cut only wood, wood like products and plastics. tion and limitations as well as the specific potential hazards peculiar to this tool. • To reduce the risk of injury from accidental contact with moving parts, don’t do layout, assembly, or set up work on the saw while any parts are moving. • Reduce the Risk of accidental starting. Make sure switch is “OFF” before plugging saw into a power outlet. Inspect your workpiece. • Make sure there are no nails or foreign objects in the part of the workpiece to be cut. Use extra caution with large, very small or awkward workpieces: • Use extra supports (tables, saw horses, blocks, etc.) for any workpieces large enough to tip when not held down to the table top. • NEVER use another person as a substitute for a table extension, or as additional support for a workpiece that is longer or wider than the basic saw table, or to help feed, support or pull the workpiece. • When cutting irregularly shaped workpieces, plan your work so it will not slip and pinch the blade. A piece of molding for example, must lie flat or be held by a fixture or jig that will not let it twist, rock or slip while being cut. • Properly support round material such as dowel rods, or tubing. They have a tendency to roll during a cut, causing the blade to “bite”. To reduce the risk of this, always use a “V” block or clamp the work to the miter gage. • Cut only one workpiece at a time. • Clear everything except the workpiece and related support devices off the table before turning the saw on. CAUTION: To reduce the risk of blade breakage, fire or other damage to the saw, NEVER use this band saw to cut metals. • Know your saw. Read and understand the operator’s manual and labels affixed to the tool. Learn its applica- Plan Ahead To Protect Your Eyes, Hands, Face and Ears Dress for safety • For dusty operations, wear a dust mask along with safety goggles. • Do not wear loose clothing, gloves, neckties or jewelry (rings, wrist watches). They can get caught and draw you into moving parts. • Wear nonslip footwear. • Tie back long hair. • Roll long sleeves above the elbow. • Noise levels vary widely. To reduce the risk of possible hearing damage, wear ear plugs or muffs when using saw for hours at a time. Plan the way you will hold the workpiece from start to finish. • Do not hand hold pieces so small that your fingers will go under the blade guard. Use jigs or fixtures to hold the work and keep your hands away from the blade. • Secure work. Use clamps to hold work when practical. It’s often safer than using your hand, and frees both hands to operate the tool. • Don’t overreach. Keep good footing and balance. WARNING: The operation of any power tool can result in foreign objects being thrown into your eyes, which can result in severe eye damage. Before beginning tool operation, always wear safety goggles or safety glasses with side shields and a full face shield when needed. We recommend Wide Vision Safety Mask for use over eyeglasses or standard safety glasses with side shields. Always wear eye protection which is marked to comply wtih ANSI Z87.1. Look for this symbol to point out important safety precautions. It means attention!!! Your safety is involved. 4 Whenever Saw Is Running WARNING: Don’t allow familiarity (gained from frequent use of your band saw) cause a careless mistake. Always remember that a careless fraction of a second is enough to cause a severe injury. Before freeing jammed material. • Turn switch “OFF”. • Unplug the saw. • Wait for all moving parts to stop. • Remove switch key. When backing up the workpiece, the blade may bind in the kerf (cut). This is usually caused by sawdust clogging up the kerf or because the blade comes out of the guides. If this happens: • Turn saw “OFF”. • Wait for all moving parts to stop. • Remove switch key. • Unplug the saw. • Remove band saw cover. • Stick flat blade screwdriver or wedge into the kerf. • Turn the upper wheel by hand while backing up the workpiece. • Before starting your cut, watch the saw while it runs. If it makes an unfamiliar noise or vibrates a lot, stop immediately. Turn the saw off. Unplug the saw. Do not restart until finding and correcting the problem. • Before removing loose pieces from the table, turn saw off and wait for all moving parts to stop. Keep Children Away. • Keep all visitors a safe distance from the table saw. • Make sure bystanders are clear of the table saw and workpiece. Don’t Force Tool. • Let the blade reach full speed before cutting. • It will do the job better and safer at its designed rate. • Feed the workpiece into the saw only fast enough to let the blade cut without bogging down or binding. Before Leaving The Saw • • • • Turn the saw off. Wait for all moving parts to stop. Unplug the saw. Make workshop child-proof. - Lock the shop. - Disconnect master switches. - Remove the yellow switch key. Store it away from children and others not qualified to use the tool. WARNING: Some dust created by power sanding, sawing, grinding, drilling, and other construction activities contains chemicals known (to the State of California) to cause cancer, birth defects or other reproductive harm. Some examples of these chemicals are: • Lead from lead-bases paints, • Crystalline silica from bricks and cement and other masonry products, and • Arsenic and chromium from chemically-treated lumber. Your risk from these exposures varies, depending on how often you do this type of work. To reduce your exposure to these chemicals: work in a well ventilated area, and work with approved safety equipment, such as those dust masks that are specially designed to filter out microscopic particles. Glossary Of Terms For Woodworking Beveling An angle cutting operation made through the face of the workpiece. Compound Cutting A simultaneous bevel and miter crosscutting operation. Crosscut A cutting operation made across the width of the workpiece. FPM Feet per minute. Used in reference to surface speed of blade. Freehand (as used for band saw) Performing a cut without the workpiece properly supported on the work table. Gum A sticky, sap based residue from wood products. Kerf The material removed by the blade in a through cut or the slot produced by the blade in a nonthrough or partial cut. Leading End The end of the workpiece which, is pushed into the cutting tool first. Mitering An angle cutting operation made across the width of the workpiece. Push Stick A device used to feed the workpiece through the saw during narrow ripping type operations and helps keep the operator’s hands well away from the blade. Resaw A cutting operation to reduce the thickness of the work5 piece to make thinner pieces. Resin A sticky, sap based substance that has dried. Ripping A cutting operation along the length of the workpiece. Sawblade Path The area of the worktable or workpiece directly in line with the saw blade. Set The distance the tip of the sawblade tooth is bent out- ward from the face of the blade. Trailing End The workpiece end last cut by the blade. Workpiece The item on which the cutting operation is being performed. The surfaces of a workpiece are commonly referred to as faces, ends, and edges. Worktable The surface on which the workpiece rests while performing a cutting or sanding operation. Motor Specifications and Electrical Requirements Power Supply and Motor Specifications The A-C motor used in this saw is nonreversible type, having the following specifications: WARNING: To reduce the risk of electrical hazards, fire hazards or damage to the tool, use proper circuit protection. Your tool is wired at the factory for operation using the voltage shown. Connect tool to a power line with the appropriate voltage and a 15-amp branch circuit. Use a 15-amp time delay type fuse or circuit breaker. To reduce the risk of shock or fire, if power cord is worn or cut, or damaged in any way, have it replaced immediately. Rated Horsepower Voltage Follow the instructions on page 7 to connect the motor for 220-240V A/C operation. 3/4 110-120 220-240 Amperes 10 5 Hertz (Cycles) 60 50/60 Phase Single RPM 1725 Rotation of Shaft Counterclockwise General Electrical Connections DANGER: To reduce the risk of electrocution: 1. Use only identical replacement parts when servicing. Servicing should be performed by a qualified service technician. 2. Do not use in rain or where floor is wet. This tool is intended for indoor residential use only. WARNING: Do not permit fingers to touch the terminals of plug when installing or removing the plug to or from the outlet. 110-120 Volt, 60 Hz. Tool Information The plug supplied on your tool may not fit into the outlet you are planning to use. Your local electrical code may require slightly different power cord plug connections. If these differences exist refer to and make the proper adjustments per your local code before your tool is plugged in and turned on. stood, or if you are in doubt as to whether the tool is properly grounded check with a qualified electrician or service personnel. WARNING: If not properly grounded, this tool can cause an electrical shock, particularly when used in damp locations, in proximity to plumbing, or out of doors. If an electrical shock occurs there is the potential of a secondary hazard, such as your hands contacting the sawblade. In the event of a malfunction or breakdown, grounding provides a path of least resistance for electric current to reduce the risk of electric shock. This tool is equipped with an electric cord having an equipment-grounding conductor and a grounding plug, as shown. The plug must be plugged into a matching outlet that is properly installed and grounded in accordance with all local codes and ordinances. Improper connection of the equipment-grounding conductor can result in a risk of electric shock. The conductor with insulation having an outer surface that is green with or without yellow stripes is the equipment-grounding conductor. If repair or replacement of the electric cord or plug is necessary, do not connect the equipment-grounding conductor to a live terminal. If the grounding instructions are not completely under- Properly Grounded 3-Prong Outlet 3-Prong Plug Grounding Prong 6 Changing Motor Voltage WARNING: If not properly grounded, this tool can cause an electrical shock, particularly when used in damp locations, in proximity to plumbing, or out of doors. If an electrical shock occurs there is the potential of a secondary hazard, such as your hands contacting the knives. “hot” plug blade terminals and connect the power cord green grounding wire to the plug ground prong terminal. 8. Plug your band saw into a 220-240V, 15 amp, 3 blade receptacle. 9. Make certain the receptacle is connected to a 240 volt A.C. power supply through a 240 volt branch circuit having at least a 15 amp capacity and protected by a 15 amp time-delay fuse or circuit breaker. NOTE: The band saw is prewired at the factory for 120V operation. Use the following procedure to change motor voltage. To change to 240V application an additional wire nut is supplied from the factory. This part is included in the loose parts. 1. Unplug the band saw before making or changing any connections. Open the motor junction box cover located on the side of the motor. 2. Remove and discard the electrical tape from the wire nuts. Remove wire nuts. 3. Reconnect the leads as shown in the “Wiring Diagram” section at the rear of manual. 4. Reinstall the wire nuts and wrap with two layers of new U.L. listed electrical tape per wire nut. 5. Recheck your wiring to the wiring diagrams. Do this so you can be sure that the wiring is correct. 6. Reinstall the junction box cover. 7. Cut off the 120 volt power cord plug and replace it with a (3 blade) 240 volt 15 amp U.L. Listed Assembled - on Plug Cap suitable for 16 AWG Type SJT Cord. (See illustration of 240V plug & receptacle.) Connect the power cord white and black leads, respectively, to the Junction Box Cover Grounding Prong Grounded Outlet Box 220-240 Volt, 60 Hz. Tool Connections Motor Safety Protection 1. Connect this tool to a power source with the appropriate voltage for your model and a 15-amp branch circuit with a 15-amp time delay fuse or circuit breaker. Using the wrong size fuse can damage the motor. 2. If the motor won't start, turn off the power switch immediately and unplug the tool. Check the saw blade to make sure it turns freely. If the blade is free, try to start the motor again. If the motor still does not start, refer to the "Motor Troubleshooting Chart." 3. If the motor suddenly stalls while cutting wood, turn off the power switch, unplug the tool and free the blade from the wood. The motor may now be restarted and the cut finished. 4. Fuses may "blow" or circuit breakers may trip frequently if: a. Motor Is Overloaded-Overloading can occur if you feed too rapidly or make too many start/stops in a short time. b. Line voltages should not be more than 10% above or below the nameplate voltage. For heavy loads, however, the voltage at motor terminals must equal the voltage specified for your model. c. Improper or dull saw blade is used. 5. Most motor troubles may be traced to loose or incorrect connections, overload, low voltage (such as small size wire in the supply circuit) or to overly long supply circuit wire. Always check the connections, the load and the supply circuit whenever motor doesn't work well. Check wire sizes and length with the Wire Size Chart. Wire Sizes NOTE: Make sure the proper extension cord is used and is in good condition. The use of any extension cord will cause some loss of power. To keep this to a minimum and to prevent overheating and motor burnout, use the table shown to determine the minimum wire size (A.W.G.) extension cord. Use only 3-wire extension cords which have 3-prong grounding type plugs and 3-pole receptacles which accept the tools plug. 7 Extension Cord Length Gauge (A.W.G.) 0-25 Ft. 26-50 Ft. 14 12 Unpacking and Checking Contents Tools Needed Combination Square Must be True Combination Wrenches 10mm, 12mm, 13mm, 14mm Straight Edge of Board 3/4” Thick This Edge Must be Perfectly Straight Draw Light Line on Board Along this Edge #1 Phillips Screwdriver Straightedge NOTE: The square and straight edge are used to align the saw. They must be accurate if the saw is to be aligned properly. #2 Phillips Screwdriver Should be no Gap or Overlap when Square is Flipped Over in Dotted Position Combination Square Adjustable Wrench List of Loose Parts Unpacking Item Description Qty. A Band Saw ...........................................................1 B Motor w/Switch ...................................................1 C Table Asm...........................................................1 D Plate Support......................................................1 E Pulley Cover .......................................................1 F Trunnion Support ................................................1 G V-Belt ..................................................................1 H Stand Top ...........................................................1 J Legs....................................................................4 K Stiffener (Long) ...................................................2 L Stiffener (Short) ..................................................2 M Bag Loose Parts ................................................. * N Operator’s Manual ..............................................1 * Number varies: bags can contain other smaller bags. NOTE: To make assembly easier keep contents of each bag together and separate from contents of other bags. NOTE: To reduce the risk of damage to the band saw leave it laying on its side in the shipping box until you are ready to mount it to the leg set. WARNING: To reduce the risk of injury from unexpected starting or electrical shock, do not plug the power cord in until all assembly and alignment steps are complete. The power cord must remain unplugged whenever you are working on the saw. 1. Separate saw and all parts from packing materials and check each one with the illustration and the “List of Loose Parts” to make certain all items are accounted for, before discarding any packing material. WARNING: If any parts are missing, do not attempt to assemble the band saw, plug in the power cord, or turn the switch on until the missing parts are obtained and are installed correctly. 2. Sometimes small parts get lost in packaging materials. Do not throw away any packaging until your saw is put together. Contact 1-866-539-1710 if any parts are damaged or missing. A B H D E J M F K N C G 8 L List of Loose Parts in Bag Screw Pan Head M4 x 0.7-10 (4) Screw Pan Head M5 x 0.8-12 (5) Washer External M4 (4) Nut Hex M4 (4) Washer Flat M5 x 10 Dia. (6) Bolt Hex Head M8 x 1.25-35 (10) Screw Hex Head M8 x 1.25-80 (1) Bolt Carriage M8 x 1.25-16 (40) Washer External M5 (2) Nut Hex 3/8-16 (8) Screw Pan Head Lock M6 x 1 (2) Washer Lock M8 (50) Screw Flat Hd. M5 x 0.8-15 (2) Nut Hex M5 (3) Washer Flat M8 x 16 (56) Bolt Hex Head M6 x 1-10 (1) Washer Flat M6 x 12 (1) Washer M5 (2) Screw Pan Head M5 x 0.8-6 (1) Nut Hex Head M8 (49) Nut Hex M5 x 0.8 (2) Rubber Grommet (4) Knob Locking (2) Leveling Foot (4) Dust Chute (1) Bevel Scale (1) Blade Hanger (2) Key-Switch (1) M3 Hex “L” Wrench (1) 9 Pointer (1) M5 Hex “L” Wrench (1) Assembly Attaching Leveling Feet 1. From the loose parts bag find the following items: 4 Leveling feet 8 Hex nut 3/8-16 2. From the loose parts find the following items: 4 Leg Hex Nut 3/8-16 Leveling Foot Leg 3. Put a hex nut on each of the leveling feet and screw it down towards the rubber foot. 4. Put the leveling feet through the holes in the bottom of each leg. 5. Put another hex nut on each of the leveling feet and hand tighten until they are next to the bottom support of the leg. Leg Hex Nut 3/8-16 WARNING: To reduce the risk of injury from unexpected saw or work movement, leveling feet must be adjusted so that saw does not rock. After the band saw has been attached to the legset, it will be necessary to adjust the leveling feet so the saw does not rock. Leveling Foot Assembling Leg Set 1. From the loose parts bag find the following hardware: 40 Carriage Bolts M8 x 1.25-16 40 M8 Washers 40 M8 Lockwashers 40 M8 Nuts 2. From the loose parts find the following items: 4 Legs (With Attached Leveling Feet) 2 Stiffeners (short) 2 Stiffeners (long) 1 Stand top Bolt Carriage Washer M8 M8 x 1.25-16 Lockwasher Nut Hex M8 M8 Legs Stand Top Stiffener (Long) 3. Place stand top upside down on a level surface. Fasten four legs to top using carriage bolts, washers, lock washers, and nuts, as shown (with nuts and washers to the inside). Note: Legs fasten to outside of top. Do not tighten at this time. 4. Fasten two long stiffeners and two short stiffeners to stand legs using carriage bolts, washers, lockwashers, and nuts, as shown. Finger tighten only at this time. Stiffener (Short) M8 Lockwasher Carriage Bolt M8 Washer M8 Nut Leg Stiffener (Long) Stand Top 10 Stiffener (Short) 5. Turn assembly over onto the legs. Be sure all four feet sit flat on the ground. Adjustment of the feet will be completed after the band saw is attached to the stand. 6. Tighten all stand fasteners at this time. 7. With the aid of a second person, lift the saw body out of the shipping container and place onto the stand top. Be sure front of saw faces stand front by aligning holes. CAUTION: Saw body is heavy! Use care when lifting and stabilize until it is firmly attached to the stand! Get help when lifting and mounting saw. Attaching Band Saw to Leg Set 1. From the loose parts bag find the following hardware: 4 M8 x 35 Hex Head Bolts (approx. 1-3/8”) 8 M8 Washers 4 M8 Lockwashers 4 M8 Nuts 2. From the loose parts find the following: 1 Support Plate 3. While one person continues to hold the saw from tipping, the other person should install mounting bolts. 4. Line up holes in saw body with holes in stand. 5. Place support plate to the underside of stand as shown. Bolt Hex Head M8 x 1.25-35 Washer M8 Support Plate Lockwasher M8 Nut Hex M8 Support Plate 6. Fasten saw body, stand, and support plate together with four hex head bolts, eight flat washers, four lockwashers, and four hex nuts. Bolt Hex Head Washer Lockwasher Nut Adjusting Leveling Feet WARNING: To reduce the risk of injury from unexpected saw or work movement, leveling feet must be adjusted so that saw does not rock. Leg To adjust leveling feet so the saw will sit properly: 1. Move saw to desired location. 2. Raise or lower leveling foot by turning the nuts clockwise or counterclockwise. 3. Tighten nuts to lock leveling foot in place. Nut Leveling Foot 11 Assembly (continued) Mounting The Motor 1. From the loose parts bag find the following items: 4 M8 x 35 Hex Cap Bolts (approx. 1-3/8”) 8 M8 Washers 4 M8 Lockwashers 4 M8 Nuts 4 Rubber Grommets 2. From the loose parts find the following items: 1 Motor 1 V-Belt Bolt Hex Head M8 x 1.25-35 Lockwasher M8 Rubber Grommet (4) Washer M8 Nut Hex M8 Motor w/Switch V-Belt 3. To mount motor, place four rubber grommets over holes in stand top. NOTE: Use of rubber grommets is essential for eliminating excessive vibration. Place motor over rubber grommets and fasten to stand top with four hex head bolts, eight washers, four lockwashers, and four hex nuts, as shown. Do not tighten at this time. Motor Bolt Washer Grommet Washer Lockwasher Nut 4. Align the inside edge of the motor pulley with inside edge of the large pulley using a straight edge. Using a 3mm hex “L” wrench, adjust one or both pulleys by loosening the set screw and moving the pulley(s) until they line up with each other. Tighten set screws. 5. Place V-belt over both pulleys. 6. Tension V-belt by moving motor away from the saw body and tighten the motor mount nuts. (Do not over-tighten motor mount bolts. Tighten just enough to tension belt.) Belt is properly tensioned when finger pressure between the two pulleys causes approximately 1/2” deflection. 12 Mounting Blade Hangers 1. From the loose parts bag find the following items. 4 Screw Pan Head M4 x 0.7-10 4 Nut Hex M4 x 0.7 4 Lockwasher External M4 2 Blade Hangers Screw Pan Head M4 x 0.7-10 (4) 2. From the loose parts find the following item. 1 Pulley Cover Nut Hex M4 (4) Lockwasher External M4 Pulley Cover Blade Hanger 3. Attach the blade hangers on the pulley cover as shown. Screw Nut Hex Lockwasher Mounting the Pulley Cover 1. From the loose parts bag find the following items. 3 Screw Pan Head M5 x 0.8-12 (approx. 1/2”) 6 M5 Washers 3 M5 Nuts Screw Pan Head M5 x 0.8-12 Washer Flat M5 x 10 Dia. Pulley Cover 2. Place pulley cover over both pulleys and fasten to stand using three pan head screws, six washers, and three hex nuts, as shown. Screw Washers Nut Mounting the Switch Box 1. From the loose parts find the following hardware: 2 Screw Pan Head M5 x 0.8-12 (approx. 1/2”) 2 Lockwasher Ext. M5 Screw Pan Head M5 x 0.8-12 2. Mount switch box assembly to frame as shown using hardware listed. Lockwasher External M5 Lockwasher Screw Lockwasher 13 Nut Hex M5 Assembly (continued) Mounting the Dust Chute 1. From the loose parts bag find the following items: 2 Screw Pan Head Lock M6 x 1 2. From the loose parts find the following items: 1 Dust Chute Screw Pan Head Lock M6 x 1 Dust Chute 3. Open lower blade guard cover and install dust chute. Use fasteners supplied. Close lower blade guard cover. Dust Chute Mounting the Table Trunnion Support To Saw Body Screw Hex Head M8 x 1.25-80 1. From the loose parts bag find the following items: 2 M8 x 35 Hex Head Bolts (approx. 1-3/8”) 2 M8 Lockwashers 1 M8 x 80 Hex Cap Bolt (table stop bolt approx. 3-1/8” long) 1 M8 Nut (For Table Stop Bolt) 2. From the loose parts find the following items: 1 Table Trunnion Support (shown below) Lockwasher M8 Bolt Hex Head M8 x 1.25-35 Nut Hex M8 Bolt Hex Head M8 x 1.25-35 Lockwasher Screw Hex Head M8 x 1.25-80 3. Attach trunnion support to saw body with two hex head bolts and two lockwashers as shown. 4. Thread nut (D) onto table stop bolt (C) and attach to trunnion support. Nut Hex M8 Mounting Bevel Scale To Table 1. From the loose parts find the following items: 2 Screw Flat Head M5 x 0.8-15 2 Washer M5 2 Nut Hex M5 x 0.8 1 Scale Bevel 2. Insert the screws through the table and bevel scale as shown. 3. Install a washer and nut. Tighten Screw Flat Hd. M5 x 0.8-15 Bevel Scale 14 Washer M5 Nut Hex M5 x 0.8 Mounting the Table To Saw Body 1. From the loose parts find the following items: 1 Table 2 Knobs 2. To mount table, remove table insert and table pin from the table. Guide sawblade through slot in table and place table screws into trunnions. Attach and lock with lock knobs. Installing Bevel Scale Indicator 1. From the loose parts find the following items: 1 Pointer 1 Screw Pan Head M5 x 0.8-6 2. Insert screw through the slot in the pointer and into the trunnion support bracket. Tighten Screw Pan Head M5 x 0.8-6 Pointer WARNING: Unit is shipped with blade installed. Do not plug in or operate unit unless the blade is adjusted and aligned per section titled “Changing Blades”. Trunnion Support Bracket 3. Replace table insert and table pin. 4. Transportation and handling may have caused some fasteners to loosen. Before operating, check all screws, bolts and nuts to make sure they are snug. Operate machine only after reading the entire manual including blade tracking, blade guide adjustments, and safety rules. 15 Getting to Know Your Band Saw 10 Upper 15 Motor Pulley Cover 1 Warning Label Cover 6 Blade Guard Support Adjustment Knob 16 Blade Hangers 18 On-Off Switch 4 Blade Guides 5 Back-Up Bearings 7 Tilting Table 2 Blade Tension Knob 8 Table Tilt 9 Tilt Table Lock Knobs Stops 14 Motor 13 Lower Blade Guard 17 Model Nameplate 3 Blade Tracking Adjustment Knob 12 Sawdust Ejection Port 11 Lower Cover 1. Warning Label 2. Blade Tension Knob - Clockwise rotation of the knob will increase the tension on the blade. Counterclockwise rotation of the knob will decrease the tension on the blade. 3. Blade Tracking, Adjustment Knob - Turn knob to adjust blade tracking. 4. Blade Guides - The guides are adjustable to provide full support of the blade. 5. Back-up Bearings - These thrust bearings support the back of the blade and are adjustable for the various blade widths. 6. Blade Guard Support Adjustment Knobs - Loosen this knob to vertically adjust the blade guard support so that it just clears the workpiece to be cut. Always adjust the guard/support before turning on the band saw. Tighten the knob to lock the guard/support in the proper location. 7. Tilting Table - Table tilts for angular cuts. Use the table tilt scale under table to measure angular settings. 8. Table Tilt Lock Knobs - Loosen knobs to move tilt table to required angle. Retighten knobs to secure table. 9. 90° Table Stops - Ensures table is perpendicular to blade. 10. Upper Cover - Pull knob to expose upper wheel during blade changes. 11. Lower Cover - Pull knob to gain access to lower wheel, remove the blade or to clean out sawdust build-up. 12. Sawdust Ejection Port - Your band saw is equipped with a vacuum hookup. This feature will allow you to attach any standard 2-1/2 inch diameter wet/dry vacuum hose into the hole provided for convenient sawdust removal. WARNING: Sawdust can clog motor. Motor could ignite sawdust. Even if saw is connected to vacuum, blow out sawdust regularly from motor. 13. Lower blade guard. Safeguards user from accidental blade contact. 14. Motor. 15. Motor pulley cover. 16. Blade Hangers - Extra blades may be stored here. 17. Model nameplate. 16 18. On-Off Switch WARNING: Before turning switch “ON”, make sure the blade guards are correctly installed and operating properly. The On-Off switch has a locking feature. This feature is intended to help prevent unauthorized and possible hazardous use by children and others. 1. To turn band saw “On” insert key into switch. NOTE: Key is made of yellow plastic, located in the loose parts bag. 2. Insert finger under switch lever and Pull end of switch out. 3. To turn band saw “Off” Push lever in. WARNING: Never leave the band saw unattended until it has come to a complete stop. 4. To lock switch in “Off” position hold switch in with one hand and remove key with other hand. WARNING: For your own safety, always lock the switch “Off” when band saw is not in use, remove the key and keep it in a safe place. In the event of a power failure (all of your lights go out) turn switch off, remove the key and store it away from the band saw. This will prevent the machine from starting up again when the power comes back on. 17 Alignments and Adjustments Tilting the Table WARNING: Unplug the machine from the power source before making any repair or adjustment. Failure to comply may cause serious injury. 90° Table Stop Jam Nut 1. Loosen two lock knobs. 2. Tilt table up to 45 degrees to the right or up to 10° to the left. 3. Tighten two lock knobs. NOTE: 90° table stop must be removed to tilt table 10° to the left. Lower Rotating Blade Guard Adjusting 90° Table Stop 1. Disconnect machine from the power source. 2. Loosen lock knobs and tilt table left until it rests against table stop. 3. Use a square placed on the table and against the blade, to see if the table is 90 degrees to the blade. 4. If an adjustment is necessary, loosen lock knobs. Tilt table to the right, and lock in place. 5. Loosen jam nut and turn table top left or right to raise or lower the stop. Tighten jam nut to hold table stop in place. 6. Unlock table, tilt back onto table rest and confirm table is 90 degrees with the blade. 7. If necessary, adjust pointer to zero. Table Pin Table Insert Changing Blades WARNING: Blade teeth are sharp. Use care when handling the sawblade. 1. Disconnect the machine from the power source. 2. Loosen blade tension by turning blade tension knob counterclockwise until it stops. 3. Remove the table insert and the table pin. 4. Open upper and lower cover. Remove screws and washers from guard blade rear. Then remove guard. 5. Insert screwdriver through table insert hole to loosen pivot screw one turn for guard under the table. Rotate guard out of the way. 6. Remove the blade from between upper and lower blade guides. Remove blade from upper and lower wheels. Turn blade so it will fit through slot in table. Remove blade. 7. Guide new blade through table slot. Place blade in upper and lower blade guides. NOTE: Make sure blade teeth point down toward table. 8. Place blade in the middle of the upper and lower wheel. 9. Replace guard blade rear and tighten screws. 10. Rotate guard under table to a closed position and tighten screw. 11. Replace table insert and table pin. 12. Tension and track blade before operating saw. Find instructions for tensioning and tracking the blade under “Adjusting Blade Tension” and “Adjusting Blade Tracking”. Blade Tension Knob 18 Adjusting Blade Tension 1. Disconnect machine from the power source. 2. Turn blade tension knob clockwise to tension blade. A gauge on the upper wheel slide bracket indicates the approximate tension according to the width of the blade. Initially, set the blade tension gauge to correspond with the blade width. 3. As you become familiar with the saw, you may find it necessary to change the blade tension from the initial setting. Changes in blade width and the type of material being cut will have an effect on blade tension. 4. Keep in mind that too little or too much blade tension can cause blade breakage. Blade Tension Knob Blade Tension Gauge Adjusting Blade Tracking WARNING: Disconnect machine from the power source. Never adjust blade tracking with the machine running. 1. Blade must be properly tensioned before adjusting blade tracking. Make sure blade guides and blade bearings do not interfere with the blade. 2. Open upper cover. Rotate the wheel forward by hand and observe the position of the blade on the wheel. It should be in the center. 3. If adjustment is necessary, loosen wing nut, tighten knob slightly to move blade toward rear of machine. Slightly loosening the knob will cause the blade to track toward the front of the machine. 4. Tighten nut after blade is tracking in the center of the wheel. Blade Tracking Knob Lock Knob Adjusting Upper Blade Guide Assembly 1. Disconnect machine from the power source. 2. Loosen lock knob and raise or lower upper blade guide assembly to just above the material being cut. 3. Tighten lock knob. Make sure blade guide blocks are still flat to the blade. If adjustment is necessary, loosen lock knob and rotate assembly until guide blocks are flat to the blade. 4. The upper blade guide is spring loaded. To adjust the tension on the spring, remove knob, tighten or loosen set screw until desired tension is reached, and replace knob. (See page 20) 19 Alignments and Adjustments (continued) Adjusting Upper Blade Guides and Blade Support Bearing WARNING: Blade guard has been removed for picture clarity. Never operate the band saw without all guards in place and in working order. Failure to comply may cause serious injury. Step 7 1. Disconnect machine from the power source. 2. Blade must already be tensioned and tracking properly. 3. Loosen thumb screws and move guide blocks as close to the blade as possible without pinching it. The thickness of a dollar bill on each side of blade is a good rule of thumb. 4. Tighten thumb screws. 5. Loosen thumb screw and turn knurled knob to move the guide block bracket in or out until the front edge of the guide blocks are just behind the “gullets” of the saw teeth. 6. Tighten thumb screw. 7. Loosen thumb screw and turn knurled knob to move the support bearing in or out until the bearing is 1/64” behind the blade. 8. Tighten thumb screw. 9. Blade support bearing should be adjusted so that the back edge of the blade overlaps the front face of the ball bearing approximately 1/8”. To change position of the bearing, remove screw bearing, and back off knurled knob completely to remove the bearing shaft. Notice the bearing holder on the shaft is eccentric. Reinstall the bearing shaft, the bearing, and the screw. Examine the overlap between the bearing face and the blade. Change the position of the bearing shaft until the overlap is approximately 1/8”. Step 3 Step 5 Blade Guides 1/8” Support Bearing Bearing Shaft Blade Step 9 (upper and lower) Adjusting Lower Blade Guides and Blade Support Bearing 1. Disconnect machine from the power source. 2. Blade must already be tensioned and tracking properly. 3. Loosen thumb screws and move guide blocks as close to blade as possible without pinching it. The thickness of a dollar bill on each side of blade is a good rule of thumb. 4. Tighten thumb screw. 5. Loosen thumb screw and move the guide block support in or out until the front edge of the guide blocks are just behind the “gullets” of the saw teeth. 6. Tighten thumb screw. 7. Loosen thumb screw and move the support bearing in or out until it is 1/64” behind the sawblade 8. Tighten thumb screw. 9. The blade support bearing should be adjusted so that the back edge of the blade overlaps the front face of the ball bearing approximately 1/8”. To change position of the bearing, remove screw and bearing. Loosen thumb screw and remove the bearing shaft. Notice the bearing holder on the shaft is eccentric. Re-install the bearing shaft, the bearing, and the screw. Examine the overlap between the bearing face and the blade. Change the position of the bearing shaft until the overlap is approximately 1/8”. Step 7 Step 5 Step 3 WARNING: Table has been removed for clarity purposes. Never operate saw without all components in place and in working order. 20 Safety Instructions for Basic Band Saw Operation Before Each Use Inspect your saw. • To reduce the risk of injury from accidental starting, turn the switch off, unplug the saw, and remove the switch key before changing the setup, removing covers, guards or blade. • Check for alignment of moving parts, binding of moving parts, breakage of parts, saw stability, and any other conditions that may affect the way the saw works. • If any part is missing, bent or broken in any way, or any electrical part does not work properly, turn the saw off and unplug the saw. • Replace damaged or missing parts before using the saw again. • Maintain tools with care. Keep the saw clean for best and safest performance. Follow instructions for lubricating. • Remove adjusting keys and wrenches. Form a habit of checking for and removing keys and adjusting wrenches from table top before turning it on. To Reduce The Risk Of Injury From Jams, Slips Or Thrown Pieces Or Broken Blades Inspect your blade. • Choose the right blade size, style and cutting speed for the material and the type of cutting you plan to do. • Make sure the blade teeth point downward, toward the table. • Make sure the blade guides and thrust bearings are properly adjusted. • Make sure the blade tension is properly adjusted. • Make sure the bevel clamp is tight and no parts have excessive play. • To reduce the risk of accidental blade contact, minimize blade breakage and provide maximum blade support, always adjust the upper blade guide and blade guard to just clear the workpiece. Inspect your work area. • Keep work area clean. • Cluttered areas and benches invite accidents. Floor must not be slippery from wax or sawdust. • To reduce the risk of burns or other fire damage, never use the saw near flammable liquids, vapors or gases. Plan your work. • Use the right tool. Don’t force tool or attachment to do a job it was not designed to do. • Use this band saw to cut only wood, wood like products and plastics. WARNING: To reduce the risk of blade breakage, personal injury, fire or other damage to the saw, NEVER use this band saw to cut metals. • Know your saw. Read and understand the operator’s manual and labels affixed to the tool. Learn its application and limitations as well as the specific potential hazards peculiar to this tool. • To reduce the risk of injury from accidental contact with moving parts, don’t do layout, assembly, or set up work on the saw while any parts are moving. • Reduce the risk of accidental starting. Make sure switch is “OFF” before plugging saw into a power outlet. Inspect your workpiece. Make sure there are no nails or foreign objects in the part of the workpiece to be cut. Use extra caution with large, very small or awkward workpieces: • Use extra supports (tables, saw horses, blocks, etc.) for any workpieces large enough to tip when not held down to the table top. • NEVER use another person as a substitute for a table extension, or as additional support for a workpiece that is longer or wider than the basic saw table, or to help feed, support or pull the workpiece. • When cutting irregularly shaped workpieces, plan your work so it will not slip and pinch the blade. A piece of molding for example, must lie flat or be held by a fixture of jig that will not let it twist, rock or slip while being cut. • Properly support round material such as dowel rods, or tubing. They have a tendency to roll during a cut, causing the blade to “bite”. To reduce the risk of this, always use a “V” block or clamp the work to the miter gage. • Cut only one workpiece at a time. • Clear everything except the workpiece and related support devices off the table before turning the saw on. Plan Ahead To Protect Your Eyes, Hands, Face and Ears Dress for safety • Any power saw can throw foreign objects into the eyes. This can result in permanent eye damage. Always wear safety goggles, not glasses, complying with ANSI Z87.1 (or in Canada CSA Z94.3-99) shown on package. Everyday eyeglasses have only impact resistant lenses. They are not safety glasses. Safety goggles are available at many local retail stores. • For dusty operations, wear a dust mask along with safety goggles. 21 • Do not wear loose clothing, gloves, neckties or jewelry (rings, wrist watches). They can get caught and draw you into moving parts. • Wear nonslip footwear. • Tie back long hair. • Roll long sleeves above the elbow. • Noise levels vary widely. To reduce the risk of possible hearing damage, wear ear plugs or muffs when using saw for hours at a time. Plan the way you will hold the workpiece from start to finish. • Do not hand hold pieces so small that your fingers will go under the blade guard. Use jigs or fixtures to hold the work and keep your hands away from the blade. • Secure work. Use clamps to hold work when practical. It’s often safer than using your hand, and frees both hands to operate the tool. • Don’t overreach. Keep good footing and balance. Whenever Saw Is Running WARNING: Don't allow familiarity gained from frequent use of your band saw to cause a careless mistake. Always remember that a careless fraction of a second is enough to cause a severe injury. • Before starting your cut, watch the saw while it runs. If it makes an unfamiliar noise or vibrates a lot, stop immediately. Turn the saw off. Unplug the saw. Do not restart until finding and correcting the problem. Keep Children Away. • Keep all visitors a safe distance from the table saw. • Make sure bystanders are clear of the table saw and workpiece. Don’t Force Tool. • Let the blade reach full speed before cutting. • It will do the job better and safer at its designed rate. • Feed the workpiece into the saw only fast enough to let the blade cut without bogging down or binding. Before freeing jammed material. • Turn switch “OFF”. • Unplug the saw. • Wait for all moving parts to stop. • Remove switch key. When backing up the workpiece, the blade may bind in the kerf (cut). This is usually caused by sawdust clogging up the kerf or because the blade comes out of the guides. If this happens: • Turn saw “OFF”. • Wait for all moving parts to stop. • Remove switch key. • Unplug the saw. • Remove band saw cover. • Stick flat blade screwdriver or wedge into the kerf. • Turn the upper wheel by hand while backing up the workpiece. Before removing loose pieces from the table, turn saw off and wait for all moving parts to stop. Before Leaving The Saw • • • • Turn the saw off. Wait for all moving parts to stop. Unplug the saw. Make workshop child-proof. - Lock the shop. - Disconnect master switches. - Remove the yellow switch key. Store it away from children and others not qualified to use the tool. 22 Basic Saw Operations General Cutting Operation CAUTION: For your safety, comply with all the safety instructions on pages 1-5 before using the band saw. A band saw is basically a “curve cutting” machine. It is not capable of doing inside cutting. It is also used for straight-line cutting operations such as crosscutting, ripping, mitering, beveling, compound cutting and resawing. This machine is fitted with a 3/8" x 93-1/2 bandsaw blade. NOTE: We recommend using non-metalic blade guide (AC5007) when using 1/8” blade. Recommended Blade Width (Inches) Cross Cutting 1/4, 3/8, 1/2, 3/4 Ripping 3/4 Mitering 1/4, 3/8, 1/2, 3/4 Beveling 1/4, 3/8, 1/2, 3/4 Compound Cutting 1/4, 3/8, 1/2, 3/4 Circle Cutting See Chart Below Resawing 3/4 Curve Cutting 1/8, 1/4 NOTE: Blade length is 93-1/2" Circle Cutting 1. Adjust the upper guides to vertically just clear the workpiece. 2. Use both hands while feeding the work into the blade. Hold the workpiece firmly against the table. Use gentle pressure, and do not force the work, but allow the blade to cut. 3. The smallest diameter that can be cut out is determined by the width of the blade. For example, a 1/4inch wide blade will cut a minimum diameter of approximately 1-1/2-inch (see chart). Blade Selection Guide for Minimum Circle Cutting Circle Dia. 1/2"D 1/8" 1"D 1-1/2"D 2"D 3/16" 1/4" 3/8" 4"D 1/2" Blade Size 23 7"D 3/4" Maintenance WARNING: For your own safety, turn switch “Off” and remove plug from power source outlet before maintaining or lubricating your band saw. Tires Pitch and sawdust that build up on the tires should be removed with a stiff brush or scrape off with a piece of wood. NOTE: To reduce the risk of damaging the tires do not use a sharp knife or any kind of solvent. When the tires become worn they should be replaced. When replacing the tires, stretch them around the wheels but do not glue them on. Adjusting The Upper Blade Guide Travel If the upper guide bar will not move up and down easily or falls when the lock knob is loosened, the following adjustment should be performed. 1. Remove the guide bar lock knob. 2. Using a 5mm hex “L” wrench, tighten or loosen the screw which is located below the lock knob. 3. Move the guide bar up and down to check for smooth movement while still holding its position when released. 4. Make further adjustments to the screw as required to get the guide bar to move smoothly and hold its position when released. 5. Reinstall guide bar lock knob. General Maintenance Keep your band saw clean. Remove the sawdust from the inside. Vacuum or blow out frequently. NOTE: Do not immerse the back-up bearings in the gum and pitch remover. Do not allow filth to build up on the table the guides or the back-up bearings. Clean them with gum and pitch remover. Put a thin coat of paste wax on the table so that the wood slides easily while cutting. Motor Frequently blow or vacuum out any sawdust from the motor. Follow lubrication instruction on the motor label. CAUTION: To reduce the risk of eye injury from blowing debris, wear safety goggles when blowing out sawdust. WARNING: To reduce the risk of electrocution or fire, immediately replace a worn, cut or damaged power cord. Lubrication All of the ball bearings are packed with grease at the factory. They require no further lubrication. RIDGID Recommends the Following Accessories WARNING: Use only accessories recommended for this saw. Using other accessories may be dangerous. Item SKU No. Band Saw Fence ................................................AC5001 Riser Block..........................................................AC5005 Cool Blocks™ .....................................................AC5007 Miter Gauge ........................................................AC1021 Key Switch ..........................................................AC1000 24 Do not use any accessory unless you have received and read complete instructions for its use. Troubleshooting Motor NOTE: Motors used on wood-working tools are particularly susceptible to the accumulation of sawdust and wood chips and should be blown out or “vacuumed” frequently to prevent interference with normal motor ventilation and proper operation of the centrifugally-operated starting switch. Trouble Probable Cause Remedy Excessive noise 1. Motor 1. Have motor checked by qualified service technician. Repair service is available your nearest Authorized Service Center store. Motor fails to develop full power. Note Low Voltage: Power output of motor decreases rapidly with decrease in voltage at motor terminals. For example, a reduction of 10% in voltage causes a reduction of 19% in maximum power output of which the motor is capable, and a reduction of 20% in voltage causes a reduction of 36% in maximum power output 1. Circuit overloaded with light, appliances and other motors. 2. Undersize wires or circuit too long. 3. General overloading of power company facilities. 1. Do not use other appliances or motors on same circuit when using the saw. 2. Increase wire sizes, or reduce length of wiring. See “Motor specifications and Electrical Requirements” section. 3. Request a voltage check from the power company. Motor starts slowly or fails to come up to full speed. 1. Low voltage. 1. Request voltage check from the power company. Check size of circuit wiring. 2. Have motor repair or replaced. 3. Blow out sawdust from motor. Have motor repaired. 2. Windings burned out or open. 3. Starting switch not operating. Motor overheats 1. Motor overloaded. 2. Improper cooling (air circulation restricted through motor due to sawdust accumulation). 1. Feed work slower into blade. 2. Clean out sawdust to provide normal air circulation through motor. See “Maintenance” section. Starting switch in motor will not operate. 1. Burned switch contacts (due to extended hold-in periods caused by low line voltage, etc.) 2. Shorted capacitor. 3. Loose or broken connections. 1. Have switch replaced and request a voltage check from the power company. Motor stalls (resulting in blown fuses or tripped circuit breakers). 1. Starting switch not operating. 2. Voltage too low to permit motor to reach operating speed. 3. Fuses or circuit breakers do not have sufficient capacity. 1. Have switch replaced. 2. Request voltage check from the power company. 3. Install proper size fuses or circuit breakers. Frequent opening of fuses or circuit breakers. 1. Motor overloaded. 2. Fuses or circuit breakers do not have sufficient capacity. 3. Starting switch not operating (motor does not reach speed). 1. Feed work slower into blade. 2. Install proper size fuses or circuit breakers. Check that wiring will handle load. 3. Have switch replaced. Blow out sawdust. 25 2. Have capacitor tested and replace if defective. 3. Have wiring checked and repaired. General WARNING: For your own safety, turn switch “Off” and remove plug from power source outlet before trouble shooting your band saw. Trouble Probable Cause Blade does not run in the approximate center of the upper wheel. Remedy 1. Not tracking properly. 1. Adjust tracking, see Assembly Section, “Adjusting Blade Tracking” section. Band Saw slows down when 1. Belt too loose. 1. Adjust belt tension, see “Assembly” section, “Mountcutting ing the Motor”. 2. Cutting too small a radius. 2. Stop feeding, and back up the material slightly, until the band saw speeds up. 3. Dull blade. 3. Replace blade. 4. Overloading motor. 4. Slow down, trying to cut too fast. Blades breaking 1. Too much tension on blade. 2. Kink in blade caused cutting too small a radius or turning the material too fast when cutting. Blade dulls too quickly. 1. Blade guides set too close 1. Adjust upper and lower blades guides. See “Assemto teeth. bly” section “Installing the blade”. 2. Cutting incorrect material Band saw vibrates. 1. Too much tension on motor belt 1. Adjust tension. See “Getting to Know Your Band Saw”. 2. Use correct cutting technique. See “Basic Saw Operation” section. 1. Adjust according to “Mounting the Motor” section. Wiring Diagram Motor Junction Box Motor Junction Box 3 2 1 3 2 4 White Black 1 Wire Nut 4 Black White Wire Nut Green Green 120V Power Cord 120V Power Cord 120V Wiring 240V Wiring 26 81 81 82 27 83 77 75 82 84 78 80 42 79 105 56 75 40 85 42 60 74 73 102 78 85 60 40 86 76 74 73 66 70 87 71 69 72 68 93 67 92 91 88 89 63 98 60 70 60 94 68 67 65 55 51 103 103 13 62 57 101 99 14 58 54 98 53 59 100 40 66 98 98 97 34 96 95 90 60 43 61 56 42 102 63 30 52 1 Parts List For RIDGID 14-inch Band Saw Model No. 14002 Figure 1 3 50 64 40 47 51 48 39 41 28 43 27 16 6 38 13 25 26 49 18 44 20 19 17 2 4 5 17 3 4 45 46 29 36 13 27 26 25 37 15 5 12 22 28 21 10 11 30 6 15 8 9 7 33 32 31 23 34 13 35 24 14 6 9 10 Repair Parts Repair Parts Parts List For RIDGID 14 Inch Band Saw Model No. BS14002 Figure 1 - Drive Assembly Parts Always Order By Part Number - Not By Key Number Key No. Part No. Description Frame Upper Arm 1 823545 Knob 2 826533 Screw Pan Hd. Lock M6 x 1-12 3 823746 Bearing Ball 4 820722-10 Sleeve Upper Spacing 5 823574 Screw Thumb M6-16 6 823744-3 Post Guide 7 823575-2 Bracket Support Post 8 823601 Screw Soc Set M8 x 1.25-40 9 823954 Nut Micro-Adjust 10 823573 Screw hex Hd. M6 x 1.0-16 11 820249-4 Guard Blade Upper 12 823596 * Washer M6 13 820238-4 Screw Hex Hd. M6 x 1.0-10 14 813307-3 Block Guide 15 823572 Bracket Support Upper 16 823745 Screw Thumb M6-12 17 823744-2 * Screw Soc. Cup M10 x 1.5-10 18 821750-1 Spring 19 823743 Ball Steel 20 823742 Pin Spring 21 813249-76 Insert Table 22 823580 Table 23 823559 Pin table 24 823579 Screw Hex Hd. M10 x 1.5-55 25 823769 Clamp Trunnion Shoe 26 823565 Trunnion 27 823586 Screw Hex Washer hd. M6 x 1-12 28 823768 * Screw Hex Hd. M8 x 1.25-80 29 813310-4 * Nut Hex M8 30 813164-6 Screw Pan Cross M5 x 0.8-9 31 816755-10 * Lockwasher M5 32 813314-8 Guard Blade Lower 33 823588 * Screw Hex Hd. M6 x 1.0-20 34 821388-2 Bracket Lower Support Post 35 826538 Guard Lower Wheel Blade 36 823750-1 Bracket Support Lower 37 823779 Knob Locking 38 826532 Pointer 39 826626 Screw Pan Hd. M5 x 0.8-6 40 813313-5 Bracket Trunnion Support 41 823587 * Lockwasher M8 42 813163-12 * Screw Hex Hd. M8 x 1.25-35 43 813310-9 Screw Flat Hd. Cross M5 x 0.8-15 44 818470-5 Scale Bevel 45 826664 * Nut Hex M5 x 0.8 46 813164-6 Belt V A40 47 817393-5 Pulley 48 828863 Screw Soc Set M6 x 1.0-10 49 817391-1 Ring Retaining 50 816782 Bearing Ball 51 817530 Pin 52 823741 Screw Hex Hd. M16 x 2.0-55 53 821732-1 * Standard hardware item. May be purchased locally. 28 Key No. Part No. 54 55 56 57 58 59 60 61 62 63 64 65 66 67 68 69 70 71 72 73 74 75 76 77 78 79 80 81 82 83 84 85 86 87 88 89 90 91 92 93 94 95 96 97 98 99 100 101 102 103 813512-1 813164-12 823756 823598 818470-3 823555 813313 819188 823584 823753 823554-1 828864 823762 823761 828864-1 823763 823595 823542 823753 823751 823583 817357 823558 826634-1 826536 823771 823552-1 816069 823760 823600 823597 820237-7 823758-9 824283 823570 826535 826534 826627 826630 823755 AC1000 826123 813313 826394 813314-8 823546 823563-1 823543-1 827589 SP6412 Description * Washer M16 * Nut M16 Stud Hinge Lower Screw Flat Hd. M5 x 0.8-10 Brush Wheel Screw Pan Hd. M5 x 0.8-12 Key 5mm x 20mm Shaft Lower Wheel * Washer M8 Base Wheel Lower Bearing Ball Ring Retaining Wheel Upper Nut Hex M12 x 1.25 Tire †Blade 3/8 x 93-1/2 Screw Hex Hd. LH M8 x 1.25-25 Bolt M10 x 1.5-15 (Special) Catch Door Screw Pan Hd. M4 x 16-8 Chute Dust Cover Lower Wheel Knob Catch Screw Pan Hd. Lock M6 x 1-8 Cover Upper Front Screw Pan Hd. Ty “AB” #6 x 5/8 Washer Guard Blade Rear Hinge Upper * Washer M5 Cover Upper Back Shaft/Hinge Upper Wheel Asm Nut Wing Knob Lock Knob Blade Adjusting Spring Coil Indicator Nut Square †Key, Switch Switch Locking * Screw Pan Hd. M5 x 0.8-12 Box Switch * Lockwasher M5 Plate Switch Backing Cord w/Plug Cord Power Stud Latch Operator’s Manual † Stock Item - May be secured through the Hardware Department of most Home Depot Stores. 21 16 8 20 22 25 23 18 24 9 19 27 8 26 28 4 29 10 14 5 15 16 7 16 13 1 18 6 7 2 Parts List For RIDGID 14 Inch Band Saws Model No. BS14002 Figure 2 17 8 9 3 14 7 11 30 29 8 11 12 10 Repair Parts Repair Parts Parts List For RIDGID 14 Inch Band Saw Model No. BS14002 Figure 2 - Base Components Always order by Part Number - Not by Key Number Key No. 1 2 3 4 5 6 7 8 9 10 11 12 13 14 15 Part No. 823592-1 826530 826632 824026-4 813314-5 813313 820237-1 823773-1 823590-1 823776 118615 803835-1 813164-6 813364-8 813303-7 Key No. Description 16 17 18 19 20 21 22 23 24 25 26 27 28 29 30 Cover Pulley Hanger Blade * Screw Pan Hd M4 x 0.7-10 * Nut Hex M4 x 0.7 * Lockwasher 4mm * Screw Pan Hd. M5 x 0.8-12 * Washer M5 Leg Stiffener Long Bolt Carriage M8 x 1.25-16 * Nut Hex 3/8-16 Foot Leveling * Nut Hex M5 * Nut Hex M8 * Lockwasher M8 * Standard hardware item. May be purchased locally. 30 Part No. 821063-2 823593-1 823589-1 828984 823747 828848 813310-9 819188 817391-1 828862 823576 823591-1 817357 813317-6 813317-8 Description * Washer M8 Plate Support Stiffener Short Stand Top Grommet Rubber Motor * Screw Hex Hd. M8 x 1.25-35 Key 5mm x 20mm Screw Set M6 x 1.0-10 Pulley Motor Pad Cover Pulley Inner * Screw Pan Hd. M4 x 16-8 Wrench Hex “L” 3mm Wrench Hex “L” 5mm Notes 31 RIDGID¨ HAND HELD AND STATIONARY POWER TOOL LIMITED THREE YEAR WARRANTY AND 90-DAY SATISFACTION GUARANTEE POLICY This product is manufactured by One World Technologies, Inc., under a trademark license from Ridgid, Inc. All warranty communications should be directed to One World Technologies, Inc., attn: RIDGID handheld and stationary power tool technical service at (toll free) 1-866-539-1710. 90-DAY SATISFACTION GUARANTEE POLICY During the first 90 days after the date of purchase, if you are dissatisfied with the performance of this RIDGID tool for any reason you may return the tool to the dealer from which it was purchased for a full refund or exchange. To receive a replacement tool you must present proof of purchase and return all original equipment packaged with the original product. The replacement tool will be covered by the limited warranty for the balance of the three year warranty period. WHAT IS COVERED UNDER THE LIMITED THREE YEAR WARRANTY This warranty covers all defects in workmanship or materials in this RIDGID tool for the three year period from the date of purchase. This warranty is specific to this tool. Warranties for other RIDGID products may vary. HOW TO OBTAIN SERVICE To obtain service for this RIDGID tool you must return it, freight prepaid, to an authorized RIDGID service center for hand held and stationary power tools. You may obtain the location of the authorized service center nearest you by calling (toll free) 1-866-539-1710 or by logging on to the RIDGID website at www.ridgid.com. When requesting warranty service, you must present the proof of purchase documentation, which includes a date of purchase. The authorized service center will repair any faulty workmanship, and either repair or replace any defective part, at our option at no charge to you. WHAT IS NOT COVERED This warranty applies only to the original purchaser at retail and may not be transferred. This warranty only covers defects arising under normal usage and does not cover any malfunction, failure or defect resulting from misuse, abuse, neglect, alteration, modification or repair by other than an authorized service center for RIDGID branded hand held and stationary power tools. RIDGID, INC. AND ONE WORLD TECHNOLOGIES, INC. MAKE NO WARRANTIES, REPRESENTATIONS OR PROMISES AS TO THE QUALITY OR PERFORMANCE OF ITS POWER TOOLS OTHER THAN THOSE SPECIFICALLY STATED IN THIS WARRANTY. ADDITIONAL LIMITATIONS To the extent permitted by applicable law, all implied warranties, including warranties of MERCHANTABILITY or FITNESS FOR A PARTICULAR PURPOSE, are disclaimed. Any implied warranties, including warranties of merchantability or fitness for a particular purpose, that cannot be disclaimed under state law are limited to three years from the date of purchase. One World Technologies, Inc. is not responsible for direct, indirect, incidental or consequential damages. Some states do not allow limitations on how long an implied warranty lasts and/or do not allow the exclusion or limitation of incidental or consequential damages, so the above limitations may not apply to you. This warranty gives you specific legal rights, and you may also have other rights which vary from state to state. Stock No. BS1400 Model No. BS14002 Serial No. __________________ Model and serial numbers may be found on a plate attached to the back side of the upper cover of your saw. You should record serial number in a safe place for future use. QUESTIONS OR COMMENTS? One World Technologies, Inc. Hwy. 8 Pickens, SC 29671 Part No. SP6412 CALL 1-866-539-1710 www.ridgid.com Please have your Model Number and Serial Number when calling. Form No. SP6412 Printed in China 8/03
advertisement
* Your assessment is very important for improving the workof artificial intelligence, which forms the content of this project