- Home
- Domestic appliances
- Climate control
- Fireplaces
- Crown Boiler
- Nassau Series (all Models)
- Product Manual
advertisement
▼
Scroll to page 2
of
23
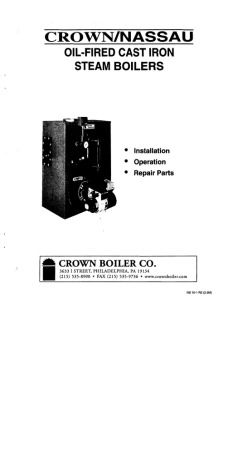
— CROWN/NASSAU OIL-FIRED CAST IRON STEAM BOILERS © Installation © Operation ® Repair Parts CROWN BOILER CO. 3633 1 STREET, PHILADELPHIA, PA 19134 (215) 535-8900 * FAX (215) 535-9736 * www.crownboiler.com NS 10-1 R2 (2.5M) Boiler Ratings and Capacities 1/2" NPT TANKLESS 1/2" NPT HEATER . „ PRESSURE TROL — ( OPTIONAL) 2-1/2" NPT 3/4 ASME PRESSURE GAUGE SUPPLY POP SAFETY - COMBINATION VALVE he 3/4 NPT o . A Low LIMIT 1 1-1/7 NPT 36 7 CONTROL ON | SKIM TAPPING | {| COIL PLATE ; 1-1/2" NPT ; RETURN : | \ | | : a В - 3 dae |! Jui ; L— 25 1/2 he A — RETURN | ( OPTIONAL ) FRONT LEFT SIDE REAR NASSAU OIL-FIRED STEAM BOILER RATINGS ** Net Net i=B=R | "Maximum | Typical DIMENSIONS-INCHES BOILER No. | Input | Heating | I=B=R Rating Firing Chimney MODEL NO.| Sec.| *MBH | Capacity | Ratin Sq. Ft. Rate Size and | *MBH *MB Radiation GPH Height A B C NS-118 3 140 118 89 369 100 |8x8x15 16 7 9 NS-145 3 175 145 109 453 125 |8x89x15 16 7 9 NS-156 3 189 156 117 488 135 |8x8'x15 16 7 9 NS-177 4 | 210 177 133 533 150 |8@x&x15 | 202 | 8 | 11 NS-204 4 245 204 153 638 1.75 |@x&@x15 | 20 8 11 NS-215 4 259 215 161 672 1.85 8" x8" x20 204 8 11 * MBH = 1,000 BTU per hour BTUH = British Thermal Unit Per Hour GPH = Gallons per Hour Oil at 140,000 BTU per Gallon ** Heating Capacity is based on a 13% CO, with a -.02" w.c. draft over fire, and a #1 smoke or less. The testing on the boilers was done in accordance with the D.O.E. (Department of Energy) test procedure. Selection of boiler size should be based upon “Net I=B=R Rating being equal to or greater than the sq. ft. of radiation already installed in the building. | The Net 1=B=R Ratings shown are based o on an allowance of 1.333 in accordance with the factors shown on the I=B=R Standard as published by The Hydronics Institute. | These boilers may not be directly installed on a combustible floor. These boilers are low pressure sectional cast iron boilers constructed and hydrostatically tested for a maximum working pressure of 15 psi in accor- dance with A.S.M.E. (American Society of Mechanical Engineers) Section IV Standards for cast iron heating boilers. They are capacity rated in accordance with the code of the I=B=R (Hydronics Institute). IMPORTANT This boiler is designed for use in closed heating systems requiring little or no make-up water. Excessive feed water will damage boiler sections and void warranty. Rules for Safe Installation and Operation 1. Read the Owners Manual for Safe Operation carefully. Failure to follow the rules for safe operation and the instructions can cause a malfunction of the boiler and result in death, serious bodily injury, and/or property damage. 2. Check your local codes and utility requirements before installation. The installation must be in accordance with their directives, or follow NFPA 31 — Installation of Oil Burning Equipment, latest revision. 3. Before servicing, allow boiler to cool. Always shut off any electricity and oil to boiler when working on it. This will prevent any electrical shocks or burns. 4. Inspect oil line and connections for leaks. | 5. Be certain oil burner nozzle is size required. Overfiring will result in early failure of the boiler sections. This will cause dangerous operation. | 6. Never vent this boiler into an enclosed space. Always vent to the outside. Never vent to another room or inside a building. Be sure there is adequate air supply for complete combustion. Follow a regular service and maintenance schedule for efficient and safe operation. 9. Keep boiler area clean and free of combustible material, gasoline and other flammable vapors and liquids. ON - WHEN SHIPMENT ARRIVES Check shipment and report any shortage immediately. The following pieces should have been received: ALL BOILERS Block (3, 4, or 5 section) Jacket (3, 4, or 5 section) Flue Collector (3, 4, or 5 section) KNOCK DOWN PACKAGE BARE Accessory Carton Bare Accessory Carton (with or less coil) (with or less coil) Burner Box WARNING Bare Boilers are not provided with Low Water Cut-Offs or Pressure Limit Controls. Both of these components are important safety devices which must be provided and instalied by the installer in accordance with this manual. ASSEMBLING KNOCK DOWN BOILER See Appendix A for instructions on the proper assembly of this boiler. | Before You Start Check to be sure you have the right size boiler before starting the installation. See rating and capacity table on preceding page. Check the rating plate on the boiler. You must see that the boiler is supplied with the proper oil, fresh air for combustion, and a suitable electrical supply. Also, the boiler must be connected to a suitable venting system and an adequate piping system. Finally, a thermostat, properly located, is needed for control of the heating system. If you have any doubts as to the various requirements, check with local authorities and obtain professional help where needed. THE OPERATING INSTRUCTIONS and THE FINAL CHECKS AND ADJUSTMENTS are vital to the proper and safe operation of the heating system. Take the time to be sure they are all done. The following steps are all necessary for proper installation and safe operation of your boiler. 1. LOCATING THE BOILER 6. ELECTRICAL WIRING 2. OIL SUPPLY AND PIPING 7. THERMOSTAT LOCATION 3. FRESH AIR FOR COMBUSTION 8. CHECKING & ADJUSTING 4. PIPING CONNECTIONS 9. MAINTENANCE 5. CHIMNEY & VENT PIPE CONNECTIONS Locating the Boiler If your boiler is part of a planned heating system, locate it as nearly as possible where shown on your plan. if boiler is to be part of an existing system, it is usually best to put it where the old one was. If you plan to change location, you will need additional materials as well as an adequate base. The following rules apply: The boiler must be level and located near piping. Use a raised base if floor can become wet or damp. The vent pipe connection should be as short as possible. Maintain clearances for fire safety as well as servicing, See Figure 2 for minimum clearances. 18” clear- ance must be maintained at a side where passage is required for access to another side for cleaning, servicing, inspection, or replacement of any parts that normally may require such attention. Boilers must be installed at least 6” from combustible material on all sides and above. Allow at least 24” front clearance for servicing. Allow at least 20” left side clearance for servicing boilers equipped with a tankless coil. 5. FRESH AIR for combustion must be available at the front of the boiler. FRESH AIR for ventilation must be available to the front AND rear of the boiler. Air passages must be free of obstructions at all times. Ventilating and combustion air must enter boiler room without restrictions. 6. If the boiler is to be installed over a combustible floor, it must be supported on either a 2” Cladlite pad or 2” concrete blocks. This pad must cover the entire area under the boiler. In addition, the boiler and burner must be installed over a pan which will catch oil from any oil leaks. 7. Be sure installation is in accordance with the requirements of the local authorities having jurisdiction. Compliance with these regulations is required. In the absence of local codes follow NFPA 31 — Installation of Oil Burning Equipment. > © № > FIGURE 2 - MINIMUM CLEARANCE DIMENSIONS » © v9 9 ey . ‘a © у © 9.5 wo 9 o зе м. | ! a" 9 * 6" MIN. 20" WITH COIL Ad © t 9, y O. 9, a u” . BOILER <5" MIN. > с =, qe 24" MIN, —} FRONT > y > —— | » ‚” 6” MIN. v - | v Installation Requirements FIGURE 3 eE i { 1 jy pr u na SERVICE LINE ELECTRIC un | LINE pa OVERCURRENT e ENTRANCE PROTECTED - SWITCH SAFETY = FILL PIPE SWITCH DRAFT = 1-1/4" REGULATOR mn { VENT PIPE | = | Nm VENT © с = LINES TO OTHER PIPE ecuador == APPLIANCES MF — м Г TO RADIATION == vy = ju res je jue TANK == Е ré pren SHUT OFF OIL BURNER 1 E je » bno — FILTER ый О =4 GENERAL PRINCIPAL REQUIREMENTS FOR A TYPICAL INSTALLATION Fresh Air for Combustion WARNING Be sure to provide enough fresh air for combustion. Enough air ensures proper combustion and assures that no hazard will develop due to the lack of oxygen. You must provide for enough fresh air to assure proper combustion. The fire in the boiler uses oxygen. It must have a continuous supply. The air in a house contains only enough oxygen to suppy the burner for a short time. Outside air must enter the house to replace that used by the burner. Study following examples 1 and 2 to determine your fresh air requirements. CASE 1: Boiler Located in Unconfined Space If your boiler is in an open area (unpartitioned basement) in a conventional house, the air that leaks through the cracks around doors and windows will usually be adequate to provide air for combustion. The doors should not fit tightly. Do not caulk the cracks around the windows. An unconfined space is defined as a space whose volume is not less than 50 cubic feet per 1,000 Btu per hour of the total input rating of all appliances installed in that space. CASE 2: Boiler Located in Confined Space A. All Air from inside the Building: The confined space shall be provided with two permanent openings communicating directly with an additional room(s) of sufficient volume so that the combined volume of all spaces meets the criteria for an unconfined space. The total input of all combustion equipment installed in the combined space shall be considered in making this determination. Each opening shall have a minimum free area of one square inch per 1,000 Btu per hour of the total input rating of all combustion equipment in the confined space, but not less than 100 square inches. One opening shall be within 12 inches of the top and one within 12 inches of the bottom of the enclosure. See Figure 4. Example: Your boiler is rated at 100,00 Btu per hour. The water heater is rated at 30,000 Btu per hour. The total is 130,000 Btu per hour. You need two grilles, each with 130 square inches of FREE opening. Metal grilles have about 60% FREE area. To find the louvered area needed, multiply the FREE area required by 1.7 (130 x 1.7 = 221.0 sq. in. louvered area). In this example two grilles, each having an 8” x 30” (240 sq. in.) louvered area would be used. Fig. 4 shows the grille locations. . All Air from Outdoors: The confined shall be provided with two permanent openings, one commenc ing within 12 inches of the top and one commencing within 12 inches of the bottom of the enclosure. The openings shall communicate directly, or by ducts, with the outdoors or spaces (craw! or attic) that freely communicate with the outdoors. 1. When directly communicating with the outdoors, each opening shall have a minimum free area of one square inch per 4,000 Btu per hour of total input rating of all equipment in the enclosure. 2. When communicating with the outdoors through vertical ducts, each opening shall have a minimum free area of one square inch per 4,000 Btu per hour of total input rating of all equipment in the enclosure. NOTE If you use a fireplace or a kitchen or bathroom exhaust fan, you should install an outside air intake. These devices will rob the boiler and water heater of combustion air. 3. When communicating with the outdoors through horizontal ducts, each opening shall have a minimum free area of one square inch per 2,000 Btu per hour of total input rating of all equipment in the enclosure. 4. When ducts are used, they shall be of the same cross-sectional area as the free area of the openings to which they connect. The minimum dimension of rectangular air ducts shall be not less than three inches. FIGURE 5 - FRESH AIR DUCT CAPACITIES FIGURE 4 - AIR OPENINGS FOR CLOSET OR Fresh Air Duct Capacities for Ducts Supplying Fresh Air UTILITY ROOM INSTALLATIONS to boiler in tightly constructed houses. British Thermal Units per hour input (Btuh)*. I | Fresh Ar 1/4” Mesh Wood Metal | za Duct Screen Louvers Louvers GRILLE TC 110 ` Size Btuh Btuh Btuh | + ! | 31” х 12” 144,000 36,000 108,000 ; I | 8" x8" 256,000 64,000 192,000 as Но 4 8” x 12” 384,000 96,000 288,000 - MB di 7 8”x 16” 512,000 128,000 384,000 L——7 SomBustION || | 7 AIR GRILLE Ll *Based on opening covered by 1/4” mesh screen, wood louvers, or metal louvers. FIGURE 6 - FRESH AIR DUCT FOR TIGHTLY SEALED HOUSE Qu FRESH AIR DUCT |- BOILER Boilers may be factory supplied with a tankless heater coil. The use of this coil eliminates the need for a hot water storage tank. Instantaneous heating of water in the coil will provide a flow of hot water for domestic use. IMPORTANT Do not use a tankless coil if your water is excessively hard with lime or other deposits which will accumulate inside the coil. TANKLESS COIL PIPING Piping is shown in Figure 7B. FIGURE 7B Boilers With Tankless Heater Coil FIGURE 7A Recommended Tankless Coil Piping Mixad Hot Water to Fixtures 8-12° NS Boiler with Coil (Aquastat not shown) Thermostatic Mixing Valve {Watts 70A or equivalent) A thermostatic mixing valve does not eliminate the risk of scalding. * Set the L4006 as low as practical. * Feel water before bathing or showering. * if anti-scaid or anti-chill protection is required, use Cold Water devices specifically designed for such service. Install these devices in accordance with their manufacturers instructions. WARNING Installation-System Piping The near boiler piping, that is the piping around the boiler, must be considered as part of the boiler for proper water level control, and to produce dry steam. Correct near boiler piping is crucial to the proper operation of the boiler and the heating system. Follow these recommendations carefully. 1. 2. Place boiler in the selected location, as near chimney as possible. Install the pop safety valve, using the furnished 3/4” 90° ell, into the 3/4” pipe nipple on the back of the ‘boiler. Make a discharge pipe, using 3/4” pipe (not fumished) to carry the water or steam to a nearby drain. Do not connect the discharge pipe directly to a drain but leave an air gap. No shutoff of any description shall be placed between the pop safety valve and the boiler, or on discharge pipes between such safety valves and the atmosphere. Installation of the pop safety valve shall conform to the requirements of the ANSI/ASME Boiler and Pressure Vessel Code, Section IV. The manufacturer is not responsible for any water damage. . This boiler is equipped with two 2-1/2” supply connections on top and two 1-1/2" retum connections, one each on front and back sides of the boiler. Unused connections must be plugged. . Recommended near boiler piping for gravity return systems is shown in Figure 8. This configuration uses one supply and one return tapping. This setup can be used on any size boiler in this series. * RECOMMENDED BUT NOT REQUIRED WATER FEED WHEN NOT IN USE FIGURE 8 << as KING — ^® \ "т a PIPE SAME SIZE AS VIVE ÓN 7 6" TL 10 BOILER TAPPING N (2 1/2" MIN) y € POP SAFETY VALVE SD ya ETURN (PIPE DISCHARGE L 1/2 MIN. TO SAFE LOCATION) OR © A pe size KIM TAP > Ll 15" MIN i 28"MIN. - DIM "А" A y | (BALL DR GATE / ` VALVE AV 6" BELOW NORMAL WATER LINE BALL OR GATE VALVE » WET RETURN (IF USED) DRAIN VALVE FOR FLUSHING SYSTEM > (BALL TR GATE VALVE RECOMMENDED) 2 CLOSE NIPPLE NO WARNING: CONNECTION FÜR PLUG BLOW DOWN & DRAIN VALVE 5. For installers choosing to use both supply tappings, Figure 8A shows the correct way to pipe this sys- tem. Figure 8B shows the wrong way to pipe a header with two risers. * Headers must be fitted with header offsets or swing joints, or be equipped with expansion joints, so that thermal expansion and contraction of the header will not damage the boiler. » System takeoffs from the header must be between the equalizer and the riser to the header nearest the equalizer. System takeoffs must never be between two risers. 6. System takeoffs from the header must never be bullheaded. If the steam main goes in two directions, there must be two takeoffs from the header, one for each main. 7. All boilers in gravity return systems must be equipped with a Hartford Loop as shown in Figures 8 and 8A. 8. When piping the vertical risers from the boiler to the header, the bottom of the header must be a mini- mum of 24 inches above the water level line on the right side of the boiler. 9. Steam riser(s) and header shall be 2-1/2” pipe size. 10. Equalizer line shall be minimum 1-1/2" pipe size. 11. The boiler has a 1-1/2” tapping in rear section for skimming. FIGURE 8A - RECOMMENDED NEAR BOILER PIPING USING TWO SUPPLY TAPPINGS WARNING: POP SAFETY VALVE & OTHER SAFETY CONTROLS NOT SHOWN. INSTALL IN ACCORDANCE WITH FIG. 8. Ва STEAM MAINS PERL SIE ue >= (2 1/2") 6° TU 10° CONNECT RISER TD BOILER WITH 2 1/2" ELBOW AND NIPPLE (NOT TT REDUCING ELL POINTING DOWN MAIN VENT (RY MAIN 1172" MIN. RETURN PIPE SIZE 15” MIN. 28° MIN. - DIM, À he — Sen, WET RETURN e ua GATE VALVE (NOT FURNISHED) DRAIN VALVE FURNISHED) | FOR FLUSHT™VG SYSTEM 1 1/2" FULL PORT BALL VALVE FOR BOTTOM BLOW DOWN AND DRAINING BOILER & SYSTEM (NOT FURNISHED) WATER FEED FIGURE 8B - COMMON NEAR BOILER PIPING MISTAKES THIS PIPING CONFIGURATION IS INCORRECT TO SHOW COMMON MISTAKES Sp WRONG - DO NOT BULLHEAD, WING - TAKE OFFS МАТ BETWEEN USE TWO TAKE FAS RISER & HRUALIZER VRONG - SWING JOINTS ARE MISSING A | de ; E — A _ + — - — a - — "nn que Fo e De Tr ET | e (+) | e y WARNING: POP SAFETY VALVE é OTHER SAFETY CONTROLS NOT SHOWN. INSTALL THESE ITEMS ON ACCORDANCE WITH FIG. 8 12. 13. 14. 15. The near boiler piping shall include a 1-1/2” ball or gate valve in the return piping as shown in Figure 8A for bottom blowdown and draining. Plug this valve when it is not in use. For gravity return systems, the bottom of the lowest steam carrying pipe, be it a dry return, or the end of the steam main, must be at least 28” above the normal water level line on the right side of the boiler. This is known as “Dimension A.” For pumped return systems, follow the condensate pump or boiler feed pump manufacturer's instructions for proper installation and hookup. In connecting the cold water supply to the water inlet valve, make sure that a clean water supply is available. When the water supply is from a well or pump, a sand strainer should be installed at the pump. куни PE A TS N sd nes ne Chimney and Chimney Connection CHECK YOUR CHIMNEY Follow local codes. In the absence of local codes, follow ANSI/NFPA 31 Installation of Oil Burning Equipment, latest edition. This is a very important part of your heating system. No boiler, however efficient its design, can perform satisfactorily if the chimney that serves it is inad- equate. Check your chimney to make certain that it is the right size, properly constructed and in sound condition. It is cheaper to rebuild a poor chimney than to pay excessive fuel bills. If yours is an old masonry chimney, a new steel liner or a new prefabricated chimney may be the best solution. The following chart shows recommended minimum chimney sizes based on Table 3 and Figure 6 of the I=B=R Testing and Rating Standard for Heating Boilers, Sixth Edition, June 1989. RECOMMENDED MINIMUM CHIMNEY SIZES FRING | cHiMNEY | NOMINAL | ROUND SQUARE RATE | HEIGHT | CHIMNEY | UNER- LINER- (gph) (ft) AREA INSIDE INSIDE 9P DIAMETER | DIMENSIONS 60-1.301 15 8” x 8” 6” | 634X634" 1.31-1.80| 15 8" x 8” 7 | 634X634 1.81-200| 20 8" x 8” 8” | 634x634 For elevations above 2,000 ft. above sea level, add 3 feet to chimney heights. (Refer to Figure 10.) For additional chimney design and sizing information, consult the ASHRAE 1992 HVAC Systems and Applications Handbook, Chapter 31, Chimney, Gas Vent and Fireplace Systems; or the National Stan- dard for Chimneys, Fireplaces, Vents and Solid Fuel Buming Appliances, ANSI/NFPA 211. CHIMNEY CONNECTOR AND DRAFT REGULATOR Your boiler requires 7” diameter chimney connector pipe on 3 section, 8” diameter chimney connector pipe on 4 section. You can also use the draft regulator packed with boiler. Properly installed, the regulator will control the draft automatically. It is better to install it in a horizontal section of the pipe; but it may be in an angled or vertical section. Just make certain that the “top” is at top — and that the short pipe section which holds the Vane is horizontal. Install it as close as practical to the boiler. 10 FIGURE 10 - CHIMNEY REQUIREMENTS MUST BE REQUIRED MINIMUM HEIGHT. MUST BE AT LEAST 3 FT. HIGHER THAN HIGHEST PART OF PASSAGE THROUGH ROOF. MUST BE AT LEAST 2 FT. HIGHER THAN ANY NEIGHBOR- ING OBJECT. MUST HAVE AN UNOBSTRUCTED TOP OPENING. MUST BE AT LEAST 4 INCHES THICK - _ mX T AND BE LINED. ALTERNATE POSITIONS MUST SLOPE UP AT LEAST 1/4 INCH PER FOOT OF HORIZONTAL RUN DRAWBAND LAST PIECE INSTALLED | x TIGHT, SMOOTH, mm — nga” Ц ( TX SEALED IN THIMBLE TIGHT CLEAN-OUT DOOR DRAFT REGULATOR VANE FH MA CRIMPED END BALANCED WEIGHT KA CORRECTLY SIZED. To install the chimney connector, start at the boiler and preferably take off from the flue collector collar with an elbow — then install the draft regulator next, making it horizontal. When the regulator is in place, start at the chimney and work back to the regulator. Join the two sections with a Drawband. The horizontal pipe must slope up toward the chimney at least 1/4 inch per foot. It must not leak and must be firmly supported. Join sections with at least three sheet-metal screws. Support every second section with a stovepipe wire. MINIMUM VENT PIPE CLEARANCE | Wood and other combustible materials must not be closer than 18” from any surface of the vent pipe. Equipment and Optional Accessories — What They Do POP SAFETY VALVE You must have a properly sized pop safety valve on your boiler. Steam expands as it is heated. If there is no place for the steam to expand into, pressure will build up inside the boiler and system. Should this happen, the pop safety valve will automatically open at a pre-determined pressure. This will relieve the strain on the boiler and system. Run a pipe from the safety valve outlet (pipe must be same size as outlet and the open end must not be threaded) to an open drain, or other suitable drainage point not subject to freezing. Failure to do so may cause water damage or injury should the relief valve open. Do not cap off the drain line from this valve! STEAM PRESSURE GAUGE Every system should have a pressure gauge installed in the boiler. This gauge enables you to monitor the pressure in the system. If the safety devices fail to shut off your boiler at the proper settings, notify your service technician immediately. WATER LEVEL GAUGE The water level in the boiler can be seen through the glass tube in the water level gauge at side of boiler. Correct water level is stamped on front jacket panel. The water level should be checked regularly for the proper level. STEAM PRESSURE CONTROL The steam pressure limit control (pressuretrol) shuts off the burner if the steam pressure in the boiler reaches the cut-off setpoint (i.e. the sum of the cut-in and the differential setpoints). Burner refires when the steam pressure drops to the cut-in setpoint. System pressure requirements are based on the size and condition of the pipes, and the load. For good system operation, the cut-in setting of the pressuretrol should never be less than twice the system pressure drop. In a typical single family residence with a clean one pipe heating system and cast iron radiation, this means that the cut-in will usually be set at the minimum setting, i.e. 1/2 psi. Steam radiation is usually sized based on square feet of equivalent direct radiation (EDR). This is based on a steam pressure in the radiator of just less than 1 psi. Therefore, in our example system from above, we would set the differential adjustment at 1 psi, i.e. the steam pressure required in the radiators. This will give us a cut-off setpoint of 1-1/2 psi. The above is an example of a typical one pipe system. For larger systems or other types of systems such as two pipe systems, or systems with convectors or fan coil units, the pressuretrol settings will need to be deter- mined on a system-by-system basis. The cut-in setpoint is determined by the system pressure drop to the furthest radiator or terminal unit. Double the system pressure drop as a safety factor, resulting in the rule that the cut-in setting should never be less than twice the system pressure drop. | The differential setpoint is the steam pressure required at the terminal heating units. Now your boiler will operate in the correct pressure range. It will maintain enough steam pressure to send the steam out to the furthest radiator, and not go over the optimum steam pressure that is required at the radiators. LOW WATER CUT-OFF The low water cut-off shuts off the burner when the water level is below a safe point. The burner will start when the water is refilled to a safe level. DRAIN VALVE This manual valve provides a means of draining all water from the boiler and system. it should be installed in the 3/4” tee where the water supply line enters the boiler (Fig. 8) You can also use this valve to lower the water level if it is too high. 11 STEAM VENTS Before a steam system will operate properly, suitable steam vents must be installed in each radiator as weli as the retum main. Some systems require steam traps in the return line at the radiation unit. The “Hartford loop” is a piping arrangement which must be included (Fig. 8) for proper operation of the steam system. Starting Your Boiler HOW A STEAM SYSTEM OPERATES The water in the boiler is heated until it reaches the boiling point. As the water boils it turns into steam. The steam rises from the top of the water through the supply main to the radiation units. As it passes through the radiators it releases its heat and condenses into water. The water returns to the boiler through the return main. FILLING SYSTEM WITH WATER On steam heating systems the boiler is partially filled with water. It is very important to the proper operation of the entire system that your boiler be filled to the proper level. The correct water level on cold start condition is about halfway up the glass water level gauge as marked on the boiler jacket. To fill: 1. Close the boiler drain valve. 2. Open the valves at the top and bottom of the glass water level gauge. Also open the drain valve at the bottom of the gauge. 3. Open the fill valve and allow water to run into the boiler. | WARNING — Never run water into a hot empty boiler. | 4. Allow boiler to fill until water runs out the gauge drain valve. Then close the gauge drain valve. 5. Continue to fill boiler until water reaches the indicated water line. This is about halfway up the glass tube. Always keep the water at this level when system is off. | IMPORTANT Skimming a new steam boiler on an existing system may need to be done several times to remove all oil, grease and sediment. The Float Low Water Cut-Off should be blown down after skimming. Following blowdown, allow the boiler to cool and then add fresh water slowly. The float chamber of the low water cut-off must be flushed clean and maintained clear of sediment to allow free movement of the float. This must be done frequently during initial operation of the boiler and at least once per week thereafter. Follow instructions on tag attached to control. Never throttle a steam radiator valve on a one-pipe system. it must be fully open or fully closed. Otherwise water is held in the radiator units. This will cause knocking sounds. Skimming may be required again after a few days operation. Checking and Adjusting WARNING The burner and control system of this boiler must be checked by a professional heating contractor prior to placing the boiler in service. This includes making sure that all safety devices work as they are supposed to. It also includes adjusting the burner using combustion test instruments. 12 aj” CROWN NASSAU BECKETT BURNER APPLICATION SHEET NS-118 NS-145 NS-156 NS-177 NS-204 NS-215 BURNER MODEL AFG AFG AFG AFG AFG AFG AIR TUBE COMBINATION MB MD MD MD MD MD BURNER HEAD SETTING 0 1 1 3 3 NOZZLE wonach | DEAN | DEAN | pes | oe | oe PUMP PRESSURE (PSI) 140 140 140 140 140 140 STARTING BAND SETTING 1 2 2 10 4 5 STARTING SHUTTER SETTING 10 10 10 10 10 10 DRAFT OVER FIRE (IN W.C.) 0.02 -0.02 -0.02 -0.02 -0.02 -0.02 SMOKE (BACHARACH SCALE) 0-TRACE 0-TRACE 0-TRACE 0-TRACE 0-TRACE O-TRACE MAXIMUM CO, 13.0 13.0 13.0 13.0 13.0 13.0 REFRACTORY BLANKET NO NO NO 17-012 17-012 17-012 Note: Best final CO, is dependent upon such field conditions as oil, chemistry, ambient temperatures and available draft. If any of these conditions are unstable, the CO, level should be reduced below 13.0% so as to reduce the likelyhood of the smoke level exceeding #1. Under no circumstances should the CO, level be left above 13.0% or under 11.0%. 13 14 CHECKING CONTROLS Co o To check the Low Water Cut-Off, tum off power to the boiler or tum the thermostat down to the lowest setting. Drain water to below the visible bottom of the water gauge glass. Turn power on and turn the thermostat to call for heat. The oil burner should not run on a call for heat when the water is low. To check the pressure limit, run the boiler until the pressure reaches system demand. Then tum the pressure screw and drop the pressure setting until the boiler shuts down. This will show that the pressure limit is operat- ing properly. OIL BURNER ADJUSTMENT Refer to the NS burner application sheet and oil burner manual provided with this manual for burner set-up information. ADJUST OPERATING CONTROLS Instructions for each control and bummer are included. Set thermostat heat anticipator at .20. Instructions for the final adjustment of the thermostat are packaged with the thermostat. CHECK THERMOSTAT OPERATION When set above temperature indicated on the thermometer, boiler burner should start. Make certain the thermo- stat turns off the boiler when room temperature reaches the selected setting and starts the boiler operating when room temperature falls a few degrees. Finally, set the thermostat for the desired temperature. Special conditions in your home and the location of the thermostat will govern this setting. Maintaining Your Boiler Check the water level every day or two. Verify the water line shown by operating the drain valve on the gauge. Be sure top and bottom valves on gauge are always open so that actual water level will be shown at all times. POP SAFETY VALVE This valve should open automatically when the steam pressure exceeds the safe limit (per instructions pack- aged with valve). Should it ever fail to open under these conditions, shut down your system. Have the valve replaced immediately. LOW WATER CUT-OFF | The Low Water Cut-Off will interrupt the electrical current to the bumer when the water line in the boiler drops to a low level. It is very important to keep the float chamber free from sediment, a condition essential to depend- ability. To keep any accumulation from interfering with float action is to ‘BLOW DOWN" or flush out the control regularly. This must be done two-three times the first week after installation and once a week thereafter during the heating season. Do it while the boiler is in operation. First note water level in gauge glass. Open blow-off valve at bottom of control; water will pour out, flushing away sediment. Drain until water is clear, about a pail, then close valve. If water level in gauge glass has dropped, add water to boiler to restore level. Consult low water cut-off manufacturer's instructions included with boiler. NOTE: Opening blow-off valve checks cut-off operation too. As float drops with falling water level, burner will shut off. After valve is closed and normal operating conditions are restored, bumers will resume firing. Boilers should not be drained between heating seasons. Only when the water in the system becomes dirty should the boiler be drained, flushed or boiled out, and refilled. Steam boilers may be entirely filled with water during the summer months to exclude air. CLEANING YOUR BOILER Under normal operating conditions, with the burner properly adjusted, we recommend that you have the flue passages, burner adjustment, and operation of the controls checked once each yearby a Service Technician. Before the start of each season (or whenever system has been shut down for some time) recheck the whole system for leaks . . . and recheck the boiler and vent pipe for leaks. Replace or patch any boiler seals that are faulty. BOILER FLUE PASSAGES Flue Passages between sections should be examined yearly and cleaned. See instructions on page 15. FOAMING, PRIMING OR SURGING These terms are used to describe a fluctuating water line — when water leaves the boiler. It is caused by any combination of the following: 1. Threading oil and organic matter in the boiler water. (Mineral oil, or core sand does not cause surging.) 2. Faulty quick vents that do not release air until a sizeable pressure is built up — replace. If dirty, clean so that you can easily blow through valve. 3. Improper header design — when steam flows in opposite direction of equalizer line on “Hartford loop.” Generally a 15” horizontal run between riser and main takeoff will allow entrained water to fall out of the steam vapor so it can return to boiler. (See page 7, Fig. 8) 4. Adjustment of steam limit control to a wide differential increases difficulty if quick vents are old style, slow- releasing type or dirty. Always set steam limit control differential as low as possible. 5. Soap and detergents cause extreme surging — clean thoroughly by skimming the boiler. CAUTION Never refill a hot boiler with cold water — thermal shock may crack a section. CAUTION Never allow electrician or oil burner mechanics to try out their work by turning on oil burner for even one second unless boiler is filled to the proper operating level. SYSTEM CHECKS AFTER FIRST STARTING — STEAM SYSTEMS Read the instructions packaged with your controls and make checks and adjustments accordingly. Start the burner and set the Thermostat for the desired room temperature. When adjusting the Steam Pressure control, watch the steam Pressure Gauge and use its pressure reading — as it will be more accurate than the control. BOILER WATER TREATMENT In steam systems where the system is tight, free from leaks, and all the steam is returned to the boiler as condensate, the amount of make up water is small. Water treatment is not required. BETWEEN HEATING SEASONS Boilers should not be drained between heating seasons. Boilers in closed hot water heating systems may be left as is. Steam boilers should be entirely filled with water during the summer months to exclude air. 15 16 A) —+ ON SQ 10. 11. 12. 13. 14. 15. 16. 17. 18. 19. 20. 21. 22. 23. Oil Boiler/Burner Cleaning Instructions Shut off all electrical power to the boiler/burner and shut off fuel supply. Remove the sheet metal smoke pipe from the top of the boiler, inspect pipe and chimney for signs of corrosion and deterioration. Clean base of chimney. Remove top jacket panel. Remove the two brass wing nuts holding the flue collector top. Check the gasket on the underside of the flue collector and replace as necessary. Remove the oil bumer - ОВ - Remove the oil burner/fire door assembly (four hex nuts). This is the recommended method, as it allows full access to the combustion chamber and less potential damage to the target wall during the cleaning process. Remove the burner drawer assembly. Clean any soot accumulations. Replace the burner nozzle with one of the exact size, type, and manufacture recommended. Note: Using a nozzle, other than is recommended, may change the performance of this boiler and/or cause a hazardous condition. Clean electrode assembly and set electrodes as per burner manufacturer's recommendations. Reinstall drawer assembly and check for proper head location as per the manufacturer's recommendations. Inspect the target wall and fire door insulation for cracking and deterioration. If there is any signs of crack- ing or deterioration, replace before reassembling the boiler. Remove soot from fireside surfaces by brushing diagonally through the flue passages (see drawing). Care should be taken not to damage the target wall with the flue brush. Carefully vacuum soot accumulations from the combustion chamber area, being particularly careful not to damage the target wall with the vacuum. Reinstall the burner/fire door assembly. Reinstall the flue collector top and secure with the two brass wing nuts. Reinstall the top jacket panel. Reconnect the flue pipe. Inspect and clean the oil burner blower wheel. Oil the bumer motor (DO NOT OVER OIL). Remove the oil pump cover and clean/replace the pump screen. Carefully reassemble. Replace the fuel filter (if applicable). Reconnect the electrical and fuel supplies. Fire the bumer, checking for proper combustion using combustion test instruments making adjustments as necessary. Insure that all safety controls and operating controls are functioning proppery. IMPORTANT OPERATING AND MAINTENANCE REQUIREMENTS ® KEEP YOUR BOILER AND THE AREA AROUND IT CLEAN ® NEVER BURN REFUSE OR ANY MATERIAL OTHER THAN THE SPECIFIED FUEL IN YOUR BOILER ® HAVE YOUR BOILER CHECKED EACH YEAR BY A QUALIFIED TECHNICIAN You may avoid inconvenience and service calls by checking these points before you call for service. IF YOUR SYSTEM IS NOT HEATING OR NOT GIVING ENOUGH HEAT... Possible Cause What to do Thermostat is not set correctly Reset thermostat above room temperature Oil Tank is empty Fill oil tank No power to boiler Check overcurrent protection. Check to be sure power supply circuit is “ON.” Water Level is too low Add water until water line reaches level indicated on jacket IF RADIATORS GET HOT WHEN THERMOSTAT IS NOT CALLING FOR HEAT (BOILERS WITH TANKLESS COILS ONLY) Possibe Cause What To Do Water level is too low Add water until water line reaches level indicated on jacket. HAVE A QUALIFIED BOILER SERVICE TECHNICIAN CHECK ANY PROBLEM YOU ARE UNABLE TO CORRECT. 18 Steam Wiring Diagram With Tankless Heater Coil 247 THERMOSTAT LEADS — PB DT EN QO) - Ie / 7 - | i | | | | | i | ( 115 VC VIRDG ——— РПОЙ. VIRING ~ = ~~ 24 К М 24VAC VIRING NOT PROVIDED — E a A. a — er ae Eee sa DIL BURNER PRIMARY [INTRIL A ry Er Te ABS = Si WY ERE e De Mis y A e #67 L.¥.C.0. — HOT CALACK) ! FROM 120/80 PINER SUPPLY n o NEUTRAL. CANTE) >— HITE (NEUTRAL) VIRE TD ARNER PRINIRY CONTROL ! Steam Wiring Diagram Less Tankless Heater Coil 24V THERMISTAT LEADS (THERMOSTAT NOT PRIVIOED) PMOL PRESSURE- TROL OPTIONAL AO Tn 120 VAC FEEDER . | | | i : | | : : | ! ! | | : | | ' : ] 1 : в | f ; L U #67 L.W.C.O, 115 UC VIRDE ————— OPTION. VIRING -——— 24 VAC VIRING 2AVAC WIRING HOT PROVIDES MILTE (NEUTRAL > VIRE TO BLRNER PRIMARY CONTROL ' Steam Block Assembly FLUE COLLECTOR 3 Sec. 796-0000) 4 Sec. 738-00-3004 COVER PLATE A) (17-003) TANKLESS HEATERCOIL — (21-003) ъ — мм GRASS WING NUTS << > { 13704007 ) А” 1/4 NUT (2) 6° NIPPLE ( 40100004 } Sv FRONT COVER GASKET = ( 1469306} ) FRONT COVER PLATE ( 14627001 ) COIL GASKET (17-001) © EB = { 14614016 ) FIRE DOOR INSULATION ya { 14614015 ) | O OBSERVATION DOOR Sa ( 40300005 ) BLOCK 7 NIPPLE ( 43300976 ) TARGET WALL FIRE DOOR ME RODS (2) INSULATION ( 40300004 ) Steam Jacket Assembly 4 >С / ОЕ 27 IT Key MODEL NUMBERS > DESCRIPTION NO. | ¿SECTION | 4SECTION 1 738-00-1030 | 738-00-1030 | FRONT PANEL > 2 638-00-1220 | 638-00-1220 | TIE BAR > ° 3 738-00-1020 | 738-00-1020 | REAR PANEL 4 738-00-1053 | 738-00-1054 | R.S. PANEL 5 738-00-1043 | 738-00-1044 | L.S. PANEL 6 738-00-1013 | 738-00-1014 | TOP PANEL 19 20 Appendix A: Knock-down Assembly Instructions Note: Bare boilers must be assembled as shown in the following instructions with the installer providing a burner, controls, and most of the fittings called for below. 1) 2) 4) 5) 6) WARNING Bare Boilers are not provided with Low Water Cut-Offs or Pressure Limit Controls. Both of these components are important safety devices which must be provided and installed by the installer in accordance with this manual. a Do not attempt to use a probe type low water cut-off on this boiler. The burner used on a bare boiler must be exactly as specified in the enclosed NS burner application sheet. Locate the block in the spot where the boiler is to be installed. Set the flue collector on top of the block. Secure with the two #14 x 3/4” sheet metal screws provided. Using the tube of silicone provided, carefully seal the flue collector to the block. Install the two 1-1/2” plugs in the tappings in the back of the boiler. If only one of the 2-1/2" taps is to be used, plug the unused tap with the plug provided. Install the jacket: Note: Jacket installation hardware is in a bag in the jacket carton. a) Mount the two 5/16 x 2-1/2 studs in the lower two tappings in the back of the block. Screw the short thread end of these studs into the block. b) Mount the four 5/16 x 1-3/8 hex studs in the upper two tappings in the back of the block and the two tappings in the front of the block. c) Slip the tie bar (key #2 on page 18) over the studs installed in Step (a). This bar should extend past the right side of the block as viewed from the front of the boiler. d) Slip the front and rear panels over the studs installed in Steps (a) and (b). Use the two 5/16 hex nuts to hold the back panel onto the lower studs. Use 5/16 acorn nuts on the remaining four studs. e) Mount the side panels. These panels have lips which fit into slots in the edges of the front and back panels. | | f) Mount the top panel. Secure it to the front and back panels with the sheet metal screws provided. Install either the tankless coil or coil cover plate. Use the gasket, 3/8 x 3/4 cap screws, and 3/8 washers. Tighten these bolts in a “cross pattern” so that the gasket is uniformly compressed. 7) If the boiler is with coil, install the control well and L4006 control in the 3/4 tapping in the coil. Make sure the control bulb is bottomed out in the well. 8) Screw the 3/4 x 3" nipple provided into the 3/4 tapping on the back of the boiler. Mount the 3/4 elbow onto this nipple and tighten so that it is directed up. Install the pop-safety valve in this elbow. 9) Install the low water cut-off and glass gauge set in the two 1/2” tappings in the front of the boiler (Fig. A1). 10) Mount a 1/2 x 1/4 bushing, 1/4 x 3" nipple, and 1/4 tee in the remaining open tapping on the front of the boiler. Install the pressure gauge in the run of the 1/4 tee. Install the straight pig tail and pressure limit control on the bull of this tee. 11) Mount the three 5/16 x 1-5/8 studs in the tappings near the burner opening. Mount the burner and secure with the 5/16 nuts and washers provided. 12) Wire the boiler in accordance with the appropriate drawing on page 17 using the wiring hamesses provided. 13) Boiler assembly is now complete. Follow the instructions starting on page 4 to complete the installation. FIG. A1: NASSAU TRIM LOCATION 2 1/2 PUB (SE IF ONLY DE SUPPLY TAPPING /— 15 PSI POP SAFETY VALVE IS USED [ L40064 CONTROL — y (ITH (OIL GUILERS DA.Y) Q VAR ya a YX AX — ON © AO VASHER (10 REID.) See J | „®’ PRESSURE LIMIT CONTROL Pe | P= V4 X 3 NIPPLE 1/4* X 1/2" BUSHING ` < 9 1/4" SIRAIGNT PIG-TAJL OQ 14" X 3* NIPPLE o „SI | 172 PLUS 1/4" TEE } > PRESSURE GUAGE Pal T „$ ` ’ PF Le NN. №7 e 40 | 1/2 CLOSE NIPALE LOY VATER CUT-0FF QL AD COLPLING > с (NOT INCLUDED - SEE NITE) VARNING! р DO NIT ATTENPT TO _ - TO LISE A PROBE TYPE | „” UN VATER OT IN | 7 THIS BOILER us Hr — MN -— | A 9/16 X 1 5/8 STD (3 READ. ) 5/16 NUT AND WASHER (3 RED.) NOTE: … 1-1/2" NIPPLE AND COUPLING MAKE PLACING A BUCKET UNDER SKIM PLUG EASTER 21 dll CROWN BOILER CO. 3633 1 STREET, PHILADELPHIA, PA 19134 (215) 535-8900 * FAX (215) 535-9736 * www.crownboiler.com
advertisement
Related manuals
Frequently Answers and Questions
What is the BTU rating for the NS-177 model?
210,00 BTU
What size is the required pressure gauge?
3/4 ASME
What is the typical heating capacity of the NS-215 model?
215 radiation
What is required to install over a combustible floor?
A minimum of 2" Cladlite pad or 2" concrete blocks which cover the entire area under the boiler.
What is the draft regulator?
Regulates the amount of air intake
What is the size of the low water cut off?
1-1/2" NPT size
advertisement