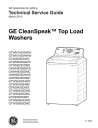
advertisement
▼
Scroll to page 2
of 93
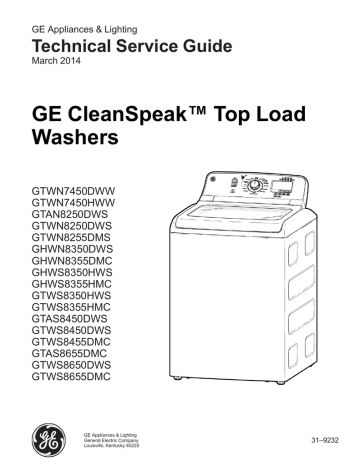
GE Appliances & Lighting Technical Service Guide March 2014 GE CleanSpeak™ Top Load Washers GTWN7450DWW GTWN7450HWW GTAN8250DWS GTWN8250DWS GTWN8255DMS GHWN8350DWS GHWN8355DMC GHWS8350HWS GHWS8355HMC GTWS8350HWS GTWS8355HMC | GTAS8450DWS » GTWS8450DWS ; GTWS8455DMC г GTAS8655DMC GTWS8650DWS ES GTWS8655DMC > GE Appliances & Lighting General Electric Company 31-9232 Louisville, Kentucky 40225 Safety Information | À WARNING Important Safety Notice The information in this service guide is intended for use by individuals possessing adequate backgrounds of electrical, electronic, and mechanical experience. Any attempt to repair a major appliance may result in personal injury and property damage. The manufacturer or seller cannot be responsible for the interpretation of this information, nor can it assume any liability in connection with its use. Warning To avoid personal injury, disconnect power before servicing this product. If electrical power is required for diagnosis or test purposes, disconnect the power immediately after performing the necessary checks. Reconnect all Grounding Devices If grounding wires, screws, straps, clips, nuts, or washers used to complete a path to ground are removed for service, they must be returned to their original position and properly fastened. GE Appliances & Lighting Technical Service Guide Copyright © 2014 All rights reserved. This service guide may not be reproduced in whole or part in any form without written permission from the General Electric Company. Table of Contents Safely REQUITEIMENTS ..... ee eee eee eee eee eee eee eee ease eee ease ener e eee ennes 5 IntroduCtiON ereeeeeee rer RRRRRRRRRRRRRERRRRRRRRRRRRRRRRRERERRRRRRRRRRREREEREEEEARRRRRREERREEEEEREREREREEERRRREEEEEEERERRRERRREEEEEEG 6 Nomenclature ….….…….….…..…........….……cceereeeeeeeeerenerr ere eee eeeee eee eeneeaar ere ee eee eenaaaaer eee eee eee rene nana eee een 8 Product Specifications.....................——.....eeeiieiecec eee erren eee ene eaeeeace cane rerereeee ener neeereeeeeee ene eeaeeeenecaneenneeeeneees 9 Electrical Specifications .......................eeeeeiieee nee eee neeeeeneee een enaeenee ener een eranereceneeeen eran eeeeeene. 9 Tools [1-70 eee eee eee eee eee eee eee eee e eee e ee eeeeeaens 10 Model GraphiCS ER 11 (Oe) ap] ole] aT=T 01 fl Mo Tor=1 (od ghY ATT YS SEE 12 UNAEISIAE TOP COVEN... cece eee eee eee rencor e neeecene reee eeeerececeneeeeaeeenecenenereraneneneeeeneena. 12 I CE 13 Basket Assembly ..........................eeeercccceee rene ee eee eee ee rene recaen ereeeeneecee ea neeeneene ceca neceneeeeeeeeeeeeene. 14 Control Panel RUS 15 BOottOM ….…..................…..…rrrecerererrer eee cree eee eee ee eanaaaa eee eee ee rene ee nana aa aae eee eee eee eee nana sara 16 Operation EE 17 Operating COntrolS.…..……..….....….....….……éirrrerrrerecereranrr serre carre eee annee eee eane eee eee nana e rene en eee cena 17 Redistribution Attempts......................... eee. n ener eee erre eee eee creen rre nenenecenereeeeeaneenecen. 23 07 [10] eee eee eee eee eee eee eee e eee eee e ee ane eee e ee nnneeaae ann, 24 DIAGNOSTICS TT 27 SEIVICE MOE... eee eee eee eee eee eee eee eeeeeenare eee eeeeeeaarrr eee eee 27 Fault COdES...........................…rrrreeecreeerrrrrr rene ee eerarr ee eeererenara eee eeeeenaare eee ee eeeeaaaa eee ne naaarr eee rene 30 Cabinet and StrUCtUre .…............…...........rrrseeeerererererr eee eeeennararr ee er ee eeerrr eee eere near eee eee eeaaaer eee eee 40 BACKS PIAS... eee eee eee eee eee eee eee eee eee eee 40 ULLOQIC BOAId ........oo eee eee eee eee eee eases eee nanas ane 42 Inverter Machine Control (IMC) Board... eee eee eee eee eee eee, 43 Lid Assembly ...........................eeeeeeeeiiiie ener ener ee eereeee een reeeeenerenereceneeeaeeeanececaneeeee ca cereeneeeeee ceca. 45 HINges.....................iieccrneerereeen ener cree rece reee erreeenerane re erereeeeee een creer eeae ren eree ee eeeeeeaeereceeeeeer cane racer eeeeee aereas 47 [Le] 0 JO 1 SR e ee 48 Lid LOCK eeeeeere rer RRRRR ER RRRRRRRRRRRRRRRRRRRRRRRRRRRRRERERRRRERREERRRRREERERERREREREREEEERERRREEEEERERRERREREEERRREREEEEEEG 50 LED TU Lig Aare RAR ERRRRRRRERRRRRRRREREERRRRRRRRREKERRRREEREREEERRERREEEERRRERRREEEEERRERREEEERERREEEEEEEEG 52 SC eee eee eee eee eee eee eee aaa ee eee nenees 54 Leveling Legs ..........................eeeeciicirerrecee e ene reee eee reee eee ear rr eee eece eee arreeeeeeeereneeeaeeeeeee ea rereeeeeaeeeececenes 55 Impeller Assembly .............................eeemeeieiinrii e e erre eee een ee een nee een enaa rene eee eee nee annee nana 55 Suspension System.....................eveereeeeeeieiicee e e ene e eee e ener eeeenee an reeeecee encore carecer ear eeeeeceeceeas 56 Basket..................—......eeececen eee eenene reee enana eaneerene ae nnreeaneeeeeecaceeee ena ——————— ee ae ee eee eae ———————————aaaaaeaeaaann, 59 Outer TUD ccc eee eee eee ease eee eee eee eee e ee eee assess eeea eee eeeaseneeeeaseansnnneeeens 60 DECESO 61 ROO OT cece eee eee eee eee eee eee eee eee ee eee eee eae a nneeenececececeeeeneeanaeneeeees 61 EC) eee eee eee eee eee eee e ee ee eee eee ee ee es aeee aa ee ee nnssneeeeeeanns 63 Mode Shiffer eee eee eee ease eee eee ee ee sane reese eases nsssneeeeeeenn, 64 Motor INSUIGLON .......eeeeeeeee eee eee eee eee eee eee eee eee ee eae eae eee anan, 67 Platform ASSEMDIY nee e enana eeeece eee reeece ee ereeecee ea reeecee ea reeeeeeee creces 67 FI SYS OM... nee nece erre n eee eeerean eee nenene oe reeeran een eeneeae ear eneneenee encarece nar eeereneaneeeeeeneeereeees 70 Water Valve Assembly ......oo eee eee eee eee eee eee eases eeeeereeceeenes 70 Pressure SEnSOF …..….…............………rrrecereeerrrereree eee eeenrarere ee eeeeeanaere eee eeeeenarere eee ee eeeaaaer eee eee ea serre eee 73 Water CA ee aa eae eee eee nsnnnnes 74 Top Cover Dispenser CUups........................eeeeeeeeeeneriiccen e erre eee eeeeenecen en eaeneeenenaneeeeeneeeee ee eeeeeeee.. 75 Bulk Dispenser TANKS... eee eee eee eee eee ee eee eee errr eee a aa aaa eee anan, 77 Bulk Tank Pressure Sensors........................ereeeeeerer eee reee eee eaeeenececeneeeneneeenee een. 80 Heater Assembly...........................e.eerceeeeeen ee e e reee e e ene eee reee eeeeeeaeecene re reeeeeeene ra neeeeneeaee ceca. 83 Tub Thermistor ….……...........rrreeerererreree eee eee re ee rene enearare ere eee eee ee enaaaaaaerer rene eee eeeeeenanaase eee eee ce rene 84 ACCES) 1 e eee ee easa eee eeeeaanee ease enneeens 86 Recirculation PUMP …….............……rreerrererrer eee e creer eee eneenaraar eee eee ee rene eeanaaaaraee eee eee eee near 86 RECIFCUIAtION TUDE... eee eee eee ea eee eee nece. 87 Drain System …...…....…....…....………crrererresenreeerrrreeeenanre nee nana eee eee ee een en rec eee eare eee eeanee eee near n eee eee een rase 88 Огаип Ритпр JR 88 Drain HOSE eee eee ee eee eee ease rene eaaa aaa eee aaa nnssnnnees 89 SchematiCS ee eneeee nene ener eneeeee ener eeeaeeneec ener eeaeeeeeee ener aaa eneeee ene eeeennececeaeereraeeeeeeneeeenes 90 GE Top Load Washer Warranty .............................ee.eeeeeeeeeie e nee e e ene reee eee eree ear eeeene ea ceeneeeeecens 92 Safety Requirements GE Factory Service Employees are required to use safety glasses with side shields, safety gloves & steel toe shoes for all repairs. — Electrically Rated Glove and Steel Toed Work Boot Dyneema® Cut Resistant Dyneema®Cut Resistant Glove Glove Keeper Plano Type Safety Glasses \ Brazing Glasses == Cut Resistant Sleeve(s) Prescription Safety Glasses Safety Glasses must be ANSI Z87.1-2003 Compliant A WARNING Prior to disassembly of the washer to access components, GE Factory Service technicians are REQUIRED to follow the Lockout / Tagout (LOTO) 6 Step Process: Step 1 Step 4 Plan and Prepare Apply LOTO device and lock Step 2 Step 5 Shut down the appliance Control (discharge) stored energy Step 3 Step 6 Isolate the appliance “Try It” verify that the appliance is locked out —5— Introduction MAKE STAINS HOWEVER YOU LIKE. WE'LL MAKE WASHING THEM SIMPLE. Getting messy is fun. We make clean-up easier with new and innovative features such as our Stain Removal Guide, designed to fight common stains with the push of a button. GE's CleanSpeak™ Top Load Washer features and appearance may vary depending upon model. SmartDispense™ TECHNOLOGY Never measure detergent again. The washer can hold about a two-month supply of detergent and fabric softener, and can automatically dispense the right amount for each load. The preferred amount for each load can be adjusted. Check the indicator to see when to refill the detergent and fabric softener. STEAM ASSIST Steam Assist protects fabrics, while penetrating and loosening tough stains like tomato and grass. STAIN REMOVAL GUIDE Remove stains with the push of a button. The Stain Removal Guide is pre-programmed with the Ideal wash settings to tackle four common stains: tomato, oil, dirt and grass. SOFT-CLOSE GLASS LID Our Soft-Close Lid uses hydraulic technology to allow the lid to open to various angles, and then close gently every time. CLEAR GLASS LID See what's going on inside the washer. The clear glass lid lets you take a peek inside without opening the washer mid-cycle. LED WASHER BASKET LIGHT Find every last sock with a bright LED light that effectively lights the wash basket CLEAN SPEAK COMMUNICATION SYSTEM Perfect drying performance is achievable thanks to the ability of the washer to communicate with the dryer to preset the dry cycle. HYDRO HEATER INTERNAL WATER HEATER Boosts water temperatures and helps achieve sanitization. QUIETPACK Enjoy a powerful clean that you won't hear thanks to noise dampening material that holds in sound for a quieter cycle. VIBRATION CONTROL Wash without the shake. Quietly washes any size load without vibration thanks to technology that optimizes spin pattern. ENERGY EFFICIENT ENERGY STAR® qualified and CEE Tier lll meets or exceeds federal guidelines for energy efficiency for year-round energy and money savings. —6— eMonitor Get the energy saving insight you need to reduce your utility bills with an electronic readout that shows the efficiency level of each load. eWash™ Energy saving option uses a cold water wash on select cycles without sacrificing performance. FLEXIBLE CAPACITY Take clean further with large, flexible capacity. GE’s largest capacity top load washer and dryer help you get more laundry done in less time. DEEP TUB ACCESS Easily reach the bottom. Deep tub access offers an ergonomically designed wash basket opening so anyone can easily reach the bottom. PERSONALIZED SETTINGS With My Settings, you can wash and dry your clothes with the settings you prefer on any cycle, and save them as favorites. Nomenclature San я Specific Color = Profile aE Engineering Digit WW =White 5 BB = Black H = Hotpoint vear CC = Bisque M = Moffat MV = Metallic Red Color MG = Metallic Gold Configuration 0 = White MS = Metallic Black T= Top Load 5 = Color WS = Silver Backguard F = Front Load L — TLestar WT = Titanium Backguard TL Derivatives Product 0 = Non eStar C = Contract W = Washer 4 = Cold Water Wash, Non eStar H=Home Depot D=Dryer 5 — eStar L = Lowes U=Unitized Key Feature M = Miscellaneous A = Canadian S = Steam H = Heater N = Stainless Tub P = PermaTuff™ Tub Series 7450 = Min. Features 81xx - 84xx = Med. Features 86xx = High Features Serial Number The nomenclature breaks down and explains what the letters and numbers mean in the model number. The first two characters of the serial number identify the month and year of manufacture. Example: LA123456S = June, 2013 A — JAN 2024 — Z D— FEB 2023 — V F — MAR 2022 —T Mini-Manual С - АРК 2021 — S H— MAY 2020 - К | — JUN 2019—M M — JUL 2018 — L R— AUG 2017—H S— SEP 2016 — G T-OCT 2015—F ras ` V_NOV 2014-D Model Serial Tag Z—-— DEC 2013-A The letter designating the year repeats every 12 years. The Model Serial ID Tag is located on the top cover, under the lid near the right rear hinge cover. The Mini Manual is in a storage bag on the inside left rear of the outer wrapper. Push down on the tub to access. —8— Product Specifications Electrical Specifications AC Voltage DC Voltage * Inverter board: 120 VAC to the J101 Ul Logic Board: 12 VDC /7.5VDC « Recirculation Pump: Should read + Lid Lock Position Locked/Unlocked: 5 VDC approximately 30.5 ohms - 120 VAC Drain Pump: Should read approximately 16.5 ohms - 120 VAC Mode Shifter Motor: Should read approximately 4k ohms - 120 VAC Tub Light: 3.8 VDC Testing the Hall Sensor: 12 VDC CAUTION: Potential of -170 VDC from Earth Ground to “P” Heater: Should read approximately 12 ohms — 10 amps — 120 VAC Water Valves: Should read approximately 1k ohms — 120 VAC NOTICE Terminal “P” at the J1001 connector on the IMC board is referred to as "V” on the mini manual. A CAUTION FOR ELECTROSTATICS, be sure to make an earth ground connection before replacing any electronic components to prevent electrostatic damage to them. This is done by touching a good earth ground on the appliance being repaired. Tools Needed The following specialized tools are referenced within this Service Guide and may be ordered from GE. Specialized Tools WX05X10022 Socket This is not an ordinary impact socket. This is a shallow wall deep well 1-5/16 impact socket, used to remove the washer hub nut. WX05X10025 Click Pliers The click pliers can be used for removing the factory installed clamps on all of the washer tube connections. These can also be used to install the click clamps. WX05X10028 Torque Limiter The torque limiter tool is used with an impact gun to achieve the proper torque. NOTE: Use the torque limiter when removing or installing the hub nut to prevent damage to the shaft and tube assembly. Standard Tools 1/4” Nut driver 5/16” Nut driver * 3/8 Socket * 7/16” Socket ° 1/2" Socket 11/16" Socket * 10mm Wrench or deep well socket — 10 — Electric impact gun Inch Ib Torque wrench Foot Ib Torque wrench T15 Torx bit Putty knife Multimeter (that can measure frequency) Needle nose pliers Model Graphics GTWN7450DWW GHWN8355DMC E я Shar ET Vimar $ VESTE “Lei Pure Damen my Ce à Er Ea Е = = El [er ; à E E Harry Parla 6 с. Que br — = == = т = ет === Ша == _ bar ¿mi sm, КН СЫ e. a Ea == | (mm a и = = mre Й === | Ema ek Ea lies = нон —= Е. E - [el | tema T = | Fira! Maia GTWN8150DWS / GTWN8155DMS GTWN8450DWS / GTWN8455DMS тет — i/o 8 a de A 2 == [lle “lalla 2 Hamel Fe: = Dee Bim eT — y Ц Iz === | A N po | | a [THERE № | — Y Come Сноу" GTWN8250DWS / GTWN8255DMS GTWS8650DWS € 9 ELE GHWN8350DWS GTWS8655DSL Adore 6 | EA Cm os — 11 — Component Locator Views Underside Top Cover Lid Switch / Lock Assembly L Zi J Ce A © % \ Orden High End Model \ me ón Hybrid Pretreat / С J Bleach Cup ЧР Low - Mid End Models Hybrid d Bulk Detergent Fabric Softener b Tank Fill Location Cup Bulk Fabric d Softener Tank D Fill Location Spring Hinge Damper Hinge Tub Light 3 O Fill Funnel 9 AIF \ O O | ® 17 e о Ss = >= Z Bulk Detergent Dispense Bulk Fabric Softener Opening Dispense Opening Water Valve Connections Bulk Tank Connecting Tubes Bulk Tank Connecting Tubes — 12 — Tub Cover Assembly Recirculation Hose — Hose Clamp Rod and Spring Assembly Tub Basket Cr Coupler Basket Assembly with Upper and (Fe N Lower Balance Rings / Heater Cover Filter SAR PAD - xD 500 O Heater — Rodand Spring Assembly Hub Nut Flat Washer Under Hub Nut =— — Rotor Nut Washer Ts Rotor Nut — 13 — Basket Assembly * This comes as a complete assembly. Balancing Ring Side Wall Balancing Ring —14 — Control Panel * The ACM Module is also referred to as RJ-45. | Backsplash Rear Cover Clean Speak oe Se Communication oara Fiatrorm Board ACM Module Backsplash Body Tano Assembly | ; æ Inverter Machine Control (IMC) a a a mr” mn Е. Knob Assembly >< | User Interface (UI) — 15 — Bottom Bulk Detergent Tank Bulk Fabric Softener Tank ы = À LA й Pl "” Fo | | | * | E | ъ || >. | EA ra a 3 FA a у ) > >. Ale , Ya M \ \ 200226 hs + E 3 4 | a Fa 1 + | id X | | + % | |! \ || || \ Li | \ ; \ \ \V/ iN \ \ Ц = | № Fo Leveling Leg Drain / Recirculation Thermistor Inlet Hose Bulk Tank Sensor Drain Pump Bulk Tank Sensor Recirculation Pump Bottom Rear Cross Bar — 16 — Operating Controls *Some features may not be available on all models. Controls © My — Vorgbla Beil Cosdrol Sribnga Tona Lg Lock (+) ©) ® OE "a SmartDispense™ Tor: Levis = SE | onto > [ soil | Temp | spin | [|| See steam Assist * "a Normal ff 5 NE Whites PC Towels/Sheets Æ - Dark Colors xt . sanitize , Bulky items Comoe, Plows « Quick Rinse * Drain & Spin BASKETclean Stain Removal Guide = Матни С ис ой ыы Вась far urn a ar. L ле че — [| 1 mato Dilly gross dirt Press Power to “wake up” the display. If the display is active, press Power to put the washer into idle mode. Power NOTE: Pressing POWER does not disconnect the appliance from the power supply. Start and Unlock Lid Press Start to begin the cycle. The lid must be closed for the washer to fill and the cycle to start. If the lid is open, “LID” will scroll across the display. If the lid is closed, the lid will lock, the LID LOCKED light will light, the detergent will be dispensed, and “FILL” will scroll across the display. Pressing Unlock Lid will Pause the cycle and the Start indicator light will blink. To continue the cycle, press Start again. If machine is paused more than 24 hours, the cycle will be cancelled. If water remains in the machine, select the Drain & Spin cycle to drain tub and spin water out of the washer tub. — 17 — Display and Status Lights Display: The display shows the approximate time remaining until the end of the cycle. NOTE: The cycle time is affected by how long it takes the washer to fill. This depends on the water pressure in the home. The “smart” timer “learns” the amount of time it takes to fill your washer and adjusts the total time accordingly. In addition, this display will scroll the washer status: bALANCINg: Start of rebalancing cycle to redistribute clothes. Stops after rebalancing is complete. CyCLE PrEP: Sensing dry load size prior to fill (normal). dELAY: Appears when Delay Wash is initiated. Replaced with estimated time when cycle starts. End: End of current cycle. ES: Washer in a delay start (4 hour maximum) awaiting lower energy rates (see the Energy Smart section in the Owners Manual Use & Care book). FILL: For the first 45 seconds of a fill, the estimated end of cycle time is displayed. For the rest of the fill time, “FILL” is scrolled until the fill completes. H20 SUPPLY: Cannot sense water level (house water supply possibly turned off). This will be displayed if the flow rate is less than 1 gallon per minute for 9 minutes. HEAt: Water being heated for Sanitize cycle. Lid Cycle: Stopped because lid is open. Close the lid. LOAd SenSE: Sensing wet load size (normal). PAUSE: Cycle paused because the Start/Pause button was pressed and the washer was set to Pause. Press Start button again to restart the cycle. Cycle status lights: Shows whether the washer is in the SOAK, WASH, RINSE or SPIN cycle. Feature status lights indicate (see sections F, G and H for more details): VY The My Settings feature is on for this The lid is locked. See the Control cycle. KE Lock description in G Additional Options. The washer is locked - will blink once if le] The eWash feature is selected. any button is pressed or if the cycle knob is turned. o The signal is on. See the Variable A Delay Wash time is set. 4) Signal description in G Additional WASH Options. Energy smart — The Energy Smart feature is selected. See About Appliance Communication section in the Owners Manual Use & Care book. — 18 — Wash Cycles-Cycle Selector Knob The wash cycle controls the type of washing process. The Cycle Selector knob can be turned in either direction. Turning the knob after starting a cycle will stop the washer and change the cycle/ options to the new selection. Press Start to begin the new cycle selection. NOTE: When the knob is turned to another cycle, the tub light is turned on to assist in loading. The chart below will help match the wash cycle setting with the clothing load. *Cycles available with Steam Assist Speedwash Р For small loads of lightly soiled items that are needed in a hurry. Provides light wash/rinse and short high speed spin. Delicates LU [| [| [| For lingerie and special-care fabrics with light to normal soil. Provides light wash and low speed spin. Hand Wash* an For items labeled hand washable with light soils. Provides an extra light wash and medium speed spin. Jeans” For washing medium to lightly soiled jeans. Provides normal wash and medium speed spin. (For heavily soiled work jeans, use Whites cycle.) Dark Colors” For non-colorfast cottons and blends or items that are labeled cold wash. Provides normal wash and medium speed spin. Whites” For heavy to lightly soiled whites, household linens, work and play clothes. Provides a heavy wash and a high speed spin. Normal/Light Colors* 9 For heavy to lightly soiled colorfast cottons, household linens, work and play clothes. This cycle provides the best overall cleaning and should be used for most everyday items. Provides normal wash and medium speed spin. Towels/Sheets* Provides periods of agitation and soak tailored for washing towels and sheets. Provides normal wash and a high speed spin. Sanitize When selecting sanitize, the washer increases the water temperature to sanitize and remove 99.9% of bacteria found in home laundry. Provides an extra heavy wash and a medium spin. и NSF Protocol P172 NSF) ee AS Bulky Items/ Comforters For large coats, bed spreads, mattress covers, sleeping bags and similar large Pillows and bulky items. Large items such as blankets, comforters, jackets and small rugs. Provides a normal wash and an extra heavy spin. uick Rinse Q Rinses and spins non-soiled items where a rinse only is desired. Provides an extra light wash and an extra high speed spin. Fabric Softener and Extra Rinse options are available with this cycle. Drain & Spin For draining the tub and spinning water out of the clothes. Provides a normal wash and a medium speed spin. — 19 — BASKETclean Use for cleaning the basket of residue and odor. The washer will fill with hot water. Use this cycle once a month with liquid chlorine bleach or Tide® Washing Machine Cleaner. NOTE: Never load laundry while using BASKETclean. The laundry may become damaged or contaminated. Steam Assist Steam Assist adds steam into the washer during Hand Wash, Jeans, Dark Cv Colors, Whites, Normal/Light Colors and Towels/Sheets cycles. This helps to Steam Assist loosen stains for better washability. To use: 1. Turn Power on and select one of the wash cycles. 2. Press the Steam Assist button to activate. 3. Press the Start button. Stain Removal Guide The Stain Removal Guide feature allows the user to indicate what stains are on the garments in the load. This feature can be used with any wash cycle except Sanitize. To use Stain Removal Guide: 1. Select the wash cycle. 2. Press the Stain Removal Guide button (the button will light up when it is on). stoin Removal Guide Continue to press to select tomato stain, oily stain, grass stain or dirt stain. The Ea a 2 indicator light will show the selected stain. To select a different stain, press the Stain Removal Guide button until desired stain to be removed is lit. To turn off Stain Removal Guide, press until the light on the button turns off. NOTE: The Soil and Temperature levels will be changed to match each stain type. Turning off Stain Removal Guide will return the settings to default. Settings Individual settings for agitation (Soil), water temperature (Temp), and spin (Spin) can be set from the minimum (lowest in column) to maximum (highest in column). In general, the higher up the column, the more washer energy will be used. NOTE: Higher Spin speeds typically reduce dryer time/energy usage (i.e.: reduces total energy when using both a washer and a dryer). — 20 — Cycle Options Soak This option begins with a brief agitation, soaks for a specified period of time, then moves through the rest of the cycle automatically. Repeated pressing of the Soak button will add 15, then 30 and then return back to 0 soak minutes. Extra Rinse When using extra detergent or bleach to clean heavily soiled clothes, use the Extra Rinse option to better remove additional residues. NOTE: This option is not allowed for some cycles. Fabric Softener Set this option to provide a deep rinse or when manually adding fabric softener to the rinse cycle. This option is not allowed for some cycles. When allowed, it may change other settings (e.g. Spin may go to a higher setting) to maximize performance. Do not use fabric softener dispensing balls with this washer. They do not work correctly in high efficiency washers. Pretreat/Bleach Set this option to add pretreatment -OR- bleach in the next load. Press once to indicate adding pretreatment (light on above button), twice to specify bleach (light on below button), three times to turn off (no light). Pretreatment or bleach will be added at the optimal time during the wash cycle (differs for pretreatment or bleach). Do NOT use pretreatment and bleach in the same load. If user forgets to dispense (did not press button once or twice), they can flush out the dispenser by pouring water into the compartment and running a Quick Rinse cycle to remove from the tub. Delay Wash When the Delay Wash button is repeatedly pressed, the delay time is set from 1 (01H) to 9 (09H) hours and back to clear (00H) hours. If the Delay Wash is pressed and held for 3 seconds, it will Immediately reset. — 21 — Additional Options My Settings As the cycle selector knob is turned, the Soil, Temp and Spin settings change to automatic pre-set default settings. If user desires a different setting, select the desired options or changes to cycle settings. Press and hold the My Settings button for 3 seconds, the washer will save these settings for that cycle and the status heart and My Settings button will light when active. In the future, when the user turns the selector knob to that cycle, their settings will be automatically recalled. To temporarily (i.e.: for this load) return to the pre-set default settings, press the My Settings button for 1/2 second. The status heart and button lights will turn off and the options will change back to these defaults. To make these default settings permanent, hold the My Settings button again for 3 seconds to make them the preferred settings (the lights will turn back on). NOTE: My Settings includes Stain Removal Guide and Steam Assist but not Delay Wash or Variable Signal - or any bulk dispense options. Variable Signal Use the Variable Signal button to change the volume of the end of cycle signal. Press the button until the desired volume is met (high, medium, low), or to off. Basket Light The basket light will turn on when the Basket Light button is pressed, the lid is lifted, or the cycle knob 15 turned. It will stay on for 5 minutes or until the Basket Light button or Power button is pressed. Control Lock The controls can be locked to prevent any selections from being made. Or the controls can be locked after a cycle has been started. Washer cannot be accidentally started by touching buttons with this option selected. To lock the washer controls, press and hold the Control Lock button for 3 seconds. The control lock icon will light up when it is on. To unlock the washer controls, press and hold the Control Lock button for 3 seconds. NOTE: The Power button can still be used when the machine is locked. eWash When the eWash button is pressed, the cycle changes to its most energy efficient settings and all of the eMonitor lights will light to indicate that the most efficient settings are on. If the settings are changed, the eWash light will go off and the number of eMonitor lights will decrease (or increase) to indicate decreased (or increased) energy efficiency settings. SmartDispense "" The SmartDispense™ feature allows the user to set their liquid h.e. (High Efficiency) detergent and/ or softener dispensing preferences for their load. This feature can be used with any wash cycle, except for Quick Rinse, Drain & Spin and BASKETclean cycles. The SmartDispense™ system automatically dispenses liquid h.e. (High Efficiency) detergent and/or concentrated liquid fabric softener into each cycle at the optimal times. To utilize the SmartDispense™ dispensers, they must first be filled. Although any liquid h.e. (High Efficiency) laundry detergent and concentrated liquid fabric softener can be used in the SmartDispense™ system, all liquid h.e. (High Efficiency) detergents and concentrated liquid fabric softeners are not the same. CAUTION! Absolutely do not store liquid chlorine bleach, powder detergent, non- concentrated liquid fabric softener or other laundry additives in any of the tanks. Use only liquid detergent which has been specifically designed for use in High Efficiency washers. — 22 — Redistribution Attempts The washer will only attempt to redistribute an out of balance load one time per cycle in the final spin up. The redistribution attempt consists of the follow sequence. The washer will try to reach the target spin speed five consecutive times. It will spin, then stop to let the clothes fall back to the bottom of the basket. Then it will attempt a second spin. This may occur up to five times, although it may not need to use all of the spin attempts if it reaches its target spin speed. If the washer cannot get to the target spin speed, it will stop, then fill the basket with water appropriate for the selected cycle load size. Once the filling is complete, the washer will switch to agitate to jog the clothes and redistribute the clothes in the basket. After this redistribution attempt is completed, the basket will drain the water. This step is considered the redistribution, not the spin attempts. The washer will then switch to spin again and make another attempt to reach the target spin speed. The target spin speed may be reached on the first attempt. However, if the target spin speed is not reached, it will go through another set of 5 sequential tries to reach the target spin speed. If it does not reach the target spin speed it will spin at the highest spin speed it was able to obtain. In this example, a customer may possibly report that their clothes came out wet. This process can add up to 30 minutes to the cycle. — 23 — Cycle Chart The information provided below is based on an example load filling the tub to just under the top balance ring. The Control Display will adjust the times according to load size and weight after the load CyCLE PrEP. Example Cycle Chart — Dark Colors Selected Description (Start to Finish) Control Display Comments 101 (minutes Settings: ( ) Bulk Detergent and Bulk Softener on. Normal Soil, Cold Wash, Extra High Spin Tub light goes out after 5 minutes. 5 Second Safety Water Spray Every time a load is started or restarted, after a short pause, the lid will lock and then a 5 second water safety spray will occur, then a load sense to recalculate the load. Lid Lock Load Sense Dry, Spin 120 RPM CyCLE PrEP (Scrolling) Water Fill, Spin 15 RPM 58 Control display reflects recalculated cycle time after load sense. Wet Clothes Load Sense LOAd SenSE (Scrolling) Water Fill FILL (Scrolling) Water valves cycle to obtain correct temperature. Adds Detergent from Bulk Dispense FILL (Scrolling) Stops Spin and Adds Water in Detergent Cup FILL (Scrolling) Starts 15 RPM Spin Again — Continues Filling FILL (Scrolling) Stops Fill and Spin SenSE (Scrolling) Mode Shift to Agitation SenSE (Scrolling) While sensing, movement of the basket or agitator is normal to ensure proper clutch engagement. Recirculation Pump and Agitation Starts 54 Agitation pushes the load up from the center to the outer — 24 — Example Cycle Chart — Dark Colors Selected Description (Start to Finish) Control Display Comments edge of the basket. Then pulls the clothes back to the center from the outer edge. Recirculation Soak, Agitation Stops 51 Programmed soak. Recirculation Pump Off, Soak 49 Recirculation Pump On, Agitation Starts 46 Recirculation Pump Off, Continues Agitation 44 Recirculation Pump On, Continues Agitation 40 Recirculation Pump Off, Agitation Stops SenSE (Scrolling) Mode Shift To Spin SenSE (Scrolling) While sensing, movement of the basket or agitation is normal to ensure proper clutch engagement. Drain Pump On 34 Will recalculate time for pump out. 450 RPM Spin 33 It is normal for the cabinet to be bumped during the initial spin while determining out of balance loads. Spin Stops 29 Add Fabric Softener, Continues Filling, 15 RPM Spin FILL (Scrolling) Stops Fill and Spin SenSE (Scrolling) Mode Shift To Agitation SenSE (Scrolling) While sensing, movement of the basket or agitator is normal to ensure proper clutch engagement. Recirculation Pump On, Agitation Starts 23 Recirculation Off, Continues Agitation 21 Agitation arc is smaller to even the clothes load. Agitation Stops SenSE (Scrolling) Mode Shift To Spin SenSE (Scrolling) While sensing, movement of the basket or agitator is normal to ensure — 25 — Example Cycle Chart — Dark Colors Selected Description (Start to Finish) Control Display Comments proper clutch engagement. Drain Pump On 19 Drain Pump On, Spin Starts 18 Ramps up to final spin speed (1,000 RPM with extra high spin selected). Spin Stops 1 Coast to stop. End (Scrolling) Communicates wash load information to the dryer (if Clean Speak communication Is connected). Cycle temperatures cannot be used to diagnose or determine proper operation of this machine. The only temperatures that can be checked are the incoming house water supply to the washer using service mode. For optimal hot water temperature from the machine, the house hot water supply should be at least 115*F degrees. Actual Sanitize Cycle time (verses what is displayed) will vary based on temperature of the hot water supply from the house. This cycle at the time of publish is certified by the Nation Sanitization Federation under their test conditions. To view the standards set by the Nation Sanitization Federation, look on the web under NSF. org. — 26 — Service Mode Test No. | Test Function 00 LED and Lid Check 01 Model ID Numb Field Service Mode ode mee 02 Ul Software Version To enter into Field Service Mode, press and hold the Start pad while rotating the Cycle Selection 03 Hot Water Valve Check knob 180 degrees (8 clicks) and then release the 04 XML Version Start pad. The Cycle Selection knob is now used р у 05 Cold Water Valve Check to control the test selection menu. The seven segment display will show the test number 06 MC Software Version according to the knob position (Example: 01 is Test 1). Upon entering the Service Mode, the control will 07 Detergent Flow-Through Test be in the test selection mode, and will display “00” 08 on the Control Panel. Inverter Software Version 09 Fabric Softener Flow-Through Test Rotating the knob clockwise will increase the test number. Rotating the knob counterclockwise will 10 Bleach Flow-Through Test decrease the test number. Rotate the knob to select the desired test and press Start to begin test. 1 Bulk Detergent Test To stop the test and/or choose the next test, turn the 12 Bulk Fabric Softener Test knob. 13 Agitate To exit Field Service Mode, press the Power pad 14 Spin or unplug the unit. The control will also exit Field Service Mode after 30 minutes. 15 Drain Pump Check Acronyms: 16 Recirculation Pump Check < Ul - User Interface 17 Heater Check ° MC — Machine Control 18 Continuity Check * SSD - Seven Segment Display 19 Lid Lock Check ° HEX- Hexadecimal (Le.: 255 = FF) | 20 Washer Communication Test NA se formula the control displays 21 UI Critical SW Version Check 22 MC Critical SW Version Check 23 Inverter Critical SW Version Check 24 Error Codes 25 Clear Error Codes 26 Clear EEPPROM — 27 — Test 00 — Lid and LED Check When the Start pad is pressed, all LEDs and . displays will be lit (should display “8:88”). When the lid is raised, all LED and displays will begin blinking indicating that the lid switch is ° reading open. Test 03 — Hot Water Valve Check Test 07 — Detergent Flow-Through Test When the Start pad is pressed, the hot water Test 11 — Bulk Detergent Test (This feature is optional and will give an invalid beep if the test is selected and the feature is not available.) When the Start pad is pressed, the bulk detergent valve will turn on for 2 seconds, off for 2 seconds, and repeat. The SSD will display “CS”. valve will open and the SSD will display an “H”. Test 12 — Bulk Fabric Softener Test Test 05 — Cold Water Valve Check ° When the Start pad is pressed, the cold water valve will open and the SSD will display a “C1”. At any time during Service Mode, if the water level reaches the lower pressure sensor levels, the Extra Light LED will come on. When the (This feature is optional and will give an invalid beep if the test is selected and the feature is not available.) When the Start pad is pressed, the bulk fabric softener valve will open and the SSD will display “CG”. water reaches the upper level, the Extra Light Test 13 — Agitate and Light LED lights come on. After all water tests fill to the upper level, it will continue filling to the overflow level set in the control logic. When the overflow level is reached, the water will shut off and the drain pump will turn on. The pump will turn off when the water ° drains to the upper level. To drain the rest of the water out, switch to the drain pump test. (This feature is optional and will give an invalid ° beep if the test is selected and the feature is not available.) When the Start pad is pressed, the detergent valve will turn on for 2 seconds, off for 2 seconds, and repeat. The SSD will display “C2”. Test 09 — Fabric Softener Flow-Through Test (This feature is optional and will give an invalid beep if the test is selected and the feature is not available.) When the Start pad is pressed, the fabric softener valve will turn on for 2 seconds, turn off for 2 seconds, and repeat. ° The SSD will display “C3”. Test 10 — Bleach Flow-Through Test (This feature is optional and will give an invalid beep if the test is selected and the feature is not available.) When the Start pad is pressed, the bleach valve will turn on for 2 seconds, off for 2 seconds, and repeat. The SSD will display “C4”. — 28 — When the Start pad is pressed, the SSD will display “A”. The test will not begin until the lid is closed. When the lid is closed, the lid will lock. After the lid is locked, if a shift is necessary, the unit will shift to agitate. When the shift is complete, the unit will start agitating. Test 14 — Spin When the Start pad is pressed the SSD will display “S”. The test will not begin until the lid is closed. When the lid is closed the lid will lock. If a shift is necessary, the unit will shift to spin. When the shift is complete, (on older software versions), the unit will start spinning at (15 RPM) with the lid unlocked. On units with newer software versions, it will ramp up to top spin speeds with the lid locked. If the lid is opened during spin, the spin will stop and will resume when the lid is closed. Test 15 — Drain Pump Check When the Start pad is pressed the SSD will display “P1”. The drain pump will turn on until the test is ended. Test 16 — Recirculation Pump Check * (This feature is optional and will give an invalid beep if the test is selected and the feature is not available.) When the Start pad is pressed the SSD will display “P2”. * The recirculation pump will turn on until the test IS ended. Test 17 — Heater Check * (This feature is optional and will give an invalid beep if the test is selected and the feature is not available.) When the Start pad is pressed the SSD will display the temperature of the tub in °F. ° A 15 RPM spin will be started during the heater test to prevent “hot spots” on the basket caused by the heater. ° At any time during the test if the water level is below the lower pressure level, the hot water valve will turn on until the water reaches the lower pressure level. + Ifthe water level is above the lower pressure level and the reported speed of the motor is greater than 10 RPM, the heater will turn on and stay on until the test is ended. ° |fthe water level falls below the lower pressure level or the reported speed of the motor is below 10 RPM, the heater will turn off. Test 18 — Continuity Check For Heater Operation * (This feature is optional and will give an invalid beep if the test is selected and the feature is not available. Models without a heater do not have the continuity check.) When the Start pad is pressed the SSD will display the following: — If continuity is good (sensor value is </= 2.4V): -—. — If continuity is NOT good (sensor value is > 2.4V): “00”. Test 19 — Lid Lock When the Start pad is pressed the lid will lock and the SSD will display “LC”. * Pressing the Start pad again will unlock the lid and the SSD will display “UL”. The lid will also unlock when the test is exited. Test 20 — Dryer Communication Test When the Start pad is pressed the SSD will display “- -” for one second. If the units are connected properly, able to communicate, and a version number is found, the display will show the major and then minor software version number of the Dryer UI. ° |fthe version number is not found (for whatever reason) the washer control will give an invalid beep and return to the Test Selection Menu. — The control will repeat the major — minor display sequence until the user exits the test. Test 24 —Error Codes When the Start pad is pressed, the SSD will display the first fault code in a HEX format. « Each press of the Start pad will advance to the next fault in the list. * Faults will only be displayed if they have occurred at least once. Test 25 — Clear Error Codes When the Start pad is pressed the SSD will display “Er”. * Pressing and holding the Start pad for 3 seconds Will clear all fault codes and sound a valid tone and update the display to “- -". On press and hold of the Start pad for 3 seconds the fault log will be cleared. Test 26 — Clear EEPROM When the Start pad is pressed the SSD will display “EE”. Next, pressing and holding the Start pad for 3 seconds will clear all EEPROM (including any fault codes), restore to default settings, and sound a valid tone and update the display to “- -". Tests 01, 02, 04, 06, 08, 21, 22 & 23 — Various Version Checks * When the Start pad is pressed, the SSD will display the major and then minor digit of the version number. * The Extra Heavy” Soil Level LED will be lit when the SSD is displaying the Major version digit. * The “Heavy” Soil Level LED will be lit when the SSD is displaying the Minor version digit. — 29 — Fault Codes Fault Code | Name Description Repair Action (Hex) 1 Ul EEPROM Board software not 1. Clear the error code using operating correctly Service Mode test T25. 2. Verify model ID # using Service Mode test TO1. If correct, go to next step. If incorrect, set the correct Model ID #. Power cycle and verify Model ID #. 3. Power cycle and check that error does not return. 4. If error comes back, replace Ul (User Interface PCB). 5 Bulk Dispense Not dispensing 1 Detergent and properly Fabric Softener . Enter Service Mode. Actuate bulk dispense valves to check water flow and dispense operation. 2. If no detergent or softener flow, check for blocked or kinked bulk dispense hose. 3. If no flow, check for frequency (Hz) change at IMC. If frequency changes, replace IMC. 4. If no frequency change, replace appropriate bulk tank pressure Sensor. 5. If no water flow, check resistance of the water valve coil (1k ohms) at IMC connector. 6. If no resistance (open), check wiring harness and appropriate water valve coil. 7. Ifresistance checks OK, check for 120 VAC at IMC connector. 8. If no voltage, replace IMC (Inverter Machine Control). If voltage, replace water valve. 9. If still no water flow, replace Ul board (User Interface PCB). 6 Bulk Dispense Not dispensing 1. Follow same actions as in Fault Detergent and properly Code 5 Fabric Softener — 30 — Fault Code (Hex) Name Description Repair Action 7 Stuck Button Buttons not operating when pressed 1. Check buttons and adjust. 2. Loosen screws on backsplash and or Ul board (User Interface PCB). 3. Replace backsplash. 4. Replace Ul (User Interface PCB). Pressure Sensor Not filling as designed 1. Check frequency (Hz) using multimeter. Validate the frequency matches table in mini manual. 2. Iffrequency is not correct, check wiring harness and pressure sensor. 3. Iffrequency is correct, but error persists, replace IMC (Inverter Machine Control). Lid Lock Will not lock or unlock or is locked while lid is opened 1. Check lid switch continuity at IMC. 2. Check continuity of lid lock position. Opened or Closed? 3. Check operation of lid lock. Plunger should slide freely in and out. 4. Check lid lock wiring harness from IMC to lock assembly. 5. Iflid lock OK, replace IMC (Inverter Machine Control). If error persists, replace User Interface PCB. No Fill Unit not filling with water properly 1. Confirm house water supply is on and has proper water pressure. 2. Check for kinked hoses. 3. Check hose screens. Make sure they are not clogged. 4. Check the lid switch continuity. The washer will not fill with the lid switch open. 5. Check pressure sensor and pressure sensor hose. — 31 — Fault Code (Hex) Name Description Repair Action . Check resistance of the water valve coll (1k ohms). . Check for 120 VAC to the water valve. . If proper voltage and resistance, replace water valve assembly. Drain Pump Water remaining in basket . Check installation instructions for proper standpipe height. . Check pressure sensor frequency (Hz) and pressure sensor hose. . Check resistance of the pump (16.5 ohms) from the Ul (User Interface PCB). . If open circuit, check wiring harness to the pump and pump motor. . Check for 120 VAC to the drain pump. . If voltage is present and pump does not operate, replace pump. . If voltage is not present, replace IMC (Inverter Machine Control). IMC (Inverter Machine Control) Communication Time-out No operation . Reset control boards by unplugging the washer for 30 seconds. . Check wiring harness connections between the IMC and Ul boards. . If still no operation, replace IMC (Inverter Machine Control). Lid Lock Will not lock or unlock or is locked while lid is opened . Check lid switch continuity at IMC. . Check continuity of lid lock position. Opened or Closed? . Check operation of lid lock. Plunger should slide freely in and out. . Check lid lock wiring harness from IMC (Inverter Machine Control) to lock assembly. — 32 — Fault Code (Hex) Name Description Repair Action 5. If lid lock OK, replace IMC (Inverter Machine Control). If error persists, replace User Interface PCB Heater Water Level Check for water in tub by continuity between heater and thermistor . With water in tub, check continuity between the heater sheath and the thermistor case from IMC. If no continuity, check harness and connections at IMC, thermistor and heater. If continuity is present, replace IMC (Inverter Machine Control). 10 Slow Fill Not enough water . Check house water supply and proper water pressure. Check for kinked hoses. Check hose and water valve screens. Make sure they are not clogged. . Check the lid switch continuity. The washer will not fill with the lid switch open. Check resistance of the water valve coll (1k ohms). . Check for 120 VAC to the water valve If proper voltage and resistance, replace water valve assembly. Check pressure sensor and pressure sensor hose. 11 Heater Not reaching target temperature . Check resistance of heater (approximately 12 ohms). . Check resistance of thermistor (approximately 12k ohms at 77F) Replace heater and/or thermistor If necessary. Energize the heater in Service Mode and check for 120 VAC/ 10amps. —33— Fault Code (Hex) Name Description Repair Action . If no voltage, and wiring harness Is OK, replace IMC (Inverter Machine Control). 12 IMC (Inverter Machine Control) Communication Time-out No operation . Reset control boards by unplugging the washer for 60 seconds. . Check wiring harness connections between the IMC and Ul boards. . If still no operation, replace IMC (Inverter Machine Control). 16 Mode Shifter Mode shifter not engaged to spin . Using an ohm meter, check to ensure mode shifter switch is in the open position. . Check resistance of mode shifter motor (approximately 3.8k ohms). . Check for 120 VAC to the mode shifter motor at the IMC. . If voltage is not present while activating the mode shifter in the service mode, replace the IMC (Inverter Machine Control). . Check mode shifter coupler for damage and ability to slide in and out freely. . Replace mode shifter assembly ¡f necessary. 17 Mode Shifter Mode shifter not engaged to agitate . Using an onm meter, check to ensure mode shifter switch is in the closed position. . Check resistance of mode shifter motor (approximately 3.8k ohms). . Check for 120 VAC to the mode shifter motor at the IMC. . If voltage is not present while activating the mode shifter in the service mode, replace the IMC (Inverter Machine Control). — 34 — Fault Code | Name Description Repair Action (Hex) 5. Check mode shifter coupler for damage and ability to slide in and out freely. 6. Replace mode shifter assembly if necessary. 18 Mode Shifter Mode shifter taking 1. Using an ohm meter, check to too long to engage ensure mode shifter switch is in the open or closed position. 2. Check resistance of mode shifter motor (approximately 3.8k ohms). 3. Check for 120 VAC to the mode shifter motor at the IMC. 4. If voltage is not present while activating the mode shifter in the service mode, replace the IMC (Inverter Machine Control). 5. Check mode shifter coupler for damage and ability to slide in and out freely. 6. Replace mode shifter assembly if necessary. 19 Flood Protection Flood level detected | 4 Check water valve is not filling washer tub in the off position. 2. If water valve is leaking, replace water valve assembly. 3. Check pressure sensor frequency (Hz). Validate the frequency matches table in mini manual. 4. If frequency is not correct, check wiring harness, pressure sensor and pressure sensor hose. 5. If frequency is correct, but error persists, replace IMC (Inverter Machine Control). 65 Lid Lock Will not lock or 1. Check lid switch continuity at unlock or is locked IMC while lid is opened 2. Check continuity of lid lock position. Opened or Closed? — 35 — Fault Code (Hex) Name Description Repair Action 3. Check operation of lid lock. Plunger should slide freely in and out. . Check lid lock wiring harness from IMC (Inverter Machine Control) to lock assembly. . If lid lock OK, replace IMC (Inverter Machine Control). If error persists, replace User Interface PCB. 66 Lid Lock Will not lock or unlock or is locked while lid is opened . Check lid switch continuity at IMC. . Check continuity of lid lock position. Opened or Closed? . Check operation of lid lock. Plunger should slide freely in and out. . Check lid lock wiring harness from IMC (Inverter Machine Control) to lock assembly. . If lid lock OK, replace IMC (Inverter Machine Control). If error persists, replace User Interface PCB. 68 Pressure Sensor Error Pressure sensor out of range . Check frequency (Hz) using multimeter. Validate the frequency matches table in mini manual. . If frequency is not correct, check wiring harness and pressure sensor. . If frequency is correct, but error persists, replace IMC (Inverter Machine Control). 6A, 6B Thermistor Error Thermistor open or short . Check thermistor resistance. Validate the resistance matches the table in mini manual. . Check wiring harness and connections. . Replace thermistor. — 36 — Fault Code (Hex) Name Description Repair Action 72 Inverter Spin Redundancy IMC detected spin speeds with either lid unlocked or open 1. Attempt to operate a Drain and Spin cycle. . If error clears itself and unit operates normally, then there is no issue. If error persists replace IMC (Inverter Machine Control). 75 Lid Lock Will not lock or unlock or is locked while lid is opened . Check lid switch continuity at IMC. . Check continuity of lid lock position. Opened or Closed? Check operation of lid lock. Plunger should slide freely in and out. Check lid lock wiring harness from IMC (Inverter Machine Control) to lock assembly. If lid lock OK, replace IMC (Inverter Machine Control). If error persists, replace User Interface PCB. 76 Detergent Bulk Dispenser Sensor Sensor not reading correctly . Check frequency (Hz) using multimeter. Validate frequency matches table in the mini manual. If frequency is correct, replace IMC (Inverter Machine Control). If frequency is incorrect, check harness and connectors. If good, replace the bulk tank sensor. 77 Softener Bulk Dispenser Sensor Sensor not reading correctly . Check frequency (Hz) using multimeter. Validate frequency matches table in the mini manual. If frequency is correct, replace IMC (Inverter Machine Control). If frequency is incorrect, check harness and connectors. If good, replace the bulk tank sensor. — 37 — Fault Code (Hex) Name Description Repair Action C9, CA, CC, CD, CE, CF, D5, DD, DE, DF IMC (Inverter Machine Control) Fault IMC (Inverter Machine Control) Fault . Reset IMC by unplugging washer from 60 seconds. Attempt to operate a Drain and Spin cycle. . Enter Service Mode and check that error has cleared. . If error persists, or unit does not spin, replace IMC (Inverter Machine Control). CB DC Bus Brownout DC bus voltage too low . Check AC line voltage is correct. . Reset IMC by unplugging washer from 60 seconds. Attempt to operate a Drain and Spin cycle. . Enter Service Mode and check that error has cleared. . If error persists, or unit does not spin, replace IMC (Inverter Machine Control). CB DC Bus High DC bus voltage too high . Check AC line voltage is correct. . Reset IMC by unplugging washer from 60 seconds. Attempt to operate a Drain and Spin cycle. . Enter Service Mode and check that error has cleared. . If error persists, or unit does not spin, replace IMC (Inverter Machine Control). CC Motor Temp high Motor Temp high . Visually check that the motor has no signs of overheating. . Reset IMC by unplugging washer from 60 seconds. Attempt to operate a Drain and Spin cycle. . Enter Service Mode and check that error has cleared. . If error persists, or unit does not spin, replace IMC (Inverter Machine Control). — 38 — Fault Code | Name Description Repair Action (Hex) De Locked Rotor Locked rotor 1. Check the motor and basket is free to spin. 2. Reset IMC by unplugging washer from 60 seconds. Attempt to operate a Drain and Spin cycle. 3. Enter Service Mode and check that error has cleared. 4. Check harness and motor connections. 5. If error persists, or unit does not spin, replace IMC (Inverter Machine Control). D3 Hall Sensor Fault Issue with pulses from hall sensor 1. Reset IMC by unplugging washer from 60 seconds. Attempt to operate a Drain and Spin cycle. 2. Enter Service Mode and check that error has cleared. 3. If error persists or unit does not spin, check hall sensor harness and module. 4. If hall sensor and harness check OK, replace IMC (Inverter Machine Control). — 39 — Cabinet and Structure Backsplash The backsplash is a separate part of the washer that houses the button fingers that press against the buttons on the User Interface (Ul) board. The Ul and the Inverter Machine Control (IMC) mounts to the backsplash. The backsplash needs to be removed from the cabinet in order to access components including the control board, water valve, and pressure sensor. Backsplash Removal 1. Open the lid completely, and then pull both hinge covers directly out. If the hinge covers do not Immediately pull out, push in on the side locking tabs through the opening provided. 2. Close the lid and lay a towel over the washer to protect the product. Remove the two 1/4 in. hex screws that secure the backsplash to the washer. — 40 — NOTICE Whenever the backsplash assembly is removed, the aluminum tape between the backsplash and the backsplash bottom under the mounting screws must remain intact. This Is used to discharge to ground any static that may occur between the two. If it is damaged or torn, it must be replaced and be secured under the screws when reassembled. Bettar monitor 3. Rotate the front of the backsplash up slightly, then push the backsplash straight back. 4. This disengages the rear cover from the two retention clips. NOTE: The following picture illustrates the clip inside the backsplash. 5. Rotate the backsplash towards the front of the washer, and lay it face down on top of the washer. 6. Remove the six dual head screws (1/4 in. hex or T15 Torx) from back cover and disconnect the harness connectors as required. NOTICE Handle the harness that goes to the RJ45 board carefully when separating the backsplash. Then disconnect all the harness connectors from the board for replacement. Backsplash Reassembly 1. Reconnect all of the wire connections to the control board. 2. Reconnect the harness to the ACM/RJ45 board on the rear half of the backsplash. 3. Refasten the rear half of the backsplash to the front half with the dual hex head 1/4 in. T15 Torx SCrews. 4. Reinstall the backsplash to the top cover, slipping the rear of the backsplash into the clips on the top cover first. Pull the backsplash towards the front of the top cover. Pull the backsplash assembly over the backsplash bottom and reinstall the two 1/4 in. hex screws, one on each side. NOTE: Be careful not to pinch the harness when reinstalling the backsplash assembly. Make sure that any torn aluminium tape has been replaced and is secured under the two screws. 5. Raise the lid to the full open position and reinstall the hinge covers. — 41 — The User Interface (Ul) board is accessible once the Ul Logic Board six dual head screws on the back cover of the Backsplash have been removed. Ul Logic Board Removal To access the board assembly, the backsplash will need to be removed and then opened (See Backsplash Removal for instructions). 1. Disconnect all of the wire connectors to the Inverter board assembly. Use needle nose pliers to remove all of the clips from the heat sink on the inverter board by placing the pliers under the clip, then pushing the handle of the pliers towards the heat sink. This will allow the clip to release from the heat sink. Remove the eight 1/4 in. hex head screws that secure the Inverter Machine Control (IMC) board assembly to the backsplash. . Transfer the Cycle Status Lights display to the new control board assembly. Use a razor safety knife and carefully separate the glue securing the Cycle Status Lights display to the Ul board. — 42 — Note: It does not have to be re-glued back to the Ul board. Extra Heavy Heavy el "= No Spin Carefully pull the Cycle Status Lights display away from the Ul board. . Lift up on the board assemblies’ plastic housing to unclip the mounting clips, then flip the board assembly over to access the Ul board. Replace the old Ul Logic Board with the new Ul Logic Board. Reinstalling the Board Assembly 1. 2. Snap the clips on the plastic housing onto the backsplash. Secure the plastic housing with the boards attached to the backsplash using the eight 1/4 in. hex head screws. Reconnect all of the harness connectors to the board assembly. Ul Logic Board Diagnostics Ul Logic Board Voltage 1. Check from the J603 connecter on the inverter board. Inverter Machine Control (IMC) Board 2. Look for approximately 12 VDC from the red The Inverter Machine Control (IMC) board is wire (pin 4) to the yellow wire (pin 1). There should also be approximately 7.5 VDC from the brown wire (pin 3) to the yellow wire (pin 1). 3. If either of these voltages are not present, replace the inverter board. accessible in the same manner as the Ul Logic board, once the six dual head screws on the back cover of the Backsplash have been removed. Inverter Machine Control (IMC) Board Removal 4. Ifthe voltages are present and correct, check for ~~ 10 access the IMC board, the backsplash will need voltage at the user interface (Ul) board. If to be removed and then opened (See Backsplash voltage is present there and the Ul board does Removal for instructions). not power on, replace the Ul board. 1. Disconnect all of the wire connectors to the UI Logic Board Strip Circuit inverter board assembly. 2. Use needle nose pliers to remove all of the clips Connector from the heat sync on the inverter board by ololó placing the pliers under the clip, then pushing the handle of the pliers towards the heat sync. This will allow the clip to release from the heat sync. eE: J603 A 5 5 3. Remove the eight 1/4 in. hex head screws that secure the Inverter Machine Control (IMC) board assembly to the backsplash. 4. Transfer the Cycle Status Lights display to the — 43 — new control board assembly. Use a razor safety knife and carefully separate the glue securing the Cycle Status Lights display to the Ul board. Note: It does not have to be re-glued back to the Ul board. Extra High 6 6 6 6 & High Colors Medium aa nl el = = Id Light =, Carefully pull the Cycle Status Lights display away from the Ul board. Lift up on the board assemblies’ plastic housing to unclip the mounting clips. Inverter Machine Control (IMC) Assembly 1. Snap the clips on the plastic housing onto the backsplash. Secure the plastic housing with the boards attached to the backsplash using the eight 1/4 in. hex head screws. Reconnect all of the harness connectors to the board assembly. — 44 — Main Control Service LED The Main Control Service LED is located, looking at the board from the front of the washer, at the upper left of the IMC/Invertor Board, alongside the heat sink. The normal status of the LED should be a steady one second on, one second off. If the LED is not lit at all, check the voltage to the inverter board. —— ai —_— Qu Main n Control - 7 Service LED © 3 N | a u A If voltage is present, and the LED still does not flash, this indicates that the IMC/Inverter Board will need to be replaced. If the LED is flashing 3 flashes and then pauses, the inverter board has an error. Try resetting the board. The board can be reset by unplugging the power cord from the wall for at least 60 seconds, and then plugging the power cord back in to the wall. If the error persists, put the control into Service Mode and check for error codes. If no error codes are present, if the Service Mode is unresponsive, or if the Ul board does not light up, check for DC voltage going to the Ul board. If there is no voltage going to the Ul board, and the boards do not light up, replace the Inverter Board. Inverter Machine Control (IMC) Board Diagnostics . First check the house outlet for the proper voltage. Check for 120 VAC to the J101 connector black to white wires from the LINE FILTER. If no voltage is present, check line voltage coming into the line filter from the power cord connector. If there is no voltage coming out of the line filter to the IMC, replace the line filter. If no voltage, check the power cord connector and harness for damage. Inverter Machine Control (IMC) Board Strip Lid Assembly Circuit All white LI {LI |} | conductors EEE ein The lid comes as a complete assembly. On all metal о И о | 5101 lids, the magnet can be ordered separately. On ol encapsulated glass lids, the glass, magnet and |: 2 hinge post comes as an assembled part. я GY-18 GY-18 — | SUBWASHER € PLATFORM B-18 "A © [В 5] LINE {ws 56, e] FILTER | { gy.18 lo la co Lid Assembly Removal 1. Toremove the lid assembly, first remove the backsplash assembly. (See Backsplash Removal for instructions). 2. Disconnect the wire connector and the pressure hose from the sensor. 3. Unclip the pressure sensor from the backsplash bottom. — 45 — 4. To remove the backsplash bottom, remove the five 1/4 in. hex screws, one on each side under the trim cap, and three along the back on 8. Lift the right side of the lid to clear the hinge and slide the lid to the right to disengage from the left hinge. backsplash bottom. gy A Г 5. Slide the backsplash bottom toward the rear of the washer and pull out. 6. Once the backsplash bottom is removed, open the lid fully to relieve the spring pressure on hinge spring. Ty E EE cals at щей Lid Assembly Reinstallation 1. When reinstalling the lid onto the top cover, make sure to center it between the hinges with the lid fully open. 2. Then reinstall the backsplash bottom before attempting to close the lid. Doing this will prevent damage to the enamel on the top cover. 3. Slide the post on the lid assembly into the left side hinge first. The left side has more of a rectangular opening on the hinge, so that when Installing the right side there is enough space to get the post into the right side hinge. 7. Slide the lid assembly to the left. 4. Slide the right side post into the right side hinge. Make sure the lid is centered between the hinges. Note: It may need to be moved to the left or the right after the backsplash bottom is in place so there is equal space on each side when the lid is closed. 5. Slip the backsplash bottom in from the back side of the lid. 6. Secure the backsplash bottom to the top cover with the five 1/4 in. hex head screws. 7. Reinstall the backsplash assembly. 8. Close the lid and install the hinge covers. — 46 — H = 2. Raise the top cover (see Top Cover Removal INges instructions). Cut the wire tie that supports the hose on the back tab of the hinge. Bulk dispense models will have wire ties on both Washers with metal lids have standard hinges that hinges. close quickly. The glass encapsulated lids are slow closing so the lid will not drop hard. The right and left hinges are specific to the side they are mounted on. From front of unit, the From front of unit, the left side is a heavy duty | right side hinge has a coll spring. damper (shock). 3. Remove the three 1/4 in. hex head screws that hold the hinge to the top cover, and the one screw facing the rear of the top cover. Hinge Removal 1. Remove the backsplash assembly, including the backsplash bottom and the lid assembly. (See Backsplash Removal and Lid Assembly Removal for instructions). 4. Remove the hinge from the underside of the top cover. — AT — Hinge Reinstallation 1. Insert the hinge from the underside of the top cover. . Reinstall the four 1/4 in. hex head screws that hold the hinge to the top cover. Raise the top cover back up, and install a zip tie back through the hinge to hold the water tube in place. Lower the top cover onto the frame of the outer washer wrapper. Reinstall lid and backsplash assembly. Top Cover The top cover is used to house the dispenser cups, lid assembly, hinges, lid lock, lid switch, and the water supply tubes. The lid lock prevents the top cover from opening during operation, providing safety by restricting access to any moving parts. Top Cover Removal 1. — 48 — Remove the Backsplash and Pressure Sensor assemblies. (See Backsplash Removal and Pressure Sensor Removal for instructions). Remove the two white 1/4 in. screws at the rear of the cover that secure the cover to the rear rod support, as well as the ground screw connecting the wire to the top cover. Use a putty knife to disengage the cover from the two clips mounted to the front flange of the apron. The front clips that hold the down the top cover to the apron are located approximately 7 inches in from the right and left sides of the washer. Once the cover is disengaged from the apron, lift up the front of the top cover from the front clips securing it to the washer. 4. Remove the hose clamps to disconnect the two Top Cover Reinstallation bulk dispenser hoses where they connect to the fill funnel. 1. At the front of the top cover, make sure to line the front clips on the wrapper and the slots on the top cover together. Once lined up, push down on the top cover to snap the clips into place. * — 2. If the clip and the slot in the top cover are not lined up, the top cover area where the slot is could be damaged or bent. This damage will result in the clip not locking into place correctly, as seen in the photograph below. If the unit being serviced is not a bulk dispenser washer, then Step 4 is unnecessary. 5. Remove the top cover. It is not necessary to remove the top cover to replace the water valve. See Water Valve Removal for further instructions. 3. Reinstall the two white 1/4 in. hex head screws at the rear of the top cover that hold the top cover to the frame. 4. Reinstall the ground screw at the rear of the top cover. 5. Reinstall the Backsplash. (See Backsplash Reinstallation for instructions). — 49 — Lid Lock The lid lock is used to prevent injuries incurred from moving parts. Once the cycle starts, the lid lock is engaged, locking the lid. The lid lock assembly also contains the lid switch. The lid lock and the lid switch are one assembly. The lid switch needs to be operational for the lid lock to activate. The lid lock assembly consists of the lock motor, lock position switches and the lid switch. Lid Lock Assembly In an unlocked state, the latch in the bezel will be in a receded state, as shown below. When the lid is closed, the magnets in the lid assembly activate the lid switch, closing the switch. When the switch circuit is closed, DC voltage is sent back to the inverter board. This prompts the lid lock motor to activate, resulting in the latch extending to a locked state, as seen in the photograph below. Lid Lock Removal To remove the lid lock assembly, the backsplash needs to be removed, and the top cover needs to be ralsed. (See Backsplash Removal and Top Cover Removal for instructions). A CAUTION When raising the top cover, be sure to tape the lid to the top cover to prevent it from opening. 1. Remove the two 1/4 in. hex head screws that mount the lock assembly to the bezel on the top cover. MATE NUS SERIE 2. Unclip the harness from the top cover and pull the rubber grommet through the top cover. — 50 — Lid Lock Reassembly 1. Insert the grommet back through the hole in the top cover. 2. When looking at the top cover from the front, route the wire harness up through the underside of the top cover into the side clips. 3. Snap the wire harness into the clips located on the side of the dispenser cup. 4. Holding the bezel in place, and reinstall the lid lock assembly back into position using the two 1/ 4 in. hex head screws. 5. Reinstall the top cover back on to the cabinet. 6. Reinstall the backsplash assembly to the top cover. Lid Lock Motor Diagnostics Check the resistance of the lid lock motor from the Inverter Board J407 connector black (pin 4) to brown (pin 5) wires. The resistance should read approximately 39 ohms. Lid Lock Motor: The resistance should read approximately 39 ohms. It operates with DC voltage, at approximately 12 VDC. Lid Lock Position Locked/Unlocked: The lid locked or unlocked signal voltage should be 5 VDC. Papal Jesuag Fra 16 ©)! a le EN = PRCT © lerne Check the lid lock position continuity from the J407 connector blue wire (position 3) to the white wires when unlocked. When the lid is locked, check the red wire (position 6) to the white wire (position 1). Lid Lock Asm Locked /° — mA 7 Motor Circuit = 12VDC pati Black - Brown = 39 Q Lid Switch VO Lid Circuit = 5VDC ЧУ) | | Lid Switch PEU CIE EN Green - White Lock Circuit = SVDC Lid Locked Si SISISIS/S Red - White œil OI ol = of = Lid Unlocked EE Blue - White PEER = © 2 5, O, = 422958 J407 — 51 — The internal lid switch actuators in the lid lock assembly are closed by the magnets in the lid, shown by the two arrows at the bottom of the photograph below. The upper arrows in the photograph display the contacts of the lid lock assembly latch in an unlocked position. \ _- -— | pu The photograph below displays the contacts of the lid lock assembly latch in an locked position. LED Tub Light The tub light is mounted to the fill funnel assembly. It receives approximately 3.8 VDC from the inverter board at the J204 connector. LED Tub Light Removal 1. Access to the inverter board is needed to disconnect the LED light harness from the inverter board. (See Backsplash Removal for Instructions). 2. Disconnect the LED light from the J204 connector on the inverter board. 3. Use pliers to pull the grommet from the bracket of the fill funnel. Then push in on the two side clips of the LED tub light to release the light assembly from the fill funnel. 4. Pull the LED tub light, harness, and the grommet through the fill funnel. — 52 — LED Tub Light Reassembly 1. Leading with the wires, route the LED tub light harness through the mounting bracket of the fill funnel and through the hole provided in the top cover. a e a 1 o = . Seat the rubber grommet into the hole in the fill funnel and top cover. The grommet will provide a moisture seal for that area. Reconnect the harness connector to the inverter board. Reinstall the backsplash assembly. LED Tub Light Diagnostics Check from the J204 connector on the board. Look for approximately 3.8 VDC. If voltage is present, but no light, disconnect power from the washer. Disconnect the J204 connector from the board. Set the meter to the DIODE setting. With your black lead on the red wire, and your red lead on the black wire, the meter should read approximately 0.727 if good. If the meter leads are reversed to red on red, there should be no reading. LED Tub Light Strip Circuit Tub Light 83XX and Higher | {| 4204 ® — 53 — Rear Panel The rear panel provides access to the rear components that are mounted to the tub assembly. This also is the only access used to remove the basket and the tub assembly. The panel provides a stiffening support for the cabinet assembly when itis screwed to the cabinet. Rear Panel Removal 1. To remove the rear panel, pull the washer out far enough to access the twelve hex head screws securing the panel to the rear of the washer. 2. Remove the twelve 1/4 in. hex head screws and remove the rear panel from the rear upper suspension bracket and lower rear leveling leg brackets. — 54 — Once the back panel has been removed, the tub assembly and components become accessible. | || hi | | Rear Panel Reinstallation 1. Fit the rear panel back into the rear upper suspension bracket and lower rear leveling leg brackets. . Reinstall the twelve 1/4 in. hex head screws. Leveling Legs Keeping the washer level is critical because the clearance of the tub to the outer cabinet is minimal. It is normal for the tub to bump against the outer wrapper during usage, which the washer uses to sense when the load is out of balance. Adjustment Move the washer into its final position. Place a level on a flat top side edge of the washer. Adjust all four leveling legs by screwing them into or out of the foot brackets until the washer is level from left to right and front to back. Should any of the leveling legs show signs of damage, order a new leg. Impeller Assembly The impeller moves the clothes in the basket. It takes the place of the tall agitator. Impellers are designed to work best moving material around in the basket with low water levels. Impeller Removal 1. Remove the center cap from the impeller. Take a pocket screwdriver or putty knife and carefully pry the cap off. 2. Remove the 7/16 hex bolt that holds the impeller in place. — 55 — 3. Lift the impeller up and off the shaft. The coupler may come off with the impeller. Impeller Reassembly 1. Reinstall the impeller and coupler onto the shaft spline. Install a new 7/16 hex bolt and torque to 60 inch pounds. A new hex bolt is required because of the specific Loctite that is on the threads of the new bolts. DO NOT REUSE THE OLD BOLT WITH REGULAR LOCTITE. USE A NEW BOLT. Suspension System Rod and Spring Suspension System The rod and spring suspension system consists of assemblies which include: four rods each with a hook at the top, and four springs and spring covers that are each supported by a ball joint and ball socket that mount onto the support bracket. They are used to support the tub assembly and assist with balancing the load being washed. The are two rod and spring suspension systems mounted toward the rear of the washer and two toward the front. Each of the four assemblies are the same for the washer they are mounted on. Suspension System Removal 1. To remove the rod and spring assembly, the top cover assembly and components mounted to it will need to be removed. (See Top Cover Removal for instructions). 2. Once the top cover assembly is removed, disengage the suspension rod assembly from the tub by lifting up slightly on the tub assembly. Then slide the rod through the slot on the tub where the spring cover is seated. — 56 — 3. Once the rod and spring are disengaged from 5. Slide the ball joint downward on the rod, until the the tub, lift the rod up to remove the upper ball hook is completely exposed. joint from the rod. i + NY ui ï ii But 1 ws 1. у MU or fa 3 A wt h Li Vie Th a PA a mid | i A a EA DATE bu Ly 1 ОЖ Lt Di 6. Rotate the ball around until the hook is in the 4. To remove the ball joint from the rod, push on the opposite direction. lower end of the ball until it snaps off. — 57 — 7. The ball socket then needs to be removed by 9. sliding it over and off the hook of the suspension rod. OR a 8. To remove the socket cup, lift up on the rod support until the cover that is over the spring hits the bottom of the cup. Pull upward with a firm pressure to pop the cup from the bracket. Then slip the ball socket off of the rod. 10. Slide the rod down through the support bracket and out of the machine. Suspension System Reassembly — 58 — 1. Slide the new rod back up through the rod support. The ball socket needs to slide over the hook of the rod, and be seated into the support bracket until it snaps into place. Then install the support rod ball back onto the hook of the rod, and rotate the hook into position, snapping the ball into place. 4. Slide the rod into position through the cup. 5. Lift slightly on the tub, and push the rod assembly through the slot on the tub where the spring cover is seated to support the tub. Reinstall the top cover assembly. B k t 6. Remove the suspension brackets that hold the asKEe tub to the apron by removing the sixteen 1/4 in. hex screws, four on each corner. The basket assembly consists of the stainless steel side wall and balance rings located at the top and bottom of the basket assembly. When ordered, this comes as a complete assembly. Basket Removal 1. The basket and tub assembly is serviced through the rear panel of the washer. The backsplash, lid and the top cover need to be removed to access the suspension brackets in the front and rear. (See Backsplash Removal, Lid Assembly Removal, Real Panel Removal, 7. Lift the rear rod support off the apron. Remove and Top Cover Removal for instructions). the rod and spring assembly from the tub and set it on the floor. Rear Brace (x 2) Front Brace [x 2) 2. The drain hose will also need to be removed from the tub. Use a pan to catch the excess 8. Remove the front rod support brackets. Place water in the drain hose. the screw hole of the bracket on the post of the 3. Be sure that the harness that goes to the outer tub. subassembly is moved to the sides of the apron so they are not damaged during the tub removal. 4. Remove the impeller. Once the impeller has been removed, remove the hub nut (1-5/16 reverse thread). 5. Roll the tub back and out of the washer apron and lay the tub on its side. Removing the tub assembly ergonomically prevents injuries. If using an impact gun to remove the hub nut, it IS required to use the torque limiter to prevent damaging the threads on the shaft from going 9. Roll the tub back and out of the washer apron the wrong direction. and lay the tub on its side. Snap Locks (x 12) 10. Remove the tub cover by lifting the twelve snap locks for the tub. 11. Slide the basket assembly out. Make sure that the flat washer under the basket remains on the shaft of the platform assembly. — 59 — Basket Reinstallation 1. Reinstall the basket by sliding it back into the tub assembly, then roll back to the upright position. 2. Reinstall the tub cover by fastening the twelve clips on the cover to the tub. 3. Reinstall the front suspension support brackets to the front outer wrapper. 4. Reconnect the suspension rod and spring assembly back to the tub and lift onto the rear of the outer wrapper. 5. Fasten both the front and rear suspension brackets onto the outer wrapper with the sixteen 1/4 In. hex head screws. 6. Install the new hub nut onto the shaft of the platform assembly in the basket and tighten to 100 ft pounds. If using an impact gun to reinstall the hub nut, It is required to use the torque limiter to prevent damaging the threads on the shaft from over tightening. 7. Reinstall the harness, top cover, rear panel and the backsplash assembly. 8. Reinstall the impeller using a new bolt. Outer Tub To access the outer tub, the rear panel must be removed (see Rear Panel Removal for instructions). The outer tub assembly is made of a plastic material that holds the water for the wash cycles. It is also used to mount components to it such as the drive motor, pumps, thermistor, heater, and platform shaft and tube assembly. The outer tub also has a built in overflow drain on it at the front of the tub assembly. Outer Tub Removal 1. Remove the basket assembly. (See Basket Removal for instructions). 2. Roll the complete tub assembly over to the upside down position. Remove all of the components, including the harnesses, from the bottom of the tub assembly. 3. Lift the outer tub off of the basket assembly. Outer Tub Reinstallation 1. Make sure the flat washer is on the bottom of the basket before setting the tub over and on the basket assembly. 2. Reinstall all of the components back onto the bottom of the tub assembly. 3. Continue by following the reinstallation of the basket assembly. (See Basket Reinstallation for instructions). — 60 — Drive System Rotor The rotor has magnets mounted within it that respond when voltage is applied to the stator. This During removal and reassembly, be careful not to pinch any fingers between the rotor and the stator as the magnetic pull on the rotor is strong. creates a pulsating magnetic field (3 phase VDC), which then creates a strong magnetic force that repels the magnets on the rotor. This will cause the 1. rotor to turn with the shaft in the platform assembly. Rotor Removal 2. 1. To access the rotor or any component on the bottom of the washer, lean the washer back or lay on the washer on its side. NOTICE If lying the washer on its side, and the model being repaired has a bulk dispense system on it, tape the vent holes on the top of the bulk tanks, and the oval opening on the fill funnel. See the NOTICE in the Bulk Dispenser Tanks section of this guide. 2. Remove the rotor by turning the 11/16 nut counter clockwise. 3. Remove the concave washer from the lower platform shaft. The washer should have a red color on one side. 4. Pull the rotor away from the washer. — 61 — Rotor Reassembly To reinstall the rotor, slide it onto the shaft of the platform assembly, over the stator. Install the concave washer onto the shaft. The side with the red color should go toward the rotor on the shaft. Install the new 11/16 rotor nut onto the shaft of the platform assembly and tighten to 500 in. pounds. Stator The stator receives three separate phases of pulsing VDC from the inverter board, which creates a magnetic force that causes the rotor to turn with the shaft. Stator Removal 1. Remove rotor. See Rotor Removal instructions. 2. Disconnect the harness from both the stator and the hall sensor. 4. Remove and transfer the hall sensor from the stator that is being replaced to the new stator. (See Hall Sensor Removal for instructions). Stator Reassembly 1. To reinstall the stator, reconnect the three phase power wire connector. 2. Reinstall the three 1/2 in. hex bolts that mount the stator to the platform assembly, and torque to 130 inch pounds. 3. Reconnect the hall sensor wire. Make sure to seat the connector until it clicks into place on the hall sensor. 4. Snap the hall sensor onto the stator. (See Hall Sensor Reassembly for instructions). Diagnosing the Stator Check from any one of the three stator phase wires to any other stator phase wires, red, yellow, or blue. On connector J1203, the resistance should be approximately 18 ohms. If no resistance is present, check the harness and connectors for damage. If the harness and connectors are good, replace the stator. Stator Strip Circuit — 62 — 3. Unclip the hall sensor from the stator by lifting up Hall Sensor from the outer edge, releasing the outer clips. Use care when releasing the outer clips, as it is possible that they may break when The hall sensor is used to measure the movement removing. Have a new hall sensor available and the speed of the rotor assembly. The hall on the truck before servicing. sensor has internal switches that open and close with the movement of the rotor magnets. The hall sensor then sends these measured, pulsating signals back to the inverter board. 4. Rotate the sensor up to release the inner clip off of the stator. Hall Sensor Removal The hall sensor can be removed without removing the stator. 1. Remove the 11/16 in. rotor nut and pull the rotor vw | LO e off to access the stator. da 2. Unplug the connector located on the center of оч the hall sensor. - es ь E = = = j E = = = я = = la i LL | AN ` — 63 — Hall Sensor Reassembly 1. Toreassemble, push the inside rears clip onto the stator and then clip the two front clips to the outside of the stator. Be sure that the front clips snap into position. 2. Plug the harness connector back onto the hall sensor. Diagnostics from the Board — Testing the Hall Sensor Check from the J1001 connector. With the power to the washer on, and the connector plugged into the inverter board, use a multimeter to verify that a 0 — 12 VDC signal from “P” goes to any one of the three HALL wires on the inverter board while very slowly moving the basket by hand. CAUTION: There is a potential of -170 VDC from earth ground to “P”. Hall Sensor Strip Circuit Motor_ Temp | af SE 20 1 V+ Е — Sense 1 E LE я Sense 2 | о : Y-20 = Sense 3) C | | c-20 pe v- | LU. J1001 Terminal “P” at the J1001 connector on the IMC board is referred to as “VV” on the mini manual. Mode Shifter The mode shifter consists of a motor, micro switch, spring and clutch. Its purpose is to switch modes of movement, spin or agitate, depending on where in the wash cycle the control is. When switching from spin to agitate, the mode shifter motor receives 120 VAC from the inverter board. The motor will rotate until the mode shifter motor sense switch closes, signaling to the inverter that the mode shifter has reached the agitate mode. Mode Shifter in spin state. This is the home position after a cycle is completed. = Ea 1 a " ‘ — 64 — Mode Shifter in agitate state — Clutch pressed 2. in A чё’ : 3. Mode Shifter Removal Remove the three 5/16 in. hex screws. Pull the mode shifter up and off the platform. Mode Shifter Reassembly The mode shifter cannot be removed without 4 removing the stator. (See Stator Removal for Instructions). 1. Disconnect the harness to the mode shifter and disengage the wire zip tie from the platform. cn № 17 e i . The mode shifter will come as a complete assembly. When replacing the mode shifter assembly, be sure to insert the flat washer before sliding the spring on to the shaft of the platform. ETT, . Slide the motor of the mode shifter into the platform housing opening. . When installing the clutch, make sure it moves freely up and down on the shaft while lining up the teeth. 4. Install the three 5/16 hex head screws. — 65 — The torque for the mode shifter screws is 54 in. pounds. Diagnostics from the Board — Mode Shifter Motor Resistance Check the Mode Shifter Motor Resistance from J701 connector orange wire to the white neutral wire on the J101 connector. Should read Diagnostics from the Board — Mode Shifter Position Switch The mode shifter motor sense switch can be tested at the J501 connector between the gray and the green wires. The switch is normally open in the idle/ spin state. It is closed in the agitate state. approximately 4k ohms. . . If Resistance is good, check for 120 VAC at the Mode Shifter Switch same locations when activated. ~~ Mode Shifter Motor OD s| 8 | x 1 | lolbiblolola 1 ‚5191917191917 G-20 5-20 Lad == — 66 — Motor Insulator Platform Assembly The Motor Insulator is a thin plastic covering required by UL, that is designed to prevent the stator coils from coming into contact with the platform. The isolator is located under the mode shifter and stator, and is held in place by sticky tabs. When the stator is installed, the isolator will roll over the sides of the platform creating a barrier between the stator and the platform assembly. The platform assembly consists of a shaft and a tube, with no gears or grease. If the wash cycle is in agitate mode, the inner shaft will have the only movement. If the cycle is in the spin mode, both the inner shaft and the outer tube will move to allow both the impeller and the basket to turn. This is done from the action of the mode shifter. The platform also acts as the mounting plate for the mode shifter and stator. Platform Assembly Removal 1. Remove the impeller. (See Impeller Removal for instructions). 2. Remove the 1-5/16 in. hub nut. Motor Insulator Removal 1. The rotor and stator must be removed before removing the insulator. (See Rotor Removal and Stator Removal for instructions). Pull the insulator off of the platform assembly, the rotor, stator and the mode shifter. Motor Insulator Reassembly 1. To reinstall the insulator, peel the paper off of the ~~ NOTICE Insulator sticky tabs. NOTICE 2. Line the insulator with the opening of the If an impact gun is not being used and a torque platform, where the motor of the mode shifter wrench is, do not use the torque limiter. The goes into it. Place the insulator to the platform torque limiter tool is used with an impact gun and apply pressure where there is adhesive. to achieve the proper torque. Use the torque limiter when removing or installing the hub nut to prevent damage to the shaft and tube assembly. NOTICE Models produce after March 2014 will not have a motor insulator on it as the newly designed stator did not require it to be there. Repairing washers that have insulators on them are required to have them reinstalled back on unless the stator had been replaced with a newly designed stator. — 67 — 3. Apply tape over the vent hole on the top of the 6. Remove the twelve 3/8 in. hex bolts. bulk tanks. Also apply tape to the oval shaped - dispense holes on the fill funnel. This will prevent detergent/softener leakage when removing the tank or laying the washer on its side. ¿ + - rr dp = je E = > я 2 i = Nu LT a Eh À E te 1 с * 2 = 7. Pry the platform off of the tub assembly. The design of the tub allows it to be used to aid with prying the platform off of it. 4. Lay the washer on its side. A CAUTION Tape the lid closed as it will spring open when laying the washer on its side. 5. Remove all of the components from the bottom of the tub assembly. — 68 — Platform Assembly Reassembly 1. When reassembling the platform, insert the 7. orientation post on the tub into the post hole on the platform. 8. 9. . Install the platform starting with the inner bolts first. They are numbered 1, 2, 3 and 4. Start with number 1 first. It is important to install the platform bolts in this pattern. It allows the tub seal to be pulled into the tub evenly without damaging it. way in. Tighten each bolt 1/4 of the way in at a time. This is done to pull the pressed on seal into the tub assembly evenly. Once the inner bolts are all pulled in, the outer bolts may then be installed. Tighten and torque each to 65 in. pounds. Reinstall all of the components back onto the bottom of the tub assembly. — 69 — 6. Stand the washer upright. Remove the tape from the vent holes on the bulk tanks and the oval shaped dispense holes on the fill funnel. Reinstall the hub nut. The torque when re- installing the hub nut is 100 ft pounds. Reinstall the impeller with coupler onto the shaft. Fill System Water Valve Assembly The water valve is a 120 VAC, compound solenoid type, and is accessed by removing the backsplash assembly. It is inserted and retained in a cutout at the rear of the top cover under the backsplash assembly. It is held in place by 1/4 in. hex head screws. lt is only available as a complete assembly. Flow rates are as follows: Gallons Per Minute (GPM) Water Valve Flow Rates Hot 2.64 Cold 2.64 Bleach 1.32 Detergent 1.32 Softener 2.00 Bulk Detergent 2.00 Bulk Softener 2.00 Water Valve Removal 1. To replace the water valve remove the backsplash assembly. (See Backsplash Removal for instructions). 2. Remove the two 1/4 in. hex screws that hold the fill funnel in place. 3. Then remove the 1/4 in. hex screws that hold the water valve to the top cover. The number of screws vary depending on the water valve in the washer, from three coils to six coils. Slide the water valve out toward the rear of the washer. Once the water valve is slid out, use pliers to grasp the clamps and turn them until the lobe of the clamp is accessible. ‚ EE A BTN a The tube the clamp is securing may turn with the clamp. This is OK. Although regular pliers will work, click pliers will work better. . Once a clamp is oriented, using pliers, grasp the lobe of the clamp and twist. The clamp will break off. Water Valve Assembly Reinstallation 4. There are two sizes of replacement clamps in clamp kit WR49X20000, needed for all the tube connections on this washer. The larger of the two clamps are only used for the Fill Funnel Tubes. The smaller of the two clamps is used for all other tubes. 1. Insert the two tubes from the fill funnel through the two large hose clamps. This will hold it in position as the clamps will not go through the hole until they are clamped closed. 2. Then using the smaller clamps, insert the tubes through the clamps and attach the tubes to the water valve barbed stems. NOTICE Be sure to have all of the clamps oriented in the same direction to prevent any difficulty getting them to go through the openings of the top cover. y Y ! 7770 3. After seating the tubes back onto the water valve, orient the click pliers where the thin edge 6. is under the lip of the clamp. That way it will slip under the hook of the clamp. If the clamp needs to be opened or removed after installing, flip the pliers over so that the thin edge is on the hump and the thick edge of the pliers is on ° the lip and clip portion of the clamp. Squeeze the pliers until the click clamp snaps open. . — 71 — Squeeze the clamp until it snaps together. Reinstall the water valve to the top cover. There are three different water valves that accommodate three different dispenser configurations. For the GTWN7450 models, the 3 coil valve is used. For the GTWN815 — GTWN845 models, the 5 coil valve is used. For the GTWS865 models, the 6 coil valve is used. Diagnosing the Water Valve ° [If no water is coming out of the valve, check the Inlet hoses and water valve screens to make sure they are not clogged. ° |f water is still not coming out of the valve, put the control into Service Mode and apply voltage to the water valve coil that is not working. Check for 120 VAC on the corresponding colored wire at the J702 connector on the inverter board to the white wire at the J101 on the inverter board. Also, the resistance of the coil can be checked at those same connectors. The resistance should read approximately 1k ohms (1000 ohms). * |f no resistance is present, check for resistance at the coil. This will verify whether or not there is an open harness. “H20 Supply” scrolling on the control is caused by the control not sensing water going into the tub. If the water is going into the tub, check the pressure sensor readings with NewFi or by checking the Hz output from the pressure sensor in approximate comparison to the amount of water in the tub. Check the harness and the connections along with the pressure sensor tube. If no water is flowing into the tub, check the house water supply. Make sure that it is turned on, and that the house doesn't just have low water pressure. If water is still not flowing into the tub, or only a low amount of water is flowing into the tub, check the hose screens for debris. If debris is present, clean the hose screens. Also check the hoses for kinks. If there is still no water or a low amount of water flowing into the tub, check or clean the water valve screens. If still no water is flowing, replace the water valve. Walter Valve Assembly Strip Circuits Water Valve Assembly 7450 HOT B-20 B-20 я C=20 Ч W-20 M-20 COLD C-20 pw | XE w-20 | Fab Soft N-20 = Xf wao | J101 Water Valve Assembly 82XX-84XX J702 HOT B-20 B-20 — NJ C-20 Y E W-20 N-20 COLD c20 A | La) e wo © X Soft N-20 4 3 w-20 Bleach | vo т wo | Det Cup v20 A J101 XE W-20 — СТО | | 6 4 W-20 [1] W-20 о с DI 3 ; Water Valve Assembly 86XX HOT B-20 AL COLD AL J101 LJ Bulk Det его A AL а NOTICE On the white neutral wire going to the water valves, there is an in-line connector between the J101 connector on the inverter board and the water valve. W-20 1 JS. = Es tw |; Ll О ео W-20 _ 72 — Pressure Sensor For models equipped with a pressure sensor, the pressure sensor status will be determined by reading the frequency coming from the pressure sensor. Pressure Sensor Removal 1. The pressure sensor is located in the backsplash area. Remove the backsplash assembly.* (See Backsplash Removal for instructions). *With the tub in an empty state. Use pliers to compress the locking tab that is holding the sensor in its housing, and onto the backsplash bottom. — Disconnect the sensor wire connector by pushing up on the tab above the wire connector and pull the connector from the sensor. Pressure Sensor Reinstallation 1. To reinstall the pressure sensor, reconnect the pressure tube to the sensor, and also to the harness connector. 2. Push the clip of the pressure sensor back onto the backsplash bottom. Pressure Sensor Diagnostics If the pressure sensor’s frequency is outside of the “Valid Values” illustrated in the Tub Water Level / Hz Conversion chart, then an error condition is set. The error condition will be logged in Service Mode. If a Pressure Sensor error occurs during a cycle, the cycle will be canceled and the control should go to an Idle state. If a cycle is started during a Pressure Sensor error, the fill cycle will be cancelled. — 73 — Pressure Sensor Testing Use a hertz meter to read the frequency at specified water levels. For testing at the pressure sensor, the pin out is as follows: 1 = Ground 2 = Signal 3=5V Test between pins 1 and 3 to verify that 5 VDC is going to the sensor. This is needed to be able to read the signal coming from the sensor. Test between pins 1 and 2 to measure the signal. Tub Pressure Sensor E ES o G-20 R-22 V-22 о оО |0 Qo и Ld o 13 a J501 ofo Tub Water Level / Hz Conversion Inches of Water Frequency Hz Pumped out tub 45.2 1” in basket 44.2 3” in basket 43.3 6” in basket 42 9” in basket 40.7 12” in basket 39.4 Water Levels Water levels can vary depending on the load being washed. This can be attributed to the weight of the items in the load, which is what sets the water level in most cycles. The level will vary from a minimum of 7 gallons to 25 gallons. NOTICE Water should always cover all valley areas (as shown below) when a cycle is run with an empty basket. There are four valley areas located between the fins of the impeller. The valley areas can be identified on the impeller by the four sections with holes, which are designed to help circulation within the basket. If there is less than 7 gallons in the basket, then water pressure from the home supply, or debris in the water valve or hose screens may be the cause. — 74 — Top Cover Dispenser Cups The dispenser cups are used to either direct the fluid into the tub assembly immediately during the cycle, or to hold the fluid and dispense at a specific time in the cycle. This occurs by flushing the dispenser cups with water from the water valve. Fabric Softener-Cup Hybrid Assembly Operation RAE Softener Water To start the flow of fabric softener, water enters the cup first, filling the reservoir and mixing with the fabric softener. A restriction in the fabric softener cup tubing (Venturi) creates a back pressure. The back pressure forces water up and around the outside edge of the cup to add water to the cup. The water then enters the cup through two openings, which begins to siphon the softener out. As the pressurized water flows through to the other side of the tube in the cup, a suction is created. The water and softener mix together, and come out of the other end of the cup and flows to the fill funnel. After the water is shut off, the softener continues to siphon out of the cup until the cup is empty. Dispenser Cup Removal 1. With the top cover still installed, place the thumb of one hand under the corner of the cup on the underside of the top cover assembly. — 75 — . Place the thumb of the other hand inside the cup from the top side of the top cover. With firm pressure, pull down with the one thumb on the underside while pushing down with the other thumb from the top side. The cup should pop free from the top cover tabs. Once the cup is free, it can be slid out from under the top cover. Remove the clamp and pull the tube off of the cup. The clamp will not be reusable, and will have to be replaced with a new clamp at reassembly. Dispenser Cup Reassembly 1. Install the tube onto the new cup using the small click clamp. (Refer to the click clamp instructions found in Water Valve Assembly Reinstallation). Straighten the tabs on the top cover hole opening so that the cup can slide into place easily around the tabs. Push up and hold the cup in place. Bend the tabs over to about a 45 degree position to hold the cup to the top cover. This can be done either thumb pressure or coated jaws or the handle of a pair of pliers. Be careful not to damage the top cover finish. Es — 76 — NOTICE Be sure to refasten the lid lock harness back into the support brackets on the cup so that it does not hang down and rub on the basket. EN o y Diagnosing Dispenser Cups To diagnose the dispenser cups, put the control into Service Mode and turn the individual water valve coll on to the dispenser cup. This will allow water into the cup to be dispensed. Depending on the type of cup (either flow through or siphon), ¡t will flow right through or fill the cup to start the siphon. Bu | K Dispenser Tan ks Set the Bulk Detergent Cup Amount Preference When the Detergent Tank On light is on, pressing the Detergent Cup Amount button will set the Bulk Dispenser Tanks Operation Detergent Cup Amount lights (1, 2, or 3). Level 1 will distribute the standard amount minus 25%. Level 2 will distribute the standard amount. * Level 3 will distribute the standard amount plus 25%. Examples: Factory default standard amount is 1.5 oz (44 ml) (Concentration Setting 15). Water enters the fill funnel from the water valve. The tube on the fill funnel narrows (Venturi), which then If Detergent Cup creates a pressure. When the pressurized water Amount shows 3 lights flows through to the oval opening in the fill funnel, it then 1.9 oz (55 ml) will causes a suction. It is this suction that pulls the be dispensed. detergent and/or softener from the bulk tank through one og 15 the bulk tank sensor, to the fill funnel mixing with the If Detergent Cup water. Amount shows 2 lights | | 3 lights: 1.9 oz then 1.5 oz (44 ml) will | Bulk Detergent/Softener Tanks be dispensed. 2 lights: 1.5 oz. The bulk detergent tank and the bulk softener tank If Detergent Cup 1 light: 1.107. each hold over a gallon (140 ounces or 4100 ml) of Amount shows 1 light liquid. After filling the tank, press the Detergent then 1.1 oz (33 ml) will Tank On button to turn on its light and designate be dispensed. bulk (rather than manual) detergent dispense. Factory default standard amount is 1.0 oz (30 ml) The Tank Levels lights (Temes (Concentration Setting 10). (five total) indicate how If Softener Cup much detergent is left. Amount shows 3 lights An empty tank is shown then 1.3 oz (37 ml) will by a single red light. A be dispensed full (or nearly full) tank Concentration 10 is shown by five lights. If Softener Cup Setting Amount shows 2 lights | | 3 lights: 1.302 then 1.0 oz (30 ml) will be dispensed. 2 lights: 1.0 oz. If Start is pressed when the tank is empty, the If Softener Cup 1 light: 0.8 oz. Detergent Tank On light and the red Tank Levels Amount shows 1 light indicator light for the tank that is empty will flash then .8 oz (22 ml) will four times, along with the Start button. be dispensed. A beep will also sound if Variable Signal Ison. The NOTE: Each cycle knob position defaults to a Start button will continue to flash approximately 30 different Detergent Cup Amount (including 0 if no seconds longer, and then will turn off the control. detergent is used). If the Soil setting is changed, the Detergent Cup Amount may change. The user can then manually change the Detergent Cup Amount, but the change will not be saved when the user Detergent will be automatically dispensed at the leaves this knob position or if a My Settings is set. optimum time at the beginning of each fill cycle. The Detergent Cup Amount lights indicate if a Low, Medium, or High amount will be dispensed. — 77 — Setting The Bulk Tank Detergent/Softener Concentration To set the concentration level you need to enter the Special Features mode: To enter the bulk tank Special Features mode: 1. Press the Power button. 2. Simultaneously press and hold either: * Detergent Tank On and Detergent Cup Amount buttons for three seconds « Softener Tank On and Softener Cup Amount buttons for three seconds Tank Levels [” ©& | | Detergent Tank т pa À 1 Softener Tank On [опий с Detergent Tank On Tank Levels Detargent Softener Cup mount § Cup Amount The My Settings and Extra Rinse lights will flash to indicate you are in the Special Features Mode. Set Concentration Settings NOTICE During initial installation, or if the household water pressure dramatically changes, the bulk dispenser will change to accommodate the homes’ unique water pressure. Wait a few wash cycles before changing concentrations. The factory default concentration settings are 1.5 oz (44 ml) for detergent and 1.0 oz (30 ml) for softener. To allow maximum user flexibility either of these can be changed to between 0.5 and 10 ounces. 1. Enter Special Features mode. 2. Press the My Settings button. The My Settings and the chosen (Detergent or Softener) three Cup Amount lights will come on and the Extra Rinse light will go out. The display will show “10 times in ounces” the current concentration setting (e.g. 15 represents 1.5 ounces). This amount will be dispensed when two (of the three) Cup Amount lights are lit. 3. Turn the cycle knob clockwise to increase or counter-clockwise to decrease the setting (within preset limits). Each click increases or decreases Level 2 (standard amount) by a 1/2 ounce. Levels 1 & 3 change proportionally. 4. Press the Cup Amount button to save the new setting. This function will then exit and the display will reflect whatever cycle the cycle knob is on. To exit without changing the setting, press the Power button. This function will automatically exit (without saving) if neither button is pressed within one minute. The following table shows the approximate amount dispensed in ounces (0z) at each Cup Amount setting (1, 2 or 3) for each Concentration Setting: Concentration Setting Number of | 200 | 100 | e7 | so | ao | 33 | 29] 25 | 22 | | зв | 17 | 15| а | 13 | 13 | г | п | а | 0 5 | 10 | 15 | 20 | 25 | 30 1-35 1 40 | 45 | 50 | 55 1 60 | 65 1 70 | 75 | 80 | 65 |] 90 | 9% | 100 = 06 | 13 119 | 25 | 31} 38 | 44 | 50 | 56| 63 1 65 | 75 | 81 (88 | 94 | 100 | 106 | 113 | 119 | 125 = 05 | 10 1 15 1 201 25 | 30 | 35 | &0 | 45 | 50 | 55 160 | 65 | 70 175 | 80 | 85 | 90 | 95 | 100 = 04 | 08 | 11 | 15 | 19 | 23 | Z6 | 30 | 3à | 38 / 41/45 | 49/53 | 56 | 60 | 64 | GB | 71 | 75 * For a 100 oz [2957 mil bottle for normal Ig setting. — 78 — NOTICE Apply tape over the vent hole on the top of the bulk tank. Also apply tape to the oval shaped dispenser hole on each end of the fill funnel. Doing this prevents detergent leakage when removing the tank or laying the washer on its side. After taping the vent hole, lay a rag under the tank flange (where the tube connects to the tank) before disconnecting the tube to catch the small amount of detergent that will come out. Then tape or plug the tank flange hole to prevent spillage. — 79 — Bulk Dispenser Tank Removal 1. The bulk dispenser tank can be removed from the bottom of the washer. 2. Lean the washer back using ergo assisting prop blocks or by laying the washer on its side. Pull the tank out from the bottom by lifting the tank up and off of the bottom apron lip. Slide the tank down and out of the outer wrapper at a 45 degree angle. E = x = Zi = | L — a a "e ; a Remove the hose clamps at the bottom of the bulk tank. (Refer to the click clamp instructions found in Water Valve Assembly Reinstallation). If there is fluid still in the tank, block the opening where the tube connects to the tank with thumb to prevent any leakage from the tank. Also have a towel under it to prevent a mess on the floor. Bulk Dispenser Tank Reassembly 1. With the washer still leaning back or laying on its side, slide the tank in at a 45 degree angle. Make sure to reconnect the hose back to the tank using a small click clamp. Slide the tank up and in alongside the front corner of the cabinet. Maneuver the top of the tank around the front suspension rod. . Once the top of the tank is in place, it will lock into position. Once locked into position at the top, apply pressure while pushing the tank in until both tank posts are secured on the bottom lip of the cabinet. Once locked in, the pressure will hold the tank in position and also prevent the tank from rattling on the cabinet. Bulk Tank Pressure Sensors The bulk tank pressure sensors, one for each tank, are located at the back of the unit. They are mounted to a plastic bracket that sits over the rear leg posts. Slots in the bracket hold them in place to the cabinet. The sensors are used to measure the amount of fluid that is in the bulk tanks. Pressure Sensor for Bulk Tanks Removal 1. To remove the pressure sensor for bulk tanks, either lean the unit back or open the rear panel. В”. тай » 7 2. Lift the sensor and bracket assembly up and off of the leg post. — 80 — 3. Using the pinch off pliers, pinch off the tube 6. Remove the remaining hose that leads to the fill coming from the bulk tank to the sensor. funnel. Disconnect the tube for the sensor by breaking Tank Pressure Sensor Reassembl the clamp off and then removing the tube. (Refer y to the click clamp instructions found in Water 1. Toreinstall the sensor, push the tubes with new Valve Assembly Reinstallation). click clamps onto the sensor. 2. Use the click pliers to click the clamps shut. (Refer to the click clamp instructions found in Water Valve Assembly Reinstallation). 3. Push the sensor back onto the plastic bracket and then slide the bracket over the leg post onto the outer wrapper. 4. Pull the sensor straight up off of the mounting bracket. — 81 — Tank Pressure Sensor Diagnostics If no liquid is being dispensed from the bulk tanks, check the water valve operation in the Service Mode. Make sure the tanks are full, and that the water pressure going to the tub is good. The hose or water valve screen could be clogged. Check the bulk tank pressure sensors to make sure that they are in range, that they are connected, and that power is going to them. If there is no power, check for a broken wire to the sensor. NOTICE If the bulk tanks are empty of either fabric softener or detergent, the tank level indicators will flash three times, and the cycle will not start. This can be bypassed by turning off the bulk tanks, and applying detergent manually. Diagnosing the bulk tank sensors can be done at the sensor or from the J502 connector on the IMC board. Use a hertz meter to read the signal at specified tank fluid levels. For testing the pressure sensor, the pin out is the same as the pressure sensor for the basket water levels and are as follows: 1 = Ground 2 = Signal 3=5V Test between pins 1 and 3 to verify that 5 VDC is going to the sensor. This is needed to be able to read the signal coming from the sensor. Test between pins 1 and 2 to measure the signal. Bulk Tank Pressure Sensors Strip Circuit Bulk Tank Sensors 86XX Bulk Bulk Detergent Softener Pressure Pressure Sensor 2 Sensor 1 [TI NIN óloz ‘И SS N z|>|o > O — J502 Bulk tank pressure sensors — 82 — Inches | Frequency of Fluid Hz 0 1380 2 1362 6 1331 9.5 1269 20 1220 Heater Assem b ly Heater Assembly Reassembly 1. The heater is 1200 watt, 12 ohms with a 10 amp draw. It is located toward the back of the washer where the sump hose connects to the tub. If there is room available, it is easiest to remove the heater after the rear panel is removed. (See Rear Panel Removal for instructions). Heater Assembly Removal 1. Disconnect the harness from the heater. 2. Loosen the 10 mm nut and slide the heater out from the tub opening. — 83 — Slide the heater assembly into the tub opening until it is seated inside the tub. Be sure that the foot at the end of the heater is pointing down. Using an inch Ib. torque wrench, tighten the 10 mm nut to 3 1/2 inch pounds. Using a 10 mm wrench or socket, tighten the 10 mm nut three more complete turns to get the proper seal between the heater and the tub. Tug on the heater assembly to make sure it will not come out. Reconnect the harness onto the heater terminals. Heater Assembly Diagnostics If diagnosing at the heater, put the control into Service Mode. Connect an amp meter to one of the wires going to the heater. The reading should read approximately 10 amps. If there is no amperage reading, check the resistance of the heater, it should read 12 ohms. To check the heater diagnostics from the IMC board, check the J803 connector from the black wire to the white wire. The resistance should be approximately 12 ohms, and the amperage draw should be approximately 10 amps. The brown wire that is on the heater sheath goes to the J501. This is the continuity circuit with the yellow wire at the thermistor. NOTICE To read continuity there needs to be water in the tub. This circuit was removed on models produced after March 2013 as it was not needed with updated programing that was used in production. Some harnesses have the connectors removed that was used for this circuit. Heater Assembly Strip Circuit Heater Circuit 84 XX to 86 XX {attached at || thermistor) 7 a THe Thermofuse | W-16 J501 Y — | ; я HTR Sheath at al | || | [| isjaf | [+f с-20 J803 Tub Thermistor The thermistor is used to sense the water temperature in the tub, and also for the steam assist cycle. IF THE TEMPERATURE NEEDS TO BE TAKEN, WAIT AT LEAST TWO MINUTES AFTER AGITATION/RECIRCULATION HAS BEGUN. Tub Thermistor Removal 1. The thermistor is located in the bottom of the outer tub assembly, next to the drain pump. Remove the two 5/16 in. hex screws to remove the thermistor. 2. Once the tub thermistor is removed, there are two different possible configurations for the harness wiring to the thermistor. Some models may present a separate yellow wire connected to a ring terminal mounted underneath one of the thermistor assembly screws. Some units may not have a separate yellow wire. Unit with no separate yellow wire. Unit with separate yellow wire. 3. If the yellow wire with the ring terminal is present, carefully lift it out of the way and protect it from damage. It will be reinstalled in the same location in a later step. — 84 — 4. Cut both azure (blue) wire leads flush with the rear black seal of the old tub thermistor to keep the azure leads coming from the harness as long as possible. 5. The leads are interchangeable when splicing so there is no need to label them. Tub Thermistor Reassembly 1. Splice the thermistor back onto the main harness. 2. Slide the new thermistor into the tub assembly. 3. Fasten the new thermistor with the two 5/15 in. hex screws. 4. If there is a yellow wire with a connector on it, slide it onto the hex screw before installing the hex screws through the thermistor. Make sure the rubber O-ring is in place before reinstalling the new thermistor into the tub. 5. Torque the hex screws to 17 in. pounds. Thermistor Diagnostics from the IMC board. To test the thermistor with the tub empty, take the ambient room temperature with a thermometer to see if the thermistor is within plus or minus 5 degrees. If good, turn on the TAP COLD water into the tub and measure the incoming water temperature at the fill funnel. The thermistor reading should drop to within what the thermometer is reading, plus or minus 5 degrees. From the J501 connector, check thermistor resistance between the two azure wires. Tub Thermistor Strip Circuit Thermistor 12k A-20 < a < 010/10 ojo Goa ojo LT 13 1 J501 Thermistor Resistance Table (These values are read from the leads while disconnected from the control PCB) Temp (degC) Temp (degF) Resistance 10 50 22166 15.5 60 17407 21 70 13840 27 80 10780 32 90 8878 38 100 7040 43 110 5610 49 120 4700 54 130 3900 66 150 2620 77 170 1840 — 85 — Wash System Recirculation Pump The recirculation pump is used to spray water over the wash load during the wash cycle, and to rinse during the rinse cycle. Recirculation Pump Removal 1. To remove the recirculation pump, access the bottom of the washer, and disconnect the wire harness from the pump. 2. Remove the recirculation tube and hose from the pump. Use the pinch off pliers to secure the hose going from the tub to the pump before disconnecting the hoses from the pump. 3. Remove one 3/8 in. hex bolt. 4. Lift up slightly and slide the pump bracket out from under the platform. Recirculation Pump Reassembly 1. To reinstall the recirculation pump, slide the pump bracket under the platform first. 2. Reinstall the 3/8 in. hex bolt. Torque is 65+/-20 In. pounds. 3. Reconnect the hose and the wire harness connector to the pump. Recirculation Pump Thermal Cut Off (TCO) The recirculation pump thermal cut off (TCO) is a safety thermostat used for this pump in case of a thermal issue with the pump. This is a one shot TCO. If it does open for any reason, replace it and the recirculation pump. Recirculation Pump Diagnostics from the IMC board 1. Disconnect power to the washer. 2. Access the control. 3. Disconnect the J701 connector. 4 . Check the resistance from the brown wire to the neutral white wire at the J101 connector. 5. Should read approximately 30.5 ohms. 6. If resistance is good, check for 120 VAC at the same locations when activated, while in Service Mode. — 86 — Recirculation Pump Strip Circuit Recirculation Pump 8XXX and Higher C-18 O 3/6 0 o | J701 01/40 W-18 | All white В conductors | are line 7 т 4 neutral J 1 01 OOo 3 1 W-18 | Thermal ap - а cut off at W-18 | 250F Recirc Pump C-18 W-18 Recirculation Tube The recirculation tube is connected to the recirculation pump with a spring clamp. From the front of the washer, the recirculation tube is mounted to the left rear side of the tub assembly, and is pushed into a rubber grommet at the top of the tub assembly. The recirculated water is then sprayed into the tub with the assistance of the tub cover at that same location. Recirculation Tube Removal 1. To remove the recirculation tube, disengage the spring clamp from the recirculation pump and pull the tube off of the pump. 2. Then pull down on the tube to remove from the tub assembly. Recirculation Tube Reassembly 1. To reinstall the recirculation tube, push the top of the tube with the rubber grommet in to the top of the tub assembly. 2. Putthe clamp onto the new tube and then push the tube onto the recirculation pump. 3. Slide the spring clamp back into position so that it holds the tube to the pump. — 87 — Drain System Drain Pump The Drain Pump is a 120 VAC pump used to expel water from the tub assembly to the house drain. The maximum drain height that it will pump out to is 8 ft. Drain Pump Removal 1. To remove the drain pump, disconnect the wire harness connector from the pump. 2. Pinch off the hose that comes from the tub to the pump. Remove the drain hoses from the pump. 3. Remove the one 3/8 in. hex bolt. 4. Lift up slightly on the bracket and then slide the drain pump out from under the platform. Drain Pump Reassembly 1. To reinstall either pump, slide the pump bracket under the platform first. 2. Reinstall the 3/8 in. hex bolt. Torque is 65+/-20 In. pounds. 3. Reconnect the hoses and the wire harness connector to the pump. Drain Pump Diagnostics Disconnect power to the washer. Access the control. Disconnect the J701 connector. Check the resistance from the yellow wire to the white wire at the J101 connector. Should read approximately 16.5 ohms. If resistance is good, check for 120 VAC at the same locations while in Service Mode. Drain Pump Diagnostics from the IMC Board 1. Disconnect power to the washer. 2. Access the control. 3. Disconnect the J701 connector. 4 . Check the resistance from the yellow wire to the white wire at the J101 connector. 5. Should read approximately 16.5 ohms. 6. If resistance is good, check for 120 VAC at the same locations while in Service Mode. Drain Pump Strip Circuit Drain Pump Motor \ = —E- - Oe W-18 F3 All white ICE conductors 6 4 are line neutral J101 Li LJ 3 1 — 88 — Drain Hose Reassembly Drain Hose 1. To reinstall, slide the drain hose into the bottom hole on the drain box. The drain hose is used to direct the water being expelled from the tub by the drain pump to the house drain or standpipe. Drain Hose Removal 1. To remove the drain hose, squeeze the spring clamp and slide it up onto the drain hose, past where it clamps onto the drain pump and then remove the drain hose from the drain pump. Have a pan or towels under the hose when disconnecting to catch any excess water in the drain hose. 2. Unclip the two wire ties that hold the drain hose to the rear of the outer wrapper and remove the drain hose from the drain box on the rear of the washer. 2. Reconnect the spring clamps onto the drain pump and hose. Install new wire ties onto the drain hose and fasten them into the rear outer wrapper. 3. Place the drain hose back into the house drain or standpipe. NOTICE Improper placing of the drain hose can cause a siphoning action. No more than seven inches of hose should be in the house stand pipe. There must be an air gap around the drain hose. A snug fit can also cause a siphoning action. The drain hose must exceed 32 in. at some point between the washer back and drain. If this height is not obtained, the washer may not operate properly. If a longer drain hose is required, order the drain hose extension kit. Connect the additional drain hose (contained in the kit) to the original hose with the hose clamp (also contained in kit). — 89 — — 90 — = + i o i FE Hi : [- АА €o8r | © qe РОГ + о y = 8 Losr | { г} vm UN aise + $ 91-8 f ME в 4057 | ALA a Carola cc |; 1e HO IN9 (og | 5 jew) TIM TS лэцб! XX98 03 XX¥8 }IN0119 Jajesy 5 Ч e 10U61H pue XXX8g —.. pue XX€8 JUDIT nl ашпа чоцертпомоэу BLAS A и [HME GE Ei AD BAD - 431713 El Hal ELE 02M LL [HA 01) 91-44 TT MD = IN OLA (ня ОБ) TE (Hw OL) ia A y ets HAADD dol Bla a 12 |= WHO4LY Id “7 : = a = HIHSYAENS = E BL-AD IA = = fl-A JOJO ше a № : 3 ë induj 3y И ЧИ a |x |3 ; f : ; BLA MÁ He = a LOLF : coer VOLF [5%] N | EH ura r A JajeaH sis a EHd ssojonpuos о = Энци У o || UY | 1883 on . TE mw do © = ix e max = - O p.eog 19. AUL/O NI ao > LOO LI НО В ВАТА Be A HO y UA A (US Deo | OE DEN CRE NO Y SAMA — 02H DEN DEA Z WEIS NOE OAMA = ОА | DEA sen oss nos stes E ee ко e Hi = io | Foro xa a | _ Lovr 20/1 = ora E a ZE0CLr РОГ 8 à cosr 6 ë 8 3 : — Ï i i ECU syue | esusdsiq MINE Эвери LOST © Г TTT] 0er : T я = т | |» 0 A = IE y PIO D = |# |= RIÑA GRR = IR e RSR ors CE г” С O ео pio |= © FREE он deg ЗВ 5 > La L { 7 Че ВМ | a og | ©) м 3 i E — | |+ В ВВ © pieog soeuaju| Jasn 5 = pao a 8 + un 1 Ke CR | , en || 9 ¡PEZ LL ele ‚© ВОВ О BRRLZED MEL JOSUSS Fl IE ala od = : A DINSA 8| |8 o payo y ani E zo | Wsy 4567 Pr MSIE | (OD) 5 EL YIUMS SYS эроуу JOIN Jays: apoyy N 10pauvos 1ahigrvas Xx LT (eseyd 07 aseud) 1o3ON CL 13123H S'O£ dwnd uoge|na1193H G'OT dung UIe1g 008€ J0JOW 13 IUs apON OOOT [109 2AJ8A 19128 M 929UejSsISay juauodwo) (92d jojuos SU wo) POJISUVOISIP 9j/YAA SPED| 94] WOÏ PES) QUE SONJEA 9SOUI) ejge | a9uejsisay 0v8T OZT LL 029¢ 0ST 99 006€ ET $5 00Z7 OCT 67 0195 OTT EV OvOZ 00T BE 8.88 06 CE 08ZOT 08 LZ OvSET oz Le LOVLT 09 SSL IITEZ 05 OT do 922ueljsisoy | (4Zap) dua| —_ (82d 1юдисо эщр шод рераииоовр энум зрее| эцу шод реа) are sonjeA asoui) OCeT Oz 69€T S'6 TEET 9 C9ET с OBET 0 ZH pIni4 Jo Acuanbaiq | sayou SJOSUBS a1nsse1d yue1 Ying cosr |. aunssaid JusBus180 “INE XX98 S1OSUSS BRE ED 0Z-M O Te Yoru 190 Ying LOLF NE E Y ven SERE i e Toza dnd leg = Xx Y ozn yoea|g | oe om De | О DEA ur Е РЕ E Foz Too aloo DEN 0Z-M 3 LE zo ; AD [=] 02-8 02-8 № cozr XX98 Ajquessy onjea 1938 M + A+ | 0Z-M Opa 7 F a ETA a о! 0Z-M De LOLF “огл dns 180 OZ-M De Toza YES DEM DO TozN HOS des 1 02-2 102 | 0Z-M e + oa JOH XX78-XX78 Álquessy sAJeA 19)EM o|qe| a9uejsIsay JOJSILUJSU | jue] jing я ZZ siajeay yw paddinba sjapoww 76€ 19ySEQ Ul ,ZT т = 3 и эбпеб элм эуешеце sajouag — (LIM YY) L'Ob Ja) seq ui 6 9 |9 = (mm Cl a ayxsea ul en ti — “lo MO|[BA YIM UBBIDIAD СЁ 1 X 9 1 19 LoLr | — enby: y uaals).©) E EV 19Yseg ul LE : De eBueso:0O MOISAZA ; Ton OS ged aldındiA ania:N cv 49MSEQq Ul ,¡T E 0 YUldid hais CS; = |gn33n0 padung pou: soe|g:g 7H | © 3 UMOJE: SIMA 191eM Jo sausu on IND Auanbal VEN 02-8 10H abneb ap AA COLT JOJ09 SUIMI:XX 10sues ainssaid ¡9n9] 1Ja3eM qn] 0S7/ Á|quessy aAJeA 19)eM AA-KXK ÑÁay 10/09 31M — 91 — GE Top Load Washer Warranty All warranty service provided by out Factory Service Centers or an authorized Customer Care® technician. To schedule service, visit us on-line at GEAppliances.com, or call 800.GE. CARES (800.432.2737). Please have serial number and model number available when calling for service. Staple your receipt here. Proof of the original purchase date is needed to obtain service under the warranty. For The Period Of: GE Will Replace: One Year Any part of the CleanSpeak™ Top Load Washer which fails due to a From the date of the defect in materials or workmanship. During this limited one-year original purchase warranty, GE will also provide free of charge, all labor and in-home service to replace the defective part. What GE Will Not Cover о Service trips to your home to teach you how « Failure of the product if it is abused, to use the product misused, or used for other than the intended * Improper installation, delivery or purpose or used commercially maintenance * Incidental or consequential damage caused * Replacement of house fuses or resetting of by possible defects with this appliance. circuit breakers « Cleaning or servicing of the air gap device in Product not accessible to provide required the drain line. service « Damage caused after delivery, including * Damage to the product caused by accident, fire, floods or acts of God. damage from items dropped on the door. one year or the shortest period allowed by law. EXCLUSION OF IMPLIED WARRANTIES — Your sole and exclusive remedy is product repair as provided in this Limited Warranty. Any implied warranties, including the implied warranties of merchantability or fitness for a particular purpose, are limited to This warranty is extended to the original purchaser and any succeeding owner for products purchased for home use within the USA. If the product is located in an area where service by a GE Authorized Servicer is not available, you may be responsible for a trip change or you may be required to bring the product to an Authorized GE Service location for service. Proof of original purchase date is needed to obtain service under the warranty. In Alaska, the warranty excludes the cost of shipping or service calls to your home. Some states do not allow the exclusion or limitation of incidental or consequential damages. This warranty gives you specific legal rights, and you may also have other rights which vary from state to state. To know what your legal rights are, consult your local or state consumer affairs office or your state's Attorney General. Warrantor: General Electric Company, Louisville, KY 40225 — 92 — — 93 —
advertisement
* Your assessment is very important for improving the workof artificial intelligence, which forms the content of this project
Related manuals
advertisement