- No category
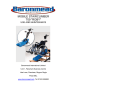
advertisement
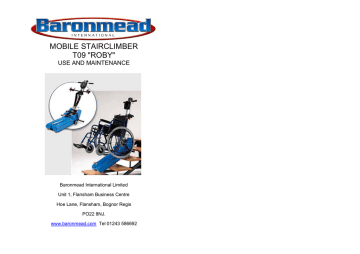
MOBILE STAIRCLIMBER
T09 "ROBY"
USE AND MAINTENANCE
Baronmead International Limited
Unit 1, Flansham Business Centre
Hoe Lane, Flansham, Bognor Regis
PO22 8NJ. www.baronmead.com
Tel 01243 586692
CE DECLARATION OF CONFORMITY
The Manufacturer:
VIMEC, Via Parri n. 7, 42045 Luzzara (R.E.) ITALY declares on its own responsibility that the mobile Stairclimbers for the transport of person on wheelchair model:
T09
comply with the following European Directives:
• Directive 89/336 "Electromagnetic Compatibility" as modified by
Directive 92/31/CE
• Directive 93/42 "Medical Devices" (Category I)
Managing Director
Ing. Pier Franco Linari
Luzzara, 01/02/2006
1
USE AND MAINTENANCE
GENERAL CONTENTS
1. Unit and manufacturer identification
2. Service
3. Description of unit
4. Technical data
5. Permitted use of the unit
6. Transport
7. Preparation for use
8. Preparation for daily use
9. Maintenance
10. Vibrations - aerial noise of unit
11. Information about components and materials disposal
12. Instruction summary.
13. Reversing wheelchair handle clamps
Page 3
Page 4
Page 4
Page 7
Page 9
Page 10
Page 11
Page 13
Page 21
Page 23
Page 24
Page 25
Page 27
STAY SAFE!
ATTENTION
This symbol indicates important instructions for safety.
While all the instructions are important, please pay particular attention to these.
Carefully read this manual before undertaking the assembly, use and maintenance of the unit.
2
3
Pay due care and attention while operating this machine to minimise the risk of accidents.
Follow all the instructions for the T09 including all the stickers applied to the unit.
Immediately replace any damaged stickers.
Only trained staff are to operate the unit.
Observe the Training level for different activities with reference to the following symbols:
O Trained operator
OS Manufacturers authorised agent
The unit should only be used by a RESPONSIBLE ADULT who is trained in all operating functions described in this manual.
1) UNIT AND MANUFACTURER IDENTIFICATION
2) SERVICE
To arrange a service for your T09 stairclimber, please contact Baronmead on Tel 01243 586692
3) DESCRIPTION OF UNIT
3.1) Description
Chassis - Fig. 1/a
It is composed of:
- light alloy frame & plastic cover
It contains:
· Motor & gearbox
· Tracks;
· Transit wheels for level surface use;
· Electrical control system.
· Battery;
· Integral battery charger.
On the chassis control panel you can find the following:
- Control handle release lever
(Fig. 2\a);
- Plug for battery charger (Fig.
2\b);
- Battery charge condition indicator led (Fig.2/c).
- Rocker switch to drive base unit
(Fig. 2/d);
4
Control handle - Fig. 3/a
The control handle secures the wheelchair onto the stairclimber while on the stairs or on landings.
The control handle also has the main controls to drive the mobile stairclimber.
It contains:
- Wheelchair attachment clamps
(Fig. 3/c);
-Height and width adjustable attachment clamp cross member
(Fig. 3/d);
- Wheelchair wheels support cross member (Fig. 3/e);
- Adjustable headrest (Fig. 3/b);
- Automatic electrical connector for the chassis (Fig. 3/f).
The drive control panel (Fig.4/f) includes:
5
- Up / Down pushbuttons (Fig. 4\a);
- Emergency stop switch (Fig. 4\b);
- Gradient indicator (Fig. 4\c);
-Battery discharge indicator (Fig.
4\d):
· Flat battery - slow flash;
· Motor high temperature
– fast flash;
· Motor jammed - double fast flash
compared to motor high temperature.
-
“ON/OFF” key (Fig. 4/e).
Battery charger on machine
Recharge the battery after use of mobile stairclimber to maintain the battery condition when the unit is not used. Technical data and the use and maintenance instructions are listed in the manual enclosed with the battery charger.
3.2) Main precautionary measures for wheelchair mounting.
Wheelchair clamping to the Control Handle
- Lock knobs clamping levers with return spring (Fig.6\a).
- Hand wheel of the wheelchair clamping cross member with return spring
(Fig. 6\c).
- Clamping hand wheel (Fig. 6/b).
3.3) Main precautionary measures for operation on stairs.
- Optical indicator of maximum gradient (Fig. 4\c).
3.4) Warning and instructions
Always comply with the following warnings and instructions:
- Always fasten safety belts.
- Use both hands whenever using the T09.
- Do not leave the unit loaded.
- Details for the wheelchair loading.
6
3.5) Operating position
The operator should always be behind the Control Handle, firmly holding the handles (Fig. 4/f).
3.6) Components
- Chassis (Fig. 1\a).
- Control Handle (Fig. 3\a).
- Charge cable (Fig. 5/a).
3.7) Technical standards
The unit complies with the following standards:
STANDARD 93/42/CEE
Concerning medical devices.
STANDARD 89/336
Electromagnetic compatibility as modified by Standard CE 92/31.
4) TECHNICAL DATA
- Drive gear
Irreversible Worm Screw reduction gear
Toothed belt with rubber tracks
Driving pulley
Transit wheels for the transfer on the level
- Performance
Running direction
Speed (upwards/downwards)
7
Capacity
Rated load
Geometrical features of the stair
Ratio 1/50
HTD-8M z=40 n° 4 wheels on ball bearings
Forward/Backward
5 m/min.
1 person with wheelchair
130 kg
See Fig. 8
- Environmental conditions
Temperature
Humidity -max.
- Overall dimensions
Machine body
Control Handle
- Weight
Machine body
Control Handle
- Electrical installation
D.C. Motor Brushless
Electrical input
Battery charger on machine
Non spillable AGM battery
Battery recharge time
Fuse
- Controls
Timed start push button (Forward/backward)
Emergency stop push button
- Indicators
Battery charge display
Gravity gradient visual signal
0° - +45°C
90%
See Fig. 7
See Fig. 7 kg 37 kg 10
24V
25 A
230V AC 50 Hz to 24V DC 3A
2x 12V 12Ah
8 hours from flat
40 A
Delay of 1 second
(Fig. 4/b)
(Fig. 4/d)
(Fig. 4/c)
8
Fig. 7
5
) Permitted use of the unit
5.1) Permitted use
Mobile stairclimber Model T09, has been designed for the transport of disabled persons on manual self propel wheelchair on staircases with the following features:
- Environment:
- Steps:
Indoor/outdoor
Parallel, without coatings
- Gradient:
- Step-riser height:
Maximum 35° (Fig. 8/a)
Maximum 180 mm, min. 100 mm (Fig. 8/A)
- Step nose radius: From 0 to 20 mm (Fig. 8/R)
- Attendant: Always present and with the following characteristics:
A physically and mentally suitable adult, familiar with the operation of the equipment and maintenance instructions.
9
5.2) Unsuitable environments
Environment: Potential problems
Use on staircases with gradient over 35°: Instability, tracks skidding
Use on steps with riser height over 180 mm: Instability, tracks skidding
Use on steps with riser less than 100 mm:
Use on steps with a nose radius higher than 20 mm:
Tracks skidding
Tracks skidding
Un-trained operator:
Transport of Power chairs
Potential Instability
Not suitable
Transport of people or things not seated on the wheelchair Not suitable
Use on wet or icy stairs: Instability, tracks skidding
Use in water or in rain:
Use on staircases with non parallel steps:
Electric installation failure
Instability, lateral tilting
WARNING: DO NOT MODIFIY FOR UNINTENDED USES.
6) TRANSPORT
6.1) Handling
The dismantled unit can be carried or for loading / unloading. The base section can be carried by using the handles on either end (Fig. 9\a and b).
Base weight complete with battery: 37 Kg
Control Handle weight: 10 Kg
For ergonomic reasons, the base will need to be lifted by two people.
6.2) In When not in use:
- Place the machine in a dry room.
- Cover to protect from dust / dirt.
- Never leave the machine open to the weather.
10
6.3) Position of the centre of mass (Fig. 10\a)
It is located between the Control
Handle and the chassis when assembled.
7) PREPERATION FOR USE
7.1) Initial Set up.
Before setting up, read the manual carefully.
Package opening
- Cut the protective film by using a knife. Do not cut or heat the box.
- Take care not to damage the surfaces of the unit.
- Clean the unit, taking away all residual packaging and dust.
7.2) Disposal of package material
Dispose of the packaging responisbly.
7.3) Preliminary checks
Checks to carry out before using:
Competence: OS - Manufacturers authorised agent.
11
MACHINE CHECK:
Check the following for correct function.
Control Handle:
- Correct clamping of the Control
Handle (Fig. 11):
- Wheel chair catches (Fig. 6/a):
Smoothness, safe return to the lock position.
- Safety belts: Condition, security and catch operation.
- Controls:
Correct action of the controls;
Correct timing of the controls;
Efficiency of the emergency stop (Fig.
4/b).
- Indicators:
Efficiency of the battery charger signal
(Fig. 4\d);
Efficiency of the gradient indicator
(Fig. 4\c).
Machine body:
- Battery charger:
Voltage and frequency as in paragraph
7.5.
7.4) Environmental conditions for the operating location.
- Temperature: From 0 °C to +45 °C
- Humidity: Max 90%
12
7.5) Electrical connection
The input for the battery charger is an IEC socket. The user should connect the battery charger to a supply conforming to the standards for the civil use electrical units, equipped with an appropriate switch.
Battery charger data:
- Input Voltage:
- Frequency:
- Output Voltage:
8) PREPARATION FOR DAILY USE
230V ac.
50 Hz
24 V dc / 3A
8.1) Control Handle assembly and clamping
a) Place the control handle (Fig. 11/a) carefully on the mounting bar (Fig.
1/b) on the base.
b) Incline the control handle (Fig. 12/a) as shown by the arrow (Fig. 11/b) until it is locked to the base.
c) Once the control handle is locked (Fig. 12/a), protect the release lever pushing on the cover (Fig. 12/b).
WARNING: Ensure that the safety cover is in its proper position.
In this position, the safety switch is activated and the Control
Handle is locked in the work position. To switch on the machine, insert the key (Fig. 4/e); the push buttons (Fig. 4/a) on the
Control Handle allows the operating of the tracks forwards - backwards.
* If the red cover is not in its proper position, drive of the
machine is inhibited.
13
8.2) Control Handle release
To release the control handle (Fig. 13/a) ,lift the red safety cover (Fig.13/b) and then, while the release pedal (Fig. 14/b) is being pressed, push the control handle (Fig. 14/a) forward as shown by the arrow (Fig. 14/c).
8.3) Wheelchair clamping
a) Insert the key (Fig. 15/a) for stair climber activation
(Fig. 15/b). into its appropriate socket
b) Lock the wheelchair brakes. By pressing down on the control handle, tilt the mobile stairclimber back onto its transit wheels and push it under the wheelchair (Fig. 16/a).
c) Holding the control handle (Fig.
13/a), lift the red cover (Fig. 13/c) with your foot, exposing the handle release lever (Fig. 13/b).
d) Press the lever (Fig. 14/b) downwards in order to release the control handle (Fig. 14/a) and, push it forward (Fig. 14/c), bring it to the wheelchair seat back (Fig. 16/c).
e) Unscrew (Fig. 17/b) the knob (Fig.
17/a) placed on the rear face of the control handle, push the metallic central pushbutton (Fig. 17/c) and slide the arms
(Fig. 17/d) until they are brought under the handgrips of the wheelchair (see Fig.
16).
NOTE: Carry out this operation holding the crosspiece as shown in Fig. 17/e.
14
f) Adjust the handle clamp width (Fig. 18/a) according to the wheelchair handle width: unscrew the knob (Fig. 18/b) and move the handle clamp sideways (Fig.18/c). Repeat for the other side.
g) Grasp the plunger (Fig. 19/a) by hand and lift it. Then swing the hook
(Fig.19/b) past the plunger and hook it to the wheelchair frame (see
Fig.16/e), then release the plunger and ensure that the hook can’t open,
Repeat for the other side.. Finally, tighten the knobs (Fig. 18/b).
IMPORTANT: do not clamp handles or other objects that are not firmly attached to the wheelchair.
h) Lean the control handle back (Fig.
11/b) until it can be locked to the drive unit. For this operation i t’s possible to place your foot on the bar provided on the base unit (Fig. 16/f).
i) Close the safety cover (Fig. 12/b) by foot.
j) Now the machine is ready (the green led on the control handle cover will light up when drive switches are pressed and the wheelchair is properly locked and anchored to the stair climber).
k) Pressing downwards on the control handle the transit wheels are activated and the first step of the flight can be reached to perform the climb or descent (Fig. 27 and 29).
WARNING: Always fasten the seat belt before use.
15
WARNING: Hold the Control Handle firmly, even when on level ground, when a passenger is on the machine.
8.4) Travel preparation a) BATTERY:
Check the battery state after having assembled the machine; activating drive for a moment when the machine is empty (with no one on board).
The use of the machine when the indicator led is blinking could damage the battery. b) SIGNALS:
Do not use the mobile stairclimber on unfamiliar stairs before checking the gradient indicator.
If the gradient indicator does not work, DO NOT USE THE
TRACK MOBILE STAIRCLIMBER! Call Baronmead operative immediately. c) EMERGENCY:
Check the emergency
STOP operation (red push-button on control panel).
- Press the push-button: the drive controls should be inhibited.
- Reset the push-button pulling it out.
If the emergency STOP does not work, DO NOT USE the mobile stairclimber! Call Baronmead operative immediately.
Do not move the mobile stairclimber with a person on board before carrying out all operations described in paragraph 8.3.
16
NEVER LEAVE THE MACHINE UNATTENDED WITH A
PASSENGER ON BOARD.
8.5) Manual operation on level surfaces
To move quickly over longer distances and to turn the machine, it is necessary to operate manually:
a) Using the Control Handle as a lever, raise the tracks off the ground to allow the machine to roll on its transit wheels.
b) Push the unit in the desired direction.
8.6) Stair gradient check
This check should be done on all new locations.
a) Check that the step riser is not greater than 180 mm (Fig. 8).
b) Operating manually, without person on board, on approaching the first stage of the stair to travel, press the push button control (Fig. 4/a), travel on a section of stair, release the push button and make sure that the gradient indicator placed (Fig. 4\c) on the
Control Handle is green (Gradient under 35°). If the indicator is red
(Gradient above 35°), it is not possible to travel on that staircase.
Green indicator: correct gradient
Red indicator: excessive gradient
8.7) Headrest adjustment
To adjust the headrest (Fig. 20/a):
Remove the headrest and adjust it using two Velcro stripes (Fig. 20/b).
17
WARNING: THE MOBILE STAIRCLIMBER OPERATOR
DETERMINES THE STABILITY OF THE UNIT. TO AVOID
UNSTABLE CONDITIONS PLEASE FOLLOW THE POINTS
BELOW.
8.8) Operation on staircase
The unit should be always placed so as the control handle is towards the upward side. If during the stair operation, the mobile stairclimber continues to operate when the push button is released, press the emergency STOP red push button on the Control Handle control panel. Afterwards follow section 8.9.
8.8.1) Stair ascent operation
a) Operate manually as in section 8.5.
Advance the mobile stairclimber with the person on board to the first step of the flight (Fig. 21/a).
- If you must travel just one flight, position the mobile stairclimber in the middle of the staircase.
- If there is more than one flight of stairs, travel as near the inside handrail as possible or near the inside wall; this position makes manual operation on landings easier.
The mobile stairclimber should be perpendicular to the steps; it is not possible to travel on staircases diagonally.
b) Press the
“up” push button holding the Control Handle firmly with two hands, travel up the flight until the STOP sticker(Fig.
22/a) aligns with the nose of the last step (Fig. 22/b).
18
c) Release the drive button, and lower the Control Handle slowly (Fig.22/c).
If the staircase comprises two or more flights, operate manually and approach the second flight. Repeat the previous operation.
WARNING: The lugs on the tracks can slide on the step nose during operation and while resting on the staircase. In extreme circumstances, this could cause the mobile stairclimber to tip forward. For this reason, firmly hold the
Control Handle firmly, even when stationary, whenever a passenger is transported.
8.8.2) Stair descent operation
a) Operate manually as in section 8.5.
Approach the first step (Fig. 22/b) of the flight you must travel on, until the mobile stairclimber has arrived with the message STOP at the beginning of the flight (Fig.22/a).
- Stair with one flight:
Locate at the centre of the staircase, with the machine placed in axis to the staircase.
- Stair with more flights:
Place the unit towards the stair well inner edge, taking care of being in square with the staircase (see
8.8.1a).
WARNING: The machine should be always perpendicular to the step.
b) Raise the Control Handle (Fig. 22/d) until the tracks have touched the lower step, press the downwards push button and travel down the stairs taking care to hold the Control Handle firmly in both hands.
c) At the end of each flight, the side mobile wheels (Fig.23/a) will automatically position for the next manual operation.
19
this reason, firmly hold the Control Handle, even when on level ground, when the user is transported.
8.9) Emergency stop on the staircase
WARNING: there is the possibility that the track lugs may slide on the nose of the stair during the operation of the mobile stair climber.
This could cause the mobile stairclimber to tip forward. For
In case of an emergency stop on a staircase flight, do not release the control handle
When the unit is locked, make sure of the vehicle stability before leaving the Control Handle.
If the track mobile stairclimber stops in the upward direction due to discharged battery, it is possible to rescue the passenger by reversing the direction and bringing him to the lower level.
8.10) Passenger release
a) At the end of the journey, release the Control Handle. b) Push the Control Handle forwards until the wheelchair touches the ground. c) Raise plunger (Fig. 24/a) and retract red lever (Fig. 24/b) outwards.
Loosen handwheels (Fig. 25/a). d) Lower the Control Handle and re-clamp it to the chassis. e) Remove the mobile stairclimber manually from under the wheelchair.
20
8.11) Passenger recovery
IMPORTANT: in case of an emergency stop on the stairs, it is absolutely forbidden to release the Control Handle.
If the mobile stairclimber stops when in the upward direction due to discharged battery, it is possible to rescue the transported user by reversing the direction and bringing him back to the lower level.
WARNING: if it’s not possible to come back to the lower floor, move the machine by using the handle control device for its handling (Fig.26/a) supplied in equipment.
9) MAINTENANCE
The unit requires maintenance and service by an approved operative every six months.
It is very important to check the following parts regularly:
Competence level: O - Trained operator
Detail / Component Check frequency
a) Rubber tracks
b) Control Handle clamping
c) Wheelchair clamping monthly
monthly monthly
d) Battery
e) Control Handle connector
f) Electrical loom & fuses
g) Indicators before every use
monthly monthly before every use
h) Emergency STOP switch before every use
The tests to carry out for every point a).....f) are the following:
a) The tracks must not show any wear or cuts or lugs excessive wear.
21
b) Make sure that the wheelchair release mechanism is intact and in working order.
c) The batteries are sealed and maintenance free. They must be kept on charge by connecting the battery charger using the cable supplied, during the periods when the machine is inactive.
d) Check the IEC charger socket is undamaged.
e) Check that the status light on the control handle is activated shortly after pressing the up / down buttons.
f) Check the emergency STOP red button operation. Push the red button: the controls should be deactivated. Reset the push button pulling it upwards.
If the result of every check is not positive, contact
BARONMEAD agent. See chapter 2.
9.1) Periodic cleaning of the unit
Competence: O - Trained operator
Frequency: Quarterly
In operations that require the removal of the covers, switch off at the mains and remove the charge cable before proceeding.
In order to maintain reliable operating, it is necessary to keep the machine clean both inside and out.
Cleaning instructions:
- Turn off the mains supply and remove the power cable.
- Remove the covers by unscrewing the 8*fixing screws.
- Remove dust, dirt and grease marks.
22
- At the end of cleaning, replace the covers and reconnect the mains connector.
Battery charger:
When the battery charger reaches the yellow led (Fig.27/a) the machine can be used because the battery has reached the 3/4 of its charge. Every 7 or 8 partial charges it’s good thing, in order to save the battery, to carry out the complete battery charge until the green led is reached (Fig.27/b) (after about 11 hours of charge).
It’s not possible to use the machine while charging the battery.
9.2) Defects - Possible causes
–
Competence: O - Trained operator
Possible cures
Defects
The unit does not move in either direction.
Possible causes
Starting key
Emergency STOP
“in”
Handle lock up (fig. 14)
Discharged battery
Damaged battery
Discharged battery
Possible cures
Insert the ON/OFF key
Pull out
Press down
Recharge
Replace
Safety lock out at a charge percentage of 10%
If the malfunction persists, contact a BARONMEAD operative.
10) UNEXPECTED MOVEMENT AND NOISE OF THE UNIT a) Unexpected movement
As every staircase can have different pitch, occasionally the T09 will move downward slightly while operating due to the track lug not engaging fully with the stair nose this is:
- infrequent with moderate acceleration;
23
-momentary disruption for the operator and passenger as the next lug locates on the stair nose.
This does not affect the safe operation of the machine. b) Aerial noise: less than 70 db.
11) INFORMATION ABOUT PARTS AND MATERIALS DISPOSAL a) Rubber and plastic materials disposal
Dispose of used parts responsibly in accordance with the local regulations in force; contact your local council if in doubt.
b) Battery disposal
Where possible, recycle batteries at an authorised recycling site, if this facility is not available, dispose of responsibly in accordance with the local regulations in force, contact your local council if in doubt.
24
12) Instruction Summary
12.1) Descent
1st phase: Once the wheelchair is properly locked (the green light must be lighted up on the panel), by a soft pressure downwards (Fig. 28/b), on the control handle, lift the nose of the machine (Fig.28/d), activating the transit wheels (Fig. 28/c). In this way it’s possible, with little effort, to move
3rd phase: gently tilt the machine forward (Fig. 29/c) until the tracks are resting on the stairs. Now, press the down pushbutton (remember that the start is delayed of about one second), the machine will start to descended the stairs.
25 the machine to the edge of the first stair of the flight (Fig. 28/a).
2nd phase: Activate the down pushbutton until the STOP sticker
(placed on the base of the cover) lines up (Fig.29/a) with the edge of the first stair (Fig.29/b).
4th phase: When end of the flight is reached, drive until the machine is flat, press the control bar downwards again to activate the transit wheels, then at the same time, push and turn the machine placing it again on the edge of the first stair of the next flight
(see Fig. 30), paying attention to stop on the STOP. Now the 3rd phase can be carried out again.
WARNING: ALWAYS
HOLD THE CONTROL
HANDLE FIRMLY!
12.2) Climb
1st phase: Remember that moving the machine on the plane it’s required to exert a soft pressure downwards on the control handle (Fig. 31/b), bring the machine to the first stair of the flight (Fig. 31/a) taking care of keeping the machine square to the staircase.
2nd phase: Now keeping the up pushbutton pushed (remember that the start is delayed of about one second), start the climb.
3rd phase: Once the last stair is reached, stop the machine when the
STOP sticker (placed on the base of the truck) (Fig. 32/a) aligns with the edge of the stair (Fig.32/b), then gently lean the machine onto the landing, tilting the machine as shown in Fig. 32/c.
4th phase: When the top of the flight is reached, once the machine is flat, press downwards on the control handle again to activate the transit wheels, then, at the same time, pull and turn the machine bringing it to the first stair of the next flight,
26
paying attention to place it square to the staircase (see Fig. 33). Now, climb the next flight or, if the final destination is reached, release the wheelchair.
WARNING: ALWAYS
HOLD THE CONTROL HANDLE
FIRMLY!
13) REVERSING WHEELCHAIR
HANDLE CLAMPS
on the market, there are not only wheelchairs equipped with push handles (Fig. 34/a) but also wheelchairs in which the push handles are replaced by a cross bar
(Fig.35/a) placed in the rear part on the seat back. In these cases the safety couplings (Fig. 36/a), because it is equipped with a second hole (Fig.
36/b), can be rotated of 90° so that the red hook (Fig. 36/c) grasps the shackle from below and not sideways, clamping the wheelchair to the control handle with the same
3) Rotate the safety coupling
(Fig.37/a) by 90° (Fig.37/b), to the left for the left one and to the right for the right one;
4) Insert the rotated coupling (Fig.
37/c) onto the arm (Fig.37/d). Rescrew the setscrew into the end of control handle arms.
5) Bring the control handle (Fig.38/a) to the seat back of the wheelchair
(Fig.38/b). Pull the safety plunger (Fig.
38/c), hook the shackle (Fig. 38/d) using the hook (Fig. 38/e) and release the plunger (Fig. 38/c).
NOTE: ensure that the plunger (Fig.
38/c) is placed under the red hook
(Fig. 38/e) so that it can’t be released from the wheelchair (Fig.
38/d);
safety of the traditional wheelchairs.
In order to carry out this operation follow this procedure:
1) Remove the clamping screw placed in the end of the control handle arm
(Fig.36/d) and loosen the locking hand-wheel (Fig. 36/e);
2) Extract the safety clamp (Fig. 36/a) toward the outside (Fig. 36/f);
27
6) Lock the coupling turning the hand-wheel (Fig. 38/f).
7) Lift the arms (Fig. 38/g) until the point in which the red hook (Fig.
38/e) is placed in contact to the shackle (Fig. 38/d) is reached.
28
29
Base Drive Unit
7801211
30
Base Drive Unit
– 7801211.1
28
29
30
31
24
25
26
27
32
33
20
21
22
23
16
17
18
19
12
13
14
15
8
9
10
11
4
5
6
7
Part
1
2
3
34
31
804035
12956
1044147
2864208
2864209
804027
10907
2864210
714016
12809
12800
904262
12170
2384099
1044146
992027
12052
1022095
12906
Code
4294642
4294643
3702021
3702020
1004017
12389
11062
2824457
1304325
992004
12041
6064163
11053
12959
10433
2
1
1
2
2
1
2
2
4
3
3
1
2
4
2
2
4
2
1
2
8
2
4
1
1
2
2
2
2
4
2
Qty. Description
1 RH GUIDE
1
2
LH GUIDE
WHEEL
WHEEL
NO STEP Sticker
5x15x1 WASHER
M8x35 SCREW
GUARD
PIN
SPACER
RING
VIMEC ADHESIVE LABEL
M5x12 SCREW
M8 NUT
M8x16 SCREW
PULLEY
8,4x17x1,6 WASHER
WHEEL
LH BRACKET
RH BRACKET
PLULLEY
M6 NUT
BRACKET
SPRING
6x6x20 TANG
5x5x50 TANG
SPACER
RING
DRIVE SHAFT
GEARWHEEL
20x28x1 WASHER
RING
BEARING
RING
55
56
57
58
59
51
52
53
54
60
61
62
63
64
65
66
47
48
49
50
43
44
45
46
39
40
41
42
35
36
37
38
12992
782012
7007426
12956
6882008
484031
1004018
10529
824005
10396
904273
904276
6882004
12918
10316
1004021
1004019
6014005
2384100
1044145
12993
10435
12807
12909
12943
10190
12373
11055
2594470
2304758
10079
2304761
1
1
1
4
2
2
1
1
1
2
2
1
4
2
2
1
1
1
7
1
1
4
4
4
2
6
1
3
2
1
1
1
STOP ADHESIVE
REDUCTION GEAR
REDUCTION GEAR SHAFT
GEARWHEEL
M6x30 SCREW
M8x20 SCREW
A6x6x45 TANG
8x32x2,5 WASHER
5x5x20 TANG
M6x20 SCREW
6,4x12,5 WASHER
M6x35 SCREW
PLATE
PLATE
M3x10 SCREW
PLATE
M6x40 SCREW
ELASTIC BELT
EMERGENCY MOVE KIT
8,4x17x1,6 WASHER
PLATE
CAP
ITALY FLAG LABEL
M5x16 SCREW
TRACK
M5x10 SCREW
SPACER
SPACER
SUPPORT
A5x5x15 TANG
8x24x2 WASHER
STICKER
32
33
Control Handle - 7801212
12
13
14
15
8
9
10
11
4
5
6
7
Part
1
2
3
20
21
22
23
24
16
17
18
19
37
38
39
40
33
34
35
36
29
30
31
32
25
26
27
28
41
42
43
44
45
Code
10007
6064342
10673
28941117
482019
4254562
782020
3424422
28941118
482020
11052
28941128
4692004
1304028
164105
1004016
2564055
902007
4692006
12376
10378
28941130
12956
12941
10648
2304798
2864941
11053
6064329
1044033
6064309
6064330
10990
4694002
12188
1304329
12984
712053
12376
10033
28941108
874150
404039
10239
10945
1
1
2
1
2
1
1
2
2
4
1
1
1
1
1
1
1
4
1
1
1
2
2
1
2
2
2
2
2
2
1
2
2
2
1
1
2
2
1
2
1
1
Qty. Description
1 M3 NUT
1
4
KEY-RING
3,5x13 SCREW
PROFILE
SUPPORT TERMINAL
WHEELCHAIR WELDED COUPLING
SAFETY BELT
M8 120x18x5 PLATE
PROFILE
CAP
M8x12 SCREW
RH BLOCK
M8x25 BALL GRIP
PIN
BUSH
ADHESIVE LABEL WITH ARROW
BRACKET
BUSH
BALL GRIP
10,5x21 WASHER
M10x45 SCREW
LH BLOCK
8,4x17x1,6 WASHER
WASHER
4,2x9,5 SCREW
PLATE
PLATE
M5x12 SCREW
INSTRUMENT BOARD STOP ADHESIVE
WHEEL
KEY ADHESIVE
PLATE
6,3x19 SCREW
BALL GRIP
RING
PIN
20x28x0,5 WASHER
SPRING
10,5x18 WASHER
M10 NUT
SUPPORT
RUDDER INSTRUMENT BOARD
VELCRUM
M3x25 SCREW
M10x35 SCREW
Base / Handle coupling - 7801213
Code
2784359
4004167
12372
712044
904260
1304325
164047
10023
992004
12041
3084070
10679
10698
10433
11053
10081
484026
2255348
10005
10007
804035
1004014
2874195
1304324
10518
1304326
2304814
12054
484030
712045
10001
12370
12956
11060
12959
10027
10893
6882009
Base / Handle coupling - 7801213.1
11
12
13
14
7
8
9
10
Part
1
2
3
4
5
6
19
20
21
22
23
15
16
17
18
32
33
34
35
36
37
38
28
29
30
31
24
25
26
27
2
1
1
2
2
2
2
2
1
2
2
1
2
1
1
1
3
2
1
1
4
2
1
1
1
2
4
2
2
2
2
2
Qty. Description
1 STRUCTURE
1
1
RUDDER COUPLING/RELEASE DEVICE
5,5x10 WASHER
2
2
1
GRIPPING SPRING
SPACER
PIN
BUSH
M8 NUT
SPACER
RING
CONNECTING ROD
M6x10 SCREW
3,5x13 SCREW
M8x16 SCREW
M5x12 SCREW
M3x12 SCREW
CAP
SHEATH
M4 NUT
M3 NUT
PULLEY
BATTERY CHARGER ADHESIVE LABEL
PEDAL COVER
PIN
M3x16 SCREW
PIN
PLATE
FIXER
CAP
GRIPPING SPRING
M3 NUT
3,2x6 WASHER
8,4x17x1,6 WASHER
DOWEL
M8 NUT
M8 NUT
M4x12 SCREW
PLATE
35
Loom components
–7801215
6
7
8
9
Part
1
2
3
4
5
10
11
12
13
14
15
37
Code
2255338
2262019
2255212
2255336
2255337
2255345
1802004
1852003
1824010
1902023
1852018
8884908
1702003
1714092
8884909
1
1
1
2
1
1
2
1
1
1
Qty. Description
1 SHEATH
1
1
1
1
TAP+CABLE+PLUG
SHEATH
SHEATH
SHEATH
PUSHBUTTON
5 mm LED-HOLDER
PUSHBUTTON
PLUG KEY+RING
MICROSWITCH
PUSHBUTTON
FEEDER
BATTERY
24 V 0,5 Kw MOTOR
DISPLAY
advertisement
* Your assessment is very important for improving the workof artificial intelligence, which forms the content of this project
Related manuals
advertisement