O.S. Engine MAX-40FX Instruction manuals
Add to My manuals22 Pages
O.S. engine MAX-91FXRING is a powerful and reliable engine that is perfect for a variety of radio-controlled aircraft. With its advanced features and precision engineering, the MAX-91FXRING delivers exceptional performance and durability.
Here are some of the key features of the MAX-91FXRING:
- Powerful 91 cubic inch displacement for plenty of power and torque
- Advanced carburetor design for precise fuel metering and smooth running
- Durable construction with high-quality materials for long life
- Easy to start and operate, even for beginners
- Versatile and can be used in a variety of aircraft types
advertisement
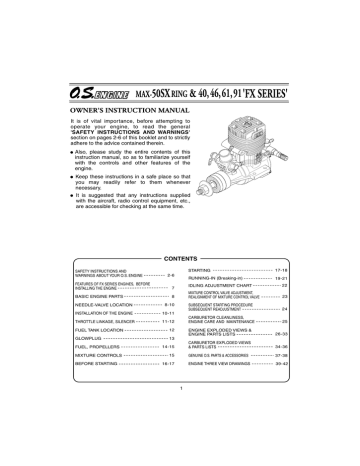
It is of vital importance, before attempting to operate your engine, to read the general
'SAFETY INSTRUCTIONS AND WARNINGS'
section on pages 2-6 of this booklet and to strictly adhere to the advice contained therein.
Also, please study the entire contents of this instruction manual, so as to familiarize yourself with the controls and other features of the engine.
Keep these instructions in a safe place so that you may readily refer to them whenever necessary.
It is suggested that any instructions supplied with the aircraft, radio control equipment, etc., are accessible for checking at the same time.
SAFETY INSTRUCTIONS AND
WARNINGS ABOUT YOUR O.S. ENGINE
FEATURES OF FX SERIES ENGINES,
BEFORE
INSTALLING THE ENGINE
BASIC ENGINE PARTS
NEEDLE-VALVE LOCATION
INSTALLATION OF THE ENGINE
THROTTLE LINKAGE, SILENCER
FUEL TANK LOCATION
GLOWPLUG
FUEL, PROPELLERS
MIXTURE CONTROLS
BEFORE STARTING
8-10
10-11
11-12
7
8
12
13
14-15
15
16-17
CONTENTS
2-6
STARTING
RUNNING-IN (Breaking-in)
IDLING ADJUSTMENT CHART
MIXTURE CONTROL VALVE ADJUSTMENT,
REALIGNMENT OF MIXTURE CONTROL VALVE
SUBSEQUENT STARTING PROCEDURE
SUBSEQUENT READJUSTMENT
CARBURETOR CLEANLINESS,
ENGINE CARE AND MAINTENANCE
ENGINE EXPLODED VIEWS &
ENGINE PARTS LISTS
CARBURETOR EXPLODED VIEWS
& PARTS LISTS
GENUINE O.S. PARTS & ACCESSORIES
ENGINE THREE VIEW DRAWINGS
17-18
19-21
22
23
24
25
26-33
34-36
37-38
39-42
1
SAFETY INSTRUCTIONS AND WARNINGS ABOUT YOUR O.S. ENGINE
Remember that your engine is not a "toy", but a highly efficient internalcombustion machine whose power is capable of harming you, or others, if it is misused.
As owner, you, alone, are responsible for the safe operation of your engine, so act with discretion and care at all times.
If at some future date, your O.S. engine is acquired by another person, we would respectfully request that these instructions are also passed on to its new owner.
The advice which follows is grouped under two headings according to the degree of damage or danger which might arise through misuse or neglect.
WARNINGS
These cover events which might involve serious (in extreme circumstances, even fatal) injury.
NOTES
These cover the many other possibilities, generally less obvious sources of danger, but which, under certain circumstances, may also cause damage or injury.
2
WARNINGS
Never touch, or allow any object to come into contact with, the rotating propeller and do not crouch over the engine when it is running.
A weakened or loose propeller may disintegrate or be thrown off and, since propeller tip speeds with powerful engines may exceed 600 feet(180 metres) per second, it will be understood that such a failure could result in serious injury, (see 'NOTES' section relating to propeller safety).
Model engine fuel is poisonous. Do not allow it to come into contact with the eyes or mouth. Always store it in a clearly marked container and out of the reach of children.
Model engine fuel is also highly flammable. Keep it away from open flame, excessive heat, sources of sparks, or anything else which might ignite it. Do not smoke or allow anyone else to smoke, near to it.
Never operate your engine in an enclosed space. Model engines, like automobile engines, exhaust deadly carbonmonoxide. Run your engine only in an open area.
Model engines generate considerable heat. Do not touch any part of your engine until it has cooled. Contact with the muffler (silencer), cylinder head or exhaust header pipe, in particular, may result in a serious burn.
3
NOTES
This engine was designed for model aircraft. Do not attempt to use it for any other purpose.
Mount the engine in your model securely, following the manufacturers' recommendations, using appropriate screws and locknuts.
Be sure to use the silencer (muffler) supplied with the engine. Frequent exposure to an open exhaust may eventually impair your hearing.
Such noise is also likely to cause annoyance to others over a wide area.
If you remove the glowplug from the engine and check its condition by connecting the battery leads to it, do not hold the plug with bare fingers.Use an appropriate tool or a folded piece of cloth.
Install a top-quality propeller of the diameter and pitch specified for the engine and aircraft. Locate the propeller on the shaft so that the curved face of the blades faces forward-i.e. in the direction of flight.
Firmly tighten the propeller nut, using the correct size wrench.
4
Always check the tightness of the propeller nut and retighten it, if necessary, before restarting the
engine, particularly in the case of four-stroke-cycle engines. If a safety locknut assembly is provided with your engine, always use it. This will prevent the propeller from flying off in the event of a
"backfire", even if it loosens. Also, check the tightness of all the screws and nuts before restarting the engine.
If you fit a spinner, make sure that it is a precision made product and that the slots for the propeller blades do not cut into the blade roots and weaken them.
Preferably, use an electric starter. The wearing of safety glasses is also strongly recommended.
NOTES
Discard any propeller which has become split, cracked, nicked or otherwise rendered unsafe. Never attempt to repair such a propeller: destroy it. Do not modify a propeller in any way, unless you are highly experienced in tuning propellers for specialized competition work such as pylon-racing.
Take care that the glow plug clip or battery leads do not come into contact with the propeller. Also check the linkage to the throttle arm. A disconnected linkage could also foul the propeller.
After starting the engine, carry out any needle-valve readjustments from a safe position behind the rotating propeller. Stop the engine before attempting to make other adjustments to the carburetor.
5
NOTES
Adjust the throttle linkage so that the engine stops when the throttle stick and trim lever on the transmitter are fully retarded.
Alternatively, the engine may be stopped by cutting off the fuel supply. Never try to stop the engine physically.
Take care that loose clothing (ties, shirt sleeves, scarves, etc.)do not come into contact with the propeller.Do not carry loose objects (such as pencils, screwdrivers, etc.) in a shirt pocket from where they could fall through the propeller arc.
Do not start your engine in an area containing loose gravel or sand.
The propeller may throw such material in your face and eyes and cause injury.
For their safety, keep all onlookers
(especially small children) well back (at least 20 feet or 6 meters) when preparing your model for flight. If you have to carry the model to the take-off point with the engine running, be especially cautious.
Keep the propeller pointed away from you and walk well clear of spectators.
Warning! Immediately after a glowplugignition engine has been run and is still warm, conditions sometimes exist whereby it is just possible for the engine to abruptly restart if the propeller is casually flipped over compression WITHOUT the glowplug battery being reconnected. Remember this if you wish to avoid the risk of a painfully rapped knuckle!
6
FEATURES OF FX SERIES ENGINES
This range of engines is ideally suited to a variety of R/C aircraft, including trainer, sports, aerobatic and scale types.
A separate precision-made needle-valve unit is installed at the rear, where manual adjustment is safely remote from the rotating propeller.
With the 50SX, 61FX and 91FX, the needle-valve assembly can be installed either horizontally or vertically.
Common to accessories
Silicone Tube, Instruction Manual
50SX, 40/46FX
61FX
91FX
873 Silencer Assembly
E-4010 Silencer Assembly
E-4020 Silencer Assembly
Needle Valve Extension Cable
Note :
With these engines, the piston will feel tight at the top of its stroke when the engine is cold. This is normal. The piston and cylinder are designed to achieve a perfect running clearance when they reach their intended running temperature.
7
BEFORE INSTALLING THE ENGINE
Installing the glowplug
Carefully insert plug, with washer, fingertight only, before final tightening with the correct size plug wrench.
Connecting fuel tubing
Connect the short length of fuel tubing (supplied) securely between the needle-valve outlet and carburetor inlet as shown in the illustration on the next page.
In the event of the tubing becoming damaged, it should be replaced with a suitable length (as indicated below) of best quality 5mm ODx2mm ID silicone tubing. Use similar material to connect the fuel inlet nipple to the fuel tank.
Type of engines
50SX
40,46FX
Length
54-56mm
44-46mm
Glow plug
Washer
Type of engines
61FX
91FX
Length
54-56mm
62mm
BASIC ENGINE PARTS
Cylinder head
Throttle Stop Screw
Carburetor
Glowplug
Fuel inlet
Needle valve
Throttle
Lever
Fuel outlet
Cover Plate
Crankshaft
Silicone Tube
Fuel inlet
Drive Hub
Beam Mount
Crankcase
Propeller washer
Propeller nut
MAX-61FX
8
NEEDLE-VALVE LOCATION
As delivered from the factory, the MAX-61FX has its needle-valve assembly installed horizontally.
However, if more convenient for a particular installation, the needle-valve may be reinstalled vertically behind the cylinder. (See sketch opposite.)
Please note that the needle-valve knob has a center hole and set-screw for the fitting of a piano-wire extension so that, when relocated vertically, the extension enables adjustments to be made without risk of burning one's fingers on the cylinder head.
The procedure for relocating the needle-valve vertically is as follows:
1.
Using 8mm wrench, remove complete needle-valve holder assembly including needle, from side of cover plate.
2.
Remove fuel inlet assembly from upper boss of cover plate.
3.
Transfer banjo type fuel inlet including washers, to needle-valve holder and carefully screw complete assembly into upper boss vacated by fuel inlet assembly. Tighten very carefully.
4.
Use hexagon-head brass inlet holder (61FX) or plug screw (50SX) to blank off side boss vacated by needle- valve assembly.
61FX
Inlet Holder
Needle Extension
Needle-Valve
Assembly
Fuel Inlet
Fuel Inlet
Inlet Holder
Needle-Valve
Assembly
50SX
Plug Screw
Fuel Inlet
Needle-Valve
Assembly
Needle Extension
Needle-Valve
Assembly
Fuel Inlet
Plug Screw
9
As delivered from the factory, the 91FX has the needle-valve assembly installed vertically. However, if more convenient for a particular installation, the needle-valve may be reinstalled horizontally.
The procedure for relocating the needle-valve is as follows:
1.
Remove the two cover-plate screws which secure the needle-valve assembly bracket, then carefully remove the two screws by which the needle-valve unit is attached to the bracket.
2.
Rotate the needle-valve unit through 90˚ and reattach it to the bracket in the required position (see sketch below).
Note:
As self-tapping screws are used for unit attachment, screw them in carefully so that screw threads match those of the unit body precisely.
3.
Finally, secure the complete assembly to rear cover plate as before.
91FX
Needle Valve unit
Cover plate fitting holes
Needle Stay
Vertical position
(Factory position)
Horizontal position
Needle Valve unit Retaining screws
INSTALLATION OF THE ENGINE
Installation in the model
A typical method of beam mounting is shown below, left.
O.S. radial motor mount
(Available as an optional extra
part. See parts list)
Rigid hardwood
(e.g. maple)
At least
15mm(5/8")
At least
15mm(5/8")
10
50SX
40, 46FX
61, 91FX
For 50SX, 40/46FX(Code No. 71913100)
For 60FP, 61, 91FX(Code No. 71905200)
Mounting Screw Size
50SX, 40, 46FX
61, 91FX
3mm
4mm
Make sure that the mounting beams are parallel and that their top surfaces are in the same plane.
CORRECT INCORRECT
Front view Side view
Top surfaces are in the same plane.
Top surfaces are not in the same plane.
Opposite beam Top surfaces are not in the same plane.
Re-align the surfaces as necessary
Engine does not rest firmly.
How to fasten the mounting screws.
3-4mm steel nuts
Spring washer or lock washer
Tighten second nut firmly down onto first nut.
Tighten this nut first.
3.5mm steel
Allen screw
Spring washer
3-4mm steel screw
Hardwood such as cherry or maple.
Steel washer
Hardwood mounting beams
Use mounting screws of a diameter
(between 3mm and 4mm) appropriate to engine size (see table left).
O.S. radial motor mount
(cast aluminum)
11
THROTTLE LINKAGE
Before connecting the throttle-lever/servo linkage, make sure that no part of the linkage interferes with the internal structure of the aircraft or wiring, etc., when the throttle is fully open or fully closed.
Set the throttle lever linkage so that the throttle rotor is
(a) fully open when the transmitter throttle stick is fully advanced and (b) fully closed when the throttle stick is fully retarded. Adjustment of the throttle rotor opening at the idling position can then be made with the throttle trim lever on the transmitter. (Select throttlelever and servo-horn hole positions that will avoid excessive pushrod travel causing the throttle to bind at either end.)
Note: When adjusting the throttle lever angle, relative to the rotor,hold the rotor at about half-way between the open and closed positions while loosening and tightening the fixing screw, otherwise the rotor, rotor guide screw,throttle stop screw or carburettor body may become burred and damaged.
SILENCER
The exhaust outlet of the silencer can be rotated to any desired position in the following manner:
E-4010 Silencer
Assembly screw
Cone baffle
Turn to requlred position
Exhaust outlet
Exhaust pressure nipple
Locknut
1)
2)
Loosen the locknut and assembly screw.
Set the exhaust outlet at the required position by rotating the rear part of the silencer.
3)
Re-tighten the assembly screw, followed by the locknut.
NOTE :
The standard expansion-chamber type silencer is quite effective, but reduces power to some degree.
Reminder!
Model engines generate considerable heat.
Do not touch any part of your engine until it has cooled. Contact with the muffler
(silencer), cylinder head or exhaust header pipe, in particular, may result in a serious burn. Keep your hands and face away from exhaust gas or you will suffer a burn.
12
FUEL TANK LOCATION
Suggested fuel tank capacities are listed opposite.
These will allow 12-13 minute flights.
Locate the fuel tank so that the top of the tank is 5-
10mm (1/4-3/8") above the level of the needle-valve.
• Be sure to use a pressurized fuel system by connecting the muffler pressure nipple to the ventpipe of the fuel tank.
50SX
40,46FX
Suggested Fuel Tank Capacities
approx 300cc
61FX
91FX approx 350cc approx 450cc
Attention to tank height
Fuel level
10mm
GLOWPLUG
Since the glowplug and fuel combination used may have a marked effect on performance and reliability, it would be worthwhile to experiment with different plug types.
Recommended O.S. plugs are Nos. 8, A5 and A3.
Carefully install plug finger-tight, before final tightening with the correct size plug wrench.
The role of the glowplug
With a glowplug engine, ignition is initiated by the application of a 1.5-volt power source. When the battery is disconnected, the heat retained within the combustion chamber remains sufficient to keep the plug filament glowing, thereby continuing to keep the engine running.
Ignition timing is 'automatic' : under reduced load, allowing higher rpm, the plug becomes hotter and, appropriately, fires the fuel/air charge earlier; conversely, at reduced rpm, the plug become cooler and ignition is retarded.
13
Glowplug life
Particularly in the case of very high performance engines, glowplugs must be regarded as expendable items.
However, plug life can be extended and engine performance maintained by careful use, i.e.:
Install a plug suitable for the engine.
Use fuel containing a moderate percentage of nitromethane unless more is essential for racing events.
Do not run the engine too lean and do not leave the battery connected while adjusting the needle.
When to replace the glowplug
Apart from when actually burned out, a plug may need to be replaced because it no longer delivers its best performance, such as when:
Filament surface has roughened and turned white.
Filament coil has become distorted.
Foreign matter has adhered to filament or plug body has corroded.
Engine tends to cut out when idling.
Starting qualities deteriorate.
FUEL
Select, by practical tests, the most suitable fuel from among the best quality fuels available in your country for model use. For the best performance, a fuel containing 5% to 20% nitromethane is preferable.
Lubricants may be either castor-oil or a suitable synthetic oil ( or a blend of both ) provided that they are always of top quality.
For consistent performance and long engine life, it is essential to use fuel containing AT LEAST 18% lubricant by volume. Some fuels containing coloring additives tend to deteriorate and may adversely affect running qualities.
Once a satisfactory fuel has been selected and used for a while, it may be unwise to needlessly change the brand or type. In any engine, a change of fuel may cause carbon deposits in the combustion chamber or on the piston head to become detached and lodged elsewhere, with the risk of this causing unreliable operation for a while. If, however, the adoption of a different fuel is unavoidable, check the engine for the first few flights on the new fuel, by temporarily reverting to the running-in procedure.
14
Reminder!
Reminder!
Model engine fuel is poisonous. Do not allow it to come into contact with the eyes or mouth. Always store it in a clearly marked container and out of the reach of children.
Model engine fuel is also highly flammable. Keep it away from open flame, excessive heat, sources of sparks, or anything else which might ignite it.
Do not smoke, or allow anyone else to smoke, near to it.
PROPELLERS
Suggested propeller sizes are listed on page 15. The suitability of the prop depends on the size and weight of the model and type of flying. Determine the best size and type after the engine has been run in. Check the balance of the propeller before fitting it to the engine. Unbalanced propellers cause vibration and loss of power. Wooden propellers are to be preferred.
Some nylon propellers are not strong enough to withstand the high power output of these engines and a thrown blade can be very dangerous.
50SX
40FX
46FX
61FX
91FX
RING
11x7-9, 12x6-7
Sport
10x6, 10.5x6, 11x6-7
10.5x6, 11x6-8, 12x6-7
12x6-8, 13x6-7
15x8, 16x6-8, 17x6, 14x7 (3-blade)
Reminder!
Never touch, or allow any object to come into contact with, the rotating propeller and do not crouch over the engine when it is running.
MIXTURE CONTROLS
Two mixture controls are provided on these engines.
The Needle Valve (at rear of engine)
When set to produce maximum power at full throttle, this establishes the basic fuel/air mixture strength. The correct mixture is then maintained by the carburetor's built-in automatic mixture control system to cover the engine's requirements at reduced throttle settings.
The Mixture Control Valve (carburetor)
This meters fuel flow at part-throttle and idling speeds to ensure reliable operation as the throttle is opened and closed. The Mixture Control Valve is factory set for the approximate best result. First run the engine as received and readjust the Mixture
Control Screw only if necessary.
Type of Carburetor
50SX
40, 46FX
40B
61FX
91FX
60C
60F
15
BEFORE STARTING
Tools, accessories, etc.
The following items are necessary for operating the engine.
1 Fuel
Model glowplug engine fuel of good quality, preferably containing a small percentage of nitromethane.
2 Glowplug
O.S. No.8 glowplug is supplied with the engine.
3 Propeller
Suggested size is 10x6(40FX), 11X6 (46FX), 12X6
(50SX, 61FX), or 15x8(91FX) .
4 Glowplug battery
The power source for heating the glowplug may be either a large heavy-duty 1.5volt dry cell, or preferably, a 2-volt rechargeable lead-acid cell (accumulator).
1.5 volt heavy-duty dry battery
If a 2-volt cell is employed, use a resistance wire, as shown, to reduce applied voltage, otherwise element will overheat and burn out.
or 2 volt rechargeable lead-acid cell (at least 5Ah)
16
Warning (Very hot)
Never touch the nichrome wire while the battery is connected.
Resistance coil
(nichrome wire)
.
Low er v reduce br
Raise voltage to increase brightness
.
Battery leads
Adjust applied voltage by changing the position of clip on resistance coil until glowplug element is glowing bright red.
5 Battery leads
These are used to conduct current
Battery leads from the battery to the glowplug.
Basically, two leads, with clips, are required, but, for greater convenience, twin leads with special glowplug connectors, as shown on the right, are commercially available.
6 Fuel tank
For installation in the model, a 300cc (10.6oz.) for 50SX and 40,46FX, a 350cc (12oz.) for 61FX, a 450cc
(15.8oz.) for 91FX tank, is suggested.
7 Fuel bottle or pump
For filling the fuel tank, a simple, polyethylene "squeeze" bottle, with a suitable spout,is all that is required. Alternatively, one of the purpose-made manual or electric fuel pumps may be used to transfer fuel directly from your fuel container to the fuel tank.
Fuel bulb
Fuel pumps
Electric Manual
8 Electric starter and starter battery
An electric starter is recommended for starting.
12V Battery
9 Fuel can filter
Fit a filter to the outlet tube of your refuelling container to prevent entry of foreign matter into the fuel tank.
Starter
Fuel Can Filter
10 Silicone tubing
This is required for the connection between the fuel tank and engine.
11 Plug wrench
Used for tightening glowplug. The
O.S. long plug wrench is available as an optional accessory.
For tightening glowplug
STARTING
1.
Install appropriate propeller and tighten securely.
2.
To facilitate electric starting, Install an O.S. solid aluminium alloy spinner-nut for centering the rubber drive insert of the starter. Alternatively, a good quality spinner, enclosing the propeller boss, may be used, but make sure that it is of precision-made and sturdy construction so that the spinner shell cannot loosen when the starter is used. Close the throttle.
17
3.
Fill the fuel tank. Do not allow fuel to overflow into the silencer, otherwise the engine may become flooded and difficult to start.
4.
Check that the needle-valve is closed. (Do not overtighten.) Now open the needle-valve counterclockwise to the starting setting:-
4-5 turns for 91FX
3-4 turns for 61FX when a tuned silencer is used.
Mark
Close
Turn needle-valve clockwise to close
(for leaner mixture)
Turn needle-valve counter-clockwise to open (for richer mixture)
Open
5. Open the throttle approx. one-quarter.
(This is to avoid unnecessarily high r.p.m. when the engine starts.)
Fully closed position
1
4
3
Fully opened position
4
Set at this point
18
6. Connect battery leads to glowplug.
7.
Bring electric starter into contact with spinner-nut or spinner and depress starter switch for one or two seconds. Repeat if necessary.
When the engine starts, withdraw the starter immediately.
Attention :
Do not choke the carburettor air intake when applying the starter. This could cause an excessive amount of fuel to be drawn into the cylinder which may initiate an hydraulic lock and damage the engine.
If the engine does not start within 10 repeat applications of the starter, remove the glow-plug, check that it glows brightly and that the cylinder is not flooded with fuel. (To eject excess fuel, close needlevalve and apply starter with glowplug removed.) Then try again.
VERY IMPORTANT!
Before being operated at full power (i.e. at full-throttle and with the needle-valve closed to its optimum setting) the engine must be adequately run-in, otherwise there is a danger of it becoming overheated and damaged.
RUNNING-IN ("Breaking-in")
All internal-combustion engines benefit from extra care when they are run for the first few timesknown as running-in or breaking-in.
This allows the working parts to mate together under load at operating temperature. Therefore, it is vitally important to complete the break-in before allowing the engine to run continuously at high speed and before finalizing carburetor adjustments.
However, because O.S. engines are produced with the aid of the finest modern precision machinery and from the best and most suitable materials, only a short and simple running-in procedure is called for and can be carried out with the engine installed in the model. The process is as follows.
1.
Install the engine with the propeller intended for your model. Open the needle-valve to the advised starting setting and start the engine. If the engine stops when the glow plug battery disconnected, open the needle-valve to the point where the engine does not stop.Run the engine for one minute with the throttle fully open, but with the needlevalve adjusted for rich, slow "four-cycle"operation.
19
2.
Now close the needle-valve until the engine speeds up to "two-cycle"operation and allow it to run for about 10 seconds, then reopen the needlevalve to bring the engine back to "fourcycle"operation and run it for another 10 seconds.
Repeat this procedure until the fuel tank is empty.
3.
Re-start and adjust the needle-valve so that the engine just breaks into "two-cycle" from "fourcycle" operation, then make three or four flights, avoiding successive "nose-up" flights.
4.
During subsequent flights, the needle-valve can be gradually closed to give more power.
However, if the engine shows signs of running too lean, the next flight should be set rich. After a total of ten to fifteen flights, the engine should run continuously, on its optimum needle-valve setting, without loss of power as it warms up.
5.
After the completion of the running-in adjust the carburetor at optimum setting referring to
MIXTURE CONTROL VALVE ADJUSTMENT section and SUBSEQUENT READJUSTMENT section.
Optimum needle setting(1)
Slowly advance the throttle to its fully open position, then gradually close the needle-valve until the exhaust note begins to change. (4-cycle to 2-cycle)
At this point, disconnect the battery from the glowplug, taking care that the battery leads or glowplug clip do not come into contact with the rotating propeller. If the engine stops when the battery is disconnected, close the needle-valve about
30˚ and restart.
Optimum needle setting(2)
As the needle-valve is closed slowly and gradually, the engine r.p.m. will increase and a continuous highpitched exhaust note, only, will be heard. Close the needle-valve 10-15˚ and wait for the change of r.p.m.
After the engine r.p.m. increases turn the needlevalve another 10-15˚ and wait for the next change of r.p.m. As the speed of the engine does not instantly change with needle-valve readjustment, small movements, with pauses between, are necessary to arrive at the optimum setting.
20
Needle-valve adjustment diagram
6
Practical best(optimum) needle-valve setting
Clear, high-pitched two-stroke 20-45
7 exhaust note
5
Intermittent, high-pitched two-stroke note
˚
Maximum rpm setting("Lean").
1 superimposed on low "four-stroke" sound.
STARTING
"Rich" needle-valve setting when starting the engine.
R e to vo lu o ti d e c re s a
4
Disconnect battery leads from glowplug at about this point.
3
Exhaust note starts to change.
2
The engine may stop if the battery leads are disconnected from the glowplug while the engine is running rich.
Note :
This diagram is for reference purposes only.
Actual needle positions may differ from those shown.
To stop the engine, close the throttle completely to cut off fuel/air supply.
Note: Although this is a two-stroke engine it fires like a four-stroke at these rich needle-valve settings-i.e. ignition of the fuel charge takes place at every fourth stroke of the piston instead of at every second stroke.
21
Disconnect the battery leads at mid speed.
22
MIXTURE CONTROL VALVE ADJUSTMENT
With the engine running, close the throttle and allow it to idle for about five seconds, then open the throttle fully. If, at this point, the engine is slow to pick up and produces an excess of exhaust smoke, the mixture is too rich. Correct this condition by turning the Mixture
Control Screw clockwise 15-30˚. If the mixture is excessively rich, engine rpm will become unstable: opening the throttle will produce a great deal of smoke and rpm may drop suddenly or the engine may stop. This condition may also be initiated by excessively prolonged idling.
If,on the other hand, the mixture is too lean, this will be indicated by a marked lack of exhaust smoke and a tendency for the engine to cut out when the throttle is opened. In this case, turn the Mixture Control
Screw counter-clockwise 90˚to positively enrich the idle mixture, then turn the screw clockwise gradually until the engine regains full power cleanly when the throttle is reopened.
Carry out adjustments patiently until the engine responds quickly and positively to the throttle control.
Note: Mixture Control Valve adjustments should be made in steps of 15-30˚ initially, carefully checking the effect, on throttle response, of each small adjustment.
REALIGNMENT OF MIXTURE CONTROL VALVE
In the course of making carburetor adjustments, it is just possible that the Mixture Control Valve may be inadvertently screwed in or out too far and thereby moved beyond its effective adjustment range.
Its basic setting can be re-established as follows:
Close the throttle rotor gradually from the fully opened position until it is just fully closed.
(Do not turn further.) Then, screw in the Mixture
Control Screw until it stops. Now unscrew the Mixture
Control Screw as indicated below.
50SX
40, 46FX
61FX
91FX
23
SUBSEQUENT STARTING PROCEDURE
Once the optimum needle-valve setting has been established (see page 19, Needle-valve adjustment diagram) the procedure for starting may be simplified as follows.
1.
Open the needle-valve one half-turn (180
°) from the optimum setting.
2.
Set the throttle one-quarter open from the fully closed position, energize the glowplug and apply the electric starter. When the engine starts, reopen the throttle and re-adjust the needle-valve to the optimum setting.
Note:
When re-starting the engine on the same day, provided that atmospheric conditions have not changed significantly, it may be practicable to restart the engine on its optimum(running) setting.
SUBSEQUENT READJUSTMENT
Once the engine has been run-in and the controls properly set up, it should be unnecessary to alter the mixture settings; except to make minor adjustments to the Needle-Valve occasionally, to take account of variations in climatic conditions.
The use of a different fuel, however, particularly one containing more, or less, nitromethane and/or a different type or proportion of lubricating oil, is likely to call for some readjustment of the Needle-Valve.
Remember that, as a safety measure, it is advisable to increase the Needle-Valve opening by an extra half-turn counter-clockwise, prior to establishing a new setting. The same applies if the silencer type is changed.
A different silencer may alter the exhaust pressure applied to the fuel feed and call for a revised Needle-
Valve setting. The use of a different glowplug may also require compensating carburetor readjustments.
24
CARBURETOR CLEANLINESS
The correct functioning of the carburetor depends on its small fuel orifices remaining clear. The minute particles of foreign matter that are present in any fuel, can easily partially obstruct these orifices and upset mixture strength so that engine performance becomes erratic and unreliable.
O.S.'Super-Filters'(large and small ) are available, as optional extras, to deal with this problem.
One of these filters, fitted to the outlet tube inside your refueling container, will prevent the entry of foreign material into the fuel tank.
It is also recommended that a good in-line filter be installed between the tank and needle-valve.
Do not forget to clean the filters regularly to remove dirt and lint that accumulate on the filter screen.
Also, clean the carburetor itself occasionally.
ENGINE CARE AND MAINTENANCE
1.
At the end of each operating session, drain out any fuel that may remain in the fuel tank.
2.
Next, energize the glowplug and try to restart the engine to burn off any fuel that may remain inside the engine. Repeat this procedure until the engine fails to fire. Remove the glowplug and eject any residue by rotating the engine with an electric starter for 4 to 5 seconds while the engine is still warm.
3.
Finally, inject some after-run oil into the engine.
Rotate the engine a few times by hand, to make sure that it is free, and then with an electric starter for 4 to 5 seconds to distribute the oil to all the working parts.
Note:
Do not inject after-run oil into the carburetor as this may cause the O-ring inside the carburettor to deteriorate.
These procedures will reduce the risk of starting difficulties and of internal corrosion after a period of storage.
25
26
27
28
29
30
31
32
33
CARBURETOR 40B (50SX,40,46FX)
1
1-2 1-1
2
2-1
3
4
5
6
7
N.+M3.5x6
8
9
Type of screw
C...Cap Screw M...Oval Fillister-Head Screw
F...Flat Head Screw N...Round Head Screw S...Set Screw
No.
6
7
4
5
1
1-1
1-2
2
2-1
3
8
9
Code No.
22781401
22781411
22781420
27783600
22781800
25681200
26781506
25681100
25681620
22681953
46215000
25081700
Description
Throttle Lever Assembly
Throttle Lever
Throttle Lever Fixing Screw
Mixture Control Valve
"O"Ring
Carburetor Rotor
Rotor Spring
Carburetor Body
Throttle Stop Screw
Fuel Inlet (No.1)
Carburetor Gasket
Carburetor Retaining Screw
The specifications are subject to alteration for improvement without notice.
34
CARBURETOR 60C (61FX)
1-2
1
1-1
2
2-1
3
4
N.+M3.5x6
5
8
9
Type of screw
C...Cap Screw M...Oval Fillister-Head Screw
F...Flat Head Screw N...Round Head Screw S...Set Screw
6
7
No.
2-1
3
4
5
1
1-1
1-2
2
6
7
8
9
Code No.
22781401
22781411
22781420
27783600
22781800
27783200
26781506
27783100
25681620
22681953
46215000
25081700
Description
Throttle Lever Assembly
Throttle Lever
Throttle Lever Fixing Nut
Mixture Control Valve Assembly
"O" Ring
Carburetor Rotor
Rotor Spring
Carburetor Body
Throttle Stop Screw
Fuel Inlet (No.1)
Carburetor Gasket
Carburetor Retaining Screw
The specifications are subject to alteration for improvement without notice.
35
CARBURETOR 60F (91FX
RING
)
N.+M3x6
1
2
3-1
3-2
N.+M3.5x6
3
8
4
7
5
6
No.
1
2
3
3-1
3-2
6
7
4
5
8
Code No.
27881400
29581200
45582300
46066319
24881824
29581100
45581820
22681953
29015019
25081700
Description
Throttle Lever Assembly
Carburetor Rotor
Mixture Control Valve Assembly
"O" Ring (L)
"O" Ring (S)
Carburetor Body
Rotor Guide Screw
Fuel Inlet (No.1)
Carburetor Gasket
Carburetor Retaining Screw
The specifications are subject to alteration for improvement without notice.
Type of screw
C...Cap Screw M...Oval Fillister-Head Screw
F...Flat Head Screw N...Round Head Screw S...Set Screw
36
O.S. GENUINE PARTS & ACCESSORIES
O.S.
GLOW PLUGS
RADIAL MOTOR
MOUNTS
SPINNER NUT NEEDLE VALVE EXTENSION
CABLE SET
(72200080)
No.8
(71608001)
A5
(71605100)
A3
(71605300)
LONG PROPELLER
NUT SETS
Code No.
Type of Engine
71913100
71905200
50SX. 40. 46FX
61FX. 91FX
Code No.
Size
23024009
45024000
1/4"-28(L)
5/16"-24
Type of Engine
50SX. 40. 46FX
61FX. 91FX
SUPER SILENCERS SILENCER EXTENSION ADAPTORS
Code No.
Size Type of Engine
73101000
73101010
1/4"-28
5/16"-24
50SX. 40. 46FX
61FX. 91FX
PROPELLER NUT SETS
FOR TRUTURN SPINNERS
(73101020)
For 50SX. 40.46FX
Code No.
Size Type of Engine
25425020 873S
50SX. 40/46FX
26028010 E-4010S
61FX
37
Code No.
25425600
26625340
26625500
Type of Engine • Silencer
50SX. 40.46FX (873)
61FX (E-4010). 91FX (E-4020)
Length 35mm
61FX (E-4010). 91FX (E-4020)
O.S. SILICONE
TUBE ASSEMBLY
EXHAUST
HEADER PIPE
(72101230)
T-4010 TUNED SILENCER
(72101120)
NON-BUBBLE WEIGHT
(71531000)
SUPER FI LTER
(72403050)
Code No.
72105337
72101338
Type of Engine
40.46FX
61FX.91FX
BLIND NUTS
(10pcs. /Sets)
For 61FX, 91FX
LOCK WASHER
(10Sets)
For 61FX
CAP SCREW SETS
(10pcs./sets)
M3.5x8
(79871060)
M3.5x10
(79871070)
LONG SOCKET WRENCH
WITH PLUG GRIP
(71521000)
Code No.
79870030
79870040
Size
M3
M4
Type of Engine
50SX. 40.46FX
61FX.91FX
Code No.
55500002
55500003
Size
M3
M4
Type of Engine
50SX. 40.46FX
61FX.91FX
The specifications are subject to alteration for improvement without notice.
38
MAX-
50SX
RING
SPECIFICATIONS
Displacement
Bore
Stroke
Practical R.P.M.
Power output
Weight
8.17 cc (0.499 cu.in.)
22.0mm (0.866 in.)
21.5mm (0.847 in.)
2,000-20,000 r.p.m.
1.8 ps / 17,000 r.p.m.
390g (13.76 oz.)
21
17.5
Dimensions(mm)
36
52
UNF1/4-28
39
28 60.7
121
25 7.5
THREE VIEW DRAWING
MAX -
40FX
SPECIFICATIONS
Displacement
Bore
Stroke
Practical R.P.M.
Power output
Weight
6.47 cc (0.395 cu.in.)
20.5mm (0.807 in.)
19.6mm (0.772 in.)
2,000-17,000 r.p.m.
1.36 ps / 16,000 r.p.m.
386g (13.6 oz.)
MAX -
46FX
SPECIFICATIONS
Displacement
Bore
Stroke
Practical R.P.M.
Power output
Weight
7.45 cc (0.455 cu.in.)
22.0mm (0.866 in.)
19.6mm (0.772 in.)
2,500-17,000 r.p.m.
1.62 ps / 16,000 r.p.m.
375g (13.2 oz.)
Dimensions(mm)
35
51
40
UNF1/4-28
17.5
60.5
19.5
MAX -
61FX
SPECIFICATIONS
Displacement
Bore
Stroke
Practical R.P.M.
Power output
Weight
9.95 cc (0.607 cu.in.)
24.0mm (0.945 in.)
22.0mm (0.866 in.)
2,000-17,000 r.p.m.
1.9 ps / 1.93 hp / 16,000 r.p.m.
550g (19.42 oz.)
43
61
25
ø4.2
42
ø4.2
UNF5/16-24
41
66.5
29.1
Dimensions(mm)
MAX -
91FX
RING
SPECIFICATIONS
Displacement
Bore
Stroke
Practical R.P.M.
Power output
Weight
14.95 cc (0.912 cu.in.)
27.7mm (1.091 in.)
24.8mm (0.976 in.)
2,000-16,000 r.p.m.
2.8 ps / 15,000 r.p.m.
550g (19.42 oz.)
24.7
4- 4.2
25
UNF 5/16-24
Dimensions(mm)
42.6
61
42
66.5
103.6
29.5
UN
EQ
UA
LLE
D Q
UALITY
PRECISION & PE
RFOR
M
AN
ES
TAB
LISHIN
G THE STANDARDS OF EX
CEL
LE
NC
E
CE
6-15 3-Chome Imagawa Higashisumiyoshi-ku
FAX. (06) 6704-2722
URL : http://www.os-engines.co.jp
C
Copyright 2001 by O.S.Engines Mfg. Co., Ltd. All rights reserved. Printed in Japan.
60090880 061106
advertisement
Key Features
- It is a highly efficient internal-combustion machine.
- It is designed for model aircraft.
- It generates considerable heat.
- Model engine fuel is poisonous.
Related manuals
Frequently Answers and Questions
What are the warnings for using this product?
What are the notes for using this product?
What is the suggested propeller?
advertisement