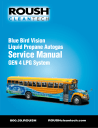
advertisement
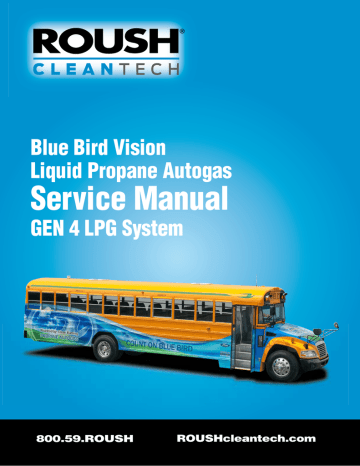
Blue Bird Vision
Liquid Propane Autogas
Service Manual
GEN 4 LPG System
800.59.ROUSH
ROUSHcleantech.com
Table of Contents
Foreward ............................................................... 1
Introduction ........................................................... 1
LPA System Overview .......................................... 1
ROUSH CleanTech Technical Assistance ............ 1
Propane ................................................................ 2
Fill Stations .......................................................... 2
Safety Information ................................................ 2
Alert Messages ..................................................... 2
Installation, Garaging and Training ....................... 3
Purging and Venting (Tanks and Lines) ................ 3
Description and Operation .................................... 3
LPA Fuel System Overview .................................. 3
Start Sequence ..................................................... 8
Stage .................................................................... 8
Name .................................................................... 8
Description ........................................................... 8
General Propane Tank Filling Procedure .............. 9
Propane Powered Motor Vehicle
Filling Overview .................................................... 9
Vehicle Filling Procedure ...................................... 9
Propane Fuel Tank .............................................. 11
Tank Fill Valve/80% Overfill Prevention
Device (OPD) ..................................................... 12
Fuel Pumps ........................................................ 12
In-Tank Fuel Filters ............................................. 12
Tank Pressure Temperature Sensor ................... 12
Fuel Level Sender ............................................... 12
Tank Bleeder Valve/Fixed Liquid Level Gauge .... 13
Pressure Relief Valve ......................................... 13
Tank Supply Circuit Assembly ........................... 13
Tank Solenoid Valve .......................................... 13
Manual Shutoff Valve .......................................... 13
Excess Flow Valve (XFV) .................................... 14
Fuel Return Valve ............................................... 14
Fuel Transfer Lines ............................................. 14
Fuel Rail Pressure Control Module (FRPCM) .... 14
Injection Pressure Temperature Sensor ............. 15
Vapor Canister Assembly .................................. 15
Vapor Lines ......................................................... 15
Fuel Rail Assemblies .......................................... 15
Remote Fill Valve ................................................ 17
Fill Line ............................................................... 17
Fill Filter .............................................................. 17
Remote Bleeder Valve ........................................ 17
Bleeder Hose ...................................................... 17
Electronic Fuel Pump Relay (EFPR) .................. 17
LPA Gateway Module ......................................... 17
Gateway Function ............................................... 17
LPA Interface Function ....................................... 18
Service Preparation ............................................ 18
Alert Messages ................................................... 18
Manual Fuel Shutoff .......................................... 18
Opening the Manual Fuel Shutoff ....................... 18
Fuel Tank Pressure Relief ................................... 19
Fuel System Purge, Evacuation and Priming Procedures .................................... 19
Fuel Line Purging ............................................... 19
Fuel Tank Draining Procedure ............................ 20
Using In-Tank Pumps ......................................... 21
Fuel Tank Purging Procedure ............................. 22
Fuel System Priming Procedure ......................... 22
Fuel System Flow Diagrams ............................... 23
Component Servicing ......................................... 26
Special Tools ....................................................... 26
Quick Disconnect Tools .................................... 26
Electronic Leak Detector ................................... 26
Flare Tower ......................................................... 26
Fuel Tank ........................................................... 26
Tank Fill Valve/80% Overfill
Prevention Device (OPD) ................................... 29
Tank Bleeder Valve ............................................. 30
Fuel Tank Pressure Relief Valve ........................ 30
Tank Supply Circuit Assembly ............................ 31
Fuel Tank Return Valve ....................................... 32
Solenoid Coil Replacement ................................ 33
Fuel Pump Assembly (In-Tank) .......................... 33
Tank Pressure Temperature Sensor ................... 33
Fuel Level Sender (located on top of the LH cylinder) .............................................. 35
Fuel Tank Wiring ................................................. 36
Remote Mounted Fuel Fill Valve ......................... 38
Remote Fuel Fill Line(s) ..................................... 38
In-Line Fuel Filters .............................................. 39
Remote Mounted Bleeder Valve ......................... 39
Remote Bleeder Line .......................................... 40
Fuel Rail Pressure Control Module (FRPCM) .... 40
Fuel Supply and Return Line .............................. 42
Fuel Rail ............................................................. 43
Fuel Injector ........................................................ 45
Injection Pressure Temperature Sensor ............. 45
Vapor Canister Assembly .................................. 46
Gateway Module ................................................. 47
System Maintenance .......................................... 47
LPA Fuel System ................................................ 47
Fuel Tank .......................................................... 47
Fuel Filters .......................................................... 48
Fuel Supply and Return Line ............................ 48
Fuel Rail Pressure Control Module ..................... 48
Fuel Rails and Injectors ...................................... 48
Electrical System ................................................ 48
Torque Chart ....................................................... 49
FAQs ................................................................... 50
ROUSH CleanTech Technical Assistance .......... 50
Special Conditions ............................................. 51
Refueling ............................................................ 51
Troubleshooting – Refueling ............................... 51
Maintenance and Specifications ........................ 53
ROUSH CleanTech System
Use and Maintenance ........................................ 53
Service Recommendations ............................... 53
Refill Capacity ................................................... 54
Jump Starting ..................................................... 54
Manual Shutoff Valve ......................................... 54
Storing the Vehicle ............................................. 54
Repainting (Vehicle or Tank) .............................. 54
DIAGNOSTIC TROUBLE CODES
(DTC) — LPA-FUELED VEHICLES .................... 56
About Diagnostic Trouble Codes ........................ 56
System and Diagnostic Terminology .................. 56
Diagnostic Trouble Code List .............................. 57
Flow Control Solenoid (FCS) .............................. 58
Bleed Solenoid ................................................... 58
Tank Solenoid ..................................................... 59
Fuel Rail Pressure Control Module Supply
Solenoid and Wiring ........................................... 60
Gateway Module, CAN Bus Circuit Wiring .......... 61
Fuel System ........................................................ 61
Heated Exhaust Gas Oxygen Sensor ................. 63
Electronic Fuel Pump Relay (A/B) ...................... 63
Integrated Pressure Temperature Sensor ........... 66
Fuel Level Sensor (FLS) ..................................... 69
Other ................................................................... 70
DIAGNOSTIC TESTS AND PROCEDURES —
LPA-FUELED VEHICLES ................................... 71
General Information ............................................ 71
No Fill ................................................................. 72
Short Fill ............................................................. 73
Slow Fill .............................................................. 75
Over Fill .............................................................. 78
Engine Does Not Crank ...................................... 80
Engine Cranks, No Start ..................................... 80
Engine Stumble, Stall, Rough Idle ...................... 82
Excess Flow Valve (XFV) Check ........................ 84
Maximum Pressure Check ................................. 85
Step Procedure Action ........................................ 85
Fuel System Fails to Bleed ................................. 86
Tank Solenoid Electrical Check .......................... 87
Fuel Rail Pressure Control
Module Electrical Check ..................................... 89
Integrated Pressure Temperature
Sensor Electrical Check ..................................... 91
IPTS Temperature/Resistance Chart .................. 92
Tank Pressure Temperature
Sensor Electrical Check ..................................... 93
Fuel Pump Electrical Test ................................... 94
Fuel Pump Control Module
Electrical Continuity Test ..................................... 96
Gateway Module Electrical Test .......................... 96
Fuel Level Indication Check ................................ 97
Fuel Level Sender (FLS) Electrical Check .......... 98
Manual Solenoid Activation Procedure ............... 99
ROUSH CleanTech Blue Bird Vision Liquid Propane Autogas (LPA)
Service Manual
FOREWARD
This manual is intended to provide technicians with the procedures required to maintain and service the unique components for the ROUSH CleanTech
Liquid Propane Autogas (LPA) system. Service procedures for other vehicle components may be referenced to, which can be found in one of the
Blue Bird Service Manuals. For base engine or transmission information, refer to the 2017 Ford
F-650 (H561) workshop manual. For access to the
Ford manual, please subscribe to www.motorcraft.
com.
Technicians working with, or around, fuel systems should be properly trained to utilize extreme care and caution at all times. Failure to exercise extreme caution and care may lead to serious accidents which can result in property damage, personal injury and/or death.
INTRODUCTION
LPA System Overview
The introduction of the Propane powered Blue Bird
Vision marks a new generation in alternative fuel powered school buses. The bus is powered by a
Ford Triton 6.8L V10 engine equipped with a Liquid
Propane Autogas (LPA) fuel system. Unlike the traditional propane powered vehicle that supplies propane to the engine in a vapor phase the LPA system delivers, meters and injects propane in a liquid phase into the engine.
Similar to a modern gasoline engine, the LPA system stores liquid propane in the fuel tank. Dual in-tank electric fuel pumps circulate the propane through fuel rails which supply fuel to the fuel injectors. The injectors meter and inject liquid propane into each of the original ten (10) inlet ports on the Triton engine. Fuel that is not used by the injectors will return to the fuel tank through a flow control solenoid.
The ROUSH CleanTech LPA system is fully integrated using Ford’s One Touch Integrated
Start (OTIS) system. When the ignition key is turned to Start and released to the On position, if the Blue Bird Multiplex start logic is satisfied, the
LPA system will begin a purge process. Once the correct pressure and temperature is detected at the fuel rail, the starter engages and the vehicle starts with no further action required from the operator.
Fueling a propane powered bus is noticeably different than on a conventional fueled vehicle.
A propane fuel system is completely sealed and the major difference is the fill nozzle. There are 2 types of fill nozzles and valves used for propane, a screw-on type and a quick-connect type (also known as “euro style”). When fueling, with the screw-on type, turn connector clockwise to tighten ensuring a good seal at the fill valve. With the quick-connect type, fully engage the nozzle to the valve ensuring a good seal at the fill valve.
The tank is equipped with an Overflow Protection
Device (OPD), which only allows to tank to be filled to 80% of the overall tank volume leaving room for the fuel to expand. At the 80% fill level the dash fuel gauge will read full. The filling times should be comparable to that of gasoline or diesel but things such as ambient temperature and filling station pressure settings can affect these filling times.
Liquid propane autogas is also called liquid (or liquefied) petroleum gas (LPG, sometimes just
LP gas). A vapor at normal room temperature and atmospheric pressure, a moderate increase in pressure produces its liquid state at ambient temperatures. It vaporizes readily when released.
Because the liquid contains so much more energy than the same volume of vapor, liquid propane autogas is stored and shipped under pressure.
A few liquid propane autogas facts:
• Liquid propane autogas is colorless.
• Liquid propane autogas is originally odorless. An odor is added to aid in leak detection.
• Liquid propane autogas is non-toxic, but very high concentrations in the air we breathe can asphyxiate, which can result in personal injury including death.
• Liquid propane autogas is slightly heavier than air.
• Liquid propane autogas will float on water briefly before vaporizing.
• Liquid propane autogas vaporizes rapidly and therefore is not a ground contaminate like gasoline and diesel products.
ROUSH CleanTech Technical Assistance
Technical issues involving starting, operating or re-fueling a propane power bus should be reported to your local qualified service provider. In the event further technical assistance is needed, you should first contact your authorized Blue Bird Dealer regarding any technical issues with your Blue Bird product.
Blue Bird Vision Service Manual
ROUSH CleanTech Blue Bird Vision Liquid Propane Autogas (LPA)
Service Manual
In emergency situations or if immediate technical assistance is needed and the above mentioned technical assistance is unavailable you can call
ROUSH CleanTech Customer Service at 800.59.
ROUSH (597-6874) with any questions regarding
ROUSH CleanTech Liquid Propane Autogas
Systems.
Propane
Propane exists as a gas in its natural state, and like diesel fuel, gasoline or natural gas, is a member of the hydrocarbon family. Propane is a by-product of refined petroleum and natural gas.
When stored under pressure, the propane turns into a liquid. Propane is colorless, odorless and non-toxic. Ethyl mercaptan is added to propane during the manufacturing process to give it a distinct, recognizable odor.
Propane is commonly referred to as LPG or LP gas. Like most liquids, liquid propane expands as its temperature increases. This is why propane tanks are only filled to 80% of its water capacity.
Even with an 80% fill capacity, due to liquid propane’s expansion ratio of 1:270 (liquid propane to a gas by volume) and its high BTU rating a large volume of energy can be stored in a relative small tank under relative low pressure.
Propane also has a very narrow range of flammability with a 2.15% threshold on the low side and a 9.6% threshold on the high side. This means that if the propane to oxygen mixture is lower than 2.15 % or higher than 9.6 % the mixture is noncombustible.
Propane is heavier than air; therefore, a leak in a propane fuel system can result in a gas accumulation in low places, such as sewers, drains or service pits. This can create a fire and health hazard as the propane will displace oxygen, potentially resulting in suffocation. For this reason, additional safety precautions should be observed when working on or around propane powered equipment or storage tanks.
Propane is stored in the vehicle fuel tank under pressure as a liquid. The pressure in the tank is determined by the temperature of the fuel, ranging from 0 psi at minus 44°F, to 312 psi at 145°F. The tank has a pressure relief valve (PRV) which vents the tank at pressures over 312 psi or 375 psi, depending on the application.
ROUSH CleanTech LPA vehicles require HD-5 propane, rated for automotive use. Use of HD-10 or other substandard propane may result in excess contamination of the system and premature failure of the fuel pump, injectors and in-tank filter.
Propane, like other fuels, must be handled safely with knowledge of its characteristics. Training in propane characteristics and handling is available through the Propane Education and Research
Council (PERC), 1140 Connecticut Avenue,
Washington, DC 20036. Their web address is www.
propanecouncil.org.
Fill Stations
Propane is readily available anywhere in the United
States. To locate the nearest station, check with www.afdc.energy.gov/afdc/locator/stations.
ROUSH CleanTech recommends facilities designed for automotive refueling. Other locations may have low output pumps, resulting in slow or no fill, or low quality fuel which can result in premature component failure.
CleanTech nor Blue Bird approve of any additions to or modifications of this fuel system. This fuel system is designed and installed to meet federal standards and engine manufacturer’s guidelines. The maintenance provider or modifier assumes all responsibility for the vehicle engine and fuel system if the fuel system is changed or modified. Some states require a special license to perform maintenance or work on propane powered vehicles. Check with local authorities or your state LP Gas Association for details. All fuel system components must be a minimum of 18 inches from any exhaust system component unless properly shielded. All service, maintenance and repairs performed on LP Gas systems must be done by an authorized LP Gas service technician.
SAFETY INFORMATION
The National Fire Protection Association (NFPA) publishes a code book of rules that apply to the storage, handling, transportation, and use of liquefied petroleum gas (LP-Gas or LPG).
The book is known as NFPA 58. It is revised as necessary and published every other year. This code is adopted as law in virtually every political subdivision in the United States. Check with your local authorities for regulations applicable to liquid propane.
Alert Messages
The following alert messages appear from time to time in the appropriate places in this manual.
Ensure that all personnel in the immediate area are aware of these reminders.
2 Blue Bird Vision Service Manual
ROUSH CleanTech Blue Bird Vision Liquid Propane Autogas (LPA)
Service Manual
Although propane is nontoxic, nonpoisonous, has the lowest flammability range of any alternative fuel and dissipates quickly when released into the atmosphere, propane vapor is heavier than air and seeks the lowest point. When the ratio of propane to air is between 2.2% and 9.6%, propane will burn in the presence of an ignition source at 940°F (504°C) or hotter. Keep away from heat, sparks, flames, static electricity or other sources of ignition. Failure to heed this danger may result in severe personal injury or death.
The fuel supply lines remain pressurized after engine shutdown. Keep away from heat, sparks, flames, static electricity or other sources of ignition. Do NOT enter storage areas or confined space unless they are adequately ventilated. Failure to heed this danger may result in severe personal injury or death.
Do NOT carry lighted smoking materials or smoke while working on fuel system components. Failure to heed this danger could result in severe personal injury or death.
Technicians working with, or around, fuel systems should be properly trained to utilize extreme care and caution at all times. Failure to exercise extreme caution and care may lead to serious accidents which can result in property damage, personal injury and/or death.
Installation, Garaging and Training
Chapter 11 of NFPA 58 applies to engine fuel systems using LP-Gas in internal combustion engines, including containers, container appurtenances, carburetion equipment, piping, hose and fittings and their installation. Additionally, this chapter applies to garaging of vehicles and to the training of personnel.
Paragraph 11.2 specifies that each person engaged in installing, repairing, filling or otherwise servicing an LP-Gas engine fuel system shall be trained. Contact the Propane Education and
Research Council to learn more about their CETP
E-Learning computer-based training program: [email protected], or vincent.
Purging and Venting (Tanks and Lines)
Venting of LP-Gas to the atmosphere is covered by paragraphs 7.3.1, General, and 7.3.2, Purging of NFPA 58, 2008 edition. Refer to NFPA 58, Local
Codes and Proper Training for specific information relating to safe venting of LPG.
Disconnect the battery ground at the battery to ensure that the vehicle electrical system has no current. Failure to heed this danger could result in severe personal injury or death.
Propane is heavier than air and seeks the lowest available level when released to the atmosphere.
Keep heat, sparks, flames, static electricity or other sources of ignition out of the area when filling, venting or purging the fuel lines or tank.
Failure to heed this danger can result in severe personal injury or property damage.
Liquid propane is cold. The temperature of propane in its liquid state is -44°F (-42°C). Wear eye and ear protection during venting and repair operations. Keep moisture away from the valves.
Failure to heed this warning can result in personal injury.
DESCRIPTION AND OPERATION
LPA Fuel System Overview
The Ford 6.8L engine fuel supply is controlled by the same Powertrain Control Module (PCM) as used on Ford medium duty trucks; however the fuel control calibration has been optimized for propane.
A Gateway Module controls the fuel system solenoids, upon command from the PCM.
Electronic Fuel Pump Relays (EFPR) control the dual fuel pumps inside the tank to deliver liquid propane to the injectors. From the pumps, the fuel flows through the supply solenoid (on the tank), into the 3/8" fuel supply line, to the supply solenoid on the Fuel Rail Pressure Control Module
(FRPCM), then to the fuel rails and injectors.
Excess fuel flows back to the tank through the
FRPCM’s check valve, into the 1/4" fuel return line and through the Flow Control Solenoid (FCS) in the tank return valve. Fuel pressure is regulated by
Blue Bird Vision Service Manual 3
ROUSH CleanTech Blue Bird Vision Liquid Propane Autogas (LPA)
Service Manual
the Flow Control Solenoid (FCS) which includes a small orifice to restrict return flow in normal conditions; and a bypass circuit to allow maximum fuel flow prior to engine starting or during extremely hot conditions.
The FRPCM also contains a bleed solenoid to control the flow of fuel vapors from the fuel rail to the carbon canister during engine off conditions when ambient temperature is above 40 degrees
F. The engine’s Vapor Management Valve (VMV) controls the purging of the vapor canister, sending the vapors back into the intake manifold for the engine to consume.
The filling process is safeguarded against overfilling by an 80% overfill prevention device
(OPD) integral to the LPA system’s fuel fill valve on the tank. In order to safely store pressurized liquid propane in the vehicle, the fill system must ensure that the tank is not filled beyond 80% of its water capacity. This ensures that sufficient expansion volume is present in case of significant tank temperature changes.
The LPA tank consists of dual cylinders connected by manifolds to store the liquid propane under pressure. Internal to the tank are dual electric fuel pumps, fuel pump housing, fuel filters, fuel level sender, fuel fill valve with OPD, fixed liquid level gauge, supply circuit assembly with excess flow valve, return circuit assembly, Fuel Pressure and
Temperature Sensor (FPTS) and a wiring harness.
There are three (3) propane filters in the system.
The primary filter is located in the fuel fill line which is intended to filter out the majority of contaminants that may be present in the fuel from the filling station. This filter must be replaced every 50,000 miles. The secondary fuel filter is a sock filter located at the bottom (inlets) of the fuel pumps.
The third filter is located in-line with the supply fuel line, mounted to the exterior of the tank, near the front of the tank. This filter should be replaced every 50,000 miles.
ROUSH CleanTech LPA vehicles require HD-5 propane, rated for automotive use. Use of HD-10 or other substandard propane may result in excess contamination of the system and failure of the fuel pump, injectors and in-tank filters.
Due to the inherent qualities of propane, a purge strategy must be employed during engine start up.
Whenever the fuel pumps are not activated, there is a potential for the liquid propane in the fuel rails to absorb heat from the engine or from ambient temperatures. This heat may cause the fuel to expand rapidly and create vapor in the fuel rails.
This vapor, if not purged from the fuel rails, can cause lean fueling or a no start condition.
4 Blue Bird Vision Service Manual
ROUSH CleanTech Blue Bird Vision Liquid Propane Autogas (LPA)
Service Manual
FRPCM
FUEL RAIL
AND LINES
CHASSIS SUPPLY
AND RETURN LINES
PRESSURE
RELIEF
VENT
FUEL TANK
AND LINE
ASSEMBLY
VAPOR
CANISTER
ASSEMBLY
FILL VALVE
REMOTE BLEEDER
AND FILL DOOR SWITCH
Figure 1 – Fuel and Evaporative System Overview
Blue Bird Vision Service Manual 5
ROUSH CleanTech Blue Bird Vision Liquid Propane Autogas (LPA)
Service Manual
FUEL PUMP RELAYS
BLEEDER
HOSE
Figure 2 – Fuel Tank and Line Assembly Installed
REMOTE
BLEEDER
VALVE
REMOTE
FILL
VALVE
6
Figure 3 – Fuel Tank and Line Assembly
Blue Bird Vision Service Manual
ROUSH CleanTech Blue Bird Vision Liquid Propane Autogas (LPA)
Service Manual
CHASSIS SUPPLY
AND RETURN LINES
FORWARD
SUPPLY AND
RETURN LINES
VAPOR
PURGE
LINES
FRESH AIR
INLET LINE
FRPCM
GATEWAY MODULE
(MOUNTED ON
DRIVER CONTROL MODULE)
VAPOR CANISTER AND BRACKET ASSEMBLY
Figure 4 – Forward Fuel System Components
Blue Bird Vision Service Manual 7
ROUSH CleanTech Blue Bird Vision Liquid Propane Autogas (LPA)
Service Manual
Start Sequence
When the engine is not running, the fuel in the rail boils and turns to vapor. For proper engine operation the vapor must be flushed from the rail prior to starting the engine. This is a fully automated process that is controlled by the PCM. This process typically takes 7-15 seconds, but depending on ambient conditions, engine off time, and engine temperature at shutdown it could take up to 43 seconds.
The cycle will begin when the operator turns the key to the crank position and released to the ON position. Upon receiving the crank request, the PCM initiates the start sequence. During this time, the PCM performs diagnostics on several of the solenoids, as well as flushing the rail of vapor. This is accomplished by monitoring the Injection Pressure and Temperature Sensor (IPTS) while opening the various solenoids in the tank and FRPCM in stages, then engaging the fuel pump (see System
Description for a more detail description of the components).
There are seven distinct stages of the start cycle:
Stage
1
2
3
4
5
6
7
Name
CAN Bus
Initialization
Bleed
Diagnostic
Pressure
Read
Description
For the sequence to work the PCM and Gateway Module need to be communicating. There is a short delay after key-up to ensure communication has been established.
The PCM measures the fuel pressure in the rail after a bleed cycle. All solenoids are still closed at this time. If the pressure is too high, the system did not bleed and a fault will set.
Open Tank
Solenoid
Open
Supply
Solenoid
The tank solenoid is energized. The pressure in the rail is measured (again).
This pressure will be used later to determine if the FRPCM supply solenoid has properly opened.
The FRPCM Supply Solenoid is energized.
Flush
Pressure
Build
Crank
The FCS is energized and the fuel pump is turned on high speed. The IPTS monitors pressure and temperature in the rail to determine when the vapor has been cleared from the rail.
The FCS is de-engergized and the pressure is allowed to rise. The IPTS is still monitoring the pressure and temperature in the rail to ensure there is liquid in the rail.
Once liquid is detected in the rail, the PCM engages the starter, and starts the vehicle.
Stage
Tank Solenoid
Supply Solenoid
Flow Control Solenoid
Fuel Pump
Starter
1 2 3 4 5 6 7
On
On
On
On
On
CAN Bus
Initialization
(0.2 sec)
Bleed
Diagnostic
Pressure Read
(0.2 sec)
Open Tank
Solenoid
Supply
Solenoid
Diagnostic
Pressure Read
(0.2 sec)
Open Supply
Solenoid
(0.2 sec)
Flush
(minimum 1 sec)
(maximum 31.875 sec)
Flow Control Solenoid Open
Pressure Build
(minimum 0.5 sec)
(maximum 10 sec)
Crank minimum – 5.5 seconds maximum – 43.075 seconds
Figure 5 – Vehicle Start Sequence
8 Blue Bird Vision Service Manual
ROUSH CleanTech Blue Bird Vision Liquid Propane Autogas (LPA)
Service Manual
General Propane Tank Filling Procedure
The most important aspect of filling a propane tank is safety. Understanding the properties and characteristics and safe handling practices of the fuel is required before conducting any propane tank filling efforts.
A propane powered vehicle is equipped with a propane tank built and certified to the regulations of the American Society of Mechanical Engineers
(ASME). These tanks have a data plate with pertinent information including the ASME stamp.
This plate must be securely attached and legible or the tank should be taken out of service and replaced. There are no requirements for recertifying ASME tanks, however, inspection is required and maintenance is recommended if there are signs of corrosion.
Propane tanks are filled to 80% water capacity to allow for the liquid fuel to expand and contract depending on ambient temperatures. All tanks built for use on motor vehicles are equipped with an overfilling prevention device (OPD). The National
Fire Protection Association (NFPA) requires motor vehicle propane tanks be equipped with an overfill prevention device to automatically prevent filling the tank beyond the maximum recommended capacity of 80%. This automatic stop fill system prevents overfilling of the fuel tanks. This requirement has been in effect since January 1,
1984.
Propane Powered Motor Vehicle Filling
Overview
The fuel fill system includes the following components:
1. Fuel fill valve, cap and mounting bracket.
a. The valve is located behind a locked fuel door. There is also a switch mounted to the fill valve bracket, which is activated by contacting the door.
NOTE: If the door is not closed and locked to activate the switch, the multiplex will not send the signal to the PCM to being the start sequence.
2. Fuel Fill hoses
3. Fuel Fill Filter and Mounting Clamp
4. Fuel tank mounted fill valve containing a mechanical Overfill Prevention Device (OPD).
5. Fuel Tank Internal Components
During a fill event, the system functions as follows:
1. Customer connects fuel filler nozzle to fill valve and activates the fill station pump.
2. Fuel pressure in the fill line causes the remote fill valve, tank fill valve and tank shutoff valve to open. In order for the valves to open, pressure in the fill line must be at least
20 psi higher than tank pressure (50 psi is recommended), otherwise no fill is possible.
3. Once the fuel reaches the 80% fill level the overfill prevention device closes the shut-off valve, not allowing additional fuel to flow into the tank.
NOTE: Some fuel station pumps may have sufficient pressure to allow a small fuel flow into the tank even with the valves closed. The operator should stop the fill as soon the fuel flow drops noticeably.
Vehicle Filling Procedure
This filling procedure is included for reference only.
All personnel conducting fills should receive safety training on proper fill procedures.
For passenger safety, Blue Bird recommends all occupants disembark to a safety zone before fuel filling procedures take place.
1. Entering the propane fueling station.
a. Park the vehicle in close proximity to the motor fuel dispensing station.
NO SMOKING ALLOWED.
2. Turn off and remove the vehicle ignition key.
Technicians working with or around, fuel systems should be properly trained to utilize extreme care and caution at all times. Failure to exercise extreme caution and care may lead to serious accidents which can result in property damage, personal injury and/or death.
3. Exit the vehicle and ask all passengers to step outside the vehicle.
a. Some stations may ask all passengers to stand outside the area where the fill process is taking place.
Blue Bird Vision Service Manual 9
ROUSH CleanTech Blue Bird Vision Liquid Propane Autogas (LPA)
Service Manual
b. Some stations could be self-service and the driver would perform the filling process; however in this case the driver has to be trained and certified to obtain an authorized filling station dispenser access card.
4. The attendant may need to inspect the propane tank for corrosion, dents and verify the data plate displays the ASME stamp and other pertinent information is correct. An attendant can refuse to fill your propane tank if it does not pass this inspection. Regular inspection and maintenance of your tank will prevent refusal to fill the tank.
5. Unlock and open the fuel door.
6. Verify the dispenser meter is set to zero.
a. If the dispenser is an electronic dispenser it will set to zero automatically once the transaction has been initiated.
7. Connect the fuel nozzle to the vehicle fueling receptacle.
a. The propane fueling nozzle must be fully engaged.
i. Wear protective gloves while fueling a propane tank.
Propane is a refrigerant. Liquid propane boils into a vapor at -44°F (-42°C) when not under pressure, causing a powerful cooling effect.
ii. Remove the protective cap from the vehicle fueling receptacle.
iii. Mate the nozzle coupling to the fueling receptacle.
iv. If using the threaded fill valve and nozzle, turn the nozzle coupling in a clockwise direction; two or three turns until secure.
A soft rubber washer or O-ring seals the connection so over tightening is not required. If using the quick-connect style fill valve and nozzle, push the nozzle firmly against the valve to fully engage the nozzle and the seal.
v. Most nozzles for motor vehicle fueling are much like a gasoline type nozzle. The nozzles are also minimum bleed type for safety and to meet hydrocarbon release requirements in certain jurisdictions.
8. Turn on the propane dispenser/pump and begin the filling process.
a. Open the nozzle to begin filling.
b. Do not fill the tank based on a mechanical float gauge reading or the fuel level gauge on the dashboard.
c. Pay attention and never walk away from the filling process.
d. When the tank is full the overfill prevention device automatically stops the filling process at the 80% liquid level capacity of the tank.
9. Release or close the fueling nozzle.
a. Turn off the fuel dispenser/pump.
b. If using the threaded fill valve and nozzle, carefully and slowly unscrew the fueling nozzle (counterclockwise). If using the quickconnect nozzle, pull the nozzle away from the valve to disengage.
i. A minimum bleed nozzle on the station’s nozzle should have released any pressure left in the space between the nozzle and the receptacle when closed and should not bleed any pressure when unscrewing the connection.
NOTE: Some nozzles will have more pressure trapped between the nozzle and the receptacle, so it is necessary to slowly unscrew the connection to allow pressure to bleed off before removing the nozzle completely
10. Replace the nozzle and fuel transfer hose on the dispenser.
11. Verify there are no leaks at the tank filling receptacle and replace the protective cap.
12. The fueling process is complete.
During a propane vehicle fueling process fuel may be emitted to the immediate area. There could be a combustible fuel mixture around this immediate area. The person performing the re-fueling process has total responsibility for safety in the immediate area.
NOTES:
• It is unlawful to fill a non-compliant tank or a tank that possesses a safety violation.
10 Blue Bird Vision Service Manual
ROUSH CleanTech Blue Bird Vision Liquid Propane Autogas (LPA)
Service Manual
• Any person performing the re-fueling process must be trained and certified in the procedures of filling propane tanks and in the procedures of safe handling.
Propane Fuel Tank
The LPA system utilizes a dual cylindrical manifold tank assembly to store the liquid propane. The two cylinders are permanently connected by mounting brackets and crossover tubes that create a single volume of fuel and are considered a single fuel tank assembly. The fuel tank is designed and certified to meet all applicable safety standards required for installation on a motor vehicle. The tank design includes structural mounting brackets, which are used for mounting the tank assembly between the frame rails. The tank assembly is secured to the chassis using specially coated and grade level fasteners.
In addition, the tank is fitted with a pressure relief valve (PRV) that will open if tank pressure exceeds
312 psi or 375 psi depending on application. The excess pressure (propane vapor) is vented off on the street side of the bus and the integrity of the tank is protected.
The following components are mounted to the outside of the fuel tank; fixed liquid level gauge
(bleeder valve), supply circuit assembly, return circuit assembly (including FCS), pressure relief valve, fill port check valve, Fuel Pressure and
Temperature Sensor (FPTS) and fuel level sender.
The LPA fuel tank is fitted with a service port flange for accessing the internals of the tank. The following components are located inside the fuel tank; dual electric fuel pumps with an inlet filter, jet pump and a wiring harness.
The tank components and their functions will be provided individually in this manual.
Figure 6 – Fuel Tank – Top
Figure 7 – Fuel Tank – Bottom
When servicing the tank or removing the tank from the vehicle be sure to reinstall the tank with the original fasteners or new like fasteners. Do not replace the fasteners with a lower grade of bolt than originally equipped as this may cause the tank to become dislodged from the vehicle and cause serious damage or injury.
Blue Bird Vision Service Manual 11
ROUSH CleanTech Blue Bird Vision Liquid Propane Autogas (LPA)
Service Manual
Tank Fill Valve/80% Overfill Prevention
Device (OPD)
Located where fuel enters into the fuel tank, the fill valve is opened mechanically by the refueling pump pressure during the fill process. It also incorporates a back flow check valve and an overfilling prevention device. The back flow check valve closes when vehicle tank pressure is greater than pressure outside of the tank to prevent fuel from escaping.
Tank Pressure Temperature Sensor
There is a Tank Pressure Temperature Sensor or (TPTS) mounted on the fuel tank assembly that reads both fuel tank pressure and fuel tank temperature and supplies these values to the
Ford PCM via the Gateway module. This sensor is utilized to help target an expected fuel rail pressure to the engine to ensure the propane in the fuel rails remains in a liquid form at all times during operation.
Figure 8 – Fuel Fill Valve/Overfill Prevention Device (OPD)
Fuel Pumps
The LPA fuel system utilizes two (2) 12-volt in-tank fuel pumps. The fuel pump assembly is mounted to brackets located in the bottom of the fuel tank. The pumps are serviceable through the service port opening on the bottom of the fuel tank.
The in-tank pumps receive a 12-volt supply when the ignition key is switched on and runs a purge cycle for up to 30 seconds. Each pump is controlled by an Electronic Fuel Pump Relay
(EFPR), which are controlled by the PCM. The pump is provided with a constant ground signal.
During operation the pump voltage will vary from
7 – 13.5V.
In-Tank Fuel Filters
There is one filter inside the tank and one outside the tank. The filter inside the tank is located on the bottom of the fuel pumps at the pump inlet ports.
This filter is part of the fuel pump assembly and is non-serviceable on it’s own. The filter on the outside of the tank is the in-line fuel filter and is located at the front end of the tank, in-line with the fuel supply line. It is recommended that this filter be replaced every 50,000 miles.
Figure 9 – Tank Pressure Temperature Sensor
Fuel Level Sender
The tank is fitted with a fuel level sender that consists of an in-tank float arm coupled to an externally mounted variable voltage sensor.
This sender provides a fuel level signal to the instrument panel, which utilizes an “anti-slosh” signal conditioner to provide a constant gauge reading. The fuel level sender is serviceable from the top of the tank through a service opening in the floor of the bus and includes a visual indicator which can be referenced during service.
NOTE: The fuel level indicator on the sender will vary slightly from actual fuel level.
12 Blue Bird Vision Service Manual
ROUSH CleanTech Blue Bird Vision Liquid Propane Autogas (LPA)
Service Manual
Figure 10 – Fuel Level Sender
Tank Bleeder Valve/Fixed Liquid Level
Gauge
The bleeder valve/fixed liquid level gauge serves two functions:
1. Offers a means to evacuate the tank for tank internal component service procedures.
2. Allows annual verification of the function on the
Overfill Prevention Device (OPD).
NOTE: The tank bleeder valve is to remain open during vehicle operation.
Figure 11 – Tank Bleeder Valve/Fixed Liquid Level Gauge
Pressure Relief Valve
The pressure relief valve will activate when tank pressure is above 312 psi or 375 psi. Propane vapor will vent through the pressure relief hose until tank pressure is between 281-309 psig.
Propane vapor is vented out of the pressure relief hose and exits the vehicle vent mounted to the body on the street side behind the rear axle. This is a safety feature designed to prevent excessive tank pressure.
Tank Supply Circuit Assembly
The Fuel Supply Circuit consists of an Excess Flow
Valve, Tank Solenoid (automatic shut off valve) and a Manual Shutoff Valve. The supply circuit Tank
Solenoid is controlled by the PCM and is activated whenever power is supplied to the fuel pump.
Figure 12 – Fuel Tank Supply Circuit
Tank Solenoid Valve
The tank solenoid is an electrically operated automatic shutoff valve. It is located downstream from the Excess Flow Valve and Manual Shutoff
Valve. The Tank Solenoid is normally in a closed position (de-energized), preventing the flow of fuel to the engine. When the ignition key is turned on to start the vehicle, power is supplied to the solenoid opening the valve and allowing fuel to flow from the tank to the engine. The tank solenoid will close when the ignition is shut off, or if the engine stalls
(with ignition on).
Manual Shutoff Valve
The Manual Shutoff Valve is used to seal the outlet of the tank during shipping, service or in case of a vehicle failure. It is located between the Excess
Flow Valve and Tank Solenoid Valve. It is manually operated by turning the knurled knob mounted on the front of the Supply Circuit Assembly. Turning the knob clockwise closes the valve and turning the knob counterclockwise opens the valve.
It should always be open when the vehicle is operating.
Blue Bird Vision Service Manual 13
ROUSH CleanTech Blue Bird Vision Liquid Propane Autogas (LPA)
Service Manual
Excess Flow Valve (XFV)
The Excess Flow Valve is located in the supply fuel path, ahead of the Tank Solenoid and Manual
Shutoff Valve. The valve is intended to shut off fuel flow from the tank in the event of a rapid pressure drop outside the fuel tank. A rapid pressure drop could be caused by a severed line or an inadvertent disconnect without shutting the
Manual Shutoff Valve. If the excess flow valve trips (may happen after servicing the system), it can be reset by closing the manual shutoff valve and then slowly opening it. The excess flow valve does not completely stop flow and will not actuate with smaller leaks, so it should not be relied on for servicing purposes. If the excess flow valve activates (such as immediately following service where the system may not be primed with fuel), turn off the key and wait 15-30 seconds then retry.
Fuel Return Valve
The fuel return valve on the tank incorporates a check valve, which prevents fuel from flowing from the tank into the return line. The fuel return valve also contains the Flow Control Solenoid (FCS) which includes a small orifice to restrict return flow in normal conditions; and a bypass circuit to allow maximum fuel flow prior to engine starting or during extremely hot conditions.
Figure 13 – Fuel Return Valve
Fuel Transfer Lines
The fuel transfer lines utilized in the LPA fuel system are made of a steel-reinforced PTFE with stainless steel hard line sections to provide long term protection and service. The 3/8" supply and 1/4" return lines contain SAE quick connect couplings, which require special tools to disconnect.
NOTE: Special tools are required to properly disconnect the quick connect fittings. Attempting to remove the lines without these tools can cause damage to the fitting and/or line.
NOTE: When replacing hoses and lines, use
Roush CleanTech replacement parts made from the same material and size. Always route and secure hoses as originally installed. All hoses and lines must be compliant and labeled per NFPA 58 requirements.
Figure 14 – Flexible Fuel Line
Fuel Rail Pressure Control Module
(FRPCM)
The FRPCM is a unit consisting of two (2) normally closed solenoids and a return check valve. The
FRPCM is controlled directly by the Gateway
Module which is governed by the PCM. Included in the FRPCM are:
Supply Solenoid — Open (energized) when the engine is running, the supply solenoid allows fuel to flow from the chassis fuel lines to the fuel rail.
The supply solenoid is closed when the engine is turned off, preventing fuel from flowing from the chassis fuel lines to the engine fuel rail.
NOTE: There is a second supply solenoid located at the fuel tank which prevents fuel from flowing into the chassis fuel lines when the engine is turned off.
Return Check Valve — Open when the engine is running, the return check valve allows fuel to return from the fuel rails to the chassis fuel lines.
The return check valve closes when the engine is turned off, isolating the fuel return line and fuel tank and preventing fuel from backfilling the engine fuel rail.
14 Blue Bird Vision Service Manual
ROUSH CleanTech Blue Bird Vision Liquid Propane Autogas (LPA)
Service Manual
Bleed Solenoid — Closed when the engine is running, the bleed solenoid seals the fuel rail from the vehicle EVAP system. When ambient temperature is above 40° F, after the engine is turned off for approximately one hour, the bleed solenoid opens for a calibrated length of time allowing all the fuel pressure to bleed from the fuel rail through a metered orifice and into the carbon canister. When the process is complete, the solenoid closes, preventing fuel from entering the
EVAP system.
Figure 15 – Fuel Rail Pressure Control Module (FRPCM)
Injection Pressure Temperature Sensor
The Injection Pressure Temperature Sensor is located in the drivers side fuel rail and is used to determine the pressure and temperature of the propane in the fuel rail. This information is supplied to the Ford PCM via the gateway module and helps to ensure the propane in the fuel rails is kept in a liquid form as well as assisting with fuel injector pulse width.
Vapor Canister Assembly
A vapor canister is being utilized to vent the fuel vapors remaining in the fuel rail during engine shut-off to eliminate the chance of propane leaking past the fuel injectors.
Figure 16 – Vapor Canister and Line Assembly
Vapor Lines
The fuel vapor hoses are flexible with quick connect fittings, which can be easily disconnected by pinching the connector release points.
Fuel Rail Assemblies
(Refer to Figures 17, 51, & 53)
Each fuel rail assembly is mounted to the intake manifold by three brackets, and is made up of the following components:
• Five fuel injectors retained in the fuel rail by a c-clip. The injectors are connected to the main engine wiring harness. Fuel metering and injection is controlled by the engine PCM as the injectors are opened and closed by switching the ground internally in the PCM.
• Five injector spacers sealed to the fuel rail and intake manifold injector ports by O-rings and retained to the fuel rail with a retention clip.
• A Fuel Pressure and Temperature Sensor
(FPTS) is mounted on the left hand rail.
Blue Bird Vision Service Manual 15
ROUSH CleanTech Blue Bird Vision Liquid Propane Autogas (LPA)
Service Manual
16
Figure 17 – Fuel Rail and Lines Installed
Blue Bird Vision Service Manual
ROUSH CleanTech Blue Bird Vision Liquid Propane Autogas (LPA)
Service Manual
Remote Fill Valve
This valve is used to connect the refueling station nozzle to the fill line during filling. It is mounted to a bracket behind the locked fuel door on the curb side of the bus and has a screw-on protective dust cap. It contains a backflow check valve to prevent propane in the line from escaping when the dispensing nozzle is removed.
Fill Line
The fill line is a flexible black line with nonserviceable fittings on either end, connecting between the remote fill valve, in-line fill filter and the tank fill valve.
Fill Filter
The fill filter is mounted to the bus body in-line between the remote fill valve and the tank fill valve.
It consists of an internal filtering cartridge capable of filtering out contaminants as small as 5 microns.
This filter should be replaced every 50,000 miles.
Remote Bleeder Valve
The remote bleeder valve is to remain closed during vehicle operation and filling.
This valve is connected to the tank bleeder valve by a bleeder hose and is used for the same functions as the tank bleeder valve.
1. Offers a means to evacuate the tank for tank internal component service procedures.
2. Allows annual verification of the function on the
Overfill Prevention Device (OPD).
Bleeder Hose
The bleeder hose is a flexible steel-reinforced line with non-serviceable fittings on either end, connecting the tank bleeder valve to the remote bleeder valve. This line is pressurized at all times and should only be serviced after closing the tank bleeder valve and opening the remote bleeder valve to release trapped pressure.
Electronic Fuel Pump Relay (EFPR)
The relay controls the fuel pump voltage, which controls the fuel pump duty cycle. Each fuel pump is controlled by a separate EFPR. The EFPRs are mounted to a bracket on the frame cross member in front of the fuel tank.
Figure 18 – Remote Bleeder Valve
Figure 19 – Electronic Fuel Pump Relays
LPA Gateway Module
The Gateway Module is an electronic control module that provides two functions within the Blue
Bird bus LPA system:
1. Communications gateway between the Blue
Bird Bus electrical system and the Engine/
Transmission controller.
2. To provide additional input/output features required for the LPA fuel system.
Gateway Function
The Gateway Module provides the following signals to the Blue Bird bus from the Ford engine/ transmission module.
• Engine data
• Transmission data
• Start in progress
• Fuel level
• Diagnostic warning light requests
Blue Bird Vision Service Manual 17
ROUSH CleanTech Blue Bird Vision Liquid Propane Autogas (LPA)
Service Manual
The Gateway Module reads the following signals from the Blue Bird bus and reports them to the engine controller.
• Front AC request
• Rear AC request
• Cruise control switch positions
• Throttle Interlock requests
• High idle speed request
LPA Interface Function
The Gateway Module controls the following functions within the LPA system
• Fuel rail pressure control module solenoids
• Fuel tank supply solenoid
The Gateway Module supplies the following information to the Ford engine controller
• Fuel rail temperature and pressure
• Fuel tank temperature and pressure
• Second fuel pump relay module fault status
• Fuel level
NOTE: Signals supplied to the Ford engine controller will be diagnosed by the engine controller and reported as engine P-Codes. Lack of communication between the Gateway Module and the engine controller will also be reported by the engine controller.
from heat, sparks, flames, static electricity or other sources of ignition. Failure to heed this danger can result in severe personal injury.
Fuel supply lines remain pressurized after engine shutdown. Keep away from heat, sparks, flames, static electricity or other sources of ignition. Do NOT enter storage areas or confined spaces unless they are adequately ventilated. Failure to heed this danger can result in severe personal injury.
Propane is heavier than air and seeks the lowest available level when released to the atmosphere. Keep heat, sparks, flames, static electricity or other sources of ignition out of the area when venting or purging the fuel lines or tank. Failure to heed this danger can result in severe personal injury or property damage.
SERVICE PREPARATION
Alert Messages
The following alert messages appear from time to time in appropriate places in this manual. Ensure that all personnel in the immediate area are aware of these reminders.
These messages consist of reminders of Dangers and Warnings. Other reminders may appear under the heading, Notes.
Propane is nontoxic, nonpoisonous, has the lowest flammability range of any alternative fuel and dissipates quickly when released into the atmosphere. Propane vapor is heavier than air and seeks the lowest point. When the ratio of propane to air is between 2.2% and 9.6%, propane burns in the presence of an ignition source at 940°F (504°C) or hotter. Keep away
Liquid propane is cold. The temperature of propane in its liquid state is -44°F (-42°C). Wear eye and ear protection during venting and repair operations. Keep moisture away from the valves.
Failure to heed this warning can result in personal injury.
NOTE: Identify the condition (good, stuck open, stuck closed or inoperable) of each solenoid valve prior to venting the fuel tank to ensure that the solenoid valves are not the reason for vehicle service and unnecessarily venting the tank.
Manual Fuel Shutoff
NOTE: This procedure ensures that no propane leaves the fuel tank during service activities.
1. Remove the supply circuit cover on the bottom of the tank, using the thumb screws.
2. With the cover removed locate the manual shutoff valve. Turn the knurled knob clockwise until it stops and is tightly bottomed out. The propane supply from the tank is now shutoff.
Opening the Manual Fuel Shutoff
1. After fuel system service is completed, open the manual shutoff valve on the tank by turning it counter-clockwise until it stops.
2. Follow the Fuel System Priming Procedure.
18 Blue Bird Vision Service Manual
ROUSH CleanTech Blue Bird Vision Liquid Propane Autogas (LPA)
Service Manual
3. Leak-check the fuel lines and fuel rails with an electronic leak detector or leak detection solution. Repair as necessary.
4. Install the supply circuit cover back onto the tank.
5. Start and run the engine and check for diagnostic trouble codes. Repair as necessary.
NOTE: Starting the engine for the first time after the fuel supply line has been evacuated may cause the Excess Flow Valve to close which may cause the engine to run rough or stall. If this occurs turn off the ignition and wait about 30 seconds, then restart. This may have to be repeated multiple times until the fuel supply line comes up to pressure.
Technical issues involving starting, operating or re-fueling a propane power bus should be reported to your local qualified service provider. In the event further technical assistance is needed, you should first contact your authorized Blue Bird Dealer regarding any technical issues with your Blue Bird product.
In emergency situations or if immediate technical assistance is needed and the above mentioned technical assistance is unavailable you can call
ROUSH CleanTech Customer Service at 800.59.
ROUSH (597-6874) with any questions regarding
ROUSH CleanTech Liquid Propane Autogas
Systems.
Fuel Tank Pressure Relief
To relieve excess pressure in the tank the remote bleeder valve inside the fuel door can be used.
Fuel System Purge, Evacuation and
Priming Procedures
During any fuel system maintenance or repair in which the fuel pressure must be released from the system or the system completely evacuated, use the following procedures.
Technicians working with, or around, fuel systems should be properly trained to utilize extreme care and caution at all times. Failure to exercise extreme caution and care may lead to serious accidents which can result in property damage, personal injury and/or death.
LPG is under pressure, wear adequate eye protection. When LPG is discharged into the atmosphere the rapid change in pressure can cause a refrigerant condition in the fuel (quick cooling) and can harm your skin or cause serious burns much like frostbite, Always wear gloves.
When releasing the fuel pressure be sure to place the discharge point of the drain hose in a safe area free from any combustible material or ignition source. Be sure that no one is in the immediate area of the discharge hose.
Propane is heavier than air and seeks the lowest available level when released to the atmosphere. Keep heat, sparks, flames, static electricity or other sources of ignition out of the area when venting or purging the fuel lines or tank. Failure to heed this danger can result in severe personal injury or property damage.
Liquid propane is cold. The temperature of propane in its liquid state is -44°F (-42°C). Wear eye and ear protection during venting and repair operations. Keep moisture away from the valves. Failure to heed this warning can result in personal injury.
Fuel Line Purging
Clearing the propane out of the fuel lines (purging) is required before working on many fuel system components. Following the suggested techniques for purging the fuel lines will reduce the amount of vapor released harmlessly into the atmosphere and will produce the least risk to life and property.
1. Close the manual shut-off valve on the tank supply valve.
2. Disconnect the fuel pump electrical connectors at the frame rail on the curb-side near the fuel tank. This disconnects the power to the fuel pumps.
3. Start the engine and let it run until it stalls.
This purges the supply and return fuel lines of liquid propane.
4. Turn off the ignition.
Blue Bird Vision Service Manual 19
ROUSH CleanTech Blue Bird Vision Liquid Propane Autogas (LPA)
Service Manual
5. Slowly open the fuel line connection at in-line filter and at return valve on tank to allow the remaining fuel to bleed off.
6. Turn key on to cycle supply solenoid, but turn off before the engine cranks.
7. Tighten fuel line fitting at the filter to xx Nm and the fuel line at the return valve to xx Nm.
8. Disconnect the negative battery cables from the batteries.
NOTE: There may still be a small amount of propane in the lines after running this procedure.
Open the lines slowly and cautiously to bleed off any remaining propane.
When releasing the fuel pressure be sure to keep the discharge point of the line or hose in a safe area free from any combustible material or ignition source. Be sure that no one is in the immediate area of the discharge hose.
Propane is nontoxic, nonpoisonous, has the lowest flammability range of any alternative fuel and dissipates quickly when released into the atmosphere. Propane vapor is heavier than air and seeks the lowest point. When the ratio of propane to air is between 2.2% and 9.6%, propane burns in the presence of an ignition source at 940°F (504°C) or hotter. Keep away from heat, sparks, flames, static electricity or other sources of ignition. Failure to heed this danger can result in severe personal injury.
The fuel tank on an LPA fuel system utilizes an electric fuel pump to deliver fuel to the fuel injectors during normal operation. If you are shipping the tank, servicing one of the valves or to service in-tank components you must follow the procedures listed below.
Draining the LPA tank should be performed by a trained technician only. When draining a fuel tank use all the following precautions to prevent serious bodily injury, death and/or property damage.
Liquid propane is cold. The temperature of propane in its liquid state is -44°F (-42°C). Wear eye and ear protection during venting and repair operations. Keep moisture away from the valves. Failure to heed this warning can result in personal injury.
Fuel Tank Draining Procedure
Propane is heavier than air and seeks the lowest available level when released to the atmosphere. Keep heat, sparks, flames, static electricity or other sources of ignition out of the area when venting or purging the fuel lines or tank. Failure to heed this danger can result in severe personal injury or property damage.
Technicians working with or around, fuel systems should be properly trained to utilize extreme care and caution at all times. Failure to exercise extreme caution and care may lead to serious accidents which can result in property damage, personal injury and/or death.
NOTE: A propane fuel tank must be empty of propane before it can be transported by a carrier.
Due to the volume of fuel likely to be retained in the fuel tank, releasing the vapor to the atmosphere would be wasteful, unsafe and is an extremely slow procedure without special equipment. It is suggested that a local, certified propane handling company be engaged to purge the fuel tank and recapture the fuel as the need requires.
Liquid propane is cold. The temperature of propane in its liquid state is -44°F (-42°C). Wear eye and ear protection during venting and repair operations.
Keep moisture away from the valves. Failure to heed this warning can result in personal injury.
• Wear protective eye wear, gloves and clothing
• Perform the process in a well ventilated area only
• Remove all potential ignition sources from the area
• Use only the recommended processes
• Use the proper tools
• Drain the tank on the vehicle into a tank of equivalent or larger capacity
20 Blue Bird Vision Service Manual
ROUSH CleanTech Blue Bird Vision Liquid Propane Autogas (LPA)
Service Manual
Using In-Tank Pumps
Use of the in-tank pumps to drain the tank is an acceptable method assuming at least one of the two pumps and the supply valve are functioning normally. Temperature can affect transfer rates.
NOTE: This method will not completely drain the tank and a final process of venting the tank will still be required. In some areas it is not allowed or may not be safe to vent the fuel to the atmosphere. In this case, the fuel must be burned off.
1. Move the vehicle to a well ventilated area free of any external ignition sources.
2. Place the tank in which the fuel is to be captured close to the tank to be drained.
3. Purge the fuel lines by using the Fuel Line
Purge Procedure.
4. Disconnect supply line from forward side of inline filter at front of fuel tank.
5. Connect the fuel transfer hose to the receiving tank fill valve or other appropriate valve.
6. Connect the transfer hose to the forward side of filter that line was removed from in Step 4.
7. Disconnect the fuel pump wire harness in vehicle and connect a switch to the fuel pump wire connectors.
8. Open the manual supply valve on the tank to be drained.
9. Open the automatic supply valve on the tank to be drained, this requires 12V power to the supply solenoid.
10. Turn the switch on the jumper harness to the
ON position, you should hear the pumps in the fuel tank running and fuel will begin to transfer to the capture fuel tank.
11. When the liquid propane level in the fuel tank drops below the fuel pumps pickup tube the pump will make a different sound. Turn the switch off to stop the pump. NOTE: Running fuel pumps without liquid in them will cause damage to the pumps and lead to premature failure.
12. The remaining fuel in the tank will now need to be evacuated through the bleed valve.
13. Manually close the supply valve on the vehicle tank.
14. Loosen the fuel transfer hose and bleed off the fuel pressure.
Fuel may be under pressure in the transfer line; use caution when disconnecting the fittings, slowly loosen the fittings and use gloves and protective eye wear.
15. Disconnect the transfer hose from the receiving tank and place the other end of the transfer hose in a safe, well ventilated location away from any area where the fuel could create a volatile condition.
16. Slowly open the manual supply valve and allow the tank to vent until the pressure has been released completely from the tank. If the excess flow closes during this operation simply close the supply valve and re-open it slowly.
NOTE: The tank can be evacuated using a flare stand, if the service center is equipped with a stand and has received the proper training.
17. If using a flare stand to burn off the remaining fuel in the tank this would require approximately a 50 foot clearance from the vehicle, other vehicles, a building or any combustible materials. Slowly open the valve on the flare stand and light the escaping gas; open the valve little by little to decrease the time to evacuate.
Some states and municipalities may have regulations preventing the release of LPG into the atmosphere. Check with your local fire marshal or your local LPG supplier prior to venting or burning off a tank.
18. When the pressure in the tank has reduced to a point that it does not support the flame turn the liquid supply valve off and disconnect the hoses. Open the remote bleeder valve to vent the remaining pressure to the atmosphere.
Do not have any sources of ignition within a minimum of 50 foot of the area.
19. Once the tank has vented, close the supply valve and bleeder valves on the tank.
NOTE: If you have any questions or concerns or you feel unqualified to perform the process of venting the tank contact your local fuel system provider or ROUSH CleanTech (800) 59-ROUSH.
Blue Bird Vision Service Manual 21
ROUSH CleanTech Blue Bird Vision Liquid Propane Autogas (LPA)
Service Manual
Fuel Tank Purging Procedure
The following procedure is required to purge the air from the fuel tank after servicing.
1. Fill the tank with one (1) gallon of propane and cycle the ignition key to the crank position and then to the off position. (Do not allow the vehicle to start during this step.)
2. Inspect and monitor the tank for any leaks.
3. Open the bleeder valve for 20 minutes or until propane stops bleeding, whichever comes first.
Close the bleeder valve.
4. Fill with 25+ gallons of propane.
5. Close the bleeder valve.
NOTE: When filling an empty tank start filling at a slow rate to build up pressure inside the tank. An initial fast fill may trip the OPD, creating a slow or no fill condition.
6. Perform a final leak inspection at all fuel fill and fuel line connections to ensure no leaks are present using an electronic leak detector or leak detection solution.
7. Install supply circuit cover on tank. Apply antiseize to the thumb screws and hand tighten.
Fuel System Priming Procedure
After performing any fuel system service work air will have entered the system through the open connections and ports. You will need to prime the fuel system to expel all the air from the fuel lines and rails. To prime the fuel system turn the ignition key to the Key On Engine Off (KOEO) position,
NOT THE START POSITION.
See Fuel System Description and Operation at the beginning of this chapter for detailed operation of the purge cycle.
1. Make sure the battery is connected.
2. Check to make sure there is fuel in the tank and manual shutoff valve is closed.
3. Turn the key to the KOEO position for 5 seconds.
4. Turn the key to the start position. When the
“Start In Progress” light comes on, slowly open the manual shutoff valve.
5. If vehicle does not start, close the manual shutoff valve and repeat the process.
NOTE: If the engine fails to start refer to the Fuel
System Pressure Check Procedure in this manual.
22 Blue Bird Vision Service Manual
ROUSH CleanTech Blue Bird Vision Liquid Propane Autogas (LPA)
Service Manual
Fuel System Flow Diagrams
Figure 20 – In-Tank Lines and Filters
FUEL PUMP
ASSEMBLY
Figure 21 – Fuel Pump and Filter Assembly
Blue Bird Vision Service Manual 23
ROUSH CleanTech Blue Bird Vision Liquid Propane Autogas (LPA)
Service Manual
Figure 22 – Fuel Tank Bottom View
24
Figure 23 – Fuel System Remote Valves and Lines
Blue Bird Vision Service Manual
ROUSH CleanTech Blue Bird Vision Liquid Propane Autogas (LPA)
Service Manual
Blue Bird Vision Service Manual
Figure 24 – Fuel Rail and Lines
Figure 25 – Fuel Evaporative System
25
ROUSH CleanTech Blue Bird Vision Liquid Propane Autogas (LPA)
Service Manual
COMPONENT SERVICING
Special Tools
Quick Disconnect Tools
The fuel lines in the LPA system use quick connect fittings, which require special tools to disconnect the supply lines. The supply lines use the 3/8" tool which can be purchased from any automotive service tool supplier.
Some states and municipalities may have regulations preventing the release of LPG into the atmosphere. Check with your local fire marshal or your local LPG supplier prior to venting or burning off a tank.
Fuel Tank
The cylindrical tank assembly for the LPA fuel system is mounted in the rear overhang between the frame rails parallel to the vehicle frame.
Figure 26 – Quick Disconnect Tools
Electronic Leak Detector
If purchasing an electronic leak detector, it is recommended to use a tester capable of detecting down to 35 PPM of propane vapor.
Flare Tower
A flare stand/tower can be used to burn off vented propane during servicing. If using a flare tower we recommend purchasing one from a reputable supplier, such as: www.flameengineering.com/Propane_Flare.htm
Figure 27 – Fuel Tank and Frame Supports
Do not attempt to build your own flare tower.
Failure to exercise extreme caution and care may lead to serious accidents which can result in property damage, personal injury and/or death.
Figure 28 – Fuel Tank Installed – Rear View
NOTE: To service the tank or any valves, make sure the vehicle is in a well ventilated area and ensure the tank is in a stable position prior to starting work.
26 Blue Bird Vision Service Manual
ROUSH CleanTech Blue Bird Vision Liquid Propane Autogas (LPA)
Service Manual
Technicians working with, or around, fuel systems should be properly trained to utilize extreme care and caution at all times. Failure to exercise extreme caution and care may lead to serious accidents which can result in property damage, personal injury and/or death.
LPG Propane Gas is flammable. DO NOT vent propane in an enclosed area, or close to service pits, drainage ditches or low lying areas. DO NOT vent propane within 25 feet of any source of ignition, spark, open flame or heat. When venting propane liquid, it will vaporize at a very cold temperature (-44 F).
Always wear safety goggles and gloves when handling systems venting gas. Always perform a complete system leak test after completing any service or maintenance.
Be sure the tank has been completely drained before removing any valves or fittings from the tank. See Fuel Tank Draining Procedure.
Be fully aware of the local regulations, NFPA codes and safety requirements for handling propane fuel prior to working on this vehicle.
REAR FRONT
Figure 29 – Fuel Tank and Line Assembly
Removal
1. Purge the fuel lines using the Fuel Line
Purging Procedure.
2. If the tank is being replaced or will be opened for service, drain the fuel tank using the Fuel
Tank Draining Procedure.
NOTE: If the tank does not need to be serviced and will be removed with propane inside, be sure the manual shutoff and tank bleeder valves are securely closed.
3. Carefully disconnect the chassis flex lines from the tank mounted hard lines using the appropriate disconnect tools.
4. Remove bleed hose from the bleeder valve on the back of the tank.
5. Remove the fill hose from the fill valve on the back of the tank.
Blue Bird Vision Service Manual 27
6. Loosen and remove all nuts and carriage fasteners attaching the rear bumper to the vehicle.
7. Carefully remove rear bumper to prevent damage to the vehicle.
ROUSH CleanTech Blue Bird Vision Liquid Propane Autogas (LPA)
Service Manual
17. Using suitable lifting device (hydraulic table, transmission jack, etc) lift tank from tank support cross members approximately 1”.
(Note: Using 4x4 wooden blocks makes this much easier.)
8. Remove the rear tow hooks and the tow hook cross member.
Ensure tank is securely fastened to lifting device to prevent accidental dropping.
18. When tank is fully supported and stable on the lifting device, remove the four (4) tank support cross members toward the rear of the vehicle.
The forward most bracket does not need to be removed for this operation.
Replacement
Reverse the above procedure (refer to torque chart for proper torques)
Once installed,
1. If the tank was drained and/or opened during the servicing, purge the fuel tank using the
Fuel Tank Purging Procedure.
2. Confirm all fuel and electrical connections are secure, the battery is connected and the manual shut off valve is open.
3. Add 10 gallons of propane to the tank.
4. Leak Check the valves and fuel lines using an electronic leak detector or leak detection solution.
5. Reinstall fuel supply circuit cover.
Figure 30 – Frame Brackets
9. Detach back up alarm harness from vehicle frame and ensure it is safely out of the way.
10. Remove six (6) fasteners attaching the rear tank cross member to the frame.
11. Remove four (4) fasteners attaching the rear tank cross member to the tank end guard.
12. Remove three (3) fasteners attaching the tank end guard to the tank support cross member.
Remove the tank end guard and rear tank cross member.
13. Unplug the tank electrical connectors from the vehicle wiring harness located at the rear tank support cross member. Cut any nylon ties that will prevent easy removal.
14. Remove eight (8) fasteners attaching the tank to the tank support cross members.
15. Remove every other nut and bolt attaching the tank support cross members to the right and left hand tank barriers.
16. Loosen but DO NOT remove remaining nuts and fasteners.
Figure 31 – Fuel Tank Frame Brackets and Shields
28 Blue Bird Vision Service Manual
ROUSH CleanTech Blue Bird Vision Liquid Propane Autogas (LPA)
Service Manual
Tank Fill Valve/80% Overfill Prevention
Device (OPD)
Located at the top of the tank, near the center of the tank, and can be accessed through the service door in the floor of the bus.
NOTCH
TOP MARKING
Be sure the tank has been completely drained before removing the fill valve from the tank.
Removal
1. Purge the fuel lines using the Fuel Line Purge
Procedure.
2. Drain the fuel tank using the Fuel Tank
Draining Procedure.
3. Remove the fill line from the tank fill valve.
4. Remove the 90 degree fitting from the fill valve.
5. Remove the fill valve from the tank.
Replacement
NOTE: The mark on the fill valve needs to face vertically upwards to work properly when installed.
For ease of visibility after installation, a punch mark
(disregard paint markings) has been added to the face at the hex end of the fill valve see Figures 32 and 33.
Figure 32 – Fuel Fill Valve/Overfill Prevention Device (OPD)
Installation
SCALE 1:2
PIN
POSITION
FLOAT
DIRECTION
Figure 33 – Tank Fill Valve/Overfill Prevention Device
1. Install the new fill valve assembly into the tank.
Torque to 75 Nm minimum, plus orientation, reverse torque not permissible.
2. If reusing, clean the threads and apply pipe thread sealant (PLS2 Everseal 183) to the threads of the 90-degree fitting. Assemble the 90-degree fitting to the fill valve in the orientation shown in Figure 34. Torque fitting to 31 Nm minimum, plus orientation, reverse rotation is not permissible.
3. Reinstall the fill line to the valve and torque fill line to 45 +/- 0.4 Nm.
4. Purge the fuel tank using the Fuel Tank
Purging Procedure.
5. Reconnect the battery.
6. Fill tank and leak check the fitting using an electronic leak detector or an approved leak detection solution.
NOTE: The mark on the fill valve connector needs to face straight up to work properly when installed.
For ease of visibility (after installation) add a mark at the end of the fitting with a marker before it is installed.
Blue Bird Vision Service Manual 29
ROUSH CleanTech Blue Bird Vision Liquid Propane Autogas (LPA)
Service Manual
4. Purge the fuel tank using the Fuel Tank
Purging Procedure
5. Reconnect the battery.
6. Fill tank and leak check the fitting using an electronic leak detector or an approved leak detection solution.
Fuel Tank Pressure Relief Valve
Figure 34 – OPD Orientation
Tank Bleeder Valve
Located at the bottom of the tank, see Figure 35.
Figure 35 – Tank Bleeder Valve
Be sure the tank has been completely drained before removing the fill valve from the tank.
Removal
1. Purge the fuel lines using the Fuel Line Purge
Procedure.
2. Drain the fuel tank using the Fuel Tank
Draining Procedure.
3. Remove the bleeder line from the tank bleeder valve.
4. Remove the bleeder valve from the tank.
Replacement
1. Apply pipe thread sealant (PLS-2 or Everseal
183) ONLY to the threads going into the tank.
2. Install the new bleeder valve assembly into the tank. Torque to 20 +/- 4.0 Nm minimum, plus orientation, reverse torque not permissible
(see Figure 35).
3. Reinstall the bleeder line to the valve and torque to 18.5 +/- 3.0 Nm.
Be sure the tank has been completely drained before removing the pressure relief valve from the tank.
Removal
1. Purge the fuel lines using the Fuel Line
Purging Procedure.
2. Drain the fuel tank using the Fuel Tank
Draining Procedure.
3. Remove the frame cross-member and shield behind the tank.
4. Disconnect the fuel pressure relief hose from the pipe away fitting on the tank.
5. Remove the pipe away fitting from Pressure
Relief Valve (PRV).
6. Remove pressure relief valve from tank.
Replacement
1. Install the new pressure relief valve (thread sealant pre-applied) into the threaded coupling, torque to 120 Nm minimum plus
180-degrees.
2. Clean the threads of the pipe away fitting.
3. Apply thread sealant (PLS-2 or Everseal 183) to the threads of the pipe away fitting.
4. Assemble the pipe away fitting to the pressure relief valve and Torque to 95 +/- 5 Nm.
5. Purge the fuel tank using the Fuel Tank
Purging Procedure.
6. Reconnect the fuel pressure relief valve hose and clamp.
7. Install the frame cross-member and tank shield.
8. Reconnect the battery.
9. Perform the Fuel System Priming Procedure.
30 Blue Bird Vision Service Manual
ROUSH CleanTech Blue Bird Vision Liquid Propane Autogas (LPA)
Service Manual
Tank Supply Circuit Assembly
Located on the bottom of the LH tank cylinder behind the supply circuit cover.
Be sure the tank has been completely drained before removing any of the supply valve components from the tank.
Figure 36 – Supply Circuit Assembly
Removal
1. Purge the fuel lines using the Fuel Line
Purging Procedure.
2. Drain the fuel tank using the Fuel Tank
Draining Procedure.
Ensure the battery ground wires are disconnected before proceeding.
3. Disconnect the chassis flex line from the supply line on the tank using the appropriate disconnect tool.
4. Remove the supply line bolt from the front tank support.
5. Remove the supply line at the valve using the appropriate disconnect tool.
6. Disconnect the supply solenoid electrical connection.
7. Open the remote bleeder valve to ensure there is no remaining pressure in the tank.
8. Remove the four (4) bolts securing the valve to the tank.
9. Pull the Supply Circuit Assembly away from the tank.
10. Disconnect the internal fuel pump supply line by depressing the colored tabs on either side of the quick connect fitting and pulling it off the stem.
NOTE: Retain the fuel supply line with a clip to prevent it from slipping back into the fuel tank.
11. Remove and discard the o-ring from the bottom of the supply valve.
Replacement
NOTE: When replacing the Supply Circuit
Assembly, the tank seat o-ring must be replaced.
1. Inspect the o-ring sealing surface and remove any debris.
2. Apply silicone o-ring lubricant (Parker Super
Lube or equivalent) to the o-ring and install to the supply solenoid.
3. Lubricate the tip of the brass stem quick connect with a small amount of motor oil.
4. Connect the internal fuel pump supply line, push on until a “click” is heard, then tug to insure it is secured.
5. Slide the supply valve assembly to the tank seat.
6. While holding the supply circuit valve assembly, install the four (4) bolts and hand tighten.
7. Torque the bolts using the sequence and torques shown in Figure 37.
a. Initial Torque: Crossing pattern
2.5 +/- 0.5 Nm b. Final Torque: Crossing pattern 10 +/- 1 Nm
8. Install the threaded fitting of the supply line to the supply valve, torque to 29 to 33 Nm.
9. Close the remote bleeder valve.
10. Connect the wiring harness to the tank solenoid coil.
11. Secure the supply line to the front mounting bracket on the tank.
12. Connect the chassis flex line to the tank supply line.
13. Purge the fuel tank using the Fuel Tank
Purging Procedure.
14. Connect the vehicle battery.
15. Install 10 gals of propane into the tank.
Blue Bird Vision Service Manual 31
16. Check the supply valve and tank lines for leaks using an electronic leak detector or leak detection solution.
17. Reinstall the supply circuit cover and hand tighten the thumb screws.
18. Perform the Fuel System Priming Procedure.
BOLT TORQUE SEQUENCE
1-4-3-2 SNUG 2-3 Nm
1-4-3-2 9-11 Nm
2
Figure 37 – Supply Circuit Torque Sequence
Fuel Tank Return Valve
Located on the bottom of the LH tank cylinder behind the supply circuit cover.
Be sure the tank has been completely drained before removing the return line or valve from the tank.
4
ROUSH CleanTech Blue Bird Vision Liquid Propane Autogas (LPA)
Service Manual
Figure 38 – Tank Return Circuit Assembly
3
1
Removal
1. Purge the fuel lines using the Fuel Line
Purging Procedure.
2. Drain the fuel tank using the Fuel Tank
Draining Procedure.
3. Disconnect the chassis flex fuel line from the hard lines on the tank
4. Remove the supply and return line bolts from the front tank support
5. Remove the fuel supply and return lines from the valves.
6. Remove the return valve from the tank.
7. Remove the return hose from the return valve quick connect fitting.
NOTE: Retain the fuel return line with a clip to prevent it from slipping back into the fuel tank.
Replacement
1. Slide the return valve assembly to the tank seat.
2. While holding the return valve assembly, install the four (4) bolts and hand tighten.
3. Torque the bolts using the sequence and torques shown in Figure 37.
a. Initial Torque: Crossing pattern
2.5 +/- 0.5 Nm.
b. Final Torque: Crossing pattern 10 +/- 1 Nm.
4. Install the threaded fitting of the return line to the return valve, torque to 29 to 33 Nm.
5. Secure fuel return line to the front tank support.
6. Lubricate the end of the fuel tank hard lines with oil and connect to the chassis flex lines and tug on them gently to confirm they are secure.
7. Purge the fuel tank using the Fuel Tank
Purging Procedure.
8. Check line connections for leaks using an electronic leak detector or leak detection solution.
9. Reinstall the supply circuit cover apply antiseize and hand tighten the thumb screws.
10. Connect vehicle batteries.
11. Perform the Fuel System Priming Procedure.
32 Blue Bird Vision Service Manual
ROUSH CleanTech Blue Bird Vision Liquid Propane Autogas (LPA)
Service Manual
Solenoid Coil Replacement
Removal
1. Disconnect vehicle battery and remove 2-pin connection from solenoid to be serviced.
2. Remove the nut holding the coil onto the solenoid post.
3. Slide coil off of the post.
Installation
1. Slide new coil onto the post.
2. Install the nut which holds on the coil and torque to 47.5-48.5 in-lb.
3. Reconnect electrical connector to solenoid coil.
4. Reconnect vehicle battery.
5. Start vehicle and perform KOEO/KOER self test to ensure vehicle is repaired and solenoid faults do not persist.
Fuel Pump Assembly (In-Tank)
Removal
1. Purge the fuel lines using the Fuel Line Purge
Procedure
.
2. Drain the fuel tank using the Fuel Tank
Draining Procedure
.
Ensure the battery ground wires are disconnected before proceeding.
3. Remove tank service cover from the tank, loosening bolts in a star-pattern.
4. Reach into fuel tank and disconnect fuel pump electrical connectors.
5. Release pump hose quick connects from intank fi lters.
6. Remove the center bolt and the two (2) nuts that secure pump housing to tank bracket.
7. Remove pump assembly from fuel tank.
NOTE:
Pumps are to be serviced as an assembly.
Replacement
1. Attach new pump assembly to tank bracket using center bolt (5.8 +/- 0.3 Nm) and two (2) nuts (8.5 +/- 0.5 Nm).
2. Attach pump hose quick connects to in-tank fi lters.
3. Connect fuel pump electrical connectors.
4. Lubricate the tank supply cover O-ring with a small amount of motor oil and install it to the tank, driving bolts in a star-pattern.
NOTE:
It is recommended to replace the service cover O-ring whenever the cover is removed.
5. Purge the fuel tank using the Fuel Tank
Purging Procedure
.
6. Reconnect battery.
7. Check the supply valve and tank lines for leaks using an electronic leak detector or leak detection solution.
8. Reinstall the supply circuit cover and hand tighten the thumb screws.
the .
Tank Pressure Temperature Sensor
Removal
1. Disconnect vehicle battery and refer to fuel tank evacuation procedure.
2. Once tank is properly drained remove the connector from the TPTS and remove the sensor from the fuel tank.
Replacement
1. Install new TPTS into the fuel tank assembly and torque to 7 +/- 1 Nm.
2. Reinstall connector to the TPTS.
3. Perform the fuel tank purge procedure and ensure there are no leaks present from the fuel tank assembly.
4. Reconnect vehicle battery and clear all DTCs.
Blue Bird Vision Service Manual 33
ROUSH CleanTech Blue Bird Vision Liquid Propane Autogas (LPA)
Service Manual
Figure 39 – In-Tank Lines and Filters
NOT
SERVICEABLE
RETURN
LINE
34
SUPPLY
LINE
Figure 40 – Fuel Pump and Filter Assemblies Installed
Blue Bird Vision Service Manual
ROUSH CleanTech Blue Bird Vision Liquid Propane Autogas (LPA)
Service Manual
Fuel Level Sender (located on top of the LH cylinder)
Removal
1. Purge the fuel lines using the Fuel Line Purge
Procedure.
2. Drain the fuel tank, using the Fuel Tank
Draining Procedure.
Ensure the battery ground wires are disconnected before proceeding.
3. Open the service door on the floor of the interior of the bus.
4. Disconnect the wiring connector to the fuel level sender.
5. Open the tank bleeder valve.
6. Remove the four (4) fasteners securing the level sender to the cylinder.
7. Slide the level sender out of the tank.
Replacement
1. Install the new fuel level sender into the tank aligning it properly, see Figure 41. Apply silicone lubricant to the O-ring on the sender.
2. Secure the level sender to the tank with four
(4) bolts hand tight.
3. Torque the bolts using the sequence and torques shown in Figure 42.
a. Initial Torque: Crossing pattern
2.5 +/- 0.5 Nm b. Final Torque: Crossing pattern 10 +/- 1 Nm
4. Connect wiring to fuel level sender.
5. Close the tank bleeder valve.
6. Close and secure the service door in the floor on the interior of the bus.
NOTE: Since the tank was opened to replace the level sender, perform the Fuel Tank Purging
Procedure.
7. Reconnect vehicle batteries.
8. Leak check all fuel line joints with an electronic leak detector or leak detection solution.
9. Perform Fuel System Priming Procedure.
FRONT OF
TANK
Figure 41 – Fuel Level Sender Installation
1
1/4
3
TOP OF TANK
1/2
3/4
F
2
4
Figure 42 – Fuel Level Sender Torque Sequence
Blue Bird Vision Service Manual 35
ROUSH CleanTech Blue Bird Vision Liquid Propane Autogas (LPA)
Service Manual
Fuel Tank Wiring
Two wiring harnesses are used on the fuel tank assembly. The pass-through harness connects the in-tank pumps and routes outside the tank through the tank service cover where it connects to the fuel tank harness. The fuel tank harness connects the tank components to the vehicle wiring harness.
Figure 43 – Fuel Tank Connectors
36 Blue Bird Vision Service Manual
ROUSH CleanTech Blue Bird Vision Liquid Propane Autogas (LPA)
Service Manual
FUEL PUMP
HARNESS
O-RING
SEAL
INLINE CONNECTOR (PUMP-1)
A PK/BLK 12 AWG FUEL_PUMP_1 (V+)
B BR/WH 12 AWG FUEL_PUMP_1 (V–)
DELPHI CONNECTOR 1205792 (BLACK)
DELPHI 12 AWG TERMINAL 12124581
DELPHI CABLE SEAL 15324981
INLINE CONNECTOR (PUMP-2)
A DR BLU 12 AWG FUEL_PUMP_2 (V+)
B BLACK 12 AWG FUEL_PUMP_2 (V–)
DELPHI CONNECTOR 12103784 (LIGHT GRAY)
DELPHI 12 AWG TERMINAL 12124581
DELPHI CABLE SEAL 15324981
Figure 44 – Fuel Pump Wire Harness
TANK SERVICE
COVER
Blue Bird Vision Service Manual 37
ROUSH CleanTech Blue Bird Vision Liquid Propane Autogas (LPA)
Service Manual
Remote Mounted Fuel Fill Valve
The LPA fuel system on this vehicle utilizes a remote mounted fill valve. The fill valve is located on the curb side of the vehicle attached to a bracket behind a locked fuel door. This valve connects to a fill hose, through a filter, to a second fill hose, then to the fill valve on the tank. The following procedure must be done outside and 50 feet away from any source of ignition.
Figure 45 – Remote Fill Valve (threaded version shown),
Remote Bleeder Valve and Fuel Door Switch
Figure 46 – Fill Valves
Removal
1. Drain the fill line by carefully loosening the fill hose that is connected to the back side of the fill valve. Allow all of the propane to drain before removing the fill hose from the valve.
NOTE: The tank overpressure prevention device
(OPD) includes a back check valve, which only allows fuel flow into the tank. This will allow the fill hoses to be bled without losing any fuel in the tank.
38
2. If equipped with a threaded fill valve, remove the fill valve to mounting bracket nut and separate the valve from the bracket. If equipped with quick-connect valve, remove the four (4) retaining screws and remove the valve from the bracket.
Replacement
1. Attach the fill valve to the mounting bracket.
Install the nut and tighten to the specified torque.
2. Attach the fill hose to the fitting on the fill valve and torque to 45 +/- 0.4 Nm.
3. Connect the fill valve to a fuel dispensing source to charge the line.
4. Leak check the fill line fitting at the valve using an electronic leak detector or leak detection solution.
Remote Fuel Fill Line(s)
This vehicle utilizes a remote fill device mounted on the curbside. The fill valve will be mounted to a bracket and a fuel line will be connected from the remote fill valve, through a filter, to the tank fill valve. To replace the remote line(s) use the following steps.
Removal
1. Remove any clamps or retainers on the fill line(s).
2. Slowly loosen the fitting(s) at the filter and drain the fill lines.
NOTE: The tank overpressure prevention device
(OPD) includes a back check valve, which only allows fuel flow into the tank. This will allow the fill hoses to be bled without losing any fuel from the tank.
3. Loosen the fill line(s) at the remote mounted fill valve or tank OPD and remove the line.
Replacement
1. Connect the fill line to the fill valve or tank OPD and torque to 45 +/- 0.4 Nm.
NOTE: Thread sealant is NOT required on flare or compression fittings.
2. Connect the fill line(s) to the filter and torque to
57 +/- 0.4 Nm.
3. Connect the fill valve to a fuel dispensing source to charge the line.
4. Check all fittings for leaks using an electronic leak detector or leak detection solution.
Blue Bird Vision Service Manual
ROUSH CleanTech Blue Bird Vision Liquid Propane Autogas (LPA)
Service Manual
5. Secure the fuel filter using the originally installed clamp and torque to 23 +/- 1.4 Nm.
Figure 47 – Fuel Fill Circuit and Bleeder Line
In-Line Fuel Filters
Propane fuel will be released on loosening the fittings. It will settle to the lowest available surface before it dissipates into the atmosphere. Keep heat, sparks, flames, static electricity or other sources of ignition out of the area when venting or purging the fuel lines or tank. Failure to heed this danger can result in severe personal injury or property damage.
Removal of the Fill Filter
1. Slowly loosen the fitting(s) at the filter to drain the fill lines.
2. Disconnect the fuel fill line from the fuel filter inlet and outlet.
3. Remove the clamp retaining the fuel filter to the body.
4. Remove and discard the filter.
Replacement of the Fill Filter
1. Connect the fuel fill lines to the filter inlet and outlet and torque to 57 +/- 0.4 Nm. Note filter orientation.
2. Connect the fill valve to a fuel dispensing source to charge the line.
3. Check all fittings for leaks using an electronic leak detector or leak detection solution.
4. Secure the fuel filter using the originally installed clamp and torque.
Removal of the In-Line Supply Filter
1. Close the manual shutoff valve on the tank.
2. Disconnect the two fuel pump connectors at the tank access panel.
3. Perform starting procedure and let vehicle run until it stalls.
4. Using two (2) wrenches, slowly loosen the fittings on the in-line supply filter.
5. Remove filter from bracket.
Replacement of the In-Line Supply Filter
1. Install a new filter in the bracket. Note filter orientation.
2. Install the fuel supply lines to the filter.
3. Torque the supply line from the tank to the filter to 53-61 Nm and the supply line from the filter to the FRPCM to 24-32 Nm.
4. Perform the Fuel System Priming Procedure.
Remote Mounted Bleeder Valve
The LPA fuel system on this vehicle utilizes a remote mounted bleeder valve. The bleeder valve is located on the curb side of the vehicle attached to a bracket behind a locked fuel door. This valve connects to a bleeder hose connected to the bleeder valve on the tank. The following procedure must be done outside and 50 feet away from any source of ignition.
Removal
1. Close the tank bleeder valve.
2. Open the remote bleeder valve to vent the line.
NOTE: If the remote bleeder valve does not stop venting within a few seconds, then the tank bleeder valve is not fully closed.
3. Disconnect the bleeder line from the back of the remote bleeder valve.
4. Remove the bleeder valve to mounting bracket nut and separate the valve from the bracket.
Replacement
1. Attach the bleeder valve to the mounting bracket. Install the nut and tighten to the specified torque.
2. Attach the bleeder hose to the fitting on the bleeder valve and torque to 18.5 +/- 3.0 Nm.
3. Confirm the remote bleeder valve is closed and open the tank bleeder valve.
Blue Bird Vision Service Manual 39
ROUSH CleanTech Blue Bird Vision Liquid Propane Autogas (LPA)
Service Manual
4. Leak check the bleeder line fitting at the valve using an electronic leak detector or leak detection solution.
Remote Bleeder Line
Removal
1. Close the tank bleeder valve.
2. Open the remote bleeder valve to vent the line.
NOTE: If the remote bleeder valve does not stop venting within a few seconds, then the tank bleeder valve is not fully closed.
3. Disconnect the bleeder line from the back of the remote bleeder valve.
4. Disconnect the bleeder line from the tank bleeder valve.
5. Remove line from vehicle.
Replacement
1. Route line in vehicle.
NOTE: 90-degree fitting connects to remote bleeder valve.
2. Attach the bleeder line to the tank valve and torque to 18.5 +/- 3.0 Nm.
3. Attach the bleeder hose to the remote bleeder valve and torque to 18.5 +/- 3.0 Nm.
4. Confirm the remote bleeder valve is closed and open the tank bleeder valve.
5. Leak check the bleeder line fittings using an electronic leak detector or leak detection solution.
Fuel Rail Pressure Control Module
(FRPCM)
Removal
1. Purge the fuel lines using the Fuel Line
Purging Procedure.
4. Remove the vapor line from the FRPCM by squeezing the release tabs on either side of the connector.
5. Remove the two (2) fasteners securing the
FRPCM to the bracket.
Replacement
1. Install the new FRPCM to the bracket and torque to 8-12 Nm.
2. Install fuel lines starting with the line closest to the bleed port, working forward.
Torque specifications:
Forward Return Line: 18-20 Nm
Fuel Rail Supply Line: 23-26 Nm
Forward Supply Line: 29-33 Nm
Fuel Rail Return Line: 20-22 Nm
3. Connect the wiring harness wiring connectors.
Ensure correct connector locations or vehicle will not start.
4. Connect the vehicle batteries.
5. Open the manual shut-off valve on the fuel tank and install the supply circuit cover.
6. Perform the Fuel System Priming Procedure.
7. Check the fuel line connections for leaks using an electronic leak detector or leak detection solution.
Ensure the battery ground wires are disconnected before proceeding.
2. Disconnect the FRPCM electrical connectors.
Note connector locations when removing.
3. Remove the fuel lines from the FRPCM.
NOTE: Start by removing forward most fuel line and working toward the rear line next to the bleed port.
40 Blue Bird Vision Service Manual
ROUSH CleanTech Blue Bird Vision Liquid Propane Autogas (LPA)
Service Manual
FUEL
RETURN
TO TANK
FUEL
SUPPLY
TO RAILS
BLEED
PORT
FUEL RETURN
FROM RAILS
FUEL SUPPLY
FROM TANK
Figure 48 – Fuel Rail Pressure Control Module (FRPCM) Connections
Blue Bird Vision Service Manual 41
ROUSH CleanTech Blue Bird Vision Liquid Propane Autogas (LPA)
Service Manual
Fuel Supply and Return Line
4. Disconnect the other end of the hose/line to be replaced.
5. Remove the hose/line from the vehicle.
Technicians working with, or around, fuel systems should be properly trained to utilize extreme care and caution at all times. Failure to exercise extreme caution and care may lead to serious accidents which can result in property damage, personal injury and/or death.
The fuel supply and return lines are made of special material and should only be replaced or repaired using original equipment parts. The fuel line can be removed using the following procedure.
Removal (Fuel Line)
1. Purge the fuel lines using the Fuel Line
Purging Procedure.
Ensure the battery ground wires are disconnected before proceeding.
2. Remove any securing clamps or retainers from the hose/line to be replaced.
3. Slowly disconnect one of the fuel line joints, using the appropriate disconnect tool, allowing any excess propane to dissipate into the atmosphere.
LPG is under pressure, wear adequate eye protection. When LPG is discharged into the atmosphere the rapid change in pressure can cause a refrigerant condition in the fuel and can harm your skin or cause serious burns, always wear gloves.
Replacement (Fuel Line)
1. Install hose/line in vehicle using the same routing and loosely secure the retaining features.
2. Connect the quick connect fitting and gently tug on the lines to make sure the connection is secure.
3. Tighten the hose/line retaining features.
4. Connect the vehicle batteries.
5. Open the manual shut-off valve on the fuel tank and install the supply circuit cover.
6. Perform the Fuel System Priming Procedure.
7. Check the fuel line and rail connections for leaks using an electronic leak detector or leak detection solution.
42
Figure 49 – Fuel Line Routing Along Frame
Blue Bird Vision Service Manual
ROUSH CleanTech Blue Bird Vision Liquid Propane Autogas (LPA)
Service Manual
Figure 50 – Fuel Tank Hard Lines
Fuel Rail
When removing or replacing any fuel delivery components which include: Fuel Rails,
Injectors, or Supply Lines, thoroughly clean the work area with solvents and compressed air to remove any debris or contaminants. Always insure your hands are clean when handling fuel injection components to prevent contaminating the fuel delivery systems.
Contamination may cause the injectors to stick, leak, or become damaged, delivering incorrect amounts of fuel and causing the fuel control system to be non-compliant.
NOTE: Always cap any open ports after disconnecting fuel lines, removing injectors or the fuel rails to prevent contamination of the fuel delivery system.
When removing the fuel rails use the following procedure.
Removal
1. Purge the fuel lines using the Fuel Line
Purging Procedure.
Ensure the battery ground wires are disconnected before proceeding.
2. Disconnect the Injection Pressure and
Temperature Sensor (IPTS) electrical connector.
3. Disconnect the fuel injector electrical connectors.
4. Disconnect the fuel rail supply and return hoses from the fuel rails.
5. Remove bolt connecting right side fuel rail to
FRPCM bracket.
6. Remove the two (2) bolts connecting the
FRPCM bracket to the intake manifold.
7. Remove fuel rail mounting brackets from intake manifold.
8. Remove the fuel rail assembly.
Replacement
1. Lubricate injector spacer lower O-rings using
SAE 5W20 motor oil or equivalent.
NOTE: It is recommended to replace the fuel rail
O-rings during servicing.
2. Position fuel rail assemblies onto the intake manifold and fully seat the injector spacers.
Blue Bird Vision Service Manual 43
ROUSH CleanTech Blue Bird Vision Liquid Propane Autogas (LPA)
Service Manual
3. Install and tighten fuel rail to intake manifold mounting brackets to the specified torque.
a. M5 Bolt: 5.8 +/- 1.2 Nm b. M6 Bolts: 10 +/- 2 Nm
4. Install the two (2) bolts connecting the FRPCM bracket to the intake manifold. Torque to 10 +/-
2 Nm.
5. Install the bolt connecting the right side fuel rail to the FRPCM bracket. Torque to 25 +/- 5 Nm.
6. Install fuel rail supply and return lines on the fuel rail. Torque to: Fuel Rail Supply Line
23-26 Nm, Fuel Rail Return Line 20-22 Nm.
7. Connect the fuel injector electrical connectors.
8. Connect the Injection Pressure and
Temperature Sensor (IPTS) electrical connector.
9. Connect the vehicle batteries.
10. Open the manual shut-off valve on the fuel tank and install the supply circuit cover.
11. Perform the Fuel System Priming Procedure.
12. Check the fuel line and rail connections for leaks using an electronic leak detector or leak detection solution.
FUEL RAIL
SUPPLY LINE
BRACKET
SUPPLY LINE
RH RAIL
ASSEMBLY
FUEL RAIL
RETURN LINE
LH RAIL
ASSEMBLY
BOLT
M6 (QTY. 22)
44
Figure 51 – Fuel Rail and Line Assembly
Blue Bird Vision Service Manual
ROUSH CleanTech Blue Bird Vision Liquid Propane Autogas (LPA)
Service Manual
Fuel Injector
NOTE: It is possible to service the injector on the vehicle. However, clean the area thoroughly and blow the area clean with compressed air before starting.
When removing or replacing any fuel delivery components which include: Fuel Rails,
Injectors, or Supply Lines, thoroughly clean the work area with solvents and compressed air to remove any debris or contaminants. Always insure your hands are clean when handling fuel injection components to prevent contaminating the fuel delivery systems.
If replacing one or more injectors use the following procedure.
Removal
1. Purge the fuel lines using the Fuel Line
Purging Procedure.
Ensure the battery ground wires are disconnected before proceeding.
2. To release any residual propane in the lines, disconnect one of the fuel lines connected to the fuel rail. Once pressure is released, reconnect the line. Torque to: Fuel Rail Supply
Line 23-26 Nm, Fuel Rail Return Line
20-22 Nm.
3. Disconnect the fuel injector electrical connector.
4. Remove the fuel injector retention c-clip.
5. Using a twisting motion, pull the fuel injector straight upward out of the fuel rail (a pair of pliers might be necessary to help remove the fuel injector). Use care to prevent damage to the fuel injector.
6. Repeat steps 2-5 as needed for the remaining fuel injectors.
Replacement
NOTE: Before removing the injector assembly from the package, clean the work area and your hands. Do not remove the protective caps until it is necessary.
1. Lubricate the upper and lower injector O-rings using SAE 5W20 motor oil or equivalent.
2. Install the fuel injector into the fuel rail, so that the electrical connection faces away from the intake manifold when the injector is fully seated. Place injector in position, then push straight down to ensure it is fully seated.
3. Install the fuel injector retention c-clip and ensure it is fully engaged in the groove.
4. Connect the fuel injector electrical connector.
5. Repeat steps 1-4 as needed for the remaining fuel injectors.
6. Connect the vehicle batteries.
7. Perform the Fuel System Priming Procedure.
8. Check the fuel line and rail connections for leaks using an electronic leak detector or leak detection solution.
Injection Pressure Temperature Sensor
Removal
1. Disconnect vehicle battery and refer to the fuel line purging procedure.
2. Once the system is properly drained remove the connector from the IPTS and remove the sensor from the fuel rail.
Replacement
1. Install new IPTS into the fuel rail assembly and torque to 7 +/- 1 Nm.
2. Reinstall connector to the IPTS.
3. Perform the fuel system priming procedure and ensure there are no leaks present from the fuel system.
4. Reconnect vehicle battery and clear all DTCs.
Figure 52 – Injection Pressure Temperature Sensor
Blue Bird Vision Service Manual 45
INJECTION PRESSURE
TEMPERATURE SENSOR
(IPTS)
ROUSH CleanTech Blue Bird Vision Liquid Propane Autogas (LPA)
Service Manual
CLAMP
FITTING – 1/4"
QUICK CONNECT
INJECTOR
NOZZLE CLIP
O-RING PLUG
FUEL RAIL
BRACKET – RAIL
MOUNTING
FUEL RAIL
SPACER
O-RING
Figure 53 – Fuel Rail Assembly Detail
Vapor Canister Assembly (see Figure 4)
Removal
1. Disconnect load/purge hose from canister by disconnecting the quick connect fitting.
2. Disconnect fresh air line from canister by disconnecting quick connect fitting.
3. Remove canister to bracket mounting bolts and remove the canister.
4. Remove bracket to frame rail mounting bolts and remove the brackets.
Replacement
1. Install the canister mounting brackets onto the frame rail and tighten to the specified torque.
2. Place the canister onto the mounting brackets and tighten bolts to the specified torques.
a. M6 Bolts: 6.0 +/- 0.3 Nm b. Thread Cutting Bolts: 2.75 Nm +/- 0.25 Nm
3. Install the fresh air line to the canister.
4. Install the load/purge hose onto the canister.
NOTE: There is an audible “click” when the quick connects are installed properly.
46 Blue Bird Vision Service Manual
ROUSH CleanTech Blue Bird Vision Liquid Propane Autogas (LPA)
Service Manual
Gateway Module
Removal
1. Disconnect the negative ground cables from the vehicle batteries.
Ensure battery is disconnected before proceeding.
2. Disconnect the main harness connector at the
Gateway Module.
3. Remove the four (4) mounting bolts and retain.
4. Remove the Gateway Module.
Replacement
1. Install the Gateway Module to the isolators using the four bolts and torque to 11.5 +/- 0.5
Nm.
2. Connect the main harness connector to the
Gateway Module.
3. Push until the connector is fully seated, then close lever until the tab locks it in place as seen in Figure 54.
4. Connect the vehicle batteries.
SYSTEM MAINTENANCE
LPA Fuel System
This section covers the items in the LPA fuel system, which requires regularly scheduled maintenance. For maintenance of the base engine or transmission refer to the 2017 Ford F650 service manual at www.motorcraft.com or consult the local Ford Medium Duty Truck Service Center.
Fuel Tank
The fuel tank equipped has been certified to ASME
Tank and Pressure vessel requirements and the installation complies with all NFPA Pamphlet 58
Standards in affect at the time of certification. State and or local regulatory agencies may require a periodic inspection of the LPG tank. At a minimum of every 12 months the LPG tank should be inspected by a trained technician for the following items:
• Check for impact damage, dents, cuts or severe gouging or any tank deformation.
• Check for cracks in the welded seams or mounting brackets.
• Check to insure the service valves or shut off valves are functioning and manually closes the valve.
• Check to insure the pressure relief valve vent is clear of any obstructions and is properly orientated.
• Check all electrical connections to insure they are properly seated and have not become corroded.
• Check all mounting fasteners and brackets to insure the tank is properly fitted to the chassis.
• Leak check all external fittings and connection.
If during the tank inspection any or all the above have been observed you should have the tank repaired by a certified LPG Tank Repair Facility or replace the tank.
Figure 54 – Gateway Module
Never cut or weld on or near the LPG fuel tank.
Repairs to the fuel tank should only be made by a certified LPG tank repair facility. Failure to observe this warning could result in serious bodily injury, death and/or serious property damage.
Blue Bird Vision Service Manual 47
ROUSH CleanTech Blue Bird Vision Liquid Propane Autogas (LPA)
Service Manual
Fuel Filters
The fuel fill filter and fuel supply filter are the only filters that require periodic maintenance. Filters should be replaced every 50,000 miles. The fuel pump includes a sock filter that is rated for the lift of the fuel pump.
Fuel Supply and Return Line
It is recommended that the fuel line connections be inspected for damage annually or anytime the lines have been removed. The routing of the lines should also be inspected annually to ensure that the lines have not come into contact with any sharp edges, rotating devices, hot surfaces or are located where they may be impacted by road debris.
Fuel Rail Pressure Control Module
The FRPCM does not require any periodic adjustment. You should annually inspect the following items:
• Check the mounting of the FRPCM to make sure the body, valves and fuel lines are secure.
• Check the FRPCM wiring to make sure the wiring and connectors are not damaged.
• Leak check the fuel line connectors using an electronic leak detector or an approved leak detection solution.
Fuel Rails and Injectors
The fuel rails and injectors require no periodic adjustment. You should annually inspect the following items on the fuel rails and injectors:
• Check to make sure the rail brackets are securely attached to the intake manifold.
• Check to make sure the rail brackets have no signs of cracks or breaks.
• Check to make sure that each injector is retained in the fuel rail.
• Leak check all of the connections on the fuel rail at each injector connector and the inlet and outlet fitting at the rail using an electronic leak detector or an approved leak detection soap solution.
With the engine running use an electronic leak detector or an approved leak detection soap solution to check the FRPCM to intake manifold and all hose connections for leaks.
Electrical System
The electrical system and wiring harnesses do not require any periodic adjustments. You should annually inspect the following items:
• Check the Gateway Module fasteners to ensure they are securely fastened and the rubber is in good condition.
• Check the Gateway Module electrical connector and insure the connector is securely attached and locked.
• Check the wire harness routing under the hood to ensure the main harness and injector harness have not come into contact with any rotating devices, hot surfaces or have come loose from their securing points and are hanging in an unsafe location.
• Check all electrical connectors by lightly pulling on each connector to ensure the connector is fully locked and seated.
• Check all wire ties used to secure the harness for cracking, splitting or breakage and replace if necessary.
• Check the harness routing to the fuel tank connector and ensure the harness is securely attached to the frame and protected from any hot surfaces, rotating devices or road debris and repair any unsafe conditions.
• Check the wiring on the fuel tank to make sure it is secure and undamaged.
48 Blue Bird Vision Service Manual
ROUSH CleanTech Blue Bird Vision Liquid Propane Autogas (LPA)
Service Manual
TORQUE CHART
Component
Remote Fill Valve
Remote Pressure Relief Outlet
Remote Bleeder Valve
Fuel Fill Line
Fuel Tank and Vehicle Components
Quantity
1
1
1
Torque (Nm)
Hand Tight + 1/4 to 1/2 turn
Hand Tight + 1/4 turn
Hand Tight + 1/4 to 1/2 turn
At Filter: 57 +/- 4
At Valve: 45 +/- 4
Fill Filter Clamp Bolt
Bleeder Hose
Fuel Tank Assembly
Fuel Tank Line Bolts – M6
Pressure Relief Outlet
Fuel Level Sender Screws – 1/4"
Bleeder Nozzle
Tank Access Cover Bolts – 3/8"
2
1
4
1
8
1
1
1
23.0 +/- 1.4
18.5 +/- 3.0
-----
11 +/- 1
95 +/- 5
See Procedure
Fuel Filler – Tank OPD
Fuel Return Circuit Screws – 1/4"
Fuel Supply Circuit Screws – 1/4"
Fuel Pump Housing to Tank Bolt – M5
Fuel Pump Wiring Bolts - M4
Fuel Pump Housing to Tank – M6 nuts
1
1
3
4
4
2
20 +/- 4 MIN plus Orientation
See Procedure
P/N 66-1290B: 75 MIN plus Orientation
P/N A10110098: 104 MIN plus Orientation
See Procedure
See Procedure
5.8 +/- 0.3
2.7 +/- 0.4
8.5 +/- 0.5
Fuel Pump Housing – #6 Screw
Pressure Relief Valve
4
1
5.0 +/- 0.5 in-lbs
213.5 Min.
Hand Tight Supply Circuit Cover – M5 Thumb Screw 4
Fuel Rail and Line Assembly
Component
Fuel Rail & Supply Line Bolts – M6
O-Ring Plug
Quantity
22
1
Torque (Nm)
11 +/- 1
8.9 +/- 0.9
19 +/- 1 Fitting – 1/4" and 3/8" Threaded 4
Fuel Pressure and Temperature Sensor 1 7 +/- 1
Evaporative System and Forward Fuel Components
Component
Vapor Canister Bracket Bolts – Self Threading
Quantity
3
Torque (Nm)
2.75 +/- 0.25
Vapor Canister Bracket Bolts – M6
Vapor Canister to Frame Fasteners – M10
Gateway Module Bolt – 1/4"
FRPCM Bracket Assembly Bolts
M6 Bolts
M8 Bolt
Bleeder Port
2
4
4
2
1
1
6.0 +/- 0.3
65.0 +/- 13.3
11.5 +/- 0.5
10 +/- 2
25 +/- 5
19 +/- 1
Blue Bird Vision Service Manual 49
ROUSH CleanTech Blue Bird Vision Liquid Propane Autogas (LPA)
Service Manual
FAQS
ROUSH CleanTech Technical Assistance
Technical issues involving starting, operating or re-fueling a propane power bus should be reported to your local qualified service provider. In the event further technical assistance is needed, you should first contact your authorized Blue Bird Dealer regarding any technical issues with your Blue Bird product.
In emergency situations or if immediate technical assistance is needed and the above mentioned technical assistance is unavailable you can call
ROUSH CleanTech Customer Service at 800.59.
ROUSH (597-6874) with any questions regarding
ROUSH CleanTech Liquid Propane Autogas
Systems.
Q) How long should it take for my vehicle to start once I have cycled the key to on?
A) Typically the time will vary between seven
(7) and fifteen (15) seconds, depending on the temperature of the fuel. Under severe operating circumstances (hot day, hot engine), the delay could be up to forty-three (43) seconds. Do not hold ignition in start position or engage starter multiple times. See “Starting” section under
Features and Controls.
Q) How long will it take to fill my ROUSH
CleanTech System fuel tank?
A) Normal refueling rates are typically between five
(5) and eight (8) gallons per minute but may vary depending on the ambient temperature conditions and pump capacity of the refueling equipment being used.
Q) Why does my refueling take longer when it’s
hot out?
A) On a hot day, refueling may take longer than usual because the heat will raise the pressure inside the fuel tank, which must be overcome by the refueling equipment.
Q) Is any special liquid propane autogas fuel required?
A) Yes, motor vehicles require the use of HD-5 automotive grade liquid propane autogas.
Other grades of propane (including HD-10 or
“commercial-grade”) may contain higher levels of contaminants and could cause premature failure of fuel pumps and injectors, or clogging of system components. If you are unsure about the quality of your propane, check with your retailer or distributor.
Q) Where are liquid propane autogas filling stations located?
A) There are over 3,000 liquid propane autogas retail outlets available around the country to fill your vehicle. Liquid propane autogas filling locations can be found at these websites: www.afdc.energy.gov/afdc/locator/stations www.roushcleantech.com
Q) Can I perform my own service or repair on the Roush CleanTech System?
A) Not recommended. Most states require a licensed technician to work on liquid propane autogas systems. We recommend that you go to a Blue Bird/Roush CleanTech Authorized Service
Center for any service or repair to your vehicle. To locate a ROUSH CleanTech Authorized Service
Center near you, visit us at www.roushcleantech.
com or call us between the hours of 8 AM and
5 PM Eastern Time, Monday through Friday, at
800.59.ROUSH (800.597.6874).
Q) Can I add additional liquid propane autogas tanks?
A) No. Adding tanks to the vehicle would potentially violate emissions compliance of the vehicle and could result in drivability and emissions issues.
Q) Are there any unique maintenance
requirements for the ROUSH Propane System?
A) Yes. There is a fuel filter in the fuel fill line and supply line to prevent contamination during refueling and operation. These filters are replaced at 50,000 mile intervals. No other
ROUSH CleanTech System parts require periodic service. Some states require periodic certification of the tank or filling systems, see your local gas association or state regulating agency for additional information.
NOTE: To maintain your warranty coverage, you must follow the normal maintenance schedule for your Blue Bird vehicle.
Q) Who do I contact for LPA warranty-related
issues?
A) Take your vehicle to a Blue Bird/Roush
CleanTech Authorized Service Center or, if not readily available, to any Ford dealer that is authorized to repair ROUSH CleanTech propane vehicles.
50 Blue Bird Vision Service Manual
ROUSH CleanTech Blue Bird Vision Liquid Propane Autogas (LPA)
Service Manual
For further information about ROUSH CleanTech
Systems or to locate a ROUSH CleanTech
Authorized Service Center near you, visit us at www.roushcleantech.com or call us between the hours of 8 AM and 5 PM Eastern Time, Monday through Friday, at 800.59.ROUSH (800.597.6874).
Q) Can I use any fuel additives?
A) No. It will void your warranty and harm the operation of the ROUSH CleanTech System installed on your vehicle.
SPECIAL CONDITIONS
Refueling
Before refueling, extinguish all open flames and smoking materials. Ensure that no electrical sparks are present. Failure to heed this danger may result in serious personal and property damage.
Stop refueling if there is any difficulty with the refueling process or the dispensing equipment.
Notify the station operator at once. Failure to heed this danger may result in serious personal injury and property damage.
The filler cap screws on and off the filler valve. The filler nozzle either screws on or quick connects to the fill valve. Before attaching the filler nozzle, inspect the valve O-ring. If the O-ring is missing or damaged, replace it before attaching the filler nozzle.
Allow a station attendant to refuel your vehicle if you are not trained in proper liquid propane autogas refueling procedures and safety precautions. Ensure that the vehicle rests on level ground and that the engine is not running.
NOTE: Failure to refuel on a level surface may result in an incomplete or overfill condition.
Troubleshooting – Refueling
My vehicle does not fill at all:
• In order for the system to fill, the fuel supply pressure from the pump must be at least 50 psi higher than tank pressure (required to open the check valve in the fill system). Check the following:
– If the vehicle fuel tank is significantly warmer than the station storage tank, the station fuel pump may not be able to provide sufficient pressure (either due to insufficient pump capacity or a low bypass pressure setting).
This can be a particular problem if the station fuel tank is underground and the vehicle is fueling on a hot day.
– If the fuel tank is over 3/4 full (indicated), or if the fuel tank is over 1/2 full and the vehicle is not level, it may be possible that the OPD is in the closed position due to fuel level at the location of the OPD. If vehicle is not level, turn the vehicle around and try to refill with vehicle pointed in the opposite direction. If vehicle is level, or if this does not change behavior, drive vehicle until indication is under 1/2 tank and attempt to fill again. If behavior repeats, take vehicle to qualified service center for diagnosis and repair.
– If fuel tank is under 1/2 full (indicated), and there is sufficient fuel pressure from the fuel pump (minimum 50 psi over tank), the OPD may be stuck closed. Diagnosis and repair by qualified service center is likely required.
My vehicle fills slowly (less than three (3) gallons/minute):
• If the vehicle is filling slowly, it indicates that the
OPD is functioning properly but something in the system is preventing normal flow.
– Confirm that fueling station has fueling equipment rated for Autogas applications
(5-7.5 hp pump set at a minimum differential pressure of 125 psi). Lower capacity pumps may be acceptable for cylinder fills but can result in slow fills in automotive applications.
– If tank temperature is very high, the density of propane in the tank is relatively low which can result in higher than normal restriction and slow fill. This is most likely at temperatures above 100ºF ambient, especially if station has underground storage tanks. This does not indicate any problem with the vehicle.
We suggest trying to fill in the morning
(when vehicle and station are at similar temperatures), or trying another filling station.
– Fuel filter may be clogged. The inline fuel filter should be changed every 50,000 miles.
If it has not been changed on schedule, have it changed by qualified technician. The
Blue Bird Vision Service Manual 51
ROUSH CleanTech Blue Bird Vision Liquid Propane Autogas (LPA)
Service Manual
technician should measure pressure drop to determine whether it has clogged prematurely
(this is possible if the fuel has unusually high levels of contaminants).
– If filter has less than 50,000 miles, take vehicle to qualified service center for fuel fill system diagnosis/repair.
My vehicle does not fill completely (shuts off early):
• During the fill event, it is possible for the tank pressure to increase causing the check valves to close. See “My vehicle does not fill at all”.
– Make sure vehicle is level (either due to the fill station pavement, or to loading of the vehicle), the shutoff may occur early.
• The OPD system is required to be inspected annually to verify proper function, and may be inspected more frequently based on local or fleet-specific requirements. Check the OPD inspection label (located on driver’s door pillar) to determine whether OPD has been recently inspected.
• Verify fuel tank is level. If tank is tilted away from the fill valve, some overfilling could result. Within reason, this should not result in any issues, but if fill area is severely non-level, it should be corrected.
• If consistent overfill is suspected, have the full
OPD inspection procedure performed to verify correct operation.
• Fuel tanks which are overfilled may vent propane unexpectedly, due to normal ambient temperature changes. Use caution if overfilled tank is suspected.
Troubleshooting – Starting
If the engine does not start within a few seconds of cranking, one touch integrated starting (OTIS) will disengage the starter. Check the fuel gauge before attempting to start again. If there is adequate liquid propane autogas fuel and the engine fails to start after several attempts, obtain the assistance of a qualified liquid propane autogas service technician to diagnose the problem. We recommend that you take your vehicle to a Blue Bird/ROUSH CleanTech
Authorized Service Center to have such diagnosis performed. To locate a ROUSH CleanTech
Authorized Service Center near you, visit us at www.roushcleantech.com or call us between the hours of 8 AM and 5 PM Eastern Time, Monday through Friday, at 800.59.ROUSH (800.597.6874).
THE VEHICLE DOES NOT START:
The starter does not engage even after 40 seconds:
• Most common cause of no-start/no-crank is either that the PCM did not recognize the request for crank, or that the key did not remain in the
“on” position after being turned to start. Turn key to off and repeat start sequence, making sure to firmly turn the key to the start position, and then allowing the key to return to “on” without overshooting back to “off” or “accy”.
• Ensure transmission is in Neutral with parking brake engaged.
• Confirm vehicle battery is sufficiently charged and no other issues present.
• Refer to to Blue Bird multiplex vehicle starting diagnostics.
• If fuel pumps can be heard (roughly 1-2 seconds after turning the key to start), but starter does not engage, it likely indicates an issue with the vehicle unrelated to the propane system. If fuel pumps are not heard, there may be an issue where the propane system is not recognizing the start attempt. In either case, vehicle likely will need to be serviced.
THE VEHICLE DOES NOT START:
The starter engages but engine does not start or starts and will not keep running:
• Confirm adequate fuel in the tank. On level road, tank indication at or above indicated “E” should be sufficient for starting; vehicles parked on grades (either front/rear or side/side) may experience lack of starting at indication of 1/8 tank.
• Ensure battery is properly charged, and turn off all electrical accessories. Propane fuel injectors operate at higher pressures than gasoline and can fail to open in low battery conditions (such as experienced in crank), especially in hot conditions. Turn off headlights, radio, A/C, etc. If issue is repeatedly seen, take vehicle to qualified service center for investigation/repair of charging system or propane system.
• The ROUSH CleanTech starting system attempts to achieve liquid conditions in the fuel rail prior to engaging the starter. However, if the system does not achieve known liquid conditions in under forty-three (43) seconds, it will attempt to start the engine (to avoid excessively long delays
52 Blue Bird Vision Service Manual
ROUSH CleanTech Blue Bird Vision Liquid Propane Autogas (LPA)
Service Manual
in extreme conditions). If the engine cranks but does not start, and there are no other indications of faults, key the engine off and attempt to start again. If vehicle continues not to start, or frequently requires multiple attempts, vehicle should be taken to qualified dealer for service.
The vehicle does start and run, but delay seems excessive:
• Due to the unique properties of liquid propane, vaporization in the rail is not always easy to predict and therefore long delays may be encountered unexpectedly. The following conditions are likely to result in longer delays:
– Vehicle fully warm, engine off for 5-90 minutes. This is a long enough condition for heat to build in the rail, but not so long for engine to cool down.
– Engine compartment fully warm, with tank relatively cool (below 60°F). In this condition, the rail needs to cool significantly prior to start. Generally starting in this condition is not a problem, but the delay may seem unusually long.
– Engine compartment fully warm, tank very warm (above 110°F). In this condition, rail pressure is extremely high and the fuel is not much cooler than the rail.
• If you do believe that the crank delay times are consistently excessive, take the vehicle to qualified service center for inspection and repair if necessary.
MAINTENANCE AND
SPECIFICATIONS
ROUSH CleanTech System Use and
Maintenance
Use, maintenance, service and repair of the
ROUSH CleanTech System must be in accordance with regulations put forth by the NFPA in their pamphlets #54 and #58, by the American Society of Mechanical Engineers (ASME), the Department of Transportation (DOT), the American National
Standards Institute (ANSI) and all applicable federal, state, provincial and local authorities.
Among those responsible for compliance are the maintenance provider, refueler and end-user personnel.
Service Recommendations
It is strongly recommended that all service needs for the engine and fuel system of the ROUSH
CleanTech System installed on your vehicle be referred to a qualified liquid propane autogas service technician. Working with pressurized liquid propane autogas that fuels an internal combustion engine requires special training. Technical issues involving starting, operating or re-fueling a propane power bus should be reported to your local qualified service provider. In the event further technical assistance is needed, you should first contact your authorized Blue Bird Dealer regarding any technical issues with your Blue Bird product.
In emergency situations or if immediate technical assistance is needed and the above mentioned technical assistance is unavailable you can call
ROUSH CleanTech Customer Service at 800.59.
ROUSH (597-6874) with any questions regarding
ROUSH CleanTech Liquid Propane Autogas
Systems.
The installation, service or repair of the ROUSH
CleanTech System by a person who is not licensed or registered to perform installation, service or repair to liquid propane autogas systems may result in personal injury, harm, or loss or damage to property. Contact a person licensed or registered to fit install, service or repair a liquid propane autogas system. A person licensed to install, service or repair a liquid propane autogas system may not be liable for damages caused by the modification of a liquid propane autogas system by an unlicensed person except as otherwise provided by applicable law. Failure to heed this warning may void your ROUSH CleanTech
System warranty. We recommend that you go to a Blue Bird/ROUSH CleanTech Authorized
Service Center for installation or repair of the
ROUSH CleanTech System.
Blue Bird Vision Service Manual 53
ROUSH CleanTech Blue Bird Vision Liquid Propane Autogas (LPA)
Service Manual
Each ROUSH CleanTech System has been specially developed and designed by ROUSH
CleanTech for its intended vehicle application.
Therefore, the ROUSH CleanTech System must not be installed on vehicles other than the intended vehicle application designated by
ROUSH CleanTech. Additionally, the ROUSH
CleanTech System must not be modified or altered (either before installation or at any time after installation, or as part of any service, maintenance or repair, etc., to the vehicle or the ROUSH CleanTech System), except as specifically directed by ROUSH CleanTech as part of a safety recall, technical service bulletin or other formal written direction by ROUSH
CleanTech. Modification or alteration of the
ROUSH CleanTech System without ROUSH’s prior written authorization may void the ROUSH
CleanTech Limited Warranty.
Refill Capacity
The Blue Bird bus is designed with a dual cylindrical manifold tank assembly, which will hold approximately 93, 67, or 45 gallons of usable capacity, depending on application.
NOTE: There is typically 8-10% of the usable tank capacity remaining once “Low Fuel” lamp light illuminates below this level. It is possible to experience drivability issues related to fuel pressure when operating on grades, hard accelerating and cornering.
NOTE: The density of the liquid propane changes significantly with temperature. On a hot day, it is not unusual for vehicle to apparently fill less than usual, and for the fuel gauge to read less than full after the tank cools off. This is normal and does not indicate a problem with the fill system.
Jump Starting
Before attempting electrical connections for jump starting, check for battery and liquid propane autogas fumes. If there is any indication of a propane leak (rotten egg smell, ice buildup or visible vapor around fittings, audible hiss, etc.), follow the leak reporting procedure. Do not attempt to start the vehicle
— sparks from the electrical connections may ignite the vapors. Failure to heed this danger may result in serious personal injury, including death and property damage.
Follow the jump starting procedures in the Driver’s
Manual.
NOTE: It may take up to forty-three (43) seconds for the engine to crank after initiating the start sequence.
Manual Shutoff Valve
Should the need arise (leaking or electrical failure, etc.) to stop the flow of liquid propane autogas manually, there is a manual shutoff valve on the liquid supply line of the ROUSH CleanTech
System. The supply valve is located on the bottom of the ROUSH CleanTech System fuel tank; specific location of the valve is labeled on the tank. An access cover may be removed to allow access to the manual shutoff valve. Turn the knob clockwise, until it stops, to stop the flow of liquid propane autogas.
NOTE: Open this valve slowly when the system is restored to normal. Releasing liquid propane autogas quickly into an empty line may set off a special check valve restricting proper fuel flow. If difficulty occurs, close the valve completely and then open it slowly.
NOTE: This valve must always be fully open during vehicle operation.
Service needs for the liquid propane autogas fuel system should be referred to a qualified liquid propane autogas service technician for inspection and correction. We recommend that you see a Blue
Bird/ROUSH CleanTech Authorized Service Center to address any service needs you may have.
Storing the Vehicle
If the vehicle is to be stored for more than sixty
(60) days, close the manual shutoff valve of the
ROUSH CleanTech System and consult the
Driver’s Manual for information about protecting the base vehicle.
NOTE: Remember to open this valve slowly before returning the vehicle to operation.
Repainting (Vehicle or Tank)
The fuel tank should not be repainted. Touchups, if required, should be performed according to
National Fire Protection Association (NFPA)
NFPA58. Repainting the tank for purposes other than touching up or repair may result in voiding the tank warranty.
54 Blue Bird Vision Service Manual
ROUSH CleanTech Blue Bird Vision Liquid Propane Autogas (LPA)
Service Manual
Remove the ROUSH CleanTech System fuel tank before attempting to paint the vehicle.
The high temperatures used in the painting process can set off the pressure relief valve, discharging liquid propane autogas into the hot chamber causing asphyxiation that could result in personal injury, including death.
Tank removal should be performed by a qualified liquid propane autogas service technician. We recommend that you see a Blue Bird/ROUSH
CleanTech Authorized Service Center to have this procedure performed.
Technical issues involving starting, operating or re-fueling a propane power bus should be reported to your local qualified service provider. In the event further technical assistance is needed, you should first contact your authorized Blue Bird Dealer regarding any technical issues with your Blue Bird product.
In emergency situations or if immediate technical assistance is needed and the above mentioned technical assistance is unavailable you can call
ROUSH CleanTech Customer Service at 800.59.
ROUSH (597-6874) with any questions regarding
ROUSH CleanTech Liquid Propane Autogas
Systems.
Blue Bird Vision Service Manual 55
ROUSH CleanTech Blue Bird Vision Liquid Propane Autogas (LPA)
Service Manual
DIAGNOSTIC TROUBLE CODES (DTC) — LPA-FUELED VEHICLES
About Diagnostic Trouble Codes
All diagnostic trouble codes (DTCs) known to be affected by the liquid propane autogas (LPA) system are covered in this manual. For all other DTCs, refer to the Ford Powertrain Control/Emissions Diagnosis
Service Manual at www.motorcraft.com.
System and Diagnostic Terminology
FTS
GRD
HEGO
IC
IPTS
KOEO
KOER
LPA
MAF
OEM
OPD
PCM
PID
PWR GND
SIG RTN
BS
CAN
Acronym or Abbreviation
DTC
EFPR
ERFS
EVAP
FCS
FLIM
FLS
FP
FPCM
FRP
FRPCM
Gateway Module
SS
TPTS
TS
VMV
VPWR
VREF
WOT
Description
Bleed Solenoid
Controller Area Network
Diagnostic Trouble Code
Electronic Fuel Pump Relay
Electronic Returnless Fuel System
Evaporative
Flow Control Solenoid
Fuel Level Interface Module
Fuel Level Sender
Fuel Pump
Fuel Pump Control Module
Fuel Rail Pressure
Fuel Rail Pressure Control Module
Fuel Temperature Sensor
Ground
Heated Exhaust Gas Oxygen
Instrument Cluster
Injection Pressure Temperature Sensor
Key On Engine Off
Key On Engine Running
Liquid Propane Autogas
Mass Air Flow
Original Equipment Manufacturer
Overfill Protection Device
Powertrain Control Module
Parameter Identification
Power Ground
Signal Return
Gateway Module
Supply Solenoid
Tank Pressure Temperature Sensor
Tank Solenoid
Vapor Management Valve
Voltage Power
Voltage Reference
Wide Open Throttle
56 Blue Bird Vision Service Manual
ROUSH CleanTech Blue Bird Vision Liquid Propane Autogas (LPA)
Service Manual
P2197
P25B0
P2665
P26B3
P26B5
U0108
U0109
U210B
P0461
P0462
P0463
P0627
P064A
P116E
P1453
P2195
P0005
P0090
P009B
P009E
P0148
P0171
P0172
P0174
P0175
P0181
P0182
P0183
P0190
P0192
P0193
P025A
P025B
P03xx
Diagnostic Trouble Code List
Code Description
Fuel Shutoff Valve “A” Control Circuit/Open
Fuel Pressure Regulator Circuit/Open
Fuel Pressure Relief Control Circuit/Open
Fuel Pressure Relief Control Performance/Stuck Off
Fuel Delivery Error
System Too Lean (Bank 1)
System Too Rich (Bank 1)
System Too Lean (Bank 2)
System Too Rich (Bank 2)
Fuel Temperature Sensor “A” Circuit Range/Performance
Fuel Temperature Sensor “A” Circuit Low
Fuel Temperature Sensor “A” Circuit High
Fuel Rail Pressure Sensor Circuit (Bank 1)
Fuel Rail Pressure Sensor Circuit Low (Bank 1)
Fuel Rail Pressure Sensor Circuit High (Bank 1)
Fuel Pump Module “A” Control Circuit/Open
Fuel Pump Module “A” Control Circuit Range/Performance
Misfire
Fuel Level Sender “A” Circuit Range/Performance
Fuel Level Sender “A” Circuit Low
Fuel Level Sender “A” Circuit High
Fuel Pump “A” Control Circuit Open
Fuel Pump Control Module “A”
Fuel Pressure Relief Valve Actuated
Fuel Tank Pressure Relief Valve Malfunction
Heated Exhaust Gas Oxygen Sensor Stuck
Heated Exhaust Gas Oxygen Sensor Stuck
Fuel Level Sensor “A” Stuck
Fuel Shutoff Valve “B” Control Circuit/Open
Fuel Shutoff Valve “A” Control Circuit Performance/Stuck Off
Fuel Shutoff Valve “B” Control Circuit Performance/Stuck Off
Lost Communication with Alternative Fuel Control Module
Lost Communication with Fuel Pump Control Module “A”
Lost Communication Between Fuel Pump Control Module “A” and
Restraint Control Module
Blue Bird Vision Service Manual 57
ROUSH CleanTech Blue Bird Vision Liquid Propane Autogas (LPA)
Service Manual
Flow Control Solenoid (FCS)
P0090 — Fuel Pressure Regulator Circuit Open
Description
Possible Causes
Symptom
Diagnostic Aid
Action
FCS circuit fault. Gateway Module monitors FCS circuit for open and short circuit faults.
• Short to voltage
• Water in the harness connector
• Open power circuit
• Open ground (GND) circuit
• Low battery voltage
• Corrosion
• Incorrect connections
• Damaged FCS coil
• Blown fuse
Fuel pressure in the rail does not change when commanded. Extended fuel rail flush time.
Check the FRPCM and Gateway Module electrical connector for damage, corrosion and water intrusion.
Refer to the Fuel Rail Pressure Control Module Electrical Check procedure in
Diagnostic Tests and Procedures.
Bleed Solenoid
P009E/P26B3 — Fuel Pressure Relief Control Performance Stuck Off/Fuel Shutoff Valve “A”
Control Circuit Performance Stuck Off
Description
Possible Causes
Symptom
Diagnostic Aid
Action
Fuel rail failed to bleed. The PCM measures fuel rail pressure on key-up to determine if fuel rail has been properly bled.
• BS did not open
• FRPCM check valve leaked (P26B3)
• FRPCM supply solenoid leaked (P26B3)
• Bleed port (bleed rate restrictor in outlet to VMV) clogged
• EVAP line kinked
• Blown fuse
Fuel pressure present in the fuel rail after bleed event should have occurred; this may result in hard starts.
Check that FRPCM bleeds fuel from rail. Leaks to FRPCM can also trigger a fault.
Refer to the Fuel System Fails to Bleed procedure in Diagnostic Tests and
Procedures.
58 Blue Bird Vision Service Manual
ROUSH CleanTech Blue Bird Vision Liquid Propane Autogas (LPA)
Service Manual
P009B — Fuel Pressure Relief Control Circuit Open
Description
Possible Causes
Symptom
Diagnostic Aid
Action
Bleed solenoid circuit fault. The Gateway Module monitors bleed solenoid circuit for open and short circuit faults.
• Short to voltage
• Water in the harness connector
• Open power circuit
• Open GND circuit
• Low battery voltage
• Corrosion
• Incorrect connections
• Damaged BS coil
Fuel rail bleed system does not operate correctly. There is a potential for fuel odor or hard start.
Check the FRPCM and Gateway Module electrical for damage, corrosion and water intrusion.
Refer to the Fuel Rail Pressure Control Module Electrical Check procedure in
Diagnostic Tests and Procedures.
Tank Solenoid
P0005 — Fuel Shutoff Valve “A” Control Circuit Open
Description
Possible Causes
Symptom
Diagnostic Aid
Action
TS circuit fault. The Gateway Module monitors tank solenoid circuit for open and short circuit faults.
• Short to voltage
• Water in the harness connector
• Open power circuit
• Open GND circuit
• Low battery voltage
• Corrosion
• Incorrect connections
• Damaged TS coil
• Blown fuse
Vehicle does not start. The pump runs but no pressure builds in the fuel rail.
Check the FRPCM and Gateway Module electrical connectors for damage, corrosion and water intrusion.
Refer to the Tank Solenoid Electrical Check procedure in Diagnostic Tests
and Procedures.
Blue Bird Vision Service Manual 59
ROUSH CleanTech Blue Bird Vision Liquid Propane Autogas (LPA)
Service Manual
Fuel Rail Pressure Control Module Supply Solenoid and Wiring
P26B5 — Fuel Shutoff Valve “B” Control Circuit Performance/Stuck Off
Description
Possible Causes
Symptom
Diagnostic Aid
Action
Fuel supply solenoid stuck. The Gateway Module monitors fuel rail pressure before and after the solenoid was commanded open. If the pressure rise is below a threshold, the fault is set.
• Electrical fault
• Damaged SS coil
• Damaged SS armature
• Excess flow valve tripped
• Tank solenoid stuck closed
• Tank manual valve closed
• Fuel pumps do not power on
• Blown fuse
Vehicle does not start. The pumps run (or may not) but no pressure builds in the fuel rail.
Check the FRPCM and Gateway Module electrical connectors for damage, corrosion and water intrusion.
Refer to the Engine Cranks, No Start procedure in Diagnostic Tests and
Procedures.
P2665 — Fuel Shutoff Valve “B” Control Circuit/Open
Description
Possible Causes
Symptom
Diagnostic Aid
Action
FRPCM supply solenoid circuit fault. Gateway Module monitors supply solenoid circuit for open and short circuit faults.
• Short to voltage
• Water in the harness connector
• Open power circuit
• Open GND circuit
• Low battery voltage
• Corrosion
• Incorrect connections
• Damaged SS coil
• Blown fuse
Vehicle does not start. The pump runs but no pressure builds in the fuel rail.
Check the FRPCM and Gateway Module electrical connectors for damage, corrosion and water intrusion.
Refer to the Fuel Rail Pressure Control Module Electrical Check procedure in
Diagnostic Tests and Procedures.
60 Blue Bird Vision Service Manual
ROUSH CleanTech Blue Bird Vision Liquid Propane Autogas (LPA)
Service Manual
Gateway Module, CAN Bus Circuit Wiring
U0108 — Lost Communication with Alternative Fuel Control Module
Description
Possible Causes
Symptom
Diagnostic Aid
Action
Lost communication with Gateway Module. The PCM monitors CAN bus communication for missing messages from the Gateway Module. If the messages are continuously missing, a fault is set.
• Wiring between the Gateway Module and PCM
• No power to the Gateway Module
• Blown fuse
Rough idle.
Check the FRPCM and Gateway Module electrical connectors for damage, corrosion and water intrusion. Check for power at the Gateway Module.
Refer to the Gateway Module Electrical Check procedure under Diagnostic
Tests and Procedures.
Fuel System
P0148 — Fuel Delivery Error
Description
Possible Causes
Symptom
Diagnostic Aid
Action
LPA system is operating in vapor space. At least one bank is lean at WOT.
• Severely restricted fuel filter
• Severely restricted fuel supply line
• Damaged or worn fuel pump
• Damaged or contaminated MAF sensor
• Excess flow valve tripped
• TS or SS closed
• Tank manual shutoff valve not completely open
Vehicle hesitation or stall condition.
—
Refer to the Engine Cranks, No Start procedure under Diagnostic Tests and
Procedures.
P116E — Fuel Pressure Relief Valve Actuated
Description
Possible Causes
Symptom
Diagnostic Aid
Action
Maximum injection pressure reached. The PCM monitors fuel rail pressure and battery voltage. Based on these measurements, the PCM adjusts fuel pump speed to stay below the maximum operating pressure of the injectors.
• Operating the vehicle in high ambient conditions
• Vehicle operated in a low voltage condition
Vehicle hesitation, stall, rough idle, misfire or no start.
The P116E code is meant as an indication that the fuel system was operated at the limits of the system. The customer may have experienced drive issues although the system is performing as expected.
Refer to the Maximum Pressure Check procedure under Diagnostic Tests and
Procedures.
Blue Bird Vision Service Manual 61
ROUSH CleanTech Blue Bird Vision Liquid Propane Autogas (LPA)
Service Manual
P0171, P0174 — System Too Lean (Bank 1 and Bank 2 respectively)
Description
Possible Causes
Symptom
Diagnostic Aid
Action
Refer to the Ford Powertrain Control/Emissions Diagnosis Service Manual for more descriptive information.
• The LPA system was operated in the vapor region
• Refer to the Ford Powertrain Control/Emissions Diagnosis Service Manual for a list of other causes.
—
Verify that no LPA system faults are present and then follow the Ford service manual procedure.
Refer to the Engine Stumble, Stall, Rough Idle procedure under Diagnostic
Tests and Procedures.
P0172, P0175 — System Too Rich (Bank 1 and Bank 2 respectively)
Description
Possible Causes
Symptom
Diagnostic Aid
Action
Refer to the Ford Powertrain Control/Emissions Diagnosis Service Manual for more descriptive information.
• The LPA system was operated in the vapor region
• Refer to the Ford Powertrain Control/Emissions Diagnosis Service Manual for a list of other causes.
—
Verify that no LPA system faults are present and then follow the Ford service manual procedure.
Refer to the Engine Stumble, Stall, Rough Idle procedure under Diagnostic
Tests and Procedures.
P1453 — Fuel Tank Pressure Relief Valve Malfunction
Description
Possible Causes
Symptom
Diagnostic Aid
Action
The Gateway Module reads the FPTS and passes the voltage reading over the CAN bus to the PCM. If the pressure value of the propane fuel tank approaches the Pressure Relief Valve “pop-off” pressure, a fault is set.
• High ambient temperature operation
• Propane tank fill is contaminated with nitrogen or other constituents.
• Vehicle is parked over heat source.
The Engine Warning Light is illuminated to notify the driver there is an issue with the vehicle.
—
Discontinue use of the vehicle allowing tank pressure to cool, inspect the fuel tank pressure sensor for any faults or false readings and ensure the tank pressure is in spec per the pressure chart in the service manual to ensure there is not nitrogen or oxygen inside the tank which could cause excess tank pressures.
62 Blue Bird Vision Service Manual
ROUSH CleanTech Blue Bird Vision Liquid Propane Autogas (LPA)
Service Manual
P03xx – Misfire
Description
Possible Causes
Symptom
Diagnostic Aid
Action
Refer to the Ford Powertrain Control/Emissions Diagnosis Service Manual for more descriptive information.
• The LPA system was operated in the vapor region
• Refer to the Ford Powertrain Control/Emissions Diagnosis Service Manual for a list of other causes.
—
Verify that no LPA system faults are present and then follow the Ford service manual procedure.
Refer to the Engine Stumble, Stall, Rough Idle procedure under Diagnostic
Tests and Procedures.
Heated Exhaust Gas Oxygen Sensor
P2195, P2197 — Heated Exhaust Gas Oxygen Sensor Stuck
Description
Possible Causes
Symptom
Diagnostic Aid
Refer to the Ford Powertrain Control/Emissions Diagnosis Service Manual for more descriptive information.
• The LPA system was operated in the vapor region
• Refer to the Ford Powertrain Control/Emissions Diagnosis Service Manual for a list of other causes.
—
Verify that no LPA system faults are present and then follow the Ford service manual.
Electronic Fuel Pump Relay (A/B)
U0109 — Lost Communication with Fuel Pump Control Module A/B
Description
Possible Causes
Symptom
Diagnostic Aid
Action
The Gateway Module repeats the signal from the second EFPR to the PCM over the CAN bus. The PCM monitors this communication. If there is a lack of communication for a long enough period of time, a fault is set.
• Wire fault between the EFPR and Gateway Module
• Wire fault between Gateway Module and PCM
• No power to the EFPR
• Gateway Module fault
• CAN bus fault
• Blown fuse
• Refer to the Ford Powertrain Control/Emissions Diagnosis Service Manual for a list of other causes.
—
—
Refer to the Fuel Pump Control Module Electrical Continuity Test procedure and also the Gateway Module Electrical Test procedure in Diagnostic Tests
and Procedures.
Blue Bird Vision Service Manual 63
ROUSH CleanTech Blue Bird Vision Liquid Propane Autogas (LPA)
Service Manual
P025A — Fuel Pump Module “A” Control Circuit/Open
Description
Possible Causes
Symptom
Diagnostic Aid
Action
The Gateway Module receives the output of the second fuel pump monitor line and repeats the output over the CAN bus to the PCM. The PCM monitors the commanded output versus the monitor’s feedback. If the monitor is out-ofrange, a fault is set.
Refer to the Ford Powertrain Control/Emissions Diagnosis Service Manual for a list of other causes.
Poor starts, rough idle, hesitation/surge.
—
Refer to the Fuel Pump Control Module Electrical Continuity Test procedure in Diagnostic Tests and Procedures.
P025B — Fuel Pump Module “A” Control Circuit Range/Performance
Description
Possible Causes
Symptom
Diagnostic Aid
Action
The Fuel Pump Control Module (FPCM) A receives control commands from the PCM on a Fuel Pump Command (FPC) pin. The FPCM A passes diagnostic information on the CAN bus to the PCM. If the FPCM A receives an invalid control command from the PCM on the FPC, it sends a corresponding signal to the PCM on the CAN bus and the fault is set.
Refer to the Ford Powertrain Control/Emissions Diagnosis Service Manual for a list of other causes.
—
—
Refer to the Fuel Pump Control Module Electrical Continuity Test procedure in Diagnostic Tests and Procedures.
U210B — Lost Communication Between Fuel Pump Control Module “A” and Restraint Control
Module
Description
Possible Causes
Symptom
Diagnostic Aid
Action
The FPCM A constantly receives either an OK signal or a disable signal from the RCM on a dedicated “disable” wire. The FPCM A passes diagnostic information on the CAN bus to the PCM. If the FPCM A fails to receive a signal from the RCM, the FPCM A passes a signal, indicating it lost communication with the RCM, to the PCM and the fault is set.
• Wire fault between EFPR “A” and RCM
• Wire fault between Gateway Module and PCM
• No power to the EFPR “A”
• Gateway Module fault
• CAN fault
• Blown fuse
• RCM failure
• EFPR “A” failure
—
—
—
64 Blue Bird Vision Service Manual
ROUSH CleanTech Blue Bird Vision Liquid Propane Autogas (LPA)
Service Manual
P0627 — Fuel Pump “A” Control Circuit Open
Description
Possible Causes
Symptom
Diagnostic Aid
Action
The Fuel Pump Control Module (FPCM) A diagnoses faults of fuel pump A.
The FPCM A passes diagnostic information on the CAN bus to the PCM. If the PCM receives a FPCM A signal indicating a fuel pump problem, the fault is set.
• Wiring fault between FPCM A and fuel pump A
• Open circuit
• FPCM A fault
• CAN fault
—
—
Refer to the Fuel Pump Control Module Electrical Continuity Test procedure in Diagnostic Tests and Procedures.
P064A — Fuel Pump Control Module “A”
Description
Possible Causes
Symptom
Diagnostic Aid
Action
The Fuel Pump Control Module (FPCM) A has its own internal diagnostics.
The FPCM A passes diagnostic information on the CAN bus to the PCM. If the PCM receives a FPCM A signal indicating an internal problem, the fault is set.
• FPCM A fault
• CAN fault
—
—
Refer to the Fuel Pump Control Module Electrical Continuity Test procedure in Diagnostic Tests and Procedures.
Blue Bird Vision Service Manual 65
ROUSH CleanTech Blue Bird Vision Liquid Propane Autogas (LPA)
Service Manual
Integrated Pressure Temperature Sensor
P0181 — Fuel Temperature Sensor “A” Circuit Range/Performance
Description
Possible Causes
Symptom
Diagnostic Aid
Action
The Gateway Module reads the IPTS and passes the voltage reading over the CAN bus to the PCM. The PCM monitors the voltage as if the sensor were plugged into the vehicle.
• CAN bus fault between the Gateway Module and PCM
• Wiring fault between IPTS and Gateway Module
• Short in harness
• Short in harness
• Open circuit
• Open or short to voltage in harness
• Incorrect harness connection
• Damaged IPTS
• IPTS failure
• Gateway Module failure
—
Verify the fuel rail temperature PID value to determine open or short.
Refer to the Injection Pressure Temperature Sensor Electrical Check procedure in Diagnostic Tests and Procedures.
P0182 — Fuel Temperature Sensor “A” Circuit Low
Description
Possible Causes
Symptom
Diagnostic Aid
Action
The Gateway Module reads the IPTS and passes the voltage reading over the CAN bus to the PCM. The PCM monitors the voltage as if the sensor were plugged into the vehicle.
• CAN bus fault between the Gateway Module and PCM
• Wiring fault between IPTS and Gateway Module
• Short in harness
• VREF open or short
• Low ambient temperature operation
• Incorrect harness connection
• Damaged IPTS (or FTS)
• IPTS failure
• Gateway Module failure
—
Verify the fuel rail temperature PID value to determine open or short.
Refer to the Injection Pressure Temperature Sensor Electrical Check procedure in Diagnostic Tests and Procedures.
66 Blue Bird Vision Service Manual
ROUSH CleanTech Blue Bird Vision Liquid Propane Autogas (LPA)
Service Manual
P0183 — Fuel Temperature Sensor “A” Circuit High
Description
Possible Causes
Symptom
Diagnostic Aid
Action
The Gateway Module reads the IPTS and passes the voltage reading over the CAN bus to the PCM. The PCM monitors the voltage as if the sensor were plugged into the vehicle.
• CAN bus fault between the Gateway Module and PCM
• Wiring fault between IPTS and Gateway Module
• Open circuit
• Open or short to voltage in harness
• Incorrect harness connection
• Damaged IPTS (FTS)
• IPTS failure
• Gateway Module failure
—
Verify the fuel rail temperature parameter ID (PID) value to determine open or short.
Refer to the Injection Pressure Temperature Sensor Electrical Check procedure in Diagnostic Tests and Procedures.
P0190 — Fuel Rail Pressure Sensor Circuit
Description
Possible Causes
Symptom
Diagnostic Aid
Action
The Gateway Module reads the IPTS and passes the voltage reading over the CAN bus to the PCM. The PCM monitors the voltage as if the sensor were plugged into the vehicle.
• CAN bus fault between the Gateway Module and PCM
• Wiring fault between IPTS and Gateway Module
• VREF open in harness
• VREF open in sensor
• Vacuum leaks
• IPTS failure
• Gateway Module failure
—
VREF should be between 4–6 volts.
Refer to the Injection Pressure Temperature Sensor Electrical Check procedure in Diagnostic Tests and Procedures.
Blue Bird Vision Service Manual 67
ROUSH CleanTech Blue Bird Vision Liquid Propane Autogas (LPA)
Service Manual
P0192 — Fuel Rail Pressure Sensor Circuit Low
Description
Possible Causes
Symptom
Diagnostic Aid
Action
The Gateway Module reads the IPTS and passes the voltage reading over the CAN bus to the PCM. The PCM monitors the voltage as if the sensor were plugged into the vehicle.
• CAN bus fault between the Gateway Module and PCM
• Wiring fault between IPTS and Gateway Module
• IPTS FRP signal short to SIG RTN or PWR GND
• Damaged IPTS (or FRP)
• IPTS failure
• Gateway Module failure
—
A FRP PID value during ignition ON, engine OFF, or ignition ON, engine running is less than 0.3 volt. This indicates a concern is present.
Refer to the Injection Pressure Temperature Sensor Electrical Check procedure in Diagnostic Tests and Procedures.
P0193 — Fuel Rail Pressure Sensor Circuit High
Description
Possible Causes
Symptom
Diagnostic Aid
Action
The Gateway Module reads the IPTS and passes the voltage reading over the CAN bus to the PCM. The PCM monitors the voltage as if the sensor were plugged into the vehicle.
• CAN bus fault between the Gateway Module and PCM
• Wiring fault between IPTS and Gateway Module
• IPTS FRP signal short to VREF or VPWR
• IPTS (or FRP) open signal
• Damaged IPTS (or FRP)
• IPTS failure
• Gateway Module failure
—
Verify the FRP PID value to determine open or short.
Refer to the Injection Pressure Temperature Sensor Electrical Check procedure in Diagnostic Tests and Procedures.
68 Blue Bird Vision Service Manual
ROUSH CleanTech Blue Bird Vision Liquid Propane Autogas (LPA)
Service Manual
Fuel Level Sensor (FLS)
P0461 — Fuel Level Sender “A” Circuit Range/Performance
Description
Possible Causes
Symptom
Diagnostic Aid
Action
Refer to the Ford Powertrain Control/Emissions Diagnosis Service Manual for more descriptive information.
Refer to the Ford service manual. Causes are the same except that communication is between the sender and the Gateway Module and not the
IC.
—
The Gateway Module reads fuel level sender input and broadcasts it to the IC and PCM.
Refer to the Fuel Level Indication System Check procedure in Diagnostic
Tests and Procedures.
P0462 — Fuel Level Sender “A” Circuit Low
Description
Possible Causes
Symptom
Diagnostic Aid
Action
This DTC sets when the Fuel Level Gauge signal is electrically less than the minimum allowable sender value.
• Fuel level sender wiring shorted to ground
• Damaged Fuel Level Sender
• Gateway Module
P0462 — Fuel gauge may read empty all the time
P2067 — Fuel gauge will only show primary tank
The Gateway Module reads fuel level sender input and broadcasts it to the
PCM and IC.
Refer to the following tests located later in this manual.
• Gateway Module Electrical Test
• Fuel Level Sender Test
• Fuel Level Interface Module
Blue Bird Vision Service Manual 69
ROUSH CleanTech Blue Bird Vision Liquid Propane Autogas (LPA)
Service Manual
P0463 — Fuel Level Sender “A” Circuit High
Description
Possible Causes
Symptom
Diagnostic Aid
Action
This DTC sets when the Fuel Level Gauge signal is electrically less than the minimum allowable sender value.
• Fuel level sender wiring shorted to ground
• Damaged Fuel Level Sender
• Gateway Module
P0463 — Fuel gauge may read full all the time
P2068 — Fuel gauge will only show primary tank
The Gateway Module reads fuel level sender input and broadcasts it to the
PCM and IC.
Refer to the following tests located later in this manual.
• Gateway Module Electrical Test
• Fuel Level Sender Test
• Fuel Level Interface Module
P25B0 — Fuel Level Sensor “A” Stuck
Description
Possible Causes
Symptom
Diagnostic Aid
Action
The Gateway Module reads Fuel Level Sender (FLS) input and broadcasts it to the IC and PCM. If the vehicle is driven a considerable distance and the
FLS value doesn’t change, the fault is set.
• Fuel Level Sender fault
• Wire fault between FLS and Gateway Module
• Gateway Module fault
The driver is unaware of a low fuel condition.
—
Refer to the Fuel Level Indication System Check procedure in Diagnostic
Tests and Procedures.
Other
All diagnostic trouble codes (DTCs) known to be affected by the liquid propane autogas system
(LPA) are covered in this document. For all other
DTCs, refer to the Ford Powertrain Control/
Emissions Diagnosis Service Manual at www.
motorcraft.com (2012 F-650 H561).
70 Blue Bird Vision Service Manual
ROUSH CleanTech Blue Bird Vision Liquid Propane Autogas (LPA)
Service Manual
75
80
85
90
95
100
105
110
115
120
30
35
40
45
50
0
5
10
15
20
25
55
60
65
70
DIAGNOSTIC TESTS AND
PROCEDURES — LPA-FUELED
VEHICLES
General Information
Measuring Fuel Rail and Tank Pressure
Expected Fuel Tank Pressure
Fuel tank pressure can be measured two ways:
Method 1 — Install a 0–500 psi gauge on the bleeder valve.
Method 2 — Measure fuel rail pressure immediately after vehicle shutdown.
On a tank at ambient temperature conditions, the following pressures can be expected:
Temperature (°F)
111
121
131
142
153
165
178
191
205
219
55
62
69
77
84
93
102
28
33
38
43
49
Pressure (psi)
Min.
Nominal Max.
15 25 35
19
23
29
33
39
43
38
43
48
53
59
48
53
58
63
69
65
72
79
87
94
103
112
75
82
89
97
104
113
122
121
131
141
152
163
175
188
201
215
229
131
141
151
162
173
185
198
211
225
239
On vehicles that have been operated for extended periods of time, the tank can be much warmer and higher pressures are to be expected.
Expected Fuel Rail Pressure
The fuel pressure controls are designed to keep the rails at a certain pressure over tank pressure, therefore, it is important to measure tank pressure prior to collecting fuel rail pressure data. For example, if the fuel tank is at 150 psi (1034 kPa) and pressure in the rail is measured at 200 psi
(1379 kPa), the rail is running at 50 psi (345 kPa) over tank. The fuel pumps are fully variable voltage and can run anywhere between 7-13.5 volts to maintain a certain fuel rail pressure increase over fuel tank pressure which will keep the propane in the fuel rails in a liquid form for injection.
Once a fuel demand threshold is met, typically during wide open throttle (WOT) operation, the pump is switched to high speed. The pump is also operated at high speed during the pre-start flush sequence.
The fuel pressure controls are designed to keep the rails at a certain pressure over tank pressure, therefore, it is important to measure tank pressure prior to collecting fuel rail pressure data. For example, if the fuel tank is at 150 psi and pressure in the rail is measured at 200 psi, the rail is running at 50 psi above tank pressure.
Condition
Engine Off Off
Idle Low
Part Throttle Low
Part Throttle High
WOT High
<10
>30
<25
>25
>25
Blue Bird Vision Service Manual 71
ROUSH CleanTech Blue Bird Vision Liquid Propane Autogas (LPA)
Service Manual
Under extreme operating conditions, there is a third pump mode. In the event that the fuel system has degraded and the sensor detects vapor, or if the fuel rail pressure is approaching the limit of the fuel system, the pump runs in a variable speed mode, controlling to a target pressure. In this mode there is no predicted rise over tank pressure. The fuel pump will adjust the pressure to maintain a required operating pressure. This condition will likely result in a
P116E or P0148 code.
No Fill
Step Procedure
1
Check the fuel gauge in the instrument cluster.
Is the gauge indicating less than 3/4 full?
Action
Yes — Go to Step 2.
No — Drive bus until fuel gauge is below 3/4 full and retest.
2
If this is a first time fuel fill event after an in-tank repair, go to step 5.
Inspect vehicle to check for kinked fill lines.
Are any fill lines kinked?
3
Remove in-line fuel filter and inspect for restriction using shop air in direction of flow per arrow on filter.
4
Does the filter allow air to flow through it?
Check body side fuel fill valve; it may be stuck
closed. a. Make sure that the fuel fill line is disconnected from the fill valve.
b. Attempt to push open the piston in the fill valve to determine if it is stuck closed.
Is the fill valve piston stuck closed?
Yes — Replace damaged lines and retest.
No — Go to Step 3.
Yes — Go to Step 4.
No — Replace in-line filter and retest.
Yes — Replace body-side fill valve and retest.
No — Go to Step 5.
72 Blue Bird Vision Service Manual
ROUSH CleanTech Blue Bird Vision Liquid Propane Autogas (LPA)
Service Manual
Step Procedure
5
Check to see if the OPD is being activated.
First time fuel fill event with an empty tank could be activating the OPD and shutting off fuel flow in the fill line.
a. Loosen the fuel fill line at the fill valve or at the inlet to the fuel filter to relieve any pressure in the fill line. Retighten the fill line.
b. Confirm that the bleeder valve is open.
c. Connect the fuel dispensing nozzle to the fill valve and turn on the pump. d. Open the fill nozzle handle slow as possible to allow fuel to slowly enter the fill line and fill tank with 5 gallons of fuel only.
e. If vehicle does accept the 5 gallons of fuel?
Yes — Continue with diagnostic Step “F” below.
No — Replace OPD per Service Manual and retest.
f. Close the bleeder valve and inspect all tank connections for leaks using approved leak detecting solution or electronic tester.
g. Fill with another 20 gallons of fuel and verify vehicle starts and runs with no issues?
6
Fill the fuel tank with fuel.
Does the vehicle fuel tank fill to capacity?
Action
Step “E” Unable to fill with fuel.
Replace OPD per Service Manual and retest.
Step “G”
Yes — Go to Step 6.
No — Review repairs performed and repair as needed.
Note that fuel tank may require being emptied and make sure not to fill with more fuel.
Yes — Diagnostic is complete.
No — Go to Short Fill diagnostic.
Short Fill
Step Procedure
1
Confirm Bus is level front to back and side to side during fuel filling.
Is the bus level?
2
Check fuel gauge.
Does fuel gauge read full?
3
Confirm the following has been performed.
a. Using the tables provided at the front of this section, determine expected propane tank pressure based on ambient temperature.
Is the vehicle fuel tank pressure greater than 20 psi
(138 kPa) over the nominal expected pressure?
Action
Yes — Go to Step 2.
No — Level the bus and retest.
Yes — Diagnostic complete.
No — Go to Step 3.
Yes — Go to Step 4.
No — Go to Step 5.
Blue Bird Vision Service Manual 73
74
ROUSH CleanTech Blue Bird Vision Liquid Propane Autogas (LPA)
Service Manual
Step Procedure
4
Vehicle fuel tank is at a higher pressure than
expected.
Action
When tank pressure is within 10 psi
(69 kPa) of expected tank pressure, go to Step 5.
If this is a new vehicle, there may be nitrogen in the tank causing pressure to be greater than expected. Make sure tank is at ambient temperature and then confirm pressure reading, if greater than expected.
a. Higher pressure is likely caused by heavy vehicle usage heating the fuel.
b. Allow the vehicle (fuel tank) to cool to ambient temperature and then recheck pressure in the fuel tank.
c. If pressure is still higher than expected, place vehicle in a well-ventilated area away from any ignition source and open the bleeder valve for
30 minutes.
d. Close the bleeder valve and allow fuel tank to stabilize the temperature for 30 minutes and recheck tank pressure.
e. Repeat steps A-D until tank pressure is within the 10 psi expected tank pressure.
5
Check for pressure gauges on fill station.
Is the filling station equipped with an inlet and outlet pressure gauge?
Yes — Go to Step 6.
No — Contact filling station provider to assist with this diagnostic step.
6
Check for sufficient filling pressure on fill station.
a. Record vehicle tank pressure. Static vehicle tank pressure = __________ (example: 250 psi).
b. With fill hose connected to vehicle, start pump and during fuel fill monitor and record the outlet pump pressure gauge. Pump pressure during fuel fill =_________ (example: 350 psi).
c. Is fill station pump pressure at least 50 psi (345 kPa) greater than tank pressure?
(example: pump psi minus vehicle tank psi
350-250 = 100 psi over vehicle tank pressure).
Yes — Go to Step 7.
No — Contact filling station provider to repair pressure concern and retest.
Blue Bird Vision Service Manual
ROUSH CleanTech Blue Bird Vision Liquid Propane Autogas (LPA)
Service Manual
Step Procedure
7
Attempt to fill the vehicle fuel tank.
Does the fuel tank fill full?
Action
Yes — Diagnostic is complete.
No — Call ROUSH CleanTech
Customer Service at 800-597-
6874 with the following information documented.
Results from:
Fuel sending unit electrical test
Filling station pressure test
Slow Fill
Step Procedure
1
Inspect vehicle to check for kinked fill lines.
Are lines kinked?
2
Determine flow rate at which the vehicle fuel system fills.
a. Time the fill station pump for 10 seconds and record the number of gallons dispensed. b. Multiply the gallons dispensed by six to determine the flow rate in gallons per minute. c. Is the fill station pump flow rate at least 6 gallons per minute?
3
Check for sufficient filling pressure on fill station.
a. Record vehicle tank pressure. Static vehicle tank pressure = __________ (example: 250 psi).
b. With fill hose connected to vehicle, start pump and during fuel fill monitor and record the outlet pump pressure gauge. Pump pressure during fuel fill =_________ (example: 350 psi).
c. Is fill station pump pressure at least 50 psi (345 kPa) greater than tank pressure?
(example: pump psi minus vehicle tank psi
350-250 = 100 psi over vehicle tank pressure).
4
Check fuel fill valve; it may not be opening completely.
a. Loosen the fuel fill line connection at the fill valve or at the inlet to the fuel filter to relieve any pressure in the fill line. b. Attempt to push open the piston in the fill valve to determine if it is opening completely. Piston should travel 1/4 inch. c. Is the fill valve piston opening completely?
Action
Yes — Replace kinked lines.
No — Go to Step 2.
Yes — System fill rate is OK; diagnostic is complete.
No — Fill station is not providing enough pressure to fill vehicle tank. Go to Step 3.
Yes — Go to Step 4.
No — Fill station is not providing enough pressure to fill vehicle tank. Go to Step 10.
Yes — Replace the filter in the fuel fill line and then go to Step 7.
No — Replace the fuel fill valve and then go to Step 5.
Blue Bird Vision Service Manual 75
76
ROUSH CleanTech Blue Bird Vision Liquid Propane Autogas (LPA)
Service Manual
Step Procedure
5
Attempt to fill the vehicle fuel tank.
Does the fuel tank fill at greater than 6 gal (23 L) per minute?
6
Replace the in-line fuel filter.
Does the vehicle fuel tank fill at greater than 6 gal
(23 L) per minute?
7
Replace the overfill protection device (OPD) valve in the vehicle fuel tank.
Action
Yes — Diagnostic is complete.
No — Go to Step 6.
Yes — Diagnostic is complete.
No — Go to Step 7.
Go to Step 8.
8
Attempt to fill the vehicle fuel tank as follows:
Yes — Go to Step 9.
No — Call ROUSH CleanTech
Customer Service at 800-597-6874.
First time fuel fill event with an empty tank could be activating the OPD and shutting off fuel flow in the fill line.
a. Confirm that the bleeder valve is open.
b. Connect the fuel dispensing nozzle to the fill valve and turn on the pump. c. Open the fill nozzle handle as slow as possible to allow fuel to slowly enter the fill line and fill tank with 5 gallons of fuel only. d. Close the bleeder valve and inspect all tank connections for leaks using approved leak detecting solution or electronic tester.
e. Fill with another 20 gallons of fuel and verify vehicle starts and runs with no issues.
Attempt to fill the vehicle fuel tank.
9
Does the fuel tank fill at greater than 6 gal (23 L) per minute?
10
Fill station is not providing enough pressure to fill.
a. Using the tables provided at the front of this section, determine expected propane tank pressure based on ambient temperature. b. Is the vehicle fuel tank pressure greater than
20 psi (38 kPa) over the nominal expected pressure?
Yes — Diagnostic is complete.
No — Call ROUSH CleanTech
Customer Service at 800-597-6874.
Yes — Go to Step 11.
No — Locate a dispensing facility with pump output capacity in excess of 50 psi (345 kPa) over vehicle fuel tank pressure. Then, go to Step 2.
Blue Bird Vision Service Manual
ROUSH CleanTech Blue Bird Vision Liquid Propane Autogas (LPA)
Service Manual
Step Procedure
11
Vehicle fuel tank is at a higher pressure than expected.
Action
When tank pressure is within 10 psi (69 kPa) of expected tank pressure, go to
Step 12.
If this is a new vehicle, there may be nitrogen in the tank causing pressure to be greater than expected. Make sure tank is at ambient temperature and then confirm pressure reading, if greater than expected.
a. Higher pressure is likely caused by heavy vehicle usage heating the fuel. b. Allow the vehicle (fuel tank) to cool to ambient temperature and then recheck pressure in the fuel tank.
c. If pressure is still higher than expected, place vehicle in a well-ventilated area away from any ignition source and open the bleeder valve for
30 minutes.
d. Close the bleeder valve and allow fuel tank to stabilize the temperature for 30 minutes and recheck tank pressure.
e. Repeat steps A-D until tank pressure is within the 10 psi expected tank pressure.
12
Check for sufficient filling pressure on fill station.
a. Record vehicle tank pressure. Static vehicle tank pressure = __________ (example: 250 psi).
b. With fill hose connected to vehicle, start pump and during fuel fill monitor and record the outlet pump pressure gauge. Pump pressure during fuel fill =_________ (example: 350 psi).
c. Is fill station pump pressure at least 50 psi (345 kPa) greater than tank pressure?
(example: pump psi minus vehicle tank psi
350-250 = 100 psi over vehicle tank pressure).
13
Attempt to fill the vehicle fuel tank.
Does the fuel tank fill at greater than 6 gal (23 L) per minute?
Yes — Go to Step 13.
No — Fill station is not providing enough pressure to fill vehicle tank. Go to Step 14.
Locate a dispensing facility with pump output capacity in excess of 50 psi
(345 kPa) over vehicle fuel tank pressure or contact your fueling provider to assist with filling site concern.
Yes — Diagnostic is complete.
No — Go to Step 4.
Blue Bird Vision Service Manual 77
ROUSH CleanTech Blue Bird Vision Liquid Propane Autogas (LPA)
Service Manual
Over Fill
Step Procedure
1
Suspect overfill because fuel fill volumes achieved during refueling exceed the rated fuel capacity or excessive vehicle range between refueling.
a. Check the fuel gauge. b. Is the gauge reading below 3/4 tank?
2
Open the bleeder valve on the fuel tank and in the fuel fill door.
a. Listen at valve to verify propane vapor is venting. b. Is propane vapor venting?
3
Park the vehicle at the refueling station.
a. Check to determine if the vehicle is level using the vehicle frame as reference. b. Does the vehicle set level?
4
Locate the American Society of Mechanical
Engineers (ASME) inspection plate on the fuel
tank. a. Note the tank water capacity listed on the plate. b. Multiply the listed capacity by 0.05 (5%) and record the value.
Example:
WC on tank reads 86.5 gallons
86.5x0.05 = 4.325 gallons
Action
Yes — Go to Step 2.
No — Drive vehicle until gauge reads below 3/4 tank.
Yes — Go to Step 3.
No — Bleeder valve is not functioning properly. Replace the valve.
Yes — Go to Step 4.
No — Using a jack, raise the vehicle to obtain a level condition. Then, go to
Step 4.
With the value recorded, go to Step 5.
78 Blue Bird Vision Service Manual
ROUSH CleanTech Blue Bird Vision Liquid Propane Autogas (LPA)
Service Manual
Step Procedure
5
Refuel the vehicle as follows:
Action
Pump stopped prior to 5% value —
If the key is on during refueling, it will take the fuel level gauge in the instrument cluster longer to register full.
Tank did not overfill. Go to Step 7.
Pump did not stop and 5% value was
passed — Tank is overfilling. Replace the OPD fill valve in the fuel tank; then, go to Step 6.
a. Verify that the ignition is in the OFF position.
b. Connect the fuel dispensing nozzle to the vehicle. Verify that the bleeder valve is open.
c. With the bleeder valve open, turn on the pump.
Open the fill nozzle handle as slow as possible to allow fuel to slowly enter the fill line and fill tank.
NOTE: If tank has vented from the
Pressure Relief Valve (PRV), then you must also replace it at the same time as OPD replacement.
d. While refueling, observe the bleeder valve for fuel discharge.
e. Start to record gallons being filled when a solid stream of liquid fuel flows from the bleeder valve.
6 f. Continue filling until you have reached the 5% value determined by tank size (example 4.325 gal) from Step 4 or the pump stopped filling.
g. Did the pump continue to pump and the 5% value reached or did the pump stop prior to the 5% value?
Refuel the vehicle as follows after OPD replacement.
If the key is on during refueling, it will take the fuel level gauge in the instrument cluster longer to register full.
a. Verify that the ignition is in the OFF position. b. Connect the fuel dispensing nozzle to the vehicle. Verify that the bleeder valve is open.
c. Open the fill nozzle handle as slow as possible to allow fuel to slowly enter the fill line and fill tank with 5 gallons of fuel only and stop pump.
Pump stopped prior to 5% value
and liquid was present — Vehicle is repaired and can be placed back into service.
Pump stopped prior to 5% value and
no liquid was present — Go to Step 7.
d. Close the bleeder valve and inspect all tank connections for leaks using approved leak detecting solution or electronic tester.
e. Fill with another 20 gallons of fuel and verify vehicle starts and runs with no issues.
f. Open the bleeder and fill until the pump stops filling and monitor the bleeder for fuel discharge.
Blue Bird Vision Service Manual 79
ROUSH CleanTech Blue Bird Vision Liquid Propane Autogas (LPA)
Service Manual
Step Procedure
7
The dispensing pump stopped automatically and a liquid fuel stream was not observed flowing from bleeder valve.
a. Document number of gallons filled and verify that the tank was filled to the 80% volume – full capacity?
Action
Yes — Tank does not overfill.
Diagnostic is complete.
No — Call ROUSH CleanTech
Customer Service at 800-597-6874.
Engine Does Not Crank
Step Procedure
1 Is battery voltage above 12 volts?
2 Refer to the Blue Bird Multiplex Diagnostics.
Is the problem corrected?
Action
Yes — Go to Step 2.
No — Determine cause of low battery voltage.
Yes — Diagnostic is complete.
No — Call ROUSH CleanTech
Customer Service at 800-597-6874.
Engine Cranks, No Start
Step Procedure
1
Verify the following:
a. Is there fuel in the tank of at least 1/8 tank or more? (add fuel if necessary).
b. Is the tank supply manual shut-off valve fully open?
c. Does battery voltage stay above 10 volts during crank? d. Check fuel pump fuse, tank solenoid fuse, and
FRPCM fuse in the Blue Bird PDU.
2
Check for diagnostic trouble codes (DTC).
Are any codes present?
3
Is the DTC identified on the ROUSH LPA DTC
list?
Action
Yes — Go to Step 2.
No — Correct fault and retry.
Yes — Go to Step 3.
No — Go to Step 4.
Yes — Refer to Diagnostic Trouble
Codes — LPA-Fueled Vehicles.
No — Refer to Ford service manual
DTC chart.
Yes — Go to Step 9.
No — Go to Step 5.
4
Check fuel pressure.
a. Measure and record fuel rail and fuel tank pressure, key on, engine off (KOEO). b. While monitoring fuel pressure, attempt to start engine. c. Record the highest pressure observed. d. Does fuel pressure rise 25 psi before engine crank?
80 Blue Bird Vision Service Manual
ROUSH CleanTech Blue Bird Vision Liquid Propane Autogas (LPA)
Service Manual
Step Procedure
5
Check fuel pump operation.
a. Turn the ignition switch to start. b. During the fuel system flush, use a current clamp and check current draw to determine if fuel pumps run when engine cranks. When measuring fuel pump current a minimum of 2 amps should be recorded. c. Do fuel pumps draw current when engine cranks?
6 Check excess flow valve (XFV). a. Turn off engine.
7 b. Wait 1 minute and then restart engine. c. Measure and record fuel pressure, using a scan tool, at integrated pressure temperature sensor (IPTS). d. Is problem resolved?
Verify that there is power and proper grounding in the tank solenoid (TS) and supply solenoid
(SS) wiring circuits. Refer to the Blue Bird
Service Manual.
a. Check for +12 volts at the TS and SS connectors. See the Tank Solenoid Electrical
Check procedure. b. Is +12 volts present at the TS connector? c. Is +12 volts present at the SS connector?
8
Verify that there is power and proper grounding in the wiring circuit to the tank. Refer to the Blue
Bird Service Manual.
a. Check for +12 volts at the fuel pump 1 (FP1) and fuel pump 2 (FP2) connectors. See the
Fuel Pump Electrical Check procedure. b. Is +12 volts present at the FP1 connector? c. Is +12 volts present at the FP2 connector?
9
Integrated Pressure Temperature Sensor (IPTS)
Rationality
Is the temperature and pressure reading in the expected range as outlined in the verification procedure?
Action
Yes — Go to Step 6.
No — Check OEM fuel pump (FP) fuse and replace fuse, if necessary. If OK, go to Step 8.
Yes — Go to Step 9.
No — Go to Step 7.
Yes — Voltage present at SS, replace
FRPCM. Voltage present at TS, replace fuel supply valve assembly.
No — Check for an open(s) in the wiring circuits and repair. Diagnostic is complete.
Yes — Go to Step 9.
No — Check for an open(s) in the wiring circuits and repair.
Yes — Refer to the Integrated Pressure
Temperature Sensor (IPTS) Electrical
Check.
No — Verify that wiring in circuit is
OK. See the Integrated Pressure
Temperature Sensor (IPTS) Electrical
Check procedure. If not, repair wiring. If
OK, replace sensor.
Blue Bird Vision Service Manual 81
ROUSH CleanTech Blue Bird Vision Liquid Propane Autogas (LPA)
Service Manual
Step Procedure
10
Inspect the tank pass-through harness.
a. Drain the propane from the fuel tank. Refer to the Fuel Tank Draining Procedure in the appropriate ROUSH CleanTech Service
Manual for more information. b. Remove tank service cover. c. Check for open or short circuits on tank passthrough harness. d. Is a wiring problem present?
11
Check fuel hoses and quick-connect fittings.
Are in-tank fuel hoses and quick-connect fittings connected and in good condition?
Engine Stumble, Stall, Rough Idle
Action
Yes — Replace harness.
No — Go to Step 11.
Yes — Replace fuel pump assembly.
No — Replace hose assemblies as needed.
Step Procedure
1 Verify the following: a. Is there fuel in the tank of at least 1/8 tank or more? (Add fuel if necessary.) b. Is the tank supply manual shut-off valve fully open? c. Is battery voltage above 11 volts with engine running? d. Check for air restrictions and un-metered air leaks (air filter, vacuum leaks).
2
Check for diagnostic trouble codes (DTCs).
Are any codes present?
3
Identify the DTC.
a. Is the DTC covered in the ROUSH CleanTech
DTC listing for LPA-fueled vehicles? b. Correct all DTCs before continuing.
4
Determine fuel pressure.
a. Measure tank pressure with key on and engine off (KOEO). b. Measure fuel rail pressure with key on and engine running (KOER). c. Substract the KOEO pressure from the KOER pressure to obtain the difference. Compare to the chart in Expected Fuel Rail Pressure. d. Is the resulting fuel pressure reading within the expected range?
Action
Yes — Go to Step 2.
No — Correct the fault and retry.
Yes — Go to Step 3.
No — Go to Step 4.
Yes — Refer to ROUSH CleanTech
DTC procedure.
No — Refer to the Ford Powertrain
Control/Emissions Diagnosis Service
Manual at www.motorcraft.com (F-650).
Yes — Go to Step 6.
No — Go to Step 5.
82 Blue Bird Vision Service Manual
ROUSH CleanTech Blue Bird Vision Liquid Propane Autogas (LPA)
Service Manual
Step Procedure
5
Determine if the excess flow valve (XFV) is tripped.
a. Turn off the engine. b. Wait one minute and then restart the engine. c. Is the fault condition resolved?
6
Determine fuel pressure at time of fault.
a. While driving the vehicle, determine and record the fuel pressure during stumble. b. Does the pressure drop more than 10 psi during stumble?
7
Check fuel pump operation.
a. Turn the ignition switch to start and wait for engine to crank. b. Using a current clamp, check current draw to determine if fuel pumps run when engine cranks. When measuring fuel pump current a minimum of 2 amps should be recorded. Do fuel pumps run?
8
Check Blue Bird fuel pump fuse. Refer to the
Blue Bird Service Manual.
Is fuel pump fuse intact and OK?
9
Check tank solenoid (TS) and supply solenoid
(SS) fuses.
a. Locate the TS and SS fuses. b. Are the fuses blown?
10
Verify that there is power and grounding in the tank solenoid (TS) and supply solenoid (SS) wiring circuits. Refer to the Blue Bird Electrical
Manual.
a. Check for +12 volts at the TS and SS connectors. See the Tank Solenoid Electrical
Check procedure. b. Is +12 volts present at the TS connector? c. Is +12 volts present at the SS connector?
11
Verify that there is power and proper grounding in the wiring circuit to the tank. Refer to the Blue
Bird Electrical Manual.
a. Check for +12 volts at the fuel pump 1 (FP1) and fuel pump 2 (FP2) connectors. See the
Fuel Rail Pressure Control Module (FRPCM)
Electrical Check procedure. b. Is +12 volts present at the FP1 connector? c. Is +12 volts present at the FP2 connector?
Action
Yes — Go to Excess Flow Valve (XFV)
Check procedure.
No — Go to Step 6.
Yes — Go to Step 7.
No — Go to Step 13.
Yes — Go to Step 4.
No — Check OEM fuel pump (FP) fuse and replace fuse if necessary. If OK, go to Step 9.
Yes — Go to Step 5.
No — Repair short and replace fuse.
Yes — Find and repair the short; replace the fuse.
No — Go to Step 10.
Yes — Voltage present at SS, replace
FRPCM. Voltage present at TS, replace fuel supply valve assembly.
No — Check for an open/short in the wiring circuit and repair.
Yes — Go to Step 12.
No — Check for an open/short in the wiring circuit and repair.
Blue Bird Vision Service Manual 83
ROUSH CleanTech Blue Bird Vision Liquid Propane Autogas (LPA)
Service Manual
Step Procedure
12
Inspect the tank pass-through harness.
a. Drain the propane from the fuel tank. See the Fuel Tank Draining Procedure in the appropriate ROUSH CleanTech Service
Manual for more information. b. Remove tank service cover. c. Check for open or short circuits on tank passthrough harness. d. Is a wiring problem present?
13
Check fuel hoses and quick-connect fittings.
Are in-tank fuel hoses and quick-connect fittings connected and in good condition?
14
Integrated Pressure Temperature Sensor (IPTS)
Rationality
Does temperature and pressure make sense to verification? See the Integrated Pressure
Temperature Sensor (IPTS) Electrical Check
procedure.
15
Refer to the Ford Powertrain Control/Emissions
Diagnosis Service Manual at www.motorcraft.
com (2016 F-650).
Excess Flow Valve (XFV) Check
The excess flow valve (XFV) is designed to restrict fuel exiting the tank if the pump is energized while the fuel lines are not connected to the fuel tank.
Under normal circumstances, the XFV should not trip. The XFV will reset itself after the fuel pumps have been off for about one minute.
It is common to trip the XFV after the fuel lines have been serviced and contain no pressure. If the
XFV trips, turn the vehicle off, wait one minute, and restart. This may take more than one attempt.
If the PCM determines that the XFV is checked based on input from TPTS and IPTS, then it will cycle voltage to the tank solenoid and fuel pumps three times to attempt to reset the XFV.
If the fuel lines have not been serviced recently and the problem persists, there may be a leak in the supply side fuel line. If the problem is only present after the vehicle has been sitting for a length of time, but not present during a short soak, or there is a propane odor when the vehicle is running, see the Fuel Line Leak Detection procedure.
Action
Yes — Replace harness.
No — Go to Step 13.
Yes — Replace fuel pump assembly.
No — Replace hose assemblies as needed.
Yes — Go to Step 15.
No — Verify that wiring in circuit is
OK. If not, repair wiring. If OK, replace sensor.
—
84 Blue Bird Vision Service Manual
ROUSH CleanTech Blue Bird Vision Liquid Propane Autogas (LPA)
Service Manual
Step Procedure
1
Verify fuel supply line pressure prior to cranking
engine. a. Read fuel rail pressure and tank pressure. b. Energize bleed solenoid until rail pressure is at least 50 psi below tank pressure. If rail is bled, skip to Step D. c. Let pressure stabilize for 1 minute. d. Open the supply solenoid. e. Read fuel rail pressure and tank pressure. f. Does fuel rail pressure jump to tank pressure?
Action
Yes — Check is OK.
No — Repair the leak in the fuel supply line.
Maximum Pressure Check
The LPA system operates over a wide range of pressures depending on ambient temperature, driving mode, etc. When the vehicle is subjected to a severe drive cycle in high ambient temperatures, the fuel rail pressure can rise to the limit of the injectors capabilities. This limit is a function of injector voltage and fuel rail pressure. The PCM protects for this condition by reducing the fuel pump speed when the condition is sensed, however, there still may be drive concerns. When the PCM starts controlling the fuel pump, a
P116E code is set. While this condition can occur in a normally functioning vehicle, it can also be exacerbated by several factors. If the fuel tank was not properly bled during the first fill, trapped air in the vapor space can increase tank pressure.
In this condition there is often only a faint smell of propane when the bleeder valve is opened.
The tank should be vented until there is a strong propane odor coming from the bleeder valve. The tank pressure should be confirmed against the expected pressure.
Allow the fuel tank to cool to ambient temperature before performing the following procedure.
Step Procedure Action
Step Procedure
1
Measure tank pressure and tank surface temperature.
Is tank pressure more than 15 psi (103 kPa) over expected tank pressure?
Action
Yes — Vent the tank until pressure is within the expected range.
No — Vehicle is working properly; inform and explain operating characteristics to customer.
Blue Bird Vision Service Manual 85
ROUSH CleanTech Blue Bird Vision Liquid Propane Autogas (LPA)
Service Manual
Fuel System Fails to Bleed
Step Procedure
1
Check for diagnostic trouble codes (DTC).
a. Are both DTC 26B3 and P009E present?
2
Check for oil contamination at vapor port/EVAP
line. a. Disconnect EVAP line from vapor port. b. Is oil present in EVAP line or vapor port?
3
Determine if fault condition repeats.
a. START the engine and allow it to run for a few minutes. b. Turn OFF the engine and wait one minute.
c. Measure and record the fuel rail pressure, fuel rail temperature and fuel tank pressure with the Key ON Engine OFF (KOEO).
Action
Yes — Go to Step 8.
No — Go to Step 2.
Yes — Replace vapor port and perform
Step 3.
No — Go to Step 3.
Yes — Potential intermittent fault.
Return vehicle to customer and see if problem persists.
No — Go to Step 4. d. Energize the bleed solenoid. Refer to the
Manual Solenoid Activation Procedure. Verify wiring integrity and voltage to solenoid.
e. With the engine OFF, monitor fuel rail pressure for 15 minutes.
f. Does fuel rail pressure drop more than 20 psi
(138 kPa)?
4
Verify vapor port function.
a. Disconnect the EVAP line from the FRPCM port. b. Energize the bleed solenoid. Refer to the
Manual Solenoid Activation Procedure. Verify wiring integrity and voltage to solenoid.
c. Is there propane flowing from the port?
5
Verify bleed solenoid function.
a. Disconnect the EVAP line from the FRPCM port. b. Remove the vapor port.
6 c. Energize the bleed solenoid. Refer to the
Manual Solenoid Activation Procedure. Verify wiring integrity and voltage to solenoid.
d. Is there propane flowing from the port?
Verify that wiring is in good condition and functioning.
a. Perform wiring checks of the FRPCM harness.
b. Is the wiring OK?
Yes — Go to Step 7.
No — Go to Step 5.
Yes — Replace vapor port and repeat
Step 3.
No — Go to Step 6.
Yes — Bleed solenoid stuck closed.
Replace the FRPCM.
No — Repair wiring and repeat Step 3.
86 Blue Bird Vision Service Manual
ROUSH CleanTech Blue Bird Vision Liquid Propane Autogas (LPA)
Service Manual
Step Procedure
7
Check for a kinked EVAP line.
a. Inspect the EVAP line between the FRPCM and EVAP canister.
8 b. Are there kinks in the line?
Check for leaks to the FRPCM.
a. START the engine and allow it to run for a few minutes.
b. Turn OFF the engine.
c. Measure and record fuel rail pressure.
d. Activate bleed solenoid to bleed pressure from fuel rail until fuel pressure drops more than 50 psi (345 kPa). Refer to the Manual
Solenoid Activation Procedure.
e. De-energize bleed solenoid.
f. Disconnect the FRPCM and wait 120 minutes.
g. Measure fuel rail pressure and fuel tank pressure.
h. Does fuel rail pressure rise more than 10 psi
(69 kPa)?
Action
Yes — Replace the kinked EVAP line and then repeat Step 3.
No — Go to Step 8.
Yes — FRPCM leaks at either supply solenoid or return check valve. Replace
FRPCM.
No — Potential intermittent fault. Return vehicle to customer and see if problem persists.
Tank Solenoid Electrical Check
For harness and connector layout diagrams and system electrical schematics, refer to
Wiring Diagrams and Electrical Schematics.
CONNECTORS
C1
30
1
31
2
32
PBT/ASA-GF20
18
3
44
29
45
A1
46
15
16 17
PIN 1
Figure 55 — Underhood Harness Connectors
100446a
Blue Bird Vision Service Manual 87
ROUSH CleanTech Blue Bird Vision Liquid Propane Autogas (LPA)
Service Manual
SUPPLY SOLENOID
(BLACK)
2 1
C7
100477a
Figure 56 — Tank Harness Connector
PROCEDURE
Step Procedure
1
Unplug the solenoid harness connector C7 from the tank solenoid.
2
Using a multimeter, measure resistance of the solenoid.
Is the measured resistance within 6–11 ohms?
3
Use a multimeter to check the voltage at the tank solenoid.
a. With the ignition key ON, check for voltage present at pin-1, connector C7 (tank harness).
Use the body as the reference ground.
b. Is battery (B+) voltage present?
4
Check fuse in the PDU fuse box for supply solenoid power. (Refer to Blue Bird wiring schematic).
Is fuse blown?
5
Check relay in the PDU.
a. Check continuity between pin-1 of the solenoid harness and the fuse box. Refer to the Blue Bird Service Manual for fuse box and circuit information.
b. Is there good continuity in the circuit?
6
Check ground circuit continuity from solenoid harness to smart relay module (SRM) connector.
Refer to the Blue Bird Service Manual for SRM circuit information.
a. Check continuity between pin-2 connector
C7 of solenoid harness to pin-1 at Gateway
Module connector.
b. Is there good continuity in the circuit?
Action
Go to Step 2.
Yes — Go to Step 3.
No — Replace the tank solenoid.
Yes — Supply circuit OK.
No — Go to Step 4.
Yes — Replace the fuse.
No — Fuse OK. Go to Step 5.
Yes — Go to Step 6.
No — Repair circuit wiring.
Yes — Go to Gateway Module Electrical
Test procedure.
No — Repair circuit wiring.
88 Blue Bird Vision Service Manual
ROUSH CleanTech Blue Bird Vision Liquid Propane Autogas (LPA)
Service Manual
Fuel Rail Pressure Control Module
Electrical Check
For harness and connector layout diagrams and system electrical schematics, refer to
Blue Bird Wiring Diagrams and Electrical
Schematics.
CONNECTORS
C1
33
46
C5
SUPPLY
SOLENOID
(BLACK)
32
30 31
PBT/ASA-GF20
18
1 2
3
44
45
29
A1
46
15
16 17
2 1 2
C6
BLEED
SOLENOID
(GRAY)
1
17
100449a
Figure 57 — Underhood Harness Connectors
PROCEDURE
Step Procedure
1
Unplug the fuel rail pressure control module
(FRPCM) connector.
2
Using a multimeter, check the resistance of each solenoid.
a. Check resistance across the terminals of the
FRPCM solenoid in sequence as follows:
• Supply Solenoid — Pin-1 and pin-2
• Bleed Solenoid — Pin-1 and pin-2 b. Is resistance value between 6-11 ohms?
3
Check supply voltage to FRPCM solenoids.
4
Using a multimeter, measure voltage between the terminal for each solenoid at the harness side connectors and ground as follows:
Supply Solenoid — Pin-1 and body ground
5
Bleed Solenoid — Pin-1 and body ground
Action
Go to Step 2.
Yes — Go to Step 3.
No — Replace the FRPCM if resistance for any one of the solenoids is not within the specified range.
Go to Steps 4–6.
B+ Voltage — Go to Step 5.
No Voltage — Go to Step 5.
B+ Voltage — Continue with Step 8.
No Voltage — Go to Step 7 if Step 4 has voltage; if Step 4 has no voltage, go to Step 6.
Blue Bird Vision Service Manual 89
90
ROUSH CleanTech Blue Bird Vision Liquid Propane Autogas (LPA)
Service Manual
Step Procedure
6
Check fuses for the Supply Solenoid and Bleed
Solenoid in the Blue Bird PDU fuse box (refer to the Blue Bird Wiring Diagram).
7
Is a fuse blown?
Check solenoid supply circuit continuity.
a. Check continuity between:
• Supply Solenoid — Pin-1, connector C5
(underhood harness) and fuse location in the Blue Bird PDU
• Bleed Solenoid — Pin-1, connector C6
(underhood harness) and fuse location in the Blue Bird PDU
8 b. Is there good continuity in both circuits?
Check solenoid ground circuit continuity.
a. Check continuity in the underhood harness between:
• Supply Solenoid — Pin-2, connector C5 and pin-32, connector C1 at Gateway
Module
• Bleed Solenoid — Pin-2, connector C6 and pin-33, connector C1 at Gateway Module b. Is there good continuity in both circuits?
Action
Yes — Replace fuse.
No — Go to Step 7.
Yes — Go to Step 8.
No — Repair wiring circuit (refer to the
Blue Bird wiring schematic).
Yes — Refer to the Gateway Module
Electrical Test procedure.
No — Repair wiring circuit (refer to the
Blue Bird wiring schematic).
Blue Bird Vision Service Manual
ROUSH CleanTech Blue Bird Vision Liquid Propane Autogas (LPA)
Service Manual
Integrated Pressure Temperature Sensor
Electrical Check
For harness and connector layout diagrams and system electrical schematics, refer to
Wiring Diagrams and Electrical Schematics.
CONNECTORS
C1
40
30
1
31
2
32
PBT/ASA-GF20
18
3
18 20 25
44
29
45
A1
46
15
16 17
C3
4
2
3
1
IPTS CONNECTOR
INSERTION VIEW
C3
1
2 4
3
IPTS CONNECTOR
FACEVIEW
POWER TERMINAL
(VOLTAGE IN)
PRESSURE OUTPUT
TERMINAL
(VOLTAGE OUT)
4
TEMPERATURE
OUTPUT TERMINAL
(VOLTAGE OUT)
C3
1
IPTS SENSOR PINOUT
GROUND
TERMINAL
(GROUND)
100485a
Figure 58 — Underhood Harness Connectors
PROCEDURE
Step Procedure
1
Unplug the connector 3 (underhood harness) to the IPTS.
2
Check resistance of the injection pressure temperature sensor (IPTS).
a. With vehicle at ambient room temperature
(20–30°C, 68–86°F) and using a multimeter, measure resistance across the IPTS terminals
(between pin-1 and pin-3).
b. Is the resistance value between 8K–12K ohms?
Action
Go to Step 2.
Yes — Go to Step 3.
No — Replace the IPTS.
Blue Bird Vision Service Manual 91
Step Procedure
3
ROUSH CleanTech Blue Bird Vision Liquid Propane Autogas (LPA)
Service Manual
Check circuit continuity between the IPTS and the Gateway Module (Gateway Module).
a. Using a multimeter, check continuity in the underhood harness between:
• Pin-1, connector C3 and pin-40, connector C1
• Pin-2, connector C3 and pin-20, connector C1
• Pin-3, connector C3 and pin-18, connector C1
• Pin-4, connector C3 and pin-25, connector C1 b. Is there good continuity in the circuits?
IPTS Temperature/Resistance Chart
90
100
110
120
130
135
10
20
25
30
40
50
60
70
80
Temp, °C A R, Nom. A R, Min. A R, Max.
-40 316181 301183 331179
-30
-20
-10
0
169149
94143
54308
32014
162304
90938
52781
31290
175994
97349
55836
32738
19691
12474
10000
8080
5372
3661
2536
1794
1290
19346
12315
8900
7977
5282
3585
2474
1744
1250
20036
12633
10100
8182
5462
3737
2598
1844
1330
941.8
697.2
524.9
399.6
308.4
271.3
909.8
671.3
504.0
382.6
294.6
258.6
974.0
723.1
545.9
416.6
322.3
283.9
Action
Yes — Refer to the Gateway Module
Electrical Test procedure.
No — Repair circuit wiring.
92 Blue Bird Vision Service Manual
ROUSH CleanTech Blue Bird Vision Liquid Propane Autogas (LPA)
Service Manual
Tank Pressure Temperature Sensor
Electrical Check
For harness and connector layout diagrams and system electrical schematics, refer to
Wiring Diagrams and Electrical Schematics.
CONNECTORS
C1 40
32
30 31
PBT/ASA-GF20
18
1 2
3
44
45
29
A1
46
15
16 17
19 21 25
100476a
Figure 59 — Underhood Harness Connectors
C3
1
2 4
3
TPTS CONNECTOR
FACEVIEW
POWER
TERMINAL
(VOLTAGE IN)
PRESSURE
OUTPUT
TERMINAL
(VOLTAGE OUT)
4
TEMPERATURE
OUTPUT
TERMINAL
(VOLTAGE OUT)
1
TPTS SENSOR PINOUT
GROUND
TERMINAL
(GROUND)
100480a
Figure 60 — Fuel Tank Connectors
PROCEDURE
Step Procedure
1
Unplug the connector 3 (underhood harness) to the TPTS.
2
Check resistance of the tank pressure temperature sensor (TPTS).
a. With vehicle at ambient room temperature
(20–30°C, 68–86°F) and using a multimeter, measure resistance across the TPTS terminals (between pin-1 and pin-3).
b. Is the resistance value between 8K–12K ohms?
Action
Go to Step 2.
Yes — Go to Step 3.
No — Replace the IPTS.
Blue Bird Vision Service Manual 93
Step Procedure
3
Check circuit continuity between the TPTS and the Gateway Module.
a. Using a multimeter, check continuity in the underhood harness between:
• Pin-3, connector C2 and pin-40, connector C1
• Pin-6, connector C2 and pin-21, connector C1
• Pin-5, connector C2 and pin-19, connector C1
• Pin-4, connector C2 and pin-25, connector C1 b. Is there good continuity in the circuits?
Fuel Pump Electrical Test
ROUSH CleanTech Blue Bird Vision Liquid Propane Autogas (LPA)
Service Manual
Action
Yes — Refer to the Gateway Module
Electrical Test procedure.
No — Repair circuit wiring.
For harness and connector layout diagrams and system electrical schematics, refer to
Wiring Diagrams and Electrical Schematics.
CONNECTORS
C9 C11
4 1
8
100451a
5
Figure 61 — Rear Frame Harness Connector
A
1 2
B
4A 4B
A
B
100076a
Figure 62 — In-Tank Harness Connectors
94 Blue Bird Vision Service Manual
ROUSH CleanTech Blue Bird Vision Liquid Propane Autogas (LPA)
Service Manual
Step Procedure
1
Check fuel pump circuit continuity.
a. Unplug the EFPR connector C11 for fuel pump 1. Check fuel pump circuit continuity.
b. Using a multimeter, measure resistance between pin-5 and pin-8.
c. Is resistance between 0.4–1.0 ohm?
2
Check continuity for each fuel pump.
a. Unplug connectors 1 and 4 of in-tank harness.
b. Check continuity across connector 1 pins
A and B. Is the resistance between 0.4-1.0 ohms?
c. Check continuity across connector 4 pins
A and B. Is the resistance between 0.4-1.0 ohms?
3
Check for voltage and ground to fuel pump connectors.
4 a. Unplug both fuel pump connects and check for B+ voltage across pins a and b.
b. If voltage is present at both fuel pumps?
Verify continuity between fuel pump connectors and EFPRs.
a. Check continuity between EFPR 1 pin-5 and fuel pump 1 pin-a.
b. Check for continuity between EFPR 1 pin-8 and fuel pump 1 pin-b.
c. Check continuity between EFPR 2 pin-5 and fuel pump 2 pin-a.
d. Check for continuity between EFPR 2 pin-8 and fuel pump 2 pin-b.
e. Is continuity present on all 4 circuits?
Action
Yes — Go to Step 3.
No — Go to Step 2.
Yes — Go to Step 3.
No — Replace fuel pump assembly.
Yes — Replace fuel pump assembly.
No — Go to Step 4.
Yes — Go to Fuel Pump Control
Module Electrical Test.
No — Repair circuit wiring (refer to Blue
Bird wiring schematic).
Blue Bird Vision Service Manual 95
ROUSH CleanTech Blue Bird Vision Liquid Propane Autogas (LPA)
Service Manual
Fuel Pump Control Module Electrical
Continuity Test
PROCEDURE
Step Procedure Action
For FPCM functional testing and diagnostic trouble codes, refer to the Ford Powertrain Control/
Emissions Diagnosis Service Manual at www.motorcraft.com.
Verify the following:
1
Check FPCM circuit continuity to Blue Bird fuse box. Refer to the Blue Bird Service Manual for
circuit information. a. Using a multimeter, check VPWR (V+) circuit to fuse box. b. Is there good continuity in the circuit?
2
Check fuse for FPCM at Blue Bird fuse box.
Refer to the Blue Bird Service Manual for fuse
box and circuit information.
Yes — Go to Step 2.
No — Repair circuit wiring.
Yes — Replace fuse with the correct value fuse.
No — Go to Step 4. a. Check the fuse at the fuse box. b. Is the fuse blown?
3
Check for continuity in the circuits.
a. Check for continuity in the circuits. b. Is there good continuity in the circuits?
Yes — Refer to Ford Powertrain
Control/Emissions Diagnosis Service
Manual for functional testing of the
FPCM.
No — Repair circuit wiring.
Gateway Module Electrical Test
CONNECTORS
31
30
1
31
2
32
PBT/ASA-GF20
18
3
44
29
45
A1
46
15
16 17
2
Figure 63 — Underhood Harness Connectors
PROCEDURE
100124a
Step Procedure
1
Disconnect the Gateway Module connector.
Refer to the BlueBird Service Manual for circuit information.
Action
Go to Step 2.
96 Blue Bird Vision Service Manual
ROUSH CleanTech Blue Bird Vision Liquid Propane Autogas (LPA)
Service Manual
2
Check for battery voltage (B+) to the Gateway
Module.
a. Using a multimeter, check for B+ voltage at cavity 2 of the SRM connector. Use the body as a reference ground.
b. Is there voltage (B+)?
3
Check for continuity in the circuits.
a. Check circuit continuity between cavity 2 of the Gateway Module connector and the Blue
Bird fuse box. Refer to the Blue Bird Service
Manual for fuse box and circuit information.
b. Is there good continuity in the circuit?
4 Check Gateway Module fuse at fuse box. a. Check condition of Gateway Module power fuse in the Blue Bird fuse box. Refer to the Blue Bird Service Manual for circuit information. b. Is fuse blown?
5
Check the Gateway Module ground circuit for continuity.
a. Using a multimeter, check ground at cavity 31 of the Gateway Module connector. Use the body as a reference ground.
b. Is there good continuity?
6
Check CAN wiring for Gateway Module circuit continuity. Refer to the Blue Bird Service Manual for circuit information.
a. Check Gateway Module for continuity.
b. Is there good continuity in the circuits?
Yes — Go to Step 5.
No — Go to Step 3.
Yes — Go to Step 4.
No — Repair circuit wiring.
Yes — Replace fuse.
No — Go to Step 5.
Yes — Go to Step 6.
No — Repair circuit wiring.
Yes — Call ROUSH Technical Support at 800-59-ROUSH.
No — Repair circuit wiring.
Fuel Level Indication Check
The ROUSH LPA fuel level indication system differs from the gasoline system because the fuel level sender is not wired directly to the instrument cluster. Instead, the fuel level sender is wired to the Gateway Module (Gateway Module), which reads the fuel level and transmits the signal to the instrument cluster via the controller area network
(CAN) bus.
Symptom Cause/Action to be taken
P-code?
There is a circuit fault that has been identified by the PCM. Initially follow the Ford service manual, whenever a circuit check is called for.
Doesn’t read full after a fill?
This could be the result of either a fuel level indicator fault or an overflow protection device (OPD) valve triggering prematurely. Go to Short Fill diagnostic test.
Blue Bird Vision Service Manual 97
ROUSH CleanTech Blue Bird Vision Liquid Propane Autogas (LPA)
Service Manual
Fuel Level Sender (FLS) Electrical Check
For harness and connector layout diagrams and system electrical schematics, refer to
Wiring Diagrams and Electrical Schematics.
CONNECTORS
C1
30
1
31
2
32
PBT/ASA-GF20
18
3
44
29
45
A1
46
15
16 17
100455a
Figure 64 — Underhood Harness Connectors
C2
100479a
Figure 65 — Tank Harness Connectors
PROCEDURE
Step Procedure
When performing the following continuity test, make sure to verify off-set of DVOM being used.
When you touch the leads together, a value will be present, this could be 0.1 or greater.
Remember to deduct this value from reading for actual resistance value.
All continuity (ohms) readings should be less than
0.5 ohms.
1
If any Gateway Module, IPTS, TPTS DTCs present go to Pin Point test and resolve those faults prior to diagnosing the Fuel Level Sender fault.
Action
Example — DVOM off-set value is 0.2 ohms. When a circuit reading is taken and the value is 0.6 ohms, you would subtract the 0.2 from 0.6 for an actual value of 0.4 ohms.
Yes — Go to Gateway Module or TPTS
PPT.
2
Check for 5v vref present at pin-A harness side of FLS connector.
No — Go to Step 2.
Yes — Go to Step 4.
No — Go to Step 3.
98 Blue Bird Vision Service Manual
ROUSH CleanTech Blue Bird Vision Liquid Propane Autogas (LPA)
Service Manual
Step Procedure
3
Check for continuity of harness for 5v vref circuit and ground circuit of Fuel Level Sender.
a. Check for continuity from FLS pin-A frame side harness to pin-4 of Gateway Module connector: Continuity present - Yes, go to Step
3b.
Action
Yes — Go to Step 4.
No — Locate and repair open circuit or replace harness. b. Check for continuity from FLS pin-C frame harness at FLS and pin-40 of Gateway
Module connector.
c. Is there good continuity in each circuit?
4
Perform output voltage check using a universal probe on pin-B at FLS connector.
a. With harness fully connected and KOEO, place the universal probe into pin-B of sending unit connector and monitor for voltage.
b. Is voltage present?
5
Perform sending unit range voltage test.
a. Remove the sending unit electronic portion by removing the two (2) phillips screws securing it and use a magnet to move sender from full to empty: Make sure the voltage is within 0-5v.
b. Was there any concern with voltage range output test?
Yes — Go to Step 5.
No — Replace electronic portion of sending unit.
Yes — Replace electronic portion of sending unit, clear faults and test.
No — Refer to the Fuel Tank Draining
Procedure and In-Tank Sending Unit
Replacement Procedure to replace the in-tank sending unit.
Manual Solenoid Activation Procedure
For harness and connector layout diagrams and system electrical schematics, refer to
Wiring Diagrams and Electrical Schematics.
CONNECTORS
C1
33
46
30 31
32
PBT/ASA-GF20
18
1 2
3
44
29
45
A1
46
15
16 17
17
100351a
Figure 66 — Connector End View
Blue Bird Vision Service Manual 99
BLEED SOLENOID
ROUSH CleanTech Blue Bird Vision Liquid Propane Autogas (LPA)
Service Manual
SUPPLY SOLENOID
BLEED/
VAPOR
PORT
RETURN
PORT
Figure 67 — FRPCM Solenoid Locations
SUPPLY
PORT
100458a
Step Procedure
1
Disconnect the Gateway Module (Gateway
Module) wire harness connector at the Gateway
Module.
2
Energize the individual solenoids on the FRPCM by providing a ground to the following pins in the Gateway Module connector:
• Pin 33 – Bleed Solenoid
• Pin 32 – Supply Solenoid
Action
—
—
100 Blue Bird Vision Service Manual
Copyright © 2016 ROUSH CleanTech, LLC. All Rights Reserved.
advertisement
* Your assessment is very important for improving the workof artificial intelligence, which forms the content of this project
Related manuals
advertisement
Table of contents
- 5 Foreward
- 5 Introduction
- 5 LPA System Overview
- 5 ROUSH CleanTech Technical Assistance
- 6 Propane
- 6 Fill Stations
- 6 Safety Information
- 6 Alert Messages
- 7 Installation, Garaging and Training
- 7 Purging and Venting (Tanks and Lines)
- 7 Description and Operation
- 7 LPA Fuel System Overview
- 12 Start Sequence
- 12 Stage
- 12 Description
- 13 General Propane Tank Filling Procedure
- 13 Filling Overview
- 13 Vehicle Filling Procedure
- 15 Propane Fuel Tank
- 16 Device (OPD)
- 16 Fuel Pumps
- 16 In-Tank Fuel Filters
- 16 Tank Pressure Temperature Sensor
- 16 Fuel Level Sender
- 17 Tank Bleeder Valve/Fixed Liquid Level Gauge
- 17 Pressure Relief Valve
- 17 Tank Supply Circuit Assembly
- 17 Tank Solenoid Valve
- 17 Manual Shutoff Valve
- 18 Excess Flow Valve (XFV)
- 18 Fuel Return Valve
- 18 Fuel Transfer Lines
- 18 Fuel Rail Pressure Control Module (FRPCM)
- 19 Injection Pressure Temperature Sensor
- 19 Vapor Canister Assembly
- 19 Vapor Lines
- 19 Fuel Rail Assemblies
- 21 Remote Fill Valve
- 21 Fill Line
- 21 Fill Filter
- 21 Remote Bleeder Valve
- 21 Bleeder Hose
- 21 Electronic Fuel Pump Relay (EFPR)
- 21 LPA Gateway Module
- 21 Gateway Function
- 22 LPA Interface Function
- 22 Service Preparation
- 22 Alert Messages
- 22 Manual Fuel Shutoff
- 22 Opening the Manual Fuel Shutoff
- 23 Fuel Tank Pressure Relief
- 23 and Priming Procedures
- 23 Fuel Line Purging
- 24 Fuel Tank Draining Procedure
- 25 Using In-Tank Pumps
- 26 Fuel Tank Purging Procedure
- 26 Fuel System Priming Procedure
- 27 Fuel System Flow Diagrams
- 30 Component Servicing
- 30 Special Tools
- 30 Quick Disconnect Tools
- 30 Electronic Leak Detector
- 30 Flare Tower
- 30 Fuel Tank
- 33 Prevention Device (OPD)
- 34 Tank Bleeder Valve
- 34 Fuel Tank Pressure Relief Valve
- 35 Tank Supply Circuit Assembly
- 36 Fuel Tank Return Valve
- 37 Solenoid Coil Replacement
- 37 Fuel Pump Assembly (In-Tank)
- 37 Tank Pressure Temperature Sensor
- 39 of the LH cylinder)
- 40 Fuel Tank Wiring
- 42 Remote Mounted Fuel Fill Valve
- 42 Remote Fuel Fill Line(s)
- 43 In-Line Fuel Filters
- 43 Remote Mounted Bleeder Valve
- 44 Remote Bleeder Line
- 44 Fuel Rail Pressure Control Module (FRPCM)
- 46 Fuel Supply and Return Line
- 47 Fuel Rail
- 49 Fuel Injector
- 49 Injection Pressure Temperature Sensor
- 50 Vapor Canister Assembly
- 51 Gateway Module
- 51 System Maintenance
- 51 LPA Fuel System
- 51 Fuel Tank
- 52 Fuel Filters
- 52 Fuel Supply and Return Line
- 52 Fuel Rail Pressure Control Module
- 52 Fuel Rails and Injectors
- 52 Electrical System
- 53 Torque Chart
- 54 ROUSH CleanTech Technical Assistance
- 55 Special Conditions
- 55 Refueling
- 55 Troubleshooting – Refueling
- 57 Maintenance and Specifications
- 57 Use and Maintenance
- 57 Service Recommendations
- 58 Refill Capacity
- 58 Jump Starting
- 58 Manual Shutoff Valve
- 58 Storing the Vehicle
- 58 Repainting (Vehicle or Tank)
- 60 (DTC) — LPA-FUELED VEHICLES
- 60 About Diagnostic Trouble Codes
- 60 System and Diagnostic Terminology
- 61 Diagnostic Trouble Code List
- 62 Flow Control Solenoid (FCS)
- 62 Bleed Solenoid
- 63 Tank Solenoid
- 64 Solenoid and Wiring
- 65 Gateway Module, CAN Bus Circuit Wiring
- 65 Fuel System
- 67 Heated Exhaust Gas Oxygen Sensor
- 67 Electronic Fuel Pump Relay (A/B)
- 70 Integrated Pressure Temperature Sensor
- 73 Fuel Level Sensor (FLS)
- 74 Other
- 75 LPA-FUELED VEHICLES
- 75 General Information
- 76 No Fill
- 77 Short Fill
- 79 Slow Fill
- 82 Over Fill
- 84 Engine Does Not Crank
- 84 Engine Cranks, No Start
- 86 Engine Stumble, Stall, Rough Idle
- 88 Excess Flow Valve (XFV) Check
- 89 Maximum Pressure Check
- 89 Step Procedure Action
- 90 Fuel System Fails to Bleed
- 91 Tank Solenoid Electrical Check
- 93 Module Electrical Check
- 95 Sensor Electrical Check
- 96 IPTS Temperature/Resistance Chart
- 97 Sensor Electrical Check
- 98 Fuel Pump Electrical Test
- 100 Electrical Continuity Test
- 100 Gateway Module Electrical Test
- 101 Fuel Level Indication Check
- 102 Fuel Level Sender (FLS) Electrical Check
- 103 Manual Solenoid Activation Procedure