Master-force CLIPPED HEAD FRAMING NAILER Operator's Manual
Add to my manuals
16 Pages
Master-force ANGLED FINISH NAILER is a versatile tool designed for precise and efficient fastening in various woodworking projects. Its angled design allows for easy access to tight corners and hard-to-reach areas, making it ideal for intricate trim work, cabinetry, and furniture making. The tool features a lightweight and compact body for better maneuverability and reduced user fatigue during prolonged use.
advertisement
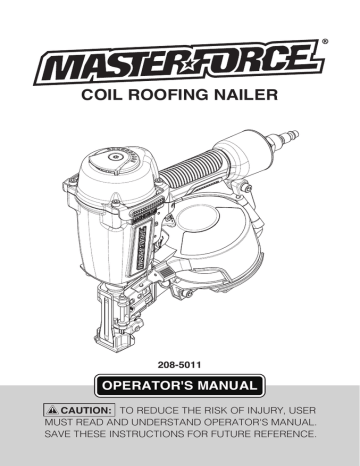
COIL ROOFING NAILER
208-5011
OPERATOR'S MANUAL
CAUTION: TO REDUCE THE RISK OF INJURY, USER
MUST READ AND UNDERSTAND OPERATOR'S MANUAL.
SAVE THESE INSTRUCTIONS FOR FUTURE REFERENCE.
TABLE OF CONTENTS
Safety Instructions .......................................................... Page 2
Air Supply: Fittings, Hoses, Filters, Air Consumption, Regulators,
Operation Pressure, Setting Correct Pressure ............... Page 5
Production specifications ................................................ Page 6
Depth Adjustment ........................................................... Page 7
Loading the Tool ............................................................. Page 8
Tool Operation ................................................................ Page 9
Maintaining the Pneumatic Tool ..................................... Page 11
Trouble Shooting ............................................................ Page 12
Page 1
SAFETY INSTRUCTIONS
The purpose of safety symbols is to attract our attention to possible dangers. The safety symbols, and the explanations with them, deserve your careful attention and understanding.
The symbol warnings do not by themselves eliminate any danger. The instructions and warnings they give are no substitutes for proper accidents prevention measures.
Be sure to read and understand all safety instruction in this manual, including all safety alert symbols such as "DANGER", "WARNING" and
"CAUTION", before using this pneumatic tool.
SYMBOL SAFETY ALERT: Indicates DANGER, WARNING, or CAUTION. May be used in conjunction with other symbols or photographs.
Failure to obey this safety warning WILL result in death or serious injury to yourself or others. Always follow the safety precaution to reduce the risk of fire and personal injury.
Failure to obey this safety warning CAN result in death or serious injury to yourself or others. Always follow the safety precaution to reduce the risk of fire and personal injury.
Failure to obey this safety warning MAY result in personal injury to yourself or others, or property damage. Always follow the safety precaution to reduce the risk of fire and personal injury.
Page 2
SAFETY INSTRUCTIONS
1. EYE PROTECTION which conforms to
ANSI specifications and provides protection against flying particles both from the FRONT and SIDE should ALWAYS be worn by the operator and others in the work area when connecting to air supply, loading, operating or servicing this tool. Eye protection is required to guard against flying fasteners and debris, which could cause severe eye injury.
2. The employer and/or user must ensure that proper eye protection is worn. Eye protection equipment must conform to the requirements of the American National
Standards Institute, ANSI Z87.1 and provide both frontal and side protection.
3. NOTE: Non-side shielded spectacles and face shields alone do not provide adequate protection.
Additional Safety
Protection will be required in some environments. For example, the working area may include exposure to noise level which can lead to hearing damage. The employer and user must ensure that any necessary hearing protection is provided and used by the operator and others in the work area. Some environments will require the use of head protection equipment. When required, the employer and user must ensure that head protection conforming to ANSI Z89.1 is used.
4.
Dress properly. Do not wear loose clothing or jewelry. Contain long hair. Keep your hair, clothing, and gloves away from moving parts.
5. Keep fingers away from trigger when not driving fasteners to avoid accidental firing.
6. Do not overreach. Keep proper footing
Page 3 and balance at all times. Proper footing and balance enables better control of the tool in unexpected situations.
6. Do not use on a ladder or unstable support. Stable footing on a solid surface enables better control of the tool in unexpected situations.
7. Tool service must be performed only by qualified repair personnel. Service or maintenance performed by unqualified personnel may result in a risk of injury.
8. When servicing a tool, use only identical replacement parts. Use of unauthorized parts may create a risk of injury.
9.
Know your pneumatic tool. Read operator's manual carefully. Learn its applications and limitations, as well as the specific potential hazards related to this tool. Following this rule will reduce the risk of electric shock, fire, or serious injury.
10. Always wear safety glasses with side shields. Everyday glasses have only impact resistant lenses. They are NOT safety glasses. Following this rule will reduce the risk of eye injury.
11. Protect your lungs. Wear a face or dust mask if the operation is dusty. Following this rule will reduce the risk of serious personal injury.
12. Protect your hearing. Wear hearing protection during extended periods of operation. Following this rule will reduce the risk of serious personal injury.
13.
Make sure the hose is free of obstructions or snags. Entangled or snarled hoses can cause loss of balance or footing and may become damaged.
14. Use the tool only for its intended use.
Do not discharge fasteners into open air.
15. Use the MENARDS pneumatic tool only for the purpose for which it was designed.
16. Use only the fasteners recommended for this tool. Use of the wrong fasteners could result in poor fastener feeding, jammed fasteners, and nails leaving the tool at erratic angles. If fasteners are not feeding smoothly and properly, discontinue their use immediately. Jammed and
SAFETY INSTRUCTIONS
improperly feeding fasteners could result in serious personal injury.
17. Never use this tool in a manner that could cause a fastener to be directed toward the user or others in the work area.
Do not use the tool as a hammer.
18.
19. Always be aware that misuse and improper handling of this tool can cause injury to yourself and others.
20. Never leave a tool unattended with the air hose attached.
21. Do not operate this tool if it does not contain a legible warning label.
22. Do not continue to use a tool that leaks air or does not function properly.
1. Do not use supply sources which can potentially exceed 200 P.S.I. as tool may burst, possibly causing injury.
2. The connector on the tool must not hold pressure when air supply is disconnected. If a wrong fitting is used, the tool can remain charged with air after disconnecting and thus will be able to drive a fastener even after the air line is disconnected possibly causing injury.
3. Do not pull trigger or depress contact arm while connected to the air supply as the tool may cycle, possibly causing injury.
4. Always disconnect air supply: 1.) Before making adjustments; 2.) When servicing the tool; 3.) When clearing a jam; 4.) When tool is not in use; 5.) When moving to a different work area, as accidental actuation may occur, possibly causing injury.
When loading tool: 1.) Never place a hand or any other part of the body in fastener discharge area of tool; 2.) Never point tool at anyone; 3.) Do not pull the trigger or depress the trip as accidental actuation may occur, possibly causing injury.
1. Always handle the tool with care: 1.)
Never engage in horseplay; 2.) Never pull the trigger unless nose is directed toward the work; 3.) Keep others a safe distance from the tool while tool is in operation as accidental actuation may occur, possibly causing injury.
2. The operator must not hold the trigger pulled on contact arm tools except during fastening operation as serious injury could result if the trip accidentally contacted someone or something, causing the tool to cycle.
3. Keep hands and body away from the discharge area of the tool. A contact arm tool may bounce from the recoil of driving a fastener and an unwanted second fastener may be driven possibly causing injury.
4. Check operation of the contact arm mechanism frequently. Do not use the tool if the arm is not working correctly as accidental driving of a fastener may result.
Do not interfere with the proper operation of the contact arm mechanism.
5. Do not drive fasteners on top of other fasteners or with the tool at an overly steep angle as this may cause deflection of fasteners which could cause injury.
6. Do not drive fasteners close to the edge of the work piece as the wood may split, allowing the fastener to be deflected possibly causing injury.
7. Do not point the tool toward yourself or anyone whether it contains fasteners or not.
8.
Always ensure that the workpiece contact is fully positioned above the workpiece. Positioning the workpiece contact on ly partially above the workpiece could cause the fastener to miss the workpiece completely and result in serious personal injury.
Page 4
Do not use oxygen, combustible gases, or bottled gases as a power source for this tool as tool may explode, possibly causing injury. Keep the tool pointed away from yourself and others when connecting air source.
A pressure regulator with an operating pressure of 0 - 125 p.s.i. (0 - 8.79 kg/cm2) is required to control the operating pressure for safe operation of this tool. Do not connect this tool to air pressure which can potentially exceed 200 p.s.i. (14 kg/cm2) as tool may fracture or burst, possibly causing injury.
Install a male plug on the tool which is free flowing and which will release air pressure from the tool when disconnected from the supply source.
Air hoses should have a minimum of 150 p.s.i. (10.6 kg/cm2) working pressure rating or
150 percent of the maximum pressure that could be produced in the air system. The supply hose should contain a fitting that will provide "quick disconnecting" from the male plug on the tool.
Do not exceed recommended maximum operating pressure wear will be greatly increased. The air supply must be capable maintaining the operating pressure at the tool. Pressure drops in supply can reduce the tool's driving power. Refer to
SPECIFICATIONS" for setting the correct operating pressure tool.
Use only clean regulated compressed air as a power source for this tool. NEVER USE
OXYGEN, COMBUSTIBLE GASES, OR
BOTTLED GASES, AS A POWER SOURCE
FOR THIS TOOL AS TOOL MAY EXPLODE.
Dirt and water in the air supply are major causes of wear in pneumatic tools. A filter will help to get the best performance and minimum wear from the tool. The filter must have adequate flow capacity for the specific installation. The filter has to be kept clean to be effective in providing clean compressed air to the tool. Consult the manufacturer's instructions on proper maintenance of your filter. A dirty and clogged filter will cause a pressure drop which will reduce the tool's performance.
Page 5
DRIVING POWER . . . . . . . . . . . . . . . . . . . . . . . . . . . . . . . . . . . . . . . . . . . . . . . . . . . . . 455 in.lbs
FASTENER TYPE . . . . . . . . . . . . . . . . . . . . . . . . . . . . . . . . . . . . . . . . . . 0.120" ROOFING NAIL
FASTENER RANGE . . . . . . . . . . . . . . . . . . . . . . . . . . . . . . . . . . . . . . . . . . . . . . . . . 3/4" to 1 3/4"
MAGAZINE CAPACITY. . . . . . . . . . . . . . . . . . . . . . . . . . . . . . . . . . . . . . . . . . . . . . . . . 120 NAILS
WEIGHT. . . . . . . . . . . . . . . . . . . . . . . . . . . . . . . . . . . . . . . . . . . . . . . . . . . . . . . . . . . . . . . . 5 LBS
OPERATION PRESSURE . . . . . . . . . . . . . . . . . . . . . . . . . . . . . . . . . . . . . . . . . . . . 70 to 120 PSI
AIR INLET. . . . . . . . . . . . . . . . . . . . . . . . . . . . . . . . . . . . . . . . . . . . . . . . . . . . . . . . . . . . . 1/4" NPT
TOOL-FREE
MULTI-DIRECTIONAL
EXHAUST
LIGHT WEIGHT
MAGNESIUM
HOUSING
SWIVEL
CONNECTOR
NAIL GUIDE
CARBIDE
TIPPED NOSE
PIECE
SELECTABLE
TRIGGER
TOOL-FREE DRIVE
DEPTH ADJUST
TOOL-FREE MULTI-DIRECTIONAL EXHAUST
The tool-free exhaust can be adjusted to any positions depending on operator preference.
SELECTABLE TRIGGER
The selectable trigger lets the operator choose between from Contact Actuation and Single
Sequential Actuation.
LIGHT WEIGHT MAGNESIUM HOUSING
The light weight magnesium housing helps reduce work fatigue.
TOOL-FREE DRIVE DEPTH ADJUST
The tool-free depth adjust lets the operator select precise driving depth of the fastener.
CARBIDE TIPPED NOSE PIECE
The carbide tipped nose piece can prevent from wearing when driving nails.
SWIVEL CONNECTOR
The swivel connector helps prevent hose tangles.
NAIL GUIDE
Patented nail guide to ensure the nails are always driven straight.
Page 6
DEPTH ADJUSTMENT
Always disconnect air supply: 1. Before making adjustments; 2.
When servicing the tool; 3. When clearing a jam; 4. When tool is not in use; 5. When moving to a different work area, as accidental actuation may occur, possibly causing injury.
The depth adjustment feature provides close control of the fastener drive depth; from flush with the work surface to shallow or deep countersink. First, set the air pressure for consistent drive in the specific work. Then use the depth adjustment to give the desired depth of drive.
1. Disconnect the tool from the air supply.
2. Turn the depth selector left or right to change the driving depth.
3. Reconnect the tool to the air supply.
4. Drive a test nail after each adjustment until the desired depth is set.
Page 7
LOADING
• Never place a hand or any other part of the body in nail discharge area of tool while the air supply is connected.
• Never point the tool at anyone else.
• Never engage in horseplay.
• Never pull the trigger unless nose is directed at the work.
• Always handle the tool with care.
• Do not pull the trigger or depress the trip mechanism while loading the tool.
1. Push latch, open feeder cover and magazine cover.
2. Remove retainer from a coil of roofing nails, and position coil onto nail support with the second nail in the feed fingers.
3. Close magazine cover, close latch and feeder cover.
Page 8
TOOL OPERATION
EYE PROTECTION which conforms to ANSI specifications and provides protection against flying particles both from the FRONT and SIDE should ALWAYS be worn by the operator and others in the work area when connecting to air supply, loading, operating or servicing this tool. Eye protection is required to guard against flying fasteners and debris, which could cause severe eye injury.
The employer and/or user must ensure that proper eye protection is worn. Eye protection equipment must conform to the requirements of the American National
Standards Institute, ANSI Z87.1 and provide both frontal and side protection.
NOTE: Non-side shielded spectacles and face shields alone do not provide adequate protection.
Additional Safety Protection will be required in some environments. For example, the working area may include exposure to noise level which can lead to hearing damage. The employer and user must ensure that any necessary hearing protection is provided and used by the operator and others in the work area. Some environments will require the use of head protection equipment. When required, the employer and user must ensure that head protection conforming to ANSI Z89.1 is used.
I. READ AND UNDERSTAND THE WARNINGS CONTAINED IN THIS MANUAL.
II. REFER TO "TOOL SPECIFICATIONS" IN THIS MANUAL TO IDENTIFY THE OPERATING SYSTEM ON
YOUR TOOL.
OPERATION
A. SINGLE FASTENER PLACEMENT: To operate the tool in this manner, first position the contact trip on the
work surface, WITHOUT PULLING THE TRIGGER. Depress the contact trip until the nose touches the work
surface and then pull the trigger to drive a fastener. Do not press the tool against the work with extra force.
Instead, allow the tool to recoil off the work surface to avoid a second unwanted fastener. Remove your
finger from the trigger after each operation.
B. RAPID FASTENER OPERATION: To operate the tool in this manner, hold the tool with the contact trip
pointing towards but not touching the work surface. Pull the trigger and then tap the contact trip against the
work surface using a bouncing motion. Each depression of the contact trip will cause a fastener to be driven.
The operator must not hold the trigger pulled on contact trip tools except during fastening operation, as serious injury could result if the trip accidentally contacted someone or something, causing the tool to cycle.
Keep hands and body away from the discharge area of the tool. A contact trip tool may bounce from the recoil of driving a fastener and an unwanted second fastener may be driven, possibly causing injury.
The SEQUENTIAL TRIP MODEL contains a contact trip that operates in conjunction with the trigger to drive a fastener. To operate a sequential trip tool, first position the contact trip on the work surface WITHOUT PULLING
THE TRIGGER. Depress the contact trip and then pull the trigger to drive a fastener. As long as the contact trip is contacting the work and is held depressed, the tool will drive a fastener each time the trigger is depressed.
If the contact trip is allowed to leave the work surface, the sequence described above must be repeated to drive another fastener.
Page 9
Sequential Trip Operation Contact Trip Operation
TOOL OPERATION CHECK
Keep the tool away from yourself and others when connecting air source.
Remove all fasteners from tool before performing tool operation check.To reduce the risk of injury to yourself and others, check the tool before beginning work each day or if the tool is dropped, receive a sharp blow, been run over, etc. If the tool does not work as it should, contact Menards service center immediately.
1. CONTACT TRIP OPERATION:
A. With finger off the trigger, press the contact trip against the work surface.
THE TOOL MUST NOT CYCLE.
B. Hold the tool off the work surface, and pull the trigger.
THE TOOL MUST NOT CYCLE.
C. With the tool off the work surface, pull the trigger. Press the contact trip against the work surface.
THE TOOL MUST CYCLE.
D. Without touching the trigger, press the contact trip against the work surface, then pull the trigger.
THE TOOL MUST CYCLE.
2. SEQUENTIAL TRIP OPERATION:
A. Press the contact trip against the work surface, without touching the trigger.
THE TOOL MUST NOT CYCLE.
B. Hold the tool off the work surface and pull the trigger.
THE TOOL MUST NOT CYCLE.
Release the trigger. The trigger must return to the trigger stop on the frame.
C. Pull the trigger and press the contact trip against the work surface.
THE TOOL MUST NOT CYCLE.
D. With finger off the trigger, press the contact trip against the work surface. Pull the trigger.
THE TOOL MUST CYCLE.
IN ADDITION TO THE OTHER WARNINGS CONTAINED IN THIS MANUAL
OBSERVE THE FOLLOWING FOR SAFE OPERATION
• Use the Masterforce pneumatic tool only for the purpose for which it was designed.
• Never use this tool in a manner that could cause a fastener to be directed toward the user or others in the work area.
• Do not use the tool as a hammer.
• Always carry the tool by the handle. Never carry the tool by the air hose.
• Always be aware that misuse and improper handling of this tool can cause injury to yourself and others.
• Never clamp or tape the trigger or contact trip in an actuated position.
• Never leave a tool unattended with the air hose attached.
• Do not operate this tool if it does not contain a legible WARNING LABEL.
• Do not continue to use a tool that leaks air or does not function properly.
• Notify Menards service center if your tool continues to experience functional problems.
Page 10
Do not store tools in a cold weather environment to prevent frost or ice formation on the tools operating valves and mechanisms that could cause too failure.
could cause
TROUBLE SHOOTING
PROBLEM
Frame/nose leaks air
CAUSE CORRECTION
Loose nose screws . . . . . . . . . . . . . . . .Tighten and recheck
Frame/cap leaks air
Failure to cycle
O-ring or Gasket is cut or cracked . . .Replace O-ring or gasket
Bumper cracked/worn . . . . . . . . . . . . .Replace bumper
Damaged gasket or seal . . . . . . . . . . .Replace gasket or seal
Loose cap screws . . . . . . . . . . . . . . . .Tighten and recheck
Air supply restriction . . . . . . . . . . . . . . .Check air supply equipment
Tool dry, lack of lubrication . . . . . . . . .Use Lubricant
Worn head valve O-rings . . . . . . . . . . .Replace O-rings
Head valve stuck in cap . . . . . . . . . . . .Disassemble/Check/Lubricate
Lack of power; slow to cycle Tool dry, lacks lubrication . . . . . . . . . . .Use Lubricant
O-rings/seals cut or cracked . . . . . . . .Replace O-rings/seals
Trigger assembly worn/leaks . . . . . . . .Replace trigger assembly
Dirt/tar build up on driver . . . . . . . . . . .Disassemble nose/driver to clean
Cylinder sleeve not seated correctly on bottom bumper . . . . . . . . . . . . . . . .Disassemble to correct
Head valve dry . . . . . . . . . . . . . . . . . . .Disassemble/lubricate
Air pressure too low . . . . . . . . . . . . . . .Check air supply equipment
Skipping fasteners; intermittent feed Worn bumper . . . . . . . . . . . . . . . . . . . .Replace bumper
Tar/dirt in driver channel . . . . . . . . . . . .Disassemble and clean nose and driver
Air restriction/inadequate air flow through quick disconnect socket and plug . . . .Replace quick disconnect fittings
Worn piston O-ring . . . . . . . . . . . . . . . .Replace O-ring, check driver
Tool dry, lacks lubrication . . . . . . . . . . .Use Lubricant
Fasteners jam in tool
Low air pressure . . . . . . . . . . . . . . . . . .Check air supply system to tool
Loose magazine nose screws . . . . . . .Tighten all screws
Fasteners too short for tool . . . . . . . . .Use only recommended fasteners
Bent fasteners . . . . . . . . . . . . . . . . . . .Discontinue using these fasteners
Wrong size fasteners . . . . . . . . . . . . . .Use only recommended fasteners
Leaking head cap gasket . . . . . . . . . . .Tighten screws/replace gasket/ O-ring
Trigger valve O-ring cut/worn . . . . . . . .Replace O-ring
Broken/chipped driver . . . . . . . . . . . . .Replace driver (check piston O-ring)
Dry/dirty magazine . . . . . . . . . . . . . . . .Clean/lubricate use Lubricant
Wrong size fasteners . . . . . . . . . . . . . .Use only recommended fasteners
Bent fasteners . . . . . . . . . . . . . . . . . . .Discontinue using these fasteners
Loose magazine/nose screws . . . . . . .Tighten all screws
Broken/chipped driver . . . . . . . . . . . . .Replace driver
Page 12
Page 13
NOTES
COIL ROOFING NAILER
COIL ROOFING NAILER
WARRANTY
90-DAY MONEY BACK GUARANTEE
This MASTERFORCE® brand power tool carries our 90-DAY Money Back Guarantee. If you are not completely satisfied with your MASTERFORCE® brand power tool for any reason within ninety (90) days from the date of purchase, return the tool with your original receipt to any
MENARDS® retail store, and we will provide you a refund - no questions asked.
3-YEAR LIMITED WARRANTY
This MASTERFORCE® brand power tool carries our famous No Hassle 3-Year Limited
Warranty to the original purchaser. If, during normal use, this MASTERFORCE® power tool breaks or fails due to a defect in material or workmanship within three (3) years from the date of original purchase, simply bring this tool with the original sales receipt back to your nearest
MENARDS® retail store. At its discretion, MASTERFORCE® agrees to have the tool or any defective part(s) repaired or replaced with the same or similar MASTERFORCE® product or part free of charge, within the stated warranty period, when returned by the original purchaser with original sales receipt.
Not withstanding the foregoing, this limited warranty does not cover any damage that has resulted from abuse or misuse of the Merchandise. This warranty: (1) excludes expendable parts including but not limited to blades, brushes, belts, bits, light bulbs, and/or batteries; (2) shall be void if this tool is used for commercial and/or rental purposes; and (3) does not cover any losses, injuries to persons/property or costs. This warranty does give you specific legal rights and you may have other rights, which vary from state to state. Be careful, tools are dangerous if improperly used or maintained. Seller's employees are not qualified to advise you on the use of this Merchandise. Any oral representation(s) made will not be binding on seller or its employees. The rights under this limited warranty are to the original purchaser of the
Merchandise and may not be transferred to any subsequent owner. This limited warranty is in lieu of all warranties, expressed or implied including warranties or merchantability and fitness for a particular purpose. Seller shall not be liable for any special, incidental, or consequential damages. The sole exclusive remedy against the seller will be for the replacement of any defects as provided herein, as long as the seller is willing or able to replace this product or is willing to refund the purchase price as provided above. For insurance purposes, seller is not allowed to demonstrate any of these power tools for you.
For questions / comments, technical assistance or repair parts -
Please Call Toll Free at: 1-888-728-0800
SAVE YOUR RECEIPTS
THIS WARRANTY IS VOID WITHOUT THEM.
Page 14
Menards, Inc., Eau Claire, WI 54703 Rev. A
advertisement
* Your assessment is very important for improving the workof artificial intelligence, which forms the content of this project
Related manuals
advertisement