Miller ROUGHNECK 1F Owner’s Manual
Add to my manuals
27 Pages
Miller ROUGHNECK 1F is a powerful and versatile welding machine designed for professional and industrial use. This robust machine delivers excellent welding performance and is suitable for a wide range of welding applications. Its advanced features and user-friendly design make it an ideal choice for both experienced welders and those new to the field.
advertisement
▼
Scroll to page 2
of 27
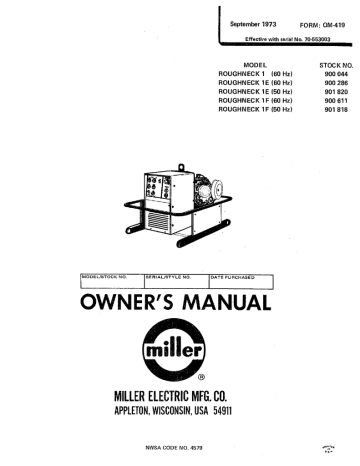
— September 1973 MODEL ROUGHNECK 1 (60 Hz) ROUGHNECK 1E (60 Hz) ROUGHNECK 1E (50 Hz) ROUGHNECK 1F (60 Hz) ROUGHNECK 1F (50 Hz) MODEL/STOCK NO. SERIAL/STYLE NO. DATE PURCHASED OWNER'S MANUAL MILLER ELECTRIC MFG. CO. APPLETON, WISCONSIN, USA 54911 NWSA CODE NO, 4579 FORM: OM-419 Effective with serial No. 70-553003 STOCK NO. 900 044 900 236 901 820 200 611 901 818 ERRATA SHEET After this manual was printed, refinements in equipment design occurred. This sheet lists exceptions to data appearing later in this manual. item Part No. Listed Replaced with No. In Parts List Part No. Description: | Quantity 6 603 945 010 681 KEY, woodruff 1/4 x 1 When ordering this key be sure to measure the length of the key as they are not interchangable. Order the same length key as is in your unit. | OM-419 Page А Paragraph No, SECTION 1 — SAFETY RULES FOR OPERATION OF ARC WELDING MACHINE - 1. General ..... -2. Welding Cables - 7. Polarity Switch - 8. Range Switch - 9. Exhaust Gases EOS EEE SERE 4% “ t = FE + NR N няни ни к я на ни в. вн ни ян кана кв % # 1 * a7 414 = = =m w= - 3. Electrode Holder . ............... ea ee - 5. Parallel Connections ............... ee ean er eee aaa naa - 6. Power Disconnect Switch .......e.eereeeeroarenen e. PA # LA OF FF RE RE 2 я + ка нии вм кии вн Ан & F 4 ®% EH #& #% wm & ¥# ¥ 4 a Fk * mE E E ENE mH ENE BB FF NE ENE ®wW в -10. Power Circuit Ground ........ anadanaronradanmenavaaoanusooon 1-12. Hollow Castings (Welding of) ......... aire 1-13. Explosion Hazards . .......... eee eee eee eee 1-14. Ventilation .. 1-15. Solvents..... 1-16. Fire Hazards ..............m0mneniroarasearerara deaoverrorede, "= = = = EEK EEE KK ото м ов о от око mw ov =m 4 F¥ = 2 = ® = # 4 =% F =m 4 + = #* =m 1 = & % EFD = =m a & ®= = ENE mE =m -17. Electrical Shock-Voltage ................. eer ere eae -18. Electrical Shock-Dampness .............. e. eee eee 1 1 1-19. Starting Under 1 Load .................... eee ee a aa 18006 -20. Face Protection ......120220002 000121111110 PS 1-21. Eve Protection 1-22. Clothing .... mm Fm ok % wor om oh wok mo mo ok mod ow ok NH EEE Mara aan EEE TR ON REE & wom op + вы ня + EB = & 4 w BE ¥ & ¥ 4 & FOV ON OF ве нк ви ии & & #& mom ow om ww ouw mom mE =m & 1-23. Hot Metal Burns ............ eaaaadonnoandoararanarerarereraaro 1-24. Grinding and Chipping .........e.eeee.evracareraenneao0nanra e neo 1-25. Compressed Gas Cylinder ..........eeenearrenvone a. RS SECTION 2 — INTRODUCTION General ..... и и = к инки и нашей и ши т Ш а нА вы ин ня им ны ян ин ви ин ан в вн вн + Receiving-Handling ................. ee RR RR ea 2-1. 2-2. 2-3. Description .. 2-4. Safety ...... OREA ET TL LL EA EA - - - - - - - - = = a - a“ - a - + =" + - = a - || - = a + - - = a - =" a - + - - - = = = = = = SECTION 3 — INSTALLATION и. ин и наи ди да кин А a = EN EN BB BB NE mE SS NE ия ни вн в 4 NE mB & "=" FB & 4 +. 3-1. 3-2. Generator Chassis Ground .. 1.112202 4 24 0 4 44 4 4 4 4 4 4 4 4 4 0 4 4 4 4 4 a a 2e 14 à 3 - 3. SECTION 4 — ENGINE PREPARATION 4-1. Engine Lubrication .................... eee eee 4-2. Fuel........ a J = пи тмин к 4 i % H 4 # ® WN § WN & WN EN Hy EN EN FB ® EN & = ® NF FN EN FON mR OE & & EN & HN ON # & 4 4 - 3. Readying New Battery For Service 122004000044 4044 ae a aa aa 20 à SECTION 5 — FUNCTION OF GENERATOR CONTROLS 5-1, Current Control ....... anaddoarasreruoorarndannaneneoaarnaa nena 5.2 Weld/Power Switch ........e_rescreonverereoredrarereororener. 5-3, 115 Volts AC Receptacies ......._ o .e.eecorcarrrenodeorormoronereoa 5-4. VoltAmpere Curves ....... .eeneovoaarvaran0nearanorarmaco armo SECTION 6 — FUNCTION - 3. Stop Switch .. - 4, Start Button . с) M GO CO) OF ENGINE CONTROLS и вы к § wm # = zx x 4 ке ня = & = = m » ww =m = & 4d #& + & #& 8 Ad FF F #& тан ки ти 3 я в кн и ри риа к mm mm x йе ини дин ый и на та в ан ти в ка та + =m om + & 4 =m = ан ¥ = + и и & ® 4 § ри в ви к ин ни т 4 4 & & #& ни тв Мм F F EH ® F ad в ен в 4 F + MN ¥ Page No. Bb BAR (0 (0 0 0 0) 00 ©) № №3 № № = = = aed + 00 — QT O1 du сл nf = O o do cda © © © © SECTION 7 — SEQUENCE GF OPERATION - 1. Starting The Engine ........... aa naaa naaa naaa -2. Stopping The Engine .......... a aredondecoreraoa nadan - 3. Shielded Metal-Arc Welding........... oe ee ei E wd SECTION 8 — GENERATOR MAINTENANCE 8-1. General .................. ee aaa 8-2. Collector Ring Brushes ............... adadereraraae aaron 8-3. Welding Cables ............. Daanearererovenca are rene a ora ee. SECTION 9 — ENGINE MAINTENANCE . Lubricatión ©. ee ee LL LL LL ALL ALL an Cleaning The Engine ........ RR RR LL 1100 . Spark Plugs ........ 2.2... .0erese een. ee eae (О © © © © SECTION 10 — GENERATOR TROUBLESHOOTING SECTION 17 — ENGINE TROUBLESHOOTING PARTS LIST -4. 115 Volts AC Power Operation . ......... iii iin. - 1 -2 3 -4. Fuel Filter .......... RK KR 4 a a eee a 4 ae ea ea ae | 5 | | | 6 10 10 10 10 10 10 10 11 11 11 11 11 11 - === SECTION 1- SAFETY RULES FOR OPERATION OF ARC WELDING MACHINE seme 1-1. GENERAL These rules apply to ac and dc welding generators, sc trans- former and ac/dc welding machines, and dc transformer recti- fier welding machines. In arc-welding operations, where electrically energized parts are exposed, obsarve the following safety rules to insure max- imum personal safety and protect nearby persons. Failure to observe these safety precautions may expose not only you, but fellow workers as well, to serious injuries. Once these rules are learned and kept in mind, proceed with maxi- mum assurance, 1-2. WELDING CABLES DON'T overload cables, (Figure 1-1) Figure 1-1. Don't overload cables NEVER use welding cables at currents in excess of their rated capacity. it will cause overheating and rapid deterioration of the insutation. 1t is also uneconomical. DON'T use worn or poorly connected cables. (Figure 1-2) Figure 1-2. Don’t use worn or poorly connected cables Inspect the cables frequently. Immediately repair all breaks in the insulation with rubber and friction tapes. Tighten all cable connections and adequately insulate any joints where a connector may have an exposed conductive part. In addition to the potential hazard to life, a hazard occurs when exposed sections of cable come in contact with grounded metallic objects, causing an arc. Unprotected eyes may be injured and fire may result if combustible materials such as oil or grease are in the vicinity. The efficiency and quality of welding will be improved by elimination of these dangerous grounds, and by keeping connections tight, . ELECTRODE HOLDER DON'T use electrode holders with defective jaws. (Figure 1-3) Keep the jaws of the electrode holder tight and the gripping surfaces in good condition to provide close contact with the electrodes, Defective jaws will permit the electrode to wob- ble, making control of the welding operations difficult. Figure 1-3. Don’t use Electrode Holder with defective jaws ' DON'T use electrode holder with loose cable connections. Keep the connections of the electrode lead to the holder tight at all times. Use only fully insulated electrode holders {and without pro- truding screwheads.) Never touch two electrode holders from two separate welding machines at the same time. CODE CONFORMANCE The machine and its equipment must be installed and main- tained in accordance with the National Electrical Code and local requirements. . PARALLEL CONNECTIONS See diagrams in the instruction manual applying to the weld- ing machine used. 1-6. POWER DISCONNECT SWITCH If the welding machine does not include a power disconnect switch, install one at or near the machine, 1-7.POLARITY SWITCH 1-8. DON'T operate the polarity switch under load. The polarity switch {when supplied} is provided for changing the electrode lead from positive (reverse polarity} to negative {straight polarity). Never move it while under the load of a welding current. Operate this switch only while the machine is idling and the welding circuit is open. The potential dan- gers of opening the circuit while carrying high current are: 1. An arc will form between the contact surfaces of the switch and severely burn them. 2. The person throwing the switch may receive a severe burn from this arcing. RANGE SWITCH DON "T operate the range switch under load, | The range switch {when supplied} is provided for obtaining required current settings, 1t must never be operated while the machine is under the load of welding current, Operate the range switch only while the machine is idling and the welding circuit is open. The potential danger of switching the circuit while carrying high current is the formation of an arc be- tween the contact surface which will severely burn them, Repeated occurrences of this arcing will eventually prevent operation of the contacts. . EXHAUST GASES DON'T use gas engine units in confined spaces without vent- ing the exhaust gases, (Figure 1-4} if gasoline or other fuel driven welding machines are operated indoors, provide means to pipe the exhaust gases to the out- side air to avoid carbon monoxide poisoning. OM-419 Page 1 Figure 1-4. Vent exhaust gases 1-10. POWER CIRCUIT GROUND DONT use welding machine without grounding frame or case. (Figure 1-5) Figure 1-5. Ground frame or case Ground the ground cable of every power circuit to prevent accidental shock by stray current. The potential danger is that development of a stray current may give a fatal shock should a person, for example, place one hand on the welding machine and the other on the switch box, or other grounded equipment. Do not ground to pipelines carrying gases or flammable liquids and conduits carrying electrical condue- tors. Be sure conductors can safely carry the ground current. When connecting the welding machine, properly ground the machine frame or case. 1-11. CONTAINERS WHICH HELD COMBUSTIBLES Page 2 DON'T weld on containers which have held combustible or flammable materials or materials. which, when heated, give off flammable or toxic vapors without proper cleaning, p purg- ing, or inerting. Welding containers which have held flammable or combust- ible materials may be extremely dangerous. To prevent a fire or explosion of the container, follow the recommendations of the American Welding Society Pamphiet A6.0 “Welding or Cutting Containers Which Have Held Combustibles”. DON'T depend on your eyes or nose to decide if it is safe to weld on a closed container. . Find out what was in the container or use an explosimeter. A very small amount of residusl flammable gas or liquid can cause a serious explosion, NEVER use oxygen to ventilate a container. When you know the container held a gas or liquid which will readily dissolve in water: 1. Flush out with water several times and then fill with water as far as work permits, positioning container to permit introduction of as much water as possible, 2. Before welding be sure there is a vent or opening to pro- vide for release of air pressure. 1-12. — When you know the container held a gas or liquid which wil! not readily dissolve in water; 1. Clean out thouroughly with steam or a cleansing agent and purge all air or inert with a gas such as carbon dioxide or nitrogen before repairing. Carbon dioxide is heavier than air and wil! tend to remain in the container if the opening is at the top. 2. Use steam to clean out light material, 3. Use a strong caustic soda solution to clean out heavy oils or grease, 4. Be sure to purge all air or inert with a gas, such as nitro- gen or carbon dioxide, no matter how well you have cleaned. There may still be traces of oil, grease, or other readily oxidizable material under the seams. Be careful when cleaning with steam or caustic soda wear goggles and gloves. DON'T clean where there is poor ventilation. Ventilation is necessary to carry away harmful or explosive . Vapors. DONT clean where there are open flames. When scraping or hammering to remove heavy sludge or scale, use a spark resistive tool and keep it wet to avoid sparks. | Keep your head and arms as far away from your work as possible. HOLLOW CASTINGS DON'T weld on hollow {cored} castings that have not been properly vented. The casting may explode. (Figure 1-6) Ш — ча - Figure 1-6. Don't weld on hollow (cored) castings 1-13. EXPLOSION HAZARDS NEVER weld in or near explosive atmospheres. Such atmos- pheres can be created by flammable gas leaks or by vapors from flammable liquids (gasoline, alcohol, etc.) or by com- bustibie dusts. 1-14. VENTILATION . DON'T weld in confined spaces without adequate ventilation. When welding in confined spaces, provide ventilation in accordance with United States of American Standard Z49.1, 1967. Always provide adequate ventilation by blowers, air lines, Or other acceptable means. Never use compressed ox- ygen. The depletion of the oxygen supply, the heat of weld- ing, and the fumes given off may cause severe discomfort or a serious iliness. When toxic fumes from lead or cadmium bearing materials or any other substances are present in harmful concentrations, always use an air supplied respirator. 1-15. SOLVENTS 1-16. 1-17. Do not weld where chlorinated hydrocarbon vapors from de- greasing, cleaning, or spraying may reach or be drawn into air surrounding the welding operation, The heat of the arc can decompose solvent vapors to form phosgene, a highly toxic gas and other irritating decomposition products, Do not weld where ultraviolet light from the electric arc can penetrate air containing even minute amounts of vapors from solvents such as trichtoroethylene or perchloroethylene, Ul- traviolet light can decompose the vapors to form phosgene, a highly toxic gas and other irritating products. FIRE HAZARDS DON'T weld near flammable or combustible materials. Fires can be caused by the arc, by contact with the heated metal, by slag, or sparks, Keep combustibles at least 35 feet from the arc or suitably protected. If welding must be done in a particular area, move the combustibles away, If they cannot be moved, cover them completely with fire resistive screens, Cover cracks or openings in floors or walls: sweep floor free of combustibles and wet down, if wood, being sure welder wears insulation shoe coverings. Avoid welding on par- tion walls in contact with combustibles. Heated metal on the other side of partition wall being welded upon can ignite combustibles in contact with the partition. Where other than a minor fire might develop, have a fire watcher stand-by with suitable fire extinguishing equipment for at least one-half hour after the welding is completed, ELECTRICAL SHOCK-VOLTAGE . OPEN power circuits before checking machines. - Before working on the wiring, switches, controls, etc., open the power line disconnect switch. In most welding shops the power supply used for arc welding machines is 230 or 460 volts, Open circuit voltages are usually less than 100 volts and welding or arc voltage drops are still lower. However, all of these voltages are capable of developing a harmful or fatal current to the body. DON'T touch electrically “hot” parts, NEVER touch any exposed or non-insulated part of the cables, cable connectors, clamps, electrode holders, elec- trodes, or the power supply equipment to prevent harmful or fatal electric shock or burns. . ELECTRICAL SHOCK-DAMPNESS NEVER work in a damp area without suitable insulation a- gainst shock. Keep hands, feet, and clothing dry at all times. To prevent harmful body shocks, keep hands, feet and cloth- ing dry. Never stand or lie in puddles of water, damp ground, or against grounded metal when welding without suitable in- sulation against shock. Always find a dry board or rubber mat to stand on when water, moisture, or perspiration cannot be avoided. Dampness between the body and an energized or grounded metallic part iowers the resistance to the passage of current to the body which may produce a harmful or fatal shock. Salt in perspiration or sea water dangerously lowers contact resistances. Figure 1-7. Don’t leave electrode in contact with grounded metallic surface. 1-19. STARTING UNDER LOAD DON'T leave an uninsulated electrode holder, or a “live” 1-20. 1-21. Se electrode on the table top or in contact with a grounded metallic surface. {Figure 1-7} When it is not in use, never place an electrode hotder in contact with the tabletop or other metailic surface in contact with welding ground. Provide an insulated hook or holder for the electrode holder. A potential danger is that a holder in contact with the ground circuit provides a dead short circuit on the welding machine, If the machine should be started up, this short ctreuit would cause an excessive load on the ma- chine and may darnage the insulation. FACE PROTECTION DON'T use cracked or defective helmets or shields. Keep the helmet, hand shields, or face shield in good condi- tion. If cracks occur in the fibre material, replace the shield, since the leakage of arc rays may cause serious burns. EYE PROTECTION NEVER under any circumstances, look at an electric arc without eye protection. , Me — к Do = Figure 1-8. Use eye protection at all times Make sure that flash goggles are used under the weld- ing heimet at ali times, particularly while gas shielded- arc weiding. In some type of arc welding, such as gas shielded-arc welding, ultra-violet and infra-red radiation from the arc is particularly intense and requires constant attention to avoid arc flashes to the weider when striking an arc and to avoid exposure to other welders. NEVER strike an arc without ascertaining that nearby per- sons either have the necessary protective equipment or are looking in the opposite direction. For weiding operations in open areas, provide portable, non- reflecting screens to shieid persons nearby from the rays of the arc. Eye burns from the arc, through not generally per- manent injuries, are exceedingly painful. Such burns fre- quently referred to as “flashes”, feel like hot sand in the eye. If the eye is focused on the arc without filterglass protec- tion, infra-red radiation can cause retinal scarring and im- paired vision. For eye burns consult your first aid station or doctor. NEVER use cracked, ill-fitting, or defective plates. The filter glass plate provided in the helmets and shields must be of reputable manufacture conforming to the latest Ameri- can National Standards Institute, Standard Z2.1. Replace cracked or ili-fitting fiiter plates promptly. NEVER use filter plates without a protecting cover glass. OM-419 Page 3 Keep a clean cover giass in front of the fiiter plate for the protection thereof. Frequent renewal of these cover glasses is necessary, since they become covered with spatter, reducing vision, 1-22, CLOTHING NEVER use poor, inadequate, or worn-out clothing. Wear heavy shoes, tightly laced. Keep clothing dry. | Proper and dry, oil-free clothing is essential for the weider's 1-23, protection, Clothing must not only keep off the spatter and molten particles, but must also obstruct the rays of the arc and, when nacessary, insuiate the body from harmful electri- cal currents, Wear leather or asbestos gloves at all times to protect the hands and wrists. Dark colored shirts are preferred to light cones because light ones reflect arc rays to exposed parts of the body. in the case of gas shielded-arc welding, light colors are more reflective and may cause eye burns due to the in- tense ultra-violet rays given off by the process. Avoid cotton fabrics when gas shielded-arc welding. An arc burn on the skin resembles a sunburn, except that it is usually more severe. Clothing can be made flame resistant by treatment with a solution of 3/4 pound of sodium stannate in 1 gallon of water, then wrung out and dipped in a solution of 1/4 pound ammonium sulphate per galion of water. Don't wash clothing so prepared in water, but dry clean, When welding operations are to be performed in vertical and overhead positions, leather sleevelets, aprons, and in some . cases leggings and ear plugs should be used to prevent severe burns from spatter and molten metal, HOT METAL BURNS NEVER pick up hot objects. (Figure 1-9) Figure 1-9. Never pick up hot objects NEVER pick up pieces of metal which have just been welded or heated, or the stub ends of electrodes which have been discarded. 1-24. GRINDING AND CHIPPING Figure 1-10. Never do any chipping or grinding without NEVER do any chipping or grinding without protective goggles. (Figure 1-10) protective goggles. Page 4 Whenever it is necessary to grind or chip metal, wear protec- tive goggles specifically designed for this purpose. Serious eye Injuries may result from failure to wear protective goggles, 1-25. COMPRESSED GAS CYLINDERS NEVER strike an arc on a compressed gas cylinder. Always observe the following precautions in regards to compressed gas cylinders: 1. Avoid accidental contact of the electrodes, electrode holder, or other electrically energized parts with a compressed gas cylinder or any other pressure vessel. Serious accidents or fires may result, 2. Use I.C.C.or D.O.T. cylinders. They are manufactured and maintained in accordance with D.O.T. require- ments and are safe so long as they are properly handled. Don’t drop cylinders, 3. Identify gas content by the name marked on the cylin- der, If the cylinder is unmarked, do not use it. Return it to the supplier. Do not rely on a color code. 4. Never use a cylinder or its contents for other than intended purposes. 5. Keep oil and grease away from oxygen cylinders and cylinder valves. 6. Keep cylinders away from exposure to sparks, hot slag, open flame and all possible sources of ignition or excessive heat. 7. Be careful that cylinders are not placed so as to be- come a part of an electrical circuit. Avoid third rails, wires and electric welding circuits. 8. When transporting cylinders by crane, use cradle plat- form or other suitable support. 9. Never hift the cylinders by slings, by the caps or by electric magnets. 10. Never use cylinders as supports or rollers. 11, Never try to mix any gases in a cylinder, 12. Never try to refill a cylinder. 13. Mark or tag empty cylinders “Empty” or “MT”. 14. Send “Emptys” back to the supplier prompthy. 15. 15. Keep “Emptys” and“ Fulis” separate. 16. Never tamper with or alter cylinder numbers or other markings, This is not only foolish but may be illegal. 17. Do not tamper with or change fittings on cylinders, 18. tf valves cannot be opened by hand, do not use ham- mer or wrench. Notify supplier. 19. Protect cylinder valves from bumps, falls, falling ob- jects, and from weather. Keep them covered with cylinder caps when moving cylinders. 20. Keep valves closed on empty cylinders. 21. See that your cylinders are clear of passageways and active work areas and that they are secured against falling. 22. If adapter is required between cylinder and regulator, always use a standard adapter. These may be obtained from your supplier. Where right and left hand threads are used on“ adapter, use two wrenches to insure leak proof connections, - 23. Do not store cylinders in unventilated areas. — SECTION 2 - INTRODUCTION DOMESTIC MODELS EXPORT MODELS Rope Start Electric Start Electric Start Rope Start Rope Start 60 Hz. 60 Hz. 50 Hz. 50 Hz. 60 Hz, WELDING CURRENT RANGE 45-190 45-190 45-190 45-190 45-190 RATED QUTPUT AMPERES 180 180 180 180 180 DUTY CYCLE 100% 100% 100% 100% 100% OPEN CIRCUIT VOLTAGE 80 80 80 80 80 115 VOLTS AC POWER 3.5kva 3.5kva 1.5kva 1.5kva 3.5kva WELD RPM NO LOAD 3600 3600 3600 3600 3600 POWER RPM NO LOAD 1950 1950 1600 1600 1950 24 in. 24 in. 24 in. 24 in. 24 in. HEIGHT 61cm. 61cm. 61cm. 61cm. 61cm. 22-3/4 in. | 22-3/4 in. 22.3/4 in. 16 in. 16 in. WIDTH 57 cm. 57 cm. 57 em. 41em, 41cm. 37 in. 37 in, 37 in. 24 in. 24 in. LENGTH 94 em. 94 cm. 94 cm. 79cm. 73cm. 350 Ibs. 385 165. 385 165. 353 Ibs. 353'Ibs. APPROX. NET WEIGHT 158.8 kgs. | 174.7 kas. 174.7 kgs. 160 kgs. 160 kgs. 375 Ibs. 410 Ibs. 410 tbs. 465 Ibs. 465 Ibs. APPROX. SHIPPING WEIGHT 170 kgs. 186 Kgs. 186 kgs. 217 kas. 211 kgs. 2-1. GENERAL ` This manual has been prepared especially for use in familiar- izing personnel with the design, installation, operation, main- tenance, and troubleshooting of this equipment. All informa- tion presented herein should be given careful consideration to assure optimum performance of this equipment. 2-2. RECEIVING-HANDLING Prior to installing this equipment, clean all packing material from around the unit and carefully inspect for any damage that may have occurred during shipment. Any claims for loss or damage that may have occurred in transit must be filed by the purchaser with the carrier. À ccpy of the bill of lading and freight bill will be furnished by the carrier on request if occasion to file claim arises. When requesting information concerning this equipment, it is essential that Model Designation and/or Stock Number and Serial lor Style) Number of the equipment be supplied. 2-3. DESCRIPTION ENGINE Figure 2-1. Specifications STATIC EXCITER RHEOSTAT REVOLVING FIELD WE LD/POWER SWITCH 115VOLTSAC RECEPTACLE AC REACTOR WELD STATOR OUTPUT TA-300 044-1A Figure 2-2. Block Diagram four cycle engine which is manufactured to specifications which are required for use with this generator, The engine features an automatic compression release camshaft for easy starting. This engine driven welding generator is designed to be used as the power source for the ac Shielded Metal-Arc Welding pro- cess. From 45 to 190 amperes of ac weld current may be obtained by means of the five coarse range receptacles and the Fine Current Control. . 115 volts ac power is available at the 3 prong duplex recep- tacle on the front panel when the generator is being operated at 1950 rpm on 60 Hz models or 1600 rpm on 50 Hz modeis {throttle in power position}. The engine used to drive this generator is a single cylinder SAFETY Before the equipment is put into operation, the safety sec- tion at the front of this manual should be read completely. This will help avoid possible injury due to misuse or improper welding applications. The following definitions apply to CAUTION, IMPORTANT, and NOTE blocks found throughout this manual: E Installation, operating, and maintenance procedures, practices, etc., which will result in personnel injury ог L loss of life if not carefully fotfowed. B IMPORTANT Installation, operating, and maintenance procedures, practices, etc., which will result in damage to equip- | ment, i Installation, operating, and maintenance procedures, i practices, etc., which it is essential 1c emphasize. i OM-419 Page 5 3-1. | | о 3-3. ¡ TA-013 597 TA-013 596 TIONS Figure 3-1, Allowable Tiit Angles Use Table 3-1 as a guide for selecting correct cable size for ~ the anticipated maximum weld current which will be used. Mounting holes are provided in the welding generator base Table 3-1 takes into account total cable length, which means for installations which require fixed mountings. Figure 3-2 the length given in the table includes the electrode and work gives base mounting hole and overall unit dimensions, cable. Exampie: If the electrode holder cable is 75 feet (23 meters) long and work cable 25 feet (8 meters! long, you A lifting eye is provided on top of the unit for moving pur- would select the size cable that is recommended for 100 feet poses, (31 meters) at the maximum weid current you wil be using. y Table 3-1. Welding Cable Sizes If this unit is to be operated indoors, it should be Welding *Total Length of Cable {copper} in Weld Circuit) 206 located in a place where the engine exhaust fumes can Ampere 2 0 д = = > A == = 1/0 be vented out of the building. Failure to comply with 150 | 2 2 > "e 1/0 2/0 3/0 3/0 this recommendation may result in serious bodily in- 200 [1 14 q 140 2/0 2/0 4/01 . 4/0 I jury or loss of life. | 250 1/0 1/0 1/0 2/0 3/0 4/0 ‘4/6| 2-2/0) | . ТА-901 181-10 3-2. GENERATOR CHASSIS GROUND (Figure 3-3) | 8 NOTE: “A. SO FEET OR LESS , - . -8. CABLE SIZE IS BASED ON DIRECT CURRENT (DC), 100% DUTY Normally engine driven welding generators are not required CYCLE AND El THER A 4 VOLTS OR LESS DROP OR A CURRENT {о be grounded. However, this machine has auxiliary power .. DENSITY OF NOT OVER 300 CIRCULAR MILS PER AMP. SA plant capability, therefore, grounding of the frame and case is STAND TES rea AU CL TAR eo OR me recommended, For this reason a convenient grounding ter- WELDING POWER GENERATOR MUST BE USED. WHILE MOST minal is provided on ali weider/power plant units. For de- O NE GENERATORS HAVE AN. OPEN Cle T tailed grounding instructions consult your local or state codes ENE Ras ome OF SPECIAL Ces TSS Nave NIZA OPEN or the latest issue of the National Electric Code. CIRCUIT VOLTAGE. : | : — | | | 12-1/2" ai * (20cm) (31.8cm) 24 : | | (61cm) rr - *(230m) (22.9em) | To. 10-1/8" + *(22.5em] (26.0cm) | | 23/8" р” + | 4” (8.0cm) co or *{14.9cm) le ; a - a > -.. i Ú 22-3/4 SEE {94cm} | 5 (57cm) | *(79em) GENERATOR END *{41em) . . EE (5.1em) | *Export Model Page 6 LOCATION A good installation is essential if the generator and engine are to provide satisfactory and dependable service. To ensure proper carburetor and engine lubrication, the engine manu- facturer recommends that the unit be set on a fairly level plain when operating. Tilting not to exceed 23° on the car- buretor side and 309 on the other three sides is recom- mended by the engine manufacturers. Figure 3-1 shows the maximum allowable tilt of the unit during operation. IMPORTANT MAX. FORE AND AFT TILT IMPORTANT MAXIMUM SIDE TILT Equipment Grounding Terminal TB-906G 044-3 Figure 3-3. Generator Chassis Grounding WELDING CABLES AND JACK PLUG INSTALLA- Figure 3-2. Dimensional Drawing - —TB-900 044-1 Two jack plugs are furnished with this unit. Follow instruc- tions carefully for proper installation of the jack plugs to the welding cables. See Table 3-1 for proper welding cable size. Standard jack plugs furnished with the unit will accommo- date cable ranging from Size 6 to Size 1. 1. Clamp the welding cable in a vise with the uninsulated end protruding upward out of the vise approximately 1-3/4 inches (45mm). 2. Place the steel tie wire (See A Figure 34) approxi- matety 1/4 inch (6.4mm) from the end of the insula- tion, UN TA-901 024-4 Figure 3-4. Jack Plug installation 3. Make a half turn around the cable bringing the {coped ends of the tie wire together. 4. insert a rod of approximately 3/8 inch {10mm) dia- meter through the two looped ends of the tie wire. 5, Twist the tie wire (B) until the entire tie wire is twisted and is tight around the insulation of the weld- ing cable. : 6. Clip off the looped ends of the tie wire. 7. Bend the untwisted tie wire over along the side (C) of the uninsulated portion of the welding cable. 8. Wrap the strip of copper foil tightly around the unin- sulated end of the welding cable and the twisted tie wire (D). 9. Place the jack plug on the end of the welding cable and push it onto the welding cable over the copper coil (E). 10. — Insert the 1/4-20 set screws into the center and upper . holes in the jack plug and tighten. 11. Remove the welding cable from the vise and insert the jack plug into the fiber sleeve. Slide the fiber sleeve over the jack plug and welding cable until the hole in the fiber sleeve lines up with the 1/4 inch (6.4mm) hole in the jack plug. ' 12. Insert the 1/4 inch (6.4mm) self tapping screw through the hole in the fiber sleeve into the jack plug. Tighten the screw with a screw driver. mme SECTION 4 - ENGINE PREPARATION rm res See the Engine Manufacturer's manual for complete De Core, o I ENGINE LUBRICATION All engines are shipped from the factory with their crankcase filed with the required type and amount of break-in oil. Before attempting to operate the engine, make sure the oil level is checked. The break-in oit should be drained after about 40 to 50 hours of operation. If service or loading is at an extremely high duty cycle during this period, or air and environmental condi- tions are dusty and dirty, the oil should be drained after about 2b hours of operation. Also, continued operation of the unit in high temperature (above 909F or 32.29C.} wil! necessitate an oil change after about 25 hours of running time. When changing the break-in oil, use a good detergent type cil having an A.P.i. service designation of ms’. Refer to Figure 4-1, "Temperature-0il Viscosity Guide’, for proper weight ol! to use in various operating temperatures, The oil capacity of this engine crankcase is 5 U.S. (4.16 Brit) pints. Always check the oil fevel after a change with the bayonet type indicator in the oil filler tube. CHECK OIL LEVEL La] F {-1.11°C) OE (17.8%) т 4 НЧ "pp USE API i SERVICE MS OIE e TA-900 044-2 Figure 4-1. Temperature - Oil Viscosity Guide 4-2. 4-3. IMPORTANT | Check oil level daily. During the break-in period, check the oil level several times per operating day as some new engines may use oil until the piston rings etc. have seated. If oil must be added to the break-in oil, use an oil type and weight as explained in the I preceeding paragraph and Figure 4-1; I FUEL IMPORTANT & = Do not mix oil with the gasoline. I Use a good grade of “regular” gasoline, rated at least at 85 octane, for this engine. Fuels of lower octane ratings may cause detonations {knocking} which could result in damage to the engine bearings and head gasket. The fue! capacity of the fuel tank is 1.5 gallons {U.S. Measure}. CAUTION | "A. Never allow the fuel to drain on the engine, the generator, or other components. Arrange provisions for catching the fuel when being drained and if the tank must be drained frequently, install a valve and drain line in the tank. When filling the fuel tank, do not fili completely full. The reason being that the cold fuel will expand due to engine heat and the outside air when operating in a warm climate. If the tank is too full, it will overflow causing a potential fire hazard. Also, do not attempt to fill the fuel tank with the | engine running, always shut the engine down first. I READYING NEW BATTERY FOR SERVICE (Elec- tric Start Models Only} This battery is shipped from the factory in a dry state, A sufficient amount of electrolyte is shipped along in separate OM-419 Page 7 — SECTION 5-FUNCTION OF GENERATOR CONTROLS containers to activate the dry charge battery. To prepare the new battery for operation, proceed : as follows: Put on protective eye cover and clothing prior to pour- ing the electrolyte solution, 1. Remove the battery from the unit and’ place | rf on a level work table or other suitable area. 2. Filt the battery cells to the required level with electrolyte. Do not dilute this electrolyte as it is pre-mixed to the | required strength. I 3. Place a battery thermometer in one of the center cells and check the specific gravity of each cell with a battery hydrometer, 4. The battery temperature must be above 80°F and the specific gravity reading above 1.240 prior to installation. If both conditions are not met, charge the battery follow- ing the beiow instructions: a. Use an automotive type battery charger. This battery should be charged at about a 3.5 ampere rate until Weld-Power | — Switch — Fine Current Coarse Current 45.60 100-140 Control Range > Receptacles ` ceptace 115 Volts ac 51. . Electrode And Work Receptacles Page 8 Work — Receptacle L— Receptacies | = 3 т a Figure 5-1. Control Panel View CURRENT CONTROL (Figure 5-1) . This welding generator is equipped with five Electrode receptacies and one Work receptacie. The five Electrode receptacles provide five ac welding coarse amperage ranges. To select the amperage range desired, insert the electrode cable jack plug into the desired Electrode receptacle. The work cable jack plug must be inserted into the Work recep- tacie and the opposite end connected to the workpiece. Fine Current Control The Fine Current Control permits selection of the eXact amount of weld current desired within the range being used. As the Fine Current Control is rotated in a clockwise direc- tion, weld current will increase. When utilizing the 115 volts ac receptacle, the Fine Current Control must be set at the 100 (maximum) 1 position. : ; The scale which surrounds the Fine Current Control is cali- brated in increments of ten from Q to 100 percent. Due to this percentage calibration, it should be noted that if the operator is using this scale to select a fine amperage setting, TA-900 044-6 5-2. 5-3. correct electrolyte conditions are met. Lower charging rates can be used, however, the time to obtain the correct electrolyte conditions will ba longer. b. When the battery is charged, remove it from the charger and re-check the electrolyte level, Add if necessary. С. Rinse out the empty electrolyte containers with water before discarding. Since battery acid is corrosive to metals, do not pour into a metal sink or drain. Rinse and mutilate the empty electrolyte container before discarding. If acid has accidentally spilled on the bat tery or work. area during filling or charging, flush and mutilate the empty electrolyte container before dis- carding. If acid has accidentally spilled on the battery or work area during filling or charging, flush off with clear water and neutralize with soda or ammonia solu- tion. Use the same procedure if acid is spilled on cloth- ing. 5. Re-install the battery in the unit making sure that the negative (—) terminal of the battery is connected to the ground cable. IMPORTANT Do not attempt to operate the engine without the battery connected. Also, do not attempt to remove the battery while the engine is running | the operator is selecting a percentage of the coarse range in use and not an actual amperage value, WELD/POWER SWITCH (Figure 5-1} | A Weld/Power Selector Switch, located on the front panel! of the generator, is provided to select either weld power or 115 volts ac power output from the generator. When the generator is operated as a welding generator the Weld/Power Switch must be in the WELD position and the throttle lever in the WELD position. When . operated as a power plant, the weld/power switch -must be placed in the POWER position and the throttle lever placed in the POWER position, 115 VOLTS AC RECEPTACLES (Figure 5-1) 115 volts ac is considered standard power. However, if special output voltages and frequency were ordered in the unit, refer to the nameplate on the unit for fre- quency and output voltage and required engine rpm for the given output, In some cases, the duplex recep- tacle may be replaced with a receptacie designated by the purchaser or customer. The basic instructions for connection and operation as a power plant remain the 1 same. i This generator is capable of furnishing up to 3.5kva of 115 — volts ac power on 60 Hertz models and 1.5kva of 115 volts ac power on 50 Hertz models for operating various motors and other 115 volts ac equipment. This is single phase power. - AC voltage will decrease in accordance with the {oad applied to the 115 volts ac Receptacles. This generator is designed to deliver 30.5 amperes at 115 volts ac on 60 Hertz models and 13 amperes at 115 voits ac on 50 Hertz models provided the engine rpm is up to specifications. 5-4. (ELECTRIC START MODELS ONLY) 6-1. 6-2. VOLT-AMPERE CURVES (Figure 5-2) These volt-ampere curves show the ac output voltage avail- able at any given output current within the limits of the minimum and maximum Fine Current Control setting. Load voltage Is predetermined to a large degree by arc character- istics. Wi th the use of the volt-ampere curves, itis possible to determine the amperage required for a particular load volt age. START BUTTON - STOP SWITCH (ELECTRIC START MODELS ONLY) STOP SWITCH (MANUAL START MODELS ONLY) 80 70 MW © o AC YOLTS in = o oo SECTION 6- FUNCTION OF ENGINE CONTROLS NAMEPLATE RANGE MARKINGS A 45-60 в 60-7 5 с 75-100 D 100-140 E 135-MAX. a “ “ . ` D x \ \ A pe LA Г | 1, E $d 1 1 100 125 150 175 200 225 250 А С AMPERES B-002 312 Figure 5-2. Volt-Ampere Curves CHOKE CONTROL. THROTTLE CONTROL T8-900 044-7 Figure 6-1. Engine Controls CHOKE CONTROL {Figure 6-1) A CHOKE Control is provided for varying the fuel-air mix- ture to the engine. When the CHOKE Control is rotated fully counterclockwise, very little air will be admitted to the en- gine thru the carburetor, thereby supplying a richer mixture of fuel. This position is required if the engine is cold when started. As the engine warms up it will be necessary to rotate the CHOKE Control clockwise siowly untit it is rotated clockwise as far as it will go. When the CHOKE Control is fully rotated clockwise the engine should be ready for opera- von. - THROTTLE CONTROL (Figure 6-1) The Throttle Control provides the operator with the capa- bility of selecting either WELD or POWER engine speed, 6-3. 6-4. To place the engine at WELD rpm, push the Throttle Control in a downward direction as Tar as it will rotate. To obtain POWER rpm, push the Throttle Control in an upward direc- tion as far as it will rotate, STOP SWITCH (Figure 6-1) A Stop Button is provided on the engine for shutting the engine down. To stop the engine, depress the Stop Button until the engine ceases to rotate, START BUTTON (Figure 6-1){Electric Start Models Only - Depressing the Start Button wiil engage the engine starter and thereby start the engine. The Start Button must be released as soon as the engine starts or resulting damage to the starter will occur, OM-419 Page 9 — SECTION 7 - SEQUENCE OF OPERATION 7-1. 7-2. 7-3. Never operate the unit with the wrapper removed. If the wrapper is removed, a safety hazard exists to per- sonnel from moving and electrical components. Also, weather protection to the internal components of the y unit will be greatly reduced. ' STARTING THE ENGINE IMPORTANT $ Make sure all electrical equipment connected to the 115 volts receptacle is turned off before starting the engine. The engine when starting has low speed which causes low voltage at the output receptacle of the generator. This could result in damage to electrical E equipment. 1, Fill the fuel tank and check to ensure that the oil leve! is adequate. 2. Rotate the Choke Control fully counterciockwise. Lesser degrees of choking may be required if the engine is warm. 3. Place the Throttle Control in the POWER position. ~ 4. On models without electric start, give a quick steady pull on the starter rope. For models with electric start, depress the Starter Button, B. Once the engine has started, siowly rotate the Choke Con- trol clockwise, 6. Allow the engine to run for a few minutes before applying a load. This is necessary to enable the engine to properly warm up and ensure proper lubrication, 7. Place the Throttle Control in the desired position. STOPPING THE ENGINE 1. Remove the load from the welding generator. 2. Place the Throttle Control in the POWER position. Operate the engine at this speed for 2 minutes; this will allow internal engine temperature to equalize. 3. To stop the engine, depress the Stop Button. SHIELDED METAL-ARC WELDING 1. Prepare the engine for operation as instructed in the en- gine preparation section. 2, Make weld connections from the electrode holder jack plug to the desired range receptacle and from the work clamp jack plug to the work receptacle. 3. Rotate the Fine Current Control to the desired setting. 4. Place the Weld/Power Switch in the WELD position. 5. Start the engine as instructed in paragraph 7-1. Prior to welding, it is imperative that proper protective clothing (welding coat and gloves) and eye protection (glasses and/or welding helmet) be put on. Failure to comply may result in serious and even permanent bodily damage. 6. Connect the work clamp to the object to be welded, place the desired electrode into the electrode holder, and com- mence welding. TB-800 044-5 Figure 5-1. Shielded Metal-Arc Welding Connection Diagram 7-4. 115 VOLTS AC POWER OPERATION 1. Prepare the engine for operation as instructed in the En- gine Preparation Section, 2. Rotate the Fine Current Control fully clockwise to the 100% setting. 3. Place the Throttle Control on the Engine in the POWER postition, 4. Start the engine as instructed in paragraph 7-1. 5. Connect the auxiliary equipment or desired load to the receptacle and commence operation. 8-1. Page 10 - CAUTION If any work is to be done on the rotor of the genera- tor, remove the spark plugs from the engine. This witl prevent engine compression from turning the rotor and catching the repairman's hand between the rotor . fan casting and the stationary adapter casting. I GENERAL Economical operation and trouble-free service of this welding generator are based upon regular inspections and reasonable attention. Occasional blowing out of the unit with clean dry com- pressed air is recommended, This should be performed peri- odically, depending upon the location of the unit and the amount of dust and dirt in the atmosphere. 8-2. 8-3. COLLECTOR RING BRUSHES The brushes should be inspected periodically to ensure their proper function. The brush life 1s very good under nomnal conditions. If the generator has been operating in an ex- tremely dusty or dirty location, a close check of the brushes for freedom of movement and cleanliness should be made weekly. Under normal use the slip rings will discolor to a dark brown. If it should become necessary to clean the slip rings, use a 3/0 or finer sandpaper followed by a crocus cloth. Never use emery cloth as part of the emery will embed itself into the exciter or collector rings and in turn destroy the carbon brushes. WELDING CABLES Check connections periodically for tightness. The cables should be inspectéd frequently. and all breaks in the insula- tion should be repaired with electrical insulating tape or the cables replaced. 9-1. 9-2. 9-3. LUBRICATION This engine will require at least 10 hours of running time to become fully broken in. During this period, the load on the engine should be kept as light as possible. The oil level should be checked a number of times during an operating day, as some engines will use oil during the break-in period. After about 40 to 50 hours of running time on the break-in oil, drain the oil. Premium heavy duty oil, manufactured by any one of the major oil companies, should be used as a replace- ment ail. Tabie 4-1 gives a list of recommended grades and types of oi! to use to keep oil level up during break-in and to use after the break-in oil is drained. The oil capacity of the engine is 5 pints, Check the dip stick to make sure oil level is up to the required operating level. In normal operation, oil should be changed after about 25 hours of operation. The oil should be drained after the engine has been warmed up to normal operating temperature, thus promoting foreign particle suspension in the oil and thereby removal when the oil is drained. Foreign particles tend to settle at the bottom of the crankcase when the oil is allowed to cool, thereby avoiding removal and thus contaminating the new oil added, | CLEANING THE ENGINE This air cooled engine operates most efficiently when kept clean. Maintain cleanliness at all times. Wipe oil spills from engine immediately to avoid accumulation of dust. SPARK PLUGS IMPORTANT Do not attempt to clean the spark plug electrode by sandblasting. Particles of abrasive may stick to the spark plug and thereby enter the engine and cause damage to the internai engine components. Also, the I spark plug gap shouid be kept at .025”. | ] The area around the base of the spark plug should be cleaned 95. 9-4. 9-6. prior to removal of the spark plug to help avoid dirt getting into the engine, Remove the plug periodically and clean the electrode with a wire brush or knife blade. Take care so as not to crack the porcelain insulator-on the spark ptug. FUEL FILTER The fuel fiiter is located below the fuel tank. Check the sediment bowl periodically for water and dirt deposits. How often the filter has to be checked will depend on the grade of gascline used and how dusty and dirty the location in which the engine is being used. AIR CLEANER The air cleaner is one of the most important parts of the engine from the standpoint of engine life. If dirty air gets into the engine, it can wear out a set of piston rings within a few operating hours. . This engine is equipped with a dry paper type filter element. Dry paper element type cleaners can be cleaned by removing the element and tapping lightly, causing loose dirt to fall off. The element should be replaced if dirt does not drop off easily. The paper element should be handled with care to avoid perforations. Removing the dirt with compressed air can rup- ture the paper element. Check to ensure that gasket surfaces of element are not bent or damaged in any way. Gasket surfaces must seal tightly at top and bottom of cleaner shell to prevent foreign matter from entering the carburetor. Whenever air cleaner is removed, cover air intake hole to prevent dirt from falling into carburetor. PERIODIC SERVICE The efficiency of the engine depends a great deal on the care and attention given it. By following a definite schedule of - inspection and service, engine failure caused by neglect can be avoided. Service periods are based on hours of running time and are for normal operating conditions, For extreme conditions of load, dust, dirt, etc., service more often. Table 9-1. Periodic Engine Maintenance Chart Each Every Every Every Every PERFORM SERVICE AT INTERVALS INDICATED (X) Day 25 Hours 50 Hours 100 Hours 500 Hours CHECK OIL LEVEL (maintain in safe operating range) ..... к) X CLEAN AIR INTAKE SCREEN (plus other external surfaces). ..|.. X REPLENISH FUEL SUPPLY (Use clean, fresh fuel) ..........}.. X CHANGE OIL (Use API Service MS of proper weight) ........L.........}.. > € SERVICE FUEL FILTER (remove and clean sediment bowl) ...|........[.... X CHECK AIR CLEANER ELEMENT ..... vinnie anche oe. X SERVICE SPARKPLUG {gap for.025”) .... o.oo oi, X SERVICE BREAKER POINTS (gap .020”) .......... 2.222 rene ros, X NOTE: Intervals stated are for good, clean operating conditions — perform services more frequentiy if dusty or dirty conditions prevail. ——— SECTION 10. GENERATOR TROUBLESHOOTING mes INTRODUCTION This data collected here, discusses some of the common problems which may occur in this welding generator. A little thought will probably solve the problem involved through the information pro vided. The assumption of this data 1s that a proper welding condition has been achieved and has been used until trouble developed. In atl cases of equipment malfunction, the manufacturer's recommendations should be strictly adhered to and followed. If after performing the following procedures the trouble is still not remedied, it is recommended that a serviceman be called. It is recommended that the circuitdiagram be used for reference during the troubleshooting. OM-419 Page 11 TROUBLE PROBABLE CAUSE REMEDY No weld output. Weld/Power Switch in POWER position. Place Weld/Power Switch in WELD Position. Poor connections on WELD/P OWER Switch. Fuse F1 biown. Replace fuse and check for defective associated circuitry, Low weld output. Throttie control is in POWER position. Place Throttle ono in WELD position. Low engine speed with Throttle Control in WELD position, load speed). Check engine speed which should be 3600 mm (no Engine may require servicing or overhaul- Ä Poor coilector ring connections or defective brushes, Check collector ring for good brush contact. Use 3/0 sandpaper if it is necessary to clean sip rings. install new brushes if necessary. Fine Current Control defective. Check for defective or loose connections on rheostat R1. Replace rheostat If defective. Low or no power output. WELD/POWER Switch is in WELD position, Place WELD/POWER Switch in POWER position. Engine speed below normal power engine throttle setting. Check engine speed. If it is incorrect (1900 fom on 60 Hz models and 1600 rpm on 50 Hz models) see engine manual for adjustment procedure, Erratic weld current. Damp, defective or wrong type welding electrodes. Try different electrodes. Improper connection to workpiece. Check and tighten any loose connections, Jack plugs connected to WORK and COURSE CURRENT RANGE Receptacle are loose. Twist jack plug in a clockwise direction to insure tight fit. Page 12 SECTION e CARBURETION Сре) | FAILURE TO START | ENGINE TROUBLESHOOT! NG Mechanical 1 |. IGNITION [compression] Cylinders dry. Sticking valve, Loose or broken spark plugs. Cylinder head gasket leaking, Piston rings stuck, Warped or broken valves, Poor grade] [Restricted air cleaner, Plugs wet Breaker points pitted of fuel Fue! pump diaphragm or dirty. or fused. Water Choke Condensation | ISpark plug insulation bad, in fuel Flooded on electrodes, | [Breaker arm sticking. Gum Birt or gum holding Weak battery [ lImproper timing, in fuel float needle valve Broken ignition cables. Dirt Damaged HS needle valve. Ignition cables in fuel Fuel line clogged. disconnected. Improper Air vent, filler cap plugged. Wires to wrong plugs. volatility Manifold gasket leak. No fuel Muffler clogged. | KNOCKING | L CARBURETION MECHANICAL | | IGNITION | Poor grade of fue! Octane rating to low | -- Heavy load at slow speed. “1 Carbon or lead deposits in -) Breaker points too far advanced cylinder head, Loose connecting rod, Loose main bearings. : Burned out connecting rod, Worn or loose piston pin, Worn or loose timing gears, Improper piston fit. Valve fash too great. Vaives sticking. | | MISSING | CARBURETION Water in fuel Gum in fuel Dirty fuel system. Vapor lock. improper needle valve. Improper carburetor Improper fuel mixture. Inoperative fual pump (Dirt or mechanical). Air leaks in system. Defective float mechanism Inoperative choke control COMPRESSION | Scored cylinders, Improper valve lash, Sticking valves, Loose or broken spark plugs. Cylinder head gasket leaking, - | Piston rings stuck. Warped or broken valves. Sand hole in casting, Valve springs weak or broken. | OVERHEATING | "= CARBURETION| — [LUBRICATION] | Low grade of fuel. Engine operated white detonating, due to low octane fuel or heavy load. Improper carburetor setting. Plugged air filter. Leak in intake system. ENGINE FLYWHEEL ALTERNATOR On supply low, Dirty or incorrect grade of oil, Engine overicaded, Carbon deposits in engine, Restricted exhaust, Choke control partially pulled out, Valves leaking. Restricted air cleaner, Recirculation of hot air. Improper break-in, | SURGING ___| Improper heat range in plug. Loose plug. Poor insulation om plug. Spark plug gap incorrect. Worn and leaking ignition cables, Wealk spark, Loose electrical connections. Breaker points pitted or worn, Breaker paints sticking. Improper tension of breaker point spring. ‚ Improper breaker point gap. Bad condenser. Weak cout, Worn out plug . Defective ignition switch, Grounding of ignition adcessories, Moisture Carburetor flooding. Improper adjustment. intake leaks. Sticky controls Improper lubrication, WELD 52 78 OPERATED BY ENGINE THROTTLE POWER No E GROUND — FE - POWER 79 POWER WINDING WINDING STATIC EXCITER PANEL ELECTRODE 16 e WORK Circuit Diagram No. CB-900 044-1P Figure 7-1. Circuit Diagram For Manual Start Model OM-419 Page 13 |Эроу 34218 211309) 104 wesberq anon) ‘7-7 esnb14 AL-987 006-949 “ON WeaBeIQ 1119419 MHOM 100412373 JaNYd HALIDX3 DILYLSE ONION IM To - м OAM IDHYHD < £ INIGNIM ce re HIMOd 6 es _L I SI EZ | No 6 ) [ 2 | 3 1 ot 15 \— — ——= -+ — — + — — — — ¢ | | J LJ Tamod) QM HAMOd TIIM € Но Y or I — = Zl À À Bl ‘ tq о ANNOND 2NVUd vzs | Ш o be A SN | 7 AillowHi aNon3 A 0319m3do” [> YN — | — 90000 — It. HIMOd а HIMOd qm, TAE оно HOLYNYI LY Эа НМА | {2 135 “ANTONI Page 14 September 1973 FORM: OM-419 Effective with serial No. 71-593696 MODEL STOCK NO. ROUGHNECK 1 900 044 ROUGHNECK 1E 900 286 ROUGHNECK 1F 900 611 MODEL/STOCK NO, SERIAL/STYLE NO. DATE PURCHASED PARTS LIST MILLER ELECTRIC MFG. CO. APPLETON, WISCONSIN, USA 54911 RIN TE, 1 NWSA CODE NO. 4579 TD-200 286A Main Assembly Figure A — ОМ-419 Раде 1 Quantity Model Manual “| Electric Item Dia. Factory Start Start No. Mkgs. PartNo. Description Export | Domestic | Domestic Figure A Main Assembly 1 014313 WRAPPER............eorroveroroccereoomeracoeoo 1 1 1 2 Figure B GENERATOR & REACTOR (SeePage 3) .............. 1 1 1 3 602 018 SCREW, cap-sockethd 7/16-14x 1-1/2. ,.............. 1 1 1 4 602 215 WASHER, lock-split 7/16 .........—r—resresorencaras 1 1 1 5 602 226 WASHER, flat-7/16 ID x 2-1/4 OD x 3/16 ............. 1 1 1 6 603 945 KEY, 1/4x 7/8 ..L1120 40040 0 4 0 40 a aa a кк кк какие о . 1 1 1 7 017742 ADAPTER, fan ........eeoererverororeseorerrenea. 1 1 1 8 FigureC PANEL, rear with components (See Page 4) ............ i 1 1 9 038107 ENGINE (consisting Of). ........rre=errareorreerec.. 1 1 10 020251 , SWITCH, with leads {consistingof) .................. 1 1 11 015503 ..BRACKET mountingswitch ...................... 1 1 12 52 *027 878 ..SWITCH, limit-leaf actuator SPDT ................. 1 1 13 010298 .NIPPLE, 1x3 ........iremeresvsarereroarecncero, 1 1 14 *015 621 .MUFFLER .......ce.e.eemerereccioraareamavonor i 1 9 026 526 ENGINE (consisting of) ...........ece.esomrerevcameea i 10 022 496° . SWITCH, with leads (consisting of) .................. 1 11 015503 .,.BRACKET, mountingswiteh ...................... 1 12 S2 *012 879 ..SWITCH, limit-dual actuator DPDT . . ............... 1 13 010 298 .NIPPLE,1x3....... _—ererereserarecarercereree.. 1 14 *015 621 MUFFLER .....i..recrarareanoom0necndrovmacaroeno 1 15 024117 ADAPTER, engine.........esronmeacanesne, FU eee = 1 1 1 16 025576 PAN, base ......o_ecececdcracrorereve norvrreocareco. 1 i 1 17 010955 WASHER, flat 13/32IDx20Dx 1/8 244100000000 0 3 3 3 18 015754 MOUNT, engine......eoeracreararoro0serareseamarne. 2 2 2 19 021993 BASE... 101224 20 1e a a 4 a 4 0 4 a a a ee ea a ae a a en eue» 1 19 021990 BASE.......reareserecvoeserecrserarocnarmedvorere, 1 1 20 017175 PANEL, side ..........errrececarerareeroce cea. 2 2 2 21 022017 MOUNT, generator ......r_eereesrorvoresvvreonerec. 1 1 1 22 010 954 WASHER, flat 13/32 ID x 1-1/4 0D x 1/8 .........e..e. 3 3 3 23 604 435 BOLT, carriage 5/16-18x 7 ............ coun... ... 2 24 Batt *604 207 BATTERY, 12 volt 95 amp-hour........e s_ereeresneoo. 1 023652 CABLE, battery-positive .....1044400 0000000 an en ua 0 + 1 023 653 CABLE, battery-negative ......_e.ecoreroroenesonoorane. 1 25 017222 FHOLDDOWN, battery ........—._eceremorvororereara, 1 26 Figure D PANEL, front with components (See Page 5) ........... 1 1 1 022152 SWITCH ASSEMBLY, stop .......oeaarooroerorvera. 1 039608 PLUG ASSEMBLY, jack (consistingof) ............... 2 2 2 019833 STRIP, copper ..........o.eresasrarerecdereoreo. 1 1 1 101 219 PLUG, J2CK ........er—eedonvoreroreoresereerean. 1 1 1 602 814 INSULATOR, molded-red ........... PARA 1 1 1 602 160 .SCREW, self-tapping filister hd 8-32 x 1/4 ............ 1 1 1 602 178 SCREW, set-sockethd 1/4-20x 3/8 ......... 0... 2 2 2 025 918 KIT, label (includes alllabels) ....................... 1 1 1 *Recommended Spare Parts. BE SURE TO PROVIDE STOCK, MODEL, AND SERIAL NUMBERS WHEN ORDERING REPLACEMENT PARTS. OM-419 Page 2 Quantity Model Manual Start Electric Start Item Dia. Factory 50 Hz 60 Hz 50 Hz 60 Hz No. Mkgs. Part No. Description 115V !230V |115V| 230V | 115V | 230V | 115V1 230V Figure B Generator 8: Reactor (See Fig. A Page 2 Item 2) 36 018614 BRUSH SET, electrical (consisting of) Lea 2 2 2 2 2 2 2 2 37 *020 034 . BRUSH, withspring .......... 1 1 1-1 1 1 1 1 38 600270 HOLDER, brush ............. 1 1 1 1 1 1 1 1 .39 018665 .CAP, holder ................ 1 1 1 1 1 1 1 1 40 018 641 BRACKET, mountingbrush holder 1 1 1 1 1 Л 1 1 41 Z 036 182 REACTOR .................. 1 1 1 а 1 1 1 1 42 017756 ROTOR (consistingof)......... 1 1 1 1 1 1 1 1 43 OL7 624 .FAN ... ..emerrorarerean ea 1 1 1. 1 1 1 1 1 44 024616 BEARING ................. 1 1 1 1 1 1 1 1 45 024 617 . RING, retaining-bearing ....... 1 1 1 1 1 1 1 1 46 022 040 STATOR ................... 1 46 **022 041 STATOR ................... 1 46 **022 038 STATOR. ................... 1 46 **022 039 STATOR ............. ea 1 46 **022 036 STATOR ................... 1 46 **022 037 STATOR ................... 1 46 **022 034 STATOR ......... eee 1 46 **022 035 STATOR ................... 1 47 017763 ENDBELL .................. 1 1 1 1 1 1 1 1 *Recommended Spare Parts. **R otor and Stator Replacements are available on exchange basis. Contact Factory Service Department for details. BE SURE TO PROVIDE STOCK, MODEL, AND SERIAL NUMBERS WHEN ORDERING REPLACEMENT PARTS. Page 3 Figure B — Generator & Reactor TE-018 223 Quantity - Model Item Dia. Factory | Manual | Electric No. Mkgs. Part No. Description Start Start Figure C Panel, Rear With Components (See Fig. A Page 2 Item 8) 51 038 432 CIRCUIT CARD ASSEMBLY (consisting of) ...... PARA 1 1 52 Cl 604 005 .,CAPACITOR, metalized-paper 4 uf 150 volt de ..........e.ece o. 1 1 53 C2 031643 CAPACITOR, ceramic 0.01 uf 500voltde .................... 1 1 54 Fl 023014 FUSE ............... enano. eee eae era eee 1 1 556 01-10 027 369 . DIODE, 3 amp 600 volt straight polarity ................... a 10 10 56 022112 PANEL, rear ......eecoeeoenorerorerercóreneoo eee eee 1 1 57 015 712 GROMMET, rubber 5/8 ID x 7/8 hole x 1/16 groove ............. 1 1 58 CB +*012 612 CIRCUIT BREAKER, 10 amp (Spencer) or | | 58 CB +*027 889 CIRCUIT BREAKER, 10 amp (ETA) ...........eemenmanarac 2. 1 59 DH 027 856 DIODE, withlead &terminal ......... viverra. 1 60 C4 031722 CAPACITOR, mylar 1uf200volt. ........ coins. 1 1 61 010 311 CLAMP, steel nylon coated 3/4 dia .........e.eesrersmoró reo. 1 1 62 014159 BRACKET, mounting-capacitor...........o._ec-e—r.. enreda. 1 1 63 C38 031601 CAPACITOR, paper-oill 10 uf600voltde ...................... 1 1 64 Ll 036 011 CHOKE, 30 milli-henry .........e_eeeenaadonaoanvaranoaarorna 1 1 Figure C — Panel, Rear With Components тс-022 115 *Recommended Spare Parts. +Be sure to order correct circuit breaker, as the mounting holes are different. BE SURE TO PROVIDE STOCK, MODEL, AND SERIAL NUMBERS WHEN ORDERING REPLACEMENT PARTS, OM-419 Page 4 *Recommended Spare Parts | BE SURE TO PROVIDE STOCK, MODEL, AND SERIAL NUMBERS WHEN ORDERING REPLACEMENT PARTS. Page 5 / Figure D — Panel, Front With Components Item Dia. Factory No, Mkgs. PartNo. Description Quantity Figure D Panel, Front With Components (See Fig. A Page 2 Item 26) 91 Work 039 800 RECEPTACLE ASSEMBLY, jack-red (consistingof) ............... 1 92 039 768 NUT, terminal-red ,.......oe_eseauenaraaaaaoononad—anararira 1 93 010 291 | WASHER, flatmylafil 5/81 Dx 1-1/40Dx 1/8 .................. 1 94 604 668 -.NUT, steel-self locking hex hd 1/2-20 .............. 2... a. .... 1 95 020 015 .RECEPTACLE ..........esrecsrorerrenvoreroovedroneono ne 1 96 601 881 NUT, steel-hex jam 1/2-20 . ci eee, 1 97 Elect 039 801 RECEPTACLE ASSEMBLY, jack-black (consisting of} ............. 5 98 032 796 NUT, terminal-black .............. eee eee 1 99 010 291 .WASHER, flat mylafil 5/8 ID x 1-1/4 OD x 1/8 .................. 1 100 604 668 1 NUT, steel-self locking hex hd 1/2-20......... .... eee eee 1 101 038198 .RECEPTACLE ......ee..0resonvacaeervanedrerernaonarerene a 1 102 601 881 .NUT, steel-hex jam 1/2-20 .............000000edo0orie.o aaa 1 108 Si *011 622 SWITCH, togele 3PDT 15 amp 125 volt ........._e-r.erorerereoo. 1 104 Ri *030 987 RHEOSTAT, WW 50 watt 25 ohm ......oeeeeonrerdaresvananerdoo ‚1 105 RC1 604176 RECEPTACLE, duplex-ground straight 2P3W 115 volt or 105 RC1 604103 RECEPTACLE, duplex-ground straight 2P3W 230 volt ............. 1 106 010 014 CLAMP, steel-cushioned 11/16 dia ........e.eecreoresrerveeraroo 1 107 017180 PANEL, front........................ eae 1 108 NAMEPLATE (order by stock, model & serial numbers) ............ 1 109 024 366 KNOB, pointer line indicator 1-1/8 OD x 1/4 bore.............e... 1 TC-018 247
advertisement
* Your assessment is very important for improving the workof artificial intelligence, which forms the content of this project
Key Features
- Delivers excellent welding performance for a wide range of applications.
- Robust construction ensures durability and reliability in demanding environments.
- User-friendly design with intuitive controls for ease of operation.
- Suitable for both experienced welders and those new to the field.
- Provides precise current control for optimal weld quality.
- Equipped with 115 Volts AC receptacles for added versatility.
Related manuals
Frequently Answers and Questions
What is the power input for the Miller ROUGHNECK 1F?
The power input for the Miller ROUGHNECK 1F is not specified in the provided manual.
What is the duty cycle of the Miller ROUGHNECK 1F?
The duty cycle of the Miller ROUGHNECK 1F is not specified in the provided manual.
What type of welding processes can be performed with the Miller ROUGHNECK 1F?
The provided manual does not specify the welding processes that can be performed with the Miller ROUGHNECK 1F.
What safety features are included with the Miller ROUGHNECK 1F?
The safety features of the Miller ROUGHNECK 1F are not specified in the provided manual.
What accessories are included with the Miller ROUGHNECK 1F?
The accessories included with the Miller ROUGHNECK 1F are not specified in the provided manual.
advertisement