- No category
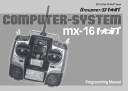
advertisement
▼
Scroll to page 2
of 200
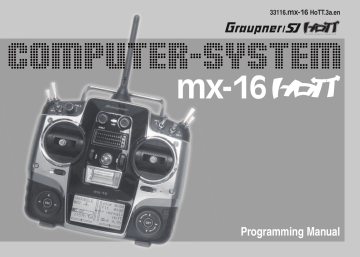
33116.mx-16 HoTT.3a.en mx-16 Programming Manual Contents General Information Contents......................................................................... 2 Warning and information symbols a. their meaning........ 3 Environmental protection notes...................................... 3 Safety Notes................................................................... 4 Safety notes and handling instructions relating to Nickel-Metal-Hydride rechargeable batteries............. 8 Disposal of exhausted dry and rechargeable batt.......... 9 Foreword....................................................................... 10 Description of radio control set..................................... 11 Technical specifications................................................ 13 Recommended battery chargers.................................. 13 Operating notes Transmitter power supply......................................... 14 Receiver power supply............................................ 16 Adjusting the stick length......................................... 17 Opening the transmitter case.................................. 17 Changing the stick mode......................................... 18 Description of transmitter.......................................... 20 Front of transmitter.................................................. 20 Rear of transmitter................................................... 21 Headphone socket................................................... 21 Mini-USB socket...................................................... 21 Data socket.............................................................. 21 DSC socket.............................................................. 22 Card slot / data storage........................................... 22 Screen and keypad.................................................. 24 Operating the “Data Terminal”.................................. 25 Short-cuts................................................................ 25 Hidden Mode Language selection Voice messages............................................ 26 Changing the screen language...................... 27 Firmware update from SD card.......................... 27 2 Contents Stick calibration.................................................. 27 Telemetry data displays........................................... 30 On-screen warnings................................................ 36 On-screen function fields......................................... 36 Position indicator of rotary controls CTRL 7 + 8...... 37 Input lock................................................................. 37 Using the transmitter for the first time..................... 38 Downloading a firmware package........................... 40 Firmware-update of the transmitter......................... 41 Restoring the transmitter firmware.......................... 44 Using the receiver for the first time.......................... 46 Firmware-update of the receiver.............................. 48 Backing up receiver settings.................................... 52 Installation notes........................................................ 54 Receiving system power supply.............................. 55 Definition of terms........................................................ 58 Switch and transmitter control assignment................... 59 Digital trims................................................................... 60 Fixed-wing model aircraft.......................................... 62 Receiver socket sequence....................................... 63 Servo with incorrect direction of rotation................. 63 Model helicopters....................................................... 64 Receiver socket sequence....................................... 65 Program descriptions Setting up a new model memory.................................. 66 “Model memories”....................................................... 70 “Base settings” (model) Fixed-wing model aircraft........................................ 74 Binding receivers.............................................. 80 Range-checking............................................... 80 Model helicopter...................................................... 82 Binding receivers.............................................. 88 Range-checking............................................... 89 “Servo settings”........................................................... 92 “Transmitter control settings” Fixed-wing model aircraft........................................ 94 Model helicopter...................................................... 96 Throttle limit function.......................................... 99 Basic idle setting................................................. 99 “D/R Expo” Fixed-wing model aircraft...................................... 102 Model helicopter.................................................... 104 “Phase trim” (fixed-wing)........................................... 106 What is a mixer?......................................................... 108 “Wing mixer”............................................................. 108 “Heli mixer”............................................................... 114 Adjusting throttle and collective pitch curves......... 120 Auto-rotation setting.............................................. 124 General notes re. freely programmable mixers........... 126 “Free mixers”............................................................ 127 Examples............................................................... 131 “Swashplate mixers”................................................ 132 “Servo display”.......................................................... 133 “Basic settings”......................................................... 134 “Fail-Safe”.................................................................. 136 “Telemetry”................................................................ 137 Setting & Data view............................................... 138 Satellite operation with two receivers............... 148 Sensor select......................................................... 150 RF status view....................................................... 151 Selecting voice output........................................... 152 “Trainer mode”.......................................................... 154 Wiring diagrams..................................................... 157 Wireless HoTT system.......................................... 158 “Info display”............................................................ 162 Warning and information symbols and their meaning Programming examples WARNING: This symbol calls attention to the information next to it and perhaps following it, with which the user must absolutely comply! Any failure to comply with this information can impair the reliable functioning and the safety of the operator as well as third parties. Introduction................................................................. 164 Fixed-wing model aircraft First steps.............................................................. 166 Including an electric power system........................ 170 E-motor and Butterfly (crow) using Ch1 stick........ 172 Operating timers.................................................... 175 Use of flight phases............................................... 176 Servos running in parallel...................................... 177 Deltas and flying wings............................................... 178 F3A models................................................................ 182 Model helicopters....................................................... 186 Appendix Appendix..................................................................... 194 Conformity declaration................................................ 197 FCC Information......................................................... 198 Guarantee certificate.................................................. 199 ATTENTION: This symbol calls attention to the information next to it and perhaps following it, which the user must absolutely observe! Any failure to observe this information can result in damage of all kinds, nullify the warranty, et cetera. This symbol WITHOUT a specific heading calls attention to the information next to it and perhaps following it, or any tips, which the user should absolutely observe! Any failure to observe such information or tip can result in damage of all kinds. Environmental protection This symbol on the product, in the operating instructions or the packaging indicates that the product must not be discarded via the normal household refuse at the end of its useful life. Instead it must be taken to a collection point for the recycling of electrical and electronic apparatus. The materials can be re-used according to their identification code. You can make an important contribution to the protection of our shared environment by recycling old equipment and making use of its basic materials. Dry and rechargeable batteries must be removed from the device and taken to the appropriate collection point. Please ask your local authority for the location of your nearest waste disposal site. This symbol calls attention to information and tips of all kinds, which should be observed by the user. P This symbol calls attention to information on the maintenance of the device, which should absolutely be observed by the user in order to ensure the long service life of the device. The sole purpose of this manual is to provide information; it is subject to amendment without prior notification. Graupner accepts no responsibility or liability for errors or inaccuracies which may occur in the information section of this manual. Contents 3 Safety Notes Please read carefully! We all want you to have many hours of pleasure in our mutual hobby of modelling, and safety is an important aspect of this. It is absolutely essential that you read right through these instructions and take careful note of all our safety recommendations. We also strongly recommend that you register without delay at https:// www.graupner.de/en/service/product_registration.aspx, as this ensures that you automatically receive the latest information relating to your product by e-mail. If you are a beginner to the world of radio-controlled model aircraft, boats and cars, we strongly advise that you seek out an experienced modeller in your field, and ask him or her for help and advice. If you ever dispose of this transmitter, these instructions must be passed on to the new owner. Application This radio control system may only be used for the purpose for which the manufacturer intended it, i. e. for operating radio-controlled models which do not carry humans. No other type of use is approved or permissible. ATTENTION: SAFETY IS NO ACCIDENT and RADIO-CONTROLLED MODELS ARE NOT PLAYTHINGS Even small models can cause serious personal injury and damage to property if they are handled incompetently, or if an accident occurs due to the fault of others. Technical problems in electrical and mechanical systems can cause motors to rev up or burst into life unexpectedly, with the result that parts may fly off at great speed, causing considerable injury. Short-circuits of all kinds must be avoided at all times. Safety Notes 4 Short-circuits can easily destroy parts of the radio control system, but even more dangerous is the acute risk of fire and explosion, depending on the circumstances and the energy content of the batteries. Aircraft and boat propellers, helicopter rotors, open gearboxes and all other rotating parts which are driven by a motor or engine represent a constant injury hazard. Do not touch these items with any object or part of your body. Remember that a propeller spinning at high speed can easily slice off a finger! Ensure that no other object can make contact with the driven components. Never stand in the primary danger zone, i. e. in the rotational plane of the propeller or other rotating parts, when the motor is running or the drive battery is connected. Please note that a glowplug engine or electric motor could burst into life accidentally if the receiving system is switched on when you are transmitting the transmitter. To be on the safe side, disconnect the fueltank or the flight battery. Protect all electronic equipment from dust, dirt, damp, and foreign bodies. Avoid subjecting the equipment to vibration and excessive heat or cold. Radio control equipment should only be used in “normal” ambient temperatures, i. e. within the range -10°C to +55°C. Avoid subjecting the equipment to shock and pressure. Check the units at regular intervals for damage to cases and leads. Do not re-use any item which is damaged or has become wet, even after you have dried it out thoroughly. Use only those components and accessories which we expressly recommend. Be sure to use only genuine matching Graupner connectors of the same design with contacts of the same material. When deploying cables ensure that they are not under strain, are not tightly bent (kinked) or broken. Avoid sharp edges, as they can chafe through insulating materials. Before you use the system, check that all connectors are pushed home firmly. When disconnecting components, pull on the connectors themselves – not on the wires. It is not permissible to carry out any modifications to the RC system components, as any such changes invalidate both your operating licence and your insurance cover. Installing the receiving system In a model aircraft the receiver must be packed in soft foam and stowed behind a stout bulkhead, and in a model boat or car it should be protected effectively from dust and spray. The receiver must not make direct contact with the fuselage, hull or chassis at any point, otherwise motor vibration and landing shocks will be transmitted directly to it. When installing the receiving system in a model with a glowplug or petrol engine, be sure to install all the components in well-protected positions, so that no exhaust gas or oil residues can reach the units and get inside them. This applies above all to the ON / OFF switch, which is usually installed in the outer skin of the model. Secure the receiver in such a way that the aerial, servo leads and switch harness are not under any strain. The receiver aerial should be at least 5 cm away from all large metal parts and any wiring which is not connected directly to the receiver. This includes steel and carbon fibre components, servos, electric motors, fuel pumps, cabling of all kinds, etc.. Ideally the receiver should be installed well away from any other installed equipment in the model, but in an easily accessible position. Under no circumstances allow servo leads to run close to the aerial, far less coiled round it! Ensure that cables are fastened securely, so that they cannot move close to the receiver aerial when the model is flying. Deploying the receiver aerial(s) The receiver and its aerials should be installed as far away as possible from all kinds of power system. If your model has a carbon fibre fuselage, the aerial tips must always be deployed outside the fuselage. The orientation of the aerial(s) is not critical, but we recommend installing them vertically (upright) in the model. If the receiver features aerial diversity (two aerials), the second aerial should be arranged at 90° to the first. Installing the servos Always install servos using the vibration-damping grommets supplied. The rubber grommets provide some degree of protection from mechanical shock and severe vibration. Installing control linkages The basic rule is that all linkages should be installed in such a way that the pushrods move accurately, smoothly and freely. It is particularly important that all servo output arms can move to their full extent without fouling or rubbing on anything, or being obstructed mechanically at any point in their travel. It is essential that you should be able to stop your motor at any time. With a glow motor this is achieved by adjusting the throttle so that the barrel closes completely when you move the throttle stick and trim to their end-points. Ensure that no metal parts are able to rub against each other, e. g. when controls are operated, when parts rotate, or when motor vibration affects the model. Metal-to-metal contact causes electrical “noise” which can interfere with the correct working of the receiver. Directing the transmitter aerial Transmitter field strength is at a minimum in an imaginary line extending straight out from the transmitter aerial. It is therefore fundamentally misguided to “point” the transmitter aerial at the model with the intention of obtaining good reception. When several radio control systems are in use on adjacent channels, the pilots should always stand together in a loose group. Pilots who insist on standing away from the group endanger their own models as well as those of the other pilots. However, if two or more pilots operating 2.4 GHz radio control systems stand closer together than 5 m, the down-link channel may be swamped, triggering a very premature range warning. If this should occur, walk away from the other pilots until the range warning ceases again. Pre-flight checking Before you switch on the receiver, ensure that the throttle stick is at the stop / idle end-point. Always switch on the transmitter first, and only then the receiver. Always switch off the receiver first, and only then the transmitter. ATTENTION: If you do not keep to this sequence, i. e. if the receiver is at any time switched on when “its” transmitter is switched OFF, then the receiver is wide open to signals from other transmitters and any interference, and may respond. The model could then carry out uncontrolled movements, which could easily result in personal injury or damage to property. Please take particular care if your model is fitted with a mechanical gyro: before you switch your receiver off, disconnect the power supply to ensure that the motor cannot run up to high speed accidentally. As it runs down, the gyro can generate such a high voltage that the receiver picks up apparently valid throttle commands, and the motor could respond by unexpectedly bursting into life. Range checking Before every session check that the system works properly in all respects, and has adequate range. Secure the model adequately, and ensure that no persons are standing in front of the model. Before you fly the model, carry out at least one complete check of all the working systems, and one complete simulated flight, in order to eliminate any possible system faults or model programming errors. In this regard it is essential to read the notes on pages 80 and 89. When operating a model, i. e. when flying or driving, do not operate the transmitter without the aerial fitted. Check that the transmitter aerial is firmly seated. Safety Notes 5 Safety Notes Operating your model aircraft, helicopter, boat or car WARNING: Never fly directly over spectators or other pilots, and take care at all times not to endanger people or animals. Keep well clear of high-tension overhead cables. Never operate your model boat close to locks and full-size vessels. Model cars should never be run on public streets or motorways, footpaths, public squares etc.. WARNING: Never switch off the transmitter while the model is in operation! However, if this does happen, keep calm and wait until the transmitter display goes off and the transmitter has shut down completely. This takes at least three seconds. Don’t switch the transmitter back on until then. Otherwise, there is a danger that the transmitter will get “hung up” immediately after being switched back on, causing you to lose control of the model. Then it will not be possible to restart the transmitter until you have switched it off again and have carried out the described procedure correctly. Towing operations WARNING: When operating towed models, keep a minimum distance of about 50 cm between the receiver units involved, or their aerials. If necessary, use satellite receivers. Otherwise, malfunctions caused by the return channel can not be excluded. 6 Safety Notes Checking the transmitter and receiver batteries It is essential to stop using the radio control system and recharge the batteries well before they are completely discharged. In the case of the transmitter this means – at the very latest – when the message “battery needs charging” appears on the screen, and you hear an audible warning signal. It is vital to check the state of the batteries at regular intervals – especially the receiver pack. When the battery is almost flat you may notice the servos running more slowly, but it is by no means safe to keep flying or running your model until this happens. Always replace or recharge the batteries in good time. Keep to the battery manufacturer’s instructions, and don’t leave the batteries on charge for longer than stated. Do not leave batteries on charge unsupervised. Never attempt to recharge dry cells, as they may explode. Rechargeable batteries should always be recharged before every session. When charging batteries it is important to avoid short-circuits. Do this by first connecting the banana plugs on the charge lead to the charger, taking care to maintain correct polarity. Only then connect the charge lead to the transmitter or receiver battery. Disconnect all batteries and remove them from your model if you know you will not be using it in the near future. Capacity and operating times This rule applies to all battery types: capacity diminishes with each charge. At low temperatures the battery’s internal resistance rises, and capacity falls. This means that its ability to deliver current and maintain voltage is reduced. Frequent charging, and / or the use of maintenance programs, tends to cause a gradual reduction in battery capacity. We recommend that you check the capacity of all your rechargeable batteries at least every six months, and replace them if their performance has fallen off significantly. Use only genuine Graupner rechargeable batteries! Suppressing electric motors All conventional (brushed) electric motors generate sparks between the commutator and the brushes, which cause more or less serious interference to the radio control system, depending on the type of motor. If an RC system is to work correctly, it is therefore important to suppress the electric motors, and in electric-powered models it is essential that every motor should be effectively suppressed. Suppressor filters reliably eliminate such interference, and should always be fitted where possible. Please read the notes and recommendations supplied by the motor manufacturer. Refer to the main Graupner FS catalogue or the Internet website at www.graupner.de/en for more information on suppressor filters. Servo suppressor filter for extension leads Order No. 1040 Servo suppressor filters are required if you are obliged to use long servo extension leads, as they eliminate the danger of de-tuning the receiver. The filter is connected directly to the receiver input. In very difficult cases a second filter can be used, positioned close to the servo. Using electronic speed controllers The basic rule is that the electronic speed controller must be chosen to suit the size of the electric motor it is required to control. There is always a danger of overloading and possibly damaging the speed controller, but you can avoid this by ensuring that the controller’s current-handling capacity is at least half the motor’s maximum stall current. Particular care is called for if you are using a “hot” (i. e. upgrade) motor, as any low-turn motor (small number of turns on the winding) can draw many times its nominal current when stalled, and the high current will then burn out the speed controller. Caution • Electrical ignition systems Ignition systems for internal combustion engines can also produce interference, which has an adverse effect on the working of the radio control system. Electrical ignition systems should always be powered by a separate battery – not the receiver battery. Be sure to use effectively suppressed spark plugs and plug caps, and shielded ignition leads. Keep the receiving system an adequate distance away from the ignition system. • Static charges warning: Lightning causes magnetic shock waves which can interfere with the operation of a radio control transmitter even if the thunderstorm actually occurs several kilometres away. For this reason … … cease flying operations immediately if you notice an electrical storm approaching. Static charges through the transmitter aerial can be life-threatening! • • • In order to fulfil the FCC RF radiation regulations applicable to mobile transmitting apparatus, the equipment’s aerial must be at least 20 cm from any person when the system is in use. We therefore do not recommend using the equipment at a closer range than 20 cm. Ensure that no other transmitter is closer than 20 cm from your equipment, in order to avoid adverse effects on the system’s electrical characteristics and radiation pattern. The radio control system should not be operated until the Country setting has been set correctly at the transmitter. This is essential in order to fulfil the requirements of various directives - FCC, ETSI, CE etc. Please refer to the instructions for your particular transmitter and receiver for details of this procedure. Check all working systems and carry out at least one full range check on the ground before every flight, in order to show up any errors in the system and the model’s programming. Never make any changes to the programming of the transmitter or receiver whilst operating a model. Care and maintenance Don’t use cleaning agents, petrol, water or other solvents to clean your equipment. If the case, the aerial etc. gets dirty, simply wipe the surfaces clean with a soft dry cloth. P Components and accessories attention: As manufacturers, the company of Graupner GmbH & Co. KG recommends the exclusive use of components and accessories which have been tested by Graupner and approved for their capability, function and safety. If you observe this rule, Graupner accepts responsibility for the product. Graupner cannot accept liability for non-approved components or accessories made by other manufacturers. It is not possible for Graupner to assess every individual item manufactured by other companies, so we are unable to state whether such parts can be used without incurring a safety risk. Liability exclusion / Compensation The sole purpose of this manual is to provide information; it is subject to amendment without prior notification. Graupner accepts no responsibility or liability for errors or inaccuracies which may occur in the information section of this manual. It is not possible for Graupner to ensure that the user observes the installation and operation instructions, and the recommended conditions and methods when installing, operating, using and maintaining the radio control components. For this reason Graupner denies all liability for loss, damages or costs which arise through misuse or mishandling of this equipment, or are connected with such use in any way. Unless obliged by law, Graupner’s obligation to pay compensation, regardless of the legal argument employed, is limited to the invoice value of that quantity of Graupner products which were immediately involved in the event in which the damage occurred, unless the Safety Notes 7 Safety notes and handling instructions relating to NickelMetal-Hydride rechargeable batteries company is deemed to have unlimited liability on account of deliberate or gross negligence. Furthermore, any claims can be considered only if there is a log file, see under “Data recording / storage” on page 23. Likewise, the transmitter must always be updated with the latest software. To always be informed without delay of important software updates, you should therefore be sure to register at www.graupner.de/en/service/product_registration. aspx. That is the only way for you to be informed of new updates by email automatically. As with all sophisticated technical products, it is vitally important that you observe the following safety notes and handling instructions if you wish the equipment to operate safely and reliably for an extended period. • Safety notes • • • • • • • • 8 Safety Notes attention: Individual cells and rechargeable batteries are not playthings, and must be kept well away from children. Store rechargeable cells and batteries out of the reach of children. Check that the batteries are in perfect, serviceable condition before every use. Do not re-use defective or damaged cells or batteries. Rechargeable cells and batteries must be used within the specified limits stated for the corresponding cell type. Do not heat, incinerate or short-circuit rechargeable cells or batteries, and never charge them with excessive currents or reversed polarity. Never use rechargeable batteries consisting of parallel-wired cells, combinations of old and new cells, cells of different construction, size, capacity, make, brand or cell type. Batteries installed inside equipment should always be removed from the device when it is not in use and not about to be used. Always keep equipment switched off in order to avoid deep-discharged cells. Batteries must be recharged in good time. The battery to be charged should be placed on a non-inflammable, heat-resistant, non-conductive surface for the whole of the charge period. Keep inflammable and volatile objects and materials well • • • • • • • • clear of the charging area. Batteries must always be supervised when on charge. Never exceed the maximum fast-charge current specified for the cell type in use. If the battery heats up to more than 60°C whilst on charge, halt the charge process immediately and allow the pack to cool down to about 30°C. Never recharge a battery which is already charged, hot, or not completely discharged. Do not make any modifications to batteries. Never solder or weld directly to cells. If incorrectly handled, rechargeable batteries are at risk of combustion, explosion, corrosive action and burns. Suitable extinguishing materials include fire blankets, CO2 fire extinguishers and sand. Escaped electrolyte is corrosive - do not allow it to contact skin or eyes. In an emergency rinse the area immediately with plenty of clean water before seeking medical help. The cells’ air vents must never be blocked or sealed, e. g. by solder. When soldering, the iron temperature should not exceed 220°C, and each joint should be completed in less than twenty seconds. To avoid cell deformation, do not exert excessive mechanical pressure on battery cells. If a battery should be accidentally overcharged, use the following procedure: Simply disconnect the battery and leave it on a non-inflammable surface (e. g. stone floor) until it has cooled down. Never hold the battery in your hand, as there is a risk that cells might explode. Always observe the recommended rates for charging and discharging. General information The capacity of your rechargeable battery diminishes with every charge / discharge process. Stored batteries may eventually exhibit reduced capacity. Storage Batteries should not be stored in a completely discharged state. Store them in a dry enclosed space at an ambient temperature of +5°C to +25°C. If you are storing a battery for a period longer than four weeks, ensure that the cell voltage does not fall below 1.2 V Balancing individual battery cells • To balance new battery cells, i. e. to bring them all to the same state of charge, charge them at what is known as the ‘normal’ rate until they are full. As a general guideline a fully discharged battery needs to be charged for a period of twelve hours at a current corresponding to one tenth of the capacity printed on the cell label (the “1/10C” method). After this treatment all the cells will be fully charged, and exhibit the same voltage. This method of balancing battery cells should be repeated after every ten fast-charge processes, so that the cells are repeatedly balanced; this helps to ensure an extended useful life for your batteries. • If you have the facilities to discharge individual cells, we recommend that you make use of this before every charge process. Otherwise the battery pack should be run down to a discharge voltage of 0.9 V per cell. For example, this corresponds to a final discharge voltage of 3.6 V in the case of the four-cell pack used in the transmitter. Charging NiMH batteries should only be charged using the specified currents, charge times and temperature range, and should be supervised constantly when on charge. If you do not have access to a suitable fast charger, i. e. one which allows you to set the charge current accurately, then the battery should always be recharged using the “normal” charge rate of 1/10C; see the example stated above. Wherever possible, transmitter batteries should always be recharged at the 1/10C rate, in order to avoid differences in cell states. The charge current must never exceed the maximum permissible value stated in the transmitter instructions. Fast charging • If your charger offers these facilities, then set the Delta Peak trigger voltage to 5 mV per cell. However, most battery chargers are set to a fixed value of 15 … 20 mV per cell, and can therefore be used equally well for NiCd batteries and for NiMH batteries. If you are unsure, refer to the operating instructions or ask your dealer whether the charger is also suitable for NiMH batteries. If you are still not sure, charge your batteries at half of the stated maximum charge current. Discharging All rechargeable batteries sold by Graupner and GM-Racing are suitable for a maximum continuous current load of 6C … 13C, according to battery type (refer to the manufacturer’s specification!). The higher the continuous current load, the shorter the batteries’ useful life. • Use your battery until its performance falls off, or until the low voltage warning is triggered. attention: When stored for a long period, the cell voltage should not be allowed to fall below 1.2 V. This means that you may have to recharge the battery before storing it. • Reflex charging and charge / discharge (cycle) programs shorten the effective life of batteries unnecessarily, and are only suitable for checking battery quality or “reviving” relatively old cells. It also makes no sense to charge / discharge a battery before using it - unless you simply wish to check its quality. Disposal of exhausted dry and rechargeable batteries The German Battery Order places a legal requirement on every consumer to return all used and exhausted dry cells and rechargeable batteries. It is prohibited to dispose of these items in the ordinary domestic waste. At no charge to the user, old dry and rechargeable batteries can be surrendered at local authority collection points, Graupner retail outlets, and any other shop where dry and rechargeable batteries of the same type are sold. You can also send batteries supplied by us to the following address - with adequate pre-paid postage - for disposal: Graupner GmbH & Co. KG Service: Gebrauchte Batterien (Used batteries) Henriettenstr. 94 - 96 D-73230 Kirchheim unter Teck You can make an important contribution to environmental protection in this way. Caution: Damaged batteries may require special packaging before despatch, as some contain highly toxic materials!!!!! Safety Notes 9 mx-16 the latest generation of radio control technology HoTT (Hopping Telemetry Transmission) is the synthesis of expertise, engineering and world-wide testing by professional pilots. The equipment operates on the 2.4 GHz band, and offers bi-directional communication between transmitter and receiver via a down-link channel integrated into the receiver. The mx-16 HoTT RC system is based on the Graupner/JR mc-24 computer radio control system which was introduced back in 1997. It has been developed specifically for the beginner, but the mx-16 HoTT is still capable of controlling all current model types without problem - whether fixed-wing model or helicopter, model boat or car. In the area of fixed-wing models and helicopters it is often necessary to employ complex mixer functions for the control surfaces or the swashplate actuation system. Computer technology enables you to activate a vast range of functions to cope with special model requirements – just by pressing a button. With the mx16 HoTT all you do is select the appropriate model type, and the software then presents you automatically with the appropriate mixer and coupling functions. This means that the transmitter requires no additional modules in order to implement complex coupled functions, and you can forget all about old-fashioned mechanical mixers in the model. The mx-16 HoTT provides an extremely high level of safety and reliability in use. The mx-16 HoTT offers twenty model memories, each of which can store model settings for different flight phases. Individual phases can be called up in flight simply by operating a switch, so that you can try out various settings quickly and without risk. This can be for test purposes or for varying parameters for different phases of flight. 10 Introduction The large graphic screen makes operating the transmitter a simple, intuitive process. Mixers and other functions can be displayed in graphic form, and this is extraordinarily helpful. The beginner quickly becomes familiar with the different functions thanks to the clear, logically arranged program structure. Four-way touch-sensitive buttons to left and right of the high-contrast screen are used to enter settings, allowing the user to exploit all the options he needs, in accordance with his experience in handling radio-controlled models. In theory the Graupner|SJ HoTT process allows more than 200 models to be operated simultaneously. Although in practice the mixed operation of different technical systems in the 2.4 GHz ISM band – as required by the approval regulations – reduces this number considerably. Generally, however, it will always be possible to operate even more models simultaneously on the 2.4 GHz band than on the 35 / 40 MHz frequency bands which we have used to date. However, the actual limiting factor – as it has always been – is likely to remain the size of the (air-) space available. The simple fact that no frequency control procedure is necessary equates to an enormous gain in safety, especially at flying sites such as gliding slopes where groups of pilots may be distributed over a large area, with nobody in overall control. The integral Telemetry menu provides a simple means of accessing data and programming HoTT receivers. For example, this method can be used to map receiver outputs, distribute control functions to multiple servos, and match servo travels and directions to each other. This manual describes each menu in detail, and also provides dozens of useful tips, notes and programming examples to complement the basic information. More general modelling terms, such as Transmitter controls, Dual-Rates, Butterfly (Crow) and many others, are all explained in the manual. Please refer to the Appendix for additional information on the HoTT system. This manual concludes with the transmitter’s conformity declaration and guarantee certificate. Please read the safety notes and the technical information. We recommend that you read right through the instructions with great care, and check all the functions as described in the text. This can be carried out simply by connecting servos to the supplied receiver, and watching their response as you program the transmitter. However, please read the notes on page 20 in this regard. This is the quickest method of becoming familiar with the essential procedures and functions of the mx16 HoTT. Always handle your radio-controlled model with a responsible attitude to avoid endangering yourself and others. The Graupner team wishes you great pleasure and success with your mx-16 HoTT - a radio control system of the latest generation. Kirchheim-Teck, February 2013 mx-16 Computer System Eight-channel radio control set with Graupner|SJ HoTT 2.4 GHz technology (Hopping Telemetry Transmission) Graupner|SJ HoTT technology offers extreme reliability in use, with bi-directional communication between transmitter and receiver, integrated telemetry, speech output via earphone socket and ultrafast response times. Simplified programming technology with capacitive programming touch-buttons. High-contrast, eight-line graphic screen with blue backlighting for ultra-clear display of all set-up parameters and telemetry data. Telemetry data is stored on a micro-SD memory card. USB socket for reading out and saving model memory data, and loading firmware updates. • Micro-computer radio control system exploiting the latest Graupner|SJ HoTT 2.4 GHz technology • Bi-directional communication between transmitter and receiver • Five different languages English, French, German, Italian and Spanish • Ultra-fast response times through direct, ultra-reliable data transmission from the main processor to the 2.4 GHz RF module. No additional delay caused by detours through a module processor. • Telemetry menu for displaying telemetry data, and programming receiver outputs and optional sensors. • Telemetry display shows numerous programming and analysis functions directly on the transmitter screen. • Speech output can be called up using freely programmable switches • User-selectable servo cycle times for digital servos, min. 10 ms • Short, folding aerial • Methods of operation and programming based on the proven concepts of the mc-19 to mc-24 • High-contrast graphic screen with blue backlighting ensures perfect monitoring of set-up parameters, such as model type, model memory, timers and operating voltage. • Function encoder with two four-way touch-sensitive buttons for simplified programming and accurate settings • Key-Lock function to guard against accidental operation. • Four programmable flight phases • Twenty model memories, with storage of all model-specific programming and set-up parameters Description of radio control set 11 mx-16 Computer System Eight-channel radio control set with Graupner|SJ HoTT 2.4 GHz technology (Hopping Telemetry Transmission) • Seven switches (two three-way switches, three twoway switches and two momentary switches), plus three digital controls - already installed and extremely versatile • Unrestricted assignment of all switches to switched functions simply by operating the appropriate switch • Internal real-time clock for dating log files • User-replaceable CR2032 buffer battery for internal real-time clock • Storage of model memories using the latest battery-free back-up system • Eight control functions with simplified, very convenient assignment of transmitter controls for auxiliary functions, such as switches and proportional controls • Convenient mode selector provides simple method of changing the stick mode (modes 1 - 4, e. g. throttle right / throttle left). When you change modes, all the affected settings are switched at the same time. • Graphical servo display provides a straightforward overview of the servo set-up, and a swift method of checking servo travels • Receiver output swap • Comprehensive programs for fixed-wing model aircraft and helicopters: Fixed-wing menu for: 1 AIL, 1 AIL + 1 FLAP, 2 AIL, 2 AIL + 1 or 2 FLAP, V-tail, delta / flying wing, two elevator servos Fixed-wing mixer: diff aile, diff.flaps, ail rudd, ail flaps, brake elev, brake flap, brake aile, elev flap, elev aile, flap elev, flap aile and diff. reduction • Heli menu: 1-point, 2-point, 3-point and 4-point 12 Description of radio control set • • • • • • • • linkages (1 servo, 2 servo, 3sv(2roll), 3sv(140°), 3sv(2nick (pitch-axis)), 4 SV (90°)) Swashplate limiter Servo travel adjustment +/- 150% for all servo outputs, variable separately for each side (Single Side Servo Throw) Variable sub-trim, range +/- 125%, for adjusting the neutral position of all servos Servo reverse, programmable for all servos EXPO / DUAL-RATE system, separately variable, can be switched in-flight, flight phase programmable Stopwatch / count-down timer with alarm function Model memory copy function Integral DSC socket for use with flight simulators and Trainer systems General features of the HoTT system • Simple, ultra-fast binding of transmitter and receiver • Multiple receivers can be bound per model for parallel operation • Extremely fast re-binding, even at maximum range • Two-receiver satellite operation using special cable connection • Range-check and warning function • Receiver low-voltage warning on transmitter screen • Ultra-wide receiver operating voltage range: 3.6 V to 8.4 V (fully operational down to 2.5 V) • Fail-Safe • Unrestricted channel assignment (channel-mapping), mixer functions and all servo settings programmable in the Telemetry menu • Up to four servos can be actuated simultaneously as a block, with a servo cycle time of 10 ms (digital • • • • • servos only) Optimised frequency hopping and broad channel spread for maximum interference rejection Intelligent data transmission with corrective function Real-time telemetry analysis More than 200 systems can be operated simultaneously Future-proof update capability using USB port The set Order No. 33116 contains mx-16 HoTT micro-computer transmitter with integral 4NH-2000 RX RTU flat-pack NiMH transmitter battery, Order No. 33116.2 (specification reserved), plug-type battery charger (5,6 V / 200 mAh), Graupner|SJ GR-16 HoTT bi-directional receiver, Order No. 33508, micro-SD card, USB interface, Order No. 7168.6 and adapter lead, Order No. 7168.6S. Recommended battery chargers (optional) Order No. Description 6411 6463 6464 6466 6468 6469 6470 6475 6478 6480 Ultramat 8 Ultramat 12 plus Ultramat 14 plus Ultra Trio plus 14 Ultramat 16S Ultra Trio Plus 16 Ultramat 18 Ultra Duo Plus 45 Ultra Duo Plus 60 Ultra Duo Plus 80 220 V mains conn. 12 V DC connect. NiCd NiMH LiPo Lead-ac. Integral charge. lead Suitable for the following battery types x x x x x x x x x x x x x x x x x x x x x x x x x x x x x x x x x x x x x x x x x x x x x x x x x x x x x x x x x x x x x x x x x x To charge the batteries you will also need the transmitter charge lead, Order No. 3022 and the receiver charge lead, Order No. 3021. For details of additional battery chargers, and details of the chargers listed here, please refer to the main Graupner FS catalogue, or our Internet site at www.graupner.de/en. Specification, mx-16 HoTT transmitter Specification, GR-16 HoTT receiver Frequency band 2,4 … 2,4835 GHz Operating voltage 3,6 … 8,4 V* Modulation FHSS Current drain ca. 70 mA Transmitter power 100 mW EIRP Frequency band 2,4 … 2,4835 GHz Control functions Eight functions; four with trims Modulation FHSS Temperature range -10 … +55°C Aerial Aerial folding Operating voltage 3,4 … 6 V Current drain approx. 180 mA Diversity aerials, 2 x approx. 145 mm long, approx. 115 mm encapsulated and approx. 30 mm active Dimensions approx. 190 x 195 x 90 mm Servo sockets 8 Weight approx. 770 g with transmitter battery Sensor socket 1 Temperature range approx. -10° … +55°C Dimensions approx. 46 x 21 x 14 mm Weight approx. 12 g Accessories Order No. Description 1121 Neckstrap, 20 mm wide Neckstrap, 30 mm wide 70 3097 Wind-shield for hand-held transmitter * The permissible operating voltage range stated above applies to the receiver only! Please note in this regard that the receiver’s input voltage is passed directly (i.e. unregulated) to the servo sockets, but the permissible operating voltage range of the overwhelming majority of servos, speed controllers, gyros etc. which can be connected to the receiver is only 4.8 to 6 Volt! Trainer leads for mx-16 HoTT: see page 157 Replacement parts Order No. Description 2498.4FBEC 4NH-2000 RX RTU, flat-pack 33800 HoTT transmitter aerial For information on additional accessories please refer to the Appendix or visit our Internet site at www.graupner. de/en. Alternatively you can enquire at your local model shop, where the staff will be pleased to advise you. Description of radio control set 13 Operating Notes Transmitter power supply The mx-16 HoTT transmitter is fitted as standard with a high-capacity rechargeable 4NH-2000 RX RTU NiMH battery (Order No. 2498.4FBEC) (specification reserved). When delivered, the standard rechargeable battery is not charged. When you are using the transmitter you can monitor the battery voltage on the LCD screen. If the voltage of the transmitter battery falls below a certain voltage (default 4.7 V), which can be set in the “Battery warning threshold” line of the “Basic settings” menu, page 134, you will hear an audible warning signal. The screen then displays a message reminding you that the transmitter battery needs to be recharged. stop batter y needs 4.7 charging!! x Mx 0:22h #01 0:00 0:00 HoTT 0.0V Always recharge the transmitter battery in good time. When you see this message, cease operations immediately and recharge the transmitter battery. Note: Ensure that the correct battery type is set in the “Basic settings” menu on page 134! NIMH must be set as the standard value. Charging the transmitter battery The rechargeable NiMH transmitter battery can be recharged with the battery charger (Order No. 33116.2) supplied in the set, using the charge socket located on the right-hand side of the transmitter. Leave the battery 14 Operating Notes inside the transmitter for charging, to avoid premature damage to the internal battery socket. As an approximate guideline a discharged battery should be charged for twelve hours at a current corresponding to one tenth of the capacity printed on the pack. If you are using the standard transmitter battery and the charger supplied in the set, this current is 200 mA. Never use charger plugs of other manufacturers or chargers designed for other battery types. If the output voltage is too high, or if the plug has any incorrect polarity (see below), immense damage can result. We recommend labelling the charger plug accordingly as needed. The transmitter must be switched “OFF” for the whole period of the charge process. Never switch on the transmitter when it is still connected to the charger; even a very brief interruption in the process can cause the charge voltage to rise to the point where the transmitter is immediately damaged. For this reason check carefully that all connectors are secure, and are making really good contact. Polarity of the mx-16 HoTT charge socket Commercially available battery charge leads produced by other manufacturers are often made up with the opposite polarity. For this reason it is essential to use only the genuine Graupner charge lead, Order No. 3022. Using automatic battery chargers As standard the charge socket is protected against short-circuit by a diode. However, genuine Graupner automatic battery chargers are still able to detect the voltage of the battery. The maximum charge current must not exceed 1 A, otherwise the diode and possibly other components may be damaged. If possible, set the delta peak voltage difference of your fast charger to a value in the range 10 mV … 20 mV or equivalent, as described in the charger’s instructions; this ensures that it is suitable for fast-charging NiMH cells. attention: First connect the banana plugs on the charge lead to the charger, and only then connect the other end of the charge lead to the charge socket on the transmitter. When the charge lead is connected to the transmitter, never allow the bare ends of the plugs to touch! To avoid damage to the transmitter, the charge current must never exceed 1 A. If necessary, limit the current on the charger itself. Removing the transmitter battery To remove the transmitter battery, first disengage the cover over the battery compartment on the back of the transmitter, then lift it off: Remove the battery, then carefully pull on the power lead to disconnect the transmitter battery connector. Installing the transmitter battery Hold the connector attached to the transmitter battery in such a way that the black or brown wire faces the aerial, and the unused socket of the battery connector is on the side facing the bottom, then push the battery connector onto the three pins projecting out of the inside of the transmitter, in the direction of the circuit board. (The battery connector is protected against reversed polarity by two chamfered edges; see illustration). Polarity of Finally place the battery in the comtransmitter battery connector partment, and close the cover. The purpose of this battery is to protect the system from loss of date and time if the transmitter’s power supply is disconnected; for example, when the transmitter battery is replaced. Battery timer, bottom left corner of the screen This timer displays the cumulative operating time of the transmitter since the last time the transmitter battery was charged. This timer is automatically reset to “0:00” when the transmitter detects that the voltage of the transmitter battery is significantly higher than the last time it was switched on, e. g. as a result of a charge process. #01 5.6V 0:00h stop flt 0:00 0:00 Mx HoTT 0.0V CR 2032 lithium battery On the left-hand side of the transmitter circuit board you will find a holder fitted with a user-replaceable CR 2032 lithium battery: Operating Notes 15 Operating Notes Receiver power supply A wide range of rechargeable four-cell and five-cell NiMH batteries varying in capacity is available for use as the receiver power supply. If you are using digital servos we recommend that you use a five-cell (6 V) pack of generous capacity. If your model is fitted with a mixture of digital and analogue servos, it is important to check the maximum permissible operating voltage of all the types. The PRX unit, Order No. 4136, provides a stabilised receiver power supply with a user-variable voltage from one or two receiver batteries; see Appendix. For reasons of safety battery boxes or dry cells should never be used. The voltage of the airborne power supply is displayed on the transmitter screen while the model is flying: #01 5.2V 2:22h stop flt 0:00 0:00 M HoTT 5.5V If the voltage falls below the pre-set warning threshold - 3.8 Volt as standard, but variable in the Telemetry menu; see page 146 - a visual and audible low-voltage warning is triggered. Nevertheless it is important to check the state of the batteries at regular intervals. Don’t put off charging the batteries until the warning signal is triggered. Note: 16 Please refer to the main Graupner FS catalogue or visit the Internet site at www. graupner.de/en for full details of batteries, Operating Notes chargers, measuring equipment and battery monitor units. Charging the receiver battery The charge lead, Order No. 3021, can be connected directly to the NC receiver battery for charging. If the battery is installed in a model and you have installed one of the following switch harnesses: Order No. 3046, 3934 or 3934.1 or 3934.3, the battery can be charged via the separate charge socket, or the charge socket which is built into the switch. The switch on the switch harness must be left at the “OFF” position for charging. Polarity of the receiver battery connector General notes on battery charging • Observe the recommendations provided by the charger manufacturer and the battery manufacturer at all times. • Keep to the maximum permissible charge current stated by the battery manufacturer. • The maximum charge current for the transmitter battery is 1.5 A. Limit the charge current to this value on the charger. • If you wish to charge the transmitter battery at a current higher than 1.5 A, you must first remove the pack from the transmitter, otherwise you risk damaging the circuit board through overloading the conductor tracks, and / or overheating the battery. • Carry out a series of test charges to ensure that the automatic charge termination circuit works correctly with your battery. This applies in particular if you are using an automatic charger designed for NiCd batteries to recharge the standard NiMH battery. • You may need to adjust the charger’s termination behaviour, if it provides this option. • Do not discharge the battery or carry out a battery maintenance program via the integral charge socket. The charge socket is not suitable for this application. • Always connect the charge lead to the charger first, and only then to the transmitter or receiver battery. Observing this rule eliminates the danger of accidental short-circuits between the bare contacts of the charge lead plugs. • If the battery becomes hot when on charge, it is time to check the pack’s condition. Replace it if necessary, or reduce the charge current. • Never leave batteries unsupervised when on charge. • Read and observe the safety notes and handling information in the section starting on page 8. Adjusting stick length Both sticks are infinitely variable in length over a broad range, enabling you to set them to suit your personal preference. Hold the bottom half of the knurled grip firmly, and unscrew the top section: Now screw the stick top in or out (shorter or longer) to the length you prefer before tightening the top and bottom sections against each other to fix the stick top. Opening the transmitter case Please read the following notes carefully before you open the transmitter. If you have no experience in such matters, we recommend that you ask your nearest Graupner Service Centre to carry out the work for you. The transmitter should only be opened in the following cases: • When a self-neutralising stick needs to be converted to non-neutralising action, or a non-neutralising stick to a self-neutralising action. • If you wish to adjust the stick centring spring tension. Before opening the transmitter check that it is switched off (move Power switch to “OFF”). Open the battery compartment and remove the transmitter battery as described on the previous double page, together with any micro-SD card already installed. After this, use a PH1-size cross-point screwdriver to undo the six screws recessed into the back panel of the transmitter, as shown in the illustration: Arrangement of the case back screws Hold the two case sections together with your hand, and turn the unit over to allow these six screws to fall out onto the table. Now carefully raise the case back and fold it open to the right, as if you were opening a book. attention: Two multi-core cables connect the lower shell to the transmitter electronics located in the top section. Please take great care not to damage this cable! Important: • Do not modify the transmitter circuit in any way, as this invalidates your guarantee and official approval for the system. • Do not touch any part of the circuit boards with any metal object. Avoid touching the contacts with your fingers. • Never switch the transmitter on while the case is open. Please note the following points when closing the transmitter: • Make sure that no cables are jammed between the transmitter case sections when you close the back. • Check that the two case sections fit together flush all round before fitting the retaining screws. Never force the two case components together. • Fit the case screws in the existing threads, and tighten them gently. Over-tightening them will strip the threads in the plastic. • Remember to re-connect the battery. Operating Notes 17 Operating Notes Converting the dual-axis stick units Self-centring action Either or both sticks can be converted from self-neutralising to non self-neutralising action: start by opening the transmitter as described on the previous page. If you wish to change the standard stick unit arrangement, start by locating the screw on the left-hand stick unit shown circled in white in the photo below. Folding aerial Adjuster screws for stick centring force Self-centring screw Note: The right-hand stick unit is buitl-in turned of about 180 °, i. e. the screw you require is located on the right, below centre. Self-centring screw Do not touch transmitter circuit board Brake springs Brake springs Adjuster screws Adjuster screws Right-hand stick unit Charge socket User-replaceable CR2032 lithium cell, acting as buffer battery for the integral real time clock 18 Operating Notes Left-hand stick unit Turn this screw clockwise until the stick on that side moves freely from one end-stop to the other; alternatively unscrew it until the stick is fully self-centring again. Do not touch transmitter circuit board Memory card slot Brake spring and ratchet You can alter the braking force of the stick by adjusting the outer of the two screws circled in white in the next picture; adjusting the inner screw alters the strength of the ratchet: Stick centring force The centring force of the sticks is also variable to suit your preference. The adjustment system is located adjacent to the centring springs; see the white circles in the following photo. You can set the preferred centring spring force by rotating the corresponding adjuster screw using a cross-point screwdriver: • Turn to the right = harder spring tension; • Turn to the left = softer spring tension. vertical Note: The right-hand stick unit is buitl-in turned of about 180 °, i. e. the screw you require is located on the right, below centre. horizontal Note: The right-hand stick unit is buitl-in turned of about 180 °, i. e. the screw you require is located on the right, below centre. Operating Notes 19 Description of transmitter Front of transmitter Attaching the transmitter neckstrap You will find a strap lug mounted in the centre of the front face of the mx-16 HoTT transmitter, as shown in the drawing on the right. This lug is positioned in such a way that the transmitter is perfectly balanced even when suspended from a neckstrap. Order No. 1121 Neckstrap, 20 mm wide Order No. 70 Neckstrap, 30 mm wide Central Status LED Aerial with folding / rotating base Rotary proportional control CTRL 8 Rotary proportional control CTRL 7 Carry handle 2-position switch SW 8 2-position switch SW 9 3-position switch SW 4/5 2-position switch SW 2 2-position momentary switch SW 1 3-position switch SW 6/7 2-position switch SW 3 Rotary proportional control CTRL 6 Left-hand stick Important note: In the transmitter’s standard form any servos connected to the receiver can initially only be operated using the dual-axis sticks. For maximum flexibility, all the other transmitter controls (CTRL 6 ... 8, SW 1 ... 9) are “free” in software terms, and can be assigned to any channels you like, enabling you to set up the system to suit your personal preference or the requirements of a particular model. This is carried out in the “contr set.” menu, as described on pages 94 (fixed-wing models) and 96 (model helicopters). 20 Description of transmitter Neckstrap lug Right-hand stick Trim Trim ON / OFF switch Right-hand touch-button Left-hand touch-button LCD screen Rear of transmitter Case screw Case screw Earphone / headphone socket Data socket for connecting Smart-Box, Order No. 33700 Five-pin mini-USB socket for connecting transmitter to a PC DSC socket for connecting flight simulators and for Teacher mode Case screw Case screw mini-USB socket This socket can be used to connect the transmitter to a PC running Windows XP, Vista or 7. The software required at the PC, including a suitable USB driver, can be found in the Download section for that product at www.graupner.de/en. Once you have installed the software required, you can update the transmitter via this connection as and when required, or simply set the correct date and time of day. Data socket For connecting the optional Smart-Box, Order No. 33700. For more details about the Smart-Box please refer to the main Graupner FS catalogue, or refer to that product on the Internet at www.graupner.de/en. Transmitter battery charge socket Battery compartment cover Case screw Headphone socket The central socket at the bottom edge of the back panel name plate is intended for connecting a standard commercial earphone or headphones fitted with a 3.5 mm barrel plug (not included in the set). Signals and voice messages associated with the Telemetry menu are generated via this socket, as are the transmitter’s audible signals. The default language for speech output is German. For more information on this please refer to “Voice messages” in the “HIDDEN MODE” section starting on page 26, and the “Telemetry” section starting on page 137. The volume of the headphone output can be adjusted in the “Voice volume” line of the “Basic settings” menu; see page 135. Case screw Description of transmitter 21 DSC socket Card slot Connenction socket for flight simulators or trainer systems The original function of this socket was for “Direct Servo Control”, and that’s why the abbreviation is still in use. However, for technical reasons “direct servo control” is no longer possible with the HoTT system using a diagnosis lead. The mx-16 HoTT transmitter’s standard two-pole DSC socket is now used as a Trainer (buddy box) socket (Teacher or Pupil), and as an interface for flight simulators. For the DSC connection to work you must check the following: 1. Carry out any adjustments required in the appropriate menus: See page 154 for information on setting up the mx-16 HoTT transmitter to work as part of a Trainer system. 2. ALWAYS leave the transmitter’s On / Off switch in the “OFF” position when using a flight simulator, and when using the mx-16 HoTT transmitter as a Pupil unit in a Trainer system, for only in this position is the RF section of the transmitter module switched off (no RF signal) even when the DSC lead is plugged in. At the same time the transmitter’s current drain is reduced slightly. The central Status LED should now glow a constant red, and the abbreviation “DSC” appears in the transmitter’s base display on the left, below the model number. At the same time the display of telemetry symbols is suppressed: 22 Description of transmitter PUPIL #11 DSC 5.6V 0:01h Data storage stop flt 0:00 0:00 HoTT The transmitter is now ready for use. In contrast, when the mx-16 HoTT is used in Teacher mode, the transmitter must be switched on before the appropriate cable is plugged in. 3. Connect the other end of the connecting lead to the appropriate apparatus, taking into account the operating instructions supplied with that device. Important: Ensure that all connectors are firmly seated in their sockets. Note regarding flight simulators: The range of flight simulators available commercially is now very wide, and you may find that it is necessary to swap over certain contacts at the barrel connector or the DSC module. This work must be carried out by a Graupner Service Centre. micro-SD and micro-SDHC When you switch off the mx-16 HoTT transmitter and remove the battery compartment cover, you will see the card slot for memory cards (of the micro-SD and micro-SDHC type) in the right-hand side of the compartment: In addition to the memory card supplied as standard, it is possible to use any standard commercial micro-SD memory card with a capacity of max. 2 GB, and any micro-SDHC card with a capacity of up to 32 GB. However, the manufacturer recommends the use of memory cards with capacities up to only 4 GB, as these are completely adequate in all normal circumstances. The memory cards for which the transmitter is intended are familiar from their use in digital cameras and mobile telephones. Place the card in the slot with the contacts facing up, towards the back panel, and push it in until it locks. When the battery has been installed and the battery compartment closed, switching the transmitter on causes a number of folders to be created on the memory card. At the same time a stylised memory card graphic appears in the base display to indicate that a memory card is inserted. #01 5.2V 3:33h stop flt 0:00 0:00 M HoTT 5.5V Note: If there is an SD card installed, withdraw it BEFORE you remove the transmitter’s back panel, otherwise there is a risk that you will damage the card. Prepare the memory card as described, remove it from the transmitter, and insert it in a suitable card reader. Make sure the reader is connected to your PC or laptop, and copy the files previously downloaded from the Download page for your transmitter into the appropriate folder. Finally remove the memory card from the card reader, and replace it in the transmitter. Data recording / storage The process of saving data on the SD card is coupled to the flight timer: if the timer is started, then data saving commences - provided that a suitable memory card is in the card slot, and a telemetry connection to the receiver exists - and ceases again when the flight timer is stopped. The flight timer is started and stopped as described in the “Timers” section on page 77 for fixedwing models, and pages 86 for model helicopters. When data is being recorded, the card symbol flashes constantly and slowly. When data is being written to the memory card, the memory card symbol swells from left to right to indicate the process. When a data storage process is concluded, you will find an (empty) “Models” folder and a “Log-Data” folder on the memory card. The latter contains the log files, stored in sub-folders named “Model name”, using the format 0001 Year-Month-Day.bin, 0002 Year-Month-Day.bin etc. However, if a model memory has not yet been named, then you will find the associated log files in a sub-folder named “NoName” when you remove the memory card from the transmitter and insert it in the card slot of a PC or laptop. The data can subsequently be analysed on a compatible PC using the PC program available on the Download page for the transmitter at www.graupner.de/ en. Firmware updates / Changing the screen language It is possible to replace and / or update the transmitter’s firmware - and the transmitter’s screen language, if necessary - under menu control, as described in detail on page 27 under the title “Firmware update” in the “Hidden Mode” chapter. In addition to a German version of the firmware, the SD card supplied in the set as standard also contains firmware versions in English, French, Italian and Spanish; this information was correct at the time these instructions went to press. Corresponding updates and information can be found in the Download area of www.graupner.de/en under the product concerned. can be replaced by a voice package in another language at any time. For more information on this please refer to the “HIDDEN MODE” section starting on page 26. Importing and exporting model memories Any model memories can be copied onto a memory card in the transmitter, or copied from the card into the transmitter, so that you can exchange data between identical transmitters, and also back up your data. For more information please see the “Model memories” section starting on page 70. Note: Some of the special characters used in certain model names cannot be accepted due to specific limitations of the FAT or FAT32 file system used by memory cards. During the copy process they are replaced by a tilde (~) character. Importing voice files As mentioned in the “Headphone socket” section on page 21, the signals associated with the Telemetry menu and voice messages can be generated via this socket, in addition to the transmitter’s audible signals. These voice messages are collected in a voice package and stored in the transmitter’s internal memory, but they Description of transmitter 23 Screen and keypad Visual display of the trim lever positions; alternatively - if rotary controls CTRL 7 … 9 are operated - display of the current settings of these two controls Model name Model type display (fixed-wing / helicopter) See page 36 for possible warnings Stopwatch in min:sec (count-up / count-down) Model memory 1 … 20 Left-hand touch-key leaf through pressed briefly together: switches to Servo display menu Right-hand touch-key leaf through / alter values SET Select / Confirm ESC = interrupt / back ESC touched for about three seconds; Switches to the Telemetry menu, and back to the base display Simultaneous brief press of or = CLEAR Battery voltage (If battery voltage falls below a particular level, you will see a warning display - see “Warning notes” on page 36. At the same time the transmitter emits an audible warning signal.) Battery operating time since last battery charge, in hr:min 24 Flight timer in min:sec (count-up / count-down) Description of transmitter - screen and keypad Receiver power supply voltage Flight phase name Switching between flight phases using switch Signal strength indicator Operating the “Data Terminal” Input buttons ESC and SET symbols On-screen telemetry symbols The active model memory has not yet been “bound” to a HoTT receiver. See page 80 or 88 for more information on the “binding” process. Not flashing: RF switched off at transmitter Flashing aerial symbol: The last receiver bound to the active model is inactive, or out of range >M x No telemetry signal detected >M Signal strength display >P Display of Pupil signal strength on the Teacher transmitter’s screen. Buttons to the left of the screen • ESC button A brief press on the ESC button returns you step by step within the function select system, taking you right back to the basic display. If you make a change in the meantime, the change is retained. If touched for about three seconds in the base display, ESC opens and closes the Telemetry menu. • Arrow buttons 1. A brief press on one of these buttons allows you to leaf through lists, such as the Model Select or Multi-Function list, always moving in the direction of the arrow; the arrow buttons are also used to move through menu lines within menus. 2. A brief simultaneous press of the buttons switches from the base transmitter display, and from almost any menu position, into the “Servo display” menu. Short-Cuts Buttons to the right of the screen • SET button 1. Starting from the base screen display - as it appears when you switch the transmitter on - a brief press of the SET button takes you to the multi-function menus. You can also call up a selected menu using the SET button. 2. Within the set-up menus you can activate (confirm) and disable the corresponding set-up fields with a brief press of the SET button. • Arrow buttons 1. “Leafs through” the multi-function menu and the menu lines within the set-up menus, in the same manner as the left-hand touch-key’s arrow buttons. 2. Selects and adjusts parameters in set-up fields after you have activated them by briefly pressing the SET button; the buttons and are assigned the same function in each case, i. e. it makes absolutely no difference which of the two buttons you use. 3. A brief simultaneous press of the or buttons resets an altered parameter value in the active input field to the default value (CLEAR). Notes: • It is not the contact with the touch-key itself that triggers the corresponding action, but the cessation of the touch. • If you switch the transmitter off and then immediately on again, you may find that the touch-keys have no effect. This is not a fault! Switch the transmitter off again, and wait a few seconds before switching it on once more. You can call up particular menus or options directly using the following button combinations: • CLEAR A brief simultaneous press of the or buttons of the right-hand touch-key resets an altered parameter value in the active input field to the default value. • “Servo display” A brief simultaneous press of the buttons of the left-hand touch-key switches from the transmitter’s base display, and from almost any menu position, to the “Servo display”, menu; see page 133. • “Telemetry” Hold the central ESC button of the left-hand touchkey pressed in for about one second in order to call up the “Telemetry” menu from the transmitter’s base display - see section starting on page 137 - and also to return to it again. • Graphic display of telemetry data Briefly pressing the or button of the left or righthand touch-key switches directly from the transmitter’s base display to the graphic telemetry data display, and also leafs to and fro between the individual graphic displays. Press ESC to return to the base display. • “HIDDEN MODE” (language selection and contrast) Simultaneously press the arrow buttons of the left-hand touch-key AND the central SET button of the right-hand touch-key; see next pagees. • Input lock Can be activated and disabled at the transmitter’s basic display by simultaneously holding the ESC and SET buttons pressed in for about two seconds. Description of transmitter - screen and keypad 25 HIDDEN MODE Language selection and screen contrast The “HIDDEN MODE” (VERSTECKTER MODUS) menu of the mx-16 HoTT transmitter can be accessed from virtually any menu position by holding the arrow buttons of the left-hand touch-key and the SET button of the right-hand touch-key pressed in; after about one second this display appears: VERSTECKTER MODUS ANSAGEN FIRMWARE UPDATE KNÜPPEL KALIBRIER. VOICE As mentioned in the “Headphone socket” section on page 21, the signals associated with the Telemetry menu and voice messages can be generated via this socket, in addition to the transmitter’s audible signals. The default language for these messages is German. These voice messages are collected in a voice package and stored in the transmitter’s internal memory, but they can be replaced by a voice package in another language at any time. When this manual went to press, the following langua­ ges were available: • English • French • German • Italian • Spanish The currently active voice package can be exchanged using either the PC program which is available at www. graupner.de/en on the Download page for the transmit26 Description of transmitter ter, or using the SD card supplied in the set, as described in the following section. If you have not already done so, insert your SD or SDHC card in the transmitter, as described on page 22. Switch the transmitter on with RF switched off: RF ON/OFF? ON OFF Changing the language Use the arrow buttons of the left or right-hand touch-key to move to the “VOICE” (“ANSAGEN”) line: VERSTECKTER MODUS ANSAGEN FIRMWARE UPDATE KNÜPPEL KALIBRIER. DATEILISTE VOICE2_ENGLISH.VDF VOICE2_FRANCE.VDF VOICE2_GERMAN.VDF VOICE2_ITALIANO.VDF VOICE2_SPAIN.VDF Confirm your selection by briefly pressing the central SET button of the right-hand touch-key again: the selected voice package is now loaded into the transmitter’s memory: HIDDEN MODE 0 CONTRAST ENGLISH LANGUAGE VOICE ENGLISH 22/100% I Press the central SET button of the right-hand touch-key to move to the Select page of the “VOICE” option: DATEILISTE VOICE2_ENGLISH.VDF VOICE2_FRANCE.VDF VOICE2_GERMAN.VDF VOICE2_ITALIANO.VDF VOICE2_SPAIN.VDF Now use the arrow buttons of the left or right-hand touch-key to select the language you prefer, for example: The loading process is finished when the progress bar at the bottom edge of the screen disappears: VERSTECKTER MODUS ANSAGEN FIRMWARE UPDATE KNÜPPEL KALIBRIER. Finally switch the transmitter off to conclude the procedure. All the settings stored in the transmitter are retained in full even after you have switched languages. Notes: • If the warning message … RF MUST BE OFF OK … appears, then the transmitter’s RF section is still active. Switch this section off in the “RF module” line of the “Base settings” menu, and repeat the procedure. • If the warning … SD-CARD INSERT OK … appears, then there is no memory card in the card slot, or the card cannot be read. • If the Select window is empty … FILE LIST … then the transmitter cannot find a suitable voice file on the SD card in the transmitter. If this should happen, check the contents of the “VoiceFile” folder by inserting the SD card in a PC or laptop. FIRMWARE UPDATE / Changing the screen language Important note: It is essential to check the state of charge of your transmitter battery before you carry out any update. For safety’s sake recharge it and back up all occupied model memories, so that you can restore them if anything goes wrong. DATEILISTE MX-12_1V234_ENGLISH. MX-12_1V234_FRANCE.B MX-12_1V234_GERMAN.B MX-12_1V234_ITALIANO MX-12_1V234_SPAIN.BI Use the arrow buttons of the left or right-hand touch-key to select the firmware version you wish to use, for example: VERSTECKTER MODUS ANSAGEN FIRMWARE UPDATE KNÜPPEL KALIBRIER. DATEILISTE MX-12_1V234_ENGLISH. MX-12_1V234_FRANCE.B MX-12_1V234_GERMAN.B MX-12_1V234_ITALIANO MX-12_1V234_SPAIN.BI It is possible to update and / or replace the transmitter’s firmware, and with it the screen language, using this menu point; the procedure is similar to that described in the section entitled “VOICE”. When this manual went to press, the following languages were present on the SD card supplied as standard in the set: • German • English • French • Italian • Spanish Corresponding updates and further information can be found at www.graupner.de/en on the mx-16 HoTT pro­ duct page under Download. Confirm your choice by briefly pressing the central SET button of the right-hand touch-key once more. The selected firmware now starts to load into the transmitter’s memory, and after two brief screen displays (which only concern the start of the firmware update) you will see … Firmware Download Prozess Start Please Wait.... Description of transmitter 27 Boot Download Success!!! Please Wait.... … then there is no memory card in the card slot, or the card cannot be read. • If the Select window is empty … FILE LIST … this display: Firmware Downloading... Progress 023/123 The loading process is complete when the counter to the left of “/” reaches “Data quantity” to the right of it, and this message appears: Firmware Upgrade success!!! If this warning message appears … SD-CARD INSERT OK 28 Description of transmitter STICK CALIBRATION HIDDEN MODE VOICE FIRMWARE UPDATE STICK CALI. After a few seconds the message disappears, and the transmitter re-starts. The system is now ready for use again. Notes: • … then the transmitter cannot find a suitable firmware file on the SD card in the slot. If this should happen, check the contents of the “Firmware” folder on the SD card by inserting it into a PC or laptop. If you suspect that the centre point of your self-centring sticks (transmitter controls 1 … 4) does not correspond exactly to 0% travel of the transmitter control, you can check and - if necessary - correct it using the following procedure: Move to the “Model select” menu and set up a free model memory, as described on page 66. It makes no difference whether you select a fixed-wing or helicopter model type. Wait for the usual on-screen messages which appear in the base display after switching models, then move to the “Servo display” menu with, for example, a simultaneous brief press of the buttons of the left-hand touch-key, but WITHOUT moving the trims, or carrying out any other programming procedures. If all four of your primary stick functions are still set to self-centring action, the screen display should look like this: 1 0% 2 0% 3 0% 4 0% 5 0% 6 0% 7 0% 8 0% Otherwise the bar and % figure for the non self-centring stick function - usually that of the throttle / brake or throttle / collective pitch stick “Ch 1” - will correspond to the stick’s current position. For example, if the throttle / brake stick is at the “quarter-throttle” position, then the screen will look like this: 1 – 50 % 2 0% 3 0% 4 0% 5 0% 6 0% 7 0% 8 0% Now move each of the two primary sticks to each of the four possible end-points in turn, but without exerting pressure at the end-points. At each of the end-points eight in total - the screen should show exactly -100% or +100%, depending on the side of centre. For example, if transmitter control 2 is at its right-hand end-point, and the three other stick functions are all at centre, then your transmitter’s screen display should look like this: 3 0% 4 0% 5 0% 6 0% 7 0% 8 0% 0% STICK CALIBRATION +100% … and briefly press the central SET button of the right-hand touch-key. In our example this completes the calibration of the “left-hand” end-point of the right-hand stick, and the circle in the centre of the stylised stick plane flashes to confirm this: Now repeat the calibration procedure for the right-hand end-point of the right-hand stick. Repeat the procedure for the other stick planes. Notes: • If you make a mistake in the calibration process, simply repeat the appropriate step. • Within any one stick plane each of the three calibration positions can be selected directly using the arrow buttons of the left or right-hand touch-key. Conclude the procedure by briefly pressing the central ESC button of the left-hand touch-key, then quit the “Stick calibration” sub-menu. STICK CALIBRATION With the arrow buttons of the right-hand touch-key you can now select in turn the positions of the four stick planes to be calibrated, for example, those of the left / right plane of the right-hand stick: Move the “left” flashing arrow marker to the left-hand end-point using the right-hand stick - again without exerting pressure … STICK CALIBRATION 0% If this checking procedure shows a result of up to four times 0% and eight times 100% - depending on the number of your transmitter’s self-centring stick functions - then the transmitter’s sticks are perfectly calibrated. You can conclude the procedure and - if you wish erase the model memory you have just created. If this is not the case, move to the “Stick calibration” line of the “HIDDEN MODE” menu as described at the start of the preceding double page, and briefly press the central SET button of the right-hand touch-key: 0% –100 % 2 STICK CALIBRATION 0% 1 STICK CALIBRATION +100% Now release the self-centring stick, so that it can take up its centre position, and again press briefly the central SET button to calibrate the centre position. The “right” triangular marker now starts to flash: Description of transmitter 29 Telemetry data display As described on page 150, as part of the “SENSOR SELECT” sub-menu of the “Telemetry” menu … SENSOR SELECT RECEIVER GENERAL MODULE ELECTRIC AIR.MOD VARIO MODULE GPS … and selecting the line for the desired sensor after superimposing the Select window by pressing one of the two buttons. If no sensor is currently active, all the other displays / sensors described in the following section are suppressed from the Select list, with the exception of the “RECEIVER” display, which is described in the next column: RECEIVER … the graphic displays of one or more sensors can be activated. The “Receiver” display, and other graphic displays activated in accordance with your choice of sensors, is accessed from the transmitter’s base display by briefly pressing the or button of the left or right-hand touch-key: RX–S QUA: 100% RX–S ST : 100% RX–dBm: –33dBm TX–dBm: –33dBm L–PACK: 10ms RX–VOLT:4.8V TMP R–LOW V:4.6V +22°C You can switch between the displays for the sensors activated in the “SELECT SENSOR” sub-menu of the “Telemetry” menu by briefly pressing one of the arrow buttons of the left or right-hand touch-key … RECEIVER GENERAL ELECT. AIR VARIO GPS 30 Description of transmitter - Telemetry data display If you wish, you can confirm your choice immediately after this by pressing the central SET button of the right-hand touch-key; alternatively you can simply wait until, after a brief interval, the selected display appears automatically. Note: The displays are described below in the sequence which occurs when you press the button. For more information on these modules please see the Appendix, or refer to the product on the Internet at www. graupner.de/en. RECEIVER RX–S QUA: 100% RX–S ST : 100% RX–dBm: –33dBm TX–dBm: –33dBm L–PACK: 10ms RX–VOLT:4.8V TMP R–LOW V:4.6V +22°C This screen displays the data which can also be viewed in the “RX DATAVIEW” screen of the telemetry menu “SETTING & DATA VIEW” (see page 138), but in graphic form. The meanings are as follows: Value Explanation RX-S QUA Signal quality in % RX-S STR Signal strength in % RX-dBm Receive performance in dBm TX-dBm Transmit power in dBm L-PACK Shows the longest period in ms in which data packets were lost in transmission from transmitter to receiver RX-VOLT Actual receiver operating voltage in Volts R-LOW V Lowest receiver operating voltage in Volts since the last time it was switched on TMP The thermometer indicates the receiver’s current operating temperature GENERAL MODUL RECEIVER GENERAL ELECT. AIR VARIO GPS BAT1 E FUEL F 0.0V T1 BAT2 0.0V T2 0°C 0°C CELL.V 1:0.00 2:0.00 3:0.00 4:0.00 5:0.00 6:0.00 0 ALT 0m 0m1 BAT1 E FUEL F 0m3 0.0V POWER T1 0°C 0.0V 0.0A BAT2 0 0.0V T2 0°C This display visualises the data from a General-Engine module, Order No. 33610, or a General-Air module, Order No. 33611, connected to the receiver. For more information on these modules please see the Appendix, or refer to the product on the Internet at www.graupner. de/en. Depending on the sensors connected to the modules, the following data may be generated constantly on the screen: The actual voltage of up to two batteries (BAT1 and BAT2); the measurement results from up to two temperature sensors (T1 and T2); also a fluid level indicator for the fueltank. At the right-hand margin you will see an alternating display either of the actual cell voltages of a battery pack (up to six cells), or the current altitude relative to the pilot’s location, climb / descent in m/1 s and m/3 s, the actual current in Ampere and the actual voltage of the battery connected to the sensor. The meanings are as follows: Value Explanation BAT1 / BAT2 Battery 1 / Battery 2 FUEL Fuel level / Fueltank indicator E/F Empty / full T1 / T2 Temperature of sensor 1 / sensor 2 CELL V Cell voltage of cell 1 … max. 6 ALT Current altitude 0m1 m/1 sec climb / descent 0m3 m/3 sec climb / descent 0.0V Actual voltage of drive battery 0.0A Actual current in Ampere Battery and consumption display 0.0V 0.0A 0mAh 0ml Engine module (Order No. 33610) or the General Air module (Order No. 33611), or the consumed fuel in ml. SENSOR 1 SENSOR 1 0.0V 0°C This display visualises the actual voltage and temperature measured by a temperature / voltage sensor, Order No. 33612 or 33613, connected to the “T(EMP)1” socket of the General Engine module (Order No. 33610) or the General Air module (Order No. 33611). SENSOR 2 SENSOR 2 0.0V 0°C This display visualises the actual voltage and temperature measured by a temperature / voltage sensor, Order No. 33612 or 33613, connected to the “T(EMP)2” socket of the General Engine module (Order No. 33610) or the General Air module (Order No. 33611). This display visualises the actual voltage, the actual current drain and the consumed capacity of any battery connected to the “Battery 1” socket of the General Description of transmitter - Telemetry data display 31 Rev-count sensor ELECTRIC AIR MODUL 0 0 rpm 0 This display visualises the rotational speed measured by a rev-count sensor, Order No. 33615 or 33616, connected to the General Engine module (Order No. 33610) or the General Air module (Order No. 33611). Note: For correct display of rotational speed you must first set the appropriate number of blades by accessing the Telemetry menu for the sensor. Vario 0 mm 0.0 s This display visualises the data for altitude in m relative to the location or launch point, and the actual climb / sink rate in m/s, generated by the integral vario in the General Engine module (Order No. 33610) or the General Air module (Order No. 33611). 32 Description of transmitter - Telemetry data display RECEIVER GENERAL ELECT. AIR VARIO GPS 0.0V 0A ALT 0m BAT1 0m/1s 0.0V 0m/3s T1 0°C BAT2 0.0V T2 0°C 0.0V 0A ALT 0m BAT1 0m/1s 0.0V 0m/3s T1 0°C BAT2 0.0V T2 0°C m/1 s and m/3 s, and - in the centre of the screen - the actual current drawn from a power source. At the right-hand margin you will see an alternating display of the actual cell voltages of the battery packs (up to seven cells) connected to balancer sockets 1 (L) or 2 (H). The meanings are as follows: Value Value 0 1L0.00 2L0.00 3L0.00 4L0.00 5L0.00 6L0.00 7L0.00 V Actual voltage A Actual current BAT1 / BAT2 Battery 1 / Battery 2 ALT Current altitude m/1s m/1 sec climb / descent 0 1H0.00 2H0.00 3H0.00 4H0.00 5H0.00 6H0.00 7H0.00 m/3s m/3 sec climb / descent T1 / T2 Temperature at sensor 1 / 2 L/H Cell voltage of cell 1 … max. 14 L = balancer socket 1 H = balancer socket 2 This display visualises the data from an Electric-Air module, Order No. 33620, connected to the receiver. For more information on this module please see the Appendix, or refer to the product on the Internet at www. graupner.de/en. Depending on the sensors connected to the modules, the following data may be generated constantly on the screen: The actual voltage of up to two batteries (BAT1 and BAT2); the measurement results from up to two temperature sensors (T1 and T2); the current altitude relative to the pilot’s location, the model’s climb / descent rate in BAT 1 0.0V 0.0A 0mAh This display visualises the actual voltage, the actual current drain and the consumed capacity of any battery connected to the “Battery 1” socket of the Electric Air module (Order No. 33620). SENSOR 1 SENSOR 1 0.0V 0°C to the location or launch point, and the actual climb / sink rate in m/s, generated by the integral vario in the Electric Air module (Order No. 33620). RECEIVER GENERAL ELECT. AIR VARIO GPS m/1s 0.0 SENSOR 2 This display visualises the actual voltage and temperature measured by a temperature / voltage sensor, Order No. 33612 or 33613, connected to the “T(EMP)2” socket of the Electric Air module (Order No. 33620). Vario 0 mm 0.0 s The pre-set altitude limit below the launch point; below this altitude the transmitter emits audible warning signals m/1s m/1 sec climb / descent m/3s m/3 sec climb / descent m/10s m/10 sec climb / descent H High L Low VARIO This display visualises the actual voltage and temperature measured by a temperature / voltage sensor, Order No. 33612 or 33613, connected to the “T(EMP)1” socket of the Electric Air module (Order No. 33620). SENSOR 2 0.0V 0°C MIN H ALT 0 m/3s 0.0 m/10s 0.0 RXSQ 0 L Vario 0 mm 0.0 s MAX 0m MIN 0m This display visualises the data from a Vario module, Order No. 33601, connected to the receiver. The meanings are as follows: Value Explanation ALT Current altitude RXSQ Signal quality of the signal picked up by the receiver in % MAX The pre-set altitude limit relative to the launch point; above this altitude the transmitter emits audible warning signals This display visualises the data for altitude in m relative to the location or launch point, and the actual climb / sink rate in m/s, generated by a Vario module (Order No. 33601) connected to the Telemetry socket of a receiver. GPS RECEIVER GENERAL ELECT. AIR VARIO GPS This display visualises the data for altitude in m relative Description of transmitter - Telemetry data display 33 RXSQ 0 DIS 0m ALT 0m 0.0m/1s 0m/3s N W 0 Kmh E S N E Vario 0 mm 0.0 s 0°00.0000 0°00.0000 This display visualises the data delivered by a GPS module with integral vario, Order No. 33600, connected to the receiver. In addition to the model’s current positional data and speed, shown in the centre of the screen, the display also includes the current altitude in relation to the launch point and the model’s climb / sink rate in m/1 s, m/3 s and m/10 s. The current reception quality and the model’s distance from the launch point are also displayed. The meanings are as follows: This display visualises the data for altitude in m relative to the location or launch point, and the actual climb / sink rate in m/s, generated by the integral vario in the GPS / Vario module (Order No. 33600). GPS N W 0 Kmh E 0km/h m 0DIS 0.0m/s 0ALT m Value Explanation W/N/E/S West / North / East / South Kmh Speed RXSQ Signal quality of downlink channel DIS Distance ALT Current altitude relative to launch point This display visualises the data delivered by a GPS module with integral vario, Order No. 33600, connected to the receiver. The meanings are as follows: m/1s m/1 sec climb / descent Value Explanation m/3s m/3 sec climb / descent W/N/E/S West / North / East / South km/h Speed DIS Horizontal distance in m m/s Climb / descent in m/s ALT Altitude relative to launch point in m 34 Description of transmitter - Telemetry data display S For your notes 35 On-screen warnings Warnings BIND N/A OK RF ON/OFF? ON OFF batter y needs charging fail safe setup t.b.d MISSING IMPORT DATA OK 36 “Binding not present” No receiver is bound to the currently active model memory. A brief touch of the SET button takes you directly to the corresponding option. Do you want the RF signal to be “ON” or “OFF? Battery must be charged Operating voltage too low Fail-Safe not yet set up On-screen function fields CAN‘T RECEIVE DATA OK no student signal SD-CARD INSERT OK The throttle stick (or helicopter limiter) is set too far in the direction of full-throttle RF MUST BE OFF OK Request to switch off the RF section (voice files can only be loaded with the RF section switched off) No connection between Teacher and Pupil transmitters No SD or SDHC memory card in the card slot, or card cannot be read. TRAINER Wireless Link ACT INH A “wireless Trainer connection” was used before the transmitter was last switched off; do you wish that connection to be continued (ACT), or switched OFF (INH)? No suitable voice files found on the memory card throttle too high ! No bound receiver in range. Description of transmitter - On-screen warnings and function fields SEL, STO, SYM, ASY, , The bottom line of the screen displays function fields which vary according to the menu selected. SEL STO SYM ASY The function fields are activated by touching the SET button. Function fields • SELselect • STO store (e. g. transmitter control position) • SYM adjust values symmetrically adjust values asymmetrically • ASY Switch symbol field • (assigning switches of all kinds) Switch to second page (next menu) • within a menu Position display Rotary proportional controls CTRL 7 and 8 As soon as you operate one of the two rotary controls CTRL 7 + 8 on the centre console, a small symbol appears to the right of the two vertical position indicators: At the same time the position display of the two central vertical bars switches for the duration of the actuation from the display of the current trim position to the current position of the rotary controls CTRL 7 + 8. As you would expect, the left-hand bar represents the position of the left-hand rotary control CTRL 7, and the right-hand bar reflects the position of CTRL 8 (however, both horizontal bars continue to show the current position of the corresponding transmitter stick trim levers): #01 5.2V 3:33h stop flt M 0:00 0:00 Input lock To prevent programming errors, it is possible to lock the touch-keys, and with them access to all the set-up options, from the base display of the mx-16 HoTT transmitter by touching the ESC and SET buttons for about two seconds. This is indicated by an inverted key symbol at the centre point of the trim bars: #01 5.2V 3:33h stop flt 0:00 0:00 M HoTT 5.5V The lock is immediately active, but the control system remains ready for use. Touching the ESC and SET buttons again for about two seconds disengages the lock: the next time you switch the transmitter on, the lock is also disengaged. HoTT About two seconds after you cease operating one of the two rotary controls, the screen reverts to a display of the current position of the four trim levers for the two dual-axis stick units. Description of transmitter - Position display and Input lock 37 Using the transmitter for the first time Preliminary notes regarding the mx-16 HoTT transmitter For more information please visit our Internet site at www.graupner.de/en Preliminary notes RF ON/OFF? In theory the Graupner|SJ HoTT system permits the ON OFF simultaneous operation of more than 200 models. Within this period you can switch off the RF signal if However, in practice the mixed operation of different required by moving the black field to the right using the technical systems in the 2.4 GHz ISM band - as required or arrows of the right-hand touch-key; when you by the approval regulations - reduces this number condo this, ON should appear normal, and OFF in inverse siderably. Generally, however, it will always be possible form (black background). to operate even more models simultaneously on the 2.4 GHz band than on the 35 / 40 MHz frequency bands RF ON/OFF? ON OFF which we have used to date. However, the actual limiting factor - as it has always been - is likely to remain the You can now switch the RF module off by briefly presssize of the (air-) space available. The simple fact that ing the central SET button of the right-hand touch-key. no frequency control procedure is necessary - a great Until this point the central LED glowed blue, but it now convenience in itself - equates to an enormous gain in changes to red, and at the same time the screen switchsafety, especially at flying sites where groups of pilots es to the transmitter’s base display: may be distributed over a large area, with nobody in overall control. 0:00 stop Battery charged? When you take receipt of your transmitter, the battery will be in the discharged state, so you must first charge it as described on page 14. If you do not do this, the battery will soon fall below the pre-set threshold voltage, and you will see and hear a warning signal to remind you to recharge it. The threshold voltage can be adjusted in the batter y needs “Battery warning threshold” line charging of the “Basic settings” menu; see page 134. Switching the transmitter on When you switch the transmitter on, the following display appears in the centre of the transmitter screen for about two seconds: 38 Using the transmitter for the first time #01 5.2V 0:33h flt M 0:00 HoTT 0.0V The symbol combination means that the currently active model memory is already “bound” to a Graupner|SJ HoTT receiver, but there is currently no connection with this receiver. (In our example we - of course - switched off the RF signal!) In contrast, if you switch the transmitter on without switching off the RF signal, the central LED glows an intense blue, and the symbolic transmitter mast flashes. At the same time the transmitter emits an audible warning until a connection is made with the corresponding receiver. Once this connection exists, a field strength indicator appears instead of the “x” at the base of the symbolic aerial, for example , and the visual and audible warnings cease. At the right of the same line a display in the same format appears when a telemetry connection is made, showing the strength of the telemetry signal picked up from the receiver (>M ) together with the actual voltage of the receiver power supply. appears, and However, if the symbol combination the central LED glows a constant red, the currently active model memory is not “bound” to any receiver. Low-voltage warning If the transmitter voltage falls below a particular value, a visual and audible low-voltage warning is generated. The default value is 4.7 V, but this can be varied in the “Basic settings” menu (page 134). Important notes: The transmitter included in the set is • prepared at the factory with the correct settings for most European countries (except France). If you wish to operate the RC system in France, you MUST first set the Country setting on the transmitter to “FRANCE” mode; see page 135. IT IS PROHIBITED to use the system IN FRANCE using the Universal / EUROPE mode! • You can operate up to eight servos using the mx-16 HoTT transmitter and the receiver supplied in the set, which is already bound to the transmitter. However, in the interest of maximum possible flexibility, control channels 5 … 8 are not assigned to transmitter controls by default; this also helps to eliminate the danger of inadvertently using them incorrectly. This means that any servos connected to these channels will simply “stay put” at their centre position until a transmitter control is assigned to the channel in question. For the same reason virtually all the mixers are inactive by default. For more details of this please refer to page 86 (fixed-wing model) or 88 (helicopter). • The basic procedure for programming a new model memory can be found on page 66, and in the programming examples starting on page 164. • When switching on, binding or setting up the radio control system, please ensure at all times that the transmitter aerial is an adequate distance from the receiver aerials. If the transmitter aerial is too close to the receiver aerials, the receiver will be swamped, and the red LED on the receiver will begin to glow. At the same time the downlink channel will stop working. As a result the field strength bars on the transmitter screen are replaced by “x”, and the receiver battery voltage is displayed as 0.0 V. At the same time the radio control system switches to Fail-Safe mode, see page 136, i.e. the servos remain fixed in their current position for as long as reception is not possible, and until a new, valid signal is picked up. If this should happen, simply increase the distance between transmitter and receiver until the displays revert to “normal”. warning: Never switch off the transmitter while the model is in operation! However, if this does happen, keep calm and wait until the transmitter display goes off and the transmitter has shut down completely. This takes at least three seconds. Don’t switch the transmitter back on until then. Otherwise, there is a danger that the transmitter will get “hung up” immediately after being switched back on, causing you to lose control of the model. Then it will not be possible to restart the transmitter until you have switched it off again and have carried out the described procedure correctly. Using the transmitter for the first time 39 Downloading and updating the transmitter firmware The transmitter firmware can be updated at the owner’s risk using either of two methods: • As described under “FIRMWARE UPDATE / Changing the screen language” in the section entitled “Hidden mode” on page 27. • As described in the next section, using the five-pin mini-USB port on the back of the transmitter, in conjunction with a PC or laptop running Windows XP, Vista or 7. Downloading a software package Current software and information can be found in the Download section for the corresponding product at www. graupner.de/en. Note: Once you have registered your transmitter at https://www.graupner.de/en/service/ product_registration.aspx you will automatically be informed of new updates by e-mail as they become available. Press the ENTER key of the PC or laptop once more, and the page you require will appear: This takes you to the home page of the Graupner company website, where you will find an input field at top right below the title “Suchen / Search”: The easiest method of accessing the “corresponding” product page, as mentioned above, is to enter www. graupner.de/en in the address line of your Internet browser, and then press the ENTER button of your PC or laptop: Place the mouse pointer in this field and then enter a search term, for example, the article number printed on the type placard on the back of your transmitter: 40 Downloading and updating the transmitter firmware If you now use the mouse to move your browser’s lateral scroll bar down a little, you will see the tabs “Features”, “Replacement parts”, “Accessories” and “Downloads”. Click on the “Download” tab to move to the Download area: of the download file initially tells you whether firmware updates are present, and the version numbers of the relevant firmware files also change. Select the required file(s) and start the downloading process by double-clicking on “Download” below the selected file. Selecting “HoTT-Software VX” downloads the file “HoTT_Software_VX.zip”. This compressed file contains all the files required to update the transmitter, HoTT receiver, sensors, etc. Please note: at the time of revising this manual the current version of the program package is version “4” “HoTT-Software V4”. If the last update you loaded is version “V3” or older, all components of the radio control system MUST be updated to version “V4”. If you ignore this, you may encounter malfunctions in individual components. The same applies to future download packages “V5” or higher. If individual firmware files change within a version “VX”, all you need to do is install the new, later firmware version for the corresponding product. The date of creation Now save the file in a folder of your choice, and unpack it using a suitable program. If a transmitter update does not function as described below, please continue reading the section entitled “Restoring the transmitter firmware” on page 44. Updating the mx-16 HoTT software To update the transmitter software you only need the USB lead supplied as standard with the USB interface, Order No. 7168.6. This can be plugged directly into the five-pin mini-USB socket on the back of the transmitter. Important notes: Please note that reliable communica• tion between your system’s HoTT components is only guaranteed if the firmware is compatible. That is why the programs required to update all the HoTT components and files are grouped in a single file, which is currently named HoTT_Software_V4.zip”. • It is essential to check the state of charge of your transmitter battery before you carry out any update. For safety’s sake recharge it and back up all occupied model memories, so that you can restore them if anything goes wrong. • The connection between the transmitter and the PC or laptop must not be interrupted during the update process, so please ensure that there is reliable contact between the transmitter and the computer. 1. Unpacking the program package Unpack the file “HoTT_Software_VX.zip” into a convenient folder. For example, you might name the folder “HoTT_Software_VX”, the “X” standing for the current version number. 2. Installing the driver If you have not already done so, install the driver software which is included in the program package in the “USB driver” folder; this is necessary in order to use the transmitter’s integral USB port. Start the driver installation by double-clicking on the corresponding file, and follow the instructions. After a successful installation the computer will need to be restarted. Note that the driver only has to be installed once. 3. Connecting the transmitter to the PC Connect the USB lead to the PC or laptop and the five-pin mini-USB socket on the back of the transmitter, with the transmitter switched off. Check that the USB lead is making solid contact. Downloading and updating the transmitter firmware 41 4. Updating the mx-16 HoTT transmitter software Start the program “Firmware_Upgrade_grStudio_VerX.X.exe”, which is now stored in the folder you have just named “HoTT_Software_VX” (or similar). (Note: version 1.9, which is current at the time this manual went to press, starts without being installed beforehand.): Open the “Controller Menu” and click on “Port Select” in the “Upgrade” folder. Alternatively select the “Port Select” entry under “Menu”: window, i.e. the port to which the USB interface is connected. You can recognise this by the name “Silicon Labs CP210x USB to UART Bridge” in the “Device Name” column. In the screen-shot above this would be the “COM 3” port. Now call up the “Firmware Upgrade” option in the “Transmitter” folder under “Controller Menu”. Alternatively select the “Firmware Upgrade” entry under “Menu”: When you have called up the program, you will see the number “1” flashing red in the numeric row 1 … 7 at the top of the window, indicating that the program is currently operating at “[Process Step] 1”. In each case the meaning of the currently flashing step is indicated immediately below the numeric row: For example, at Step 1: “Connect USB lead to PC and transmitter” and “Press File Browse button and select Update file”, as shown here. Now select the correct COM port in the “Port select” 42 Downloading and updating the transmitter firmware Note: At any time you can call up an explanation of any step in the form of Quick-Info by positioning the mouse pointer over a number. If you have not already done so, connect your transmitter to the PC or laptop at this point. Now click on the button marked “File Browse” and select the firmware update file matching your transmitter in the “Open file” dialogue which now appears; the file suffix will be “bin”. In the case of the zip file “HoTT_Software_VX” which you have already downloaded and unpacked, this will usually be found in the folder “Official Version \ 33112_ …_ 33032_mx-xx_mc-32 \ SD card \ Firmware”, and is called “mx-16_1vXXX_German.bin” (or “… English.bin”). The file appears in the associated window. At the same time the “2” starts to flash red instead of the “1”. The firmware files are encoded in a manner speci­ fic to each product, i.e. if you accidentally select a file which does not match the product (e.g. receiver update file instead of transmitter update file), the popup window “Product code error” appears, and you will be unable to continue the update process. Follow the instructions for “[Process Step] 2”. If you have not already done so, switch the transmitter on at this point, and then start the transmitter update by clicking on the “Download Start” button. Shortly after this you will see a warning that the transmitter’s RF signal is being disabled: “RF will be switched OFF.” Before clicking on “Yes” you should therefore switch the receiving system off if it is currently operating. At this point the actual update process begins, and a progress bar starts to advance above the constantly changing lines of text. At the same time the flashing red number continues to indicate the current “Process Step”. You must not interrupt the connection between the transmitter and the PC during the update process! Click on “OK”, then switch the transmitter off and finally disconnect the lead between the transmitter and the PC or laptop. If the progress bar fails to advance, or if the update process terminates before it reaches the 100% mark, close the program and repeat the update procedure, i.e. carry out each of the steps described above once more. If an update fails repeatedly, please read the following section. If you accidentally attempt to load a version of the firmware which is correct, but older than the one currently in the transmitter, the screen will display a corresponding warning: The update is finished when the progress bar reaches the right-hand end, and the message “Firmware Download Success” appears. At the same time the [Process Steps] display moves on to “7” “Update Process Finish”: Unless you really want to load older firmware, click on “No” with the mouse, and load the correct *.bin file using the “File Browse” button. Downloading and updating the transmitter firmware 43 Restoring the transmitter’s firmware „Emergency“ program Restoring the mx-16 HoTT transmitter software If a transmitter firmware update should fail, or if the transmitter software “hangs” (in which case you may not be able to switch the transmitter off using the “POWER” switch), then you can restore the earlier firmware using the “Emergency” program segment. If you switch the transmitter off, but the screen continues to be active, then please set the switch to the “POWER=OFF” position, unplug the transmitter battery, wait a few seconds, then plug it in again - but leave the POWER switch at the “OFF” position! 1. Starting the “Emergency” program Now move to the “Controller Menu” and select the “Emergency” entry under the heading “Transmitter”: Ensure that the transmitter is switched off! Connect the USB lead to the PC or laptop, and to the USB socket on the back of the transmitter. 2. Restoring the mx-16 transmitter software Press the “File Browse” button and search for the current firmware in the program window which now opens; as mentioned earlier, you will find this in the “Official Version \ 33112_…_33032_mx-xx_mc-32 \ SD card \ Firmware” folder of the unpacked “HoTT_ Software_VX” file. The file matching the mx-16 transmitter is called: “mx-16_1vXXX_German.bin” (or “…English.bin”). Now press the “Download Start” button to initiate the update process. Wait for a moment until the status 44 Restoring the transmitter’s firmware bar starts to advance, and only then switch the transmitter on. Don’t be surprised if the screen comes to life, but displays no information. (If the progress bar reaches the right-hand end before the transmitter is switched on, you will have to click on the “Download Start” button again.) After you switch the transmitter on, there may well be a wait lasting a minute before the process actually starts. The transmitter’s signal melody sounds, the transmitter screen switches itself on with the start display “mx-16 HoTT”, and the current firmware version is shown on the screen. Finally click on “OK”. Switch the transmitter off, and disconnect the USB lead from the transmitter and the PC or laptop. The progress bar indicates that the data transfer process is under way, and the screen displays [Process Step] “No 4, Firmware downloading …”. Ensure that the USB lead is making reliable contact, and do not interrupt the update process. The firmware transfer is finished when the progress bar reaches the right-hand end; you will then see the message “File Transfer Success” to indicate that the transfer has been successful. For your notes 45 Using the receiver for the first time Preliminary notes regarding the GR-16 receiver For more information please visit the Internet at www.graupner.de/en. Receiving system about one second. The mx-16 HoTT radio control set includes a GR-16 Servo connections and polarity 2.4 GHz bi-directional receiver which is suitable for The servo sockets of Graupner|SJ HoTT receivers are connection to a maximum of eight servos. numbered. The connector system is polarised: look for If you switch a HoTT receiver on, and “its” transmitter is the small chamfers when inserting the connectors, and switched off or not within range, the red LED on the reon no account force the plugs into the sockets. ceiver lights up steadily for about one second, and then The sockets marked “1+B-” and “6+B-” are intended starts to flash slowly. This means that no connection with for the connection of the battery. It is also possible to a Graupner|SJ HoTT transmitter exists (at this stage). connect the appropriate servos to both these sockets in When the connection is made, the green LED glows parallel with the power supply by using a Y-lead, Order constantly, and the red LED goes out. No. 3936.11. In order to create a connection, the Graupner|SJ HoTT Do not connect the battery to these receiver must first be “bound” to “its” model memory in sockets with reversed polarity, as this is “its” Graupner|SJ HoTT transmitter; this procedure is likely to ruin the receiver and any devices known as “binding”. However, binding is only necessary connected to it. once for each receiver / model memory combination The power supply voltage is through-connected via all (see pages 80 or 88), and has been carried out at the numbered sockets. The function of each individual the factory for model memory 1 using the components channel is determined by the transmitter you are using, supplied in the set. You therefore only need to carry out rather than by the receiver. Example: the throttle servo the “binding” process - as described later - with additionsocket is defined by the radio control system, and may al receivers, or if you switch to a different model memdiffer according to the make and type. ory. The procedure can also be repeated whenever you In the case of Graupner radio control systems the wish - for instance, if you change the transmitter. throttle function is assigned to channels 1 or 6, whereas Receiver voltage display it is allocated to channel 3 in the case of Futaba radio Once a telemetry connection exists, the actual voltage control systems, for example. of the receiver power supply is displayed on the rightObserve the installation notes regarding the receiver, hand side of the transmitter screen. receiver aerial and servos, which you will find on page 54. Temperature warning If the temperature of the receiver falls below a limit value set on the receiver (the default is -10°C), or exceeds the upper warning threshold, which is also set on the receiver (the default is +55°C), the transmitter generates a warning in the form of steady beeps at intervals of 46 Using the receiver for the first time Concluding notes: The much higher servo resolution of the • HoTT system results in a substantially more direct response compared with previous technologies. Please take a little time to be- come accustomed to the finer control characteristics offered by the system! • If you wish to use a speed controller with integral BEC* system in parallel with a separate receiver battery, in most cases (depending on the speed controller) the positive terminal (red wire) must be removed from the three-pin connector, as shown in the diagram. Be sure to read the appropriate notes in the instructions supplied with your speed controller before doing this. Carefully raise the central lug of the connector slightred ly (1), withdraw the red 1 wire (2) and insulate the bare contact with tape 3 2 to avoid possible short circuits (3). Reset To carry out a receiver reset, locate the SET button on the top of the receiver and hold it pressed in while you switch the receiver power supply on. Hold the receiver’s SET button pressed in until the green and the red LED goes out; this takes about four seconds. If you carried out the reset with the transmitter switched off, or with an unbound receiver, the receiver LED will flash red slowly after a pause lasing about two seconds. At this point it is immediately possible to initiate a Bind process at the transmitter. If the reset is carried out with an already bound receiver, if the transmitter is switched on, and if the associated model memory is active, then the LED lights up green after a short interval to indicate that your transmitter / receiving system is ready for use once more. * Battery Elimination Circuit Please note the following: Resetting the receiver resets ALL the settings stored in the receiver to the default settings, with the exception of the binding information! If you carry out a RESET by mistake, this means that you will have to restore all the receiver settings entered using the Telemetry menu. On the other hand, a deliberate RESET is particularly useful if you wish to “re-house” a receiver in a different model, as it represents an easy method of avoiding the transference of unsuitable settings. Using the receiver for the first time 47 Firmware update of the receiver Firmware updates for the receiver are carried out using the telemetry socket on the side of the receiver, in conjunction with a PC running Windows XP, Vista or 7. For this you require the optional USB interface, No. 7168.6 and the optional adapter lead, Order No. 7168.6S. The software and files also required for the process can be found in the Download area for the corresponding product at www.graupner.de/en. Note: Once you have registered your transmitter at https://www.graupner.de/en/service/ product_registration.aspx you will automatically be informed of new updates by e-mail as they become available. Updating the receiver firmware Important notes: Please note that reliable communica• tion between your system’s HoTT components is only guaranteed if the firmware is compatible. That is why the programs required to update all the HoTT components and files are grouped in a single file, which is currently named HoTT_Software_V4.zip”. • It is essential to check the state of charge of your receiver battery before you carry out any update. For safety’s sake recharge it before updating. • The connection between the receiver and the PC or laptop must not be interrupted during the update process, so please ensure that there is reliable contact between the receiver and the computer. 48 Updating the receiver firmware 1. Installing the driver The driver software for the USB interface, Order No. 7168.6, is identical to the driver software of the interface fitted to the mx-16 transmitter. This means that the driver only has to be installed once; the procedure is described on page 41. 2. Connecting the receiver to the PC Connect the USB interface, Order No. 7168.6 to the receiver socket marked “- + T” using the adapter lead, Order No. 7168.6S. The connectors are polarised: look for the small chamfer on the side. The connectors should engage easily; on no account use force. al went to press, starts without being installed beforehand.): Adapter lead Order No. 7168.6A If a central red wire is present, cut through it Open the “Controller Menu” and click on “Port Select” in the “Upgrade” folder. Alternatively select the “Port Select” entry under “Menu”: Caution: If your adapter lead is of the earlier three-core type, first cut the central red wire in the adapter lead, Order No. 7168.6A. Now connect the USB interface to the PC or laptop using the USB lead (PC USB / mini-USB) also supplied in the set. When the components are connected correctly, a red LED on the interface circuit board should light up red for a few seconds. The receiver should be left switched off. 3. Firmware update Start the program “Firmware_Upgrade_grStudio_ Ver-X.X.exe” by double-clicking on it, as described for updating the transmitter software; see page 42. (Version 1.9, which is current at the time this manu- Now select the correct COM port in the “Port select” window, i.e. the port to which the USB interface is connected. You can recognise this by the name “Silicon Labs CP210x USB to UART Bridge” in the “Device Name” column. In the screen-shot above this would be the “COM 3” port. Now call up the “HoTT Receiver” option in the “Device” folder under “Controller Menu”. Alternatively select the “HoTT Receiver Upgrade” entry under “Menu”: the button marked “File Browse” and select the firmware update file matching your receiver in the “Open file” dialogue which now appears; the file suffix will be “bin”. In the case of the zip file “HoTT_Software_VX” which you have already downloaded and unpacked, this will usually be found in the folder whose name starts with the Order Number of the receiver to be updated. If your receiver is the GR-16 which is supplied in the set as standard, this would be the folder “33508_8CH_RX”. The file appears in the associated window. At the same time the “2” starts to flash red: with the SET button pressed in. After a few seconds “Line 3” appears in the column “No” of the Status display, with the message: “Found target device …”. Release the button at this point. The actual firmware update process now starts automatically: “11, Start Firmware upgrade…”. If the device is not detected, a pop-up window appears with the message “Target device ID not found”. If this should happen, check your update arrangements and try again: When you have called up the program, you will see the number “1” flashing red in the numeric row 1 … 5 at the top of the window, indicating that the program is currently operating at “[Process Step] 1”. In each case the meaning of the currently flashing step is indicated immediately below the numeric row: Note: For example, at Step 1: “Connect USB lead to HoTT receiver” and “Press File Browse button and select Update file”, as shown here. Note: At any time you can call up an explanation of any step in the form of Quick-Info by positioning the mouse pointer over a number. If you have not already done so, connect your receiver to the PC or laptop at this point. Now click on The firmware files are encoded in a manner specific to each product, i.e. if you accidentally select a file which does not match the product (e.g. transmitter update file instead of receiver update file), the pop-up window “Product code error” appears, and you will be unable to continue the update process. Follow the instructions for “[Process Step] 2”. With the receiver still switched off, click on the “Download Start” button in the “HoTT Receiver Upgrade” window. (The display changes to “[Process Step] 3”.) Wait until the progress bar starts to advance; this may take several seconds, depending on your computer. Only at this point should you switch the receiver on In the Status display the progress of the firmware update is indicated by the progress bar. During the update process the green and the red LED on the receiver glows a constant green and red. You must not interrupt the connection between the transmitter and the PC during the update process! The update is finished when the progress bar reaches the right-hand end, and the message “12, Complete !!” appears in the bottom line of the Status display. At the same time the [Process Steps] display moves on to “5”. Updating the receiver firmware 49 When the update is completed, the green LED goes out, and the red LED starts to flash. If the process terminates before the 100% mark is reached, switch the receiver power supply off and repeat the update procedure, i.e. carry out each of the steps described above once more. If you accidentally attempt to load a version of the firmware which is correct, but older than the one currently in the receiver, the screen will display a corresponding warning: Unless you really want to load older firmware, click on “No” with the mouse, and load the correct *.bin file using the “File Browse” button. Finally you MUST initialise the receiver, i.e. reset it to the factory default settings. This is accomplished by switching the receiver off and removing the interface lead. 4. Initialising the receiver In the interests of safety you should now re-initialise the receiver before re-using it. The screen-shot shown above indicates this: Hold the SET button on the receiver pressed in while you switch the receiver on. The red and green LEDs flash four times, followed by a pause lasting about two seconds. At this point the red LED starts flash50 Updating the receiver firmware ing on its own. At this point you can release the SET button. Switch the transmitter on again, and wait until RF transmission is active: about two or three seconds after this the green LED of the bound receiver will glow constantly. If you have not yet bound the receiver to the transmitter, you can now do so as described on pages 80 and 88. Important note: With the exception of the binding information, all the receiver’s previously programmed settings are now reset to the default values. You must therefore enter the data again if necessary; see the section entitled “Reset” on page 46. If you wish to “save” the data, you should run the program “Receiver Setup” before updating the receiver. This will spare you the trouble of re-programming the receiver under the “Telemetry” menu. For your notes 51 Backing up receiver settings The “Receiver Setup” segment of the program “Firmware_Upgrade_grStudio” can be used to save all the data programmed in the receiver in a file on your computer, so that you can transfer the data set back into the receiver in an emergency; this eliminates the need to re-program the receiver using the “Telemetry” menu, as would otherwise be necessary. We recommend that you call up the “Receiver Setup” program from the “Firmware_Upgrade_grStudio” program. Alternatively you can start the application directly. You will find the file “Receiver_Setup.exe” in the “Graupner_PC-Software” folder. Note: If you call up “Receiver Setup” from the Firmware_Upgrade program, ensure that the sub-program “Receiver_Setup.exe” is located in the same folder as the “Firmware_Upgrade_grStudio” program; see the screen-shot above! For this program you need the USB interface, Order No. 7168.6, and the interface lead, Order No. 7168.S, supplied in the mx-16 radio control set, Order No. 33116. Backing up receiver settings 1. Connecting the receiver to the PC With the receiver switched off, connect the USB interface, Order No. 7168.6, to the socket marked “-+T” on the receiver using the adapter lead, Order No. 7168.6S. 52 Backing up receiver settings The connector system is polarised: note the small chamfers on the edges. Do not use force under any circumstances; the plugs should engage easily. Adapter lead Order No. 7168.6A the “Controller Menu” (see earlier), and note the Com port number at the entry “Silicon Labs CP210x USB to UART Bridge”. In accordance with the previous update descriptions this would be the port “COM 3”. If a central red wire is present, cut through it Caution: If you are using the - earlier - adapter lead, Order No. 7168.6A, and this is fitted with a three-core lead, cut through the central red wire of the adapter lead before using it. Now connect the USB interface to the PC or laptop using the USB lead supplied in the set (PC-USB / mini-USB). If connected correctly, a red LED on the interface circuit board should light up. The receiver should be left switched off at this point. 2. Receiver Setup: selecting the port Start the program “Firmware_Upgrade_grStudio_ Ver-X.X.exe” by double-clicking on it, as described for updating the transmitter software (see page 42). (Version 1.9, which is current at the time this manual went to press, starts without being installed beforehand.) Open the “Controller Menu” and click on “Receiver Setup” in the “Upgrade / Link” folder. Alternatively select the “Receiver Setup” entry under “Menu”. A program window now appears, in which you should start by setting the “correct” COM port for the USB interface, Order No. 7168.6. If you are not sure of this, check the COM port in the “Port select” window in (If you select the wrong port, the program will alert you to the error.) 3. Reading out receiver data Click on the “Connect” button and wait until the Status bar below it starts to advance: Locate the SET button on the receiver and hold it pressed in while you switch it on. After about three seconds the receiver’s current values will be displayed in the corresponding fields. If the progress bar is “faster than you are”, and reaches the end before you have switched the receiver on, the pop-up window shown here appears. In this case repeat the procedure. backed up when you click on the “Save” button. When the process is complete, this message appears: Important: The active connection is terminated using the “Disconnect” button, but you should only do this if you wish to initialise the receiver directly, as described on page 46 or 50, and do not wish to overwrite it with a data set you have already saved. 4. Saving receiver data The “File Save” button backs up the current servo configuration on the PC. The Windows “Save as” dialogue now opens: First select a folder of your choice in which to save the file, and enter under “File name” an appropriate and unambiguous name, so that you can easily find the file again at a later date. The program automatically appends the file suffix “rdf”. The data set is Click on “OK” to close the window. You can now reset the receiver to the default settings, as mentioned earlier and described on page 46. not be used at present. You can find out about the latest state of the software in the Download area for the mx-16 on the Graup­ner website. A separate manual for the whole “Firm• ware_Upgrade_grStudio_Ver-X.X” program package is in preparation, and will be updated constantly as soon as new options are available. Copying a data set to the receiver You can re-load the backed-up data into the receiver using the “File Load” function of the Receiver Setup program. The first step is to connect the receiver as described under point 3 “Reading out receiver data”, and click on the “Connect” button. Assuming that the receiver has been previously initialised, the program reads out the default settings. Now select the desired “rdf” file from the appropriate folder and click on “OK” in the “File Load” pop-up window. Click on the “Write” button to transfer the data to the receiver connected to the PC. When the data transfer is complete, the pop-up window “Receiver Data Write Success” appears. Finally you can click on “OK” to confirm the action, then on the “Disconnect” button to disconnect the Receiver Setup program from the receiver. Important notes: The “Receiver Setup” program in• cludes additional functions which are currently still in preparation; they must Backing up receiver settings 53 Installation notes Installing the receiver Regardless of which Graupner receiving system you are using, the procedure is always the same: Please note that the receiver aerials must be arranged at least 5 cm away from all large metal parts and leads which are not attached or connected directly to the receiver. This includes steel and carbon fibre components, servos, fuel pumps, cables of all sorts, etc. Ideally the receiver should be installed in an easily accessible position in the model, away from all other installed components. Under no circumstances run servo leads immediately adjacent to the receiver aerials, far less coil them round it! Tests have shown that a vertical (upright) position of a single aerial produces the best results when long approaches are flown with a model. If the receiver features a diversity aerial system (two aerials), the second aerial should be deployed at an angle of 90° to the first. The servo sockets of Graupner receivers are numbered. The power supply is through-connected via all the numbered sockets, and in principle can be connected to any of the servo sockets. It is also possible to connect the power supply via a Y-lead, Order No. 3936.11, in parallel with a servo. The function of each individual channel is determined by the transmitter in use, rather than by the receiver. However, it is possible to alter the channel assignment (mapping) by changing the programming in the Telemetry menu. Nevertheless, we recommend that you carry out this process using the “Receiver output” option; see page 79 or 87. The following section contains notes and helpful ideas on installing radio control components in the model: 1. Wrap the receiver in foam rubber at least 6 mm thick. Fix the foam round the receiver using rubber bands, to protect it from vibration, hard landings and crash damage. 2. All switches must be installed in a position where they will not be affected by exhaust gases or vibration. The switch toggle must be free to move over its full range of travel. 3. Always install servos using the vibration-damping grommets and tubular metal spacers supplied. The rubber grommets provide some degree of protection from mechanical shock and severe vibration. Don’t over-tighten the servo retaining screws, as this will compress the grommets and thereby reduce the vibration protection they afford. The system offers good security and vibration protection for your servos, but only if the servo retaining screws are fitted and tightened properly. The drawing below shows how to install a servo correctly. The brass spacers should be pushed into the rubber grommets from the underside. Servo mounting lug Retaining screw Rubber grommet Tubular brass spacer 4. The servo output arms must be free to move over their full arc of travel. Ensure that no parts of the me54 Installation notes chanical linkage can obstruct the servo’s movement. The sequence in which the servos are connected to the receiver is dictated by the model type. Please see the socket assignments listed on pages 63 and 65. Be sure to read the additional safety notes on pages 4 … 9. If the receiver is ever switched on when the transmitter is off, the servos may carry out uncontrolled movements. You can avoid this by switching the system on in this order: Always switch the transmitter on first, then the receiver. When switching the system off: Always switch the receiver off first, then the transmitter. When programming the transmitter you must always ensure that any electric motors in the system cannot possibly burst into life accidentally, and that an I.C. engine fitted with an automatic starter cannot start unintentionally. In the interests of safety it is always best to disconnect the flight battery, or cut off the fuel supply. Receiving system power supply A reliable power supply is one of the basic essentials for reliable model control. Free-moving pushrods, a fully-charged battery, battery connecting leads of adequate cross-section, minimal transfer resistance at the connectors etc. all help to minimise energy consumption, but if you have attended to all this, and the receiver voltage displayed on the transmitter screen still collapses repeatedly, or is generally (too) low, then please note the following: The first point to check is that your batteries are always fully charged at the start of each flying session. Check that contacts and switches are low in resistance. It is a good idea to measure the voltage drop over the installed switch harness under load, as even a new, heavy-duty switch can cause a voltage drop of up to 0.2 Volt. Ageing effects and oxidation of the contacts can increase this several times over. Constant vibration and movement at the contacts also “gnaws away” at the contacts, and tends to produce a creeping increase in transfer resistance. It is also true that even small servos, such as the Graupner/JR DS-281, can draw currents of up to 0.75 Ampere when stalled (mechanically obstructed). Just four servos of this type in a “foamy” can therefore place a load of up to 3 Amps on the airborne power supply ... For this reason you should always choose a receiver battery which constantly delivers an adequate voltage, i. e. which does not collapse under severe load. To “calculate” the necessary battery capacity we recommend as a starting point that you provide 350 mAh for each analogue servo, and at least 500 mAh for each digital servo. For example, a 1400 mAh battery would represent an absolute minimum as the power supply for a receiving system with a total of four analogue servos. When making your calculations, however, please bear the receiver in mind as well, as it draws a current of around 70 mA due to its bi-directional function. Regardless of these considerations, it is generally advisable to connect the power supply to the receiver using two leads: lead “1” is connected to the 6+B receiver socket in the usual way, and lead “2” to the opposite socket, marked 1+B, at the other end of the receiver socket bank. For example, you could use a switch or voltage regulator with two power supply leads running to the receiver. You might install a Y-lead, Order No. 3936.11, between lead and receiver, as shown in the diagram below, if you wish to use one or both of the receiver sockets to connect a servo, speed controller, etc. The dual connection at the switch or voltage regulator not only reduces the risk of a cable fracture, but also ensures a more even energy supply to the servos connected to the receiver. Auxiliary function Y-lead, Order No. 3936.11 PRX stabilised receiver power supply, Order No. 4136 Four-cell NiMH battery packs Traditional four-cell packs are a good choice for powering your Graupner|SJ HoTT receiving system, provided that you observe the conditions described above, i. e. you must ensure that the packs have adequate capacity and maintain their voltage well. Five-cell NiMH battery packs Five-cell batteries offer a wider margin of safety in terms of voltage compared with four-cell packs. However, please note that not all servos available on the market can tolerate the voltage of a five-cell pack (in the longterm), especially when the battery is freshly charged. For example, many of these servos respond to the high voltage with a clearly audible “rumble”. It is therefore important to check the specification of the servos you intend to use before you make the decision to use five-cell packs. Two-cell LiFe 6.6 V batteries Taking into account the current situation, these new cells are now regarded as the optimum choice for receiver packs. LiFe cells are also available in plastic hard-case housings, to protect them from mechanical damage. Like LiPo cells, LiFe cells can be fast-charged in conjunction with a suitable battery charger, and are comparatively robust. It is also true that a much higher number of charge / discharge cycles is attributed to this cell type than, for example, to LiPo cells. The nominal voltage of 6.6 Volt of a two-cell LiFe pack presents no problems to Graupner|SJ HoTT receivers, nor to those servos, speed controllers, gyros, etc. which are expressly approved for use at these higher voltages. Please note, however, that virtually all servos, speed controllers, gyros etc. sold in the past, and also most of those currently available, are only approved for use on an operating voltage in the range 4.8 to 6 Volt. If you wish to connect these devices to the receiver, it is essential to use a stabilised regulated power supply, such as the PRX, Order No. 4136; see Appendix. If you neglect this, there is a danger that the connected devices will quickly suffer permanent damage. Installation notes 55 Two-cell LiPo battery packs For a given capacity LiPo batteries are lighter than NiMH batteries. To protect them from mechanical damage LiPo batteries are also available in plastic hard-case housings. Moreover LiPo batteries only have a limited ability to be fast-charged, and generally do not survive such a high number of charge / discharge cycles as is claimed for other batteries, such as Nanophosphate® types. The comparatively high nominal voltage of 7.4 Volt of a two-cell LiPo pack presents no problems to Graupner|SJ HoTT receivers, nor to those servos, speed controllers, gyros, etc. which are expressly approved for use at these higher voltages. Please note, however, that virtually all servos, speed controllers, gyros etc. sold in the past, and also most of those currently available, are only approved for use on an operating voltage in the range 4.8 to 6 Volt. If you wish to connect these devices to the receiver, it is essential to use a stabilised regulated power supply, such as the PRX, Order No. 4136; see Appendix. If you neglect this, there is a danger that the connected devices will quickly suffer permanent damage. 56 Installation notes For your notes 57 Definition of terms Control functions, transmitter controls, function inputs, control channels, mixers, switches, control switches To make it easier for you to understand the mx-16 HoTT manual, the following section contains definitions of many terms which crop up again and again in the remainder of the text. Control function The term “control function” can be thought of as the signal generated for a particular function which needs to be controlled - initially independent of its subsequent progress through the transmitter. In the case of fixedwing model aircraft the control functions include throttle, rudder and aileron, whereas collective pitch, roll and pitch-axis are typical of those used for helicopters. The signal of a control function may be assigned directly, or to several control channels simultaneously via mixers. A typical example of the latter is separate aileron servos, or pairs of roll-axis or pitch-axis servos in a model helicopter. The essential feature of a control function is its influence on the mechanical travel of the corresponding servo. Transmitter control The term “transmitter control” refers to the mechanical elements on the transmitter which are operated directly by the pilot. Their movements in turn generate corresponding movements in the servos, speed controllers etc. at the receiver end. The transmitter controls include the following: • The two dual-axis stick units for the control functions 1 to 4; for both model types (“fixed-wing” and “helicopter”) these four functions can be interchanged in any way you wish using the “Mode” function, e. g. throttle left or right, without having to re-connect the servos. The dual-axis stick function for throttle (or airbrakes) is often referred to as the Ch 1 (Channel 1) control. • The three rotary proportional controls CTRL 6, 7 + 8 58 Definition of terms • The switches SW 4/5 and 6/7, and CTRL 9 and 10 • The switches SW 1 … 3, plus 8 and 9, if they have been assigned to a control channel in the “Transmitter control settings” menu. When a proportional transmitter control is operated, the servo or servos follow the position of the control directly, whereas a switched channel provides just the two or three set servo positions. Function input This is an imaginary point on the signal path, and must not be considered the same as the point on the circuit board where the transmitter control is connected! The two menus “Stick mode” and “Transmitter control settings” affect the course of the signal “after” this point, and it is possible (and likely) that there will be differences between the number of the transmitter control (as stated above) and the number of the subsequent control channel. Control channel There is a point on the signal path where the signal contains all the control information required for a particular servo – this may be directly generated by a transmitter control or indirectly via a mixer – and from this point on we call the signal a “control channel”. This signal is only affected by any adjustments carried out in the “Servo settings” menu before leaving the transmitter via the RF module. Once picked up at the receiver, this signal may be modified by any settings made in the Telemetry menu before finally passing to the corresponding servo in the model. Mixer The transmitter’s software includes a wide range of mixer functions. Their purpose is to enable a control function to affect multiple servos at the branching point of the mixer input, or alternatively to allow several control functions to affect one servo. For more information please refer to the numerous mixer functions as described in the section starting on page 108 of the manual. Switch The three standard switches SW 2, 3 and 8, the two three-position switches SW 4/5 and 6/7 and the two momentary buttons SW 1 and 9 can also be incorporated into the programming of the transmitter controls. However, all these switches are also generally intended for switching program options, e. g. starting and stopping timers, switching mixers on and off, transferring control in Trainer mode etc. Each physical switch function can be assigned to as many functions as you wish. Numerous examples are described in the manual. Transmitter control switch It is often desirable to switch a function on or off automatically at a particular position of another transmitter control, e. g. at a defined position of one of the dual-axis sticks. Typical examples are switching a stopwatch on and off to allow you to record the motor run time, extending spoilers automatically (and many others). The mx16 HoTT software includes a total of two (three - for helicopters) “control switches” of this type. Two transmitter control switches are available for the Ch 1 stick in each model memory, both for fixed-wing model aircraft and helicopters. For helicopters a third is present in the form of the throttle limiter; see the right-hand side and page 86. This manual includes a range of instructive examples which make programming as simple as child’s play. Please refer to the programming examples in the section starting on page 164. Assigning switches and control switches The basic procedure At many points in the program there is the option of using a switch (SW 1 … 9) or a control switch (G1 … 3; see below) to operate a function, or to switch between settings, such as the DUAL RATE / EXPO function, flight phase programming, mixers and more. The mx-16 HoTT allows you to assign several functions to a single switch. The process of assigning switches is exactly the same in all the relevant menus, and we will explain the basic programming procedure at this point so that you can concentrate on the special features when reading the detailed menu descriptions. A switch symbol appears in the bottom line of the screen at all programming points where switches can be assigned: Move to the appropriate column using the arrow buttons of the left or right touch-key. This is the procedure for assigning a switch: 1. Briefly press the SET button of the right-hand touchkey. The following message appears on the screen: push desired switch into position ON 2. Now simply move the switch you wish to use to the “ON” position, press the push-button, or move the Ch 1 stick from the “OFF” position in the direction of “ON”. Please note: the so-called control switches assigned to this transmitter control (see right) carry out the task of an ON / OFF switch in software; the same applies to the throttle limiter (see page 99) which is available in the “Helicopter” model type. This completes the assignment process. Changing the direction of switching: If the switch turns out to work in the wrong direction, you can correct it as follows: move the switch to the desired OFF position, activate switch assignment once more and assign the switch again, this time with the switch direction you prefer. Erasing a switch: Activate the switch symbol as described under Point 2, then briefly press the button combination or of the right-hand touch-key (CLEAR) simultaneously Transmitter control switches Many functions are best controlled automatically by a particular (freely programmable) position of the Ch 1 transmitter stick (or the throttle limiter in the case of helicopters), rather than by a conventional physical switch. Typical applications: • Automatically switching an on-board glowplug energizer on and off according to the throttle position of the Ch 1 stick (“G1” or “G2”). In this case the switch for the plug energizer is controlled by a mixer at the transmitter. • Automatically switching a stopwatch on and off to record the pure “flight time” of a model helicopter; this is accomplished using the “G3” switch of the throttle limiter. • Automatically switching the “AIL RUD” mixer off when the airbrakes are extended, in order to keep the wings parallel with the ground when landing on a slope face, without the (usually coupled) rudder affecting the model’s heading. • Automatically extending landing flaps with coupled elevator trim adjustment on the landing approach, as soon as the throttle stick is reduced below the set threshold point. • Automatically switching a stopwatch on and off in order to time the run of an electric motor. For both model types the mx-16 HoTT transmitter’s software caters for these purposes with two “control switches” of this type; they can be assigned to the Ch 1 stick: “G1” is switched on at around -80% of full travel, while “G2” is switched on at around +80%. The Helicopter program also includes an extra control switch “G3” on the throttle limiter close to the 100% point; see page 99. All these control switches can be included without restriction in the free programming of the switches, i. e. they can be assigned to a function instead of a physical switch. This means that you are able to assign one of the control switches G1 … G2 (or G1 … G3) instead of a physical switch at any point in the software where switches are assigned. All you have to do is move the Ch 1 stick or the throttle limiter control (by default the rotary proportional control CTRL 6) from the desired “OFF” position in the direction of “ON”. Assigning switches and control switches 59 Digital trims Description of function, and Ch 1 cut-off trim 60 Digital trims 1. Fixed-wing models The Ch 1 trim features a special cut-off trim which is designed for glowplug motors: you initially use the trim lever in the usual way to select a reliable idle setting for the motor. If you now move the Ch 1 trim lever to its end-point in the direction of “motor cut-off”, pushing the lever in a single movement, a marker appears on the screen in the last position. You can now return to the idle setting for starting the motor simply by pushing the stick one click in the direction of “open throttle”. Last idle position Current trim position 2. Model helicopters In helicopter mode the Ch 1 trim has another feature in addition to “cut-off trim”, as described under “Fixedwing models” on the left; this time in conjunction with the “Throttle limit function” (see page 99): while the throttle limit slider is in the bottom half of its travel, i. e. in the “start-up range”, the Ch 1 trim lever acts as idle trim on the throttle limit, and the idle trim is displayed on the screen: Last idle position Current trim position stop flt Throttle limit control M CTRL 6 Ch 1 trim lever stop flt Idle direction Digital trims with visual and audible indicators Both the dual-axis stick units are fitted with digital trim systems. When you give the trim lever a brief push (one “click”), the neutral position of the associated stick channel changes by one increment. If you hold the trim lever in one direction, the trim value changes continuously in the corresponding direction with increasing speed. The degree of trim offset is also “audible”, as the pitch of the tone changes to reflect the setting. When you are flying a model, you can find the trim centre position easily without having to look at the screen: if you over-run the centre setting, the trim stays in the centre position for a moment. The current trim values are automatically stored when you switch from one model memory to another. The digital trims are also stored separately for each flight phase within a model memory, with the exception of the “Ch 1” (Channel 1) trim, which is the throttle / airbrake trim on a fixed-wing model. The Ch 1 trim includes another special function which makes it easy to re-locate the idle throttle setting of a glowplug motor. However, since the trim functions described in these instructions only affect the “Motor off” direction, the trim display on the transmitter’s screen will vary according to your individual set stick mode, i. e. the “forward” or “back” throttle / collective pitch minimum position of the Ch 1 stick, and also according to “left stick” or “right stick” for throttle / collective pitch. The illustrations in these instructions always refer to “Throttle / Collective pitch right” for both model types, and to “Throttle back” for fixed-wing models and “Collective pitch forward” for model helicopters. M Trim at motor OFF position In contrast to a fixed-wing model aircraft, this display is suppressed if the throttle limit control is moved to the “right” half of its travel. Trim at motor OFF position The cut-off trim feature is disabled if you enter “none” or “none / inv” in the “Motor at Ch 1” line within the “Base settings” menu (page 74 / 75). Note: Since this trim function is only effective in the “Motor off” direction, the above illustration will not apply if you change the direction of the Ch 1 stick for throttle minimum from “back” (which is reflected in the illustration above) to “forward” in the “Motor at Ch1” line of the “Base settings” menu. stop flt M Throttle limit control CTRL 6 Note regarding helicopters: The Ch 1 trim only affects the throttle servo and not the collective pitch servos; it also works evenly over the full stick travel. Please note that the helicopter throttle servo must be connected to receiver output 6 (see Receiver socket assignment, page 65). For your notes 61 Fixed-wing model aircraft This program provides convenient support for normal model aircraft with up to two aileron servos and two flap servos, V-tail models, flying wings and deltas with two elevon (aileron / elevator) servos and two flap servos. The majority of power models and gliders belong to the “normal” tail type with one servo each for elevator, rudder, ailerons and throttle or electronic speed controller (airbrakes on a glider). There is also the special model type “2 EL Sv” which provides a means of connecting two elevator servos to channels 3 and 8 in parallel. If your model features two separate aileron servos (and also in some cases two flap servos), the aileron travel of both pairs of control surfaces can be set up with differential movement in the “Wing mixers” menu, i. e. the down-travel can be set independently of the up-travel. Finally the program caters for camber-changing flaps, which can be operated by any of the transmitter controls “CTRL 6 … 10”. Alternatively a phase-specific trim is available for flaps, ailerons and elevator in the “Phase trim” menu. If the model features a V-tail instead of a conventional tail, you need to select the tail type “V-tail” in the “Base settings” menu, as this automatically superimposes the elevator and rudder control functions in such a way that each tail panel can be actuated by a separate servo. For deltas and flying wings it is easy to set up mixed elevons, i. e. the aileron and elevator functions can be carried out via common control surfaces at the trailing edge of the right and left wing. As standard the program contains the appropriate mixer functions for the two servos. Up to four flight phases can be programmed in each of the twenty model memories. The digital trim positions are stored separately for each flight phase, with the exception of the Ch 1 trim. The Ch 1 trim provides a simple means of re-locating the correct idle throttle setting. Two timers are available at all times when flying. The screen also displays the transmitter operating time since the battery was last charged. All the transmitter controls (CTRL) and switches (SW) can be assigned to virtually any of the inputs 5 … 8 in the “Transmitter control settings” menu. “Dual Rate” and “Exponential” can be programmed separately for aileron, rudder and elevator, giving two modes of control. Depending on the model type you have selected, the “Wing mixers” menu presents you with up to twelve additional pre-defined mixers and coupling functions which you can simply select and set up when necessary, in addition to three free mixers: 1. Aileron differential (switchable) 2. Flap differential (switchable) 3. Aileron rudder (switchable) 4. Aileron flap (switchable) 5. Airbrake elevator (switchable) 6. Airbrake flap (switchable) 7. Airbrake aileron (switchable) 8. Elevator flap (switchable) 9. Elevator aileron (switchable) 10. Flap elevator (switchable) 11. Flap aileron (switchable) 12. Differential reduction Airbrake-Function 1 ro n Ai le Ail e r o t va er Ele A il Flap left le v a tor Airbrake Flap Airbrake Elevator r Flap F la p E va Ele to l e ro n r Elevator Flap right left Rudder/Elevator V-Tail F la p E le v ator right A il e r o n R u dder E le v at or A ileron 62 Fixed-wing model aircraft Aileron Airbrake Flap Airbrake Elevator A leron F la p Fl a p Ai dde A il e r o n n Ru n Ailero n Rudder A il e ro F la p Fl ap at or E l ev on Airbrake n Flap Ail e r o E ev ato r Fla p Fl a p or F la p A leron Installation notes The servos MUST be connected to the receiver outputs in the order shown on this page. Outputs not required are simply left vacant. Please note the following points in particular: • If you are using only one aileron servo, receiver output 5 (right aileron) is left unused; it can also be used for another purpose if you select “1 AIL” in the line “aile/flap” of the “Base settings” menu. • If you are using only one flap servo, receiver output 7 (right flap) MUST be left unused, assuming that you have selected “2 FL” in the line “aile/flap” of the “Base settings” menu. Please also read the information on the following pages. Winged aircraft with and without motor, having up to 4 aileron servos and up to 4 fl ap servos … … and tail plane type “normal” or “2 elevator servos” 2nd elevator or aux. function or free Flap or left flap or free Receiver power supply Right aileron or aux. function Rudder Elevator or 1st elevator Aileron or left aileron Receiver power supply Airbrake or throttle servo or speed controller (electric motor) Right flap or free or aux. function … and tail plane type “V tail unit” Aux. function or free Flap or left flap or free Receiver power supply Right aileron or aux. function Right rudder / elevator Left rudder / elevator Aileron or left aileron Receiver power supply Airbrake or throttle servo or speed controller (electric motor) Right flap or free or aux. function As there are several possible combinations of servo orientation and control surface linkage, you may find that the direction of rotation of one or more servos is incorrect. Use the following table to solve the problem. Model type V-tail Delta/flying wing aircraft models with and without motor having up to two aileron/elevator servos and up to 2 fl ap/elevator servos Free or aux. function Free or left flap / elevator Receiver power supply Free or aux. function Free or rudder Right elevon Left elevon Receiver power supply Airbrake or throttle servo or speed controller (electric motor) Free or right flap / elevator Delta, flying wing Servo rotating in wrong direction Remedy Rudder and elevator reversed Reverse servos 3 + 4 in the “servo set.” menu Rudder correct, elevator reversed Swap over servos 3 + 4 at the receiver Elevator correct, rudder reversed Reverse servos 3 + 4 in the “servo set.” menu, AND swap over at the receiver Elevator and ailerons Reverse servos 2 + 3 in reversed the “servo set.” menu Elevator correct, ailerons reversed Reverse servos 2 + 3 in the “servo set.” menu, AND swap over at the receiver Ailerons correct, elevator reversed Swap over servos 2 + 3 at the receiver All menus which are relevant to fixed-wing models are marked with an “aeroplane” symbol in the “Program descriptions”: This means that you can easily skip irrelevant menus when programming a fixed-wing model aircraft. Fixed-wing models: receiver assignment 63 Model helicopters The continued development of model helicopters and helicopter components, such as gyros, speed governors, rotor blades etc., has led to the current position where helicopters are capable of sophisticated 3-D aerobatics. In contrast, if you are a beginner to helicopter flying, you need a simple set-up so that you can quickly get started on the initial stages of hovering practice, and then gradually learn to exploit all the options provided by the mx-16 HoTT. The helicopter program of the mx-16 HoTT can cope with all current model helicopters equipped with 1 … 4 servos for collective pitch control, entirely regardless of whether they are powered by a fuel-driven or electric motor. Each model memory can include three flight phases plus auto-rotation. Two timers are constantly included in the basic screen display. At the same time the period which has elapsed since the last charge process is also displayed. You can return to the correct idle position for the digital Ch 1 trim simply by pressing a button. “Dual Rate” and “Exponential” are available for roll, pitch-axis and tail rotor; they can be coupled together, and programmed to provide two settings. All the transmitter controls (CTRL) and switches (SW) can be assigned to inputs 5 … 8 in virtually any order. This is carried out in the “Transmitter control settings” menu. In addition to three linear mixers, which can be assigned to any functions and can also be switched on and off, the “Helicopter mixers” menu provides five-point curves for the collective pitch, throttle and tail rotor mixers, variable separately for each flight phase; these provide non-linear mixer characteristics. 1. Collective pitch 2. Ch 1 throttle 3. Ch 1 tail rotor Such advanced features are not needed by the beginner, who will initially simply set the hover point to coin- Collective Pitch Curve Channel 1 64 Model helicopters Throttle cide with the centre point of the stick arc, and adjust the collective pitch travel as required. Moreover the “Heli mixers” menu offers two additional set-up options in the lines “Gyro” and “Inp8”, plus a “swashplate limiter”. The mixer inputs for collective pitch, roll and pitch-axis can then be adjusted in the “Swashplate mixers” menu. The throttle limit function in the “Transmitter control settings” menu provides an effective means of starting the motor in any flight phase. By default the proportional rotary control CTRL 7 is assigned to this input, and this control function determines the maximum throttle servo position, i. e. the trim lever controls the motor over the idle range. Only when this rotary knob is turned in the direction of full-throttle do the programmed throttle curves take effect. If you have set up the two timers, they also start recording the flight time automatically at this point. See page 99 for more information on this. Channel 1 Tail Rotor Note for modellers upgrading from earlier Graupner systems: Compared with the previous receiver channel sequence, servo socket 1 (collective pitch servo) and servo socket 6 (throttle servo) have been interchanged. The servos must be connected to the receiver output sockets in the order shown at bottom right. Outputs not required are simply left vacant. For more information on the different types of swashplate, please refer to the “Base settings” menu described on page 82 / 83. Installation notes The servos MUST be connected to the receiver outputs in the order shown on this page: Outputs not required are simply left vacant. Please note the additional information on the following pages. Note: To be able to exploit all the convenience and safety features of the throttle limiter (see page 99), the speed controller should be connected to receiver output “6”, and not to receiver output “8”, as shown in the drawing on the left. See page 117 for more details. Receiver layout for helicopter models … … with 1 to 3 swashplate servos Free or speed governor or aux. funct. Throttle servo or speed controller Receiver power supply Free or aux. function Tail rotor servo (gyro system) Pitch-axis 1 servo Roll 1 servo Receiver power supply Collective pitch or roll 2 or Pitch-axis 2 servo Gyro gain … with 4 swashplate servos Free or speed governor or aux. funct. Throttle servo or speed controller Receiver power supply Pitch-axis 2 servo Tail rotor servo (gyro system) Pitch-axis 1 servo Roll 1 servo Receiver power supply Roll 2 servo Gyro gain All menus which are relevant to model helicopters are marked with a “helicopter” symbol in the “Program descriptions”: This means that you can easily skip irrelevant menus when programming a model helicopter. Model helicopters: receiver assignment 65 Detailed description of programming Setting up a new model memory If you have already read through the manual to this point, you will undoubtedly have made your first attempt at programming the system already. Even so, it is important to describe each menu here in detail, to ensure that you have comprehensive instructions for each application you are likely to encounter. In this section we start with setting up a “free” model memory prior to “programming” a new model: #01 5.6V 0:00h stop flt M 0:00 0:00 HoTT 0.0V From the basic display press the central SET button of the right-hand touch-key to move to the “Multi-function list”. (You can return to the basic screen at any time by pressing the central ESC button of the left-hand touchkey.) By default the menu point “Model memory” is displayed inverse (black background) and is therefore active when you first call up the multi-function select menu after switching the transmitter on. If this is not the case, select the “Model memory” menu using the arrow buttons (, ) of the left or right-hand touch-key, then briefly press the central SET button of the righthand touch-key: mod.mem. ser vo set. D/R expo wing mixer ser vo disp fail-safe 66 base sett. contr set. phase trim free mixer basic sett telemetr y Program description: reserving a new memory select model clear model copy mod–>mod expor t to SD impor t from SD => => => => => Now touch the central SET button of the right-hand touch-key once more to move on to the “select model” sub-menu. 01 02 03 04 05 06 free free free free free R08 In the transmitter’s default state the first model memory is already initialised with the “Fixed-wing model” model type, and the receiver supplied in the set is “bound” to it. This is indicated by the receiver code displayed at top right of the screen; in the example above this is R08. If, on the other hand, the model memory is “unbound”, you will see “---”. The remainder of the model memories are not yet occupied, and are “unbound”; these are entitled “ free”. If you want to set up a fixed-wing model, then you can immediately start the programming procedure after leaving the “select model” sub-menu and the “Model memory” menu by pressing the central ESC button of the left-hand touch-key each time … alternatively you can select one of the free model memories using the left or right-hand touch-key … 01 02 03 04 05 06 free free free free free R08 ... and then briefly press the central SET button of the right-hand touch-key to confirm your choice. After this you are invited to select the basic model type, i. e. either “Fixed-wing” or “Helicopter”: Sel model type ( empty mod mem ) Use the or button of the left or right-hand touchkey to select the appropriate basic model type, then touch the central SET button of the right-hand touch-key to confirm your choice. Your chosen model memory is now initialised with the selected basic model type, and the screen switches back to the basic display. The model memory is now reserved for that use. However, if you wish to get started with a helicopter, then use the or button of the left or right-hand touch-key to select one of the model memories marked as “free”, and confirm your choice with a brief touch of the central SET button of the right-hand touchkey. You are now requested to define the basic model type, i. e. either “fixed-wing” or “helicopter”. Use the or button of the left or right touch-key to select the corresponding symbol, then again press the central SET button of the right-hand touch-key briefly in confirmation. This initialises the selected model type for the model memory you have just selected, and you can now start programming your model in this memory. It is now only possible to change this memory to a different model type if you first erase the model memory (“Model memory” menu, page 70). Notes: • If you wish to erase the model memory which is currently active in the basic display, you will have to define one of the two model types “fixed-wing” or “heli­copter” immediately after completing the erase procedure. You cannot avoid making this choice by switching the transmitter off. If you wish to remove a model memory which you inadvertently occupied, you can simply erase it from a different model memory. However, if you erase a model memory which is not currently active, after the procedure you will see the memory marked as “free” under Model Select. • After the selected model memory has been initialised with your preferred basic model type, the screen shifts to the newly reserved model memory. At the same time the following warning appears for a few seconds … BIND N/A OK … as an indication that this memory has not yet been bound to a receiver. With a brief touch of the central SET button of the right-hand touch-key you can move directly to the corresponding option. For more detailed information on binding a receiver please refer to pages 80 and 88. • The warning “BIND. n/v” just described is now followed for a few seconds by this warning … fail safe setup t.b.d … as an indication that no Fail-Safe settings have been entered. For more information on this please refer to page 136. • If the warning … throttle too high ! … appears on the screen, move the throttle stick (or the limiter - by default the rotary knob CTRL 6 - if setting up a helicopter) back to idle. This warning only appears in accordance with the settings you have entered in the “Motor at Ch1” or “Collective pitch min.” section of the “Base settings” menu, as described on pages 74 and 85. If you are setting up a non-powered fixed-wing model, enter “none” or “none/inv” at this point; this disables the throttle warning message, and makes available the “Brake NN *“ mixers in the “Wing mixers” menu, which would otherwise be suppressed. • If the transmitter’s model memories are already occupied, then a pictogram of the selected model type appears in the appropriate model memory, followed by a blank line, or the model’s name if a name has already been entered in the “Base settings” menu (pages 74 and 82), together with an indicator that the memory is bound to a receiver, if appropriate. • If the battery voltage is too low, the software prevents you switching model memories in the interests of safety. In this case the screen displays this message: not possible now voltage too low Basically there are now four different options for assigning the four control functions aileron, elevator, rudder and throttle / airbrakes (fixed-wing model), and roll, pitch-axis, tail rotor and throttle / collective pitch (model helicopter) to the two primary dual-axis sticks. Which of these options is adopted depends on the personal preference of the individual model pilot. This function is set in the “Stick mode” line for the currently active model memory in the “Base settings” menu (page 74 or 82): mod Name stick mode motor at C1 CH8 delay tail type 1 no yes normal As mentioned earlier, for maximum flexibility the transmitter controls 5 … 8 are by default not assigned to transmitter controls, and can be assigned to any channels you like; this also helps to avoid accidental mishandling. This means that in the default state of the equipment only those servos connected to receiver outputs 1 … 4 can usually be controlled by the two dual-axis sticks, whereas servos connected to sockets 5 … max. 8 remain steadfastly at their centre position. If you set up a * NN = Nomen Nominandum (name to be stated) Program description: reserving a new memory 67 new model helicopter, servo 6 may also respond to some extent to the controls - depending on the position of the throttle limiter CTRL 6. For both model types this situation only changes once you have carried out the appropriate assignments in the “Transmitter control settings” menu. If you wish to use a newly initialised model memory, then this MUST first be “bound” to a (further) receiver before any servos connected to the receiver can be controlled from the transmitter. For more information on this please refer to the “Binding” section on pages 80 and 88. You will find a description of the basic steps for programming a fixed-wing model aircraft in the Programming Examples section starting on page 164; for model helicopters the equivalent section starts on page 186. The following menu descriptions are arranged in the order that they are listed in the individual menus in the multi-function list. 68 Program description: reserving a new memory For your notes 69 Model memories Calling up a model, erasing a model, copying model model The section on pages 24 and 25 explains the basic method of using the buttons, while the previous two double-pages explains how to move to the Multi-function list and reserve a new model memory. At this point we wish to start with the “normal” description of the individual menu points in the sequence in which they occur on the transmitter itself. For this reason we start with the menu … select model Model memory If you now briefly press the SET button again, you move to the “Call up model” sub-menu: mod.mem. ser vo set. D/R expo wing mixer ser vo disp fail-safe select model clear model copy mod–>mod expor t to SD impor t from SD base sett. contr set. phase trim free mixer basic sett telemetr y The transmitter can store up to twenty complete sets of model data, including the digital trim values set by the four trim levers. The trims are automatically stored, which means that the settings you have carefully established through test-flying are never lost when you swap models. A pictogram of the selected model type, and - if you have entered a model name in the “Base settings” menu (pages 74 and 82) - the name appears in all three sub-menus of the “Model memory” menu following the model number. If necessary, use the arrow buttons of the left or righthand touch-key to select the “Model memory” menu, then briefly touch the SET button of the right-hand touch-key: clear model 01 02 03 04 05 06 GRAUBELE ULTIMATE STARLET BELL47G free free Program description: model memories R08 R08 R08 ––– Now use the arrow buttons of the left or right-hand touch-key to select from the list the model memory you wish to use, and confirm your selection by pressing the SET button. Pressing ESC takes you back to the previous menu page without switching models. Notes: • If the warning message “Throttle too high” appears when you switch models, the throttle or collective pitch stick (Ch 1), or the throttle limiter, is positioned too far towards full-throttle. • If the battery voltage is too low, it may not be possible to switch model memories for safety reasons. In this case the screen displays the following message: not possible now voltage too low 70 => => => => => select model clear model copy mod–>mod expor t to SD impor t from SD => => => => => Use the arrow buttons of the left or right-hand touch-key to select the “clear model” sub-menu, then touch the SET button. Select the model to be erased using the arrow buttons of the left or right-hand touch-key, … model 01 02 03 04 to be cleared: R08 GRAUBELE R08 ULTIMATE R08 STARLET ––– BELL47G … then touch the SET button again; the program responds with the security query: model GRAUBELE 01 to be erased ? NO YES If you answer NO, the process is interrupted, and you are returned to the previous screen page. If you answer YES with the button of the left or right-hand touchkey and confirm your choice with the SET button, then the selected model memory is erased. The erasure process is irrevocable. All data in the selected model memory is reset to the factory default settings. Note: If you wish to erase the currently active model memory in the basic display, you will be required to define the model type “Helicopter” or “Fixed-wing” immediately. However, if you erase a non-active model memory, then the message “free” appears in the Model select menu. copy model model Use the arrow buttons of the left or right-hand touch-key to select the “copy model model” submenu, then touch the SET button. => select model > l l SWITCHING RF OFF > > OK > impor t from SD If this message appears, the transmitter’s RF module is active. You can interrupt the process by briefly pressing the central ESC button of the left-hand touch-key. Alternatively a short press of the SET button of the right-hand touch-key switches the RF circuit off, and the menu you called up opens. For safety’s sake you should switch the receiving system off at this point, if it is already operating. Select the model to be copied using the arrow buttons of the left or right-hand touch-key … copy from model: 01 GRAUBELE ULTIMATE 02 03 STARLET 04 BELL47G model memory. R08 R08 R08 ––– … then briefly press the SET button of the right-hand touch-key in the “Copy to model” window. You can now select the target memory using the arrow buttons of the left or right-hand touch-key, and confirm your choice with SET. Alternatively you can interrupt the process with ESC. It is possible to overwrite a model memory which already contains model data. copy to model: 01 GRAUBELE ULTIMATE 02 03 STARLET 04 BELL47G free 05 R08 R08 R08 ––– When you confirm the selected model memory by touching the SET button, the security query appears: model 01 ULTIMATE free 03 to be copied ? NO YES Selecting NO interrupts the process, and returns you to the previous page. If you select YES with the button, and confirm your choice by touching the SET button, then the selected model is copied into the chosen target Note: When you copy a model memory, the binding data is copied together with the model data, so that a receiving system bound to the original model memory can also be operated with the copy of the memory, i. e. it does not require another binding process. Export to SD Use the arrow buttons of the left or right-hand touch-key to select the “Export to SD” sub-menu, then touch the SET button. select model clear model copy mod–>mod expor t to SD impor t from SD => => => => => Use the arrow buttons of the left or right-hand touch-key to select the model to be exported: expor t 01 02 03 04 to SD-CARD: GRAUBELE ULTIMATE STARLET BELL47G R08 R08 R08 ––– When you confirm the selected model memory with a brief press of the SET button, this security query appears: Program description: model memories 71 model 01 ULTIMATE SD-CARD expor t ? NO YES You can interrupt the process with NO; if you do this, you are returned to the starting screen. However, if you select YES with the button, and confirm your choice by touching the SET button, then the selected model is copied to the SD card. Notes: • If the warning … SD-CARD INSERT OK … appears instead of a model selection, there is no SD card in the card slot; see page 22. • When you copy a model memory, the binding data is copied along with the model data, so that the receiving system associated with the original model memory can also be operated using the SAME transmitter and the copied memory without repeating the binding procedure. • An exported fixed-wing model is stored on the memory card under \\Models\mx-16 with the format “aModelname.mdl” and a model helicopter with the format “hModelname.mdl”. However, if you export a “nameless” model, then you will find its data stored on the memory card under “a-” and “hNoName.mdl”. • Some of the special characters used in certain model names cannot be accepted due to specific limita72 Program description: model memories tions of the FAT or FAT32 file system used by memory cards. During the copy process they are replaced by a tilde (~) character. • If the memory card already contains a model file of the same name, it will be overwritten without warning. Import from SD Use the arrow buttons of the left or right-hand touch-key to select the “Import from SD” sub-menu, then briefly press the SET button. => > SWITCHING RF OFF > > OK > impor t from SD select model If this message appears, the transmitter’s RF module is active. You can interrupt the process by briefly pressing the central ESC button of the left-hand touch-key. Alternatively a short press of the SET button of the right-hand touch-key switches the RF circuit off, and the menu you called up opens. For safety’s sake you should switch the receiving system off at this point, if it is already operating. Use the arrow buttons of the left or right-hand touch-key to select the model to be imported from the SD memory card: impor t from SD-CARD: 11/03/10 ALPINA 11/03/11 EXTRA 11/03/11 COBRA 11/03/12 BELL47G Note: The export date displayed to the right of the model name is shown in the format “Year/ Month/Day”. When you do this, and briefly press the SET button of the right-hand touch-key again, an “Import to model:” window is displayed. Use the arrow buttons of the left or right-hand touch-key to select the target memory, confirm your choice with SET, or press ESC to interrupt the process. An occupied memory can be overwritten: impor t 01 02 03 04 05 to model : GRAUBELE ULTIMATE STARLET BELL47G free E08 E08 E08 ––– When you confirm the selected model memory by touching the SET button, this security query is displayed: model 01 03 impor t ? NO ULTIMATE free YES You can interrupt the process with NO; if you do this, you are returned to the starting screen. However, if you use the button to select YES, and confirm your choice by touching the SET button, then the selected model is imported into the selected model memory. Notes: • If the warning … SD-CARD INSERT OK … appears instead of a model selection, there is no SD card in the card slot; see page 22. • When you import a model memory, the binding data is copied along with the model data, so that the receiving system associated with the original model memory can also be operated using the SAME transmitter and the copied memory without repeating the binding procedure. Program description: model memories 73 Base settings Basic model-specific settings for fixed-wing model aircraft Before you start programming specific parameters, some basic settings must be entered which apply only to the currently active model memory. Select the “Base settings” (basic model settings) menu using the arrow buttons of the left or right-hand touch-key, then touch the central SET button of the right-hand touch-key: base sett. contr set. phase trim free mixer basic sett telemetr y model name “MODE 1” (Throttle at right stick) left aileron left aileron left rudder right aileron idle “MODE 3” (Throttle at right stick) “MODE 4” (Throttle at left stick) idle elev. down idle left rudder right rudder elev. up full throttle left aileron Motor Vollgas left rudder elev. down GRAUBELE mod name stick mode 1 no motor at C1 CH8 delay yes tail type normal Briefly press the SET button to highlight the current stick mode (black background). Now use the arrow buttons of the right-hand touch-key to select one of the options 1 to 4. Simultaneously pressing the buttons or the buttons of the right-hand touch-key (CLEAR) returns the display to stick mode “1”. Touching the SET button again disables the select field once more, so that you can switch lines. motor at C1 GRAUBELE mod name stick mode 1 no motor at C1 CH8 delay yes tail type normal elev. up Basically there are four possible ways of arranging the principal control functions of a fixed-wing model on the two dual-axis sticks: the primary functions are aileron, elevator, rudder and throttle (or airbrakes). Which of these options you select depends on your individual preferences and flying style. Use the arrow buttons of the left or right-hand Use the arrow buttons of the left-hand touch-key to select the desired character, then move to the next position 74 Program description: base settings - fixed-wing model touch-key to move to the “Stick mode” line. You will see the select field framed: elev. up right aileron GRAUB idle elev. down right rudder model name full throttle right rudder 0123456789 : ; ? ABCDEFGHIJKLMNO PQRSTUVWXYZ elev. up right aileron Touch the SET button of the right-hand touch-key to move to the next screen page, where you can select characters to assemble the model name. You can enter up to nine characters to define a model name: “MODE 2” (Throttle at left stick) full throttle right aileron no yes normal elev. down left rudder 1 right rudder mod name stick mode motor at C1 CH8 delay tail type stick mode left aileron mod.mem. ser vo set. D/R expo wing mixer ser vo disp fail-safe in the name by pressing the arrow button of the righthand touch-key, or its central SET button, where you can select the next character. Simultaneously pressing the or buttons of the right-hand touch-key (CLEAR) inserts a space at that point. You can move to any character position within the input field using the buttons of the right-hand touch-key. Touching the central ESC button of the left-hand touchkey returns you to the previous menu page. The model name entered in this way appears in the basic display, and also in the sub-menus of the “Model memory” menu. When you select “motor at C1” using the arrow buttons of the left or right-hand touch-key, you will see the corresponding input field framed. Touch the central SET button of the right-hand touch-key to highlight the current setting. Now use the arrow buttons of the right-hand touch-key to switch between the four possible options: “idle fr.”: The idle position of the throttle / airbrake stick (C1) is forward, i. e. away from the pilot. The throttle warning message “Throttle too high”, see page 36, and the – following – option “cut off” are activated. In the “Wing mixer” menu the “Brake NN *” mixers and the option “CH8 delay” are disabled. “idle re.”: The idle position of the throttle / airbrake stick (C1) is back, i. e. towards the pilot. The throttle warning message “Throttle too high”, see page 36, and the – following – option “cut off” are activated. In the “Wing mixer” menu the “Brake NN *” mixers and the option “CH8 delay” are disabled. “no”: The brake system is “retracted” in the forward position of the throttle / brake stick. In the “Wing mixer” menu the “Brake NN *” mixers are activated. The throttle warning message “Throttle too high”, see page 36, and the option “cut off” are disabled. „no/inv“ The brake system is “retracted” in the back position of the throttle / brake stick. In the “Wing mixer” menu the “Brake NN *” mixers are activated. The throttle warning message “Throttle too high”, see page 36, and the option “cut off” are disabled. * NN = Nomen Nominandum (name to be stated) Notes: • During the programming process it is important to ensure that any internalcombustion engine or electric motor cannot start running accidentally. The safe option is always to disconnect the fuel supply or the flight battery. Depending on your choice in this menu, • the Ch 1 trim acts “normally” (over the full control travel), or just at the idle end of the range, i. e. only at the “back” or “forward” end of the stick travel. • Please note the Cut-off trim function, which is described on page 60. CH8 delay Notes: • If you select “Idle forward / back” in the “Motor at C1” line, this menu line is suppressed. • This option is also only effective if you have activated at least one flight phase; see below under “Phases”. GRAUBELE mod name stick mode 1 no motor at C1 CH8 delay yes tail type normal If you select “no”, the transition delay for control channel 8 of about one second, which takes effect every time you switch flight phases, is switched off; selecting “yes” switches it on. When you select the “K8 delayed” line using the arrow buttons of the left or right-hand touch-key, the corresponding input field is framed. Briefly press the central SET button of the right-hand touch-key to highlight the current setting (black background). Now use the arrow buttons of the right-hand touch-key to select one of the two options. cut off Note: This menu line is suppressed if you choose “none” or “none/inv” in the “Motor at Ch 1” line. If you select “Idle forward / back” in the “Motor at Ch1” line, you can make use of the “Motor stop” option by assigning a physical switch to it. When the switch is operated, the speed controller or throttle servo move to a pre-set position, i.e. the throttle setting of the speed controller is reduced, or the carburettor control (throttle) servo moves to the motor OFF position (or idle position). The motor OFF (or idle) position is entered in the lefthand column above the “SEL” field; the optimum setting must be found experimentally. However, the speed controller or throttle servo only takes up this defined position in response to the switch if the throttle signal is below a particular servo position or switching threshold. This point is defined by entering the desired servo position (switching threshold) in the centre column above the “STO” field. Your preferred ON / OFF switch can be selected in the right-hand column. • If the % value entered in the centre column is higher than the current servo position, i.e. the current servo position is below the switching threshold, then the change takes effect as soon as you move the switch Program description: base settings - fixed-wing model 75 to the ON position. • If the % value entered in the centre column is lower than the current servo position, i.e. the current servo position is above the switching threshold, and you move the assigned switch to the ON position, then the change (speed controller reduces motor speed, or throttle servo closes the carburettor to the point defined in the left-hand column) only takes effect when the servo position first falls below the switching threshold (max. +150%). The speed controller or throttle servo remains at this motor OFF position until you operate the selected switch again, and use the throttle / brake stick to move the throttle servo or speed controller beyond the pre-programmed switching threshold. The default value in the left-hand column for the “motor OFF” position of the throttle servo is -100%; the default switching threshold in the centre column is a servo position of +150%: GRAUBELE mod name stick mode 1 idle re. motor at C1 cut off –100% +150% ––– tail type normal STO it is important to ensure that the throttle servo does not strike its mechanical end-stop, e.g. -125%: GRAUBELE mod name stick mode 1 idle re. motor at C1 cut off –125% +150% ––– tail type normal STO The default value in the centre column is deliberately high, as this enables you to stop the motor over the maximum possible range of servo travel (or speed controller range) simply by operating the switch; the switch is assigned in the right-hand column later. However, if you prefer to set a lower switching threshold, so that the switch only takes effect when the throttle servo or speed controller is below a certain point, then you should reduce the pre-set servo travel from +150%. This is accomplished by moving the throttle / brake stick until the throttle servo or speed controller is at the position you prefer, then briefly pressing the central SET button of the right-hand touch-key: GRAUBELE mod name stick mode 1 idle re. motor at C1 cut off –125% +100% ––– tail type normal STO Programming This is the procedure for changing the default value for the “motor OFF” position of the throttle servo: briefly The final step is to move to the right-hand column press the central SET button of the right-hand touch-key: and assign a switch which you would like to use to cut the current setting is now highlighted (dark background). the motor (in an emergency) or activate the switching Now use the arrow buttons of the left or right-hand threshold. touch-key to enter a value at which the motor is reliably “off”. If you are controlling a throttle servo (carburettor) 76 Program description: base settings - fixed-wing model GRAUBELE mod name stick mode 1 idle re. motor at C1 cut off –125% +100% 9 tail type normal STO Notes: • You must ensure that the throttle servo does not strike its mechanical end-stop when the motor stop switch is operated. • To set a switching threshold higher than +100%, temporarily increase the travel of servo 1 to more than 100% in the “Servo settings” menu, and then restore the original value once you have stored the switching threshold. tail type GRAUBELE mod name stick mode 1 idle re. motor on C1 cut off –125% +100% 9 tail type normal When you select “tail type” using the arrow buttons of the left or right-hand touch-key, you will see the corresponding input field framed. Touch the central SET button of the right-hand touch-key to highlight the current setting. Now use the arrow buttons of the righthand touch-key to select the option which matches your model: „normal“: This setting caters for all models in which each of the functions elevator and rudder „V-tail“: „Delt/FlW“: „2elev sv“: is operated by one servo. The elevator and rudder functions are operated by two control surfaces set in a V-shape, each controlled by a separate servo. The two-way coupling function for the rudder and elevator control systems is automatically carried out by the transmitter software. If necessary, the ratio of rudder travel to elevator travel can be adjusted in the “Dual Rate” menu (page 102). The mixed elevon (aileron and elevator) control system requires two or four separate servos, one or two in each wing. However, the elevator trim only affects servos 2 + 3, even if you select “2ail2fl” see below. This option is designed for model aircraft with two elevator servos. When the elevator stick is moved, the servo connected to receiver output 8 moves in parallel with servo 3. The elevator trim lever affects both servos. Note regarding “2elev sv”: In this mode a transmitter control which is assigned to input 8 in the “Transmitter control settings” menu is de-coupled from servo “8”; this is for safety reasons. Ailerons / Camber-changing flaps When you select the “Aileron / Flap” line using the arrow buttons of the left or right-hand touch-key, you will see the corresponding input field framed: stick mode 1 idle re. motor at C1 cut off –125% +100% 9 tail type normal aile/flap 1aile Touch the central SET button of the right-hand touchkey to highlight the current setting. Now use the arrow buttons of the right-hand touch-key to select one of the three options , which are. “1aile” Both ailerons are actuated by a single servo. “1ail1fl” Both ailerons are actuated by a single servo, and both flaps are actuated by a single servo, “2aile” Each aileron is actuated by one servo. 2ail1fl” Aileron actuation as above, but with one flap servo, “2ail2fl” Each aileron is actuated by a separate servo; there are also one or two camber-changing flap servos. The mixers and associated adjustment facilities which appear in the “Wing mixers” menu (see section starting on page 108) vary according to the data you enter here. The software provides a maximum of twelve ready-made mixers for up to two aileron servos and two camber-changing flap servos. timer Two timers are shown in the basic display: one stopwatch and one flight timer: GRAUBELE #01 stop flt 5.6V 0:00h M 0:00 0:00 HoTT 0.0V You can assign a physical switch or a control switch to these two timers in the right-hand column of the “timer” line, indicated by the switch symbol at the bottom edge of the screen. idle re. motor at C1 cut off –125% +100% 9 tail type normal aile/flap 2aile timer 0:00 ––– The assigned switch starts both timers, and also halts the stopwatch. The method of assigning a physical switch or a control switch is described on page 59. The flight timer, and the saving of telemetry data on a memory card fitted in the card slot (see page 22), always starts simultaneously with the stopwatch, but continues to run even when the stopwatch is halted (switched off). It can only be stopped by touching the central ESC button of the left-hand touch-key when the stopwatch is already halted. Once the timers are stopped, you can reset both timers to their initial value by briefly pressing the or Program description: base settings - fixed-wing model 77 buttons of the right-hand touch key (CLEAR). Switching between “count-up” and “count-down” Count-up timer (stopwatch function) If you assign a switch and start the stopwatch with the initial value of “0:00”, the timer runs up until the maximum of 180 minutes and 59 seconds, then re-starts at 0:00. Count-down timer (alarm timer function) You can select a starting time within the range 0 to 180 minutes in the left-hand minutes field, and a starting time within the range 0 to 59 seconds in the right-hand seconds field. Any combination of times can also be selected. Simultaneously touching the or buttons of the right-hand touch-key (CLEAR) resets any settings you have made to “0” or “00”. idle re. motor at C1 cut off –125% +100% 9 tail type normal aile/flap 2aile timer 2 0:00 5. Once you have switched back to the basic display by touching the central ESC button of the lefthand touch-key the required number of times, touch the or buttons of the right-hand touchkey (CLEAR) simultaneously, with the stopwatch stopped, to switch the stopwatch to the “Timer” function; see top right in the following illustration: GRAUBELE #01 stop flt 10:01 0:00 5.6V 0:00h M HoTT 0.0V When you operate the assigned switch, the stopwatch now starts from the set initial value, counting down (“Timer function”). When the set time has elapsed, the timer does not stop, but continues to run so that you can read off the time elapsed after reaching zero. To make this clear, the over-run time is shown highlighted (black background). Sequence of sounds 30 sec. before zero: triple beep single beep every two seconds 20 sec. before zero: double beep single beep every two seconds 10 sec. before zero: single beep single beep every second 5 sec. before zero: single beep every second at higher rate zero: longer beep; display switches to inverse video The “alarm timer” is reset by simultaneously touching Procedure 1. Select the desired input field using the arrow buttons of the left or right-hand touch-key. 2. Touch SET in the centre of the right-hand touch-key. 3. Select the required time in the highlighted minutes and seconds fields using the arrow buttons of the right-hand touch-key. 4. Touch the central SET button to conclude the input process. 78 Program description: base settings - fixed-wing model the or buttons of the right-hand touch-key (CLEAR), once you have halted the timer. Note: A count-down timer is indicated in the basic display by a flashing colon (:) between the minutes field and the seconds field. Phase 2, Phase 3 and Phase 4 You will automatically be in the “normal” flight phase 1 unless you have already assigned a switch to phases 2, 3 or 4. Both the number and name of this flight phase are fixed permanently as “normal”, and cannot be changed. For this reason the “normal” phase is simply concealed, i. e. it is not displayed as phase 1. aile/flap timer phase 2 phase 3 phase 4 10:01 takeoff speed landing 2aile 2 ––– ––– ––– It is also important to understand that the flight phases have their own inherent priorities which need to be observed, particularly when assigning individual switches. The underlying scheme can be described as follows: • If all assigned flight phase switches are closed or open, the “normal” flight phase is active. • If only one switch is closed, then the flight phase assigned to the currently closed switch is active. • If two switches are closed, then the flight phase with the lower number is active. For example, this would be phase 2, if one of the switches assigned to phase 3 or 4 is also closed, or phase 3, if the switches assigned to phases 3 and 4 are closed. • As a result you may wish to take the inherent phase priorities into account when assigning names to the flight phases; see below. • At the servo end the transition does not occur “abruptly”, but with a fixed transition period of about one second. Programming When you select “phase 2”, “phase 3” or “phase 4” using the arrow buttons of the left or right-hand touchkey, the “Name” field for that flight phase is already framed. If the default name does not seem appropriate, touch the central SET button of the right-hand touch-key, and the current setting is shown highlighted. Now use the arrow buttons of the right-hand touch-key to select an appropriate name from those available. Touch the SET button to conclude the input process. Now press the button of the left or right-hand touchkey to move to the right-hand column at the bottom of , and the screen, indicated by the switch symbol briefly touch the central SET button. You can now assign a switch to the phase as described on page 59. We recommend one of the two three-position switches SW 4/5 or SW 6/7, in each case starting from the centre toggle position. For more information on flight phase programming please refer to page 106, in the section entitled “Phase trim”. Receiver output For maximum flexibility in terms of receiver socket assignment, the mx-16 HoTT software provides the means to swap over the servo outputs 1 to max. 8; this is carried out on the second page of the “Receiver output” sub-menu. timer phase phase phase receiv 2 3 4 out 10:01 takeoff speed landing 2 7 ––– 6 Note: Touch the central SET button of the right-hand touch-key to move to the next page of the display. Here you can assign the “control channels” for servos 1 … 8 to any receiver output you wish to use. However, please note that the display in “Servo display” - which you can access from virtually any menu position by simultaneously touching the and buttons of the left-hand touchkey - refers exclusively to the “control channels”, i. e. the outputs are NOT swapped over. S S S S S 1 2 3 4 5 output output output output output arrow buttons, and confirm your choice with SET … or alternatively touch the or buttons of the righthand touch-key (CLEAR) simultaneously to revert to the default sequence. Please note that any subsequent changes to servo settings, such as servo travel, Dual Rate / Expo, mixers etc., must be carried out according to the original (default) receiver socket sequence. 1 2 3 4 5 Use the arrow buttons of the left or right-hand touch-key to select the servo / output combination you wish to change, then touch the central SET button of the right-hand touch-key. Now you can assign the desired servo (S) to the selected output using the right-hand It is also possible to distribute the control functions amongst as many receivers as you wish, using the channel-mapping function in the mx-16 HoTT’s integral Telemetry menu, or even to assign the same control function to multiple receiver outputs. For example, you might wish to actuate each aileron with two servos instead of just one, etc. However, we strongly recommend that you use only one of the two options, as a combination will soon lead to confusion. rx bind Graupner|SJ HoTT receivers have to be “instructed” to communicate exclusively with a particular model (i. e. model memory) of a Graupner|SJ HoTT transmitter. This process is known as “binding”, and is only necessary once for each new combination of receiver and model. It can be repeated at any time. Important note: When carrying out the binding procedure, please ensure that the transmitter aerial is always an adequate distance from the receiver aerials: keeping the aerials about 1 m apart is safe in this respect. Otherwise you risk a failed connection to the down-link channel, and consequent malfunctions. Program description: base settings - fixed-wing model 79 “Binding” multiple receivers to one model If necessary, it is possible to bind more than one receiver to a single model. This is accomplished by initially binding the receivers individually, as described in the next section. When operating the system, please note that only the receiver which was bound last will establish a telemetry link to the transmitter. For this reason all telemetry sensors installed in the model must be connected to this receiver, since only the last bound receiver is able to transmit their data via the down-link channel. The second, and all other receivers, run in parallel to the receiver last bound to the transmitter, but completely independently of it; they operate in Slave mode with the down-link channel switched off. The receiver is in Bind mode as long as the LED flashes red / green. Within this period of about three seconds briefly touch the central SET button of the right-hand touch-key to initiate the so-called binding process between a receiver and the current model memory. At the same time the word “BINDING” starts flashing on the screen in the frame of the “Bound receiver” line, instead of the three “---”: “Binding” transmitter and receiver Use the arrow buttons of the left or right-hand touch-key to move to the “rx bind” line: The receiver LED is now flashing red again, and if it goes out without about ten seconds, and instead glows a constant green, then the binding process has been completed successfully. Your model / receiver combination is now ready for use. In parallel with this the screen displays the code number for the receiver now “bound” to this model memory. For example: phase 2 phase 3 phase 4 receiv out rx bind takeoff speed landing 7 ––– 6 phase 2 phase 3 phase 4 receiv out rx bind ––– If you have not already done so, switch on the power supply to your receiver now: the red LED on the receiver flashes. Press and hold the SET button on the receiver until, after about three seconds, the red-flashing LED starts to flash red / green; this will last for a further three seconds. You can now release the SET button on the receiver. 80 phase 2 phase 3 phase 4 receiv out rx bind takeoff speed landing 7 ––– 6 BINDING takeoff speed landing 7 ––– 6 R08 If, in contrast, the red LED on the receiver flashes for longer than about ten seconds, then the binding process has failed. In parallel with this the screen will display three “---” once more. If this should occur, alter Program description: base settings - fixed-wing model the relative position of the aerials, and repeat the whole procedure. range test The integral range-check reduces the transmitter’s output power in such a way that you can test the system’s operation at a distance of less than hundred metres. Carry out the range-check of the Graupner|SJ HoTT system in accordance with the following instructions. We recommend that you ask a friend to help with range-checking. 1. Install the receiver in the model as required, preferably after completing the binding process with the transmitter. 2. Switch the radio control system on and wait until the green LED on the receiver glows. Now you can observe the servo movements. 3. Place the model on a flat surface (paving, close-mown grass or earth), with the receiver aerials at least 15 cm above the ground. This means that you may have to place the model on a raised object for the period of the check. 4. Hold the transmitter at hip-height, and away from your body. However, do not point the aerial straight at the model; instead rotate and / or angle the tip of the aerial so that it is vertical while you carry out the check. 5. If you have not already done so, use the arrow buttons of the left or right-hand touch-key to move to the “Test range” line, and initiate range-check mode by briefly pressing the central SET button of the righthand touch-key: phase 3 phase 4 receiv out rx bind range test speed landing ––– 6 R08 99sec When you start the range-check, the transmitter’s output power is significantly reduced, and the blue LED on the aerial base starts to flash. At the same time the time display on the transmitter screen starts counting down, and a double beep sounds every five seconds. From five seconds before the end of the range-check you will hear a triple beep every second. When the 99 seconds of the range-check period have elapsed, the transmitter switches back to full power, and the blue LED glows constantly once more. 6. Within this period walk away from the model, moving the sticks all the while. If at any point within a distance of about fifty metres you notice a break in the connection, attempt to reproduce it. 7. If the model is fitted with a motor, switch it on in order to check the system’s interference rejection. 8. Walk further away from the model until you no longer have full control over it. 9. At this point wait until the test period has elapsed, with the model still switched on and ready for use. When the range-check period is over, the model should respond again to control commands. It this is not 100% the case, do not use the system. Contact your nearest Service Centre of Graupner GmbH & Co. KG. 10.Carry out the range-check before every flight, and simulate all the servo movements which are likely to occur in a typical flight. To ensure safe operation of the model, the range must always be at least fifty metres on the ground. attention: Never initiate a range-check when you are actually operating a model! RF transmit In this menu line you can manually switch the transmitter’s RF transmission on and off again for a specific model for the current period that the transmitter is switched on. For example, you might wish to do this to save power when demonstrating the programming of a model. If you switch the transmitter off with the RF module switched off, next time you switch the transmitter on it will be switched back on again. Use the arrow buttons of the left or right-hand touch-key to move to the “RF module” line, and touch the central SET button of the right-hand touch-key to activate the value window: phase 4 landing 6 receiv out rx bind R08 range test 99sec RF transmit OFF Now you can use the right-hand arrow buttons to switch between OFF and ON. Touch the central SET button of the right-hand touch-key again to conclude the input. Program description: base settings - fixed-wing model 81 Base settings Basic model-specific settings for model helicopters Before you start programming specific parameters, some basic settings must be entered which apply only to the currently active model memory. Select the “Base settings” (Basic model settings) menu using the arrow buttons of the left or right-hand touch-key, and press the central SET button of the right-hand touch-key: mod.mem. ser vo set. D/R expo free mixer ser vo disp fail-safe base sett. contr set. heli mixer swashp. mix basic sett telemetr y Model name mod name stick mode 1 1 ser vo swashplate cut off –100% +150% ––– right rotor direct tons of the right-hand touch button, or its central SET button, to move to the next position in the name, at which point you can again select a character. Simultaneously touching the or buttons of the righthand touch-key (CLEAR) inserts a space at that point. You can move to any character position within the input field using the buttons of the right-hand touch-key. You can return to the previous menu page by briefly pressing the central ESC button of the left-hand touchkey. The model name entered in this way appears in the basic display, and also in the sub-menus of the “Model memory” menu point. Stick mode Basically there are four possible ways of arranging the principal control functions of a model helicopter on the two dual-axis sticks: the primary functions are roll, pitch-axis, tail rotor and throttle / collective pitch. Which of these options you select depends on your individual preferences and flying style: Touch the SET button of the right-hand touch-key to move to the next screen page, where you can select characters to assemble the model name. You can enter up to nine characters to define a model name: “MODE 1” (Throttle at right stick) “MODE 2” (Throttle at left stick) 0123456789 : ; ? ABCDEFGHIJKLMNO PQRSTUVWXYZ “MODE 3” (Throttle at right stick) “MODE 4” (Throttle at left stick) throttle tail rotor roll tail rotor roll tail rotor pitch axis tail rotor roll throttle STARLET mod name stick mode 1 1 ser vo swashplate cut off –100% +150% ––– right rotor direct Briefly press the SET button: the current stick mode appears highlighted. Now use the arrow buttons of the right-hand touch-key to choose one of the options 1 to 4. By simultaneously touching the or buttons of the right-hand touch-key (CLEAR) the display reverts to stick mode “1”. A further brief press on the SET button disables the select field again, so that you can change to a different line. Swashplate type STARLET mod name stick mode 1 1 ser vo swashplate cut off –100% +150% ––– right rotor direct roll Motor/Pitch throttle pitch axis roll pitch axis tail rotor pitch axis pitch axis throttle tail rotor STAR throttle roll model name roll tail rotor pitch axis throttle tail rotor throttle roll pitch axis is now framed: pitch axis Use the arrow buttons of the left or right-hand Use the arrow buttons of the left-hand touch-key to touch-key to select the “Stick mode” line; the select field select the desired character. Touch one of the arrow but82 Program description: base settings - model helicopter You will require a particular program variant to suit the number of servos which operate the collective pitch function. Select “Swashplate” with the arrow buttons of the left or right-hand touch-key, and the select field is framed. Touch the SET button: the current number of collective pitch servos is highlighted on the screen. You can now determine the required variant using the arrow buttons of the right-hand touch-key: “1 servo”: The swashplate is tilted by one roll servo and one pitch-axis servo. Collective pitch is controlled by one separate servo. The “Swashplate mixer” menu point is suppressed in the multi-function menu if you select “1 servo” as the swashplate type. This is because model helicopters with only one collective pitch servo are controlled WITHOUT transmitter mixers for the swashplate functions collective pitch, pitch-axis and roll. The swashplate is moved axially by two “2 servo”: roll servos for collective pitch control; pitch-axis control is de-coupled by a mechanical compensating rocker. “3sv(2rol)”: A symmetrical three-point swashplate linkage using three linkage points arranged equally at 120°, actuated by one pitch-axis servo (front or rear) and two roll servos (left and right). For collective pitch control all three servos move the swashplate axially. “3sv(140)”: Asymmetrical three-point swashplate linkage using three linkage points, connected to one pitch servo (rear) and two roll servos (front left and right). For collective pitch control all three servos move the swashplate axially. “3sv(2nic)”: A symmetrical three-point linkage as above, but rotated through 90°, i. e. one roll servo on one side, and two pitch-axis servos front and rear. “4sv(90)”: Four-point swashplate linkage using two roll and two pitch-axis servos. Simultaneously pressing the or buttons of the right-hand touch-key (CLEAR) resets the swashplate type to “1 servo”. Swashplate type: 1 servo Swashplate type: 3 servos (pitch-axis) 1 3 2 Swashplate type: 4 servos (90°), 2 pitch / 2 roll 2 Swashplate type: 2 servos 2 5 3 1 Note: 2 1 Swashplate type: 3 servos (2 roll) 2 3 1 Swashplate type: 3 servos (140°) 2 3 1 With the exception of the “1 servo” pre-set, the swashplate mixer ratios are set in the “Swashplate mixers” menu; see page 132. Cut off The auto-rotation settings of the mx-16 HoTT transmitter’s Helicopter program include a facility for defining a “motor OFF” position for the throttle servo or speed controller for use in an emergency; see the programming suggestion on page 180. However, you may wish to set an idle position instead of an (emergency) OFF position in the “Throttle” line of the “Helimix” menu, perhaps in order to avoid having to re-start the engine after every practice auto-rotation landing. This effectively circumvents the “motor cut” facility, but there is an alternative method of setting up an emergency OFF system: this is the “Motor stop” option, which is described in the following section. If you select “front / rear” in the “Collective pitch min.” Program description: base settings - model helicopter 83 line of the “Base settings” menu, you can make use of the “Motor stop” option by assigning a physical switch to it. When the switch is operated, the speed controller or throttle servo move to a pre-set position, i.e. the throttle setting of the speed controller is reduced, or the carburettor control (throttle) servo moves to the motor OFF position (or idle position). The motor OFF (or idle) position is entered in the lefthand column above the “SEL” field; the optimum setting must be found experimentally. However, the speed controller or throttle servo only takes up this defined position in response to the switch if the throttle signal is below a particular servo position or switching threshold. This point is defined by entering the desired servo position (switching threshold) in the centre column above the “STO” field. Your preferred ON / OFF switch can be selected in the right-hand column. • If the % value entered in the centre column is higher than the current servo position, i.e. the current servo position is below the switching threshold, then the change takes effect as soon as you move the switch to the ON position. • If the % value entered in the centre column is lower than the current servo position, i.e. the current servo position is above the switching threshold, and you move the assigned switch to the ON position, then the change (speed controller reduces motor speed, or throttle servo closes the carburettor to the point defined in the left-hand column) only takes effect when the servo position first falls below the switching threshold (max. +150%). The speed controller or throttle servo remains at this motor OFF position until you operate the selected switch again, and use the throttle / brake stick to 84 move the throttle servo or speed controller beyond the pre-programmed switching threshold. The default value in the left-hand column for the “motor OFF” position of the throttle servo is -100%; the default switching threshold in the centre column is a servo position of +150%: STARLET mod name stick mode 1 3sv(2rol) swashplate cut off –100% +150% ––– right rotor direct STO Programming This is the procedure for changing the default value for the “motor OFF” position of the throttle servo: briefly press the central SET button of the right-hand touch-key: the current setting is now highlighted (dark background). Now use the arrow buttons of the left or right-hand touch-key to enter a value at which the motor is reliably “off”. If you are controlling a throttle servo (carburettor) it is important to ensure that the throttle servo does not strike its mechanical end-stop, e.g. -125%: STARLET mod name stick mode 1 3sv(2rol) swashplate cut off –125% +150% ––– right rotor direct STO The default value in the centre column is deliberately high, as this enables you to stop the motor over the maximum possible range of servo travel (or speed controller range) simply by operating the switch; the switch Program description: base settings - model helicopter is assigned in the right-hand column later. However, if you prefer to set a lower switching threshold, so that the switch only takes effect when the throttle servo or speed controller is below a certain point, then you should reduce the pre-set servo travel from +150%. This is accomplished by moving the throttle / brake stick until the throttle servo or speed controller is at the position you prefer, then briefly pressing the central SET button of the right-hand touch-key: STARLET mod name stick mode 1 3sv(2rol) swashplate cut off –125% +100% ––– right rotor direct STO The final step is to move to the right-hand column and assign a switch which you would like to use to cut the motor (in an emergency) or activate the switching threshold. STARLET mod name stick mode 1 3sv(2rol) swashplate cut off –125% +100% 1 right rotor direct STO Notes: • You must ensure that the throttle servo does not strike its mechanical end-stop when the motor stop switch is operated. • To set a switching threshold higher than +100%, temporarily increase the travel of servo 1 to more than 100% in the “Servo settings” menu, and then restore the original value once you have stored the switching threshold. Direction of rotation of main rotor STARLET mod name stick mode 1 3sv(2rol) swashplate cut off –125% +100% 1 right rotor direct In the “Rotor direction” line you enter the direction of rotation of the main rotor using the arrow buttons of the right-hand touch-key, after briefly pressing the central SET button: “right”: the main rotor spins clockwise as viewed from above. the main rotor spins anti-clockwise as viewed “left”: from above. Simultaneously touching the or buttons of the right-hand touch-key (CLEAR) switches to “right”. right-hand rotation the mixers which compensate for rotor torque and motor power. You will find these in the “Helicopter mixer” menu: Pitch Ch1 throttle Ch1 tail rotor Pitch Collective pitch min. stick mode 1 3sv(2rol) swashplate cut off –125% +100% 1 right rotor direct pitch min rear In the “Collective pitch min.” line you can set up the direction of operation of the throttle / collective pitch stick to suit your preference. This setting is crucial to the correct operation of all the other options in the helicopter program which affect the throttle and collective pitch functions, i. e. the throttle curve, idle trim, tail rotor mixer etc. Briefly touch the central SET button of the right-hand touch-key, and the direction of operation of the throttle / collective pitch stick is highlighted. Now you can select the required variant using the arrow buttons of the righthand touch-key: The meaning is as follows: “front”: minimum collective pitch when the collective pitch stick (Ch 1) is “forward” (away from you); “rear”: minimum collective pitch when the collective pitch stick (Ch 1) is “back” (towards you). Simultaneously pressing the or buttons of the right-hand touch-key (CLEAR) returns the collective pitch min. position to “rear”. Notes: • By default what is known as the “throttle limiter” is set (see page 99); this limits the travel of the throttle servo in the direction of maximum throttle, acting separately from the collective pitch servos. This point can be programmed using the “Lim” input in the “Transmitter control settings” menu. • The Ch 1 trim always affects the throttle servo only. left-hand rotation The program requires this information in order to set up the mixers to work in the correct “sense”; this applies to Program description: base settings - model helicopter 85 timer Two timers are shown in the basic display: one stopwatch and one flight timer. STARLET #02 stop flt 5.6V 0:00h M 0:00 0:00 HoTT 0.0V A physical switch or a control switch - e. g. the control switch G3 located on the throttle limiter - can be assigned to these two timers in the “Timers” line … 3sv(2rol) swashplate cut off –125% +100% 1 right rotor direct pitch min rear timer 0:00 ––– the right-hand touch-key (CLEAR). Switching between “count-up” and “count-down” Count-up timer (stopwatch function) If you assign a switch and start the stopwatch with the initial value of “0:00”, the timer runs up until the maximum of 180 minutes and 59 seconds, then re-starts at 0:00. Count-down timer (timer function) In the left-hand minutes field you can select a starting time within the range 0 to 180 minutes; in the right-hand seconds field the range is 0 to 59 seconds. Any combination of times can also be selected. Simultaneously pressing the buttons of the righthand touch-key (CLEAR) resets any settings you have entered to “0” or “00”. 3sv(2rol) swashplate cut off –125% +100% 1 right rotor direct pitch min rear timer 10:01 G3 … using the switch symbol at the bottom right-hand side of the screen. The assigned switch starts both timers, and also halts the stopwatch. The method of assigning a physical switch or a control Procedure switch is described on page 59. 1. Select the desired input field using the arrow buttons The flight timer, and the saving of telemetry data on a of the left or right-hand touch-key. memory card inserted in the card slot (see page 22) 2. Touch SET in the centre of the right-hand touch-key. always starts simultaneously with the stopwatch, but continues to run even when the stopwatch is halted 3. Select the required time in the highlighted minutes (switched off). It can only be stopped by touching the and seconds fields using the arrow buttons of the central ESC button of the left-hand touch-key with the right-hand touch-key. stopwatch halted. 4. Touch the central SET button to conclude the input Once stopped, both timers can be reset to the initial process. value by simultaneously touching the buttons of 86 Program description: base settings - model helicopter 5. Switch back to the basic display by repeatedly touching the central ESC button of the left-hand touch-key. With the stopwatch halted, press the buttons of the right-hand touch-key simultaneously (CLEAR) to switch the stopwatch to the “Timer” function; see top right in the next illustration: STARLET #02 stop flt 10:01 0:00 5.6V 0:00h M HoTT 0.0V If you now operate the assigned switch, the stopwatch starts from the set initial value, counting down (“Timer function”). When the set time has elapsed, the timer does not stop, but continues to run to allow you to read off the time elapsed after reaching zero. To make this clear, the over-run time is shown highlighted (black background). Sequence of sounds 30 sec. before zero: triple beep single beep every two seconds 20 sec. before zero: double beep single beep every two seconds 10 sec. before zero: single beep single beep every second 5 sec. before zero: single beep every second at higher rate zero: longer beep; display switches to inverse video The “alarm timer” is reset by simultaneously pressing the or buttons of the right-hand touch-key (CLEAR) after you have halted the timer. Note: A count-down timer is indicated in the basic display by a flashing colon (:) between the minutes field and the seconds field. Phase 2 / Phase 3 You will automatically be in the “normal” flight phase 1 unless you have already assigned a switch to phases 2 or 3. Both the number and name of this flight phase are fixed permanently as “normal”, and cannot be changed. For this reason the “normal” phase is simply concealed, i. e. it is not displayed as phase 1. rotor direct pitch min timer phase 2 phase 3 right rear 10:01 G3 hover ––– speed ––– It is also important to understand that the flight phases have their own inherent priorities which need to be observed, particularly when assigning individual switches. The underlying scheme can be described as follows: • If all assigned flight phase switches are closed or open, the “normal” flight phase is active. • If only one switch is closed, then the flight phase assigned to the currently closed switch is active. • If two switches are closed, then the flight phase with the lower number is active. For example, this would be phase 2 if the switches assigned to phase 2 and 3 are closed. • The “auto-rotation phase” ALWAYS has precedence over all other flight phases, regardless of the priorities outlined above. When the auto-rotation phase is selected, the switch is always made WITHOUT DELAY. • With this in mind, you may wish to take the inherent phase priorities into account when assigning names to the flight phases; see below. • At the servo end the transition does not occur “abruptly”, but with a fixed transition period of about one second. Programming When you select “Phase 2” or “Phase 3” using the arrow buttons of the left or right-hand touch-key, the “Name” field for that flight phase is already framed. If the default name does not seem appropriate, touch the central SET button of the right-hand touch-key, and the current setting is shown highlighted. Now use the arrow buttons of the right-hand touch-key to select an appropriate name from those available. Touch the SET button to conclude the input process. Now press the button of the left or right-hand touchkey to move to the right-hand column at the bottom of , and the screen, indicated by the switch symbol briefly touch the central SET button. You can now assign a switch to the phase as described on page 59. We recommend one of the two three-position switches SW 4/5 or SW 6/7, in each case starting from the centre toggle position. For more information on flight phase programming please refer to page 114, in the section entitled “Flight phase specific settings for collective pitch, throttle and tail rotor”. Auto-rotation pitch min timer phase 2 phase 3 autorotat. rear 10:01 G3 hover 5 speed 4 ––– The name “Auto-rotation” is permanently assigned to Phase 4, and CANNOT be altered. The only available option is to assign a switch to it using the switch symbol at the right of the screen. For more information on programming flight phases please refer to the “Helicopter mixers” section starting on page 114. Receiver output For maximum flexibility in terms of receiver socket assignment, the mx-16 HoTT software provides the means to swap over the servo outputs 1 to max. 8; this is carried out on the second page of the “Receiver output” sub-menu. timer phase 2 phase 3 autorotat. receiv out 10:01 G3 hover 5 speed 4 2 Touch the central SET button of the right-hand touchkey to move to the next page of the display. Here you can assign the “control channels” for servos 1 … 8 to any receiver output you wish to use. However, please note that the display in “Servo display” - which you can Program description: base settings - model helicopter 87 access from virtually any menu position by simultaneously touching the and buttons of the left-hand touch-key - refers exclusively to the “control channels”, i. e. the outputs are NOT swapped over. S S S S S 1 2 3 4 5 output output output output output 1 2 3 4 5 Use the arrow buttons of the left or right-hand touch-key to select the servo / output combination you wish to change, then touch the central SET button of the right-hand touch-key. Now you can assign the desired servo (S) to the selected output using the right-hand arrow buttons, and confirm your choice with SET … or alternatively touch the or buttons of the righthand touch-key (CLEAR) simultaneously to revert to the default sequence. Please note that any subsequent changes to servo settings, such as servo travel, Dual Rate / Expo, mixers etc., must be carried out according to the original (default) receiver socket sequence. Typical application: In the helicopter program of the mx-16 HoTT the outputs for one collective pitch servo and the throttle servo have been interchanged compared to all earlier GRAUPNER/JR mc-systems. The throttle servo is now assigned to receiver output “6” and the collective pitch servo to output “1”. However, you may wish to retain the earlier configuration. 88 S S S S S S 6 2 3 4 5 1 output output output output output output 1 2 3 4 5 6 Note: It is also possible to distribute the control functions amongst as many receivers as you wish, using the channel-mapping function in the mx-16 HoTT’s integral Telemetry menu, or even to assign the same control function to multiple receiver outputs. However, we strongly recommend that you use only one of the two options, as a combination will soon lead to confusion. rx bind (Bound receiver) Graupner|SJ HoTT receivers have to be “instructed” to communicate exclusively with a particular model (i. e. model memory) of a Graupner|SJ HoTT transmitter. This process is known as “binding”, and is only necessary once for each new combination of receiver and model. It can be repeated at any time. Important note: When carrying out the binding procedure, please ensure that the transmitter aerial is always an adequate distance from the receiver aerials: keeping the aerials about 1 m apart is safe in this respect. Otherwise you risk a failed connection to the down-link channel, and consequent malfunctions. Program description: base settings - model helicopter “Binding” multiple receivers to one model If necessary, it is possible to bind more than one receiver to a single model. This is accomplished by initially binding the receivers individually, as described in the next section. When operating the system, please note that only the receiver which was bound last will establish a telemetry link to the transmitter. For this reason all telemetry sensors installed in the model must be connected to this receiver, since only the last bound receiver is able to transmit their data via the down-link channel. The second, and all other receivers, run in parallel to the receiver last bound to the transmitter, but completely independently of it; they operate in Slave mode with the down-link channel switched off. “Binding” transmitter and receiver Use the arrow buttons of the left or right-hand touch-key to move to the “rx bind” line: phase 2 phase 3 autorotat. receiv out rx bind hover speed 5 4 2 ––– If you have not already done so, switch on the power supply to your receiver now: the red LED on the receiver flashes. Press and hold the SET button on the receiver until, after about three seconds, the red-flashing LED starts to flash red / green; this will last for a further three seconds. You can now release the SET button on the receiver. The receiver is in Bind mode as long as the LED flashes red / green. Briefly touch the central SET button of the right-hand touch-key within this period of about three seconds: this initiate the binding process between a receiver and the current model memory. At the same time the word “BINDING” starts flashing in the frame of the “rx bind” line on the screen, instead of the three “---”: phase 2 phase 3 autorotat. receiv out rx bind hover speed 5 4 2 BINDING The receiver LED is now flashing red again, and if it goes out within about ten seconds, and instead glows a constant green, then the binding process has been completed successfully. Your model / receiver combination is now ready for use. In parallel with this the screen displays the code number for the receiver now “bound” to this model memory. For example: phase 2 phase 3 autorotat. receiv out rx bind hover speed 5 4 2 R08 If, in contrast, the red LED on the receiver flashes for longer than about ten seconds, then the binding process has failed. In parallel with this the screen will display three “---” once more. If this should occur, alter the relative position of the aerials and repeat the whole procedure. Range test The integral range-check reduces the transmitter’s output power in such a way that you can test the system’s operation at a distance of up to about fifty metres. Carry out the range-check of the Graupner|SJ HoTT system in accordance with the following instructions. We recommend that you ask a friend to help with range-checking. 1. Install the receiver in the model as required, preferably after completing the binding process with the transmitter. 2. Switch the radio control system on and wait until the green LED on the receiver glows. Now you can observe the servo movements. 3. Place the model on a flat surface (paving, close-mown grass or earth), with the receiver aerials at least 15 cm above the ground. This means that you may have to place the model on a raised object for the period of the check. 4. Hold the transmitter at hip-height, and away from your body. Do not point the aerial straight at the model; instead rotate and / or angle the aerial tip so that it is vertical while you carry out the check. 5. If you have not already done so, use the arrow buttons of the left or right-hand touch-key to move to the “Test range” line, and initiate range-check mode by briefly pressing the central SET button of the right-hand touch-key: phase 3 autorotat. receiv out rx bind range test speed 4 2 R08 99sec When you start the range-check, the transmitter’s output power is significantly reduced, and the blue LED on the aerial base starts to flash. At this point the time display on the transmitter screen starts counting down, and a double beep sounds every five seconds. From five seconds before the end of the range-check you will hear a triple beep every second. When the 99 seconds of the range-check period have elapsed, the transmitter switches back to full power, and the blue LED glows constantly once more. 6. Within this period walk away from the model, moving the sticks all the while. If at any point within a distance of about fifty metres you notice a break in the connection, attempt to reproduce it. 7. If the model is fitted with a motor, switch it on in order to check the system’s interference rejection. 8. Walk further away from the model until you no longer have full control over it. 9. At this point wait until the test period has elapsed, with the model still switched on and ready for use. When the range-check period is over, the model should respond again to control commands. It this is not 100% the case, do not use the system. Contact your nearest Graupner Service Centre. 10.Carry out a range-check before every flight, and simulate all the servo movements which are likely to oc- Program description: base settings - model helicopter 89 cur in a typical flight. To ensure safe operation of the model, the range must always be at least fifty metres on the ground. attention: Never initiate a range-check when you are actually operating a model! RF transmit In this menu line you can manually switch the transmitter’s RF transmission on and off again for a specific model for the period that the transmitter is currently switched on. For example, you might wish to do this to save power when demonstrating the programming of a model. If you switch the transmitter off with the RF module switched off, next time you switch the transmitter on it will be switched back on again. Use the arrow buttons of the left or right-hand touch-key to move to the “RF transmit” line, and touch the central SET button of the right-hand touch-key to activate the value window: autorotat. receiv out rx bind range test RF transmit 2 R08 99sec ON Now you can use the right-hand arrow buttons to switch between OFF and ON. Touch the central SET button of the right-hand touch-key again to conclude the input. 90 Program description: base settings - model helicopter For your notes 91 Servo settings Servo direction, centre, travel S1 S2 S3 S4 S5 rev 0% 0% 0% 0% 0% cent 100% 100% 100% 100% 100% 100% 100% 100% 100% 100% trav + In this menu you can adjust parameters which only affect the servo connected to a particular receiver output, namely the direction of servo rotation, neutral point and servo travel. Always start with the servo setting in the left-hand column.v Basic procedure: 1. Use the arrow buttons of the left or right-hand touch-key to select the relevant servo (1 to 8). 2. If necessary, use the arrow buttons of the left or right-hand touch-key to select the desired column, and move the associated transmitter control from its centre position if you wish to define an asymmetrical setting. 3. Touch the central SET button of the right-hand touchkey, and the corresponding input field is highlighted (black background). 4. Set the appropriate value using the arrow buttons of the right-hand touch-key. 5. Touch the central SET button of the right-hand touchkey to conclude the input process. 6. Simultaneously pressing the arrow buttons or of the right-hand touch-key (CLEAR) resets any settings you have entered to the default value. 92 Program description: servo settings Important: The numbers in the servo designations refer to the receiver output socket to which a particular servo(s) is connected, assuming that these have not been swapped over. This means that changing the stick mode does not affect the numbering of the servos. Column 2 “Rev.” The direction of servo rotation can be adjusted to suit the actual installation in your model. This means that you don’t need to concern yourself with servo directions when installing the mechanical linkages in the model, as you can reverse them as and when necessary. The direction of rotation is indicated by the symbols “=>” and “<=”. Be sure to set the direction of servo rotation before you make adjustments to the remaining options! Simultaneously pressing the arrow buttons or of the right-hand touch-key (CLEAR) resets the direction of rotation to “=>”. normal normal reversed reversed Column 3 “Centre” The facility to offset the servo travel centre is intended for adjusting servos whose centre setting is not standard (servo centre point at 1.5 ms or 1500 μs), and also for minor adjustments, e. g. when fine-tuning the neutral position of the model’s control surfaces. The neutral position can be shifted over the range -125% to +125% of normal servo travel, within the maximum servo travel of +/- 150%, regardless of the trim lever position and any mixers you have set up. The setting affects the associated servo directly, independently of all other trim and mixer settings. However, please note that an extreme shift of the servo’s neutral point may result in servo travel to one side of neutral only, as total servo travel is limited to +/- 150% for both electronic and mechanical reasons. Simultaneously pressing the arrow buttons or of the right-hand touch-key (CLEAR) resets the value in the highlighted input field to “0%”. Ser vo travel tre adjustment Cen +1 % 25 25 % -1 Column 4 “- Servo travel +” In this column you can adjust servo travel symmetrically or asymmetrically (different each side of neutral). The adjustment range is 0 … 150% of normal servo travel. The reference point for the set values is the setting in the “Centre” column. To set symmetrical travel, i. e. to adjust travel equally on both sides of neutral, move the associated transmitter control (stick, proportional rotary knob or switch) to a position in which the marking frame encloses both sides of the travel setting. the control signal for this servo is generated, i. e. either directly by a stick channel, or by means of any type of mixer function. Note: To set up asymmetrical travel, move the associated transmitter control (stick, rotary proportional knob or switch) to the side to be adjusted, so that the marking frame only encloses the value you wish to change. Touch the central SET button of the right-hand touchkey to activate value adjustment; the value field is now highlighted. Use the arrow buttons of the right-hand touch-key to change the values. A further brief press on the central SET button of the right-hand touch-key concludes the input process. Simultaneously pressing the arrow buttons or of the right-hand touch-key (CLEAR) resets the parameter in the highlighted input field to 100%. Important: In contrast to the “Transmitter control settings” menu, this setting affects the servo directly, regardless of how Servo travel You may need to assign a transmitter control to a servo which is connected to one of the control channels 5 … 8; this is accomplished in the “Transmitter control settings” menu; see next page. The graph alongside shows an example of asymmetrical servo travel, with a setting of -50% and +150%. Transmitter control travel Program description: servo settings 93 Transmitter control settings Basic procedures for assigning transmitter controls and switches I5 I6 I7 I8 free free free free +100% +100% +100% +100% +100% +100% +100% +100% tr v + In addition to the two dual-axis stick units for the control functions 1 to 4, the mx-16 HoTT is fitted as standard with a range of supplementary controls: • Two three-position switches: SW 4/5 or CTRL 9 and SW 6/7 or CTRL 10. These are assigned in this menu as “CTRL 9” and “CTR 10” respectively. • Three rotary proportional controls: CTRL 6, 7 and 8. These are included in the menu as “CTRL 6”, “CTRL 7” and “CTRL 8”. • Three two-position switches: SW 2, 3 and 8. These are indicated in the menu by “2”, “3” and “8” plus a switch symbol, which indicates the direction of operation of the switch. • Two momentary switches: SW 1 and SW 9. These are indicated by “1” and “9” plus a switch symbol and direction indicator, as mentioned above. The two dual-axis stick units directly affect the servos connected to receiver outputs 1 … 4 (assuming that you have set up a newly initialised model memory with the model type “Fixed-wing model”). In contrast, the “supplementary” transmitter controls listed above are inactive when the transmitter is in its default state (as delivered). As already mentioned on page 20, this means that the transmitter in its basic form only controls servos connected to receiver outputs 1 … 4 using the primary sticks - even when you have initialised a new model memory with the model type “Fixed-wing model” and 94 “bound” it to the receiver you intend to install. Any servos connected to receiver sockets 5 … 8 simply stay at their centre point when you operate the associated transmitter controls. This may seem rather inconvenient at first sight, but it is the only way to ensure that you can select any of the “supplementary” transmitter controls for any task you like, and that you are not required deliberately to “program away” the transmitter controls which are not required for a particular model. Any superfluous transmitter control will have an effect on your model if you operate it by mistake - unless it is inactive, i. e. unless no function is assigned to it. That is why you can select these “supplementary” transmitter controls with complete freedom in the “Transmitter control settings” menu and assign them to any function input (see page 58) you like, as this method ensures that the transmitter meets your own requirements exactly. This also means that each of these transmitter controls can be assigned to several functions simultaneously. For example, the same toggle switch SW X, which you assign to an input in this menu, can also be assigned as the On / Off switch controlling the “Timers” in the “Base settings” menu. Important: In contrast to servo travel adjustments, changing the transmitter travel setting affects all mixer and coupling inputs derived from it, i. e. in the final analysis all the servos which can be operated using the associated transmitter control. Program description: transmitter control settings - fixed-wing model The basic procedure: 1. Select the appropriate input I5 … I8 using the arrow buttons of the left or right-hand touch-key. 2. If necessary, use the arrow buttons of the left or right-hand touch-key to switch to the desired column. 3. Touch the central SET button of the right-hand touchkey, and the corresponding input field is highlighted. 4. Operate the transmitter control you wish to use, and set the desired value using the arrow buttons of the right-hand touch-key. 5. Touch the central SET button of the right-hand touchkey to conclude the input process. 6. Simultaneously pressing the or buttons of the right-hand touch-key (CLEAR) resets any settings you have entered to the appropriate default value. Column 2 “Assigning transmitter controls and switches” Select one of the function inputs 5 to 8 using the buttons of the right-hand touch-key. Touch the central SET button of the right-hand touch-key to activate the assignment facility. I5 free +100% +100% operate desired switch or control I8 free +100% +100% tr v + Now move the appropriate transmitter control (CTRL 6 to 10), or operate the selected switch (SW 1 to 3, 8 or 9). Note that the rotary proportional controls are not detected until they have moved a few “ratchet clicks”, i. e. they need to be operated for slightly longer. If the travel is not sufficient for the transmitter to detect it, move the control in the opposite direction. If you assign one of the two-position switches, then this control channel works like an On / Off switch. It is then possible to switch to and fro between two end-point values using this simple switch, e. g. motor ON / OFF. The three-position switches SW 4/5 and 6/7, which you will find in the “Transmitter control settings” menu as “Control 9” and “Control 10”, provide a centre position in addition to the two end-points. Simultaneously pressing the or buttons of the right-hand touch-key (CLEAR) with the switch assignment activated - see illustration above - resets the input to “free”. Tips: • When assigning the switches please take care to set them to the appropriate direction of travel, and ensure that all inputs not required are left at or set to “free”, to eliminate the possibility of errors if unused transmitter controls are operated accidentally. • You can alter the effective end-points of an assigned switch by adjusting servo travel, as described in the next section. The screen now displays either the transmitter control number or the switch number, followed by a switch symbol which indicates the direction of operation, e. g.: I5 +100% +100% 3 I6 ctrl 7 +100% +100% +100% +100% I7 free +100% +100% I8 free tr v + Column 3 “-Travel+” In this column the transmitter control can be adjusted symmetrically or asymmetrically, i. e. different to either side. The available range is +/-125% of the normal servo travel. Use the arrow buttons of the left or right-hand touch-key to select one of the inputs 5 to 8. If you wish to set up symmetrical travel, i. e. the same in both directions, move the associated transmitter control (rotary proportional controls CTRL 6 … 8 or switches 4/5 and 6/7) to a position at which the marking frame encloses both sides of the travel setting: +100% +100% I5 3 I6 ctrl 7 +100% +100% +100% +100% I7 free +100% +100% I8 free tr v + If you wish to set up asymmetrical travel, i. e. different for both directions, move the associated transmitter control (rotary proportional control or switch) to a position at which the marking frame encloses the side of the travel setting you wish to change: I5 +100% +100% 3 I6 ctrl 7 +100% +100% +100% +100% I7 free +100% +100% I8 free tr v + Touch the central SET button of the right-hand touch-key to activate the value setting; the value field is now shown highlighted. Use the arrow buttons of the right-hand touch-key to alter the values: +100% +100% I5 3 I6 ctrl 7 +111% +111% I7 free +100% +100% +100% +100% I8 free tr v + I5 +100% +100% 3 +88% +111% I6 ctrl 7 +100% +100% I7 free I8 free +100% +100% tr v + Touch the central SET button of the right-hand touch-key to conclude the input process. Negative and positive parameter values are possible; this enables you to set the appropriate direction of movement of the transmitter control or its direction of effect to suit your model. Simultaneously pressing the arrow buttons or of the right-hand touch-key (CLEAR) resets the altered parameter in the highlighted input field to +100%. Program description: transmitter control settings - fixed-wing model 95 Transmitter control settings Basic procedures for assigning transmitter controls and switches I5 thr gyr I8 lim free free free free ctrl 6 +100% +100% +100% +100% +100% +100% +100% +100% +100% +100% tr v + In addition to the two dual-axis stick units for the control functions 1 to 4, the mx-16 HoTT is fitted as standard with a range of supplementary controls: • Two three-position switches: SW 4/5 or CTRL 9 and SW 6/7 or CTRL 10. These are assigned in this menu as “CTRL 9” and “CTR 10” respectively. • Three rotary proportional controls: CTRL 6, 7 and 8. These are included in the menu as “Control 6”, “Control 7” and “Control 8”. • Three two-position switches: SW 2, 3 and 8. These are indicated in the menu by “2”, “3” and “8” plus a switch symbol, which indicates the direction of operation of the switch. • Two momentary switches: SW 1 and SW 9. These are indicated by “1” and “9” plus a switch symbol and direction indicator, as mentioned above. The two dual-axis stick units directly affect servos connected to receiver outputs 1 … 4 and 6 (assuming that you have set up a newly initialised model memory with the model type “Helicopter”). In contrast, the “supplementary” transmitter controls listed above are inactive when the transmitter is in its default state (as delivered). The exception is the rotary proportional knob CTRL 7 (throttle limiter), which acts upon servo 6 by default. As already mentioned on page 20, this means that the transmitter in its basic form only controls servos connected to receiver outputs 1 … 4 using the primary 96 sticks, plus servo 6 - depending on the position of the throttle limiter - even when you have initialised a new model memory with the model type “Helicopter” and “bound” it to the receiver you intend to install. Any servos connected to receiver sockets 5, 7 and 8 simply stay at their centre point when you operate the associated transmitter controls. This may seem rather inconvenient at first sight, but it is the only way to ensure that you can select any of the “supplementary” transmitter controls for any task you like, and that you are not required deliberately to “program away” the transmitter controls which are not required for a particular model. Any superfluous transmitter control will have an effect on your model if you operate it by mistake, unless it is inactive, i. e. unless no function is assigned to it. That is why you can select these “supplementary” transmitter controls with complete freedom in the “Transmitter control settings” menu, and assign them to any function input (see page 58) you like, as this method ensures that the transmitter meets your own requirements exactly. This also means that each of these transmitter controls can be assigned to several functions simultaneously. For example, the same toggle switch SW X which you assign to an input in this menu, can also be assigned as the On / OFF switch controlling the “Timers” in the “Base settings” menu. Notes: • For model helicopters input 6 must always be left “free”. Please see the section entitled “Throttle” on the next double-page. • In contrast to servo travel adjustments, changing the Program description: transmitter control settings – model helicopter transmitter travel setting affects all mixer and coupling inputs derived from it, i. e. in the final analysis all the servos which can be operated using the associated transmitter control. The basic procedure 1. Select the appropriate input I5, throttle, gyro, I8 or Lim using the arrow buttons of the left or righthand touch-key. 2. If necessary, use the arrow buttons of the left or right-hand touch-key to switch to the desired column. 3. Touch the central SET button of the right-hand touchkey, and the corresponding input field is highlighted. 4. Operate the transmitter control you wish to use, and set the desired value using the arrow buttons of the right-hand touch-key. 5. Touch the central SET button of the right-hand touchkey to conclude the input process. 6. Simultaneously pressing the or buttons of the right-hand touch-key (CLEAR) resets any settings you have entered to the appropriate default value. Column 2 “Assigning transmitter controls and switches” Select one of the function inputs I5, throttle, gyro, I8 or lim using the buttons of the left or right-hand touch-key. Touch the central SET button of the right-hand touch-key to activate the assignment facility. I5 free +100% +100% operate desired switch or control I8 free +100% +100% lim ctrl 6 +100% +100% tr v + Now move the appropriate transmitter control (CTRL 6 to 10), or operate the selected switch (SW 1 to 3, 8 or 9). Note that the rotary proportional controls are not detected until they have moved a few “ratchet clicks”, i. e. they need to be operated for slightly longer. If the travel is not sufficient for the transmitter to detect it, move the control in the opposite direction. If you assign one of the two-position switches, then this control channel works like an On / Off switch. It is then possible to switch to and fro between two end-point values using this simple switch, e. g. motor ON / OFF. The three-position switches SW 4/5 and 6/7, which you will find in the “Transmitter control settings” menu as “CTRL 9” and “CTR 10”, provide a centre position in addition to the two end-points. Simultaneously pressing the or buttons of the right-hand touch-key (CLEAR) with the switch assignment activated - see illustration above - resets the input to “free”. Tips: • When assigning the switches please take care to set them to the appropriate direction of travel, and ensure that all inputs not required are left at or set to “free”, to eliminate the possibility of errors if unused transmitter controls are operated accidentally. • You can alter the effective end-points of an assigned switch by adjusting servo travel as described in the next section. The screen now displays either the transmitter control number or the switch number, followed by a switch symbol which indicates the direction of operation, e. g.: I5 thr gyr I8 lim 3 +100% +100% +100% +100% free ctrl 7 +100% +100% free +100% +100% ctrl 6 +100% +100% tr v + Column 3 “-Travel+” In this column the transmitter control can be adjusted symmetrically or asymmetrically, i. e. different to either side. The available range is +/-125% of the normal servo travel. Use the arrow buttons of the left or right-hand touch-key to select one of the inputs I5, throttle, gyro, I8 or lim. If you wish to set up symmetrical travel, i. e. the same in both directions, move the associated transmitter control (rotary proportional control or switches 4/5 and 6/7) to a position at which the marking frame encloses both sides of the travel setting: I5 thr gyr I8 lim 3 +100% +100% +100% +100% free ctrl 7 +100% +100% +100% +100% free ctrl 6 +100% +100% tr v + If you wish to set up asymmetrical travel, i. e. different for both directions, move the associated transmitter control (rotary proportional control or switch) to a position at which the marking frame encloses the side of the travel setting you wish to change: I5 thr gyr I8 lim 3 +100% +100% free +100% +100% ctrl 7 +100% +100% free +100% +100% ctrl 6 +100% +100% tr v + Touch the central SET button of the right-hand touch-key to activate the value setting; the value field is now shown highlighted. Use the arrow buttons of the right-hand touch-key to alter the values: I5 thr gyr I8 lim +100% +100% 3 +100% +100% free ctrl 7 +111% +111% free +100% +100% ctrl 6 +100% +100% tr v + I5 thr gyr I8 lim +100% +100% 3 +100% +100% free +88% +111% ctrl 7 +100% +100% free ctrl 6 +100% +100% tr v + Touch the central SET button of the right-hand touch-key to conclude the input process. Negative and positive parameter values are possible; this enables you to set the appropriate direction of movement of the transmitter control or its direction of Program description: transmitter control settings – model helicopter 97 effect to suit your model. Simultaneously pressing the arrow buttons or of the right-hand touch-key (CLEAR) resets the altered parameter in the highlighted input field to +100%. “Throttle” „Gyr“ I5 thr gyr I8 lim 3 +100% +100% free +100% +100% ctrl 7 +100% +100% free +100% +100% ctrl 6 +100% +100% tr v + In principle all transmitter controls (rotary proportional knob) and switches present on the transmitter can be assigned to the individual inputs within the Helicopter program. However, please note that some inputs available in this menu are already pre-defined for helicopter-specific functions, and for this reason cannot be used without restriction. For example, the receiver sequence printed on page 65 shows that the throttle servo (or the speed controller of an electric-powered model helicopter) must be connected to receiver output “6”, i. e. control channel “6” is reserved for motor speed control. However, in contrast to a fixed-wing aircraft, the throttle servo or speed controller is not directly controlled by the throttle stick or any other transmitter control, but via a complex mixer system - see “Helicopter mixers” menu, starting on page 114. The “throttle limit function” (described on the next page) also has an influence on this mixer system. Assigning a transmitter control or switch in the “Throttle” 98 line, or its supplementary control signal, would only unnecessarily “confuse” this complex mixer system. For this reason the “Throttle” input MUST always be left “free” when you are programming a model helicopter. I5 thr gyr I8 lim 3 +100% +100% +100% +100% free ctrl 7 +100% +100% free +100% +100% ctrl 6 +100% +100% tr v + If the gyro you are using features infinitely variable gain control, then you can pre-set the static gyro effect by setting an “offset” within the range +/-125%, separately for each flight phase, in the “Gyro” line of the “Helicopter mixers” menu - see the section starting on page 118. Once you have entered these pre-defined - static - gain settings (set separately for each flight phase in the “Helicopter mixers” menu), you can use a transmitter control such as one of the rotary proportional controls CTRL 7 or 8 to vary gyro gain around the set “offset point”; all you have to do is assign that transmitter control in the “Gyro” line of this menu: in the centre position of the transmitter control this corresponds to the setting selected in the “Helicopter mixers” menu (see section starting on page 118). If the transmitter control is moved from this centre point in the direction of full travel, gyro gain is increased; towards the opposite end-point it is reduced. This is a fast, simple method of fine-tuning gyro gain when the model is in flight - perhaps to suit varying weather conditions - or alternatively to find the optimum setting. In software terms you can also limit the Program description: transmitter control settings – model helicopter gain range to both sides by restricting the transmitter control travel. However, please be sure to read the set-up notes provided with your gyro before carrying out these adjustments, as you could render your helicopter uncontrollable if you make a mistake. Throttle limit function “Lim” input By default the “lim” input is assigned to the rotary proportional control CTRL 6, which is located at top left on the transmitter: I5 thr gyr I8 lim 3 +100% +100% free +100% +100% ctrl 7 +100% +100% free +100% +100% ctrl 6 +100% +100% tr v + This pre-defined assignment eliminates the need to program two flight phases - “with idle-up” and “without idle-up” - as are often used by other radio control systems for this purpose, since the method of raising the system rotational speed below the hover point is more flexible with the mx-16 HoTT program, and can be fine-tuned more accurately than using the conventional “idle-up” function. However, if you prefer to program your helicopter “with idle-up”, then switch off the “throttle limit” function, described below, by setting the “Lim” input to “free”. Meaning and application of “throttle limit” As mentioned previously under “Throttle”, the power output of the engine or motor of a model helicopter is not controlled directly using the throttle (Ch 1) stick - in contrast to fixed-wing model aircraft. Instead it is controlled indirectly by the throttle curve settings which you set up in the “Helicopter mixers” menu. Alternatively the throttle is controlled by the speed controller if the unit you are using is a governor or regulator. Note: Naturally it is possible to set up different throttle curves to suit different stages of flight using flight phase programming. By their very nature, both methods of controlling power have the same result, i. e. that a helicopter’s motor never gets anywhere near its idle speed during “normal” flying, so it is impossible to start or stop the motor easily unless some other means is used. The “Throttle limiter” function solves this problem in an elegant manner: a separate transmitter control - as standard this is the rotary proportional control CTRL 6 located at top left on the transmitter - is employed to limit the setting of the throttle servo or the speed controller, which means that you can throttle right back to the idle position. At this setting the trim of the throttle / collective pitch stick assumes control, and can be used to switch off an electric motor directly. At the other extreme, the throttle servo or speed controller can, of course, only reach its full-throttle position if you release full servo travel using the throttle limit control. That is why the “lim” input is reserved in the Helicopter program for the “Throttle limiter” function. For this reason the right-hand positive value in the “Travel” column must be large enough to ensure that it does not limit the full-throttle setting available via the throttle curve settings when the throttle limit control is at its maximum position. Usually this means a value in the range +100% to +125%. The left-hand negative value in the “Travel” column should be set in such a way that the throttle limit control reliably cuts the electric motor, or closes the throttle to the point where you can cut the I.C. motor using the (digital) Ch 1 trim. For this reason you should leave this value at +100%, at least for the time being. This variable “limiting” of throttle travel provides a convenient means of starting and stopping the motor. However, it also gives an additional level of safety if, for example, you have to carry your helicopter to the flight line with the motor running: you simply move the control to its minimum position, and this prevents any accidental movement of the Ch 1 stick affecting the throttle servo. If the carburettor is too far open (or the speed controller not at “stop”) when you switch the transmitter on, you will hear an audible warning, and the screen displays the message: throttle too high ! Tip: You can call up the “Servo display” menu to check the influence of the throttle limit slider. This menu can be accessed from virtually any menu points by simultaneously pressing the buttons of the left-hand touch-key. Bear in mind that servo output 6 controls the throttle servo on the mx-16 HoTT. Basic idle setting Start by turning the throttle limiter - by default the rotary proportional knob CTRL 6 located at top left on the transmitter - clockwise to its end-point. Move the throttle / collective pitch stick to the maximum position, and ensure that a standard throttle curve is active in the “Channel 1 throttle” sub-menu of the … “Heli mixer” (page 114 … 125) … menu. If you have already altered the standard Program description: transmitter control settings – model helicopter 99 throttle curve which is present when you first initialise a model memory, then this should be reset to the values “Point 1 = 0%”, “Point 3 = +50%” and “Point 5 = +100%” - at least temporarily. ch1 input output point 3 thr +50% +50% +50% Note: Since the throttle trim lever has no effect when the throttle limiter is open, its position is not relevant at this point. Now - without starting the glow motor - adjust the mechanical linkage of the throttle servo so that the carburettor barrel is fully open; if necessary, carry out fine-tuning using the travel setting for servo 6 in the “Servo settings” menu. Close the throttle limiter completely by turning the rotary proportional knob CTRL 6 anti-clockwise to its endpoint. Use the trim lever of the throttle / collective pitch stick to move the trim position marker to the motor OFF position (see illustration in the right-hand column of the next page). Note: In contrast, when the throttle limiter is closed, the position of the throttle / collective pitch stick is not relevant; it can therefore be left in the maximum collective pitch position, i. e. the throttle linkage can be adjusted between full-throttle (throttle limiter open) and “motor OFF” (throttle limiter closed) using just the throttle limiter. Now, with the throttle limiter closed, adjust the mechanical throttle linkage so that the carburettor is just fully closed. However, do check carefully that the throttle servo is not stalled at either of its extreme end-points (full-throttle / motor OFF). To complete this basic set-up you still have to adjust the idle trim range to coincide with point “1” of the throttle curve. This is accomplished by setting point “1” of the “Ch 1 throttle” mixer in the “Heli mixer” menu to a value of about +15 to +18%: ch1 input output point 1 0% +16% +16% Throttle limit in conjunction with the digital trim When used with the throttle limit control CTRL 6, the Ch 1 trim places a marker at the set idle position of the motor; at this point the motor can be stopped using the Last idle position Current trim position thr To check that the setting is exact, i. e. that there is a seamless transition from idle trim to the throttle curve, you need to close the throttle limiter and move the collective pitch stick to and fro slightly at the minimum end-point. When you do this, the throttle servo must not move! In any case fine-tuning must be carried out with the model flying. The motor is always started with the throttle limiter completely closed; this has the effect that the idle speed is adjusted solely using the trim lever of the throttle / collective pitch stick. 100 Program description: transmitter control settings – model helicopter trim. If the trim is in its end-range (see screen-shot: top picture in the right-hand column), then a single click immediately takes you back to the marker, i. e. to the pre-set idle position (see also page 60). The cut-off trim only acts as idle trim in the left-hand half of the travel of the throttle limit control, i. e. the marker is only set and stored within this range. stop flt Throttle limit control M CTRL 6 Trim at motor OFF position For this reason the Ch 1 trim display is also completely suppressed as soon as the throttle limit control is moved to the right of the centre position. stop flt M Throttle limit control CTRL 6 Note: Since this trim function is only effective in the “Motor off” direction, the illustration above changes if you alter the transmitter control direction for the collective pitch minimum position of the Ch 1 stick from “back” (reflected in the picture above) to “forward” in the “Collective pitch min.” line of the “Base settings” menu. In the same way the effects shown in the illustration swap sides if you change the stick mode from collective pitch right (reflected in the pictures above) to collective pitch left in the “Stick mode” line of the “Base settings” menu; see page 82. Program description: transmitter control settings – model helicopter 101 D/R Expo Switchable control characteristics for aileron, elevator and rudder Use the arrow buttons of the left or right-hand touchkey to leaf through to the “D/R Expo” menu point of the multi-function menu: mod. mem. ser vo set. D/R expo wing mixer ser vo disp fail-safe base sett. contr set. phase trim free mixer basic sett telemetr y A brief press on the central SET button of the right-hand touch-key opens this menu point: aile 100% elev 100% rudd 100% 0% 0% 0% DUAL EXPO ––– ––– ––– The Dual Rate / Expo function provides a means of switching to reduced control travels, and of influencing the travel characteristics, for aileron, elevator and rudder (control functions 2 ... 4). Dual Rate works in a similar way to transmitter control travel adjustment in the “Transmitter control settings” menu, i. e. it affects the corresponding stick function, regardless of whether that function controls a single servo or multiple servos via any number of complex mixer and coupling functions. For each switch position the servo travels can be set to any value within the range 0 to 125% of full travel. Expo works in a different way. If you set a value greater than 0%, exponential provides fine control of the model around the centre position of the primary control func102 Dual Rate / Expo - fixed-wing model tions (aileron, elevator and rudder), without forfeiting full travel at the end-points of stick movement. If you set a value lower than 0%, travel is increased around the neutral position, and diminishes towards the extremes of travel. The degree of “progression” can therefore be set to any value within the range -100% to +100%, where 0% equates to normal, linear control characteristics. Another application for exponential is to improve the linearity of rotary-output servos, which are the standard nowadays. With a rotary servo the movement of the control surface is inevitably non-linear, as the linear movement of the output disc or lever diminishes progressively as the angular movement increases, i. e. the rate of travel of the control surface declines steadily towards the extremes, dependent upon the position of the linkage point on the output disc or lever. You can compensate for this effect by setting an Expo value greater than 0%, with the result that the angular travel of the output device increases disproportionately as stick travel increases. Like Dual Rates, the Expo setting applies directly to the corresponding stick function, regardless of whether that function controls a single servo or multiple servos via any number of complex mixer and coupling functions. The Dual Rate and Expo functions can be switched on and off together if you assign a switch to the function. The result of this is that Dual Rates and Expo can be controlled simultaneously using a single switch, and this can be advantageous - especially with high-speed models. Flight phase dependent Dual-Rate and Expo settings If you have assigned a switch and - if you wish - a more appropriate name to one of the phases 2 to 4 in the “Base settings” menu (see page 78), then this appears at bottom left, e. g. “normal”. If necessary, operate the associated switch in order to switch between the flight phases. The basic set-up procedure 1. Switch to the desired flight phase, and then select the desired line “aile”, “elev” or “rudd” using the arrow buttons of the left or right-hand touch-key. 2. If necessary, use the buttons of the left or righthand touch key to select the desired column. 3. Briefly press the central SET button of the right-hand touch-key: the corresponding input field is now highlighted (black background). 4. Set the desired value using the arrow buttons of the right-hand touch-key. 5. Touch the central SET button of the right-hand touchkey to conclude the input process. 6. Simultaneously press the or buttons of the right-hand touch-key (CLEAR) to reset any changed settings to the default values. Dual Rate function If you wish to switch between two possible D/R settings, use the button of the left or right-hand touch-key to move to the right-hand column, marked at the bottom , then edge of the screen with the switch symbol briefly touch the central SET button … ––– 0% aile 100% push desired switch into position ON normal DUAL EXPO attention: For safety reasons the Dual Rate value should always be at least 20% of total control travel. aile 100% elev 100% rudd 100% normal DUAL Examples of different Dual Rate values: Simultaneously touching the or buttons of the right-hand touch-key (CLEAR) resets an altered value in the highlighted input field to 0%. Servo travel Servo travel Servo travel EXPO Dual Rate = 20% Dual Rate = 50% Dual Rate = 100% 2 2 ––– +11% +22% 0% Examples of different Expo values: Stick deflection Stick deflection Expo = –100%, DR = 50% Expo = +100%, DR = 50% Expo = +100%, DR = 125% Servo travel Stick deflection Stick deflection e. g. “switch back”: 88% aile 77% elev rudd 100% 0% 0% 0% normal DUAL EXPO 2 2 ––– and after moving switch “2” to the “forward” position: aile 122% elev 111% rudd 100% +11% +22% 0% normal DUAL EXPO 2 2 ––– Servo travel Exponential function If you wish to switch between two settings, use the button of the left or right-hand touch-key to move to the right-hand column, marked at the bottom edge of the screen with the switch symbol , then briefly touch the central SET button and assign a switch to the function, as described in the section “Assigning switches and control switches” on page 59. The assigned switch Expo = –100% Expo = +50% Expo = +100% Stick deflection Servo travel Stick deflection Servo travel Stick deflection Combined Dual Rate and Expo If you enter values for both Dual Rates and Expo, the two functions are superimposed as follows: Servo travel appears on the screen together with a switch symbol which indicates the direction of operation when you move the switch. For example, the system enables you to fly with a linear curve characteristic in the one switch position, and to pre-set a value other than 0% in the other switch position. Select the right-hand column, marked with EXPO at the bottom edge of the screen, in order to change the Dual-Rate value for each of the two switch positions in the highlighted field, using the arrow buttons of the righthand touch-key. Servo travel … and assign a physical switch as described in the section “Assigning switches and control switches” on page 59. The assigned switch appears on the screen together with a switch symbol which indicates the direction of operation of the switch. Select the left-hand column, marked DUAL at the bottom edge of the screen, and set the values for each of the two switch positions separately in the highlighted field using the arrow buttons of the right-hand touch-key. Simultaneously touching the or buttons of the right-hand touch-key (CLEAR) resets an altered value in the highlighted field to 100%. Stick deflection Stick deflection In these examples the Dual Rate value is 100% in each case. Dual Rate / Expo - fixed-wing model 103 D/R Expo Switchable control characteristics for roll, pitch-axis and tail rotor roll nick tail 100% 100% 100% 0% 0% 0% DUAL EXPO ––– ––– ––– The Dual Rate / Expo function provides a means of switching to reduced control travels, and influencing the travel characteristics, for the roll, pitch-axis and tail rotor servos (control functions 2 … 4). A separate curve for control function 1 (motor / collective pitch) can be set individually for throttle, collective pitch and tail rotor in the “Helicopter mixers” menu. These curves feature up to five separately programmable points; see the sections starting on page 114 and 189. Dual Rate works in a similar way to transmitter control travel adjustment in the “Transmitter control settings” menu, i. e. it affects the corresponding stick function, regardless of whether that function controls a single servo or multiple servos via any number of complex mixer and coupling functions. For each switch position the servo travels can be set to any value within the range 0 to 125% of full travel. Expo works in a different way. If you set a value greater than 0%, exponential provides fine control of the model around the centre position of the primary control functions (roll, pitch-axis and tail rotor), without forfeiting full travel at the end-points of stick movement. If you set a value lower than 0%, travel is increased around the neutral position, and diminishes towards the extremes of travel. The degree of “progression” can be set within the range -100% to +100%, where 0% equates to normal, linear control characteristics. Another application for exponential is to improve the linearity of rotary-output servos, which are the standard nowadays. With a rotary servo the movement of the control surface is inevitably non-linear, as the linear movement of the output disc or lever diminishes progressively as the angular movement increases, i. e. the rate of travel of the control surface declines steadily towards the extremes, dependent upon the position of the linkage point on the output disc or lever. You can compensate for this effect by setting an Expo value greater than 0%, with the result that the angular travel of the output device increases disproportionately as stick travel increases. Like Dual Rates, the Expo setting applies directly to the corresponding stick function, regardless of whether that function controls a single servo or multiple servos via any number of complex mixer and coupling functions. The Dual Rate and Expo functions can also be switched on and off together if you assign a switch to the function. The result of this is that Dual Rates and Expo can be controlled simultaneously using a single switch, and this can be advantageous - especially with high-speed models. Flight phase dependent Dual-Rate and Expo settings If you have assigned a switch and - if you wish - a more appropriate name to one of the phases 2, 3 or Auto-rotation in the “Base settings” menu (see page 87), then this appears at bottom left, e. g. “normal”. If necessary, operate the associated switch in order to switch between the flight phases. 104 Program description: Dual Rate / Expo – model helicopter The basic set-up procedure 1. Switch to the desired flight phase, and then select the desired line “Roll”, “Nick” or “Tail” using the arrow buttons of the left or right-hand touch-key. 2. If necessary, use the buttons of the left or righthand touch key to select the desired column. 3. Briefly press the central SET button of the right-hand touch-key: the corresponding input field is now highlighted (black background). 4. Set the desired value using the arrow buttons of the right-hand touch-key. 5. Touch the central SET button of the right-hand touchkey to conclude the input process. 6. Simultaneously press the or buttons of the right-hand touch key (CLEAR) to reset any changed settings to the default values. Dual Rate function If you wish to switch between two possible D/R settings, use the button of the left or right-hand touch-key to move to the right-hand column, marked at the bottom , briefly edge of the screen with the switch symbol touch the central SET button … 0% ––– roll 100% push desired switch into position ON DUAL EXPO … and assign a physical switch as described in the section “Assigning switches and control switches” on page 59. The assigned switch appears on the screen together with a switch symbol which indicates the direc- attention: For safety reasons the Dual Rate value should always be at least 20% of total control travel. Examples of different Dual Rate values: Servo travel +11% +22% 0% normal DUAL EXPO roll nick tail Examples of different Expo values: Expo = –100% Expo = +50% Exponential function If you wish to switch between two settings, use the button of the left or right-hand touch-key to move to the right-hand column, marked at the bottom edge of the screen with the switch symbol , then briefly touch the central SET button and assign a switch to the function, as described in the section “Assigning switches and control switches” on page 59. The assigned switch appears on the screen together with a switch symbol which indicates the direction of operation when you move the switch. Servo travel Stick deflection Servo travel Stick deflection Stick deflection Stick deflection Servo travel Stick deflection Stick deflection e. g. “switch back”: Simultaneously touching the or buttons of the right-hand touch-key (CLEAR) resets an altered value in the highlighted input field to 0%. Expo = +100% Stick deflection Expo = –100%, DR = 50% Expo = +100%, DR = 50% Expo = +100%, DR = 125% Stick deflection 2 2 ––– Servo travel Servo travel Servo travel Dual Rate = 20% Dual Rate = 50% Dual Rate = 100% 100% 100% 100% roll nick tail Combined Dual Rate and Expo If you enter values for both Dual Rates and Expo, the two functions are superimposed as follows: Servo travel For example, the system enables you to fly with a linear curve characteristic in the one switch position, and to pre-set a value other than 0% in the other switch position. Select the right-hand column, marked with EXPO at the bottom edge of the screen, in order to change the Dual-Rate value for each of the two switch positions in the highlighted field, using the arrow buttons of the righthand touch-key. Servo travel tion of operation of the switch. Select the left-hand column, marked DUAL at the bottom edge of the screen, and set the values for each of the two switch positions separately in the highlighted field using the arrow buttons or of the right-hand touch-key. Simultaneously press the or buttons of the right-hand touch key (CLEAR) resets an altered value in the highlighted field to 100%. 88% 77% 100% 0% 0% 0% normal DUAL EXPO 2 2 ––– and after moving switch “2” to the “forward” position: 122% 111% 100% +11% +22% 0% normal DUAL EXPO roll nick tail 2 2 ––– Stick deflection In these examples the Dual Rate value is 100% in each case. Program description: Dual Rate / Expo – model helicopter 105 Phase trim Flight phase-specific trims for flaps, ailerons and elevator If you have not assigned a switch to phases 2, 3 and 4 in the “Base settings” menu, i. e. you have not assigned switches to these alternative phases, you automatically remain in flight phase 1 - “normal”. The number and name (“normal”) of this flight phase are permanently assigned, and cannot be altered. For this reason the “normal” phase is not stated as Phase 1 “normal” in the “Base settings” menu; it is simply concealed. aile/flap timer phase 2 phase 3 phase 4 10:01 takeoff speed landing 2aile 2 ––– ––– ––– If you select the “Phase trim” menu with this basic arrangement, you will find just the “normal” line on the screen, whose pre-set values of 0% are not usually altered. P H A S E T R I M normal 0% 0% 0% FLA AIL ELE Note: In this menu you will have at least one control function (ELE), and a maximum of three functions (ELE, AIL and FLA), available for phase-specific trim settings, depending on the settings you have entered in the “Aileron / flap” line of the “Base settings” menu (see page 77). If you wish to enter values other than “0”, e. g. to have more lift at launch, or to be able to fly more slowly when thermalling, or faster when flying speed tasks, but WITHOUT having to change the basic settings each time, then you need to use alternative flight phases. This is done by activating “Phase 2” and, if necessary, “Phase 3” in the “Base settings” menu. You might then use “Phase 4” for the “thermal” settings. This is accomplished by moving to the “Base settings” menu and assigning a switch to the selected phase or phases. If you decide to use one of the three-position switches SW 4/5 or 6/7 as the phase switch, then it is advisable to assign it to the “Speed” phase and “Landing” phase at the extremes, with “normal” at the centre position. In our example phase 2 contains the “Launch” settings, and since this has top priority, you can shift to this phase from any other phase using a two-position switch. Notes: • At the centre position of SW 4/5 or 6/7 the switch symbols on the screen should look as in the picture at top right. • Please note the priorities of the individual flight phases, as described in detail on page 78. The default name for “Phase 2” is “take off”, that for “Phase 3” is “speed”, and that for “Phase 4” is “landing”. However, you can assign your own choice of names at any time by selecting the appropriate line, pressing the central SET button of the right-hand touch-key, and selecting one of the following names in the highlighted field using the arrow buttons of the right-hand touch-key. • take off • thermal 106 Program description: Phase trim – fixed-wing model • • • • • • dist(ance) speed acro landing air-tow test timer phase phase phase receiv 2 3 4 out 10:01 takeoff speed thermal 2 2 7 6 These names will appear in the transmitter’s basic display … GRAUBELE #01 5.2V 2:22h 0:00 stop flt 0:00 «normal » HoTT M 5.5V … and in the “Phase trim” menu - see lower picture. Setting up flight phase trims In the “Phase trim” menu you can adjust the trims for the previously selected flight phases. The first step is to use the phase switch you have already assigned to move to the phase which you wish to adjust (the “*” at far left indicates the currently active phase). P H A S E T R I M normal 0% 0% 0% takeoff 0% 0% 0% speed 0% 0% 0% thermal 0% 0% 0% FLA AIL ELE Note: In this menu you will have at least one control function (ELE), and a maximum of three functions (ELE, AIL and FLA), available for phase-specific trim settings, depending on the settings you have entered in the “Aileron / flap” line of the “Base settings” menu (see page 77). Select the desired control surface function using the arrow buttons of the left or right-hand touch-key, then briefly press the central SET button of the righthand touch-key. The trim values in the highlighted value field can now be adjusted using the arrow-buttons of the right-hand touch-key. You can activate each phase by operating the assigned phase select switch or switches. Note that the servos do not change from one setting to another abruptly; they move smoothly with a transition time of around one second. With this option, which works in a similar way to transmitter control sub-trim or offset settings with other radio control systems, it is possible to set values within the range -99% to +99%. However, typical values are normally in single figures or low double figures. P H A S E T R I M normal 0% 0% 0% takeoff +8% 4% +2% speed –7% –5% –3% thermal +10% +5% +2% FLA AIL ELE If you have made any changes, simultaneously pressing the or buttons of the right-hand touch-key (CLEAR) resets them to the default value of 0%. Program description: Phase trim – fixed-wing model 107 What is a mixer? Fixed-wing mixers The basic function In many models it is often desirable to use a mixer to couple various control systems, e. g. to link the ailerons and rudder, or to inter-connect a pair of servos where two control surfaces are actuated by separate servos. In all these cases the signal which flows directly from the “output” of a transmitter stick to the associated servo is “bled off” at a particular point - this effect can also be “concealed” in transmitter control options such as “D/R Expo” or “Transmitter control settings” - and the derived signal is then processed in such a way that it affects the “input” of another control channel, and therefore eventually another receiver output. For more information please refer to the general notes on “Free mixers” in the section of this manual starting on page 126. Example: V-tail mixer 48V e C 577 48V es N 410 Right rudder / elevator C 577 4 Left rudder / elevator Se v er dd Ru er dd r Ru vato Ele 4 Control channels (receiver outputs) r V-tail mixer B s N 410 3 Ru Ele dder vat or 3 o vat Ele Control function inputs Elevator stick Rudder stick The mx-16 HoTT transmitter software contains a large number of pre-programmed coupling functions as standard, designed to mix together two (or more) control channels. The mixer required in this example is supplied “ready-made” in the software, and just has to be activated in the “tail” line of the “Base settings” menu in the form of “V-tail”. The software also includes three freely programmable linear mixers in the fixed-wing and helicopter programs, all of which can be used in each model memory. diff aile. diff flaps ail rudd ail flaps brak elev brak flap brak aile elev flap elev aile elev flap aile flap diff–red 0% 0% 0% 0% 0% 0% 0% 0% 0% 0% 0% 0% The display varies according to the information you have entered in the “Motor at Ch 1” and “Ail / Flap” lines in the “Base settings” menu. The selection above shows the maximum number of options, and equates to the setting “No (motor)” and “2AIL 2FL”. The mx-16 HoTT transmitter’s program contains a series of pre-programmed coupling functions, and all you have to do is set the mixer ratios and (optionally) assign a switch. The number of pre-programmed mixer functions in the mixer list will vary according to the pre-set “model type” (tail type, number of wing servos, with or without motor - see the section starting on page 74). For example, if your model is not fitted with camber-changing flaps, and you have not entered any flap servos in the “Base settings” menu, the software automatically suppresses all the flap mixers, as are the “Brake NN *“ mixers if you enter “Idle forward” or “Idle back” in the “Motor at Ch 1” line. This makes the menus clearer and easier to understand, and also avoids potential programming errors. * NN = Nomen Nominandum (name to be stated) 108 Program description: wing mixers – fixed-wing model ––– ––– ––– ––– ––– ––– ––– ––– ––– ––– ––– Notes: • There are various alternative methods of positioning the camber-changing flaps; these include: a) settling on just one position per flight phase, simply by setting appropriate trim values in the “Phase trim” menu, as described on the preceding double-page; b) controlling the flaps manually using any transmitter control assigned to “Input 6” (in the “Transmitter control settings” menu - see page 94), after setting the basic flap positions in the “Phase trim” menu, as described earlier. Ideally the transmitter control would be one of the rotary proportional controls CTRL 6 … 8. The selected transmitter control directly operates the two flap servos connected to receiver outputs 6 and 7, assuming that you have specified flaps in the “Ail. / Flap” line of the “Base settings” menu. The same control determines the flap setting of the ailerons via the percentage value entered in the “FL AIL” mixer line. However, for finer control of the flap positions, we recommend that you reduce their travel to about 25% in the “E6” line of the “Transmitter control settings” menu. c) It is also possible to leave the default setting of “0%” in the appropriate line of the “FL AIL” menu, and to assign the same transmitter control to both input 6 and input 5 in the “Transmitter control settings” menu. The magnitude of the effect on the two pairs of wing flaps can then be adjusted using the servo travel adjustment facility. • If a transmitter control is assigned to input “7”, it will be de-coupled by the software if two camber-changing flaps are defined; this is intentional, as it eliminates the danger of errors when a flap command is given. The basic programming procedure 1. Use the buttons of the left or right-hand touchkey to select the desired mixer. 2. Use the button of the left or right-hand touch-key to move to the right-hand column, marked by the at the bottom edge of the screen. switch symbol 3. Touch the central SET button of the right-hand touchkey; the corresponding input field is now highlighted (black background). 4. Use the arrow buttons of the right-hand touch-key to set the desired value, and assign the switch if necessary, as described on page 59. With the exception of the “Diff. red.” line, negative and positive parameter values are possible; this may be necessary to obtain the correct direction of servo rotation (control surface deflection). Simultaneously pressing the or buttons of the right-hand touch-key (CLEAR) resets an altered value to the default value. 5. Touch the central SET button of the right-hand touchkey to conclude the input process. Mixer neutral point (offset) The neutral point of the mixers … Aileron NN * Elevator NN * Elevator NN * … is by default the zero point of the transmitter control, i. e. that is the point at which they have no effect. At the end-point of the transmitter control the full mixer value is applied. The default neutral point (“offset”) of the mixers … Airbrake NN * … at which the airbrakes are always retracted, is the forward position of the Ch 1 stick (throttle / airbrakes) if you select “none” in the “Motor at Ch 1” line of the “Base settings” menu, and is the back position of the Ch 1 stick if you select “none/inv”. diff aile (differential aileron travel) Aileron differential compensates for an unwanted side-effect which occurs when ailerons are deflected: the problem known as “adverse yaw”. When ailerons are deflected, the drag generated by the down-going aileron is greater than that produced by the up-going aileron. The differential drag causes a yawing motion around the vertical axis in the opposite direction to the desired turn. This effect is much more pronounced in model gliders with high aspect ratio wings than in power models with their much shorter moment arms, and usually has to be countered by giving a simultaneous rudder deflection in the opposite direction to the yaw. However, this in turns causes additional drag and reduces the aircraft’s efficiency even further. Aileron differential reduces the angular travel of the down-going aileron relative to the up-going aileron, and this reduces the drag and therefore the adverse yaw. However, electronic differential can only be applied if each aileron is actuated by its own servo, usually mounted in the wings themselves. The shorter pushrods also result in virtually slop-free aileron linkages with reliable centring. * NN = Nomen Nominandum (name to be stated) Program description: wing mixers – fixed-wing model 109 Mechanical solutions are also possible, but they usually have to be “designed in” when the model is built, and the degree of differential cannot be altered subsequently. In any case significant mechanical differential tends to cause additional slop in the control system. Electronic differential offers several important advantages: 0% (normal) 50% (differential) 100% (split) It is easily possible to vary the degree of differential without affecting the travel of the up-going aileron. At one extreme it is possible to suppress the down-aileron deflection completely, i. e. only the up-going aileron moves at all, and this arrangement is sometimes called the “split” setting. Split ailerons not only tend to suppress adverse yaw, but can even generate positive yaw, which means that the model yaws in the direction of the turn when an aileron command is given. In the case of large model gliders, smooth turns can then be flown using ailerons alone, which with most models of this type is usually by no means the case. The adjustment range of -100% to +100% makes it possible to set the correct direction of differential regardless of the direction of rotation of the aileron servos. “0%” corresponds to a normal linkage, i. e. no differential, while “-100%” or “+100%” represents the “split” function. For aerobatic flying it is necessary to set low absolute differential values, to ensure that the model rotates exactly along its longitudinal axis when an aileron command is given. Moderate values around -50% or +50% are typical for making thermal turns easier to fly. The split setting (-100%, +100%) is popular with slope flyers, when ailerons alone are often used for turning the model. Simultaneously pressing the or buttons of the right-hand touch-key (CLEAR) resets an altered value to 0%. Note: Negative values are not usually necessary if the correct channels are used. Note: In this case the rudder automatically “follows” when an aileron command is given, and the mixer ratio (degree of following) can be set by the user. Coupled aileron / rudder (also known as “combi-switch”) is especially useful for suppressing adverse yaw in conjunction with aileron differential, and this combination usually makes smooth turns very easy to fly. Naturally, the rudder can still be controlled separately by means of its dedicated stick. The adjustment range of +/- 150% enables the user to set up the correct direction of travel according to the direction of rotation of the flap servos. If an (optional) non-centring switch (SW 2 … 8) is assigned to this function, the mixer can be turned on and off in flight, so that you can control the ailerons and rudder separately if and when you so desire. Simultaneously pressing the or buttons of the right-hand touch-key (CLEAR) resets an altered value to 0%. This mixer is usually set up in such a way that the rudder deflects automatically to the side of the up-going aileron; a setting around 50% is likely to be approximately correct. Although it is possible to enter negative values in order to reverse the direction of servo rotation, this is not usually necessary if the correct channels are used. diff flaps (Camber-changing flap differential) The aileron / flap mixer (see below) is designed to superimpose an aileron function on the flaps. Flap differential works like aileron differential, and produces a reduced flap movement in the down-direction when these surfaces are used as supplementary ailerons. The adjustment range of -100% to +100% makes it possible to set the correct direction of differential regardless of the direction of rotation of the servo. “0%” corresponds to a normal linkage, i. e. the servo travel is the same up and down. A setting of “-100%” or “+100%” means that the down-travel of the flaps is reduced to zero when an aileron command is given (“split” setting). Simultaneously pressing the or buttons of the right-hand touch-key (CLEAR) resets an altered value to 0%. 110 Program description: wing mixers – fixed-wing model ail rudd(Aileron rudder) ail flaps(Aileron flap) This mixer feeds a variable amount of the aileron signal into the flap channel. When an aileron command is given, the flaps “follow” the ailerons, although usually through a smaller angle, i. e. the mixer ratio is generally less than 100%. The adjustment range of -150% to +150% allows the user to set up the flap direction to match that of the ailerons. The flaps should not deflect more than about 50% of the (mechanical) travel of the ailerons. Simultaneously pressing the or buttons of the right-hand touch-key (CLEAR) resets an altered value to 0%. brak elev(Airbrake elevator) or Extending any form of airbrakes usually generates an unwanted change in airspeed; this is especially marked when a butterfly (crow) braking system is deployed (see next page). This mixer feeds a corrective signal to the elevator to compensate for such an effect. The adjustment range is -150% to +150%. Simultaneously pressing the or buttons of the right-hand touch-key (CLEAR) resets an altered value to 0%. “Usual” values are generally in single to low double figures. It is essential to check and adjust this setting at a safe height, and it is also important to ensure that the model does not slow down too much when the airbrakes are extended. The danger is that you might need to retract the brakes again on the landing approach when you realise the model will “land short”; if its airspeed is too low when you retract the brakes, the model will just fall to the ground at that point. brak flap(Airbrake flap) of the servos concerned strikes its mechanical endstops (servos stalled). To achieve this, you may need to limit the servo travel(s) using the “Travel -/+” option, which is found on the “RX SERVO” display page of the “Telemetry” menu. brak aile (Airbrake aileron) When you operate the brake function, both aileron servos move together for the landing approach; the mixer ratio can be set to any value in the range -150% to +150%. Simultaneously pressing the or buttons of the right-hand touch-key (CLEAR) resets an altered value to 0%. Note: It can also be useful to deflect both ailerons up slightly when the airbrakes are extended; in most cases this significantly reduces the risk of a tip-stall. When you operate the brake function (Ch 1 stick), both flap servos move together for the landing approach; the mixer ratio can be set to any value in the range -150% to +150%. Down-flap is usually selected. Combination of the “Brake NN *” mixers: “Crow” or “Butterfly” setting Simultaneously pressing the or buttons of the right-hand touch-key (CLEAR) resets an altered value If you have set up all three airbrake mixers for your to 0%. model, it is then possible to program a special configuration known as the “crow” or “butterfly” arrangement for At this point you select the value which causes the flaps glide path control. In the butterfly setting both ailerons to deflect down as far as possible when the airbrake are deflected up by a moderate amount, and both flaps function is deployed. However, please ensure that none Program description: wing mixers – fixed-wing model 111 down by the maximum possible amount. The third mixer provides elevator trim to counteract any unwanted pitch trim change and maintain the model’s airspeed at a safe level. This is necessary to avoid the danger of the model slowing up excessively; if the landing approach is started too soon, and has to be extended by retracting the airbrakes again, the model could then stall abruptly. This inter-action between the flaps, ailerons and elevator is used to control the glide angle on the landing approach. Optionally the butterfly setting can also be used without the airbrakes or spoilers; nowadays this is very commonly used for sports and competition aircraft. Note: If your model features full-span (strip) ailerons which also double as camber-changing flaps, the two mixers “Brake aileron” and “Brake elevator” can be combined for glide path control. In this case up-flap is applied, but the flaps can still be controlled as ailerons. Elevator pitch trim compensation is generally required. If you have programmed aileron differential, the response of the ailerons will inevitably be adversely affected by the extreme “up” deflection of the ailerons in the butterfly setting, because the differential travel reduces or entirely suppresses the down-aileron deflection. However, the “up” travel of the ailerons is also greatly restricted because they are already at or close to their “up” end-point. The remedy here is to apply “differential reduction”, which is explained in its own section later. elev flap (Elevator flap) response in the same way as the previous mixer. Simultaneously pressing the or buttons of the right-hand touch-key (CLEAR) resets an altered value to 0%. The adjustment range is +/- 150%. For this mixer the “usual” settings are again in the low two-digit range. flap elev The flaps can be used to enhance the effect of the elevator in tight turns and aerobatics, and this mixer feeds part of the elevator signal to the flap servos. The mixer direction must be set so that the flaps move down when up-elevator is applied, and vice versa. Simultaneously pressing the or buttons of the right-hand touch-key (CLEAR) resets an altered value to 0%. The “usual” settings for this mixer are in the low two-digit range. elev aile (Elevator aileron) This mixer allows the ailerons to reinforce the elevator * NN = Nomen Nominandum (name to be stated) 112 Program description: wing mixers – fixed-wing model (Flap elevator) When the camber-changing flaps are lowered, either using “Phase trim” or by means of a transmitter control assigned to input “6”, a pitch trim change (up or down) may occur. Alternatively it may be desirable for slight down-elevator to be applied automatically when the flaps are raised by a small amount, in order to increase the model’s basic airspeed. This mixer can be used to achieve both purposes. When the flaps are deployed, this mixer causes the elevator setting to be corrected automatically in proportion to the flap deflection. The adjustment range is +/- 150%. For this mixer the “usual” settings are in the single to low two-digit range. Simultaneously pressing the or buttons of the right-hand touch-key (CLEAR) resets an altered value to 0%. flap aile (Flap aileron) This mixer causes a variable proportion of the flap signal to be mixed in with the aileron channels 2 and 5 so that the ailerons follow the movement of the flaps, albeit normally with a smaller deflection. The adjustment range is +/- 150%. For this mixer the “usual” settings are around 50%. Simultaneously pressing the or buttons of the right-hand touch-key (CLEAR) resets an altered value to 0%. Note: If you assign a transmitter control to inputs 5 and 6 in the “Transmitter control settings” menu for adjusting the flap positions, then you should leave the value for this mixer at 0%. See the notes on page 109 in this regard. reduced aileron response compared with the normal setting of the control surfaces. In this case you really should use “differential reduction” if at all possible. This reduces the degree of aileron differential when you invoke the butterfly setting using the airbrake stick. Differential is reduced progressively, or even eliminated altogether, as the airbrake stick is moved towards its end-point. A value of 0% at this point means that the full programmed aileron differential is retained. A value of 100% means that the aileron differential is completely eliminated at the maximum butterfly setting, i. e. when the airbrakes and other glide path control surfaces are fully extended. If you set a value above 100%, the aileron differential is eliminated even before full travel of the airbrake stick is reached. The adjustment range is 0 to 150%. Simultaneously pressing the or buttons of the right-hand touch-key (CLEAR) resets an altered value to 0%. diff red (Differential reduction) The problem of reduced aileron response in the butterfly configuration has been mentioned earlier: if aileron differential is employed, the aileron response on the landing approach may be adversely affected through the extreme “up” deflection of the ailerons, permitting virtually no further up-movement; on the other hand the “down” travel has already been reduced by the programmed differential setting. The overall result is significantly Program description: wing mixers – fixed-wing model 113 Helicopter mixers Flight phase-specific mixers for collective pitch, throttle and tail rotor In the “Base settings” menu a method of switching flight phases can be activated by assigning the appropriate switches to “Phase 2”, “Phase 3” and “Auto-rotation”. You can then switch between the phases “normal” and a second and third phase - to which you can assign more appropriate names yourself, if necessary - using one of the non-centring switches SW 2 … 8; a further switch then selects “Auto-rotation”. However, “Phase 2” always has precedence over the “normal”-phase and “Phase 3” and auto-rotation always has precedence over all other phases; see pages 87. If you have not yet assigned switches for the flight phases, you should do so now. Use the arrow buttons of the left-hand touch-key to move to the right-hand column, symbol at the bottom of the marked by the switch screen, then touch the central SET button of the righthand touch-key. The switches are assigned as described on page 59: pitch min timer phase 2 phase 3 autorotat. rear 10:01 C3 hover 5 speed 4 2 Phase 1 always bears the designation “normal”. Both the number and name of this phase are permanently assigned, and cannot be altered. For this reason the “normal” phase is not stated as Phase 1 in the “Base settings” menu; it is simply concealed. By default “Phase 2” is assigned the phase name “hover”, and “Phase 3” the name “speed”, but you can change these at any time if you prefer: touch the central SET button with the right-hand touch-key, and use the arrow buttons of the right-hand touch-key to select one of the following names: • hover • acro • acro 3D • speed • test Description of the helicopter mixers Five-point curves are available for setting up the control characteristics of “collective pitch”, “Ch 1 throttle” and “Ch 1 tail rotor”. Using these curves it is possible to program non-linear mixer ratios along the travel of the transmitter stick for these mixers. Move to the display page for setting 5-point curves by touching the central SET button of the right-hand touch-key (see below). In contrast, the mixers “Ch 1 throttle” and “Ch 1 tail rotor” are not required for the “Auto-rotation” flight phase (described in the section starting on page 124); instead they are automatically switched to a (user-variable) pre-defined value. A value must be entered in the “Gyro” and “Input 8” lines: touch the central SET button of the right-hand touchkey, then enter a value in the highlighted field using the arrow buttons of the right-hand touch key - in a similar fashion to changing the transmitter centre position or the offset position with other radio control systems. This set-up facility is rounded off with the “Swashplate limit” option: this restricts the maximum travel of the swashplate servos to the value you set, in the form of a limiter. All these options are required for the basic process of setting up a model helicopter. Altered parameters can be reset to the corresponding 114 Program description: helicopter mixers – model helicopter default values at any time by simultaneously pressing the or buttons of the right-hand touch-key (CLEAR). The name of the currently selected flight phase is displayed in the “Helicopter mixers” menu as well as in the transmitter’s basic display; this is designed to ensure that any changes you make actually apply to the appropriate flight phase. Note that the servos do not change from one setting to another abruptly; they move smoothly with a transition time of around one second. This does not apply to auto-rotation: when you switch INTO auto-rotation, the change takes place immediately. If you operate the switch selected for a particular flight phase, the associated flight phase is superimposed at the left-hand bottom edge of the screen, e. g. “normal”. ptch ch1 thro tail ch1 gyro inp8 normal 0% 0% Now you can program the settings for this flight phase. Basic programming procedure 1. Use the arrow buttons of the left or right-hand touch-key to select the desired option. 2. Touch the central SET button of the right-hand touchkey, and the screen switches to the set-up page ( symbol at the bottom edge of the screen), or the corresponding input field is highlighted (black background). 3. Define the mixer values using the arrow buttons of the right-hand touch-key, moving the throttle / collec- tive pitch stick at the same time if necessary. 4. Simultaneously pressing the or buttons of the right-hand touch-key (CLEAR) resets an altered value to the default value. 5. Touch the central SET button of the right-hand touchkey to conclude the input process. ptch (Collective pitch (ch1 pitch)) Select the “Collective pitch” line using the arrow buttons of the left or right-hand touch key, then touch the central SET button of the right-hand touch-key: ptch input output point 3 normal 0% 0% 0% The control curve can be based on a maximum of five nodes, known as “reference points”, which can be placed along the length of the control travel; separate curves can be programmed for each flight phase. However, in most cases it is sufficient to use a smaller number of reference points when defining the collective pitch curve. As a basic rule we recommend that you start with the three default reference points offered by the software. These three points, i. e. the two end-points “Point 1” (collective pitch minimum) and “Point 5” (collective pitch maximum), and “Point 3”, exactly in the centre of the travel, initially describe a linear characteristic for the collective pitch curve; this is represented in the picture above. The programming procedure in detail The throttle / collective pitch stick can now be used to move the vertical line in the graph between the two end-points “Point 1” and “Point 5”; at the same time the momentary position of the stick is displayed in numeric form in the “Input” line (-100% to +100%). The point where the vertical line crosses the curve is termed the “Output”, and this point can be varied within the range -125% and +125% at a maximum of five reference points. The control signal, modified in this way, affects the collective pitch servos only. In the picture on the left the stick is exactly at the 0% position at “Point 3”, and also generates an output signal of 0% due to the linear nature of the graph. By default only points “1” (collective pitch minimum at -100%), “3” (hover point at 0%) and “5” (collective pitch maximum at +100% travel) are active. To set a point you use the associated stick to move the vertical line to the point you wish to change. The number and current curve value of this point are displayed in the bottom line in the left-hand half of the screen in the “Point” line. The arrow buttons of the right-hand touchkey can now be used to change the current curve value in the highlighted field to any value within the range -125% to +125%, without affecting the adjacent points. ptch input output point 3 normal 0% +75% +75% However, the optional points “2” and “4” can also be activated. In the next example we activate point “2” at -50% … ptch input output point 2 normal –50% –12% deact … and point “4” at +50% … ptch input output point 4 normal +50% +88% deact This is accomplished using the stick to move the vertical line to the appropriate area. As soon as the message “inactive” appears in the highlighted value field, you can activate the associated point with the arrow buttons of the right-hand touch-key; it can then be adjusted in the same manner as the other points … ptch input output point 4 normal +50% –50% –50% … or reset to “inactive” by simultaneously pressing the or buttons of the right-hand touch-key (CLEAR). In this example we have moved reference point “3” to +75%. Program description: helicopter mixers – model helicopter 115 ch1 thro Points “1” and “5”, however, CANNOT be disabled. Note: ch1 The following illustration, and all the other pictures on this page, show a control curve which we prepared for illustration purposes only. Please note that the curve characteristics by no means represent real collective pitch curves! input output point 3 normal ptch input output point 3 normal 0% –50% –50% Typical collective pitch curves for different flight phases: +100% Output Output +100% Output +100% 100% 100% 100% 1 2 3 4 5 1 2 3 4 5 1 2 3 4 Control travel Control travel Control travel Hover Aerobatics 3D 5 (throttle curve) thro +50% +50% +50% Helicopter with glow engine or electric motor and STANDARD SPEED CONTROLLER This setting only affects the control curve of the throttle servo or speed controller. The method of setting up a throttle curve for a model helicopter fitted with a speed governor or regulator is discussed later. The throttle curve can be defined using up to five points, in a similar way to the collective pitch curve (see previous page). • In all cases the control curve must be set up in such a way that the throttle is fully open, or the speed controller of an electric helicopter is at full power, at the end-point of the throttle / collective pitch stick, (exception: auto-rotation - see page 124). • The hover point is normally located at the centre of the stick travel, and the throttle setting should be adjusted relative to the collective pitch curve in such a way that the correct system rotational speed is obtained at this point. • At the minimum position of the throttle / collective pitch stick the throttle curve should initially be set up so that the (glow) motor runs at a distinctly higher speed compared to the idle setting, with the clutch reliably engaged. 116 Program description: helicopter mixers – model helicopter In all flight phases the motor (glow or electric) is started and stopped using the throttle limiter (see below). If you are used to a different radio control system which uses two separate flight phases for this - “with idle-up” and “without idle-up”; therefore incurring the “loss” of one complete flight phase - please note that the throttle limiter renders this complication superfluous, as the increased system rotational speed below the hover point in the mx-16 HoTT program is more flexible, and can be fine-tuned more accurately, than the “idle-up” system used with earlier mc radio control systems. Ensure that the throttle limiter is closed before you start the glow motor, i. e. the throttle can only be adjusted within its idle range using the idle trim. Be sure to read the safety notes on page 122 which refer to this. If the idle is set too high when you switch the transmitter on, you will see and hear a clear warning! 0:00 STARLET stop throttle #02 0:00 too mal » high ! HoTT 5.2 5.5V 2:22h M The following three diagrams show typical 3-point throttle curves for different flight phases, such as hover, aerobatics and 3-D flying. Typical throttle curves for different flight phases: +100% Output Output +100% Output +100% 0% 0% 0% 1 2 3 4 Control travel Hover 5 1 2 3 4 Control travel Aerobatics 5 1 2 3 4 Control travel 3D 5 Notes on using the “Throttle limit” function: We strongly recommend that you make • use of the throttle limit function (“Transmitter control settings” menu, page 99). When you use this function the throttle servo is completely disconnected from the throttle / collective pitch stick when the proportional throttle limit control is at its left-hand end-point; the motor runs at idle and only responds to the Ch 1 trim. This feature enables you to start the motor from within any flight phase. Once the motor is running, turn the throttle limiter slowly to the opposite end-point, so that full control of the throttle servo is returned to the throttle / collective pitch stick. It is important that the throttle limiter should not restrict the throttle servo at its upper endpoint; you can avoid this by setting the control travel to +125% in the “Lim” line of the “Transmitter control settings” menu. • Since electric motors by their nature require no idle setting, the only important point when setting up an electric-powered model helicopter is that the adjustment range of the throttle limiter should be set significantly higher and lower than the adjustment range of the speed controller, which is usually from -100% to +100%. It may therefore be necessary to set the “Travel” value of the throttle limiter to an appropriate point in the “Lim” line of the “Transmitter control settings” menu. However, the throttle curve itself has to be finetuned with the helicopter in flight, just like a glow-powered machine. • Releasing the full throttle range, and imposing the throttle limiter again, trips the switching threshold of the control switch “C3” (i. e. in either direction); this switch can be used for automatically starting and stopping the stopwatch to record the flight time, or some similar purpose; see page 59. When you select auto-rotation, the mixer automatically switches the value to a variable pre-set value; see the section starting on page 124. Helicopter with speed GOVERNOR (REGULATOR) In contrast to speed controllers, which simply adjust power output in the same way as a carburettor, speed governors maintain a constant rotational speed in the system which they regulate; they accomplish this by adjusting the power output as required. In the case of a glow-powered helicopter the governor automatically controls the throttle servo; in an electric-powered machine the governor does the same with the speed controller. For this reason speed governors do not require a classic throttle curve; they just need a pre-set rotational speed. Once this is set, the system rotational speed does not alter unless the system calls for more power from the motor than is available. In most cases a speed governor is connected to receiver output 8; see the receiver socket sequence on page 65. If this socket is already in use, then the throttle limiter function is not used, since this only affects output 6 - which is now not occupied - via the “Ch 1 throttle” mixer. However, if you wish to be able to exploit the convenience and safety features of the throttle limiter, the speed governor should be connected to receiver output 6 - in contrast to the usual socket sequence - and the throttle curve adjusted so that it can simply assume the role of the “usual” transmitter control. In this case the “throttle curve” only determines the nominal rotational speed of the speed controller, and this nominal value is required to remain constant over the full range of collective pitch; for this reason a horizontal line should be set in the “Ch 1 throttle” mixer, i. e. every (collective pitch) input value results in the same (“throttle”) output value. The “height” of the line in the graph determines the nominal system rotational speed. Initially, then, reference point “3” should be erased, and reference points “1” (input = 0%) and “5” (input = +100%) set to the same value; for example: ch1 input output point 1 normal thro 0% +65% +65% The value to be set varies according to the speed governor you are using, and also to the desired nominal rotational speed; you may wish to vary it, of course, in the various flight phases. When you select auto-rotation, the mixer automatically switches the value to a variable pre-set value; see the section starting on page 124. Program description: helicopter mixers – model helicopter 117 Ch1 tail rotor Ch1 input output point 3 normal (static torque compensation) CH1 tail input output point 3 normal 0% 0% 0% The default setting is a torque compensation curve with a uniform linear mixer input of 0%, as is required for a gyro sensor operating in “heading lock mode”; see illustration above. attention: It is absolutely essential to read and observe the set-up instructions supplied with your gyro before entering any settings at this point, as a mistake here could render your helicopter uncontrollable. If you use your gyro sensor in “normal” operating mode, or if the gyro only offers “normal mode”, then you should set up the mixer as follows: The tail rotor control curve can be defined using up to five points, in a similar way to the collective pitch curve (see previous page). You can therefore modify the mixer at any time when required, and enter symmetrical or asymmetrical mixer inputs both above and below the hover point. However, please ensure at the outset that you have entered the correct direction of main rotor rotation in the “Base settings” menu. tail 0% 0% 0% Starting from -30% at Point 1 and +30% at Point 5, this mixer should be set up in such a way that the helicopter does not rotate around the vertical (yaw) axis (i. e. does not deviate from the hover heading) during a long vertical climb or descent, due to the change in torque of the main rotor. At the hover the yaw trim should be set using the (digital) tail rotor trim lever only. For a reliable torque compensation setting it is essential that the collective pitch and throttle curves have been set up correctly, i. e. that main rotor speed remains constant over the full range of collective pitch. When you select auto-rotation, this mixer is automatically switched off. Gyro (adjusting gyro gain) Most modern gyro systems feature proportional, infinitely variable adjustment of gyro gain as well as a means of selecting either of two different methods of working from the transmitter. If the gyro you wish to use features at least one of these options, then it offers you the possibility of pre-setting both “normal” gyro effect and - if available - “heading lock mode”, and also of flying normal, slow circuits with maximum gyro stabilisation, but reducing the gyro effect for high-speed circuits and aerobatics. This is generally similar to the transmitter control centre adjustment or 118 Program description: helicopter mixers – model helicopter offset adjustment provided by other radio control systems. We recommend that you set up switchable flight phases for this, and set different gain settings for each phase in the “Gyro” line; values between -125% and +125% are possible. ptch ch1 thro tail ch1 gyro inp8 normal 0% 0% Based on the offset values determined for each flight phase, gyro gain can be varied proportionally by means of a transmitter control assigned in the “Gyro” line of the “Transmitter control settings” menu (see page 98). This could be CTRL 8, which would provide infinitely variable gyro gain control: • At the centre position of this transmitter control the gyro effect always corresponds to the settings selected here. • If you turn the rotary proportional control CTRL 8, which we are using in our example, in the direction of full travel (away from centre), the gyro gain increases accordingly … • … and diminishes again if you turn it in the direction of the opposite end-point. attention: It is absolutely essential to read and observe the set-up instructions supplied with your gyro before entering any settings at this point, as a mistake here could render your helicopter uncontrollable. Adjusting the gyro sensor If you wish to set up a gyro to achieve maximum possible stabilisation of the helicopter around the vertical axis, please note the following points: • The mechanical control system should be as free-moving and accurate (slop-free) as possible. • There should be no “spring” or “give” in the tail rotor linkage. • You must use a powerful and - above all - fast servo for the tail rotor. When the gyro sensor detects a deviation in yaw, the faster it adjusts the thrust of the tail rotor, the further the gyro gain adjuster can be advanced without the tail of the model starting to oscillate, and the better the machine’s stability around the vertical axis. If the corrective system is not fast enough, there is a danger that the model’s tail will start to oscillate even at low gyro gain settings, and you then have to reduce gyro gain further using the rotary proportional control CTRL 8, as used in our example, to adjust the pre-set “Gyro” value to eliminate the oscillation. If the model is flying forward at high speed, or hovering in a powerful headwind, the net result of the stabilising effect of the vertical fin combined with the gyro’s stabilising effect may be an over-reaction which manifests itself as tail oscillation. In order to obtain optimum stabilisation from a gyro in all flight situations, you should make use of the facility to adjust gyro gain from the transmitter. inp8 (Input 8) ptch Ch1 thro tail Ch1 gyro inp8 normal 0% 0% The adjustment facilities in this line of the menu are only relevant if your model helicopter is fitted with a speed governor (regulator) which maintains a constant system rotational speed, and you wish to control it using the “classic” method. The settings should then be entered in accordance with the instructions supplied with the governor you intend to use. However, it is more convenient - and also safer - to adopt the method described on the preceding double-page, using the “Ch1 thro” mixer. Swashplate limiter Ch1 thro Ch1 tail gyro inp8 swash lim. normal 0% 0% off This function acts like a circular mechanical gate acting upon the swashplate control stick, restricting its range of travel - which is usually rectangular - to a circular pattern. This is designed to solve the following problem: if the helicopter is set up in such a way that the roll and pitch-axis travels extend to the maximum possible in mechanical terms, e. g. for 3-D helicopter flying, then at simultaneous full travel of roll and pitch-axis the actual movement of the swashplate is higher (theoretically 141%). In this situation the mechanical swashplate system may strike its end-stops, and in the extreme case the ball-links may even be forced off the linkage balls. In the mx-16 HoTT transmitter a software function has the effect of limiting the overall swashplate travel, i. e. the tilt angle of the swashplate between 100% (the travel is limited to the value which can be reached by one function - roll or pitch-axis - alone) and 149% (no limiting in force) is switched “off” (the function is completely disabled). Swashplate limiting can also be adjusted to suit individual models and flight phases. This software solution is far more flexible than a physical limiter disc attached to the stick unit, and such a disc can only be used in any case if the roll and pitch-axis functions are controlled by one of the two primary sticks. The sketch alongside shows the effect of the limiter at a setting of 100%: the dotted area of travel is cut off, and appears as a dead zone. If this function is used, you should leave “Dual Rate” at 100%, and you should not set Dual Rate values greater than 100%, otherwise travel will be limited on the roll or pitch-axis individually if the swashplate limiter is set to 100%. Adjustment range: 100 ... 149% and “off”. Program description: helicopter mixers – model helicopter 119 Adjusting the throttle and collective pitch curves A practical procedure Although the throttle and collective pitch control systems are based on separate servos, they are always operated in parallel by the throttle / collective pitch stick (except when auto-rotation is invoked). The Helicopter program automatically couples the functions in the required way. In the mx-16 HoTT program the trim lever of control function 1 only affects the throttle servo, i. e. it acts as idle trim (see “Digital trims” on page 60). The process of adjusting “throttle” and collective pitch correctly, i. e. setting the motor’s power curve to match the collective pitch setting of the main rotor blades, is the most important aspect of setting up any model helicopter. The program of the mx-16 HoTT provides independent adjustment facilities for the throttle, collective pitch and torque compensation curves. These curves can be defined using a maximum of five reference points. To define the control curves all you have to do is set individual values for these five points in order to determine each control curve. However, before you set up the throttle / collective pitch function it is important to adjust the mechanical linkages to all the servos accurately, in accordance with the setup notes provided by the helicopter manufacturer. of the throttle and collective pitch curve(s) must still be carried out as described here, in a similar way to a glow-powered helicopter. Note: Different throttle curves are programmed for each flight phase, so that you can use the optimum set-up both for hovering and aerobatics: • Low system rotational speed with smooth, gentle control response and low noise at the hover. • Higher speed for aerobatics with motor power settings close to maximum. In this case the throttle curve also has to be adjusted in the hover range. The hover point should always be set to the centre position of the throttle / collective pitch stick. Idle setting and throttle curve Note: Since electric power systems by their nature require no idle setting, it is not necessary to adjust the idle value. However, the matching The idle setting is adjusted solely using the trim lever of the Ch 1 function, with the throttle limiter closed, as described in detail on pages 99 to 101. Reference point 1 of the throttle curve defines the throttle setting when the helicopter is in a descent, but without affecting the hover setting. This is a case where you can exploit flight phase programming to use different throttle curves. An increased system rotational speed below the hover point proves to be useful in certain circumstances; for example, for fast, steep landing approaches with greatly reduced collective pitch, and for aerobatics. The diagram shows a curve with a slightly altered throttle setting below the hover point at the centre of stick travel. OUTPUT +100% 0% 1 2 3 4 Control travel The basic set-up procedure Although the mx-16 HoTT transmitter provides a 120 Program description: helicopter mixers – model helicopter 5 broad range of adjustment for the collective pitch and throttle curves, it is essential that you first adjust all the mechanical linkages in the model according to the information supplied by the helicopter manufacturer, i. e. all the system linkages should already be approximately correct in mechanical terms. If you are not sure of how to do this, any experienced helicopter pilot will be glad to help you with the basic set-up. The throttle linkage must be adjusted in such a way that the throttle is just at the “fully open” position at the full-throttle setting, or the speed controller of an electric helicopter is set to full-power. When the throttle limiter is at the idle position, the Ch 1 trim lever should just be able to close the throttle completely, without the servo striking its mechanical end-stop (quick throttle adjustment using the “digital trim”: see page 60). With an electric helicopter the motor should stop reliably when the throttle limiter is closed. Take your time, and carry out these adjustments very carefully by adjusting the mechanical linkage and / or changing the linkage point on the servo output arm or the throttle lever. Only when you are confident that all is well should you think about fine-tuning the throttle servo using the transmitter’s electronic facilities. warning: Read all you can about motors and helicopters, so that you are aware of the inherent dangers and the cautionary measures required before you attempt to start the motor for the first time! With the basic set-up completed, it should be possible to start the motor in accordance with the operating instructions supplied with it, and adjust the idle setting using the trim lever of the throttle / collective pitch stick. The Hover point 0% 1 3 4 Control travel 5 +100% OUTPUT b) Rotational speed too high Remedy: on the “Collective pitch” graphic page, increase the blade pitch angle for collective pitch by increasing the value at Point 3. 2 Hover point 0% 1 2 3 4 Control travel 5 2. The model lifts off below the centre point. +100% OUTPUT a) Rotational speed too high Remedy: on the “Ch 1 throttle” graphic page, reduce the throttle opening by reducing the value at Point 3. Hover point 0% 1 2 3 4 Control travel Hover point 0% 1 2 3 4 Control travel 5 Important: It is important to persevere with this adjustment procedure until the model hovers at the correct rotational speed at the centre point of the throttle / collective pitch stick. All the other model settings depend upon the correct setting of these parameters! +100% OUTPUT a) Rotational speed too low Remedy: on the “Ch 1 throttle” graphic page, increase the value at Point 3. +100% 5 The standard set-up The remainder of the standard adjustment procedure is completed on the basis of the fundamental set-up which you have just carried out, i. e. we now assume that the model hovers in normal flight at the centre point of the throttle / collective pitch stick, with the correct rotor speed. This means that your model helicopter is capable of hovering and also flying circuits in all phases whilst maintaining a constant system rotational speed. The climb setting The combination of throttle hover setting, collective pitch setting for the hover and the maximum collective pitch setting (Point 5) now provides you with a simple method of achieving constant system rotational speed from the hover right to maximum climb. Start by placing the model in an extended vertical climb, holding the collective pitch stick at its end-point: motor speed should not alter compared with the hover setting. If motor speed falls off in the climb, when the throttle is already fully open and no further power increase is possible (this assumes that the motor is correctly adjusted), then you should reduce the maximum blade pitch angle at full deflection of the collective pitch stick, i. e. the value at Point 5. Conversely, if motor speed rises during the vertical climb, you should increase the pitch angle. This is done on the “Collective pitch” graphic page by moving the vertical line to Point 5 using the collective pitch stick, and changing its value accordingly using the arrow buttons of the right-hand touch-button. +100% OUTPUT 1. The model does not lift off until the collective pitch stick is above the centre point. b) Rotational speed too low Remedy: on the “Collective pitch” graphic page, reduce the blade pitch angle by reducing the value at Point 3. OUTPUT idle position which you set is indicated in the transmitter’s basic screen display by a horizontal bar in the display of the Ch 1 trim lever’s position. Refer to page 60 of this manual for a full explanation of the digital trims. Around the mid-point of the collective pitch stick the model should lift off the ground and hover at approximately the rotational speed you wish to use. If this is not the case, correct the settings as follows: This diagram shows the changes to the collective pitch maximum value only. Hover point 100% 1 2 3 4 Control travel 5 Now bring the model back to the hover, which again should coincide with the mid-point of the Ch 1 stick. If you find that the collective pitch stick now has to be moved from the mid-point in the direction of “higher”, then you should correct this deviation by slightly increasing the collective pitch angle at the hover - i. e. Point 3 - until the model again hovers at the stick centre point. Conversely, if the model hovers below the mid-point, correct this by reducing the pitch angle once more. You may find that it is also necessary to correct the throttle opening at the hover point (Point 3) in the “Ch 1 throttle” menu. Program description: helicopter mixers – model helicopter 121 Important final notes +100% OUTPUT warning: Before you start the motor, check carefully This diagram only shows the change in the hover point, i. e. colthat the throttle limiter is completely closed, lective pitch minimum and maxiso that the throttle can be controlled by the mum have been left at -100% and Ch 1 trim lever alone. If the throttle is too far open when Control travel +100% respectively. you switch the transmitter on, you will see and hear a Continue adjusting these settings until you really do warning. If you ignore this and start the motor with the achieve constant main rotor speed over the full control throttle too far advanced, there is a danger that the range between hover and climb. motor will immediately run up to speed after starting, and the centrifugal clutch will at once engage. Descent setting For this reason you should: The descent adjustment should now be carried out always grasp the rotor head firmly from a safe height by fully reducing collective pitch to when starting the motor. place the model in a descent from forward flight; adjust However, if you accidentally start the motor with the the collective pitch minimum value (Point 1) so that the throttle open, the rule is this: model descends at an angle of 60 … 80°. This is done Don’t panic! on the “Collective pitch” graphic page by moving the vertical line to Point 1 using the collective pitch stick, and Hang on to the rotor head regardless! adjusting the value accordingly using the arrow buttons Don’t let go! of the right-hand touch-key. Immediately reduce the throttle limiter, even though there may be a risk of damaging the helicopter’s drive train, because: Hover it is vital that YOU ensure point that the helicopter cannot possibly move off by itself in an uncontrolled manner. As an example, this diagram The cost of repairing a clutch, a gearbox or even the shows the changes in the collecControl travel tive pitch minimum value only. motor itself is negligible compared with the damage which a model helicopter can cause if its spinning rotor Once the model descends reliably as described, adjust blades are allowed to wreak havoc. the value for “Throttle minimum” - the value of Point 1 Make sure that nobody else is standing on the graph of the “Ch 1 throttle” mixer - so that in the primary hazard zone around the helicopter. system rotational speed neither increases nor declines. This completes the set-up procedure for throttle and You must never switch abruptly from idle to the flight setcollective pitch. ting by suddenly increasing system rotational speed, as 122 Program description: helicopter mixers – model helicopter 100% 1 2 3 4 5 2 3 4 5 OUTPUT +100% 100% 1 this would cause the rotor to accelerate quickly, resulting in premature wear of the clutch and gear train. The main rotor blades are generally free to swivel, and they may be unable to keep pace with such swift acceleration, in which case they might respond by swinging far out of their normal position, perhaps resulting in a boom strike. Once the motor is running, you should s l o w l y increase system rotational speed using the throttle limiter. For your notes 123 Helicopter mixers Auto-rotation settings Auto-rotation allows full-size and model helicopters to land safely in a crisis, i. e. if the power plant should fail. It can also be used if the tail rotor should fail, in which case cutting the motor and carrying out an auto-rotation landing is the only possible way of avoiding a highspeed uncontrollable rotation around the vertical axis, invariably terminating in a catastrophic crash. And that is the reason why switching INTO auto-rotation occurs with zero delay. When you switch to the auto-rotation phase the helicopter mixers change as shown in this screen shot: ptch thro tail gyro inp8 Autorot –90% 0% 0% 0% During an auto-rotation descent the main rotor is not driven by the motor; it is kept spinning only by the airflow through the rotor disc caused by the speed of the descent. The rotational energy stored in the still spinning rotor can be consumed to allow the machine to flare out, but this can only be done once. For this reason “autos” are only likely to be successful if the pilot has plenty of experience in handling model helicopters, and has also set up the appropriate functions with great care. Once you have sufficient experience you should practise auto-rotation landings at regular intervals, not only so that you can demonstrate your all-round flying skill by flying the manoeuvre in competitions, but also so that you are in a position to land the helicopter undamaged from a great height if the motor should fail. For this purpose the program provides a range of adjustment fa- cilities which are designed to help you fly your helicopter in its unpowered state. Please note that the auto-rotation setting takes the form of a complete fourth flight phase, for which all the adjustment facilities are available which can be varied separately for all flight phases, especially trims, collective pitch curve settings etc. ptch (Collective pitch curve (Ch1 pitch)) In powered flight the maximum blade pitch angle is limited by the motor power which is available; however, in auto-rotation the angle is only limited by the point at which the airflow over the main rotor blades breaks away. Nevertheless, to provide sufficient upthrust even when rotational speed is falling off, it is necessary to set a greater maximum collective pitch value. Touch the central SET button of the right-hand touch-key to select the graph page of “Collective pitch”, and then move the vertical line to Point 5 using the transmitter stick. Start by setting a value which is about 10 to 20% higher than your normal collective pitch maximum. Do NOT set a much higher value compared with normal flight initially, because collective pitch control will then differ too greatly from the machine’s usual response after you have thrown the switch. The danger is that you will over-control the helicopter, and it may balloon up again during the flare following the auto-rotation descent. If this happens, the rotational speed of the main rotor will quickly decline to the point where it collapses, and the helicopter ends up crashing to the ground from a considerable height. Later, after a few trial autos, you may wish to adjust the value again. Under certain circumstances the collective pitch minimum setting may also differ from the normal flight setting; this depends on your piloting style for normal flying. In any case you must set a sufficiently generous collec- 124 Program description: helicopter mixers / auto-rotation settings tive pitch minimum value at Point 1 to ensure that your model can be brought from forward flight at moderate speed into a descent of around 60 ... 70° when collective pitch is reduced to minimum. Most helicopter pilots already use such a setting for normal flying, and if this applies to you, you can simply adopt the same value. If you normally allow your model to “fall” at a shallower angle, increase the value for “Point 1”, and vice versa. Approach angle in strong wind in moderate wind no wind Approach angle under varying wind conditions. 75° 60° 45° For auto-rotation the collective pitch stick itself may not be positioned right at the bottom of its travel; typically it will be between the hover position and the bottom endpoint, giving the pilot scope for correction if necessary, i. e. the chance to adjust the model’s pitch inclination using the pitch-axis control. You can shorten the approach by pulling back slightly on the pitch-axis stick and gently reducing collective pitch, or alternatively extend the approach by pushing forward on the pitch-axis stick and gently increasing collective pitch. Throttle (throttle curve) In a competition the pilot is expected to cut the motor completely, but for practice purposes this is certainly inconvenient, as after every practice “auto” landing you would have to start the motor again. For practice, then, you should set the value in this line so that the motor runs at a reliable idle during auto-rotation, but without the clutch engaging, so that you can open the throttle immediately to recover from an emergency; for an electric helicopter the motor should be reliably “off”. Tail rotor (static torque compensation) For normal flying the tail rotor is set up in such a way that it compensates for motor torque when the helicopter is hovering. This means that it already generates a certain amount of thrust even in its neutral position. The level of thrust is then varied by the tail rotor control system, and also by the various mixers which provide all manner of torque compensation, while the tail rotor trim is also used to compensate for varying weather conditions, fluctuations in system rotational speed and other influences. However, in an auto-rotation descent the main rotor spins according to the windmill principle, i. e. it is not driven by the motor, and therefore there is no torque effect for which compensation is required, i. e. which the tail rotor would have to correct. For this reason all the appropriate mixers are automatically switched off in auto-rotation mode. However, the basic tail rotor setting therefore has to be different for auto-rotation, as the compensatory thrust described above is no longer required: Stop the motor and place the helicopter horizontal on the ground. With the transmitter and receiving system switched on, select the “Auto-rotation” flight phase. Fold both tail rotor blades down and change the blade pitch angle to zero degrees in the “Tail rotor” line. Viewed from the rear, the tail rotor blades should now lie parallel to each other. Depending on the friction and running resistance of the gearbox, you may find that the fuselage still yaws slightly in an auto-rotation descent. If necessary, the relatively slight torque which causes this effect must then be corrected by adjusting the tail rotor blade pitch angle. This value will always be a small figure between zero degrees and a pitch angle opposed to the direction of tail rotor pitch required for normal flight. Program description: helicopter mixers / auto-rotation settings 125 General notes regarding freely programmable mixers The two menus “Fixed-wing mixers” and “Helicopter mixers”, as described on the preceding pages, contain a wide range of ready-programmed coupling functions. The basic meaning of mixers has already been explained on page 108, together with the principle on which they work. In the following section you will find information relating to “free mixers”: In addition to the pre-programmed mixers mentioned above, the mx-16 HoTT offers three freely programmable linear mixers which can be used in every model memory; their inputs and outputs can be selected to suit your exact requirements. Any control function (1 to 8), or what is known as a “switch channel” (see below), can be assigned as the input signal of a “free mixer”. The signal present at the control channel, and passed to the mixer input, is determined by the transmitter control and any control characteristics as defined, for example, in the “D/R Expo” and “Transmitter control settings” menus. The mixer output acts upon a freely selectable control channel (1 to max. 8 - depending on receiver type). Before the signal is passed to the associated servo, the only influences which can act upon it are those defined in the “Servo settings” menu, i. e. the servo reverse, centre and travel functions. One control function can be set up to affect several mixer inputs simultaneously, if, for example, you wish to arrange several mixers to operate in parallel. Conversely it is possible for several mixer outputs to affect one and the same control channel. The following description of the free mixers includes examples of such arrangements. In software terms the default setting for any “free mixer” is that it is constantly switched on, but it is also possible to assign an optional ON / OFF switch to it. However, since there are so many functions to which switches can potentially be assigned, you should take care not to assign dual functions to particular switches accidentally. The two important mixer parameters are as follows: • … the mixer ratio, which defines the extent to which the input signal acts on the output of the control channel which is programmed as the mixer output. • … the neutral point, which is also termed the “offset”. The offset is that point on the travel of a transmitter control (stick, rotary proportional knob CTRL 6 … 8 and SW 1 … 9) at which the mixer has no influence on the control channel connected to its output. Normally this is the centre point of the transmitter control, but the offset can be placed at any point on the control’s travel. Switch channel “S” as mixer input In some cases a constant control signal is all that is required as the mixer output; a typical application would be for slight up-elevator trim when an aero-tow coupling is closed - completely independently of the normal elevator trim. If you then assign a switch, you can switch to and fro between the two mixer end-points, and adjust the supplementary elevator trim deflection by altering the mixer ratio. To identify this special arrangement, this mixer input control function is designated “S” for “switch channel” in the software. If you do not want the “target channel” to be affected by the “normal” transmitter control, the control can be de-coupled from the function input of the associated control channel by entering “free” in the “Transmitter control settings” menu; see pages 94 126 General notes regarding freely programmable mixers and 96. The following menu description again includes an example which makes this function clear. Now use the arrow buttons of the left or right-hand touch-key to leaf through to the “Free mixers” menu point of the multi-function menu: mod. mem. ser vo set. D/R expo wing mixer ser vo disp fail-safe base sett. contr set. phase trim free mixer basic sett telemetr y mod. mem. ser vo set. D/R expo free mixer ser vo disp fail-safe base sett. contr set. heli mixer swashp.mix basic sett telemetr y Touch the central SET button of the right-hand touch-key to open this menu point. Free mixers Linear mixers Regardless of the selected model type, three linear mixers are available for each of the twenty model memories, with the additional possibility of setting up non-linear characteristic curves. In this first section we will concentrate on the programming procedure for the first screen page. We will then move on to the method of programming mixer ratios, as found on the second screen page of this menu. The basic programming procedure 1. Use the arrow buttons of the left or right-hand touch-key to select the desired mixer. 2. Briefly press the central SET button of the righthand touch-key: the input field in the column marked “fro(m)” at the bottom edge of the screen is now highlighted (black background). 3. Use the arrow buttons of the right-hand touch-key to define the mixer input “fro(m)”. 4. Touch the central SET button of the right-hand touchkey; switch to the “to” column using the button of the left or right-hand touch-key, then touch the central SET button of the right-hand touch-key once more: the input field “to” is now highlighted. 5. Use the arrow buttons of the right-hand touch-key to define the mixer input “to”. 6. Touch the central SET button of the right-hand touchkey, and (optionally) use the button of the left or right-hand touch-key to move to the column marked “Type” at the bottom edge of the screen; you can now include the Ch1 … Ch 4 trim lever for the mixer input signal (“Tr” for trim) … 7. … and / or use the arrow button of the left or righthand touch-key to move to the column marked with at the bottom edge of the the switch symbol screen, touch the central SET button of the righthand touch-key again, and assign a switch if desired, as described on page 59. 8. Use the arrow button of the left or right-hand touch-key to move to the => column, then touch the central SET button of the right-hand touch-key. 9. Define the mixer ratios on the second screen page. 10.Press the central ESC button of the left-hand touchkey to switch back to the first page. “fro(m)” After briefly pressing the central SET button of the right-hand touch-key, select the highlighted field of the selected mixer line using the arrow buttons of the same touch-key, and select one of the control functions 1 … 8 or S. In the interests of clarity, the control functions 1 … 4 are abbreviated as follows when dealing with the fixed-wing mixers: c1 Throttle / airbrake stick ar Aileron stick el Elevator stick rd Rudder stick Note: Don’t forget to assign transmitter controls to the selected control functions 5 … 8 for a fixed-wing model, or 5, 7 and 8 for a model helicopter, in the “Transmitter control settings” menu. “S” for switch channel The letter “S” (switch channel) in the “from” column has the effect of passing a constant input signal to the mixer input, e. g. in order to apply a little extra up-elevator trim when an aero-tow coupling is closed, as mentioned earlier. Once you have assigned a control function or the letter “S” in the “from” column, an additional … “to” … appears at the bottom edge of the screen. In the input field of this column you can define the control channel as the mixer destination, i. e. the mixer output. At the same time additional fields appear at the bottom line of the screen: M1 M2 M3 6 c1 S el el el fro to 1 c1 2 … and in the Heli program: 1 Throttle / collective pitch stick 2 Roll stick 3 Pitch-axis stick 4 Tail rotor stick typ In this example three mixers have already been defined. The second mixer (“Brake el”) is already familiar to us from the “Fixed-wing mixers” menu. As a general rule you should always start by using these pre-programmed mixers if possible. However, if you need asymmetrical mixer ratios on both sides of centre, or have to offset the mixer neutral point, Program description: Free mixers 127 then you should set or leave the pre-set mixers at “0”, and program one of the free mixers instead. Erasing mixers If you need to erase a mixer that you have already defined, use the arrow buttons of the left or righthand touch-key to select its line, then use the arrow buttons to move to the “from” column before touching the central SET button of the right-hand touch-key. The field in the “from” column of the mixer to be erased is now highlighted: simultaneously touch the two arrow buttons or of the right-hand touch-key (CLEAR). Mixer switches In our example above, a physical switch “2” and the control switch “C1” have been assigned to the two linear mixers 1 and 2, and switch “3” to mixer 3. The switch symbol to the right of the switch number shows the current status of that switch. Any mixer to which no switch has been assigned in the column marked by the switch symbol at the bottom of the screen is permanently switched on. “Type” (including the trim) If you wish, and if you are using one of the primary control functions 1 … 4, you can set the trim value of the digital trim lever for the associated stick to affect the mixer input. This is accomplished by touching the central SET button of the right-hand touch-key, then using its arrow buttons to select “Tr” in the highlighted field. Note: The effect of the Ch 1 trim lever on the mixer output varies according to the function which has been assigned to it in the “Base settings” menu (pages 74) in the “Motor at Ch 1” column for fixed-wing models. Additional special features of free mixers If you set up a mixer whose input is the same as its output, e. g. “c1 c1”, exotic results can be obtained in conjunction with the option of switching a free mixer on and off. You will find one typical example of this on pages 172 … 174. Before we come to setting mixer ratios, we have to consider what happens if a mixer input is allowed to act on the pre-set coupling of aileron servos, flap servos or collective pitch servos: • Fixed-wing models: Depending on the number of wing servos set in the “Aileron / Flap” line of the “Base settings” menu, receiver outputs 2 and 5 are reserved for the aileron servos, and outputs 6 and 7 for the two flap servos, as special mixers are assigned to these functions. If mixer outputs are programmed to this type of coupled function, you have to consider their effect on the associated pair of wing flaps, according to the “receiving” control channel: Mixer Wirkung NN * 2 Servo pair 2 + 5 responds with aileron function NN * 5 Servo pair 2 + 5 responds with flap function * NN = Nomen Nominandum (name to be stated) 128 Program description: Free mixers NN * 6 Servo pair 6 + 7 responds with flap function NN * 7 Servo pair 6 + 7 responds with aileron function • Model helicopters: Depending on the type of helicopter, up to four servos may be employed for collective pitch control; these will be connected to receiver outputs 1, 2, 3 and 5. The transmitter software links them together to provide the functions collective pitch, roll and pitch-axis. It is not advisable to mix one of the transmitter controls into these occupied channels using the free mixers available outside the “Heli mixers” menu, as you may inadvertently generate some extremely complex and unwanted interactions. “Collective pitch trim via a separate transmitter control” counts as one of the few exceptions to this rule; see example 2 at page 131. Important note: When dealing with the interaction of multiple mixers on one control channel, it is essential to remember that the mixed travels of the individual mixers are cumulative when multiple stick commands are made simultaneously, and this brings a danger that the servo concerned may strike its mechanical end-stops. If you encounter this problem, simply reduce the servo travel in the “Servo settings” menu, and / or reduce the mixer values. However, if you do not wish to reduce the travels in this way, because this method would unnecessarily reduce the control travels you normally use, then you may prefer an alternative method of preventing the servos striking their end-stops: set a suitable travel limit in the “LIMIT -/+” lines of the “RX SERVO” display page of the “Telemetry” menu. Mixer ratios and mixer neutral point Now that we have explained the wide-ranging nature of the mixer functions, we can move on to the method of programming linear and non-linear mixer curves. For each of the three available mixers the mixer curves are programmed on a second page of the screen display. Use the arrow buttons of the left or right-hand touch-key to select the desired mixer line, use its arrow buttons to move to the right-hand column (=>), then touch the central SET button of the right-hand touch-key to switch to the graphic page. Setting up linear mixer values In the next section we will describe a typical practical application, by defining a linear mixer curve intended to solve the following problem: We have a powered model with two flap servos connected to receiver outputs 6 and 7, which were programmed as “… 2FL” in the “Ail / Flap” line of the “Base settings” menu. These control surfaces are to be employed as landing flaps, i. e. when the associated transmitter control is operated, they deflect down only. However, this flap movement requires an elevator trim correction to counteract the resultant pitch trim change. In the “Transmitter control settings” menu, assign the rotary proportional control CTRL 7 to input 6. The control assigned to input 6 now operates the two servos connected to receiver outputs 6 and 7 in the standard way, operating as simple wing flaps. “Transmitter control settings” menu I5 I6 I7 I8 MIX1 6 el off free +100% +100% ctrl 7 +100% +100% +100% +100% free free +100% +100% tr v + Note: If you assign a transmitter control to input 7 and select two flap servos, input 7 is automatically de-coupled to avoid possible flap malfunctions. Start by rotating the transmitter control to its left-hand end-point, and adjust the landing flap linkages so that they are in the neutral position at this setting. If you now turn the knob to the right, the flaps should deflect down; if they move up, you must reverse the direction of servo rotation. Now we turn to the first mixer on the screen on page 127; this is the mixer “6 el”, to which switch 2 has been assigned: M1 M2 M3 typ 6 c1 S el el el fro to 1 C1 2 If this display appears, you have not activated the mixer by operating the assigned external switch - in this case “2”. To correct this, operate the switch: MIX1 tr v offs 6 el 0% 0% 0% SYM ASY The full-height vertical line in the graph represents the current position of the transmitter control assigned to input 6. (In the above graph this is located at the lefthand edge because CTRL 7 is at its left-hand end-point, as already mentioned.) The full-length horizontal line shows the mixer ratio, which currently has the value of zero over the whole of stick travel; this means that the elevator will not “follow” when the flaps are operated. The first step is to define the offset (mixer neutral point). To do this press the arrow button of the left or righthand touch-key and move to the “Offs” line: Touch the central SET button of the right-hand touch-key to open the second screen page: Program description: Free mixers 129 MIX1 tr v offs 6 Notes: • el 0% 0% 0% STO SEL The dotted vertical line indicates the position of the mixer neutral point (“offset”), i. e. that point along the control travel at which the mixer has NO influence on the channel connected to its output. By default this point is set to the centre position. However, in our example the neutral (retracted) position of the flaps is located at the left-hand end-stop of the rotary proportional control, and in this position the elevator must not be affected. We therefore have to shift the mixer neutral point exactly to that position. If you have not already done so, turn the control - in our example this is CTRL 7 - to the left-hand end-stop and touch the central SET button of the right-hand touch-key. The dotted vertical line now moves to this point - the new mixer neutral point - which always retains the “OUTPUT” value of zero in accordance with the mixer definition. As it happens, this setting is difficult to show in a screen shot, so we will change the “offset” value to only -75%. MIX1 tr v offs 6 el 0% 0% –75% STO SEL 130 Program description: Free mixers If you wish, you can move the offset value back to centre or otherwise adjust it as follows: select SEL using the arrow button of the left or right-hand touch-key, followed by briefly pressing the central SET button of the righthand touch-key; … MIX1 tr v offs 6 el 0% 0% –75% STO SEL • … you can now use the arrow buttons of the left or right-hand touch-key to move the offset value. • You can also return the mixer neutral point to centre automatically as follows: select SEL using the arrow button of the left or right-hand touch-key, then simultaneously press the two arrow buttons or of the right-hand touch-key (CLEAR). Symmetrical mixer ratios The next step is to define the mixer values above and below the mixer neutral point, starting from its current position. Use the arrow button of the left or right-hand touch-key to move to the “Travel” line: if necessary, use the arrow buttons of the left or right-hand touchkey to select the SYM field, so that you can set the mixer value symmetrically relative to the offset point you have just programmed. Touch the central SET button of the right-hand touch-key, then set the values in the two highlighted fields within the range -150% to +150% using the arrow buttons of the right-hand touch-key. Remember that the set mixer value always refers to the input signal from the associated transmitter control (control signal)! Setting a negative mixer value reverses the direction of the mixer. Simultaneously pressing the two arrow buttons or of the right-hand touch-key (CLEAR) erases the mixer ratio in the highlighted field. The “optimum” value for our purposes will inevitably need to be established through a flight testing programme. MIX1 6 el tr v +20% +20% offs –75% SYM ASY Since we previously set the mixer neutral point to -75% of control travel, the elevator (“el”) will already exhibit a (slight) “down-elevator effect” at the neutral point of the landing flaps, and this, of course, is not wanted. To correct this we shift the mixer neutral point back to -100% of control travel, as described earlier. MIX1 6 el tr v +20% +20% offs –100% STO SEL If you were now to reset the offset from -75% to, say, 0% control travel, by selecting the SEL field using the arrow buttons of the left or right-hand touch-key, and then briefly pressing the two arrow buttons or of the right-hand touch-key (CLEAR) simultaneously, the screen would look like this: MIX1 6 el tr v +20% +20% offs 0% STO SEL Asymmetrical mixer ratios For many applications it is necessary to set up different mixer values on either side of the mixer neutral point. Start by resetting the offset of the mixer used in our example (“6 el”) to 0%, as shown in the picture above. Now use the arrow button of the left or righthand touch-key to select the ASY field, and then touch the central SET button of the right-hand touch-key. If you now turn the rotary proportional control CTRL 7 assigned in our example to input 6 - in the appropriate direction, the mixer ratio for each direction of control can be set separately, i. e. to left and right of the selected offset point using the arrow buttons of the right-hand touch-key: MIX1 6 el tr v +55% +20% offs 0% Note: If you are setting up a switch channel mixer of the “S NN *” type, you must operate the assigned switch to achieve this effect. The vertical line then jumps between the left and right sides. Examples: 1. The switch SW 2 has already been assigned to control channel 8 in the “Transmitter control settings” menu, in order to open and close the aero-tow release. +100% I5 free I6 ctrl 7 +100% +100% I7 free +100% 2 I8 +100% +100% +100% +100% tr v + In the meantime you have carried out a few aero-tow flights, which showed that you always needed to hold in slight up-elevator during the tow. You now wish to set the elevator servo (connected to receiver output 3) to slight “up” trim when the tow release is closed. In the screen display familiar from page 127 we have set up the third linear mixer to accomplish this, using the switch channel “S” as the mixer input. Now move the selected switch to the OFF position, and move to the … M1 M2 M3 6 c1 S el el el fro to typ 1 C1 2 … mixer set-up page. Use the arrow button of the left or right-hand touch-key to select the “Offs” line, then touch the central SET button of the right-hand touch-key. According to the travel setting selected in the “Transmitter control settings” menu and the switch position, the offset value now jumps to +X% or -X%, e. g.: MIX3 tr v offs S el 0% 0% +100% STO SET Use the arrow button of the left or right-hand touch-key to move to the “Travel” line, then touch the central SET button of the right-hand touch-key. After moving the selected switch to the mixer ON position, set the required mixer ratio in the now highlighted value fields using the arrow buttons of the right-hand touch-key. SYM ASY * NN = Nomen Nominandum (name to be stated) Program description: Free mixers 131 Swashplate mixers Collective pitch, roll and pitch-axis mixers MIX3 S el SP – MIXER ptch roll nick tr v +10% +10% offs +100% +61% +61% +61% Note: SYM ASY 2. The following example applies to model helicopters: In the Helicopter program you may wish to assign one of the rotary proportional controls (CTRL 6 … 8) to the collective pitch trim function. This is the procedure: in the “Transmitter control settings” menu assign one of these two transmitter controls to input “E8”. Now simply define a free mixer “8 1” with a symmetrical mixer ratio of, say, 25%. Due to the internal coupling, this transmitter control now acts equally on all the collective pitch servos you are using, without affecting the throttle servo. MIX1 8 1 tr v +25% +25% offs 0% SYM ASY and pitch-axis) does not follow the transmitter sticks in the proper manner, then the first step is to change the mixer directions (“+” or “-”), before you attempt to correct the directions of servo rotation. In the “Swashplate” line of the “Base settings” menu you have already defined the number of servos which are installed in your helicopter to provide collective pitch control; see page 82. With this information the transmitter software automatically superimposes the functions for roll, pitch-axis and collective pitch as required, i. e. you do not need to define any additional mixers yourself. If you have a model helicopter which only has a single collective pitch servo, the “Swashplate mixer” menu point is - of course - superfluous, since the three swashplate servos for collective pitch, pitch-axis and roll are controlled independently of each other, i. e. no mixers are used. In this case the swashplate mixer menu does not appear in the multi-function list. With all other swashplate linkages employing 2 … 4 collective pitch servos, the mixer ratios and directions are set up by default, as can be seen in the screen shot above. The pre-set value is +61% in each case, but the value can be varied within the range -100% to +100% using the arrow buttons of the right-hand touch-key, after touching the central SET button of the same touch-key. Simultaneously pressing the two arrow buttons or of the right-hand touch-key (CLEAR) resets the mixer input in the highlighted field to the default value of +61%. If the swashplate control system (collective pitch, roll 132 Program description: Swashplate mixers - model helicopter Ensure that the servos do not strike their mechanical end-stops if you change the mixer values. Servo display Use the arrow buttons of the left or right-hand touch-key to leaf through to the “Servo display” menu point of the multi-function menu: mod.mem. ser vo set. D/R expo wing mixer ser vo disp fail-safe base sett. contr set. phase trim free mixer basic sett telemetr y Open the menu point by touching the central SET button of the right-hand touch-key. However, this visual display of the current servo positions can be called up not only by selecting this menu, but also directly by simultaneously pressing the buttons of the left-hand touch-key from the transmitter’s basic display, and also from almost any menu position. Touching the central ESC button of the left-hand touchkey returns you to your starting point again. 1 –100 % 2 0% 3 0% 4 +100 % 5 0% 6 0% 7 0% 8 0% The current position of any servo is displayed in barchart form, which takes into account the transmitter control and servo settings, the Dual-Rate / Expo functions, the interaction of all active mixers etc., within the range -150% to +150% of normal travel. 0% corresponds exactly to the servo centre position. The servo display provides a quick method of checking your settings, without having to switch on the receiving system. However, this does not relieve you of the need to check all your programming steps carefully on the model before operating it for the first time, as this is the only safe method of excluding possible programming errors. The display is based on the following scheme for fixed-wing models: Bar 1 = throttle / brake servo Bar 2 = aileron or left aileron Bar 3 = elevator Bar 4 = rudder Bar 5 = right aileron Bar 6 = (left) flap / free channel Bar 7 = right flap / free channel Bar 8 = free channel / second elevator servo menu. • The number of channels shown in this menu corresponds to the eight control channels available at the mx-16 HoTT transmitter. However, the actual number of channels you can use varies according to the type of receiver in the model, and to the number of servos connected to the receiver; the number may therefore be much smaller. • Use this display during the model programming procedure, so that you can immediately check all the settings at the transmitter. However, this does not release you from the responsibility to check all the programming steps on the model itself before operating it for the first time, in order to exclude the possibility of errors! and for model helicopters: Bar 1 = collective pitch or roll (2) or pitch-axis (2) servo Bar 2 = roll (1) servo Bar 3 = pitch-axis (1) servo Bar 4 = tail rotor servo (gyro) Bar 5 = pitch-axis (2) servo / free channel Bar 6 = throttle servo or speed controller Bar 7 = gyro gain / free channel Bar 8 = speed governor / free channel Notes: • Please note, however, that the servo display always applies to the original servo sequence, i.e. it takes no account of any outputs swapped over in the “Receiver output” menu of the “Basic model settings” menu, nor changes made directly at the receiver using the “Telemetry” Program description: servo position 133 Basic settings Use the arrow buttons of the left or right-hand touch-key to leaf through to the “basic settings” menu point of the multi-function menu: mod. mem. ser vo set. D/R expo wing mixer ser vo disp fail-safe base sett. contr set. phase trim free mixer basic sett telemetr y Touch the central SET button of the right-hand touch-key to open the menu point: Batt type Batt warning Touch Sense Contrast Display light RF Countr y Voice volume Beep volume Ni-MH 4.7V 2 0 unlim Euro 3 3 can use the arrow buttons of the right-hand touch-key to alter the default value. Pressing the central SET button once more concludes the entry process. Battery type Batt type Batt war ning Touch Sense Contrast Display light Ni-MH 4.7v 2 0 unlim In this line you inform the transmitter whether its power is to be drawn from a four-cell NiMH battery or a single-cell LiPo battery. The voltage range offered in the (next) line “Battery warning threshold” will vary according to this setting. Simultaneously pressing the arrow buttons or of the right-hand touch-key (CLEAR) resets the value in the highlighted field to NiMH. Battery warning threshold In this menu you can enter basic settings which are specific to the transmitter. Note: Settings in this menu only need to be entered once, and apply to the whole transmitter. This means that the last valid settings always appear when you call up this menu from another model memory. Use the arrow buttons of the left or right-hand touch-key to select the appropriate line, then touch the central SET button of the right-hand touch-key. The value field is now highlighted (black background), and you 134 Program description: basic settings Batt type Batt war ning Touch Sense Contrast Display light Ni-MH 4.7v 2 0 unlim In this line you can enter any voltage you like … batter y needs charging … within the range 4.5 to 5.5 V (NiMH battery) or 3.4 to 4.2 V (LiPo battery) - according to your choice of battery type - in increments of 0.1 Volt. However, never be tempted to enter too low a value here, to ensure that you always have ample time to land your model safely if a battery warning should be triggered. Simultaneously pressing the arrow buttons or of the right-hand touch-key (CLEAR) resets the value in the highlighted field to 4.7 V or 3.4 V respectively. Touch sensitivity Batt type Batt war ning Touch Sense Contrast Display light Ni-MH 4.7v 2 0 unlim In this line you can select the touch sensitivity of the touch-keys within the range 1 to 10. Simultaneously pressing the arrow buttons or of the right-hand touch-key (CLEAR) resets the value in the highlighted field to “2”. Contrast You can adjust the contrast of the mx-16 HoTT’s integral screen to optimise its legibility in varying weather and temperatures: #01 5.2V 3:33h stop flt 0:00 0:00 M HoTT 5.5V #01 stop flt 0:00 0:00 M HoTT 5.5V 5.2V 3:33h This is accomplished by selecting the “Contrast” line using the arrow buttons of the left or right-hand touch-key: Batt type Batt war ning Touch Sense Contrast Display light Ni-MH 4.7v 2 0 unlim Now briefly touch the central SET button of the righthand touch-key: the value field is now highlighted, and you can adjust the screen contrast within the range +/20 using the arrow buttons of the right-hand touch-key: Simultaneously pressing the arrow buttons or of the right-hand touch-key (CLEAR) resets the value in the highlighted field to “0”. Screen backlight Batt type Batt war ning Touch Sense Contrast Display light Ni-MH 4.7v 2 0 unlim remains on when you switch the transmitter on, and after the last button-press. The available values are “unlimited” “30 s”, 60 s” and “120 s”. Simultaneously pressing the arrow buttons or of the right-hand touch-key (CLEAR) resets the value in the highlighted field to “unlimited”. Country setting Batt war ning Touch Sense Contrast Display light RF Country 4.7v 2 0 unlim Euro Voice volume Touch Sense Contrast Display light RF Country Voice volume 2 0 unlim Euro 3 In this line you can define the volume of the speech output which is generated through earphones; the available range is “0” to “10”. Simultaneously pressing the arrow buttons or of the right-hand touch-key (CLEAR) resets the value in the highlighted field to “3”. Beep volume The purpose of the country setting is to fulfil the requirements of various directives (FCC, ETSI, IC, etc.). For example, radio control systems operated in France must be set to a restricted frequency band. For this reason the transmitter’s country setting MUST be set to “France” mode before the system is used in that country. It is prohibited to use the Universal / EURO mode in France. Simultaneously pressing the arrow buttons or of the right-hand touch-key (CLEAR) resets the value in the highlighted field to “Euro”. Contrast Display light RF Country Voice volume Beep volume 0 unlim Euro 3 3 This line determines the volume of the transmitter’s internal sounder within the range “0” to “6”. Simultaneously pressing the arrow buttons or of the right-hand touch-key (CLEAR) resets the value in the highlighted field to “4”. This line determines how long the screen backlighting Program description: basic settings 135 Fail-Safe FAIL SAFE Pos hold 1 2 3 4 5 6 7 8 Delay 0.25s STO The inherently higher operational security of the HoTT system compared with classic PPM technology is due to the ability of the HoTT receiver’s integral micro-processor to process the signals from “its” transmitter exclusively, and also to process any “dirty” control signals which it picks up. The receiver constantly stores the latest valid signals, and invalid signals are automatically replaced by the stored signals - but only if the control signal is seriously inaccurate or even damaged, e. g. due to interference from an outside source. This process is dependent upon various settings which are described later in this section. For example, the receiver suppresses brief interference such as field strength “holes” and similar effects which would otherwise result in the familiar “glitches”. When this happens, the red LED on the receiver lights up. If you have not yet programmed any Fail-Safe settings in the currently active model memory, the following warning display will appear in the basic display for a few seconds when you switch the transmitter on: fail safe setup t.b.d Programming The “Fail-Safe” function determines the receiver’s beha­ viour when interference occurs in the transmission from 136 Program description: Fail-Safe transmitter to receiver. The receiver outputs 1 … 8 can optionally … 1. maintain (“hold”) their current position: If interference should occur, all servos programmed to “hold” mode remain at the position last assessed by the receiver as correct until such time as a new, correct control signal arrives at the receiver, or 2. move to a user-selectable position (“Pos”) if interference occurs, after a “delay” time has elapsed. Use the arrow buttons of the left or right-hand touch-key to select the desired servo socket 1 to 8 (), then touch the central SET button of the right-hand touch-key to switch between “hold” ( ) and “position” ( ) mode: FAIL SAFE and 1 s). Simultaneously pressing the arrow buttons or of the right-hand touch-key (CLEAR) resets the highlighted field to the default value of 0.75 s. Now use the arrow buttons of the left or right-hand touch-key to select the STO field at bottom right of the screen; SIMULTANEOUSLY move the servos for which you have selected Position mode to the desired positions using the associated transmitter controls. A touch of the central SET button of the right-hand touch-key stores these positions in the receiver as the Fail-Safe settings, so that it can revert to these if interference should strike. The transmitter informs you of the stored data by briefly displaying: FAIL SAFE Pos hold 1 2 3 4 5 6 7 8 STO Delay 0.25s Now select the “Delay” option at bottom left of the screen using the arrow buttons of the left or righthand touch-key … FAIL SAFE Pos hold 1 2 3 4 5 6 7 8 STO Delay 0.25s … touch the central SET button of the right-hand touchkey, and use its arrow buttons to select your preferred delay period from the four on offer (0.25 s, 0.5 s, 0.75 s Pos hold Position stored 1 2 3 4 5 6 7 8 Delay 0.25s STO attention: We strongly recommend that you make use of the safety potential of this option by at least setting the throttle position (glow-powered models) to idle, or the electric motor to stop, if a fail-safe event should be triggered. Model helicopters should be programmed to “hold”. This simple precaution ensures that the model is much less likely to cause havoc and cause property damage or personal injury. Telemetry The “Telemetry” menu provides a means of calling up receiver settings, and settings for any telemetry sensors connected to the system, and programming them in real-time. The transmitter is linked to the receiver via the downlink channel which is an integral feature of the HoTT receiver. If Y-leads are used, a maximum of four sensors can be connected to the Telemetry sockets of the following receivers; this assumes that the current firmware is loaded: GR-12S HoTT (Order No. 33505), GR-12 HoTT (Order No. 33506), GR-16 (Order No. 33508), GR-24 HoTT (Order No. 33512) and GR-32 DUAL (Order No. 33516). Since the system can be updated by the user, the associated “Telemetry” menus can constantly be kept up-todate, and expanded with the introduction of additional functions or languages in future. ing products at the website www.graupner.de/en. We always recommend that you load the latest firmware into your equipment, to ensure that your system is constantly kept up-to-date. Important information: • • Note: If you register your product under https:// www.graupner.de/en/service/product_registration.aspx you will automatically be informed about new updates by e-mail. Before updating the transmitter software you should always back up all occupied model memories to a compatible laptop or PC in order to avoid a possible loss of data. As mentioned earlier, firmware can be updated and data backed up via the transmitter’s PC socket using the USB interface, Order No. 7168.6, and the connecting lead, Order No. 6466.S, which are supplied in the set as standard. This requires the use of a PC running Windows XP, Vista or 7 as operating system. The programs required for this and related information can be found in the Download area for the correspond- • • • These instructions cover the functions available at the time of going to press. As mentioned in the sections entitled “Binding multiple receivers” on pages 80 and 88, it is possible to bind more than one receiver per model. However, in subsequent operations only the receiver which was bound last is able to make a telemetry connection to the transmitter. On the other hand, this also means that only the last bound receiver can be addressed using the Telemetry menu. You may therefore need to change the binding sequence before you can enter settings which relate to a particular receiver. Since the transmitter and receiver only exchange telemetry data after each fourth data packet, data transmission inevitably requires a certain amount of time, which means that there will be some delay in responding to button-presses and set-up changes. This does not constitute an error. When setting up the radio control system, please ensure at all times that the transmitter aerial is an adequate distance from the receiver aerials. A safe distance is about one metre. If you neglect this, you risk interference with the downlink channel, and consequent malfunctions. When operating towed models, keep a minimum distance of about 50 cm between the receiver units involved, or their aerials. If necessary, use satellite receivers. Otherwise, malfunctions caused by the return channel can not be excluded. • Changes to model and sensor programming must only be carried out when the model is on the ground. Do not make any alterations unless the motor is switched off and the flight battery is disconnected. If you ignore this, unwanted effects of programming changes cannot be excluded. For example, if you accidentally initiate an active servo test at the receiver, the model could crash and cause personal injury or property damage. Please see the Safety Notes on pages 4 … 9 of this manual and the various individual instructions. • All settings which you enter using the “Telemetry” menu, such as Fail-Safe, servo direction, servo travel, mixer and curve settings etc., are stored exclusively in the receiver, and are therefore carried over if you install the receiver in a different model. For this reason we strongly recommend that you re-initialise your HoTT receiver if you wish to use it in another model; see “Reset” on page 46 and 47. We therefore recommend that you program directions of servo rotation, servo travel, mixer and curve settings using only the mx-16-specific standard menus “Servo settings” (page 92), “Free mixers” (page 127) and “D/R Expo” (pages 102 and 104). If you ignore this, the settings may overlap and interfere with each other; in the most favourable case this can result in confusion when operating the model, and in the least favourable case it could cause problems. • The channel-mapping function of the mx-16 HoTT’s integral “Telemetry” menu can be used to Program description: Telemetry menu 137 SETTING & DATA VIEW share out control functions between multiple receivers in any way, or even to assign the same control function to several receiver outputs; for example, you may wish to operate each aileron with two servos instead of just one, etc. Once again we strongly recommend that you act as cautiously as possible when carrying out the programming. Telemetry The menus grouped together under the overall heading “Telemetry” are called up from the basic display of the mx-16 HoTT transmitter by holding the central ESC button of the left-hand touch-key pressed in for about one seconds. An alternative method of calling up this menu, which also applies to the transmitter’s other menus, is to briefly press the central SET button of the right-hand touch-key in the multi-function list: mod. mem. ser vo set. D/R expo wing mixer ser vo disp fail-safe base sett. contr set. phase trim free mixer basic sett telemetr y Basic menu operation In general terms the “Telemetry” menu is operated just like the other menus of the mx-16 HoTT transmitter. The few differences are described below: You can switch between the individual pages of the Telemetry menu using the arrow buttons of the left or right-hand touch-key: the corresponding direction indicators can be found at top right of every screen page in the form of pointed brackets (<>); see the following illustrations. If only one angle bracket is visible, then you 138 Program description: Telemetry menu are currently at the first or last page. In this case it is only possible to switch pages in the direction indicated by the angle bracket. Menu lines in which parameters can be altered are marked with an angle bracket prefix (>). Pressing the arrow buttons of the left or right-hand touch-key causes the “>” pointer to jump forward or back by one line. Lines to which you cannot jump contain no user-variable values. If you wish to change a parameter, touch the central SET button of the right-hand touch-key to highlight the parameter (black background)). Change the value within the possible range using the arrow buttons of the righthand touch-key, and then press the SET button again briefly to accept the value. At this point you can use the arrow buttons of the left or right touch-key to select the desired sub-menu. However, if the message … CAN‘T RECEIVE DATA OK … appears instead of the desired sub-menu when you touch the central SET button of the right-hand touch-key, then the transmitter has no connection to a receiver. In this case, switch your receiving system on, or re-bind the receiver you wish to address, as described on page 72 and 80; alternatively activate the receiver as described on the previous page under “Important notes”. On the first screen, headed … RX DATAVIEW … of the sub-menu “SETTING & DATA VIEW” of the “Telemetry” menu … TELEMETRY SETTING & DATA VIEW SENSOR SELECT RF STATUS VIEW VOICE TRIGGER … you cannot enter any settings. This page is for information purposes only: RX DATAVIEW S–QUA100%S–dBM–030dBM S–STR100% R–TEM.+28°C L PACK TIME 00010msec R-VOLT :05.0V L.R-VOLT:04.5V SENSOR1 :00.0V 00°C SENSOR2 :00.0V 00°C Value Explanation S-QUA Signal quality in % S-dBm Receive performance in dBm S-STR Signal strength in % R-TEM. Receiver temperature in °C L PACK TIME Indicates the time in ms for which the longest data packet was lost in transmission between transmitter and receiver R-VOLT Current receiver operating voltage, in Volt L.R-VOLT Lowest receiver operating voltage since the last power-on, in Volt SENSOR1 Shows the values of the optional telemetry sensor 1 in Volt and °C SENSOR2 Shows the values of the optional telemetry sensor 2 in Volt and °C Signal quality (S-QUA) The signal quality (S-QUA) is sent “live” to the transmitter via the receiver’s downlink channel, and shows the signal quality in %. Receive performance (S-dBm) The receive performance (S-dBm) is displayed as a negative value, i. e. a value approaching zero is the highest value (= best reception). The lower the value falls, the worse is the receive performance. This is an important item of information, particularly when you are carrying out a range-check before operating the model. Note: In the case of negative numbers the value is reversed: the higher the number following the minus sign, the lower the value. This means that a receive performance of, say, -80 dBm is worse than one of -70 dBm. Carry out a range-check as described on pages 80 and 89 before every flight, and remember to simulate all the servo movements which are likely to occur in the air. In active range-check mode the range must be at least fifty metres on the ground. To guarantee safe operation of your model, a value no higher than -80 dBm must be displayed in the “RX DATA” display under “S-dBm” at this distance. If the value falls below this (e. g. -85 dBm), you should under no circumstances fly your model. Instead check the receiving system installation and the aerial positions. When operating a model this value should not fall below -90 dBm; if it does, reduce the distance between the pilot and the model. However, the audible range warning (beeping at one-second intervals) will normally be triggered before this value is reached, in order to ensure safe operation. Signal strength (S-STR) The value for signal strength (S-STR) is displayed in %. An audible range warning (beeping at one-second intervals) will always be generated as soon as the receiver signal in the downlink channel is too weak. However, since the transmitter has a much higher transmitting power than the receiver, the model can still be operated safely at this point. Nevertheless, in the interests of safety the distance to the model should be reduced until the audible warning ceases. Receiver temperature (R-TEM.) Ensure under all flight conditions that the receiver stays within its specified temperature range (ideally between -10 and +55°C). The limit values for receiver temperature after which a warning occurs can be set in the “SERVO TEST” sub-menu under “ALARM TEMP+” (50 … 80°C) and “ALARM TEMP-” (-20 … +10°C). If the temperature exceeds or falls below the set limit, an audible signal (continuous beeping) is triggered, and “TEMP.E” is displayed at top right in all the “RX” receiver sub-menus. At the same time the “R-TEM“ parameter is highlighted on the “RX DATAVIEW” screen page. packets were lost in transmission from the transmitter to the receiver. In practice this means the longest time in which the radio control system went into Fail-Safe mode. Operating voltage (R-VOLT) Check the receiver’s operating voltage constantly. If it is too low, you must under no circumstances continue to operate your model, and certainly not launch it. The low receiver voltage warning can be adjusted within the range 3.0 to 6.0 Volt in the “SERVO TEST” sub-menu under “ALARM VOLT”. If the voltage falls below the threshold, an audible signal (repeated double beep, long / short) is generated, and in all the receiver sub-menus “RX …” you will see “VOLT.E” at top right. At the same time the parameter “R-VOLT” is highlighted in the “RX DATAVIEW” sub-menu. The current receiver battery voltage is also shown in the basic display; see page 24. Minimum operating voltage (L.R-VOLT) “L.R-VOLT” shows the receiver’s minimum operating voltage since the last time it was switched on. If this voltage differs significantly from the current operating voltage “R-VOLT”, this could mean that the receiver battery is being overstressed by the servos, causing collapses in battery voltage. If this should occur, we recommend installing a higher-performance receiver battery to ensure maximum operating safety. Sensor 1 + 2 Shows the values of the optional telemetry sensor 1 and, if present, sensor 2 in Volt and °C. You will find a description of these sensors in the Appendix. Data packets (L PACK TIME) This displays the longest period in ms in which data Program description: Telemetry menu 139 RX SERVO RX SERVO OUTPUT CH: REVERSE : CENTER : TRIM : LIMIT– : LIMIT+ : PERIOD : 01 OFF 1500µsec –000µsec 150% 150% 20msec Before you carry out any programming at this screen display be sure to read the information on page 137. Value Explanation Possible settings OUTPUT CH Channel select 1 … according to receiver REVERSE Servo reverse OFF / ON CENTER Servo centre in μs If active (high­ lighted), according to transmitter control position TRIM Trim position in μs -120 … +120 µs deviating from the CENTRE position LIMIT– Travel limit on the “-” side of servo travel in % servo travel 30 … 150% LIMIT+ Travel limit on the “+” side of servo travel in % servo travel 30 … 150% Cycle time in ms 10 or 20 ms PERIOD 140 Program description: Telemetry menu OUTPUT CH (Channel select) Select the “Channel” line if necessary using the arrow buttons. Touch the SET button of the right-hand touchkey to highlight the value field. Now use the arrow buttons of the right-hand touch-key to set the desired channel (e. g. 01). The following parameters always refer to the channel which you set at this point: REVERSE (servo reverse) Sets the direction of rotation of the servo connected to the selected control channel: ON / OFF CENTER (servo centre) The “CENTRE” line displays the current pulse width in μs of the control channel selected in the “OUTPUT CH” line. The displayed value varies according to the current position of the transmitter control which affects this control channel, and also its trim position. A pulse width of 1500 μs corresponds to the standard centre position, and therefore the usual servo centre setting. If you wish to alter this value, select the “CENTER” line and touch the SET button. Now move the corresponding transmitter control, stick and / or trim lever in the desired direction, and touch the SET button again to store the current position. This position will be stored as the new neutral position. TRIM (trim position) The purpose of the “TRIM” line is to provide fine adjustment of the neutral position of a servo connected to the control channel selected in the “OUTPUT CH” line. Adjustments are made in 1 μs increments using the arrow buttons of the right-hand touch-key. The value in the “CENTRE” line can be adjusted over the range +/- 120 μs around the TRIM value set here. Default setting: 0 μs LIMIT–/+ (travel reduction, separate for each side) This option can be used to place a limit on servo travel (control surface travel) for the servo connected to the control channel selected in the “OUTPUT CH” line. The value is set separately for each side of centre. The setting can be altered separately for both directions within the range 30 ... 150%. Default setting: 150% on both sides. PERIOD (cycle time) In this line you can determine the frame time for the individual channel signals. This setting applies to all control channels. If you use digital servos exclusively, it is safe to set a cycle time of 10 ms. If you are using a mixture of servo types, or exclusively analogue servos, it is essential to set 20 ms, otherwise the servos will be “over-stressed” and may response by jittering or making rumbling noises. RX FAIL SAFE RX FAIL SAFE OUTPUT CH: 01 INPUT CH: 01 MODE : HOLD F.S.POS. : 1500µsec DELAY : 0.75sec FAIL SAFE ALL: NO POSITION : 1500µsec Before we describe this menu a few words as a reminder: “Doing nothing” is the worst thing you can do in this regard. The default setting for the HoTT receiver is “HOLD” mode. If interference should occur with hold-mode in force, and if you are very lucky, the model aircraft will fly straight ahead for an indefinite period and then “land” somewhere or other without causing major damage. However, if the interference strikes in the wrong place and at the wrong time, then a power model could become uncontrollable and tear wildly across the flying field, endangering pilots and spectators. For this reason you really must consider whether you should at least program the throttle to “motor stopped”, to avoid the worst of these risks. If you are unsure of this, please ask a competent model pilot for advice on how to find a “sensible” setting for your model. After that warning we present a brief description of the three possible Fail-Safe variants offered by the mx-16 HoTT transmitter: The simplest way of setting Fail-Safe - and the one we recommend - is to use the “Fail-Safe” menu, which is accessed from the multi-function list; see page 136. A similar alternative, albeit slightly more difficult to access, is to use the “FAIL-SAFE ALL” option described on the next double-page. And finally there is the relatively complex method of entering individual settings using the “MODE”, “F.S.Pos.” and “DELAY” options. The description of this variant starts below with the “MODE” option. Value Explanation Possible settings OUTPUT CH Output channel (receiver servo socket) 1 … according to receiver INPUT CH Input channel (control channel coming from transmitter) 1 … 16 MODE Fail-Safe mode HOLD FAIL SAFE OFF F.S.Pos. Fail-Safe position 1000 … 2000 µs DELAY Response time (delay) 0,25, 0,50, 0,75 and 1,00 s FAIL SAFE ALL Stores fail-safe positions for all control channels NO / SAVE POSITION Displays stored Fail-Safe position between approx. 1000 and 2000 µs OUTPUT CH (servo socket) In this line you select the OUTPUT CH (receiver servo socket) which is to be adjusted. INPUT CH (input channel select) As already mentioned on page 137, the eight control functions of the mx-16 HoTT transmitter can be shared out between several receivers if necessary, or alternatively several receiver outputs can be assigned to the same control function; for example, you may wish to be able to operate each aileron with two servos, or to control an oversized rudder using two coupled servos instead of a single one. Sharing control functions amongst multiple HoTT receivers is a useful idea for large-scale models, for example, to avoid long servo leads. In this case bear in mind that only the last bound receiver can be addressed using the “Telemetry” menu. The eight control channels (INPUT CH) of the mx-16 HoTT can be managed in the appropriate manner using the facility known as “channel mapping”, i. e. by assigning a different control channel in the INPUT CH line to the receiver servo socket selected in the OUTPUT CH line. attention: If, for example, you have entered “2AIL” in the “Aileron/flap” line of the “Base settings” menu at the transmitter, then control function 2 (aileron) is already divided to control channels 2 + 5 for the left and right ailerons. In this case the corresponding receiver INPUT CH, i.e. the channels to be mapped, would then be channels 02 + 05; see the following example. Examples: • You wish to assign two or more servos to each aileron of a large-scale model aircraft: Assign the two standard aileron control channels 2 or 5 as INPUT CH to the appropriate OUTPUT CH (servo sockets), maintaining the correct sequence for the left and right wings. • You wish to control the rudder of a large-scale model aircraft using two or more servos: Assign one and the same INPUT CH (control channel) to each of the appropriate OUTPUT CH (servo sockets); in this case the default rudder channel 4. Program description: Telemetry menu 141 MODE The settings you enter for the options “MODE”, “F.S. Pos.” and “DELAY” determine the receiver’s behaviour if interference should affect the transmission from transmitter to receiver. The setting programmed under “MODE” always refers to the channel you have set in the OUTPUT CH line. The default setting for all servos is “HOLD”. For each selected OUTPUT CH (receiver servo socket) you can choose between: • FAI(L) SAFE If interference occurs, the corresponding servo moves to the position displayed in the “POSITION” line for the duration of the interference, after the “delay time” set in the “DELAY” line. • HOLD If interference occurs, a servo set to “HOLD” maintains the position last assessed as correct for the duration of the interference. • OFF If set to “OFF” when interference occurs, the receiver continues to send the last correct control signals (which it has stored) to the corresponding servo output for the duration of the interference. This can be imagined as the receiver switching the signal wire “off”. attention: If the control signal is absent, analogue servos and many digital servos offer no resistance to the forces acting on the control surfaces, with the result that the model’s control surface positions are more or less quickly lost. 142 Program description: Telemetry menu F.S.Pos. (Fail-Safe position) For each OUTPUT CH (receiver servo socket) activate (highlight) the value field by briefly pressing the central SET button of the right-hand touch-key, then use the arrow buttons of the right-hand touch-key in the “F.S.POS.” line to set the servo position which the servo is to take up in “FAIL-SAFE” mode if interference should occur. The setting can be entered in increments of 10 μs. Default setting: 1500 μs (servo centre) Important note: The “F.S.POS.” function is also significant if the receiver is switched on, but is (not yet) receiving a valid signal; this applies to all three modes “OFF”, “HOLD” and “FAIL-SAFE”: The servo immediately runs to the Fail-Safe position previously set in the “Position” line. This can be exploited, for example, to prevent the operation of a retractable undercarriage or similar function if the receiver is switched on accidentally. However, during normal model operations the corresponding servo behaves in accordance with the set “MODE” if interference should strike. DELAY (fail-safe response time or delay) At this point you can set the delay time after which the servos are to run to their previously selected positions if the signal should be interrupted. This setting applies to all channels, but only affects the servos programmed to “FAIL-SAFE” mode. Default setting: 0.75 s FAIL SAFE ALL (global fail-safe setting) This sub-menu can be used to define the Fail-Safe position of the servos simply by “pressing a button”; it operates in a similar manner to the “Fail-Safe” menu described on page 136, and is simple to use: Move to the “FAIL-SAFE ALL” line and press the central SET button of the right-hand touch-key to activate the value field; “NO” is highlighted (black background). Now set the parameter to “SAVE” using one of the arrow buttons of the right-hand touch-key. Use the transmitter controls to move all the servos which you have assigned - or intend to assign later - in the “MODE - FAIL-SAFE” line, to the desired fail-safe positions. In the extreme bottom line “Position” displays the current position of the transmitter control for the channel you have just set: RX FAIL SAFE OUTPUT CH: 01 INPUT CH: 01 MODE : FAI-SAFE F.S.POS. : 1500µsec DELAY : 0.75sec FAIL SAFE ALL: SAVE POSITION : 1670µsec After touching the central SET button of the right-hand touch-key once more, the display reverts from “SAVE” to “NO”. This indicates that the position of all the servos affected by the procedure have now been stored, and have also been adopted in the “F.S.Pos.” line. At the same time the position for the current OUTPUT CH (servo socket) is immediately displayed on the screen. RX FAIL SAFE OUTPUT CH: 01 INPUT CH: 01 MODE : FAI-SAFE F.S.POS. : 1670µsec DELAY : 0.75sec FAIL SAFE ALL: NO POSITION : 1670µsec Switch the transmitter off, and check the Fail-Safe positions by observing the servo movements. “Fail-Safe” in combination with “channel mapping” It is clearly desirable that mapped servos - i. e. servos which are controlled by a common control channel (INPUT CH) - should respond in the same way when interference occurs, so the corresponding settings of the INPUT CH determine the behaviour of mapped servos. For example, if receiver servo sockets 6, 7 and 8 are mapped together, i. e. if the same control channel “04” is assigned to OUTPUT CH (servo sockets) 06, 07 and 08 … for INPUT CH 04: RX FAIL SAFE OUTPUT CH: 04 INPUT CH: 04 MODE : FAI-SAFE F.S.POS. : 1500µsec DELAY : 0.75sec FAIL SAFE ALL: NO POSITION : 1500µsec This also applies, for example, if it is mapped in turn to INPUT CH 01: RX FAIL SAFE OUTPUT CH: 04 INPUT CH: 01 MODE : FAI-SAFE F.S.POS. : 1500µsec DELAY : 0.75sec FAIL SAFE ALL: NO POSITION : 1500µsec RX FAIL SAFE OUTPUT CH: 06 INPUT CH: 04 MODE : OFF F.S.POS. : 1670µsec DELAY : 0.75sec FAIL SAFE ALL: NO POSITION : 1670µsec RX FAIL SAFE OUTPUT CH: 07 INPUT CH: 04 MODE : OFF F.S.POS. : 1230µsec DELAY : 0.75sec FAIL SAFE ALL: NO POSITION : 1670µsec In this case servo socket 04 would respond in accordance with the Fail-Safe settings for CH 01. In contrast, the response or delay time set in the “DELAY” line always applies uniformly to all channels which are set to “FAIL-SAFE”. RX FREE MIXER RX FREE MIXER MODE : 1 MASTER CH: 00 SLAVE CH : 00 S–TRAVEL–: 100 S–TRAVEL+: 100 RX WING MIXER TAIL TYPE: NORMAL RX FAIL SAFE OUTPUT CH: 08 INPUT CH: 04 MODE : HOLD F.S.POS. : 1770µsec DELAY : 0.75sec FAIL SAFE ALL: NO POSITION : 1670µsec … then INPUT CH 04 determines the Fail-Safe behaviour of the three servos connected to control channel 4, regardless of the individual settings of the OUTPUT CH Value Explanation Possible settings MODE Mixer select 1…5 MASTER CH Primary channel 0, 1 … according to transmitter SLAVE CH Secondary channel 0, 1 … according to receiver S-TRAVEL– Mix value on the “-” side of servo travel in % servo travel 0 … 100% S-TRAVEL+ Mix value on the “+” side of servo travel in % servo travel 0 … 100% RX WING MIXER Tail type NORMAL, V-TAIL ELEVON (aileron / elevator mixer for deltas and flying wings) MIXER Up to three mixers can be programmed simultaneously. You can switch between mixer 1, mixer 2 and mixer 3 using “MIXER”. The following settings on this screen always apply to the mixer selected in the MIXER line. Important note: If you have already programmed mixer functions in the “Wing mixers” or “Free mixers” menus, check very carefully that those mixers do not overlap with those of the “RX FREE MIXER” menu. MASTER CH (“from”) The signal present at the MASTER CH (master chanProgram description: Telemetry menu 143 TRAVEL–/+ (mixer ratio in %) The mixer ratio in relation to the MASTER signal is determined separately for each direction by the values entered in these two lines. RX WING MIXER TAIL TYPE The following model types are also available in the “Tail” line of the “Base settings” menu (see page 76), and should normally be set up at that point. If you have done this, you should always leave the TAIL TYPE at NORMAL. However, if you prefer to use the receiver’s integral mixers, you can select the pre-set mixer function for the corresponding model type: • NORMAL This setting corresponds to the classic aircraft type with tail-mounted stabiliser panels and separate rudder and elevator. No mixer function is required for this model type. • V-TAIL For this model type the control functions elevator and rudder are linked together in such a way that each of 144 Program description: Telemetry menu RX CURVE RX CURVE CURVE1 CH TYPE CURVE2 CH TYPE CURVE3 CH TYPE : : : : : : 02 B 03 B 04 B Value Explanation Possible settings CURVE1, 2 or 3 CH Channel assign­ 1 … according to ment of the selec­ receiver ted curve setting TYPE Curve type A, B, C see illustration TYPE A Expo = –100% DR = 125% TYPE C Expo = +100% DR = 70% Servo travel +100% 0 Servo travel +100% 0 –100% –100% TYPE B linear Servo travel +100% 0 SLAVE CH (“to”) A proportion of the signal of the MASTER CH (master channel) is mixed into the SLAVE CH (slave channel); the mixer ratio is determined by the percentage figures entered in the “TRAVEL-” and “TRAVEL+” lines. Select “00” if no mixer is to be set. the two control surfaces - actuated by a separate servos - carries out superimposed elevator and rudder functions. The servos are usually connected to the receiver as follows: OUTPUT CH 3: left V-tail servo OUTPUT CH 4: right V-tail servo If you find that the servos rotate in the wrong direction, please see the notes on page 63. • ELEVON (delta / flying wing models) The servos connected to outputs 2 and 3 assume superimposed aileron and elevator functions. The servos are usually connected to the receiver as follows: OUTPUT CH 2: left elevon OUTPUT CH 3: right elevon If you find that the servos rotate in the wrong direction, please see the notes on page 63. –100% nel) is mixed into the SLAVE CH (slave channel) to a user-variable extent, following the same principles as described in detail in the section entitled “Free mixers” on page 127. Select “00” if no mixer is to be set. –100% 0 +100% Transmitter control travel –100% 0 +100% Transmitter control travel –100% 0 +100% Transmitter control travel In most cases a non-linear control function is used for aileron (channel 2), elevator (channel 3) and rudder (channel 4), and the default settings assume that this is the case. BUT CAUTION: This assignment only applies if you have not set either “2 ELE Sv” in the “Tail” line of the “Base settings” menu, or “2AIL” or “2AIL 2FL” in the “Ail / flap” line, at the transmitter. Otherwise control function 3 (elevator) is already split over control channels 3 + 8, and control function 2 (aileron) is split over control channels 2 + 5 for the left and right ailerons. In both these cases the corresponding receiver control channels (INPUT CH) would then be channels 03 + 08 or 02 + 05. For example, if you have set “2AIL” at the transmitter, and wish to use the RX CURVE option discussed here instead of the “D/R Expo” menu (see page 102) of the mx-16 HoTT transmitter - which offers more individual adjustment options - then two curves must be set: RX CURVE CURVE1 CH TYPE CURVE2 CH TYPE CURVE3 CH TYPE 5CH FUNCTION: “SERVO” or “SENSOR” : : : : : : 02 A 05 A 04 B If you ignored this, the left and right ailerons would exhibit different control characteristics. The RX CURVE function can be used to manage the control characteristics for up to three servos: • CURVE 1, 2 or 3 CH Select the desired control channel (INPUT CH) for the first servo. The following setting in TYPE only affects the channel you select at this point. TYPE Select the servo curve: A: EXPO = -100% and DUAL RATE = 125% The servo responds slowly to stick movements around the neutral position, but the curve becomes steeper with increasing control travel. B: Linear setting The servo follows the stick movement with a linear response. C: EXPO = +100% and DUAL RATE = 70% The servo responds slowly to stick movements around the neutral position, but the curve becomes steeper with increasing control travel. RX CURVE CURVE1 CH : 02 TYPE : A CURVE2 CH : 05 TYPE : A CURVE3 CH : 04 TYPE : B 5CH FUNCTION:SERVO Certain receivers feature one switchable servo socket instead of an independent telemetry socket. For example, servo socket 5 of the GR-12 receiver, which is supplied with the mx-12 HoTT, Order No. 33112, bears the suffix “T” … Servo OR sensor … and has two additional uses: a telemetry sensor can be connected to it, and also the adapter lead, Order No. 7168.A, can be connected to it for the purpose of updating the receiver. To ensure that the receiver correctly detects the device connected to this receiver socket, servo socket 5 MUST be switched from “SERVO” to “SENSOR” and vice versa. This is accomplished by shifting the arrow button of the left or right-hand touch-key the “>” symbol at the lefthand margin of the bottom line, followed by pressing the central SET button of the right-hand touch-key: RX CURVE CURVE1 CH : 02 TYPE : A CURVE2 CH : 05 TYPE : A CURVE3 CH : 04 TYPE : B 5CH FUNCTION:SERVO Now use one of the two arrow buttons of the right-hand touch-key to select the alternative “SENSOR” setting. RX CURVE CURVE1 CH : 02 TYPE : A CURVE2 CH : 05 TYPE : A CURVE3 CH : 04 TYPE : B 5CH FUNCTION:SENSOR A further press on the central SET button of the righthand touch-key concludes the selection process. You can now return to the transmitter’s base display by repeatedly pressing the central ESC button of the lefthand touch-key. Note: The control characteristics programmed at this point also affect mapped receiver outputs. Program description: Telemetry menu 145 RX SERVO TEST RX SERVO TEST ALL–MAX : 2000µsec ALL–MIN : 1000µsec TEST : STOP ALARM VOLT : 3.8V ALARM TEMP+: 55°C ALARM TEMP–:–10°C CH OUTPUT TYPE:ONCE ALL MAX (Servo travel on the “+” side) In this line you can set the maximum servo travel for the servo test on the plus side of control travel. 2000 μs corresponds to full travel, 1500 μs corresponds to the neutral position. Ensure that the servos do not strike their mechanical end-stops during the test routine. Value Explanation Possible settings ALL-MAX Servo travel on the “+” side for all servo outputs in the servo test 1500 … 2000 µs ALL MIN (Servo travel on the “-” side) In this line you can set the maximum servo travel for the servo test on the minus side of control travel. 1000 μs corresponds to full travel, 1500 μs corresponds to the neutral position. ALL-MIN Servo travel on the “-” side for all servo outputs in the servo test 1500 … 1000 µs Note: Ensure that the servos do not strike their mechanical end-stops during the test routine. TEST Test procedure START / STOP ALARM VOLT Alarm limit for the receiver lowvoltage warning 3,0 … 6,0 V Default setting: 3,8 V ALARM TEMP+ Alarm limit for 50 … 80 °C excessive receiver Default setting: temperature 55 °C ALARM TEMP– Alarm limit for excessively low receiver temperature -20 … +10 °C Default setting: -10 °C CH OUTPUT Channel sequence ONCE, SAME, TYPE SUMI, SUMO 146 Program description: Telemetry menu TEST In this line you can start and stop the receiver’s integral servo test. Touch the central SET button of the right-hand touch-key to activate the input field: RX SERVO TEST ALL–MAX : 2000µsec ALL–MIN : 1000µsec TEST : STOP ALARM VOLT : 3.8V ALARM TEMP+: 55°C ALARM TEMP–:–10°C CH OUTPUT TYPE:ONCE Now select START with one of the arrow buttons of the right-hand touch-key: RX SERVO TEST ALL–MAX : 2000µsec ALL–MIN : 1000µsec TEST : START ALARM VOLT : 3.8V ALARM TEMP+: 55°C ALARM TEMP–:–10°C CH OUTPUT TYPE:ONCE Touch the central SET button of the right-hand touchkey to start the test-run. The input field now reverts from highlighted to “normal”: RX SERVO TEST ALL–MAX : 2000µsec ALL–MIN : 1000µsec TEST : START ALARM VOLT : 3.8V ALARM TEMP+: 55°C ALARM TEMP–:–10°C CH OUTPUT TYPE:ONCE To stop the servo test, re-activate the input field as described previously, then select STOP and confirm your choice with the SET button of the right-hand touch-key. ALARM VOLT (low receiver voltage warning) ALARM VOLT monitors the receiver voltage. The threshold can be set to any value within the range 3.0 to 6.0 Volt. If the voltage falls below the set alarm limit, an audible signal (interval beeping, long / short) is triggered, and “VOLT.E” flashes at top right in all “RX …” screen displays: RX SERVO OUTPUT CH: REVERSE : CENTER : TRIM : TRAVEL– : TRAVEL+ : PERIOD : VOLT.E 01 OFF 1500µsec –000µsec 150% 150% 20msec The parameter “R-VOLT“ is also highlighted in the “RX DATAVIEW” display: RX DATAVIEW VOLT.E S–QUA100%S–dBM–030dBM S–STR100% R–TEM.+28°C L PACK TIME 00010msec R-VOLT :03.7V L.R-VOLT:03.5V SENSOR1 :00.0V 00°C SENSOR2 :00.0V 00°C ALARM TEMP +/- (receiver temperature monitor) These two options monitor the temperature of the receiver: a lower limit value “ALARM TEMP-” (-20 ... +10°C) and an upper limit value “ALARM TEMP+” (50 ... 80°C) can be programmed. If the temperature exceeds the upper limit or falls below the lower one, an audible signal (continuous beeping) is triggered, and “TEMP.E” appears at top right in all receiver displays. The parameter “R-TEM“ is also highlighted in the “RX DATAVIEW” display. Ensure that the receiver remains within the permitted temperature range under all flight conditions (ideally between -10 and +50°C). CH OUTPUT TYPE At this point you can select how the receiver outputs are to be addressed. • ONCE RX SERVO TEST ALL–MAX : 2000µsec ALL–MIN : 1000µsec TEST : START ALARM VOLT : 3.8V ALARM TEMP+: 55°C ALARM TEMP–:–10°C CH OUT TYPE:ONCE The receiver servo sockets are addressed in sequence; this is recommended for use with analogue servos. At this setting the servos are automatically operated at a frame rate of 20 ms (30 ms with the twelve-channel receiver, Order No. 33512) - regardless of what is set or displayed in the “PERIOD” line of the “RX SERVO” display. • SAME RX SERVO TEST ALL–MAX : 2000µsec ALL–MIN : 1000µsec TEST : START ALARM VOLT : 3.8V ALARM TEMP+: 55°C ALARM TEMP–:–10°C CH OUT TYPE:SAME The receiver servo sockets are addressed in parallel blocks of four, i. e. channels 1 to 4 and channels 5 to 8 each receive their control signals simultaneously. This is recommended for use with digital servos, and especially where multiple servos are employed for a single function (e. g. ailerons), to ensure that the groups of servos run absolutely synchronously. If you are using digital servos exclusively, it is advisable to set a value of 10 ms in the “PERIOD” line of the “RX SERVO” screen, as this enables you to exploit the fast response of digital servos. If you are using analogue servos, or a mixture of both types, it is essential to select “20 ms”! If you choose the faster setting, please take particular care when selecting the receiver power supply: since up to four servos can start moving simultaneously, the load on the battery is fairly severe, so it must be a high-performance type. • SUMO (Sum signal OUT) RX SERVO TEST ALL–MAX : 2000µsec ALL–MIN : 1000µsec TEST : START ALARM VOLT : 3.8V ALARM TEMP+: 55°C ALARM TEMP–:–10°C CH OUTPUT TYPE:SUMO A HoTT receiver configured as SUMO constantly generates what is known as a sum signal from the control signals of all its control channels, and - in the case of the GR-16 receiver supplied in the set as standard - makes this available at servo socket 8. If the receiver’s display shows a two-digit number to the right of “SUMO” … RX SERVO TEST ALL–MAX : 2000µsec ALL–MIN : 1000µsec TEST : START ALARM VOLT : 3.8V ALARM TEMP+: 55°C ALARM TEMP–:–10°C CH OUT TYPE:SUMO 08 … then the active field shifts to the right - to channel select - when you confirm “SUMO” with a brief press of the central SET button of the right-hand touch-key. This choice determine the highest of the transmitter channels contained in the SUMO signal: RX SERVO TEST ALL–MAX : 2000µsec ALL–MIN : 1000µsec TEST : START ALARM VOLT : 3.8V ALARM TEMP+: 55°C ALARM TEMP–:–10°C CH OUT TYPE:SUMO 08 Program description: Telemetry menu 147 You can confirm the pre-set number with a further brief press of the central SET button of the right-hand touch-key, or use the arrow buttons to select one of the other channels between 04 and 16, and then confirm your choice with SET. The receiver outputs are addressed in sequence at a frame rate of 20 ms (30 ms with the GR-24 receiver, Order No. 33512), even if you have set 10 ms in the “PERIOD” line of the “RX SERVO” screen page. Although primarily intended for “satellite mode” with two HoTT receivers, as described below, the sum signal generated by the receiver defined as SUMO can also be used, for example, to control a flybarless system, or to control a flight simulator (using the adapter lead, Order No. 33310). In … Satellite mode … two HoTT receivers are inter-connected using a three-core connecting lead (Order No. 33700.1 (300 mm) or 33700.2 (100 mm)) using servo sockets determined according to the specific receiver types. For example, GR-16 and GR-24 receivers are inter-connected using servo output 8. For more details on this please refer to the Internet at www.graupner.de/en. All channels of the HoTT receiver which is configured as SUMO, and is defined as the satellite receiver, are constantly transferred to the second HoTT receiver the primary receiver - via this connection. The primary receiver must be programmed as the … 148 Program description: Telemetry menu • SUMI (Sum signal IN) RX SERVO TEST ALL–MAX : 2000µsec ALL–MIN : 1000µsec TEST : START ALARM VOLT : 3.8V ALARM TEMP+: 55°C ALARM TEMP–:–10°C CH OUT TYPE:SUMI Note that the signal only ever moves in one direction: towards the SUMI. However, if reception fails, the receiver defined as SUMI only uses the sum signal coming from the SUMO if at least one channel at the SUMI is programmed to Fail-Safe. If the receiver programmed as the satellite (SUMO) suffers signal reception failure, the servos connected to that receiver take up the Fail-Safe positions programmed in the satellite receiver, regardless of the primary receiver. If, in contrast, reception fails at both receivers simultaneously, then the receiver software (the version current at the time of printing these instructions) always reverts to the SUMO’s fail-safe settings. However, mutual interactions can certainly not be ruled out in individual cases, and for this reason we urgently advise you to carry out appropriate tests BEFORE flying a model. This receiver configuration is recommended in particular circumstances: for example, if one of the two receivers has to be installed in an unfavourable position in the model, or if there is a danger that the received signal will be weak in certain flight attitudes, perhaps due to a turbine, carbon fibre in the airframe, or a similar problem, with the result that sporadic range problems might be expected. For this reason it is essential to connect the most important control functions to the primary receiver (the one programmed as SUMI), so that interference to the satellite receiver (SUMO) does not cause the model to go out of control. Telemetry data, such as the voltage of the airborne power supply, are only sent to the transmitter by the satellite receiver (configured as SUMO), i. e. all telemetry sensors must be connected to the satellite receiver (SUMO). Each receiver should be connected to the shared power supply using its own power lead. If high currents can be expected, duplicated power connections are recommended. However, if each of the two receivers is to be powred ered by its own battery, 1 then it is essential to withdraw the central 3 2 (red) wire from one of the two satellite lead connectors, as shown in the illustration. If you wish to carry out further programming, such as the Fail-Safe settings, disconnect the three-core satellite connection between the two receivers, and switch on just the receiver you wish to address. Note that you may also need to change the binding sequence. Setting up / displaying sensor(s) If you select at least one sensor in addition to “Receiver” in the “SELECT SENSOR” sub-menu of the “Telemetry” menu, which is described below, then you can read out and alter its settings following on from the receiver pages described in the previous sections. However, if you wish to have actual access to these data, then you must connect the selected sensor or sensors to a receiving system, and set up a working tele­metry link. If you activate at least one sensor, as described in the next section, you can switch directly between the individual modules - provided that the sensor is loaded with the current firmware. However, if you are using sensors with earlier firmware, it may be necessary to select “etc.” instead of selecting the sensor directly. In either case press the Select button or of the left-hand touch-key … further screen pages are available: RX SERVO TEST ALL–MAX : 2000µsec ALL–MIN : 1000µsec TEST : START ALARM VOLT : 3.8V ALARM TEMP+: 55°C ALARM TEMP–:–10°C CH OUT TYPE:ONCE Now use the Select button of the left or right-hand touch-key to switch to the displays for the selected sensor, where you can check or alter its settings as described in the instructions supplied with the sensor. etc. RECEIVER VARIO … and then select the desired module using the same buttons, working either up or down, e.g.: RECEIVER GENERAL ELECT. AIR If the General Module is active, as selected in our example, you will also see the right-pointing arrow “ ” at top right on the last receiver page (“RX SERVO TEST”), in addition to the left-pointing arrow “ ”; this indicates that Program description: Telemetry menu 149 SENSOR SELECT When you select the desired menu line using the arrow buttons of the left or right-hand touch-key … TELEMETRY SETTING & DATA VIEW SENSOR SELECT RF STATUS VIEW VOICE TRIGGER … and then briefly press the central SET button of the right-hand touch-key, the selected sub-menu opens: SENSOR SELECT RECEIVER GENERAL MODULE ELECTRIC AIR.MOD VARIO MODULE GPS At this menu point you can determine separately for each model memory which graphic displays are available for selection, and which are to be suppressed, as described in the section starting on page 30 and the previously described “SETTING & DATA VIEW” submenu. Once you have selected the appropriate line using the arrow buttons of the left or right-hand touch-key, and then pressed the central SET button of the righthand touch-key, you can activate ( ) or disable ( ) the displays for the corresponding sensors, e.g.: 150 Program description: Telemetry menu SENSOR SELECT RECEIVER GENERAL MODULE ELECTRIC AIR.MOD VARIO MODULE GPS This choice is a requirement for superimposing the sensor in the “VOICE TRIGGER” sub-menu, and for displaying telemetry data in the corresponding graphic display; see page 30. RF STATUS VIEW After you select the desired menu line using the arrow buttons of the left or right-hand touch-key … TELEMETRY SETTING & DATA VIEW SENSOR SELECT RF STATUS VIEW VOICE TRIGGER … a brief press on the central SET button of the righthand touch-key opens the selected sub-menu. This visualises the quality of the connection between transmitter and receiver: (S-dbm)” on page 139. • The dots above the bar indicate the worst-case receive performance since the transmitter was switched on, or since the display was reset by simultaneously pressing the or buttons of the right-hand touch-key (CLEAR). Additional information in numeric form is generated to the left of the graphic display of receive performance. The meaning of these figures is as follows: Value Explanation R Signal quality in % for the signal arriving from the receiver R100% S 90% TD 40 S Signal quality in % for the signal arriving at the receiver TD Reception performance in dBm E 10 RD 51 4.8VC 4.8VM 0123456789ABCDE E Number of lost receiver data packets RD Reception performance in dBm of the signal picked up by the receiver VC Actual receiver operating voltage in Volt VM Lowest receiver operating voltage in Volt since the last time it was switched on Top row: Bottom row: Receive performance of channels 1 … 75 in the 2.4 GHz band in dBm, coming from the receiver, picked up at the transmitter. Receive performance of channels 1 … 75 in the 2.4 GHz band in dBm, coming from the transmitter, picked up at the receiver. Notes: • Since the receive performance is measured and displayed in dBm, the higher the bar, the worse the receive performance, and vice versa; see also under “Receive performance Program description: Telemetry menu 151 VOICE TRIGGER Once you have selected the appropriate menu line using the arrow buttons of the left or right-hand four-way button … TELEMETRY SETTING & DATA VIEW SENSOR SELECT RF STATUS VIEW VOICE TRIGGER … and then pressed the central SET button of the righthand four-way button, the selected sub-menu appears: VOICE TRIGGER REPEAT 10SEC ––– TRIG ––– VARIO ––– TRANSMITTER RECEIVER GENERAL MODULE ELECTRIC AIR.MOD. VARIO MODULE GPS Note: This display will vary according to the choices you have made in the “Select sensor” sub-menu; as described on page 150. The illustration above shows the maximum number of options, and indicates that the user has selected all the sensors. 152 Program description: Telemetry menu REPEAT VOICE TRIGGER REPEAT 10SEC TRIG VARIO TRANSMITTER RECEIVER ––– ––– ––– Speech output is available via the headphone socket, but not until you have at least assigned a switch in the “REPEAT” line. This is accomplished as described in the section entitled „Assigning switches and control switches“ on page 59: TRIG If you assign a switch in this line - preferably the momentary switch SW 1 - you can cycle through the voice outputs selected in the options “TRANSMITTER”, “RECEIVER” and under “Sensors”, as described in the following sections. However, please note that any warnings can only be generated by the sensor which is currently active! VOICE TRIGGER REPEAT 10SEC TRIG VARIO TRANSMITTER RECEIVER 3 1 ––– VOICE TRIGGER REPE T 10SEC push into desired switch position ON TRANSMITTER RECEIVER VOICE TRIGGER REPEAT 10SEC TRIG VARIO TRANSMITTER RECEIVER 3 ––– ––– All the time the assigned switch is closed, the last speech output is repeated for the period set to the left of the switch. Simultaneously pressing the Select buttons or of the right-hand four-way button (CLEAR) causes the time setting to revert to “10SEC”. VARIO If you activate the “VARIO” ( ) line in the “SELECT SENSOR” sub-menu, as described on page 150, you can use a switch assigned in this line to call up vario-specific voice outputs, i.e. those triggered by altitude changes, such as “slow climb / descent” etc. via the transmitter’s earphone socket; these outputs are completely independent of the other voice messages. VOICE TRIGGER REPEAT 10SEC TRIG VARIO TRANSMITTER RECEIVER 3 1 7 TRANSFER Select the desired menu line using the arrow buttons of the left or right-hand four-way button … VOICE TRIGGER REPEAT 10SEC TRIG VARIO TRANSMITTER RECEIVER 3 1 7 … then briefly press the central SET button of the righthand four-way button to open the selected sub-menu: VOLT: MODELTIME: BATTERYTIME: STOPWATCH: RUNTIME: In this menu you can activate ( ) or disable ( ) the chosen speech output after using the arrow buttons of the left or right-hand four-way button to select the desired line, followed by a brief press of the central SET button of the right-hand four-way button: VOLT: MODELTIME: BATTERYTIME: STOPWATCH: RUNTIME: RECEIVER Select the desired menu line with the arrow buttons of the left or right-hand four-way button … VOICE TRIGGER REPEAT 10SEC TRIG VARIO TRANSMITTER RECEIVER 3 1 7 „Sensors“ These lines only appear if you previously activated at least one sensor in the “SELECT SENSOR” sub-menu of the “TELEMETRY” menu; see page 150. The corresponding voice outputs are selected using the procedure described in the previous sections. Note: The selection you make here is completely independent of the “VARIO” voice outputs. … then touch the central SET button of the right-hand four-way button to call up the selected sub-menu: TEMP: STRENGTH: VOLT: LOWVOLT: In this menu you can activate ( ) or disable ( ) the chosen speech output after using the arrow buttons of the left or right-hand four-way button to select the desired line, followed by a brief press of the central SET button of the right-hand four-way button: TEMP: STRENGTH: VOLT: LOWVOLT: Program description: Telemetry menu 153 Trainer Mode Connecting two transmitters for trainer mode operations using a Trainer lead Use the arrow buttons of the left or right-hand touch-key to leaf through to the “Trainer” menu point of the multi-function menu: ser vo set. D/R expo wing mixer ser vo disp fail-safe teach/pupi ser vo set. D/R expo free mixer ser vo disp fail-safe teach/pupi contr set. phase trim free mixer basic sett telemetr y info disp contr set. heli mixer swashp.mix basic sett telemetr y info disp Touch the central SET button of the right-hand touch-key to open the menu: TRAINER/Pupil –P T 1 2 3 4 5 6 7 8 N/A SW: ––– BIND: The illustration above shows the initial state of this menu: transmitter controls have not been released ( ) to the pupil, and a switch has not been assigned (SW: --- at bottom right and -P on the left of the display). 154 Program description: Trainer system Teacher transmitter settings Up to eight transmitter control functions (see „Definition of terms“ on page 58) of the Teacher transmitter “T” can be transferred to the pupil transmitter “P”, either individually or in any combination. For this reason the bottom line of the screen, marked “L”, indicates those function inputs which are permanently associated with control functions 1 … 4 (dual-axis stick functions on fixed-wing models and helicopters), as well as the freely assignable inputs 5 … 8 of the “Transmitter control settings” menu. buttons of the left or right-hand touch-key to place the marker next to “SW” at bottom right, and assign a switch as described on page 59. We recommend that you use one of the two momentary switches SW 1 or SW 9 as the transfer switch, to ensure that the Teacher transmitter can regain control instantly at any time. TRAINER/Teach No student signal 1 2 3 5 6 7 8 N/A SW: 9 BIND: –P T Note: In principle it makes no difference which individual transmitter controls are assigned to the inputs which are to be transferred to the pupil. However, they can only be assigned in the “Transmitter control settings” menu with the Trainer connection switched off. Use the arrow buttons of the left or right-hand touch-key to select the transmitter controls 1 to 8 () to be transferred to the pupil, and briefly press the central SET button of the right-hand touch-key in each case, so that they switch from “T (Teacher)” ( ) to “P (Pupil)” ( ): Since it is very unlikely that a prepared (i. e. ready for use) Pupil transmitter will already be connected to a Teacher transmitter at this early stage of programming a Trainer system, the transmitter will generate appropriate visual and audible warnings when the switch is operated as part of the switch assignment procedure. You should therefore re-open the switch once you have assigned it: TRAINER/Teach P T TRAINER/Pupil 1 2 3 4 5 6 7 8 N/A SW: 9 BIND: –P T 1 2 3 4 5 6 7 8 N/A SW: ––– BIND: You still have to assign a Trainer transfer switch on the right of the screen so that you can actually transfer control to the Pupil. This is accomplished by using the arrow Note: The switch assignment procedure described above determines which transmitter provides the Teacher function, and which provides the Pupil function. For this reason a switch must NEVER be assigned to the Pupil transmitter in this menu. To underline this, the menu headline switches from “TRAINER / pupil” to “TRAINER / teacher” as soon as a switch is assigned. The model to be controlled by the pupil must be programmed completely in a model memory of the mx16 HoTT Teacher transmitter, i. e. with all its functions including trims and any mixer functions. The HoTT receiver in the model must also be “bound” to the Teacher transmitter, since it is this transmitter which actually controls the model in Pupil mode - even in Trainer mode operations. The mx-16 HoTT Teacher transmitter MUST ALWAYS BE SWITCHED ON FIRST. ONLY THEN MAY THE CONNECTING LEAD BE PLUGGED INTO IT. If you neglect this, the RF module will not be activated. The mx-16 HoTT Teacher transmitter can be linked to any suitable Pupil transmitter - even those operating on the “classic” 35 / 40 MHz band. However, if the connection at the pupil end is NOT made using a two-pole DSC socket, but instead - for example - using a three-pin Trainer socket from the Graupner range, the basic requirement for a correct connection with a Pupil transmitter is that PPM (18 or 24) modulation must ALWAYS be set on the Pupil transmitter, regardless of the modulation used by the Teacher transmitter. Pupil transmitter settings The model to be controlled by the pupil must be programmed completely in a model memory of the Teacher transmitter, i. e. with all its functions including trims and any mixer functions, and the HoTT receiver in the model must be “bound” to the Teacher transmitter. In principle, however, an mx-16 HoTT Pupil transmitter can also be linked to a Teacher transmitter operating on the “classic” 35 / 40 MHz band. The Pupil transmitter can be virtually any transmitter from the former and current Graupner range with at least four control functions. More information on this is available in the main FS catalogue, and on the Internet under www.graupner.de/en. Some transmitters will need to be retro-fitted with the appropriate module in order to act as the Pupil transmitter. This should be connected to the transmitter circuit board as described in the installation instructions supplied in the set. Information on the Pupil module required can be found in the main Graupner FS catalogue and on the Internet at www.graupner.de/en. The Pupil transmitter must be connected to the Teacher transmitter using the appropriate lead - see next double page. The control functions of the Pupil transmitter MUST act directly on the control channels, i. e. the receiver outputs, without the intervention of any mixers. If you are using an “mc” or “mx” series transmitter, it is best to set up a free model memory in the Pupil transmitter with the required model type (“Fixed-wing” or “Helicopter”). Assign the model name “Pupil” to the memory, and set up the stick mode (Mode 1 … 4) and “Throttle min. forward / back” to suit the pupil’s preference. All the other settings should be left at the appropriate default values. If you select the “Helicopter” model type, the throttle / collective pitch direction and idle trim must also be set accordingly on the Pupil transmitter. All other functions, including mixer and coupling functions, are carried out by the Teacher transmitter, which transmits them to the receiver in the model. If you are using an mx-20 or mc-32 HoTT Pupil transmitter, it is also necessary to match the type of modulation to the numbers of the control channels to be transferred; this is carried out in the “DSC output” line of the “Basic model settings” menu. For example, “PPM10” modulation carries control channels 1 … 5, and its signal packet only contains control channels 1 … 5 - but not channel 6. If you also wish the pupil to be able to use this channel, then you must select a type of modulation which includes it! If you are using a “D” or “FM” type transmitter, you should check the servo directions and stick mode, and alter them by re-connecting the appropriate leads if required. All mixers should be switched off or set to “zero”. When assigning the control functions the usual conventions should be observed: Channel Function 1 Throttle / Collective pitch 2 Aileron / Roll 3 Elevator / Pitch-axis 4 Rudder / Tail rotor If you wish to transfer other control functions to the Pupil transmitter, in addition to the functions of the two dual-axis sticks (1 … 4), then you will need to assign additional transmitter controls in the Pupil transmitter’s “Transmitter control settings” menu to those inputs which correspond to transmitter control numbers 5 … 8, as released in the Teacher transmitter’s “Trainer” menu. Program description: Trainer system 155 Important: • If you forget to assign a transmitter control, then the servo or servos concerned will remain in the centre position when control is transferred to the Pupil transmitter. • The Pupil transmitter must always be operated in PPM mode, regardless of the type of RF link between the Teacher transmitter and the model. • If the Pupil transmitter is connected using a DSC socket, then you should ALWAYS leave the Pupil transmitter’s On / Off switch at the “OFF” position, as this is the only way to ensure that the Pupil transmitter module does not generate an RF signal even when the DSC lead is plugged in. Trainer mode operations Connect the two transmitters using the appropriate lead; see the overview on the next page: connect the plug marked “M” (Master) to the socket on the Teacher transmitter, and the plug marked “S” (Student) (not present on all leads) to the appropriate socket on the Pupil transmitter. Important notes: It is essential to check that all func• tions are transferred correctly to the prepared model BEFORE initiating Trainer mode operations. • If you are using a Trainer lead with three-pole barrel connectors, on no account connect one of the ends marked “S” or “M” to a DSC system socket, as it is not suitable for this purpose. The DSC socket is only suitable for leads fitted with twopole barrel connectors. 156 Program description: Trainer system Checking the system Operate the assigned Trainer transfer switch: • If the screen display changes from „T“ to „P“, the Trainer system is working properly. • However, if the central LED flashes blue / red at a high rate, and at the same time the transmitter emits audible signals, then there is a problem with the connection between Pupil and Teacher transmitter. At the same time the following warning appears in the base display … no student signal … and in the “Trainer” menu the display changes to “-P” on the left. If this should happen, note that all the functions automatically remain under the control of the Teacher transmitter, regardless of the position of the Trainer transfer switch; this ensures that the model is not out of control at any time. Possible errors: • Pupil transmitter not ready • The interface in the Pupil transmitter, which replaces the RF module, is not connected correctly • Incorrect cable connection: see next section for cable selection • Pupil transmitter not set to PPM (10, 18, 24) mode. Further possible errors: • Teacher transmitter and HoTT receiver in trainer model not correctly “bound”. Trainer leads 4179.1 For Trainer mode operations between any two Graupner transmitters equipped with a DSC socket - identifiable by two-pole barrel connectors at both ends. 3290.7 Trainer lead for connecting a Teacher transmitter with DSC socket (e. g. mx-16 HoTT), or a transmitter retro-fitted with the optional DSC module, Order No. 3290.24, to a Graupner Pupil transmitter with opto-electronic Pupil socket - identifiable by the letter “S” at the end with the three-pole barrel connector. 3290.8 Trainer lead for connecting a Pupil transmitter with DSC socket (e. g. mx-16 HoTT) or a transmitter retro-fitted with the optional DSC module, Order No. 3290.24, to a Graupner Teacher transmitter with opto-electronic Teacher socket - identifiable by the letter “M” at the end with the three-pole barrel connector. For more detailed information about the leads and modules for the Teacher and Pupil transmitters listed on this page, please refer to the operating instructions supplied with your transmitter, the main Graupner FS catalogue, or the Internet at www.graupner.de/en. Trainer mode operations with the mx-16 HoTT transmitter Due to the constant expansion of our range of products please visit the Internet at www.graupner.de/en for the latest information. mx-16 HoTT Teacher transmitter mx-16 HoTT Pupil transmitter Trainer lead, Order No. 4179.1 Trainer lead, Order No. 3290.8 Trainer lead, Order No. 3290.7 Trainer lead, Order No. 4179.1 M Teacher transmitter with DSC socket mx-12 HoTT, mx-16 HoTT, mx-20 HoTT mx-32 HoTT mc-16 HoTT mc-20 HoTT and mc-32 HoTT S Teacher transmitter with Teacher module Order No. 3290.2, 3290.19, 3290.22 mc-19 to mc-24, mx-22(iFS), mx-24s Pupil transmitter with DSC socket mx-12 HoTT, mx-16 HoTT, mx-20 HoTT mx-32 HoTT mc-16 HoTT mc-20 HoTT and mc-32 HoTT Pupil transmitter with Pupil module Order No. 3290.3, 3290.10, 3290.33 D 14, FM 414, FM 4014, FM 6014, mc-10 … mc-24, mx-22(iFS), mx-24s Note: These lists represent the transmitters and transmitter combinations which are possible at time of going to press. Program description: Trainer system 157 Wireless HoTT system The mx-16 HoTT Trainer system can also be operated by wireless means. In this case the Teacher transmitter is “connected” to a Pupil transmitter as described in the following section. However, the trainer model must first be bound to the PUPIL transmitter. This configuration is possible between transmitters which feature the “BIND:” option in the “Trainer” menu. mits them to the receiver in the model. When assigning the control functions the usual conventions should be observed: Channel Function 1 Throttle / Collective pitch 2 Aileron / Roll Preparations for Trainer mode operations 3 Elevator / Pitch-axis Teacher transmitter The trainer model must be programmed completely, i. e. with all its functions including trims and any mixer functions, in a model memory of the HoTT Teacher transmitter. This means that it must be possible to control the trainer model fully, without restriction, by the Teacher transmitter. However, the preparations are concluded by binding the training model to the Pupil transmitter; you will find a detailed description of the binding procedure on pages 80 and 88. 4 Rudder / Tail rotor Pupil transmitter If you are using an “mc” or “mx” series transmitter, it is best to set up a free model memory in the Pupil transmitter with the required model type (“Fixed-wing” or “Helicopter”). Assign the model name “Pupil” to the memory, and set up the stick mode (Mode 1 … 4) and “Throttle min. forward / back” to suit the pupil’s preference. All the other settings should be left at the appropriate default values. If you select the “Helicopter” model type, the throttle / collective pitch direction and idle trim must also be set accordingly on the Pupil transmitter. All other functions, including mixer and coupling functions, are carried out by the Teacher transmitter, which trans158 Program description: Trainer system If you wish to transfer further control functions to the Pupil transmitter, i.e. in addition to the functions of the two dual-axis stick units (1 … 4), then you will need to assign transmitter controls to those inputs which correspond to the function or transmitter control inputs 5 … 8, as selected in the Teacher transmitter’s “Trainer” menu; this has to be carried out in the Pupil transmitter’s “Transmitter control settings” menu. Important: If you should forget to assign a transmitter control at the Pupil end, the servo or servos concerned will remain at their centre position when control is transferred to the Pupil transmitter. Preparing the Teacher and Pupil transmitters Once you have bound the trainer model to the Pupil transmitter, the Teacher transmitter should also be switched on. Now use the arrow buttons or the left or right-hand touch-key to leaf through on both transmitters to the “Trainer” menu point in the multi-function menu: ser vo set. D/R expo wing mixer ser vo disp fail-safe teach/pupi contr set. phase trim free mixer basic sett telemetr y info disp ser vo set. D/R expo free mixer ser vo disp fail-safe teach/pupi contr set. heli mixer swashp.mix basic sett telemetr y info disp Touch the central SET button of the right-hand touch-key to open the following menu point: TRAINER/Pupil –P T 1 2 3 4 5 6 7 8 N/A SW: ––– BIND: The illustration above shows the initial state of this menu: no transmitter controls have been released to the Pupil ( ), and no switches have been assigned (SW: --- bottom right and -S on left of illustration). Pupil transmitter Use the arrow buttons of the left or right-hand touch-key to move the marker / cursor to the input field marked “Bind”. If a switch is displayed adjacent to “SW” on the right, then it is essential to erase this: see the following illustration: –P T TRAINER/Teach TRAINER/Pupil TRAINER/Pupil P T –P T 1 2 3 4 5 6 7 8 SW: ––– BIND: N/A 1 2 3 4 5 6 7 8 N/A SW: ––– BIND: Teacher transmitter Up to eight of the Teacher transmitter’s (“Teacher”) transmitter control functions can be transferred to the Pupil transmitter (“Pupil”), either individually or in any combination. For this reason the bottom line of the screen, marked “L”, indicates those function inputs which are permanently associated with control functions 1 … 4 (dual-axis stick functions on fixed-wing models and helicopters), as well as the freely assignable inputs 5 … 8 of the “Transmitter control settings” menu. You still have to assign a Trainer transfer switch on the right of the screen so that you can actually transfer control to the Pupil. This is accomplished by using the arrow buttons of the left or right-hand touch-key to place the marker frame next to “SW” at bottom left, and assign a switch as described on page 49. We recommend that you use one of the two momentary switches SW 1 or SW 9 as the transfer switch, to ensure that the Teacher transmitter can regain control instantly at any time: Note: In principle it makes no difference which individual transmitter controls are assigned to the inputs which are to be transferred to the pupil. However, they can only be assigned in the “Transmitter control settings” menu with the Trainer connection switched off. Use the arrow buttons of the left or right-hand touch-key to select the transmitter controls 1 to 8 () to be transferred to the pupil, and briefly press the central SET button of the right-hand touch-key in each case, so that they switch from “T (Teacher)” ( ) to “P (Pupil)” ( ): TRAINER/Teach –P T No student signal 1 SW: 9 BIND: 1 2 3 4 5 6 7 8 N/A SW: 9 BIND: Note: The switch assignment procedure described above determines which transmitter provides the Teacher function, and which provides the Pupil function. For this reason a switch must NEVER be assigned to the Pupil transmitter in this menu. To underline this, the menu headline switches from “TRAINER / pupil” to “TRAINER / teacher” as soon as a switch is assigned. Now use the arrow buttons of the left or right-hand touch-key to move the marker to “BIND: N/A” on the right: TRAINER/Teach 7 8 N/A Since it is very unlikely that a prepared (i. e. ready for use) Pupil transmitter will already be connected to a Teacher transmitter at this early stage of programming a Trainer system, the transmitter will generate appropriate visual and audible warnings when the switch is operated as part of the switch assignment procedure. You should therefore re-open the switch once you have assigned it: P T 1 2 3 4 5 6 7 8 N/A SW: 9 BIND: Binding the Pupil transmitter to the Teacher transmitter Note: During the binding procedure the distance between the two transmitters should not be too great. You may need to change the relative position of the two transmitters and initiate the Program description: Trainer system 159 binding process a second time. TRAINER/Pupil First initiate the “BINDING” process at the Pupil transmitter by briefly pressing the central SET button of the right-hand four-way button … –P T 1 2 3 4 5 6 7 8 SW: ––– BIND: ON TRAINER/Pupil –P T 1 2 3 4 5 6 7 8 SW: ––– BIND: BINDING … and immediately afterwards that of the Teacher transmitter: TRAINER/Teach P T 1 2 3 4 5 6 7 8 SW: 9 BIND: BINDING As soon as this process is concluded, both screens display “ON” instead of the flashing message “BINDING”: TRAINER/Teach P T 1 2 3 4 5 6 7 8 SW: 9 BIND: ON 160 Program description: Trainer system GRAUBELE #01 RFC–Teach 5.2V 2:22h 0:00 stop flt 0:00 «normal » HoTT P 5.5V This concludes the binding process, and you can return to the basic display of both transmitters, and start trainer mode operations - once you have checked the operation of all the functions. However, if neither transmitter, or only one of the transmitters, displays “ON”, indicating that the binding procedure has failed, try changing the relative position of the two transmitters, and repeat the whole procedure. … and that of the Pupil transmitter typically like this: Important note: It is essential to check that all functions are transferred correctly to the prepared model BEFORE initiating Trainer mode operations. If it should occur that the link between the Teacher and Pupil transmitters is lost during Trainer mode operations, note that the Teacher transmitter automatically assumes control of the model. In this situation, if the Trainer change-over switch is in the “Pupil” position, then the central LED on the Teacher transmitter starts to flash blue / red for the duration of the signal loss, and the transmitter emits audible warning signals. At the same time “RFC-” flashes in the basic display, and the following warning is displayed: During … Trainer mode operations … it is no problem for the Teacher and Pupil to stand a little way apart. However, you should never exceed a distance of 50 m (this is known as the call range), and no other persons should stand between the Teacher and Pupil, as this could reduce the effective range. In this mode of operation the basic display of the Teacher transmitter looks like this … GRAUBELE #09 RFC-Pupil 4.9V 1:11h stop flt 0:00 0:00 HoTT no student signal However, if only “RFC-” flashes in the basic transmitter display, and - relatively quiet - audible signals are heard … GRAUBELE #01 RFC–Teach 5.2V 2:22h 0:00 stop flt 0:00 «normal » HoTT P 5.5V … then this indicates that the Pupil signal has also been lost, but the Trainer transfer switch is in the “Teacher” position. In either situation your first recourse should be to reduce the distance between the two transmitters. If this does not help, land the model immediately, and seek the cause. However, if both transmitters are operating with the receiving system switched off, then the “familiar” symbol appears in the basic display of the Teacher transmitter instead of the two symbols. buttons of the left or right-hand touch-key … TRAINER Wireless Link ACT INH … and confirm your choice by briefly pressing the central SET button of the right-hand touch-key, this resets that transmitter to “normal” operation. In this case you will have to repeat the binding process with a Teacher or Pupil transmitter as and when required. Resuming Trainer mode operations If - for whatever reason - one or both transmitters are switched off during a Trainer mode session, then the screen displays the following query when the transmitter or transmitters are switched on again: TRAINER Wireless Link ACT INH Touch the central SET button of the right-hand touch-key to confirm “ACT(ivate)”, or alternatively wait for about two seconds until the message disappears; the last link you created with a Teacher or Pupil transmitter is now restored. However, if you select “INH(ibit)” using one of the arrow Program description: Trainer system 161 Info Display Date, time, transmitter ID and memory card Use the arrow buttons of the left or right-hand touch-key to leaf through to the “Info” menu point of the multi-function menu: ser vo set. D/R expo wing mixer ser vo disp fail-safe teach/pupi contr set. phase trim free mixer basic sett telemetr y info disp ser vo set. D/R expo free mixer ser vo disp fail-safe teach/pupi contr set. heli mixer swashp.mix basic sett telemetr y info disp Touch the central SET button of the right-hand touch-key to open the menu point: ABCDEF12 RFID 1.234 firmware ver. 2012/03/01(THU) date 11:22:33s time 0Mb SD-CARD 0Mb available 0% This menu displays transmitter-specific information, some of which can be altered where necessary and sensible. Use the arrow buttons of the left or right-hand touch-key to select the appropriate line, then touch the central SET button of the right-hand touch-key. In the 162 Program description: Info display highlighted value field you can now alter the default value using the arrow buttons of the right-hand touchkey, and conclude your input with a further touch of the central SET key. In some circumstances our Service department may also ask you for the version number. Date ABCDEF12 RFID 1.234 firmware ver. 2012/03/01(THU) date 11:22:33s time 0Mb SD-CARD RFID ABCDEF12 RFID 1.234 firmware ver. 2012/03/01(THU) date 11:22:33s time 0Mb SD-CARD This line displays the transmitter’s identification number. This number is specific to the transmitter, and is only issued once for each transmitter. During the binding process this ID is transmitted to the receiver (amongst other data), so that it is able at any time to identify the radio signals of “its” transmitter. Version ABCDEF12 RFID 1.234 firmware ver. 2012/03/01(THU) date 11:22:33s time 0Mb SD-CARD This line displays the version number of the transmitter software currently installed. By comparing the number shown here with the update version available for the same product on the Internet at www.graupner.de/en you can judge whether an update to the transmitter’s operating system is necessary and useful. If necessary, select this line using the arrow buttons ** of the left or right-hand touch-key, then select the month or day field. A brief press of the central SET button of the right-hand touch-key activates the corresponding value field, and you can then set the year, month or day using the arrow buttons of the right-hand touch-key. A further brief press of the central SET button of the right-hand touch-key concludes the input process. The available range of years runs from 2000 to 2135. The weekday, shown in brackets at far right in abbreviated form, is automatically generated from the date. Notes: • The date and time of day can also be set using the PC program available for the corresponding product on the Internet at www.graupner.de/en; this requires that the transmitter should be connected to a PC in the appropriate manner. • The date and time are protected from data loss due to power failure - for example, when the battery is swapped - by a user-replaceable buffer battery. Time SD card ABCDEF12 RFID 1.11 firmware ver. 2011/03/11 (FRI) date 11:22:33s time 0MB SD-CARD If necessary, you can select this line, and the minutes field, using the arrow buttons of the left or right-hand touch-key. A brief press on the central SET button of the right-hand touch-key activates the corresponding value field, and you can then adjust the hours or minutes using the arrow buttons of the right-hand touch-key. A further brief press on the central SET button of the righthand touch-key concludes the entry process. Note that the seconds display cannot be set directly; instead it can be reset to “00” with a touch of the central SET button of the right-hand touch-key. Notes: • The date and time of day can also be set using the PC program available for the corresponding product on the Internet at www.graupner.de/en; this requires that the transmitter should be connected to a PC in the appropriate manner. • The date and time are protected from data loss due to power failure - for example, when the battery is swapped - by a user-replaceable buffer battery. ABCDEF12 RFID 1.234 firmware ver. 2012/03/01(THU) date 11:22:33s time 2048Mb SD-CARD This line displays the storage capacity in MB of a memory card installed in the transmitter. Depending on the memory capacity of the micro-SD or micro-SDHC memory card fitted in the transmitter, it may take several minutes for the display to show the correct value after you switch the transmitter on. 2012/03/01(THU) date time 11:22:33s SD-CARD 2048Mb available 1234Mb 60% As already mentioned, it may take a certain amount of time for the available memory to be displayed after you switch the transmitter on, depending on the total capacity of the installed memory card. available 1.234 firmware ver. 2012/03/01(THU) date time 11:22:33s 2048Mb SD-CARD available 1234Mb Display of the available memory in MB. As already mentioned, it may take a certain amount of time for the available memory to be displayed after you switch the transmitter on, depending on the total capacity of the installed memory card. The next line down displays the available memory in relation to the total memory capacity: Program description: Info display 163 mx-16 HoTT programming techniques Preparation, using a fixed-wing model aircraft as an example Programming model data into an mx-16 HoTT … … is easier than it might appear at first sight. There is one basic rule which applies equally to all programmable radio control transmitters, and not just to the mx-16 HoTT: if the programming is to go “smoothly” and the systems work as expected, the receiving system components must first be installed correctly in the model, i. e. the mechanical systems must be firstrate. This means: ensure that each servo is at its correct neutral position when you fit the output lever or disc and connect the linkage to it. If you find this is not the case, correct it! Remove the output arm, rotate it by one or more splines and secure it again. If you use a servo tester, e. g. the RC-Tester, Order No. 2894.12, to centre the servos, you will find it very easy to find the “correct” position. Virtually all modern transmitters offer facilities for offsetting the neutral position of servos, but this is no substitute for a correct mechanical installation; this function is only intended for fine tuning. Any substantial deviation from the “0” position may result in additional asymmetry when the signal undergoes further processing in the transmitter. Think of it this way: if the chassis of a car is distorted, you may be able to force the vehicle to run straight by holding the steering wheel away from centre, but it does not make the chassis any less bent, and the basic problem remains. Another important point is to set up the correct control travels wherever possible by using the appropriate linkage points in the mechanical system; this is much more efficient than making major changes to the travel settings at the transmitter. The same rule applies: electronic travel adjustment facilities are designed primarily to compensate for minor manufacturing tolerances in the 164 Programming example - fixed-wing model servos and for fine adjustment, and not to compensate for poor-quality construction and defective installation methods. If two separate aileron servos are installed in a fixedwing model aircraft, the ailerons can also be employed as flaps by deflecting both of them down, and as airbrakes by deflecting both of them up - simply by setting up a suitable mixer (see the section starting on the next double page). Such systems are generally more often used in gliders and electric gliders than in power models. braking effect of the crow system is provided primarily by the down-movement of the flaps rather than the up-movement of the ailerons, so in this case the servo output arms should be angled aft, i. e. offset towards the trailing edge of the wing, as this makes greater travel available for the down-movement. When this combination of lowered flaps and raised ailerons is used, the ailerons should only be raised by a moderate extent, as their primary purpose in this configuration is to stabilise and control the model rather than act as brakes. You can “see” the difference in terms of braking effect by deploying the crow system, then looking over and under the wing from the front: the larger the projected area of the deflected control surfaces, the greater the braking effect. Outboard ailerons In such cases the servo output arms should be offset forward by one spline relative to the neutral point, i. e. towards the leading edge of the wing, and fitted on the servo output shaft in that position. The mechanical differential achieved by this asymmetrical installation takes into account the fact that the braking effect of the up-going ailerons increases with their angle of deflection, and this means that much less travel is usually required in the down-direction than the up-direction. Similar reasoning applies to the installation of the flap linkage when separately actuated flap servos are installed, designed to be used in a butterfly (crow) system. Here again an asymmetrical linkage point is useful. The Inboard camber-changing flaps (This type of asymmetrical installation of the servo output arms can also make sense when you are setting up split flaps or landing flaps on a power model.) Once you have completed your model and set up the mechanical systems accurately in this way, you are ready to start programming the transmitter. The instructions in this section are intended to reflect standard practice by describing the basic model settings first, and then refining and specialising them to complete the set-up. After the initial test-flight, and in the course of continued test-flying, you may need to adjust one or oth- er of the model’s settings. As your piloting skills improve and you gain experience, it is very likely that you will feel the need to try out refinements such as expanded control systems, and to cater for these requirements you may find that the text deviates from the obvious order of options, or that one or other of the options is mentioned more than once. On the other hand, it can certainly occur that not every step described in these instructions is relevant to a particular model, just as some users might miss the description of a particular step which is relevant to his model only … Regardless of all this, it is worthwhile thinking carefully about a sensible layout of the transmitter controls at this point, just before you start programming the model data. If the model in question is one with the emphasis on “power” - whether the power of an electric motor or internal-combustion engine (glow motor) - you will probably encounter few problems in this matter, because the two stick units are primarily employed to control the four basic functions “power control (= throttle)”, “rudder”, “elevator” and “aileron”. Nevertheless, you still have to call up the … “Base settings” menu (pages 74 … 81) GRAUBELE mod name stick mode 1 no motor at C1 CH8 delay yes tail type normal … and define your preferred throttle direction, i. e. throttle minimum forward (“Idle forward”) or back (“Idle back”), because the program’s default setting is “none” (i. e. no motor) when you first set up a model memory. The basic difference between “none” or “none/inv” and “throttle min. forward / back” is the effect of the Ch 1 trim. The trim is effective over the full stick travel if “none (/ inv)” is entered, but it only affects the idle range if you enter “throttle min. forward or back”. However, it also affects the “direction of effect” of the Ch 1 stick, i. e. if you switch from “forward” to “back” or vice versa, you do not also have to reverse the direction of the throttle (or brake) servo. For safety reasons you will also see a warning message, and hear an audible warning, if you switch the transmitter on with the throttle stick positioned towards “full-throttle” - but only if you have already set “throttle min. forward or back”. stop throttle too high ! 5.2 0:33h M 0:00 0:00 #01 HoTT 0.0V Your choice of “none” (no motor) or “throttle min. forward or back” also affects the range of mixers available in the “Fixed-wing mixers” menu. The mixers “Brake NN *” are only present if you choose “none” (no motor) or “none/inv”; otherwise they are suppressed. In addition to these basic matters you will certainly need to consider carefully how best to control any “auxiliary functions” present on your model. In contrast, if your model is a glider or electric glider the whole situation may be rather different. The immediate question is: what is the best way of operating the motor and braking system? Now, some solutions have proved to be practical, and others less so. For example, it is not a good idea to be forced to let go of one of the primary sticks in order to extend the airbrakes or deploy the crow braking system when your glider is on the landing approach. It surely makes more sense to set up switchable functions for the Ch 1 stick (see example 4 on page 172), or to assign the braking system to the throttle stick, and shift the motor control to a slider - or even a switch. With this type of model the electric motor is often little more than a “self-launching system”, and is used either to haul the model into the sky at full power, or to pull it from one area of lift to the next at, say half-power, and for such models a three-position switch is usually quite adequate. If the switch is positioned where you can easily reach it, then you can turn the motor on and off without having to let go of the sticks - even on the landing approach. Incidentally, similar thinking can be applied to flap control systems, regardless of whether they are “just” the ailerons, or full-span (combination) control surfaces which are raised and lowered in parallel. Once you are satisfied that all these preparations have been completed successfully, programming can commence. * NN = Nomen Nominandum (name to be stated) Programming example - fixed-wing model 165 First steps in programming a new model Example: non-powered fixed-wing model aircraft When programming a new model you should start by activating the … “select model” sub-menu (page 70) … in the “Model memory” menu. Use the arrow buttons of the left or right-hand touch-key to select a free model memory … 01 02 03 04 05 06 free free free free free R08 … then touch the central SET button of the right-hand touch-key. You are now immediately requested to select the type of model you wish to program. Sel model type • Once you have called up the “Model select” option it is not possible to interrupt the process, i. e. you must choose one or other model type. Even if you switch off the transmitter at this point, you cannot avoid this select procedure. However, if you make a mistake you can always correct it simply by erasing the model memory. • If the battery voltage is too low, you will not be able to change model memories for safety reasons. The screen then displays an appropriate message: not possible now voltage too low Once you have overcome this initial hurdle, you may need to bind the receiver installed in the model to this model memory in the … “Base settings” menu (pages 74 … 81) This is accomplished by moving to the “rx bind” line: ( empty mod mem ) Since in this example we are setting up a fixed-wing model, we simply confirm the fixed-wing model symbol with a brief press on the central SET button of the righthand touch-key; the screen now reverts to the basic display. Notes: • Naturally you can also use the pre-defined model memory 01 for programming your first model; this is the “fixed-wing model” type by default. 166 Programming example - fixed-wing model phase 2 phase 3 phase 4 receiv out rx bind takeoff ––– speed ––– landing ––– ––– button of the right-hand touch-key, you automatically move to this line: In this line you trigger the bind process between model memory and receiver, as described in detail on pages 80. Without this step you cannot address the receiver. The next step is to press the arrow button of the left-hand or right-hand four-way touch-key to move up into the first line, where you can start the actual model programming in the “mod name” line: mod name stick mode motor at C1 CH8 delay tail type When you confirm the model selection the following message appears in the basic display for a few seconds: BIND N/A OK If you confirm your choice by briefly pressing the SET no yes normal At this point you can enter the “Model name” by touching the central SET button of the right-hand touch-key in order to move to the character table: 0123456789 : ; ? ABCDEFGHIJKLMNO PQRSTUVWXYZ model name Note: 1 GRAUB You should also check the settings for “Stick mode” and “Motor at Ch 1” and change them if necessary: • “none”: The brake system is “retracted” at the forward position of the throttle / brake stick; the “Ch8 delayed” option and the “Brake NN*” mixers in the “Wing mixers” menu are activated. * NN = Nomen Nominandum (name to be stated) In the “Aileron / flap” line of the “Basic settings” menu you can select “1AIL”, “2AIL” and “1/2AIL 1/2FL”, and in the “Wing mixer” menu the mixer “Brake NN*”, plus all mixers “from” and “to” flaps, are activated. The warning message “Throttle too high” - see pages 36 and 67 - and the “Motor stop” option in the “Basic settings” menu are disabled. • “none/inv”: The brake system is “retracted” at the back position of the throttle / brake stick; the “Ch8 delayed” option and the “Brake NN*” mixers in the “Wing mixers” menu are activated. In the “Aileron / flap” line of the “Basic settings” menu you can select “1AIL”, “2AIL” and “1/2AIL 1/2FL”, and in the “Wing mixer” menu the mixer “Brake NN*”, plus all mixers “from” and “to” flaps, are activated. The warning message “Throttle too high” - see pages 36 and 67 - and the “Motor stop” option in the “Basic settings” menu are disabled. • “Throttle min. forward or rear”: Ch1 trim takes effect forward or back, and the “Motor stop” option in the “Basic settings” menu is activated. If the throttle stick is too far towards full-throttle when the transmitter is switched on, the warning “Throttle too high” appears to alert you to this; see pages 36 and 67. In the “Basic settings” menu the “Ch8 delayed” option and the “Brake N.N.*” mixers in the “Wing mixers” menu are disabled. Note: As mentioned previously, selecting “motor” or “no motor” also affects the range of mixers available in the “Fixed-wing mixers” menu. For this reason we shall initially consider “none” (no motor) in the following programming example. In the next two lines you select the basic arrangement of the servos in the model, and inform the transmitter of your choice: stick mode motor at C1 CH8 delay tail type aile/flap 1 no yes normal 2aile tail type: “normal”, “V-tail”, “delt/FlW” or “2elev sv” aile/flap: 1 or 2 aileron servos and 0, 1 or 2 flap servos At this juncture - if not before - you should check that the servos are connected to the receiver in the standard Graupner sequence: Receiver power supply Auxiliary function Flap servo or left flap servo Right aileron servo Rudder servo or V-tail Elevator servo or V-tail Aileron servo or left aileron servo Airbrakes or throttle / speed controller or speed controller (electric) Right flap servo Notes: • If you set up a V-tail, but the “up / down” and / or “left / right” functions work the wrong way round, please refer to the table in the right-hand column on page 63 for the remedy. The same procedure can be used if you set up flaperons (superimposed ailerons and flaps), and they work the wrong way round. • The following settings apply to a model with a “normal” tail and no motor (“none”); if your model has a V-tail, the settings can be adopted virtually unchanged. However, if the model is a delta or flying wing, the situation is not quite so straightforward. A special programming example covering this model type will be found in the section starting on page 178. In the … “Servo settings” menu S1 S2 S3 S4 S5 rev 0% 0% 0% 0% 0% cent (page 92) 100% 100% 100% 100% 100% 100% 100% 100% 100% 100% trav + … ... you can set various parameters relating to the servos, i. e. “direction of rotation”, “neutral setting” and “servo travel”, to suit the requirements of the model. By “requirements” we mean adjustments to servo centre and servo travel which are needed to compensate for minor tolerances in servos and slight inaccuracies on the model itself. Programming example - fixed-wing model 167 Note: Note: The facilities provided in this menu for setting asymmetrical servo travels are NOT intended as a means of setting up differential travel on ailerons and / or camber-changing flaps. There are more suitable options for this in the form of specific functions in the “Fixed-wing mixers” menu; see the first two options in the picture on the right. This menu will show a varying range of options depending on the information you have entered in the “Base settings” menu. In the illustration above, the full range is shown, as generated by the entries “2AIL 2FL” in the “Ail/Flap” line, and “none (/inv) in the “Motor at Ch 1” line. Once you have completed the settings described thus far, a fixed-wing or powered model aircraft (the latter if you enter the idle direction of the throttle stick in the “Motor at Ch 1” line of the “Base settings” menu) will, in principle, fly. However, there are no “refinements” in this set-up, and it is the refinements which will give you more long-term pleasure in your flying. Assuming that you are already capable of controlling your model safely, it’s time to get a taste of these extra facilities; to this end we now move on to the … “Wing mixers” menu diff aile. diff flaps ail rudd ail flaps brak elev brak flap brak aile elev flap elev aile elev flap aile flap diff–red (pages 108 … 113) 0% 0% 0% 0% 0% 0% 0% 0% 0% 0% 0% 0% ––– ––– ––– ––– ––– ––– ––– ––– ––– ––– ––– 168 Programming example - fixed-wing model Of particular interest at the moment are “AIL-Diff.” (aileron differential) and the “AIL RUD” (aileron rudder) mixer, sometimes known as a combi-switch, and perhaps the mixers “Brake AIL” and “Brake FLAP”. As already described in detail on pages 109 and 110, the purpose of “AIL-Diff.” (aileron differential) is to eliminate adverse yaw. When a model aircraft turns, the down-going aileron produces more drag than the up-going one if both move through the same angle, and this causes the model to yaw in the opposite direction to the turn. This can be eliminated by setting differential aileron travel. A value between 20% and 40% is usually a good starting point, but the “perfect” setting nearly always has to be established by practical testing. The same applies to the “FL-Diff.” (flap differential) option if your model also features two camber-changing flap servos, assuming that the flaps are also to be used as ailerons, e. g. using the “AIL FL” mixer. The “AIL RUD” (aileron rudder) mixer serves a similar purpose, but also makes many models generally easier to handle when turning. A value of around 50% is usually a practical starting point. However, it is advisable to be able to switch this function off, particularly if you have ambitions as an aerobatic pilot; this is done by assigning a physical switch to the mixer (for example, the writer switches this mixer off “automatically” when he switches into the “Speed” flight phase, simply by assigning the same switch to both options). It is usually only necessary to set up a “Brake ELE” (brake elevator) mixer if your model suffers an excessive change of speed when you deploy the braking system. The danger is that you might need to retract the brakes again on the landing approach when you realise the model will “land short”; if its airspeed is too low when you retract the brakes, the model will just fall to the ground at that point. If you set up such a mixer it is important to test the setting at a safe height, and adjust the trim compensation if necessary. If you have selected “2AIL” or “2AIL 2FL” in the “Aileron / Flap” line of the “Base settings” menu … stick mode motor at C1 CH8 delay tail type aile/flap 1 no yes normal 2aile … and if you wish to be able to deflect both ailerons up using the throttle / brake stick (Ch 1), then a suitable value should be entered in the “Brake AIL” line. diff aile. ail rudd brak elev brak aile elev aile 0% 0% 0% 0% 0% ––– ––– ––– ––– ––– In principle the same applies to the “Brake FL” line, which also becomes available if you have selected “2AIL 2FL”, although the set value should cause the flaps to deflect as far as possible in the downward direction when the brake stick is operated. It is important to ensure that the servos do not strike their mechanical end-stops. To achieve this, you may need to limit the servo travel(s) for the servos concerned using the “LIMIT-” or “LIMIT+” line on the “RX SERVO” display page of the “Telemetry” menu. If the ailerons are set up to act as simple brakes, as described previously, or as part of the braking arrangement in a butterfly (crow) system, then you should always enter a value for “Diff.-Red.” (“differential reduction” - see page 113) - selecting 100% is the safe option here! Differential reduction means that aileron differential is suppressed proportionally only when you operate the airbrake stick. The purpose of this is to increase the down-going aileron travel on the landing approach, with the aim of improving aileron response. If the wing is equipped with two camber-changing flap servos in addition to two separately actuated ailerons, then the “AIL FL” (aileron flap) mixer transfers the aileron movements to the flaps; we suggest that the flaps should not follow the movement of the ailerons to a greater extent than about 50%. Note: If you have only installed one flap servo, you should leave this mixer at 0%. … 8) should be used for this. Note: We strongly recommend that you reduce the travel of the flaps to about 25% in the “Transmitter control settings” menu, as this gives finer control of the flap positions using the selected transmitter control. The remaining options in the “Fixed-wing mixers” menu are designed to provide further fine-tuning of multi-flap wing systems, and are largely self-explanatory. When you have completed the model-specific settings up to this point, you are probably ready to consider the model’s first flight. At this juncture you should certainly take the time to carry out a series of “dry runs”, i. e. check all the settings thoroughly while the model is still on the ground. Remember that a serious programming error may damage more than just the model. If you are not sure of any point, please ask an experienced model pilot for advice. “D/R Expo” menu (page 102) aile 122% elev 111% rudd 100% +11% +22% 0% DUAL EXPO 2 2 ––– … in order to adjust the overall set-up to suit your requirements and flying style. The Dual Rate function is used to adjust the relationship between stick travel and control surface travel (see page 102). However, if it is only the model’s control response around neutral which is too powerful for comfortable flying, i. e. the maximum travels are acceptable, then “Exponential” can be employed, either instead of Dual Rates or in addition to them. If a physical switch is assigned to this function, you can switch between two Dual Rate / Expo settings while the model is flying. If during the test phase you realise that one or other of the settings needs to be changed in order to tailor the model’s control response to your preferences - perhaps the servo travels are too great or too small overall - then we suggest that you turn to the … The “FL AIL” (flap aileron) mixer works in the opposite direction; depending on the layout of the model we suggest values between about 50% and 100% for this option. The flaps are controlled using the transmitter control or switch assigned to the input “E6”. Preferably, however, one of the rotary proportional controls (CTRL 6 Programming example - fixed-wing model 169 Including an electric power system when programming a model your speed controller to receiver output 8, moving to the … “Base settings” menu,(pages 74 … 81) … and setting the “Ch8 delayed” option to “no”: An electric power system can be controlled in various ways: The simplest method of including such a power plant in a model program is to use the throttle / brake stick (Ch 1). However, in the preceding programming instructions we have already reserved the Ch 1 transmitter control for the airbrakes, which means that we have to explore other possibilities for controlling the motor: one is to use the switchable solution described in the section starting on page 172, and another is to use an alternative transmitter control. A suitable option is one of the two three-position switches SW 4/5 or 6/7, and another is one of the rotary proportional controls CTRL 6 … 8. However, another alternative would be one of the two-position switches. The main reason for your choice ought to be that the switch is within easy reach of your fingers. Before we turn to the individual examples, it is very important to note that the “transition delay” which occurs when you change flight phases also affects other switching processes which are triggered simultaneously, for example motor ON / OFF. However, you may wish - especially in an emergency to be able to switch the motor off instantly, i. e. without the transition delay. In this case it is advisable to make use of the “Ch8 delayed yes / no” option in the “Base settings” menu. This is accomplished by connecting 170 Programming example - fixed-wing model GRAUBELE mod name stick mode 1 no motor at C1 no CH8 delay tail type normal Example 1 Using one of the rotary proportional controls CTRL 6 … 8 If one of these transmitter controls is used, the set-up is extremely easy. All you have to do is connect the speed controller to any of the receiver servo sockets 5 … 8 which is vacant. However, please bear in mind that outputs 2 + 5 and 6 + 7 may already be linked together, depending on the model type you have selected and the number of aileron and flap servos in your model. Connect your speed controller to the next vacant input, and assign one of the rotary proportional controls CTRL 6 … 8 - in our example CTRL 7 - to the selected input for example, “I8”. This is accomplished in the … “Transmitter control settings” menu (page 94) Use the arrow buttons of the left or right-hand touch-key to select the desired line. Touching the central SET button of the right-hand touch-key activates “Switch / transmitter control assignment”. Now turn the knob of the rotary proportional control: after a brief delay the entry “Transmitter control 7” will appear in the highlighted field: I5 I6 I7 I8 free free free ctrl 7 +100% +100% +100% +100% +100% +100% +100% +100% tr v + In the third column you can adjust servo travel to suit the speed controller you are using; alternatively you could use the “-Travel+” column in the … “Servo settings” menu S4 S5 S6 S7 S8 rev 0% 0% 0% 0% 0% cent (page 92). 100% 100% 100% 100% 100% 100% 100% 100% 100% 100% trav + The last stage is to check the settings, so move from the basic display to “Servo display”, typically by simultaneously touching the buttons of the left-hand touchkey: In the “OFF” position of the rotary control CTRL 7 the control channel you have selected - in this example channel “8” - should be at -100%, and at the “full-throttle” setting at +100%. Example 2 Using a two-position switch, SW 2, 3 or 8 This variant implements a pure ON / OFF function, and results in the motor starting “abruptly” … unless the speed controller you are using features what is known as a “soft start” function. At the receiving end you need either a simple electronic switch or - if you want a smoother motor start - a suitable speed controller. The settings for this arrangement are entered in the … “Transmitter control settings” menu (page 94) First check which receiver socket (5 or higher) is available for connection to your speed controller. If you have assigned two aileron servos in the “Base settings” menu, and if you have not connected any other auxiliary function, then this would be channel 6; if your model features two aileron servos and two flap servos, then channel 8 would be available for connecting the speed controller; the latter option is the one we wish to use in this example. First set the selected switch to the “OFF” position, then use the arrow buttons of the left or right-hand touch-key to select the desired line in the menu. Touch the central SET button of the right-hand touch-key to activate “Switch / transmitter control assignment”, then move the selected switch from the “OFF” position to the “ON” position. The highlighted field now shows the switch number together with a symbol which indicates the direction of switching: I5 free I6 free I7 free I8 3 +100% +100% +100% +100% +100% +100% +100% +100% tr v + In the third column you can adjust servo travel to suit the speed controller you are using; alternatively you could use the “Servo travel” column in the … “Servo settings” menu S4 S5 S6 S7 S8 rev 0% 0% 0% 0% 0% cent (page 92). 100% 100% 100% 100% 100% 100% 100% 100% 100% 100% trav + The last stage is to check the settings, so move from the basic display to “Servo display” by simultaneously touching the buttons of the left-hand touch-key: in the switch’s “OFF” position, the control channel you have selected - in our example this is channel “8” - should be at -100%, and at the “full-throttle” setting at +100%. Example 3 Using one of the three-position switches SW 4/5 or 6/7 This variant implements a three-stage solution for switching an electric motor on and off, and also results in an “abrupt “ motor start-up … unless the speed controller you are using features what is known as a “soft start” function. At the receiving end you need a suitable speed controller. First check which receiver socket (5 or higher) is available to connect your speed controller. If you have assigned two aileron servos in the “Base settings” menu, and if you have not connected any other auxiliary function, then this would be channel 6; if your model features two aileron servos and two flap servos, then channel 8 would be available for connecting the speed controller; the latter option is the one we will use in this example. Move to the … “Transmitter control settings” menu (page 94) … and use the arrow buttons of the left or righthand touch-key to select the desired line. Briefly press the central SET button of the right-hand touch-key to activate “Switch / transmitter control assignment”. Move the selected three-position switch; the highlighted field now shows the number of this transmitter control, for example “Transmitter control 9”. I5 I6 I7 I8 free free free ctrl 9 +100% +100% +100% +100% +100% +100% +100% +100% tr v + In the third column you can adjust servo travel to suit the speed controller you are using; alternatively you could use the “Servo travel” column in the … Programming example - fixed-wing model 171 Controlling the electric motor and butterfly (crow) system using the Ch 1 stick “Servo settings” menu S4 S5 S6 S7 S8 rev 0% 0% 0% 0% 0% cent (page 92). 100% 100% 100% 100% 100% 100% 100% 100% 100% 100% trav + The last stage is to check the settings, so move from the basic display to “Servo display” by simultaneously touching the buttons of the left-hand touch-key: in the (upper) “OFF” position of the three-position switch the control channel you have selected - in our example this is channel “8” - should be at -100%. If you now move the switch toggle to the centre position, the bar should be in the middle, and at the (lower) “full-throttle” setting it should be at +100%. 172 Programming example - fixed-wing model Example 4 Butterfly / crow system as landing aid: ailerons up, flaps down Before we start the programming of this fourth example, and turn our attention to expanding the basic programming we have already discussed, we need to consider briefly the position of the throttle / brake stick at “motor OFF” or “brake OFF”. Usually the Ch 1 stick is moved forward to open the throttle, and back to extend the brakes. However, if you adopt this “classic” configuration, and switch, say, from “motor OFF” (stick “back”) to the braking system, “full brake” would immediately be applied, and vice versa: if you switch from “brakes retracted” to power, this would instantly switch to “full power”. It is certainly possible to make a “virtue” out of this “vice”: a “glider pilot” - usually flying with “brakes retracted = forward” will only switch to motor “ON” when necessary, and then reduce power to suit the situation (and we hope - does not forget to move the Ch 1 stick back to the “forward” position when switching back). In contrast, a typical “power pilot” would probably operate with the reverse priority, i. e. he would only switch to “brake” when necessary, etc. In any case, it is possible to avoid these inter-connected effects by positioning the “zero point” of both systems so that they coincide. The above considerations mean that a “glider pilot” will probably prefer the “zero point forward” arrangement, while a “power pilot” might well decide on “zero point back”. The mx-16 HoTT transmitter can cope with whichever arrangement you prefer. However, the following section assumes that both “OFF” positions will be set to “forward”. If you prefer the alternative arrangement, there is no problem: the only difference compared with the version described here is that you would select “none/ inv” in the “Motor at Ch 1” line of the “Base settings” menu instead of “none”. All the other settings can be adopted as described. In the … “Transmitter control settings” menu (page 94) GRAUBELE mod name stick mode 1 no motor at C1 CH8 delay yes tail type normal … leave the “motor at Ch 1” line at “none” if you have set “Motor ON = forward”, or switch to “none/inv” if preferred. This is essential, otherwise the “Brake 1 NN *” mixers which we need will be suppressed in the “Fixed-wing mixers” menu. Important Note: As it is essential to set the motor to “none”, this also automatically disables the “Throttle too high” power-on warning! For this reason please take great care to set the Ch 1 stick to the correct position before you switch the receiving system on. The next step is to ensure that the speed controller connected to receiver output 1 is switched off “at the right end”. To accomplish this you may have to move to the … * NN = Nomen Nominandum (name to be stated) “Servo settings” menu S1 S2 S3 S4 S5 rev 0% 0% 0% 0% 0% cent (page 92) 100% 100% 100% 100% 100% 100% 100% 100% 100% 100% trav + … and reverse the direction of servo 1. For safety’s sake you should check this setting now, before you continue with the programming procedure. Take the transmitter and model to a location where it is safe to run the motor. Switch the transmitter on, and move the Ch 1 stick to the motor “OFF” position, i. e. either fully forward or back. Hold your model firmly, or ask a friend to hold it for you. Check that the propeller is free to rotate without causing havoc, then connect the flight battery and switch your model’s receiving system on. If the motor does NOT run when the stick is in the “forward” or “back” position (as appropriate), then everything is in order. However, please check the system anyway by gradually advancing the stick until the motor begins to run. When you are satisfied, stop the motor, then switch off the receiving system in the model and finally switch off the transmitter. Note: If the motor does not start, or spins in the wrong direction, this indicates that there are other problems which you must correct before you continue with programming. For example, check the wiring of your motor, and refer to the operating instructions supplied with your speed controller. Once you are confident that the direction of the Ch 1 stick is “correct” as far as the motor is concerned, the next step is to ensure that you can switch its effect on the motor on and off, so that you can also control the braking system. This is carried out in the … “Free mixers” menu M1 M2 M3 typ MIX1 c1 ?? ?? fro to 2 … where you need to program a free mixer “c1 c1”. When you have done this, use the arrow button of the left or right-hand touch-key to move to the column above symbol, and assign your selected “change-over the switch” to this mixer; for example SW 2. This is done by activating the switch assignment by touching the central SET button of the right-hand touch-key, and moving the switch from “forward” to “back”, i. e. towards you. With the mixer switched on, move to the column above symbol using the arrow button of the left or the right-hand touch-key, and then on to the second screen page by touching the central SET button of the righthand touch-key. At this point you should set an initial SYMmetrical mixer value of -100%. c1 tr v –100% –100% offs 0% SYM ASY (pages 127 … 132) c1 ?? ?? c1 Now move to the “Offs” line: when you do this, the SYM and ASY fields are replaced by STO and SET. With the STO button highlighted, move the Ch 1 stick to the “OFF” position you have selected, and then touch the central SET button of the right-hand touch-key: the value to the right of “Offs” now changes from 0% to approx. +100%, and the graphic display of the mixer curve displayed on the right also changes accordingly: MIX1 c1 c1 tr v –100% –100% offs +100% STO SET If you now touch the buttons of the left-hand touchkey simultaneously to move to the … (page 133), “Servo display” menu … you can immediately check the effect of the settings you have entered so far: with the mixer switched off, the bar display for Channel 1 follows the movement of the Ch 1 stick. With the mixer switched on it stops - as shown - at around -100%. Programming example - fixed-wing model 173 1 –100 % 2 0% 3 0% 4 0% 5 0% 6 0% 7 0% 8 0% Note: If you carry out this test with the receiving system and power system switched on, please take great care that you operate the change-over switch only in the “motor OFF” position! If you ignore this, there is a danger that the power system will be severely overloaded by being switched on abruptly, and it could even suffer damage. For the same reason you should be careful only to use the change-over switch at the “motor OFF” setting when you are flying the model. To conclude the programming procedure, return the selected “change-over switch” to the “motor ON” position, i. e. “forward”; move back to the multi-function menu and from there to the … “Fixed-wing mixers” menu (pages 108 … 113) where - assuming that you have not already done this in your general model programming - you can select the “Brake AIL” line and set the desired aileron travel when the Ch 1 stick is operated in the up direction (“Brake”). In the column above the symbol touch the central SET button of the right-hand touch-key before assigning your selected “change-over switch” by moving your preferred switch from “forward” to “back”. 174 Programming example - fixed-wing model diff aile. ail rudd brak elev brak aile elev aile +33% +55% –5% +44% 0% ––– ––– ––– 2 ––– Note: The settings shown here are just examples, and must not be adopted under any circumstances without careful checking. If your model also features camber-changing flaps, and you have therefore selected “2AIL 2FL” in the “Aile / flap” line of the “Base settings” menu, locate the “change-over switch” you have just operated (in this case switch 2), move it “forward” again and switch to the “Brake FL” line using the arrow buttons of the left or right-hand touch-key. You can now set the desired down-deflection of the flaps when the Ch 1 stick is moved (this flap position is termed “crow” or “butterfly”; see also page 111), and assign the external switch which also acts as the change-over switch by moving it from the “forward” to the “back” position, as already described. If you now return to the “Servo display” menu and move the Ch 1 stick alone, you will see that the bar display for Channel 1 either remains at around -100% while the displays for channels 2 + 5 (and also the flaps 6 + 7, if set up) follow the stick movement, or the other way round: when the switch is operated, the latter stay at around the mid-point, and only the Channel 1 display moves. 1 –100 % 2 + 88 % 3 0% 4 0% 5 – 88 % 6 0% 7 0% 8 0% Operating the timers using the Ch 1 stick or a switch SW 1 … 9 If, following on from the model programming described on the preceding pages, you have decided on Example 4 from the previous page, or you are using the Ch 1 stick (throttle / brake stick) to control motor power - independently of this programming example - then you can use the associated control switch to turn the stopwatch on and off automatically. To assign this control switch, move the Ch 1 stick to the Idle position, then move to the “Timers” line in the … “Base settings” menu(pages 74 … 81) Briefly touch the central SET button of the right-hand touch-key to activate the switch assignment, then select the input field above the switch symbol and move the throttle / brake stick from its idle position in the direction of “full throttle”. Depending on the direction of movement, the switch “C1l” or “C2l” will appear on the screen at a particular position of the Ch 1 stick: motor at C1 C8 delay tail type aile/flap timer no no normal 2aile 0:00 C2 If you now move the stick back towards idle, you will see that the switch symbol changes again at around 80% of stick travel: between the “idle position” and the switching point the switch symbol is “open”, beyond this it is “closed” (see “Control switches” on page 59). If you now repeatedly press the central ESC button of the left-hand touch-key to return to the transmitter’s basic display, in order to check the system, you will see that the stopwatch and flight timer start running when you move the stick past the switching point in the direction of full-throttle, and that the stopwatch alone halts again when you move the stick back to the idle position. When the stopwatch is halted, you can stop the flight timer by touching the central ESC button of the left-hand touch-key, and then reset both timers to their starting value by simultaneously touching the two arrow buttons of the right-hand touch-key (CLEAR) … or re-start them by moving the stick beyond the switching point again. GRAUBELE #01 5.2V 3:33h stop flt 2:22 11:11 M HoTT 5.5V With the stopwatch halted, touch the central ESC button of the left-hand touch-key (CLEAR) button in the basic display, so that the stopwatch switches to the “Timer” function. The timer can now be started and stopped using the throttle control. Alternatively, if you control your motor using one of the switches SW 1 … 4 or 6/7, as described in Examples 2 or 3, you do not need any of the previously described control switches. All you need to do is locate the switch which you use to turn your motor on and off, and assign the same switch to the “Timers”, with the same switching direction, so that they start running at the same moment you turn the motor on. In contrast, if you have decided on the solution described in Example 1, then unfortunately there is no alternative but to operate the motor and timers separately. Tip: When using an electric motor the motor run is usually limited by the capacity of the battery, and in this case you would normally set the stopwatch to “count down”. Simply enter the maximum permitted motor run, e. g. “5 min.”. As described on pages 77 and 86, the transmitter’s sounder starts to emit warning tones “30 sec” before “zero”. motor at C1 C8 delay tail type aile/flap timer no no normal 2aile 5:00 C2 Programming example - fixed-wing model 175 Using flight phases Within any of the twenty model memories you can program up to four different flight phases (states of flight), each incorporating settings which can be entirely different from the others. Each flight phase can be called up by means of a switch. Flight phases represent the simplest and most convenient method of switching between different model settings in flight, and are programmed for different stages of a typical flight, such as “normal”, “thermal”, “speed”, “distance” etc. We assume that you have already programmed the model in the transmitter’s model memory, set it up carefully, test-flown it and trimmed it out properly. First move to the … three-position switches SW 4/5 or 6/7, located at front left and right on the transmitter. Each of the two end-points of this switch should be assigned to one flight phase, starting from the centre position. We recommend that the switch direction should match the phase numbering: as shown in the left-hand illustration, for example, “Phase 2” is “forward” from the centre position, while “Phase 3” is “back” (towards you). Select the appropriate line, name, and switch assignment in the “usual” way, i. e. using the various touchkeys. aile/flap timer phase 2 phase 3 phase 4 “Base settings” menu(pages 74 … 81) aile/flap timer phase 2 phase 3 phase 4 5:00 takeoff speed landing 2ail2fl 2 ––– ––– ––– … and then to the line “Phase 2”, “Phase 3” and / or “Phase 4”, where you can either accept the default name or assign a specific, more appropriate, name to each flight phase. The purpose of this name is just to help you differentiate between the flight phases; it has no significance in terms of programming. It will later appear in the transmitter’s basic screen display, and also in the “Phase trim” and “D/R Expo” menu. A physical switch must be assigned so that you can select the different flight phases. The ideal one for switching a maximum of three flight phases is one of the 176 Programming example - fixed-wing model 5:00 takeoff speed landing the control surfaces, and especially the wing flaps, are the same. To change these settings, call up the … “Phase trim” menu (page 106) … move the phase switch (or switches) to the appropriate position, and enter the desired values in the standard way by touching the input buttons, in a similar way to the method of adjusting transmitter control centres and offsets with other radio control systems. P H A S E T R I M normal 0% 0% 0% takeoff +8% 4% +2% speed –7% –5% –3% thermal +10% +5% +2% FLA AIL ELE 2ail2fl 2 4 ––– 5 Note: In principle it makes no difference which names you assign to the various phases with the exception of Phase 1, which is assigned the name “normal”, and is always active when flight phases 2, 3 and 4 are disabled. For general model flying three flight phases are usually quite sufficient: • “Launch” or “Thermal” for launch and “staying up”, • “Normal” for normal conditions, and • “Speed” for flying in “top gear”. At this point all three phases have been set up and assigned names, and you can switch between them; however … if you operate the phase switch you will soon notice that nothing has changed, i. e. all the settings for If you now switch the receiving system on and select the different phases in turn, you will see a difference in control surface response. The differences are also reflected in the bar display for the servos in the “Servo display” menu, which you can call up from virtually any menu position by simultaneously touching the buttons of the left-hand touch-key. Note: Depending on the information you have entered in the “aile/flap” line of the “Base settings” menu, the “ELE” column alone, the “AIL” and “ELE” columns, or - as shown above - “FLAP”, “AIL” and “ELE” may appear on the screen for “Phase trimming”. Programming example: servos running in parallel In some cases a second servo is required to run in parallel with an existing servo; for example, if a second elevator or rudder is to be actuated by a separate servo, or where a second servo is needed to cope with very high control forces, or where two servos are required for a large control surface due to the high forces involved. This task could be solved simply by connecting both servos together in the model using a conventional Y-lead. However, this has the drawback that the linked servos cannot be adjusted individually from the transmitter, i. e. you forfeit the basic advantage of the computer radio control system: separate adjustment of individual servos from the transmitter. Another option would be to call up the Telemetry menu and use its “Channel mapping” option instead of a simple Y-lead; see page 140. However, the simplest method is to use the transmitter’s software facilities. For example, it is easy to set up … Two elevator servos … to operate in parallel. First move to the … “Base settings” menu(page 74 … 81) mod name stick mode 1 idle re. motor at C1 cut off –100% +150% ––– tail type 2elev sv … and set “2elev sv” in the “tail type” line. The two elevator servos are then connected to receiver output sockets 3 and 8. Two rudder servos In this example we will connect two rudders “in parallel” using the “Free mixers” menu. The second rudder could be connected to receiver output 8, which is not already in use. The first step is to move to the … “Free mixers” menu M1 M2 M3 second rudder control channel”, with suitable servo travel settings. An offset of +100% is then selected for both mixers, as the Ch 1 stick is (usually) at its top endpoint when the airbrakes are retracted, and the winglet rudders are only required to deflect outwards proportionally when the brakes are extended. (pages 127 … 132) tr rd ?? ?? 8 ?? ?? typ fro to … and set up a mixer “Tr RUD 8”. In the “Type” column select the “Tr” setting, so that the rudder trim affects both rudder servos. Finally switch to the graphics page and set a SYMmetrical mixer input of +100%: MIX1 tr rd 8 tr v +100% +100% Offs 0% SYM ASY Once again, for safety reasons it is really essential that you set input 8 to “free” in the “Transmitter control settings” menu. As an added refinement, you may want both rudders to deflect outwards only, as part of a braking system controlled by the Ch 1 stick. This can be accomplished by setting up two additional mixers “c1 4” and “c1 Programming example - fixed-wing model 177 Programming example: Delta / flying wing On page 164, where the section on fixed-wing model programming starts, you will find general notes regarding the installation and set-up of the RC system in a model, and - of course - this applies equally to deltas and flying wings. The information on test-flying and refining the settings is also relevant, including the section on programming flight phases. left right Receiver power supply Auxiliary function Left flap Auxiliary function Rudder (if present) Right elevon (ail. / elev.) servo Left elevon (ail. / elev.) servo Airbrakes or throttle or speed controller (electric motor) Right flap If your delta or flying wing is of more “modern” configuration, the “normal” servo sequence has proved useful; this arrangement can also be used for canards: Receiver power supply Auxiliary function In their characteristic shape and geometry, deltas and flying wings differ very significantly from “normal” models even at first sight, but the differences in the requisite servo arrangement are rather more subtle. The “classic” model delta or flying wing generally has only two control surfaces, which act both as ailerons (in opposite directions) and as elevators (in the same direction), in a similar way to the superimposed rudder / elevator functions of a V-tail. More modern designs tend to be more complex; one (or two) inboard control surfaces may be used purely as elevators, while the outboard ailerons also act as elevators, but to a reduced extent. If a flying wing has four or even six wing control surfaces, it is certainly feasible nowadays to set them up with camber-changing flap functions and / or even a butterfly (crow) system. However, most of these models still rank as “classic” deltas and flying wings, and for them the servos should be connected to the receiver as follows (see also page 63): 178 Programming example: delta and flying wing Left flap (/ elevator) Right elevon (aileron / elevator) Rudder (if present) Elevator (if present) Left elevon (aileron / elevator) Airbrakes or throttle or speed controller (electric motor) Right flap (/ elevator) Depending on the receiver servo sequence you select, you should first move to the … “Base settings” menu(pages 74 … 81) … and select the following options in the line “motor at C1”: • “none”: The brake system is “retracted” at the forward position of the throttle / brake stick; the “Ch8 delayed” option and the “Brake NN*” mixers in the “Wing mixers” menu are activated. In the “Aileron / flap” line of the “Basic settings” menu you can select “1AIL”, “2AIL” and “1/2AIL 1/2FL”, and in the “Wing mixer” menu the mixer “Brake NN*”, plus all mixers “from” and “to” flaps, are activated. The warning message “Throttle too high” - see pages 36 and 67 - and the “Motor stop” option in the “Basic settings” menu are disabled. • “none/inv”: The brake system is “retracted” at the back position of the throttle / brake stick; the “Ch8 delayed” option and the “Brake NN*” mixers in the “Wing mixers” menu are activated. In the “Aileron / flap” line of the “Basic settings” menu you can select “1AIL”, “2AIL” and “1/2AIL 1/2FL”, and in the “Wing mixer” menu the mixer “Brake NN*”, plus all mixers “from” and “to” flaps, are activated. The warning message “Throttle too high” - see pages 36 and 67 - and the “Motor stop” option in the “Basic settings” menu are disabled. • “Idle forward” or “Idle rear” The Ch 1 trim operates either forward or back. If you switch the transmitter on with the throttle stick too far in the direction of full-throttle, you will see the warning message “Throttle too high” on the screen. In the “Basic settings” menu the “Motor stop” option is activated. In the same menu the “Ch8 delayed” option and the “Brake NN*” mixers in the “Wing mixers” menu are disabled. “tail type”: “Delta / flying wing” or “Normal” “aile/flap”: Two ailerons “2ail” and - if present two flaps “2fl”. The primary function of these settings is to define the * NN = Nomen Nominandum (name to be stated) range of wing mixers which the software makes available. If you select the “Delta / flying wing” tail type, the software automatically superimposes the elevator and aileron functions. In this case the mixer ratios can be adjusted by varying the Dual Rate settings in the “D/R / Expo” menu (see page 102). If you select “Delta / flying wing”, all settings of the “NN * elev” wing mixers in the … “Fixed-wing mixers” menu diff aile. ail rudd brak elev diff–red (pages 108 … 113) 0% ––– 0% ––– 0% ––– 0% Programming a model delta using the “normal” tail setting Alternatively, if you select the “normal” tail type in the “Base settings” menu, and connect the servos to the receiver as shown in the lower of the two receiver socket sequence diagrams on the left-hand page, then the aileron function of the two elevon servos will work correctly, but not the elevator function. In the “normal” tail type you have to force the two aileron servos and the two flap servos to move in the same direction and provide an elevator effect when an elevator command is given. This requires the “elev NN *” wing mixers, whose effect can be adjusted separately. The procedure starts by selecting the … “Fixed-wing mixers” menu … affect the elevator (up / down) function of the two elevon (combined aileron / elevator) servos, as well as the flap / elevator servos. Notes: • The flap mixers and flap differential only appear in the list if you have also entered “2fl” in the “aile/flap” line at the “Delta / Flying wing” model type; see illustration on the right. • In principle the same applies to the “Brake NN *” mixers. These are also suppressed if you have decided on “Throttle min forward / back” in the “motor at C1” line of the “Base settings” menu. • Even if you have selected “2aile2fl”, the (digital) elevator and aileron trims only affect aileron / elevator. If you wish to circumvent this, it is simpler to program your model as described in the following section. * NN = Nomen Nominandum (name to be stated) (pages 108 … 113) The following settings are model-specific, and you must check carefully that they work correctly on your model before accepting them. diff aile. diff flaps ail rudd ail flaps brak elev brak flap brak aile elev flap elev aile elev flap aile flap diff–red 0% 0% 0% +55% 0% +55% +66% +77% +77% 0% 0% 0% ––– ––– ––– ––– ––– ––– ––– ––– ––– ––– ––– With this set-up the tailless model is considered to be a “normal” four-flap wing (two ailerons and two flaps), and therefore has all the options associated with this wing type. The method involves the “elev NN *” mixers, which were originally intended only for pitch trim compensation and non-standard applications. In this case they are “abused” by setting higher values than normal, in order to transfer the elevator signal to the control surfaces of the tailless model. However, none of the fixed-wing mixers includes the digital trim of the elevator stick - so an alternative has to be found. Start by switching to the … “Transmitter control settings” menu I5 I6 I7 I8 (page 94) ctrl 6 +15% +15% ctrl 6 +15% +15% +100% +100% free free +100% +100% tr v + … and assign the same transmitter control to the inputs 5 and (if required) 6, e. g. the rotary proportional control CTRL 6. Now move to the “Travel” column and reduce the travel of the transmitter control for these two inputs symmetrically to around 50%, or even less, because: the lower this value, the finer the trim control. However, if you prefer to use the normal elevator trim lever, set - or leave - the “elev NN *” mixers to 0%, and instead set up free linear mixers to do the job. This is done by calling up the … … where you set values other than zero for these mixers. Programming example: delta and flying wing 179 “Free mixers” menu M1 M2 M3 (pages 127 … 132) tr tr el el ?? 5 6 ?? typ fro to … and setting up one linear mixer “Tr elev 5”, and - if necessary - “Tr elev 6”. Move to the graphic page of this menu to set the required mixer ratios. Check the settings, and above all the direction of effect, in the “Servo display”, or on the model itself, and change the prefixes if necessary. If you carry out the programming as described above, the ailerons will also move in the same direction, like flaps, when you move the elevator stick. The effect of the “tr” option is that the elevator trim lever also affects the associated mixer when you operate the elevator stick. Since an additional transmitter control is no longer required for this arrangement, you should disable input 5 and (if used) input 6 in the second column of the “Transmitter control settings” menu; simply set these inputs to “free”. Many years ago, the author flew a model delta programmed exactly in this way using the mc-20, with the following additional refinements: “flap settings” used as trim, and butterfly (crow) as landing aid - the latter exploiting the “Brake AIL” and “Brake FL” wing mixers to provide complete compensation for pitch trim changes in both directions. In this case the term “ailerons” means the outboard wing control surfaces, and “flaps” the inboard pair of control surfaces. A modern sweptback flying wing can be controlled in 180 Programming example: delta and flying wing a similar fashion. These models also feature inboard and outboard control surfaces: the former forward of the Centre of Gravity, the latter aft of it. Deflecting the inboard control surface(s) down increases lift and produces an up-elevator effect; deflecting them up creates the opposite effect. In contrast, the outboard ailerons act in the reverse direction: a down-deflection produces a down-elevator effect, and vice versa. There are really no limits to what can be achieved with appropriate settings of the system’s sophisticated mixers. However, please note that you should be extremely careful when setting differential travel with such a configuration, regardless of your model’s set-up, its tail type and the number of servos you are using. This is because differential travels on a tailless model tend to produce an asymmetrical elevator effect, rather than the desired adverse yaw reduction. For this reason it is advisable to start with a differential setting of 0% - at least for the first few flights. When you are familiar with the model and feel the need to experiment, it may then be feasible under certain circumstances to try differential settings deviating from zero. For larger models it could be advisable to install winglets fitted with rudders, i. e. small vertical surfaces at the wingtips. If these are actuated by two separate servos, they can be controlled as described in the example on page 177 dealing with “Servos running in parallel”, or using “Channel mapping” in the “Telemetry” menu; see page 140. You may also want both rudders to deflect outwards when a braking system is operated using the Ch 1 stick, and this can be accomplished as follows: if you have selected the “normal” tail type, set up two further mixers “c1 4” and “c1 second rudder control channel” with suitable travel settings. The offset for both mixers should be +100%, as the Ch 1 stick is usually at the forward end-point when the airbrakes are retracted, and the winglet rudders are only required to deflect outwards proportionally when the brakes are extended. For your notes 181 Programming example: F3A model aircraft F3A models belong to the category of powered fixedwing model aircraft designed for competition flying. They may be powered by an internal combustion engine or an electric motor. Electric-powered models are eligible and totally competitive in the international F3A “pattern” class, and also in the F5A electric aerobatic class. fixed-wing models we have already described. The auxiliary function “Retracts” is usually assigned to one of the auxiliary channels 6 to 8. Ideally the retracts are operated using one of the two switches without a centre detent (SW 3 or SW 8). An optional “extra” - used only if necessary - is mixture adjustment control for the carburettor. This is generally operated by one of the rotary proportional controls CTRL 6 … 8, connected to one of the auxiliary channels not already in use. Receiver power supply Auxiliary function In this programming example we assume that you have already read through the description of the individual menus, and are therefore familiar with the general method of handling the transmitter. On page 164, where the section on fixed-wing model programming starts, you will find general notes on installing and setting up the RC system in a model, and - of course - this applies equally to F3A models, and therefore does not need to be repeated at this point. If an F3A model is accurately built, it usually exhibits flying characteristics which are almost completely neutral. The perfect aerobatic model has a very smooth but precise control response, and any movement around any one of its flight axes should not affect the other axes. F3A models are flown using aileron, elevator and rudder controls. The use of separate servos for each aileron is almost universal. The flying controls are supplemented by control of motor power (throttle function) and in many cases a retractable undercarriage. As a result the servo assignment for channels 1 to 5 is no different from the 182 Programming example: F3A model Retracts Right aileron Rudder Elevator Aileron or left aileron Throttle or speed controller (electric motor) Mixture adjustment When assigning functions to the auxiliary channels at the transmitter, it is advisable to ensure that the controls required are within easy reach, since the advanced aerobatic pilot has very little time to think about letting go of the sticks - especially when flying under competition conditions. Programming The basic programming of the transmitter has already been described in detail in the section starting on page 166, so this section concentrates on tips specific to F3A models. In the … “Servo settings” menu S1 S2 S3 S4 S5 rev 0% 0% 0% 0% 0% cent (page 92) 100% 100% 100% 100% 100% 100% 100% 100% 100% 100% trav + … you can adjust the servo settings to suit your model. It has proved advisable to use at least 100% servo travel, as precision of control can be perceptibly better if relatively large servo travels are employed. This should be borne in mind when building the model and designing the control surface linkages. Any minor corrections required can be made in the third column during the initial test flights. The next step is to select the … “Base setting” menu (page 74 … 81) … and activate the idle trim for Channel 1 (normally “Idle back”; i. e. full-throttle forward). The digital trim now works at the idle end of stick travel. The “cut-off trim” enables you to switch immediately from the “motor stopped” position to the idle position you have previously established just by applying a single “click” on the trim lever (see page 60). stick mode 1 motor at C1 idle re. cut off –100% +150% 9 tail type normal aile/flap 2aile The remaining settings should be adjusted as required to suit your personal preferences. You may find it necessary to assign transmitter controls to particular inputs to operate the retractable undercarriage and carburettor mixture adjustment. This is carried out in the … “Transmitter control settings” menu (page 94). For example, you may like to assign a particular transmitter control - perhaps one of the ON / OFF switches SW 2 or 8 - to the input “E8” for the retracts, and a rotary proportional control - e. g. CTRL 6 - to the input “E7”, for mixture adjustment. I5 free +100% +100% I6 free I7 ctrl 6 +100% 8 +100% I8 +100% +100% +100% +100% tr v + The retracts are extended and retracted when you operate the switch “SW 8”. You may need to adjust the travel of the transmitter control, and perhaps reverse that channel by setting a negative prefix for servo travel. F3A models fly fairly fast, and respond very “solidly” to corrective movements of the servos. However, in competition flying it is vital that all abrupt control movements and corrections should be kept to a minimum, as the judges will invariably notice any lack of smoothness and dock a few points, so it is advisable to set exponential control characteristics on the stick functions. Move to the … “D/R Expo” menu (page 102). Exponential values of around +30% on aileron, elevator and rudder have proved to be a good starting point, and you can set them in the right-hand column of this menu. These values provide smooth, well-defined control of the typical F3A model. Many experts use higher values; even up to +60% exponential. aile 100% elev 100% rudd 100% +33% +33% +33% DUAL EXPO ––– ––– ––– Since F3A models generally have two aileron servos, it has proved useful to deflect both ailerons “up” slightly for the landing. In most cases this causes the model to fly a little more slowly and with a more stable attitude on the landing approach. To achieve this you will need to program mixers in the … “Free mixers” menu (section starting on page 127). Both ailerons are usually required to deflect “up” as a landing aid, in parallel with the movement of the throttle stick, but only from the half-throttle setting in the direction of idle. From that point on, the further the stick is moved towards the idle position, the more the ailerons deflect up. The reverse occurs when you open the throttle: the ailerons are returned to neutral to avoid the model suddenly ballooning up. A little down-elevator must usually be mixed in to ensure that the aeroplane does not climb when the ailerons / flaps are deployed. To meet these requirements you need the two mixers shown in the illustration below. M1 M2 M3 typ c1 c1 ?? 5 el ?? fro to 3 3 The mixers are activated using one and the same external switch, e. g. “SW 3”, which therefore has to be assigned to both mixers, with the same direction of effect. Touch the central SET button of the right-hand touch-key to move to the mixer inputs on the second screen page, and set the appropriate mixer ratios. In both cases the mixer neutral point should be left at the centre position of the Ch 1 stick travel. For this reason you should now move the Ch 1 stick to the Idle range, select the ASY field, and enter the following values: MIX 1: -60% … -80% and MIX 2: -5% … -10%. Programming example: F3A model 183 Example of MIX 1: MIX1 c1 5 tr v –66% 0% offs 0% SYM ASY This completes the basic set-up for a typical F3A model. Correcting model-specific errors It is an unfortunate fact of life that even very carefully built models exhibit minute faults and inaccuracies which produce unwanted deviations when the model is flying; the mixers of a computer radio control system are then needed to compensate for these deficiencies. In this section we will describe how to carry out the adjustments required, but please note the following points before we get started: it is vital to ensure that the model is built as accurately as humanly possible, is balanced perfectly around the lateral and longitudinal axes, and that motor downthrust and sidethrust are set correctly. 1. Rudder causes unwanted movement around the longitudinal and lateral axes It is often the case that a rudder command causes the model to rotate slightly around the longitudinal and / or lateral axis. This is particularly troublesome in what is known as knife-edge flight, where the model’s total lift is generated by the fuselage, aided by the rudder deflection. The result is that the model rotates and changes heading slightly, as if the pilot were applying aileron or elevator at the same time. These tendencies have to be corrected with compensation around the lateral axis (elevator) and around 184 Programming example: F3A model the longitudinal axis (aileron). These corrections can be achieved easily with the mx-16 HoTT, exploiting the “free mixers” once again. For example, if the model rotates to the right around the longitudinal (roll) axis when the rudder is deflected to the right for a knife-edge pass, then a mixer is set up which deflects the ailerons slightly to the left. Heading changes around the lateral (elevator) axis can be corrected in a similar way using a mixer acting upon the elevator: a) Correction around the lateral axis (elevator) MIX “rd el” ASYmmetrical setting. The exact values required must be found by flight testing. b) Correction around the longitudinal axis (aileron) MIX “rd al” ASYmmetrical setting. The exact values required must be found by flight testing. In most cases relatively small mixer values are called for - typically below 10% - but this does vary from model to model. 2. Vertical climb and descent Many models exhibit a tendency to deviate from the ideal line in vertical climbs and descents. To correct this we need an elevator neutral position which varies according to the throttle setting. For example, if the model tends to pull out of a vertical descent by itself when the motor is throttled back, slight down-elevator must be mixed in at this throttle setting. MIX “c1 el” As a rule you will need to set mixer values below 5%, but once again there is no substitute for test-flying. 3. Rolling (movement around the longitudinal axis) at idle When you reduce the throttle setting, the model may tend to roll slightly in one direction. Clearly an aileron correction must be made. However, it is much more elegant to let a mixer correct this effect for you than to move the stick manually. Once again, a mixer needs to be set up: MIX “c1 al” As a rule you will need to set mixer values below 5%, but once again test-flying is called for. The adjustment process should only be carried out in calm weather. Often all you need to do is apply the mixer in the control segment between half-throttle and idle. To achieve this, leave the Offset point at the centre position, and set up the mixer ASYmetrically. 4. Rolling when ailerons and flaps are extended If you fly the landing approach with both ailerons deflected up, the model may show a tendency to roll slightly due to minor variations in aileron servo travel (or constructional inaccuracies); i. e. the model may turn to either side by itself. Once again, this tendency can easily be corrected using a mixer to vary the compensation according to the position of the ailerons / landing flaps. MIX ”c1 al” It is essential to provide a means of switching the mixer on and off using the switch which controls the aileron / landing flap function (see previous page), to ensure that this mixer only has any effect when the aileron / landing flap function is activated. The optimum value has to be found by test-flying. And finally a few words on the … “FAIL-SAFE settings” We strongly recommend that you make use of the safety potential of this option by at least setting the throttle position (glow-powered models) to idle, or the electric motor to stop, if a fail-safe event should be triggered. This simple precaution ensures that the model is much less likely to create havoc and cause property damage or personal injury. If you also program the fail-safe positions of the control surfaces in such a way that the model flies steadily descending circles in case of interference, then you have a good chance that it will land relatively gently even if the radio link fails for a protracted period. This also gives you plenty of time to restore the connection, should the whole 2.4 GHz frequency band suffer interference for a while. In the receiver’s default state, however, the servos remain in their last valid position (“hold mode”) when interference occurs. You can program any individual servo output of your receiver to a “fail-safe position” (fail-safe mode), as described on page 136. characteristics you desire. Summary The settings described on this page are intended primarily for the expert flyer. Please bear in mind that refining the flying characteristics of a model aeroplane to this extent involves tremendous effort, time, sensitivity and expertise. Some experts continue the programming procedure even when they are flying, although it is not advisable to try this if you are just a moderately advanced pilot making your first attempt with an F3A aerobatic model. You would be well advised to request help from an experienced pilot, and carry out the fine-tuning adjustments mentioned here one by one, with the expert at your side, until your model exhibits the neutral flying Programming example: F3A model 185 Programming example: model helicopter In this programming example we assume that you have already read and understood the descriptions of the individual menus, and are by now familiar with the general handling of the transmitter. We also assume that you have assembled and adjusted the helicopter exactly according to the kit instructions. The electronic facilities provided by the transmitter should never be used to compensate for major mechanical inaccuracies. As so often in life, there are various ways and means of reaching a particular destination when programming the mx-16 HoTT. In this example our intention is to provide a sensibly structured course of action, so that you have a clear idea of logical programming techniques. Where there are several possible methods, we first describe the simplest and most easily understood solution. It is likely that the helicopter will work perfectly when set up in this way, but naturally you are still free to try out other solutions at a later stage, in case they suit you better. We have deliberately chosen this simple programming project in order to demonstrate that it is possible to set up a helicopter which flies extremely well with relatively little programming effort. Nevertheless, we do not want to forfeit all the possible refinement facilities: after the basic description you will also find set-up notes on gyro gain, speed governors and flight phase programming. Note: If, in contrast to the glow-powered machine described here, your main interest lies in electric-powered model helicopters, then please read on! Apart from the idle adjustments, which naturally do not apply, you can adopt most of the settings described in the following section virtually unchanged. To initiate this typical programming exercise move to the “Model memory” menu, then to the … “select model” sub-menu (page 70), … where you select a free model memory using the arrow buttons of the left or right-hand touch-key: As our programming example we take the Graupner STARLET 50 helicopter, with right-hand rotation, three swashplate linkage points distributed evenly at 120° (“3Sv (2 roll)” type), a beginner’s set-up without enhanced throttle curve, without heading-lock gyro system, no method of influencing the gyro’s “normal operating mode” from the transmitter, and with no speed governor (regulator). 186 Programming example: model helicopter 01 02 03 04 05 06 free free free free free R08 After touching the central SET button of the right-hand touch-key, you can use the button of the left or righthand touch-key to select … Sel model type ( empty mod mem ) … the “Helicopter” model type. Confirm your choice by touching the central SET button of the right-hand touchkey, and the screen immediately switches to the basic display. Notes: • Once you have called up the “Model select” option it is not possible to interrupt the process, i. e. you must choose one or other model type. Even if you switch the transmitter off, then on again, you still have to make this choice. However, if you make a mistake you can always correct it simply by erasing the model memory. • If the warning message “Throttle too high” appears, you can erase it by turning the rotary proportional knob CTRL 6 anti-clockwise to its end-point. • If the battery voltage is too low, you will not be able to change model memories for safety reasons. In this case the screen displays an appropriate message: not possible now voltage too low Once you have overcome this initial hurdle, it is essential to bind the receiver installed in the model to this model memory in the … “Base settings” menu (pages 82 … 90) This is accomplished by moving to the “rx bind” line: phase 2 phase 3 autorotat. receiv out rx bind hover speed ––– ––– ––– ––– Note: When you confirm the model selection the following message appears in the basic display for a few seconds: BIND N/A OK If you confirm your choice by briefly pressing the SET button of the right-hand touch-key, you automatically move to this line: In this line you trigger the bind process between model memory and receiver, as described in detail on page 88. Without this step you cannot address the receiver. The next step is to press the arrow button of the left-hand or right-hand four-way touch-key to move up into the first line, where you can start the actual model programming in the “mod name” line. Now enter a suitable name for the model memory, … mod name stick mode 1 1 ser vo swashplate cut off –100% +150% ––– right rotor direct all subsequent mixers, and it is therefore vital that you do not change it later in order to alter individual mixer directions, such as the direction of collective pitch or throttle. stick mode 1 3sv(2rol) swashplate cut off –100% +150% 1 right rotor direct pitch min rear … by selecting the characters available on the second page of the “mod name” line: 0123456789 : ; ? ABCDEFGHIJKLMNO PQRSTUVWXYZ model name At this point, if you have not already done so, the servos should be connected to the receiver in the following sequence: STAR Receiver power supply Auxiliary function (speed governor) Once you have entered the “Model name” you should check that the “Stick mode” is correct: STARLET mod name stick mode 1 1 ser vo swashplate cut off –100% +150% ––– right rotor direct In the next four lines we come to the first settings which are specific to helicopters: In the “Swashplate type” line select the number of servos which are used to actuate the swashplate. See page 82 for more details of this. In the “Rotor direction” line we enter the direction of rotation of the main rotor as viewed from above. In the “Collective pitch min.” line set “forward” or “rear” to suit your personal preference. This setting applies equally to Throttle servo Free or auxiliary function Tail rotor servo (gyro system) Pitch-axis servo Roll 1 servo Roll 2 servo Gyro gain Note: Please note one important difference in later Graupner mc and mx radio control systems compared with earlier equipment: the first collective pitch servo and the throttle servo have been interchanged. The mixer ratios and mixer directions for the swashplate servos for collective pitch, roll and pitch-axis are set in the … Programming example: model helicopter 187 “Swashplate mixer” menu SP – MIXER ptch roll nick (page 132), “Transmitter control settings” menu +61% +61% +61% I5 thr gyr I8 lim … where you will find that they are pre-set to +61% in each case. If the swashplate does not respond correctly to the stick movements, the first step is to change the mixer directions from “+” to “-” if necessary. The second recourse is to reverse the servo directions in the “Servo settings” menu. Now move to the … “Servo settings” menu S1 S2 S3 S4 S5 rev 0% 0% 0% 0% 0% cent A glance at the … (page 92), 100% 100% 100% 100% 100% 100% 100% 100% 100% 100% trav + … where you can set up the travels and directions of rotation of the individual servos. The basic aim here should be to keep servo travels at 100% wherever possible, as this maintains best possible resolution and accuracy. Use “Rev.” if necessary to change the direction of rotation of any servo; do check carefully that the direction you set really is correct. The tail rotor servo, in particular, must operate in such a way that the nose (!) of the helicopter moves in the direction which corresponds to the movement of the tail rotor stick. 188 Programming example: model helicopter free free free free ctrl6 (page 96) +100% +100% +100% +100% +100% +100% +100% +100% +100% +100% tr v + … will show you that transmitter control “6”, i. e. the rotary proportional control CTRL 6, is assigned to the “Lim” input, whereas all other inputs are programmed to “free” by default. The “Lim” input serves as throttle limiter. It acts solely on output “6”, to which the throttle servo is connected. Just to remind you: • Using the “Throttle limiter” function eliminates the need to program an “Idle-up” flight phase. • The throttle limiter does not control the throttle servo; it simply limits the travel of this servo in the forward direction, according to the setting of the throttle limiter, when required. The throttle servo is usually controlled by the collective pitch stick via the throttle curve or curves you have set in the “Helimix” menu, for which reason input 6 should always be left “free”. For more details please refer to the sections on pages 116 and 117 of the manual. • Moreover the Ch 1 trim only affects a helicopter’s throttle servo. This section does not describe the special features of this trim (“cut-off trim”) again, as it is covered on page 60. (Thanks to the digital trims, trim values are automatically stored when you switch models and when you switch between flight phases.) • You will find a detailed description of the basic idle set-up procedure and the method of adjusting idle and throttle limit in the section starting on page 99. Now use the arrow button of the left or right-hand touch-key to move to the “Travel” column, and increase the value in the highlighted field from 100% to 125%, with the throttle limiter at its forward end-stop. I5 thr gyr I8 lim free free free free ctrl6 +100% +100% +100% +100% +100% +100% +100% +100% +100% +125% tr v + This ensures that the throttle limiter cannot possibly restrict the full throttle travel dictated by the collective pitch stick when the model is in flight. Set-up note for electric helicopters: Since electric motors by their nature require no idle setting, the only important point when setting up an electric-powered model helicopter is that the adjustment range of the throttle limiter should be set significantly higher and lower than the adjustment range of the speed controller, which is usually from -100% to +100%. It may therefore be necessary to adjust the “Travel” value of the throttle limiter to an appropriate value, such as a symmetrical 110% setting. However, further fine-tuning can be carried out exactly as described here for the glow-powered machine. An additional function needs to be activated in the … “Base settings” menu (pages 82 … 90). Even if you are a beginner to flying and are not yet ready for this, it is advisable at least to define the auto-rotation switch, so that you have an “emergency cut” switch for the motor. This is carried out by selecting the “Auto-rotation” line using the arrow buttons of the left or right-hand touch-key, briefly touching the central SET button of the right-hand touch-key, and then moving one of the two-position switches (SW 2 or 8) to the “ON” setting. The switch number (in our example “2”) now appears on the right of the screen. pitch min timer phase 2 phase 3 autorotat. rear 5:00 C3 hover ––– speed ––– 2 This switch should be located at a position on the transmitter where you can easily reach it without letting go of the stick, e. g. above the collective pitch stick. Note: For more information on setting up this “emergency OFF switch” please refer to the section in the centre column of the following page. And another tip: Please make it a habit to give all the switches a common “on” direction; then a quick glance at the transmitter before flying will soon reassure you that all switches are “off”. If you wish, you could at this point move up two lines and assign a flight phase switch for flight phase 2, which is already assigned the name “Hover”, but this simple programming example deliberately excludes such refinements. You have now completed the basic settings at the transmitter, i. e. the procedure which you will need to use time and again when setting up a new model. The actual helicopter-specific set-up is carried out primarily in the … “Heli mixers” menu ptch ch1 thro tail ch1 gyro inp8 normal (pages 114 … 125). 0% 0% In the very first line you will see the “Collective pitch” function, and a brief press on the central SET button of the right-hand touch-key takes you to the appropriate sub-menu. At this point you will see a graphic representation of the collective pitch curve. This is initially defined by only three reference points, and in most cases this is quite adequate. Tip: Always try to manage with these three reference points initially, as additional points just complicate matters, and extra complexity is just what you don’t need at the moment. The reference point for hovering should generally be the mechanical centre-point of the collective pitch stick, as this position feels completely natural to most pilots. You can, of course, set up the curve to locate the hover at a different point, but you should not be tempted to do this unless you know exactly what you are doing. Start by setting the collective pitch stick to centre. Assuming that you previously adjusted the servos in accordance with the manufacturer’s instructions, the servo output arms will now (usually) be at right-angles to the servo case. If you have not already done so, adjust the mechanical linkages to the rotor head so that all the blades are set to a collective pitch angle of 4° to 5° positive for the hover. All known helicopters will fly at this setting. Now push the collective pitch stick fully forward to the maximum collective pitch point (the full-length vertical line indicates the current position of the stick). Adjust Point 5 on the collective pitch curve using the arrow buttons of the right-hand touch-key, with the aim of obtaining a maximum collective pitch setting of around 9° at the main rotor blades. This point should be at a value of around +50%. Note: A rotor blade set-up gauge, e. g. the Graupner item, Order No. 61, is very useful when setting up blade pitch angles, as you can read off the angles directly. Now pull the collective pitch stick right back to the collective pitch minimum position. Set the blade pitch angle for Point 1 to 0 to -4°, depending on your piloting ability. This produces a graph line with a slight angle at the hover point, forming what is known as the collective pitch curve. It might look approximately like this: ptch input –100% output –80% point 1 –80% normal Programming example: model helicopter 189 If you now switch to the auto-rotation phase - you will see the name of the flight phase “Autorot” at bottom left on the screen - the “old” collective pitch curve will re-appear. In this phase you should set the same values as in the normal phase, with the following exception: increase the pitch angle at Point 5 (collective pitch maximum) by about 2°. This gives slightly more pitch for flaring the model when practising “autos” at a later (!) date. Once you have set up the collective pitch curve, operate the auto-rotation switch again, then briefly touch the central ESC button of the left-hand touch-key to return to the helicopter mixer menu select point. Now we move on to the “Ch1 thro” line, where you can set up the throttle curve. The first step here is to enter the idle trim range by adjusting the throttle curve. Move the collective pitch stick to the minimum position, and set Point 1 to a value of around +16%. c1 thro input output point 1 normal 0% +16% +16% With the throttle limiter closed and the idle trim fully open, pull the collective pitch stick to the “fully back” position and move it slightly to and fro: the throttle servo should not respond to this movement. This arrangement gives you a seamless transition from idle trim to the throttle curve. You will probably need to make further adjustments to the throttle curve, but this process must be carried out later as part of the flight-testing procedure. If you now switch temporarily from this graph to the 190 Programming example: model helicopter auto-rotation flight phase, you will see - instead of the usual display - the following: c1 thro off Autorot This means that the throttle servo has switched to a fixed value, which can be adjusted as follows: Press ESC to return to the menu list. Assuming that you are still in the auto-rotation phase, this will now include new sub-menus. The important line is “Throttle”, where you should set a value of around +125% or -125%, depending on the direction of servo rotation. ptch thro tail gyro inp8 Autorot –125% 0% 0% 0% This setting ensures that the motor stops reliably in the auto-rotation phase (to allow you to cope with an emergency). Later, when you have gained sufficient experience to practise auto-rotation landings, the setting should be changed to a value which provides a reliable idle. Set-up note for electric helicopters: Since the motor must be stopped completely if an emergency occurs with an electric-powered model helicopter, this setting can be adopted unchanged. At present the remaining sub-menus are of no interest. Simply switch “Auto-rotation” off, and move back to the first menu list. Call up the set-up page of the “Ch1 tail rotor” menu: this is where you set static torque compensation (DMA) for the tail rotor. Once again, please restrict yourself to the three default reference points; everything else is the preserve of the experienced pilot. For the initial set-up - intended for a heading-lock gyro system - the uniform pre-set values of 0% should be changed to -30% at Point 1 (collective pitch minimum) and +30% at the opposite end, Point 5 (collective pitch maximum), although you may find it necessary to adjust the settings slightly later. c1 tail input –100% output –30% point 1 –30% normal Now switch back to the auto-rotation phase for a moment. The set-up curve is disabled here, with the result that the tail rotor servo no longer responds to collective pitch commands (when the main rotor is not powered, there is no rotor torque to be corrected). The - static - pre-set of the gyro effect principle (“normal” or “heading lock” mode), and also the gyro gain can now be altered by setting a value other than “0” in the “Gyro” line: ptch ch1 thro tail ch1 gyro inp8 normal I5 thr gyr I8 lim 0% 0% Please be sure to read and observe the set-up instructions supplied with your gyro at this point, as there is a possibility that your helicopter will be uncontrollable if you set it up incorrectly! If your gyro features gain control from the transmitter unlike the type we are using in this example - you will need another free proportional control for it, e. g. CTRL 7. This can be assigned to the “Gyro” input in the … “Transmitter control settings” menu I5 thr gyr I8 lim free free ctrl 7 free ctrl 6 (page 96). +100% +100% +100% +100% +100% +100% +100% +100% +100% +100% tr v + Turn the rotary control until its number (transmitter control number) appears on the screen, then use the arrow button of the left or right-hand touch-key to move to the ASY field in the “Travel” column. Briefly press the central SET button of the right-hand touch-key, and you will be able to set a maximum gyro gain such as 50% in the now highlighted field: free free ctrl 7 free ctrl 6 +100% +100% +100% +100% +50% +50% +100% +100% +100% +100% tr v + This represents a safe fixed value which is maintained as long as the rotary control is at its right-hand end-stop. You will probably need to adjust the value in the course of flight-testing. Additional notes on setting up gyros can be found on pages 118 / 119. Further adjustments If you have followed this programming example, you will have a helicopter which is set up properly, and in an ideal state for hovering practice and simple circuits. Of course, you may wish to activate further functions depending on your skill and flying experience. If you wish to fly using different rotor speeds and trim set-ups, you will need to activate a series of “flight phases”, which can be called up via switches which you assign. The first step in this process is to call up the … “Base settings” menu pitch min timer phase 2 phase 3 autorotat. (pages 82 … 90), rear 10:01 C3 8 hover acro ––– 2 … assign a switch to “Phase 2”, e. g. SW 8, and enter a relevant name (if you wish). It is important to be quite clear in your mind that auto-ro- tation always has absolute precedence over any other phases. This simply means: if you operate the auto-rotation switch, you immediately move to the auto-rotation phase from either of the other two flight phases (“normal” phase and “phase 2”). Now move back to the “Helimix” menu, switch to “Phase 2” (which you have just set up), and modify the settings accordingly. Since the mx-16 HoTT features digital trims, in the Heli program all the trim positions for the control functions “roll”, “pitch-axis” and “tail rotor” are stored separately for each flight phase, in addition to the other menu settings which you entered separately for each flight phase (see page 114). For example, if the motor run is limited by the fueltank size or battery capacity, you should set the stopwatch to count down. Enter the maximum possible motor run time, e. g. “5 min.”. The transmitter’s sounder now starts emitting warning sounds starting at “30 s” before “zero”, as described on page 86. You could assign the transmitter control switch “G3” to this timer, by first activating switch assignment and then turning the throttle limit control from its idle position in the direction of full-throttle: 3sv(2rol) swashplate cut off –100% +150% 1 right rotor direct pitch min rear 5:00 C3 timer With the stopwatch halted, touch the or buttons of the left-hand touch-key (CLEAR) simultaneously at the basic display, so that the stopwatch switches to the “Timer” function. The timer then starts automatically when you move the throttle limit slider towards full-throtProgramming example: model helicopter 191 tle, and stops again when you move the limiter back to the idle range. Suggested refinement: speed governor At some time you may wish to install a speed governor (regulator) in your helicopter, e. g. the mc-Heli-Control, to try flying with a system rotational speed which is automatically maintained at a constant value. It makes sense to couple the individual rotor speeds with the flight phases, as this enables you to carry out further fine-tuning. The initial requirement when programming the transmitter is to install and program the speed governor exactly in accordance with the manufacturer’s instructions. Of course, the mx-16 HoTT provides further facilities to allow you to implement different rotational speeds in the individual flight phases. A practical suggestion, which includes the throttle limiter function, can be found in the section starting on page 117. If you have set up your helicopter as described in this programming example, you will find that it is capable of carrying out extremely challenging flight tasks even though it is not suitable for competition work. We suggest that you should not make use of additional functions until your model is flying perfectly, so that you will be in a position to recognise and appreciate any improvements. Whenever possible, it is always best to implement additional refinements one at a time, otherwise you won’t know which change has brought about any improvement. Bear in mind that the good pilot is not recognised by the number of complex functions with which he can cope, but by the results he can obtain when flying a relatively simple set-up. 192 Programming example: model helicopter For your notes 193 Appendix PRX (Power for Receiver) Order No. 4136 Graupner|SJ HoTT GPS / Vario module Order No. 33600 Graupner|SJ HoTT Vario module Order No. 33601 A highly developed stabilised receiver power supply with intelligent power management. The unit constitutes a stabilised user-selectable power supply for the receiver, and provides a further enhancement in the reliability of the airborne power supply. It is designed for use with different types of receiver battery, to ensure that it is straightforward and versatile in use. When the model is operating, even brief collapses in battery voltage are stored and displayed, offering the user the means of detecting a receiver battery which is not “up to the job”, or failing. • For use with one or two receiver batteries (simultaneous discharge if two batteries are employed) • Suitable for five-cell or six-cell NiMH batteries, or two-cell LiPo or LiFe packs. Graupner/JR, G3.5, G2 and BEC connector systems. • Three user-selectable receiver power voltage levels: 5.1 V / 5.5 V / 5.9 V. • Two ultra-bright LEDs indicate the operational status of batteries 1 and 2 separately. • Integral high-quality On / Off switch. • Constructed to cope with high-current applications. • Low-profile switch and LEDs to avoid spoiling the appearance and efficiency of the model. • Straight-through design of mounting lugs, LEDs and switch for simple installation using drilling template (supplied). Vario with altitude signals and five different tones for climb and descent, plus GPS with range measurement, distance measurement, speed indicator, display of flight direction and co-ordinates • Additional warning thresholds for min. altitude, max. altitude, twostage climb and descent rate • Altitude display, storage of min. and max. altitude • Variable warning time: OFF, 5, 10, 15, 20, 25, 30 seconds, constant • Variable warning repeat time: constant, 1, 2, 3, 4, 5 min, once • The GPS / Vario sensor can be connected directly to the receiver’s telemetry input. Vario with altitude signals and five different tones for climb and descent; altitude display and storage of min. and max. altitude. • Additional warning thresholds for min. altitude, max. altitude, twostage climb and descent rate • Variable warning time: OFF, 5, 10, 15, 20, 25, 30 seconds, constant • Variable warning repeat time: constant, 1, 2, 3, 4, 5 min, once • The vario sensor can be connected directly to the receiver’s telemetry input. 194 Appendix Specification, vario • Altitude measurement: -500 m ... +3000 m • Resolution: 0.1 m • Sensitivity, vario: 0.5 m/3s, 1 m/3s, 0.5 m/s, 1 m/s, 3 m/s, programmable per beep • Calculated average value: 4 - 20 measurements per measured value, programmable Specification • Altitude measurement: -500 m ... +3000 m • Resolution: 0.1 m • Sensitivity, vario: 0.5 m/3s, 1 m/3s, 0.5 m/s, 1 m/s, 3 m/s, programmable per beep • Calculated average value: 4 - 20 measurements per measured ­value, programmable Graupner|SJ HoTT General Engine Module Order No. 33610 Graupner|SJ HoTT General Air Module Order No. 33611 Graupner|SJ HoTT Electric Air-Module Order No. 33620 General sensor for Graupner|SJ HoTT receivers and models with internal-combustion or electric power system: • 2 x temperature and voltage measurements with warning thresholds for min. and max. voltage and min. and max. temperature • Individual cell measurement with min. voltage warning thresholds • Voltage, current and capacity measurement with warning thresholds for min. and max. voltage, max. capacity and max. current • Programmable current limiting • Current measurement with 2 x 1 mOhm shunt resistors in parallel = 0.5 mOhm • Rev-count measurement and warning thresholds for min. and max. rotational speed • Fuel measurement with warning thresholds in 25% increments (requires software update) • User-variable warning time: OFF, 5, 10, 15, 20, 25, 30 seconds, constant • User-variable warning repeat time: constant, 1, 2, 3, 4, 5 min, once • 2 x temperature measurement, optionally 0 to 120°C or 200°C, also voltage measurement up to 80 V DC • 1 x rev-count measurement up to 100,000 rpm with two-blade propeller • 1 x speed controller / servo input, 1 x speed governor input, 1 x speed controller / servo output for rotational speed governor • etc. see product at www.graupner.de/en General sensor for Graupner|SJ HoTT receivers and models with internal-combustion or electric power system: • Vario with altitude signals, climb and descent signals, and additional warning thresholds for min. altitude, max. altitude, climb and twostage descent rate • Altitude indicator (-500 … +3000 m), storage of min. and max. altitude • 2 x temperature and voltage measurements with warning thresholds for min. and max. voltage and min. and max. temperature • Individual cell measurement with min. voltage warning thresholds • Voltage, current and capacity measurement with warning thresholds for min. and max. voltage, max. capacity and max. current • Rev-count measurement and programmable speed governor, also warning thresholds for min. and max. rotational speed • Fuel measurement with warning thresholds in 25% increments (requires software update) • User-variable warning time: OFF, 5, 10, 15, 20, 25, 30 seconds, constant • User-variable warning repeat time: constant, 1, 2, 3, 4, 5 min, once • 2 x temperature measurement, optionally 0 to 120°C or 200°C, also voltage measurement up to 80 V DC • 1 x rev-count measurement up to 100,000 rpm with two-blade propeller • etc. see product at www.graupner.de/en General sensor for Graupner|SJ HoTT receivers and electric-powered models: • Vario with altitude signals, climb and descent signals, and additional warning thresholds for min. altitude, max. altitude, two-stage climb and descent rate • Altitude indicator (-500 … +3000 m), storage of min. and max. altitude. • 2 x temperature and voltage measurements with warning thresholds for min. and max. voltage and min. and max. temperature • Individual cell measurement 2 ... 14S with min. voltage warning thresholds • Voltage, current and capacity measurement with warning thresholds for min. and max. voltage, max. capacity and max. current • User-variable warning time: OFF, 5, 10, 15, 20, 25, 30 seconds, constant • User-variable warning repeat time: constant, 1, 2, 3, 4, 5 min, once • 2 x temperature measurement, optionally 0 to 120°C or 200°C, also voltage measurement up to 80 V DC • 1 x speed controller input, 1 x speed controller output for power reduction due to low voltage of individual cells • 1 x current, voltage and capacity measurement, up to 150 A (peak 1 sec. 320 A) and up to 60 V • 1 x individual cell monitoring for 2 - 14S Lithium batteries (LiPo, LiIo, LiFe) • etc. see product at www.graupner.de/en Appendix 195 Graupner|SJ HoTT magnetic rev-count sensor Order No. 33616 Graupner|SJ HoTT Smart-Box Order No. 33700 Graupner|SJ HoTT USB interface Order No. 7168.6 For connection to the General-Engine module (Order No. 33610), General-Air module (Order No. 33611) or Electric-Air module (Order No. 33620). The number of blades must be selected beforehand in the module’s Telemetry menu. A vast range of different functions combined in a single device: that’s what destines the SMART-BOX to be your intelligent companion in future. Whether you want to display telemetry data in real time, or enter changes to your HoTT system, the large-area screen with 8 x 21 characters makes the task simple. The flexible Smart-Box includes an integral buzzer for generating audible signals and warnings for even greater flexibility and practicality. The installation set supplied makes it easy to mount the unit on the support bars of hand-held transmitters, allowing you to position it in such a way that you can read off telemetry data in real time while you control your model. The user-update facility ensures that the SMART-BOX is always up-todate, and provides a route for expanded functions in future. • Transmitter voltage display with • Country setting user-variable warning threshold • Signal quality • Range check • Receiver temperature • Receiver voltage • Servo neutral position • Servo reverse • Servo travel • Cycle time • Channel swap • Fail-Safe settings • Mixer settings • Servo test Dimensions: approx. 76 mm x 72 mm x 17 mm (L x W x H) Weight: approx. 55g This USB interface is required in conjunction with the adapter lead, Order No. 7168.6A (available separately) for updating receivers and sensors. The mx-16 HoTT transmitter can be updated directly using the USB lead included in the interface set. Graupner|SJ HoTT optical rev-count sensor Order No. 33615 For connection to the General-Engine (Order No. 33610), General-Air (Order No. 33611) or Electric-Air module (Order No. 33620). The number of blades must be selected beforehand in the module’s Telemetry menu. 196 Appendix Graupner|SJ HoTT adapter lead Order No. 7168.6A This adapter lead is required in conjunction with the USB interface, Order No. 7168.6 (available separately) for updating receivers and sensors. The mx-16 HoTT transmitter can be updated directly using the USB lead included in the interface set. mx-10 HoTT - No. 33110, mx-12 HoTT - No. 33112, mx-16 HoTT - No. 33116, mx-20 HoTT - No. 33124, mc-16 HoTT - No. 33016, mc-20 HoTT - No. 33020, mc-32 - No. 33032 GR-12S HoTT - No. 33505, GR-12 HoTT - No. 33506, GR-16 HoTT - No. 33508, GR-24 HoTT - No. 33512, GR-32 HoTT - No. 33516 2 Geräteklasse: V1.7.1 Stefan Graupner, Managing Director Stefan Graupner, Geschäftsführer Measures for the efficient use of the radio frequency spectrum § 3 (2) (Article 3 (2)) Maßnahmen zur effizienten Nutzung des Frequenzspektrums § 3 (2) (Artikel 3 (2)) Graupner GmbH & Co. KG Henriettenstraße 94-96 D-73230 Kirchheim/Teck Germany Tel: 07021/722-0 Fax: 07021/722-188 EMail: [email protected] Kirchheim, 07. August 2012 0678 EN 300 328 Schutzanforderungen in Bezug auf elektromagnetische Verträglichkeit § 3 (1) 2, Artikel 3 (1) b)) EN 301 489-1 V1.9.2 EN 301 489-17 V2.1.1 Protection requirement concernig electromagnetic compatibility § 3 (1) 2, Artikel 3 (1) b)) Health and safety requirements pursuant to § 3 (1) 1. (Article 3 (1) a)) Gesundheit und Sicherheit gemäß § 3 (1) 1. (Artikel 3 (1)a)) EN 60950-1:2006+A11: 2009+A1:2010+A12: 2011 Harmonised standards applied Angewendete harmonisierte Normen: complies with the essential requirements of § 3 and the other relevant provisions of the FTEG (Article 3 of the R&TTE Directive). den grundlegenden Anforderungen des § 3 und den übrigen einschlägigen Bestimmungen des FTEG (Artikel 3 der R&TTE) entspricht. Equipment class declares that the product erklärt, dass das Produkt: Graupner GmbH & Co. KG Henriettenstraße 94-96 D-73230 Kirchheim/Teck Declaration of Conformity in accordiance with the Radio and Telecomunikations Terminal Equipment Act (FTEG) and Directive 1999/5/EG (R&TTE) Konformitätserklärung gemäß dem Gesetz über Funkanlagen und Telekomunikationsendeinrichtungen (FTEG) und der Richtlinie 1999/5/EG (R&TTE) Conformity declaration Conformity declaration 197 FCC Information Graupner|SJ mx-16 HoTT #33116 FCC ID: ZGZ-mx-16-20 FCC Label Compliance Statement This device complies with Part 15C of the FCC Rules. Operation is subject to the following two conditions: 1. This device may not cause harmful interference. 2. This device must accept any interference received, including interference that may cause undesired operation. WARNING: Changes or modifi cations not expressly approved by the party responsible for compliance could void the user‘s authority to operate the equipment. NOTE This equipment has been tested and found to comply with the limits for a Class B digital device, pursuant to Part 15C of the FCC Rules. These limits are designed to provide reasonable protection against harmful interference in a residential installation. This equipment generates uses and can radiate radio frequency energy and, if not installed and used in accordance with the instructions, may cause harmful interference to radio communications. However, there is no guarantee that interference will not occur in a particular installation. If this equipment does cause harmful interference to radio or television reception, which can be determined by turning the equipment off and on, the user is encouraged to try to correct the interference by one or more of the following measures: • Reorient or relocate the receiving antenna. • Increase the separation between the equipment and receiver. 198 FCC Information • Connect the equipment into an outlet on a circuit different from that to which the receiver is connected. • Consult the dealer or an experienced radio/TV technician for help. RF Exposure Statement This device has been evaluated to meet the FCC RF exposure requirement when used in combination with the genuine Graupner|SJ HoTT accessoires and operated with a minimum distance of 20 cm between the antenna and your body. Guarantee certificate Servicestellen / Service / Service après-vente http://www.graupner.de/en/service/servicepoints.aspx Graupner Zentralservice Graupner GmbH & Co. KG Henriettenstrasse 94 - 96 D-73230 Kirchheim [email protected] Servicehotline (+49) 0 18 05 47 28 76* Mo - Do: 09:15 - 18:00 Freitag: 09:15 - 16:00 Uhr Belgie/Belgique/Nederland Jan van Mouwerik Slot de Houvelaan 30 NL 3155 Maasland VT (+31) 10 59 13 59 4 [email protected] Luxembourg Kit Flammang 129, route d’Arlon L 8009 Strassen (+35) 23 12 23 2 [email protected] Ceská Republika Slovenská Republika RC Service Z. Hnizdil Letecka 666/22 CZ 16100 Praha 6 - Ruzyne (+420) 2 33 31 30 95 [email protected] Schweiz Graupner Service Schweiz CD-Electronics GmbH Kirchweg 18 CH-5614 Sarmenstorf (+41) 56 667 14 91 [email protected] Espana Anguera Hobbies C/Terrassa 14 E 43206 Reus (Tarragona) (+34) 97 77 55 32 0 [email protected] United Kingdom Graupner Service UK Brunel Drive GB, NEWARK, Nottingham­shire NG242EG (+44) 16 36 61 05 39 [email protected] France Graupner Service France Gérard Altmayer 86, rue St. Antoine F 57601 Forbach-Oeting (+33) 3 87 85 62 12 [email protected] Italia GiMax Via Manzoni, no. 8 I 25064 Gussago (+39) 030 25 22 73 2 [email protected] * 0.14 cent / minute from a German Telecom land-line. Calling price variations possible for calls from cell phones or from the land-lines of other providers. Wir gewähren auf dieses Erzeugnis eine Garantie von This product is warrantied for Sur ce produit nous accordons une garantie de Die Fa. Graupner GmbH & Co. KG, Henriettenstraße 94 - 96, D-73230 Kirchheim/Teck gewährt ab dem Kaufdatum auf dieses Produkt eine Garantie von 24 Monaten. Die Garantie gilt nur für die bereits beim Kauf des Produktes vorhandenen Material- oder Funktionsmängel. Schäden, die auf Abnützung, Überlastung, falsches Zubehör oder unsachgemäße Behandlung zurückzuführen sind, sind von der Garantie ausgeschlossen. Die gesetzlichen Rechte und Gewährleistunsansprüche des Verbrauchers werden durch diese Garantie nicht berührt. Bitte überprüfen Sie vor einer Reklamation oder Rücksendung das Produkt genau auf Mängel, da wir Ihnen bei Mängelfreiheit die entstandenen Unkosten in Rechnung stellen müssen. 24 Monaten months mois Garantie-Urkunde Warranty certificate / Certificat de garantie mx-16 HoTT Set Order No. 33116 Graupner GmbH & Co. KG, Henriettenstraße 94 - 96. D-73230 Kirchheim/Teck, Germany guarantees this product for a period of 24 months from date of purchase. The guarantee applies only to such material or operational defects witch are present at the time of purchase of the product. Damage due to wear, overloading, incompetent handling or the use of incorrect accessories is not covered by the guarantee. The user´s legal rights and claims under guarantee are not affected by this guarantee. Please check the product carefully for defects before you are make a claim or send the item to us, since we are obliged to make a charge for our cost if the product is found to be free of faults. Übergabedatum: Date of purchase/delivery: Date d’achat : La société Graupner GmbH & Co. KG, Henriettenstraße 94-96, D-73230 Kirchheim/Teck, accorde sur ce produit une garantie de 24 mois à compter de la date d’achat. La garantie ne s’applique qu’aux défauts de matériel et de fonctionnement du produit acheté. Les dommages dus à une usure, à une surcharge, à l’emploi d’accessoires non compatibles ou à une manipulation non conforme sont exclus de la garantie. Cette garantie ne remet pas en cause les droits légaux des consommateurs. Avant toute réclamation ou retour de matériel, vérifiez précisément les défauts ou vices constatés, car si le matériel est conforme et qu’aucun défaut n’a été constaté par nos services, nous nous verrions contraints de facturer le coût de cette intervention. Firmenstempel und Unterschrift des Einzelhändlers: Stamp and signature of dealer: Cachet et signature du détaillant : Name des Käufers: Owner´s name: Nom de I`acheteur : Straße, Wohnort: Complete address: Adresse complète : Guarantee certificate 199 H O P P I N G . T E L E M E T R Y . T R A N S M I S S I O N GRAUPNER GMBH & CO. KG POSTFACH 1242 D-73220 KIRCHHEIM/TECK GERMANY Modifications and availability reserved. Graupner products are only available through model shops. We will gladly inform you of your nearest stockist. We accept no liability for printing errors. www.graupner.de/en Printed in Germany PN.RC-03a (V6de) Although we have carefully checked the information contained in these instructions and checked that it is correct, we can accept no liability of any kind for mistakes, incomplete information and printing errors. Graupner reserves the right to alter the characteristics and features of the software and hardware at any time and without prior notification.
advertisement
* Your assessment is very important for improving the workof artificial intelligence, which forms the content of this project
Related manuals
advertisement