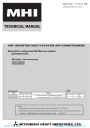
advertisement
▼
Scroll to page 2
of 157
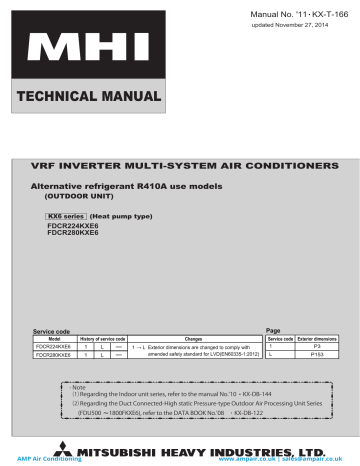
Manual No. '11 • KX-T-166 updated November 27, 2014 TECHNICAL MANUAL VRF INVERTER MULTI-SYSTEM AIR CONDITIONERS Alternative refrigerant R410A use models (OUTDOOR UNIT) KX6 series (Heat pump type) FDCR224KXE6 FDCR280KXE6 Page Service code Model History of service code FDCR224KXE6 1 L FDCR280KXE6 1 L • Changes 1 → L Exterior dimensions are changed to comply with amended safety standard for LVD(EN60335-1:2012) Note ⑴ Regarding the Indoor unit series, refer to the manual No.'10 Service code Exterior dimensions 1 P3 L P153 KX-DB-144 ⑵ Regarding the Duct Connected-High static Pressure-type Outdoor Air Processing Unit Series (FDU500 AMP Air Conditioning 1800FKXE6), refer to the DATA BOOK No.'08 KX-DB-122 www.ampair.co.uk | [email protected] '11 • KX-T-166 CONTENTS 1 GENERAL INFORMATION ............................................................................... 1 1.1 Increased indoor unit connection capacity ................................................... 1 1.2 How to read the model name ....................................................................... 1 1.3 Branch pipe set and Header pipe set ........................................................... 1 2 OUTDOOR UNIT ............................................................................................... 2 2.1 Specifications ............................................................................................... 2 2.2 Exterior dimensions ..................................................................................... 3 2.3 Electrical wiring ............................................................................................ 6 2.4 Noise level ................................................................................................... 7 3 RANGE OF USAGE & LIMITATIONS .............................................................. 8 4 SELECTION CHART ...................................................................................... 10 5 PIPING SYSTEM ............................................................................................ 17 6 APPLICATION DATA ..................................................................................... 19 6.1 Cautions for reuse of existing pipes ......................................................... 19 6.2 Installation of outdoor unit .......................................................................... 22 6.3 Method for connecting the accessory pipe ................................................ 38 6.4 Installation work check sheet (For heat pump unit) ................................... 39 6.5 Check operation procedure ........................................................................ 41 6.6 Instructions for installing the branch pipe set (option) ................................ 49 6.7 Service valve kit installation manual .......................................................... 53 6.8 Pipe washing check sheet ......................................................................... 55 6.9 Instruction manual piping re-fresh kit ......................................................... 56 7 OUTLINE OF OPERATION CONTROL BY MICROCOMPUTER .................. 58 7.1 Operation control function by the outdoor controller .................................. 58 8 SYSTEM TROUBLESHOOTING PROCEDURE ............................................ 89 8.1 Basics of troubleshooting ........................................................................... 89 8.2 Explanation of troubleshooting ................................................................... 90 8.3 Contents of troubleshooting ....................................................................... 91 8.4 Outdoor unit control PCB replacement procedure ................................... 146 8.5 Inverter PCB replacement procedure ...................................................... 148 9 OUTDOOR UNIT (Service code L) ............................................................. 153 9.1 Exterior dimensions .................................................................................. 153 # AMP Air Conditioning www.ampair.co.uk | [email protected] '11 • KX-T-166 1 GENERAL INFORMATION 1.1 Increased indoor unit connection capacity • Capacity from 50% to 130% is possible Item Number of connectable Connectable capacity FDCR224KXE6 1 to 13 units 112 ~ 292 FDCR280KXE6 1 to 16 units 140 ~ 364 Model 1.2 How to read the model name (1) Outdoor unit Example: FDCR 224 KX E 6 Series No. Application power source...See the specifications Multi KX series Nominal capacity (nominal cooling capacity : 22.4kW) Model name (Outdoor unit) 1.3 Branch pipe set and Header pipe set (1) Branch pipe set (Option) Total capacity downstream Branching pipe set Less than 180 DIS-22-1G 180 or more but less than 371 DIS-180-1G (2) Header pipe set (Option) Total capacity downstream Header set model type Number of branches Less than 180 HEAD4-22-1G 4 branches at the most 180 or more but less than 371 HEAD6-180-1G 6 branches at the most Note This unit complies with EN61000-3-3. For outdoor unit, EN61000-3-2 is not applicable as consent by the utility company or notification to the utility company is given before usage. - AMP Air Conditioning www.ampair.co.uk | [email protected] '11 • KX-T-166 2 OUTDOOR UNIT 2.1 Specifications Models Nominal cooling capacity*1 Nominal heating capacity*2 Power source Power consumption Running current Sound Pressure Level(Cool/Heat) Exterior dimensions Height × Width × Depth Exterior appearance (Munsell color) Net weight Refrigerant equipment compressor type & Q'ty Motor Starting method connectable capacity capacity control range Crankcase heater Refrigerant equipment Heat exchanger Refrigerant control Refrigerant Quantity Refrigerant oil Defrost control Air handling equipment fan type & Q'ty Motor Starting method Air flow(Standard) Static Pressure Shock & vibration absorber Notes FDCR280KXE6 22.4 25.0 28.0 31.5 kW Cool Heat Cool Heat 380-415V 3N∼ 50Hz 5.60 6.03 9.25/8.47 9.85/9.02 58/58 kW A dB(A) stucco white (4.2 Y 7.5 / 1.1)near equivalent 224 kg GTC5150NH40K×1 kW 3.81 % % W 50-130 27-114 GTC5150NH40K×1 5.22 Direct line start 50-130 20-115 33 Straight fin & inner grooved tubing Electronic expansion valve R410A 11.5 1.7(M-MA32R) MC controlled De-Icer kg l Propeller fan × 2 W 144×2 Direct line start 200 Max.35 Rubber mount(for compressor) Compressor over current protection / abnormal high pressure protection abnormal low pressure protection / abnormal discharge temperture protection / over current protection φ9.52(3/8")∼φ15.88(5/8") φ19.05(3/4")∼φ25.4(1") φ22.22(7/8")∼φ28.58(1 1/8") Liquid:Flare / Gas:Brazing Hole for drain(φ20 ×4) Necessary(both Liquid & Gas lines) CMM Pa Liquid Line Gas Line mm(in) (1) The data are measured at the following conditions. (The piping length is 7.5m) Item 8.09 8.21 13.22/12.10 13.41/12.28 59/60 1675×1080×480 mm safety equipment Installation data Refrigerant piping size Connecting method Drain Insullation for piping Accessories FDCR224KXE6 Indoor air temperature Outdoor air temperature Operation DB WB DB WB Cooling*1 27: 19: 35: 24: Heating*2 20: - 7: 6: Adapted to RoHS directive Standards ISO-T1 (2) This packaged air-conditioner is manufactured and tested in conformity with the following standard. ISO-T1 "UNITARY AIR-CONDITIONERS" (3) Refer to the technical data about below. ・Reusability of the existing pipes. ・Necessity of Re-fresh kit and Service valve kit when washing existing pipes. PCB003Z361 - AMP Air Conditioning www.ampair.co.uk | [email protected] Intake L4 Outlet F1 F2 F3 F4 43※ 60 120 69 48 L1 Service space B C D E 69※ Intake A Minimum installation space G Content Service valve connection of the attached connecting pipe(gas side) Service valve connection(liquid side) Pipe/cable draw-out hole Drain discharge hole Anchor bolt hole Cable draw-out hole Cable draw-out hole Cable draw-out hole Cable draw-out hole Connecting position of the local pipe.(gas side) φ19.05(3/4") (Flare) φ12.7(1/2") (Flare) 4places φ20×4places M10×4places φ30 φ45 φ22 φ34 φ25.4(1") (Brazing) 22 Notes (1)It must not be surrounded by walls on the four sides. (2)The unit must be fixed with anchor bolts. An anchor bolt must not protrude more the 15mm. (3)Where the unit is subject to strong winds, lay it in such a direction that the blower outlet faces perpendicularly to the dominant wind direction. (4)Leave 1m or more space above the unit. (5)A wall in front of the blower outlet must not exceed the units height. (6)The model name label is attached on the lower right corner of the front. (7)Connect the Service valve with local pipe by using the pipe of the attachment. (Gas side only) (8)Mark ※ shows the connecting posotion of the local pipe.(Gas side only) 1675 Terminal Block B A 690 50 80 D 42 34 155 161 55 84 55 174 84 553 634 35 159 194※ 30 30 C 105 520 480 19 39 E F3 989 67 42 701 C 50 124 F4 461 421 8 56 F 4 64 Examples of installation Dimensions L1 L2 L3 L4 Unit:mm I Open 300 300 250(5) *2 I I I I I Open 5 300 250(5) *2 1500(500) Open 300 250(5) *2 *1 *1 Figure in( )shows the value applicable when the flex flow adaptor is installed. *2 Under the setting condition as specified in( ),it is necessary to secure 250 mm for the dimension L4 when replacing the compressor. Establish this for example by moving the unit during the work. '11 • KX-T-166 PCB003Z362 AMP Air Conditioning 195 F2 C 141 241 321 361 195 19 39 E 55 20 1080 54 14 G 84 - F3 F 1 C 51 2.2 Exterior dimensions L2 Symbol B A G (1) Outdoor unit Models FDCR224KXE6, 280KXE6 L3 www.ampair.co.uk | [email protected] Connecting hole (Ø25.4)for pipe at refrigerant gas side (To outdoor unit) 476 506 150 430 22 37 150 Connecting hole (Ø25.4)for pipe at refrigerant gas side (To indoor unit) 62 160 215 Indoor 27 Outdoor (2) Service valve kit Hole for 4- anchor bolt (for M10 bolt) 63 300 - - Notes 1.Install the Service valve kit when carrying out the washing operation utilizing existing pipes. For the outdoor units which can use this kit, refer to the technical data. 2.The Service valve kit cannot be installed upside-down. Install the kit at level. 3.Use new pipes to connect between the Service valve kit and the outdoor unit. It is prohibited to use existing pipes. Restrict the actual pipe lenght no longer than 3m. 4.Secure the service spaces shown in the figure below. (Rear) 1350 Service space (Necessary for washing operation) Secure also an overhead space sufficient for working in a standing position. Model FDCR-V-KIT-E Weight 10.7kg '11 • KX-T-166 PCB003Z365 AMP Air Conditioning 500 (Front) www.ampair.co.uk | [email protected] 25 125 (3) Pipe Re-fresh Kit Model : FDCR-KIT-E 404 Accessory 602 62 351 (189) Flexible tube x 2pcs. Accumulator - Check joint L Check valve Flange fixing bolt x 8pcs. Check joint R Bypass gas pipe service valve Bypass gas pipe service valve 158 Flange Oil drain hole 201 151 126 '11 • KX-T-166 PCB003Z366 AMP Air Conditioning Gasket x 4pcs. 47 Flange Oil drain hole 1283 - Strainer www.ampair.co.uk | [email protected] 52X1 52X2 SA CNN9 (BK) CNN4 (OR) CNQ3 (Y) CNL1 (BL) 7SEG2 SW3 1 2 3 4 5 6 7 8 - - MS 3∼ CNL2 CNZ1 (WH) (RD) EEVH EEVSC t° t° Silent mode input External CNS1 WH (GN) input t° CNP1 (YE) BK BK BK BK BK Y t° Tho-H FMo2 t° t° Tho-C1 FMo1 t° Tho-R2 M Tho-A M Tho-D1 M Cooling/Heating forced input CNG2 WH (WH) PC (RS232C) LED3 CNB2 CNF1 CNF2 CNU1 (RD) (WH) (GN) (BL) CNTH (WH) t° M LED2 WH CNS2 WH (RD) Black Blue Brown Green Gray Orange Red White Yellow Pink Yellow/Green Demand input BK LED1 Tho-SC J15 BK J14 Tho-S J13 CNEEV2 (BL) RD CNEEV1 (RD) BL OR Y WH CNFAN_2 (WH) J12 BK SW7 RD CNFAN_1 (WH) CNG1 (BL) 1 2 3 4 5 6 7 8 CNV J11 Operation output Trouble CNY (WH) output SW6 1 2 3 4 5 6 7 8 Reseave output BK BL BR GN GR OR RD WH Y P Y/GN t° W SW1 SW2 SW3-1 SW3-2 SW3-3 SW3-4,5 SW3-6 SW3-7 SW3-8 SW4-1∼4 SW4-5,6 SW4-7,8 SW5-1 SW5-2 SW5-3 SW5-4 SW5-5 SW5-6∼8 SW6-1∼8 SW7 SW8 SW9 ON OFF ON OFF ON OFF ON OFF ON OFF ON OFF ON OFF Address setting SW outdoor unit No.(2 digits) Address setting SW outdoor unit No.(1 digit) Inspection LED reset Spare Model setting Spare Pipe washing operation Normal operation Forced heating/cooling mode Normal operation Test mode Normal operation Model setting Demand switching Spare Test run Normal operation Cooling at test run Heating at test run Pump-down operation Normal operation Spare Super Link communication Super Link communication Spare Spare Data delete/write 7-segment indication up(1 digit) 7-segment indication up(2 digits) TB1,2 Tho-A Tho-C1 Tho-D1 Tho-H Tho-P1 Tho-R1 Tho-R2 Tho-S Tho-SC X01∼03,06∼09 7SEG1 7SEG2 20S 52X1,2 63H1-1 63H1-R1,2 Terminal block External air thermistor Under-dome thermistor Discharge pipe thermistor Super-cooling coil thermistor 2 Power transistor thermistor Heat exchanger thermistor 1(Exit/front) Heat exchanger thermistor 1(Exit/rear) Suction pipe thermistor Super-cooling coil thermistor 1 Aux. relay 7-segment LED(Data display) 7-segment LED(Function display) 4-way switching solenoid Solenoid for CM High pressure switch High pressure switch '11 • KX-T-166 PCB003Z364 Crankcase heater Compressor motor Connector Current sensor Electrolytic capacitor Diode module Heating expansion valve Super-cooling coil expansion valve Fan motor Fuse Intelligent power module Power supply, voltage switching External input switching level/pulse Spare Defrosting start temperature selection, normal/cold region Inspection(Red) Normal(Yellow) Flashing Normal(Green) Service(Green) DC reactor High pressure sensor Low pressure sensor PCB Rush current suppression resistor Solenoid valve(fluid return) Solenoid valve(oil return) Solenoid valve(gas bypass) Solenoid valve(gas bypass) V 1 2 3 4 5 6 7 8 Tho-R1 LED1(INV) SW5 SW8 CONTROL PWB1 RD CNI1 (WH) SW4 SW9 WH OR BR BL CNA2 (BR) PSL BK WH RD BK WH RD PSH CNQ1 (WH) Color symbol 63H1-R2 BK BK RD BL BL BL BL CNN2 (GN) 63H1-R1 63H1-1 SV12 SV11 Tho-P1 CNA1 (WH) RD R3 RD 7SEG1 RD RD R1 R2 BL Y YYE RD YE RD + C1 RD CNA BL P (WH) IPM U V W CNI2 (WH) U CM AMP Air Conditioning CNN6 (PK) N RD INVERTER PWB2 RD WH R4 BL CNR (WH) RD BL BL A2 B2 SW2 ON OFF WH + C2 WH BETWEEN THE OUTDOOR UNITS shows local wiring. CNN1 (RD) CNM1 (GY) SV6 CNH (BL) SW1 F1(10A) L1 L2 A1 B1 LED1 LED1(INV) LED2 LED3 L1~L3 PSH PSL PWB1~3 R1 SV1 SV6 SV11 SV12 +4 NETWORK CONNECTOR BETWEEN THE INDOOR UNIT AND THE OUTDOOR UNIT CH1 CM CNA-Z1 CT1 C1 DM EEVH EEVSC FMo1,2 F1 IPM J11,12 J13 J14 J15 DM R5 CNSL1,2 BK CNR1 (WH) SV1 CNX1 (YE) BK BK BK BK WH BK GN BK SIGNAL LINE K -6 WH RDRD AC1 AC2 AC3 G BL 20S BL OR Y WH BL POWER SOURCE WH 52X2 WH 380/415V 3N∼ 50Hz TB2 A1 B1 A2 B2 CNW (RD) WH OR BR BL Earth leakage breaker 52X1 CH1 BK No BK E L3o GN Circuit breaker for cabling Ni Va1 Va2 Va3 GN L2o WH BR L3i BK L3 RD L1o RD BK WH BL NOISE FILTER PWB3 RD WH L2i RD WH BL L1i WH 2.3 Electrical wiring 4 RD Models FDCR224KXE6, 280KXE6 TB1 L1 L2 L3 N www.ampair.co.uk | [email protected] '11 • KX-T-166 2.4 Noise level Measured based on JIS B 8616 Mike position as highest noise level in position as below Distance from front side1m Height1m Model FDCR224KXE6 㪝㪛㪚㪧㪉㪉㪋㪊㪟㪣㪯㪰 Noise level 58 dB (A) ಄ᚱ Cooling Noise level 58 dB (A) Heating 㪏㪇 80 㪏㪇 80 N80 㪎㪇 Souud Pressure Level (dB) -5 (standard 2×10 Pa) Souud Pressure Level (dB) 㖸䊧䊔䊦䋨㪻䌂䋩 -5 (standard 2×10 Pa) 䋨ၮḰ㖸㪇㪅㪇㪇㪇㪉䊙䉟䉪䊨䊋䊷䊦䋩 㪥㪏㪇 㪎㪇 㪥㪎㪇 㪍㪇 㪍㪇 㪥㪍㪇 㪌㪇 㪌㪇 㪥㪌㪇 㪋㪇 㪋㪇 㪥㪋㪇 㪥㪊㪇 㪊㪇 㪍㪊 㪈㪉㪌 㪉㪌㪇 㪌㪇㪇 㪈㪇㪇㪇 㪉㪇㪇㪇 㪋㪇㪇㪇 70 70 N70 60 60 N60 50 50 N50 40 40 30 㪊㪇 㪏㪇㪇㪇 N40 N30 63 Mid Octave Band Frequency (Hz) 䉥䉪䉺䊷䊑ਛᔃᵄᢙ㩷䋨䌈㫑䋩㩷 125 250 500 1000 2000 4000 Model FDCR280KXE6 Noise level 59 dB (A) Cooling Noise level 60 dB (A) Heating 80 80 80 80 70 N80 Souud Pressure Level (dB) -5 (standard 2×10 Pa) Souud Pressure Level (dB) -5 (standard 2×10 Pa) N80 70 N70 60 60 N60 50 50 N50 40 40 N40 N30 30 63 125 250 500 1000 2000 4000 30 8000 70 70 N70 60 60 N60 50 50 N50 40 40 N40 N30 30 63 Mid Octave Band Frequency (Hz) 125 250 500 1000 2000 4000 80 80 80 70 N80 Souud Pressure Level (dB) -5 (standard 2×10 Pa) Souud Pressure Level (dB) -5 (standard 2×10 Pa) N80 70 N70 60 60 N60 50 50 N50 40 40 N40 N30 63 125 250 500 1000 2000 4000 30 8000 70 70 N70 60 60 N60 50 50 N50 40 40 N40 N30 30 63 Mid Octave Band Frequency (Hz) 125 250 500 1000 2000 4000 30 8000 Mid Octave Band Frequency (Hz) - AMP Air Conditioning 30 8000 Mid Octave Band Frequency (Hz) 80 30 30 8000 Mid Octave Band Frequency (Hz) www.ampair.co.uk | [email protected] '11 • KX-T-166 3 RANGE OF USAGE & LIMITATIONS System FDCR280KXE6 FDCR224KXE6 Item Indoor intake air temperature (Upper, lower limits) Please see the next page. Outdoor air temperature (Upper, lower limits) Indoor units that can be used in combination Number of connected units 1 to 13 unit 1 to 16 unit Connectable capacity (1) 112 ~ 292 140 ~ 364 Total piping length 510m or less Main pipe length 130m or less Single direction piping length Actual length : 160m or less, Eguivalent length : 185m or less 90m or less (However, difference between the longest and shortest piping : 40m or less) Allowable pipe length from the first branching Elevation difference between the first branching point and the indoor unit 18m or less Difference in height between indoor and outdoor units Outdoor unit is higher 50m or less Outdoor unit is lower 40m or less 15m or less Difference in the elevation of indoor units in a system Indoor unit atmosphere (behind ceiling) temperature and humidity Only models FDT, FDTC, FDTW, FDTS, FDTQ, FDU, FDUM, FDQS, FDUH Compressor stop/start frequency Dew point temperature 28 or less, relative humidity 80% or less (FDE, FDK, FDFL, FDFU : Dew point temperature 23 or less, relative humidity 80% or less) 6 min or more (3 minutes or more from start to stop or 3 minutes or more from stop to start) 1 cycle time 3 min or more Stop time Power source voltage Voltage fluctuation Within 10% of rated voltage Voltage drop during start Within 15% of rated voltage Phase unbalance Within 3% of rated voltage Allowable length of refrigerant piping, height difference between indoor and outdoor unit (1) Branch pipe method (using branch piping) Outdoor Outdoor unit unit Indoor unitunit Indoor First branch First branch At the most, 90 m or less MAX. 90m (2) Header System (Header used) Outdoor unit 40 m or less (2) MAX. 15m MAX. 18m MAX. 130m MAX. 15m MAX. 18m MAX. 18m (Highest indoor unit) (Highest indoor unit) MAX. 18m At the most, 130m or less 50m (Outdoor unit is lower : 40m) 50m (Outdoor unit is lower : 40m) MAX. 90m denotes denotes (Lowest indoor unit) (Lowest indoor unit) Indoor unit Outdoor unit Indoor unit 40 m or less (2) (Header) 18m First branch At the most, 90m or less MAX. 15m (Header) MAX. 15m MAX. 18m (Highest indoor unit) MAX. 18m MAX.MAX. 18m First branch At the most, 130m or less MAX. 130m 50m (Outdoor unit is lower : 40m) 50m (Outdoor unit is lower : 40m) (Highest indoor unit) (Lowest indoor unit) Note (1) A branch piping system cannot be connected after a header system. (Lowest indoor unit) (2) 90m or less (However, difference between the longest and shortest piping : 40m or less) MAX. 90m - AMP Air Conditioning www.ampair.co.uk | [email protected] '11 • KX-T-166 (3) Mixed System (Branch piping and Header used) Outdoor unit Indoor unit (Highest indoor unit) MAX.40m(2) Ⅱ Ⅲ (Header) Ⅳ MAX.18m First branch Ⅴ MAX.15m MAX.18m Ⅰ MAX.130m (Outdoor unit is lower: 40m) 50m MAX.90m(2) Ⅵ MAX.90m(2) (Lowest indoor unit) Note (1) A branch piping system cannot be connected after a header system. (2) 90m or less (However, difference between the longest and shortest piping : 40m or less) Operating temperature range Cooling operation Outdoor air D.B. temperature ˚C D.B. Applicable range 43 40 35 30 25 20 26 24 0 Heating operation Indoor air D.B. temperature ˚C D.B. -5 -15 14 16 18 20 22 Indoor air W.B. temperature ˚C W.B. 27 25 20 15 10 -25 -20 -15 -10 -5 0 5 10 15 Outdoor air W.B. temperature ˚C W.B. “CAUTION” Cooling operation under low outdoor air temperature conditions KXE6 models can be operated in cooling mode at low outdoor air temperature condition within above temperature range. However in case of severely low temperature conditions if the following precaution is not observed, it may not be operated in spite of operable temperature range mentioned above and cooling capacity may not be established under certain conditions. [Precaution] In case of severely low temperature condition 1) Install the outdoor unit at the place where strong wind cannot blow directly into the outdoor unit. 2) If there is no installation place where can prevent strong wind from directly blowing into the outdoor unit, prepare a windbreak fence or something like that locally in order to divert the strong wind from the outdoor unit. [Reason] Under the low outdoor air temperature conditions of -5 or lower, if strong wind directly blow into the outdoor unit, the outdoor heat exchanger temperature will drop, even though the outdoor fan is stopped by outdoor fan control. This makes high and low pressures to drop as well. This low pressure drop makes the indoor heat exchanger temperature to drop and will activate anti-frost control at indoor heat exchanger at frequent intervals, that cooling operation may not be established for any given time. - AMP Air Conditioning www.ampair.co.uk | [email protected] '11 • KX-T-166 4 SELECTION CHART (1) Equipment selection flow Calculate the load for each room separately, then determine the indoor load. Select an indoor unit that matches the indoor load (tentative). Calculate the temperature compensation, then calculate the indoor unit capacity. (See item (2) (a) for the calculation method.) Indoor unit capacity (tentative) Indoor Load Change the indoor unit. Select the outdoor unit (tentative). NO Calculate temperature compensation and piping compensation, etc., then calculate the outdoor unit capacity. (See item (2) (b) for the calculation method.) YES Calculate the total indoor unit capacity. Calculate the system capacity (See item (2) (c) for the calculation method.) NO Total indoor unit capacity System Capacity Change the outdoor unit. YES Calculate the indoor unit capacity. (See item (2) (d) for the calculation method.) Indoor unit capacity Indoor Load NO YES Equipment selection complete. - AMP Air Conditioning 10 www.ampair.co.uk | [email protected] '11 • KX-T-166 (2) Capacity calculation method (a) Calculating the indoor unit capacity compensation Indoor unit capacity (cooling, heating) = Indoor unit total rated capacity × Capacity compensation coefficient according to temperature conditions See item (3) (a) concerning the capacity compensation coefficient according to temperature conditions. (b) Calculating the outdoor unit capacity compensation Outdoor Unit Capacity (Cooling, Heating) = Outdoor unit rated capacity (rated capacity when 100% connected) × Capacity compensation coefficient according to temperature conditions × Capacity compensation coefficient according to piping length × Capacity compensation coefficient according to height difference × Correction of heating capacity in relation to the frost on the outdoor unit heat exchanger × Capacity compensation coefficient according to indoor unit connection capacity See item (3) (a) concerning the capacity compensation coefficient according to temperature conditions. See item (3) (c) concerning the capacity compensation coefficient according to piping length. See item (3) (d) concerning the capacity compensation coefficient according to height difference. This compensation should be carried out only in cases where the outdoor unit is lower during cooling and higher during heating. See item (3) (e) correction of heating capacity in relation to the frost on the outdoor unit heat exchanger. This compensation should be carried out only when calculating the heating capacity. See item (3) (f) concerning the capacity compensation coefficient according to indoor unit connected capacity. This compensation should be carried out only in cases where the indoor unit total capacity is 100% or higher. (c) Calculating system capacity Compare the capacities determined in items (a) and (b) above and let the smaller value be the system capacity (cooling, heating). In cases where indoor unit total capacity (cooling, heating) > outdoor unit capacity (cooling, heating) System capacity (cooling, heating) = Outdoor unit capacity (cooling, heating) In cases where indoor unit total capacity (cooling, heating) < outdoor unit capacity (cooling, heating) System capacity (cooling, heating) = Indoor unit capacity (cooling, heating) (d) Calculating indoor unit capacity [item (c) 1 only] Indoor unit capacity (cooling, heating) = System capacity (cooling, heating) × [(Indoor unit capacity) / (Indoor unit total capacity)] Capacity calculation examples Example 1 Cooling (when the indoor unit connected total capacity is less than 100%) • Outdoor unit FDCR224KXE6...................................................... 1 Unit • Indoor unit FDT56KXE6D.......................................................... 3 Units • Piping length ............................................................................... 60 m (Equivalent length) • Indoor, outdoor unit height difference......................................... 15 m (Outdoor unit is lower) • Temperature conditions ............................................................... Outdoor temperature: 33˚C DB • Temperature conditions................................................................ Indoor temperature: 19˚C WB <Indoor unit total cooling capacity>: Item (2) (a) calculation. • Indoor unit rated cooling capacity: 5.6 kW • Capacity compensation coefficient according to temperature conditions: 1.02 (Calculated according to Indoor 19˚C WB / Outdoor 33˚C DB); (See page 13) . Indoor unit cooling capacity: 5.6 kW × 1.02 =. 5.7 kW • Indoor unit total cooling capacity calculation; indoor unit total cooling capacity: 5.7 kW × 3 units = 17.1 kW <Outdoor unit maximum cooling capacity> : Item (2) (b) calculation • Outdoor unit rated cooling capacity: 22.4 kW • Capacity compensation coefficient according to temperature conditions: 1.02 (Calculated according to Indoor 19˚C WB / Outdoor 33˚C DB); (See page 13) . Outdoor unit cooling capacity: 22.4 kW × 1.02 =. 22.8 kW • Capacity compensation coefficient according to piping length: 0.92 (calculated according to 60 m length); (See page 15) . 22.8 kW × 0.92 =. 21.0 kW - AMP Air Conditioning 11 www.ampair.co.uk | [email protected] '11 • KX-T-166 • Capacity compensation coefficient according to height difference: 0.97 (calculated according to 15 m difference); (See page 16) . 21.0 kW × 0.97 =. 20.4 kW • Capacity compensation coefficient according to indoor unit connected total capacity: 1.0 , (56 × 3) / 224 < 100%) No compensation <System cooling capacity>: Item (2) (c) calculation Compare the indoor unit total cooling capacity and the outdoor unit maximum cooling capacity. The smaller value is the actual system cooling capacity. • Indoor unit total cooling capacity: 17.1 kW e System cooling capacity: 17.1 kW • Outdoor unit maximum cooling capacity: 20.4 kW <Indoor unit capacity compensation> No compensation (5.7 kW) Example 2 Cooling (when the indoor unit connected total capacity is 100% or higher) • Outdoor unit FDCR224KXE6...................................................... 1 Unit • Indoor unit FDT56KXE6D.......................................................... 5 Units • Piping length ............................................................................... 60 m (Equivalent length) • Indoor, outdoor unit height difference......................................... 15 m (Outdoor unit is higher) • Temperature conditions ............................................................... Outdoor temperature: 35˚C DB • Temperature conditions................................................................ Indoor temperature: 18˚C WB <Indoor unit total cooling capacity>: Item (2) (a) calculation. • Indoor unit rated cooling capacity: 5.6 kW • Capacity compensation coefficient according to temperature conditions: 0.95 (Calculated according to Indoor 18˚C WB / Outdoor 35˚C DB); (See page 13) . Indoor unit cooling capacity: 5.6 kW × 0.95 =. 5.3 kW • Indoor unit total cooling capacity calculation; . indoor unit total cooling capacity: 5.3 kW × 5 units =. 26.5 kW <Outdoor unit maximum cooling capacity> : Item (2) (b) calculation • Outdoor unit rated cooling capacity: 22.4 kW • Capacity compensation coefficient according to temperature conditions: 0.95 (Calculated according to Indoor 18˚C WB / Outdoor 35˚C DB); (See page 13) . Outdoor unit cooling capacity: 22.4 kW × 0.95 =. 21.3 kW • Capacity compensation coefficient according to piping length: 0.92 (calculated according to 60 m length); (See page 15) . 21.3 kW × 0.92 =. 19.6 kW • Capacity compensation coefficient according to height difference: 1.0 (the outdoor unit is higher during cooling) No compensation . • Capacity compensation coefficient according to indoor unit connected total capacity: 1.08 , (56 × 5) / 224 =. 125%) (See page 16) .. 19.6 kW × 1.08 = 21.2 kW <System cooling capacity>: Item (2) (c) calculation Compare the indoor unit total cooling capacity and the outdoor unit maximum cooling capacity. The smaller value is the actual system cooling capacity. • Indoor unit total cooling capacity : 26.5 kW e System cooling capacity: 21.2 kW • Outdoor unit maximum cooling capacity: 21.2 kW <Indoor unit cooling capacity Compensation>: Item (2) (d) calculation. 21.2 kW × 5.3 kW . =. 4.2 kW 26.5 kW Example 3 Heating (when the indoor unit connected total capacity is 100% or higher) • Outdoor unit FDCR224KXE6...................................................... 1 Unit • Indoor unit FDT56KXE6D.......................................................... 5 Units • Piping length ............................................................................... 60 m (Equivalent length) • Indoor, outdoor unit height difference......................................... 20 m (Outdoor unit is higher) • Temperature conditions ............................................................... Outdoor temperature: 6˚C WB • Temperature conditions................................................................ Indoor temperature: 19˚C DB <Indoor unit total heating capacity>: Item (2) (a) calculation. • Indoor unit rated heating capacity: 6.3 kW • Capacity compensation coefficient according to temprature conditions: 1.04 (Calculated according to Outdoor 6˚C WB / Indoor 19˚C DB); (See page 14) . Indoor unit heating capacity: 6.3 kW × 1.04 =. 6.6 kW • Indoor unit total heating capacity calculation; . indoor unit total heating capacity: 6.6 kW × 5 units =. 33.0 kW AMP Air Conditioning - 12 www.ampair.co.uk | [email protected] '11 • KX-T-166 <Outdoor unit maximum heating capacity> : Item (2) (b) calculation • Outdoor unit rated heating capacity: 25.0 kW • Capacity compensation coefficient according to temperature conditions: 1.04 (Calculated according to Outdoor 6˚C WB / Indoor 19˚C DB); (See page 14) Outdoor unit heating capacity: 25.0 kW × 1.04 = 26.0 kW • Capacity compensation coefficient according to piping length: 0.982 (calculated according to 60 m length); (See page 15) . 26.0 kW × 0.982 =. 25.5 kW • Capacity compensation coefficient according to height difference: 0.96 (calculated according to 20 m difference); (See page 16) . 25.5 kW × 0.96 =. 24.5 kW • Correction of heating capacity in relation to the frost on the outdoor unit heat exchanger: 1.0 (calculated according to 6˚C WB); (See page 000) . 24.5 kW × 1.0 =. 24.5 kW. . • Capacity compensation coefficient according to indoor unit connected total capacity: 1.0, (56 × 5) / 224 =. 125%) (See page 16) . 24.5 kW × 1.0 =. 24.5 kW. <System heating capacity>: Item (2) (c) calculation Compare the indoor unit total heating capacity and the outdoor unit maximum heating capacity. The smaller value is the actual system heating capacity. : 33.0 kW e System heating capacity: 24.5 kW • Indoor unit total heating capacity • Outdoor unit maximum heating capacity: 24.5 kW <Indoor unit heating capacity compensation> (Item (2) (d) calculation 24.5 kW × 6.6 kW . =. 4.9 kW 33.0 kW (3) Capacity compensation coefficient (a) Capacity compensation coefficient and power consumption compensation coefficient according to indoor and outdoor temperature conditions. 1) Capacity compensation coefficient SCooling 1.40 Indoor air W.B. temperature 24˚CWB 1.35 Indoor air W.B. temperature 26˚CWB Capacity compensation conefficient 1.30 1.25 Indoor air W.B. temperature 22˚CWB 1.20 Indoor air W.B. temperature 21˚CWB 1.15 1.10 Indoor air W.B. temperature 20˚CWB 1.05 Indoor air W.B. temperature 19˚CWB 1.00 Indoor air W.B. temperature 18˚CWB 0.95 0.90 Indoor air W.B. temperature 17˚CWB 0.85 0.80 Indoor air W.B. temperature 16˚CWB Indoor air W.B. temperature 15˚CWB 0.75 Indoor air W.B. temperature 14˚CWB 0.70 0 2 4 6 8 10 12 14 16 18 20 22 24 26 28 30 32 34 36 38 40 42 Outdoor air D.B. temperature (˚CDB) Note (1) The above-mentioned table shows a typical condition among conditions to occur via controlling an air-conditioning equipment. (2) When performing the cooling operation with the outdoor air temperature being -5°C or under, a windbreak fence must be installed. - AMP Air Conditioning 13 www.ampair.co.uk | [email protected] '11 • KX-T-166 SHeating 1.20 1.15 Outdoor air W.B. temperature 18˚CWB Capacity compensation coefficient 1.10 Outdoor air W.B. temperature 10˚CWB 1.05 Outdoor air W.B. temperature 14˚CWB 1.00 Outdoor air W.B. temperature 6˚CWB 0.95 Outdoor air W.B. temperature 2˚CWB 0.90 Outdoor air W.B. temperature -2˚CWB 0.85 Outdoor air W.B. temperature -6˚CWB 0.80 0.75 Outdoor air W.B. temperature -10˚CWB 0.70 0.65 Outdoor air W.B. temperature -15˚CWB Outdoor air W.B. temperature -20˚CWB 0.60 0.55 17 16 18 19 20 21 22 23 24 Indoor air D.B. temperature(˚CDB) Note (1) The above-mentioned table shows a typical condition among conditions to occur via controlling an air-conditioning equipment. 2) Power consumption correction factor SCooling 1.25 Power consumption compensation coefficient 1.25 1.20 1.15 Indoor air W.B. temperature 26˚CWB 1.10 Indoor air W.B. temperature 24˚CWB 1.05 1.00 Indoor air W.B. temperature 22˚CWB 0.95 Indoor air W.B. temperature 21˚CWB 0.90 0.85 Indoor air W.B. temperature 20˚CWB 0.80 Indoor air W.B. temperature 19˚CWB 0.75 Indoor air W.B. temperature 18˚CWB 0.70 0.65 Indoor air W.B. temperature 17˚CWB 0.60 Indoor air W.B. temperature 16˚CWB 0.55 0.50 Indoor air W.B. temperature 15˚CWB 0 2 4 6 8 Indoor air W.B. temperature 14˚CWB 10 12 14 16 18 20 22 24 26 28 30 32 34 36 38 40 42 Outdoor air D.B. temperature(˚CDB) Note (1) The above-mentioned table shows a typical condition among conditions to occur via controlling an air-conditioning equipment. - AMP Air Conditioning 14 www.ampair.co.uk | [email protected] '11 • KX-T-166 ◆ Heating 1.25 Power consumption compensation coefficient Outdoor air W.B. temperature 6˚CWB 1.20 Outdoor air W.B. temperature -2˚CWB Outdoor air W.B. temperature 2˚CWB Outdoor air W.B. temperature -6˚CWB 1.15 1.10 Outdoor air W.B. temperature 10˚CWB 1.05 1.00 0.95 Outdoor air W.B. temperature -15˚CWB 0.90 0.85 Outdoor air W.B. temperature -10˚CWB 0.80 Outdoor air W.B. temperature -20˚CWB Outdoor air W.B. temperature 14˚CWB 0.75 Outdoorair W.B. temperature 18˚CWB 0.70 16 17 18 19 20 21 22 23 24 Indoor air D.B. temperature(˚CDB) Note (1) The above-mentioned table shows a typical condition among conditions to occur via controlling an air-conditioning equipment. (c) Correction of cooling and heating capacity in relation to one way length of refrigerant piping. (Note) This table is for reference only. If the refrigerant piping one way equivalent after the first branch is extended longer than 40 m, it could drop further by about 10% in the worst case. 1) Cooling Model : FDCR224KXE6 Model : FDCR280KXE6 1.00 Capacity compensation coefficient Capacity compensation coefficient 1.00 0.95 Liquid line:φ12.7 0.90 Gas line:φ25.4 Liquid line:φ12.7 Gas line:φ22.22 0.85 Liquid line:φ9.52 Gas line:φ19.05 0.80 0 20 40 60 80 90 100 120 140 160 0.95 Liquid line:φ15.88 Gas line:φ28.58 0.90 0.85 0.80 180 Refrigerant piping one way equivalent length (m) Liquid line:φ12.7 Gas line:φ25.4 Liquid line:φ9.52 Gas line:φ22.22 0 20 40 60 80 90 100 120 140 160 180 Refrigerant piping one way equivalent length (m) 2) Heatling All models Capacity compensation coefficient 1.00 0.98 0.96 0.94 0.92 0.90 0 20 40 60 80 100 120 140 160 180 Refrigerant piping one way equivalent length (m) - AMP Air Conditioning 15 - # www.ampair.co.uk | [email protected] '11 • KX-T-166 Note (1) Equivalent piping length can be obtained by calculating as follows. Equivalent piping length = Real gas piping length + Number of bends in gas piping × Equivalent piping length of bends. Unit : m/one part Equivalent length of each joint φ9.52 0.15 φ12.7 0.20 φ15.88 0.25 φ19.05 0.30 φ22.22 0.35 φ25.4 0.40 φ28.58 0.45 φ31.8 0.55 (d) When the outdoor unit is located at a lower height than the indoor unit in cooling operation and when the outdoor unit is located at a higher height than the indoor unit in heating operation, the following values should be subtracted from the values in the above table. Height difference between the indoor unit and outdoor unit in the vertical height difference Adjustment coefficient Height difference between the indoor unit and outdoor unit in the vertical height difference Adjustment coefficient 5m 10 m 15 m 20 m 25 m 30 m 0.99 0.98 0.97 0.96 0.95 0.94 35 m 40 m 45 m 50 m 0.93 0.92 0.91 0.90 (e) Correction of heating capacity in relation to the frost on the outdoor unit heat exchanger Air inlet temperature of outdoor unit in ˚C WB Adjustment coefficient -20 -15 -13 -11 -9 -7 -5 -3 -1 1 3 5 or more 0.96 0.96 0.96 0.95 0.94 0.93 0.91 0.88 0.86 0.87 0.92 1 The correction factors will change drastically according to weather conditions. So necessary adjustment should be made empirically according to the weather data of the particular area. (f) The capacity compensation coefficient and power consumption compensation coefficient vary according to the total capacity of concurrently operating indoor units, as shown below. (Note) This table shows typical values. Model FDCA140HKXEN4A, 140HKXES4A ◆ Capacity coefficient Modelscompensation : FDCR 224KXE6, 280KXE6 � Capability compensation coefficient 1.2 1.0 1.0 0.8 0.6 0.4 Heating Heating Capability compensation Capacity compensation coefficient coefficient 1.2 Capability compensation coefficient Capacity compensation coefficient Cooling Cooling 0.8 0.6 0.4 0.2 0.2 0 0 0 20 40 60 80 100 120 1.0 1.0 0.8 0.8 0.6 0.6 0.4 0.4 0.2 0.2 0 20 40 60 80 100 120 00 0Total capacity 20 40 60operating 80indoor 100 of concurrently units (%) 120 20capacity40of concurrently 60 80 100 units120 Total operating indoor (%) 0 1.2 1.2 Total capacity of concurrently operating indoor unit (%) Total capacity of concurrently operating indoor unit (%) � Power consumption compensation coefficient Cooling 1.2 Power consumption compensation coefficient Power consumption compensation coefficient 1.2 1.0 0.8 0.6 0.4 0.2 0 0 10 20 30 40 50 60 70 80 90 100 110 120 130 Total capacity of concurrently operating indoor units (%) Heating 1.0 0.8 0.6 0.4 0.2 0 0 10 20 30 40 50 60 70 80 90 100 110 120 130 Total capacity of concurrently operating indoor units (%) (Note) If the connecting capacity of the indoor unit exceeds 130%, consider the connecting capacity as 130%. - AMP Air Conditioning 16 www.ampair.co.uk | [email protected] 㪟㪼㪸㫋 㪼㫏㪺㪿㪸㫅㪾㪼㫉 㪫㪼㫉㫄㫀㫊㫋㫆㫉 㪫㪼㫉㫄㫀㫊㫋㫆㫉 㩿㪫㪿㫆㪄㪘㪀 㩿㪫㪿㫆㪄㪩㪈㪃㪉㪀 㪧㫀㫇㪼㩷㫉㪼㪄㪽㫉㪼㫊㪿㩷㫂㫀㫋 㪫㪼㫉㫄㫀㫊㫋㫆㫉 㪫㪿㫀㪄㪩㪊 㪠㫅㪻㫆㫆㫉㩷㪘㩷㫌㫅㫀㫋 㪟㪼㪸㫋 㪼㫏㪺㪿㪸㫅㪾㪼㫉 㪫㪼㫉㫄㫀㫊㫋㫆㫉 6JK# 㪫㪼㫉㫄㫀㫊㫋㫆㫉 㪫㪿㫀㪄㪩㪉㪀 㪫㪼㫉㫄㫀㫊㫋㫆㫉 㩿㪫㪿㫀㪄㪩㪊㪀 㪪㫋㫉㪸㫀㫅㪼㫉 㪫㪼㫉㫄㫀㫊㫋㫆㫉 6JK4 㪘㪺㪺㫌㫄㫃㪸㫋㫆㫉 㪪㫆㫃㪼㫅㫆㫀㪻 㪪㪼㫉㫍㫀㪺㪼㩷㪭㪸㫃㫍㪼 㫍㪸㫃㫍㪼 㩿㪮㫀㫋㪿㩷㪺㪿㪸㫉㪾㪼㩷㫇㫆㫉㫋㪀㪚㪸㫇㫀㫃㫃㪸㫉㫐 㩿㪪㪭㪈㪉㪀 㫋㫌㪹㪼 㪪㫋㫉㪸㫀㫅㪼㫉 㪚㪿㪼㪺㫂 㫍㪸㫃㫍㪼 㪪㪼㫉㫍㫀㪺㪼㩷㪭㪸㫃㫍㪼 㪚㪿㪼㪺㫂 㩿㪮㫀㫋㪿㩷㪺㪿㪸㫉㩷㪾㪼㩷㫇㫆㫉㫋㪀 㩷㫁㫆㫀㫅㫋 㪜㫃㪼㪺㫋㫉㫆㫅㫀㪺 㪼㫏㫇㪸㫅㫊㫀㫆㫅 㫍㪸㫃㫍㪼㩷㩿㪜㪜㪭㪀 㪪㫋㫉㪸㫀㫅㪼㫉 㪪㪼㫉㫍㫀㪺㪼㩷㪭㪸㫃㫍㪼 㩿㪮㫀㫋㪿㩷㪺㪿㪸㫉㪾㪼㩷㫇㫆㫉㫋㪀 㪠㫅㪻㫆㫆㫉㩷㪙㩷㫌㫅㫀㫋 㪟㪼㪸㫋 㪼㫏㪺㪿㪸㫅㪾㪼㫉 㪚㪿㪼㪺㫂㩷㫍㪸㫃㫍㪼 - 17 - 㪪㫋㫉㪸㫀㫅㪼㫉 㪚㪿㪼㪺㫂㩷㫁㫆㫀㫅㫋 㪣㫆㫎㩷㫇㫉㪼㫊㫊㫌㫉㪼 㫊㪼㫅㫊㫆㫉㩷㩿㪧㪪㪣㪀 㪫㪼㫉㫄㫀㫊㫋㫆㫉 㩿㪫㪿㫆㪄㪛㪈㪀 㪪㫋㫉㪸㫀㫅㪼㫉 㪪㫆㫃㪼㫅㫆㫀㪻 㫍㪸㫃㫍㪼 㩿㪪㪭㪍㪀 㪚㫆㫄㫇㫉㪼㫊㫊㫆㫉 㪪㫌㪹㪄 㪺㫆㫆㫃㫀㫅㪾㩷㪺㫆㫀㫃 㪫㪼㫉㫄㫀㫊㫋㫆㫉 㩿㪫㪟㫆㪄㪪㪀 㪟㫀㪾㪿㩷㫇㫉㪼㫊㫊㫌㫉㪼㩷㫊㫎㫀㫋㪺㪿 㩿㪍㪊㪟㪈㪄㪈㪀 1KN UGRCTCVQT 㪫㪼㫉㫄㫀㫊㫋㫆㫉 㩿㪫㪿㫆㪄㪚㪈㪀 㪫㪼㫉㫄㫀㫊㫋㫆㫉 㩿㪫㪿㫀㪄㪘㪀㩷 㪫㪼㫉㫄㫀㫊㫋㫆㫉㪀 㩿㪫㪿㫀㪄㪩㪉㪀 㪪㫋㫉㪸㫀㫅㪼㫉 㪪㫆㫃㪼㫅㫆㫀㪻 㫍㪸㫃㫍㪼 㩿㪪㪭㪈㪈㪀 㪟㫀㪾㪿㩷㫇㫉㪼㫊㫊㫌㫉㪼 㫊㪼㫅㫊㫆㫉㩷㩿㪧㪪㪟㪀 㪚㪿㪼㪺㫂㩷㫁㫆㫀㫅㫋 㪚㪸㫇㫀㫃㫃㪸㫉㫐 㫋㫌㪹㪼 㪫㪼㫉㫄㫀㫊㫋㫆㫉 㩿㪫㪿㫀㪄㪩㪈 㪋㫎㪸㫐㩷㫍㪸㫃㫍㪼 㪪㫋㫉㪸㫀㫅㪼㫉 㪚㪸㫇㫀㫃㫃㪸㫉㫐 㫋㫌㪹㪼 㪪㫆㫃㪼㫅㫆㫀㪻 㫍㪸㫃㫍㪼 㩿㪪㪭㪈㪀 㪚㪸㫇㫀㫃㫃㪸㫉㫐 㫋㫌㪹㪼 㪘㪺㪺㫌㫄㫃 㪸㫋㫆㫉 㪫㪼㫉㫄㫀㫊㫋㫆㫉 㩿㪫㪿㫆㪄㪟㪀 㪜㫃㪼㪺㫋㫉㫆㫅㫀㪺 㩷㪼㫏㫇㪸㫅㫊㫀㫆㫅㩷㫍㪸㫃㫍㪼 㩷㩿㪜㪜㪭㪟㪀 㪪㫋㫉㪸㫀㫅㪼㫉 㪪㫋㫉㪸㫀㫅㪼㫉 㪩㪼㪺㪼㫀㫍㪼㫉 㪜㫃㪼㪺㫋㫉㫆㫅㫀㪺 㪼㫏㫇㪸㫅㫊㫀㫆㫅 㫍㪸㫃㫍㪼㩷㩿㪜㪜㪭㪀 㪫㪼㫉㫄㫀㫊㫋㫆㫉 㪪㫌㪹㪄㪺㫆㫆㫃㫀㫅㪾㩷㪺㫆㫀㫃 㪪㪼㫉㫍㫀㪺㪼㩷㪭㪸㫃㫍㪼㩿㪮㫀㫋㪿㩷㪺㪿㪸㫉㪾㪼㩷㫇㫆㫉㫋㪀㩿㪫㪟㫆㪄㪪㪚㪀 㪟㫀㪾㪿㩷㫇㫉㪼㫊㫊㫌㫉㪼㩷㫊㫎㫀㫋㪺㪿 㩿㪍㪊㪟㪈㪄㪩㪈㪀 㪣㫀㫈㫌㫀㪻㩷㫃㫀㫅㪼 㪫㫆㩷㫅㪼㫏㫋㩷㫌㫅㫀㫋㫊㩷㪹㫐 㫋㫌㫉㫅 0QVGU 2TGUGVRQKPVQHRTQVGEVKXGFGXKEGU *1RGP/2C%NQUG/2C HQTRTQVGEVKQP *ޓޓޓޓ41RGP/2C%NQUG/2C HQTEQPVTQN *ޓޓޓޓ41RGP/2C%NQUG/2C HQTEQPVTQN (WPEVKQPQHVJGTOKUVQT 25*10/2C (QTEQORTGUUQTQHEQPVTQNEQQNKPI 10/2C (QTEQORTGUUQTQHEQPVTQNJGCVKPI 25.10/2C1((/2C (QTEQORTGUUQTQHEQPVTQN 10/2C1((/2C (QTRTQVGEVKQP 㪪㫋㫉㪸㫀㫅㪼㫉 㪪㫋㫉㪸㫀㫅㪼㫉 㪪㫋㫉㪸㫀㫅㪼㫉 㪜㫃㪼㪺㫋㫉㫆㫅㫀㪺㩷㪼㫏㫇㪸㫅㫊㫀㫆㫅㩷㫍㪸㫃㫍㪼 㩿㪜㪜㪭㪪㪚㪀 5 PIPING SYSTEM 㪪㪼㫉㫍㫀㪺㪼㩷㪭㪸㫃㫍㪼㩿㪮㫀㫋㪿㩷㪺㪿㪸㫉㪾㪼㩷㫇㫆㫉㫋㪀 㪟㫀㪾㪿㩷㫇㫉㪼㫊㫊㫌㫉㪼㩷㫊㫎㫀㫋㪺㪿 㩿㪍㪊㪟㪈㪄㪩㪉㪀 Models FDCR224KXE6, 280KXE6 㪤㫌㪽㪽㫃㪼㫉 㪞㪸㫊㩷㫃㫀㫅㪼 5.1 Including service valve kit and pipe re-fresh kit 㪦㫌㫋㪻㫆㫆㫉㩷㫌㫅㫀㫋 㪪㪼㫉㫍㫀㪺㪼㩷㫍㪸㫃㫍㪼㩷㫂㫀㫋 6JK44*GCVKPIQRGTCVKQP+PFQQTHCPEQPVTQN %QQNKPIQRGTCVKQP(TQUVRTGXGPVKQPEQPVTQN 5WRGTJGCVEQPVTQN 6JK4(QTUWRGTJGCVEQPVTQNQHEQQNKPIQRGTCVKQP 6JQ&(QTEQPVTQNQHFKUEJCTIGRKRGVGORGTCVWTG 6JQ%(QTEQPVTQNQHVGORGTCVWTGWPFGTVJGFQOG 6JQ5(QTEQPVTQNQHUWEVKQPRKRGVGORGTCVWTG 6JQ44(QTEQPVTQNQHFGHTQUVKPI 6JQ#(QTEQPVTQNQHFGHTQUVKPI 6JQ5%'NGEVTQPKEGZRCPUKQPXCNXG ''85%EQPVTQNQHEQQNKPIQRGTCVKQP 6JQ*(QTUWRGTJGCVEQPVTQNQHUWDEQQNKPIEQKN '11 • KX-T-166 AMP Air Conditioning www.ampair.co.uk | [email protected] 㪤㫌㪽㪽㫃㪼㫉 㪫㪼㫉㫄㫀㫊㫋㫆㫉 㩿㪫㪿㫀㪄㪩㪊㪀 㪠㫅㪻㫆㫆㫉㩷㪘㩷㫌㫅㫀㫋 㪟㪼㪸㫋 㪼㫏㪺㪿㪸㫅㪾㪼㫉 㪫㪼㫉㫄㫀㫊㫋㫆㫉 6JK# 㪫㪼㫉㫄㫀㫊㫋㫆㫉 㩿㪫㪿㫀㪄㪩㪉㪀 㪫㪼㫉㫄㫀㫊㫋㫆㫉 㩿㪫㪿㫀㪄㪩㪊㪀 㪞㪸㫊㩷㫃㫀㫅㪼 㪪㫋㫉㪸㫀㫅㪼㫉 㪫㪼㫉㫄㫀㫊㫋㫆㫉 6JK4 㪜㫃㪼㪺㫋㫉㫆㫅㫀㪺 㪼㫏㫇㪸㫅㫊㫀㫆㫅 㫍㪸㫃㫍㪼㩷㩿㪜㪜㪭㪀 㪪㫆㫃㪼㫅㫆㫀㪻 㪪㪼㫉㫍㫀㪺㪼㩷㪭㪸㫃㫍㪼 㫍㪸㫃㫍㪼 㩿㪮㫀㫋㪿㩷㪺㪿㪸㫉㪾㪼㩷㫇㫆㫉㫋㪀㪚㪸㫇㫀㫃㫃㪸㫉㫐 㩿㪪㪭㪈㪉㪀 㫋㫌㪹㪼 㪚㪸㫇㫀㫃㫃㪸㫉㫐 㫋㫌㪹㪼 㪚㫆㫄㫇㫉㪼㫊㫊㫆㫉 - 㪫㪼㫉㫄㫀㫊㫋㫆㫉 㩿㪫㪿㫆㪄㪚㪈㪀 18 - 㪫㪼㫉㫄㫀㫊㫋㫆㫉 㩿㪫㪿㫀㪄㪘㪀 㪫㪼㫉㫄㫀㫊㫋㫆㫉㪀 㩿㪫㪿㫀㪄㪩㪉㪀 㪪㫋㫉㪸㫀㫅㪼㫉 㪣㫆㫎㩷㫇㫉㪼㫊㫊㫌㫉㪼 㫊㪼㫅㫊㫆㫉㩷㩿㪧㪪㪣㪀 㪪㫌㪹㪄 㪺㫆㫆㫃㫀㫅㪾㩷㪺㫆㫀㫃 㪫㪼㫉㫄㫀㫊㫋㫆㫉 㩿㪫㪟㫆㪄㪪㪀 㪪㫋㫉㪸㫀㫅㪼㫉 㪚㪸㫇㫀㫃㫃㪸㫉㫐 㫋㫌㪹㪼 㪪㫆㫃㪼㫅㫆㫀㪻 㫍㪸㫃㫍㪼 㩿㪪㪭㪈㪀 㪚㪸㫇㫀㫃㫃㪸㫉㫐 㫋㫌㪹㪼 㪘㪺㪺㫌㫄㫃 㪸㫋㫆㫉 㪫㪼㫉㫄㫀㫊㫋㫆㫉 㩿㪫㪿㫆㪄㪟㪀 㪜㫃㪼㪺㫋㫉㫆㫅㫀㪺 㩷㪼㫏㫇㪸㫅㫊㫀㫆㫅㩷㫍㪸㫃㫍㪼 㩷㩿㪜㪜㪭㪟㪀 㪩㪼㪺㪼㫀㫍㪼㫉 㪫㪼㫉㫄㫀㫊㫋㫆㫉 㪪㫌㪹㪄㪺㫆㫆㫃㫀㫅㪾㩷㪺㫆㫀㫃 㪪㪼㫉㫍㫀㪺㪼㩷㪭㪸㫃㫍㪼㩿㪮㫀㫋㪿㩷㪺㪿㪸㫉㪾㪼㩷㫇㫆㫉㫋㪀㩿㪫㪟㫆㪄㪪㪚㪀 㪟㫀㪾㪿㩷㫇㫉㪼㫊㫊㫌㫉㪼㩷㫊㫎㫀㫋㪺㪿 㩿㪍㪊㪟㪈㪄㪩㪈㪀 㪣㫀㫈㫌㫀㪻㩷㫃㫀㫅㪼 㪫㫆㩷㫅㪼㫏㫋㩷㫌㫅㫀㫋㫊㩷㪹㫐 㫋㫌㫉㫅 0QVGU 2TGUGVRQKPVQHRTQVGEVKXGFGXKEGU *1RGP/2C%NQUG/2C HQTRTQVGEVKQP *ޓޓޓޓ41RGP/2C%NQUG/2C HQTEQPVTQN *ޓޓޓޓ41RGP/2C%NQUG/2C HQTEQPVTQN (WPEVKQPQHVJGTOKUVQT 25*10/2C (QTEQORTGUUQTQHEQPVTQNEQQNKPI 10/2C (QTEQORTGUUQTQHEQPVTQNJGCVKPI 25.10/2C1((/2C (QTEQORTGUUQTQHEQPVTQN 10/2C1((/2C (QTRTQVGEVKQP 㪪㫋㫉㪸㫀㫅㪼㫉 㪪㫋㫉㪸㫀㫅㪼㫉 㪪㫋㫉㪸㫀㫅㪼㫉 㪜㫃㪼㪺㫋㫉㫆㫅㫀㪺 㪼㫏㫇㪸㫅㫊㫀㫆㫅 㫍㪸㫃㫍㪼㩷㩿㪜㪜㪭㪀 㪪㫋㫉㪸㫀㫅㪼㫉 㪪㫋㫉㪸㫀㫅㪼㫉 㪜㫃㪼㪺㫋㫉㫆㫅㫀㪺㩷㪼㫏㫇㪸㫅㫊㫀㫆㫅㩷㫍㪸㫃㫍㪼 㩿㪜㪜㪭㪪㪚㪀 6JK44*GCVKPIQRGTCVKQP+PFQQTHCPEQPVTQN %QQNKPIQRGTCVKQP(TQUVRTGXGPVKQPEQPVTQN 5WRGTJGCVEQPVTQN 6JK4(QTUWRGTJGCVEQPVTQNQHEQQNKPIQRGTCVKQP 6JQ&(QTEQPVTQNQHFKUEJCTIGRKRGVGORGTCVWTG 6JQ%(QTEQPVTQNQHVGORGTCVWTGWPFGTVJGFQOG 6JQ5(QTEQPVTQNQHUWEVKQPRKRGVGORGTCVWTG 6JQ44(QTEQPVTQNQHFGHTQUVKPI 6JQ#(QTEQPVTQNQHFGHTQUVKPI 6JQ5%'NGEVTQPKEGZRCPUKQPXCNXG ''85%EQPVTQNQHEQQNKPIQRGTCVKQP 6JQ*(QTUWRGTJGCVEQPVTQNQHUWDEQQNKPIEQKN '11 • KX-T-166 AMP Air Conditioning 㪚㪿㪼㪺㫂㩷㫁㫆㫀㫅㫋 㪫㪼㫉㫄㫀㫊㫋㫆㫉 㩿㪫㪿㫆㪄㪛㪈㪀 㪪㫋㫉㪸㫀㫅㪼㫉 㪪㫆㫃㪼㫅㫆㫀㪻 㫍㪸㫃㫍㪼 㩿㪪㪭㪍㪀 㪫㪼㫉㫄㫀㫊㫋㫆㫉 㩿㪫㪿㫀㪄㪩㪈㪀 㪪㫋㫉㪸㫀㫅㪼㫉 㪫㪼㫉㫄㫀㫊㫋㫆㫉 㪫㪼㫉㫄㫀㫊㫋㫆㫉 㩿㪫㪿㫆㪄㪘㪀 㩿㪫㪿㫆㪄㪩㪈㪃㪉㪀 㪪㫆㫃㪼㫅㫆㫀㪻 㫍㪸㫃㫍㪼 㩿㪪㪭㪈㪈㪀 㪟㫀㪾㪿㩷㫇㫉㪼㫊㫊㫌㫉㪼㩷㫊㫎㫀㫋㪺㪿 㩿㪍㪊㪟㪈㪄㪈㪀 1KN UGRCTCVQT 㪪㫋㫉㪸㫀㫅㪼㫉 㪋㫎㪸㫐㩷㫍㪸㫃㫍㪼 㪟㪼㪸㫋 㪼㫏㪺㪿㪸㫅㪾㪼㫉 㪟㫀㪾㪿㩷㫇㫉㪼㫊㫊㫌㫉㪼 㫊㪼㫅㫊㫆㫉㩷㩿㪧㪪㪟㪀 㪚㪿㪼㪺㫂㩷㫁㫆㫀㫅㫋 㪚㪿㪼㪺㫂㩷㫍㪸㫃㫍㪼 㪠㫅㪻㫆㫆㫉㩷㪙㩷㫌㫅㫀㫋 㪟㪼㪸㫋 㪼㫏㪺㪿㪸㫅㪾㪼㫉 㪪㪼㫉㫍㫀㪺㪼㩷㪭㪸㫃㫍㪼㩿㪮㫀㫋㪿㩷㪺㪿㪸㫉㪾㪼㩷㫇㫆㫉㫋㪀 㪟㫀㪾㪿㩷㫇㫉㪼㫊㫊㫌㫉㪼㩷㫊㫎㫀㫋㪺㪿 㩿㪍㪊㪟㪈㪄㪩㪉㪀 5.2 Without service valve kit and pipe re-fresh kit 㪦㫌㫋㪻㫆㫆㫉㩷㫌㫅㫀㫋 www.ampair.co.uk | [email protected] '11 • KX-T-166 6 APPLICATION DATA 6.1 Cautions for reuse of existing pipes ① Procedure of installation work for reuse of existing pipes Check & consideration Confirmation of the scope of replacement Before installation work at site Confirmation of reusability of existing refrigerant pipes Confirmation of reusability of existing control wires Confirmation of reusability of existing power supply equipment Existing unit operability Pipe washing method by cooling operation of existing unit ◦Please note that we cannot warrant the reliability (improper properties owing to deterioration, etc.) of refrigerant pipes, control wires, electric equipment, etc., for reuse. ◦Check existing refrigerant pipes for reusability according to “② Flowchart of the confirmation of reusability of existing pipes”. ◦Regarding restrictions on the refrigerant pipe length, applicable pipe diameter, etc., refer to the product catalogs and manuals. ◦When reusing existing control wires between outdoor units, indoor units and remote controller, check them according to “ ③ Check and consideration for reuse of existing wires and power supply equipment”. ◦Power supply equipment must use the voltage and number of phases adequate for outdoor units and indoor units and have the circuit breaker capacity and wire diameters as specified on the power supply wiring diagram. ◦When reusing existing power supply equipment (including power supply wiring), extent of deterioration of and damages on the equipment must be checked. ◦When wires or power supply equipment are aged, sufficient care must be taken to prevent risk of fire or earth leakage. Not operable Pipe washing method by re-fresh kit Operable Implementation of pump-down operation after cooling operation with old system for more than 30 minutes (Existing unit cooling washing operation) Recovery of old refrigerant and removal of existing outdoor unit, indoor unit, remote controller, etc. Check & consideration Recovery of old refrigerant and removal of existing outdoor unit, indoor unit, remote controller, etc. ・If refrigerant cannot be recovered completely with the pump-down, recover remaining refrigerant using Installation work at site the refrigerant recovery unit. Installation of outdoor unit, indoor unit, remote controller, etc., and electrical work <Installation of service valve kit is not necessary.> Airtight test of pipes Vacuumizing of pipes System check after the address setting Additional refrigerant charge Installation of outdoor unit, indoor unit, remote controller, etc., and electrical work <Installation of service valve kit is necessary.> ・If the existing unit is not operable, install the ser- Connection of pipe re-fresh kit mm or more in front of the kit) Airtight test of pipes Vacuumizing of pipes vice valve kit. Make sure to secure a space to install the re-fresh kit in front of the service valve kit. (500 ・When implementing the pipe washing operation using the re-fresh kit, consult our dealer. ・Test the air tightness at 3.24 MPa. System check after the address setting ・Turn the power supply on after the address setting. Additional refrigerant charge there is no error display on the remote controller or Pipe washing operation using re-fresh kit Confirm that the system operates properly and that indoor unit. Removal of pipe re-fresh kit Test run & adjustment - AMP Air Conditioning 19 www.ampair.co.uk | [email protected] '11 • KX-T-166 ② Flowchart of the confirmation of reusability of existing pipes Judge if existing pipes are reusable or not according to the following flowchart. Start No Are outdoor units and indoor units connected to existing pipes for reuse? Are olds units MHI products? Yes No Yes Is any of followings used for the refrigerating machine oil on old unit? Suniso, MS, Barrel Freeze, HAB Freol, ether oil, ester oil No Consult us to confirm if they can be used or not. Yes Not usable Usable Are the length, diameter and wall thickness of existing pipes for reuse and difference of elevation between units within the ranges of our specification? No Yes Are branch pipes and header on the existing pipeline for reuse supplied from Mitsubishi? *Any special parts like a branch pipe with orifice, or other, cannot be used, even if they are supplied from MHI. No Consult us to confirm if they can be used or not. Usable – Replace with MHI products. Yes Is there any corrosion, damage or dent on existing pipes for reuse? Yes Repair defective sections. Yes Test existing pipes for air tightness at site. Yes Remove the branch pipe. No Yes Repair defective sections. Unable to repair Repair Loosened Check pipe support hardware for looseness. Repair defective sections. Tightened firmly Repair When existing unit is: ・Operable → Pipe washing method by cooling operation of existing unit. ・Not operable → Pipe washing method by re-fresh kit Existing pipes can be reused by the above methods. - AMP Air Conditioning Unable to remove Remove No Check the insulator on existing pipes to be reused for peeling or deterioration. (Both gas and liquid pipes need insulation.) Poor air tightness Good air tightness No Is there any branch pipe which is not connected to indoor unit? Unable to repair Repair No Does gas leak from existing pipes for reuse? (Check if refrigerant was recharged frequently.) Not usable Unable to replace Existing pipes cannot be reused. Use new pipes. Select the standard specification for indoor units. 20 www.ampair.co.uk | [email protected] '11 • KX-T-166 ③ Check and consideration for reuse of existing wires and power supply equipment Keep in mind the following contents when reusing existing ⑷ Confirmation of conductivity of existing wires wires and power supply equipment. Check existing wires for conductivity and voltage and ⑴ Confirmation of existing wires the circuit breaker for proper operation. Check existing wires not only for kinds of wire and If any anomaly is detected, replace wires or parts and number of core wires but also for the length of wire put them in appropriate condition. extension and number of branches with reference to ⑸ C onfirmation of compatibility of power supply the equipment drawings or other. Take notice of the equipment following points for connecting wires. Since the circuit breaker capacity or other may ● When using a shielding wire, make sure to earth one vary depending on systems, check if the power supply equipment is compatible or not according to side only. ● Do not use shielding wires and other kinds of wire the procedure for wiring at outside of unit. Check simultaneously also for deterioration or damages on the in the same system. ● Do not use multi-core wires having a number of equipment and, if any anomaly is detected, repair such appropriately. cores more than necessary. ● C onfirm that wires are separated sufficiently from Confirm that the existing earth leakage breaker is adaptable to the inverter (high frequency). If it is not, the power supply cable. ● Confirm that the wire diameter is larger than 0.75 replace it with a breaker adaptable to the inverter. ⑹ Confirmation of failure history 2 mm . ⑵ Confirmation of existing power supply equipment Check if there are records of failure such as transmission Confirm the voltage, number of phases, circuit breaker or conductivity error owing to anomalies on wires or capacity, etc. for existing power supply equipment. power supply equipment. If there is any, check if such When reusing existing power supply equipment, make failure had been repaired properly. If it is not, repair it sure to check the degree of aging and damages on them. properly. Sufficient care must be taken to prevent earth leakage or ⑺ Confirmation of the procedure for wiring at outside of unit fire when using old wires or power supply equipment. ⑶ Confirmation of reliability of existing wires Wiring problem could cause failures of equipment, In so far as there is no problem on the above ⑴ and ⑵, earth leakage or fire. When considering a reuse of the existing wires and power supply equipment can be existing wires or power supply equipment, check them utilized basically. sufficiently according to the procedure for wiring at outside of unit. If any trace of defect is detected on parts or wires, replace them or use new equipment. - AMP Air Conditioning 21 www.ampair.co.uk | [email protected] '11 • KX-T-166 6.2 Installation of outdoor unit PCB012D015M KX SERIES INSTALLATION MANUAL r Outdoor unit capacity FDCR224∼280 ◎This installation manual deals with outdoor units and general installation specifications only. For indoor units, please refer to the respective installation manuals supplied with your units. ◎Please read this manual carefully before you set to installation work and carry it out according to the instructions contained in this manual. ◎When washing existing pipes using the re-fresh kit, refer to the instruction manual packed with the re-fresh kit for the procedures, etc. Application data When install the unit, be sure to check whether the selection of installation place, power supply specifications, usage limitation (piping length, height differences between indoor and outdoor units, power supply voltage and etc.) and installation spaces. SAFETY PRECAUTIONS ●We recommend you to read this "SAFETY PRECAUTIONS" carefully before the installation work in order to gain full advantage of the functions of the unit and to avoid malfunction due to mishandling. CAUTIONS . The matters with possibilities leading to serious consequences such as death or serious personal WARNINGS and ●The precautions described below are divided into injury due to erroneous handling are listed in the WARNINGS and the matters with possibilities leading to personal injury or damage of the unit due to erroneous handling including CAUTIONS . These are very important precautions for safety. Be sure to observe all of them without fail. probability leading to serious consequences in some cases are listed in ●The meaning of"Marks"used here are as shown on the right. Always do it according to the instruction. Never do it under any circumstance. ●Be sure to confirm no anomaly on the equipment by commissioning after completed installation and explain the operating methods as well as the maintenance methods of this equipment to the user according to the owner's manual. ●Keep the installation manual together with owner's manual at a place where any user can read at any time. Moreover if necessary, ask to hand them to a new user ●This unit complies with EN61000-3-3. For outdoor unit, EN61000-3-2 is not applicable as consent by the utility company or notification to the utility company is given before usage. CAUTION WARNING ●Installation must be carried out by the qualified installer. ●Use the circuit breaker for all pole with correct capacity. Using the incorrect circuit breaker, it can cause the unit malfunction and fire. If you install the system by yourself, it may cause serious trouble such as water leaks, electric shocks, fire and personal inju ry, as a result of a system malfunction. ●Install the system in full accordance with the instruction manual. Incorrect installation may cause bursts, personal injury, water leaks, electric shocks and fire. ●Use the original accessories and the specified components for installation. If parts other than those prescribed by us are used, It may cause fall of the unit, water leaks, electric shocks, fire, refrigerant leak, substanard performance, contrl failure and personal injury. ●When installing in small rooms, take prevention measures not to exceed the density limit of refrigerant in the event of leakage accordance with ISO5149. Consult the expert about prevention measures. If the density of refrigerant exceeds the limit in the event of leakage, lack of oxygen can occur, which can cause serious accidents. ●Ventilate the working area well in the event of refrigerant leakage during installation. If the refrigerant comes into contact with naked flames, poisonous gas is produced. ●After completed installation, check that no refrigerant leaks from the system. If refrigerant leaks into the room and comes into contact with an oven or other hot surface, poisonous gas is produced. ●Hang up the unit at the specified points with ropes which can support the weight in lifting for portage. And to avoid jolting out of alignment, be sure to hang up the unit at 4-point support. An improper manner of portage such as 3-point support can cause death or serious personal injury due to falling of the unit. ●Install the unit in a location with good support. Unsuitable installation locations can cause the unit to fall and cause material damage and personal injury. ●Ensure the unit is stable when installed, so that it can withstand earthquakes and strong winds. Unsuitable installation locations can cause the unit to fall and cause material damage and personal injury. ●The electrical installation must be carried out by the qualified electrician in accordance with "the norm for electrical work" and "national wiring regulation", and the system must be connected to the dedicated circuit. Power supply with insufficient capacity and incorrect function done by improper work can cause electric shocks and fire. ●Be sure to shut off the power before starting electrical work. Failure to shut off the power can cause electric shocks, unit failure or incorrect function of equipment. ●Be sure to use the cables conformed to safety standard and cable ampacity for power distribution work. Unconformable cables can cause electric leak, anomalous heat production or fire. ●Use the prescribed cables for electrical connection, tighten the cables securely in terminal block and relieve the cables correctly to prevent overloading the terminal blocks. Loose connections or cable mountings can cause anomalous heat production or fire. ●Arrange the wiring in the control box so that it cannot be pushed up further into the box. Install the service panel correctly. Incorrect installation may result in overheating and fire. ●In connecting the power cable, make sure that no anomakies such as dust deposits, socket clogging or wobble are found and insert the plug securely. Accumulation of dust, clogging on the socket, or looseness of plugging can cause electric shocks and fire. ●Do not perform brazing work in the airtight room It can cause lack of oxygen. ●Tighten the flare nut by using double spanners and torque wrench according to prescribed method. Be sure not to tighten the flare nut too much. Loose flare connection or damage on the flare part by tightening with excess torque can cause burst or refrigerant leaks which may result in lack of oxygen. ●Do not open the service valves for liquid line and gas line until completed refrigerant piping work, air tightness test and evacuation. If the compressor is operated in state of opening service valves before completed connection of refrigerant piping work, you may incur frost bite or injury from an abrupt refrigerant outflow and air can be sucked into refrigerant circuit, which can cause burst or personal injury due to anomalously high pressure in the refrigerant. ●Do not put the drainage pipe directly into drainage channels where poisonous gases such as sulphide gas can occur. Poisonous gases will flow into the room through drainage pipe and seriously affect the user's health and safety. It can also cause the corrosion of the indoor unit and resultant unit failure or refrigerant leak. ●Only use prescribed optional parts. The installation must be carried out by the qualified installer. If you install the system by yourself, it can cause serious trouble such as water leaks, electric shocks, fire. ●Do not perform any change of protective device itself or its setup condition The forced operation by short-circuiting protective device of pressure switch and temperature controller or the use of non specified component can cause fire or burst. ●Be sure to switch off the power supply in the event of installation, inspection or servicing. If the power supply is not shut off, there is a risk of electric shocks, unit failure or personal injury due to the unexpected start of fan. ●Consult the dealer or an expert regarding removal of the unit. Incorrect installation can cause water leaks, electric shocks or fire. ●Stop the compressor before closing valve and disconnecting refrigerant pipes in case of pump down operation. If disconnecting refrigerant pipes in state of opening service valves before compressor stopping, you may incur frost bite or injury from an abrupt refrigerant outflow and air can be sucked, which can cause burst or personal injury due to anomalously high pressure in the refrigerant circuit. ●Take care when carrying the unit by hand. If the unit weights more than 20kg, it must be carried by two or more persons. Do not carry by the plastic straps, always use the carry handle when carrying the unit by hand. Use gloves to minimize the risk of cuts by the aluminum fins. ●Dispose of any packing materials correctly. Any remaining packing materials can cause personal injury as it contains nails and wood. And to avoid danger of suffocation, be sure to keep the plastic wrapper away from children and to dispose after tear it up. ●Pay attention not to damage the drain pan by weld spatter when welding work is done near the indoor unit. If weld spatter entered into the indoor unit during welding work, it can cause pin-hole in drain pan and result in water leakage. To prevent such damage, keep the indoor unit in its packing or cover it. ●Be sure to insulate the refrigerant pipes so as not to condense the ambient air moisture on them. Insufficient insulation can cause condensation, which can lead to moisture damage on the ceiling, floor, furniture and any other valuables. ●Be sure to perform air tightness test by pressurizing with nitrogen gas after completed refrigerant piping work. If the density of refrigerant exceeds the limit in the event of refrigerant leakage in the small room, lack of oxygen can occur, which can cause serious accidents. ●Perform installation work properly according to this installation manual. Improper installation can cause abnormal vibrations or increased noise generation. ●Earth leakage breaker must be installed If the earth leakage breaker is not installed, it can cause fire or electric shocks. ●Carry out the electrical work for ground lead with care. Do not connect the ground lead to the gas line, water line, lightning conductor or telephone line's ground lead. Incorrect grounding can cause unit faults such as electric shocks or fire due to short-circuiting. Never connect the grounding wire to a gas pipe because if gas leaks, it could cause explosion or ignition. ●Do not use any materials other than a fuse with the correct rating in the location where fuses are to be used. Connecting the circuit with copper wire or other metal thread can cause unit failure and fire. ●Do not install the unit near the location where leakage of combustible gases can occur. If leaked gases accumulate around the unit, it can cause fire. ●Do not install the unit where corrosive gas (such as sulfurous acid gas etc.) or combustible gas (such as thinner and petroleum gases) can accumulate or collect, or where volatile combustible substances are handled. Corrosive gas can cause corrosion of heat exchanger, breakage of plastic parts and etc. And combustible gas can cause fire. ●Secure a space for installation, inspection and maintenance specified in the manual. Insufficient space can result in accident such as personal injury due to falling from the installation place. ●When the outdoor unit is installed on a roof or a high place, provide permanent ladders and handrails along the access route and fences and handrails around the outdoor unit. If safety facilities are not provided, it can cause personal injury due to falling from the installation place. ●Do not install nor use the system close to the equipment that generates electromagnetic fields or high frequency harmonics Equipment such as inverters, standby generators, medical high frequency equipments and telecommunication equipments can affect the system, and cause malfunctions and breakdowns. The system can also affect medical equipment and telecommunication equipment, and obstruct its function or cause jamming. ●Do not install the outdoor unit in a location where insects and small animals can inhabit. Insects and small animals can enter the electric parts and cause damage or fire. Instruct the user to keep the surroundings clean. ●Do not use the base flame for outdoor unit which is corroded or damaged due to long periods of operation. Using an old and damage base flame can cause the unit falling down and cause personal injury. ●Do not install the unit in the locations listed below • Locations where carbon fiber, metal powder or any powder is floating. • Locations where any substances that can affect the unit such as sulphide gas, chloride gas, acid and alkaline can occur. • Vehicles and ships • Locations where cosmetic or special sprays are often used. • Locations with direct exposure of oil mist and steam such as kitchen and machine plant. • Locations where any machines which generate high frequency harmonics are used. • Locations with salty atmospheres such as coastlines • Locations with heavy snow (If installed, be sure to provide base flame and snow hood mentioned in the manual) • Locations where the unit is exposed to chimney smoke • Locations at high altitude (more than 1000m high) • Locations with ammonic atmospheres • Locations where heat radiation from other heat source can affect the unit • Locations without good air circulation. • Locations with any obstacles which can prevent inlet and outlet air of the unit • Locations where short circuit of air can occur (in case of multiple units installation) • Locations where strong air blows against the air outlet of outdoor unit It can cause remarkable decrease in performance, corrosion and damage of components, malfunction and fire. ●Do not install the outdoor unit in the locations listed below. • Locations where discharged hot air or operating sound of the outdoor unit can bother neighborhood. • Locations where outlet air of the outdoor unit blows directly to an animal or plants. The outlet air can affect adversely to the plant etc. • Locations where vibration can be amplified and transmitted due to insufficient strength of structure. • Locations where vibration and operation sound generated by the outdoor unit can affect seriously. (on the wall or at the place near bed room) • Locations where an equipment affected by high harmonics is placed. (TV set or radio receiver is placed within 5m) • Locations where drainage cannot run off safely. It can affect surrounding environment and cause a claim ●Do not use the unit for special purposes such as storing foods, cooling precision instruments and preservation of animals, plants or art. It can cause the damage of the items. ●Do not touch any buttons with wet hands It can cause electric shocks ●Do not shut off the power supply immediately after stopping the operation. Wait at least 5 minutes, otherwise there is a risk of water leakage or breakdown. ●Do not control the system with main power switch. It can cause fire or water leakage. In addition, the fan can start unexpectedly, which can cause personal injury. ●Do not touch any refrigerant pipes with your hands when the system is in operation. During operation the refrigerant pipes become extremely hot or extremely cold depending the operating condition, and it can cause burn injury or frost injury. ●Do not operate the outdoor unit with any article placed on it. You may incur property damage or personal injure from a fall of the article. ●Do not step onto the outdoor unit. You may incur injury from a drop or fall. ●Ensure that no air enters in the refrigerant circuit when the unit is installed and removed. If air enters in the refrigerant circuit, the pressure in the refrigerant circuit becomes too high, which can cause burst and personal injury. ●Do not run the unit with removed panels or protections Touching rotating equipments, hot surfaces or high voltage parts can cause personal injury due to entrapment, burn or electric shocks. ●Be sure to fix up the service panels. Incorrect fixing can cause electric shocks or fire due to intrusion of dust or water. ●Do not perform any repairs or modifications by yourself. Consult the dealer if the unit requires repair. If you repair or modify the unit, it can cause water leaks, electric shocks or fire. - AMP Air Conditioning 22 www.ampair.co.uk | [email protected] '11 • KX-T-166 Notabilia as a unit designed for R410A Do not use any refrigerant other than R410A. R410A will rise to pressure about 1.6 times higher than that of a conventional refrigerant. ● A unit designed for R410A has adopted a different size outdoor unit service valve charge port and a different size check joint provided in the unit to prevent the charging of a wrong refrigerant by mistake. The processed dimension of the flared part of a refrigerant pipe and a flare nut's parallel side measurement have also been altered to raise strength against pressure. Accordingly, you are required to arrange dedicated R410A tools listed in the table on the right before installing or servicing this unit. ● Do not use a charge cylinder. The use of a charge cylinder will cause the refrigerant composition to change, which results in performance degradation. ● In charging refrigerant, always take it out from a cylinder in the liquid phase. ● All indoor units must be models designed exclusively for R410A. Please check connectable indoor unit models in a catalog, etc. (A wrong indoor unit, if connected into the system, will impair proper system operation) ● Dedicated R410A tools a) Gauge manifold b) Charge hose c) Electronic scale for refrigerant charging d) Torque wrench e) Flare tool f) Protrusion control copper pipe gauge g ) Vacuum pump adapter h) Gas leak detector 1. BEFORE BEGINNING INSTALLATION (Check that the models, power supply specifications, piping, wiring are correct.) Caution ●Be sure to read this manual before installation to follow the proper installation methods. ●When installing the indoor unit, read the installation manual of indoor unit. ●Optional distribution parts are required for the piping (Branch pipe set, header set). For details, refer to the catalog, etc. ●Make sure to install the earth leakage breaker. (Select a product compatible with high frequency.) ●There is risk of damaging the compressor if the unit is operated while the discharge pipe thermistor, suction pipe thermistor, pressure sensor, etc. are removed. Never attempt to operation in such condition. ●With this air-conditioning system, room temperature may rise, depending on installation conditions, while indoor units are stopped, because small quantity of refrigerant flows into the stopped indoor units if heating operation is conducted on the system. Accessory Name Location of use Quantity Insert this in CNG on the outdoor unit PCB when using the silencing mode or forced cooling mode Secured in the control box with adhesive tape. 1 Use it for protection of a knock-out hole. It is attached to the bracket with an adhesive tape in the proximity of the service valve. Attached pipe 1 Use this when connecting gas pipe. Attached on the base below the operation valve. Instruction manual 1 When the installation work is completed, give instructions to the customer and ask him/her to keep it. Attached on the base below the operation valve. 2 Wire Edging Combination pattern ●Combination pattern of outdoor units, number of indoor units connected and capacity of connection are as show in the table at right. ●It can be used in combination with the following indoor unit. Remote controller Connection OK/NO RC-E3(2 cores), RC-E4(2 cores) OK Indoor unit FD○△△KXE6 FD○A△△KXE4R, KXE4BR, KXE5R RC-E1R(3 cores) OK FD○A△△KXE4, KXE4(A), KXE4A RC-E1(3 cores) NO Outdoor unit Indoor unit Capacity Combination pattern Number of units connected (unit) Range of total capacity of connected indoor units 224 Single 1~13 112~292 280 Single 1~16 140~364 [Items sold separately] Refrigerant pipe distribution parts, which are not contained in the package, will be required for installation. As for refrigerant pipe distribution parts, we offer branching pipe sets (Model type: DIS) and header sets (Model type: HEAD) as parts used on the indoor side of piping. Please select one suiting your application. In selecting distribution parts, please also refer to “4. REFRIGERANT PIPING.” If you are not sure which parts to select, please consult with your dealer or the manufacture. When washing existing pipes using the re-fresh kit, it is necessary to install the service valve kit (Model: FDCR-V-KIT-E). 2. INSTALLATION LOCATION (Obtain approval from the customer when selecting the installation area.) 2-1. Selecting the installation location 〇 Where air is not trapped. 〇 Where the installation fittings can be firmly installed. 〇 Where any object does not prevent inlet or outlet air. 〇 Out of the heat range of other heat sources. 〇 Where strong winds will not blow against the outlet air. Please note 〇 〇 〇 〇 〇 A place where stringent regulation of electric noises is applicable. Where it is safe for the drain water to be discharged. Where noise and hot air will not bother neighboring residents. Where snow will not accumulate. A place where no TV set or radio receiver is placed within 5m. (If electrical interference is caused, seek a place less likely to cause the problem) a) If there is a possibility of a short-circuit, then install a flex flow adapter. b) When installing multiple units, provide sufficient intake space so that a short-circuit does not occur. c) In areas where there is snowfall, install the unit in a frame or under a snow hood to prevent snow from accumulating on it. (Inhibition of collective drain discharge in a snowy country) d) Do not install the equipment in areas where there is a danger for potential explosive atmosphere. e) Install the equipment in a location that can sufficiently support the weight of the equipment. f) If a unit is installed into a special environment as shown below, there will be a danger that the corrosion of the outdoor unit or its malfunctioning is caused. If this is the case, please consult with the distributor from whom you have purchased the unit. ・Where corrosive gas is generated (such as a hot-spring resort area). ・Where the unit is subject to sea breezes (coastal area). ・Where the unit is subject to oil mists. ・Where equipment generating electromagnetic waves exists in the vicinity. g) When strong winds occur ● Where it is likely that the unit is subjected to strong winds, provide wind guards according to the following guidelines. Strong winds can cause performance degradation, an accidental stop due to a rise of high pressure and a broken fan. ②Please install so the direction of the air from the blowing outlet will be perpendicular to the direction of the wind. ①Place the unit outlet pipe perpendicular to the wind direction. When installing units side by side, install the flex flow adaptor. (This is not required if a distance of 1,500 mm may be secured between the blowing outlet and the wall.) ③When the foundation is not level, use wires to tie down the unit. Wind direction Wind direction Ove r 50 0m Fasten with anchor bolts m - AMP Air Conditioning CAUTION Please leave sufficient clearance around the unit without fail. Otherwise, a risk of compressor and/or electric component failure may arise. 23 www.ampair.co.uk | [email protected] '11 • KX-T-166 2-2. Installation space (Ex. servicing space) a) Minimum installation space (Please select an installation point with due attention to the direction of installation of the refrigerant pipe) (If the installation conditions shown in this drawing are not satisfied, please consult with your dealer or the manufacturer.) b) When units are installed side by side, leave a 10 mm or wider service space between the units. c) Don’t install at a place where it will be surrounded with walls in four directions. Even when it is not surrounded with walls in four directions and it is met the installation conditions as shown by this figure, if there is risk of short-circuit, install the flex flow adaptor to prevent the short-circuit. d) There must be a 1-meter or larger space in the above. e) A barrier wall placed in front of the exhaust diffuser must not be higher than the unit. (Unit : mm) Air inlet L2 Size L3 L4 Air inlet Service space Air outlet L1 Sample Ⅱ Ⅰ Ⅲ *1 L1 Open L2 300 5 L3 300 300 L4 250 (5) Open 1500 (500) *2 Open 300 *2 250 (5) 250 (5) *2 *1 Figure in ( ) shows the value applicable when the flex flow adaptor is installed. *2 Under the setting condition as specified in ( ) , it is necessary to secured 250 mm for the dimension L4 when replacing the compressor. Establish this for example by moving the unit during the work. 3. Unit delivery and installation Caution Attach the ropes on the unit and carry it in avoiding displacement of gravity center. Wear plate Improper slinging may cause the unit to lose balance and fall. 3-1. Delivery ●Deliver the unit in the packing to the specified installation place. ●To hoist the unit, attach a pair of textile ropes with cushion materials attached to protect it. Request Put cushion materials between the unit and the ropes to avoid damages. Wooden base 20 3-2. Cautions for installation ●Make sure to lock the fixing legs of outdoor unit with 4 pieces of anchor bolt (M10). Best margin of protrusion for bolt above the floor is 20 mm. ● When installing the unit, make sure to lock its legs with the following bolts. 20 520 Blowout 195 20 690 Foundation bolt position (4 places) Important Suction Lock with bolt (M10-12) Blowout 195 The protrusion of an anchor bolt on the front side must be kept within 15 mm. ● Securely install the unit so that it does not fall over during earthquakes or strong winds, etc. ● Refer to the above illustrations for information regarding concrete foundations. ● Install the unit in a level area. (With a gradient of 5 mm or less.) Improper installation can result in a compressor failure, broken piping within the unit and abnormal noise generation. ● Suction Use a thicker block to anchor deeper. Use a long block to extend the width. In case that the unit operates in cooling mode, when the outdoor temperature is –5°C or lower, please equip a flex flow adapter and a snow guard hood (option) on the unit. 4. REFRIGERANT PIPING 4-1. Determination of piping specifications (Please select from the following matrix according to indoor unit specifications and installation site conditions) (1) Limitation on use of pipes ●When arranging pipes, observe the restrictions on use concerning the longest distance of (1), total piping length, allowable pipe length from initial branching and allowable difference of height (difference between heads). ●Avoid any trap ( ) or bump ( ) in piping as they can cause fluid stagnation. ●Maximum length (To the furthest indoor unit) … Actual length Less than 160 m (Actual length less than 185 m) It is required to change the pipe diameter when the actual length exceeds 90 m. Determine the size of main pipe, referring to the table of main pipe selection table of (3) (a). ●Total piping length ………………………………………………………… 510 m or less ●Length of main pipe ……………………………………………………… 130 m or less ●Allowable pipe length from initial branching …………………………… 90 m or less Difference in pipe lengths between indoor units, however, is 40 m or less. ●Allowable difference in height (Difference of heads) (a) When an indoor unit is positioned at a higher place ……………… 50 m or less (b) When an outdoor unit is positioned at a lower place ……………… 40 m or less (c) Difference of heights between indoor units in a system …………… 15 m or less (d) Difference of heights between initial branching and indoor unit … 18 m or less (2) Selection of pipe material ●Use pipes with the inside clean and free from any harmful sulfur, oxides, dirt, chips & oil, or moisture (contamination). Height difference ●Use following refrigerant pipes. Actual length Material … Phosphate deoxidation treated seamless pipe (C1220T-O, 1/2H, JIS H3300) Equivalent length Total piping length C1220T-1/2H for O.D. ø25.4 or more, or C1220T-O for ø22.22 or less ●Wall thickness and size - Select according to the guide for pipe size selection (This product uses R410A. Since, in case of pipes in the size of ø25.4 or more, materials of -O lacks sufficient capacity to withstand pressure, make sure to use pipes of 1/2H material and thickness larger than the minimum thickness.) ●When a pipe is branched, make sure to use our branching set or header set. ●When setting branching pipes, take care of the mounting direction and consult carefully with the instruction manual. ●Regarding the handling of operation valve, refer to 4-3 (1) Operating method of operation valve. - AMP Air Conditioning CAUTION Make sure to install within the range of limitation. Otherwise, resulting malfunction of compressor may not be warranted. Observe always the limitation of use during installation. Outdoor unit Height difference between indoor units: 15 m 50 m 160 m 185 m 510 m Indoor unit 24 www.ampair.co.uk | [email protected] '11 • KX-T-166 (3) Pipe size selection WARNING Make sure that the materials of existing pipes, pipe diameters and pipe wall thickness are appropriate and that the design pressure (allowable pressure) is 3.24 MPa or higher. ●When selecting pipe sizes to install additional indoor units, refer to the technical data of KXE6 SERIES. Use C1220T-1/2H material for ø25.4 or larger. Branch pipe set at indoor side Model: DIS Outdoor unit Header set at indoor side Model: HEAD B B C C C C Branch pipe set at indoor side Model: DIS Indoor unit B A B C C C C Fig. 1 Indoor unit (a) Main pipe (Between outdoor unit and initial branch at indoor unit side): Section A in Fig.1 Outdoor unit Main pipe Liquid pipe size ø6.4 ø9.5 ø12.7 ø15.9 ø19.1 ø22.2 224 *1 *2 280 *1 *2 Gas pipe size ø9.5 ø12.7 ø15.9 ø19.1 ø22.2 ø25.4 ø28.6 ø31.8 ø34.7 *1 *1 (b) Between the initial branch at indoor unit side and the indoor unit side: Section B in Fig.1 Indoor unit capacity Liquid pipe size ø6.4 ø9.5 ø12.7 ø15.9 ø19.1 ø22.2 Gas pipe size ø9.5 – 101 or less Pipe diameter between indoor Over 101 – 180 or less branch and main pipe (Combined capacity of indoor units) Over 180 – 364 or less ø12.7 ø15.9 ø19.1 ø22.2 ø25.4 ø28.6 ø31.8 ø34.7 *3 *3 *4 *5 (c) Between indoor unit branch and indoor unit: Section C in Fig.1 Indoor unit capacity Liquid pipe size ø6.4 ø9.5 ø12.7 ø15.9 ø19.1 ø22.2 Gas pipe size ø9.5 ø12.7 ø15.9 ø19.1 ø22.2 ø25.4 ø28.6 ø31.8 ø34.7 22 *6 28 *6 36 45 56 Indoor branch pipe 71 80 90 112 140 160 224 280 *1. It cannot be used when the pipe length exceeds. 90 m *2. It cannot be used when the main pipe length exceeds. 80 m *3. It can be used when the capacity of indoor unit connected with φ15.9 Gas pipe size is 44 or less and difference of height between the indoor units is within 10m. It can be used when the capacity of indoor unit connected with φ12.7 Gas pipe .size is 35 or less and difference of height between the indoor units is within 10m. *4. It can be used when the capacity of indoor units connected at the down stream is higher than 280. *5. It can be used when the capacity of indoor units connected at the down stream is higher than 335. *6. Vertical length of φ12.7 gas pipe size must be within 10m. . - AMP Air Conditioning 25 - # www.ampair.co.uk | [email protected] '11 • KX-T-166 4-2. Piping work (1) Pipe connecting position and pipe outgoing direction 120 B A G A B 155 124 Legend A Attached pipe connecting outlet at refrigerant gas side B Pipe connection outlet at liquid refrigerant side C Refrigerant pipe outlet (Slot 64x109) D Power cable outlet (ø30) E Power cable outlet (ø45) F Refrigerant pipe connection outlet (Slot 50x105) G Pipe connection outlet at gas refrigerant side H Signal cable outlet (ø22) I Power cable outlet (ø34) Outdoor unit 45 D 34 42 43 I I 161 640 174 C 45 30 45 69 30 H 54 H E 45 14 51 68 159 35 286 D C F 43 G 54 553 60 14 C Liquid service valve (To indoor unit) Outdoor unit ( Bypass gas pipe service valve Flared connection to re-fresh kit ) A Drain outlet (ø20) Service valve shown in Fig. A is used only when the pipe washing operation is carried out using the re-fresh kit. Take note that the valve is not use during normal operation. Hook Pipe fastening position Over 1.5m Rear connection Right-hand side connection Front connection Outdoor gas pipe To pipe at outdoor unit ( side of service valve kit ) Bottom connection First remove the five screws ( mark) of the service panel and push it down into the direction of the arrow mark and then remove it by pulling it toward you. The pipe can be laid in any of the following directions: side right, front, rear and downward. ● Remove a knock-out plate provided on the pipe penetration to open a minimum necessary area and attach an edging material supplied as an accessory by cutting it to an appropriate length before laying a pipe. ● ● In laying pipes on the installation site, cut off the casing’s half blank that covers a hole for pipe penetration with nippers. If there is a risk of small animals entering from the pipe penetration part, close the part with some sealing material or the like (to be arranged on the installer’s part). ● In the case of an installation using a collective drain system, use a port other than the bottom one to take out cables and pipes. If the bottom port is used, seal it thoroughly so that drain water may not spill out. ● Use an elbow (to be arranged on the user’s part) to connect control valves to the piping. ● In anchoring piping on the installation site, give 1.5m or a longer distance between an outdoor unit and an anchoring point where the piping is secured as illustrated below. (A failure to observe this instruction may result in a pipe fracture depending on a method of isolating vibrations employed.) ● The pipe should be anchored every 1.5m or less to isolate the vibration. ● ● CAUTION If you tighten it without using double spanners, you may deform the service valve, which can cause an inflow of nitrogen gas into the outdoor unit. (2) Field piping work Important Please take care so that installed pipes may not touch components within a unit. During the pipe installation at site, keep the service valves shut all the time. ● Give sufficient protections (compressed and brazed or by an adhesive tape) to pipe ends so that any water or foreign matters may not enter the pipes. ● In bending a pipe, bend it to the largest possible radius (at least four times the pipe diameter). Do not bend a pipe repeatedly to correct its form. ● An outdoor unit’s pipe and refrigerant piping are to be flare connected. Flare a pipe after engaging a flare nut onto it. A flare size for R410A is different from that for conventional R407C. Although we recommend the use of flaring tools developed specifically for R410A, conventional flaring tools can also be used by adjusting the measurement of protrusion B with a protrusion control gauge. ● Be sure to use the accessory pipe for connection to the gas operation valve. For details, refer to the installation manual of the accessory pipe. ● Tighten a flare joint securely with two spanners. Observe flare nut tightening torque specified in the table below. ● Flare nut parallel side measurement: H (mm) Copper H pipe outer diameter 17 ø6.35 H A Flared pipe end: A (mm) Copper pipe outer A 0 -0.4 diameter B ● Copper pipe protrusion for flaring: B (mm) Copper In the case of a rigid (clutch) type pipe outer With an R410A tool With a conventional tool diameter ø6.35 9.1 ø6.35 ø9.52 22 ø9.52 13.2 ø9.52 ø12.7 26 ø12.7 16.6 ø12.7 ø15.88 29 ø15.88 19.7 ø15.88 - AMP Air Conditioning 0~0.5 0.7~1.3 26 www.ampair.co.uk | [email protected] '11 • KX-T-166 For operation valves both at the fluid and gas sides, fix the valve body and tighten to adequate torque as shown at right. Operation valve size Tightening torque Tightening angle Recommended length of tool handle (N・m) (mm) (mm) (° ) ø6.35 (1/4") ø9.52 (3/8") ø12.7 (1/2") ø15.88(5/8") ø19.05 (3/4") 14∼18 45∼60 150 34∼42 30∼45 200 49∼61 30∼45 250 68∼82 15∼20 300 100∼120 15∼20 450 Do not hold the valve cap area with a spanner. Use a torque wrench. If a torque wrench is not available, fasten the flare nut manually first and then tighten it further, using the left table as a guide. Do not apply any oil on a flare joint. Blazing must be performed under a nitrogen gas flow. Without nitrogen gas, a large quantity of foreign matters (oxidized film) are created, causing a critical failure from capillary tube or expansion valve clogging. ● Brazing of the service valve and the pipes should be performed while cooling the valve body with a wet towel. ● Perform flushing. To flush the piping, charge nitrogen gas at about 0.02MPa with a pipe end closed with a hand. When pressure inside builds up to a sufficient level, remove the hand to flush. (in flushing a pipe, close the other end of the pipe with a plug). ● ● Plug the end of the pipe with tape, or other material, and fill the pipe with nitrogen gas. Operation procedure ① During the pipe installation at site, keep the service valves shut all the time. ② Blazing must be performed under a nitrogen gas flow. Without nitrogen gas, a large quantity of foreign matters (oxidized film) are created, causing a critical failure from capillary tube or expansion valve clogging. <N2> Taping Only use nitrogen gas (N2) Brazing Nitrogen Flatten ③ Give sufficient protections (compressed and brazed or with an adhesive tape) so that water or foreign matters may not enter the piping. Brazing ④ Perform flushing. To flush the piping, charge nitrogen gas at about 0.02MPa with a pipe end closed with a hand. When pressure inside builds up to a sufficient level, remove the hand to flush. (in flushing a pipe, close the other end of the pipe with a plug). 4-3. Air tightness test and air purge Primary side Secondary side Station valve 0.02MPa Hand Nitrogen gas (1) Air tightness test Adhesive tape Relief valve ① Although an outdoor unit itself has been tested for air tightness at the factory, please check the connected pipes and indoor units for air tightness from the check joint of the service valve on the outdoor unit side. While conducting a test, keep the service valve shut all the time. ② Since refrigerant piping is pressurized to the design pressure of a unit with nitrogen gas for testing air tightness, please connect instruments according the drawing below. Under no circumstances should chlorine-based refrigerant, oxygen or any other combustible gas be used to pressurize a system Keep the service valve shut all the time. Do not open it under any circumstances. Be sure to pressurize all of the liquid, gas pipes. CAUTION ③ In pressurizing the piping, do not apply the specified level of pressure all at once, but gradually raise pressure. Applying excessive pressure can cause an a) Raise the pressure to 0.5 MPa, and then stop. Leave it for five minutes or more to see if the pressure drops. inflow of nitrogen gas into an outdoor unit. b) Then raise the pressure to 1.5 MPa, and stop. Leave it for five more minutes to see if the pressure drops. c) Then raise the pressure to the specified level (3.24 MPa), and record the ambient temperature and the pressure. d) If no pressure drop is observed with an installation pressurized to the specified level and left for about one day, it is acceptable. When the ambient temperature changes 1℃, the pressure also changes approximately 0.01 MPa. The pressure, if changed, should be compensated for. e) If a pressure drop is observed in checking e) and a) – d), a leak exists somewhere. Find a leak by applying bubble test liquid to welded parts and flare joints and repair it. After repair, conduct an air-tightness test again. ④Always pull air from the pipes after the airtightness test. Standard torque at sections on operation valve Operation valve Liquid pipe To indoor unit Operation valve size Shaft tightening torque Cap tightening torque (mm) (N·m) (N·m) Gas pipe Gauge manifold Lo Hi Nitrogen gas Lo knob Hi knob ø9.52 (3/8") ø12.7 (1/2") ø19.05 (3/4") Service point (check joint) 6~8 20~30 10~12 14~16 25~35 10~12 3 30~35 12~14 Securely tighten the cap and the blind nut after the adjustment. Avoid applying any excessive force when operating the shaft or when tightening the cap or blind nut. Otherwise, it could cause malfunction or leakage from the shaft, cap or blind nut. Outdoor unit Pin type ▲ ▲ Allen wrench type Check joint blind nut tightening torque (N·m) Remove the cap and adjust as shown below Allen wrench (M4) Stopper Open Pin State at shipping (closed) Fluid/gas operation valve ・Open the valve stem till it hits the stopper. No need to apply force more than that. ・ After the adjustment, replace the blind nut as it was. - AMP Air Conditioning State of open ・After the adjustment, replace the cap as it was. 27 www.ampair.co.uk | [email protected] '11 • KX-T-166 (2) Air purge (When washing pipes using the re-fresh kit, do not air purge before connecting the kit.) CAUTION Insufficient degree of vacuum causes a capacity shortage, clogging by remaining moisture or malfunction of compressor Refrigerant charge after achieving -101 kPa or under (-755 mmHg or under. After letting it alone for more than 1 hour, the pointer needle of vacuum gauge should not creep up. Degree of vacuum check Operate the vacuum pump for more than 1 hour Completion of air purge Completion of air tightness test <Work flow> Start of air purge Perform the air purge from both the operation check joints at fluid side and gas side. When the needle pointer of vacuum gauge has crept up, it means that there is moisture in or leakage from the system. Identify and repair the leaking position and then perform the air purge again. This product uses R410A. Take care of the following points. To avoid contamination with different type of oil, use separate tools depending on the type of refrigerant. It is prohibited especially to use the gauge manifold and the charge hose for different types of refrigerant (R22, R407C). Use a reverse flow prevention adaptor to prevent the contamination of refrigerant system with vacuum pump oil. 4-4. Additional charge of refrigerant (When washing pipes using the re-fresh kit, do not charge additional refrigerant before connecting the kit.) ●Refrigerant must be in the state of fluid when charging. ●Make sure to use a measuring device when charging the refrigerant. When it cannot charge whole required quantity because the outdoor unit is stopped, operate the unit in the test run mode and charge. (See Section 8 for the method of test run.) Operating the unit for a long period of time with insufficient quantity of refrigerant could cause malfunction on the compressor. (When charging while operating the unit, especially, complete the charge within 30 minutes.) This unit contains 11.5 kg of refrigerant. Calculate necessary quantity of additional charge with the following formula, and record the quantity of additionally charged refrigerant on the refrigerant quantity list provided on the back of service panel. ●Charge the additional refrigerant depending on the size and length of fluid pipe. Determine the quantity of additional charge by rounding the second place after decimal point, which means in the unit of 0.1 kg. Additional charge quantity (kg) =2.5+ (L3×0.17) + (L4×0.11) + (L5×0.054) Standard additional refrigerant quantity Make sure to charge this quantity in addition to the charge quantity for the refrigerant piping. L3: Tot al length of ø15.88 pipes (m), L4: Total length of ø12.7 pipes (m) L5: Total length of ø0.952 pipes (m), L6: Total length of ø6.35 pipes (m) + (L6×0.022) Charge quantity for the refrigerant piping Refrigerant pipe size ø15.88 ø12.7 ø9.52 ø6.35 0.17 0.11 0.054 0.022 Additional charge quantity(kg/m) Remark ●This product uses R410A. Take care of the following points. ∙ To avoid contamination with different type of oil, use separate tools depending on the type of refrigerant. It is prohibited especially to use the gauge manifold and the charge hose for different types of refrigerant (R22, R407C). ∙ Type of refrigerant is indicated with the color painted on the container (Yellow for R410A). Sufficient care must be taken to use correct refrigerant only. ∙ Never use a charge cylinder. Otherwise, the composition of refrigerant may change when introducing R410A into the cylinder. ∙ Make sure to charge the refrigerant in the state of fluid. CAUTION ●Request Record the refrigerant quantity calculated based on the piping length in the refrigerant quantity list provided on the back of service panel. Make sure to enter the data. The data is required at maintenance or service. Attached on the back of service panel. Refrigerant quantity label 4-5. Heat insulation and moisture condensation proof (1) Dress refrigerant pipes (both gas and liquid pipes) for heat insulation and prevention of dew condensation. Improper heat insulation/anti-dew dressing can result in a water leak or dripping causing damage to household effects, etc. (2) Use a heat insulating material that can withstand 120℃ or a higher temperature. Poor heat insulating capacity can cause heat insulation problems or cable deterioration. ● All gas pipes must be securely heat insulated in order to prevent damage from dripping water that comes from the condensation formed on them during a cooling operation or personal injury from burns because their surface can reach quite a high temperature due to discharged gas flowing inside during a heating operation. ● Wrap indoor units’ flare joints with heat insulating parts (pipe cover) for heat insulation (both gas and liquid pipes). ● Give heat insulation to both gas and liquid side pipes. Bundle a heat insulating material and a pipe tightly together so that no gaps may be left between them and wrap them together with a connecting cable by a dressing tape. ● Although it is verified in a test that this air conditioning unit shows satisfactory performance under JIS condensation test conditions, both gas and liquid pipes need to be dressed with 20mm, or over, heat insulation materials additionally above the ceiling where relative humidity exceeds 70%. Wires for connecting indoor and outdoor units Liquid piping Exterior tape Gas piping Insulation Band (accessory) Pipe cover (accessory) 5. Drainage ● ● ● ● ● Where water drained from the outdoor unit may freeze, connect the drain pipe using optional drain elbow and drain grommet. Outdoor unit has 4 drain outlets on the bottom. When guiding drain water to a scupper, etc, install the parts on a flat stand (optional item), blocks, or other. Connect the drain elbow as shown by the figure. Seal remaining holes with grommets. When draining water collectively, use holes for wires and pipes opened other than on the bottom. When this is impracticable, sufficiently seal the drain pipe to prevent water leakage. Drain elbow (1 pc) Drain grommet (3 pcs.) Commercial general purpose hard polycarbonate pipe, VP-16 - AMP Air Conditioning 28 www.ampair.co.uk | [email protected] '11 • KX-T-166 6. Electric wiring Electrical installation work must be performed by an electrical installation service provider qualified by a power provider of the country. Electrical installation work must be executed according to the technical standards and other regulations applicable to electrical installations in the country. Please install an earth leakage breaker without fail. The installation of an earth leakage breaker is compulsory in order to prevent electric shocks or fire accidents. (Since this unit employs inverter control, please use an impulse withstanding type to prevent an earth leakage breaker’s false actuation.) Please note a) Use only copper wires. Do not use any supply cord lighter than one specified in parentheses for each type below. - braided cord (code designation 60245 IEC 51), if allowed in the relevant part 2; - ordinary tough rubber sheathed cord (code designation 60245 IEC 53); - flat twin tinsel cord (code designation 60227 IEC 41) - ordinary polyvinyl chloride sheathed cord (code designation 60227 IEC 53). Please do not use anything lighter than polychloroprene sheathed flexible cord (cord designation 60245 IEC57) for supply cords of parts of appliances for outdoor use. b) Use separate power supplies for the indoor and outdoor units. c) The power supplies for indoor units in the same system should turn on and off simultaneously. d) Ground the unit. Do not connect the grounding wire to a gas pipe, water pipe, lightning rod or telephone grounding wire. A grounding wire must be connected before connecting the power cable. Provide a grounding wire longer than the power cable. If improperly grounded, an electric shock or malfunction may result. e) The installation of an impulse with standing type earth leakage breaker is necessary. A failure to install an earth leakage breaker can result in an accident such as an electric shock or a fire. Do not turn on the power until the electrical work is completed. Be sure to turn off the power when servicing. f ) Please do not use a condensive capacitor for power factor improvement under any circumstances. (It does not improve power factor, while it can cause an abnormal overheat accident) g) For power supply cables, use conduits. h) Please do not lay electronic control cables (remote control and signaling lines) and other high current cables together outside the unit. Laying them together can result in malfunctioning or a failure of the unit due to electric noises. i ) Power cables and signaling lines must always be connected to the terminal block and secured by cable fastening clamps provided in the unit. j ) Fasten cables so that they may not touch the piping, etc. k) When cables are connected, please make sure that all electrical components within the electrical component box are not free or not loose on the terminal connection and then attach the cover securely. (Improper cover attachment can result in malfunctioning or a failure of the unit, if water penetrates into the box.) l ) Make sure to use circuit breakers (earth leakage breaker and circuit breaker) of proper capacity. Use of breakers of larger capacity could result in trouble on components or fire accident. The circuit breaker should isolate all poles under over current. m) Install isolator or disconnect switch on the power supply wiring in accordance with the local codes and regulations. The isolator should be locked in OFF state in accordance with EN60204-1. n) After maintenance, all wiring, wiring ties and the like, should be returned to their original state and wiring route, and the necessary clearance from all metal parts should be secured. 6-1. Wiring system drawing (Example of combination) Power supply (outdoor unit side) 380/415V 3N ∼ 50Hz Power supply (indoor unit side) 220/240V ∼ 50Hz 220V ∼ 60Hz Earth leakage breaker Grounding work 6-2. Power supply connection ● Signal wire (between outdoor - indoor units〈Ⅰ〉) 1 A・B ・ 2 X・Y 1 A・B ・ 2 X・Y 〈Ⅰ〉 Remote controller wire (1) Method of leading out cables ● Outdoor unit A1・B1 ・・・ ・・・ Circuit breaker for cabling Indoor unit ● L1・L2・L3・N Earth leakage Circuit breaker Grounding work breaker for cabling Signal wire (between indoor units) X・Y If the earth leakage breaker is exclusively for ground fault protection, then you will need to install a circuit breaker for wiring work. 〈Ⅷ〉 〈Ⅱ〉 X・Y Remote controller CAUTION 1 A・B ・ 2 X・Y ・・・ ・・・ X・Y As shown on the drawing in Section 4-2, cables can be laid through the front, right, left or bottom casing. In wiring on the installation site, cut off a half-blank covering a penetration of the casing with nippers. In the case of an installation using a collective drain system, use a port other than the bottom one to take out cables and pipes. If the bottom port is used, seal it thoroughly so that drain water may not spill out. (2) Notabilia in connecting power cables Connect the ground wire before you connect the power cable. When you connect a grounding wire to a terminal block, use a grounding wire longer than the power cable so that it may not be subject to tension. Do not turn on power until installation work is completed. Turn off power to the unit before you service the unit. ● Ensure that the unit is properly grounded. ● Always connect power cables to the power terminal block. ● To connect a cable to the power terminal block, use a round crimp contact terminal. If two cables are to be connected to one terminal, arrange cables in such a manner that you put their crimp contact terminals together back to back. Further, put the thinner cable above the thicker one in arranging cables for such connection. ● Use specified wires in wiring, and fasten them securely in such a manner that the terminal blocks are not subject to external force. ● In fastening a screw of a terminal block, use a correct-size driver. Fastening a screw of a terminal block with excessive force can break the screw. ● When electrical installation work is completed, make sure that all electrical components within the electrical component box are free of loose connector coupling or terminal connection. ● Round crimp contact terminal ● Terminal block Crimp contact terminal Wire Diameter of a cable:thin Diameter of a cable:thick (3) Outdoor unit power supply specification: 380/415V 3N~ 50Hz 380V 3N~ 60Hz Moulded-case circuit breaker (A) Model Power source Cable size for power source (mm2) Wire length (m) Rated current Switch capacity 224KXE6 280KXE6 Three-phase 380/415V 50Hz 380V 60Hz 5.5 54 30 30 Please note Earth leakage breaker 30A, 30mA less than 0.1 sec Earth wire Size (mm2) Screw type 2 M5 a) The method of laying cables has been determined pursuant to the Japanese indoor wiring regulations (JEAC8001). (Please adapt it to the regulations in effect in each country) b) For details, please refer to the installation manual supplied with the indoor unit. (4) Indoor unit power source (Outdoor unit is another power source.) & signal line Request Combined total capacity Cable size for power source(mm2) of indoor units less than 7A 2 less than 11A 3.5 less than 12A less than 16A Wire length(m) Moulded-case circuit breaker (A) Signal line (mm2) Earth leakage breaker outdoor-indoor indoor-indoor Rated current Switch capacity 21 20 5.5 33 20 5.5 24 30 20A, 30mA less than 0.1 sec 30 30A, 30mA less than 0.1 sec 2 core × 0.75 ※ (a) Table at left shows the standard specification. Use the power supply of single phase 220/240V. (b) Distance in the table shows the value obtained when indoor units are connected in series. The table shows the wire size and the distance provided voltage drop is within 2% for each total current of indoor unit. Where the current exceeds the values in the table, change the wire size according to the extension wiring regulations. (c) Wires connected to indoor units are allowed up to 5.5 mm2. For 8 mm2 or more, use a dedicated pull box and branch to indoor units with 5.5 mm2 or less. ※ Please use a shielded cable. - AMP Air Conditioning 29 www.ampair.co.uk | [email protected] '11 • KX-T-166 6-3. How to connect signal cables The communication protocol can be choosen from following two types. One of them is the conventional Superlink (hereinafter previous SL) and the other is the new SuperlinkⅡ (hereinafter new SL) . These two communication protocols have the following advantages and restrictions, so please choose a desirable one meeting your installation conditions such as connected indoor units and centralized controller. When signal cables are connected into a network involving outdoor units, indoor units or centralized control equipment that do not support new SL, please select communications in the previous SL mode, even if the refrigerant system is separated from theirs. Communication protocol New communication protocol (new SL) Conventional communication protocol (previous SL) Outdoor unit setting (SW5-5) ON OFF (Factory default) No. of connectable indoor units Max. 48 Max. 128 No. of connectable outdoor unitsin a network Max. 48 Max. 32 No. of connectable outdoor units Up to 1000m Up to 2,000 m for wires other than shielding wire Up to 1,500 m for 0.75 mm2 shielding wire (MVVS) Up to 1,000 m for 1.25 mm2 shielding wire (MVVS) Signal cable (furthest length) Up to 1000m Up to 1000m Connectable units to a network Units not supporting new SL (FD A KXE4 series) Units supporting new SL (FD KXE6 series) Can be used together. Units supporting new SL (FD KXE6 series) Note: For FDT224 and 280 models, calculate the number of units taking 1 indoor unit as 2 units for the sake of communication. ● Signal cables are for DC 5 V. Never connect wires for 220/240 V or 380/415 V. Protective fuse on the PCB will trip. ① Confirm that signal cables are prevented from applying 220/240 V or 380/415 V ② Before turning the power on, check the resistance on the signal cable terminal block. If it is less than 100Ω, power supply cables may be connected to the signal cable terminal block. When the FD KXE6 Series unit(s) only is connected; Standard resistance value = 5,100/number of connected units When the FD A KXE4 Series unit(s) only is connected: Standard resistance value = 9,200/number of connected units When the FD A KXE4 Series and type FD KXE6 Series units are connected in a mixture: Standard resistance value = 46,000/{(Number of FD A KXE4 Series units connected x 5) + (Number of FD KXE6 Series units connected x 9)} Number of connected units includes the indoor unit, outdoor unit and SL devices. If the resistance value is less than 100Ω, disconnect the signal cables temporarily to divide to more than one network, to reduce the number of indoor units on the same network, and check each network Indoor and outdoor units signal cables Connect the signal line between indoor unit and outdoor unit to A1 and B1. Connect the signal line between outdoor units to A2 and B2. ● Please use a shielded cable for a signal line and connect a shielding earth at all the indoor units and outdoor units. ● ● (2) When plural outdoor units are used (1) When one outdoor unit is used. Outdoor signal line terminal block A1 B1 Outdoor unit Outdoor unit Outdoor unit A1∙B1 A1∙B1 A1∙B1 Network connector Indoor signal line terminal block A B A B A B Indoor unit ○Indoor and outdoor signal lines do not have a polarity. Any of the connections in the following illustration can be made. A1 A A1 A B1 B B1 B A2∙B2 Indoor unit Outdoor unit Outdoor unit Indoor unit Indoor unit Indoor unit Indoor unit Indoor unit Indoor unit A2∙B2 Indoor unit A A A B B B Indoor unit Indoor unit Indoor unit A A A B B B (1) The signal lines can also be connected using the method shown below. Outdoor unit A2∙B2 Refrigerant pipe Signal line Important Outdoor unit Outdoor unit ○Loop wiring prohibited. Outdoor unit Outdoor unit The signal lines cannot form a loop, so the wirings shown as ....... in the diagram are prohibited. Indoor unit Indoor unit Indoor unit Indoor unit Power cable and signal cable connection Network connector Earth wire is giving slack. Wiring clamp ● Fix the cables not to exert external force to the terminal connection. ● Give adequate slack to cables in fastening them. ● Fix power cables separately from signal cables. Outgoing cable direction ● As like the refrigerant pipe, it can be let out in any of 4 directions of right-hand side, front, rear and bottom. Wiring label The wiring label is attached on the back of the service panel. ● Request ● When connecting to the power supply terminal block, use the crimp terminals for M5 as shown at right. ● When connecting to the signal terminal block, use the crimp terminals for M3.5 as shown at right. Remote controller wiring specifications ● For the remote controller the standard wire is 0.3 mm2. The max. length is up to 600 m. When the wire is more than 100 m long, use the wire shown in the table. ● Use 3-core wires for FD A KXE4 or 2-core wires for FD KXE6. - AMP Air Conditioning Length (m) Wire size Within 100 - 200 0.5mm2 Within - 300 0.75mm2 Within - 400 1.25mm2 Within - 600 2.0mm2 12.5 mm or less 7 mm or less 30 www.ampair.co.uk | [email protected] '11 • KX-T-166 7. CONTROLLER SETTINGS 7-1. Unit address setting This control system controls the controllers of more than one air conditioner's outdoor unit, indoor unit and remote control unit through communication control, using the microcomputers built in the respective controllers. Address setting needs to be done for both outdoor and indoor units. Turn on power in the order of the outdoor units and then the indoor units. Use 1 minute as the rule of thumb for an interval between them. The communication protocol can be chosen from following two types. One of them is the conventional communication protocol (previous SL) and the other is the new communication protocol (new SL). These two communication protocols have their own features and restrictions as shown by Table 6-3. Select them according the indoor units and the centralized control to be connected. When signal cables are connected into a network involving outdoor units, indoor units or centralized control equipment that do not support new SL, please select communications in the previous SL mode, even if the refrigerant system is separated from theirs. When communication is established after setting addresses, check the communication protocol with the 7 segment display panel of the outdoor unit. ●Address setting methods The following address setting methods can be used. The procedure for automatic address setting is different from the conventional one. Please use the automatic address setting function after reading this manual carefully. new SL previous SL Automatic Manual Automatic Manual Communication protocol Address setting method When plural refrigerant systems are linked with signal lines (e.g., to implement centralized control) Case 1 When signal lines linking plural refrigerant systems are provided between outdoor units. (When the network connector is disconnected, refrigerant systems are separated each other) OK※1 OK × OK Case 2 When signal lines linking plural refrigerant systems are provided between indoor units. ×※2 OK × OK OK OK OK OK When only one refrigerant system is involved (signal lines do not link plural refrigerant systems) ※1 Do not connect the signal line between outdoor units to A1 and B1. This may interrupt proper address setting. (Case 3) Do not connect the signal line between indoor unit and outdoor unit to A2 and B2. This may interrupt proper address setting. (Case 4) ※2 In Case 2, automatic address setting is not available. Set addresses manually. Outdoor unit Outdoor unit Outdoor unit Outdoor unit Outdoor unit Outdoor unit A1·B1 A1·B1 A1·B1 Network connector A1·B1 Signal line A2·B2 A1·B1 A2·B2 A1·B1 Network connector A2·B2 A2·B2 A2·B2 A2·B2 Indoor unit Indoor unit Indoor unit Indoor unit Indoor unit Indoor unit A B A B A B A B A B A B Indoor unit Indoor unit Indoor unit Indoor unit Indoor unit Indoor unit A B A B A B A B A B A B Refrigerant pipe CASE 1 Outdoor unit CASE 2 Outdoor unit Outdoor unit Outdoor unit Outdoor unit Outdoor unit Network connector A1·B1 A2·B2 A1·B1 A2·B2 A1·B1 Network connector × A2·B2 A1·B1 A2·B2 A1·B1 Indoor unit Indoor unit Indoor unit A B A B A B Indoor unit Indoor unit A B A B Indoor unit Indoor unit Indoor unit Indoor unit Indoor unit A B A B A B A B A B A1·B1 A2·B2 Indoor unit A B Indoor unit A B CASE 4 CASE 3 Incorrect cable connection (The signal line between outdoor units is connected to A1 and B1) ●Address A2·B2 Incorrect cable connection (The signal line between indoor unit and outdoor units is connected to A2 and B2) No. setting Set SW1 through 4 and SW5-2 provided on the PCB and SW1 & 2 provided on the outdoor unit PCB as shown in the drawings below. SW2 (SW4) SW1 (SW3) For setting indoor No. (The ten’s and one’s) 8 8 7 7 4 5 6 For ten’s place ●Summary of address setting methods (figures in [ Automatic address setting for single refrigerant system installation (previous SL/new SL) Automatic address setting for multiple refrigerant systems installation (with new SL only) By inserting a flat driver (precision screw driver) into this groove and turn the arrow to point a desired number. For one’s place ] should be used with previous SL) Units supporting new SL Indoor unit address setting Indoor No. switch Outdoor No. switch Manual address setting (previous SL/new SL) 6 Indoor No. switch (The hundred’s Place) [OFF : 0, ON : 1] 5 SW5-2 3 SW1, 2 (green) For setting outdoor No. (The ten’s and one’s) 0 1 2 Outdoor PCB 9 3 SW3, 4 (green) For setting outdoor No. (The ten’s and one’s) 0 1 2 Indoor PCB 9 4 SW1, 2 (blue) Outdoor unit address setting Outdoor No. switch Units NOT supporting new SL Indoor unit address setting Outdoor unit address setting Indoor No. switch Outdoor No. switch Outdoor No. switch 000~127 [47] 00~31 [47] 00~31 [47] 00~47 00~47 00~47 000 49 49 49 49 49 000 49 00~31 × × × Do not set numbers other than those shown in the table, or an error may be generated. Note: When units supporting new SL are added to a network using previous SL such as one involving FD A KXE4 series units, choose previous SL for the communication protocol and set addresses manually. Since the models FDT224 and 280 have 2 PCBs per unit, set different indoor unit No. and SW on each PCB. ● An outdoor unit No., which is used to identify which outdoor unit and indoor units are connected in a refrigerant system, is set on outdoor unit PCB and indoor unit PCB. Give the same outdoor unit No. to all outdoor unit and indoor units connected in same refrigerant system. ● An indoor unit No. is used to identify individual indoor units. Assign a unique number that is not assigned to any other indoor units on the network. - AMP Air Conditioning 31 www.ampair.co.uk | [email protected] '11 • KX-T-166 Unless stated otherwise, the following procedures apply, when new SL is chosen for the communication protocol. When previous SL is chosen, use figures shown in [ ] in carrying out these procedures. Manual address setting Generally applicable to new SL/previous SL, use figures in [ ] with previous SL. ① Outdoor unit address setting Set as follows before you turn on power. Upon turning on power, the outdoor unit address is registered. Set the Outdoor Unit No. switch to a number 00 - 31 [in the case of previous SL: 00 - 47]. Set a unique number by avoiding the numbers assigned to other outdoor units on the network. ② Indoor unit address setting Set as follows before you turn on power. Upon turning on power, the indoor unit address is registered. Set the Indoor Unit No. switch to a number 000 - 127 [in the case of previous SL: 00 - 47]. Set the Outdoor Unit No. switch to the outdoor unit No. of the associated outdoor unit within the range of 00 - 31 [in the case of previous SL: 00 - 47]. Set a unique number by avoiding the numbers assigned to other indoor units on the network. ③ Turn on power in order from the outdoor unit to indoor units. Give a one-minute or longer interval for them. * When there are some units not supporting new SL connected in the network, set SW5-5 to ON to choose the previous SL communication mode. In the case of previous SL, the maximum number of indoor units connectable in a network is 48. Automatic address setting Generally applicable to new SL/previous SL, use figures in [ ] with previous SL. With new SL, you can set indoor unit addresses automatically even for an installation involving multiple refrigerant systems connected with same network, in addition to the conventional automatic address setting of a single refrigerant system installation. However, an installation must satisfy some additional requirements such as for wiring methods, so please read this manual carefully before you carry out automatic address setting. (1) In the case of a single refrigerant system installation (Generally applicable to new SL/previous SL, use figures in [ ] with previous SL.) ① Outdoor unit address setting Set as follows before you turn on power. Make sure that the Outdoor Unit No. switch is set to 49 (factory setting) ② Indoor unit address setting Set as follows before you turn on power. Make sure that the Indoor Unit No. switch is set to 000 [in the case of previous SL: 49] (factory setting) Make sure that the Outdoor Unit No. switch is set to 49 (factory setting) ③ Turn on power in order from the outdoor unit to indoor units. Give a one-minute or longer interval for them. Unlike the procedure set out in (2) below, you need not change settings from the 7 segment display panel. ④ Make sure that the number of indoor units indicated on the 7 segment display panel agrees with the number of the indoor units that are actually connected to the refrigerant system. (2) In the case of a multiple refrigerant systems installation (Applicable to new SL only. In the case of previous SL, set addresses with some other method.) (This option is available when the interconnection wiring among refrigerant systems is on the outdoor side and new SL is chosen as the communication protocol.) Address setting procedure (perform these steps for each outdoor unit) [STEP1] (Items set before turning on power) ① Outdoor unit address setting Set as follows before you turn on power. Set the Outdoor Unit No. switch to a number 00 - 31. Set a unique number by avoiding the numbers assigned to other outdoor units on the network. ② Indoor unit address setting Set as follows before you turn on power. Make sure that the Indoor Unit No. switch is set to 000 (factory setting) Make sure that the Outdoor Unit No. switch is set to 49 (factory setting) ③ Isolate the present refrigerant system from the network. Disengage the network connectors (white 2P) of the outdoor units. (Turning on power without isolating each refrigerant system will result in erroneous address setting.) [STEP2] (Power on and automatic address setting) ④ Turn on power to the outdoor unit Turn on power in order from the outdoor unit to indoor units. Give a one-minute or longer interval for them. ⑤ Select and enter “1” in P31 on the 7 segment display panel of each outdoor unit to input “Automatic address start.” ⑥ Input a starting address and the number of connected indoor units. Input a starting address in P32 on the 7 segment display panel of each outdoor unit. ⑦ When a starting address is entered, the display indication will switch back to the “Number of Connected Indoor Units Input” screen. Input the number of connected indoor units from the 7 segment display panel of each outdoor unit. Please input the number of connected indoor units for each outdoor unit. (You can input it from P33 on the 7 segment display panel.)When the number of connected indoor units is entered, the 7 segment display panel indication will switch to “AUX” and start flickering. [STEP3] (Automatic address setting completion check) ⑧ Indoor unit address determination When the indoor unit addresses are all set, the 7 segment display panel indication will switch to “AUE” and start flickering. If an error is detected in this process, the display will show “A○○.” Check the 7 segment display panel of each outdoor unit. Depending on the number of connected indoor units, it may take about 10 minutes before the indoor unit addresses are all set. [STEP4] (Network definition setting) ⑨ Network connection When you have confirmed an “AUE” indication on the display of each outdoor unit, engage the network connectors again. ⑩ Network polarity setting After you have made sure that the network connectors are engaged in ⑧, select and enter “1” in P34 on the 7 segment display panel of any outdoor unit (on only 1 unit) to specify network polarity. ⑪ Network setting completion check When the network is defined, “End” will appear on the 7 segment display panel. An “End” indication will go off, when some operation is made from the 7 segment display panel or 3 minutes after. - AMP Air Conditioning 32 www.ampair.co.uk | [email protected] '11 • KX-T-166 STEP1 STEP2 STEP3 STEP4 Indoor unit power source ②OFF ④ON Outdoor unit power source ①OFF ④ON Indoor unit (indoor/outdoor No.SW) ②indoor000/outdoor 49 (factory setting) – ー Outdoor unit (outdoor No.SW) ①01,02(Ex) – ー ー Network connectors ③Disconnect(each outdoor unit) – ⑤ Select “Automatic Address Start” on each outdoor unit. ⑥outdoor 01:「01」(Ex) outdoor 02:「04」(Ex) ⑦outdoor 01:「03」(Ex) outdoor 02:「03」(Ex) ー ⑨Connect(each outdoor unit) ー ー ー ー – ー ⑩ Set in P34 on the 7 segment display panel of any outdoor unit. Start automatic address setting Set starting address Set the number of indoor unit Polarity setting ー ー ー [STEP1] ー ⑪「End」 ⑧ “AUE”(blink), or “A○○” in error events. ⑦[AUX](Blink) 7 segment display – [STEP2] Outdoor unit [01] Outdoor unit [02] Outdoor unit [01] Outdoor unit [02] Start [01] Number [03] Start [04] Number [03] Refrigerant pipe Indoor unit Indoor unit Indoor unit (00)+01 Indoor unit (00)+04 Indoor unit Indoor unit Indoor unit (01)+01 Indoor unit (01)+04 Indoor unit Indoor unit Indoor unit (02)+01 Indoor unit (02)+04 Signal line [STEP3] [STEP4] Outdoor unit [01] Outdoor unit [02] Outdoor unit [01] Polarity setting Outdoor unit [02] Indoor unit 01 Indoor unit 04 Indoor unit 01 Indoor unit 04 Indoor unit 02 Indoor unit 05 Indoor unit 02 Indoor unit 05 Indoor unit 03 Indoor unit 06 Indoor unit 03 Indoor unit 06 ・Within a refrigerant system, indoor units are assigned addresses in the order they are recognized by the outdoor unit. Therefore, they are not necessarily assigned addresses in order from the nearest to the outdoor unit first as depicted in drawings above. ・Make sure that power has been turned on to all indoor units. ・When addresses are set, you can have the registered indoor unit address No.’s and the outdoor unit address No. displayed on the remote control unit by pressing its Inspection switch. ・Automatic address setting can be used for an installation in which prulal indoor units are controlled from one remote control unit. ・Once they are registered, addresses are stored in microcomputers, even if power is turned off. ・If you want to change an address after automatic address setting, you can change it from the remote control unit with its “Address Change” function or by means of manual setting. Set a unique address by avoiding the address assigned to other indoor unit on the network when the address is changed. ・Do not turn on power to centralized control equipment until automatic address setting is completed. ・When addresses are set, be sure to perform a test run and ensure that you can operate all indoor and outdoor units normally. Also check the addresses assigned to the indoor units. Address change (available only with new SL) “Address Change” is used, when you want to change an indoor unit address assigned with the “Automatic Address Setting” function from a remote control unit. Accordingly, the conditions that permit an address change from a remote control unit are as follows. Indoor unit address setting Outdoor unit address setting Indoor No.SW Outdoor No.SW Automatic address setting forsingle refrigerant system installation 000 49 49 Automatic address setting for multiple refrigerant systems installation 000 49 00~31 Outdoor No.SW If “CHANGE ADD. ▼” is selected with some addresses falling outside these conditions, the following indication will appear for 3 seconds on the remote controller ”INVALID OPER” . - AMP Air Conditioning 33 www.ampair.co.uk | [email protected] '11 • KX-T-166 Operating procedure (1) When single indoor unit is connected to the remote controller. Item 1 2 3 Address change mode To set a new indoor unit No. To set a new outdoor unit No. Operation Display ① Press the AIR CON No. switch for 3 seconds or longer. [CHANGE ADD.▼] ② Each time when you press the [CHANGE ADD.▼] ⇔[MASTER I/U▲] switch, the display indication will be switched. ③ Press the Set switch when the display shows “CHANGE ADD. ▼” and then start the address change mode, changing the display indication to the “Indoor Unit No. Setting” screen from the currently assigned address. [I/U 001 O/U 01] (1sec) →[ SET I/U ADD.] (1sec) →[I/U 001 ] (Blink) ④ Set a new indoor unit No. with the switch. A number indicated on the display will increase or decrease by 1 upon pressing the ▲ or ▼ switch respectively. [I/U 000▲」 ⇔[I/U 001 ] ⇔[I/U 002 ] ⇔ ・・・ ⇔[I/U 127▼] ⑤ After selecting an address, press the Set switch, and then the indoor unit address No. is defined. [I/U 002] (2sec) ⑥ After showing the defined indoor address No. for 2 seconds, the display will change to the “Outdoor Address No. Setting” screen. The currently assigned address is shown as a default value. [I/U 002] (2sec Lighting) →[ SET O/U ADD.] (1sec) →[O/U 01 ] (Blink) ⑦Set a new outdoor unit No. with the switch. A number indicated on the display will increase or decrease by 1 upon pressing the ▲ or ▼ switch respectively. [O/U 00▲] ⇔[O/U 01 ] ⇔[O/U 02 ] ⇔ ・・・ ⇔[O/U 31▼] ⑧ After selecting an address, press the Set switch, and then the outdoor unit No. and the indoor unit No. are defined. [I/U 002 O/U 02] (2sec Lighting) →[SET COMPLETE] (2sec Lighting) →Returns to normal condition. (2) When plural indoor units are connected to the remote controller. When plural indoor units are connected, you can change their addresses without altering their cable connection. Item 1 2 3 4 5 Address change mode Operation Display ① Press the AIR CON Unit No. switch for 3 seconds or longer. [CHANGE ADD▼] ② Each time when you press the [CHANGE ADD▼] ⇔[MASTER I/U▲] switch, the display indication will be switched. ③ Press the Set switch when the display shows “CHANGE ADD. ▼” The lowest indoor unit No. among the indoor units connected to the remote control unit will be shown. [ SELECT I/U] (1sec) →[I/U 001 O/U 01▲] (Blink) ④ Pressing the switch will change the display indication cyclically to show the unit No.’s of the indoor units connected to the remote controller and the unit No.’s of the outdoor units connected with them. [I/U 001 O/U 01▲」 ⇔[I/U 002 O/U 01 ] ⇔[I/U 003 O/U 01 ] ⇔ ・・・ ⇔[I/U 016 O/U 01▼」 ⑤ Then the address No. of the indoor unit to be changed is determined and the screen switches to the display “ SET I/U ADD.” [ SET I/U ADD.] (1sec) →[I/U 001 ](Blink) Setting a new indoor unit No. ⑥ Set a new indoor unit No. with the switch. A number indicated on the display will increase or decrease by 1 upon pressing the ▲ or ▼ switch respectively. [I/U 000▲] ⇔[I/U 001 ] ⇔[I/U 002 ] ⇔ ・・・ ⇔[I/U 127▼] ⑦ After selecting an address, press the Set switch. Then the address No.of the indoor unit is determined. [I/U 002] (2sec) Setting a new outdoor unit No. ⑧ The display will indicate the determined indoor address No. for 2 seconds and then switch to the “ SET O/U ADD.” screen. A default value shown on the display is the current address. [I/U 002] (2sec lighting) ⇔[ SET O/U ADD.](1sec) ⇔[O/U 01 ] (Blink) ⑨ Set a new outdoor unit No. with the switch. A number indicated on the display will increase or decrease by 1 upon pressing the ▲ or ▼ switch respectively. [O/U 00▲] ⇔[O/U 01 ] ⇔[O/U 02 ] ⇔ ・・・ ⇔[O/U 31▼] ⑩ After selecting an address, press the Set switch. Then the address of the indoor unit and outdoor unit are determined. [I/U 002 O/U 02](2sec lighting) →[ SELECT](1sec lighting) →[I/U SELECTION▼](lighting) ⑪ If you want to continue to change addresses, return to step ④. [Press the switch](1sec) →[SET COMPLETE] (2∼10sec lighting) ⑫ If you want to end the session (and reflect new address settings) In Step ⑩, press the ▼ switch to select “END ▲.” If you have finished changing addresses, press the Set switch while “END ▲” is shown. While new settings are being transmitted, “SET COMPLETE” will be indicated. Then the remote controller display will change to the normal state. [END▲] →[SET COMPLETE] (2∼10sec lighting) →Normal state ⑬ If you want to end the session (without reflecting new address settings) Before you complete the present address setting session, press the “ON/OFF” switch. Then the display is change to exit from this mode and switch the display to the normal state. All address settings changed in the session will be aborted and not reflected. [ON/OFF] →Forced termination Selecting an indoor unit to be changed address Ending the session The switch will continuously change the display indication to the next one in every 0.25 seconds when it is pressed for 0.75 seconds or longer. If the Reset switch is pressed during an operation, the display indication returns to the one that was shown before the last Set switch operation. Even if an indoor unit No. is changed in this mode, the registered indoor unit No. before address change mode is displayed when [I/U SELECTION ▼] is shown. When “SET COMPLETE” is shown, indoor unit No.’s are registered. NOTICE Turn on power to centralized control equipment after the addresses are determined. Turning on power in wrong order may result in a failure to recognize addresses. - AMP Air Conditioning 34 www.ampair.co.uk | [email protected] '11 • KX-T-166 ● 7 segment display indication in automatic address setting Items that are to be set by the customer Code P30 P31 Contents of a display Communication protocol 0: Previos SL mode 1: New SL mode Automatic address start Specify a starting indoor unit address in automatic address setting. P32 Input starting address P33 Input number of connected indoor units P34 (The communication plotocol is displayed ; display only) Polarity difinition Specify the number of indoor units connected in the refrigerant system in automatic address setting. 0: Network polarity not defined. 1: Network polarity defined. 7 segment display indication in automatic address setting. Code Contents of a display AUX During automatic address setting. X: The number of indoor units recognized by the outdoor unit. AUE Indoor unit address setting is completed normally. End Polarity is defined. (Automatic address) Completed normally. Address setting failure indication Code Contents of a display Please check A00 Unable to find any indoor unit that can be actually communicated with. Are signal lines connected properly without any loose connections? Is power for indoor units all turned on? A01 The number of the indoor units that can be actually communicated with is less than the number specified in P33 on the 7 segment display panel. Are signal lines connected properly without any loose connections? Input the number of connected indoor units again. A02 The number of the indoor units that can be actually communicated with is more than the number specified in P33 on the 7 segment display panel. Are signal lines connected properly without any loose connections? Are the network connectors coupled properly? Input the number of connected indoor units again. A03 Starting address (P32) + Number of connected indoor units (P33) > 128 Input the starting address again. Input the number of connected indoor units again. A04 While some units are operating in the previous SL mode on the network, the automatic address setting on multiple refrigerant systems is attempted. Perform manual address setting. Separate old SL setting unit from the network Arrange all units to operate in the new SL. Error indication Contents of a display Code Cause E2 Duplicating indoor unit address. ・Incorrect manual address setting E3 Incorrect pairing of indoor-outdoor units. ・An outdoor unit number that does not exist in the network is specified ・No master unit exists in combination outdoor unit. E11 Address setting for plural remote controllers. ・Indoor unit address is set from plural remote controllers. E12 Incorrect adderess setting of indoor units. E31 Duplicating outdoor unit address. ・Automatic address setting and manual address setting are mixed. ・Plural outdoor units are exist as same address in same network. E46 Incorrect setting. ・Automatic address setting and manual address setting are mixed. - AMP Air Conditioning 35 www.ampair.co.uk | [email protected] '11 • KX-T-166 7-2. Selection of controls Controls of outdoor unit may be selected as follows using the dip switches on the PCB and P○○ on the 7-segment. To change P○○ on the 7-segment, hold down SW8 (7-segement display increment up: 1-digit), SW9 (7-segment increment up: 10-digit) and SW7 (Data write/Enter). Content of control Control selecting method SW setting on PCB P○○ on 7-segment SW3-7 to ON=1 *1 Set external input function allocation to “2” *1 Forced cooling mode (It can be fixed at cooling with external input terminals open, or at heating with them short-circuited.) SW5-1 to ON + SW5-2 to ON ー Cooling test run SW5-1 to ON + SW5-2 to OFF ー Heating test run ー Pump down operation Close the fluid operation valve on outdoor unit and set as follows: (1) SW5-2 on PCB to ON (2) SW5-3 on PCB to ON (3) SW5-1 on PCB to ON SW4-5:OFF, SW4-6:OFF*1 80% (Factory default) SW4-5:ON , SW4-6:OFF*1 60% SW4-5:OFF, SW4-6:ON*1 40% SW4-5:ON , SW4-6:ON*1 00% Set allocation of external input function to “1” *1 Inputting signals to external input terminals selects the demand mode. (J13 short-circuited: Level input, J13 open: Pulse input) SW5-5 ー Communication method selection ON: Previous SL communication, OFF: New SL communication J13: Closed (Factory default), J13: Open ー External input switing (CnS1, CnS2 only) Closed: Level input, Open: Pulse input) J14: Closed (Factory default), J14: Open Defrost recover temperature Closed: normal, Open: cold weather district Defrost start temperature Closed: normal, Open: cold weather district Operation priority selection 0: First push priority (at shipping) 1: Last push priority ー J15: Closed (Factory default), J15: Open ー P01 ー P02 ー P03 ー P04 ー P05 Silencing mode setting 0 (at shipping) - 3: Larger values for larger effect ー P06 Allocation of external output (CnZ1) ー P07 Allocation of external input (CnS1) ー P08 Allocation of external input (CnS2) ー P09 Allocation of external input (CnG1) ー P10 Allocation of external input (CnG2) ー P11∼ Spare Outdoor unit fan snow protection control 0: Control disabled (at shipping) 1: Control enabled Outdoor unit fan snow protection control ON time setting - 30 sec (at shipping) 10, 30-600 sec Energy saving mode *2 OFF: Disabled (at shipping) 2 stage demand mode 000, 040, 060, 080 [%] *1 Control is switched when both the allocation of external input function (P07-10) and SW are changed. (Example: To use CnS1 for the input of forced cooling mode, set P07 at 2 and SW3-7 at ON. To use CnS2 for the input of forced cooling mode, set P08 at 2 and SW3-7 at ON.) *2 In the energy saving mode, the capacity restriction becomes effective even if no signals are input at external input terminals. By changing the allocation of external input functions (P07-19) on the 7-segment, functions of external input terminals may be selected. Inputting signals to external input terminals enable the following functions. Setting value for allocation of external input function The external output function of CnZ1 can be changed by changing the setting in P06 on the 7 segment display panel. "0" : Operation output With external input terminals short-circuited With external input terminals open "0" : External operation input Invalid Valid "1" : Error output "1" : Demand input Invalid Valid "2" : Compressor ON output "2" : Cooling/heating forced input Valid Invalid "3" : Fan ON output "3" : Silent mode 1 *1 Valid Invalid "4 – 9" : Spare "5" : Outdoor fan snow guard control input Valid Invalid "6" : Test run external input 1 (equivalent to SW5-1) Test run start Normal "7" : Test run external input 2 (equivalent to SW5-2) Cooling Heating "8" : Silent mode 2 *2 Valid Invalid "9" : 2 stage demand input Invalid Valid "4" : Spare *1 Valid/invalid is changed depending on outdoor temperature. *2 It is always Valid, regardless of outdoor temperature. 7-3. External input and output terminals specifications Name Purpose (Factory default) Specification Operating side connector External input CnS1 External operation input (Closed at shipping) Non-voltage contactor (DC12V) J.S.T (NICHIATSU) B02B-XAMK-2 (LF) (SN) External input CnS2 Demand input (Closed at shipping) Non-voltage contactor (DC12V) J.S.T (NICHIATSU) B02B-XARK-2 (LF) (SN) External input CnG1 Forced refrigerant input (Open at shipping) Non-voltage contactor (DC12V) J.S.T (NICHIATSU) B02B-XAEK-2 (LF) (SN) External input CnG2 Silencing mode input (Open at shipping) Non-voltage contactor (DC12V) J.S.T (NICHIATSU) B02B-XASK-2 (LF) (SN) External output CnZ1 Spare output (External output) DC12V output MOLEX 5566-02A-RE External output CnH Operation output DC12V output MOLEX 5566-02A-BU External output CnY Error output DC12V output MOLEX 5266-02A - AMP Air Conditioning 36 www.ampair.co.uk | [email protected] '11 • KX-T-166 8. TEST OPERATION AND TRANSFER 8-1. Before starting operation (1) Make sure that a measurement between the power supply terminal block and ground, when measured with a 500V megger tester, is greater than 1 MΩ. When the unit is left for a long time with power OFF or just after the installation, there is possibility that the refrigerant is accumulated in the compressor and the insulation resistance between the contact terminals for power supply and grounding decreases to 1MΩ or around. When the insulation resistance is 1MΩ or more, the insulation resistance will rise with crank case heater power ON for 6 hours or more because the refrigerant in the compressor is evaporated. (2) When the resistance of the signaling line terminal block is 100Ω or less before turning the power on, the power cables may be connected to the signaling line terminal block. Check the wiring referring to the standard resistance value of 6-3. (3) Be sure turn ON the power supply to supply power to the crank case heater 6 hours before operation. After supplying the power to the crank case heater, the compressor may not start unless the time mentioned above elapses. (For protection of compressor) In such occasion, the 7-segment LED shows “dL○○○○”. Wait till the temperature in the compressor rises sufficiently after turning power on to the crank case heater, before starting the test run. (4) Make sure that the bottom of the compressor casing is warm. (5) Be sure to fully open the service valves (liquid, gas) for the outdoor unit. Operating the outdoor unit with the valves closed may damage the compressor. (6) Confirm that the power is supplied to all indoor units. It could cause trouble if there is any indoor unit which is not powered. CAUTION Please make sure that the service valves (gas, liquid) are full open before a test run. Conducing a test run with any of them in a closed position can result in a compressor failure. 8-2. Test run (When washing pipes using the re-fresh kit, refer to the instruction manual packed with the ref-fresh kit for the procedures, etc.) (1) Test run from an outdoor unit. Whether CnS1 is set to ON or OFF, you can start a test run by using the SW5-1 and SW5-2 switches provided on the outdoor unit PCB. Select the test run mode first. Please set SW5-2 to ON for a cooling test run or OFF for a heating test run. (It is set to OFF at the factory for shipment) Turning SW5-1 from OFF to ON next will cause all connected indoor units to start. When a test run is completed, please set SW5-1 to OFF. Note: During a test run, an indoor unit cannot be operated from the remote control unit (to change settings). (“Under centralized control” is indicated) (2) Method of starting a test run for a cooling operation from an outdoor unit: please operate a remote control unit according to the following steps. (a) Start of a cooling test run ○Operate the unit by pressing the START/STOP button. ○Select the “COOLING” mode with the MODE button. ○Press the TEST RUN button for 3 seconds or longer. The screen display will be switched from “Select with ITEM ”→“Determine with SET ”→“Cooling test run▼.” ○When the SET button is pressed while “Cooling test run▼ ” is displayed, a cooling test run will start. The screen display will be switched to “COOLING TEST RUN.” (b) Termination of a cooling test run ○When the START/STOP button or the “TEMP SET ” button is pressed, a cooling test run will be terminated. 8-3. Transfer After completing the installation and test run, explain methods of use and maintenance to the customer, referring to the Instruction Manual. Ask the customer to keep the installation manual safely together with the Instruction Manual. ● Instruct the customer that the power should not be turned off even if the unit is not to be used for a long time. This will enable operation of the air conditioner any time. (Since the compressor bottom is warmed by the crank case heater, seasonal compressor trouble can be prevented.) ● 9. CAUTIONS FOR SERVICING (for R410A and compatible machines) (1) To avoid mixing of different types of oil, use separate tools for each type of refrigerant. (2) To avoid moisture from being absorbed by the ice machine oil, the time for when the refrigerant circuit is open should be kept as short as possible. (Within 10 min. is ideal.) (3) For other piping work, airtighteness testing , vacuuming, and refrigerant charging, refer to section 4, REFRIGERANT PIPING. (4) Diagnostic Inspection Procedures For the meanings of failure diagnosis messages, please refer to the technical manual. (5) 7-segment LED indication Data are indicated when so chosen with the indication selector switch. For the details of indication, please refer to the technical manual. (6) Internal wiring After maintenance, all wiring, wiring ties and the like, should be returned to their original state and wiring route, and the necessary clearance from all metal parts should be secured. - AMP Air Conditioning 37 www.ampair.co.uk | [email protected] Method for connecting the accessory pipe About brazing 1 Referring to Table 1 and Table 2 , prepare the straight pipe and the elbow in the field, which are used in the construction examples A-D applicable to the connecting direction. 2 Firstly, use the accessory pipe to assemble the connecting pipe assembly outside the outdoor unit. As shown in the figures of construction examples A∼D applicable to the connecting direction (chain double dashed line), braze the accessory pipe and the parts prepared in the above 1 . ●Orient the accessory pipe according to the dimensions as shown in of Fig. 1. 3 After assembly of the connecting pipe, connect it to the operation valve on the gas side inside the outdoor unit. Tighten the flare nut with appropriate torque. 4 After connection of the connecting pipe assembly to the operation valve on the gas side, braze the connecting pipe assembly and the field pipe. 5 After the brazing, insulate using the attached heat insulating material and band as shown by Fig. 2. Be sure to braze while supplying nitrogen gas. If no nitrogen gas is supplled, a large amount of impurity (oxidized film) will be generated, which may clog the capillary tube and the expansion valve, resulting in fatal malfunction. Heat insulating material x 1 pc Accessory pipe x 1 pc Band x 2 pcs Heat insulating material is attached to the accessory pipe with band. When installing the heat insulating material, cut the band and retrieve it. Two pieces of fig. 2 band for installation are found in a bag. Proper torque 100~120N·m Operation valve connecting position at gas side 67 Table 1 Parts used for the connecting pipe assembly Remark Heat insulating material (Accessory) Band (Accessory) Accessory pipe Accessory Internal face of base Accessory Internal face of base - 38 - No. Quantity Name 1 1 Accessory pipe 2 Heat insulating material 1 3 2 Band 4 Straight pipe 1 1 5 Straight pipe 2 1 or 0 6 1 or 0 Elbow ø19.05 Accessory Procured at the field Procured at the field (Not required for downward direction) Accessory pipe position Procured at the field (Not required for downward direction) (Fig. 1) 40 Heat insulating method (Fig. 2) Straight pipe 1 (Procured in the field, 270 mm or more) Table 2 Length and specification of straight pipe (Procured in the field) A Downward B Forward C Rightward D Backward Straight pipe1 270 mm or over 70∼120mm 70∼120mm 70∼120mm Straight pipe2 — 125mm or over 125mm or over 515mm or over Be sure to use pipes of 1/2H material, and wall thickness above 1mm. (Pressure resistance of O-type pipe is not enough) Pipe specification 224 280 Braze the refrigerant pipe here. ø19.05-ø25.4 ø22.22-ø28.58 6.3 Method for connecting the accessory pipe Be sure to use the accessory pipe to connect the operation valve on the gas side with the field pipe. Connection example of refrigerant pipe - A Select and use the pipes, which are procured in the field, according to the specification that corresponds to the outdoor unit capacity as described in the installation manual. (Downward connection) Accessory pipe Accessory pipe Braze the refrigerant pipe here. Straight pipe 1 (Procured in the field, 70 - 120 mm) Straight pipe 1 (Procured in the field, 70 - 120 mm) Straight pipe 2 (Procured in the field, 125 mm or more) Connection example of refrigerant pipe - B (Forward connection) AMP Air Conditioning Accessory pipe Braze the refrigerant pipe here. Straight pipe 2 (Procured in the field, 125 mm or more) Elbow, procured in the field Braze the refrigerant pipe here. Connection example of refrigerant pipe - C (Rightward connection) '11 • KX-T-166 Elbow, procured in the field Straight pipe 1 (Procured in the field, 70 - 120 mm) Straight pipe 2 (Procured in the field, 515 mm or more) Elbow, procured in the field Connection example of refrigerant pipe - D (Backward connection) PSB012D917G k www.ampair.co.uk | [email protected] '11 • KX-T-166 6.4 Installation work check sheet (For heat pump unit) - AMP Air Conditioning 39 www.ampair.co.uk | [email protected] '11 • KX-T-166 Pressure:4.15MPa(in case of FDCR:3.24MPa)No fluctuation of pressure for 24 hours. Refer to the technical manual about the pressure fluctuation caused from temperature. - AMP Air Conditioning 40 www.ampair.co.uk | [email protected] '11 • KX-T-166 6.5 Check operation procedure (1) Check operation The following ① – ③ can be checked automatically with this operation. ① Checking of operation valves opened/closed. Checks to see if operation valves are opened. ② Checking of mismatch on wiring or piping. Checks to see if refrigerant piping or signal wiring between indoor and outdoor units in the same refrigerant system are connected properly. ③ Checking of indoor expansion valve operation. Checks to see if indoor expansion valve operates properly. * Check operation should be performed before initial test run after completion of installation. When any corrective measure for nonconformity has been taken, perform the check operation again after repair. Operational condition Temperature range: Outdoor air temperature … 0 㨪 43℃, Indoor air temperature … 10 㨪 32℃. Connecting capacity of indoor units: 80% or more of outdoor unit capacity. Precautions Check each outdoor unit system for single use or each refrigeration system for combination use. Outdoor units in other refrigerant system shall not be operated. After turning on power supply to outdoor unit and connected indoor units, start check operation with all connected indoor units stopped. In combination use, check the setting and the result displayed on the 7-segment display of master outdoor unit. If the unit has been operating before check operation, wait for 5 minutes after stopping the unit operation before starting check operation, in order to avoid misjudgment. In combination use, judging operation valves opened or closed by check operation can be done as no good (NG), when all of operation valves in liquid line, gas line and oil equalizing line of both master and slave outdoor units are closed. However, in other cases than the above, judgment may not be done. During check operation it is impossible to stop operation from remote controller. Accordingly, before starting check operation, be sure to confirm that no one working near the indoor unit especially near the rotating part such as fan of indoor unit or something is remaining near the fan of indoor unit. Purpose ޓThe purpose of this check operation is only to verify any overlooked items to be checked during the ordinary checking done at the site after installation. Accordingly it has no function to substitute the ordinary checking to be done during or after installation work and to restore automatically as a result of checking operation. ޓTherefore be sure to conduct the checking in ordinary way after installation firstly, and then to perform this check operation. We believe that this checking method could prevent from overlooking any items to be checked. - AMP Air Conditioning 41 www.ampair.co.uk | [email protected] '11 • KX-T-166 (2) Flow of the check operation Check operation is performed as follows. Start Preliminary check Note (1) Auto checking Note (2) Judgment of checked result Note (3) NG OK End Note (1) For preliminary check method, refer to “(3) Confirmation before check operation”. (2) For details of check operation, refer to “(4) Check operation procedure”. (3) For measures to be taken in case of NG, refer to “(5) Measures to be taken after check operation”. - AMP Air Conditioning 42 www.ampair.co.uk | [email protected] '11 • KX-T-166 (3) Confirmation before check operation ・Confirm the installation has been completed properly by hearing, actual inspection or other method. ・This preliminary confirmation is indispensable to prevent troubles during or after check operation. ・Check operation can be performed only when the following conditions (1) – (8) are established. ・Check the following contents listed in the table with 7-segment display and MentePC. (1) Item Preparation Content Supply power to outdoor and indoor units. Check method Check result No outdoor unit in other refrigerant systems is operating. All indoor units are stopped. It has elapsed more than 5 minutes after the stopping. (2) Connecting capacity of Connecting capacity of indoor Check capacities of outdoor and indoor units. indoor units units is 80% or more of outdoor unit capacity. (3) Address setting Addresses of outdoor unit Check the number of connected units. (in combination use, both of master and slave outdoor units) and indoor units have been set. (4) Temperature range Outdoor air temperature is 0 – Check outdoor air temperature with 7-segment 43℃. Indoor air temperature is display and indoor air temperature with 10 – 32℃. MentePC. (5) Others System communicating method Check the model name of outdoor unit, indoor is of new SL. units, central control device, etc. System is not in error stop condition. Check to see if any error code (E??) is displayed on indoor or outdoor unit. (6) Outdoor unit operation valve Outdoor unit operation valve is Check visually. opened. *1 (7) Refrigerant amount Proper amount of refrigerant is Check the additional charged amount of charged. refrigerant is written in the plate for specifying refrigerant charging amount on the back of outdoor service panel. (8) Number of connected indoor units It is same as the number of Check with 7-segement display or MentePC. connected indoor units installed. *1 ・Be sure to open the operation valves in both liquid and gas lines of outdoor unit before starting check operation. In combination use, open the operation valves not only in liquid and gas lines but also in oil equalizing line of both master and slave outdoor units. ・Operating with operation valves closed causes vacuum operation that results in a compressor fault. ・If the operation valves are “closed” before test run, be sure to verify whether the evacuation, air tightness test and additional refrigerant charge have been completed by hearing to installation contractor, before opening the operation valves. Otherwise, it may cause such trouble as mixing air (non-condensation gas and water) in, forgetting to charge additional refrigerant at the site, or others. - AMP Air Conditioning 43 www.ampair.co.uk | [email protected] '11 • KX-T-166 (4) Check operation procedure Flow Preliminary check Work Operation status (Displayed on 7-segment) Meaning of 7-segment display Check in advance as per “(3) Confirmation before check operation”. Remarks Don’t operate any outdoors unit in other refrigerant systems during check operation. Start of check Turn “Chek operation switch “H1 Max. remaining time” Remaining time: Max. This operation status is displayed operation (SW3-5)” on outdoor control remaining time for check during preparation for check operation. PCB from OFF to ON. operation Depending on conditions, it may not When “H0-HE” is “H0 HE” be displayed. In combination use, turn displayed for more then 10 In combination use, “H0---” is “Chek operation switch minutes, then check displayed on the slave outdoor unit. (SW3-5) on master control operation is not started yet. *Be sure to start check operation PCB from OFF to ON. In such case refer to “(3) when all indoor units are stopping. confirmation before check Implementing auto checking End of auto checking, judgment result “H2 Max. remaining time” Remaining time: Max. In combination use, “H0---” is remaining time for auto displayed on the slave outdoor unit. checking. Record the indication of “CHO End” 7-segment indicator on outdoor unit. “CHL---” Result of check operation End the check operation. is judged normal. Operation valve may be Refer to “(5) Measures to be closed. taken after check operation”. “CHU Anomalous indoor Refrigerant piping or unit No.” signal wiring between indoor and outdoor units may not be connected correctly. “CHJ Anomalous indoor Indoor expansion valve unit No.” may not be operating properly. “CHE---” Check operation has not ended properly. All judgment results at the end are displayed. Other display Check of Check for anomalous condition nonconforming as per “(5) Measures to be item taken after check operation” When any display other than Refer to “(5) Measures to be “CHO-End” is displayed taken after check operation”. after auto checking. End of check operation Returns to normal display. Turn off “Chek operation run switch (SW3-5)” on outdoor control PCB. Notes (1) W hen “HO-HE” is displayed for more than 10 minutes, or any displays other than “CHO-End” is displayed at the end of cheek operation, turn SW3-5 to OFF and take necessary measures. And then turn SW3-5 to ON again and perform the check operation. (2) During check operation it is impossible to stop operation from remote controller. Accordingly, before starting check operation, be sure to confirm that no one working near the indoor unit especially near the rotating part such as fan of indoor unit or something is remaining near the fan of indoor unit. When interrupting check operation, turu SW3-5 to OFF, Compressor stops and 7-segment display returns to normal display. - AMP Air Conditioning 44 www.ampair.co.uk | [email protected] '11 • KX-T-166 (5) Measures to be taken after check operation When any display other than “CHO-End” is displayed after completing the judgment of check operation, the meanings of each display are shown as follows. After checking the contents of inspection and repairing nonconforming items, perform check operation again. Code display Data display CHL --- Meaning of display Contents of Inspection Refrigerant circuit is choked at certain Operation valve on outdoor unit may be left closed. place. Low pressure sensor may be anomalous. Check the detected pressure displayed on 7-segment and compare it with the value measured with gauge manifold. Refrigerant piping or signal wiring may not be connected properly. *1 (See page 47.) Check with Mente PC, etc. Indoor heat exchanger temperature thermistor may be anomalous or disconnected. *2 (See page 47.) Refrigerant may not be charged correctly. Indoor unit expansion valve may not be operating properly. Connector of indoor unit expansion valve coil may not be connected. *3 (See page 47.) Indoor unit expansion valve coil may be disconnected from main body of expansion valve. *4 (See page 47.) Outdoor unit PCB may be defective. CHU Anomalous Refrigerant is not circulated in the Refrigerant piping or signal cables may not be connected properly between indoor indoor unit indoor unit of indicated No. and outdoor units. *1 (See page 47.) Check with Mente PC, etc. No. Indoor heat exchanger temperature thermistor may be anomalous or disconnected. *2 (See page 47.) Operation valve on outdoor unit may be left closed. Check it especially when many indoor units No. are displayed in data display column of CHU. it may be displayed by influence of liquid flooding due to the trouble on any other indoor unit. If CHJ is displayed at the same time, check preferentially the indoor unit displaying CHJ and after repairing, perform check operation again. Refrigerant may not be charged correctly. Indoor unit expansion valve may not be operating properly. Connector of indoor unit expansion valve coil may not be connected. *3 (See page 47.) Indoor unit expansion valve coil may be disconnected from main body of expansion valve. *4 (See page 47.) CHJ Anomalous Expansion valve on the indoor unit Indoor heat exchanger temperature thermistor may be anomalous or disconnected. indoor unit of indicated No. does not operate *2 (See page 47.) No. properly. it may be displayed by influence of liquid flooding due to the trouble on any other indoor unit. Contamination may be trapped in expansion valve due to installation or transitional cause. Indoor unit expansion valve may not be operating properly. Connector of indoor unit expansion valve coil may not be connected. *3 (See page 47.) Indoor unit expansion valve coil may be disconnected from main body of expansion valve. *4 (See page 47.) Refrigerant may not be charged correctly. CH1 --- Indoor heat exchanger temperature Indoor heat exchanger temperature thermistor may be anomalous or disconnected. anomaly. *2 (See page 47.) CH3 --- Unable to do indoor EEV trouble check. Unable to do indoor EEV trouble check because of unstable operation. - AMP Air Conditioning 45 www.ampair.co.uk | [email protected] '11 • KX-T-166 Code display Data display CHH --- Meaning of display Contents of Inspection It may be liquid flooding. Refrigerant piping or signal cables may not be connected properly between indoor and outdoor units. *1 (See next page.) Power switch may be turned off on some indoor units. Check if power is supplied to all indoor units. Indoor unit expansion valve may not be operating properly. Connector of indoor unit expansion valve coil may not be connected. *3 (See next page) Indoor unit expansion valve coil may be disconnected from main body of expansion valve. *4 (See next page.) If no indoor unit indicates CHJ, check also indoor units which are not showing CHJ. Refrigerant may not be charged correctly. CHE --- Anomalous stop of check operation. Some error may happen on indoor or outdoor units. Check if any error code “E??” is displayed on indoor or outdoor units. There may be anomalous on signal wire connection. Check if signal wire is connected firmly. SW setting on outdoor PCB might have been changed. Check if any SW setting has been changed during check operation. CHE Anomalous Anomalous stop of check operation. indoor unit No. Indoor unit indicated its No. has anomaly. Some error may happen on indoor or outdoor units. Check if any error code “E??” is displayed on indoor or outdoor units. There may be anomalous on signal wire connection. Check if signal wire is connected firmly. Power switch may be turned off on some indoor units. Check if power is supplied to indoor units. E 40 High pressure anomaly. Refrigerant circuit may be choked at a certain place. Refer to the technical manual or the above. E 42 Current cut. Refrigerant circuit may be choked at a certain place. Refer to the technical manual or the above. It might have been started operation while bottom of compressor was still cold. Perform check operation again after the bottom of compressor has been enough warm. E 49 Low pressure anomaly. Refrigerant circuit may be choked at a certain place. Refer to the technical manual or the above. E 36-3 Liquid flooding anomaly. It may be in the same condition as “CHH---”. Refer to the technical manual or the above. Note (1) W hen an error code (E??) is displayed, press SW9 to display all indicalions other than the error code in series. Press SW9 again to return to error display. (2) When check operation has been suspended, the followings listed in below table are displayed depending on judgment at the time of stoppage. Code display Data display HL --- Refrigerant circuit is choked at a certain place. Contents of display HL LPL Refrigerant circuit is choked at a certain place. (In combination use) HU Anomalous indoor unit No. Refrigerant is not circulated in the indoor unit of indicated No. HJ Anomalous indoor unit No. Expansion valve does not operate on the indoor unit of indicated No. UU Anomalous indoor unit No. Refrigerant is not circulated in the indoor unit of indicated No. U Anomalous indoor unit No. Refrigerant was not circulated in the indoor unit of indicated No. just after starting but it has been confirmed that it is now circulated. (3) If refrigerant circuit is choked at a certain place, it may be stopped with error code E40 (High pressure anomaly), E42 (Current cut) or E49 (Low pressure anomaly). (4) When it has stopped with error code E36-3 (Liquid flooding anomaly), it may be in the same condition as “CHH---”. (5) When it has stopped with error code E42 (Current cut), it might have been started operation while bottom of compressor was still cold. Perform check operation again after the bottom of compressor has been enough warm. - AMP Air Conditioning 46 www.ampair.co.uk | [email protected] '11 • KX-T-166 *1 Piping Wiring ・ Wrong wiring ・Normal Outdoor unit 1 Outdoor unit 1 Indoor unit 1 Indoor unit 2 Outdoor unit 2 Indoor unit 1 Indoor unit 2 Indoor unit 3 Outdoor unit 2 Indoor unit 4 Indoor unit 3 Indoor unit 4 *2 (If the connector comes off by a weak pull, it’s no good. If not come off, It’s OK) The connector of indoor heat exchanger temperature thermistor. Normal Disconnected *3 (If the connector comes off by a weak pull, it’s no good. If not come off, It’s OK) The connector of indoor expansion valve coil. Normal Disconnected *4 The indoor expansion valve coil itself. Normal Disconnected from main body - AMP Air Conditioning 47 www.ampair.co.uk | [email protected] (6) Data sheet <Check Operation Data Sheet> Project name Outdoor unit Location Fill necessary data in advance Model Address Master FDC Slave FDC Checked by Date of checking Weather Outdoor air temperature Start time of check operation Completion time of check operation Date of installation (d/m/y) Superlink version Name of installer Superlink II Superlink I* * In case of Superlink I, the check operation cannot be implemented. Fill necessary data in advance No. Indoor unit - 48 - FD FD FD FD FD FD FD FD FD FD FD FD FD FD FD FD FD FD FD FD FD FD FD FD FD FD FD FD FD FD FD FD FD FD FD FD FD FD FD FD AMP Air Conditioning Address Piping length O/U-I/U Elevation difference O/U-I/U No. 41 42 43 44 45 46 47 48 49 50 51 52 53 54 55 56 57 58 59 60 61 62 63 64 65 66 67 68 69 70 71 72 73 74 75 76 77 78 79 80 Model FD FD FD FD FD FD FD FD FD FD FD FD FD FD FD FD FD FD FD FD FD FD FD FD FD FD FD FD FD FD FD FD FD FD FD FD FD FD FD FD Address Piping length O/U-I/U ℃ (h/m/) (h/m/) Elevation difference O/U-I/U 【Judgment】 Checked items Result ① No anomaly allowed. → If anomaly occurred: Error code E② 7-segment display at completion ③ Others (Comment/Measures to be taken/etc.) '11 • KX-T-166 1 2 3 4 5 6 7 8 9 10 11 12 13 14 15 16 17 18 19 20 21 22 23 24 25 26 27 28 29 30 31 32 33 34 35 36 37 38 39 40 Model (d/m/y) www.ampair.co.uk | [email protected] '11 • KX-T-166 6.6 Instructions for installing the branch pipe set (option) PSB012D855B a G G G G - AMP Air Conditioning 49 www.ampair.co.uk | [email protected] '11 • KX-T-166 - AMP Air Conditioning 50 www.ampair.co.uk | [email protected] '11 • KX-T-166 G G G G - AMP Air Conditioning 51 www.ampair.co.uk | [email protected] '11 • KX-T-166 G G G G 326 280 22 (22+22+22+22+22+36+36 +36+36+36+36)=326 (22+22+22+22+36+36 +36+36+36+36)=304 (36+36+36+36+36+36)=216 (36+36+36+36+36)=180 22 22 22 36 DIS-180-1G 2 36 36 (22+22+22+22)=88 DIS-180-1G 2 (36+36+36+36)=144 36 HEAD4-22-1G HEAD4-22-1G2 DIS-180-1G 2 DIS-22-1G2 - AMP Air Conditioning 36 52 www.ampair.co.uk | [email protected] '11 • KX-T-166 PCB012D021A 6.7 Service valve kit Installation Manual B •Read these “Precautions for safety” carefully before starting installation work and do it in the proper way. •Safety instructions listed here are grouped into Warnings and Cautions . If a non-compliant installation method is likely to result in a serious consequence such as death or major Warnings to emphasize its importance. However, a failure to observe a safety instruction listed under injury, the instruction is grouped into consequence depending on the circumstances. Please observe all these instructions, because they include important points concerning safety. Cautions can also result in a serious •When you have completed installation work, perform a test run and make sure that the installation is working properly. Then, explain the customer how to operate and how to take care of the air-conditioner according to the user’s manual. Please ask the customer to keep this installation manual together with the user’s manual. CAUTION WARNING •Take care when carrying the unit by hand. If the kit weights more than 20kg, it must be carried by two or more persons. Do not carry by the plastic straps, always use the carry handle when carrying the unit by hand. Use gloves to minimize the risk of cuts by the aluminum fins. •Dispose of any packing materials correctly. Any remaining packing materials can cause personal injury as it contains nails and wood. And to avoid danger of suffocation, be sure to keep the plastic wrapper away from children and to dispose after tear it up. •Be sure to insulate the refrigerant pipes so as not to condense the ambient air moisture on them. Insufficient insulation can cause condensation, which can lead to moisture damage on the ceiling, floor, furniture and any other valuables. •Be sure to perform air tightness test by pressurizing with nitrogen gas after completed refrigerant piping work. If the density of refrigerant exceeds the limit in the event of refrigerant leakage in the small room, lack of oxygen can occur, which can cause serious accidents. •Perform installation work properly according to this installation manual. Improper installation can cause abnormal vibrations or increased noise generation. •Installation must be carried out by the qualified installer. If you install the system by yourself, it may cause serious trouble such as water leaks, electric shocks, fire and personal injury, as a result of a system malfunction. •Install the system in full accordance with the instruction manual. Incorrect installation may cause bursts, personal injury, water leaks, electric shocks and fire. •Use the original accessories and the specified components for installation. If parts other than those prescribed by us are used, It may cause fall of the unit, water leaks, electric shocks, fire, refrigerant leak, substanard performance, contrl failure and personal injury. •When installing in small rooms, take prevention measures not to exceed the density limit of refrigerant in the event of leakage accordance with ISO5149. Consult the expert about prevention measures. If the density of refrigerant exceeds the limit in the event of leakage, lack of oxygen can occur, which can cause serious accidents. •Ventilate the working area well in the event of refrigerant leakage during installation. If the refrigerant comes into contact with naked flames, poisonous gas is produced. •After completed installation, check that no refrigerant leaks from the system. If refrigerant leaks into the room and comes into contact with an oven or other hot surface, poisonous gas is produced. •Hang up the unit at the specified points with ropes which can support the weight in lifting for portage. And to avoid jolting out of alignment, be sure to hang up the unit at 4-point support. An improper manner of portage such as 3-point support can cause death or serious personal injury due to falling of the unit. •Install the unit in a location with good support. Unsuitable installation locations can cause the unit to fall and cause material damage and personal injury. •Ensure the unit is stable when installed, so that it can withstand earthquakes and strong winds. Unsuitable installation locations can cause the unit to fall and cause material damage and personal injury. •Be sure not to reuse existing refrigerant pipes Conventional refrigerant oil or chlorine contained in the conventional refrigerant which is remaining in the existing refrigerant pipes can cause deterioration of refrigerant oil of new unit. And 1.6 times higher pressure of R410A refrigerant than conventional one can cause burst of existing pipe, personal injury or serious accident. •Do not perform brazing work in the airtight room It can cause lack of oxygen. •Use the prescribed pipes, flare nuts and tools for R410A. Using existing parts (for R22 or R407C) can cause the unit failure and serious accidents due to burst of the refrigerant circuit. •Tighten the flare nut by using double spanners and torque wrench according to prescribed method. Be sure not to tighten the flare nut too much. Loose flare connection or damage on the flare part by tightening with excess torque can cause burst or refrigerant leaks which may result in lack of oxygen. •Do not open the service valves for liquid line and gas line until completed refrigerant piping work, air tightness test and evacuation. If the compressor is operated in state of opening service valves before completed connection of refrigerant piping work, you may incur frost bite or injury from an abrupt refrigerant outflow and air can be sucked into refrigerant circuit, which can cause burst or personal injury due to anomalously high pressure in the refrigerant. •Do not put the drainage pipe directly into drainage channels where poisonous gases such as sulphide gas can occur. Poisonous gases will flow into the room through drainage pipe and seriously affect the user's health and safety. It can also cause the corrosion of the indoor unit and resultant unit failure or refrigerant leak. •Only use prescribed optional parts. The installation must be carried out by the qualified installer. If you install the system by yourself, it can cause serious trouble such as water leaks, electric shocks, fire. •Do not perform any change of protective device itself or its setup condition The forced operation by short-circuiting protective device of pressure switch and temperature controller or the use of non specified component can cause fire or burst. •Be sure to switch off the power supply in the event of installation, inspection or servicing. If the power supply is not shut off, there is a risk of electric shocks, unit failure or personal injury due to the unexpected start of fan. •Consult the dealer or an expert regarding removal of the kit. Incorrect installation can cause water leaks, electric shocks or fire. •Do not install the kit near the location where leakage of combustible gases can occur. If leaked gases accumulate around the unit, it can cause fire. •Do not install the kit where corrosive gas (such as sulfurous acid gas etc.) or combustible gas (such as thinner and petroleum gases) can accumulate or collect, or where volatile combustible substances are handled. Corrosive gas can cause corrosion of heat exchanger, breakage of plastic parts and etc. And combustible gas can cause fire. •Secure a space for installation, inspection and maintenance specified in the manual. Insufficient space can result in accident such as personal injury due to falling from the installation place. •Do not install nor use the system close to the equipment that generates electromagnetic fields or high frequency harmonics Equipment such as inverters, standby generators, medical high frequency equipments and telecommunication equipments can affect the system, and cause malfunctions and breakdowns. The system can also affect medical equipment and telecommunication equipment, and obstruct its function or cause jamming. •Do not install the kit in the locations listed below • Locations where carbon fiber, metal powder or any powder is floating. • Locations where any substances that can affect the unit such as sulphide gas, chloride gas, acid and alkaline can occur. • Vehicles and ships • Locations where cosmetic or special sprays are often used. • Locations with direct exposure of oil mist and steam such as kitchen and machine plant. • Locations where any machines which generate high frequency harmonics are used. • Locations with salty atmospheres such as coastlines • Locations with heavy snow (If installed, be sure to provide base flame and snow hood mentioned in the manual) • Locations where the unit is exposed to chimney smoke • Locations at high altitude (more than 1000m high) • Locations with ammonic atmospheres • Locations where heat radiation from other heat source can affect the unit • Locations without good air circulation. It can cause remarkable decrease in performance, corrosion and damage of components, malfunction and fire. •Do not use the kit for special purposes such as storing foods, cooling precision instruments and preservation of animals, plants or art. It can cause the damage of the items. •Do not touch any refrigerant pipes with your hands when the system is in operation. During operation the refrigerant pipes become extremely hot or extremely cold depending the operating condition, and it can cause burn injury or frost injury. •Do not operate the kit with any article placed on it. You may incur property damage or personal injure from a fall of the article. •Do not step onto the kit. You may incur injury from a drop or fall. •Ensure that no air enters in the refrigerant circuit when the kit is installed and removed. If air enters in the refrigerant circuit, the pressure in the refrigerant circuit becomes too high, which can cause burst and personal injury. •Do not run the kit with removed panels or protections Touching rotating equipments, hot surfaces or high voltage parts can cause personal injury due to entrapment, burn or electric shocks. •Be sure to fix up the service panels. Incorrect fixing can cause electric shocks or fire due to intrusion of dust or water. •Do not perform any repairs or modifications by yourself. Consult the dealer if the unit requires repair. If you repair or modify the unit, it can cause water leaks, electric shocks or fire. 1. BEFORE BEGINNING INSTALLATION 2 Confirmation of accessory Connecting hole (ø25.4) for pipe at refrigerant gas side 160 Hole for 4- anchor bolt (for M10 bolt) Gasket To outdoor unit To indoor unit 215 Check sheet 62 Installation manual Connecting hole (ø25.4) for pipe at refrigerant gas side (To indoor unit) 1 Install the service valve kit when carrying out the washing operation utilizing existing pipes. For the outdoor units which can use this kit, refer to the technical data – Installation manual of outdoor unit. Service space (Necessary for washing operation) Secure also an overhead space sufficient for working in a standing position. 476 506 500 2 pcs. 27 (To outdoor unit) 1350 - AMP Air Conditioning 53 www.ampair.co.uk | [email protected] '11 • KX-T-166 PCB012D021A 2. INSTALLATION OF SERVICE VALVE KIT Selection of installation place Panel Open the cover when operating the service valves A, B and C at the inside. Where the service spaces shown in the figure at right are available. ٤Use new pipes to connect between the service valve kit and the outdoor unit. It is prohibited to use existing pipes. Restrict the actual pipe length no longer than 3 m. 63 300 ٤ Request B 20 (1) Fix the kit securely using the fixing holes (for M10 bolt) at four places shown in the figure at right. (2) The service valve kit cannot be installed upside-down. Install the main unit at level such that the labels attached to the pipes are positioned upward. 150 430 150 Level Level 3. REFRIGERANT PIPING On the gas pipes of the service valve kit, the marking “To outdoor unit” is indicated on the gas pipe at outdoor unit side and the marking “To indoor unit” gas pipe is indicated on the gas pipe at indoor unit side. Be sure not to misconnect the gas pipes. ٤It is not necessary to connect to the liquid pipe. ٤Before connecting the pipes, make sure to open the panel and close the service valves A and C while open the service valve B. ٤Make sure to substitute with nitrogen gas when doing brazing. ٤When a pipe has been connected by means of brazing, make sure to heat insulate the pipe. ٤ * Tighten the service valve to the following torques. Service valve cap Check joint cap Service valve C 30 N·m 11~13 N·m Service valve A To outdoor unit To indoor unit Service valve B Pipe connection When the size of connecting pipe is not same as the pipe diameter (ø25.4) of the service valve kit, use a joint of which size is different at both ends. (Work at site) ٤Install the service valve kit at the same level as or lower than the outdoor unit. ٤Connect the service valve kit and the outdoor unit with actual pipe length no longer than 3 m. ٤Install it on the main pipe between the outdoor unit and the initial branch. (See following figure.) ٤Close the panel after connecting pipes. (During the washing operation, open the cover to control the service valves.) ٤ Outdoor unit Indoor unit Service valve kit Less than 3m Initial branch Indoor unit - AMP Air Conditioning 54 www.ampair.co.uk | [email protected] '11 • KX-T-166 * Use this Check Sheet when washing pipes using the re-fresh kit. * Original Sheet: Carefully handle the original Check Sheet because it is retained by the distributor. 6.8 Pipe washing check sheet Customer : J Date of washing operation Outdoor unit model/Serial No. : / Additional refrigerant charge amount/Total pipe length : Check Person in Checked charge by PSB012D869G kg / m Person who washed : (Affiliation) (Name) Checked by : (Name) (Affiliation) Description of operation Caution, etc. ① Delivery and installation of indoor and outdoor units Turn on the circuit breakers on the indoor and outdoor units. Remove the front panels from the outdoor unit, service valve kit and re-fresh kit. Confirm that there is no anomaly in the number of indoor units to be connected, their address numbers and appearance. Check the outdoor air temperature and the indoor air temperature. ② Connection of the re-fresh kit Confirmation of oil draining Oil drain port is opened upward. Connect the flared fitting and lead the pipe to the drain oil container. (Work at site) Open the service valve at the oil drain hole on the re-fresh kit. Supply pressurized nitrogen from the check joint of re-fresh kit to drain oil. [Open] the [Service valve at the oil drain hole on the re-fresh kit]. Connection of the flexible tube Remove the plate and the gasket from the flange on the service valve kit. Remove the plate and the gasket from the re-fresh kit. Remove the vinyl from the flexible tube. Using the attached bolts and gasket (supplied items), connect the flexible tube to the flange of service valve kit. Using the attached bolts and gasket (supplied items), connect the flexible tube to the flange of re-fresh kit. Connection of bypass gas pipe (Flared: ø9.52) Connect the bypass gas pipe to the bypass gas service valve of outdoor unit. (Flared connection) • Confirm that pipes connected to the indoor and outdoor units have been vacuumized. • Turn on the switch of crankcase heater. • Use 7 SEG display, Mente PC, etc. • Use the code No. C02 of 7 SEG to display the outdoor air temperature. • Record the temperature on the “Outdoor air temperature” in the following table. • It will not be washed properly if it is out of the range of use. (Indoor: 10 – 35°C, outdoor: 5 – 35°C.) • Size of oil drain hole is ø15.88. • The plate must be attached to the flange of re-fresh kit. • Raise the pressure gradually. Confirm that oil has been drained, before going to next step. • Bolt tightening torque is 25 – 30 (N·m). • Width across flat on the bolt is 17 mm. • Retain the plate with care to protect from dust, till the end of washing. • Retain the vinyl and rubber ring with care to protect from dust, till the end of washing. • Always use new gasket (Parts No.: PCA005A061). • Coat the gasket with refrigerating machine oil before installation. (For ease of attachment) • Flare the end of bypass gas pipe at site. • Tightening torque is 38±4 (N·m). • Retain the removed flare nut and flare cap with care to protect from dust, till the end of washing. • Different flange hole pitches are used on both ends to prevent misconnection. • Tightening torque is 38±4 (N·m). Connect the bypass gas pipe to the bypass gas service valve of re-fresh kit. (Flared connection) Connect the gauge manifolds or pressure gauges (work at site) at two places of the left (Inlet side) and right (Outlet side) check joints on the re-fresh kit. ③ Air tightness test (Airtight test of the re-fresh kit, flexible tube and bypass gas pipe) [Open] the [Bypass gas service valve of re-fresh kit]. Check the air-tightness at the [Check joint of service valve A] on the service valve kit. (2.21 MPa) • Pressurize gradually. ④ Air purge Release the pressure in the re-fresh kit through the [Check joint of service valve C] on the service valve kit to atmosphere. Vacuumize through the [Check joint of service valve C] on the service valve kit to atmosphere. Open the [Service valve A] on the service valve kit to confirm that the inside of the pipe connected at site is vacuumized. ⑤ Additional charge of refrigerant Charge the refrigerant for the pipe through the [Check joint of liquid service valve]. • Make the additional charge from the liquid side. Follow the step ⑥ if it cannot be charged fully. (Never charge from the gas side.) • Record the charge amount. (“Additional charge amount ①” in the following table) ⑥ Pipe washing operation • Turn off the SW3-6 to stop the operation in the event of an emergency. [Open] the [Service valve C] on the service valve kit and the [Bypass gas service valve] on the outdoor unit. [Close] the [Service valve B] on the service valve kit. [Open] only the [Liquid service valve]. (Keep closing the gas service valve B on the service valve kit.) Make sure to insert the [CNS1] (External operation input) connector. • It cannot be washed properly if the connector CNS1 is disconnected. • Outdoor fan is turned on, and 7 SEG shows the remaining time (approximate value). • Compressor starts to run 2 minutes later, and the washing operation starts. • Indoor unit start the cooling operation if the remaining time is reduced to about 75 minutes. Turn [ON] the [SW3-6]. (Pipe washing operation starts.) • Avoid touching the bypass gas pipe because it could become very hot. • Since it is now controlled with the central control (the center mode) from the outdoor unit, controls from individual indoor units are disabled. Charge additionally the portion of refrigerant, which could not be charged at the step ⑤, through the [Check joint of • Charge in the liquid phase, and record the charge amount. (“Additional charge amount ②” in the following table) service valve C] on the service valve kit. Never use the check joints of service valves A and B for the additional charge. Record the reading on the pressure gauge when the remaining time on 7 SEG is 60 – 65 minutes. • Record the readings on the pressure gauges connected to the check joints. (“Pressure gauge (check joint L)” and “Pressure gauge (check joint R)” in the following table) • It is completed at about 60 minutes. (It may take about 120 minutes at the maximum when the outdoor air temperature is low.) • The gas pipe is in the state of pump down, at the end of washing. • When the display ② is shown, check to see if oil has been drained from the re-fresh kit, and repeat the washing operation. Washing operation is completed if the followings are displayed on 7 SEG. (Up to 2 times at the maximum) Display ①: PCL End Display ②: PCL --[Steps] Close the service valves A and C and the bypass gas service valve at outdoor side. � Collect refrigerant through the check joint of service valve C. � Confirmation of oil draining by the step ② above � Vacuumizing through the check joint of service valve C � Open the service valves A and C and the bypass gas service valve. � Turn off SW3-6 once and then back on again. [Close] the [Service valves A, C] on the service valve kit and the [Bypass gas service valve] on the outdoor unit. [Open] the [Service valve B] on the service valve kit. Turn [OFF] the [SW3-6]. • It can be input from individual indoor units. ⑦ Removal of the re-fresh kit Removal of the flexible tube and the bypass gas pipe • Collect a small amount of refrigerant remaining in the re-fresh kit. (Provide a refrigerant collecting device.) [Collect refrigerant] in the re-fresh kit through the check joint on the service valve C of service valve kit. • Make an additional charge to the system for the amount of collected refrigerant, and record the amount. (“Additional charge amount ③” in the following table) Open up the inside of re-fresh kit to atmosphere. [Close] the [Bypass gas service valve of re-fresh kit]. Remove the flexible hose and the bypass gas pipe. Install the flare nut and flare cap on the bypass gas service valve of outdoor unit. • Tightening torque is 38±4 (N∙m). Install the flare nut and flare cap on the bypass gas service valve of re-fresh kit. • Use the new gasket (Parts No.: SSA932A004T), which is attached to the outdoor unit. • Bolt tightening torque is 25 – 30 (N·m). Install the plate and gasket on the flange of service valve kit. Tighten the bolt homogeneously by tightening alternately at top and bottom for more than 2 times. Finish up the tightening by retightening the bolt to the specified torque. [Vacuumize] through the [Check joints of service valves A, C] on the service valve kit. [Open] the [Service valves A, C] on the service valve kit. Check then the flange section of service valve kit for leakage, using soap water or other. Install the plate and gasket on the flange of re-fresh kit. • Insert the used gasket, which has been removed for pipe washing, between the flange and the plate. Install the vinyl, which has been removed at the step ②, on the flexible hose flange. • Take care to protect the flange face and the inside of flexible tube from dust. Remove the gauge manifolds from the check joints. ⑧ Oil draining from the re-fresh kit • This is necessary whenever the washing operation has been completed. Drain oil from the re-fresh kit by opening the service valve at the oil drain hole. • Check this in the same way as the confirmation of oil draining of the step ②. ⑨ Replacement of the filter of filter dryer Replace the filter when the differential pressure on the pressure gauge has exceeded 0.1 MPa. • For the replacement method, refer to the instruction manual of the re-fresh kit. ⑩ Replenishment of refrigerating machine oil to the unit • Replenish 450 mL of refrigerating machine oil (new MA32R oil) after completing the washing operation. • For the replenishment method, refer to the instruction manual of the re-fresh kit. Liquid service valve (To indoor unit) Service valve A Bypass gas pipe service valve Check joint L (Inlet side) connection (Flared ) to re-fresh kit To outdoor unit <Outdoor unit> Service valve C Service valve B °C Additional charge amount ① kg Additional charge amount ② kg Additional charge amount ③ kg Check joint R (Outlet side) Pressure gauge (check joint L) MPa Bypass gas service valve Pressure gauge (check joint R) MPa Differential pressure (L-R) MPa Collected oil amount g Oil drain hole service valve <Service valve kit> <Inside of re-fresh kit> - AMP Air Conditioning °C Indoor air temperature To indoor unit Outdoor gas pipe outdoor unit side pipe ( ofTo service ) valve kit Outdoor air temperature 55 www.ampair.co.uk | [email protected] '11 • KX-T-166 6.9 Instruction manual piping re-fresh kit Applicable model: FDCR KXE6 PSA012B703A C <Environment conditions for operation of the unit> • Ambient temperature: Indoor side 10 – 35˚C, outdoor side 5 – 35˚C • Pipe length: Total of main and branch pipes 510 m or less Existing pipe cannot be reused in the following cases. It is necessary to use new pipes. • When existing pipes have been open to atmosphere (When existing units have been disconnected) • When size and length of existing pipes run out the allowable range for new unit. For allowable combinations of pipe size and length, refer to the technical data or catalog. • When there is corrosion, damage or dent unable to repair • When there is peering or deterioration unable to repair on the heat insulator of pipe • When there are branch pipes, which are not used and cannot be removed • When we consider that branch pipes do not fit to reuse and when they cannot be replaced with the pipes compatible with R410A specified by us. CAUTION This pipe re-fresh kit is designed to use when existing units meet the following conditions. When any other conditions apply, comply with the “Confirmation and caution items for reuse of existing pipes” given in the technical data or catalog. • When existing units are in trouble and do not operate <Reusable branch pipe> <Accessory> Branch pipes are reusable if they are produced by us and correspond to the following models. (~ is filled with numerals that stand for the capacity.) FDC~HKXES FDC~HKXE1 FDC~HKXE2 FDCJ~HKXE2 FDCP~HKXE2 FDCJ~HKXE2B FDCP~HKXE2B • Flexible tube (PCA324C004): 2 pcs. • Flange fixing bolt (SSA911C056A): 8 pcs. • Gasket (SSA932A004J) x 4 pcs. FDCJ~HKXE2D FDCP~HKXE2D PCA324C004 <Necessary parts> Re-fresh Multi (PCA006A061 set) • Gasket (SSA932A004J) x 4 pcs. SSA932A004J SSA911C056A SSA932A004J In addition to the above set, provide at site also joints having different diameters at both ends, elbows and pipes as required. Outdoor unit $[RCUUICURKRGUGTXKEGXCNXG $[RCUUICURKRG UGTXKEGXCNXG (NCTGFEQPPGEVKQP VQTGHTGUJMKV .KSWKFUGTXKEGXCNXG 6QKPFQQTWPKV )CUMGV 55##, 7. Test-run 6. Removal of the kit 5. Additional charge of refrigerant/pipe washing operation 4. Air tightness test/electric wiring/air purge 3. Pipe repair/installation of the kit 2. Installation of new unit 1. Removal of existing unit <Procedure of use> 5GTXKEGXCNXGMKV 6Q㧌CPIGQHUGTXKEGXCNXG% 1. Removal of existing unit Service valve kit • Collect refrigerant using a refrigerant collecting device. For details, refer to the instruction manual of refrigerant collecting device. • When refrigerant has been collected, close the service valve and disconnect the flared connection of gas pipe and brazed connection. Cure the end faces of removed pipe to protect from dust or moisture. 5GTXKEGXCNXGMKV 6Q㧌CPIGQHUGTXKEGXCNXG# 5GTXKEGXCNXG# 1WVFQQTICURKRG 6QQWVFQQTWPKV 2. Installation of new unit 6QKPFQQTWPKV 6QRKRGCVQWVFQQTWPKV UKFGQHUGTXKEGXCNXGMKV • Bring in a new unit. Regarding the installation and fixing methods, refer to the installation manual of new unit. 5GTXKEGXCNXG% 3. Pipe repair and installation of the kit (Replacement of flare nut, rework of flare and installation of pipes to kit) 2) Connect the gauge manifolds or pressure gauges (work at site) at two places of the left (Inlet side) and right (Outlet side) check joints on the re-fresh kit. 1) Machining of pipes provided at site and connections of the service valve kit and the pipe re-fresh kit i ) Connect the pipes according to the installation manual of the unit. ii ) Connect the service valve kit to the pipe re-fresh kit. Use the flexible tube for the suction gas pipe and a pipe with flare nut (provided at site) for the bypass gas pipe. Gauge manifold Lo Hi Lo valve Hi valve CLOSED CLOSED CAUTION • Install the kit at the same level as or lower than the outdoor unit. If the kit is installed higher than the outdoor unit, the refrigerating machine oil salvaged by washing may not be collected in the container of kit. • Connect the gas pipe to the pipe re-fresh kit as illustrated. • Flexible tube should not be bent larger than R200. The tube may be broken if it is bet excessively. • Rework the flared connection such that it will fit to R410A. 1 When the pipe size is same as the standard pipe size of new unit, use the flare nut attached to the unit. (Do not use the flare nut attached to existing unit.) 2 When the pipe size is different from the standard pipe size of new unit, use a flare nut compatible with R410A. (Do not use the flare nut attached to existing unit.) • Braze the gas pipe according to the installation manual. Sufficient care must be taken not to overheat the service valve of flange pipe. Overheat by brazing may damage the seal on the service valve, resulting in gas leakage. %JGEMLQKPV. +PNGVUKFG %JGEMLQKPV4 1WVNGVUKFG 4. Air tightness test, electrical wiring and air purge CAUTION • Always use a gasket when connecting a pipe with flange. When it is difficult to attaché a gasket, tighten at the specified position after coating refrigerating machine oil. • Tighten bolts to a torque of 25 – 30 N-m. If it is tightened beyond the specified range, it could cause gas leakage. • Tighten the flare nut of bypass gas pipe to 38±4 N-m. <Common> • When facing the front of the pipe re-fresh unit, the entrance is positioned at left and the exit is positioned at right. Take care of this difference when connecting the kit. If it is connected in reverse, it cannot wash. - AMP Air Conditioning 5GTXKEGXCNXG$ 1) Air tightness test Check the air-tightness according to the procedure described in the installation manual of outdoor unit. After checking the air-tightness on existing pipes and the indoor unit, test for the air-tightness of bypass pipe (2.21 MPa) through the check joint of service valve A. Open the bypass gas service valve at the re-fresh kit side during the test. CAUTION • When pressurizing the inside of pipe re-fresh kit, take care to restrict the pressure no higher than 3.24 MPa. 56 www.ampair.co.uk | [email protected] '11 • KX-T-166 7BDVVNJ[JOH $"65*0/ $"65*0/ t 6TF B HBTLFU XIFO JOTUBMMJOH UIF nBOHF QMBUF t #PMU UJHIUFOJOH UPSRVF JT o /N *G UJHIUFOFE CFZPOE UIJT SBOHF JU DPVME DBVTF HBT MFBLBHF t #F TVSF UP UVSO PO UIF QPXFS TVQQMZ UP UIF PVUEPPS VOJU CFGPSF TUBSUJOH BJS QVSHF 1JQF XBTIJOH PQFSBUJPO DBOOPU TUBSU UJMM JU FMBQTFT BCPVU IPVST BGUFS UVSOJOH PO UIF PVUEPPS VOJU t"GUFS SFMFBTJOH UIF BSJHIU QSFTTVSF UP BUNPTQIFSF UISPVHI UIF DIFDL KPJOUT PG TFSWJDF WBMWFT # BOE $ WBDVVNJ[F UISPVHI UIF DIFDL KPJOUT PG TFSWJDF WBMWF $ BOE MJRVJE TFSWJDF WBMWF ,FFQ PQFO UIF TFSWJDF WBMWF" EVSJOH UIF WBDVVNJ[JOH 4FSWJDFWBMWFLJU 4UPSJOH PG UIF LJU 1 %JTDPOOFDU UIF nBOHF DPOOFDUJPO BU UIF LJU TJEF 2 $MPTF UIF TFSWJDF WBMWF PG UIF CZQBTT HBT QJQF BOE EJTDPOOFDU UIF nBSFE DPOOFDUJPO"GUFS EJTDPOOFDUJOH UIF nBSFE DPOOFDUJPO NBLF TVSF UP JOTFSU UIF nBSF DBQ BOE UJHIUFO UIF nBSF OVU 3 *OTUBMM UIF QMBUF PO UIF nBOHF 6TF B HBTLFU BOE UJHIUFO CPMUT UP B UPSRVF PG o /N 4 3FNPWF UIF HBVHF NBOJGPMET GSPN UIF DIFDL KPJOUT 4FSWJDFWBMWF" 5PPVUEPPSVOJU 5PJOEPPSVOJU 4FSWJDFWBMWF$ 4FSWJDFWBMWF# 5FTUSVO J .BLF TVSF UP DIFDL PS JNQMFNFOU UIF GPMMPXJOHT CFGPSF TUBSUJOH UFTUSVO "EEJUJPOBMDIBSHFPGSFGSJHFSBOUBOEQJQFXBTIJOHPQFSBUJPO "EEJUJPOBM DIBSHF $IBSHF BO BEEJUJPOBM BNPVOU PG SFGSJHFSBOU BDDPSEJOH UP UIF QJQF MFOHUI 'PS UIF DIBSHF BNPVOU SFGFS UP UIF JOTUBMMBUJPO NBOVBM PG PVUEPPS VOJU 0QFO UIF TFSWJDF WBMWF $ BOE UIF CZQBTT HBT QJQF TFSWJDF WBMWF BU PVUEPPS VOJU TJEF BOE UIFO DIBSHF UIF BEEJUJPOBM SFGSJHFSBOU UISPVHI UIF DIFDL KPJOU PG MJRVJE TFSWJDF WBMWF $"65*0/ 4UBSU UIF BEEJUJPOBM DIBSHF GSPN UIF MJRVJE QJQF 8IFO OFDFTTBSZ DIBSHF BNPVOU DPVME OPU CF BEEFE GVMMZ DPOUJOVF UP DIBSHF GSPN UIF HBT QJQF XIJMF DBSSZJOH PVU UIF QJQF XBTIJOH PQFSBUJPO 8IFO DIBSHJOH GSPN UIF HBT QJQF VTJOH UIF SFGSFTI NVMUJ DIBSHF UIF SFGSJHFSBOU UISPVHI UIF DIFDL KPJOU PG TFSWJDF WBMWF $ %P OPU DIBSHF GSPN UIF TFSWJDF WBMWFT" BOE # UP QSFWFOU UIF MJRVJE BDDVNVMBUJPO 8IFO JNQMFNFOUJOH UIF XBTIJOH PQFSBUJPO UVSO PO UIF QPXFS TVQQMZ IPVST FBSMJFS 1 *T UIF QJQF XBTIJOH PQFSBUJPO TXJUDI 48 UVSOFE PGG 2 4FSWJDF WBMWFT" BOE $ BSF DMPTFE XIJMF UIF TFSWJDF WBMWF # JT PQFOFE 3 *T UIF CZQBTT HBT QJQF TFSWJDF WBMWF DMPTFE 4 *T UIF nBSF OVU PG CZQBTT HBT QJQF UJHIUFOFE BGUFS JOTFSUJOH UIF nBSF DBQ 5 *T UIF QMBUF JOTUBMMFE PO UIF nBOHF *T HBTLFU JOTUBMMFE VOEFS UIF QMBUF JJ "GUFS BMM DIFDL QPJOUT BSF DPNQMFUFE WBDVVNJ[F UISPVHI UIF DIFDL KPJOUT PG TFSWJDF WBMWFT" BOE $ JJJ 5IFO PQFO UIF TFSWJDF WBMWFT" BOE $ $IFDL UIFO UIF nBOHF TFDUJPO GPS MFBLBHF VTJOH TPBQ XBUFS PS PUIFS JW "GUFS DPNQMFUJOH UIF QJQF XBTIJOH PQFSBUJPO CZ NFBOT PG UIF SFGSFTI LJU SFQMFOJTI CZ B QVNQ N- PG OFX ."3 PJM UISPVHI UIF DIFDL KPJOU PG TFSWJDF WBMWF # PO UIF TFSWJDF WBMWF LJU W $BSSZ PVU UIF UFTUSVO BDDPSEJOH UP UIF QSPDFEVSFT EFTDSJCFE JO UIF JOTUBMMBUJPO NBOVBM PG PVUEPPS VOJU 5SBOTQPSUBUJPOPGUIFLJU t8IFO DBSSZJOH UIF QJQF SFGSFTI LJU UJMU JU TVDI UIBU UIF IPMEFS BOE UIF DBTUFST BSF QPTJUJPOFE BU UIF CPUUPN *G JU JT DBSSJFE XJUI UIF GSPOU PS TJEF JT QPTJUJPOFE BU UIF CPUUPN UIF LJU DPVME CF EBNBHFE t8IFO DBSSZJOH UIF LJU CZ UXP QFSTPOT IPME JU XJUI UIF UJSF TJEF EPXO *G JU JT IFME XJUI UIF UJSF TJEF VQ JOTUFBE SFGSJHFSBUJOH NBDIJOF PJM SFNBJOJOH JO UIF BDDVNVMBUPS NBZ TQJMM PVU 1JQF XBTIJOH PQFSBUJPO $"65*0/ t %P OPU FOUFS UIF QJQF XBTIJOH PQFSBUJPO NPEF XJUIPVU DPOOFDUJOH UIF QJQF SFGSFTI LJU *U DPVME CSFBL EPXO UIF VOJU t %P OPU TUBSU GSPN UIF SFNPUF DPOUSPMMFS XIJMF UIF QJQF SFGSFTI LJU JT DPOOFDUFE *U DPVME CSFBL EPXO UIF VOJU t 0QFO VQ UIF GPMMPXJOH TFSWJDF WBMWFT 4&(JOEJDBUPS 48 t -JRVJE TFSWJDF WBMWF PG PVSEPPS VOJU t #ZQBTT HBT TFSWJDF WBMWF PG PVUEPPS VOJU t 4FSWJDF WBMWF $ PG TFSWJDF WBMWF LJU t #ZQBTT HBT TFSWJDF WBMWF PG SFGSFTI LJU 5VSO PO UIF 48 UP FOUFS UIF QJQF XBTIJOH PQFSBUJPO NPEF *U JT DPOUSPMMFE DFOUSBMMZ GSPN UIF PVUEPPS VOJU 5VSO PGG UIF 48 BGUFS DPNQMFUJOH UIF QJQF XBTIJOH PQFSBUJPO $FOUSBM DPOUSPM GSPN UIF PVUEPPS VOJU JT SFTFU .BJOUFOBODF 1 %SBJOJOH PG DPMMFDUFE PJM t %SBJO UIF SFGSJHFSBUJOH NBDIJOF PJM DPMMFDUFE JO UIF QJQF SFGSFTI LJU BGUFS FBDI XBTIJOH PQFSBUJPO 4JODF UIF BNPVOU PG SFNBJOJOH SFGSJHFSBUJOH NBDIJOF PJM WBSJFT EFQFOEJOH PO TZTUFNT CFJOH XBTIFE JG OFYU XBTIJOH JT DBSSJFE PVU XJUIPVU ESBJOJOH DPMMFDUFE SFGSJHFSBUJOH NBDIJOF PJM PME PJM NBZ PWFSnPX BOE NJY JO OFX VOJU t8IFO ESBJOJOH SFGSJHFSBUJOH NBDIJOF PJM QMBDF B DPOUBJOFS VOEFS UIF PJM ESBJO IPMF 4FF mHVSF t8IFO ESBJOJOH PJM TVQQMZ QSFTTVSJ[FE OJUSPHFO HSBEVBMMZ UISPVHI UIF DIFDL KPJOU - UP ESBJO PJM GPSDJCMZ GSPN UIF PJM ESBJO IPMF PQFOJOH VQXBSE t %JTQPTF ESBJOFE SFGSJHFSBUJOH NBDIJOF PJM BDDPSEJOH UP BQQMJDBCMF MBXT PS SFHVMBUJPOT t 3FDPSE UIF SFBEJOH PO UIF QSFTTVSF HBVHF XIFO UIF SFNBJOJOH UJNF PO 4&( JT o NJOVUFT (SFFO-&% 3FE-&% %JTQMBZT CZ 4&( BOE -&%T JO UIF QJQF XBTIJOH PQFSBUJPO NPEF BSF BT TIPXO JO UIF GPMMPXJOH UBCMF 4&( 3FNBJOJOHUJNFUPFOE (SFFO-&% 3FE-&% 2VJDLnBTIJOH %BSL "UFOEPGQJQFXBTIJOHNPEF 1$-&OE 1$-ooo l l "UBCOPSNBMTUPQ &SSPSDPEF l #ZFSSPSDPEF /PSNBMNPEF $POUJOVPVTnBTIJOH "UFNFSHFODZTUPQ 3FQMBDFNFOUPGTUSBJOFS (BTLFU J 3FNPWF UIF nBOHF CPMU BOE QBOFM CPBSE BOE UBLF PVU UIF mMUFS FMFNFOU JJ 3FNPWF UIF TQSJOH BOE UBLF PVU PME FMFNFOU JJJ $MFBO JOUFSOBM QBSUT JW *G HBTLFUT JOTUBMMFE BU UIF QBOFM CPBSE BOE VOEFS UIF NBJO VOJU BSF EBNBHFE SFQMBDF UIFN 3FQMBDFNFOU HBTLFUT BSF QBDLFE UPHFUIFS XJUI OFX FMFNFOU W 4FU OFX FMFNFOU BOE JOTUBMM UIF TQSJOH WJ 4FU UIF FMFNFOU PO UIF NBJO VOJU BOE JOTUBMM UIF QBOFM CPBSE 5JHIUFO CPMUT UP B UPSRVF PG o /N IPNPHFOFPVTMZ WJJ 5FTU GPS BJSUJHIUOFTT UP DPOmSN UIBU UIFSF JT OP MFBLBHF 3FNBJOJOH UJNF UP UIF FOE PG QJQF XBTIJOH PQFSBUJPO TIPXT BO BQQSPYJNBUF WBMVF BOE B MJUUMF MPOHFS UIBO BDUVBM UJNF 8IFO UIF UJNF CFDPNFT MFTT UIBO NJOVUFT TUBOECZ OFBS UIF PVUEPPS VOJU QSFQBSFE GPS XPSL BGUFS UIF FOE PG PQFSBUJPO &NFSHFODZ TUPQ 1JQF XBTIJOH PQFSBUJPO DBO CF TUPQQFE CZ PQFSBUJOH UIF EJQ TXJUDI *U JT TUPQQFE JG UIF 48 JT UVSOFE PGG 'PS EJTQMBZT CZ 4&( BOE -&%T SFGFS UP UIF UBCMF TIPXO BCPWF "GUFS BO FNFSHFODZ TUPQ UIF QJQF XBTIJOH PQFSBUJPO DBO CF SFTUBSUFE CZ UVSOJOH PO UIF 48 3FNPWBMPGLJU 3FNPWBM PG UIF LJU "GUFS DPOmSNJOH UIF FOE PG QJQF XBTIJOH PQFSBUJPO XJUI 4&( BOE -&%T SFNPWF UIF QJQF SFGSFTI LJU J 0QFO BOE DMPTF UIF HBT QJQF TFSWJDF WBMWFT POMZ 0QFSBUF UIJT JO UIF GPMMPXJOH PSEFS *U JT OPU OFDFTTBSZ UP DMPTF UIF MJRVJE QJQF 0VUEPPSVOJU 1 $MPTF UIF TFSWJDF WBMWF $ #ZQBTTHBTQJQFTFSWJDFWBMWF 2 $MPTF UIF CZQBTT HBT QJQF TFSWJDF WBMWF BU PVUEPPS VOJU 'MBSFEDPOOFDUJPO UPSFGSFTILJU 3 $MPTF UIF TFSWJDF WBMWF" -JRVJETFSWJDFWBMWF 4 0QFO UIF TFSWJDF WBMWF # 5PJOEPPSVOJU &SSPSDPEF %FTDSJQUJPO PSA012B703A△C.indd "COPSNBMEJTDIBSHF )BT UIF BEEJUJPOBM DIBSHF CFFO EPOF QSPQFSMZ UFNQFSBUVSF *T UIF PVUEPPS BJS UFNQFSBUVSF XJUIJO UIF SBOHFPGVTF & 5PJOEPPSVOJU & 4FSWJDFWBMWF# "COPSNBMMZIJHI QSFTTVSF )USJQT "COPSNBMMZMPX QSFTTVSF 3FNFEZ 0QFOUIFTFSWJDFWBMWF $BSSZPVUUIFBEEJUJPOBMDIBSHF *NQMFNFOUXJUIJOUIFSBOHFPGVTF 6OJUTFSWJDFWBMWFNBZCFDMPTFE 0QFOUIFTFSWJDFWBMWF /PODPOEFOTFEHBTNBZCFNJYFE $IFDLUIFCBMBODFQSFTTVSFBUUIFUJNFPGTUPQ*GUIF TBUVSBUJPO QSFTTVSF UFNQFSBUVSF EJGGFST MBSHFMZ GSPN UIFBNCJFOUUFNQFSBUVSFSFQFBUUIFDIBSHF 6OJUTFSWJDFWBMWFNBZCFDMPTFE 0QFOUIFTFSWJDFWBMWF 'PS PUIFS FSSPS EJTQMBZT SFGFS UP UIF JOTUBMMBUJPO NBOVBM PG PVUEPPS VOJU 0VUEPPSHBTQJQF 5PQJQFBUPVUEPPSVOJU TJEFPGTFSWJDFWBMWFLJU 3 2011/06/17 - AMP Air Conditioning $IFDLJUFN 6OJUTFSWJDFWBMWFNBZCFDMPTFE & JJ $MPTF UIF CZQBTT HBT QJQF TFSWJDF WBMWF BU SFGSFTI LJU TJEF JJJ $PMMFDU B TNBMM BNPVOU PG SFGSJHFSBOU SFNBJOJOH JO UIF QJQF SFGSFTI LJU VTJOH B SFGSJHFSBOU DPMMFDUJOH EFWJDF JW %JTDPOOFDU UIF nBSFE DPOOFDUJPO PG CZQBTT HBT QJQF "GUFS EJTDPOOFDUJOH UIF nBSFE DPOOFDUJPO NBLF TVSF UP JOTFSU BOE UJHIUFO UIF nBSF DBQ W %JTDPOOFDU UIF nBOHF DPOOFDUJPO UP UIF QJQF SFGSFTI LJU WJ *OTUBMM UIF QMBUF PO UIF nBOHF *OTUBMM UIF DBQT PO UIF TFSWJDF WBMWFT" UP $ BOE UIF DBQ PO UIF DIFDL KPJOU (BTLFU &SSPSEJBHOPTJT 4FSWJDFWBMWF" 4FSWJDFWBMWF$ &MFNFOU t8IFO UIF QJQF XBTIJOH IBT CFFO TUPQQFE CZ UIF BCOPSNBM TUPQ DIFDL UIF DBVTF SFGFSSJOH UP UIF GPMMPXJOH UBCMF 4FSWJDFWBMWFLJU 5PPVUEPPSVOJU 0JMESBJOIPMF 2 3FQMBDFNFOU PG TUSBJOFS t8IFO UIF EJGGFSFOUJBM QSFTTVSF CFUXFFO UIF UXP DIFDL KPJOUT EVSJOH QJQF XBTIJOH PQFSBUJPO FYDFFET .1B SFQMBDF UIF TUSBJOFS 3FGSFTINVMUJ *OQJQFXBTIJOHNPEF $IFDLKPJOU- 57 10:25:09 - www.ampair.co.uk | [email protected] '11 • KX-T-166 7 OUTLINE OF OPERATION CONTROL BY MICROCOMPUTER 7.1 Operation control function by the outdoor controller (A) Normal control (1) Operation of major functional components under each operation mode Operation mode Cooling/Dehumidifying Fan Stopped Heating Thermostat ON Thermostat OFF Thermostat Thermostat Defrost ON OFF Fonctional item Compressor (CM) 〇 × × 〇 × 〇 Solenoid for CM (52X1, 52X2) 〇 〇 ×/〇 〇 〇 〇 Outdoor unit fan mortor (FMo-1) 〇 ×/〇 ×/〇 〇/× ×/〇 〇→× Outdoor unit fan mortor (FMo-2) 〇/× ×/〇 ×/〇 〇/× ×/〇 〇→× 4 way solenoid valve (20S) × × × 〇 〇 〇→× Heating electronic expansion valve Opening Angle Fully closed / Fully open Fully open ※1 ※2 (EEVH) Control Fully open Super cooling coil electronic expansion Opening Angle Fully closed Fully closed Fully closed Fully closed Fully closed valve (EEVSC) Control Solenoid valve (SV6) (oil return) 〇/× × × 〇/× × 〇/× Solenoid valve (SV1) (fluid return) 〇/× 〇/× × 〇/× 〇/× 〇/× Solenoid valve (SV11) (gas bypass) × × × 〇/× × × Solenoid valve (SV12) (gas bypass) 〇/× × × × × × Crankcase heater (CH1) 〇/× 〇/× 〇 〇/× 〇/× 〇/× Note (1) It means 〇 : ON, × : OFF, 〇/× : -, ×/〇 : ON or OFF. (2) This shows the state of output when all indoor units are under the same mode. (3) ※1 : When stopped from cooling, it is fully open When stopped from heating, it is fully closed unless another degree of opening is specified by the electronic expansion valve (EEV) control at the stop. ※2 : When stopped from heating, it is fully closed unless another degree of opening is specified by the electronic expansion valve (EEV) control at the stop. ESP-FP-1736 R - AMP Air Conditioning 58 www.ampair.co.uk | [email protected] '11 • KX-T-166 (2) Compressor pre-start control (a) Remote controller full stop → Operation (i) Start conditions • When it has changed to the compressor operation frequency command > 0 Hz from the state of compressor stopping. (ii) Control contents • It sets the compressor operation frequency command = 0 Hz, and then after this control ends, It starts the compressor. (iii) End conditions When all of following conditions are satisf ied ① It has elapsed 15 seconds after the start of this control. Operation Stop ON OFF 52X1, 52X2 CM 15 seconds Orps 6 seconds Opening at stop Normal control Initial opening EEVH 2 minutes EEVSC Initial opening O pulse Normal control 3 minutes ON SV6 OFF Time Start condition established • Meaning of marks 52X1, 52X2 EEVH SV6 Solenoid for compressor CM Heating electronic expansion valve Subcooling coil electronic expansion valve Solenoid valve [Oil return] - AMP Air Conditioning EEVSC Compressor 59 www.ampair.co.uk | [email protected] '11 • KX-T-166 (b) Cooling → Heating (i) Start conditions • When the outdoor unit operation mode is changed from the cooling operation to heating operation (ii) Control contents 1) When the compressor is operating, it makes the compressor stopped. 2) Each functional component operates according to the sequence shown below. (iii) End conditions • End of sequence Heating Cooling 3 minutes Any state 15 seconds CM Initial speed Any state FMo1, FMo2 OFF ON 20S OFF Fully open Initial opening EEVH Normal control Fully closed Any state EEVSC Fully closed Time Start conditions established • Meaning of marks CM FMo1, FMo2 20S Compressor EEVH Heating electronic expansion valve Fan motor EEVSC Subcooling coil electronic expansion valve 4-way solenoid valve - AMP Air Conditioning 60 www.ampair.co.uk | [email protected] '11 • KX-T-166 (c) Heating → Cooling (i) Start conditions • When the outdoor unit operation mode is changed from the heating operation to cooling operation (ii) Control contents 1) When the compressor is operating, it makes the compressor stopped. 2) Each functional component operates according to the sequence shown below. (iii) End conditions • End of sequence Heating Cooling 3 minutes Any state 15 seconds CM Initial speed Any state FMo1, FMo2 OFF ON 20S OFF Fully open Any state EEVH Fully closed(※) Initial opening EEVSC Normal control Fully closed Time Start conditions established Note (1) ※ : It is fully closed till the end of 3-minute delay after the automatic reset. • Meaning of marks CM Compressor EEVH Heating electronic expansion valve FMo1, FMo2 Fan motor EEVSC Subcooling coil electronic expansion valve ― ――― 20S 4-way solenoid valve - AMP Air Conditioning 61 www.ampair.co.uk | [email protected] '11 • KX-T-166 (3) Compressor control (a) 4-way valve switching safeguard In order to switch 4-way valve completely, it makes the compressor speed increasing as follows. (i) This control starts to increase the compressor speed from 10Hz after the compressor pre-start control ends. (ii) The target compressor speed is shown in following table. Item Model 4-way valve switching safeguard/Target compressor speed Frequency (Fk) Speed (rps) 224 280 70 50 (b) Compressor protection start After the 4-way valve switching safeguard, the compressor is controlled with the following compressor protection start. Compressor protection start, normal Compressor protection start A Compressor protection start B Thermostat ON start Compressor ON Initial Compressor ON Second & later Initial start remote controller ON error reset Operation mode is changed during thermostat OFF Operation mode is not changed during thermostat OFF Less than 45 min after power ON Compressor protection start B Compressor protection start B Compressor protection start B 45min. or more after power ON Compressor protection start A Compressor protection start A Compressor protection start A Less than 45 min after stop Compressor normal protection start Compressor normal protection start Compressor normal protection start Compressor protection start A Compressor protection start A Compressor protection start A 45min. or more after stop (i) Compressor protection start, normal < Control contents > Compressor maintains operation at lower limit frequency, after 4-way valve switching safeguard ends. (During this control, compressor speed is prohibited to increase.) After this control ends, comperssor speed is governed by the compressor speed control. < End conditions > When either one of the following conditions is established a) When it has elapsed 1 minute and 45 seconds after the start Compressor inverter frequency (Hz) Speed control 60 40 Lower limit frequency 20 10 Start 10 20 25 30 40 50 60 70 80 90 105 120 Time (second) (ii) Compressor protection start A < Control contents > Compressor maintains operation at lower limit frequency, after 4-way valve switching safeguard ends. If the time from starting till reaching the lower limit frequency after 4-way valve switching safeguard operation has elapsed 1minute, the target frequency is changed to that of 1minute later from the lower limit frequency. During this control, the target frequency is increased at a rate of 5Hz/minute from the lower limit frequency. (Note) The starting point of this control is the completion point of inverter start (10Hz). - AMP Air Conditioning 62 www.ampair.co.uk | [email protected] '11 • KX-T-166 < End conditions > When either one of following conditions is established a) When the frequency upper limit increase by this control continued for 15 minutes in total When the inverter has stopped within 15 minutes after the start and is started again, it starts with the normal protection start and increases the frequency upper limit at a rate of 5 Hz/minute till the frequency increase continues for 15 minutes in total. Speed control 120 100 Upper limit frequency Compressor inverter frequency (Hz) 80 60 40 Lower limit frequency 20 0 Start 1 2 3 4 5 6 7 8 9 10 11 12 13 14 15 Time (minute) (iii) Compressor protection start B < Control contents > Compressor maintains operation at lower limit frequency, after 4-way valve switching safeguard ends. If the time from starting till reaching the lower limit frequency after 4-way valve switching safeguard operation has elapsed 2 minutes, the target frequency is changed to that of 2 minutes later from the lower limit frequency. For 18 minutes after starting, the target frequency is increased at a rate of 5Hz/2 minutes from the lower limit frequency. For 18 minutes after starting, the starting point of this control is the completion point of inverter start (10 Hz). From 18 minutes to 24 minutes, it is increased at a rate of 5 Hz/minute. < End conditions > When either one of the following conditions is established (a) This frequency-up control will end when the cumulative operation time after starting becomes 24 minutes. If the inverter stopped within 24 minutes after starting and starts again, it starts with “Compressor protection start, normal”and increases the frequency at a rate of 5Hz/minute till the cumulative operation time after starting becomes 24 minutes. However, if 45 minutes have been elapsed since inverter stopped and starts again, it starts with“Compressor protection start A”. Speed control 120 100 Compressor inverter frequency (Hz) 80 Upper limit frequency 60 40 Lower limit frequency 20 0 Start 2 4 6 8 10 12 14 18 20 22 24 Time (minute) - AMP Air Conditioning 16 63 www.ampair.co.uk | [email protected] '11 • KX-T-166 (4) Outdoor fan control (a) Outdoor fan speed and fan motor rotation speed. The 7th outdoor fan speed in the following table is specified as the rated speed. Under the normal control, the speeds up to 8th level (800 min−1) are used. Outdoor fan tap Cooling FMo1 [min−1] Heating FMo2 [min−1] FMo1 [min−1] FMo2 [min−1] 0th speed 0 0 0 0 1st speed 200 0 200 0 2nd speed 200 200 200 200 3rd speed 300 300 300 300 4th speed 400 400 400 400 5th speed 500 500 500 500 6th speed 575 575 575 575 7th speed 700 700 700 700 8th speed 800 800 800 (780) 800 (780) Note (1) Figures in the parentheses in the above table are applicable to FDCR224KXE6. (b) Fan control during cooling During cooling and dehumidifying, fan speed is controlled in accordance with the high pressure (sensed by PSH) and the outdoor air temperature (sensed by Tho-A). (i) Initial fan speeds are as follows. Initial ourdoor fan speed at cooling Model Outdoor air temp ≤ 10ºC 10ºC < Outdoor air Temp. < 15ºC 15ºC ≤ Outdoor air Temp. All models 2nd speed 4th speed 6th speed (ii) During normal operation, the speed is changed in accordance with the high pressure value. When it has detected HP ≧ 2.2 MPa for 1 minute continuously, the fan speed is raised by one tap. When it is 1.5 MPa < HP < 2.2 MPa, the present fan speed is maintained. When it has detected HP ≦ 1.5 MPa for 1 minute continuously, the fan speed is dropped by one tap. Control range of fan speed is 1th – 8th speeds. One tap up Maintained One tap down 1.5 2.2 High pressure (MPa) (iii) When states under this control change from HP < 3.3 MPa to HP ≧ 3.3 MPa, the fan speed is changed preferentially to the followings. (After the change it returns to the normal control.) When the outdoor air temperature ≧ 30ºC, it changes to 7th or higher speed. When the outdoor air temperature < 30ºC, it changes to 3rd or higher speed. When the fan speed was higher than the above before the change of states, the fan speed is not changed. - AMP Air Conditioning 64 www.ampair.co.uk | [email protected] '11 • KX-T-166 (c) Outdoor fan cooling control at low outdoor air temperature. (i) Start conditions This control is performed when all of following conditions is established. When the ordinary outdoor fan control is performed Outdoor air temperature ≦ 10ºC (It is reset with the hysteresis of the outdoor air temperature > 15ºC.) Va lid Invalid 10 15 Outdoor air temperature Outdoor fan speed = 1st speed (200 min−1) (ii) Control contents Initial fan speed is 200 min−1 If the following high pressure is detected for 20 seconds continuously, fan speed will be changed +10 min−1 Maintained −10 min−1 1.7 1.4 High pressure (MPa) Outdoor fan speed is in a range of 130 min−1 – 300 min−1. (iii) End conditions When either one of following conditions is established When the ordinary outdoor unit fan cooling control ends Outdoor air temperature > 15ºC Outdoor fan speed ≧ 2nd speed (Note) This control range is not more than 300 min−1 × 1fan. (d) Outdoor fan heating control The fan speed control is performed based on the low pressure (detected with PSL) during heating operation. (i) Initial fan speed is 6th speed. (ii) Speed is changed depending on the low pressure value. When it is detected LP ≦ 0.75 MPa for 30 seconds continuously, the fan speed is raised by 1 tap. When it is 0.75 MPa < LP < 0.85 MPa, the present fan speed is maintained. When it is detected LP ≧ 0.85 MPa for 30 seconds continuously, the fan speed is dropped by 1 tap. Control range of fan speed is 1st – 8th speeds. One tap up Maintained One tap down 0.75 0.85 Low pressure (MPa) (iii) When states change from LP < 1.0 MPa to ≧ HP 1.0 MPa during this control, the fan speed is changed preferentially to the following. (It returns to the normal control after the change.) It changes to 4th or lower speed. If the fan speed was lower than the above speed before the change of states, the fan speed does not change. - AMP Air Conditioning 65 www.ampair.co.uk | [email protected] '11 • KX-T-166 (5) Defrost control (a) Temperature condition of defrosting 1) Start conditions (Standard specification or cold region specification can be selected by switching the jumper wire J15.) Defrost operation will start, when outdoor unit whose compressor is operating under heating mode has satisfied all the following conditions. (i) When 33 minutes of cumulative compressor operation time has passed since heating operation started. (ii) When 33 minutes of cumulative compressor operation time has passed since the previous defrosting ended. (iii) When 8 minutes has passed since the compressor turned ON from OFF status. (iv) When 8minutes has passed since one outdoor fan turned ON from OFF status. (v) After all above conditions have been met, when any of the following conditions is satisfied. When the outdoor heat exchanger temperature (sensed by Tho-R) and the outdoor air temperature (sensed by Tho-A) dropped below the defrosting start temperature in Fig. 1 for 30 seconds continuously When the suction pressure saturated temperature calculated by the low pressure (sensed by PSL) and the outdoor air temperature (sensed by Tho-A) dropped below the defrosting start temperature in Fig. 2 for 3 minutes continuously TR: Heat exchanger temperature. (°C) Fig. 1 -2 Without J15 Cold region specification -6 With J15 Cold region -15 Standard (Factory setting) -19 -21 Defrost start zone -25 SST: Suction pressure saturated temperature. (°C) -20 -15 6 TA: Outdoor air temperature. (°C) Fig. 2 Without J15 Cold region specification -6 With J15 -10 Cold region -19 -23 Standard (Factory setting) -25 Defrost start zone -29 -20 -15 6 TA: Outdoor air temperature. (°C) 2) End conditions - AMP Air Conditioning 66 www.ampair.co.uk | [email protected] '11 • KX-T-166 (b) Time condition of defrosting 1) Start conditions Defrosting operation start when all of the following conditions are satisfied. (i) When 33 minutes of cumulative compressor operation time has passed since heating operation started. (ii) When 33 minutes of cumulative compressor operation time has passed since the previous defrosting ended. (iii) When 105 seconds has passed since the compressor turned ON from OFF status in heating mode. (iv) When the oil return condition has been established (v) Following cases are excluded. When the upper limit frequency of the compressor protection start A or B is lower than the defrosting frequency During the normal compressor protection start 2) End conditions Defrosting operation stops when any of the following conditions is satisfied. (i) When 12 minutes has passed since defrost started (ii) When the outdoor heat exchanger temperature (sensed by Tho-R) is detected 10°C or higher continuously for 10 seconds (iii) When it has detected the high pressure (HP) ≥3.0MPa (6) Protective control (a) Discharge pipe temperature (Td) control Discharge pipe temperature sensor (Tho-D1) monitors the discharge pipe temperature (Td) to avoid the rise of discharge pipe temperature. 1) Compressor capacity control (i) Start conditions When all of following conditions are satisfied When the compressor is ON state. When it detects the discharge pipe temperature (sensed by Tho-D1) is higher than 120ºC (ii) Control contents Whenever it detects the discharge pipe temperature is higher than 120ºC for 5 seconds, the capacity is decreased. (iii) End conditions When any of the following conditions is satisfied When the discharge pipe temperature (sensed by Tho-D1) drops below 110ºC When the compressor is OFF state. During the defrosting control 2) Indoor EEV slightly open control at heating stop. Rise of discharge pipe temperature (Td) is restarined by opening the indoor EEV during heating stop. (b) Over-current protection control (Current safe) 1) If the input current value at the inverter inlet (converter inlet L3-phase) exceeds the setting value, the compressor speed is reduced. If the higher value persists even after the speed reduction, the speed is reduced further. 2) This control terminates when it is lower than the reset value for 3 minutes continuously or lower than the setting value for 6 minutes continuously. (c) Power transistor temperature (PT) protective control If the power transistor temperature exceeds 75°C, the compressor speed is controlled. Speed is reduced once each minute Retention Release 72 75 Power transistor temp.(°C) - AMP Air Conditioning 67 www.ampair.co.uk | [email protected] '11 • KX-T-166 (7) Test run (a) Start conditions (i) Turn ON the test run switch (SW5-1). The switch is invalid if it is turned ON before the power ON. (ii) Pump down switch (SW5-3) must be turned OFF. (b) Contents of control (i) Turning ON the dip switch (SW5-2) conducts cooling operation and turning OFF (SW5-2) conducts heating operation. 1) Cooling operation Compressor operation frequency control is conducted by the cooling low pressure control. 2) Heating operation Compressor operation frequency control is conducted by the heating high pressure control. (ii) Test run start signal under corresponding operation mode is transmitted to all indoor units connected. (c) End conditions (i) When the test run switch (SW5-1) is turned OFF, it stops. (ii) When it has stopped anomalously by the error control during test run, the error is displayed in the same way as the case of normal operation and the state of anomalous stop is kept ON even if the test run switch (SW5-1) is turned OFF. (B) Optional controls • Functions of outdoor PCB connector CNS1 and CNZ1 CNS1, CnS2, CnG1, CnG2 connector : By changing the allocation of external input functions [P07-10- X ] on the 7-segment, following functions can be selected. Function No. X “0” : External operation input CNS1 short circuited CNS1 open Operation permission Operation prohibition “1” : Demand input Invalid Valid “2” : Forced cooling/heating input Heating Cooling Valid Invalid “3” : Silent mode input 1 “4” : Spare “5” : Outdoor fan snow guard control input Valid Invalid “6” : Test run external input 1 (SW5‒1) Test run start Normail operation “7” : Test run external input 2 (SW5‒2) Cooling test run Heating test run “8” : Silent mode input 2 Valid Invalid “9” : 2‒step demand input Invalid Valid CNZ1 connector: By changing the allocation of external output functions [P06-“X”] on the 7-segment, following functions can be selected. “0” : Operation output “1” : Error output “2” : Compressor ON output “3” : Fan ON output “4” : Oil return operation output “5” : High pressure control output to water spray unit, etc. “6∼9” : Spare P○○ on the 7-segment P06 P07 P08 P09 P10 Content of control Allocation of external output (CnZ1) Allocation of external input (CnS1) Allocation of external input (CnS2) Allocation of external input (CnG1) Allocation of external input (CnG2) - AMP Air Conditioning 68 www.ampair.co.uk | [email protected] '11 • KX-T-166 (1) External input and demand input (a) Operation permission and prohibition modes (Note) With 7-segment display [P07]-[0] 1) 2) Operation permission or operation prohibition mode is switched with the connector (CnS1) and the jumper wire (J13) on the outdoor PCB. J13: Switching of CnS1 input method J13 short-circuited: CNS1 is for the level input. J13 open: CnS1 is for the pulse input. Operation permission/prohibition control by the external input CnS1 of outdoor unit Input: CnS1 Switching with J13 Short-circuit Short-circuit (Level input) Short-circuit Operation prohibition mode Operation permission mode Switching of operation permission/ operation prohibition modes (Reversal) Open (Pulse input) Open CnS1: Switching of operation permission/ prohibition modes Short-circuit (Level input) Operation permission mode Operation prohibition mode Open (Pulse input) Open (NOP) Note (1) Factory setting – J13: Short-circuit, CnS1: Short-circuit (Short-circuit pin connected) 3) 4) 5) The operation condition is desplayed on the LCD of remote controller and is transferred to optional centralised controller. When the control comand from remote controller is not accepted (Under the condition of the system all stop status by external input), “Center” is dispalyed. See Item 5) mentioned below. CnS1 performs the following operations depending on the short-circuit or open of the jumper wire (J13). In case of pulse input, the pulse width is 500ms or larger. J13 – Short-circuit Air-conditioner ON OK CnS1 input OFF (Open) ON (Short-circuit) PUSH PUSH OFF (Open) PUSH PUSH Remote controller operation Remote controller display Air-conditioner operation/stop Remote Center OFF Center ON OFF ON OFF J13 - Open ON OFF ON OFF CnS1 input Air-conditioner ON OK PUSH Remote controller operation Center PUSH PUSH Remote Center PUSH PUSH Remote Center Remote controller display Air-conditioner operation/stop OFF ON OFF ON OFF (b) Demand control (Note) With 7-segment [P07] = [1] 1) Demand control and normal operation are switched with the dip switches (SW4‒5,4‒6) and the jumper wire (J13) on the outdoor PCB. J13 short-circuit: CnS1 is for the level input J13 open: CnS1 is for the pulse input - AMP Air Conditioning 69 www.ampair.co.uk | [email protected] '11 • KX-T-166 2) Operation/ stop control by the demand input CnS2 of outdoor unit Input: CnS2 CnS2: Switching of demand control/ normal operation Switching with J13 Short-circuit Demand control Normal operation Short-circuit (Level input) Switching of normal operation/ demand control (Reversal) Open (Pulse input) Open Short-circuit Normal operation Demand control Short-circuit (Level input) Open (Pulse input) Open NOP Note (1) Factory setting – J13: Short-circuit, CnS2: Short-circuit (Short-circuit pin connected) 3) The operation condition is desplayed on the LCD of remote controller and is transferred to optional centralised controller. 4) Demand control Demand ratio can be switched with the dip switches (SW4-5, 4-6) on the outdoor PCB. SW4-5, SW4-6 demand switching: 0 : Open, 1 : Short-circuit (Factory default is open) SW4-5 SW4-6 Compressor Out put(%) 0 0 80 1 0 60 0 1 40 1 1 0 5) CnS2 performs the following operations depending on the short circuited or open of the jumper wire (J13). In the case of pulse input, the pulse width is 500ms or larger. J13 – Short-circuit ON (Short-circuit) CnS2 input OFF (Open) Normal ON (Short-circuit) Normal Demand control PUSH PUSH PUSH PUSH Remote controller operation Remote Remote controller display ON Air-conditioner operation/stop OFF Compressor OFF ON Compressor OFF OFF OFF J13 - Open OFF ON CnS2 input PUSH OFF ON Demand control Demand control PUSH PUSH PUSH Remote controller operation Remote Remote controller display Air-conditioner operation/stop Compressor OFF Compressor OFF - AMP Air Conditioning 70 www.ampair.co.uk | [email protected] '11 • KX-T-166 6) 2-step demand control (i) Starting conditions 1) When all of the followings are met a) When the 7-segment [P04] is set at any other than OFF b) Under the demand control c) When the outdoor unit external input terminal “2-step demand input” is valid (The external demand input is valid when it is opened) d) To make valid the demand 2, the demand 1 also must be set to be valid. (ii) Contents of control ・ Same as (5) Energy saving mode control (See page 74.) (iii) Ending condition ・ When starting conditions are not met ompressor Hz is restricted with the setting of P04 on the 7-segment, instead of external Energy saving mode control : C input. Demand control : C ompressor Hz is restricted with the external input ON. Demand rate is set with the dipswitch SW4-5 and SW4-6. 2-step demand control : C ompressor Hz is restricted with the external input ON. Demand rate is set with P04 on the 7-segment. External input (Demand input) External input (2-step demand input) Normal Invalid (short-circuited) Normal Air-conditioner operation/stop Valid (opened) Normal 2-step demand control PUSH Remote controller operation Remote controller operation Normal Invalid (short-circuited) Demand control PUSH PUSH PUSH Demand control Valid (opened) (short-circuited) 2-step demand control (Opened) PUSH PUSH Remote ON OFF Demand 1 ON ON OFF Demand 2 Demand 1 Demand 2 OFF OFF Demand 1: Demand control with the compressor output as set by SW4-5 and SW4-6 Demand 2: Demand control with the compressor output as set by [P04] - AMP Air Conditioning 71 www.ampair.co.uk | [email protected] '11 • KX-T-166 (2) Silent mode control (a) Start conditions When all of the following conditions is established (i) At the start of silent mode initiated by the indoor unit or when the silent mode input is made effective (short-circuited) at the external input terminal (Factory default: CnG2) on the outdoor unit (ii) When the outdoor unit operation mode is cooling or heating (iii) When the outdoor air temperature satisfies the following conditions 1) Silent setting 0, 1: Effective in zone A and B 2) Silent setting 2, 3: Effective in zone B (Note) Silent setting 0 to 3 can be swiched by [P05] of 7-segment display. <Outdoor operation mode - Cooling> Valid (zone B) Valid (zone A) Invalid 27 29 31 Outdoor air temperature (°C) <Outdoor operation mode - Heating> Valid (zone B) Valid (zone A) Invalid 2 4 6 Outdoor air temperature (°C) (iv) It is excluded when the following invalid conditions are established (For prevention of anomalous pressure rise at start) • For 30 seconds after either compressor has been turned ON (During a special operation) • During the 4-way valve switching safeguard • During the defrost control • During the oil return control • During the moved pump down control • During the pump down control for removal of the unit (Note) Any controls affected by the restriction of compressor and outdoor fan capcity during the silent mode are excluded. (b) Control contents Setting values can be changed with the silent setting as follows. (i) Upper limit of compressor speed is restricted. (ii) Upper limit of outdoor fan speed is restricted. Item Upper limit of compressor speed Upper limit of outdoor fan speed min−1 rps Setting P224 P280 P224 P280 Silent setting 0 (Factory default) 80 100 780 800 Silent setting 1 74 88 700 700 Silent setting 2 64 80 575 575 Silent setting 3 50 60 540 540 (c) End condition • When the starting conditions are not established - AMP Air Conditioning 72 www.ampair.co.uk | [email protected] '11 • KX-T-166 (3) Outdoor fan snow protection control (a) This control is enabled/disabled by entering data into 7-segment display. (b) Setting method of outdoor fan control [Starting conditions] When following conditions are established for 10 minutes continuously. (i) Snow protection control setting is valid ([P02]-1) and outdoor air temperature < 3°C or external input of outdoor fan snow protection control ON. ([P07]-5 and CnS1 is shorted) Set the Code No. to “P02”. “0” or “1” is displayed at the data display area. “0”: Outdoor fan control disabled (Factory setting) “1”: Outdoor fan control enabled Press SW7 (Data write/delete) for 3 seconds continuously. “0” or “1” blinks every 0.5 second at the data display area. Press SW8 (one digit) to toggle the display back and forth between “0” and “1” (blinking). If SW7 is pressed for 3 seconds or longer continuously while “0 “ and “1” is blinking, the blinking stops. With this operation, the enabled/disabled setting of outdoor fan control is stored in memory of EEPROM, and henceforth the outdoor fan is controlled according to the contents of memory. Contents of the outdoor fan control are retained even if the power is turned off and backed on again. (c) Contents of outdoor fan snow protection control If the outdoor air temperature drops 3°C or lower when the unit is all stop or error stop, the outdoor fan runs at the rating speed (7th speed) once every 10 minutes. The outdoor fan runs for 30 seconds.* *Operation time outdoor fan is changeable from 10 to 600 seconds by [P03] During this snow protection control, the compressor’s magnetic contactor (52X1 52X2) is ON. (d) End conditions of outdoor fan snow protection control When folowing conditions are established. (i) Snow protection control setting is invalid ([P02]-0) or outdoor air temperature > 5°C and external input of outdoor fan snow protection control OFF ([P07]-[5]and CnS1is opend). (ii) Compressor ON (iii) During all stop by anomaly <Outdoor air temperature condition at snow protection control> Valid Invalid 3 5 Outdoor air temperature (°C ) (4) External output This function is used in order to operate the external optional devices in conjunction with relay outputs of the respective operation information from outdoor unit. [External output function] External output function of CnZ1 can be switched by changing of [P06] on 7-segment display as mentioned below. 0: Operation output • When the outdoor unit operation mode is “Operation”, the external output relay is turned ON. (Note) The “Operation” includes not only compressor ON mode but also Fan mode and thermostat OFF mode under the condition of remote controller ON. But the anomalous stop is excluded. 1: Error output • It is turned ON at anomalous stop, and turned OFF when “CHECK” and “RESET” buttons on remote controller are pressed simutaneously after recovering from the anomaly. Even if “CHECK” and “RESET” buttons are pressed before recovering from the anomaly, it is not turned OFF, but when recovering from the anomaly later, it is automatically turned OFF. 2: Compressor ON output • It is turned ON when the compressor is ON. 3: Fan ON output • It is turned ON when the outdoor fan speed command > 0. - AMP Air Conditioning 73 www.ampair.co.uk | [email protected] '11 • KX-T-166 (5) Energy saving mode control This control is effective, when [P04] of 7-segment display is set 000, 040, 060, 080 (except OFF) Control contents (i) Compressor upper limit speed is changed according to the setting ratio. (ii) Compressor upper limit speed is obtained by multiplying the rating speed (at cooling/heating) with the setting ratio as follows. OFF: Normal (Factory setting) 80%: 80% of rating compressor upper limit speed 60%: 60% of rating compressor upper limit speed 40%: 40% of rating compressor upper limit speed 0%: 0% of rating compressor upper limit speed (stop) (iii) Except 0% of energy saving ratio, the following controls take precedence over this control. • 4-way valve switching safeguard • Defrosting control • Oil return control • During the pump down control for removal of the unit • Pump down control at start/stop (6) Forced cooling/heating operation (i) With this control, SW3-7 on the outdoor PCB is turned ON and CnG1 (equipped with short circuit pin) is shorted or opened so as to forcibly determined whether the indoor unit is operated for cooling or heating. (ii) If any operation mode other than the forcible mode is commanded from indoor unit, the mode unmatch message is displayed on the remote controller or others and operation enters in the FAN mode. SW3-7 ON (7) CnG1 Operation Open Cooling only Close Heating only Emergency stop control When one of indoor units receives the emergency stop signal from optional device like as refrigerant leakage detector and the information is transmitted to the outdoor unit, the outdoor unit stops operation and an emergency stop error is transmitted to all indoor units running. Make the emergency stop effective by remote controller indoor function setting. (i) When it receives the “Emergency stop” command from the indoor unit, it makes all stop by error. (ii) It shows the Error display “E63” and transmits the “Emergency stop” command to all indoor units. (iii) If the “Emergency stop reset” command is received from the indoor unit, the “Emergency stop reset” command is transmitted to all indoor units. - AMP Air Conditioning 74 www.ampair.co.uk | [email protected] '11 • KX-T-166 (8) Pump down operation control for removal of the unit When an outdoor unit is discarded or removed, the pump down control is performed at the outdoor unit side in order to recover the refrigerant quickly to the outdoor unit. (a) Start conditions This is implemented with the liquid service valve closed. (i) Outdoor unit operation mode – Stop (ii) Turn ON the test run cooling switch SW5-2 (cooling). (iii) Turn ON the pump down switch SW5-3 (pump down). (iv) Turn ON the test run switch SW5-1 when the above (i)-(iii) statuses are satisfied. Note (1) Input before the power ON is invalid. (b) Control contents (i) Compressor starts under compressor start protection control and runs at target speed of pump down operation. However, when the operation start conditions have been established during the 3-minute delay control of compressor, the compressor starts after completing the 3-minute delay control. Item Hp Target compressor speed at pump down operation 224 8 50HZ 280 10 62HZ Model (ii) As the start conditions are established, both red LED and green LED on the outdoor PCB flash continuously. 7-segment display shows “PdS” (Channel 0) at the code display area. (iii) During the pump down operation control, the protective controls (excluing low pressure protective control, anomalous low pressure control and pressure ratio protection control) and the error detection control are effective. (iv) The sub-cooling coil expansion valve (EEVSC) closes fully during the pump down control. (c) End conditions If any of the following conditions is satisfied, this control ends. (i) If a low pressure (LP) ≤ 0.01MPa is detected for 5 seconds continuously, it ends normally and initiates the followings. Red LED: keeps lighting Green LED: keeps flashing 7-segment display: PdE Remote controller: Stop (ii) Anomalous all stop by the error detection control (iii) If the cumulative compressor operation time under the pump down control totals 15 minutes (ending by time count up), it stops and initiates the following. Red LED: stays OFF Green LED: keeps flashing 7-segment display: No display Remote controller: Stop (iv) When any of setting switches (SW5-1, SW5-2 and SW5-3) has been turned OFF during pump down. (Note) Even if only the pump down switch SW5-3 is turned OFF, it does not recognized as the cooling test run mode , but stops - AMP Air Conditioning 75 www.ampair.co.uk | [email protected] '11 • KX-T-166 (C) Data output (1) 7-segment and operation data retention (a) 7-segment display Operation information is displayed for checking various operation data during test run and for helping malfunction diagnosis at servicing. Input data to microcomputer, contents of outdoor unit control, indoor unit registration information, or other, are mainly displayed on the 7-segment LED. (i) Operation information display Displays each item at 7-segment of 3-digit × 2 on the outdoor unit PCB. Display is controlled with the following buttons. SW9: Setting button for order of 10 of display code SW8: Setting button for order of 1 of display code SW7: Data erase/write button Select the order of 10 for the code No. of each item with SW9 or SW8 for the order of 1. Following identification alphabets are used at the code display. “C”: “C00” – “C99” “P”: “P00” – “Pxx” (up to a place where content is specified) Code [C96]is operable item. It is possible to delete the retained operation data (data of 30 minutes preceding an anomalous stop) by following resetting procedure. <Resetting operation> • Select code [C96]. If any anomalous data is retained, the data display [dEL] is shown. • Pressing SW7 for 3 seconds erases the memory data on RAM. (EEPROM data are not erased.) • As the data are erased, the data display shows [- - -]. When no anomalous data are retained, it displays [---] as well. • Unless the reset operation is performed, data are retained. Therefore, if normal operation is resumed without the reset operation and an anomalous stop occurs again, no new anomalous data cannot be retained, but former anomalous data are still retained unchanged. If you press SW8 (order of 1), the number changes 0 1 2 ... 9 0. If you press SW9 (order of 10), the number jumps to the leading code of each order of 10. Data display [Cxx] and setting value display [Pxx] are considered to be continuous. Example: Pressing SW9 at [C07] it changes to [C10] : Pressing SW9 at [C90], it changes to [P00] Codes [C44] are operable items. With the following reset operation, the cumulative compressor operation time corresponding to the code No. can be erased (reset). (Reset of operation time after replacing the compressor) <Resetting operation> • Select codes [C44]. Cumulative compressor operation time up to present is displayed. • Pressing SW7 for 3 seconds erases the memory data. However, the cumulative compressor operation time data in the 30 minutes log data preceding an anomalous stop (if this retained log data are not deleted) are not erased by this procedure. Data display for spare items is left in blank. (ii) When the temperature is below -10.0°C for the display of discharge pressure saturated temperature and suction pressure saturated temperature, the fraction after decimal point is rounded up. (Because the range of 7-segment display is 3-digit.) (iii) Return the error No. display after an error to the normal display by turning ON the dipswitch SW3-1. - AMP Air Conditioning 76 www.ampair.co.uk | [email protected] '11 • KX-T-166 (iii) Precedence of display [Exx] > [Related to check operation ([CHJ] > [CHU])] > [PdE] > [PdS]> [oPx] > [Cxx] If resetting from the display of , it is switched to [C00]. If SW8 or SW9 is pressed during the display of , it changes to [C00]. However, unless no button input is done for 10 seconds after change to [C00], it changes to the display of automatically according to the precedence. Display switching Special display is the display other than [CXX]. When special display occurs Special display [CXX] Button operation Special display reset or button operation No operation for 10 seconds* Automatic feeding Button operation [C99] * If the special display is reset in the meanwhile, it remains as [CXX]. - AMP Air Conditioning 77 www.ampair.co.uk | [email protected] '11 • KX-T-166 (b) List of 7-segment displays Code No. Contents of display Data display range Minimum unit Remarks Error display [Exx] Caution [Axx] display Special display [PdS][PdE][CH][CHF][CO][HE][PCL][dLP][dLC][dLH][oPE][CAP] Code No. Data display range Minimum unit Contents of data display Remarks <Sensor value, actuator information> C00 CM1 operation frequency 0 ~ 130 1Hz C01 (Spare) C02 Tho-A Outdoor air temperature L,-20 ~ 43 1°C C03 Tho-R1 Heat exchanger temperature 1 L,-25 ~ 73 1°C C04 Tho-R2 Heat exchanger temperature 2 L,-25 ~ 73 1°C C05 (Spare) C06 (Spare) C07 Tho-D1 Discharge pipe temperature (CM1) L,31 ~ 136 1°C C08 (Spare) C09 (Spare) C10 Tho-C1 Under-dome temperature (CM1) L,5 ~ 90 1°C C11 (Spare) C12 Tho-P1 Power transistor temperature (CM1) L,5 ~ 136 1°C C13 (Spare) C14 Tho-SC Sub-cooling coil temperature 1 L,18 ~ 73 1°C C15 Tho-H Sub-cooling coil temperature 2 L,-25 ~ 73 1°C C16 Tho-S Suction pipe temperature L,-25 ~ 73 1°C C17 Inverter secondary current 0 ~ 50 1A C18 CT1 (CM1) current 0 ~ 50 1A C19 (Spare) C20 EEVH1 Heating expansion valve opening angle 0 ~ 500 1 pulse C21 (Spare) C22 EEVSC Sub-cooling coil expansion valve opening angle 0 ~ 500 1 pulse C23 FMo1 Actual fan speed 0 ~ 999 10min-1 C24 FMo2 Actual fan speed 0 ~ 999 10min-1 C25 PSH High pressure sensor 0 ~ 4.15 0.01MPa C26 PSL Low pressure sensor 0 ~ 1.70 0.01MPa C27 (Spare) C28 (Spare) C29 (Spare) C30 C31 Pressure switch External input 0,1 (0: Open, 1: Close) 0,1 (0: Open, 1: Close) - AMP Air Conditioning Order of 100: 63H1-1 – Order of 10: (Spare) Order of 1: (Spare) Order of 100: CNS1 – Order of 10: CNS2 Order of 1: CNG1 78 www.ampair.co.uk | [email protected] '11 • KX-T-166 Code No. Contents of data display C32 External input C33 Relay output C34 Relay output C35 Relay output C36 Relay output Data display range Minimum unit 0,1 (0: Open, 1: Close) – 0,1 (0: Open, 1: Close) – 0,1 (0: Open, 1: Close) – 0,1 (0: Open, 1: Close) 0,1 (0: Open, 1: Close) Order of 100: CNG2 Order of 10: (Spare) Order of 1: (Spare) Order of 100: 52C-1 Order of 10: 20S Order of 1: Crankcase heater 1 Order of 100: SV6 Order of 10: (Spare) Order of 1: (Spare) Order of 100: SV1 – Order of 10: SV11 Order of 1: SV12 Order of 100: (Spare) – Order of 10: (Spare) Order of 1: (Spare) Order of 100: External output (CNZ1) 0,1 (0: Open, 1: Close) – C38 (Spare) – – C39 (Spare) – – C40 Number of connected indoor units 0 ~ 50 1 C41 Capacity of connected indoor units 0 ~ 200 1 C37 External output Remarks Order of 10: CnH Operation output Order of 1: CnY Anomalous output <Outdoor unit information> C42 Number of indoor units with thermostat ON 0 ~ 50 1 C43 Required Hz total Cumulative compressor operation time C44 (CM1) C45 (Spare) 0 ~ 999 1Hz 0 ~ 655 100h C46 Discharge pressure saturated temperature -50 ~ 70 0.1°C Range unable to display (-10°C or under) is in the unit of 1°C. C47 Suction pressure saturated temperature -50 ~ 30 0.1°C Range unable to display (-10°C or under) is in the unit of 1°C. -0.68 ~ 4.15 0.01 MPa 0 is omitted in negative range. -0.68 [-.68] C49 Super cooling 0 ~ 50 0.1deg C50 Super heat 0 ~ 50 0.1deg C51 Sub-cooling coil overheat 0 ~ 50 0.1deg C52 Discharge pipe overheat 1 0 ~ 50 0.1deg C53 Under-dome overheat 1 0 ~ 50 0.1deg C54 Target cooling low pressure 0.00 ~ 2.00 0.01MPa C55 Target heating high pressure 1.60 ~ 4.15 0.01MPa C48 Sub-cooling coil temperature sensor 1 saturated pressure C56 Target Fk 0 ~ 999 1Hz C57 Inverter 1 operation frequency command 0 ~ 130 1Hz C58 (Spare) 0 ~ 130 1Hz C59 FMo1 Fan Speed command 0 ~ 999 10min-1 C60 FMo2 Fan Speed command 0 ~ 999 10min-1 - AMP Air Conditioning 79 www.ampair.co.uk | [email protected] '11 • KX-T-166 code No. Contents of data display Data display range Minimum unit Remarks <Control status> C61 C62 C63 C64 C65 C66 C67 C68 C69 Control status Control status Control status Spare Protection control status Protection control status Protection control status 1-digit: Spare – 0.1 3-digit: Under test run control 2-digit: Under the demand control (0:OFF,1:ON) 1-digit: Under the silent mode control – 0.1 3-digit: In the capacity measuring mode 2-digit: Spare (0:OFF,1:ON) 1-digit: Spare – 0.1 3-digit: Spare 2-digit: Spare (0:OFF,1:ON) 1-digit: Spare – 0.1 3-digit: Under the HP speed reduction control 2-digit: Under the LP speed reduction control (0:OFF,1:ON) 1-digit: Under the Td speed reduction control – 0.1 3-digit: Compression ratio speed reduction control 2-digit: Under the CS speed reduction control (0:OFF,1:ON) 1-digit: Under the PT speed reduction control – 0.1 3-digit: Under the Tc speed reduction control 2-digit: Spare (0:OFF,1:ON) 1-digit: Spare 0 ~ 127 0.1 1 See page 83 – 3-digit: Spare 2-digit: Spare (0:OFF,1:ON) 1-digit: Spare - AMP Air Conditioning 3-digit: Under the oil return control 2-digit: During defrosting (0:OFF,1:ON) Cause of compressor stop Spare – 0.1 80 www.ampair.co.uk | [email protected] '11 • KX-T-166 Data display range Minimum unit C70 Counter · Sensor wire disconnected 0 ~ 3 1 C71 Counter · High pressure protection 0 ~ 5 1 0 ~ 5 1 Code No. Contents of data display Remarks <Anomalous counter information> C72 Counter · Anomalous low pressure (During operation) C73 Counter · Anomalous low pressure(During stop) 0 ~ 5 1 C74 Counter · Discharge pipe 1 anomalous temperature 0 ~ 5 1 C75 Counter · Anomalous FMo1 stop 0 ~ 5 1 C76 Counter · Anomalous FMo2 stop 0 ~ 5 1 C77 Counter · Current cut (CM1) 0 ~ 4 1 C78 Counter · Compressor 1 starting failure 0 ~ 20 1 C79 Counter · Inverter 1 comunication error 0 ~ 4 1 C80 Counter · Power transistor 1 overheat 0 ~ 4 1 C82 Counter · Inverter 1 desynchronism error 0 ~ 127 1 C81 (Spare) C83 Counter · Inverter 1 comunication error cumulative 0 ~ 127 1 C84 Counter · Indoor/outdoor comunication error 0 ~ 255 1 C85 Counter · CPU reset 0 ~ 255 1 0 ~ 3 1 C97 Program · Sub version 0 ~ 991 – C98 Program · POL version 0.00 ~ 9.99 0.01 C86 (Spare) C87 (Spare) C88 (Spare) C89 (Spare) C90 (Spare) C91 (Spare) C92 (Spare) C93 Counter – Liquid-back error C94 (Spare) <Others> C95 (Spare) C96 Data reset C99 Auto feed display – - AMP Air Conditioning 81 www.ampair.co.uk | [email protected] '11 • KX-T-166 Code No. Contents of data display Data display range Minimum unit Remarks <User setting> P00 (Spare) P01 Operation priority selection – – – – – 0,1 – 0: First push priority (at shipping) 1: Last push priorit P02 Outdoor unit fan snow protection control 0,1 – 0: Control disabled (at shipping) 1: Control enabled P03 Outdoor unit fan snow protection control ON time setting 30 : (Factory default) 10, 30 ~ 600 [Sec] 30 Changes like 10, 30, 60 90 … 600 P04 Energy saving mode OFF,000,040, 060,080 0: OFF, 1: 0%, 2: 40%. 3: 60%, 4: 80% Factory default is 0: OFF. P05 Silent mode setting 0 : (Factory default) 0 ~ 3 1 P06 Allocation of external output (CnZ1) 0 : (Factory default) 0 ~ 9 1 P07 Allocation of external input (CnS1) 0 : (Factory default) 0 ~ 9 1 P08 Allocation of external input (CnS2) 1 : (Factory default) 0 ~ 9 1 P09 Allocation of external input (CnG1) 2 : (Factory default) 0 ~ 9 1 P10 Allocation of external input (CnG2) 3 : (Factory default) 0 ~ 9 1 <Service engineer setting> Preferencial switch to ensure certain P19 indoor outlet air temperature at heating 0 : (Factory default) 0.1 Allowable total capacity of thermostat 110 : (Factory default) ON indoor units to ensure certain P20 indoor outlet temperature at heating 100, 090, 080 Allowable number of thermostat ON indoor units to ensure certain indoor 0 : (Factory default) P21 0 ~ 9 outlet temperature at heating <Newsuper link setting> 0,1 P30 Superlink communication status Automatic address setting 0 : (Factory default) P31 start input 0,1 Input the starting indoor 1 : (Factory default) P32 address for automatic address 1 ~127 setting P33 Input the number of connected indoor units P34 Polarity difinition – Changes to 110, 100, 090, 080, 110 … 1 – – 0: 1: 0: 1: Previous superlink New superlink Automatic address setting standby Automatic address setting start 1 Specify the starting indoor address connected in one refrigerant system for automatic address setting. 1 : (Factory default) 1 ~24 (*) 1 Specify the number of indoor units connected in one refrigerant system for automatic address setting. (*) Maximum connectable number of indoor units for each outdoor unit 0 : (Factory default) 0,1 – 0: Network polarity not defined 1: Network polarity defined - AMP Air Conditioning – 0: Control for ensuring certain indoor outlet air temperature at heating is valid 1: Control for ensuring certain indoor outlet air temperature at heating is invalid 82 www.ampair.co.uk | [email protected] '11 • KX-T-166 Compressor stop cause (Cord No. C68) It shows the latest comprressor anomalous stop cause Compressor stop cause At power on Outdoor air temperature Outdoor heat exchanger temperture 1 Outdoor heat exchanger temperture 2 Discharge pipe temperature sensor 1(CM1) Suction pipe temperature sensor Sensor disconnection Sub-cooling temperature sensor 1(liquid side) and/or short-circuit Sub-cooling temperature sensor 2(gas side) Under-dome temperature sensor 1 Power transistor temperature sensor 1 Active filter temperature sensor High pressure sensor Low pressure sensor HP anomaly LP anomaly Td1 anomaly FMo1 anomaly FMo2 anomaly Inverter 1 current cut Anomaly detection Inverter 1 startup failure Inverter 1 communication error Inverter 1 anomalous compressor induced voltage and torque Inverter 1 power tansistor overheat Inverter 1 rotor lock Liquid flooding anomaly Outdoor operation mode heating/cooling switching Heating overload protection Stop by restriction Stopping time by compressor dilution ratio protection control (Less than 30 minutes) *3 Stopping time by compressor dilution ratio protection control (Over 30 minutes) *3 No 0 1 2 3 4 5 6 7 8 9 10 11 12 20 21 22 23 24 25 26 27 28 29 30 31 40 41 50 51 *3 As the actual operation, write the stop factor 50 at the start of power supply and, when the accumulated compressor start inhibition time (counted only when the remote controller is turned on) has exceeded 30 minutes, overwrite on it with the stop factor with 51. The code of this stop factor is retained even after the protective start inhibition has been released, until it is overwritten with another stop factor. - AMP Air Conditioning 83 www.ampair.co.uk | [email protected] '11 • KX-T-166 (c) Saving of Operation Data Mainly for investigating the causes of market claims, operation data are always saved in memory. If any trouble occurs, the data writing is stopped and only the operation data prior to the time when the trouble occurs are recorded. These data can be loaded to a PC via RS232C connector of PCB and utilized for identifying causes. (i) Operation data for a period of 30minutes prior to the present operation are saved and updated continuously. (ii) If an anomalous stop occurs, the data are not updated any more. (iii) Data are written in based on 1 minute sampling interval and following data is transmitted to PC upon demand. Data Software version PID (Program ID) Outdoor unit capacity Power supply frequency Outdoor address Indoor address × 16 units Indoor capacity × 16 units Outdoor unit composition Single type Ascii Ascii Ascii Ascii Ascii Ascii Ascii Data range 15 bytes 2 bytes 3 bytes 2 bytes 2 bytes 2 bytes × 16 units 3 bytes × 16 units Example KD3C218######## (# : NULL) 5D As listed blow 60 00 ~ 3F 40 ~ 7F 022 ~ 280 Outdoor unit capacity data Remarks Example: 10HP - [S10] S: Display with Horse Power of single type (iv) Error retention and monitoring data Code No. 00 01 02 03 04 05 Indoor Indoor Indoor Indoor Indoor Indoor 06 Indoor 07 08 09 Indoor Indoor Indoor 10 11 Indoor Indoor 12 Indoor Record data Data write range Unit of write Number of bytes Contents 1 Thi-A –14 ~ 50 A/D value 1 Return air 1 Thi-R1 0 ~ 72 A/D value 1 Heat exchanger 1 1 Thi-R2 0 ~ 72 A/D value 1 Heat exchanger 2 1 Thi-R3 0 ~ 72 A/D value 1 Heat exchanger 3 1 EEV 0 ~ 470 1 pulse 2 1 operation/stop 0,1 – 1 0 Stop 1 Operation 1 operation mode 0 ~ 4 – 1 0 Auto 1 Dehumidifying 2 Cooling 3 Fan 4 Heating 1 request Hz 0 ~ 255 1Hz 1 1 answer Hz 0 ~ 255 1Hz 1 1 indoor local – – 1 Bit0 Anti-frost Bit1 EEV opening angle implementation 1 Thi spare –14 ~ 50 A/D value 1 Discharge 1 type 0 ~ 67 – 1 0 FDT 1 FDK 2 Others 3 FDE 4 FDTC 5 6 7 60 ~ 1PID – – 1 Write contents - AMP Air Conditioning 84 www.ampair.co.uk | [email protected] '11 • KX-T-166 Code No. Write contents Record data Number of Unit of write Data write range bytes 0 Error code 00 ~ 99 – 1 1 Error existing unit address 00 ~ FF – 1 <Sensor value> 2 Tho-A Outdoor air temperature -20 ~ 70 A/D value 1 3 Tho-R1 Heat exchanger temp. 1 -40 ~ 75 A/D value 2 4 Tho-R2 Heat exchanger temp. 2 -40 ~ 75 A/D value 2 5 Tho-D1 Discharge pipe temp. (CM1) -20 ~ 140 A/D value 1 6 Tho-S Suction pipe temperature -40 ~ 75 A/D value 2 7 Tho-SC Sub-cooling coil temp. 1 -40 ~ 75 A/D value 2 8 Tho-H Sub-cooling coil temp. 2 -40 ~ 75 A/D value 2 -20 ~ 140 A/D value 1 0 ~ 50 A/D value 1 -40 ~ 90 A/D value 1 9 Tho-P1 Power transistor temp. (Radiator fin) 10 Inverter secondary current 11 Tho-C1 Under-dome temp. (CM1) 12 CT1 Current 0 ~ 50 A/D value 1 13 High pressure sensor 0 ~ 4.15 A/D value 1 14 Low pressure sensor 0 ~1.70 A/D value 1 <Outdoor unit information> 15 Number of connected indoor units 16 Capacity of connected indoor units 17 Number of indoor units with thermostat ON 18 19 20 Total capacity of indoor units with cooling thermostat ON Total capacity of indoor units with heating thermostat ON Operation mode 0 ~ 127 1 unit 1 0 ~ 65535 – 2 0 ~ 255 1 unit 1 0 ~ 65535 2 0 ~ 65535 2 0 ~ 2 – 1 21 Inverter CM1 actual operation frequency 0 ~ 255 1Hz 1 22 FMo1 Actual fan speed 0 ~ 65535 10min-1 2 23 FMo2 Actual fan speed 0 ~ 65535 10min-1 2 24 Required Hz total 0 ~ 65535 1Hz 2 25 Discharge pressure saturated temperature -50 ~ 70 0.01°C 2 26 Suction pressure saturated temperature -50 ~ 30 0.01°C 2 -0.68 ~ 4.15 0.01MPa 2 1.0 ~ 10.0 0.1 1 28 Sub-cooling coil temp. sensor 1 saturated pressure Pressure ratio 29 Cooling sub-cooling 0 ~ 50 0.1deg 2 30 Suction overheat 0 ~ 50 0.1deg 2 31 Sub-cooling coil overheat 0 ~ 50 0.1deg 2 32 Discharge pipe overheat 0 ~ 50 0.1deg 2 33 Compressor 1 under-dome overheat 0 ~ 50 0.1deg 2 34 Target Fk 0 ~ 65535 1Hz 2 35 Answer Hz total 0 ~ 65535 1Hz 2 36 Inverter 1 operation frequency command 0 ~ 120 1Hz 1 27 Contents 00: No error on outdoor unit 01-99: All errors 00 – 3F: Outdoor 40 – 6F: Indoor 0 Stop 1 Cooling 2 Heating See below※mark ※ Definition of signals No.28: Pressure ratio Pressure ratio = (High pressure sensor + 0.101) [MPa] / (Low pressure sensor + 0.101) [MPa] - AMP Air Conditioning 85 www.ampair.co.uk | [email protected] '11 • KX-T-166 Code Write contents No. 37 FMo1 Fan speed command Record data Unit of Number of Data write range write bytes 0 ~ 65535 10min-1 2 Contents 38 FMo2 Fan speed command 0 ~ 65535 10min-1 2 39 EEVH1 opening degree 0 ~ 65535 1 pulse 2 40 EEVSC opening degree 0 ~ 65535 1 pulse 2 41 Compressor target cooling low pressure Compressor target heating high pressure Outdoor EEVH target superheat 0.00 ~ 2.00 0.01MPa 1 0.00 ~ 4.15 0.01MPa 2 0 ~ 25.5 0.1°C 1 0 ~ 255 1 pulse 1 45 Outdoor EEVH initial learning opeing position Outdoor EEVSC target superheat 0 ~ 25.5 0.1°C 1 46 Cumulative amount of hold-up oil. 0 ~ 2550 10cc 1 Actual range: 0cc – 1100cc 47 Oil return count down 0 ~ 255 3 min. 1 Actual range: 0 – 600min (10 hour) – – 1 42 43 44 Actual range: 5°C – 11°C <PCB hardware input> 48 49 50 51 External input Dip SW [SW3] Dip SW [SW4] Dip SW [SW5] – – – – – 1 – - AMP Air Conditioning 1 1 Bit0 63H1 0: Open, 1: Short-circuit Bit1 (Spare) 0: Open, 1: Short-circuit Bit2 CNS1 0: Open, 1: Short-circuit Bit3 CNS2 0: Open, 1: Short-circuit Bit4 CNG1 0: Open, 1: Short-circuit Bit5 CNG2 0: Open, 1: Short-circuit Bit6 (Spare) 0: Open, 1: Short-circuit Bit7 (Spare) 0: Open, 1: Short-circuit Bit0 SW3-1 0 : OFF, 1 : ON Bit1 SW3-2 0 : OFF, 1 : ON Bit2 SW3-3 0 : OFF, 1 : ON Bit3 SW3-4 0 : OFF, 1 : ON Bit4 SW3-5 0 : OFF, 1 : ON Bit5 SW3-6 0 : OFF, 1 : ON Bit6 SW3-7 0 : OFF, 1 : ON Bit7 SW3-8 0 : OFF, 1 : ON Bit0 SW4-1 0 : OFF, 1 : ON Bit1 SW4-2 0 : OFF, 1 : ON Bit2 SW4-3 0 : OFF, 1 : ON Bit3 SW4-4 0 : OFF, 1 : ON Bit4 SW4-5 0 : OFF, 1 : ON Bit5 SW4-6 0 : OFF, 1 : ON Bit6 SW4-7 0 : OFF, 1 : ON Bit7 SW4-8 0 : OFF, 1 : ON Bit0 SW5-1 0 : OFF, 1 : ON Bit1 SW5-2 0 : OFF, 1 : ON Bit2 SW5-3 0 : OFF, 1 : ON Bit3 SW5-4 0 : OFF, 1 : ON Bit4 SW5-5 0 : OFF, 1 : ON Bit5 SW5-6 0 : OFF, 1 : ON Bit6 SW5-7 0 : OFF, 1 : ON Bit7 SW5-8 0 : OFF, 1 : ON 86 www.ampair.co.uk | [email protected] '11 • KX-T-166 Code No. 52 53 Write contents Dip SW [SW6] Jumper SW Record data Unit of Number of Data write range write bytes – – – 1 – 1 Contents Bit0 SW6-1 0 : OFF, 1 : ON Bit1 SW6-2 0 : OFF, 1 : ON Bit2 SW6-3 0 : OFF, 1 : ON Bit3 SW6-4 0 : OFF, 1 : ON Bit4 SW6-5 0 : OFF, 1 : ON Bit5 SW6-6 0 : OFF, 1 : ON Bit6 SW6-7 0 : OFF, 1 : ON Bit7 SW6-8 0 : OFF, 1 : ON Bit0 J11 0: Open, 1: Short-circuit Bit1 J12 0: Open, 1: Short-circuit Bit2 J13 0: Open, 1: Short-circuit Bit3 J14 0: Open, 1: Short-circuit Bit4 J15 0: Open, 1: Short-circuit Bit5 J16 0: Open, 1: Short-circuit Bit6 (Spare) Bit7 (Spare) Bit0 52X1, 52X2 0 : OFF, 1 : ON Bit1 20S 0 : OFF, 1 : ON Bit2 CH1 0 : OFF, 1 : ON Bit3 SV1 0 : OFF, 1 : ON Bit4 SV6 0 : OFF, 1 : ON Bit5 SV11 0 : OFF, 1 : ON Bit6 (Spare) 0 : OFF, 1 : ON Bit7 (Spare) FMC1,2 0 : OFF, 1 : ON Bit0 Operation output (CnH) 0 : OFF, 1 : ON <PCB hardware output> 54 55 Relay output Relay output – – – 1 – 1 Bit1 Error output (CnY) 0 : OFF, 1 : ON Bit2 External output (CnZ) 0 : OFF, 1 : ON Bit3 (Spare) 0 : OFF, 1 : ON Bit4 (Spare) 0 : OFF, 1 : ON Bit5 (Spare) 0 : OFF, 1 : ON Bit6 (Spare) 0 : OFF, 1 : ON Bit7 (Spare) 0 : OFF, 1 : ON <Related to compressor> 56 CM1 Cumulative operation hours (Approx.) 0 ~ 65535 1h 2 57 CM1 Starting times 0 ~ 65535 × 20 times 2 58 CM1 3-minute delay timer 0 ~ 180 1 sec 1 59 Energizing time count down 0 ~ 255 1 min 1 60 Control status CH Compressor protection timer 0 ~ 360 3 min 1 61 Control status CH Compressor protection start 0 ~ 15 – 1 Protection start complete 0 ~ 14 Protection start ON - AMP Air Conditioning 15 87 www.ampair.co.uk | [email protected] '11 • KX-T-166 Record data Data write range Unit of write Number of bytes Control status HP (63H1) anomaly counter Control status LP anomaly counter while 73 running Control status LP anomaly counter while 74 stopping 75 Control status Td1 error counter 0~5 1 1 0~5 1 1 0~5 1 1 0~5 1 1 76 Control status DC fan motor 1 error counter 0~5 1 1 77 Control status DC fan motor 2 error counter Control status sensor wire disconnected 78 counter 79 Control status INV1 current cut error counter 0~5 1 1 0~3 1 1 0~4 1 1 80 Control status INV1 starting failure counter Control status INV1 communication error 81 counter Control status INV1 desynchronism error 82 counter Control status INV1 communication error 83 counter cumulative (Spare) Control status INV1 power transistor 84 overheat error counter 85 Control status INV1 rotor lock error counter 0 ~ 20 1 1 0~4 1 1 0~4 1 1 0 ~ 255 1 1 0~4 1 1 0 ~ 127 1 1 0,1 – 1 Code No. Write contents Contents <Error counter information> 72 <Setting value display> 86 Operation priority switching outsoor fan snow protection control 87 Outdoor fan snow protection control 0,1 88 Outdoor fan snow protection control ON time setting 30: (Factory default) 10, 30 – 600 [sec] 89 Demand ratio change value 90 1 10 sec 1 OFF, 000, 040, 060, 080 Factory default 0: OFF – 1 Silent mode setting 0~9 – 1 91 CNS1 function quota value 0~9 – 1 92 CNS2 function quota value 0~9 – 1 93 CNG1 function quota value 0~9 – 1 94 CNG2 function quota value 0~9 – 1 95 External output function quota 0~9 – 1 96 Target cooling low pressure compensation -0.20 ~ +0.20 0.01MPa 1 97 Target cooling high pressure compensation 0.00 ~ 0.40 0.01MPa 1 98 Heating setting 1 (Target outlet temperature) 40 ~ 50 1 [°C] 1 99 Heating setting 2 (Target high pressure) 3.15 ~ 2.75 0.05[Mpa] 1 30 ~ 38 1 [℃] 1 0~ - 1 0~4 - 8 100 Heating setting 3 (Judgment temperature) 0 First push priority 1 Last push priority 0 Invalid 1 Valid 0 Auto 1 Humidifying 2 Cooling 3 Fan 4 Heating <Other> 104 Override number <Indoor unit information> 106 Registered indoor 1-8 operation mode 107 Registered indoor 1-8 request Hz 0 ~ 255 1Hz 8 108 Registered indoor 1-8 answer Hz 0 ~ 255 1Hz 8 - AMP Air Conditioning 88 www.ampair.co.uk | [email protected] '11 • KX-T-166 8 SYSTEM TROUBLESHOOTING PROCEDURE 8.1 Basics of troubleshooting Basic troubleshooting is to check/analyze/save data by connecting the Mente PC. Whenever arriving at the site, always connect the Mente PC before starting work. Method of error data analysis (Basic procedure) • Identify whether particular error occurred during operation or stopping. • Is it caused by the installation conditions of outdoor/indoor unit? (Refrigerant quantity, pipe length, short-circuit, clogged filter, etc.) • Isn’t there any beginner’s mistake at the installation? (Wrong address, mistake in piping or wiring, etc.) • Is the failure related to any hardware (parts)? (SV main body, coil, capillary, check valve, sensor, etc.) • Is it a major component. Compressor, inverter PCB and outdoor DC fan motor. • Is it a failure of electrical component? Error on indoor unit or outdoor unit? Indoor unit Outdoor unit Is the remote controller connected? Was the power supply reset after the error occurred? Save the momentary data just before the error occurred in Mente PC Connect the Mente PC and restart operation Save the data for 30 minutes before the error occurred in Mente PC Check and write down the momentary data (retained in the remote controller) just before the error occurred Connect the Mente PC and restart operation Connect the Mente PC and restart operation Connect the Mente PC and restart operation - AMP Air Conditioning 89 www.ampair.co.uk | [email protected] '11 • KX-T-166 8.2 Explanation of troubleshooting (a) Checking 15V on the control PCB (Step to check if the inverter PCB fails or not) Use this to diagnose E41, E42, E45 and E48. Fan motor check Power OFF (Power supply circuit breaker OFF) *Be sure to check both fan motor 1 and 2 Be sure to wait for 3 minutes after turning the power circuit breaker off. Disconnect the fan motor wires. (Both the power cable and control wires) Even if DC15Vis detected, affection by fan motor anomaly is suspected. Implement following check. Turn the power circuit breaker OFF Wait 3 minutes Turn the power ON (power circuit breaker ON) and start operation with the test run SW. Connect the wires of fan motor 1 or 2 Check between #1 and #2 of CNA2 on the control PCB to see if DC 15V is detected. ③ Power ON Test run switch ON Check whether DC15V betten ①-② of CNA2 on the control PCB is detected. Since, unless DC15V is detected, faulty inverter PCB is suspected, check CNI at the control PCB side, the connector connection of CNA at the inverter side and breakage of communication wires. If everything is all right, replace the inverter PCB. If DC15V is detected, primary check is completed. Return to ① and check fan motor (Between ①-③ of CNI3). If no problem on both fan motor 1 and 2, go to further diagnosis of E41, E42, E45, E48 sequentially. Check E41, 42, 45, 48 If DC15V is not detected, the connected fan motor has anomaly. Turn the power OFF and disconnect the wires. If the check of fan motor 2 is not completed, return to ① and check fan motor 2 (Between ①-③ of CNI3). *After completion of checking both fan motor 1 and 2, replace the anomalous fan moto r. (b) Inspection of short-circuit on the power transistor module terminals Disconnect the wiring of compressor and check for short-circuit with a tester. Inspect between terminals of: P-U, P-V, P-W, N-U, N-V, N-W and P-N It will be easier to contact the tester at the following place at each terminal. P: P terminal of power transistor N: N terminal of power transistor U: End of red harness to compressor V: End of white harness to compressor W: End of blue harness to compressor Terminal (+) P N P P P N N N U V W U V W Terminal (-) N P U V W U V W P P P N N N Normal value (Ω) Several 10 M Several M Several 10 M Several 100K Several 100K Several 10 M Note (1) When a measured value is 0 ­ a few kΩ, the element may be broken. Replace the power transistor part. - AMP Air Conditioning 90 www.ampair.co.uk | [email protected] '11 • KX-T-166 8.3 Contentsoftroubleshooting (a) List of inspection displays 1) Indoor and outdoor units Remote 7-segment controller display error code E1 – E2 – E3 – E5 – E6 – E7 – E9 – E10 – E12 – – – – E16 E18 Name of inspection Classification Remote controller communication error Duplicated indoor unit address Outdoor unit signal line error Communication error during operation Indoor heat exchanger temperature thermistor anomaly (Thi-R) Indoor return air temperature thermistor anomaly (Thi-A) Drain trouble Excessive number of indoor units (more than 17 units) by controlling one remote controller Address setting error by mixed setting method Indoor fan motor anomaly (FDT series) Indoor fan motor anomaly (FDK series) Address setting error of master and slave indoor untis Indoor unit operation check drain motor check mode anomaly Indoor fan motor rotion speed anomaly (FDT, FDTC, FDFW and FDK series) Remote controller temperature thermistor anomaly (Thc) Unmatch connection of indoor and outdoor unit Duplicated outdoor unit address No. Open L3 Phase on power supply at primary side Discharge pipe temperature error (Tho-D1) E36 Liquid flooding anomaly Outdoor heat exchanger temperature thermistor (Tho-R) E37-1, 2 and subcooling coil temperature thermistor (Tho-SC, -H) E37 E37-5, 6 anomaly E38 E38 Outdoor air temperature thermistor anomaly (Tho-A) E39 E39-1 Discharge pipe temperature thermistor anomaly (Tho-D1) E40 E40 High pressure anomaly (63H1-1 activated) E41 (E51) E41 (E51)-1 Power transister overheat E42 E42-1 Current cut (CM1) Excessive number of indoor units connected, excessive total E43-1 E43 capacity of connection E43-2 Communication error between inverter PCB and outdoor E45 E45-1 control (PCB) Mixed address setting methods coexistent in same network E46 E46 E48-1 E48 Outdoor DC fan motor anomaly E48-2 E49 E49 Low pressure anomaly Suction pipe temperature thermistor anomaly (Tho-S), E53/E55 E53/E55-1 Under-dome temperature thermistor anomaly (Tho-C1) High pressure sensor anomaly (PSH)/Low pressure sensor E54-1 E54 anomaly (PSL) E54-2 E56 E56-1 Power transitor temperature thermistor anomaly (Tho-P1) E19 E20 E28 E30 E31 E32 – – – E30 E31 E32 E36-1 E36-3 E58 E59 E60 E63 2) E58-1 E59-1 E60-1 E63 Anomalous compressor by loss of synchronism Compressor startup failure (CM) Rotor position detection failure (CM) Emergency stop Page 108 Communication error Address setting error 109 Address pairing setting error 110 Communication error 110・111 Thermistor wire breakage 112 Thermistor wire breakage 113 System error 114 Communication error 115 Address DC fan DC fan Address 116 117 118 119 120 121 122 123 124 125 126 127 setting error motor error motor error setting error Setting error DC fan motor error Thermistor wire breakage System error Address setting error Site setting error System error System error Thermistor wire breakage 128 Thermistor wire breakage Thermistor wire breakage System error System error System error 129 130 131 132 133 Site setting error 134 Communication error 135 Address setting error 136 DC fan motor error 137 System error Thermistor wire breakage Thermistor wire breakage Thermistor wire breakage 138 System error System error System error Site setting error 142 143 144 145 139 140 141 Optional controller in-use SL-1N-E SL-2N-E SL-3N-E Error Red code LED E75 Indoor unit control PCB Red LED Green LED Outdoor unit control PCB Red LED Green LED Keeps Stays Keeps Stays Keep flashing OFF flashing OFF flashing Location of trouble Repair method SL-1N-E ・ Communication enor (Deflective communication circuit on the main unit of Replacoment SL-2N-E SL1N-E, SL2N-Eor SL3N-E) SL-3N-E - AMP Air Conditioning Description of trouble 91 - # www.ampair.co.uk | [email protected] '11 • KX-T-166 (b) Troubleshooting Error code Remote controller: None 7-segment display: 1. Applicable model LED Green Red Content Indoor Keeps flashing Stays Off Operates but does not cool Outdoor Keeps flashing Stays Off 5. Troubleshooting All models Diagnosis Countermeasure Check the indoor fan operation Check the temperature difference between return and suction air of indoor unit 2. Error detection method Is the temperature differnce between return and suction air 10-20ºC at cooling? YES Does the heat load increase after installtion? NO It is normal (This unit is designed to start in the soft start mode by detecting the compressor under-dome temperature when it restart after power reset) YES NO It is necessary to replace to higher capacity unit or to install additional unit Mistake in model selection. Calculate heat load once more. Is the compressor operating? NO " WAIT " message is displayed [for 3 seconds] when performing cooling, defumidifying or heating operation from remote controller? YES YES Compressor may be stopped by the error detection control. For the contents of control, refer to anomalous stop control by controlling compressor rotation speed of microcomputer control function Is the compressor rotation speed low? Check the followings • Minor clogging of filter • Minor fouling of heat exchanger • Minor short-circuit of airflow • Slightly insufficient or excessive refrigerant amount • Poor compression of compressor NO 3. Condition of error displayed NO YES 4. Presumable cause • Poor compression of compressor • Expansion valve anomaly Compressor refrigerant oil protective control at starting is activated. For the contents of control, refer to the compressor start control. Check suspicious points considering appropriate operation control Check following operation control function. . Control for determing compressor rotation speed . Protective control by controlling compressor rotation speed Which control is appropriate to this phenomenon Is the operating conditions of indoor/outdoor unit under rated condition? YES Note (1) Outdoor: 35ºC Indoor : 27ºCDB/19ºCWB NO The unit is operating normally, but is operating under the protective control of compressor or other respective components Check the followings for reference • Severe clogging of filter • Severe clogging of heat exchanger • Severe short-circuit of airflow • Severely insufficient or excessive refrigerant amount • Under protective control of compressor • Indoor unit fan tap setting • Valid setting of silent mode Note: - AMP Air Conditioning 92 www.ampair.co.uk | [email protected] '11 • KX-T-166 Error code Remote controller: None 7-segment display: 1.Applicable model LED Green Red Content Indoor Keeps flashing Stays Off Operates but does not heat Outdoor Keeps flashing Stays Off 5.Troubleshooting All models Diagnosis Countermeasure Check the indoor fan operation Check the temperature difference between return and suction air of indoor unit 2.Error detection method Is the temperature differnce between return and suction air 10-30ºC at heating? YES Does the heat load increase after installtion? NO It is normal (This unit is designed to start in the soft start mode by detecting the compressor under-dome temperature when it restart after power reset) YES NO It is necessary to replace to higher capacity unit or to install additional unit Mistake in model selection. Calculate heat load once more. Is the compressor operating? NO " WAIT " message is displayed [for 3 seconds] when performing cooling, defumidifying or heating operation from remote controller? YES NO YES 3. Condition of error displayed Is the compressor rotation speed low? • 4-way valve anomaly • Poor compression of compressor • Expansion valve anomaly Check following operation control function. . Control for determing compressor rotation speed . Protective control by controlling compressor rotation speed Which control is appropriate to this phenomenon Is the operating conditions of indoor/outdoor unit under rated condition? Check suspicious points considering appropriate operation control YES Note (1) Outdoor: 7ºC Indoor : 20ºC NO The unit is operating normally, but is operating under the protective control of compressor or other respective components Compressor may be stopped by the error detection control. For the contents of control, refer to anomalous stop control by controlling compressor rotation speed of microcomputer control function Check the followings • Minor clogging of filter • Minor fouling of heat exchanger • Minor short-circuit of airflow • Slightly insufficient or excessive refrigerant amount • Poor compression of compressor NO YES 4.Presumable cause Compressor refrigerant oil protective control at starting is activated. For the contents of control, refer to the compressor start control. Check the followings for reference • Severe clogging of filter • Severe clogging of heat exchanger • Severe short-circuit of airflow • Severely insufficient or excessive refrigerant amount • Under protective control of compressor • Indoor unit fan tap setting • Valid setting of silent mode Note: - AMP Air Conditioning 93 www.ampair.co.uk | [email protected] '11 • KX-T-166 Error code Remote controller: None 7-segment display: 1.Applicable model LED Green Red Content Indoor Stays Off Stays Off Earth leakage breaker activated Outdoor Stays Off Stays Off 5.Troubleshooting All models Diagnosis Are the insulation resistance and and coil resistance of compressor OK? Countermeasure NO Replace compressor. * NO Secure insulation resistance. YES Secure insulation resistance. YES 2.Error detection method Is insulation of respective harnesses OK? YES Is any hamess bitten between pannel and casing or etc? NO 3. Condition of error displayed Check the outdoor unit grounding wire and earth leakage breaker Check of the outdoor unit grounding wire and earth leakage breaker ① Run an independent grounding wire from the grounding screw of outdoor unit to the grounding terminal on the distribution panel. (Do not connect to another grounding wire.) ② In order to prevent malfunction of the earth leakage breaker itself, confirm the conformity of high harmonic regulation. 4.Presumable cause • Compressor anomaly • Noise * Insulation resistance of compressor • Immediately after installation or when the unit has been left for long period without power supply, the insulation resistance may drop to a few M because of refrigerant migrated in the compressor. When the earth leakage breaker is activated at lower insulation resistance, check the following points. ① 6 hours after power ON, check if the insulation resistance recovers to normal. When power ON, crankcase heater heat up compressor and evaporates the refrigerant migrated in the compressor. ② Check if the earth leakage breaker is conformed to higher harmonic regulation or not. Since the unit has inverter, it is necessary to use components conformed to high harmonic regulation in order to prevent malfunction of earth leakage breaker. Note: - AMP Air Conditioning 94 www.ampair.co.uk | [email protected] '11 • KX-T-166 Error code Remote controller: None 7-segment display: 1.Applicable model LED Green Red Indoor – – Outdoor – – Content Excessive noise/vibration (1/3) 5.Troubleshooting All models Diagnosis Does noise/ vibration occur during or soon after stopping operation of air-conditioner? 2.Error detection method Countermeasure If excessive noise/vibration persists when sufficient time has elapsed after stopping the unit, it is considered that the airconditioner is not the source. NO YES Does the installation of indoor/outdoor unit have looseness? YES YES [Installation work] Does the noise/vibration occur not only from the air-conditioner but also from entire building? NO Are pipes touching the wall and etc? YES NO NO Check the installed condition carefully, and correct the installed position or insert rubber cushions into the gap or take other measure in order to eliminate looseness. Prevent the vibration from transmitting to wall and etc by fixing pipes on the wall tightly or wrapping rubber cushion around the pipe which goes through the hole in the wall or applying other appropriate means. Strength of ceiling wall, floo , etc. may be insufficient. Review the installation place or apply reinforcement to increase the strength. 3. Condition of error displayed [Units] Does noise/vibration occur when only the fan is operating? YES Is fan or louver touching other components? YES Check for leaning of installed unit or incorrect mounting of fan, louver or motor, and then specify the contacting point and correct it. NO When th eheat exchanger or filter is clogged, clean them. In case that the unit is installed at the site where background noise is very low, even the low level noise from indoor unit like as refrigerant flow noise can be heard, but it is normal. Before installation, check for background noise. If background noise is very low, convince client prior to installation. NO To next page 4.Presumable cause ① Improper installation work ・Improper vibration-proof work at instllation ・Insufficient strength of mounting surface ② Anomaly of product ・Before/after shipment from factory ③ Improper adjustment during commissioning ・Excessive/insufficient refrigerant. Note: - AMP Air Conditioning 95 www.ampair.co.uk | [email protected] '11 • KX-T-166 Error code Remote controller: None 7-segment display: 1.Applicable model LED Green Red Indoor – – Outdoor – – Content Excessive noise/vibration (2/3) 5.Troubleshooting All models Diagnosis Countermeasure From previous page Are the pipes contacting with the casing? 2.Error detection method [Unit] Does noise/vibration occur when the cooling/ heating operation is performing normally? YES Rearrange the piping to avoid contact with the casing. YES NO Is continuous hissing or roaring sound occurred? YES NO NO Noise/vibration is generated when the refrigerant gas or liquid flows through inside of piping of air-conditioner. It is likely to occur particularly during cooling or defrosting in the heating mode. It is normal. To next page Is hissing sounds occurred at the startup or stopping? YES NO Is blowing sound occurred at the start/stop of defrost operation during heating mode? 3. Condition of error displayed YES NO Is cracking noise occurred during heating operation? YES NO 4.Presumable cause Is hissing noise occurred during cooling operation or after operation stopped? NO YES The noise/vibration occurs when the refrigerant starts or stops flowing. It is normal. When the defrosting starts or stops during heating mode, the refrigerant flow is reversed due to switching 4-way valve. This causes a large change in pressure wich produces a blowing sound. It may also accompany the hissing sound as mentioned above. This is normal. After the start or stop of heating operation or during defrosting, abrupt changes in temperature cause resin parts to shrink or expand. This is normal. It is the sound produced by the drain pump that discharges drain from indoor unit. The pump continues to run for 5 minutes after stopping the cooling operation. This is normal. Apply the damper sealant at the place considered to be the sources such as the pressure reducing mechanism (Expansion valve, capillary tube, etc.) Note: - AMP Air Conditioning 96 www.ampair.co.uk | [email protected] '11 • KX-T-166 Error code Remote controller: None 7-segment display: 1.Applicable model All models LED Green Red Indoor – – Outdoor – – Content Excessive noise/vibration (3/3) 5.Troubleshooting Diagnosis Countermeasure From previous page 2.Error detection method [Adjustment during commissioning] Does noise/vibration occur when the cooling/heating operation is performed under anomalous condition? YES If insufficient cooling/ heating problem happens due to anomalous operating conditions at cooling /heating, followings are suspicious. • Excessive charged amount of refrigerant • Insufficient charge amount of refrigerant • Intrusion of air, nitrogen, etc. In such case, it is necessary to recover refrigerant, vacuum-dry and recharge refrigerant. 3. Condition of error displayed * Since there could be many causes of noise/ vibration, the above may not cover all. In such case, check the conditions when, where, how the noise/vibration occurs according to following check points and ask our consultation 4.Presumable cause • Indoor/outdoor unit • Cooling/heating/fan mode • Startup/stop/during operation • Operating condition (Indoor/outdoor temperatures and pressures) • Time it occurred • Operation data retained by remote controller or Mente PC such as compressor rotation speed, heat exchanger temperature, EEV opening degree and etc. • Tone (If available, record the noise) • Any other anomalies Note: - AMP Air Conditioning 97 www.ampair.co.uk | [email protected] '11 • KX-T-166 Error code Remote controller: None 7-segment display: 1.Applicable model LED Green Red Content Indoor Keeps flashing Stays Off Louver motor anomaly Outdoor Keeps flashing Stays Off 5.Troubleshooting All models Diagnosis Countermeasure -Check at the indoor unit side. Operate after waiting for more than 1 minute. Does the louver operate when power on? NO Is there any disconnection or breakage of LM connector? 2.Error detection method YES Correct it NO YES NO Is LM harness broken? NO Repair harness Check connector (CNJ) Replace Louver Motor NO Correct it YES Correct it YES Is LM locked? YES Does LM turn smoothly? NO Is there any problem on the connection link? 3. Condition of error displayed Replace indoor control PCB NO Is the setting of airflow direction change prohibited? NO YES Correct it Check the remote controller whether it is fixed free flow setting. In cases of FDTW, FDTS and FDTQ 4.Presumable cause It is normal if LM can be stopped by pressing LS two times. Check how LS reacts when the power is turned OFF and ON again NO • Louver motor anomaly • Disconnection/breakage of LM harness • Limit switch anomaly Does the louver link press LS till crick sound can be heard? NO YES Note (1) LM: Louver motor (2) LS: Limit switch Adjust LM lever and then check again. • LS anomalyReplace • Indoor control PCB anomalyReplace. In cases of FDT, FDTC, FDE and FDK Check the remote controller whether it is fixed free flow setting or not. Note: - AMP Air Conditioning 98 www.ampair.co.uk | [email protected] '11 • KX-T-166 Error code Remote controller: None 7-segment display: 1.Applicable model LED Green Red Content Power supply system anomaly (Power supply to indoor unit PCB) Indoor Stays Off Stays Off Outdoor Stays Off 2 times flash 5.Troubleshooting All models Diagnosis Is AC 220-240V/220V detected between L-N on the indoor terminal block? 2.Error detection method Countermeasure NO Is AC 380/415V for 3-phase unit detected between L1, L2 and L3 on the outdoor tarminal block respectively? YES NO YES Note (1) FDT and FDTC series: F200, F201 Other than FDT and FDTC: Fuse between wires Outdoor Noise filter PCB anomaly Replace it Wrong wiring or broken wires between outdoor and indoor units (1) Are fuses OK? (2 pcs) NO (2) Is power supply between① - ③of CNW0 OK? NO YES Indoor power PCB anomaly Replace it Note (2) Remove YES transformer for other than FDT and FDTC series (CNW1) (3) Is power supply to FM, LM and etc. OK? 3. Condition of error displayed YES NO Other than FDT and FDT and FDTC series FDTC series (4) NO Note (4) ⑤ • Wrong connection or breakage of connecting wires • Blown fuse • Transformer anomaly • Indoor power PCB anomaly • Broken harness • Indoor control PCB anomaly Indoor power PCB anomaly Replace it for GND YES 4.Presumable cause Replace fuse Note (3) LM: Louver motor FM: Fan motor Is DC5V detected between ④- ⑤ of CNW2? Is DC18V or higher detected between RedRed (CNW2) at the transformer secondary side? Replace FM, LM and etc. NO YES Indoor control PCB anomaly Replace it Replace transformer Indoor control PCB anomaly Replace it Note: - AMP Air Conditioning 99 www.ampair.co.uk | [email protected] '11 • KX-T-166 Error code Remote controller: None 7-segment display: 1.Applicable model LED Green Red Content Power supply system error (Power supply to remote controller) Indoor Stays Off Keeps lighting Outdoor Stays Off Keeps lighting 5.Troubleshooting All models Diagnosis Countermeasure Isn't there any loose connection of remote controller wires? YES Correct it. YES Replace wires. YES Replace remote controller. NO 2.Error detection method Isn't remote controller wire broken or short-circuited? NO Disconnect the remote controller wires. Is DC15V or higher detected between X-Y of indoor unit terminal block? 3. Condition of error displayed Other than NO FDT and FDT and FDTC Series FDTC Series Is DC18V detected between ①- ② of CNW2? YES 4.Presumable cause • Remote controller wire breakage/short-circuit • Remote controller anomaly • Malfunction by noise • Indoor power PCB anomaly • Broken harness • Indoor control PCB anomaly Is 23V or higher detected between Brown-Brown at the transformer secondary side? NO Indoor power PCB anomaly Replace it. Indoor control PCB anomaly Replace it. NO Replace transformer. YES Indoor control PCB anomaly Replace it. Note: - AMP Air Conditioning 100 www.ampair.co.uk | [email protected] '11 • KX-T-166 LED Error code Remote controller: 7-segment display: WAIT 1.Applicable model Green Red Content Indoor Keeps flashing Stays Off (1) Outdoor Keeps flashing Keeps flashing 5.Troubleshooting All models (In case that is kept WAIT on displaying on the remote controller for more than 2 minutes after power ON) WAIT Diagnosis WAIT is kept on displaying on the remote controller for more than 2 minutes after power ON Countermeasure Once turn OFF the breaker and turn ON it again at 3 minute after power OFF Does it become normal? NO 2.Error detection method Isn't the power fuse (5A) on the outdoor control PCB blown? YES Replace fuse Refer next page NO Is AC380-415V detected at the secondary side of noise filter PCB terminal? NO Replace noise filter PCB NO Connect wires correctly NO Indoor control PCB anomaly Replace it YES Is the connection of wire between noise filter and inverter PCBs OK? YES 3. Condition of error displayed Does indoor green LED keep flashing? YES Does indoor green LED flash 2 times? NO YES Are the wires between indoor and outdoor units connected properly ? NO Correct the connecting wires between indoor and outdoor units NO Outdoor control PCB anomaly Replace it NO Breakage of connecting wire Noise YES Indoor control PCB anomaly Replace it YES 4.Presumable cause • Fuse blown • Noise filter anomaly • Anomalous connection of wire between PCBs • Indoor control PCB anomaly • Remote controller anomaly • Breakage of connecting wires of remote controller • Outdoor control PCB anomaly Is AC380-415V detected between L1-L2, L2-L3, L3-L1 respectively at outdoor terminal block? Indoor/outdoor control PCB anomaly Replace it Remote controller anomaly Replace it Breakage of wires for remote controller Replace it YES Is AC220-240V detected between L-N at indoor teminal block? Note: (1) When anomaly occurs during establishing communication betweeen indoor and outdoor unit, error code E5 is displayed (outdoor red LED flash 2-times) In case of E5, the way of troubleshooting is same as above mentioned (except for checking of connecting wire) When reset the power after E5 occurs, if this anomaly recurs, WAIT is displayed on remote controller. If power ON/OFF is repeated in a short period (within 1 minute), WAIT may be displayed. In such case, please wait for 3 minute after the power breaker OFF. (2) If any error is detected 30 minutes after displaying“ WAIT ”on the remote controller, the display changes to“INSPECT I/U” . - AMP Air Conditioning 101 www.ampair.co.uk | [email protected] '11 • KX-T-166 LED Error code Remote controller: 7-segment display: WAIT 1.Applicable model Green Red Content Indoor Keeps flashing Stays Off WAIT Outdoor Keeps flashing Keeps flashing (2) 5.Troubleshooting All models Diagnosis Countermeasure (In case of fuse blown, how to check the unit before replacement of fuse) Isn't there any short circuit between phases of noise filter? YES Replace noise filter NO 2.Error detection method Isn't there any crack or damage on power transistor module or diode stack? YES Replace inverter PCB NO Isn't there any anomaly on reactor? YES Replace reactor 3. Condition of error displayed NO Replace fuse 4.Presumable cause • Fuse blown • Noise filter anomaly • Anomalous connection of wire between PCBs • Indoor control PCB anomaly • Remote controller anomaly • Breakage of connecting wires of remote controller • Outdoor control PCB anomaly Note: - AMP Air Conditioning 102 www.ampair.co.uk | [email protected] '11 • KX-T-166 LED Error code Remote controller: 7-segment display: WAIT 1.Applicable model Green Red Content Indoor Keeps flashing Stays Off WAIT Outdoor Keeps flashing Keeps flashing (3) 5.Troubleshooting All models Diagnosis Countermeasure (No display on the remote controller after power ON) No display on the remote controller after power ON 2.Error detection method Does indoor green LED keep flashing? NO Is The fuse on indoor control PCB OK? NO Fuse blown Replace fuse YES Is AC18V or higher is detected between RedRed at secondary side of indoor transformer? (1) YES NO Transformer anomaly Note (1) except FDT and FDTC YES Is DC10-11V between X-Y at indoor control PCB side when removing remote controller ? NO Remote controller wire short-circuited YES 3. Condition of error displayed Remote controller anomaly Does outdoor red LED flash 2-times? NO Indoor control PCB anomaly Remote controller anomaly Brakage of connecting wires of remote controller NO Correct the connecting wires properly YES Is the connecting wires between indoor and outdoor units comnnected properly? YES 4.Presumable cause • Fuse blown • Noise filter anomaly • Anomalous connection of wire between PCBs • Indoor control PCB anomaly • Remote controller anomaly • Breakage of connecting wires of remote controller • Outdoor control PCB anomaly Is AC380-415V detected between L1-L2, L2-L3, L3-L1 respectively at outdoor terminal block? NO Outdoor control PCB anomaly Replace it YES Is AC220-240V detected between L-N at indoor teminal block? NO Breakage of connecting wire Noise YES Indoor control PCB anomaly Replace it Note: - AMP Air Conditioning 103 www.ampair.co.uk | [email protected] '11 • KX-T-166 LED Error code Remote controller: 7-segment display: WAIT 1.Applicable model Green Content Indoor Keeps flashing Stays Off WAIT Outdoor Keeps flashing Keeps flashing (4) 5.Troubleshooting All models (In case that is kept WAIT on displaying on the remote controller for more than 2 minutes after power ON) Red Countermeasure Diagnosis is kept on WAIT displaying on the remote controller for more than 2 minutes after power ON To next page A 2.Error detection method Does outdoor green LED keep flashing? NO YES Does indoor green LED keep flashing? NO Indoor control PCB anomaly Replace it NO Indoor control PCB anomaly Replace it Remote controller anomaly Replace it Breakage of wires for remote controller Replace it YES Does outdoor red LED flash 2 times? YES 3. Condition of error displayed Are the wires between indoor and outdoor units connected properly ? NO Correct the connecting wires between indoor and outdoor units YES Is AC380-415V detected between L1-L2, L2-L3, L3-L1 respectively at outdoor terminal block? NO Outdoor control PCB anomaly Replace it YES Is AC220-240V detected between L-N at indoor teminal block? NO 4.Presumable cause YES • Fuse blown • Noise filter anomaly • Anomalous connection of wire between PCBs • Indoor control PCB anomaly • Remote controller anomaly • Breakage of connecting wires of remote controller • Outdoor control PCB anomaly Breakage of connecting wire Noise Indoor control PCB anomaly Replace it Note: - AMP Air Conditioning 104 www.ampair.co.uk | [email protected] '11 • KX-T-166 LED Error code Remote controller: 7-segment display: WAIT 1.Applicable model Green Red Indoor Stays OFF Stays Off WAIT Outdoor Stays OFF Stays Off (5) 5.Troubleshooting All models (In case that LED on outdoor control PCB stays OFF) Content Diagnosis Countermeasure In case that LED on outdoor control PCB stays OFF From previous page A Once turn OFF the breaker and turn ON it again at 3 minute after power OFF 2.Error detection method Does it become normal? NO YES Is power fuse (5A) on the outdoor conrol PCB blown? Normal (Malfunction by temporary noise) NO Check inverter before replacement of 52C YES B 3. Condition of error displayed Is AC380-415V detected at secondary side of noise filter? To next page NO Replace noise filte NO Connect the connecting wire properly YES Are connecting wires between noise filter and inverter PCB connected properly? YES 4.Presumable cause • Fuse blown • Noise filter anomaly • Anomalous connection of wire between PCBs • Indoor control PCB anomaly • Remote controller anomaly • Breakage of connecting wires of remote controller • Outdoor control PCB anomaly Is the connection of connecting wire of reactor OK? NO Correct connection (In case of breakage of wire replace it) YES Is there any anomaly on outdoor fan motor? NO YES Outdoor control PCB anomaly Replace it Outdoor fan motor anomaly Replace it Note: - AMP Air Conditioning 105 www.ampair.co.uk | [email protected] '11 • KX-T-166 LED Error code Remote controller: 7-segment display: WAIT 1.Applicable model Green Red WAIT Outdoor Stays Off Stays Off (6) 5.Troubleshooting All models (In case of fuse blown, how to check the unit before replacement of fuse) Content Indoor Stays Off Stays Off Diagnosis Countermeasure From previous page B Isn't there any short circuit between phases of noise filter? 2.Error detection method YES Replace Noise filter NO Isn't there any short circuit between phases at input terminal of inverter PCB? YES NO Isn't there any crack or damage on power transistor module or diode stack? YES Replace inverter PCB NO 3. Condition of error displayed Isn't there any anomaly on reactor? Replace reactor NO Isn't there any anomaly on electrolytic capacitor? 4.Presumable cause YES Replace electrolytic capacitor NO • Fuse blown • Noise filter anomaly • Anomalous connection of wire between PCBs • Indoor control PCB anomaly • Remote controller anomaly • Breakage of connecting wires of remote controller • Outdoor control PCB anomaly YES Replace power fuse Note: - AMP Air Conditioning 106 www.ampair.co.uk | [email protected] '11 • KX-T-166 Error code Remote controller:〔No display〕 7-segment display: 1.Applicable model LED Green Red [No display] Outdoor Stays OFF Stays Off 5.Troubleshooting All models (No display on the remote controller after power ON) Content Indoor Stays OFF Stays Off Diagnosis No display on the remote controller after power ON Is DC10V or higher between X-Y detected at remote controller terminal? 2.Error detection method Countermeasure NO Remote controller anomaly NO Remote controller anomaly NO Correct connecting wire YES Is DC10V or higher between X-Y wires detected when removing remote controller? YES Are connecting wires between indoor and outdoor units connected properly? 3. Condition of error displayed YES Indoor control PCB anomaly 4.Presumable cause • Fuse blown • Noise filter anomaly • Anomalous connection of wire between PCBs • Indoor control PCB anomaly • Remote controller anomaly • Breakage of connecting wires of remote controller • Outdoor control PCB anomaly Note: - AMP Air Conditioning 107 www.ampair.co.uk | [email protected] '11 • KX-T-166 Error code Remote controller: E1 7-segment display: - 1.Applicable model LED Green Red Content Remote controller communication error Indoor Keeps flashing Stays Off Outdoor Keeps flashing Stays Off 5.Troubleshooting All models Diagnosis (2) Is it possible to reset normally by the power supply reset? Countermeasure Malfunction by temporary noise. Check peripheral environment YES NO 2.Error detection method When normal communication between remote controller and indoor unit is interrupted for more than 2 minutes (Detectable only with the remote controller) (1) Note (1) SW7-1: OFF ON Turn SW7-1 OFF.ON Disconnect the wire ③ between indoor and outdoor units Reset power supply Does the drain pump start automatically at one minutes after power ON? Indoor control PCB anomaly Replace it YES NO 3. Condition of error displayed Note (2) Does the remote controller displays “Internal check ON” even after 3 minutes? Remote controller anomaly Replace it Same as above 4.Presumable cause • Anomalous communication circuit between remote controller and indoor unit • Noise Note: If the indoor unit cannot communicate normally with the remote controller for 180 seconds, the indoor unit PCB starts to reset automatically. - AMP Air Conditioning 108 www.ampair.co.uk | [email protected] '11 • KX-T-166 Error code Remote controller: E2 7-segment display: - 1.Applicable model LED Green Red Content Indoor Keeps flashing Keeps flashing Duplicated indoor unit address Outdoor Keeps flashing Stays Off 5.Troubleshooting All models Diagnosis Is the number of connected indoor units up to 128 units? Countermeasure Review number of connected units. NO 2.Error detection method YES More than 129 indoor units are connected in the same superlink system. Duplicated indoor unit address Is the different address No. assigned to each indoor unit? NO Correct indoor unit address setting. YES Reset the power supply and restart. Caution: Unless the power supply is reset, addresses will not be confirmed. 3. Condition of error displayed Is E2 displayed? NO Implement test run. YES Replace indoor control PCB. * Same as above * Before replacement, confirm whether the rotary switch for address setting is not damaged. (It was experienced that No. 5 on rotary switch was not recognized.) 4.Presumable cause • Number of connected indoor units exceeds the limitation. • Duplicated indoor unit address • Indoor control PCB anomaly Note: - AMP Air Conditioning 109 www.ampair.co.uk | [email protected] '11 • KX-T-166 Error code Remote controller: E3/5 7-segment display: - 1.Applicable model LED Green Red Content Indoor Keeps flashing 2 times flash Outdoor unit signal line error Outdoor Keeps flashing Stays Off 5.Troubleshooting All models Diagnosis Countermeasure E3 is a communication error that occurs when communication between indoor and outdoor units is not established at all. Once the communication between indoor and outdoor units is established, it changes to E5. In both cases, check signal wires (between indoor outdoor units) locally Reset the power supply and restart. NO Temporary malfunction by noise. Identify the source of noise and correct it. YES Change to spare circuit. NO Indoor control PCB anomaly Replace it NO Correct it. NO Correct it. NO Correct it. YES Outdoor control PCB anomaly Replace it 2.Error detection method Does E3/E5 occurs? No outdoor unit exists in the same superlink system. YES Is protective fuse for the super link circuit blown? NO Is the LED on indoor control PCB OK? 3. Condition of error displayed Same as above YES Is the power supply to outdoor unit OK? YES Is the outdoor unit address set on the indoor unit OK? 4.Presumable cause • Power is not supplied to the outdoor unit • Unmatch of pairing between indoor and outdoor units • Indoor control PCB anomaly • Outdoor control PCB anomaly • Missing local wiring YES signal wires (between indoor ~ outdoor units) connection OK? Note: - AMP Air Conditioning 110 www.ampair.co.uk | [email protected] '11 • KX-T-166 Error code Remote controller: E5 7-segment display: - 1.Applicable model LED Green Red Content Indoor Keeps flashing *See below Communication error during operation Outdoor Keeps flashing 2 time flash 5.Troubleshooting All models Diagnosis Countermeasure * In case that indoor red LED flashes 2 times Note (1) Check the connection (disconnection, looseness) of signal wires at outdoor terminal block Is the connection of signal wires at the outdoor unit side OK? 2.Error detection method When the communication between indoor and outdoor units is interupted for more than 2 minutes Repair signal wires. NO YES Note (2) Check the connection (disconnection, looseness, brakage) of signal wires (between indoor and Is the outdoor units) connection of signal wires NO (between indoor and outdoor units) OK? Repair signal wires. YES Reset the power supply and restart. Does the remote controller LCD becomes normal? NO Go to the diagnosis of (1) WAIT YES Unit is normal. (Malfunction by temporary noise, etc.) 3. Condition of error displayed * In case that indoor red LED stays OFF When this anomaly is detected during operation. Reset the power supply and restart. Does the remote controller LCD becomes normal? NO YES Outdoor control PCB anomaly (Network communicaion circuit anomaly) Replace it Unit is normal. (Malfunction by temporary noise, etc.) 4.Presumable cause • Unit address No. setting error • Remote controller wires broken • Poor connection/disconnection of remote controller wires • Indoor control PCB anomaly Note: When the pump down switch is turned on, communication between indoor and outdoor units is cancelled so that "Communication error E5" will be displayed on the remote controller and indoor control PCB, but this is normal. - AMP Air Conditioning 111 www.ampair.co.uk | [email protected] '11 • KX-T-166 Error code LED Green Indoor heat exchanger temperature thermistor anomaly (Thi-R) Red Content Indoor Keeps flashing 1 time flash Remote controller: E6 7-segment display: - Outdoor Keeps flashing Stays Off 1. Applicable model 5.Troubleshooting All models Diagnosis Countermeasure Is the connector of thermistor connected properly ? NO Insert the connector securely YES 2. Error detection method Detection of anomalously low temperature (resistance) of Thi-R1, R2, R3 Regarding the characteristics of the thermistor, see the following chart Are the characteristics of thermistor OK? *1 NO Replace thermistor (Thi-R) YES Replace indoor control PCB *1 Check several times to prove any poor connection 3. Condition of error displayed Temperature-resistance characreristics of indoor heat exchanger temperature thermistor (Thi-R1, R2, R3) Ω • If -50ºC or lower is detected for 5 seconds continuously, compressor stops. After 3-minute delay, the compressor is restarted automatically, but if this anomaly occurs again within 60 minutes after the initial detection. • Or if 70ºC or higher is detected for 5 seconds continuously. 4. Presumable cause Ω Te • Anomalous connecion of indoor heat exchanger temperature thermistor • Indoor heat exchanger temperature thermistor anomaly • Indoor control PCB anomaly Temperature (ºC) Note: - AMP Air Conditioning 112 www.ampair.co.uk | [email protected] '11 • KX-T-166 Error code Remote controller: E7 7-segment display: - 1.Applicable model LED Green Red Indoor Keeps flashing 1 time flash Outdoor Keeps flashing Stays Off Content Indoor return air temperature thermistor anomaly (Thi-A) 5.Troubleshooting All models Diagnosis Countermeasure Is the connector of thermistor connected properly ? NO Insert the connector securely YES Regarding the characteristics of the thermistor, see the following chart 2.Error detection method Are the characteristics of thermistor OK? *1 Detection of anomalously low temperature (resistance) of Thi-A NO Replace thermistor (Thi-A) YES Replace indoor control PCB *1 Check several times to prove any poor connection 3. Condition of error displayed 4.Presumable cause • Anomalous connection of indoor return air temperature thermistor • Indoor return air temperature thermistor anomaly • Indoor control PCB anomaly Temperature-resistance characreristics of indoor return air temperature thermistor (Thi-A) Temperature thermistor resistance (kΩ) • If -50°C or lower is detected for 5 seconds continuously, compressor stops. After 3-minutes delay the compressor is restarted automatically, but if this anomaly occurs again within 60 minutes after the initial detection. • Or if 48°C or higher is detected for 5 seconds continuously. 15 10 5 0 10 20 30 40 50 Temperature (°C) Note: - AMP Air Conditioning 113 www.ampair.co.uk | [email protected] '11 • KX-T-166 Error code Remote controller: E9 7-segment display: - 1.Applicable model LED Green Red Content Indoor Keeps flashing 1 time flash Drain trouble Outdoor Keeps flashing Stays Off 5.Troubleshooting FDT, FDTC, FDTW, FDTQ, FDTS, FDR, FDU, FDUM, and FDQS series Diagnosis Countermeasure Check the error data in the remote controller. Is there any overflow? NO Is DC 12V detected at CN1 connector? 2.Error detection method Float switch is activated YES NO YES Check float switch. Is the CN1 connected firmly NO Check the connection of CNI If it is loose, connect it securely NO Replace indoor control PCB. YES Check optional equipment YES NO Is the humidifier connected? Is there any anomaly on the optional equipment? YES 3. Condition of error displayed If the float switch OPEN is detected for 3 seconds continuously or if float switch connector is disconnected or wire broken. Is the humidifier Drain Motor interlocked by the indoor unit function setting of remote controller? Correct setting to "Humidifier drain motor interlock" NO YES Drain motor ON from the remote controller Does the drain motor operate? NO Is AC220/240V detected at CNR? NO YES YES 4.Presumable cause • Indoor control PCB anomaly • Mistake in setting of float switch • Mistake in setting of humidifier drain motor interlock • Mistake in setting of optional equipment • Mistake in drain piping • Drain motor anomaly • Disconnection/breakage of drain motor wires Is the drain piping unclogged? Is the drain pipe slop OK? Indoor control PCB anomaly Replace it Check the wiring of drain motor NO Correct it. YES Check drain motor Note: When this anomaly occurs at power ON, disconnection of connector or breakage of wire of float switch is suspected. Check and correct it (or replace it, if necessary). - AMP Air Conditioning 114 www.ampair.co.uk | [email protected] '11 • KX-T-166 Error code Remote controller: E10 7-segment display: - 1.Applicable model LED Green Red Indoor Keeps flashing Stays Off Outdoor Keeps flashing Stays Off Content Excessive number of indoor units (moe than 17 units) by controlling one remoto controller 5.Troubleshooting All models Diagnosis Aren't more than 17 indoor units connected to one remote controller? 2.Error detection method Countermeasure NO Remote controller anomaly Replace it. YES Reduce to 16 or less units. When it detects more than 17 of indoor units connected to one remote contorller 3. Condition of error displayed Same as above 4.Presumable cause • Excessive number of indoor units connected. • Remote controller anomaly. Note: - AMP Air Conditioning 115 www.ampair.co.uk | [email protected] '11 • KX-T-166 Error code Remote controller: E12 7-segment display: - 1.Applicable model LED Green Red Content Indoor Keeps flashing Keeps flashing Outdoor Keeps flashing Stays Off Address setting error by mixed setting method 5.Troubleshooting All models Diagnosis Countermeasure Isn't the automatic setting and manual setting mixed in the address setting method for indoor units? YES Review address setting. 2.Error detection method Automatic address setting and manual adress setting are mixed when setting adress of indoor units Replace indoor control PCB. NO Address setting method list (Figures in [ ] are for Previous superlink models) Models for new superlink protocol Models for Previous superlink protocol Outdoor unit Outdoor unit Indoor unit address setting address setting address setting Indoor unit No. SW Outdoor unit No. SW Outdoor unit No. SW Indoor unit No. SW Outdoor unit No. SW Outdoor unit No. SW (New SL) 000-127 00-31 00-31 00-47 00-47 00-47 (Previous SL) [00-47] [00-47] [00-47] (New SL) 000 49 49 49 49 49 (Previous SL) (New SL) 000 49 00-31 Not available (Previous SL) Not available Indoor unit address setting Manual address setting Automatic address setting for single refrgerant system Automatic address setting for multiple refrgerant systems 3. Condition of error displayed Same as above 4.Presumable cause Mistake in address setting for indoor unit Note: - AMP Air Conditioning 116 www.ampair.co.uk | [email protected] '11 • KX-T-166 Error code Remote controller: E16 7-segment display: - 1.Applicable model LED Green Red Content Indoor Keeps flashing 1 time flash Indoor fan motor anomaly (FDT series) Outdoor Keeps flashing Stays Off 5.Troubleshooting FDT series only Diagnosis Countermeasure Does any foreign matter intervene in rotational area of fan propeller? YES Remove foreign matter. NO Replace the fan motor. NO 2.Error detection method Does the fan rotate smoothly when turned by hand? Detected by revolution speed of indoor fan motor YES Note (1)④ is GND (1) Is DC280V detected between ① - ④ of fan motor connector CNM? YES NO NO Is the fuse F202 blown? Reset the power supply and restart. YES 3. Condition of error displayed When actual revolution speed of indoor fan motor drops to lower than 200min-1 for 30 seconds continuously, the compressor and the indoor fan motor stop. After 2-seconds delay, fan motor starts again automatically, but if this anomaly occurs 4 times within 60 minutes after the initial detection. NO Does it become normal? YES Check power supply voltage. Replace fan motor and power PCB. Replace fan motor. (If the anomaly persists after replacing the fan motor, replace the indoor control PCB.) Malfunction by temporary noise 4.Presumable cause • Indoor fan motor anomaly • Foreign matter at rotational area of fan propeller • Fan motor anomaly • Dust on control PCB • Blown fuse • External noise, surge Note: - AMP Air Conditioning 117 www.ampair.co.uk | [email protected] '11 • KX-T-166 Error code Remote controller: E16 7-segment display: - 1.Applicable model LED Green Red Content Indoor Keeps flashing 1 time flash Indoor fan motor anomaly (FDK series) Outdoor Keeps flashing Stays Off 5.Troubleshooting FDK series only Diagnosis Countermeasure Does any foreign matter intervene in rotational area of fan impeller? YES Remove foreign matter. NO 2.Error detection method Does the fan rotate smoothly when turned by hand? NO Replace fan motor. Detected by revolution speed of indoor fan motor YES Note (1) ③ for GND (1) Is DC280V detected between ① - ③ of fan motor connector CNM? NO Replace fan motor and power PCB YES Reset the power supply and restart. 3. Condition of error displayed When actual revolution speed of indoor fan motor drops to lower than 200min-1 for 30 seconds continuously, the compressor and the indoor fan motor stop. After 3-seconds delay, fan motor starts again automatically, but if this anomaly occurs 4 times within 60 minutes after the initial detection. Does is become normal? NO YES Replace fan motor. (If this anomaly persists after replacing the fan motor, replace indoor control PCB.) Malfunction by temporary noise 4.Presumable cause • Indoor fan motor anomaly • Foreign matter at rotational area of fan impeller • Fan motor anomaly • Dust on control PCB • Blown fuse • External noise, surge Note: - AMP Air Conditioning 118 www.ampair.co.uk | [email protected] '11 • KX-T-166 Error code Remote controller: E18 7-segment display: - 1.Applicable model LED Green Red Content Indoor Keeps flashing 1 time flash Outdoor Keeps flashing Stays Off Address setting setting error error of of Address master and and slave slave indoor indoor units units master 5. Troubleshooting All models Diagnosis Is the address setting for the master indoor unit correct? Countermeasure NO Correct the address setting of the master indoor unit NO Supply the power to the master indoor unit NO Connect the superlink signal wires correctly㪅㩷 YES 2. Error detection method (1) When the address setting for the master indoor unit is not existing in the same superlink system. (2) When the address setting for the slave indoor unit is set for the master indoor unit redundantly. Is the power surely supplied to the master indoor unit ? YES Are the superlink signal wires connected between master and slave indoor units? YES 3. Condition of Error displayed Same as above NO Indoor control PCB anomaly → Replace it (Firstly replace PCB on the slave indoor unit. If it is not recovered, replace PCB on the master indoor unit as well.) 4. Presumable cause Address setting error of the master indoor unit No power supply to the master indoor unit No connection of superlink signal wires between master and slave indoor unit. Note: - AMP Air Conditioning 119 www.ampair.co.uk | [email protected] '11 • KX-T-166 Error code Remote controller: E19 7-segment display: - 1.Applicable model LED Green Red Content Indoor unit operation check, drain motor check mode anomaly Indoor Keeps flashing 1 time flash Outdoor Keeps flashing Stays Off 5.Troubleshooting All models Diagnosis Countermeasure E19 occurs when the power ON 2. Error detection method E19 occurs Is SW7-1 on the indoor control PCB ON? YES NO Indoor control PCB anomaly (Anomalous SW7) Replace Turn SW7-1 on the indoor control PCB OFF and reset the power 3. Condition of error displayed Same as above 4. Presumable cause Mistake in SW7-1 setting Due to forgetting to turn OFF SW7-1 after indoor operation check) Note: Indoor operation check/drain pump check mode If the power is ON after SW7-1ON. indoor operation check/drain pump check mode can be established. 1) When the communication between remote controller and indoor PCB is established 15 seconds after power ON, it goes to indoor operation check. 2) When the communication between remote controller and indoor PCB is not established, it goes to drain pump check (CnB connector should be open before power ON) - AMP Air Conditioning 120 www.ampair.co.uk | [email protected] '11 • KX-T-166 Error code Remote controller: E20 7-segment display: - 1.Applicable model LED Green Red Content Indoor Keeps flashing 1 time flash Indoor fan motor rotation speed anomaly (In case of FDT,FDTC,FDFW and FDK series) Outdoor Keeps flashing Stays Off 5.Troubleshooting FDT,FDTC,FDFW and FDK series only Diagnosis Countermeasure Does any foreign matter intervene in rotational area of fan propeller? Remove foreign material. YES NO 2. Error detection method Detected by rotation speed of indoor fan motor Does the fan rotate smoothly when turned by hand? Replace the fan motor. NO YES Note (1) ③,④ for GND (2) Valve in ( ) are for the model FDFW and FDK (1) (2) Is DC280V FDK, FDFW series detected between①-④(①-③) of NO fan motor connector CNM? FDTC, FDT series YES NO Is the fuse F202 blown? Reset the power supply and restart. YES 3. Condition of error displayed When the actual fan rotation speed does not reach to the speed of [required speed ─50min−1] after 2 minutes have been elapsed since the fan motor rotation speed command was output, the unit stops by detecting indoor fan motor anomaly. NO Does it become normal? YES Replace fan motor and power PCB. Check power supply voltage. Replace fan motor and power PCB. Replace fan motor. (If the anomaly persists after replacing the fan motor, replace the indoor control PCB.) Malfunction by temporary noise 4. Presumable cause • Indoor fan motor anomaly • Foreign matter at rotational area of fan propeller • Fan motor anomaly • Dust on control PCB • Blown fuse • External noise, surge Note: - AMP Air Conditioning 121 www.ampair.co.uk | [email protected] '11 • KX-T-166 Error code Remote controller: E21 LED Green Red Content Defective panel switch operation (FDT) Indoor Keeps flashing 1 time flash Outdoor Keeps flashing Stays OFF 1.Applicable model 5. Troubleshooting FDT series only Diagnosis Is grill opened? Countermeasure YES Reset the error and close the grill. YES Insufficient push on the panel switch at the internal face of grill ➞Attach 3 mm thick rubber sheet at the section where the panel switch touches the inside of grill. Close then the grill. NO 2. Error detection method Panel switch (PS) has detected Open for more than 1 second. Does matter improve if panel switch is turned ON forcibly after resetting error? NO Are connectors at right inserted properly? <Forced panel switch ON> Put the switch in the state of ON by fixing the silicone section of panel switch with adhesive tape while it is held down. NO <Connectors on PCBs> Indoor control PCB: CNV Disconnected, poorly connected connectors ➞Reinsert properly. →To CNY1 YES Panel switch 3. Condition of Error displayed Same as above Is there continuity between #1 – #4 of CNV on indoor control PCB when panel switch operation is checked? Silicone guide Push to turn ON. NO ・Defective panel switch or incorrect panel switch wiring ➞ Replace panel switch. ・Broken wire between panel PCB (CNV) ➞ Correct or replace wire. YES Defective indoor control PCB ➞ Replace indoor control PCB. 4. Presumable cause •Defective panel switch •Disconnection of wiring •Defective indoor control PCB Note: -121-1 - AMP Air Conditioning # www.ampair.co.uk | [email protected] '11 • KX-T-166 Error code Remote controller: E28 7-segment display: - 1.Applicable model LED Green Red Indoor Keeps flashing Stays Off Outdoor Keeps flashing Stays Off Content Remote controller temperature thermistor anomaly (Thc) 5.Troubleshooting All models Diagnosis Is the connector of thermistor connected properly ? YES 2. Error detection method Insert the connector securely NO Regarding the characteristics of the thermistor, see the following table Are the characteristics of thermistor OK? Is the thermistor wire OK *1 Detection of anomalously low temperature (resistance) of Thc Countermeasure NO Replace thermistor (Thc) YES Replace indoor control PCB *1 Check several times to prove any poor connection Temperature-resistance characreristics of remote controller temperature thermistor (Thc) Temperature (°C) Resistance (kΩ) Temperature (°C) Resistance (kΩ) Temperature (°C) Resistance (kΩ) Temperature (°C) Resistance (kΩ) 3. Condition of error displayed • If -50ºC or lower is detected for 5 seconds continuously, compressor stops. After 3-minutes delay, the compressor is restarted automatically, biut if this anomaly occurs again within 60 minutes after the initial detection. 0 1 2 4 6 8 10 12 65 62 59 53 48 44 40 36 14 16 18 20 22 24 26 28 33 30 27 25 23 21 19 18 30 32 34 36 38 40 42 44 16 15 14 13 12 11 9.9 9.2 46 48 50 52 54 56 58 60 8.5 7.8 7.3 6.7 6.3 5.8 5.4 5.0 4. Presumable cause • Anomalous connection of remote controller temperature thermistor • Remote controller temperature thermistor anomaly • Remote controller PCB anomaly Note: After 10 seconds has elapsed since remote controller temperature thermistor was switched from invalid to valid, E28 will not be displayed even if the thermistor harness is disconnected or broken. However, in such case, the indoor return air temperature thermistor (Thi-A) will be valid instantly instead of the remote controller temperature thermistor (Thc). Please note that even though the remote controller temperature thermistor (Thc) is valid, the displayed return air temperature on the remote controller LCD shows the value detected by the indoor return air temperature thermistor (Thi-A), not by the remote controller temperature thermistor (Thc). - AMP Air Conditioning 122 www.ampair.co.uk | [email protected] '11 • KX-T-166 Error code Remote controller: E30 7-segment display: E30 1.Applicable model LED Green Red Content Indoor Keeps flashing Stays Off Outdoor Keeps flashing 1 time flash Unmatch connection of indoor and outdoor unit 5.Troubleshooting Outdoor unit Diagnosis Is the wiring connection between indoor and outdoor units correctly? Countermeasure NO Correct the wiring NO Replace outdoor control PCB NO Disconnection or breakage of wire between indoor and outdoor unit 2. Error detection method YES Is the voltage between L1-L2, L2-L3 and L3-L1 at the terminal brock on outdoor unit AC380/415V respectively? YES 3. Condition of error displayed Is the voltage between L1-N at the terminal block on indoor unit AC220/240V? YES Replace indoor unit PCB 4. Presumable cause • Indoor control PCB anomaly • Outdoor control PCB anomaly Note: - AMP Air Conditioning 123 www.ampair.co.uk | [email protected] '11 • KX-T-166 LED Error code Green Red Content Indoor Keeps flashing Stays Off Remote controller: E31 7-segment display: E31 Outdoor Keeps flashing 1 time flash Duplicated outdoor unit address No. 5.Troubleshooting 1.Applicable model Outdoor unit Diagnosis Countermeasure Check and save the data of operating condition. Check the conditions whether it occurs immediately after the power on or during operation. Check the current address Nos. of outdoor units. Save data for 30 minutes before stopping in Mente PC 2. Error detection method Reset the power supply and restart operation. When the microcomputer of outdoor control PCB recognizes the dupplicated address No. by scanning all adresses of outdoor units in the same superlink system. Does E31 recur? Caution: Unless the power is reset after changing address, the set address will not be confirmed NO Test run *No action is taken because it is judged that the power reset is not done after changing address YES Correct address. NO Replace outdoor control PCB. * YES Check outdoor address No. in the same superlink system Does the same address No. exist? 3. Condition of error displayed When duplicated outdoor unit address No. exists in the same superlink system. * Before replacement, please confirm whether the rotary switch for address setting is not damaged. (It was experienced that No. 5 on rotary switch was not recognized.) 4. Presumable cause • Mistake in the address setting of outdoor units • More than 129 indoor units connected Maximum number can be set by address switch is 128 units • No setting of Master/Slave setting switch for combination use [ ] Note: After taken above measure, reset the power and confirm no error is displayed occurs Unless the power is reset after changing address, the set address will not be confirmed In case of combination use, set the same address to both master and slave units. Distinction of master or slave unit is done by setting SW4-7. (Refer the instruction manual and technical manual for details) - AMP Air Conditioning 124 www.ampair.co.uk | [email protected] '11 • KX-T-166 Error code Remote controller: E32 7-segment display: E32 1.Applicable model LED Green Red Content Open L3 Phase on power supply at primary side Indoor Keeps flashing Stays Off Outdoor Keeps flashing 1 time flash 5.Troubleshooting Outdoor unit Diagnosis Countermeasure Check and save the data of operating condition. Check the conditions whether it occurs immediately after the power on or during operation or stopping. (It will be useful to persuade the customer why an improvement of power supply is required by showing these data) Save data for 30 minutes before stopping in Mente PC 2. Error detection method By Checking the power supply voltage at primary side of the outdoor control PCB (Check only L3 phase) Is the power supply voltage (between phases) at the primary side OK? NO Check it, as much as possible, under the operating conditions for 30 minutes before error occurred. YES Reset the power supply and restart operation. Does E32 recur? Propose an improvement to the customer. YES Replace outdoor control PCB. NO Wait and see without taking any action. 3. Condition of error displayed When the power supply voltage between L1-L3 or L2-L3 becomes 0V and/or the current of L3 decrease to 0A 4. Presumable cause • Anomalous power supply at primary side • Outdoor control PCB anomaly. Note: - AMP Air Conditioning 125 www.ampair.co.uk | [email protected] '11 • KX-T-166 Error code Remote controller: E36 7-segment display: E36-1 1.Applicable model LED Green Red Content Indoor Keeps flashing Stays Off Outdoor Keeps flashing 1 time flash Discharge pipe temperature error (Tho-D1) 5.Troubleshooting Outdoor unit Diagnosis Countermeasure Check and save the data of operating condition Check the ROM version Confir ation of SV1 operation Save data for 30 minutes before stopping in Mente PC Is the unit installation environment within the range of limitation? NO Propose an improvement to the customer. YES 2. Error detection method When anomalously high temperature is detected by the discharge pipe temperature thermistor (Tho-D1) Are the refrigerant amount and piping length OK? NO YES Is the insertion of the thermistor connector into the connector on outdoor control PCB OK? NO Insert connector securely. NO Check if the characteristics are correct by referring the characteristics chart of E39. And if necessary, replace the discharge pipe temperature thermistor. YES Is the discharge pipe temperature thermistor OK? 3. Condition of error displayed When 130°C or higher is detected by the discharge temperature thermistor, the compressor stops. After 3 minutesdelay, the compressor starts again automatically, but if this anomaly occurs 2 times within 60 minutes after the initial detection, or 130°C or higher is detected continuously for 60 minutes. 4. Presumable cause • Discharge pipe temperature anomaly • SV1 (liquid refrigerant by-pass valve ) anomaly • Beakage of coil • Faulty main body. • Outdoor control PCB anomaly • Insufficient amount of refrigerant • Insufficient airflow volume • Short-circuit of airflow YES Check it, as much as possible, under the operating conditions for 30 minutes before error occurred. Reset the power supply and restart operation. Is the error recur when restarting? NO YES Is there AC200V of output signal for SV1 from outdoor control PCB? Adjust the refrigerant amount poperly (Check whether the refrigerant amount is insufficient or not. (Check the gas leakage) Wait and see. Continue to obtain data, if possible. (Keep connecting the Mente PC) NO Replace outdoor control PCB NO Replace the coil SV1 YES Is the coil of SV1 energized? YES Does the refrigerant flow through SV1 main body ? YES NO Replace the SV1 main body (If there is no refrigerant in liquid line, charge refrigerant additionall) Check refrigerant amount again. Note: - AMP Air Conditioning 126 www.ampair.co.uk | [email protected] '11 • KX-T-166 Error code Remote controller: E36 7-segment display: E36-3 1.Applicable model LED Green Red Content Indoor Keeps flashing Stays Off Liqiud flooding anomal Outdoor Keeps flashing 3 times flash 5.Troubleshooting Outdoor units Diagnosis Countermeasure Check and save the data of operating condition Check the ROM version Comfirmation of SV1 operatio Save data for 30 minutes before stopping in Mente PC Are there any wrong connection of refrigerant piping and/or signal wiring ? . Check the numbers of connected indoor units recognized by outdoor unit in comparison with those numbers in utility drawing YES Correct the connection of refrigerant piping and/or signal wiring properly YES Adjust refrigerant amount properly NO 2. Error detection method When 5ºC or lower of the under-dome temperature superheat is detected for 15 minutes continuously or for 30 minutes continuously. 3. Condition of error displayed When above anomaly is detected 3 times within 90 minutes. Are there any excessive refrigerant charged at site? . Check the calculation result of additional refrigerant charging amount and the record of additional refrigerant charged amount NO Are there any leakage of refrigerant through valve sheet of SV1? . Check the temperature difference between before and after SV1 YES NO Are there any fault in subcooling coil circuit ? . Check whether the EEVSC is kept open . Check whether the thermistor of Tho-H is inserted in the thermistor holder properly (at cooling mode) . Check whether the characteristics of Tho-H and PSL is OK YES NO 4. Presumable cause • Unmatching of refrigerant piping and/or signal wiring • Overcharging of refrigerant • Anomalous control of superheat • Anomalous circuit of liquid refrigerant by-pass • Anomalous refrigerant circuit of subcool coil • Under-dome temperature (Tho-D1) anomaly Replace SV1 Replace the coil of SV1 Is the superheat control of indoor unit OK at cooling mode? . Check whether the indoor EEV is kept open or not . Check whether Thi-R1, R2 are installed at proper position or the characteristics of them are OK . Check whether the air filter is clogged . Check whether the indoor fan rotates NO YES Is the superheat control of outdoor unit OK at heating mode? . Check whether EEVH1 is kept open or not . Check whether Tho-R1, R2 are installed at proper position or the characteristics of them is OK . Check whether the characteristics of PSL are OK . Check whether the fin of outdoor heat exchanger is clogged with snow, ice or dust . Check whether the outdoor fan rotates NO YES Is the characteristics of Tho-C1 OK ? • Replace EEVSC • Check the coil of EEVSC Replace the coil of EEVSC • Replace Tho-H • Replace PSL • Replace indoor EEV • Check the coil of EEV Replace the coil of EEV • Check the installed position of Thi-R1, R2, R3 Replace Thi-R, if necessary • Check the air filter • Check the connection of indoor fan motor connector Replace indoor fan motor * By checking Thi-R1, R2, R3 from indoor unit operation data of Mente PC, specify the indoor unit which tends .to be liquid flooding (Thi-R3=.Thi-R2 shows the probability of liquid flooding) • Replace EEVH1 • Check the coil of EEVH1 Replace the coil of EEVH1 • Check the installed position of Tho-R1, R2, R3 Replace Tho-R, if necessary • Clean the fin of outdoor heat exchanger • Check the connection of outdoor fan motor connector Replace outdoor fan motor NO • Replace Tho-C1 YES Correct the data with Mente PC and ask our consultation Note:If the error does not recur, connect the Mente PC and continue to collect data. - AMP Air Conditioning 127 www.ampair.co.uk | [email protected] '11 • KX-T-166 Error code Remote controller: E37 7-segment display: E37-1, 2, 5, 6*1 LED Green Red Outdoor Keeps flashing Outdoor heat exchanger temperature termistor (Tho-R) and subcooling coil temperature thermistor (Tho-SC,-H) anomaly Content Indoor Keeps flashing Stays Off *1 *1 E37-1: one time flash (Tho-R1), E37-2: 2 time flash (Tho-R2), E37-5: 5 time flash (Tho-SC), E37-6: 6 time flash (Tho-H) 1.Applicable model 5.Troubleshooting Outdoor unit Diagnosis Countermeasure Check and save the data of operating conditions Check the conditions whether it occurs immediately after the power on or during operation or stopping. Check the sensed value. Compare the temperature on Mente PC with actual measured value Save data for 30 minutes before stopping in Mente PC 2. Error detection method Detection of anomalously low temperature (resistance) of Tho-R or Tho-SC or Tho-H Is the connector of thermistor connected properly? NO Insert the connector securely NO Replace Thermistor (Tho-SC, Tho-H, Tho-R) YES Replace outdoor control PCB YES Are the characteristics of thermistor OK?*2 *2 Check several times to prove any poor connection 3. Condition of error displayed 4. Presumable cause • Broken thermistor harness or the internal wire of sensing section (Check the molded section as well) • Disconnection of thermistor harness connection (connector) • Outdoor control PCB anomaly Temperature thermistor resistance (kΩ) • If -50°C or lower is detected for 5 seconds continuously within 2-minutes to 2-minutes 20-seconds after the compressor ON, the compressor stops.And after 3-minutes delay, the compressor starts again automatically, but if this anomalous temperature is detected 3 times within 40 minutes after the initial detection. • If -50°C or lower is detected for 5 seconds continuously within 20 seconds after power ON Outdoor heat exchanger temperature thermistor (Tho-R1, R2, R5, R6) Sub-cooling coil thermistor (Tho-SC,Tho-H) Temperature-resistance characteristics Temperature (°C) Note: - AMP Air Conditioning 128 www.ampair.co.uk | [email protected] '11 • KX-T-166 Error code Remote controller: E38 7-segment display: E38 1.Applicable model LED Green Red Content Outdoor air temperature thermistor anomaly (Tho-A) Indoor Keeps flashing Stays Off Outdoor Keeps flashing 1 time flash 5.Troubleshooting Outdoor unit Diagnosis Countermeasure Check and save the data of operating condition. Check the conditions whether it occurs immediately after the power on or during operation or stopping. Check the sensed value. Compare the temperature on Mente PC with actual measured value. Save data for 30 minutes before stopping in Mente PC 2. Error detection method Detection of anomalously low temperature (resistance) of Tho-A Is the connector of thermistor connected properly? Insert the connector securely NO YES Are the characteristics of thermistor OK?*1 Replace thermistor (Tho-A). NO Replace outdoor control PCB. YES *1 Check several times to prove any poor connection 100 • If -30°C or lower is detected for 5 seconds continuously within 2-minutes to 2-minutes 20-seconds after the compressor ON, the compressor stops. And after 3-minutes delay, the compressor starts again automatically, but if this anomalous temperature is detected 3 times within 40 minutes after the initial detection. • If -30°C or lower is detected for 5 seconds continuously within 20 seconds after power ON. 4. Presumable cause Temperature thermistor resistance (kΩ) 3. Condition of error displayed Temperature-resistance characteristics of Outdoor air temperature thermistor (Tho-A) 90 80 70 60 50 40 30 20 10 0 -20 -10 • Broken thermistor harness or the internal wire of sensing section (Check the molded section as well) • Disconnection of thermistor harness connection (connector) • Outdoor control PCB anomaly 0 10 20 30 Temperature (°C) 40 50 Note: - AMP Air Conditioning 129 www.ampair.co.uk | [email protected] '11 • KX-T-166 Error code Remote controller: E39 7-segment display: E39-1 1.Applicable model LED Green Red Content Discharge pipe temperature thermistor anomaly (Tho-D1) Indoor Keeps flashing Stays Off Outdoor Keeps flashing 1 time flash 5.Troubleshooting Outdoor unit Diagnosis Countermeasure Save data for 30 minutes before stopping in Mente PC 2.Error detection method Detection of anomalously low temperature (resistance) of Tho-D1 Is the connector of thermistor connected properly? Check and save the data of operating condition. Check the conditions whether it occurs immediately after the power on or during operation or stopping. Check the sensed value. Compare the temperature on Mente PC with actual measured value. Insert the connector securely NO YES Are the characteristics of thermistor OK? *3 NO Replace thermistor (Tho-D1). Replace outdoor control PCB. YES *3 Check several times to prove any poor connection Temperature-resistance characteristics of discharge pipe temperature thermistor (Tho-D1) • If 3°C or lower is detected for 5 seconds continuously within 10-minutes to 10-minutes 20-seconds after the compressor ON, the compressor stops. And after 3-minutes delay, the compressor starts again automatically, but if this anomalous temperature is detected 3 times within 40 minutes after the initial detection. Temperature thermistor resistance (k ) 3. Condition of error displayed 200 180 160 140 120 100 80 60 40 20 0 0 20 40 60 80 100 120 140 160 Temperature (°C) 4.Presumable cause • Broken thermistor harness or the internal wire of sensing section (Check the molded section as well) • Disconnection of thermistor harness connection (connector) • Outdoor control PCB anomaly Note: - AMP Air Conditioning 130 www.ampair.co.uk | [email protected] '11 • KX-T-166 Error code Remote controller: E40 7-segment display: E40 1.Applicable model LED Green Red Content High pressure anomaly (63H1-1activated) Indoor Keeps flashing Stays Off Outdoor Keeps flashing 1 time flash 5.Troubleshooting Outdoor unit Diagnosis Countermeasure Check and save the data of operating condition Check the sensed value of high pressure sensor when the 63H1-1 is activated Check whether the high pressure switch is activated at the sensed value of high pressure sensor. Save data for 30 minutes before stopping in Mente PC Was 63H1 activated at 4.15MPa or higher? NO 2.Error detection method YES Does the sensed value of the high pressure sensor show 4.15MPa? (Normal?) When high pressure switch 63H1-1 is activated NO YES Are the 63H1-1 OK? Are the connector and/or harnesse OK? YES Are the service valves fully open? 3. Condition of error displayed • If high pressure exceeds 4.15MPa • If 63H1-1 is activated 5 times within 60 minutes • If 63H1-1 is activated for 60 minutes continuously NO If the connector is disconnected or the harness is broken, correct it. Also check whether the high pressure switch is properly mounted or not Open operation valve. Check it, as much as possible, under the operating conditions for 30 minutes before error occurred. YES Connect a pressure gauge and restart operation. Is it stop at 4.15MPa of gauge pressre ? NO High pressure sensor anomaly is suspicious. Check high pressure sensor itself according to the troubleshooting procedure of E54, after retarting operation. (If the high pressure sensor [PSH] fails, replace it) NO Replace outdoor control PCB. YES Remove clogs. YES Is there any clogging in the refrigerant circuit ? 4.Presumable cause NO Check items (condenser side): • Filter clogging • Airflow volume (Fan motor) • Short-circuit of airflow • Short-circuit of airflow at condenser side of heat exchanger/Disturbance of airflow/Clogging filter/Fan motor anomaly • Disconnection of high pressure switch connector • Breakage of high pressure switch harness • Closed service valves • High pressure sensor anomaly • High pressure switch anomaly Note:If the error does not recur, connect the Mente PC and continue to collect data. - AMP Air Conditioning 131 www.ampair.co.uk | [email protected] '11 • KX-T-166 Error code Remote controller: E41(E51) 7-segment display: E41(E51)-1 1.Applicable model LED Green Red Content Indoor Keeps flashing Stays Off Power transistor overheat Outdoor Keeps flashing 1 time flash 5.Troubleshooting Outdoor unit Diagnosis Countermeasure Check and save the data of operating conditions Check the temperature of power transistor Check the operation of outdoor fan and cooling fan Save data for 30 minutes before stopping in Mente PC Does the outdoor fan run ? 2.Error detection method NO YES Reset power supply and restart When anomalously high temperature is detected by power transistor temperature thermistor (Tho-P1) Does the error recur when restarting? NO YES Is the cooling fan for inverter running? Anomalously high temperature of power transistor is detected 5 times within 60 minutes (E41). Or it is detected for 15 minutes continuously (E51) Is 15V of power for control PCB detected? If the cooling fan does not run in spite of the operation ON range, check the voltage at the connector of cooling fan. If the 220/240V is detected, repalce cooling fan motor. If 0V is detected, replace outdoor control PCB NO After checking the loose connection of connetor or breakage of harness, replace inverter PCB NO Connect the connector of thermistor securely. Or replace power transistor temperature thermistor NO Replace power transistor temperature thermistor YES After power OFF Is the connection of power transistor temperature thermistor OK? (Check short-circuit or breakage of harness) YES 4.Presumable cause • Power transistor anomaly • Power transistor temperature thermistor anomaly • Improperly fixing of power transistor to radiator fin • Inverter PCB anomaly • Outdoor fan motor anomaly • Anomalous cooling fan motor for inverter • Inadequate installation space of outdoor unit Is the characteristics of power transitor temperature thermistor OK? * * Refer the characterristics of power transistor temperature thermistor to E56 YES Is the fixing of power transistor OK? (Check tightening of screws or application of radiation silicon) NO YES Note: The operating conditions of cooling fan for inverter is shown in the right figure If the error does not recur, connect the Mente PC and continue to collect data. - AMP Air Conditioning Wait and see. Continue to obain data, if possible (Keep connecting the Mente PC) NO YES 3. Condition of error displayed Repair it according to the troubleshooting procedure of E48 Check it as much as possible under the operating conditions for 30 minutes before error occurred Fix power transistor on to the radiation f n with proper application of radiation silicon Replace power transistor ON OFF 81°C 85°C Power transistor thermistor temperature 132 www.ampair.co.uk | [email protected] '11 • KX-T-166 Error code Remote controller: E42 7-segment display: E42-1 1.Applicable model LED Green Red Content Indoor Keeps flashing Stays Off Current cut (CM1) Outdoor Keeps flashing 1 time flash 5.Troubleshooting Outdoor unit Diagnosis Countermeasure Check and save the data of operating conditions Check pressure anomaly Check the operation of outdoor fan Save data for 30 minutes before stopping in Mente PC Is the coil resistance and insulation (megger check) of compressor motor OK? 2.Error detection method When anomalously high output current of inverter is detected by the current sensormounted in the power transistor NO YES Does the outdoor fan run ? NO Repair it according to the troubleshooting of E48 NO Replace inverter PCB or outdoor fan motor YES Is 15V of power for control PCB detected? Is the outdoor fan motor OK? (Refer the checking method of 15V in page 90) Check it as much as possible under the operating conditions for 30 minutes before error occurred YES Reset power supply and restart NO Does E42 recur? 3. Condition of error displayed YES When 88A or higher output current of inverter is detected 4 times within 15 minutes. Replace compressor. Check the capillary tube and stariner of oil separator. If necessary, replace the capillary tube and strainer as well. Do you have inverter checker for judging whether inverter PCB is OK or not? NO YES After power OFF, Remove the 1-3 layers of control box Wait and see. Continue to obain data, if possible (Keep connecting the Mente PC) YES Is the checked result by inverter checker OK? NO Replace power transistor module Replace inverter PCB 4.Presumable cause • Compressor anomaly • Leakage of refrigerant • Power transistor module anomaly • Anomalous power supply for inverter PCB • Outdoor fan motor anomaly Is the checked result by measuring the resistance beween each terminal of power transistor module OK? (Are there any shortcircuit?) NO YES Replace power transistor module. Refer Page 90. (Remove the power cable from compressor and check the resistance between P-U, P-V, P-W, N-U, N-V, N-W respectively. Replace inverter PCB Note: In case that there is no the insulation resistance anomaly, the compressor anomaly could be considered. If this anomaly occurs after replacement of power transistor module and/or inverter PCB, try to replace compressor as well. If the error does not recur, connect the Mente PC and continue to collect data - AMP Air Conditioning 133 www.ampair.co.uk | [email protected] '11 • KX-T-166 Error code Remote controller: E43 7-segment display: E43-1, 2 *1 LED Green Red Content Excessive number of indoor units connected, excessive total capacity of connection Indoor Keeps flashing Stays Off Outdoor Keeps flashing *1 *1 E43-1:1 time flash (Excessive number of indoor units connected), E43- :2 time flash (Excessive capacity of indoor units connection) 1.Applicable model 5.Troubleshooting Outdoor unit Diagnosis Countermeasure Check and save the data of operating condition. Save data for 30 minutes before stopping in Mente PC Reset the power. Does E43 recur? Caution Unless the power is reset after changing address, the set address will not be confirmed NO 2.Error detection method YES When the number of connected indoor units exceeds the limitation. When the total capacity of connected indoor units exceeds the limitation. Does the number of indoor units connected and/or total capacity of connected indoor units exceed the limitation? Check the number of connected indoor units by the code No.C50 of 7-segment display or Mente PC with reference to the utility drawing (check not only one system, but also other systems) 3. Condition of error displayed • Excessive number of connected indoor units • Excessive total capacity of connected indoor units • The total capacity of connected indoor units exceeds the limitation 4.Presumable cause Check the resistance between A and B of signal line as well. YES Check indoor unit addresses and correct it. In case that total capacity of connected indoor units exceeds the limitation if tentative operation is required, turn ON the dip switch SW5-4 on the outdoor control PCB. (However since this tentative solution could cause trouble, be sure to correct it as soon as possible) YES Signal wire may be connected to other outoor unit system. NO Is there any indoor units which is not expected to exsist in that signal line? Test run. No action is taken because it is judged that the power reset was not done after changing address. NO Throughly checking of the addresses of indoor/outdoor units by means of • Outdoor unit: Mente PC, 7-segment display and rotary switch (SW1, SW2) • Indoor unit: Remote controller and rotary switch (SW1, 2, 3, 4) * Recommend to use means other than the rotary switch which could be faulty • Mistake in setting of indoor/ outdoor unit addresses • Mistake in signal wire connection Correct addresses. (Either one of addresses is wrong.) If the address corrected by rotary switch is still wrong, replace control PCB (rotary switch anomaly) * Before replacement, please confirm whether the rotary switch for address setting is not damaged. (It was experienced that No. 5 on rotary switch was not recognized.) Note: After completing the above procedure, reset the power and confirm that the error display does not recur. Unless the power is reset for both indoor unit and outdoor unit, the set addresses will not be confirmed - AMP Air Conditioning 134 www.ampair.co.uk | [email protected] '11 • KX-T-166 Error code Remote controller: E45 7-segment display: E45-1 1.Applicable model LED Green Red Content Communication error between inverter PCB and outdoor control PCB Indoor Keeps flashing Stays Off Outdoor Keeps flashing 1 time flash 5.Troubleshooting Outdoor unit Diagnosis Countermeasure Check and save the data of operating conditions Save data for 30 minutes before stopping in Mente PC Is 15V of power for control PCB detected? Is the outdoor fan motor OK? (Refer the checking method of 15V in page 90) 2.Error detection method NO Check it as much as possible under the operating conditions for 30 minutes before error occurred YES Reset power supply and restart When the communication between inverter PCB and outdoor control PCB is not established. Does E45 recur? NO Wait and see. Continue to obain data, if possible (Keep connecting the Mente PC) NO Check whether the harness is broken? Check whether the connector is loose? If there is problem, correct it. YES Turn off the power. IS the harness and/or connector between inverter PCB and outdoor control PCB OK ? YES 3. Condition of error displayed Same as above. Is the rush current prevention resistor broken? YES NO Is the harness and/or connector between inverter PCB and diode module OK? Check whether the harness is broken? Check whether the connector is loose? If there is problem, correct it. NO Correct the setting of switches on the inverter PCB 4.Presumable cause • Signal wire anomaly • Outdoor control PCB anomaly • Inverter PCB (INV1) anomaly • Rush current prevention resistor anomaly Disconnect the harness from the resistor and measure the resistance. If broken, replace the resistor. In such case check the harness between diode module and inverter PCB as well NO YES Is the setting of switches on the inverter PCB OK? * Replace inverter PCB or outdoor fan motor YES Replace outdoor control PCB * Switch setting of inverter PCB SW1-1 SW1-2 SW1-3 SW1-4 JSW1-1 JSW1-2 JSW1-3 JSW1-4 OFF OFF OFF OFF ON OFF OFF OFF Note: If the error does not recur, connect the Mente PC and continue to collect data. - AMP Air Conditioning 135 www.ampair.co.uk | [email protected] '11 • KX-T-166 Error code Remote controller: E46 7-segment display: E46 1.Applicable model LED Green Red Content Mixed address setting methods coexistent in same network. Indoor Keeps flashing Stays Off Outdoor Keeps flashing Stays Off 5.Troubleshooting Outdoor unit Diagnosis Countermeasure Save data for 30 minutes before stopping in Mente PC Reset power supply and restart Caution: Unless the power is reset after changing address, the set address will not be confirmed. 2.Error detection method If the signal line of a outdoor unit system applied automatic address setting is connected to other outdoor unit system (Detected at indoor unit side) Check and save the data of operating conditions Check the address setting method of faulty network whether it is automatic setting or manual setting. Does E46 recur? NO Test run. * No action is taken because it is judged that the power rest is not done after changing address YES Correct signal line *In case of automatic address setting, signal line cannot be connected to other outdoor unit system NO Test run YES Is't the signal line of a outdoor unit system applying automatic address setting connected to other outdoor unit system? NO If signal line is connected to more than 2 outdoor unit systems, address setting should be done by manually. 3. Condition of error displayed Same as above. Is E46 still displayed? YES Turn ON the power of each outdoor unit one by one and search the outdoor unit that can start up with automatic address setting 4.Presumable cause • Mistake in the address setting • Mistake in the connection of signal wire Replace outdoor control PCB* (Rotary switch anomaly) <Reference> Error display at mixed address setting Auto Manual Auto address setting E31 E46 Manual address setting E46 Normal * Before replacement, please confirm whether the rotary switch for address setting is not damaged. (It was experienced that No.5 on rotary switch was not recognized ) Note: After completing the above procedure, reset the power and confirm that the error display does not recur. Unless the power is reset for both indoor unit and outdoor unit, the set addresses will not be confirmed - AMP Air Conditioning 136 www.ampair.co.uk | [email protected] '11 • KX-T-166 Error code Remote controller: E48 7-segment display: E48-1, 2 *1 LED Green Red Content Indoor Keeps flashing Stays Off Outdoor Keeps flashing Outdoor DC fan motor anomaly *1 *1 E48-1: 1 time flash (FMO1), E48-2 : 2 time flash (FMO 1.Applicable model 5.Troubleshooting also the fan motor 2 even if it is E48-1. ( Inspect Inspect also the fan motor 1 even if it is E48-2. ) Outdoor unit Diagnosis Countermeasure Check and save the data of operating conditions Save data for 30 minutes before stopping in Mente PC Does the fan rotate smoothly when turned by hand? NO Replace fan motor NO Replace inverter PCB or fan motor YES 2.Error detection method • If 400min-1 or lower of the fan rotation command and the state of overcurent are detected for 10 times continueously • If 100min-1 of the actual fan rotation speed is detected for 30 seconds (Fan motor is locked) Is 15V of power for control PCB detected? Is the outdoor fan motor OK? (Refer the checking method of 15V in page 90) Check it as much as possible under the operating conditions for 30 minutes before error occurred YES Reset power supply and restart Is E48 restored at 10 seconds after compressor starting? NO Wait and see. Continue to obain data, if possible (Keep connecting the Mente PC) NO Replace fan motor YES Replace outdoor control PCB YES 3. Condition of error displayed Same as above. Turn the power supply OFF Interchange the connectors of fan motor harnesses at the connectors on outdoor control PCB side Start operation again Is the fan motor failed to start up switched? 4.Presumable cause • Breakage of harness or loose conection of connector • Outdoor fan motor anomaly • Inverter PCB anomaly • Outdoor control PCB anomaly Note: If the error does not recur, connect the Mente PC and continue to collect data. - AMP Air Conditioning 137 www.ampair.co.uk | [email protected] '11 • KX-T-166 Error code Remote controller: E49 7-segment display: E49 1.Applicable model LED Green Red Content Indoor Keeps flashing Stays Off Low pressure anomaly Outdoor Keeps flashing 1 time flash 5.Troubleshooting Outdoor unit Diagnosis Countermeasure Check and save the data of operating conditions Check error status. Is the refrigerant amount OK Check additional refrigerant amount charged at site according to the piping length instructed on the label pasted on the panel of the unit. Save data for 30 minutes before stopping in Mente PC Reset power supply and restart. 2.Error detection method Does the error occur immediately after the startup? NO Detection of anomalously low pressure Does the low pressure fluctuate after the startup? NO YES Is the connection of sensor connector OK? Check whether the service valves are open. NO Correct the connection of low pressure sensor connector NO Replace low pressure sensor. YES Are the sensor characteristics OK?* YES * The sensor characteristics is shown in Page 140 3. Condition of error displayed • At start up after power on: When the low pressure sensor detects lower than 0.003MPa for 60 seconds continuously. And if this anomaly occurs 2 times. • During operation: When the low pressure sensor detects 0.134MPa or lower for 30 seconds coninuously. And if this anomaly occurs 5 times within 60 minutes 4.Presumable cause • Low pressure sensor (PSL) anomaly • Service valves closed • EEV anomaly (EEV closed) • Insufficient refrigerant amount • Clogging at EEV or strainer Is the opening degree of EEV for evaporator side flucturing? NO YES Replace outdoor control PCB. YES Is the connection of thermistor connector for heat exchanger OK? NO YES Is the checked result of harness and insulation of EEV coil OK? Are the thermistor characteristics OK? NO YES YES NO YES Replace temperature thermistor of heat exchanger at evaporator side. Replace control PCB at evaporator side. Replace EEV coil. NO Does the EEV operate normally by judging from Mente PC data, etc? Correct the connection of temperature thermistor connector of heat exchanger Isn’t EEV or strainer clogged? YES Replace EEV main body or strainer. Check for short circuit of airflow of heat exchanger at evaporator side and for fan motor anomaly NO Note: Check whether the indoor unit is connected to other outdoor superlink network. If the error does not recur, connect the Mente PC and continue to collect data. - AMP Air Conditioning 138 www.ampair.co.uk | [email protected] '11 • KX-T-166 Error code Remote controller: E53/E55 7-segment display: E53/E55-1 LED Green Red Content Suction pipe temperature thermistor anomaly (Tho-S), Under-dome temperature thermistor anomaly (Tho-C1) Indoor Keeps flashing Stays Off Outdoor Keeps flashing 1 time flash E53: Tho-S, E55-1: Tho-C1 1.Applicable model 5.Troubleshooting Outdoor unit Diagnosis Countermeasure Check and save the data of operating conditions Check the conditions whether it occurs immediately after the power on or during operation or stopping. Check the sensed value. Compare the temperature on Mente PC with actual measured value Save data for 30 minutes before stopping in Mente PC 2. Error detection method Is the connector of thermistor connected properly ? Detection of anomalously low temperature (resistance) of Tho-S or Tho-C YES Regarding the characteristics of the thermistor, see the following chart Are the characteristics of thermistor OK? *1 3. Condition of error displayed • Broken thermistor harness or the internal wire of sensing section (Check the molded section as well) • Disconnection of thermistor harness connection (connector) • Outdoor control PCB anomaly Temperature-resistance characreristics of suction pipe temperature thermistor (Tho-S) Replace thermistor (Tho-S or Tho-C1) YES Replace outdoor control PCB 5kΩ at 25Cº Temperature-resistance characreristics of under-dome temperature thermistor (Tho-C1) Tempearture thermistor resistance (kΩ) 4. Presumable cause NO *1 Check several times to prove any poor connection Tempearture thermistor resistance (kΩ) • if -50°C or lower is detected for 5 seconds continuously within 2 minutes to 2 minutes 20 seconds after compressor ON, compressor stops. When the compressor is restarted automatically after 3-minutes delay, if this anomaly occurs 3 times within 40 minutes Insert the connector securely NO 200 180 160 140 120 100 80 60 40 20 0 0 20 40 60 80 100 120 140 160 Temperature (Cº) Temperature (Cº) Note: - AMP Air Conditioning 139 www.ampair.co.uk | [email protected] '11 • KX-T-166 LED Error code Remote controller: E54 7-segment display: E54-1, 2 *1 *1 E54-1: 1 time flash (PSL), Green Red Content High pressure sensor anomaly (PSH) Low pressure sensor anomaly (PSL) Indoor Keeps flashing Stays Off Outdoor Keeps flashing *1 E54-2 : 2 time flash (PSH) 5.Troubleshooting 1.Applicable model Outdoor unit Diagnosis Countermeasure Check and save the data of operating conditions Check the conditions whether it occurs immediately after the power on or during operation or stopping. Check the sensed value. Save data for 30 minutes before stopping in Mente PC Check the data for 30 minutes before stopping YES Is anomalous pressure detected? 2.Error detection method Detection of anomalous pressure (valtage) of PSH or PSL [ Operation range High pressure : 0-4.15MPa Low pressure : 0-1.7MPa Is the connector of the sensor inserted properly to the connector on the outdoor control PCB? NO ] NO Insert the connector securely and restart operation YES Reset the power and restart operation. NO E54 Does it recur? YES Does the pressure converted from the sensor output voltage match the actual pressure measure by pressure gauge? 3. Condition of error displayed If anomalous sensor output voltage (0V or lower or 3.49V or higher) is detected for 5 seconds within 2 minutes to 2 minutes 20 seconds after the compressor ON • Broken sensor harness • Disconnection of sensor harness connection (connector) • Sensor (PSH, PSL) anomaly • Outdoor control PCB anomaly • Anomalous installation conditions • Insufficient airflow volume • Excessive or insufficient refrigerant amount YES Replace sensor (PSH, PSL) Replace outdoor control PCB Low pressure sensor output characteristics Output voltage (V) High pressure sensor output characteristics Output voltage (V) 4.Presumable cause NO Temporary malfunction by noise. Correct if the source of noise is specified Pressure (MPa) Pressure (MPa) Sensor output Black (GND) – White; Output voltage (Black – Red; DC5V) Note: - AMP Air Conditioning 140 www.ampair.co.uk | [email protected] '11 • KX-T-166 Error code Remote controller: E56 7-segment display: E56-1 1.Applicable model LED Green Red Content Power transitor temperature thermistor anomaly (Tho-P1) Indoor Keeps flashing Stays Off Outdoor Keeps flashing 1 time flash 5.Troubleshooting Outdoor unit Diagnosis Countermeasure Check and save the data of operating condition. Check the conditions whether it occurs immediately after the power on or during operation or stopping. Check the sensed value. Compare the temperature of Mente PC data with actual measured value Save data for 30 minutes before stopping in Mente PC 2.Error detection method Is the connector of thermistor connected properly OK ? Detection of anomalously low temperature (resistance) of Tho-P1 Insert the connector securely NO YES Are the characteristics of thermistor OK? *1 Replace power transistor temperature thermistor (Tho-P1). NO Replace outdoor control PCB. YES *1 Check several times to prove any poor connection Temperature-resistance characteristics of power transistor temperature thermistor (Tho-P1) 3. Condition of error displayed When the outdoor air temperature is above 0ºC, if -10ºC or lower is detected for 20 seconds continuously within 10 minutes to 10 minutes 30 seconds after compressor ON, compressor stops. When the compressor is restarted automatically after 3-minutes delay, if this anomaly occurs 3 times within 40 minutes Power transistor thermistor 200 180 160 140 120 100 80 60 40 20 0 0 20 40 60 80 100 120 140 Temperature (°C) 4.Presumable cause • Broken thermistor harness or the internal wire of sensing section (Check the molded section as well) • Disconnection of thermistor harness connection (connector) • Outdoor control PCB anomaly Note: - AMP Air Conditioning 141 www.ampair.co.uk | [email protected] '11 • KX-T-166 Error code Remote controller: E58 7-segment display: E58-1 1.Applicable model LED Green Red Content Indoor Keeps flashing Stays Off Outdoor Keeps flashing 1 time flash Anomalous compressor by loss of synchronism 5.Troubleshooting Outdoor unit Diagnosis Countermeasure Save data for 30 minutes before stopping in Mente PC Check and save the data of operating condition Check the data for 30 minutes before stopping 2.Error detection method E58 is displayed on 7-segment LED Is this the first startup within one hour after power is supplied? YES NO Is there any replacement record of inverter PCB ? 3. Condition of error displayed YES Refrigerant might be migrated in the refrigerant oil in the compressor. Wait for about one hour under the condition of power ON and start again. ( Turn the on crankcase heater ON and evaporate the liquid refrigerant migrated in the compressor. The model setting could be wrong. Check the dip switch for model setting on the outdoor control PCB. NO This anomaly is established 4 times within 15 minutes. Compressor could be locked -Replace the compressor 4.Presumable cause • Insufficient time elapsed after the power supplied, before compressor startup. (Startup the compressor wihtout crankcase heater ON) • Compressor anomaly Note: If the error does not recur, connect the Mente PC and continue to collect data. - AMP Air Conditioning 142 www.ampair.co.uk | [email protected] '11 • KX-T-166 Error code Remote controller: E59 7-segment display: E59-1 1.Applicable model LED Green Red Content Indoor Keeps flashing Stays Off Compressor startup failure (CM) Outdoor Keeps flashing 1 time flash 5.Troubleshooting Outdoor unit Diagnosis Countermeasure Check and save the data of operating conditions Save data for 30 minutes before stopping in Mente PC Check the data for 30 minutes before stopping Is power supply voltage OK? 2.Error detection method When it fails to change over to the operation for rotor position detection of compressor motor (If the compressor speed cannot increase 11Hz or higher) YES NO specification of power supply voltage 380/415V Is the pressure equalized during 3-minute delay before startup? NO YES Is there any loose connection or breakage of cable connected to the terminal of the compressor? NO Check the power supply voltage and correct it Check the version No. of software (Is it latest?) Check whether the solenoid valve SV6 at the exit of oil separator is open during compressor stopping. (Is the pressure equalized?) Replace the cable (If there is a problem on the terminal of compressor, replace the compressor YES Under the condition of no pressure difference, startup by test operation mode 3. Condition of error displayed If the compressor fails to startup for 20 times (10 patterns x 2 times) continuously. Is it the unit with one compressor? NO Check the Model YES Wait and see YES Replace compressor NO Replace inverter PCB or power transistor module. (Check 15V on the outdoor control PCB and check power transistor by inverter checker. If the power transistor is OK, replace inverter PCB) YES Can startup? NO Is there any output of inverter? 4.Presumable cause • Anomalous voltage of power supply • Anomalous components for refrigerant circuit • Inverter PCB anomaly • Loose connection of connector or cable • Compressor anomaly (Motor or bearing) Note: If the error does not recur, connect the Mente PC and continue to collect data. - AMP Air Conditioning 143 www.ampair.co.uk | [email protected] '11 • KX-T-166 Error code Remote controller: E60 7-segment display: E60-1 1.Applicable model LED Green Red Content Rotor position detection failure (CM) Indoor Keeps flashing Stays Off Outdoor Keeps flashing 1 time flash 5.Troubleshooting Outdoor unit Diagnosis Countermeasure Check and save the data of operating conditions Save data for 30 minutes before stopping in Mente PC Is power supply voltage OK? Correct it NO YES Check it as much as possible under the operating conditions for 30 minutes before error occurred Reset the power supply and restart operation 2.Error detection method Detection of the compressor rotor position. YES YES Can the compressor startup? Correct it according to the troubleshooting procedure of E59 Does E59 occur? NO NO Does E42 occur? YES Correct it according to the troubleshooting procedure of E42 YES Replace compressor Is the sound and vibration of the compressor normal? 3. Condition of error displayed If it fails to detect the rotor position of compressor, after changinging over to the operation of compressor rotor position detection, the compressor stops. When it is restart automatically after 3 minutes delay, this anomaly occurs 4 times within 15 minute after the initial detection NO ( anomalous sound and vibration ) YES Is it operated normally without occurrence of E60? Check the insulation resistance and coil resistance of compressor. If necessary, replace compressor NO Replace compressor YES Temporary malfunction by noise. 4.Presumable cause • Compressor anomaly • Inverter PCB anomaly • Anomaly of power supply Note: If the error does not recur, connect the Mente PC and continue to collect data. - AMP Air Conditioning 144 www.ampair.co.uk | [email protected] '11 • KX-T-166 Error code Remote controller: E63 7-segment display: E63 1.Applicable model LED Green Red Content Indoor Keeps flashing Stays Off Emergency stop Outdoor Keeps flashing 1 time flash 5.Troubleshooting Indoor unit Diagnosis Countermeasure Check and save the data of operating conditions Check the conditions whether it occurs immediately after the power on or during operation. Save data for 30 minutes before stopping in Mente PC 2.Error detection method Is the remote controller setting of Emergency Stop "Valid"? Replace remote control PCB NO YES When ON signal is inputted to the CnT terminal of indoor control PCB Is ON signal inputted to the CnT terminal of indoor control PCB? NO YES Replace indoor control PCB Check the cause of emergency stop. (It is better to have the data for 30 minutes before stopping, when instructing the installer) 3. Condition of error displayed Same as above 4.Presumable cause Factors for emergency stop Note: Indoor unit detected emergency stop signal gives command "all stop" - AMP Air Conditioning 145 www.ampair.co.uk | [email protected] '11 • KX-T-166 8.4 Outdoor unit control PCB replacement procedure PCB012D017A j Precautions for Safety Since the following precaution is the important contents for safety, be sure to observe them. WARNING and CAUTION are described as follows: Indicates an imminently hazardous situation which will result in death or serious injury if WARNING proper safety procedures and instructions are not adhered to. CAUTION Indicates a potentially hazardous situation which may result in minor or moderate injury if proper safety procedures and instructions are not adhered to. WARNING Securely replace PCB according to this following instruction. If PCB is incorrectly replace, it will cause an electric shock or -re . Be sure to check that the power source for the outdoor unit is turned OFF before replace PCB, The PCB replacement under current-carrying will cause an electric shock. After -nishing PCB replacement, check that wiring is correctly c onnected with the PCB before power distribution, If PCB is incorrectly replace, it will cause an electric shock or -re. CAUTION Bundle the wiring so as not to tense because it will cause an electric shock. (Note) If cut the tie, the wiring cables should be bound with new tie again. Exchange the control PCB according to the following procedure. 1. Replace the control PCB after elapsing 3 minutes from power OFF. (Be sure to measure voltage (DC) at both capacitor terminals (1. Power supply for PCB 2. Power supply for fan motor) and check that the voltage is discharged completely. (Refer to Fig.1)) 2. Disconnect the connectors from the PCB. 3. Disconnect the blue wiring passing through CT1 on the PCB before replace the coutrol PCB. 4. Set the setting switches (SW1-6) of new PCB same as previous PCB. 5. Tighten up a screw after passing blue wiring through CT1 of the changed. 6. Connect the connectors to the PCB. (Contirm the connectors are not half inserted.) CNEEV2 CNEEV1 CNFAN_2 CNA2 CNFAN_1 CNQ3 2 2 CNQ1 CNTH CNW CNX1 After elapsing 3 minutes from power OFF CT1 CNB2 CNU1 CNF2 CNF1 CNP1 CNA2 CNQ3 CNL1 CN 2 CNS1 CNS2 CNG1 CNG2 CNI CNN2 CNN1 CNN9 CNN6 CNN4 CNR1 CNM1 Parts arrangement view - AMP Air Conditioning 1 Reuse the parts used before the PCB exchange. 2 Please do not carry out wrong insertion. The PCB will be destroyed if a mistake is made in putting CNA2 (brown) and CNQ3 (yellow). 146 www.ampair.co.uk | [email protected] '11 • KX-T-166 Fan motor voltage measurement point (between L63, L64) PCB voltage measurement point (between F1, DS1(-)) Fig.1 Voltage measurement points Target PCB Appearance of the controller - AMP Air Conditioning 147 www.ampair.co.uk | [email protected] '11 • KX-T-166 8.5 Inverter PCB replacement procedure PCB012D018AB H Precautions for Safety f Since the following precaution is the important contents for safety, be sure to observe them. WARNING and CAUTION are described as follows: Indicates an imminently hazardous situation which will result in death or serious injury if WARNING proper safety procedures and instructions are not adhered to. CAUTION Indicates a potentially hazardous situation which may result in minor or moderate injury if proper safety procedures and instructions are not adhered to. WARNING f Securely replace PCB according to this following instruction. If PCB is incorrectly replace, it will cause an electric shock or fire. f Be sure to check that the power source for the outdoor unit is turned OFF before replace PCB, The PCB replacement under current-carrying will cause an electric shock. f After finishing PCB replacement, check that wiring is correctly connected with the PCB before power distribution, If PCB is incorrectly replace, it will cause an electric shock or fire. CAUTION f Bundle the wiring so as not to tense because it will cause an electric shock. (Note) If cut the tie, the wiring cables should be bound with new tie again. fExchange the inverter PCB according to the following procedure. 1. Replace the inverter PCB after elapsing 3 minutes from power OFF. (Be sure to measure voltage (DC, AC) of two places ((A)(B)) and check that the voltage is discharged completely. (Refer to Fig.1)) 2. Disconnect all of terminals and connectors from the inverter PCB before replace the invertor PCB. 3. Replace to the new PCB. 4. Set the setting switches (JSW 10, 11) of new PCB as shown in table 1. 5. Connect all of terminals and connectors to the new PCB securely. (Check the secure connection of terminals and connectors again) CNR CNI2 CNA JSW10,11 Table.1 Switch Setting JSW10 Model All models JSW11 1 2 3 4 all OFF OFF ON OFF OFF After elapsing 3 minutes from power OF F Connectors are not half inserted Parts Arrangement View - AMP Air Conditioning 148 www.ampair.co.uk | [email protected] '11 • KX-T-166 PCB voltage measurement point PCB PCB voltage measurement point Fig.1 Voltage Measurement Points Terminal Harness Snubber capacitor Inverter PCB Connection binder (Metallic pillar) Power transistor Installation Method to Power transistor • Procedure on tightening harness (snubber capacitor) and power transistor with screw. A metallic connection binder is set in each hole of the inverter PCB of "P", "N", "U", "V", and "W" beforehand. Then tighten the harness (snubber capacitor) and the power transistor with the screw together. (Connect snubber capacitor with "P" and "N".) - AMP Air Conditioning 149 www.ampair.co.uk | [email protected] '11 • KX-T-166 8.6 Outdoor unit transistor module replacement procedure PCB012D008A Precautions for Safety ¡Since the following precaution is the important contents for safety, be sure to observe them. WARNING and CAUTION are described as follows: Indicates an imminently hazardous situation which will result in death or serious injury if WARNING proper safety procedures and instructions are not adhered to. CAUTION Indicates a potentially hazardous situation which may result in minor or moderate injury if proper safety procedures and instructions are not adhered to. WARNING ¡Securely exchange the transistor module according to this procedure. If the transistor module is incorrectly exchanged, it will cause an electric shock or fire. ¡Be sure to check that the power source for the outdoor unit is turned OFF before exchanging the transistor module. The transistor module exchange under current-carrying will cause an electric shock. ¡After finishing the transistor module exchange, check that wiring is correctly connected with the transistor module before power distribution. If the transistor module is incorrectly exchanged, it will cause an electric shock or fire. CAUTION ¡Band the wiring so as not to tense because it will cause an electric shock. It is recommended to exchange the transistor module according to the following procedure. 1. S tart the replacing work ten minutes after turning off the power. (Be sure to measure the voltage (DC) between the capacitor terminals (P,N of transistor module or connector terminals of fan motor power etc.) to check that the capacitor have been discharged completely.) 2. Disassemble the control box. 3. Disconnect with the wire (U,V,W,P,N ) to the transistor module. (See Fig 1.Parts Arrangement View) 4. Pull up the inverter substrate from transistor module. Remove transistor module after removing the screw for transistor module. 5. Attach the transistor module. Coat the transistor module where its reverse-side all over with accessories silicone grease (MRE equipment SA03434 or SA01846)uniformly. 6. Set the inverter substrate with make sure of connect connector. 7. Connect with the wire (U,V,W,P,N ) to the transistor module. 8. Assemble the control box as before. Connector connected by inverter substrate P wire (red) N wire (blue) W wire (blue) V U wire (white) wire (red) Fig.1Part Arrangement View - AMP Air Conditioning 150 www.ampair.co.uk | [email protected] '11 • KX-T-166 Function of Dip switch for contorl (SW3, 4, 5) • SW3 (Function setting) Switch • SW4 (Change demand ratio) Function SW3-1 SW3-7 Switch ON Inspection LED reset OFF Normal ON Forced cooling/heating OFF Normal Function ON SW4-5 SW4-6 OFF OFF Compressor capacity 60% ON Compressor capacity 0% OFF Compressor capacity 80% ON Compressor capacity 40% • SW5 (Function setting) ON/OFF Function of Jumper wire (J13, 15) (With: Shorted / None: Opened) Jumper J13 J15 SW5-1 Function SW5-2 With External input Level input None External input Pulse input With Defrost time Normal None Defrost time Cold weather region SW5-3 SW5-5 • SW4 (Model selection) Switch Test run switch Test run OFF Test run switch Normal ON Test run operation mode Cooling ON OFF Test run operation mode Heating ON Pump down switch Pump down OFF Pump down switch Normal ON Super link protocol: Previos SL OFF Super link protocol: New SL • SW7, 8, 9 (Function setting) SW4 Switch 1 2 3 4 224 OFF OFF OFF OFF 280 ON OFF OFF OFF Model Function Function SW7 Data erase/data write SW8 7-segment dispalay No.UP order of 1 SW9 7-segment dispalay No.UP order of 10 Function of Connector Connector Function CNEEV1 Heating EEV CNEEV2 Sub-cooling coil EEV CNA2 Power fan motor CNFAN1 Fan motor 1 CNFAN2 Fan motor 2 CNQ1 High pressure switch (CM1) CNTH Color Connector Function Color Red CNF2 Sub-cooling coil thermistor 1 Green White CNP1 Power transistor thermistor (CM) Yellow - CNL1 High pressure sensor Blue White CNL2 Low pressure sensor White Red CNS1 External input - White CNS2 Demand input - Heat exchanger thermistor 1 (Exit/front) CNN1 4-way switching solenoid valve Discharge pipe thermistor CNN2 Solenoid valve・oil return (CM1) Green CNN4 Solenoid valve (gas by pass) Orange Suction pipe thermistor White External air thermistor Red CNN6 Solenoid valve (liquid bypass) Pink Red CNN9 Solenoid valve (gas bypass) Black Under-dome thermistor (CM1) Blue CMM1 Solenoid valve for CM Gray Sub-cooling coil thermistor 1 White CNR1 Crankcase heater White CNB2 Heat exchanger thermistor 2 CNU1 CNF1 - AMP Air Conditioning 151 www.ampair.co.uk | [email protected] '11 • KX-T-166 ٨DIP Switch setting list (1) Outdoor unit (a) Control PCB 㪪㫎㫀㫋㪺㪿㪼㫊 㪛㪼㫊㪺㫉㫀㫇㫋㫀㫆㫅 㪦㫌㫋㪻㫆㫆㫉㩷㪸㪻㪻㫉㪼㫊㫊㩷㪥㫆㪅㩷㩿㪦㫉㪻㪼㫉㩷㫆㪽㩷㪈㪇㪀㩷 㪦㫌㫋㪻㫆㫆㫉㩷㪸㪻㪻㫉㪼㫊㫊㩷㪥㫆㪅㩷㩿㪦㫉㪻㪼㫉㩷㫆㪽㩷㪈㪀㩷 㪠㫅㫊㫇㪼㪺㫋㫀㫆㫅㩷㪣㪜㪛㩷㫉㪼㫊㪼㫋㩷㩷㩷㩷㩷㩷㩷㩷㩷 㪪㫇㪸㫉㪼 㪩㪼㪽㫉㪼㫊㪿㩷㫄㫆㪻㪼㫃㩷㫊㪼㫃㪼㪺㫋㫀㫆㫅 㪩㪼㫊㪼㫉㫍㪼㪻 㪚㪿㪼㪺㫂㩷㫆㫇㪼㫉㪸㫋㫀㫆㫅㩷㫊㫋㪸㫉㫋 㪧㫀㫇㪼㩷㫎㪸㫊㪿㫀㫅㪾㩷㫆㫇㪼㫉㪸㫋㫀㫆㫅 㪝㫆㫉㪺㪼㪻㩷㪿㪼㪸㫋㫀㫅㪾㪆㪺㫆㫆㫃㫀㫅㪾㩷 㪩㪼㫊㪼㫉㫍㪼㪻 㪪㪮㪈 㪪㪮㪉 㪪㪮㪊㪄㪈 㪪㪮㪊㪄㪉 㪪㪮㪊㪄㪊 㪪㪮㪊㪄㪋 㪪㪮㪊㪄㪌 㪪㪮㪊㪄㪍 㪪㪮㪊㪄㪎 㪪㪮㪊㪄㪏 㪪㪮㪋㪄㪈 㪪㪮㪋㪄㪉 㪪㪮㪋㪄㪊 㪪㪮㪋㪄㪋 㪪㪮㪋㪄㪌 㪪㪮㪋㪄㪍 㪪㪮㪋㪄㪎 㪪㪮㪋㪄㪏 㪪㪮㪌㪄㪈 㪪㪮㪌㪄㪉 㪪㪮㪌㪄㪊 㪪㪮㪌㪄㪋 㪪㪮㪌㪄㪌 㪪㪮㪌㪄㪍 㪪㪮㪌㪄㪎 㪪㪮㪌㪄㪏 㪪㪮㪍㪄㪈 㪪㪮㪍㪄㪉 㪪㪮㪍㪄㪊 㪪㪮㪍㪄㪋 㪪㪮㪍㪄㪌 㪪㪮㪍㪄㪍 㪪㪮㪍㪄㪎 㪪㪮㪍㪄㪏 㪪㪮㪎 㪪㪮㪏 㪪㪮㪐 㪡㪈㪇 㪡㪈㪈 㪡㪈㪉 㪡㪈㪊 㪡㪈㪋 㪡㪈㪌 㪡㪈㪍 㪛㪼㪽㪸㫌㫃㫋㩷㫊㪼㫋㫋㫀㫅㪾 㪇㪄㪐 㪇㪄㪐 㪋 㪐 㪦㪝㪝 㪦㪝㪝 㪦㪥 㪦㪝㪝 㪦㪝㪝 㪦㪝㪝 㪦㪝㪝 㪦㪝㪝 㪥㫆㫉㫄㪸㫃㪁㪆㪩㪼㫊㪼㫋 㪥㫆㫉㫄㪸㫃㪁㪆㪪㫋㪸㫉㫋 㪥㫆㫉㫄㪸㫃㪁㪆㪪㫋㪸㫉㫋 㪥㫆㫉㫄㪸㫃㪁㪆㪝㫆㫉㪺㪼㪻 㪤㫆㪻㪼㫃㩷㫊㪼㫃㪼㪺㫋㫀㫆㫅 㪩㪼㫄㪸㫉㫂㫊 㪥㫆㫉㫄㪸㫃 㫂㪼㪼㫇㩷㪦㪝㪝㩷 㫂㪼㪼㫇㩷㪦㪥㩷 㫂㪼㪼㫇㩷㪦㪝㪝㩷 㪥㫆㫉㫄㪸㫃 㪥㫆㫉㫄㪸㫃 㪥㫆㫉㫄㪸㫃 㫂㪼㪼㫇㩷㪦㪝㪝㩷 㪘㫊㩷㫇㪼㫉㩷㫄㫆㪻㪼㫃 㪦㪝㪝 㪦㪝㪝 㪩㪼㫊㪼㫉㫍㪼㪻 㪦㪝㪝 㪪㫇㪸㫉㪼 㪦㪝㪝 㪫㪼㫊㫋㩷㫉㫌㫅㩷㪪㪮 㪥㫆㫉㫄㪸㫃㪁㪆㪫㪼㫊㫋㩷㫉㫌㫅 㪦㪝㪝 㪫㪼㫊㫋㩷㫉㫌㫅㩷㫄㫆㪻㪼 㪟㪼㪸㫋㫀㫅㪾㪁㪆㪚㫆㫆㫃㫀㫅㪾 㪦㪝㪝 㪧㫌㫄㫇㩷㪻㫆㫎㫅㩷㫆㫇㪼㫉㪸㫋㫀㫆㫅 㪥㫆㫉㫄㪸㫃㪁㪆㪧㫌㫄㫇㩷㪻㫆㫎㫅 㪦㪝㪝 㪩㪼㫊㪼㫉㫍㪼㪻 㪦㪝㪝 㪪㫌㫇㪼㫉㫃㫀㫅㫂㩷㫊㪼㫃㪼㪺㫋㫀㫆㫅 㪥㪼㫎㩷㪪㪣㪁㪆㪧㫉㪼㫍㫀㫆㫌㫊㩷㪪㪣 㪦㪝㪝 㪩㪼㫊㪼㫉㫍㪼㪻 㪦㪝㪝 㪩㪼㫊㪼㫉㫍㪼㪻 㪦㪝㪝 㪩㪼㫊㪼㫉㫍㪼㪻 㪦㪝㪝 㪩㪼㫊㪼㫉㫍㪼㪻 㪦㪝㪝 㪩㪼㫊㪼㫉㫍㪼㪻 㪦㪝㪝 㪪㫇㪸㫉㪼 㪦㪝㪝 㪪㫇㪸㫉㪼 㪦㪝㪝 㪪㫇㪸㫉㪼 㪦㪝㪝 㪪㫇㪸㫉㪼 㪦㪝㪝 㪪㫇㪸㫉㪼 㪦㪝㪝 㪪㫇㪸㫉㪼 㪦㪝㪝 㪜㫉㪸㫊㪼㪁㪆㪮㫉㫀㫋㪼 㪛㪸㫋㪸㩷㩷㩷㪜㫉㪸㫊㪼㪆㪮㫉㫀㫋㪼 㪦㪝㪝 㪎㪄㫊㪼㪾㫄㪼㫅㫋㩷㪻㫀㫊㫇㫃㪸㫐㩷㪺㫆㪻㪼㩷㪥㫆㪅㩷㫀㫅㪺㫉㪼㪸㫊㪼㩷㩷㩿㪦㫉㪻㪼㫉㩷㫆㪽㩷㪈㪀 㪇 㪎㪄㫊㪼㪾㫄㪼㫅㫋㩷㪻㫀㫊㫇㫃㪸㫐㩷㪺㫆㪻㪼㩷㪥㫆㪅㩷㫀㫅㪺㫉㪼㪸㫊㪼㩷㩷㩿㪦㫉㪻㪼㫉㩷㫆㪽㩷㪈㪇㪀 㪇 㪪㫌㫇㪼㫉㫃㫀㫅㫂㩷㫋㪼㫉㫄㫀㫅㪸㫃㩷㫊㫇㪸㫉㪼 㪥㫆㫉㫄㪸㫃㪁㪆㫊㫎㫀㫋㪺㪿㩷㫋㫆㩷㫊㫇㪸㫉㪼 㪮㫀㫋㪿 㪪㪼㪼㩷㫋㪸㪹㫃㪼㩷䋱 㪛㪼㫄㪸㫅㪻㩷㫉㪸㫋㫀㫆㩷㫊㪼㫃㪼㪺㫋㫀㫆㫅 㪧㫆㫎㪼㫉㩷㫍㫆㫃㫋㪸㪾㪼㩷㫊㪼㫃㪼㪺㫋㫀㫆㫅 㪪㪼㪼㩷㫋㪸㪹㫃㪼㩷㪉 㪢㪼㪼㫇㩷㪦㪝㪝 㪢㪼㪼㫇㩷㪦㪝㪝 㪥㫆㫉㫄㪸㫃 㪟㪼㪸㫋㫀㫅㪾 㪥㫆㫉㫄㪸㫃 㪢㪼㪼㫇㩷㪦㪝㪝 㪥㪼㫎㩷㪪㪣㩿㪘㫌㫋㫆㪀 㪢㪼㪼㫇㩷㪦㪝㪝 㪢㪼㪼㫇㩷㪦㪝㪝 㪢㪼㪼㫇㩷㪦㪝㪝 㪢㪼㪼㫇㩷㪦㪝㪝 㪢㪼㪼㫇㩷㪦㪝㪝 㪢㪼㪼㫇㩷㪦㪝㪝 㪢㪼㪼㫇㩷㪦㪝㪝 㪢㪼㪼㫇㩷㪦㪝㪝 㪢㪼㪼㫇㩷㪦㪝㪝 㪢㪼㪼㫇㩷㪦㪝㪝 㪢㪼㪼㫇㩷㪦㪝㪝 㪜㫉㪸㫊㪼 㪥㫆㫉㫄㪸㫃 㪘㫊㩷㫇㪼㫉㩷㫍㫆㫃㫋㪸㪾㪼 㪜㫏㫋㪼㫉㫅㪸㫃㩷㫀㫅㫇㫌㫋 㪪㫇㪸㫉㪼 㪛㪼㪽㫉㫆㫊㫋㩷㫊㫋㪸㫉㫋㩷㫋㪼㫄㫇㪼㫉㪸㫋㫌㫉㪼 㪦㫌㫋㪻㫆㫆㫉㩷㫌㫅㫀㫋㩷㫋㫐㫇㪼㩷㫊㪼㫃㪼㪺㫋㫀㫆㫅 㪣㪼㫍㪼㫃㪁㪆㪧㫌㫃㫊㪼 㪪㪼㪼㩷㫋㪸㪹㫃㪼㩷㪊 㪣㪼㫍㪼㫃 㪮㫀㫋㪿 㪮㫀㫋㪿 㪥㫆㫉㫄㪸㫃 㪮㫀㫋㪿 㪘㪪㩷㫇㪼㫉㩷㫄㫆㪻㪼㫃 㪥㫆㫉㫄㪸㫃㪁㪆㪚㫆㫃㪻㩷㫉㪼㪾㫀㫆㫅 㪢㪼㪼㫇㩷㪮㫀㫋㪿 㪪㪼㪼㩷㫋㪸㪹㫃㪼㩷㪈 㪁㩷㪛㪼㪽㪸㫌㫃㫋㩷㫊㪼㫋㫋㫀㫅㪾 Table 1㪑㩷㪤㫆㪻㪼㫃㩷㫊㪼㫃㪼㪺㫋㫀㫆㫅㩷㫎㫀㫋㪿㩷㪪㪮㪋㪄㪈㪄㪪㪮㪋㪄㪋㩷㪸㫅㪻㩷㪡㪈㪍 㪇㪑㩷㪦㪝㪝㩷 㪈㪑㪦㪥 㪉㪉㪋 㪉㪏㪇 㪪㪮㪋㪄㪈 㪇 㪈 㪪㪮㪋㪄㪉 㪇 㪇 㪪㪮㪋㪄㪊 㪇 㪇 㪪㪮㪋㪄㪋 㪇 㪇 㪡㪈㪍 㪥㫆㫅㪼 㪥㫆㫅㪼 Table 2㪑㩷㪛㪼㫄㪸㫅㪻㩷㫉㪸㫋㫀㫆㩷㫊㪼㫃㪼㪺㫋㫀㫆㫅㩷㫎㫀㫋㪿㩷㪪㪮㪋㪄㪌㪃㩷㪪㪮㪋㪄㪍 㪇㪑㩷㪦㪝㪝 㪈㪑㪦㪥 㪪㪮㪋㪄㪌 㪪㪮㪋㪄㪍 㪚㫆㫄㫇㫉㪼㫊㫊㫆㫉㩷㪺㪸㫇㪸㪺㫀㫋㫐㩷㩿㩼㪀 㪇 㪇 㪏㪇 㪈 㪇 㪍㪇 㪇 㪈 㪋㪇 㪈 㪈 㪇 Table 3㪑㩷㪧㫆㫎㪼㫉㩷㫍㫆㫃㫋㪸㪾㪼㩷㫊㪼㫃㪼㪺㫋㫀㫆㫅㩷㫎㫀㫋㪿㩷㪡㪈㪈㪃㩷㪡㪈㪉 㪦㫌㫋㪻㫆㫆㫉㩷㫌㫅㫀㫋 㪊㪏㪇㪆㪋㪈㪌㪭㩷㪌㪇㪟㫑 㪇㪑㩷㪥㫆㫅㪼 㪈㪑㩷㪮㫀㫋㪿 㪡㪈㪉 㪇 㪡㪈㪈 㪇 (2) Indoor unit 㪪㫎㫀㫋㪺㪿㪼㫊 㪪㪮㪈 㪪㪮㪉 㪪㪮㪊 㪪㪮㪋 㪪㪮㪌㪄㪈 㪪㪮㪌㪄㪉 㪪㪮㪍㪄㪈 㪪㪮㪍㪄㪉 㪪㪮㪍㪄㪊 㪪㪮㪍㪄㪋 㪪㪮㪎㪄㪈 㪪㪮㪎㪄㪉 㪪㪮㪎㪄㪊 㪪㪮㪎㪄㪋 㪡㪪㪣㪈 㪛㪼㫊㪺㫉㫀㫇㫋㫀㫆㫅 㪠㫅㪻㫆㫆㫉㩷㫌㫅㫀㫋㩷㪸㪻㪻㫉㪼㫊㫊㩷㪥㫆㪅㩷㩿㪦㫉㪻㪼㫉㩷㫆㪽㩷㪈㪇㪀 㪠㫅㪻㫆㫆㫉㩷㫌㫅㫀㫋㩷㪸㪻㪻㫉㪼㫊㫊㩷㪥㫆㪅㩷㩿㪦㫉㪻㪼㫉㩷㫆㪽㩷㪈㪀 㪦㫌㫋㪻㫆㫆㫉㩷㫌㫅㫀㫋㩷㪸㪻㪻㫉㪼㫊㫊㩷㪥㫆㪅㩷㩿㪦㫉㪻㪼㫉㩷㫆㪽㩷㪈㪇㪀 㪦㫌㫋㪻㫆㫆㫉㩷㫌㫅㫀㫋㩷㪸㪻㪻㫉㪼㫊㫊㩷㪥㫆㪅㩷㩿㪦㫉㪻㪼㫉㩷㫆㪽㩷㪈㪀 㪪㫌㫇㪼㫉㫃㫀㫅㫂㩷㫊㪼㫃㪼㪺㫋㫀㫆㫅 㪘㫌㫋㫆㫄㪸㫋㫀㪺㪁㪆㪧㫉㪼㫍㫀㫆㫌㫊㩷㪪㪣 㪠㫅㪻㫆㫆㫉㩷㫌㫅㫀㫋㩷㪸㪻㪻㫉㪼㫊㫊㩷㪥㫆㪅㩷㩿㪦㫉㪻㪼㫉㩷㫆㪽㩷㪈㪇㪇㪀 㪇 㪇 㪋 㪐 㪦㪝㪝 㪦㪝㪝 㪤㫆㪻㪼㫃㩷㫊㪼㫃㪼㪺㫋㫀㫆㫅 㪘㫊㩷㫇㪼㫉㩷㫄㫆㪻㪼㫃 㪫㪼㫊㫋㩷㫉㫌㫅㪃㩷㪛㫉㪸㫀㫅㩷㫄㫆㫋㫆㫉 㪩㪼㫊㪼㫉㫍㪼㪻 㪪㫇㪸㫉㪼 㪩㪼㫊㪼㫉㫍㪼㪻 㪪㫌㫇㪼㫉㫃㫀㫅㫂㩷㫋㪼㫉㫄㫀㫅㪸㫃㩷㫊㫇㪸㫉㪼 㪥㫆㫉㫄㪸㫃㪁㪆㪫㪼㫊㫋㩷㫉㫌㫅 㪛㪼㪽㪸㫌㫃㫋㩷㫊㪼㫋㫋㫀㫅㪾 㪦㪝㪝 㪦㪝㪝 㪦㪝㪝 㪦㪝㪝 㪥㫆㫉㫄㪸㫃㪁㪆㫊㫎㫀㫋㪺㪿㩷㫋㫆㩷㫊㫇㪸㫉㪼 㪮㫀㫋㪿 㪁㩷㪛㪼㪽㪸㫌㫃㫋㩷㫊㪼㫋㫋㫀㫅㪾 㪫㪸㪹㫃㪼㩷㪈㪑㩷㪠㫅㪻㫆㫆㫉㩷㫌㫅㫀㫋㩷㫄㫆㪻㪼㫃㩷㫊㪼㫃㪼㪺㫋㫀㫆㫅㩷㫎㫀㫋㪿㩷㪪㪮㪍㪄㪈㪄㪪㪮㪍㪄㪋 㪪㪮㪍㪄㪈 㪪㪮㪍㪄㪉 㪪㪮㪍㪄㪊 㪪㪮㪍㪄㪋 㪧㪉㪉 㪇 㪇 㪇 㪇 㪧㪉㪏 㪈 㪇 㪇 㪇 AMP Air Conditioning 㪧㪊㪍 㪇 㪈 㪇 㪇 㪧㪋㪌 㪇 㪇 㪈 㪇 㪧㪌㪍 㪇 㪈 㪈 㪇 㪧㪎㪈 㪇 㪇 㪇 㪈 㪧㪐㪇 㪇 㪈 㪇 㪈 㪩㪼㫄㪸㫉㫂㫊 㪇㪄㪐 㪇㪄㪐 㪇㪄㪐 㪇㪄㪐 㪘㫌㫋㫆㫄㪸㫋㫀㪺 㪇 㪦㪝㪝㪑㩷㪇㪃㩷㪦㪥㪑㩷㪈 㪪㪼㪼㩷㫋㪸㪹㫃㪼㩷㪈 㪥㫆㫉㫄㪸㫃 㫂㪼㪼㫇㩷㪦㪝㪝 㫂㪼㪼㫇㩷㪦㪝㪝 㫂㪼㪼㫇㩷㪦㪝㪝 㪥㫆㫉㫄㪸㫃 㪧㪈㪈㪉 㪈 㪈 㪇 㪈 㪧㪈㪋㪇 㪇 㪇 㪈 㪈 㪧㪈㪍㪇 㪈 㪇 㪈 㪈 - 152 - 㪇㪑㩷㪦㪝㪝 㪈㪑㪦㪥 㪧㪉㪉㪋 㪧㪉㪏㪇 㪇 㪈 㪈 㪈 㪈 㪈 㪈 㪈 www.ampair.co.uk | [email protected] '11 • KX-T-166 9 OUTDOOR UNIT (Service code L) 9.1 Exterior dimensions (1) Outdoor unit Models FDCR224KXE6, 280KXE6 PCB003Z362 A - AMP Air Conditioning 153 - # www.ampair.co.uk | [email protected] VRF INVERTER MULTI-SYSTEM AIR CONDITIONERS Air-Conditioning & Refrigeration Systems Headquarters 16-5, Konan 2-chome, Minato-ku, Tokyo, 108-8215 Japan http://www.mhi.co.jp Because of our policy of continuous improvement, we reserve the right to make changes in all specifications without notice. C Copyright MITSUBISHI HEAVY INDUSTRIES, LTD. AMP Air Conditioning www.ampair.co.uk | [email protected]
advertisement
* Your assessment is very important for improving the workof artificial intelligence, which forms the content of this project