
advertisement
▼
Scroll to page 2
of 382
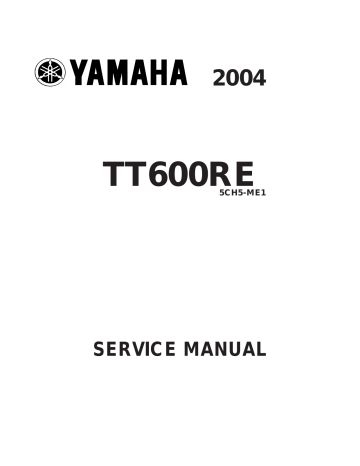
2004 TT600RE 5CH5-ME1 SERVICE MANUAL EASB0000 TT600RE SERVICE MANUAL © 2003 by Belgarda S.p.A. First edition, July 2003 All rights reserved. Any reproduction or unauthorized use without the written permission of Belgarda S.p.A. is expressly prohibited. Printed in Italy EASB0001 NOTICE This manual was produced by the Belgarda S.p.A. primarily for use by Yamaha dealers and their qualified mechanics. It is not possible to include all the knowledge of a mechanic in one manual. Therefore, anyone who uses this book to perform maintenance and repairs on Yamaha vehicles should have a basic understanding of mechanics and the techniques to repair these types of vehicles. Repair and maintenance work attempted by anyone without this knowledge is likely to render the vehicle unsafe and unfit for use. Belgarda S.p.A. is continually striving to improve all of its models. Modifications and significant changes in specifications or procedures will be forwarded to all authorized Yamaha dealers and will appear in future editions of this manual where applicable. NOTE: Designs and specifications are subject to change without notice. EAS00004 IMPORTANT MANUAL INFORMATION Particularly important information is distinguished in this manual by the following. The Safety Alert Symbol means ATTENTION! BECOME ALERT! YOUR SAFETY IS INVOLVED! WARNING CAUTION: NOTE: Failure to follow WARNING instructions could result in severe injury or death to the motorcycle operator, a bystander or a person checking or repairing the motorcycle. A CAUTION indicates special precautions that must be taken to avoid damage to the motorcycle. A NOTE provides key information to make procedures easier or clearer. EAS00007 HOW TO USE THIS MANUAL This manual is intended as a handy, easy-to-read reference book for the mechanic. Comprehensive explanations of all installation, removal, disassembly, assembly, repair and check procedures are laid out with the individual steps in sequential order. 1 The manual is divided into chapters. An abbreviation and symbol in the upper right corner of each page indicate the current chapter. Refer to "SYMBOLS". 2 Each chapter is divided into sections. The current section title is shown at the top of each page, except in Chapter 3 ("PERIODIC CHECKS AND ADJUSTMENTS"), where the sub-section title(s) appears. 3 Sub-section titles appear in smaller print than the section title. 4 To help identify parts and clarify procedure steps, there are exploded diagrams at the start of each removal and disassembly section. 5 Numbers are given in the order of the jobs in the exploded diagram. A circled number indicates a disassembly step. 6 Symbols indicate parts to be lubricated or replaced. Refer to "SYMBOLS". 7 A job instruction chart accompanies the exploded diagram, providing the order of jobs, names of parts, notes in jobs, etc. 8 Jobs requiring more information (such as special tools and technical data) are described sequentially. 1 ILLUSTRATED SYMBOLS 2 GEN INFO SPEC 3 4 INSP ADJ CHAS 5 6 ENG CARB 7 8 TRBL SHTG ELEC 9 0 q w e r t y u i o p a s d The following symbols are not relevant to every vehicle. Illustrated symbols 1 to 8 are printed on the top right of each page and indicate the subject of each chapter. 1 General information 2 Specifications 3 Periodic inspections and adjustments 4 Chassis 5 Engine 6 Carburetor 7 Electrical system 8 Troubleshooting ? f New Illustrated symbols 9 to y are used to identify the specifications appearing in the text. 9 Can be serviced with engine mounted 0 Filling fluid q Lubricant w Special tool e Torque r Wear limit, clearance t Engine speed y Electrical data Illustrated symbols u to s in the exploded diagrams indicate the types of lubricants and lubrication points. u Apply engine oil i Apply gear oil o Apply molybdenum disulfide oil p Apply wheel bearing grease a Apply lightweight lithium-soap base grease s Apply molybdenum disulfide grease Illustrated symbols d to f in the exploded diagrams indicate the following: d Apply locking agent (LOCTITE®) f Replace the part E004000 TABLE OF CONTENTS GENERAL INFORMATION SPECIFICATIONS PERIODIC INSPECTION AND ADJUSTMENTS CHASSIS ENGINE CARBURETION ELECTRICAL TROUBLESHOOTING GEN INFO 1 SPEC 2 INSP ADJ 3 CHAS 4 ENG 5 CARB 6 ELEC 7 ? TRBL SHTG 8 GEN INFO 1 GEN INFO CHAPTER 1. GENERAL INFORMATION MOTORCYCLE IDENTIFICATION ......................................................................................1-1 VEHICLE IDENTIFICATION NUMBER..........................................................................1-1 MODEL LABEL ..............................................................................................................1-1 IMPORTANT INFORMATION ..............................................................................................1-2 PREPARATION FOR REMOVAL PROCEDURES ........................................................1-2 REPLACEMENT PARTS ..............................................................................................1-2 GASKETS, OIL SEALS AND O-RINGS ........................................................................1-2 LOCK WASHERS/PLATES AND COTTER PINS ........................................................1-3 BEARINGS AND OIL SEALS ........................................................................................1-3 CIRCLIPS ......................................................................................................................1-3 CHECKING OF CONNECTIONS ........................................................................................1-4 SPECIAL TOOLS..................................................................................................................1-5 GEN INFO VEHICLE IDENTIFICATION GEN INFO GENERAL INFORMATION VEHICLE IDENTIFICATION VEHICLE IDENTIFICATION NUMBER The vehicle identification number 1 is stamped into the frame. MODEL LABEL The model label 1 is affixed to the frame under the seat. This information will be needed to order spare parts. 1 1-1 IMPORTANT INFORMATION GEN INFO EB101000 IMPORTANT INFORMATION PREPARATION FOR REMOVAL PROCEDURES 1. Remove all dirt, mud, dust and foreign material before removal and disassembly. 2. Use proper tools and cleaning equipment. Refer to the “SPECIAL TOOLS” section. 3. When disassembling the machine, always keep mated parts together. This includes gears, cylinders, pistons and other parts that have been “mated” through normal wear. Mated parts must always be reused or replaced as an assembly. 4. During machine disassembly, clean all parts and place them in trays in the order of disassembly. This will speed up assembly and allow for the correct installation of all parts. 5. Keep all parts away from any source of fire. EB101010 REPLACEMENT PARTS 1. Use only genuine Yamaha parts for all replacements. Use oil and grease recommended by Yamaha for all lubrication jobs. Other brands may be similar in function and appearance, but inferior in quality. EB101020 GASKETS, OIL SEALS AND O-RINGS 1. Replace all gaskets, seals and O-rings when overhauling the engine. All gasket surfaces, oil seal lips and O-rings must be cleaned. 2. Properly oil all mating parts and bearings during reassembly. Apply grease to the oil seal lips. 1-2 IMPORTANT INFORMATION GEN INFO EB101030 LOCK WASHERS/PLATES AND COTTER PINS 1. Replace all lock washers/plates 1 and cotter pins after removal. Bend lock tabs along the bolt or nut flats after the bolt or nut has been tightened to specification. OR EB101040 BEARINGS AND OIL SEALS 1. Install bearings and oil seals so that the manufacturer’s marks or numbers are visible. When installing oil seals, apply a light coating of lightweight lithium base grease to the seal lips. Oil bearings liberally when installing, if appropriate. 1 Oil seal CAUTION: Do not use compressed air to spin the bearings dry. This will damage the bearing surfaces. 1 Bearing EB101050 CIRCLIPS 1. Check all circlips carefully before reassembly. Always replace piston pin clips after one use. Replace distorted circlips. When installing a circlip 1, make sure that the sharp-edged corner 2 is positioned opposite the thrust 3 it receives. See sectional view. 4 Shaft 1-3 CHECKING OF CONNECTIONS GEN INFO EB801000 CHECKING OF CONNECTIONS Check the connectors for stains, rust, moisture, etc. 1. Disconnect: • connector 2. Check: • connector Moisture → Dry each terminal with an air blower. Stains/rust → Connect and disconnect the terminals several times. 3. Check: • connector leads Looseness → Bend up the pin 1 and connect the terminals. 4. Connect: • connector terminals NOTE: The two terminals “click” together. 5. Check: • continuity (using a pocket tester) NOTE: • If there is no continuity, clean the terminals. • When checking the wire harness be sure to perform steps 1 to 3. • As a quick remedy, use a contact revitalizer available at most part stores. • Check the connector with a pocket tester as shown. 1-4 SPECIAL TOOLS GEN INFO SPECIAL TOOLS The following special tools are necessary for complete and accurate tune-up and assembly. Use only the appropriate special tools; this will help prevent damage caused by the use of inappropriate tools or improvised techniques. When placing an order, refer to the list provided below to avoid any mistakes. Tool No. Tool name / Usage Engine tachometer 90890-03113 This tool is needed for detecting engine rpm. Timing light 90890-03141 This tool is needed for detecting ignition timing. Pocket tester 90890-03112 These instruments are invaluable for checking the electrical system. Ignition checker 90890-06754 This instrument is necessary for checking the ignition system components. Compression gauge 90890-03081 These tools are used to measure the engine compression. Adapter (compression gauge) 90890-04082 This tool serves to measure the engine compression. Fuel level gauge 90890-01312 This gauge is used to measure the fuel level in the float chamber. Piston pin clip puller 90890-01304 This tool serves for removing the piston pin clip. 1-5 Illustration SPECIAL TOOLS Tool name / Usage Tool No. Rocker arm shaft puller bolt 90890-01083 These tools are used when removing the rocker arm shafts. Weight 90890-01084 These tools are used when removing the rocker arm shafts. Valve spring compressor 90890-04019 These tools are used when removing or installing the valve and the valve spring. 7 mm (0.28 in) valve guide puller 90890-01225 This tool is used to remove the valve guides. 7 mm (0.28 in) valve guide installer 90890-04017 This tool is necessary to install the valve slides properly. 7 mm (0.28 in) valve guide reamer 90890-01227 This tool is used to re-ream the new valve guide. Valve adjusting tool 90890-01311 This tool is necessary for adjusting valve clearance. Rotor holder 90890-01701 This tool is used for loosing and tightening the rotor nut. Rotor screw puller 90890-01362 This tool is used to disassemble the magneto flywheel rotor. 1-6 GEN INFO Illustration SPECIAL TOOLS Tool No. Tool name / Usage All-purpose clutch holder 90890-04086 This tool is used to lock the clutch, when the clutch boss lock nut is being loosened or tightened. Crankcase separating tool 90890-01135 This tool is necessary to disassemble the crankcase. Crankshaft installation hose 90890-01274 This tool is used to install the crankshaft. Crankshaft installation bolt 90890-01275 This tool is used to install the crankshaft. #10 (M14) adapter 90890-04059 This tool is used to install the crankshaft. Crank spacer 90890-04081 This tool is used to install the crankshaft. SEALANT (QUICK GASKET) ® Yamaha Bond No. 1215 ® 90890-85505 This sealant (adhesive) is used for crankcase mating surfaces etc. Ringnut wrench 90890-01268 This tool is used to loosen and tighten the steering ringnut. Ringnut wrench 90890-01348 This tool is used to loosen and tighten the steering ringnut. 1-7 GEN INFO Illustration SPECIAL TOOLS Tool name / Usage Tool No. T-handle 90890-01326 This tool is needed to loosen and tighten the front fork damper rod holding bolt. Front fork damper rod holder 90890-01460 This tool is needed to hold the front fork damper rod when loosening and tightening the holding bolt. DU bush/oil seal guide 90890-11043 This tool is used to install the DU bush and the fork oil seal. 1-8 GEN INFO Illustration SPEC 2 SPEC CHAPTER 2. SPECIFICATIONS GENERAL SPECIFICATIONS ............................................................................................ 2-1 MAINTENANCE SPECIFICATIONS ....................................................................................2-4 ENGINE ........................................................................................................................2-4 CHASSIS ....................................................................................................................2-12 ELECTRICAL ..............................................................................................................2-17 GENERAL TORQUE SPECIFICATIONS............................................................................2-19 CONVERSION TABLE........................................................................................................2-19 LUBRICATION POINTS AND LUBRICANT TYPES..........................................................2-20 ENGINE ......................................................................................................................2-20 CHASSIS ....................................................................................................................2-21 LUBRICATION LAYOUT ....................................................................................................2-22 CABLE ROUTING ..............................................................................................................2-26 SPEC GENERAL SPECIFICATIONS SPEC SPECIFICATIONS GENERAL SPECIFICATIONS Item Standard Limit TT600RE: 5CH5 Model Dimensions Overall length Overall width Overall height Seat height Wheelbase Ground clearance Minimum turning radius 2,220 mm 865 mm 1,195 mm 890 mm 1,480 mm 280 mm 3,300 mm (right) 3,100 mm (left) ••• ••• ••• ••• ••• ••• Basic weight (with oil and full fuel tank) 164.5 kg ••• Engine Engine type Cylinder arrangement Displacement Bore x stroke Compression ratio Starting system Lubrication system Air cooled 4-stroke, SOHC Forward inclined single cylinder 595 cm3 95.0 x 84.0 mm 8.5 : 1 Electric starter Dry sump with separate oil tank ••• ••• ••• SAE20W40SE or SAE10W30SE ••• Recommended engine oil classification Quantity: Without oil filter cartridge replacement With oil filter cartridge replacement Total amount (dry engine) API Service SE, SF, SG or higher ••• 2.4 L ••• 2.5 L 3.0 L ••• ••• Air filter Wet type element Fuel Type Fuel tank capacity Fuel reserve amount Regular unleaded gasoline 10 L 3.0 L Carburetor Manufacturer Model x quantity TEIKEI Y30PV-2ATK x 1 Engine oil Type Temp. °C 2-1 ••• ••• ••• GENERAL SPECIFICATIONS Item Standard Limit Spark plug Manufacturer/model Gap NGK/DPR8EA-9 or NGK/DPR9EA-9 0.8–0.9 mm Clutch type Wet. Multiple-disc Transmission Primary reduction system Primary reduction ratio Secondary reduction system Secondary reduction ratio Number of drive chain sprocket teeth (front/rear) Transmission type Operation Gear ratio Chassis Frame type Caster angle Trail Tires Front: Type Size Manufacturer/model Rear: Type Size Manufacturer/model Maximum load* Tire air pressure (measured on cold tires): Up to 90 kg* Front Rear 90 kg–maximum* Front Rear Off-road riding Front Rear High-speed riding Front Rear * Total weight of rider, passenger, cargo and accessories Wheels Front: Type Size Rear: Type Size SPEC ••• Spur gear 71/34 (2.088) Chain drive 47/15 (3.133) 1st 2nd 3rd 4th 5th 15/47 Constant mesh 5-speed Left foot 2.583 1.588 1.200 0.955 0.792 Open cradle backbone frame/detachable rear frame 27° 117 mm ••• ••• With tube 90/90-21-(54R) / 90/90-21-(54S) Pirelli / MT70 - Michelin / T63 With tube 130/80-18-(66R) / 130/80-18-(66S) Pirelli / MT70 - Michelin / T63 180 kg ••• 200 220 210 240 150 160 210 240 ••• ••• ••• ••• ••• ••• ••• ••• kPa; kPa; kPa; kPa; kPa; kPa; kPa; kPa; 2.00 2.20 2.10 2.40 1.50 1.60 2.10 2.40 Spoke wheel 21” x 1.85 Spoke wheel 18” x MT 2.50 2-2 kgf/cm2; kgf/cm2; kgf/cm2; kgf/cm2; kgf/cm2; kgf/cm2; kgf/cm2; kgf/cm2; 2.00 2.20 2.10 2.40 1.50 1.60 2.10 2.40 bar bar bar bar bar bar bar bar GENERAL SPECIFICATIONS Item Brakes Front: Type Operation Fluid Rear: Type Operation Fluid Suspension Front Rear Spring/shock absorber Front Rear Wheel travel Front Rear SPEC Standard Limit Single Ø 267 mm disk brake, 2 x 28 mm Right hand DOT 4 Single Ø 220 mm disk brake, 1 x 34 mm caliper Right foot DOT 4 Telescopic fork Outside tube dia. 46 mm Deltabox Swingarm with adjustable shock absorber Coil spring / oil damper Coil spring / gas-oil damper, spring preload adjustable 230 mm 230 mm ••• ••• Electrical system Ignition system Charging system: Type Standard output Battery: Model Voltage, capacity A.C. magneto 14V, 13.5A at 5.000 r/min ••• GT9B-4 12V, 8Ah ••• Headlight type Quartz bulb (halogen) Bulb voltage, wattage x quantity Headlight Tail/brake light Turn signal light Auxiliary light Meter lighting Turn signal indicator light Neutral indicator light Auxiliary indicator light High beam indicator light 12V 12V 12V 12V 12V 12V 12V 12V 12V Fuse 20A Transistorized coil ignition (digital) 60W / 55W x 1 5W / 21W x 1 10W x 4 5W x 1 3W x 1 1.2W x 1 1.2W x 1 1.2W x 1 1.2W x 1 ••• ••• ••• ••• ••• ••• ••• ••• ••• ••• 2-3 MAINTENANCE SPECIFICATIONS SPEC MAINTENANCE SPECIFICATIONS ENGINE Item Standard Limit Cylinder head Max. warpage ••• 0.03 mm Cylinder Bore Measuring point 94.970 - 95.020 mm 50 mm 95.10 mm ••• Chain drive (left) 23.000 - 23.021 mm 22.967 - 22.980 mm ••• ••• 0.020 - 0.054 mm ••• Camshaft Drive system Camshaft cap inside diameter Camshaft journal diameter Camshaft-journal-to-camshaft-cap clearance Camshaft lobe dimensions: Intake-measurement Intake-measurement Intake-measurement A B C 36.470 - 36.570 mm 30.060 - 30.160 mm 6.41 mm ••• ••• ••• Exhaust-measurement Exhaust-measurement Exhaust-measurement Max. camshaft runout A B C 36.620 - 36.720 mm 30.110 - 30.210 mm 6.51 mm ••• ••• ••• ••• 0.030 mm 2-4 MAINTENANCE SPECIFICATIONS Item SPEC Standard Limit Timing chain Model/number of links Tensioning system 75-010/126 Automatic Rocker arm/rocker arm shaft Arm inside diameter Shaft outside diameter Arm-to-shaft clearance 12.000 - 12.018 mm 11.976 - 11.991 mm 0.009 - 0.042 mm ••• ••• ••• Valve, valve seat, valve guide Valve clearance (cold) intake exhaust 0.05 - 0.10 mm 0.12 - 0.17 mm ••• ••• intake exhaust intake exhaust intake exhaust intake exhaust intake exhaust 36.90 - 37.10 mm 31.90 - 32.10 mm 2.260 mm 2.260 mm 1.00 - 1.20 mm 1.00 - 1.20 mm 1.00 - 1.40 mm 0.80 - 1.20 mm 6.975 - 6.990 mm 6.955 - 6.970 mm ••• ••• ••• ••• 1.80 mm 1.80 mm 0.80 mm 0.65 mm 6.995 mm 6.925 mm intake exhaust 7.000 - 7.012 mm 7.000 - 7.012 mm 7.042 mm 7.042 mm intake exhaust 0.010 - 0.037 mm 0.030 - 0.057 mm 0.08 mm 0.10 mm ••• 0.010 mm 1.10 mm 1.10 mm 1.80 mm 1.80 mm Valve dimensions: Valve head diameter A Valve face width B Valve seat width C Valve margin thickness D Valve stem diameter Valve guide inside diameter Valve stem to valve guide clearance Valve stem runout Valve seat width intake exhaust 2-5 MAINTENANCE SPECIFICATIONS Item Valve spring Inner spring: Free length Installed length (valve closed) Compressed spring force (installed) Standard Winding direction (top view) Outer spring: Free length intake Installed length (valve closed) Compressed spring force (installed) 40.10 mm 40.10 mm 38.10 mm 38.10 mm intake exhaust 22.70 mm 22.70 mm ••• ••• intake intake exhaust 164.80 - 190.20 N 16.80 - 19.39 kg 164.80 - 190.20 N 16.80 - 19.39 kg ••• ••• ••• ••• ••• ••• 2.5 °/1.7 mm 2.5 °/1.7 mm intake exhaust Clockwise Clockwise intake exhaust 43.80 mm 43.80 mm 38.10 mm 38.10 mm intake exhaust intake intake exhaust 34.20 mm 34.20 mm 71.60 - 87.30 N 7.3 - 8,9 kg 149.10 - 182.40 N 15.2 - 18.6 kg ••• ••• ••• ••• ••• ••• ••• ••• 2.5 °/1.7 mm 2.5 °/1.9 mm intake exhaust Counterclockwise Counterclockwise exhaust Spring tilt Winding direction (top view) Limit intake exhaust exhaust Spring tilt intake SPEC Piston Piston-to-cylinder clearance Diameter D Height H Piston pin bore inside diameter Offset Offset direction Piston pin outside diameter 0.045 - 0.065 mm 94.915 - 94.965 mm 5.0 mm 0.15 mm ••• ••• 22.004 - 22.015 mm 2.00 mm Intake side 21.991 - 22.000 mm ••• ••• 2-6 ••• MAINTENANCE SPECIFICATIONS Item SPEC Standard Limit Piston ring Top ring: Ring type Dimensions (B x T) End gap (installed) Ring side clearance 2nd ring: Ring type Dimensions (B x T) End gap (installed) Ring side clearance Oil ring: Dimensions (B x T) End gap (installed) Ring side clearance Barrel 1.20 x 3.80 mm ••• 0.30 - 0.45 mm 0.040 - 0.080 mm 0.70 mm 0.130 mm Plain 1.20 x 3.80 mm ••• 0.30 - 0.45 mm 0.030 - 0.070 mm 0.80 mm 0.130 mm 2.50 x 3.40 mm ••• 0.20 - 0.70 mm 0.020 - 0.060 mm ••• ••• 74.95 - 75.00 mm ••• 0.350 - 0.650 mm 0.010 - 0.025 mm 0.80 mm ••• 0.030 mm ••• ••• ••• Crankshaft Width A Max. runout C Big end side clearance D Big end radial clearance Small end free play F 2-7 MAINTENANCE SPECIFICATIONS Item SPEC Standard Limit Ballancer Ballancer drive method Gear Clutch Clutch release method Friction plate thickness Wear limit Plate quantity Friction plate thickness Wear limit Plate quantity Clutch plate thickness Plate quantity Max. warpage Clutch spring free length Plate quantity Clutch housing thrust clearance Inner push, cam push 2.72 - 2.88 mm ••• 6 pcs 2.94 - 3.06 mm ••• 2 pcs 1.20 mm 7 pcs ••• 42.8 mm 5 pcs 0.070 - 0.071 mm Transmission Max. main axle runout Max. drive axle runout Shift mechanism type ••• ••• Cam drum and guide bar Carburetor ID mark Main jet Main air jet Jet needle Needle jet Cutaway Pilot air jet 1 Pilot jet Bypass 1 Pilot screw turns out Valve seat size Starter jet 1 Float height 5CH5 10 #1:#150 #2:#145 #1:1.0 #2:0.9 #1:5C5A-3/5 #2:5Y18-3/5 2.600 4.00 # 0.8 mm # 50 # 1.0 2-3/4 +/- 1/2 2.5 # 74 6.0 - 8.0 mm ••• Engine idle speed CO% Intake vacuum 1,150-1,450 r/min 1.5 - 3 30.6-33.36 kPa - 230-250 mm Hg ••• ••• ••• Lubrication system Oil filter type Oil pump: Oil pump type Inner rotor to outer rotor tip clearance Outer rotor to pump housing clearance Bypass valve opening pressure Relief valve operating pressure Oil pressure (hot) Pressure check location Dry sump Paper type ••• 2.60 mm ••• 2.8 mm ••• 0.20 mm ••• ••• 0.08 mm 0.08 mm Trochoid type 0.12 mm 0.20 mm 0.030 - 0.080 mm 80.0 - 120.0 kPa (0.8 - 1.2 kgf/cm2) 80.0 - 120.0 kPa (0.8 - 1.2 kgf/cm2) 13.0 kPa (0.13 kgf/cm2)/1,300 r/min Oil filter chamber 0.150 mm ••• ••• ••• ••• 2-8 MAINTENANCE SPECIFICATIONS SPEC ENGINE Cylinder head tightening steps: Crankcase tightening steps: Left crankcase Right crankcase 2-9 MAINTENANCE SPECIFICATIONS SPEC Tightening torques Part to be tightened Cylinder head Cylinder head Cylinder head Cylinder head Cylinder head: Cap (oil check) Spark plug Cylinder head cover Tappet cover (intake) Tappet cover (exhaust) Cylinder Cylinder Cylinder Weight drive gear Rotor (A.C. magneto) Lock nut (valve adjusting screw) Cam chain sprocket Cam chain stopper guide Cam chain stopper guide Rocker shaft Oil pump Oil delivery/retrieval pipe Oil draining pipe Oil filter cover Bleed screw (oil filter cover) Push lever (clutch) Push rod (clutch) Sprocket Lock washer (oil seal) Stop lever Shift cam Stator Part name Thread size Washer based bol Stud bolt Hexagon socket head screw Stud bolt Union bolt – Hexagon socket head screw Hexagon socket head screw – Crown nut Nut Hexagon socket head screw Hexagon nut Hexagon nut Hexagon nut Washer based bolt Hexagon socket head screw Washer based screw Hexagon socket head screw Hexagon socket head screw Pan screw Washer based screw Hexagon socket head screw Hexagon screw Pan screw Hexagon nut Hexagon nut Hexagon screw Bolt Hexagon screw Pan head (+) screw 2-10 Tightening torque Nm mkg M8 x 1.25 M10 x 1.25 29 20 2.9 2.0 M6 x 1.0 M6 x 1.0 10 7 1.0 0.7 M6 x 1.0 M12 x 1.25 7 18 0.7 1.8 M6 x 1.0 10 1.0 M6 x 1.0 M32 x 1.5 M8 x 1.25 M10 x 1.25 10 12 22 42 1.0 1.2 2.2 4.2 M6 x 1.0 M16 x 1.0 M14 x 1.5 M6 x 1.0 10 60 120 14 1.0 6.0 12.0 1.4 M7 x 1.0 20 2.0 M6 x 1.0 10 1.0 M16 x 1.0 20 2.0 M6 x 1.0 10 1.0 M6 x 1.0 M6 x 1.0 10 7 1.0 0.7 M14 x 1.5 30 3.0 M6 x 1.0 M5 x 0.8 M8 x 1.0 M6 x 1.0 M18 x 1.0 M6 x 1.0 M6 x 1.0 M6 x 1.0 10 5 12 8 115 10 10 10 1.0 0.5 1.2 0.8 11.5 1.0 1.0 1.0 M5 x 0.8 5 0.5 Remarks MAINTENANCE SPECIFICATIONS Part to be tightened Part name Thread size Hexagon socket head screw SPEC Tightening torque Nm mkg M6 x 1.0 7 0.7 Hexagon socket head screw M6 x 1.0 10 1.0 Engine oil pipe 2 Union screw M12 x 1.25 35 3.5 Oil delivery pipe Union bolt M8 x 1.25 18 1.8 Carburetor joints Hexagon socket head screw M6 x 1.0 10 1.0 Air filter case (frame) Hexagon screw M6 x 1.0 10 1.0 Air filter case (frame) Washer based screw M6 x 1.0 10 1.0 Washer based nut M6 x 1.0 10 1.0 Pan head (+) screw M6 x 1.0 7 0.7 Hexagon socket head screw M8 x 1.25 23 2.3 Nut, nylon M8 x 1.25 23 2.3 Washer based screw Stator (pick-up coil) Engine oil pipe 1 Exhaust pipe Exhaust pipe protector Muffler Muffler (band) Muffler M8 x 1.25 23 2.3 Crankcase Hexagon socket head screw M6 x 1.0 10 1.0 Crankcase Stud bolt M10 x 1.25 20 2.0 Hexagon socket head screw M6 x 1.0 10 1.0 Hexagon socket head screw M6 x 1.0 10 1.0 Hexagon socket head screw M6 x 1.0 10 1.0 Stop washer (bearing) Flat headscrew M6 x 1.0 7 0.7 Pressure plate Washer based screw M6 x 1.0 8 0.8 Clutch housing Hexagon nut M20 x 1.0 90 9.0 Primary drive gear Hexagon nut M20 x 1.0 120 12.0 Crankcase cover (right) Crankcase cover (left) Sprocket cover 2-11 Remarks MAINTENANCE SPECIFICATIONS SPEC CHASSIS Item Standard Steering Steering bearing type Lock to lock angle (left) Lock to lock angle (right) Front suspension Front fork travel Fork spring free length Spring rate Spring stroke Spring rate Optional spring available Recommended oil Quantity Level < min - max > Taper roller bearing 45° 45° (K1) (K1) (K2) Rear suspension Rear shock absorber assembly travel Spring free length Installed length Spring rate (K) Optional spring available 277 - 283 mm 530 mm 7.0 N/mm (0.71 kgf/mm) 330 mm 11.2 N/mm (1.14 kgf/mm) No Liqui Moly Racing suspension oil SAE 7,5 650 cc 180 mm 170-190 mm (from upper edge of inner tube, fully compressed without spring) Limit ••• ••• ••• ••• ••• ••• ••• ••• ••• ••• 83 mm 224 mm 211 mm 80 N/mm (8.1 kgf/mm) No ••• ± 1.5 mm ••• Swingarm Free play limit (at the end of the swingarm)-radial Free play limit (at the end of the swingarm)-axial ••• 1.0 mm 0.4 - 0.7 mm ••• Front wheel Wheel type Rim size Rim material Max. radial wheel runout Max. lateral wheel runout Spoke wheel 21 x 1.85 Aluminium 1.0 mm 0.5 mm ••• ••• Rear wheel Wheel type Rim size Rim material Max. radial wheel runout Max. lateral wheel runout Spoke wheel 18 x MT2.50 Aluminium 1.0 mm 0.5 mm ••• ••• 2-12 MAINTENANCE SPECIFICATIONS Item SPEC Standard Limit Drive chain Type/manufacturer Link quantity Drive chain slack 520 135ORSB / Regina Chain 114 30.0 - 40.0 mm ••• Front disc brake Disc outside diameter x thickness Max. deflection Brake pad lining thickness-inner Brake pad lining thickness-outer 267 x 4 mm ••• 7.5 mm 7.5 mm ••• 0.15 mm * 3.7 mm * 3.7 mm Master cylinder inside diameter Caliper cylinder inside diameter Recommended fluid 13 mm 28 mm x 2 DOT 4 Rear disc brake Disc outside diameter x thickness Max. deflection Brake pad lining thickness-inner Brake pad lining thickness-outer Master cylinder inside diameter Caliper cylinder inside diameter Recommended fluid 220.0 x 5.0 mm ••• 9.0 mm 9.0 mm ••• 0.15 mm * 4.5 mm * 4.5 mm 12.7 mm 34 mm DOT 4 Front brake lever Adjustable Brake pedal lever Brake pedal position 10 mm (below the footrest plane) ••• Clutch lever Clutch lever free play (lever end) 10.0 - 15.0 mm ••• Throttle grip Throttle cable free play 3.0 - 5.0 mm ••• 2-13 MAINTENANCE SPECIFICATIONS SPEC Tightening torques Thread size Part to be tightened Tightening torque N·m m·kg Engine mounting and rear frame: Engine front/Stay engine Stay engine (engine front)/Frame Engine rear under/Frame Engine top/Stay engine Engine protector/Frame Chain tensioner top/Frame Chain tensioner under/Frame Frame/Rear frame (upper) Frame/Rear frame (under) Rear frame/Air filter assy M10 x 1.25 M10 x 1.25 M10 x 1.25 M10 x 1.25 M6 x 1.0 M8 x 1.25 M8 x 1.25 M8 x 1.25 M8 x 1.25 M6 x 1.0 64 64 68 64 7 23 23 23 23 5 6.4 6.4 6.8 6.4 0.7 2.3 2.3 2.3 2.3 0.5 Front fork and steering: Handle crown/Inner tube Handle crown/Steering shaft Steering shaft/Ring nut Holder handle upper/Crown handle Holder handle under/Crown handle Front fork under bracket/Inner tube Front master cylinder/Cap Front master cylinder/Handle Union bolt tightening Front fender/Front fork Stay headlight/Handle crown Stay headlight/Bracket meter Headlight/Stay headlight M8 x 1.25 M28 x 1.5 M36 x 1.5 M8 x 1.25 M10 x 1.5 M8 x 1.25 M4 x 0.7 M6 x 1.0 M10 x 1.0 M6 x 1.0 M6 x 1.0 M6 x 1.0 M6 x 1.0 28 4 115 20 40 23 1.5 9 20 7 10 6 10 2.8 0.4 11.5 2.0 4.0 2.3 0.15 0.9 2.0 0.7 1.0 0.6 1.0 Rear arm and cushion: Pivot shaft/Frame Arm relay/Frame Arm relay/Rod connecting Arm relay/Shock absorber Rod connecting/Rear arm Shock absorber upper/Frame Seal guard/Rear arm Support chain/Rear arm Chain case/Rear arm M14 x 1.5 M10 x 1.25 M10 x 1.25 M10 x 1.25 M12 x 1.25 M12 x 1.25 M6 x 1.0 M6 x 1.0 M6 x 1.0 90 60 52 59 66 66 4 9 9 9.0 6.0 5.2 5.9 6.6 6.6 0.4 0.9 0.9 Front wheel: Front wheel shaft/Front fork Axle holder//Front fork M16 x 1.5 M6 x 1.0 59 9 5.9 0.9 Rear wheel: Rear wheel shaft/Nut M18 x 1.5 115 11.5 Clutch hub/Sprocket M10 x 1.25 48 4.8 2-14 Remarks See “NOTE” MAINTENANCE SPECIFICATIONS Thread size Part to be tightened Tightening torque N·m m·kg Front brake: Front hub/Disc brake Front caliper/Front fork Front caliper/Bleeder tightening Union bolt tightening (front) M6 x 1.0 M8 x 1.25 M10 x 1.0 M10 x 1.0 12 25 14 20 1.2 2.5 1.4 2.0 Rear brake: Rear hub/Disc brake Rear master cylinder/Frame Rear stop switch/Rear master cylinder Rear caliper/Bleeder tightening Protector rear caliper/Rear caliper Union bolt tightening (rear) Rear brake tank reserve/Air cleaner assy Brake pedal/Frame M6 x 1.0 M6 x 1.0 M10 x 1.0 M10 x 1.0 M6 x 1.0 M10 x 1.0 M6 x 1.0 M10 x 1.25 12 10 20 14 10 20 5 48 1.2 1.0 2.0 1.4 1.0 2.0 0.5 4.8 Sidestand/Footrest: Sidestand mounting bolt/Frame Sidestand mounting bolt/Nut Sidestand switch/Frame Rear footrest/Rear frame Bracket 1 (main footrest)/Frame Bracket 2 (main footrest)/Frame Footrest cover/Footrest M12 x 1.25 M12 x 1.25 M5 x 0.8 M8 x 1.25 M10 x 1.25 M10 x 1.25 M6 x 1.0 40 40 8 30 48 48 10 4.0 4.0 0.8 3.0 4.8 4.8 1.0 Seat, fuel tank and oil tank: Seat/Frame Bolt (guide seat)/Fuel tank Fuel tank/Rear frame Damper fuel tank (front)/Frame Fuel tank/Fuel cock Oil tank/Sub-oil tank Union bolt (oil hose 2)/Oil tank assy/Engine Oil hose 1/Oil tank/Engine Oil tank/Rear frame M6 x 1.0 M6 x 1.0 M6 x 1.0 M8 x 1.25 M6 x 1.0 M6 x 1.0 M12 x 1.25 M6 x 1.0 M12 x 1.5 10 5 12 15 7 7 35 10 20 1.0 0.5 1.2 1.5 0.7 0.7 3.5 1.0 2.0 Frame, rear fender compl. and lights: Rear fender compl. (under)/Rear frame Rear fender compl. (upper)/Rear frame Bracket, license/Rear frame Bracket, license/Rear flasher Horn/Frame Regulator/Frame Igniton coil/Frame Battery box/Rear frame Igniter cover/Battery box Main switch/Frame Tail light (lense)/Rear fender compl. Starter switch/Red wire M6 x 1.0 M6 x 1.0 M6 x 1.0 M6 x 1.0 M6 x 1.0 M8 x 1.25 M5 x 0.8 M6 x 1.0 M4 M24 x 1.0 M3.5 M6 x 1.0 2 7 10 10 13 7 13 7 1 1 1 7 0.2 0.7 1.0 1.0 1.3 0.7 1.3 0.7 0.1 0.1 0.1 0.7 2-15 SPEC Remarks MAINTENANCE SPECIFICATIONS Thread size Part to be tightened Starting motor cord/Starting motor Wire minus lead (-)/Starting motor Front flasher lights/Stay, headlight Clutch wire/Engine Assist grip (Standing handle)/Rear frame Speedometer Air filter case 1/Air filter case 2 (L = 13 mm) Air filter case 1/Air filter case 2 (L = 19 mm) Hose clamp/Joint, carburator Hose clamp/Air cleaner/Carburator Battery (+)/(-) M6 x 1.0 M6 x 1.0 M6 x 1.0 M6 x 1.0 M8 x 1.25 M5 x 0.8 M3.9 M3.9 M4 x 0.7 M5 x 0.8 M6 x 1.0 Tightening torque N·m m·kg 11 10 1.5 7 23 4 0.5 1 0.6 0.8 2.5 1.1 1.0 0.15 0.7 2.3 0.4 0.05 0.1 0.06 0.08 0.25 SPEC Remarks NOTE: 1. First tighten the ring nut approximately 38 Nm (3.8 mkg) by using the torque wrench, then loosen the ring nut one turn. 2. Final tighten the ring nut at the torque of 4 Nm (0.4 mkg). 2-16 MAINTENANCE SPECIFICATIONS SPEC ELECTRICAL Item Standard Limit Ignition system Ignition timing (B.T.D.C.) Advanced timing (B.T.D.C.) Advancer type 12° / 1,300 r/min 31° / 7,500 r/min Electrical type ••• ••• Transistorized coil ignition Pickup coil resistance T.C.I. unit model/manufacturer 230 Ω ± 20% L/Y-G/W TNDF09 / NIPPON DENSO ••• Ignition coil Model/manufacturer Primary coil resistance Secondary coil resistance JO300 / NIPPON DENSO 4 Ω ± 15% 13 kΩ ± 20% ••• ••• Spark plug cap Material Resistance Resin 10 kΩ ••• Charging system Type Model/manufacturer Standard output Stator coil resistance A.C. magneto TLMZ48 / NIPPON DENSO 14.0 V 13.5 A 5,000 r/min 0.65 Ω ± 20% W-W ••• ••• Rectifier/regulator Regulator type Model/manufacturer No load regulated voltage Rectifier capacity Withstand voltage Semi conductor-short circuit SH629A-12/SHINDENGEN 14.5 ± 0.4 V 25 A 240 V ••• ••• ••• Battery Specific gravity 1.320 ••• Electric starting system System type Starter motor: Model/manufacturer Power output Armature coil resistance Brush overall length Brush spring force Commutator diameter Mica undercut (depth) Starter relay: Model/manufacturer Amperage Coil resistance Constant mesh SM-13/MITSUBA 0.80 kW 0.03 - 0.04 Ω 10.0 mm 8.82 N (899 gf) 28.0 mm 0.70 mm ••• ••• 5 mm ••• 27 mm ••• MS5F-721 / JIDECO 180 A 4,4 Ω ± 5% ••• ••• 2-17 MAINTENANCE SPECIFICATIONS Item SPEC Standard Limit Horn Horn type Quantity Manufacturer Max. amperage Plane 1 pcs LEONELLI 1.5 A ••• Flasher relay Type Model/manufacturer Self cancelling device Flasher frequency Wattage Semi-transistor FB222M/NIPPONDENSO No 75 - 95 cycle/min 10 W 2 + 3.4 W ••• ••• ••• ••• ••• Daylight switch relay Model/manufacturer ACA12151-1-MATSUSHITA DENKOU Circuit breaker Type Amperage for fuse Reserve Fuse 20 A 20 A ••• ••• 2-18 GENERAL TORQUE SPECIFICATIONS/ CONVERSION TABLE SPEC GENERAL TORQUE SPECIFICATIONS CONVERSION TABLE This chart specifies torque for standard fasteners with standard I.S.O. pitch threads. Torque specifications for special components or assemblies are provided for each chapter of this manual. To avoid warpage, tighten multi-fastener assemblies in a crisscross fashion, in progressive stages, until the specified torque is reached. Unless otherwise specified, torque specifications require clean, dry threads. Components should be at room temperature. All specification data in this manual are listed in SI and METRIC UNITS. Use this table to convert METRIC unit data to IMPERIAL unit data. Ex. METRIC MULTIPLIER IMP ** mm 0.03937 = ** in 2 mm 0.03937 = 0.08 in CONVERSION TABLE METRIC TO IMP Known A: Distance between flats B: Outside thread diameter A (nut) B (Bolt) m·kg 10 mm 6 mm 6 0.6 12 mm 8 mm 15 1.5 14 mm 10 mm 30 3.0 17 mm 12 mm 55 5.5 19 mm 14 mm 85 8.5 22 mm 16 mm 130 13.0 2-19 Result Torque m·kg m·kg cm·kg cm·kg 7.233 86.794 0.0723 0.8679 ft·lb in·lb ft·lb in·lb Weight kg g 2.205 0.03527 lb oz Distance km/hr km m m cm mm 0.6214 0.6214 3.281 1.094 0.3937 0.03937 mph mi ft yd in in Volume/ Capacity cc (cm3) cc (cm3) lt (liter) lt (liter) 0.03527 0.06102 0.8799 0.2199 oz (IMP liq.) cu·in qt (IMP liq.) gal (IMP liq.) Miscellaneous kg/mm 55.997 lb/in 14.2234 psi (lb/in2) kg/cm2 Centigrade 9/5 (°C) + 32 Fahrenheit (°F) General torque specifications N·m Multiplier LUBRlCATlON POINTS AND LUBRICANT TYPE SPEC LUBRlCATlON POINTS AND LUBRICANT TYPES ENGINE Lubrication points (part name) Lubricant type Oil seal edges (completely) Bearing retainer Rod pins Rod (big end) Piston and piston rings Hub (weight drive sprocket) Piston pin Valve stim and guide Oil seal (valve stim end) Rocker shaft and rocker arm Cam and bearing (camshaft) Rotor and rotor housing (oil pump) Push rod (clutch) Primary driven gear and main shaft Sliding gear (transmission) Idle gear (transmission) Shift forks and bar Shift cam and bearing (gearshift cam) Shift shaft Rod housing coupled surfaces Bonding agent (rapid seal adhesive)® Yamaha bond No. 1215® Coupled surfaces (cylinder head and cylinder head cover) Bonding agent (rapid seal adhesive)® Yamaha bond No. 1215® 2-20 LUBRlCATlON POINTS AND LUBRICANT TYPE SPEC CHASSIS Lubrication points (part name) Lubricant type Gear unit (tachometer) Oil seal edges (completely) Wheel axle (front and rear wheels) Rear wheel hub and clutch Bearings brasses (rear arm) and bearing push cover Front footrest Pivot points (brake pedal and shift pedal) Bearings (steering head) Pivot points (brake lever and clutch lever) Clutch cable end Pivot points (sidestand) Grease nipples (rear arm-front axle) 2-21 LUBRICATION LAYOUT LUBRICATION LAYOUT (1) (2) (3) (4) (5) (6) Oil Oil Oil Oil Oil Oil tank pump filter (oil tank) strainer (engine) vapour retrieval hose blow-by retrieval hose [A] DELIVERY [B] RETRIEVAL 2-22 SPEC LUBRICATION LAYOUT (1) (2) (3) (4) (5) (6) Oil pump Oil filter Camshaft Oil delivery hose Main driving shaft Drive shaft SPEC [A] DELIVERY [B] RETRIEVAL A B 2-23 LUBRICATION LAYOUT (1) (2) (3) (4) (5) (6) Oil filter Camshaft Connecting rod pin Main driving shaft Secondary drive shaft Drain plug SPEC [A] DELIVERY [B] RETRIEVAL A B 2-24 LUBRICATION LAYOUT (1) (2) (3) (4) (5) Oil pump Oil filter Oil delivery hose Transmission Oil strainer [A] DELIVERY [B] RETRIEVAL A B 2-25 SPEC CABLE ROUTING SPEC CABLE ROUTING (1) Clutch cable (2) Brake hose holder (3) Brake hose (4) Throttle cables (10) Socket cover (5) Bands (6) Lighting wire harness (11) Engine stop switch connector (7) Brake and engine stop switch wire harness (8) Tachometer/ odometer cable (14) Right turn light connector (20) Clutch switch connector (9) Complete wire harness (15) Meter wire harness connector (21) Brake switch connector (16) Main switch wire harness connector (22) Clip [A] (17) Clutch switch (12) Headlight wire harness connector (18) Headlight connector (19) Side/taillight connector (13) Left turn light connector A2 3 4 1 4 22 6 3 1 Lay the brake hose throught the holder on the handle crown. 5 5 5 7 17 6 21 5 5 16 14 9 11 20 8 13 15 12 10 19 18 2-26 CABLE ROUTING (1) (2) (3) (4) (5) (6) Front brake hose Brake hose holder Left tube guard Plastic plate Throttle cables Tachometer/ odometer cable (7) Clutch cable (8) Clutch cable holder (9) Throttle cables holder (10) Wire harness band (11) Fuel pipe from fuel cock (12) Flasher relay (13) Main relay (14) Sidestand switch (15) Diodes (n. 3) (16) A.C. generator wire harness (engine) (17) Engine oil breather pipe (to engine oil tank) (18) Main switch (19) Oil hose (oil tank to engine) (20) Oil hose (engine to oil tank) (21) C.D.I. unit (22) Starting motor plus cable (23) Starting motor minus cable (24) Battery (25) Starting relay (26) Fuse (reserve) (27) Fuse (main) 23 SPEC (28) Wire extension (29) Battery plus cable [A] [B] [C] [D] Lay the brake hose behind the left tube guard and fasten it down by means of the plate 4. Attach throttle cables 5. Fasten the fuel pipe 11 to the tank. Fit the 3 diodes inside the chassis, against the coil clip. 28 30 29 22 25 26 27 24 1 2 D 18 9 15 13 12 10 A3 B 10 11 C 5 17 20 4 8 6 16 7 19 2-27 14 CABLE ROUTING (1) (2) (3) (4) (5) (6) Tachometer/ odometer cable Tachometer/ odometer cable holder Tachometer/ odometer cable band Right tube guard Spark plug cable Horn (7) Carburetor suction pipe (8) Main wire harness band (9) Rear brake switch wire harness (10) Rear brake fluid tank hose (11) Hose from rear master cylinder to caliper (12) Rear brake hose holders (13) Pipe (14) Air breather pipe (15) Spark plug ignition coil (16) Chassis ground (17) Engine oil breather pipe (to air filer case) 7 8 [A] SPEC Insert the tachometer/ odometer cable into the band 3 and the holder 2. 15 16 3A 9 4 10 5 11 6 12 A2 1 17 13 14 2-28 SPEC CABLE ROUTING (1) Rectifier (2) Wire harness bands (3) Protection (4) Left turn wire harness (5) Right turn wire harness (6) Tail light wire harness (7) Air breather pipe (carburetor) (8) Wire extension (9) Starter power cables [A] Screw protection 3 after setting wiring properly. (10) Engine cables and side stand switch 1 2 7 2 4 10 5 8 6 9 3 A 2-29 SPEC INSP ADJ 3 INSP ADJ CHAPTER 3. PERIODIC INSPECTION AND ADJUSTMENTS INTRODUCTION..........................................................................................................3-1 PERIODIC MAINTENANCE/LUBRICATION INTERVALS ........................................3-1 SEAT, FUEL TANK AND REAR COWLING ................................................................3-3 REMOVAL ............................................................................................................3-3 INSTALLATION ....................................................................................................3-3 ENGINE ........................................................................................................................3-4 VALVE CLEARANCE ADJUSTMENT ..................................................................3-4 DRIVE CHAIN ADJUSTMENT ..............................................................................3-7 IDLE SPEED ADJUSTMENT ................................................................................3-7 THROTTLE CABLE FREE PLAY ADJUSTMENT ................................................3-8 SPARK PLUG INSPECTION ................................................................................3-9 IGNITION TIMING CHECK ................................................................................3-11 COMPRESSION INSPECTION ..........................................................................3-12 ENGINE OIL LEVEL CHECK ..............................................................................3-15 ENGINE OIL REPLACEMENT............................................................................3-17 ENGINE OIL PRESSURE CHECK ....................................................................3-21 CLUTCH ADJUSTMENT ....................................................................................3-21 AIR FILTER CLEANING......................................................................................3-24 FUEL FILTER CLEANING ..................................................................................3-25 ENGINE OIL TANK FILTER CLEANING ............................................................3-26 SUCTION HOSE AND MANIFOLD INSPECTION..............................................3-28 FUEL LINE INSPECTION ..................................................................................3-28 CRANKCASE VENTILATION HOSE INSPECTION ..........................................3-29 EXHAUST SYSTEM INSPECTION ....................................................................3-29 CHASSIS ....................................................................................................................3-30 ADJUSTING THE FRONT BRAKE ....................................................................3-30 ADJUSTING THE REAR BRAKE ......................................................................3-31 CHECKING THE BRAKE FLUID LEVEL ............................................................3-32 BRAKE PAD WEAR INSPECTION ....................................................................3-33 BRAKE HOSING INSPECTION..........................................................................3-33 BRAKE CIRCUIT BLEEDING ............................................................................3-34 DRIVE CHAIN SLACK INSPECTION AND ADJUSTMENT ..................................3-35 DRIVE CHAIN LUBRICATION ............................................................................3-36 FRONT FORK INSPECTION ..............................................................................3-37 ADJUSTING THE FRONT FORK ......................................................................3-37 REAR SHOCK ABSORBER ADJUSTMENT ......................................................3-38 STEERING INSPECTION ..................................................................................3-40 TYRE INSPECTION............................................................................................3-41 WHEEL INSPECTION ........................................................................................3-44 SPOKE INSPECTION AND TIGHTENING ........................................................3-44 CABLE INSPECTION..........................................................................................3-45 LEVER AND PEDAL LUBRICATION ..................................................................3-45 SIDESTAND LUBRICATION ..............................................................................3-46 REAR SUSPENSION LUBRICATION ................................................................3-46 INSP ADJ ELECTRICAL SYSTEM ............................................................................................3-47 CHECKING AND CHARGING THE BATTERY ..................................................3-47 CHECKING THE FUSES ....................................................................................3-53 REPLACING THE HEADLIGHT BULBS ............................................................3-54 REPLACING THE TURN INDICATOR LIGHT BULB..........................................3-56 REPLACING THE TAIL/BRAKE LIGHT BULB....................................................3-57 INTRODUCTION/PERIODIC MAINTENANCE/ LUBRICATION INTERVALS INSP ADJ PERIODIC INSPECTION AND ADJUSTMENTS INTRODUCTION This chapter includes all information necessary to perform recommended inspections and adjustments. These preventive maintenance procedures, if followed, will ensure more reliable vehicle operation and a longer service life. The need for costly overhaul work will be greatly reduced. This information applies to vehicles already in service as well as to new vehicles that are being prepared for sale. All service technicians should be familiar with this entire chapter. PERIODIC MAINTENANCE/LUBRICATION INTERVALS ODOMETER READING (x 1,000 km) N0. 1 ITEM * 2 CHECK OR MAINTENANCE JOB 1 10 20 30 40 ✓ ✓ ✓ Fuel line • Check fuel hoses for cracks or damage. ✓ • Check condition. • Clean and regap. ✓ Spurk plug 3 * Valves • Check valve clearance. • Adjust. ✓ • Clean. ✓ ✓ ✓ ✓ ✓ ✓ 4 Air filter element 5 Clutch • Check operation. • Adjust. ✓ ✓ ✓ ✓ ✓ Front brake • Check operation, fluid level and vehicle for fluid leakeage. • (See NOTE). ✓ ✓ ✓ ✓ ✓ 6 * ✓ • Replace. • Replace brake pads. 7 * Rear brake 8 * Brake hoses 9 * Wheels 10 * Tyres 11 * Wheel bearings 12 * ✓ • ✓ ✓ • Replace. ANNUAL CHECK ✓ ✓ • Whenever worm to the limit • Check operation, fluid level and vehicle • for fluid leakage. • (See NOTE). ✓ ✓ ✓ ✓ ✓ • Replace brake pads. Whenever worm to the limit • Check for cracks or damage. ✓ • Replace. (See NOTE). ✓ ✓ ✓ ✓ ✓ Every 4 years • Check runout, spoke tightness and for damage. • Tighten spokes if necessary. ✓ ✓ ✓ ✓ ✓ ✓ ✓ ✓ ✓ • Check bearing for looseness or damage. ✓ ✓ ✓ ✓ Swingarm • Check operation and for excessive play. ✓ ✓ ✓ ✓ • Check chain slack. • Make sure that the rear wheel is properly aligned. • Clean and lubricate. • • • • Check tread depth and for damage. Replace if necessary. Check air pressure. Correct if necessary. Every 500 km and after washing the motorcycle or riding in the rain. 13 * Drive chain 14 * Steering bearings • Lubrificate with lithium-soap-based grease. 15 * Chassis fasteners • Make sure that all nuts, bolts and screws are properly • tightened. ✓ ✓ ✓ ✓ ✓ Sidestand • Check operation. • Lubricate. ✓ ✓ ✓ ✓ ✓ Sidestand switch • Check operation and for oil leakage. ✓ ✓ ✓ ✓ ✓ 16 17 * • Check bearing play and steering for roughness. ✓ ✓ ✓ ✓ Every 20,000 km ✓ 3-1 ✓ INTRODUCTION/PERIODIC MAINTENANCE/ LUBRICATION INTERVALS INSP ADJ ODOMETER READING (x 1,000 km) N0. ITEM CHECK OR MAINTENANCE JOB 1 10 20 30 40 18 * Rear brake • Check operation, fluid level and vehicle for fluid leakage. ✓ ✓ ✓ ✓ 19 Rear shock * absorber assembly • Check operation and shock absorber for oil leakage. sull’ammortizzatore. ✓ ✓ ✓ ✓ Rear suspension • Check operation. * relay arm and connecting arm • Lubricate with lithium-soap-based grease. pivoting points ✓ ✓ ✓ ✓ 20 21 * Carburator ✓ ✓ ✓ ✓ ✓ ✓ ✓ ✓ ✓ ✓ ✓ ✓ Engine oil • Change. • Check oil level and oil leakage. ✓ 23 Engine oil filter element • Replace. ✓ •• Check operation. ✓ Front and rear * brake switches 25 Moving parts and cables ✓ • Check starter (choke) operation. • Adjust engine idling speed. 22 24 ANNUAL CHECK ✓ ✓ ✓ ✓ ✓ ✓ ✓ • Lubricate. ✓ ✓ ✓ ✓ ✓ ✓ ✓ ✓ ✓ ✓ ✓ ✓ ✓ ✓ ✓ 26 Throttle grip * housing and cable • Check operation and free play. • Adjust the throttle cable free play if necessary. • Lubricate the throttle grip housing and cable. 27 Muffler and * exhaust pipe • Check the screw clamp for looseness. ✓ 28 Lights, signals * and switches • Check operation. • Adjust headlight beam. ✓ * Items marked with an asterisk should be performed by a Yamaha dealer as they require special tools, data and technical skills. NOTE: • The annual checks must be performed every year, except if a kilometer-based maintenance is performed instead. • From 50,000 km, repeat the maintenance intervals starting from 10,000 km. • The air filter needs more frequent service if you are riding in unusually wet or dusty areas. • Hydraulic brake system: • Check the brake fluid level regularly and fill as required. • Replace the oil seals on the inner parts of the master cylinder and caliper cylinder every two years. • Replace the brake hoses every four years or if cracked or damaged. 3-2 SEAT, FUEL TANK AND REAR COWLING INSP ADJ SEAT, FUEL TANK AND REAR COWLING Order Job name/Part name Q.ty Remarks Remove the parts in order. Seat, fuel tank and rear cowling removal 1 Seat 1 2 Fuel pipe 1 3 Fuel tank 1 4 Lamp connector 1 Disconnect. 5 Rear cowling 1 NOTE: Widen the rear cowling body sides carefully to extract rear cowling from the chassis. NOTE: Be sure the cap is properly tightened and the fuel cock is in the “OFF” position before removing the tank. Reverse the removal procedure for installation. 3-3 VALVE CLEARANCE ADJUSTMENT INSP ADJ ENGINE VALVE CLEARANCE ADJUSTMENT NOTE: Valve clearance must be adjusted when the engine is at ambient temperature. • Adjust valve clearance with the piston under compression at top dead centre (T.D.C.). • WARNING Hold the motorcycle firmly in place to prevent it falling over during the operation. 2 1. Remove: • Seat • Fuel tank See the section “ SEAT, FUEL TANK AND REAR COWLING”. 2. Disconnect: • Spark plug cap (1) 3. Remove: • Spark plug • Tappet cover (2) (intake) • Tappet covers (3) (exhaust) 1 3 CAUTION: When removing the spark plug and tappet cover, be careful not to drop foreign objects inside the engine. 1 4. Remove: • Cap (1) • Cap (2) 2 5. Turn the crankshaft anticlockwise using a wrench. 3-4 VALVE CLEARANCE ADJUSTMENT INSP ADJ 6. Align: • Reference mark “T” on the flywheel (1) with the fixed reference mark on the crankcase (2). NOTE: Check that the piston is under compression at top dead centre (T.D.C.). (3) Ignition timing reference mark 7. Check: • Valve clearance Out of specification ➔ Adjust. Valve clearance (cold): Intake: 0.05 ~ 0.10 mm Exhaust: 0.12 ~ 0.17 mm 8. Adjust: • Valve clearance ▼▼▼▼▼▼▼▼▼▼▼▼▼▼▼▼▼▼▼▼▼▼▼▼▼▼▼▼ Adjustment: • Loosen the lock nut (1). • Fit a thickness gauge (2) between the rocker arm and the valve stem. • Turn the adjuster (1) clockwise or anticlockwise using the special tool (2) to obtain the required clearance. Special tool: P/N. 90890-01311 • Holding the adjuster firmly in place, lock tighten lock nut. Lock nut: 14 Nm (1.4 mkg) • Measure valve clearance. If the clearance is incorrect, repeat the previous stages to achieve the required value. ▲▲▲▲▲▲▲▲▲▲▲▲▲▲▲▲▲▲▲▲▲▲▲▲▲▲▲▲▲ 3-5 VALVE CLEARANCE ADJUSTMENT INSP ADJ 9. Reassemble: • Caps • Tappet cover (intake) • Tappet covers (exhaust) • Spark plug Tappet cover (exhaust): 12 Nm (1.2 mkg) Bolt (tappet cover - intake): 10 Nm (1.0 mkg) Spark plug: 18 Nm (1.8 mkg) NOTE: The tappet cover (intake) should be mounted with arrow (1) pointing upwards. 10. Connect: • Spark plug cap 11. Reassemble: • Fuel tank • Seat See section “SEAT, FUEL TANK AND REAR COWLING”. Seat screws: 10 Nm (1.0 mkg) 3-6 DRIVE CHAIN ADJUSTMENT IDLE SPEED ADJUSTMENT INSP ADJ DRIVE CHAIN ADJUSTMENT The drive chain does not need to be adjusted. IDLE SPEED ADJUSTMENT 1. Start the engine and let it heat. 2. Connect: • The inductive engine speed indicator to the spark plug cable Special tool: P/N. 90890-03113 3. Check: • The engine idle speed. Out of specification ➔ Adjust. Engine idle speed: 1,150 ~ 1,450 rpm 4. Adjust: • Engine idle speed ▼▼▼▼▼▼▼▼▼▼▼▼▼▼▼▼▼▼▼▼▼▼▼▼▼▼▼▼ Adjustment: • Turn the throttle stop screw (1) either way to obtain the idle speed required. Screwing (a) Increases idle speed Unscrewing (b) Decreases idle speed ▲▲▲▲▲▲▲▲▲▲▲▲▲▲▲▲▲▲▲▲▲▲▲▲▲▲▲▲▲ NOTE: After setting the idle speed, adjust the accelerator cable free play. 5. Disconnect: • Inductive engine speed indicator 3-7 THROTTLE CABLE FREE PLAY ADJUSTMENT INSP ADJ THROTTLE CABLE FREE PLAY ADJUSTMENT NOTE: Before adjusting the throttle cable free play, adjust the engine idle speed. 1. Remove: • Seat • Fuel tank See section “SEAT, FUEL TANK AND REAR COWLING”. 2. Check: • Throttle cable free play (a) Out of specification ➔ Adjust. Throttle cable free play: 3 ~ 5 mm (at the grip flange) a 3. Adjust: • Throttle cable free play 2 1 ▼▼▼▼▼▼▼▼▼▼▼▼▼▼▼▼▼▼▼▼▼▼▼▼▼▼▼▼ 5 Adjustment: • Loosen the throttle cable (2) lock nuts (1). • Turn the adjuster (3) clockwise or anticlockwise to obtain the required free play. • If after loosening the adjuster by 5 mm, the free play is still not correct, tighten the adjuster (4) on the throttle cable (5) once more. • Tighten the lock nuts. 3 4 6 (1), (6) Lock nuts ▲▲▲▲▲▲▲▲▲▲▲▲▲▲▲▲▲▲▲▲▲▲▲▲▲▲▲▲▲ 4. Reassemble: • Fuel tank • Seat See section “SEAT, FUEL TANK AND REAR COWLING”. Seat screws: 10 Nm (1,0 mkg) 3-8 SPARK PLUG INSPECTION INSP ADJ SPARK PLUG INSPECTION 1. Remove: • Seat • Fuel tank See section “SEAT, FUEL TANK AND REAR COWLING”. 2. Disconnect: • Spark plug cap 3. Remove: • Spark plug (1) CAUTION: 1 Before removing the spark plug, use compressed air to blow away any dirt accumulated in the spark plug wells to prevent it from falling into the cylinder. CAUTION: When removing the spark plug, be careful not to drop foreign objects inside the engine. 4. Inspect: • Type of spark plug Incorrect ➔ Replace. Standard spark plug: DPR8EA-9 (N.G.K.) or DPR9EA-9 (N.G.K.) 5. Inspect: • Electrodes (1) Wear and tear/damage ➔ Replace. • Insulator (2) Normal insulator (2) colour is light tan. 6. Clean the spark plug with a suitable tool and a steel brush. 7. Measure: • Spark plug electrode gap (a) Use a wire or thickness gauge. Out of specification ➔ Regap. Electrode gap: 0.8 ~ 0.9 mm 3-9 SPARK PLUG INSPECTION INSP ADJ 8. Lock tighten: • Spark plug Before installing the spark plug, clean the surface and thread. Spark plug: 18 Nm (1.8 mkg) NOTE: Tighten the spark plug by hand before torquing to specification. 9. Connect: • Spark plug cap 10. Install: • Fuel tank • Seat See section “SEAT, FUEL TANK AND REAR COWLING”. Seat screws: 10 Nm (1.0 mkg) 3-10 IGNITION TIMING CHECK INSP ADJ IGNITION TIMING CHECK 1. Start the engine and let it heat. 2. Connect: • Inductive rev counter • Stroboscopic lamp to spark plug cable Inductive engine speed indicator: P/N. 90890-03113 Stroboscopic lamp: P/N. 90890-03141 3. Remove: • Cap (1) CAUTION: 1 In certain conditions, the oil might spray out when the cap is removed. Be careful therefore when removing the cap. 4. Check: • Ignition advance ▼▼▼▼▼▼▼▼▼▼▼▼▼▼▼▼▼▼▼▼▼▼▼▼▼▼▼▼ Check: • Heat engine and let it run to the number of revs required. Engine idle speed: 1,150 ~ 1,450 rpm • Check that reference (1) is in the mobile field of reference (2) on the flywheel. Incorrect ignition timing ➔ Check the ignition coil unit. NOTE: Ignition timing cannot be adjusted. ▲▲▲▲▲▲▲▲▲▲▲▲▲▲▲▲▲▲▲▲▲▲▲▲▲▲▲▲▲ 5. Install: • Cap 6. Remove: • Stroboscopic lamp • Inductive engine speed indicator 3-11 COMPRESSION INSPECTION INSP ADJ COMPRESSION INSPECTION NOTE: Insufficient compression causes a loss of performance. WARNING Set the motorcycle firmly in place to prevent it falling during the operation. 1. Remove: • Seat • Fuel tank See section “SEAT, FUEL TANK AND REAR COWLING”. 2. Check: • Valve clearance Out of specification ➔ Adjust. See section “VALVE CLEARANCE ADJUSTMENT”. 3. Install: • Secondary fuel tank 4. Start engine and let it heat. • Switch off engine. 5. Disconnect: • Spark plug cap 6. Remove: • Spark plug (1) CAUTION: When removing the spark plug, be careful to prevent foreign bodies from dropping inside the engine. 1 7. Apply: • Pressure gauge (1) • Adapter (2) Pressure gauge: P/N. 90890-03081 Adapter: P/N. 90890-04082 3-12 COMPRESSION INSPECTION INSP ADJ 8. Check: • Pressure under compression ▼▼▼▼▼▼▼▼▼▼▼▼▼▼▼▼▼▼▼▼▼▼▼▼▼▼▼▼ Inspection: • Turn the main switch to "ON". • With the throttle wide open, crank the engine until the reading on the compression gauge stabilized. WARNING While operating the starter, disconnect the spark plug cap to avoid sparks. • Compare the pressure reading with those in the table. Pressure under compression: Standard 1,100 kPa (11 kg/cm2, 156 psi) Minimum 900 kPa (9 kg/cm2, 128 psi) Maximum 1.200 kPa (12 kg/cm2, 171 psi) • If the pressure reading is lower than minimum: 1) Add a few drops of oil to the cylinder through the hole in the spark plug. 2) Measure the compression again. 3) Compare the new reading with the first, then proceed according to the indications in the table. 3-13 COMPRESSION INSPECTION INSP ADJ Pressure under compression: (after adding oil to the cylinder) Reading Diagnosis Pressure higher than before Piston worn or damaged. Pressure same as before Cylinder head or piston rings, valves, gaskets may be faulty. Pressure above maximum value Inspect cylinder head, valve surfaces, piston rim to check for carbon deposits. ▲▲▲▲▲▲▲▲▲▲▲▲▲▲▲▲▲▲▲▲▲▲▲▲▲▲▲▲▲ 9. Remove: • Secondary fuel tank • Pressure gauge (with adapter) 10. Reassemble: • Spark plug See section “SPARK PLUG INSPECTION”. Spark plug: 18 Nm (1.8 mkg) 11. Connect: • Spark plug cap 12. Reassemble: • Fuel tank • Seat See section “SEAT, FUEL TANK AND REAR COWLING”. Seat screws: 10 Nm (1.0 mkg) 3-14 ENGINE OIL LEVEL CHECK INSP ADJ ENGINE OIL LEVEL CHECK CAUTION: Do not put additives into the engine oil. The latter also lubricates the clutch and additives might cause it to slide. WARNING Never remove the oil tank cap when the engine is hot. The boiling oil might spill over, causing burns. Wait for the oil to cool to at least 60°C (140°F) or thereabouts. This model is fitted with a dry crankcase lubrication system. A feed pump delivers oil to the engine; after fully lubricating the latter, the oil is returned to the tank by a scavenge pump. The oil level must therefore be checked in the oil tank. 1. Start the engine and warm up until the oil temperature rises to approximately 60°C (140°F). 2. Idle the engine for at least 10 seconds while keeping the motorcycle upright. After stop the engine and check the oil level through the level window (3) located on the left side of the oil tank assy and(or) by oil level gauge. NOTE: Be sure the motorcycle is positioned straight up when checking the oil level. A slight tilt toward the side can result in false readings. 3. The oil level should be between the maximum (1) and minimum (2) marks. 3-15 ENGINE OIL LEVEL CHECK INSP ADJ If the oil level is below minimum ➔ Add oil up to maximum level. Recommended oil: SAE20W40SE or SAE10W30SE Refer to the chart for selection of the oils suited to the atmospheric temperature. API Standard: API SE, SF, SG or higher grade CAUTION: • • • Do not put in any chemical additives or use oils with a grade of CD (a) or higher. Be sure not to use oils labeled “ENERGY CONSERVING II” (b) or higher. Engine oil also lubricates the clutch and additives could cause clutch slippage. Be sure no foreign material enters the crankcase. 4. Reassemble the oil tank cap. CAUTION: Never start the engine when the oil tank is empty. Oil capacity: Total: 3.0 litres Periodic oil change: 2.4 litres With oil filter change: 2.5 litres 3-16 ENGINE OIL REPLACEMENT INSP ADJ ENGINE OIL REPLACEMENT CAUTION: Do not put additives into the engine oil. The latter also lubricates the clutch and additives might cause it to slide. WARNING Never remove the oil tank cap when the engine is hot. The boiling oil might spill over, causing burns. Wait for the oil to cool to at least 60°C (140°F) or thereabouts. Engine oil replacement (without replacing filter oil) 1. Warm up the engine for a few minutes. 2. Stop the engine. Place an oil pan under the engine and remove the oil filler cap. 3. Remove the drain plug (1) and drain the engine oil. 4. Remove two bolts (2) and O-ring of the oil hose flange, and drain the oil from oil tank. 5. Remove the air bleed screw (3) attached to the oil filter cover (4). 6. Wait until the oil has completely drained. 3 4 7. Inspect: • All gaskets Damaged ➔ Replace. 8. Reassemble: • Oil filter cover bleeder screw • Engine oil drain plug • Oil tank hose and O-ring 3-17 ENGINE OIL REPLACEMENT INSP ADJ Fastening torques: Drain plug (engine): 30 Nm (3.0 mkg) Oil tank hose (flange): 10 Nm (1.0 mkg) Oil filter cover air bleeder screw: 5 Nm (0.5 mkg) 9. Fill: • Oil tank Recommended oil: SAE20W40SE or SAE10W30SE Refer to the chart for selection of the oils suited to the atmospheric temperature. API Standard: API SE, SF, SG or higher grade Oil capacity: Periodic change = 2.4 litres CAUTION: • • • Do not put in any chemical additives or use oils with a grade of CD (a) or higher. Be sure not to use oils labeled “ENERGY CONSERVING II” (b) or higher. Engine oil also lubricates the clutch and additives could cause clutch slippage. Be sure no foreign material enters the crankcase. 10. Install: • Oil tank tap 11. Check: • Oil level See section “ENGINE OIL LEVEL CHECK”. • Oil pressure See section “ENGINE OIL PRESSURE CHECK”. • Oil leakage 3-18 ENGINE OIL REPLACEMENT INSP ADJ Engine oil replacement (with oil filter replacement) 1. Warm up the engine for a few minutes. 2. Stop the engine. Place an oil pan under the engine and remove the oil filler cap. 3. Remove the drain plug (1) and drain the engine oil. 4. Remove two bolts (2) and O-ring of the oil hose flange, and drain the oil from oil tank. 5. Remove the air bleed screw (3) attached to the oil filter cover (4). 6. Wait until the oil has completely drained. 3 NOTE: The oil filter cover is secured by three screws (5). The lower one should be removed so that the filter cavity will drain. 4 5 7. Remove the other filter cover screws and remove the oil filter cover. 8. Remove the oil filter (6) and O-ring (7). 9. Inspect: • All gaskets • O-rings Damaged ➔ Replace. 6 7 10. Reassemble: • (New) filter cartridge • Filter cover screw • Oil filter cover bleeder screw • Engine drain plug • Oil tank hose Fastening torques: Drain plug (engine): 30 Nm (3.0 mkg) Oil tank hose (flange): 10 Nm (1.0 mkg) Filter cover screw: 10 Nm (1.0 mkg) Oil filter cover bleeder screw: 5 Nm (0.5 mkg) 3-19 ENGINE OIL REPLACEMENT INSP ADJ 11. Fill: • Oil tank Recommended oil: SAE20W40SE or SAE10W30SE Refer to the chart for selection of the oils suited to the atmospheric temperature. API Standard: API SE, SF, SG or higher grade Oil capacity: Total: 3.0 litres Periodic oil change: 2.4 litres With oil filter change: 2.5 litres CAUTION: • • • Do not put in any chemical additives or use oils with a grade of CD (a) or higher. Be sure not to use oils labeled “ENERGY CONSERVING II” (b) or higher. Engine oil also lubricates the clutch and additives could cause clutch slippage. Be sure no foreign material enters the crankcase. 12. Install: • Oil tank cap 13. Check: • Oil level See section “ENGINE OIL LEVEL CHECK”. • Oil pressure See section “ENGINE OIL PRESSURE CHECK”. • Oil leakage 3-20 ENGINE OIL PRESSURE CHECK/ CLUTCH ADJUSTMENT INSP ADJ ENGINE OIL PRESSURE CHECK 1. Remove: • Bleeder screw (1) 1 2. Start the engine and keep it idling until oil flows out of the bleed hole. 3. Inspect: • Conditions of oil at bleeder hole. Oil leakage ➔ Oil pressure good. No leakage ➔ Pressure insufficient. CAUTION: If the oil does not come out after one minute, stop the engine immediately to prevent seizure. 4. Tighten: • Bleeder screw Bleeder screw: 5 Nm (0.5 kgm) 2 CLUTCH ADJUSTMENT Cable free play adjustment 1 1. Check: • Clutch free play adjustment (a) Out of specification ➔ Adjust. a Free play: 10 ~ 15 mm 2. Adjust: • Clutch cable free play ▼▼▼▼▼▼▼▼▼▼▼▼▼▼▼▼▼▼▼▼▼▼▼▼▼▼▼▼▼ Adjustment: 1 • • 2 • Loosen lock nuts (1). Turn the adjuster (2) either way to obtain correct free play. Tighten lock nuts after adjustment. ▲▲▲▲▲▲▲▲▲▲▲▲▲▲▲▲▲▲▲▲▲▲▲▲▲▲▲▲▲ 3-21 CLUTCH ADJUSTMENT INSP ADJ NOTE: After adjustment, recheck lever free play to make sure that it works smoothly and progressively. If it is impossible to obtain the required adjustment or if the clutch does not work properly, adjust the internal mechanism. Internal mechanism adjustment 1. Loosen: • Lock nuts on the lever cable adjuster and crankcase adjuster 2. Fully tighten: • Adjusters 3. Drain off: • Engine oil See section “ENGINE OIL REPLACEMENT”. 4. Remove: • Footrest (right) (1) • Engine protector (2) 5. Disconnect: • Brake pedal return spring (3) 6. Remove: • Rear master cylinder fastening screws (4) • Oil delivery hose fastening screw (5) • Right crankcase cover fastening screws • Right crankcase cover (6) 7. Loosen: • Lock nut (1) 8. Push the engine clutch control lever forward to the stop point. 9. Adjust: • Free play With the lever in this position, turn the adjuster (2) either way until the marks on the lever (3) and crankcase (4) are aligned. 10. Tighten: • Lock nut (1) Lock nut: 8 Nm (0.8 mkg) 3-22 CLUTCH ADJUSTMENT INSP ADJ 11. Install: • Right crankcase cover • Right crankcase cover fastening screws • Oil delivery hose fastening screw Screw (crankcase cover): 10 Nm (1.0 mkg) Oil delivery hose screw: 18 Nm (1.8 mkg) 12. Connect: • Brake pedal return spring • Rear master cylinder Screw (rear master cylinder): 10 Nm (1.0 mkg) 13. Reassemble: • Footrest (right) Bolt (footrest): 48 Nm (4.8 mkg) • Engine protector 14. Fill: • Engine oil tank See section “ENGINE OIL REPLACEMENT”. 15. Adjust: • Clutch cable free play Free play (at lever tip): 10 ~ 15 mm See section “Cable free play adjustment”. 3-23 AIR FILTER CLEANING INSP ADJ AIR FILTER CLEANING 1. Remove: • Fast screws (1) • Air filter box cap (2) 2. Pull out: • Filtering element (3) from its seat 3. Wash: • Filtering element (with water biodegradable liquid soap) 1 2 and NOTE: Rinse properly and dry perfectly by squeezing the filtering element, without twisting it! 3 4. Inspect: • Filtering element Damaged ➔ Replace. 5. Apply: • SAE 20W50 engine oil or special filter oil all over filter surface 6. Squeeze out: • Excess oil NOTE: The filtering element should be wet but not dripping. 7. Install: • Filtering element (4) in its case 4 NOTE: When installing the filtering element in its case, follow the direction indicated by the arrows, make sure that the flame-trap net is set forward and that the cap is properly assembled. 8. Reassemble: • Air filter box cap • Fast screws CAUTION: Make sure the air filter is properly seated in the air filter case. The engine should never be run without the air filter installed. Excessive piston and/or cylinder wear may result. 3-24 AIR FILTER CLEANING/ FUEL FILTER CLEANING INSP ADJ CAUTION: Periodically check wheter the sleeve on the bottom of the air filter case is empty. Remove the plug (5) and clean it if dirt or water accumulate. 5 FUEL FILTER CLEANING OFF 1. Turn the fuel cock to "OFF". 2. Disconnect: • Fuel pipe from cock 3. Place a fuel pan under the fuel tank and turn the fuel cock to "RES" to drain the fuel. OFF CAUTION: Do not bring naked flames or possible sources of sparks near to the fuel tank: FIRE AND EXPLOSION RISK! Be careful not to spill fuel from the tank. Always wipe off spilled fuel immediately with a dry and clean soft cloth. Fuel may deteriorate painted surfaces or plastic. RES RES 4. Disassemble: • The fuel cock from the fuel tank 5. Wash: • Fuel filter (1) with solvent 6. Inspect: • Fuel filter (1) • Gasket (2) Damaged ➔ Replace. 7. Reassemble: • Fuel cock to tank • Fuel pipe to cock NOTE: When reassembling the cock, be careful not to tighten the fastening screws unduly, as the gasket might leave its housing and cause fuel leakage. 3-25 ENGINE OIL TANK FILTER CLEANING INSP ADJ ENGINE OIL TANK FILTER CLEANING WARNING Securely support the motorcycle so there is no danger of it falling over. 1. Drain: • Engine oil See section “ENGINE OIL REPLACEMENT”. 2. Remove: • Seat • Rear cowling See section “SEAT, FUEL TANK AND REAR COWLING”. • Rear wire harness • Exhaust muffler • Exhaust pipe • Rear shock absorber See section “REAR SHOCK ABSORBER” in Chapter 4. • Joint air cleaner clamps • Rear frame • Engine oil tank 3. Loosen: • Stay (rear left side cover) fastening screws 4. Remove: • Oil tank cap (1) • Oil return hose (2) • Oil return hose flange (4) fastening screw (3) • Oil delivery hose flange (6) fastening screws (5) • Oil tank filter (7) • OR gaskets (8) 5. Clean: • Oil tank filter (with solvent) • Oil tank (with solvent) NOTE: After cleaning the inside of the oil tank, remove the remaining solvent. 6. Inspect: • OR gaskets Damaged ➔ Replace. 3-26 ENGINE OIL TANK FILTER CLEANING INSP ADJ 7. Reassemble: • OR gaskets • Oil tank filter • Oil delivery hose flange fastening screws Screw (oil delivery hose flange): 10 Nm (1.0 mkg) • • Oil return hose Oil return hose flange fastening screws Screw (oil return hose flange): 35 Nm (3.5 mkg) 8. Tighten: • Stay (rear left side cover) fastening screws 9. Reassemble: • Engine oil tank • Rear frame • Joint air cleaner clamps • Rear shock absorber See section “REAR SHOCK ABSORBER” in Chapter 4. • Exhaust pipe • Exhaust muffler • Rear wire harness • Rear cowling • Seat See section “SEAT, FUEL TANK AND Screw (seat): 10 Nm (1.0 mkg) REAR COWLING”. 10. Fill: • Engine oil See section “ENGINE OIL REPLACEMENT”. 11. Reassemble: • Engine tank cap 3-27 SUCTION HOSE AND MANIFOLD INSPECTION/ FUEL LINE INSPECTION INSP ADJ SUCTION HOSE AND MANIFOLD INSPECTION 1. Remove: • Seat • Fuel tank See section “SEAT, FUEL TANK AND REAR COWLING”. 2. Inspect: • Suction hoses (1) Cracked/damaged ➔ Replace. Screw (2) (carburetor manifold): 10 Nm (1.0 mkg) Screw (3) (clamp): 2 Nm (0.2 mkg) 3. Reassemble: • Fuel tank • Seat See section “SEAT, FUEL TANK AND REAR COWLING”. Seat screws: 10 Nm (1.0 mkg) FUEL LINE INSPECTION 1 1. Inspect: • Fuel pipe (1) Cracked/Damaged ➔ Replace. 3-28 CRANCKCASE VENTILATION HOSE INSPECTION/ EXHAUST SYSTEM INSPECTION INSP ADJ CRANCKCASE VENTILATION HOSE INSPECTION 1. Inspect: • Crankcase ventilation hoses (1) Cracked/Damaged ➔ Replace. EXHAUST SYSTEM INSPECTION 1. Inspect: • Exhaust pipe (1) • Muffer (2) Cracks/Damage ➔ Replace. • Gaskets (3) Exhaust gas leakage ➔ Replace. Nut (4) (exhaust pipe): 10 Nm (1.0 mkg) Screw (5) (muffler): 23 Nm (2.3 mkg) Bolt (6) (flange): 23 Nm (2.3 mkg) (apply molybdenum disulfide grease) Screw (7) (protection): 7 Nm (0.7 mkg) Use LOCTITE®. Nut (8) (muffler): 23 Nm (2.3 mkg) 3-29 ADJUSTING THE FRONT BRAKE INSP ADJ CHASSIS ADJUSTING THE FRONT BRAKE 1. Adjust: • Brake lever position (distance a between the brake lever and the handlebar grip) 2 a ▼▼▼▼▼▼▼▼▼▼▼▼▼▼▼▼▼▼▼▼▼▼▼▼▼▼▼▼▼ a. Turn the adjusting dial 1 while holding the lever pushed away from the handlebar grip 1 NOTE: Align the setting on the adjusting dial with the arrow mark 2 Posizione n. 1 La distanza a è la massima. Posizione n. 4 La distanza a è la minima. WARNING After adjusting the brake lever position, make sure the pin on the brake lever holder is firmly inserted in the hole in the adjusting dial. ▲▲▲▲▲▲▲▲▲▲▲▲▲▲▲▲▲▲▲▲▲▲▲▲▲▲▲▲▲ WARNING A soft or spongy feeling in the brake lever can indicate the presence of air in the brake system. Before the vehicle is operated, the air must be removed by bleeding the brake system. Air in the brake system will considerably reduce braking performance and could result in loss of control and possibly an accident. Therefore, inspect and, if necessary, bleed the brake system. After adjusting the brake lever free play, make sure that there is no brake drag. 3-30 ADJUSTING THE REAR BRAKE INSP ADJ ADJUSTING THE REAR BRAKE 1. Check: • Brake pedal position (distance a from the top of the rider footrest to the top of the brake pedal) Out of specification ➔ Adjust. a Brake pedal position (below the top of the rider footrest): 10 mm 2. Adjust: • Brake pedal position 1 ▼▼▼▼▼▼▼▼▼▼▼▼▼▼▼▼▼▼▼▼▼▼▼▼▼▼▼▼▼ 2 • • Loosen lock nut (1). Turn the adjuster (2) either way to obtain the correct pedal height. Unscrewing Height (a) diminishes. Screwing Height (a) increases. • Tighten lock nut. Lock nut: 20 Nm (2.0 mkg) CAUTION: After adjusting the brake pedal position, make sure the brake doesn't oppose resistance. ▲▲▲▲▲▲▲▲▲▲▲▲▲▲▲▲▲▲▲▲▲▲▲▲▲▲▲▲▲ WARNING If the brake brake pedal has a soft or slack feel, this means that there is air in the brake system. It should be bled away before using the motorcycle. Air in the system seriously affects the effectiveness of braking and may cause loss of control of the motorcycle. 3-31 CHECKING THE BRAKE FLUID LEVEL INSP ADJ CHECKING THE BRAKE FLUID LEVEL 1. Stand the motorcycle on a level surface. NOTE: • Place the motorcycle on a suitable stand. • Make sure that the motorcycle is upright. 2. Check: • Brake fluid level Below the minimum level mark a ➔ Add the recommended brake fluid to the proper level. A MIN Recommended brake fluid: DOT4 a [A] Front brake [B] Rear brake 2 3 4 WARNING • B • a • Use only the designated brake fluid. Other brake fluids may cause the rubber seals to deteriorate, causing leakage and poor brake performance. Refill with the same type of brake fluid that is already in the system. Mixing brake fluids may result in a harmful chemical reaction, leading to poor brake performance. When refilling, be careful that water does not enter the reservoir. Water will significantly lower the boiling point of the brake fluid and could cause vapor lock. CAUTION: Brake fluid may damage painted surfaces and plastic parts. Therefore, always clean up any spilt brake fluid immediately. NOTE: In order to ensure a correct reading of the brake fluid level, make sure that the top of the reservoir is horizontal. 3-32 1 BRAKE PAD WEAR INSPECTION/ BRAKE HOSING INSPECTION INSP ADJ 1. Operate the brake lever or brake pedal. 2. Check: • Thickness of frictional material Out of specification ➔ Replace. A Wear limit (a): Front: 1.0 mm Rear: 1.0 mm a For brake pad replacement, see section “BRAKE PAD REPLACEMENT” in Chapter 4. B [A] Front brake [B] Rear brake a BRAKE HOSING INSPECTION A 1. Inspect: • Brake hosing Cracks/Damage ➔ Replace. To replace hosing, see section “FRONT AND REAR BRAKE” in Chapter 4. [A] Front brake [B] Rear brake B 3-33 BRAKE CIRCUIT BLEEDING INSP ADJ BRAKE CIRCUIT BLEEDING WARNING If the brake lever or brake pedal has a soft or slack feel, this means that there is air in the brake system. It should be bled away before using the motorcycle. Air in the system seriously affects the effectiveness of braking and may cause loss of control of the motorcycle. In all cases, bleed the brake system if: • The system has been disassembled. • A brake hose has been loosened or removed. • The brake fluid in the tank is at a very low level. • Brake operation is faulty. Air bleeding procedures: A 1 B a. Top up the level of the fluid in the tank to maximum. b. Install the diaphragm. Be careful not to spill fluid or let it overflow from the tank. c. Connect the clear plastic hose (1) to the caliper bleeder screw. [A] Front [B] Rear d. Place the other end of the hose in a container. e. Slowly pull the brake lever or press the brake pedal several times. f. Pull the brake lever right in or press the pedal right down and hold in position. g. Loosen the bleeder screw and allow the lever or pedal to travel slowly towards its limit. h. Tighten the bleeder screw when the lever or pedal limit has been reached, then release the lever or pedal. 1 Bleeder screw: 14 Nm (1.4 mkg) i. 3-34 Repeat operations (e) to (h) until all the air bubbles have disappeared from the clear plastic hose (1). DRIVE CHAIN SLACK INSPECTION AND ADJUSTMENT INSP ADJ NOTE: If bleeing proves difficult, it may be necessary to allow the brake fluid system to stabilise for a few hours. Repeat the bleeding procedure when the tiny bubbles in the system have disappeared. j. Top up fluid to the maximum level. DRIVE CHAIN SLACK INSPECTION AND ADJUSTMENT Inspecting slack: NOTE: Before checking and/or adjusting the chain, rotate the rear wheel through several revolutions and check the slack several times to find the point on the wheel where chain slack is highest. Check and/or adjust chain slack with rear wheel in this “tight chain” position. 1. Check: • Drive chain slack (a) Out of specification ➔ Adjust. Drive chain slack: 30 ~ 40 mm NOTE: To check chain slack, the motorcycle must stand in an upright position with its two wheels touching the ground and no one sitting on it. Check slack in the position shown in the figure. a 2. Adjust: • Drive chain slack Slack adjustment: CAUTION: Too little chain slack will overload the engine and other vital parts. Keep the slack within the specified limits. 3-35 DRIVE CHAIN SLACK INSPECTION AND ADJUSTMENT/ DRIVE CHAIN LUBRICATION • • 2 ➩ a ➩ b • 1 3 INSP ADJ Loosen the axle nut (1). Loosen the locknuts (2) on each side. To tighten the chain, turn the chain adjusting bolts (3) in direction (a). Loosen the locknuts on each side. To loosen the chain, turn the chain adjusting bolts in direction (b) and push the wheel forward. After adjusting, tighten the locknuts (2). Then tighten the axle nut (1) to the specified torque. Rear wheel axle nut: 115 Nm (11.5 mkg) • Turn each adjusting bolt exactly the same amount to maintain correct axle alignment. There are marks on each side of the swingarm. Use these marks to align the rear wheel. DRIVE CHAIN LUBRICATION The chain consists of many parts which work with each other. If the chain is not maintained properly, it will wear out quickly. Therefore, the chain must be serviced regularly. This service is especially necessary when riding in dusty areas. This motorcycle has a drive chain with small rubber O-Rings between the chain plates. Steam cleaning, highpressure washing and certain solvents can damage these O-Rings. Use only kerosene to clean the drive chain. Wipe it dry, and thoroughly lubricate it with SAE 80 ~ 90W motor oil or special lubricant for O-Ring chains. Do not use any other lubricants on the drive chain. They may contain solvents that could damage the O-Rings. Recommended lubricant: SAE 80W/90 engine oil or special lubricant for O-Ring chains. (1) O-Rings 3-36 FRONT FORK INSPECTION/ FRONT FORK ADJUSTMENT INSP ADJ FRONT FORK INSPECTION WARNING When inspecting the front fork, hold the motorcycle firmly to prevent it falling over. 1. Place the motorcycle on a level surface. 2. Check: • Inner tube Scratches/Damage ➔ Replace. • Oil seal Undue oil leakage ➔ Replace. 3. With the motorcycle in a level upright position operate the front brake. 4. Check: • Proper functioning Compress and release the front fork several times. Irregular/jerky functioning ➔ Repair. See section “FRONT FORK” in Chapter 4. ADJUSTING THE FRONT FORK This front fork is equipped with spring pre-load adjusting bolts. WARNING0 b a 1 b Always adjust both fork legs equally, otherwise poor handling and loss of stability may result. a Adjust the spring preload as follows. To increase the spring preload and thereby harden the suspension, turn the adjusting bolt on each fork leg in direction a. To decrease the spring preload and thereby soften the suspension, turn the adjusting bolt on each fork leg in direction b. Minimum (soft) Standard Maximum (hard) 3-37 Setting 1-2-3 4 5-6-7-8-9-10 REAR SHOCK ABSORBER ADJUSTMENT INSP ADJ REAR SHOCK ABSORBER ADJUSTMENT WARNING 2 a b This shock absorber contains highly pressurized nitrogen gas. For proper handling, read and understand the following information before handling the shock absorber. The manufacturer cannot be held responsible for property damage or personal injury that may result from improper handling. • Do not tamper with or attempt to open the gas cylinder. • Do not subject the shock absorber to an open flame or other high heat sources, otherwise it may explode due to excessive gas pressure. • Do not deform or damage the gas cylinder in any way, as this will result in poor damping performance. A 1 This shock absorber assembly is equipped with a spring preload adjusting nut. CAUTION: Never attempt to turn an adjusting mechanism beyond the maximum or minimum settings. Adjust the spring preload as follows. 1. Loosen the locknut. 2. To increase the spring preload and thereby harden the suspension, turn the adjusting nut in direction a. To decrease the spring preload and thereby soften the suspension, turn the adjusting nut in direction b. 3-38 REAR SHOCK ABSORBER ADJUSTMENT INSP ADJ NOTE: • Use the special wrench included in the owner's tool kit to make the adjustment. • The spring preload setting is determined by measuring distance A, shown in the illustration. The longer distance A is, the lower the spring preload; the shorter distance A is, the higher the spring preload. With each complete turn of the adjusting nut, distance A changes by 1.5 mm. Spring preload: Minimum (soft): Distance A = 217 mm Standard: Distance A = 211 mm Maximum (hard): Distance A = 205 mm 2. Tighten the locknut to the specified torque. Locknut: 45 Nm (4.5 m·kgf) CAUTION: Always tighten the locknut against the adjusting nut, and then tighten the locknut to the specified torque. 3-39 STEERING INSPECTION INSP ADJ STEERING INSPECTION WARNING Hold the motorcycle firmly in place to prevent it falling over. 1. Raise the front wheel and place a support under the engine. 2. Check: • Steering bearings Grasp the bottoms of the front fork legs and rock back and forward. Free play ➔ Adjust steering bearing. 3. Adjust: • Steering bearing ▼▼▼▼▼▼▼▼▼▼▼▼▼▼▼▼▼▼▼▼▼▼▼▼▼▼▼▼▼ 2 Adjustment: • 2 • 1 3 • Remove the fuel tank. See section “SEAT, FUEL TANK AND REAR COWLING”. Loosen steering axle nut (1) and fork upper bracket screws (2). Tighten the ring nut (3) with the special wrench. Ringnut wrench: P/N. 90890-01268 P/N. 90890-01348 NOTE: The torque wrench and the ringnut wrench should form a right angle. Ring nut (initial tightening): 38 Nm (3.8 mkg) • • Loosen the ring nut one turn. Retighten the ring nut using the special wrench. WARNING Do not tighten the ring nut excessively. Ring nut (final tightening): 4 Nm (0.4 mkg) 3-40 STEERING INSPECTION/ TYRE INSPECTION • INSP ADJ Tighten the steering axle nut and the front fork bracket screws. Nut (steering axle): 115 Nm (11.5 mkg) Screws (front fork bracket): 28 Nm (2.8 mkg) • Reassemble the fuel tank. See section “SEAT, FUEL TANK AND REAR COWLING”. NOTE: Check the steering head for looseness or binding by turning it all the way in both directions. If it binds, remove the steering axle assembly and inspect the steering bearings. Refer to “STEERING HEAD” in Chapter 6. ▲▲▲▲▲▲▲▲▲▲▲▲▲▲▲▲▲▲▲▲▲▲▲▲▲▲▲▲▲ TYRE INSPECTION WARNING • • • • • 3-41 Tyre pressure must be checked when the tyres are at ambient temperature. Pressure must be adjusted according to the total weight of luggage, driver, passenger and accessories (fairings, bags, if approved for this model) and speed of the motorcycle. A list of tyres approved for this model following severe testing by Yamaha is provided. There can be no guarantee of safe roadholding if a combination of tyres different from those indicated is used. Front and rear tyres must have the same design and be of the same make. The use of valves and valve stems other than those indicated might cause the loss of tyre pressure at high speeds. Use only original or compatible spare parts. Replace the valve cap securely to prevent losses of tyre pressure at high speed. TYRE INSPECTION INSP ADJ 1. Check: • Tyre pressure Out of specification ➔ Adjust. Tire air pressure (measured on cold tires) Load* Front Rear 200 kPa 220 kPa Up to 90 kg (2.00 kgf/cm2, (2.20 kgf/cm2, 2.00 bar) 2.20 bar) 210 kPa 240 kPa 90 kg-maximum (2.10 kgf/cm2, (2.40 kgf/cm2, 2.10 bar) 2.40 bar) 150 kPa 160 kPa Off-road riding (1.50 kgf/cm2, (1.60 kgf/cm2, 1.50 bar) 1.60 bar) 210 kPa 240 kPa High-speed (2.10 kgf/cm2, (2.40 kgf/cm2 riding 2.10 bar) 2.40 bar) Maximum load* 180 kg * Total weight of rider, passenger, cargo and accessories. 2. Adjust: • Air pressure ▼▼▼▼▼▼▼▼▼▼▼▼▼▼▼▼▼▼▼▼▼▼▼▼▼▼▼▼▼ Adjustment: • Remove the valve cap. • Use an air pump or compressed air pistol. Increase air pressure Eliminate air by pressing valve tube stem Air pressure diminishes Install valve caps securely. ▲▲▲▲▲▲▲▲▲▲▲▲▲▲▲▲▲▲▲▲▲▲▲▲▲▲▲▲▲ 3. Inspect: • Tyre surface Wear/Damage ➔ Replace. 3-42 TYRE INSPECTION INSP ADJ Minimum track thickness: (front and rear) 1,6 mm NOTE: These limits may be different by regulation from country to country. If so, conform to the limits specified by the regulations of your own country. (1) Track thickness (2) Side (3) Wear indicators WARNING The use of worn tyres reduces stability and may cause a loss of control. It is not advisable to repair a punctured air tube. If absolutely necessary, repair with the utmost care and replace the tube as quickly as possible with another with the same characteristics. 4. Tighten: • Valve stem lock nut Lock nut (valve stem) 1.5 Nm (0.15 kgm) FRONT: Manufacture PIRELLI MICHELIN Size 90/90-21 54R 90/90-21 54S Type MT70 T63 Size 130/80-18 66R 130/80-18 66S Type MT70 T63 REAR: Manufacture PIRELLI MICHELIN WARNING After assembling the new tyres, drive slowly to allow them to adapt well to the rim and yjus ensure maximum holding. 3-43 WHEEL INSPECTION/ SPOKE INSPECTION AND TIGHTENING INSP ADJ WHEEL INSPECTION 1. Inspect: • Wheels Damage/Deformation ➔ Replace. NOTE: Always balance the wheel after the replacement or reassembly of a tyre or rim. WARNING Never try to repair a rim in any way. Bearing inspection Check the front and rear wheel bearings periodically to make sure that they do not have free play in the hub and that the wheel turns smoothly without sticking. Wheel bearings must always be checked in accordance with the maintenance table. SPOKE INSPECTION AND TIGHTENING 1. Inspect: • Spokes (1) Curvature/Damaged ➔ Replace. Loose spoke ➔ Tighten. 2. Tighten: • Spoke (s) NOTE: Tighten the spokes before and after the break-in period. Spoke: 3 Nm (0.3 mkg) 3-44 CABLE INSPECTION/ LEVER AND PEDAL LUBRICATION INSP ADJ CABLE INSPECTION WARNING If the cable sheath is damaged, corrosion might ensue or the cable might not run freely. To avoid such drawbacks, replaced damaged cables as quickly as possible. 1. Inspect: • Cable sheath Damaged ➔ Replace the cable assembly. 2. Check: • Cable functioning Does not run freely ➔ Replace the cable assembly. LEVER AND PEDAL LUBRICATION 1. Lubricate the pivoting parts: • Clutch lever • Front brake lever • Rear brake pedal • Shift pedal Recommended lubricant: SAE 10W30 motor oil 3-45 SIDESTAND LUBRICATION/ REAR SUSPENSION LUBRICATION INSP ADJ SIDESTAND LUBRICATION Lubricate the sidestand pivoting and mating parts. Check to see that the sidestand moves up and down smoothly. Recommended lubricant: SAE 10W30 motor oil REAR SUSPENSION LUBRICATION Lubricate the pivoting parts. 1 Recommended lubricant: Molybdenum disulfide grease 3-46 CHECKING AND CHARGING THE BATTERY INSP ADJ ELECTRICAL SYSTEM CHECKING AND CHARGING THE BATTERY WARNING Batteries generate explosive hydrogen gas and contain electrolyte which is made of poisonous and highly caustic sulfuric acid. Therefore, always follow these preventive measures: • Wear protective eye gear when handling or working near batteries. • Charge batteries in a well-ventilated area. • Keep batteries away from fire, sparks or open flames (e.g., welding equipment, lighted cigarettes). DO NOT SMOKE when charging or han• dling batteries. • KEEP BATTERIES AND ELECTROLYTE OUT OF REACH OF CHILDREN. • Avoid bodily contact with electrolyte as it can cause severe burns or permanent eye injury. First aid in case of bodily contact: External • SKIN – Wash with water. • EYES – Flush with water for 15 minutes and get immediate medical attention. Internal Drink large quantities of water or milk followed with milk of magnesia, beaten egg or vegetable oil. Get immediate medical attention. CAUTION: • • 3-47 This is a sealed battery. Never remove the sealing caps because the balance between cells will not be maintained and battery performance will deteriorate. Charging time, charging amperage and charging voltage for a MF battery are different from those of conventional batteries. The MF battery should be charged as explained in the charging method illustrations. If the battery is overcharged, the electrolyte level will drop considerably. Therefore, take special care when charging the battery. CHECKING AND CHARGING THE BATTERY INSP ADJ NOTE: Since MF batteries are sealed, it is not possible to check the charge state of the battery by measuring the specific gravity of the electrolyte. Therefore, the charge of the battery has to be checked by measuring the voltage at the battery terminals. 1 1. Remove: • Seat • Panel 1 2. Disconnect: • Battery leads (from the battery terminals) 1 2 CAUTION: First, disconnect the negative lead 1, then the positive lead 2. 3. Remove: • Battery 4. Check: • Battery charge ▼▼▼▼▼▼▼▼▼▼▼▼▼▼▼▼▼▼▼▼▼▼▼▼▼▼▼▼▼ a. Connect a pocket tester to the battery terminals. Open-circuit voltage Battery positive terminal Tester negative ➔ lead Battery negative terminal NOTE: • The charge state of a MF battery can be checked by measuring its open-circuit voltage (i.e., the voltage when the positive terminal is disconnected). • No charging is necessary when the open-circuit voltage equals or exceeds 12.8 V. Voltmeter 13,0 Tester positive ➔ lead b. Check the charge of the battery, as shown in the charts and the following example. Example c. Open-circuit voltage = 12.0 V d. Charging time = 6.5 hours e. Charge of the battery = 20 ~ 30 % Relationship between open-circuit voltage and charging time at 20 °C 12,5 12,0 ▲▲▲▲▲▲▲▲▲▲▲▲▲▲▲▲▲▲▲▲▲▲▲▲▲▲▲▲▲ 5. Charge: • Battery (refer to the appropriate charging method illustration) 11,5 5 6,5 10 Charging time (Hours) • This varies depending on the temperature, the state of charge in battery plates and the electrolyte level. 3-48 CHECKING AND CHARGING THE BATTERY WARNING 14 Ambient temperature 20 °C Open-circuit voltage (V) 13 Do not quick charge a battery. 12 CAUTION: 11 • • 10 100 75 50 30 2520 Condition of charge in battery (%) Charging 0 • Ambient temperature 20 °C 18 Open-circuit voltage (V) INSP ADJ 17 • 16 15 14 13 12 11 10 0 10 20 30 40 50 60 Time (minutes) • Check the open-circuit voltage • • • • 3-49 Never remove the MF battery sealing caps. Do not use a high-rate battery charger. They force a high-amperage current into the battery quickly and can cause battery overheating and battery plate damage. If it is impossible to regulate the charging current on the battery charger, be careful not to overcharge the battery. When charging a battery, be sure to remove it from the motorcycle (if charging has to be done with the battery mounted on the motorcycle, disconnect the negative lead from the battery terminal). To reduce the chance of sparks, do not plug in the battery charger until the battery charger leads are connected to the battery. Before removing the battery charger lead clips from the battery terminals, be sure to turn off the battery charger. Make sure that the battery charger lead clips are in full contact with the battery terminal and that they are not shorted. A corroded battery charger lead clip may generate heat in the contact area and a weak clip spring may cause sparks. If the battery becomes hot to the touch at any time during the charging process, disconnect the battery charger and let the battery cool before reconnecting it. Hot batteries can explode! As shown in the following illustration, the open-circuit voltage of a MF battery stabilizes about 30 minutes after charging has been completed. Therefore, wait 30 minutes after charging is completed before measuring the open-circuit voltage. CHECKING AND CHARGING THE BATTERY INSP ADJ Charging method using a variable-current (voltage) type charger Charger AMP meter YES Measure the open-circuit voltage prior to charging. NOTE: Voltage should be measured 30 minutes after the machine is stopped. Connect a charger and AMP meter to the battery and start charging. NOTE: Set the charging voltage at 16 ~ 17 V (if the setting is lower, charging will be insufficient. If too high, the battery will be over-charged.) Make sure the current is higher than the standard charging current written on the battery. NO By turning the charging voltage adjust dial, set the charging voltage at 20 ~ 25 V. Adjust the voltage so that current is at standard charging level. YES Monitor the amperage for 3 ~ 5 minutes to check if the standard charging current is reached. NO Set the timer according to the charging time suitable for the open-circuit voltage. Refer to "Battery condition checking steps." If the current does not exceed standard charging current after 5 minutes, replace the battery. In case that charging requires more than 5 hours, it is advisable to check the charging current after a lapse of 5 hours. If there is any charge in the amperage, readjust the voltage to obtain the standard charging current. Measure the battery open-circuit voltage after having left the battery unused for more than 30 minutes. 12.8 V or more --- Charging is complete. 12.7 V or less --- Recharging is required. Under 12.0 V --- Replace the battery. 3-50 CHECKING AND CHARGING THE BATTERY INSP ADJ Charging method using a constant-voltage type charger Measure the open-circuit voltage prior to charging. NOTE: Voltage should be measured 30 minutes after the machine is stopped. Connect a charger and AMP meter to the battery and start charging. YES Make sure the current is higher than the standard charging current written on the battery. Charge the battery until the battery’s charging voltage is 15 V. NO This type of battery charger cannot charge the MF battery. A variable volt- NOTE: Set the charging time at 20 hours (maximum). Measure the battery open-circuit voltage after having left the battery unused for more than 30 minutes. 12.8 V or more --- Charging is complete. 12.7 V or less --- Recharging is required. Under 12.0 V --- Replace the battery. Charger AMP meter Voltmeter Charging method using a constant-current type charger This type of battery charger cannot charge the MF battery. 3-51 CHECKING AND CHARGING THE BATTERY INSP ADJ 6. Connect: • Battery leads (to the battery terminals) 1 2 CAUTION: First, connect the positive lead 2, then the negative lead 1. 7. Check: • Battery terminals Dirt ➔ Clean with a wire brush. Loose connection ➔ Connect properly. 8. Lubricate: • Battery terminals Recommended lubricant Dielectric grease 9. Install: • Panel • Seat 3-52 CHECKING THE FUSES INSP ADJ CHECKING THE FUSES CAUTION: To avoid a short circuit, always turn the main switch to "OFF" when checking or replacing a fuse. 1 1. Remove: • Seat • Panel 1 2. Check: • Fuse ▼▼▼▼▼▼▼▼▼▼▼▼▼▼▼▼▼▼▼▼▼▼▼▼▼▼▼▼▼ a. Connect the pocket tester to the fuse and check it for continuity. NOTE: Set the pocket tester selector to “Ω 1”. Pocket tester 90890-03112 b. If the pocket tester indicates "∞", replace the fuse. ▲▲▲▲▲▲▲▲▲▲▲▲▲▲▲▲▲▲▲▲▲▲▲▲▲▲▲▲▲ 3. Replace: • Blown fuse ▼▼▼▼▼▼▼▼▼▼▼▼▼▼▼▼▼▼▼▼▼▼▼▼▼▼▼▼▼ a. Turn off the ignition. b. Install a new fuse of the correct amperage rating. c. Turn on the switches to verify if the electrical circuit is operational. d. If the fuse immediately blows again, check the electrical circuit. ▲▲▲▲▲▲▲▲▲▲▲▲▲▲▲▲▲▲▲▲▲▲▲▲▲▲▲▲▲ 1 Fuses 2 Main (1) Reserve (2) 3-53 Amperage rating 20 A 20 A Quantity 1 1 CHECKING THE FUSES/ REPLACING THE HEADLIGHT BULBS INSP ADJ WARNING Never use a fuse with an amperage rating other than that specified. Improvising or using a fuse with the wrong amperage rating may cause extensive damage to the electrical system, cause the lighting and ignition systems to malfunction and could possibly cause a fire. 4. Install: • Pannel • Seat REPLACING THE HEADLIGHT BULBS 1 Low beam/high beam 3 1. Remove: • Cowling screws (1) 2. Remove: • Cowling (from the meter bracket) 4 1 NOTE: Remove the cowling from the meter bracket by lowering it to disengage it, and then lifting it up. 2 a b 3. Remove: • Headlight (2) 4. Disconnect: • Headlight coupler (3) 5. Remove: • Headlight bulb cover (4) 6. Remove: • Headlight bulb holder (5) (by turning it counterclockwise (a)) • Headlight bulb 5 WARNING Headlight bulbs get very hot. Therefore, keep flammable products away from a lit headlight bulb, and do not touch the bulb until it has cooled down. 3-54 REPLACING THE HEADLIGHT BULBS INSP ADJ 7. Install: • Headlight bulb (new) • Headlight bulb holder (by turning it clockwise (b)) CAUTION: Do not touch the glass part of the headlight bulb to keep it free from oil, otherwise the transparency of the glass, the luminosity of the bulb, and the bulb life will be adversely affected. Thoroughly clean off any dirt and fingerprints on the headlight bulb using a cloth moistened with alcohol or thinner. 8. Install: • Headlight bulb cover 9. Connect: • Headlight coupler 10. Install: • Upper side of the cowling (onto the meter bracket) • Headlight (adjust the headlight beam if necessary) 11. Install: • Cowling screws Cowling screws: 10 Nm (1.0 kgm) 1 Auxiliary light bulb 1. Remove: • Cowling screws (1) 2. Remove: • Cowling (from the meter bracket) 3 1 NOTE: Remove the cowling from the meter bracket by lowering it to disengage it, and then lifting it up. 2 3. Remove: • Headlight (2) • Auxiliary light socket (3) NOTE: Remove the auxiliary light socket (together with the bulb) without disconnecting the leads. • 3-55 Bulb (by pushing it in and turning it counterclockwise) REPLACING THE TURN INDICATOR LIGHT BULB INSP ADJ 4. Install: • Bulb (new) (by pushing it in and turning it clockwise) • Bulb holder • Upper side of the cowling (onto the meter bracket) • Headlight (adjust the headlight beam if necessary) 5. Install: • Cowling screws Cowling screws: 10 Nm (1.0 kgm) REPLACING THE TURN INDICATOR LIGHT BULB 2 1. Remove: • Lens screw (1) • Lens (2) • Bulb (3) 1 NOTE: To remove the bulb press it into place and turn it counterclockwise. 2. Install: • New bulb NOTE: To install the bulb press it into place and turn it clockwise. 3 • • Lens Lens screw CAUTION: Do not overtighten the screw, otherwise the lens may break. 3-56 REPLACING THE TAIL/ BRAKE LIGHT BULB INSP ADJ REPLACING THE TAIL/BRAKE LIGHT BULB 1. Remove: • Screws (1) (lens fixing) • Lens (2) • Bulb (3) 2 NOTE: To remove the bulb press it into place and turn it counterclockwise (a). 1 2. Install: • New bulb NOTE: To install the bulb press it into place and turn it clockwise (b). 3 • • a b Lens Screws (lens fixing) CAUTION: Do not overtighten the screws, otherwise the lens may break. 3-57 INSP ADJ CHAS 4 CHAS CHAPTER 4. CHASSIS FRONT WHEEL AND BRAKE DISC . . . . . . . . . . . . . . . . . . . . . . . . . . . . . . . . . . . . . . . FRONT WHEEL AND BRAKE DISC REMOVAL . . . . . . . . . . . . . . . . . . . . . . . . . . . FRONT WHEEL DISASSEMBLY . . . . . . . . . . . . . . . . . . . . . . . . . . . . . . . . . . . . . . . FRONT WHEEL INSPECTION . . . . . . . . . . . . . . . . . . . . . . . . . . . . . . . . . . . . . . . . . BRAKE DISC INSPECTION . . . . . . . . . . . . . . . . . . . . . . . . . . . . . . . . . . . . . . . . . . FRONT WHEEL ASSEMBLY . . . . . . . . . . . . . . . . . . . . . . . . . . . . . . . . . . . . . . . . . . FRONT WHEEL INSTALLATION . . . . . . . . . . . . . . . . . . . . . . . . . . . . . . . . . . . . . . . WHEEL STATIC BALANCE ADJUSTMENT . . . . . . . . . . . . . . . . . . . . . . . . . . . . . . . 4-1 4-1 4-3 4-3 4-5 4-5 4-6 4-6 FRONT BRAKE . . . . . . . . . . . . . . . . . . . . . . . . . . . . . . . . . . . . . . . . . . . . . . . . . . . . . . . 4-8 BRAKE PAD REMOVAL . . . . . . . . . . . . . . . . . . . . . . . . . . . . . . . . . . . . . . . . . . . . . 4-8 BRAKE PAD REPLACEMENT . . . . . . . . . . . . . . . . . . . . . . . . . . . . . . . . . . . . . . . . 4-9 MASTER CYLINDER . . . . . . . . . . . . . . . . . . . . . . . . . . . . . . . . . . . . . . . . . . . . . . 4-11 MASTER CYLINDER INSPECTION . . . . . . . . . . . . . . . . . . . . . . . . . . . . . . . . . . . 4-13 MASTER CYLINDER ASSEMBLY . . . . . . . . . . . . . . . . . . . . . . . . . . . . . . . . . . . . . 4-13 MASTER CYLINDER INSTALLATION . . . . . . . . . . . . . . . . . . . . . . . . . . . . . . . . . . 4-14 BRAKE CALIPER . . . . . . . . . . . . . . . . . . . . . . . . . . . . . . . . . . . . . . . . . . . . . . . . . 4-16 BRAKE CALIPER DISASSEMBLY . . . . . . . . . . . . . . . . . . . . . . . . . . . . . . . . . . . . 4-18 CALIPER INSPECTION . . . . . . . . . . . . . . . . . . . . . . . . . . . . . . . . . . . . . . . . . . . . 4-18 CALIPER ASSEMBLY . . . . . . . . . . . . . . . . . . . . . . . . . . . . . . . . . . . . . . . . . . . . . . 4-19 CALIPER INSTALLATION . . . . . . . . . . . . . . . . . . . . . . . . . . . . . . . . . . . . . . . . . . . 4-19 REAR WHEEL AND BRAKE DISC . . . . . . . . . . . . REAR WHEEL AND BRAKE DISC REMOVAL . REAR WHEEL DISASSEMBLY . . . . . . . . . . . . REAR WHEEL INSPECTION . . . . . . . . . . . . . BRAKE DISC INSPECTION . . . . . . . . . . . . . . REAR WHEEL ASSEMBLY . . . . . . . . . . . . . . . REAR WHEEL INSTALLATION . . . . . . . . . . . . WHEEL STATIC BALANCE ADJUSTMENT . . . . . . . . . . . . . . . . . . . . . . . . . . . . . . . . . . . . . . . . . . . . . . . . . . . . . . . . . . . . . . . . . . . . . . . . . . . . . . . . . . . . . . . . . . . . . . . . . . . . . . . . . . . . . . . . . . . . . . . . . . . . . . . . . . . . . . . . . . . . . . . . . . . . . . . . . . . . . . . . . . . . . . . . . . . . . . . . . . . . . . . . . . . . . . . . . . . . . . . . . . . . . . . . . . . . . . . . . . . REAR BRAKE. . . . . . . . . . . . . . . . . . . . . . . . . . . . . . . . . . . . . . . . . . . . . . . . . . . . . . . . BRAKE PAD REMOVAL . . . . . . . . . . . . . . . . . . . . . . . . . . . . . . . . . . . . . . . . . . . . BRAKE PAD REPLACEMENT . . . . . . . . . . . . . . . . . . . . . . . . . . . . . . . . . . . . . . . MASTER CYLINDER . . . . . . . . . . . . . . . . . . . . . . . . . . . . . . . . . . . . . . . . . . . . . . MASTER CYLINDER INSPECTION . . . . . . . . . . . . . . . . . . . . . . . . . . . . . . . . . . . MASTER CYLINDER ASSEMBLY . . . . . . . . . . . . . . . . . . . . . . . . . . . . . . . . . . . . . MASTER CYLINDER INSTALLATION . . . . . . . . . . . . . . . . . . . . . . . . . . . . . . . . . . BRAKE PEDAL REMOVAL . . . . . . . . . . . . . . . . . . . . . . . . . . . . . . . . . . . . . . . . . . BRAKE CALIPER . . . . . . . . . . . . . . . . . . . . . . . . . . . . . . . . . . . . . . . . . . . . . . . . . BRAKE CALIPER DISASSEMBLY . . . . . . . . . . . . . . . . . . . . . . . . . . . . . . . . . . . . CALIPER INSPECTION . . . . . . . . . . . . . . . . . . . . . . . . . . . . . . . . . . . . . . . . . . . . CALIPER ASSEMBLY . . . . . . . . . . . . . . . . . . . . . . . . . . . . . . . . . . . . . . . . . . . . . . CALIPER INSTALLATION . . . . . . . . . . . . . . . . . . . . . . . . . . . . . . . . . . . . . . . . . . . 4-21 4-21 4-23 4-23 4-24 4-25 4-25 4-27 4-29 4-29 4-30 4-32 4-33 4-33 4-34 4-35 4-36 4-38 4-38 4-39 4-39 CHAS FRONT FORK . . . . . . . . . . . . . . . . . . . . . . FRONT FORK REMOVAL . . . . . . . . . . FRONT FORK DISASSEMBLY . . . . . . FRONT FORK REMOVAL . . . . . . . . . . OIL REPLACEMENT . . . . . . . . . . . . . . CLEANING THE DUST SEAL . . . . . . . SEAL AND BUSH REPLACEMENT . . . OIL LEAKAGE FROM DUST SEAL . . . ANOMALOUS HYDRAULIC BRAKING FRONT FORK INSPECTION . . . . . . . FRONT FORK INSTALLATION . . . . . . FRONT FORK ADJUSTMENT . . . . . . . . . . . . . . . . . . . . . . . . . . . . . . . . . . . . . . . . . . . . . . . . . . . . . . . . . . . . . . . . . . . . . . . . . . . . . . . . . . . . . . . . . . . . . . . . . . . . . . . . . . . . . . . . . . . . . . . . . . . . . . . . . . . . . . . . . . . . . . . . . . . . . . . . . . . . . . . . . . . . . . . . . . . . . . . . . . . . . . . . . . . . . . . . . . . . . . . . . . . . . . . . . . . . . . . . . . . . . . . . . . . . . . . . . . . . . . . . . . . . . . . . . . . . . . . . . . . . . . . . . . . . . . . . . . . . . . . . . . . . . . . . . . . . . . . . . . . . . . . . . . . . . . . . . . . . . . . . . . . . . . . . . . . . . . . . . . . . . . . . . . . . . . . . . . . . . . . . . . . . . . . . . . . . . . . . . . . . . . . . . . . . . . . . . . . . . . . . . . 4-42 4-42 4-43 4-45 4-46 4-49 4-50 4-56 4-56 4-57 4-59 4-60 STEERING . . . . . . . . . . . . . . . . . STEERING REMOVAL . . . . STEERING INSPECTION . . STEERING INSTALLATION . . . . . . . . . . . . . . . . . . . . . . . . . . . . . . . . . . . . . . . . . . . . . . . . . . . . . . . . . . . . . . . . . . . . . . . . . . . . . . . . . . . . . . . . . . . . . . . . . . . . . . . . . . . . . . . . . . . . . . . . . . . . . . . . . . . . . . . . . . . . . . . . . . . . . . . . . . . . . . . . . . . . 4-61 4-64 4-65 4-65 REAR SHOCK ABSORBER . . . . . . . . . . NOTE ON DISPOSAL . . . . . . . . . . . SHOCK ABSORBER REMOVAL . . . SHOCK ABSORBER INSPECTION . SHOCK ABSORBER ADJUSTMENT . . . . . . . . . . . . . . . . . . . . . . . . . . . . . . . . . . . . . . . . . . . . . . . . . . . . . . . . . . . . . . . . . . . . . . . . . . . . . . . . . . . . . . . . . . . . . . . . . . . . . . . . . . . . . . . . . . . . . . . . . . . . . . . . . . . . . . . . . . . . . . . . . . . . . . . . . . . . . . . . . . . . . . . . . . . . . . . 4-69 4-72 4-73 4-74 4-74 SWINGARM . . . . . . . . . . . . . . . . . . . . . . . SWINGARM REMOVAL . . . . . . . . . . . . SWINGARM INSPECTION . . . . . . . . . LATERAL FREE PLAY ADJUSTMENT SWINGARM INSTALLATION . . . . . . . . . . . . . . . . . . . . . . . . . . . . . . . . . . . . . . . . . . . . . . . . . . . . . . . . . . . . . . . . . . . . . . . . . . . . . . . . . . . . . . . . . . . . . . . . . . . . . . . . . . . . . . . . . . . . . . . . . . . . . . . . . . . . . . . . . . . . . . . . . . . . . . . . . . . . . . . . . . . . . . . . . . . . 4-76 4-77 4-78 4-79 4-80 DRIVE CHAIN, DRIVE SPROCKET AND REAR WHEEL SPROCKET DRIVE CHAIN REMOVAL . . . . . . . . . . . . . . . . . . . . . . . . . . . . . . DRIVE CHAIN INSPECTION . . . . . . . . . . . . . . . . . . . . . . . . . . . DRIVE CHAIN INSTALLATION . . . . . . . . . . . . . . . . . . . . . . . . . . . . . . . . . . . . . . . . . . . . . . . . . . . . . . . . . . . . . . . . . . . . . . . . . . . . . . 4-82 4-82 4-83 4-85 FRONT WHEEL AND BRAKE DISC CHAS CHASSIS - FRONT WHEEL AND BRAKE DISC Order Job name/Part name Q.ty Remarks Remove the parts in order. Front wheel and brake disc removal WARNING Securely support the motorcycle so there is no danger of it falling over. 1 2 3 4 5 6 7 8 9 Speedometer cable Pinch bolt Wheel axle Front wheel assembly Collar Gear unit assembly Brake disc screw Brake disc Ring 1 2 1 1 1 1 6 1 1 4-1 Disconnect. Loosen. Refer to “FRONT WHEEL INSTALLATION” section. Reverse the removal procedure for installation. FRONT WHEEL AND BRAKE DISC CHAS 1 2 3 4 5 Order 1 2 3 4 5 Job name/Part name Q.ty Remarks Remove the parts in order. Front wheel disassembly Oil seal Bearing Spacer Oil seal Bearing 1 1 1 1 1 Refer to “FRONT WHEEL DISASSEMBLY/ ASSEMBLY” section. Reverse the removal procedure for installation. 4-2 FRONT WHEEL AND BRAKE DISC CHAS FRONT WHEEL DISASSEMBLY 1. Remove: • Oil seal • Bearing (1) • Spacer ▼▼▼▼▼▼▼▼▼▼▼▼▼▼▼▼▼▼▼▼▼▼▼▼▼▼▼▼▼ Removal procedure: • Clean the outside of the hub. • Remove the dust cover with a flat-headed screwdriver. NOTE: Place a rag on the outside to avoid damaging the hub. • Disassemble the bearing (1) with a normal puller (2). ▲▲▲▲▲▲▲▲▲▲▲▲▲▲▲▲▲▲▲▲▲▲▲▲▲▲▲▲▲ FRONT WHEEL INSPECTION 1. Inspect: • Front wheel axle (by rolling it on a flat surface) Bends ➔ Replace. WARNING Do not attempt to straighten a bent axle. 2. Inspect: • Front tire Wear/damage ➔ Replace. Refer to “TIRE INSPECTION” in CHAPTER 3. • Front wheel Refer to “WHEEL INSPECTION” in CHAPTER 3. 3. Inspect: • Spoke(s) Bent/Damaged ➔ Replace. Loose spoke(s) ➔ Tighten. Turn the wheel and hit the spokes gently with a screwdriver. NOTE: A well tightened spoke makes a distinct, sharp noise: a loose spoke makes a dull, muffled noise. 4-3 FRONT WHEEL AND BRAKE DISC CHAS 4. Tighten: • Loose spokes Spoke: 2 Nm (0.2 mkg) NOTE: After tightening the spokes, check the centring of the wheel. 5. Measure: • Front wheel runout Over the specified limits ➔ Replace. Front wheel runout limits: Radial (1) : 1.0 mm Lateral (2) : 0.5 mm 6. Inspect: • Front wheel bearings Bearings allow free play in the wheel hub or the wheel does not turn smoothly ➔ Replace. • Oil seal Wear/damage ➔ Replace. WARNING • • After assembling a tyre, drive slowly to allow it to adapt to the rim. If this precaution is not observed, damage might be caused to the motorcycle and accidents to the driver. After repairing or changing a tyre, do not forget to tighten the valve lock nut (1) to the prescribed torque. Valve lock nut: 1.5 Nm (0.15 mkg) 4-4 FRONT WHEEL AND BRAKE DISC CHAS BRAKE DISC INSPECTION 1. Inspect: • Brake disc Wear/Damage ➔ Replace. 2. Measure: • Brake disc deflection (a) If over envisaged limits ➔ Verify wheel centring. If the wheel centring is correct, replace the brake disc. Maximum deflection (brake disc): 0.15 mm • Misure at 2 mm from disc edge Brake disc thickness (b) If out of specified limits ➔ Replace. Minimum thickness (brake disc): 3.6 mm IFRONT WHEEL ASSEMBLY 1. Install: • Spacer • Bearings • Oil seal ▼▼▼▼▼▼▼▼▼▼▼▼▼▼▼▼▼▼▼▼▼▼▼▼▼▼▼▼▼ Assembly procedure: • Install the new bearing and the dust cover by following the disassembly procedures in reverse order. NOTE: Use a wrench (1) with an external diameter equal to that of the bearing and dust cover. CAUTION: Do not strike the bearing inner race (2) or balls (3). The contact must only be made with the outer race (4). ▲▲▲▲▲▲▲▲▲▲▲▲▲▲▲▲▲▲▲▲▲▲▲▲▲▲▲▲▲ 4-5 FRONT WHEEL AND BRAKE DISC CHAS FRONT WHEEL INSTALLATION 1. Install: • Brake disc (1) Screw (brake disc): 12 Nm (1.2 mkg) NOTE: • Apply LOCTITE® to the threads of brake disc screw. • Tighten the screws (brake disc) in stage using a crisscross pattern. 1 2. Install: • Speedometer gear unit (1) NOTE: Make sure that the wheel hub and the speedometer gear unit are installed with the projections meshed into the slots. 3. Tighten: • Front wheel • Front wheel axle Front wheel axle: 59 Nm (5.9 mkg) NOTE: Make sure that the slot (a) in the speedometer gear unit fits under the stopper on the front fork outer tube. a • Pinch bolt Pinch bolt: 9 Nm (0.9 mkg) WHEEL STATIC BALANCE ADJUSTMENT NOTE: • After replacing the tire and/or rim, the wheel static balance should be adjusted. • Adjust the front wheel static balance with the brake disc installed. 1. Remove: • Balancing weight 2. Set: • Wheel (on a suitable stand) 3. Find: • Heavy spot 4-6 FRONT WHEEL AND BRAKE DISC CHAS ▼▼▼▼▼▼▼▼▼▼▼▼▼▼▼▼▼▼▼▼▼▼▼▼▼▼▼▼▼ Procedure: a. Spin the wheel and wait for it to rest. b. Put an “X1” mark on the wheel’s bottom spot. c. Turn the wheel so that the “X1” mark is 90° up. d. Release the wheel and wait for it to rest. Put an “X2” mark on the wheel’s bottom spot. e. Repeat the above b., c., and d. several times until all marks come to the same spot. f. This spot is the wheel’s heavy spot “X”. ▲▲▲▲▲▲▲▲▲▲▲▲▲▲▲▲▲▲▲▲▲▲▲▲▲▲▲▲▲ 4. Adjust: • Wheel static balance ▼▼▼▼▼▼▼▼▼▼▼▼▼▼▼▼▼▼▼▼▼▼▼▼▼▼▼▼▼ Adjusting steps: • Install a balancing weight (1) on the rim exactly opposite to the heavy spot “X”. NOTE: Start with the smallest weight. • • Turn the wheel so that the heavy spot is 90° up. Check that the heavy spot is at rest there. If not, try another weight until the wheel is balanced. ▲▲▲▲▲▲▲▲▲▲▲▲▲▲▲▲▲▲▲▲▲▲▲▲▲▲▲▲▲ 5. Check: • Wheel static balance ▼▼▼▼▼▼▼▼▼▼▼▼▼▼▼▼▼▼▼▼▼▼▼▼▼▼▼▼▼ Checking steps: • Turn the wheel so that it comes to each point as shown. • Check that the wheel is at rest at each point. If not, readjust the front wheel static balance. ▲▲▲▲▲▲▲▲▲▲▲▲▲▲▲▲▲▲▲▲▲▲▲▲▲▲▲▲▲ 4-7 FRONT BRAKE CHAS FRONT BRAKE BRAKE PAD 2 6 3 1 4 5 25 Nm (2.5 m•kg) Order Job name/Part name Q.ty Remove the parts in order. Brake pad removal 1 2 3 4 5 6 Remarks Brake caliper screw Brake caliper Pad pin retainer Pad pin Brake pad Pad spring 2 1 2 1 2 2 Refer to “BRAKE PAD REPLACEMENT” section. Reverse the removal procedure for installation. 4-8 FRONT BRAKE CHAS CAUTION: Brake components must not be disassembled. The builder declines every responsibility after brake components disassembly (brake master cylinder or brake caliper) or in case of use of non original parts. DO NOT: • Remove brake components from the motorcycle unless is absolutely necessary. • Use solvents on internal brake components. • Use brake fluid already used for bleeding. • Allow brake fluid to come into contact with the eyes as it may cause injury. • Allow brake fluid to come into contact with painted or plastic parts as it may damage them. • Disconnect any hydraulic connection, otherwise the whole system must be disassembled, drained, cleaned, then properly filled and bled after reassembly. BRAKE PAD REPLACEMENT NOTE: It is unnecessary to disassemble the brake hose to replace the pads. 1. Remove: • Caliper bracket fastening screws (1) (deplace the caliper) 2. Remove: • Pin retainers (2) • Pad fastening pin (3) • Brake pads (4) • Pad springs (5) • Caliper bracket (6) NOTE: • If you replace the pads, also replace the springs. • If one of the two pads has to be replaced because it is worn, replace both. Wear limit (a): 3.7 mm 4-9 FRONT BRAKE CHAS 3. Lubricate: • Guide pins (1) 1 Lithium-base grease 4 4. Install: • Pin bracket (2) (on the caliper body (3)) NOTE: Fit the rubber protections (4) when installing the caliper body. 5. Install: • Pad springs (1) (new) • Brake pads (2) (new) • Pad fastening pin (3) • Pin retainers (4) ▼▼▼▼▼▼▼▼▼▼▼▼▼▼▼▼▼▼▼▼▼▼▼▼▼▼▼▼▼ Installation procedure: • Connect the hose (1) firmly to the caliper bleeder screw (2). Place the other end of the hose in an open container. • Loosen the caliper bleeder screw and push the pistons into the caliper with your finger. • Retighten the bleeder screw (2). Caliper bleeder screw: 14 Nm (1.4 mkg) • • • • Install the (new) brake pads and (new) springs. Fit the pad fastening pin well into its housing by hammering with a punch with a suitable diameter. Install the (new) pin retainers. Install the caliper and screws. Caliper fastening screw: 25 Nm (2.5 kgm) ▲▲▲▲▲▲▲▲▲▲▲▲▲▲▲▲▲▲▲▲▲▲▲▲▲▲▲▲▲ 6. Check: • Level of brake fluid in reservoir. See section “BRAKE FLUID LEVEL INSPECTION” in CHAPTER 3. (a) Lower minimum level “MIN” 7. Check: • Brake lever operation Lever soft and spongy ➔ Bleed air from brake circuit. See section “AIR BLEEDING (HYDRAULIC BRAKE SYSTEM)” in CHAPTER 3. a 4-10 FRONT BRAKE CHAS MASTER CYLINDER 9 Nm (0.9 m•kg) 1 6 2 7 4 20 Nm (2.0 m•kg) 3 5 New Order 1 2 3 4 5 6 7 Job name/Part name Master cylinder removal Brake fluid Rear view mirror (right)/ Master cylinder bracket Brake lever Brake switch Union bolt Plain washer Brake hose Master cylinder Q.ty Remarks Remove the parts in order. Drain. 1/1 1 1 1 2 1 1 Refer to “MASTER CYLINDER INSTALLATION” section. Reverse the removal procedure for installation. 4-11 FRONT BRAKE CHAS 1.5 Nm (0.15 m•kg) 1 6 3 2 4 5 Order Job name/Part name Q.ty Remove the parts in order. Master cylinder disassembly 1 2 3 4 5 6 Remarks Reservoir cap Diaphragm Master cylinder boot Circlip Master cylinder assembly Spring 1 1 1 1 1 2 Refer to “MASTER CYLINDER ASSEMBLY” section. Reverse the disassembly procedure for assembly. 4-12 FRONT BRAKE CHAS MASTER CYLINDER INSPECTION 1. Inspect: • Master cylinder assembly Wear/scratches ➔ Replace the master cylinder assembly. • Master cylinder body Cracks/damage ➔ Replace the master cylinder assembly. • Fluid delivery passage (master cylinder) Obstruction ➔ Clean with a jet of compressed air. 2. Inspect: • Master cylinder piston unit (1) Scratches/wear/damage ➔ Replace the master cylinder assembly. 3. Inspect: • Diaphragm Wear/damage ➔ Replace. 4. Inspect: • Brake hose Cracks/wear/damage ➔ Replace. MASTER CYLINDER ASSEMBLY WARNING • All internal brake components should be cleaned and lubricated with new brake fluid only before installation. Recommended brake fluid: DOT 4 • In case of non correct operation of the brake master cylinder, replace the master cylinder assembly. 1. Install: • Spring (1) • Master cylinder (2) 4-13 FRONT BRAKE CHAS 2. Install: • Circlip (1) • Master cylinder boot (2) MASTER CYLINDER INSTALLATION 1. Install: • Master cylinder (1) • Master cylinder bracket (2) Screw (master cylinder bracket): 9 Nm (0.9 mkg) 2. Install: • Plain washer (1) (new) • Brake hose (2) • Union bolt (3) 2 Union bolt (brake hose): 20 Nm (2.0 mkg) 3 NOTE: • When tightening the union bolt be sure to put the brake hose in the correct position. • Check that the brake hose has stayed in the correct position. Adjust if necessary. 1 WARNING • • Check that the brake hose routing is as described. Refer to “CABLE ROUTING” section. Always use new plain washers. 3. Fill: • Brake fluid reservoir Recommended brake fluid: DOT 4 4-14 FRONT BRAKE CHAS CAUTION: Brake fluid may deteriorate painted surfaces or plastic parts. Always clean up spilled fluid immediately. WARNING • • • Use only designated quality brake fluid. Otherwise, the rubber seals may deteriorate, causing leakage and poor brake performance. Refill with the same type of brake fluid: mixing fluids may result in a harmful chemical reaction and lead to poor performance. Be careful that water does not enter the significantly lower the boiling point of the fluid may result in vapor lock. 4. Air bleed: • Brake system Refer to “AIR BLEEDING (HYDRAULIC BRAKE SYSTEM)” section in CHAPTER 3. 5. Inspect: • Brake fluid level Lower than “MIN” mark ➔ Fill. Refer to “BRAKE FLUID INSPECTION” section in CHAPTER 3. (a) Minimum level mark “MIN” a 2 6. Install: • Diaphragm (1) • Master cylinder cap (2) • Screw (3) (cap) 3 1 Screw (master cylinder cap): 1.5 Nm (0.15 mkg) 4-15 FRONT BRAKE CHAS BRAKE CALIPER 20 Nm (2.0 m•kg) 1 3 2 New 4 5 25 Nm (2.5 m•kg) Order 1 2 3 4 5 Job name/Part name Q.ty Remarks Remove the parts in order. Drain. Caliper removal Brake fluid Union bolt Plain washer Brake hose Caliper support bolt Caliper assembly 1 2 1 2 1 Refer to “CALIPER INSTALLATION” section Reverse the removal procedure for installation. 4-16 FRONT BRAKE CHAS 1 14 Nm (1.4 m•kg) 3 4 5 2 Order Job name/Part name Q.ty Remove the parts in order. Refer to “BRAKE PAD” section. Caliper disassembly Brake pad 1 2 3 4 5 Remarks Pad spring Caliper piston Dust seal Piston seal Bleed screw 2 2 2 2 1 Refer to “BRAKE CALIPER DISASSEMBLY/ASSEMBLY” section. Refer the disassembly procedure for assembly. 4-17 CHAS FRONT BRAKE BRAKE CALIPER DISASSEMBLY 1. Remove: • Brake caliper piston • Dust seal (1) • Piston seal (2) ▼▼▼▼▼▼▼▼▼▼▼▼▼▼▼▼▼▼▼▼▼▼▼▼▼▼▼▼▼ Removal procedure: Blow compressed air into the hose joint opening to force out the caliper piston from the brake caliper body. • WARNING • • Never try to pry out the caliper piston. Cover the caliper piston with a rag. Be careful not to get injured when the piston is expelled from the master cylinder. • Remove the piston seal. ▲▲▲▲▲▲▲▲▲▲▲▲▲▲▲▲▲▲▲▲▲▲▲▲▲▲▲▲▲ CALIPER INSPECTION Recommended programme for the replacement of brake system components: Brake pads When necessary Brake hoses Every four years Brake fluid Replace every 24,000 km or 24 months and whenever the brake is disassembled. WARNING All internal brake components should be cleaned and lubricated with new brake fluid only before installation. Do not use solvents to prevent sealing elements from becoming misshapen or swollen. 1. Inspect: • Caliper piston (1) Scratches/wear/rust ➔ Replace caliper assembly. • Caliper cylinder (2) Scratches/wear ➔ Replace caliper assembly. • Caliper (3) Cracks/damaged ➔ Replace the brake caliper assembly.. 4-18 FRONT BRAKE • CHAS Fluid delivery passage (caliper) Obstruction ➔ Clean with compressed air. WARNING In case of non correct operation of the brake caliper, replace the brake caliper assembly. CALIPER ASSEMBLY WARNING • All internal brake components should be cleaned and lubricated with new brake fluid only before installation. Recommended brake fluid: DOT 4 • In case of non correct operation of the brake caliper, replace the brake caliper assembly. 1. Install: • Piston seals (1) • Dust seals (2) 2. Install: • Brake caliper pistons (1) CALIPER INSTALLATION 1. Install: • Brake caliper (1) • Caliper support bolts (2) 3 4 Bolt (caliper support): 25 Nm (2.5 mkg) 5 • • • 2 Brake hose (3) Plain washers (4) (new) Union bolt (5) Union bolt: 20 Nm (2.0 mkg) 1 4-19 FRONT BRAKE CHAS WARNING Check that the brake hose routing is correct. Refer to “CABLE ROUTING” section. 2. Fill: • Brake fluid reservoir Recommended brake fluid: DOT 4 CAUTION: Brake fluid may deteriorate painted surfaces or plastic parts. Always clean up spilled fluid immediately. WARNING • • • Use only designated quality brake fluid. Otherwise, the rubber seals may deteriorate, causing leakage and poor brake performance. Refill with the same type of brake fluid: mixing fluids may result in a harmful chemical reaction and lead to poor performance. Be careful that water does not enter the significantly lower the boiling point of the fluid may result in vapor lock. 3. Air bleed: • Brake system Refer to “AIR BLEEDING (HYDRAULIC BRAKE SYSTEM)” section in CHAPTER 3. 4. Inspect: • Brake fluid level Lower than “MIN” mark ➔ Fill. Refer to “BRAKE FLUID INSPECTION” section in CHAPTER 3. (a) Minimum level mark “MIN” a 4-20 REAR WHEEL AND BRAKE DISC CHAS REAR WHEEL AND BRAKE DISC Order Job name/Part name Q.ty Remarks Remove the parts in order. Rear wheel and brake disc removal WARNING Securely support the motorcycle so there is no danger of it falling over. 1 Axle nut 1 2 Wheel axle 1 3 Drive chain - 4 Collar 2 5 Rear wheel assembly 1 6 Brake disc 1 4-21 Push the wheel forward and remove the chain. Refer to “REAR WHEEL INSTALLATION” section. Reverse the installation. removal procedure for REAR WHEEL AND BRAKE DISC Order 1 2 3 4 5 6 7 8 9 10 11 Job name/Part name Q.ty CHAS Remarks Remove the parts in order. Rear wheel disassembly Driven sprocket Hub Damper Spacer Oil seal Bearing Bearing Hub dust cover Oil seal Bearing Bearing spacer 1 1 4 1 1 1 1 1 1 1 1 4-22 Refer to “REAR WHEEL DISASSEMBLY/ASSEMBLY” section. Reverse the removal procedure for installation. REAR WHEEL AND BRAKE DISC CHAS REAR WHEEL DISASSEMBLY 1. Remove: • Hub and driven sprocket • Dampers • Hub spacer • Oil seal • Hub bearing • Wheel bearing • Wheel spacer • Wheel bearing • Dust cover • Oil seal • Wheel bearing • Wheel spacer ▼▼▼▼▼▼▼▼▼▼▼▼▼▼▼▼▼▼▼▼▼▼▼▼▼▼▼▼▼ Removal procedure: • Clean the outside of the hub. • Remove the dust cover with a flat-headed screw driver. NOTE: Place a rag on the outside to avoid damaging the hub. • Disassemble the bearing (1) with a normal puller (2). ▲▲▲▲▲▲▲▲▲▲▲▲▲▲▲▲▲▲▲▲▲▲▲▲▲▲▲▲▲ REAR WHEEL INSPECTION 1. Inspect: • Rear wheel axle (by rolling it on a flat surface) Bends ➔ Replace. WARNING Do not attempt to straighten a bent axle. 2. Inspect: • Rear tire Refer to “TIRE INSPECTION” in CHAPTER 3. • Rear wheel Refer to “WHEEL INSPECTION” in CHAPTER 3. 3. Inspect: • Spoke(s) Bent/Damaged ➔ Replace. Loose spoke(s) ➔ Tighten. Turn the wheel and hit the spokes gently with a screwdriver. NOTE: A well tightened spoke makes a distinct, sharp noise: a loose spoke makes a dull, muffled noise. 4-23 REAR WHEEL AND BRAKE DISC CHAS 4. Tighten: • Loose spokes Spoke: 2 Nm (0.2 mkg) NOTE: After tightening the spokes, check the centring of the wheel. 5. Measure: • Rear wheel runout Over the specified limits ➔ Replace. Rear wheel runout limits: Radial (1) : 1.0 mm Lateral (2) : 0.5 mm 6. Inspect: • Rear wheel bearings Bearings allow free play in the wheel hub or the wheel does not turn smoothly ➔ Replace. • Hub dust cover Wear/damage ➔ Replace. • Oil seal Wear/damage ➔ Replace. BRAKE DISC INSPECTION 1. Inspect: • Brake disc Wear/Damage ➔ Replace. 2. Measure: • Brake disc deflection (a) If over envisaged limits ➔ Verify wheel centring. If the wheel centring is correct, replace the brake disc. Maximum deflection (brake disc): 0.15 mm • Misure at 2 mm from disc edge Brake disc thickness (b) If out of specified limits ➔ Replace. Minimum thickness (brake disc): 4.5 mm 4-24 REAR WHEEL AND BRAKE DISC CHAS REAR WHEEL ASSEMBLY 1. Install: • Wheel spacer • Wheel bearing • Oil seal • Dust cover • Wheel bearing • Wheel spacer • Wheel bearing • Hub bearing • Oil seal • Hub spacer • Dampers • Hub and driven sprocket ▼▼▼▼▼▼▼▼▼▼▼▼▼▼▼▼▼▼▼▼▼▼▼▼▼▼▼▼▼ Assembly procedure: • Install the new bearing, the dust cover and the oil seal by following the disassembly procedures in reverse order. NOTE: Use a wrench (1) with an external diameter equal to that of the bearing, dust cover and oil seal. CAUTION: Do not strike the bearing inner race (2) or balls (3). The contact must only be made with the outer race (4). ▲▲▲▲▲▲▲▲▲▲▲▲▲▲▲▲▲▲▲▲▲▲▲▲▲▲▲▲▲ REAR WHEEL INSTALLATION 1. Install: • Brake disc (1) Screw (brake disc): 12 Nm (1.2 mkg) NOTE: • Apply LOCTITE ® to the threads of brake disc screw. • Tighten the screws (brake disc) in stage using a crisscross pattern. 2. Install: • Hub spacer (1) • Driven sprocket (2) • Hub and driven sprocket Screw (driven sprocket): 48 Nm (4.8 mkg) 3. Install: • Collar 4-25 REAR WHEEL AND BRAKE DISC CHAS 4. Lubricate: • Wheel axle • Bearings • Edge of hub dust cover Lithium-base grease CAUTION: Check that the brake caliper support has stayed in the correct position on the rear arm. 5. Install: • Rear wheel assembly (in the rear arm) • Bearing • Edge of the hub dust cover CAUTION: Check that the brake disc is driving through the brake pads. 6. Install: • Drive chain (on the driven sprocket) • Rear wheel axle (left side) CAUTION: Make sure the collars and chain pullers are positioned correctly. 7. Adjust: • Drive chain slack Drive chain slack: 30 ~ 40 mm Refer to “DRIVE CHAIN SLACK INSPECTION AND ADJUSTMENT” section in Chapter 3. 8. Tighten: • Wheel axle nut Wheel axle nut: 115 Nm (11.5 mkg) 4-26 REAR WHEEL AND BRAKE DISC CHAS WHEEL STATIC BALANCE ADJUSTMENT NOTE: • After replacing the tire and/or rim, the wheel static balance should be adjusted. • Adjust the rear wheel static balance with the brake disc installed. 1. Remove: • Balancing weight 2. Set: • Wheel (on a suitable stand) 3. Find: • Heavy spot ▼▼▼▼▼▼▼▼▼▼▼▼▼▼▼▼▼▼▼▼▼▼▼▼▼▼▼▼▼ Procedure: a. Spin the wheel and wait for it to rest. b. Put an “X1” mark on the wheel’s bottom spot. c. Turn the wheel so that the “X1” mark is 90° up. d. Release the wheel and wait for it to rest. Put an “X2” mark on the wheel’s bottom spot. e. Repeat the above b., c., and d. several times until all marks come to the same spot. f. This spot is the wheel’s heavy spot “X”. ▲▲▲▲▲▲▲▲▲▲▲▲▲▲▲▲▲▲▲▲▲▲▲▲▲▲▲▲▲ 4. Adjust: • Wheel static balance ▼▼▼▼▼▼▼▼▼▼▼▼▼▼▼▼▼▼▼▼▼▼▼▼▼▼▼▼▼ Adjusting steps: • Install a balancing weight (1) on the rim exactly opposite to the heavy spot “X”. NOTE: Start with the smallest weight. • • Turn the wheel so that the heavy spot is 90° up. Check that the heavy spot is at rest there. If not, try another weight until the wheel is balanced. ▲▲▲▲▲▲▲▲▲▲▲▲▲▲▲▲▲▲▲▲▲▲▲▲▲▲▲▲▲ 4-27 REAR WHEEL AND BRAKE DISC CHAS 5. Check: • Wheel static balance ▼▼▼▼▼▼▼▼▼▼▼▼▼▼▼▼▼▼▼▼▼▼▼▼▼▼▼▼▼ Checking steps: • Turn the wheel so that it comes to each point as shown. • Check that the wheel is at rest at each point. If not, readjust the rear wheel static balance. ▲▲▲▲▲▲▲▲▲▲▲▲▲▲▲▲▲▲▲▲▲▲▲▲▲▲▲▲▲ 4-28 REAR BRAKE CHAS REAR BRAKE BRAKE PAD Order Job name/Part name Q.ty Remove the parts in order. Refer to “REAR WHEEL REMOVAL” section. Remove from clamp. Brake pad removal Rear wheel Brake hose 1 2 3 4 5 6 Remarks Caliper protector Pad pin retainer Pad pin Brake pad Brake caliper (remove from caliper support) Brake pad support 1 1 1 1 2 Refer to “BRAKE PAD REPLACEMENT” section. 1 Reverse the removal procedure for installation. 4-29 REAR BRAKE CHAS CAUTION: Brake components must not be disassembled. The builder declines every responsibility after brake components disassembly (brake master cylinder or brake caliper) or in case of use of non original parts. DO NOT: • Remove brake components from the motorcycle unless is absolutely necessary. • Use solvents on internal brake components. • Use brake fluid already used for bleeding. • Allow brake fluid to come into contact with the eyes as it may cause injury. • Allow brake fluid to come into contact with painted or plastic parts as it may damage them. • Disconnect any hydraulic connection, otherwise the whole system must be disassembled, drained, cleaned, then properly filled and bled after reassembly. 3 BRAKE PAD REPLACEMENT 4 6 2 NOTE: It is unnecessary to disassemble the brake hose to replace the pads. 5 1 1. Remove: • Rear wheel (refer to “REAR WHEEL REMOVAL” section). • Bolt (caliper protector) (1) • Brake caliper protector (2) • Pad pin retainer (3) • Brake pad pin (4) Remove the caliper in the illustrated direction. 2. Remove: • Brake pads (5) • Pad support (6) NOTE: • If you replace the pads, also replace the pad support. • If one of the two pads has to be replaced because it is worn, replace both. 4-30 REAR BRAKE CHAS 3. Install: • Brake pads • Pad support ▼▼▼▼▼▼▼▼▼▼▼▼▼▼▼▼▼▼▼▼▼▼▼▼▼▼▼▼▼ Installation procedure: • Connect the hose (1) firmly to the caliper bleeder screw (2). Place the other end of the hose in an open container. • Loosen the caliper bleeder screw and push the piston into the caliper with your finger. • Retighten the bleeder screw (2). Caliper bleeder screw: 14 Nm (1.4 mkg) • • • • 5 6 Install the (new) brake pads and (new) pad support. Install the caliper (3) and the pad pin (4). Install the (new) pin retainer (5) Install the caliper protector (6). Caliper protector bolt: 10 Nm (1.0 mkg) 4 ▲▲▲▲▲▲▲▲▲▲▲▲▲▲▲▲▲▲▲▲▲▲▲▲▲▲▲▲▲ 2 3 4. Check: • Brake fluid level Refer to “BRAKE FLUID INSPECTION” section in Chapter 3. (a) Minimum level mark “MIN” (b) Maximum level mark “MAX” b a 5. Check: • Brake pedal operation Pedal soft and spongy ➔ Bleed air from brake circuit. Refer to “AIR BLEEDING (HYDRAULIC BRAKE SYSTEM)” section in Chapter 3. 4-31 REAR BRAKE CHAS MASTER CYLINDER 20 Nm (2.0 m•kg) New 4 Nm (0.4 m•kg) 10 Nm (1.0 m•kg) New 45 Nm (4.5 m•kg) Order Job name/Part name 1 2 3 4 5 6 Master cylinder removal Brake fluid Rear stop switch connector Rear stop switch Plain washer Brake hose Brake fluid reserve tank Brake master cylinder 7 Brake pedal/spring Q.ty Remarks Remove the parts in order. Drain. 1 1 2 1 1 1 Refer to “MASTER CYLINDER INSTALLATION” section. 1/1 Refer to “BRAKE PEDAL REMOVAL” section. Reverse the removal procedure for installation. 4-32 REAR BRAKE CHAS MASTER CYLINDER INSPECTION 1. Inspect: • Master cylinder assembly Wear/scratches ➔ Replace the master cylinder assembly. • Master cylinder body Cracks/damage ➔ Replace the master cylinder assembly. • Fluid delivery passage (master cylinder) Obstruction ➔ Clean with a jet of compressed air. 2. Inspect: • Master cylinder piston unit Scratches/wear/damage ➔ Replace the master cylinder assembly. 3. Inspect: • Diaphragm (1) Wear/damage ➔ Replace. 4. Inspect: • Brake hose Cracks/wear/damage ➔ Replace. MASTER CYLINDER ASSEMBLY WARNING • All internal brake components should be cleaned and lubricated with new brake fluid only before installation. Recommended brake fluid: DOT 4 • In case of non correct operation of the brake master cylinder, replace the master cylinder assembly. 1. Install: • Spring • Master cylinder piston unit 4-33 REAR BRAKE CHAS MASTER CYLINDER INSTALLATION 1. Install: • Brake pedal (refer to “BRAKE PEDAL REMOVAL” section in this Chapter). NOTE: Lubricate the pin of the brake pedal with lithiumbase grease. • • • • • New Master cylinder Brake fluid reserve tank Plain washers (1) (new) Brake hose (2) Stop switch (to mount the brake hose) (3) Brake switch (brake hose): 20 Nm (2.0 mkg) Master cylinder mounting bolt: 10 Nm (1.0 mkg) Reserve tank mounting bolt: 4 Nm (0.4 mkg) 2. Fill: • Brake fluid reserve tank Recommended brake fluid: DOT 4 CAUTION: Brake fluid may deteriorate painted surfaces or plastic parts. Always clean up spilled fluid immediately. WARNING • • • 4-34 Use only designated quality brake fluid. Otherwise, the rubber seals may deteriorate, causing leakage and poor brake performance. Refill with the same type of brake fluid: mixing fluids may result in a harmful chemical reaction and lead to poor performance. Be careful that water does not enter the significantly lower the boiling point of the fluid may result in vapor lock. REAR BRAKE CHAS 3. Air bleed: • Brake system Refer to “AIR BLEEDING (HYDRAULIC BRAKE SYSTEM)” in Chapter 3. 4. Inspect: • Brake fluid level Lower than “MIN” mark (1) ➔ Fill. Refer to “BRAKE FLUID INSPECTION” section in Chapter 3. (1) Minimum level mark “MIN” 1 5. Adjust: • Brake pedal height (a) (below the top of the footrest) a Brake pedal height: 10 mm BRAKE PEDAL REMOVAL 1. Remove: • Split pin (1) (new) • Plain washer (2) • Pin (3) 2. Unscrew: • Bolt (4) 3. Remove: • Spring (5) 4. Remove: • Brake pedal (6) from chassis NOTE: Pull the brake pedal from the lower part of the chassis, causing it to rotate progressively as it comes away. 4-35 REAR BRAKE CHAS BRAKE CALIPER Order Job name/Part name Q.ty Remove the parts in order. Refer to “REAR WHEEL REMOVAL” section. Drain. Remove from clamp. Caliper removal Rear wheel Brake fluid Brake hose 1 2 3 4 5 6 Remarks Caliper protector Brake caliper Union bolt Plain washer Brake hose Brake pad support 1 1 1 2 1 1 Remove from caliper support. Refer to “BRAKE CALIPER INSTALLATION” section. Reverse the removal procedure for installation. 4-36 REAR BRAKE CHAS New 14 Nm (1.4 m•kg) 2 10 Nm (1.0 m•kg) Order Job name/Part name Q.ty Remove the parts in order. Caliper disassembly 1 2 3 4 5 6 7 8 Remarks Caliper protector Brake pad support Brake pad Pad support Caliper piston Dust seal Piston seal Bleed screw 1 1 2 1 1 1 1 1 Refer to “BRAKE PAD” section. Refer to “BRAKE CALIPER DISASSEMBLY/ASSEMBLY” section. Reverse the removal procedure for installation. 4-37 REAR BRAKE CHAS BRAKE CALIPER DISASSEMBLY 1. Remove: • Brake caliper piston (1) • Dust seal (3) • Piston seal (2) ▼▼▼▼▼▼▼▼▼▼▼▼▼▼▼▼▼▼▼▼▼▼▼▼▼▼▼▼▼ Removal procedure: • Blow compressed air into the hose joint opening to force out the caliper piston from the brake caliper body. WARNING • • Never try to pry out the caliper piston. Cover the caliper piston with a rag. Be careful not to get injured when the piston is expelled from the master cylinder. • Remove the piston seal ▲▲▲▲▲▲▲▲▲▲▲▲▲▲▲▲▲▲▲▲▲▲▲▲▲▲▲▲▲ CALIPER INSPECTION Recommended programme for the replacement of brake system components: Brake pads When necessary Brake hose Every four years Replace every 24,000 km or 24 Brake fluid months and whenever the brake is disassembled. WARNING All internal brake components should be cleaned and lubricated with new brake fluid only before installation. Do not use solvents to prevent sealing elements from becoming misshapen or swollen. 1. Inspect: • Caliper piston Scratches/wear/rust ➔ Replace caliper assembly. • Caliper cylinder Scratches/wear ➔ Replace caliper assembly. • Caliper Cracks/damaged ➔ Replace. 4-38 REAR BRAKE • CHAS Fluid delivery passage (caliper) Obstruction ➔ Clean with compressed air. WARNING In case of non correct operation of the brake caliper, replace the brake caliper assembly. BRAKE CALIPER ASSEMBLY WARNING • All internal brake components should be cleaned and lubricated with new brake fluid only before installation. Liquido freni raccomandato: DOT 4 • In case of non correct operation of the brake caliper, replace the brake caliper assembly. 1. Install: • Piston seal (1) • Dust seal (2) • Caliper piston (3) 5 4 CALIPER INSTALLATION 1. Install: • Brake caliper (1) • Caliper support (2) • Brake hose (3) • Plain washers (4) (new) • Union bolt (5) 1 2 3 Union bolt: 20 Nm (2.0 mkg) • 4-39 Caliper protector REAR BRAKE CHAS CAUTION: Check that the brake hose has stayed in correct position with the pipe-fitting matching the projection (a) of the caliper. WARNING Check that the brake hose routing is correct. Refer to “CABLE ROUTING” section. a 2. Fill: • Brake fluid reserve tank Recommended brake fluid: DOT 4 CAUTION: Brake fluid may deteriorate painted surfaces or plastic parts. Always clean up spilled fluid immediately. WARNING • • • Use only designated quality brake fluid. Otherwise, the rubber seals may deteriorate, causing leakage and poor brake performance. Refill with the same type of brake fluid: mixing fluids may result in a harmful chemical reaction and lead to poor performance. Be careful that water does not enter the significantly lower the boiling point of the fluid may result in vapor lock. 3. Air bleed: • Brake system Refer to “AIR BLEEDING (HYDRAULIC BRAKE SYSTEM)” section in CHAPTER 3. 4-40 REAR BRAKE CHAS 4. Inspect: • Brake fluid level Lower than “MIN” mark (1) ➔ Fill. Refer to “BRAKE FLUID INSPECTION” section in Chapter 3. (1) Minimum level mark “MIN” 1 4-41 FRONT FORK CHAS FRONT FORK FRONT FORK REMOVAL Order Job name/Part name Q.ty Remarks Remove the parts in order. Refer to “FRONT WHEEL” section. 1 2 3 4 5 6 7 Front fork removal Front wheel Inner tube protector Brake hose guide Protector guide Brake caliper assembly Cowling (displace) Pinch bolt (upper bracket) Cap bolt (loosen) 1 1 2 1 1 4 2 8 9 Pinch bolt (under bracket) (loosen) Fork leg 4 2 Refer to "FRONT FORK INSTALLATION" section. Reverse the removal procedure for installation. 4-42 FRONT FORK CHAS FRONT FORK DISASSEMBLY Order Job name/Part name Q.ty Remove the parts in order. Refer to “FRONT FORK REMOVAL/INSTALLATION”. Front fork disassembly 1 2 3 4 5 6 7 8 9 10 11 Remarks Cap bolt Seat Spacer Seat Fork spring Bolt O-ring Damper adjusting cylinder Taper spindle Dust seal Snap ring 1 1 1 1 1 1 1 1 1 1 1 4-43 Refer to “OIL REPLACEMENT” section. Refer to “SEAL AND BUSH REPLACEMENT” section. FRONT FORK Order 12 13 14 15 16 17 Job name/Part name CHAS Q.ty Remarks 1 1 1 1 1 1 Refer to “SEAL AND BUSH REPLACEMENT” section. Inner tube Inner tube bushing Oil seal Washer Outer tube bushing Outer tube Reverse the removal procedure for installation. 4-44 FRONT FORK CHAS OIL CAPACITY (IN EACH FORK LEG): 650 cm3 RECOMMENDED OIL: Liqui Moly Racing suspension oil SAE 7,5 FRONT FORK OIL LEVEL STANDARD 180 mm MINIMUM 190 mm MAXIMUM 170 mm From top of inner tube with inner tube fully compressed without spring. MINIMUM FORK SPRING FREE LENGTH: 530 mm INNER TUBE BENDING LIMIT: 0.2 mm FRONT FORK REMOVAL WARNING Securely support the motorcycle so there is no danger of it falling over. 1. Park the motorcycle on a level surface. 2. Raise the front wheel by placing a suitable support under the engine. 3. Remove: • Front wheel Refer to “FRONT WHEEL REMOVAL” section. 4. Remove: • Inner tube protector • Protector guide • Gear unit assembly and cable • Brake caliper and hose 5. Loosen: • Cap bolt • Pinch bolt (upper and lower bracket) 4-45 FRONT FORK CHAS OIL REPLACEMENT NOTE: The quality of the fork oil is of fundamental importance for obtaining the maximum performance and functioning. For this reason it needs to be replaced after the first 3÷4 hours to eliminate any residues due to the adaptation of the internal components and successively every 8 hours for motor-cross and every 20 hours for enduro. CAUTION: Using oil with different technical specifications will compromise the good efficiency of the fork. 1. Generally clean the front fork. 2. Loosen: • Cap bolt (inner tube) 3. Remove: • Fork leg 4. Unscrew: • Cap bolt (1) (completely) NOTE: Place the components in a clean area. 5. Withdraw: • Seat (2) • Spacer (3) • Spring (4) (from the inner tube (5)) NOTE: The spring, being immersed in oil could cause oil to drip onto the work surface when withdrawn. It is advisable therefore to withdraw it slowly and to dry it with a clean cloth. 6. Pour the oil into a tray whilst at the same time moving the inner tube (1) backwards and forwards. CAUTION: In order not to cause damage to the environment collect the used oil and take it to a collection centre. 4-46 FRONT FORK CHAS 7. Fill: • Part of the new oil (with the fork leg in a vertical position) Recommended oil: Liqui Moly Racing suspension oil SAE 7,5 8. Using the inner tube pump back and forth until a regular drag is felt on the return stroke. 9. With the fork leg in a perfectly upright position, insert the inner tube (1) in the outer tube (2) completely to the end of the stroke. 10. Finish topping up the oil bringing it to the prescribed level from the upper edge measured with a graduated dipstick or ruler (3). Recommended oil: Liqui Moly Racing suspension oil SAE 7,5 Oil level: Standard 180 mm Minimum 190 mm Maximum 170 mm From top of inner tube with inner tube fully inserted without spring. 11. Insert: • Spring (1) (into the inner tube (2)) • Seat (3) • Spacer (4) NOTE: Usually there is no particular sense in which the spring is mounted and so it may be inserted from either end. If there is a hem, however mount it keeping the hemmed parts towards the top. 12. Screw: • Cap bolts (5) (on inner tube, without tighten) 13. Install: • Fork leg 4-47 FRONT FORK CHAS 14. Tighten: • Pinch bolt (upper and lower bracket) Pinch bolt (upper bracket): 28 Nm (2.8 mkg) Pinch bolt (under bracket): 23 Nm (2.3 mkg) NOTE: Always tighten the lower pinch bolt (to the prescribed torque) and then the upper one (to the prescribed torque) and then retighten the lower one (to the prescribed torque). 15. Tighten: • Cap bolt (on inner tube) Cap bolt (on inner tube): 20 Nm (2.0 mkg) 4-48 FRONT FORK CHAS CLEANING THE DUST SEAL 1 NOTE: After using the motorcycle it is necessary to clean the dust seal carefully in order to maintain the fork at maximum efficiency. In fact, if dust infiltrates to the inside of the dust seal it can compromise the smoothness and therefore the sensitivity of the fork, and also cause the premature wear of the underlying oil seal. Just a few simple operations then, guided by the following indications are necessary to maintain the optimum functioning of the fork with time. 2 1 1. With a screwdriver prise the dust seal (1) from the oil seal seat (2) and then withdraw it using force. 1 2 2 2. Using a low pressure jet of compressed air clean the inside of the dust seal and the oil seal seat. 3. Insert the edge of a cloth under the lip and keeping the cloth steady, carefully clean the lip by rotating the dust seal. 4-49 FRONT FORK CHAS 4. Using a small screwdriver take a small amount of silicon grease and insert it under the lip paying attention not to scratch it. Lubricate the dust seal by rotating it in such a manner that the grease is distributed in the inner part of the lip. 5. Remount the dust seal inserting it with force into the oil seal seat. CAUTION: Check that the oil seal housing edge of the dust seal adheres perfectly to the oil seal seat. SEAL AND BUSH REPLACEMENT NOTE: To ensure maximum efficiency to the fork and therefore a longer duration and greater safety, every year (unless there are leakages) it is necessary to replace all the seals and slide bushes. To carry out this operation it is recommended to use the proper tools. CAUTION: To remove the fork leg from the steering unit, the cap bolt, the spring and to drain and refill the oil, follow the procedures indicated in the preceding pages scrupulously. 1. Drain: • Fork leg oil Refer to “OIL REPLACEMENT”section. 2. Clamp: • Fork leg in a vice (in a horizontal position) CAUTION: Protect the outer tube with a clean rag to avoid damaging. 4-50 FRONT FORK CHAS 2 1 3 3. Insert an Allen key in the bolt (3) at the bottom of the outer tube and the special tool (1) with the holder (2) on the damper cylinder assembly and unscrew the bolt completely. CAUTION: Before unscrewing the bolt ensure that the end of the damper rod holder is correctly engaged on the damper cylinder assembly. T-handle (1): 90890-01326 Front fork damper rod holder (2): 90890-01460 4. Remove: • Damper cylinder assembly (from inner tube) 5. Clean the inside of the outer tube and the outside of the damper cylinder assembly with petrol. CAUTION: Taking care not to let petrol enter the inside of the damper cylinder assembly as it would seriously compromise its functioning. 4-51 FRONT FORK CHAS WARNING Never tamper with the damper cylinder assembly! Tampering with the damper cylinder assembly by non authorized personnel can compromise tha safety of the fork. In order not to cause damage to the environment collect the used oil and take it to a collection centre. 6. Tightly clamp the fork leg horizontally fastening it by caliper attachment on the outer tube. 4 5 7. Using a screwdriver prise the dust seal (4) from the edge of the oil seal seat (5). Then withdraw the dust seal using force. 5 4 1 2 8. Remove: • Snap ring (1) (using a screwdriver) 1 4-52 FRONT FORK 9. With a few sharp blows withdraw the inner tube (2) from the outer tube (3). 3 7 NOTE: The oil seal (4), the washer (5), the outer tube DU bush (6) and the inner tube DU bush (7) are installed on the inner tube and must be removed and replaced with new one. 6 4 2 CHAS 5 10. Install: • Outer tube DU bush (6) (new) • Inner tube DU bush (7) (new) 6 CAUTION: Check that the inner tube bush (7) is inserted correctly in its seat on the end of the inner tube. 7 3 11. Mount the tool (1) on the inner tube (2) with the side (3) matching the DU outer tube bush (4) and clamp it keeping the two joints (5) at the top and bottom (never towards the jaws of the vice) and make it protrude by at least 40 mm at the sides. 4 DU bush/oil seal driver (1): 90890-11043 3 4 1 2 4-53 FRONT FORK 5 CHAS 12. The vice tightened, grip the outer tube and with a few strong blows hit it against the tool (3) until the DU outer tube bush (4) is correctly positioned in its seat. 4 3 ~ 40 mm 1 2 13. Remove the fork leg from the vice and remove the tool (1). Insert the new washer (3) and the new oil seal (4) as shown on the inner tube (2). 4 NOTE: Apply lightweight lithium-soap base grease to the oil seal before installing it. 14. Mount the tool (1) on the inner tube (2) with the side (5) matching the oil seal (4) and clamp it keeping the two joints (6) at the top and bottom (never towards the jaws of the vice) and make it protrude by at least 40 mm at the sides. 5 DU bush/oil seal driver (1): 90890-11043 3 4 1 2 15. The vice tightened, grip the outer tube and with a few strong blows hit it against the tool (1). After each blow rotate the outer tube slightly in order to install the oil seal (4) correctly and until it is completely inserted in its seat. 3 6 4 1 2 ~ 40 mm 4-54 FRONT FORK CHAS 16. Tightly clamp the fork leg horizontally fastening it by caliper attachment on the outer tube. 17. Install: • Snap ring (1) 1 CAUTION: Check that the snap ring is correctly seated. 18. Install: • Dust seal (1) (new) 1 NOTE: Apply lightweight lithium-soap base grease to the dust seal before installing it. NOTE: Taking care to insert completely the dust seal (1) with force in the outer tube (2). 2 1 2 1 3 4-55 FRONT FORK CHAS 19. Insert: • Damper cylinder assembly (in the inner tube) 20. Insert an Allen key in the bolt (3) at the bottom of the outer tube and the special tool (1) with the holder (2) on the damper cylinder assembly and screw the bolt completely. CAUTION: During tightening the bolt ensure that the end of the damper rod holder is correctly engaged on the damper cylinder assembly. T-handle (1): 90890-01326 Front fork damper rod holder (2): 90890-01460 Damper cylinder assembly bolt (3): 25 Nm (2.5 kgm) 21. Fill: • Fork leg oil Refer to “OIL REPLACEMENT”section. OIL LEAKAGE FROM DUST SEAL If there is a leakage of oil from between the dust seal (1) and the inner tube (2) replace the oil seal (refer to “SEAL AND BUSH REPLACEMENT” section). 2 ANOMALOUS HYDRAULIC BRAKING If the fork shows an anomalous hydraulic braking effect it is necessary to overhaul the damper cylinder assembly. 1 WARNING Never tamper with the damper cylinder assembly! This operation should be done by authorized personnel. Tampering with the damper cylinder assembly by non authorized personnel can compromise the safety of the front fork. The building firm will not assume any responsibility for any damages resulting from such action. 4-56 FRONT FORK CHAS FRONT FORK INSPECTION CAUTION: The front fork has a very sophisticated internal construction and is particularly sensitive to foreign bodies. Use enough care to prevent foreign bodies entering when replacing oil or disassembling and reassembling the front fork. 1. Inspect: • Cap bolt (inner tube) Wear/Damage ➔ Replace. • O-Rings Damage ➔ Replace. 2. Measure: • Fork spring free length (a) Out of specification ➔ Replace. Fork spring free length: 530 mm 3. Inspect: • Inner tube surface Score marks ➔ Repair or replace. Use #1.000 grit wet sandpaper. Damaged oil seal surface ➔ Replace. • Inner tube bending Out of specification ➔ Replace. Use a dial gauge (1). Inner tube bending limit: 0.2 mm NOTE: The bending value is shown by one half of the dial gauge reading. 4-57 FRONT FORK CHAS WARNING Do not attempt to straighten a bent inner tube as this may have dangerous consequences. 4. Inspect: • Outer tube (1) Score marks/Wear/Damage ➔ Replace. 5. Inspect: • Cap bolt • O-ring Wear/Damage ➔ Replace. 4-58 FRONT FORK CHAS FRONT FORK INSTALLATION 1. Install: • Front fork (1) Temporarily tighten the pinch bolts (lower). 2. Tighten: • Cap bolt Cap bolt: 20 Nm (2.0 kgm) NOTE: Do not tighten the pinch bolt (upper) yet. 3. Adjust: • Front fork top end (a) Front fork top end (a) (Standard): 0 mm 4. Tighten: • Pinch bolt (upper and lower bracket) Pinch bolt (upper bracket): 28 Nm (2.8 mkg) Pinch bolt (under bracket): 23 Nm (2.3 mkg) NOTE: Always tighten the lower pinch bolt (to the prescribed torque) and then the upper one (to the prescribed torque) and then retighten the lower one (to the prescribed torque). 5. Install: • Front wheel • Caliper • Brake hose • Tachometer cable Refer to “FRONT WHEEL” and “FRONT BRAKE” sections in this CHAPTER. 4-59 FRONT FORK CHAS ADJUSTING THE FRONT FORK This front fork is equipped with spring pre-load adjusting bolts. WARNING b a 1 b Always adjust both fork legs equally, otherwise poor handling and loss of stability may result. a Adjust the spring preload as follows. To increase the spring preload and thereby harden the suspension, turn the adjusting bolt on each fork leg in direction a. To decrease the spring preload and thereby soften the suspension, turn the adjusting bolt on each fork leg in direction b. Minimum (soft) Standard Maximum (hard) 4-60 Setting 1-2-3 4 5-6-7-8-9-10 STEERING CHAS TIGHTENING PROCEDURE • Initial tightening 38 Nm (3.8 mkg) • Loosen 1 turn • Final tightening 4 Nm (0.4 mkg) Order Job name/Part name Q.ty Remarks Remove the parts in order. Park the motorcycle on a level surface. Steering removal WARNING Securely support the motorcycle to prevent it falling over. Front wheel 1 2 3 4 5 6 7 8 Fork legs Cowling/Meter unit Front fender Handle upper holder Handle lower holder Handlebar Nut Upper bracket Special washer 1 1 2 1 1 1 1 1 4-61 Refer to “FRONT WHEEL REMOVAL” section. Refer to “FRONT FORK” section. Displace. Displace. STEERING CHAS TIGHTENING PROCEDURE • Initial tightening 38 Nm (3.8 mkg) • Loosen 1 turn • Final tightening 4 Nm (0.4 mkg) Order 9 10 11 12 13 14 Job name/Part name Q.ty Remarks 1 1 1 1 1 1 Refer to “STEERING REMOVAL/INSTALLATION” section. Upper ring nut Lower ring nut Ball race cover Lower bracket/Steering axle Bearing (upper) Bearing (lower) Reverse the removal procedure for installation. 4-62 STEERING (1) (2) (3) (4) (5) (6) Handle upper holder Handle lower holder Spacer Nut Plate washer Upper bracket (7) Brake hose holder (8) Plate washer (9) Special washer (10) Upper ring nut (11) Lower ring nut (12) Ball race cover (13) (14) (15) (16) CHAS Bearings Steering lock Steering axle Wire guide TIGHTENING PROCEDURE • Initial tightening 38 Nm (3.8 mkg) • Loosen 1 turn • Final tightening 4 Nm (0.4 mkg) 4-63 STEERING CHAS STEERING REMOVAL 1. Park the motorcycle on a level surface. WARNING Support the motorcycle securely to prevent it falling over. 2. Raise the front wheel placing a suitable support under the engine. 3. Remove: • Front wheel Refer to “FRONT WHEEL-REMOVAL” section. • Front fork Refer to “FRONT FORK-REMOVAL” section. 4. Remove: • Front fender • Cowling • Handlebar • Meter assembly 5. Remove: • Steering axle nut (1) Use the ring nut wrench (3). Ring nut wrench (3): 90890-01348 6. Remove: • Ring nut (upper) (1) • Use the ring nut wrench (2) Ring nut wrench (2): 90890-01268 4-64 STEERING CHAS 7. Remove: • Ring nut (lower) (1) • Use the ring nut wrench (2) Ring nut wrench (2): 90890-01268 WARNING Support the steering axle to prevent it falling. STEERING INSPECTION 1. Wash the bearings in solvent. 2. Inspect: • Bearing (upper and lower) (1) Corrosion/Damage ➔ Replace races and bearing. Install the bearings in the races. Spin the bearing by hand. If the bearing rises or fails to run freely in the race, replace bearing and race. 3. Inspect: • Steering axle (1) Bend/Damage ➔ Replace. STEERING INSTALLATION 1. Install: • Bearing (1) • Ball race cover (2) NOTE: Apply lithium soap-base grease to the bearing and ball race cover lip. 2. Install: • Lower bracket (1) NOTE: Apply lithium soap-base grease to the bearing. 4-65 STEERING CHAS 3. Install: • Ring nut (lower) (1) Use the ring nut wrench (2). Ring nut wrench: 90890-01268 NOTE: Apply the lithium soap-base grease to the steering axle thread. ▼▼▼▼▼▼▼▼▼▼▼▼▼▼▼▼▼▼▼▼▼▼▼▼▼▼▼▼▼ Lower ring nut tightening steps: • Tighten the ring nut (1) using the ring nut wrench. Ring nut (lower) (initial tightening): 38 Nm (3.8 mkg) • Loosen the ring nut completely and retighten it to specification. WARNING Do not tighten excessively. Ring nut (lower) (final tightening): 4 Nm (0.4 mkg) ▲▲▲▲▲▲▲▲▲▲▲▲▲▲▲▲▲▲▲▲▲▲▲▲▲▲▲▲▲ 4. Check the steering axle by turning it lock to lock. If there is any binding, remove the steering axle assembly and inspect the steering bearings. 5. Install: • Ring nut (upper) (1) • Special washer (2) 4-66 STEERING CHAS ▼▼▼▼▼▼▼▼▼▼▼▼▼▼▼▼▼▼▼▼▼▼▼▼▼▼▼▼▼ Installation steps: • • • Install the ring nut (upper) (1). Finger tighten the ring nut (upper), then align the slots of both ring nuts. If not aligned, hold the lower ring nut and tighten the other until they are aligned. Install the special washer. NOTE: Make sure the special washer tabs are in the slots. ▲▲▲▲▲▲▲▲▲▲▲▲▲▲▲▲▲▲▲▲▲▲▲▲▲▲▲▲▲ 6. Install: • Upper bracket • Fork legs (left and right) (1) NOTE: Temporarily install the under bracket pinch bolt to achieve the correct fork position. Front fork top end (a) (standard): 0 mm 7. Install: • Plate washer (1) • Steering axle nut (2) Use the lock nut wrench (4). Lock nut wrench (4): 90890-01348 NOTE: Set the torque wrench to the lock nut wrench so that they form a right angle. Steering axle nut: 115 Nm (11.5 mkg) 4-67 STEERING CHAS 8. After tightening the nut, check the steering for smooth movement. If it is not smooth, adjust by progressively loosening the (lower) ring nut. 9. Tighten: • Pinch bolts (upper and lower bracket) Pinch bolt (upper bracket): 28 Nm (2.8 mkg) Pinch bolt (under bracket): 23 Nm (2.3 mkg) NOTE: Always tighten the lower pinch bolt (to the prescribed torque) and then the upper one (to the prescribed torque) and then retighten the lower one (to the prescribed torque). CAUTION: Tighten the pinch bolt to specified torque. If torqued too much, it may cause malfunctioning of the front fork. 10. Install: • Handlebar holder • Handlebar • Handlebar upper holder Fitting nut (handle lower holder): 40 Nm (4.0 mkg) Flange bolt (handlebar holder): 20 Nm (2.0 mkg) CAUTION: First tighten the front bolt on the handlebar holder, then tighten the rear bolt. 4-68 REAR SHOCK ABSORBER Order Job name/Part name Q.ty CHAS Remarks Remove the parts in order. Shock absorber removal WARNING Securely support the motorcycle so there is no danger of it falling over. 1 2 3 4 5 Seat Fuel tank Rear cowling Battery leads 2 Muffler Exhaust pipe assembly Rear frame Brake fluid reserve tank Air filter case 1 1 1 1 1 Refer to “SEAT, FUEL TANK AND REAR COWLING” section in Chapter 3. 4-69 Disconnect. NOTE: First, disconnect the negative lead, then the positive lead. Refer to “REAR SHOCK ABSORBER REMOVAL” section. Secure the brake fluid tank to the frame in an upright position to avoid air entering the hydraulic system. REAR SHOCK ABSORBER Order 6 7 Job name/Part name Q.ty Lower bolt Upper bolt CHAS Remarks 1 1 Reverse the removal procedure for installation. 4-70 REAR SHOCK ABSORBER (1) (2) (3) (4) (5) (6) Rear shock absorber Spring Spring adjuster ring nut Lock ring nut End of stroke buffer Special spanner 4-71 CHAS REAR SHOCK ABSORBER CHAS WARNING This shock absorber contains high-pressure nitrogen gas. Read the following information carefully before handling it. The manufacturer cannot be held responsible for any damage or injury that may result from improper handling. • Never tamper with or attempt to open the cylinder or the tank. • Never expose the shock absorber to a naked flame or other source of heat. This might cause the pressurised gas to explode. • Do not deform or damage the cylinder in any way. Damage to the cylinder would impair the damping effect. • Be careful not to scratch the surface of the rod: this would cause the oil to leak. • Before disposing of the shock absorber, read the section “NOTES ON DISPOSAL”. NOTE ON DISPOSAL ▼▼▼▼▼▼▼▼▼▼▼▼▼▼▼▼▼▼▼▼▼▼▼▼▼▼▼▼▼ Before neutralising the rear shock absorber: The gas pressure must be discharged before disposing of the shock absorber it is necessary to discharge the gas pressure. To do this, bore a hole of 2~3 mm through the cylinder wall about 15~20 mm from the bottom of the gas chamber. WARNING Wear protective goggles to avoid eye injuries from escaping gas and/or metal chips. ▲▲▲▲▲▲▲▲▲▲▲▲▲▲▲▲▲▲▲▲▲▲▲▲▲▲▲▲▲ 4-72 REAR SHOCK ABSORBER CHAS SHOCK ABSORBER REMOVAL WARNING Support the motorcycle securely to prevent it from falling over. 1. Park the motorcycle on a level surface. 2. Remove: • Seat • Rear cowling • Fuel tank See section “SEAT, FUEL TANK AND REAR COWLING” in CHAPTER 3. 3. Disconnect: • Battery leads NOTE: First, disconnect the negative lead, then the positive lead. 4. Remove: • Exhaust pipe assembly • Rear frame • Air filter case 5. Raise the rear wheel placing a suitable support under the engine. 6. Remove: • Rear wheel Refer to “REAR WHEEL REMOVAL” section. 7. Remove: • Shock absorber fastening nut (1) • Lower mounting bolt 1 8. Remove: • Upper mounting bolt (1) • Rear shock absorber 4-73 REAR SHOCK ABSORBER CHAS SHOCK ABSORBER INSPECTION 1. Inspect: • Shock absorber Oil leak/Damaged ➔ Replace. REAR SHOCK ABSORBER ADJUSTMENT This shock absorber is equipped with a spring preload adjuster. 2 a b CAUTION: A Never attempt to turn an adjusting mechanism beyond the maximum or minimum settings. 1 Adjust the spring preload as follows. 1. Loosen the locknut. 2. To increase the spring preload and thereby harden the suspension, turn the adjusting nut in direction a. To decrease the spring preload and thereby soften the suspension, turn the adjusting nut in direction b. NOTE: • Use the special wrench included in the owner's tool kit to make the adjustment. • The spring preload setting is determined by measuring distance A, shown in the illustration. The longer distance A is, the lower the spring preload; the shorter distance A is, the higher the spring preload. With each complete turn of the adjusting nut, distance A changes by 1.5 mm. Spring preload: Minimum (soft): Distance A = 217 mm Standard: Distance A = 211 mm Maximum (hard): Distance A = 205 mm 4-74 REAR SHOCK ABSORBER CHAS 2. Tighten the locknut to the specified torque. Locknut: 45 Nm (4.5 m·kgf) CAUTION: Always tighten the locknut against the adjusting nut, and then tighten the locknut to the specified torque. 4-75 SWINGARM CHAS SWINGARM (1) Upper chain case (2) Swingarm (3) Chain support (4) Swingarm guard seal (5) Connecting rod (6) Relay arm 4-76 [A] LATERAL FREE PLAY (END): 1.0 mm [B] LATERAL FREE PLAY: 0.4 ~ 0.7 mm SWINGARM CHAS SWINGARM REMOVAL NOTE Check free play and remove swingarm, if necessary, after removing the rear shock absorber. 1. Remove: • Swingarm connecting rod bolt (1) 1 1 2. Check: • Swingarm free play ▼▼▼▼▼▼▼▼▼▼▼▼▼▼▼▼▼▼▼▼▼▼▼▼▼▼▼▼▼ Inspection procedure: • Check the tightening torque of the nut which fastens the swingarm pivot shaft (1). Nut (pivot shaft): 90 Nm (9.0 mkg) • Check the lateral free play [A] of the swingarm moving it laterally. If the free play seems excessive, verify the collar, bearings, washer and thrust cover. Lateral free play (at end of swing arm): Limit: 1.0 mm • Check the vertical movement [B] of the swingarm, moving it up and down. If the movement seems rigid, unsmooth or jerky, inspect the internal collar, the bearings, the washer and the thrust cover. ▲▲▲▲▲▲▲▲▲▲▲▲▲▲▲▲▲▲▲▲▲▲▲▲▲▲▲▲▲ 4-77 SWINGARM CHAS 3. Remove: • Upper chain case (1) • Chain support (2) 1 2 4. Remove: • Swingarm pivot shaft • Swingarm SWINGARM INSPECTION 1. Inspect: • Swingarm Deformation/Cracks/Damage ➔ Replace. 2. Inspect: • Connecting rod (1) • Relay arm (2) Deformation/Cracks/Damage ➔ Replace. 3. Inspect: • Oil seals Wear/Damaged ➔ Replace. • Washers • Thrust cover Wear/Damaged ➔ Replace. • Bushes Scratches/Damaged ➔ Replace. • Bearings Pitting/Damaged ➔ Replace. 4. Inspect: • Chain guard seal • Chain case and support Wear/Damage ➔ Replace. 4-78 SWINGARM CHAS LATERAL FREE PLAY ADJUSTMENT 1. Measure: • Length of bushes A1 and A2 Out of specification ➔ Replace. Length of bushes: A1 = 76.70 ~ 76.85 mm A2 = 74.90 ~ 75.00 mm 2. Measure: • Length B1 and B2 3. Calculate: • Lateral swing arm side play C. Out of specification ➔ Adjust free play with special shims. Use the following formula: C = (A1+A2) – (B1+B2) Swing arm lateral free play C: 0.4 ~ 0.7 mm 4. Adjust: • Lateral side play using one or more adjust shims (1) Measurement of adjust shim (1): 0.3 mm NOTE: When only one shim is used, install it on the left side; when two shims are used, install one on each side. 4-79 SWINGARM CHAS SWINGARM INSTALLATION Perform “removal” operations in reverse order. Note the following points. 1. Lubricate: • Bearings • Bushes • Thrust cover (inside) • Flange • Swingarm pivot shaft • Bolt (connecting rod) • Bolt (relay arm) • Bolt (shock absorber) Lithium-base grease 2. Tighten: Nut (relay arm-swingarm): 66 Nm (6.6 mkg) Nut (relay arm - connecting rod): 52 Nm (5.2 mkg) Bolt (chain case): 9 Nm (0.9 mkg) Nut (swingarm pivot shaft): 90 Nm (9.0 mkg) Bolt (chain support): 4 Nm (0.4 mkg) Nut (relay arm-frame): 60 Nm (6.0 mkg) Bolt (rear shock absorber): 59 Nm (5.9 mkg) Screw (chain case): 4 Nm (0.4 mkg) 3. Install: • Rear wheel Refer to “REAR WHEEL INSTALLATION” section. 4-80 SWINGARM CHAS 4. Adjust: • Drive chain slack Drive chain slack: 30 ~ 40 mm Refer to “DRIVE CHAIN SLACK ADJUSTMENT” in CHAPTER 3. 5. Install: • Fuel tank • Rear cowling • Seat Bolt (seat): 10 Nm (1.0 mkg) Refer to “SEAT, FUEL TANK AND REAR COWLING” section in CHAPTER 3. 4-81 DRIVE CHAIN, DRIVE SPROCKET AND REAR WHEEL SPROCKET CHAS DRIVE CHAIN, DRIVE SPROCKET AND REAR WHEEL SPROCKET NOTE: Before removing the drive chain, drive sprocket and rear wheel sprocket, it is necessary to measure the free play and length of the 10 links in the chain. DRIVE CHAIN REMOVAL 2 1. Park the motorcycle upright on an even surface. 2. Remove: • Shift pedal (1) • Cover (2) (drive sprocket) 1 3. Remove: • Drive sprocket (1) NOTE: • Before removing the sprocket nut, straighten the tab on the lock washer. • Loosen the nut with the rear brake pulled. 4. Raise the rear wheel placing a suitable support under the engine. WARNING Set the motorcycle up securely to prevent it falling over. 5. Remove: • Rear wheel • Rear wheel sprocket • Hub • Damper • Spacer Refer to “REAR WHEEL REMOVAL” section. 4-82 DRIVE CHAIN, DRIVE SPROCKET AND REAR WHEEL SPROCKET CHAS 6. Remove: • Swingarm • Drive chain Refer to “REAR SHOCK ABSORBER REMOVAL” and “SWINGARM REMOVAL” sections. DRIVE CHAIN INSPECTION 1. Measure: • Length of 10 links (drive chain) Out of specification ➔ Replace drive chain. Maximum lenght of 10 links (a): 150.2 mm a NOTE: • Stretch the chain by hand to measure it. • The length of the 10 links is recorded between the inside of the link pins (1) and (11) as shown. • The length of the 10 links is measured at various points. 2. Clean: • Drive chain Immerge in kerosene and brush thoroughly to remove as much dirt as possible. Remove from kerosene and allow to dry. CAUTION: This motorcycle is fitted with a chain with small O-Rings (1) fitted between its plates. Vapour cleaning, pressurised washing and certain types of solvents may damage these seal rings. To clean the transmission chain use only kerosene. 4-83 DRIVE CHAIN, DRIVE SPROCKET AND REAR WHEEL SPROCKET CHAS 3. Inspect: • Seal rings (1) (drive chain) Damaged ➔ Replace drive chain. • Rollers (2) • Lateral plates (3) Damage/Wear ➔ Replace drive chain. 4. Lubricate: • Drive chain Lubricant for drive chain: SAE 80W/90 engine oil or special lubricant for O-Ring chains. 5. Inspect: • Drive chain Rigid ➔ Clean and lubricate, replace if necessary. 6. Inspect: • Drive sprocket • Rear wheel sprocket Wear over 1/4 tooth (1) ➔ Replace. Teeth bent ➔ Replace. (2) Undamaged tooth profile (3) Roller (4) Sprocket ▼▼▼▼▼▼▼▼▼▼▼▼▼▼▼▼▼▼▼▼▼▼▼▼▼▼▼▼▼ How to replace the rear wheel sprocket: With wheel removed: 1. Remove: • Hub (1) • Sprocket fastening bolts (2) • Rear wheel sprocket (3) 2. Install: • New sprocket (3) • Sprocket fastening bolts (2) • Hub (1) 4-84 DRIVE CHAIN, DRIVE SPROCKET AND REAR WHEEL SPROCKET CHAS 3. Tighten: • Rear wheel sprocket fastening bolts Rear wheel sprocket fastening bolts: 48 Nm (4.8 mkg) ▲▲▲▲▲▲▲▲▲▲▲▲▲▲▲▲▲▲▲▲▲▲▲▲▲▲▲▲▲ DRIVE CHAIN INSTALLATION Perform “REMOVAL” operations in reverse order. Pay special attention to the following points. 1. Install: • Drive chain • Swingarm Nut (swingarm pivot shaft): 90 Nm (9.0 mkg) Nut (frame-relay arm): 60 Nm (6.0 mkg) 2. Install: • Rear wheel Refer to “REAR WHEEL INSTALLATION” section. 3. Install: • Drive sprocket Nut (drive sprocket): 110 Nm (11.0 mkg) WARNING Always use a new lock washer. NOTE: • Tighten the drive sprocket nut with the rear brake pulled. • After tightening the nut, bend the tab on the lock washer once more over the faces of the nut. 4. Adjust: • Drive chain slack Refer to “DRIVE CHAIN SLACK ADJUSTMENT” section in CHAPTER 3. Drive chain slack: 30 ~ 40 mm 4-85 DRIVE CHAIN, DRIVE SPROCKET AND REAR WHEEL SPROCKET CHAS 5. Tighten: • Rear wheel axle nut Rear wheel axle nut: 115 Nm (11.5 mkg) Refer to “REAR WHEEL INSTALLATION” section. 7. Install: • Cover (drive sprocket) • Shift pedal Screws (drive sprocket cover): 10 Nm (1.0 mkg) Bolt (shift pedal): 10 Nm (1.0 mkg) 4-86 ENG 5 ENG CHAPTER 5. ENGINE ENGINE REMOVAL . . . . . . . . . . . . . . . . . . . . . . . . . . . . . . . . . . . . . . . . . . . . . . . . . . . . . 5-1 MUFFLER, EXHAUST PIPE, ENGINE PROTECTOR, DRIVE SPROCKET, CRANKCASE COVER, DRIVE SPROCKET AND SHIFT PEDAL . . . . . . . . . . . . . . . 5-1 ENGINE MOUNTING BOLT . . . . . . . . . . . . . . . . . . . . . . . . . . . . . . . . . . . . . . . . . . . 5-4 ENGINE DISASSEMBLY . . . . . . . . . . . . . . . . . . . . . . . . . . . . . . . . . . . . . . . . . . . . . . . . . 5-5 CYLINDER HEAD, CYLINDER, CAMSHAFT AND PISTON. . . . . . . . . . . . . . . . . . . . 5-5 INTERMEDIATE STARTER GEAR, CRANKCASE COVER (L) AND GENERATOR STATOR. . . . . . . . . . . . . . . . . . . . . . . . . . . . . . . . . . . . . . . . . . . 5-8 CRANKCASE COVER (R), CLUTCH, PRIMARY DRIVE GEAR AND BALANCER SHAFT GEAR . . . . . . . . . . . . . . . . . . . . . . . . . . . . . . . . . . . . . . . . 5-9 OIL PUMP AND SHIFT LEVER . . . . . . . . . . . . . . . . . . . . . . . . . . . . . . . . . . . . . . . . 5-12 AC GENERATOR AND TIMING CHAIN. . . . . . . . . . . . . . . . . . . . . . . . . . . . . . . . . . 5-13 CRANKCASE(R). . . . . . . . . . . . . . . . . . . . . . . . . . . . . . . . . . . . . . . . . . . . . . . . . . . 5-14 GEARBOX AND TRANSMISSION. . . . . . . . . . . . . . . . . . . . . . . . . . . . . . . . . . . . . . 5-16 BALANCER SHAFT AND CRANKSHAFT . . . . . . . . . . . . . . . . . . . . . . . . . . . . . . . . 5-17 OILSTRAINER . . . . . . . . . . . . . . . . . . . . . . . . . . . . . . . . . . . . . . . . . . . . . . . . . . . . 5-17 ROCKER ARMS . . . . . . . . . . . . . . . . . . . . . . . . . . . . . . . . . . . . . . . . . . . . . . . . . . . 5-18 VALVES . . . . . . . . . . . . . . . . . . . . . . . . . . . . . . . . . . . . . . . . . . . . . . . . . . . . . . . . . 5-19 INSPECTION AND REPAIR . . . . . . . . . . . . . . CYLINDER HEAD. . . . . . . . . . . . . . . . . . VALVES AND VALVE GUIDES . . . . . . . . VALVESEAT . . . . . . . . . . . . . . . . . . . . . . VALVE SPRINGS . . . . . . . . . . . . . . . . . . CAMSHAFT . . . . . . . . . . . . . . . . . . . . . . ROCKER ARMS AND ROCKER SHAFT . CAMSHAFT CHAIN AND SPROCKET . . CAMSHAFT CHAIN GUIDE . . . . . . . . . . CYLINDER AND PISTON . . . . . . . . . . . . PISTON RINGS . . . . . . . . . . . . . . . . . . . PISTONPIN . . . . . . . . . . . . . . . . . . . . . . CLUTCH. . . . . . . . . . . . . . . . . . . . . . . . . OILPUMP . . . . . . . . . . . . . . . . . . . . . . . . PRIMARY TRANSMISSION . . . . . . . . . . TRANSMISSION AND GEARBOX. . . . . . SHIFT SHAFT AND STOPPER LEVER . . STARTER TRANSMISSION . . . . . . . . . . CRANKSHAFT . . . . . . . . . . . . . . . . . . . . BALANCER SHAFT DRIVE AND DRIVEN GEARS . . . . . . . . . . . . . . CRANKCASE . . . . . . . . . . . . . . . . . . . . . BEARING AND OIL SEAL . . . . . . . . . . . . . . . . . . . . . . . . . . . . . . . . . . . . . . . . . . . . . . . . . . . . . . . . . . . . . . . . . . . . . . . . . . . . . . . . . . . . . . . . . . . . . . . . . . . . . . . . . . . . . . . . . . . . . . . . . . . . . . . . . . . . . . . . . . . . . . . . . . . . . . . . . . . . . . . . . . . . . . . . . . . . . . . . . . . . . . . . . . . . . . . . . . . . . . . . . . . . . . . . . . . . . . . . . . . . . . . . . . . . . . . . . . . . . . . . . . . . . . . . . . . . . . . . . . . . . . . . . . . . . . . . . . . . . . . . . . . . . . . . . . . . . . . . . . . . . . . . . . . . . . . . . . . . . . . . . . . . . . . . . . . . . . . . . . . . . . . . . . . . . . . . . . . . . . . . . . . . . . . . . . . . . . . . . . . . . . . . . . . . . . . . . . . . . . . . . . . . . . . . . . . . . . . . . . . . . . . . . . . . . . . . . . . . . . . . . . . . . . . . . . . . . . . . . . . . . . . . . . . . . . . . . . . . . . . . . . . . . . . . . . . . . . . . . . . . . . . . . . . . . . . . . . . . . . . . . . . . . . . . . . . . . . . . . . . . . . . . . . . . . . . . . . . . . . . . . . . . . . . . . . . . . . . . . . . . . . . . . . . . . . . . . . . . . . . . . . . . . . . . . . . . . . . . . . . . 5-21 5-21 5-22 5-23 5-27 5-28 5-28 5-29 5-30 5-30 5-32 5-33 5-33 5-35 5-35 5-36 5-37 5-38 5-39 . . . . . . . . . . . . . . . . . . . . . . . . . . . . . . . . 5-40 . . . . . . . . . . . . . . . . . . . . . . . . . . . . . . . . 5-40 . . . . . . . . . . . . . . . . . . . . . . . . . . . . . . . . 5-40 ENG ENGINE ASSEMBLY AND SETTING . . . . . . . . . . . . . . . . . . . . . . VALVES AND ROCKER ARMS . . . . . . . . . . . . . . . . . . . . . . . VALVES . . . . . . . . . . . . . . . . . . . . . . . . . . . . . . . . . . . . . . . . ROCKER ARMS . . . . . . . . . . . . . . . . . . . . . . . . . . . . . . . . . . CRANKSHAFT AND BALANCER SHAFT . . . . . . . . . . . . . . . TRANSMISSION. . . . . . . . . . . . . . . . . . . . . . . . . . . . . . . . . . GEARBOX . . . . . . . . . . . . . . . . . . . . . . . . . . . . . . . . . . . . . . TRANSMISSION AND GEARBOX. . . . . . . . . . . . . . . . . . . . . ENGINE OIL PUMP AND OIL STRAINER . . . . . . . . . . . . . . . CRANKCASE . . . . . . . . . . . . . . . . . . . . . . . . . . . . . . . . . . . . ENGINE OIL STRAINER. . . . . . . . . . . . . . . . . . . . . . . . . . . . CRANKCASE . . . . . . . . . . . . . . . . . . . . . . . . . . . . . . . . . . . . SHIFT SHAFT AND OIL PUMP . . . . . . . . . . . . . . . . . . . . . . . TIMING CHAIN . . . . . . . . . . . . . . . . . . . . . . . . . . . . . . . . . . . PISTON AND RINGS . . . . . . . . . . . . . . . . . . . . . . . . . . . . . . CYLINDER . . . . . . . . . . . . . . . . . . . . . . . . . . . . . . . . . . . . . . CYLINDER HEAD. . . . . . . . . . . . . . . . . . . . . . . . . . . . . . . . . CAMSHAFT AND TIMING CHAIN . . . . . . . . . . . . . . . . . . . . . PISTON, CYLINDER, CYLINDER HEAD AND CAMSHAFT. . AC GENERATOR.. . . . . . . . . . . . . . . . . . . . . . . . . . . . . . . . . OIL FILTER AND OIL HOSES . . . . . . . . . . . . . . . . . . . . . . . . BALANCER SHAFT GEAR AND PRIMARY TRANSMISSION GEAR . . . . . . . . . . . . . . . . . . . . . . . . . . . . CLUTCH. . . . . . . . . . . . . . . . . . . . . . . . . . . . . . . . . . . . . . . . STARTER GEARS . . . . . . . . . . . . . . . . . . . . . . . . . . . . . . . . STARTER NEUTRAL GEAR AND CRANKCASE COVER (L) . . . . . . . . . . . . . . . . . . . . . . . . . . . . . . . . . . . . . . . . . . . . . . . . . . . . . . . . . . . . . . . . . . . . . . . . . . . . . . . . . . . . . . . . . . . . . . . . . . . . . . . . . . . . . . . . . . . . . . . . . . . . . . . . . . . . . . . . . 5-41 . . . . . . . . . . . 5-41 . . . . . . . . . . . 5-42 . . . . . . . . . . . 5-43 . . . . . . . . . . . 5-44 . . . . . . . . . . . 5-46 . . . . . . . . . . . 5-47 . . . . . . . . . . . 5-48 . . . . . . . . . . . 5-49 . . . . . . . . . . . 5-50 . . . . . . . . . . . 5-51 . . . . . . . . . . . 5-51 . . . . . . . . . . . 5-52 . . . . . . . . . . . 5-54 . . . . . . . . . . . 5-55 . . . . . . . . . . . 5-56 . . . . . . . . . . . 5-57 . . . . . . . . . . . 5-58 . . . . . . . . . . . 5-59 . . . . . . . . . . . 5-65 . . . . . . . . . . . 5-67 . . . . . . . . . . . . . . . . . . . . . . . . . . . . . . . . . . . . . . . . . . . . . . . . . . . . . 5-68 . . . . . 5-70 . . . . . 5-73 . . . . . 5-74 ENGINE REASSEMBLY. . . . . . . . . . . . . . . . . . . . . . . . . . . . . . . . . . . . . . . . . . . . . . . . . 5-76 ENGINE REMOVAL ENG ENGINE ENGINE REMOVAL MUFFLER, EXHAUST PIPE, ENGINE PROTECTOR, DRIVE SPROCKET CRANKCASE COVER, DRIVE SPROCKET AND SHIFT PEDAL Order Job name/Part name Q.ty Muffler, exhaust pipe, engine protector, drive sprocket crankcase cover, drive sprocket and shift pedal removal Remarks Remove the parts in order. Park the motorcycle in a stable and level position. WARNING Securely support the motorcycle so there is no danger of it falling over. 5-1 ENGINE REMOVAL Order 1 2 3 4 5 6 7 8 9 Job name/Part name Q.ty Battery leads connector Muffler Exhaust pipe Engine protector Shift pedal Drive sprocket crankcase cover Drive sprocket Clutch cable Plug cap 1 1 1 1 1 1 1 1 1 5-2 ENG Remarks Drain the engine oil (refer to “ENGINE OIL REPLACEMENT” section in CHAPTER 3). Remove the seat, the fuel tank and the rear cowling (refer to “SEAT, FUEL TANK AND REAR COWLING” section in CHAPTER 3). Disconnect. Displace the drive chain. Disconnect. Disconnect. ENGINE REMOVAL Order Job name/Part name Q.ty ENG Remarks – Starter leads 2 Disconnect. – Starter 1 Remove. 10 Connectors of engine wire harness 2 Disconnect. 11 Oil delivery hose 1 Disconnect. 12 Oil return hose 1 Disconnect. 13 Oil breather pipe (to oil tank) 14 Oil breather pipe (to air filter box) – Disconnect. – 5-3 Disconnect. Reverse the installation. removal procedure for ENGINE REMOVAL ENG ENGINE MOUNTING BOLT Order Job name/Part name Q.ty Remarks CAUTION: The engine and rear arm are assembled together on the rear pivot shaft. When removing the pivot shaft, it is thus necessary to pay special care with the rear arm. 1 Stay of oil tank – Remove the mounting screws (to engine). 2 Hose clamp (carburetor) 2 Loosen. 3 Pivot shaft (rear - top) 1 4 Engine mounting bolt (rear - lower) Engine stay (front - lower) Engine stay (front - top/right/left) Engine assembly 1 5 6 7 1 1 1 5-4 NOTE: Remove the engine from the lower side. Reverse the installation. removal procedure for ENGINE DISASSEMBLY ENG ENGINE DISASSEMBLY CYLINDER HEAD, CYLINDER, CAMSHAFT AND PISTON NOTE: The cylinder head, cylinder, camshaft and piston can be examined with the engine installed by removing the following parts. • Seat • Fuel tank • Rear cowling • Carburetor • Exhaust pipe 1. Remove: • Spark plug (1) • Tappet cover (2) (intake) • Tappet covers (3) (exhaust) • Cylinder head cover (4) • Cap (5) • Pins (6) 2. Loosen: • Bolt (1) (chain tensioner) 3. Remove: • Chain tensioner (2) 5-5 ENGINE DISASSEMBLY ENG 4. Remove: • Cam sprocket (1) • Camshaft (2) • Caps (left crankcase cover) NOTE: Fix a safety wire (3) to the timing chain to prevent it falling into the crankcase. 5. Remove: • Chain stopper guide (1) 6. Remove: • Cylinder head NOTE: Loosen all bolts by a 1/4 turn and remove once all are loosened. 5-6 ENGINE DISASSEMBLY ENG 7. Remove: • Gasket (1) (cylinder head) • Pins (2) • Cylinder (3) • Gasket (4) (cylinder) 8. Remove: • Pins (1) 9. Remove: • Pin ring (1) NOTE: Before removing the pin ring, cover the crankcase with a clean cloth to prevent the ring falling into the crankcase cavity. 10. Remove: • Pin (1) • Piston (2) NOTE: Before removing the pin, burr the pin housing groove. If it is hard to pull out the pin even with the groove burred, use the pin puller. 5-7 ENGINE DISASSEMBLY ENG Piston pin puller set: P/N. 90890-01304 CAUTION: Avoid using the hammer to pull the pin out. INTERMEDIATE STARTER GEAR, CRANKCASE COVER (L) AND GENERATOR STATOR NOTE: With the engine installed, maintenance of the intermediate starter gear and the crankcase cover (L) may be performed by removing the following parts. • Exhaust pipe • Starter • Sprocket cover 1. Remove: • Cover (1) intermediate starter gear • Centring pins • Gasket 2. Remove: • Intermediate starter gear (1) • Bearing (2) • Distributor shaft (3) 3. Remove: • Neutral gear switch cable (1) 5-8 ENGINE DISASSEMBLY ENG 4. Remove: • Crankcase cover gasket (1) (L) • Centring pins • Seal ring and O-ring • Gasket 5. Remove: • Intermediate starter gear (1) • Bearing (2) • Distributor shaft (3) 6. Remove: • Cable clamp (1) • Coil (2) • Stator (3) CRANKCASE COVER (R), CLUTCH, PRIMARY DRIVE GEAR AND BALANCER SHAFT GEAR NOTE: The clutch, the primary gear and the balance gear may be inspected with the engine installed by removing the following parts. • Footrest (R) • Oil delivery hose screw 5-9 ENGINE DISASSEMBLY ENG 1. Remove: • Engine oil delivery hose screw • Copper washer • Oil filter cover (1) • Oil filter • Seal ring and O-Ring • Crankcase cover (2) (R) 2. Remove: • Compression spring (1) • Pressure plate (2) • Ball (3) • Friction plate (4) • Clutch plate (5) • Clutch boss spring (6) • Clutch boss (7) • Thrust plate (8) • Clutch shroud (9) • Push rod (10) NOTE: • Before loosening the nut (11) (clutch shroud), straighten the washer lock tab. • To loosen the nut (clutch boss), block the clutch boss using the special tool (12). Clutch holding tool: P/N. 90890-04086 5-10 ENGINE DISASSEMBLY ENG 3. Remove • Primary drive gear (1) • Disc (2) • Balancer drive gear (3) • Disc (4) • Key (5) • Disc washer (6) • Disc (7) • Balancer gear (8) • Straight key (9) NOTE: Before loosening the nut (9) (primary drive gear) and nut (10) (balancer gear), straighten the wash lock tab. NOTE: To loosen nuts (9) and (10), hold the rotor (CA magneto) firmly in place using special tool (11). Sheave holder: P/N. 90890-01701 CAUTION: Be careful not to touch jutting edges (12) on the rotor with the sheave holder. 4. Remove: • Push lever (1) • Spring • Flat washer NOTE: Loosen the screw to remove the push rod. 5-11 ENGINE DISASSEMBLY ENG OIL PUMP AND SHIFT LEVER NOTE: The oil pump and shift lever may be checked with the engine installed by removing the following parts: • Footrest (R) • Oil delivery hose screw • Crankcase (R) • Clutch 1. Remove: • Circlip (1) • Oil pump gear (2) • Oil pump (3) • O-rings (4) 2. Remove: • Circlip (1) (from drive shaft) • Ring (2) • Circlip (3) 3. Remove: • Circlip (1) • Shift lever (2) • Spring (3) • Flat washer (4) 4. Remove: • Stopper lever (1) • Ring (2) • Spring (3) 5-12 ENGINE DISASSEMBLY ENG AC GENERATOR AND TIMING CHAIN NOTE: The AC generator may be inspected with the engine installed by removing the following parts: • Crankcase (L) 1. Remove: • Nut (1) • Washer (2) • Rotor (3) (with starter gear) • Bearing (4) • Shim adjustment washer (5) • Key (6) NOTE: To loosen the nut (rotor), lock the rotor with the special tool (7). Sheave holder: P/N. 90890-01701 CAUTION: Be careful not to touch the jutting edges (8) on the rotor with the special tool. NOTE: Remove the rotor with the puller (1). Flywheel puller: P/N. 90890-01362 2. Remove: • Chain guide (1) • Timing chain (2) 5-13 ENGINE DISASSEMBLY ENG CRANKCASE (R) 1. Remove: • Crankcase (R) NOTE: Loosen nuts starting from the one with the highest number. • Loosen all by 1/4 turn and then remove. • ▼▼▼▼▼▼▼▼▼▼▼▼▼▼▼▼▼▼▼▼▼▼▼▼▼▼▼▼▼ Removal procedure: • Set the crankcase separating tool (1) in place. Crankcase separating tool: P/N. 90890-01135 NOTE: When tightening the support bolts of the separating tool, be sure to keep the tool body parallel to the engine crankcase. If necessary, a screw may be slightly loosened to put the tool body on level. • Applying pressure, strike the front engine assembly flange, the drive shafts and the gear cam plate with a rubber hammer. Then remove the crankcase. NOTE: • If the crankcase fails come out, lever at points (2), being careful not to damage the crankcase. • Turn the gear cam plate as shown in the figure to prevent it interfering with the crankcase. 5-14 ENGINE DISASSEMBLY ENG CAUTION: • • 5-15 Be careful not to damage surfaces in contact with the crankcase. Use a soft hammer to hit the engine crankcase. Only hit the reinforced parts. Do not hit the surface in contact with the gasket. Work slowly and carefully. Be careful to perform the separation uniformly. If one end locks, remove pressure from the thrust screw, realign and recommence. If it is impossible to separate the crankcase, check that all screws and components have been disassembled. Do not use force. ENGINE DISASSEMBLY ENG GEARBOX AND TRANSMISSION 1. Remove: • Guide bar (1) • Shift cam (2) • Selector fork # 3 (3) • Selector fork # 2 (4) • Selector fork # 1 (5) 2. Remove: • Transmission assembly unit (1) 3. Remove: • Shift shaft # 1 (1) • Shift shaft # 2 (2) 5-16 ENGINE DISASSEMBLY ENG BALANCER SHAFT AND CRANKSHAFT 1. Remove: • Balancer shaft (1) 2. Remove: • Crankshaft (1) NOTE: • Remove the crankshaft by crankcase separating tool (2). using the Crankcase separating tool: P/N. 90890-01135 • Tighten the separating tool bolts, making sure that the tool body is parallel with the engine crankcase. If necessary, a screw may be backed out slightly to level tool body. OIL STRAINER NOTE: It is advisable to replace the oil strainer every time the engine is disassembled. 1. Remove: • Oil strainer (1) • Oil passage cover (2) • Gasket 5-17 ENGINE DISASSEMBLY ENG ROCKER ARMS NOTE: The rocker arms may be examined with the engine installed by removing the following parts. • Seat • Fuel tank • Cylinder head cover 1. Remove: • Cap (1) 2. Remove: • Bolts (1) (rocker shaft) 3. Remove: • Rocker shaft • Rocker arms NOTE: Remove the rocker shaft using sliding hammer (1) and weight (2). Sliding hammer bolt: P/N. 90890-01083 Weight: P/N. 90890-01084 5-18 ENGINE DISASSEMBLY ENG VALVES NOTE: The valves may be inspected with the engine installed by removing the following parts. • Seat • Fuel tank • Exhaust pipe • Carburetor • Cylinder head cover • Cylinder head 1. Check: • Valve seal Leakage from valve seats’ Inspect the valve surface, the seat and seat width. See section “VALVE SEAT INSPECTION AND REPAIR”. NOTE: Check the valve seal before assembling the internal parts of the cylinder head (valves, valve springs, spring retainer etc). ▼▼▼▼▼▼▼▼▼▼▼▼▼▼▼▼▼▼▼▼▼▼▼▼▼▼▼▼▼ Inspection steps: • Pour clean solvent (1) into the intake and exhaust ports. • Check the valve seal. There must be no blowbys from the valve seats (2). ▲▲▲▲▲▲▲▲▲▲▲▲▲▲▲▲▲▲▲▲▲▲▲▲▲▲▲▲▲ 5-19 ENGINE DISASSEMBLY ENG 2. Remove: • Cotters (1) • Top spring retainer (2) • Internal spring (3) • External spring (4) • Lower spring retainer (5) • Valve (6) • Valve stem seal (7) NOTE: Mark each part and its position so that each may reassembled as before. NOTE: Compress the valve spring using tool (8) to remove the cotters. Valve spring compressor: P/N. 90890-04019 5-20 INSPECTION AND REPAIR ENG INSPECTION AND REPAIR CYLINDER HEAD 1. Eliminate: • Carbon deposits (from combustion chamber) Use a rounded scraper (1). NOTE: Do not use a pointed tool to avoid damaging or scratching: • spark plug thread • valve seats • combustion chamber 2. Inspect: • Cylinder head Scratches/Damage ➔ Replace. 3. Measure: • Deformation Out of specification ➔ Rework the surface. Cylinder head deformation: Less than 0.03 mm 4. Surface: • Cylinder head ▼▼▼▼▼▼▼▼▼▼▼▼▼▼▼▼▼▼▼▼▼▼▼▼▼▼▼▼▼ Levelling: Level the cylinder head with wet 400 ~ 600 emery paper in a figure-8 direction. NOTE: To avoid removing too much material on one side only, turn the cylinder head a number of times. ▲▲▲▲▲▲▲▲▲▲▲▲▲▲▲▲▲▲▲▲▲▲▲▲▲▲▲▲▲ 5-21 INSPECTION AND REPAIR ENG VALVES AND VALVE GUIDES 1. Measure: • Clearance between stem and guide Clearance between stem and guide = Internal diameter of valve guide (a) – Diameter of valve stem (b) Out of specification ➔ Replace valve guide. Clearance between stem and guide: Intake: 0.010 ~ 0.037 mm <Limit>: 0.08 mm Exhaust: 0.030 ~ 0.057 mm <Limit>: 0.10 mm (1) Bore gauge ▼▼▼▼▼▼▼▼▼▼▼▼▼▼▼▼▼▼▼▼▼▼▼▼▼▼▼▼▼ Replacement steps: NOTE: Heat the cylinder head in an oven at 100°C to facilitate the removal and installation of the guides and to maintain correct locking interference. • • • Remove the valve guide using the special punch (1). Install the new guide using the special installation tool (2). After installing the valve guide, bore with special tool (3) to obtain valve-guide free play. Valve guide remover (7 mm): P/N. 90890-01225 Valve guide installer: P/N. 90890-04017 Valve guide reamer (7 mm): P/N. 90890-01227 ▲▲▲▲▲▲▲▲▲▲▲▲▲▲▲▲▲▲▲▲▲▲▲▲▲▲▲▲▲ 5-22 INSPECTION AND REPAIR ENG 2. Clean the valve surfaces of the carbon deposits. 3. Inspect: • Valve seal surface Pitting/Wear ➔ Grind the valve seal surface. 4. Measure: • Edge thickness (a) Out of specification ➔ Replace valve. Edge thickness (a): Intake: 1.0 ~ 1.4 mm <Limit>: 0.8 mm Exhaust: 0.8 ~ 1.2 mm <Limit>: 0.65 mm 5. Check: • Valve stem tip Deformed, mushroom-shaped or with a higher diameter than the rest of the stem ➔ Replace valve. • Misalignment: Out of specification ➔ Replace valve. Stem offsetting: <Limit>: 0.01 mm NOTE: • Changing the valve, replace also the valve guide. • Pulling the valve out, replace the stem seal. VALVE SEAT 1. Clean the valve surface and seat of carbon deposits. 2. Inspect: • Valve seat Pitting/Wear ➔ Renew valve seat. 5-23 INSPECTION AND REPAIR ENG 3. Measure: • Valve seat width (a) Out of specification ➔ Renew valve seat. Valve seat width (a): Intake: 1.0 ~ 1.2 mm <Limit>: 1.8 mm Exhaust: 1.0 ~ 1.2 mm <Limit>: 1.8 mm ▼▼▼▼▼▼▼▼▼▼▼▼▼▼▼▼▼▼▼▼▼▼▼▼▼▼▼▼▼ Measurement steps: • • • • • Apply Prussian blue (Dykem) to the valve seat. Install the valve in the cylinder head. Press the valve onto the housing through the guide to leave a clear outline. Measure the width of the valve seat. Where there is contatc between valve and seat the Prussian blue is wiped away. If the valve seat is too narrow, wide or off-centre, the valve seat must be renewed. ▲▲▲▲▲▲▲▲▲▲▲▲▲▲▲▲▲▲▲▲▲▲▲▲▲▲▲▲▲ 4. Renew: • Valve seat Use the special tool (1) to renew the valve seat with 30°, 45° and 60° mills. CAUTION: Turning the cutter, maintain uniform pressure (about 4-5 kg) to avoid leaving marks on the valve seat. 5-24 INSPECTION AND REPAIR ENG Mill the valve seat as follows: Section Cutter A 30° B 45° C 60° ▼▼▼▼▼▼▼▼▼▼▼▼▼▼▼▼▼▼▼▼▼▼▼▼▼▼▼▼▼ Valve seat faults recorded by analysing the valve seal surface: [A] If the valve surface resembles that shown in the figure, this means that the valve seat is centred on the surface but is too wide. Intervention on the valve seat Cutter type: 30° 60° Desired effect Reduce valve seat width to 1.0 mm [B] If the valve surface is like this, it means that the valve seat is centred on the valve surface but is too narrow. Intervention on the valve seat Cutter type: 45° Desired effect Centring of seat and attainment of 1.0 mm width [C] If the valve surface is like this, it means that the valve seat is too narrow and close to the edge of the valve. Intervention on the valve seat Cutter type: Desired effect 30° (before) Centring of seat and attainment of 1.0 mm 45° width [D] If the valve surface is like this, it means that the valve seat is too narrow and situated low down near the lower edge of the valve surface. Intervention on the valve seat Cutter type: 5-25 60° (first) 45° Desired effect Centring of seat and attainment of 1.0 mm width INSPECTION AND REPAIR ENG 5. Emery: • Valve seal surface • Valve seat NOTE: If the valve seat is renewed or the valve and guide replaced, the valve seat and seal surface must be lapped. ▲▲▲▲▲▲▲▲▲▲▲▲▲▲▲▲▲▲▲▲▲▲▲▲▲▲▲▲▲ Lapping steps: • Apply rough-lapping compound to the valve seal surface. CAUTION: Make sure the lapping compound does not run into the space between the guide and valve stem. • • • Apply oil to the molybdenum disulfide on the valve stem. Install the valve in the cylinder head. Turn the valve until face and surface are not evenly polished. Then clean away all the lapping compound. NOTE: For best results, during lapping, repeatedly apply (light) pressure to the valve seat, turning the valve backwards and forwards by hand. • Apply a fine-lapping compound on the valve seal surface and repeat the procedures described above. NOTE: Be sure to remove all the lapping compound from the valve surface after every lapping operation. 5-26 INSPECTION AND REPAIR • • • • ENG Apply Prussian blue (Dykem) to the valve seal surface. Install the valve in the cylinder head. Press the valve onto the housing through the guide to leave a clear outline. Measure the valve seat width once more. If the width of the valve is out of specification alter and relap. ▲▲▲▲▲▲▲▲▲▲▲▲▲▲▲▲▲▲▲▲▲▲▲▲▲▲▲▲▲ VALVE SPRINGS 1. Measure: • Free width of valve springs (a) Out of specification ➔ Replace. Free width of valve springs (intake and exhaust): Internal spring External spring 40.1 mm 43.8 mm 2. Measure: • Spring load Out of specification ➔ Replace. (b) Length of loaded spring Valve spring load: Internal spring (intake and exhaust) 164.8 ~ 190.2 N (16.80 ~ 19.39 kgf) at 22.7 mm External spring (intake) 71.6 ~ 87.3 N (7.3 ~ 8.9 kgf) at 34.2 mm External spring (exhaust) 149.1 ~ 182.4 N (15.2 ~ 18.6 kgf) at 34.2 mm 3. Measure: • Inclination of spring (a) Out of specification ➔ Replace. Spring inclination limit: 5-27 Internal spring External spring 2.5°/1.7 mm 2.5°/1.9 mm INSPECTION AND REPAIR ENG CAMSHAFT 1. Inspect: • Cam eccentrics Pitting/Scratches/Blue colour ➔ Replace camshaft. 2. Measure: • Cam eccentrics Out of specification ➔ Replace camshaft. (a) (b) Intake: 36.47~36.57 mm 30.06~30.16 mm Exhaust: 36.62~36.72 mm 30.11~30.21 mm ROCKER ARMS AND ROCKER SHAFT 1. Inspect: • Rocker shafts Blue colour/Grooves ➔ Replace shafts and check lubrication system. 2. Inspect: • Rocker shaft slot (1) • Surface in contact with cam eccentric (2) • Adjuster surface (3) Pitting/Wear/Scratches/Blue colour ➔ Replace and check lubrication system. 5-28 INSPECTION AND REPAIR ENG 3. Measure: • Rocker arm-shaft clearance Rocker arm-shaft clearance Internal diameter (a) of rocker arm – External diameter (b) of shaft Out of specification ➔ Replace whole unit. Rocker shaft clearance: 0.009 ~ 0.042 mm CAMSHAFT CHAIN AND SPROCKET 1. Inspect: • Chain Stiffness/Cracks ➔ Replace timing chain and sprocket. 2. Inspect: • Sprocket Wear/Damage ➔ Replace timing chain and sprocket. (1) (2) (3) (4) 5-29 1/4 tooth (maximum) New sprocket tooth profile Roller Sprocket INSPECTION AND REPAIR ENG CAMSHAFT CHAIN GUIDE 1. Inspect: • Side chain guide (exhaust) (1) • Side chain guide (intake) (2) Wear/Damage ➔ Replace. CYLINDER AND PISTON 1. Inspect: • Piston and cylinder walls Vertical scratches ➔ Replace cylinder liner and piston. 2. Measure: • Piston-cylinder clearance ▼▼▼▼▼▼▼▼▼▼▼▼▼▼▼▼▼▼▼▼▼▼▼▼▼▼▼▼▼ Measurement steps: First step C X • Measure cylinder bore “C” with a cylinder gauge. (1) 50 mm from top of cylinder Y NOTE: Measure bore parallel and at right angles to the driving shaft. Then calculate average measurement. Cylinder bore “C” Standard Wear limit 94.97 ~ 95.02 mm 95.1 mm C=X+Y 2 • If the measurements are out of tolerance, replace the cylinder liner, piston and circlips all together. Second step • Measure diameter “P” of the piston skirt with a micrometer. (1) 5 mm from the lower edge of the piston Piston “P” size: Standard 5-30 94.915 ~ 94.965 mm INSPECTION AND REPAIR • ENG If the measurements are out of tolerance, replace the piston and circlips all together. Third step • Calculate the piston-cylinder free play according to the following formula. Piston-cylinder clearance = Cylinder boring “C” – Piston skirt diameter “P” Piston-cylinder clearance: 0.045 ~ 0.065 mm <Limit>: 0.15 mm • If the measurements are out of tolerance, replace the cylinder liner, piston and circlips all together. ▲▲▲▲▲▲▲▲▲▲▲▲▲▲▲▲▲▲▲▲▲▲▲▲▲▲▲▲▲ 5-31 ENG INSPECTION AND REPAIR PISTON RINGS 1. Measure: • Side clearance of rings Use a thickness gauge. Out of specification ➔ Replace piston. NOTE: Before measuring side clearance, remove carbon deposits from the piston ring seats and from the rings themselves. Piston ring side clearance (installed): Upper ring 0.04 ~ 0.08 mm Lower ring 0.03 ~ 0.07 mm <Limit>: 0.13 mm Oil scraper 0.02 ~ 0.06 mm 2. Install: • Ring (into the cylinder) NOTE: Fit each ring into the cylinder and push it to about 20 mm from the top edge of the cylinder. Push the ring into the cylinder with the piston so that it is perfectly perpendicular to the cylinder axis. (a) 20 mm 3. Measure: • Ring end gap Out of specification ➔ Replace. NOTE: It is impossible to measure the oil scraper end gap. If the oil scraper port appears too large, replace all three rings. Piston ring end gap (fitted into cylinder): 5-32 Upper ring 0.30 ~ 0.45 mm <Limit>: 0.7 mm Lower ring 0.30 ~ 0.45 mm <Limit>: 0.8 mm Oil scraper (tracks) 0.20 ~ 0.70 mm INSPECTION AND REPAIR ENG PISTON PIN 1. Check: • Piston pin Blue colour/Grooves ➔ Replace and check lubrication system. 2. Measure: • External diameter (a) of pin Out of specification ➔ Replace. External diameter (pin): 21.991 ~ 22.000 mm 3. Measure: • Clearance between piston pin and pin seat Out of specification ➔ Replace. Clearance between piston pin and piston = Diameter of pin seat on piston (b) – Diameter of pin (a) Clearance between piston pin and pin seat on piston: 0.004 ~ 0.024 mm <Limit>: 0.07 mm CLUTCH 1. Inspect: • Clutch gear assy teeth Cracks/Pitting (on edges): Moderate ➔ Burr. Accentuated ➔ Replace clutch gear assy. NOTE: Pitting of the gear assy teeth causes irregular functioning. 5-33 INSPECTION AND REPAIR ENG 2. Inspect: • Clutch gear assy bearing Damaged ➔ Replace. 3. Inspect: • Groove in clutch boss. Pitting: Moderate ➔ Burr. Accentuated ➔ Replace clutch boss. NOTE: Pitting of the clutch boss grooves causes irregular functioning. 4. Measure: • Thickness of friction plates Out of specification ➔ Replace all plates. Thickness Wear limit Type “A” (2 parts) 2.94 ~ 3.06 mm 2.8 mm Type “B” (6 parts) 2.72 ~ 2.88 mm 2.6 mm 5. Measure: • Deformation of clutch plates Out of specification ➔ Replace all plates. Clutch plates deformation: <Limit>: 0.2 mm 6. Measure: • Runout limit of clutch push rod. Turn clutch push rod on two V blocks. Clutch push rod runout: <Limit>: 0.2 mm 5-34 ENG INSPECTION AND REPAIR 7. Measure: • Free length of clutch compression springs (a) Out of specification ➔ Replace all springs. Free length of clutch compression spring (a): 42.8 mm OIL PUMP 1. Measure: • Clearance between rotors (a) (Between the internal rotor (1) and the external rotor (2)) • Side clearance (b) (Between the external rotor (2) and the pump stator (3)) Out of specification ➔ Replace oil pump. Oil pump clearances: Clearance between rotors (a) 0.12 mm <Limit>: 0.2 mm Side clearance (b) 0.03 ~ 0.08 mm <Limit>: 0.15 mm 2. Inspect: • Oil pump drive gear (1) • Oil pump driven gear (2) Wear/Cracks/Damage ➔ Replace. PRIMARY TRANSMISSION 1. Inspect: • Primary drive gear teeth (1) • Primary driven gear teeth (2) Wear/Damage ➔ Replace both gears. Excess noise during functioning ➔ Replace both gears. 5-35 INSPECTION AND REPAIR ENG TRANSMISSION AND GEARBOX 1. Inspect: • Shift fork pin (1) • Shift fork pawl (2) Lines/Creases/Wear ➔ Replace. 2. Inspect: • Shift cam groove • Shift cam pins Wear/Damage ➔ Replace. 3. Check: • Shift fork movement Rough functioning ➔ Replace shift forks and/or guide bars. 4. Inspect: • Guide bar Turn on a flat surface. Curvature ➔ Replace. WARNING Do not attempt to straighten the deformed guide bar. 5. Measure: • Transmission shaft eccentricity. Use the centring tool and micrometer. Out of specification ➔ Replace bent shaft. Transmission shaft eccentricity: <Limit>: 0.08 mm 5-36 INSPECTION AND REPAIR ENG 6. Inspect: • Gear teeth Brown colouring/Pitting/Wear ➔ Replace. • Mating clutches Rounded edges/Cracks/Missing fragments ➔ Replace. 7. Check: • Proper mating of each gear (with corresponding part) • Gear movement Roughness ➔ Replace. ▼▼▼▼▼▼▼▼▼▼▼▼▼▼▼▼▼▼▼▼▼▼▼▼▼▼▼▼▼ Transmission gear assembly steps: • Fit the second gear (2) to the propeller shaft (1) as shown in the figure. (a) 60.0 mm • Fit the second sprocket (4) and fifth sprocket (5) to the main shaft (3). (b) 90.5 mm ▲▲▲▲▲▲▲▲▲▲▲▲▲▲▲▲▲▲▲▲▲▲▲▲▲▲▲▲▲ 8. Inspect: • Circlip Damage/Loosening/Bending ➔ Replace. SHAFT AND STOPPER LEVER 1. Inspect: • Shift shaft Bent/Wear/Damage ➔ Replace. 2. Inspect: • Stopper lever (1) The roller rotates jerkily ➔ Replace. Bent/Damage ➔ Replace. 3. Inspect: • Return spring (2) Damage/Cracks ➔ Replace. 5-37 INSPECTION AND REPAIR ENG STARTER TRANSMISSION 1. Check: • Starter clutch functioning (1). Turn the clutch in the direction indicated by the arrow. Irregular functioning/Damage ➔ Replace the clutch. ▼▼▼▼▼▼▼▼▼▼▼▼▼▼▼▼▼▼▼▼▼▼▼▼▼▼▼▼▼ • • • Install the starter rim on the gear and hold the gear firm. When turning the gear rim in a clockwise direction (A), the gear and rim must be meshed. Otherwise, the gear is faulty and must be replaced. When the gear rim is turned in a anticlockwise direction (B), it must turn freely. Otherwise, the gear is faulty and must be replaced. ▲▲▲▲▲▲▲▲▲▲▲▲▲▲▲▲▲▲▲▲▲▲▲▲▲▲▲▲▲ 2. Inspect: • Starter neutral gear teeth (1) • Starter neutral gear teeth (2) • Starter rim teeth (3) Burrs/Shavings/Roughness/Wear ➔ Replace. 3. Inspect: • Starter rim (contact surfaces) Pitting/Wear/Damage ➔ Replace. 5-38 INSPECTION AND REPAIR ENG CRANKSHAFT 1. Measure: • Width of crank (A) Out of specification ➔ Replace crankshaft. Width of crank: 74.95 ~ 75.00 mm • Runout (B) Out of specification ➔ Replace crankshaft and/or crank bearing. Crankshaft runout: <Limit>: 0.03 mm • Connecting rod small end clearance (C) Out of specification ➔ Replace connecting rod big end bearing, connecting rod pin and/or connecting rod. Connecting rod small end clearance: 0.8 mm • Side clearance (D) Out of specification ➔ Replace connecting rod. Connecting rod big end clearance: 0.35 ~ 0.65 mm Crankshaft assembly procedure: The passages of crankshaft (1) oil and connecting rod pin (2) oil must coincide with a tolerance of less than 1.0 mm. 5-39 INSPECTION AND REPAIR ENG BALANCER SHAFT DRIVE AND DRIVEN GEARS 1. Inspect: • Drive gear teeth (1) • Driven gear teeth (2) Wear/damage ➔ Replace both gears. 2. Check: • Marks (1) If they are not aligned ➔ Align the marks as shown in the figure. CRANKCASE 1. Inspect: • Crankcase • Bearing housing Damaged ➔ Replace. BEARING AND OIL SEAL 1. Inspect: • Bearing Roughness/Pitting/Damage ➔ Replace. • Oil seal edge Damage/Wear ➔ Replace. 5-40 ENGINE ASSEMBLY AND SETTING ENGINE ASSEMBLY AND SETTING VALVES AND ROCKER ARMS (1) (2) (3) (4) (5) (6) Rocker arm n. 2 Wave washer Rocker shaft (intake) Rocker arm n. 1 Valve cotters Upper valve spring retainer (7) Oil seal (8) Inner valve spring (9) Outer valve spring (10) Valve (intake) (11) Lower valve spring retainer (12) Rocker shaft (exhaust) (13) Rocker arm n. 4 (14) Rocker arm n. 3 (15) Rocker shaft (exhaust) (16) Valve (exhaust) 5-41 ENG ENGINE ASSEMBLY AND SETTING ENG VALVES 1. Burrs: • Valve stem tip (leave the valve stem tip with an oil stone). 2. Lubricate: • Valve stem and oil seal (apply high quality molybdenum disulfide oil) 3. Install: • Oil seal (1) • Valves (2) • Lower valve spring retainer (3) • Inner valve spring (4) • Outer valve spring (5) • Upper valve spring retainer (6) NOTE: Install the innner and outer springs with the widest thread upwards. (7) Higher pitch (8) Lower pitch 4. Install: • Valve cotters (1) NOTE: Compress the valve spring with the specific tool (2) to fit the cotters. Valve spring compressor: P/N. 90890-04019 5-42 ENGINE ASSEMBLY AND SETTING ENG ROCKER ARMS 1. Lubricate: • Rocker shaft (apply engine oil) 2. Install: • Rocker arm • Rocker shaft Screws (1) (rocker shaft): 10 Nm (1.0 kgm) NOTE: Each rocker arm is numbered. (1) (2) (3) (4) # # # # 1 2 3 4 3. Install: • Cap (1) 5-43 ENGINE ASSEMBLY AND SETTING CRANKSHAFT AND BALANCER SHAFT (1) (2) (3) (4) Connecting rod pin (5) Bearing Crank (left) (6) Bearing Connecting rod (7) Balancer shaft Bearing (8) Bearing 5-44 ENG ENGINE ASSEMBLY AND SETTING ENG CRANKSHAFT AND BALANCER SHAFT 1. Install: • Crankshaft Crankshaft installation tool (1): P/N. Y U-90050 Crankshaft installation tool spacer (2): P/N. 90890-01274 Crankshaft installation tool bolt (3): P/N. 90890-01275 Adapter # 10 (Ml 4) (4): P/N. Y M-90069 P/N. 90890-04059 Crank spacer (5): P/N. YM-91044 P/N. 90890-04081 Spacer (6): P/N. 90890-01016 NOTE: Hold the connecting rod at top dead centre with one hand and turn the assembly tool nut with the other. Work on the assembly tool until the lower part of the crankshaft enters into contact with the bearings. CAUTION: To protect the crankshaft from scratches and facilitate assembly operations, apply grease to the edges of the oil seals and engine oil to the bearings. 2. Install: • Balancer shaft (1) 5-45 ENGINE ASSEMBLY AND SETTING TRANSMISSION (1) Sprocket (2) Oil seal (3) Bearing (4) Second wheel gear (5) Secondary shaft (6) Fifth wheel gear (7) Third wheel gear (8) Fourth wheel gear (9) First wheel gear (10) (11) (12) (13) (14) (15) (16) (17) Bearing Bearing Second sprocket gear Fifth sprocket gear Third sprocket gear Fourth sprocket gear Main shaft Bearing 5-46 ENG ENGINE ASSEMBLY AND SETTING GEARBOX (1) Stopper lever (2) Guide bar (3) Shift fork #3 (4) Shift fork #1 (5) Shift cam (6) Guide bar (7) Shift fork #2 (8) (9) (10) (11) Shift shaft #1 Shift shaft #2 Oil seal Shift lever 5-47 ENG ENGINE ASSEMBLY AND SETTING ENG TRANSMISSION AND GEARBOX 1. Install: • Transmission assembly (1) 2. Install: • Shift fork #1 (1) • Shift fork #2 (2) • Shift fork #3 (3) • Shift cam (4) • Guide bar (5) NOTE: Each shift fork is identified by the number stamped on its side. All numbers must face left. 3. Install: • Shift shaft #1 (1) • Shift shaft #2 (2) NOTE: Align mark (3) on the shift lever shaft with that on the shift shaft. 4. Check: • Transmission functioning Jerky functioning ➔ Repair. 5-48 ENGINE ASSEMBLY AND SETTING ENGINE OIL PUMP AND OIL STRAINER (1) Oil strainer (2) Oil pump (3) Oil pump gear 5-49 ENG ENGINE ASSEMBLY AND SETTING CRANKCASE (1) (2) (3) (4) (5) (6) (7) (8) (9) Crankcase (R) Crankcase (L) Crankcase ventilation hose Dowel pin Dowel pin Dowel pin Bearing cover plate Collar Lock plate 5-50 ENG ENGINE ASSEMBLY AND SETTING ENG ENGINE OIL STRAINER 1. Install: • Oil strainer (1) • Oil passage cover (2) Screw (oil strainer): 7 Nm (0.7 mkg) Screw (oil passage cover): 7 Nm (0.7 mkg) WARNING Always use a new gasket. CRANKCASE 1. Apply: • Yamaha bond N° 1215® (1) (on the crankcase mating surfaces) Yamaha bond N° 1215®: P/N. 90890-85505 2 Install: • Dowel pin (2) 3. Assemble the left crankcase to the right. Beat gently with a soft hammer. NOTE: Turn the shift cam as shown in the figure so that it does not interfere with the crankcase during assembly. CAUTION: Before installing and tightening the fastening screws, be sure that the transmission is working properly by hand, turning the shift cam in both directions. 5-51 ENGINE ASSEMBLY AND SETTING ENG 4. Tighten: • Screws (crankcase) (1) ~ (14) NOTE: Tighten the screws beginning with the one with the lowest number. Screw (crankcase): 10 Nm (1.0 mkg) 5. Apply: • 4-stroke engine oil (to the connecting rod pin, the bearing and the oil passage). 6. Check: • Gearbox and transmission functioning Jerky functioning ➔ Replace. SHIFT SHAFT AND OIL PUMP 1. Install • Spring (1) • Collar (2) • Stopper lever (3) Stopper lever screw (4): 10 Nm (1.0 mkg) NOTE: Place the stopper lever and the spring in the correct position. 2. Install: • Plate washer (1) • Spring (2) • Shift lever (3) • Circlip (4) 5-52 ENGINE ASSEMBLY AND SETTING ENG NOTE: When installing the shift lever, align the mark on the lever with that on the shift shaft. 3. Install: • Circlip (1) (to the driving axle) • Spacer (2) • Circlip (3) 4. Apply: • 4-stroke engine oil (oil pipes in crankcase) CAUTION: To avoid damage to the engine, lubricate the oil pump pipes in the crankcase liberally with 4-stroke engine oil. 5. Apply: • 4-stroke engine oil (oil pump pipes) 6. Apply: • O-Ring (1) • Oil pump (2) • Oil pump gear (3) • Circlip (4) Screw (5) (oil pump): 10 Nm (1.0 mkg) 5-53 ENGINE ASSEMBLY AND SETTING TIMING CHAIN 1. Install: • Timing chain (1) • Chain guide (2) 5-54 ENG ENGINE ASSEMBLY AND SETTING PISTON AND RINGS (1) (2) (3) (4) (5) (6) ENG PISTON SIZE: 94.915 ~ 94.965 mm PISTON RING END GAP: TOP: 0.30 ~ 0.45 mm 2ND: 0.30 ~ 0.45 mm OIL: 0.20 ~ 0.70 mm PISTON RING SIDE CLEARANCE: TOP: 0.04 ~ 0.08 mm 2ND: 0.03 ~ 0.07 mm Ring (upper) Ring (lower) Scraper Piston Piston pin Circlip 5-55 ENGINE ASSEMBLY AND SETTING CYLINDER (1) Gasket (2) Cylinder (3) O-Ring (4) Gasket (5) Dowel pin (6) Dowel pin 5-56 ENG ENGINE ASSEMBLY AND SETTING ENG CYLINDER HEAD (1) Cylinder head cover (2) O-Ring (3) Tappet cover (intake) (4) Tappet covers (exhaust) (5) O-Ring (6) Cap (7) Cylinder head (8) Valve guide (intake valve) (9) Valve guide (exhaust valve) (10) Spark plug (11) Dowel pin 10 Nm (1.0 m•kg 7.2 ft•lb) 10 Nm (1.0 m•kg 7.2 ft•lb) 10 Nm (1.0 m•kg 7.2 ft•lb) 12 Nm (1.2 m•kg 8.7 ft•lb) 10 Nm (1.0 m•kg 7.2 ft•lb) 10 Nm (1.0 m•kg 7.2 ft•lb) 18 Nm (1.8 m•kg 13 ft•lb) 7 Nm (0.7 m•kg 5.1 ft•lb) ® A SEALANT (QUICK GASKET) 20 Nm (2.0 m•kg 14 ft•lb) 5-57 ENGINE ASSEMBLY AND SETTING CAMSHAFT AND TIMING CHAIN (1) (2) (3) (4) (5) (6) (7) Camshaft Cam chain sprocket Chain stopper guide Timing chain Chain stopper guide Gasket Chain tensioner 5-58 ENG ENGINE ASSEMBLY AND SETTING ENG PISTON, CYLINDER, CYLINDER HEAD AND CAMSHAFT 1. Apply: • 4-stroke engine oil (on piston pin). 2. Install: • Piston (1) • Pin (2) • Circlip (3) NOTE: Arrow (4) on the piston must point towards the front of the engine. • Before installing the piston pin circlips, cover the crankcase with a clean cloth to prevent foreign bodies falling into it. • WARNING Always use new circlips for the piston pin. 3. Install: • Dowel pins (1) • O-Ring (2) 4. Install: • Gasket (1) (cylinder) NOTE: Install the cylinder gasket as shown in the illustration. 5-59 ENGINE ASSEMBLY AND SETTING ENG 5. Offset the piston ring end gaps as illustrated in the figure. NOTE: • Check that the marks and numbers stamped by the manufacturer on the piston rings face upwards. • Before installing the cylinder, lubricate the piston rings liberally with 4-stroke engine oil. (1) (2) (3) (4) Upper ring Scraper (lower ring) Scraper (upper ring) Lower ring 6. Install: • Cylinder (1) NOTE: • Install the cylinder to the piston with one hand while one hand while compressing the piston rings with the other. • Bind the timing chain with wire and slip it through the appropriate slot. Cylinder: Screw (2): 10 Nm (1.0 mkg) Cap nut (3): 42 Nm (4.2 mkg) Nut (4): 42 Nm (4.2 mkg) 5-60 ENGINE ASSEMBLY AND SETTING ENG 7. Install: • Dowel pins (1) • O-Ring (2) • Gasket (3) (cylinder head) 8. Install: • Cylinder head NOTE: Tighten screws beginning with the one with the lowest number. Cylinder head: Screw (l), (2), (3) and (4): 29 Nm (2.9 mkg) Nut (5) and (6): 22 Nm (2.2 mkg) Screw (7): 10 Nm (1.0 mkg) 9. Install: • Chain stopper guide • Camshaft • Cam chain sprocket ▼▼▼▼▼▼▼▼▼▼▼▼▼▼▼▼▼▼▼▼▼▼▼▼▼▼▼▼▼ Timing chain installation: • • 5-61 Install the cam chain on the cylinder head as illustrated (compression phase timing). Run the cam shaft in an anticlockwise direction until the mark on the crankcase (1) and the point on the cam chain gearwheel (2) are aligned. ENGINE ASSEMBLY AND SETTING ENG • Install the gear wheel with the timing marks as shown in the figure and tighten the screws on the gear wheel by hand. (3) Upper cylinder head surface (4) Timing marks (5) Upper position mark • • When pushing the chain tensioner be sure that the marks on the cam chain sprocket are aligned with the top surface of the cylinder head. If the marks are aligned, tighten the cam chain sprocket bolts. Bolt (cam chain sprocket): 20 Nm (2.0 mkg) • If the marks are not aligned, replace the chain sprocket mating piston and chain. ▲▲▲▲▲▲▲▲▲▲▲▲▲▲▲▲▲▲▲▲▲▲▲▲▲▲▲▲▲ 10. Apply: • Yamaha Bond N° 1215® (1) (on the mating surfaces) Sigillante (Quick Gasket)® Yamaha bond N° 1215®: P/N. 90890-85505 11. Install: • Dowel pins (2) 12. Install: • Cap • Cylinder head cover NOTE: Cross-tighten the screws repeatedly. Bolt (cylinder head cover): 10 Nm (1.0 mkg) 5-62 ENGINE ASSEMBLY AND SETTING ENG 13. Install: • Chain tensioner ▼▼▼▼▼▼▼▼▼▼▼▼▼▼▼▼▼▼▼▼▼▼▼▼▼▼▼▼▼ Assembly steps: • • • Remove the chain tensioner screw (1), the washer (2) and the spring (3). Release the chain tensioner unidirectional cam (4) and push the thrust rod (5). Install the chain tensioner in the cylinder with a new gasket. Screw (chain tensioner body): 10 Nm (1.0 mkg) WARNING Always use a new gasket. • Install the spring, the washer and the chain tensioner. Chain tensioner screw: 20 Nm (2.0 mkg) ▲▲▲▲▲▲▲▲▲▲▲▲▲▲▲▲▲▲▲▲▲▲▲▲▲▲▲▲▲ 14. Adjust: • Valve clearance Valve clearance: Intake 0.05 ~ 0.10 mm Exhaust 0.12 - 0.17 mm See section “VALVE CLEARANCE ADJUSTMENT” in CHAPTER 3. 5-63 ENGINE ASSEMBLY AND SETTING ENG 15. Install: • Tappet covers (1) (exhaust) • Tappet cover (2) (intake) • Spark plug (3) Tappet cover (exhaust): 12 Nm (1.2 mkg) Screw (tappet cover-intake): 10 Nm (1.0 mkg) Spark plug: 18 Nm (1.8 mkg) NOTE: The tappet cover (intake) should be assembled with the arrow (4) pointing upwards. 5-64 ENGINE ASSEMBLY AND SETTING AC GENERATOR ENG PICKUP COIL RESISTANCE: 230 Ω ± 20% at 20°C (68°F) (Blue/Yellow - Green/White) (1) Rotor (2) Pick-up coil (3) Stator winding CHARGING COIL RESISTANCE: 0.65 Ω ± 20% at 20°C (68°F) (White - White) 5-65 ENGINE ASSEMBLY AND SETTING ENG AC GENERATOR 1. Install: • Woodruff key (1) • Washer (2) • Bearing (3) • Rotor (4) • Washer (5) • Nut (6) NOTE: When installing the AC generator rotor, check that the woodruff key fits properly into its seat on the crankshaft. Apply a thin layer of lithium soapbased grease on the conical tip of the crankshaft. 2. Tighten: • Nut (rotor) Nut (rotor): 120 Nm (12.0 mkg) NOTE: To tighten the nut, lock the rotor with the special tool (1). Sheave holder: P/N. 90890-01701 CAUTION: Be careful not to touch the jutting edges (2) on the rotor with the sheave holder. 5-66 ENGINE ASSEMBLY AND SETTING OIL FILTER AND OIL HOSES (1) (2) (3) (4) (5) (6) Oil filter Filter cover Oil hose Oil hose Oil delivery hose Oil drain plug 5-67 ENG ENGINE ASSEMBLY AND SETTING BALANCER SHAFT GEAR AND PRIMARY TRANSMISSION GEAR (1) (2) (3) (4) (5) (6) (7) (8) Straight key Balancer shaft gear Breather plate Lock washer Nut Plate washer Straight key Plate (9) (10) (11) (12) (13) 5-68 Balancer shaft drive gear Plate Primary drive gear Lock washer Nut ENG ENGINE ASSEMBLY AND SETTING ENG BALANCER SHAFT GEAR AND PRIMARY TRANSMISSION GEAR 1. Install: • Key (1) • Balancer shaft gear (2) • Plate (3) • Lock washer (4) • Nut (5) (balancer shaft gear) • Washer (6) • Key (7) • Plate (8) • Balancer shaft drive gear (9) • Plate (10) • Primary drive gear (11) • Lock washer (12) • Nut (13) (primary drive gear) Nut (balancer shaft gear): 60 Nm (6.0 mkg) Nut (primary drive gear): 120 Nm (12.0 mkg) NOTE: When installing the drive gear, align the mark on it (14) with that of the balancer shaft gear (15). WARNING Always use a new lock washer. NOTE: To tighten nuts (5) and (13), keep the AC generator rotor still with the special tool (16). Sheave holder: P/N. 90890-01701 CAUTION: Be careful not to touch the jutting part (17) of the rotor with the sheave holder. 2. Bend the lock washer tab along the face of the nut. 5-69 ENGINE ASSEMBLY AND SETTING CLUTCH (1) (2) (3) (4) (5) (6) (7) (8) Compression spring Pressure plate Push rod Ball Friction plate (type A) Clutch boss spring Clutch plate Friction plate (type B) (9) Clutch boss (10) Thrust plate (11) Primary driven gear comp. (12) Push rod (13) Push lever (14) Primary drive gear 5-70 ENG ENGINE ASSEMBLY AND SETTING ENG CLUTCH 1. Install: • Plain washer • Spring • Push lever (1) Screw (push lever): 12 Nm (1.2 mkg) 2. Install: • Push rod (1) • Primary driven gear comp. (2) • Thrust plate (3) • Clutch boss (4) • Lock washer (5) • Nut (6) (clutch boss) • Clutch boss spring (7) • Clutch plate (8) • Friction plate (9) • Ball (10) • Pressure plate (11) • Compression spring (12) • Screw (pressure plate) (13) Nut (clutch boss): 90 Nm (9.0 mkg) Pressure plate screw: 8 Nm (0.8 mkg) NOTE: • To tighten the nut (clutch boss), lock the clutch drum with the special tool (14). Clutch holding tool: P/N. 90890-04086 • Bend the lock washer tab along the face of the nut. WARNING Always use a new lock washer. 5-71 ENGINE ASSEMBLY AND SETTING ENG NOTE: Install the friction and clutch plates to the clutch boss, beginning and ending with a friction plate. CAUTION: • • The two friction plates (type A) (15) with the widest internal diameter should be assembled in second and last place. The clutch boss spring (16) should be placed inside the second friction plate. 16 15 Friction plate Type “A” Type “B” Quantity Internal diameter “D” 2 6 116 mm 113 mm NOTE: Align the mark on the clutch boss (17) with the arrow (18) on the pressure plate. 3. Adjust: • Clutch (free play) See section “CLUTCH ADJUSTMENT” in CHAPTER 3. 4. Install: • Straight key • Gasket • Crankcase cover (right) (1) • O-Ring • Oil filter • Filter cover (2) (with O-Ring) See section “Engine oil replacement (with oil filter change)” in CHAPTER 3. Bolt (crankcase cover): 10 Nm (1.0 mkg) 5-72 ENGINE ASSEMBLY AND SETTING STARTER GEARS (1) (2) (3) (4) (5) Starter Starter Starter Starter Starter gear neutral gear 1 neutral gear 2 gear clutch 5-73 ENG ENGINE ASSEMBLY AND SETTING ENG STARTER NEUTRAL GEAR AND CRANKCASE COVER (L)) 1. Install: • Stator winding (1) • Pick-up coil (2) • Cable clamp (3) Screws (stator and coil): 7 Nm (0.7 mkg) Use LOCTITE ® Screw (cable clamp): 7 Nm (0.7 mkg) 2. Install: • Bearing (1) • Intermediate starter gear 2 (2) 3. Install: • Centring pin (1) • Gasket (2) • O-Ring (3) • Crankcase cover (L) (4) • Plugs Bolt (crankcase cover): 10 Nm (1.0 mkg) WARNING Always use a new gasket. 5-74 ENGINE ASSEMBLY AND SETTING ENG 4. Install: • Neutral switch cable (1) 5. Install: • Shaft (1) • Bearing (2) • Starter intermediate gear 1 (3) 6. Install: • Centring pins • Gasket • Cover (1) (starter intermediate gear) Screw (cover): 10 Nm (1.0 mkg) 5-75 ENGINE REASSEMBLY ENG ENGINE REASSEMBLY To reassemble the engine, repeat the procedures described in the paragraph “ ENGINE REMOVAL” in this chapter in reverse order. Pay attention to the following points. 1. Install: • Sprocket (1) • Drive chain Nut (sprocket): 110 Nm (11.0 mkg) NOTE: Bend the lock washer tab along the face of the nut. WARNING Always use a new lock washer. 2. Install: • Cover (sprocket) • Shift pedal • Footrest (L) Screw (sprocket cover): 10 Nm (1.0 mkg) Use LOCTlTE® Screw (shift ptidal): 10 Nm (1.0 mkg) Screw (footrest): 48 Nm (4.8 mkg) 3. Adjust: • Drive chain slack Drive chain slack: 30 ~ 40 mm See section “DRIVE CHAIN SLACK INSPECTION AND ADJUSTMENT” in CHAPTER 5-76 ENGINE REASSEMBLY ENG 4. Install: • Oil delivery hose (1) Union bolt: 18 Nm (1.8 mkg) 5. Remove: • Tappet cover (intake) • Air bleeder screw (oil filter cover) 6. Apply: • 4-stroke engine oil • (on the top side of the camshaft and in the oil filter housing). CAUTION: Liberally apply 4-stroke engine oil in the oil passage in the crankcase to prevent damage to the engine. Amount of oil: Camshaft 0.1 litres Oil filter housing 0.06 litres 7. Install: • Tappet cover (intake) • Air bleeder screw (oil filter cover) Screw (tappet cover): 10 Nm (1.0 mkg) Air bleeder screw (oil filter cover): 5 Nm (0.5 mkg) 8. Adjust: • Clutch cable free play Free play (at end of lever): 10 ~ 15 mm See section “CLUTCH ADJUSTMENT” in CHAPTER 3. 5-77 ENGINE REASSEMBLY ENG 9. Install: • Carburetor Screw (clamp): 2 Nm (0.2 mkg) See section “CARBURETOR-INSTALLATION” in CHAPTER 6. 10. Adjust: • Throttle cable free play Free play: 3 ~ 5 mm See section “THROTTLE CABLE FREE PLAY ADJUSTMENT” in CHAPTER 3. 11. Install: • Fuel tank CAUTION: Do not start the engine until it is filled with oil. 12. Fill with: • Engine oil Amount of oil (total): 3.0 litres See section “ENGINE OIL REPLACEMENT” in CHAPTER 3. 13. Check: • Engine idle speed Engine idle speed: 1.150 ~ 1.450 rpm See section “IDLE SPEED ADJUSTMENT” in CHAPTER 3. 14. Install: • Seat Screw (seat): 10 Nm (1.0 mkg) 5-78 CARB 6 CARB CHAPTER 6 CARBURETOR CARBURETOR REMOVAL................................................................................................ 6-1 TECHNICAL SPECIFICATIONS/TIGHTENING TORQUES/EXPLODED VIEW .............. 6-3 SECTION VIEW .......................................................................................................... 6-5 CARBURETOR DISASSEMBLY ........................................................................................ 6-6 CARBURETOR INSPECTION .......................................................................................... 6-9 CARBURETOR ASSEMBLY .............................................................................................. 6-11 FUEL LEVEL ADJUSTMENT (CARBURETOR INSTALLED) .......................................... 6-16 CARB CARBURETOR REMOVAL CARB CARBURETOR CARBURETOR REMOVAL Order Job name/Part name Q.ty Remarks Carburetor removal Remove the parts in order. Seat Refer to “SEAT, FUEL TANK AND REAR COWLING" section in CHAPTER 3. NOTE: Be sure the cap is properly tightened and the fuel cock is in the “OFF” position before removing the fuel tank. Fuel pipe Fuel tank 1 Lock nut 4 Loosen. 2 Throttle cable adjuster 2 Screw. 3 Throttle cable 2 4 Hose clamp 2 6-1 Loosen. CARBURETOR REMOVAL Order Job name/Part name CARB Q.ty Remarks Loosen. NOTE: Move carburetor manifold clamps towards the rear side. 5 Hose clamp 2 6 Carburetor 2 Reverse the removal procedure for installation. Adjust throttle cable free play (refer to THROTTLE CABLE FREE PLAY ADJUSTMENT” section in CHAPTER 3). Adjust idle speed (refer to “IDLE SPEED ADJUSTMENT” section in CHAPTER 3). 6-2 CARBURETOR CARB TYPE: Y30PV-2ATK MANUFACTURER: TEIKEI 2 Nm (0.2 m.kg, 1.4 ft.lb) 3 Nm (0.3 m.kg, 2.1 ft.lb) 2 Nm (0.2 m.kg, 1.4 ft.lb) 9 Nm (0.9 m.kg, 6.3 ft.lb) 2 Nm (0.2 m.kg, 1.4 ft.lb) 6 Nm (0.6 m.kg, 4.3 ft.lb) 8 Nm (0.8 m.kg, 5.9 ft.lb) 3,5 Nm (0.35 m.kg, 2.5 ft.lb) 2 Nm (0.2 m.kg, 1.4 ft.lb) 6-3 CARBURETOR (1) Carburetor assembly (2) Cover gasket (3) Gasket, nozzle (4) Float (5) Float pin (6) Float chamber gasket (7) Screw (8) Float chamber fastening screw (9) Spring washer (10) Collar (11) Screw (12) Gasket (27) (28) (29) (30) (31) (32) (33) (34) (35) (36) (37) (38) (39) (40) (41) (13) Throttle valve spring (14) Spring washer (15) Nut (16) Gasket (17) Screw (18) Stop screw (19) Nut (20) Screw (21) Hose (22) Diaphragm (23) Cover (24) Bracket (25) O-ring (26) Spring washer SPECIFICATIONS Main jet #150 FIRST #145 SEC. Starter jet #74 Needle jet 5C5A-3/5 ( FIRST) 5Y18-3/5 (SEC.) Main nozzle ø 2,6 Pilot jet #50 Pilot air screw 2,75 ± 0,5 revs approx., open Float height 27~29 mm Fuel level 6~8 mm Engine idle speed 1.150~1.450 r/min Throttle valve seat ø 2,5 mm 6-4 Spring Drain valve Pipe Pipe Screw Screw Pipe Clip Main jet 1 Main nozzle 1 Throttle valve Pilot jet Main jet 2 Main nozzle 2 Pilot screw set (42) (43) (44) (45) (46) (47) (48) (49) (50) (51) (52) (53) (54) (55) (56) CARB Needle valve set Stop screw set Throttle screw set Diaphragm Needle set 1 Needle set 2 Starter set Way 3 Hose Hose Hose Clip Breather pipe O-ring Pipe CARBURETOR CARB SECTION VIEW (1) (2) (3) (4) (5) (6) (7) (8) Main nozzle (secondary) (9) Main jet (secondary) Needle jet (primary) Valve seat Needle valve Main nozzle (primary) Main jet (primary) Pilot air screw Needle jet (secondary) [A] Primary carburetor [B] Secondary carburetor Air Fuel Mixture A B 6-5 CARBURETOR DISASSEMBLY CARB CARBURETOR DISASSEMBLY 1. Remove: • Support plate (1) (front) • Support plate (2) (rear) 2. Separate: • Primary carburetor • Secondary carburetor Primary carburetor 1. Remove: • Float chamber (1) • Float pin (2) • Float (3) NOTE: Remove the float needle in the direction of the arrow. 6-6 CARBURETOR DISASSEMBLY CARB 2. Remove: • Needle valve set/Valve seat (1) • Main jet/Main nozzle 1 (2) • Pilot jet (3) • Pilot screw set (4) • O-Ring (5) 3. Remove: • Stop screw (1) • Starter set (2) 4. Remove: • Cover (1) (enrichment) • Spring (2) • Diaphragm (3) 5. Remove: • Top cover (1) • Cover gasket (2) • Screw (3) (connecter comp.) 6. Remove: • Throttle lever (1) • Collar (2) • Cable holder (3) 6-7 CARBURETOR DISASSEMBLY 7. Remove: • Throttle shaft (1) • Spring (2) 8. Remove: • Connecter comp. (1) • Needle jet (2) • Throttle valve (3) Secondary carburetor 1. Remove: • Drain plug (1) • Main jet (2) 2. Remove: • Top cover (1) • Spring (2) 3. Remove: • Diaphragm (1) • Needle jet 2 (2) 6-8 CARB CARBURETOR INSPECTION CARB CARBURETOR INSPECTION 1. Inspect: • Carburetor body Soiled ➔ Clean. NOTE: Use petroleum-based solutions to clean. Clean all passages and jets with compressed air. 2. Inspect: • Valve seat (1) • Needle valve set (2) Wear/Corrosion ➔ Replace. • O-Ring (3) Damaged ➔ Replace. NOTE: Always replace the needle valve set and the valve seat together. 3. Inspect: • Starter piston (1) Wear/Damage ➔ Replace • Stop screw (2) Damaged ➔ Replace. 4. Inspect: • Diaphragm (1) (piston valve) • Diaphragm (2) (enrichment) Damaged ➔ Replace. 5. Inspect: • Needle jet (1) (primary) • Needle jet (2) (secondary) Curvature/Wear ➔ Replace. 6-9 CARBURETOR INSPECTION CARB 6. Inspect: • Throttle valve (1) (primary) • Diaphragm (2) (secondary) ear/Damaged ➔ Replace. 7. Check: • Free movement Hampered ➔ Replace. Fit the throttle valve and diaphragm into the carburetor body and check that movement is free. [A] Primary carburetor [B] Secondary carburetor 8. Inspect: • Float (1) Damaged ➔ Replace. 9. Inspect: • Main jet (1) (primary) • Main jet (2) (secondary) • Main nozzle (3) (primary) • Main nozzle (4) (secondary) • Pilot jet (5) NOTE: Clean jets with compressed air. 6-10 CARBURETOR ASSEMBLY CARB CARBURETOR ASSEMBLY Perform “CARBURETOR DISASSEMBLY” operations in reverse order. Pay attention to the following points. CAUTION: Wash all parts with clean petrol prior to reassembly. Secondary carburetor 1. Install: • Needle jet (1) • Diaphragm (2) • Spring NOTE: Draw the diaphragm tab level with the notch on the secondary carburetor. 2. Install: • Top cover Screw (top cover): 2 Nm (0.2 mkg) 3. Install: • Main jet (secondary) • Drain vavle Main jet (secondary): 2 Nm (0.2 mkg) Drain valve: 9 Nm (0.9 mkg) 6-11 CARBURETOR ASSEMBLY CARB Primary carburetor 1. Install: • Needle jet (1) • Connecter comp. (2) NOTE: Check that the connecter comp. (1) is in the position shown in the figure. 2. Install: • Throttle valve 3. Install: • Spring • Throttle shaft NOTE: Assemble the spring as shown in the illustration. 4. Install: • Screw (connecter comp.) NOTE: Turn the throttle shaft clockwise (1/2 turn) to preload the spring and then, holding it in position, assemble the screw (connecter comp.). Screw (connecter camp.): 2 Nm (0.2 mkg) 6-12 CARBURETOR ASSEMBLY CARB 5. Install: • Cable holder • Collar • Throttle lever NOTE: Check that the throttle shaft lever (2) and the adjuster bolt (3) are aligned when tightening the throttle nut (1). Screw (cable holder): 3 Nm (0.3 mkg) 6. Install: • Top cover Screw (top cover): 2 Nm (0.2 mkg) 7. Install: • Diaphragm (1) (enrichment) NOTE: Make the diaphragm tab coincide with the gravity enricher notch. 8. Install: • Starter set • Stop screw Starter piston: 6 Nm (0.6 mkg) 9. Install: • Pilot screw set (1) • Pilot jet (2) • Main nozzle 1 (3) • Main jet (primary) (4) • Valve seat (5) Main nozzle 1: 2 Nm (0.2 mkg) Screw (valve seat): 2 Nm (0.2 mkg) 6-13 CARBURETOR ASSEMBLY CARB 10. Install: • Float pin (1) NOTE: Assemble the float pin in the opposite direction to the arrow. 11. Measure: • Float height (a) Out of specification ➔ Adjust. Float height: 27.0 - 29.0 mm ▼▼▼▼▼▼▼▼▼▼▼▼▼▼▼▼▼▼▼▼▼▼▼▼▼▼▼▼▼ Measurement and adjustment: • Hold the carburetor upside down. • Measure the distance from the joint plane of the float chamber (without the gasket) and the top of the float. NOTE: The float arm must rest on the neeedle valve without being pressed. • • • • If the float height is out of tolerance, check the valve seat and the needle valve. If either is worn, replace both. If both are perfect, adjust the float height by bending the wing tab of the float itself (1). Recheck the float height. ▲▲▲▲▲▲▲▲▲▲▲▲▲▲▲▲▲▲▲▲▲▲▲▲▲▲▲▲▲ 12. Install: • Float chamber Screw (float chamber): 2 Nm (0.2 mkg) 13. Adjust: • Pilot air screw (1) ▼▼▼▼▼▼▼▼▼▼▼▼▼▼▼▼▼▼▼▼▼▼▼▼▼▼▼▼▼ Adjustment: • • Turn the screw until it is slightly locked. Unscrew by 3 and 1/2 turns. ▲▲▲▲▲▲▲▲▲▲▲▲▲▲▲▲▲▲▲▲▲▲▲▲▲▲▲▲▲ 6-14 CARBURETOR ASSEMBLY CARB 14. Install: • Primary carburetor • Secondary carburetor 15. Install: • Support plate (front) (1) • Support plate (rear) (2) Screw (support plate): 3.5 Nm (0.35 mkg) 16. Adjust: • Synchronisation of secondary carburetor ▼▼▼▼▼▼▼▼▼▼▼▼▼▼▼▼▼▼▼▼▼▼▼▼▼▼▼▼▼ Adjustment: • Move the primary throttle valve (1) to a height of 7.0 mm as shown in the figure. • Tighten or loosen the synchronisation screw (1) until the secondary throttle valve (2) starts to open. • Check that the secondary throttle valve is open horizontally (a)=(b) when the primary throttle valve is completely open ▲▲▲▲▲▲▲▲▲▲▲▲▲▲▲▲▲▲▲▲▲▲▲▲▲▲▲▲▲ 6-15 CARBURETOR ASSEMBLY CARB FUEL LEVEL ADJUSTMENT (CARBURETOR INSTALLED 1. Place the motorcycle on a level surface. 2. Make sure that the carburetor is in a horizontal position by placing a hydraulic jack under the engine. 3. Connect the fuel level gauge (1) to the carburettor nipple. Fuel level gauge: P/N. 90890-01312 4. Loosen drain screw (2) and heat the engine. 5. Measure: • Fuel level (a) Out of specification ➔ Adjust. Fuel level: 6.0 ~ 8.0 mm Under the edge of the carburetor body. 6. Adjust: • Fuel level ▼▼▼▼▼▼▼▼▼▼▼▼▼▼▼▼▼▼▼▼▼▼▼▼▼▼▼▼▼ Fuel level adjustment: • • • • • Remove carburetor assembly. Inspect valve seat and needle valve set. If either of the two is worn, replace both. If both are perfect, adjust float height by bending the wing tab of the float itself (1). Recheck the fuel level. ▲▲▲▲▲▲▲▲▲▲▲▲▲▲▲▲▲▲▲▲▲▲▲▲▲▲▲▲▲ 6-16 ELEC 7 ELEC CHAPTER 7 ELECTRICAL ELECTRICAL CIRCUIT DIAGRAM . . . . . . . . . . . . . . . . . . . . . . . . . . . . . . . . . . . . . . . . . 7-1 COLOUR CODE . . . . . . . . . . . . . . . . . . . . . . . . . . . . . . . . . . . . . . . . . . . . . . . . . . . 7-2 ELECTRICAL COMPONENTS . . . . . . . . . . . . . . . . . . . . . . . . . . . . . . . . . . . . . . . . . . . . 7-3 SWITCH CHECK . . . . . . . . . . . . . . . . . . . . . . . . . . . . . . . . . . . . . . . . . . . . . . . . . . . . . . 7-5 SWITCH CONNECTION . . . . . . . . . . . . . . . . . . . . . . . . . . . . . . . . . . . . . . . . . . . . . 7-5 MAIN SWITCH INSPECTION. . . . . . . . . . . . . . . . . . . . . . . . . . . . . . . . . . . . . . . . . . 7-5 LIGHT INSPECTION (HEADLIGHTS, TAIL LIGHT AND BRAKE LIGHTS, DIRECTION INDICATOR LIGHTS, INSTRUMENT LIGHTS, ETC) . . . . . . . . . . . . . . . . . 7-8 BULB TYPES. . . . . . . . . . . . . . . . . . . . . . . . . . . . . . . . . . . . . . . . . . . . . . . . . . . . . . 7-8 BULB INSPECTION . . . . . . . . . . . . . . . . . . . . . . . . . . . . . . . . . . . . . . . . . . . . . . . . . 7-8 IGNITION SYSTEM . . . . . . . . . . . . . . . . . . . . . . . . . . . . . . . . . . . . . . . . . . . . . . . . . . . . 7-11 CIRCUIT DIAGRAM . . . . . . . . . . . . . . . . . . . . . . . . . . . . . . . . . . . . . . . . . . . . . . . . 7-11 DIAGNOSTICS . . . . . . . . . . . . . . . . . . . . . . . . . . . . . . . . . . . . . . . . . . . . . . . . . . . 7-13 ELECTRICAL STARTING SYSTEM. . . . CIRCUIT DIAGRAM . . . . . . . . . . . . STARTING CIRCUIT OPERATION . DIAGNOSTICS . . . . . . . . . . . . . . . STARTER MOTOR. . . . . . . . . . . . . . . . . . . . . . . . . . . . . . . . . . . . . . . . . . . . . . . . . . . . . . . . . . . . . . . . . . . . . . . . . . . . . . . . . . . . . . . . . . . . . . . . . . . . . . . . . . . . . . . . . . . . . . . . . . . . . . . . . . . . . . . . . . . . . . . . . . . . . . . . . . . . . . . . . . . . . . . . . . . . . . . . . . . . . . . . . . . . . . . . . 7-21 7-21 7-23 7-24 7-30 CHARGING SYSTEM . . . . . . . . . . . . . . . . . . . . . . . . . . . . . . . . . . . . . . . . . . . . . . . . . . 7-35 CIRCUIT DIAGRAM . . . . . . . . . . . . . . . . . . . . . . . . . . . . . . . . . . . . . . . . . . . . . . . . 7-35 DIAGNOSTICS . . . . . . . . . . . . . . . . . . . . . . . . . . . . . . . . . . . . . . . . . . . . . . . . . . . 7-37 LIGHT SYSTEM . . . . . . . . . . . . . . . CIRCUIT DIAGRAM . . . . . . . . . DIAGNOSTICS . . . . . . . . . . . . LIGHT SYSTEM INSPECTION . . . . . . . . . . . . . . . . . . . . . . . . . . . . . . . . . . . . . . . . . . . . . . . . . . . . . . . . . . . . . . . . . . . . . . . . . . . . . . . . . . . . . . . . . . . . . . . . . . . . . . . . . . . . . . . . . . . . . . . . . . . . . . . . . . . . . . . . . . . . . . . . . . . . . . . . . SIGNALLING SYSTEM . . . . . . . . CIRCUIT DIAGRAM . . . . . . . DIAGNOSTICS . . . . . . . . . . . SIGNAL SYSTEM CONTROL . . . . . . . . . . . . . . . . . . . . . . . . . . . . . . . . . . . . . . . . . . . . . . . . . . . . . . . . . . . . . . . . . . . . . . . . . . . . . . . . . . . . . . . . . . . . . . . . . . . . . . . . . . . . . . . . . . . . . . . . . . . . . . . . . . . . . . . . . . . . . . . . . . . . . . . . . . . . . . . . . . . . 7-41 7-41 7-43 7-46 7-51 7-51 7-53 7-55 ELEC W W W 7-1 20 W W W B R WB BrL W 2 W W BrL WB W W 1 B B B WB GW LY GW GW B R 4 B 28 B BrL WB Br P GB Y Y GB B BrL G BrW BrB P BrB BrW G 5 B BrL B 18 BrL Br 3 6 R ON OFF 21 26 LW LW Br Br L L Y G B B 12V5W B A B B G Y OFF OFF RUN R BrB BrB B B GB B BrB B BrB B B LW 27 LY BY B GB B GB B LB RB B GB GB B B B LY B B 12V10W B B B GW LY B B B B L GY GY GY Br GY B GW LY - B L L LR Sb B 31 Or LB - - 15 L LR Sb Sb LY BY GY 30 Sb Sb LY - B Or RB 16 GW LY 14 11 B B BY GB B (BLUE) B B LY B B RB LB 12 12V10W LY B 13 GB GB B Br BrW BY GB B 12V10W BrB 12V10W BrB BrB B BrB BrB R N L OFF B Br BrW 23 ON LW BY P 19 BY RB BY GY RB Br GY Br BrW B GY Br 25 187 187 RB P Br Br Br L START 29 9 10 24 LW 8 12V60/55W G G A Y A L A L L G Y BrL Y LOW HIGH 22 RB B B RB Br RB LW R 7 R PARK RB L Br BrL R OFF ON Or RW 205 17 Y Ch Dg Br TURN HIGH NEU. ILL. B BrB GB Y BrSb 32 467C4B5CAMP403D494A4856 172320-2 B Y GB BrB B LRBr LR OrLW EXT. CORD B MAIN HARNESS R B R RB LY LB GW LY RB GW LB HEAD LIGHT LW Or MAIN HARNESS G Y L B B L B A G Y ELECTRICAL - W W W W W W R W LY LY ELECTRICAL CIRCUIT DIAGRAM ELEC ELECTRICAL CIRCUIT DIAGRAM ELECTRICAL CIRCUIT DIAGRAM (17) Ignition coil (18) Left handlebar switch (19) Horn switch (20) Diode (21) Pass switch (22) Dimmer switch (23) Flasher switch (24) Horn (25) Flasher relay (26) Headlight (27) Flasher light (28) Relay assy (29) Front brake switch (30) Rear brake switch (31) Tail/stop light (32) Meter (1) AC generator/Pickup coil (2) Rectifier/Regulator (3) Battery (4) Starter relay (5) Starting motor (6) Fuse (7) Main switch (8) Right handlebar switch (9) Engine stop switch (10) Starter switch (11) Diode (12) Clutch switch (13) Sidestand switch (14) Neutral switch (15) Diode (16) Ignitor unit COLOUR CODE B Black B/Y Black/Yellow Br Brown Br/B Brown/Black Ch Chocolate Br/W Brown/White Dg Deep green G/B Green/Black G Green G/R Green/Red Gy Grey G/W Green/White L Blue G/Y Green/Yellow Or Orange L/R Blue/Red P Pink L/W Blue/White R Red L/Y Blue/Yellow Sb Sky-blue R/B Red/Black W White R/W Red/White Y Yellow R/Y Red/Yellow B/R Black/Red W/L White/Blue B/W Black/White Y/R Yellow/Red 7-2 ELEC ELECTRICAL COMPONENTS ELECTRICAL COMPONENTS (1) (2) (3) (4) (5) (6) (7) (8) ELEC BATTERY: CAPACITY 12V – 8Ah SPECIFIC GRAVITY: 1.320 Main wire harness Diodes Extension wire harness Rectifier/Regulator CDI ignition unit Battery (12V – 8Ah) Starter relay Fuse (20A) 7-3 ELECTRICAL COMPONENTS (1) (2) (3) (4) (5) (6) (7) (8) (9) Ignition coil Spark plug cap Flasher relay Horn Clutch switch Relay assy Sidestand switch Neutral switch Main switch ELEC IGNITION COIL: Primary winding resistance: 4 Ω ± 15% at 20°C (68°F) Secondary winding resistance: Ω ± 20% at 20°C (68°F) 13 kΩ 7-4 SWITCH CHECK ELEC SWITCH CHECK Check the continuity between the switch terminals to verify whether connections are correct. To check the switch, read the following points. SWITCH CONNECTION The table shown here contains the connections between the switch terminals (eg main switch, handlebar switches, brake switch, light switch etc). The column on the far left shows the positions of the main switch and the top line indicates the colours of the cables connected with the terminals of the switch itself. “o––––o” indicates the terminals between which there is electrical continuity, ie a closed circuit on the respective switch positions. For example, in this table: “R” and “Br” are continuous when the switch is at ON. “L” and “R/B” are continuous when the switch is at ON. R Br L R/B “R” and “L” are continuous when the switch is at PARK. ON Terminals are not continuous when the switch is at OFF. OFF PARK MAIN SWITCH INSPECTION Before inspecting the switch, see the connection table shown above and check the terminal connections (closed circuit) by the colour combination. 7-5 SWITCH CHECK ELEC 1. Detach the main switch connector from the harness connector. CAUTION When detaching the connector, do not pull by the cables. This way the cables might disconnect from the terminals inside the connector itself. 2. Check to see if any cables are disconnected from their terminal inside the connector. Reconnect, if necessary. NOTE: If the connector is blocked up with mud or dust, clean it with a jet of compressed air. R Br L 3. Use the connection table to check the combination of colours for continuity (closed circuit). In this example, continuity is as follows: “R” and “Br” are continuous when the switch is at ON. “L” and “R/B” are continuous when the switch is at ON. “R” and “L” are continuous when the switch is at PARK. Note that there is no continuity (open circuit) for any of the combinations of a colour different from those mentioned and when the switch is at OFF. R/B ON OFF PARK 4. Check the switch component for continuity between “R” and “Br”. ▼▼▼▼▼▼▼▼▼▼▼▼▼▼▼▼▼▼▼▼▼▼▼▼▼▼▼▼▼ R Control procedure: • Repeatedly shift the switch key to the various positions - ON, OFF and PARK. • Shift the tester selector to “Ωx1”. • Connect the tester positive cable (+) to the terminal of cable “R” of the connector, and the negative cable (–) to cable terminal “Br”. L Br 7-6 SWITCH CHECK ELEC NOTE: Use the thin tester terminals to check continuity, as the terminals might come into contact with others inside the connector. • Check continuity between “R” and “Br” at switch positions ON (1), OFF (2) and PARK (3). There must be continuity (ie the tester must show “0”) at ON and there must be no continuity (ie the tester must show “∞” ) at OFF and PARK. Something is not working between “R and Br” if there is no continuity between these two points at position ON, or if there is some continuity in one of the other positions OFF or PARK. NOTE: Check switch continuity various times. ▲▲▲▲▲▲▲▲▲▲▲▲▲▲▲▲▲▲▲▲▲▲▲▲▲▲▲▲▲ 1 5. Continue to check continuity between “R” and “L” and “L” and “Br” in the respective switch positions in the manner described above. 3 6. If anything wrong is noted in any of the combinations, replace the switch component. OF F 2 IGNICTION 7-7 LIGHT INSPECTION ELEC LIGHT INSPECTION (HEADLIGHTS, TAIL LIGHT AND BRAKE LIGHTS, DIRECTION INDICATOR LIGHTS, INSTRUMENT LIGHTS, ETC) Check the continuity between the bulb terminals to see that they are undamaged. BULB TYPES The bulbs used are classified as shown to the left according to type of attachment. (B) is H4 type halogen bulb (12V - 55/60W) and it is used for headlight. CAUTION: A B Avoid touching the glass part of a bulb. Keep it free from oil; otherwise, the transparency of the glass, life of the bulb, and luminous flux will be adversely affected. If oil gets on a bulb, thoroughly clean it with a cloth moistened with alcohol or lacquer thinner. C (A) and (C) are used mainly for headlights. (D) is used mainly for direction indicator lights and the rear and braking lights. (E) and (F) are used especially for instrument and other indication lights. D E BULB INSPECTION F 1. Remove the bulb. NOTE: • Bulbs of type (B) and (C) use special supports (bulbholders). Remove the bulbholder before removing the bulb. Most of these bulbholders may be removed by turning in an anticlockwise direction. • Most bulbs of type (A), (D) and (E) may be removed from their housing by pushing them and turning them in an anticlockwise direction. • Bulbs of type (F) may be removed simply by pulling them out. 7-8 LIGHT INSPECTION ELEC CAUTION: When removing a bulb be careful to hold the bulbholder or its housing firmly. Never pull the cable, as it might detach from the terminal inside the connector. WARNING Keep inflammable products and hands well away from bulbs when they are on (danger of burns and fire). Do not touch the bulb before it is cool. 2. Check the continuity between the bulb terminals. ▼▼▼▼▼▼▼▼▼▼▼▼▼▼▼▼▼▼▼▼▼▼▼▼▼▼▼▼▼ Control procedure: • Set the tester selector to Ω x 1”. • Connect the tester terminals to the bulb pins. Take, for example, a three pin bulb as shown in the figure. First check continuity between pins (1) and (2), connecting tester terminal (+) to pin (1) and terminal (–) to pole (2). Then check the continuity between poles (1) and (3), again connecting tester terminal (+) to pole (1), and terminal (–) to pole (3). If the tester indicates “∞”, even in one case only, the bulb must be replaced. ▲▲▲▲▲▲▲▲▲▲▲▲▲▲▲▲▲▲▲▲▲▲▲▲▲▲▲▲▲ 3. . Check the bulb attachment by installing a test bulb. Furthermore, during inspection of the bulbs, connect the tester terminals to the respective socket cables and check continuity as described. 7-9 ELEC 7-10 W W W 7-11 20 W W W W W W R W W W W B R WB BrL W 2 W W BrL WB W W 1 B B B GW GW WB GW LY LY LY B R 4 B 28 B BrL WB Br P GB Y Y GB B BrL G BrW BrB P BrB BrW G 5 B BrL B 18 BrL Br 3 6 R ON OFF 21 26 LW LW Br Br L L RB Y G B B 12V5W B A B B G Y OFF OFF RUN R Br BrB B Br BrB B B BrB B BrB B B LW 27 LY BY B GB B GB B LB RB B GB GB B B B LY B B 12V10W B B B GW LY B B B B L B GY GY GY GY Br B L L LR Sb B 31 Or LB - - GW LY - 15 L LR Sb Sb LY BY GY 30 Sb Sb LY - B Or RB 16 GW LY 14 11 B B BY GB B (BLUE) B B LY B B RB LB 12 12V10W LY B 13 GB GB B Br BrW BY GB B 12V10W BrB 12V10W BrB BrB B GB BrB R BrB L OFF N 23 ON LW BY BrW 19 BY RB BY GY RB Br GY Br P B GY Br 25 187 187 RB BrW Br L P Br B START 29 9 10 24 LW 8 12V60/55W G G A Y A L A L L G Y BrL Y LOW HIGH 22 RB B B RB Br RB LW R BrL R PARK 7 L Br OFF ON R Or RW 205 17 Y Ch Dg Br TURN HIGH NEU. ILL. B BrB GB Y BrSb 32 467C4B5CAMP403D494A4856 172320-2 B Y GB BrB B LRBr LR B OrLW EXT. CORD B MAIN HARNESS R B R RB LY LB GW LY RB GW LB HEAD LIGHT LW Or MAIN HARNESS G Y L B G B L Y A IGNITION SYSTEM ELEC IGNITION SYSTEM - CIRCUIT DIAGRAM ELEC IGNITION SYSTEM The diagram illustrates the ignition circuit inside the motorcycles electric system. NOTE: For the colour code and legend, see page 7-2. (1) (2) (3) (6) (7) (9) (11) AC generator/Pickup coil Rectifier/Regulator Battery Fuse Main switch Engine stop switch Diode 12 (12) (13) (14) (15) (16) (17) Clutch switch Sidestand switch Neutral switch Diode Ignitor unit Ignition coil 11 15 6 3 1 14 13 9 17 2 7-12 7 16 IGNITION SYSTEM ELEC DIAGNOSTICS IF THE IGNITION SYSTEM WERE TO STOP WORKING (NO OR INTERMITTENT SPARK) Procedure Check: 1. Fuse 2. Battery 3. Spark plug 4. Amplitude of ignition spark 5. Spark plug cap resistance 6. Ignition winding resistance 7. Main switch 8. Engine stop switch 9. Sidestand switch 10. Neutral switch 11. Clutch switch 12. Pick-up coil resistance 13. Wiring connections (whole connection system) NOTE: Before making the inspections mentioned, remove the following parts: 1. Seat 2. Rear cowling • 3. Fuel tank 4. Cowling (headlight) To check functioning defects use the following special tools. Dinamic spark tester: P/N. 90890-06754 Pocket tester: P/N. 90890-03112 1. Fuse • • NO Check the fuse for continuity. Refer to “CHECKING THE FUSES” in Chapter 3. Is the fuse OK? Replace the fuse. YES 2. Battery • Check the condition of the battery. Refer to “CHECKING AND CHARGING THE BATTERY” in Chapter 3. NO Min. open-circuit voltage: 2.8 V or more at 20°C (68°F) • • • Is the battery OK? YES * 7-13 Clean the battery terminals. Recharge or replace the battery. IGNITION SYSTEM ELEC * 3. Spark plug. • Check the conditions of the spark plug. • Check the type of spark plug used. • Check the electrodes gap. Standard spark plug: DPR8EA-9 (NGK), DPR9EA-9 OUT OF SPECIFICATION Electrodes gap: DPR8EA-9, DPR9EA-9 (NGK) 0.8 ~ 0.9 mm Correct the electrodes gap or replace the spark plug. YES 4. Amplitude of the ignition spark. • Detach the spark plug cap from the spark plug. • Connect the dynamic spark tester (1) as shown in the figure. (2) Spark plug cover (3) Spark plug • Turn the main switch ON. • • Check the amplitude of the ignition spark. Start the engine and increase the amplitude until the ignition becomes discontinuous. IN COMPLIANCE WITH SPECIFICATIONS Minimum spark amplitude. Spark amplitude if the ignition system is efficient: 6.0 mm THE IGNITION SYSTEM IS INEFFICIENT OR THERE IS NO SPARK * 7-14 IGNITION SYSTEM ELEC * 5. Spark plug cap resistance. • • Remove the spark plug cap. Connect the pocket tester (Ω x 1k) to the spark plug cap. OUT OF SPECIFICATION • The spark plug cap is defective. Replace. Check that the spark plug cap has the specified resistance. Resistance of spark plug cap: 10 kΩ at 20°C (68°F) IN COMPLIANCE WITH SPECIFICATIONS 6. Ignition winding resistance. • • Disconnect the ignition coil cables from the wire harness. Connect the pocket tester (Ω x 1) to the ignition coil. Tester terminal (+) ➔ Pole (+) Tester terminal (–) ➔ Pole (–) • Check that the primary coil has the specified resistance. 7-15 IGNITION SYSTEM ELEC Primary winding resistance: 4 Ω ± 15% at 20°C (68°F) (Terminal (+) – Terminal (–)) • Connect the pocket tester (Ω x 1) to the ignition coil. Tester terminal (+) ➔ Spark plug cable (1) Tester terminal (–) ➔ Pole (+) • OUT OF SPECIFICATION Check that the secondary coil has the specified resistance Secondary winding resistance: 13 kΩ ± 20% at 20°C (68°F) (Spark plug cable – Terminal (–)) The ignition coil is defective. Replace. BOTH RESISTANCE VALUES ARE CORRECT 7. Main switch. • • Disconnect the main switch connector from the wire harness. Connect the pocket tester (Ω x 1) to the main switch cables. Refer to “SWITCH CHECK” in Chapter 3. ON OFF PARK INCORRECT Br L R Br L R The main switch is defective. Replace. CORRECT * 7-16 IGNITION SYSTEM ELEC * 8. Emergency stop engine switch. • • Disconnect the emergency stop engine switch connector (Brown, Green/Yellow and Red/Black) from the wire harness. Connect the pocket tester (Ω x 1) to the switch cables. Refer to “SWITCH CHECK” in Chapter 3. Tester terminal (+) ➔ Red/Black (1) cable Tester terminal (–) ➔ Brown cable (2) OFF RUN INCORRECT 1 2 Br GY RB The emergency stop engine switch is defective. Replace the right handlebar switch. Br GY RB CORRECT 9. Sidestand switch. • • Disconnect the sidestand switch connector (Black and Black) from the wire harness. Connect the pocket tester (Ω x 1) to the sidestand switch cables. Refer to “SWITCH CHECK” in Chapter 3. Tester terminal (+) ➔ Black cable (1) Tester terminal (–) ➔ Black cable (2) B B UP DOWN INCORRECT B 1 B 2 The sidestand switch is defective. Replace. CORRECT * 7-17 IGNITION SYSTEM ELEC * 10. Neutral switch. • • Disconnect the neutral switch cable (Sky blue). Connect the pocket tester (Ω x 1) to the neutral switch cables. Refer to “SWITCH CHECK” in Chapter 3. Tester terminal (+) ➔ Sky blue cable (1) Tester terminal (–) ➔ Earth Sb In gear Neutral INCORRECT Sb 1 The neutral switch is defective. Replace. CORRECT 11. Clutch switch. • Disconnect the clutch switch connector from the harness. • Connect the pocket tester (Ω x 1) to the clutch switch cable. • Check the clutch switch component for continuity between “Black (1)” and “Black (2)”. Refer to “SWITCH CHECK” in Chapter 3. B B Release Hold INCORRECT 1 B B 2 The clutch switch is defective. Replace. CORRECT * 7-18 IGNITION SYSTEM ELEC * 12. Pick-up coil resistance. • • Disconnect the generator connector (Green/White and Blue/Yellow). Connect the pocket tester (Ω x 100) to pick-up coil cables. Tester terminal (+) ➔ Blue/Yellow cable (1) Tester terminal (–) ➔ Green/White cable (2) • Check that the pick-up coil resistance is as specified. OUT OF SPECIFICATIONS Pick-up coil resistance: 230 Ω ± 20% at 20°C (68°F) (Green/White - Blue/Yellow) The pick-up coil is defective. Replace. COMPLY WITH SPECIFICATIONS UNCERTAIN CONNECTIONS 13. Wiring connections. Check the connections of the entire ignition system. Refer to “ELECTRICAL CIRCUIT DIAGRAM” section. Correct. CORRECT The CDI unit is defective. Replace. 7-19 ELEC 7-20 W W W 7-21 20 W W W W W W R W W W W B R WB BrL W 2 W W BrL WB W W 1 B B B GW GW WB GW LY LY LY B 28 B BrL GB Y P BrB BrW G BrL B R 4 B WB Br 18 BrL Br 3 6 R B BrL Y GB P G BrW BrB 5 B ON OFF 21 26 LW LW Br Br L L Y G B B 12V5W B A B B G Y OFF OFF RUN R Br BrB B BrB B B BrB B BrB B B LW 27 LY BY B GB B B B GB B B RB LB B GB GB B B B LY B B 12V10W B B B GW LY B B B B L B GY GY GY GY Br B L L LR Sb B 31 Or LB - - GW LY - 15 L LR Sb Sb LY BY GY 30 Sb Sb LY - B Or RB 16 GW LY 14 11 B BY GB B (BLUE) B B LY RB LB 12 12V10W LY B 13 GB GB B Br BrW BY GB B 12V10W BrB 12V10W BrB BrB B GB BrB R BrB L OFF N 23 ON Br BY LW BrW 19 BY RB BY RB GY Br GY Br P B GY 25 187 187 Br RB BrW Br L P Br B START 29 9 10 24 LW 8 12V60/55W G G A Y A L A L L G Y BrL Y LOW HIGH 22 RB B B RB Br RB LW R 7 R PARK RB L Br BrL R OFF ON Or RW 205 17 Y Ch Dg Br TURN HIGH NEU. ILL. B BrB GB Y BrSb 32 467C4B5CAMP403D494A4856 172320-2 B Y GB BrB B LRBr LR B MAIN HARNESS EXT. CORD R B RB LY B OrLW LY RB R LB GW LW Or HEAD LIGHT GW LB MAIN HARNESS G Y L B G B L Y A ELECTRICAL STARTING SYSTEM ELEC ELECTRICAL STARTING SYSTEM - CIRCUIT DIAGRAM ELECTRICAL STARTING SYSTEM ELEC The diagram illustrates the electrical starting system-circuit inside the motorcycles electric system. NOTE: For the colour code and legend, see page 7-2. (3) (4) (5) (6) (7) (9) (10) (11) (12) (13) (14) (15) Battery Starter relay Starting motor Fuse Main switch Engine stop switch Starter switch Diode Clutch switch Sidestand switch Neutral switch Diode 12 5 11 15 14 3 6 4 13 9 10 7 7-22 ELECTRICAL STARTING SYSTEM ELEC STARTING CIRCUIT OPERATION The starting circuit on this model consists of the starter motor, starter relay, and the starting circuit cut-off relay. If the engine stop switch is on “RUN” and the main switch is on “ON” (both switches are closed), the starter motor can operate only if: The transmission is in neutral (the neutral switch is closed). or if The clutch lever is pulled to the handlebar (the clutch switch is closed) and the sidestand is up (the sidestand switch is closed). The starting circuit cut-off relay prevents the starter from operating when neither of these conditions have been met. In this instance, the starting circuit cut-off relay is open so current cannot reach the starter motor. When at least one of the above conditions have been met however, the starting circuit cut-off relay is closed, and the engine can be started by pressing the starter switch. WHEN THE TRANSMISSION IS IN NEUTRAL WHEN THE SIDESTAND IS UP AND THE CLUTCH LEVER IS PULLED IN 1 2 3 4 5 6 7 8 9 0 7-23 Battery Main switch Engine stop switch Starter relay Starting circuit cut-off relay Start switch Starter motor Neutral switch Clutch switch Sidestand switch ELECTRICAL STARTING SYSTEM ELEC DIAGNOSTICS THE STARTER FAILS TO WORK Procedure Inspect: (1) Fuse (2) Battery (3) Starting motor (4) Starter relay (5) Main switch (6) Engine stop switch (7) Sidestand switch (8) Neutral switch (9) Clutch switch (10) Starter switch (11) Harness connections NOTE: Before starting inspections, remove the following parts: 1. Seat 2. Rear cowling • 3. Fuel tank 4. Cowling (headlight) To check for defects use the following special tools. Pocket tester: P/N. 90890-03112 1. Fuse. • Remove fuse. • Connect the pocket tester (Ω x 1) to the fuse. • Check the fuse for continuity. Refer to “CHECKING THE FUSES” in Chapter 3. DISCONTINUTY Replace the fuse. CONTINUITY INCORRECT 2. Battery. • Check the condition of the battery. Refer to “CHECKING AND CHARGING THE BATTERY” in Chapter 3. • • Min. open-circuit voltage: 12.8 V or more at 20°C (68°F) CORRECT * 7-24 Clean the battery terminals. Recharge or replace the battery. Refer to “BATTERY INSPECTION” in Chapter 3. ELECTRICAL STARTING SYSTEM ELEC * * WARNING 3. Starter • • A wire that is used as a jumper lead must have at least the same capacity of the battery lead, otherwise the jumper lead may burn. • This check is likely to produce sparks, therefore make sure that no flammable gas or fluid is in the vicinity. Connect the positive terminal of the battery (1) and the starter cable (2) using a connection cable (3) *. IT FAILS TO RUN • The starter is defective. Repair or replace. Check the functioning of the starter. IT RUNS 4. Starter relay. • • Disconnect the starter relay connector. Connect the battery and frame to the starter relay connector, using a connection cable (1) as shown. Battery terminal (+) (2) ➔ Red/Black terminal (3) Frame ➔ Blue/White terminal (4) IT FAILS TO RUN The starter relay is defective. Replace. • Check the functioning of the starter. IT RUNS * 7-25 ELECTRICAL STARTING SYSTEM ELEC * 5. Main switch • • Disconnect the main switch connector from the wire harness. Connect the pocket tester (Ω x 1) to the main switch cables. Refer to “SWITCH CHECK” in Chapter 3. ON OFF PARK INCORRECT Br L R Br L R The main switch is defective. Replace. CORRECT 6. Emergency stop engine switch. • • Disconnect the emergency stop engine switch connector (Brown, Green/Yellow and Red/Black) from the wire harness. Connect the pocket tester (Ω x 1) to the switch cables. Refer to “SWITCH CHECK” in Chapter 3. Tester terminal (+) ➔ Red/Black (1) cable Tester terminal (–) ➔ Brown cable (2) OFF RUN INCORRECT 1 2 Br GY RB The emergency stop engine switch is defective. Replace the right handlebar switch. Br GY RB CORRECT * 7-26 ELECTRICAL STARTING SYSTEM ELEC * 7. Sidestand switch. • • Disconnect the sidestand switch connector (Black and Black) from the wire harness. Connect the pocket tester (Ω x 1) to the sidestand switch cables. Refer to “SWITCH CHECK” in Chapter 3. Tester terminal (+) ➔ Black cable (1) Tester terminal (–) ➔ Black cable (2) B B UP DOWN INCORRECT B B 2 1 The sidestand switch is defective. Replace. CORRECT 8. Neutral switch. • • Disconnect the neutral switch cable (Sky blue). Connect the pocket tester (Ω x 1) to the neutral switch cables. Refer to “SWITCH CHECK” in Chapter 3. Tester terminal (+) ➔ Sky blue cable (1) Tester terminal (–) ➔ Earth Sb In gear Neutral INCORRECT Sb 1 The neutral switch is defective. Replace. CORRECT * 7-27 ELECTRICAL STARTING SYSTEM ELEC * 9. Clutch switch. • Disconnect the clutch switch connector from the harness. • Connect the pocket tester (Ω x 1) to the clutch switch cable. • Check the clutch switch component for continuity between “Black (1)” and “Black (2)”. Refer to “SWITCH CHECK” in Chapter 3. B B Release Hold INCORRECT 1 B B 2 The clutch switch is defective. Replace. CORRECT 10. Start switch. • Disconnect the start switch connector from the harness. • Connect the pocket tester (Ω x 1) to the handlebar switch terminal. • Check the start switch component for continuity between “Blue/White (1)” and “Black/Yellow (2)”. Refer to “SWITCH CHECK” in Chapter 3. L/W BY Free Pushed in INCORRECT LW BY 1 The start switch is defective. Replace the right handlebar switch. 2 CORRECT * 7-28 ELECTRICAL STARTING SYSTEM ELEC * 11. Harness connections. Check the connections of the entire starter system. See the “ELECTRIC CIRCUIT DIAGRAM”. UNCERTAIN CONNECTIONS Correct. 7-29 ELECTRICAL STARTING SYSTEM STARTER MOTOR ELEC BRUSH LENGHT LIMIT 5 mm (0.20 in) (1) Brushes (2) Armature (3) Stator (4) O-Ring COMMUTATOR WEAR LIMIT: 27 mm (1.06 in) MICA UNDERCUT: 0.7 mm (0.027 in) ARMATURE COIL RESISTANCE: 0.03 ~ 0.04 Ω at 20°C (68°F) 7-30 ELECTRICAL STARTING SYSTEM ELEC Removal 1. Remove: • The starter motor Refer to the “ENGINE REMOVAL” section in CHAPTER 5. Disassembly 1. Remove: • Circlip (1) • Drive gear (2) • Screws (3) • Rear bracket (4) • Washers (5) • Brushes housing (6) • Brushes (7) • Front bracket (8) • Washers (9) • Armature (10) • Stator (11) Inspection and repair 1. Inspect: • Manifold Dirty ➔ Clean with sandpaper no. 600. 2. Measure: • Diameter of the commutator Out of specification ➔ Replace the motor. Wear limit of commutator (a): 27 mm 3. Measure: • The mica undercut (b). Out of specification ➔ Level the undercut to the correct value using a hacksaw. Mica undercut (b): 0.7 mm NOTE: The mica insulation of the commutator must have an undercut to ensure proper functioning of the commutator. 7-31 ELECTRICAL STARTING SYSTEM ELEC 4. Inspect: • Armature coils (insulation/continuity). Out of specification ➔ Replace the motor. ▼▼▼▼▼▼▼▼▼▼▼▼▼▼▼▼▼▼▼▼▼▼▼▼▼▼▼▼▼ How to inspect the excitation coils: • Connect the pocket tester and check continuity (1) and insulation (2). Check the armature resistance: • Armature coil resistance: Continuity check (1): 0 Ω at 20°C (68°F) Insulation check (2): Over 1 MΩ at 20°C (68°F) • If the resistance is not correct, replace the starter motor. ▲▲▲▲▲▲▲▲▲▲▲▲▲▲▲▲▲▲▲▲▲▲▲▲▲▲▲▲▲ 5. Measure: • Brush lenght Out of specification ➔ Replace all brushes at once. Brush lenght limit (a): 5.0 mm 6. Inspect: • Brush spring strength Worn out ➔ Replace all springs at once. Brush spring strength: 8.82 N (899 gf) 7. Inspect: • Bearings (1) • Oil seal (2) • O-Rings • Bush (3) 7-32 ELECTRICAL STARTING SYSTEM ELEC Assembly Revert the disassembly procedure. Pay attention to the following points: 1. Install: • Brush housing NOTE: Align the jutting surface on the brush housing with the slot (2). 2. Install: • Stator (1) • Front bracket (2) NOTE: Align the reference marks (3) on the stator with the corresponding reference marks on the cover (4). 3. Install: • Screws (1) Screw (stator): 7 Nm (0.7 kgm) Installation 1. Install: • Starter motor. NOTE: Slightly grease the O-Ring (1) Screw (starter motor): 10 Nm (1.0 kgm) 7-33 ELEC 7-34 W W W 7-35 20 W W W W W W R W W W W B R WB BrL W 2 W W BrL WB W W 1 B B B GW GW WB GW LY LY LY B R 4 B 28 B BrL WB Br P GB Y Y GB B BrL G BrW BrB P BrB BrW G 5 B BrL B 18 BrL Br 3 6 R ON OFF 21 26 LW LW Br Br L Y G B B 12V5W B A B B G Y OFF OFF RUN R Br BrB B BrB B B BrB B BrB B B LW 27 LY BY B GB B B B GB B LB RB B GB GB B B B LY B B 12V10W B B B GW LY B B B B L B GY GY GY GY Br B L L LR Sb B 31 Or LB - - GW LY - 15 L LR Sb Sb LY BY GY 30 Sb Sb LY - B Or RB 16 GW LY 14 11 B B BY GB B (BLUE) B B LY RB LB 12 12V10W LY B 13 GB GB B Br BrW BY GB B 12V10W BrB 12V10W BrB BrB B GB BrB R BrB L OFF N 23 ON Br BY LW BrW 19 BY RB RB BY GY Br GY Br P B GY Br 25 187 187 RB BrW Br L P Br B START 29 9 10 24 LW 8 12V60/55W G G A Y A L A L L G Y BrL Y LOW HIGH 22 RB B B RB Br RB LW R L RB R PARK 7 L Br BrL R OFF ON Or RW 205 17 Y Ch Dg Br TURN HIGH NEU. ILL. B BrB GB Y BrSb 32 467C4B5CAMP403D494A4856 172320-2 B Y GB BrB B LRBr LR B MAIN HARNESS EXT. CORD R B RB LY B OrLW LY RB R LB GW GW LB HEAD LIGHT LW Or MAIN HARNESS G Y L B G B L Y A CHARGING SYSTEM ELEC CHARGING SYSTEM – CIRCUIT DIAGRAM ELEC CHARGING SYSTEM The diagram illustrates the charging circuit inside the motorcycles electric system. NOTE: For the colour code and legend, see page 7-2. (1) (2) (3) (6) AC generator/Pickup coil Rectifier/Regulator Battery Fuse 6 2 1 7-36 3 CHARGING SYSTEM ELEC DIAGNOSTICS THE BATTERY IS NOT BEING CHARGED Procedure Inspect: 1. Fuse 2. Battery 3. Charging voltage 4. Stator winding resistance 5. Harness connection (whole connection system) NOTE: Before starting inspections, remove the following parts: 1. Seat 2. Rear cowling • To check for defects use the following special tools. Inductive rev counter: P/N. 90890-03113 Pocket tester: P/N. 90890-03112 1. Fuse • • NO Check the fuse for continuity. Refer to “CHECKING THE FUSES” in Chapter 3. Is the fuse OK? Replace the fuse. YES 2. Battery • Check the condition of the battery. Refer to “CHECKING AND CHARGING THE BATTERY” in Chapter 3. NO Min. open-circuit voltage: 12.8 V or more at 20°C (68°F) • • • Is the battery OK? YES * 7-37 Clean the battery terminals. Recharge or replace the battery. CHARGING SYSTEM * 3. Charging voltage • Connect the inductive rev counter to the spark plug cable. • Connect the pocket tester (DC 20V) to the battery, as shown. Tester terminal (+) ➔ Battery terminal (+) Tester terminal (-) ➔ Battery terminal (-) • • Start the engine and rev to about 5,000 rpm. Check the charging voltage. IN COMPLIANCE WITH SPECIFICATIONS Charging voltage: 14.0V at 5,000 rpm NOTE: Use a fully charged battery. Replace the battery. OUT OF SPECIFICATIONS 4. Stator coil resistance. • Disconnect the AC generator connector from the harness. • Connect the pocket tester (Ω x 1) to the stator coils. Stator coils (1) Tester terminal (+) ➔ White cable (1) Tester terminal (-) ➔ White cable (2)) 7-38 ELEC CHARGING SYSTEM ELEC Stator coils (2) Tester terminal (+) ➔ White cable (1) Tester terminal (-) ➔ White cable (3) 2 3 W W W 1 • Check that the winding resistance of the stator complies with specifications. Stator coil resistance: White (1) – White (2) 0.65 Ω ± 20% at 20°C (68°F) White (1) – White (3) 0.65 Ω ± 20% at 20°C (68°F) OUT OF SPECIFICATIONS Stator winding is defective. Replace. IN COMPLIANCE WITH SPECIFICATIONS 5. Wiring connections. • UNCERTAIN CONNECTIONS Check the connections of the entire charging system. Refer to “ELECTRICAL CIRCUIT DIAGRAM” section. Correct. CORRECT The rectifier/regulator is defective. Replace. 7-39 ELEC 7-40 W W W 7-41 20 W W W W W W R W W W W B R WB BrL W 2 W W BrL WB W W 1 B B B GW GW WB GW LY LY LY B 28 B BrL GB Y P BrB BrW G BrL B R 4 B WB Br 18 BrL Br 3 6 R B BrL Y GB P G BrW BrB 5 B ON OFF 21 26 LW LW Br Br L Y G B B 12V5W B A B B G Y OFF OFF RUN R Br BrB B BrB B B BrB B BrB B B LW 27 LY BY B GB B B B GB B LB RB B GB GB B B B LY B B 12V10W B B B GW LY B B B B L B GY GY GY GY Br B L L LR Sb B 31 Or LB - - GW LY - 15 L LR Sb Sb LY BY GY 30 Sb Sb LY - B Or RB 16 GW LY 14 11 B B BY GB B (BLUE) B B LY RB LB 12 12V10W LY B 13 GB GB B Br BrW BY GB B 12V10W BrB 12V10W BrB BrB B GB BrB R BrB L OFF N 23 ON Br BY LW BrW 19 BY RB RB BY GY Br GY Br P B GY Br 25 187 187 RB BrW Br L P Br B START 29 9 10 24 LW 8 12V60/55W G G A Y A L A L L G Y BrL Y LOW HIGH 22 RB B B RB Br RB LW R L RB R PARK 7 L Br BrL R OFF ON Or RW 205 17 Y Ch Dg Br TURN HIGH NEU. ILL. B BrB GB Y BrSb 32 467C4B5CAMP403D494A4856 172320-2 B Y GB BrB B LRBr LR B MAIN HARNESS EXT. CORD R B RB LY B OrLW LY RB R LB GW GW LB HEAD LIGHT LW Or MAIN HARNESS G Y L B G B L Y A LIGHT SYSTEM ELEC LIGHT SYSTEM - CIRCUIT DIAGRAM ELEC LIGHT SYSTEM The diagram shows the light system circuit inside the electric system of the motorcycle. NOTE: For the colour codes and complete legend, see page 7-2. (3) Battery (6) Fuse (7) Main switch (18) Left handlebar switch (20) Diode (21) Pass switch (22) Dimmer switch (26) Headlight (28) Relay assy (31) Tail/stop light (32) Meter 18 21 22 28 3 6 26 20 32 7 7-42 31 LIGHT SYSTEM ELEC DIAGNOSTICS THE HIGH BEAM LIGHT, PARKING INDICATOR LIGHT, REAR LIGHT, FRONT PARKING LIGHT AND/OR INSTRUMENT LIGHTS FAIL TO TURN ON. Procedure Inspect: 1. Fuse 2. Battery 3. Main switch 4. Dipped/high beam light and dimmer switch 5. Relay assy 6. Harness connections (full system of connections) NOTE: • Before starting inspections, remove the following parts: 1. Seat 2. Rear cowling 3. Cowling (headlight) 4. Tail light cover • To check for defects use the following special tools. Pocket tester: P/N. 90890-03112 1. Fuse • • NO Check the fuse for continuity. Refer to “CHECKING THE FUSES” in Chapter 3. Is the fuse OK? Replace the fuse. YES 2. Battery • Check the condition of the battery. Refer to “CHECKING AND CHARGING THE BATTERY” in Chapter 3. NO Min. open-circuit voltage: 12.8 V or more at 20°C (68°F) • • • Is the battery OK? YES * 7-43 Clean the battery terminals. Recharge or replace the battery. LIGHT SYSTEM ELEC * 3. Main switch. • • Disconnect the main switch connector from the wire harness. Connect the pocket tester (Ω x 1) to the switch cables. Refer to “SWITCH CHECK” in CHAPTER 3. ON OFF PARK INCORRECT Br L R Br L R The main switch is defective. Replace. CORRECT 4. Dipped/high beam commutator and dimmer switch. • • • Disconnect the left handlebar switch connector from the wire harness. Connect the pocket tester (Ω x 1) to the left handlebar switch terminals. Check the switch component for continuity between “Brown (1)” and “Yellow (2)”, “Brown/Blue (3)” and “Green (4)”, “Brown/Blue (3)” and “Yellow (2)”. Refer to “SWITCH CHECK” in CHAPTER 3. 4 3 G BrW BrB P B BrL Y GB 2 BrL Br OFF ON INCORRECT HIGH LOW Y The dipped/high beam commutator and/or the dimmer switch are defective. Replace the left handlebar switch. G CORRECT * 7-44 LIGHT SYSTEM ELEC * 5. Starter circuit cut-off relay. • Connect the pocket tester (DC 20V) and the battery (12V) to the cut-off relay connector terminal of the starter circuit. Battery terminal (+) ➔ White/Black terminal (1) Battery terminal (–) ➔ Black terminal (2) Tester terminal (+) ➔ Brown terminal (3) Tester terminal (–) ➔ Earth DISCONTINUITY The starter circuit cut-off relay is defective. Replace. • • Turn the main switch to ON. Check the voltage (12V) on the “Brown/Blue” and “Brown” cable to the connector terminal of the starter circuit cut-off relay. IN COMPLIANCE WITH SPECIFICATIONS (12V) DEFECTIVE CONNECTIONS 6. Harness connections. • Check the connections of the entire light system. Repair. CORRECT Check the conditions of each circuit for the entire light system. See the “ELECTRIC CIRCUIT DIAGRAM”. 7-45 LIGHT SYSTEM ELEC LIGHT SYSTEM INSPECTION NOTE: To proceed to the control of the light system, start the engine and then stop it by the emergency engine stop switch. In this way the light relay remains excited and it is possible to check the light system. 1. The front headlight and the high beam light fail to turn on. DISCONTINUITY 1. Bulb and bulbholder. • Check the continuity of the bulb and bulbholder. Refer to “BULB INSPECTION” section. Replace the bulb and/or the bulbholder. CONTINUITY 2. Voltage. • Connect the pocket tester (DC 20V) to the front headlight connectors and the high beam switch. Headlight: Tester terminal (+) ➔ Green (2) or Yellow (1) cable Tester terminal (–) ➔ Black cable (3) High beam light: Tester terminal (+) ➔ Yellow cable (4) Tester terminal (–) ➔ Black cable (5) A OUT OF SPECIFICATION The circuit from the main switch to the bulbholder connector is defective. Repair. B [A] When the lights switch (commutator) is at position “HI”. [B] When the lights switch (commutator) is at position “LO”. 7-46 LIGHT SYSTEM • • • ELEC Turn the main switch to ON. Turn the lights switch to “LO” or “HI”. Check the voltage (12V) on the “Green” and “Yellow” cable at the bulbholder terminals. IN COMPLIANCE WITH SPECIFICATIONS (12V) The circuit is efficient. 2. The instrument light and/or the parking indicator light fails to turn on. DISCONTINUITY 1. Bulb and bulbholder. • Check the continuity of the bulb and bulbholder. Refer to “BULB INSPECTION” section. Replace the bulb and/or the bulbholder. CONTINUITY 2. Voltage. • Connect the pocket tester (DC 20V) to the bulbholder connector. Tester terminal (+) ➔ Blue cable (1) Tester terminal (–) ➔ Black cable (2) OUT OF SPECIFICATION • • The circuit from the main switch to the bulbholder connector is defective. Repair. Turn the main switch to ON. Check the voltage (12V) on the “Blue” cable of the bulbholder connector. IN COMPLIANCE WITH SPECIFICATIONS (12V) The circuit is efficient. 7-47 LIGHT SYSTEM ELEC 3. The parking light fails to turn on. DISCONTINUITY 1. Bulb and bulbholder. • Check the continuity of the bulb and bulbholder. Refer to “BULB INSPECTION” section. Replace the bulb and/or bulbholder. CONTINUITY 2. Voltage. • Connect the pocket tester (DC 20V) to the bulbholder connector. Tester terminal (+) ➔ Blue terminal (1) Tester terminal (–) ➔ Black terminal (2) OUT OF SPECIFICATION • • The circuit from the main switch to the bulbholder connector is defective. Repair. Turn the main switch to ON. Check the voltage (12V) on the “Blue” cable of the bulbholder connector. IN COMPLIANCE WITH SPECIFICATIONS (12V) The circuit is efficient. 7-48 LIGHT SYSTEM ELEC 4. The rear light fails to turn on. DISCONTINUITY 1. Bulb and bulbholder. • Check the continuity of the bulb and bulbholder. Refer to “BULB INSPECTION” section. Replace the bulb and/or bulbholder. CONTINUITY 2. Voltage. • Connect the pocket tester (DC 20V) to the bulbholder connector. Tester terminal (+) ➔ Blue terminal (1) Tester terminal (–) ➔ Black terminal (2) OUT OF SPECIFICATION • • The circuit from the main switch to the bulbholder connector is defective. Repair. Turn the main switch to ON. Check the voltage (12V) on the “Blue” cable of the bulbholder connector. IN COMPLIANCE WITH SPECIFICATIONS (12V) The circuit is efficient. 7-49 ELEC 7-50 W W W 7-51 20 W W W W W W R W W W W B R WB BrL W 2 W W BrL WB W W 1 B B B GW GW WB GW LY LY LY B 28 B BrL GB Y P BrB BrW G BrL B R 4 B WB Br 18 BrL Br 3 6 R B BrL Y GB P G BrW BrB 5 B ON OFF 21 26 LW LW Br Br L Y G B B 12V5W B A B B G Y OFF OFF RUN R Br BrB B BrB B B BrB B BrB B B LW 27 LY BY B GB B B B GB B LB RB B GB GB B B B LY B B 12V10W B B B GW LY B B B B L B GY GY GY GY Br B L L LR Sb B 31 Or LB - - GW LY - 15 L LR Sb Sb LY BY GY 30 Sb Sb LY - B Or RB 16 GW LY 14 11 B B BY GB B (BLUE) B B LY RB LB 12 12V10W LY B 13 GB GB B Br BrW BY GB B 12V10W BrB 12V10W BrB BrB B GB BrB R BrB L OFF N 23 ON Br BY LW BrW 19 BY RB RB BY GY Br GY Br P B GY Br 25 187 187 RB BrW Br L P Br B START 29 9 10 24 LW 8 12V60/55W G G A Y A L A L L G Y BrL Y LOW HIGH 22 RB B B RB Br RB LW R L RB R PARK 7 L Br BrL R OFF ON Or RW 205 17 Y Ch Dg Br TURN HIGH NEU. ILL. B BrB GB Y BrSb 32 467C4B5CAMP403D494A4856 172320-2 B Y GB BrB B LRBr LR B MAIN HARNESS EXT. CORD R B RB LY B OrLW LY RB R LB GW GW LB HEAD LIGHT LW Or MAIN HARNESS G Y L B G B L Y A SIGNAL SYSTEM ELEC SIGNAL SYSTEM - CIRCUIT DIAGRAM SIGNAL SYSTEM ELEC The diagram shows the signal system circuit inside the electric system of the motorcycle. NOTE: For the colour codes and complete legend, see page 7-2. (23) Flasher switch (24) Horn (25) Flasher relay (27) Flasher light (29) Front brake switch (30) Rear brake switch (31) Tail/stop light (32) Meter (3) Battery (6) Fuse (7) Main switch (11) Diode (14) Neutral switch (15) Diode (18) Left handlebar switch (19) Horn switch 18 19 23 25 3 6 27 11 15 14 29 31 32 24 7 30 7-52 27 SIGNAL SYSTEM ELEC DIAGNOSTICS • THE FLASHER LIGHTS, BRAKE LIGHT AND/OR WARNING LIGHTS FAIL TO TURN ON. • THE HORN FAILS TO SOUND. Procedure Check: 1. Fuse 2. Battery 3. Main switch 4. Harness connections (entire system of connections) NOTE: • Before starting inspections, remove the following parts: 1. Seat 2. Rear cowling 3. Cowling (headlight) 4. Tail light cover • To check for operating faults use the following special tools. Pocket tester: P/N. 90890-03112 1. Fuse • • NO Check the fuse for continuity. Refer to “CHECKING THE FUSES” in Chapter 3. Is the fuse OK? Replace the fuse. YES 2. Battery. • Check the condition of the battery. Refer to “CHECKING AND CHARGING THE BATTERY” in Chapter 3. NO Min. open-circuit voltage: 12.8 V or more at 20°C (68°F) • • • Is the battery OK? YES * 7-53 Clean the battery terminals. Recharge or replace the battery. SIGNAL SYSTEM ELEC * 3. Main switch. • • Disconnect the main switch connector (Blue, Red and Brown) from the wire harness. Connect the pocket tester (Ω x 1) to the main switch cables. Refer to “SWITCH CHECK” section. Tester terminal (+) ➔ Red cable (1) Tester terminal (–) ➔ Brown cable (2) Tester terminal (–) ➔ Blue cable (3) ON OFF PARK 3 L Br 2 DISCONTINUITY R 1 Br L R The main switch is defective. Replace. CORRECT UNCERTAIN CONNECTIONS 4. Harness connections • Check the connections of the entire signal system. Repair. CORRECT Check the condition of each signal system. Refer to “ELECTRICAL CIRCUIT DIAGRAM” section. 7-54 SIGNAL SYSTEM ELEC SIGNAL SYSTEM CONTROL 1. The horn does not work. 1. Horn switch. • • • Disconnect the left handlebar switch connector from the wire harness. Connect the pocket tester (Ω x 1) to the switch terminals. Check the switch component for continuity between “Pink (1)” and “Black (2)”. Refer to “SWITCH CHECK” section. P B OFF ON DISCONTINUITY 1 G BrW BrB P 2 B BrL The horn switch is defective. Replace the left handlebar switch. Y GB CORRECT 2. Voltage. • Connect the pocket tester (DC 20V) to the horn cable. Tester terminal (+) ➔ Brown terminal (1) Tester terminal (–) ➔ Earth OUT OF SPECIFICATIONS • • The circuit from the main switch to the horn terminal is defective. Repair. Turn the main switch to ON. Check the voltage (12V) on the “Brown” terminal of the horn. IN COMPLIANCE WITH SPECIFICATIONS (12V) * 7-55 SIGNAL SYSTEM ELEC * 3. Horn. • • • Disconnect the “Pink” cable from horn terminal. Connect a special cable (1) to the horn terminal and earth the cable. Turn the main switch to ON. THE HORN WORKS The horn is efficient. THE HORN DOES NOT WORK 4. Voltage. • Connect the pocket tester (DC 20V) to the “Pink” terminal of the horn. Tester terminal (+) ➔ Pink cable (1) Tester terminal (–) ➔ Earth OUT OF SPECIFICATION The horn is defective. Repair. • • Turn the main switch to ON. Check the voltage (12V) on the “Pink” terminal of the horn. IN COMPLIANCE WITH SPECIFICATIONS (12V) Repair or replace the horn. 7-56 SIGNAL SYSTEM ELEC 2. The rear stop light fails to turn on. DISCONTINUITY 1. Bulb and bulbholder. • Check the continuity of the bulb and bulbholder. Refer to “BULB INSPECTION” section. Replace the bulb and/or bulbholder. CONTINUITY 2. Brake switch. • • • Disconnect the brake switch cables and the connector from the wire harness. Connect the pocket tester (Ω x 1) to the brake switch terminals. Check the switch component for continuity between “Green/Yellow (1)” and “Brown (2)”, or “Black (3)” and “Black (4)”. Refer to “SWITCH CHECK” section. A Br G/Y OFF (Free) ON (Pull in) Br G/Y RW 1 2 B B B B B ON (Step down) OFF (Free) 3 4 G/Y INCORRECT Br [A] Front brake switch [B] Rear brake switch The brake switch is defective. Replace. * 7-57 SIGNAL SYSTEM ELEC * 3. Voltage. • Connect the pocket tester (DC 20V) to the bulbholder connector. Tester terminal (+) ➔ Green/Yellow cable (1) Tester terminal (–) ➔ Black terminal (2) OUT OF SPECIFICATION • • • The circuit from the main switch to the bulbholder connector is defective. Repair. Turn the main switch to ON. The brake lever is pulled or the brake pedal is pressed. Check the voltage (12V) on the “Green/Yellow” cable of the bulbholder connector. IN COMPLIANCE WITH SPECIFICATIONS (12V) The circuit is efficient. 3. The direction indicator light and/or the direction indicator light fail to flash. DISCONTINUITY 1. Bulb and bulbholder. • Check the continuity of the bulb and bulbholder. Refer to “BULB INSPECTION” section. Replace the bulb and/or bulbholder. CONTINUITY 2. Direction indicator switch. • • Disconnect the left handlebar switch connector from the wire harness. Connect the pocket tester (Ω x 1) to the left handlebar switch cables. 7-58 SIGNAL SYSTEM • ELEC Check the switch component for continuity between “Brown/White (1)” and “Brown/Black (2)” and “Brown/White (1)” and “Green/Black (3)”. Refer to “SWITCH CHECK” section. 1 3 2 G BrW BrB P B BrL Y GB INCORRECT L N R The direction indicator switch is defective. Replace. CORRECT 3. Direction indicator lamp relay. • Connect the pocket tester (DC 20V) to the indicator lamp relay. Tester terminal (+) ➔ Brown terminal (1) Tester terminal (–) ➔ Earth OUT OF SPECIFICATION • • Turn the main switch to ON. Check the voltage (12V) on the “Brown” cable to the indicator lamp relay terminal. The circuit from the main switch to the lamp relay connector is defective. Repair. IN COMPLIANCE WITH SPECIFICATIONS (12V) * 7-59 SIGNAL SYSTEM ELEC * 4. Voltage. • Connect the pocket tester (DC 20V) to the bulbholder connector. Tester terminal (+) ➔ Brown/White terminal (1) Tester terminal (–) ➔ Earth OUT OF SPECIFICATION • • The direction indicator lamp relay is defective. Replace. Turn the main switch to ON. Check the voltage (12V) on the “Blue” cable to the bulbholder connector. IN COMPLIANCE WITH SPECIFICATIONS (12V) * 7-60 SIGNAL SYSTEM ELEC * 5. Voltage. • • Connect the pocket tester (DC 20V) to the bulbholder connector. Connect the left handlebar switch connector to the wire harness. To the left flasher light: Tester terminal (+) ➔ Green/Black terminal (1) Tester terminal (–) ➔ Earth To the right flasher light: Tester terminal (+) ➔ Brown/Black terminal (1) Tester terminal (–) ➔ Earth OUT OF SPECIFICATION GB BrB The circuit from the direction indicator switch to the bulbholder is defective. Repair. • • • Turn the main switch to ON. Turn the direction indicator switch to “L” or “R”. Check the voltage (it flashes at 2-8V) on the “Green/Black” or “Brown/Black” cable at the bulbholder connector. IN COMPLIANCE WITH SPECIFICATIONS (12V) The circuit is efficient. 7-61 SIGNAL SYSTEM ELEC 4. The “N” neutral light fails to turn on. DISCONTINUITY 1. Bulb and bulbholder. • Check the continuity of the bulb and bulbholder. Refer to “BULB INSPECTION” section. Replace the bulb and/or bulbholder. CONTINUITY 2. Neutral switch. • • • Disconnect the neutral switch cable from the wire harness. Connect the pocket tester (Ω x 1) to the neutral switch cables. Check the switch component for continuity between “Sky blue (1)” and “earth”. Refer to “SWITCH CHECK” section. Sb In gear Neutral INCORRECT Sb 1 The neutral switch is defective. Replace. CORRECT 3. Voltage. • Connect the pocket tester (DC 20V) to the bulbholder connector. Tester terminal (+) ➔ Brown cable (1) Tester terminal (–) ➔ Earth 1 Br Y BrB LR B GB LR B GB Br Y BrB 7-62 SIGNAL SYSTEM • • Turn the main switch to ON. Check the voltage (12V) on the Brown cable of the bulbholder connector. IN COMPLIANCE WITH SPECIFICATIONS (12V) ELEC OUT OF SPECIFICATION The circuit from the main switch to the bulbholder connector is defective. Repair. 4. Neutral switch cable. • • Disconnect the neutral switch connector from the wire harness and the bulbholder connector. Connect the pocket tester (Ω x 1) to the neutral switch cable (on the harness side) and the bulbholder connector (1). DISCONTINUITY The circuit from the bulb to the neutral switch cable is defective. Repair. CONTINUITY The circuit is efficient. 7-63 ELEC 7-64 ? TRBL SHTG 8 ? TRBL SHTG CHAPTER 8° TROUBLESHOOTING FAILURE TO START/DIFFICULTIES IN STARTING FUEL SYSTEM . . . . . . . . . . . . . . . . . . . . . . . . ELECTRICAL SYSTEM . . . . . . . . . . . . . . . . . . POOR ENGINE COMPRESSION . . . . . . . . . . . . . . . . . . . . . . . . . . . . . . . . . . . . . . . . . . . . . . . . . . . . . . . . . . . . . . . . . . . . . . . . . . . . . . . . . . . . . . . . . . . . . . . . . . . . . . . . . . . . . . . . . . . . . . . . . . . 8-1 8-1 8-2 8-2 POOR PERFORMANCE AT IDLE SPEED . . . . . . . . . . . . . . . . . . . . . . . . . . . . . . . . . . . 8-3 UNSATISFACTORY PERFORMANCE AT MEDIUM-HIGH SPEED . . . . . . . . . . . . . . . . . 8-3 DIFFICULTIES IN SHIFTING . . . . . . . . . . SHIFTING IMPOSSIBLE . . . . . . . . . . THE SHIFT PEDAL FAILS TO MOVE DISENGAGING GEARS . . . . . . . . . . . . . . . . . . . . . . . . . . . . . . . . . . . . . . . . . . . . . . . . . . . . . . . . . . . . . . . . . . . . . . . . . . . . . . . . . . . . . . . . . . . . . . . . . . . . . . . . . . . . . . . . . . . . . . . . . . . . . . . . . . . . . . . . . . . . . . . . . . . . . . 8-4 8-4 8-4 8-4 CLUTCH SLIDES OR FAILS TO RELEASE . . . . . . . . . . . . . . . . . . . . . . . . . . . . . . . . . . 8-5 CLUTCH SLIDES . . . . . . . . . . . . . . . . . . . . . . . . . . . . . . . . . . . . . . . . . . . . . . . . . . 8-5 CLUTCH FAILS TO RELEASE . . . . . . . . . . . . . . . . . . . . . . . . . . . . . . . . . . . . . . . . . 8-5 DEFECTIVE BRAKES . . . . . . . . . . . . . . . . . . . . . . . . . . . . . . . . . . . . . . . . . . . . . . . . . . . 8-6 POOR BRAKING . . . . . . . . . . . . . . . . . . . . . . . . . . . . . . . . . . . . . . . . . . . . . . . . . . . 8-6 OIL LEAKS OR MALFUNCTIONING OF FRONT FORK . . . . . . . . . . . . . . . . . . . . . . . . . 8-6 OIL LEAKS . . . . . . . . . . . . . . . . . . . . . . . . . . . . . . . . . . . . . . . . . . . . . . . . . . . . . . . 8-6 MALFUNCTIONING . . . . . . . . . . . . . . . . . . . . . . . . . . . . . . . . . . . . . . . . . . . . . . . . . 8-6 UNSTABLE STEERING . . . . . . . . . . . . . . . . . . . . . . . . . . . . . . . . . . . . . . . . . . . . . . . . . 8-7 DEFECTIVE FUNCTIONING OF LIGHTS AND INDICATORS . . POOR HEADLIGHT ILLUMINATION . . . . . . . . . . . . . . . . . FREQUENT BURNING OF BULB . . . . . . . . . . . . . . . . . . . DIRECTION INDICATORS FAIL TO TURN ON . . . . . . . . . . DIRECTION INDICATORS FAIL TO TURN OFF . . . . . . . . . DELAYED TURNING ON OF INDICATORS . . . . . . . . . . . . EXCESSIVE INDICATOR INTERMITTENCE FREQUENCY THE HORN FAILS TO WORK . . . . . . . . . . . . . . . . . . . . . . . . . . . . . . . . . . . . . . . . . . . . . . . . . . . . . . . . . . . . . . . . . . . . . . . . . . . . . . . . . . . 8-8 . . . . . . . . . . . . . 8-8 . . . . . . . . . . . . . 8-8 . . . . . . . . . . . . . 8-8 . . . . . . . . . . . . . 8-8 . . . . . . . . . . . . . 8-9 . . . . . . . . . . . . . 8-9 . . . . . . . . . . . . . 8-9 OVERHEATING OF ENGINE . . . . . . . . . . . . . . . . . . . . . . . . . . . . . . . . . . . . . . . . . . . . . 8-9 TRBL SHTG ? FAILURE TO START/ DIFFICULTIES IN STARTING TRBL SHTG ? TROUBLESHOOTING NOTE: The troubleshooting tables that follow do not identify every cause of trouble. They may however prove helpful as a guide to identifying trouble. To inspect, adjust or replace parts, refer to the appropriate section in the manual. FAILURE TO START/DIFFICULTIES IN STARTING FUEL SYSTEM PROBABLE CAUSES Fuel tank • • • • Empty Fuel filter obstructed Fuel tank air cap passage obstructed Petrol contains water or impurities or is adulterated Fuel cock • • Hose obstructed Fuel filter obstructed Carburetor • • • • • • • • • • • Petrol contains water or impurities or is adulterated Pilot jet obstructed Pilot air passage obstructed Infiltrations of air Deformation of float Needle valve worn or scratched Needle valve seat insufficiently sealed Fuel level set wrongly Pilot jet set wrongly Starter jet obstructed Malfunctioning of the starter piston Air filter • Air filter element obstructed 8-1 FAILURE TO START/ DIFFICULTIES IN STARTING ELECTRICAL SYSTEM TRBL SHTG ? PROBABLE CAUSES Spark plug • • • • • Electrodes gap not correct Electrodes worn Feed cable interrupted Wrong thermal grading of spark plug Defective spark plug cap Ignition coil • • • Primary or secondary winding interrupted High voltage cable defective Defective coil Ignition unit • • • Defective unit Defective pick-up coil Woodruff key broken Switches and cables • • • • • • • Main switch defective Emergency stop engine switch defective Harness with cable interrupted Neutral switch defective Sidestand switch defective Clutch switch defective Starter switch defective Starter motor • Starter motor defective • Starter motor relay defective • Diodes defectives • Starter one-way bearing defective POOR ENGINE COMPRESSION PROBABLE CAUSES Cylinder and cylinder head • • • • • Spark plug tightening insufficiently Cylinder head or cylinder insufficiently tightened Cylinder head gasket broken Cylinder gasket broken Cylinder worn, damaged or seized Piston and piston rings • • • • Piston Piston Piston Piston Crankcase and valves, crankshaft • • • • • • • • Poor crankcase sealing Crankshaft oil seal edge damaged Poor valve sealing Valve and seat with insufficient contact Valve timing wrongly Valve spring broken Crankshaft seized Camshaft seized 8-2 rings wrongly assembled rings worn, yielded or broken rings stuck together seized or damaged POOR PERFORMANCE AT IDLE SPEED/ UNSATISFACTORY PERFORMANCE AT MEDIUM-HIGH SPEED POOR PERFORMANCE AT IDLE SPEED Carburetor Valves ? PROBABLE CAUSES • • • • • • • Electrical system TRBL SHTG The starter piston fails to return freely Pilot jet obstructed or loose Pilot jet obstructed Pilot air screw wrongly set Idle speed wrongly set (throttle valve stop screw) Throttle cable free play wrongly set Carburetor flooded • • • • • Defective battery • Valve clearance wrongly set Defective spark plug Defective ignition unit Defective AC magneto Defective ignition coil UNSATISFACTORY PERFORMANCE AT MEDIUM-HIGH SPEED See “FAILURE TO START/DIFFICULTIES IN STARTING”. (FUEL SYSTEM, ELECTRICAL SYSTEM, COMPRESSION SYSTEM and Valve clearance) PROBABLE CAUSES Carburetor Air filter • • • • • • • • • • Petrol contains water or impurities or is adulterated • Air filter element obstructed 8-3 Infiltrations of air Deformation of float Defective diaphragm Needle valve worn or scratched Needle valve seat insufficiently sealed Needle stop position incorrect Fuel level set wrongly Main jet obstructed or loose Main nozzle obstructed or loose DIFFICULTIES IN SHIFTING TRBL SHTG ? DIFFICULTIES IN SHIFTING PROBABLE CAUSES SHIFTING IMPOSSIBLE • • • Clutch • • • • • • • • • • • • Engine oil THE SHIFT PEDAL FAILS TO MOVE Clutch cable wrongly set Wrong position of push lever Irregular engagement of push lever and push rod Pressure plate deformed Clutch springs not preloaded uniformly Reference marks not aligned Push rod broken Clutch gear assy nut loose or push rod deformed Primary driven gear bearing defective Driven plates deformed Driving plates deformed Clutch cable damaged Oil level over maximum Incorrect gradation (high viscosity) Degradation PROBABLE CAUSES Shift shaft • Shift shaft deformed Shift cam, shift fork • • • Groove with impurities or foreign bodies • • • Transmission gears struck Transmission DISENGAGING GEARS Shift fork stuck Shift fork guide bar deformed Gears stuck by impurities or foreign bodies Wrong transmission assembly PROBABLE CAUSES • • Shift lever set wrongly Shift fork • Shift forks worn Shift cam • • Shaft cam with thrust free play • Gear clutches worn Shift shaft Transmission 8-4 Shift cam stop lever fails to return freely Shift cam groove worn CLUTCH SLIDES OR FAILS TO RELEASE TRBL SHTG CLUTCH SLIDES OR FAILS TO RELEASE CLUTCH SLIDES Clutch Engine oil PROBABLE CAUSES • • • • • • • • • CLUTCH FAILS TO RELEASE Refer to “SHIFTING IMPOSSIBLE” section. 8-5 Clutch cable wrongly set Clutch springs loose Clutch spring yielded Friction plates worn Clutch plates worn Clutch improperly assembled Oil level below minimum Incorrect gradation (low viscosity) Degradation ? DEFECTIVE BRAKES/ OIL LEAKS OR MALFUNCTIONING OF FRONT FORK TRBL SHTG ? DEFECTIVE BRAKES POOR BRAKING PROBABLE CAUSES • • • • • • • • • • • Brake pads worn Brake disc worn Water in the brake fluid Brake fluid leak Brake fluid tank defective Bleed cap not sealed to calipers Union bolt loose Brake hose cracked Brake disc dirty or greasy Brake pads dirty or greasy Incorrect brake fluid level OIL LEAKS OR MALFUNCTIONING OF FRONT FORK OIL LEAKS PROBABLE CAUSES • • • • • • • MALFUNCTIONING Inner tube deformed, damaged or rusty Outer tube damaged or cracked Oil seal lip damaged Oil seal assembled incorrectly Oil level incorrect (excessive) Shock-absorber rod stop bolt loose O-ring on cap bolt broken PROBABLE CAUSES • • • • • • • 8-6 Inner tube deformed, damaged or rusty Outer tube deformed or damaged Fork spring damaged Piston worn or damaged Shock-absorber rod deformed or damaged Incorrect oil viscosity Incorrect oil level UNSTABLE STEERING TRBL SHTG ? UNSTABLE STEERING PROBABLE CAUSES Handlebar • Assembled crooked or incorrectly Steering • • • Handlebar crown assembled incorrectly Front fork Tyres Wheels Frame Rear arm Rear shock absorber Drive chain Lower bracket crooked Lower steering column installed incorrectly (threaded ring nuts not tightened correctly) • Bearing or bearing tracks damaged • • • Oil level not the same in both tubes • • • Tyre pressure incorrect for type of road • • • • • Wheels balanced incorrectly • • • Deformed • • Bushes or bearings consumed • • • Spring yielded • Chain set incorrectly 8-7 Spring broken Front fork crooked Tyre pressure incorrect Tyres worn non-uniformly Wheel deformed Bearing loose Wheel axle deformed or loose Wheels excessively off-centre Head tube damaged Ball track installed incorrectly Deformed or damaged Spring preloaded Oil leak DEFECTIVE FUNCTIONING OF LIGHTS AND INDICATORS TRBL SHTG ? DEFECTIVE FUNCTIONING OF LIGHTS AND INDICATORS HEADLIGHT DOES NOT LIGHT PROBABLE CAUSES • • • • • • • FREQUENT BURNING OF BULB Difficulties in charging (charging coil broken and/or rectifier/regulator defective) Uncertain connections Wrong negative earthing Insufficient contacts (main switch) Bulb gone Light relay/diode defective Incorrect bulb Rectifier/regulator defective Wrong negative earthing Main switch defective Bulbs gone PROBABLE CAUSES • • • • • • • DIRECTION INDICATORS FAIL TO TURN OFF Excessive absorption of electrical accessories PROBABLE CAUSES • • • • • • DIRECTION INDICATORS FAIL TO TURN ON Incorrect bulb Wrong negative earthing Battery flat Defective direction indicator switch Indicator lamp relay defective Harness cut off Connector loose Bulb gone PROBABLE CAUSES • • • • 8-8 Indicator lamp relay defective Insufficient battery capacity (battery almost flat) Bulb (front or rear) burnt out Direction indicator switch defective DEFECTIVE FUNCTIONING OF LIGHTS AND INDICATORS/ OVERHEATING OF ENGINE DELAYED TURNING ON OF INDICATORS TRBL SHTG ? PROBABLE CAUSES • • • • Indicator lamp relay defective Insufficient battery capacity (battery almost flat) Incorrect bulb Main switch or direction indicator switch defective EXCESSIVE INDICATOR INTERMITTENCE FREQUENCY PROBABLE CAUSES • • THE HORN FAILS TO WORK Indicator lamp relay defective PROBABLE CAUSES • • • • • OVERHEATING OF ENGINE Incorrect bulb Battery flat Main switch or horn switch defective Horn wrongly set Defective horn Harness cut off PROBABLE CAUSES • • • Incorrect electrode gap of spark plug • • • Incorrect carburetor main jet (incorrect setting) Air filter element obstructed Engine compression • Excess of carbon deposits Engine oil • • • Incorrect oil level • Pads fail to return freely (remains blocked) Ignition system Fuel feed system Brake 8-9 Spark plug thermal gradation wrong Ignition unit defective Incorrect fuel level Incorrect oil viscosity Incorrect oil gradation TRBL SHTG ? ELECTRICAL SYSTEM DIAGRAM TT600RE WIRING DIAGRAM LY LY GW GW LY GW Br L L Br R LY W W W ON OFF PARK GW W B W W B W Or RB LY W GW W R 1 - B GW LY LB - - A 467C4B5CAMP403D494A4856 172320-2 R L Br G Y L B RB B RB LB B LB Or 16 B Or MAIN HARNESS HEAD LIGHT 205 LY BB 17 B 7 2 RB BrL R W W W W W RW B W R G B L Y W Br R 11 R 9 RUN Br Br OFF GY GY RB RB 10 OFF RB LW 3 RB B RB LW B LW 12 START BY BY BY BY B LY B B GY LW BY Sb B B 187 LY B 13 14 B B LY B R B B MAIN HARNESS EXT. CORD LR B 29 R Sb LY 5 RB LY 15 Sb 187 B B Br 4 LW OrLW LY RB Sb B LW LB GW LW Or LR 6 LY BY Sb B GW LB BY R RB B 8 B (BLUE) Br Br WB ILL. Br WB Br Br 25 BrL W WB 24 Br Dg TURN 21 18 BrB BrW G G BrW BrB BrL B P BrW GY 30 Y HIGH 23 19 BrSb OFF HIGH OFF L ON LOW ON N B BrL Y B BrB GB LRBr B Y GB BrB R Y GB GB B GY G L GB GB L L GY GY B B B B B B B B BrB BrB GB GB GB GB COLOR CODE B ...........Black Br ..........Brown Ch .........Chocolate Dg .........Dark green G...........Green Gy .........Gray L............Blue Lg..........Light green O...........Orange P ...........Pink R...........Red Sb .........Sky blue W..........White Y ...........Yellow B/L ........Black/Blue B 27 B B B B B B A B G Y 31 B B BrB B B BrB B B B B 12V10W 12V10W GB BrB GB BrB BrB G BrB 12V10W 26 12V10W 12V5W 12V60/55W L Y GY Y G A L L A Y A Y G BrB GB Y 22 Ch L P P Br BrL BrL BrW P B 28 BrL 20 LR NEU. BrW Br B BrL W B WB Br L 32 B/W.......Black/White B/Y........Black/Yellow Br/B.......Brown/Black Br/L .......Brown/Blue Br/W......Brown/White Br/Y.......Brown/Yellow L/B ........Blue/Black L/R ........Blue/Red L/W .......Blue/White L/Y ........Blue/Yellow R/B........Red/Black R/G .......Red/Green R/W.......Red/White R/Y........Red/Yellow 1 2 3 4 5 6 7 8 9 0 q w e r t y u i o p a s d f g h j k l ; z x AC generator/Pickup coil Rectifier/Regulator Battery Starter relay Starting motor Fuse Main switch Right handlebar switch Engine stop switch Starter switch Diode Clutch switch Sidestand switch Neutral switch Diode Ignitor unit Ignition coil Left handlebar switch Horn switch Diode Pass switch Dimmer switch Flasher switch Horn Flasher relay Headlight Flasher light Relay assy Front brake switch Rear brake switch Tail/stop light Meter
advertisement
* Your assessment is very important for improving the workof artificial intelligence, which forms the content of this project