advertisement
▼
Scroll to page 2
of 10
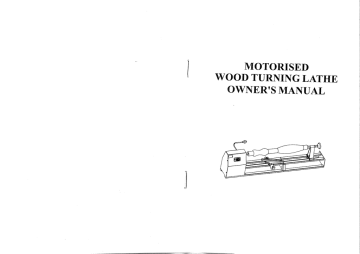
MOTORISED WOOD TURNING LATHE OWNER'S MANUAL CONGRATULATIONS You have just purchased one of our growing family of Bench Power Tools. Each is engineered and manufactured to the highest standards of quality. You will find your new Wood Turning Lathe a very useful tool. It will perform between centre turning and faceplate turning, and is especially suited to high speed sanding and polishing of finished work. This Wood Turning Lathe is a self-contained power tool not requiring the purchase of a seperater motor. MAIN FEATURES 1. HEAD 8. HAND WHEEL 2. CABLE 9. TAIL STOCK 3. DRIVE CENTER 10. LOCKING HANDLE 4. TOOL RESTHOLDER 11. FACE PLATE 5. TOOL REST 12. WRENCH 6. REAR PART-BED RAIL 13. SWITCH 7. LIVE CENTER A a AT TT TZ SAFETY RULES FOR ALL POWER TOOLS . READ AND BECOME FAMILIAR With the entire operating manual. . KEEP GUARDS AND COVER In place and in working order. . ALWAYS USE SAFETY GLASSES. Also use face or dust mask if cutting. operations is dusty. Everyday eyeglasses only have impact resistant lenses. They are not safely glasses. . KEEP WORK AREA CLEAN. Cluttered areas and benches invite accidents. . DON'T FORCE TOOL. It will do a better and safer job at the rate for which was designed. . AVOID ACCIDENTAL STARTING. Make sure switch is in "OFF" position before plugging in. . DISCONNECT TOOLS BEFORE SERVICING and when changing accessories such as spindle, centre, chuck etc. . DON'T OVER REACH. Keep your proper footing and balance at all times. For best footing wear rubber soled footwear. Keep floor clear of all, scrap wood, etc. . WEAR PROPER APPRAEL. Loose clothing or jewelry may get caught in moving parts. Wear protective hair covering to contain long hair. 10. MAKE WORKSHOP KIDPROOF. 11. 12. Place a padlock on the switch when the machine is not in use and store the key in a safe location. REMOVE ADJUSTING KEYS AND WRENCHES. Form habit of checking to see that keys and adjusting wrenches are removed from tool before turning it on. AVOID DANGEROUS ENVIRONMENT. Don't use power tools in damp or wet locations. Keep your work area well 13. 14. 15. 16. 17. 18. 19. 20. 21. illuminated. DO NOT USE in explosive atmosphere(around paint. flammable liquids, etc). KEEP CHILDREN AWAY. All visitors should be kept a safe distance from work area, especially while operation unit. USE THE PROPER TOOL. Don't force tool or attachment to do a job for which it was not designed. MAINTAIN TOOLS IN TOP CONDITION. Keep tools sharp and clean for best and safest performance. Follow instructions for lubricating and changing * accessories. SECURE WORK. Use clamps or a vise to hold work. when practical. It's safer than using your hand and prevents round or irregularly shaped pieces from turning. CHECK DAMAGED PARTS. Before further use of the tool, a guard or other part that is damaged should be checked to assure that it will operate properly and perform its intended function - check for alignment of moving parts, breakage of parts, mounting, any other conditions that may affect its operations. A guard or other part that is damaged should be properly repaired or replaced. USE RECOMMENDED ACCESSORIES - Consult Owner's Manual. Use of improper accessories could be hazardous. NEVER STAND ON TOOL. Injury could occur from a fall. NEVER LEAVE TOOL RUNNING AND UNATTENDED. ALWAYS REMOVE CORD PLUG from electrical outlet when adjusting, changing parts or working on tool. BED RAIL CONNECTION As per instruction showed in Fig.1,connecting the two part bed rails. | Fig.1 TOOL REST HOLDER ASSEMBLY Put the tool rest holder properly on the bed rail, and fasten it with guide track plate by screw. See Fig.2 TOOL REST ASSEMBLY Insert the tool rest into the holder and lock it with locking handle, See Fig.3 TAIL STOCK ASSEMBLY Assemble the tail stock as per Fig.4 = Fig.4 INSTALLATION The wood lathe should be bolted to a solidly built work bench. Mouting holes are provided in the base at both the headstock and tailstock end of the lathe. Large flat was hers should be used between the bolt heads and the housing to fasten the wood [athe more | | | securely and prevent damage. Tighten snugly but do not overtighten. Fig.5 q HOLES MOUNTING HOLES Fig.5 CHANGING SPEEDS 1. Turn the power off at the main switch. 2. Loosen motor mounting bolts under pulley cover. 3. Change belt to the desired pulley steps. 4. Lift belt tension lever to tighten belt. 5. Retighten motor mounting bolts. CHANGING FACEPLATE AND DRIVE CENTRE The adjustment spanner has jaws which fit across flats on the headstock spindle. Locate the spanneracross the flats and unsrew th faceplate or drive centre towards you. See Fig.7 MOVING TAILSTOCK AND TOOLREST The taiistock and toolrest are held to the bed with lock nuts underneath the bed rails. To move them to a new position, loosen the nut with the adjustment spanner, slide the tailstock or toolrest along the bed and retighten the nut, The toolrestis held in place by the lockknob. See Fig.8 MOTOR : An induction type motor is provided with the lathe. The rear cover of the lathe has ventilation slots to provide additional air movement over the motor. ; | The rear cover can be removed by simply undoing four screws to Inspect the motor when needed. Always keep motor ventilations slots clear, cleaning woodchips frequently. See Fig. 9 Fig.9 CHISELS FOR WOODTURNING 1. Large skew 2. Medium skew 3. Largé gouge 4. Medium gouge 5. Small gouge 6. Round nose 7. Spearpoint 3. Parting too! Successful woodturners investin good quality chisels and keep them ~ well maintained. Figure 7 shows a typical 8 piece chisel set which will cover most of your needs. Use the gouges for roughing in round nose for shaping, skews for planing and fine line detailing, spear point for V grooves, and the parting tool for cutting off finished work. After using your chisels maintain their fine cutting edge with an ollstone, taking care to keep the original angles. Or use a profes sional sharpening tool with a holder to set angles, a fine | grinding wheel for resharpening and a stropping wheel or polishing th cutting edge. See Fig11 — Fig. 11 TURNING BETWEEN CENTRES Turning between centres is the operation of turning a long workpiece supported at one end by the driving centre, and by the tail stock centre at the other. MARKING THE CENTRES-Draw two diagonal lines across each end of the workpiece, from corner to corner, The junction ofthe lines - will be the correct centre, Mark the centres with an awl or a drill. See Fig.12 | CO Les FA Fig.12 : REMOVING WASTE STOCK-With a jack plane or bandsaw remove the four corners of the timber along its length to form an octagonal workpiece. This speeds the operation of turning down to round. See Fig.13 | MOUNTING THE WORK BETWEEN CENTRES-Unscrew driving centre from the lathe spindle. Locate the point ofthe driving centre in the hole marked at one end of the timber, and hammer home with a wooden mallet of soft hammer. See Fig.14 Fig.14 Screw the timber and driving centre onto the headstock spindle, and move the tailstock up to the opposite end of the timber, locating the tailstock spindle in the centre hole marked previcusty. Tighten the tail stock lock nut underneath the bed rails Turn the tailstock spindle until the work is held firmly but still rotates freely. Tighten the spindle lock nut. POSITIONING TOOL REST-The position of the chisel and operator comfortis more important than the actual height of the tool rest. Set it at centre height to begin with, and adjust it slightly higher or lower after trial to suit the operation. See Fig.15 Always rotate the work one full turn before switching on the motor to be sure that the timber is free of all obstructions. FACEPLATE TURNING N Faceplate turning is the operation of turning a large workpiece supported by the faceplate only. MAKING A BACKING PIECE-Use a piece of 1"(25mm) thick timber larger than the diameter of the faceplate. Screw the backing piece to the faceplate using woodscrews through the holes in the back of the faceplate. Mount the faceplate and backing piece onto the lathe spindle and carefully turn the timber until itis completely circular and slightly larger in diameter than the faceplate. See Fig.16 Fig.16 The backing piece provides a surface on which to mountthe workpiece and is also a protective spacer between your chisels and the metal faceplate MOUNTING WORK TO THE BACKING PIECE-Spread wood-working adhesive over the packing piece. Place brown paper overthe adhesive and apply adhesive to the outside of the paper. Spread adhesive on the workpiece, press the workpiece against the brown paper. Allow the adhesive to dry completely, Clamping may be required, Follow the adhesive manufacturer's instructions carefully. When turning is completed the finished article can be easily pried off the face plate with a flat chisel. Work can also be screwed directly to the faceplate by drilling from the holes in the back of the faceplate completly through the backing piece. Make sure that enough material is allowed so that the chisel will not hit a screw during the turning operation. Excess timber can be cut off with a handsaw or fret saw when turning is completed. TURNING THE TIMBER TURNING BETWEEN CENTRES- Use a gouge or round nose chisel to rough the timber to the desired shape. Hold the chisel firmly against the tool rest. Use the hand holding the handle of the chisel to raise of lower the cutting point, with the tool rest as a fulcrum. When the rough shape is ready use other chisels for final shaping and decorative grooving as required. See Fig1/ [ FACEPLATE TURNING-Mount the faceplate and workpiece to the lathe spindle. Start by turning the outside of the work first. Whenever possible bring the tailstock up to support the workpiece. Move the tailstock well clear when turning the inside of the work. Extra care must be taken that the chisel does not catch on the work, particularly when the inside turning is long and narrow. See Fig.18 FINISHING. Turned timber can be power sanded on the lathe using a folded strip of sandpaper across the work. Remove the tool rest so that you have proper access to the workpiece. e wa CONDO AWN =F о Description Power cable Ball bearing Bearing block Bearing block Bali bearing Washer Boit Main shaft L athe tip Jip Cap screw Tool carriage Locking screw Tip Ball bearing Screw axis Tailstock Nut Locking screw Hand wheel Rear rail Guide track plate Spring washer Nut Screw 45 2 el +. DD $ DNA a AAA ANY AAA (0 не = нА AA M18x60 12" 60201 M18 M18 M6x8 M8 M8x16 Description Switch Screw Switch bracket Window Lath body. Nut Nut Washer s teeth Washers Spring washers Wire bracket Screw Belt pulley Belt pulley Cover Motor Screw Cord clamp Washers Belt Tool handle instruction manus! Screw driver Chuck Protecting crust Size M4x10 M4 M5 M5x16 M5x10 2500
advertisement
* Your assessment is very important for improving the workof artificial intelligence, which forms the content of this project
Related manuals
advertisement