advertisement
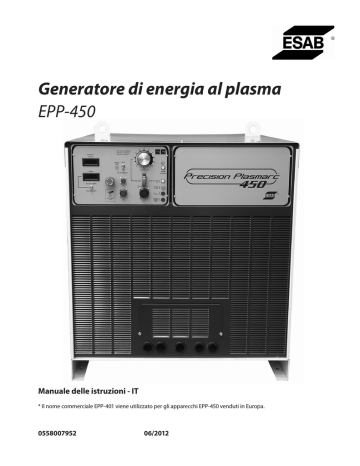
Generatore di energia al plasma
EPP-450
Manuale delle istruzioni - IT
* Il nome commerciale EPP-401 viene utilizzato per gli apparecchi EPP-450 venduti in Europa.
0558007952 06/2012
ACCERTARSI CHE L’OPERATORE RICEVA QUESTE INFORMAZIONI.
È POSSIBILE RICHIEDERE ULTERIORI COPIE AL PROPRIO FORNITORE.
ATTENZIONE
Queste ISTRUZIONI sono indirizzate a operatori esperti. Se non si conoscono perfettamente i principi di funzionamento e le indicazioni per la sicurezza delle apparecchiature per la saldatura e il taglio ad arco, è necessario leggere l’opuscolo “Precauzioni e indicazioni per la sicurezza per la saldatura, il taglio e la scultura ad arco,” Modulo 52-529. L’installazione, l’uso e la manutenzione devono essere effettuati SOLO da persone adeguatamente addestrate. NON tentare di installare o utilizzare questa attrezzatura senza aver letto e compreso totalmente queste istruzioni. In caso di dubbi su queste istruzioni, contattare il proprio fornitore per ulteriori informazioni. Accertarsi di aver letto le Indicazioni per la sicurezza prima di installare o utilizzare questo dispositivo.
RESPONSABILITÀ DELL’UTENTE
Questo dispositivo funzionerà in maniera conforme alla descrizione contenuta in questo manuale e nelle etichette e/o gli allegati, se installato, utilizzato o sottoposto a manutenzione e riparazione sulla base delle istruzioni fornite. Questa attrezzatura deve essere controllata periodicamente. Non utilizzare attrezzatura che funzioni male o sottoposta a manutenzione insufficiente. Sostituire immediatamente i componenti rotti, mancanti, usurati, deformati o contaminati. Nel caso in cui tale riparazione o sostituzione diventi necessaria, il produttore raccomanda di richiedere telefonicamente o per iscritto assistenza al distributore autorizzato presso il quale è stata acquistata l’attrezzatura.
Non modificare questo dispositivo né alcuno dei suoi componenti senza previo consenso scritto del produttore.
L’utente di questo dispositivo sarà il solo responsabile per un eventuale funzionamento errato, derivante da uso non corretto, manutenzione erronea, danni, riparazione non corretta o modifica da parte di persona diversa dal produttore o dalla ditta di assistenza indicata dal produttore.
NON INSTALLARE NÉ UTILIZZARE L’ATTREZZATURA PRIMA DI AVER LETTO E COMPRESO
IL MANUALE DI ISTRUZIONI.
PROTEGGERE SE STESSI E GLI ALTRI!
4
INDICE
Sezione / Titolo Pagina
1.0 Precauzioni di sicurezza . . . . . . . . . . . . . . . . . . . . . . . . . . . . . . . . . . . . . . . . . . . . . . . . . . . . . . . . . . . . . . . . . . . . . . . . . . . . . . .7
2.0 Descrizione . . . . . . . . . . . . . . . . . . . . . . . . . . . . . . . . . . . . . . . . . . . . . . . . . . . . . . . . . . . . . . . . . . . . . . . . . . . . . . . . . . . . . . . . . . .9
2.1 Introduzione. . . . . . . . . . . . . . . . . . . . . . . . . . . . . . . . . . . . . . . . . . . . . . . . . . . . . . . . . . . . . . . . . . . . . . . . . . . . . . . . . . . . . .9
2.2 Caratteristiche tecniche generali . . . . . . . . . . . . . . . . . . . . . . . . . . . . . . . . . . . . . . . . . . . . . . . . . . . . . . . . . . . . . . . . . .9
2.3 Dimensioni e peso. . . . . . . . . . . . . . . . . . . . . . . . . . . . . . . . . . . . . . . . . . . . . . . . . . . . . . . . . . . . . . . . . . . . . . . . . . . . . . .10
3.0 Installazione . . . . . . . . . . . . . . . . . . . . . . . . . . . . . . . . . . . . . . . . . . . . . . . . . . . . . . . . . . . . . . . . . . . . . . . . . . . . . . . . . . . . . . . . .11
3.1 Generale . . . . . . . . . . . . . . . . . . . . . . . . . . . . . . . . . . . . . . . . . . . . . . . . . . . . . . . . . . . . . . . . . . . . . . . . . . . . . . . . . . . . . . . .11
3.2 Svuotamento della cassa. . . . . . . . . . . . . . . . . . . . . . . . . . . . . . . . . . . . . . . . . . . . . . . . . . . . . . . . . . . . . . . . . . . . . . . . .11
3.3 Posizionamento . . . . . . . . . . . . . . . . . . . . . . . . . . . . . . . . . . . . . . . . . . . . . . . . . . . . . . . . . . . . . . . . . . . . . . . . . . . . . . . . .11
3.4 Connessione dell’alimentazione di ingresso. . . . . . . . . . . . . . . . . . . . . . . . . . . . . . . . . . . . . . . . . . . . . . . . . . . . . . .12
3.4.1 Alimentazione primaria . . . . . . . . . . . . . . . . . . . . . . . . . . . . . . . . . . . . . . . . . . . . . . . . . . . . . . . . . . . . . . . . . . . .12
3.4.2 Conduttori di ingresso. . . . . . . . . . . . . . . . . . . . . . . . . . . . . . . . . . . . . . . . . . . . . . . . . . . . . . . . . . . . . . . . . . . . .13
3.4.3 Procedura di connessione di ingresso . . . . . . . . . . . . . . . . . . . . . . . . . . . . . . . . . . . . . . . . . . . . . . . . . . . . . .13
3.5 Connessione di uscita. . . . . . . . . . . . . . . . . . . . . . . . . . . . . . . . . . . . . . . . . . . . . . . . . . . . . . . . . . . . . . . . . . . . . . . . . . . .14
3.5.1 Cavi di uscita (forniti dal cliente) . . . . . . . . . . . . . . . . . . . . . . . . . . . . . . . . . . . . . . . . . . . . . . . . . . . . . . . . . . . .14
3.5.2 Procedura di connessione di uscita - Generatore di energia singolo. . . . . . . . . . . . . . . . . . . . . . . . . .14
3.6 Installazione parallela . . . . . . . . . . . . . . . . . . . . . . . . . . . . . . . . . . . . . . . . . . . . . . . . . . . . . . . . . . . . . . . . . . . . . . . . . . . .15
3.6.1 Connessioni per due EPP-450 in parallelo . . . . . . . . . . . . . . . . . . . . . . . . . . . . . . . . . . . . . . . . . . . . . . . . . .16
3.6.2 Marcatura con due EPP-450 paralleli . . . . . . . . . . . . . . . . . . . . . . . . . . . . . . . . . . . . . . . . . . . . . . . . . . . . . . .19
3.7 Cavi di interfaccia . . . . . . . . . . . . . . . . . . . . . . . . . . . . . . . . . . . . . . . . . . . . . . . . . . . . . . . . . . . . . . . . . . . . . . . . . . . . . . . 20
3.7.1 Cavi di interfaccia CNC con generatore di energia di alimentazione di accoppiamento e
con interfaccia CNC non terminato . . . . . . . . . . . . . . . . . . . . . . . . . . . . . . . . . . . . . . . . . . . . . . . . . . . . . . . .21
3.7.2 Cavi di interfaccia CNC con connettori del generatore di energia di alimentazione di accoppiamento su entrambe le estremità. . . . . . . . . . . . . . . . . . . . . . . . . . . . . . . . . . . . . . . . . . . . . . . .21
3.7.3 Cavi di interfaccia del refrigerante ad acqua con connettori del generatore di energia di alimentazione di accoppiamento su entrambe le estremità. . . . . . . . . . . . . . . . . . . . . . . . . . . . . . 22
4.0 Funzionamento . . . . . . . . . . . . . . . . . . . . . . . . . . . . . . . . . . . . . . . . . . . . . . . . . . . . . . . . . . . . . . . . . . . . . . . . . . . . . . . . . . . . . 23
4.1 Descrizione del circuito del diagramma a blocchi. . . . . . . . . . . . . . . . . . . . . . . . . . . . . . . . . . . . . . . . . . . . . . . . . 23
4.2 Pannello di controllo. . . . . . . . . . . . . . . . . . . . . . . . . . . . . . . . . . . . . . . . . . . . . . . . . . . . . . . . . . . . . . . . . . . . . . . . . . . . 26
4.2.1 Modalità di funzionamento: Modalità di taglio e di marcatura. . . . . . . . . . . . . . . . . . . . . . . . . . . . . . 29
4.3 Sequenza del funzionamento . . . . . . . . . . . . . . . . . . . . . . . . . . . . . . . . . . . . . . . . . . . . . . . . . . . . . . . . . . . . . . . . . . . 30
4.4 Impostazioni di avviamento dell’arco . . . . . . . . . . . . . . . . . . . . . . . . . . . . . . . . . . . . . . . . . . . . . . . . . . . . . . . . . . . . .31
4.4.1 Attivazione / disattivazione delle condizioni di avviamento dell’arco. . . . . . . . . . . . . . . . . . . . . . . . .32
4.4.2 Regolare il timer di sosta dell’avviamento dell’arco. . . . . . . . . . . . . . . . . . . . . . . . . . . . . . . . . . . . . . . . . .32
4.4.3 Regolazione della corrente di avvio minima . . . . . . . . . . . . . . . . . . . . . . . . . . . . . . . . . . . . . . . . . . . . . . . .32
4.4.4 Controlli dell’avviamento dell’arco . . . . . . . . . . . . . . . . . . . . . . . . . . . . . . . . . . . . . . . . . . . . . . . . . . . . . . . . .33
4.4.5 Avvio della corrente e del timer di aumento della corrente . . . . . . . . . . . . . . . . . . . . . . . . . . . . . . . . . .33
4.5 Curve V-I EPP-450. . . . . . . . . . . . . . . . . . . . . . . . . . . . . . . . . . . . . . . . . . . . . . . . . . . . . . . . . . . . . . . . . . . . . . . . . . . . . . . 34
4.5.1 Curve V-I EPP-450 per tutti i modelli . . . . . . . . . . . . . . . . . . . . . . . . . . . . . . . . . . . . . . . . . . . . . . . . . . . . . . . 34
5.0 Manutenzione . . . . . . . . . . . . . . . . . . . . . . . . . . . . . . . . . . . . . . . . . . . . . . . . . . . . . . . . . . . . . . . . . . . . . . . . . . . . . . . . . . . . . . .35
5.1 Generale . . . . . . . . . . . . . . . . . . . . . . . . . . . . . . . . . . . . . . . . . . . . . . . . . . . . . . . . . . . . . . . . . . . . . . . . . . . . . . . . . . . . . . . .35
5.2 Pulizia. . . . . . . . . . . . . . . . . . . . . . . . . . . . . . . . . . . . . . . . . . . . . . . . . . . . . . . . . . . . . . . . . . . . . . . . . . . . . . . . . . . . . . . . . . .35
5.3 Lubrificazione . . . . . . . . . . . . . . . . . . . . . . . . . . . . . . . . . . . . . . . . . . . . . . . . . . . . . . . . . . . . . . . . . . . . . . . . . . . . . . . . . . 36
5
INDICE
Sezione / Titolo Pagina
6.0 Risoluzione dei guasti . . . . . . . . . . . . . . . . . . . . . . . . . . . . . . . . . . . . . . . . . . . . . . . . . . . . . . . . . . . . . . . . . . . . . . . . . . . . . . . .37
6.1 Generale . . . . . . . . . . . . . . . . . . . . . . . . . . . . . . . . . . . . . . . . . . . . . . . . . . . . . . . . . . . . . . . . . . . . . . . . . . . . . . . . . . . . . . . .37
6.2 Indicatori dei guasti. . . . . . . . . . . . . . . . . . . . . . . . . . . . . . . . . . . . . . . . . . . . . . . . . . . . . . . . . . . . . . . . . . . . . . . . . . . . . .37
6.3 Isolamento dei guasti . . . . . . . . . . . . . . . . . . . . . . . . . . . . . . . . . . . . . . . . . . . . . . . . . . . . . . . . . . . . . . . . . . . . . . . . . . . 40
6.3.1 Nessuna uscita con il segnale del contattore applicato . . . . . . . . . . . . . . . . . . . . . . . . . . . . . . . . . . . . . 40
6.3.2 Uscita limitata a 100 A . . . . . . . . . . . . . . . . . . . . . . . . . . . . . . . . . . . . . . . . . . . . . . . . . . . . . . . . . . . . . . . . . . . . 40
6.3.3 Ventole guaste . . . . . . . . . . . . . . . . . . . . . . . . . . . . . . . . . . . . . . . . . . . . . . . . . . . . . . . . . . . . . . . . . . . . . . . . . . . 40
6.3.4 Alimentazione non accesa o bassa tensione . . . . . . . . . . . . . . . . . . . . . . . . . . . . . . . . . . . . . . . . . . . . . . . .41
6.3.5 Accensione della luce dei guasti . . . . . . . . . . . . . . . . . . . . . . . . . . . . . . . . . . . . . . . . . . . . . . . . . . . . . . . . . . .41
6.3.6 Il cannello non si accende. . . . . . . . . . . . . . . . . . . . . . . . . . . . . . . . . . . . . . . . . . . . . . . . . . . . . . . . . . . . . . . . . 45
6.3.7 Fusi F1 e F2 saltati . . . . . . . . . . . . . . . . . . . . . . . . . . . . . . . . . . . . . . . . . . . . . . . . . . . . . . . . . . . . . . . . . . . . . . . . 46
6.3.8 Funzionamento intermittente, interrotto o parziale . . . . . . . . . . . . . . . . . . . . . . . . . . . . . . . . . . . . . . . . 46
6.4 Controllo e sostituzione dei componenti . . . . . . . . . . . . . . . . . . . . . . . . . . . . . . . . . . . . . . . . . . . . . . . . . . . . . . . . 48
6.4.1 Raddrizzatori di alimentazione . . . . . . . . . . . . . . . . . . . . . . . . . . . . . . . . . . . . . . . . . . . . . . . . . . . . . . . . . . . . 49
6.4.2 Sostituzione dell’IGBT / Diodo di marcia per inerzia (FWD - Freewheeling Diode). . . . . . . . . . . . .51
6.4.3 Installazione del derivatore di alimentazione . . . . . . . . . . . . . . . . . . . . . . . . . . . . . . . . . . . . . . . . . . . . . . .53
6.4.4 Procedura per la verifica della calibrazione dei misuratori digitali . . . . . . . . . . . . . . . . . . . . . . . . . . . 54
6.5 Interfaccia del circuito di controllo con i connettori J1 e J6. . . . . . . . . . . . . . . . . . . . . . . . . . . . . . . . . . . . . . . . 54
6.6 Contattore principale ausiliario (K3) e circuiti del contattore di stato solido . . . . . . . . . . . . . . . . . . . . . . . . 56
6.7 Circuito di attivazione del contattore principale (K1A, K1B e K1C). . . . . . . . . . . . . . . . . . . . . . . . . . . . . . . . . . 57
6.8 Circuiti del rilevatore della corrente dell’arco . . . . . . . . . . . . . . . . . . . . . . . . . . . . . . . . . . . . . . . . . . . . . . . . . . . . . 58
6.9 Potenziometro e telecomando di controllo della corrente Vref. . . . . . . . . . . . . . . . . . . . . . . . . . . . . . . . . . . . .59
6.10 Circuiti dell’arco pilota HI / LO (alto/basso) e di Taglio / Marcatura . . . . . . . . . . . . . . . . . . . . . . . . . . . . . . . . 60
6.11 Bassa gamma della corrente . . . . . . . . . . . . . . . . . . . . . . . . . . . . . . . . . . . . . . . . . . . . . . . . . . . . . . . . . . . . . . . . . . . . .61
7.0 Parti di sostituzione . . . . . . . . . . . . . . . . . . . . . . . . . . . . . . . . . . . . . . . . . . . . . . . . . . . . . . . . . . . . . . . . . . . . . . . . . . . . . . . . . 63
7.1 Generale. . . . . . . . . . . . . . . . . . . . . . . . . . . . . . . . . . . . . . . . . . . . . . . . . . . . . . . . . . . . . . . . . . . . . . . . . . . . . . . . . . . . . . . . 63
7.2 Come ordinare. . . . . . . . . . . . . . . . . . . . . . . . . . . . . . . . . . . . . . . . . . . . . . . . . . . . . . . . . . . . . . . . . . . . . . . . . . . . . . . . . . 63
6
SEZIONE 1 INDICAZIONI PER LA SICUREZZA
1.0 Indicazioni per la sicurezza
Gli utenti dell’attrezzatura per la saldatura e il taglio al plasma ESAB hanno la responsabilità di accertarsi che chiunque lavori al dispositivo o accanto ad esso adotti tutte le idonee misure di sicurezza. Le misure di sicurezza devono soddisfare i requisiti che si applicano a questo tipo di dispositivo per la saldatura o il taglio al plasma.
Attenersi alle seguenti raccomandazioni, oltre che ai regolamenti standard che si applicano al luogo di lavoro.
Tutto il lavoro deve essere eseguito da personale addestrato, perfettamente al corrente del funzionamento dell’attrezzatura per la saldatura o il taglio al plasma. Il funzionamento errato dell’attrezzatura può determinare situazioni pericolose con conseguenti lesioni all’operatore e danni al dispositivo stesso.
1. Chiunque utilizzi attrezzatura per la saldatura o il taglio al plasma deve conoscerne perfettamente:
- il funzionamento
- la posizione degli arresti di emergenza
- la funzione
- le idonee misure di sicurezza
- la saldatura e/o il taglio al plasma
2. L’operatore deve accertarsi che:
- nessuna persona non autorizzata si trovi nell’area operativa dell’attrezzatura quando questa viene messa in
funzione.
- tutti siano protetti quando si esegue l’arco.
3. Il luogo di lavoro deve essere:
- idoneo allo scopo
- privo di correnti d’aria
4. Attrezzature per la sicurezza personale:
- indossare sempre l’attrezzatura di sicurezza personale raccomandata, come occhiali di sicurezza, abbigliamento ignifugo, guanti di sicurezza.
- non indossare oggetti sporgenti, come sciarpe, braccialetti, anelli, ecc., che potrebbero rimanere intrappolati o causare ustioni.
5. Precauzioni generali:
- accertarsi che il cavo di ritorno sia collegato saldamente;
- il lavoro su apparecchiature ad alta tensione può essere effettuato sono da parte di tecnici qualificati;
- i dispositivi antincendio idonei devono essere indicati chiaramente e a portata di mano;
- durante il funzionamento non effettuare lavori di lubrificazione e manutenzione.
Classe del contenitore
Il codice IP indica la classe del contenitore, cioè il livello di protezione contro la penetrazione di oggetti solidi o acqua. La protezione viene fornita per evitare l’inserimento di dita, la penetrazione di oggetti solidi più grandi di
12 mm e gli spruzzi di acqua fino a 60 gradi di inclinazione rispetto alla verticale. Le attrezzature marcate IP23S possono essere immagazzinate, ma non devono essere usate all’aperto in presenza di precipitazione senza un adeguato riparo.
ATTENZIONE
Se l’apparecchiatura è collocata su una superficie inclinata più di 15° si potrebbe verificare un ribaltamento, con conseguenti rischi di lesioni personali e/o danni rilevanti all’attrezzatura.
Inclinazione massima consentita
15°
7
SEZIONE 1 INDICAZIONI PER LA SICUREZZA
AVVERTENZA
LA SALDATURA E IL TAGLIO AL PLASMA POSSONO ESSERE
PERICOLOSI PER L’OPERATORE E COLORO CHE GLI SI TROVANO
ACCANTO. ADOTTARE LE OPPORTUNE PRECAUZIONI DURANTE
LA SALDATURA O IL TAGLIO. INFORMARSI DELLE MISURE DI
SICUREZZA ADOTTATE DAL PROPRIO DATORE DI LAVORO, CHE
SI DEVONO BASARE SUI DATI RELATIVI AL PERICOLO INDICATI
DAL PRODUTTORE.
SCOSSA ELETTRICA - Può essere mortale
- Installare e collegare a terra (massa) l’unità di saldatura o taglio al plasma sulla base degli standard applicabili.
- Non toccare le parti elettriche o gli elettrodi sotto tensione con la pelle nuda e guanti o abbigliamento bagnato.
- Isolarsi dalla terra e dal pezzo in lavorazione.
- Accertasi che la propria posizione di lavoro sia sicura.
FUMI E GAS - Possono essere pericolosi per la salute.
- Tenere la testa lontano dai fumi.
- Usare la ventilazione, l’estrazione fumi sull’arco o entrambe per mantenere lontani fumi e gas dalla propria zona di respirazione e dall’area in genere.
I RAGGI DELL’ARCO - Possono causare lesioni agli occhi e ustionare la pelle.
- Proteggere gli occhi e il corpo. Usare lo schermo di protezione per saldatura/taglio al plasma e lenti con filtro idonei e indossare abbigliamento di protezione.
- Proteggere le persone circostanti con schermi o barriere di sicurezza idonee.
PERICOLO DI INCENDIO
- Scintille (spruzzi) possono causare incendi. Accertarsi quindi che nelle immediate vicinanze non siano pre senti materiali infiammabili.
RUMORE - Il rumore in eccesso può danneggiare l’udito.
- Proteggere le orecchie. Usare cuffie antirumore o altre protezioni per l’udito.
- Informare le persone circostanti del rischio.
GUASTI - In caso di guasti richiedere l’assistenza di un esperto.
NON INSTALLARE NÉ UTILIZZARE L’ATTREZZATURA PRIMA DI AVER LETTO E COMPRESO
IL MANUALE DI ISTRUZIONI. PROTEGGERE SE STESSI E GLI ALTRI!
ATTENZIONE
Questo prodotto è destinato esclusivamente al taglio del plasma. Qualsiasi altro utilizzo potrebbe provocare lesioni personali e/o danni alle apparecchiature.
ATTENZIONE
Per evitare lesioni personali e/o danni alle apparecchiature, sollevare utilizzando il metodo e i punti di aggancio indicati a fianco.
8
SEZIONE 2 DESCRIZIONE
2.1 Introduzione
Il generatore di energia EPP è stato ideato per applicazioni di marcatura e di taglio meccanizzato a getto di plasma ad alta velocità. Può essere usato con altri prodotti ESAB, come i cannelli PT-15, PT-19XLS, PT-600 e PT-36 e con Smart Flow II, un sistema di regolazione e commutazione del gas computerizzato.
• Da 10 a 100 ampere per la marcatura in gamma di corrente bassa
• Taglio da 50 a 450 ampere in gamma di corrente alta
• Taglio da 35 a 100 ampere in gamma di corrente bassa
• Raffreddamento a circolazione forzata d’aria
• Alimentazione CC a stato solido
• Protezione della tensione di ingresso
• Controllo del pannello anteriore remoto o locale
• Protezione dell’interruttore termale per il trasformatore principale e per i componenti del semiconduttore di alimentazione
• Spazio degli anelli di sollevamento superiori o dell’elevatore a forca per il trasporto
• Capacità del generatore di energia supplementare parallela per estendere la gamma di uscita della corrente.
2.2 Caratteristiche tecniche generali
Numero della parte
Tensione di ingresso (trifase)
Corrente di ingresso (trifase)
Frequenza di ingresso kVa di ingresso
Alimentazione di ingresso
Fattore dell’alimentazione di ingresso
Cavo dell’alimentazione di ingresso consigliato
Fusibile di ingresso (Consigliato)
Tensione del circuito aperto di uscita
(OCV-Open Circuit Voltage) (Taglio a gamma alta)
Tensione del circuito aperto di uscita
(Taglio a gamma bassa)
Tensione del circuito aperto di uscita
(OCV-Open Circuit Voltage) (Marcatura)
Gamma alta del taglio di uscita (100% lavoro)
Gamma bassa del taglio di uscita (100% lavoro)
Gamma bassa della marcatura di uscita
(100% lavoro)
Alimentazione di uscita (100% lavoro)
Informazioni sull’ingresso/uscita di EPP-450
EPP-450
380V 50/60HZ
380V TAPS
EPP-450
380V 50/60HZ
400V TAPS
EPP-450
400V 50/60HZ
380 V CA
167 A RMS
(valore efficace)
0558007730
380 V CA
167 A RMS
(valore efficace)
400 V CA
159 A RMS
(valore efficace)
50/60 HZ
109,9 kVA
50/60 HZ
109,9 kVA
50/60 HZ
110,2 kVA
98,9 KW
90%
98,9 KW
90%
99,1 KW
90%
*2/0 AWG *2/0 AWG *2/0 AWG
200 A
430 V CC
414 V CC
360 V CC
200 A
406 V CC
393 V CC
342 V CC
200 A
427 V CC
413 V CC
369 V CC
90 KW
EPP-450
460V 60HZ
0558007731
460 V CA
138 A RMS
(valore efficace)
60 HZ
110,0 kVA
99,0 KW
90%
*1/0 AWG
Da 50 A a 100 V a 450 A a 200 V
Da 35 A a 94 V a 100 A a 120 V
Da 10 A a 84 V a 100 A a 120 V
200 A
431 V CC
415 V CC
360 V CC
EPP-450
575V 60HZ
0558007732
575 V CA
110 A RMS
(valore efficace)
60 HZ
109,6 kVA
98,6 KW
90%
*2/0 AWG
150 A
431 V CC
415 V CC
360 V CC
* Misure dei fusibili in base al Codice Elettrico Nazionale per conduttori in rame classificati per 90° C (194˚ F) ad una temperatura ambiente di 40° C (104˚ F). Non più di tre conduttori nel canalino o nel cavo. I codici locali devono essere seguiti, se specificano misure diverse da quelle indicate in alto.
9
SEZIONE 2
2.3 Dimensioni e peso
1143 mm
45,00 pollici
DESCRIZIONE
946 mm
37,25 pollici
1022 mm
40,25 pollici
Peso = 850 kg (1870 libbre)
10
SEZIONE 3 INSTALLAZIONE
3.1 Generale
AVVERTIMENTO
UNA MANCATA OSSERVANZA DELLE ISTRUZIONI POTREBBE CAU-
SARE LA MORTE, LESIONI O DANNI ALLE PROPRIETÀ. SEGUIRE LE
ISTRUZIONI PER PREVENIRE LE LESIONI O I DANNI ALLE PROPRIETÀ.
È NECESSARIO RISPETTARE I CODICI DI SICUREZZA ED ELETTRICI
LOCALI, STATALI E NAZIONALI.
3.2 Svuotamento della cassa
L’utilizzo di un solo anello di sospensione danneggerà la lastra di metallo e la struttura.
Utilizzare entrambi gli anelli quando si effettua il trasporto a sospensione.
• Al momento della ricezione, ispezionare immediatamente il materiale per eventuali danni.
• Rimuovere tutti i componenti dalla cassa di spedizione ed accertarsi che nessuna parte si sia staccata e sia rimasta nel contenitore.
• Ispezionare le feritoie per accertarsi che non siano presenti ostruzioni dell’aria.
3.3 Posizionamento
Nota:
Utilizzare entrambi gli anelli di sospensione quando si effettua il trasporto dall’alto.
• È necessario uno spazio minimo di 1 M (3 piedi) sul davanti e sul retro per il flusso d’aria di raffreddamento.
• Ricordare che il pannello superiore e i pannelli laterali devono essere rimossi per la manutenzione, la pulizia e l’ispezione.
• Posizionare l’EPP-450 relativamente vicino ad una fonte di alimentazione elettrica con fusibile.
• Mantenere libera l’area al di sotto del generatore di energia per il flusso d’aria di raffreddamento.
• L’ambiente deve essere relativamente privo di polvere, fumi e calore eccessivo. Questi fattori influenzeranno l’efficienza del raffreddamento.
PRECAUZIONE
La polvere e lo sporco conduttivi all’interno del generatore di energia potrebbero causare una scarica dell’arco.
Potrebbero verificarsi danni all’apparecchiatura. Un corto circuito elettrico potrebbe verificarsi se si verifica un accumulo di polvere all’interno del generatore di energia. Consultare la sezione sulla manutenzione.
11
SEZIONE 3 INSTALLAZIONE
3.4 Connessione dell’alimentazione di ingresso
AVVERTIMENTO
LE SCOSSE ELETTRICHE POSSONO UCCIDERE!
GARANTIRE UNA MASSIMA PROTEZIONE DALLE SCOSSE ELETTRICHE.
PRIMA CHE QUALSIASI CONNESSIONE VENGA EFFETTUATA ALL’IN-
TERNO DELLA MACCHINA, APRIRE IL SEZIONATORE A PARETE PER
SPEGNERE L’ALIMENTAZIONE.
3.4.1 Alimentazione primaria
EPP-450 è un’unità a tre fasi. L’alimentazione di ingresso deve essere fornita da un sezionatore (a parete) che contiene fusibili o interruttori differenziali conformi alle normative locali.
Nota:
Si prega di fare riferimento alla tabella alla voce “Caratteristiche tecniche generali” nel Paragrafo 2.2 per le misure dei fusibili del cavo e di ingresso.
Per preventivare la corrente di ingresso per una vasta gamma di condizioni di uscita, usare la formula in basso.
Corrente di ingresso =
(arco V) x (arco l) x 0,688
(linea V)
AVVISO
Potrebbe essere necessario disporre di una linea di alimentazione dedicata.
EPP-450 è dotato di una compensazione della tensione della linea ma, per evitare prestazioni alterate dovute ad un circuito sovraccarico, potrebbe essere necessario disporre di una linea di alimentazione.
12
SEZIONE 3 INSTALLAZIONE
3.4.2 Conduttori di ingresso
• Forniti dal cliente
• Potrebbe trattarsi di conduttori in rame pesanti ricoperti di gomma (tre di alimentazione e uno di messa a terra) o che scorrono in un condotto solido o flessibile.
• Le dimensioni devono corrispondere a quelle riportate nella tabella “Caratteristiche tecniche generali” nel
Paragrafo 2.2.
AVVISO
Le estremità dei conduttori di ingresso devono consistere di terminali ad anello.
Le estremità dei conduttori di ingresso devono consistere di terminali ad anello per componenti metallici di 12,7 mm (0,50 pollici), prima di essere attaccati all’EPP-450.
PRECAUZIONE
Ispezionare lo spazio tra i terminali ad anello del cavo di alimentazione ed il pannello laterale. I cilindri di alcuni terminali di grandi dimensioni potrebbero avvicinarsi al pannello laterale o toccarlo se il terminale non è montato correttamente. I cilindri dei terminali montati su TB4 e TB6 devono essere ruotati in modo che siano rivolti nella direzione contraria a quella del pannello laterale.
3.4.3 Procedura di connessione di ingresso
2
1
1. Rimuovere il pannello laterale dell’EPP-450
2. Infilare i cavi attraverso l’apertura di accesso nel pannello posteriore.
3. Fissare i cavi con un serracavo sull’apertura di accesso.
4. Collegare il cavo di massa al perno sulla base del telaio.
5. Collegare i terminali ad anello del cavo di alimentazione ai terminali primari con i bulloni, le rondelle e i dadi forniti.
6. Collegare i conduttori di ingresso al sezionatore (a parete).
3
1 = Terminali primari
2 = Messa a terra del telaio
3 = Apertura di accesso del cavo di ingresso dell’alimentazione (Pannello posteriore)
13
SEZIONE 3 INSTALLAZIONE
AVVERTIMENTO
LE SCOSSE ELETTRICHE POSSONO UCCIDERE!
I TERMINALI AD ANELLO DEVONO AVERE UNO SPAZIO TRA IL PAN-
NELLO LATERALE ED IL TRASFORMATORE PRINCIPALE. LO SPAZIO
DEVE ESSERE SUFFICIENTE IN CASO DI EVENTUALE CONTATTO
D’ARCO. ACCERTARSI CHE I CAVI NON INTERFERISCANO CON LA
ROTAZIONE DELLA VENTOLA DI RAFFREDDAMENTO.
AVVERTIMENTO
UNA MESSA A TERRA ERRATA PUÒ RISULTARE IN MORTE O LESIONE.
IL TELAIO DEVE ESSERE COLLEGATO AD UNA MESSA A TERRA ELET-
TRICA APPROVATA. ACCERTARSI CHE IL CAVO DI MASSA NON SIA
COLLEGATO AD ALCUN TERMINALE PRIMARIO.
3.5 Connessioni di uscita
AVVERTIMENTO
LE SCOSSE ELETTRICHE POSSONO UCCIDERE! TENSIONE E CORRENTE
PERICOLOSI!
QUANDO SI LAVORA INTORNO AD UN GENERATORE DI ENERGIA AL
PLASMA CON I COPERCHI RIMOSSI:
• DISINNESTARE IL GENERATORE DI ENERGIA NEL SEZIONATORE
(A PARETE).
• UN INDIVIDUO QUALIFICATO DOVREBBE CONTROLLARE LE SBAR-
RE COLLETTRICI (POSITIVE E NEGATIVE) CON UN VOLTMETRO.
3.5.1 Cavi di uscita (forniti dal cliente)
Scegliere i cavi di uscita del taglio a getto di plasma (forniti dal cliente) sulla base di un cavo di rame 4/0 AWG isolato da 600 volt per 400 ampere di corrente di uscita. Per 450 ampere, devono essere usati cavi a 600 volt, taglio 100% lavoro, due 2/0 AWG paralleli.
Nota:
Non usare un cavo di saldatura isolato da 100 volt.
3.5.2 Procedura di connessione di uscita - Generatore di energia singolo
1. Rimuovere il pannello di accesso sul lato anteriore inferiore del generatore di energia.
2. Infilare i cavi di uscita attraverso le aperture sul fondo del pannello anteriore o sul fondo del generatore di energia subito dietro il pannello anteriore.
3. Collegare i cavi ai terminali specificati montati all’interno del generatore di energia, usando i connettori del cavo di pressione classificata UL.
4. Riposizionare il pannello rimosso nel corso del primo procedimento.
14
SEZIONE 3 INSTALLAZIONE
Pannello di accesso aperto lavoro
(+)
EPP-450
Generatore di energia arco pilota elettrodo
(-) * Si consigliano due cavi paralleli 2/0 AWG per il funzionamento 100% lavoro 450 A. Per il funzionamento a 400 A 100% lavoro (o inferiore), è possibile usare un cavo 4/0. Anche per il funzionamento a 450 A 80% lavoro (o inferiore), è possibile usare un cavo 4/0. 80% lavoro massimo equivale ad un funzionamento non superiore agli 8 minuti in qualsiasi intervallo di tempo di 10 minuti.
* 2 - 2/0 AWG 600V cavi positivi al pezzo da lavorare
1 - 14 AWG 600V cavo alla connessione dell’arco pilota nella cassetta di avviamento dell’arco (generatore alta frequenza)
* 2 - 2/0 AWG
600V cavi negativi nella cassetta di avviamento dell’arco
(generatore alta frequenza)
3.6 Installazione parallela
Due generatori di energia EPP-450 possono essere collegati in parallelo, per ampliare la gamma della corrente di uscita.
PRECAUZIONE
Utilizzare un solo generatore di energia per il taglio inferiore a 100 A.
Consigliamo di disconnettere il cavo negativo dal generatore di energia supplementare, quando si passa a correnti inferiori a 100 A. Questo cavo deve essere correttamente isolato per la protezione dalle scosse elettriche.
15
SEZIONE 3 INSTALLAZIONE
3.6.1 Connessioni per due EPP-450 in parallelo
Nota:
Il generatore di energia primario è dotato di conduttore di elettrodo (-) ponticellato. Il generatore di energia supplementare è dotato di lavoro (+) ponticellato.
1. Collegare i cavi di uscita negativi (-) alla cassetta di avviamento dell’arco (generatore alta frequenza).
2. Collegare i cavi di uscita positivi (+) al pezzo da lavorare.
3. Collegare i conduttori di uscita positivi (+) e negativi (-) tra i generatori di energia.
4. Collegare il cavo dell’arco pilota al terminale dell’arco pilota nel generatore di energia primario. La connessione dell’arco pilota nel generatore di energia supplementare non viene usata. Il circuito dell’arco pilota non scorre parallelo.
5. Impostare l’interruttore dell’arco pilota ALTO / BASSO sul generatore di energia supplementare su “BASSO”.
6. Impostare l’interruttore dell’arco pilota ALTO / BASSO sul generatore di energia primario su “ALTO”.
7. Se un segnale di riferimento della corrente da 0,00 a +10,00 V CC viene usato per impostare la corrente di uscita, fornire lo stesso segnale a entrambi i generatori di energia. Unire J1-G (positivo da 0,00 a 10,00 V CC) di entrambi i generatori di energia e unire J1-P (negativo) di entrambi i generatori di energia. Quando entrambi i generatori di energia funzionano, la corrente di uscita può essere prevista usando la seguente formula: [corrente di uscita (ampere)] = [tensione di riferimento] x [100]
L’EPP-450 non è dotato di un interruttore ON/OFF (ACCESO/SPENTO). L’alimentazione principale è controllata tramite il sezionatore (a parete)
NON ATTIVARE L’EPP-450 CON I COPERCHI RIMOSSI.
I COMPONENTI AD ALTA TENSIONE SONO ESPOSTI ED AUMENTANO I
RISCHI DI SCOSSA ELETTRICA.
IL COMPONENTE INTERNO POTREBBE ESSERE DANNEGGIATO SE LE
VENTOLE DI RAFFREDDAMENTO PERDONO EFFICIENZA.
LE SCOSSE ELETTRICHE POSSONO UCCIDERE!
AVVERTIMENTO
I CONDUTTORI ELETTRICI ESPOSTI POSSONO ESSERE PERICOLOSI!
NON LASCIARE ESPOSTI I CONDUTTORI ELETTRICAMENTE “CALDI“.
QUANDO SI EFFETTUA LA DISCONNESSIONE DEL GENERATORE DI
ENERGIA SUPPLEMENTARE DA QUELLO PRIMARIO, ACCERTARSI CHE I
CAVI GIUSTI SIANO SCONNESSI. ISOLARE LE ESTREMITÀ SCONNESSE.
QUANDO SI UTILIZZA SOLO UN GENERATORE DI ENERGIA IN UNA
CONFIGURAZIONE PARALLELA, IL CONDUTTORE DELL’ELETTRODO
NEGATIVO DEVE ESSERE DISINNESTATO DAL GENERATORE DI ENER-
GIA SUPPLEMENTARE E DALLA CASSETTA IDRAULICA. UNA MANCA-
TA OSSERVANZA DI QUESTA PROCEDURA LASCERÀ IL GENERATORE
DI ENERGIA SUPPLEMENTARE ELETTRICAMENTE “CALDO”.
16
SEZIONE 3 INSTALLAZIONE
Connessioni per l’installazione parallela di due generatori di alimentazione EPP-450 con entrambi i generatori di alimentazione attivi.
Le connessioni descritte in basso sono idonee per il funzionamento parallelo di un massimo di 800 A a 100% lavoro o di 900 A a 80% lavoro (o meno). 80% lavoro significa 8 minuti di tempo dell’arco “on” (acceso) in un qualsiasi periodo di 10 minuti.
EPP-450 EPP-450
Generatore di energia supplementare lavoro
(+) elettrodo
(-) lavoro
(+)
Generatore di energia primario arco pilota elettrodo
(-)
2 - 4/0 600V cavi positivi al pezzo da lavorare
1 - 14 AWG 600V cavo alla connessione dell’arco pilota nella cassetta di avviamento dell’arco
(generatore alta frequenza)
2 - 4/0 600V cavi negativi nella cassetta di avviamento dell’arco
(generatore alta frequenza)
Per funzionamento a 100% lavoro al di sopra di 800 A, fare riferimento al diagramma di connessione in basso.
EPP-450
Generatore di energia supplementare lavoro
(+) elettrodo
(-) lavoro
(+)
EPP-450
Generatore di energia primario arco pilota elettrodo
(-)
3 - 2/0 AWG 600V cavi positivi al pezzo da lavorare
2/0 AWG 600V cavi di connessione tra unità
17
1 - 14 AWG 600V cavo alla connessione dell’arco pilota nella cassetta di avviamento dell’arco
(generatore alta frequenza)
3 - 2/0 AWG 600V cavi negativi nella cassetta di avviamento dell’arco (generatore alta frequenza)
SEZIONE 3 INSTALLAZIONE
3.6.1 Connessioni per due EPP-450 in parallelo (segue)
Connessioni per l’installazione parallela di due generatori di alimentazione EPP-450 con un solo generatore di energia attivo.
Connessioni per il funzionamento del generatore di energia di un massimo di 400 A a 100% lavoro o di 450 A a
80% lavoro (massimo). 80% lavoro massimo equivale ad un funzionamento non superiore agli 8 minuti in qualsiasi intervallo di tempo di 10 minuti.
EPP-450
Generatore di energia supplementare
EPP-450
Generatore di energia primario lavoro elettrodo lavoro elettrodo
2 - 4/0 600V cavi positivi al pezzo da lavorare
Staccare la connessione negativa dal generatore di energia secondaria ed isolare per convertire da due a uno i generatori di energia
2 - 4/0 600V cavi negativi nella cassetta di avviamento dell’arco
(generatore alta frequenza)
18
SEZIONE 3 INSTALLAZIONE
3.6.1 Connessioni per due EPP-450 in parallelo (segue)
Connessioni per l’installazione parallela di due generatori di alimentazione EPP-450 con un solo generatore di energia attivo.
Le connessioni descritte in basso sono idonee per il funzionamento della fornitura di alimentazione singola di un massimo di 450 A e 100% lavoro.
EPP-450
Generatore di energia supplementare
EPP-450
Generatore di energia primario lavoro elettrodo lavoro elettrodo
3 - 2/0 AWG 600V cavi positivi al pezzo da lavorare
Staccare la connessione negativa dal generatore di energia supplementare ed isolare per convertire da due a uno i generatori di energia
3 - 2/0 AWG 600V cavi negativi nella cassetta di avviamento dell’arco (generatore alta frequenza)
3.6.2 Marcatura con due EPP-450 paralleli
Due EPP-450, collegati in parallelo, ed utilizzabili per l’abbassamento della marcatura a 20 A e per il taglio da 100 A fino a 900A. Due semplici modifiche possono essere effettuate al Generatore di energia supplementare, per poter effettuare l’abbassamento della marcatura a 10 A. Queste modifiche devono essere effettuate solo se la marcatura al di sotto di 20 A
è necessaria.
MODIFICHE DEL CAMPO PER CONSENTIRE L’ABBASSAMENTO DELLA MARCATURA A 10 A:
1. MODIFICHE AL GENERATORE DI ENERGIA PRIMARIO: Nessuna
2. MODIFICHE AL GENERATORE DI ENERGIA SUPPLEMENTARE:
A. Staccare il filo WHT dalla bobina i K12
B. Rimuovere il cavo di connessione tra TB7-7 e TB7-8. Il cavo di connessione è un collegamento incorporato nella striscia del terminale.
NOTA:
Queste modifiche disattivano l’uscita della corrente del generatore di energia secondario soltanto nella modalità di marcatura. Le modifiche non hanno alcun effetto sulla corrente di uscita del secondo generatore di energia, quando si effettua il taglio nelle modalità di taglio a corrente ALTA o BASSA.
19
SEZIONE 3 INSTALLAZIONE
3.6.2 Marcatura con due EPP-450 paralleli (segue)
FUNZIONAMENTO DI DUE EPP-450 PARALLELI:
1. Fornire i segnali Contattore On/Off (Acceso/Spento), taglio/marcatura, gamma della corrente Alta/Bassa ad entrambi i generatori di energia primario e supplementare. Fornire lo stesso segnale V
REF
in entrambi i generatori di energia.
2. Quando si effettua la marcatura con i generatori di energia paralleli, e il generatore di energia secondario non è modificato, la funzione di trasferimento della corrente di uscita corrisponde alla somma delle funzioni di trasferimento per ciascun generatore di energia. I
OUT
= 20 x V
REF
. Ciascun generatore di energia fornirà la stessa corrente di uscita.
Quando si effettua la marcatura con i generatori di energia paralleli, e il generatore di energia secondario è modificato, la funzione di trasferimento della corrente è quella del generatore di energia primario. I
OUT
= 10 x V
REF
. Entrambi i generatori di energia si accenderanno quando è presente il segnale del Contattore, ma la corrente di uscita di un generatore di energia secondario è disattivata nella modalità di marcatura.
3. Quando si effettua il taglio nella modalità di corrente bassa, la funzione di trasferimento della corrente è la somma delle funzioni di trasferimento per ciascun generatore di energia: I
OUT
= 20 x V
REF
. Per i tagli con correnti al di sotto di
100 A, staccare il(i) cavo(i) negativo dal generatore di energia secondario ed accertarsi che le estremità siano isolate, per protezione dalle scosse elettriche. Quando il generatore di energia è staccato, la funzione di trasferimento della corrente è quella del generatore di energia primario: I
OUT
= 10 x V
REF
.
4. Quando si effettua il taglio nella modalità di corrente alta, la funzione di trasferimento della corrente è la somma delle funzioni di trasferimento per ciascun generatore di energia: I
OUT
= 100 x V
REF
. Per i tagli con correnti al di sotto di 100
A, staccare il(i) cavo(i) negativo dal generatore di energia secondario ed accertarsi che le estremità siano isolate, per protezione dalle scosse elettriche. Usare la modalità di taglio a corrente Bassa.
3.7 Cavi di interfaccia
Interfaccia CNC (24 conduttori)
Interfaccia del refrigerante ad acqua (8 conduttori)
20
SEZIONE 3 INSTALLAZIONE
3.7.1 Cavi di interfaccia CNC con generatore di energia di alimentazione di accoppiamento e con interfaccia CNC non terminato
Connettore maschio
N. parte: 647032
GRN/YEL
RED #4
3.7.2 Cavi di interfaccia CNC con connettori del generatore di energia di accoppiamento e connettore CNC di accoppiamento
Connettore CNC
N. parte: 2010549
Connettore maschio
N. parte: 647032
GRN/YEL
21
RED #4
SEZIONE 3 INSTALLAZIONE
3.7.3 Cavi di interfaccia del refrigerante ad acqua con connettori del generatore di energia di alimentazione di accoppiamento su entrambe le estremità
Connettore femmina
N. parte: 2062105
Connettore maschio
N. parte: 647257
22
SEZIONE 4
4.1 Descrizione del circuito del diagramma a blocchi
FUNZIONAMENTO
23
SEZIONE 4 FUNZIONAMENTO
4.1 Descrizione del circuito del diagramma a blocchi (segue)
Il circuito di alimentazione utilizzato nell’EPP-450 viene comunemente definito Buck Converter o Chopper. Gli interruttori elettronici ad alta velocità si accendono e si spengono varie migliaia di volte al secondo e forniscono impulsi di energia all’uscita. Un circuito del filtro, che consiste essenzialmente di un induttore (chiamato a volte una bobina) converte gli impulsi in un’uscita CC (Corrente Continua) relativamente costante.
Anche se l’induttore del filtro rimuove la maggior parte delle fluttuazioni dall’uscita “chopped” (spezzettata) degli interruttori elettronici, alcune piccole fluttuazioni di uscita, chiamate ondulazioni, rimangono L’EPP-450 utilizza un circuito di alimentazione brevettato che unisce l’uscita dei due chopper (ciascuno dei quali fornisce circa la metà dell’uscita totale), in modo da ridurre testa a getto d’inchiostro ondulazioni. I chopper sono sincronizzati in modo che quando l’ondulazione del primo chopper aumenta l’uscita, il secondo chopper diminuisce l’uscita. Questo risulta nell’ondulazione del primo chopper che parzialmente annulla l’ondulazione dell’altro chopper. Il risultato è quindi un’ondulazione molto bassa con un’uscita stabile e omogenea. L’ondulazione bassa è altamente desiderabile perché la durata consumabile del cannello migliora spesso con un’ondulazione bassa.
Il grafico in basso mostra l’effetto della riduzione dell’ondulazione brevettata di ESAB che utilizza due chopper sincronizzati e la commutazione alternata. A confronto con i due chopper che si alternano in sincronia, la commutazione alternata tipicamente riduce il fattore ondulazione da 4 a 10.
9.0
8.0
7.0
6.0
5.0
4.0
3.0
2.0
1.0
0.0
0 50 100 150
P. K. Higgins: Current_Ripple_ESP-600C; RMS CURRENT RIPPLE Chart 17
24
200 250 300 350
SEZIONE 4 FUNZIONAMENTO
4.1 Descrizione del circuito del diagramma a blocchi (segue)
Il diagramma a blocchi dell’EPP-450 (dopo il Paragrafo 4) mostra gli elementi funzionali principali del generatore di energia.
T1, il trasformatore principale, fornisce isolamento dalla linea di alimentazione primaria, oltre alla corretta tensione per il
*375 V CC Bus. Il rettificatore bus converte l’uscita a tre fasi di T1 in tensione *375 V bus. Un banco di condensatori fornisce il filtraggio e la conservazione dell’energia che garantisce alimentazione agli interruttori elettronici ad alta velocità. Gli interruttori sono IGBT (Transistor bipolari della gate isolati). Il *375 V bus garantisce l’alimentazione sia al Chopper sinistro
(Primario) che a quello destro (Asservito).
Ciascun chopper contiene IGBT, Diodi a funzionamento libero, un Sensore del vano, un Induttore del filtro e Diodi di blocco.
Gli IGBT sono gli interruttori elettronici che, nell’EPP-450 effettuano l’accensione e lo spegnimento 10.000 volte al secondo
(25.000 volte al secondo in modalità di corrente bassa e di marcatura). Questi offrono gli impulsi dell’alimentazione filtrati dall’induttore. I Diodi a funzionamento libero assicurano il percorso per il flusso della corrente quando gli IGBT sono spenti.
I Sensori del vano sono trasduttori di corrente che effettuano il monitoraggio delle correnti di uscita e che forniscono i segnali di feedback per il circuito di controllo.
I Diodi di blocco offrono due funzioni. Questi si occupano innanzitutto di evitare che il 430 V CC dal Circuito di avviamento della spinta ritorni indietro agli IGBT e al *375 V Bus. In secondo luogo, si occupano di fornire isolamento dei due chopper l’uno dall’altro. Questo consente un funzionamento indipendente di ciascun chopper, senza che l’altro chopper sia in funzione.
Il Circuito di controllo contiene servomeccanismi per entrambi i chopper. Contiene inoltre un terzo servomeccanismo che effettua il monitoraggio del feedback del segnale della corrente di uscita dal derivatore di precisione. Questo terzo servomeccanismo regola i servomeccanismi dei due chopper, per conservare una corrente di uscita accuratamente controllata e comandata dal segnale V
REF
.
La circuiteria V
REF
è isolata galvanicamente dal resto del generatore di energia. L’isolamento previene i problemi che potrebbero scaturire dai loop “di terra”.
Ciascun chopper, il sinistro Primario ed il destro Asservito, contiene una scheda PC PWM / Unità gate montata accanto agli
IGBT. Questa circuiteria fornisce i segnali PWM (Pulse Width Modulation - Modulazione della larghezza dell’impulso) on / off (acceso / spento) per la conduzione degli IGBT. Il PWM sinistro (Primario) fornisce un segnale di orologio sincronizzato alla propria circuiteria dell’Unità gate, oltre che alla circuiteria dell’Unità gate destra (Asservito). Tramite questo segnale sincronizzato gli IGBT dai due lati commutano alternativamente e riducono l’ondulazione di uscita.
L’EPP-450 fornisce una spinta per l’approvvigionamento di circa 430 V CC per l’avviamento dell’arco. Dopo la stabilizzazione dell’arco di taglio, la Fornitura della spinta viene spenta con i contatti sul Contattore (K10).
Un Ammortizzatore polarizzato riduce i transitori della tensione creati durante la terminazione dell’arco di taglio. Riduce inoltre le tensioni dei transitori da un generatore di energia parallelo, evitando quindi danni alla fonte di alimentazione.
Il Circuito dell’arco pilota consiste dei componenti necessari per l’istituzione di un arco pilota. Questo circuito è disattivo quando l’arco di taglio o di marcatura è stato istituito.
* La tensione bus per il modello 380/400 V, 50 Hz è di circa 360 V CC durante il funzionamento con un ingresso di 380 V.
25
SEZIONE 4 FUNZIONAMENTO
4.2 Pannello di controllo
I
J
H F
C
D
G
A
B
E
K
N L M
A - Alimentazione principale
L’indicatore si accende quando l’alimentazione di ingresso è applicata al generatore di energia.
B - Contattore acceso
L’indicatore si accende quando il contattore principale è energizzato.
C - Temperatura eccessiva
L’indicatore si accende quando il generatore di energia si è surriscaldato.
D - Guasto
L’indicatore si accende quando ci sono anormalità nel processo di taglio o quando la tensione della linea di ingresso scende al di sotto del valore nominale necessario di più di ±10%.
E - Guasto di ripristino dell’alimentazione
L’indicatore si accende quando si è verificato un grave guasto. L’alimentazione di ingresso deve essere disinnestata per almeno 5 secondi e quindi riapplicata.
F - Indicatore della corrente (Potenziometro)
Indicatore dell’EPP-450 mostrato. EPP-450 ha una gamma di 10-100 A, in gamma di corrente bassa, e di 50-400 A in gamma di corrente alta. Il potenziometro è usato solo in modalità pannello.
G - Interruttore remoto del pannello
Verifica l’ubicazione del controllo della corrente.
• Collocare nella posizione PANNELLO per il controllo tramite il potenziometro della corrente.
• Collocare nella posizione REMOTO per il controllo tramite un segnale esterno (CNC).
26
SEZIONE 4 FUNZIONAMENTO
4.2 Pannello di controllo (segue)
H e L - Connessioni remote
H - Spina a 24 perni per la connessione del generatore di energia al CNC (telecomando)
L - Spina a 8 perni per la connessione del generatore di energia al circolatore di refrigerante.
I - Interruttore dell’arco pilota ALTO / BASSO
Usato per selezionare la quantità di corrente dell’arco pilota desiderata. Come regola generale, per 100 ampere e meno, viene usata un’impostazione di BASSO. Questo potrebbe variare in base al gas, al materiale e al cannello usati. Le impostazioni
Alto/Basso sono specificate nei dati di taglio inclusi nel manuale del cannello. Quando l’EPP-450 è impostato sulla modalità di marcatura, questo interruttore deve trovarsi nella posizione in basso.
M - Connettore E-stop
Il connettore E-stop offre un contatto normalmente chiuso dell’interruttore E-stop. Il contatto è collegato a J4-A e J4-B.
Il contatto si apre dopo che il pulsante E-stop viene premuto. Questa procedura fornisce un segnale al controllo del plasma per indicare che la fonte di alimentazione è in condizione E-stop.
N - Pulsante e-stop
Il pulsante E-stop attiva l’interruttore E-stop. Quando il pulsante viene premuto ed esiste la condizione E-stop che impedisce alla fonte di alimentazione di fornire un’uscita, perfino quando un segnale di avvio viene fornito.
NOTA:
Il generatore di energia EPP-450 è solitamente in “Gamma di corrente bassa”, 100 A massimo. Il controllo esterno deve fornire una connessione (chiusura del contatto) tra J1-R e J1-T per collocare la fornitura di alimentazione in una “Gamma di corrente alta”, massimo 450 A. Se l’EPP-450 sarà permanentemente collegato nella “Gamma di corrente alta”, spostare il filo rosso da TB8-1 a TB8-2. TB8 è situato accanto alla parte superiore del generatore di energia sul retro della cassa della lastra di metallo che contiene la scheda PC di controllo.
J
I H F
G
A
B
C
D
E
K
N L M
27
SEZIONE 4
4.2 Pannello di controllo (segue)
FUNZIONAMENTO
J - Misuratori
Mostra la tensione e gli ampere durante il taglio. L’amperometro può essere attivato con l’interruttore Effettivo / Preimpostato, quando non si effettua il taglio, per visualizzare un’approssimazione della corrente di taglio prima dell’inizio del taglio.
K - Interruttore effettivo / preimpostato
L’interruttore di commutazione a molla AMP EFFETTIVI / AMP PREIMPOSTATI,
S4, ritorna alla posizione EFFETTIVE (SU). Nella posizione EFFETTIVO, l’AMPE-
ROMETRO DI USCITA mostra la corrente di taglio di uscita.
Nella posizione PREIMPOSTATO (GIÙ), l’AMPEROMETRO DI USCITA mostra un’approssimazione della corrente di taglio di uscita, monitorando il segnale di riferimento della corrente di marcatura o di taglio da 0,00 a 10,00 V CC
(Vref). Il segnale di riferimento deriva dal POTENZIOMETRO ATTUALE con l’interruttore PANNELLO/REMOTO nella posizione PANNELLO (SU) e da un segnale di riferimento remoto (J1-J / J1-L(+)) con l’interruttore PANNELLO/RE-
MOTO nella posizione REMOTO (GIÙ). Il valore che appare sull’AMPEROMETRO
DI USCITA sarà il valore della corrente di uscita effettiva approssimativo per entrambe le modalità di corrente Alta e Bassa.
L’interruttore può essere spostato tra le posizioni EFFTTIVO e PREIMPOSTATO in qualsiasi momento, senza influenzare in alcun modo il processo di taglio.
AVVERTIMENTO
TENSIONE E CORRENTE PERICOLOSI!
LE SCOSSE ELETTRICHE POSSONO UCCIDERE!
PRIMA DI ATTIVARE, ACCERTARSI CHE LE PROCEDURE DI ISTALLA-
ZIONE E MESSA A TERRA SIANO STATE ESEGUITE. NON ATTIVARE
L’UNITÀ CON I COPERCHI RIMOSSI.
28
SEZIONE 4 FUNZIONAMENTO
4.2.1 Modalità di funzionamento: Modalità di taglio e di marcatura alte e basse
1. L’EPP-450 funziona nella modalità di taglio in due gamme di corrente. La gamma di corrente inferiore è 35-100 A e corrisponde al segnale V
REF
di 3,50-10,00 V. Nella gamma di corrente alta, l’uscita di corrente è continuamente regolabile da 50 A fino a 450 A utilizzando o il Potenziometro della corrente, sul pannello anteriore, o un segnale di riferimento della corrente remoto inviato al connettore, J1. La modalità di taglio predefinita per l’EPP-450 è quella bassa. Per attivare l’apparecchio in modalità di taglio alta, alimentare il J1-T con 115 Volt CA, collegando il J1-T al J1-R con un contatto isolato.
Quando si utilizza un segnale remoto, 50 A corrisponde ad un segnale di riferimento della corrente di 1,00 V CC, e
450 A corrisponde ad un segnale di 9,00 V CC. Per i segnali oltre 9,00 V, la fonte di alimentazione internamente limita la corrente di uscita ad un valore di 475 A.
I valori predefiniti dell’EPP-450 sono impostati sulla Modalità di funzionamento di taglio, a meno che venga fornito un segnale di comando proveniente da un telecomando.
2. Il generatore di energia è posizionato in Modalità di marcatura con un relè esterno isolato o con un contatto di interruttore che collega J1-R (115VAC) a J1-M. Vedere il diagramma schematico nel coperchio posteriore. Questa chiusura del contatto deve essere effettuata prima (50 mS o più a lungo) di emettere un comando di Avvio
(Contattore acceso).
In Modalità di marcatura, la corrente di uscita è regolata attraverso una gamma continuamente regolabile singola da
10 A a 100 A, usando o il Potenziometro della corrente, sul pannello anteriore, o un segnale di riferimento della corrente remoto inviato al connettore, J1. L’EPP-450 passa automaticamente alla gamma della corrente bassa in modalità di marcatura.
Nella gamma della corrente bassa, quando si utilizza un segnale remoto, 10 A corrisponde ad un segnale di riferimento della corrente di 1,00 V CC e 100 A corrisponde ad un segnale di 10.00 V CC. Nella gamma della corrente alta, quando si utilizza il segnale di riferimento della corrente remoto (V corrente di uscita ad un valore tipico di 475 A.
REF
), la corrente di uscita da 50 a 450 A corrisponde ad un segnale di riferimento da 1,00 a 9,00 V CC. Per i segnali di riferimento oltre 9,00 V, la fonte di alimentazione limita la
Nella Modalità di marcatura, la Fornitura della spinta usata per l’avvio dell’arco nella Modalità di taglio viene disattivata. La tensione del Circuito aperto risultante equivale a circa 360 V nella tensione della linea di ingresso nominale*.
Inoltre, K12 si chiude e collega R60 a R67 nel circuito di uscita. Queste resistenze aiutano a stabilizzare l’uscita per le correnti di marcatura basse. Il generatore di energia è in grado di fornire un’uscita di 10-100 A al 100% lavoro nella modalità di marcatura.
L’uscita di 10 Amp viene fornita tramite le resistenze R60-R67. La Corrente di avvio minima (SW2) impostata in sede di fabbrica è di 3 Ampere. Le impostazioni predefinite dell’Interruttore due (SW2) sulla Scheda PC di controllo montata dietro il coperchio di accesso sul lato destro superiore del pannello anteriore equivale alle posizioni 5, 6, 7 e
8 spente (giù).
* Circa 345V per il modello 380/400 V che funziona con 380 V.
29
SEZIONE 4 FUNZIONAMENTO
4.3 Sequence of Operation
SECTION 4 Operation
Apply Power
1. Applicare l’alimentazione chiudendo il sezionatore (a parete).
(L’EPP-450 non è dotato di un interruttore on / off (acceso/
1.
Apply power by closing the line (wall) switch.
(The ESP-400C does not have an on/off
4.3 Sequence of Operation
2. Il pulsante E-stop viene estratto.
and the fault light will flash and then go out.
PANEL
PILOT
ARC
REMOTE
Apply Power
HIGH
PANEL
LOW
REMOTE
ACTUAL AMPS
2.
3.
Select the Panel/Remote setting.
Set pilot arc High/Low switch. (Refer to cutting data in the torch manual.)
1.
Apply power by closing the line (wall) switch.
(The ESP-400C does not have an on/off
4.
If using panel mode, view preset amps with the pere preimpostati con l’interruttore degli AMP EFFETTIVI /
PREIMPOSTATI. Regolare la corrente fino a quando il valore approssimativo desiderato appaia sull’amperometro. Se si
5.
3.
ACTUAL/PRESET AMPS switch. Adjust current until the approximate desired value is shown on the ammeter.
Begin plasma cutting operation. This may
Set pilot arc High/Low switch. (Refer to cutting depending on the total plasma package.
PILOT
ARC
HIGH
PRESET AMPS
LOW
Begin
Cutting
ACTUAL AMPS
6.
7.
If using panel mode, after cutting has begun, adjust current to desired amount.
until the approximate desired value is shown on the ammeter.
Note: The fault light flashes when the contactor is first turned on signifying the DC Bus powered up normally.
6.
If using panel mode, after cutting has begun,
Nota:
PRESET AMPS
7.
Check for fault light. If a fault light illuminates, refer to troubleshooting section.
Begin
4.4 Arc Initiation Settings
4.4 Arc Initiation Settings
4-4
30
Note: The fault light flashes when the contactor is first turned on signifying the DC Bus powered up normally.
The time to achieve full current can be adjusted to suit your particular system. This feature uses 50% of the cutting current to start, dwell and then gradually (less than a second) achieve full current.
The ESP-400C is factory shipped with this feature enabled. The default settings are:
Minimum Start Current 40A
50% of cut current
Timing to achieve full current
Dwell Time
800 msec
50 msec
The ESP-400C is factory shipped with this feature enabled. The default settings are:
Minimum Start Current 40A
Start Current 50% of cut current
Timing to achieve full current 800 msec
Dwell Time 50 msec
4-4
SEZIONE 4 FUNZIONAMENTO
4.4 Impostazioni di avviamento dell’arco
Il tempo di ottenimento della corrente completa può essere regolato per un avvio progressivo. Questa funzione utilizza una corrente ridotta per l’avvio e quindi gradualmente aumenta la corrente fino al massimo. L’EPP-450 viene spedito con l’avvio progressivo attivo impostato in sede di fabbrica. Le impostazioni predefinite sono:
Corrente di avvio minima . . . . . . . . . . . . . . . . . . . . . . . . . . . . . . . . . . . . . 3 A
Corrente di avvio . . . . . . . . . . . . . . . . . . . . . . . . . . . . . . . . . . . . . . . . . . . . . 50% della corrente di taglio
Tempo per il raggiungimento del massimo della corrente. . . . . . 800 msec
Tempo di sosta . . . . . . . . . . . . . . . . . . . . . . . . . . . . . . . . . . . . . . . . . . . . . . . 2 msec min.
Queste funzioni dei tempi possono essere disattivate o regolate in base alle necessità del sistema individuali.
Forma della corrente di avvio con Avvio rapido OFF (SPENTO)
I
Corrente di taglio
OUT
= 50 V
I
OUT
= 10 V
REF
REF
(Alto)
(Basso)
Circa 2 msec fino al massimo della corrente
Tempo
Forma della corrente di avvio con Avvio rapido ON (ACCESO)
Corrente di avvio
Tempo di sosta
Tempo per il raggiungimento del massimo della corrente
800 msec
I
I
Corrente di taglio
OUT
OUT
= 50 V
REF
= 10 V
REF
(Alto)
(Basso)
Tempo
AVVERTIMENTO
LE SCOSSE ELETTRICHE POSSONO UCCIDERE!
SPEGNERE L’ALIMENAZIONE NEL SEZIONATORE (A PARETE) PRIMA
DI RIMUOVERE QUALSIASI COPERCHIO O DI EFFETTUARE QUA-
LUNQUE REGOLAZIONE AL GENERATORE DI ENERGIA.
31
SEZIONE 4 FUNZIONAMENTO
4.4.1 Attivazione / disattivazione delle condizioni di avviamento dell’arco
1 2 3 4 5 6 7
On (acceso)
Off (spento)
8 7
SW1
6 5 4 3 2 1
1. Rimuovere il pannello di accesso sull’angolo superiore destro del pannello anteriore. Riposizionare il pannello dopo aver effettuato le regolazioni.
SW2
2. Individuare SW1 e PCB1 e spingere entrambi gli interruttori a bilico verso il basso per disattivare. Per attivare, spingere gli interruttori verso l’alto. (Se un interruttore è in alto e l’altro è in basso, il tempo di avviamento dell’arco è considerato acceso).
Le impostazioni predefinite in sede di fabbrica vengono mostrate
1 2 3 4 5 6 7 8
On (acceso)
Off (spento)
SW2
4.4.2 Regolazione del timer di sosta dell’avviamento dell’arco
Il Tempo di sosta è controllato tramite la selezione delle posizioni da 1 a 4 di SW2 su PCB1. Quando un interruttore viene spento, il suo valore è aggiunto al tempo di sosta minimo di 2 msec.
Interruttore N. 1 = 2 msec tempo di sosta
Interruttore N. 2 = 4 msec tempo di sosta
Interruttore N. 3 = 8 msec tempo di sosta
Interruttore N. 4 = 16 msec tempo di sosta
Tutti gli interruttori spenti. 2 msec è il tempo di sosta predefinito in sede di fabbrica.
4.4.3 Regolazione della corrente di avvio minima
Il Tempo di avvio minimo è controllato tramite la selezione delle posizioni da 5 a 8 di SW2. Quando un interruttore viene spento, il suo valore è aggiunto al valore minimo impostato in sede di fabbrica di 3 A.
Interruttore N. 5 = 25 A min. corrente di avvio
Interruttore N. 6 = 12 A min. corrente di avvio
Interruttore N. 7 = 6 A min. corrente di avvio
Interruttore N. 8 = 3 A min. corrente di avvio
L’impostazione predefinita è con 5, 6, 7 e 8 spenti (giù) 0 A + 0 A + 0 A + 0 A + 3 A = 3 A
32
8
SEZIONE 4
4.4.4 Controlli dell’avviamento dell’arco
Potenziometro della corrente di avvio
Timer di aumento della corrente
FUNZIONAMENTO
SW1
SW2
4.4.5 Avvio della corrente e del timer di aumento della corrente
Rapporto corrente di avvio (%) e impostazione potenziometro
90%
80%
70%
60%
50%
40%
30%
20%
10%
Corrente di avvio
Impostare utilizzando il potenziometro situato in alto e a sinistra del centro di PCB1. L’impostazione in sede di fabbrica di 7 risulta in una corrente di avviamento che corrisponde al 50% della corrente di taglio.
Timer di aumento della corrente
Tre interruttori situati accanto al potenziometro della corrente di avviamento. Il tempo è quello trascorso tra la corrente di avviamento (dopo la fine della sosta) e la corrente massima.
Predefinito in sede di fabbrica = 800 msec.
Predefinito in sede di fabbrica = 250 msec.
Posizione centrale = 800 msec.
Posizione a destra = 1200 msec
0%
0 1 2 3 4 5 6 7 8 9 10
Impostazione del potenziometro della corrente di avvio
MAX.
33
38
SEZIONE 4
4.5.1 Curve approssimative V-I EPP-450 per tutti i modelli
FUNZIONAMENTO
V
VREF = 5.00 HIGH RANGE
V
REF
= 9,000
VREF = 9.000
34
section 5 maintenance
5.1 General
warninG electric shock can kill!
shut off power at the line (wall) disconnect before attemptinG any maintenance.
warninG eye hazard when usinG compressed air to clean.
• Wear approved eye protection with side shields when cleaning the power source.
• Use only low pressure air.
caution maintenance on this equipment should only be performed by trained personnel.
5.2 cleaning
Regularly scheduled cleaning of the power source is required to help keep the unit running trouble free. The frequency of cleaning depends on environment and use.
1. Turn power off at wall disconnect.
2. Remove side panels.
3. Use low pressure compressed dry air, remove dust from all air passages and components. Pay particular attention to heat sinks in the front of the unit. Dust insulates, reducing heat dissipation. Be sure to wear eye protection.
35
section 5 maintenance caution air restrictions may cause epp-450 to over heat.
thermal switches may be activated causing interruption of function. do not use air filters on this unit. keep air passages clear of dust and other obstructions.
5.3 lubrication
• Some units are equipped with oil tubes on the fans. These fans should be oiled after 1 year of service.
• All other EPP-450s have fan motors that are permanently lubricated and require no regular maintenance.
warninG electric shock hazard!
be sure to replace any covers removed durinG cleaninG before turninG power back on.
36
section 6
6.1 General
troubleshootinG warninG electric shock can kill!
do not permit untrained persons to inspect or repair this equipment. electrical work must be performed by an experienced electrician.
caution stop work immediately if power source does not work properly.
have only trained personnel investigate the cause.
use only recommended replacement parts.
6.2 fault indicators
Front Panel Fault
Indicators
PCB1 Located behind this panel.
Fault indicators are found on the front panel Used with the LEDs on PCB1 (located behind the cover with the
EPP label) problems can be diagnosed.
note:
It is normal for momentary lighting (flashing) of the fault indicator and LED 3 when a “contactor on” signal is applied at the beginning of each cut start.
Fault Indicator used with:
LED 3 - Bus Ripple
LED 4 - High Bus
LED 5 - Low Bus
LED 7 - Arc Voltage Saturation
LED 8 - Arc Voltage Cutoff
Power Reset Fault Indicator used with:
LED 6 - Right Overcurrent
LED 9 - Left Overcurrent
LED 10 - Left IGBT Unsaturated
LED 11 - Right IGBT Unsaturated
LED 12 - Left -12V Bias Supply
LED 13 - Right -12V Bias Supply
37
section 6
38
troubleshootinG
Fault Indicator (Front Panel)
Illuminates when there are abnormalities in the cutting process or when the input voltage falls ±10% outside the normal value. Momentary illumination is normal. If continuously lit, check LEDs 3, 4, 5, 7, and 8 on PCB1 for further diagnosis.
LED 3 – (yellow) Bus Ripple Fault - Momentarily illuminates at the beginning of each cut. Continuously lit during single-phasing or imbalanced line-to-line voltages of the three phase input line (Excessive Ripple). Power Source is shut down.
LED 4 – (yellow) High Bus Fault – Illuminates when input line voltage is too high for proper operation (approximately 20% above nominal line voltage rating).
Power source is shut down.
LED 5 – (yellow) Low Bus Fault – Illuminates when input line voltage is lower than 10% below nominal line voltage rating.
Power Source is shut down.
LED 7 – (yellow) Arc Voltage Saturation Fault – Illuminates when the cutting arc voltage is too high and cutting current drops below preset level. LED will extinguish after voltage decreases and current rises.
LED 8 – (yellow) Arc Voltage Cutoff Fault – Illuminates when arc voltage increases over the preset value. PS is shut down.
38
38
section 6 troubleshootinG
Power Reset Fault Indicator (on front panel)
Illuminates when a serious fault is detected. Input power must be disconnected for a least 5 seconds to clear this fault. Check PCB1 Red LEDs 6, 9, 10, 11, 12, and 13 if this fault is illuminated for further diagnosis.
LED 6 – (red) Right Overcurrent Fault – Illuminates when the current out of the right side chopper is too high (300 amps). This current is measured by the right-side hall sensor. The power source is shut down.
LED 9 – (red) Left Overcurrent Fault – Illuminates when the current from the left side chopper is too high (300 amps). Measured by the left hall sensor. Power source is shut down.
LED 10 _ (red) Left IGBT Unsaturated Fault – Illuminates when left IGBT is not fully conducting. PS (PS) is shut down.
LED 11 – (red) Right IGBT Unsaturated Fault – Illuminates when right IGBT is not fully conducting. Power Source (PS) is shut down.
LED 12 – (red) Left -(neg) 12V Bias Supply Fault – Illuminates when negative 12 V bias supply to the left side IGBT gate drive circuit (located on PWM-drive board PCB2) is missing.
PS is shut down.
LED 13 – (red) Right –(neg) 12V Bias Supply Fault - Illuminates when negative 12 V bias supply to the right side IGBT gate drive circuit (located on PWM drive board PCB3) is missing. PS is shut down.
39
38
section 6 troubleshootinG
6.3 fault isolation
Many of the most common problems are listed by symptom.
6.3.1 No output with contactor signal applied
6.3.2 Output limited to 100A
6.3.3 Fans not working
6.3.4 Power not on or low voltage
6.3.5 Fault light illumination
6.3.6 Torch won’t fire
6.3.7 Fusses blown - F1 and F2
6.3.8 Intermittent, interrupted or partial operation
6.3.1 no output with contactor signal applied problem possible cause action
Contactor signal is applied, contactor lamp on front panel is illuminated, K2 and
K3 contactors do not close and low bus fault light, LED
5 illuminates.
External emergency stop (E-stop) is open.
E-stop button on front panel is pushed in.
Power reset lamp on front panel indicates a serious fault condition.
Connect isolated contact of E-stop switch to provide connection between J1-E and J1-F.
Twist and pull out to reset E-stop condition.
Refer to section under fault light illumination.
6.3.2 output limited to 100a problem possible cause
Power source will not go over
100A.
High current range signal missing.
action
External control should connect J1-R to J1-T. As an alternative, in the power source, move the red wire on TB8-1 to TB8-2.
6.3.3 fans not working problem
All 4 fans do not run
1, 2 or 3 fans do not run.
possible cause
This is normal when not cutting.
Fans run only when “Contactor On” signal is received.
Broken or disconnected wire in fan motor circuit.
Faulty fan(s)
None
Repair wire.
Replace fans
40
action
section 6 troubleshootinG
6.3.4 power not on or low voltage problem possible cause
Power source inoperable:
Main power lamp is off.
Low open circuit voltage
Missing 3-phase input voltage
Missing 1 of 3-phase input voltage
Fuse F3/F4 blown
Pilot arc Contactor (K4) faulty
Faulty Control PCB1
action
Restore all 3 phases of input voltage to within
±10% of nominal line.
Restore all 3 phases of input voltage to within
±10% of nominal line.
Replace F3/F4
Replace K4
Replace Control PCB1 (P/N 0558038312)
6.3.5 fault light illumination problem
Fault light illuminates at the end of cut but goes off at the start of the next.
LED 3 – (amber) Bus Ripple
LED 4 – (amber) High Bus
LED 5 – (amber) Low Bus
possible cause action
Normal condition caused when terminating the arc by running the torch off the work or the arc being attached to a part that falls away.
Imbalance of 3-phase input power
Momentary loss of one phase of input power
Faulty control PCB1
One or more phases of input voltage exceed nominal line voltage by more than 15%.
Faulty control PCB1
One or more shorted diode rectifiers
(D25-D28) on the “Electrode Plate”
One or more phases of input voltage are lower than nominal by more than 15%.
Blown F1 and F2 fuses
Over temp Light comes on.
Imbalanced 3-phase input power
Momentary loss of one phase of input power
Faulty Main Contactor (K1)
FAULTY Control PCB1
Reprogram cutting process to ensure arc is terminated only by removing the “Contactor On” signal.
Maintain phase voltage imbalance of less than 5%.
Restore and maintain input power within ±10% nominal
Replace PCB1 P/N 0558038312
Restore and maintain line voltage within ±10%
Replace PCB1 P/N 0558038312
Replace shorted diode rectifiers
Restore and maintain within
±10% of nominal
See F1 and F2 in Blown
Fuses Section
See over temp in Fault Light Section
Maintain phase voltage imbalance of less than 5%
Restore and maintain within
±10% of nominal
Replace K1
Replace PCB1 P/N 0558038312
41
section 6 troubleshootinG problem possible cause action
LED 6 – (red) Right Over Current
note:
If operation at 275A or less is possible, then the LEFT side is not working.
LED 9 – (red) Left Over Current
note:
If operation at 275A or less is possible, then the Right side is not working.
Cutting at over 275A with a faulty left side
(left side output = 0)
Right current transducer connector loose or unplugged. PCB loose.
Loose or unplugged connector at right
PWM/Drive Printed circuit board.
P2 at left of PWM / Drive PCB loose or unplugged.
Check voltage between P7-6 and P7-7. A voltage in either polarity of greater than
0.01 V indicates a faulty right current transducer (TD2).
Faulty PCB1
Faulty right PWM / Drive PCB
See faulty left or right side
Secure connections
Secure connection
Secure connection
Replace right current transducer
(TD2)
Replace PCB1 P/N 0558038312
Replace right PWM / Drive PCB P/N
0558038324
Cutting at over 275A with a faulty right side
(right side output = 0)
Left current transducer connector loose or unplugged. PCB loose.
Loose or unplugged connector at left PWM
/ Drive Printed circuit board.
P2 at right of PWM / Drive PCB loose or unplugged.
Check voltage between P7-2 and P7-3. A voltage in either polarity of greater than
0.01 V indicates a faulty left current transducer (TD1).
Faulty PCB1
Faulty left PWM / Drive PCB
See faulty right side
Secure connections
Secure connection
Secure connection
Replace left current transducer (TD1)
Replace PCB1 P/N 0558038312
Replace left PWM / Drive PCB P/N
0558038324
caution never attempt to power-up or operate the power source with any
Gate / emitter iGbt plug disconnected from it’s pwm / Gate drive board. attempting to operate the power source with any open (unplugged) iGbt Gate / emitter connector may damage the iGbt and the plasma cutting torch.
42
section 6 troubleshootinG problem possible cause action
Very high Output current accompanied by either a left or right over current (LED 6)
LED 10 - (red) Left IGBT Unsaturated
LED 11 - (red) Right IGBT
Unsaturated
Shorted IGBT
Current pot set too high
Faulty left PWM / Drive PCB
High remote current signal
Faulty PCB1
Black wire connecting IGBT (Q2) collector to P3 of the left PWM / Drive PCB (PCB2) is disconnected.
Shorted Freewheeling Diode(s)
Loose or unplugged P1 connector at the left PWM /
Drive PCB
Loose or unplugged P10 connector at PCB1
Faulty PCB1
Faulty left PWM / Drive PCB
Black wire connecting IGBT (Q5) collector to P3 of the right PWM / Drive PCB (PCB3) is disconnected.
Shorted Freewheeling Diode(s)
Loose or unplugged P1 connector at the left PWM /
Drive PCB
Loose or unplugged P10 connector at PCB1
Faulty PCB1
Faulty right PWM / Drive PCB
Replace the IGBTs
Lower the current setting
Replace left PWM / Drive PCB
Decrease remote current signal
Replace PCB1 P/N 0558038312
Secure connector
Replace freewheeling diode(s)
Secure P1
Secure P10
Replace PCB1 P/N 0558038312
Replace PCB2 P/N 0558038324
Secure connector
Replace freewheeling diode(s)
Secure P1
Secure P11
Replace PCB1 P/N 0558038312
Replace PCB3 P/N 0558038324
43
section 6 troubleshootinG problem possible cause action
LED 12 – (red) Left –12V Missing
LED 12 – (red) Right –12V Missing
Very high Output current accompanied by either a left or right over current (LED 9 or LED 6 respectively)
Over Temp Lamp illuminates
Loose or unplugged P1 connector at the left PWM / Drive PCB
Loose or unplugged P10 connector at PCB1
Secure P1 connector
Secure P10 connector
Faulty left PWM / Drive PCB
Replace left PWM / Drive PCB P/N
0558038324
Loose or unplugged P1 connector at the right PWM / Drive PCB
Loose or unplugged P11 connector at PCB1
Secure P1 connector
Secure P11 connector
Faulty right PWM / Drive PCB
Shorted IGBT
Current pot set too high
Faulty left PWM / Drive PCB
High remote current signal
Faulty PCB1
One or more fans inoperable
Broken wire or unplugged connector at thermal switch.
Obstruction to air flow closer than 3 feet
(1 m) to rear of power source.
Excessive dirt restricting cooling air flow
Obstructed air intake
Replace right PWM / Drive PCB P/N
0558038324
Replace the IGBTs
Lower the current setting
Replace left PWM / Drive PCB P/N
0558038324
Decrease remote current signal
Replace PCB1 P/N 0558038312
Repair or replace fan(s)
Repair broken wires and unplugged connector
Allow 3 ft. (1 m) minimum between the rear of the power source and any object that may restrict air flow.
Clean out excessive dirt, especially in the extrusions for the IGBTs and freewheeling diodes, the POS, NEG and Electrode Plates, the main transformer (T1) and the filter inductors (L1 and L2).
Check and clear any obstructions from the bottom, front, and top rear of the Power
Source.
44
section 6 troubleshootinG
6.3.6 torch will not fire problem possible cause action
Main Arc Transfers to the work with a short “pop”, placing only a small dimple in the work.
Arc does not start. There is no arc at the torch. Open circuit voltage is OK.
Remote control removes the start signal when the main arc transfers to the work.
Place Panel/Remote switch in “Panel” position
Panel/Remote switch in “Remote” with no remote control of the current
Remote current control present but signal missing.
Check for current reference signal at TB1-
4(+) and TB1-5(-). See Signal vs. Output
Current Curve this section.
Increase current pot setting.
Current pot set too low.
Start current pot, located behind the cover for the control PCB is set too low.
Increase the start current post setting to “7”.
Open connection between the power source positive output and the work.
Repair connection
Fuse F6 in the Pilot arc circuit is blown. Replace F6
Fuse F7 in the pilot arc circuit is blown. Replace F7
Pilot arc High/Low switch is in the ”LOW” position when using consumables for
100A or higher (Refer to process data included in torch manuals)
Change Pilot arc to “High” position.
(Refer to process data included in torch manuals)
Pilot arc contactor (K4) faulty.
Faulty PCB1
Replace K4
Replace PCB1 P/N 0558038312
45
section 6 troubleshootinG
6.3.7 fuses f1 and f2 blown problem
Fuses F1 and F2 blown.
possible cause action
Process controller ignites pilot arc too soon after providing the “Contactor
On” signal
Process controller must allow at least
300MS to lapse between the application of the “Contactor On” signal and the ignition of the pilot arc. Fix process controller logic and replace diodes.
Faulty negative (Electrode) output cable shorting to earth ground.
Repair cable
Shorted freewheeling diode.
One or more shorted diode rectifiers
(D13-D18) on “POS Plate”.
One or more shorted diode rectifiers
(D7-D12) on “NEG Plate”.
Replace shorted freewheeling diode and F1-F2
Replace all diode rectifiers on the “POS
Plate”.
Replace all diode rectifiers on the “NEG
Plate”.
6.3.8 intermittent, interrupted or partial operation problem possible cause action
Works OK at 275A or less - Over current right side when cutting over 275A. LED 6 on control board illuminated.
Loose or unplugged connector at left PWM /
Drive PCB (PCB2)
Secure connector
Faulty left PWM / Drive PCB
Replace right PWM / Drive PCB P/N
0558038324
Check voltage between P5-1 and P5-2 at the left PWM / Drive PCB (PCB2). Should be 20V
AC. Between P5-1 and P5-3 should be 40V AC.
If not the control transformer (T5) is faulty.
Replace control transformer T5
Works OK at 275A or less - Over current left side when cutting over 275A. LED 9 on control board illuminated.
Loose or unplugged connector at Right PWM
/ Drive PCB (PCB3)
Secure connector
Faulty Right PWM / Drive PCB
Replace right PWM / Drive PCB P/N
0558038324
Check voltage between P5-1 and P5-2 at the right PWM / Drive PCB (PCB3). Should be 20V
AC. Between P5-1 and P5-3 should be 40V AC.
If not the control transformer (T7) is faulty.
Replace control transformer T7
caution never attempt to power-up or operate the power source with any
Gate / emitter iGbt plug disconnected from it’s pwm / Gate drive board. attempting to operate the power source with any open (unplugged) iGbt Gate / emitter connector may damage the iGbt and the plasma cutting torch.
46
section 6 troubleshootinG problem possible cause action
Power Supply turns off prematurely in the middle of the cut.
Momentary loss of primary input power.
Faulty condition, indicated by illumination of the fault lamp.
Faulty condition, indicated by the illumination of the power reset fault lamp.
Current setting too low.
Restore and maintain input voltage within ±10% of nominal.
Remove control PCB (PCB1) access panel to determine the fault causing the shutdown. Refer to fault light illumination section.
Remove control PCB (PCB1) access panel to determine the fault causing the shutdown. Refer to fault light illumination section.
Increase current setting
Remote current signal removed during cut. Fix remote current signal
problem possible cause action
Output current is unstable and drifts above or below the setting.
Place the PANEL / REMOTE switch in the “PANEL” position. Adjust current control pot. If current no longer drifts, the remote current control signal is faulty.
Select “PANEL” on the PANEL / REMOTE switch and adjust the current control pot. The current still drifts, measure the current reference signal at TB1-4 (+) and TB1-5 (-). If the signal drifts, the current control pot is faulty. If the signal does not drift, the Control PCB (PCB1) is faulty.
Fix the remote current control signal to operate the PANEL / REMOTE switch in the “PANEL” position.
Replace the current control pot.
Replace the control PCB (PCB1) P/N
0558038312
47
section 6 troubleshootinG
6.4 testing and replacing components notice
• Replace a PC board only when a problem is isolated to that board.
• Always disconnect power before removing or installing a PC board.
• Do not grasp or pull on board components.
• Always place a removed board on a static free surface.
• If a PC board is found to be a problem, check with your ESAB distributor for a replacement. Provide the distributor with the part number of the board as well as the serial number of the power source.
• Do not attempt to repair the board yourself. Warranty will be voided if repaired by the customer or an unauthorized repair shop.
power semiconductor components
Categories of power semiconductors include;
• Power Rectifiers
• Modules containing the free wheeling diodes and IGBTs
48
section 6
6.4.1 power rectifiers and blocking diodes
Power Rectifiers
troubleshootinG
Power Rectifiers
Procedure to access behind the front panel
1. Remove top cover and side panels
2. Locate and disconnect plug in rear of ammeter (attached tone red and one black wire)
3. Remove pilot arc switch
4. Disconnect voltmeter
5. Disconnect orange and yellow wires from relay K4.
6. Remove two bolts holding the left side of the front panel to the base.
7. Remove three bolts holding across the center base of the front panel. These are accessed from underneath.
8. Remove one of the bolts holding the right side of the front panel to the base. Loosen the second bolt. Of these two bolts, remove the bolt on the left and loosen the bold on the right.
9. Swing the front panel out to gain access to power rectifier components.
Blocking Diodes
troubleshooting procedures –negative plate
Location of Neg. Plate
1. Visually inspect fuses F8 and F9. Replace if they show signs of being blown or melted. Inspect diodes. If ruptured or burned, replace all diodes on the NEG Plate. If diodes appear to be OK, proceed to next step.
Location of fuses F8 and F9
49
section 6
NEG Plate
Electrode Plate
Location of fuses F8 and F9
Diode Rectifier
POS Plate
troubleshooting pos plate
Location of Pos. Plate
troubleshootinG
1. Check ohms between NEG Plate and BR “A” Bus. A reading of 2 ohms or less indicates one or more shorted diodes.
Replace all Diodes on NEG Plate.
2. If fuses F8 and/or F9 were open in the first step, make two more ohmmeter readings.
A. Measure resistance between the NEG Plate and
BR “B” bus.
B. Measure between NEG Plate and BR “C” bus.
If resistance is 2 ohms or less in either case, replace all the diodes on the NEG Plate.
1. Check ohms between POS Plate and BR “A” Bus. A reading of 2 ohms or less indicates one or more shorted diodes.
Replace all Diodes on POS Plate.
2. If fuses F8 and/or F9 were open in the first step, make two more ohmmeter readings.
A. Measure resistance between the POS Plate and BR
“B” bus.
B. Measure between POS Plate and BR “C” bus.
If resistance is 2 ohms or less in either case, replace all the diodes on the POS Plate.
troubleshooting electrode plate
Bus
Cathode Leads
1. Visually inspect for ruptured or burned diodes. Replace only those damaged.
2. Check resistance between Electrode Plate and the parallel pig tails (cathode leads) of D25 and D26. If reading is 2 ohms or less, disconnect leads from bus and check each diode. Replace only shorted diodes.
Repeat procedure for D27 and D28. Replace only shorted diodes.
blocking diodes d25, d26, d27 and d-28
50
section 6
6.4.2 iGbt / freewheeling diode (fwd) replacement troubleshootinG caution the emitter and the gate of each affected iGbt must be jumpered together to prevent electrostatic damage. each power source is supplied with six jumper plugs that mate to the iGbt
Gate / emitter plug.
caution electrostatic discharge hazard electrostatic discharge may damage these components.
• Damage is accumulative and may only appear as shortened component life and not as a catastrophic failure.
• Wear a protective ground strap when handling to prevent damage to PCB components.
• Always place a pc board in a static-free bag when not installed.
removal:
A. Insure that input power is removed by two actions such as a disconnect switch and removal of fuses. Tag and lock any disconnect switch to prevent accidental activation.
B. Remove the top panel to gain access to the modules located in the top rear of the power source.
C. Clean the compartment containing the modules with dry, oil-free compressed air.
D. Unplug the gate drive leads connecting the IGBT Gates to the PWM/Gate Drive PC Board. In order to prevent damage to the IGBT, install jumper plugs into the IGBT Gate Drive Connector. See Caution below. Jumper plugs are supplied with each power source.
E. Remove the copper buss plates and bars connected to the IGBT’s. Save the M6 hardware connecting the bus structure to the module terminals. You may need to re-use the hardware. Longer hardware can damage the module by contacting the circuitry directly below the terminals.
F. Remove the M6 hardware mounting the modules to the heat sink. Save the hardware because you may need to re-use it. Hardware too short can strip the threads in the Aluminum heat sink. Hardware too long can hit the bottom of the holes causing the modules to have insufficient thermal contact to the heat sink. Hardware too long or too short can cause module damage due to over heating.
caution the module gate plugs must be plugged into the pwm/Gate drive pc board whenever the power source is in operation. failure to plug them in will result in damage to the module and possible damage to the torch.
51
section 6 troubleshootinG replacement:
A. Thoroughly clean any thermal compound from the heat sink and the modules. Any foreign material trapped between the module and heat sink, other than an appropriate thermal interface, can cause module damage due to over heating.
B. Inspect the thermal (interface) pad, P/N 951833, for damage. A crease or deformity can prevent the module from seating properly, impeding the heat transfer from the module to the heat sink. The result can be module damage due to over heating.
If a thermal pad is not available, a heat sink compound such as Dow Corning® 340 Heat Sink Compound may be used. It’s a good idea to mount all paralleled modules located on the same heat sink using the same thermal interface. Different interfaces can cause the modules to operate at different temperatures resulting in un-equal current sharing. The imbalance can shorten module life.
C. Place a thermal pad, and an IGBT module on the heat sink. Carefully align the holes in the thermal pad with the heatsink and module holes. If heat sink compound is used in place of a thermal pad, apply a thin coat of even thickness to the metal bottom of the module. A thickness of 0.002” – 0.003” (0.050mm – 0.075mm) is optimum. Too much compound impedes heat transfer from the module to the heat sink resulting in short module life due to over heating.
D. Insert the four M6 mounting bolts, but do not tighten. Leave them loose a few turns. Be certain that the threads from the mounting bolts do not bend the edges of the thermal pad clearance holes. A bent thermal pad can prevent the module from seating properly, impeding the heat transfer from the module to the heat sink. The result can be module damage due to over heating.
E. Partially tighten the four mounting bolts a little more than finger tight in the order: A-B-C-D. See figure below.
F. Fully tighten, in the same order above, to a torque of 35 – 44 in-lbs (4.0 – 5.0 N-M). See figure below.
G. Install the bus plates and bus bars. Be careful that the sheets of insulation separating the bus plates are still in their original positions. It’s a good idea to tighten the mounting hardware only after getting it all started. Torque the M6 module terminal hardware to 35 – 44 in-lbs (4.0 – 5.0 N-M).
H. Remove the jumper plugs from the module gate lead plugs, and plug into the appropriate plugs from the PWM/Gate
Drive PC Board. See Caution below.
I. Replace the top panel.
caution the module gate plugs must be plugged into the pwm/Gate drive pc board whenever the power source is in operation. failure to plug them in will result in damage to the module and possible damage to the torch.
1 - IBGT Collector, Free Wheeling
Diode (FWD) Anode
2 - IGBT Emitter
3 - FWD Cathode
6 - IGBT Gate
7 - IGBT Emitter
d a
1
Four-Point Mounting Type
Partial tightening - a
-
b
-
c
-
d
Fully tightening - a
-
b
-
c
-
d c
2 b
3
6 (red)
7 (wht) key plug position 1 (red)
52 three leads
section 6 troubleshootinG
6.4.3 power shunt installation caution instability or oscillation in cutting current can be caused by improper dressing of shunt pick-up leads.
poor torch consumable life will be the result.
There are two cables that attach to the shunt pick-up points: a two conductor cable drives the ammeter a three conductor which provides the current feedback signal to PCB1 (control PCB).
Dressing of the 2 conductor cable is not critical.
The following is the dressing procedure for the 3 conductor cable.
• The breakout point should be physically at the middle of the shunt. The breakout point is the place where the conductors exit from the outer insulation jacket.
• The black and clear insulated wires must be kept next to the shunt and under the cable ties.
• The wire terminals for the black and clear insulated wires should be oriented in parallel with bus bars as shown.
three leads clear insulation
Terminals parallel to bus bars two leads
53
• It is important to have the barrels of the black and clear insulated wires, from the three lead cable, be pointing in opposite directions.
• The third wire attaches to the bus bar on the left with the shunt mounting hardware. Orientation of this wire is not critical.
section 6 troubleshootinG
6.4.4 procedure for verifying calibration of digital meters.
Voltmeter
1. Connect a digital meter known to be calibrated to the positive and negative output bus bars.
2. Compare the power source voltmeter reading to the calibrated meter reading. Readings should match within
±0.75%.
Ammeter
1. External to the power source, connect a precision shunt in series with the work lead(s). The best shunt is one with a value of 100 micro-ohms (50mV / 500A or 100mV / 1000A) and a calibrated tolerance of 0.25%.
2. Use a calibrated 4 ½ digit meter to measure the output of the shunt. The amperage indicated with the external shunt and meter should match power source ammeter to within 0.75%.
6.5 control circuit interface using J1, J4 and J6 connectors
Interface to the EPP-450 control circuitry is made with connectors J1, J4 and J6 on the front panel. J1 has 24 conductors, J4 has 2 and J6 has 10.
J1-P and J1-G provide access to the galvanically isolated transistor output signal indicating an “Arc On” condition. See
Subsection 6.8, Arc Current Detector Circuits. J1-L and J1-J are the inputs for the remote Voltage Reference Signal that commands the EPP-450 output current Subsection 6.9, Current Control Pot & Remote Vref. J1-R and J1-Z supply 115V AC for remote controls. See Subsection 6.6, Auxiliary Main Contactor (K3 and K33) & Solid State Contactor Circuits and Subsection
6.10, Pilot Arc Hi/lo & Cut/mark Circuits.
J1-E and J1-F are the input connections for the Emergency Stop function. For Emergency Stop to operate, the Jumper between TB8-18 and TB8-19 must be removed.
J1-S is the input to K8 that parallels S1 switch contact. When 115V AC from J1-R is fed into J1-S, K8 activates placing the Pilot
Arc in High.
J4-A and J4-B are from an isolated contact on the emergency stop (E-stop) switch. This signal can be used by the plasma control to indicate the state of the E-stop switch on the power source.
Cut / Mark selection: The power source defaults to Cutting mode when there is no signal fed into J1-C. When 115V AC from
J1-R is fed into J1-C, K11 is activated placing the EPP-450 in the Marking mode. For more details concerning the operation of K11 and the Cut / Mark modes, refer to Subsection 6.10, High / Low Cut Current Modes and Mark Mode.
High / Low current ranges: The power source defaults to low cutting current range (35-100A) when no signal is fed into
J1-T. High range (50A to maximum current rating) is selected whenever 115VAC is fed into J1-T by connecting J1-R to J1-T.
J6 connects to the water cooler. J6-A and J6-B are 115VAC hot and neutral respectively. This 115VAC activates the contactor for the pump. J6-C and J6-D connect to the flow switch. The flow switch is closed when coolant is flowing. J6-E and
J6-H connect to the coolant level switch. The switch is closed when the coolant reservoir contains sufficient coolant and it is open when the reservoir is low.
54
section 6 troubleshootinG
CONTROL CIRCUIT INTERFACE USING J1, J4, & J6 CONNECTORS
CONTROL
J4-A
REMOTE EMERGENCY STOP
ISOLATED CONTACT
E-STOP LOOP MUST BE
CLOSED FOR POWER
SOURCE TO FUNCTION
J4-B
J1-F
RED 06
J1-E
RED 05
ISOLATED CONTACT
22 21
TB8-19
E-STOP RELAY
K15
S5
12
E-STOP BUTTON
11
TB8-18
24 VAC
T2
3A
CB2
PILOT ARC HI/LO
PLASMA START
J1-D
GRN/YEL
J1-Z
RED 04
J1-R
RED 16
J1-S
RED 17
J1-M
RED 12
CHASSIS
115V AC NEUTRAL
H
115V AC HOT
S1
HI
LO
OFF: PILOT ARC LOW
ON: PILOT ARC HIGH
K8
115V AC CONTACTOR INPUT
T2
115 VAC
K3
NOTE: Panel S1
MUST BE in LOW position for remote contact to function
K33
CUT/MARK MODE SELECT
CUT
MARK
HI/LO CURRENT RANGE
LO
HI
J1-C
RED 03
J1-T
RED 18
J1-B
115V AC MARK MODE INPUT
K11
K11
K13 K14
115 VAC HI
RANGE
INPUT
IN MARK MODE, K11 FORCES
THE LO CURRENT RANGE
J6-B J1-B
115 VAC
CONTACTOR FOR
PUMP & FAN
H
J6-A J1-A
COOLANT LEVEL
J1-K
RED 10
J6-H J1-H
COOLANT FLOW
RED 02
J6-C
J6-D
J1-C
J1-D
FLOW
SWITCH
OK
LEVEL
SWITCH
OK
LO
15 - 50 VDC
- +
J1-G
RED 07
J6-E J1-E
K1
LO
COOLANT CIRCULATOR
CUT/MARK
CURRENT DETECT
J1-P
RED 14
100V
50mA
MAX
CURRENT
DETECTOR
REMOTE
0 - 10V Vref
J1-Y
RED 23
J1-L
RED 11
J1-J
RED 09
10 OHMS
100 OHMS
+
ELECTRODE CURRENT SIGNAL 1.0V = 100A
-
200K
Ohms
REMOTE CUTTING CURRENT
REFERENCE VOLTAGE (Vref)
Icut = (Vref) x (50) hi current range
Icut = (Vref) x (10) lo current range
55
section 6 troubleshootinG
6.6 auxiliary main contactor (k3 & k33) and solid state contactor circuits
K3 and K33, activated by supplying a Contactor Signal, initiate and controls the operation of K2 (Starting Contactor) and
K4 (Pilot Arc Contactor). K3/K33 are called the Auxiliary Main Contactors because they must be activated before the
Main Contactor (K1) power-up sequence can occur. The Contactor Signal is supplied through a remote contact connecting 115VAC from J1-R to J1-M. If K6 is closed (no fault), K3 will activate. The closing of K3(6, 9) activates K2, the Starting
Contactor, and K4, the Pilot Arc Contactor, provided the power source is not over heated. See Subsection 6.7, E-stop and
Main Contactor Circuits for more information on the operation of K2. K4 is turned off when the Current Detector senses arc current and opens the contact connecting P2-5 to P2-6 on the Control PC Board.
In addition to operating K3/K33, the Contactor Signal also activates the Solid State Contactor. The Solid State Contactor is a logic and interlock circuit permitting the IGBT’s to conduct whenever the remote Contactor Signal is present. The 115V
AC Contactor Signal is fed to TB1-9, TB7-8, and resistors R45 and R45A. These resistors reduce the 115V to approximately
16V AC fed into the Control PC Board at P6-1 and P6-2. The Control PC Board sends a signal to both the Left and Right PWM
/ Gate Drive PC Boards. Illumination of LED3 on both of the PWM / Gate Drive PC Boards is indication that the Solid State
Contactor is functioning.
AUXILLARY MAIN CONTACTOR (K3 & K33) & SOLID STATE CONTACTOR CIRCUITS
115V AC
LEFT PWM/GATE
DRIVE PC BOARD
RIGHT PWM/GATE
DRIVE PC BOARD
PILOT ARC
CONTACTOR
TB7-8
K4
P2-5
I
P2-6
IGBT DRIVE
ON/OFF
LED3
IGBT DRIVE
ON/OFF
LED3
Current Detector
Contact on
Control PCB
TB9-16
TB9-13
P1-9 P1-10 P1-9 P1-10
6
K3 K7
9 6 9
K2
6
K33 K15
6 9
TB9-18
3
1
TB1-7
Over Heat Relay - Closed during normal operation
STARTING
CONTACTOR
FN4
115V
AC
2
4
TB8-7
J1-H
K3 K33
(AMC)
P6-2
+15V
Solid State Contactor
680
T
CONTROL
PC BOARD
J1-R
H
J1-Z
N
TB1-8
J1-M
K6
Fault Relay
9 6
Open with fault or main line power off
TB1-9
P6-1
TB7-9
R45A
10K
8W
TB7-8
R45B
10K
8W
56
section 6 troubleshootinG
6.7 e-stop (emergency stop) and main contactor (k1a, k1b and k1c) circuits
A power-up sequence takes place before the Main Contactor (K1) activates. K1 is actually three separate contactors – one for each primary input phase. Thus, K1A, K1B, and K1C switch phases A, B, and C respectively to the Main Transformer, T1.
The power-up sequence begins with a remote Contactor Signal activating K3 and K33. Refer to the description entitled,
Section 6.6, Auxiliary Main Contactor (K3 and K33) & Solid State Contactor Circuits for more information. K3 and K33 activates K2 closing the three contacts of K2. K2 bypasses K1 contacts providing primary input power to the Main Transformer,
T1. This current is limited by three one Ohm resistors, R1, R2, and R3. The resistors eliminate the high surge currents typical of the turn-on inrush transients associated with large transformers. The high current surge of charging the Bus Capacitor
Bank is also eliminated by initially powering the Main Transformer through K2 and the resistors.
The discharged Bus Capacitor Bank initially prevents the output of the Main transformer from reaching its normal value.
As the Bus Capacitor Bank charges, the Main Transformer output voltage rises and becomes high enough for K1A, K1B, and
K1C to close. Once the K1’s are closed, the contacts of the Starting Contactor, K2, are bypassed, and full primary line power is supplied to the Main Transformer through the contacts of the K1’s.
Because the starting sequence takes time, it is important at least 300 mS lapse between applying the Contactor Signal and applying load to the power source. Applying load too soon will prevent the K1’s from closing and fuses F1 and F2 will open.
K15, the E-Stop relay must be closed for the power-up sequence to take place. K15 contains one contact in the K2 coil circuit and another contact in the K1A, K1B, & K1C circuits. There is no power supplied to the Main Transformer, T1, until K15 is activated. For K15 to activate, S5, the E-Stop switch on the front panel must be closed. Also, the Plasma Control must complete the E-stop loop by closing an isolated contact between J1-E and J1-F.
The E-Stop switch is closed whenever the E-Stop button, on the front panel, is pulled out. For troubleshooting purposes only, a jumper can be connected between TB8-18 and TB8-19. If a jumper is installed, it MUST be removed before placing the power source back into service. If the jumper is not removed, the power source E-Stop condition will not function when the E-Stop button for the Plasma Control is pushed.
J4-A and J4-B are connected together whenever the E-Stop button on the power source is pulled out. This signal can be sent to the Plasma Control so that the control senses the state of the power source E-Stop switch.
57
E-STOP (EMERGENCY STOP) & MAIN CONTACTOR (K1A, K1B, & K1C) CIRCUITS
section 6 troubleshootinG
6.7 e-stop (emergency stop) and main contactor (k1a, k1b and k1c) circuits (continued)
7 4
115 VAC WINDING ON "A" COIL OF MAIN TRANSFORMER
7 4
STARTING CONTACTOR
TOP E-S
E-STOP LOOP MUST BE CLOSED FOR POWER SOURCE TO FUNCTION
58
section 6 troubleshootinG
6.8 arc current detector circuits
There are three Arc Current Detector circuits in the EPP-450. One is used internally to control the Pilot Arc Contactor, K4.
The other two are available for remote use.
A galvanically isolated transistor Current Detector Output is accessible at J1-G (-) and J1-P (+). J1 is the 24 conductor connector on the EPP-450 front panel. The transistor is best suited for switching small relays or low current logic signals like those utilized by PLC’s (Programmable Logic Controllers). The transistor can withstand a maximum peak voltage of 150V.
It can switch a maximum of 50 mA. The transistor turns on whenever the arc current through the Work Lead exceeds 3A.
Pilot arcs not establishing main arcs will not turn on the transistor.
A second current detector output is available at TB8-3 and TB8-4. This output is supplied by an isolated relay contact rated for 150V, 3 Amperes. This contact is closed when the primary input power to the EPP-450 is off. It opens whenever primary power is supplied to the power source, and it closes when main arc current is established. Like the transistor output, the relay contact closes whenever the arc current through the Work Lead exceeds 3A. Pilot arcs not establishing main arcs will not close the contact.
J6-D J6-E J1-G J1-P
59
section 6 troubleshootinG
6.9 current control pot and remote vref
A Reference Voltage, V
REF
, is used to command the output current of the EPP-450. V
REF
fed into J1-L (+) and J1-J (-). The EPP-450 Output Current, I
OUT
, will follow V
I
OUT
= (50) x (V
REF
) in the high output current mode and I
OUT
= (10) x (V
REF
REF
is a DC voltage that can come from either the Current Control Potentiometer on the front panel or from a remote source. In the “Panel” position, S2, the Panel
/ Remote switch selects the Current Control Potentiometer. In the “Remote” position, the Panel/Remote switch selects the
V
REF
with the following relationship:
) in the low output current mode.
PCB10 is the analog signal scaling board. If 115VAC is fed into P1-2 and P1-3 the output current range is in the high mode used for cutting from 50 to 450A. With the 115VAC absent, the output current range is in the low mode used for marking between 10 and 100A and cutting between 35 and 100A.
The Control PC Board contains two inputs for V
REF
: High Speed; and Normal. When the negative of the V the High Speed input (P8-3), the EPP-450 will respond to a change in V
REF
REF
signal is fed into
within 10 mS. When the negative of the V is fed into the Low Speed input (P8-1), the EPP-450 will respond to a change in V
REF
REF
signal
within 50 mS. The slower response of the “Normal” input helps filter electrical noise sometimes encountered in industrial environments.
CONTROL
BOARD
0558038313
P4-11
P4-10
JUMPER
P4-9
220
P4-12
S
P3-3
S BIAS
P3-4 P3-5
20V
T10
20V
PRI: 120V
SEC: 40VCT
H1 H2
H
120V
N
+15S
0.00-10.00V
CURRENT REFERENCE
EPP-600: I(out) = (80) X Vref
EPP-450: I(out) = (50) X Vref
200K 200K
HIGH
SPEED
NRM
P8-3
-
P8-1
-
+
P8-2
S
S
TB8-11
TB1-4
J1-L
+
P4-8
-
+10T
PRECISION
REFERENCE
P5-8
JUMPER FOR
EPP-600
P2-1 P2-2
+
P4-7
50 50
SIGNAL:
LO: 10V = 100A
S
HI EPP-450: 1V = 50A
HI EPP-600: 1V = 80A
PCB10
ANALOG
SCALING
BOARD
0558038326
P4-2
22
11
0-10V
200K
200K
-
NRM
P4-1
55
S2
66
TB1-6
+
-
HIGH
SPEED
P4-3
-
TB8-12
TB1-5
J1-J
J1-J, DC SIGNAL
COMMON (NEG)
ALSO SHOWN
ON PAGE 1
60
D
SEE PAGE 1, K13-6
N
T
TB1-3
CURRENT
CONTROL
POT
R50
10K
section 6 troubleshootinG
6.10 high / low cut current modes and mark mode
A remote contact connecting 115V AC from J1-R to J1-S places the Pilot Arc in High by operating K8. Note, that for this function to operate, the Pilot Arc Hi/Lo switch on the front panel must be in the “LO” position.
The EPP-450 is placed in the Marking mode when a remote contact connecting 115V AC from J1-R to J1-C operates K11. In the Marking mode, a normally closed contact on K11 opens turning off K10. When K10 turns off, the Boost supply is disconnected lowering the normal Cutting Mode 430V DC Open Circuit Voltage to 360VDC for Marking. A normally open contact on K11 activates K12. K12 connects the I (min) resistors necessary for stabilizing the low currents required for marking. In the Cutting mode, the minimum stable output current is 50A in the high current range, 35A in the low current range and
HIGH/LOW CUT CURRENT MODES & MARK MODE
SEE PAGE 2
PCB10 P1-2
H
115 VAC
9
K13
6
D
Z BIAS
P5-3 P5-2
20V 20V
P5-1
SEC 40VCT
PRI 120V
T7
PCB3 Right
PWM/Gate Drive
FAN
M5
N
G
K13
9
9
9
S1
LO
6
HI
5
3
K11
6
3
K11
5
K3
8
T3
K4
L3
PILOT ARC
HI/LO
N
K8
A
K12
R70
10 2W
1µF
600V
I(min) RESISTORS
WHT
A
K10
BOOST
K13
5 8
TB9-18
TB9-13
PL2
N
TB8-8
3
FN4
1
115V
AC
4
2
TB1-8
K11
A
K14 K13
N
TB8-7
J1-S
J1-C
TB1-7
J1-Z
TB8-7
J6-B
HI
MARK
TB8-2
7
1
K11
H
TB1-7
LO
PILOT
ARC
CUT
CUT/
MARK
TB8-1
LO
MOVE RED WIRE FROM
TB8-1 TO TB8-2 FOR
FOR HI CURRENT RANGE CUT HI
CURRENT
RANGE
J1-T
61
section 6 troubleshootinG
6.11 low current range
The EPP-450 operates in either LOW or HIGH current output ranges. The LOW range is used for marking from 10 to 100 amperes and cutting from 35 to 100 amperes. The HIGH range is used for cutting from 50 to 450 amperes.
In the HIGH range, both the left and right power sources are used. Each side contributes 50% of the total output current.
The left side acts as a master power source by synchronizing the switching of the right side to its own switching frequency of 10 KHz.
In the LOW range, only the left power source is used. The normally open contact, K13(6, 9) prevents T7 from supplying bias supply power to PCB-3, the right PWM / IGBT Gate Drive PC Board. This disables the right side.
The same K13 contact (square labeled “D” on the schematic diagrams) places the EPP-450 in the HIGH current mode. In addition to providing bias power to PCB-3 in the HIGH current mode, this 115 VAC is fed into PCB-10 P1-2.
PCB-10 performs two functions. With no input on PCB-10 P1-2, PCB-10 scales the 0 to 10 VDC current reference signal for 0 to 100 amperes (LOW range). In the LOW range, PCB-10 P4-11 / P4-12 provides a signal to PCB-2 P4-1 / P4-2. This signal commands PCB-2, the left (master) PWM / IGBT Gate Drive PC Board to change the switching frequency from 10 KHz to 25 KHz.
The higher switching frequency results in the more power dissipation by the heat sinks on PCB-3. Therefore, in the LOW current mode, a small fan, M5, turns on to provide additional cooling. M5 does not operate in the HIGH current mode.
6.12 electrode current transducer circuit
The Electrode Current Transducer Circuit provides a galvanically isolated signal to the plasma control indicating the power source output current. The scaling of the signal is: VOUT = IELECTRODE/100. For example, 200A results in 2.0V output. The scaling is the same for both high and low current ranges. The output signal resistance is 100 Ohms.
PCB11 receives the signal from the Hall Effect Transducer and sends the signal through FN5 to J1-Y (+) and J1-J (-). PCB11 sup-
ELECTRODE CURRENT TRANSDUCER CIRCUIT
4
TO SHUNT NEG.
J1-J & TB1-5, DC
SIGNAL COMMON
(NEG), ALSO
SHOWN ON PAGE 2
J1-Y
J1-J
1V=100A
TB1-5
+
-
FN5
3
+
P4-7
TO PILOT ARC CONTACTOR, K4-T1
P4-8
-
50
50
ELECTRODE
CURRENT
TRANSDUCER
P4-6 -15S
HALL ARROW
TD3
P1-4
P1-3
P4-5 S COM
P4-1 SIGNAL -
S
PCB11
ANALOG
SCALING
BOARD
P4-2 SIGNAL +
S BIAS
ELECTRODE
1
FN1
3
2
WORK
+
1
FN2
3
2
P4-4 +15S
P1-2 P1-1 P3-1 P3-2
20V 20V
T11
PRI: 120V
H2
SEC: 40VCT
H1
N
120V
H
62
section 6 troubleshootinG
63
section 7 replacement parts
7.0 replacement parts
7.1 General
Always provide the serial number of the unit on which the parts will be used. The serial number is stamped on the unit serial number plate.
7.2 ordering
To ensure proper operation, it is recommended that only genuine ESAB parts and products be used with this equipment. The use of non-ESAB parts may void your warranty.
Replacement parts may be ordered from your ESAB Distributor.
Be sure to indicate any special shipping instructions when ordering replacement parts.
Refer to the Communications Guide located on the back page of this manual for a list of customer service phone numbers.
part number epp-450
380v 50/60hz
380v taps epp-450 information epp-450
380v 50/60hz
400v taps
0558007730 epp-450
400v 50/60hz epp-450
460v 60hz
0558007731 epp-450
575v 60hz
0558007732 note
Items listed in the following Bill of Materials that do not have a part number shown are not available from ESAB as a replaceable item and cannot be ordered. Descriptions are shown for reference only. Please use local retail hardware outlets as a source for these items.
Note
Replacement Parts, Schematics and Wiring Diagrams are printed on 279.4mm x 431.8mm (11” x 17”) paper and are included inside the back cover of this manual.
64
notes
65
notes
66
revision history
1. Original release - 02/2008.
2. Revision 05/2008 - added E-stop information throughout manual. Included Replacement Parts section in Schematic / Wiring Diagram package.
3. Revision 08/2010 - Added new DOC form.
4. Revision 09/2010 - Removed 401 references.
5. Revision 06/2012 - dimensions changes section 2.3.
67
esab subsidiaries and representative offices europe austria
ESAB Ges.m.b.H
Vienna-Liesing
Tel: +43 1 888 25 11
Fax: +43 1 888 25 11 85
italy
ESAB Saldatura S.p.A.
Mesero (Mi)
Tel: +39 02 97 96 81
Fax: +39 02 97 28 91 81
belGium
S.A. ESAB N.V.
Brussels
Tel: +32 2 745 11 00
Fax: +32 2 745 11 28
the netherlands
ESAB Nederland B.V.
Utrecht
Tel: +31 30 2485 377
Fax: +31 30 2485 260
the czech republic
ESAB VAMBERK s.r.o.
Prague
Tel: +420 2 819 40 885
Fax: +420 2 819 40 120
norway
AS ESAB
Larvik
Tel: +47 33 12 10 00
Fax: +47 33 11 52 03
denmark
Aktieselskabet ESAB
Copenhagen-Valby
Tel: +45 36 30 01 11
Fax: +45 36 30 40 03
poland
ESAB Sp.zo.o.
Katowice
Tel: +48 32 351 11 00
Fax: +48 32 351 11 20
finland
ESAB Oy
Helsinki
Tel: +358 9 547 761
Fax: +358 9 547 77 71
portuGal
ESAB Lda
Lisbon
Tel: +351 8 310 960
Fax: +351 1 859 1277
france
ESAB France S.A.
Cergy Pontoise
Tel: +33 1 30 75 55 00
Fax: +33 1 30 75 55 24
slovakia
ESAB SIovakia s.r.o.
Bratislava
Tel: +421 7 44 88 24 26
Fax: +421 7 44 88 87 41
Germany
ESAB GmbH
Solingen
Tel: +49 212 298 0
Fax: +49 212 298 218
spain
ESAB Ibérica S.A.
Alcalá de Henares (MADRID)
Tel: +34 91 878 3600
Fax: +34 91 802 3461
Great britain
ESAB Group (UK) Ltd
Waltham Cross
Tel: +44 1992 76 85 15
Fax: +44 1992 71 58 03
sweden
ESAB Sverige AB
Gothenburg
Tel: +46 31 50 95 00
Fax: +46 31 50 92 22
ESAB Automation Ltd
Andover
Tel: +44 1264 33 22 33
Fax: +44 1264 33 20 74
ESAB International AB
Gothenburg
Tel: +46 31 50 90 00
Fax: +46 31 50 93 60
hunGary
ESAB Kft
Budapest
Tel: +36 1 20 44 182
Fax: +36 1 20 44 186
switzerland
ESAB AG
Dietikon
Tel: +41 1 741 25 25
Fax: +41 1 740 30 55
esab ab se-695 81 laxÅ sweden phone: +46 584 81 000
www.esab.com
north and south america arGentina
CONARCO
Buenos Aires
Tel: +54 11 4 753 4039
Fax: +54 11 4 753 6313
brazil
ESAB S.A.
Contagem-MG
Tel: +55 31 2191 4333
Fax: +55 31 2191 4440
canada
ESAB Group Canada Inc.
Missisauga, Ontario
Tel: +1 905 670 02 20
Fax: +1 905 670 48 79
mexico
ESAB Mexico S.A.
Monterrey
Tel: +52 8 350 5959
Fax: +52 8 350 7554
usa
ESAB Welding and
Cutting Products
Florence, SC
Tel: +1 843 669 44 11
Fax: +1 843 664 57 48
asia/pacific china
Shanghai ESAB A/P
Shanghai
Tel: +86 21 5308 9922
Fax: +86 21 6566 6622
india
ESAB India Ltd
Calcutta
Tel: +91 33 478 45 17
Fax: +91 33 468 18 80
indonesia
P.T. ESABindo Pratama
Jakarta
Tel: +62 21 460 0188
Fax: +62 21 461 2929
Japan
ESAB Japan
Tokyo
Tel: +81 3 5296 7371
Fax: +81 3 5296 8080
malaysia
ESAB (Malaysia) Snd Bhd
Shah Alam Selangor
Tel: +60 3 5511 3615
Fax: +60 3 5512 3552
sinGapore
ESAB Asia/Pacific Pte Ltd
Singapore
Tel: +65 6861 43 22
Fax: +65 6861 31 95
south korea
ESAB SeAH Corporation
Kyungnam
Tel: +82 55 269 8170
Fax: +82 55 289 8864
united arab emirates
ESAB Middle East FZE
Dubai
Tel: +971 4 887 21 11
Fax: +971 4 887 22 63
representative offices bulGaria
ESAB Representative Office
Sofia
Tel/Fax: +359 2 974 42 88
eGypt
ESAB Egypt
Dokki-Cairo
Tel: +20 2 390 96 69
Fax:+20 2 393 32 13
romania
ESAB Representative Office
Bucharest
Tel/Fax: +40 1 322 36 74
russia-cis
ESAB Representative Office
Moscow
Tel: +7 095 937 98 20
Fax: +7 095 937 95 80
ESAB Representative Office
St Petersburg
Tel: +7 812 325 43 62
Fax: +7 812 325 66 85
distributors
For addresses and phone numbers to our distributors in other countries, please visit our home page
www.esab.com
advertisement
* Your assessment is very important for improving the workof artificial intelligence, which forms the content of this project
Related manuals
advertisement
Table of contents
- 7 1.0 Precauzioni di sicurezza
- 9 2.0 Descrizione
- 9 2.1 Introduzione
- 9 2.2 Caratteristiche tecniche generali
- 10 2.3 Dimensioni e peso
- 11 3.0 Installazione
- 11 3.1 Generale
- 11 3.2 Svuotamento della cassa
- 11 3.3 Posizionamento
- 12 3.4 Connessione dell’alimentazione di ingresso
- 12 3.4.1 Alimentazione primaria
- 13 3.4.2 Conduttori di ingresso
- 13 3.4.3 Procedura di connessione di ingresso
- 14 3.5 Connessione di uscita
- 14 3.5.1 Cavi di uscita (forniti dal cliente)
- 14 3.5.2 Procedura di connessione di uscita - Generatore di energia singolo
- 15 3.6 Installazione parallela
- 16 3.6.1 Connessioni per due EPP-450 in parallelo
- 19 3.6.2 Marcatura con due EPP-450 paralleli
- 20 3.7 Cavi di interfaccia
- 21 con interfaccia CNC non terminato
- 21 di accoppiamento su entrambe le estremità
- 22 di alimentazione di accoppiamento su entrambe le estremità
- 23 4.0 Funzionamento
- 23 4.1 Descrizione del circuito del diagramma a blocchi
- 26 4.2 Pannello di controllo
- 29 4.2.1 Modalità di funzionamento: Modalità di taglio e di marcatura
- 30 4.3 Sequenza del funzionamento
- 31 4.4 Impostazioni di avviamento dell’arco
- 32 4.4.1 Attivazione / disattivazione delle condizioni di avviamento dell’arco
- 32 4.4.2 Regolare il timer di sosta dell’avviamento dell’arco
- 32 4.4.3 Regolazione della corrente di avvio minima
- 33 4.4.4 Controlli dell’avviamento dell’arco
- 33 4.4.5 Avvio della corrente e del timer di aumento della corrente
- 34 4.5 Curve V-I EPP
- 34 4.5.1 Curve V-I EPP-450 per tutti i modelli
- 35 5.0 Manutenzione
- 35 5.1 Generale
- 35 5.2 Pulizia
- 36 5.3 Lubrificazione