- No category
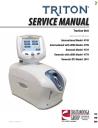
advertisement
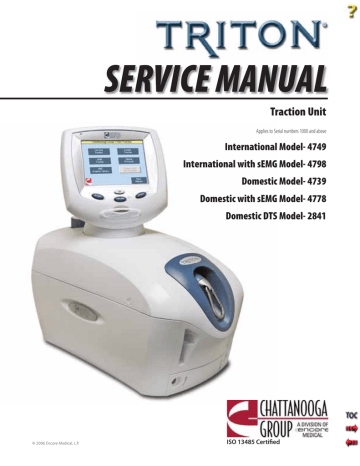
SERVICE MANUAL
Traction Unit
Applies to Serial numbers 1000 and above
International Model- 4749
International with sEMG Model- 4798
Domestic Model- 4739
Domestic with sEMG Model- 4778
Domestic DTS Model- 2841
© 2006 Encore Medical, L.P.
ISO 13485 Certifi ed
TABLE OF CONTENTS
Triton® Traction Unit
FOREWORD . .. .. .. .. .. .. .. .. .. .. .. .. .. .. .. .. .. .. .. .. .. .. .. 1
1 THEORY OF OPERATION .. .. .. .. .. .. .. .. .. .. .. .. .. .. 2
1.1 OVERVIEW .. .. .. .. .. .. .. .. .. .. .. .. .. .. .. .. .. .. .. .. ..2
2 SAFETY PRECAUTIONS .. .. .. .. .. .. .. .. .. .. .. .. .. .. .. 3
3 NOMENCLATURE . .. .. .. .. .. .. .. .. .. .. .. .. .. .. .. .. ..67
4 SPECIFICATIONS .. .. .. .. .. .. .. .. .. .. .. .. .. .. .. .. .. .. .. 8
4.1 PHYSICAL SPECIFICATIONS . .. .. .. .. .. .. .. .. .. ..8
5 TROUBLESHOOTING . .. .. .. .. .. .. .. .. .. .. .. .. .. .. 929
5.2 TRITON TRACTION UNIT TESTING . .. .. .. .. .. 14
REMOVAL & REPLACEMENT . .. .. .. .. .. .. .. 41-46
REMOVAL & REPLACEMENT .. .. .. .. .. .. 47-48
REMOVAL & REPLACEMENT .. .. .. .. .. .. .. .. 49
REMOVAL & REPLACEMENT .. .. .. .. .. .. 50-51
6.13 MOTOR ASSEMBLY
REMOVAL & REPLACEMENT .. .. .. .. .. .. 52-53
REMOVAL & REPLACEMENT .. .. .. .. .. .. .. .. 54
REMOVAL & REPLACEMENT .. .. .. .. .. .. .. .. 55
7 CALIBRATION.. .. .. .. .. .. .. .. .. .. .. .. .. .. .. .. .. .. .. .. 56
7.1 UNIT CALIBRATION.. .. .. .. .. .. .. .. .. .. .. .. .. 56-58
8 PARTS . .. .. .. .. .. .. .. .. .. .. .. .. .. .. .. .. .. .. .. .. .. .. .. .. 61
5.6 ON/OFF SWITCH TEST .. .. .. .. .. .. .. .. .. .. .. .. .. 16
5.7 ON/OFF SWITCH TROUBLESHOOTING . .. .. 16
8.2 SIDE COVERS . .. .. .. .. .. .. .. .. .. .. .. .. .. .. .. .. .. .. 62
5.9 CORD RELEASE AND RETRACT TEST .. .. .. .. 18
5.10 CORD RELEASE TROUBLESHOOTING . 19-20
8.4 BASE AND EXTRUSION ASSEMBLY .. .. .. .. .. 64
AND POWER SUPPLY.. .. .. .. .. .. .. .. .. .. .. .. .. .. 66
6 REMOVAL & REPLACEMENT .. .. .. .. .. .. .. .. .. 3055
6.1 SIDE COVER REMOVAL & REPLACEMENT .. 30
6.2 TOP AND CORD GUIDE COVER
REMOVAL & REPLACEMENT . .. .. .. .. .. .. .. .. .. 31
REMOVAL & REPLACEMENT . .. .. .. .. .. .. .. .. .. 32
REMOVAL & REPLACEMENT . .. .. .. .. .. .. .. 33-34
6.5 MOTOR CONTROL BOARD
REMOVAL & REPLACEMENT . .. .. .. .. .. .. .. .. .. 35
REMOVAL & REPLACEMENT . .. .. .. .. .. .. .. 36-37
REMOVAL & REPLACEMENT . .. .. .. .. .. .. .. 38-39
6.8 CLAMP SPRING ASSEMBLY
REMOVAL & REPLACEMENT . .. .. .. .. .. .. .. .. .. 40
SPOOL ASSEMBLY . .. .. .. .. .. .. .. .. .. .. .. .. .. .. .. 68
9 SCHEMATICS .. .. .. .. .. .. .. .. .. .. .. .. .. .. .. .. .. .. 6979
9.1 TRITON TRACTION UNIT SCHEMATICS . 69-79
CONTROL BOARD .. .. .. .. .. .. .. .. .. .. .. .. .. .. 70-72
MOTOR CONTROL BOARD.. .. .. .. .. .. .. .. .. 73-74
PATIENT INTERRUPT SWITCH .. .. .. .. .. .. .. .. .. 75
SERIAL INTERFACE . .. .. .. .. .. .. .. .. .. .. .. .. .. .. .. 76
SMART CARD.. .. .. .. .. .. .. .. .. .. .. .. .. .. .. .. .. .. .. 77
sEMG BOARD.. .. .. .. .. .. .. .. .. .. .. .. .. .. .. .. .. .. .. 78
BLOCK DIAGRAM .. .. .. .. .. .. .. .. .. .. .. .. .. .. .. .. 79
10- SPECIAL FIXTURES .. .. .. .. .. .. .. .. .. .. .. .. .. .. .. 80-83
CALIBRATION FIXTURE .. .. .. .. .. .. .. .. .. .. .. .. .. 80-83
11 WARRANTY .. .. .. .. .. .. .. .. .. .. .. .. .. .. .. .. .. .. .. .. .. 84
FOREWORD
Triton® Traction Unit
Read, understand, and follow the Safety Precautions and all other information contained in this manual.
This manual contains the necessary safety and field service information for those field service technicians, certified by Chattanooga Group, to perform field service on the Triton unit.
At the time of publication, the information contained herein was current and up-to-date. However, due to continual technological improvements and increased clinical knowledge in the field of traction therapy, as well as Chattanooga Group’s policy of continual improvement, Chattanooga
Group reserves the right to make periodic changes and improvements to their equipment and documentation without any obligation on the part of Chattanooga Group.
It is the sole responsibility for certified field technicians to stay informed and trained in the latest technology utilized in the Triton units by Chattanooga Group. From time to time, as significant improvements are incorporated, service bulletins will be produced and made available on our web site (chattgroup.com) in lieu of reprinting a complete manual prematurely. These service bulletins will provide updated service information and technological improvements to the Triton unit for use by certified service technicians.
Due to the complex nature of the technology utilized by Chattanooga Group, the recommended troubleshooting techniques are to determine “Bad Board” and board replacement only. No board component level troubleshooting is recommended, nor will information or parts be supplied by
Chattanooga Group.
Any board component level troubleshooting performed will be at the sole risk and liability of the certified field service technician performing such troubleshooting techniques. Performance of such techniques may render the warranty null and void.
Triton® are prescription devices to be used only under the supervision of and by the order of a physician or other licensed health care provider.
©2006 Encore Medical Corporation or its affiliates, Austin, Texas, USA. Any use of editorial, pictorial, or layout composition of this publication without express written consent from the Chattanooga Group of Encore Medical, L.P. is strictly prohibited. This publication was written, illustrated, and prepared for print by the Chattanooga Group of
Encore Medical, L.P.
1
1 THEORY OF OPERATION
Triton® Traction Unit
1.1 OVERVIEW
The Triton traction unit is comprised of several pieces of proprietary hardware and software causing the unit to function as required allowing administration of traction therapy under the prescription and supervision of a licensed medical practitioner.
The Touch Screen Assembly houses the necessary hardware and software to communicate to the Motor
Control Board. Communicates commands and limits as established by the user through use of the Touch
Screen. The Touch Screen Assembly, in conjunction with the Motor Control Board, monitors the functionality of the entire system during the course of the traction therapy being administered. Should the unit malfunction or a communication error occur, the unit will stop treatment and generate an error message to notify the operator of a possible problem.
The Touch Screen Assembly communicates to the Motor Control Board Assembly via a proprietary bus.
The Motor Control Board communicates to the Touch Screen Assembly throughout the therapy session all parameters via feedback from the Motor Assembly and the Load Cell Assembly.
The Touch Screen Assembly incorporates a Patient Data Card Reader/Writer for the purpose of storing Patient
Treatment Data that can then be downloaded to a PC equipped with the optional PDMS System.
2
2 SAFETY PRECAUTIONS
2.1 PRECAUTIONARY DEFINITIONS
The precautionary instructions found in this section and throughout this manual are indicated by specific symbols. Understand these symbols and their definitions before operating this equipment. The definition of these symbols are as follows:
A. Caution
Text with a “CAUTION” indicator will explain possible safety infractions that could have the potential to cause minor to moderate injury or damage to equipment.
2.2 PRECAUTIONARY INSTRUCTIONS
A. Cautions
B. Warning
Text with a “WARNING” indicator will explain possible safety infractions that will potentially cause serious injury and equipment damage.
C. Danger
Text with a “DANGER” indicator will explain possible safety infractions that are imminently hazardous situations that would result in death or serious injury.
D. Dangerous Voltage
Text with a “Dangerous Voltage” indicator serves to inform the technician of possible hazards resulting in the electrical charge disbursement from certain components if handled or serviced improperly.
E. NOTE
Throughout this manual, “NOTE” may be found.
These Notes are helpful information to aid in the particular area or function being described.
Triton® Traction Unit
•
Read, understand, and practice all precautionary instructions found in this manual. Know the limitations and hazards associated with using any electrical traction device. Observe the precautionary and operational decals placed on the unit.
•
Do not use accessories other than those supplied with the unit or recommended by Chattanooga
Group. The safety of other products has not been established, and their use could result in injury to the patient.
•
This unit should be transported and stored in temperatures between 0°F and 140°F (-18°C and 60°C) to prevent damage to the unit or its components.
•
DO NOT operate this unit in an environment where other devices are being used that intentionally radiates electromagnetic energy in an unshielded manner. Portable and mobile RF communications equipment can affect Medical
Electrical Equipment.
•
This unit generates, uses, and can radiate radio frequency energy and, if not installed and used in accordance with the instructions, may cause harmful interference to other devices in the vicinity. However, there is no guarantee that interference will not occur in a particular installation. Harmful interference to other devices can be determined by turning this (table, unit, device, etc.) on and off. Try to correct the interference using one or more of the following: reorient or relocate the receiving device, increase the separation between the equipment, connect the equipment to an outlet on a different circuit from that which the other device(s) are connected and consult the Chattanooga Group
Service Department for help.
•
The unit should be routinely checked before each use to determine all controls function normally.
•
Handle the unit with care. Inappropriate handling of the unit may adversely affect its characteristics.
•
Before each use, inspect the Traction Cord for wear. Prolonged wear on the cord will cause it to break, which may cause sudden release of traction pressure on a patient.
•
Test the Patient Interrupt Switch before each use for power operation.
3
2 SAFETY PRECAUTIONS
2.2 PRECAUTIONARY INSTRUCTIONS (continued)
B. Warnings
Triton® Traction Unit
•
Do not remove the cover. This may cause unit damage, malfunction, electrical shock, fire, or personal injury. There are no user-serviceable parts inside the unit. If a malfunction occurs, discontinue use immediately, disconnect the Mains Power Cord from the outlet, and consult the dealer for repair service.
•
Do not use sharp objects such as a pencil point or ballpoint pen to operate the buttons on the LCD base as damage may result.
•
Do not permit any foreign materials or liquids to enter the unit. Take care to prevent any foreign materials including, but not limited to, inflammables, water, and metallic objects from entering the unit. These may cause unit damage, malfunction, electrical shock, fire, or personal injury.
•
Do not disassemble, modify, or remodel the unit or accessories. This may cause unit damage, malfunction, electrical shock, fire, or personal injury.
•
Do not use the traction unit near devices such as
X-ray units or diathermy units. These units may emit high frequency noise that may affect the operation of the unit.
•
Failure to use and maintain the traction unit and its accessories in accordance with the instructions outlined in this manual will render the warranty void.
•
In the event of a loss of power to the unit or when quick release is needed, traction tension should only be released by having the patient move towards the traction head to release the tension on the rope. Once the tension on the rope has been released, loosen the patient harness adjustment straps.
•
The tool, lubrication, and locking compound requirements listed are critical to component removal and replacement of the unit.
•
The hardware, bolts, nuts, and screws used to assemble the Triton are SAE and Metric. Therefore, it will be necessary to obtain both SAE and Metric tools for removal and replacement of components.
•
The lubricant and locking compound listed are crucial in the assembly of certain components to ensure patient safety and efficient operation of the unit.
•
Use of controls or adjustments or performance of procedures other than those specified herein may result in a hazardous traction related injury.
•
Before connecting the unit to an electrical outlet, make certain the unit is electrically grounded by connecting only to a grounded electrical service receptacle conforming to the applicable national and local electrical codes.
•
Do not use a damaged Mains Power Cord. Using a damaged Mains Power Cord may cause unit damage, malfunction, electrical shock, fire, or personal injury. If the Mains Power Cord becomes damaged, discontinue use immediately and contact the dealer for replacement of the Mains Power Cord.
•
This device should be kept out of the reach of children.
•
Always hand tighten the Lock Knob securely to avoid any slippage.
•
Care must be taken when operating this unit, adjacent to or stacked with other equipment.
Potential electromagnetic or other interference could occur to this or other equipment. Try to minimize this interference by not using other equipment in conjunction with it.
•
In the event of a loss of power to the unit, traction tension should only be released by gradually lengthening the patient harness adjustment straps.
•
Dispose of all products in accordance with local and national regulations and codes.
•
In the event that an Error message or Warning appears beginning with a 2 or 3, immediately stop all use of the system and contact the dealer or
Chattanooga Group for service. Errors and Warnings in these categories indicate an internal problem with the unit that must be tested by Chattanooga
Group or a Field Service Technician certified by
Chattanooga Group before any further operation or use of the unit. Use of a unit that indicates an Error or Warning in these categories may pose a risk of injury to the patient, user, or may cause extensive internal damage to the unit.
•
Unit failing Dielectric Withstand and/or Leakage
Tests could indicate serious internal problems.
DO NOT place the back into service! Send unit to factory for repair! DO NOT attempt to repair the unit in the field!
•
Unplug the unit from the power source before attempting removal or replacement procedures to prevent electrical shock.
•
When performing Unit Calibration Procedure, the
Calibration Fixture Load Cell must be set to US lbs.
4
2 SAFETY PRECAUTIONS
2.2 PRECAUTIONARY INSTRUCTIONS (continued)
C. Dangers
•
Use only accessories that are specially designed for this unit. Do not use accessories manufactured by other companies on this (table, unit, device, etc.). Chattanooga Group is not responsible for any consequence resulting from using products manufactured by other companies. The use of other accessories or cables may result in increased emissions or decreased immunity of this (table, unit, device, etc.).
•
This component removal and replacement procedure requires that the following be performed after component or assembly replacement to ensure proper alignment and operation of the unit:
COMPLETE CALIBRATION OF UNIT
Refer to Section 7
AND
MINIMUM OF 2 HOUR BURN IN OF UNIT AFTER
SUCCESSFUL CALIBRATION Refer to Section 7
Failure to perform either of these procedures, after
a component or assembly replacement will void
warranty and may result in injury to patients
and/or severe equipment damage.
• It is not recommend tying a new knot in a cord that has frayed or failed in use or is worn in an area from constant use. The cord must be replaced.
Triton® Traction Unit
• DO NOT connect the unit to an electrical supply without first verifying that the power supply is the correct voltage.
Incorrect voltage may cause unit damage, malfunction, electrical shock, fire, or personal injury. Your unit was constructed to operate only on the electrical voltage specified on the Voltage Rating and Serial
Number Plate. Contact the Chattanooga
Group dealer if the unit is not properly rated.
• Power Supplies retain High Voltage!
• Discharge the C4 Capacitor prior to complete removal of the Power Supply.
• Discharge the C4 Capacitor prior to handling of the new Power Supply.
• Triton® is a prescription device to be used only under the supervision of and by the order of a physician or other licensed health care provider.
• Do not use any other knot styles in the
Cord other than those specified in this manual. Use of other knot styles could cause Cord to completely disengage from the system and may cause serious injury to patient and personnel.
5
3 NOMENCLATURE
3.1 TRITON UNIT EXTERNAL COMPONENTS
The nomenclature graphics below, Figure 3.1, indicate the general locations of the major external components of the Triton traction unit.
1
Triton® Traction Unit
Know the components and their functions before performing any operation of or service to the
Triton traction unit.
2
3
7
6
4
5
1.
2.
3.
4.
5.
Touch Screen Assembly
Top and Cord Guide Cover
Traction Cord Knuckle
Front Cover
Patient Interrupt Switch Receptacle
10
9
FIGURE 3.1
6.
7.
8.
Side Cover
Clamp Assembly Knob
Rear Cover
9.
Mains Power Cord Receptacle
10.
On/Off Power Switch
6
8
3 NOMENCLATURE
3.2 INTERNAL COMPONENTS
The nomenclature graphics below, Figure 3.2, indicate the locations of the major internal components of the Triton traction unit.
9
Triton® Traction Unit
Know the components and their functions before performing any operation of or service to the
Triton traction unit.
1
2
3
4
5
8
7
10
6
12
11
4.
5.
6.
1.
2.
3.
Chassis
Load Cell
Top Front Traction Cord Guide
Traction Cord
Front Cover Mounting Bracket
Motor Control Board
FIGURE 3.2
7.
8.
9.
Motor Assembly
Power Supply
Cord Tension Spring and Housing
10.
Clamp Spring Assembly
11.
Large Driven Gear
12.
Solenoid Assembly
7
4 SPECIFICATIONS
4.1 PHYSICAL SPECIFICATIONS
Triton® Traction Unit
HEIGHT
DEPTH
WIDTH
FIGURE 4.1
Width . . . . . . . . . . . . . . . . . . . . . . . . . . . . . . . . . 24 cm (9.5 in)
Depth . . . . . . . . . . . . . . . . . . . . . . . . . . . . . . . 45 cm (17.5 in)
Height . . . . . . . . . . . . . . . . . . . . . . . . . . . . . . . 45 cm (17.5 in)
Weight
Standard Weight . . . . . . . . . . . . . . . . . . . . . . . .14 kg (30 lbs)
Shipping Weight . . . . . . . . . . . . . . . . . . . . . . . .18 kg (40 lbs)
Power
Voltage. . . . . . . . . . . . . . . . . . . . . . . . 100 V-240 V (50/60 Hz)
Power Consumption . . . . . . . . . . . . . . . . . . . . . . . . . . . 75 VA
Current Consumption . . . . . . . . . . . . . . . . . . . . . . 3.2 A Max
Electrical Class . . . . . . . . . . . . . . . . . . . . . . . . . . . . . . . . .Class I
Traction Unit Electrical Type . . . . . . . . . . . . . . . . . .Type B sEMG Electrical Type . . . . . . . . . . . . . . . . . . . . . . Type BF
Traction Modes. . . . . . . . . . . . . . . . . Static, Intermittent,
Cyclic, and their combinations.
Traction Type . . . . . . . . . . . . . . . . . . . . . . . . . . . Mechanical
LCD Display . . . . . . . . . . . . .High contrast monochrome
Touch Screen
Regulatory Compliance
Meets Directive 93 /42 /EEC
IEC/UL/EN: 60601-1 and 60601-1-2
CAN C22.2 No. 601.1-M90w/AZ
0 4 1 3
Traction Period
Hold Period
Rest Period
Traction Tension
Progrssive and
Regressive Steps
TRACTION TENSION SPECIFICATIONS
1 minute
0 seconds
0 seconds
0 kg (0 lb/0 N)
1 step
99 minutes
99 seconds
99 seconds
90 kg (200 lb/890 N)
9 steps
1 minute
1 second
1 second
1 kg (1 lb/5 N)
1 step
8
5 TROUBLESHOOTING
5.1 TRITON ERROR MESSAGES
A. The following information is provided
as an aid in defining the Software Error
Messages of the Triton traction unit.
Once a particular Error Message is defined,
the information will also list probable causes
and possible remedies. Once the problem
area is determined, subsequent tests for
verification will be necessary to determine
the subassembly or PC Board to be replaced.
Triton® Traction Unit
In the case of PC Boards, all troubleshooting
and tests will be to validate a “Bad Board”
only. No component level troubleshooting
information is or will be provided by
Chattanooga Group for field troubleshooting
of PC board components.
B. Once a particular subassembly or PC Board
has been determined as bad, refer to the
appropriate Removal & Replacement
Section for the board affected and follow the
instructions for replacement of the board.
ERROR
CODE
100
101
102
104
105
106
107
112
113
114
108
109
110
111
115
ERROR
TYPE
DEFINITION PROBABLE CAUSES POSSIBLE REMEDY
USER CORRECTABLE WARNING MESSAGES
WARNING Treatment has been running for 8 seconds, but no tension is detected on the Cord.
WARNING Patient pressed Patient Switch.
WARNING Patient Switch is unplugged.
Too much slack in Traction Cord
Patient Interrupt Switch button pressed.
Patient Interrupt Switch not properly connected to unit.
Wrong or bad Patient Data Card inserted into unit.
Remove Traction Cord Slack.
Touch the Touch Screen to clear message.
Properly connect Patient Interrupt Switch and touch Touch
Screen to clear message.
Insert correct Patient Data Card.
WARNING User selected Patient Card button on utilities screen, but no traction treatments were found on the card.
No Patient Data Card inserted.
Properly insert correct Patient Data Card into unit.
WARNING User selected save to card, but no card is inserted into the unit.
WARNING User selected save to card, but the card currently inserted is not a Patient Card.
WARNING User selected save to card, but the card currently inserted is full.
WARNING User typed in a blank patient name.
WARNING User typed in a blank protocol name.
WARNING User attempted to access a MMC function, but no MMC is inserted into the unit.
WARNING User attempted to upgrade software, but the MMC in the unit is not a software upgrade MMC.
WARNING Error upgrading Control Board software.
WARNING Error upgrading motor board software.
WARNING User pressed START, but has not yet set the Max Level value to a value greater than zero.
WARNING User pressed HOME button from treatment review screen while a treatment was running.
Wrong or bad Patient Data Card inserted into unit.
Memory full on Patient Data Card used.
No Patient ID assigned.
No Protocol name entered.
No Multimedia Card (MMC) inserted into unit.
Wrong Multimedia Card (MMC) inserted into unit.
Unknown
Unknown
User has not completed Treatment Set Up.
Home button has been pressed.
Insert correct Patient Data Card.
Save Data to PDMS and erase Patient Data Card.
Enter Patient ID.
Enter Protocol name.
Insert Multimedia Card (MMC) into unit.
Insert proper Mutimedia Card (MMC).
Contact Dealer or Chattanooga Group for Service.
Contact Dealer or Chattanooga Group for Service.
Complete Treatment Set Up prior to pressing START.
Press STOP to end treatment prior to pressing HOME.
9
5 TROUBLESHOOTING
5.1 TRITON ERROR MESSAGES (continued)
Triton® Traction Unit
In the event that an Error message or Warning appears beginning with a 2 or 3, immediately stop all use of the unit and contact the dealer or Chattanooga
Group for service. Errors and Warnings in these categories indicate an internal problem with the unit that must be tested by Chattanooga Group or a Field
Service Technician certified by Chattanooga Group before any further operation or use of the unit. Use of a unit that indicates an Error or Warning in these categories may pose a risk of injury to the patient, user, or may cause extensive internal damage to the unit.
ERROR
CODE
200
201
202
203
204
205
206
207
208
209
210
211
212
213
ERROR
TYPE
DEFINITION PROBABLE CAUSES POSSIBLE REMEDY
ERROR MESSAGES (200-223) REQUIRING TECHNICAL ASSISTANCE
ERROR The motor PCB has reset.
ERROR Error communicating with the realtime clock chip.
ERROR The motor PCB returned an error while performing the zero Load Cell function.
Motor Control Board is bad.
Control Board Communication Error.
Bad Load Cell Assembly
Motor Control Board Communication Error.
If the Error repeats routinely, replace Motor Control Board.
If the Error repeats routinely, replace Touch Screen Assembly.
ERROR Timeout waiting for the motor PCB to perform the zero Load Cell calibration.
ERROR Timeout waiting for the motor PCB to perform the motor current calibration.
Bad Load Cell
Bad Motor Control Board
Motor Control Board Communication Error.
1. Check Cables and Harnesses for proper seating and
connection on Motor Control Board.
2. Replace Load Cell Assembly.
3. Replace Motor Control Board.
4. Replace Touch Screen Assembly.
1. Ensure there is slack in the Cord.
2. Check Cables and Harnesses for proper seating and
connection on Motor Control Board.
3. Replace Load Cell.
4. Replace Motor Control Board.
1. Ensure there is no slack in the Cord.
2. Check Cables and Harnesses for proper seating and
connection on Motor Control Board.
3. Replace Load Cell.
4. Replace Motor Control Board.
ERROR A Motor fault error has occurred while a treatment was running.
ERROR We have detected a motor current error
(MC_MON pin on motor PCB).
Internal mechanical jam of unit.
Bad Motor Control Board or Motor Assembly.
ERROR The Motor PCB cannot get to the desired tension.
Internal Mechanical Jam of unit.
Bad Motor Control Board or Motor Assembly.
Unit out of calibration.
ERROR We have detected a Load Cell limit error
(LC_MON pin on motor PCB).
ERROR Error erasing a patient card.
Unit is out of calibration.
Bad Motor Control Board.
Bad Load Cell Assembly.
Bad Patient Data Card.
Bad Touch Screen Assembly.
ERROR CRC not correct on treatment just read from
Patient Card.
ERROR Error reading default protocol on power up so must rebuild protocols to factory presets.
Bad Patient Data Card.
Bad Touch Screen Assembly.
EEPROM is corrupt.
ERROR The Motor PCB fl agged a comm watchdog error.
Touch Screen Assembly did not poll Motor Control
Board in a reasonable amount of time.
ERROR Motor PCB has indicated that the zero calibration value is invalid and needs to be calibrated.
Unit is out of calibration.
1. Correct any internal mechanical jam.
2. Replace bad Motor Control Board or bad Motor Assembly.
1. Correct any internal mechanical jam.
2. Replace bad Motor Control Board or bad Motor Assembly.
Perform Unit Calibration and Burn In procedures.
1. Perform Unit Calibration and Burn In procedures.
2. Replace Motor Control Board.
3. Replace Load Cell Assembly.
1. Try known good Patient Data Card.
2. Check Cables and Harnesses for proper seating and
connection on Motor Control Board.
3. Replace Touch Screen Assembly.
1. Try known good Patient Data Card.
2. Replace Touch Screen Assembly.
If the Error repeats routinely, replace Touch Screen Assembly.
1. Check Cables and Harnesses for proper seating and
connection on Motor Control Board.
2. If the Error repeats routinely, replace Touch Screen
Assembly.
Perform Unit Calibration and Burn In procedures.
10
5 TROUBLESHOOTING
5.1 TRITON ERROR MESSAGES (continued)
Triton® Traction Unit
In the event that an Error message or Warning appears beginning with a 2 or 3, immediately stop all use of the unit and contact the dealer or Chattanooga
Group for service. Errors and Warnings in these categories indicate an internal problem with the unit that must be tested by Chattanooga Group or a Field
Service Technician certified by Chattanooga Group before any further operation or use of the unit. Use of a unit that indicates an Error or Warning in these categories may pose a risk of injury to the patient, user, or may cause extensive internal damage to the unit.
ERROR
CODE
214
215
217
218
219
220
221
222
223
ERROR
TYPE
DEFINITION PROBABLE CAUSES POSSIBLE REMEDY
ERROR MESSAGES (200-223) REQUIRING TECHNICAL ASSISTANCE (continued)
ERROR User has confi gured a treatment such that it takes too much memory to compute the treatment steps. Unit will default back to the default power up protocol.
ERROR Internal error, unit cannot get the next treatment step information, treatment is terminated.
Under normal operating conditions, this Error should never appear.
Multimedia Card (MMC) Data is corrupt.
Multimedia Card (MMC) interface not working.
Remove unit from service and report exact treatment parameters to Chattanooga Group.
ERROR Error reading a MMC.
ERROR Error upgrading Control Board software.
Bad Mutimedia Card (MMC).
Improper cable connection to Motor Control Board.
Bad Touch Screen Assembly.
Bad Mutimedia Card (MMC).
Improper cable connection to Motor Control Board.
Bad Touch Screen Assembly.
1. Try known good Multimedia Card (MMC).
2. Remove unit from service and report exact treatment
parameters to Chattanooga Group.
1. Try known good Multimedia Card (MMC).
2. Check Cables and Harnesses for proper seating and
connection on Motor Control Board.
3. Replace Touch Screen Assembly.
1. Try known good Multimedia Card (MMC).
2. Check Cables and Harnesses for proper seating and
connection on Motor Control Board.
3. Replace Touch Screen Assembly.
ERROR Error upgrading Control Board software.
ERROR Error upgrading Motor Control Board software.
Bad Mutimedia Card (MMC).
Improper cable connection to Motor Control Board.
Bad Motor Control Board.
Bad Touch Screen Assembly.
ERROR Error upgrading Motor Control Board software.
Bad Mutimedia Card (MMC).
Improper cable connection to Motor Control Board.
Bad Motor Control Board.
Bad Touch Screen Assembly.
ERROR Patient switch is shorted.
ERROR Beta version evaluation period has expired.
Bad Mutimedia Card (MMC).
Improper cable connection to Motor Control Board.
Bad Touch Screen Assembly.
Patient Interrupt Switch not completely seated in connector.
Bad Patient Interrupt Switch.
Bad Patient Interrupt Switch Connector.
Unit is designated BETA Test Unit.
1. Try known good Multimedia Card (MMC).
2. Check Cables and Harnesses for proper seating and
connection on Motor Control Board.
3. Replace Touch Screen Assembly.
1. Try known good Multimedia Card (MMC).
2. Check Cables and Harnesses for proper seating and
connection on Motor Control Board.
3. Replace Motor Control Board.
4. Replace Touch Screen Assembly.
1. Try known good Multimedia Card (MMC).
2. Check Cables and Harnesses for proper seating and
connection on Motor Control Board.
3. Replace Motor Control Board.
4. Replace Touch Screen Assembly.
1. Properly connect Patient Interrupt Switch to unit.
2. Use a known good Patient Interrupt Switch.
3. Replace Patient Interrupt Switch Connector on unit.
Immediately return unit to Chattanooga Group.
11
5 TROUBLESHOOTING
5.1 TRITON ERROR MESSAGES (continued)
Triton® Traction Unit
In the event that an Error message or Warning appears beginning with a 2 or 3, immediately stop all use of the unit and contact the dealer or Chattanooga
Group for service. Errors and Warnings in these categories indicate an internal problem with the unit that must be tested by Chattanooga Group or a Field
Service Technician certified by Chattanooga Group before any further operation or use of the unit. Use of a unit that indicates an Error or Warning in these categories may pose a risk of injury to the patient, user, or may cause extensive internal damage to the unit.
ERROR
CODE
300 through
307
308
309
310
311
312
313
314
ERROR
TYPE
DEFINITION PROBABLE CAUSES POSSIBLE REMEDY
CRITICAL
ERROR
CRITICAL
ERROR
CRITICAL
ERROR
CRITICAL
ERROR
CRITICAL
ERROR
CRITICAL
ERROR
CRITICAL
ERROR
CRITICAL
ERROR
CRITICAL ERRORS (300-314) DEMANDING TECHNICAL SERVICE
Communication Error between Touch Screen and Motor
Control Board.
We are supposed to be increasing tension, but tension is not increasing.
We are supposed to be decreasing tension, but tension is actually increasing.
Communication Error.
Slack in Cord.
Bad Load Cell.
Bad Motor Control Board.
Unit out of calibration.
Bad Harness connection.
Bad Load Cell.
Bad Motor Control Board.
Unit out of calibration.
1. Check Cables and Harnesses for proper seating and
connection on Motor Control Board.
2. Replace Motor Control Board.
3. Replace Touch Screen Assembly.
1. Remove slack in Cord.
2. Check Cables and Harnesses for proper seating and
connection on Motor Control Board.
3. Replace Load Cell.
4. Replace Motor Control Board.
1. Perform Unit Calibration and Burn In procedures.
2. Check Cables and Harnesses for proper seating and
connection on Motor Control Board.
3. Replace Load Cell.
4. Replace Motor Control Board.
Perform Unit Calibration and Burn In procedures.
We are reading > 0 tension when we should be reading zero.
We are reading < 0 tension when we should be reading zero.
We have detected that the motor is running too fast.
Internal memory error.
Error reading EEPROM.
Unit out of calibration.
Bad Load Cell.
Bad Motor Control Board.
Bad Motor Control Board.
Bad Motor Assembly.
Bad Touch Screen.
Bad Touch Screen.
1. Perform Unit Calibration and Burn In procedures.
2. Check Cables and Harnesses for proper seating and
connection on Motor Control Board.
3. Replace Load Cell.
4. Replace Motor Control Board.
1. Replace Motor Control Board.
2. Replace Motor Assembly.
Replace Touch Screen Assembly.
Cycle power to unit. If the Error repeats, then replace
Touch Screen Assembly.
12
NOTES
Triton® Traction Unit
13
5 TROUBLESHOOTING
5.2 TRITON TRACTION UNIT TESTING
A. General- Electronic
1. Information within this section in respect to
electronic components is intended to aid
in troubleshooting the PCB's of the Triton units
These tests are the standard testing
procedures and methods used at the factory
before shipment of the unit.
2. Due to the complex nature of the technology
utilized by Chattanooga Group, the
recommended PCB troubleshooting
techniques are to determine “Bad Board” and
board replacement only. No PCB
component level troubleshooting is
recommended nor will information or parts
be supplied by Chattanooga Group. Any PC
board component level troubleshooting
performed will be at the sole risk and liability
of the Service Technician performing such
3. Once a particular PCB has been
determined as bad, replace the PCB. Use
only Chattanooga Group replacement parts
B. General- Replacement Components
Critical component replacement parts for the
traction unit are available as subassemblies only.
This is due to the accuracy required and the
critical nature of the subassembly within the
unit for power function and operation. Individual
components of these subassemblies will not be
made available by Chattanooga Group.
C. General- Tests and Repair Procedures
1. Certain tests and repair procedures require the use of special tools and/or fixtures.
These will be listed at the particular test where they are required. Testing with any other special tool or fixture other than those stated could give erroneous readings or test results. Always perform the tests exactly as stated to ensure accurate results.
2. Test equipment settings will be listed for each test performed prior to the respective test to ensure the test is performed to
Chattanooga Group standards and ensure
3. The troubleshooting and repair of the units are to be performed only by authorized technicians trained and certified by
Triton® Traction Unit
NOTE:
Adjust Dielectric Withstand tester to indicate fault with
120 kOhm load across the output when at specified test voltage.
2. Milliohm Meter
3. Digital Multimeter
4. Required Hand Tool
•
•
#1 Phillips Screwdriver
#2 Phillips Screwdriver
•
•
Flat Blade Screwdriver
• Calibrated Torque Wrench- 200 inch pound or 2,500 Newton meter minimum capacity.
Allen Wrenches
•
•
• SAE- 3/32, 5/32, and 9/64 in
Metric- 3 mm
Hex Key Sockets for Torque Wrench
The tool, lubrication, and locking compound requirements listed are critical to component removal and replacement of the unit.
The hardware, bolts, nuts, and screws used to assemble the Triton are SAE and Metric. Therefore, it will be necessary to obtain both SAE and Metric tools for removal and replacement of components.
The lubricant and locking compound listed are crucial in the assembly of certain components to ensure patient safety and efficient operation of the unit.
•
•
•
•
• SAE- 3/32 and 5/32 in
• Metric- 4 mm
Needle Nose Pliers
Tape Measure- 12 ft (3 meter) minimum
Ratchet
7mm Box End Wrench
• Pick for removing connector wires.
5. Touch Screen to Cover Assembly Jig
6. Calibration Fixture with calibrated Strain
Meter.
7. Solenoid Assembly Mounting Jig. P/N 48139.
8. Attenuator
9. Calibrated Audio Signal Generator, B-K
10. Test leads for Audio Generator to Attenuator.
D. Tools, Fixtures, and Equipment Required
1. Dielectric Withstand (Hi-Pot) and ground
resistance tester.
14
5 TROUBLESHOOTING
5.3 VISUAL INSPECTION
A. General
Visually inspect the unit. A visual
inspection can, to an experienced Technician,
indicate possible abuse of the unit and
5.4 GROUND RESISTANCE TEST
A. Voltage Specifications
Models 4759 and 4779 . . . . . . . . . Input: 100-240 VAC
50/60 Hz, 75 VA
B. Specification
Maximum Acceptable Resistance: 100 milliohms
C. Equipment Required
5.5 LEAKAGE TESTS
Triton® Traction Unit
UNIT FAILING DIELECTRIC WITHSTAND AND/OR
LEAKAGE TESTS COULD INDICATE SERIOUS
INTERNAL SYSTEM PROBLEMS.
DO NOT PLACE UNIT BACK INTO SERVICE!
SEND UNIT TO FACTORY FOR REPAIR! DO NOT
ATTEMPT TO REPAIR IN THE FIELD!
Test Voltage Spec . . . . . . . . . . . . . . . . . . . . . . . . . . . . . .1000 V
Conduct all necessary leakage tests as required per
“Chapter 7 Electrical Equipment” of the 1999, or later, edition of the NFPA (National Fire Protection
Association) “Health Care Facilities” standards.
See Figure 5.2.
D. Test
Place unit on level work surface.
Place one meter probe on the ground prong of
power supply and the other to any exposed
metal or screw on the unit. See Figure 5.1.
EXPOSED METAL
GROUND PRONG
FIGURE 5.1
NOTE:
U.S.A. Power Cord Illustrated.
Unit is illustrated on its side.
FIGURE 5.2
NOTE:
The NFPA "Health Care Facilities" standards are specific to the U.S.A. All other technicians should verify their country's requirements for these tests.
15
5 TROUBLESHOOTING
5.6 ON/OFF SWITCH TEST
A. Specification
Unit turns Off and On
B. Equipment Required
None
C. On/Off Switch Test Procedure
1. Place unit on level work surface.
2. Plug Power Cord into grounded power source
with appropriate voltage. See Specifications
3. Turn unit Off and back On with Power Switch.
D. Test Result
1. If unit turns Off and On, unit passed test.
2. If unit does not turn Off and On, unit failed
test. Refer to: 5.7 On/Off Switch
5.7 ON/OFF SWITCH TROUBLESHOOTING
A. Specification
Appropriate AC voltage.
B. Equipment Required
Digital Multimeter
3/32 in Allen Wrench
C. On/Off Switch Troubleshooting Procedure
1. Disconnect unit from power source.Remove
Side Covers. Refer to 6.1 Side Cover Removal &
Replacement.
2. Remove Top Cover. Refer to 6.2 Top and Cord
Guide Cover Removal & Replacement.
3. Remove Rear Cover leaving harnesses
connected. Refer to 6.3 Rear Cover Removal
4. Disconnect the Blue and Red wires from the
Power Supply to the Power Switch. See
5. Set Multimeter to AC and to the appropriate
voltage setting. Connect Multimeter Leads
to the Blue and Brown wire Connectors from
the Power Switch. See Figure 5.5.
6. Plug unit into a grounded power source with
appropriate voltage. Turn Power Switch On
and take reading from Multimeter.
D. Test Result
1. If Multimeter reads appropriate voltage, unit
passed test. If unit will not power up, refer to
2. If Multimeter does not read appropriate
voltage.
ON/OFF
SWITCH
ON/OFF
SWITCH
FIGURE 5.3
DISCONNECT RED AND BLUE
POWER SUPPLY WIRES
FIGURE 5.4
MULTIMETER
CONNECTED TO BLUE
AND BROWN WIRES
FIGURE 5.5
Triton® Traction Unit
16
5 TROUBLESHOOTING
5.8 PATIENT INTERRUPT SWITCH TEST
A. Specification
Unit displays Error 101 or 102 at the
B. Equipment Required
None
C. Patient Interrupt Switch Test Procedure
1. Place unit on level work surface. Plug Power
Cord into grounded power source with
2. Connect Patient Interrupt Switch to unit
making certain it is completely seated in the
Patient Interrupt Switch connector. See
3. Turn unit On with Power Switch. After unit
has completely booted up, disconnect the
Patient Interrupt Switch. Unit should display
Error 102. See Figure 5.7.
4. Reconnect the Patient Interrupt Switch. Touch
the Touch Screen anywhere to clear the Error.
5. Turn unit Off. with Patient Interrupt Switch
connected to the unit, turn unit On with
6. After unit has completely booted up, depress
the Patient Interrupt Switch button. The unit
should display Error 101. Touch the Touch
Screen anywhere to clear the Error. See
D. Test Result
1. If unit displays Errors 101 or 102 at the
respective test, unit passed test.
2. If unit does not display Errors 101 or 102 at
the respective test, unit failed test. Repeat
test with a known good Patient Interrupt
Switch.
3. If known good Patient Interrupt Switch
resolves the problem, replace existing Patient
Interrupt Switch with new part.
4. If the known good Patient Interrupt Switch
does not remedy the problem, Replace
Patient Interrupt Switch Jack.
FIGURE 5.6
FIGURE 5.7
Triton® Traction Unit
17
FIGURE 5.8
5 TROUBLESHOOTING
5.9 CORD RELEASE AND RETRACT TEST
A. Specification
Release . . . . . . . . . . . . . . . . . . . . Cord releases with less than 5 lbs tension
Retract . . . . . . . . . . . . . . . . . .Cord completely retracts
B. Equipment Required
Calibration Fixture with calibrated Strain Meter.
C. Cord Release and Retract Test Procedures
1. Secure unit to the Calibration Fixture. See
5.9.
2. Plug unit into approved power source and
turn unit On.
3. After unit has completely booted, press and
hold Rope Release on Touch Screen, and
pull Cord out. Release Rope Release while
holding Cord out. See Figure 5.10.
NOTE:
It may be necessary to pull and release slight tension on the Cord to allow the internal mechanism to release the stop on the Cord.
4. While holding on to extended Cord, press
Rope Release on the Touch Screen and
guide Cord back into unit.
5. Repeat step 3 above to connect the Cord to
the Calibration Fixture. See Figure 5.11.
6. Set up unit for a static pull of 100 lbs. Refer
to User Manual if necessary.
7. Press the START button. After the 100 lbs has
been reached, press the STOP Button
and view the Rope Release on the Touch
Screen, it should be inactive.
8. Watch as the tension decreases. Once the
tension decreases to below 5 lbs, the Rope
Release should become active. Immediately
press the Rope Release on the Touch Screen,
pull enough Cord out to facilitate
disconnection from the Calibration Fixture.
Release the Rope Release control.
Disconnect the Cord from the Calibration
Fixture.
NOTE:
It may be necessary to apply and release slight tension on the Cord to allow the internal mechanism to release the stop on the Cord.
Repeat step 4.
D. Test Result
1. If Cord fails to release, unit failed test.
Refer to 5.10 Cord Release
Troubleshooting.
2. If Cord fails to completely retract, unit
failed test. Adjust Cord Retraction Spring.
Refer to page 42 beginning with step 13
for adjustment procedures.
18
FIGURE 5.9
FIGURE 5.10
FIGURE 5.11
Triton® Traction Unit
5 TROUBLESHOOTING
5.10 CORD RELEASE TROUBLESHOOTING
A. Specification
Solenoid Gear . .Properly engages Driven Gear
Required
1. Digital Multimeter
2. #1 Phillips Screwdriver
3. 3/32 in Allen Wrench
4. Solenoid Assembly Mounting Jig
C. Cord Release Troubleshooting Procedure
1. Solenoid Assembly
Cover Removal & Replacement.
b. Manually move solenoid shaft in and out
to ensure gears are not locked and the
Solenoid Shaft moves and properly
engages the large Driven Gear. See
Figure 5.12. If Solenoid moves and
engages properly, procede to step c. below.
If Solenoid Shaft will not move or
properly mesh with the Large Driven
Gear, adjust Solenoid Assembly. Refer
to page 46, parts A-D for adjustment. If
problem persists, replace Solenoid
Assembly. Refer to 6.11 Solenoid
Assembly Removal & Replacement procedures.
c. With unit connected to an approved
power supply and turned on, press the
Rope Release on the Touch Screen.
Repeat several times to ensure the
solenoid properly engages and
disengages the large Driven Gear.
1) Touch Screen Control does not activate
Solenoid. Troubleshoot Motor Control
Board. Refer to page 20 for instructions.
2) Solenoid Gear does not properly
engage the large Driven Gear. See
Figure 5.13. Adjust Solenoid
Assembly. Refer to page 46, parts A
through D for adjustment.
FIGURE 5.12
FIGURE 5.13
Triton® Traction Unit
19
5 TROUBLESHOOTING
5.10 CORD RELEASE TROUBLESHOOTING (continued)
2. Motor Control Board
a. Disconnect Solenoid Harness from J8 on
Motor Control Board. See Figure 5.14.
b. Make certain unit is connected to an
approved power supply outlet and turn
unit On with Power Switch.
c.
connect leads to the J8 connector pins.
See Figure 5.15.
d. Push and hold the Rope Release on the
Touch Screen and take reading from
Multimeter.
1. If no voltage is present or low voltage
is present, replace Motor Control
Board. Refer to 6.5 Motor Control
Board Removal & Replacement.
2. If proper voltage is present and
problem persists, replace Touch
Screen Assembly. Refer to 6.6 Touch
Screen Removal & Replacement.
FIGURE 5.14
Triton® Traction Unit
FIGURE 5.15
20
5 TROUBLESHOOTING
5.11 LOAD CELL TEST
A. Specification
Touch Screen Reading . . . . . . . . . . . . . . . . . . ±10%
Required
1. Calibration Fixture with calibrated Load Cell
C. Load Cell Test Procedure
2. Plug unit into an approved power source
and turn unit On with Power Switch.
3. After unit is completely booted, Press Cord
Release on the Touch Screen and pull out
enough Cord to connect Cord to
the Load Cell. See Figure 5.16.
4. After connecting Cord to Load Cell, allow
any slack Cord back into the unit. Release
the Rope Release on the Touch Screen.
5. Set up unit for a 100 lbs static pull. Refer to
User Manual if necessary.
6. Zero the Load Cell according to the
7. Press the START button just below the Touch
Screen. See Figure 5.17.
8. During the pull, compare and record the
reading on the Touch Screen to the reading
on the Load Cell at 25, 50, 75, and 100 lb intervals.
9. After 100 lbs has been reached, press the
STOP button. See Figure 5.18. Allow unit to
release the Cord.
D. Test Result
1. If reading of Load Cell is within ±10% of the
Touch Screen reading, unit passed test.
2. If readings are higher or lower than the
±10% tolerance, unit failed test. Calibrate
unit and re-test. Refer to Section 7
Calibration for Procedures.
3. If problem persists, perform Load
Cell Troubleshooting. Refer to 5.12 Load Cell
Troubleshooting for procedures.
FIGURE 5.16
FIGURE 5.17
Triton® Traction Unit
21
FIGURE 5.18
5 TROUBLESHOOTING
5.12 LOAD CELL TROUBLESHOOTING
A. Specification
Voltage to Load Cell . . . . . . . . . . . . . . . . . .10 VDC
Voltage from Load Cell . . . . . . . . . . . . . . Variable
Motor Control Board Voltage (U3) . . . Variable
Required
1. Calibration Fixture with calibrated Load Cell
2. 3/32 in Allen Wrench
3. Digital Multimeter
4. Pick for removing wires from connectors.
C. Voltage to Load Cell Test
Cover Removal & Replacement.
3. Plug unit into an approved power source and turn unit On with Power Switch.
4. After unit is completely booted, press Cord
Release on the Touch Screen and pull out enough Cord to connect Accessory Clip to the Load Cell. See Figure 5.19.
5. Guide any Cord slack back into unit.
Release the Rope Release on the Touch
Screen.
6. Remove Load Cell Connector from J11 on
Motor Control Board. See Figure 5.20.
7. Set Multimeter to read 10 VDC and connect leads to Pins 1 and 2 of the J11 connector on the Motor Control Board.
8. Multimeter should read 10 VDC.
If reading is 10 VDC, procede to step 9.
If reading is not 10 VDC, replace Motor
Control Board. Refer to 6.5 Motor Control
Board Removal & Replacement.
9. Reconnect Load Cell Connector to J11 on
Motor Control Board. Make certain the
Pink Wire on the Connector is positioned onto Pin 1 of the Motor Control Board. See
10. Set Multimeter to read 10 VDC. Make connection with Pins 1 and 2 from the side of the connector with Multimeter
Leads and take reading. See Figure 5.22.
11. If reading is not 10 VDC, replace unit Load
Cell. Refer to 6.7 Load Cell Removal and
Replacement. If reading is 10 VDC proceed
22
FIGURE 5.21
FIGURE 5.19
FIGURE 5.20
Triton® Traction Unit
FIGURE 5.22
5 TROUBLESHOOTING
5.12 LOAD CELL TROUBLESHOOTING (continued)
D. Voltage from Load Cell Tests
NOTE:
It will be necessary to have two people available for the following test.
1. Set Multimeter to read 10 VDC. Make connection with Pin 3 (Blue wire) and Pin 4
(Green wire) from the side of the connector with Multimeter Leads. See
2. Press the START button. The voltage reading on Multimeter should increase as
3. Press the STOP button. The voltage reading on Multimeter should decrease as Cord
4. If voltage does not increase and decrease as described in steps 2 and 3, continue
5. Turn unit Off. Using the Pick, remove Blue wire and Green wire from connector. See
6. Connect the Multimeter Leads to the Blue and Green wires. Repeat steps 2 and 3.
7. If voltage does not increase or decrease as described in steps 2 and 3, replace unit
Load Cell. Refer to 6.7 Load Cell Removal
8. If voltage does increase and decrease as described in steps 2 and 3, replace wires into connector. Make certain the Blue wire is in the Pin 3 position and the Green wire is in the Pin 4 position. Repeat steps 2 and
3. If problem persists, proceed to step 9.
9. Locate U3 on Motor Control Board.
Connect the Red (+) Multimeter Lead to
Pin 7 of U3 and the Black (-) Lead to Pin 4 of U3. See Figure 5.25.
10. Repeat steps 2 and 3. If voltage does not increase and decrease as described in steps 2 and 3, replace Motor Control
Board. Refer to 6.5 Motor Control Board
Removal & Replacement.
RED LEAD
TO PIN 4
BLACK LEAD
TO PIN 3
FIGURE 5.23
USE PICK TO
REMOVE WIRES
FIGURE 5.24
Triton® Traction Unit
FIGURE 5.25
23
5 TROUBLESHOOTING
5.13 TOUCH SCREEN TEST
A. Specification
Control . . . . . . . . . . Touch Screen Dims and Brightens
Touch Screen . . . . . . . . . Displays proper Screen
None
C. Touch Screen Test Procedure
1. Place unit on level work surface.
2. Plug Power Cord into grounded power
source with appropriate voltage. See
Specifications on page 8.
3. Turn unit On with Power Switch. After the
unit has completely booted, adjust the
Touch Screen Contrast with the Contrast
Control on the back of the Touch Screen
Housing. See Figure 5.26.
4. Press Touch Screen controls to verify the
Touch Screen responds and displays the
correct screen. See Figure 5.27.
D. Test Result
1. If when adjusting, Contrast Control dims
and brightens Touch Screen, unit passed
test. If Contrast Control does not dim and
brighten Touch Screen, refer to 5.14 Touch
2. If when pressing controls on Touch Screen
the proper screen does not display,
unit failed test. Calibrate Touch Screen. Refer
to 7.2 Touch Screen Calibration.
3. If nothing is visible on Touch Screen, adjust
Contrast Control. If problem persists, unit
failed test. Refer to 5.14 Touch Screen
Troubleshooting.
CONTRAST
KNOB
FIGURE 5.26
FIGURE 5.27
Triton® Traction Unit
24
5 TROUBLESHOOTING
5.14 TOUCH SCREEN TROUBLESHOOTING
A. Specification
Voltage to Touch Screen:
J6 Connector . . . . . . . . . . . . . . . . . 5 VDC ±5%
Display Connector . . . . . . . . . . .24 VDC ±5%
B. Equipment Required
1. 3/32 in Allen Wrench
2. Digital Multimeter
C. Touch Screen Troubleshooting Procedure
1. Remove Side Covers. Refer to 6.1 Side Cover
Removal & Replacement.
2. Plug unit into an approved power source
and turn unit On with Power Switch.
3. Observe Motor Control Board LEDs. The
"5V OK" LED should be illuminated and
LED 3 should be flashing. See Figure 5.28.
a. If LEDs are not working properly, proceed
to step 4.
b. If LEDs are working properly, proceed to
steps 5 through 9.
4. Turn unit Off. Remove Touch Screen Ribbon
Cable from "Display" on Motor Control
Board. See Figure 5.29. Turn unit On.
a. If LEDs begin working properly, replace
Touch Screen assembly. Refer to 6.6
Touch Screen Assembly Removal and
Replacement.
b. If LEDs are not working properly, refer to
5.15 Power Supply Troubleshooting.
c. If Power Supply is functioning properly,
replace Motor Control Board. Refer to 6.5
Motor Control Board Removal and
Replacement.
5. Turn unit Off. Remove Touch Screen Ribbon
Cable from "Display" on Motor Control
Board. See Figure 5.29. Turn unit On.
6. Set Multimeter to VDC. On Connector J6,
connect the Red (+) Multimeter Lead to
Pin 1 and the Black (-) Lead to Pin 2. See
Figure 5.28. Take reading from Multimeter.
Reading should be +5 VDC.
7. Connect the Red (+) Multimeter Lead to Pin
6 and the Black (-) Lead to Pin 1 on the
Motor Control Board "Display" Connector.
See Figure 5.30 reading on Multimeter
should be 24 VDC.
8. If the voltage reads correctly from steps
5 and 6, replace the Touch Screen Assembly.
Refer to 6.6 Touch Screen Removal
9. If either of the voltages are not reading
properly as in steps 6 and 7, replace Motor
Control Board. Refer to 6.5 Motor Control
Board Removal & Replacement.
25
PIN 1
Triton® Traction Unit
PIN 2
J6
LED 3
FIGURE 5.28
5V OK LED
FIGURE 5.29
CAUTION
Make certain Multimeter Leads are on the correct pins and do not short across any other pins to prevent destruction of the
Motor Control Board.
FIGURE 5.30
5 TROUBLESHOOTING
5.15 POWER SUPPLY TROUBLESHOOTING
A. Specification
Power Supply Input . . 100 V-240 V (50/60 Hz)
Power Supply Output . . . . . . . . . . .24 VDC ±5%
1. 3/32 in Allen Wrench
2. Digital Multimeter
C. Power Supply Troubleshooting Procedure
1. Remove Side Covers. Refer to 6.1 Side Cover
Removal & Replacement.
2. Plug Power Cord into grounded power
source with appropriate voltage. See
Specifications on page 8.
3. Set Multimeter to read appropriate VAC.
4. Connect Multimeter Leads to the Power
Supply Fuses at the rear of Power Supply.
See Figure 5.31. Multimeter should read
same voltage as the approved power source.
a. If reading is the same as approved power
source, proceed to step 5.
b. If VAC reading is not the same as
approved power source, replace Power
Supply. Refer to 6.12 Power Supply
Removal & Replacement.
5. Remove Power Supply Output Harness from
Motor Control Board J5. See Figure 5.32.
6. Set Multimeter to read VDC. Connect
Multimeter Leads to the Power Supply
Output Harness. See Figure 5.33. Multimeter
reading should be 24 VDC ±5%.
a. If reading is within the specified range as
stated above, unit passed test.
b. If reading is not within the specified
range as stated above, replace Power
Supply. Refer to 6.12 Power Supply
Removal & Replacement.
FIGURE 5.31
FIGURE 5.32
Triton® Traction Unit
26
FIGURE 5.33
5 TROUBLESHOOTING
5.16 sEMG TESTS
This test is to be performed on the Triton Traction unit only with the sEMG Module properly installed.
Perform this test on all Channels with sEMG.
A. Test Equipment Required
1.
It will be necessary to build an Attenuator for this test. See Figure 5.34 for schematic of the required Attenuator. The Attenuator must be contained in shielded enclosure.
Input connection and output connections should be separated from each other as far as possible within the confines of the shielded enclosure.
2.
Calibrated Audio Signal Generator, B-K
Precision, Model 3001.
3.
Test leads for Audio Generator to
Attenuator.
NOTE:
Audio Signal Generator must produce a sine waveform.
4.
Known good sEMG Lead Wires.
B. sEMG Test Procedures
1.
Figure 5.35 depicts the controls of the
Audio Signal Generator. Set up Audio Signal
Generator as follows:
a) Plug the Audio Signal Generator Test
Leads into Generator SYNC Ports.
b) Set the FREQ. RANGE Hz to X1.
c) Turn the amplitude knob up to
maximum.
d) Set the WAVEFORM to Sine waveform.
e) Set the ATTEN to O.
f) Set the FREQUENCY DIAL to 100.
g) Turn Audio Signal Generator On.
2.
Turn Triton On. View Home Screen for the presence of the sEMG icon. See Figure 5.36.
If icon is grey, stop test and make necessary repairs to the sEMG Module and System.
a) Make certain sEMG Module is completely
seated in unit.
b) Replace sEMG Module with a known
good sEMG Module. Refer to 6.15 sEMG
Module Removal and Replacement.
Triton® Traction Unit
RED
ATTENUATOR SCHEMATIC
100K 1%
RED
49.9 OHM 1%
GREEN
TO AUDIO WAVEFORM
GENERATOR
49.9 OHM 1%
BLACK
BLACK
100K 1%
SET FREQUENCY RANGE
HZ TO X1
AMPLITUDE TO
MAXIMUM
TO SEMG LEAD WIRES
FIGURE 5.34
FREQUENCY
DIAL TO 100
WAVEFORM
TO SINE
ATTEN TO 0
FIGURE 5.35
sEMG ICON
TEST LEADS TO
SYNC PORTS
FIGURE 5.36
27
5 TROUBLESHOOTING
5.16 sEMG TESTS (continued)
3. If icons are present, connect known good
sEMG Lead Wire to the Triton Traction unit.
See Figure 5.37.
Triton® Traction Unit
FIGURE 5.37
4. Connect the sEMG Lead Wires into the
Attenuator. Make certain the sEMG Lead
is connected to its respective color on the
Attenuator. See Figure 5.38.
NOTE:
Make certain that nothing is touching the sEMG lead wires or the attenuator box. Signals used in sEMG are very small and signal can be induced from external sources that create an unbalanced input.
5. Press the sEMG Traction icon on Home
Screen. See Figure 5.39 Reading should be
7 or less.
6. If the reading is greater than 7, replace
the sEMG Module and re-test. Refer to 6.15
sEMG Module Removal and Replacement.
FIGURE 5.38
LEAD WIRES TO THEIR
RESPECTIVE COLORS
ON ATTENUATOR
28
FIGURE 5.39
5 TROUBLESHOOTING
5.16 sEMG TESTS (continued)
7. Make certain the Audio Signal Generator
is set up per 5.16, part B, steps 1, a) through
1, g). Connect the Audio Signal Generator
Test Leads from the Generator SYNC Ports to
the Attenuator (make certain test leads are
connected red to red and black to black).
5.40.
8. View the Triton sEMG Screen. The Channel
should read between 604 and 738.
If the Channel reads below 604 or greater
than 738, replace the sEMG Module and
re-test. Refer to 6.15 sEMG Module Removal
Replacement.
C. sEMG Test Results
If the sEMG Channel fails any part of the tests as described in 5.16, B, steps 2 through 8, then the module fails the test.
1.
Make certain the sEMG Module is completely seated in the Triton unit.
2.
Replace the sEMG Module and re-test.
Refer to 6.15 sEMG Module Removal and
Replacement. If the problem continues, perform step 3 below.
3.
Replace the Motor Control Board and re-test. Refer to 6.5 Motor Control Board
Removal and Replacement. If the problem continues after performing steps 2 and 3 above proceed to step 4 below.
4.
Replace the Touch Screen Assembly and re-test. Refer to 6.6 Touch Screen Assembly
Removal and Replacement.
FIGURE 5.40
Triton® Traction Unit
29
6 REMOVAL & REPLACEMENT
6.1 SIDE COVER REMOVAL & REPLACEMENT
Unplug the unit from the power source before attempting removal or replacement procedures to prevent electrical shock.
A. Part Numbers
Side Cover (2 Req'd) . . . . . . . . . . . . . . . . . . . 47857
• 3/32 in Allen Wrench
• Flat Blade Screwdriver
• #1 Phillips Screwdriver
C. Removal of Side Covers
1. Remove Patient Interrupt Switch Hook
Screw Cover with a Flat Blade Screwdriver.
See inset at Figure 6.1.
2. Remove Patient Interrupt Switch Hook
Screw using a #1 Phillips Screwdriver. See
3. Lay unit on its side on a clean, soft work surface.
4. Using the 3/32 in Allen Wrench, remove the
three Side Cover Mounting Screws from the
bottom of the unit. See Figure 6.2.
5. Slide side cover from under Top Cover.
6. Turn unit over onto opposite side and
repeat steps 2-5.
D. Replacement of Side Covers
1. Position Side Cover Top Mounting Tab
between plastic of Top Cover and Touch
Screen Mounting Plate. See Figure 6.3.
2. Slide cover into position and secure with
three socket head screws using the 3/32 in
Allen Wrench. Refer to Figure 6.2.
NOTE:
Do not overtighten mounting screws.
Triton® Traction Unit
FIGURE 6.1
SIDE COVER
MOUNTING SCREWS
FIGURE 6.2
30
FIGURE 6.3
6 REMOVAL & REPLACEMENT
6.2 TOP AND CORD GUIDE COVER REMOVAL & REPLACEMENT
Unplug the unit from the power source before attempting removal or replacement procedures to prevent electrical shock.
A. Part Numbers
•
Top Cover . . . . . . . . . . . . . . . . . . . . . . . . . . . . 47856
•
Cord Guide Cover . . . . . . . . . . . . . . . . . . . . 47872
•
3/32 in Allen Wrench
•
#2 Phillips Screwdriver
•
Touch Screen to Cover Assembly Jig
C. Removal of Top and Cord Guide Covers
1. Remove Side Covers. Refer to 6.1 Side Cover
Removal & Replacement.
2. Position unit upright on base and untie
Traction Cord from Knuckle. Refer to
page 41, step 11 Traction Cord Removal &
Replacement.
3. Disconnect the Touch Screen Ribbon
Cable from the Motor Control Board. See
4. Using the #1 Phillips Screwdriver, remove
the two Top Cover Mounting Screws from
each side of the unit. See Figure 6.5.
NOTE:
To remove the Touch Screen Assembly from the
Top Cover refer to 6.6 Touch Screen Removal &
Replacement.
5. Carefully lift the Top Cover away from unit
and position into Touch Screen to Cover
Assembly Jig. See Figure 6.6.
6. Using the #2 Phillips Screwdriver, remove
the four Cord Guide Cover Mounting
Screws. See Figure 6.6.
D. Replacing Top and Cord Guide Covers
1. With Top Cover positioned onto the Touch
Screen to Cover Assembly Jig, place the
Cord Guide Cover into position. Secure with
the four Cord Guide Cover Mounting
Screws. See Figure 6.6.
2. Position the Top Cover Assembly onto the
unit chassis. Secure into position on the
standoffs with the four Top Cover Mounting
Screws (two on each side). See Figure 6.5.
3. Connect the Touch Screen Ribbon Cable to
the "Display" Connector on the Motor
Control Board. See Figure 6.4.
4. Install Side Covers. Refer to 6.1 Side Cover
Removal & Replacement.
31
WHEN INSTALLING, RIBBON CABLE BLACK STRIP MUST BE
TOWARD THE TOP OF THE MOTOR CONTROL BOARD.
FIGURE 6.4
TOP COVER MOUNTING SCREWS
TWO ON EACH SIDE
FIGURE 6.5
FIGURE 6.6
Triton® Traction Unit
CORD GUIDE COVER
MOUNTING SCREWS
6 REMOVAL & REPLACEMENT
6.3 REAR COVER REMOVAL & REPLACEMENT
Triton® Traction Unit
Unplug the unit from the power source before attempting removal or replacement procedures to prevent electrical shock.
A. Part Numbers
Rear Cover Assembly . . . . . . . . . . . . . . . . . .48110
•
3/32 in Allen Wrench
•
Touch Screen to Cover Assembly Jig
C. Removal of Top and Cord Guide Covers
1. Remove IEC Connector Cover. See
2. Remove Side Covers. Refer to 6.1 Side Cover
Removal & Replacement.
3. Remove Top Cover Assembly. Refer to 6.2,
part C, steps 1-5.
4. Using the 3/32 in Allen Wrench, remove
the four Rear Cover Mounting Screws. See
NOTE:
To replace the Rear Cover with a new part, remove the
Power Switch, Mains Connector, and USB Board from the old Rear Cover for re-installation onto the new part. See Figure 6.9.
It is not necessary to remove Harnesses from Power
Switch, Mains Connector, or USB Board unless these components are to be replaced.
D. Replacing Rear Cover
1. Replace existing Rear Cover
a. Secure Rear Cover to chassis with four
Rear Cover Mounting Screws. See
b. Install Top Cover Assembly. Refer to 6.2,
part D, steps 2 and 3.
c. Install Side Covers. Refer to 6.1, part D,
steps 1 and 2.
2. Replace with new Rear Cover
a. Install existing Power Switch, Mains
Connector, and USB Board to new Rear
Cover.
b. Secure Rear Cover to chassis. See
c. Install Top Cover Assembly. Refer to 6.2,
part D, steps 2 and 3.
d. Install Side Covers. Refer to 6.1, part D,
steps 1 and 2.
NOTE:
Do not overtighten mounting screws.
32
REAR COVER
MOUNTING SCREWS
FIGURE 6.7
FIGURE 6.8
USB BOARD
FIGURE 6.9
IEC CONNECTOR COVER
POWER SWITCH
MAINS CONNECTOR
6 REMOVAL & REPLACEMENT
6.4 FRONT COVER REMOVAL & REPLACEMENT
Unplug the unit from the power source before attempting removal or replacement procedures to prevent electrical shock.
A. Part Numbers
Front Cover . . . . . . . . . . . . . . . . . . . . . . . . . . . .47858
•
3/32 in Allen Wrench
•
Touch Screen to Cover Assembly Jig
•
Needle Nose Pliers
C. Removal of Front Cover
1. Remove Side Covers. Refer to 6.1 Side Cover
Removal & Replacement.
2. Remove Top Cover Assembly. Refer to 6.2,
part C, steps 2-5.
3. Disconnect the Patient Interrupt Switch
Jack from the Motor Control Board. See
4. Using the 3/32 in Allen Wrench, remove
the four Front Cover Mounting Screws. See
NOTE:
To replace the Front Cover with a new part, remove the Patient Interrupt Switch Jack from the old Front
Cover for re-installation onto the new part. See
Figure 6.12.
D. Replacing Front Cover
1. Replacing existing Front Cover
a. Connect Patient Interrupt Switch Jack to
the Motor Control Board. See Figure 6.10.
b. Secure the Front Cover to the chassis
with the four Front Cover Mounting
Screws. See Figure 6.11.
c. Install Top Cover Assembly. Refer to 6.2,
part D, steps 2 and 3.
d. Install Side Covers. Refer to 6.1, part D,
steps 1 and 2.
2. Replacing with new Front Cover
a. Install Patient Interrupt Switch Jack into
new Front Cover. See Figure 6.12.
b. Perform steps 3-4 above in reverse order.
c. Install Top Cover Assembly. Refer to 6.2,
part D, steps 2 and 3.
d. Install Side Covers. Refer to 6.1, part D,
steps 1 and 2.
NOTE:
Do not overtighten mounting screws.
33
Triton® Traction Unit
PATIENT INTERRUPT
SWITCH HARNESS
FIGURE 6.10
FRONT COVER
MOUNTING SCREWS
FIGURE 6.11
PATIENT INTERRUPT
SWITCH JACK
FIGURE 6.12
6 REMOVAL & REPLACEMENT
Triton® Traction Unit
The remaining removal and replacement procedures in this section require that the following be performed after component or assembly replacement to ensure proper alignment and operation of the unit:
1. COMPLETE CALIBRATION OF UNIT
AND
2. MINIMUM OF 2 HOUR BURN IN OF UNIT AFTER SUCCESSFUL CALIBRATION
Failure to perform either of these procedures after a component or assembly replacement will void warranty and may result in injury to patients and severe equipment damage.
34
6 REMOVAL & REPLACEMENT
6.5 MOTOR CONTROL BOARD REMOVAL & REPLACEMENT
Unplug the unit from the power source before attempting removal or replacement procedures to prevent electrical shock.
A. Part Numbers
Motor Control Board . . . . . . . . . . . . . . . . . .47803
•
3/32 in Allen Wrench
•
#2 Phillips Screwdriver
C. Removal of Motor Control Board
1. Remove Side Covers. Refer to 6.1 Side Cover
Removal & Replacement.
2. Disconnect all seven harnesses from the
Motor Control Board. See Figure 6.13.
3. Using the #2 Phillips Screwdriver, remove
the four Motor Control Board Mounting
Screws. See Figure 6.14.
D. Replacing Motor Control Board
1. Position Motor Control Board over chassis
standoffs and secure into position with the
screws removed in step 3 above.
2. Install Harnesses to the Motor Control
Board. See Figure 6.13.
3. Perform complete Calibration and Burn In
NOTE:
Do not overtighten mounting screws.
This component removal and replacement procedure requires that the following be performed after component or assembly replacement to ensure proper alignment and operation of the unit:
COMPLETE CALIBRATION OF UNIT Refer to
Section 7
AND
MINIMUM OF 2 HOUR BURN IN OF UNIT AFTER
SUCCESSFUL CALIBRATION Refer to Section 7
Failure to perform either of these procedures, after a component or assembly replacement will void warranty and may result in injury to patients and/or severe equipment damage.
LOAD CELL HARNESS
USB HARNESS
TOUCH SCREEN
HARNESS
SOLENOID HARNESS
MOTOR HARNESS
PATIENT INTERRUPT
SWITCH HARNESS
POWER SUPPLY
HARNESS
FIGURE 6.13
MOTOR CONTROL
BOARD MOUNTING
SCREWS
FIGURE 6.14
35
Triton® Traction Unit
6 REMOVAL & REPLACEMENT
6.6 TOUCH SCREEEN ASSEMBLY REMOVAL & REPLACEMENT
Unplug the unit from the power source before attempting removal or replacement procedures to prevent electrical shock.
A. Part Numbers
Touch Screen Assembly . . . . . . . . . . . . . . .48063
•
3/32 in Allen Wrench
•
Flat Blade Screwdriver
•
Touch Screen to Cover Assembly Jig
C. Removal of Touch Screen Assembly
1. Remove Side Covers. Refer to 6.1 Side Cover
Removal & Replacement.
2. Remove the Top Cover. Refer to 6.2 Top and
Cord Guide Cover Removal & Replacement,
part C, steps 2-5.
3. Using the Flat Blade Screwdriver, remove
the four Top Moulding Plate Mounting
Screws. When removing the Top Moulding
Plate, guide the Touch Screen Ribbon Cable
through the opening. See Figure 6.15.
4. Using the Flat Blade Screwdriver, remove
the four Turn Table Plate Retaining Screws.
5. Squeeze the two Touch Screen Assembly
Tabs and push the Touch Screen Assembly
out of the Top Cover. See Figure 6.17.
TOP MOULDING PLATE
MOUNTING SCREWS
FIGURE 6.15
TURN TABLE PLATE
MOUNTING SCREWS
Triton® Traction Unit
FIGURE 6.16
36
FIGURE 6.17
6 REMOVAL & REPLACEMENT
6.6 TOUCH SCREEN ASSEMBLY REMOVAL & REPLACEMENT (continued)
Unplug the unit from the power source before attempting removal or replacement procedures to prevent electrical shock.
D. Replacing Touch Screen Assembly
1. Place new Touch Screen Assembly into
Touch Screen to Cover Assembly Jig.
2. Position Top Cover over the Touch Screen
Assembly aligning the mounting hole to the
Touch Screen Assembly.
3. Slide the Top Cover over the Touch Screen
Assembly until the Mounting Tabs click into
position. See Figure 6.18.
4. Position the Turntable Plate and secure the
four screws with the #2 Phillips Screwdriver.
5. Position the Top Moulding Plate. Thread the
Touch Screen Ribbon Cable through the
opening in the Top Moulding Plate as
shown in Figure 6.20. Secure the four Top
Moulding Plate screws with the #2 Phillips
Screwdriver. Refer to Figure 6.15.
6. Install Top Cover Assembly. Refer to 6.2,
part D, steps 2 and 3.
7. Install Side Covers. Refer to 6.1, part D,
steps 1 and 2.
8. Perform complete Calibration and Burn In
NOTE:
Do not overtighten mounting screws.
This removal and replacement procedure requires that the following be performed after component or assembly replacement to ensure proper alignment and operation of the unit:
1. COMPLETE CALIBRATION OF UNIT
Refer to Section 7
AND
2. MINIMUM OF 2 HOUR BURN IN OF UNIT
AFTER SUCCESSFUL CALIBRATION
Refer to Section 7
Failure to perform either of these procedures after a component or assembly replacement will void warranty and may result in injury to patients and severe equipment damage.
37
FIGURE 6.18
TURN TABLE PLATE
MOUNTING SCREWS
FIGURE 6.19
FIGURE 6.20
Triton® Traction Unit
6 REMOVAL & REPLACEMENT
6.7 LOAD CELL ASSEMBLY REMOVAL & REPLACEMENT
LOAD CELL HARNESS
Unplug the unit from the power source before attempting removal or replacement procedures to prevent electrical shock.
A. Part Numbers
Load Cell Assembly . . . . . . . . . . . . . . . . . . . .48009
•
3/32 in Allen Wrench
•
4 mm Hex Key Socket and Ratchet
•
Calibrated Torque Wrench- 200 inch pound or 2,500 Newton meter minimum capacity.
C. Removal of Load Cell Assembly
1. Remove Side Covers. Refer to 6.1 Side Cover
Removal & Replacement.
2. Remove the Top Cover. Refer to 6.2 Top and
Cord Guide Cover Removal & Replacement,
part C, steps 2-5.
3. Remove Rear Cover. Refer to 6.3 Rear Cover
Removal & Replacement.
4. Remove the Clamp Spring Assembly.
Refer to 6.8 Clamp Spring Assembly
Removal & Replacement.
5. Disconnect the Load Cell Harness from the
Motor Control Board. See Figure 6.21.
6. Using the 4 mm Hex Key Socket and
Ratchet, remove the two Load Cell
Mounting Screws and Flat Washers from
each side of the Chassis. See Figure 6.22.
7. Lift Load Cell Assembly out of Chassis. See
LOAD CELL HARNESS
MOUNTING SCREWS
2 EACH SIDE
FIGURE 6.21
FIGURE 6.22
LOAD CELL
ASSEMBLY
Triton® Traction Unit
38
FIGURE 6.23
6 REMOVAL & REPLACEMENT
6.7 LOAD CELL ASSEMBLY REMOVAL & REPLACEMENT (continued)
Unplug the unit from the power source before attempting removal or replacement procedures to prevent electrical shock.
D. Replacement of Load Cell Assembly
1. Place Load Cell Assembly into Chassis and
hold in position while hand starting the
Load Cell Mounting Screws and Flat
Washers. See Figure 6.24.
2. Hand tighten the Load Cell Mounting
Screws.
3. Install the Clamp Spring Assembly.
Refer to 6.8 Clamp Spring Assembly
4. Use the Torque Wrench and 4 mm Hex
Key Socket to torque the Load Cell
Mounting Screws to 35 Nm (84 in lbs).
5. Route Load Cell Harness through Harness
Clips on the Chassis and connect to Motor
Control Board. See Figure 6.25.
6. Route Traction Cord through the Load Cell
Assembly Pulley and through the Chassis
Upper Guide Pulley. See Figure 6.26.
7. Install Rear Cover. Refer to 6.3 Rear Cover
8. Install Top Cover. Refer to 6.2 Top and Cord
Guide Cover Removal & Replacement.
9. Install Side Covers. Refer to 6.1 Side Cover
10. Perform complete Calibration and Burn In unit.
FIGURE 6.24
FIGURE 6.25
Triton® Traction Unit
This removal and replacement procedure requires that the following be performed after component or assembly replacement to ensure proper alignment and operation of the unit:
1. COMPLETE CALIBRATION OF UNIT
Refer to Section 7
AND
2. MINIMUM OF 2 HOUR BURN IN OF UNIT
AFTER SUCCESSFUL CALIBRATION
Refer to Section 7
Failure to perform either of these procedures after a component or assembly replacement will void warranty and may result in injury to patients and severe equipment damage.
39
FIGURE 6.26
6 REMOVAL & REPLACEMENT
6.8 CLAMP SPRING ASSEMBLY REMOVAL & REPLACEMENT
Triton® Traction Unit
Unplug the unit from the power source before attempting removal or replacement procedures to prevent electrical shock.
A. Part Numbers
Clamp Spring Assembly . . . . . . . . . . . . . . .48023
3/32 in Allen Wrench
C. Clamp Spring Assembly Removal
1. Remove Side Covers. Refer to 6.1 Side Cover
Removal & Replacement.
2. Remove the Top Cover. Refer to 6.2 Top and
Cord Guide Cover Removal & Replacement,
part C, steps 2-5.
3. Remove Rear Cover. Refer to 6.3 Rear Cover
Removal & Replacement.
4. Remove the four Clamp Spring Assembly
Mounting Screws. See Figure 6.27.
5. Turn the Clamp Knob Counterclockwise
until it is completely disengaged from the
Clamp Plate. See Figure 6.28.
D. Clamp Spring Assembly Replacement
1. Position the Clamp Spring Assembly at the
Chassis and rotate Clamp Knob until the
threaded portion is fully engaged in the
Clamp Plate and the Clamp Spring
Assembly Mounting Bracket is aligned with
the respective mounting holes in the
Chassis. Secure with the four Clamp Spring
Assembly Mounting Screws.
2. Install Rear Cover. Refer to 6.3 Rear Cover
Removal & Replacement.
3. Install Top Cover. Refer to 6.2 Top and
Cord Guide Cover Removal & Replacement.
4. Install Side Covers. Refer to 6.1 Side Cover
Removal & Replacement.
5. Perform complete Calibration and Burn In
FIGURE 6.27
FIGURE 6.28
CLAMP SPRING
ASSEMBLY
SCREWS
2 EACH SIDE
CLAMP KNOB
CLAMP SPRING
ASSEMBLY
MOUNTING SCREWS
2 EACH SIDE
CLAMP PLATE
This removal and replacement procedure requires that the following be performed after component or assembly replacement to ensure proper alignment and operation of the unit:
1. COMPLETE CALIBRATION OF UNIT
Refer to Section 7
AND
2. MINIMUM OF 2 HOUR BURN IN OF UNIT
AFTER SUCCESSFUL CALIBRATION
Refer to Section 7
Failure to perform either of these procedures after a component or assembly replacement will void warranty and may result in injury to patients and severe equipment damage.
40
6 REMOVAL & REPLACEMENT
6.9 TRACTION CORD REMOVAL & REPLACEMENT
Unplug the unit from the power source before attempting removal or replacement procedures to prevent electrical shock.
A. Part Numbers
Traction Cord . . . . . . . . . . . . . . . . . . . . . . . . . .48031
•
•
3/32 in Allen Wrench
5/32 in Allen Wrench
•
Needle Nose Pliers
•
Tape Measure
C. Clamp Spring Assembly Removal
1. Remove Side Covers. Refer to 6.1 Side Cover
Removal & Replacement.
2. Remove the Top Cover. Refer to 6.2 Top and
Cord Guide Cover Removal & Replacement,
part C, steps 2-5.
3. Remove Rear Cover. Refer to 6.3 Rear Cover
Removal & Replacement.
4. Remove the Clamp Spring Assembly. Refer
to 6.8 Clamp Spring Removal and
Replacement.
5. While holding the Cord Tension Spring
Housing in position with one hand, loosen
the retaining screw with the other hand.
6. Gradually release the spring tension by
allowing the Spring Housing to slowly
rotate in the hand. Leave the Housing
Retaining Screw loose.
7. Manually release the Solenoid from the
Large Driven Gear and simultaneously
pull the Traction Cord through the unit
front until the Traction Cord stops. See
NOTE:
Make certain the Traction Cord Knot is facing the rear of the unit.
8. Release the Solenoid, making certain it fully
engages the teeth of the Large Driven Gear.
NOTE:
It may be necessary to slightly jog the Large Driven
Gear to facilitate tooth engagement.
9. Remove the Traction Cord Knuckle. Refer to
page 41, step 11. Using the Needle Nose
Pliers, pull the Traction Cord Knot from the
Traction Cord Spool and completely pull the
Traction Cord out of unit. See Figure 6.31.
41
FIGURE 6.29
FIGURE 6.30
FIGURE 6.31
Triton® Traction Unit
6 REMOVAL & REPLACEMENT
Triton® Traction Unit
6.9 TRACTION CORD REMOVAL & REPLACEMENT (continued)
D. Traction Cord Replacement
1. Route Traction Cord through the Traction
Cord Spool, Load Cell Pulley, and Top Guide
• Unplug the unit from the power source before attempting removal or replacement procedures to
• prevent electrical shock.
It is not recommend tying a new knot in a cord that has frayed or failed in use or is worn in an area from constant use. The cord must be replaced.
NOTE:
The left side of the Chassis incorporates a Window to facilitate proper routing of the Traction Cord.
TOP GUIDE PULLEY
LOAD CELL PULLEY
TRACTION CORD SPOOL
TRACTION CORD
ROUTING WINDOW
FIGURE 6.32
42
6 REMOVAL & REPLACEMENT
6.9 TRACTION CORD REMOVAL & REPLACEMENT (continued)
Unplug the unit from the power source before attempting removal or replacement procedures to prevent electrical shock.
2. Pull enough of the Traction Cord through
the Traction Cord Spool to allow the knot
to be tied.
3. Tie a Figure Eight (Flemish, Savoy) Knot
in the end of the Cord passing through the
Traction Cord Spool. See Figure 6.33.
1
Do not use any other knot styles in the Cord other than those specified in this manual. Use of other knot styles could cause Cord to completely disengage from the system causing serious injury to patient and personnel.
4. Trim any fraying from the Traction Cord
leaving 19 mm (0.75 in) of Cord outside the
Figure Eight (Flemish, Savoy) Knot.
5. Singe the Cord end until the outer jacket
and inner core of the Traction Cord melt
together. See Figure 6.34A.
6. Pull other end of Traction Cord until the
Figure Eight (Flemish, Savoy) Knot is
completely seated within the Traction Cord
Spool. See Figure 6.34B.
NOTE:
It may be necessary to use a long, thin tool such as a
Flat Blade Screwdriver to properly tuck the Figure Eight
(Flemish, Savoy) Knot into the Traction Cord Spool.
3
FIGURE 6.33
4
Triton® Traction Unit
2
43
FIGURE 6.34A
FIGURE 6.34B
6 REMOVAL & REPLACEMENT
6.9 TRACTION CORD REMOVAL & REPLACEMENT (continued)
Unplug the unit from the power source before attempting removal or replacement procedures to prevent electrical shock.
7. Route Traction Cord through the Front
Cord Guide Support.
8. Route Traction Cord through the Top
Cover and place the Top Cover in Position
on the Chassis. See Figure 6.35. Do not
secure Top Cover at this time.
9. Inspect Traction Cord Knuckle for damage
and wear. Replace if damaged or worn.
10. Route Traction Cord through Traction
Cord Knuckle Cover and Cord Knuckle. Tie
an Overhand or Half Knot in the end of
the Traction Cord leaving 25.5 mm
(1.00 in) of Traction Cord outside the
knot. See Figure 6.36.
11. Trim any fraying from the end of the
Traction Cord and singe the Cord end
until the outer jacket and inner core of
the Traction Cord melt together. Make
certain at least 19 mm (0.750 in) of
Traction Cord still remains outside the
knot. See Figure 6.36 inset.
FIGURE 6.35
Triton® Traction Unit
Do not use any other knot styles in the Cord other than those specified in this manual. Use of other knot styles could cause Cord to completely disengage from the system and may cause serious injury to patient and personnel.
12. Secure the knot inside the Traction Cord
Knuckle ensuring the loose end enters
the Bore inside the Traction Cord
Knuckle. See Figure 6.37. Slide Traction
Cord Knuckle Cover into position over the
knot. See Figure 6.37 inset.
NOTE:
It may be necessary to use a long, thin tool such as a
Flat Blade Screwdriver to properly tuck the loose end of the Traction Cord into the Bore of the Traction Cord
Knuckle.
FIGURE 6.36
FIGURE 6.37
44
6 REMOVAL & REPLACEMENT
6.9 TRACTION CORD REMOVAL & REPLACEMENT (continued)
Unplug the unit from the power source before attempting removal or replacement procedures to prevent electrical shock.
NOTE:
If adjusting Spring Tension only and not replacing the
Traction Cord, it will be necessary to remove the Side
Covers and have available the Tools required in 6.9, B.
13. Manually release the Solenoid and
simultaneously fully extend the Traction
Cord. Release Solenoid and make certain
the Solenoid Gear fully engages the
Large Driven Gear. See Figure 6.38.
14. With the Cord fully extended, rotate the
Cord Spring Housing clockwise until
the Cord Spring is completely wound,
then rotate counterclockwise 1/4 to 1/2
turn. Hold the Cord Spring Housing in
position and tighten the Retaining Screw
using the 5/32 in Allen Wrench. See
NOTE:
Overtightening of the Cord Spring Housing Retaining
Screw will break the housing and cause the spring to lose tension.
15. While holding on to the Traction Cord,
manually release the Solenoid and allow
the Traction Cord to retract.
16. Manually release the Solenoid and
simultaneously fully extend the Traction
Cord. Release Solenoid and make certain
it fully engages the Large Driven Gear.
17. Using Tape Measure, measure the length
of the Cord from the Cord Guide Cover to
the end of the Harness Clip. See
Figure 6.40. Measurement should be
96.5 cm to 106.5 cm (38 in to 42 in).
a) If measurement is less than 96.5 cm
(38 in), Spring Tension is too tight.
Loosen the Spring Housing Retaining
Screw and allow the housing to release
no more than 1/2 revolution of tension.
Tighten Spring Housing Retaining
Screw and repeat steps 15 and 16.
b) If measurement is more than 106.5 cm
(42 in), increase Traction Cord Spring
Tension by no more than 1/2
revolution.
18. Repeat step 17 a or b until Cord
dimension is correct.
45
FIGURE 6.38
FIGURE 6.39
FIGURE 6.40
Triton® Traction Unit
6 REMOVAL & REPLACEMENT
6.9 TRACTION CORD REMOVAL & REPLACEMENT (continued)
Unplug the unit from the power source before attempting removal or replacement procedures to prevent electrical shock.
19. Install Clamp Spring Assembly. Refer to
6.8 Clamp Spring Assembly Removal &
Replacement.
20. Install Rear Cover. Refer to 6.3 Rear Cover
Removal & Replacement.
21. Install Top Cover. Refer to 6.2 Top and
Cord Guide Cover Removal &
Replacement.
22. Install Side Covers. Refer to 6.1 Side Cover
Removal & Replacement.
23. Perform complete Calibration and Burn In unit.
This removal and replacement procedure requires that the following be performed after component or assembly replacement to ensure proper alignment and operation of the unit:
1. COMPLETE CALIBRATION OF UNIT
Refer to Section 7
AND
2. MINIMUM OF 2 HOUR BURN IN OF UNIT
AFTER SUCCESSFUL CALIBRATION
Refer to Section 7
Failure to perform either of these procedures after a component or assembly replacement will void warranty and may result in injury to patients and severe equipment damage.
Triton® Traction Unit
46
6 REMOVAL & REPLACEMENT
6.10 CORD TENSION SPRING REMOVAL & REPLACEMENT
Unplug the unit from the power source before attempting removal or replacement procedures to prevent electrical shock.
A. Part Numbers
Cord Tension Spring . . . . . . . . . . . . . . . . . . .80653
•
3/32 in Allen Wrench
•
5/32 in Allen Wrench
C. Cord Tension Spring Removal
1. Remove Side Covers. Refer to 6.1 Side Cover
Removal & Replacement.
2. Remove the Top Cover. Refer to 6.2 Top and
Cord Guide Cover Removal & Replacement,
part C, steps 2-5.
3. While holding the Cord Tension Spring
Housing with one hand. Loosen the
retaining screw with the other hand using
the 5/32 in Allen Wrench. See Figure 6.41.
4. Gradually allow the Spring Housing to
rotate in the hand releasing spring tension.
5. Rotate the Cord Tension Spring Housing
until the hole in the face aligns with the
Spring Mounting Screw. Remove screw with
the 3/32 in Allen Wrench. See Figure 6.42.
6. Remove the Cord Tension Spring Housing
Mounting Screw. See Figure 6.43.
7. Remove Cord Tension Spring and Housing
SPRING
MOUNTING
SCREW
FIGURE 6.41
FIGURE 6.42
Triton® Traction Unit
47
FIGURE 6.43
6 REMOVAL & REPLACEMENT
6.10 CORD TENSION SPRING REMOVAL & REPLACEMENT (continued)
Unplug the unit from the power source before attempting removal or replacement procedures to prevent electrical shock.
D. Cord Tension Spring Replacement
1. Position new Cord Tension Spring in
Housing as shown in Figure 6.44.
2. Place Spring Mounting Screw through hole
in face of the Housing and through the
Cord Tension Spring Mounting Loop. Leave
the head of the Spring Mounting Screw
protruding through the Housing. See
3. Position the Spring and Housing assembly
in the mounting position on the Chassis.
Start the Spring Mounting Screw using the
3/32 in Allen Wrench. Tighten Mounting
Screw until Cord Tension Spring Mounting
Loop is secure then, back the screw out one
complete revolution. See Figure 6.46.
4. Position the Spring and Housing so that the
Housing Mounting Screw can be started.
Start screw with the 5/32 in Allen Wrench.
5. Adjust Spring Tension. Refer to page 42.
6. Install Top Cover. Refer to 6.2 Top and
Cord Guide Cover Removal &
Replacement.
7. Install Side Covers. Refer to 6.1 Side Cover
Removal & Replacement.
8. Perform complete Calibration and Burn In
FIGURE 6.44
FIGURE 6.45
Triton® Traction Unit
This removal and replacement procedure requires that the following be performed after component or assembly replacement to ensure proper alignment and operation of the unit:
1. COMPLETE CALIBRATION OF UNIT
Refer to Section 7
AND
2. MINIMUM OF 2 HOUR BURN IN OF UNIT
AFTER SUCCESSFUL CALIBRATION
Refer to Section 7
Failure to perform either of these procedures after a component or assembly replacement will void warranty and may result in injury to patients and severe equipment damage.
48
FIGURE 6.46
6 REMOVAL & REPLACEMENT
6.11 SOLENOID ASSEMBLY REMOVAL & REPLACEMENT
Unplug the unit from the power source before attempting removal or replacement procedures to prevent electrical shock.
A. Part Numbers
Solenoid Assembly . . . . . . . . . . . . . . . . . . . . 48014
B. Equipment Required
•
9/64 in Allen Wrench
•
Solenoid Assembly Mounting Jig(P/N 48139)
C. Solenoid Assembly Removal
1. Remove Side Covers. Refer to 6.1 Side Cover
Removal & Replacement.
2. Make certain the Cord is fully retracted. If
necessary, manually retract. Refer to
3. Disconnect the Solenoid Assembly Harness
from Motor Control Board. See Figure 6.47.
4. Using the 9/64 in Allen Wrench, remove the
two Solenoid Assembly Mounting Screws.
D. Solenoid Assembly Replacement
1. Position the Solenoid Assembly Mounting
Jig onto the Shafts of the Large Driven Gear
and the Motor Gear. See Figure 6.49.
2. Position the Solenoid Assembly so gears are
fully seated and the front and bottom of the
Bracket are against the Solenoid Assembly
Mounting Jig. Secure with screws. See
3. Connect Solenoid Assembly Harness to
Motor Control Board. See Figure 6.47.
4. Install Side Covers. Refer to 6.1 Side Cover
Removal & Replacement.
5. Perform complete Calibration and Burn In
This removal and replacement procedure requires that the following be performed after component or assembly replacement to ensure proper alignment and operation of the unit:
1. COMPLETE CALIBRATION OF UNIT
Refer to Section 7
AND
2. MINIMUM OF 2 HOUR BURN IN OF UNIT AFTER
SUCCESSFUL CALIBRATION
Refer to Section 7
Failure to perform either of these procedures after a component or assembly replacement will void warranty and may result in injury to patients and severe equipment damage.
49
SOLENOID
MOUNTING
SCREWS
FIGURE 6.47
SOLENOID
MOUNTING
SCREWS
FIGURE 6.48
SOLENOID ASSEMBLY
MOUNTING JIG P/N 48139
FIGURE 6.49
Triton® Traction Unit
6 REMOVAL & REPLACEMENT
6.12 POWER SUPPLY REMOVAL & REPLACEMENT
Triton® Traction Unit
Unplug the unit from the power source before attempting removal or replacement procedures to prevent electrical shock.
A. Part Numbers
Power Supply . . . . . . . . . . . . . . . . . . . . . . . . . .27265
Power Supply Shield . . . . . . . . . . . . . . . . . .27592
•
3/32 in Allen Wrench
•
#2 Phillips Screwdriver
•
Digital Multimeter (Set to VDC)
C. Power Supply Removal
1. Remove Side Covers. Refer to 6.1 Side Cover
Removal & Replacement.
2. Remove the Top Cover. Refer to 6.2 Top and
Cord Guide Cover Removal & Replacement.
3. Remove Rear Cover. Refer to 6.3 Rear Cover
Removal & Replacement.
4. Disconnect the Power Supply Input
Harnesses from the Mains Connector. See
5. Disconnect Power Supply Output
Harness from the Motor Control Board. See
6. Using the 3/32 in Allen Wrench, remove the
Ground Harnesses from the Chassis. See
7. Using the Multimeter set to VDC discharge
the Power Supply Capacitor at C4. See
POWER SUPPLY
INPUT HARNESSES
FIGURE 6.50A
FIGURE 6.50B
FIGURE 6.51
• Power Supplies retain High Voltage!
• Discharge the C4 Capacitor prior to complete removal of the Power Supply.
8. Using the #2 Phillips Screwdriver, remove
the four Power Supply Mounting Screws.
9. Grasp the sides of the Power Supply and
carefully remove from the chassis.
FIGURE 6.52
50
6 REMOVAL & REPLACEMENT
6.12 POWER SUPPLY REMOVAL & REPLACEMENT (continued)
POWER SUPPLY
MOUNTING SCREWS
Unplug the unit from the power source before attempting removal or replacement procedures to prevent electrical shock.
GROUND
HARNESSES
D. Power Supply Replacement
1. Prior to handling new Power Supply,
discharge the Capacitor at C4. Refer to
Triton® Traction Unit
SHIELD
BLACK SIDE TOWARD
POWER SUPPLY
• Power Supplies retain High Voltage!
• Discharge the C4 Capacitor prior to handling of the new Power Supply.
2. Make certain the Shield is in place with
the nonconductive (black) side toward
the Power Supply. Position the Power
Supply on the Chassis. Secure with the
four Power Supply Mounting Screws. See
3. Using the 3/32 in Allen Wrench and Ground
Harness Mounting Screw, secure the
Ground Harnesses from the Power Supply
and the Mains Connector to the Chassis.
4. Connect the Power Supply Input Harnesses
to the Mains Connector Harnesses. See
5. Connect the Power Supply Output
Harness to the Motor Control Board. See
6. Install Rear Cover. Refer to 6.3 Rear Cover
Removal & Replacement.
7. Install Top Cover. Refer to 6.2 Top and
Cord Guide Cover Removal &
Replacement.
8. Install Side Covers. Refer to 6.1 Side Cover
Removal & Replacement.
9. Perform complete Calibration and Burn In
POWER SUPPLY
MOUNTING SCREWS
FIGURE 6.53
POWER SUPPLY
INPUT HARNESSES
FIGURE 6.54A
FIGURE 6.54B
This removal and replacement procedure requires that the following be performed after component or assembly replacement to ensure proper alignment and operation of the unit:
1. COMPLETE CALIBRATION OF UNIT
Refer to Section 7
AND
2. MINIMUM OF 2 HOUR BURN IN OF UNIT
AFTER SUCCESSFUL CALIBRATION
Refer to Section 7
Failure to perform either of these procedures after a component or assembly replacement will void warranty and may result in injury to patients and severe equipment damage.
51
6 REMOVAL & REPLACEMENT
6.13 MOTOR ASSEMBLY REMOVAL & REPLACEMENT
Unplug the unit from the power source before attempting removal or replacement procedures to prevent electrical shock.
A. Part Numbers
Motor Assembly . . . . . . . . . . . . . . . . . . . . . . .48019
•
3/32 in Allen Wrench
•
3 mm Allen Wrench
•
7 mm Box End Wrench
•
Solenoid Assembly Mounting Jig
C. Motor Assembly Removal
1. Remove Side Covers. Refer to 6.1 Side Cover
Removal & Replacement.
2. Make certain Traction Cord is completely
retracted. If necessary, manually release
Solenoid to retract Cord.
3. Loosen the Solenoid Mounting Screws
enough to rotate Solenoid Gear up and off
of the Motor Gear. See Figure 6.55.
4. Disconnect the Motor Harness from the
Motor Control Board. See Figure 6.56.
5. Using the 3 mm Allen Wrench and 7 mm
Boxed End Wrench, remove the four Motor
Assembly Mounting Screws. See Figure 6.57.
6. Remove Motor Assembly from Chassis.
NOTE:
It may be necessary to remove the Motor Control
Board. Refer to 6.5 Motor Control Board Removal &
Replacement.
FIGURE 6.55
FIGURE 6.56
Triton® Traction Unit
52
FIGURE 6.57
6 REMOVAL & REPLACEMENT
6.13 MOTOR ASSEMBLY REMOVAL & REPLACEMENT (continued)
Unplug the unit from the power source before attempting removal or replacement procedures to prevent electrical shock.
D. Motor Assembly Replacement
1. Position new Motor Assembly into Chassis
and secure with the four Motor Assembly
Screws, Lock washers, and Nuts. See
2. Position and adjust the Solenoid. Refer to
6.11 Solenoid Assembly Removal &
Replacement.
NOTE:
If Motor Control Board was removed, re-install before proceeding to step 3 below.
3. Connect the Motor Assembly Harness to
the Motor Control Board. See Figure 6.59.
4. Install Side Covers. Refer to 6.1 Side Cover
Removal & Replacement.
5. Perform complete Calibration and Burn In
FIGURE 6.58
Triton® Traction Unit
This removal and replacement procedure requires that the following be performed after component or assembly replacement to ensure proper alignment and operation of the unit:
1. COMPLETE CALIBRATION OF UNIT
Refer to Section 7
AND
2. MINIMUM OF 2 HOUR BURN IN OF UNIT
AFTER SUCCESSFUL CALIBRATION
Refer to Section 7
Failure to perform either of these procedures after a component or assembly replacement will void warranty and may result in injury to patients and severe equipment damage.
FIGURE 6.59
53
6 REMOVAL & REPLACEMENT
6.14 MOTOR DRIVE GEAR REMOVAL & REPLACEMENT
SOLENOID REMOVED
FOR CLARITY
Unplug the unit from the power source before attempting removal or replacement procedures to prevent electrical shock.
A. Part Numbers
Motor Drive Gear . . . . . . . . . . . . . . . . . . . . . .48024
•
3/32 in Allen Wrench
•
Solenoid Assembly Mounting Jig
•
Tape Measure
C. Motor Drive Gear Removal
1. Remove Side Covers. Refer to 6.1 Side Cover
Removal & Replacement.
2. Make certain Traction Cord is completely
retracted. If necessary, manually release
Solenoid to retract Cord.
3. Rotate Motor until Drive Gear Set Screw is
accessible. See Figure 6.60.
4. Using the 3/32 in Allen Wrench, loosen the
Drive Gear Set Screw and pull the Drive
Gear from Motor Shaft.
D. Motor Drive Gear Replacement
1. Install new Motor Drive Gear onto Motor
Shaft. Align Set Screw with the Key Slot in
the Motor Shaft. See Figure 6.61.
2. Adjust the Gear position until the face of
the gear is 9.5 mm (3/8 in) from the face of
the shaft. See Figure 6.61.
3. Tighten the Set Screw with the 3/32 in Allen
Wrench.
4. Install Side Covers. Refer to 6.1 Side Cover
Removal & Replacement.
LOOSEN SET SCREW
TIGHTEN SET SCREW
9.5 MM
3/8"
FIGURE 6.60
FIGURE 6.61
Triton® Traction Unit
This removal and replacement procedure requires that the following be performed after component or assembly replacement to ensure proper alignment and operation of the unit:
1. COMPLETE CALIBRATION OF UNIT
Refer to Section 7
AND
2. MINIMUM OF 2 HOUR BURN IN OF UNIT
AFTER SUCCESSFUL CALIBRATION
Refer to Section 7
Failure to perform either of these procedures after a component or assembly replacement will void warranty and may result in injury to patients and severe equipment damage.
54
6 REMOVAL & REPLACEMENT
6.15 sEMG MODULE REMOVAL & REPLACEMENT
Unplug the unit from the power source before attempting removal or replacement procedures to prevent electrical shock.
A. Part Numbers
sEMG Module . . . . . . . . . . . . . . . . . . . . . . . . . .48019
B. Equipment Required
•
3/32 in Allen Wrench
•
3 mm Allen Wrench
•
7 mm Box End Wrench
•
Solenoid Assembly Mounting Jig
C. sEMG Module Removal
1. Lay the Triton Traction unit on its side. See
2. Depress the two sEMG mounting tabs in
and simultaneously pull the sEMG Module
free from the Triton Traction unit. See
D. sEMG Module Replacement
1. Position the sEMG Module so that the
sEMG Module Contacts align with the sEMG
Module Connector inside the Triton Traction unit.
2. Push the sEMG Module into the Triton unit
until the sEMG Module is completely seated
and the Mounting Tabs snap into position
locking the sEMG module in place. See
Triton® Traction Unit
FIGURE 6.62
PRESS TABS AND PULL
OUT sEMG MODULE
FIGURE 6.63
55
7 CALIBRATION
7.1 UNIT CALIBRATION
Triton® Traction Unit
Certain removal and replacement procedures require that complete Unit Calibration and Burn In be performed prior to placing the unit back into service.
Failure to perform either of these procedures after certain component or assembly replacement will void warranty and may result in injury to patients and severe equipment damage.
A. General Information
1. The Calibration and Burn-In Procedures in
this section must be performed annually
and when field service requires removal and
replacement of certain components.
2. The Calibration Procedure requires use of
US lb Weight Measurements. The software
is fixed and will not perform conversions of
Metric Weight Measurements for this critical
procedure. Therefore, when constructing
and equipping the Calibration Fixture, it is
required that the Electronic Load Cell
Components be capable of expressing
US lbs.
3. The fabrication of a Calibration Fixture is
required for these units.
FIGURE 7.1
Calibration Fixture with calibrated Strain Meter
C. Unit Calibration Procedure
1. Place unit on Calibration Fixture and secure
in position by tightening the unit Lock
Knob. See Figure 7.1.
2. Connect unit to an approved power source.
3. Turn unit On.
4. Release Traction Cord and connect
Accessory Clip to the Strain Meter. Leave
slack in Cord. See Figure 7.2.
5. Zero Strain Meter LCD.
SLACK IN
CORD
STRAIN METER
ACCESSORY CLIP TO
LOAD CELL
FIGURE 7.2
When performing Unit Calibration Procedure, the
Calibration Fixture Load Cell must be set to US lbs.
56
7 CALIBRATION
7.1 UNIT CALIBRATION (continued)
6. Press the Clinical Resources button. See
7. Simultaneously press the START, STOP, and
Clinical Resources buttons. See Figure 7.4.
FIGURE 7.3
Triton® Traction Unit
8. Press "Zero the Load Cell" on Touch Screen.
9. When the screen message appears, "Load
Cell has been zero calibrated!", touch the
Touch Screen anywhere to continue.
FIGURE 7.4
57
FIGURE 7.5
7 CALIBRATION
7.1 UNIT CALIBRATION (continued)
10. Hold onto Traction Cord and press Rope
Release to remove all slack from Traction
Cord.
11. Press Calibrate Load Cell Bias on the Touch
Screen. See Figure 7.6.
CALIBRATE LOAD CELL
BIAS
Triton® Traction Unit
12. While watching the Strain Meter LCD,
Figure 7.7A, press the Up and Down
Arrow buttons, Figure 7.7B until 100 lbs is displayed on LCD.
13. Press Back icon on Touch Screen to set and accept calibration measurement.
NOTE:
Unit will display a validation message reading
"Returning to zero" while releasing tension on the
Traction Cord.
14. Press Rope Release and pull enough Cord out to connect the Accessory Hook to the
Lower Ring on the Calibration Fixture. See
7.8.
15. Allow excess Traction Cord to feed back into unit and release Rope Release.
STRAIN METER LCD
FIGURE 7.7A
FIGURE 7.6
FIGURE 7.7B
58
ACCESSORY CLIP TO
LOWER RING
FIGURE 7.8
7 CALIBRATION
7.1 UNIT CALIBRATION (continued)
16. Press Calibrate Motor Current on the
Touch Screen. See Figure 7.9.
17. Unit will display "Motor Current
Calibration completed OK." When Motor
Current Calibration is complete. Touch
anywhere to continue.
7.2 TOUCH SCREEN CALIBRATION
NOTE:
If the unit is not in the Calibration Mode, refer to 7.1, C, steps 6-7 to place unit in Calibration Mode.
A. Equipment Required
None
B. Touch Screen Calibration Procedure
1. Press Touch Screen Calibration on Touch
Screen. See Figure 7.10.
2. Follow instructions on Touch Screen.
FIGURE 7.9
FIGURE 7.10
Triton® Traction Unit
CALIBRATE MOTOR
CURRENT
59
7 CALIBRATION
7.3 UNIT BURN IN
Triton® Traction Unit
Certain removal and replacement procedures require that complete Unit Calibration and Burn In be performed prior to placing the unit back into service.
Failure to perform either of these procedures after certain component or assembly replacement will void warranty and may result in injury to patients and severe equipment damage.
The following Burn In procedure must be allowed to cycle for a minimum of two hours after Calibration
Procedures have been performed, but prior to placing the unit back into service.
A. Specifications
Burn In Intermittent Pull . . . 0-200 US lbs ±10%
Burn In Time Period . . . . . . . . .2 hours minimum
B. Equipment Required
Calibration Fixture with calibrated Strain Meter.
C. Burn In Set Up
1. Place unit on Calibration Fixture and secure
in position by tightening the unit Lock
Knob. See Figure 7.11.
2. Connect unit to an approved power source.
3. Turn unit On.
4. Release Traction Cord and connect
Accessory Clip to the Load Cell. See
5. Zero Load Cell.
D. Burn In Procedure
1. Perform Burn In Set Up.
2. Press the Clinical Resources button.
3. Simultaneously press the STOP, Clinical
Resources, and PAUSE buttons to access the
4. Press Start Burn-In on the Touch Screen. See
5. After unit has cycled for a minimum of two
hours, press the STOP button. Unit will
return to the Home Screen.
6. Set up unit for a 100 lb Static pull. Start the
pull and verify the readout for the Load Cell
is 100 lbs ±10%.
E. Burn-In Result
1. If Load Cell Readout is outside the specified
range during the Static pull, perform Unit
Calibration Procedure and Burn In
procedure. Refer to pages 51-55.
2. If Load Cell Readout is within Specified
Range during Static pull, unit is ready to be
placed into service.
START BURN IN
FIGURE 7.11
FIGURE 7.12
60
8 PARTS
8.1 TOP COVER ASSEMBLY
1
8
3
7
3
6
Triton® Traction Unit
2
3
4
5
ITEM PART
NO.
1 47856
6
7
8
4
5
2
3
48007
27137
60803
48072
48062
47896
47873
Top Cover
Top Moulding Plate
Screw
Screw
Touch Screen Assembly
Turn Table Plate
Hook Cover
Cord Guide Cover
DESCRIPTION
61
QTY
1
1
2
1
4
1
1
10
8 PARTS
8.2 SIDE COVERS
6
1
See Page 61
Triton® Traction Unit
1
2
2
ITEM PART
NO.
1 47857
4
5
2
3
6
47884
47871
47870
27306
48115
Side Cover
Side Badge
Knob Cap
Lock Knob
IEC Connector Cover
Triton Badge
DESCRIPTION
62
5
3
4
QTY
2
1
1
2
1
1
8 PARTS
8.3 FRONT AND REAR COVERS
5
8
5
7-7A
6
1
2
1
3
3
3
Triton® Traction Unit
4
ITEM PART
NO.
1 47858
4
5
2
3
48038
48070
48110
47851
7A
8
6
7
48054
47878
48123
48040
DESCRIPTION
Front Cover
Left Spring
Stand Off
Rear Cover Assembly (includes wiring and hardware)
Screw
Right Spring
Front Infi ll (Not Illustrated) eEMG Module (Not Illustrated)
Patient Switch Receptacle
63
5
QTY
1
1
1
1
4
1
1
1
8
8 PARTS
8.4 BASE AND EXTRUSION ASSEMBLY
7
6
5
6
3
4
7
ITEM PART
NO.
1 47833
2 70208
21387
47832
60014
62951
48019
Extrusion
Hex Nut
Flat Washer
Base Plate
Anti Skid Feet
Screw
Motor Assembly
DESCRIPTION
64
1
2
Triton® Traction Unit
3
4
5
QTY
4
8
8
1
1
1
8
8 PARTS
8.5 CHASSIS ASSEMBLY
1
2
3
2
4
5
14
6
7
Triton® Traction Unit
8
13
ITEM PART
NO.
1 48009
10
11
12
13
14
15
8
9
6
7
4
5
2
3
48097
47850
47803
70777
78155
48008
21387
48102
70369
48078
47998
48031
47851
47889
Load Cell Assembly
Flat Washer
Shoulder Bolt
Top Guide Pulley
Top Guide Mounting Spacer
Top Guide Pulley Axle
Traction Cord
Screw
Spring Housing
Front Cover Mounting Bracket
Stand Off
Motor Control Board
Screw
Cable Guide
E-Clip
15
12
11
DESCRIPTION
8
65
10
9
QTY
1
4
2
1
1
1
2
4
4
1
4
1
4
2
2
8 PARTS
8.6 TRACTION CORD SPRING ASSEMBLY AND POWER SUPPLY
12
13
14
1
Triton® Traction Unit
2
3
4
5
6
11
ITEM PART
NO.
1 54758
2 48106
7
8
9
5
6
3
4
10
11
12
13
14
73146
48104
71934
80653
80634
21384
47846
47823
72559
31768
27592
27265
Snap Ring
Mounting Hub
Square Key
Screw
Bearing
Traction Cord Spring
Spring Cover
Flat Washer
Screw
Spring Mounting Screw
Stand Off
Screw
Power Supply Shield
Power Supply
10
DESCRIPTION
66
7
8
9
QTY
1
1
1
1
1
1
4
4
1
1
4
1
1
1
8 PARTS
8.7 SOLENOID AND CLAMP ASSEMBLIES
6
2
1
Triton® Traction Unit
2
5
4
3
ITEM PART
NO.
1 48023
2
5
6
3
4
47851
48014
21384
47851
48097
Clamp Assembly
Screw
Solenoid Assembly
Flat Washer
Screw
Front Traction Cord Guide
DESCRIPTION
67
QTY
1
8
2
1
1
2
8 PARTS
8.8 LARGE DRIVEN GEAR AND SPOOL ASSEMBLY
Triton® Traction Unit
1
2
3
8
7
6
9
7
8
9
5
6
3
4
ITEM PART
NO.
1 47997
2 48103
72017
47851
80158
47840
48104
71934
47839
Retaining Bar
Spool
Set Screw
Screw
Clamp Foot
Hub
Screw
Bearing
Large Driven Gear with Shaft Assembly
DESCRIPTION
68
5
4
3
QTY
4
1
1
1
1
2
2
1
1
9 SCHEMATICS
Triton® Traction Unit
9.1 TRITON TRACTION UNIT SCHEMATICS
A. General Information
1. Due to the complex nature of the technology utilized by Chattanooga Group, the recommended
PCB troubleshooting techniques are to determine “Bad Board” and board replacement only. No PCB
component level troubleshooting is recommended, nor will information or parts be supplied by
Chattanooga Group. Any PCB component level troubleshooting performed will be at sole risk and
liability of the Service Technician performing such troubleshooting techniques.
2. Once a particular PCB has been determined as bad, replace the PCB. Use only Chattanooga
Group replacement parts and hardware. Refer to Section 8 Parts for replacement parts and assemblies.
69
9 SCHEMATICS
70
Control Board- 47801
1 of 3
Triton® Traction Unit
9 SCHEMATICS
71
Control Board- 47801
2 of 3
Triton® Traction Unit
9 SCHEMATICS
72
Control Board-47801
3 of 3
Triton® Traction Unit
9 SCHEMATICS
73
Triton® Traction Unit
Motor Control Board- 47803
1 of 2
9 SCHEMATICS
74
Triton® Traction Unit
Motor Control Board- 47803
2 of 2
9 SCHEMATICS
75
Triton® Traction Unit
Patient Interrupt Switch- 48056
1 of 1
9 SCHEMATICS
76
Serial Interface- 47022
1 of 1
Triton® Traction Unit
9 SCHEMATICS
77
Smart Card- 47807
1 of 1
Triton® Traction Unit
9 SCHEMATICS
78
sEMG Module- 48123
1 of 1
Triton® Traction Unit
9 SCHEMATICS
79
Block Diagram
1 of 1
Triton® Traction Unit
10 SPECIAL FIXTURES
80
Calibration Fixture
1 of 4
Triton® Traction Unit
10 SPECIAL FIXTURES
81
Calibration Fixture
2 of 4
Triton® Traction Unit
10 SPECIAL FIXTURES
82
Calibration Fixture
3 of 4
Triton® Traction Unit
10 SPECIAL FIXTURES
83
Calibration Fixture
4 of 4
Triton® Traction Unit
11 WARRANTY
Triton® Traction Unit
Chattanooga Group (“Company”) warrants that the Triton Traction Unit (“Product”) is free of defects in material and workmanship. This warranty shall remain in effect for two years (24 months) from the date of original consumer purchase. If this Product fails to function during the two year warranty period due to a defect in material or workmanship, Company or the selling dealer will repair or replace this Product without charge within a period of thirty days from the date on which the Product is returned to the Company or the dealer.
All repairs to the Product must be performed by a service center authorized by the Company. Any modifications or repairs performed by unauthorized centers or groups will void this warranty.
The warranty period for accessories is 180 days. Accessories consist of Patient Interrupt Switch shipped with the unit.
To participate in warranty coverage, this Product’s warranty registration card (included with Product) must be filled out and returned to the Company by the original owner within ten business days of purchase.
This Warranty Does Not Cover:
• Replacement parts or labor furnished by anyone other than the Company, the selling dealer, or a certified
Company service agent.
• Defects or damage caused by labor furnished by someone other than Company, the selling dealer, or a certified Company service agent.
• Any malfunction or failure in the Product caused by product misuse, including, but not limited to, the failure to provide reasonable and necessary maintenance or any use that is inconsistent with the Product User
Manual.
COMPANY SHALL NOT BE LIABLE IN ANY EVENT FOR INCIDENTAL OR CONSEQUENTIAL DAMAGES.
Some states do not allow the exclusion or limitation of incidental or consequential damages, so the above limitation or exclusion may not apply to you.
To obtain service from Company or the selling dealer under this warranty:
1. A written claim must be made within the warranty period to the Company or the selling dealer. Written claims
made to the Company should be sent to:
4717 Adams Road
Phone: USA: (800) 592-7329
Fax: (423) 875-5497
Canada: (800) 361-6661
Outside USA: +1 (423) 870-7200
Outside USA Fax: +1 (423) 870-2046
2. The Product must be returned to the Company or the selling dealer by the owner.
This warranty gives you specific legal rights and you may also have other rights which vary from state to state or location to location.
The Company does not authorize any person or representative to create for it any other obligation or liability in connection with the sale of the Product. Any representation or agreement not contained in the warranty shall be void and of no effect.
THE FOREGOING WARRANTY IS IN LIEU OF ALL OTHER WARRANTIES, EXPRESSED OR IMPLIED,
INCLUDING ANY WARRANTY OR MERCHANTABILITY OR FITNESS FOR A PARTICULAR PURPOSE.
84
© 2006 Encore Medical, L.P.
ISO 13485 Certifi ed
4717 Adams Road
P.O. Box 489
Hixson, TN 37343
U.S.A.
1-423-870-2281
1-800-592-7329
U.S.A.
1-800-361-6661
CANADA
+1-423-870-7200
OUTSIDE U.S.A
+1 423-870-2046
OUTSIDE U.S.A. FAX chattgroup.com
Medical Device Safety Service (MDSS)
Burckhardtstr. 1
D-30163 Hannover
Germany
Telephone: +49-5103-939430
48160A
0 4 1 3
advertisement
* Your assessment is very important for improving the workof artificial intelligence, which forms the content of this project