ClimateMaster Tranquility Large (TMW) 360, 600, 840 Water-to-Water Heat Pump Installation, Operation & Maintenance
Tranquility Large (TMW) 360, Tranquility Large (TMW) 600, Tranquility Large (TMW) 840 are commercial water-to-water heat pumps designed for a variety of applications. This manual covers installation, operation and maintenance procedures. The units have a high-efficiency scroll compressor and are designed for both heating and cooling.
PDF
Document
Advertisement
Advertisement
Tranquility® Large Water-to-Water (TMW) Series Models 360 - 840 Table of Contents Commercial EarthPure® Water-to-Water Water-Source Heat Pumps - 60Hz Installation, Operation & Maintenance 97B0090N01 Revised: 12 February, 2016 Model Nomenclature General Information Unit Physical Data Unit Dimensional Data Unit Installation Piping Installation Load Plumbing Installation Water Temperature Requirements Water-Loop Heat Pump Applications Ground-Water Heat Pump Applications Ground-Loop Heat Pump Applications Electrical - Line Voltage Wiring Diagram Matrix Typical Wiring Diagram Refrigeration Circuit Diagram Heat Exchangers Control System Control System Optional Features Control Sequence of Operation from BAS BACnet, Modbus, N2 Points List Unit Commissioning & Operating Conditions Piping System Cleaning & Flushing Pre-Start Up Procedures Pre Start-up Check List Unit Start Up Procedures Operation and Maintenance Operational Limitations Compressor Information Refrigeration System Recharging Sequence of Operation Factory Installed Options Field Installed Options Troubleshooting Guide Start Up and Warranty Form Refrigeration Troubleshooting Form Warranty (US & Canada) Revision History 3 4 6 7 8 9 10 10 11 12 13 14 17 18 21 22 23 31 32 33 38 39 40 42 43 46 48 49 50 51 52 52 53 54 57 58 60 CLIMATEMASTER WATER-SOURCE HEAT PUMPS Tranquility ® Large Water-to-Water (TMW) Series Rev.: 12 February, 2016 This Page Intentionally Left Blank 2 C l i m a t e M a s t e r Wa t e r - S o u r c e H e a t P u m p s THE SMART SOLUTION FOR ENERGY EFFICIENCY Tranquility ® Large Water-to-Water (TMW) Series Rev.: 12 February, 2106 Model Nomenclature 1 2 3 4 5 6 7 8 9 10 11 12 13 14 15 T MW 360 B F S S A R S 0 S MODEL TYPE TMW = TRANQUILITY® MEDIUM TEMPERATURE WATER TO WATER MODEL CONFIGURATION S = STANDARD UNIT SIZE 360 600 840 REFRIGERANT OPTIONS 0 = NONE REVISION LEVEL B = CURRENT WATER ISOLATION VALVES VOLTAGE 0 = NONE B = LOAD & SOURCE MOTORIZED VALVES* C = LOAD MOTORIZED VALVES S = SOURCE MOTORIZED VALVES* F = 460/60/3 H = 208-230/60/3 N = 575/60/3 *If ESWT is 60ºF or below in cooling mode CONTROLS S = SINGLE UNIT CONTROL L = LON COMPRESSOR TYPE S = SCROLL APPLICATION R = REVERSE CYCLE HEAT PUMP REFRIGERANT A = HFC-410A *- Source MWV is required if ESWT is 60ºF or below in cooling mode. c l i m a t e m a s t e r. c o m 3 CLIMATEMASTER WATER-SOURCE HEAT PUMPS Tranquility ® Large Water-to-Water (TMW) Series Rev.: 12 February, 2016 General Information Safety Warnings, cautions, and notices appear throughout this manual. Read these items carefully before attempting any installation, service, or troubleshooting of the equipment. DANGER: Indicates an immediate hazardous situation, which if not avoided will result in death or serious injury. DANGER labels on unit access panels must be observed. WARNING: Indicates a potentially hazardous situation, which if not avoided could result in death or serious injury. CAUTION: Indicates a potentially hazardous situation or an unsafe practice, which if not avoided could result in minor or moderate injury or product or property damage. NOTICE: Notification of installation, operation, or maintenance information, which is important, but which is not hazard-related. DANGER (OHFWULFVKRFNKD]DUG 0D\UHVXOWLQLQMXU\RUGHDWK 'LVFRQQHFWSRZHUVXSSO\LHV EHIRUHVHUYLFLQJ 5HIHUVHUYLFLQJWRTXDOLILHG VHUYLFHSHUVRQQHO &$87,21 8QLWWREHVHUYLFHGE\TXDOLILHG SHUVRQQHORQO\ 5HIULJHUDQWV\VWHPXQGHU SUHVVXUH 5HOLHYHSUHVVXUHEHIRUHXVLQJ WRXUFK 5HFRYHUUHIULJHUDQWDQGVWRUHRU GLVSRVHRISURSHUO\ 4 DANGER 5LVTXHGHFKRFpOHFWULTXH 5pVXOWDWGHPDLGDQVGRPPDJHV RXODPRUW 'HEUDQFKHUDYDQWGҋHQWUHSUHQGUH OHGpSDQQDJHGHOҋDSSDUHLO &RQVXOWHUXQUpSDUDWHXUTXDOLILH SRXUOHGpSDQQDJH 5(&29(5 5()5,*(5$17 WARNING! WARNING! To avoid the release of refrigerant into the atmosphere, the refrigerant circuit of this unit must be serviced only by technicians who meet local, state, and federal proficiency requirements. WARNING! WARNING! All refrigerant discharged from this unit must be recovered WITHOUT EXCEPTION. Technicians must follow industry accepted guidelines and all local, state, and federal statutes for the recovery and disposal of refrigerants. If a compressor is removed from this unit, refrigerant circuit oil will remain in the compressor. To avoid leakage of compressor oil, refrigerant lines of the compressor must be sealed after it is removed. WARNING! WARNING! The installation of water-source heat pumps and all associated components, parts, and accessories which make up the installation shall be in accordance with the regulations of ALL authorities having jurisdiction and MUST conform to all applicable codes. It is the responsibility of the installing contractor to determine and comply with ALL applicable codes and regulations. CAUTION! $77(17,21 &RQILHUODPDLQWHQDQFHiXQ WHFKQLFLHQTXDOLILH /HV\VWpPHIULJRULILTXHVRXV SUHVVLRQ 'pFRPSULPHUDYDQWGҋH[SRVHUi ODIODPPH 5pFXSHUpUOHIULJRULJHQHHWOH VWRFNHURXOHGpWULUH FRUUHFWHPHQW CAUTION! To avoid equipment damage, DO NOT use these units as a source of heating or cooling during the construction process. The mechanical components and filters will quickly become clogged with construction dirt and debris, which may cause system damage. C l i m a t e M a s t e r Wa t e r - S o u r c e H e a t P u m p s THE SMART SOLUTION FOR ENERGY EFFICIENCY Tranquility ® Large Water-to-Water (TMW) Series Rev.: 12 February, 2106 General Information Inspection - Upon receipt of the equipment, carefully check the shipment against the bill of lading. Make sure all units have been received. Inspect the carton or crating of each unit, and inspect each unit for damage. Assure the carrier makes proper notation of any shortages or damage on all copies of the freight bill and completes a common carrier inspection report. Concealed damage not discovered during unloading must be reported to the carrier within 15 days of receipt of shipment. If not filed within 15 days, the freight company can deny the claim without recourse. Note: It is the responsibility of the purchaser to file all necessary claims with the carrier. Notify the ClimateMaster Traffic Department of all damage within fifteen (15) days of shipment. Storage - Equipment should be stored in its original packaging in a clean, dry area. Store units in an upright position at all times. Do not stack. Unit Protection - Cover units on the job site with either shipping packaging, vinyl film, or an equivalent protective covering. Cap the open ends of pipes stored on the job site. In areas where painting, plastering, and/or spraying has not been completed, all due precautions must be taken to avoid physical damage to the units and contamination by foreign material. Physical damage and contamination may prevent proper start-up and may result in costly equipment clean-up. Examine all pipes, fittings, and valves before installing any of the system components. Remove any dirt or trash found in or on these components. Pre-Installation - Installation, Operation, and Maintenance instructions are provided with each unit.. The installation site chosen should include adequate service clearance around the unit. Before unit startup, read all manuals and become familiar with the unit and its operation. Thoroughly check the system before operation. Prepare units for installation as follows: 1. Compare the electrical data on the unit nameplate with ordering and shipping information to verify that the correct unit has been shipped. 2. Keep the cabinet covered with the shipping packaging until installation is complete and all plastering, painting, etc. is finished. 3. Verify refrigerant tubing is free of kinks or dents and that it does not touch other unit components. 4. Do not apply power to compressors until startup. Verify isolation switches (at bottom of low voltage section) are off. 5. Verify I/O Flex 6126 board has jumper set to 5 Vac. See Wire Diagram. CAUTION! CAUTION! All three phase scroll compressors must have direction of rotation verified at start-up. Verification is achieved by checking compressor Amp draw. Amp draw will be substantially lower compared to nameplate values. Additionally, reverse rotation results in an elevated sound level compared to correct rotation. Reverse rotation will result in compressor internal overload trip within several minutes. Verify compressor type before proceeding. CAUTION! CAUTION! DO NOT store or install units in corrosive environments or in locations subject to temperature or humidity extremes (e.g., attics, garages, rooftops, etc.). Corrosive conditions and high temperature or humidity can significantly reduce performance, reliability, and service life. Always move and store units in an upright position. Tilting units on their sides may cause equipment damage. CAUTION! CAUTION! CUT HAZARD - Failure to follow this caution may result in personal injury. Sheet metal parts may have sharp edges or burrs. Use care and wear appropriate protective clothing, safety glasses and gloves when handling parts and servicing heat pumps. Handling - Carefully remove the unit’s packaging. The steel base cut-outs provide maneuverability by forklift or pallet jack into its final position (See Rigging and Lifting Procedures). Rigging and Lifting - Each unit should be lifted by using a pallet jack or fork lift in base slots. If it is necessary to utilize a crane for rigging or lifting, use lifting straps and spreader bars. c l i m a t e m a s t e r. c o m 5 CLIMATEMASTER WATER-SOURCE HEAT PUMPS Tranquility ® Large Water-to-Water (TMW) Series Rev.: 12 February, 2016 Unit Physical Data Model TMW360 Compressor (qty) Scroll (2) Compressor Oil Type Factory Charge HFC-410A (lbs) [kg] / circuit TMW600 TMW 840 Scroll (2) Scroll (2) ALL REVA REVB ALL POE POE PVE PVE 15 [6.8] 27.5 [12.5] 33.8 [15.4] Indoor / Load Water connection sizes FPT (in) 2 2-1/2 2-1/2 Outdoor / Source Water connection size FPT (in) 2 2-1/2 2-1/2 Weight - Operating (lbs) [kg] 1400 [635] 2055 [932] 2305 [1042] Weight - Shipping (lbs) [kg] 1325 [601] 1925 [873] 2175 [983] 4.7 [17.8] 8.3 [31.4] 9.5 [36] 4.4 [16.7] 7.3 [27.6] 8.5 [32.2] Water Volume (Source) Gallons [Liters] Water Volume (Load) Gallons [Liters] Insulated Source and Load Water Coils standard. Insulated Refrigerant Circuit standard. Status Lights Power on (green), fault (red), compressor 1 on (green), and compressor 2 on (green). Unit Maximum Water Working Pressure Options Max Working Pressure PSIG [kPa] Base Unit 300 [2,068] Motorized Valves 300 [2,068] Unit Corner Weights (lbs) [kg] 6 Model Left Front Left Rear Right Front Right Rear TMW360 345 [156] 350 [159] 275 [125] 355 [161] TMW600 492 [223] 500 [227] 400 [181] 533 [242] TMW840 557 [252] 565 [255] 452 [204] 601 [271] C l i m a t e M a s t e r Wa t e r - S o u r c e H e a t P u m p s THE SMART SOLUTION FOR ENERGY EFFICIENCY Tranquility ® Large Water-to-Water (TMW) Series Rev.: 12 February, 2106 Unit Dimensional Data HIGH VOLTAGE MINIMUM 2-1/2 ft. [76cm] REQUIRED SERVICE ACCESS LOW VOLTAGE RV ACCESS PANEL MINIMUM 18” REQUIRED SERVICE ACCESS 2 ft. [61cm] OPTIONAL SERVICE ACCESS (BOTH SIDES) NOTE 4 HIGH VOLTAGE CONTROL BOX LOW VOLTAGE CONTROL BOX COMPRESSOR ACCESS PANEL [860] FRONT NOTE: 1. DIMENSIONS SHOWN IN INCHES AND [MILLIMETERS]. 2. TMW360 WATER CONNECTIONS ARE 2” FPT. 3. TMW600 AND 840 WATER CONNECTIONS ARE 2.5” FPT. 4. FOR MULTIPLE UNITS PLACED SIDE BY SIDE. ALLOW SUFFICIENT SPACE FRONT OR BACK TO REMOVE UNIT. c l i m a t e m a s t e r. c o m 7 CLIMATEMASTER WATER-SOURCE HEAT PUMPS Tranquility ® Large Water-to-Water (TMW) Series Rev.: 12 February, 2016 Unit Installation TMW Unit Location - These units are not designed for unconditioned indoor or outdoor installation. Locate the unit in an INDOOR dry, conditioned air (see Operational Limits Table - 9) area that allows enough space for service personnel to remove access panels and to perform typical maintenance or repairs in the future. The installation of water-source heat pump units and all associated components, parts and accessories which make up the installation must be in accordance with the regulations of ALL authorities having jurisdiction and MUST conform to all applicable codes. It is the responsibility of the Installing Contractor to determine and comply with ALL applicable codes and regulations. ClimateMaster recommends locking down the TMW to a concrete base or to three 4” field supplied base rails that can support the unit weight. Base pan has 6 bolt holes for securing to base or rail. Recommended service clearances are 36” (91cm) at front, 30” (76cm) at rear, and 18” (46cm) above. Optional service clearances 24” (61cm) each side. Provide sufficient room to make water and electrical connections. Access panel screws are for shipping and may be removed prior to setting the unit. These units are not approved for outdoor installation and, therefore, must be installed inside the structure being conditioned. Note: Do not apply power to compressors until startup. Verify isolation switches (at bottom of low voltage section) are off. The Load side should have a minimum capacity of 6 gallons per ton of cooling ouput capacity to prevent compressor short cycling. Note: If springs or vibration isolation pads are used, size and weight distribution must be determined by a qualified structural engineer. 8 C l i m a t e M a s t e r Wa t e r - S o u r c e H e a t P u m p s THE SMART SOLUTION FOR ENERGY EFFICIENCY Tranquility ® Large Water-to-Water (TMW) Series Rev.: 12 February, 2106 Piping Installation Installation of Supply and Return Piping for Load and Source Follow these piping guidelines. 1. Install a drain valve at the base of each supply and return riser to facilitate system flushing. 2. Install shut-off / balancing valves and unions at each unit to permit unit removal and for servicing. 3. Install shut off valves to isolate strainers. 4. Install 60 mesh strainers on unit inlet for both Source and Load. Recommend basket strainer on Source. 5. Select the proper hose length to allow slack between connection points. Hoses may vary in length by +2% to -4% under pressure. 6. Exceeding the minimum bend radius may cause the hose to collapse which reduces water flow rate. Install an angle adapter to avoid sharp bends in the hose when the radius falls below the required minimum and causes a slight kink. 7. Install (4) petes ports, install on both Source and Load inlets and outlets. 8. Both Load and Source must adhere to Water Quality Standards. See Table 5. Copy of water test to be sent to ClimateMaster technical service department. Optional pressure-rated hose assemblies designed specifically for use with ClimateMaster units are available. Similar hoses can be obtained from alternate suppliers. Supply and return hoses are fitted with swivel-joint fittings at one end to prevent kinking during installation. Refer to Figure 1 for an illustration of a Supply/Return Hose Kit. Male adapters secure hose assemblies to the unit. Install hose assemblies properly and check them regularly to avoid system failure and reduced service life. WARNING! WARNING! Polyolester Oil, commonly known as POE oil, or Polyvinylether, commonly known as PVE oil, are synthetic oils used in many refrigeration systems including those with HFC-410A refrigerant. POE, or PVE oil, if it ever comes in contact with PVC or CPVS piping, may cause failure of the PVC/CPVC. PVC/CPVC piping should never be used as supply or return water piping with water source heat pump products containing HFC-410A as system failures and property damage may result. CAUTION! CAUTION! Corrosive system water requires corrosion resistant fittings and hoses and possibly water treatment. WARNING! WARNING! Piping must comply with all applicable codes. Figure 1: Supply/Return Hose Kit WARNING! Rib Crimped Swivel Brass Fitting Brass Fitting WARNING! Do not bend or kink supply lines or hoses. Insulation is not required on loop water piping except where the piping runs through unheated areas or outside the building or when the loop water temperature is below the minimum expected dew point of the pipe ambient temperature. Insulation is required if loop water temperature drops below the dew point. Length (2 ft [0.6m] Length Standard) MPT MPT (Typical Both Hoses) Figure 2: Connection Locations Pipe joint compound is not necessary when Teflon threaded tape is pre-applied to hose assemblies or when flared-end connections are used. If pipe joint compound is preferred, use compound only in small amounts on the pipe threads of the fitting adapters. Prevent sealant from reaching the flared surfaces of the joint. Source connections Load connections Field-supplied power disconnect Field-supplied flex-conduit Note: When antifreeze is used in the loop, assure that any Teflon® tape or pipe joint compound used is compatible. Maximum allowable torque for brass fittings is 30 ft-lbs [41 N-m]. If a torque wrench is not available, tighten fingertight plus one quarter turn. Tighten steel fittings as necessary. c l i m a t e m a s t e r. c o m 9 CLIMATEMASTER WATER-SOURCE HEAT PUMPS Tranquility ® Large Water-to-Water (TMW) Series Rev.: 12 February, 2016 Load Plumbing Installation TMW Unit Load Plumbing - The applications are too varied to describe in this document. However, some basic guidelines will be presented. Much of the discussions on water loop applications would be valid for the load plumbing discussion as well. All plumbing must conform to local codes with the following considerations: Wide temperature variation applications such as heating/cooling coils: • Employ piping materials that are rated for the maximum temperature and pressure combination. This excludes PVC for most heating applications. • Ensure that load water flow in high temperature heating applications is at least 3 gpm per ton [3.9 l/m per kW] to improve performance and reduce nuisance high pressure faults. • DO NOT employ plastic to metal threaded joints • Utilize a pressure tank and air separator vent system to equalize pressure and remove air. Potable Water Applications: • Load exchanger should be isolated with secondary heat exchanger. • Ensure load water flow in high temperature heating applications is at least 3 gpm per ton to improve performance and reduce nuissance to high pressure faults. Note: The manufacturer strongly recommends all piping connections, both internal and external to the unit, be pressure tested by an appropriate method prior to any finishing of the interior space or before access to all connections is limited. Test pressure may not exceed the maximum allowable pressure for the unit and all components within the water system. The manufacturer will not be responsible or liable for damages from water leaks due to inadequate or lack of a pressurized leak test, or damages caused by exceeding the maximum pressure rating during installation. Swimming Pool Hot Tub Applications: • Load exchanger should be isolated with secondary heat exchanger constructed of anti-corrosion material for chlorine/bromine fluid applications. Figure 3: Load Water System (Not all components of system shown. See engineering specifications and drawings) AHK Hose Kit (1) 2” (360) 2.5” (600) Pressure taps with shutoff valves and gages Pressure Relief Valve Manual Isolation Valves Flow to Load Field Pump Backflow Preventer Hose Unions AYS30060 Y-Strainer (3” - 60 mesh) In Out Flow from Load Field Bypass Valve (Not required if unit has Source MWV) Revision A Models Only TMW Front 60” (No Scale) ADPS (1) KIT Differential Pressure Sensor Kit (Wire to LVTB2 15, 16, 17) Note: Rev B ADPS Factory installed and wired internal WATER TEMPERATURE REQUIREMENTS Cooling Water Temperature - Unit is designed for a leaving water temperature range from 40°F to 62°F. TMW360-840 units can operate safely in this range without the need of special controls or glycol additives. Leaving water temperatures below 40°F can result in evaporator suction temperatures below the freezing point of water. Therefore, a glycol solution additive is required that will protect the evaporator from freeze ups at lower operating suction temperatures. The full range of leaving fluid temperature using glycol is 24°F to 62°F. 10 C l i m a t e M a s t e r Wa t e r - S o u r c e H e a t P u m p s THE SMART SOLUTION FOR ENERGY EFFICIENCY Tranquility ® Large Water-to-Water (TMW) Series Rev.: 12 February, 2106 Water-Loop Heat Pump Applications Commercial systems typically include a number of units plumbed to a common piping system. Any unit plumbing maintenance work can introduce air into the piping system, therefore air elimination equipment is a major portion of the mechanical room plumbing. In piping systems expected to utilize water temperatures below 50°F [10°C], 1/2" [13mm] closed cell insulation is required on all piping surfaces to eliminate condensation. Metal to plastic threaded joints should never be employed due to their tendency to leak over time. Teflon tape thread sealant is recommended for NPT water connections (commercial class) to minimize internal fouling of the heat exchanger. Do not overtighten connections and route piping so as not to interfere with service or maintenance access. Hose kits are available from ClimateMaster for connection between the TMW Series and the piping system. The piping system should be flushed to remove dirt, piping chips, and other foreign material prior to operation. See Piping System Cleaning and Flushing Procedures later in this document. The flow rate is usually set between 2.25 gpm and 3 gpm per ton [2.9 l/m and 4.5 l/m per kW] of cooling capacity. ClimateMaster recommends 2.5 gpm per ton [3.2 l/m per kW] for most applications of water loop heat pumps. To insure proper maintenance and servicing, P/T ports are imperative for temperature and flow verification, as well as performance checks. Cooling Tower/Boiler Systems typically utilize a common loop maintained 60-90°F [16-32°C]. The use of a closed circuit evaporative cooling tower with a secondary heat exchanger between the tower and the water loop is recommended. If an open type cooling tower is used continuously, chemical treatment and filtering will be necessary. Figure 4: Source Water System (Not all components of system shown. See engineering specifications and drawings). Pressure taps with shutoff valves and gages ABS30060Basket Strainer (3”- 60 mesh) AHK Hose Kit (1) 2” (360) 2.5” (600) Flow from Source Flow to Source Hose Unions Revision A Models Only In Out TMW Front ADPS (1) KIT Differential Pressure Sensor Kit (Wire to LVTB2 13, 14, 17) 60” Note: Rev B ADPS Factory installed and wired internal (No Scale) c l i m a t e m a s t e r. c o m 11 CLIMATEMASTER WATER-SOURCE HEAT PUMPS Tranquility ® Large Water-to-Water (TMW) Series Rev.: 12 February, 2016 Ground-Water Heat Pump Applications Shut off valves should be included for ease of servicing. Unit has internal flush valves to allow alkaline flushing of just the heat exchanger. Pressure temperature plugs should be used so that flow and temperature can be measured. Supply and return water piping materials should be limited to copper, PE, or similar material. PVC or CPVC should never be used as they are incompatible with the POE and PVE oils used in HFC-410A products and piping system failure and property damage may result. WARNING! WARNING! Polyolester Oil, commonly known as POE oil, or Polyvinylether, commonly known as PVE oil, are synthetic oils used in many refrigeration systems including those with HFC-410A refrigerant. POE, or PVE oil, if it ever comes in contact with PVC or CPVS piping, may cause failure of the PVC/CPVC. PVC/CPVC piping should never be used as supply or return water piping with water source heat pump products containing HFC-410A as system failures and property damage may result. Water quantity should be plentiful and of good quality. Consult Table 5 for water quality guidelines. The unit has stainless steel braze plate heat exchangers. In ground water situations where scaling could be heavy or where biological growth such as iron bacteria will be present, a closed loop system is recommended. It is mandatory to install an intermediate heat exchanger to isolate an open loop from the heat pump loop on open well systems. Heat exchangers may over time lose heat exchange capabilities due to a build up of mineral deposits inside. These can be cleaned only by a qualified service mechanic as acid and special pumping equipment are required. Table 5: Water Quality Standards Water Containing Ammonia CaCO3 Alkalinity CaCO3 Hardness Chlorides Dissolved Solids Iron Manganese Nitrate pH Sulphate Concentration Less than 2.0 mg/l 30 - 500 mg/l 30 - 500 mg/l Less than 200 mg/l Less than 1000 mg/l Less than 5.0 mg/l Less than 4.0 mg/l Less than 100 mg/l 7.0 - 9.0 Less than 200 mg/l In areas with extremely hard water, the owner should be informed that the intermediate heat exchanger may require occasional flushing. Use a 2% phosphoric or sulfamic acid solution, on the unit side and manufacturer’s recommendation on ground water side. 12 Expansion Tank and Pump - Use a closed, bladder-type expansion tank to minimize mineral formation due to air exposure. The expansion tank should be sized to handle at least one minute run time of the pump to prevent premature pump failure using its drawdown capacity rating. Discharge water from the unit is not contaminated in any manner and can be disposed of in various ways depending on local building codes; i.e. recharge well, storm sewer, drain field, adjacent stream or pond, etc. Most local codes forbid the use of sanitary sewer for disposal. Consult your local building and zoning department to assure compliance in your area. Water Control Valve - Note the placement of the water control valve. Always maintain water pressure in the heat exchanger by placing water control valves at the outlet of the unit to prevent mineral precipitation. Slow opening and closing valves are recommended to reduce water hammer. If water hammer persists, a mini-expansion tank can be mounted on the piping to help absorb the excess hammer shock. Ensure that the total ‘VA’ draw of any field-supplied valve can be supplied by the unit transformer. Flow Regulation - Flow regulation can be accomplished by two methods. First, most water control valves have a built in flow adjustment. By measuring the pressure drop through the unit heat exchanger, flow rate can be determined and compared to Table 6. Since the pressure is constantly varying, two pressure gauges might be needed. Simply adjust the water control valve until the desired flow of 1.5 to 2 gpm per ton is achieved. Secondly, a flow control device may be installed. The devices are typically an orifice of plastic material that is designed to allow a specified flow rate. These are mounted on the outlet of the water control valve. On occasion, these valves can produce a velocity noise that can be reduced by applying some back pressure. This is accomplished by slightly closing the leaving isolation valve of the well water setup. Table 6 Model TMW360 TMW600 TMW840 Flow GPM 45 68 90 75 113 150 105 158 210 C l i m a t e M a s t e r Wa t e r - S o u r c e H e a t P u m p s Pressure Drop PSI (FT) 1.2 (2.7) 2.4 (5.6) 4.2 (9.6) 1.7 (3.9) 3.6 (8.3) 6.3 (14.5) 2.7 (6.2) 6.0 (13.7) 10.4 (23.7) THE SMART SOLUTION FOR ENERGY EFFICIENCY Tranquility ® Large Water-to-Water (TMW) Series Rev.: 12 February, 2106 Ground-Loop Heat Pump Applications CAUTION! CAUTION! The following instructions represent industry accepted installation practices for Closed Loop Earth Coupled Heat Pump Systems. They are provided to assist the contractor in installing trouble free ground loops. These instructions are recommendations only. State and Local Codes MUST be followed and installation MUST conform to ALL applicable Codes. It is the responsibility of the Installing contractor to determine and comply with ALL applicable Codes and Regulations. Pre-Installation - Prior to installation, locate and mark all existing underground utilities, piping, etc. Install loops for new construction before sidewalks, patios, driveways, and other construction has begun. During construction, accurately mark all ground loop piping on the plot plan as an aid in avoiding potential future damage to the installation. Antifreeze - In areas where minimum entering loop temperatures drop below 40°F [5°C] or where piping will be routed through areas subject to freezing, anti-freeze is needed. Alcohols and glycols are commonly used as antifreezes, however your local sales manager should be consulted for the antifreeze best suited to your area. Low temperature protection should be maintained to 15°F [9°C] below the lowest expected entering loop temperature. For example, if 30°F [-1°C] is the minimum expected entering loop temperature, the leaving loop temperature would be 25 to 22°F [-4 to -6°C] and low temperature protection should be at 15°F [-10°C] e.g. 30°F - 15°F = 15°F [-1°C - 9°C = -10°C]. All alcohols should be premixed and pumped from a reservoir outside of the building when possible or introduced under water level to prevent fuming. Initially calculate the total volume of fluid in the piping system. Then use the percentage by volume shown in Table 7 for the amount of antifreeze. Antifreeze concentration should be checked from a well mixed sample using a hydrometer to measure specific gravity. Table 7: Antifreeze Percentages by Volume Type Minimum Temperature for Low Temperature Protection 10°F [-12.2°C] 15°F [-9.4°C] 20°F [-6.7°C] 25°F [-3.9°C] Methanol 25% 21% 16% 10% 100% USP Food Grade Propylene Glycol 38% 25% 22% 15% Ethanol 29% 25% 20% 14% * Must not be denatured with any petroleum based product Piping Installation - All earth loop piping materials should be limited to only polyethylene fusion for inground sections of the loop. Galvanized or steel fitting should not be used at any time due to their tendency to corrode. All plastic to metal threaded fittings should be avoided due to their potential to leak in earth coupled applications and a flanged fitting substituted. P/T plugs should be used so that flow can be measured using the pressure drop of the unit heat exchanger in lieu of other flow measurement means. Earth loop temperatures can range between 25 to 110°F [-4 to 43°C], and 2.25 to 3 gpm of flow per ton [2.9 l/m to 3.9 l/m per kW] of cooling capacity is recommended in these applications. Upon completion of the ground loop piping, pressure test the loop to assure a leak free system. Horizontal Systems: Test individual loops as installed. Test entire system when all loops are assembled. Vertical U-Bends and Pond Loop Systems: Test Vertical U-bends and pond loop assemblies prior to installation with a test pressure of at least 100 psi [689 kPa]. Flushing the Earth Loop - Upon completion of system installation and testing, flush the system to remove all foreign objects and purge to remove all air. Flush the loop first with the unit isolated to avoid flushing debris from the loop into the unit heat exchanger. Water Control Valve - Note the placement of the water control valve. Always maintain water pressure in the heat exchanger by installing water control valves at the source out of the unit to prevent mineral precipitation. Position water high pressure switch between unit and valve. Pilot operated or slow closing valves are recommended to reduce water hammer. If water hammer persists, a mini-expansion tank can be mounted on the piping to help absorb the excess hammer shock. Insure that the total ‘VA’ draw of the valve can be supplied by the unit transformer. For instance, some slow closing valves can draw up to 35VA. This can overload smaller transformers depending on the other controls employed. A typical pilot operated solenoid valve draws approximately 15VA. Flow Regulation - Install on source in of unit. Flow regulation can be accomplished by two methods. First, most water control valves have a built in flow adjustment. By measuring the pressure drop through the unit heat exchanger, flow rate can be determined and compared to Table 6. Since the pressure is constantly varying, two pressure gauges might be needed. Simply adjust the water control valve until the desired flow of 2.5 to 3 gpm per ton [2.0 to 2.6 l/m per kW] is achieved. Secondly, a flow control device may be installed. The devices are typically an orifice of plastic material that is designed to allow a specified flow rate. These are mounted on the outlet of the water control valve. On occasion, these valves can produce a velocity noise that can be reduced by applying some back pressure. This is accomplished by slightly closing the leaving isolation valve of the well water setup. c l i m a t e m a s t e r. c o m 13 CLIMATEMASTER WATER-SOURCE HEAT PUMPS Tranquility ® Large Water-to-Water (TMW) Series Rev.: 12 February, 2016 Electrical - Line Voltage WARNING! To avoid possible injury or death due to electrical shock, open the power supply disconnect switch and secure it in an open position during installation. Electrical Connection - The compliance of the installation to relevant local and national codes is the responsibility of the installer. Before carrying out any electrical work, confirm that the main supply is isolated. The installer must ensure that the correct electrical drawing is available. Before power is applied to the system, the wiring should be visually inspected for loose connections or frayed terminal connections. All control wiring should follow wiring instructions supplied in the project submittal package. General Line Voltage Wiring - Be sure the available power is the same voltage and phase as that shown on the unit serial plate. Line and low voltage wiring must be done in accordance with local codes or the National Electric Code, whichever is applicable. Consult the unit wiring diagram located on the inside of the compressor access panel to ensure proper electrical hookup. All final electrical connections must be made with a length of flexible conduit to minimize vibration and sound transmission to the building. TMW Power Connection - Line voltage connection is made by connecting the incoming line voltage wires to L1, L2, and L3 on power distribution block. Consult electrical data table 8 for correct fuse size. Incoming Power Wiring - The power for all units is taken from a suitable fused disconnect power supply within the main panel and the electrical service enters the individual units through the top into the units control panel enclosure. Proper grounding is mandatory. The power supply shall be in compliance with all local and national codes. CAUTION! CAUTION! Use only copper conductors for field installed electrical wiring. Unit terminals are not designed to accept other types of conductors. WARNING! 208 Volt Operation - All 208-230 Volt units are factory wired for 208 Volt. The transformers may be switched to 230V operation as illustrated on the wiring diagram by switching the Red wire from H2 to H3 terminal on the transformer. All field installed wiring, including electrical ground, must comply with the National Electrical Code as well as all applicable local codes. Refer to the unit wiring diagrams for fuse sizes and a schematic of the field connections which must be made by the installing (or electrical) contractor. Table 8: TMW Large Electrical Data Model Voltage Code Voltage H 208-230/60/3 F TMW360 TMW600 TMW840 Voltage Min/Max Compressor Total Unit FLA Min Circuit Amps Max UL/CSA HACR Qty RLA (EA) LRA (EA) 187/254 2 56.4 425 113 127 175 460/60/3 414/506 2 25.5 173 51 57 80 N 575/60/3 518/633 2 20.4 128 41 46 60 H 208-230/60/3 187/254 2 94.7 605 189 213 300 F 460/60/3 414/506 2 42.8 272 86 96 125 N 575/60/3 518/633 2 34.3 238 69 77 110 H 208-230/60/3 187/254 2 124.3 599 249 280 400 F 460/60/3 414/506 2 56.2 310 112 126 175 N 575/60/3 518/633 2 45.0 239 90 101 125 HACR circuit breaker in USA only 14 C l i m a t e M a s t e r Wa t e r - S o u r c e H e a t P u m p s THE SMART SOLUTION FOR ENERGY EFFICIENCY Tranquility ® Large Water-to-Water (TMW) Series Rev.: 12 February, 2106 Electrical - Line Voltage (Continued) SAFETY WARNING WARNING! High voltage is used to operate this equipment. Failure to observe standard electrical safety procedures may result in serious injury. Only persons qualified and / or properly trained should attempt to install, operate and maintain this equipment. These units come fully charged with refrigerant. Installation, and start – up should be accomplished by technicians who are fully certified to handle refrigerants, as required by 40 CRF Part 82, subpart F of the Recycling and Emissions Reduction Act. Scroll compressors are used in this equipment. Phase verification is required for proper rotation direction. Incorrect rotation will result in elevated sound and internal overload trip failure. Proper Voltage Balance - Occasionally, in three phase circuits, a voltage imbalance occurs between phases. It is not recommended to operate equipment when an imbalance greater that 2% occurs. This causes motors to run at high temperatures and may affect their longevity. The following example describes how to calculate the average voltage of the three phases to see if the imbalance is greater than 2%. Example: Line one = 226v Line two = 230v Line three = 228v The average is: 226+230+228 = 228v Next, 100(228-226) = 0.9% 228 The voltage imbalance of the three phase circuit is 0.9%. This is well under the 2% range. c l i m a t e m a s t e r. c o m 15 CLIMATEMASTER WATER-SOURCE HEAT PUMPS Tranquility ® Large Water-to-Water (TMW) Series Rev.: 12 February, 2016 Electrical - Low Voltage DDC Control Wiring - Control wiring cannot be installed in the same conduit as line voltage wiring or with wires that switch highly inductive loads such as contactor and relay coils. All wiring shall be in compliance with all local and national codes. Electrical Phase Sequencing - Proper clockwise rotation for scroll compressor motors is important to prevent damaging the compressors. ClimateMaster recommends the use of a phase sequence indicating instrument following the manufactures directions. Another alternative would be to “bump test” the compressors one at a time with pressure gauges attached to the high and low gauge ports of the compressors to check for proper rotation. Energize the compressor for a few seconds to ensure the discharge pressure gauge increases significantly. If the discharge pressure does not increase, proper rotation is reversed. Compressor rotation can be reversed by opening the main electrical disconnect and switching any two of the main power supply leads feeding that compressor’s contactor. ATTENTION INSTALLER 3 Phase Scroll Compressor Units • If this unit uses a 3 Phase Scroll Compressor, the following instructions MUST BE followed: - Unit power supply MUST BE wired in the proper sequence to avoid damage to the 3 Phase Scroll Compressor; - Scroll Compressors with INCORRECT rotation show the following characteristics: 1) High sound level; 2) High suction pressure and low discharge pressure; 3) Low current draw. - If any of the three above characteristics exist, swap two of the three supply wires at the disconnect/fuse block and recheck compressor for incorrect rotation. Low Voltage Knockouts are provided on top, sides, or front of unit. Run wires into low voltage section. Connect to terminal strips per wire diagram. 16 C l i m a t e M a s t e r Wa t e r - S o u r c e H e a t P u m p s THE SMART SOLUTION FOR ENERGY EFFICIENCY Tranquility ® Large Water-to-Water (TMW) Series Rev.: 12 February, 2106 Wiring Diagram Matrix All diagrams can be located online at climatemaster.com using the part numbers below. Model Refrigerant Wiring Diagram Part Number Electrical Agency TMW360-840 EarthPure® HFC-410A 96B0152N01 208-230/60/3 460/60/3 575/60/3 UL c l i m a t e m a s t e r. c o m 17 CLIMATEMASTER WATER-SOURCE HEAT PUMPS Tranquility ® Large Water-to-Water (TMW) Series Rev.: 12 February, 2016 Typical Wiring Diagram 18 C l i m a t e M a s t e r Wa t e r - S o u r c e H e a t P u m p s THE SMART SOLUTION FOR ENERGY EFFICIENCY Tranquility ® Large Water-to-Water (TMW) Series Rev.: 12 February, 2106 Typical Wiring Diagram (Continued) c l i m a t e m a s t e r. c o m 19 CLIMATEMASTER WATER-SOURCE HEAT PUMPS Tranquility ® Large Water-to-Water (TMW) Series Rev.: 12 February, 2016 Typical Wiring Diagram 20 C l i m a t e M a s t e r Wa t e r - S o u r c e H e a t P u m p s THE SMART SOLUTION FOR ENERGY EFFICIENCY Tranquility ® Large Water-to-Water (TMW) Series Rev.: 12 February, 2106 Refrigeration Circuit Diagram c l i m a t e m a s t e r. c o m 21 CLIMATEMASTER WATER-SOURCE HEAT PUMPS Tranquility ® Large Water-to-Water (TMW) Series Rev.: 12 February, 2016 Heat Exchangers Draining - When performing standard maintenance procedures such as flushing a heat exchanger, it will be necessary to close off each heat exchanger. This can easily be done if factory mounted water isolation valves are provided. Access to a floor drain is helpful when performing standard maintenance procedures. Back Washing - It may become evident from the recorded weekly log data that the performance of the TMW is gradually degrading. This could be due to a buildup of debris or sludge obstructing the free passage of flow through the heat exchangers. This debris can be removed by a back washing process, which involves the introduction of a forced, violent, backwards flow through the heat exchanger, using a carefully formulated flushing solution. To be effective, this back flow should be slightly higher than the normal flow, and in the opposite direction. The difficulties and practicality of this method depends on the back wash pumping system itself. Another method would be to back flush each heat exchanger using city water as opposed to system water (see Figure 5 – City Water Cleaning Arrangement). The back washing procedure is accomplished by isolating each individual heat exchanger and introducing the city water using a connection hose to the ¾” service port to flow in an opposite direction from the normal heat exchanger flow direction. On the opposite ¾” service port, connect a drain hose to run to a suitable floor drain. Continue back flow until all debris is removed. Chemical Clean In Place Washing Without Water Isolation Valves - Chemical Clean in place washing will typically provide the best debris removal, even from severely clogged heat exchangers. The cleaning tank, pump and pump strainer should be arranged in the manner shown in Figure 6 - In Place Cleaning Arrangement. The flow of the cleaning is arranged in the opposite flow to the normal operational direction. Connection points are provided using the 3/4” service ports at each heat exchanger. The cleaning solution used can be either a detergent or hot water to remove particles and simple cleaning. If correct water treatment has been implemented this should provide adequate cleaning for most situations. The solution can be pumped through the heat exchangers and allowed to “soak” for a time and then pumped again. CAUTION! CAUTION! Do not chemically clean heat exchangers with chloride based solutions. Figure 5: City Water Cleaning Arrangement Connected to City Water Isolation Ball Valve (2”) Refrigerant Circuit #1 Service Port (3/4”) To Cooling Tower Header Refrigerant Circuit #2 From Cooling Tower Header Service Port (3/4”) Isolation Ball Valve (2”) Heat Exchanger To Drain Figure 6: In Place Cleaning Arrangement Connected to City Water Cleaning Tank Isolation Ball Valve (2”) Refrigerant Circuit #1 Service Port (3/4”) To Cooling Tower Header Refrigerant Circuit #2 From Cooling Tower Header Cleaning Pump 22 Service Port (3/4”) Isolation Ball Valve (2”) Heat Exchanger C l i m a t e M a s t e r Wa t e r - S o u r c e H e a t P u m p s THE SMART SOLUTION FOR ENERGY EFFICIENCY Tranquility ® Large Water-to-Water (TMW) Series Rev.: 12 February, 2106 Control System The Control System provides leaving chilled and hot water liquid temperature control algorithms which maintain precise temperature control for heating and cooling applications. A compressor run time equalization sequence is given to ensure even distribution of compressor run time. Unit power consumption is minimized by indexing the most efficient stages of cooling, optimizing heat transfer surface. The controls are two separate boards; the IO FLEX6126 and EX8160 expander board. The controls govern all significant events, timing and compressor staging, providing operator interface for all levels of setting and retrieving data. The controller directly senses the control parameters that govern the unit operation, such as Load and Source entering and leaving temperatures, both compressors’ winding temperatures, suction and discharge temperatures and pressures. Field Component Connections to the Controller Field integration is simplified by the use of the following minimum input devices: • A remote OFF, HEAT, COOL input for scheduling is required for unit operation. (not required if BAS is used) Connect 3 wires to 7, 9, 10 plus add jumper between 8 and 10. • Differential pressure sensors ADPS for both Load and Source water flows are required for unit operation (connect 6 wires to 13-17 at LVTB2, see wire diagram). • Voltage/phase monitor (phase loss/phase reversal, brown-out/black-out device) is recommended for unit operation. (If not used, add jumper wire, connect between 1 and 2 at LVTB2, see wire diagram.) • BAS or BacView6 (one per site). • Optional fault reset switch can be connected between 11 and 12 at LVTB2, see wire diagram. Controller Connections and Settings - Before wiring to, setting or changing the hardware address, make sure the controller power is off. The controller only reads the address when the unit is turned on. The controller has two rotary switches for assigning the module’s hardware address. One switch corresponds to the “tens” digit and the second switch corresponds to the “ones” digit, allowing for hardware-based addresses of 02 to 99. For example, if the unit’s address is two, set the tens switch to zero and the ones switch to two, as shown in Figure 7. The station ID for each MS/TP node must be unique on a MS/TP segment. The rotary address switches are used to set this unique ID. Set the communication BAUD rate with DIPS 1 and 2, see figure 7. 9600, 19.2K, 38.4K, or 76.8K available. Set the protocol with DIPS 5, 7, and 8, see figure 7. MSTP, N2, and Modbus are available. c l i m a t e m a s t e r. c o m 23 CLIMATEMASTER WATER-SOURCE HEAT PUMPS Tranquility ® Large Water-to-Water (TMW) Series Rev.: 12 February, 2016 Control System (continued) Alarm Codes - I/O FLEX6126 Board has LED near AO-2 that will flash alarm code. 1. Compressor 1 Fault. (2 Flashes) 2. Compressor 2 Fault. (3 Flashes) 3. Compressor 1 Out of Range Sensor. (4 Flashes) 4. Compressor 2 Out of Range Sensor. (5 Flashes) 5. Compressor No Run Alarm or Motorized Valve Alarm. (6 Flashes) 6. Hot Water Temperature Alarm. (7 Flashes) 7. Cold Water Temperature Alarm. (8 Flashes) 8. Load or Source flow failure or main power phase loss. (9 Flashes) Figure 7: Controller Connections and Settings N01 N02 +5V +24V UI-01 + 3 x Gnd 2 Out + 1 3 2 1 Ensure Jumper at 5 VDC All Other Jumpers Are Factory Preconfigured (Do Not Change). Plug in BacView Fault LED Set Unit Address Set Baud Rate (DIPS 1,2) Field Connection to BAS 24 Set Protocol (DIPS 5,6,7,8) C l i m a t e M a s t e r Wa t e r - S o u r c e H e a t P u m p s THE SMART SOLUTION FOR ENERGY EFFICIENCY Tranquility ® Large Water-to-Water (TMW) Series Rev.: 12 February, 2106 Control System (continued) BACView6 Interface - The BACView6 offers an easy-touse operator interface keypad (Figure 8) which includes a four-line by 40 character, back-lit LCD display panel, which is easy to navigate using logically grouped menus. This enables the user to access important information concerning setpoints, active temperatures, pressures, operating modes, alarm conditions, unit scheduling, servicing, diagnostics and more. See Figure 9 - 14 for the screen menus. Figure 8 Figure 9: Hierarchy Menu HOME (See Fig. 10) STATUS SETUP (FN2) SERVICE (FN7) (See Fig. 11) (See Fig. 12) (See Fig. 13) ALARM (See Fig. 14) Figure 10: Home Screen Sourc Water In:0000.0F / Tot Stg On: 00 Sourc WaterOut:0000.0F/Tot Cool Stg: 00 Load Water In:0000.0F /Tot Heat Stg: 00 Load WaterOut:0000.0F/ Load Wtr Flow: Yes /Source Wtr Flow:Yes Unit Status: Off /UnitMode:No Flo/Phas [→ STATUS] [→SETUP] [→SERVICE] [→ALARM] c l i m a t e m a s t e r. c o m 25 26 OPERATING STATUS List of Function (FN) Menus FN(0) Bacnet Network #’s & IP Assign FN(2) System Setup Menu FN(3) Alarm Lockout Reset Menu FN(4) Bacnet Device Instance #’s FN(5) Compressor Unload Menu FN(6) Module Level Factory Setup FN(7) Service Menu FN(8) Master Level Factory Setup FN(9) Customer Password Assignment NOTE: To access the hidden functions, hold the FN key down, then press desired number key, then release both. [→Prev] [→ALARM] [→SETUP][→CLOCKSET] COMPR ON/OFF STATUS LOAD WATER STATUS [→SETUP] [→HOME] [→Prev] [→SETUP] [→HOME] [→ALARM] TMW Load Water Temp Status Load WtrIn:0000.0F/LoadWaterOut:0000.0F Load Flo Status:Off/Src Flow Status:Off Load Water Diff Press Sensor: 00.0 PSID [→Prev] [→SETUP] [→STATUS] [→ALARM] TMW Compressor Cycles Status M1C1 Cycles: 00000 /M1C2 Cycles: 00000 [→Prev] TMW Compressor ON/OFF Status M1C1 Status: Off / M1C2 Status: Off TMW Compressor Runtime Status M1C1 Runtm: 000000 hours M1C2 Runtm: 000000 hours [→Prev] [→SETUP] [→HOME] [→ALARM] Diagnostic Flash Code Descriptions No Flashes System Operation Normal 2 Flashes Compr #1 Lockout in Alarm 3 Flashes Compr #2 Lockout in Alarm 4 Flashes Compr #1 Sensor Circuit OOR 5 Flashes Compr #2 Sensor Circuit OOR 6 Flashes Mot Vlv SW Fail or HPC Trip 7 Flashes Load Water Alarm Condition 8 Flashes Source Water Alarm Condition 9 Flashes Phase or Flow Failure or DPS [→Prev] [→ALARM] [→SETUP][→CLOCKSET] SOURCE WATER STATUS TMW Source Water Temp Status Src Wtr In :0000.0F/Src Wtr Out:0000.0F Load Flo Status:Off/Src Flow Status:Off Sourc Water Diff Press Sensor:00.0 PSID Load Water Diff Press Sensor: 00.0 PSID [→Prev] [→SETUP] [→STATUS] COMPR RUNTIMES STATUS COMPR CYCLES STATUS MODULE 1 COMP 1 OPERATING STATUS M1 in Heat Mode?Yes/M1 in Cool Mode?Yes Load Wtr Flow: Yes /Source Wtr Flow:Yes Hot Water In:000.0F/ Cold Wat In:000.0F Hot Wat Out :000.0F/ Cold WatOut:000.0F Suc SuperHt:000.0 F/ M1C1 DisPr:000 psi M1C1 Suc Tp:000.0 F/M1C1 SucPr:000.0psi M1C1 Discharge Temp: 000.0F M1C1 Status: Off /M1C1 Fail : Off Load Wat Out:000.0F/SourcWat Out:000.0F M1C1 Runtime:00000h/M1C1 Cycles:00000 M1C1 Min OffTm :Off/M1C1 Min Runtm:Off MV PID VdcOut:00.00/ Lowest Hd Pres:000 [→Prev] [→STATUS] [→HOME] [→ALARM] MOD COMP 1 DATA TMW Operating, Loading & PID Status Stg1 Clg PID:000.0/ Stg1 Htg PID:000.0 Src Wtr Out:0000.0F/Load WtrOut:0000.0F Status:Unit OFF/Unit Mode:NoFlo/Phas [→Prev] [→SETUP] [→HOME] [→ALARM] TMW Module 1 Compr Unload Status M1C1 Low Suct Press Unload : Off M1C2 Low Suct Press Unload : Off M1C1 XLow Suct Press Unload : Off M1C2 XLow Suct Press Unload : Off M1C1 Low Suct Temp Unload : Off M1C2 Low Suct Temp Unload : Off M1 Evap Freeze Temp Unload : Off M1 Cond WatOut Temp Unload : Off M1C1 High Dis Press Unload : Off M1C2 High Dis Press Unload : Off M1C1 High Dis Temp Unload : Off M1C2 High Dis Temp Unload : Off [→Prev] [→SETUP] [→HOME] [→ALARM] MODULE COMPR UNLOAD FUNCTIONS F5 TMW Unit Status Menu [→All Module Compr Unload Status] FN5 [→Unit Oper Stat] / [→Load Water Stat]/[→Source Water Stat] [→Modl Compl Data]/ [→Modl Comp2 Data] [→Compr Runtimes] / [→Compr Cycles] [→Compr ON/OFF Status] [→Alarm Flash Code Descriptions] [→List of Function Menus] [→Prev] [→CLOCKSET] [→Home] [→Alarm] CLIMATEMASTER WATER-SOURCE HEAT PUMPS Tranquility ® Large Water-to-Water (TMW) Series Rev.: 12 February, 2016 Control System (continued) Figure 11: Status Menu C l i m a t e M a s t e r Wa t e r - S o u r c e H e a t P u m p s THE SMART SOLUTION FOR ENERGY EFFICIENCY Tranquility ® Large Water-to-Water (TMW) Series Rev.: 12 February, 2106 Control System (continued) Figure 12: Setup Menu GENERAL SYSTEM SETTINGS (FN4) TMW System Setup FN2 [→General System Settings] [→Heat & Cool Setpoint Menus] [→Lead Compr Rotation Setup] [→Alarm Lockout Reset ] [→Unit Loading Status] [→Schedules] [→Prev] [→STATUS] [→HOME] [→ALARM] LEAD COMPR ROTATION SETUP TMW Lead Compr Rotation Setup Lead Compr Rotation Method: [Monthly] Manual Rotate LeadCompr:[Do Not Rotate] Rotate Cmpr Lead on Runtime Hrs: [0000] Refresh Runtime Hours: [000] [→Prev] [→SETUP] [→HOME] [→ALARM] HEAT-COOL SETPOINTS MENU TMW General System Settings Enable BAS Cool Control?[Yes] Enable BAS Heat Control?[Yes] Mod Ref Type[407C] Unit Model Type: [TMW] Software Version: TMW-HP.SDAM.04a.11 [→Prev] [→SETUP] [→HOME] [→ALARM] ALARM LOCKOUT RESET (FN3) TMW Alarm Lockout Reset FN3 [→Reset All Module Alarms at Once] [→Reset Comp Alarms] [→Reset Module Freeze &Hot Alarms] [→Reset Comp Runtime & Cycles] [→Reset All Module Sensor OOR Alarms] Master Pnl Out-of-Range Alm Reset:[Off] Master Pnl Temp Lockout Reset: [Off] [→Prev] [→SETUP] [→HOME] [→ALARM] [→HOME] Reset All Module Alarms at Once Reset All Alarms at Once? [Yes] [→SETUP] TMW Reset Mod Wtr Hot&Freeze Alarms M1 inFreezAlm? Yes/M1 Frz-CWReset?[Yes] M1 in CWR Alm? Yes/ [→Prev] [→SETUP] [→HOME] TMW Reset Module Sensor OOR Alms M1C1 inOOR Alm? Yes/ Reset M1 OOR?[Yes] M1C2 inOOR Alm? Yes/ [→Prev] [→SETUP] [→HOME] Compr Runtime & Cycles Menu Runtm[Yes]/M1C1Reset Cycl[Yes] Runtm[Yes]/M1C2Reset Cycl[Yes] [→SETUP] [→HOME] [→Prev] Reset M1C1Reset M1C2Reset [→Prev] TMW Reset Compr Alarms M1C1 in Alarm? Yes /M1C1Reset Alm?[Yes] M1C2 in Alarm? Yes /M1C2Reset Alm?[Yes] [→Prev] [→SETUP] [→HOME] COOL MODE SETPOINT MENU TMW Cool Mode Setpoint Menu Local Evap Wat Out Setpt:[0000.0]F Min Evap Wat Out Setpt:[0000.0]F Max Evap Wat Out Setpt:[0000.0]F Active Evap Wat Out Setpt:0000.0F [→Prev] [→SETUP] [→HOME] [→ALARM] TMW Heat and Cool Setpoints [→Cool Setpoint Menu] [→Heat Setpoint Menu] [→Diff Press Chnls 1-13&1-14 Setup] [→Lead Compr Rotation Setup] [→Prev] [→SETUP] [→HOME] [→ALARM] HEAT MODE SETPOINT MENU TMW Heat Mode Setpoint Menu Local Cond Wat Out Setpt:[0000.0]F Min Cond Wat Out Setpt:[0000.0]F Max Cond Wat Out Setpt:[0000.0]F Active Cond Wat Out Setpt: 0000.0 F [→Prev] [→SETUP] [→HOME] [→ALARM] 27 c l i m a t e m a s t e r. c o m 28 C l i m a t e M a s t e r Wa t e r - S o u r c e H e a t P u m p s M1 Manual Mode [Off] M1C1 Manual ON [Off] M1C1 Status: Off M1C2 Manual ON [Off] M1C2 Status: Off Max Time Allowed in Manual Mode:[000] s Force a Reset from Manual Mode: [Off] [→Prev] [→SERVICE] [→HOME] TMW Module 1 Compr Unload Status M1C1 Low Suct Press Unload : Off M1C2 Low Suct Press Unload : Off M1C1 XLow Suct Press Unload : Off M1C2 XLow Suct Press Unload : Off M1C1 Low Suct Temp Unload : Off M1C2 Low Suct Temp Unload : Off M1 Evap Freeze Temp Unload : Off M1 Cond WatOut Temp Unload : Off M1C1 High Dis Press Unload : Off M1C2 High Dis Press Unload : Off M1C1 High Dis Temp Unload : Off M1C2 High Dis Temp Unload : Off [→Prev] [→SETUP] [→HOME] [→ALARM] MODULE COMPR UNLOAD FUNCTIONS F5 Diagnostics Manual Mode [ Manual Mode M1] /[ Lock Water Temps] SWAP LEAD COMPR: [Do Not Refresh Lead] [→Prev] [→SETUP] [→HOME] [→ALARM] DIAGNOSTIC & MANUAL MODE RESET ALL MODULE SENSOR OORʼS TMW Module 1 Water Calibrations SrcOutCalib:[0000.0]F/SrcOutSta:0000.0F SrcIn Calib:[0000.0]F/SrcInStat:0000.0F LdOutCal:[0000.0]F/ LoadOutStat:0000.0F LoadInCal:[0000.0]F/LoadIn Stat:0000.0F TMW Module 1 Refrig Calibrations C1DisPresCal:[0000]psi/C1DisPr: 0000psi C2DisPresCal:[0000]psi/C2DisPr: 0000psi C1SucPresCal:[0000]psi/C1SucPr:0000.0ps C2SucPresCal:[0000]psi/C2SucPr:0000.0ps C1DisTmpCal:[0000.0]ºF/C1DisTp:0000.0ºF C2DisTmpCal:[0000.0]ºF/C2DisTp:0000.0ºF C1SucTempCal:[0000.0]F/C1SucTp:0000.0F C2SucTempCal: [0000.0]F/C2SucTp:0000.0F [→Prev] [→SETUP] [→HOME] CALIBRATE ALL MODULE SENSORS TMW Service Menu Setup FN7 [→Diagnostics Manual Mode] [→All Module Compr Unload Status] FN5 [→All Modules Sensor Calibration Menu] [→Reset All Module Sensor OOR Alarms] [→Reset Comp Alarms] [→Reset All Module Alarms at Once] [→TMW Module Water Temp Limits] [→Lock Water Temps] [→Reset Comp Runtimes & Cycles] [→Prev] [→SETUP] [→HOME] [→ALARM] WATER TEMP LIMITS TMW Lock Water Temps Wat In Lock :[Off] Wat In Lock Value :[0000.0]F Wat Out Lock :[Off] Wat Out Lock Value :[0000.0]F Wat In Lock :[Off] Wat In Lock Value :[0000.0]F Wat Out Lock :[Off] Wat Out Lock Value :[0000.0]F Wat In Lock :[Off] Wat In Lock Value :[0000.0]F Wat Out Lock :[Off] Wat Out Lock Value :[0000.0]F Wat In Lock :[Off] Wat In Lock Value :[0000.0]F Wat Out Lock :[Off] Wat Out Lock Value :[0000.0]F [→SETUP] [→HOME] TMW Module Water Temp Limits Cool Mode Cold Wtr Low Limit: [0000.0]F Cool Mode Cold Wtr High Limit:[0000.0]F Cool Mode Hot Wtr Low Limit : [0000.0]F Cool Mode Hot Wtr High Limit :[0000.0]F Heat Mode Cold Wtr Low Limit: [0000.0]F Heat Mode Cold Wtr High Limit:[0000.0]F Heat Mode Hot Wtr Low Limit : [0000.0]F Heat Mode Hot Wtr High Limit :[0000.0]F [→Prev] [→SETUP] [→HOME] TMW Alarm Lockout Reset FN3 [→Reset All Module Alarms at Once] [→Reset Comp Alarms] [→Reset Module Freeze &Hot Alarms] [→Reset Comp Runtime & Cycles] [→Reset All Module Sensor OOR Alarms] [→Prev] [→SETUP] [→HOME] [→ALARM] RESET COMPR ALARMS Cool Evap Cool Evap Cool Evap Cool Evap Cool Cond Cool Cond Cool Cond Cool Cond Heat Evap Heat Evap Heat Evap Heat Evap Heat Cond Heat Cond Heat Cond Heat Cond [→Prev] LOCK WATER TEMPS CLIMATEMASTER WATER-SOURCE HEAT PUMPS Tranquility ® Large Water-to-Water (TMW) Series Rev.: 12 February, 2016 Control System (continued) Figure 13: Service Menu THE SMART SOLUTION FOR ENERGY EFFICIENCY Tranquility ® Large Water-to-Water (TMW) Series Rev.: 12 February, 2106 Control System (continued) Figure 14: Alarm Screen (FN+3 resets the alarm) EVENT HISTORY (100 MOST RECENT ) =====================ACTIVE ALARMS===================== Service Menu - TMW service and limits can be checked (figure 13) Sub-menus NONE IN BUFFER. =====================ACTIVE FAULTS====================== NONE IN BUFFER. ================RETURNED-TO-NORMAL (RTN)================ NONE IN BUFFER. ================MANUALLY CLEARED (CLR)================== NONE IN BUFFER. [- -> PREV ] Operating Unit with BacView6 Connect to I/O FLEX6126 at J6 with cable BACView6A. When power is first applied to the BACView6 a 45 second initialization period will occur. The display will show the home screen (Figure 10). Various display screens are accessible by several methods. From the “Home” screen, you are easily guided to the main menu listings for the following categories by pressing one of the four menu buttons: Status, Setup, Service, Alarm. At the end of this delay, the first compressor will start and after a 5 minute timeout, the display will change to the default screen. (Figure 15) Figure 15: Default Screen ClimateMaster Model TMW Date: MM/DD/YYYY Time: HH:MM AM Sourc WtrOut:0000.0F/LoadWtrOut:0000.0F press any key to continue • • • • • • • Diagnostic and manual mode Compressor unload functions F5 Calibrate sensors Reset sensor OOR’s Reset compressor alarms Water temperature limits Lock water temperatures Alarm Menu - Up to 100 of the most recent occurrences stored with date and time. Access to this log is available through the keypad. (Figure 14) Chilled Water Flow Sensor - The controller has an input for a differential pressure sensor configured for sensor, which measures and displays pressure drops across the entering and leaving water. If the differential pressure drops below a predetermined setting for a fixed period of time, after the unit receives a “RUN” input signal, the unit will not be allowed to run and a water flow alarm condition is displayed. The alarm condition must be resolved, flow re-established, and a minimum pressure differential acknowledged by the differential pressure sensor. The alarm clears automatically (the alarm condition is logged for retention in the most recent 100 alarms) which constitutes an “OK to RUN” status. Setup Menu - System operation is determined by the values assigned to the system variables, as predominantly found in the Setup menu (Figure 12). The Setup menu lists a series of sub-menus: • • • • General System Settings Heating and Cooling Setpoint Menus Lead Compressor Rotation Setup Alarm Lockout Reset (or FN + 3) These variables are initially assigned a default value. For most applications, these values will provide optimum results. Once these values have been set, they are put in permanent memory and will remain, even when all power is removed from the TMW. c l i m a t e m a s t e r. c o m 29 CLIMATEMASTER WATER-SOURCE HEAT PUMPS Tranquility ® Large Water-to-Water (TMW) Series Rev.: 12 February, 2016 Control System (continued) Condenser Water Flow Sensor - The controller has an input for a differential pressure sensor, which measures and displays pressure drops across the condenser water main headers. If the differential pressure drops below a predetermined setting for a fixed period of time after the unit receives a “RUN” input signal, the unit will not be allowed to run, and a Source water flow alarm condition is displayed. This alarm condition must be resolved and flow re-established, and a minimum pressure differential acknowledged by the differential pressure sensor. The alarm clears automatically; however, the alarm condition is logged for permanent retention of the most recent 100 alarms. This will constitute an “OK to RUN” status. Alternatively, the controller can configure to accept a differential pressure sensor indicating proper Source water flow (refer to the wiring diagram), set to differential pressure sensor. Alarm Output - The relay output contact is closed whenever there is an active latching or non-latching alarm condition present relative to a fault parameter. TMW Status Output - The relay output contact is closed whenever all input signals to the unit are present and normal, indicating the requirement for the unit to operate when able. 30 C l i m a t e M a s t e r Wa t e r - S o u r c e H e a t P u m p s THE SMART SOLUTION FOR ENERGY EFFICIENCY Tranquility ® Large Water-to-Water (TMW) Series Rev.: 12 February, 2106 Control System Optional Features Building Automation System (BAS) Interface - Internal operational information is available where the TMW is to be integrated into a building system and monitored by the equipment of a controls manufacturer. Available protocols built into the Control System as standard are: • BACnet over MSTP • MODBUS • N2 High Discharge Temperature - During operation, should this temperature rise above 225ºF, the compressor will shut down. This requires resetting at the Controller after the temperature has cooled to below 175ºF. See Setup Menu for Alarm Menu display or press FN+3. Low Leaving Chilled Water Temperature - Below 36ºF - Evaporator freeze protection requires resetting at the Controller after the temperature has risen to 40ºF See Setup Menu for Alarm Menu display or press FN+3. Compressor Unloading - Compressor unloading routines are programmed into the controller. When any one of the compressor control parameters approaches a pre-limit condition, the Control System executes appropriate compressor unloading commands to avoid compressor lockout, thus maximizing the unit on time. High Leaving Condenser Water Temperature - Above 140ºF This requires resetting at the Controller after the temperature has fallen below 135ºF. See Setup Menu for Alarm Menu display or press FN+3. Compressor Minimum Off Delay - When a compressor is turned off, the compressor will remain off for this period of time. Communications Error - This signifies a loss of communication between any TMW controller and the BAS or BACView6. Compressor Minimum On Delay - When a compressor is turned on, the compressor will remain on for this period of time. This time can be cut short if an alarm condition is predicted. Miscellaneous Alarm Functions of the Control System • Loss of flow through the evaporator • Loss of flow through the condenser • Electrical voltage/phase failure • Temperature Sensor “Out-of-Range” error detects when an open or shorted sensor condition exists. ALARM FUNCTIONS OF THE CONTROL SYSTEM High Pressure Cutout - This requires resetting at both the TMW manual reset high pressure control switch and at the Controller’s software reset to resume operation See Setup Menu for Alarm Menu display or press FN+3. Low Pressure Cutout - This requires resetting at the Controller to resume operation.See page 5 Setup Menu for Alarm Menu display or press FN+3. Compressor Thermal Protector Fault - This would occur if the motor protector sensed an overload trip in the compressor motor. It would also occur if any component in the motor protector circuit failed to open. This requires resetting at the Controller. See Setup Menu for Alarm Menu display or press FN+3. Low Suction Temperature - During operation, should this temperature drop to 28ºF, the compressor will shut down. This requires resetting at the Controller after the temperature has risen above 33ºF. See Setup Menu for Alarm Menu display or press FN+3. c l i m a t e m a s t e r. c o m 31 CLIMATEMASTER WATER-SOURCE HEAT PUMPS Tranquility ® Large Water-to-Water (TMW) Series Rev.: 12 February, 2016 Control Sequence of Operation from BAS A. Heat Pump Module #1 Startup in Cool Mode: B. Heat Pump Module #1 Startup in Heat Mode: 1. Ensure all “local” binary inputs at the heat pump are in the open state for the following points: • “dig_cool_enable_1”, (B1:4); • “dig_heat_enable_1”, (B1:5); 1. Ensure all “local” binary inputs at the heat pump are in the open state for the following points: • “dig_cool_enable_1”, (B1:4); • “dig_heat_enable_1”, (B1:5); 2. Adjust the cool leaving target by writing to the following point, “cool_temp_stp_1”. Valid adjustment values are from 42 to 62 in deg. F. 2. Adjust the heat leaving target by writing to the following point, “heat_temp_stp_1”. Valid adjustment values are from 80 to 135 in deg. F. 3. Command the BBV point (BV:53), “heat_enable_ bas_1” to the “OFF” or “0” position”. 3. Command the BBV point (BV:52), “cool_enable_ bas_1” to the “OFF” or “0” position”. 4. Command the BBV point (BV:52), “cool_enable_ bas_1” to the “ON” or “1” position. 4. Command the BBV point (BV:53), “heat_enable_ bas_1” to the “ON” or “1” position. 5. The above four steps (1 through 4) will signal to open the motorized valves inside the module to allow for water flow to both the load and source loops. When the motorized valve(s) aux. switches detect the valve(s) are opened, (when the BBV point (BV: 107), “mot_ valve_status_1” is in the “ON” or “1” state), then start the load and source water pumps for the heat pump module. 5. The above four steps (1 through 4) will signal to open the motorized valves inside the module to allow for water flow to both the load and source loops. When the motorized valve(s) aux. switches detect the valve(s) are opened, (when the BBV point (BV: 107), “mot_ valve_status_1” is in the “ON” or “1” state), then start the load and source water pumps for the heat pump module. 6. When load flow is established, the BBV point (BV:9), “load_flow_1” will show in the “ON” or “1” state. 6. When load flow is established, the BBV point (BV:9), “load_flow_1” will show in the “ON” or “1” state. 7. When source flow is established, the BBV point (BV:73), “source_flow_1” will show in the “ON” or “1” state. 7. When source flow is established, the BBV point (BV:73), “source_flow_1” will show in the “ON” or “1” state. 8. When #8 and #9 above are both “ON”, the combined flow point (BV:38), “flow_1” will show in the “ON” or “1” state. 8. When #8 and #9 above are both “ON”, the combined flow point (BV:38), “flow_1” will show in the “ON” or “1” state. 9. When the following conditions are all met: • all inlet and outlet load and source water temperatures are within acceptable limits; • the heat mode is not currently commanded ON; • the phase monitor detects normal operation,; • the delay before a change in heat mode to cool mode has expired, or when BBV point (BV:23), “clg_ok_1” will show in the “ON” or “1” state; 9. When the following conditions are all met: • all inlet and outlet load and source water temperatures are within acceptable limits; • the heat mode is not currently commanded ON; • the phase monitor detects normal operation,; • the delay before a change in cool mode to heat mode has expired, or when BBV point (BV:70), “htg_ok_1” will show in the “ON” or “1” state; 10. Then you will see the BBV point (BV:21), “run_cool_1” will show in the “ON” or “1” state. 10. Then you will see the BBV point (BV:22), “run_ heat_1” will show in the “ON” or “1” state. 11. Finally, the 100-digit, Cool PID routine will then begin counting, and you will see the AV point, (AV:634), “stg1_clg_pid_1” count up from 0. When the count reaches 50, the lead compressor will turn “ON”, and when the count reaches 100, the lag compressor will turn ON. 11. Finally, the 100-digit, Heat PID routine will then begin counting, and you will see the AV point, (AV:635), “stg1_htg_pid_1” count up from 0. When the count reaches 50, the lead compressor will turn “ON”, and when the count reaches 100, the lag compressor will turn ON. 32 C l i m a t e M a s t e r Wa t e r - S o u r c e H e a t P u m p s THE SMART SOLUTION FOR ENERGY EFFICIENCY Tranquility ® Large Water-to-Water (TMW) Series Rev.: 12 February, 2106 BACnet, Modbus, N2 Points List Name Note C1-C2 Status Inputs C1 Discharge Pressure C1 Discharge Temp C1 Suction Pressure C1 Suction Temp C2 Discharge Pressure C2 Discharge Temp Load Inlet Temp Cool Mode C2 Suction Pressure C2 Suction Temp Load Inlet Temp Heat Mode Load Outlet Temp Cool Mode Mot Valve Status Inputs Load Outlet Temp Heat Mode Diff Press Hi Range Load Flow 0-5VDC Diff Press Hi Range Source Flow 0-5VDC Diff Press Low Range Load Flow 0-5VDC Diff Press Low Range Source Flow 0-5VDC Source Inlet Temp Cool Mode Source Inlet Temp Heat Mode Source Outlet Temp Cool Mode Source Outlet Temp Heat Mode Remote Cool Setpoint 0-10VDC Remote Heat Setpoint 0-10VDC Phase Input OK Load Water Flow Switch Source Water Flow Switch Digital Input Cool Enable Digital Input Heat Enable Reset All Alarms Source Cond Mot Valve AO Alarm Flash Code AO Cool Reversing Valve S/S Chiller Status Comp 1 S/S Comp 2 S/S Load Mot Vlv S/S Alarm # Cool Comp Requested # Heat Comp Requested Active Cool Setpoint Active Heat Setpoint C1 Disch Pressure Status C1 Discharge Temp Status Cond Mot Valve PID I-gain C1 Suction Pressure Status C1 Suction Temp Status C2 Discharge Pressure Status Cond Mot Valve PID Min Percent Cond Mot Valve PID P-gain Cond In Temp Status Cond Wtr Inlet Temp Status Alarm Flash Code number Cool Mode PID Deadband1 Cool Mode PID Fall Rate Cool Mode PID I-gain Cool Mode PID P-gain Cool Mode PID Rise Rate Cond Wtr Outlet Temp Status C2 Discharge Temp Status Cool Mode Evap Wtr Low Alm Temp Cool Mode Cond Wtr Hi Alm Temp Cool Mode Evap Wtr Hi Alm Temp Cool Mode Low Cond Alarm Temp Load Water Header Diff Pressure Evap Mot Vlv PID Deadband Evap Mot Valve PID I-gain Evap Mot Valve PID Min Percent BACnet MSTP Object Type ID BAI AI:1 BAI AI:2 BAI AI:3 BAI AI:4 BAI AI:5 BAI AI:6 BAI AI:7 BAI AI:8 BAI AI:9 BAI AI:10 BAI AI:11 BAI AI:12 BAI AI:13 BAI AI:14 Object Name Value 1 1 1 1 1 1 1 1 1 1 1 1 1 1 c1-2_inputs_1 c1_disch_pres_1 c1_disch_temp_1 c1_suc_pres_1 c1_suct_temp_1 c2_disch_pres_1 c2_disch_temp_1 load_in_temp_cool_1 c2_suc_pres_1 c2_suct_temp_1 load_in_temp_heat_1 load_out_temp_cool_1 valve_in_1 load_out_temp_heat_1 -60.2 128.4 76.9 °F 130.6 77.0 °F -3.7 77.3 °F 77.3 °F 130.6 77.4 °F 77.3 °F 42.2 °F 99.2 42.2 °F 1 diff_pr_hi_range_load_010_1 15.23 BAI D D D D D D D D D D D D D D Modbus Object Register Type float value 40001 float value 40003 float value 40005 float value 40007 float value 40009 float value 40011 float value 40013 float value 40027 float value 40015 float value 40017 float value 40029 float value 40031 float value 40047 float value 40033 analog analog analog analog analog analog analog analog analog analog analog analog analog analog in in in in in in in in in in in in in in 1 2 3 4 5 6 7 14 8 9 15 16 24 17 DEV:2460xx D float value 40019 analog in 10 D float value 40021 analog in 11 D D D D D D D D D float value float value float value float value float value float value discrete in discrete in discrete in 40039 40041 40043 40045 40035 40037 10008 10007 10010 analog in analog in analog in analog in analog in analog in binary in binary in binary in 20 21 22 23 18 19 6 5 8 D discrete in float value float value discrete in discrete in discrete in discrete in discrete in discrete in float value float value float value float value float value float value float value float value float value float value float value float value float value float value float value float value float value float value float value float value float value float value 10009 40051 40049 10014 10003 10012 10013 10015 10002 40059 40061 40063 40065 40069 40093 40147 40103 40107 40109 40171 40175 40211 40209 40067 40073 40079 40085 40089 40091 40213 40113 binary in analog out analog out binary out binary out binary out binary out binary out binary out data float data float data float data float data float data float data float data float data float data float data float data float data float data float data float data float data float data float data float data float data float data float 7 2 1 5 2 3 4 6 1 3 4 5 6 8 11 48 14 16 17 50 52 76 74 7 18 21 24 26 27 77 31 Exp: Num 0:12 0:03 0:07 0:01 0:05 0:04 0:08 1:09 0:02 0:06 1:09 1:10 0:11 1:10 I/O Type Device ID Read Only Thermistor 0-5 Volt Thermistor 0-5 Volt Thermistor 0-5 Volt Thermistor Thermistor 0-5 Volt Thermistor Thermistor Thermistor Thermistor Thermistor DEV:2460xx DEV:2460xx DEV:2460xx DEV:2460xx DEV:2460xx DEV:2460xx DEV:2460xx DEV:2460xx DEV:2460xx DEV:2460xx DEV:2460xx DEV:2460xx DEV:2460xx DEV:2460xx AI:15 1:14 0-5 Volt N2 Type ID 1 diff_pr_hi_range_source_010_1 15.23 BAI AI:16 1:13 0-5 Volt DEV:2460xx 1 diff_pr_load_010_1 5.07 BAI AI:17 1:14 0-5 Volt DEV:2460xx 1 diff_pr_source_010_1 5.07 BAI AI:18 1:13 0-5 Volt DEV:2460xx 1 1 1 1 1 1 1 1 1 1 1 1 1 1 1 1 1 1 1 1 2 2 2 2 2 2 src_in_temp_cool_1 src_in_temp_heat_1 src_out_temp_cool_1 src_out_temp_heat_1 rem_chw_stp_010_1 rem_cw_stp_010_1 phase_in_ok_1 ld_water_flow_1 src_water_flow_1 dig_cool_enable_1 dig_heat_enable_1 reset_all_alrm_1 cnd_vlv_ao_1 alm_flash_code_ao_1 cool_rev_vlv_bo_1 chlr_stat_1 comp_1_ss_bo_1 comp_2_ss_bo_1 load_vlv_ss_bo_1 o245_1 cool_comp_req_1 heat_comp_req_1 cool_stp_stat_1 heat_stp_stat_1 c1_disch_pres_stat_1 c1_disch_temp_stat_1 cdmv_i_gain_1 c1_suc_pres_stat_1 c1_suct_temp_stat_1 c2_disch_pres_stat_1 cdmv_pid_mnpct_1 cdmv_p_gain_1 cond_in_tmp_stat_1 cond_in_temp_stat_1 alarm_code_1 clg_db1_1 clg_fall_1 clg_i_gain_1 clg_p_gain_1 clg_rise_1 cond_out_temp_stat_1 c2_disch_temp_stat_1 77.3 °F 77.3 °F 105.5 °F 105.5 °F 7.7 7.8 On Off Off Off Off Off 4.80% 0.00% On On Off Off On Off 0.0 0.0 44.0 °F 120.0 °F 128.4 76.9 0.01 130.7 77.0 -3.9 35.0 2.0 77.3 °F 77.3 1.0 1.0 40.0 0.8 16.0 10.0 sec 105.5 77.3 BAI BAI BAI BAI BAI BAI BBI BBI BBI BBI BBI BBI BAO BAO BBO BBO BBO BBO BBO BBO BAV BAV BAV BAV BAV BAV BAV BAV BAV BAV BAV BAV BAV BAV BAV BAV BAV BAV BAV BAV BAV BAV AI:19 AI:20 AI:21 AI:22 AI:23 AI:25 BI:1 BI:2 BI:3 BI:4 BI:5 BI:7 AO:1 AO:2 BO:1 BO:2 BO:3 BO:4 BO:5 BO:6 AV:3 AV:4 AV:5 AV:6 AV:7 AV:9 AV:14 AV:16 AV:19 AV:20 AV:22 AV:23 AV:26 AV:29 AV:31 AV:32 AV:35 AV:38 AV:40 AV:41 AV:42 AV:43 1:11 1:11 1:12 1:12 1:15 1:16 1:01 1:02 1:03 1:04 1:05 1:06 0:01 0:02 0:03 0:06 0:01 0:02 0:04 0:05 Thermistor Thermistor Thermistor Thermistor 0-10 Volt 0-10 Volt Binary Input Universal Input Universal Input Universal Input Universal Input Universal Input Electrical 0-10 Volt Electrical 0-10 Volt Relay / Triac Output Relay / Triac Output Relay / Triac Output Relay / Triac Output Relay / Triac Output Relay / Triac Output DEV:2460xx DEV:2460xx DEV:2460xx DEV:2460xx DEV:2460xx DEV:2460xx DEV:2460xx DEV:2460xx DEV:2460xx DEV:2460xx DEV:2460xx DEV:2460xx DEV:2460xx DEV:2460xx DEV:2460xx DEV:2460xx DEV:2460xx DEV:2460xx DEV:2460xx DEV:2460xx DEV:2460xx DEV:2460xx DEV:2460xx DEV:2460xx DEV:2460xx DEV:2460xx DEV:2460xx DEV:2460xx DEV:2460xx DEV:2460xx DEV:2460xx DEV:2460xx DEV:2460xx DEV:2460xx DEV:2460xx DEV:2460xx DEV:2460xx DEV:2460xx DEV:2460xx DEV:2460xx DEV:2460xx DEV:2460xx cool_evap_lo_tmp_1 38.0 BAV AV:44 DEV:2460xx float value 40245 data float 97 cool_high_cond_tmp_1 140.0 BAV AV:45 DEV:2460xx float value 40249 data float 99 100 2 2 2 2 2 2 2 2 D D D D D D D D D D D D D D cool_hi_evap_tmp_1 90.0 BAV AV:47 DEV:2460xx float value 40251 data float cool_lo_cond_tmp_1 40.0 BAV AV:48 DEV:2460xx float value 40257 data float 103 diff_press_ld_1 evmv_pid_db_1 evmv_i_gain_1 evmv_pid_mnpct_1 15.23 0.0 0.01 35.0 BAV BAV BAV BAV AV:49 AV:50 AV:52 AV:54 DEV:2460xx DEV:2460xx DEV:2460xx DEV:2460xx float float float float 40279 40299 40303 40307 data data data data 108 124 126 128 D value value value value float float float float Note 1: Indicates Physical Inputs/Outputs to/from Master Controller. Note 2: Indicates Recommended Status Indication of important parameters. Note 3: Indicates Command Inputs from Bacview/BAS system. Note 4: Indicates Customer Alarm Reset Functions from Bacview/BAS System. Note 5: Indicates all System Alarms possible. Table Continued on Next Page c l i m a t e m a s t e r. c o m 33 CLIMATEMASTER WATER-SOURCE HEAT PUMPS Tranquility ® Large Water-to-Water (TMW) Series Rev.: 12 February, 2016 Name Evap Mot Valve PID P-gain Evap Mot Valve PID Ramp Source Water Header Diff Pressure Note 2 Value evmv_p_gain_1 evmv_pid_ramp_1 2.0 1.0 diff_press_src_1 15.23 BACnet MSTP Object Type ID BAV AV:55 BAV AV:56 BAV Exp: Num I/O Type AV:57 Read Only DEV:2460xx DEV:2460xx DEV:2460xx D Modbus Object Register Type float value 40311 float value 40313 Type N2 ID data float data float 130 131 float value 40283 data float 109 155.0 BAV AV:63 DEV:2460xx float value 40385 data float 166 1.0 40.0 0.8 16.0 10.0 sec 105.5 77.3 265.0 41.9 BAV BAV BAV BAV BAV BAV BAV BAV BAV AV:64 AV:67 AV:70 AV:72 AV:73 AV:75 AV:76 AV:78 AV:80 DEV:2460xx DEV:2460xx DEV:2460xx DEV:2460xx DEV:2460xx DEV:2460xx DEV:2460xx DEV:2460xx DEV:2460xx float float float float float float float float float value value value value value value value value value 40151 40157 40163 40167 40169 40215 40285 40409 40293 data data data data data data data data data float float float float float float float float float 57 60 63 65 66 78 110 178 120 man_mode_time_1 900.0 BAV AV:81 DEV:2460xx float value 40411 data float 179 2 max_cool_load_stp_1 62.0 °F BAV AV:82 DEV:2460xx float value 40413 data float 180 2 cool_temp_stp_1 44.0 °F BAV AV:83 DEV:2460xx float value 40277 data float 107 heat_evap_lo_tmp_1 38.0 BAV AV:84 DEV:2460xx float value 40355 data float 151 2 2 2 2 D D D c2_suc_pres_stat_1 130.7 BAV AV:86 DEV:2460xx float value 40119 data float 34 min_cool_load_stp_1 40.0 °F BAV AV:87 DEV:2460xx float value 40417 data float 182 heat_temp_stp_1 mod_cmpr_off_delay_1 mod_cmpr_min_run_1 mod_default_hp_1 mod_default_sp_1 mod_cool_lo_suc_press_ sp_410_1 120.0 °F 220.0 90.0 200.0 125.0 BAV BAV BAV BAV BAV AV:88 AV:89 AV:90 AV:93 AV:94 DEV:2460xx DEV:2460xx DEV:2460xx DEV:2460xx DEV:2460xx float float float float float value value value value value 40371 40423 40425 40121 40125 data data data data data float float float float float 159 185 186 32 33 92.0 BAV AV:98 DEV:2460xx float value 40267 data float 105 heat_high_cond_tmp_1 140.0 BAV AV:99 DEV:2460xx float value 40359 data float 153 mod_hi_disch_press_sp_1 560.0 BAV AV:100 DEV:2460xx float value 40443 data float 195 mod_hi_disch_tmp_1 225.0 BAV AV:101 DEV:2460xx float value 40445 data float 196 cool_lo_suct_tmp_1 32.0 BAV AV:104 DEV:2460xx float value 40275 data float 106 float value 40361 data float 154 float value 40123 data float 36 float value 40363 data float 155 D D D heat_hi_evap_tmp_1 90.0 BAV AV:105 DEV:2460xx c2_suct_temp_stat_1 77.4 BAV AV:107 DEV:2460xx heat_lo_cond_tmp_1 40.0 BAV AV:110 DEV:2460xx mod_high_suct_press_sp_1 155.0 BAV AV:111 DEV:2460xx D float value 40451 data float 199 mod_lo_disch_press_sp_1 265.0 BAV AV:112 DEV:2460xx D float value 40453 data float 200 201 D mod_low_low_press_sp_1 5.0 BAV AV:113 DEV:2460xx float value 40455 data float mod_lo_suc_psi_delay_1 60.0 BAV AV:114 DEV:2460xx float value 40457 data float 202 2 2 2 load_in_tmp_stat_1 comp_on_1 failed_comp_1 mod_low_press_sp_1 mod_lo_suction_tmp_1 mod_startup_delay_1 77.3 0.0 0.0 92.0 38.0 60.0 sec BAV BAV BAV BAV BAV BAV AV:118 AV:121 AV:123 AV:124 AV:125 AV:135 DEV:2460xx DEV:2460xx DEV:2460xx DEV:2460xx DEV:2460xx DEV:2460xx float float float float float float value value value value value value 40393 40273 40281 40465 40467 40483 data data data data data data float float float float float float 170 119 122 206 207 215 2 max_heat_temp_stp_1 135.0 °F BAV AV:137 DEV:2460xx float value 40415 data float 181 min_heat_temp_stp_1 75.0 °F BAV AV:138 DEV:2460xx float value 40419 data float 183 rem_cool_stp_stat_1 62.0 °F BAV AV:139 DEV:2460xx D float value 40493 data float 220 rem_heat_stp_stat_1 135.0 °F BAV AV:140 DEV:2460xx D float value 40495 data float 221 c1_suc_sat_tmp_1 c1_suc_superheat_1 mod_heat_lo_suc_press_ sp_410_1 load_out_tmp_stat_1 45.4 31.6 °F BAV BAV AV:141 AV:142 DEV:2460xx DEV:2460xx 92.0 BAV AV:145 DEV:2460xx float value 40367 data float 157 42.2 BAV AV:146 DEV:2460xx D float value 40397 data float 172 heat_lo_suct_tmp_1 32.0 BAV AV:147 DEV:2460xx float value 40369 data float 158 2 lo_ld_diff_pr_1 1.5 BAV AV:148 DEV:2460xx float value 40399 data float 173 2 lo_src_diff_pr_1 1.5 BAV AV:149 DEV:2460xx float value 40401 data float 174 mod_cool_low_press_sp_1 92.0 BAV AV:150 DEV:2460xx D float value 40429 data float 188 mod_heat_low_press_sp_1 92.0 BAV AV:152 DEV:2460xx D float value 40441 data float 194 reset_alm_delay_1 source_in_tmp_stat_1 source_out_tmp_stat_1 10.0 77.3 105.5 BAV BAV BAV AV:153 AV:154 AV:156 DEV:2460xx DEV:2460xx DEV:2460xx D D float value float value float value 40497 40505 40511 data float data float data float 222 226 229 2 2 2 2 2 Note 1: Indicates Physical Inputs/Outputs to/from Master Controller. Note 2: Indicates Recommended Status Indication of important parameters. Note 3: Indicates Command Inputs from Bacview/BAS system. Note 4: Indicates Customer Alarm Reset Functions from Bacview/BAS System. Note 5: Indicates all System Alarms possible. Table Continued on Next Page 34 Device ID mod_high_suct_press_ sp_410_1 htg_db1_1 htg_fall_1 htg_i_gain_1 htg_p_gain_1 htg_rise_1 cond_out_tmp_stat_1 evap_in_temp_stat_1 mod_lo_disch_press_sp_410_1 evap_out_stat_1 High Suction Press Alm Sp 410a Heat Mode PID Deadband1 Heat Mode PID Fall Rate Heat Mode PID I-gain Heat Mode PID P-gain Heat Mode PID Rise Rate COND Out Temp Status Evap Wtr Inlet Temp Status Low Discharge Press Sp 410a EVAP Out Temp Status Max Allowed Time in Manual Mode Cool Mode Max Water Out Setpoint Cool Mode Outlet Water Setpoint Heat Mode Evap Wtr Low Alm Temp C2 Suction Pressure Status Cool Mode Min Water Out Setpoint Heat Mode Outlet Water Setpoint Compr Min Off-Cycle Delay Compr Min Run Time Module Default Head Pressure Module Default SP Cool Low Suction Press Alrm Sp 410a Heat Mode Cond Wtr Hi Alm Temp Hi Compr Discharge Press Alarm Stp Hi Compr Discharge Alarm Temp Cool Mode Low Suction Alarm Temp Heat Mode Evap Wtr Hi Alm Temp C2 Suction Temp Status Heat Mode Cond Wtr Low Alm Temp High Compr Suction Pressure Stp Low Compr Discharge Pressure Stp Extra-Low Suction Pressure Alarm Stp Time Delay Before Low Suction Pressure Alm Load Water In Temp Status Num of Comp ON Num of Failed Comp Low Suction Pressure Alarm Stp Low Compr Suction Alarm Temp Module Start-Up Delay Heat Mode Max Water Out Setpoint Heat Mode Min Water Out Setpoint Cool Mode Remote Water Out Setpoint Heat Mode Remote Water Out Setpoint C1 Saturated Suction Temp C1 Suction Superheat Heat Low Suction Press Alm Sp 410a Load Water Out Temp Status Heat Mode Low Suction Alm Temp Load Water Header Low Diff Alm Pressure Source Water Header Low Diff Alm Pressure Cool Mode Low Suction Press Alm Stp Heat Mode Low Suction Press Alarm Stp Reset Alarm DELAY Source Wtr In Temp Status Source Wtr Out Temp Status Object Name C l i m a t e M a s t e r Wa t e r - S o u r c e H e a t P u m p s D D D D THE SMART SOLUTION FOR ENERGY EFFICIENCY Tranquility ® Large Water-to-Water (TMW) Series Rev.: 12 February, 2106 Name Evap In Temp Status Evap Wtr Outlet Temp Status Num of Stages ON Actual Low Diff Press Trip Load Actual Low Diff Press Trip Source C1 Comp Cycle Count C2 Comp Cycle Count Diff Pressure Trip Multiplier Estimated Kw Per Ton Estimated Tons Estimated Watts Load Water Diff Pr Cali Point Max Delta Temp- Load Max Delta Temp- Source Num 32.5 Ton Comps Req Stg1 C2 Saturated Suction Temp PID Differential Factor Source Water Diff Pr Cali Point Default HP Using High Head Pressure Default HP Using Low Head Pressure C2 Suction Superheat Cool Mode Setpoint Offset Comp 1 Cycles Comp 1 Runtime Comp 2 Cycles Comp 2 Runtime Cool Mode Setpoint Offset Heating Setpoint Offset Heat Mode Setpoint Offset Max Cool Ramp Rate Maximum Heat Ramp Rate Num of Cooling Comp Requested Num of Heating Comp Requested Time Interval Before Compr Runtime Refresh Source Mot Valve PID Out % Cool Mode PID Count Heat Mode PID Count Step PID Value for 65T C1 Cycles Reset System Run Command Status C1 Hi Discharge Pressure Unload C1 Hi Discharge Temp Unload C1 Extra-Low Suction Pressure Unload C1 Low Suction Pressure Unload Alarm Status Output Cool Mode Enable Input Load Water Flow Switch Status C1 Low Suction Temp Unload C1 Runtime Reset C2 Cycles Reset C2 Hi Discharge Pressure Unload C2 Hi Discharge Temp Unload C2 Extra-Low Suction Pressure Unload C2 Low Suction Pressure Unload C2 Low SuctionTemp Unload C2 Manual Mode Lock On C2 Runtime Reset Cool Mode Run Command Status Heat Mode Run Command Status Cool Mode OK to Run Compr 1 Fail Status Comp 1 High Go Command Compr 1 Min Runtime Status Compr 1 Off Delay Status Compr 1 Start/Stop Compr 1 Sensor Out-O-Range Compr 1 Run Status Compr 2 Min Runtime Status Compr 2 Off Delay Status Compr 2 Start/Stop Note BACnet MSTP Object Type ID BAV AV:157 BAV AV:158 BAV AV:185 BAV AV:186 Exp: Num Object Name Value 2 evap_in_tmp_stat_1 evap_out_temp_stat_1 stages_on_1 act_lo_diff_press_ld_1 77.3 41.9 0.0 2.0 °F 2 act_lo_diff_press_src_1 3.9 °F BAV AV:187 DEV:2460xx 2 2 c1_comp_cyc_count_1 c2_comp_cyc_count_1 diff_pr_trip_mult_1 est_kw_per_ton_1 est_tons_1 est_watts_1 ldpsi_cali_point_1 max_delta_temp_ld_1 max_delta_temp_src_1 num65t1req_1 c2_suc_sat_tmp_1 pid_diff_fact_1 srcpsi_cali_point_1 0.0 0.0 0.6 1.0896169 °F 46.08453 °F 50214.48 °F 0.0 10.0 10.0 0.0 45.4 5.0 0.0 BAV BAV BAV BAV BAV BAV BAV BAV BAV BAV BAV BAV BAV AV:188 AV:189 AV:190 AV:191 AV:192 AV:193 AV:194 AV:195 AV:196 AV:197 AV:200 AV:201 AV:202 DEV:2460xx DEV:2460xx DEV:2460xx DEV:2460xx DEV:2460xx DEV:2460xx DEV:2460xx DEV:2460xx DEV:2460xx DEV:2460xx DEV:2460xx DEV:2460xx DEV:2460xx mod_defaulthp_usehihp_1 200.0 BAV AV:203 DEV:2460xx mod_defaulthp_uselowhp_1 350.0 BAV AV:204 DEV:2460xx c2_suc_superheat_1 cool_stp_with_offset_1 c1_cycles_1 c1_runtime_1 c2_cycles_1 c2_runtime_1 cool_stp_offset_1 heat_stp_offset_1 heat_stp_with_offset_1 max_cool_ramp_rate_1 max_heat_ramp_rate_1 32.0 °F 44.0 0.0 2.215 0.0 2.1 0.0 0.0 120.0 10.0 10.0 BAV BAV BAV BAV BAV BAV BAV BAV BAV BAV BAV AV:447 AV:581 AV:583 AV:584 AV:585 AV:586 AV:588 AV:589 AV:609 AV:615 AV:616 DEV:2460xx DEV:2460xx DEV:2460xx DEV:2460xx DEV:2460xx DEV:2460xx DEV:2460xx DEV:2460xx DEV:2460xx DEV:2460xx DEV:2460xx 2 clg_comp_req_1 0.0 BAV AV:627 DEV:2460xx 2 htg_comp_req_1 0.0 BAV AV:628 DEV:2460xx runtime_refresh_1 84.0 hr BAV AV:631 DEV:2460xx 2 2 2 4 source_mv_pidout_1 stg1_clg_pid_1 stg1_htg_pid_1 step_pid_65t_1 c1_cycles_reset_1 run_1 4.8 0.0 0.0 50.0 Off On BAV BAV BAV BAV BBV BBV AV:633 AV:634 AV:635 AV:638 BV:1 BV:2 c1_hi_dis_psi_unld_1 Off BBV c1_hi_dis_tmp_unld_1 Off c1_lolo_suc_psi_unld_1 c1_lo_suc_psi_unld_1 alarm_bo_1 cool_enable_1 load_flow_1 c1_lo_suc_tmp_unld_1 reset_c1_rtim_1 c2_cycles_reset_1 2 2 2 2 2 2 2 2 2 2 2 4 4 4 2 2 2 I/O Type Modbus Read Object Device ID Register Only Type DEV:2460xx float value 40287 D DEV:2460xx float value 40289 D DEV:2460xx float value 40129 D DEV:2460xx float value 40023 D N2 Type data data data data float float float float ID 112 114 37 1 float value 40025 data float 2 float float float float float float float float float float float float float value value value value value value value value value value value value value 40071 40077 40087 40095 40097 40099 40101 40111 40115 40127 40137 40131 40133 data data data data data data data data data data data data data float float float float float float float float float float float float float 9 10 15 19 20 22 23 28 29 35 43 38 39 float value 40081 data float 12 float value 40083 data float 13 float float float float float float float float float float float value value value value value value value value value value value 40139 40189 40193 40195 40205 40207 40253 40255 40387 40105 40117 data data data data data data data data data data data float float float float float float float float float float float 44 67 69 70 71 72 101 102 167 25 30 D float value 40487 data float 217 D float value 40489 data float 218 float value 40499 data float 223 DEV:2460xx DEV:2460xx DEV:2460xx DEV:2460xx DEV:2460xx DEV:2460xx D D D D float value float value float value float value discrete out discrete in 40507 40317 40319 40135 1 10023 data float 227 data float 140 data float 141 data float 40 binary out 7 binary in 21 BV:3 DEV:2460xx D discrete in 10018 binary in 12 BBV BV:4 DEV:2460xx D discrete in 10021 binary in 13 Off BBV BV:5 DEV:2460xx D discrete in 10022 binary in 14 Off Off On On Off No Off BBV BBV BBV BBV BBV BBV BBV BV:6 BV:7 BV:8 BV:9 BV:10 BV:12 BV:13 DEV:2460xx DEV:2460xx DEV:2460xx DEV:2460xx DEV:2460xx DEV:2460xx DEV:2460xx D D D D D discrete in discrete in discrete in discrete in discrete in discrete out discrete out 10025 10004 10016 10049 10028 3 4 binary in binary in binary in binary in binary in binary out binary out 15 2 10 43 16 9 10 D D D D D D D D D D D D D D c2_hi_dis_psi_unld_1 Off BBV BV:14 DEV:2460xx D discrete in 10029 binary in 19 c2_hi_dis_tmp_unld_1 Off BBV BV:15 DEV:2460xx D discrete in 10030 binary in 20 c2_lolo_suc_psi_unld_1 Off BBV BV:16 DEV:2460xx D discrete in 10031 binary in 23 c2_lo_suc_psi_unld_1 c2_lo_suc_tmp_unld_1 c2_manual_1 reset_c2_rtim_1 Off Off Off No BBV BBV BBV BBV BV:17 BV:18 BV:19 BV:20 DEV:2460xx DEV:2460xx DEV:2460xx DEV:2460xx D D discrete in discrete in discrete out discrete out 10006 10011 5 6 binary in binary in binary out binary out 4 9 11 12 run_cool_1 On BBV BV:21 DEV:2460xx D discrete in 10019 binary in 17 run_heat_1 clg_ok_1 comp1_fail_1 comp_1h_go_1 cmpr1_min_run_1 cmpr1_delay_on_1 comp_1_ss_1 comp1_oor_1 comp1_status_1 cmpr2_min_run_1 cmpr2_delay_on_1 comp_2_ss_1 Off On Off Off Off On Off Off Off Off On Off BBV BBV BBV BBV BBV BBV BBV BBV BBV BBV BBV BBV BV:22 BV:23 BV:24 BV:25 BV:26 BV:27 BV:29 BV:31 BV:32 BV:33 BV:34 BV:36 DEV:2460xx DEV:2460xx DEV:2460xx DEV:2460xx DEV:2460xx DEV:2460xx DEV:2460xx DEV:2460xx DEV:2460xx DEV:2460xx DEV:2460xx DEV:2460xx D D D discrete in discrete in discrete in discrete out discrete in discrete in discrete in discrete in discrete in discrete in discrete in discrete in 10020 10024 10026 7 10027 10032 10033 10034 10035 10036 10037 10038 binary in binary in binary in binary out binary in binary in binary in binary in binary in binary in binary in binary in 18 22 24 13 25 26 27 28 29 30 31 32 D D D D D D D D Note 1: Indicates Physical Inputs/Outputs to/from Master Controller. Note 2: Indicates Recommended Status Indication of important parameters. Note 3: Indicates Command Inputs from Bacview/BAS system. Note 4: Indicates Customer Alarm Reset Functions from Bacview/BAS System. Note 5: Indicates all System Alarms possible. Table Continued on Next Page c l i m a t e m a s t e r. c o m 35 CLIMATEMASTER WATER-SOURCE HEAT PUMPS Tranquility ® Large Water-to-Water (TMW) Series Rev.: 12 February, 2016 Name Compr 2 Sensor Out-Of-Range All Water Flows Status Heat Mode Enable Input Cool Mode Status Heat Mode Run Status Cond Water Out Sensor Available Command Cond Water Out Enable High Temp Limit Cond Water Out Enable Low Temp Limit Compr Discharge Pressure Available Command Compr Discharge Temp Available Command Compr Suction Pressure Available Command Compr Suction Temp Avalable Command Cool Enable BAS Command Heat Enable BAS Command COOL BIN RESET Unit Status Use Water Hdr Diff Press Flow Sensors Use Hi Range Water Hdr Diff Press Flow Sensors Compr 2 Run Status Compr 2 Fail Status Compressor New Lead 1 Fix Mot Valves as Open Command Load Mot Valve Start/Stop HEAT BIN RESET Cond Wtr Inlet Hi Temp Alarm Hi Cond Wtr Out Temp Unload Cond Wtr Inlet Lo Temp Alarm Reset Alarm Timeout Load Mot Valve Aux Switch Status Low Evap Water Out Temp Unload Heat Mode OK to Run Cond Water Inlet Temp Out-OfRange Alarm Source Water Flow Switch Status Compr1 Lead Status Reset All Alarm Compr2 Lead Status Use Pre-Calc Diff Pr Cutout Use Hi Head Pressure Compr for Low HP Ctrl Note 2 Exp: Num I/O Type Modbus Object Register Type discrete in 10039 discrete in 10045 discrete in 10017 discrete in 10043 discrete in 10047 N2 comp2_oor_1 flow_1 heat_enable_1 cool_mode_1 heat_mode_1 Off On Off On Off mod_cwr_avail_1 On BBV BV:44 DEV:2460xx discrete out 22 binary out 28 mod_chs_hi_enable_1 On BBV BV:45 DEV:2460xx discrete out 23 binary out 29 DEV:2460xx DEV:2460xx DEV:2460xx DEV:2460xx DEV:2460xx Type binary binary binary binary binary in in in in in ID 33 39 11 37 41 mod_cwr_lo_enable_1 On BBV BV:46 DEV:2460xx discrete out 24 binary out 30 mod_disch_psi_avail_1 On BBV BV:47 DEV:2460xx discrete out 25 binary out 31 mod_disch_tmp_avail_1 On BBV BV:48 DEV:2460xx discrete out 26 binary out 32 mod_suc_psi_avail_1 On BBV BV:50 DEV:2460xx discrete out 27 binary out 33 mod_suc_tmp_avail_1 On BBV BV:51 DEV:2460xx discrete out 28 binary out 34 cool_enable_bas_1 heat_enable_bas_1 cool_bin_reset_1 unit_status_1 On Off Off On BBV BBV BBV BBV BV:52 BV:53 BV:54 BV:55 DEV:2460xx DEV:2460xx DEV:2460xx DEV:2460xx discrete out discrete out discrete out discrete in 8 10 2 10068 binary out binary out binary out 14 16 8 3 use_diff_pr_flow_sens_1 Yes BBV BV:56 DEV:2460xx discrete out 11 3 use_hi_range_diff_pr_sens_1 Yes BBV BV:57 DEV:2460xx discrete out 12 2 comp2_status_1 comp2_fail_1 newcmplead1_1 Off Off Off BBV BBV BBV BV:58 BV:59 BV:60 DEV:2460xx DEV:2460xx DEV:2460xx discrete in discrete in discrete in 10040 10041 10042 binary in binary in binary in 34 35 36 discrete out 9 binary out 15 10050 13 10092 10044 10093 10063 binary in binary out binary in binary in binary in binary in 44 19 86 38 87 57 45 4 5 5 5 2 D D D D fix_open_mod_1 Off BBV BV:61 DEV:2460xx load_mv_ss_1 heat_bin_reset_1 cond_in_hi_tmp_alm_1 cwr_trg_unld_1 cond_in_lo_tmp_alm_1 reset_alm_timeout_1 On Off Normal Off Normal Off BBV BBV BALM BBV BALM BBV BV:62 BV:63 BV:64 BV:65 BV:66 BV:67 DEV:2460xx DEV:2460xx DEV:2460xx DEV:2460xx DEV:2460xx DEV:2460xx D D D D discrete in discrete out discrete in discrete in discrete in discrete in D load_vlv_status_1 On BBV BV:68 DEV:2460xx D discrete in 10051 binary in freeze_trg_unld_1 Off BBV BV:69 DEV:2460xx D discrete in 10046 binary in 40 htg_ok_1 Off BBV BV:70 DEV:2460xx D discrete in 10048 binary in 42 cond_in_oor_1 Off BALM BV:71 DEV:2460xx D discrete in 10089 binary in 83 src_flow_1 On BBV BV:73 DEV:2460xx D discrete in 10054 binary in 48 On No Off Yes BBV BBV BBV BBV BV:74 BV:75 BV:76 BV:77 DEV:2460xx DEV:2460xx DEV:2460xx DEV:2460xx D 3 m01c1lead_1 reset_all_1 m01c2lead_1 use_pre_calc_dif_pr_setpt_1 discrete in discrete out discrete in discrete out 10052 29 10053 15 binary in binary out binary in binary out 46 35 47 21 3 use_hi_hp_comp_1 Yes BBV BV:78 DEV:2460xx discrete out 14 binary out 20 man_refr_cmplead_1 Do Not Refresh Lead BBV BV:79 DEV:2460xx discrete out 21 binary out 27 4 D 5 c1t1_oor_1 Off BALM BV:81 DEV:2460xx D discrete in 10069 binary in 63 5 c1t2_oor_1 Off BALM BV:82 DEV:2460xx D discrete in 10072 binary in 66 5 cond_out_oor_1 Off BALM BV:83 DEV:2460xx D discrete in 10091 binary in 85 5 5 evap_in_hi_tmp_alm_1 evap_in_lo_tmp_alm_1 Normal Normal BALM BALM BV:84 BV:85 DEV:2460xx DEV:2460xx D D discrete in discrete in 10098 10099 binary in binary in 92 93 5 c2t1_oor_1 Off BALM BV:86 DEV:2460xx D discrete in 10073 binary in 67 5 c2t2_oor_1 Off BALM BV:87 DEV:2460xx D discrete in 10076 binary in 70 5 no_flow_1 Off BALM BV:88 DEV:2460xx D discrete in 10104 binary in 98 5 ld_dif_pr_oor_1 Off BALM BV:89 DEV:2460xx D discrete in 10102 binary in 96 5 phase_alarm_1 Off BALM BV:90 DEV:2460xx D discrete in 10105 binary in 99 5 evap_in_oor_1 Off BALM BV:91 DEV:2460xx D discrete in 10095 binary in 89 5 evap_out_oor_1 Off BALM BV:92 DEV:2460xx D discrete in 10097 binary in 91 5 cd_wtr_out_hi_alm_1 Normal BALM BV:97 DEV:2460xx D discrete in 10100 binary in 94 5 ev_wtr_out_hi_alm_1 Normal BALM BV:98 DEV:2460xx D discrete in 10101 binary in 95 5 cd_wtr_out_lo_alm_1 Off BALM BV:99 DEV:2460xx D discrete in 10103 binary in 97 5 nomodsavail_1 Off BALM BV:100 DEV:2460xx 5 src_dif_pr_oor_1 Off BALM BV:101 DEV:2460xx D discrete in 10106 binary in 100 Note 1: Indicates Physical Inputs/Outputs to/from Master Controller. Note 2: Indicates Recommended Status Indication of important parameters. Note 3: Indicates Command Inputs from Bacview/BAS system. Note 4: Indicates Customer Alarm Reset Functions from Bacview/BAS System. Note 5: Indicates all System Alarms possible. Table Continued on Next Page 36 Device ID Read Only D D D D D Value 3 3 4 2 Manually Refresh Lead Compr C1 Discharge Temp Out-OfRange Alarm C1 Suction Temp Out-Of-Range Alarm Cond Water Outlet Temp Out-OfRange Alarm Evap Wtr Inlet Hi Temp Alarm Evap Wtr Inlet Low Temp Alarm C2 Discharge Temp Out-OfRange Alarm C2 Suction Temp Out-Of-Range Alarm No Flow Alarm Load Water Diff Pressure Out-OfRange Alarm Phase Alarm Evap Water Inlet Temp Out-OfRange Alarm Evap Water Outlet Out-Of-Range Alarm Cond Water Outlet Hi Temp Alarm Evap Water Outlet Hi Temp Alarm Cond Water Outlet Low Temp Alarm No Modules Available Alarm Source Water Diff Pressure OutOf-Range Alarm BACnet MSTP Object Type ID BBV BV:37 BBV BV:38 BBV BV:39 BBV BV:40 BBV BV:41 Object Name C l i m a t e M a s t e r Wa t e r - S o u r c e H e a t P u m p s THE SMART SOLUTION FOR ENERGY EFFICIENCY Tranquility ® Large Water-to-Water (TMW) Series Rev.: 12 February, 2106 Name Module Failure Mot Valve Module Failure Water Out Temp Manual Heat Mode Command Module Here Module Ok Mot Vlv Aux Sw Status Reset Force Man Mode Terminate Request to Run Status Reset C1 Alarms Reset C2 Alarms Reset Freeze or Hot Wtr Alm or Mot Valve Alarm Reversing Valve Reset Sensor Out-Of-Range Alarm Compr OK to Stage Down Compr OK to Stage Up Module OK after Startup Delay Source Mot Valve Aux Switch Status Phase Loss Status C1 Discharge Pressure Out- OfRange Alarm C1 Suction Pressure Out-OfRange Alarm C2 Discharge Pressure Out-OfRange Alarm C2 Suction Pressure Out-OfRange Alarm Compressor 1 Excessive Pump Downs Compr1 High Discharge Temp Alarm Compr1 High Discharge Pressure Alarm Compr1 Extra-Low Suction Pressure Alarm Compr1 Low Suction Pressure Alarm Compressor 1 Low Suction Superheat Compr1 Low Suction Temp Alarm Compr1 No-Run Alarm Compressor 2 Excess Pump Downs Compr2 High Discharge Temp Alarm Compr2 High Discharge Pressure Alarm Compr2 Extra-Low Suction Pressure Alarm Compr2 Low Suction Pressure Alarm Compressor 2 Low Suction Superheat Compr2 Low Suction Temp Alarm Compr2 NO-Run Alarm Cond Water Motorized Valve Status Alarm Evap Water Outlet Low Temp Alarm Evap Water Motorized Valve Status Alarm Superheat Notice Note Object Name Value mod_fail_mot_vlv_1 mod_fail_wat_out_1 reset_manheatmode_1 module_here_1 module_ok_1 mot_vlv_status_1 Off Off Off On On On BACnet MSTP Object Type ID BBV BV:102 BBV BV:103 BBV BV:104 BBV BV:105 BBV BV:106 BBV BV:107 Exp: Num I/O Type Modbus Read Object Device ID Register Only Type DEV:2460xx discrete in 10056 D DEV:2460xx discrete in 10057 D DEV:2460xx discrete in 10058 D DEV:2460xx discrete in 10059 D DEV:2460xx discrete in 10060 D DEV:2460xx discrete out 32 4 reset_forceman_1 No BBV BV:108 DEV:2460xx 4 4 m2457_1 reset_c1_alrm_1 reset_c2_alrm_1 On No No BBV BBV BBV BV:109 BV:110 BV:111 DEV:2460xx DEV:2460xx DEV:2460xx 4 4 reset_freeze_1 No BBV BV:112 DEV:2460xx reversing_vlv_1 On BBV BV:113 DEV:2460xx 50 51 binary in binary in binary in 52 53 54 discrete in 10062 binary out 38 discrete out discrete out discrete out 30 31 33 binary in binary out binary out 56 36 37 discrete in 10064 binary out 39 discrete out 34 binary in 58 reset_oorsl_1 No BBV BV:114 DEV:2460xx D discrete in 10065 binary out 40 Off On On BBV BBV BBV BV:115 BV:116 BV:117 DEV:2460xx DEV:2460xx DEV:2460xx D D D discrete in discrete in discrete in 10066 10067 10070 binary in binary in binary in 59 60 61 source_vlv_status_1 On BBV BV:122 DEV:2460xx D discrete in 10071 binary in 49 phasestat_1 On BBV BV:235 DEV:2460xx D discrete in 10061 binary in 55 5 c1p1_oor_1 Off BALM BV:118 DEV:2460xx D discrete in 10074 binary in 64 5 c1p2_oor_1 Off BALM BV:119 DEV:2460xx D discrete in 10075 binary in 65 D discrete in 10055 5 c2p1_oor_1 Off BALM BV:120 DEV:2460xx 5 c2p2_oor_1 Off BALM BV:121 DEV:2460xx 5 c1_ex_pump_dns_1 Off BALM BV:123 DEV:2460xx binary in 68 binary in 68 5 c1_hi_disch_tmp_1 Off BALM BV:127 DEV:2460xx D discrete in 10077 binary in 71 5 c1_hi_pres_alm_1 Off BALM BV:128 DEV:2460xx D discrete in 10078 binary in 72 5 c1_lolo_suc_pres_alm_1 Off BALM BV:129 DEV:2460xx D discrete in 10079 binary in 73 5 c1_low_suc_pres_alm_1 Off BALM BV:130 DEV:2460xx D discrete in 10080 binary in 74 5 c1_low_suc_supht_1 Off BALM BV:131 DEV:2460xx 5 c1_lo_suc_tmp_1 Off BALM BV:132 DEV:2460xx D discrete in 10081 binary in 75 5 c1_no_run_1 Off BALM BV:136 DEV:2460xx D discrete in 10082 binary in 76 5 c2_ex_pump_dns_1 Off BALM BV:141 DEV:2460xx 5 c2_hi_disch_tmp_1 Off BALM BV:181 DEV:2460xx D discrete in 10083 binary in 77 5 c2_hi_pres_alm_1 Off BALM BV:182 DEV:2460xx D discrete in 10084 binary in 78 5 c2_lolo_suc_pres_alm_1 Off BALM BV:196 DEV:2460xx D discrete in 10085 binary in 79 5 c2_low_suc_pres_alm_1 Off BALM BV:210 DEV:2460xx D discrete in 10086 binary in 80 5 c2_low_suc_supht_1 Off BALM BV:211 DEV:2460xx 5 c2_lo_suc_tmp_1 Off BALM BV:212 DEV:2460xx D discrete in 10087 binary in 81 5 c2_no_run_1 Off BALM BV:213 DEV:2460xx D discrete in 10088 binary in 82 5 cond_vlv_al_1 Off BALM BV:215 DEV:2460xx D discrete in 10090 binary in 84 5 freeze_trg_1 Normal BALM BV:218 DEV:2460xx D discrete in 10094 binary in 88 5 evap_vlv_al_1 Off BALM BV:219 DEV:2460xx D discrete in 10096 binary in 90 40055 data int 3 3 Compr Runtime Refresh Method Selector Remote Cool Trg AI Type- None or 0-5VDC Remote Heat Trg AI Type- None or 0-5VDC dis_suct_superht_1 Off BALM BV:226 DEV:2460xx chiller_model_type_1 TMW600 BMSV MSV:1 DEV:2460xx refresh_cmplead_method_1 Runtime BMSV MSV:2 DEV:2460xx an_inp15_typ_1 NONE BMSV MSV:3 DEV:2460xx an_inp16_typ_1 NONE BMSV MSV:4 DEV:2460xx Compr Refrigerant Type 3 mod_comp_ref_type_1 410a BMSV MSV:5 DEV:2460xx Motorized Valve Options 3 mot_vlv_opt_1 MVCONDEVAP BMSV MSV:6 DEV:2460xx Unit Operating Mode Status D ID binary in binary in stagedn_ok_1 stageup_ok_1 startup_ok_1 Chiller Model Type Remote Cool Mode Setpoint AI Chnl 1-15 Remote Heat Mode Setpoint AI Chnl 1-16 D N2 Type unit_mode_1 Normal Run BMSV MSV:7 DEV:2460xx inp_15_point_type_1 NONE BMSV MSV:8 DEV:2460xx inp_16_point_type_1 NONE BMSV MSV:9 DEV:2460xx D unsigned int unsigned int unsigned int unsigned int unsigned int unsigned int unsigned int unsigned int unsigned int 40076 data int 8 40053 data int 1 40054 data int 2 40058 data int 6 40075 data int 7 30001 data int 9 40056 data int 4 40057 data int 5 Note 1: Indicates Physical Inputs/Outputs to/from Master Controller. Note 2: Indicates Recommended Status Indication of important parameters. Note 3: Indicates Command Inputs from Bacview/BAS system. Note 4: Indicates Customer Alarm Reset Functions from Bacview/BAS System. Note 5: Indicates all System Alarms possible. c l i m a t e m a s t e r. c o m 37 CLIMATEMASTER WATER-SOURCE HEAT PUMPS Tranquility ® Large Water-to-Water (TMW) Series Rev.: 12 February, 2016 Unit Commissioning & Operating Conditions Environment -This unit is designed for indoor installation only. Do not install in an area subject to freezing or where humidity levels can cause cabinet condensation. Power Supply - A voltage variation of +/- 10% of nameplate utilization voltage is acceptable. Operation and performance is primarily dependent upon water temperatures, water flow rates and ambient air temperature. This water to water heat pump is capable of operating over a wide temperature range and with flow rates of between 1.5 GPM (.1 l/s) and 3 GPM (.19 l/s) per ton, however usually no more than one of these factors may be at a minimum or maximum level at a time. The commissioning table indicates water temperatures which are suitable for initial unit commissioning in an environment where the flow rate and water temperature is not yet stable and to avoid nuisance shut down of the units freeze and refrigerant pressure safeties. For more specific unit performance reference the product catalog, the submittal data sheets or contact your supplier for assistance. BUILDING COMMISSIONING Heating 360/600/840 Unit Size 360/600/840 Source Min/Max 80/125 ºF 50/70 ºF Load Min/Max 50/70 ºF 80/125 ºF 45/104 ºF 39/85 ºF Ambient Min/Max BUILDING OPERATING Cooling Heating Unit Size 360/600/840 360/600/840 Source Min/Max 60/120 ºF 30/70 ºF Load Min/Max 30/70 ºF 60/120 ºF Ambient Min/Max 45/104 ºF 39/85 ºF The operating table indicates the maximum and minimum ranges of the unit. 38 Cooling C l i m a t e M a s t e r Wa t e r - S o u r c e H e a t P u m p s THE SMART SOLUTION FOR ENERGY EFFICIENCY Tranquility ® Large Water-to-Water (TMW) Series Rev.: 12 February, 2106 Piping System Cleaning & Flushing Cleaning by flushing water through the Load and Source piping system, bypassing unit, is the single most important step to ensure proper start-up and continued efficient operation of the system. Proper maintenance of strainers and checking pH are also as important. Follow the instructions below to properly clean and flush the system: 1. Verify electrical power to the unit is disconnected. 2. Install the system with the supply hose connected directly to the return riser valve. Use a single length of flexible hose. 3. Open all air vents. Fill the system with the water. DO NOT allow system to overflow. Bleed all air from the system. Pressurize and check the system for leaks and repair appropriately. 4. Verify all strainers are in place. Start the pumps, and systematically check each vent to ensure all air is bled from the system. 5. Verify make-up water is available. Adjust make-up water appropriately to replace the air which was bled from the system. Check and adjust the water/air level in the expansion tank. 6. If possible, raise the Source loop temperature to approximately 85ºF (29ºC). Open the a drain at the lowest point in the system. Adjust the make-up water replacement rate to equal the rate of bleed. 7. Refill the system and add phosporic or sulfamic acid for a 2% solution. If possible, raise the Source loop temperature to approximately 100°F [38°C]. Circulate the solution for a minimum of 8 to 24 hours. At the end of this period, shut off the circulating pump and drain the solution. Repeat system cleaning if desired. 8. When the cleaning process is complete, remove the short-circuited hoses. Reconnect the hoses to the proper supply, and return connections to each of the units. Refill the system and bleed off all air. 9. Test the system pH with litmus paper. The system water should be slightly alkaline (pH 7.0-9.0). Add chemicals, as appropriate, to maintain acidity levels. WARNING! WARNING! Polyolester Oil, commonly known as POE oil, or Polyvinylether, commonly known as PVE oil, are synthetic oils used in many refrigeration systems including those with HFC-410A refrigerant. POE, or PVE oil, if it ever comes in contact with PVC or CPVS piping, may cause failure of the PVC/CPVC. PVC/CPVC piping should never be used as supply or return water piping with water source heat pump products containing HFC-410A as system failures and property damage may result. 10. When the system is successfully cleaned, flushed, refilled and bled, check the main system panels, safety cutouts and alarms. Set the controls to properly maintain loop temperatures. 11. Extract three water samples from the Load and Source water system using bottles provided from the Water Sample test kit. Confirm that the sample bottles are filled to the top leaving no air in the bottles. All six sample bottles must have labels filled out per instruction included with the bottles. Ship the bottles immediately to the appropriate water testing laboratory as per the instructions included with the bottles. CAUTION! CAUTION! DO NOT use 'stop leak' or any similar chemical agent in this system. Addition of these chemicals to the loop water will foul the system and inhibit unit operation. c l i m a t e m a s t e r. c o m 39 CLIMATEMASTER WATER-SOURCE HEAT PUMPS Tranquility ® Large Water-to-Water (TMW) Series Rev.: 12 February, 2016 Pre-Start Up Procedures WARNING! WARNING! Do Not operate compressors for pre-start check. Prior to unit start up, there are certain essential checks which must be completed. Failure to carry out these checks could result in damage to the TMW voiding the warranty. Assembly - ClimateMaster recommends locking down the unit to a concrete base or to three 4” base mounting rails using the six bolt holes provided in each base pan. Confirm that bolts have been properly tightened during installation. Electrical - It is imperative to turn off the main electrical power supply and follow proper lock-out, tag-out procedures prior to servicing any of the TMW electrical components. The following procedures can be performed only after the electrical power is confirmed to be off: 1. The installation must be inspected and approved by the respective agent and be in compliance with all local and national electrical codes. 2. Check and tighten as required all electrical terminal connections. Utilize any lock-out/ tag-out procedures required for your project location when performing this operation. If no procedure exists take all precautions necessary to prevent the power from being turned on. A systematic tightening of all terminals inside the electrical control panel should be carried out. This will include the compressor motor terminals, which would require removal of the compressor terminal cover. Check connections at each safety and every termination in the panel. 3. Low voltage wiring can enter top, left hand side, or front. Control wires should be #18 AWG minimum up to 50 feet, #16 AWG minimum up to 100 feet, rated at 60°C minimum. Tag wire inside control box with component it is coming from. 4. All field connections should be checked for tightness. 5. Check all fuses for proper sizing as indicated on the data plate and/or the electrical diagram on the inside door of the electrical panel. 6. Verify line voltage is within acceptable range, see electrical table 8. 7. 208/230 model, verify transformer is wired to correct TAP, shipped for 208V, rewire if needed. 40 DANGER (OHFWULFVKRFNKD]DUG 0D\UHVXOWLQLQMXU\RUGHDWK 'LVFRQQHFWSRZHUVXSSO\LHV EHIRUHVHUYLFLQJ 5HIHUVHUYLFLQJWRTXDOLILHG VHUYLFHSHUVRQQHO &$87,21 8QLWWREHVHUYLFHGE\TXDOLILHG SHUVRQQHORQO\ 5HIULJHUDQWV\VWHPXQGHU SUHVVXUH 5HOLHYHSUHVVXUHEHIRUHXVLQJ WRXUFK 5HFRYHUUHIULJHUDQWDQGVWRUHRU GLVSRVHRISURSHUO\ DANGER 5LVTXHGHFKRFpOHFWULTXH 5pVXOWDWGHPDLGDQVGRPPDJHV RXODPRUW 'HEUDQFKHUDYDQWGҋHQWUHSUHQGUH OHGpSDQQDJHGHOҋDSSDUHLO &RQVXOWHUXQUpSDUDWHXUTXDOLILH SRXUOHGpSDQQDJH 5(&29(5 5()5,*(5$17 $77(17,21 &RQILHUODPDLQWHQDQFHiXQ WHFKQLFLHQTXDOLILH /HV\VWpPHIULJRULILTXHVRXV SUHVVLRQ 'pFRPSULPHUDYDQWGҋH[SRVHUi ODIODPPH 5pFXSHUpUOHIULJRULJHQHHWOH VWRFNHURXOHGpWULUH FRUUHFWHPHQW 8. Verify I/O Flex 6126 board has jumper set to 5Vac. See Wire Diagram. 9. Verify proper installation of the mandatory field installed water pressure differential flow sensors. 10. Verify BAS and or BACview6 11. If phase monitor is not used make sure jumper wire is connected, LVTB2 - 1 and 2 (See wire diagram). Refrigeration 1. Refrigerant piping and components should be inspected for damage. 2. Place refrigerant gauges on the discharge and suction access ports of each refrigerant circuit to ensure a refrigerant charge is present. 3. Confirm the settings on all pressure switches. Note: The manufacturer strongly recommends all piping connections, both internal and external to the unit, be pressure tested by an appropriate method prior to any finishing of the interior space or before access to all connections is limited. Test pressure may not exceed the maximum allowable pressure for the unit and all components within the water system. The manufacturer will not be responsible or liable for damages from water leaks due to inadequate or lack of a pressurized leak test, or damages caused by exceeding the maximum pressure rating during installation. C l i m a t e M a s t e r Wa t e r - S o u r c e H e a t P u m p s THE SMART SOLUTION FOR ENERGY EFFICIENCY Tranquility ® Large Water-to-Water (TMW) Series Rev.: 12 February, 2106 Pre-Start Up Procedures Water System 1. Confirm that leak testing has been carried out. 2. Confirm that the system has been flushed and is clean. 3. Confirm that the results of both Load and Source water analysis does not conflict with the acceptable constituent ppm levels as indicated in Water Quality Table - 5. 4. Confirm that appropriate water analysis has been conducted and treated if required by the end-user or facility manager. 5. Confirm that necessary water treatment systems are in place with both the Load and Source water systems. pH should be 7-9. 6. Confirm that both the Load and Source circulating pumps are operational and water is flowing through both exchangers. (Manually open any motorized valve). 7. Shut entering water valve and blow out some water to check for particles or coloration from suspended particles. Record the pressure differential across the load and source heat exchangers, measured at the Pete’s ports. 8. Confirm correct water flow rates through the Source and Load. Compare the measured differential pressures with the predicted flow rates to ensure proper correlation to the flow results. 9. Confirm entering water temperature is within operating limits in table 9. 10. Confirm installation of mandatory field installed Source and Load water strainers with minimum of 60 mesh screens. 11. Cooling Tower/Boiler: Check equipment for proper setpoints and operation. 12. Standby Pumps: Verify the standby pump is properly installed and in operating condition. Pre-start form - complete all information and send to ClimateMaster. Keep a copy for your records. WARNING! WARNING! To avoid equipment damage, DO NOT leave system filled in a building without heat during the winter unless antifreeze is added to system water. Heat exchangers never fully drain by themselves and will freeze unless winterized with antifreeze. c l i m a t e m a s t e r. c o m 41 CLIMATEMASTER WATER-SOURCE HEAT PUMPS Tranquility ® Large Water-to-Water (TMW) Series Rev.: 12 February, 2016 Pre Start-up Check List NOTICE! RECOMMEND FACTORY START UP Requires chiller start up experience and knowledge of service tool - ABACVIEW6 Project Name: Project Address: Phone No. Date: Sales Order: Quantity of TMWs: WARNING! IMPORTANT! WARNING! Only trained, qualified personnel should install and or service ClimateMaster equipment. Verify both compressor switches in low voltage control box are “OFF”. Do not operate compressor during pre start checks. YES NO 1. I have read the Installation Manual. All Pre-start up procedures and checks are complete? (Installation, Operation, & Maintenance Manual is available at climatemaster.com. 2. Are units installed properly “per all codes and installation manual”? 3. Is there a 60-mesh strainer on Source and Load inlet water? 4. Is Source water system filled and flushed? (See “Filling the Water System” in I.O.M). 5. Is Load water system filled, flushed and all air purged from the system? (All air must be purged from system prior to startup. See “Filling the Water System” in I.O.M). 6. Are proof of flow devices installed on Load and Source? 7. Are all pumps tested, and operational? 8. Are required Load GPM’s (verified by pressure differential) supplied to the unit? 9. Are required Source GPM’s (verified by pressure differential) being provided to the unit? 10. Is there water presently circulating through the unit? 11. Water test results within quality parameter table? 12. Was water treated if results indicated treatment required? 13. Verified power suppy agrees with unit nameplate? 14. Is power and communication wiring complete to each unit? 15. Verify that wiring and devices meet with approved electrical submittal drawings? 16. Electrical power available to run multiple compressors at start-up? 17. Is there a BACView6? 18. If TMW is connected to BAS, what is protocol? If you answered “No” to any question above, provide the line reference number and the date of scheduled completion below. Please note, all conditions must be complete prior to ClimateMaster approval. This form must be completed and submitted to ClimateMaster, a minimum of three (3) weeks prior to final scheduling of any Start-up. Email [email protected] or fax 405-745-2006. Note: If any of the above items are not complete at time of start-up, backcharges will be assessed for additional costs. Number of TMW units that I am requesting optional paid factory start-up Will there be additional start-ups required for this project Contractor Name: Address: (Authorized Signature) Phone No. Date: 42 C l i m a t e M a s t e r Wa t e r - S o u r c e H e a t P u m p s THE SMART SOLUTION FOR ENERGY EFFICIENCY Tranquility ® Large Water-to-Water (TMW) Series Rev.: 12 February, 2106 Unit Start Up Procedures Phase Check Procedure 1. Turn compressor selector switches inside the TMW control panel (low voltage side) to the off position. 2. Ensure the correct fuses are installed in the control transformer fuse blocks. Turn on the power. The “Power” light should be on. 3. Connect BACView6 to I/O flex board at J6 (see wire diagram E-4). 4. Override the Controller’s DDC outputs to the compressors. Within the “Service Menu” of the BACView6 index to the “Diagnostics Manual Mode” section to engage the compressors individually for startup purposes. Index to the “M1 Manual Mode” prompt so the cursor is at the “Off” prompt to the right. Press “Enter”. Use the increment key so the “Off” prompt changes to “On” and then press “Enter”, or press the “OK” key. Index down to the “MC1 Manual Mode On” prompt so the cursor is at the “Off” prompt to the right. Press “Enter”. Use the increment key so the “Off” prompt changes to “On” and then press “Enter”, or press the “OK” key. Inside the low voltage control section (left-most control door),turn the Compressor 1 switch ON to bump compressor 1 and check for proper rotation using pressure gauges. Once this is complete and correct rotation is verified, turn the compressor 1 switch off and reverse the manual mode for M1C1 compressor so it is “Off” by similar prompts as outlined above. Use this same technique to manually override the M1C2 compressor to the “On” state. Turn on the switch marked “Compressor 2” to bump the compressor and verify that circuit 2 compressor has correct rotation. Always use proper electrical safety precautions. 5. Slowly close the Load water inlet isolating valve and note that the pressure differential flow sensor stops the machine. Note the flow rate at which this occurs. If too much flow is lost before unit is stopped, reset switch setting. The pressure differential flow sensor should be set so the unit shuts down when the flow rate to each water circuit drops below 60% of rated AHRI full load conditions (indicating a 10°F temperature change through the Load heat exchanger). 6. 7. 8. Slowly close the source water inlet isolating valve and note that the pressure differential flow sensor stops the unit. Note the flow rate at which this occurs. If too much flow is lost before unit is stopped, reset switch setting. The pressure differential flow sensor should be set so the unit shuts down when the flow rate to each Source water circuit drops below 25% of rated AHRI full load conditions (indicating a 10°F temperature change through the Source heat exchanger). Repeat the tests of all other safety interlocks which may be connected. The antifreeze temperature sensor at the Load outlet should be set to stop the compressors from operating when the leaving chilled water temperature drops below 36°F. WARNING! WARNING! To avoid possible injury or death due to electric shock, open the power supply disconnect switch and secure it in an open position during installation. CAUTION! CAUTION! Use only copper conductors for field installed electrical wiring. Unit terminals are not designed to accept other types of conductors. WARNING WARNING! This unit contains HFC-(R410A), an azeotropic mixture of R-32 (Difluoromethane) and R-125 (Pentafluoroethane). DO NOT VENT HFC-(R410A) to the atmosphere. The U.S. Clean Air Act requires the recovery of any residual refrigerant. Do not use R-22 service equipment or components on R410A systems. c l i m a t e m a s t e r. c o m 43 CLIMATEMASTER WATER-SOURCE HEAT PUMPS Tranquility ® Large Water-to-Water (TMW) Series Rev.: 12 February, 2016 Unit Start Up Procedure WARNING! WARNING! When the disconnect switch is closed, high voltage is present in some areas of the electrical panel. Exercise caution when working with energized equipment. Unit Start Up (Continued) 1. Built into the logic of the ClimateMaster DDC Controller is an anti-short cycle timer which will prevent the compressors from re-starting immediately following a compressor shutdown. 2. If the chilled water temperature is above the normal operating level (greater than 90°F), all load should be removed from the chilled water system and the suction temperature should be monitored to prevent high current draw. 3. If the Source water temperature is below the normal operating level (less that 60°F), ensure that the Source water temperature control is in the correct position. 4. When all temperatures are within operating limits, all high and low pressure safety switches should be tested for each refrigeration system. 5. The Source temperature controller should be checked. Once stable conditions have been achieved, the refrigeration system’s high and low pressures, compressor amp draw, voltage input level, and water system temperatures and pressures should be logged for each unit module separately. 6. Check that oil level is between 1/3 and 1/2 of the sight glass. 7. The action of the controller should be checked for correct operation and control. Adjusting Unit Charge and TXV’s Using Superheat and Subcooling Method - Due to varying installation conditions/applications and to optimize performance, proper refrigerant charge and TXV adjustment must be confirmed. After checking compressor rotation, choose a circuit to be tested first. Connect test equipment to monitor the suction Line and Liquid Line temperatures simultaneously. Place a manifold gauge set on the suction line and liquid line. Start the compressor. As long as the suction pressure is high enough to prevent the low pressure switch from tripping, run compressor. After compressor runs at least five minutes, verify proper superheat by subtracting the saturated evaporative temperature from the suction line temperature. The saturated evaporative temperature is found by converting the suction pressure reading on the manifold gauge, to the related temperature. Proper superheat temperature range is 6-12°F. If superheat is low, this may indicate that TXV is overfeeding. To adjust the TXV, turn the adjustment stem clockwise. This will cause the superheat to rise. Wait five minutes before checking results of adjustment. Repeat until desired superheat is achieved. After verifying proper superheat, then verify proper subcooling. This is accomplished by subtracting liquid line temperature from the saturated condensing temperature. Saturated condensing temperature is found by converting the liquid line pressure reading on the manifold gauge, to the related temperature. Normal subcooling temperature range, at the condenser, is 5-15°F BUT for total accuracy please follow the charge recommendations found in the selection program. If subcooling is too low, then refrigerant must be added to the system. Add charge and wait five minutes before checking results. If subcooling is too high, then refrigerant must be removed from the system. CAUTION! CAUTION! Do not charge to achieve subcooling temperature when the TXV is overfeeding. If the TXV is overfeeding, readings may still indicate low subcooling and low superheat, but circuit may not be undercharged. WARNING! WARNING! Verify ALL water controls are open and allow water flow prior to engaging the compressor. Freezing of the brazed plate heat exchangers or water lines will permanently damage the heat pump. 44 C l i m a t e M a s t e r Wa t e r - S o u r c e H e a t P u m p s THE SMART SOLUTION FOR ENERGY EFFICIENCY Tranquility ® Large Water-to-Water (TMW) Series Rev.: 12 February, 2106 Unit Start Up Procedure Run Compressor for 5 Minutes Is Superheat in Range? No Yes Is Superheat Low or High? Low Turn TXV Adjustment Stem Clockwise Is Subcooling in Range? High No Is Subcooling Low or High? Is Subcooling Low or High? Low Low High Yes Recheck Superheat and Complete Start-up and Warranty Form High Add Refrigerant Remove Refrigerant Turn TXV Adjustment Stem Counter Clockwise Add Refrigerant All start up paperwork and documentation must be submitted to ClimateMaster. Future warranty claims cannot be processed without a completed Start Up and Warranty Registration form on file (See pages 54-56). c l i m a t e m a s t e r. c o m 45 CLIMATEMASTER WATER-SOURCE HEAT PUMPS Tranquility ® Large Water-to-Water (TMW) Series Rev.: 12 February, 2016 Operation and Maintenance Maintaining a Daily Log Date: Unit No. Technician Sun. Mon. Tue. Wed. Thur. Fri. Sat. Load Water Entering Temperature Load Water Leaving Temperature Source Water Entering Temperature Load Water Pressure Drop Source Water Pressure Drop Faults Pressure and Temperature Log A log of temperatures and pressures should be taken regularly. Periodically conduct a visual inspection of the unit to identify problems before they reach the point of failure. As with any mechanical system, it is necessary to conduct a series of checks to the TMW unit to confirm correct operation. Daily • A daily operational log should be kept. • Perform visual inspection. • Record entering and leaving Load water and Source water temperatures and pressures. • Note any problems that may exist and immediately plan for further investigation. If repair is necessary, schedule for earliest possible date. • Properly document all data taken. Weekly • Perform visual inspection. • Properly document all data taken. • Note any problems that may exist. Immediately plan for further investigation. If repair is necessary, schedule for earliest possible date. • Review daily log from previous week. Quarterly • Check controller operating parameters and setpoints. • Check temperature drop/rise on each individual heat exchanger.* • Check compressor oil level. • Check compressor oil color. • Check water flow rates and pressure drops across Load and Source heat exchangers. • Properly document all data taken. 46 * The temperature drop/rise on a fully loaded (both compressors) heat exchanger is generally 10°F. If only one compressor is running the temperature drop/rise will be approximately 5°F. Some projects are designed to have a higher temperature drop on either the Load or the Source depending on application. Consult log sheet for your project for these values. If the temperature drop/ rise is greater than the design, your heat exchanger may need to be back flushed or the strainer may need to be cleaned. Annual • Back flush all heat exchangers. If fouling is suspected use only ClimateMaster recommended descalers (see Chemical Clean In Place Washing). • Remove and clean all waterside strainers. • Manually operate all waterside isolation valves, if provided, on each module. • Check all electrical connections for tightness. • Perform leak check on all refrigerant circuits. • Check all header piping couplings for tightness. • Check oil level and color on each compressor. • Check and test all refrigerant safeties for proper operation. • Check all peripheral systems for proper operation. • Verify setpoints, sensors, and general control configuration. • Properly document all data taken. C l i m a t e M a s t e r Wa t e r - S o u r c e H e a t P u m p s THE SMART SOLUTION FOR ENERGY EFFICIENCY Tranquility ® Large Water-to-Water (TMW) Series Rev.: 12 February, 2106 Operation and Maintenance Chemical Clean in Place Washing with Water Isolation Valves - Chemical Clean in place washing will typically provide the best debris removal, even from severely clogged heat exchangers. The cleaning tank, pump and pump strainer should be arranged in the manner shown in Figure 6 - In Place Cleaning Arrangement. The flow of the cleaning is arranged in the opposite flow to the normal operational direction. Connection points are provided using the ¾” service ports at each heat exchanger. The cleaning solution used can be either a detergent or hot water to remove particles and simple cleaning. If correct water treatment has been implemented this should provide adequate cleaning for most situations. The solution can be pumped through the heat exchangers and allowed to soak for a time and then pumped again. If it is required to remove carbonates, then an acidic wash should be used. A 2% solution of phosphoric or sulfamic acid in pure water is generally acceptable. These acid solutions should only be allowed to circulate within the heat exchanger for 10 to 15 minutes, followed by a thorough pure water flush for 10 to 15 minutes. Hydrochloric or sulfuric acids must not be used. In any case, consult the chemical supplier to establish the correct handling process. Once the washing is complete, the solution should be flushed out completely by pumping clean, fresh water through the unit. To achieve a reasonable level of dilution, it may be required to change the water several times. After cleaning, the water quality and water treatment should be confirmed. c l i m a t e m a s t e r. c o m 47 CLIMATEMASTER WATER-SOURCE HEAT PUMPS Tranquility ® Large Water-to-Water (TMW) Series Rev.: 12 February, 2016 Operational Limitations Table 9 Voltage Limitations Compressor Operating Limitations TMW Maximum Compression Ratio The following voltage limitations are absolute and operation beyond these limitations may cause serious damage to the compressor. 5.7:1 Minimum Operating Pressure Differential (PSI) 85 Maximum Operating Pressure Differential (PSI) 475 Minimum Discharge Pressure (PSIG) 215 Maximum Discharge Pressure (PSIG) 590 Minimum Suction Pressure (No Glycol) (PSIG) 105 Minimum Suction Pressure (With Glycol) (PSIG) 70 Maximum Suction Pressure (PSIG) 175 Maximum Discharge Temperature (ºF) 265 Minimum Subcooling (ºF) 5 Maximum Subcooling (ºF) 15 Nominal Voltage Minimum Voltage Maximum Voltage Minimum Superheat at Compressor (ºF) 6 208/230/3/60 187 253 Maximum Superheat at Compressor (ºF) 12 460/3/60 414 506 Maximum Oil Temperature (Max) (ºF) 200 575/3/60 518 632 Maximum Saturation Discharge Temperature (ºF) 145 Water Flow Data TMW360 TMW600 TMW840 Minimum Load Water Flow (GPM) 45 75 105 Maximum Load Water Flow (GPM) 90 150 210 Minimum Source Water Flow (GPM) 45 75 105 Maximum Source Water Flow (GPM) 90 150 210 Minimum Leaving Load Water Temperature (No Glycol) (ºF) C 40 40 40 Minimum Leaving Load Water Temperature (with Glycol) (ºF) C 20 20 20 C 62 62 62 H 135 135 135 Minimum Load Water Differential Temperature (ºF) 5 5.4 5.9 Maximum Load Water Differential Temperature (ºF) 20 20 20 C 60 60 60 H (with Glycol) 30 30 30 Minimum Source Water Differential Temperature (ºF) 6.5 6.9 7.2 Maximum Source Water Differential Temperature (ºF) 30 30 30 C 135 135 135 H 62 62 62 Maximum Leaving Load Water Temperature (ºF) Minimum Entering Source Water Temperature (ºF) Maximum Leaving Source Water Temperature (ºF) Equipment Room Data Minimum Equipment Room Ambient Temperature (ºF) 55 55 55 Maximum Equipment Room Ambient Temperature (ºF) 104 104 104 C=Cooling, H=Heating 48 C l i m a t e M a s t e r Wa t e r - S o u r c e H e a t P u m p s THE SMART SOLUTION FOR ENERGY EFFICIENCY Tranquility ® Large Water-to-Water (TMW) Series Rev.: 12 February, 2106 Compressor Information Compressor Information - The compressors used in the ClimateMaster heat pumps are scroll compressors. They are highly efficient and extremely reliable. However, the information contained in this manual will be useful for their care. Compressor Rotation - All scroll-type machines are unidirectional and will only compress in one direction. Operating in the reverse rotation can be destructive and will be indicated by a load operating noise together with a lack of compression. Compressor Lubrication - The compressor operates on a sealed system and oil can only be lost if leak occurs. There are few cases when oil will need to be added to a machine in normal operation. Oil Type - The oil in TMW scroll compressors is either polyester type oil, (POE), or polyvinylester oil (PVE), and is intended for R-410A refrigerant use. All refrigerant oils require special handling and should be protected from contamination. They are extremely hygroscopic and will absorb moisture rapidly from the air. It is strongly recommended to store and dispense all refrigerant oil from sealed metal cans. Oil Type POE PVE Oil Levels - The oil level in the compressor should be checked with the compressor running. The compressor oil level may vary during operation and particularly on the start-up. The normal operating compressor oil level should be between 1/3 and 1/2 of the sight glass. During operation a certain amount of oil maybe carried out into the refrigerant system. The system has been designed to allow the oil to return back to the compressor. If the level in the sight glass falls, it may be due to the operating conditions and enough time should be given to allow the oil to return before more oil is added. This could take up to 6 hours of operation. The compressor should not be allowed to operate with oil level less than 1/8 of the sight glass for an extended period of time. (Longer than 4-6 hours). Adding Oil - The compressor must never be run in a vacuum. A suitable hydraulic pump should be used to add oil and reserved for this process. Oil should only be added to a compressor while it is operating to observe valid oil sight glass levels. Oil is pressure-injected either into a gauge connection on the suction line or injected into the oil process port at the bottom of the compressor housing. Only enough oil should be added to raise the level above the sight glass point. Models TMW TMW TMW TMW 360 600 REV A 600 REV B 840 c l i m a t e m a s t e r. c o m 49 CLIMATEMASTER WATER-SOURCE HEAT PUMPS Tranquility ® Large Water-to-Water (TMW) Series Rev.: 12 February, 2016 Refrigeration System Recharging Refrigeration System Recharging - Conforming to local and national codes is the responsibility of the service technician or installing contractor. The service technician should be familiar with the following codes: • ASHRAE Standard Safety Code for Mechanical Refrigeration, ANSI/ASHRAE 15-1978 • American National Standard Code for Pressure Piping, ANSI B31.5-1974 Factory Tested - ClimateMaster units have been pressure-tested, evacuated and fully charged and run tested at design water flow rates prior to shipment. In the unlikely event that a refrigerant leak is detected at startup, the following guidelines should be consulted before reprocessing the refrigeration systems. Refrigerant System Recharging - Debris and moisture can enter copper tubing in a matter of minutes. All tubing, coil connections, or any refrigerant containing portions should be temporarily capped or sealed to keep contaminants to a minimum. Filter driers should be opened just prior to brazing into the system to prevent moisture infiltration whenever possible. After all of the repairs have been made to the refrigeration system, a pressure test using refrigerant and nitrogen should be performed. Pressurize the system with dry nitrogen to 20 psi and check for any obvious leaks. If no leaks are present introduce a “trace” amount of refrigerant to the system (raise system pressure to 30-40 psi). With a dry nitrogen tank equipped with a regulator set to 150 psi, continue to pressurize the system to 150 psi. Using a leak detector, carefully check the system for any remaining leaks. If the system is free of leaks you may release the pressure. Evacuating the System - The compressors should never be run while the system is in a vacuum. This could cause immediate failure to the compressors. After the system has been leak tested and sealed, any moisture that entered the system should be dehydrated and removed. While the pressure is reduced under a vacuum, the boiling point of moisture trapped inside the lines is reduced also. A pressure of .0095 PSIA, or 500 microns absolute pressure or better must be reached and sustained for several hours in order for the system to be considered free from moisture. It is necessary to use a micron meter equipped with an absolute pressure gauge (or transducer) to take this reading. ClimateMaster recommends the double evacuation process to ensure the proper removal of moisture and contaminants from the refrigeration system. After the initial vacuum is reached and held on the system, allow dry nitrogen back into the system until the pressure reaches zero PSIG or slightly higher. Then, repeat the entire evacuation process described above. The 50 evacuation process is considered complete ONLY after a successful “blank-off” test is performed. A “blank-off” test is defined as: a) pulling a vacuum level less than 500 microns on the system and holding it for several hours; b) record the vacuum level in the system in microns, then close off the vacuum pump from the system for 15 minutes, and continue to monitor the micron level inside the refrigeration system; c) if the vacuum level inside the system does NOT rise more than 400 microns above the recorded vacuum level at the start of the 15 minute period, then the evacuation process is complete. If the vacuum level rises more than 400 microns in 15 minutes, then continue to evacuate the system for 1-2 hours, and then repeat a “blank-off” test. Recharging the System - After all repairs have been completed, the system has been leak tested, and proper vacuum pressures have been reached and maintained, refrigerant may be recharged into the system. With a known weight of refrigerant in the cylinder, use the gage manifold set to connect the cylinder’s liquid charging port to the charging access port near the refrigerant liquid line valve. Open the compressor suction and discharge line valves. Gradually meter the appropriate weight of liquid refrigerant into the condenser side of the system first, until no additional refrigerant can be dispensed. Accurate refrigerant charge per circuit may be found in the Physical Data information on page 6. Then continue the charging process by filling the evaporator side of the system with refrigerant. Close the refrigerant cylinder charging port, close all gage manifold ports and start the compressor. Be careful when continuing to charge the balance of the refrigerant, constantly maintaining a positive compressor suction pressure (>25 PSIG) at all times. WARNING! WARNING! To avoid the release of refrigerant into the atmosphere, the refrigerant circuit of this unit must be serviced only by technicians who meet local, state and federal proficiency requirements. WARNING! WARNING! All refrigerant discharged from this unit must be recovered WITHOUT EXCEPTION. Technicians must follow industry accepted guidelines and all local, state and federal statutes for the recovery and disposal of refrigerants. WARNING! WARNING! If a compressor is removed from this unit, system refrigerant circuit oil will remain in the compressor. To avoid leakage of compressor oil, the refrigerant lines of the compressor must be sealed after it is removed. C l i m a t e M a s t e r Wa t e r - S o u r c e H e a t P u m p s THE SMART SOLUTION FOR ENERGY EFFICIENCY Tranquility ® Large Water-to-Water (TMW) Series Rev.: 12 February, 2106 Sequence of Operation Generic Interface - TMW shall be enabled locally via field-installed selector switch or from enable/disable contact by Building Automation System (BAS). Pumps for Load and Source water supply shall be started by others. When proof of flow is established in both the Load and Source water lines, the TMW shall start. The “Chilled Water Supply” (CHWS) temperature sensor (TS1), located in the discharge line, shall be used to cycle compressor stages sequentially to maintain setpoint of 44°F (adjustable from the LED Display/Keypad of the BACView6, or remotely through a BAS communications protocol (e.g. BACnet, Modbus or N2). TMW will be disabled until “Chilled Water Return” (CHWR) temperature sensor is below 90°F and “Source Water Supply” (SWS) temperature sensor is above 60°F. The compressor with most run time will de-energize as the setpoint is satisfied, and compressor with least run time will energize as additional capacity is required. If a fault is detected the compressor will be disabled and displayed on the DDC Controller LED display. (Faults must be manually reset at the unit by momentary contact between 11 and 12 on terminal block LVTB2). The Unit Status and Run Time in hours for each compressor can be displayed on the BACView6. Common Alarm contact and Unit Status contact is provided at the panel. Each unit has 2 compressors. Stage 1 compressors shall be started first on lead week and stage 2 compressors shall be started first on lag weeks to equalize run hours between compressors 1 and 2 of the modules automatically. c l i m a t e m a s t e r. c o m 51 CLIMATEMASTER WATER-SOURCE HEAT PUMPS Tranquility ® Large Water-to-Water (TMW) Series Rev.: 12 February, 2016 Factory Installed Options FACTORY INSTALLED OPTIONS Strainer Removal Instructions Water Isolation Valves and Flush Ports - Water isolation valves provide isolation to the unit for maintenance and cleaning of load and source heat exchangers. Optional motorized valves includes ¾” fill and flush valves. Y Type Strainers: 1. Drain piping. 2. Vent line to relieve pressure. 3. Loosen flange bolts (flanged ends). 4. Secure necessary lifting equipment to strainer assembly. 5. Remove inlet/outlet flange bolts (flanged end), or unthread (threaded ends) and carefully remove strainer. 6. Tighten cover. The strainer is ready for line start-up. Motorized source water valve provide head pressure regulation for low entering condenser water temperature applications (less than 60°F), in cooling. This is required for units intended for both heating and cooling, optional for other applications. Motorized Load water valve is optional, would be required for variable speed pumping. FIELD INSTALLED OPTIONS Strainer Installation Instructions 1. Ensure all machined surfaces are free of defects and that the inside of the strainer is free of foreign objects. 2. The strainer should be installed so that the drain connection is pointed downwards. 3. For flanged end strainers the flange bolting should be tightened gradually in a back and forth clockwise motion. Threaded end strainers should use an appropriate sealant. 4. Once installed increase line pressure gradually and check for leakage around joints. 5. If the strainer is supplied with a start-up screen monitor pressure drop carefully. 6. Isolation valves should be installed for ease of maintenance of strainers. IMPORTANT: Ultimate responsibility for strainer and material selection rest with the end-user or facility manager, as only the end-user or facility manager knows the particular application and operating parameters to which the strainer will be subjected. ClimateMaster recommends basket type for Source side. Basket Type Strainers 1. Drain Piping. 2. Vent line to relieve pressure. 3. Loosen cover and open to access basket. 4. Remove, clean and replace basket in original position. (Note: In some instances a high pressure water jet or steam may be required for effective cleaning). 5. Inspect cover gasket for damage. If necessary replace. (Note: If spiral wound gaskets have been used, they must be replaced and cannot be used again). 6. Tighten cover. The strainer is ready for line start-up. Maintenance Instructions - For maximum efficiency determine the length of time it takes for the pressure drop to double that in the clean condition. Once the pressure drop reaches an unacceptable value, shut down line and follow the Strainer Removal Instructions above. A pressure gauge installed before and after the strainer in-line will indicate pressure loss due to clogging and may be used to determine when cleaning is required. Troubleshooting Guides and Diagnostic Techniques - After pressurizing inspect cover and other joints for leakage. Gasket replacement or cover tightening is necessary if leakage occurs. If the required filtration is not taking place, ensure the screen is installed in the correct position, and that the screen is mounted flush to the upper and lower seating surfaces. CAUTION! CAUTION! CAUTION! Prior to dismantling the strainer for cleaning, it is imperative that the strainer assembly is isolated and completely de-pressurized. 52 CAUTION! Caution should be taken due to possible emission of process material from piping. Always ensure no line pressure exists when opening cover C l i m a t e M a s t e r Wa t e r - S o u r c e H e a t P u m p s THE SMART SOLUTION FOR ENERGY EFFICIENCY Tranquility ® Large Water-to-Water (TMW) Series Rev.: 12 February, 2106 Troubleshooting Guide Unit Will Not Start Possible Cause Remedy Power off Check main disconnect switch Main Line open Check main fuses Incorrect wiring Check the wiring diagram Loose terminals/connections Tighten the terminal connections Control Circuit open Check interlocks with auxiliary Improper phasing of main power Change any two of three phases of main power Compressor Hums but Does Not Start Possible Cause Low voltage Remedy Check at main power entry and power entry at unit (consult power company if low) Phase Loss Check power wiring and fuses Compressor Runs but Does Not Cool or Heat Possible Cause Improper phasing of main power Remedy Switch any two of three phases of main power Compressor Cuts Out on Low Pressure Safety Control Possible Cause Remedy Main water valve closed or restricted Open valve to full open position Water isolation valves, if provided, closed or restricted Open valves to full open position Low water flow Check water pump operation Low water flow Check water flow through the unit Refrigerant shortage Check for leaks - add refrigerant Fouled Load brazed plate heat exchanger Clean-in-place heat exchanger. See section on heat exchangers. Restriction in liquid line Plugged liquid line drier - replace liquid line drier Expansion valve clogged or inoperative Repair/Replace the expansion valve Low discharge pressure Raise and control discharge pressure within design limits Load water temperature too cold or hot Check water temperature setpoint Improper Load water circulation Use an ample sized cleanable strainer in the water circuit; make certain the strainer is clean to ensure full flow of water (strainer screen must be 60 mesh minimum) Faulty suction pressure transducer Verify transducer calibration using a calibrated manifold gauge and replace if defective. Wrong suction pressure cutout setpoint Verify suction pressure cutout setpoint to be set equal to the corresponding leaving chilled solution freeze temperature equivalent pressure on a PT chart. (i.e. if the solution freeze point is 32°F the equivalent pressure setpoint will be 101 PSIG) Compressor Cycles on High Pressure Control Possible Cause Main Source water valve closed or restricted Remedy Open valve to full open position Source water isolation valves, if provided, closed or restricted Open valves to full open position Water regulating valve incorrectly set or defective Reset or replace Compressor discharge valve partially closed Open valve to full open position Non-condensable gases in hydronic system Purge non-condensable gases from bleed valve on condenser or at bleed valve of the building condenser water system Overcharge of refrigerant Purge refrigerant from system while in operation until the first sign of bubbles are shown in the sight glass. Add back refrigerant just until bubbles clear. Source water temperature high Check water supply temperature against requirements; if cooling tower is used check spray nozzles on cooling tower Improper condenser water circulation Use an ample sized cleanable strainer in the condenser water circuit; make certain the strainer is clean to ensure full flow of condenser water (strainer screen must be 60 mesh minimum) Insufficient water flow through the Source Check water flow through condenser against design requirements Fouled Source brazed plate heat exchanger Clean-in-place heat exchanger as described on page 32 Defective high pressure switch Replace high pressure switch Causes and Prevention of Freeze-Up Possible Cause Prevention Improper charging Charge per data plate information, located on the unit, following the Superheat and Subcooling procedure described on page 27. Improper Load water circulation Use an ample sized cleanable strainer in the chilled water circuit; make certain the strainer is clean to ensure full flow and velocity of chilled water (strainer screen must be 60 mesh minimum). It may sometimes be necessary to treat the water to prevent formation of deposits. Not draining for winter shutdown When the system is shut down for the winter, remove the drain plugs, and drain the cooler. Blow out remaining water with air. Faulty leaving Load water solution temperature sensor Verify sensor calibration using a calibrated thermometer and replace if defective. Wrong freeze-up protection temperature setpoint Verify leaving chilled solution freeze protection temperature setpoint to be set at 8°F above solution freeze point. c l i m a t e m a s t e r. c o m 53 CLIMATEMASTER WATER-SOURCE HEAT PUMPS Tranquility ® Large Water-to-Water (TMW) Series Rev.: 12 February, 2016 Start Up and Warranty Form Commissioning Report, Tranquility TMW 360/600/840 Heat Pumps Pg. 1 IMPORTANT: For warranty validation and activation a copy of Water Test Lab Results, Pre Start Up Form, and this form must be completed for each ClimateMaster TMW 360/600/840 unit and forms must be returned to ClimateMaster Technical Service Department immediately after completion of commissioning. Warranty shall not be considered valid or active withoutverification from the ClimateMaster Technical Service Dept. For warranty status contact: ClimateMaster Inc. C/0 Service and Warranty Dept. 7300 S.W. 44th Street Oklahoma City, OK, 73179 (405) 745-6000 ¾ Prior to Commissioning read and become familiar with the TMW 360/600/840 unit Installation and Operation Manual (IOM). If you do not fully understand the manuals or require additional information contact the ClimateMaster Technical Service Dept. Be prepared to quote unit model number(s) and serial number(s). ¾ Use one (1) each Commissioning Report per unit. One report will be required for each DOAS unit. Clearly print all required information. Additional comments or pages may be attached as needed. Location and Unit Information Job Name: Installation Address: ClimateMaster Sales Representative: Unit Model #: Unit Serial #: Compressor Model #: Compressor #1 Serial Number: Compressor #2 Serial Number: Form Completed By: Company Name: Company Address: Phone# Date: WARNING! ONLY TRAINED, QUALIFIED PERSONNEL SHOULD INSTALL AND/OR SERVICE CLIMATEMASTER EQUIPMENT. SERIOUS INJURY, PROPERTY DAMAGE, AND/OR DEATH CAN RESULT FROM IMPROPER INSTALLATION AND/OR SERVICE OF THIS EQUIPMENT. HIGH VOLTAGE ELECTRICAL COMPONENTS, MOVING PARTS, AND HIGH REFRIGERANT PRESSURES ARE PRESENT. 54 C l i m a t e M a s t e r Wa t e r - S o u r c e H e a t P u m p s THE SMART SOLUTION FOR ENERGY EFFICIENCY Tranquility ® Large Water-to-Water (TMW) Series Rev.: 12 February, 2106 Start Up and Warranty Form Commissioning Report, Tranquility® TMW 360/600/840 Heat Pumps Pg. 2 Installation Check List Installation Manual read and understood Tighten/Check all wiring connections Verify Power Supply Matches Data Plate Check for internal Damage Verify Proper compressor rotation Verify Water Flow & GPM Verify Flow device safety shuts off at 25% or less Verify 60 Mesh Strainers are Installed and Clean Verify Low Limit, Low pressure, and High pressure safeties Verify Low Limit, Low Pressure, and High pressure safeties Verify Flow device safety shuts off at 25% or less Compressor Operation Warm Weather Operation (Cooling Mode) Compressor 1 Voltage @ Compressor Contactor during operation. Voltage @ Compressor to ground Compressor Amps Cold Weather Operation (Heating mode) Compressor 2 Compressor 1 Compressor 2 T1-T2 T1-T2 T1-T2 T1-T2 T2-T3 T2-T3 T2-T3 T2-T3 T1-T3 T1-T3 T1-T3 T1-T3 L1 L1 L1 L1 L2 L2 L2 L2 L3 L3 L3 L3 L1 L1 L1 L1 L2 L2 L2 L2 L3 L3 L3 L3 Transformer Voltage Refrigerant Discharge Pressure Psig Psig Psig Psig Liquid Line Temperature ºF ºF ºF ºF Sub-cooling ºF ºF ºF ºF Refrigerant Suction Pressure Psig Psig Psig Psig Suction Line Temperature ºF ºF ºF ºF Superheat ºF ºF ºF ºF Evaporator EWT / LWT T °F ºF ºF ºF ºF Condenser EWT / LWT T °F ºF ºF ºF ºF Evaporator P P Condenser P P Oil Level Sight glass F 3/4 1/2 E F 3/4 1/2 E c l i m a t e m a s t e r. c o m F 3/4 1/2 E F 3/4 1/2 E 55 CLIMATEMASTER WATER-SOURCE HEAT PUMPS Tranquility ® Large Water-to-Water (TMW) Series Rev.: 12 February, 2016 Start Up and Warranty Form Commissioning Report, Tranquility® TMW 360/600 Heat Pumps Pg. 3 Water System ” Water Pipe Sizing GPM Through Load Side Cooling T / Heating Antifreeze T Type % ºF ºF Loop Type GPM Through Source Side Cooling T / Heating 60 Mesh Strainers Installed AFR Installed GPM AFR Installed Has water been tested? Has water been treated if needed? Notes: 56 T C l i m a t e M a s t e r Wa t e r - S o u r c e H e a t P u m p s ºF ºF THE SMART SOLUTION FOR ENERGY EFFICIENCY Tranquility ® Large Water-to-Water (TMW) Series Rev.: 12 February, 2106 Refrigeration Troubleshooting Form Refrigeration Troubleshooting Form Water-to-Water Units Customer: Loop Type: Model #: Serial #: Startup Date: Antifreeze Type & %: Complaint: REFRIGERANT: HFC-410A OPERATING MODE: HEATING POSITION HEATING REFRIG FLOW - HEATING COOLING REFRIG FLOW - COOLING REVERSING VALVE 11 13 2 1 SUCTION CONDENSER (COOLING) EVAPORATOR (HEATING) Load COOLING POSITION COMPRESSOR 10 12 EXPANSION VALVE CONDENSER (HT G) EVAPORAT OR (CLG) 3 FILTER DRIER DISCHARGE 4 Source 5 LT2 : **Turn off HWG before troubleshooting. 5 LT1: HEATING LIQUID LINE COOLING LIQUID LINE 6 7 8 9 CIRCUIT 1 Description Heating Cooling CIRCUIT 2 Heating Cooling Notes Voltage Compressor Amps 1 Suction Temp 2 Suction Press 2a Saturation Temp 2b Superheat 3 Discharge Temp 4 Discharge Press 4a Saturation Temp 4b Subcooling 5 Liquid Line Temp 6 Source Water In Tmp 7 Source Water Out Tmp 8 Source Water In Pres 9 Source Water Out Pres 9a Press Drop 9b Flow Rate GPM [l/s] 10 Load Water In Temp 11 Load Water Out Temp 12 Load Water In Pres 13 Load Water Out Pres 13a Press Drop 13b Flow Rate GPM [l/s] Heat of Extraction (Absorption) or Heat of Rejection: HE or HR = Flow Rate x Temp. Diff x Fluid Factor Temp Diff.= Temp Diff.= Fluid Factor: (for Btuh) Fluid Factor: (for kW) 500 (Water); 485 (Antifreeze) 4.18 (Water); 4.05 (Antifreeze) c l i m a t e m a s t e r. c o m 57 58 C l i m a t e M a s t e r Wa t e r - S o u r c e H e a t P u m p s Rev.: 11/09 Please refer to the CM Installation, Operation and Maintenance Manual for operating and maintenance instructions. LC083 *LC083* NOTE: Some states or Canadian provinces do not allow limitations on how long an implied warranty lasts, or the limitation or exclusions of consequential or incidental damages, so the foregoing exclusions and limitations may not apply to you. This warranty gives you speciÀc legal rights, and you may also have other rights which vary from state to state and from Canadian province to Canadian province. Climate Master, Inc. • Customer Service • 7300 S.W. 44th Street • Oklahoma City, Oklahoma 73179 (405) 745-6000 OBTAINING WARRANTY PERFORMANCE Normally, the contractor or service organization who installed the products will provide warranty performance for the owner. Should the installer be unavailable, contact any CM recognized dealer, contractor or service organization. If assistance is required in obtaining warranty performance, write or call: LIMITATION OF LIABILITY CM shall have no liability for any damages if CM’s performance is delayed for any reason or is prevented to any extent by any event such as, but not limited to: any war, civil unrest, government restrictions or restraints, strikes or work stoppages, Àre, Áood, accident, shortages of transportation, fuel, material, or labor, acts of God or any other reason beyond the sole control of CM. CM EXPRESSLY DISCLAIMS AND EXCLUDES ANY LIABILITY FOR CONSEQUENTIAL OR INCIDENTAL DAMAGE IN CONTRACT, FOR BREACH OF ANY EXPRESS OR IMPLIED WARRANTY, OR IN TORT, WHETHER FOR CM’s NEGLIGENCE OR AS STRICT LIABILITY. LIMITATION OF REMEDIES In the event of a breach of the Limited Express Warranty, CM will only be obligated at CM’s option to repair the failed part or unit or to furnish a new or rebuilt part or unit in exchange for the part or unit which has failed. If after written notice to CM’s factory in Oklahoma City, Oklahoma of each defect, malfunction or other failure and a reasonable number of attempts by CM to correct the defect, malfunction or other failure and the remedy fails of its essential purpose, CM shall refund the purchase price paid to CM in exchange for the return of the sold good(s). Said refund shall be the maximum liability of CM. THIS REMEDY IS THE SOLE AND EXCLUSIVE REMEDY OF THE BUYER OR THEIR PURCHASER AGAINST CM FOR BREACH OF CONTRACT, FOR THE BREACH OF ANY WARRANTY OR FOR CM’S NEGLIGENCE OR IN STRICT LIABILITY. Limitation: This Limited Express Warranty is given in lieu of all other warranties. If, notwithstanding the disclaimers contained herein, it is determined that other warranties exist, any such warranties, including without limitation any express warranties or any implied warranties of Àtness for particular purpose and merchantability, shall be limited to the duration of the Limited Express Warranty. CM is not responsible for: (1) The costs of any Áuids, refrigerant or other system components, or associated labor to repair or replace the same, which is incurred as a result of a defective part covered by CM’s Limited Express Warranty; (2) The costs of labor, refrigerant, materials or service incurred in removal of the defective part, or in obtaining and replacing the new or repaired part; or, (3) Transportation costs of the defective part from the installation site to CM or of the return of any part not covered by CM’s Limited Express Warranty. This warranty does not cover and does not apply to: (1) Air Àlters, fuses, refrigerant, Áuids, oil; (2) Products relocated after initial installation; (3) Any portion or component of any system that is not supplied by CM, regardless of the cause of the failure of such portion or component; (4) Products on which the unit identiÀcation tags or labels have been removed or defaced; (5) Products on which payment to CM is or has been in default; (6) Products which have defects or damage which result from improper installation, wiring, electrical imbalance characteristics or maintenance; or are caused by accident, misuse or abuse, Àre, Áood, alteration or misapplication of the product; (7) Products which have defects or damage which result from a contaminated or corrosive air or liquid supply, operation at abnormal temperatures, or unauthorized opening of refrigerant circuit; (8) Mold, fungus or bacteria damages; (9) Products subjected to corrosion or abrasion; (10) Products manufactured or supplied by others; (11) Products which have been subjected to misuse, negligence or accidents; (12) Products which have been operated in a manner contrary to CM’s printed instructions; or (13) Products which have defects, damage or insufÀcient performance as a result of insufÀcient or incorrect system design or the improper application of CM’s products. GRANT OF LIMITED EXPRESS WARRANTY CM warrants CM products purchased and retained in the United States of America and Canada to be free from defects in material and workmanship under normal use and maintenance as follows: (1) All complete air conditioning, heating and/or heat pump units built or sold by CM for twelve (12) months from date of unit start up or eighteen (18) months from date of shipment (from factory), whichever comes Àrst; (2) Repair and replacement parts, which are not supplied under warranty, for nintey (90) days from date of shipment (from factory). All parts must be returned to CM’s factory in Oklahoma City, Oklahoma, freight prepaid, no later than sixty (60) days after the date of the failure of the part; if CM determines the part to be defective and within CM’s Limited Express Warranty, CM shall, when such part has been either replaced or repaired, return such to a factory recognized dealer, contractor or service organization, F.O.B. CM’s factory, Oklahoma City, Oklahoma, freight prepaid. The warranty on any parts repaired or replaced under warranty expires at the end of the original warranty period. EXCEPT AS SPECIFICALLY SET FORTH HEREIN, THERE IS NO EXPRESS WARRANTY AS TO ANY OF CM’S PRODUCTS. CM MAKES NO WARRANTY AGAINST LATENT DEFECTS. CM MAKES NO WARRANTY OF MERCHANTABILITY OF THE GOODS OR OF THE FITNESS OF THE GOODS FOR ANY PARTICULAR PURPOSE. It is expressly understood that unless a statement is speciÀcally identiÀed as a warranty, statements made by Climate Master, Inc., a Delaware corporation, (“CM”) or its representatives, relating to CM’s products, whether oral, written or contained in any sales literature, catalog or any other agreement, are not express warranties and do not form a part of the basis of the bargain, but are merely CM’s opinion or commendation of CM’s products. CLIMATE MASTER, INC. LIMITED EXPRESS WARRANTY/ LIMITATION OF REMEDIES AND LIABILITY CLIMATEMASTER WATER-SOURCE HEAT PUMPS Tranquility ® Large Water-to-Water (TMW) Series Rev.: 12 February, 2016 Warranty (US & Canada) THE SMART SOLUTION FOR ENERGY EFFICIENCY Tranquility ® Large Water-to-Water (TMW) Series Rev.: 12 February, 2106 Notes: c l i m a t e m a s t e r. c o m 59 CLIMATEMASTER WATER-SOURCE HEAT PUMPS Tranquility ® Large Water-to-Water (TMW) Series Rev.: 12 February, 2016 Revision History Date: Item: Action: Unit Physical Data Table Added Compressor Oil Type POE & PVE Oil Warning Added 08/21/12 ALL Added TMW 840 and Misc. Revisions 11/14/11 Dimensional Data Unit Commissioning & Building Operating Conditions Updated 08/09/11 Unit Maximum Working Water Pressure Updated to Reflect New Safeties Control System Information Added Start-up Form Revised 12/12/12 07/01/11 04/29/11 Created 7300 S.W. 44th Street Oklahoma City, OK 73179 Phone: 405-745-6000 *97B0090N01* Fax: 405-745-6058 climatemaster.com 97B0090N01 ClimateMaster works continually to improve its products. As a result, the design and specifications of each product at the time for order may be changed without notice and may not be as described herein. Please contact ClimateMaster’s Customer Service Department at 1-405-745-6000 for specific information on the current design and specifications. Statements and other information contained herein are not express warranties and do not form the basis of any bargain between the parties, but are merely ClimateMaster’s opinion or commendation of its products. The management system governing the manufacture of ClimateMaster’s products is ISO 9001:2008 certified. ClimateMaster is a proud supporter of the Geothermal Exchange Organization - GEO. For more information visit geoexchange.org. © ClimateMaster, Inc. 2006 60 C l i m a t e M a s t e r Wa t e r - S o u r c e H e a t P u m p s ">
/
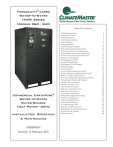
Download
Just a friendly reminder. You can view the document right here. But most importantly, our AI has already read it. It can explain complex things in simple terms, answer your questions in any language, and help you quickly navigate even the longest or most compilcated documents.
Advertisement
Key features
- High-efficiency scroll compressor
- Heating and cooling capabilities
- Commercial grade
- Water-to-water operation
- Multiple operating modes
- Easy to install and maintain
Frequently asked questions
The unit is designed for a leaving water temperature range from 40°F to 62°F. Lower temperatures require a glycol solution additive.
The maximum working pressure is 300 PSIG [2,068 kPa].
Recommended service clearances are 36” (91cm) at front, 30” (76cm) at rear, and 18” (46cm) above. Optional service clearances 24” (61cm) each side.
Consult the unit wiring diagram located on the inside of the compressor access panel to ensure proper electrical hookup.