Great Plains 1993-1996 TM500 & TM700 Tractor Mounted Sprayer Operator Manual
Below you will find brief information for TM500 Tractor Mount Sprayer, TM700 Tractor Mount Sprayer. This manual provides safety, assembly, operation, adjustments, troubleshooting, and maintenance information for the sprayer. Follow the recommendations to help ensure safe and efficient operation. Covers tractor requirements, setup, plumbing, controls, calibration, troubleshooting, and storage procedures.
Advertisement
Advertisement
Operator’s Manual
1993-1996 TM500 & TM700
Tractor Mount Sprayer
Manufacturing, Inc.
!
Read the operator’s manual entirely. When you see this symbol, the subsequent instructions and warnings are serious - follow without exception. Your life and the lives of others depend on it!
12303
Cover illustration may show optional equipment not supplied with standard unit.
© Copyright 1997 Printed 5/13/2003 500-052M
Table of Contents
Important Safety Information . . . . . . . . . . . . . . . . . 1
Wear Protective Equipment . . . . . . . . . . . . . . . . . 5
Handle Chemicals Properly . . . . . . . . . . . . . . . . . 6
Safety Decals. . . . . . . . . . . . . . . . . . . . . . . . . . . . 8
Introduction . . . . . . . . . . . . . . . . . . . . . . . . . . . . . . 10
Intended Usage . . . . . . . . . . . . . . . . . . . . . . 10
Models Covered . . . . . . . . . . . . . . . . . . . . . 10
Using This Manual . . . . . . . . . . . . . . . . . . . . . . . 10
Definitions . . . . . . . . . . . . . . . . . . . . . . . . . . 10
Owner Assistance . . . . . . . . . . . . . . . . . . . . . . . 10
Preparation and Setup . . . . . . . . . . . . . . . . . . . . . . 11
Tractor Requirements . . . . . . . . . . . . . . . . . . . . 11
Before You Start. . . . . . . . . . . . . . . . . . . . . . . . . 11
Case/IH 7110 - 7150 Tractor Mount Assembly
Instructions . . . . . . . . . . . . . . . . . . . . . . . . . . . . 11
John Deere 4240 - 4455 Tractor Mount Assembly
Instructions . . . . . . . . . . . . . . . . . . . . . . . . . . . . 13
John Deere 4630 - 4960 Tractor Mount Assembly
Instructions . . . . . . . . . . . . . . . . . . . . . . . . . . . . 14
Plumbing & Controls Instructions. . . . . . . . . . . . 15
Agitation & Gauge Plumbing . . . . . . . . . . . . . . . 19
Boom & Attachment Plumbing Instructions . . . . 20
Tractor / PTO Pump Hook-Up . . . . . . . . . . . . . . 20
Tractor / Hydraulic Pump Hook-Up . . . . . . . . . . 20
Quad-Jet Agitators {S.S. Tanks Only} . . . . . . . . 21
Control Box Assembly {Manual Control
Systems Only} . . . . . . . . . . . . . . . . . . . . . . . . . . 22
Control Box Wiring Assembly Instructions
{Manual Control System Only}. . . . . . . . . . . . . . 23
Operating Instructions. . . . . . . . . . . . . . . . . . . . . . 24
Basic Sprayer Operating Procedures . . . . . . . . 24
Plumbing Operations {Manual Control
System Only} . . . . . . . . . . . . . . . . . . . . . . . . . . . 24
Operating Pump. . . . . . . . . . . . . . . . . . . . . . . . . 25
Filling Tank Procedures . . . . . . . . . . . . . . . . . . . 25
Using Handwash Tank . . . . . . . . . . . . . . . . . . . . 26
Operating Whirlfilter® . . . . . . . . . . . . . . . . . . . . . 26
To clean-out the solution . . . . . . . . . . . . . . . 26
To clean out the tank-fill . . . . . . . . . . . . . . . . 26
Transporting . . . . . . . . . . . . . . . . . . . . . . . . . . . . 26
General Notes For Field Operation . . . . . . . . . . 27
Adjustments . . . . . . . . . . . . . . . . . . . . . . . . . . . . . . 28
Sprayer Pre-Calibrations . . . . . . . . . . . . . . . . . . 28
Calibration Procedures . . . . . . . . . . . . . . . . . . . . 28
Basic Sprayer Calibration . . . . . . . . . . . . . . . . . . 29
Miles Per Hour Calibration . . . . . . . . . . . . . . . . . 29
Worn Nozzles & Flow Table Information. . . . . . . 30
TeeJet® Worn Nozzles & Flow Table . . . . . . . . . 31
MeterCone® Worn Nozzles & Flow Table . . . . . 31
Spraying Solutions Other Than Water . . . . . . . . 32
Useful Formulas . . . . . . . . . . . . . . . . . . . . . . . . . 32
Check Valve Restriction Data . . . . . . . . . . . . . . . 33
Miscellaneous Conversion Factors. . . . . . . . . . . 33
General Field Adjustments . . . . . . . . . . . . . . . . . 51
Boom Height . . . . . . . . . . . . . . . . . . . . . . . . 51
Nozzle Pressure. . . . . . . . . . . . . . . . . . . . . . 51
Solenoid Throttling Valve {Manual Control
System Only} . . . . . . . . . . . . . . . . . . . . . . . . . . . 51
Pressure Adjustments {Manual Control
System Only} . . . . . . . . . . . . . . . . . . . . . . . . . . . 52
Troubleshooting . . . . . . . . . . . . . . . . . . . . . . . . . . . 53
Maintenance and Lubrication . . . . . . . . . . . . . . . . 54
Maintenance . . . . . . . . . . . . . . . . . . . . . . . . . . . . 54
Equipment Cleanup . . . . . . . . . . . . . . . . . . . 54
General Information . . . . . . . . . . . . . . . . . . . 54
Pump Maintenance & Repair . . . . . . . . . . . . 54
Lubrication . . . . . . . . . . . . . . . . . . . . . . . . . . . . . 56
Storage . . . . . . . . . . . . . . . . . . . . . . . . . . . . . . . . 56
Specifications and Capacities . . . . . . . . . . . . . . . . 57
Appendix . . . . . . . . . . . . . . . . . . . . . . . . . . . . . . . . . 58
Torque Values Chart. . . . . . . . . . . . . . . . . . . . . . 58
Warranty . . . . . . . . . . . . . . . . . . . . . . . . . . . . . . . 59
©
Copyright 1997 All rights Reserved
Great Plains Manufacturing, Inc. provides this publication “as is” without warranty of any kind, either expressed or implied. While every precaution has been taken in the preparation of this manual, Great Plains Manufacturing, Inc. assumes no responsibility for errors or omissions. Neither is any liability assumed for damages resulting from the use of the information contained herein. Great Plains Manufacturing, Inc. reserves the right to revise and improve its products as it sees fit. This publication describes the state of this product at the time of its publication, and may not reflect the product in the future.
Great Plains Manufacturing, Incorporated Trademarks
The following are trademarks of Great Plains Mfg., Inc.: Application Systems, Ausherman, Land Pride, Great Plains
All other brands and product names are trademarks or registered trademarks of their respective holders.
Printed in the United States of America.
5/13/2003
500-052M
5/13/2003
Important Safety Information 1
Important Safety Information
Look for Safety Symbol
The SAFETY ALERT SYMBOL indicates there is a potential hazard to personal safety involved and extra safety precaution must be taken. When you see this symbol, be alert and carefully read the message that follows it. In addition to design and configuration of equipment, hazard control and accident prevention are dependent upon the awareness, concern, prudence and proper training of personnel involved in the operation, transport, maintenance and storage of equipment.
Be Aware of Signal Words
Signal words designate a degree or level of hazard seriousness.
DANGER indicates an imminently hazardous situation which, if not avoided, will result in death or serious injury. This signal word is limited to the most extreme situations, typically for machine components that, for functional purposes, cannot be guarded.
WARNING indicates a potentially hazardous situation which, if not avoided, could result in death or serious injury, and includes hazards that are exposed when guards are removed. It may also be used to alert against unsafe practices.
CAUTION indicates a potentially hazardous situation which, if not avoided, may result in minor or moderate injury. It may also be used to alert against unsafe practices.
!
!
DANGER
!
WARNING
!
CAUTION
500-052M
2 Tractor Mount Sprayer
Be Familiar with Safety Decals
▲
Read and understand “Safety Decals,” page 8,
thoroughly.
▲ Read all instructions noted on the decals.
Keep Riders Off Machinery
Riders obstruct the operator’s view. Riders could be struck by foreign objects or thrown from the machine.
▲
Never allow children to operate equipment.
▲
Keep all bystanders away from machine during operation.
Shutdown and Storage
▲
Fold the Tractor Mount Sprayer Boom, put tractor in park, turn off engine, and remove the key.
▲
Secure Tractor Mount Sprayer using blocks and supports provided.
▲
Detach and store Tractor Mount Sprayer in an area where children normally do not play.
Use Safety Lights and Devices
Slow-moving tractors and towed implements can create a hazard when driven on public roads.
They are difficult to see, especially at night.
▲ Use flashing warning lights and turn signals whenever driving on public roads.
▲ Use lights and devices provided with implement.
Use A Safety Chain
▲ Use a safety chain to help control drawn machinery should it separate from tractor drawbar.
▲ Use a chain with a strength rating equal to or greater than the gross weight of towed machinery.
▲ Attach chain to tractor drawbar support or other specified anchor location. Allow only enough slack in chain to permit turning.
▲ Replace chain if any links or end fittings are broken, stretched or damaged.
▲ Do not use safety chain for towing.
500-052M
OFF
5/13/2003
Transport Machinery Safely
Maximum transport speed for implement is 20 mph. Some rough terrains require a slower speed. Sudden braking can cause a towed load to swerve and upset.
▲
Do not exceed 20 mph. Never travel at a speed which does not allow adequate control of steering and stopping. Reduce speed if towed load is not equipped with brakes.
▲
Comply with state and local laws.
▲
Do not tow an implement that, when fully loaded, weighs more than 1.5 times the weight of towing vehicle.
▲
Carry reflectors or flags to mark Tractor Mount
Sprayer in case of breakdown on the road.
▲
Keep clear of overhead power lines and other obstructions when transporting. Refer to transport dimensions under “Specifications and
▲
Do not fold or unfold the Tractor Mount
Sprayer Boom while the tractor is moving.
Avoid High Pressure Fluids
Escaping fluid under pressure can penetrate the skin, causing serious injury.
▲ Avoid the hazard by relieving pressure before disconnecting hydraulic lines.
▲ Use a piece of paper or cardboard, NOT
BODY PARTS, to check for suspected leaks.
▲ Wear protective gloves and safety glasses or goggles when working with hydraulic systems.
▲ If an accident occurs, see a doctor immediately. Any fluid injected into the skin must be surgically removed within a few hours or gangrene may result.
5/13/2003
Important Safety Information 3
500-052M
4 Tractor Mount Sprayer
Practice Safe Maintenance
▲
Understand procedure before doing work. Use proper tools and equipment. Refer to this manual for additional information.
▲
Work in a clean, dry area.
▲
Fold the Tractor Mount Sprayer, put tractor in park, turn off engine, and remove key before performing maintenance.
▲
Make sure all moving parts have stopped and all system pressure is relieved.
▲
Allow Tractor Mount Sprayer to cool completely.
▲
Disconnect battery ground cable (-) before servicing or adjusting electrical systems or before welding on Tractor Mount Sprayer.
▲
Inspect all parts. Make sure parts are in good condition and installed properly.
▲
Remove buildup of grease, oil or debris.
▲
Remove all tools and unused parts from Tractor Mount Sprayer before operation.
Prepare for Emergencies
▲
Be prepared if a fire starts.
▲
Keep a first aid kit and fire extinguisher handy.
▲
Keep emergency numbers for doctor, ambulance, hospital and fire department near phone.
Tire Safety
Tire changing can be dangerous and should be performed by trained personnel using correct tools and equipment.
▲ When inflating tires, use a clip-on chuck and extension hose long enough for you to stand to one side–not in front of or over tire assembly. Use a safety cage if available.
▲ When removing and installing wheels, use wheel-handling equipment adequate for weight involved.
OFF
911
500-052M
5/13/2003
Wear Protective Equipment
Great Plains advises all users of chemical pesticides or herbicides to use the following personal safety equipment.
▲ Waterproof, wide-brimmed hat.
▲ Waterproof apron.
▲ Face shield, goggles or full face respirator.
▲ Goggles with side shields or a full face respirator is required if handling or applying dusts, wettable powders, or granules or if being exposed to spray mist.
▲ Cartridge-type respirator approved for pesticide vapors unless label specifies another type of respirator.
▲ Waterproof, unlined gloves. Neoprene gloves are recommended.
▲ Cloth coveralls/outer clothing changed daily; waterproof items if there is a chance of becoming wet with spray.
▲ Waterproof boots or foot coverings.
▲ Do not wear contaminated clothing. Wash protective clothing and equipment with soap and water after each use. Personal clothing must be laundered separately from household articles.
▲ Clothing contaminated with certain pesticides must be destroyed according to state and local regulations. Read chemical label for specific instructions.
▲ Wear clothing and equipment appropriate for the job.
Avoid loose-fitting clothing.
▲ Prolonged exposure to loud noise can cause hearing impairment or loss. Wear suitable hearing protection such as earmuffs or earplugs.
▲ Avoid wearing radio headphones while operating machinery. Operating equipment safely requires the full attention of the operator.
5/13/2003
Important Safety Information 5
500-052M
6 Tractor Mount Sprayer
Handle Chemicals Properly
▲ Read and follow chemical manufacturer’s instructions.
▲ Wear protective clothing.
▲ Handle all chemicals with care.
▲ Agricultural chemicals can be dangerous.
Improper use can seriously injure persons, animals, plants, soil and property.
▲ Inhaling smoke from any type of chemical fire is a serious health hazard.
▲ Store or dispose of unused chemicals as specified by the chemical manufacturer.
▲ Before adding chemical to the tank, make sure tank is at least half full. Do not pour concentrate into an empty tank.
▲ Never leave fill hose attached to the sprayer after filling tank. Chemicals in tank can siphon out of tank and contaminate freshwater source.
▲ Always keep hand-wash tank filled with clean water and have soap available in case of an emergency. Immediately and thoroughly flush any area of the body that is contaminated by chemicals.
▲ Do not touch sprayer components with mouth or lips.
▲ If chemical is swallowed, carefully follow the chemical manufacturer’s recommendations and consult with a doctor.
▲ If persons are exposed to a chemical in a way that could affect their health, consult a doctor immediately with the chemical label or container in hand. Any delay could cause serious illness or death.
▲ Dispose of empty chemical containers properly. By law rinsing of the used chemical container must be repeated three times. Puncture the container to prevent future use. An alternative is to jet-rinse or pressure rinse the container.
▲ Wash hands and face before eating after working with chemicals. Shower as soon as spraying is completed for the day.
▲ Spray only with acceptable wind conditions.
Wind speed must be below 5 mph. Make sure wind drift of chemicals will not affect any surrounding land, people or animals.
▲ Never wash out the sprayer tank within 100 feet of any freshwater source or in a car wash.
▲ Rinse out the tank. Spray rinse water on last field sprayed.
500-052M
5/13/2003
Safety At All Times
Thoroughly read and understand the instructions in this manual before operation. Read all instructions noted on the safety decals.
▲ Be familiar with all Tractor Mount Sprayer functions.
▲ Operate machinery from the driver’s seat only.
▲ Do not leave Tractor Mount Sprayer unattended with tractor engine running.
▲ Do not dismount a moving tractor. Dismounting a moving tractor could cause serious injury or death.
▲ Do not stand between the tractor and Sprayer
Boom during hitching.
▲ Keep hands, feet and clothing away from power-driven parts.
▲ Wear snug-fitting clothing to avoid entanglement with moving parts.
▲ Watch out for wires, trees, etc., when folding and raising Sprayer Boom. Make sure all persons are clear of working area.
▲ Do not turn tractor too tightly, causing Sprayer
Boom to ride up on wheels. This could cause personal injury or equipment damage.
▲ Use only water without pesticides added to calibrate the sprayer. Do not exceed the calibrated sprayer speed and pressure when operating.
▲ When using a PTO pump, be sure that PTO shield is in place on the tractor, PTO coupler bolts are torqued to the correct specification, and torque bar is properly chained to tractor drawbar.
▲ Spray with the boom in the unfolded position only.
▲ The boom has many pinch points during field operation and folding. Keep all bystanders away.
5/13/2003
Important Safety Information 7
500-052M
8 Tractor Mount Sprayer
Safety Decals
Your implement comes equipped with all safety decals in place. They were designed to help you safely operate your implement.
▲
Read and follow decal directions.
▲
Keep all safety decals clean and legible.
▲
Replace all damaged or missing decals. Order new decals from your Great Plains dealer.
Refer to this section for proper decal placement.
▲
When ordering new parts or components, also request corresponding safety decals.
▲
To install new decals:
1.
Clean the area where the decal is to be placed.
2.
Peel backing from decal. Press firmly on surface, being careful not to cause air bubbles under decal.
818-324C
Caution! General Sprayer Safety Information.
818-367C
Danger! Power line hazard.
12538
12538
818-323C
Caution! Use proper personal safety equipment. Also, refer to previous page.
500-052M
12219
5/13/2003
Important Safety Information 9
12538
818-307C
Caution! Do Not run pump dry.
5/13/2003
12539
818-344C
Notice! Gauge protector.
12540
818-326C
Notice! Control box power leads.
500-052M
10 Tractor Mount Sprayer
Introduction
Great Plains welcomes you to its growing family of new product owners. This Tractor Mount Sprayer has been designed with care and built by skilled workers using quality materials. Proper setup, maintenance and safe operating practices will help you get years of satisfactory use from the machine.
Intended Usage
Use this Tractor Mount Sprayer as part of a pressurized sprayer system to apply liquid pesticides, herbicides or fertilizers to production-agriculture crops only. Do not modify sprayer for use with attachments other than those approved by Great
Plains.
Models Covered
TM500 & TM700 Tractor Mount Sprayer
Using This Manual
This manual will familiarize you with safety, assembly, operation, adjustments, troubleshooting and maintenance. Read this manual and follow the recommendations to help ensure safe and efficient operation.
The information in this manual is current at printing. Some parts may change to assure top performance.
Definitions
The following terms are used throughout this manual.
Right-hand and left-hand as used in this manual are determined by facing the direction the machine will travel while in use unless otherwise stated.
IMPORTANT: A crucial point of information related to the preceding topic. For safe and correct operation, read and follow the directions provided before continuing.
NOTE: Useful information related to the preceding topic.
Owner Assistance
If you need customer service or repair parts, contact a Great Plains dealer. They have trained personnel, repair parts and equipment specially designed for Tractor Mount Sprayer products.
Your machine’s parts were specially designed and should only be replaced with Tractor Mount Sprayer parts. Always use the serial and model number when ordering parts from your Great Plains dealer.
Record your sprayer model and serial number here for quick reference:
Model Number:__________________________
Serial Number: ___________________________
Your Great Plains dealer wants you to be satisfied with your new machine. If you do not understand any part of this manual or are not satisfied with the service received, please take the following actions.
1.
Discuss the matter with your dealership service manager. Make sure they are aware of any problems so they can assist you.
2.
If you are still unsatisfied, seek out the owner or general manager of the dealership.
3.
For further assistance write to:
Product Support
Great Plains Mfg. Inc., Service Department
PO Box 5060
Salina, KS 67402-5060
5/13/2003
500-052M
Preparation and Setup 11
Preparation and Setup
Tractor Requirements
To operate your Great Plains Sprayer, a tractor using a
12 volt electrical system must be used.
The tractor will need two hydraulic outlets (one pair) if the sprayer is equipped with a hydraulic pump.
Before You Start
Read and understand the owners manual for your sprayer. A basic understanding of how the sprayer works will aid in the assembly, setup and operation of your sprayer.
Before attempting to assemble the sprayer, use the following as a checklist. Having all the needed parts and equipment readily at hand will speed up your assembly task and will make the job as safe as possible.
1.
❑
Check for all sprayer components and hardware.
2.
❑
If a bolt, pin or other component has been removed, or if you are unsure about where it is used, refer to the parts manual to identify it.
Case/IH 7110 - 7150 Tractor Mount
Assembly Instructions
Refer to Figure 2 on page 12
To assemble the side-mount tanks, you will need to remove the steps, the front fenders (if equipped) and possibly other components to fit the tanks onto the tractor.
1.
Assemble the right (1) and left (2) side plates onto the front of the tractor frame using the twelve 5/8" x
5" long bolts, flat washers and flange nuts.
2.
Remove the two front bolts from the tractor drawbar support (3).
3.
Assemble the rear bracket support (4) with the two longer M16.2.0x75 metric bolts (5) and 5/8" flat washers included.
4.
Bolt together the right (1) and left (2) side plates to the rear bracket support (4) with the six 5/8" x 2" long bolts, flat washers and flange nuts.
5.
Assemble the two tank rails (6) onto the right (1) and left (2) side plates with the backup plates (7), 5/8" x
6" long bolts, flat washers, and flange nuts. There are three locations to bolt these rails. Make sure that when you fasten the rails on that you bolt them in the same perspective hole locations or else the tanks won’t fit on the rails.
6.
Position the notched tank on the left rails and the full tank on the right rails with the tank caps toward the outside.
!
WARNING
Lifting Hazard
-Use a crane or hoist to lift and position the tanks.
-The tanks can fall causing potential injury if not handled correctly.
Move the tanks so that there is sufficient clearance between the tanks and the tractor.
Refer to Figure 1
7.
Assemble the angles (8) onto the outer holes in the tank saddles using the 3/4" x 1 3/4" long bolts, and flange nuts. There are four angles on each saddle that support the four corners of the saddle.
8.
Hook the four angle brackets (9) onto the rails for each tank and bolt them to the angles (8) using the
1/2" x 1 3/4" long bolts, and flange nuts. Release the overhead support of the tanks after they are securely fastened.
9.
Check and make sure all nuts are torqued to the correct specs listed in the “Torque Values Table” on
10. Proceed with the “Plumbing & Controls Instruc-
12527
Figure 1
Angles on Saddle
500-052M
5/13/2003
12 Tractor Mount Sprayer
12526
500-052M
Figure 2
Case/IH 7110 - 7150 Tractor Mount Assembly Instructions
5/13/2003
Preparation and Setup 13
John Deere 4240 - 4455 Tractor
Mount Assembly Instructions
Refer to Figure 3
To assemble the side-mount tanks, you will need to remove the steps, the front fenders (if equipped) and possibly other components to fit the tanks onto the tractor.
1.
Assemble the left (1) and right (2) side plates onto the front of the tractor frame using the eight 5/8" x 2" long carriage bolts, flat washers and flange nuts.
2.
Mount the spreader bar (3) onto the left and right side plates with the u-bolts, 5/8" flange nuts, and washers but do not tighten the nuts completely.
3.
Determine where the left (4) right (5) side rails will be positioned so that when the tanks are mounted, there will be sufficient clearance between the tires and the tanks. You will have to slide the spreader bar
(3) to position where the rails will be.
4.
Fasten the left (4) and right (5) side rails to the spreader bar (3) with four 5/8" x 2" long carriage bolts, flat washers, and flange nuts on each rail.
Support the rear of the rails by assembling a few of the bolts in step 5.
5.
After determining where the left and right rails (4 &
5) will be positioned, use the optimum holes in the rear portion of the rails (4 & 5) with the two spacer blocks (6), four backup angles (7), eight 5/8" x 11
1/2" long bolts (8), and the eight 5/8" flange nuts and washers.
6.
Tighten all the hardware on all the components assembled to the correct torque specifications listed on page 58.
7.
Assemble the four tank rails (9) using the 5/8" x 2" long bolts, flat washers and flange nuts.
8.
Position the notched tank on the left rails and the full tank on the right rails with the tank caps toward the outside.
!
WARNING
Lifting Hazard
-Use a crane or hoist to lift and position the tanks.
-The tanks can fall causing potential injury if not handled correctly.
Move the tanks so that there is sufficient clearance between the tanks and the tractor.
9.
Assemble the angles (10) onto the outer holes in the tank saddles (refer to Figure 1 on page 11) using the
3/4" x 1 3/4" long bolts, and flange nuts. There are four angles on each saddle that support the four corners of the saddle.
10. Hook the four angle brackets (11) onto the rails for each tank and bolt them to the angles (10) using the
1/2" x 1 3/4" long bolts, and flange nuts. Release the overhead support of the tanks after they are securely fastened.
11. Check and make sure all nuts are torqued to the correct specs listed in the “Torque Values Table” on
12. Proceed with the “Plumbing & Controls Instruc-
Figure 3
John Deere 4240 - 4455 Tractor Mount
Assembly Instructions
12528
500-052M
5/13/2003
14 Tractor Mount Sprayer
John Deere 4630 - 4960 Tractor
Mount Assembly Instructions
Refer to Figure 4
To assemble the side-mount tanks, you will need to remove the steps, the front fenders (if equipped) and possibly other components to fit the tanks onto the tractor.
1.
Assemble the left (1) and right (2) side plates onto the front of the tractor frame using the eight 5/8" x 2" long carriage bolts, flat washers and flange nuts.
2.
Mount the spreader bar (3) onto the left and right side plates with the u-bolts, 5/8" flange nuts, and washers but do not tighten the nuts completely.
3.
Determine where the left (4) right (5) side rails will be positioned so that when the tanks are mounted, there will be sufficient clearance between the tires and the tanks. You will have to slide the spreader bar
(3) to position where the rails will be.
4.
Fasten the left (4) and right (5) side rails to the spreader bar (3) with four 5/8" x 2" long carriage bolts, flat washers, and flange nuts on each rail.
Support the rear of the rails by assembling a few of the bolts in step 5.
5.
After determining where the left and right rails (4 &
5) will be positioned, use the optimum holes in the rear portion of the rails (4 & 5) with the two spacer blocks (6), four backup angles (7), and the eight 5/8" x 10" long bolts (8), flange nuts and washers.
6.
Tighten all the hardware on all the components assembled to the correct torque specifications listed on page 56.
7.
Assemble the front two tank rails (9) using the eight
5/8" x 2" long bolts, flat washers and flange nuts.
8.
Assemble the rear to tank rails (10) using the four
5/8" x 5" bolts, four 5/8" x 2" long bolts and the eight
5/8" flange nuts and flat washers.
9.
Position the notched tank on the left rails and the full tank on the right rails with the tank caps toward the outside.
!
WARNING
Lifting Hazard
-Use a crane or hoist to lift and position the tanks.
-The tanks can fall causing potential injury if not handled correctly.
Move the tanks so that there is sufficient clearance between the tanks and the tractor.
10. Assemble the angles (11) onto the outer holes in the tank saddles (refer to Figure 1 on page 11) using the
3/4 x 1 3/4" long bolts, and flange nuts. There are four angles on each saddle that support the four corners of the saddle.
11. Hook the four angle brackets (12) onto the rails for each tank and bolt them to the angles (11) using the
1/2" x 1 3/4" long bolts, and flange nuts. Release the overhead support of the tanks after they are securely fastened.
12. Check and make sure all nuts are torqued to the correct specs listed in the “Torque Values Table” on
13. Proceed with the “Plumbing & Controls Instruc-
Figure 4
John Deere 4630 - 4960 Tractor
Mount Assembly Instructions
12529
5/13/2003
500-052M
Preparation and Setup 15
Plumbing & Controls Instructions
Refer to Figure 5
1.
Measure the distance “A” to determine where the tank union tee should be placed.
2.
The length “B” and length “C” should be as follows:
Length “B”
Length “C”
75% of Length “A”
25% of Length “A”
!
CAUTION
Chemical Hazard
Make sure the tank union tee is assembled according to instructions. Failure to place the tee in the correct position may cause water overflow out of a tank when filling the tanks.
Chemical residue previously in the tank could be exposed to the environment if the fill-water is spilled.
Refer to Figure 6 on page 16
3.
Assemble the 1 1/2" hose barb tank union tee (1) with the correct length of 1 1/2" ID hose according to the measurements you determined in step 2. It is recommended to use petroleum jelly or some type of lubricant in the inside diameter of the hose before it is assembled on the hose barbs. It will make the assembly much easier. Tighten the #28 hose clamps after the hose is assembled.
4.
Mount the quick-fill bracket (2) on the front of your tractor so that the fill-coupler is easily accessed. You may be able to place the quick-fill bracket in-between two tractor weights.
5.
Cut a short section of 1 1/2" hose (3) and assemble a second 1 1/2" hose barb tee (4) on the section of hose. Fasten the hose with the #28 hose clamps when finished.
6.
Measure out and cut a section of 1 1/2" ID hose from the tee (4) to the hose barb (5). Secure the #28 hose clamps when finished. Use plastic cable-ties 6) to secure the hose to the tractor. Make sure the hose does not droop below the tractor where it could get caught.
7.
Attach another short section of 1 1/2" ID hose (7) in between tee (4) and the tee assembly (8). Tighten the #28 hose clamps.
8.
Follow the “Tractor/PTO Pump Hook-Up” on
page 20 {if equipped} and mount the pump onto the
tractor.
9.
Measure and assemble a section of 1 1/2" ID hose from the tee assembly (8) to the pump with a 1 1/2" hose barb elbow (9) just below the pump. The section of hose in-between the hose barb elbow (9) and the pump should be less than a foot long. Tighten the #28 hose clamps.
10. Use cable ties (6) to secure the hose under the tractor.
5/13/2003
Figure 5
Tank Union Tee
12545
500-052M
16 Tractor Mount Sprayer
500-052M
12534
Figure 6
Plumbing Assembly Instructions
5/13/2003
Preparation and Setup 17
Refer to Figure 7
11. Cut a 1" ID hose (10) that leads from the pump to the solution Whirlfilter
® hose barb. You will need to place 1" elbow hose-barbs (11) as shown to orient the hose up the side of the tank. Measure out and cut a length of hose guard material (14) along the area between the tractor and the tank, and route hose from pump to Whirlfilter
® hose barb through the hose guard material. Pump suction and pressure line should also be routed through the hose guard material where sharp corners exist under the tractor transmission area. Tighten the #16 hose clamps.
12. Use cable ties (6) to secure the hose under the tractor.
5/13/2003
Figure 7
Pressure Head Assembly
13229
500-052M
18 Tractor Mount Sprayer
Refer to Figure 8
13. Cut a 1" ID hose (12) that leads from the tee assembly (8) to the bypass elbow. A 1" hose-barb elbow will need to be in place at the bottom and top of the tank as shown. An additional 1" elbow
(13) will need to be assembled so that the hose can be connected without kinking. Also route this hose through hose guard material between tractor and tank. Tighten the #16 hose clamps on all hose ends after assembling the hose.
14. Use cable ties (6) to secure the two hoses.
500-052M
Figure 8
Solenoid Valve Assembly
12537
5/13/2003
Preparation and Setup 19
Agitation & Gauge Plumbing
Refer to Figure 9
1.
Assemble a section of 1" hose (1) on to the agitation hose barb (2). Route the hose along the other two hoses assembled in Figure 6 on page 16.
2.
Place the 1" hose barb elbow (3) so that the vertical section of the 1" hose guard material {Figure 6 (14)} that secures the other two hoses {Figure 6 (10) &
(12)} assembled vertically along the side of the tank.
3.
Secure the hose to the hose barbs with the number
16 hose clamps. After all the hoses are routed through the hose guard material {Figure 6 (14)}, fold the ends of the hose guard material back underneath and tie with cable ties {Figure 6 (6)}.
4.
Attach the tee assembly (4) to the vertical 1" hose.
5.
Measure and cut two pieces of hose 3/4" (5) so that they are assembled from the tee assembly (4) to the agitation elbow (6) on both tanks. Secure the number 12 hose clamps on the 3/4" hose.
6.
Cut a section of 3/8" hose (7) to a length that is satisfactory for where you will place the gauge on the tractor. Route the hose from the 3/8" hose barb on the solenoids to the 3/8" hose barb on the gauge assembly as shown. Secure the hose with the number
5 hose clamps.
5/13/2003
Figure 9
Agitation Assembly
12595
500-052M
20 Tractor Mount Sprayer
Boom & Attachment
Plumbing Instructions
Refer to Figure 8 on page 18
1.
If the 3-point boom is being mounted on a tractor with Great Plains side-mount tanks remove the cap plugs on the solenoid hose barbs and route the left boom feed-line hose from the corresponding female fluid connector to the right solenoid (right being as you sit in the tractor) marked with red tape. Connect the center boom feed-line hose from the corresponding female fluid connector to the middle solenoid marked with yellow tape. Now aconite the right feed-line hose from the corresponding female fluid connector to the left solenoid marked with green tape. Take care when routing the boom hoses to the tractor to ensure there will be no kinking, drooping, hanging bellow the tractor, or rubbing on the tractor frame when in operation. Route boom hoses through the remaining hose guard material along the front side of the left-hand tank.
2.
If the Great Plains side-mount tanks are being mounted with another implement, route and connect the hoses to the solenoid valve as described in (1) above.
Tractor / PTO Pump Hook-Up
1.
With the tractor not running, position the PTO pump on the tractor’s PTO shaft with the coupler bolt loose on the splined end.
2.
Push the coupler of the pump on to align with notch in the tractor PTO shaft and install bolt.
3.
Make sure there is adequate hose length to reach the pump.
4.
If you have a 540 RPM pump or a 1000 RPM 1 3/8 inch spline pump, torque the 1/2 inch Grade 8 coupler bolts to 105 ft-lbs. If you have a 1000 RPM
1 3/4 inch spline PTO pump, torque the 5/8 inch
Grade 8 coupler bolt to 210 ft-lbs and the other 1/2 inch Grade 8 coupler bolt to 105 ft-lbs.
5.
Rotate the PTO shaft by hand to make sure the bolts clear the PTO shielding.
6.
Attach the torque bar chain to the drawbar securely.
7.
Hook the tarp strap in such a way that the slack in the chain is taken up slowly when the PTO is engaged so the torque bar does not bang.
8.
Tie up any loose hoses with cable ties to prevent hose damage.
Tractor / Hydraulic Pump Hook-Up
1.
Your tractor should be equipped with at least two remote outlets (one pair).
2.
If your tractor has an open-center hydraulic system, remove the orifice restrictor in the pressure line. If your open-center hydraulic system produces more than 15 GPM, it is not recommended to hook this hydraulic pump up to your tractor. Without a flow divider of adequate capacity the pump will spin too fast. If your open-center hydraulic system is 15 GPM or less, it is recommended to install a hydraulic flow divider so that you can adjust the speed of the pump.
A Gresen model number CFDA or similar flow divider will work. The maximum flow for the hydraulic motor is 6 GPM.
3.
For the hydraulic motor to turn in the right direction, the pressure hose must be connected to the "A" port of the motor and the return line connected to the "B" port. Install hydraulic hose clamp label provided {refer to hydraulic pump section in parts manual} approximately18 inches from tractor quick couplers so that the hydraulic cylinder retract symbol and arrow aligns with the pressure hose going to motor port "A". If your tractor is a John Deere, leave the restrictor in the pressure side of the hydraulic pump.
If your tractor has a closed center hydraulic system and is not a John Deere, remove the restrictor.
4.
If your tractor has a closed-center system, or a flow divider has been installed in your tractor’s open-center system, set the hydraulic flow control valve at a minimum flow for the pair of outlets that operates the pump.
5.
With water in the sprayer tank, and water in the pump, place the hydraulic lever in the float position and start the tractor.
6.
Place a stop in the neutral position of your tractor hydraulics so that the lever can only be moved to the float and down positions. Refer to your tractor operator’s manual or tractor dealer on information for the neutral stop.
IMPORTANT: DO NOT move the hydraulic lever into the neutral position while the hydraulic pump is running. To do so may cause damage to the hydraulic pump.
7.
To set the hydraulic flow control on the tractor, first engage the pump by placing the hydraulic lever in the down position. Once the system builds pressure, close the agitation valve, shut off the boom section switches and close throttling valves {if applicable}.
500-052M
5/13/2003
Sprayers with Raven Automatic Monitors do not have throttling valves. The pump is now at dead head pressure. Adjust the hydraulic flow control valve so that the spray pressure reaches 80 PSI maximum on the nozzle pressure gauge. If so equipped, reset the solenoid throttling valves as described in the "Solenoid Throttling Valve" on
Quad-Jet Agitators {Stainless Steel
Tanks Only}
Refer to Figure 10
The Quad-Jet agitator is the agitator in the stainless steel tank. Each agitator has four holes that shoot jets of water out at a high velocity. The agitator head is oriented at 45 degrees, with reference to the tank ends, so that the water jets are aimed at the corners of the tank. To ensure proper agitation, make sure that the agitator head is always kept in the orientation as shown.
Preparation and Setup 21
12546
Figure 10
Tank Top View
Quad-Jet Agitator Head Orientation
5/13/2003
500-052M
22 Tractor Mount Sprayer
Control Box Assembly {Manual Control Systems Only}
Refer to Figure 11
1.
Remove the solenoid cover to gain access to the solenoid terminals.
2.
Mount the control box on your tractor. Connect the red wire (1) to the positive terminal of the 12 volt battery and the white wire (2) to the negative terminal.
You will need to pull the red and white wires out of the black harness (3) until there is enough wire to reach the battery.
Note: You may want to attach the battery leads (4) to the battery terminals and the control box power leads so that the control box can be disconnected easily.
After the power leads (1) & (2) are hooked to the battery, you should be able to turn on the master switch and see the red power light come on. Turn the master switch OFF
BEFORE proceeding to the next step.
3.
Attach the electric solenoid cord (5) to the solenoids as shown. The green wire attaches to the front solenoid {front being toward the hitch}. The yellow wire attaches to the middle solenoid and the brown wire attaches to the rear solenoid. Connect the other wire
{white} to all three solenoids.
4.
Hook up the electric solenoid cord (5) to the solenoid plug (6). You may need to use the extension cord included to reach the solenoid valves more easily. Turn the master switch on and flip the boom section switches to see if the solenoids are operating properly. The left boom switch should operate the front solenoid, the center boom switch should operate the middle solenoid, and the right boom switch should operate the rear solenoid. If the switches don’t correspond with the correct solenoids, check your electric cord assembly in step 3, or the wiring of the control box under "Control Box
Wiring Assembly Instructions" on page 23.
5.
Attach the electric ball valve cord (7) to the terminals
(8) on the electric ball valve.
6.
Hook up the electric ball valve cord (7) to the ball valve plug (9). You may need to use the extension cord included to reach the ball valve. Turn the master boom switch and flip the pressure adjust switch.
The ball valve should operate when the switch is flipped.
7.
Reassemble the solenoid cover over the top of the solenoids.
11953
Figure 11
Control Box Assembly
500-052M
5/13/2003
Preparation and Setup 23
Control Box Wiring Assembly
Instructions {Manual Control System
Only}
Refer to 12
The electrical assembly schematic is shown for the control box in a view that is looking into the back of the box with the cover off. There are four separate wiring harnesses that enter into the control box along with the positive and negative power leads. In this control box, the red wires are always positive and the white wires are always negative. Other colored wires could be positive or negative. Make sure that all wires are attached as shown in the schematic. There are two wire nuts that attach several wires at once and are displayed by the large asterisk (*) signs in the drawing.
Attach the wires as shown in the drawing for any electrical repair work. This will also serve as a guide for replacing the electrical wiring. Refer to "Sprayer Con-
trol Box Assembly" in the parts manual.
IMPORTANT: Disconnect battery leads before working on any electrical components in this control box. Failure to do so may result in damage to the electrical components.
5/13/2003
Figure 12
Control Box Wiring Assembly
11473
500-052M
24 Tractor Mount Sprayer
Operating Instructions
Basic Sprayer Operating
Procedures
1.
Make sure to read the label on the chemical compound that is to be applied. It is the law.
2.
Consider how the chemical will be stored and how you will dispose of the chemical, according to the chemical label.
3.
When calibrating, filling the tank, or working around chemicals, wear protective clothing that covers the body. Refer to "Personal Safety Equipment" on
page 5. Have soap and clean water available to
wash any exposed areas. Never open a container with your bare hands.
4.
When filling the sprayer, it is better to mix the chemical in the field where it is to be applied. Position the sprayer 100 feet from any well or other water source
BEFORE mixing chemical.
5.
By law, you must repeat the rinsing of the chemical container 3 times. The container should then be punctured to prevent future use. An alternative is to jet-rinse or pressure rinse the container.
6.
Check the condition of hoses and connections frequently. Release system pressure BEFORE working on the sprayer by shutting off the pump and flipping the individual boom section switches on the control box. ALWAYS wear rubber gloves when making repairs or adjustments.
7.
If equipped with level-float boom, remove the level float pin and place in the storage position after unfolding the boom. Refer to your Great Plains Boom
Manual for more information.
Note: If possible, do not operate your Great Plains
Sprayer Boom without first unlocking the level-float pin.
The boom will float over the contours of the ground more effectively and minimize stress on the boom.
8.
Apply spray when the wind is 5 m.p.h. or less. Minimize drift by using nozzle tips with the largest practical openings and by operating the sprayer boom at the lowest practical height and lowest practical pressure.
9.
Drive at the same speed you used in your calibra-
tion. Refer to "Sprayer Calibrations" on page 28.
Keep your sprayer calibrated.
10. If possible work crosswise to the wind, starting from the downwind side of the field. Do this so you won’t ever be heading directly into chemical fumes.
11. Take note of adjoining crops, houses, gardens, people, etc.
12. When you are finished spraying, empty the tank and flush the sprayer with water, including the pump, the nozzles and the bypass line from the solenoids.
Properly store the chemical emptied from the tank or dispose of it by the recommendations on its label.
13. When turning at the end of a field, make sure you are correct on the rows so that the boom will not overlap on crop previously sprayed.
Plumbing Operations {Manual Control System Only}
The basic plumbing diagrams are shown for the tractor mount plumbing. A basic knowledge of how the sprayer is plumbed will help you to understand how to operate you Great Plains Sprayer. Throughout this manual, the components on this diagram will be described with the terminology labeling these components. For further details about the plumbing components, refer to the parts manual.
Fluid is drawn out of the sump in the tank and passes through the pump. From the pump it passes through the solution Whirlfilter
® and filters out or grinds up all undissolved chemical and solid particles. The fluid then passes through the agitation ball valve or proceeds through the electric pressure adjustment ball valve. If the fluid passes through the electric ball valve, it proceeds to the 3-way solenoid valves. If a solenoid valve is on, the fluid passes to its perspective boom section and is sprayed out the individual nozzles. If that solenoid is off, the fluid bypasses back into the pump inlet.
You can monitor the nozzle pressure gauge and adjust the pressure to the booms by adjusting the pressure switch on the control box. The pressure switch rotates the electric ball valve. To decrease the sensitivity of the pressure adjustment switch the manual pressure adjustment valve must be set. To set this valve, run the pump at the same rpm you would when spraying. Open the electric ball valve completely and adjust the manual pressure adjustment valve down so that the nozzle pressure gauge reads 10 to 20 psi greater than the pressure you will spray at. This will decrease the amount of flow to the electric ball valve and reduce its sensitivity.
Note: When pressure is increased at a later date, the manual pressure adjustment valve will need to be opened.
500-052M
5/13/2003
Operating Instructions 25
The agitation can be set by adjusting the agitation pressure valve while the pump is at operating speed. Adjust the valve until you get the desired agitation pressure you would like on the agitation pressure gauge.
There are tank shut off valves everywhere there is an outlet from the tank so that if there is a leak, the source can be shut off and the chemical spill reduced. These valves need to be wide open when the sprayer is in use.
IMPORTANT: Do not move the hydraulic lever to the neutral position while the hydraulic pump is running.
To do so may cause damage to the hydraulic pump.
12547
Plumbing Diagrams Stainless Steel Tank
{Manual Control System Only}
!
WARNING
Never operate the PTO pump without the tractor PTO shield in place, and the pump torque bar firmly chained in place.
To operate the hydraulic pump, first make sure that the hydraulic hoses are routed correctly so that the pump turns in the correct direction. See the “Tractor/Hydrau-
lic Pump Hook-Up” on page 20, for more details. To run
the pump, push the hydraulic lever in the “down” position. When you want to stop the pump, push the hydraulic lever in the “float” position.
Filling Tank Procedures
!
CAUTION
When filling the sprayer tank, use a check valve or anti-siphon device to prevent the solution in the tank from infiltrating into the fresh water source and contaminating it.
Your Great Plains Sprayer fills the tank from the bottom of the tank and uses a standard 2 inch Cam-Lock coupler to connect to the freshwater hose. An 1 1/2 inch camlock coupler is also available as an accessory. Refer to "Quick Fill Assembly" in the parts manual.
1.
To fill the tank, hook up the freshwater hose to the quick-fill camlock coupler with the quick-fill ball valve in the closed position.
2.
Turn the water on and open the quick-fill ball valve for the freshwater to enter the tank. When using a positive displacement pump to fill the tank, open the quick fill ball valve first and then pump water into the tank.
!
CAUTION
Do not add the chemical until you are at the field, just prior to spraying. When you add the chemical, follow the manufacturer’s instructions for mixing the spray solution in order to achieve the desired application rate.
Operating Pump
To operate the PTO pumps, engage the PTO shaft slowly at the tractor’s idle throttle position. Slowly accelerate to the desired PTO RPM (On a 540 RPM pump it is recommended to operate the pump at 540 RPM and on a
1000 RPM pump it is recommended to operate the pump at 1000 RPM). Disengage the PTO at any RPM to stop the pump.
!
CAUTION
Read the manufacturer’s label carefully before handling chemicals.
3.
Before you add the chemical to the tank, make sure the tank is at least one half full. The concentrate should not be poured into an empty tank.
4.
Keep the spray solution away from all skin. Wear protective clothing and goggles. If the solutions comes in contact with the body, wash off the contaminated area with soap and water.
5.
Keep chemical containers low when pouring.
6.
Let the wind blow fumes and dust away from you while pouring the chemical.
7.
DO NOT smoke while handling chemicals.
500-052M
5/13/2003
26 Tractor Mount Sprayer
Using Handwash Tank
In the event when an accident occurs and chemical is spilled on your skin or in your eyes, use the Handwash
Tank to flush away the chemical.
1.
Open the tank valve and use the hose to direct the clean water on all contaminated areas. Wash all areas of skin that has been contaminated with soap and water. To flush your eyes, point the hose and water stream upward while you lower your eye into the stream of flowing water.
2.
Close the tank valve and refill the handwash tank with fresh water when you are finished.
3.
Periodically refill the handwash tank with fresh water. ALWAYS keep the handwash tank clean.
Operating Whirlfilter
®
There are two Whirlfilters
® on your Great Plains Sprayer.
One filters the water entering the tank and the other filters the chemical solution being sprayed.
To clean-out the solution Whirlfilter
®
, proceed with the following:
1.
Fill the sprayer tank with water and turn the pump on.
2.
With the pump running, slowly open the clean-out valve and allow the grit to flow out into a bucket.
Clean out the solution Whirlfilter
® only when the sprayer tank is filled with water and no chemical has been added.
3.
Close the clean-out valve and turn off the pump.
4.
Dispose of the grit and water in the same manner described on the manufacturer’s label of the latest chemical used in the sprayer.
To clean out the tank-fill Whirlfilter
®
, proceed with the following:
1.
Start with an empty sprayer tank.
2.
Position a bucket under the plug in the sump of the
Whirlfilter
® and allow the grit to fall out.
3.
Screw the plug back in using pipe thread sealant to seal the plug.
4.
Dispose of the grit and water in the same manner described on the manufacturer’s label of the latest chemical used in the sprayer.
Transporting
1.
Park your sprayer in an open area where you will not hit power lines, buildings, etc. when the boom is folded.
2.
Secure the level-float pin in the lock position, if using a level float boom.
3.
NEVER allow riders when transporting the sprayer.
4.
When transporting your sprayer, be sure to watch the height clearances of your folded boom to prevent damage to the boom and possible injury.
!
DANGER
Contact with electrical power lines can cause death by electrocution.
5.
DO NOT exceed 20 mph transporting your sprayer.
6.
DO NOT transport sprayer while filled with chemical mixture.
5/13/2003
500-052M
General Notes For Field Operation
1.
Check the tire pressure in each tractor tire. The recommended tire pressure should be listed in your tractor’s owner’s manual.
2.
Lubricate the sprayer as needed. Refer to "Lubrica-
tion & Maintenance" on Page 56.
3.
Hook-Up the pump to the tractor. Follow the instruc-
tions in “Operating Pump” on page 25.
4.
When transporting the sprayer, DO NOT exceed 20 mph and DO NOT transport with chemical in the tank. Fasten the level-float pin in the lock position
BEFORE folding the boom and transporting it if equipped with a level-float boom
5.
NEVER allow anyone to ride on the sprayer.
6.
Make sure all tank shut off valves are turned on.
7.
Calibrate sprayer with water only, not chemical and water. Calibrate with the sprayer tank half full of water.Refer to the calibration procedures in the Appli-
cation Guide, or the Adjustments section of this manual.
8.
Adjust throttling valves on the solenoids, and the manual pressure adjustment valve {if applicable}.
Adjust the boom height required for the nozzles and spacing to be used. {Refer to nozzle tables starting
on page 28 of this manual or the Application
Guide.}
9.
Check and clean, if necessary, pump, nozzles and
Whirlfilters
®
.
10. Safely and carefully add the chemical to the sprayer tank. ALWAYS wear "Personal Safety Equipment"
as shown on Page 5. By law, you must repeat the
rinsing of the chemical container three times. The container should then be punctured to prevent future use. An alternative is to jet-rinse or pressure rinse the container. When adding chemical, remain at least 100 feet from any water well or fresh water source. Follow chemical manufacturer’s recommendations for safe handling of chemicals.
11. Check the sprayer initially and periodically for loose bolts, pins and hose clamps. Check the hoses, pumps, valves and fittings for leaks.
12. Make sure that the hand wash tank is full of clean water.
5/13/2003
Operating Instructions 27
500-052M
28 Tractor Mount Sprayer
Adjustments
Sprayer Pre-Calibrations
1.
Wear the proper protective clothing as indicated on
page 5 in "Personal Safety Equipment".
2.
From the crop protectant label and field conditions, select a spray application rate and an operating speed.
3.
Be familiar with the type of crop protectant you are using. READ THE LABEL.
4.
Have all equipment ready BEFORE starting your sprayer calibrations.
5.
Make sure all spray parts are free from foreign material and are functioning properly. Carefully inspect nozzles and internal parts for wear, defects, proper size and type.
6.
Fill spray tank with water at least one quarter full, and preferably half full.
7.
Use only water to calibrate the sprayer.
8.
With the sprayer stationary, operate the pump at the desired spraying pressure. Check for leaks and improper spray patterns from the nozzles.
9.
Read the following pages to determine which method of calibration you will use and have a clear understanding of how the procedure works.
10. Use Calibration kit provided with booms to calibrate.
Calibration Procedures
Average
Nozzle
Spacing
{Inches}
Distance
{Feet}
Average
Nozzle
Spacing
{Inches}
Distance
{Feet}
6
8
10
12
14
15
681
510
408
340
292
272
22
24
30
36
38
40
186
170
136
113
107
102
16
18
255
227
42
48
97
85
20 204
Table 1: Distance for each nozzle to spray 1/128 acre {One ounce discharge per nozzle equals one gallon per acre}
This method gives you the distance driven to cover
1/128 acre {because there are 128 ounces per gallon}.
The time required to drive that distance is measured first, and the volume of spray in ounces caught in the time you measured is your application rate in gallons per acre. From the chart below, determine the distance to drive in the field {three runs are suggested} to obtain your average time in seconds. You will generally use 15,
20, or 30 inch nozzle spacing on standard booms.
1.
Determine your nozzle size, spacing, and pressure to achieve your desired rate from the application guide.
2.
Measure the nozzle spacing on your boom and determine the distance to drive to calibrate your sprayer.
3.
Mark off the distance with two markers provided, tie twine at distance needed for nozzle spacing {Table
#1} and time how many seconds it takes to drive this distance at the speed you will be spraying at. Make sure you are at spraying speed when you cross both marks. Two or more runs are suggested with the sprayer half full. Simulate your field conditions to take into account wheel slippage.
5/13/2003
500-052M
Adjustments 29
4.
With the sprayer filled with water {no chemical added}, park in an open area with the booms unfolded.
Prepare to collect samples at the individual nozzles.
Turn on the pump and run it at the operation pressure. If applicable, correctly set the solenoid throttling valves. Refer to “Solenoid Throttling Valve”
on page 51. Flip on the boom section switch{es} on
the control box and catch the water being sprayed out of the nozzle{s} with cup provided as you are calibrating.
5.
Measure the volume of the sample in ounces over the time it took to travel the distance in Step #3. The number of ounces caught is the exact number of gallons per acre you will apply with that perspective nozzle.
EXAMPLE #1: With a 20 inch spacing, it took 28 seconds to travel the 204 feet {refer to Table #1}. Using a
MeterCone
®
1.875 nozzle at 35 psi, the volume caught in 28 seconds was 21 ounces. This illustrates you would apply 21 gallons per acre with this nozzle.
EXAMPLE #2: With a 30 inch spacing, it took 15 seconds to travel 136 feet {refer to Table #1}. Using a
TeeJet
XR11003 nozzle at 30 psi, the volume caught in
15 seconds was 13 ounces. This means you will apply
13 gallons per acre with the XR11003 nozzle at the same ground speed as when you drove the 136 feet.
Step 2: Place graduated container, provided with boom calibration kit, under one nozzle and catch the discharge for 1 minute. Divide 128 into the number of fluid ounces caught. 128 fluid ounces equals one gallon. EXAMPLE:
64 ounces caught in one minute.
64.0
÷
128 = 0.50 gallons/minute
Step 3: Net determine your nozzle spacing in inches.
EXAMPLE: 1 nozzle every 40".
SOLUTION:
Gallons per acre = 5940 x Gallon per minute
Nozzle spacing in inches x
Miles Per Hour
GPA = 5940 x .50
40 x 5
GPA = 2970
200
GPA = 14.9
The above information will assure you of a check for accurate application in the event there is an error in the gauge nozzle spacing, nozzle height, tractor speed or nozzle wear.
Miles Per Hour Calibration
To determine true ground speed, use Table #2 with the sprayer half-filled with water.
When measuring the MPH of your tractor, always simulate current field conditions as close as possible, taking care to account for wheel slippage.
See application chart when M.P.H. is obtained.
Basic Sprayer Calibration
To double check the accuracy of your Great Plains
Sprayer, the following instructions provide another method of calibration:
Step 1: Measure 200 feet and determine the number of seconds required to travel this distance under field conditions with implements in working condition.
EXAMPLE: It takes 27 seconds to travel the 200 feet which equals 5 mph.
mph
Seconds to Travel
200 feet mph
Seconds to Travel
200 feet
4.5
5.0
6.0
2.5
3.0
3.5
4.0
30
27
23
55
45
39
34
7.0
8.0
9.0
10.0
11.0
12.0
Table 2: Miles per Hour Calibration
19
17
15
14
12.5
11.5
5/13/2003
500-052M
30 Tractor Mount Sprayer
Worn Nozzles & Flow Table
Information
1.
Determine nozzle size and desired spraying pressure using this application guide.
2.
Find fluid ounces per minute (OPM) in Table #3 or
Table #4.
3.
Catch flow at pressure desired for 1 minute {for large nozzles catch the flow for 30 seconds and multiply by 2}.
4.
If the OPM caught are within the
+ limit in the chart
on page 31, the nozzle is accurate and G.P.A. charts
should be followed.
5.
If the nozzle is not within the
+ limit, check for obstructions or wear in the orifices of the nozzle. Take the cap off the nozzle, clean the orifices with a toothpick or brush and retest. If several nozzles test the same, but are not within the
+ limits, a faulty gauge may be the problem. If two or more nozzles are outside the limit, it is a good indication that all your nozzles may be worn. In this case, it would be advisable to replace ALL the nozzles with new nozzles.
6.
FOR HEAVIER SOLUTIONS USE DENSITY FLOW
500-052M
5/13/2003
Adjustments 31
TeeJet
®
Worn Nozzles & Flow Table
PSI
8001 & 11001 80015 & 11015 8002 & 11002 8003 & 11003 8004 & 11004 8005 & 11005 8006 & 11006 8008 & 11008
GPM
15
.06
OPM GPM OPM GPM OPM GPM OPM GPM OPM GPM OPM GPM OPM GPM
8.0
+
1 .09 12.0
+
1 .12
15.0
+
2 .18
23.0
+
2 .24
31.0
+
3 .31
40.0
+
4 .37
47.0
+
5 .49
20
.07
9.0
+
1 .11 14.0
+
1 .14
18.0
+
2 .21
27.0
+
3 .28
36.0
+
4 .35
45.0
+
5 .42
54.0
+
5 .57
25
.08
10.0
+
1 .12 15.5
+
2 .16
20.0
+
2 .23
30.0
+
3 .32
40.5
+
4 .39
50.0
+
5 .47
60.5
+
6 .63
OPM
63.0
+
6
73.0
+
7
80.5
+
8
30
.09
11.0
+
1 .13 17.0
+
2 .17
22.0
+
2 .26
33.0
+
3 .35
45.0
+
5 .43
55.0
+
6 .52
67.0
+
7 .69
88.0
+
9
35
.09
12.0
+
1 .14 18.0
+
2 .19
24.0
+
2 .28
35.5
+
4 .38
48.0
+
5 .46
59.5
+
6 .56
72.0
+
7 .74
95.0
+
10
40
.10
13.0
+
1 .15 19.0
+
2 .20
26.0
+
3 .30
38.0
+
4 .40
51.0
+
5 .50
64.0
+
6 .60
77.0
+
8 .80 102.0
+
10
45
.11
13.5
+
1 .16 20.5
+
2 .21
27.5
+
3 .32
41.0
+
4 .43
54.5
+
5 .53
68.0
+
7 .64
81.5
+
8 .84 108.0
+
11
50
.11
14.0
+
1 .17 22.0
+
2 .23
29.0
+
3 .34
44.0
+
4 .45
58.0
+
6 .56
72.0
+
7 .67
86.0
+
9 .89 114.0
+
11
55
.11
14.5
+
1 .18 22.5
+
2 .24
30.5
+
3 .36
45.5
+
5 .47
60.5
+
6 .59
75.0
+
8 .71
90.5
+
9 .93 119.5
+
12
60
.12
15.0
+
2 .18 23.0
+
2 .25
32.0
+
3 .37
47.0
+
5 .49
63.0
+
6 .61
78.0
+
8 .74 95.0
+
10 .98 125.0
+
13
Table 3: TeeJet® Worn Nozzles & Flow Table
DISCARD NOZZLES NOT WITHIN THE
+
LIMITS
NOTE: The
+
value shown is a
+
10% value of the OPM
OPM = Ounces Per Minute
GPM = Gallons Per Minute
MeterCone
®
Worn Nozzles & Flow Table
30
35
40
45
10
15
20
25
50
55
60
PSI MC1.25
MC1.875
MC2.5
MC3.75
MC5.0
MC7.5
MC10 MC12.5
MC15
GPM OPM GPM OPM GPM OPM GPM OPM GPM OPM GPM OPM GPM OPM GPM OPM GPM OPM
.13
16.0
+
2 .19
24.0
+
2 .25
32.0
+
3 .38
48.0
+
5 .50
64.0
+
6 .75
96.5
+
9 1.00 128.0
+
13 1.25
160.0
+
16 1.50
192.0
+
19
.18
22.4
+
2 .23
29.1
+
3 .31
39.7
+
4 .46
58.6
+
6 .61
78.1
+
8 .92 117.8
+
12 1.22 156.2
+
15 1.53
195.8
+
20 1.84
235.5
+
23
.19
23.7
+
2 .26
33.0
+
3 .35
44.8
+
4 .53
67.5
+
6 .71
90.9
+
10 1.06 135.7
+
14 1.41 180.5
+
18 1.77
226.6
+
21 2.12
271.4
+
27
.20
25.0
+
2 .28
35.5
+
3 .40
51.2
+
5 .59
75.2
+
8 .79 101.1
+
10 1.19 152.3
+
15 1.57 201.0
+
20 1.98
253.4
+
25 2.37
303.4
+
30
.22
27.5
+
2 .33
41.9
+
4 .43
55.0
+
5 .65
82.9
+
8 .87 111.4
+
11 1.30 166.4
+
16 1.73 221.4
+
22 2.18
279.0
+
28 2.60
332.8
+
33
.23
28.8
+
2 .35
44.5
+
4 .46
58.9
+
6 .71
90.6
+
9 .92 117.8
+
12 1.39 177.9
+
18 1.85 236.8
+
24 2.31
295.7
+
30 2.78
355.8
+
35
.25
31.4
+
3 .38
48.3
+
5 .50
64.0
+
6 .75
95.7
+
9 1.0 128.0
+
13 1.50 192.0
+
19 2.00 256.0
+
25 2.50
320.0
+
32 3.00
384.0
+
38
.26
32.6
+
3 .39
50.9
+
5 .50
64.0
+
6 .79 101.5
+
10 1.06 135.5
+
13 ---
.28
35.2
+
3 .42
53.3
+
5 .51
65.3
+
6 .82 105.5
+
10 1.10 141.0
+
14 ---
.29
37.1
+
4 .43
55.7
+
5 .51
72.5
+
7 .87 111.9
+
11 1.16 149.0
+
15 ---
.31
39.0
+
4 .45
58.1
+
5 .61
78.1
+
8 .92 117.3
+
12 1.20 153.3
+
15 ---
---
---
---
---
---
---
---
---
---
---
---
---
---
---
---
---
---
---
---
---
---
---
---
---
---
---
---
---
Table 4: MeterCone® Worn Nozzles & Flow Table
DISCARD NOZZLES NOT WITHIN THE
+
LIMITS
NOTE: The
+
value shown is a
+
10% value of the OPM
GPM TO OPM CONVERSION
GPM {Gallons Per Minute} x 128 = OPM {Ounces Per
Minute}
EXAMPLE: 0.5 GPM x 128 = 64 OPM
OPM = Ounces Per Minute
GPM = Gallons Per Minute
OPM TO GPM CONVERSION
OPM {Ounces Per Minute}
÷
128 = GPM {Gallons Per
Minute}
EXAMPLE: 32 OPM
÷
128 = 0.25 GPM
5/13/2003
500-052M
32 Tractor Mount Sprayer
Spraying Solutions Other Than
Water
Calculations are based on spraying water, which weighs
8.34 pounds per US gallon. The following conversion factors must be used when spraying solutions which are heavier or lighter than water. In order to determine the proper size nozzle for the solution to be sprayed, multiply the desired GPM or GPA of solution by the water rate conversion factor. Then use the new converted GPM or
GPA rate to select the proper size nozzle.
Weight of
Solution
{lbs/Gal.}
7.00
7.50
8.00
8.34 {Water}
8.50
9.00
9.50
10.00
10.50
10.65 {Nitrogen 28%}
11.00
11.50
12.00
14.00
Solution
Specific
Gravity
1.02
1.08
1.14
1.20
.84
.90
.96
1.00
1.26
1.28
Conversion
Factor
1.01
1.04
1.06
1.10
.92
.95
.98
1.00
1.12
1.13
1.32
1.38
1.44
1.68
1.15
1.18
1.20
1.30
Table 5: Density Conversion Table
EXAMPLE: It is desired to apply 22 GPA {gallons per acre} of nitrogen in 30" rows. {28% N, density is 10.65 lb/ gal from the chart above}
From theTable 5, “Density Conversion Table,”, the conversion factor is 1.13.
GPA {Solution} x Conversion Factor = GPA
(22 gal/acre) (1.13) = 24.86 gal/acre
To choose a nozzle and a pressure, use 24.86 gal/acre on the nozzle charts.
Useful Formulas
GPM = GPA x MPH x W*
5940
*W = Row Spacing.....in inches.
GPA = 5940 x GPM {Per Nozzle}
MPH x W*
Let’s assume you are using TeeJet ® XR8006 nozzles and want to spray at 40 psi pressure. From the nozzle chart at a 30" spacing, determine the desired speed of travel.
If the value of 24.86 GPA is not an exact number shown on the nozzle chart. Interpolation to find an exact figure in needed. Interpolation is simple once you have an understanding of how it works {don’t be intimidated}. From the XR8006 nozzle chart at 30" spacing and 40 psi 24.86
GPA falls between 29.70 GPA at 4 mph and 23.76 GPA at 5 mph.
GPA MPH
-5.94
Difference
-4.84
Difference
29.70
at 4
24.86
at
?
23.76
at 5
1.0
Difference
Basically, you need to find the percentage that 24.86
GPA is between 23.76 GPA & 29.70 GPA. To do this, take a factor of the differences.
24.86 - 29.70 = -4.84 = 0.81or 81%
23.76 - 29.70
-5.94
In order to find the value for the mph that is 81% between 4 mph & 5 mph, take the fraction 0.81 times the difference in miles per hour.
(0.81) (1 mph) = 0.81 mph
Therefore, the speed of travel needed is:
4 mph + 0.81 = 4.81 mph
From the same example, determine the pressure needed to spray at 5 mph. From the XR8006 chart at 30",
24.86 GPA falls between 25.15 GPA at 45 psi and 23.76
500-052M
5/13/2003
Adjustments 33
GPA at 40 psi.
1.39
Difference
GPA PSI
1.10
Difference
23.76
at 40
24.86
at
25.15
at 45
?
5.0
Difference
The 43.95 PSI value is the pressure you should attempt to maintain on the pressure gauge. It is always a good idea to interpolate. Attempting to guess what the value should be, generally gives you an inaccurate result.
When using chemicals, ACCURACY IS CRITICAL.
24.86 - 23.76 = 1.10 = 0.79
25.15 - 23.76
1.39
(0.79) (5 PSI) = 3.95 PSI
40 PSI + 3.95 PSI = 43.95 PSI
Check Valve Restriction Data
OPM and GPM in the charts are shown at a PSI without the use of restriction no-drip check valves. Note the characteristics of the check valves below:
Diaphragm Check Valves may cause = a 2 to 3 PSI pressure drop at the nozzle. Catch nozzle flow to insure accuracy.
If you are using a nozzle spacing different than 15”, 20”, or 30”, you will need to convert the values in the nozzle charts to determine the correct GPA you will apply. Multiply the GPA factors in the existing tables by the given conversion factor for your nozzle spacing.
Where Tables are Based on 20" Nozzle Spacing
Other Spacing 8" 10" 12" 14" 16" 18" 22" 24" 30"
Conversion Factor 2.5
2 1.67 1.43 1.25 1.11 .91 .83 .66
Where Tables are Based on 30" Nozzle Spacing
Other Spacing 26" 28" 32" 34" 36" 38" 40" 42" 44"
Conversion Factor 1.15 1.07 .94 .88 .83 .79 .75 .71 .68
Where Tables are Based on 40" Nozzle Spacing
Other Spacing 28" 30" 32" 34" 36" 38" 42" 44" 48"
Conversion Factor 1.43 1.33 1.25 1.18 1.11 1.05 .95 .91 .83
Table 6: Nozzle Spacing
Miscellaneous Conversion Factors
One Acre = 43,560 Square Feet = 0.405 Hectares
One Hectare = 2.471 Acres
One Gallon Per Acre = 9.35 Liters Per Hectare
One Mile = 5,280 Feet = 1,610 Meters = 1.61 Kilometers
Table 7: Miscellaneous Information
One Gallon = 128 Fluid Ounces = 8 Pints = 4 Quarts
One Gallon = 3.79 Liters = 0.83 Imperial Gallons
One Pound Per Square Inch = 0.069 bar = 6.896 Kilopascal
One Mile Per Hour = 1.609 Kilometers Per Hour
Table 7: Miscellaneous Information
5/13/2003
500-052M
34 Tractor Mount Sprayer
MeterCone
®
Nozzles 15" Spacing - Height 12" to 13" or 24" to 26" Angle Fixed 20˚
Nozzle Size
1.25
Pressure
PSI
4.00
10.00
12.38
Gallons Per Acre At Miles Per Hour
5.00
6.00
7.00
8.00
9.00
10.00
11.00
12.00
9.90
8.25
7.07
6.19
5.50
4.95
4.50
4.13
15.00
17.33
13.86
11.55
9.90
8.66
7.70
20.00
18.32
14.65
12.21
10.47
9.16
8.14
6.93
7.33
6.30
6.66
5.78
6.11
25.00
19.31
15.44
12.87
11.03
9.65
8.58
30.00
21.29
17.03
14.19
12.16
10.64
9.46
35.00
22.28
17.82
14.85
12.73
11.14
9.90
40.00* 24.26
19.40
16.17
13.86
12.13
10.78
7.72
8.51
8.91
9.70
7.02
7.74
8.10
8.82
6.44
7.10
7.43
8.09
45.00* 25.25
20.20
16.83
14.43
12.62
11.22
10.10
9.18
50.00* 27.23
21.78
18.15
15.56
13.61
12.10
10.89
9.90
8.42
9.08
55.00* 28.71
22.97
19.14
16.41
14.36
12.76
11.48
10.44
9.57
60.00* 30.20
24.16
20.13
17.25
15.10
13.42
12.08
10.98
10.07
Nozzle Size
1.875
Pressure
PSI
Gallons Per Acre At Miles Per Hour
4.00
5.00
6.00
7.00
8.00
9.00
10.00
11.00
12.00
10.00
18.56
14.85
12.38
10.61
9.28
8.25
15.00
22.52
18.02
15.02
12.87
11.26
10.01
7.43
6.75
9.01
8.19
20.00
25.49
20.39
17.00
14.57
12.75
11.33
10.20
9.27
25.00
27.47
21.98
18.32
15.70
13.74
12.21
10.99
9.99
6.19
7.51
8.50
9.16
30.00
32.42
25.94
21.62
18.53
16.21
14.41
12.97
11.79
10.81
35.00
34.40
27.52
22.94
19.66
17.20
15.29
13.76
12.51
11.47
40.00* 37.37
29.90
24.92
21.36
18.69
16.61
14.95
13.59
12.46
45.00* 40.59
32.47
27.06
23.19
20.30
18.04
16.24
14.76
13.53
50.00* 43.56
34.85
29.04
24.89
21.78
19.36
17.42
15.84
14.52
55.00* 46.53
37.22
31.02
26.59
23.27
20.68
18.61
16.92
15.51
60.00* 50.49
40.39
33.66
28.85
25.25
22.44
20.20
18.36
16.83
Nozzle Size
2.5
Pressure
PSI
Gallons Per Acre At Miles Per Hour
4.00
5.00
6.00
7.00
8.00
9.00
10.00
11.00
12.00
10.00
24.75
19.80
16.50
14.14
12.38
11.00
9.90
9.00
8.25
15.00
30.69
24.55
20.46
17.54
15.35
13.64
12.28
11.16
10.23
20.00
34.65
27.72
23.10
19.80
17.33
15.40
13.86
12.60
11.55
25.00
39.60
31.68
26.40
22.63
19.80
17.60
15.84
14.40
13.20
30.00
42.57
34.06
28.38
24.33
21.29
18.92
17.03
15.48
14.19
35.00
45.54
36.43
30.36
26.02
22.77
20.24
18.22
16.56
15.18
40.00* 49.50
39.60
33.00
28.29
24.75
22.00
19.80
18.00
16.50
45.00* 51.08
40.87
34.06
29.19
25.54
22.70
20.43
18.58
17.03
50.00* 55.64
44.51
37.09
31.79
27.82
24.73
22.26
20.23
18.55
55.00* 58.41
46.73
38.94
33.38
29.21
25.96
23.36
21.24
19.47
60.00* 60.39
48.31
40.26
34.51
30.20
26.84
24.16
21.96
20.13
*For Post Emerge Applications where finer droplets are required use 40 PSI or greater.
5/13/2003
500-052M
Adjustments 35
Nozzle Size
3.75
Nozzle Size
5.0
Pressure
PSI
Gallons Per Acre At Miles Per Hour
4.00
5.00
6.00
7.00
8.00
9.00
10.00
11.00
12.00
10.00
37.13
29.70
24.75
21.21
18.56
16.50
14.85
13.50
12.38
15.00
45.29
36.23
30.20
25.88
22.65
20.13
18.12
16.47
15.10
20.00
52.22
41.78
34.82
29.84
26.11
23.21
20.89
18.99
17.41
25.00
58.16
46.53
38.78
33.24
29.08
25.85
23.27
21.15
19.39
30.00
64.10
51.28
42.74
36.63
32.05
28.49
25.64
23.31
21.37
35.00
70.04
56.03
46.70
40.02
35.02
31.13
28.02
25.47
23.35
40.00* 74.00
59.20
49.34
42.29
37.00
32.89
29.60
26.91
24.67
45.00* 80.19
64.15
53.46
45.82
40.10
35.64
32.08
29.16
26.73
50.00* 85.14
68.11
56.76
48.65
42.57
37.84
34.06
30.96
28.38
55.00* 91.08
72.86
60.72
52.05
45.54
40.48
36.43
33.12
30.36
60.00* 97.02
77.62
64.68
55.44
48.51
43.12
38.81
35.28
32.34
Pressure
PSI
4.00
Gallons Per Acre At Miles Per Hour
5.00
6.00
7.00
8.00
9.00
10.00
11.00
12.00
10.00
49.50
39.60
33.00
28.29
24.75
22.00
19.80
18.00
16.50
15.00
60.39
48.31
40.26
34.51
30.20
26.84
24.16
21.96
20.13
20.00
70.29
56.23
46.86
40.17
35.15
31.24
28.12
25.56
23.43
25.00
78.21
62.57
52.14
44.69
39.11
34.76
31.28
28.44
26.07
30.00
86.13
68.90
57.42
49.22
43.07
38.28
34.45
31.32
28.71
35.00
91.08
72.86
60.72
52.05
45.54
40.48
36.43
33.12
30.36
40.00* 99.00
79.20
66.00
56.57
49.50
44.00
39.60
36.00
33.00
Nozzle Size
7.5
Pressure
PSI
Gallons Per Acre At Miles Per Hour
4.00
5.00
6.00
7.00
8.00
9.00
10.00
11.00
12.00
10.00
74.25
59.40
49.50
42.43
37.13
33.00
29.70
27.00
24.75
15.00
91.08
72.86
60.72
52.05
45.54
40.48
36.43
33.12
30.36
20.00
104.94
83.95
69.96
59.97
52.47
46.64
41.98
38.16
34.98
25.00
117.81
94.25
78.54
67.32
58.91
52.36
47.12
42.84
39.27
30.00
128.70
102.96
85.80
73.54
64.35
57.20
51.48
46.80
42.90
35.00
137.61
110.09
91.74
78.63
68.81
61.16
55.04
50.04
45.87
40.00* 148.50
118.80
99.00
84.86
74.25
66.00
59.40
54.00
49.50
Gallons Per Acre At Miles Per Hour
Nozzle Size
Pressure
PSI
10.0
10.00
15.00
4.00
99.00
120.78
5.00
6.00
79.20
66.00
96.62
80.52
20.00
139.59
111.67
93.06
25.00
155.43
124.34
103.62
7.00
8.00
9.00
10.00
11.00
12.00
56.57
49.50
44.00
39.60
36.00
33.00
69.02
60.39
53.68
48.31
43.92
40.26
79.77
69.80
62.04
55.84
50.76
46.53
88.82
77.72
69.08
62.17
56.52
51.81
30.00
171.27
137.02
114.18
97.87
85.64
76.12
68.51
62.28
57.09
35.00
183.15
146.52
122.10
104.66
91.58
81.40
73.26
66.60
61.05
40.00* 198.00
158.40
132.00
113.14
99.00
88.00
79.20
72.00
66.00
*For Post Emerge Applications where finer droplets are required use 40 PSI or greater.
500-052M
5/13/2003
36 Tractor Mount Sprayer
Nozzle
Size
12.5
Pressure
PSI
Gallons Per Acre At Miles Per Hour
4.00
5.00
6.00
7.00
8.00
9.00
10.00
11.00
12.00
10.00
123.75
99.00
82.50
70.71
61.88
55.00
49.50
45.00
41.25
15.00
151.47
121.18
100.98
86.55
75.74
67.32
60.59
55.08
50.49
20.00
175.23
140.18
116.82
100.13
87.62
77.88
70.09
63.72
58.41
25.00
196.02
156.82
130.68
112.01
98.01
87.12
78.41
71.28
65.34
30.00
215.82
172.66
143.88
123.33
107.91
95.92
86.33
78.48
71.94
35.00
228.69
182.95
152.46
130.68
114.35
101.64
91.48
83.16
76.23
40.00* 247.50
198.00
165.00
141.43
123.75
110.00
99.00
90.00
82.50
Nozzle
Size
15.0
Pressure
PSI
4.00
5.00
Gallons Per Acre At Miles Per Hour
6.00
7.00
8.00
9.00
10.00
11.00
12.00
10.00
148.50
118.80
99.00
84.86
74.25
66.00
59.40
54.00
49.50
15.00
182.16
145.73
121.44
104.09
91.08
80.96
72.86
66.24
60.72
20.00
209.88
167.90
139.92
119.93
104.94
93.28
83.95
76.32
69.96
25.00
234.63
187.70
156.42
134.07
117.32
104.28
93.85
85.32
78.21
30.00
257.40
205.92
171.60
147.09
128.70
114.40
102.96
93.60
85.80
35.00
275.22
220.18
183.48
157.27
137.61
122.32
110.09
100.08
91.74
40.00* 297.00
237.60
198.00
169.71
148.50
132.00
118.80
108.00
99.00
*For Post Emerge Applications where finer droplets are required use 40 PSI or greater.
500-052M
5/13/2003
Adjustments 37
MeterCone
®
Nozzles 20" Spacing - Height 19" to 21" Angle Fixed 20˚
Nozzle Size
1.25
Pressure
PSI
10.00
4.00
9.28
5.00
7.43
Gallons Per Acre At Miles Per Hour
6.00
6.19
7.00
5.30
8.00
4.64
9.00
4.13
15.00
12.99
10.40
8.66
7.43
6.50
5.78
10.00
3.71
5.20
11.00
3.38
4.73
12.00
3.09
4.33
20.00
13.74
10.99
9.16
7.85
6.87
6.11
25.00
14.48
11.58
9.65
8.27
7.24
6.44
5.49
5.79
5.00
5.27
4.58
4.83
30.00
15.96
12.77
10.64
9.12
7.98
7.10
35.00
16.71
13.37
11.14
9.55
8.35
7.43
40.00* 18.19
14.55
12.13
10.40
9.10
8.09
45.00* 18.93
15.15
12.62
10.82
9.47
8.42
6.39
6.68
7.28
7.57
5.81
6.08
6.62
6.89
5.32
5.57
6.06
6.31
50.00* 20.42
16.34
13.61
11.67
10.21
9.08
55.00* 21.53
17.23
14.36
12.30
10.77
9.57
60.00* 22.65
18.12
15.10
12.94
11.32
10.07
8.17
7.43
8.61
7.83
9.06
8.24
6.81
7.18
7.55
Nozzle Size
1.875
Pressure
PSI
4.00
Gallons Per Acre At Miles Per Hour
5.00
6.00
7.00
8.00
9.00
10.00
11.00
12.00
10.00
13.92
11.14
9.28
7.96
6.96
6.19
15.00
16.89
13.51
11.26
9.65
8.45
7.51
20.00
19.12
15.30
12.75
10.93
9.56
8.50
25.00
20.60
16.48
13.74
11.77
10.30
9.16
5.57
5.06
6.76
6.14
7.65
6.95
8.24
7.49
4.64
5.63
6.37
6.87
30.00
24.32
19.45
16.21
13.90
12.16
10.81
9.73
8.84
35.00
25.80
20.64
17.20
14.74
12.90
11.47
10.32
9.38
8.11
8.60
40.00* 28.03
22.42
18.69
16.02
14.01
12.46
11.21
10.19
9.34
45.00* 30.44
24.35
20.30
17.40
15.22
13.53
12.18
11.07
10.15
50.00* 32.67
26.14
21.78
18.67
16.34
14.52
13.07
11.88
10.89
55.00* 34.90
27.92
23.27
19.94
17.45
15.51
13.96
12.69
11.63
60.00* 37.87
30.29
25.25
21.64
18.93
16.83
15.15
13.77
12.62
Nozzle Size
2.5
Pressure
PSI
Gallons Per Acre At Miles Per Hour
4.00
5.00
6.00
7.00
8.00
9.00
10.00
11.00
12.00
10.00
18.56
14.85
12.38
10.61
9.28
8.25
15.00
23.02
18.41
15.35
13.15
11.51
10.23
7.43
6.75
9.21
8.37
20.00
25.99
20.79
17.33
14.85
12.99
11.55
10.40
9.45
25.00
29.70
23.76
19.80
16.97
14.85
13.20
11.88
10.80
6.19
7.67
8.66
9.90
30.00
31.93
25.54
21.29
18.24
15.96
14.19
12.77
11.61
10.64
35.00
34.16
27.32
22.77
19.52
17.08
15.18
13.66
12.42
11.39
40.00* 37.13
29.70
24.75
21.21
18.56
16.50
14.85
13.50
12.38
45.00* 38.31
30.65
25.54
21.89
19.16
17.03
15.33
13.93
12.77
50.00* 41.73
33.38
27.82
23.84
20.86
18.55
16.69
15.17
13.91
55.00* 43.81
35.05
29.21
25.03
21.90
19.47
17.52
15.93
14.60
60.00* 45.29
36.23
30.20
25.88
22.65
20.13
18.12
16.47
15.10
*For Post Emerge Applications where finer droplets are required use 40 PSI or greater.
500-052M
5/13/2003
38 Tractor Mount Sprayer
Nozzle Size
3.75
Pressure
PSI
Gallons Per Acre At Miles Per Hour
4.00
5.00
6.00
7.00
8.00
9.00
10.00
11.00
12.00
10.00
27.84
22.28
18.56
15.91
13.92
12.38
11.14
10.13
9.28
15.00
33.97
27.18
22.65
19.41
16.98
15.10
13.59
12.35
11.32
20.00
39.17
31.33
26.11
22.38
19.58
17.41
15.67
14.24
13.06
25.00
43.62
34.90
29.08
24.93
21.81
19.39
17.45
15.86
14.54
30.00
48.08
38.46
32.05
27.47
24.04
21.37
19.23
17.48
16.03
35.00
52.53
42.03
35.02
30.02
26.27
23.35
21.01
19.10
17.51
40.00* 55.50
44.40
37.00
31.72
27.75
24.67
22.20
20.18
18.50
45.00* 60.14
48.11
40.10
34.37
30.07
26.73
24.06
21.87
20.05
50.00* 63.86
51.08
42.57
36.49
31.93
28.38
25.54
23.22
21.29
55.00* 68.31
54.65
45.54
39.03
34.16
30.36
27.32
24.84
22.77
60.00* 72.77
58.21
48.51
41.58
36.38
32.34
29.11
26.46
24.26
Nozzle Size
5.0
Pressure
PSI
Gallons Per Acre At Miles Per Hour
4.00
5.00
6.00
7.00
8.00
9.00
10.00
11.00
12.00
10.00
37.13
29.70
24.75
21.21
18.56
16.50
14.85
13.50
12.38
15.00
45.29
36.23
30.20
25.88
22.65
20.13
18.12
16.47
15.10
20.00
52.72
42.17
35.15
30.12
26.36
23.43
21.09
19.17
17.57
25.00
58.66
46.93
39.11
33.52
29.33
26.07
23.46
21.33
19.55
30.00
64.60
51.68
43.07
36.91
32.30
28.71
25.84
23.49
21.53
35.00
68.31
54.65
45.54
39.03
34.16
30.36
27.32
24.84
22.77
40.00* 74.25
59.40
49.50
42.43
37.13
33.00
29.70
27.00
24.75
Nozzle Size
7.5
Pressure
PSI
Gallons Per Acre At Miles Per Hour
4.00
5.00
6.00
7.00
8.00
9.00
10.00
11.00
12.00
10.00
55.69
44.55
37.13
31.82
27.84
24.75
22.28
20.25
18.56
15.00
68.31
54.65
45.54
39.03
34.16
30.36
27.32
24.84
22.77
20.00
25.00
78.71
62.96
52.47
44.97
39.35
34.98
31.48
28.62
26.24
88.36
70.69
58.91
50.49
44.18
39.27
35.34
32.13
29.45
30.00
96.53
77.22
64.35
55.16
48.26
42.90
38.61
35.10
32.18
35.00
103.21
82.57
68.81
58.98
51.60
45.87
41.28
37.53
34.40
40.00* 111.38
89.10
74.25
63.64
55.69
49.50
44.55
40.50
37.13
Nozzle Size
10.0
Pressure
PSI
Gallons Per Acre At Miles Per Hour
4.00
5.00
6.00
7.00
8.00
9.00
10.00
11.00
12.00
10.00
15.00
74.25
90.59
20.00
104.69
25.00
116.57
59.40
49.50
42.43
37.13
33.00
29.70
27.00
24.75
72.47
60.39
51.76
45.29
40.26
36.23
32.94
30.20
83.75
69.80
59.82
52.35
46.53
41.88
38.07
34.90
93.26
77.72
66.61
58.29
51.81
46.63
42.39
38.86
30.00
128.45
102.76
85.64
73.40
64.23
57.09
51.38
46.71
42.82
35.00
137.36
109.89
91.58
78.49
68.68
61.05
54.95
49.95
45.79
40.00* 148.50
118.80
99.00
84.86
74.25
66.00
59.40
54.00
49.50
*For Post Emerge Applications where finer droplets are required use 40 PSI or greater.
5/13/2003
500-052M
Adjustments 39
Nozzle
Size
12.5
Pressure
PSI
Gallons Per Acre At Miles Per Hour
4.00
5.00
6.00
7.00
8.00
9.00
10.00
11.00
12.00
10.00
92.81
74.25
15.00
113.60
90.88
20.00
131.42
105.14
25.00
147.02
117.61
61.88
53.04
46.41
41.25
37.13
33.75
30.94
75.74
64.92
56.80
50.49
45.44
41.31
37.87
87.62
75.10
65.71
58.41
52.57
47.79
43.81
98.01
84.01
73.51
65.34
58.81
53.46
49.01
30.00
161.87
129.49
107.91
92.49
80.93
71.94
64.75
58.86
53.96
35.00
171.52
137.21
114.35
98.01
85.76
76.23
68.61
62.37
57.17
40.00* 185.63
148.50
123.75
106.07
92.81
82.50
74.25
67.50
61.88
Nozzle
Size
15.0
Pressure
PSI
4.00
5.00
Gallons Per Acre At Miles Per Hour
6.00
7.00
8.00
9.00
10.00
11.00
12.00
10.00
111.38
89.10
74.25
63.64
55.69
49.50
44.55
40.50
37.13
15.00
136.62
109.30
91.08
78.07
68.31
60.72
54.65
49.68
45.54
20.00
157.41
125.93
104.94
89.95
78.71
69.96
62.96
57.24
52.47
25.00
175.97
140.78
117.32
100.56
87.99
78.21
70.39
63.99
58.66
30.00
193.05
154.44
128.70
110.31
96.53
85.80
77.22
70.20
64.35
35.00
206.42
165.13
137.61
117.95
103.21
91.74
82.57
75.06
68.81
40.00* 222.75
178.20
148.50
127.29
111.38
99.00
89.10
81.00
74.25
*For Post Emerge Applications where finer droplets are required use 40 PSI or greater.
5/13/2003
500-052M
40 Tractor Mount Sprayer
MeterCone
®
Nozzles 30" Spacing - Height 24" to 26" Angle Fixed 20˚
Nozzle Size
1.25
Pressure
PSI
4.00
5.00
Gallons Per Acre At Miles Per Hour
6.00
7.00
8.00
9.00
10.00
11.00
12.00
10.00
15.00
20.00
25.00
6.19
8.66
9.16
9.65
4.95
4.13
3.54
3.09
2.75
6.93
5.78
4.95
4.33
3.85
7.33
6.11
5.23
4.58
4.07
7.72
6.44
5.52
4.83
4.29
30.00
10.64
35.00
11.14
8.51
7.10
6.08
5.32
4.73
8.91
7.43
6.36
5.57
4.95
40.00* 12.13
9.70
8.09
6.93
6.06
5.39
45.00* 12.62
10.10
8.42
7.21
6.31
5.61
50.00* 13.61
10.89
9.08
7.78
6.81
6.05
55.00* 14.36
11.48
9.57
8.20
7.18
6.38
60.00* 15.10
12.08
10.07
8.63
7.55
6.71
2.48
2.25
3.47
3.15
3.66
3.33
3.86
3.51
4.26
3.87
4.46
4.05
4.85
4.41
5.05
4.59
5.45
5.74
6.04
4.95
5.22
5.49
2.06
2.89
3.05
3.22
3.55
3.71
4.04
4.21
4.54
4.79
5.03
Nozzle Size
1.875
Pressure
PSI
4.00
5.00
Gallons Per Acre At Miles Per Hour
6.00
7.00
8.00
9.00
10.00
11.00
12.00
10.00
9.28
15.00
11.26
7.43
6.19
5.30
4.64
4.13
9.01
7.51
6.44
5.63
5.01
20.00
12.75
10.20
8.50
7.28
6.37
5.67
25.00
13.74
10.99
9.16
7.85
6.87
6.11
30.00
16.21
12.97
10.81
9.26
8.11
7.21
35.00
17.20
13.76
11.47
9.83
8.60
7.65
40.00* 18.69
14.95
12.46
10.68
9.34
8.31
45.00* 20.30
16.24
13.53
11.60
10.15
9.02
3.71
4.50
5.10
5.49
6.48
6.88
7.47
8.12
3.38
4.10
4.64
5.00
5.90
6.26
6.80
7.38
50.00* 21.78
17.42
14.52
12.45
10.89
9.68
55.00* 23.27
18.61
15.51
13.29
11.63
10.34
8.71
9.31
7.92
8.46
60.00* 25.25
20.20
16.83
14.43
12.62
11.22
10.10
9.18
3.09
3.75
4.25
4.58
5.40
5.73
6.23
6.77
7.26
7.76
8.42
Nozzle Size
2.5
Pressure
PSI
Gallons Per Acre At Miles Per Hour
4.00
5.00
6.00
7.00
8.00
9.00
10.00
11.00
12.00
10.00
12.38
9.90
8.25
7.07
6.19
5.50
15.00
15.35
12.28
10.23
8.77
7.67
6.82
20.00
17.33
13.86
11.55
9.90
8.66
7.70
25.00
19.80
15.84
13.20
11.31
9.90
8.80
4.95
4.50
6.14
5.58
6.93
6.30
7.92
7.20
30.00
21.29
17.03
14.19
12.16
10.64
9.46
35.00
22.77
18.22
15.18
13.01
11.39
10.12
8.51
7.74
9.11
8.28
40.00* 24.75
19.80
16.50
14.14
12.38
11.00
9.90
9.00
45.00* 25.54
20.43
17.03
14.60
12.77
11.35
10.22
9.29
50.00* 27.82
22.26
18.55
15.90
13.91
12.36
11.13
10.12
55.00* 29.21
23.36
19.47
16.69
14.60
12.98
11.68
10.62
9.27
9.74
60.00* 30.20
24.16
20.13
17.25
15.10
13.42
12.08
10.98
10.07
4.13
5.12
5.78
6.60
7.10
7.59
8.25
8.51
*For Post Emerge Applications where finer droplets are required use 40 PSI or greater.
500-052M
5/13/2003
Adjustments 41
Nozzle Size
3.75
Pressure
PSI
Gallons Per Acre At Miles Per Hour
4.00
5.00
6.00
7.00
8.00
9.00
10.00
11.00
12.00
10.00
18.56
14.85
12.38
10.61
9.28
8.25
7.43
6.75
6.19
15.00
22.65
18.12
15.10
12.94
11.32
10.07
9.06
8.24
7.55
20.00
26.11
20.89
17.41
14.92
13.06
11.61
10.44
9.50
25.00
29.08
23.27
19.39
16.62
14.54
12.93
11.63
10.58
8.70
9.69
30.00
32.05
25.64
21.37
18.32
16.03
14.25
12.82
11.66
10.68
35.00
35.02
28.02
23.35
20.01
17.51
15.57
14.01
12.74
11.67
40.00* 37.00
29.60
24.67
21.14
18.50
16.45
14.80
13.46
12.33
45.00* 40.10
32.08
26.73
22.91
20.05
17.82
16.04
14.58
13.37
50.00* 42.57
34.06
28.38
24.33
21.29
18.92
17.03
15.48
14.19
55.00* 45.54
36.43
30.36
26.02
22.77
20.24
18.22
16.56
15.18
60.00* 48.51
38.81
32.34
27.72
24.26
21.56
19.40
17.64
16.17
Nozzle Size
5.0
Pressure
PSI
10.00
15.00
20.00
25.00
30.00
35.00
40.00*
Gallons Per Acre At Miles Per Hour
4.00
5.00
6.00
7.00
8.00
9.00
10.00
11.00
12.00
24.75
19.80
16.50
14.14
12.38
11.00
9.90
9.00
8.25
30.20
24.16
20.13
17.25
15.10
13.42
12.08
10.98
10.07
35.15
28.12
23.43
20.08
17.57
15.62
14.06
12.78
11.72
39.11
31.28
26.07
22.35
19.55
17.38
15.64
14.22
13.04
43.07
34.45
28.71
24.61
21.53
19.14
17.23
15.66
14.36
45.54
36.43
30.36
26.02
22.77
20.24
18.22
16.56
15.18
49.50
39.60
33.00
28.29
24.75
22.00
19.80
18.00
16.50
Nozzle Size
7.5
Pressure
PSI
10.00
15.00
20.00
25.00
30.00
35.00
40.00*
4.00
37.13
45.54
52.47
58.91
64.35
68.81
74.25
Gallons Per Acre At Miles Per Hour
5.00
6.00
7.00
8.00
9.00
10.00
11.00
12.00
29.70
24.75
21.21
18.56
16.50
14.85
13.50
12.38
36.43
30.36
26.02
22.77
20.24
18.22
16.56
15.18
41.98
34.98
29.98
26.24
23.32
20.99
19.08
17.49
47.12
39.27
33.66
29.45
26.18
23.56
21.42
19.64
51.48
42.90
36.77
32.18
28.60
25.74
23.40
21.45
55.04
45.87
39.32
34.40
30.58
27.52
25.02
22.94
59.40
49.50
42.43
37.13
33.00
29.70
27.00
24.75
*For Post Emerge Applications where finer droplets are required use 40 PSI or greater.
5/13/2003
500-052M
42 Tractor Mount Sprayer
Nozzle
Size
10.0
Pressure
PSI
4.00
5.00
10.00
49.50
39.60
15.00
60.39
48.31
20.00
69.80
55.84
25.00
77.72
62.17
30.00
85.64
68.51
35.00
91.58
73.26
40.00* 99.00
79.20
Gallons Per Acre At Miles Per Hour
6.00
7.00
8.00
9.00
10.00
11.00
12.00
33.00
28.29
24.75
22.00
19.80
18.00
16.50
40.26
34.51
30.20
26.84
24.16
21.96
20.13
46.53
39.88
34.90
31.02
27.92
25.38
23.27
51.81
44.41
38.86
34.54
31.09
28.26
25.91
57.09
48.93
42.82
38.06
34.25
31.14
28.55
61.05
52.33
45.79
40.70
36.63
33.30
30.53
66.00
56.57
49.50
44.00
39.60
36.00
33.00
Nozzle
Size
12.5
Pressure
PSI
4.00
10.00
15.00
20.00
25.00
61.88
75.74
87.62
98.01
30.00
107.91
35.00
114.35
40.00* 123.75
Gallons Per Acre At Miles Per Hour
5.00
6.00
7.00
8.00
9.00
10.00
11.00
12.00
49.50
41.25
35.36
30.94
27.50
24.75
22.50
20.63
60.59
50.49
43.28
37.87
33.66
30.29
27.54
25.25
70.09
58.41
50.07
43.81
38.94
35.05
31.86
29.21
78.41
65.34
56.01
49.01
43.56
39.20
35.64
32.67
86.33
71.94
61.66
53.96
47.96
43.16
39.24
35.97
91.48
76.23
65.34
57.17
50.82
45.74
41.58
38.12
99.00
82.50
70.71
61.88
55.00
49.50
45.00
41.25
Nozzle Size
15.0
Pressure
PSI
Gallons Per Acre At Miles Per Hour
4.00
5.00
6.00
7.00
8.00
9.00
10.00
11.00
12.00
10.00
15.00
74.25
91.08
20.00
104.94
25.00
117.32
59.40
49.50
42.43
37.13
33.00
29.70
27.00
24.75
72.86
60.72
52.05
45.54
40.48
36.43
33.12
30.36
83.95
69.96
59.97
52.47
46.64
41.98
38.16
34.98
93.85
78.21
67.04
58.66
52.14
46.93
42.66
39.11
30.00
128.70
102.96
85.80
73.54
64.35
57.20
51.48
46.80
42.90
35.00
137.61
110.09
91.74
78.63
68.81
61.16
55.04
50.04
45.87
40.00* 148.50
118.80
99.00
84.86
74.25
66.00
59.40
54.00
49.50
*For Post Emerge Applications where finer droplets are required use 40 PSI or greater.
500-052M
5/13/2003
Adjustments 43
TeeJet
®
Nozzles 15" Spacing - Height 13" to 15" for XR80; 10" to 12" for XR110
Nozzle Size
XR
8001
&
XR
1100
1
Pressure
PSI
4.00
15.00
20.00
25.00
30.00
5.94
6.93
7.92
8.91
35.00
40.00
9.41
9.90
45.00
10.40
50.00
10.89
55.00
11.39
60.00
11.88
Gallons Per Acre At Miles Per Hour
5.00
6.00
7.00
8.00
9.00
10.00
11.00
12.00
4.75
3.96
3.39
2.97
2.64
5.54
4.62
3.96
3.47
3.08
6.34
5.28
4.53
3.96
3.52
7.13
5.94
5.09
4.46
3.96
7.52
6.27
5.37
4.70
4.18
7.92
6.60
5.66
4.95
4.40
8.32
6.93
5.94
5.20
4.62
8.71
7.26
6.22
5.45
4.84
9.11
7.59
6.51
5.69
5.06
9.50
7.92
6.79
5.94
5.28
2.38
2.77
3.17
3.56
3.76
3.96
4.16
4.36
4.55
4.75
2.16
2.52
2.88
3.24
3.42
3.60
3.78
3.96
4.14
4.32
1.98
2.31
2.64
2.97
3.14
3.30
3.47
3.63
3.80
3.96
Nozzle Size
XR
80015
&
XR
11015
Pressure
PSI
4.00
Gallons Per Acre At Miles Per Hour
5.00
6.00
7.00
8.00
9.00
10.00
11.00
12.00
15.00
8.91
20.00
10.89
7.13
5.94
5.09
4.46
3.96
8.71
7.26
6.22
5.45
4.84
25.00
11.88
9.50
7.92
6.79
5.94
5.28
30.00
12.87
10.30
8.58
7.35
6.44
5.72
35.00
13.86
11.09
9.24
7.92
6.93
6.16
40.00
14.85
11.88
9.90
8.49
7.43
6.60
45.00
15.59
12.47
10.40
8.91
7.80
6.93
50.00
16.34
13.07
10.89
9.33
8.17
7.26
55.00
17.08
13.66
11.39
9.76
8.54
7.59
60.00
17.82
14.26
11.88
10.18
8.91
7.92
3.56
4.36
4.75
5.15
5.54
5.94
6.24
6.53
6.83
7.13
3.24
3.96
4.32
4.68
5.04
5.40
5.67
5.94
6.21
6.48
2.97
3.63
3.96
4.29
4.62
4.95
5.20
5.45
5.69
5.94
Nozzle Size
XR
8002
&
XR
1100
2
Pressure
PSI
4.00
Gallons Per Acre At Miles Per Hour
5.00
6.00
7.00
8.00
9.00
10.00
11.00
12.00
15.00
11.88
9.50
7.92
6.79
5.94
5.28
20.00
13.86
11.09
9.24
7.92
6.93
6.16
25.00
15.35
12.28
10.23
8.77
7.67
6.82
30.00
16.83
13.46
11.22
9.62
8.42
7.48
35.00
18.32
14.65
12.21
10.47
9.16
8.14
40.00
19.80
15.84
13.20
11.31
9.90
8.80
45.00
21.04
16.83
14.03
12.02
10.52
9.35
50.00
22.28
17.82
14.82
12.73
11.14
9.90
55.00
23.51
18.81
15.68
13.44
11.76
10.45
60.00
24.75
19.80
16.50
14.14
12.38
11.00
4.75
5.54
6.14
6.73
7.33
7.92
8.42
8.91
9.41
9.90
4.32
5.04
5.58
6.12
6.66
7.20
7.65
8.10
8.55
9.00
3.96
4.62
5.12
5.61
6.11
6.60
7.01
7.43
7.84
8.25
500-052M
5/13/2003
44 Tractor Mount Sprayer
500-052M
Nozzle Size
XR
8003
&
XR
1100
3
Pressure
PSI
4.00
Gallons Per Acre At Miles Per Hour
5.00
6.00
7.00
8.00
9.00
10.00
11.00
12.00
15.00
17.82
14.26
11.88
10.18
8.91
7.92
20.00
20.79
16.63
13.86
11.88
10.40
9.24
7.13
6.48
8.32
7.56
25.00
23.27
18.61
15.51
13.29
11.63
10.34
9.31
8.46
30.00
25.74
20.59
17.16
14.71
12.87
11.44
10.30
9.36
5.94
6.93
7.76
8.58
35.00
27.72
22.18
18.48
15.84
13.86
12.32
11.09
10.08
40.00
29.70
23.76
19.80
16.97
14.85
13.20
11.88
10.80
9.24
9.90
45.00
31.43
25.15
20.96
17.96
15.72
13.97
12.57
11.43
10.48
50.00
33.17
26.53
22.11
18.95
16.58
14.74
13.27
12.06
11.06
55.00
34.90
27.92
23.27
19.94
17.45
15.51
13.96
12.69
11.63
60.00
36.63
29.30
24.42
20.93
18.32
16.28
14.65
13.32
12.21
Nozzle Size
XR
8004
&
XR
1100
4
Pressure
PSI
Gallons Per Acre At Miles Per Hour
4.00
5.00
6.00
7.00
8.00
9.00
10.00
11.00
12.00
15.00
23.76
19.01
15.84
13.58
11.88
10.56
9.50
8.64
20.00
27.72
22.18
18.48
15.84
13.86
12.32
11.09
10.08
7.92
9.24
25.00
31.19
24.95
20.79
17.82
15.59
13.86
12.47
11.34
10.40
30.00
34.65
27.72
23.10
19.80
17.33
15.40
13.86
12.60
11.55
35.00
37.13
29.70
24.75
21.21
18.56
16.50
14.85
13.50
12.38
40.00
39.60
31.68
26.40
22.63
19.80
17.60
15.84
14.40
13.20
45.00
41.83
33.46
27.89
23.90
20.91
18.59
16.73
15.21
13.94
50.00
44.06
35.24
29.37
25.17
22.03
19.58
17.62
16.02
14.69
55.00
46.28
37.03
30.86
26.45
23.14
20.57
18.51
16.83
15.43
60.00
48.51
38.81
32.34
27.72
24.26
21.56
19.40
17.64
16.17
Nozzle Size
XR
8005
&
XR
1100
5
Pressure
PSI
Gallons Per Acre At Miles Per Hour
4.00
5.00
6.00
7.00
8.00
9.00
10.00
11.00
12.00
15.00
30.69
24.55
20.46
17.54
15.35
13.64
12.28
11.16
10.23
20.00
34.65
27.72
23.10
19.80
17.33
15.40
13.86
12.60
11.55
25.00
38.61
30.89
25.74
22.06
19.31
17.16
15.44
14.04
12.87
30.00
42.57
34.06
28.38
24.33
21.29
18.92
17.03
15.48
14.19
35.00
46.04
36.83
30.69
26.31
23.02
20.46
18.41
16.74
15.35
40.00
49.50
39.60
33.00
28.29
24.75
22.00
19.80
18.00
16.50
45.00
52.22
41.78
34.82
29.84
26.11
23.21
20.89
18.99
17.41
50.00
54.95
43.96
36.63
31.40
27.47
24.42
21.98
19.98
18.32
55.00
57.67
46.13
38.45
32.95
28.83
25.63
23.07
20.97
19.22
60.00
60.39
48.31
40.26
34.51
30.20
26.84
24.16
21.96
20.13
5/13/2003
Adjustments 45
Nozzle Size
XR
8006
&
XR
1100
6
Pressure
PSI
Gallons Per Acre At Miles Per Hour
4.00
5.00
6.00
7.00
8.00
9.00
10.00
11.00
12.00
15.00
36.63
29.30
24.42
20.93
18.32
16.28
14.65
13.32
12.21
20.00
41.58
33.26
27.72
23.76
20.79
18.48
16.63
15.12
13.86
25.00
46.53
37.22
31.02
26.59
23.27
20.68
18.61
16.92
15.51
30.00
51.48
41.18
34.32
29.42
25.74
22.88
20.59
18.72
17.16
35.00
55.44
44.35
36.96
31.68
27.72
24.64
22.18
20.16
18.48
40.00
59.40
47.52
39.60
33.94
29.70
26.40
23.76
21.60
19.80
45.00
62.87
50.29
41.91
35.92
31.43
27.94
25.15
22.86
20.96
50.00
66.33
53.06
44.22
37.90
33.17
29.48
26.53
24.12
22.11
55.00
69.80
55.84
46.53
39.88
34.90
31.02
27.92
25.38
23.27
60.00
73.26
58.61
48.84
41.86
36.63
32.56
29.30
26.64
24.42
Nozzle Size
XR
8008
&
XR
1100
8
Pressure
PSI
Gallons Per Acre At Miles Per Hour
4.00
5.00
6.00
7.00
8.00
9.00
10.00
11.00
12.00
15.00
48.51
38.81
32.34
27.72
24.26
21.56
19.40
17.64
16.17
20.00
56.43
45.14
37.62
32.25
28.22
25.08
22.57
20.52
18.81
25.00
62.37
49.90
41.58
35.64
31.19
27.72
24.95
22.68
20.79
30.00
68.31
54.65
45.54
39.03
34.16
30.36
27.32
24.84
22.77
35.00
73.76
59.00
49.17
42.15
36.88
32.78
29.50
26.82
24.59
40.00
79.20
63.36
52.80
45.26
39.60
35.20
31.68
28.80
26.40
45.00
83.66
66.92
55.77
47.80
41.83
37.18
33.46
30.42
27.89
50.00
88.11
70.94
58.74
50.35
44.06
39.16
35.24
32.04
29.37
55.00
92.57
74.05
61.71
52.89
46.28
41.14
37.03
33.66
30.86
60.00
97.02
77.62
64.68
55.44
48.51
43.12
38.81
35.28
32.34
500-052M
5/13/2003
46 Tractor Mount Sprayer
TeeJet
®
Nozzles 20" Spacing - Height 17" to 19" for XR80; 15" to 18" for XR110
Nozzle Size
XR
8001
&
XR
11001
Nozzle Size
XR
80015
&
XR
110015
Pressure
PSI
15.00
20.00
25.00
30.00
35.00
40.00
45.00
50.00
55.00
60.00
Pressure
PSI
15.00
20.00
25.00
30.00
35.00
40.00
45.00
50.00
55.00
60.00
Nozzle Size
XR
8002
&
XR
11002
Pressure
PSI
15.00
20.00
25.00
30.00
35.00
40.00
45.00
50.00
55.00
60.00
4.00
8.91
10.40
11.51
12.62
13.74
14.85
15.78
16.71
17.63
18.56
4.00
4.46
5.20
5.94
6.68
7.05
7.43
7.80
8.17
8.54
8.91
4.00
6.68
8.17
8.91
9.65
10.40
11.14
11.69
12.25
12.81
13.37
Gallons Per Acre At Miles Per Hour
5.00
6.00
7.00
8.00
9.00
10.00
11.00
12.00
3.56
2.97
2.55
2.23
1.98
4.16
3.47
2.97
2.60
2.31
4.75
3.96
3.39
2.97
2.64
5.35
4.46
3.82
3.34
2.97
5.64
4.70
4.03
3.53
3.14
5.94
4.95
4.24
3.71
3.30
6.24
5.20
4.46
3.90
3.47
6.53
5.45
4.67
4.08
3.63
6.83
5.69
4.88
4.27
3.80
7.13
5.94
5.09
4.46
3.96
1.78
2.08
2.38
2.67
2.82
2.97
3.12
3.27
3.42
3.56
1.62
1.89
2.16
2.43
2.57
2.70
2.84
2.97
3.11
3.24
1.49
1.73
1.98
2.23
2.35
2.48
2.60
2.72
2.85
2.97
Gallons Per Acre At Miles Per Hour
5.00
6.00
7.00
8.00
9.00
10.00
11.00
12.00
5.35
6.53
7.13
7.72
8.32
8.91
9.36
9.80
10.25
10.69
4.46
5.45
5.94
6.44
6.93
7.43
7.80
8.17
8.54
8.91
3.82
4.67
5.09
5.52
5.94
6.36
6.68
7.00
7.32
7.64
3.34
4.08
4.46
4.83
5.20
5.57
5.85
6.13
6.40
6.68
2.97
3.63
3.96
4.29
4.62
4.95
5.20
5.45
5.69
5.94
2.67
3.27
3.56
3.86
4.16
4.46
4.68
4.90
5.12
5.35
2.43
2.97
3.24
3.51
3.78
4.05
4.25
4.46
4.66
4.86
2.23
2.72
2.97
3.22
3.47
3.71
3.90
4.08
4.27
4.46
Gallons Per Acre At Miles Per Hour
5.00
6.00
7.00
8.00
9.00
10.00
11.00
12.00
7.13
8.32
9.21
10.10
5.94
6.93
7.67
8.42
10.99
11.88
9.16
9.90
12.62
10.52
13.37
11.14
5.09
5.94
6.58
7.21
7.85
8.49
9.02
9.55
14.11
11.76
10.08
14.85
12.38
10.61
4.46
5.20
5.75
6.31
6.87
7.43
7.89
8.35
8.82
9.28
3.96
4.62
5.12
5.61
6.11
6.60
7.01
7.43
7.84
8.25
3.56
4.16
4.60
5.05
5.49
5.94
6.31
6.68
7.05
7.42
3.24
3.78
4.19
4.59
5.00
5.40
5.74
6.08
6.41
6.75
2.97
3.47
3.84
4.21
4.58
4.95
5.26
5.57
5.88
6.19
Nozzle Size
XR
8003
&
XR
11003
Pressure
PSI
15.00
20.00
25.00
30.00
35.00
40.00
45.00
50.00
55.00
60.00
4.00
13.37
15.59
17.45
19.31
20.79
22.28
23.57
24.87
26.17
27.47
Gallons Per Acre At Miles Per Hour
5.00
6.00
7.00
8.00
9.00
10.00
11.00
12.00
10.69
8.91
12.47
10.40
7.64
8.91
13.96
11.63
9.97
15.44
12.87
11.03
6.68
7.80
8.72
9.65
5.94
6.93
7.76
8.58
16.63
13.86
11.88
10.40
17.82
14.85
12.73
11.14
9.24
9.90
18.86
15.72
13.47
11.79
10.48
19.90
16.58
14.21
12.44
11.06
20.94
17.45
14.96
13.09
11.63
21.98
18.32
15.70
13.74
12.21
5.35
6.24
6.98
7.72
8.32
8.91
9.43
9.95
10.47
10.99
4.86
5.67
6.35
7.02
7.56
8.10
8.57
9.05
9.52
9.99
4.46
5.20
5.82
6.44
6.93
7.43
7.86
8.29
8.72
9.16
5/13/2003
500-052M
Adjustments 47
Nozzle Size
XR
8004
&
XR
11004
Pressure
PSI
15.00
20.00
25.00
30.00
35.00
40.00
45.00
50.00
55.00
60.00
4.00
17.82
20.79
23.39
25.99
27.84
29.70
31.37
33.04
34.71
36.38
Gallons Per Acre At Miles Per Hour
5.00
6.00
7.00
8.00
9.00
10.00
11.00
12.00
14.26
11.88
10.18
8.91
16.63
13.86
11.88
10.40
7.92
9.24
18.71
15.59
13.37
11.69
10.40
20.79
17.33
14.85
12.99
11.55
22.28
18.56
15.91
13.92
12.38
23.76
19.80
16.97
14.85
13.20
25.10
20.91
17.93
15.69
13.94
26.43
22.03
18.88
16.52
14.69
27.77
23.14
19.84
17.36
15.43
29.11
24.26
20.79
18.19
16.17
7.13
8.32
9.36
10.40
6.48
7.56
8.51
9.45
11.14
10.13
11.88
10.80
12.55
11.41
13.22
12.02
13.88
12.62
14.55
13.23
5.94
6.93
7.80
8.66
9.28
9.90
10.46
11.01
11.57
12.13
Nozzle Size
XR
8005
&
XR
11005
Pressure
PSI
15.00
20.00
25.00
30.00
35.00
40.00
45.00
50.00
55.00
60.00
4.00
23.02
25.99
28.96
31.93
34.53
37.13
39.17
41.21
43.25
45.29
Gallons Per Acre At Miles Per Hour
5.00
6.00
7.00
8.00
9.00
10.00
11.00
12.00
18.41
15.35
13.15
11.51
10.23
20.79
17.33
14.85
12.99
11.55
23.17
19.31
16.55
14.48
12.87
25.54
21.29
18.24
15.96
14.19
27.62
23.02
19.73
17.26
15.35
29.70
24.75
21.21
18.56
16.50
31.33
26.11
22.38
19.58
17.41
32.97
27.47
23.55
20.60
18.32
34.60
28.83
24.71
21.63
19.22
36.23
30.20
25.88
22.65
20.13
9.21
10.40
8.37
9.45
11.58
10.53
12.77
11.61
13.81
12.56
14.85
13.50
15.67
14.24
16.48
14.99
17.30
15.73
18.12
16.47
7.67
8.66
9.65
10.64
11.51
12.38
13.06
13.74
14.42
15.10
Nozzle Size
XR
8006
&
XR
11006
Pressure
PSI
15.00
20.00
25.00
30.00
35.00
40.00
45.00
50.00
55.00
60.00
4.00
27.47
31.19
34.90
38.61
41.58
44.55
47.15
49.75
52.35
54.95
Gallons Per Acre At Miles Per Hour
5.00
6.00
7.00
8.00
9.00
10.00
11.00
12.00
21.98
18.32
15.70
13.74
12.21
24.95
20.79
17.82
15.59
13.86
27.92
23.27
19.94
17.45
15.51
30.89
25.74
22.06
19.31
17.16
33.26
27.72
26.76
20.79
18.48
35.64
29.70
25.46
22.28
19.80
37.72
31.43
26.94
23.57
20.96
39.80
33.17
28.43
24.87
22.11
41.88
34.90
29.91
26.17
23.27
43.96
36.63
31.40
27.47
24.42
10.99
9.99
12.47
11.34
13.96
12.69
15.44
14.04
16.63
15.12
17.82
16.20
18.86
17.15
19.90
18.09
20.94
19.04
21.98
19.98
9.16
10.40
11.63
12.87
13.86
14.85
15.72
16.58
17.45
18.32
Nozzle Size
XR
8008
&
XR
11008
Pressure
PSI
15.00
20.00
25.00
30.00
35.00
40.00
45.00
50.00
55.00
60.00
4.00
36.38
42.32
46.78
51.23
55.32
59.40
62.74
66.08
69.42
72.77
Gallons Per Acre At Miles Per Hour
5.00
6.00
7.00
8.00
9.00
10.00
11.00
12.00
29.11
24.26
20.79
18.19
16.17
33.86
28.22
24.18
21.16
18.81
37.42
31.19
26.73
23.39
20.79
40.99
34.16
29.28
25.62
22.77
44.25
36.88
31.61
27.66
24.59
47.52
39.60
33.94
29.70
26.40
50.19
41.83
35.85
31.37
27.89
52.87
44.06
37.76
33.04
29.37
55.54
46.28
39.67
34.71
30.86
58.21
48.51
41.58
36.38
32.34
14.55
13.23
16.93
15.39
18.71
17.01
20.49
18.63
22.13
20.12
23.76
21.60
25.10
22.82
26.43
24.03
27.77
25.25
29.11
26.46
12.13
14.11
15.59
17.08
18.44
19.80
20.91
22.03
23.14
24.26
500-052M
5/13/2003
48 Tractor Mount Sprayer
Teejet
®
Nozzles 30" Spacing - Height 26" to 28" for XR80; 20" to 22" for XR110
Nozzle Size
XR
8001
&
XR
11001
Pressure
PSI
15.00
20.00
25.00
30.00
35.00
40.00
45.00
50.00
55.00
60.00
4.00
2.97
3.47
3.96
4.46
4.70
4.95
5.20
5.45
5.69
5.94
Gallons Per Acre At Miles Per Hour
5.00
6.00
7.00
8.00
9.00
10.00
11.00
12.00
2.38
2.77
3.17
3.56
3.76
3.96
4.16
4.36
4.55
4.75
1.98
2.31
2.64
2.97
3.14
3.30
3.47
3.63
3.80
3.96
1.70
1.98
2.26
2.55
2.69
2.83
2.97
3.11
3.25
3.39
1.49
1.73
1.98
2.23
2.35
2.48
2.60
2.72
2.85
2.97
1.32
1.54
1.76
1.98
2.09
2.20
2.31
2.42
2.53
2.64
1.19
1.39
1.58
1.78
1.88
1.98
2.08
2.18
2.28
2.38
1.08
1.26
1.44
1.62
1.71
1.80
1.89
1.98
2.07
2.16
0.99
1.16
1.32
1.49
1.57
1.65
1.73
1.82
1.90
1.98
Nozzle Size
XR
80015
&
XR
110015
Pressure
PSI
15.00
20.00
25.00
30.00
35.00
40.00
45.00
50.00
55.00
60.00
4.00
4.46
5.45
5.94
6.44
6.93
7.43
7.80
8.17
8.54
8.91
5.00
3.56
4.36
4.75
5.15
5.54
5.94
6.24
6.53
6.83
7.13
Gallons Per Acre At Miles Per Hour
6.00
7.00
8.00
9.00
10.00
11.00
12.00
2.97
3.63
3.96
4.29
4.62
4.95
5.20
5.45
5.69
5.94
2.55
3.11
3.39
3.68
3.96
4.24
4.46
4.67
4.88
5.09
2.23
2.72
2.97
3.22
3.47
3.71
3.90
4.08
4.27
4.46
1.98
2.42
2.64
2.86
3.08
3.30
3.47
3.63
3.80
3.96
1.78
2.18
2.38
2.57
2.77
2.97
3.12
3.27
3.42
3.56
1.62
1.98
2.16
2.34
2.52
2.70
2.84
2.97
3.11
3.24
1.49
1.82
1.98
2.15
2.31
2.48
2.60
2.72
2.85
2.97
Nozzle Size
XR
8002
&
XR
11002
Pressure
PSI
15.00
20.00
25.00
30.00
35.00
40.00
45.00
50.00
55.00
60.00
4.00
5.94
6.93
7.67
8.42
9.16
9.90
10.52
11.14
11.76
12.38
Gallons Per Acre At Miles Per Hour
5.00
6.00
7.00
8.00
9.00
10.00
11.00
12.00
4.75
5.54
6.14
6.73
7.33
7.92
8.42
8.91
9.41
9.90
3.96
4.62
5.12
5.61
6.11
6.60
7.01
7.43
7.84
8.25
3.39
3.96
4.38
4.81
5.23
5.66
6.01
6.36
6.72
7.07
2.97
3.47
3.84
4.21
4.58
4.95
5.26
5.57
5.88
6.19
2.64
3.08
3.41
3.74
4.07
4.40
4.68
4.95
5.23
5.50
2.38
2.77
3.07
3.37
3.66
3.96
4.21
4.46
4.70
4.95
2.16
2.52
2.79
3.06
3.33
3.60
3.83
4.05
4.28
4.50
1.98
2.31
2.56
2.81
3.05
3.30
3.51
3.71
3.92
4.13
5/13/2003
500-052M
Adjustments 49
Nozzle Size
XR
8003
&
XR
11003
Pressure
PSI
15.00
20.00
25.00
30.00
35.00
40.00
45.00
50.00
55.00
60.00
4.00
8.91
10.40
11.63
12.87
13.86
14.85
15.72
16.58
17.45
18.32
Gallons Per Acre At Miles Per Hour
5.00
6.00
7.00
8.00
9.00
10.00
11.00
12.00
7.13
8.32
9.31
10.30
5.94
6.93
7.76
8.58
11.09
11.88
9.24
9.90
12.57
10.48
13.27
11.06
5.09
5.94
6.65
7.35
7.92
8.49
8.98
9.48
13.96
11.63
9.97
14.65
12.21
10.47
4.46
5.20
5.82
6.44
6.93
7.43
7.86
8.29
8.72
9.16
3.96
4.62
5.17
5.72
6.16
6.60
6.99
7.37
7.76
8.14
3.56
4.16
4.65
5.15
5.54
5.94
6.29
6.63
6.98
7.33
3.24
3.78
4.23
4.68
5.04
5.40
5.72
6.03
6.35
6.66
2.97
3.47
3.88
4.29
4.62
4.92
5.24
5.53
5.82
6.11
Nozzle Size
XR
8004
&
XR
11004
Pressure
PSI
15.00
20.00
25.00
30.00
35.00
40.00
45.00
50.00
55.00
60.00
4.00
11.88
13.86
15.59
17.33
18.56
19.80
20.91
22.03
23.14
24.26
Gallons Per Acre At Miles Per Hour
5.00
6.00
7.00
8.00
9.00
10.00
11.00
12.00
9.50
11.09
7.92
9.24
12.47
10.40
13.86
11.55
6.79
7.92
8.91
9.90
5.94
6.93
7.80
8.66
14.85
12.38
10.61
15.84
13.20
11.31
9.28
9.90
16.73
13.94
11.95
10.46
17.62
14.69
12.59
11.01
5.28
6.16
6.93
7.70
8.25
8.80
9.30
9.79
18.51
15.43
13.22
11.57
10.29
19.40
16.17
13.86
12.13
10.78
4.75
5.54
6.24
6.93
7.43
7.92
8.37
8.81
9.26
9.70
4.32
5.04
5.67
6.30
6.75
7.20
7.61
8.01
8.42
8.82
3.96
4.62
5.20
5.78
6.19
6.60
6.97
7.34
7.71
8.09
Nozzle Size
XR
8005
&
XR
11005
Pressure
PSI
15.00
20.00
25.00
30.00
35.00
40.00
45.00
50.00
55.00
60.00
4.00
15.35
17.33
19.31
21.29
23.02
24.75
26.11
27.47
28.83
30.20
Gallons Per Acre At Miles Per Hour
5.00
6.00
7.00
8.00
9.00
10.00
11.00
12.00
12.28
10.23
13.86
11.55
8.77
9.90
7.67
8.66
15.44
12.87
11.03
9.65
17.03
14.19
12.16
10.64
6.82
7.70
8.58
9.46
18.41
15.35
13.15
11.51
10.23
19.80
16.50
14.14
12.38
11.00
20.89
17.41
14.92
13.06
11.61
21.98
18.32
15.70
13.74
12.21
23.07
19.22
16.48
14.42
12.82
24.16
20.13
17.25
15.10
13.42
6.14
6.93
7.72
8.51
9.21
9.90
10.44
10.99
5.58
6.30
7.02
7.74
8.37
9.00
9.50
9.99
11.53
10.49
12.08
10.98
5.12
5.78
6.44
7.10
7.67
8.25
8.70
9.16
9.61
10.07
500-052M
5/13/2003
50 Tractor Mount Sprayer
Nozzle Size
XR
8006
&
XR
11006
Pressure
PSI
15.00
20.00
25.00
30.00
35.00
40.00
45.00
50.00
55.00
60.00
4.00
18.32
20.79
23.27
25.74
27.72
29.70
31.43
33.17
34.90
36.63
Gallons Per Acre At Miles Per Hour
5.00
6.00
7.00
8.00
9.00
10.00
11.00
12.00
14.65
12.21
10.47
9.16
16.63
13.86
11.88
10.40
8.14
9.24
18.61
15.51
13.29
11.63
10.34
20.59
17.16
14.71
12.87
11.44
22.18
18.48
15.84
13.86
12.32
23.76
19.80
16.97
14.85
13.20
25.15
20.96
17.96
15.72
13.97
26.53
22.11
18.95
16.58
14.74
27.92
23.27
19.94
17.45
15.51
29.30
24.42
20.93
18.32
16.28
7.33
8.32
9.31
10.30
6.66
7.56
8.46
9.36
11.09
10.08
11.88
10.80
12.57
11.43
13.27
12.06
13.96
12.69
14.65
13.32
6.11
6.93
7.76
8.58
9.24
9.90
10.48
11.06
11.63
12.21
Nozzle Size
XR
8008
&
XR
11008
Pressure
PSI
15.00
20.00
25.00
30.00
35.00
40.00
45.00
50.00
55.00
60.00
4.00
24.26
28.22
31.19
34.16
36.88
39.60
41.83
44.06
46.28
48.51
Gallons Per Acre At Miles Per Hour
5.00
6.00
7.00
8.00
9.00
10.00
11.00
12.00
19.40
16.17
13.86
12.13
10.78
22.57
18.81
16.12
14.11
12.54
24.95
20.79
17.82
15.59
13.86
27.32
22.77
19.52
17.08
15.18
29.50
24.59
21.07
18.44
16.39
31.68
26.40
22.63
19.80
17.60
33.46
27.89
23.90
20.91
18.59
35.24
29.37
25.17
22.03
19.58
37.03
30.86
26.45
23.14
20.57
38.81
32.34
27.72
24.26
21.56
9.70
8.82
11.29
10.26
12.47
11.34
13.66
12.42
14.75
13.41
15.84
14.40
16.73
15.21
17.62
16.02
18.51
16.83
19.40
17.64
8.09
9.41
10.40
11.39
12.29
13.20
13.94
14.69
15.43
16.17
500-052M
5/13/2003
Adjustments 51
General Field Adjustments
Boom Height
After calibrating your sprayer for the specific nozzle you will use at a desired pressure, and tractor speed, the main field adjustment is the boom height. Depending on which type of nozzle you are using, you need to set your boom height so that you achieve the correct overlap for that specific nozzle. If the crop canopy is taller in some fields than others, you will need to adjust the boom height accordingly. Refer to the nozzle charts located in this manual to determine the height of the boom needed.
EXAMPLE: A 2.5 MeterCone
®
nozzle at 20 inch spacing is being used. From the nozzle chart {refer to the Adjustments section of this manual or the Application Guide}, a height of 19 to 21 inches above the top of the crop is required. If the crop is 6 inches off the ground, the boom height should be set to 25 to 27 inches off the ground.
Nozzle Pressure
Another area that will need some field adjustments is the nozzle pressure. As your tank level decreases, you may have to adjust the boom pressure to keep the pressure at the same magnitude for what the sprayer was calibrated for if your sprayer is not equipped with a monitor.
Watch your pressure gauge and be aware of changes in the pressure.
To set the three solenoid throttling valves complete the following:
Refer to Figure 13
1.
Loosen the lock collar and adjust all three of the throttling valves until they are closed.
CLOSE
Solenoid Throttling Valve {Manual
Control System Only}
The electric solenoids used to turn on the individual boom sections are three way valves. These valves route the flow to the boom sections or back into the tank, depending on whether the boom section switches on the control box are turned on or off.
When a boom section switch is turned to the off position, the electric solenoid for that switch diverts the flow back into the inlet of the pump. {Refer to "Plumbing Dia-
grams" beginning on page 24}. To insure that the flow
going to the boom section and the flow going back to the inlet of the pump are the same, a throttling valve is used to adjust the flow going to the inlet of the pump. If these flows were not equal, every time the boom section switch if flipped, the pressure will either rise or decrease in the other boom sections, causing the sprayer to over or under apply chemical in those boom sections.
OPEN
11465
Figure 13
Solenoid Throttling Valve
2.
Turn all the boom section switches on with the tank filled with water {no chemical added} and the pump running. Adjust the boom pressure until the boom pressure gauge reaches the selected calibration pressure.
3.
Turn the left boom section switch off and keep the center and right section switches on. Unscrew the throttling valve for the left boom section until the pressure on the boom pressure gauge reaches the calibration pressure. Flip the left boom section switch a few times and adjust the throttling valve so that the pressure remains at the selected calibration pressure.
4.
Turn the left boom section switch on. With the left and right boom sections on, turn the center boom section off and adjust the throttling valve as described in step 3.
5.
Adjust the throttling valve for the right boom section with the left and center boom sections on as described in step 3.
6.
With all throttling valves adjusted, it should be possible to flip any combination of boom section switches with the pressure remaining constant.
5/13/2003
500-052M
52 Tractor Mount Sprayer
Pressure Adjustments {Manual Control System Only}
One of the most important areas of controlling the sprayer accuracy is to have the proper pressure when spraying. The pressure is determined when the sprayer is calibrated. Refer to "Calibration Procedures", start-
The electric ball valve is used to adjust the pressure to the booms. It is controlled with the pressure adjust switch on the control box. The boom pressure is displayed by the boom pressure gauge.
To adjust the pressure, hold the pressure adjust toggle switch up for more pressure, down for less pressure. If holding the switch up decreases pressure, reverse wires at the ball valve. Refer to Figure 11 on page 22 (8).
As the tank level decreases, the boom pressure may change. Check your boom pressure gauge frequently and make sure that the pressure doesn’t change. Generally, the boom pressure will need to be adjusted up slightly when the tank level decreases.
When the manual pressure adjustment valve {refer to
"Plumbing Diagrams" beginning on page 24} is wide
open, the pressure adjust switch is very sensitive. To decrease the sensitivity of the pressure adjust, set the manual pressure adjustment valve.
To set the manual pressure adjustment valve, open the electric ball valve wide open with the pressure adjustment switch. Shut the manual pressure adjustment valve down so the pressure is about 20 psi greater than the pressure you will spray at {the pressure the spray will be applied at is determined when you calibrate your spray-
er. Refer to "Calibration Procedures" on page 28}.
With this valve set, it will decrease the flow through the electric ball valve and reduce the sensitivity of the pressure adjustment switch.
500-052M
5/13/2003
Troubleshooting 53
Troubleshooting
Area of Concern
Pressure
Decreasing
Pressure
Fluctuating
Pressure
Increasing
Pressure
Cannot
Increase
No
Pressure
No
Pressure
Pressure
Cannot
Decrease
Problem
Area
Between gauge & liquid supply
Between pump outlet & liquid
Between gauge & nozzle
Pump or electric ball valve
Plumbing
Pump
Pump or electric ball valve
Specific Checks Corrections
1. Pump wearing.
2. Plugged suction or pump to pressure head hose.
3. Plugged Whirlfilter
®
.
4. Plugged gauge.
3. Collapsed suction hose to pump.
4. Obstruction in suction hose or tank.
1. Hydraulic pump running in the wrong direction.
2. PTO pump coupler loose.
1. Tank agitation restricted.
1. Rebuild or replace pump.
2. Clean hose and reduce cause of clogging.
3. Clean out Whirlfilter
®
, refer to
4. Open gauge clean-out valve and flush gauge protector.
1. Remove obstruction from clogged area.
1. Check suction hose & fittings for air leaks. Air in system is indicated by buffs of air at nozzles.
2. Vortex in tank suction.
3. Cracked pump housing.
1. Nozzle screens clogged.
2. Nozzle orifices plugged.
3. Boom hoses becoming clogged.
4. Boom hoses pinched.
1. From nozzle charts check liquid demand against pump capacity {Nozzle requirement + agitation requirement}.
2. Electric ball valve or gauge not functional.
3. Pressure adjust switch faulty.
4. Fuse is out in the control box.
5. Manual pressure adjustment valve not all the way open.
1. Tank shut-off valves off.
2. Loose fittings.
2. Align agitator properly.
3. Replace pump housing.
1. Clean screens.
2. Remove material with soft brush or air.
3. Remove obstruction from clogged area.
4. Use cable ties to position hose so it will not kink.
1. Reduce swath width by nozzle reduction; install smaller nozzles & drive at a lower rate of speed.
2. Replace or repair.
3. Test switch & replace if faulty.
4. Replace fuse.
5. Open the manual pressure valve all the way & allow the electric ball valve to govern the pressure.
1. Make sure all tank shut-off valves are open.
2. Tighten fittings so pump can prime.
3. Replace hose.
4. Remove obstruction.
1. Switch hydraulic hoses in the tractor outlet.
2. Tighten PTO coupler.
1. Check that the agitator valve is open & that the liquid is being agitated.
500-052M
5/13/2003
54 Tractor Mount Sprayer
Maintenance and Lubrication
Maintenance
Proper servicing and adjustment is the key to the long life of any farm implement. With careful and systematic inspection, you can avoid costly maintenance, time and repair.
Equipment Cleanup
Nozzles should be cleaned with a low pressure {less than 30 psi} air hose, and periodically replaced. Haul a supply tank of water so you can clean the spray tank and applicator out in the field. NEVER wash tank out in the yard or at a car wash. Rinse out tank and spray the rinse water on the last field that was sprayed.
Dispose of leftover chemical in the same manner described on the manufacturer’s label of the chemical last used in the sprayer. Rinse out the tank and spray the rinse water on the last field that was sprayed.
Flush the sprayer with fresh water and spray the water in the field that was last sprayed. While the sprayer is being flushed at the field, turn the boom section switches "on" to flush the nozzles, then turn them "off" to flush out the throttling valves and bypass lines {if equipped}. Repeat this procedure several times. Periodically clean each throttling valve by unscrewing its gray knob until it stops.
Flush it with the fresh water by operating the pump with the boom section switches "off". Reset the solenoid throttling valves as described in "Solenoid Throttling
The boom pressure gauge has a ball valve that is used to clean out any chemical that has built up under the gauge protector. With the sprayer tank full of water and the pump running, open the ball valve and allow the water to run in a bucket. After the liquid coming out of the hose turns clear, turn off the ball valve and dump the contents of the bucket into the sprayer tank.
General Information
If equipment is to be used in freezing or near freezing conditions, protect pump and plumbing system by thoroughly draining liquid and pumping antifreeze {Great
Plains strongly recommends the use of recreational vehicle antifreeze} solution through the plumbing system.
Before working on, servicing or making adjustments on sprayer, ALWAYS disengage power, shut off tractor engine, make sure all moving parts have stopped, and all pressure in the system is relieved.
Check the conditions of hoses and connections frequently. Release the system pressure BEFORE working on the sprayer. To release the pressure flip the boom section switches on an off without the pump running.
ALWAYS wear rubber gloves when making repairs or adjustments. Make sure all "Personal Safety Equip-
ment" {gloves, goggles, etc.} listed on Page 5, are
stored in an easily accessible place but protected from potential contamination from dust or chemicals.
Check the sprayer for any loose bolts, pins, and hose clamps.
Check the hoses, pumps, valves, and fittings for any leaks.
Inspect all parts of the sprayer for wear and rust. Repair and paint parts as necessary.
Pump Maintenance & Repair
This Great Plains pump is designed for long life and service. Through the years, there may be a need to replace the mechanical seal or service some component of the pump. A mechanical seal may weep slightly, but if it starts to drip, the pump will have to be disassembled.
Before you disassemble the pump, be sure to wash it out with fresh water.
The following is an instruction list for how to reassemble the pump after it has been disassembled and repaired.
Refer to the parts manual for the components of the pump.
Refer to Figure 14
If your pump is leaking, before you remove it from the sprayer, run the pump with adequate water in the tank to diagnose the actual pump problem. If fluid leaks out between the front suction housing (5) and the rear volute housing (8), the housing gasket may be dried out. Give the gasket (6) adequate time to absorb moisture and swell up. If necessary, retighten the volute housing (8) by alternating on opposite sides until all nuts (9) are torqued to 16 - 18 ft.-lbs. It is a good practice to apply grease to both sides of the gasket (6) to prevent shrinkage.
If seal replacement is required:
1.
Disassemble pump and clean all components.
2.
Assemble the ceramic ring seat of the mechanical seal (7) into the volute housing (8) of the pump.
Make sure the ceramic seat is positioned square into the volute housing.
5/13/2003
500-052M
Maintenance and Lubrication 55
3.
Clean off any grease or dirt from the pump shaft (10) and dry the shaft so the rubber bellows on the mechanical seal will adhere to the shaft properly when assembled.
4.
Bolt up the pump input bearing housing (not shown) to the volute housing (8) using bolts (2), (3) and (4) with spacers (not furnished) for alignment and assembly of the shaft seal.
5.
Assemble the seal (7) without its spring, on the pump shaft by pushing on the inside rubber portion of the seal using water as the lubrication. The graphite seal face should touch the white ceramic seat face. The rubber bellows adhering to the pump shaft should not protrude more than 1/16" beyond the stainless steel ring located on the impeller side of the seal.
6.
Assemble the seal’s spring and the impeller, being careful not to move the mechanical seal that has been positioned on the pump shaft. Torque the impeller bolt (1) 16 - 18 ft./lbs.
7.
Remove the three bolts and spacers. Using gun grease, lubricate the gasket (6). Assemble the gasket (6) and suction housing (5) using bolts, flat washers and locknuts. Torque nuts 16 - 18 ft./lbs.
5/13/2003
Figure 14
Centrifugal Pump Assembly
11591
500-052M
56 Tractor Mount Sprayer
Lubrication
Universal Lubrication Symbols
10
Lubrication is required every 10 hours of operation.
10
Lubrication is required every 10 hours of operation.
As
Required
Use a multipurpose spray lub. Use as required.
Do not over lubricate.
Seasonally
Lubrication is required ______________.
10
PTO Pump {if applicable}
The grease zerk is located on the gear case cover and is marked with a decal. Grease with five shots of grease.
Type of Lubrication: NLGI grade 2 or 3 grease lubricant
12229
Storage
1.
Empty solution from the tank and store or dispose of the chemical as recommended by the manufacturer’s chemical label.
2.
Flush the entire sprayer system with clean water.
3.
Clean out Whirlfilters
®
. Refer to "Operating Whirl-
filter
®
4.
Circulate 3 - 5 gallons of antifreeze {Great Plains strongly recommends the use of recreational vehicle antifreeze} through the system including the pump, hoses and nozzles. Drain the sprayer and properly dispose of antifreeze.Keep antifreeze in the pump to prevent gasket shrinkage.
Note: Regular antifreeze is harmful or fatal to animals and humans. Use carefully according to the label’s instructions. We strongly recommend the use of recreational vehicle antifreeze which does not exhibit these harmful side effects.
5.
Remove nozzles, disconnect the control box, and place them indoors.
6.
Change filters in the tractor cab after finished.
7.
Wash off the exterior of the sprayer thoroughly using a safe solvent or soap and water.
8.
Inspect all parts of the sprayer for wear and rust. Repair and paint parts as necessary.
9.
Store the sprayer in a dry area away from direct sunlight.
500-052M
5/13/2003
Specifications and Capacities 57
Tank Size
Pumps
Specifications and Capacities
Tractor Mount Sprayer 500 Gallons
2 Tanks Totalling 500 gallons
Tractor Mounted PTO Pump - 540 rpm
Tractor Mounted PTO Pump - 1,000 rpm 1 3/8" Spline
Tractor Mounted PTO Pump - 1,000 rpm 1 3/4" Spline
Hydraulic Pump
5/13/2003
500-052M
58 Tractor Mount Sprayer
Appendix
Torque Values Chart
Bolt Head Identification
Bolt Head Identification
Bolt Size
(Inches)
in-tpi
1
5.8
8.8
10.9
1/4" - 20
1/4" - 28
5/16 - 18
5/16" - 24
3/8" - 16
3/8" - 24
7/16" - 14
7/16" - 20
1/2" - 13
1/2" - 20
9/16" - 12
9/16" - 18
5/8" - 11
5/8" - 18
3/4" - 10
3/4" - 16
7/8" - 9
7/8" - 14
1" - 8
1" - 12
Grade 2
N · m
2 ft-lb
3
7.4
8.5
15
17
27
31
43
49
66
75
95
105
130
150
235
260
225
250
340
370
5.6
6
11
13
20
22
32
36
49
55
70
79
97
110
170
190
165
185
250
275
Grade 5
N · m
11
13
24
26
42
47
67
75
105
115
150
165
205
230
360
405
585
640
875
955 ft-lb N · m
8
10
17
19
31
35
49
55
76
85
110
120
150
170
265
295
16
18
33
37
59
67
95
105
145
165
210
235
285
325
510
570
Grade 8 ft-lb
12
14
25
27
44
49
70
78
105
120
155
170
210
240
375
420
430
475
820
905
605
670
645 1230 910
705 1350 995
Bolt Size
(Metric)
mm x pitch
M 5 X 0.8
M 6 X 1
M 8 X 1.25
M 8 X 1
M10 X 1.5
M10 X 0.75
M12 X 1.75
M12 X 1.5
M12 X 1
M14 X 2
M14 X 1.5
M16 X 2
M16 X 1.5
M18 X 2.5
M18 X 1.5
M20 X 2.5
M20 X 1.5
M24 X 3
M24 X 2
M30 X 3.5
4
Class 5.8
N · m
4
7
17
18
33
39
58
60
90
92
99
145
155
195
220
280
310
480
525
960 ft-lb
3
5
12
13
24
29
42
44
66
68
73
105
115
145
165
205
230
355
390
705
Class 8.8
N · m
6
11
26
28
52
61
91
95
105
145
155
225
240
310
350
440
650
760
830
1510 ft-lb
5
8
19
21
39
45
67
70
77
105
115
165
180
230
260
325
480
560
610
1120
Class 10.9
N · m
9
15
36
39
72
85
125
130
145
200
215
315
335
405
485
610
900
1050
1150
2100 ft-lb
7
11
27
29
245
300
355
450
665
780
845
1550
1-1/8" - 7
1 1/8" - 12
1 1/4" - 7
1 1/4" - 12
1 3/8" - 6
1 3/8" - 12
1 1/2" - 6
1 1/2" - 12
480
540
680
750
355 1080 795 1750 1290
395 1210 890 1960 1440
500 1520 1120 2460 1820
555 1680 1240 2730 2010
M30 X 2
M36 X 3.5
M36 X 2
1060
1730
1880
785
1270
1380
1680
2650
2960
1240
1950
2190
2320
3660
4100
1710
2700
3220
890
1010
1180
1330
655
745
870
980
1990
2270
2640
2970
1470
1670
1950
2190
3230
3680
4290
4820
2380
2710
3160
3560
1
in-tpi = nominal thread diameter in inches-threads per inch
2
N· m = newton-meters
3
ft-lb= foot pounds
4 mm x pitch = nominal thread diameter in millimeters x thread pitch
Torque tolerance + 0%, -15% of torquing values. Unless otherwise specified use torque values listed above.
105
150
160
230
53
62
93
97
5/13/2003
500-052M
5/13/2003
Warranty
Great Plains Manufacturing, Incorporated warrants to the original purchaser that this spraying equipment will be free from defects in material and workmanship for a period of one year from the date of original purchase when used as intended and under normal service and conditions for personal use; 90 days for commercial or rental purposes. This Warranty is limited to the replacement of any defective part by Great Plains
Manufacturing, Incorporated and the installation by the dealer of any such replacement part. Great Plains reserves the right to inspect any equipment or part which are claimed to have been defective in material or workmanship.
This Warranty does not apply to any part or product which in Great
Plains’ judgement shall have been misused or damaged by accident or lack of normal maintenance or care, or which has been repaired or altered in a way which adversely affects its performance or reliability, or which has been used for a purpose for which the product is not designed. This Warranty shall not apply if the product is towed at a speed in excess of 20 miles per hour.
Claims under this Warranty must be made to the dealer which originally sold the product and all warranty adjustments must by made through such dealer. Great Plains reserves the right to make changes in materials or design of the product at any time without notice.
This Warranty shall not be interpreted to render Great Plains liable for damages of any kind, direct, consequential, or contingent, to property.
Furthermore, Great Plains shall not be liable for damages resulting from any cause beyond its reasonable control. This Warranty does not extend to loss of crops, losses caused by harvest delays or any expense or loss for labor, supplies, rental machinery or for any other reason.
No other warranty of any kind whatsoever, express or implied, is made with respect to this sale; and all implied warranties of merchantability and fitness for a particular purpose which exceed the obligations set forth in this written warranty are hereby disclaimed and excluded from this sale.
This Warranty is not valid unless registered with Great Plains Manufacturing, Incorporated within 10 days from the date of original purchase.
Appendix 59
500-052M
Great Plains Manufacturing, Inc.
Corporate Office: P.O. Box 5060
Salina, Kansas 67402-5060 USA
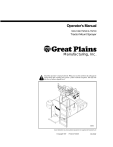
Download
Advertisement
Key features
Designed for applying liquid pesticides, herbicides, or fertilizers.
Compatible with various tractor models.
Includes plumbing and control instructions for ease of use.
Provides calibration procedures for accurate application.
Offers guidance on maintenance and troubleshooting.
Frequently asked questions
Use this Tractor Mount Sprayer as part of a pressurized sprayer system to apply liquid pesticides, herbicides or fertilizers to production-agriculture crops only.
To operate your Great Plains Sprayer, a tractor using a 12 volt electrical system must be used. The tractor will need two hydraulic outlets (one pair) if the sprayer is equipped with a hydraulic pump.
Before adding chemical to the tank, make sure tank is at least half full. Do not pour concentrate into an empty tank.