- No category
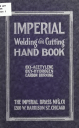
advertisement
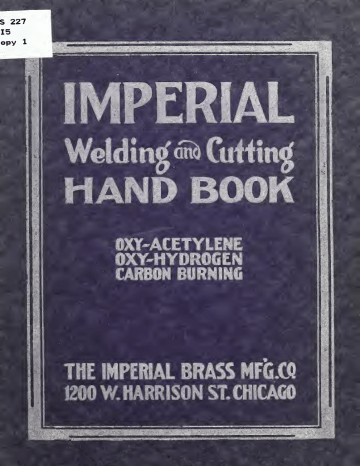
IMPERIAL
Weldings
Cutting
HAND
BOOK
THE
IMPERIAL
BRASS
MFG.CQ
1200
W.HARRISON
ST.CHICAffiO
IMPERIAL
We laing and Cutting
HAND
BOOK
OXY-ACETYLENE
OXY-HYDROGEN
CARBON
BURNING
Price,
$1.00
per copy
The
Imperial
Brass
Mfg.
Co.
1200
West
Harrison
Street,
....
Chicago
1>
Copyright
1916 by
The
Imperial Brass
Mfg.
Co.,
Chicago oil r<
AUG
24
1916
©CI.A43.6
510
c
V
-%
*>
THE IMPERIAL BRASS
MFG.
CO.
PREFACE
With proper or intelligent use,
Imperial Apparatus is practically indestructible.
So far as engineering knowledge, carefully selected materials, modern machinery and skilled mechanics can make them, the regulators, gauges, torches and other parts which comprise the equipment, are built for service
— to give the proper kind of a flame and to stand up under ordinary wear year in and year out.
We have done our part
; but unless you acquire an elementary knowledge of the apparatus, its use and how to properly keep it in good working condition, the best possible results cannot be expected.
To give this necessary elementary knowledge is the purpose of this booklet.
Its careful reading will help to effect a better understanding of
Imperial
Equipment and its use and will probably save annoying mistakes, due to lack of knowledge.
The text is free from technical verbiage and while volumes could be written on the subject, we believe this covers the fundamentals.
Following along the lines described, the operator will be on the way to becoming a successful user of oxy-acetylene equipment.
Following out the rules and directions of this booklet will make your work not only a success but a pleasure as well.
THE IMPERIAL
BRASS
MFG.
CO.
SUGGESTIONS FOR BEGINNERS
NE of the things
NOT to do after purchasing an oxy-acetylene welding outfit is to immediately solicit work.
Note that word immediately.
There is no quicker way of hurting your own reputation and of giving oxy-acetylene welding a general black eye than to fall down on a job for a customer.
In several instances, novices have solicited work before their apparatus arrived.
Others, without even connecting the equipment, announce they are ready for all the castings of any metal
— and into the shop come malleable iron, aluminum, bronze and cast iron
— metals with which the newly enlisted operator is probably unfamiliar, to be welded by a process totally different from the method he has been acquainted with.
Now the oxy-acetylene flame will certainly join all these metals, but, given the proper equipment, it is essential that some judgment and some practice be added.
To practice on a customer's job means the enmity of that customer.
So, before tackling oxy-acetylene on a commercial scale, put the apparatus in the back of the shop or in a separate room, master the principles and practice on scrap material.
Then make a noise.
There are certain fundamental principles which must be understood and mastered before commercial welding, even upon a simple scale, is undertaken.
following pages,
These fundamental principles are given on the but one can't become a welder by reading alone
— it is necessary to do actual welding, though reading practical articles will certainly help.
Whenever possible, by all means secure some training, a week or two, in a repair
'-.hop.
If this is not possible, practice on junk material until you are competent to operate the oxy-acetylene equipment.
THE IMPERIAL BRASS
MFG.
CO.
PRINCIPLE OF
WELDING
Welding with the oxy-acetylene flame is a fusing process.
With a temperature of over 6,000°
F., concentrated in a comparatively small point, the flame is held on the edges to be united
UNTIL
THEY
MELT
TOGETHER.
Since by this process, no hammering or compression is necessary, it is applicable to all the metals: cast iron, malleable iron, steel, aluminum, bronze and copper.
Oxygen is purchased in conveniently handled cylinders or drums which are charged to a pressure of approximately
1,800 pounds.
Purity is essential to the successful and economical operation of the oxy-acetylene process and the oxygen purchased in these high pressure drums is considerably cheaper and much purer than that made by chemicals on the premises.
The proper manufacture and testing of both the oxygen and acetylene cylinders is supervised by an
U.
S.
Government commission and if ordinary precautions are employed by the user, the tank system of gases is ideal.
Acetylene in tanks is more properly known as dissolved acetylene.
The cylinder is filled with a porous material and also with a liquid known as acetone, which has the quality of absorbing many times its own volume of acetylene.
Acetylene, in a free state, is dangerous at pressures greater than fifteen pounds.
Dissolved, however, this hazard is removed and the gas in cylinders, while costing a little more than that generated on the premises, is considerably purer, is always ready for use merely by opening the valve and requires no care.
In addition, the use of dissolved acetylene feature makes the entire equipment portable, a many times of real value for repair purposes.
Pressures of acetylene cylinders vary with the different manufacturers and temperatures, but the average is around
225 pounds to the square inch.
With pure gases, it is necessary that the equipment regulators, torches, etc.
— that is, the
— be scientifically constructed and used with intelligence to effect satisfactory results.
principles of this equipment
An understanding of the we believe is essential.
As you become acquainted with Imperial Apparatus, and precision it is constructed, you will realize with what care how the factor of strength has been obtained without clumsiness
; hazard possible except one how we have removed every danger
— the human element
— so that we have considered it necessary to devote a part of these instructions to the care of the apparatus.
—
THE IMPERIAL
BRASS
MFG.
CO.
PLATE
1
SHOWING
IMPERIAL
WELDING
OUTFIT CONNECTED TO TANKS
A—
Acetylene
Inlet to Torch.
AV—
Acetylene Valve on Torch.
B—
Tank
Coupling.
C
—
Hose
Coupling.
D
—
Outlet Valve to
Hose.
E
—
Acetylene
Regulating Screw.
Tank
Coupling.
Regulating Screw.
Torch.
P
J
F
—
Acetylene
Tank
Valve.
G
—
Oxygen Tank
Valve.
H
—
Hose
Coupling.
K
—
Outlet
Valve to
Hose.
L
M ing Pressure Gauge.
—
Acetylene
O
Tank
Pressure Gauge.
N
—
—
Acetylene
Oxygen
Work-
—
Oxygen
Inlet to Torch.
OV
—
Oxygen
Valve on
—
Oxygen Tank
Pressure
Gauge.
R
—
Oxygen Working
Pressure
Gauge.
Note
—
When either the Searchlight or
Commercial Companies'
Acetylene
Tanks are used, the Acetylene Regulator stands out at right angle to the tank, shown in center tank.
as
When
Prest-O-Lite
Tanks are used, the regulator stands up on end, as shown in partial view of tank at left.
THE IMPERIAL BRASS
MFG.
CO.
OXYGEN
CARE OF APPARATUS
—
The use of a truck for the apparatus is very desirable.
Even though the portable feature may not be desired, the oxygen cylinder then, should be firmly clamped or strapped to avoid falling.
If, you are not a user of the truck, which secures both cylinders, see that the oxygen cylinder is made secure to a wall or bench, for reason that because of its small base, it is very easily tipped over the and a broken regulator would be the result.
Keep the cylinders in a reasonably cool place, away from fires or the direct rays of the sun, remembering that heat causes the gas to expand and while the factor of safety of the cylinder is a big one, it pays to be cautious.
Bear in mind that oil and oxygen under any considerable pressure make a very dangerous combination.
Oil burns
— oxygen is the generator and supporter of combustion; therefore, it would be quite a simple bination.
matter to secure spontaneous combustion through this com-
NEVER
USE
OIL
ON ANY PART OF
THE OXYGEN
SUPPLY, the tank valve, the regulator, the connections or the torch.
Before the regulator is attached to the drum, open the valve the cylinder quickly and close it immediately, thus blowing on away any dirt that may be present on the seat of the outlet valve.
If, after attaching the regulator, the valve on the drum or cylinder leaks, quickly open it as far as possible.
If it still leaks, close it and take off the regulator and return the cylinder to the manufacturers, with a statement of the trouble.
DO NOT ATTEMPT TO
REPAIR
THIS
VALVE.
Remember there is
1,800 pounds pressure per square inch behind it and the sudden release of this gas, caused by carelessness in repairing the valve, workman.
would probably result in an injury to the
This tank valve is provided with a safety in the form of a hex.
PLATE
2
Adantor f° r connecting
Imperial
Acetylene Regulator to
Prest-O-Lite
100,
150 and
300foot
Tanks
PLATE
3 or connecting
Acetylene light
Tanks
Regulator to
Searchor
Commercial
Co.'s
THE IMPERIAL BRASS
MFG.
CO.
nut, which is sealed.
thread, without
The connection for the regulator is a male any nut.
It would hardly seem necessary to warn the user against taking off the safety nut, yet instances have been recorded where the results.
workman attempted to do this with very unsatisfactory
LEAVE THE SAFETY ALONE.
If it at any time leaks, with a letter of explanation.
return the cylinder,
LEAKS
—
While oxygen itself will not burn, and has no odor, oxygen will feed leaks should be guarded against, for the reason that a fire rag with considerable energy.
GEN
TO USE
MATCHES OR
A
FLAME
IN
FINDING
AN
OXY-
LEAK
IS
HAZARDOUS.
Soapy water used with a brush or may better be employed.
OXYGEN
REGULATOR—
As we have already learned, the initial oxygen pressure is
1,800 pounds to the square inch, decreasing, of course, as the contents of the tank are used.
The pressure at the welding torch varies from a few pounds on the small tips to eighteen on the large size and in cutting reaches 125 pounds.
The duty of the
Imperial
PLATE
4
Oxygen
Regulator
—
Type
C
L
H—
Tank
Coupling.
J
—
Hose
Connection.
K—
Outlet
Valve to
Hose.
—
Regulating
Screw.
P
—
Tank
Pressure Gauge showing pressure in tank and contents in cubic feet.
R
—
Working
Pressure
Gauge showing pressure delivered to torch.
THE IMPERIAL
BRASS
MFG.
CO.
regulator then is to reduce the tank pressure to the to deliver amount required, an absolutely steady flow of gas at this pressure and to maintain the necessary volume, irrespective of the tank pressure.
Imperial regulators will do all these things and keep doing them if they are properly treated.
Note carefully the explanation following and so avoid the troubles of those not understanding what an oxygen regulator is.
The principle of operation is very simple.
After the regulator is attached to cylinder and the tank valve has been opened, the flexible metal diaphragm is interposed between the pressure of the cylinder and the heavy springs, the tension of which may be set at the pressure desired by means of the regulating screw.
If, for instance, the pressure of the gas desired is twenty-five pounds, the regulating screw is turned to the right and the springs forced against the diaphragm to this tension, which will so register on the small gauge directly over the body of the regulator.
As the gas enters the body of the regulator from the cylinder it passes through the seat and presses up against the diaphragm.
It will quite readily be seen that sure whenever the presfrom the cylinder exceeds the spring tension, the gas pressing against the diaphragm will overcome the spring tension, thus forcing the diaphragm outward
(against the springs) and as the plunger of valve is attached to the diaphragm, it is drawn against the seat of valve and the gas from the cylinder shut off.
The oxy-acetylene flame must at all times have a steady, even flow of gas.
Therefore, the regulator, which is an instrument of very delicate manufacture, must be handled carefully by the operator to maintain this object.
Before turning on the gas at the cylinder,
SPRING
BE SURE
THAT THE
TENSION
IS
RELEASED, i.
e., the regulating screw turned to the left, which brings the plunger of valve down onto the seat, thus closing the regulator.
After opening the tank valve, turn the regulating screw to the right until the small gauge registers the pressure desired.
NEVER TURN ON THE
GAS
AT CYLINDER
WITH THE
REGULATING SCREW
TIGHT, AS THIS PUTS
SPRING TENSION
ON THE DIAPHRAGM and allows the gas from the cylinder to enter the body of the regulator very suddenly
(because the plunger of valve is away from the seat) and as the sudden pressure strikes the diaphragm, the plunger is thrown violently against the seat, often causing the seat to become cracked or broken.
With the motor of an automobile racing, you wouldn't throw the
THE IMPERIAL
BRASS
MFG.
CO.
10
___ gears in mesh for high speed direct from neutral and attempt to start away from the curb
— not if you want to keep your automobile very long
— yet turning on the oxygen with the spring tension on the regulator has about the same effect on the regulator.
Bear in mind that the regulator is a steadying device
— that the diaphragm is the balance between the high pressure of the cylinder movement of this gas and the spring tension and that at all times the diaphragm should be slow
— never violent.
The low pressure gauge
(R), Plate
4, is a positive index of regulator trouble.
If you are operating, say at fifteen pounds, and after shutting off the valve on the torch, the hand on the dial keeps moving to that the seat is damaged pounds without stopping, it means twenty-five or thirty or forty
— that the high pressure of the cylinder is and the regulator should be immeleaking past the plunger of valve diately sent back to the factory for repairs.
Only by violating some of the rules previously given would you be likely to damage this seat but once damaged, it should be immediately repaired.
ACETYLENE
—
The acetylene cylinder usually has a broad base; and, therefore, is not so easily tipped over as the oxygen; yet, even in this instance, especially where the smaller tanks are used, it is advisable to have it clamped and the truck is therefore a desirable and a wise investment.
ACETYLENE DOUBLES
IN
PRESSURE
AS
THE
TEM-
PERATURE
IS
DOUBLED—
Therefore, keep the cylinder away from any excessively hot place.
Do not carry this idea so far, however, as to keep the cylinder cold, as better and more economical welding results are secured with the cylinder in a
WARM place
; i.
e., with a temperature of around
90°
F.
sure decreased, this temperature
As the gas is used, and the presmay be increased without danger, especially as in using the gas there is considerable refrigeration, which is offset by having the cylinder warm.
Remember, that besides the acetylene in the tank, there is also a very volatile liquid.
When the gas in the tank is exhausted,
CLOSE
THE
VALVE, as the vaporizing of the liquid and its escape might cause an explosive mixture.
DON'T
CEPT
IN
USE
AUTOMOBILE
LIGHTING CYLINDERS
EX-
EMERGENCY.
They are much more expensive to operate than regular welding cylinders and in addition, the liquid absorbent in the cylinder is liable to be withdrawn, thereby lowering the heat of the welding flame and adversely affecting the weld.
Acetylene
;
THE IMPERIAL BRASS
MFG.
CO.
11 should not be used at a rate greater than one-seventh the tank capacity per hour.
If a tip consumes
20 feet of acetylene per hour and the acetylene cylinder used is a
100-foot size, it will readily be seen that the rate of withdrawal of gas is much too rapid and a 225-foot size should be employed, or if small cylinders only are available, connect two or more by means of a manifold, attaching the regulator to the manifold, to insure getting the necessary volume of gas without drawing out the acetone.
LEAKS
—
Acetylene has a decided odor, quickly recognized even if the leak is a very small one.
If such a leak cannot be located by the odor, it is advisable to hunt for it with soap suds, just as when looking for an oxygen leak.
Should the acetylene ignite around the packing nut or between the regulator and the connection, do not be unnecessarily alarmed, as the flame will not go back into the tank.
Simply blow it out and tighten the nut where the gas is escaping, if the leak is a small one.
tinued escape of gas
The chief danger to guard against is the conand its ignition when an explosive mixture is formed.
Such a condition could only occur through extreme carelessness.
ACETYLENE REGULATOR—
The principle of this regulator is the same as that used for oxygen, and while the initial pressure to be reduced is comparatively small, it is well to be governed by the same rules in its care as apply to the oxygen regulator.
It is equipped with two gauges, one 500 pounds to indicate tank pressure and one
50 pounds, showing the line or torch pressure.
Note that the 500-pound gauge indicates tank
PRESSURE, not
CON-
TENTS.
This pressure will vary according to temperature
; and a cylinder having
150 pounds may have the same cubical contents as one having
300 pounds pressure.
This is fully explained later in the chapter devoted to
Figuring
Costs,
Page
43.
WELDING TORCH—
The
Imperial torch is so constructed that the factor of strength is considerably greater than in any other on the market
— this for the reason that a welding torch is very often carelessly handled; if it receives very ordinary care, it is practically indestructible.
The oxygen hose is attached to the upper connection (marked
O), the acetylene to the lower
(marked
A).
Both are ground joints and
12
THE IMPERIAL
BRASS
MFG.
CO.
PLATE
5
Imperial
Acetylene Regulator
—
Type
AA
B
—
Tank
Coupling.
C
—
Hose
Connection.
D
—
Outlet
Valve to
Hose.
E
—
Regulating Screw.
M
—
Tank
Pressure
Gauge showing pressure in tank.
N
—
Working
Pressure
Gauge showing pressure delivered to torch.
AV-
€
EXTENSION
OV
IMPERIAL
10
9
8
6
54321
PLATE
6
Imperial
Welding Torch
—
Type
B
A
—
Acetylene
Inlet.
B
—
Removable Welding
Tip.
AV
—
Acetylene Valve.
O
—
Oxygen
Inlet.
OV
—
Oxygen
Valve.
Nos.
1-10 are the
Welding
Tips.
THE IMPERIAL BRASS
MFG.
CO.
13 make up easily.
The shut-offs are so situated as to enable the operator to adjust the flame while welding, with the thumb or fore finger of the hand grasping the handle.
LEAKS—
After attaching the hose, see that the connection is tight before lighting the torch.
Make sure of this, as a leak at this point may burn the hand.
Then see that the valves are tight and do not leak, either open or shut.
After continued use, it may be found necessary to clean these small valves and to repack.
Be careful not to use oil and for packing use graphite-asbestos.
ABUSE OF as a pair of
TORCH—
Don't attempt to use the welding torch tongs in helping to turn a casting while welding.
Rememand is made to weld bronze composition ber that it is constructed of with
— not for use as a crowbar.
working on a hot casting, where there is little escape for the
In heat waves, except directly against the torch, keep it cool by having a bucket of water acetylene handy and shut off and the
SLOWLY immersing the torch, with the
OXYGEN
PARTLY SHUT
OFF.
Proper judgment in this respect will prevent the burning of tips and the fouling of the mixing tube, due to heating the mixed gases to the ignition point.
FLASHBACK
—
Due to the long mixing chamber of the Imperial and the natural cooling effect of the gases under pressure, the torch flashback is an almost contact unknown occurrence.
Bringing the tip in close with the metal will not (as it does in most welding torches) cause the Imperial to burn back to the
There are only mixing chamber.
two ways in which a flashback will occur
— both easily prevented by the operator, if he is careful.
The first is lack of acetylene
— that is, giving the flame too lean a mixture.
Since
The adjustment of the gases is fully explained on Page
21.
good welding can only be obtained with the correct flame, which is neutral in character, it adjustment behooves the operator to be careful in his and not allow the oxygen to be in excess of the acetylene, which would give a lean mixture and so invite a flashback.
The second is heat.
A mixture of acetylene and oxygen will ignite at a comparatively low temperature.
Therefore, if the torch is heated to a fairly high degree, the gases will burn back to the mixing chamber.
This degree of heat may be obtained by holding the torch over a heavy, hot casting
(previously described) or by bringing the torch in continued close proximity to the metal ping; i.
e., the and causing a snap-
TEMPORARY burning back of the gases.
If this
—
U
THE IMPERIAL BRASS
MFG.
CO.
snapping is continued, the tube or mixing chamber eventually becomes hot enough to ignite the mixed gases and a flashback results.
lene
When a flashback occurs, shut off the oxygen first, then the acetyand cool the torch.
Then relight and adjust the flame,
BUT the flashback may be almost entirely obviated by attention to the two reasons given.
It is better to eliminate the
CAUSE than to allow it to flashback, as the continued burning back of the gases may seriously affect the proper regulation of the torch.
BURNED
TIPS
—
Welding in a corner, or in a depression, where there is no escape for the heat waves, except against the torch tip, may cause the tip to become heated to such an extent that it will melt.
By a study of local conditions, we are usually able to plan to avoid this by proper manipulation of the torch.
If we are not able to do this, cool the tip frequently, as a burned tip is not again usable.
RAGGED
TIPS—
By flying sparks or molten flux, the end of the tip at times becomes partially clogged and the flame then assumes a ragged shape.
Clean these tips with soft wire or wood, using care not to get the aperture out of round.
pand
CARE OF
TIPS
—
Bear in mind that heat causes metals to ex-
— use care in screwing up or unscrewing the tips while they are hot, since tips in a carelessness in this respect clean place, away from dirt may strip the thread.
Keep the
— in the apparatus box or in a small rack near the welding table.
HOSE, GOGGLES, SUPPLIES—
Examine the hose at intervals for leakage, especially ing at this point where it clamps to the torch.
Either gas leakmay cause a serious burn.
So far as possible, keep the hose off the floor trampled upon.
away from oil and possible damage by being
And while welding, see that it is in such a position that no one may trip over it, not especially because it will hurt the hose, but more for the reason that such an occurrence might bad burn to the operator by pulling the torch from his hand.
mean a
It is always necessary to watch each detail of the molten metal keep the welding glasses clean to enable
NEVER you to do this properly.
WELD
WITHOUT
THESE
GLASSES, since to do so means an impairment of the vision.
Welding rods should be kept clean and in a place convenient to the operator
; moisture as they become short, weld them together in leisure time, to closed be ready when the job is started upon.
Keep the flux cans when not in use
— especially the aluminum, as this absorbs from the air and is useless as a flux when this happens.
THE IMPERIAL
BRASS
MFG.
CO.
15
EXPANSION
AND
CONTRACTION
As we heat metal, we expand it
; as it cools, it contracts.
The degree of expansion is not the same with all metals, aluminum expanding and contracting more than cast iron for instance.
per
Different metals
CONDUCT HEAT with varying degrees, cophaving the greatest conductivity of the metals we have to deal with in welding, so conductivity of the we must take into consideration the expansion and metal we are welding in order that we may allow for the shrinkage when the metal cools.
Since cold metal must occupy a smaller space than hot metal, it follows that unless we recognize this and plan to offset it in some way, this shrinkage is likely to distort the article we are welding or in some cases break it.
NOTHING
CAN
PREVENT THE
EXPANSION OF
METALS
HEATED OR
CONTRACTION
WHEN
WHEN
THEY COOL OFF
AGAIN.
PLATE
7
The effect of expansion and contraction is illustrated in
Plate
7.
Suppose that we weld a bar at the break shown.
As we heat it, the metal expands
; but there is opportunity for it to since they are free to expand on the ends, move, or towards the break, and when the weld cools, shorter the ends will move back or perhaps the bar will be slightly
— it depends upon how much care we have used in setting the job up.
16
THE IMPERIAL
BRASS
MFG.
CO.
PLATE
8
Now, suppose that this bar is the middle member of a frame, as illustrated in
Plate
8, with the ends are permanently attached same character of break.
Here the and as we heat the bar at the break, the ends being rigidly held, have expansion is all no opportunity to move and the toward the break.
Since cold metal must occupy a smaller space than hot metal, as the metal cools, the middle bar contracts and shortens and results in breaking the bar or some portion of the frame or the distortion of the frame in the general shape as shown by the dotted lines.
Whether it breaks or bends depends upon the
DUCTILITY of the metal, i.
e., the ability of the metal to stretch.
Wrought iron or steel, for instance, would probably bend out of shape.
Cast iron bend would probably break.
Aluminum might break or it might
— it would depend upon the alloy used in the casting.
But irrespective of whether the article is broken or bent, it would be considered class.
an unsuccessful welding job, even though the weld itself is first
It is, therefore, evident that this must be overcome in some manner before
The most we can do successful welding.
common form is to heat the article all over in order to set up an equal expansion throughout and consequently have the metal cool equally all over.
This is not possible in all cases, however, or practical.
heat the
In the figure illustrated, it is not necessary, since two side bars about as we may much as we would heat the middle bar in welding and thus take care of contraction, since in heating the side bars, the break in the middle bar would open up.
Perhaps conditions are such that we are unable to heat either a portion of the article
THE IMPERIAL BRASS
MFG.
CO.
17 or all of it.
We may then use a jack to open the break in the middle bar a short distance, make the weld, and then slowly loosen the tension on the jack as the metal contracts.
Or we may wrap wet cloths or wet asbestos or clay around the middle bar, close to the weld, make the
US ed weld and while making it keep cold water running on the material
— this method simply holds the expansion to a limited area and should be employed only when no other method is possible.
Undoubtedly the better method in nearly all cases is the preheating of the article or a portion of it, though in each case proper judgment must be exercised.
The fact to bear strongly in mind and to understand thoroughly before proceeding to actual welding is, that expansion and contraction must always take place and that shafts or angle irons.
we cannot prevent it with jigs, vises,
We may offset its ill effects by one of the methods outlined in the preceding paragraph and we will do well to thoroughly digest this, since most failures in welding may be traced directly to lack of knowledge of expansion and contraction.
CHEMICAL ACTION OF
THE FLAME
Metals are susceptible to certain chemical actions, especially under the influence of heat.
Particularly, they have a high affinity for oxygen
; that is, oxygen, either from the flame, from the air, or from wet gas, may unite with the metal and form an oxide.
This oxide is detrimental to the weld, exactly the same as iron rust, which is one form of iron oxide, weakens iron
; hence we must guard against oxidation.
Since acetylene is rich in carbon and the presence of carbon in steel or iron makes them hard and brittle, the flame must be properly adjusted to prevent an excess of carbon being deposited in the weld in other words, to prevent carbonization.
Oxygen also has an affinity for the carbon in iron and steel and the loss of it changes the character of the metal.
This action, however, is so like oxidation that we may consider it practically the same in guarding against it.
MECHANICAL
EFFECT OF
THE FLAME
Case hardened or tempered steel cease to be hard after being melted, as happens when a bond is made with the oxy-acetylene flame.
In the welding of brass or bronze, we may melt out some of the alloy, changing the color ing.
Copper and composition of the casting in the line of weldmay lose its ductility
— cast iron become brittle.
To a
;
18
THE IMPERIAL BRASS
MFG.
CO.
large extent we may prevent many of these detrimental chemical and mechanical changes by proper selection and use of the welding rods and fluxes, plus proper use of the torch and careful heating and cooling.
PREHEATING
AGENCIES
Since it is often necessary to preheat an article, either in sections or all over, to prevent breakage or distortion and in some instances also to prevent detrimental chemical actions, we must decide upon an agency to do this.
PLATE
9
The simplest form of preheating is undoubtedly a temporary fire brick furnace, with charcoal, as shown in
Plate
9.
But we may also use gas to decided advantage, if we are properly equipped with a blower to furnish air for it, or we may use kerosene oil.
The choice of a preheating agency must be governed entirely by our needs.
Any of the three methods are usable, but for reasons which are obvious, the oil or gas torch offers at times many advantages over charcoal, i.
e., the ability to concentrate the flame when it is advisaable to for do so, as example.
when only a section of a casting requires preheating,
We may also use charcoal in a hearth which we may construct ourselves, similar to Plate
10, covering the article with asbestos paper while heating and welding.
THE IMPERIAL
BRASS
MFG.
CO
PLATE
10
Care
SLOW
COOLING must also be exercised in cooling slowly to effect a uniform distribution of the heat in order to prevent breaks or strains welded to cool with the dying fire
; and also for one other important reason
Iron.
Sometimes later more fully described under Cast we are able to use the preheating furnace for cooling, allowing the article but a box
PLATE
11
•
v.
>
}:.
u' if
-f'.'-VjA''"'
20
THE IMPERIAL BRASS
MFG.
CO.
made of sheet iron, with seams welded, similar to Plate
11, and filled with a little to good non-conductor, such as asbestos, mica, or even ashes, costs make and the hot casting may be placed in it to insure even cooling, away from draughts.
WELDING
TABLES
For welding small pieces or as an aid in securing the proper alignment of articles with flat surfaces, a table with a heavy cast iron top is indispensable.
Such a table may be purchased from the Imperial
Brass Mfg.
Co.
In addition to this, we should have a table with a fire brick top, the size of which will depend upon the kind of work handled, but which should be large enough to construct upon it temporary heating furnaces if we so desire.
Such a table may be made from pipe, angle or channel iron, with all connections welded, as in
Plate
12.
PLATE
12
CLAMPING DEVICES—TOOLS
No specific advice can be given regarding shop equipment, as this will depend wholly upon the character of work to be welded.
In some instances, we need nothing but the welding outfit.
In others, we should have clamps to aid us in securing alignment,
V blocks for the same reason in shaft welding, etc.
A stationary grinder is a necessity both in preparing and finishing castings and a portable grinder may be classed as desirable in most cases but not essential.
Asbestos paper, purchased cheaply by the roll, should always be on hand to shelter the castings from draughts while heating and also to protect the operator from intense heat radiation.
THE IMPERIAL BRASS
MFG.
CO.
21 aids.
Hammers, chisels, files, tongs, etc., are inexpensive but necessary
A
REGULATION OF
B
THE FLAME
C
D
B C
D
PLATE
13
A
—
Acetylene turned on with sufficient pressure, so that it blows away from
On the
No.
1 the tip.
This space depends upon the size of tip being used.
the interval between tip and acetylene flame would be about re
; on the
No.
10, an inch.
34 of to
B
—
Oxygen partly turned on, united with the acetylene.
The flame has begun assume two different shapes and two different colors.
The center flame is white and is shaped somewhat like a rosebud.
Not enough oxygen has yet been given the acetylene and the flame is called carbonizing.
has
C
—
This is the neutral welding flame.
The rosebud cone of the upper figure become blunt, with no ragged edges and of a beautiful blue-white color.
D
—
An oxidizing flame
— ruinous to welding.
This is obtained by turning on much oxygen and the cone has become shorter, of a darker, dirtier blue, too and is to more pointed.
This view is exaggerated.
The utmost care is necessary guard against this flame, as even a slight excess of oxygen is detrimental.
Imperial welding tips are marked on the flat sides with letters and numbers to indicate size of tips and pressure required in pounds
22
THE IMPERIAL
BRASS
MFG.
CO.
and kind of gas.
For example
:
Welding
Tip No.
1 has on one side the figure
(1), referring to size.
On the next side is
(A-2), which means a pressure of 2 lbs.
of acetylene is required, and on the next side is
(0-3), showing that 3 lbs.
of oxygen are required, etc.
The pressures to use on each tip, as explained above, are meant for the guidance of the operator.
Conditions beyond the control of the manufacturer, such as the possible clogging or partial clogging of one or both of the gas lines, the slight derangement of the indicating gauge, etc., prohibit at times an exact compliance with these pressures.
Since the adjustment of the flame is of the utmost importance in successful welding, we must learn the various forms the flame is known to take, so as to familiarize ourselves with the correct one by observing its shape.
In Plate
13 are four views of flames which we should earnestly study.
Particularly watch at all times the character of the flame, remembering that even though adjusted properly at the welding, various conditions
START of
— expansion of the gases by the heat arisfrom the weld, refrigeration of the gas caused by its release from ing pressure, enlargement or decrease in the sizes of the orifices by heat or dirt
— tend to change the character of the flame
DURING welding.
With only one flame
— the neutral
— are we able to successfully weld.
During the weld, then, we should find out if the flame is neutral by slightly opening the acetylene valve (or increasing the pressure on the acetylene the by means of the diaphragm valve regulating screw) until cone begins to assume the ragged shape shown in
Plate
13-B
(carbonizing).
We may, without particular harm, set the pressure on the regulating valves, say at ten pounds each, and adjust the flame by means of the valve on the torch, if we are using tips up to the No.
7 size.
For the larger sizes, it will be better if we adjust the flame at the regulators.
It will be noted there are two distinct shapes to the welding flame, the inner, short, very brilliant, and the other, long and of faint luminosity.
We call the inner the
CONE and the outer the
ENVELOPE.
We will frequently refer to the
CONE in our text; let us understand, then, that it is the short, brilliant flame shown at "C," Plate
13.
BEVELING OR CHAMPFERING
Since oxygen-acetylene welding is the joining of metals by fusion only and without hammering, it is necessary to bevel each edge of the
THE
IMPERIAL BRASS
MFG.
CO.
23
PLATE
14 break on an angle of about
45 degrees, as in Plate
14, so that the heat of the gether.
welding cone?
is sufficient in all places to flow the
On very thin sections, this beveling is metal tonot necessary, but the beginner should not attempt the welding of anything over one-eighth inch without first grinding the edges on about the angle stated.
heavy work, where it is possible to do so, this beveling or
On champ-
PLATE
15 fering should be done from each side, as in
Plate
15.
To do this, we may use the grinder, a hammer and chisel, possibly the drill press with a proper shape of drill, and in the case of wrought iron or over a quarter inch thick, the cutting torch.
If this is steel done, it is well to thoroughly clean the edges to be welded, as well as a space each side of the weld, varying with the thickness of the casting, but ranging from one to three inches, to eliminate any possibility of dirt, including rust, from an outside source entering the line of welding.
24
THE IMPERIAL
BRASS
MFG.
CO.
PLATE
16
Many times the shape of the article does not permit us to make this bevel all the way without danger of losing the alignment of the pieces.
In a case like this, leave two or three places on the bottom of the casting to permit setting up, which is more clearly outlined in
Plate
16.
Beveling is very important
; unless we appreciate the necessity of doing it, good welding becomes extremely difficult and even very experienced operators will execute bad welds.
HOW
TO
HOLD THE WELDING TORCH
PLATE
17 in
Theoretically, the proper way is to hold the torch as illustrated
Plate
17, so that the flame is directed in the line of welding, with
THE IMPERIAL BRASS
MFG.
CO.
25 the work progressing doubtedly is the
AWAY from the operator.
This method unmost economical, since the
ENVELOPE of the flame preheats the section to be welded and a weld made in this manner takes advantage of this preheating, which costs nothing.
As we become expert, and where conditions permit it, this is the proper way to execute the weld.
For the beginner, however, it is rather dangerous, since there is every likelihood of flowing the metal the welding rod from
ON TO the line of welding, without getting it in fusion with it.
PLATE
18
Another method recommended by some is directly opposite to this idea, as in of welding,
Plate
18.
Here we work in the same direction as the line but our flame is pointing
TOWARD the area already welded.
In this fusing the metal, manner there is but this much less chance of not properly method not only does not take advantage of the preheating effect of the envelope, but keeps the cone on the welded section after it is welded, which is a serious objection.
all metals,
With we want to properly fuse the particular section we are working upon, but once fused, we must move on to the next spot immediately to prevent oxidation or burning of the material.
Both of the above methods have a very serious disadvantage when working upon hot, heavy material, inasmuch as the channel beveling offers a made by pathway for the sweep of intensely hot waves and the position of the operator in these two methods places his hands and face directly over this channel.
There is considerable discomfort in
26
THE IMPERIAL BRASS
MFG.
CO.
some cases, even though the article is protected by asbestos paper; and since we cannot do proper welding unless we are watching the weld carefully, it seems to us that the best manner of holding the torch is as follows:
PLATE
19
Note carefully
Plate
19.
Here we are working at right angles with the line of welding, with the flame on an angle, pointing from the line of welding.
To prevent flowing hot metal away
ON TO comparatively cold metal, we would advise that the article welded be slightly raised slightly on one end, so that the operator is always welding
UP
HILL.
Note carefully the angle of the
HEAD of the torch in relation to the angle of the being bonded.
break or the sides of the metal
The torch is held so that the flame strikes
BOTH edges at once.
We may quite easily arrange the height of the welding table or the position of the casting to effect this position discomfort.
without
MAKE
CERTAIN
THAT THE FLAME DOES
STRIKE
BOTH
EDGES, since failure to do this means that the material from the welding rod is brought into fusion only with one side and merely sticks, without welding, to the other.
CHOICE OF
PROPER
SIZE
TIPS
Thickness of i
32
» i «
A"
%" v± Vs"
M" S
A"
%" l'and over
Size of
Use
Tip to
No.
1
No.
2
No.
3
No.
4
No.
5
No.
fi
No.
7
No.
8
No.
9
No.
10
Above will be found a table giving approximately the size tip to use on mild steel plate of a given thickness.
It will be understood that this table cannot be exact, but is meant as a help to the
:
THE IMPERIAL BRASS
MFG.
CO.
27 beginner.
It is made up on the basis of welding without preheating and it will help us in arriving at a decision as to
ABOUT which size to use.
than
As we become more skilled, we may use a slightly larger tip we do when learning to weld, and this results in faster welding, with a consequent saving of gas, since there is less radiation of heat, i.
e., we bring the weld into fusion and get away quicker with a large tip than we do with a small one and there is less lost heat, due to the conductivity of the metal.
More will be said about the choice of tips under the various
Metal subjects.
Let us carefully read the different subjects, the whether or not we are interested in the actual welding of metal covered, since the same
GENERAL ideas of cast iron welding, for instance, would apply to other metals and we will save ourselves a little considerable trouble study first, by mastering the principles of welding by and afterwards some practice.
CAST IRON
The welding of cast iron with the oxy-acetylene flame is comparatively easy, if attention is paid to the simple rules, which to a large extent, have already been outlined.
The cast iron in common use is known as "grey;" it is quite soft, easily machined and has a lower melting point than wrought iron or steel.
It contains two kinds of carbon, combined and graphitic.
If we change the graphitic into combined, we have white cast iron, extremely hard, very brittle and practically impossible to machine.
Because of certain chemical actions which take place when cast iron is melted, we may obtain a very brittle weld in this manner unless we pay strict attention to
ALL of the following requirements
Heat or cool slowly.
Use a proper welding rod.
Employ a good flux.
Handle the torch carefully.
We have already learned the value of preheating to overcome the ill effects of expansion and contraction.
Preheating is also an economical factor, since nary means of oxygen and acetylene are more costly than ordiheating, and with cast iron it is essential that it be carefully heated and as carefully cooled to prevent hardening.
The casting to be welded should be beveled as previously described.
If entirely broken through we should slightly separate and the ends are free to move,
THE
EDGES before we start welding to allow for contraction.
This separation, if we have properly champ-
THE IMPERIAL BRASS
MFG.
CO.
28 fered the break, will be quite short
— about l/32d of an inch will be found about correct.
The utmost care should be exercised in preparation and in setting the article up to prevent its moving while it is being welded.
Since we have a comparatively light edge from beveling, it is advisable to flow the metal together at this spot,
"Tacking" it, as it is called in the welding shop.
Especial care should be used to heat slowly, in the construction often employed, remembering that we will find heavy sections adjoining light and the heavy section requires more heat than the light.
Whatever means we may employ to preheat then, arrange to have the casting heated evenly and this can only be done by heating slowly.
The size of the welding tip will be about the same as we would use for the same thickness of steel.
While cast iron melts at a lower temperature than steel, its ability to absorb heat is slightly greater than steel and this will offset the lower melting point.
The welding rod is furnished in three sizes
; thicknesses we will choose for the the one best adapted to the work that size which is somewhere near same thickness of the metal
— up to one-half inch in thickness.
Beyond this thickness, we will use a rod of about
^ths and on extreme we may tack two or three together, though this is rarely necessary.
PLATE
20
Now, with the welding rod in one hand and the torch, with the
fflillllllllll!
llllWIlllllli
IS
I
III
Imperial
Oxy-Acetylene
Equipment llllllllllinililllllB
No.
1
Imperial
Welding
Outfit with
Truck
UJiniiiDiiiniiiiiiiiiiiiiiniiiiiiiw
NOTE
—
See catalog for full description and listing
iiniiiiiii
.":!i
:.?:
.:
^IlLMiii-MIIM^iih
Hill: Hi!
.JIM
:ilii .:lll:
.!» :!!
ilii.-iilll/iii.
.HII.iiiinilHilHiill!:'!il!: i!li; :!
ii :
1 i
; fi'f
I
If
I"
2
'Wit^ilMMMM
IMPERIAL
WELDING
i
PATEr
Type
B—
\
Www niiiiwiniinniiiiniiiiiniiiiiiniiiiinii!iiiniin
Type
D
—
Combination r
™
r f
Type E
NOTE-See catalog
lillllllllliillillll
D
CUTTING
TORCHES
ENDING ing
Torch
[ding and
Cutting
Torch tting
Torch
IlillllllEI description
BEE!
Illll and listing
IllllllllfflllllffllllllllllllllilllSllllllllllIlllllllffllllllllllfflllfflllllffllllll
aiimiiL, iiiiiiiniii i;
I
I
1:
III
IP
:l ill
HI!
I ill iiiiiinii
Imperial
Oxy-Acetylene Regulators
:'" illMllllllllllltllllllllllillli
NOTE —
See catalog for full description and listing
THE IMPERIAL BRASS
MFG.
CO.
29 flame properly reach, adjusted in the other, and the flux can in convenient we are ready to start welding.
Presumably the casting is at a red heat in the furnace and we may protect ourselves from any excessive heat as by using the asbestos paper to cover such portions of it may be necessary.
PLATE
21
Bring the welding flame down to the metal until the end of the welding rod is placed near the flame to slightly heat it
The cone is almost, but not quite, touching the edges, as in
Plate
20.
— then it is dipped in the flux can and the flux picked up by the hot rod is placed in the spot the flame is playing upon.
Usually this is sufficient to break the film of oxide that and to cause the metal to flow together.
Note we have added no material from the welding rod as
YET.
Now, we melt the until the
SIDES of the break and flow them towards the bottom, weld has the general appearance of
Figure
21.
Then we are ready to use the material in contact with the from the welding rod, which should be kept weld at all times to avoid loss of heat.
REMEM-
BER
THAT THE
ARTICLE
AND THE WELDING ROD ARE
THE SAME
METALS,
MELTING AT
THE SAME
TEMPERA-
TURE.
We must, then, keep the article and the rod in fusion at all times to effect a bond.
Be very careful that the metal is actually melting while the rod is being added.
Avoid the habit of pulling the torch away from the weld
— rather use a slow circular with loss of heat.
movement which insures fusion and does away
Use the flux sparingly
— never throwing it in with the hands
— the amount picked up by the hot welding rod is sufficient at all times.
At times it may be necessary to break the oxide by
30
THE IMPERIAL
BRASS
MFG.
CO.
stirring the molten iron with the rod and if the metal is very dirty, by pulling it out of the line of welding by means of the rod.
PLATE
22
Do not move away from the section being worked upon until the weld on that section is complete, as is shown in Plate
22.
Never reweld without first grinding out the old material.
Don't bring the cone in direct contact with the metal
— hold it just a little distance away.
As we progress with the welding, we note that the metal always does not flow where we want it to; i.
e., where we are holding the flame.
metal where join
The force of the flame usually prevents this and from the welding rod at a point a little distance we add the away from we actually want it to flow, and when we are ready to have it the casting, we remove the flame from that point and swing the metal to the section desired by the circular motion described.
Cast iron does not immediately solidify the removed moment the flame is
— it remains liquid for some little time and this condition presents two difficulties
; one the danger of allowing this fluid metal to flow over, without bonding to other metal, lapsing of the weld.
The first difficulty and the other the colmay be offset by watching the weld carefully and bringing all parts into fusion.
The second one is usually experienced by beginners and is caused by their lack of knowledge of the metal and the force of the flame with the metal in a liquid condition is sufficient to cause the metal to collapse and create a hole.
When we get this condition, it is sometimes discouraging, as our efforts to fill up the hole usually result in making it larger.
THE IMPERIAL
BRASS
MFG.
CO.
31
PLATE
23
Remember that one of the reasons for the collapse is the force or velocity of the flame
— the metal is fluid all the way through and this force is sufficient to let it drop.
We must, therefore, have a solid base at all times, welding torch which may be secured by the circular motion of the
— not keeping the flame in one spot too long.
To fill a down the sides the same as we have done in starting the hole, work weld, then tip the torch on an angle as illustrated in Plate
23, being careful, is, as however, to keep the metal in fusion all the time.
The idea may readily be seen, to divert the direction of the force of the flame.
This same method is applicable where small sections may be missing.
Where large sections are gone, we may make a rough pattern by the use of plaster paris and cast the desired design, or from useless castings of approximately the same thickness, break several pieces and by properly tacking them, form the general shape required.
The user of the oxy-acetylene torch a should realize that he has at his very powerful agent capable of replacing missing command parts— a true
"putting on" tool.
THE IMPERIAL BRASS
MFG.
CO.
32
If we have carefully followed out the directions given for cast iron welding, we have a joint which is even stronger than the original article, and we can make it considerable stronger by adding additional metal to the line of welding, as it.
If we may desire, to strongly reinforce we have had trouble, if the metal is hard, or if we get contraction cracks, it is because we have not properly heeded the suggestions given.
Since the does not have a choice of conditions.
is,
He must take the article as it study carefully its construction with a view of determining the effects of welding of cast iron is usually repair work, the welder expansion and contraction and plan to overcome them; he must use a welding rod which will prevent hardness; a flux which will make the metal fluid and remove the oxide
; and use judgment in and careful cooling.
These are not difficult conditions
— they slow simply call for that little study judgment which is sometimes called a knack.
means a good weld
A
— the lack of knowledge means a failure, and since foresight is a great deal more valuable than second guesses, let us understand these conditions so we may intelligently use the welding torch.
MALLEABLE
CAST IRON
This metal is originally white cast iron, very brittle and hard.
By heat treatment, the carbon content is changed, and instead of the brittle casting, it becomes ductile, fairly soft and changes to a darker color.
Just how far into the body of the metal this change penetrates depends upon the size of the casting and the length of the heat treatment, so that a malleable casting, as it is generally called, may be steel at on the surface, a semi-steel part the core way through and white cast iron
— better outlined in
Plate
24.
Stee
demi-steel
White
Iron
PLATE
24
THE IMPERIAL BRASS
MFG.
CO.
33
Very small castings sometimes are steel all the way through and we may weld them without flux, using
Norway iron or mild steel as the welding rod.
In nearly all cases, however, it will be found that the casting is composed of different metals
— if the break is examined, we can tell this by the different colors.
It is obvious that such a casting cannot be welded, since it would be extremely difficult to determine just where one metal left off and another began.
The practice of using cast iron as a welding rod on malleable castings is not a good one, since sired the bond is very brittle and in all cases where strength is dewe will better use manganese or
Tobin bronze
— in this way welded one, of a different color securing a brazed joint instead of a than the casting but with the factor of strength a big one.
The break is prepared exactly the same as for any welding job, cleanliness in this instance being especially desirable, since the metal is not to expansion be melted.
Allowance should be made for the effects of and contraction
; malleable iron is less liable to break than cast iron, since it is ductile, but will be distorted unless such provisions are made.
Use for a flux the same powder that is used for brass.
As with cast iron, do not let the end of the cone touch the casting, but hold it just a little distance away.
Watch the metal carefully and when the spot the flame is playing upon reaches a bright red heat, bring the flux, bronze welding rod, which has previously picked up some down upon this section, being careful that the cone does not come directly in contact with the bronze rod.
Bronze melts at a lower temperature than malleable iron and with the iron at a bright red heat, and with plenty of flux used, it will be found that the bronze attaches itself to the iron.
We must not, however,
MELT any portion of the malleable iron and we must not play the cone directly on the iron or on the bronze.
There are standpoint they
STEEL
AND
IRON many different varieties of steel, but from a welding may be classified by their carbon content.
Those having a high carbon content are called hard steels
; those with a low carbon content, soft steels.
Wrought iron may be treated the same as mild or soft steel.
To be sure, there are various alloys, such as vanadium, tungsten, nickel, manganese, chromium, etc., but in general these alloys will not seriously bother us, except in special instances and we will not take them into consideration, but will keep in mind whether the steel is soft, medium or hard.
Soft or mild steel is in the widest use.
More than any other
34
THE IMPERIAL
BRASS
MFG.
CO.
metal, the welder will have to study it, since from previous understanding or training he has learned that it is the easiest metal to weld whereas, it is by all means the most difficult and frequent failures result if the operator lacks certain elementary knowledge of it.
Mild steel is very ductile
— it may be hammered cold or hot without fracture, and this fact is an invitation to the careless workman to disregard the effects of expansion and contraction.
We should bear in mind, then, that while it may not break, it will bend or distort, unless traction, and we take into consideration expansion and conwe are very likely to have failures or leave a strain in the weld or in some section of the article welded, which will break while in use.
Since the metal is ductile, it is not necessary at all times to preheat it in order to offset expansion and contraction
— we may bend certain sections before welding, with a view of having the contraction straighten use water or them and thus allow for contraction
; wet asbestos, clay, etc., to
LIMIT the expansion we may
— these methods are sometimes essential, where we cannot preheat, due to size or location of the weld, but in all cases where we may do so, the proper of way is to preheat.
Where we cannot do so, we will choose one the other methods, but
ALWAYS we must allow for expansion and contraction.
Previously we have spoken of the danger of oxidation and decarbonization.
rapid, if
The oxidation, or we might say burning, of steel is very we in any way neglect essential requirements, chiefly the proper adjustment of the torch to secure a neutral welding flame, a welding rod without injurious elements and the proper handling of the torch.
mild steel,
Decarbonization is caused in the steels but not particularly if we are reasonably careful.
But particular care must be taken to adjust the welding flame to secure a neutral flame and to keep it neutral during the welding.
Make sure you understand this.
is
PREPARATION
OF
THE
WELD
Particular care especially wide.
must be taken in beveling steel to see that the
V
We are not able to burn out this
V with the torch, as we are sometimes able in other metals, since to do so means severe oxidation or burning.
On metal under one-eighth inch no beveling necessary.
is
The proper preparation will depend weld, using no welding rod.
largely on whether we are constructing or repairing.
If instance, we are welding new sheet metal, for we may butt the edges and make what is termed a "flash"
Such a weld will naturally not be as strong as the material, since it will not be as thick.
;
THE IMPERIAL
BRASS
MFG.
CO.
35
PLATE
25
Or we may upset the edges, as shown in
Plate
25, and these upset edges take the place of the welding rod and melt down, as shown in
Plate
26.
PLATE
26
As the metal becomes thicker, this is impractical, and bevel and use a welding rod approximately of the we then same material as however.
the metal welded, being sure it is of the right quality,
No flux is necessary on mild steel and torch should be held in the position previously described, particular care sity of having the flame directed to being given to the neces-
BOTH edges of the material.
36
THE IMPERIAL BRASS
MFG.
CO.
PLATE
27
Much of the mild steel welding done is impractical or impossible to preheat, and a frequent mistake of the beginner is to too quickly try and start fusion.
To avoid this, we first play the torch in a gradually decreasing circle, as shown in
Plate
27, with the end of the cone just
PLATE
28
THE IMPERIAL
BRASS
MFG.
CO.
37 a short distance from the surface, until the metal becomes red in the vicinity of the weld for a distance about three times as wide as the metal is thick.
Then we bring the cone down as shown in
Plate 28 until the end of it just steel is touches the surfaces to be joined.
the
Note this carefully, since
ONLY metal with which we bring the cone
INTO
ACTUAL
CONTACT.
On all other metals we hold the cone a little distance away.
torch to the
Do not make the mistake of bringing the tip of the metal
— hold the torch so that the end of the cone just
LICKS the surface.
PLATE
29
As the bottom of the bevel melts together, the welding rod is brought down until it touches that spot and a small portion of it is melted while it is in contact with the material, as in
Plate
29.
Now, we fuse this small portion to the material by a short circular motion, making sure that the flame actually comes into contact with every portion of it that it and that it is thoroughly fused to the material and has penetrated.
As we finish the circular motion, we start melting the spot immediately adjoining.
Unlike cast iron, steel does not remain a liquid
— it solidifies almost the instant the flame is removed, and it is for this reason that we are able to weld it in a vertical or overhead position, as well as horizontal.
38
THE IMPERIAL
BRASS
MFG.
CO.
If there is an excess of sparks, the flame is improperly adjusted and contains an excess of oxygen.
If the metal melts too rapidly and is difficult to control, the tip is too large.
If it does not keep in fusion and there is difficulty in getting the welding rod material to actually fuse to the article, the tip is too small.
The beginner will be troubled with the welding rod sticking to the metal
— don't attempt to pull it away
; let it stay there until it is necessary to melt a portion of it in the weld.
Steel until after welding on a commercial scale should never be attempted the operator has proved to his own satisfaction that the weld is strong by welding together mild steel plates of one-eighth to one-quarter inch, sawing them through the weld to make sure that the material is really bonded and testing them by bending back and forth in a vise.
The practice of twisting several pieces of wire together to form a welding rod is not a oxidation or good one, since this exposes more surface to burning and for the same reason have the rod in contact with the material welded as it is added to the weld, so the article will prevent burning by its ability to conduct the heat away from the rod.
In welding two pieces of unequal thickness, suggestions previously given we must bear in mind
— that the large piece requires more heat than the smaller one, and that care must be used to cool equally to prevent strains.
MEDIUM AND HARD
STEELS
With the increase of carbon content, welding becomes more difficult, yet by no means is it impossible, even on those steels containing a large percentage.
Whether or not we should employ the oxyacetylene flame article welded.
depends entirely upon our skill and the use of the
Crank shaft welding is usually practical, if we are proficient
; yet most crank shafts have a high carbon content.
But it is by all means the best practice to become a good mild steel welder before attempting higher carbon steels.
To prevent, as far as possible, decarbonization, we should use the cast iron flux on steels of high carbon carbon content if and a welding rod of a higher we want about the same hardness.
If the bond be one which will bend without harm, use a mild steel welding rod, since it is easier to make a weld of this character.
welded to tool steel
Common steel may be
— for instance, an auto spring may be welded with high carbon steel, if retempering is necessary
; end, it but if broken on the may be welded with mild steel with good results.
The welding
THE
IMPERIAL BRASS
MFG.
CO.
39 of steels of high carbon call for a great deal of skill and it is impossible to lay down any hard and fast rule governing all cases.
After we have become good mild steel welders, we are usually able to determine whether we should or should not weld steels of higher carbon.
ALUMINUM
While aluminum has a melting point less than half that of steel, its conductivity is over three times as great, so we use a tip about the same size for this metal as ductivity, we do for steel, and because of this conwe should realize that the effects of expansion and contraction must be particularly guarded against, since there is a large area which is heated and expanded and consequently a large area which must cool and contract.
The manufacture of sheet aluminum articles is daily becoming larger
— the requirements in preparation practically the same as for iron or steel sheets, with the addition of a proper flux.
Aluminum castings vary in their composition, and success in welding them will depend somewhat upon the alloy used.
Copper increases the strength, but machine work is made difficult
; many times there is percentage of zinc, which makes machine work easy, but the a large casting is more or less brittle.
An aluminum case, welded without or it expansion and contraction, may distort attention paid to the effects of may break
— it depends upon the alloy used.
The first considera-
We have tion in aluminum repair work is expansion and contraction.
previously studied this principle remembering that with and should realize its importance, aluminum the shrinkage is a great deal more than the metals we have already dealt with and warpage or breakage are certain unless we understand it.
Plan, then, to heat and cool slowly and evenly.
Oxidation takes place very easily
— more so than with other metals
— and this oxide has a very high melting point.
As the metal comes to the melting point, this oxide forms a film which prevents edges flowing together and it must be destroyed before a bond can the be effected.
The method generally practiced by experienced welders is the to destroy this oxide edges joined by means of a small iron rod or paddle and by puddling the metal with this rod.
This method is the cheapest, but it calls for the exercise of considerable skill and is not so effective as the destruction of the oxide by a flux, since it introduces the oxide into the weld.
4Q
THE IMPERIAL BRASS
MFG.
CO.
Beveling aluminum is not so important as other metals, since the action of the flame causes the other.
edges to slightly draw apart from each
At this moment, the welding rod coated with flux, the same as with cast iron, is added, the flux chemically removes the oxide and the edges are bonded and material added from the rod at the same time.
With aluminum, we are especially likely to cause the metal to collapse because the heated area, due to the high conductivity, is large and the metal is without
"strength" when it is very hot.
For this reason, it is advisable for the beginner to make a mould consisting of approximately two-thirds asbestos fibre and one-third plaster paris to back up the broken section.
let it
Have this mould about one inch thick and dry thoroughly before starting to weld.
Asbestos paper or ordinary paper may be put between this mould and the case if desired and if this will help in keeping dirt out of the weld.
How hot shall we preheat aluminum castings?
It depends upon the alloy used.
Ordinarily, a safe rule to follow is to stop heating when the casting gives off a dull sound when tapped lightly with a hammer.
We can tell little by its color, as we can with iron and steel and even with the welding flame playing upon the break, it gives practically no warning that it is in a melting condition, other than when it is ready to add the flux and welding rod, it has a wrinkled appearance, dull grey in color.
Special care must be given to even heating, since most castings have bosses thinner or thicker than adjoining sections and we are likely to melt the thin part unless we particularly guard against it, or, on the other hand, not give the heavy section enough heat and so cause an unequal expansion.
Remember that aluminum must be carefully supported when preheating, since it is very brittle when hot, and as well keep it protected from draughts, as with other castings.
Aluminum is not a difficult metal to weld
— the difficulty lies in properly taking care of this subject carefully, expansion and contraction, and if we study we will avoid many of the failures of the beginner.
In finishing the nary wheel quickly welded fills section of an aluminum casting, the ordiup with chips.
If this wheel is kept well oiled with a heavy lubricant, to a large extent this will be overcome.
Ordinary files are useless and a
Vixen should be used.
COPPER
Copper conducts heat more rapidly than any other commercial
—
THE IMPERIAL
BRASS
MFG.
CO.
41 metal.
It will oxidize very easily and this oxidation is not easily apparent to the operator, but the melting point is under that of steel weld becomes very brittle.
and iron, yet because of its
The high conductivity a larger tip for the same size material is necessary.
Cold, copper is very ductile
; hot, it is brittle
; so care welding, since at a must be used in its high heat it is very likely to fracture, either at the weld or some distance away, since the heat is conducted so rapidly that the temperature of the metal some distance from the weld is but little less than at the weld.
the
The metal should be prepared for welding the same as others
V properly made, and the metal thoroughly clean.
Besides the advantage of preheating to prevent contraction cracks or strains, owing to the high conductivity of copper, it will cheapen the welding operation considerably to heat it by other means than the oxyacetylene flame.
The welding of copper is quite difficult to realize and maintain ductility.
A special welding rod is necessary containing an element opposing the action of oxygen on the copper and a flux for the same purpose as well.
The cone should not come in direct contact with the metal at any time.
For repair purposes, it is sometimes impossible or impractical to weld the break, and we then braze it, either with brass or bronze, using the brass flux for this purpose and following the same general directions as for brazing malleable iron.
BRASS
AND BRONZE
Brasses and bronzes are composed of copper, with lower melting metals as alloys, zinc, tin, etc.
Since these metals have different melting points, considerable care must be exercised in welding not to change the character of the metal too much by burning out these alloys.
The metal should be prepared the same as any other, with particular care in setting up to prevent moving while being welded and to prevent collapse of the heated area.
The metal should not be brought to fusion by bringing the cone in contact with it, but as with copper, the end of the cone should be slightly above the metal.
For repair purposes,
Tobin bronze or brass should be used for the welding rod
— for foundries or in manufacturing where the weld must be practically the same color and the same material as the metal, more judgment is necessary in the choice of the rod, with a view of replac-
42
THE IMPERIAL
BRASS
MFG.
CO.
ing, by means of the material in the welding rod, those metals burnt out of the line of welding by the flame.
MISCELLANEOUS METALS
Galvanized Iron
—
Cannot be welded, since the iron is covered with and to a greater or less extent impregnated with, a lower melting metal.
German
Silver
—
In many cases considered unweldable, due to its absorption of gases.
For practically all commercial purposes, it may be bonded, using the same flux as for brass and a strip of
German silver for the welding rod.
Especial care must be given to expansion and contraction.
Nickel
—
Extremely difficult to weld, but in many cases not impossible.
Anodes, used in nickel plating, may be fused together without flux and while there are considerable blow holes in the bond, the conductivity is little affected.
Where a bond is required free from blow holes, it is possible to effect it by a combination of the blacksmith weld with oxy-acetylene.
White
Metal
—
Castings used for die moulded purposes usually are composed of aluminum, tin and zinc in varying proportions, but nearly always with the lower melting metals in the larger proportion.
While the castings have a good deal the same appearance as aluminum, they are considerably heavier.
They may be considered unweldable.
Lead
—
Is perfectly feasible.
The objection here is on the ground of heat
; i.
e., the oxy-acetylene flame is too hot.
This merely calls for speed on the operator's part and this metal is easily joined.
The most successful flame for lead burning, however, is oxygen-hydrogen, for which special apparatus is furnished.
See
Page
52.
Different
Metals
—
Sometimes we are required to bond two different metals.
Cast iron may be welded to iron or steel, for instance.
The bond is brittle, to be sure, but sometimes this is not an objection.
Some authorities recommend the use of
Norway iron as a welding rod, but we would prefer using cast iron.
Copper may be bonded to cast iron or steel, with copper used as a welding rod.
Brass to copper, using brass as a welding rod, etc.
THE IMPERIAL BRASS
MFG.
CO.
43
FIGURING COSTS
The high pressure oxygen gauge is registered in pounds.
All oxygen cylinders are charged to a pressure of 1,800 pounds and at that pressure contain 100 cubic feet or 200 cubic feet, depending upon the size used.
The pressure, however, is the same in all cases.
The
Imperial torch uses practically equal volumes of oxygen and acetylene, so it is only necessary to determine the cubic feet of oxygen used and estimate the same number of cubic feet of acetylene to determine cubic feet of both gases.
As we know the cost per foot of each, F.
O. B. the factory, it is necessary only to add freight or expressage to find out the cost per foot in the shop, and we are then in a position to figure exactly the cost of both gases on any job.
The gauge pressure on the acetylene cylinder
DOES
NOT indicate cubical contents.
As acetylene is dissolved in acetone, the contents of volume.
and its the cylinder varies with the purity of the absorbent
Temperature is also an important factor
— in the winter a full cylinder will register, say,
150 pounds, and in the summer may register
300 pounds.
We can determine the contents by weight, as there are
11% cubic feet of acetylene in a pound.
If a cylinder weighs, when received,
160^ pounds and when empty
145 pounds, we have used
15^2 pounds of gas.
Multiplying this by
14^ we have
22434, which is the number of cubic feet.
This procedure is not necessary to estimate costs, since we can figure acetylene consumption by our oxygen gauge reading.
It is advisable at intervals, at least, to check up the invoices in this manner to see we are getting the exact amount of gas for which we are paying.
On
Page
44 is a suggestion for a cost card, the principles of which may be adapted to your particular requirements.
Overhead is largely a matter of local conditions, but in a repair shop it would be wise to figure this overhead at a fairly high percentage.
44
— —
THE IMPERIAL
BRASS
MFG.
CO.
SUGGESTION
FOR
COST
CARD
Oxygen gauge, start.
.
.
.
Oxygen gauge, finish.
.
.
Oxygen used
1800 lbs.=
=100 cu.
ft.
900 lbs.=
= 50 cu.
ft.
900 lbs.= = 50 cu.
ft.
Acetylene used
50 cubic feet
@
2%
Oxygen used
50 cubic feet
@
2
PREHEATING
COST
Charcoal
Gas, y
2 hour,
2 burners.
Kerosene
@
60
LABOR
(Preparing)—
1 hour 30 min
@
60
LABOR
(Welding)—
1 hour
30 min
@
60
LABOR
(Finishing and testing)-
1 hour min
@
30
RODS—
15
Lbs.
Steel
Lbs.
Lbs.
Cast Iron
.
.
.
Bronze
@
@
10
@
Lbs.
Copper
Lbs.
Aluminum
.
(a)
@
FLUX—
^2
Cans
Cast
Iron.
.
.
M
@
50
$1.25
1.00
.30
.90
.90
.30
1.50
.25
«
M
«
Total
$6.40
REMARKS
THE IMPERIAL
BRASS
MFG.
CO.
CUTTING
WITH
IMPERIAL APPARATUS ov-
45
Imperial Cutting
Torch
—
Type
E for
A
—
Acetylene
Inlet.
AV
—
Acetylene Valve.
C
—
Lever Operating Valve
Oxygen
Cutting
—
Thumb
Screw.
F
—
Removable Housing that protects Cutting Tips.
Jet.
O
D
—
Oxygen
Inlet.
Nos.
2,
3 and
4 are Cutting
Tips.
SETTING
UP APPARATUS
The same general care is required for the cutting equipment which has been outlined for the welding apparatus, particular care being given to tight hose connections and valves which will not leak, since the oxygen is used at a higher pressure and a leak, in combination with the flying sparks, is likely to cause a serious burn.
The oxygen hose is attached to the upper tube, as with the welding torch, and the acetylene to the lower.
The pressure used on the oxygen line is considerably higher than in welding, since we need an excess of oxygen, which is conducted through an inner tube, to
OXIDIZE or burn the metal.
ess.
PLATE
30
SPECIAL IMPERIAL
TIPS
FOR STRAIGHT CUTTING
For cutting of plates, I-beams, straight, etc., where the line of cutting is always we have designed a special flat tip, with only two preheating flames
(Plate
30).
By this method a smaller surface of the metal is being preheated, a narrower, smoother cut results and a considerable amount of gas is saved.
46
:
THE IMPERIAL
BRASS
MFG.
CO.
PLATE
31
SPECIAL
For rivet cutting
IMPERIAL
TIP
FOR RIVET CUTTING we furnish a flat tip slightly curved, which allows quick and clean cutting of rivets without injury to the plate.
These tips are furnished on application with regular Cutting Outfits.
SELECTION OF CUTTING
TIPS
Each
Imperial cutting tip is marked on the flat sides with letters and numbers to indicate size of tip, thickness of metal it will cut, pressure in pounds and kind of gas.
For example
:
Cutting Tip No.
1 has the figure
1 on one side, meaning size
No.
1
; on next side are
Y% and
3, meaning it will cut wrought iron or steel from y%" to
3" in thickness
; on the next side is
A-15, meaning the small acetylene gauge should register
15 lbs., small and then the marking
O-70, which oxygen gauge should register
70 lbs.
means the the
Note that the markings
A-15 and
O-70, referred to above, indicate
MAXIMUM gas pressures needed for cutting the thickest metal that particular size of tip is intended for.
To illustrate:
When cutting y^" or thinner about
10 lbs.
metal with the
No.
1 tip, an acetylene pressure of and an oxygen pressure of about 40 lbs.
are required.
These pressures are varied according to the thickness of the metal and the conditions to be met.
Select the proper size of cutting tip according to the thickness of metal to be cut as follows
Thickness of
Metal
...:
34" to
3"
3" to
6"
6" to
9"
9" to
12"
Size of
Tip to
Use
...1
No.
1
No.
2
No.
3
No.
4
After screwing the tip into the torch, screw the housing (F) down and be sure the face of the housing is flush with the end of the tip.
The preheating flame is adjusted exactly the same as for welding, but in this case we have six small flames instead of one and we must control the adjustment by means of the shut-off valve on the torch.
The valve with the lever handle is the one which controls the independent comes oxygen supply, the one which does the cutting, and which down in the center of the tip.
This is a diaphragm control, shutting off the gas the lever is when the lever is pressed down and open when allowed to spring up.
A small knurled wheel controls the
THE IMPERIAL
BRASS
MFG.
CO.
47 distance this lever cutting torch is moves and may be adjusted simply a welding torch with an by the operator.
A added tube through which comes oxygen alone under pressure to oxidize the metal.
Imperial
Combination
Welding and
Cutting
Torch
Valve.
Tip.
A
—
Acetylene
Inlet.
B
—
Valve for
Oxygen
Cutting
Jet.
AV—
Acetylene
OV
—
Oxygen
Valve.
No.
5
Tip is attached to
F
—
Removable
Welding Head.
Housing that protects Cutting
O—
Oxygen
Inlet.
Nos.
1-10 on right are the
Attachment
Welding
Tips.
Nos.
1 and
2 on left removed is shown at top of illustration.
are Cutting Tips.
Cutting
In combination with the welding torch, the Imperial
Brass
Manufacturing
Company also furnish an attachment for cutting, which can be attached to the welding torch, as lever control is supplanted shown in
Plate
32.
Here the by a push button, the principle of which is exactly the same as the lever control of the cutting torch.
In planning the job, have the tanks firmly secured to prevent tipping over and hose
BEHIND you so as to protect it as far as possible from damage due to flying sparks.
Make certain also that the hose is not in a location where it may be cut or otherwise damaged.
PRINCIPLE OF
CUTTING
Beginners often mistake cutting for melting.
Since the only visible agency to do work is the flame, it is assumed that the flame is melting the iron or steel.
This is not so, however.
Previously we have spoken of oxidation and how we must guard against it in welding; that oxidation is the burning of a metal and takes place by oxygen uniting with the metal and forming an oxide.
Cutting, then,
48
THE IMPERIAL
BRASS
MFG.
CO.
is simply the rapid oxidation or burning of the metal and the flame is used merely to get the metal hot
Since all enough so that it will oxidize quickly.
metals are subject to oxidation in welding, it is natural to assume that all metals could be cut by cutting torch
; but this is not so, and means of oxygen from the we are limited to those metals where the oxide is of a lower melting point than the metal itself, this being the case in wrought iron and steel.
Other metals, such as cast iron, aluminum, copper, brass, etc., cannot be cut.
The flame is of use simply to get the metal hot enough so that oxidation takes place rapidly
; the oxide having a lower melting point than the metal, runs off the metal to the cutting jet of oxygen.
and leaves a new surface exposed
Once started, this oxygen jet theoretically should be sufficient to keep
— the oxygen up oxidation, since there is considerbeing the supporter of combustion and able heat created the metal the fuel
— in other words, the metal is burnt up, but because the area.
stream of oxygen is small, this burning is confined to a narrow
We need the flame because other influences, scale, dirt, the air, sand, blowholes, etc., may stop this oxidation and the flame then heats the metal to a sufficient point to again start oxidation.
PLATE
34
HOW
TO CUT
When the flame is adjusted, as described above, hold the torch as shown in
Plate
34, the left hand grasping it well toward the head and
THE IMPERIAL
BRASS
MFG.
CO.
49 the right hand on the handle with the fingers controlling the lever valve.
The elbow or forearm should rest on the material being cut whenever possible to steady the torch.
possible.
When we are cutting free hand, that is without the wheel guide,
IT
IS
DESIRABLE TO
AR-
RANGE TO CUT EITHER RIGHT TO LEFT OR LEFT TO
RIGHT
— not toward or away from the operator.
Start on an edge
— not in the center of a plate
— whenever it is
Now hold the flame on the edge until it gets to a white heat release metal.
the lever valve and the oxygen immediately starts burning the
Hold the torch steady until the cut goes through
— then move the torch jerky one.
along the line to be cut with a steady movement
— not a
WATCH
THE
DIRECTION OF
THE
SPARKS.
If they fly in the direction as shown in
Plate
35, the cut is not going through.
At the start, they should appear about as
Then the torch head is slightly inclined
TION
WE
ARE
CUTTING.
shown in
Plate
36.
TOWARD
THE
DIREC-
;
PLATE
35
50
THE IMPERIAL
BRASS
MFG.
CO.
PLATE
36
Previously we have remarked that various reasons cause the stopping of oxidation.
The chief reason
(for beginners, at least) is the unsteadiness of the hand.
Just the moment this oxidation stops, use the right hand to close the lever valve on the oxygen supply, then start heating an edge exactly the same as in the beginning of the cut and when at the white heat again release the lever valve and start cutting.
When the cut to be made must be reasonably smooth, use the wheel guides, and if a straight line must be followed, clamp a suitable bar of metal to the article to be cut, as shown in
Plate
37.
THE IMPERIAL
BR
ASS MFG.
CO.
—
51
PLATE
37
GENERAL
HINTS
ON CUTTING
Hold the flame so that the end of the cone just licks the metal don't attempt to plunge it down into the cut.
When cutting two plates or more, or where there is a lap joint, remember that there is more or less of an insulation (air, dirt, etc.) between these plates and that the oxidation cannot be as fast as where only one thickness is cut.
THE
SLIGHT
TIPPING
OF
THE
TORCH
TOWARD THE
DIRECTION
TO BE CUT
IS
A
HELP
IN
CUTTING
MORE THAN ONE
THICKNESS.
Remember that the flame does not do the cutting
— therefore, work with the smallest flame possible
— it means a neater cut.
Keep the oxygen pressure as low as possible and yet maintain speed.
A high pressure is spectacular and there are a great number of sparks, but it is not economical and a wider scarf is made.
Don't use the torch with greasy gloves
— a spark in combination with a leak on the oxygen supply will badly burn the hand.
If a cut must be started in any place except on an edge, drill a hole or use a cold chisel and a hammer to roughen up the surface, the idea being to get an edge to quickly start oxidation.
POINTS
TO BE
OBSERVED
Never use oil or lubricant of any kind on tank valves, gauges, regulators or other fittings, as this may result in spontaneous combustion and explosions.
Be careful that there are no leaks in any of the connections, or in the rubber tubing, and that the torch tip is free from obstruction.
52
THE IMPERIAL
BRASS
MFG.
CO.
Always have an ample supply of gases, before commencing a job, as it is injurious to stop in the middle of the work.
It is necessary to wear tinted glasses or goggles to prevent eye strain.
In doing heavy work, if the burner is used continuously for a long time, or held in a confined space, it will become heated.
In such cases, turn off the gases and dip the torch head into cold water.
When working inside a boiler or tank, or any small enclosure, two operators should be employed, so that one will be available to quickly turn off the gases in case of accident, such as the bursting of the hose.
No one but a thoroughly instructed, experienced operator should attempt boiler welding.
We believe the time will soon come when the officials of shops will require a Certificate of
Competence from every operator who is entrusted turing with that kind of work, and
The
Imperial Brass
Manufac-
Company is opening a school with competent teachers to qualify students for every kind of welding and cutting.
In very heavy welding, two operators should be used, so that one can relieve the other, and the work continued until finished without interruption.
An excessive discharge of sparks indicates that too much oxygen is being used, and that the metal is being burned or oxidized.
In very heavy welding, there will, of course, be a considerable volume of spark even when the flame is neutral.
Butt welding is preferable to lap welding and easier to perform.
In clearing the torch tips, do not use steel
; other soft metal.
employ copper or some
Never tighten up regulating screws on either regulator except when tank valves are open, as otherwise you might distort the diaphragm.
OXY-HYDROGEN
PROCESS
The foregoing directions are applicable specially to the use of oxygen and acetylene gas for welding and cutting.
Imperial Torches are also adapted for the use of hydro-carbon gases and of hydrogen in connection with oxygen gas for welding and cutting.
Special tips and special regulators are furnished for these purposes with
Imperial
Equipment on request.
We do not recommend welding of steel above
*4" and of cast iron
THE IMPERIAL BRASS
MFG.
CO.
53 above Y^" in for thickness with, anything but welding of light sheet steel of
No.
16 acetylene gauge and and oxygen, but up, light cast iron and especially aluminum, the oxy-hydrogen process offers vantages provided the many adhydrogen can be purchased at a reasonable price.
The oxy-hydrogen flame having a temperature of about 4,000°
F., the metal is not so easily burned, and as hydrogen contains no carbon, the weld is softer and very uniform.
In welding with oxygen and hydrogen, the torch has to be held somewhat further away from the work than is practiced in oxy-acetylene welding, because the flame is not so pointed and less concentrated.
When a black spot appears in the weld, it proves that the torch is too near the work and the distance has to be slightly increased.
Otherwise the same directions given in the former chapters on oxyacetylene welding apply also on oxy-hydrogen welding and an experienced oxy-acetylene operator will soon become proficient in this branch of his trade.
For cutting of steel and wrought iron, the oxy-hydrogen flame is decidedly superior to the oxy-acetylene flame.
Hydrogen does not deposit carbon products in the seam, it lessens the formation of slag, therefore a much cleaner and smoother cut results and much thicker material can be cut with the same amount of gas.
A drawback to the novice in the use of hydrogen is the circumstance that the hydrogen flame is not easily visible and it seems harder to properly adjust the flame.
However, Imperial tips are all marked with the required gas pressures and the operator quickly gets used to the different conditions.
CARBON BURNING
We have already learned that oxygen and carbon have a great affinity for each other
; that is, that oxygen will unite with carbon very easily.
Carbon in a cylinder of a motor is caused by imperfect combustion
— it may be there because the carburetor was not adjusted may be because too much oil was properly to give sufficient air or it motor had received enough air, used in proportion to the air.
If the it would not be there, and since the element in the air necessary to completely burn it is oxygen, we may remove it quite easily by the use of oxygen.
54
THE
IMPERIAL BRASS
MFG.
CO.
PLATE
38
A
Imperial
—
Oxygen Tank
Valve.
B ing pressure delivered to
Torch.
F
—
Trigger Valve.
G
Decarbonizing
Outfit
—
D
Tank
Coupling.
C
—
Pressure
—
Regulating Screw.
E
—
Hose
Gauge show-
Connection.
—
Hose
Connection.
H
—
Flexible
Copper
Tip.
THE APPARATUS
The
Imperial
Carbon Burning Equipment consists of one oxygen regulator with gauge and the decarbonizing torch with hose.
REMEMBER THAT OXYGEN ALONE
IS
NECESSARY TO
DO CARBON BURNING
—
NO ACETYLENE
BEING EM-
PLOYED.
Connect the one end to outlet oxygen regulator to oxygen tank and the hose at
E of the regulator and at the other end to the carbon burning torch G.
—
THE IMPERIAL BRASS
MFG.
CO.
55
Now, with the motor running, shut off the gasoline and allow the engine to run down.
If the engine is particularly dirty, it may be advisable to protect the carburetor and pan by placing some asbestos paper at points to prevent fires from flying sparks.
Remove spark plugs from cylinders
— not the valve caps.
Crank the motor until the cylinder to be started upon has the piston at the top, with both valves closed.
Set the pressure on the regulator at about fifteen pounds and
PARTIALLY depress the lever on the handle of the carbon burner.
Use a wax taper or drop a lighted match into the spark plug opening of cylinder, at the the same time directing the copper tube of carbon burner at that point.
This ignites the carbon, and if it is not too dry, the oxygen should thereafter be sufficient to completely consume it without again lighting it.
At the start, particularly if the cylinder is oily, there will be some flame as well as considerable sparks.
Hold the pressure appeared, press down until the flame has practically disdown the lever all the way and move the tubing back and forth around the walls until sparks stop.
Sometimes the cylinder is very dry and the carbon is rather difficult to burn.
This can be more or less determined by the appearance of the spark plug.
If it is dry, squirt about a teaspoonful of kerosene into the cylinder, spreading it over as large a surface as possible, to
AID the burning.
The tube is flexible and may be bent as desired to reach any portion of the cylinder.
is not necessary to
Actual contact with the carbon consume it by the tube
— carbon burns in an atmosphere of oxygen after it is ignited.
_ too
The only possible danger to the cylinder, valves or piston is a high pressure of oxygen on an extremely oily cylinder
— there would be considerable heat generated in this instance.
Hold the pressure down, then, until the flames have gone and sparks only are being thrown out before opening the lever on the handle full.
When through cleaning, it is desirable to and blow out any solid particles there remove the valve cap may be present
; these solid particles cannot be carbon, but may be graphite, pieces of iron, etc.
The appearance of the cylinder will be considerably improved by swabbing off the top of the piston and valves with an oily rag.
care
Carbon burning is a very practical solution of carbon deposits and horse sense must be applied, however, though the process calls for no particular degree of skill.
56
THE
IMPERIAL BRASS
MFG.
CO.
With every Imperial
Welding
Outfit a decarbonizing torch is furnished.
For removing carbon from engine necessary to connect this torch with the regular follow otherwise the directions given above.
cylinders oxygen it hose is only and to
INDEX
Beveling
Carbon Burning
Care of
Apparatus
Champfering
Contraction of
Metal
Costs,
Figuring
Cutting
Expansion of
Metal
Flash
Back
How to
Hold Torch
Oxy-Hydrogen
Process
Regulation of
Flame
Regulators,
Acetylene
" Oxygen
Tips, Selection of
Torch,
Combination
Cutting
Welding
Welding,
Aluminum
Brass and Bronze
Cast Iron
Copper
Malleable Iron
Medium and
Hard
Steel
Miscellaneous Metals
Preparation for
Steel and
Iron
•
•
•
•
.
.
12
39
41
27
40
8
26
47
45
52
21
12
43
45
15
13
24
22
53
7
22
15
32
38
42
34
33
advertisement
* Your assessment is very important for improving the workof artificial intelligence, which forms the content of this project
Related manuals
advertisement