- No category
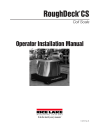
advertisement
▼
Scroll to page 2
of
15
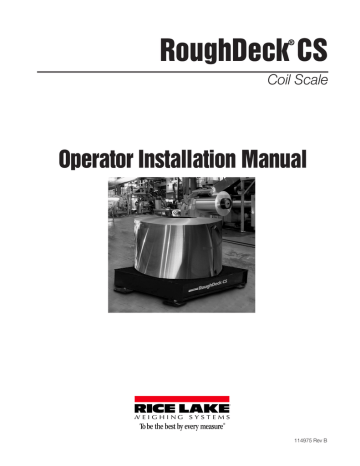
RoughDeck CS ® Coil Scale Operator Installation Manual 114975 Rev B Contents 1.0 Installation ................................................................................................................................... 1 1.1 Recommended Equipment and Tools (Steel Deck) . . . . . . . . . . . . . . . . . . . . . . . . . . . . . . . . . . . . . . . 1 1.2 Lifting and Handling (Steel Deck) . . . . . . . . . . . . . . . . . . . . . . . . . . . . . . . . . . . . . . . . . . . . . . . . . . . . 1 1.3 Temporary Setting Blocks . . . . . . . . . . . . . . . . . . . . . . . . . . . . . . . . . . . . . . . . . . . . . . . . . . . . . . . . . 2 2.0 Load Cell Mount Installation........................................................................................................ 3 2.1 Install Baseplate and Load Cell. . . . . . . . . . . . . . . . . . . . . . . . . . . . . . . . . . . . . . . . . . . . . . . . . . . . . . 3 2.2 Mount Block and Grout Installation. . . . . . . . . . . . . . . . . . . . . . . . . . . . . . . . . . . . . . . . . . . . . . . . . . . 3 3.0 Load Cell Wiring .......................................................................................................................... 5 3.1 Trimming & Calibration . . . . . . . . . . . . . . . . . . . . . . . . . . . . . . . . . . . . . . . . . . . . . . . . . . . . . . . . . . . . 6 4.0 Load Cell Replacement................................................................................................................ 7 5.0 Troubleshooting ........................................................................................................................... 8 Technical training seminars are available through Rice Lake Weighing Systems. Rice Lake continually offers web-based video training on a growing selection Course descriptions and dates can be viewed at www.ricelake.com/training of product-related topics at no cost. Visit www.ricelake.com/webinars. or obtained by calling 715-234-9171 and asking for the training department. © 2010 Rice Lake Weighing Systems. All rights reserved. Printed in the United States of America. Specifications subject to change without notice. Rice Lake Weighing Systems is an ISO 9001 registered company. Version 1.0, October 2014 i Technical training seminars are available through Rice Lake Weighing Systems. Course descriptions and dates can be viewed at www.ricelake.com/training or obtained by calling 715-234-9171 and asking for the training department. ii RoughDeck® CS Operator Installation Manual Introduction This manual is intended for use by technicians responsible for installing and servicing the RoughDeck® CS. Authorized distributors and their employees can view or download this manual from the Rice Lake Weighing Systems distributor site at www.ricelake.com. Site Consideration: The opening of the V-Top coil cradle option runs parallel with the load cell pocket CAUTION cover plate. See Figure 2-3 on page 18 Package includes: Assembled weighbridge module and weighbridge fasteners; load cells; load cell mounts with leveling bolts and anchor bolts; junction box; homerun cable to indicator (20' long). 1.0 Installation The general assembly order is summarized below: 1. Set deck module into position on setting blocks. 2. Install load cell mounts in pockets and anchor bolts in baseplates. 3. Run cabling and connect electrical wiring to J-box. 4. Connect indicator and peripheral devices. 1.1 Recommended Equipment and Tools (Steel Deck) • • • • • • • • • • • • • • 1.2 Crane with a minimum 5000 lb. capacity Four chains or cables (8' minimum length each) with hooks or clevises 3/4" rotary hammer drill 3/4" x 24" masonry carbide bit One low-profile 4-ton bottle jack 3" minimum setting blocks Torque wrench to 100 ft-lb Socket wrenches to 1 1/2" (drive compatible with torque wrench) Box end wrenches to 1 1/4" Open end wrench set (7/16" – 1 1/4") 4' bubble level Small torpedo level Hammers, maul, pry bar Hand tools for pulling and connecting electrical wiring Lifting and Handling (Steel Deck) Deck modules are lifted using four chains or cables attached to the four lifting straps mounted on the top of the weighbridge. The lifting straps provide balanced lifting of the modules. Note A set of lifting lugs are provided with the scale. Lifting straps must always be inserted into the top of the scale. Lifting should always occur WARNING with the top plate facing up and the lifting straps securely attached through the nuts welded to the bottom side of the top plate. Lifting from the bottom of the plate could cause nuts to break loose and the scale to fall. Installation 15 1.3 Temporary Setting Blocks Most installers use setting blocks that are approximately 3" high for the initial placement and connecting of the deck module. Use leveling bolts in base plate to level the scale. Setting blocks are only used in the corners of the module where the load cell mounts are installed. Weighbridge Module 7.5" 3" Figure 1-1. Setting Blocks Under Weighbridge Module When placing module on setting blocks, place blocks in locations close to, but not at, the pocket (to allow Note room for mount). It is important to consider the orientation of the scale if using the V-Top coil cradle option. The V-Top coil Note cradle runs parallel with the load cell pocket cover plate. See Figure 2-3 on page 2. 16 RoughDeck HE AutoLift 2.0 Load Cell Mount Installation Load cell mount components (baseplate, mount blocks, anchor bolts, link, load cell, and upper mount blocks) are shipped in the hardware box and need to be assembled while in the load cell pocket. Remove the printed load cell Certificate of Conformance (CC) forms (included with load cells) and store them in a safe place for future reference. The following sections contain step-by-step instructions on mount installation, including the baseplate, load cells, upper mount blocks, ground straps, and anchor bolts. 2.1 Install Baseplate and Load Cell Use the following steps for installing the mount baseplate and load cell in the load cell mount pockets: 1. Remove load cell mount components from the packing box and position one set at each mount location. Figure 2-1. Baseplate 2. Remove load cell pocket covers. 3. Working with the baseplate first, lower baseplate through pocket opening and onto concrete foundation. 4. Place the load cell link over the end of the cell and install load cell/link assembly onto the top of the baseplate. 5. Place the load link on top of the load cell and the upper mount block on top of the load link. 6. Place the load cell and load link assembly onto the two stands of the base stand and screw in the load cell mounting bolts (finger tight). The loose bolts allow freer movement for better weighing accuracy. 7. Adjust the load link so it is vertical and centered side to side (in a balanced condition). If the load link is not vertical and centered side to side, adjust the base stand. 8. Apply anti-seize compound to threads of load cell bolts before installing. Torque load cell bolts 55 ft-lb. Figure 2-2. Cut-Out View of Load Cell Access Area Shown with Optional Flexible Conduit 2.2 Mount Block and Grout Installation Use the following steps to install mount blocks and baseplate grout. It is important to consider the orientation of the scale if using the V-Top coil cradle option. The V-Top coil Note cradle runs parallel with the load cell pocket cover plate. See Figure 2-3 Load Cell Mount Installation 17 . Figure 2-3. V-Top coil cradle option showing orientation 9. Adjust leveling bolts until radius of block comes in contact with rocker link radius. 10. Jack the weigh module and remove setting blocks. 11. Slowly lower the weigh module until it rests on the load cell links. After the weigh module is lowered into final position, check each load cell mount assembly to ensure that the Note link is plumb and that there is no binding or misalignment. 12. Use an industrial hammer drill to drill a 3/4" hole into the concrete at least 6" deep on one side of the mount frame. 13. Drill a second anchor bolt hole on the opposite side of the mount frame. 14. Each mount requires two anchor bolts to prevent longitudinal motion of the baseplate. Anchor bolts (7" x 3/4") with expansion heads are supplied with the scale. 15. Insert bolts into holes drilled in foundation. 16. Install one washer and one nut on each anchor bolt. Place a driver pipe on top of the anchor bolt and use the long punch to seat anchor bolts against baseplate. Note Do not apply excessive force to the anchor bolts-- bending of the baseplate could occur. When installing anchor bolts, make sure that there is adequate bolt length to extend into the concrete foundation. 17. Attach one end of the ground strap to the upper block. 18. Insert a bolt through the wire terminal on the loose end and thread the bolt into the hole on the baseplate. Tighten the bolt securely with a wrench. 19. Pour 9000 PSI, non-shrinking, epoxy or cement grout under and around the baseplate. A funnel with a long tube can be used to pour grout under and around the baseplate while working from above the access hole. 20. Grout should be allowed to set for at least 24 hours before removing the wooden forms. 21. After grout has hardened, tighten anchor bolt nuts. 18 RoughDeck HE AutoLift 3.0 Load Cell Wiring Before the weigh module wiring can be completed, all load cell cables have to be routed through the conduit beginning at the load cell outlet. Use the following steps to route load cell cables through conduit to the J-box: 1. Before routing load cell cables, mark each load cell cable at the end to help identify each load cell. 2. Working from the J-box corner, insert a fish tape or similar tool and pull each load cell cable through the rigid conduit until all excess cable is taken in. 1 2 Pocket 1 Conduit Pocket 2 Conduit J-box corner Pocket 2 Conduit 4 3 Pocket 3 Conduit Figure 3-1. J-box location 3. Wire each load cell to the J-box terminal strip in accordance with the wiring code contained in the Certificate of Conformance. 4. Cable should not be routed near heat sources greater than 400°F. Do not shorten any load cell cable. The load cell is temperature compensated with the supplied length of cable. Cutting the cable will affect temperature compensation. Coil and protect excess cable so it will not be mechanically damaged or sit in water. 5. Provide a drip loop in all cables so that water or other liquids will not run directly down the cables onto either the load cells or the junction box. 6. If conduit protection is necessary against mechanical or rodent damage to the load cell cables, use flexible conduit and conduit adapters at the load cells. Note Flexible conduit and conduit adapters are an optional item and not included with the standard setup. 7. Connect cables for load cells to the summing board in the junction box according to the guide shown below and the labels on the terminal strips of the junction box. To verify the wiring scheme, see the certification shipped with each load cell. 8. For better performance, use positive and negative remote sense lines if the wiring running from the junction box to the indicator is longer than 25 feet Load Cell Wiring 19 Drip Loop Figure 3-2. Load Cell Wiring Drawing Load Cell Wire Color Function Red + EXC Black - EXC Green + SIG White - SIG Gray or Bare Shield Table 3-1. Load Cell Wiring 3.1 Trimming & Calibration Refer to the JB4SS TuffSeal™ Signal Trim Junction Box manual for trimming details. Refer to indicator manual for connection and calibration details. 20 RoughDeck HE AutoLift 4.0 Load Cell Replacement Use the following steps to replace load cells in the RoughDeck® CS coil scale: 1. Position jack on the concrete foundation beneath one of the weighbridge’s main frame members close to the load cell mount. (Allow Upper Mount Block room for load cell removal and installation.) Raise jack approximately 1/2" and put setting block(s) under the scale deck. Shim As a safety precaution, always use Note setting blocks when jacking scale Load Cell Bolts Load Cell Link Anchor Bolt Load Plate Baseplate module. Grout (optional) 2. Disconnect the load cell terminal connections in the junction box. Pull the load cell cable out of the conduit. Attach a pull cord to the load cell Note cable at the junction box before pulling the cable through the conduit. Figure 4-1. Load Cell Mount 3. Remove the two load cell bolts and lift out load cell and link assembly. 4. Install link over new load cell. Reinstall load cell and link assembly onto the baseplate. Install load cell mount bolts. Torque bolts to 55 ft-lb. 5. Pull load cell cable through conduit using pull cord. 6. Remove setting blocks and lower scale module so that it rests on the link. Check link to verify that it is centered and plum. 7. Connect wiring to terminals in junction box. Load Cell Replacement 21 5.0 Troubleshooting If the system powers up and gives some type of stable digital readout that varies with the load on the system, any system problems are probably caused by factors other than the load cells. The load cells are often blamed for a malfunctioning system, but the majority of the time, the problem lies elsewhere. Look for mechanical causes for your problem first. If the system can be calibrated but doesn't return to zero, loses calibration, or demonstrates non-linearity or non-repeatability, see the following chart for possible causes and do the following checks. Symptom Possible Cause No return to zero Mechanical binding or debris in seals or under load cells; may have lost system calibration. Non-linearity Thermal expansion or deflection under load causing binding or side load. Non-repeatability Loose load cell mount; drifting caused by moisture, load cell overload or shock damage; mechanical binding. Lost calibration Out of level or plumb; moisture problem; mechanical binding. Drifting readout Moisture in junction box, cables, or load cell; mechanical binding. Table 5-1. Troubleshooting 1. Check load cell mount for debris restricting load cell movement or debris between scale and structure. 2. Check that tank/vessel and mounts are plumb, level, and square at the critical areas. 3. Check all piping and conduit for connections that restrict movement. 4. If check rods are used, loosen all connections to finger tight only for testing. 5. Check load cell cables for physical or water damage. If after all these checks the problem still cannot be isolated, reconnect all but one load cell. Replace the load cell with a load cell simulator. Alternate so that each load cell is individually disconnected and replaced with a simulator. If there is a problem with a particular load cell, the symptom should disappear when that load cell is disconnected and replaced with the simulator. 22 RoughDeck HE AutoLift RoughDeck Limited Warranty Rice Lake Weighing Systems (RLWS) warrants that all RLWS equipment and systems properly installed by a Distributor or Original Equipment Manufacturer (OEM) will operate per written specifications as confirmed by the Distributor/OEM and accepted by RLWS. RoughDeck fabricated platforms and weldments are warranted against defects in materials and workmanship for five (5) years. Load cells and all other components are warranted for two (2) years. RLWS warrants that the equipment sold hereunder will conform to the current written specifications authorized by RLWS. RLWS warrants the equipment against faulty workmanship and defective materials. If any equipment fails to conform to these warranties, RLWS will, at its option, repair or replace such goods returned within the warranty period subject to the following conditions: • Upon discovery by Buyer of such nonconformity, RLWS will be given prompt written notice with a detailed explanation of the alleged deficiencies. • Individual electronic components returned to RLWS for warranty purposes must be packaged to prevent electrostatic discharge (ESD) damage in shipment. Packaging requirements are listed in a publication, “Protecting Your Components From Static Damage in Shipment,” available from RLWS Equipment Return Department. • Examination of such equipment by RLWS confirms that the nonconformity actually exists, and was not caused by accident, misuse, neglect, alteration, improper installation, improper repair or improper testing; RLWS shall be the sole judge of all alleged non-conformities. • Such equipment has not been modified, altered, or changed by any person other than RLWS or its duly authorized repair agents. • • RLWS will have a reasonable time to repair or replace the defective equipment. Buyer is responsible for shipping charges both ways. In no event will RLWS be responsible for travel time or on-location repairs, including assembly or disassembly of equipment, nor will RLWS be liable for the cost of any repairs made by others. THESE WARRANTIES EXCLUDE ALL OTHER WARRANTIES, EXPRESSED OR IMPLIED, INCLUDING WITHOUT LIMITATION WARRANTIES OF MERCHANTABILITY OR FITNESS FOR A PARTICULAR PURPOSE. NEITHER RLWS NOR DISTRIBUTOR WILL, IN ANY EVENT, BE LIABLE FOR INCIDENTAL OR CONSEQUENTIAL DAMAGES. RLWS AND BUYER AGREE THAT RLWS’ SOLE AND EXCLUSIVE LIABILITY HEREUNDER IS LIMITED TO REPAIR OR REPLACEMENT OF SUCH GOODS. IN ACCEPTING THIS WARRANTY, THE BUYER WAIVES ANY AND ALL OTHER CLAIMS TO WARRANTY. SHOULD THE SELLER BE OTHER THAN RLWS, THE BUYER AGREES TO LOOK ONLY TO THE SELLER FOR WARRANTY CLAIMS. No terms, conditions, understanding, or agreements purporting to modify the terms of this warranty shall have any legal effect unless made in writing and signed by a corporate officer of RLWS and the Buyer. © Rice Lake Weighing Systems, Inc. Rice Lake, WI USA. All Rights Reserved. RICE LAKE WEIGHING SYSTEMS • 230 WEST COLEMAN STREET • RICE LAKE, WISCONSIN 54868 • USA Troubleshooting 23 230 W. Coleman St. • Rice Lake, WI 54868 • USA U.S. 800-472-6703 • Canada/Mexico 800-321-6703 • International 715-234-9171 • Europe +31 (0)26 472 1319 ww.ricelake.com www.ricelake.mx www.ricelake.eu www.ricelake.co.in m.ricelake.com © Rice Lake Weighing Systems October 24, 2014 PN 114975 Rev B
advertisement
Related manuals
advertisement