- Home
- Domestic appliances
- Small kitchen appliances
- Ice cube makers
- Cornelius
- SID851W/250S-BC
- User manual
advertisement
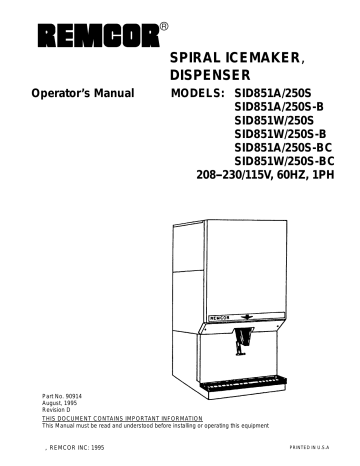
Operator’s Manual
SPIRAL ICEMAKER
â
DISPENSER
MODELS: SID851A/250S
SID851A/250S-B
SID851W/250S
SID851W/250S-B
SID851A/250S-BC
SID851W/250S-BC
208--230/115V, 60HZ, 1PH
Part No. 90914
August, 1995
Revision D
THIS DOCUMENT CONTAINS IMPORTANT INFORMATION
This Manual must be read and understood before installing or operating this equipment
â
REMCOR INC: 1995
PRINTED IN U.S.A
TABLE OF CONTENTS
GENERAL INFORMATION . . . . . . . . . . . . . . . . . . . . . . . . . . . . . . . . . . . . . . . . . . . . . . . . . .
Page
1
DESCRIPTION . . . . . . . . . . . . . . . . . . . . . . . . . . . . . . . . . . . . . . . . . . . . . . . . . . . . . . . .
INSTALLATION INSTRUCTIONS . . . . . . . . . . . . . . . . . . . . . . . . . . . . . . . . . . . . . . . . . . . .
UNPACKING INSTRUCTIONS . . . . . . . . . . . . . . . . . . . . . . . . . . . . . . . . . . . . . . . . . .
INSTALLATION INSTRUCTIONS . . . . . . . . . . . . . . . . . . . . . . . . . . . . . . . . . . . . . . . .
BEVERAGE SYSTEM
INSTALLATION
. . . . . . . . . . . . . . . . . . . . . . . . . . . . . . . . . . . . . . . . . . . . . . . . . .
. . . . . . . . . . . . . . . . . . . . . . . . . . . . . . . . . . . . . . . . . . . . . . . . . .
START -UP . . . . . . . . . . . . . . . . . . . . . . . . . . . . . . . . . . . . . . . . . . . . . . . . . . . . . . . . . . .
OPERATING INSTRUCTIONS . . . . . . . . . . . . . . . . . . . . . . . . . . . . . . . . . . . . . . . . . . . . . . .
MAINTENANCE . . . . . . . . . . . . . . . . . . . . . . . . . . . . . . . . . . . . . . . . . . . . . . . . . . . . . . . . . . .
7
10
2
2
7
7
1
2
14
REGULAR BASIS (OR AS REQUIRED) . . . . . . . . . . . . . . . . . . . . . . . . . . . . . . . . . .
EVERY THREE MONTHS (OR AS REQUIRED) . . . . . . . . . . . . . . . . . . . . . . . . . . .
PERIODICALLY (OR AS REQUIRED)
CLEANING INSTRUCTIONS
. . . . . . . . . . . . . . . . . . . . . . . . . . . . . . . . . . . .
. . . . . . . . . . . . . . . . . . . . . . . . . . . . . . . . . . . . . . . . . . .
ICE MAKER SECTION
DISPENSER SECTION
. . . . . . . . . . . . . . . . . . . . . . . . . . . . . . . . . . . . . . . . . . . .
. . . . . . . . . . . . . . . . . . . . . . . . . . . . . . . . . . . . . . . . . . .
FOR UNITS WITH BEVERAGE SYSTEM . . . . . . . . . . . . . . . . . . . . . . . . . . . .
TROUBLESHOOTING GUIDE . . . . . . . . . . . . . . . . . . . . . . . . . . . . . . . . . . . . . . . . . . . . . . .
MAINTENANCE/ADJUSTMENT PROCEDURES . . . . . . . . . . . . . . . . . . . . . . . . . . .
THERMOSTAT ALTITUDE ADJUSTMENTS . . . . . . . . . . . . . . . . . . . . . . . . .
BIN THERMOSTAT . . . . . . . . . . . . . . . . . . . . . . . . . . . . . . . . . . . . . . . . . . . . . . .
CLEARING EVAPORATOR FREEZE-UP . . . . . . . . . . . . . . . . . . . . . . . . . . . .
ICE THICKNESS ADJUSTMENT . . . . . . . . . . . . . . . . . . . . . . . . . . . . . . . . . . .
CLEANING/REPLACE THE FILTER . . . . . . . . . . . . . . . . . . . . . . . . . . . . . . . .
CLEANING THE CONDENSER
HARVEST TIME ADJUSTMENT
. . . . . . . . . . . . . . . . . . . . . . . . . . . . . . . . . . . .
. . . . . . . . . . . . . . . . . . . . . . . . . . . . . . . . . . . .
MANUAL FILLING
PARTS LIST
. . . . . . . . . . . . . . . . . . . . . . . . . . . . . . . . . . . . . . . . . . . . . . . .
. . . . . . . . . . . . . . . . . . . . . . . . . . . . . . . . . . . . . . . . . . . . . . . . . . . . . . . . . . . . . .
31
31
31
32
30
30
30
30
32
34
14
15
15
17
14
14
14
14
LIST OF FIGURES
FIGURE 1. ELECTRICAL WIRING INSTALLATION INSTRUCTIONS
FIGURE 2. INSTALLATION DIMENSIONS
. . . . . . . . .
. . . . . . . . . . . . . . . . . . . . . . . . . . . . . . . .
FIGURE 3. MOUNTING TEMPLATE MODEL SID 851/250-B
FIGURE 4. MOUNTING TEMPLATE MODEL SID 851/250-BC
. . . . . . . . . . . . . . . .
. . . . . . . . . . . . . . .
FIGURE 5. BEVERAGE SYSTEM SCHEMATIC B MODELS
FIGURE 6. BEVERAGE SYSTEM SCHEMATIC -BC MODELS
. . . . . . . . . . . . . . . .
. . . . . . . . . . . . . .
FIGURE 7. WIRING SCHEMATIC SID 850/250 . . . . . . . . . . . . . . . . . . . . . . . . . . . .
FIGURE 8. WIRING DIAGRAM SID 850/250 (208--230/115V, 1PH, 60HZ) . . . . .
FIGURE 9. REFRIGERATION SCHEMATIC
FIGURE 10. HARVEST TIMER
. . . . . . . . . . . . . . . . . . . . . . . . . . . . . . .
. . . . . . . . . . . . . . . . . . . . . . . . . . . . . . . . . . . . . . . . . .
11
12
8
9
13
33
3
4
5
6 i
90914
TABLE OF CONTENTS (cont’d)
LIST OF TABLES
TABLE 1. SPECIFICATIONS . . . . . . . . . . . . . . . . . . . . . . . . . . . . . . . . . . . . . . . . . . . .
TABLE 2. LBS./24-HOUR ICE PRODUCTION . . . . . . . . . . . . . . . . . . . . . . . . . . . . .
TABLE 3. HARVEST CYCLE . . . . . . . . . . . . . . . . . . . . . . . . . . . . . . . . . . . . . . . . . . . .
Page
1
1
1
90914 ii
GENERAL INFORMATION
DESCRIPTION
The Remcor S.I.D. (Spiral Ice Maker/Dispenser) is a unique, self-contained, counter top style unit that automatically makes hard, clear cube-quality ice and stores it in a sealed hopper for sanitary dispensing. The ice is made by a new, patented process on a spiral-shaped, stainless steel evaporator and produces true cube quality ice on the outside of the tubes. There are no augers; no compressing of flaked ice; no bearings; and no high gear motor loads in the ice-making process. The unit has been designed to be simple, yet effective, to provide many years of trouble-free operation.
Compressor:
Refrigerant:
Voltage:
AMPS:
Circuit Ampacity:
Fuse Size:
Ice Storage Capacity:
Ice Making Capacity:
Shipping Weight:
Table 1. SPECIFICATIONS
1 Horsepower
R-502/2.25 lbs. (Air Cooled); 2.75 lbs. (Water Cooled)
208-230/115, 1 phase, 60 Hertz
18
25
20A Time-Delay
225 lbs.
Up to 964 lbs./24 Hours
550 lbs.
Air Temp.
60 °
70 °
80 °
90 °
40 °
964
916
817
725
Table 2. LBS./24-HOUR ICE PRODUCTION
50 °
901
858
756
680
Water Temperature
60 °
861
820
731
650
70 °
806
777
700
630
80 °
755
728
656
590
90 °
712
687
619
556
1
90914
INSTALLATION INSTRUCTIONS
UNPACKING INSTRUCTIONS
1. With the unit upright, carefully remove the shipping crate. Inspect for shipping damage and report any such damage to the shipper immediately.
2. Open the hinged service door and remove shipping tape from the ice drop cover, storage hopper cover and agitator in the storage hopper.
3. Remove shipping tape from air inlet filter and sink grill.
INSTALLATION
NOTE: An Everpure Model 9320-42 Systems IV, Model B1000 (or equal) ice maker quality water treatment unit MUST BE INSTALLED in the water supply line to the ice maker. Failure to do so may result in poor quality ice, low production output, and may cause premature failure of the ice maker evaporator and void the extended evaporator warranty.
This ice maker is provided with a stainless steel evaporator designed to last the life of the product. But, some of the chemicals in treated and untreated water, specifically chlorine and sulphur (sulphide), have the ability to attach stainless steel and cause premature failure. An initial investment in proper water treatment will pay for itself in increased production, quality and long life of the product.
1. Location
Locate the ice maker/dispenser indoors in a well-ventilated area. Avoid exposure to direct sunlight and/or heat caused by radiation.
Ambient room temperature must be in the range of 60 ° to 90 ° F. Do not install unit in an enclosed area where heat build up could be a problem. For proper air flow for the refrigeration system, allow a 6 clearance at the back of the unit and a 12
?
Consult Figure 1 for utility connection location.
Consult Figure 2 for dimensions for mounting unit to the counter with the hardware provide.
Note that the unit must be level for proper operation.
The unit must be sealed to the counter. The mounting template drawing (Figure 2) indicated the openings which must be cut in the counter. Locate the desired position for the unit, then mark the outline dimensions and cut-out locations using the template drawing. Cut openings in counter.
Apply a continuous bead of NSF International (NSF) listed silastic sealant (Dow 732 or equal) approximately 1/4
?
inside of the unit outline dimensions and around all openings. Then position the unit on the counter within the outline dimensions. All excess sealant must be wiped away.
2. Plumbing
Connect the ice maker to a cold, potable water source suitable for drinking. Do not install unit on a water softener line. It is recommended that a hand shut-off valve, strainer, and backflow preventer be used on the incoming supply line. For Models: SID851/250S and SID851/250S-B, a 3/8
?
tube fitting is provided at the back of the unit for the water supply hook up (See Figure 1). For model
SID851/250S-BC, a 3/8
?
through the bottom opening in the unit to the water supply (See Figure 2).
90914
2
IMPORTANT: To ensure proper ice maker operation and also to reduce the frequency of water-related service problems, a water filter should be installed. Remcor recommends the use of one of the following basic systems:
1
.
Everpure, Inc.
660 No. Blackhawk Drive
Westmont, IL 60559
(708) 654-4000
Insurlce Twin System #9320-42
2. System IV
16632 Burke Lane
Huntington Beach, CA 92647
(714) 842-4221
Basic Water System #B1000
For specific recommendations on these filter systems for your local conditions, consult with a distributor in your area or contact the filter manufacturer.
Models SID851/250S & SID851/250S-B
Connect two (2) 3/4
?
IPS (or equal) drain lines to the 3/4
?
threaded drain connections at the lower rear of the unit. These lines must pitch downward to an open drain and must contain no traps or improper drainage will result.
Model SID851/250S-BC
A 1
?
OD tubing drain elbow is provided at the bottom of the unit for the sink drain. Connect this elbow to a 7/8
?
ID plastic drain tube.
A 3/4
?
IPS threaded drain connection for the ice maker is also provided at the bottom of the unit. Connect this to a 3/4
?
IPS drain line (or equal).
These lines must pitch downward to an open drain and must contain no traps or improper drainage will result.
NOTE: In areas where consistently warm water temperatures are encountered, the use of a Remcor Pre-
Cooler in the water line is recommended to maximize the ice production of this unit. Contact Remcor for more information on this product.
2. Electrical
A 4 x 2 junction box is located at the rear of the unit for the supply hook-up. Connect the ice maker to its own circuit per the national electric code and local code. See SPECIFICATIONS for ampacity and fuse size.
IMPORTANT: The wire size must be adequate for the ampacity rating, and the supply voltage must be within a range of ± 10% for proper ice maker operation.
NOTE: The units require a 3 wire system plus earth ground for proper operations.
115/208-230V
1 PHASE
60 HERTZ
SUPPLY CONDUIT
BLACK (HOT)
RED (HOT)
WHITE (NEUTRAL)
GREEN (GROUND)
FIGURE 1. ELECTRICAL WIRING INSTALLATION INSTRUCTIONS
3
90914
4
90914
15 7/8-IN.
2 1/8-IN.
UNIT OUTLINE FRONT
27 11/16-IN.
32-IN.
NOTE: Shaded area indicates opening in bottom for beverage tubing.
14-IN.
3/8 DIA.
2 3/4-IN.
10 1/2-IN.
32 1/2-IN.
36-IN.
16-IN.
FIGURE 3. MOUNTING TEMPLATE MODEL SID 851/250-B
5
90914
1/2 DIA.
32-IN.
27 11/16-IN.
3 1/16-IN.
10 1/2-IN.
14 1/8-IN.
36-IN.
16-IN.
11 1/4-IN.
19 5/8-IN.
FRONT
NOTE: Shaded area indicates opening in bottom for beverage tubing and utilities.
UNIT OUTLINE
5 7/8-IN.
90914
FIGURE 4. MOUNTING TEMPLATE MODEL SID 851/250-BC
6
BEVERAGE SYSTEM
“B”models contain beverage faucets only and must be supplied with cold product from any remote cold plate or refrigerated soda factory. “BC”units have a built-in cold plate, in addition to the beverage faucets and are designed to be supplied directly from syrup tanks and carbonator with no additional cooling required.
Installation
1. Locate the required openings in the counter top for the beverage lines as shown in Figure 3 (for “B”models) or Figure 4 (for “BC”models).
2. For “B”models, carefully pull the beverage tubers through the bottom opening in the unit and through the clearance opening in the counter.
3. For “BC”models, 1/4
?
and 3/8
?
plate for syrup and water line hook-up respectively.
To access these inlet tubes, remove the lower front panel above the sink. Remove the sink by disconnecting the sink drain connection; lifting the two (2) sink side mounting pins and pulling the sink forward.
4. Connect the beverage system product lines as indicated in Figure 5 (“B”units) and Figure 6 (“BC”units).
This work should be done by a qualified service person. Note that the hoses are marked with numbers
(1through 8) for syrup connection and “CW”for carbonated water connection.
5. For “BC”models, reverse the procedure in step 3 to reconnect the sink. Make sure that all drain connections are properly positioned before installing the lower front panel.
START-UP
1. Open the hinged service door. Remove ice drop cover and storage hopper cover.
2. Turn on water to ice maker.
3. Depress the flush switch to verify that the water dump valve operates and that the water drain lines are open and not plugged.
WARNING: To prevent possible injury, do not stick fingers or hand into ice maker nozzle or hopper with power applied to unit.
4. Put the “Stop/Run”switch in the “run”position. Observe that the ice maker goes through proper ice making and harvest cycles. If unit malfunctions, consult the
Troubleshooting Guide.
NOTE: Due to meltage loss because of a warm storage hopper, it will take longer to fill the hopper the first time than when the ice maker has been operating continuously.
5. Depress the vend switch lever. Check that both the gate solenoid and agitator motor are energized simultaneously to lift the gate slide and rotate the agitator in the storage hopper, respectively. If either component malfunctions, consult the
Troubleshooting Guide.
Replace the ice drop and hopper covers.
6. For beverage units, start up the beverage system and adjust the faucets to the proper brix. Contact your local syrup distributor for complete information on the beverage system. For units with a built in cold plate, it will take approximately one (1) hour from the initial machine start-up for the cold plate to be at full capacity.
7. The bin thermostat is calibrated at an atmospheric pressure equivalent at 500 feet above sea level. For locations at higher elevations, it may be necessary to re-adjust these controls. Consult the
Maintenance/
Adjustment Procedures
section.
7
90914
90914
8
9
90914
OPERATING INSTRUCTIONS
A temperature sensing control bulb located in the storage hopper starts and stops the ice making process in response to ice level in the hopper. With this ice level control “calling”for ice (hopper ice level is low), ice begins to form on the stainless steel tubing coils in the evaporator coils until it contacts the ice thickness probe (low voltage conductivity sensor). At this point, the conductivity probe triggers the harvest timer motor. The harvest timer contains five (5) cam operated switches which function as detailed in the table on the following pages.
Table 3. HARVEST CYCLE
Time
0--86 Seconds
Cam Switch
#1
Action
Timer motor energized
1--23 Seconds
1--37 Seconds
37--90 Seconds
±
±
1 Second
2 Seconds
#4
#2
#2
Water dump valve open
Hot gas solenoid valve open.
Air pump off.
Condenser fan motor off.
Air pump on.
Condenser fan motor on.
Hot gas solenoid valve closed.
Harvest motor on.
36--39 Seconds #3
43--47 Seconds #5 Hopper agitator motor operates.
When ice contacts the ice lever control bulb in the storage hopper, the control will shut down the refrigeration system. If this signal occurs during the harvest cycle, the harvest cycle will be completed before shutdown occurs.
To dispense ice, push the lever located on the lower front panel. Ice will flow from the ice chute until the lever is released.
For units with a built-in cold plate, ice will automatically fill the cold plate cabinet. Allow one (1) hour for the cold plate to reach its maximum capacity. Start up the beverage system and adjust the faucets to the proper brix.
Pushing the lever on any faucet will provide beverage of the appropriate flow.
90914
10
L1
CC
TP
5
START
RELAY
STOP /
RUN
2
LPS
C
NC
HT4
NO
C
C
208-230 / 115V, 1PH,
(4 WIRE SYSTEM)
C
COMPRESSOR
R
5
RUN CAP
L2
N
CC
NC
HT3
NO
NC
HT2
NO
HPS
START CAP
BIN T’STAT
1 2
CC
COMPRESSOR
CONTRACTOR
RUN
CLEAN
CAP
HARVEST MOTOR
RED
BLUE
CONDENSER FAN
AIR PUMP
HG SOL VALVE
WATER DUMP VALVE
FLUSH
WATER LEVEL
PROBE
ICE THICKNESS
PROBE
NO
NC
L N
C
HI
C
LO
COM
NO
NC
CONDUCTIVITY
CONTROL
FILL
NC
HT1
NO
C
WATER FILL VALVE
HT
HARVEST
TIMER
VEND SWITCH
NO
HT5
NC
C
AGITATOR
RELAY
AR
F
GATE SOLENOID
AGITATOR MOTOR
AR
MOTOR HEATER
R
BEVERAGE TRANSFORMER (OPTIONAL)
24 V TO BEVERAGE FAUCETS
FIGURE 7. WIRING SCHEMATIC SID 850/250
11
90914
YEL
PUR
BRN
BLK
BLUE
I
P
N
K
W
H
T
NEUTRAL
TERMINAL BOARD
MORE LOCATION MAY VARY
WHT
YEL
BLUE
LPS R
E
D
FUSE 1-1/4 AMP
TIME DELAY
AGITATOR
MOTOR CAP
BLK
CLEAN
ICE MAKER
RUN
RUN
STOP
Y
E
L
BRN
PUSH TO
FLUSH
MANUAL
WATER
FILL
BIN
T’STAT
BLK
BLK
PUR
PINK
BLK
BLK
PINK
ORN
RED
O
R
N
HARVEST
TIME
O
R
N
RED
R
E
D
BRN
YEL
RED
O
R
N
RED
PINK
FILL
VALVE
WATER
INDICATOR
L1 L2
CONDUCTIVITY
CONTROL
HI LO COM
Y
E
L
R
E
D
BRN
W
H
T
COMPRESSOR CONTACTOR
BRN
BLK
BLK
WHT
WHT
BLK
BLUE
HPS
ORANGE
RED
B
R
N
Y
E
L
GATE
SOLENOID
RED
WHT
VOID
SWITCH
Y
E
L
B
L
K
WHT
BLK
BLK
WHT
MERCURY
RELAY
Y
E
L
GRN
W
H
T
BRN
START
RELAY
1
GRN
RED
2
3
R
E
D
B
L
K
W
H
T
Y
E
L
GRN
BLK
115 VOLT
NEUTRAL
BLK
TERMINAL
BOARD
BRN
W
H
T
WHT
WHT
YEL
Y
E
L
Y
E
L
HARVEST
MOTOR CAP.
BLUE
RED
RED
WHT
BLK
BLK
BLK
COMPRESSOR
START CAP.
B
L
U
E
RED
RED
COMP.
RUN
CAP.
YEL
WHT
BLK
BLUE
WHT
HQ SOL VALVE
YEL
WATER LEVEL PROBE
PINK
WHT
RED
BLUE
WHT
WATER FILL VALVE
ORN
ICE THICKNESS PROBE
HARVEST MOTOR
ORN
BRN
S
C
RED
R
COMPRESSOR MOTOR
BLK
BLK
CONDENSER FAN MOTOR
BLK
BLK
AIR PUMP
208--230V/115V 1PH, 60HZ, 20AMP
FIELD SUPPLIED
RED
L2
BLK
L1
WHT
GRN
NO
REAR JUNCTION
BOX POWER IN
MOTOR
HEATER
B
L
K
B
L
K
W
H
T
AGITATOR
MOTOR
BEVERAGE
TRANSFORMER
(OPTIONAL)
WHT
BRN
WATER DUMP VALVE
90914
FIGURE 8. WIRING DIAGRAM SID 850/250 (208--230/115V, 1 PH, 60HZ)
12
FIGURE 9. REFRIGERATION SCHEMATIC
13
90914
MAINTENANCE
REGULAR BASIS
(or as required)
Cleaning of the ice maker is recommended on a regular basis not only for sanitary reasons, but also to maintain the performance of the unit. Build-up of lime and scale can hinder ice making production rates and interfere with proper dispensing of the ice. See
Cleaning Instructions
for the recommended procedure.
EVERY THREE MONTHS
(or as required)
It is recommended that the air inlet filter be cleaned every three (3) months or sooner depending on the operating environment for proper refrigeration system performance. On an air-cooled unit, also check that the condenser is free of dirt/foreign material that could cause air flow blockage. Consult the
Maintenance/Adjustment
Procedures
section for cleaning these items.
PERIODICALLY
(or as required)
Check the vending area sink for proper water drainage. Remove any foreign material from the sink to prevent drain blockage.
CLEANING INSTRUCTIONS
IMPORTANT: The ice maker should be cleaned at a minimum of three (3) month intervals or more frequently, depending on local water conditions. The storage hopper interior should be cleaned once a month.
CAUTION: Do not use metal scrapers, sharp objects or abrasives on the surface of the storage hopper, as damage may result. Do not use solvents or other cleaning agents, as they may attack the plastic surface. Use only the recommended chemicals and solutions for both the ice maker and hopper.
Ice Maker Section
1. Open the hinged service door.
2. Put the “Stop/Run”switch in the “stop”position at the end of the harvest cycle.
WARNING: The unit is still plugged into the electrical power during ice maker section cleaning. Therefore, do not reach into hopper, and do not contact exposed electrical wiring or components.
3. Remove the ice drop cover from the evaporator and the storage hopper cover.
4. Seal the evaporator outlet with the plastic plug provided with the unit and replace the ice drop cover.
5. Remove cleaning fill plug and add four (4) ounces of Virginia Ice Machine Cleaner to the evaporator and replace cleaning fill plug.
CAUTION: Virginia Ice Machine Cleaner is a mild acid, therefore, normal care should be taken when using. Keep out of eyes and cuts. Read warnings on package before using. Do not operate unit in the cleaning mode without the ice drop cover in place. There may be some overflow of cleaning solution through the evaporator vent tube during the cleaning cycle.
90914
14
6. Push manual water fill switch and fill evaporator with water (approximately 5 seconds).
7. Put the “Clean/Run”switch in the “clean”position. Allow unit to run in the cleaning mode for at least 30 minutes.
8. Put the “Clean/Run”switch in the “run”position.
9. Depress the “Flush”switch push button and drain evaporator for about 1-1/2 minutes. Release push button. Push manual water fill switch and allow evaporator to refill with water. Repeat Step 9 three (3) times to thoroughly remove cleaning solution from evaporator.
10. Depress the “Flush”switch push button for 1-1/2 minutes to drain the evaporator.
11. Remove the evaporator plug.
12. Put the “Stop/Run”switch in the “run”position and allow unit to run through at least three (3) complete ice making cycles or until ice is free of “sweet”taste.
WARNING: If unit fails to harvest ice, put the “Stop/Run” switch in the “stop” position.
Depress the “Flush” switch push button for 1-1/2 minutes to drain the evaporator. Flush the evaporator with hot water to thoroughly melt all the ice in the evaporator. Repeat Step 9 to remove all traces of the cleaning solution from the evaporator.
13. Dispense all ice out of storage hopper and discard.
Dispenser Section
1. Turn off main electrical power supply to machine.
2. Remove agitator assembly from storage hopper and wash and rinse it thoroughly.
3. Wash down all inside surfaces of the ice storage area, including the top cover and ice drop cover with a mild detergent solution and rinse thoroughly to remove all traces of detergent.
4. Replace agitator.
5. Remove ice chute cover as follows:
A. Flex sides outward to disengage lower pins.
B. Lift ice chute cover to disengage upper pins.
C. Lower ice chute cover down out of unit.
Note: It may be helpful to twist cover slightly.
6. Clean the inside of the ice chute and ice chute cover with a mild detergent solution. Rinse thoroughly to remove all traces of detergent.
7. Reverse steps above to reassemble ice chute.
8. Sanitize the inside of the hopper agitator, ice chute, the hopper cover and ice drop cover with a solution of
1 ounce of household bleach to 2 gallons of water. (200 PPM)
9. Replace the hopper cover and ice drop cover. Turn on the electrical power supply. The ice maker is ready for normal operation.
For Units With Beverage System
Cold Plate
1. Carefully remove the lower front panel. (Below beverage faucets).
15
90914
2. Slide the cold plate cover back. (Remove shipping tape and discard).
3. Remove any debris from the drain trough and spring. Check that drain hole is not clogged.
4. Wash down the inside of the cold plate with a mild detergent solution and rinse. A small, long handled brush will be found helpful in reaching the corners.
5. Slide the cover forward, taking care that it is securely positioned on the cold plate.
6. Replace the lower front panel.
Beverage System
1. Remove the faucet spouts, wash in mild detergent, rinse and replace.
2. Disconnect electrical power to the carbonator. Shut off the water supply and close the CO
2 carbonator.
regulator to the
3. Disconnect the syrup tanks from the system.
4. Energize the beverage faucets to purge the remaining soda water in the system.
5. Use a clean 5 gallon tank for each of the following:
Cleaning Tank: Fill with hot (120 ° - 140 ° F) potable water.
Sanitizing Tank: Fill with a chlorine sanitizing solution in the strength of 1 ounce of household bleach(sodium hypochlorite) to 2 gallons of cold (ambient) potable water (200 PPM).
6. Repeat the following procedure on each of the units’syrup product lines:
A. Connect the cleaning tank to the syrup line to be sanitized and to the CO
2 system.
B. Energize the beverage faucet until the liquid dispensed is free of any syrup.
C. Disconnect the cleaning tank and hook up the sanitizing tank to the syrup line and CO
2 system.
D. Energize the beverage faucet until the chlorine sanitizing solution is dispensed through the faucet.
Flush at least 2 cups of liquid to ensure that the sanitizing solution has filled the entire length of the syrup lines. Allow the sanitizer to remain in the line for twenty (20) minutes.
E. Disconnect the sanitizing tank. Hook up the product tank to the syrup line and to the CO
2 system.
F.
Energize the faucet to flush the sanitizing solution from the syrup line and faucet. Continue to draw on the faucet until only syrup is dispensed.
7. Repeat Step 2 in reverse order to turn on the carbonator. Dispense at least 1 cup of beverage from each faucet. Check taste. Continue to flush if needed, to obtain a satisfactory tasting drink.
90914
16
TROUBLESHOOTING GUIDE
The following pages contain troubleshooting charts designed to aid an experienced service person in diagnosing any operating problem which may be experienced. It is assumed that normal service techniques and skills are familiar to the person doing the troubleshooting. In order to gain maximum benefit from these charts please note:
1. Start at the beginning of the chart and supply the appropriate answer to each question.
2. Do not skip any section, unless instructed to do so. You might miss the solution to your problem.
3. Evaluate the possible problem causes in the sequence in which they are presented. In general, they begin with the most likely (or easiest) to check and proceed to the less likely (or more complicated).
4. If after checking all indicated causes, the problem is not resolved, it is recommended that you re-try a second time, carefully evaluating the symptoms and modifying your answers as necessary.
5. If you are unable to resolve a problem after several attempts, contact Remcor Customer Service for assistance.
17
90914
90914
START
DOES UNIT
OPERATE?
YES
IS
ICE MAKER
O.K.?
YES
IS
DISPENSER
O.K.?
YES
IS
BEVERAGE
SYSTEM
O.K.?
YES
DONE
NO
NO
NO
NO
NO OPERATION OF ANY
COMPONENT.
GO TO 1.
ICE MAKER ABNORMAL.
DISPENSER AND BEVERAGE
WORK NORMALLY.
GO TO 2.
DOES NOT DISPENSE.
ICE MAKER WORKS O.K.
GO TO 3.
PROBLEM WITH BEVERAGE
FAUCETS OR DRINK QUALITY.
GO TO 4.
18
1. TOTALLY INOPERATIVE
YES
CHECK FOR LOOSE CONNECTION
OR BROKEN WIRE INSIDE UNIT.
POWER
PRESENT AT
REAR JUNCTION
BOX?
YES
NO
IS
SUPPLY FUSE
BLOWN (OR C/B
TRIPPED)?
NO
CHECK FOR LOOSE CONNECTION
OR BROKEN WIRE IN SUPPLY
WIRING OF UNIT.
NO
IS LINE
VOLTAGE
WITHIN
±
10% OF
NAMEPLATE
VOLTAGE?
YES
1. CHECK FOR SHORT CIRCUIT IN
WIRING INSIDE UNIT.
2. CHECK COMPONENTS FOR SHORT
CIRCUIT OR GROUNDED WIRING.
YES
IS
FUSE OR C/B
SIZE PROPER?
NO
REPLACE WITH CORRECT
SIZE DEVICE.
IS
LINE VOLTAGE
HIGH OR
LOW?
HIGH
INSTALL BUCKING TRANSFORMER
TO REDUCE LINE VOLTAGE.
LOW
YES
IS
OTHER EQUIP.
ON SAME
CIRCUIT?
1. REMOVE ALL OTHER EQUIPMENT
FROM ICE MAKER CIRCUIT.
2. INSTALL NEW DEDICATED CIRCUIT
FOR ICE MAKER.
NO
1. CHECK FOR LOOSE OR CORRODED CON-
NECTION IN SUPPLY WIRING.
2. CHECK SUPPLY WIRING FOR UNDER-
SIZED WIRE, AND REPLACE.
3. INSTALL BOOSTING TRANSFORMER TO
RAISE LINE VOLTAGE.
19
90914
90914
2. ICE MAKER PROBLEM
DOES
ICE MAKER
OPERATE?
YES
NO
GO TO 2.A
YES
IS ICE
PRODUCED?
NO
DOES
COMPRESSOR
RUN?
NO
GO TO 2.B
YES
IS
ICE ON
EVAPORATOR?
NO
GO TO 2.C
YES
GO TO 2.D
DONE
YES
IS ICE
PRODUCTION
NORMAL?
YES
IS ICE
QUALITY
NORMAL?
NO
GO TO 2.E
NO
GO TO 2.F
20
2.A ICE MAKER PROBLEM
YES
IS
HOPPER
FULL?
NO
RUN
RUN/STOP
SWITCH?
STOP
PUT SWITCH IN
RUN POSITION.
NORMAL SHUTOFF ON
BIN THERMOSTAT.
YES
IS BIN
THERMOSTAT
OPEN?
YES
1. CHECK THERMOSTAT ADJUST-
MENT.
2. REPLACE BIN THERMOSTAT.
IS
WATER
LEVEL NORMAL
IN EVAP.?
NO
YES
IS LOW-
PRESSURE
SWITCH
OPEN?
NO
CHECK FOR LOOSE CONNECTION
OR BROKEN WIRE.
NO
NO
1. CHECK THAT WATER SUPPLY IS OPEN.
2. CHECK WATER SUPPLY FILTER.
3. CHECK FOR PLUGGED WATER SOLENOID
VALVE.
4. CHECK ADJUSTMENT OF TIMER CAM #4.
(WATER DUMP)
5. CHECK TIMER SWITCH #4.
6. CHECK IF WATER DUMP VALVE IS STUCK
OPEN.
1. CHECK FOR REFRIGERANT UN-
DER-CHARGE
2. CHECK TXV VALVE.
IS HIGH-
PRESSURE
SWITCH
OPEN?
YES
AIR-COOLED UNITS
1. CHECK FOR RESTRICTED AIR FLOW AT TOP
OR REAR OF UNIT.
2. CHECK FOR HOT AIR RECIRCULATING TO TOP
INLET. ELIMINATE BY BAFFLING.
3. CHECK FOR DIRTY INLET AIR FILTER.
4. CHECK FOR DIRTY AIR-COOLED CONDENSER.
5. CHECK CONDENSER FAN MOTOR.
6. CHECK FOR REFRIG. OVER-CHARGE.
WATER-COOLED UNITS
1. CHECK WATER SUPPLY TO CONDENSER.
2. CHECK FOR FAULTY WATER REG. VALVE.
3. CHECK FOR REFRIG. OVER-CHARGE.
4. CHECK FOR FOULED CONDENSER.
21
90914
2.B COMPRESSOR INOPERATIVE
YES
IS
LINE VOLTAGE
WITHIN
±
10%
OF NAMEPLATE
VOLTAGE?
YES
IS
THERMAL
PROTECTOR
OPEN?
YES
IS
COMPRESSOR
BODY
COLD?
NO
NO
NO
CHECK VOLTAGE
PROBLEMS IN 1.
IS
CONTACTOR
PULLED
IN?
NO
YES
1. CHECK FOR LOOSE OR BROKEN WIRING
CONNECTION IN COMPRESSOR POWER
CIRCUIT.
2. CHECK CONTACTOR.
3. CHECK STARTING RELAY.
4. CHECK CAPACITOR(S).
5. CHECK COMPRESSOR MOTOR.
REPLACE
THERMAL
PROTECTOR.
YES
IS
120V.
PRESENT AT
CONTACTOR
COIL
TERMINAL?
NO
REPLACE CONTACTOR.
1. CHECK FOR LOOSE OR BROKEN
WIRING CONNECTION IN CONTROL
CIRCUIT.
2. GO TO 2.A.
90914
22
2.C NO ICE ON EVAPORATOR
NO
IS
HARVEST
TIMER
RUNNING?
YES
YES
CHECK
REFRIGERATION
SYSTEM.
IS
WATER LEVEL
NORMAL?
YES
NO
CHECK WATER
PROBLEMS IN 2.A.
IS
EVAPORATOR
COLD?
NO
YES
IS
HOT GAS SOLENOID
ENERGIZED?
NO
1. CHECK FOR REFRIGERANT
UNDER-CHARGE.
2. CHECK HOT GAS SOLENOID
FOR LEAKING SEAT.
3. GO TO 2.A.
YES
IS
COND. CONTROL
ENERGIZED?
NO
CHECK TIMER
SWITCH #1.
1. CHECK FOR OPEN CONDUCT
PROBE WIRING.
2. CHECK CONDUCTIVITY
CONTROL.
YES
IS
HARVEST TIMER
HOME?
NO
1. CHECK ADJUSTMENT OF
TIMER CAM #2. (HOT GAS)
2. CHECK TIMER SWITCH #2.
1. CHECK ADJUSTMENT OF TIMER
CAM #1. (TIMER HOME)
2. CHECK TIMER SWITCH #1.
3. CHECK TIMER MOTOR.
23
90914
90914
2.D FROZEN EVAPORATOR
1. SHUTOFF ICE MAKER AND THAW EVAPORATOR.
2. START ICE MAKER.
IS
AMBIENT ABOVE
60
°
F?
YES
NO
IS
VOLTAGE WITHIN
±
10%?
YES
DISCONNECT PROBE WIRE FROM
CONDUCTIVITY CONTROL.
NO
1. ARRANGE TO MAINTAIN MINIMUM
60
°
F AMBIENT.
2. CONDUCT FACTORY REGARDING
SPECIAL APPLICATION.
CHECK VOLTAGE ITEMS IN 1.
DOES
TIMER
START?
NO
1. CHECK TIMER MOTOR.
2. CHECK CONDUCTIVITY CONTROL.
YES
HOT
GAS OPERATION
O.K.?
YES
WATER
DUMP
O.K.?
YES
DOES
ICE HARVEST
NORMALLY?
YES
NO
1. CHECK ADJUSTMENT OF TIMER
CAM #2. (HOT GAS)
2. CHECK TIMER SWITCH #2.
3. CHECK HOT GAS SOLENOID.
NO
1. CHECK ADJUSTMENT OF TIMER
CAM #4. (WATER DUMP)
2. CHECK TIMER SWITCH #4.
3. CHECK DUMP SOLENOID.
NO
24
YES
2.D (CONT’D)
NO
1. CHECK ADJUSTMENT OF TIMER CAM
#3. (HARVEST MOTOR)
2. CHECK TIMER SWITCH #3.
3. CHECK HARVEST MOTOR CAPACITOR.
4. CHECK HARVEST MOTOR.
REPLACE PROBE WIRE ON
CONDUCTIVITY CONTROL
DURING HARVEST CYCLE.
DOES
TIMER RETURN
HOME?
YES
WAIT ONE FULL FREEZING
CYCLE (APPROX. 6-10 MIN.)
NO
DOES
HARVEST
INITIATE?
YES
DOES
ICE HARVEST
NORMALLY?
YES
DONE
NO
NO
1. CHECK ADJUSTMENT OF TIMER
CAM #1. (TIMER HOME)
2. CHECK TIMER SWITCH #1.
1. CHECK PROBE WIRING FOR
SHORTED CONNECTION.
2. CHECK CONDUCTIVITY CONTROL.
1. REPEAT PREVIOUS CHECK OF OPERATION OF HARVEST
COMPONENTS IN 2.D.
2. ADJUST ICE THICKNESS PROBE ONLY AFTER ALL OTH-
ER FACTORS HAVE BEEN CHECKED THOROUGHLY.
25
90914
90914
2.E LOW ICE PRODUCTION
IS
WATER LEVEL
NORMAL?
YES
NO
CHECK WATER ITEMS IN 2.A.
IS
WATER TEMP.
HIGH?
NO
YES
NORMAL EFFECT. INSTALL
REMCOR PRE-COOLER TO
INCREASE CAPACITY.
IS
AMBIENT TEMP.
HIGH?
NO
YES
NORMAL EFFECT. ARRANGE
FOR LOWER AMBIENT AIR
TEMP. IF POSSIBLE.
IS
ICE THIN?
NO
YES
GO TO 2.C.
CHECK REFRIGERATION
SYSTEM.
26
2.F POOR ICE QUALITY
YES
IS
ICE CLOUDY?
NO
IS
ICE SOFT?
YES
NO
1. CHECK AIR PUMP.
2. CHECK ADJUSTMENT OF TIMER CAM #4. (WATER
PUMP)
3. CHECK TIMER SWITCH #4.
4. CHECK WATER DUMP VALVE.
5. CHECK WATER FILTER.
6. INCREASE WATER DUMP BY ADJUSTING TIMER
CAM #4.
7. INSTALL ADDITIONAL WATER TREATMENT DE-
VICES FOR SPECIFIC PROBLEM WATER.
DONE
27
90914
3. DISPENSER PROBLEM
YES
DOES
AGITATOR
ROTATE?
NO
YES
1. CHECK MOTOR CAPACITOR.
2. CHECK TIMER SWITCH #5.
3. CHECK AGITATOR MOTOR.
DOES
GATE OPEN?
NO
MECHANISM.
IS
VOLTAGE AT
SOLENOID
103-126V.?
NO
1. CHECK FOR BURNED OUT SOLENOID.
2. CHECK FOR STUCK OR BINDING GATE
YES
IS
HOPPER LEVEL
TOO HIGH?
YES
1. CHECK BIN THERMOSTAT
ADJUSTMENT.
2. REPLACE BIN THERMOSTAT.
NO
1. CHECK FOR BLOWN SOLENOID FUSE IN ELEC-
TRICAL BOX. IF FUSE IS BLOWN, CHECK FOR
STUCK GATE MECHANISM, BURNED OUT SOLE-
NOID, OR LOW VOLTAGE.
2. CHECK VEND SWITCH.
3. CHECK FOR LOOSE OR BROKEN WIRE CONNEC-
TION IN SOLENOID CIRCUIT.
4. CHECK VOLTAGE PROBLEMS IN 1.
IS
ICE SLUSHY?
NO
DONE
YES
1. CHECK HOPPER DRAINS.
2. CHECK LEVEL OF UNIT.
3. CHECK FOR WATER OVERFLOW FROM EVAP-
ORATOR. SEE SECTION 2.
4. CHECK ADJUSTMENT OF TIMER CAM #5.
(AGITATION)
5. CHECK TIMER SWITCH #5.
90914
28
4. BEVERAGE SYSTEM PROBLEM
IS
ONE OR MORE
FAUCETS
INOPERATIVE?
NO
IS
BEVERAGE
COLD?
YES
IS
BEVERAGE
PROPERLY
CARBONATED?
YES
IS
BEVERAGE
TOO SWEET?
NO
IS
BEVERAGE
TOO WATERY?
NO
DONE
YES
NO
NO
1. CHECK WIRING CONNECTIONS TO IN-
OPERATIVE FAUCETS.
2. REPLACE INOPERATIVE FAUCETS.
3. CHECK WIRING CONNECTIONS FROM
24V. TRANSFORMER.
4. CHECK 24V. TRANSFORMER.
1. CHECK REMOTE COOLING
SYSTEM. (-B MODELS)
2. CHECK FOR ICE ON COLD
PLATE. (-BC MODELS)
3. CHECK CO
2
PRESSURE.
4. CHECK CARBONATOR.
YES
1. CHECK WATER SUPPLY PRESSURE.
2. CHECK SUPPLY FILTER.
3. CHECK CARBONATOR.
4. CHECK FAUCET BRIX.
YES
1. CHECK IF SYRUP TANK IS EMPTY.
2. CHECK CO
2
PRESSURE.
3. CHECK FAUCET BRIX.
29
90914
MAINTENANCE/ADJUSTMENT PROCEDURES
THERMOSTAT ALTITUDE ADJUSTMENTS
IMPORTANT: Adjust the bin thermostat setting only if storage hopper over fill is a problem.
BIN THERMOSTAT
1. Open the hinged service door.
2. The adjustment screw is located below the “Flush”switch on the left side of the electrical box.
3. For altitudes up to 6,000 feet, turn the adjustment screw COUNTERCLOCKWISE as follows:
ELEVATION (FEET)
2,000
4,000
6,000
COUNTERCLOCKWISE TURN
1/13
1/6
1/4
4. For altitudes above 6,000 feet, consult the factory.
CLEARING EVAPORATOR FREEZE-UP
WARNING: To prevent possible injury, do not place fingers or hand into ice maker nozzle or hopper with power applied to the unit.
1. Open the hinged service door.
2. Place the “Stop/Run”switch in the “Stop”position.
3. Close the water supply valve to the ice maker.
4. Remove the ice drop and hopper covers.
5. Depress the “Flush”switch push button and drain the evaporator.
6. Pour hot water into the evaporator ice exit opening. It will be necessary to use either a funnel or a container with a spout. Fill the evaporator completely.
7. Drain the evaporator. Repeat steps 5 and 6 as required to ensure that all the ice in the evaporator is melted.
8. Open the water supply valve. Depress the fill switch and refill evaporator.
9. Replace the ice drop and hopper covers.
10. Consult
TROUBLESHOOTING GUIDE
to determine cause of freeze-up before putting unit back in service.
90914
30
ICE THICKNESS ADJUSTMENT
WARNING: Do not adjust ice thickness probe unless all other problem causes have been evaluated.
1. Open the hinged service door and remove the ice drop and hopper covers.
2. Collect and weigh the ice produced during the harvest cycle. The amount of ice harvested should weigh approximately five (5) pounds. Use the following procedure to adjust the probe to obtain this weight. (A clockwise adjustment will reduce the harvest weight while counterclockwise turns will increase the amount).
CAUTION: Do not turn the screw on the end of the probe. Rotate the plastic probe body only using a 3/8 inch open end wrench. Make adjustments in 1/8 inch turn increments.
A. Place the “Stop/Run”switch in the “Stop”position. (If unit is in the ice-making cycle, stop the unit at the end of the harvest cycle).
B. Access to the probe is obtained by removing the rear service panel. (For units without beverage faucets, the probe can be adjusted from the front by removing the lower front panel if rear access is blocked).
C. Adjust the probe.
D. Place the “Stop/Run”switch in the “Run”position.
E. Collect and weigh the ice harvested. Repeat step A through E as necessary to obtain the required amount of ice.
3. In making an initial adjustment (for example, if the probe has been removed and replaced for any reason), turn probe clockwise until it just touches the evaporator coil (a slight back pressure will be felt). Turn probe counterclockwise 2-1/2 turns. Follow procedure in step 2 to obtain the required ice harvest weight.
CLEANING/REPLACE THE FILTER
1. Remove the filter from the cabinet panel by sliding it forward toward the front of the unit.
2. Wash the filter in a solution of warm water and a mild detergent. Do not use caustic detergents as they may attack the aluminum filter elements.
3. Dry filter thoroughly.
4. For maximum effectiveness, reactivate the filter with an air filter coating (see Parts List, Miscellaneous
Components).
CLEANING THE CONDENSER
Air-Cooled Units.
1. Disconnect power to the unit.
2. Remove the upper right side panel.
3. Remove all dirt/foreign material built up from the condenser fins (fan side). Be careful not to damage the fins. It is recommended that a power vacuum cleaner with a “crevice”tool attachment be used.
31
90914
HARVEST TIME ADJUSTMENT
WARNING: Disconnect electrical power to the unit before servicing the timer in the electrical box.
1. Disconnect power to ice maker.
2. Open the hinged service door and remove the electrical control box cover.
3. Place the “Stop/Run”switch in the “Stop”position.
4. Using Figure 10 as a guide, set the timer cam tabs as follows, starting with cam wheel No.1 (all cam tab positions are in relation to No.1 left cam tab).
NOTE: Timer cam wheels can be manually rotated only in the normal direction of rotation-downward as viewed from the front of the unit.
A. “Manually”adjust the cam tabs by using each “click”as the cam tab is rotated, as equivalent to .75
seconds.
B. Set up cam wheel No.1 with the left and right cam tabs back-to-back as shown in Figure 7A.
C. Adjust the cam tabs on wheels No. 2 through No. 5 in sequence as shown on the chart. Rotate the cam wheels manually downward to set each wheel.
D. After the cam tabs are manually set, reconnect power to the ice maker.
E. Rotate the cam wheels slightly to activate the timer motor (No. 1 telltale down).
F.
Using a stop watch, time the cam switch telltales. Adjust the cam tabs as necessary for the required cycle times.
MANUAL FILLING
In the event that the ice maker is not functioning, the hopper may be manually filled with ice.
1. Open the hinged service door.
2. Place the “Stop/Run”switch in the “Stop”position.
WARNING:
Electrical power is on to the agitator motor and the gate solenoid.
Avoid contact with these components.
3. Remove the ice drop and storage hopper covers.
4. Fill hopper with ice and replace covers. Unit is now ready for dispensing.
CAUTION: Do not use crushed or flaked ice. Use of bagged ice, which has frozen into large chunks, can void warranty. The agitator is not designed to be an ice crusher. Use of large chunks of ice which “jam up” inside the hopper will cause failure of the agitator motor and damage the hopper. If bagged ice is used, it must be carefully and completely broken into small, cube size pieces before filling into the storage hopper. Do not allow foreign material to enter the ice storage hopper.
90914
32
FIGURE 10. HARVEST TIMER
33
10A
90914
DESCRIPTION
Dispenser Components
Gate Slide
Depressor Lever
Depressor Retainer
Agitator
Vend Switch
Switch Boot
Agitator Motor with Gasket
Agitator Motor Shaft Seal
Agitator Motor Plate Insulation
Sink
Sink Grill
Ice Chute, Back Section
Ice Chute Cover
Gate Gasket
Gate Solenoid Assembly
Gate Rebuilding Kit
Agitator Motor Heater
Agitator Motor Gasket
DESCRIPTION
Electrical Controls
Contactor
Toggle Switch
Flush Switch
Bin Thermostat
Fuse, 1-1/4 Amps (Gate Solenoid)
Timer, Harvest
Conductivity Control
Capacitor, Harvest Motor
Compressor Start Relay
Capacitor, Compressor Start
Capacitor, Compressor Run
Compressor Overload
High Pressure Control
Low Pressure Control
Transformer, Beverage
Relay, Agitator Motor
PARTS LIST
PART NUMBERS
250
Air Cooled
250 “BC”
21491
22777
21491
22777
22644
23692
30895
31007
31197-1
50891
50967
51024
70496
53015
53016
50770
31470
70438
----------
50481
22644
23692
30895
31007
31197-1
50891
50967
52208
70496
53015
53016
50770
31470
70438
30794
50481
Water Cooled
250 250 “BC”
21491
22777
21491
22777
22644
23692
30895
31007
31197-1
50891
50967
51024
70496
53015
53016
50770
31470
70438
----------
50481
22644
23692
30895
31007
31197-1
50891
50967
52208
70496
53015
53016
50770
31470
70438
30794
50481
PART NUMBERS
250
30379
30385
Air Cooled
250 “BC”
30379
30385
Water Cooled
250
30379
30385
250 “BC”
30379
30385
30895
31001
31406
31840
31743
31673
31671
31741
31673
31742
60501
60369
----------
31375
30895
31001
31406
31840
31743
31673
31671
31741
31673
31742
60501
60369
31091
31375
30895
31001
31406
31840
31743
31673
31671
31741
31673
31742
60501
60369
----------
31375
30895
31001
31406
31840
31743
31673
31671
31741
31673
31742
60501
60369
31091
31375
90914
34
DESCRIPTION
Refrigeration Components
Compressor
Compressor Mounting Kit
Air Pump
Hose Adaptor, 3/8 NPT X 3/8 Barb
Hose Adaptor 90
°
, 3/8 NPT X 3/8 Barb
Condenser Fan Motor
Condenser Fan Blade
Water Valve Inlet
Condenser Air-Cooled
Condenser Shroud
Tinnerman Clip, Shroud
Filter (Drier)
Hot Gas Solenoid Valve
Hot Gas Solenoid Coil (115 Volt)
TXV R-502
Condenser, Water Cooled
Water Regulating Valve
Water Drain Valve
Tubing, Water Drain, 1/2 inch I.D.
Tubing, Air Pump, 3/8 inch I.D.
PARTS LIST (CONT’D)
PART NUMBERS
250
Air Cooled
250 “BC”
51388
70704
60623
60620
32576
60947
----------
----------
40653
50351
50096
60678
31607
31568
51189
51190
31738
31739
40672
60679
51388
70704
60623
60620
32576
60947
----------
----------
40653
50351
50096
60678
31607
31568
51189
51190
31738
31739
40672
60679
Water Cooled
250 250 “BC”
----------
----------
60623
60620
32576
60947
60309
40122
40653
50351
50096
60678
31607
31568
51189
51190
----------
----------
40672
----------
----------
----------
60623
60620
32576
60947
60309
40122
40653
50351
50096
60678
31607
31568
51189
51190
----------
----------
40672
----------
DESCRIPTION
Evaporator Components
Evaporator Assembly
Evaporator Housing, Foamed
Evaporator Coil Assembly
Harvest Bar Assembly With Gaskets
Gasket Kit
Ice Thickness Probe
Harvest Motor With Gaskets
Hose Adaptor, 1/4 NPT X 3/8 Barb
Hose Adaptor, 1/4 NPT X 1/2 Barb
10-32 X 5/8 Phillips Flat Head Screw
Miscellaneous Components
Filter
Filter Coating, 16 Ounces
Label “Press For Ice”
Wiring Diagram
Manual
Cleaning Label
PART NUMBERS
250
Air Cooled
250 “BC”
61023
51368
60680
51369--1
51356
51179
31560--1
51191
51192
70746
61023
51368
60680
51369--1
51356
51179
31560--1
51191
51192
70746
250
Air Cooled
250 “BC”
70551 70551
51355
90906
90915
90914
90916
51355
90906
90915
90914
90916
Water Cooled
250 250 “BC”
61023
51368
60680
51369--1
51356
51179
31560--1
51191
51192
70746
61023
51368
60680
51369--1
51356
51179
31560--1
51191
51192
70746
Water Cooled
250 250 “BC”
70551 70551
51355
90906
90915
90914
90916
51355
90906
90915
90914
90916
35
90914
IMI CORNELIUS INC
.
O
NE
C
ORNELIUS
P
LACE
A
NOKA,
MN
. 55303--6234
T
ELEPHONE (800) 238--3600
F
ACSIMILE (612) 422--3232
T
ECH
S
VC 1-800-535-4240
WARRANTY
IMI Cornelius Inc. and Remcor Products Company warrants that all equipment and parts are free from defects in material and workmanship under normal use and service. For a copy of the warranty applicable to your
Cornelius and or Remcor product, in your country, please write, fax or telephone the IMI Cornelius office nearest you. Please provide the equipment model number, serial number and the date of purchase.
IMI Cornelius Offices
AUSTRALIA
AUSTRIA
D P.O. 210, D RIVERWOOD, D NSW 2210, AUSTRALIA D (61) 2 533 3122 D FAX (61) 2 534 2166
D AM LANGEN FELDE 32 D A-1222 D VIENNA, AUSTRIA D (43) 1 233 520 D FAX (43) 1-2335-2930
BELGIUM
BRAZIL
D BOSKAPELLEI 122 D B-2930 BRAASCHAAT, BELGIUM D (32) 3 664 0552 D FAX (32) 3 665 2307
D
RUA ITAOCARA 97
D
TOMAS COELHO
D
RIO DE JANEIRO, BRAZIL
D
(55) 21 591 7150
D
FAX (55) 21 593 1829
ENGLAND
FRANCE
D
TYTHING ROAD ALCESTER
D
WARWICKSHIRE, B49 6 EU, ENGLAND
D
(44) 789 763 101
D
FAX (44) 789 763 644
D
71 ROUTE DE ST. DENIS
D
F-95170 DEUIL LA BARRE
D
PARIS, FRANCE
D
(33) 1 34 28 6200
D
FAX (33) 1 34 28 6201
GERMANY
GREECE
D
CARL LEVERKUS STRASSE 15
D
D-4018 LANGENFELD, GERMANY
D
(49) 2173 7930
D
FAX (49) 2173 77 438
D
488 MESSOGION AVENUE
D
AGIA PARASKEVI
D
153 42
D
ATHENS, GREECE
D
(30) 1 600 1073
D
FAX (30) 1 601 2491
HONG KONG
ITALY
D
1104 TAIKOTSUI CENTRE
D
11-15 KOK CHEUNG ST
D
TAIKOKTSUE, HONG KONG
D
(852) 789 9882
D
FAX (852) 391 6222
D
VIA PELLIZZARI 11
D
1-20059
D
VIMARCATE, ITALY
D
(39) 39 608 0817
D
FAX (39) 39 608 0814
NEW ZEALAND
SINGAPORE
D
20 LANSFORD CRES.
D
P.O. BOX 19-044 AVONDALE
D
AUCKLAND 7, NEW ZEALAND
D
(64) 9 8200 357
D
FAX (64) 9 8200 361
D
16 TUAS STREET
D
SINGAPORE 2263
D
(65) 862 5542
D
FAX (65) 862 5604
SPAIN
USA
D
POLIGONO INDUSTRAIL
D
RIERA DEL FONOLLAR
D
E-08830 SANT BOI DE LLOBREGAT
D
BARCELONA, SPAIN
D
(34) 3 640 2839
D
FAX (34) 3 654 3379
D
ONE CORNELIUS PLACE
D
ANOKA, MINNESOTA
D
(612) 421-6120
D
FAX (612) 422-3255
36
Manual number
CORPORATE HEADQUARTERS:
Remcor Incorporated
500 Regency Drive
Glendale Heights, IL 60139
708. 980.6900
advertisement
Related manuals
advertisement