Duerkopp Adler 975-1-5 Program
Add to My manualsDURKOPP ADLER 975-1-5 offers a wide range of capabilities to enhance your sewing and testing processes. With its comprehensive MULTITEST testing and monitoring system, this microcomputer-controlled device ensures fault-free functioning by conducting self-tests at startup and displaying error messages when necessary. Multiple programs aid in mechanical settings, testing input and output elements, and monitoring the sewing procedure. You can also reset the summation counter and receive cycle displays for the clamping tables and sewing process.
advertisement
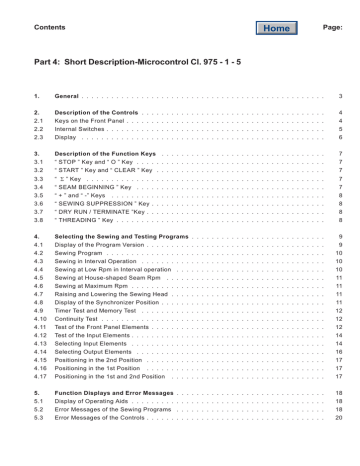
Contents
Home
Page:
Part 4: Short Description-Microcontrol Cl. 975 - 1 - 5
Description of the Function Keys . . . . . . . . . . . . . . . . . . . . . . . . . . . . . . . . .
“ START ” Key and “ CLEAR ” Key . . . . . . . . . . . . . . . . . . . . . . . . . . . . . . . . . .
“ SEAM BEGINNING ” Key . . . . . . . . . . . . . . . . . . . . . . . . . . . . . . . . . . . . . .
“ SEWING SUPPRESSION ” Key . . . . . . . . . . . . . . . . . . . . . . . . . . . . . . . . . . .
“ DRY RUN / TERMINATE ”Key . . . . . . . . . . . . . . . . . . . . . . . . . . . . . . . . . . . .
Selecting the Sewing and Testing Programs . . . . . . . . . . . . . . . . . . . . . . . . . . .
Sewing at Low Rpm in Interval operation . . . . . . . . . . . . . . . . . . . . . . . . . . . . . .
Sewing at House-shaped Seam Rpm . . . . . . . . . . . . . . . . . . . . . . . . . . . . . . . .
Sewing at Maximum Rpm . . . . . . . . . . . . . . . . . . . . . . . . . . . . . . . . . . . . . . .
Raising and Lowering the Sewing Head . . . . . . . . . . . . . . . . . . . . . . . . . . . . . . .
Timer Test and Memory Test . . . . . . . . . . . . . . . . . . . . . . . . . . . . . . . . . . . . .
Function Displays and Error Messages . . . . . . . . . . . . . . . . . . . . . . . . . . . . . .
Error Messages of the Sewing Programs . . . . . . . . . . . . . . . . . . . . . . . . . . . . . .
1.
General
The MICROCONTROL controls of the DÜRKOPP ADLER 975 - 1 - 5 have as an integral part the comprehensive MULTITEST testing and monitoring system.
A microcomputer assumes the control tasks, monitors the sewing procedure and displays operator errors and malfunctions.
Special programs aid in making mechanical settings and make possible a quick inspection of the input and output elements without additional measuring equipment.
Errors and testing results are shown in a 2 x 16-digit display.
During fault-free operation the display shows information to the operating and the sewing sequences.
For program testing and error diagnosis it is possible to blank out the summation counter and to alternatively receive a cycle display of the parallel-operating PROM components for the left and right clamping tables as well as for the sewing process.
With an operator error or a malfunction the function sequence is interrupted. The cause is shown in the display by the appropriate error symbol. In most cases the error symbol disappears after the cause of the error is remedied and the CLEAR key pressed.
In some cases the main switch must be turned off when the error is corrected for safety reasons.
A number of error messages are meant only for the maintenance staff.
All functions can be called up and changed by pressing the appropriate key. The sewing unit must be in its base position for this.
When the sewing unit is turned on the controls conduct a number of self-tests. At this time the program and data memory and the display, among other things, are checked as to fault-free functioning.
After the sewing unit is turned off the set values for the individual functions are stored in the program and data memory (battery buffered) and automatically activated when next turned on again.
ATTENTION !
This short description of the Microcontrol 975 - 1 - 5 is valid for the
Program Version 975A03 !
3
2.
Description of the Controls
2.1
Keys on the Front Panel
I C auto
4
Key Function Key
Selecting sewing and testing programs
Stopping the current program
Activating the selected program
Threading
- Reserve -
Start
Clear
( Cancelling an error message )
Reset counter
Activating the function
Seam beginning
Function
Activating the function
- Reserve -
- Reserve -
Increasing the parameter value
Decreasing the parameter value
Sewing suppression
Dry run / Terminate
2.2
Internal Switches
DIP-switch b417 b401 b402
I C auto
On the controls behind the display there are 3 pre-selector switches for setting various machine parameters.
ATTENTION !
The switches are evaluated only once after the sewing unit is turned on.
After changing a switch position turn the main switch off and on again or press the “ STOP ” key.
DIP-switch b417 b417
1
2
3...8
Function
Display
Sewing sequence
- Reserve -
OFF
Piece counter
Normal
—————
ON
Program cycle
Continuous test
—————
Dials b401 and b402
With these switches the sewing rpms for the sewing of the house-shaped seam ( b401 ) and for sewing at maximum rpm
( b402 ) are set.
Switch position
0
1
2
3
4 - 9
Sewing rpm
960 min -1
1 280 min -1
1 700 min -1
2 260 min -1
3 000 min -1
5
2.3
Display
The Microcontrol controls are equipped with a 2 x 16-digit display.
It shows program numbers, piece counts, status reports, error messages, seam beginning delay, among other items.
The sewing unit is ready for operation when the prompt to press the
“ START ” key appears in the display.
Example 1:
P01
1234
OK
= Program number
= Piece count
= Status report
Example 2:
P01 = Program number
L07R00Z03 = Program cycle
ERROR 01 = Error message
Example 3:
P01
1234
Begin: 600 msec
= Program number
= Piece counter
= Seam beginning delay
6
3.
Description of the Keys
3.1
“ STOP ” Key and “ O ” Key
By pressing the “ STOP ” key all current procedures of the sewing unit and the clamping tables are immediately interrupted.
By pressing the “ STOP ” key the sewing, aid and testing programs set with the “ PROGRAM ” switch are activated.
By pressing the “ O ” key the selected output and input elements or the front panel elements in the various testing programs are activated.
3.2
“ START ” Key and “ CLEAR ” Key
By pressing the “ START ” key the command for the initial run of the clamping tables is issued after the sewing unit is turned on.
By pressing the “ START ” key a STOP command is cancelled.
By pressing the “ CLEAR ” key slight errors are cancelled after the malfunction has been corrected.
If, after pressing the “ CLEAR ” key, the error message does not disappear, then the service technician must be notified.
3.3
“
Σ
” Key
By pressing the “
Σ
” key the piece count ( in the upper right of the display ) is reset to 0000.
The piece count shows the number of pieces finished since the last reset.
In program 40 the sewing process is activated by pressing the “
Σ
” key, if one of the two clamping tables is in sewing position.
3.4
“ SEAM BEGINNING ” Key
By pressing the “ SEAM BEGINNING ” key the set delay is shown in the display.
With the “ SEAM BEGINNING ” key held down, the delay can be set with the “ + ” and “ - ” keys.
Setting range: 0....600 msec
The set value remains in the memory even after the sewing unit is turned off.
7
3.5
“ + ” and “ - ” Keys
With “ SEAM BEGINNING ” key held down the delay can be set using the “ + ” and “ - ” keys.
The set value remains stored in the memory even after the sewing unit is turned off.
3.6
“ SEWING SUPPRESSION ” Key
By pressing the “ SEWING SUPPRESSION ” key the cloth can be checked before being swung in for sewing.
By pressing the “ SEWING SUPPRESSION ” key again the function is cancelled.
When the function is active the LED above the key is lit.
3.7
“ DRY RUN / TERMINATE ” Key
By pressing the “ DRY RUN / TERMINATE ” key the clamping table which is next to be swung in for sewing is not sewn ( dry run ).
If sewing is already occuring, then this is interrupted and the thread cut.
When the function is active the LED above the key is lit.
3.8
“ THREADING ” Key
By pressing the “ THREADING ” key the unit is automatically run into the threading position.
The “ THREADING ” key can only be used in program 01 ( sewing ) before a sewing process has been started, this is when the display shows “ PRESS START ”.
Turn the main switch off or press the “ STOP ” key in program 01.
See also the Program Description in the Operating Instructions !
8
4.
Selecting the Sewing and Testing Programs
The sewing and testing programs listed below are selected with the
“ PROGRAM ” switch.
– Set the “ PROGRAM ” switch to the desired program.
– Turn the main switch on or press the “ STOP ” key.
The selected program is active.
– If “ P? ” appears in the display, then an invalid program number was set.
A sewing process running at the time that the “STOP ” key is pressed will be terminated.
– Correct the setting and press the “ STOP ” key.
61
62
63
45
59
60
64
66
67
68
Program
00
01
40
41
42
43
44
Function
Display of the program version
Sewing program
Sewing in interval operation
Sewing at low rpm in interval operation
Sewing at house-shaped seam rpm
Sewing at maximum rpm
Raising and lowering the sewing head, needle plate and sewing foot
Display of the synchronizer position
Timer test and memory test
Continuity test
Test of the front panel elements
Test of the input elements
Selecting input elements
Selecting output elements
Positioning in the 2nd position
Positioning in the 1st position
Positioning with cutting
4.1
Display of the Program Version
– Set the “ PROGRAM ” switch to 00.
– Press the “ STOP ” key.
The program is active. The lower line of the display shows the program version and a check sum.
e.g.
975A01 0000
975
A
= Class designation of the sewing unit
= Identification letter
01 = Version number
0000 = Check sum
By program versions with the same class designation and the same identification letter the higher version replaces all lower versions
( Example: 975A03 replaces 975A01 and 975A02 ).
The check sum is meant only for the factory service staff.
Specialists can see by this sum if the program memory ( EPROM ) of the sewing unit flautlessly contains the complete program.
9
4.2
Sewing Program
Only the sewing program 01 can be called up.
The work sequence is comprehensively described in the Operating
Instructions.
– Set the “ PROGRAM ” switch to 01.
– Turn the main switch on or press the “ STOP ” key.
The sewing program is active.
4.3
Sewing in Interval Operation
This program is generally the same as program 01.
The clamping table is, however, controlled in interval operation.
– Set the “ PROGRAM ” switch to 40.
– Press the “ STOP ” key.
The program is activated.
– Press the “ REPEAT / INTERVAL ” key on the clamping table.
While the key is pressed the folding sequence is initiated.
If the key is released the folding device immediately ceases movement.
– In the sewing position press the"
Σ
“ key.
The sewing process is initiated.
If the ”
Σ
“ key is not pressed at this point, then the folding sequence runs completely through to the end ( base position ) without sewing.
4.4
Sewing at Low Rpm in Interval Operation
This program is identical with program 40. Sewing, however, occurs only at low rpm ( house-shaped seam rpm ).
– Set the “ PROGRAM ” switch to 41.
– Press the “ STOP ” key.
The program is activated.
– Press the “ REPEAT / INTERVAL ” key on the clamping table.
While the key is pressed the folding sequence is initiated.
If the key is released the folding device immediately ceases movement.
– In the sewing position press the “
Σ
” key.
The sewing process is initiated.
If the “
Σ
” key is not pressed at this point the folding sequence will run through to the end ( base position ) without sewing.
10
4.5
Sewing at House-shaped Seam Rpm
With this program a check of the sewing, of the thread trimming and the house-shaped seam rpm ( b401 ) is made.
A clamping-in of the cloth on the clamping tables is not required.
– Set the “ PROGRAM ” switch to 42.
– Press the “ STOP ” key.
The program is activated.
4.6
Sewing at Maximum Rpm
This program is identical to program 42. Sewing, however, is conducted at maximum rpm ( b402 ).
– Set the “ PROGRAM ” switch to 43.
– Press the “ STOP ” key.
The program is activated.
4.7
Raising and Lowering the Sewing Head
Program 44 makes possible adjustment work on the machine head during which the sewing head, needle plate and sewing foot must be raised or lowered.
– Set the “ PROGRAM ” switch to 44.
– Press the “ STOP ” key.
The program is activated.
The sewing head is lowered and the needle plate and sewing foot raised.
– Press the “ START ” key.
– With the “
Σ
” key the sewing head can now be raised or lowered as often as desired.
4.8
Display of the Synchronizer Position
Program 45 shows the position of the synchronizer.
– Set the “ PROGRAM ” switch to 45.
– Press the “ STOP ” key.
The program is activated.
Display: P45 POS 1 , 2 , 3
* *
The asterisks in the lower line of the display show the current position of the synchronizer.
11
4.9
Timer Test and Memory Test
Program 59 checks the working memory ( RAM ) and all timer switchings of the controls.
– Set the “ PROGRAM ” switch to 59.
– Press the “ STOP ” key.
The program is activated.
Display
OK
ERROR 0
ERROR 6
ERROR 7
ERROR 8
ERROR 9
Explanation
Working memory and all timer switchings are okay
RAM error
Timer 1 defective
Timer 2 defective
Timer 3 defective ( expansion card )
Timer 4 defective ( expansion card )
4.10 Continuity Test
Program 60 checks if the 24 V electrical supply delivers current with the output drivers turned off. Then the program checks all existing output elements ( including output drivers and installation) as to continuity.
– Set the “ PROGRAM ” switch to 60.
– Press the “ STOP ” key.
The program is activated.
Display
V?
OK s23
( Example )
Explanation
Short circuit in the installation or one of the output drivers is defective.
All circuits have continuity
Interruption in the output element s23, in its installation or driver.
Output element s23 does not exist because it is part of the special accessories.
Continue the check at the next element by pressing the “
Σ
” key.
4.11 Test of the Front Panel Elements
Program 61 checks the front panel elements.
– Set the “ PROGRAM ” switch to 61.
– Press the “ STOP ” key.
The program is activated.
Continued on the next page !
12
– Operate the pre-selector switch on the front panel.
The display shows the current setting value of the last operated pre-selector switch.
When pressing a key on the front panel ( Exception: STOP key ) the number assigned to this switch ( 1, 2, 4, 8 ) is shown.
– The light diodes on the front panel are selected by code number.
The short designations of the circuit diagram ( 1...8 ) serve as the code numbers.
The light diodes are turned on by pressing the “ O ” key.
Designation b825 b814 b815 b816 b817 b818 b819 b820 b821
LED
H3
H4
H5
H6
Switch b417 b401 b402 b413/b412 b416
Function
Function switch
House-shaped seam rpm
Maximum rpm
Program switch
Stop ( Key 13 )
Key b415
Function
Stop ( Off )
Threading
Relocate seam beginning
Reset counter
Clear ( Cancel )
Start ( On )
Dry run / Terminate
Sewing suppression
Minus
Plus
Function Indicator
Indicator “ Sewing suppression ”
Indicator “ Start ready ”
Indicator “ Dry run ”
Indicator “ Sewing suppression ”
PROGRAM
STOP
Symbol Indicator display display
LED
LED
LED
13
4.12 Test of the Input Elements
Program 62 shows the switching status of any desired input element.
– Set the “ PROGRAM ” switch to 62.
– Press the “ STOP ” key.
The program is activated.
– Press the input element to be checked.
The display shows the circuit diagram designation and the switching status of the input element ( e.g. “ +B25 ” ).
The display changes when the switching status of any other input element is changed.
The switching status “ + ” means: by contact switches by proximity switches
= open contact
= Metal in front of the switches by reflected light barrier = No reflection by light beam barrier = Light beam not interrupted
4.13 Selecting Input Elements
ATTENTION !
All input elements have been carefully set at the factory.
Adjustment and correction may only be carried out by trained service personnel.
Program 63 sets the input elements.
– Set the “ PROGRAM ” switch to 63.
– Press the “ STOP ” key.
The program is activated.
– Set the “ PROGRAM ” switch to the code number of the desired input element.
The short designations of the circuit diagram serve as the code numbers ( see table ). This does not apply for the keys on the front panel ( see “ Test of the Front Panel Elements ” ).
– The display shows the circuit diagram designation and the switching status of the input element ( e.g. “ B14 ” ).
– Adjust the input element ( e.g. proximity switches ) until the desired switching status is shown in the display.
The meaning of the switching statuses corresponds to the switching statuses in program P62.
The table for the input elements is to be found on the next page !
14
Input element b8 b9 b10 b11 b12 b14 b1 b2 b3 b4 b5 b6 b7 b15 b16 b17 b18 b19 b20 b21 b22 b23 b24 b25 b26 b27 b28 b29 b30 b31 b32 b44 b45
Function
Right pedal
Initiator-Cross seam/right
Initiator-Sewing/base position right
Inititator-Sewing/quickly right
Initiator-Intermediate position/right clamping table
Initiator-Sewing position/right clamping table
Initiator-Base position/right clamping table
Left pedal
Initiator-Sewing/quickly left
Initiator-Base position/left
Initiator-Pinner/right ( Option )
Initiator-Pinner/left ( Option )
Phase monitor
Reserve/right clamping table
Initiator-Cross seam/left
Limit switch-Sewing head/up
Limit switch-Sewing head/down
Limit switch-Needle plate/down
Limit switch-Needle plate/up
Pressure monitor
Key-Interval/right clamping table
Hold-down forward/right clamping table
Hold-down to the back/right clamping table
Interior slide/right clamping table
Key-interval/left clamping table
Hold-down to the back/left clamping table
Hold-down forward/left clamping table
Interior slide/left clamping table
Base position/left clamping table
Initiator-Sewing position/left clamping table
Initiator-Intermediate position/left clamping table
Light barrier/left clamping table
Light barrier/right clamping table
15
4.14 Selecting Output Elements
Caution Risk of Injury !
During function testing of the output elements do not reach into the running sewing unit.
Select your position so that no injury is possible.
s1 s2 s3 s4 s7 s8 s9 s10 s11 s12 s14 s17 s18 s19 s21 s22 s23 s24 s25 s26 s30 s31
Program 64 tests the output elements.
– Set the “ PROGRAM ” switch to 64.
– Press the “ STOP ” key.
The program is activated.
– Set the “ PROGRAM ” switch to the code number of the desired output element.
The short designations of the circuit diagram apply as the code numbers ( see table ).
– Press the “ O ” key.
The output element is turned on or off.
Output element Function
Brake-Left clamping table/Output 1
Brake-Left clamping table/Output 2
Coupling-Left clamping table/Output 1
Coupling-Left clamping table/Output 2
Valve-Pinner/right clamping table
Valve-Pinner/left clamping table
Thread tension ( Power output )
Thread trimmer ( Power output )
Coupling-Sewing head ( Power output )
Coupling-Left corpus ( Power output )
Coupling-Right corpus ( Power output )
Brake-Right clamping table/Output 1
Coupling-Right clamping table/Output 2
Coupling-Right clamping table/Output 2
Brake-Right clamping table/Output 2
Valve-Sewing head/raise
Valve-Brake
Valve-Sewing foot/lower
Valve-Sewing head/lower
Valve-Sewing foot/raise
Valve-Beard clamp/Left clamping table
Valve-Beard clamp/Right clamping table
16
4.15 Positioning in the 2nd Position
Program 66 runs the needle into the 2nd position.
– Set the “ PROGRAM ” switch to 66.
– Press the “ STOP ” key.
The program is activated. Display shows “ SW ? ”.
– Set the drive rpm with the “ PROGRAM ” switch at 01 to 13.
01 = Minimum rpm
13 = Maximum rpm
– Press the “ O ” key.
The drive runs at the desired rpm.
The actual rpm is displayed after a few seconds.
– Release the “ O ” key.
The needle is positioned in the 2nd position ( thread lever high position ).
4.16 Positioning in the 1st Position
Program 67 runs the needle into the 1st position.
– Set the “ PROGRAM ” switch to 67.
– Press the “ STOP ” key.
The program is activated. The display shows “ SW ? ”.
– Set the drive rpm with the “ PROGRAM ” switch at 01 to 13.
01 = Minimum rpm
13 = Maximum rpm
– Press the “ O ” key.
The drive runs at with the desired rpm.
The actual rpm is displayed after a few seconds.
– Release the “ O ” key.
The needle is positioned in the 1st position.
4.17 Positioning in the 1st and 2nd Position
Program 68 positions the needle in the 1st and 2nd positions.
– Set the “ PROGRAM ” switch to 68.
– Press the “ STOP ” key.
The program is activated. The display shows “ SW ? ”.
– Set the drive rpm with the “ PROGRAM ” switch at 01 to 13.
01 = Minimum rpm
13 = Maximum rpm
– Press the “ O ” key.
The drive runs at the desired rpm.
The actual rpm is displayed after a few seconds.
– Release the “ O ” key.
The needle is positioned in the 1st position. Then, after a short pause, the needle is positioned in the 2nd position.
17
5.
Function Displays and Error Messages
5.1
Display of the Operating Aids
Display
P?
975A01
Σ
= xxxx
Explanation
Invalid program selected
Display of the program version
Piece counter
Remedy
Reset the “ Program ” switch
—————-
—————-
5.2 Error Messages of the Sewing Program
Display
ERROR 10
Explanation
Phase direction of rotation incorrect
ERROR 11
ERROR 12
ERROR 13
ERROR 14
ERROR 15
ERROR 16
ERROR 17
ERROR 18
ERROR 19
ERROR 20
ERROR 21
ERROR 22
ERROR 23
ERROR 24
Air pressure too low
Base position-left is missing
Base position-right is missing
Thread lever is not up
By units with 2 synchronizers, also synchronizers interchanged
Hold-down/left is displaced
Hold-down/right is displaced
Machine head is not up
(inspite of having been called up)
Needle plate is not down
(inspite of having been called up)
Light barrier/left is not free
Light barrier/right is not free
Interior slide/left is not to the back
Interior slide/right is not to the back
Machine head is not down
(inspite of having been called up)
Needle plate is not up
(inspite of having been called up)
ERROR 25
ERROR 26
ERROR 27
ERROR 28
ERROR 29
ERROR 30
ERROR 31
ERROR 32
ERROR 33
Keypad pressed when turning on
Pedal/left pressed when turning on
Pedal/right pressed when turning on
Both switches/ hold-down left triggered
No switches/hold-down left triggered
Both switches/hold-down right triggered
No switches/hold-down right triggered
Both switches/needle plate triggered
No switches/needle plate triggered
Continued on the next page !
18
Remedy
Power supplie x1: change phases L1+L2
Bridge X3.1 - X3.2 is missing.
See Componect Connection Diagram !
Increase the compressed air supply.
Bring the clamping table into the base position with the hand crank.
Bring the clamping table into the base position with the hand crank.
Turn the handwheel.
Interchange synchronizer.
Bring into the base position manually.
Bring into the base position manually.
Check the cylinder.
Check the cylinder
Remove sewing piece or foreign object.
Remove sewing piece or foreign object.
Bring into position manually.
Bring into position manually.
Check the cylinder.
Check the cylinder.
Re-start the sewing unit.
Re-start the sewing unit.
Re-start the sewing unit.
Check the limit switches.
Check the limit switches.
Check the limit switches.
Check the limit switches.
Check the limit switches.
Check the limit switches.
Display
ERROR 34
ERROR 35
Explanation
Both switches/sewing head triggered
No switches/sewing head triggered
ERROR 36
ERROR 37
More than 1 initiator on the left clamping table triggered.
More than 1 initiator on the right clamping table triggered.
ERROR 38
ERROR 39
ERROR 40
ERROR 41
ERROR 42
ERROR 43
Timing error
Sewing position-left reached too late
Timing error
Sewing position left reached too soon
Timing error
Sewing position right reached too late
Timing error
Sewing position right reached too soon
Sewing position-right left while sewing
Sewing position-left left while sewing
ERROR 44 Both large guide disks have left the base position
ERROR 45
ERROR 46
Interior slide-left does not move forward
Interior slide-right does not move forward
ERROR 47
ERROR 48
Thread lever error when leaving the base position of the large guide disk-left
Thread lever error when leaving the base position of the large guide disk-right
ERROR 49
ERROR 50
Synchronizer does not work correctly
Sewing head is not down when sewing
ERROR 51
ERROR 52
Reasonableness error in the initiator evaluation of the large guide disk-left
Reasonableness error in the initiator evaluation of the large guide disk-right
Remedy
Check the limit switches.
Check the limit switches.
Check the initiators, switching disks and aluminium strips.
Check the initiators, switching disks and aluminium strips.
Check the coupling/ clamping table-left.
Check the coupling/ clamping table-left.
Check the coupling/ clamping table-right.
Check the coupling/ clamping table-right.
Check the coupling ( s18 / s19 ).
Check the coupling ( s3 / s4 ).
Check the aluminium strips, initiators and coupling/clamping table.
Check the limit switches.
Check the limit switches.
Check the synchronizer and coupling/ machine head.
Check the synchronizer and coupling/ machine head.
Check the synchronizer.
Check the limit switch on the sewing head.
Check the initiators and aluminium strips.
Check the initiators and aluminium strips.
19
5.3
Error Messages of the Controls
Display Explanation
DISP-Err Display error when turning on
ERROR 0
ERROR 2
ERROR 3
ERROR 4
ERROR 5
ERROR 6
ERROR 7
ERROR 8
ERROR 9
RAM error in program 59
Error in reading the front panel elements
Program switch defective
Regulator card for sewing drive defective
Short voltage drops in the mains
Timer 1 defective
Timer 2 defective
Timer 3 defective ( expansion card )
Timer 4 defective ( expansion card )
ERR B...
no SIO
ERR
Error in reading the input elements:
Defective or incorrectly set limit switches are shown in the display by their circuit diagram designations ( e.g. “ ERR B31 ” )
The controls have no SIO component
Interruption in the SIO send/receive loop
Remedy
—————-
Replace the controls
Check the front panel elements
Replace the program switch
Replace the controls
Stabilize the voltage supply
Replace the controls
Replace the controls
Replace the expansion card
Replace the expansion card
Replace defective switches
Reset the switches
Press the STOP key
Press the STOP key
20
advertisement
Related manuals
Frequently Answers and Questions
What are the primary functions of the Microcontrol 975-1-5?
How does the device display information and errors?
What is the purpose of the DIP-switch b417?
How do you activate the sewing suppression function?
What does pressing the 'Threading' key do?
advertisement