advertisement
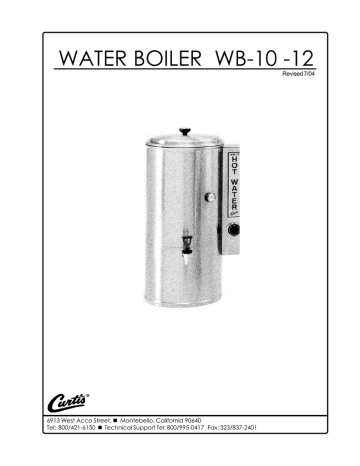
WATER BOILER WB-10 -12
Revised 7/04
6913 West Acco Street, Montebello, California 90640
Tel: 800/421-6150 Technical Support Tel: 800/995-0417 Fax: 323/837-2401
WATER BOILER - WB-10 -12
INSTALLATION INSTRUCTIONS
1. Unpack equipment carefully, inspect for any freight damage. Be sure to promptly put a claim into the freight company if any damage is found.
2. Connect faucet securely to the faucet adapter.
Electrical and plumbing hook-ups should be made by authorized installers only.
INSTALLATION MUST COMPLY WITH ALL NATIONAL AND LOCAL ELECTRICAL AND
PLUMBING CODES.
3. This water boiler can operate on 120, 208 or 220 volt power supply. To ground equipment, connect the ground wire to the green screw on inside bottom of wrap.
4. This boiler comes wired for 208 or 220 volt, single phase, 3 wire plus ground, see wiring diagram.
5. To connect the water boiler for 120 volt operation:
A. The facility will have two wires, one WHITE (neutral) and the other BLACK. Plus
GREEN for ground.
B. Splice the BLACK wire from power source, to both the heavy RED (#10 AWG) and thin BLACK (#18 AWG) wires from the WB-10.
C. Take the WHITE wire from the facility power source and splice it to the BLUE wire
(#10 AWG) and WHITE wire (#18 AWG) from the machine (see wiring diagram).
6. Water Hook-Up: Use a 1/4" copper line with a female flare fitting. Water inlet fitting is located on the back of the WB-10.
CAUTION Before turning thermostat dial to ON position, fill equipment with water up to the probe tip. This will prevent heating elements from burning out.
1
TROUBLE SHOOTING
PROBLEM: WATER WILL NOT REFILL
POSSIBLE CAUSE
1 . Water line closed or clogged filter
SOLUTION
Check the water system at your facility to make sure the line is open. Replace the water filter.
2 . Valve coil burned o u t
Turn machine off. Disconnect wires from water inlet coil terminals and connect a power cord to the terminals. Plug cord into a 120V outlet and verify if water flows when plugged in and stops when power is disconnected. If valve fails this test, replace valve.
3. Grounded probe When the water level gets below the probe tip, water should automatically refill the unit. If not, pull wire off the probe terminal. Water should now start flowing into the water boiler.
4 . Defective water level control board
Disconnect wire from probe terminal. With a voltmeter, check voltage at the water inlet coil terminals. This should read 110-120 volts. If no voltage is present, check liquid level control (L.L.C.) board. Make sure the L.L.C. board is supplied by 120V across terminals T2 & T3. The L.L.C. board is grounded to the body of the machine by contacting the board to the mounting bracket.
Make sure board is grounded here. Check for loose connections at terminals. Replace board.
PROBLEM: WATER OVERFLOWING.
POSSIBLE CAUSE
1 . Defective water inlet valve
SOLUTION
Turn power off and observe water level. If water continues to flow into the heating tank, clean or replace leaky valve.
2 . Probe limed up Disconnect wire from probe terminal. Touch the body of the heating tank with the terminal at the end of this wire. If water stops, try cleaning the probe. Probe may have to be replaced.
3 . Non-grounded or loose terminal connections at liquid level control board
Liquid level control board must be securely grounded through the back of the board and the mounting bracket. Check for loose connections at the terminals. Check for voltage across the inlet valve terminals. If there is 110 to 120 volts present at the inlet valve terminals when water level is touching the probe tip, replace the L.L.C. board.
PROBLEM: WATER DOES NOT REACH PROPER TEMPERATURE
POSSIBLE CAUSE
1 . Thermostat turned OFF (or set too low)
SOLUTION
Check thermostat to make sure the shaft is knob is rotated clockwise to the desired temperature.
2
TROUBLE SHOOTING CONTINUED:
PROBLEM: WATER DOES NOT REACH PROPER TEMPERATURE
POSSIBLE CAUSE
2 . Defective thermostat
SOLUTION
Replace thermostat if contacts are open when knob is fully clockwise and water temperature is less than 190º F. You will measure 120 volts (approximately) to ground from both thermostat terminals when it is ON and from only one terminal when it is OFF.
3 . Burned out heating element
In this water boiler there are two elements in parallel. Failure of either will cause very slow heating. Perform the following tests: a. Clamp-on ammeter test: If both elements are good, you will measure about 21 amps at 240 volts, 24 amps at
208 volts or 29 amps at 120 volts. If you measure only 10 to 12 amps, check the current to each element to identify the defective part.
b . Ohmmeter or continuity test: Disconnect all power by unplugging unit. Disconnect one terminal to measure each element. They should each have continuity or measure about 20 ohms.
PROBLEM: WATER OVERHEATS, ELEMENTS DO NOT SHUT OFF
POSSIBLE CAUSE
1 . Defective thermostat
SOLUTION
Replace the thermostat. You can sometimes operate temporarily by turning the thermostat knob to off until the boiling stops.
3
ILLUSTRATED PARTS LIST
Water Boiler – WB-10-12
B
4
WATER BOILER - WB-10-12
INDEX
N º
27
28
29
30
31
22
23
24
25
26
32
33
34
35
36
17
18
19
20
21
12
13
14
15
16
5
6
7
8
9
10
11
1
2
3
4
PART N º
WC-3205
WC-5602
WC-4600
WC-4204
WC-5502
WC-4383
WC-2966
WC-5386
WC-2401
WC-4392
WC- 801
WC- 511
WC- 922
WC-4304
WC-1800HW
WC-1906
WC-3217
WC-3220
WC- 501
WC-4426
WC-3914
WC-4439
WC- 409
WC-3700
WC- 813
WC- 608
WC-1903
WC-4211
WC-4237
WC-4320
WC-3402
WC-1901
WC-3705HW
WC-1902
WC-5611
WC-4203
DESCRIPTION
KNOB, LID . . . . . . . . . . . . . . . . . . . . . . . . . . . . . . . . . . .
LID WITH KNOB . . . . . . . . . . . . . . . . . . . . . . . . . . . . . .
SCREW, 1/4"-20 x 3/8" ROUND HEAD . . . . . . . . . . . . . . . .
NUT, 1/8" BRASS LOCK . . . . . . . . . . . . . . . . . . . . . . . . . .
PROBE, WATER LEVEL . . . . . . . . . . . . . . . . . . . . . . . . . .
SPACER, 1/2" DIA. ALUMINUM, 8-32 TAP. . . . . . . . . . . . . .
FITTING, WATER INLET 1/4" FLARE . . . . . . . . . . . . . . . . .
TUBING ASSEMBLY, 1/4" WATER INLET . . . . . . . . . . . . .
FITTING, 1/4" x 3/8" FLARE BRASS ELBOW . . . . . . . . . . . .
BUSHING, 1" SNAP IN . . . . . . . . . . . . . . . . . . . . . . . . . .
VALVE, WATER INLET S-45 . . . . . . . . . . . . . . . . . . . . . .
THERMOMETER, DIAL . . . . . . . . . . . . . . . . . . . . . . . . . .
HEATING ELEMENT, 3500 WATT, 220VOLT .. . . . . . . . . . .
WASHER, TEFLON 3/8" I.D. . . . . . . . . . . . . . . . . . . . . . .
S-FAUCET, RED HANDLE . . . . . . . . . . . . . . . . . . . . . . . . .
C- RING . . . . . . . . . . . . . . . . . . . . . . . . . . . . . . . . . . . . .
KNOB, THERMOSTAT . . . . . . . . . . . . . . . . . . . . . . . . . . . .
BEZEL, THERMOSTAT . . . . . . . . . . . . . . . . . . . . . . . . . . .
THERMOSTAT, D-18 . . . . . . . . . . . . . . . . . . . . . . . . . . .
SCREW, 8-32 x 3/8" PAN HEAD TRUSS . . . . . . . . . . . . .
LABEL, "HOT WATER" (WB-10) . . . . . . . . . . . . . . . . . . . . .
SCREW, 6-32 x 1/4" PH PAN HEAD SS . . . . . . . . . . . . . .
COIL, 115V (DOLE VALVES) . . . . . . . . . . . . . . . . . . . . . .
KIT, REPAIR INLET VALVE . . . . . . . . . . . . . . . . . . . . . . .
WASHER, 1/2" FLOW .5 G.P.M. (S-45) . . . . . . . . . . . . . . . .
CONTROL BOARD, WATER LEVEL . . . . . . . . . . . . . . . . . .
NUT, SHANK UNION . . . . . . . . . . . . . . . . . . . . . . . . . . . . .
NUT, 3/8" JAM PLATED . . . . . . . . . . . . . . . . . . . . . . . . . .
NUT, 7/16-20" HEX BRASS . . . . . . . . . . . . . . . . . . . . . . .
O- RING . . . . . . . . . . . . . . . . . . . . . . . . . . . . . . . . . . . . . .
SPRING, RETURN "S" SERIES FAUCET . . . . . . . . . . . . . .
NUT, CHROME PLATED . . . . . . . . . . . . . . . . . . . . . . . . . .
KIT, REPAIR FAUCET . . . . . . . . . . . . . . . . . . . . . . . . . . . . .
NUT, SHANK FLANGED . . . . . . . . . . . . . . . . . . . . . . . . . .
COVER, BOTTOM . . . . . . . . . . . . . . . . . . . . . . . . . . . . . . .
NUT, 3/8-24 JAM PLATED . . . . . . . . . . . . . . . . . . . . . . . .
5
Water Boiler WB 10 -12
120 VOLTS, 2100 WATTS, 17.5 AMPS, 1Ø
THERMOSTAT
6 3
L1
N
GND
BLACK
WHITE
GRN z z
RED #10
BLUE #10
INLET
VALVE
1 2
BLUE
BLACK #18
WHITE
WHITE
ORANGE
PROBE
T1
T2
T3
T4
L
WATER
LEVEL
CONTROL
BOARD
{
2 - 3.5 KW HEATING
ELEMENTS z z z z z
{
Rev. 4/15/98
Single Phase 3 Wire
208 VOLT, 6300 WATT, 30 AMP
220 VOLT, 7000 WATT, 32 AMP
240 VOLT, 8400 WATT, 35 AMP
L1
NEUTRAL
L2
GROUND
INLET
VALVE z z z
RED #10
PROBE
BLUE #10
BLUE
BLACK #10
WHITE
WHITE
ORANGE
THERMOSTAT
6 3
1 2
T3
T4
T1
T2
6
L
WATER
LEVEL
CONTROL
BOARD
{
2 - 3.5 KW HEATING
ELEMENTS z z z z
{ z
Rev. 4/15/98
Product Warranty Information
The Wilbur Curtis Company certifies that its products are free from defects in material and workmanship under normal use. The following limited warranties and conditions apply:
Additionally, the Wilbur Curtis Company warrants its Grinding Burrs for Forty (40) months from date of purchase or 40,000 pounds of coffee, whichever comes first. Stainless Steel components are warranted for two (2) years from date of purchase against leaking or pitting and replacement parts are warranted for ninety (90) days from date of purchase or for the remainder of the limited warranty period of the equipment in which the component is installed.
All in-warranty service calls must have prior authorization. For Authorization, call the Technical Support Department at 1-800-995-0417. Effective date of this policy is April 1, 2003.
Additional conditions may apply. Go to www.wilburcurtis.com to view the full product warranty information.
CONDITIONS & EXCEPTIONS
The warranty covers original equipment at time of purchase only. The Wilbur Curtis Company, Inc., assumes no responsibility for substitute replacement parts installed on Curtis equipment that have not been purchased from the
Wilbur Curtis Company, Inc. The Wilbur Curtis Company will not accept any responsibility if the following conditions are not met. The warranty does not cover and is void under the following circumstances: electrical, mechanical and plumbing codes.
responsibility of the equipment owner. The owner is responsible for proper cleaning and regular maintenance of this equipment.
Dama ged in transit: for variation in equipment operation due to excessive lime or local water conditions. The equipment must be maintained according to the manufacturer’s recommendations.
gaskets, silicone tube, canister assemblies, whipper chambers and plates, mixing bowls, agitation assemblies and whipper propellers.
normal use. All labor shall be performed during regular working hours. Overtime charges are the responsibility of the owner. Charges incurred by delays, waiting time, or operating restrictions that hinder the service technician’s ability to perform service is the responsibility of the owner of the equipment. This includes institutional and correctional facilities. The Wilbur Curtis Company will allow up to 100 miles, round trip, per in-warranty service call.
RETURN MERCHANDISE AUTHORIZA TION: All claims under this warranty must be submitted to the Wilbur Curtis Company Technical
Support Department prior to performing any repair work or return of this equipment to the factory. All returned equipment must be repackaged
WILL BE ACCEPTED A RETURN MERCHANDISE
Technical Support Department to find an agent near you.
AUTHORIZA TION (RMA).
RMA NUMBER MUST BE MARKED ON
WILBUR CURTIS CO., INC.
Factory & RMA Address:
Web Address:
Fax:
6913 Acco St., Montebello, CA 90640 Customer Service Tel: 800/421-6150 www.wilburcurtis.com
323/837-2406 Technical Support E-Mail: [email protected] Technical Support Tel: 800/995-0417
7/12/04 F-1984 rev B
advertisement
Related manuals
advertisement