- Home
- Domestic appliances
- Large home appliances
- Water heaters & boilers
- Carrier
- 58SX040-IBC
- User manual
Carrier 58SX040-IBC Furnace User Manual
Add to my manuals
8 Pages
Carrier 58SX040-IBC is a deluxe gas-fired condensing furnace designed for indoor installation. It features a compact size, making it suitable for confined spaces without special ventilation requirements. With its efficient operation, the furnace minimizes energy consumption and reduces heating costs. The unit comes with a 2-1/2 x 2-1/2-inch rubber coupling and an optional 2-1/2 x 2-inch coupling for flexible installation options. The furnace is equipped with a tuning valve for precise adjustment and optimization of performance.
advertisement
▼
Scroll to page 2
of 8
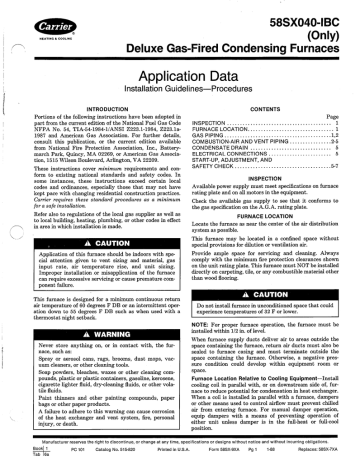
ED HEATING & COOLING 58SX040-IBC (Only) Deluxe Gas-Fired Condensing Furnaces Application Data Installation Guidelines—Procedures INTRODUCTION Portions of the following instructions have been adopted in part from the current edition of the National Fuel Gas Code NFPA No. 54, TIA-54-1984-1/ANSI Z223.1-1984, Z223.1a- 1987 and American Gas Association. For further details, consult this publication, or the current edition available from National Fire Protection Association, Inc, Battery- march Park, Quincy, MA 02269, or American Gas Associa- tion, 1515 Wilson Boulevard, Arlington, VA 22209. These instructions cover minimum requirements and con- form to existing national standards and safety codes. In some instances, these instructions exceed certain local codes and ordinances, especially those that may not have kept pace with changing residential construction practices. Carrier requires these standard procedures as a minimum for a safe installation. Refer also to regulations of the local gas supplier as well as to local building, heating, plumbing, or other codes in effect in area in which installation is made. A CAUTION Application of this furnace should be indoors with spe- cial attention given to vent sizing and material, gas input rate, air temperature rise, and unit sizing. Improper installation or misapplication of the furnace can require excessive servicing or cause premature com- ponent failure. This furnace is designed for a minimum continuous return air temperature of 60 degrees F DB or an intermittent oper- ation down to 55 degrees F DB such as when used with a thermostat night setback. A WARNING Never store anything on, or in contact with, the fur- nace, such as: Spray or aerosol cans, rags, brooms, dust mops, vac- uum cleaners, or other cleaning tools. | Soap powders, bleaches, waxes or other cleaning com- pounds, plastic or plastic containers, gasoline, kerosene, cigarette lighter fluid, dry-cleaning fluids, or other vola- tile fluids. Paint thinners and other painting compounds, paper bags or other paper products. A failure to adhere to this warning can cause corrosion of the heat exchanger and vent system, fire, personal injury, or death. CONTENTS Page INSPECTION ........... неее. La ee ea ea ea ee ae ea ane» 1 FURNACE LOCATION. «o.oo icici cee 1 GAS PIPING «oi etter eee 1,2 COMBUSTION-AIRAND VENTPIPING ................ 2-5 CONDENSATE DRAIN ............esrenedrerereorec.. 5 ELECTRICAL CONNECTIONS .... iia 5 START-UP, ADJUSTMENT, AND SAFETY CH ECK rear re 5-7 INSPECTION Available power supply must meet specifications on furnace rating plate and on all motors in the equipment. Check the available gas supply to see that it conforms to the gas specification on the A.G.A. rating plate. FURNACE LOCATION Locate the furnace as near the center of the air distribution system as possible. This furnace may be located in a confined space without special provisions for dilution or ventilation air. Provide ample space for servicing and cleaning. Always comply with the minimum fire protection clearances shown on the unit rating plate. This furnace must NOT be installed directly on carpeting, tile, or any combustible material other than wood flooring. A CAUTION Do not install furnace in unconditioned space that could experience temperatures of 32 F or lower. NOTE: For proper furnace operation, the furnace must be installed within 1/2 in. of level. | When furnace supply ducts deliver air to areas outside the space containing the furnace, return air ducts must also be sealed to furnace casing and must terminate outside the space containing the furnace. Otherwise, a negative pres- sure condition could develop within equipment room or space. Furnace Location Relative to Cooling Equipment—Instali cooling coil in parallel with, or on downstream side of, fur- nace to reduce potential for condensation in heat exchanger. When a coil is installed in parallel with a furnace, dampers or other means used to control airflow must prevent chilled air from entering furnace. For manual damper operation, equip dampers with a means of preventing operation of either unit unless damper is in the full-heat or full-cool position. Manufacturer reserves the right to discontinue, or change at any time, specifications or designs without notice and without incurring obligations. Catalog No. 515-820 Book 1 PC 101 Tab |6a Printed in U.S.A. Form 58SX-9XA Pg 1 1-88 Repiaces: 58SX-7XA Special Locations—When installing furnace in a residential garage, protect it from physical damage by vehicles. Fur- naces installed in public garages, airplane hangers, or other buildings having hazardous atmospheres must comply with requirements of the National Fire Protection Association, Inc.- GAS PIPING Gas piping must be installed in accordance with national and local codes. Run a separate gas supply line directly from the meter to the furnace, if possible. Table 1 shows recommended gas pipe sizing. Slope all pipe 1/4 inch in 15 ft to prevent traps. Slope all horizontal runs away from meter and toward risers. Use risers to connect lines to furnace and meter. Apply joint compounds (pipe dope) sparingly and only to male threads of joints. Consult local gas supplier for com- pound recommendations. . NOTE: Use only compounds resistant to the action of LP (propane) gas. Install a sediment trap in the riser leading to the furnace to trap dirt and condensate. Connect a tee to the riser leading to the furnace, keeping straight-through section of tee verti- cal. Connect a capped nipple into lower end of tee, so that nipple extends below level of gas controls (Fig. 1). Where a gum filter is required by local codes, install it in accordance with their requirements. An accessible manual shutoff valve must be installed upstream of furnace gas controls and within 6 ft of furnace. A 1/8-in. NPT plugged tapping, accessible for test-gage con- nection, must also be installed immediately upstream of gas supply connection to furnace and downstream of manual shutoff valve. Install a ground joint union between gas control manifold and manual gas shutoff valve (Fig. 1). A CAUTION Use a backup wrench when connecting gas pipe to fur- nace to avoid damaging gas controls. A WARNING Use the proper length of pipes to avoid stress on the gas control manifold. A failure to adhere to this warn- ing can cause a gas leak resulting in a fire, explosion, physical injury, or death. Protect all segments of the piping system against physical and thermal damage. Support all piping with appropriate straps or hangers (one hanger every 6 ft minimum). For pipe Table 1—Maximum Capacity of Pipe* NOMINAL INTERNAL IRON PIPE DIAMETER LENGTH OF PIPE (ft) SIZE (in.) (in.) 10 20 30 40 50 12 _ 0.6022 175 120 97 82 13 3/4 0.824 360 250 200 | 170 | 151 1 1.049 680 465 375 | 320 | 285 1-1/4 1.380 1400 950 770 | 660 | 580 1-1/2 1.610 2100 | 1460 | 1180 | 990 | 900 Ref; Table C4 NFPA 54-1984 *Cubic ft of gas per hour, for gas pressures of 0.5 psig (14 in. wc) or less, and a pressure drop of 0.5 in. wc (based on a 0.60 specific gravity gas). GAS SUPPLY MANUAL SHUTOFF VALVE SEDIMENT TRAP UNION A84218 Fig. 1—Ground Joint Union and Sediment Trap sizes larger than 1/ 21 in., follow recommendations of national codes. A CAUTION If a flexible connector is required or allowed by the authority having jurisdiction, black iron pipe must be installed at the gas valve and extend a minimum of 2 in. outside the furnace casing. Pressure-test piping in accordance with local and national plumbing and gas codes before attaching furnace. Crack ground joint union before pressure testing. If pressure “exceeds 0.5 psig (14 in. we), disconnect gas supply line from furnace before performing pressure test. If test pressure is equal to or less than 0.5 psig (14 in. wc), close manual shut- off valve located on gas valve before testing. After final connection to the furnace has been made, purge lines and check for leakage with regulated gas supply pressure. A WARNING Never purge line into combustion chamber. Never use matches, candles, flame, or other sources of ignition to check for gas leakage. Use a soap-and-water solution to check for leaks. A failure to adhere to this warning can cause a fire, explosion, physical injury, or death. COMBUSTION-AIR AND VENT PIPING The combustion-air and vent pipe and fittings must con- form to American National Standards Institute (ANSI) standards and American Society for Testing and Materials (ASTM) standards D1785 (schedule-40 PVC), D2665 (PVC- DWV), D2441 (SDR-21 and SDR-26 PVC) or D2661 (ABS- DWYV). Pipe cement and primer must conform to ASTM standards D2564 (PVC) or D2235 (ABS). See Table 3 for pipe sizing and Fig. 3 through 5 for exterior piping arrange- ments. See “High-Altitude Pipe Sizing Procedures’ section for high-altitude applications. The unit is shipped with a 2-1/2 x 2-1/2-in. rubber coupling. An optional coupling size 2-1/2 x 2-in. is available through the Distributor or Branch. See the Replacement Parts cata- log for the part number. —2— a da Ea Aa = 4/2-1N. fa =] ARMAFLEX || В VALVE iQ! | a | Ц IS IN. т y I Ee LEFT SIDE OPTIONAL LJ f A84219 Fig. 2— Tuning Valve Location The accessory vent terminal kit described below must be used in constructing the vent terminal for this unit. Pipes must terminate through either the roof or the sidewall; roof termination is preferable. Locate sidewall terminations to prevent damage to shrubs, condensing unit, and siding materials. Table 2 gives clearance requirements. A CAUTION Combustion air must not be taken from inside the structure because that air frequently is contaminated by halogens, which include fluorides, chlorides, bro- mides, and iodides. These elements are found in aero- sols, detergents, bleaches, cleaning solvents, salts, air fresheners, and other household products. Vapors from these products are highly corrosive to gas-fired fur- naces, even in extremely low concentrations (as low as 0.5 ppm). | Maintain a minimum of 36-in. between combustion-air inlet and clothes-dryer vent. Locate the combustion-air inlet as far as possible from the swimming pool and swimming pool pump house. NOTE: When a previously common-vented system (furnace and water heater) is converted to water heater only, the vent system may be drastically oversized for the water heater. Consult the National Fuel Gas Code for proper siz- ing of the vent and revise the system if necessary. Table 2—Combustion-Air and Vent Terminal Clearances LOCATION CLEARANCE Dryer vent 3ft From plumbing vent stack 3 ft Gas appliance vent terminal | 4 ft From any opening where vent gases 12 in. could enter building Above grade and anticipated snow depth 12 in. Above grade when adjacent to public 7 ft walkway | A CAUTION When the vent pipe is exposed to temperatures below freezing i.e. when it passes through an unheated space or when a chimney is used as a raceway, the pipe must be insulated with 1/2-inch thick Armaflex-type insulation. NOTE: The vent pipe must be insulated with 1/2-in. thick Armaflex insulation from the tuning valve to the point where the pipe exits the structure. A CAUTION When the combustion-air pipe is installed above a sus- pended ceiling, the pipe must be installed with 1/2-in. Armaflex insulation. | The combustion-air pipe should also be insulated in warm, humid spaces such as basements. A WARNING Solvent cements are combustible. Keep away from heat, sparks, and open flame. Use only in well ventilated areas. DO NOT breathe vapors. Avoid contact with the skin or eyes. À failure to adhere to this warning can cause a fire or physical injury. A WARNING All combustion-air and vent pipes must be airtight and watertight. Pipes must terminate exactly as shown in - Fig. 3 through 5. A failure to adhere to this warning can cause property damage, physical injury, or death. Furnace is shipped from factory assembled for right-hand vent pipe connection. When left-hand vent connection is desired, remove cap from left-hand side of inducer outlet box and install over hole in right-hand side of box. Remove plastic plug from left-hand casing side panel and install plug in unused hole in the right-hand casing side panel. Install the turning valve in the vertical riser of the vent pipe 18 in. above the elbow, as shown in Fig. 2. To install piping: Table 3— Pipe Diameter (in.) PIPE NUMBER OF 90° ELBOWS LENGTH (See Notes) (ft) 1 2 3 4 5 5 2 2 2 2 2 10 2 2 2 2 2 15 2 2 2 2 2 20 2 2 2 2 2 25 2 2 2 2 2 30 2 2 2 2 2 35 2 2 2 2 2 . NOTES: 1. Assume two 45° elbows equal one 90° elbow. 2. Diameters listed are for schedule-40 PVC, PVC-DWV or ABS-DWV pipe. 3. Long radius elbows are desirable. | 4. Elbows and pipe sections supplied in vent terminal kit should not be included in count. . Do not exceed 35 linear feet. on ROOF | q COUPLING LA < BRACKET = N В | COMBUSTION ns N | AIR VERTICAL SEPARATION — : BETWEEN COMBUSTION ” AIR AND VENT. 63 FOR 3"KIT 4: FOR 2" KIT ( \ MAINTAIN 12 IN. MINIMUM CLEARANCE ABOVE HIGHEST ANTICIPATED SNOW LEVEL. MAXIMUM OF 24 [N. ABOVE ROOF. A87224 Fig. 3— Rooftop Vent Terminal Installation ss OVERHANG | — — — m OVERHANG Da — — N - = So 12 IN. MINIMUM TT 12 IN. MINIMUM — — dd — LT 7 — 190° - | » COUPLING = > 12 IN. SEPARATION - BRACKET [2 iN. SEPARATION — BETWEEN BOTTOM OF — 90° | BETWEEN BOTTOM OF A, COMBUSTION AIR AND ——_____| — - ~~ COMBUSTION AIR AND BOTTOM OF VENT —_—_ COMBUSTION— BOTTOM OF VENT, : _AIR (ELBOW _.. ~~ PARALLEL TO т M7 ) _ WALL) ЗО MAINTAIN 12 IN. MAINTAIN 12 IN. CLEARANCE A (PA Y e CLEARANCE ABOVE ABOVE HIGHEST ANTICIPATED — AT ye ~~ HIGHEST ANTICIPATED SNOW LEVEL OR GRADE — | 15 N SNOW LEVEL OR GRADE — | MAXIMUM -— bc > 5. 6. A87225 Fig. 4—Sidewall Vent Terminal Installation (12 in. above snow level or grade) Attach factory-supplied flexible coupling to furnace combustion-air inlet connection and secure with stain- less steel hose clamp. Ensure that factory-supplied, perforated metal combustion-air disc is installed in the flexible coupling. Working from furnace to outside, cut PVC pipe to required length(s). Deburr inside and outside of pipe. Chamfer outside edge of pipe for better distribution of primer and cement. Clean and dry all surfaces to be joined. Check dry fit of pipe and mark insertion depth on pipe. NOTE: Al pipe should be cut, prepared, and preassembled before any joint is permanently cemented. 7. After pipes have been cut and preassembled, apply 10. 11. —A— A87226 Fig. 5—Sidewall Vent Terminal Installation (iess than 12 in. above snow level or grade) generous layer of PVC primer to pipe fitting socket and end of pipe to insertion mark. Quickly apply PVC cement (over primer) to end of pipe and fitting socket. Apply cement in light, uniform coat on inside of socket to prevent buildup of excess cement. Apply second coat of cement to end of pipe. . While the PVC cement is still wet, insert pipe into socket with a 1/4-turn twist. Be sure pipe is fully inserted into fitting socket. . Wipe excess cement from joint. A continuous bead of cement is visible around perimeter of a properly made joint. | Handle pipe joints carefully until cement sets. Support piping every 5 ft (minimum) using perforated metal hanging strap. Slope combustion-air and vent pipes toward furnace a minimum of 1/4-in./lineal ft with no sags between hangers. O 12. Use appropriate methods to seal openings where vent and combustion-air pipes pass through roof or sidewall. Vent Terminal Kit Installation—The combustion-air and vent pipes must terminate outside the structure. The Car- rier accessory vent termination kit for 2-in. diameter pipe (required) must be installed as shown in Fig. 3, 4 or 5. Roof termination, shown in Fig. 3, is preferred. The kit contains extra parts for the various applications. NOTE: The shaded portions of Fig. 8, 4 and 5 are consid- ered part of the vent terminal and are provided in the vent terminal kit. They should not be counted, therefore, in pipe diameter calculations. ROOFTOP VENT TERMINAL INSTALLATION (Fig. 3) NOTE: The solid-line arrangement in Fig. 3 is the preferred arrangement; the dashed-line arrangement is an option for the combustion-air pipe. 1. Remove one 90° elbow from elbow and bracket assem- bly provided in kit. Loosen screw so other elbow can turn. 2. Loosely install elbow with bracket on combustion-air pipe. 3. Loosely install pipe coupling, provided in kit, on prop- erly cut vent pipe. Position coupling so that bracket ~ will mount as shown in Fig. 3. 4. Disassemble loose pipe fittings. Clean them and apply cement using procedures described in Combustion-Air and Vent Piping. 5. Install bracket as shown in Fig. 3. | 6. For applications using combustion-air pipe option (indi- cated by dashed lines in Fig. 3), install 90-degree street ell into 90-degree elbow, making a U-fitting. Install the open end of 90-degree street ell onto combustion-air pipe. | SIDEWALL VENT TERMINAL INSTALLATION - Install kit as follows when combustion-air and vent pipes exit through sidewall 12 in. or more above highest antici- pated snow level or grade (Fig. 4). NOTE: The solid-line arrangement in Fig. 4 is preferred. The dashed-line arrangement is an option for the vent pipe only. 1. Loosely install elbow and bracket assembly on combustion-air and vent pipes. 2. Remove and disassemble elbow and bracket assembly. 3. Install elbows as shown in Fig. 4. Clean them and apply cement using procedures described in Com- bustion-Air and Vent Piping. 4. Install bracket as shown in Fig. 4. 5. Position vent-pipe assembly, maintaining a 12-in. sepa- ration. Cement vent pipe in elbow as shown in Fig. 4. 6. For applications using vent-pipe option (indicated by dashed lines in Fig. 4), rotate elbow 90° from position shown. Install kit as follows when combustion-air and vent pipes exit through sidewall less than 12 in. above highest antici- pated snow level or grade (Fig. 5): NOTE: The solid-line arrangement in Fig. 5 is preferred. The dashed-line arrangement shown is an option for the vent pipe only. 1. Remove one elbow from the elbow and bracket assem- bly. (The elbow remaining will be connected to combustion-air pipe). 2. Install the 90-degree street ell into the 90-degree elbow remaining in elbow and bracket assembly, making a U-fitting. . Loosely install coupling on end of vent pipe. 4. Loosely install U-fitting and bracket as shown in Fig. 5. Position U-fitting so that open end is against building wall. 5. Loosely install vent-pipe assembly in coupling as shown in Fig. 5. 6. Check required dimension as shown in Fig. 5. 7. Disassemble loose pipe fittings. Clean them and apply cement using procedures described in Combustion-Air and Vent Piping. 8. Install bracket as shown in Fig. 5. CONDENSATE DRAIN Route the condensate to a nearby floor drain or condensate pump. If a condensate pump is required, it should have a corrosion-resistant impeller and tank. The 1/2-inch diameter schedule 40 PVC or CPVC condensate drain pipe fittings must conform to ANSI standards and ASTM D1785 and D2846. The schedule 40 PVC or CPVC cement and primer must conform to ASTM F493 or D2564. For proper condensate drainage, furnace must be within 1/2-in. of level. Highest corner of furnace must not be more than 1/2-in. above lowest corner. NOTE: The furnace contains an internal condensate trap; do NOT install external trap. 1. Determine the side of furnace from which drain will exit. Cut and preassemble drain piping (field-supplied) directly to an open drain. Refer to Combustion-Air and Vent Piping for instructions on preparing and cement- ing plastic pipe. 2. Cement elbow on pipe assembly (factory supplied) to condensate trap mounted on blower housing. 3. Using a second wrench to hold assembly, attach first section of field-supplied drain pipe to compression cou- pling provided. 4. When using schedule 40 PVC drain pipe, connect adapter provided to end of pipe installed in compres- sion fitting. 5. Attach field-supplied schedule 40 PVC adapter to threaded factory adapter. 6. Cement remaining pipe joints. START-UP, ADJUSTMENT, AND SAFETY CHECK Adjusting Tuning Valve—Before firing the furnace, adjust the pressure drop through the heat exchanger for maximum efficiency, following the steps below. o A CAUTION Bes sure gas supply to furnace i is turned off. 1. Install field-supplied plastic tee between pressure tap on bottom of gas valve and pressure tube as shown in Fig. 6. 2. Install second field-supplied plastic tee between pres- sure switch and pressure tube from collector box. See Fig. 6. 3. Connect slope gage to tees (Fig. 6.) 4. Close R-W circuit to start inducer motor. 5. Adjust tuning valve to obtain 0.83 + 0.01 in. negative water column. 6. Remove handle from tuning valve and recheck pres- sure. Store handle in safe place. —5— 7. Open R-W circuit. . Disconnect slope gage. 9. Remove plastic tees and reconnect factory pressure tubes to gas valve and pressure switch. 10. Turn on gas supply to furnace. oo Ignition System Check—When all connections have been checked, light the furnace using procedure outlined on light- ing instruction attached to furnace. When lighting the fur- nace for the first time, however, perform the following addi- tional steps: 1. If gas supply was not purged before connecting fur- nace, line will be full of air. Loosen ground joint union and allow supply line to purge until gas odor is detected. Never purge gas lines into a combustion chamber. Immediately upon detection of gas odor, retighten union. After 5 minutes, light furnace in accordance with instructions on furnace rating plate. 2. Main burners should light 25 to 75 seconds after pilot. If main burners do not light within prescribed time period, check pilot flame. 3. The pilot flame should be soft blue in color and it must provide good impingement on the pilot switching ele- ment. The flame should extend above the burner carry- ‘over port to provide a proper burner ignition. When the pilot flame requires adjustment: a. Locate adjustment screw marked “PILOT ADJ” on top of gas valve. b. Remove cap and turn adjustment screw clockwise to decrease pilot gas flow. Turn screw counterclock- wise to increase pilot gas flow. c. When proper adjustment is obtained, replace screw cap. Gas Input NOTE: Be sure reference pressure tube, combustion-air and vent pipes, and burner enclosure front are in place when clocking the gas meter. 1. Determine gas input. a. Turn off all other gas appliances and pilots. b. Measure time (in seconds) for gas meter test dial to complete one revolution. c. Refer to Table 4 for cu ft of gas per hour. d. Multiply cu ft/hr by heating value of gas (Btu/cu ft) obtained from local gas utility. EXAMPLE: Btu heating input = Btu/cu ft times cu ft/hr Heating value of gas = 1070 Btu/cu ft Time for one revolution of 2-cu-ft dial = 72 sec Gas rate = 100 cu ft/hr (from Table 4) Btu heating input = 1070 x 100 = 107,000 Btuh e. Measured gas input must not exceed gas input on unit rating plate. 2. To adjust input rate: a. Remove burner enclosure front and cap that con- ceals adjustment screw for gas valve regulator. b. Turn adjusting screw either counterclockwise (out) to decrease input rate or clockwise to increase rate. When adjusting input rate, do NOT change mani- fold pressure more than 3.2 minimum to 3.8 maxi- mum in. wc. Make any major adjustments by changing main burner orifices. NOTE: Manifold pressure must always be measured with burner enclosure front removed. The gas meter must always be clocked with burner enclosure front installed. BURNER TUBE ASSY Dog PLASTIC TEES "a COLLECTOR BOX TUBE SLOPE GAGE OR DIGITAL MANOMETER 484500 Fig. 6—Tuning Valve Adjustment c. Replace burner enclosure front and measure adjusted gas input rate using method outlines in step 1. d. Replace cap that conceals gas valve regulator adjustment screw. NC ULI Be sure burner enclosure front is in place after adjust- ments have been made. 3. Look through sight glass in burner enclosure and check burner and pilot flame. The main burner flame should be clear blue, almost transparent. The pilot flame should be well defined. See Fig. 7. Table 4— Gas Rate in Cu Ft/Hr SECONDS SIZE OF SECONDS SIZE OF FOR ONE TEST DIAL FOR ONE TEST DIAL REVOLU- 1 2 5 REVOLU- 1 2 5 TION cu ft | cu ft | cu ft TION cu ft | cu ft | cu ft 10 360 | 720 | 1800 50 72 144 | 360 11 327 | 655 | 1636 51 71 141 | 355 12 300 | 600 | 1500 52 69 138 | 346 13 277 | 555 | 1385 53 68 136 | 340 14 257 | 514 | 1286 54 67 133 | 333 15 240 | 480 | 1200 55 65 131 | 327 16 225 | 450 | 1125 56 64 129 | 321 17 212 | 424 | 1059 57 63 126 | 316 18 200 | 400 | 1000 58 62 124 | 310 19 189 | 379 947 59 61 122 | 305 20 180 | 360 900 60 60 120 | 300 21 171 | 343 857 62 58 116 | 290 22 164 | 327 818 64 56 112 | 281 23 157 i 313 783 66 54 109 | 273 24 150 | 300 750 68 53 106 | 265 25 144 | 288 720 70 51 103 | 257 26 138 | 277 692 72 50 100 | 250 27 133 | 267 667 74 48 97 | 243 28 129 | 257 643 76 47 95 | 237 29 124 | 248 621 78 46 92 | 231 30 120 | 240 600 80 | 45 90 | 225 31 116 | 232 581 82 44 88 | 220 32 113 | 225 563 84 43 86 | 214 33 109 | 218 545 86 42 84 | 209 34 106 | 212 529 88 41 82 | 205 35 103 | 206 514 90 40 80 | 200 36 100 | 200 500 92 39 78 | 196 37 97 | 195 486 94 38 76 | 192 38 95 | 189 474 96 38 75 | 188 39 92 | 185 462 98 37 ‘| 74 | 184 40 90 | 180 450 100 36 72 | 180 41 88 | 176 439 102 35 71 | 178 42 86 | 172 429 104 35 69 | 173 43 84 | 167 419 106 34 68 | 170 44 82 | 164 409 108 33 67 | 167 45 80 | 160 400 110 33 65 | 164 46 78 | 157 391 112 | 32 64 | 161 47 76 | 153 383 116 31 62 | 155 48 75 | 150 375 120 30 60 | 150 49 73 | 147 367 —6— 5 PILOT FLAME BURNER FLAME MANIFOLD A84076 Fig. 7—Proper Pilot and Burner Flames 4. High Altitude—Input ratings apply for altitudes up to 2000 feet. Ratings for altitudes above 2000 ft must be 4% less for each 1000 ft above sea level. Temperature Rise—Do NOT operate furnace outside range of temperature rise specified on unit rating plate. Determine air temperature rise as follows: 1. Place thermometers in return and supply ducts as near furnace as possible. Thermometers must not “see” heating element or radiant heat may affect readings. This practice is particularly important with straight- run ducts. 2. When thermometer readings stabilize, subtract return- air temperature from supply-air temperature to deter- mine air temperature rise. 3. Adjust temperature rise by adjusting blower speed. Increase blower speed to reduce temperature rise. Decrease blower speed to increase temperature rise. Thermostat Heat Anticipator Adjustment—Thermostat heat anticipator must be set to match amp draw of compo- nents in R-W circuit. Accurate amp draw measurements can be obtained at thermostat subbase terminals R and W. Fig- ure 8 illustrates an easy method of obtaining these measure- ments. Amp reading should be taken after blower has started on its heating speed. | Safety Check of Limit Control—Control shuts off combus- tion gas supply and energizes circulating-air blower motor if furnace overheats. THERMOSTAT TERMINALS FROM UNIT LOW-VOLTAGE TERMINAL BLOCK OF FAN COIL 5.0 AMPS ON AMMETER 10 TURNS AROUND JAWS EXAMPLE: = 0.5 AMPS FOR THERMOSTAT SETTING A80201 Fig. 85— Amp Draw Measurements Recommended method of checking this limit control is to gradually block off return air after furnace has been operat- ing for at least 5 minutes. As soon as limit control func- tions, return-air opening should be unblocked to permit normal air circulation. By using this method to check limit control, proper functioning can be determined and furnace will fail-safe if circulating air supply is restricted or motor fails. If limit control does not function during this test, iden- tify and correct cause of malfunction. Safety Check of Flow-Sensing Switch—This control proves operation of draft inducer. Check switch operation as follows: 1. Turn off 115-v power supply to furnace. 2. Remove control access panel and disconnect inducer- motor lead wires from inducer printed-circuit board. 3. Turn on 115-v power supply to furnace. 4. Close thermostat switch as if making normal furnace start. When flow-sensing switch is functioning prop- erly, gas should not flow to pilot and ignitor should not operate. If either pilot gas flow or ignitor operation occurs when inducer motor is disconnected, shut fur- nace down immediately. Determine cause of malfunc- tion and correct condition. 5. Turn off 115-v power supply to furnace. 6. Reconnect inducer-motor leads, reinstall control access panel, and turn on 115-v power supply. Manufacturer reserves the right to discontinue, or change at any time, specifications or designs without notice and without incurring obligations. Book 1 PC 101 Catalog No. 515-820 Printed in U.S.A. Form 58SX-9XA Pg8 1-88 Replaces: 585X-7XA Tab |6a
advertisement
* Your assessment is very important for improving the workof artificial intelligence, which forms the content of this project