advertisement
▼
Scroll to page 2
of 10
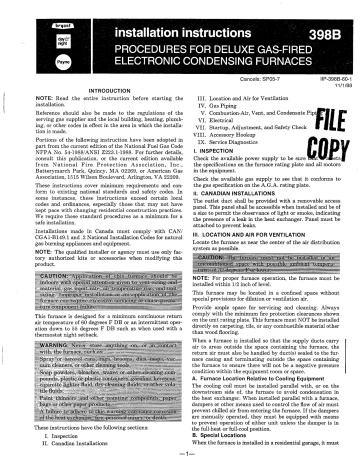
- |. и nstal lation instr ru ctior ns |. PROCEDURES FOR DELUXE GAS: sao” a ELECTRONIC CONDENSING FU RNACES © INTRODUCTION NOTE: Read the entire instruction before starting the installation. Reference should also be made to the regulations of the serving gas supplier and the local building, heating, plumb- ing, or other codes in effect in the area in which the installa- tion is made. Portions of the following instruction have been adopted in part from the current edition of the National Fuel Gas Code NFPA No. 54-1988/ANSI Z223.1-1988. For further details, consult this publication, or the current edition available from National Fire Protection Association, Inc., Batterymarch Park, Quincy, MA 02269, or American Gas Association, 1515 Wilson Boulevard, Arlington, VA 22209. These instructions cover minimum requirements and con- form to existing national standards and safety codes. In some instances, these instructions exceed certain local codes and ordinances, especially those that may not have kept pace with changing residential construction practices. We require these standard procedures as a minimum for a safe installation. Installations made in Canada must comply with CAN/ CGA1-B149.1 and .2 National Installation Codes for natural gas burning appliances and equipment. NOTE: The qualified installer or agency must use only fac- tory authorized kits or accessories when modifying this product. This furnace is designed for a minimum continuous return air temperature of 60 degrees F DB or an intermittent oper- ation down to 55 degrees F DB such as when used with a thermostat t night setback. These instructions have the following sections: I. Inspection IT. Canadian Installations _398B Cancels: : SPOS- 7 11/1/88 III. Location and Air for Ventilation IV. Gas Piping V. Combustion-Air, Vent, and Condensate =n ] [ УТ. Electrical УП. Startup, Adjustment, and Safety Check Е VIII. Accessory Hookup | IX. Service Diagnostics | |. INSPECTION | i р Check the available power supply to be sure t ets the specifications on the furnace rating plate and all motors in the equipment. Check the available gas supply to see that it conforms to the gas specification on the A.G.A. rating plate. It. CANADIAN INSTALLATIONS The outlet duct shall be provided with a removable access panel. This panel shall be accessible when installed and be of a size to permit the observance of light or smoke, indicating the presence of a leak in the heat exchanger. Panel must be attached to prevent leaks. Ш. LOCATION AND AIR FOR VENTILATION Locate the furnace as near the center of the air distribution system as possible. NOTE: For proper - furnace “operation, the furnace must be installed within 1/2 inch of level. This furnace may be located in a confined space without special provisions for dilution or ventilation air. Provide ample space for servicing and cleaning. Always comply with the minimum fire protection clearances shown on the unit rating plate. This furnace must NOT be installed directly on carpeting, tile, or any combustible material other than wood flooring. When a furnace is installed so that the supply ducts carry air to areas outside the space containing the furnace, the return air must also be handled by duct(s) sealed to the fur- | nace casing and terminating outside the space containing : the furnace to ensure there will not be a negative pressure condition within the equipment room or space. A. Furnace Location Relative to Cooling Equipment The cooling coil must be installed parallel with, or on the downstream side of, the furnace to avoid condensation in the heat exchanger. When installed parallel with a furnace, dampers or other means used to control the flow of air must prevent chilled air from entering the furnace. If the dampers are manually operated, they must be equipped with means to prevent operation of either unit unless the damper is in the full-heat or full-cool position. B. Special Locations When the furnace is installed in a residential garage, it must —1— HIP. 398B- 60- 1 be installed so that it is protected from physical damage by vehicles. When a furnace is installed in public garages, airplane han- gars, or other buildings having hazardous atmospheres, the unit must be installed in accordance with the requirements of the National Fire Protection Association, Inc. IV. GAS PIPING Gas piping must be installed in accordance with national and local codes. The gas supply line should be a separate line running directly from the meter to the furnace, if possible. Refer to Table I for the recommended gas pipe sizing. It is best to slope all pipe 1/4-inch in 15-feet to prevent traps. All hori- : ¿ong ab Tans should slope away from the meter to risers. Ris- . ess в j ot compounds (pipe dope) should be applied sparingly and we Ep..the male threads of the joints. Consult your 5 local Sas $ Shpplier for the type of compound to be used. This PC ipé done müst be resistant to the action of propane gas. Bh, Kopie be used to connect to the furnace and to the ES ¿Instala " dient trap in the riser leading to the furnace. This trap will serve as a trap for dirt and condensate. The trap can be installed by connecting a tee to the riser leading to the furnace, so that the straight-through section of the tee is vertical. Then connect a capped nipple into the lower - end of the tee. The capped nipple should extend below the level of the gas controls. See Figure 1. Where a gum filter is required by local codes, install it in accordance with their requirements. An accessible manual shut-off valve must be installed upstream of the furnace. A 1/8-inch NPT plugged tapping, accessible for test gauge connection, must be installed immediately upstream of the gas supply connection to the furnace and downstream of the manual shut-off valve. Place a ground joint union between the gas control manifold and the manual gas shut-off valve. See AN 1. Protect all segments of the piping system against physical and thermal damage. Support all piping with appropriate straps, hangers, etc. Use a minimum of one hanger every 6 feet. For pipe sizes larger than 1/2 inch, follow the recom- mendations of national codes. Piping should be pressure-tested in accordance with local and national plumbing and gas codes before the furnace has been attached. If the pressure exceeds 0.5 psig (14 inch wc), the gas supply pipe must be disconnected from the furnace before the pressure test. If the test pressure is equal to or less than 0.5 psig (14 inch we), close the manual shut-off valve located on the gas valve before the test. It is recom- ` mended that the ground joint union be loosened before pres- sure testing. TABLE I—MAXIMUM CAPACITY OF PIPE* Nominal Internal iron Pipe Diameier Length of Pipe (ft) Size (in.) п.) 10 20 30 40 50 1/2 0.622 175 120 97 82 73 3/4 0.824 360 250 200 170 151 1 1.049 680 465 375 320 285 1-1/4 1.380 1400 950 | 770 660 580 1-1/2 1.610 2100 1460 1180 990 900 Ref: Table C-4 NFPA 54-1988 *Cubic ft of gas per hour, for gas pressures of 0.5 psig (14 inch we) or less, and a pressure drop of 0.5 inch we (based on a 0.60 specific gravity gas). Fi i | After final connection to the furnace has been made, purge the lines and check for leakage with regulated gas supply pressure. V. COMBUSTION-AIR, VENT, AND CONDENSATE PIPING Combustion-air and vent pipes for this unit can be of schedule-40 PVC, PVC-DWV, SDR-21 PVC, SDR-26 PVC, or ABS-DWV pipe and terminate through either the roof or a sidewall. In Canada construct all combustion-air and vent pipes for this unit of CSA or ULC certified schedule-40 PVC, PVC- DWV or ABS-DWV pipe and pipe cement. Roof termination is preferable. Sidewall terminations must be located to prevent damage to shrubs and siding materi- als. See Table II for clearance requirements. EE ВЕБЕ == ЕКО = NOTE: When a previously common-vented system (furnace and water heater) is converted to water heater only, the vent system may be drastically oversized for the water heater. Consult the National Fuel Gas Code or CAN/CGAI- B149.1 and .2 Codes in Canada for proper sizing of the vent and revise the system if necessary. ЕЕ = E Te = ARE = == OR ER EE CHOSES pis ЕЕ НЕЕ: ЕЕ aa Siete МЕНЕЕ PASTE CREE WERDEN OYE TESpaCO WA _2_ SUPPLY Pn] MANUAL | SHUTOF F | VALVE SEDIMENT TRAP UNION С А84218 Figure 1—Gas Piping Arrangement TABLE II—COMBUSTION-AIR AND VENT TERMINAL CLEARANCES Location Dryer vent 3 From plumbing vent stack Gas appliance vent terminal From any opening where vent gases could enter building Above grade and anticipated snow depth Above grade when adjacent to public walkway Clearance Feet ~y} = | a] a} oo A. Combustion-Air and Vent Piping The combustion-air and vent pipes and fittings must con- form to American National Standards Institute (ANSI) standards and American Society for Testing and Materials (ASTM) standards D1785, D2661, D2241, or D2665. The pipe cement and primer must conform to > ASTM D2235 or D2564. In Canada construct all combustion-air vent pipes for this unit of CSA or ULC certified schedule-40 PVC, PVC-DWV or ABS-DWYV pipe and pipe cement. See Table TIT for maximum allowable pipe lengths and Fig- ures 2 through 7 for piping arrangements. ene oS Seo == We H=v weievenEH ЗЕ ЕЕ areas Von rea Peak ang of ae OA Te ЕЕ = === ==] > = = = The furnace is shipped from the factory assembled for right-hand vent pipe connection. When left-hand vent con- nection is desired, interchange the rubber vent pipe connec- tor with the rubber seal cap. Both the vent pipe connector and the seal cap are located on the inducer outlet box. Remove the plastic plug from the left-hand casing side panel and install it in the right-hand casing side panel. 1. Determine maximum allowable pipe length (for applica- tions from 0 to 10,000 feet above sea level) using Table ITI. EXAMPLE: A 100-size furnace located in Indianapolis, ele- _ vation 650 feet above sea level, could be installed in an application requiring three elbows and 28 feet of pipe. Table III indicates this application would require 2-1/2-inch pipe since 2-inch pipe is good only for lengths up to 15 feet. If the same 100-size furnace, requiring three elbows and 28 _ feet of pipe, was to be installed in Albuquerque, elevation 5250 feet above sea level, the pipe diameter required would be 3-inches, because Table ПТ shows 2-1/2-inch diameter pipe and three elbows can only be used up to 26 feet of pipe. Consult Application Engineering when pipe length of combustion-air or vent pipe needed is longer than allowed i in Table ITI. NOTE: Do not count the elbows to which the terminal bracket attaches or any elbow between the bracket and open end of the pipe. 2. Working from furnace to outside, cut pipe to required length(s). 3. Deburr inside and outside of pipe. Remove all dirt and debris from inside of pipe. 4. Chamfer outside edge of pipe for better distribution of primer and cement. | 5. Clean and dry all surfaces to be joined. 6. Check “dry fit” of pipe and mark insertion depth on pipe. NOTE: It is recommended that all pipes be cut,.prepared, and preassembled before permanently cementing any joint. TABLE Ili—MAXIMUM ALLOWABLE PIPE. LENGTH | Altitude (feet Furnace Pipe Number of 90 Degree Elbows above sea level) Size Size 1 2 3 4 5 060 & 080 2 35 35 35 35 35 0-2000 100 2 25 20 15 — — 21/2 35 35 35 35 35 060 & 2 35 35 35 32 29 080 2 1/2 35 35 35 35 35 2001-3000 2 22 16 12 — — 100 2 1/2 35 35 35 32 29 3 35 35 35 35 35 060 & 2 35 35 31 28 24 080 2 1/2 35 35 35 35 35 3001-4000 2 20 14 9 — — 100 21/2 35 35 31 28 24 3 35 35 35 35 35 060 & 2 35 33 29 26 22 080 2 1/2 35 35 35 35 35 4001-5000 2 18 12 8 — — 400 2 1/2 35 33 29 26 22 3 35 35 35 35 35 060 & 2 34 30 26 22 18 080 2 1/2 35 35 35 35 35 5001-6000 2 16 10 6 — — 100 21/2 34 30 26 22 18 3 35 35 35 35 35 060 & 2 32 28 24 20 16 080 21/2 35 35 35 35 35 6001-7000 2 15 8 5 — — 100 21/2 32 28 24 20 16 3 35 35 35 35 35 060 & 2 29 25 20 16 11 080 2 1/2 35 35 35 35 35 7001-8000 2 13 6 — — — 100 21/2 29 25 20 16 11 3 35 35 35 35 35 060 & 2 27 23 18 14 9 080 21/2 35 35 35 35 35 8001-9000 2 11 — — — — 100 2 1/2 27 23 18 14 9 3 35 35 35 35 35 060 & 2 25 20 15 10 5 080 21/2 35 35 35 35 35 9001-10,000 2 9 — — — — 100 2 1/2 25 20 15 10 5 3 35 35 35 35 35 NOTES: 1. Pipe length applies to individual combustion-air or vent pipe. 2. Elbows and pipe section supplied in the vent terminal kit should not be included in the count. 3. Two 45-degree elbows are equal to one 90-degree elbow. Long radius elbows are desirable. 4. The installer may use one pipe size larger than what is specified (up to 3-inches diameter maximum). 5. The minimum air pipe length on the 060 size with 2-inch diameter pipe and one elbow is 10-feet. — 3 7. After pipes have been cut and preassembled, apply generous layer of cement primer to pipe fitting socket and end of pipe to insertion mark. Quickly apply approved cement to end of pipe and fitting socket (over primer). Apply cement in light, uniform coat on inside of socket to prevent buildup of excess cement. Apply second coat. 8. While the cement is still wet, insert pipe into socket with a 1/4-turn twist. Be sure pipe is fully inserted into the fitting socket. 9. Wipe excess cement from joint. A continuous bead of cement will be visible around the perimeter of a prop- erly made joint. 10. Handle pipe joints carefully until cement sets. 11. Support piping at minimum of every 5 feet (3 feet for SDR-21 or -26 PVC) using perforated metal hanging strap. Slope combustion-air and vent pipes toward fur- nace a minimum of 1/4 inch per lineal foot with no sags between hangers. 12. Use appropriate methods to seal openings where vent and combustion-air pipes pass through roof or sidewall. B. Vent Terminal Kit Installation NOTE: If these instructions differ from those packaged with the vent terminal kit, follow the kit instructions. The combustion-air and vent pipes must terminate outside the structure. A factory-supplied termination kit must be installed as in one of the installations shown in Figures 2 through 7. Roof termination is preferred. See Figure 2. Two terminal kits are available. The 2-inch kit is for 1-1/2-inch and 2-inch diameter pipe systems. The 3-inch kit is for 2-1/2- inch and 38-inch diameter pipe systems. Each kit will have extra parts. See Figures 2 through 7 for the different applications. The shaded parts in Figures 2 through 7 are provided in the termination kit; therefore, do not count them when deter- mining the pipe diameter. 1. Rooftop terminal installation. See Figures 2 and 3. a. Remove one 90-degree elbow from elbow-and- bracket assembly provided in kit and loosen screw so other elbow can turn. b. Loosely install elbow with bracket on combustion- air pipe. | N N N 8-INCH MAXIMUM | > BRACK т-| K N ' y > N SA N LA Ey 11 \ NS > T4 N MI QE fi < N < > N VERTICAL SEPARATION | L Y >| N < BETWEEN BOTTOM OF. <> AT y Q COMBUSTION AIR AND LIA < TOP OF VENT: >> < = < = — А. FOR ZIN. TERMINAL < < SQ 6 SIN. FOR 31N. TERMINAL N ARK Ñ N + MN N ROOF: \ LE 12-INCH CLEARANCE MUST BE MAINTAINED ABOV HIGHEST ANTICIPATED SNOW LEVEL. MAXIMUM NOT TO EXCEED 24 INCHES ABOVE ROOF. . . A84143 Figure 2—Rooftop Termination —A— c. Loosely install pipe coupling, provided in kit, on properly cut vent pipe. The position of the coupling must be so that the bracket will mount as shown in Figure 2. d. Disassemble loose pipe fittings. Clean and cement using same procedures as used for system piping. e. Install bracket as shown in Figure 2. f. For applications using combustion-air pipe option as shown in Figure 3, install 90-degree street ell into 90-degree elbow, making a U-fitting. g. Install open end of street ell on combustion-air pipe. . Sidewall terminal installation when combustion-air and vent pipes exit through sidewall 12 inches or more above highest anticipated snow level or grade. See Fig- ures 4 and 5. In Canada, pipes must exit a minimum of 36 inches above grade. a. Loosely install elbow and bracket assembly on combustion-air and vent pipes. b. Remove and disassemble elbow and bracket assembly. c. Install elbows as shown in Figure 4 or 5 using same procedures for cementing as used for system piping. d. Install bracket as shown in Figure 4 or 5. e. Position vent outlet pipe and elbow as to maintain 12-inch separation between vent pipe outlet and combustion-air inlet. Cement vent pipe in elbow as shown in Figure 4 or 5. f. For applications using vent pipe option as shown in : Figure 5, rotate vent elbow 90 degrees from position shown in Figure 4. . Sidewall terminal installation when combustion-air and vent pipes exit through sidewall below highest antici- pated snow level or grade. See Figures 6 and 7. a. Remove one elbow from bracket assembly. b. Install 90-degree street ell into elbow remaining in bracket, making U-fitting. c. Loosely install coupling on end of vent pipe. d. Loosely install U-fitting and bracket as shown in Figure 6. Position U-fitting so open end is against structure wall. e. Loosely install vent outlet pipe and elbow in cou- pling as shown in Figure 6 or 7. > < SESS Sn BR SS \ \ > N | IN 7 - < | ti VERTICAL SEPARATION BETWEEN BOTTOM OF COMBUSTION AIR AND TOP OF VENT: 4 IN. FOR 2IN. TERMINAL 6 Zn. FOR 3 IN, TERMINAL Е 12-INCH CLEARANCE MUST BE MAINTAINED ABOVE HIGHEST ANTICIPATED SNOW LEVEL. MAXIMUM NOT TO EXCEED 24 INCHES ABOVE ROOF, . | . A84144 Figure 3—Rooftop Termination f. Check required dimensions as shown in Figure 6 or 7. g. Disassemble loose pipe fittings. Clean and cement using same procedures as used for system piping. h. Install bracket as shown in Figure 6 or 7. C. Condensate Drain NOTE: Condensate must be disposed of in a nonfreezing area. The 1/2-inch diameter schedule 40 PVC or CPVC condensate drain pipe fittings must conform to ANSI standards and ASTM D1785 and D2846. The schedule 40 PVC or CPVC cement and primer must conform to ASTM F493 or D2564. In Canada use CSA or ULC certified schedule 40 PVC or CPVC drain piping and cement. For proper condensate drainage from the furnace, the fur- nace must be within 1/2 inch of level. That is, the highest corner of the furnace must not be more than 1/2 inch higher OVERHANG 12-INCH MINIMUM 12-INCH SEPARATION BETWEEN BOTTOM OF COMBUSTION AIR AND ac „о BOTTOM OF VENT. — Do Y Soon a À BRACKET>~<—" |. Je ! Е SV AT AT > 12- INCH CLEARANCE MUST > BE MAINTAINED ABOVE HIGHEST ANTICIPATED SNOW COMBUSTION LEVEL OR GRADE. a AT IN CANADA: MAINTAIN 36 IN. CLEARANCE ABOVE GRADE OR [2 IN Pe | CLEARANCE ABOVE HIGHEST ae ANTICIPATED SNOW LEVEL A84145 Figure 4—Sidewall Termination Above Snow Level or Grade OVERHANG 12- INER MINIMUM 12-INCH SEPARATION BETWEEN BOTTOM OF COMBUSTION AIR AND BOTTOM OF VENT. 12- INCH CLEARANCE MUST BE MAINTAINED ABOVE HIGHEST ANTICIPATED SNOW LEVEL OR GRADE COMBUSTION AIR Г a Figure 5—Sidewall Termination Above Snow Level or Grade IN CANADA: MAINTAIN 36 IN. CLEARANCE ABOVE GRADE OR 12 IN CLEARANCE ABOVE HIGHEST ANTICIPATED SNOW LEVEL WHICHEVER IS GREATER . A84146 than the lowest corner. When a condensate pump is required to dispose of conden: sate, use a pump with parts that are resistant to acidic water. NOTE: The furnace contains an internal condensate trap; an external trap must not be installed. 1. Determine which side of furnace drain will exit, then cut and preassemble drain piping (not provided) directly to an open drain. Refer to Section IV A, “Combustion-Air and Vent Piping”, for instructions on preparing and cementing plastic pipe. 2. Cement elbow on pipe assembly (provided) to conden- sate trap mounted on blower housing. OVERHANG 12- INCH MINIMUM ¡A Г )—COMBUSTION AIR | (OPEN END AGAINST STRUCTURE WALL) 12-INCH CLEARANCE MUST BE MAINTAINED ABOVE HIGHEST ANTIC- IPATED SNOW LEVEL | OR GRADE. IN CANADA: MAINTAIN 36 IN. CLEARANCE ABOVE GRADE OR 12 IN, CLEARANCE ABOVE HIGHEST ANTICIPATED SNOW LEVEL WHICHEVER 1$ GREATER A84147 Figure 6—Sidewall Termination Below Snow Level or Too Close to Grade OVERHANG 12-INCH MINIMUM 12- [NCH IÓN E COMBUSTION А ANO PJ COMBUSTION AIR (OPEN END AGAINST STRUCTURE WALL) 12-INCH CLEARANCE MUST BE MAINTAINED ABOVE HIGHEST ANTIC- IPATED SNOW LEVEL 1 OR GRADE. IN CANADA: 18 INCH MAINTAIN 36 IN. CLEARANCE MAXIMUM ABOVE GRADE O CLEARANCE ABOVE HIGHEST ANTICIPATED SNOW LEVEL WHICHEVER IS GREATER , A84148 Figure 7 —Sidewall Termination Below Snow Level or Too Close to Grade —5— 3. Using backup wrench, attach first section of drain pipe to compression coupling (provided). 4. When using schedule 40 PVC drain pipe, connect adapter (provided) to end of pipe installed in compres- sion fitting. 5. Attach schedule 40 PVC adapter (field-supplied) to threaded factory adapter. 6. Cement remaining pipe joints. VI. ELECTRICAL IMPORTANT: Before proceeding with the electrical con- nections, make certain that voltage, frequency, and phase correspond to that specified on the unit rating plate. Also, check to be sure that the service provided by the utility is sufficient to handle the load imposed by this equipment. Refer to the unit rating plate for equipment electrical requirements. The specific furnace Installation Instructions contain wir- ing diagrams which show the proper field 115- and 24-volt- age wiring. Make all connections in accordance with the National Electrical Code, CSA C22.1 Electrical Code in Can- ada, and any local codes and ordinances that might apply. proKen- srounda sr A A A A _———_EE- > — _— === __—_ NOTE: Use only copper conductors between the disconnect switch and the furnace. Check all electrical connections (both factory and field) for tightness. This check should also be done after the unit has reached operating temperatures. VIL STARTUP, ADJUSTMENT, AND SAFETY CHECK A. Fill condensate trap with water. 1. Disconnect condensate drain tube from inducer outlet box. 2. Insert funnel into tube and pour one quart of water into tube. This should overfill the trap and flow into an open drain. 3. Reconnect drain tube to inducer outlet box. B. Ignition System Check Check to be sure that all connections have been properly made, then proceed as follows: Start the furnace using the procedure outlined on the Light- ing Instructions attached to the furnace; however, when starting the furnace for the first time, perform the following additional steps: 1. If the gas supply was not purged before connecting the furnace, the line will be full of air. It is recommended that the ground joint union be loosened, and the supply line be allowed to purge until the odor of gas is detected. Never purge gas lines into a combustion chamber. Immediately upon detection of a gas odor, retighten the union. Check gas supply pressure Lo be sure it is within rating plate limits. Allow 5 minutes to elapse, then start the furnace in accordance with the lighting instructions on the furnace. 2. After the pilot lights, the main burners should light in | 25 to 75 seconds. If the main burners do not light within the prescribed time period check; the pilot flame, electrical supply to gas valve, burner crossover alignment, gas supply pressure, manifold, and orifice alignment. 3. The pilot flame should be soft blue in color and it must provide good impingement on the pilot switching ele- ment. The flame should extend above the burner carry- over port to provide proper burner ignition. When the pilot flame requires adjustment: a. Locate adjustment screw marked “PILOT ADJ” on top of gas valve. b. Remove cap and turn adjustment screw clockwise to decrease pilot gas flow. Turn screw counter- clockwise to increase pilot gas flow. ‘с. When proper adjustment is obtained, replace screw cap. C. Gas Input 1. Determine natural gas orifice size and manifold pres- sure for correct input during high- and low-heat opera- tion by using Table V. Adjust manifold pressure per step 3. | NOTE: Be sure all pressure tubing, combustion-air and vent pipes, and burner enclosure front are in place when checking input. a. Obtain average yearly heat value for local gas supply. TABLE IV—GAS RATE—CU FT/HR Seconds SIZE OF TEST DIAL Seconds SIZE OF TEST DIAL for One 1 2 5 for One 1 2 5 Revolution | cu ft cu ft cu ft Revolution cu ft cu ft cu ft 10 360 720 1800 50 72 144 360 11 327 655 1636 51 71 141 355 12 300 600 1500 52 69 138 346 13 277 555 1385 53 68 136 340 14 257 514 1286 54 67 133 333 15 240 480 1200 55 65 131 327 16 225 450 1125 56 64 129 321 17 212 424 1059 57 63 126 316 18 200 400 1000 58 62 124 310 19 189 379 947 59 61 122 305 20 180 360 900 60 60 120 300 21 171 343 857 62 58 116 290 22 164 327 818 64 56 112 | 281 23 157 313 783 66 54 109 273 24 150 300 750 68 53 106 265 25 144 288 720 70 51 103 257 26 138 277 692 72 50 100 250 27 133 267 667 74 48 97 243 28 129 257 643 76 47 95 237 29 124 248 621 78 46 ‚ 92 231 30 120 240 600 80 45 90 225 31 116 232 581 82 44 88 220 32 113 225 563 84 43 86 214 33 109 218 545 86 42 84 209 34 106 212 529 88 41 82 205 35 103 206 514 90 40 80 200 36 100 200 500 92 39 78 196 37 97 195 486 94 38 76 192 38 95 189 474 96 38 75 188 39 92 185 462 98 37 74 184 40 90 180 450 100 36 72 180 41 88 176 439 102 35 71 178 42 86 | 172 429 104 35 69 173 43 84 167 419 106 34 68 170 44 82 164 409 108 33 67 167 A5 80 160 400 110 33 65 164 46 78 157 391 112 32 64 161 47 76 153 383 116 31 62 155 48 75 . 150 375 120 30 60 150 49 73 147 367 _6— im —— mn? b. Obtain average yearly specific gravity for local gas supply. c. Verify the furnace model. Table V can only be used for Model 398B Furnaces. Check and verify orifice size in furnace. NEVER ASSUME THE ORIFICE SIZE, ALWAYS CHECK AND VERIFY. | e. Find natural gas heat value and specific gravity in Table V. f. Follow heat value line and specific gravity line to point of intersection to find orifice size and manifold pressure settings for proper operation at given natu- ral gas condition. | EXAMPLE: Heat value 1050 Btu/cu feet Specific gravity 0.58 Therefore; Orifice No. 45* High-heat manifold pressure 3.8-inch we Low-heat manifold pressure 1.8-inch we *The furnace is shipped with No. 44 orifices. Therefore, in this example all main burner orifices must be changed. g. Check input rate by clocking meter as described in step 2. 2. Determine natural gas input rates during high- and low-heat operation by clocking gas meter and adjusting manifold pressure per step 3. NOTE: Be sure all pressure tubing, combustion-air and vent pipes, and burner enclosure front are in place when checking input. a. Turn off all other gas appliances and pilots. b. Measure time (in seconds) for gas meter test dial to complete one revolution. c. Refer to Table IV for cubic ft of gas per hour. Multiply gas rate (cu ft/hr) x heating value (Btu/cu ft). Obtain heating value from local gas utility. e. Measured gas input must not exceed gas input on unit rating plate. ea EXAMPLE: Btu heating input = Btu/cu ft times cu ft/hr Heating value of gas = 1070 Btu/cu ft Time for one revolution of 2-cu-ft dial = 72 sec Gas rate = 100 cu ft/hr (from Table IV) Btu heating input = 100 x 1070 = 107,000 Btuh 3. To adjust input rate: NOTE: Manifold pressure must always be measured with the burner enclosure front removed. The gas meter must always be clocked with the burner enclosure front installed. TABLE V—MODEL 398B ORIFICE SIZE AND MANIFOLD PRESSURE FOR CORRECT INPUT RATE* (Tabulated data based on altitude up to 2000 feet.) Gas SPECIFIC GRAVITY OF NATURAL GAS Heat 0.54 0.56 0.58 0.60 0.62 0.64 0.66 0.68 0.70 0,72 Value Or| Heat ;Or| Heat |Orl Heat |Or| Heat |Or! Heat |Or| Heat |Or! Heat |Ori Heat |Ог| Heat |Or! Heat a (Btu/cu ft) No. High/Low Мо. High/Low No. High/Low No. High/Low No. High/Low |No.| High/Low No. High/Low |No.| High/Low ¡No.| High/Low No. High/Low . 900 43| 3.5/1.7 |43| 3.6/1.7 ¡43| 3.7/1.8 142| 3.21.5 |42| 3.31.6 |42| 3.4/1.6 142| 3.5/1.7 [42] 3.6/1.7 |42| 3.74.8 142| 3.8/1.8 | 41| 3.2/1.5 |41| 3.3/1.6 [41] 3.4/1.6 915 44| 3.8/1.8 |43) 3.5/1.7 143! 3.6/1.7 |43| 3.7/1.8 !42| 3.2/1.5 1421 3.3/1.6 |42i 3.4/1.6 |42! 3.5/1.7 142| 3.6/1.7 |42| 3.7/1.8 43| 3.4/1.6 | 41| 3.21.5 !41| 3.3/1.6 930 441 3.7/1.8 |43| 3.4/1.6 143] 3.5/1.7 |43| 3.6/1.7 |43! 3.7/1.8 |42| 3.2/1.5 |42| 3.3/1.6 [42] 3.4/1.6 |42| 3.5/1.7 142! 3.6/1.7 43| 3.3/1.6 41| 3.2/1.5 945 44| 3.6/1.7 |44; 3.7/1.8 |43| 3.41.6 |43| 3.5/1.7 [43] 3.6/1.7 (48) 3.7/1.8 |42| 3.2/1.5 [42] 3.3/1.6 142] 3.4/1.6 142| 3.4/1.6 43| 3.2/1.5 |43] 3.3/1.6 960 44| 3.5/1.6 |44| 3.6/1.7 |44| 3.8/1.8 |43| 3.4/1.6 |431 3.5/1.7 |43| 3.6/1.7 |43! 3.7/1.8 la2| 3.21.5 |42| 3.2/1.5 |42] 3.3/1.6 43! 3.2/1.5 |43| 3.3/1.6 975 44| 3.4/1.6 |44| 3.5/1.7 1441 3.6/1.7 |44) 3.8/1.8 143| 3.49.6 |43| 3.5/1.7 143| 3.6/7.7 148] 3.74.8 |43| 3.8/1.8 143) 3.2/1.5 43| 3.2/1.5 143| 3.3/1.6 990 44| 3.3/1.5 |44) 3.4/1.6 |44| 3.5/1.7 |44| 3.6/1.7 |44;) 3.8/1.8 143] 3.4/1.6 |43| 3.5/1.7 |43| 3.6/1.7 143| 3.7/1.8 [43] 3.8/7.8 43! 3.2/1.5 143| 3.31.5 |. 1005 . |441 3.2/1.5 |44| 3.3/1.6 [44] 3.4/1.6 (44| 3.5/1.7 |44| 3.7/1.7 |44| 3.8/1.8 |43| 3.49.6 (43| 3.51.7 143] 3.69.7 \a3| 3.7/1.8 43! 3.2/1.5 143] 3.3/1.6 1020 45| 3.8/1.8 |44) 3.21.5 |44| 33/16 |44| 3.41.6 |44| 3.6/1.7 |44| 3.7/1.7 144| 3.8/1.8 |43| 3.4/1.6 |43| 35/17 143| 36/17 43| 3.2/1.5 [43] 3.3/1.6 1035 45| 3.7/1.7 |45| 3.8/1.8 |44) 3.2/1.5 |44| 3.3/1.6 |44| 3.4/1.6 |44| 3.6/1.7 |44! 3.7/1.7 \44| 38118 |43] 3.4/1.6 [438] 3.5/1.7 ; 143; 3.2/1.5 |43| 3.3/1.6 o 1050 46| 3.7/1.8 |45| 3.7/1.8 |45| 3.8/1.8 144! 3.2/1.5 |44| 3.4/1.6 |44| 3.5/1.6 144| 3.6/1.7 144| 3.7/1.8 |44! 38/18 |[43! 3.4/1.6 45! 3.5/1.7 | | 43; 3.2/1.5 |43| 3.3/1.6 | 1065 46| 3.6/1.7 146! 3.8/1.8 145] 3.7/1.8 |45| 3.8/1.8 144! 3.3/1.6 [44] 3.4/1.6 144! 3.5/1.7 |44| 3.6/1.7 144] 37/18 |44] 38/18 | 45| 3.4/1.6 |145¡ 3.6/1.7 44! 3.2/1.5 43; 3.2/1.5 [43) 3.3/1.6 | | ; 1080 46| 3.51.7 |46| 3.7/1.7 |46| 3.8/1.8 |45| 3.7/1.8 |44| 3.2/1.5 |44] 3.3/1.6 |44| 3.4/1.6 |44| 3.5/1.7 |44| 3.6/1.7 |44! 3.7/1.8 | 45| 3.41.6 |45| 3.5/1.7 |45 3.6/1.7 43| 3.2/1.5 | 1095 46| 3.4/1.6 |46| 3.6/1.7 ¡46| 3.7/1.8 146| 3.8/1.8 (45; 3.71.8 |44) 3.2/1.5 |44| 3.3/1.6 |44| 3.4/1.6 |44| 3.5/1.7 |44| 3.6/1.7 45| 3.3/1.6 145| 3.4/1.6 |45| 3.5/1.7 145| 3.6/1.7 1110 46; 3.3/1.8 |46| 3.5/1.6 |46| 3.6/1.7 |46| 3.7/7.8 |46| 3.8/1.8 145| 3.8/1.8 |44! 3.2/1.5 |44| 3.3/1.6 144| 3.4/7.6 |44| 3.5/1.7 45| 3.2/1.5 |45! 3.3/1.6 45| 3.4/1.6 |45| 3.5/1.7 |45¡| 3.6/1.7 1125 47| 3.7/1.6 !46| 3.4/1.6 ¡46| 3.5/1.7 146) 3.6/1.7 146| 3.74.8 |45| 3.7/1.7 |45| 3.8/1.8 [44] 3.2715 |44! 331.6 |44! 3.4/1.6 46; 3.2/1.5 145| 3.2/1.5 |45| 3.3/1.6 ¡45| 3.4/1.6 |45| 3.5/1.7 a, | 1140 47| 3.6/1.7 |47| 3.71.8 146] 3.4/1.6 |46| 3.5/1.7 1|46| 3.6/1.7 146] 3.7/1.8 145) 3.7/1.8 145| 3.8/1.8 [44] 3.2/1.5 [44] 3.3/1.6 46| 3.2/1.5 |46! 3.3/1.6 (45) 3.2/1.5 145! 3.3/1.6 (45! 3.5/1.6 145] 3.6/1.7 1155 471 3.5/1.7 ¡47| 3.6/1.7 |47| 3.71.8 146| 3.4/1.6 |46| 3.5/1.7 |46| 3.7/1.7 |46| 3.8/1.8 |45| 3.7/1.8 145| 3.8/1.8 |44] 3.2/1.5 46| 3.2/1.5 |46| 3.3/1.6 |45| 3.3/1.6 |45| 3.4/1.6 |45| 3.5/1.7 145! 3.6/1.7 1170 47| 3.4/1.6 |47! 3.5/1.7 |47| 3.6/11.7 |46] 3.3/1.6 !46| 3.4/1.6 ¡46! 3.6/1.7 |46| 3.7/1.7 |46| 3.8/1.8 l45| 37/18 |45] 38/18 46| 3.2/1.5 ¡45| 3.2/1.5 145| 3.31.6 |45| 3.4/1.6 145| 3.5/1.7 |45| 3.6/1.7 1185 48| 3.8/1.8 |47| 3.4/1.6 |47) 3.6/1.7 ¡47| 3.7/1.8 |46| 3.4/1.6 |46| 3.5/1.7 |46! 3.6/1.7 |46| 3.7/1.8 [46] 3.8/1.8 145! 3.7/1.8 47| 3.3/1.6 46; 3.3/1.6 |45! 3.2/1.5 145! 3.3/1.6 |45| 3.4/1.6 145! 3.5/1.7 145| 3.6/1.7 *The correct input rate per burner is: high-heat 21,000 Btuh; low-heat 14,500 Btuh. _ 7 a. Remove burner enclosure front and low-fire regula- tor adjustment seal cap. See Figure 10. b. Put setup switch No. 2 on microprocessor control board in ON position to provide continuous low-fire operation. See Figure 11. c. Turn Allen-head adjustment screw either counter- clockwise (out) to decrease low-input rate or clock- wise (in) to increase low-input rate. DO NOT set manifold pressure less than 1.4 or more than 1.8 inches we for natural gas. If manifold pressure can- not be obtained with these settings, replace the main burner orifices within one size of that pres- ently installed. NOTE: If orifice hole appears damaged or it is suspected to have been redrilled, check the orifice hole with the correct size numbered drill. Never redrill an orifice. A burr-free and squarely aligned orifice hole is essential for proper flame characteristics. d. Return setup switch No. 2 on microprocessor con- trol board to OFF position and put setup switch No. 3 to the ON position to provide continuous high-fire operation. See Figure 11. e. Replace low-fire regulator adjustment seal cap, and remove high-fire regulator adjustment seal cap. See Figure 10. £ Turn Allen-head adjustment screw either counter- clockwise (out) to decrease high-input rate or clock- wise (in) to increase high-input rate. DO NOT set BURNER FLAME PILOT FLAME BURNER MANIFOLD A84076 Il И TERMINALS —>|_®© © ® © | HOOK-AROUND et VOLT/AMMETER FROM UNIT LOW-VOLTAGE TERMINAL BLOCK OF FURNACE 5.0 AMPS ON AMMETER 10 TURNS AROUND JAWS = 0.5 AMPS FOR THERMOSTAT SETTING EXAMPLE: A80201 Figure 9—Amp Draw Check With Ammeter manifold pressure less than 3.2 or more than 3.8 inches we for natural gas. If manifold pressure can- not be obtained with these settings, replace the main burner orifices within one size of that pres- ently installed. g. Return setup switch No. 3 on microprocessor con- trol board to OFF position and replace high-fire reg- ulator adjustment seal cap. h. Replace burner enclosure front and recycle furnace , before measuring adjusted gas input using method outlined in step 1 or 2. 4. Look through sight glass in burner enclosure and check burner and pilot flame. The main burner flame should be clear blue, almost transparent. The pilot flame should be well defined. See Figure 8. 5. High Altitude Input ratings are for altitudes up to 2000 feet. Ratings for altitudes over 2000 feet must be 4% less for each 1000 feet above sea level. To obtain the altitude adjusted rating, adjust the manifold pressure and replace the main burner orifices as needed. In Canada, from 2000 to 4500 feet above sea level, derate the unit 10%. D. Temperature Rise The furnace must not be operated outside the range of tem- LOW-FIRE ADJUSTMENT ALLEN SCREW HIGH" FIRE ADJUSTMENT ALLEN SCREW A88322 Figure 10—Gas Valve ACCESSORY LED FAULT LEADS DISPLAY ACCESSORY HOOKUP RELAY SETUP SWITCHES | COOLING AIR-FLOW ADJUSTMENT BLOWER OFF-TIME ADJUSTMENT A87335 Figure 11— Microprocessor Control Center perature rise specified on the unit rating plate. Determine the air temperature rise as follows: 1. Place thermometers in return and supply ducts as near furnace as possible. Be sure thermometers do not ‘‘see”’ heating element so that radiant heat does not affect readings. This practice is particularly important with straight-run ducts. 2. When thermometer readings stabilize, subtract return- air temperature from supply-air temperature to deter- mine air temperature rise. | NOTE: Temperature rise can be determined for low-fire operation by placing setup switch No. 2 on microprocessor control board in the ON position. For high-fire operation return setup switch No. 2 to the OFF position and place setup switch No. 3 in the ON position. DO NOT forget to return setup switches to OFF position upon completion. See Figure 11. 3. This furnace is capable of automatically providing the proper airflow to maintain the temperature rise within the range specified on the unit rating plate. If the tem- perature rise is outside this range do the following: a. Check gas input for low- and high-fire operation. b. Check derate for altitude if applicable. c. Check all return and supply ducts for excessive restrictions causing static pressure greater than 0.5 inch we. d. Check to make sure bypass humidifier switch (marked BPH) on microprocessor control board is in ON position when a bypass humidifier has been installed. See Figure 11. e. Check “Troubleshooting Guide for Deluxe Gas- Fired Condensing Furnace.” E. Thermostat Heat Anticipator Adjustment The thermostat heat anticipator must be set to match the amp draw of the components in the R-W circuit while oper- ating in low heat. Accurate amp draw measurements can be obtained at the thermostat subbase terminals R & W. Figure 9 illustrates an easy method of obtaining these measurements. The amp reading should be taken while the furnace is operating in the low-heat mode. To operate the furnace in low heat reset the power and energize the thermo- stat, low heat will last for 6 minutes which should be suffi- cient time to obtain the amp draw readings. F. Safety Check of Limit Control The control shuts off the combustion gas supply and ener- gizes the circulating-air blower motor if the furnace overheats. The recommended method of checking this limit control is to gradually block off the return air after the furnace has been operating for a period of at least 5 minutes. As soon as the limit control functions, the return-air opening should be ACCESSORY RELAY CONTACTS 120-VOLT 0 —————— STA ELECTRONIC POWER SUPPLY COM NO AIR CLEANER = ee ee ee ee ee ee ee ee ee ee ee ——— FIELD LOW - VOLTAGE WIRING —— FACTORY WIRING — —- FIELD HIGH - VOLTAGE WIRING QUICK CONNECTS - FIELD CONNECTIONS Figure 12—Electronic Air Cleaner ^87330 unblocked to permit normal air circulation. By using this method to check the limit control, it can be established that the limit is functioning properly and the furnace will “fail- safe” if there is a restricted circulating air supply or motor failure. If the limit control does not function during this test, the cause must be determined and corrected. G. Safety Check of Flow-Sensing Switch This control proves operation of the draft inducer. Check switch operation as follows: 1. Turn off 115-volt power to furnace. 2. Remove control access panel and disconnect ECM inducer motor leads at 6-circuit connector on ECM inducer control box. 3. Turn on 115-volt power to furnace. 4. Set thermostat to “call for heat.” When the flow-sens- ing switches are functioning properly, fault 42 will flash on the LED fault display 10 seconds after the thermostat switch is closed. If either fault 31 or 32 is flashed when the ECM inducer motor is disconnected, the furnace will shut itself down immediately. Deter- mine the reason the flow-sensing switches did not func- tion and correct the condition. 5. Turn off 115-volt power to furnace. 6. Reconnect inducer motor leads, reinstall control access panel, turn on 115-volt power supply, and reset thermo- stat to desired temperature. Vill. ACCESSORY HOOKUP (Electronic Air Cleaner and/ or Humidifier) An isolated set of normally open contacts (not connected to 24V AC or 120VAC) are available to operate any accessory such as an electronic air cleaner or humidifier. The relay contact will close whenever the blower motor is operat- ing. These contacts are accessible by two 1/4-inch quick- connects mounted directly on the relay as shown in Figure 11. Wire leads with quick-connects have been supplied as ACCESSORY RELAY CONTACTS 120-VOLT AO "=== HH MARS ELECTRONIC POWER SUPPLY _____ | COM. NO AIR CLEANER j Lux) 124 МАС 40 VA === _ | TRANSFORMER CA — — HUMIDIFIER ——— FIELD LOW - VOLTAGE WIRING —— FACTORY WIRING ——— FIELD HIGH - VOLTAGE WIRING QUICK CONNECTS - FIELD CONNECTIONS A87328 Figure 13—Electronic Air Cleaner and Humidifier ACCESSORY RELAY CONTACTS 24- VOLT POWER SUPPLY COM NO HUMIDIFIER — i ee ee eee ee ee ——— FIELD LOW - VOLTAGE WIRING —— FACTORY WIRING ——— FIELD HIGH - VOLTAGE WIRING QUICK CONNECTS - FIELD CONNECTIONS Figure 14—Humidifier eee —9— THE FOLLOWING TABLE CAN BE USED TO KEEP ALOG OF ANY SERVICES PERFORMED. DATE TECHNICIAN COMPANY SERVICE PERFORMED FAULT HISTORY Carrier Corporation —12— Catalog Мо. BDP-3339-812
advertisement
* Your assessment is very important for improving the workof artificial intelligence, which forms the content of this project