Singer 1263 Owner Manual
Add to My manuals73 Pages
SINGER 1263 is a versatile sewing machine that offers a wide range of features to help you create beautiful garments and home décor items. It is a top-of-the-line model that is perfect for both beginners and experienced sewers. With its easy-to-use controls and clear instructions, you'll be able to start sewing right away.
advertisement
▼
Scroll to page 2
of
73
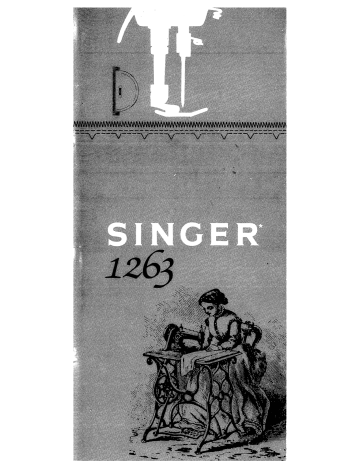
For Treadle Machine Owners To adjust your machine for treadle sewing, loosen hand wheel knob A by turning it toward you with the right hand while holding hand wheel With the left hand. | Place both feet on the treadle as illustrated. Turn hand wheel over toward you, allowing your feet to move freely with the motion of the treadle. Prac - tice this motion until you are able to start and keep the machine in operation with the hand wheel turning toward you. Remember that the faster you operate the treadle, the faster the machine will sew. When you have become accustomed to the treadle motion, tighten the hand wheel knob by turning it away from you. Place a piece of material under the presser foot and ‘lower the presser foot lifter. Now operate the machine (without thread) until you become accustomed to guiding the material. Enjoy Sewing! Arde на = SI E a A Copyright O 1981 THE SINGER COMPANY All Rights Reserved Throughout the World *A Trademark of the Singer Company For European Territories — This product is suppressed for radio and television interference in accordance with the International Electrotechnical Commission of the CISPR. IMPORTANT: Machines for Great Britain and some other countries having similar wiring standards are shipped from the factory without a plug for connection to the mains. The wire in this mains lead are coloured in accordance with the following code: Blue: neutral (N) Brown: live (L) As the colours of the wires in the mains lead of this appliance may not correspond with the coloured mark- ings identifying the terminals in your plug, proceed as follows: The wire which is coloured blue must be connected - to the terminal which is marked with the letter N or coloured black. The wire which is coloured brown must be connected to the terminal which is marked with the letter L or coloured red. If a 13 Amp. (BS 1363) plug is used, a 3 Amp. fuse must be fitted, or if any other type of plug is used, a 5 Amp. fuse must be fitted either in the plug or adaptor or at the distribution board. Dear Customer: We recommend that for future reference you record the serial number of your Sewing Machine in the space provided. Serial No. Refer to illustration at right for location of serial number on your machine. Serial No. Contents . Getting to Know Your Machine ........... 4 Principal Parts ............... 4 Accessories ......... 0... .... 6 . Getting Ready to Sew .................. 8 Choosing and Changing Accessories ........ 8 Operating Machine ..................... 16 The Bobbin Thread ............. В 18 Threading the Machine .................. 22 . Straight Stitching ....... PU 26 Setting Selectors ..... aaa 26 Sewing a Seam . 0.00. 30 Applications ........... 20000000... 32 . Zig-Zag Pattern Stitching ............. .. 36 Setting Selectors ................. Fe 36 Satin Stitching ............. 2... 40 Stiteh Usage .......................... 42 . Buttonholes and Buttons ............... 50 Garment Preparation ..... Ms 50 Four-Step Buttonholing ................ ..54 Buttons ........ as 58 6. Caring for Your Machine ................ 60 7. Tin-Needie Stitching .................. 68 Home Service Hints ................... 70 Index ........ 72 1. Getting to Know Your Machine Principal Parts N N N N = = = = mh mh wb = 50ND No oO IZRpNHENAS N сл N ©) © ENDO HONS Spool Pin Thread Guide Bobbin Winder Tension Disc Take-up Lever Needle-Thread Tension Dial Face Plate Presser Foot Lifter Thread Cutter . Presser Foot Screw . General Purpose Presser Foot . Thread Guides . Feed . General Purpose Needle Plate . Slide Plate . Bobbin Case . Bobbin Needle Clamp . Electrical Connections and Speed Controller . Hand Wheel . Hand Wheel Knob . Bobbin Winder Spindle . Stitch Width Selector Needle Position Selector . Stitch Length Selector . Reverse Stitch Push Button and Buttonhole Balance Knob . Stitch Pattern Selector e E Sy ere HEE Ti = DTO o > ES o rre E ERE TEE = re ara pg sent EEE te re Sot EE BRR fee: se o e om 4 Accessories The accessories provided with your sewing machine are designed to help you do many kinds of sewing easily. | 1. Transparent Bobbins (No. 172336) 2. Singer* Needles e Style 2020 for general sewing. e Style 2045 for sewing knits, stretch fabrics and elastic. * Style 202571 for twin-needle decorative stitching. ‘3. Button Foot holds most flat buttons securely for fastening. 4. Zipper Foot for inserting zippers and stitching corded seams. 5. Blindstitch Hem Guide. Use this with the gen- eral purpose foot to position and guide the hem. 6. Straight Stitch Foot and Straight Stitch Needle Plate are used when your fabric or sewing pro- cedure requires close control. These accessories are recommended for all straight stitch sewing. 7. Buttonhole Foot is used to make bar tack but- tonholes in four steps. 8. Special Purpose Foot. Use this for all kinds of decorative stitching. 9. Snap-in Feed Cover for button sewing, free- motion work and darning. 10. General Purpose Foot and General Purpose Needle Plate are on your machine when deliv- ered. Use them for alternating between straight and zig-zag stitching. | 11. Tube of Oil for oiling the machine.. 12. Spool Pin is used for twin-needle sewing. 13. Lint Brush for cleaning your sewing machine. TCAUTION: Use this needle with the general pur- pose needle plate and general purpose or special pur- pose foot only. Do not use any other accessories with this needle as needle breakage will occur. To ensure that you are always provided with the most modern sewing capabilities, THE MANUFACTURER reserves the right to change the appearance, design or accessories of this sewing machine when con- sidered necessary. 2. Getting Ready to Sew Choosing and Changing Accessories CAUTION: Disconnect the power line plug from the socket outlet when changing needles, feet, or needle plates, or when leaving the machine unattended. This eliminates the possibility of starting the machine by accidentally pressing the speed controller. Changing Presser Feet e Raise needle to highest position by turning the hand wheel toward you. ® Raise presser foot. 1. Press toe of presser foot upward as far as it will go until it snaps free. | 2. Centre the new presser foot under the shank A. Lower the presser foot lifter so that the shank fits over the presser foot pin. 3. Press presser foot screw down firmly until foot snaps into place. Removing and Replacing the Button Foot and Presser Foot Shank ¢ Raise needle to highest position by turning the hand wheel toward you. e Raise the presser foot. ¢ Loosen presser foot screw A and remove the shank B, guiding it to the right. * To replace the accessory, hook shank around the presser bar and tighten the presser foot screw. NOTE: Insert the edge of a coin in the seat of the presser foot screw to loosen it and tighten it securely. Attaching Blindstitch Hem Guide ® Raise presser foot, loosen presser foot screw and slip blindstitch hem guide between screw and shank of the general purpose foot. * Be sure underside of the guide clears the slide plate and front of foot. e Tighten screw with a coin. 10 or A TAS YE ris cr PRI ee em orl EL ieee Tue 4 hs ANS La liter iy RB tid Du a Aap, Pm ое pr } В A AAA и ALS: ZN © г pu bf ro oon es E a Pa у E 11 Changing Needle Plates NOTE: Remove bobbin if it contains thread in order to prevent thread being caught when plate is replaced. e Raise needle to highest position by turning the hand wheel toward you. | e Raise presser foot. * Open slide plate. Place thumb under right side of needle plate, lift it up and withdraw it to right. * Replace needie plate under clamping pin A, push it firmly to the left and press down until it snaps into place. | e Close slide plate. Attaching Snap-in Feed Cover * Raise needie to highest position by turning hand wheel toward you. * Raise presser foot, open slide plate and insert gen- eral purpose needie plate. e Slide snap-in feed cover away from you over needie plate until points B and C are positioned directly over holes in needie plate as illustrated. Snap in point B. Then push point C in toward point B until it snaps into place. Close slide plate. e To remove, open slide plate, then simply lift up front edge of feed cover and remove. Close slide plate. Changing the Needle * Raise needle to its highest position by turning the hand wheel toward you. Loosen the needle-ciamp screw D and remove the needle. e Insert new needle with the flat side of the needle to the back, up into clamp E as far as it will go. * Tighten needle-clamp screw. 12 13 Fabric, Thread The needle and thread you choose will depend upon the fabric to be stitched. The needle should be fine enough to prevent the fabric from being marred with large punctures, yet heavy enough to pierce the fabric without being bent or deflected. and Needle Table The eye of the needle must be large enough for the thread to pass through it freely: too fine a needle will cause the thread to fray. The table below is a guide to needle and thread selec- tion. Refer to it before starting a sewing project. Be sure to use the same size and type of thread in both needle and bobbin. Operating Machine Connecting Machine Before plugging in your machine, be sure that the volt- age and number of cycles indicated on the electrical nameplate A, conform to your electrical power supply. If your speed controller cord has a motor discon- nect plug, push plug B into the receptacle at the right end of machine. Then connect plug C to your socket outlet. | | If the speed controller cord is wired directly to the motor, simply connect plug C to your socket outlet. CAUTION: Disconnect the power line plug from the socket outlet when changing needles, feet, or needle: -. N plates or when leaving the machine unattended. This eliminates the possibility of starting the machine by accidentally pressing the speed controller. If your machine has a sewing light switch, pressor ~~ turn switch on the machine, as required. If machine has a three-position switch: * The OFF setting (switch moved to о symbol). e The MIN. setting (switch moved to 1 symbol) al- lows the maximum control for special jobs. * The MAX. setting (switch moved to 11 -symbol) al- lows for full il speed capacity of the machine. To run the machine and control speed, press the speed controller D with your foot. The harder you press, the faster the machine will sew. To stop ma- chine, remove foot from controller. CAUTION: Because of the up and down movement of the needle, you must work carefully and watch the sewing area when operating the machine. 16 17 The Bobbin Thread Winding the Bobbin Preparation Steps 1. Raise the presser foot and turn hand wheel toward you until needle is in highest position. 2. Loosen hand wheel knob A by turning it toward you with the right hand while holding hand wheel with the left hand. 3. Place thread spool on spool pin with thread retain- ing slit B on top. (Break paper at the end of Spool if necessary.) Winding Steps ® Lead thread around bobbin winder tension disc C, as illustrated, and through small hole in bobbin from inside out. * Place bobbin on spindie and move bobbin winder D to right. e Hold thread end and start the machine. Cut off thread end after a few coils have been wound. e When required amount of thread has been wound (winding will stop when bobbin is full) stop machine and cut connecting thread. e Move bobbin winder to the left and remove bobbin. * Hold hand wheel and tighten hand wheel knob. 18 19 Threading the Bobbin Case 1. Hold bobbin so that thread unwinds in direction shown, and insert bobbin in bobbin case. 2. Pull thread into notch A in bobbin case, draw | toward left and into slot B. 3. Draw approximately 10cm (4 inches) of thread diag- onally across the bobbin. 4. Close slide plate, allowing thread to extend through the slot between the slide plate and the needle plate. 20 Threading the Machine ¢ Place spool of thread on spool pin over spool pin felt. If spool being used has a thread retaining slit A, it should be placed at the top, as illustrated. e Raise the presser foot, to release thread tension. ¢ Raise the take-up lever to highest position by turn- ing hand wheel toward you. e Holding thread ends in each hand, snap thread into upper thread guide 1. e Pass thread through thread guide 2. e With right hand on thread spool, thread the needle thread tension 3. Slide thread over metai plate be- tween tension discs with left hand. Lead thread under tension and tension wire. Thread tension wire by firmly pulling thread up and over to the right. * Guide thread through point 4. ® Thread take-up lever 5, as illustrated. e Draw thread through points 6 and 7, guiding thread from rear of each guide to the right. e Pass thread through guide 8. Thread the needle 9 from front to back, drawing 10cm (4 inches) of thread through the needle eye. 22 N \ X 1 1 PA a 1 E 1 1 49 rd 1 CSREES q Pi р NE | t за : AAC TONO ‘ AS wa я "e i д > < © 7 Ad ' = СЫ ' «к Te 7 ' ! 1 1 1 ' t 1 1 1 1 t J E. ' Г i Ро 23 "Raising the Bobbin Thread Hold needle thread lightly with left hand and turn hand wheel slowly toward you until the needle enters plate. Continue turning hand wheel and holding needle thread until needle rises. Tighten your hold on the needle thread and bring up bobbin thread in a loop. Open the loop with your fingers. Draw approximately 10 cm (4 inches) of both threads under the presser foot and place them diagonally to left. Close slide plate. 24 25 3. Straight Stitching Setting Selectors | Before you move the selectors to set your machine for straight stitching, turn the hand wheel toward you until the needle is above the needle plate. * Needle Position: |. À * Stitch Width: [:) $ 1 £ E e Stitch Length: 1.5-4 to suit fabric Straight stitching can be performed with pattern selec- tor in either position and stitch width leverat ¡ only. Adjusting Stitch Length The stitch length dial controls the length of stitches. The numbers around the edge of the dial express stitch length in mm; the lower the number, the shorter the stitch. Generally, shorter stitches are best for light- weight fabric. The area from 0 to 1 is used for the adjustment of zig-zag satin stitching (see page 40). Setting the Dial e Turn dial so that stitch length desired is positioned under w symbol. * To shorten stitch length, turn dial toward a lower number. » To lengthen stitch length, turn dial toward a higher number. For reverse stitching, depress push button located in centre of dial, hold in until reverse stitching is com- pleted, then release push button. 26. 27 Needle Thread Tension Having selected the correct needle and thread com- bination for the fabric being used, it may be necessary to adjust the tension of the sewing machine to insure a well-balanced stitch. A well-balanced stitch is produced when the top and under thread appear the same on the fabric. Your machine has an adjustable top tension control system. This control exerts tension on the threads as they pass through the machine to form a stitch. * Too much tension will produce a tight stitch which” Will cause puckered seams. * Too little tension will produce a loose stitch. When an even amount of tension is exerted on both threads, a smooth even stitch known as a balanced stitch, is produced. Tension Test To help understand the effect of tension on fabric and thread, try this simple test: * Take two pieces of a medium weight woven fabric in a solid light colour about 15cm (6 inches) long. Place a 2020 size 14 needle in the machine. e Thread the top of your machine with a polyester or cotton dark colour thread and use a lighter colour thread of the same fibre and size in the bobbin. e select straight stitch. * Seam the two pieces of fabric together starting with the top tension control at 1. Then as you sew, slowly turn the tension control from 1 through 9. * Sew another row turning the dial back to 1. You should have a balanced stitch on each row between the start and finish in each case. e The different coloured threads will help you to see the effect that the tension has on the top and bottom threads. Now that you have observed the effects of tension, we suggest that you perform a similar test on a scrap of fabric you plan to use, being sure to duplicate the number of thicknesses of your garment. 28 29 Sewing a Seam 1. Select straight stitch and set the stitch length dial on desired setting. Raise presser foot. Pull thread back under presser foot leaving at least 10cm (4 inches) of thread. 2. Position needle approximately 1.3cm (1/2 inch) from fabric edge. Then lower presser foot and backstitch almost to the edge of the fabric for reinforcement by stitching in reverse direction. For additional in- formation on reverse stitching refer to page 26. Stitch forward to end of seam and stop machine before the end of stitching line. (Do not sew beyond edge of fabric.) CAUTION: Do not pull the fabric while you are stitching as this may deflect the needle causing it to break. | 3. Raise needle by turning hand wheel toward you. Press reverse stitch push button, and back stitch 1.3cm (1/2 inch) to reinforce end of stitching. 4. Raise needle by turning hand wheel toward you. Raise foot and remove fabric by drawing it to the back and to the left. Cut threads on thread cutter at rear of presser bar. 30 Applications Darning with an Embroidery Hoop e Needle Position: da A e Stitch Width: []] 1 ® ® e Stitch Length: O e No Presser Foot * Snap-in Feed Cover * Embroidery Hoop Designed for Machine Use * Position work under needle and lower presser bar. * Hold needle thread loosely with left hand, turn hand wheel toward you, and draw bobbin thread up through fabric. Hold both thread ends and lower needle into fabric. e Stitch across opening, moving hoop under needle at a slight angle from lower left to upper right. Keep lines of stitching closely spaced and even in length. When opening is filled, cover area with crosswise lines of stitching. Quilting Quilting is the art of stitching two or more thicknesses of fabric together in a planned design. A padding is stitched to the underside of the fabric to produce a soft, puffed effect that is becoming to some wearing apparel and to many fabric furnishings. Preparing the Fabric — Baste a light padding of cotton flannel, synthetic quilt batting, sheet wadding, or a lightweight wool interlin- ing to the underside of the fabric. When using sheet wadding, first back it with voile, batiste, or net to pre- serve the sheet wadding through wear. Baste the lay- ers-of fabric and padding together on the lengthwise and crosswise grains. Basic Procedure * Draw both threads under the foot and diagonally across feed to left. * Position the needle, lower the foot and start stitching. 32 Zipper Insertion How the zipper is inserted will depend on the type of garment and the location of the zipper. With the adjust- able zipper foot, you will find it easy to sew an even line of stitching close to the zipper. For instructions on inserting zipper foot on machine, see page 8. * Needle Position: 4 [L] L e Stitch Width: [1] 1 $ £ € e Stitch Length: To suit fabric * General Purpose Needle Plate e Zipper Foot | e Speed: MIN. The zipper foot can be used either to the left or right of the needle, depending on where the teeth of the zipper are placed. Adjusting the Zipper Foot When the zipper is to the right of the needle: A. Attach right side of zipper foot to shank (needle will enter right notch in foot). | When the zipper is to the left of the needle: B. Attach the left side of zipper foot to shank (needle will enter left notch in foot). 34 4. Zig-Zag Pattern Stitching JAVAVAVAVAVAVAVAVAVAVAVAVAVAVAVAVAVAVAVAVAVAVA. ANANNANNANANANANANANANANAN Setting Selectors Before turning selector, make sure needle is out of the fabric. 1. Stitch Pattern Selector With your sewing machine you can do two kinds of zig-zag stitching: plain zig-zag = and blind- stitching 3 . The pattern selector, located on the control panel, controls stitch selection. To Select Pattern e First make sure needle is above fabric. e For plain zig-zag stitching, slide pattern selector level to = For blindstitching, slide pattern selector lever to _ . Needle Position Selector Most of your zig-zag stitching will be done in centre J. needle position. Left da and right a settings are used for spe- cial stitch placement. | Stitch Width Selector To produce a plain zig-zag or a decorative stitch, the stitch width selector is moved from its straight stitch position | to any of its other four positions. The further you move the selector toward the right, the wider your stitch will be. 36 4. Adjusting Stitch Length Any stitch length setting from 1 to 4 mm will give you an open zig-zag stitch. The higher the number, the more open, or farther apart your stitches will be. The area between 0 and 1 on the dial is used for the adjustment of zig-zag satin stitching, a series of closely spaced plain zig-zag stitches that form a smooth, satin-like surface. (Refer to page 40 for information on satin stitching.) | Needle -Thread Tension The needle-thread tension dial regulates the amount of tension on the needle thread and lets you select just the right setting for your fabric and thread. The numbers on the dial eliminate guess- work in duplicating settings. Zig-zag stitching requires less tension than straight stitching. Notice the stitching on your test sample. The stitches should lie flat against the fabric with- out causing the fabric to pucker. lí the stitches are not flat and the fabric is puckering, lower the ten- sion by turning the dial to a lower number. Bobbin Thread Tension Bobbin thread tension is controlled by screw A, located on the bobbin case. The tension is set at the factor for regular sewing and should not be adjusted unless the corners of a zig-zag stitch can- not be locked by adjusting the needle-thread tension. On those rare occasions when it becomes neces- sary to adjust the bobbin thread tension, use a very small screwdriver. A very slight turn of screw A will change the appearance of your stitching. ¢ To increase tension, turn screw to the right. * To decrease tension, turn screw to the left. 38 Satin Stitching When you wish to produce a satin stitch, make a test sample first so you can adjust stitch length and thread tension properly. Soft fabric may require a backing to insure a firm stitch. Crisp organdy, lawn or a fusible interfacing are suitable for this purpose. Accessory and Selector Settings e Pattern: Zig-Zag Needle Position: & a e Stitch Width: : [$ $ $ | e Stitch Length: 0 to 1 * General Purpose Needle Plate * General Purpose Foot Adjusting Stitch Length o Turn stitch length selector dial to 1. * Run the machine at a slow speed and slowly turn stitch length dial toward the right until stitches are closely spaced and form a smooth surface. Adjusting Needle Thread Tension Zig-zag stitching usually requires less needle thread tension than straight stitching. Thread machine cor- rectly and make a test sample with the same fabric, thread, needle and stitch pattern combination you plan to use. Stitches should lie flat without causing fabric to pucker. If puckering occurs, lower the tension by turning dial to a lower number. An underlay or tissue paper back- ing may be needed. Satin stitching requires less tension than straight stitching or open zig-zag stitching. Furthermore, the wider the stitch, the lighter the tension on the thread must be. Notice the stitching on your sample. If the fabric is puckered, lower the needle-thread tension by turning the tension dial to a lower number. 40 Stitch Usage Applique The stitch most commonly used in appliqué is a plain zig-zag, closely spaced to form a satin stitch. The width of this stitch can be varied to accommodate fabrics of different weaves and textures. Other stitch patterns can also be used. | Preparation Make a test sample to decide which of the following methods is the most appropriate for your fabric and design. Mark design on piece of fabric to be appliquéd. Cut out design leaving about 2 cm (3/4 inch) margin — all around. Position the design. Baste it to the fabric. Method 1 e Select pattern and adjust stitch width dial for desired appliqué stitch. Adjust stitch length to fine setting, between 1 and 0. e Follow the outer edge of the design with a decora- tive stitch. | * Trim away the excess fabric on the outer edges of the stitching. | Method 2 e Select straight stitch. e Outline the entire design with a short stitch. e Trim raw edges to the stitching and remove basting. e Select stitch pattern and stitch width desired, and set stitch length on a satin stitch setting for a closely spaced stitch, between 1 and 0. e Stitch, following the straight stitch outline. This method will produce a smooth overedged finish, with no raw edges to be trimmed after stitching. Method 3 e Purchased motifs can be appliquéd quickly and easily by using either a straight or decorative stitch. 42 Zig-Zag Seam Finishes Seam edges support the garment and should be given a durable finish if the fabric is likely to ravel. There are two methods of finishing seams in such fabrics: trim- ming seam edge or overedging. Make a test sample to determine which method best suits your fabric. * Pattern: Zig-Zag | *e Needle Position: de e Stitch Width: | 3[£ E E] —* Stitch Length: 1 to 3 to suit fabric * General Purpose Needle Plate ¢ General Purpose Foot Method 1 — Trimmed Seam Finish ¢ Adjust stitch width and length to give you the most open stitch that will secure the fabric edge; avoid harsh overstitching. e Stitch near the edge of seam allowance and trim seam edges evenly after stitching. Method 2— Overedge Seam Finish . Adjust needle thread tension, stitch width and stitch length to suit fabric. * Trim seam edges evenly. ¢ Place trimmed seam under the foot and overedge the seam allowance as illustrated. | Lingerie Seams To make a lingerie seam durable and flexible use the plain zig-zag stitch at a narrow width setting. This seam treatment is particularly suitable for bias seams. When seaming nylon tricot insert a 2045 needle in the machine before you begin to sew. e Straight stitch the seam line on wrong side of fabric. e Press both seam allowances in the same direction. e From the right side, topstitch with narrow zig-zag stitching, letting the needle alternately enter the seam line and seam thickness. (Stitch width narrow; stitch length 1 to 1.5.) 44 45 Blindstitch Hems Blindstitching provides a durable hem finish that is almost invisible. While it is best suited to straight or slightly curved hems, taped, bound, or turned hem edges can also be blindstitched with ease. e Stitch: Blindstitch e Needle Position: de 4 e Stitch Width: | JE iE * Stitch Length: To suit fabric * General Purpose Needle Plate * General Purpose Foot e Blindstitch Hem Guide 1. Raise presser foot, loosen screw, and slip blind- stitch hem guide between screw and shank of foot. Make sure underside of the guide clears the slide plate and front of foot. Tighten screw with coin. 2. Prepare hem in the usual way. It is advisable to baste the hem. Place the basting at least 1.3 cm (V2 inch) below the edge of hem allowance to avoid catching the flange of guide as you stitch. 3. With the wrong side of work uppermost, turn the hem under, creating a soft fold from the top edge of hem. 4. Position hem ynder the foot with the soft fold resting against the wall of guide. Make sure the flange of the guide is between soft fold and top of hem, as shown. 5. Lower presser foot. Stitch so that the straight stitches fall on the hem allowance and zig-zag stitches pierce the soft fold of work. Adjust stitch width if necessary. While stitching, guide hem edge in a straight line and feed soft fold evenly against wall of the guide. 46 — Ladder Seam The blindstitch ladder seam is particularly appropriate for knit and stretch fabrics. It is ideal for stretchable construction seams, and edge finishes for necklines, pockets and collars in sportswear and swimsuits. e Pattern: Blindstitch * Needle Position: L À e Stitch Width: ¡[TÍ £ El e Stitch Length: 1.5 t0 2.5 — e General Purpose Needle Plate e General Purpose Foot e Make a test sample to adjust stitch width and length and needle thread tension to suit the fabric. Needle thread tension should be lighter than normal. e Cut and fit garment, allowing for 1.5 cm (5/8 inch) seam allowance. Baste seam line. * Place fabric under presser foot so that the straight stitches fall on the seam line basting and the points toward the centre of the garment. e After stitching, open seam by pulling fabric back on opposite sides of the seam to produce ladder effect. Press seam allowance after opening. 48 5. Buttonholes and Buttons Buttonholes can be made easily with the built-in four- step method. Before sewing on your garment, always make a test buttonhole duplicating the number of thicknesses of fabric and interfacing if appropriate. Garment Preparation Buttonhole Position Accurate guidelines are essential to keep buttonholes at a uniform distance from the edge of the garment, evenly spaced, and on the grain of the fabric. 1. Mark the centre line on the garment. This guideline can be made by machine or hand basting or using tailor’'s chalk. Be sure that the space from the centre line to the finished edge of the garment is at least equal to three-quarters the diameter of the button. With this spacing, the button will not extend beyond the edge when the garment is buttoned. Make sure that the centre line marking follows a ~ lengthwise fabric thread. A. Centre line B. Buttonhole C. Finished Edge of Garment D. Diameter of Button 2. Mark a position guideline for each buttonhole. Horizontal buttonholes B are placed to extend 3mm (1/8 inch) beyond the centre line A of the garment, as shown, so that the buttons will be in the centre of the figure when the garment is fastened. Horizontal buttonhole guidelines should follow a crosswise fabric thread. * Mark the horizontal buttonhole guideline for each buttonhole. It should be longer than the finished length of the buttonhole. e Mark the starting point for each buttonhole 3mm (1/8 inch) beyond the centre line (see illustration). 50 Vertical buttonholes C are placed so that the centre line A of the garment is in the centre of the buttonhole, as shown. * Mark the ends of each buttonhole horizontally across the centre line basting and use the centre line marking as the buttonhole guide when stitching. Buttonhole Length * The buttonhole length should be just long enough to allow the button to slip through the opening without stretching it. * To make sure the measurement is correct, cut a slit in a scrap of fabric equal to the diameter of the but- ton you intend to use. * Increase length of opening until button slips through easily. This test is particularly advisable for buttons of un- usual shape or thickness. 52 Four-Step Buttonholing The four dial settings for buttonholing are located on the stitch length selector. As you turn the dial for each step, your machine is automatically set for the correct needle position, stitch width, and stitch length, as well as for stitching direction for that step. You need not turn the fabric during buttonholinc. e Pattern: Zig-Zag e General Purpose Needle Plate ~* Buttonhole Foot Preparation e Prepare and mark your garment, as instructed on page 50. Ш e Position work under needle, aligning centre marking of buttonhole with centre line on the foot. Align end marking of buttonhole with the horizontal lines on the foot. e Set the buttonhole balance knob K in neutral posi- tion, as illustrated. The buttonhole balance knob, when turned slightly to the right or left, enables you to balance the stitch density of both sides of the buttonhole. Refer to the next page for information on balancing buttonhole stitch density. Step 1: Side Stitching | Raise needle above the fabric and turn the buttonhole dial to step 1. Position needle in fabric at point A. Lower the footand stitch to end of buttonhole (point B). The end marking should be aligned with the horizonta! lines on the foot. Step 2: Bar Tack Raise the needle out of the fabric. Turn buttonhole dial to step 2 and take at least four stitches. Stop at point С. Step 3: Side Stitching Raise the needle out of the fabric. Turn buttonhole dial to step 3. Complete work to point D. Raise needle. Step 4: Bar Tack Raise the needle out of the fabric and turn buttonhole dial to step 4. Take at least four stitches ending at point E. For a smooth, satin appearance and greater durability, stitch around the buttonhole a second time by repeating the four-step sequence. 54 55 ~ Balancing the Buttonhole Stitch density on left and right sides of the buttonhole may be balanced by adjusting the buttonhole balance knob K. Use the buttonhole balance knob to obtain similar stitch appearance on left and right sides of the buttonhole. A very slight turn will produce a noticeable density change. | To change the density on either side of your test but- tonhole follow the procedure below. Before sewing ON your garment, be sure to make a test but- tonhole on a sample of your fabric to check that the stitch density is similar on left and right sides of your buttonhole. 1. Make a test buttonhole with the balance knob in neutral position (indicator line or dot directly below Y symbol on control panel). 2. If the stitches on the right side of the buttonhole are too open, turn the balance knob from its neutral position to the right to increase density of the side stitching. 3. If the stitches on the left side of the buttonhole are too open, turn the blance knob from its neutral position to the left to increase ‘density of the side stitching. After buttonhole stitching is completed, return bal- ance knob to its neutral position (indicator line or dot directly below Y symbol on control panel). 56 Buttons Most flat buttons can be sewn quickly and easily using the zig-zag stitch. e Pattern: Zig-Zag | * Needie Position: da A * Stitch Width: ; $ SE) £ * Stitch Length: 0 e General Purpose Needle Plate e Snap-in Feed Cover e Button Foot Sewing on a Button e Set your machine up according to the code above. e Mark position of button on garment. Place garment under foot. Align garment so that the button is directly under the foot. Lower the presser foot to grip button centrally. 1. Turn hand wheel very slowly toward you until nee- dle point aligns with hole of the button. Adjust zig- zag stitch width, if necessary to permit clean entry of the needle. | | 2. Continue turning hand wheel one complete revolution and observe that the needie point 1s pro- perly positioned to enter the other hole. * Take six to twelve stitches. e Remove garment from machine. Pull threads to un- derside of garment and trim. 58 6. Caring for Your Machine Cleaning the Machine CAUTION: Before cleaning your machine, discon- nect the power line plug from the socket outlet. Periodically, depending on machine use, clean | and oil 8 your machine, using one drop of oil on illustrated areas. We suggest that you check your machine after completing every two or three sewing projects. | Top and Bottom Covers Clean and oil the top and bottom areas marked on the illustrations. Use a screwdriver to remove the screws. To replace the covers, simply line up the screwholes and replace screws with a screwdriver. 60 Face Plate Area To clean В апа ой & the front interior of machine, remove screw from face plate. With a soft cloth or lint brush, clean and oil points indicated by arrows. Re- place face plate and screw. Bobbin and Feed Areas To clean bobbin and feed areas, remove needle plate, as instructed on page 12. Remove bobbin case as in- structed on next page. Using soft cloth or brush, clean area as illustrated. Replace needle plate and bobbin case, as instructed on page 12 and 64. Exterior Areas If necessary, a mild solution of soap and water may be used on exterior areas to remove stubborn stains. No other cleaning liquid or powder should be used. CAUTION: Do not attempt to adjust the motor belt. Contact your nearest Service Centre should any ad- justment be required. 62 Removing and Replacing Bobbin Case CAUTION: Before removing bobbin case, dis- connect the power-line plug from-the socket out- let. IMPORTANT: The bobbin case is manufac- tured from a special phenolic compound specially designed to provide smooth friction-free sewing. With proper handling the bobbin case will give you years of reliable, trouble-free sewing. The bobbin case is the most important part of your sewing machine. Please handle with care and do not force when removing and replacing it. e Turn hand wheel toward you to raise needle to its highest position. 1. Open slide plate, remove needle plate and remove bobbin. 2. Insert screwdriver into bobbin case holder A and turn it toward the rear as illustrated. 3. To remove bobbin case: e Insert index finger into centre of bobbin case. With index finger and thumb gently lift and push bobbin case away from you until the case IS released from holder. 4. To replace bobbin case: e Insert index finger into centre of case and grip with thumb above the screws. Gently slide the flat tab at the rear of the bobbin case under- neath the curved section of feed B while main- taining slight upward pressure, then slide bob- bin case all the way to the rear. Lower the bob- bin case and draw it toward you so that tab C is positioned under plate D. Gently wiggle case to insure proper seating in the rim of the rotating hook. In this position bobbin case should be free to float slightly from side to side. * When you are sure bobbin case is properly seated lock case into position by turning holder A back, as illustrated. Replace bobbin, needle plate and close slide plate. 64 65 Changing the Light Bulb CAUTION: Before changing light bulb make sure you have disconnected power line plug from socket outlet. This machine is designed to use a 15-watt max- imum bayonet base bulb only. The screw located on the machine face plate must be removed before the face plate can be opened. * Remove face plate. e Do not attempt to unscrew the bulb. 1. Press it up into the socket and at the same time turn bulb over in direction shown to unlock the bulb pin and guide out of socket. e Press new bulb into socket, with bulb pins enter- ing slot of socket. | 2. Turn it over in direction shown to lock bulb in position. * Replace face plate. Replacing the Slide Plate You will not have any occasion to remove the slide plate. However, if it should accidentally become dis- engaged from the machine, it is easily replaced. ® Raise the presser foot and make sure needle is in its highest position. e Place slide plate in slide way with the front edge close to, but not covering, the retaining spring (as shown). e With a small screwdriver, lift each end of the spring into each of the side grooves on 1the underside of the plate. e Draw the plate gently toward you and fully engage the spring. e Close slide plate. 66 7. Twin-Needle Stitching Twin-needle sewing capability has been built into this sewing machine. The twin-needle simultaneously produces two parallel, closely spaced lines of pattern stitching. You can stitch with either one or two colours of thread. | e Stitch: Pattern desired Needle Position: & À only e Stitch Width: $ # onlyt e Stitch Length: .5-4 to suit fabric e General Purpose Needie Plate e General Purpose Foot TCAUTION: Do not use a stitch width greater than what is recommended. A wider stitch will result in needle breakage. Procedure e insert twin-needle. e Thread as for single-needle stitching, except pass thread between centre and back tension discs A, and through eye of left needle. | * Insert a second spool pin into hole on the top cover of machine, as illustrated. e Place second spool of thread on right spool pin and felt. e Thread machine in usual way, except pass thread from second spool between centre and front ten- sion discs B, as shown. e Thread through remaining points, making certain to omit the thread guide above the needle and pass thread through eye of right needle. 68 RE 69 8. Home Service Hints Whenever sewing difficulty is encountered, review the sections of the instruction book that explain the opera- tion you are performing to make sure you are using the machine correctly. If the problem still exists, the fol- lowing checklist may help you to correct it. If you still have difficulties, call your nearest Sewing Centre. What to Do If... Needie Breaks * Make sure needie is fully in- serted into needle clamp ..... ....seepage 12,13 * Make sure needle is not being pulled to one side as fabric is removed from the machine ....... see page 30,31 * Make sure presser foot or accessory is securely fas- tenedto presserbar............. see page 10,11 * Make sure fabric is not being pulled while sewing ............. see page 30,31 e Make sure stitch width does not exceed[:11] £ E when a twin-needle iIsused . . see page 68,69 Thread Breaks e Make sure machine is prop- | erly threaded ................. see page 22,23 e Make sure needle-thread ten- sion isnottootight......... see page 28,29,40,41 * Make sure thread is unwind- ing freely from spool ...... ..See page 1819,22,23 ® Маке sure bobbin case area is free of lint and loose threads... .......... .. .. see page 62,63,64,65 e Make sure the needle is straight andsharp .............. see page 14,15 70 Fabric Does Not Feed Properly e Make sure presser foot is cor- rectly attached to machine ........ see page 10,11 e Make sure stitch length dial is correctly set ............. see page 26,27,40,41 * Make sure lint has not accu- mulated around feed. ........... see page 62,63 Skipped Stitches e Make sure needle is correct style for machine and size for thread... ... ....... ........ … See page 14,15 e Make sure machine is cor- rectly threaded................ see page 22,23 * Make sure needle is securely fastenedto needle bar ........... see page 12,13 e Make sure the needle is nei- ther bent nor damaged. .......... see page 14,15 Fabric Puckers e Make sure needle-thread ten- sionis not tootight......... see page 28,29,40,41 Thread Breaks While Winding Bobbin ® Make sure machine is cor- | rectly threaded ................ see page 18,19 * Make sure thread is unwind- ing freely from spool............. see page 18,19 71 Index ACCeSSOories. . . . 10 6,7 АррИдиё ................. ВЕ EERE 42,43 Bobbin ...... aa 6,718,119 Winding.......... 18,19 BobbinCase. . ...... LL LL 64,65 Removing . .... LL LL 64,65 Threading... .. ..... LL LL 20,21 Bobbin Thread. . . . . . Lo LL LL 18,19,20,21,24 25 Raising. ........ I 24,25 Buttons . LL LL LL LL 58,59 Buttonholes ........ aa 50-57 Position ......... LL LL LL LL 50-53 Procedure . . LL LL 54-57 Caring for Your Machine . .... 60-67 Cleaningthe Machine. . ...... .. ..... . .. ..... 60-63 Connecting the Machine . . .. .... 16,17 Darning . a 32,33 Fabric, Thread and Needie Table. ................. 14,15 FeedCover............ a 6,712,13 Attaching and Removing . | 12,13 HandWheel . . .. 11110 4,5 Light Bulb....... LL ... 66,67 Needle ..................:6,712-15,22,23,28,29,38-41 Changing ..... 12,13 Position ....... aaa 2. . 36,37 Thread Tension .................. 28,29,38,39,40,41 Threading ........... . ..... . ...... 22,23 Needle PlatesS . 6,712,13 Changing Plates .......... aa 12,13 General Purpose ......... 6,7 Operating the Machine . 16,17 Olling the Machine . 60-63 PresserFeet. . .. 6-11 Changing Feet... 8,9,10,11 Presser Foot Lifter . .. 4,5 PrincipalParts . . .......... LL LL LL 4,5 Quilting .......... LL LL 32,33 Reverse Stitching... .............. ... ‚|. 26,27,30,31 Satin Stitching ................. a 40,41 Seams ....... a 30,31,48,49 Seam Finishes . . .. 44 45 Speed Controller .......................... 4,5,16,17 Stitch Length ................... 4,5,26,27,38,39,40,41 StitchWidth .................. .... .. ..... 4,5,36,37 Straight Stitching ........ a 26,27 Take-up Lever LL LL 110 4,5 Threading the Machine . 0... 22,23 Twin-Needie Stitching ............. .. ....... 68,69 Zig-Zag Stitching .................... LL LL 36-39 Form No. 21894 Printed in Taiwan - Part No. 173497-001 | 72
advertisement
Key Features
- Computerized sewing machine with built-in stitches
- Easy-to-use controls and clear instructions
- Variety of stitches for different fabrics and projects
- Adjustable stitch length and width
- Built-in needle threader
- Automatic bobbin winder
- Reverse stitch button
- Free arm for sewing sleeves and cuffs
- Hard cover included
Related manuals
Frequently Answers and Questions
What types of stitches does the SINGER 1263 have?
The SINGER 1263 has a variety of stitches, including basic stitches, decorative stitches, and stretch stitches.
Can the SINGER 1263 sew different types of fabric?
Yes, the SINGER 1263 can sew a variety of fabrics, including cotton, polyester, silk, and denim.
What is the maximum stitch width on the SINGER 1263?
The maximum stitch width on the SINGER 1263 is 6mm.
advertisement