advertisement
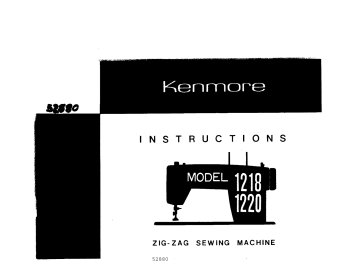
I N
R U C T I 0 N S
ZIGZAG SEWING
52880
MACHINE
@ ©
!
FRONT VIEW
I
@
®
®
-®
2
1. Bobbin Winder
2.
Special Stitch Control and Width Control
3.
Stitch Length Control
4.
Light Switch
5.
Feed Dog Control
6.
Nomenclature Plate
7.
Needle Plate
8.
Feed Dog
9. Needle Clamp Screw
10. Hand Hole Cover Plate
11. Presser Foot
12, Presser Foot Screw
13. Thread Guides
14.
Upper Thread Tension Control
15.
Thread Take-up Lever
16. Bobbin Winder Thread Guide
17. Upper Thread Guide
@
BACK VIEW
@
18.
Presser Foot Pressure Regulator
19.
Face Plate
20.
Presser Foot Lever
21, Thread Cutter
22.
Hand Wheel
23.
Clutch Knob
24, Thread Spool Pins
@
3
o
e
INSTALLING MACHINE
1, Loosen the two hinge screws under holes in the rear edge
of the machine bed.
2,
Raise hinge pins in the cabinet or case.
S!ip machine head onto pins.
3.
Tighten
hinge screws securely.
Lower
machine head to front
flap.
Screw spool pins in place.
Place
the plastic spool
holder
onto the spool pin.
Holder and pins are
packed
in the accessory box.
CONNECTING MACHINE
Push the connector
of the speed control onto three-prong connector
under
the machine bedplate.
See illustration 4.
Push the two prong
plug of the speed control
into
any
110-120V.
wall outlet,
4
FEED DOG CONTROL
The feed dog control is located on the right front of the machine
bedplate.
There are a few times when
you
want to control the feeding of the fabric yourself. When the control is turned to the left,
the feed dogs drop and do not move the fabric.
For most of your
sewing
the feed dog control is turned to "'U".
(Feed dog up)
Fig.
1
Fig. 2
SEWING LIGHT
The light and power
switch shown above
in Fig. 1 provides
the
electric current for the motor as well as the light. In order to operate the machine this switch must be on.
To turn on the light, depress the switch.
If you are interrupted while
sewing and must leave the machine
unattended, just turn off the
switch and the machine cannot be started
accidentally.
The sewing
light is located
inside the face cover plate as shown.
To replace the bulb, turn light off, and swing the face cover plate
open. Push up on the bulb slightly and turn bulb to the left.
Remove bulb from socket. Push in new bulb and turn to the right.
5
NEEDLES
Use KENMORE needles. The size of the needle should conform with
the size of the thread and both should be suitable to the fabric (See
next page). Never use a bent needle or one with a blunt point.
Fig. 1 shows you the exact length of your needle. Be sure you never use in
your machine
one that is not this exact length.
t
I
|
l
It
|
It I
Fig. 1
You will find among your accessories "'Q NEEDLE ''_ with blue shank. This special needle is to be used when
sewing certain knits and certain difficult synthetic fabrics. If you experience skipped stitches in any of your
sewing, use "'Q NEEDLE ''T".
PLACEMENT OF NEEDLE
Raise needle bar to its highest position
by turning the hand wheel toward you.
Loosen the needle clamp screw. Holding the needle with the flat side
away from you, slip the needle into the needle bar. When it is in as
far as it will go, tighten the needle clamp screw with a screwdriver.
Flat side faces to right
6
NEEDLE, THREAD, FABRIC CHART
THREAD SIZE
NEEDLE SIZE
,, ,,,,, ,,,,,,
FABRIC
POLYESTER CORE/COTTON
FINE MERCERIZED
POLYESTER
SILK A
COTTON
SYNTHETIC
WRAP
9or 1!
Lightweight: Batiste, Dimity,
Chiffon, Silks, Synthetic
Jerseys, Fine Lace, Organza,
Crepe. Taffetta, Voile,
Organdy
50 MERCERIZED COTTON
POLYESTER SYNTHETIC
SILK A
t4
Medium Weight: Cotton, Cotton
Blends, Percale, Gingham,
Shantung, Pique, Seersucker,
Satin, Knits. Vinyl, Suitings,
Linen, Wool Crepe, Leather
50 MERCERIZED
MERCERIZED
POLYESTER
SILK A
COTTON
HEAVY DUTY sYhrTHETIC
14 or 16
Medium Heavy Weight: Corduroy,
Denim, Wool, Sailcloth,
Wool
Flannel, Gabardine, Velvets,
Leather
HF_AVY DUTY MERCERIZED COTTON
POLYESTER SYNTHETIC
SILK A
SILK BUTTONHOLE
POLYESTER
TWIST
SYNTHETIC
50 MERCERIZED COTTON
18
Heavy Weight: Coatings,
Upholstery, Cotton Duck.
Heavy Twills, Canvas
16, 18 or
"Q NEEDLE"TM ilUll lUUllllll
Decorative Top-stitching on all
"Q SET"TM
("Q
NEEDLE'TM and
"Q
FOOT"TM)
Synthetic Knits and Stretch
Fabrics: Polyester Double
Knits, Nylon Tricot, Jersey,
Stretch Terry, Sl_ndex,
Cire Tricot
7
Take up
lever
at its
highest position.
_J
I I l! tt'_r _
I l't
Pull
out latch.
REMOVING BOBBIN CASE FROM SHUTTLE
Pull bobbin case straight
out.
8
O
@
@
O
@
O
WINDING THE BOBBIN
1.
Release
clutch
by turning
clutch
knob toward you.
2.
Draw thread from spool through bobbin winder tension discs as shown.
3.
Pull end of thread through hole in bobbin as shown.
4.
Place bobbin onto bobbin winder shaft with end of thread coming from-the top of the bobbin.
Push bobbin winder latch against bobbin until it clicks.
Holding onto end of
thread,
start machine.
When bobbin is slightly filled, snip off end of thread.
5.
Start machine.
Wind thread until bobbin winder latch releases.
6.
Tighten clutch knob and remove bobbin.
Two
spool
pins
have
been
included
with
this machine
to aid in bobbin winding, By placing a spool of thread on the second spool pin, you may wind your bobbin without unthreading the machine.
9
THREADING THE BOBBIN CASE
INSERTING BOBBIN INTO BOBBIN CASE
........
CASE INTO SHUI"rLE
O
O
L
@
@
i
@
t.
Insert bobbin into bobbin case making sure thread is coming from bobbin as shown.
.
Pull thread through slot of case as shown.
.
Pull thread under tension spring.
4.
Turn hand wheel to raise needle to its highest position.
Holding latch open, position case into shuttle, and release latch.
Case should lock into place when latch is released.
,
Hold needle thread loosely in ieft hand and rotate hand wheel toward you one complete turn.
Bring bobbin thread up by pulling upper thread.
10
Fig.I
Fig. 2
THREADING UPPER MACHINE
Place thread on spool pin as shown with the thread coming from the back of the
spool. Guide thread into top thread guide A as shown in Fig. 1 and Fig. 2.
Holding the spool with the right hand pull thread between tension discs as shc_wn in Fig. 3.
Pull the spring wire loop up and past the top hook until the thread can be slipped
into the hook. Release the spool and the spring loop will return to position for
sewing, Fig. 4.
Continue to thread mschine
through guides as illustrated, Fig. 5. Thread needle from left to right, Fig. 6.
Fig. 3 Fig. 4 Fig. 5 Fig. 6
11
12
ADJUSTING THE PRESSURE OF THE
PRESSER FOOT
Push down
outer ring of presser foot pressure
regulator (See illustration),
This will release pressure of presser foot.
To increase pressure, push down inner pin until suitable pressure is obtained.
For ordinary sewing, the inner pin should be all the way down.
Insufficient pressure may cause poor feeding of the
fabric, skipped stitches, or difficulty
in guiding
the fabric.
When sewing
multiple
thickness or heavy fabric
reduce the pressure. Increase pressure when sewing lighter
weight fabrics.
If feed
dog or presser foot marks appear on the fabric, reduce the pressure.
STITCH LENGTH CONTROL
The stitch length contrql regulates the length of the stitch you select.
THE
HIGHER THE NUMBER
-- THE SHORTER
THE STITCH,
The stitch setting you use will be determined by the thickness of the fabric you are sewing, The longer stitch setting should be used for thicker fabric or more layers of fabric. The middle range of the control is the 10-12 stitch per inch range which is the most commonly used,
The basting and stretch stitch are made by adjusting the lever to make the longest possible stitch.
When adjusting for shorter stitches, select the stitch
length and tighten the knob in the center of the lever handle to remain at the
same setting. The knob must be loosened to readjust the lever.
REVERSE STITCHING AND FASTENING A SEAM
tt is best to begin and end seams with a few stitches taken in reverse, Simply raise the Stitch Length Lever to R to sew in reverse. The fabric will start feeding backwards and the seam will be firmly fastened, Lower the lever to again stitch forward, This fastening of the seam is done both at the start and finish of a seam.
13
O
Fig. 1
@
Upper thread too tight
PROBLEM
ADJUSTING TENSIONS
A perfect
stitch will have threads Jocked between the two
layers of fabric with no loops on top or bottom.
REMEDY
Decrease Tension
!
Fig. 2
@
Upper thread too loose
Increase Tension
Fig, 3
14
NOTE: Never adjust more than one number at a time.
When
stitching
is
unsatisfactory as
in figures 2 and 3, adjust the
upper thread tension.
Lower
thread tension
requires adjustment less frequently than the upper thread tension.
When stitch is satisfactory, as in figure 1
and seam is badly puckered,
the cause may
be tight tensions and both upper and lower may be adjusted.
(See page 28)
When
adjusting the tension on the bobbin case, make slight adjustments with a screwdriver.
(See page 28)
INCREASE TENSION
'"
DECREASE TENSION
Turn
Clockwise.
Turn Counter
Clockwise.
15
16
INSERTING AND REMOVING THE MATERIAL
For all kinds of sewing, consult chart page 7.
Before placing the
material on the
machine see that:
• The presser foot
and needle clamp screws are both tight.
• The sizes of needle and thread suit the kind of work to be done.
• The needle and the thread take-up lever are at
their highest position.
a The ends of threads have been drawn about 4 inches to the rear of the machine.
• The feed dogs
are up.
• Stitch length and width controls are set at desired
settings.
Experiment by sewing on the fabric to be used to
determine tension adjustments and correct stitch settings.
Place material under the presser foot,
insert
the
needle into the material by turning the hand wheel
toward you, lower presser foot and start sewing.
To facilitate placement
of heavy fabrics under the presser foot, the presser foot lever can be raised
beyond the normal "up"
position.
To remove the work, first turn the hand wheel toward
you
until the needle is at its highest
position, then raise the presser foot,
draw material
to the rear and cut ° off
excess thread with the thread cutter located on the presser bar.
IMPORTANT:Always
turn the hand wheel toward
you ! When the machine is not being used, place a piece of material over the feed dog and lower the presser foot.
Always have fabric under the presser foot when operating the machine.
Operating
threaded machine without fabric will cause it to jam by forcing _int into the shuttle.
TURNING A CORNER
Stop your sewing machine and make sure needle is in fabric.
Raise presser foot.
Turn fabric to desired direction.
Lower
presser foot and go on with your stitching.
CHANGING THE PRESSER FEET
The various presser feet available for certain kinds of work are to be fastened to the presser bar.
To attach the foot, raise the presser bar to its highest position
by raising the presser foot lever,
Loosen the presser foot
screw, choose the proper foot, insert
frorfi the front. Tighten
the screw using the large screwdriver
and make sure that the
foot is secure.
17
18
STITCH WIDTH CONTROL
Stitch Width Control regulates the width of the stitch you select.
THE HIGHER THE NUMBER, THE WIDER THE
STITCH.
You may vary your zigzag stitch width by adjusting this control to the setting you desire.
Straight stitching is possible only with the control at the red dot.
In case fo Model 1220, this dial also has special setting in red
for sewing stretch stitch.
You may vary the width of the zigzag stitch by adjusting the dial from 1 to 5 in black for
regular stitching and from 1 to _ in red for Rick-Rack
stretch stitching.
Regular straight stitching is possible only with the control at
the red dot and straight stretch stitching at the _ mark.
Before turning the dial, make sure needle is above fabric_
Fig.
OVERCASTING
This is one of the more frequently used zigzag stitches
in garment construction.
You may want
to overcast along the raw edge of each seam
allowance or fold
the raw edge toward the garment and stitch.
Fig. 1 shows the raw edge finished.
Fig. 2 illustrates the folded edge stitched.
Stitch so the needle pierces the fabric just short of the outside edge. Raw
or worn edges of older garments can be overcast to prevent further
raveling.
i i
Fig. 2
i i,,,u
19
20
R
STRAIGHT STRETCH
STITCHING
(Model 1220 only)
Setting:
Special Stitch Control -,,
Stitch Length Control -- All the way
down
Use this specia! stretch stitch with knitted
fabrics and other fabrics that stretch.
Sew as
you
do a regular straight stitch seam.
The
machine will make triple lock stitches back and
forth of a fixed stitch length, to give the stretch to the seam. See illustration.
This stitch enables you to press
open your seam as with any straight stitched seam. The seam will stretch with the fabric without breaking the thread.
This is also a good stitch to use on curved seams that will receive a great deal of strain when worn, such as in children's shorts and slacks as well as adult sport clothes.
1
RICK-RACK STRETCH STITCHING
(Model 1220 only)
Setting:
Special Stitch Control
--
From red 1 to red
Stitch Length Control -- All the way down
Use this special stitch for all-purpose heavy duty sewing of stretch fabrics.
Sew as you do a regular plain zigzag seam. The machine will make triple lock stitches, (See enlarged illustration) to give the stretch to the seam.
21
22
I
Stitch
Width
.'--E
F l-
I-
Stitch
Length
Feed Dog
Control
Fig. 1
BUTFONHOUNG
SETTINGS:
Stitch Width Control
-- 1 H in black
Stitch Length Control -- Between 24 and white dot
Feed Dog Control Up
Satin Stitch Foot
1.
Mark
the buttonhole length at both ends and also the
center line. See Fig. 1.
2_
Position fabric under needle. The first stroke of the needle should be to the right and pierce fabric at point A. Stitch forward on left side of buttonhole until desired length is obtained.
Sto p with needle in fabric on right side of stitching.
Point B. See Fig. 2.
3.
Raise presser foot and turn material and set stitch width control to three. Lower presser foot and take one stitch to
the left manually.
Point B to C. See Fig. 3.
Fig. 3
4_
Raise presser foot with needle in fabric and turn
stitch
width control to 5, Drop feed dogs and lower presser foot.
Barrack about three stitches.
See Fig.
4.
Complete barracking with needle on the left side of stitching: Point
D. See Fig. 4.
Fig. 4
5,
Raise presser foot and reset stitch width control to original setting of 1_.
Raise feed dogs and lower presser foot.
Sew other
side
of buttonhole until desired length
is
obtained.
Stop with needle in fabric on left side of stitch-
Point E. See Fig. 5.
Fig. 5
6.
Raise presser foot, Set stitch width control to 5. Drop feed dogs.
Lower presser foot
and
barrack about three (3) stitches.
Remove fabric from machine,
DOWN
Fig. 6
if there is too much space between side stitching, increase the stitch width.
Depending
upon the fabric on
which you are sewing, or your own preference in buttonholes, you may increase
or decrease the width of the sides and the space in the center by varying the original width settings and step 5, up to a maximum of 2.
Remember,
an increase
in the number will widen the sides. A decrease will narrow the sides.
23
24
DARNING
WITH PRESSER FOOT:
1. Turn feed dog control to left.
2.
Press down outer ring of presser foot pressure regulator, see page 12. With regulator in this position mending, monogram work, etc. may be done.
3.
Stretch fabric tightly between two spring embroidery hoops and place under needle.
The presser bar can be raised to accommodate the embroidery hoops by pulling up on the presser foot lever.
4.
Lower presser bar so thread will have some tension. When you start to darn, move fabric back and forth to cover darning area. Then turn fabric and continue sewing at right-angles
to the previous
stitching.
Always use medium machine speed.
You can make any length stitches desired.
Slow movement of fabric will make short darning stitches.
Fast movement will make long stitches.
5.
When you finish darning, raise presser foot and remove fabric. Increase pressure for general sewing by pressing center pin of presser foot pressure regulator.
Turn feed dog control to right.
WITHOUT PRESSER FOOT:
1.
Turn feed dog control to left.
2.
Remove presser foot.
Proceed as directed under steps 3 and 4 above.
3.
When you finish darning, raise the presser bar and remove fabric. Replace presser foot.
Turn feed dog control to right.
O
0
0
0
BLIND HEMMING
1.
Fold material and baste hem.
2.
Make second fold overlapping basting as shown.
3.
Straight stitch for approximately
_ inch, then zigzag one
stitch using black #3 stitch width position, catching second fold as shown. Continue this procedure until hem is completed.
4.
Unfold, exposing
right side of material
with completed blind stitching.
Remove basting and press hem.
SEWING ON BUTTONS
I,
Turn feed dog control to left. Place needle into left hole of button,
align
holes with slot of presser foot and lower presser foot.
2.
Set stitch width control at width between holes of button.
Test width by turning handwheel
slowly.
Take several zigzag stitches to sew on button, ending with needle on left side.
.
Set stitch width control at the red dot. Take a few stitches
in left hole of button to lock threads.
Pull threads to wrong side,
NOTE: To make a small thread
shank when sewing
on a flat
button, place a straight pin or needle between the holes of the button.
25
26
Fig. A
CLEANING AND OILING
Keep the moving parts free from dust and thread for quiet and efficient operation.
Cleaning should be done with a small brush.
When machine runs hard or makes excessive noise,
place a drop of KENMORE sewing machine oil at the points indicated in figs. A, B and C.
Swing hinged face cover plate open to oil points indicated at end of machine head.
i u
Remove arm cover plate to oil points indicated
at top of machine head. To remove cover plate, loosen up
wvo top screws and lift cover.
Fig. B
Tilt machine head back to oil points indicated
on
underside of machine head.
Fig. C
27
shuttle driver lever i_er
Shutt_
Shuffle Race Cover hook
Shuttle
It may be necessary to clean the shuttle area occasionally.
1.
Raise the needle bar to its highest position
and remove bobbin case.
2.
Push levers sideways of the shuttle assembly and lift shuttle and shuttle race cover.out
by the center pin.
3.
Clean the shuttle race of any lint or small particles of thread with a small brush.
4.
Put a drop of oit on the center pin of the shuttle and on shuttle race (see arrows).
To reassemble,
hold shuttle by center pin and fit carefully
into assembly opposite the shuttle driver.
Slip shuttle race cover into place. Snap the levers into position.
Occasionally, remove the needle plate and clean feed dog with a soft brush.
28
ADJUSTING YOUR SEWING MACHINE FOR GOOD STITCHES
When your sewing machine does not sew a properly locked stitch, check the following:
1.
Insert a new needle of the correct size for the thread and fabric you are using.
Consult chart on page 7 for needle size.
2.
The upper and bobbin thread should be the same thread.
3.
Check threading carefully.
See page 10-11.
4.
Check the thread tension balance.
Use mercerized thread and a correct size needle for the fabric you are using. Do not try test with synthetic thread as it will not break. Begin with a full bobbin, properly threaded into the case. Set stitch length at about 12 stitches per inch. Fold a 6 inch square of your fabric in half diagonally, forming
a triangle. Make a line of stitching _"
from fold.
a. If seam is puckered -- both tensions are too tight.
b. If bottom thread is looped -- tighten upper thread tension, and repeat test.
c. If top thread lays in top of fabric-loosen upper thread tension, and repeat test.
Grasp the stitching and pull evenly and firmly until one or both threads break.
a. If both threads break -- tensions are balanced.
b. If neither thread breakboth tensions are too loose.
c. If upper thread breaks-- loosen
upper tension.
d. if lower thread breakstighten upper tension.
Both threads do not have to break at the same place, but they should break on the same snap.
bobbin tensions may also be reset by this procedure.
Start with a loose bobbin thread tension. Tighten the spring screw gradually until bobbin case and full bobbin can be gently lifted from your hand by the end of the bobbin thread.
29
I
III
PROBLEM
I IIHIII
Irregular
Stitches
Breaking
Needle
Bunching of
Thread
Puckering
IIH IIII
I
II IIIIIIIIIIIIIIIIIIIm
PROBABLE CAUSE
Incorrect size needle,
Improper threading.
Loose upper thread tension.
Pulling fabric,
Light pressure on presser foot,
Loose presser foot,
Unevenly wound bobbin.
Nicks or burrs on shuttle,
Nicks or burrs at hole of needle plate,
Pulling
fabric,
Incorrect
size needle,
Incorrect setting of needle,
Loose presser foot,
Upper and lower
threads not drawn back under presser foot before starting seam,
Incorrect thread tension(s).
Light pressure on presser foot.
Using two different sizes or kinds of thread,
Bent or blunt needle.
Loose presser foot.
Fabric too sheer or too soft.
3O
WHAT TO DO
II III II /
CORRECTION
IIIIIIIIIIIIII
Choose correct size needle for thread and fabric.
Rethread machine.
Tighten upper thread tension,
Do not pull fabric; guide it gently.
Increase pressure on presser foot.
Reset presser foot.
Rewind bobbin.
Replace shuttle, or polish off burrs completely.
Replace needle plate, or polish off burrs completely,
I!
I, ,ll,,,,,,,,,
Do not pull fabric; guide it gently.
Choose correct size needle for thread and fabric,
Reset needle.
Reset presser foot.
When starting a seam be sure to draw both threads under and
back of presser foot about 4"" and hold until a few
stitches
are formed,
Reset thread tension(s).
Increase pressure on presser foot,
Upper thread and bobbin thread should be same size and kind,, insert new needle,
Reset presser foot,
Use undeday of tissue paper.
. i
lal IIIIIIIIIIIII IIIIIIIIIIIIIIIIIIIIIIIIIII
PROBLEM
II IIII
III IIIIIIIIIIII
PROBABLE
CAUSE
Skipping
Stitches
Breaking Upper
Thread
Breaking Bobbin
Thread
Fabric not
Moving incorrect size needle.
Certain knits and synthetics.
Bent or blunt needle,
Incorrect
setting of needle.
Tight upper thread tension.
Light pressure on presser foot.
Starting to stitch too fast,
Improper threading.
Tight upper thread tension.
Incorrect size needle.
Sharp eye in needle,
Nicks or burrs on shuttle.
Nicks or burrs at hole of needle plate,
Improper bobbin case threading.
Tight bobbin thread tension.
Lint in bobbin case or shuttle.
Feed dog down.
Light pressure on presser foot.
Thread knotted under fabric.
Machine Jamming
(Knocking Noise)
Thread caught in shuttle.
WHAT TO DO
IIIIIII II
CORRECTION
I IIIIIIIIIIIIII
I
Choose correct size needte for thread and fabric,
Use "Q N 1".I:'I)LF'."
Insert new needle.
Reset needle.
Loosen upper thread tension.
Increase pressure on presser foot.
Start to stitch at a medium speed,
Rethread machine.
Loosen upper thread tension.
Choose correct size needle for thread and fabric.
Insert new needle.
Replace shuttle, or polish off burrs completely.
Replace needle plate, or polish off burrs completely,
Check bobbin case threading.
Loosen bobbin thread tension.
Clean bobbin case and shuttle.
Raise feed dog.
increase pressure on presser foot,
Place both threads back under presser foot
before
beginning to stitch.
Disassemble and clean shuttle.
I
II III
31
PARTS LIST
All parts listed herein may be ordered from any Sears, Roebuck and Co. or Simpsons- Sears Limited store or service center.
WHEN ORDERING
REPAIR PARTS,
ALWAYS GIVE THE FOLLOWING INFORMATION:
1.
PART NUMBER
3.
MODEL NUMBER
2.
4.
PART DESCRIPTION
NAME OF ITEM
If the parts you need are not stocked locally, your order will be electronically transmitted to a Sears Repair
Parts Distribution Center for expedited handling.
12
32
5
11
13
6
2
7
* These parts are not furnished may be ordered.
14
10
15
with the machine,
(See above ordering information).
but
10
11
12
13
14
15
16
Ref. No.
3
4
5
6
1
2
8
9
Parts No.
135
201201
231008
200878
200618
6873
6870
1939
*6740
"6741
"6742
"6743
*6744
"6746
5797
*6862
6510
47
6915
3015
3016
Description
Presser foot screw
Needel clamp
Thread spool pin
Spool holder
Presser foot
Straight
stitch foot
(Model 12201 only)
Satin stitch foot
(Model 12201 only)
Bobbin winder rubber ring
Pack of # 9 needles
(Orange pack)
Pack of # ! 1 needles
(Yellow pack)
Pack of # 14 needles
(Red pack)
Pack of # 16 needles
(Green pack}
Pack of # 18 needles
(Blue pack)
Pack of "O NEEDLES_ °'
(Chocolate pack)
Light bulb
Pack of bobbin (10 pcs)
Bobbin case
Shuffle hook
S_ng machine belt
Large screw driver
Small screw driver
SEWING MACHINE
SEARS, ROEBUCK AND CO., Chicago, IL 60684 U.S.A.
and
SIMPSONS-SEARS LIMITED, Toronto, Ontario, Canada
Pa_ No. 52880
_[_
advertisement
Related manuals
Frequently Answers and Questions
How do I wind the bobbin?
How do I insert the bobbin into the bobbin case?
How do I thread the upper machine?
How do I adjust the pressure of the presser foot?
How do I begin and end seams with reverse stitching?
advertisement