advertisement
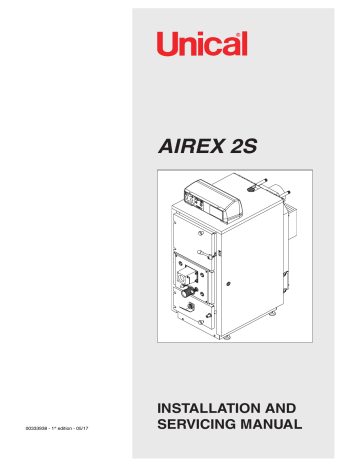
AIREX 2S
00333938 - 1 st edition - 05/17
INSTALLATION AND
SERVICING MANUAL
2
General Information
CONTENTS
1 GENERAL INFORMATION
................................................................................................................................................................................. 3
1.1 Symbols used in this manual ........................................................................................................................................................................ 3
1.2 Correct use of the appliance ......................................................................................................................................................................... 3
1.3 Water treatment ............................................................................................................................................................................................ 3
1.4 Information to be passed to the user ............................................................................................................................................................ 3
1.5 Safety warnings ............................................................................................................................................................................................ 4
1.6 Data badge ................................................................................................................................................................................................... 4
1.7 General information ...................................................................................................................................................................................... 5
1.8 The Clean Air Act 1993 and Smoke Control Areas ...................................................................................................................................... 5
2 TECHNICAL FEATURES AND DIMENSIONS
................................................................................................................................................... 6
2.1 Technical features ........................................................................................................................................................................................ 6
2.2 Dimensions and hydraulic connections ......................................................................................................................................................... 6
2.3 Main components ......................................................................................................................................................................................... 8
2.4 General Information: ..................................................................................................................................................................................... 8
Reversed flame combustion ......................................................................................................................................................................... 8
Airex boiler structure ..................................................................................................................................................................................... 9
3 INSTALLATION INSTRUCTIONS
..................................................................................................................................................................... 11
3.1 General warnings ...................................................................................................................................................................................... 11
3.2 Installation Codes of Practice .................................................................................................................................................................... 12
................................................................................................................................................................................................. 13
3.4 Transportation ............................................................................................................................................................................................ 13
3.5 Installation ................................................................................................................................................................................................. 14
3.6 Boiler system connection........................................................................................................................................................................... 14
3.7 Connection to safety heat excanger drain ................................................................................................................................................. 15
3.8 Recirculation pump .................................................................................................................................................................................... 15
3.9 Assembly instruction .................................................................................................................................................................................. 16
3.10 Flue outlet connection ................................................................................................................................................................................ 20
3.11 Electrical connections ................................................................................................................................................................................ 21
3.12 Standard panel board ................................................................................................................................................................................ 22
3.13 Hydraulic and electrical connection diagrams ........................................................................................................................................... 24
3.14 Filling the system ....................................................................................................................................................................................... 26
4 BOILER START-UP
........................................................................................................................................................................................... 27
4.1 Initial lighting ............................................................................................................................................................................................. 27
4.2 Fire wood ................................................................................................................................................................................................... 28
4.3 Wood moisture .......................................................................................................................................................................................... 28
4.4 Fire wood dimensions ................................................................................................................................................................................ 28
4.5 Initial lighting checks .................................................................................................................................................................................. 28
4.6 Start-up ...................................................................................................................................................................................................... 29
4.7 Combustion air adjustment ........................................................................................................................................................................ 30
4.8 Checks to carry out after the first start ..................................................................................................................................................... 31
4.9 Warnings ................................................................................................................................................................................................... 31
4.10 Thermostat adjustments ............................................................................................................................................................................ 32
4.11 Summer operation ..................................................................................................................................................................................... 32
4.12 Fault finding for boilers with standard control panel .................................................................................................................................. 33
5 SERVICING AND MAINTENANCE SCHEDULE
.............................................................................................................................................. 34
General Information
Warning: this manual contains instructions to be used exclusively by the installer and/or a competent person in accordance with the current laws.
The end user is NOT autorized to carry out any service work on the boiler.
Failure to follow the instructions given in this manual, which is supplied with the boiler, could cause injury to persons, animals or damage to property. UNICAL shall not be held liable for any injury and/or damage.
1 GENERAL INFORMATION
1.1 - SYMBOLS USED IN THIS MANUAL
When reading this manual particular care has to be given to the parts marked with the followings symbols:
DANGER! Indicates serious danger for your personal safety and for your life
WARNING! Indicates a potentially dangerous situation for the product and the environment
NOTE! Suggestions for the user
1.2 - A CORRECT USE OF THE APPLIANCE
The AIREX 2S appliance has been designed utilizing today’s heating technology and in compliance with the current safety regulations.
However, following an improper use, dangers could arise for the safety and life of the user or of other people, or damage could be caused to the appliance or other objects.
The appliance is designed to be used in hot water central heating systems.
Any other use of this appliance will be considered improper.
UNICAL declines any responsibility for any damages or injuries caused by an improper use; in this case the risk is completely at the user’s responsibility.
In order to use the appliance according to the foreseen scopes it is necessary to carefully follow the instructions given in this manual.
1.3 - WATER TREATMENT (refer to specific guide)
• In hard water areas where the main water can exceed 15°f total hardness, a scale reducing device is recommended. The choice of this device has to be made taking into consideration the characteristics of the water.
1.4 - INFORMATION TO BE HANDED OVER TO THE USER
The user has to instructed on the use and operation of his heating system, in particular:
- Hand over these instructions to the end user of the appliance, together with any other literature, regarding this appliance, placed inside the envelope contained in the packaging.
The user has to keep these documents in a safe place in order to always have them at hand for future reference.
- Inform the user on the importance of air openings and of the flue outlet system, stressing the fact that it is absolutely forbidden to make any alterations to the boiler.
- Inform the user how to check the system’s water pressure as well as informing him how to restore the correct pressure.
- Explain the function of temperature controls, thermostats, heating controls and radiators, to ensure the greatest possible fuel economy.
- If the appliance is sold or transferred to another owner or if the present user moves home and leaves the appliance installed, ensure yourself that the manual always follows the appliance, so that it can be consulted by the new owner and/or installer.
3
4
General Information
1.5 - SAFETY WARNINGS
WARNING!
The installation, adjustment, and servicing of this appliance must be carried out by a competent, qualified person and installed in accordance with the current standards and regulations. Failure to correctly install this appliance could cause injury to persons, animals or damage to property. The manufacturer shall not be held liable for any injury and/or damage.
DANGER!
NEVER try to carry out any repairs or service work on the boiler on your own initiative.
Servicing or repairs of the appliance must be carried out by qualified service engineers;
UNICAL recommends drawing up a service contract.
Bad or irregular servicing could compromise the safe operation of the appliance, and could cause injury to persons, animals or damage to property for which UNICAL shall not be held liable.
-
-
-
Modifications to parts connected to the appliance
Do not carry out any modifications to the following parts:
- the boiler itself to the electrical parts to the flue pipe, safety relief valve (if fitted) to the constructive components which influence the appliance’s safe operation
WARNING!
When tightening or loosening the screw pipe connections, use only adequate fork spanners.
The improper use and/or the use of inadequate equipment can cause damages.
Explosive and easily inflammable substances
Do not use or leave explosive or easily inflammable material (as for example: petrol, paint, paper) in the room where the appliance has been installed.
1.6 - DATA BADGE
The data badge is adhesive and placed inside the documentation envelope; it must be glued on to one side of the casing, on the external part, by the installer.
The boiler’s serial number is indicated on a small aluminium plate riveted on the boiler’s front plate (front side, upper right hand side).
General Information
1.7 - GENERAL WARNINGS
This instruction manual is an integral and indispensable part of the product and must be retained by the user.
Please read carefully the instructions contained in this manual, as they provide important indications regarding the safe installation, use and servicing of this appliance.
In the event of failure and/or faulty functioning of the appliance, switch off the boiler. Do not attempt to make any repairs: contact qualified technicians.
Any repairs must be carried out by Unical authorized technicians and using only original spare parts. Non-observance of the above requirement may jeopardize the safety of the appliance.
Keep this manual in a safe place for future reference.
The installation and servicing must be carried out in accordance with the regulations in force, according to the manufacturer’s instructions, and by legally competent authorized persons.
To guarantee the efficiency and correct functioning of the appliance it is indispensable to have the boiler serviced annually by a qualified person.
By a competent person, we imply a person who has a specific technical qualification in the field of components for central heating systems for domestic use, domestic hot water production and servicing. The person must have the qualifications foreseen by the current laws in force.
Bad or irregular servicing could compromise the safe operation of the appliance, and could cause injury to persons, animals or damage to property. The manufacturer shall not be held liable for any such injury and/or damage.
If the boiler remains unused for long periods, ensure that any dangerous parts are rendered innocuous.
If the appliance is sold or transferred to another owner or if the present user moves home and leaves the appliance installed, ensure yourself that the manual always follows the appliance so that it can be consulted by the new owner and/or installer.
Only original accessories must be used for all appliances supplied with optional accessories or kits (including electrical ones).
Before carrying out any cleaning or servicing, turn off the electrical supply to the boiler by means of the ON/OFF switch and/ or by means of the appropriate shutdown devices.
This appliance must be used only for the purposes for which it has been expressively designed. Any other use shall be considered incorrect and therefore dangerous
Do not obstruct the air inlet openings.
1.8 - THE CLEAN AIR ACT 1993 AND SMOKE
CONTROL AREAS
Under the Clean Air Act local authorities may declare the whole or part of the district of the authority to be a smoke control area. It is an offence to emit smoke from a chimney of a building, from a furnace or from any fixed boiler if located in a designated smoke control area. It is also an offence to acquire an “unauthorised fuel” for use within a smoke control area unless it is used in an “exempt” appliance
(“exempted” from the controls which generally apply in the smoke control area).
In England appliances are exempted by publication on a list by the Secretary of State in accordance with changes made to sections 20 and 21 of the Clean Air Act 1993 by section 15 of the Deregulation Act 2015. Similarly in Scotland appliances are exempted by publication on a list by Scottish Ministers under section 50 of the Regulatory Reform
(Scotland) Act 2014.
In Wales and Northern Ireland these are authorised by regulations made by Welsh Ministers and by the Department of the Environment respectively.
Further information on the requirements of the Clean Air
Act can be found here:
https://www.gov.uk/smoke-control-area-rules
Your local authority is responsible for implementing the
Clean Air Act 1993 including designation and supervision of smoke control areas and you can contact them for details of Clean Air Act requirements”
“The AIREX 2S 65 & 85 UK units have been recommended as suitable for use in smoke control areas when fitted with a buffer tank as specified in Technical Features and Dimensions section when burning wood logs”
5
6
2
Technical features and dimensions
TECHNICAL FEATURES
AND DIMENSIONS
2.1 - TECHNICAL FEATURES
The Airex is a steel boiler running by natural wood in logs, total gasification, flame inverted, with the combustion chamber under negative pressure.
It comes in the f ollowi ng models:
AIREX 25 2S
AIREX 40 2S
AIREX 50 2S
AIREX 65 2S
AIREX 80 2S
The boiler AIREX is complete with all the safety and control devices required by the relevant standards.
COMPONENTS DESCRIPTION :
• Steel boiler with combustion chamber partially covered with refractory
• Burner in refractory material
• Horizontal smoke channels
• Front door, for wood loading, insulated with refractory concrete
• Intermediate door complete with combustion air adjustments
• Lower door, insulated with refractory conctrete and equipped with flame sight glass
• Rear smoke chamber with side openings for inspection and ashes removal
• Smoke evacuation via a sucking fan (n° 2 fan for the model
AIREX 65 2S and AIREX 80 2S)
• Patented thermostatic valve system
• Safety heat exchanger
• Boiler body insulated with mineral wool panels with thickness of 60 mm
• Steel casing powder painted
• Recirculat ion pu mp kit (optional)
PANEL BOARD:
• Main switch with signal lamp
• Fan switch
• C.H. pump switch
• General fuse
• Working thermostat
• Safety thermostat
• Boiler thermometer
2.2 - DIMENSIONS
AND HYDRAULIC
CONNECTIONS
1 Panel board
2 Primary air setting
3 Secondary air setting
4 Cleaning openings
5 Rear smoke chamber
6 Loading door
8 Fan (n°2 fan for the model AIREX 65 2S and
AIREX 80 2S)
9 Combustion chamber door with flame sight glass
10 Prim ary & Secondary air inlet
T1 Central Heating flow
T2 Central Heating return
T3 Chimney connection
T4 Safety heat exchanger connections
T5 Connections for eventual trap sensor valve temperature relief
T6 Bulb holder for safety thermal discharge valve
T7 Bulb holder for thermostat and thermome te r
T8 Boiler drain
7
3
4
9
1
A
T3
T4
8
6
T2-T8
5
H
F
T1
B
E
T4
T5
T8
8
T1
T7
T4
T6
T3
T2
fig. 1
MODELS
AIREX 25 2S
MNOMINAL OUTPUT *
(kW) 29
E
F
C
D
DIMENSIONS:
A
B
G
H
CONNECTIONS T1 - T2
T3
T4
T5 - T6 - T7 - T8
BOILER WATER CONTENT
WATER SIDE PRESSURE DROP **
SMOKE SIDE PRESSURE DROP
MAX. WORKING PRESSURE
FIRE BOX STORAGE VOLUME
FIRE BOX DIMENSIONS
RECOMMENDED BUFFER SIZE
WEIGHT
WOOD LOGS LENGTH
(mm)
(mm)
(mm)
(mm)
(mm)
(mm)
(mm)
(mm)
UNI ISO 7/1
(Ø mm)
UNI ISO 7/1
UNI ISO 7/1
(l)
(m c.a.)
(mm c.a.)
(bar)
(l)
(mm)
(l)
(kg)
(cm)
560
700
1225
190
160
245
1030
315
Rp 1¼
150
R ½
Rp ½
90
0,10
0,3
3
95
290x340
-
396
50
* Power achieve d with good quality wood containing 15% humidity
** Pressure drop for a flow rate corresponding to a Delta T of 15K.
AIREX 40 2S
47
655
700
1355
190
160
245
1140
315
Rp 1½
200
R ½
Rp ½
110
0,08
0,4
3
135
350x440
-
485
50
Technical features and dimensions
AIREX 50 2S
58
655
900
1355
190
160
245
1140
315
Rp 1½
200
R ½
Rp ½
140
0,12
0,6
3
185
350x440
-
603
70
AIREX 65 2S
65
AIREX 80 2S
80
755
955
1405
190
160
245
1180
315
Rp 2
220
R ¾
Rp ½
170
0,06
0,3
3
235
220
R ¾
Rp ½
220
0,10
0,5
3
325
340x520 340x520
See diagram below
755
1255
1405
190
160
245
1180
315
Rp 2
760
70
927
100
Sizing of buffer
4150
4000
3850
3700
3550
3400
3250
3100
2950
2800
2650
2500
0
5950
5800
5650
5500
5350
5200
5050
4900
4750
4600
4450
4300
Sizing
Sizing of buff er for AIRE of buff er for AIRE
X 80 2
S
X 65 2S
5 10 15 20 25 30 35 40 45
Central heating
50 system
55 60 dissipation ( kW )
65 70 75 80 85
7
Technical features and dimensions
2.3 - MAIN COMPONENTS
1. Panel board
2. Casin top panel
3 N°2 side panels
4. Anti-smoke door fitted on hinges
5. Wood storage door with refractory insulation and sealing rope.
6. Central door with sealing gasket &locking screws for primary and secondary air
7. Fan ( n°2 fan for the models AIREX 65 2S and
AIREX 80 2S)
8. Combustion chamber door with sealing gasket, refractory insulat. & flame sight glass
9. Combustion chamber in thick steel
10. Heat exchange fin
11. Boiler drain
12. Thermal discharge safety heat exchanger
13. Smoke by-pass with rod
14. Boiler body insulation in mineral wool
15. Boiler body
16. Refractory burner with fire bars and grate
17. Smoke chamber
18. Thermostatic valve
M C.H. flow
R C.H. return
12
7
17
F
13
F
M
18 2
16
15
14
R
1
8
11 10 9
fig. 2
N.B.:
The fire bars and the refractory steel grate are subject to wear; it is therefore advisable to carry out an annual inspection to prevent bad boiler operation.
8
2.4 - GENERAL INFORMATION:
REVERSED FLAME COMBUSTION
Every body knows that to make a match lasting it must be held with its head upwards.
This is because it is necessary that the flame, in its convective motion, does not meet another fuel in addition to the one which has generated it. As in residential heating the fuel is in form of wood logs which are loaded from the top, the flame has to go in the opposite way, i.e. downwards.
Natural draught is a very variable source of depression, according to the type of chimney, on the weather conditions, on the type of fuel, etc.
Therefore it is necessary to integrate it with forced ventilation in order to stabilize it.
By fitting a fan it is possible to considerably reduce the section of the gas passages on the grate and furthermore there are no problems with cold starts.
The small grate permits a more controlled passage of combustion air, contrarily to what happens with the large traditional grates.
The air can be perfectly dosed because the grate, covered with fired wood, has the same crossing resistance and thus the combustion will be always optimal.
Unical has already used this principal for many years with the
GASOGEN G3 2S boiler.
The AIREX 2S boiler today has reached such a high level of perfection that it can pass all the most stringent tests foreseen by the European Standards in force concerning the environment.
3
5
4
6
AIREX BOILER STRUCTURE
The hydraulic system inside the boiler is designed in such a way that a thermostatic system keeps always the water temperature high that surrounds the wood storage room so as to eliminate the dangerous phenomenon of condensation.
The boiler is composed of two oval elements placed inside each other, so that between the two a cavity of water (Fig. 3) is formed.
We can distinguish the following parts (fig.3):
1. Fire wood storage and drying area
2. Gasification zone
3. Embers zone
4. Refractory burner
5. Combustion chamber
6. Heat exchange surface
7. Refractory steel cradle
8. Boiler water
9. Thermostatic system
10. Safety heat exchanger
M C.H. system flow
R C.H. system return
Technical features and dimensions
M
9
10
1
2
3
4
5
6
7
GASIFICATION ZONE (2)
The gasification takes place in the lower part of the firewood storage.
It is very important that the gasification is as regular as possible, so as not to overload the burner with gas. The gasification speed depends on the quantity of the wood and the dimensions of the drying area. Generally, it is better to use large logs if they are dry and small logs if the wood is wet . The quantity of primary air, proportional to the delivered output, is regulated via the adjustment system.
R
8
fig. 3
EXCHANGE SURFACE (6)
As the boiler operates on wood, and because the sulphur concentrations are not very high , it is important to obtain very low smoke temperatures in order to increase the water efficiency.
To obtain this Unical has opted for an exchange surface with dry smoke passes (fig. 4), which have already been extensively tested in oil fired boilers working at low water temperature, thus permitting low smoke temperatures without danger of condensate forming.
The surfaces of the dry passages “A” (fig. 4) have had incisions made on them in order to avoid dilatation problems.
The solid residues of combustion (ashes), which lie on the high temperature refractory-lined cradle (fig. 3, pos. 7,) will become, with the time, always lighter until they will be dragged by the gas speed and will be deposited in the lowest area of the rear smoke chamber, from which they will be removed during the cleaning operation.
REFRACTORY BURNER (4)
The burner is made up of refractory stone (fig. 3, pos. 4).
This stone has an oval central opening through which the flame passes.
The embers lie directly on the main stone which divides the fire wood storage from the lower combustion chamber.
Furthermore the main refractory stone has a rectangular seat in which the opportunely grooved cast iron fire bars are placed (fig.
5, pos. 2), which receive the secondary air from a front distributor.
A
A
fig. 4
9
10
Technical features and dimensions
The embers are prevented from falling by cylindrical pieces of refractory steel. The combustion gases, poor in oxygen and still rich in carbon not yet combined, travel across the embers and enter the opening in the centre of the main stone.
Inside this pre-combustion chamber, the gases combine with the pre-heated secondary air coming through the grooves of the two cast iron fire bars.
The resulting flame will be highly oxygenated and have a light blue colour. This flame comes out from the oval opening and invades the combustion chamber.
Due to the high temperatures the refractory burner will become a bright red colour.
COMBUSTION CHAMBER (5)
The combustion is optimised by increasing the flame temperature and producing a strong turbulence in the bottom chamber.
For this reason the flame, in addition to not to touching cold walls irrigated by the water, rebounds and is divided on a semicircular cradle which rests on the lower exchange surfaces (baffles), which, as well delimiting the smoke passages, also has the task of collecting the ashes and possible embers.
The flames, after having bounced off the walls of the bottom area and the refractory ones, direct themselves with a whirling motion towards the front part of the combustion chamber and enter the flue ducts. The combustion will be complete and clean and the dominant colour will be that of the ashes: white.
THERMOSTATIC VALVE (9)
As well known, wood normally has a high moisture content when compared with other types of fuels. The first operation which occurs inside the fire wood storage is therefore the drying phase.
The high moisture content can then cause condensation phenomena within the boiler and also in the chimney.
To limit the inconvenience in the boiler it is necessary to maintain high working temperatures.
For this reason the boiler is equipped with a patented thermostatic system (fig. 6) which permits the boiler temperature to be kept constantly high and in particular, in the fire wood storage, where the condensation phenomena is more likely to occur.
In order to reduce the consequences of condensate formation
(formation of layers of tar, corrosion, etc.) it is advantageous to dimension, time by time, the wood load to the actual needs, so as to prevent long stop overs with the wood storage completely full of humid wood.
Nevertheless all these expedients do not impede the formation of condensate in the chimney. Therefore we suggest, when building the chimney, to use air-tight components, to avoid the condensate damaging the building structure.
R
1. Metallic grate
2. Cast iron fire bars
F
F
F
M = C.H. flow
R = C.H. return
P = Primary air
S = Secondary air
F = Flue
M
3
2
1
S
T1
S
P
S
1
2
fig. 5
P
F
P
P-S
S
fig. 6 fig. 7
3
INSTALLATION
INSTRUCTIONS
3.1 - GENERAL WARNINGS
WARNING!
This boiler is to be destined only to the use for which it has expressly been designed for.
Every other use is to be considered improper and therefore dangerous.
This boiler is designed to heat water at a temperature inferior to boiling point at an atmospheric pressure.
WARNING!
These appliances are exclusively designed for indoor installations or installed in adequate sitings. Therefore these appliances must not be installed and operated outdoors. An outdoor installation could cause malfunctioning and could be dangerous.
Before installing the boiler the following points have to be carried out by a professionally qualified person: a) The whole system should be thoroughly flushed in order to remove any residual dirt or grime which could compromise correct boiler operation. b) Check that the chimney/flue pipe has an adequate draught, does not have any constrictions, and that no other appliance’s flue outlets have been fitted, unless the chimney is serving more than one heating appliance, according to the specific standards and regulations in force. The connection between the boiler and chimney/flue outlet can be made only after this verification has been carried out.
WARNING!
The appliance must be installed by a qualified, registered engineer, whom, under his own responsibility, guarantees the compliance of the standards according to the latest regulations.
NOTE:
The boiler must be connected to a heating system which is compatible to its performance and output.
Instructions for the installer
11
12
Instructions for the installer
3.2 - INSTALLATION CODES OF PRACTICE
The AIREX 2S
is a boiler foreseen for operation with firewood.
The appliance must be installed in compliance with all local applicable laws and regulations.
3.3 - PACKAGING
The AIREX 2S is supplied dismantled: the casing, the fan, the control panel, the handles and the cleaning accessories are delivered separately in carton boxes
(fig. 8).
After having unpacked everything, make sure that the consignment is intact and undamaged.
In case of doubt do not to use the appliance and inform the supplier.
1
G
Instructions for the installer
Keep the packaging material (cardboard box, plastic bags, polyester protection etc
.) out of the reach of children since they can be dangerous.
UNICAL refuses all liability for injury to persons, animals or damage to property deriving from not having respected the above mentioned recommendations.
5
2
4
3
fig. 8
Packages description:
1. Boiler body
2. Package containing the casing and boiler insulation
3. Package containing the panel board
4. Package containing the smoke extraction fan
5. Package containing: air inlet manifold , smoke chamber cleaning doors, handles, flame control mirror , screws and nuts, cleaning accessories. This package is shipped inside the fire wood storage room
In the documents, placed in the fire wood storage room, you will find:
- User’s instruction manual
- Installation and servicing instruction manual
- Guarantee card
- Adhesive data plate
- Adhesive label with ventilation requirements
If the boiler will not be used for a long period, it should be adequately protected.
3.4 - TRANSPORTATION
To facilitate the transport, the loading and unloading of the boiler, on the upper part of the boiler body there are suitable hooks
(fig. 8) for lifting.
13
14
Instructions for the installer
3.5 - INSTALLATION
The boiler does not differ from a normal solid fuel fired boiler; therefore there are no particular installation codes of practice other than the applicable national and local safety regulations and laws.
The installation room must be properly ventilated via openings, which should have a total surface of at least 0,5 m².
To facilitate cleaning of the flue circuit, a free space, not inferior to the length of the boiler, must be left in front of the boiler.
In addition ensure that the doors can open 90° without meeting any obstacles.
The boiler can be placed directly on the floor, because it is equipped with a self-supporting frame.
Nevertheless, in case of installation in very damp boiler rooms, it is preferable to fit a concrete support.
When installation is completed, the boiler should be in a horizontal position and stable so as to reduce possible vibrations and noise.
An adequate clearing must be left behind the boiler for servicing.
INSTALLATION IN BOILER ROOM
Note:
The minimum clearances indicated in figure 9 are compulsory only for boilers with an output higher than 35 kW (Italian requirement)
3.6 - BOILER SYSTEM CONNECTION
Warning!
Make sure the connection of the pipelines is free of mechanical stresses, in order to avoid water losses!
The C.H. flow and return must be connected to the respective connections in the boiler, as indicated on page 7.
When determining the size of the CH circuit pipes it is essential to bear in mind the pressure losses induced by any of the system’s components and by the configuration of the same system.
The piping route has to be designed taking all the necessary precautions in order to avoid air locks and to facilitate the continuous purging of the system.
Ensure yourself that the system’s piping is not used as earth clamps for the electrical or telephone system. They are absolutely unsuitable for this use. In a short time this could cause serious damage to the piping, boiler and radiators.
600
1300
1000
600
600
fig. 9
3.7 - CONNECTION TO SAFETY HEAT
EXCHANGER DRAIN
Solid fuel fired boilers have to be installed with the safety devices foreseen by applicable regulation and laws.
For this purpose the AIREX 2S boilers are fitted with a safety heat exchanger.
On this safety heat exchanger the installer
must
fit a
heat discharge valve
, whose control bulb has to be inserted in the bulb holder placed onto the rear wall of the wood fired boiler.
The inlet and outlet connections can be inverted.
However we recommend that the valve be fitted on the cold water inlet.
In correspondence of the safety heat exchanger outlet, we recommend fitting a drainage pipe with a funnel and siphon that lead to an adequate drainage. The drainage has to be visible.
Warning!
In absence of this precautionary measure, the eventual intervention of the heat discharge valve could cause damages to people, animals or property. The manufacturer shall not be held liable for any such injury and/or damage.
Instructions for the installer
2
1
ALIMENTAZIONE
MAINS
SCARICO
DRAIN
fig. 10
3.8 - RECIRCULATION PUMP
For correct boiler operation it is necessary to install a recirculation pump in the boiler.
The recirculation pump, supplied as an optional kit in two different versions, basic or for buffer storage tank control, will have to be connected as shown in figs. 19 and 20.
If the recirculation pump is not installed, besides limiting the boiler’s life span, it will invalidate the warranty.
WARNING!
The hardness of the mains water supply conditions the boiler’s life span.
Depending on the hardness of the of the mains water supply the possibility of installing a water softener has to be taken into consideration.
In hard water areas where the main water can exceed 15°f total hardness, water treatment is always recommended.
15
16
Instructions for the installer
3.9 - ASSEMBLY
INSTRUCTIONS
Fan assembly
Fit the fan to the smoke chamber.
(n° 2 fan for models AIREX 65 2S and AIREX 80 2S).
IMPORTANT:
When installing the fan it is necessary to check the tightness of the seal on the smoke chamber, otherwise it would cause the deformation of the wall resulting in severe damage to the impeller and / or fan motor.
This inconvenience is much more rapid as more frequent is the opening of the wood loading door.
Insulation and casing assembly
- Detail “A”: Fit the knob 4 on the upper door closing handle . Fit, in the sequence, the screw, the nut and the knob (pos. 1, 2, 3) on the upper
R.H. side corner and tighten nut and knob .
- Detail “B”: install the air collector (n°
2 collectors for the model AIREX 65
2S and AIREX 80 2S) . Ascertain that the internal non-return plate is free to move, by acting manually on the extenal lever of the air manifold.
The draft adjustment on the primary and secondary air is described on pages 29 and 30.
- Detail “C” Fit, in the sequence, the screw, the nut and the knob (pos. 1,
2, 3) on the lower R.H. side corner of the lower door and tighten nut and knob .
- Detail “D” Fit on the boiler basement the supporting feet
- Detail “E” Fit the inspection door on the smoke chamber
- Hang the mirror (pos.5) on the flame sight glass of the lower door.
B
Fit the boiler body insulation and make a suitable cut near the upper C.H. flow connection.
C
3
2
4
1
3 2
5
- Wrap on the mineral wool insulation the plastic strap and insert one of its ends in the locking slot as shown in the detail1.
- Holding the end of the strap already inserted, proceed with the other end by folding inward the plastic pin as shown in detail 2.
- Pull the two ends of the strap (as shown in details 3 and 4) until the strap adhere to all the mineral wool covering the boiler body. It is recommended not to over stretch the strap; an excessive crushing of mineral wool, would cause a not homogeneous insulation.
In case of maintenance it is possible to remove the strap by acting on the locking slots .
1
A
1
3
2
FIG. 13
fig. 11
D
fig. 12
4
fig. 13
E
Fit the microswitch onto its support and adjust the pushing washer axially in order to allow the microswitch to be regularly operated when the upper loading door is closed.
Ascertain that the by-pass disk is perfectly closed when the door is closed and the boiler in operation.
It is possible to ascertain this by simulating the closing of the upper door and observing, from the inside of the wood storage room, if, with a lamp placed in the chimney connection, there is no visible light.
If necessary, adjust the length of the by-pass rod, acting on the front threaded shaft.
Otherwise, adjust the length of the by-pass rod by acting on the threaded bar front .
Instructions for the installer
fig. 14
- Hook the casing L.H. side panel to the boiler body (pos. 1)
- Hook the casing L.H. side panel to the boiler body (pos. 2)
- Place on the ground the casing upper panel and fit on it the panel board (pos. 3, 4, 5, e 6).
- Fix to the top panel the rear profile (pos. 7)supporting the cable clamps .
- Open the panel board by acting with a screwdriver on the two side screws.
- Rotate forward the panel board cover.
Insert all the capillaries of the thermostats and thermometer (unroll them carefully), the outgoing fan(s) connecting cable(s), the incoming microswitch cable controlling the loading door opening and the outgoing electrical supply cable through the two rectangular holes on the base of the panel board.
- Place the casing upper panel on the boiler addressing the ends of the capillaries toward the rear of the boiler.
- Stick the boiler technical data badge to the most accessible side panel after having cleaned and degreased with a suitable solvent the affected area.
Remove the protecting film from the data badge and apply by sticking perfectly
Do not remove the label from the boiler because it would affect the adhesion.
1
5 4
6
3
7
2
fig. 15
17
Instructions for the installer
WORKING THERMOSTAT (Te)
DI ESERCIZIO (Te)
CONTACT SPRING
HIGH LIMIT THERMOSTAT (Tmax)
DI MASSIMA (Tmax)
SAFETY THERMOSTAT (Ts)
DI SICUREZZA (Ts)
2 1
3
The thermostats bulbs can be identified by labels stickers fixed on the respective capillary. Therefore, during any maintenance, pay attention that the labels will not be removed.
A) Place the bulb of the working thermostat (Te), of the Max thermostat, (Tmax), of the Min. Thermostat (Tsc) and of the thermometer in the central bulb holder
B) Place the bulb of the safety thermostat (Ts) in the R.H. side bulb holder
C) Fix the bracket (pos. 1), supporting the fan socket to casing L.H. side panel, using the 3 screws, supplied with
fig. 16
the product, and tighten the screw (pos. 2) on the smoke chamber.
Fit on the bracket the fan socket (pos. 3).D) Connect the fan plug to the socket (pos. 3)
E) Make the electrical connections of the supply line, the pump(s) and other possible devices according to the wiring diagrams shown in chapters 3.12 and 3.13.
Close the panel board.
Pay attention that the cables do not come in contact with the smoke chamber. During operation, this reaches high temperatures .
18
The solid fuel boilers must be installed with all the security devices foreseen by the laws in force.
For this purpose, AIREX boilers are equipped with a builtin safety heat exchanger.
A) Connect the safety discharge valve (pos. 1) and insert its temperature sensor into the bulb holder (pos.2)
The safety discharge valve may be mounted either on the right or on the left.
It is recommended to convey the discharge of the safety heat exchanger.
Remember that for the solid fuel boiler, due to the thermal inertia of the fuel, the installation of the termal discharge valve is required.
2
1
ALIMENTAZIONE
MAINS
SCARICO
DRAIN
fig. 17
For the correct operation of the AIREX range of boilers it
is necessary
to foreseen a recirculation pump, to prevent a low temperature return, which could compromise the life of the boiler.
UNICAL, to help its customers, has therefore developed a hydraulic kit for recirculation that enhances the function of the circulating water in the boiler.
This kit is supplied as an option and is available by indicating the model of your boiler.
Instructions for the installer
14
15
13
8
12
11
10
9
6
7
2
1
3
4
5
fig. 18
19
20
Instructions for the installer
3.10 - FLUE OUTLET CONNECTION
The flue system must be installed in accordance with the local regulation and national codes of practice.
The chimney is of fundamental importance for the correct boiler operation: it is therefore necessary that the chimney is impermeable and properly insulated.
Old or new chimneys, built without respecting the specific requirements can be recovered by “tubing” the chimney itself.
It will be necessary to introduce a metallic pipe inside the existing chimney and insulate the space between the metallic pipe and the chimney.
Chimneys made of prefabricated blocks must have perfectly sealed joints to avoid that flue condensate smudge the walls due to permeation.
We recommend using only flue pipes suitable to the type of fuel used.
Damages caused by installation errors and for non-observance of the instructions given by the same manufacturer will invalidate all the supplier’s contractual or extra contractual responsibilities.
The flue outlet has to meet the latest regulations in force.
The entrance to the chimney should be with an angle of 45°.
At the base of the chimney a flue inspection opening has to be made.
It is advisable to insulate the flue pipe connecting the boiler to the chimney in order to reduce the heat losses and noise.
4
7
8
5
6
5
6
2
1
3
fig. 19
1. Boiler
2. Flue outlet connection
3. Ashes collecting chamber
4. Chimney
5. External flue lining
6. Prefabricated blocks
7. Insulation
8. Flue outlet
Instructions for the installer
3.11 - ELECTRICAL CONNECTIONS
General Warnings
The appliance’s electrical safety is guaranteed only when the appliance has been correctly earthed in compliance with the regulations in force. The gas and water feeding pipes and the CH system pipes cannot be used as ground plates.
Ensure that the above safety electrical requirements have been implemented; in case of doubt, ask for a professionally qualified engineer to check the appliance’s electrical system.
UNICAL refuses responsibility for any damages arising from failure to earth the boiler correctly.
It is necessary that a qualified technician verifies that the electrical system is adequate to the appliance’s maximum absorbed power, indicated on the data plate, checking in particular that the section of the system’s cables is suitable to the appliance’s maximum absorbed power.
The use of adaptors, multiple sockets and/or extension cords for the appliance’s general electrical supply is strictly forbidden.
WARNING!
- Before opening the control panel, position the switch
(11) in the “0”pos.
- Do not connect the control panel to loads that together absorb more than 4A!
Approvals
The UNICAL panel board, code 36749 has been CE approved, according to the EN 60335-1
Standard.
Data plate and Serial number
The panel board identification data plate is glued on the base.
Use
This panel board must be used for operation of a boiler destined to heating water to a temperature that does not exceed boiling point when installed.
The use of any power supplied equipment implies the observance of he following fundamental rules:
• Do not touch the appliance with any wet part of your body and/or barefooted;
• Do not pull the supply cables
• Do not permit children or inexpert people to use the appliance
Connection to mains electrical supply 230V
The general wiring diagrams are shown on page 23 and the actual wiring diagrams on pages 24 & 25.
A mains supply of 230 V – 50 Hz is required. The wiring to the boiler must be in accordance with the current IEC regulations.
DANGER!
The electrical connections must be carried out only by a qualified engineer.
Before carrying out the connections or any other operation on the electrical parts, always switch off and disconnect the electricity supply and ensure yourself that it cannot be accidentally turned on.
Note: It is necessary to fit a double pole switch on the electrical supply line, having a 3 mm contact separation in both poles, in an easy accessible position so as to ensure quick and safe servicing.
21
22
Instructions for the installer
3.12 - STANDARD PANEL BOARD
The standard panel board (code 36749) operates in a semi-automatic way and is supplied in a cardboard with the following standard items:
- Microswitch which has to be fitted to the mechanism controlling the bypass rod (TKS) as shown in fig. 14 page 17.
- A 3 pole cable for the fan’s electrical connection (2 fans for the models AIREX 65 2S and AIREX 80 2S)
The introduction of the thermostat bulbs into the bulb holders must be carried out as shown in fig. 16, on page 18.
The connection of the loads to the panel board (C.H. pump, recirculation pump, fan, etc.) must be carried out according to the general wiring diagram in fig. 21 and/or according to the practical wiring diagrams on page 24 and 25.
Functional description
Once the main switch pos. 11 and the pump switch pos. 13 are in the ON position, it is possible to light the boiler.
Once the boiler has been fired, close the loading door; in this way the TKS microswitch, operated directly by the rod closing the smokes bypass to the chimney, will reset the temporized relay that “will begin to count.”
The factory adjusted time of the temporized relay is of 30 minutes, which can be extended to an additional 30 minutes.
The
Tsc
thermostat (minimum thermostat) is not satisfied at boiler start-up, because adjusted at 65°C, actually prevents the C.H. pump running, until this temperature is reached.
If the boiler does not reach the 65°C in the set time, the temporized relay stops the fan.
This can be due to the boiler not firing or due to an insufficient load of the firewood.
To avoid this inconvenience it is possible to increase the temporized relay’s intervention time (this operation has to be done only by trained personnel) or more firewood has to be loaded.
If the boiler fires in a regular manner, when the boiler reaches 65°C the C.H. pump is activated.
The working thermostat, pos. 32, acting on the fan(s) operation mode, will make the boiler fire in an “automatic” way.
The same thermostat will stop the fan when the preset working temperature has been reached.
In case of boiler overheating (temperature higher than 90°C), and in case of the delayed intervention of the thermal discharge valve
(remember that in solid fuel boilers, due to high thermal inertia, the installation of this valve is compulsory), the maximum thermostat
Tmax
, bypassing the microswitch
TKS
, the C.H. pump’s thermostatic control
Tsc
and the pump switch
Ipi
, will automatically allow the boiler thermal inertia to discharge into the central heating circuit. This situation could cause an undesired heating of the radiators, even if the ambient temperature does not request it.
On the fan’s electrical supply there is a safety thermostat
Ts
that will switch OFF the fan in case a temperature of 100°C is reached (safety limit temperature).
It is possible to reset this thermostat by unscrewing the cap in pos. 31 and pressing the button underneath.
A room thermostat can be connected on the terminals 19 and 20 after having removed the jumper that links them.
The recirculation pump
Pr
has to be connected to the terminals 10 and 11.
Instructions for the installer
14 15
18 19
35
11
16
33
17
20 21 22
34
31
23
42
41 12
32
13
11 Mains switch
12 Fan switch
13 C.H.pump switch
31 Safety overheat thermostat
Ph
1
230V~ 50Hz
(max 4A)
IG
11
41
F1 (max 4 A)
15
E
Rt
16 c
1
24
Te (75°÷85°C)
E
32
LL
5
9 c
2
R1
1
Ts
E
(100°C)
31
Iv
12
4
V
M
6
M
7
9
N
2
3
WIRING DIAGRAM KEY
Ph Phase (230V ~ 50Hz)
N Neutral
F1 General fuse (max 4A)
IG Mains switch with warning light
Ipi C .H. pump switch
Iv Fan switch
LL Power ON lamp
Pi C.H.system pump
Pr Recirculation pump
5 8
32 Working thermostat
41 Main fuse (4A)
42 Boiler thermometre fig. 41
13
10
Pr
12
13/21
22
14
14
TKS blu
15 c
23
1
2
Tsc
E
(65°C)
33
Rt
A2
(30 min.)
19
14
13
R1
A1
20
Ipi
13
16 c
2
Pi
18
22 21
E
34
11
17
fig. 42
Rt Temporized relay
R1 Relay
Te Working thermostat (75°C÷85°C)
TKS Microswitch on by-pass rod
Tmax Maximum thermostat (90°C
Ts Safety thermostat (100°C)
Tsc Minimum thermostat for wood fired boiler (65°C)
V Fan (s)
34
... reference to front view facia panel
23
24
Instructions for the installer
3.13 – HYDRAULIC AND ELECTRICAL WIRING DIAGRAMS
Introduction!
The diagrams below, are diagrams of principle and are subject to customization.
For special requirements, please contact our after-sales service.
Water production for heating plant with temperature controlled on the system by mixing valve with manually control.
The AIREX Standard panel board operates automatically the shut off of the fan and the recirculation pump, if the boiler temperature (after 30 minutes from the closing of the loading door, for the boiler ignition purposes) does not reache 65 ° C
(minimum temperature).
The panel board (and the cycle) can be reset only after opening the loading door for a new ignition, or by the switching off and on of the main switch pos. 11.
The same logic of the panel board will stop the fan and the recirculation pump at the end of the loaded wood.
The pump system will operate only after passing the minimum temperature of 65 °C in the boiler.
If the temperature decreases below the threshold of 65 °C, the pump system will be shut down.
VE
Pi
VM
Pr
IR
Key:
Pr = Recirculation pump (the lack of installation will void the warranty)
VM = Zone mixing valve (lack of proper management will void the warranty)
Pi = C.H. pump
VE = Open expansion tank
IR = Central heating circuit
TKS = Microswitch controlling the loading door opening
TA = Room thermostat
WOOD FIRED BOILER
CALDAIA A LEGNA
fig. 22
L1 N
Mains supply
230V – 50Hz
M
M
VE
TKS
Pi
VM
TA
Pr
IR
fig. 23
Instructions for the installer
Water production for heating circuit with temperature controlled on the system by mixing valve with manually control.
Production of hot water boiler with a coil type heat exchanger or plate heat exchanger with separate installation and dedicated loading pump.
The Standard AIREX panel board operates automatically the shut off of the fan and the recirculation pump, if the boiler temperature (after 30 minutes from the closing of the loading door, for the boiler ignition purposes) does not reache 65 °C (minimum temperature).
The panel board (and the cycle) can be reset only after opening the loading door for a new ignition, or by the switching off and on of the main switch pos. 11.
The same logic of the panel board will stop the fan and the recirculation pump at the end of the loaded wood.
The pump system will operate only after passing the minimum temperature in the boiler of 65 ° C.
If the temperature decreases below the threshold of 65 °C, the pump system will be shut down.
TheD.H.W. storage tank loading pump will work with priority on the C.H. pump.
VE
Pr
Pi
VM
Pc
IR
Ps
DOMESTIC HOT WATER
STORAGE TANK fig. 24
Key:
Pr = Recirculation pump (the lack of installation will void the warranty)
VM = Zone mixing valve (lack of proper management will void the warranty)
Pi = C.H. pump
VE = Open expansion tank
IR = Central heating circuit
TKS = Microswitch controlling the loading door opening
TA = Room thermostat
L1 N
Mains supply
230V – 50Hz
M
M
TKS
VE
Pi
VM
Pr
IR
TA
Pc
2
1
C
TB (45÷60°C)
Ps
L1 N
Mains supply
230V – 50Hz
fig. 25
25
26
Instructions for the installer
3.14 - FILLING THE SYSTEM
Warning!
Do not mix the CH system’s water with unsuitable anti-freeze products (example: antifreeze solutions for motor vehicles) or use wrong concentrations of anti-corrosion solutions!
This could cause damage to the washers and could cause noise during normal boiler operation.
UNICAL refuses all liability for injury to persons, animals or damage to property deriving from not having respected the above mentioned recommendations.
In closed heating circuits, where allowed, the water pressure in the heating system - in cold conditions
– must not be lower than one bar; if this value is lower use the filling cock on the boiler to adjust the pressure.
This operation must be carried out when the system is cold.
NOTE!
If the boiler has not been fired for a long period the pump could be jammed.
Before switching on the main switch, it is important to carry out the following un-jamming operation:
After completion of all the C.H. circuit connections fill the boiler and proceed with the inspection for soundness of all the connections, with the following procedure:
- open the radiator’s air vents
- gradually open the filling cock and check that the automatic air vents, fitted onto the system, are working properly.
- close the radiator’s air vents as soon as water begins to flow out.
- using the pressure gauge check that the pressure reaches the value of 1 bar ( this is valid only for installations equipped with a closed expansion vessel - consult local regulations if this is allowed); for installations equipped with an open expansion vessel, the reinstatement is carried out automatically via the same expansion vessel;
- close the system’s filling cock and then bleed off the air once again through the radiator’s air vents.
- check all the connections for soundness.
- after having fired the boiler for the first time and the system has reached the correct temperature, stop the pump and repeat the air bleeding operations.
- let the system cool down and, if necessary, re-establish the water pressure to 1 bar ( this is valid only for installations equipped with a closed expansion vessel - consult local regulations if this is allowed) ); for installations equipped with an open expansion vessel, the reinstatement is carried out automatically via the same expansion vessel;
NOTE!
- remove the pump vent plug positioned in the centre of the pump
- using a screwdriver, rotate the shaft in a clockwise direction.
Once this operation has been concluded, screw back the pump vent plug and check that there are no water leaks.
fig. 26
Instructions for the installer
4
BOILER START-UP
4.1 - INITIAL LIGHTING
Preliminary checks
The first ignition must be carried out by a qualified technician.
Failure to do so could cause injury to persons, animals or damage to property. UNICAL shall not be held liable for any injury and/or damage.
should be carried out.
- If the appliance is sold or transferred to another owner or if the present user moves home and leaves the appliance installed, ensure yourself that the manual always follows the appliance so that it can be consulted by the new owner and/or installer.
Before firing the boiler check that:
- the boiler installation has been carried out in accordance with the specific Standards and regulations in force;
- the air supply and the discharge of the products of combustion are carried out in the correct way in accordance to the specific Standards and regulations in force;
- the boiler is fitted with all the safety and control devices prescribed by the regulations in force;
- the electrical supply is 230 V - 50 Hz;
- the C.H. system has been filled with water;
- any gate valves of the CH system are open;
- the external mains supply switch is on;
- the boiler‘s thermal discharge valve is not blocked and that it is connected to the sewage system;
- there are no water leaks;
- all the necessary ventilation conditions and minimum clearance distances are guaranteed for subsequent servicing.
LIGHTING AND SHUTTING DOWN PROCEDURES
For lighting and shutting down the boiler refer to the “USER
INSTRUCTIONS MANUAL”
Information to be passed on to the user:
The user must be instructed on the use and operation of the boiler and the heating system, in particular:
- Hand the user the : “USERS INSTRUCTION MANUAL”, as well as all the other literature relative to the appliance, and placed in the envelope contained in the packaging.
The user must keep this literature for any future reference.
- Inform the user of the importance of the air vents and of the flue outlet system, stressing the fact that absolutely no modification can be made.
- Inform the user on the control of the system water pressure and how to restore it to the correct value.
- Inform the user on the correct adjustment of thermostats and thermostatic valves for radiators, for the economic use of the system.
- Remind the user that a regular service, once a year,
27
Instructions for the installer
4.2 - FIRE WOOD
Wood is formed mainly by cellulose and lignite. It contains other substances, such as resin
(fir - pine), tannin (oak - chestnut) and, obviously, a large quantity of water.
Good quality woods are oak, ash, beech, maple and fruit trees, except cherry; medium quality wood is: chestnut and birch; sufficient quality wood: lime tree, poplar and willow. Resinous trees are, normally, medium quality fuels.
Wood is therefore an extremely heterogeneous fuel, due to different essences (beech, oak, fruit, resinous), different moisture content, and due to different shapes and dimensions.
Boiler operation will, of course, be certainly effected by all these factors. Especially by the log dimensions, the moisture content and the way wood is loaded in the boiler.
4.3 - WOOD MOISTURE
The calorific value of the different types of wood depends on their moisture content, as shown on the table. Boiler output and autonomy will diminish as the moisture increases. In the table a reduction factor is indicated according to the moisture content of the wood used. The heat output of the AIREX 2S boiler is calculated for wood with a 15% moisture content.
As an example wood which has been dried for 2 years air in a protected area has a 25% moisture content.
Example:
Moisture content of wood used = 30%
Heat output = nominal heat output x 0,79
Correction factors for wood moisture content
% moisture
15
20
25
30
35
40
45
50
Calorific value kcal/kg
3.490
3.250
3.010
2.780
2.540
2.300
2.060
1.820
Correction factor
1
0,93
0,86
0,79
0,72
0,65
0,59
0,52
4.4 - FIRE WOOD DIMENSIONS
The dimensions, together with the moisture content, contribute to determine the boiler’s output Small pieces (with a length, however, conforming to indications hereby indicated) are more easily inflammable and therefore have the tendency to increase the boiler’s output and therefore to reduce its autonomy. Moreover, they fall with greater facility, in the lower chamber, reducing the risk of the formation of “bridges”.
The so-called “bridge” is an empty space in the fire wood storage room, where unburnt wood logs remain . In this case the bed of embers is not fed with continuity and the refractory burner’s slot is uncovered. In these conditions, preferential air passages are created with a very small flame due to an excess of air.
28
4.5 – INITIAL LIGHTING CHECKS
GENERAL CONTROLS
During the first ignition check that the C.H. system has been properly filled and properly purged, that the safety heat exchanger is connected to the water mains via the thermal safety discharge valve (fig.
10, page 15 and fig. 17 page 18), that the chimney has a sufficient draught, that the electrical connection has been made correctly (paragraph 3.12
& 3.13) and that the recirculation and boiler pumps are not blocked.
Furthermore check that the stainless steel grate and the fire bars are properly positioned.
THE BY-PASS
The by-pass is a direct passage between the fire wood storage room and the chimney. It is normally closed by a mobile shutter. The by-pass is automatically opened or closed via a pushing rod when the loading door is opened.
In this way the smoke accumulated in the fire wood storage room is aspirated and sent to the chimney directly.
The bypass, in conclusion, allows the smoke to be discharged at the chimney without escaping from the loading door when loading the wood or during lighting.
Any way, it is essential to open the loading door slowly and, as well, to rotate the antismoke flap (pos. 4, fig. 2) gradually so that the smoke is effectively aspirated.
BY-PASS CONTROL
During the installation stage and, in any case, before starting to use the boiler, check that the by-pass is correctly closed and the actuator of the microswitch, which controls the opening of the door, is correctly positioned.
In this way when the door is closed the fan has to start rotating; when the door starts to open the fan has to be OFF, otherwise all the smokes comes out.
Instructions for the installer
4.6 - STARTING
IGNITION
Make sure that the checks, listed in paragraph 4.5 have been performed.
For the models
AIREX 25 2S, AIREX 40 2S, AIREX 50 2S
(fig. 27):
Tighten the screw of primary air (P).
Fully tighten the adjustment screws of the secondary air (S) to “feel” the resistance of the spring that pushes the closing discs.
At this point, “unscrew” 10 turns the screw of primary air (P) and 4 turns the screws of secondary air (S).
For the models
AIREX 65 2S, AIREX 80 2S
(fig. 28):
The starting position of the rings (pos. 1, fig. 28), that adjust the opening or closing of the primary and secondary air, should be about halfway on the threaded rod.
Through the upper manifold the primary air is blown (P), whilst the secondary air (S) is blow through the lower manifold.
At this point, “ screw upwards” or “unscrew downwards” the rings (pos. 1, fig. 28) on the threaded rod until obtaining an optimal air adjustment, by observing the colour (yellow/white) of the flame in the lower combustion chamber.
Please note that screwing the ring in the clockwise sense (upwards), it will result in an increase of the air intake ( primary and secondary); conversely, a decrease.
Open the wood loading door and place, on the main stone, a little and thin pieces of dry wood, placed crosswise.
Use highly flammable material, and avoid large wood logs and with form of squares.
Light the wood using some sheets of paper (newspaper or similar).
Approach the top door and turn on the fan. Wait a few minutes that the fire takes and produce the embers (5 - 10 minutes).
After few minutes, if looking through the flame sight glass of lower door you will see that the flame inversion is beginning: add, now, more bigger wood logs
Close the wood loading door.
Important: during the normal operation of the boiler the by-pass must be always perfectly closed.
The fire wood logs must be of the following length:
a) 50 cm (+ 1 cm - 4 cm) for models AIREX 25 2S and 40 2S b) 70 cm (+ 1 cm - 4 cm) for the model AIREX 50 2S and
AIREX 65 2S c) 100 cm (+ 1 cm - 4 cm) for the model AIREX 80 2S
These measures must be strictly observed.
As for a good combustion it is essential that there is a uniform descent of the wood, it is necessary to ensure that the length of the wood logs introduced, the form and the manner of loading, do not prevent the regular descent of the fuel.
The wood logs must be placed longitudinally and horizontally.
No log has to be tilted or placed sideways.
C
S
P
S
C Primary/secondary air manifold
S Secondary air adjusting screws
P Primary air adjusting screw
1
C-P
C-S
C-P Primary air manifold
C-S Secondary air manifold
1 Ring nut for air adjustment fig. 27 fig. 28
SUBSEQUENT LOADINGS
Before making a new loading of wood, consume, as much as possible, the previous one.
The new loading will be done when the bed of embers, in the fire wood chamber, will be reduced to a thickness of about 5 cm.
Open slowly the loading door and the internal anti-smoke door.
It is necessary to use wood logs with the length stated in the previous paragraph.
Place the new wood logs as described above.
29
Instructions for the installer
USEFUL SUGGESTIONS and LOADING ERRORS TO BE
AVOIDED
- Logs too long do not fall down properly and can cause
„bridges“.
- Logs too short cause irregular air passages, with consequent reduction in output and efficiency.
- In case the quality of the wood causes „bridges“ it could
become necessary to cut the wood logs in two parts, as shown in fig. 29, in order that the total length “L” is as indicated in the previous paragraph.
- Always open the upper door slowly, in order to avoid blowbacks and smoke formation.
- During normal boiler operation it is absolutely forbidden to open the lower combustion chamber door.
L
=
L
=
30
fig. 29
4.7 - COMBUSTION AIR ADJUSTMENT
PRIMARY AND SECONDARY AIR ADJUSTMENT
The AIREX boiler has a combustion air intake fan (POS. 7 fig. 2), a distribution collector of the combustion air (POS. 1 fig. 27) and regulators of primary air (POS. fig. 27) and secondary air (POS.
S fig. 27).( N°2 fan for the models AIREX 65 2S and AIEREX 80 2S + N°2 collectors for primary and secondary air inlet) with their air adjustment, see fig.28)
At first start you need to adjust the primary and secondary air, bearing in mind that the primary air determines the power of the boiler and therefore the amount of wood that is burned, and the secondary air completes the combustion.
For a proper air adjustment it is necessary to observe the flame through the flame sight glass placed on the lower door.
The flame will have to fill about two-thirds of the lower combustion chamber and will have to lick the bottom cradle quietly, without dragging too much ash and without noise. The flame will have an orange-pink-white colour; will be not too clear and with the center tending to blue.
To carry the flame in optimum conditions you should then adjust the primary air by turning the knob (pos. P). Similarly it will be done for the secondary air (pos. S).
Example n.1
Thick, wet wood logs = difficult combustion
S - Very closed: try to get the maximum dimension of the flame, but not of a reddish colour.
P - Reasonably open in order to obtain a sufficient gasification.
Example n. 2
Very inflammable wood logs
S - Completely open.
P - Slightly closed in order to keep reduced the gasification, but sufficiently open to evacuate the ash that can close the combustion head.
Instructions for the installer
4.8 - CHECKS TO BE CARRIED OUT AFTER
THE FIRST START
CHECKING SEALS
During the initial start-up check the tightness of the smoke circuit and the connection to the chimney. If there is any noticeable smoke leaks alert the installer and / or the authorized After
Sale Service. If there is any noticeable aspiration of air through the door seals, tighten the handle with greater force.
Check the proper operation of the thermostat, Te (32) at full capacity (chapter 3.12) up to stop the fan.
Check for leaks from pipe connections.
After the initial start, with the boiler off, open the lower door and inspect the internal walls and insulation of the door: they should be of a light colour, indicative of a proper air adjustment.
Otherwise, if the walls are blackened, it will mean a wrong adjustment of secondary air (chapter 4.7 and 4.9).
GENERAL ADVICES
- Best performances are obtained after two/three days of operation. Refractory material must be cooked and the tar must encrust the walls of the wood storage room.
- The flame should have a good size and fairly fill the combustion chamber.
- The flame shouldn‘t be too red (lack of secondary air S).
- The flame shouldn‘t be too blue (excess of second. air S)
- The flame should not be too noisy (excess of primary air P)
- The flame must not be too small (lack of primary air P).
- If the ash doesn‘t go down well increase the primary air P).
- If too much ash falls decrease theprimary air P).
- If the chimney is smoking (open completely the secondary air S).
- If it continues smoking give max. secondary air S, and even close partially the primary air P).
AIR ADJUSTMENT FAULTS
1) If
the primary air is excessive
a lot of ash and small pieces of embers will fall through the slot into the combustion chamber: the flame is too fast, dry, of a cold colour and makes noise.
The boiler is consuming a lot of wood and the door’s refractory insulation is white.
2) If
the primary air is insufficient
the flame will be slow, hesitant, influenceable by air currents and by the chimney draught, very small, incapable of touching the lower cradle, with low ash production and the door’s refractory insulation will be of a dark colour.
3) If
the secondary air is excessive
the flame will be small, of a blueish colour and very transparent.
4) If
the secondary air is insufficient
the flame will be big, it will touch the lower cradle, it will completely fill the combustion chamber and, above all, it will be of a red colour and not transparent
4.9 - WARNINGS
HOW TO AVOID CORROSION IN THE FIRE WOOD STORAGE
The use of wood with a high moisture content
(higher than about 25%) and/or loadings not proportioned to the system’s heat request (long
OFF periods with the wood storage full) can cause considerable condensate formation in the wood storage’s internal wall.
The smokes are rich in water steam, due to combustion and the use of wood which always retains water.
If the smoke come into contact with relatively cold surfaces
(having a temperature below 60 - 70 °C), the water steam condensates and, in combination with other combustion products, originates corrosion phenomena of the metallic parts.
Check, once a week, the internal steel walls of the wood storage room: they must be covered by a slight layer of dry tar, opaque coloured, with bubbles tendind to break and fall off.
On the contrary, if the tar is bright, runny and, if removed with the fire stoke, some liquid appears, it is necessary to use wood with a lower moisture content and/or to reduce the quantity of the wood when loading the boiler.
If, in despite of these interventions the tar does not dry, you must inform of this the local After Sales Service.
The condensate inside the firewood storage room causes the corrosion of the steel plate.
Corrosion is not covered by the guarantee, because it is caused by a bad use of the boiler (wet wood, excessive loadings, etc.).
CORROSION IN THE SMOKE CIRCUIT
Every day check if there are signs of smoke condensation (black liquid on the floor and behind the boiler). In this case you must use a wood with a lower moisture content; check that the recirculation pump is working correctly and the smoke temperature at part load, and increase the working temperature. In order to control the room temperature it is therefore necessary to install a mixing valve.
The corrosion caused by the smoke condensation is not covered by the guarantee, because it is caused by the wood’s moisture content and the way the boiler is used.
PRECAUTIONS TO BE TAKEN DURING BOILER OPERATION
31
32
Instructions for the installer
After every air adjustment , wait 5 to 10 minutes before making a new adjustment. Once the best adjustment has been established, at the end of the day check that the surfaces of the combustion chamber and the door insulation are of a white colour.
In the ash deposited in the cradle there must be only a few unburnt embers. If the primary air is in excess, in the ash there will be embers and small pieces of coal, the flame will burn fast, dry, have a cold colour and be noisier, and the output will be excessive (paragraph 6.7).
If the primary air is insufficient the flame will be slow, small, it will not touch the lower cradle and will drag little ash and the output will be insufficient.
If the flame is a dark orange colour, the secondary air is insufficient and the surfaces of the combustion chamber will not be of a white colour; if it is small and blue there is too much secondary air.
Always open slowly the upper loading door and the internal antismoke flap .
If, in despite of these precautions, some blow back will occur, it will be necessary to use bigger logs of wood, with a higher moisture content, and to check that the boiler does not stop for a long time (reduce the primary air - paragraph 6.7) and make sure that the possible distortion of the cast iron fire bars or the modification of the stainless steel grates or that the presence of extraneous bodies (nails, metallic pieces) has not obstructed the refractory main stone slot.
4.10 - THERMOSTAT ADJUSTMENT
WOOD FIRED BOILER
The boiler’s adjustment thermostat must be set to the desired temperature (the adjustment range, limited by stoppers that must not be removed, varies from 75° to 85°C).
To adjust the boiler’s flow temperature to the heating system it is necessary to foresee the installation of a 3 or 4 way mixing valve.
If this mixing valve is not installed the guarantee will be void.
The manual reset safety thermostat, pos. 31, complies to the regulations in force.
At the start-up stage check if it has to be reset.
To do this unscrew the plastic protecting cap and press the reset button; then replace the plastic cap.
If the boiler safety’s thermostat, pos. 31, intervenes frequently, reduce the setting temperature of the working thermostat (pos.
32 on the control panel).
If this problem is repeated, inform the local After Sales Service.
4.11 - SUMMER OPERATION
The use of the boiler in summer season, only for the production of domestic hot water, is not advised, unless you follow these rules meticulously:
1) Use very dry wood
2) Do not load the boiler with too much wood, load the boiler partially, 2 or 3 times per day according to need.
Important.
It is absolutely wrong to load the boiler completely so as to gain very long working periods (for example 24 hours). Doing so the boiler (when the fan is OFF) will produce a lot of acid condensate and corrode the internal walls of the fire wood storage room.
Instructions for the installer
4.12 - FAULT FINDING FOR BOILER WITH
STANDARD CONTROL PANEL
WOOD FIRED BOILER:
Problem:
- The fan does not start
Remedy:
- Adjust the working thermostat (pos. 32) to maximum, by turning clockwise till the stop.
- Reset the safety thermostat (pos. 31).
Problem:
- The boiler does not reach the requested temperature. The flame is too small.
Remedy:
- Check if the by-pass is closed.
- Check the fan
- Check if the doors are properly closed
Problem:
- The fan starts, but after 30 minutes it stops; by switching OFF and ON the main switch (pos. 11) it re-starts.
Remedy:
- Increase the temporized relay’s intervention time
(this has to be done by the After Sales Service or by authorized trained personnel after switching OFF the mains supply).
If you cannot solve the problem, do no attempt any other interventions and
contact an authorized UNICAL After Sales Service.
Problem:
- When opening the loading door there are blowbacks and smoke escape.
Remedy :
- Open the door slowly.
- Use wood with a higher moisture content; make sure the boiler does not stop for long periods (see paragraph 6.9).
- Use thicker wood logs.
- Consume all the wood before loading a new batch
Problem:
- The boiler does not reach the requested temperature.
The flame is small and there is too much air.
When the fire wood storage room is checked a formation of log bridges is found.
Remedy:
- Check the length of the wood logs (see paragraph 6.6).
- Check how the wood logs are loaded in the fire wood storage room (see paragraph 6.6).
- Cut the logs in two parts (see paragraph 6.6).
- Use smaller logs (round or square, 5 to 7 cm diam. )
- Mix medium-large sized logs (15-20 cm diam.)with small sized logs (see previous point).
33
34
Servicing schedule
5
SERVICING & MAINTENANCE
SCHEDULE
To ensure the continuous, safe and efficient operation of the boiler it is highly recommended that it is checked at regular intervals and serviced when necessary, and that only original spare parts are used.
INSTRUCTIONS FOR INSPECTION AND SERVICING
To ensure a long life to all your boiler components and in order not to alter the conditions of the approved product, only original
UNICAL spare parts must be used.
Before servicing always carry out the following steps:
If the boiler is not checked and serviced regularly it could cause material and personal damages.
For this reason UNICAL recommends that a servicing contract should be made with an authorized After
Sales Service Centre.
The boiler must have regular maintenance and cleaning in order to ensure reliable and efficient operation. Regular attention will prolong the boiler’s life span.
- Disconnect the mains electricity supply.
- Separate the appliance from the electrical supply by means of a separating device with an opening contact of at least 3 mm
(for example safety devices or power switches) and ensure yourself that it cannot be accidentally reinserted.
Once all the necessary maintenance work has been completed, always follow these steps:
- Purge the boiler and, if necessary, restore the heating system’s pressure.
To ensure reliable and efficient boiler operation please refer to the table on page 37 where the “recommended servicing and maintenance operations” are indicated.
- Switch on the electrical supply to the boiler.
Servicing schedule
Servicing of the boiler body
Danger !
Before servicing the boiler body, make sure the boiler and the external components have cooled down.
ned it as described above, the cause can be attributed to bad distribution of the secondary air.
In this case:
Warnings
Do not drain any water from the boiler unless absolutely necessary. Periodically check that the chimney is working correctly and that it is in good condition.
1) Check the adjustment of the air setting, according to the instructions given in the paragraph “Combustion air adjustment”.
2) Check that the two holes for the secondary air, placed in the front part of the main stone, just in front of the two adjustment screws, are not obstructed; if they are, pass a
soft brush
in both the holes, as shown in fig. 30.
Do not clean the boiler or its parts with easily inflammable products (gasoline, alcohol, etc.).
Do not leave inflammable products in the room where the boiler is installed.
At the end of the heating season, the boiler must always be checked in order to maintain the heating system in a good working condition.
IMPORTANT
For cleaning the boiler use brushes and a vacuum cleaner. If pieces of cloths are used make sure they are all recovered.
Always keep the screws and nuts protected with grease.
CLEANING AND ORDINARY MAINTENANCE OF THE WOOD
FIRED BOILER
Every day
- Remove the ash from the lower cradle.
- Shake down, with the scraper supplied with the boiler, the embers so that the ashes, accumulated in the fire bed will fall down through the slots in the grate.
This operation will help to avoid the grate becoming obstructed and the subsequent bad operation of the boiler.
This operation has to be done when the flame decreases very much, and, in any case, before each wood loading.
fig. 30
Every week
- Remove carefully all the residues of combustion accumulated in the fire wood storage room.
- Clean, with the brush supplied, the triangular passes of the combustion chamber, below the cradle.
- Remove the ashes from the smoke chamber via the side doors, using the scraper and the vacuum cleaner.
- Make sure the grate’s slots are not obstructed; if so, free the passages using the poker.
- If the boiler continues to operate badly, even after having clea-
Every month
Check that the by-pass is working as indicated in paragraph
4.5 and that when the loading door is closed the by-pass is hermetically sealed.
EXTRAORDINARY MAINTENANCE OF THE WOOD FIRED
BOILER
At the end of each heating season perform a general cleaning of the boiler by removing all the ashes from the fire wood storage room.
During the summer season the boiler doors must be closed.
35
36
Servicing schedule
Cleaning the fan(s)
WARNING:
First of all cut the power supply to the boiler
Open the fan and clean the blades from the incrustations.
Normally with the use of compressed air and a brush it is possible to clean it properly
If the incrustations are more resistant, due to the formation of condensate or tar tears, clean very carefully in order not to bend or deform the blades. This could make the fan noisy during operation and could reduce the fan’s performances.
Cleaning the primary and secondary air distributor.
Remove the central front wall (fig. 30) where the air adjustments are placed and clean the inner space carefully from tarry residues, dust and wood flakes which have entered through the primary air holes. Clean the secondary air passages carefully with a
soft brush
.
Servicing schedule
Components to check during annual servicing
Component
Solution of inconveniente
Cast iron fire bars If necessary replace them
Stainless steel grate
Fire bars mineral wool insulation
Primary and secondary air inlets
Soundness of the bypass disk
Integrity of the combustion chamber refractory bottom
Position of bottom stainless steel craddle
Refractory insulation integrity in upper and lower doors
Integrity of doors seals
Correct operation of the loading door microswitch
Cleaning the fan blades
Fan noise
Cleaning the smoke circuit (on the rear side of boiler)
If necessary replace it
If necessary replace it
If necessary clean them
If necessary adjust it
If necessary repair it using the refractory kit (see spare parts list)
If necessary re-position it
If necessary repair and/or replace the doors
If necessary replace them
If necessary adjust it
If necessary clean them
If necessary replace the fan
If necessary clean it
37
AG
S.P.A.
46033 casteldario - mantova - italia - tel. +39 0376 57001 - fax +390376 660556 www.unical.ag - [email protected]
Unical declines any responsibility for the possible inaccuracies if due to transcription errors or press. Also reserves the right to bring to its own products those changes that it will consider necessary or useful, without jeopardizing its essential features.
advertisement
* Your assessment is very important for improving the workof artificial intelligence, which forms the content of this project
Related manuals
advertisement