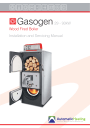
advertisement
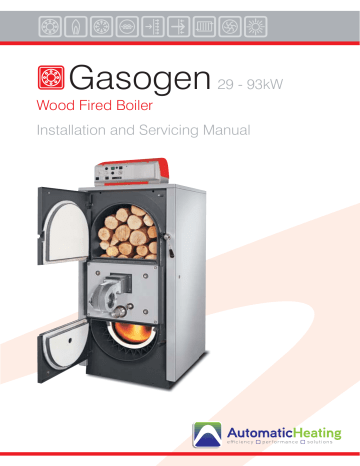
Gasogen
29 - 93kW
Wood Fired Boiler
Installation and Servicing Manual
2
Gasogen
General Information
CONTENTS
1 GENERAL INFORMATION .................................................................................................................................................................................
3
1.1 Symbols used in this manual ....................................................................................................................................................................... 3
1.2 Correct use of the appliance ........................................................................................................................................................................ 3
1.3 Water treatment ............................................................................................................................................................................................. 3
1.4 Information to be passed over to the end user or the person in charge of the appliance ......................................................................... 3
1.5 Safety warnings ............................................................................................................................................................................................. 4
1.6 Data badge .................................................................................................................................................................................................... 5
1.7 General warnings .......................................................................................................................................................................................... 5
2 TECHNICAL FEATURES AND DIMENSIONS ...................................................................................................................................................
6
2.1 Technical features ......................................................................................................................................................................................... 6
2.2 Dimensions and water connections ............................................................................................................................................................. 7
2.3 Main components .......................................................................................................................................................................................... 8
2.4 General information ...................................................................................................................................................................................... 8
3 INSTALLATION INSTRUCTIONS .....................................................................................................................................................................
12
3.1 General warnings ....................................................................................................................................................................................... 12
3.2 Installation Codes of Practice ................................................................................................................................................................... 13
3.3 Packaging ................................................................................................................................................................................................... 14
3.4 Transportation ............................................................................................................................................................................................ 14
3.5 Installation .................................................................................................................................................................................................. 15
3.6 Boiler system connection .......................................................................................................................................................................... 15
3.7 Connection to the heat exchanger’s drainage .......................................................................................................................................... 16
3.8 Recycling pump ......................................................................................................................................................................................... 16
3.9 Installation instructions .............................................................................................................................................................................. 17
3.10 Water and electrical connection diagrams with standard control panel, without hot water storage tank .............................................. 21
3.11 Water and electrical connection diagrams with optional control panel, without hot water storage tank ............................................... 23
3.12 Water and electrical connection diagrams with optional control panel, with hot water storage tank .................................................... 27
3.13 Flue outlet connection ............................................................................................................................................................................... 40
3.14 Filling the system ....................................................................................................................................................................................... 41
4-5 ELECTRICAL CONNECTIONS ........................................................................................................................................................................
42
4.1 Standard control panel .............................................................................................................................................................................. 43
5.1 Optional control panel ............................................................................................................................................................................... 45
5.2 Functional wiring diagram (Flow chart) .................................................................................................................................................... 46
5.3 Loads and sensors connection diagram ................................................................................................................................................... 48
5.4 Functional description of optional control panel ...................................................................................................................................... 49
5.4.1 Ignition ............................................................................................................................................................................................. 49
5.4.2 Normal boiler operation ................................................................................................................................................................... 49
5.4.3 No wood ........................................................................................................................................................................................... 49
5.4.4 Oil/gas boiler operation ................................................................................................................................................................... 50
5.4.5 Domestic hot water production ....................................................................................................................................................... 50
5.5 Special functions ....................................................................................................................................................................................... 51
5.5.1 Overheating ..................................................................................................................................................................................... 51
5.5.2 Combustion gas temperature control ............................................................................................................................................. 51
5.5.3 Fan overheating protection system ................................................................................................................................................ 51
5.5.4 Temperature sensor failure alarm .................................................................................................................................................. 51
5.5.5 Fireproof thermostat ........................................................................................................................................................................ 52
5.5.6 Waiting time .................................................................................................................................................................................... 52
5.5.7 Return flow sensor installation ....................................................................................................................................................... 52
5.6 Optional control panel wiring diagram ...................................................................................................................................................... 53
6 BOILER START-UP ...........................................................................................................................................................................................
54
6.1 Initial lighting ............................................................................................................................................................................................. 54
6.2 Fire wood .................................................................................................................................................................................................... 55
6.3 Wood moisture ........................................................................................................................................................................................... 55
6.4 Fire wood dimensions ................................................................................................................................................................................ 55
6.5 Initial lighting checks ................................................................................................................................................................................. 55
6.6 Start-up ...................................................................................................................................................................................................... 56
6.7 Combustion air adjustment ....................................................................................................................................................................... 57
6.8 Checks to carry out after first start-up ...................................................................................................................................................... 58
6.9 Warnings .................................................................................................................................................................................................... 58
6.10 Thermostat adjustments ............................................................................................................................................................................ 59
6.11 Summer operation ..................................................................................................................................................................................... 59
6.12 Burner adjustment on the back up boiler ................................................................................................................................................. 59
6.13 Fault finding for boilers with standard control panel ................................................................................................................................ 60
6.14 Fault finding for boilers with optional control panel .................................................................................................................................. 61
7 SERVICING AND MAINTENANCE SCHEDULE .............................................................................................................................................
62
General Information
Warning: this manual contains instructions to be used exclusively by the installer and/or a competent person in accordance with the current laws.
The end user is not qualified to carry out any service work on the boiler.
Failure to follow the instructions indicated in this manual, which is supplied with the boiler, could cause injury to persons, animals or damage to property. Automatic Heating shall not be held liable for any injury and/or damage.
1 GENERAL INFORMATION
1.1 - SYMBOLS USED IN THIS MANUAL
When reading this manual particular care has to be given to the parts marked with the followings symbols:
DANGER! Indicates serious danger for your personal safety and for your life
WARNING! Indicates a potentially dangerous situation for the product and the environment
NOTE! Suggestions for the user
1.2 - A CORRECT USE OF THE APPLIANCE
The GASOGEN G3 2S appliance has been designed utilizing today’s heating technology and in compliance with the current safety regulations.
However, following an improper use, dangers could arise for the safety and life of the user or of other people, or damage could be caused to the appliance or other objects.
The appliance is designed to be used in pumped hot water central heating systems.
Any other use of this appliance will be considered improper.
Automatic Heating declines any responsibility for any damages or injuries caused by an improper use; in this case the risk is completely at the user’s responsibility.
In order to use the appliance according to the foreseen scopes it is necessary to carefully follow the instructions indicated in this manual.
1.3 - WATER TREATMENT (refer to specific guide)
The hardness of the mains water supply conditions the frequency with which the heat exchanger is cleaned.
In hard water areas where the main water can exceed 15°f total hardness, a scale reducing device is recommended. The choice of this device has to be made taking into consideration the characteristics of the water.
We recommend you to check the state of cleanliness of the domestic hot water heat exchanger at the end of the first year and subsequently every two years; in this occasion check the state of wear of the anode.
1.4 - INFORMATION TO BE HANDED OVER TO THE USER OR PERSON IN CHARGE OF THE
APPLIANCE
The user or the person in charge has to instructed on the use and operation of his heating system, in particular:
- Hand over these instructions to the end user or person in charge of the appliance, together with any other literature regarding this appliance placed inside the envelope contained in the packaging.
The user has to keep these documents in a safe place in order to always have them at hand for future reference.
- Inform the user on the importance of air vents and of the flue outlet system, stressing the fact that it is absolutely forbidden to make any alterations to the boiler.
- Inform the user how to check the system’s water pressure as well as informing him how to restore the correct pressure.
- Explain the function of time and temperature controls, thermostats, heating controls and radiators, to ensure the greatest possible fuel economy.
- Remind the user that it is obligatory to service the appliance at least annually and to carry out a combustion analysis in compliance with the schedule indicated in the national Codes of Practice.
- If the appliance is sold or transferred to another owner or if the present user moves home and leaves the appliance installed, ensure yourself that the manual always follows the appliance so that it can be consulted by the new owner and/or installer.
3
4
Gasogen
General Information
1.5 - SAFETY WARNINGS
WARNING!
The installation, adjustment, and servicing of this appliance must be carried out by a competent, qualified person and installed in accordance with the current standards and regulations. Failure to correctly install this appliance could cause injury to persons, animals or damage to property. The manufacturer shall not be held liable for any injury and/or damage.
DANGER!
NEVER try to carry out any repairs or service work on the boiler on your own initiative.
Servicing or repairs of the appliance must be carried out by qualified service engineers;
Automatic Heating recommends drawing up a service contract.
Bad or irregular servicing could compromise the safe operation of the appliance, and could cause injury to persons, animals or damage to property for which Automatic Heating shall not be held liable.
-
-
-
-
Modifications to parts connected to the appliance
Do not carry out any modifications to the following parts: the boiler to the gas, air, water supply pipes and electrical current to the flue pipe, safety relief valve and to the central heating’s drainage pipe to the constructive components which influence the appliance’s safe operation
WARNING!
When tightening or loosening the screw pipe connections, use only adequate fork spanners.
The improper use and/or the use of inadequate equipment can cause damages (for example water or gas leakages).
Explosive and easily inflammable substances
Do not use or leave explosive or easily inflammable material (as for example: petrol, paint, paper) in the room where the appliance has been installed.
General Information
1.6 - DATA BADGE
The data badge is adhesive and placed inside the documentation envelope; it must be glued on to one side of the casing, on the external part, by the installer.
The boiler’s serial number is indicated on the plate screwed on the boiler’s front plate (front side, upper right hand side).
1.7 - GENERAL WARNINGS
This instruction manual is an integral and indispensable part of the product and must be retained by the person in charge of the appliance.
Please read carefully the instructions contained in this manual as they provide important indications regarding the safe installation, use and servicing of this appliance.
Keep this manual in a safe place for future reference.
In the event of failure and/or faulty functioning of the appliance, switch off the boiler. Do not attempt to make any repairs: contact qualified technicians.
Any repairs must be carried out by Automatic heating authorized technicians and using only original spare par ts. Nonobservance of the above requirement may jeopardize the safety of the appliance.
The installation and servicing must be carried out in accordance with the regulations in force according to the manufacturer’s instructions and by legally competent authorized persons.
To guarantee the efficiency and correct functioning of the appliance it is indispensable to have the boiler serviced annually by a qualified person.
By a competent person, we imply a person who has a specific technical qualification in the field of components for central heating systems for domestic use, domestic hot water production and ser vicing. The person must have the qualifications foreseen by the current laws in force.
Bad or irregular servicing could compromise the safe operation of the appliance, and could cause injury to persons, animals or damage to property.The manufacturer shall not be held liable for any such injury and/or damage.
If the boiler remains unused for long periods, ensure that any dangerous parts are rendered innocuous.
If the appliance is sold or transferred to another owner or if the present user moves home and leaves the appliance installed, ensure yourself that the manual always follows the appliance so that it can be consulted by the new owner and/or installer.
Before carrying out any cleaning or servicing turn off the electrical supply to the boiler by means of the ON/OFF switch and/or by means of the appropriate shutdown devices.
Only original accessories must be used for all appliances supplied with optional accessories or kits (including electrical ones).
Do not obstruct the intake/outlet terminal ducts.
This appliance must be used only for the purposes for which it has been expressively designed. Any other use shall be considered incorrect and therefore dangerous
5
6
Gasogen
Technical features and dimensions
2
TECHNICAL FEATURES
AND DIMENSIONS
2.1 - TECHNICAL FEATURES
The GASOGEN G3 2S boiler is a steel made wood fired unit
, with complete wood gasification combustion, inverted flame, with a pressurised room chamber.
The following models are available:
GASOGEN G3 25 2S
GASOGEN G3 40 2S
GASOGEN G3 50 2S
GASOGEN G3 65 2S
GASOGEN G3 80 2S
The GASOGEN G3 2S boiler is equipped with all the safety and control devices in compliance to the current standards.
DESCRIPTION OF COMPONENTS
- Steel body with a partially refractory-lined combustion chamber;
- Refractory burner;
- Horizontal flue channels;
- Front fire box lined with refractory material;
- Intermediate door complete with combustion air regulations;
- Lower cleaning door lined with refractory material and equipped with a flame inspection sight;
- Rear flue chamber with side inspection doors and ash removal
- Flue evacuation via a pressure blower.
- Patented thermostatic valves system
- Safety heat exchanger
- Insulated boiler body with 60 mm thickness mineral wool mattress
- Powder painted steel casing
- Recirculation pump kit (optional)
- Recirculation pump kit for buffer tank (optional), provided the standard control panel is replaced by the model code
23557
- Standard control panel for electromechanical operation
- Optional control panel, code 23557, for integral control of a buffer tank, according to the Standard EN 303-5 and with the possibility of operating with a back up oil or gas fired boiler.
STANDARD CONTROL PANEL COMPONENTS:
- Power On light indicator
- Boiler thermometer
- Safety thermostat in case of boiler overheating
- Boiler temperature adjustment thermostat
OPTIONAL CONTROL PANEL COMPONENTS:
- Power On light indicator
- Boiler thermometer
- Safety thermostat in case of boiler overheating
- Boiler temperature adjustment thermostat
Technical features and dimensions
2.2 - DIMENSIONS AND
WATER CONNECTIONS
1.
Control panel
2.
Primary air adjustment
3.
Secondary air adjustment
4.
Flame sight control
5.
Cleaning door
6.
Rear smoke chamber
7.
Loading door
8.
Fan
9.
Bottom inspection and cleaning door
T1. Central Heating flow
T2. Central Heating return
T3. Chimney connection
T4. Safety heat exchanger connections
T5. Bulb holder connection for heat discharge valve
T6. Bulb holder for safety thermostat
T7. Bulb holder for thermometer and high limit and minimum working thermostat,
T8. Boiler drainage
7
2
4
9
8
3
1
A
T4
T3
F
T1
B E
T4
T5
T1
T2-T8
6
5
MODELS
MINIMUM OUTPUT (kW)
GASOGEN
G3 25 2S
15
AVERAGE OUTPUT (kW) 26
29 MAXIMUM USEFUL OUTPUT* (kW)
MAXIMUM OUPUT
DIMENSIONS:
A
B
C
D
E
F
G
CONNECTIONS T1 - T2
T3
T4
(Ø mm)
UNI ISO 7/1
T5 - T6 - T7 - T8
BOILER WATER CONTENT
WATER SIDE PRESSURE DROP**
SMOKE SIDE PRESSURE DROP
UNI ISO 7/1
(l)
(m c.a.)
(mm c.a.)
MAX. WORKING PRESSURE
FIRE BOX STORAGE VOLUME
FIRE BOX DIMENSIONS
WEIGHT
WOOD LOGS LENGTH
(kW)
(mm)
(mm)
(mm)
(mm)
(mm)
(mm)
(mm)
UNI ISO 7/1
(bar)
(l)
(mm)
(kg)
(cm)
34
560
700
1225
190
315
245
1030
Rp 1¼
150
R ½
Rp ½
90
0,10
0,3
3
95
290x340
386
50
* Output obtained with good quality wood with a 15% .moisture content.
** Pressure losses for a flow rate corresponding to 15 K Delta T.
GASOGEN
G3 40 2S
23
37
47
55
655
700
1355
190
315
245
1140
Rp 1½
200
R ½
Rp ½
110
0,08
0,4
3
135
350x440
475
50
GASOGEN
G3 50 2S
29
47
58
69
655
900
1355
190
315
245
1140
Rp 1½
200
R ½
Rp ½
140
0,12
0,6
3
185
350x440
593
70
T8
GASOGEN
G3 65 2S
41
64
76
88
755
955
1405
190
315
245
1180
Rp 2
220
R ¾
Rp ½
170
0,06
0,3
3
235
340x520
630
70 fig. 1
GASOGEN
G3 80 2S
52
76
93
109
755
1255
1405
190
315
245
1180
Rp 2
220
R ¾
Rp ½
220
0,10
0,5
3
325
340x520
850
100
T2
T7
T4
T6
T3
7
Gasogen
Technical features and dimensions
2.3 - MAIN COMPONENTS
1. Control panel
2.
Upper casing panel
3.
N° 2 side casing panels
4. Smoke proof hinged door
5.
Refractory-lined loading door with sealing gasket
6.
Central door with gasket and primary and secondary air adjustment screws
7.
Fan
8.
Refractory-lined combustion chamber door, sealing gasket and flame sight
9.
Thick steel plated combustion chamber
10. Heat exchange baffle
11. Boiler drainage
12. Safety heat exchanger
13. By-pass with command rod
14. Boiler body mineral wool insulation
15. Steel boiler body
16. Refractory burner with fire bars and grate
17. Flue chamber
19. Thermostatic valve
M C.H. flow
R C.H. return
12
17
13
M
18 2 14 1
15
16
8
R
11 10 9 fig. 2
N.B.:
The fire bars and the refractory steel grate are subject to wear; it is therefore advisable to carry out an annual inspection to prevent bad boiler operation.
2.4 - GENERAL INFORMATION:
REVERSED FLAME COMBUSTION
Every body knows that to make a match last it must be held with its head upwards.
This is because it is necessary that the flame, in its convective motion, does not meet another fuel in addition to the one which it has generated it. As in residential heating the fuel is in form of wood logs which are loaded from the top, the flame has to go in the opposite way, i.e. downwards.
Natural draught is a very variable source of depression, according to the type of chimney, on the weather conditions, on the type of fuel, etc.
Therefore it is necessary to integrate it with forced ventilation in order to stabilize it.
By fitting a fan it is possible to considerably reduce the section of the gas passages on the grate and furthermore there are no problems with cold starts.
The small grate permits a more controlled passage of combustion air, contrarily to what happens with the large traditional grates.
The air can be perfectly dosed because the grate covered with fired wood has the same crossing resistance and thus the combustion will be always optimal.
Automatic Heating has already used this principal for many years with the GASOGEN G3 2S boiler.
The GASOGEN G3 2S boiler today has reached such a high level of perfection that it can pass all the most stringent tests foreseen by the European Standards in force concerning the environment.
3
5
4
6
7
8
GASOGEN G3 2S - BOILER CONSTRUCTION
The boiler body is made of two oval elements, one placed inside the other, so as to form a water cavity (fig.3).
The large fire box , in its rear wall, has a refractory insulation, which is particularly resistant to heat and mechanical stresses, in order to keep the by-pass zone dry in every working condition.
We can distinguish the following parts (fig.3):
1. Fire box, drying area
2. Gasification zone
3. Embers zone
4. Refractory burner
5. Combustion chamber
6. Heat exchange surface
7. Refractory steel cradle
8. Boiler water
9. Thermostatic system
10. Safety heat exchanger
M C.H. system flow
R C.H. system return
GASIFICATION ZONE (2)
The gasification takes place In the lower part of the fire box .
It is very important that the gasification is as regular as possible, so as not to overburden the burner with gas. The gasification speed depends on the quantity of the wood and the dimensions of the drying area. Generally, it is better to use large logs if they are dry and small logs if the wood is wet . The quantity of primary air, proportional to the delivered output, is regulated via the adjustment system.
EXCHANGE SURFACE (6)
As the boiler operates on wood, and because the sulphur concentrations are not very high , it is important to obtain very low smoke temperatures in order to increase the water efficiency.
To obtain this Automatic Heating has opted for an exchange surface with dry smoke passes (fig. 4), which have already been extensively tested in oil fired boilers working at low water temperature, thus permitting low smoke temperatures without danger of condensate forming.
The surfaces of the dry passages “A” (fig. 4) have had incisions made on them in order to avoid dilatation problems.
The solid residues of combustion (ashes), which lie on the high temperature refractory-lined cradle (fig. 3, pos. 7,) will become with time always lighter until they will be dragged by the gas speed and will deposit themselves in the lowest area of the rear smoke chamber, from which they will be removed during the cleaning operation.
REFRACTORY BURNER (4)
The burner is made up of refractory stone (fig. 3, pos. 4).
This stone has an oval central opening through which the flame passes.
The embers lie directly on the main stone which divides the fire box from the lower combustion chamber.
Furthermore the main refractory stone has a rectangular seat in which the opportunely grooved cast iron fire bars are placed
(fig. 5, pos. 2), which receive the secondary air from a front distributor.
The embers are prevented from falling by cylindrical pieces of refractory steel. The combustion gases, poor in oxygen and
Technical features and dimensions
M
9
1. Metallic grate
2. Cast iron fire bars
R
fig. 4 fig. 5
10
1
8
fig. 3
2
3
4
5
6
7
9
10
Gasogen
Technical features and dimensions still rich in carbon not yet combined, travel across the embers and enter the opening in the centre of the main stone.
Inside this pre-combustion chamber, the gases combine with the pre-heated secondary air coming through the grooves of the two cast iron fire bars.
The resulting flame will be highly oxygenated and have a light blue colour. This flame comes out from the oval opening and invades the combustion chamber.
Due to the high temperatures the refractory burner will become a bright red colour.
THERMOSTATIC VALVE (9)
As well known, wood normally has a high moisture content when compared with other types of fuels. The first operation which occurs inside the fire box is therefore the drying phase.
The high moisture content can then cause condensation phenomena within the boiler and also in the chimney.
To limit the inconvenience in the boiler it is necessary to maintain high working temperatures.
For this reason the boiler is equipped with a patented thermostatic system (fig. 6) which per mits the boiler temperature to be kept constantly high and in particular, in the fire box, where the condensation phenomena is more likely to occur.
In order to reduce the consequences of condensate formation
(formation of layers of tar, corrosion, etc.) it is advantageous to dimension, time by time, the wood load to the actual needs, so as to prevent long stop overs with the wood storage completely full of humid wood.
Nevertheless all these expedients do not impede the formation of condensate in the chimney. Therefore we suggest, when building the chimney, to use air-tight components, to avoid the condensate damaging the building structure.
COMBUSTION CHAMBER (5)
The combustion is optimised by increasing the flame temperature and producing a strong turbulence in the bottom chamber.
For this reason the flame, in addition to not to touching cold walls irrigated by the water, rebounds and is divided on a semicircular cradle which rests on the lower exchange surfaces
(baffles), which, as well delimiting the smoke passages, also has the task of collecting the ashes and possible embers.
The flames, after having bounced off the walls of the bottom area and the refractory ones, direct themselves with a whirling motion towards the front part of the combustion chamber and enter the flue ducts.The combustion will be complete and clean and the dominant colour will be that of the ashes: white.
Firewood, as is well known, normally has a high moisture content when compared to other types of fuels. The first operation which occurs inside the fire box is therefore the drying phase.
The high moisture content can cause condensate phenomenons inside the boiler and also in the chimney.
In order to limit this problem it is necessary to maintain the boiler at a high working temperature.
Therefore, in order to adjust the flow temperature it is necessary to install a 3 or 4 way mixing valve.
If the mixing valve is not installed it will make the guarantee void.
Always in order to reduce the consequences of condensate formation (tar formation , corrosion, etc.) it is advantageous to dimension, time by time, the wood load to the actual needs, so
R
F
F
M = C.H. flow
R = C.H. return
P = Primary air
S = Secondary air
F = Flue
M
3
2
1
T1
P
S S S
P
F
P
P-S
S fig. 6 fig. 7
as to prevent long stop overs with the wood storage completely full of humid wood. Nevertheless all these expedients do not impede the formation of condensate in the chimney. Therefore we suggest, when building the chimney, to use air-tight components, to avoid the condensate damaging the building structure.
Technical features and dimensions
11
12
Gasogen
Instructions for the installer
3
INSTALLATION
INSTRUCTIONS
3.1 - GENERAL WARNINGS
WARNING!
This boiler is to be destined only to the use for which it has expressly been designed for.
Every other use is to be considered improper and therefore dangerous.
This boiler is designed to heat water at a temperature inferior to boiling point at an atmospheric pressure.
WARNING!
These appliances are exclusively designed for indoor installations or installed in adequate sitings.Therefore these appliances must not be installed and operated outdoors. An outdoor installation could cause malfunctioning and could be dangerous. For outdoor installations, it is recommended to use appliances which have been specifically designed for this purpose.
Before installing the boiler the following points have to be carried out by a professionally qualified person: a) The whole system should be thoroughly flushed in order to remove any residual dirt or grime which could compromise correct boiler operation.
b) Check that the chimney/flue pipe has an adequate draught, does not have any constrictions, and that no other appliance’s flue outlets have been fitted, unless the chimney is serving more than one heating appliance, according to the specific standards and regulations in force. The connection between the boiler and chimney/flue outlet can be made only after this verification has been carried out.
WARNING!
The appliance must be installed by a qualified, registered engineer, whom, under his own responsibility, guarantees the compliance of the standards according to the latest regulations.
NOTE:
The boiler must be connected to a heating system which is compatible to its performance and output.
3.2 - INSTALLATION CODES OF PRACTICE
The GASOGEN G3 2S is a boiler foreseen for operation with firewood. The appliance must be installed in compliance with all applicable laws and regulations.
Instructions for the installer
13
14
Gasogen
Instructions for the installer
3.3 - PACKAGING
The GASOGEN G3 2S is supplied dismantled: the casing, the fan, the control panel, the handles and the cleaning accessories are delivered separately in carton boxes
(fig. 8).
After having unpacked everything, make sure that the consignment is intact and undamaged.
In case of doubt do not to use the appliance and inform the supplier.
Keep the packaging material (cardboard box, plastic bags, polyester protection etc .) out of the reach of children since they can be dangerous.
Automatic Heating refuses all liability for injury to persons, animals or damage to property deriving from not having respected the above mentioned recommendations.
1
Packages description:
1. Boiler body
2. Package containing the casing and boiler insulation
3. Package containing the control panel
4. Package containing: insulation fixing kit, fan, air manifold group, smoke chamber inspection doors, handles, flame sight mirror.
In the documents, placed in the fire box, you will find:
- User’s instruction guide
- Installation and servicing instruction manual
- Warranty
- Adhesive data plate
- Adhesive label with ventilation requirements
If the boiler will not be used for a long period, it should be adequately protected.
3.4 - TRANSPORTATION
To facilitate the transport, the loading and unloading of the boiler, on the upper part of the boiler body there are suitable hooks (fig. 8) for lifting.
2
4
3 fig. 8
Instructions for the installer
3.5 - INSTALLATION
The boiler does not differ from a normal solid fuel fired boiler; therefore there are no particular installation codes of practice other than the applicable national and local safety regulations and laws.
The installation room must be properly ventilated via openings, which should have a total surface of at least 0,5 m².
To facilitate cleaning of the flue circuit, a free space, not inferior to the length of the boiler, must be left in front of the boiler.
In addition ensure that the doors can open 90° without meeting any obstacles.
The boiler can be placed directly on the floor, because it is equipped with a self-supporting frame.
Nevertheless, in case of installation in very damp boiler rooms, it is preferable to fit a concrete support.
When installation is completed, the boiler should be in a horizontal position and stable so as to reduce possible vibrations and noise.
An adequate clearing must be left behind the boiler for servicing.
INSTALLATION IN BOILER ROOM
Note:
The minimum clearances indicated in figure 9 are compulsory only for boilers with an output higher than 35 kW.
3.6 - BOILER SYSTEM CONNECTION
Warning!
Make sure the connection of the pipelines is free of mechanical stresses, in order to avoid pressure losses!
The C.H. flow and return must be connected to the respective connections in the boiler, as indicated on page 8.
When determining the size of the CH circuit pipes it is essential to bear in mind the pressure losses induced by any of the system’s components and by the configuration of the same system.
The piping route has to be designed taking all the necessary precautions in order to avoid air locks and to facilitate the continuous purging of the system.
Ensure yourself that the system’s piping is not used as earth clamps for the electrical or telephone system. They are absolutely unsuitable for this use. In a short time this could cause serious damage to the piping, boiler and radiators.
600
1300
1000
600
600 fig. 9
15
16
Gasogen
Instructions for the installer
3.7 - CONNECTION TO SAFETY HEAT
EXCHANGER DRAIN
Solid fuel fired boilers have to be installed with the safety devices foreseen by applicable regulation and laws.
For this purpose the GASOGEN G3 2S boilers are fitted with a safety heat exchanger.
On this safety heat exchanger the installer must fit a heat discharge valve , whose control bulb has to be inserted in the bulb holder placed onto the rear wall of the wood fired boiler.
The inlet and outlet connections can be inverted.
However we recommend that the valve be fitted on the cold water inlet.
In correspondence of the safety heat exchanger outlet, we recommend fitting a drainage pipe with a funnel and siphon that lead to an adequate drainage. The drainage has to be visible.
Warning!
In absence of this precautionary measure, the eventual intervention of the heat discharge valve could cause damages to people, animals or property. The manufacturer shall not be held liable for any such injury and/or damage.
3.8 - RECIRCULATION PUMP
For correct boiler operation it is necessary to install a recirculation pump in the boiler.
The recirculation pump, supplied as an optional kit in two different versions, basic or for buffer storage tank control, will have to be connected as shown in figs. 19 and 20.
If the recirculation pump is not installed, besides limiting the boiler’s life span, it will invalidate the warranty.
WARNING!
The hardness of the mains water supply conditions the boiler’s life span.
Depending on the hardness of the of the mains water supply the possibility of installing a water softener has to be taken into consideration.
In hard water areas where the main water can exceed 15°f total hardness, water treatment is always recommended.
2
1
ALIMENTAZIONE
MAINS
SCARICO
DRAIN fig. 10
3.9 - INSTALLATION
INSTRUCTIONS
A
Installation of the insulation and casing
A) Fit the ball grip pos. 4 onto the upper door closing handle.
B) Fit the screw and nut on the upper and lower door and screw down the ball grip (pos. 1, 2, 3).
C) Fit the 4 supporting feet on the lower
L profiles of the boiler body.
D) Fit the cleaning doors onto the smoke chamber.
E) Fit the flame sight mirror (pos. 5) onto the lower door’s sight glass.
F) Fit the thermal discharge valve’s bulb holder (pos. 2, fig. 18).
G) Fit the body insulation and make a suitable hole near the flow connection pipe.
H) After fitting the fibre glass insulation onto the boiler body, pass the plastic strap provided around it, and insert an end part in the slot as shown in detail 1
(fig. 12).
Make appropr iate cuts in correspondence of the thermostatic valves.
I) Keeping the end of the plastic strap already inserted steady, proceed with the other end by bending, towards the inside, the plastic pin as shown in detail
2.
L) Pull the ends of the strap (as shown in details 3 & 4) till it adheres completely to the glass wool covering the boiler body.
Please do not pull the strap too much, as too much compression of the rock wool insulation will cause an uniformed insulation
B
3
2
4
1
3 2
5
If the boiler needs to be serviced it is possible to remove the plastic strap by removing the blocking devices.
Fit the microswitch onto its support and adjust the pushing washer axially in order to allow the microswitch to be regularly controlled when the upper loading door is closed.
Check that the by-pass disk is perfectly closed when the door is closed and the boiler in operation.
It is possible to verify this by simulating the closing of the upper door and observing, from the inside of the fire box, if there are any spaces.
If necessary, adjust the length of the by-pass shaft, acting on the front threaded shaft.
1
Instructions for the installer
FIG. 12
C fig. 11 fig. 12
D fig. 13
17
Gasogen
Instructions for the installer
- Hook the L.H. side casing panel (pos. 1) to the boiler body.
- Hook the R.H. side casing panel (pos. 2) to the boiler body.
- Before fitting the upper panel (pos. 3) to the side panel (pos.1
& 2), install the control panel (pos. 4).
- Fit the rear profile supporting the cable clamps (pos. 7).on
the upper panel
- Open the control panel by unscrewing the two side screws.
Lift the control panel’s cover, making it rotate frontwards.
Fit all the thermostat capillaries inside, unrolling them carefully, the fan(s) connecting cable(s) (outlet), the microswitch cable door opening control (inlet), and the incoming supply cable through the two rectangular slots on the base of the control panel.
- Position the upper casing panel onto the boiler by directing the capillaries towards the boiler rear.
- Stick the boiler DATA PLATE onto the R.H. side casing panel after having cleaned the interested area.
Remove the adhesive from the DATA PLATE and stick it on the boiler making it adhere perfectly.
1
Ref. fig.15 (Models GASOGEN G3 25 2S, GASOGEN G3 40
2S, GASOGEN G3 50 2S)
- Fit the air manifold (pos. 1) on to the intermediate door.
- Fit the gasket (pos. 4) and the plate (pos. 5) to the manifold.
- Fit the fan (pos. 7) to the plate.
- Make sure the air non-return plate is not blocked, by moving the air manifold’s external lever manually.
The primary and secondary air draught adjustment is described on page 57.
- Wire the electrical connections (see general wiring diagram on page 44 and practical wiring diagrams on
9
8 page 21 & 22).
1
3
2
4
On the optional control panel (code 23557)
DUPLO IT version, the wiring of the electrical connections must be carried out as indicated in the diagrams in 3.11 & 3.12, on pages 24, 26, 29, 31, 33,
36 and 39.
7
6
5
DETTAGLIO B
DETAIL B
B
Models: GASOGEN G3 25 2S
GASOGEN G3 40 2S
GASOGEN G3 50 2S
18
Ref. fig. 16 (Mod. GASOGEN G3 65 2S, GASOGEN G3 80
2S)
- Fit the air manifolds on to the intermediate door.
- Fit the gaskets and the plates to the manifolds.
- Fit the fans to the plates.
- Make sure the air non-return plates are not blocked, by moving the air manifold’s external lever manually.
The primary and secondary air adjustment is described on page 57.
- Wire the electrical connections (see general wiring diagram on page 44 and practical wiring diagrams on page 21 & 22).
On the optional control panel (code 23557)
DUPLO IT version, the wiring of the electrical connections must be carried out as shown in the diagrams in 3.11 & 3.12, on pages 24, 26, 29, 31,
33, 36 and 39.
Models: GASOGEN G3 65 2S
GASOGEN G3 80 2S
DETTAGLIO B
DETAIL B
B
5
6
4
3
7
2 fig. 14 fig. 15 fig. 16
Instructions for the installer
Wire the electrical connections as indicated on the general wiring diagram on page 44 and practical wiring diagrams on page 21 & 22).
Insert the bulbs of the thermostats in their relevant bulb holders as shown in fig. 17 and secure them in place with the fixing springs.
TERMOSTATO
DI ESERCIZIO (Te)
In the optional control panel (code 23557) DUPLO IT version, the bulbs of the sensors/thermostats to be placed in the bulb holders are the following:
- Flow sensor (Tc).
- Boiler thermometer
- Safety thermostat (small bulb holder).
TERMOMETRO
TERMOSTATO
DI MINIMA (Tsc)
MOLLA DI
FISSAGGIO
MOLLA
DI CONTATTO TERMOSTATO
DI MASSIMA (Tmax)
The flue sensor bulb must not be inserted.
MOLLA DI
FISSAGGIO
For the return sensor’s electrical connection (Tr) and for the relevant problems connected with it, see 5.5.7 (page
52) “Return sensor installation”.
TERMOSTATO
DI SICUREZZA (Ts) fig. 17
Fit the heat discharge valve (pos. 1) on the safety coil inlet and insert its sensor in the relevant bulb holder (pos. 2).
It is advisable to redirect the heat safety valve discharge to the sewage.
The heat discharge valve can be fitted , indifferently, at the inlet or outlet of the safety coil, provided the valve sensor is inserted in it relevant bulb holder.
See also chapter 3.7.
2
1
ALIMENTAZIONE
SCARICO fig. 18
TERMOSTATO DI ESERCIZIO (Te) = WORKING THERMOSTAT
TERMOMETRO = THERMOMETER
TERMOSTATO DI MINIMA (Tsc) = MINIMUM THERMOSTAT
MOLLA DI FISSAGGIO = FIXING CLIP
MOLLA DI CONTATTO = CONTACT SPRING
TERMOSTATO DI MASSIMA (Tmax) = HIGH LIMIT THERMOSTAT
MOLLA DI FISSAGGIO = FIXING CLIP
TERMOSTATO DI SICUREZZA (Ts) = SAFETY THERMOSTAT
19
Gasogen
Instructions for the installer
To ensure correct operation of the GASOGEN G3 2S boilers it is necessary to fit a recirculation pump in order to avoid low temperature water returns that could jeopardize the boiler’s life span.
Automatic Heating, to favour her clients, has developed a water recirculation kit that optimizes the water recirculation within the boiler.
This kit is supplied separately as an option and is available, on request, by indicating the appropriate part number .
The pump’s electric connection must be carried out according to the general wiring diagram shown on page 44 and the practical wiring diagrams shown on page 21 & 22.
On the optional control panel (code 23557) DUPLO IT version, the wiring of the electrical connections must be carried out as shown in the diagrams in 3.11 & 3.12, on pages 24, 26, 29, 31, 33, 36 and 39.
15
14
13
8
12
11
10
9
6
7
20
2
1
RECIRCULATION KIT FOR OPERATION WITH HOT WATER
STORAGE TANK (see 3.12 on page 27)
NOTE: For correct control of the storage tank, in addition to fitting the recirculation kit, foreseen for this purpose, the optional control panel code 23577 must be fitted.
To ensure correct operation of the GASOGEN G3 2S boilers, when a storage tank is used, it is indispensable to install the return sensor (Tr), as shown in the diagrams in figs. 29,
31, 33, 35 and 37.
Automatic Heating has developed a RECIRCULATION KIT FOR
OPERATION WITH A STORAGE TANK.
This kit is supplied separately as an option and can be ordered by indicating the code of your own boiler.
The return sensor (Tr) has to be inserted in the bulb holder pos. 26, placed in the boiler C.H. return connection.
Please refer to the control panel’s instruction manual, in 5.5.7
“Return flow sensor installation” for the return sensor’s (Tr) electrical connection and for any problems connected with it.
Note: The “MAXP” function (heat discharge pump) will be carried out by the “MKP” pump (central heating pump) (see
5.3 “Loads and sensors connection diagram”); then connect the jumper 30-38.
22
On the optional control panel (code 23557)
DUPLO IT version, the wiring of the electrical connections must be carried out as shown in the diagrams in 3.11 & 3.12, on pages 24, 26,
29, 31, 33, 36 and 39.
2
3
3
4
23
4
1
5
6
7
19
20
26
27
5
18 fig. 19
24
17
16
15
14
13
12
11
21
10
8
9
28
15
25 fig. 20
Instructions for the installer
3.10 - WATER AND ELECTRICAL CONNECTION DIAGRAMS WITH STANDARD CONTROL
PANEL, WITHOUT HOT WATER STORAGE TANK
Foreword!
The diagrams shown here below may be customized.
For particular requirements, please contact our After Sales Service.
Domestic hot water production for a central heating system with boiler temperature control via manual mixing valve.
IR
The GASOGEN G3 2S boiler’s standard control panel automatically switches off the fan and the recirculation pump in case the boiler temperature, (once 30 minutes have passed from closing the upper loading door for firing the boiler), does not reach 65°C ( minimum temperature ).
VE
Pi
VM
The control panel (and the cycle) can only be reset by opening the loading door for a new restart, or by switching OFF and ON of the switch in pos. 11.
The same control panel operation logic will switch OFF the fan and the recirculation pump when all the wood has finished.
The C.H. system pump will operate only after the minimum boiler temperature of 65°C has been reached.
When the boiler temperature falls below 65°C, the C.H. pump will shut down.
Key:
Pr = recirculation pump (if not installed the guarantee is void)
VM = zone mixing valve (if not controlled correctly the guarantee is void)
Pi = central heating system pump
VE = open water tank
IR = heating circuit
TKS = microswitch controlling the opening of the loading door
TA = room thermostat
CALDAIA A LEGNA
WOOD FIRED BOILER
Pr fig. 21
L
1
N L
1
N L
1
N L
1
N L
1
L
1
L
1
L
1
N L
1
L
1
L
1
L
1
L
1
L
1 marrone
1 2 3 4 5 6 7 8 9 10 11 12 13 14 15 16 17 18 19 20 21 22 23 24
M
4 5 6
VENTILATORE
L1 N
ALIMENTAZIONE
230V ~ 50Hz
M
7 8 9
VENTILATORE
Alimentazione: Mains supply 230V – 50Hz
Ventilatore: Fan
VE
22 14 nero
TKS blu
19
TA
20
16 17 18
Pi
IR
VM
10 11 12
Pr fig. 22
21
22
Gasogen
Instructions for the installer
Domestic Hot Water (DHW) for central heating installation with boiler temperature control via a manual mixing valve.
DHW production via a coiled hot water storage tank or plate heat exchanger with independent installation system and dedicated loading pump
The GASOGEN G3 2S boiler’s standard control panel automatically switches off the fan and the recirculation pump in case the boiler temperature, (once 30 minutes have passed from closing the upper loading door for firing the boiler), does not reach 65°C ( minimum temperature ).
VE
Pi
VM
IR
The control panel (and the cycle) can only be reset by opening the loading door for a new restart, or by switching OFF and ON of the switch in pos. 11.
The same control panel operation logic will switch OFF the fan and the recirculation pump when the wood is finished.
The C.H. system pump will operate only after the minimum boiler temperature of
65°C has been reached.
When the boiler temperature falls below
65°C, the C.H. pump will shut down.
CALDAIA A LEGNA
WOOD FIRED BOILER
Pr
Pc
PRODUTTORE ACQUA
CALDA SANITARIA fig. 23
DOMESTIC HOT WATER
STORAGE TANK
Key:
Pr = recirculation pump (if not installed the guarantee is void)
VM = zone mixing valve (if not controlled correctly the guarantee is void)
Pi = central heating pump
VE = open water tank
IR = heating circuit
TKS = microswitch controlling the opening of the loading door
TA = room thermostat
L
1
N L
1
N L
1
N L
1
N L
1
L
1
L
1
L
1
N L
1
L
1
L
1
L
1
L
1
L
1 marrone
1 2 3 4 5 6 7 8 9 10 11 12 13 14 15 16 17 18 19 20 21 22 23 24
4 5 6
M
VENTILATORE
L1 N
7 8 9
M
ALIMENTAZIONE
230V ~ 50Hz VENTILATORE
Alimentazione: Mains supply 230V – 50Hz
Ventilatore: Fan
22 14 nero
TKS blu
IR
17
Pi
VE
TA
VM
2
1
C
16
TB (45÷60°C)
10 11 12
Pr
17
Pc fig. 24
Instructions for the installer
3.11 - WATER AND ELECTRICAL CONNECTION DIAGRAMS WITH OPTIONAL CONTROL
PANEL BOARD, WITHOUT HOT WATER STORAGE TANK
Foreword!
The diagrams shown here below may be customized.
For particular requirements, please contact our After Sales Service.
Central heating installation with temperature controlled via a motorized mixing valve.
DHW is produced via a coiled hot water storage tank or plate heat exchanger with an independent installation system and dedicated loading pump.
The two boilers are hydraulically connected in series, with the wood fired boiler system flow connected to the oil/gas fired boiler’s system return.
There is no need to install a diverting valve, or DHW storage tank loading pump; the DHW tank can be incorporated in the oil/gas fired boiler.
In the summer, DHW production can be supplied only by the oil/gas fired boiler.
The heating circuit water flows through both the boilers and, in this case, the heat losses are very important.
IMPORTANT: During the installation phase make sure the jumpers’ settings in the control panel are as indicated in chapter 5.2.
The GASOGEN G3 2S boiler’s standard control panel automatically switches off the fan and the recirculation pump if the boiler temperature, (once 30 minutes have passed from closing the upper loading door for firing the boiler), does not reach 65°C ( minimum temperature ).
The logic operation of the GASOGEN G3 2S boiler’s control panel, will switch off the fan and the recirculation pump once the wood finishes.
In this case, or when the wood finishes, the auxiliary boiler will start firing automatically, provided the selector 22 of the panel board is on ( 0 ) and the burner switch 23 is in pos.
II , 30 minutes after the wood fired boiler temperature falls below 60°C.
The wood fired boiler’s door must be kept closed.
The wood fired boiler, in this case, will be excluded and it will be possible to restart it after opening the door in order to load new wood.
If the burner switch 23 is always kept on pos.
0 ), the back-up boiler’s burner will be always excluded.
Obviously, to permit operation of the back-up boiler, the control panel must be in the ON position.
The central heating system pump will operate only after the boiler exceeds the minimum temperature of 65°C.
When the boiler temperature falls below 65°C, the central heating pump will shut down.
The D.H.W. storage pump will operate in priority compared to the central heating pump.
The flow sensor (Tc) must be always placed in the boiler’s bulb holder ( see fig. 17 ).
D.H.W. production will be given priority via the storage tank loading pump (PR), controlled by a changeover thermostat.
The eventual D.H.W. recirculation pump must be connected to the mains independently from the GASOGEN G3 2S boiler’s control panel.
The GASOGEN G3 2S boiler’s control panel (and operation cycle) can be reset only after the upper door is reopened for a new restart, or by turning the mains switch 11. OFF and then
ON.
During the summer season we recommend that DHW is requested via the back-up boiler, or with the wood fired boiler, provided the indications given on paragraph 6.11, page 59, are strictly followed.
IR
VE
MKP
VM
M
B
A
AB
Tc
CALDAIA A LEGNA
WOOD FIRED BOILER
KKP
PR
CALDAIA DI SOCCORSO
GASOLIO/GAS
BACK UP BOILER
PRODUTTORE ACQUA
CALDA SANITARIA
DOMESTIC HOT
WATER STORAGE TANK fig. 25
23
24
Gasogen
Instructions for the installer
35 3334
30
29 28 27
5051-
30
20
5051-
Instructions for the installer
Central heating installation with temperature controlled via a motorized mixing valve.
Domestic hot water with a separate coil type storage tank or plate heat exchanger and dedicated loading pump.
Back-up boiler with buffer function when fire wood is finished or for domestic hot water production during summer.
In summer the D.H.W. production can be supplied only by the back up boiler.
The two boilers are hydraulically connected in parallel and the motorized UV diverting valve, will ‘direct’ the GASOGEN
G3 2S boiler in the system circuit or the auxiliary boiler alongside: in this circuit the heating circuit water will not flow through the boiler not operating, thereby reducing the heat losses.
The D.H.W. storage tank will necessarily have to be installed and connected according to the diagram below.
IMPORTANT: During the installation phase make sure the jumpers’ settings in the control panel are as indicated in 5.2.
(
The GASOGEN G3 2S boiler’s control panel automatically switches off the fan and the recirculation pump if the boiler temperature, (once 30 minutes have passed from closing the upper loading door for firing the boiler), does not reach 65°C minimum temperature ).
In this case, or when the fire wood finishes, the back-up boiler will start firing automatically, provided the selector 22 of the panel board is on ( 0 ) and the burner switch 23 is in pos.
II , 30 minutes after the wood fired boiler temperature falls below 60°C.
The door of the wood fired boiler must be kept closed.
The wood fired boiler, in this case, will be excluded and it will be possible to restart it after opening the door in order to load new wood.
If the burner switch 23 is always kept on pos.
0 ), the auxiliary boiler’s burner will be always excluded.
Obviously, to permit operation of the back-up boiler, the control panel must be in the ON position.
The GASOGEN G3 2S boiler’s control panel (and operation cycle) can be reset only after the upper door is reopened for a new restart, or by turning the mains switch 11. OFF and then
ON.
The operation logic of the GASOGEN G3 2S control panel, will switch off the fan and the recirculation pump once the fire wood finishes.
The central heating system pump will operate only after the boiler exceeds the minimum temperature of 65°C.
When the boiler temperature falls below 65°C, the central heating pump will shut down.
The D.H.W. storage pump will operate in priority compared to the central heating pump.
The diverting valve (UV) , will direct the returns towards the boiler ready to operate in that moment, thus reducing the heat losses.
The flow sensor (Tc) must be always placed in the boiler’s bulb holder ( see fig. 17 ).
D.H.W production will have priority via the storage tank’s loading pump (PR), controlled by a changeover thermostat. The D.H.W.
recirculation pump must be connected to the mains independently from the GASOGEN G3 2S boiler’s control panel.
During summer we recommend that D.H.W. is requested via the back-up boiler, or with the wood fired boiler provided the indications given in 6.11, page 59, are strictly followed.
IR
VE
MKP
Tc
VM
M
B
A
AB
CALDAIA A LEGNA
WOOD FIRED BOILER
KKP
B
M
AB
A
UV
PR
CALDAIA DI SOCCORSO
GASOLIO/GAS
BACK UP BOILER
PRODUTTORE ACQUA
CALDA SANITARIA
DOMESTIC HOT
WATER STORAGE TANK fig. 27
25
26
Gasogen
Instructions for the installer
30
20
35 3334
30
29 28 27
5051-
5051-
Instructions for the installer
3.12 - WATER CONNECTIONS AND ELECTRICAL DIAGRAMS WITH OPTIONAL CONTROL
PANEL AND ACCUMULATOR
Dimensioning of the accumulator:
The Standard EN 303-5 says that the minimum heat output for automatically fed boilers should not be higher than 30% of the nominal heat output (Qn); on the contrary, the minimum heat output can be higher than 30% on manually fed boilers. In our case the Standard foresees the installation of an accumulator with a volume V equal to:
V= 15 x Q
n
x T x (Q
min
/Q
n
-0,3)
dove:
V =
Q n
=
T =
Q min
= volume dell'accumulo (litri) potenza utile nominale (kW) autonomia (h) potenza utile minimale (kW) where:
V = accumulator (buffer tank) volume (litres)
Qn = nominal heat output (kW)
T = autonomy (h)
Qmin = minimum heat output (kW)
The boiler’s nominal heat output (Qn) must be equal to the building’s heat losses. Some of the boiler models are equipped with automatic or manual systems for the reduction of the nominal heat output in case of reduced load: the minimum heat output, in which the boiler can work, remaining within the emission levels foreseen by the EN 303-5, is exactly the minimum heat output
Qmin.
The storage tank is not necessary when the requested volume is less than 300 litres.
NOTE: to correctly install the buffer tank it is necessary to use the RECIRCULATION KIT FOR OPERATION WITH THE
ACCUMULATOR which has to be positioned as shown in fig. 20.
27
Gasogen
Instructions for the installer
Foreword!
The system designs shown in the diagrams here below may be customized.
For particular requirements, please contact our After Sales Service.
Simplified water connections diagram between the wood fired boiler and the heat storage tank.
IMPORTANT: During the installation phase make sure the jumpers settings in the control panel are as indicated in chapter 5.2.
The GASOGEN G3 2S boiler’s control panel automatically switches off the fan and the recirculation pump if the boiler temperature, (once 30 minutes have passed from closing the upper loading door for firing the boiler), does not reach 65°C
( minimum temperature ).
The flow sensor (Tc) must be always placed in the boiler’s bulb holder ( see fig. 17).
The return sensor must be always fitted (for the positioning see fig. 20); see installation mode in paragraph 5.5.7.
The GASOGEN G3 2S boiler’s control panel (and operation cycle) can be reset only after the upper door is reopened for a new restart, or by turning the mains switch 11. OFF and then
ON.
The operation logic of the GASOGEN G3 2S control panel, will switch off the fan and the recirculation pump once the fire wood finishes.
The central heating system pump will operate only after the boiler exceeds the minimum temperature of 65°C.
When the boiler temperature falls below 65°C, the central heating pump will shut down.
The thermal inertia of the wood fired boiler will always be discharged on the central heating circuit.
The jumper 71-72 on the PCB must be removed.
The introduction of an accumulator in the system of (see dimensioning on page 27), enables you to obtain a high seasonal efficiency from the GASOGEN G3 2S boiler and a better management of the heating system, as well as a longer life span of the boiler, by reducing the temperature peaks, caused by inconstant drawing-offs from the heating system itself.
Moreover, the heat accumulator, makes you save a lot on your gas bill
This type of installation is particularly effective during the “mid seasons”, since it avoids having to use reduced wood fire loads and, consequently, fire the GASOGEN G3 2S under its minimum output, with the possibility of creating flue condensate, which would damage, in a short time, the wood fired boiler.
28
VE
SVA
Tc
AB
B
RMV
A
Tr
KKP
AB
B
PMV1
A
TT (50-55°C)
MKP
VM
M
B
A
AB
KRF
CALDAIA A LEGNA
WOOD FIRED BOILER
SCAMBIATORE AD
ACCUMULO
ACCUMULATOR (BUFFER TANK)
Legend:
Tc = wood fired boiler flow temperature sensor
Tr = wood fired boiler return temperature
KKP = recirculation pump (if not installed the guarantee is void)
RMV = non-condensing thermostatic valve
KRF = RMV thermostatic valve sensor
PMV1= accumulator thermostatic valve (optional)
VM = zone mixing valve (if not installed the guarantee is void)
MKP = heating system pump
VE = open water tank
IR = heating system circuit
SVA = accumulator thermostatic valve sensor
TKS = microswitch controlling the door opening
TA = room thermostat
TT= accumulator thermostat
IR fig. 29
Instructions for the installer
PE BS RAB SK BV AGW GM MKP KKP TAMB MAXP PE NETZ TKS TR TC
L
1
N L
1
N L
1
L
1
L
1
L
1
L
1
N L
1
N L
1
N L
1
L
1
L
1
N L
1
N L
1
L
1
1 1 1 1 1 1 1 1 1 1 1 1 1 1 1 1
15 16 17 18 19 20 21 22 23 24 25 26 27 28 29 30 31 32 33 34 35 36 37 38 39 40 41 42 43 44 45 46 47 48 49 50 51
1
TKS
C 27 28 29
M
VENTILATORE 1
M
VENTILATORE 2
TT (50-55°C)
1
24 30
C
2
TA
1 C
VE
IR
SVA
Tc
MKP
32
VM
M
B
A
AB
AB
B
RMV
A
Tr
KKP
AB
B
PMV1
A
KRF fig. 30
To permit drainage of the accumulator when the firewood is finished, position the switch 23 of the control panel in pos.
II.
Otherwise, the recovery of the heat stored in the accumulator will be prevented.
In case the room thermostat (TA) does not support the MKP pump load, fit a relay that separates the room thermostat from the load.
29
30
Gasogen
Instructions for the installer
Simplified water connection layout between the wood fired boiler, with an accumulator, and D.H.W. production storage tank.
IMPORTANT: During the installation phase make sure the jumpers settings in the control panel are as indicated in chapter 5.2.
The GASOGEN G3 2S boiler’s control panel automatically switches off the fan and the recirculation pump if the boiler temperature, (once 30 minutes have passed from closing the upper loading door for firing the boiler), does not reach 65°C
( minimum temperature ).
The return sensor must be always fitted (for the positioning see fig. 20); see installation mode in paragraph 5.5.7.
The jumper 71-72 on the PCB must be removed.
The GASOGEN G3 2S boiler’s control panel (and operation cycle) can be reset only after the upper door is reopened for a new restart, or by turning the mains switch 11. OFF and then
ON.
The operation logic of the GASOGEN G3 2S control panel, will switch off the fan and the recirculation pump once the fire wood finishes.
The central heating system pump will operate only after the boiler exceeds the minimum temperature of 65°C.
When the boiler temperature falls below 65°C, the central heating pump will shut down.
The introduction of an accumulator in the heating system (see dimensioning on page 27), enables you to obtain a high seasonal efficiency from the GASOGEN G3 2S boiler and a better management of the heating system, as well as a longer life span of the boiler, by reducing the temperature peaks, caused by inconstant drawing-offs from the heating system itself.
Moreover, the accumulator, makes you save a lot on your gas bill.
This type of installation is particularly effective during the “mid seasons”, since it avoids having to use reduced wood fire loads and, consequently, fire the GASOGEN G3 2S under its minimum output, with the possibility of creating flue condensate, which would damage, in a short time, the wood fired boiler.
The thermal inertia of the wood fired boiler will always be discharged on the central heating circuit.
The flow sensor (Tc) must be always placed in the boiler’s bulb holder ( see fig. 17).
D.H.W. production will have priority and will be controlled via the buffer tank’s loading pump (PR), controlled by a changeover thermostat. The eventual D.H.W. recirculation pump shall be connected to the mains independently from the GASOGEN
G3 2S control panel.
During the summer season we recommend that D.H.W. is produced via the back-up boiler, or with the wood fired boiler, provided the indications given on paragraph 6.11, page 59, are strictly followed.
IR
VE TT (50-55°C)
SVA
Tc
MKP
VM
M
B
A
AB
AB
B
RMV
A
Tr
KKP
AB
B
PMV1
A
PR
KRF
CALDAIA A LEGNA
WOOD FIRED BOILER
ACCUMULATOR
(BUFFER TANK)
Legend:
Tc = wood fired boiler flow temperature sensor
Tr = wood fired boiler return temperature
KKP = recirculation pump (if not installed the guarantee is void)
RMV = non-condensing thermostatic valve
KRF = RMV thermostatic valve sensor
PMV1= accumulator thermostatic valve (optional)
SCAMBIATORE AD
ACCUMULO
VM = zone mixing valve (if not installed the guarantee is void)
PRODUTTORE ACQUA
CALDA SANITARIA
DOMESTIC HOT
WATER STORAGE TANK
MKP = heating system pump
VE = open water tank
IR = heating system circuit
SVA = accumulator thermostatic valve sensor
TKS = microswitch controlling the door opening
TA = room thermostat
TT= accumulator thermostat fig. 31
PE BS RAB SK BV AGW GM MKP
L
1
N L
1
N L
1
L L
1
L
1
L
1
N L
1
N
KKP
L
1
N
TAMB
MAXP
L
1
L
1
L
1
N
PE
NETZ
TKS TR
L
1
N L
1
L
1
TC
1 1 1 1 1 1 1 1 1 1 1 1 1 1 1 1
15 16 17 18 19 20 21 22 23 24 25 26 27 28 29 30 31 32 33 34 35 36 37 38 39 40 41 42 43 44 45 46 47 48 49 50 51
1
TKS
C 27 28 29
M
VENTILATORE 1
M
VENTILATORE 2
Instructions for the installer
VE
SVA
Tc
AB
B
RMV
A
Tr
KKP
AB
B
PMV1
A
TT (50-55°C)
1
24 30
C
2
31
MKP
32
VM
M
B
A
AB
TA
C 1
IR
2
1
C
TB (45÷60°C)
PR
31 32
KRF fig. 32
To allow the accumulator to discharge when the firewood is finished, position the switch 23 on the control panel in pos.
II.
Otherwise, the recovery of the heat stored in the accumulator will be inhibited.
In case the room thermostat (TA) does not support the MKP pump load, fit a relay that separates the room thermostat from the load.
31
Gasogen
Instructions for the installer
Simplified water connection layout between the wood fired boiler, accumulator, and the back- up boiler linked together.
IMPORTANT: During the installation phase make sure the jumper’s settings in the control panel are as indicated in chapter 5.2.
The jumper 71-72 on the PCB must be removed.
The GASOGEN G3 2S boiler’s control panel automatically switches off the fan and the recirculation pump if the boiler temperature, (once 30 minutes have passed from closing the upper loading door for firing the boiler), does not reach 65°C
( minimum temperature ).
The GASOGEN G3 2S boiler’s control panel (and operation cycle) can be reset only after the upper door is reopened for a new restart, or by turning the mains switch 11. OFF and then
ON.
The introduction of an accumulator in the heating system (see dimensioning/sizing on page 27), enables you to obtain a high seasonal efficiency from the GASOGEN G3 2S boiler and a better management of the heating system, as well as a longer life span of the boiler, by reducing the temperature peaks, caused by inconstant drawing-offs from the heating system itself.
Moreover, the accumulator makes you save a lot on your gas bill.
The operation logic of the GASOGEN G3 2S control panel, will switch off the fan and the recirculation pump once the fire wood finishes.
The central heating system pump will operate only after the boiler exceeds the minimum temperature of 65°C.
When the boiler temperature falls below 65°C, the central heating pump will shut down.
This type of installation is particularly effective during the “mid seasons”, since it avoids having to use reduced wood fire loads and, consequently, fire the GASOGEN G3 2S under its minimum output, with the possibility of creating flue condensate, which would damage, in a short time, the wood fired boiler.
The diverting valve (UV) , will direct the system returns towards the boiler ready to operate in that moment, thus reducing the heat losses.
The thermal inertia of the wood fired boiler will always be discharged on the central heating circuit.
The flow sensor (Tc) must be always placed in the boiler’s bulb holder ( see fig. 17).
The accumulator’s temperature , superior to 50-55°C, will prevent the back-up boiler’s burner firing.
The return sensor must be always fitted (for the positioning see fig. 20); see installation mode in paragraph 5.5.7.
32
IR
VE TT (50-55°C)
SVA
Tc
MKP
VM
M
B
A
AB
AB
B
RMV
A
Tr
KKP
AB
B
PMV1
A
UV
M
B
A
AB
KRF
CALDAIA A LEGNA
WOOD FIRED BOILER
SCAMBIATORE AD
ACCUMULO
ACCUMULATOR
(BUFFER TANK)
Key:
Tc = wood fired boiler flow temperature sensor
Tr = wood fired boiler return temperature
KKP = recirculation pump (if not installed the guarantee is void)
RMV = non-condensing thermostatic valve
KRF = RMV thermostatic valve sensor
PMV1= accumulator thermostatic valve (optional)
VM = zone mixing valve (if not installed the guarantee is void)
CALDAIA DI SOCCORSO
GASOLIO/GAS
BACK UP OIL/GAS BOILER
MKP = heating system pump
VE = open water tank
IR = heating system circuit
SVA = accumulator thermostatic valve sensor
TKS = microswitch controlling the door opening
TA = room thermostat
TT= accumulator thermostat fig. 33
Instructions for the installer
24
20
31
30
29 28 27
4849-
5051-
30
5051-
4849-
35 3334
33
34
Gasogen
Instructions for the installer
Simplified water connection layout between the wood fired boiler, accumulator and DHW production, and the back-up boiler linked together (see figs. 35 and 36)
IMPORTANT: During the installation phase make sure the jumpers settings in the control panel are as indicated in chapter 5.2.
The GASOGEN G3 2S boiler’s control panel automatically switches off the fan and the recirculation pump if the boiler temperature, (once 30 minutes have passed from closing the upper loading door for firing the boiler), does not reach 65°C
( minimum temperature ).
The GASOGEN G3 2S boiler’s control panel (and operation cycle) can be reset only after the upper door is reopened for a new restart, or by turning the mains switch 11. OFF and then
ON.
The operation logic of the GASOGEN G3 2S control panel, will switch off the fan and the recirculation pump once the fire wood finishes.
The central heating system pump will operate only after the boiler exceeds the minimum temperature of 65°C.
When the boiler temperature falls below 65°C, the central heating pump will shut down.
The thermal inertia of the wood fired boiler will always be discharged on the central heating circuit.
The flow sensor (Tc) must be always placed in the boiler’s bulb holder ( see fig. 17).
The return sensor must be always fitted (for the positioning see fig. 20); see installation mode in paragraph 5.5.7.
The jumper 71-72 on the PCB must be removed.
The introduction of an accumulator in the system of (see sizing on page 27), enables you to obtain a high seasonal efficiency from the GASOGEN G3 2S boiler and a better management of the heating system, as well as a longer life span of the boiler, by reducing the temperature peaks, caused by inconstant drawing-offs from the heating system itself.
Moreover, the accumulator makes you save a lot on your gas bill.
This type of installation is particularly effective during the “mid seasons”, since it avoids having to use reduced wood fire loads and, consequently, fire the GASOGEN G3 2S under its minimum output, with the possibility of creating flue condensate, which would damage, in a short time, the wood fired boiler.
The diverting valve (UV) , will direct the system returns towards the boiler ready to operate in that moment, thus reducing the heat losses.
The temperature of the accumulator, superior to 50-55°C, will prevent the back-up boiler’s burner firing.
La produzione di a.c.s. sarà gestita in priorità tramite la pompa di carico bollitore (PR) comandata da un termostato in scambio, la pompa di ricircolo dell’impianto sanitario dovrà essere collegata alla rete elettrica indipendentemente dal pannello strumenti della GASOGEN G3 2S.
Durante il periodo estivo si consiglia di produrre l’a.c.s. con la caldaia di soccorso, oppure con la caldaia a legna, seguendo scrupolosamente le indicazioni al cap. 6.11 a pag. 59.
D.H.W. production will have priority and be controlled via the tank’s loading pump (PR), controlled by a changeover thermostat. The eventual D.H.W. recirculation pump shall be connected to the mains independently from the GASOGEN
G3 2S control panel.
During the summer season we recommend that D.H.W. is produced with the back-up boiler, or with the wood fired boiler, provided the indications given on paragraph 6.11, page 59, are strictly followed.
Instructions for the installer
35
Gasogen
Instructions for the installer
36
24
20
35 3334
31
30
29 28 27
4849-
5051-
30
5051-
4849-
35 3334
Instructions for the installer
Simplified water connection layout between the wood fired boiler, accumulator, D.H.W. production and the back- up boiler linked together, in combination with a solar energy system for loading the D.H.W. storage tank and an eventual integration of the accumulator’s temperature (see fig. 37 & 38).
IMPORTANT: During the installation phase make sure the jumpers settings in the control panel are as indicated in chapter 5.2.
The GASOGEN G3 2S boiler’s control panel automatically switches off the fan and the recirculation pump if the boiler temperature, (once 30 minutes have passed from closing the upper loading door for firing the boiler), does not reach 65°C
( minimum temperature ).
the heating system, as well as a longer life span of the boiler, by reducing the temperature peaks, caused by inconstant drawing-offs from the heating system itself.
Moreover, the accumulator, makes you save a lot on your gas bill.
The GASOGEN G3 2S boiler’s control panel (and operation cycle) can be reset only after the upper door is reopened for a new restart, or by turning the mains switch 11. OFF and then
ON.
This type of installation is particularly effective during the “mid seasons”, since it avoids having to use reduced wood fire loads and, consequently, fire the GASOGEN G3 2S under its minimum output, with the possibility of creating flue condensate, which would damage, in a short time, the wood fired boiler.
The operation logic of the GASOGEN G3 2S control panel, will switch off the fan and the recirculation pump once the fire wood finishes.
The central heating system pump will operate only after the boiler exceeds the minimum temperature of 65°C.
When the boiler temperature falls below 65°C, the central heating pump will shut down.
The diverting valve (UV) heat losses.
, will direct the system returns towards the boiler ready to operate in that moment, thus reducing the
The accumulator’s temperature, superior to 50-55°C, will prevent the back-up boiler’s burner firing.
The thermal inertia of the wood fired boiler will always be discharged on the central heating circuit.
The flow sensor (Tc) bulb holder ( must be always placed in the boiler’s see fig. 17).
The return sensor must be always fitted (for the positioning see fig. 20); see installation mode in paragraph 5.5.7.
D.H.W. production will have priority and be controlled via the storage tank loading pump (PR), controlled by a changeover thermostat. The eventual D.H.W. recirculation pump shall be connected to the mains independently from the GASOGEN
G3 2S control panel.
The jumper 71-72 on the PCB must be removed.
The introduction of an accumulator in the heating system (see sizing on page 27), enables you to obtain a high seasonal efficiency from the GASOGEN G3 2S boiler and a better management of
During the summer season we recommend that D.H.W. is produced via the back-up boiler, or with the wood fired boiler, provided the indications given on paragraph 6.11, page 59, are strictly followed.
During the summer you can reduce energy consumption and save on your fuel bill by using a solar or photovoltaic panel, which allows you to load the D.H.W. storage tank and, in case of an over production of energy, to load the accumulator totally or partially, acting therefore as a buffer.
37
38
Gasogen
Instructions for the installer
Instructions for the installer
24
20
35 3334
31
30
29 28 27
4849-
5051-
5051-
4849-
35 3334
39
40
Gasogen
Instructions for the installer
3.13 - FLUE OUTLET CONNECTION
The flue system must be installed in accordance with the local regulation and national codes of practice.
The chimney is of fundamental importance for correct boiler operation: it is therefore necessary that the chimney is impermeable and properly insulated.
Old or new chimneys, built without respecting the specific requirements can be recovered by “tubing” the chimney itself.
It will be necessary to introduce a metallic pipe inside the existing chimney and insulate the space between the metallic pipe and the chimney.
Chimneys made of prefabricated blocks must have perfectly sealed joints to avoid that flue condensate leave the walls dirty due to permeation.
The entrance to the chimney should be at an angle of 45°.
At the base of the chimney a flue inspection opening has to be made.
It is advisable to insulate the boiler pipe connection to the chimney in order to reduce the heat losses and noise.
We recommend using only flue outlets suitable to the type of fuel used.
Damages caused by installation errors and for non-observance of the instructions given by the same manufacturer will invalidate all the supplier’s contractual or extra contractual responsibilities.
If the boiler has to be replaced ALWAYS replace the flue outlet system
The flue outlet has to meet the latest regulations in force.
4
5
6
7
8
5
6
7
8
2
1
3 fig. 39
1. Boiler
2. Flue outlet connection
3. Ashes collecting chamber
4. Chimney
5. External flue lining
6. Prefabricated blocks
7. Insulation
8. Flue outlet
Instructions for the installer
3.14 - FILLING THE SYSTEM
Warning!
Do not mix the CH system’s water with
!
unsuitable anti-freeze products (example: antifreeze solutions for motor vehicles) or use wrong concentrations of anti-corrosion solutions
This could cause damage to the washers and could cause noise during normal boiler operation.
Automatic Heating refuses all liability for injury to persons, animals or damage to property deriving from not having respected the above mentioned recommendations.
equipped with a closed expansion vessel - consult local regulations if this is allowed) ); for installations equipped with an open expansion vessel, the reinstatement is carried out automatically via the same expansion vessel;
After completing all the system’s service connections the circuits may be filled by carefully following out the following phases:
open the radiator’s air vents and check that the automatic air vent in the boiler is working properly.
gradually open the appropriate filling cock and check that the automatic air vents fitted onto the system are working properly.
close the radiator’s air vents as soon as water begins to flow out.
using the pressure gauge check that the pressure reaches the value of 1 bar (this is valid only for installations equipped with a closed expansion vessel - consult local regulations if this is allowed); for installations equipped with an open expansion vessel, the reinstatement is carr ied out automatically via the same expansion vessel;
close the system’s filling cock and then bleed off the air once again through the radiator’s air vents.
check all the connections for soundness.
after having fired the boiler for the first time and the system has reached the correct temperature, arrest the pump and repeat the air bleeding operations.
let the system cool down and, if necessary, re-establish the water pressure to 1 bar (this is valid only for installations fig. 40
NOTE!
In closed circuit heating systems, where allowed, the water pressure in the heating system - in cold conditions – must not be lower than one bar; if this value is lower use the filling cock on the boiler to adjust the pressure.
This operation must be carried out when the system is cold.
Use the pressure gauge, installed near the filling cock, to read the system’s pressure.
NOTE!
If the boiler has not been fired for a long period the pump could be jammed.
Before switching on the main switch, it is important to carry out the following un-jamming operation:
- remove the pump vent plug positioned in the centre of the pump
- using a screwdriver, rotate the shaft in a clockwise direction.
Once this operation has been concluded, screw back the pump vent plug and check that there have been no water leaks.
WARNING!
After removing the pump vent plug some slight water leakage could occur. Before replacing the front panel dry all the wet surfaces.
41
42
Gasogen
Instructions for the installer
4 - 5 ELECTRICAL CONNECTIONS
General Warnings
The appliance’s electrical safety is guaranteed only when the same appliance has been correctly earthed in compliance with the regulations in force. The gas and water feeding pipes and the CH system pipes cannot be used as ground plates.
Note: It is necessary to fit a double pole switch on the electrical supply line, having a 3 mm contact separation in both poles, in an easy accessible position so as to ensure quick and safe servicing.
Ensure that the above safety electrical requirements have been implemented; in case of doubt, ask for a professionally qualified engineer to check the appliance’s electrical system.
Automatic Heating refuses responsibility for any damages arising from failure to earth the boiler correctly.
It is necessary that a qualified technician verifies that the electrical system is adequate to the appliance’s maximum absorbed power, indicated on the data plate, checking in particular that the section of the system’s cables is suitable to the appliance’s maximum absorbed power.
The replacement of the supply cable has to be carried out by a qualified authorized engineer, using only original spare parts.
The non-observance of the above could compromise the appliance’s safety.
WARNING!
- Before opening the control panel, position the switch (11) in the “0”pos.
- Do not connect the control panel to loads that together absorb more than 4A!
The use of adaptors, multiple sockets and/or extension cords
For the appliance’s general electrical supply is strictly forbidden.
The use of any power supplied equipment implies the observance of he following fundamental rules:
Approvals
The Automatic Heating control panels code 36748 (standard) and code 23557 (electronic, optional) have according to the EN 60335-1 Standard.
been CE approved,
Data plate and factory number
The control panel’s identification data plate is glued on the base.
Do not touch the appliance with any wet part of your body and/or barefooted;
Do not pull the supply cables
Do not expose the boiler to sunlight, rain, etc., unless it is explicitly foreseen;
Do not permit children or inexpert people to use the appliance
Use
This control panel must be used for operation of a boiler destined to heating water to a temperature that does not exceed boiling point when installed.
Connection to mains electrical supply 230V
The general electric connections for the standard control panel board are shown in page 46 and for the optional control panel board in the section “ Loads and Sensors connection”
(paragraph 5.3, page 48).
A mains supply of 230 V – 50 Hz is required. The wiring to the boiler must be in accordance with the current CEI regulations.
DANGER!
The electrical connections must be carried out only by a qualified engineer.
Before carrying out the connections or any other operation on the electrical parts, always switch off and disconnect the electricity supply and ensure yourself that it cannot be accidentally turned on.
Instructions for the installer
4.1 - STANDARD CONTROL PANEL
The standard control panel (code 36748) operates in a semi-automatic way and is supplied in a cardboard with the following standard items:
- Microswitch which has to be fitted to the mechanism controlling the bypass rod (TKS) as shown in fig. 13 page 17.
- A 3 pole cable for the fan’s electrical connection (2 fans for the models G3-65 and G3-80)
The connection of the thermostat bulbs to the bulb holders must be carried out as shown in fig. 17, on page 19.
The connection of the loads to the control panel (C.H. pump, recirculation pump, fan, etc.) must be carried out according to the general wiring diagram in fig. 42 and/or according to the practical wiring diagrams on page 21 and 22.
For installation of the optional control panel (code 23557), on the boiler, with or without the possible accumulator, recommended by the EN 303-5, refer to paragraph 3.11 on page 23 and/or 3.12, on page 27.
Functional description
Once the main switch pos. 11 and the pump switch pos. 13 are in the ON position, it is possible to light the boiler.
Once the boiler has been fired, close the loading door; in this way the TKS microswitch, operated directly by the rod closing t he smokes bypass to the chimney, will reset the temporized relay that “will begin to count.”
The factory adjusted time of the temporized relay is of 30 minutes, which can be extended to an additional 30 minutes.
The Tsc thermostat (minimum thermostat) is not satisfied at boiler start-up, because adjusted at 65°C, actually prevents the
C.H. pump running, until this temperature is reached.
If the boiler does not reach the 65°C in the set time, the temporized relay stops the fan.
This can be due to the boiler not firing or due to an insufficient load of the firewood.
To avoid this inconvenience it is possible to increase the temporized relay’s intervention time (this operation has to be done only by trained personnel) or more firewood has to be loaded.
If the boiler fires in a regular manner, when the boiler reaches 65°C the C.H. pump is activated.
The working thermostat, pos. 32, acting on the fan(s) operation mode, will make the boiler fire in an “automatic” way.
The same thermostat will stop the fan when the preset working temperature has been reached.
In case of boiler overheating (temperature higher than 90°C), and in case of the delayed intervention of the heat relief valve
(remember that in solid fuel boilers, due to high thermal inertia, the installation of this valve is compulsory), the maximum thermostat Tmax , bypassing the microswitch TKS , the C.H. pump’s thermostatic control Tsc and the pump switch Ipi , will automatically allow the boiler thermal inertia to discharge into the central heating circuit. This situation could cause an und esired heating of the radiators, even if the ambient temperature does not request it.
On the fan’s electrical supply there is a safety thermostat Ts that will switch OFF the fan in case
A temperature of 100°C is reached (safety limit temperature).
It is possible to reset this thermostat by unscrewing the cap in pos. 31 and pressing the button underneath.
A room thermostat can be connected on the terminals 19 and 20 after having removed the jumper that links them.
The recirculation pump Pr has to be connected to the terminals 10 and 11.
43
Gasogen
Instructions for the installer
11 Mains switch
12 Fan switch
13 C.H.pump switch
31 Safety overheat thermostat
32 Working thermostat
41 Main fuse (4A)
42 Boiler thermometre fig. 41
44
LEGEND WIRING DIAGRAM
Ph Phase (230V ~ 50Hz)
N Neutral
F1 General fuse (max 4A)
IG Mains switch with warning light
Ipi C .H. pump switch
Iv Fan switch
LL Power ON lamp
Pi C.H.system pump
Pr Recirculation pump fig. 42
Rt Temporized relay
R1 Relay
Te Working thermostat (75°C÷85°C)
TKS By-pass shaft microswitch
Tmax Limit thermostat (90°C
Ts Safety overheat thermostat (100°C)
Tsc Minimum thermostat for wood fired boiler (65°C)
V Fan (s)
34 ... reference to front view facia panel
Instructions for the installer
5.1 - OPTIONAL CONTROL PANEL
The optional control panel (code 23557) is supplied in a cardboard box with the following standard components:
- Microswitch to be fitted integral with the opening mechanism of the loading door (TKS) (see page 17).
- Flow temperature sensor (Tc): to be fitted on the boiler’s flow connection
- Boiler fan supply cable, with 3 pole plug.
The return temperature sensor (Tr): which must be fitted on the return of the central heating system, if this is equipped with a heat storage tank , hydraulically connected in parallel to the wood fired boiler (see pages 28, 30, 32, 35 and 38), is not supplied.
The connection of the panel to the loads (C.H. pump, recirculation pump, fan, etc.) and to the sensors, has to be carried out according to the diagram shown in paragraph 5.3, page 48.
For instructions on how to install the control panel on the boiler equipped with the accumulator recommended by the
Standard EN 303-5, refer to paragraph 5.5.7, on page 52.
Functional description:
Control panel for boiler with a pushing fan : ON/OFF fan operation, with the possibility of operating with a gas/oil fired back up boiler, without part load function, with chimney sweeper switch (pos. 18 - on the facia panel), with built-in control of the he at storage tank load (see volume dimensioning of the heat storage tank volume according to EN 303-5 on page 27).
When opening the control panel, the wiring is as shown in the diagram in paragraph 5.6.
11 Mains switch
12 Fan switch
13 C.H. pump switch
18 Test push button (chimney sweeper)
22 Changeover switch (0) =wood (I)= oil/gas
23 Back up boiler burner switch
31 Safety thermostat
32 Boiler temperature range (75°÷85°C)
41 Fuse 4 A
42 Boiler thermometer
— Led indicating acoustic visual alarm fig. 43
45
46
Gasogen
Instructions for the installer
Inside the control panel there are the terminals for the following connections (see wiring diagrams on pages 48 and 53):
- Mains 230V - 50 Hz (Hertz)
- Recirculation pump (KKP) (pre-arrangement)
- Heat discharge pump (MAXP) (pre-arrangement)
- Flue thermostat (AGW) (pre-arrangement)
- Potential free contact for the auxiliary boiler’s burner (BV) (pre-arrangement)
- Back up boiler’s burner electrical supply (SK) (pre-arrangement)
- Heating controller’s electrical supply RAB) (pre-arrangement)
- Flue outlet fire-proof thermostat (BS) (pre-arrangement)
- Fan (GM)
- Central heating system pump (MKP) (pre-arrangement)
- Room thermostat (TAMB) (pre-arrangement)
- Loading door microswitch (TKS)
- Flow temperature sensor (Tc): to be fitted on the boiler flow connection
- Return temperature sensor (Tr) (see paragraph 5.5.7)
- Overheating fan protection thermostat
5.2 - FUNCTIONAL WIRING DIAGRAM (Flow-Chart)
IThe control panel code 23557 is controlled by the mother board equipped with a microprocessor (Motorola
MC68HC908JL3).
The panel’s logical control is described in paragraph 5.4.2 and in a Flow-Chart in the next page that shows its main functions.
The denominations of the single functions are the same in both the paragraph 5.4.2 and in the Flow-Chart.
In Step 0 the “IL” is displayed: it represents the jumper’s position, as described on page 47 (pos. 54 - 55).
This jumper controls the fan’s ignition when the loading door is opened.
If the fan works by pushing, as in the case of the GASOGEN G3 2S boiler, make sure that the jumper on the PINS
54 - 55 is OFF (IL=1).
The status of the logical function, which allows the transfer from the wood fired to the oil/gas fired one, is indicated in th e Flow-
Chart with “LG” and associated to the switch in pos. 22 on the facia panel:
Position “0” = LG 1
Position “1” = LG 0
In the Steps 4 and 6 “SPARE” is displayed: it represents the Jumper’s position, as described on page 47 (pos. 56 - 57, fig. 45) .
This jumper controls the auxiliary boiler’s ignition.
Make sure this jumper is ON.
In the Flow-Chart there is also the table of the constants used in the built-in program of the mother board’s microprocessor wh ich identify the working thresholds in comparison to the boiler flow temperature “Tc” and the C.H. return temperature “Tr”:
TSC-LO : Lowest threshold of the wood fired boiler’s minimum temperature.
TSC-HI : Highest threshold of the wood fired boiler’s minimum temperature.
TMAX-LO : Lowest threshold of the maximum temperature allowed for the wood and oil/gas fired boiler
TMAX-HI: Highest threshold of the maximum temperature allowed for wood and oil/gas fired boiler
DELTA: Temperature difference between boiler flow and return (only for loading of the heat storage tank combined with the wood fired boiler).
KP: Hysteresis on the set boiler temperature (Timp)
TMIN-LO : Lowest threshold of the auxiliary boiler’s minimum temperature.
TMIN-HI : Highest threshold of the auxiliary boiler’s minimum temperature.
FLOW -Chart
Instructions for the installer fig. 44
47
48
Gasogen
Instructions for the installer
5.3 - LOADS AND SENSORS CONNECTION DIAGRAM
15 = Earthing (PE)
16 = Earthing (PE)
17 = Fire proof thermostat L1 (BS)
18 = Fire proof thermostat N (BS)
19 = Outer compensator supply L1 (Rab)
20 = Outer compensator supply N (Rab)
21 = Electrical supply L1 (SK)
22 = Electrical supply N (SK)
23 = Burner tension-free contact L1 (BV)
24 = Burner tension-free contact L1 (BV)
25 = Flue thermostat L1 (AGW)
26 = Flue thermostat L1 (AGW)
27 = Fan motor L1 (GM)
28 = Fan motor N (GM)
29 = Fan motor (GM)
30 = C.H. pump L1 (MKP)
31 = C.H. Pump N (MKP)
32 = C.H. Pump ( ) (MKP)
33 = Recirculation pump L1 (KKP)
34 = Recirculation pump N (KKP)
35 = Recirculation pump ( ) (KKP)
36 = Room thermostat L1 (TAMB)
37 = Room thermostat L1 (TAMB)
38 = Heat discharge pump L1 (MAXP)
39 = Heat discharge pump N (MAXP)
40 = Heat discharge pump ( ) (MAXP)
41 = Earthing (PE)
42 = Earthing (PE)
43 = Phase L1
44 = Neutral
45 = Earthing (PE)
46 = Limit switch (TKS)
47 = Limit switch (TKS)
48 = C.H. return temperature sensor (Tr)
49 = C.H. return temperature sensor (Tr)
50 = C.H. flow temperature sensor (Tc)
51 = C.H. flow temperature sensor (Tc) fig.45
Instructions for the installer
5.4 - FUNCTIONAL DESCRIPTION OF OPTIONAL CONTROL PANEL
(see flow-chart on page 47)
5.4.1 - IGNITION (see Step 0, Step 1 page 47)
The main switch (pos. 11), the C.H. pump switch (pos. 13) and the fan switch (pos. 12) are all positioned differently to “0”; t he switch (pos. 11) is illuminated and the control panel board is ON.
The upper loading door is open: the opening of the door causes the fan to switch OFF (Step 1).
The boiler temperature is below the minimum set temperature of about 65°C.
If the installation is equipped with the accumulator foreseen by the Standard EN 303-5, the return thermostatic valve is closed
(see diagrams on pages 28, 30, 32, 35 and 38).
The opening of the loading door activates a control timer (Timer 1) via the microswitch (TKS): the default value of the Timer 1 is
30 minutes and can be increased during the installation stage of an additional 30 minutes.
If the boiler does not reach the minimum temperature (about 65°C) within the foreseen time Timer 1)), the fan and the recircula tion pump will be switched OFF; in the meantime the back-up boiler’s burner will be activated automatically if the burner switch (po s.
23) is in position “II”
The opening and the closing of the loading door will reset the Timer 1, energizing the fan and the recirculation pump again.
On the contrary, if the minimum set temperature (higher than 65°C) is reached within the control time (Timer 1), the logical control will position itself into “normal operation” (Step 3).
5.4.2 - NORMAL BOILER OPERATION (see Step 3, page 47)
The microprocessor’s logical control determines the difference between the boiler temperature (Tc) and the C.H. return temperature
(Tr) and therefore the two following situations can occur:
A - If the difference between the boiler flow temperature (Tc) and return temperature (Tr) is inferior to 6 °C (factory settin g) the time of Timer 2 is increased; if this one reaches 10 minutes, then the recirculation pump (KKP) and the fan GM are switched OFF.
B - If the difference between the boiler flow temperature (Tc) and return temperature (Tr) is higher than 6 °C (factory setting ) the
Timer 2 is reset to zero and the recirculation pump (KKP) is switched ON.
The above points A and B make up the heat storage tank’s loading strategy, if present (see on page 27).
In general, the opening and closing of the wood loading door, resets the logical control, activating the fan and the recirculat ion pump again.
In any case the ON and OFF fan function is mainly controlled by the confrontation of the boiler flow temperature (Tc) and the temperature set by the user via the knob pos. 32.
5.4.3 - NO WOOD (see Step 4, page 47)
The opening of the loading door activates the control timer (Timer 1) via the microswitch (TKS): the default value of the Timer 1 is 30 minutes and can be increased by an additional 30 minutes during the installation stage.
If the boiler does not reach the minimum temperature (about 65°C) within the foreseen time (Timer 1), due to no wood, the fan and the recirculation pump will be switched OFF; in the mean time the back up boiler’s burner, if the burner switch (pos. 23) i s in position “II”, will be automatically activated. The opening and the closing of the loading door will reset the Timer 1, switching ON again the fan and the recirculation pump.
On the contrary, if the minimum set temperature (higher than 65°C) is reached within the control time (Timer 1), the logical control will return to “normal boiler operation” (Step 3).
49
50
Gasogen
Instructions for the installer
5.4.4 - OIL/GAS BOILER OPERATION (see Step 4, Step 6, page 47)
In installations with a back up oil/gas boiler (hydraulically connected in parallel), the burner is switched ON via the potenti al free contact BV, if this has been integrated in the burner’s electrical wiring by the installer; in paragraph 3.11 an auxiliary circ uit diagram is proposed for controlling: - the C.H. pump, controlled by the back-up boiler’s control panel, - the diverting valve, which allows the water flow to be diverted from the wood fired boiler to the auxiliary one – the back up boiler’s (oil/gas) burner.
In case there is no wood, the back-up boiler is automatically fired according to the steps seen in the previous paragraph.
On the contrary, if the user needs to operate the back- up boiler without waiting the time foreseen by the Timer 1, he only nee ds to press the keys 22 and 23 respectively in position “I” and “II”.
5.4.5 - DOMESTIC HOT WATER PRODUCTION
Summer mode for only D.H.W, production is not advisable and could, if not controlled properly, cause the intervention of the safety overheat thermostat (see paragraph 6.11).
In case the user needs to produce D.H.W, to create these installation systems it is necessary to refer to the principle scheme s shown on pages 30, 35 and 38.
When designing the system for installing the wood fired boiler and the back up boiler, the engineer has to take into considerat ion the increase in output necessary for D.H.W. production; normally, in fact, D.H.W. production has priority over the request for heat and therefore the sizing of the D.H.W. storage tank volume has to be customized to the user’s needs and at the same time it has to be calculated when dimensioning the boiler in order to avoid long waiting times for the changeover from D.H.W. mode to CH mode.
As far as D.H.W. production is concerned, the electrical connection to the control panel is described in the WATER AND
ELECTRICAL CONNECTION DIAGRAMS in paragraphs 3.11 and 3.12.
Instructions for the installer
5.5 - SPECIAL FUNCTIONS
5.5.1 - OVERHEATING (see Step 5, on page 47)
The wood fired boiler with manual loading is subject to the thermal inertia phenomena which can cause transitional overheating periods which have to be contained as much as possible before the intervention of the manual reset safety thermostat.
For this purpose the panel, code 23577, is predisposed for the connection and control of a heat discharge pump via the terminals MAXP. If the boiler temperature (Tc), in spite of the fan turning off, exceeds the value of 89°C, the heat discharge pump is activated and remains running until this temperature falls below 86°C.
If the installation is not equipped with a heat discharge pump, the jumper between the MAXP and MKP terminals(see paragraph
5.3 - on page 48) must not be removed; this jumper has in fact the purpose of feeding the C.H. pump even if the room thermostat
(TAMB) is open; this could involve an unrequested heating of the radiators even if the ambient conditions apparently do not require it.
If the installation is equipped with an accumulator (see paragraph 3.12) the thermal inertia will have to be discharged through the recirculation pump KKP and therefore it is necessary that the above mentioned jumper is placed between the MAXP and KKP phase.
Obviously in order to allow any thermal discharge via the heating system, it is necessary that there are no closed gate valves between the boiler’s flow and return connections.
5.5.2 - COMBUSTION GAS TEMPERATURE CONTROL (only in case of connection to a single chimney)
For this possibility, check local requirements and rules in force.
In case of flue evacuation in a chimney serving the wood fired boiler and a back-up oil fired boiler (a gas fired boiler needs its own chimney), it is possible to fit a flue thermostat, in the part of the chimney serving only the wood fired boiler, connected to the
AGW terminals, in order to stop the burner firing in case the flue temperature of the wood fired boiler, is over 100°C.
0 °C
10 °C
15 °C
20 °C
25 °C
30 °C
35 °C
40 °C
45 °C
5.5.3 - FAN OVERHEATING PROTECTION SYSTEM
In this range of boilers (GASOGEN G3 2S) this system is not activated.
5.5.4 – TEMPERATURE SENSOR FAILURE ALARM (note for After Sales Service)
If the flow sensor (Tc) malfunctions or is not correctly connected to the relative terminals, the microprocessor’s logical co ntrol activates the acoustic-visual alarm, made up of a LED and a BUZZER, in a continuous mode: if the problem persists, consult the
After Sales Service.
The installation of a heat storage tank (see paragraph 3.12) foresees the connection of the return sensor (Tr) to the dedicated terminals: to gain access to the previously described alarm service for the Tr sensor, it is necessary that the After Sales Ser vice, during the installation stage, removes the jumper placed between the pins 71 and 72; if not, the alarm for the Tr sensor malfun ction is inhibited: the manufacturer declines any responsibility.
If the above indicated malfunctions occur, the recirculation pump (KKP), the C.H. pump (MKP) and the heat discharge pump
(MAXP) will be activated, the fan will be turned OFF and the automatic or manual transition to the auxiliary boiler will be prevented.
The temperature sensor is a NTC resistor. To check that it is in good working condition keep the following values in consideration:
MEASURED TEMPERATURE
RESISTANCE
MEASURED TEMPERATURE
RESISTANCE
33242 Ohm
19947 Ohm
15659 Ohm
12394 Ohm
9888 Ohm
7947 Ohm
6433 Ohm
5242 Ohm
4300 Ohm
50 °C
55 °C
60 °C
65 °C
70 °C
75 °C
80 °C
85 °C
90 °C
3548 Ohm
2945 Ohm
2459 Ohm
2063 Ohm
1740 Ohm
1475 Ohm
1256 Ohm
1075 Ohm
923 Ohm
51
52
Gasogen
Instructions for the installer
5.5.5 - FIRE PROOF THERMOSTAT
A fire proof thermostat can be connected to the control panel in order to switch off the fan, connected to the terminals BS so as to arrest combustion in the wood fired boiler.
5.5.6 - WAITING TIME (After Sales Service function)
The default waiting time (Timer 1) is equal to 30 minutes; to make commissioning easy at the boiler installation stage, the mot her board is equipped with a logical function that allows the waiting time to be reduced to 3 minutes: the installer to gain access to this function has to position the jumper, supplied with the boiler, between the pins 69 - 70.
WARNING : The installer, once the commissioning is finished, must remove the a.m. jumper from the terminals 69 - 70, in order to restore normal operation: the manufacturer declines any responsibility and/or additional costs connected if normal boiler operation is not restored.
5.5.7 - RETURN FLOW SENSOR (Tr) INSTALLATION
The installation of the accumulator foresees the connection of the return sensor (Tr) to the dedicated terminals (see paragraph
3.12, page 27): it is necessary that during the installation stage the After Sales Service removes the jumper placed on the pins 71 and 72. Otherwise, the Tr sensor failure alarm and the control of the KKP pump for loading the accumulator are inhibite d: the manufacturer declines any responsibility if this occurs.
5.6 - WIRING DIAGRAM OPTIONAL CONTROL PANEL
Instructions for the installer
Control panel – rear view
Mother board
LEGEND :
1÷4 Mains supply 230 V - 50 Hz
5, 6 C.H. pump
7, 8 Fuse 4A
9,10 Fan
11, 12 Safety overheat thermostat
13, 14 Back-up boiler burner
43, 45 Mains supply
58, 59 Changeover switch wood fired / auxiliary boiler
60, 61 Wood fired boiler test push button (Chimney sweeper)
REL 1 Fan (GM)
REL 2 Burner (BV)
REL 3 Recirculation pump (KKP)
REL 4 C.H. system pump (MKP)
REL 5 Heat discharge pump (MAXP)
62, 63 Acoustic-visual alarm thermostat (fan overheating)
64, 65 Acoustic-visual LED alarm (fan overheating)
66÷68 Wood fired boiler flow temperature adjustment range (75÷85 °C) fig. 46
53
54
Gasogen
Instructions for the installer
6 BOILER START-UP
6.1 - INITIAL LIGHTING
Preliminary checks
The first ignition must be carried out by a qualified technician. Failure to do so could cause injury to persons, animals or damage to property. Automatic Heating shall not be
Before firing the boiler check that:
the boiler installation has been carried out in accordance with the specific Standards and regulations in force relating to the gas part and to the electrical part;
the air supply and the discharge of the products of combustion are carried out in the correct way in accordance to the specific Standards and regulations in force;
the boiler is fitted with all the safety and control devices prescribed by the regulations in force;
the electrical supply must be 230 V - 50 Hz;
the C.H. system has been filled with water;
any gate valves of the CH system are open;
the gas for the back-up boiler corresponds to the one which the boiler has been calibrated for: otherwise convert the boiler to use the available gas; this operation must be carried out by a qualified technician in compliance to the regulations in force;
the gas supply cock for the back-up boiler, if present, is open;
there are no gas leaks;
the external mains supply switch is on;
the system’s safety valve on the boiler is not blocked and that it is connected to the sewage system;
there are no water leaks;
all the necessary ventilation conditions and minimum clearance distances are guaranteed for subsequent servicing.
Inform the user of the importance of the air vents and of the flue outlet system, stressing the fact that absolutely no modification can be made.
Inform the user about controlling the system water pressure and how to restore it to the correct value.
Explain and demonstrate to the user the correct function and adjustment of the temperature, thermostats and radiators for the economic use of the system.
Remind the user that a comprehensive service and the measurement of the combustion efficiency should be carried out regularly (as requested by the regulations in force).
If the appliance is sold or transferred to another owner or if the present user moves home and leaves the appliance installed, ensure yourself that the manual always follows the appliance so that it can be consulted by the new owner and/or installer.
LIGHTING AND SHUTTING DOWN PROCEDURES
For lighting and shutting down the boiler refer to the “USER
INSTRUCTIONS MANUAL”
Information to be passed on to the user:
The user must be instructed on the use and operation of the boiler and the hearing system, in particular:
Hand the user the : “USERS INSTRUCTION MANUAL”, as well as all the other literature relative to the appliance, and placed in the envelope contained in the packaging.
The user must keep this literature for any future reference.
Instructions for the installer
6.2 - FIRE WOOD
Wood is formed mainly by cellulose and lignite. It contains other substances, such as resin
(fir tree - pine), tannin (oak - chestnut) and, obviously, a large quantity of water.
Good quality woods are oak, ash, beech, maple and fruit trees, except cherry; medium quality wood is: chestnut and birch; sufficient quality wood: lime tree, poplar and willow. Resinous trees are, normally, medium quality fuels.
Wood is therefore an extremely heterogeneous fuel, due to different essences (beech, oak, fruit, resinous), different moisture content, and due to different shapes and dimensions.
Boiler operation will of course be certainly effected by all these factors. Especially by the log dimensions, the moisture content and the way wood is loaded in the boiler.
6.3 - WOOD MOISTURE
The calorific value of the different types of wood depends on their moisture content, as shown on the table. Boiler output and autonomy will diminish as the moisture increases. In the table a reduction factor is indicated according to the moisture content of the wood used. The heat output of the
GASOGEN G3 2S boiler is calculated for wood with a 15% moisture content.
As an example wood which has been dried for 2 years air in a protected area has a 25% moisture content.
Correction factors for wood moisture content
% moisture
15
20
25
30
35
40
45
50
Calorific value kcal/kg
3.490
3.250
3.010
2.780
2.540
2.300
2.060
1.820
Correction factor
1
0,93
0,86
0,79
0,72
0,65
0,59
0,52
Example:
Moisture content of wood used = 30%
Heat output = nominal heat output x 0,79
6.4 - FIRE WOOD DIMENSIONS
The dimensions, together with the moisture content, contribute to determine the boiler’s output
Small pieces (with a length, however, conforming to indications hereby indicated) are more easily inflammable and therefore have the tendency to increase the boiler’s output and therefore to reduce its autonomy. Moreover, they fall with greater facility, in the lower chamber, reducing the risk of the formation of “bridges”. The so-called “bridge” is an empty space in the firebox, where unburnt wood logs remain . In this case the bed of embers is not fed with continuity and the refractory burner’s slot is uncovered. In these conditions, preferential air passages are created with a very small flame due to an excess of air.
6.5 – INITIAL LIGHTING CHECKS
GENERAL CONTROLS
During the first ignition check that the C.H. system has been properly filled and properly purged, that the safety heat exchanger is connected to the water mains via the heat safety discharge valve
(fig. 10, page 16 and fig. 18 page 19) – that the chimney has a sufficient draught, that the electrical connection has been made correctly (paragraph
4 &5) and that the recirculation and boiler pumps are not blocked.
Furthermore check that the stainless steel grate and the fire bars are properly positioned.
THE BY-PASS
The by-pass is a direct passage between the fire wood storage and the chimney. It is normally closed by a mobile shutter. The by-pass is automatically opened or closed via a pushing rod when the loading door is opened.
In this way the smoke accumulated in the firebox is aspirated and sent to the chimney directly.
The bypass, in conclusion, allows the smoke to be discharged at the chimney without escaping from the loading door when loading the wood or during lighting.
Any way it is essential to open the loading door slowly and, as well, to rotate the antismoke flap (pos. 4, fig. 2) gradually so that the smoke is effectively aspirated.
BY-PASS CONTROL
During the installation stage and, in any case, before starting to use the boiler, check that the by-pass is correctly closed and the correct position of the microswitch, which controls the opening of the door. In this way when the door is closed the fan has to start rotating; when the door starts to open the fan has to be OFF, otherwise all the smokes comes out.
55
56
Gasogen
Instructions for the installer
6.6 - START-UP
IGNITION
Make sure all the controls listed in 6.5 have been carried out.
For the GASOGEN G3 25 2S, GASOGEN G3 40 2S and
GASOGEN G3 50 2S models:
Screw down completely the primary air’s ( P ) adjustment screw
Screw down completely the secondary air’s ( S ) adjustment screws until you “detect” the resistance of the spring pushing the closing discs.
Now, “ unscrew ” about 10 turns the primary
Air’s ( P ) screw and 4 turns the secondary air’s ( S ) screws.
For the GASOGEN G3 65 2S and GASOGEN G3 80 2S models:
The initial position of the ring nuts (pos. 1, fig. 48) which control the opening or closing of the primary and secondary air, has to be about in the middle of the threaded rod.
The primary air (P) is blown through the upper fan, whilst the secondary air (S) is blown through the lower one.
At this point, “screw” or “unscrew” the ring nuts (pos. 1, fig.
48) on the threaded rod until you have an optimal air regulation, by observing the colour of the flame in the combustion chamber; keep in mind that by rotating the ring nuts in a clockwise direction (that is upwards) you will have an increase of the emission of the air (primary or secondary), vice versa, a reduction.
Open the upper loading door and place above the main stone’s central slot, some thin and dry pieces of wood, in a crosswise position.
Prefer easily inflammable wood, avoiding big pieces and square shaped pieces.
Open the lower combustion chamber door.
Using sheets of thin paper (newspapers or similar) light the wood previously placed inside.
Leave the upper door ajar.
Wait several minutes until the fire starts and produces some embers (about 5 - 10 minutes).
Close the lower door first and then the upper door: at this moment the fan is automatically switched ON (point 6.1).
After some minutes, if you look through the sight glass, it is possible to see that the flame starts reversing downwards, so you can add some other larger wood pieces.
Important: during boiler operation the bypass must be always perfectly closed.
The wood has to be of the following length, according to the boiler model: a) 50 cm (+ 1 cm, - 4cm) for the GASOGEN G3 25 2S and
GASOGEN G3 40 2S models b) 70 cm (+ 1 cm, - 4 cm) for the GASOGEN G3 50 2S and
GASOGEN G3 65 2S models c) 100 cm (+ 1 cm, - 4 cm) for the GASOGEN G3 80 2S model
These dimensions must be absolutely respected.
In order to have a good combustion it is essential that the wood falls down in a uniformed way. Therefore it is necessary to make sure that the length of the wood logs introduced, their shape
C = Ventilation control box
S= Secondary air adjusting screws
P= Primary air adjusting screw
P1 = Primary air passages
S1= Secondary air passages
Models: GASOGEN G3 25 2S
GASOGEN G3 40 2S
GASOGEN G3 50 2S
S1
C
P1
S
P S
Models: GASOGEN G3 65 2S
GASOGEN G3 80 2S
1
1 = Ring nut air adjustment
P
S
P1
P= Primary air ventilation control box
S = Secondary air ventilation control box fig. 47 fig. 48 and the way they are loaded does not prevent the wood from falling down in a regular way.
The wood logs must be placed lengthwise and in a horizontal direction.
No log must be placed in an oblique or slanted direction.
SUBSEQUENT WOOD LOADINGS
Before carrying out a new loading of wood use up the previous load as much as possible.
The new load can be made when the bed of embers is about 5 cm thick.
Slowly open the upper loading door and the inner anti smoke flap.
The wood logs must have the length specified in the previous paragraph and they must be placed as previously described.
USEFUL SUGGESTIONS and LOADING ERRORS TO BE
AVOIDED
- Logs too long do not fall down properly and can cause obstructions.
- Logs too short cause irregular air passages, with consequent reduction in output and efficiency.
- In case the quality of the wood causes “obstructions” it could become necessary to cut the wood logs in two parts, as shown in fig. 49, in order that the total length “L” is as indicated in the previous paragraph.
- Always open the upper door slowly in order to avoid blowbacks and smoke formation.
- During normal boiler operation it is absolutely forbidden to open the lower combustion door.
Instructions for the installer
Cut fig. 49
6.7 - COMBUSTION AIR ADJUSTMENT
PRIMARY AND SECONDARY AIR ADJUSTMENT
The GASOGEN G3 2S boiler is equipped with a ventilation control box for combustion air (fan pos.
7 fig.2) and with primary (pos. P, fig. 47) and secondary air adjusters. (pos. S, fig. 47).
The GASOGEN G3 65 2S and GASOGEN G3 80
2S boilers are equipped with two fans (fig. 48) which incorporates a non-return valve, controlled by external ring nuts. The upper fan supplies the primary air, the lower fan the secondary air.
During the first ignition it is necessary to adjust the primary and secondary air, keeping in mind that the primar y air determines the boiler’s output and therefore the quantity of wood burnt, whilst the secondary air completes the combustion.
For correct air adjustment it will be necessary to observe the flame through the sight glass placed on the lower door. The flame will have to occupy about two thirds of the combustion chamber, and will have to quietly lick the lower cradle, without moving the ash too much and without making any noise.
The flame must be an orange-pink-white colour, not too transparent and with the centre part veering to light blue.
To bring the flame to optimal conditions, it will therefore be necessary to regulate the primary air by screwing or unscrewing the screw (pos. P); the same operation must be carried out for the secondary air (pos. S).
For the GASOGEN G3 65 2S and GASOGEN G3 80 2S boilers the primary air adjustment is achieved by acting on the upper fan’s external ring nut; for the secondary air by acting on the lower fan’s external ring nut.
Example n.1
Thick, wet wood logs = difficult combustion
S - Very closed (try to get the maximum dimension of the flame, but not a reddish colour).
P - Reasonably open in order to obtain a sufficient gasification.
Example n. 2
Very inflammable wood logs
S - Completely open.
P - Slightly closed to reduce the gasification, but sufficiently open to evacuate the ash that can close the combustion head.
GENERAL SUGGESTIONS
- Better performances are obtained after two - three days of operation. The refractory cement, in fact, needs to be baked and the tar has to cover the upper part of the fire box.
The flame has to have good dimensions and reasonably fill-up the combustion chamber.
- The flame must not be too red (lack of secondary air S).
- The flame must not be too blue (excess of secondary air S).
- The flame must not be too noisy (excess of primary air P).
- The flame must not be too small (lack of primary air P).
- If the ash does not falls down properly - increase the primary air P.
- If too much ash falls down reduce the primary air P.
- If the chimney smokes open the secondary air S completely.
- If the chimney continues smoking - adjust the secondary air S to maximum and reduce the primary air. P.
AIR ADJUSTMENT FAULTS
1) If the primary air is excessive a lot of ash and small pieces of coal will fall through the slot into the combustion chamber.
The flame is too fast, dry, a cold colour and makes a noise.
The boiler is consuming a lot of wood and the door’s refractory insulation is white.
2) If the primary air is insufficient the flame will be slow, indecisive, influenced by air currents and by the chimney draught, very small, incapable of touching the lower cradle, with low ash production and the door’s refractory insulation will be of a dark colour.
3) If the secondary air is excessive the flame will be small, a blueish colour and very transparent.
4) If the secondary air is insufficient the flame will be big, it will touch the lower cradle, it will completely fill the combustion chamber and, above all, it will be a red colour and not transparent
57
Gasogen
Instructions for the installer
6.8 - CHECKS TO CARRY OUT AFTER THE
FIRST START-UP
SOUNDNESS CHECK
During the first start-up check the soundness of the seals of the flue circuit and the chimney connection.
If you notice smoke leakages inform the installer or the After Sale Service. If you notice air suctions through the door’s seals, close the door handle with greater strength.
Check the normal operation of the working thermostat Te (32) at full capacity (paragraph 4.1 and 5.1) until it arrests the fan.
Check there are no water leaks from the water connections.
After the first start-up, with the boiler OFF, open the lower door and inspect the internal walls and the door insulation which has to be of a white colour, indication of a correct air adjustment.
On the contrary, if the walls are blackened, it means that the secondary air is not working properly (paragraph 6.7 and 6.9).
58
6.9 - WARNINGS
HOW TO AVOID CORROSION IN THE FIRE WOOD BOX
The use of wood with a high moisture content
(higher than about 25%) and/or loadings not proportioned to the system’s heat request
(long OFF periods with the wood storage full) can cause considerable condensate formation in the wood storage’s internal wall.
Check, once a week, the internal steel walls of the fire box.
They must be covered by a slight layer of opaque coloured, dry tar, with bubbles inclined to break and fall off.
On the contrary, if the tar is bright, runny and, if removed with the fire stoke, some liquid appears, it is necessary to use wood with a lower moisture content and/or reduce the quantity of the wood when loading the boiler.
If, in despite of these interventions the tar does not dry, you must inform the local After Sales Service of this.
The condensate inside the fire box causes the corrosion of the steel plates.
Corrosion is not covered by the guarantee, because it is caused by a bad use of the boiler (wet wood, excessive loadings, etc.).
CORROSION IN THE FLUE CIRCUIT
The flue is rich in water steam, due to combustion and the use of wood which always retains water.
If the flue comes into contact with relatively cold surfaces (with a minimum temperature of about 60 - 70 °C), the steam water condensates and in combination with other combustion products originates corrosion phenomena of the metallic parts.
Every day check if there are signs of smoke condensation (black liquid on the floor, behind the boiler). In this case you must use a wood with a lower moisture content; check that the recirculation pump is working correctly, the flue temperature at part load, and increase the working temperature. To control the room temperature it is therefore necessary to install a mixing valve.
The corrosion caused by flue condensation is not covered by the guarantee, because it is caused by the wood’s moisture content and the way the boiler is used.
PRECAUTIONS TO BE TAKEN DURING BOILER
OPERATION
After every air adjustment , wait 5 to 10 minutes before making a new adjustment. Once the best adjustment has been established, at the end of the day check that the surfaces of the combustion chamber and the door insulation are of a white colour.
In the ash deposited in the cradle there must be only a few unburnt embers. If the primary air is in excess, in the ash there will be embers and small pieces of coal, the flame will burn fast, dry, have a cold colour and be noisier, and the output will be excessive (paragraph 6.7).
If the primary air is insufficient the flame will be slow, small, it will not touch the lower cradle and will drag little ash; the output will be insufficient.
If the flame is a dark orange colour, the secondary air is insufficient and the surfaces of the combustion chamber will not be a white colour; if it is small and blue there is too much secondary air.
Always open the upper loading door and the internal antismoke flap slowly.
If, in despite of these precautions, some blow back will occur, it will be necessary to use bigger pieces of wood, with a higher moisture content, and to check that the boiler does not remain unused for a long time (reduce the primary air - paragraph 6.7) and make sure that the possible distortion of the cast iron fire bars or the modification of the stainless steel grates or that the presence of extraneous bodies (nails, metallic pieces) has not obstructed the refractory burner’s slot.
Instructions for the installer
6.10 - THERMOSTAT ADJUSTMENT
WOOD FIRED BOILER
The boiler’s adjustment thermostat must be set to the desired temperature (the adjustment range, limited by stoppers that must not be removed, varies from 75° to 85°C).
To adjust the boiler’s flow temperature to the heating system it is necessary to foresee the installation of a 3 or 4 way mixing valve.
If this mixing valve is not installed the guarantee will be void.
The manual reset safety thermostat, pos. 31, complies to the regulations in force.
At the start-up stage check if it has to be reset.
To do this unscrew the plastic protecting cap and press the reset button; then replace the plastic cap.
If the boiler safety’s thermostat has to intervene frequently, pos. 31, reduce the setting temperature of the working thermostat (pos. 32 on the control panel).
If this problem is repeated, inform the local After Sales Service.
6.11 - SUMMER OPERATION
Use of the boiler in summer for the production of only domestic hot water is not advised, unless you follow these rules meticulously:
1) Use very dry wood
2) Do not load the boiler with too much wood, load the boiler partially, 2 or 3 times per day according to need.
6.12 - BURNER ADJUSTMENT ON
BACK- UP BOILER
The burner must be serviced exclusively by an authorized service technician.
Important.
It is absolutely wrong to load the boiler completely so as to gain very long working periods (for example 24 hours). Doing so the boiler (when the fan is OFF) will produce a lot of acid condensate and corrode the fire box.
59
60
Gasogen
Instructions for the installer
6.13 - FAULT FINDING FOR BOILER WITH
STANDARD CONTROL PANEL
WOOD FIRED BOILER:
Problem:
- The fan does not start
Remedy:
- Adjust the working thermostat (pos. 32) to maximum.
- Reset the safety thermostat (pos. 31).
Problem:
- The fan starts, but after 30 minutes it stops; by switching OFF and ON the main switch (pos. 11) it re-starts.
Remedy:
- Increase the temporized relay’s intervention time
(this has to be done by the After Sales Service or by authorized trained personnel after switching OFF the mains supply).
Problem:
- The boiler does not reach the requested temperature. The flame is too small.
Remedy:
- Check if the by-pass is closed.
- Check the fan
- Check if the doors are properly closed
If you cannot solve the problem, do no attempt any other inter ventions and contact an authorized Automatic Heating After Sales
Service.
Problem:
- When opening the loading door there are blowbacks and flue formation.
Remedy :
- Open the door slowly.
- Use wood with a higher moisture content; make sure the boiler does not remain unused for long periods (see paragraph 6.9).
- Use thicker wood logs.
- Use up all the wood before loading a new batch
Problem:
- The boiler does not reach the requested temperature.
The flame is small and there is too much air.
When the fire box is checked a formation of log bridges is found.
Remedy:
- Check the length of the wood logs (see paragraph 6.6).
- Check how the wood logs are loaded in the fire box (see paragraph 6.6).
- Cut the logs in two parts (see paragraph 6.6).
- Use smaller logs (round or square, 5 to 7 cm diam. )
- Mix medium-large sized logs (15-20 cm diam.)with small sized logs (see previous point).
Instructions for the installer
6.14 - FAULT FINDING FOR BOILER WITH
OPTIONAL CONTROL PANEL
WOOD FIRED BOILER:
Problem:
- The fan does not start
Remedy:
- Adjust the working thermostat (pos. 32) to maximum.
- Reset the safety thermostat (pos. 31).
Problem:
- The fan starts, but after 30 minutes it stops; by switching OFF and ON the main switch (pos. 11) it re-starts.
Remedy:
- Increase the TIMER 1 intervention time
(this operation has to be carried out by the After Sales
Service or by authorized trained personnel after switching OFF the mains supply).
Problem:
- The acoustic-visual alarm system is activated in a continuous mode.
Remedy:
- Make sure the flow sensor is properly connected.
- Check that the flow sensor is working correctly.
- Inform the After Sales Service.
If you cannot solve the problem, do no attempt any other inter ventions and contact an authorized Automatic Heating After Sales
Service.
Problem:
- When opening the loading door there are blowbacks and flue formation.
Remedy:
- Open the door slowly.
- Use wood with a higher moisture content; make sure the boiler does not remain unused for long periods (see paragraph 6.9).
- Use thicker logs.
- Use up all the wood before loading a new batch
Problem:
- The boiler does not reach the requested temperature.
The flame is small and there is too much air.
When the fire box is checked a formation of log bridges is found.
Remedy:
- Check the length of the wood logs (see paragraph 6.6).
- Check how the wood logs are loaded in the fire box (see paragraph 6.6).
- Cut the logs in two parts (see paragraph 6.6).
- Use smaller logs (round or square, 5 to 7 cm diam. )
- Mix medium-large sized logs (15-20 cm diam.)with small sized logs (see previous point).
Problem:
- The boiler does not reach the requested temperature. The flame is too small.
Remedy:
- Check if the by-pass is closed.
- Check the fan
- Check if the doors are properly closed
61
62
Gasogen
Servicing schedule
7
SERVICING & MAINTENANCE
SCHEDULE
To ensure the continued safe and efficient operation of the boiler it is highly recommended that it is checked at regular intervals and serviced when necessary, and that only original spare parts are used.
Regular attention will prolong the boiler’s life span.
If the boiler is not checked and serviced regularly it could cause material and personal damages.
-
Before servicing always carry out the following steps:
Disconnect the mains electricity supply.
Separate the appliance from the electrical supply by means of a separating device with an opening contact of at least 3 mm (for example safety devices or power switches) and ensure yourself that it cannot be accidentally reinserted.
Close the on-off gas cock fitted upstream of the back up boiler.
Close any on-off valves fitted on the CH flow and return pipes, as well as the cold water inlet valve.
For this reason Automatic Heating recommends that a servicing contract should be made with one of our authorized After Sales
Service Assistance Centre.
The boiler must have regular maintenance and cleaning in order to ensure reliable and efficient operation. Regular attention will prolong the boiler’s life span.
The frequency of servicing will be determined by the service engineer and will depend on the appliance’s state of condition.
To ensure reliable and efficient boiler operation please refer to the table on page 63 where the “recommended servicing and maintenance operations” are indicated.
Once all the necessary maintenance work has been completed always follow these steps:
Open the CH flow and return valves as well as the cold water inlet valve
Purge the boiler and, if necessary, restore the heating system’s pressure.
Open the back up boiler’s on-off gas cock.
Switch on the electrical supply to the boiler.
Test for gas soundness, on the gas side (auxiliary boiler with gas burner) and on the water side.
INSTRUCTIONS FOR INSPECTION AND SERVICING
To ensure a long life to all your boiler components and in order not to alter the conditions of the approved product, only original Automatic Heating spare parts must be used.
Servicing schedule
Servicing of the boiler body
Danger !
Before servicing the boiler body, make sure the boiler has cooled down.
Warnings
Do not drain any water from the boiler unless absolutely necessary. Periodically check that the chimney is working correctly and that it is in good condition.
In case of maintenance works on structures sited near to the chimney or flue outlet system and their accessories, switch
OFF the boiler and, when the work is finished, check that they are functioning correctly.
Do not clean the boiler or its parts with easily inflammable products (gasoline, alcohol, etc.).
Do not leave inflammable products in the room where the boiler is installed.
Do not clean the boiler room when the boiler is firing.
At the end of the heating season, the boiler must always be checked in order to maintain the heating system in a good working condition.
In this case:
1) Check the adjustment of the air setting, according to the instr uctions given in the paragraph “Combustion air adjustment”.
2) Check that the two holes for the secondary air, placed in the front part of the main stone, just in front of the two adjustment screws, are not obstructed; if they are, pass a soft brush in both the holes, as shown in fig. 50.
IMPORTANT
For cleaning the boiler use brushes and a vacuum cleaner. If pieces of cloths are used make sure they are all recovered.
Always keep the screws and nuts protected with grease.
fig. 50
Every month
Check that the by-pass is working as indicated in paragraph
4.5 and that when the loading door is closed the by-pass is hermetically sealed.
CLEANING AND ORDINARY MAINTENANCE OF THE WOOD
FIRED BOILER
Every day
- Remove the ash from the lower cradle.
- Remove , with the scraper supplied with the boiler, the embers so that the ashes, accumulated in the fire bed will fall down through the holes in the grate.
This operation will help to avoid the grate becoming obstructed and the subsequent bad operation of the boiler.
This operation has to be done when there is not much flame, and, in any case, before wood loading.
Every month
Check that the by-pass is working as indicated in paragraph
4.5 and that when the loading door is closed the by-pass is hermetically sealed.
EXTRAORDINARY MAINTENANCE OF THE WOOD FIRED
BOILER
At the end of each heating season perform a general cleaning of the boiler by removing all the ashes from the fire box. During the summer season the boiler doors must be closed.
Every week
- Remove carefully all the residues of combustion accumulated in the fire box.
- Clean, with the brush supplied, the triangular passes of the combustion chamber, below the cradle.
- Remove the ashes from the flue chamber via the side doors, using the scraper.
- Make sure the grate’s slots are not obstructed; if so, free the passages using the poker.
- If the boiler continues to operate badly, even after having cleaned it as described above, the cause can be attributed to bad distribution of the secondary air.
Cleaning the fan(s)
WARNING:
First of all cut the power supply to the boiler
Remove the fan and clean the blades from the incrustations.
Normally to clean it properly we recommend you use compressed air or scrape the dirt off.
63
64
Gasogen
Servicing schedule
If the incrustations are more resistant, due to the formation of condensate or tar tears , clean very carefully in order not to bend or deform the blades. This could make the fan noisy during operation and could reduce the fan’s performances.
Cleaning the primary and secondary air distributor.
Remove the central wall (fig. 50) where the air adjustments are placed and clean the inner space carefully from tarry residues, dust and wood flakes which have entered through the primary air holes. Clean the secondary air passages carefully with a soft brush .
Servicing schedule
Components to check during annual servicing
Component
Soluzione inconveniente
Cast iron fire bars If necessary replace
Stainless steel grate
Fire bars mineral wool insulation
Primary and secondary air inlets
Soundness of the bypass disk
Integrity of the combustion chamber refractory bottom
Position of bottom stainless steel container
If necessary replace
If necessary replace
If necessary clean them
If necessary adjust it
If necessary repair it using the refractory kit (see spare parts list)
If necessary re-position it
Refractory insulation integrity in upper and lower doors If necessary repair and/or replace the doors
Integrity of doors seals If necessary replace them
Correct operation of the loading door microswitch If necessary adjust it
Cleaning the fan blades If necessary clean them
Fan noise If necessary replace the fan
Cleaning the flue circuit (on the rear side of boiler) If necessary clean it
65
notes
Gasogen
notes
DISTRIBUTED BY
51 Assembly Tullamarine Vic 3043 Australia
PO Box 356 Tullamarine Vic 3043 Australia
Telephone +61 3 9330 3300 Facsimile +61 3 9310 5655
Email [email protected]
www.automaticheating.com.au
advertisement
* Your assessment is very important for improving the workof artificial intelligence, which forms the content of this project